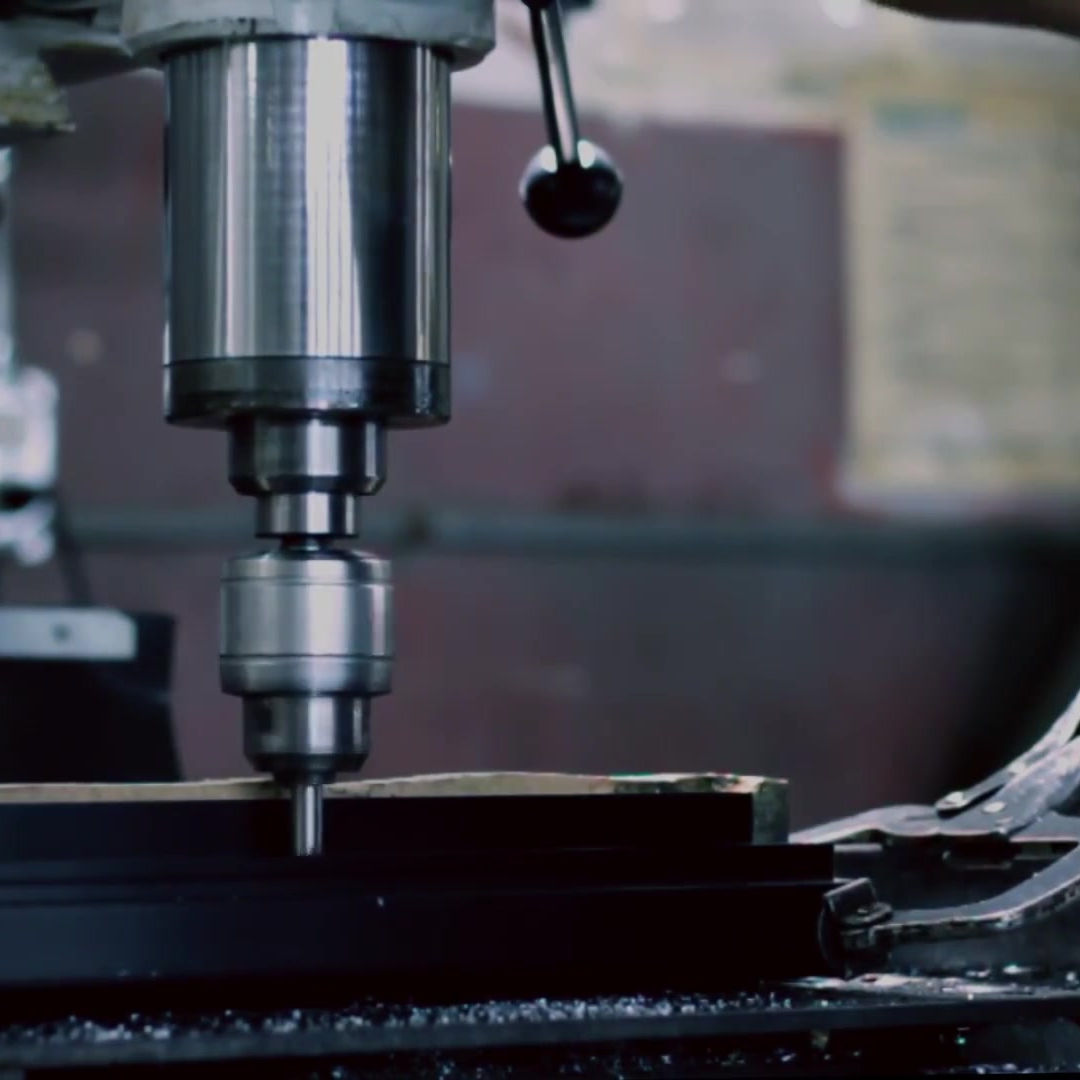
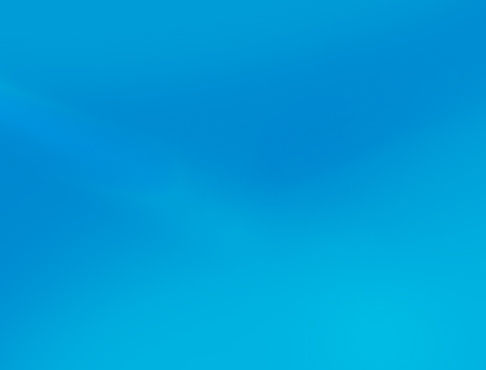
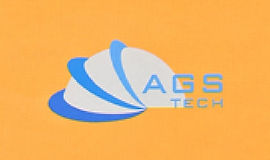
Global Custom Manufacturer, Integrator, Consolidator, Outsourcing Partner for a Wide Variety of Products & Services.
We are your one-stop source for manufacturing, fabrication, engineering, consolidation, integration, outsourcing of custom manufactured and off-shelf products & services. We also private label / white label your products with your brand name if you wish.
Choose your Language
-
Custom Manufacturing of Parts, Components, Assemblies, Finished Products, Machines and Industrial Equipment
-
Domestic & Global Contract Manufacturing
-
Manufacturing Outsourcing
-
Domestic, Global Procurement of Industrial Products
-
Private labeling / White Labeling your Products with your Brand Name
-
Product Finding & Locating Services
-
Global Design and Channel Partnership
-
Engineering Integration
-
Engineering Services
-
Global Consolidation, Warehousing, Logistics
AGS-TECH is a leading manufacturer and supplier of PNEUMATIC and HYDRAULIC ACTUATORS for assembly, packaging, robotics, and industrial automation. Our actuators are known for performance, flexibility, and extremely long life, and welcome the challenge of many different types of operating environments. We also supply HYDRAULIC ACCUMULATORS which are devices in which potential energy is stored in the form of a compressed gas or spring, or by a raised weight to be used to exert a force against a relatively incompressible fluid. Our fast delivery of pneumatic and hydraulic actuators and accumulators will reduce your inventory costs and keep your production schedule on track.
ACTUATORS: An actuator is a type of motor responsible for moving or controlling a mechanism or system. Actuators are operated by a source of energy. Hydraulic actuators are operated by hydraulic fluid pressure, and pneumatic actuators are operated by pneumatic pressure, and convert that energy into motion. Actuators are mechanisms by which a control system acts upon an environment. The control system may be a fixed mechanical or electronic system, a software-based system, a person, or any other input. Hydraulic actuators consist of cylinder or fluid motor that uses hydraulic power to facilitate mechanical operation. The mechanical motion may give an output in terms of linear, rotary or oscillatory motion. Since liquids are nearly impossible to compress, hydraulic actuators can exert considerable forces. Hydraulic actuators may have however limited acceleration. The actuator’s hydraulic cylinder consists of a hollow cylindrical tube along which a piston can slide. In single acting hydraulic actuators the fluid pressure is applied to just one side of the piston. The piston can move in only one direction, and a spring is generally used to give the piston a return stroke. Double acting actuators are used when pressure is applied on each side of the piston; any difference in pressure between the two sides of the piston moves the piston to one side or the other. Pneumatic actuators convert energy formed by vacuum or compressed air at high pressure into either linear or rotary motion. Pneumatic actuators enable large forces to be produced from relatively small pressure changes. These forces are often used with valves to move diaphragms to affect the flow of liquid through the valve. Pneumatic energy is desirable because it can respond quickly in starting and stopping as the power source does not need to be stored in reserve for operation. Industrial applications of actuators include automation, logic and sequence control, holding fixtures, and high-power motion control. Automotive applications of actuators on the other hand include power steering, power brakes, hydraulic brakes, and ventilation controls. Aerospace applications of actuators include flight-control systems, steering-control systems, air conditioning, and brake-control systems.
COMPARING PNEUMATIC and HYDRAULIC ACTUATORS: Pneumatic linear actuators consist of a piston inside a hollow cylinder. Pressure from an external compressor or manual pump moves the piston inside the cylinder. As pressure is increased, the actuator’s cylinder moves along the axis of the piston, creating a linear force. The piston returns to its original position by either a spring-back force or fluid being supplied to the other side of the piston. Hydraulic linear actuators function similar to pneumatic actuators, but an incompressible liquid from a pump rather than pressurized air moves the cylinder. The benefits of pneumatic actuators come from their simplicity. The majority of pneumatic aluminum actuators have a maximum pressure rating of 150 psi with bore sizes ranging from 1/2 to 8 in., which can be converted into approximately 30 to 7,500 lb. of force. Steel pneumatic actuators on the other hand have a maximum pressure rating of 250 psi with bore sizes ranging from 1/2 to 14 in., and generate forces ranging from 50 to 38,465 lb. Pneumatic actuators generate precise linear motion by providing accuracies such as 0.1 inches and repeatabilities within .001 inches. Typical applications of pneumatic actuators are areas of extreme temperatures such as -40 F to 250 F. Using air, pneumatic actuators avoid using hazardous materials. Pneumatic actuators meet explosion protection and machine safety requirements because they create no magnetic interference due to their lack of motors. The cost of pneumatic actuators is low compared to hydraulic actuators. Pneumatic actuators are also lightweight, require minimal maintenance, and have durable components. On the other hand there are disadvantages of pneumatic actuators: Pressure losses and air’s compressibility make pneumatics less efficient than other linear-motion methods. Operations at lower pressures will have lower forces and slower speeds. A compressor must run continuously and apply pressure even if nothing is moving. To be efficient, pneumatic actuators must be sized for a specific job and cannot be used for other applications. Accurate control and efficiency requires proportional regulators and valves, which is costly and complex. Even though the air is easily available, it can be contaminated by oil or lubrication, leading to downtime and maintenance. Compressed air is a consumable that needs to be purchased. Hydraulic actuators on the other hand are rugged and suited for high-force applications. They can produce forces 25 times greater than pneumatic actuators of equal size and operate with pressures of up to 4,000 psi. Hydraulic motors have high horsepower-to-weight ratios by 1 to 2 hp/lb greater than a pneumatic motor. Hydraulic actuators can hold force and torque constant without the pump supplying more fluid or pressure, because fluids are incompressible. Hydraulic actuators can have their pumps and motors located a considerable distance away with still minimal power losses. However hydraulics will leak fluid and result in less efficiency. Hydraulic fluid leaks lead to cleanliness problems and potential damage to surrounding components and areas. Hydraulic actuators require many companion parts, such as fluid reservoirs, motors, pumps, release valves, and heat exchangers, noise-reduction equipment. As a result hydraulic linear motion systems are large and difficult to accommodate.
ACCUMULATORS: These are used in fluid power systems to accumulate energy and to smooth out pulsations. Hydraulic system that utilize accumulators can use smaller fluid pumps because accumulators store energy from the pump during low demand periods. This energy is available for instantaneous use, released upon demand at a rate many times greater than could be supplied by the pump alone. Accumulators can also act as surge or pulsation absorbers by cushioning hydraulic hammers, reducing shocks caused by rapid operation or sudden starting and stopping of power cylinders in a hydraulic circuit. There are four major types of accumulators: 1.) The weight loaded piston type accumulators, 2.) Diaphragm type accumulators, 3.) Spring type accumulators and the 4.) Hydropneumatic piston type accumulators. The weight loaded type is much larger and heavier for its capacity than modern piston and bladder types. Both the weight loaded type, and mechanical spring type are very seldom used today. The hydro-pneumatic type accumulators use a gas as a spring cushion in conjunction with a hydraulic fluid, the gas and fluid being separated by a thin diaphragm or a piston. Accumulators have the following functions:
-Energy Storage
-Absorbing Pulsations
-Cushioning Operating Shocks
-Supplementing Pump Delivery
-Maintaining Pressure
-Acting as Dispensers
Hydro-pneumatic accumulators incorporate a gas in conjunction with a hydraulic fluid. The fluid has little dynamic power storage capability. However, the relative incompressibility of a hydraulic fluid makes it ideal for fluid power systems and provides quick response to power demand. The gas, on the other hand, a partner to the hydraulic fluid in the accumulator, can be compressed to high pressures and low volumes. Potential energy is stored in the compressed gas to be released when needed. In the piston type accumulators the energy in the compressed gas exerts pressure against the piston separating the gas and the hydraulic fluid. The piston in turn forces the fluid from the cylinder into the system and to the location where useful work needs to be accomplished. In most fluid power applications, pumps are used to generate the required power to be used or stored in a hydraulic system, and pumps deliver this power in a pulsating flow. The piston pump, as commonly used for higher pressures produces pulsations detrimental to a high pressure system. An accumulator properly located in the system will substantially cushion these pressure variations. In many fluid power applications the driven member of the hydraulic system stops suddenly, creating a pressure wave which is sent back through the system. This shock wave can develop peak pressures several times greater than normal working pressures and can be the source of system failure or disturbing noise. The gas cushioning effect in an accumulator will minimize these shock waves. An example of this application is the absorption of shock caused by suddenly stopping the loading bucket on a hydraulic front end loader. An accumulator, capable of storing power, can supplement the fluid pump in delivering power to the system. The pump stores potential energy in the accumulator during idle periods of the work cycle, and the accumulator transfers this reserve power back to the system when the cycle requires emergency or peak power. This enables a system to utilize smaller pumps, resulting in cost and power savings. Pressure changes are observed in hydraulic systems when the liquid is subjected to rising or falling temperatures. Also, there may be pressure drops due to leakage of hydraulic fluids. Accumulators compensate for such pressure changes by delivering or receiving a small amount of hydraulic liquid. In the event the main power source should fail or be stopped, accumulators would act as auxiliary power sources, maintaining pressure in the system. Lastly, accumulators mcan be used to dispense fluids under pressure, such as lubricating oils.
Please click on highlighted text below to download our product brochures for actuators and accumulators:
- YC Series Hydraulic Cyclinder - Accumulators from AGS-TECH Inc