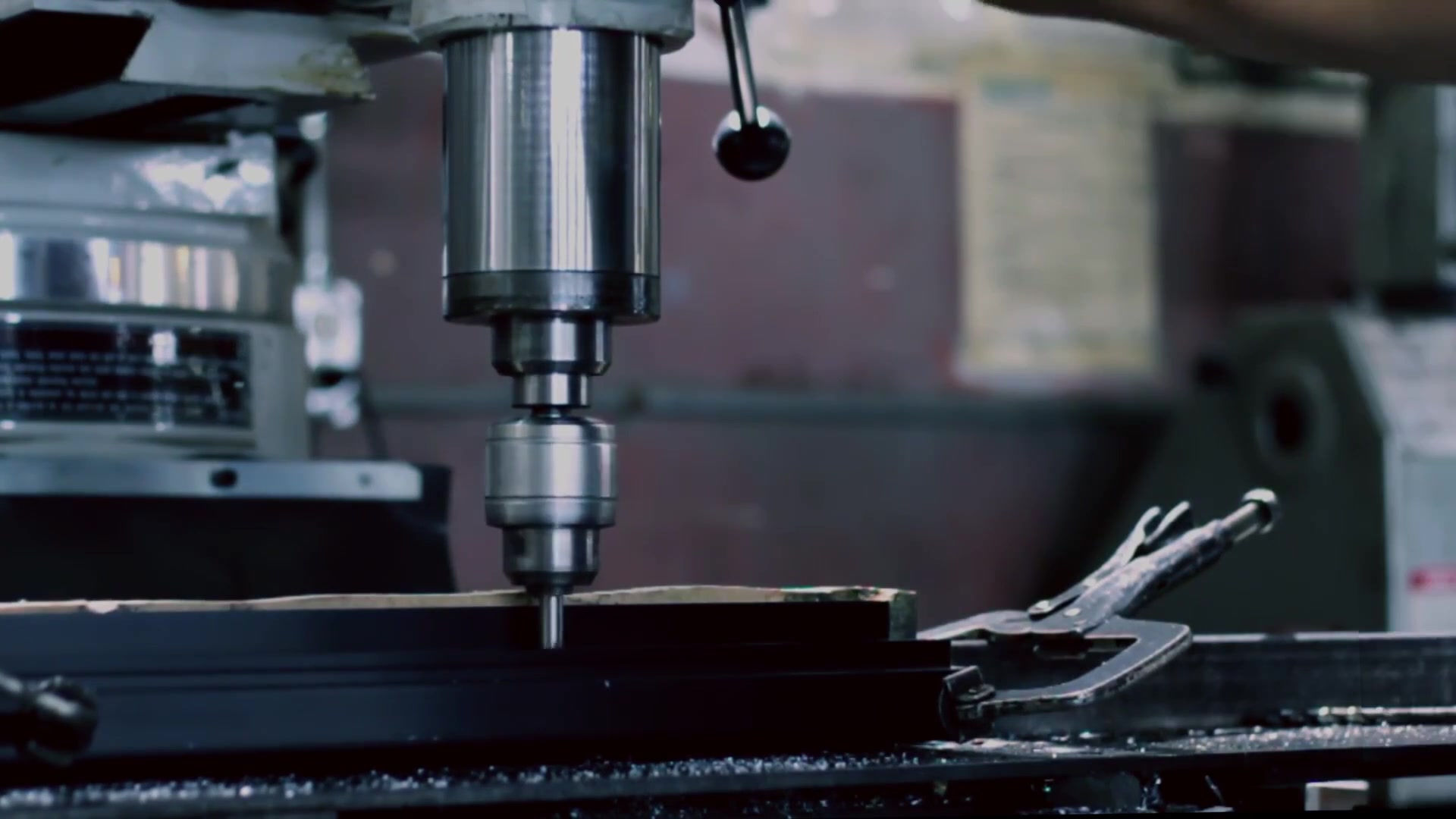
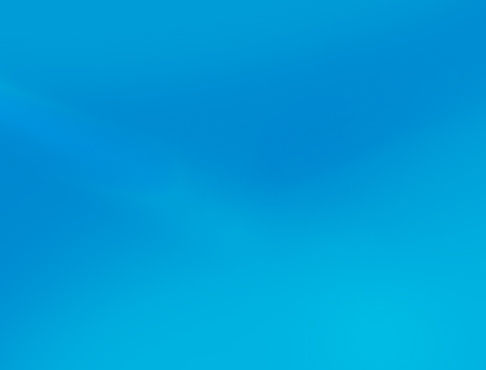
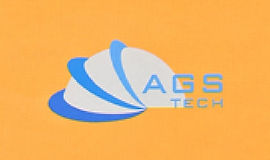
Globale pasgemaakte vervaardiger, integreerder, konsolideerder, uitkontrakteringsvennoot vir 'n wye verskeidenheid produkte en dienste.
Ons is jou eenstopbron vir vervaardiging, vervaardiging, ingenieurswese, konsolidasie, integrasie, uitkontraktering van pasgemaakte en van die rak produkte en dienste af.
Kies jou taal
-
Pasgemaakte vervaardiging
-
Binnelandse en globale kontrakvervaardiging
-
Vervaardiging Uitkontraktering
-
Binnelandse en globale verkryging
-
Consolidation
-
Ingenieursintegrasie
-
Ingenieursdienste
ELECTRICAL DISCHARGE MACHINING (EDM), also referred to as SPARK-EROSION or ELECTRODISCHARGE MACHINING, SPARK ERODING, DIE SINKING_cc781905-5cde-3194-bb3b -136bad5cf58d_or WIRE EROSION, is a NON-CONVENTIONAL MANUFACTURING process where erosion of metals takes place and desired shape is obtained using electrical discharges in the form van vonke. Ons bied ook 'n paar variëteite van EDM, naamlik NO-WEAR EDM, WIRE EDM (WEDM), EDM GRINDING (EDG), STERF-SINK EDM, ELEKTRIESE-ONTLADING, MICRO-EDM_cc -5cde-3194-bb3b-136bad5cf58d_and ELEKTROCHEMIESE-ONTLADING (ECDG). Ons EDM-stelsels bestaan uit gevormde gereedskap/elektrode en die werkstuk wat aan GS-kragbronne gekoppel is en in 'n elektries nie-geleidende diëlektriese vloeistof geplaas word. Na 1940 het elektriese ontladingsbewerking een van die belangrikste en gewildste produksietegnologieë in vervaardigingsindustrieë geword.
Wanneer die afstand tussen die twee elektrodes verminder word, word die intensiteit van die elektriese veld in die volume tussen die elektrodes groter as die sterkte van die diëlektrikum in sommige punte, wat breek en uiteindelik 'n brug vorm vir stroom om tussen die twee elektrodes te vloei. 'n Intense elektriese boog word opgewek wat veroorsaak dat aansienlike verhitting 'n gedeelte van die werkstuk en van die gereedskapmateriaal smelt. As gevolg hiervan word materiaal van beide die elektrodes verwyder. Terselfdertyd word die diëlektriese vloeistof vinnig verhit, wat lei tot verdamping van die vloeistof in die booggaping. Sodra die stroomvloei stop of dit gestop word, word hitte uit die gasborrel verwyder deur die omliggende diëlektriese vloeistof en die borrel kaviteer (ineenstort). Die skokgolf wat geskep word deur die borrel se ineenstorting en die vloei van diëlektriese vloeistof spoel puin van die werkstukoppervlak af en voer enige gesmelte werkstukmateriaal in die diëlektriese vloeistof in. Die herhalingstempo vir hierdie ontladings is tussen 50 tot 500 kHz, spannings tussen 50 tot 380 V en strome tussen 0,1 en 500 Ampere. Nuwe vloeibare diëlektrikum soos minerale olies, keroseen of gedistilleerde en gedeïoniseerde water word gewoonlik in die inter-elektrodevolume vervoer wat die vaste deeltjies (in die vorm van puin) wegdra en die isolerende eienskappe van die diëlektrikum word herstel. Na 'n stroomvloei word die potensiaalverskil tussen die twee elektrodes herstel tot wat dit was voor die onklaarraking, sodat 'n nuwe vloeibare diëlektriese afbreek kan plaasvind. Ons moderne elektriese ontladingsmasjiene (EDM) bied numeries beheerde bewegings en is toegerus met pompe en filterstelsels vir die diëlektriese vloeistowwe.
Elektriese ontladingsbewerking (EDM) is 'n bewerkingsmetode wat hoofsaaklik gebruik word vir harde metale of dié wat baie moeilik sal wees om met konvensionele tegnieke te bewerk. EDM werk tipies met enige materiaal wat elektriese geleiers is, alhoewel metodes vir die bewerking van isolerende keramiek met EDM ook voorgestel is. Die smeltpunt en latente hitte van smelt is eienskappe wat die volume metaal wat per ontlading verwyder word, bepaal. Hoe hoër hierdie waardes, hoe stadiger is die materiaalverwyderingstempo. Omdat die elektriese ontladingsbewerkingsproses geen meganiese energie behels nie, beïnvloed die hardheid, sterkte en taaiheid van die werkstuk nie die verwyderingstempo nie. Ontladingsfrekwensie of energie per ontlading, die spanning en stroom word gewissel om materiaalverwyderingstempo's te beheer. Tempo van materiaalverwydering en oppervlakruwheid neem toe met toenemende stroomdigtheid en dalende vonkfrekwensie. Ons kan ingewikkelde kontoere of holtes in voorafverharde staal sny deur gebruik te maak van EDM sonder dat dit nodig is vir hittebehandeling om dit sag te maak en weer te verhard. Ons kan hierdie metode gebruik met enige metaal of metaallegerings soos titanium, hastelloy, kovar en inconel. Toepassings van die EDM-proses sluit die vorming van polikristallyne diamantgereedskap in. EDM word beskou as 'n nie-tradisionele of nie-konvensionele bewerkingsmetode saam met prosesse soos elektrochemiese bewerking (ECM), waterstraalsny (WJ, AWJ), lasersny. Aan die ander kant sluit die konvensionele bewerkingsmetodes draai-, frees-, slyp-, boor- en ander proses in waarvan die materiaalverwyderingsmeganisme hoofsaaklik op meganiese kragte gebaseer is. Elektrodes vir elektriese-ontlading bewerking (EDM) is gemaak van grafiet, koper, koper en koper-wolfram legering. Elektrodediameters tot 0,1 mm is moontlik. Aangesien gereedskapslytasie 'n ongewenste verskynsel is wat dimensionele akkuraatheid in EDM nadelig beïnvloed, trek ons voordeel uit 'n proses genaamd NO-WEAR EDM, deur polariteit om te keer en kopergereedskap te gebruik om gereedskapslytasie te minimaliseer.
Ideaal gesproke kan die elektriese ontladingsbewerking (EDM) beskou word as 'n reeks afbreek en herstel van die diëlektriese vloeistof tussen die elektrodes. In werklikheid is die verwydering van die puin uit die interelektrode-area egter byna altyd gedeeltelik. Dit veroorsaak dat die elektriese eienskappe van die diëlektrikum in die inter-elektrode-area verskil van hul nominale waardes en wissel met tyd. Die inter-elektrode afstand, (vonk-gaping), word aangepas deur die beheeralgoritmes van die spesifieke masjien wat gebruik word. Die vonkgaping in EDM kan ongelukkig soms deur die puin kortgesluit word. Die beheerstelsel van die elektrode kan nie vinnig genoeg reageer om te verhoed dat die twee elektrodes (gereedskap en werkstuk) kortsluit nie. Hierdie ongewenste kortsluiting dra by tot materiaalverwydering anders as die ideale geval. Ons gee uiterste belang aan spoelaksie om die isolerende eienskappe van die diëlektrikum te herstel sodat die stroom altyd in die punt van die inter-elektrode area plaasvind, en sodoende die moontlikheid van ongewenste verandering van vorm (skade) van die gereedskap-elektrode tot die minimum beperk. en werkstuk. Om 'n spesifieke meetkunde te verkry, word die EDM-instrument langs die verlangde pad baie naby aan die werkstuk gelei sonder om dit aan te raak. Ons gee die grootste aandag aan die prestasie van bewegingsbeheer in gebruik. Op hierdie manier vind 'n groot aantal stroomontladings / vonke plaas, en elkeen dra by tot die verwydering van materiaal van beide gereedskap en werkstuk, waar klein kraters gevorm word. Die grootte van die kraters is 'n funksie van die tegnologiese parameters wat vir die spesifieke taak op hande gestel is en afmetings kan wissel van die nanoskaal (soos in die geval van mikro-EDM-bewerkings) tot 'n paar honderde mikrometers in ruwe toestande. Hierdie klein kraters op die werktuig veroorsaak geleidelike erosie van die elektrode wat "gereedskapslytasie" genoem word. Om die nadelige effek van die slytasie op die geometrie van die werkstuk teë te werk, vervang ons voortdurend die gereedskap-elektrode tydens 'n bewerking. Soms bereik ons dit deur 'n voortdurend vervangde draad as elektrode te gebruik (hierdie EDM-proses word ook WIRE EDM genoem). Soms gebruik ons die gereedskap-elektrode op so 'n manier dat slegs 'n klein gedeelte daarvan werklik besig is met die bewerkingsproses en hierdie gedeelte word op 'n gereelde basis verander. Dit is byvoorbeeld die geval wanneer 'n roterende skyf as 'n gereedskap-elektrode gebruik word. Hierdie proses word genoem EDM GRINDING. Nog 'n tegniek wat ons gebruik, bestaan uit die gebruik van 'n stel elektrodes met verskillende groottes en vorms tydens dieselfde EDM-operasie om vir slytasie te vergoed. Ons noem hierdie meervoudige elektrode tegniek, en word die algemeenste gebruik wanneer die gereedskapelektrode die verlangde vorm negatief herhaal en langs 'n enkele rigting na die spasie gevorder word, gewoonlik die vertikale rigting (dws z-as). Dit lyk soos die sink van die werktuig in die diëlektriese vloeistof waarin die werkstuk gedompel is, en daarom word dit na verwys as DIE-SINKING EDM_cc781905-5cde-3194-bb3b-75ccde-15cde-781905-15cde-1500-1500-1000-781905 3194-bb3b-136bad5cf58d_CONVENTIONAL EDM or RAM EDM). Die masjiene vir hierdie operasie word genoem SINKER EDM. Die elektrodes vir hierdie tipe EDM het komplekse vorms. As die finale geometrie verkry word deur gebruik te maak van 'n gewoonlik eenvoudig-vormige elektrode wat langs verskeie rigtings beweeg word en ook onderhewig is aan rotasies, noem ons dit EDM FREES. Die hoeveelheid slytasie is streng afhanklik van die tegnologiese parameters wat in die operasie gebruik word (polariteit, maksimum stroom, oopkringspanning). Byvoorbeeld, in micro-EDM, ook bekend as m-EDM, word hierdie parameters gewoonlik gestel op waardes wat ernstige slytasie genereer. Daarom is slytasie 'n groot probleem in daardie area wat ons tot die minimum beperk deur ons opgehoopte kundigheid te gebruik. Om byvoorbeeld slytasie aan grafietelektrodes te verminder, keer 'n digitale kragopwekker, beheerbaar binne millisekondes, polariteit om soos elektro-erosie plaasvind. Dit lei tot 'n effek soortgelyk aan elektroplatering wat voortdurend die geërodeerde grafiet terug op die elektrode neerlê. In 'n ander metode, 'n sogenaamde ''Zero Wear''-kring, verminder ons hoe gereeld die ontlading begin en stop, en hou dit so lank as moontlik aan. Die materiaalverwyderingstempo in elektriese ontladingsbewerking kan geskat word uit:
MRR = 4 x 10 exp(4) x I x Tw exp (-1.23)
Hier is MRR in mm3/min, I is stroom in Ampere, Tw is werkstuk smeltpunt in K-273.15K. Die exp staan vir eksponent.
Aan die ander kant kan die slytasietempo Wt van die elektrode verkry word van:
Wt = ( 1.1 x 10exp(11) ) x I x Ttexp(-2.38)
Hier is Wt in mm3/min en Tt is smeltpunt van die elektrodemateriaal in K-273.15K
Laastens kan die slytasieverhouding van die werkstuk tot elektrode R verkry word van:
R = 2,25 x Trexp(-2,38)
Hier is Tr die verhouding van smeltpunte van werkstuk tot elektrode.
SINKER EDM :
Sinker EDM, ook na verwys as CAVITY TIPE EDM or_cc781905-94cde-stuk in electro-b-bad5-8b3, vloeistof en vloeistof in vloeibare vloeistowwe en vloeibare vloeistowwe en vloeibare Die elektrode en werkstuk is aan 'n kragbron gekoppel. Die kragtoevoer genereer 'n elektriese potensiaal tussen die twee. Soos die elektrode die werkstuk nader, vind diëlektriese afbreek in die vloeistof plaas, wat 'n plasmakanaal vorm, en 'n klein vonk spring. Die vonke slaan gewoonlik een op 'n slag omdat dit hoogs onwaarskynlik is dat verskillende liggings in die interelektroderuimte identiese plaaslike elektriese eienskappe het wat dit moontlik sal maak dat 'n vonk op al sulke plekke gelyktydig kan voorkom. Honderde duisende van hierdie vonke gebeur op willekeurige punte tussen die elektrode en die werkstuk per sekonde. Soos die basismetaal erodeer, en die vonkgaping daarna toeneem, word die elektrode outomaties deur ons CNC-masjien verlaag sodat die proses ononderbroke kan voortgaan. Ons toerusting het beheersiklusse bekend as ''betyds'' en ''aftyd''. Die aan-tyd-instelling bepaal die lengte of duur van die vonk. 'n Langer tyd produseer 'n dieper holte vir daardie vonk en alle daaropvolgende vonke vir daardie siklus, wat 'n growwer afwerking op die werkstuk skep en omgekeerd. Die aftyd is die tydperk wat een vonk deur 'n ander vervang word. 'n Langer aftyd laat die diëlektriese vloeistof toe om deur 'n spuitstuk te spoel om die geërodeerde puin skoon te maak en sodoende 'n kortsluiting te vermy. Hierdie instellings word in mikro-sekondes aangepas.
WIRE EDM :
In WIRE ELECTRICAL DISCHARGE MACHINING (WEDM), also called WIRE-CUT EDM or WIRE CUTTING, we feed a dun enkelstreng metaaldraad van koper deur die werkstuk, wat in 'n tenk diëlektriese vloeistof ondergedompel is. Wire EDM is 'n belangrike variasie van EDM. Ons gebruik af en toe draadgesnyde EDM om plate so dik as 300 mm te sny en om ponse, gereedskap en matryse van harde metale te maak wat moeilik is om met ander vervaardigingsmetodes te bewerk. In hierdie proses wat soos kontoersny met 'n bandsaag lyk, word die draad, wat voortdurend van 'n spoel af gevoer word, tussen boonste en onderste diamantgeleiders vasgehou. Die CNC-beheerde gidse beweeg in die x–y-vlak en die boonste gids kan ook onafhanklik in die z–u–v-as beweeg, wat aanleiding gee tot die vermoë om tapse en oorgangsvorme te sny (soos sirkel aan die onderkant en vierkant by die bokant). Die boonste gids kan asbewegings in x–y–u–v–i–j–k–l– beheer. Dit laat die WEDM toe om baie ingewikkelde en delikate vorms te sny. Die gemiddelde snykerf van ons toerusting wat die beste ekonomiese koste en bewerkingstyd behaal, is 0,335 mm met Ø 0,25 koper-, koper- of wolframdraad. Die boonste en onderste diamantgeleiders van ons CNC-toerusting is egter akkuraat tot ongeveer 0,004 mm, en kan 'n snypad of kerf van so klein as 0,021 mm hê met behulp van Ø 0,02 mm draad. So baie smal snitte is moontlik. Die snywydte is groter as die wydte van die draad omdat vonk van die kante van die draad na die werkstuk voorkom, wat erosie veroorsaak. Hierdie ''oorsny'' is nodig, vir baie toepassings is dit voorspelbaar en kan daarom vergoed word (in mikro-EDM is dit nie dikwels die geval nie). Die draadspoele is lank—'n 8 kg-spoel van 0,25 mm-draad is net meer as 19 kilometer lank. Draaddeursnee kan so klein as 20 mikrometer wees en die geometrie-presisie is in die omgewing van +/- 1 mikrometer. Ons gebruik die draad gewoonlik net een keer en herwin dit omdat dit relatief goedkoop is. Dit beweeg teen 'n konstante snelheid van 0,15 tot 9m/min en 'n konstante kerf (gleuf) word gehandhaaf tydens 'n sny. In die draadgesnyde EDM-proses gebruik ons water as die diëlektriese vloeistof, wat die weerstand en ander elektriese eienskappe daarvan beheer met filters en de-ioniseerder-eenhede. Die water spoel die gesnyde puin weg van die snysone. Spoel is 'n belangrike faktor in die bepaling van die maksimum voertempo vir 'n gegewe materiaaldikte en daarom hou ons dit konsekwent. Snyspoed in draad-EDM word aangegee in terme van die deursnee-area gesny per tydseenheid, soos 18 000 mm2/hr vir 50 mm dik D2 gereedskapstaal. Die lineêre snyspoed vir hierdie geval sal 18 000/50 = 360 mm/hr wees. Die materiaalverwyderingstempo in draad EDM is:
MRR = Vf xhxb
Hier is MRR in mm3/min, Vf is die toevoertempo van die draad na werkstuk in mm/min, h is dikte of hoogte in mm, en b is die kerf, wat is:
b = dw + 2s
Hier is dw draaddiameter en s is gaping tussen draad en werkstuk in mm.
Saam met strenger toleransies, het ons moderne multi-as EDM draadsny bewerkingsentrums kenmerke bygevoeg soos multi koppe om twee dele gelyktydig te sny, kontroles om draadbreek te voorkom, outomatiese selfryg-eienskappe in geval van draadbreek, en geprogrammeer bewerkingstrategieë om die werking te optimaliseer, reguit en hoeksnyvermoëns.
Wire-EDM bied ons lae oorblywende spanning, want dit vereis nie hoë snykragte vir die verwydering van materiaal nie. Wanneer die energie/drywing per puls relatief laag is (soos in afrondingsbewerkings), word min verandering in die meganiese eienskappe van 'n materiaal verwag as gevolg van lae residuele spannings.
ELEKTRIESE UITLADING (EDG) : Die slypwiele bevat nie skuurmiddels nie, hulle is van grafiet of koper gemaak. Herhalende vonke tussen die roterende wiel en werkstuk verwyder materiaal van werkstukoppervlaktes. Die materiaalverwyderingskoers is:
MRR = K x I
Hier is MRR in mm3/min, I is stroom in Ampere, en K is werkstukmateriaalfaktor in mm3/A-min. Ons gebruik gereeld elektriese ontladingsslyp om smal splete op komponente te saag. Ons kombineer soms EDG (Electrical-Discharge Grinding) proses met EKG (Electrochemical Grinding) proses waar materiaal deur chemiese aksie verwyder word, die elektriese ontladings vanaf die grafietwiel breek die oksiedfilm op en spoel deur die elektroliet weg. Die proses word genoem ELECTROCHEMICAL-DISCHARGE GRINDING (ECDG). Alhoewel die ECDG-proses relatief meer krag verbruik, is dit 'n vinniger proses as die EDG. Ons slyp meestal karbiedgereedskap met hierdie tegniek.
Toepassings van elektriese ontladingsbewerking:
Prototipe produksie:
Ons gebruik die EDM-proses in vormvervaardiging, gereedskap- en matrysvervaardiging, sowel as vir die maak van prototipe en produksieonderdele, veral vir die lugvaart-, motor- en elektroniese industrieë waarin produksiehoeveelhede relatief laag is. In Sinker EDM word 'n grafiet-, koperwolfram- of suiwer koperelektrode in die verlangde (negatiewe) vorm gemasjineer en in die werkstuk aan die einde van 'n vertikale ram gevoer.
Die maak van muntstukke:
Vir die skep van matryse vir die vervaardiging van juweliersware en kentekens deur die munt (stempel) proses, kan die positiewe meester van sterling silwer gemaak word, aangesien (met toepaslike masjieninstellings) die meester aansienlik geërodeer word en slegs een keer gebruik word. Die resulterende negatiewe matrys word dan verhard en in 'n druppelhamer gebruik om gestempelde vlakke te vervaardig uit uitgesnyde velleë van brons, silwer of lae-proof goudlegering. Vir kentekens kan hierdie woonstelle verder gevorm word tot 'n geboë oppervlak deur 'n ander matrys. Hierdie tipe EDM word gewoonlik uitgevoer onder water in 'n olie-gebaseerde diëlektrikum. Die voltooide voorwerp kan verder verfyn word deur harde (glas) of sagte (verf) emaljering en/of gegalvaniseer met suiwer goud of nikkel. Sagter materiale soos silwer kan met die hand gegraveer word as 'n verfyning.
Boor van klein gaatjies:
Op ons draadgesnyde EDM-masjiene gebruik ons klein gaatjie-boor-EDM om 'n deurgat in 'n werkstuk te maak waardeur die draad geryg kan word vir die draadgesnyde EDM-bewerking. Afsonderlike EDM-koppe spesifiek vir kleingatboor word op ons draadsnymasjiene gemonteer wat toelaat dat groot geharde plate afgewerkte dele daarvan geërodeer het soos nodig en sonder om vooraf te boor. Ons gebruik ook klein gaatjie EDM om rye gate in die rande van turbinelemme wat in straalmotors gebruik word, te boor. Gasvloei deur hierdie klein gaatjies laat die enjins toe om hoër temperature te gebruik as wat andersins moontlik is. Die hoë-temperatuur, baie harde, enkelkristal-legerings waarvan hierdie lemme gemaak is, maak konvensionele bewerking van hierdie gate met 'n hoë aspekverhouding uiters moeilik en selfs onmoontlik. Ander toepassingsareas vir kleingat-EDM is om mikroskopiese openinge vir brandstofstelselkomponente te skep. Benewens die geïntegreerde EDM-koppe, ontplooi ons alleenstaande kleingat-boor-EDM-masjiene met x-y-asse om blinde of deurgate te masjien. EDM boor gate met 'n lang koper- of koperbuiselektrode wat in 'n boorkop roteer met 'n konstante vloei van gedistilleerde of gedeïoniseerde water wat deur die elektrode vloei as 'n spoelmiddel en diëlektrikum. Sommige klein-gat boor EDM's is in staat om deur 100 mm sagte of selfs geharde staal in minder as 10 sekondes te boor. Gate tussen 0,3 mm en 6,1 mm kan in hierdie booroperasie verkry word.
Metaal disintegrasie bewerking:
Ons het ook spesiale EDM-masjiene vir die spesifieke doel om stukkende gereedskap (boorpunte of krane) van werkstukke te verwyder. Hierdie proses word ''metaaldesintegrasiebewerking'' genoem.
Voordele en nadele Elektriese-ontlading bewerking:
Voordele van EDM sluit in bewerking van:
- Komplekse vorms wat andersins moeilik sou wees om met konvensionele snygereedskap te vervaardig
- Uiters harde materiaal tot baie noue toleransies
- Baie klein werkstukke waar konvensionele snygereedskap die onderdeel kan beskadig as gevolg van oormatige snygereedskapdruk.
- Daar is geen direkte kontak tussen gereedskap en werkstuk nie. Daarom kan delikate gedeeltes en swak materiale sonder enige vervorming gemasjineer word.
- 'n Goeie oppervlakafwerking kan verkry word.
- Baie fyn gate kan maklik geboor word.
Nadele van EDM sluit in:
- Die stadige tempo van materiaalverwydering.
- Die bykomende tyd en koste wat gebruik word vir die skep van elektrodes vir ram/sinker EDM.
- Om skerp hoeke op die werkstuk weer te gee is moeilik as gevolg van elektrodeslytasie.
- Kragverbruik is hoog.
- ''Oorsny'' word gevorm.
- Oormatige slytasie van gereedskap vind plaas tydens bewerking.
- Elektries nie-geleidende materiale kan slegs gemasjineer word met spesifieke opstelling van die proses.