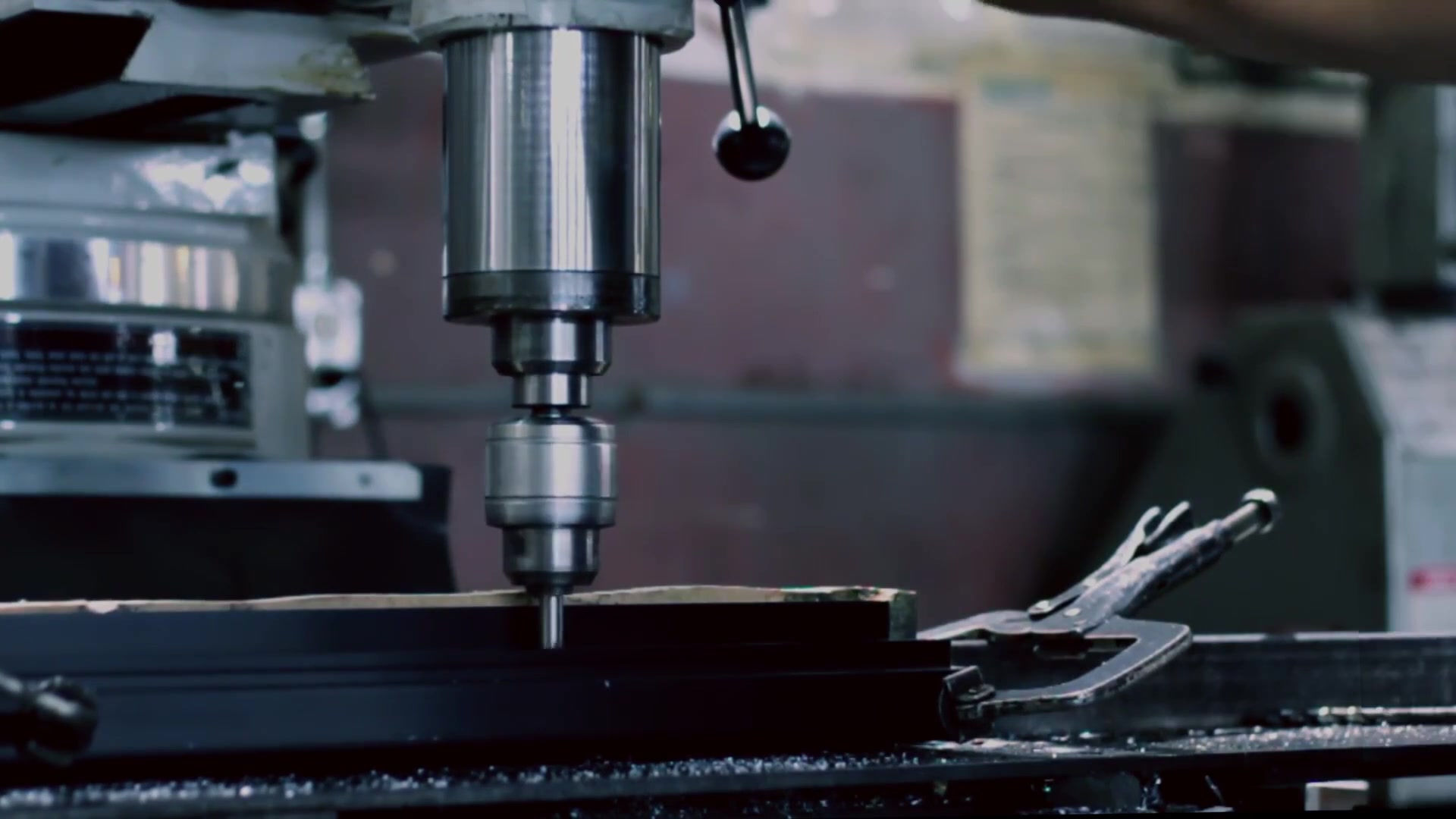
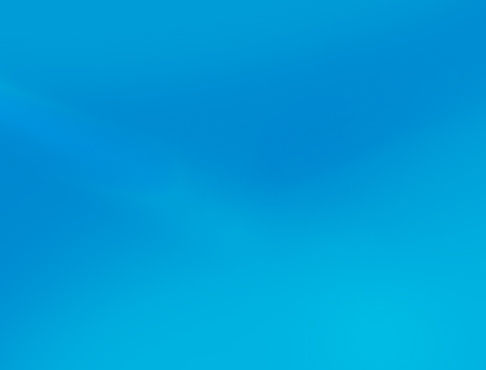
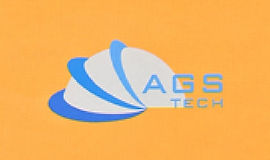
Globale pasgemaakte vervaardiger, integreerder, konsolideerder, uitkontrakteringsvennoot vir 'n wye verskeidenheid produkte en dienste.
Ons is jou eenstopbron vir vervaardiging, vervaardiging, ingenieurswese, konsolidasie, integrasie, uitkontraktering van pasgemaakte en van die rak produkte en dienste af.
Kies jou taal
-
Pasgemaakte vervaardiging
-
Binnelandse en globale kontrakvervaardiging
-
Vervaardiging Uitkontraktering
-
Binnelandse en globale verkryging
-
Consolidation
-
Ingenieursintegrasie
-
Ingenieursdienste
Search Results
164 results found with an empty search
- Transmission Components, Belts, Chains, Cable Drives, Pulleys,AGS-TECH
Transmission Components, Belts, Chains and Cable Drives, Conventional & Grooved or Serrated, Positive Drive, Pulleys Bande & kettings & kabelaandrywing samestelling AGS-TECH Inc. bied jou kragoordragkomponente, insluitend gordels & kettings & kabelaandrywingsamestelling. Met jare se verfyning het ons rubber-, leer- en ander bandaandrywings ligter en meer kompak geword, wat in staat is om hoër vragte teen laer koste te dra. Net so het ons kettingaandrywings mettertyd deur baie ontwikkeling gegaan en dit bied ons kliënte verskeie voordele. Sommige voordele van die gebruik van kettingaandrywings is hul relatief onbeperkte asmiddelafstande, kompaktheid, gemak van montering, elastisiteit in spanning sonder gly of kruip, vermoë om in hoë-temperatuur omgewings te werk. Ons kabelaandrywers bied ook voordele soos eenvoud in sommige toepassings bo ander tipe transmissiekomponente. Beide off-shelf band-, ketting- en kabelaandrywings sowel as pasgemaakte en saamgestelde weergawes is beskikbaar. Ons kan hierdie transmissiekomponente vervaardig tot die regte grootte vir jou toepassing en van die mees geskikte materiale. BORDE EN RIEM AANDRYFWERK: - Konvensionele plat bande: Dit is gewone plat bande sonder tande, groewe of tande. Platbandaandrywings bied buigsaamheid, goeie skokabsorpsie, doeltreffende kragoordrag teen hoë snelhede, skuurweerstand, lae koste. Bande kan gesplits of verbind word om groter bande te maak. Ander voordele van konvensionele plat bande is dat hulle dun is, hulle is nie onderhewig aan hoë sentrifugale vragte nie (maak hulle goed vir hoëspoedbedrywighede met klein katrolle). Aan die ander kant lê hulle hoë drabelastings op omdat plat bande hoë spanning vereis. Ander nadele van platbandaandrywings kan gly, raserige werking en relatief laer doeltreffendheid by lae en matige werkingsnelhede wees. Ons het twee tipes konvensionele bande: versterk en nie-versterk. Versterkte bande het 'n trekelement in hul struktuur. Konvensionele plat bande is beskikbaar as leer, rubberstof of koord, nie-versterkte rubber of plastiek, stof, versterkte leer. Leergordels bied lang lewe, buigsaamheid, uitstekende wrywingskoëffisiënt, maklike herstel. Leergordels is egter relatief duur, benodig gordelversorging en skoonmaak, en afhangende van die atmosfeer kan hulle krimp of rek. Rubbermateriaal of koordgordels is bestand teen vog, suur en alkalieë. Gegummeerde stofgordels bestaan uit lae katoen of sintetiese eend wat met rubber geïmpregneer is en is die mees ekonomiese. Gegummeerde koordgordels bestaan uit 'n reeks lae rubber-geïmpregneerde toue. Gegummeerde koordgordels bied hoë treksterkte en beskeie grootte en massa. Nie-versterkte rubber- of plastiekgordels is geskik vir ligte, laespoed-aandrywingtoepassings. Nie-versterkte rubber- en plastiekgordels kan oor hul katrolle in plek gespan word. Plastiek nie-versterkte gordels kan hoër krag oordra in vergelyking met rubber gordels. Versterkte leergordels bestaan uit 'n plastiese trekelement wat tussen leer bo- en onderlae vasgedruk is. Laastens kan ons materiaalgordels bestaan uit 'n enkele stuk katoen of eend wat gevou en met rye longitudinale steke toegewerk is. Stofgordels is in staat om eenvormig te volg en werk teen hoë spoed. - Gegroefde of getande bande (soos V-bande): Dit is basiese plat bande wat aangepas is om die voordele van 'n ander tipe transmissieproduk te bied. Dit is plat gordels met 'n longitudinaal geribbelde onderkant. Poli-V-bande is longitudinaal gegroefde of getande plat band met trekseksie en 'n reeks aangrensende V-vormige groewe vir spoor- en kompressiedoeleindes. Kragkapasiteit hang af van bandwydte. V-belt is die werkesel van die industrie en is beskikbaar in 'n verskeidenheid gestandaardiseerde groottes en tipes vir oordrag van byna enige laskrag. V-bandaandrywings werk goed tussen 1500 tot 6000 vt/min, maar smal V-bande sal tot 10 000 vt/min werk. V-bandaandrywings bied lang lewe soos 3 tot 5 jaar en laat groot spoedverhoudings toe, dit is maklik om te installeer en te verwyder, bied stil werking, min onderhoud, goeie skokabsorpsie tussen banddrywer en aangedrewe asse. V-bande se nadeel is hul sekere gly en kruip en daarom is dit dalk nie die beste oplossing waar sinchroniese snelhede vereis word nie. Ons het industriële, motor- en landbougordels. Voorraad standaard lengtes sowel as pasgemaakte lengtes van gordels is beskikbaar. Alle standaard V-band dwarssnitte is uit voorraad beskikbaar. Daar is tabelle waar jy onbekende parameters soos bandlengte, bandseksie (breedte en dikte) kan bereken mits jy sekere parameters van jou stelsel ken, soos dryf- en aangedrewe katroldiameters, middelafstand tussen katrolle en rotasiespoed van die katrolle. Jy kan sulke tabelle gebruik of ons vra om die regte V-riem vir jou te kies. - Positiewe dryfbande (tydband): Hierdie bande is ook plat tipe met 'n reeks tande wat eweredig gespasieer is aan die binneomtrek. Positiewe dryf- of tydbande kombineer die voordele van plat bande met die positiewe greep-eienskappe van kettings en ratte. Positiewe dryfbande toon geen gly of spoedvariasies nie. 'n Wye reeks spoedverhoudings is moontlik. Draerlaste is laag omdat hulle teen lae spanning kan werk. Hulle is egter meer vatbaar vir wanbelynings in katrolle. - Katrolle, gerwe, naaf vir bande: Verskillende tipe katrolle word gebruik met plat, geribbelde (gekartelde) en positiewe dryfbande. Ons vervaardig hulle almal. Die meeste van ons plat riem katrolle word gemaak deur yster te giet, maar staal weergawes is ook beskikbaar in verskeie rand- en naafkombinasies. Ons plat-band katrolle kan soliede, gespeke of gesplete nawe hê of ons kan vervaardig soos jy wil. Ribbe- en positiewe dryfbande is beskikbaar in 'n verskeidenheid voorraadgroottes en -breedtes. Ten minste een katrol in tydbandaandrywings moet met flens wees om die band op die aandrywing te hou. Vir lang senteraandrywingstelsels word dit aanbeveel om albei katrolle met flens te hê. Geriewe is die gegroefde wiele van katrolle en word oor die algemeen vervaardig deur yster giet, staal vorming of plastiek giet. Staalvorming is 'n geskikte proses om motor- en landbougerwe te vervaardig. Ons produseer gerwe met gereelde en diep groewe. Diepgroef-gerwe is goed geskik wanneer V-band die skeef skuins binnegaan, soos wat die geval is in kwartdraai-aandrywings. Diep groewe is ook goed geskik vir vertikale-as-aandrywings en toepassings waar vibrasie van bande 'n probleem kan wees. Ons tussenrolle katrolle is gegroefde gerwe of plat katrolle wat nie die oordrag van meganiese krag dien nie. Lepelkatrolle word meestal gebruik om gordels vas te trek. - Enkel- en veelvuldige bandaandrywings: Enkelbandaandrywings het 'n enkele groef, terwyl veelvuldige bandaandrywings veelvuldige groewe het. Deur op die toepaslike gekleurde teks hieronder te klik kan jy ons katalogusse aflaai: - Kragtransmissiebande (sluit V-bande, tydsgordels, rou randbande, toegedraaide bande en spesiale bande in) - Vervoerband - V-katrolle - Tydberekening katrolle KETTINGS EN KETTINGS: Ons kragoordragkettings het 'n paar voordele soos relatief onbeperkte asmiddelafstande, maklike montering, kompaktheid, elastisiteit onder spanning sonder gly of kruip, vermoë om onder hoë temperature te werk. Hier is die belangrikste tipes van ons kettings: - Afneembare kettings: Ons afneembare kettings word gemaak in 'n reeks groottes, steek en uiteindelike sterkte en oor die algemeen van smeebare yster of staal. Smeebare kettings word gemaak in 'n reeks groottes van 0,902 (23 mm) tot 4,063 duim (103 mm) steek en uiteindelike sterkte van 700 tot 17 000 lb/vierkante duim. Ons afneembare staalkettings word aan die ander kant gemaak in groottes van 0,904 duim (23 mm) tot ongeveer 3,00 duim (76 mm) in steek, met uiteindelike sterkte van 760 tot 5000 lb/vierkante duim._cc781905-5cde-3194-bb3b- 136bad5cf58d_ - Pintle Kettings: Hierdie kettings word gebruik vir swaarder vragte en effens hoër snelhede tot ongeveer 450 voet/min (2,2 m/sek). Pintle kettings is gemaak van individuele gegote skakels met volle, ronde loop einde met offset sidebars. Hierdie kettingskakels is met staalpenne gekoppel. Hierdie kettings wissel in toonhoogte van ongeveer 1,00 duim (25 mm) tot 6,00 duim (150 mm) en uiteindelike sterktes tussen 3600 tot 30 000 lb/vierkante duim. - Offset-sybalkkettings: Dit is gewild in dryfkettings van konstruksiemasjinerie. Hierdie kettings werk teen spoed tot 1000 voet/min en dra vragte na ongeveer 250 pk oor. Oor die algemeen het elke skakel twee verskuiwende systawe, een bus, een roller, een pen, 'n splitpen. - Rolkettings: Hulle is beskikbaar in hellings van 0,25 (6 mm) tot 3,00 (75 mm) duim. Die uiteindelike sterkte van enkelwydte-rolkettings wissel tussen 925 tot 130 000 lb/vierkante duim. Verskeie breedte weergawes van rolkettings is beskikbaar en dra groter krag teen hoër snelhede oor. Meerwydte rolkettings bied ook gladder aksie met verminderde geraas. Rolkettings word saamgestel uit rolskakels en penskakels. Splitpenne word gebruik in afneembare weergawe-rolkettings. Die ontwerp van rolkettingaandrywings vereis vakkundigheid. Terwyl bandaandrywings gebaseer is op lineêre snelhede, is kettingaandrywings gebaseer op die rotasiespoed van die kleiner kettingwiel, wat in die meeste installasies die aangedrewe lid is. Behalwe perdekrag-graderings en rotasiespoed, is die ontwerp van kettingaandrywings gebaseer op baie ander faktore. - Dubbelsteekkettings: Basies dieselfde as rolkettings, behalwe dat die toonhoogte twee keer so lank is. - Omgekeerde tand (stil) kettings: Hoëspoed kettings wat meestal gebruik word vir aandrywers, kragaftakkers. Omgekeerde tandkettingaandrywings kan kragte tot 1200 pk oordra en bestaan uit 'n reeks tandskakels, afwisselend saamgestel met óf penne óf 'n kombinasie van gewrigskomponente. Sentraalgeleidingketting het gidsskakels om groewe in die kettingwiel vas te maak, en die sygeleideketting het gidse om die kante van die kettingwiel in te skakel. - Kraal- of skuifkettings: Hierdie kettings word gebruik vir stadige spoedaandrywings en ook in handbewerkings. Deur op die toepaslike gekleurde teks hieronder te klik kan jy ons katalogusse aflaai: - Aandryfkettings - Vervoerkettings - Groot toonhoogte vervoerbandkettings - Rolkettings van vlekvrye staal - Hys kettings - Motorfietskettings - Landboumasjienkettings - Sprockets: Ons standaard sprockets voldoen aan ANSI-standaarde. Plaatkettingwiele is plat, naaflose kettingwiele. Ons klein en medium-grootte naaftandwiele word van staafvoorraad of smeewerk gedraai of gemaak deur 'n staafvoorraadnaaf aan 'n warmgewalste plaat te sweis. AGS-TECH Inc. kan tandwiele verskaf wat gemasjineer is van grys-yster gietstukke, gegote staal en gelaste naafkonstruksies, gesinterde poeiermetaal, gevormde of gemasjineerde plastiek. Vir gladde werking teen hoë snelhede, is behoorlike keuse van grootte van kettingwiele noodsaaklik. Ruimtebeperkings is natuurlik 'n faktor wat ons nie kan ignoreer wanneer ons 'n kettingwiel kies nie. Dit word aanbeveel dat die verhouding van drywer tot aangedrewe kettingwiele nie meer as 6:1 moet wees nie, en die kettingomhulsel op die drywer is 120 grade. Sentrumafstande tussen die kleiner en groter kettingwiele, kettinglengtes en kettingspanning moet ook volgens sommige aanbevole ingenieursberekeninge en riglyne gekies word en nie lukraak nie. Laai ons katalogusse af deur op gekleurde teks hieronder te klik: - Tandwiele en plaatwiele - Transmissiebussies - Kettingkoppeling - Kettingslotte KABELDRIFTE: Dit het in sommige gevalle hul voordele bo bande en kettingaandrywings. Kabelaandrywings kan dieselfde funksie as bande verrig en kan ook eenvoudiger en meer ekonomies wees om in sommige toepassings te implementeer. Byvoorbeeld, 'n nuwe reeks Synchromesh Cable Drives is ontwerp vir positiewe traksie om konvensionele toue, eenvoudige kabels en rataandrywings te vervang, veral in beperkte ruimtes. Die nuwe kabelaandrywing is ontwerp om hoë-presisie-posisionering te verskaf in elektroniese toerusting soos kopieermasjiene, plotters, tikmasjiene, drukkers, ….. ens. 'n Sleutelkenmerk van die nuwe kabelaandrywing is sy vermoë om in 3D-slangkonfigurasies gebruik te word wat dit moontlik maak. uiters miniatuur ontwerpe. Synchromesh-kabels kan met laer spanning gebruik word in vergelyking met toue en sodoende kragverbruik verminder. Kontak AGS-TECH vir vrae en mening oor bande, ketting- en kabelaandrywings. CLICK Product Finder-Locator Service VORIGE BLADSY
- Composites, Composite Materials Manufacturing, Fiber Reinforced
Composites, Composite Materials Manufacturing, Particle and Fiber Reinforced, Cermets, Ceramic & Metal Composite, Glass Fiber Reinforced Polymer, Lay-Up Process Saamgestelde en saamgestelde materiale vervaardiging Eenvoudig gedefinieer, SAAMSTELLINGS of SAAMGESTELDE MATERIALE is materiale wat bestaan uit twee of meer materiale met verskillende fisiese of chemiese eienskappe, maar wanneer dit gekombineer word, word dit 'n materiaal wat anders is as die samestellende materiale. Ons moet daarop wys dat die samestellende materiale apart en afsonderlik in die struktuur bly. Die doel met die vervaardiging van 'n saamgestelde materiaal is om 'n produk te verkry wat beter is as sy bestanddele en die gewenste eienskappe van elke bestanddeel kombineer. As 'n voorbeeld; sterkte, lae gewig of laer prys kan die motivering agter die ontwerp en vervaardiging van 'n saamgestelde wees. Die tipe komposiete wat ons aanbied, is deeltjie-versterkte komposiete, veselversterkte komposiete insluitend keramiek-matriks / polimeer-matriks / metaal-matriks / koolstof-koolstof / hibriede komposiete, strukturele & gelamineerde & toebroodjie-gestruktureerde komposiete en nanokomposiete. Die vervaardigingstegnieke wat ons in die vervaardiging van saamgestelde materiaal gebruik, is: Pultrusie, prepreg-produksieprosesse, gevorderde veselplasing, filamentwikkeling, pasgemaakte veselplasing, veselglas-spuitoplegproses, tufting, lanxied-proses, z-penning. Baie saamgestelde materiale bestaan uit twee fases, die matriks, wat aaneenlopend is en die ander fase omring; en die verspreide fase wat deur die matriks omring word. Ons beveel aan dat jy hier klik omLaai ons skematiese illustrasies af van saamgestelde en saamgestelde materiale vervaardiging deur AGS-TECH Inc. Dit sal jou help om die inligting wat ons hieronder verskaf, beter te verstaan. • PARTIKELVERSTERKTE KOMPOSIETE : Hierdie kategorie bestaan uit twee tipes: Grootdeeltjie-komposiete en dispersie-versterkte komposiete. In eersgenoemde tipe kan deeltjie-matriks-interaksies nie op atoom- of molekulêre vlak behandel word nie. In plaas daarvan is kontinuummeganika geldig. Aan die ander kant, in dispersie-versterkte komposiete is deeltjies oor die algemeen baie kleiner in die tientalle nanometerreekse. 'n Voorbeeld van groot deeltjies saamgestelde is polimere waarby vullers gevoeg is. Die vullers verbeter die eienskappe van die materiaal en kan van die polimeervolume vervang met 'n meer ekonomiese materiaal. Die volume breuke van die twee fases beïnvloed die gedrag van die saamgestelde. Groot deeltjies komposiete word gebruik met metale, polimere en keramiek. Die CERMETS is voorbeelde van keramiek/metaal-komposiete. Ons mees algemene sermet is gesementeerde karbied. Dit bestaan uit vuurvaste karbiedkeramiek soos wolframkarbieddeeltjies in 'n matriks van 'n metaal soos kobalt of nikkel. Hierdie karbiedsamestellings word wyd gebruik as snygereedskap vir geharde staal. Die harde karbieddeeltjies is verantwoordelik vir die snyaksie en hul taaiheid word versterk deur die rekbare metaalmatriks. Sodoende verkry ons die voordele van beide materiale in 'n enkele samestelling. Nog 'n algemene voorbeeld van 'n groot deeltjie-komposiet wat ons gebruik, is koolstofswart deeltjies gemeng met gevulkaniseerde rubber om 'n saamgestelde met hoë treksterkte, taaiheid, skeur- en skuurweerstand te verkry. 'n Voorbeeld van 'n dispersie-versterkte komposiet is metale en metaallegerings wat versterk en verhard word deur die eenvormige verspreiding van fyn deeltjies van 'n baie harde en inerte materiaal. Wanneer baie klein aluminiumoksiedvlokkies by aluminiummetaalmatriks gevoeg word, kry ons gesinterde aluminiumpoeier wat 'n verbeterde hoëtemperatuursterkte het. • VESELVERSTERKTE KOMPOSIETE : Hierdie kategorie komposiete is in werklikheid die belangrikste. Die doelwit om te bereik is hoë sterkte en styfheid per eenheid gewig. Die veselsamestelling, lengte, oriëntasie en konsentrasie in hierdie komposiete is krities in die bepaling van die eienskappe en bruikbaarheid van hierdie materiale. Daar is drie groepe vesels wat ons gebruik: snorbaarde, vesels en drade. WHISKERS is baie dun en lang enkelkristalle. Hulle is van die sterkste materiale. Enkele voorbeelde van snormateriale is grafiet, silikonnitried, aluminiumoksied. FIBERS aan die ander kant is meestal polimere of keramiek en is in polikristallyne of amorfe toestand. Die derde groep is fyn DRADE wat relatief groot deursnee het en dikwels uit staal of wolfram bestaan. 'n Voorbeeld van draadversterkte komposiet is motorbande wat staaldraad in rubber insluit. Afhangende van die matriksmateriaal, het ons die volgende samestellings: POLIMEER-MATRIKS-KOMPOSITEE: Dit word gemaak van 'n polimeerhars en vesels as die versterkingsbestanddeel. 'n Subgroep hiervan, genoem Glasvesel-versterkte polimeer (GFRP) Composites bevat kontinue of diskontinue glasvesels binne 'n polimeer matriks. Glas bied hoë sterkte, dit is ekonomies, maklik om tot vesel te vervaardig, en is chemies inert. Die nadele is hul beperkte styfheid en styfheid, dienstemperature is slegs tot 200 – 300 Celsius. Veselglas is geskik vir motor liggame en vervoertoerusting, mariene voertuig liggame, stoor houers. Hulle is nie geskik vir lugvaart of brug maak nie as gevolg van beperkte styfheid. Die ander subgroep word genoem Koolstofvesel-versterkte polimeer (CFRP) Saamgestelde. Hier is koolstof ons veselmateriaal in die polimeermatriks. Koolstof is bekend vir sy hoë spesifieke modulus en sterkte en sy vermoë om dit by hoë temperature te handhaaf. Koolstofvesels kan ons standaard-, intermediêre, hoë en ultrahoë trekmoduli bied. Verder bied koolstofvesels wel diverse fisiese en meganiese eienskappe en is dus geskik vir verskeie pasgemaakte ingenieurstoepassings. CFRP-komposiete kan oorweeg word om sport- en ontspanningstoerusting, drukvate en lugvaartstruktuurkomponente te vervaardig. Nog 'n ander subgroep, die Aramid-veselversterkte polimeersamestellings, is ook hoësterkte- en modulusmateriale. Hul krag-tot-gewig-verhoudings is buitengewoon hoog. Aramidvesels is ook bekend onder handelsname KEVLAR en NOMEX. Onder spanning presteer hulle beter as ander polimeriese veselmateriale, maar hulle is swak in kompressie. Aramidvesels is taai, impakbestand, kruip- en moegheidsbestand, stabiel by hoë temperature, chemies inert behalwe teen sterk sure en basisse. Aramidvesels word wyd gebruik in sportgoedere, koeëlvaste baadjies, bande, toue, optiese veselkabelsakke. Ander veselversterkingsmateriale bestaan maar word in 'n mindere mate gebruik. Dit is hoofsaaklik boor, silikonkarbied, aluminiumoksied. Die polimeermatriksmateriaal aan die ander kant is ook krities. Dit bepaal die maksimum dienstemperatuur van die samestelling omdat die polimeer oor die algemeen 'n laer smelt- en degradasietemperatuur het. Poliesters en vinielesters word wyd gebruik as die polimeermatriks. Harse word ook gebruik en dit het uitstekende vogweerstand en meganiese eienskappe. Poliimiedhars kan byvoorbeeld tot ongeveer 230 grade Celcius gebruik word. METAAL-MATRIKS-SAAMSTELLINGS: In hierdie materiale gebruik ons 'n rekbare metaalmatriks en die dienstemperature is oor die algemeen hoër as hul samestellende komponente. In vergelyking met polimeer-matriks-samestellings, kan dit hoër werkstemperature hê, nie-vlambaar wees en kan beter afbraakweerstand teen organiese vloeistowwe hê. Hulle is egter duurder. Versterkingsmateriale soos snorbaarde, deeltjies, aaneenlopende en diskontinue vesels; en matriksmateriale soos koper, aluminium, magnesium, titanium, superlegerings word algemeen gebruik. Voorbeeldtoepassings is enjinkomponente gemaak van aluminiumlegeringsmatriks wat met aluminiumoksied en koolstofvesels versterk is. KERAMIEK-MATRIKS-SAAMSTELLINGS: Keramiekmateriale is bekend vir hul uitstekende hoë temperatuurbetroubaarheid. Hulle is egter baie bros en het lae waardes vir breuktaaiheid. Deur deeltjies, vesels of snorbaarde van een keramiek in die matriks van 'n ander in te sluit, kan ons komposiete met hoër breuktaaihede bereik. Hierdie ingebedde materiale inhibeer basies kraakvoortplanting binne die matriks deur sommige meganismes soos om die kraakpunte af te buig of brûe oor kraakvlakke te vorm. As 'n voorbeeld, alumina wat met SiC-share versterk is, word gebruik as snygereedskap-insetsels vir die bewerking van harde metaallegerings. Dit kan beter werkverrigtings toon in vergelyking met gesementeerde karbiede. KOOLSTOF-KOOLSTOF KOMPOSIETE: Beide die versterking sowel as die matriks is koolstof. Hulle het hoë trekmoduli en sterktes by hoë temperature van meer as 2000 Celsius, kruipweerstand, hoë breuktaaihede, lae termiese uitsettingskoëffisiënte, hoë termiese geleidingsvermoë. Hierdie eienskappe maak hulle ideaal vir toepassings wat termiese skokweerstand vereis. Die swakheid van koolstof-koolstof-komposiete is egter die kwesbaarheid daarvan teen oksidasie by hoë temperature. Tipiese voorbeelde van gebruik is warmpersvorms, gevorderde vervaardiging van turbine-enjinkomponente. HIBRIEDE SAMESTELLINGS: Twee of meer verskillende tipes vesels word in 'n enkele matriks gemeng. 'n Mens kan dus 'n nuwe materiaal met 'n kombinasie van eienskappe pasmaak. 'n Voorbeeld is wanneer beide koolstof- en glasvesels in 'n polimeriese hars ingewerk word. Koolstofvesels bied lae digtheid styfheid en sterkte, maar is duur. Die glas aan die ander kant is goedkoop, maar het nie die styfheid van koolstofvesels nie. Die glas-koolstof-hibried-samestelling is sterker en taaier en kan teen 'n laer koste vervaardig word. VERWERKING VAN VESELVERSTERKTE SAAMSTELLINGS: Vir deurlopende veselversterkte plastiek met eenvormig verspreide vesels wat in dieselfde rigting georiënteer is, gebruik ons die volgende tegnieke. PULTRUSIE: Stawe, balke en buise van aaneenlopende lengtes en konstante deursnee word vervaardig. Deurlopende vesel rovings word geïmpregneer met 'n termohardende hars en word deur 'n staal matrys getrek om hulle voor te vorm tot 'n gewenste vorm. Vervolgens gaan hulle deur 'n presisie-gemasjineerde uithardingsmatrys om sy finale vorm te verkry. Aangesien die uithardingsmatrys verhit word, genees dit die harsmatriks. Trekkers trek die materiaal deur die matryse. Deur ingevoegde hol kerne te gebruik, is ons in staat om buise en hol geometrieë te verkry. Die pultrusie-metode is geoutomatiseer en bied ons hoë produksietempo's. Enige lengte van die produk is moontlik om te vervaardig. PREPREG PRODUKSIEPROSES: Prepreg is 'n aaneenlopende veselversterking voorafgeïmpregneer met 'n gedeeltelik uitgeharde polimeerhars. Dit word wyd gebruik vir strukturele toepassings. Die materiaal kom in bandvorm en word as 'n band gestuur. Die vervaardiger vorm dit direk en genees dit volledig sonder dat dit nodig is om enige hars by te voeg. Aangesien prepregs genesingsreaksies by kamertemperatuur ondergaan, word hulle by 0 Celsius of laer temperature gestoor. Na gebruik word die oorblywende bande by lae temperature teruggeberg. Termoplastiese en termohardende harse word gebruik en versterkingsvesels van koolstof, aramide en glas is algemeen. Om prepregs te gebruik, word die draer-rugpapier eers verwyder en dan word die vervaardiging uitgevoer deur die prepreg-band op 'n bewerkte oppervlak te lê (die oplêproses). Verskeie lae kan opgelê word om die verlangde diktes te verkry. Gereelde oefening is om die veseloriëntasie af te wissel om 'n kruislaag- of hoeklaaglaminaat te produseer. Laastens word hitte en druk toegepas vir uitharding. Beide handverwerking sowel as outomatiese prosesse word gebruik vir die sny van prepregs en oplê. FILAMENT WINDING: Deurlopende versterkende vesels is akkuraat geposisioneer in 'n voorafbepaalde patroon om 'n hol en gewoonlik silindiriese vorm te volg. Die vesels gaan eers deur 'n harsbad en word dan deur 'n geoutomatiseerde stelsel op 'n spil gewikkel. Na verskeie wikkelherhalings word verlangde diktes verkry en verharding word óf by kamertemperatuur óf binne 'n oond uitgevoer. Nou word die deurn verwyder en die produk word uit die vorm verwyder. Filamentwikkeling kan baie hoë sterkte-tot-gewig verhoudings bied deur die vesels in omtreks-, heliese en polêre patrone te wikkel. Pype, tenks, omhulsels word met hierdie tegniek vervaardig. • STRUKTURELE SAAMSTELLINGS: Oor die algemeen bestaan dit uit beide homogene en saamgestelde materiale. Daarom word die eienskappe daarvan bepaal deur die samestellende materiale en geometriese ontwerp van sy elemente. Hier is die belangrikste tipes: LAMINÊRE SAMESTELLINGS: Hierdie strukturele materiale word gemaak van tweedimensionele velle of panele met voorkeur hoë-sterkte rigtings. Lae word gestapel en saamgesement. Deur die hoësterkterigtings in die twee loodregte asse af te wissel, verkry ons 'n samestelling wat hoë sterkte in beide rigtings in die tweedimensionele vlak het. Deur die hoeke van die lae aan te pas, kan 'n komposiet vervaardig word met sterkte in die voorkeurrigtings. Moderne ski word op hierdie manier vervaardig. TOORDBROODJIE PANELE: Hierdie strukturele samestellings is liggewig, maar het tog hoë styfheid en sterkte. Toebroodjiepanele bestaan uit twee buitenste velle gemaak van 'n stywe en sterk materiaal soos aluminiumlegerings, veselversterkte plastiek of staal en 'n kern tussen die buiteplate. Die kern moet liggewig wees en die meeste van die tyd 'n lae elastisiteitsmodulus hê. Gewilde kernmateriale is stywe polimeriese skuim, hout en heuningkoeke. Toebroodjiepanele word wyd gebruik in die konstruksiebedryf as dakmateriaal, vloer- of muurmateriaal, en ook in die lugvaartnywerhede. • NANOSAAMSTELLINGS: Hierdie nuwe materiale bestaan uit deeltjies van nanogrootte wat in 'n matriks ingebed is. Met behulp van nano-samestellings kan ons rubbermateriaal vervaardig wat baie goeie hindernisse vir lugpenetrasie is, terwyl hul rubbereienskappe onveranderd behou word. CLICK Product Finder-Locator Service VORIGE BLADSY
- Joining & Assembly & Fastening Processes, Welding, Brazing, Soldering
Joining & Assembly & Fastening Processes, Welding, Brazing, Soldering, Sintering, Adhesive Bonding, Press Fitting, Wave and Reflow Solder Process, Torch Furnace Verbind & Monteer & Bevestiging Prosesse Ons heg, monteer en maak jou vervaardigde onderdele vas en verander dit in voltooide of halfvoltooide produkte deur gebruik te maak van SWEIS, BRAZING, SOLDERING, SINTERING, KLEEMVERBINDING, BEVESTIGING, PERSPASING. Sommige van ons gewildste sweisprosesse is boog, suurstofgas, weerstand, projeksie, naat, ontstel, perkussie, vastestof, elektronstraal, laser, termiet, induksie sweis. Ons gewilde soldeerprosesse is fakkel-, induksie-, oond- en dompelsoldering. Ons soldeermetodes is yster, warmplaat, oond, induksie, dip, golf, hervloei en ultrasoniese soldering. Vir kleefbinding gebruik ons gereeld termoplastiek en termo-harding, epoksieë, fenole, poliuretaan, kleeflegerings sowel as ander chemikalieë en bande. Laastens bestaan ons bevestigingsprosesse uit spyker, skroefwerk, moere en boute, klink, vasheg, vaspen, stik & kram en perspassing. • Sweiswerk: Sweiswerk behels die binding van materiale deur die werkstukke te smelt en vulmateriaal in te voer wat ook by die gesmelte sweispoel aansluit. Wanneer die area afkoel, kry ons 'n sterk gewrig. Druk word in sommige gevalle toegepas. In teenstelling met sweiswerk behels die soldeer- en soldeerbewerkings slegs die smelt van 'n materiaal met 'n laer smeltpunt tussen die werkstukke, en werkstukke smelt nie. Ons beveel aan dat jy hier klik omLaai ons skematiese illustrasies van sweisprosesse af deur AGS-TECH Inc. Dit sal jou help om die inligting wat ons hieronder verskaf, beter te verstaan. In ARRC WELDING gebruik ons 'n kragbron en 'n elektrode om 'n elektriese boog te skep wat die metale smelt. Sweispunt word beskerm deur 'n beskermende gas of damp of ander materiaal. Hierdie proses is gewild vir die sweis van motoronderdele en staalstrukture. In shelded metal arc welding (SMAW) of ook bekend as stoksweiswerk, word 'n elektrodestok naby die basismateriaal gebring en 'n elektriese boog word tussen hulle opgewek. Die elektrodestaaf smelt en dien as die vulmateriaal. Die elektrode bevat ook vloeimiddel wat as 'n laag slak optree en dampe afgee wat as die beskermende gas dien. Dit beskerm die sweisarea teen omgewingsbesoedeling. Geen ander vullers word gebruik nie. Die nadele van hierdie proses is die traagheid daarvan, die behoefte om gereeld elektrodes te vervang, die behoefte om die oorblywende slak wat van vloed afkomstig is, weg te kap. 'n Aantal metale soos yster, staal, nikkel, aluminium, koper ... ens. Kan gesweis word. Die voordele daarvan is sy goedkoop gereedskap en gemak van gebruik. Gasmetaalboogsweis (GMAW) ook bekend as metaal-inerte gas (MIG), ons het deurlopende voeding van 'n verbruikbare elektrodedraadvuller en 'n inerte of gedeeltelik inerte gas wat om die draad vloei teen omgewingsbesoedeling van die sweisgebied. Staal, aluminium en ander nie-ysterhoudende metale kan gesweis word. Die voordele van MIG is hoë sweisspoed en goeie gehalte. Die nadele is die ingewikkelde toerusting en uitdagings wat in winderige buitelugomgewings in die gesig gestaar word, want ons moet die beskermende gas rondom die sweisarea stabiel hou. 'n Variasie van GMAW is vloedkernboogsweis (FCAW) wat bestaan uit 'n fyn metaalbuis gevul met vloedmateriaal. Soms is die vloed binne die buis voldoende vir beskerming teen omgewingsbesoedeling. Submerged Arc Welding (SAW) is algemeen 'n geoutomatiseerde proses, behels deurlopende draadtoevoer en boog wat onder 'n laag vloedbedekking geslaan word. Die produksietempo en kwaliteit is hoog, sweisslak kom maklik af, en ons het 'n rookvrye werksomgewing. Die nadeel is dat dit slegs gebruik kan word om parts in sekere posisies te sweis. In gaswolframboogsweiswerk (GTAW) of wolfram-inerte gassweiswerk (TIG) gebruik ons 'n wolfraamelektrode saam met 'n aparte vuller en inerte of naby inerte gasse. Soos ons weet het wolfraam 'n hoë smeltpunt en dit is 'n baie geskikte metaal vir baie hoë temperature. Die Tungsten in TIG word nie verbruik in teenstelling met die ander metodes wat hierbo verduidelik is nie. 'n Stadige maar 'n hoë kwaliteit sweistegniek wat voordelig is bo ander tegnieke in sweis van dun materiale. Geskik vir baie metale. Plasmaboogsweiswerk is soortgelyk, maar gebruik plasmagas om die boog te skep. Die boog in plasmaboogsweiswerk is relatief meer gekonsentreerd in vergelyking met GTAW en kan gebruik word vir 'n groter reeks metaaldiktes teen baie hoër snelhede. GTAW- en plasmaboogsweiswerk kan op min of meer dieselfde materiale toegepas word. OXY-FUEL / OXYFUEL WELDING ook genoem oksiasetileen-sweiswerk, oksweisweis, gassweiswerk word uitgevoer met behulp van gasbrandstowwe en suurstof vir sweiswerk. Aangesien geen elektriese krag gebruik word nie, is dit draagbaar en kan dit gebruik word waar daar geen elektrisiteit is nie. Met 'n sweisfakkel verhit ons die stukke en die vulmateriaal om 'n gedeelde gesmelte metaalpoel te produseer. Verskeie brandstowwe kan gebruik word soos asetileen, petrol, waterstof, propaan, butaan ... ens. In suurstof-sweiswerk gebruik ons twee houers, een vir die brandstof en die ander vir suurstof. Die suurstof oksideer die brandstof (verbrand dit). WEERSTANDSWEIS: Hierdie tipe sweiswerk trek voordeel uit joule-verhitting en hitte word opgewek by die plek waar elektriese stroom vir 'n sekere tyd toegedien word. Hoë strome word deur die metaal gevoer. Poele van gesmelte metaal word op hierdie plek gevorm. Weerstandsweismetodes is gewild as gevolg van hul doeltreffendheid, min besoedelingspotensiaal. Die nadele is egter dat toerustingkoste relatief aansienlik is en die inherente beperking tot relatief dun werkstukke. SPOT WELDING is een hoof tipe weerstandsweiswerk. Hier verbind ons twee of meer oorvleuelende velle of werkstukke deur twee koperelektrodes te gebruik om die velle saam te klem en 'n hoë stroom daardeur te laat loop. Die materiaal tussen die koperelektrodes verhit en 'n gesmelte poel word op daardie plek gegenereer. Die stroom word dan gestop en die koperelektrodepunte koel die sweisplek af omdat die elektrodes waterverkoel word. Die toepassing van die regte hoeveelheid hitte op die regte materiaal en dikte is die sleutel vir hierdie tegniek, want as dit verkeerd toegepas word, sal die voeg swak wees. Puntsweiswerk het die voordele dat dit geen noemenswaardige vervorming aan werkstukke veroorsaak nie, energiedoeltreffendheid, gemak van outomatisering en uitstaande produksietempo's, en geen vullers benodig nie. Die nadeel is dat aangesien sweiswerk op kolle plaasvind eerder as om 'n aaneenlopende naat te vorm, die algehele sterkte relatief laer kan wees in vergelyking met ander sweismetodes. NAATSWEIS aan die ander kant produseer sweislasse by die vloeiende oppervlaktes van soortgelyke materiale. Die naat kan boud of oorvleuel voeg. Naatsweiswerk begin aan die een kant en beweeg progressief na die ander kant. Hierdie metode gebruik ook twee elektrodes van koper om druk en stroom op die sweisgebied toe te pas. Die skyfvormige elektrodes roteer met konstante kontak langs die naatlyn en maak 'n deurlopende sweislas. Ook hier word elektrodes deur water afgekoel. Die sweislasse is baie sterk en betroubaar. Ander metodes is projeksie-, flits- en ontstelsweistegnieke. VASTE-TOESTAND SWEIS is 'n bietjie anders as die vorige metodes wat hierbo verduidelik is. Samesmelting vind plaas by temperature onder die smelttemperatuur van die metale wat saamgevoeg is en met geen gebruik van metaalvuller nie. Druk kan in sommige prosesse gebruik word. Verskeie metodes is KOEKTRUSIESWEISING waar verskillende metale deur dieselfde matrys geëkstrueer word, KOUEDRUKSWEIS waar ons sagte legerings onder hul smeltpunte verbind, DIFFUSIESWEISING 'n tegniek sonder sigbare sweislyne, ONTPLOFFINGSWEIS vir die heg van verskillende materiale, bv. korrosiebestande legerings staal, ELEKTROMAGNETIESE PULSSWEIS waar ons buise en plate versnel deur elektromagnetiese kragte, SMEESWEIS wat bestaan uit die verhitting van die metale tot hoë temperature en dit aanmekaar te slaan, WRYWINGSSWEIS waar met voldoende wrywing sweiswerk uitgevoer word, WRYWINGSROERSWEIS wat 'n roterende nie- verbruikbare gereedskap wat die laslyn deurkruis, WARM DRUK SWEIS waar ons metale saam druk teen verhoogde temperature onder die smelttemperatuur in vakuum of inerte gasse, WARM ISOSTATIESE DRUK SWEIS 'n proses waar ons druk toepas met behulp van inerte gasse binne 'n houer, ROLSWEIS waar ons heg verskillende materiale deur hulle tussenin te dwing twee roterende wiele, ULTRASONIESE SWEIS waar dun metaal- of plastiekplate met behulp van hoëfrekwensie-vibrasie-energie gesweis word. Ons ander sweisprosesse is ELEKTRONBAAL SWEIS met diep penetrasie en vinnige verwerking, maar aangesien dit 'n duur metode is, beskou ons dit vir spesiale gevalle, ELEKTROSLAG SWEIS 'n metode wat slegs geskik is vir swaar dik plate en werkstukke staal, INDUKSIESWEIS waar ons elektromagnetiese induksie gebruik en verhit ons elektries geleidende of ferromagnetiese werkstukke, LASERSTRAALSWEIS ook met diep penetrasie en vinnige verwerking maar 'n duur metode, LASERHIBRIEDSWEIS wat LBW met GMAW in dieselfde sweiskop kombineer en in staat is om gapings van 2 mm tussen plate te oorbrug, PERKUSSIESWEIS wat behels 'n elektriese ontlading, gevolg deur die smee van die materiale met toegepaste druk, THERMIT WELDING wat eksotermiese reaksie tussen aluminium en ysteroksiedpoeiers behels., ELEKTROGASWEISING met verbruikbare elektrodes en gebruik met slegs staal in vertikale posisie, en laastens STUT BOOGSWEIS vir die heg van stoet aan basis materiaal met hitte en druk. Ons beveel aan dat jy hier klik omLaai ons skematiese illustrasies af van soldeer-, soldeer- en kleefmiddelprosesse deur AGS-TECH Inc. Dit sal jou help om die inligting wat ons hieronder verskaf, beter te verstaan. • SLIDING : Ons verbind twee of meer metale deur vulmetale tussen hulle tot bo hul smeltpunte te verhit en kapillêre werking te gebruik om te versprei. Die proses is soortgelyk aan soldering, maar die temperature wat betrokke is om die vuller te smelt, is hoër in soldering. Soos in sweiswerk, beskerm vloeimiddel die vulmateriaal teen atmosferiese besoedeling. Na afkoeling word die werkstukke saamgevoeg. Die proses behels die volgende sleutelstappe: Goeie pas en opruiming, behoorlike skoonmaak van basismateriaal, behoorlike bevestiging, behoorlike vloed- en atmosfeerkeuse, verhitting van die samestelling en laastens die skoonmaak van gesoldeerde samestelling. Sommige van ons soldeerprosesse is TORCH BRAZING, 'n gewilde metode wat met die hand of op 'n outomatiese wyse uitgevoer word. Dit is geskik vir lae volume produksiebestellings en gespesialiseerde gevalle. Hitte word toegedien met behulp van gasvlamme naby die voeg wat gesoldeer word. OONDSOLDERING vereis minder operateursvaardigheid en is 'n semi-outomatiese proses wat geskik is vir industriële massaproduksie. Beide temperatuurbeheer en beheer van die atmosfeer in die oond is voordele van hierdie tegniek, want eersgenoemde stel ons in staat om beheerde hittesiklusse te hê en plaaslike verhitting uit te skakel soos die geval is in fakkelsoldering, en laasgenoemde beskerm die onderdeel teen oksidasie. Met behulp van jigging is ons in staat om vervaardigingskoste tot 'n minimum te verminder. Die nadele is hoë kragverbruik, toerustingkoste en meer uitdagende ontwerpoorwegings. VACUUM BRAZING vind plaas in 'n oond van vakuum. Temperatuur eenvormigheid word gehandhaaf en ons verkry vloedvrye, baie skoon lasse met baie min oorblywende spanning. Hittebehandelings kan tydens vakuumsoldering plaasvind as gevolg van die lae oorblywende spanning wat tydens stadige verhitting- en verkoelingsiklusse teenwoordig is. Die groot nadeel is die hoë koste daarvan, want die skepping van 'n vakuumomgewing is 'n duur proses. Nog 'n tegniek DIP BRAZING verbind vaste dele waar soldeermiddel op parende oppervlaktes aangebring word. Daarna word die vaste onderdele in 'n bad van 'n gesmelte sout soos natriumchloried (tafelsout) gedoop wat as 'n hitte-oordragmedium en vloed dien. Lug word uitgesluit en daarom vind geen oksiedvorming plaas nie. In INDUKSIESOLDEERING verbind ons materiale deur 'n vulmetaal wat 'n laer smeltpunt as die basismateriaal het. Die wisselstroom vanaf die induksiespoel skep 'n elektromagnetiese veld wat induksieverhitting op meestal ysterhoudende magnetiese materiale veroorsaak. Die metode verskaf selektiewe verhitting, goeie voege met vullers wat net in gewenste areas vloei, min oksidasie omdat geen vlamme teenwoordig is nie en verkoeling is vinnig, vinnige verhitting, konsekwentheid en geskiktheid vir hoë volume vervaardiging. Om ons prosesse te bespoedig en om konsekwentheid te verseker, gebruik ons gereeld voorvorms. Inligting oor ons soldeerfasiliteit wat keramiek-tot-metaal-toebehore vervaardig, hermetiese verseëling, vakuumdeurvoere, hoë en ultrahoë vakuum en vloeistofbeheerkomponente kan hier gevind word:_cc781905-916-bbcd-5cde_cc781905-916-bbcd-5cdeSoldeerfabriekbrosjure • SOLDERING : By soldering het ons nie smelting van die werkstukke nie, maar 'n vulmetaal met 'n laer smeltpunt as die verbindende dele wat in die las invloei. Die vulmetaal in soldering smelt by laer temperatuur as in soldering. Ons gebruik loodvrye legerings vir soldering en voldoen aan RoHS en vir verskillende toepassings en vereistes het ons verskillende en geskikte legerings soos silwerlegering. Soldeerwerk bied ons lasse wat gas- en vloeistofdig is. In SAGTE SOLDERING het ons vulmetaal 'n smeltpunt onder 400 Celsius, terwyl ons in SILWER SOLDERING en SLOTERING hoër temperature benodig. Sagte soldering gebruik laer temperature, maar lei nie tot sterk lasse vir veeleisende toepassings by verhoogde temperature nie. Silwer soldering aan die ander kant, vereis hoë temperature wat deur fakkel verskaf word en gee ons sterk lasse wat geskik is vir hoë temperatuur toepassings. Soldering vereis die hoogste temperature en gewoonlik word 'n fakkel gebruik. Aangesien soldeerverbindings baie sterk is, is dit 'n goeie kandidate vir die herstel van swaar ystervoorwerpe. In ons vervaardigingslyne gebruik ons beide handsoldeerwerk sowel as outomatiese soldeerlyne. INDUCTION SOLDERING gebruik hoëfrekwensie WS-stroom in 'n koperspoel om induksieverhitting te vergemaklik. Strome word in die gesoldeerde deel geïnduseer en gevolglik word hitte gegenereer by die hoë weerstand joint. Hierdie hitte smelt die vulmetaal. Flux word ook gebruik. Induksie soldering is 'n goeie metode om siklusse en pype in 'n deurlopende proses te soldeer deur die spoele om hulle te draai. Om sommige materiale soos grafiet en keramiek te soldeer is moeiliker omdat dit die platering van die werkstukke met 'n geskikte metaal vereis voor soldering. Dit vergemaklik grensvlakbinding. Ons soldeer sulke materiale veral vir hermetiese verpakkingstoepassings. Ons vervaardig ons gedrukte stroombaanborde (PCB) in hoë volume, meestal deur GOLFSOLDERING te gebruik. Slegs vir klein hoeveelheid prototiperingsdoeleindes gebruik ons handsoldeer met behulp van soldeerbout. Ons gebruik golfsoldeer vir beide deurgat- sowel as oppervlakgemonteerde PCB-samestellings (PCBA). ’n Tydelike gom hou die komponente vas aan die stroombaanbord en die samestelling word op ’n vervoerband geplaas en beweeg deur ’n toerusting wat gesmelte soldeersel bevat. Eers word die PCB gevloei en gaan dan die voorverhittingsone binne. Die gesmelte soldeersel is in 'n pan en het 'n patroon van staande golwe op sy oppervlak. Wanneer die PCB oor hierdie golwe beweeg, kontak hierdie golwe die onderkant van die PCB en hou vas aan die soldeerblokkies. Die soldeersel bly slegs op penne en pads en nie op die PCB self nie. Die golwe in die gesmelte soldeersel moet goed beheer word sodat daar geen spat is nie en die golwe se toppe raak nie en besoedel ongewenste areas van die planke nie. In REFLOW SOLDERING gebruik ons 'n taai soldeerpasta om die elektroniese komponente tydelik aan die borde vas te maak. Dan word die planke deur 'n hervloei-oond met temperatuurbeheer gesit. Hier smelt die soldeersel en verbind die komponente permanent. Ons gebruik hierdie tegniek vir beide oppervlakmonteringskomponente sowel as vir deurgatkomponente. Behoorlike temperatuurbeheer en aanpassing van oondtemperature is noodsaaklik om vernietiging van elektroniese komponente op die bord te vermy deur dit oorverhit tot bo hul maksimum temperatuurlimiete. In die proses van hervloeisoldeer het ons eintlik verskeie streke of stadiums elk met 'n duidelike termiese profiel, soos voorverhittingstap, termiese weekstap, hervloei- en verkoelingstappe. Hierdie verskillende stappe is noodsaaklik vir 'n skadevrye hervloeisoldering van gedrukte stroombaansamestellings (PCBA). ULTRASONIC SOLDERING is nog 'n tegniek wat gereeld gebruik word met unieke vermoëns - Dit kan gebruik word om glas, keramiek en nie-metaal materiaal te soldeer. Byvoorbeeld, fotovoltaïese panele wat nie-metaal is, benodig elektrodes wat met hierdie tegniek aangebring kan word. In ultrasoniese soldering ontplooi ons 'n verhitte soldeerpunt wat ook ultrasoniese vibrasies uitstraal. Hierdie vibrasies produseer kavitasieborrels by die koppelvlak van die substraat met die gesmelte soldeermateriaal. Die implosiewe energie van kavitasie verander die oksiedoppervlak en verwyder die vuilheid en oksiede. Gedurende hierdie tyd word 'n legeringslaag ook gevorm. Die soldeersel by die bindingsoppervlak bevat suurstof en maak die vorming van 'n sterk gedeelde binding tussen die glas en soldeer moontlik. DIPSOLDERING kan beskou word as 'n eenvoudiger weergawe van golfsoldeer wat geskik is vir slegs kleinskaalse produksie. Eerste skoonmaakvloeimiddel word toegepas soos in ander prosesse. PCB's met gemonteerde komponente word met die hand of op 'n semi-outomatiese wyse in 'n tenk gedompel wat gesmelte soldeersel bevat. Die gesmelte soldeersel kleef aan die blootgestelde metaalareas wat nie deur soldeermasker op die bord beskerm word nie. Die toerusting is eenvoudig en goedkoop. • KLEEFBINDING: Dit is nog 'n gewilde tegniek wat ons gereeld gebruik en dit behels die binding van oppervlaktes met gom, epoksie, plastiekmiddels of ander chemikalieë. Binding word bewerkstellig deur óf die oplosmiddel te verdamp, deur hitte uitharding, deur UV-lig uitharding, deur druk uitharding óf wag vir 'n sekere tyd. Verskeie hoë werkverrigting gom word in ons produksielyne gebruik. Met behoorlik gemanipuleerde aanwendings- en uithardingsprosesse, kan gombinding lei tot baie lae spanningsbindings wat sterk en betroubaar is. Kleefmiddels kan goeie beskermers wees teen omgewingsfaktore soos vog, kontaminante, korrosiewe, vibrasie ... ens. Voordele van gombinding is: dit kan toegepas word op materiale wat andersins moeilik sou wees om te soldeer, te sweis of te soldeer. Dit kan ook verkieslik wees vir hitte-sensitiewe materiale wat deur sweiswerk of ander hoë temperatuur prosesse beskadig sal word. Ander voordele van kleefmiddels is dat dit op onreëlmatige gevormde oppervlaktes aangewend kan word en die gewig van die samestelling met baie baie klein hoeveelhede verhoog in vergelyking met ander metodes. Ook dimensionele veranderinge in dele is baie minimaal. Sommige gom het indekseienskappe en kan tussen optiese komponente gebruik word sonder om die lig of optiese seinsterkte aansienlik te verminder. Nadele aan die ander kant is langer uithardingstye wat vervaardigingslyne, bevestigingsvereistes, oppervlakvoorbereidingsvereistes en moeilikheid om uitmekaar te haal wanneer herwerk nodig is, kan vertraag. Die meeste van ons gombindingsbewerkings behels die volgende stappe: - Oppervlakbehandeling: Spesiale skoonmaakprosedures soos skoonmaak van gedeïoniseerde water, alkohol skoonmaak, plasma of korona skoonmaak is algemeen. Na skoonmaak kan ons adhesiebevorderaars op die oppervlaktes toepas om die beste moontlike lasse te verseker. -Deelbevestiging: Vir beide kleefmiddeltoepassing sowel as vir uitharding ontwerp en gebruik ons pasgemaakte toebehore. -Gomtoepassing: Ons gebruik soms handmatige, en soms, afhangende van die geval, outomatiese stelsels soos robotika, servomotors, lineêre aktueerders om die kleefmiddels op die regte plek af te lewer en ons gebruik dispensers om dit teen die regte volume en hoeveelheid te lewer. -Uitharding: Afhangende van die gom, kan ons eenvoudige droog en uitharding gebruik, sowel as uitharding onder UV-ligte wat as katalisator dien of hitte-uitharding in 'n oond of gebruik van weerstandige verhittingselemente wat op jigs en toebehore gemonteer is. Ons beveel aan dat jy hier klik omLaai ons skematiese illustrasies van bevestigingsprosesse af deur AGS-TECH Inc. Dit sal jou help om die inligting wat ons hieronder verskaf, beter te verstaan. • BEVESTIGINGSPROSESSE: Ons meganiese verbindingsprosesse val in twee soorte kategorieë: BEVESTIGINGSMIDDELS en INTEGRALE VOEGTE. Voorbeelde van hegstukke wat ons gebruik is skroewe, penne, moere, boute, klinknaels. Voorbeelde van integrale lasse wat ons gebruik is snap- en krimppassings, nate, krimpies. Deur 'n verskeidenheid hegmetodes te gebruik, maak ons seker dat ons meganiese verbindings sterk en betroubaar is vir baie jare se gebruik. SKROUE en BOUTE is van die hegstukke wat die meeste gebruik word om voorwerpe bymekaar te hou en te posisioneer. Ons skroewe en boute voldoen aan ASME-standaarde. Verskeie soorte skroewe en boute word ingespan, insluitend seskant-dopskroewe en seskantboute, lagskroewe en boute, dubbelpuntskroef, dowelskroef, oogskroef, spieëlskroef, plaatmetaalskroef, fynverstelskroef, selfboor- en selftappende skroewe , stelskroef, skroewe met ingeboude wassers,...en meer. Ons het verskeie skroefkoptipes soos versinkte, koepel, ronde, flenskoppe en verskeie skroefaandrywingtipes soos gleuf, phillips, vierkant, seskantsok. 'n RIVET aan die ander kant is 'n permanente meganiese hegstuk wat bestaan uit 'n gladde silindiriese skag en 'n kop aan die een kant. Na inbring word die ander kant van die klinknagel vervorm en sy deursnee word vergroot sodat dit in plek bly. Met ander woorde, voor installasie het 'n klinknael een kop en na installasie het dit twee. Ons installeer verskeie soorte klinknaels na gelang van toepassing, sterkte, toeganklikheid en koste soos soliede/ronde kop klinknaels, strukturele, semi-buisvormige, blinde, oscar, aandrywing, spoel, wrywingslot, selfdeurdringende klinknaels. Klinking kan verkies word in gevalle waar hittevervorming en verandering in materiaaleienskappe as gevolg van sweishitte vermy moet word. Klinknagels bied ook ligte gewig en veral goeie krag en uithouvermoë teen skuifkragte. Teen trekbelastings kan skroewe, moere en boute egter meer geskik wees. In die CLINCHING-proses gebruik ons spesiale pons en matryse om 'n meganiese grendel te vorm tussen plaatmetale wat saamgevoeg word. Die pons druk die lae plaatmetaal in die holte in en lei tot die vorming van 'n permanente las. Geen verhitting en geen verkoeling is nodig in clinching nie en dit is 'n koue werksproses. Dit is 'n ekonomiese proses wat in sommige gevalle puntsweiswerk kan vervang. In PINNING gebruik ons penne wat masjienelemente is wat gebruik word om posisies van masjienonderdele relatief tot mekaar te verseker. Die belangrikste tipes is spanpenne, splitpenne, veerpenne, pennetjies, en splitpen. In STAPLING gebruik ons kramgewere en krammetjies wat tweekantige hegstukke is wat gebruik word om materiaal te verbind of vas te bind. Kramwerk het die volgende voordele: Ekonomies, eenvoudig en vinnig om te gebruik, die kroon van die krammetjies kan gebruik word om materiaal wat saamgestamp is te oorbrug, Die kroon van die kram kan die oorbrugging van 'n stuk soos 'n kabel vergemaklik en dit aan 'n oppervlak vasmaak sonder om te steek of skadelik, relatief maklik om te verwyder. PERSPASING word uitgevoer deur dele saam te druk en die wrywing tussen hulle maak die dele vas. Perspas-onderdele wat uit 'n oormaat skag en 'n ondermaat gat bestaan, word oor die algemeen op een van twee metodes aanmekaargesit: Hetsy deur krag toe te pas of om voordeel te trek uit termiese uitsetting of sametrekking van die dele. Wanneer 'n perspassing gevestig word deur 'n krag toe te pas, gebruik ons óf 'n hidrouliese pers óf 'n handaangedrewe pers. Aan die ander kant, wanneer perspassing deur termiese uitsetting tot stand gebring word, verhit ons die omhulde dele en monteer dit op hul plek terwyl dit warm is. Wanneer hulle afkoel trek hulle saam en keer terug na hul normale afmetings. Dit lei tot 'n goeie perspassing. Ons noem dit alternatiewelik KRYMPEND. Die ander manier om dit te doen is deur die omhulde dele af te koel voordat dit saamgestel word en dit dan in hul parende dele te skuif. Wanneer die samestelling opwarm, brei hulle uit en ons kry 'n stywe pas. Laasgenoemde metode kan verkieslik wees in gevalle waar verhitting die risiko inhou om materiaal eienskappe te verander. Verkoeling is veiliger in daardie gevalle. Pneumatiese en hidrouliese komponente en samestellings • Kleppe, hidrouliese en pneumatiese komponente soos O-ring, wasser, seëls, gasket, ring, shim. Aangesien kleppe en pneumatiese komponente in 'n groot verskeidenheid kom, kan ons nie alles hier lys nie. Afhangende van die fisiese en chemiese omgewings van jou toepassing, het ons wel spesiale produkte vir jou. Spesifiseer asseblief vir ons die toepassing, tipe komponent, spesifikasies, omgewingstoestande soos druk, temperatuur, vloeistowwe of gasse wat in kontak met jou kleppe en pneumatiese komponente sal wees; en ons sal die mees geskikte produk vir jou kies of dit spesiaal vir jou toepassing vervaardig. CLICK Product Finder-Locator Service VORIGE BLADSY
- Rapid Prototyping, Desktop Manufacturing, Additive Manufacturing, FDM
Rapid Prototyping, Desktop Manufacturing, Additive Manufacturing, Stereolithography, Polyjet, Fused Deposition Modeling, Selective Laser Sintering, FDM, SLS Byvoeging en vinnige vervaardiging In onlangse jare het ons 'n toename in die vraag na VINNIGE VERVAARDIGING of VINNIGE PROTOTIPERING gesien. Hierdie proses kan ook genoem word DESKTOP VERVAARDIGING of VRYVORM VERVAARDIGING. Basies word 'n soliede fisiese model van 'n onderdeel direk van 'n driedimensionele CAD-tekening gemaak. Ons gebruik die term ADDITIEWE VERVAARDIGING vir hierdie verskeie tegnieke waar ons onderdele in lae bou. Met behulp van geïntegreerde rekenaargedrewe hardeware en sagteware voer ons bykomende vervaardiging uit. Ons vinnige prototipering en vervaardigingstegnieke is STEREOLITOGRAFIE, POLIJET, GESIGTE-DEPOSISIE MODELLERING, SELEKTIEWE LASER SINTERING, ELEKTRONSTRAAL SMELTING, DRIE-DIMENSIONELE DRUK, DIREKTE VERVAARDIGING, VINNIGE GEREEDSKAP. Ons beveel aan dat jy hier klik omLaai ons skematiese illustrasies af van bykomende vervaardiging en vinnige vervaardigingsprosesse deur AGS-TECH Inc. Dit sal jou help om die inligting wat ons hieronder verskaf, beter te verstaan. Vinnige prototipering verskaf aan ons: 1.) Die konseptuele produkontwerp word vanuit verskillende hoeke op 'n monitor met behulp van 'n 3D / CAD-stelsel beskou. 2.) Prototipes van nie-metaal- en metaalmateriale word vervaardig en bestudeer vanuit funksionele, tegniese en estetiese aspekte. 3.) Laekoste prototipering in 'n baie kort tyd word bewerkstellig. Bykomende vervaardiging kan soos die konstruksie van 'n brood gelyk word deur individuele snye bo-op mekaar te stapel en te bind. Met ander woorde, die produk word sny vir sny vervaardig, of laag vir laag op mekaar neergesit. Die meeste onderdele kan binne ure vervaardig word. Die tegniek is goed as onderdele baie vinnig benodig word of as die benodigde hoeveelhede min is en die maak van 'n vorm en gereedskap te duur en tyd neem. Die koste van 'n onderdeel is egter duur as gevolg van die duur grondstowwe. • STEREOLITOGRAFIE : Hierdie tegniek ook afgekort as STL, is gebaseer op die uitharding en verharding van 'n vloeibare fotopolimeer tot 'n spesifieke vorm deur 'n laserstraal daarop te fokus. Die laser polimeer die fotopolimeer en genees dit. Deur die UV-laserstraal volgens die geprogrammeerde vorm langs die oppervlak van die fotopolimeermengsel te skandeer, word die deel van onder af na bo in individuele skywe gevorm wat bo-op mekaar gevorm word. Die skandering van die laserkol word baie keer herhaal om die geometrieë wat in die stelsel geprogrammeer is, te bereik. Nadat die onderdeel heeltemal vervaardig is, word dit van die platform verwyder, gevlek en ultrasonies en met alkoholbad skoongemaak. Vervolgens word dit vir 'n paar uur aan UV-bestraling blootgestel om seker te maak die polimeer is ten volle uitgehard en verhard. Om die proses op te som, word 'n platform wat in 'n fotopolimeermengsel gedoop word en 'n UV-laserstraal beheer en deur 'n servo-beheerstelsel beweeg volgens die vorm van die verlangde deel en die deel word verkry deur die polimeer laag vir laag te fotoharding. Natuurlik word die maksimum afmetings van die vervaardigde onderdeel deur die stereolitografie-toerusting bepaal. • POLYJET: Soortgelyk aan inkjet-drukwerk, het ons in polyjet agt drukkoppe wat fotopolimeer op die boubak neersit. Ultraviolet lig wat langs die strale geplaas word, genees en verhard elke laag onmiddellik. Twee materiale word in polyjet gebruik. Die eerste materiaal is vir die vervaardiging van die werklike model. Die tweede materiaal, 'n jelagtige hars, word vir ondersteuning gebruik. Beide hierdie materiale word laag vir laag neergesit en gelyktydig genees. Na die voltooiing van die model word die ondersteuningsmateriaal met 'n waterige oplossing verwyder. Harse wat gebruik word is soortgelyk aan stereolitografie (STL). Die polyjet het die volgende voordele bo stereolitografie: 1.) Dit is nie nodig om onderdele skoon te maak nie. 2.) Geen behoefte aan na-proses-uitharding nie 3.) Kleiner laagdiktes is moontlik en sodoende kry ons beter resolusie en kan fyner dele vervaardig. • GESIGTE DEPOSISIE MODELLERING: Ook afgekort as FDM, in hierdie metode beweeg 'n robot-beheerde ekstruderkop in twee hoofrigtings oor 'n tafel. Die kabel word verlaag en gelig soos nodig. Uit die opening van 'n verhitte matrys op die kop word 'n termoplastiese filament geëxtrudeer en 'n aanvanklike laag word op 'n skuimfondasie neergelê. Dit word bewerkstellig deur die ekstruderkop wat 'n voorafbepaalde pad volg. Na die aanvanklike laag word die tafel laat sak en daaropvolgende lae word bo-op mekaar neergelê. Soms wanneer 'n ingewikkelde onderdeel vervaardig word, is ondersteuningstrukture nodig sodat afsetting in sekere rigtings kan voortgaan. In hierdie gevalle word 'n ondersteuningsmateriaal geëxtrudeer met 'n minder digte spasiëring van filament op 'n laag sodat dit swakker is as die modelmateriaal. Hierdie steunstrukture kan later opgelos of afgebreek word na die voltooiing van die deel. Die afmetings van die ekstrudermatrys bepaal die dikte van die geëxtrudeerde lae. Die FDM-proses produseer dele met getrapte oppervlaktes op skuins buitevlakke. As hierdie grofheid onaanvaarbaar is, kan chemiese damppolering of 'n verhitte gereedskap gebruik word om dit glad te maak. Selfs 'n poleerwas is beskikbaar as 'n deklaagmateriaal om hierdie stappe uit te skakel en redelike geometriese toleransies te bereik. • SELEKTIEWE LASER SINTERING: Word ook as SLS aangedui, die proses is gebaseer op die sintering van 'n polimeer, keramiek of metaalpoeiers selektief in 'n voorwerp. Die onderkant van die verwerkingskamer het twee silinders: 'n Deelgeboude silinder en 'n poeiervoersilinder. Eersgenoemde word inkrementeel verlaag tot waar die gesinterde deel gevorm word en laasgenoemde word inkrementeel opgelig om poeier aan die deelgeboude silinder te verskaf deur 'n rollermeganisme. Eers word 'n dun lagie poeier in die deelgeboude silinder neergesit, dan word 'n laserstraal op daardie laag gefokus, wat 'n spesifieke dwarssnit natrek en smelt/sinter, wat dan weer stol tot 'n vaste stof. Die poeier is areas wat nie deur die laserstraal getref word nie, bly los maar ondersteun steeds die soliede gedeelte. Dan word nog 'n laag poeier neergesit en die proses herhaal baie keer om die deel te verkry. Aan die einde word die los poeierdeeltjies afgeskud. Al hierdie word uitgevoer deur 'n prosesbeheerrekenaar deur gebruik te maak van instruksies wat gegenereer word deur die 3D CAD-program van die onderdeel wat vervaardig word. Verskeie materiale soos polimere (soos ABS, PVC, poliëster), was, metale en keramiek met toepaslike polimeerbinders kan neergesit word. • ELEKTRONSTRAAL MELTING : Soortgelyk aan selektiewe lasersintering, maar gebruik elektronstraal om titaan- of kobaltchroompoeiers te smelt om prototipes in vakuum te maak. Sommige ontwikkelings is gemaak om hierdie proses op vlekvrye staal, aluminium en koperlegerings uit te voer. As die vermoeiingssterkte van die vervaardigde onderdele verhoog moet word, gebruik ons warm isostatiese persing na die vervaardiging van onderdele as 'n sekondêre proses. • DRIE-DIMENSIONELE DRUK: Word ook aangedui met 3DP, in hierdie tegniek plaas 'n drukkop 'n anorganiese bindmiddel op 'n laag nie-metaal- of metaalpoeier. 'n Suier wat die poeierbed dra, word inkrementeel laat sak en by elke stap word die bindmiddel laag vir laag neergesit en deur die bindmiddel saamgesmelt. Poeiermateriaal wat gebruik word, is polimeremengsels en vesels, gieterysand, metale. Deur verskillende bindkoppe gelyktydig en verskillende kleurbinders te gebruik, kan ons verskeie kleure verkry. Die proses is soortgelyk aan inkjet-drukwerk, maar in plaas daarvan om 'n gekleurde vel te verkry, kry ons 'n gekleurde driedimensionele voorwerp. Die dele wat geproduseer word, kan poreus wees en kan daarom sintering en metaalinfiltrasie vereis om die digtheid en sterkte daarvan te verhoog. Sintering sal die bindmiddel afbrand en die metaalpoeiers saamsmelt. Metale soos vlekvrye staal, aluminium, titanium kan gebruik word om die dele te maak en as infiltrasie materiaal gebruik ons gewoonlik koper en brons. Die skoonheid van hierdie tegniek is dat selfs ingewikkelde en bewegende samestellings baie vinnig vervaardig kan word. Byvoorbeeld 'n ratsamestelling, 'n moersleutel as 'n gereedskap kan gemaak word en sal bewegende en draaiende dele hê wat gereed is om gebruik te word. Verskillende komponente van die samestelling kan met verskillende kleure en alles in een skoot vervaardig word. Laai ons brosjure af op:Metal 3D Printing Basics • DIREKTE VERVAARDIGING en VINNIGE GEREEDSKAP: Benewens ontwerpevaluering, probleemoplossing gebruik ons vinnige prototipering vir direkte vervaardiging van produkte of direkte toepassing in produkte. Met ander woorde, vinnige prototipering kan by konvensionele prosesse geïnkorporeer word om dit beter en meer mededingend te maak. Byvoorbeeld, vinnige prototipering kan patrone en vorms produseer. Patrone van 'n smeltende en brandende polimeer wat deur vinnige prototipe-bewerkings geskep word, kan saamgestel word vir beleggingsgieting en belê word. Nog 'n voorbeeld om te noem is die gebruik van 3DP om keramiekgietdop te vervaardig en dit vir dopgietbewerkings te gebruik. Selfs spuitvorms en vorm-insetsels kan geproduseer word deur vinnige prototipering en 'n mens kan baie weke of maande se vormvervaardigingstyd bespaar. Deur slegs 'n CAD-lêer van die gewenste deel te ontleed, kan ons die gereedskapgeometrie met behulp van sagteware produseer. Hier is 'n paar van ons gewilde vinnige gereedskapmetodes: RTV (Room-Temperature Vulcanizing) MOLDING / URETHANE GIET : Die gebruik van vinnige prototipering kan gebruik word om die patroon van die verlangde deel te maak. Dan word hierdie patroon met 'n skeidingsmiddel bedek en vloeibare RTV-rubber word oor die patroon gegooi om die vormhelftes te produseer. Vervolgens word hierdie vormhelftes gebruik om vloeibare uretane te spuit. Die vormlewe is kort, net soos 0 of 30 siklusse, maar genoeg vir klein bondelproduksie. ACES (Acetal Clear Epoxy Solid) INspuitgietvorm: Deur gebruik te maak van vinnige prototiperingstegnieke soos stereolitografie, vervaardig ons spuitvorms. Hierdie vorms is skulpe met 'n oop einde om vulling met materiale soos epoksie, aluminiumgevulde epoksie of metale moontlik te maak. Weereens is die vormlewe beperk tot tiene of maksimum honderde dele. GESPUIT METAAL GEREEDSKAP PROSES: Ons gebruik vinnige prototipering en maak 'n patroon. Ons spuit 'n sink-aluminiumlegering op die patroonoppervlak en bedek dit. Die patroon met die metaalbedekking word dan in 'n fles geplaas en met 'n epoksie of aluminium gevulde epoksie gepot. Laastens word dit verwyder en deur twee sulke vormhelftes te vervaardig kry ons 'n volledige vorm vir spuitgiet. Hierdie vorms het langer lewens, in sommige gevalle, afhangende van materiaal en temperature, kan hulle dele in die duisende produseer. KEELTOOL PROSES: Hierdie tegniek kan vorms produseer met 100 000 tot 10 miljoen sikluslewens. Met behulp van vinnige prototipering vervaardig ons 'n RTV-vorm. Die vorm word volgende gevul met 'n mengsel bestaande uit A6 gereedskapstaalpoeier, wolframkarbied, polimeerbindmiddel en laat uithard. Hierdie vorm word dan verhit om die polimeer af te brand en die metaalpoeiers om te versmelt. Die volgende stap is koperinfiltrasie om die finale vorm te produseer. Indien nodig, kan sekondêre bewerkings soos bewerking en polering op die vorm uitgevoer word vir beter dimensionele akkuraatheid. _cc781905-5cde-3194-bb3b-136bad_5cf58 CLICK Product Finder-Locator Service VORIGE BLADSY
- Machine Elements Manufacturing, Gears, Gear Drives, Bearings, Keys, Splines
Machine Elements Manufacturing, Gears, Gear Drives, Bearings, Keys, Splines, Pins, Shafts, Seals, Fasteners, Clutch, Cams, Followers, Belts, Couplings, Shafts Masjien Elemente Vervaardiging Lees meer Bande & kettings & kabelaandrywing samestelling Lees meer Ratte en rataandrywingsamestelling Lees meer Koppelings en laers vervaardiging Lees meer Sleutels & Splines & Pins Vervaardiging Lees meer Nokke & Volgers & Koppelings & Ratchet Wheels Vervaardiging Lees meer Skagte Vervaardiging Lees meer Meganiese seëls vervaardiging Lees meer Koppelaar- en remsamestelling Lees meer Bevestigingsmiddels vervaardiging Lees meer Eenvoudige masjiensamestelling MACHINE ELEMENTS is elementêre komponente van 'n masjien. Hierdie elemente bestaan uit drie basiese tipes: 1.) Strukturele komponente insluitend raamlede, laers, asse, splines, hegstukke, seëls en smeermiddels. 2.) Meganismes wat beweging op verskeie maniere beheer soos rattreine, band- of kettingaandrywings, skakels, nok- en volgstelsels, remme en koppelaars. 3.) Beheer komponente soos knoppies, skakelaars, aanwysers, sensors, aktueerders en rekenaarbeheerders. Die meeste van die masjienelemente wat ons aan jou bied, is gestandaardiseer tot gewone groottes, maar pasgemaakte masjienelemente is ook beskikbaar vir jou gespesialiseerde toepassings. Pasmaak van masjienelemente kan plaasvind op bestaande ontwerpe wat in ons aflaaibare katalogusse is of op splinternuwe ontwerpe. Prototipering en vervaardiging van masjienelemente kan voortgesit word sodra 'n ontwerp deur beide partye goedgekeur is. As nuwe masjienelemente ontwerp en vervaardig moet word, stuur ons kliënte óf hul eie bloudrukke per e-pos en ons hersien dit vir goedkeuring, óf hulle vra ons om masjienelemente vir hul toepassing te ontwerp. In laasgenoemde geval gebruik ons alle insette van ons kliënte en ontwerp die masjienelemente en stuur die voltooide bloudrukke aan ons kliënte vir goedkeuring. Sodra dit goedgekeur is, vervaardig ons eerste artikels en vervaardig ons daarna die masjienelemente volgens die finale ontwerp. Op enige stadium van hierdie werk, indien 'n spesifieke masjienelementontwerp onbevredigend in die veld presteer (wat skaars is), hersien ons die hele projek en maak veranderings saam met ons kliënte soos nodig. Dit is ons standaardpraktyk om nie-openbaarmakingsooreenkomste (NDA) met ons kliënte te onderteken vir die ontwerp van masjienelemente of enige ander produk wanneer dit ook al nodig of vereis word. Sodra masjienelemente vir 'n spesifieke kliënt spesiaal ontwerp en vervaardig is, ken ons 'n produkkode daaraan toe en produseer en verkoop dit slegs aan ons klant wat die produk besit. Ons reproduseer die masjienelemente met behulp van die ontwikkelde gereedskap, vorms en prosedures soveel keer as wat nodig is en wanneer ons klant dit herbestel. Met ander woorde, sodra 'n pasgemaakte masjienelement vir jou ontwerp en geproduseer is, word die intellektuele eiendom sowel as alle gereedskap en vorms deur ons gereserveer en onbepaald in voorraad vir jou en die produkte gereproduseer soos jy wil. Ons bied ook aan ons kliënte ingenieursdienste deur masjienelemente kreatief te kombineer in 'n komponent of samestelling wat 'n toepassing dien en aan ons kliënte se verwagtinge voldoen of oortref. Aanlegte wat ons masjienelemente vervaardig, is gekwalifiseer deur óf ISO9001, QS9000 of TS16949. Daarbenewens het die meeste van ons produkte wel CE- of UL-merk en voldoen aan internasionaal relevante standaarde soos ISO, SAE, ASME, DIN. Klik asseblief op submenu's om gedetailleerde inligting oor ons masjienelemente te verkry, insluitend: - Bande, kettings en kabelaandrywers - Ratte en Gear Drives - Koppelings en laers - Sleutels & Splines & penne - Nokke en koppelings - Skagte - Meganiese seëls - Industriële koppelaar en rem - Bevestigingsmiddels - Eenvoudige masjiene Ons het 'n verwysingsbrosjure voorberei vir ons kliënte, ontwerpers en ontwikkelaars van nuwe produkte, insluitend masjienelemente. U kan uself vertroud maak met 'n paar algemeen gebruikte terme in die ontwerp van masjienkomponente: Laai brosjure af vir algemene meganiese ingenieursvoorwaardes wat deur ontwerpers en ingenieurs gebruik word Ons masjienelemente vind toepassings in 'n verskeidenheid velde soos industriële masjinerie, outomatiseringstelsels, toets- en metrologietoerusting, vervoertoerusting, konstruksiemasjiene en feitlik enige plek waaraan jy kan dink. AGS-TECH ontwikkel en vervaardig masjienelemente van verskeie materiale afhangende van toepassing. Materiaal wat vir masjienelemente gebruik word, kan wissel van gevormde plastiek wat vir speelgoed gebruik word tot geharde en spesiaal bedekte staal vir industriële masjinerie. Ons ontwerpers gebruik moderne professionele sagteware en ontwerpgereedskap vir die ontwikkeling van masjienelemente, met inagneming van besonderhede soos hoeke in rattande, spannings betrokke, slytasietempo... ens. Blaai asseblief deur ons subkieslyste en laai ons produkbrosjures en katalogusse af om te sien of jy van die rak masjienelemente vir jou toepassing kan opspoor. As jy nie 'n goeie pasmaat vir jou toepassing kan vind nie, laat weet ons asseblief en ons sal saam met jou werk om masjienelemente te ontwikkel en te vervaardig wat aan jou behoeftes sal voldoen. As jy meestal belangstel in ons ingenieurs- en navorsings- en ontwikkelingsvermoëns in plaas van vervaardigingsvermoëns, dan nooi ons jou uit om ons webwerf te besoekhttp://www.ags-engineering.com waar jy meer gedetailleerde inligting oor ons ontwerp, produkontwikkeling, prosesontwikkeling, ingenieurskonsultasiedienste en meer kan vind CLICK Product Finder-Locator Service VORIGE BLADSY
- Glass and Ceramic Manufacturing, Hermetic Packages, Seals, Bonding
Glass and Ceramic Manufacturing, Hermetic Packages Seals and Bonding, Tempered Bulletproof Glass, Blow Moulding, Optical Grade Glass, Conductive Glass, Molding Vorming en vorming van glas en keramiek Die tipe glasvervaardiging wat ons aanbied, is houerglas, glasblaas, glasvesel & buise & staaf, huishoudelike en industriële glasware, lamp en gloeilamp, presisie glasgietwerk, optiese komponente en samestellings, plat & plaat & floatglas. Ons voer beide handvorming sowel as masjienvorming uit. Ons gewilde tegniese keramiekvervaardigingsprosesse is matryspers, isostatiese pers, warm isostatiese pers, warm pers, glipgiet, bandgiet, ekstrusie, spuitgiet, groen bewerking, sinter of brand, diamantslyp, hermetiese samestellings. Ons beveel aan dat jy hier klik om Laai ons skematiese illustrasies van glasvorming en -vormingsprosesse af deur AGS-TECH Inc. Laai ons skematiese illustrasies af van tegniese keramiekvervaardigingsprosesse deur AGS-TECH Inc. Hierdie aflaaibare lêers met foto's en sketse sal jou help om die inligting wat ons hieronder verskaf beter te verstaan. • HOUERGLAS VERVAARDIGING: Ons het geoutomatiseerde DRUK EN BLAAS sowel as BLAAS EN BLAAS lyne vir vervaardiging. In die blaas-en-blaas-proses laat ons 'n gob in leë vorm val en vorm die nek deur 'n blaas saamgeperste lug van bo af toe te dien. Onmiddellik hierna word saamgeperste lug 'n tweede keer van die ander rigting deur die houernek geblaas om die voorvorm van die bottel te vorm. Hierdie voorvorm word dan na die werklike vorm oorgedra, herverhit om sag te word en saamgeperste lug word toegedien om die voorvorm sy finale houervorm te gee. Meer eksplisiet word dit onder druk geplaas en teen die mure van die blaasvormholte gedruk om die gewenste vorm aan te neem. Laastens word die vervaardigde glashouer in 'n uitgloeioond oorgeplaas vir daaropvolgende herverhitting en verwydering van spanning wat tydens die gietvorm ontstaan en word op 'n beheerde wyse afgekoel. In die pers-en-blaas-metode word gesmelte gobs in 'n parison-vorm (blanko vorm) geplaas en in die parison-vorm (leë vorm) gedruk. Die spasies word dan na blaasvorms oorgeplaas en geblaas soortgelyk aan die proses wat hierbo beskryf is onder "Blas en Blaas Proses". Daaropvolgende stappe soos uitgloeiing en spanningsverligting is soortgelyk of dieselfde. • GLASBLAAIS: Ons vervaardig glasprodukte deur gebruik te maak van konvensionele handblaas sowel as die gebruik van saamgeperste lug met outomatiese toerusting. Vir sommige bestellings is konvensionele blaas nodig, soos projekte wat glaskunswerk behels, of projekte wat 'n kleiner aantal onderdele met los toleransies benodig, prototipering/demo-projekte ….ens. Konvensionele glasblaas behels die doop van 'n hol metaalpyp in 'n pot gesmelte glas en draai die pyp om 'n mate van die glasmateriaal te versamel. Die glas wat op die punt van die pyp versamel word, word op plat yster gerol, gevorm soos verlang, verleng, herverhit en lug geblaas. Wanneer dit gereed is, word dit in 'n vorm geplaas en lug word geblaas. Die vormholte is nat om kontak van die glas met metaal te vermy. Die waterfilm dien soos 'n kussing tussen hulle. Handblaas is 'n arbeidsintensiewe stadige proses en slegs geskik vir prototipering of items van hoë waarde, nie geskik vir goedkoop per stuk hoë volume bestellings nie. • VERVAARDIGING VAN HUISLIKE EN INDUSTRIËLE GLASWERK: Deur verskeie tipes glasmateriaal te gebruik, word 'n groot verskeidenheid glasware vervaardig. Sommige glase is hittebestand en geskik vir laboratoriumglasware, terwyl sommige goed genoeg is om skottelgoedwassers baie keer te weerstaan en geskik is om huishoudelike produkte te maak. Met behulp van Westlake-masjiene word tienduisende stukke drinkglase per dag vervaardig. Om dit te vereenvoudig, word gesmelte glas deur vakuum versamel en in vorms geplaas om die voorvorms te maak. Dan word lug in die vorms geblaas, dit word na 'n ander vorm oorgeplaas en lug word weer geblaas en die glas neem sy finale vorm aan. Soos in die handblaas, word hierdie vorms nat gehou met water. Verdere strek is deel van die afrondingsoperasie waar die nek gevorm word. Oortollige glas word afgebrand. Daarna volg die beheerde herverhitting en verkoelingsproses hierbo beskryf. • GLASBUIS EN -STAAFVORMING: Die hoofprosesse wat ons gebruik vir die vervaardiging van glasbuise is die DANNER- en VELLO-prosesse. In die Danner-proses vloei glas uit 'n oond en val dit op 'n skuins huls wat van vuurvaste materiale gemaak is. Die huls word op 'n roterende hol as of blaaspyp gedra. Die glas word dan om die mou gedraai en vorm 'n gladde laag wat langs die mou af en oor die punt van die skag vloei. In die geval van buisvorming word lug deur 'n blaaspyp met hol punt geblaas, en in die geval van staafvorming gebruik ons soliede punte op die as. Die buise of stawe word dan oor drarolle getrek. Die afmetings soos wanddikte en deursnee van die glasbuise word na verlangde waardes aangepas deur die deursnee van die huls te stel en lugdruk op 'n gewenste waarde te blaas, die temperatuur, tempo van vloei van glas en spoed van trek aan te pas. Die Vello-glasbuisvervaardigingsproses behels aan die ander kant glas wat uit 'n oond beweeg en in 'n bak met 'n hol deurn of klok. Die glas gaan dan deur die lugruimte tussen die deur en die bak en neem die vorm van 'n buis aan. Daarna beweeg dit oor rollers na 'n tekenmasjien en word afgekoel. Aan die einde van die koellyn vind sny en finale verwerking plaas. Die buisafmetings kan net soos in die Danner-proses aangepas word. Wanneer ons die Danner- met Vello-proses vergelyk, kan ons sê dat die Vello-proses beter geskik is vir groot hoeveelhede produksie, terwyl die Danner-proses beter geskik is vir presiese kleiner volume buisbestellings. • VERWERKING VAN PLAAT- & PLAT- & FLATGLAS: Ons het groot hoeveelhede plat glas in diktes wat wissel van submilimeterdiktes tot etlike sentimeters. Ons plat glase is van byna optiese perfeksie. Ons bied glas met spesiale bedekkings soos optiese bedekkings, waar chemiese dampneerslagtegniek gebruik word om bedekkings soos antirefleksie of spieëlbedekking te plaas. Ook deursigtige geleidende bedekkings is algemeen. Ook beskikbaar is hidrofobiese of hidrofiele bedekkings op glas, en bedekking wat glas selfreinigend maak. Geharde, koeëlvaste en gelamineerde glase is nog ander gewilde items. Ons sny glas in gewenste vorm met verlangde toleransies. Ander sekondêre bewerkings soos buiging of buiging van plat glas is beskikbaar. • PRESISIE GLAS VOER: Ons gebruik hierdie tegniek meestal vir die vervaardiging van presisie optiese komponente sonder die behoefte aan duurder en tydrowende tegnieke soos slyp, lap en poleer. Hierdie tegniek is nie altyd voldoende om die beste van die beste optika te maak nie, maar in sommige gevalle, soos verbruikersprodukte, digitale kameras, mediese optika, kan dit 'n goedkoper goeie opsie wees vir hoëvolume-vervaardiging. Dit het ook 'n voordeel bo die ander glasvormingstegnieke waar komplekse geometrieë vereis word, soos in die geval van asfere. Die basiese proses behels die laai van die onderkant van ons vorm met die glas leeg, ontruiming van die proseskamer vir suurstofverwydering, naby sluiting van die vorm, vinnige en isotermiese verhitting van die matrys en glas met infrarooi lig, verdere sluiting van die vormhelftes om die versagte glas stadig op 'n beheerde wyse tot die verlangde dikte te druk, en uiteindelik die glas af te koel en die kamer met stikstof te vul en die produk te verwyder. Presiese temperatuurbeheer, vorm sluiting afstand, vorm sluiting krag, wat ooreenstem met die koëffisiënte van uitsetting van die vorm en glas materiaal is die sleutel in hierdie proses. • VERVAARDIGING VAN OPTIESE KOMPONENTE EN SAMESTELLINGS VAN GLAS: Benewens presisie glasgietwerk, is daar 'n aantal waardevolle prosesse wat ons gebruik om optiese komponente en samestellings van hoë gehalte vir veeleisende toepassings te maak. Slyp, lap en poleer van optiese graad glase in fyn spesiale skuur slurries is 'n kuns en wetenskap vir die maak van optiese lense, prismas, flats en meer. Oppervlakvlakheid, golwendheid, gladheid en defekvrye optiese oppervlaktes vereis baie ondervinding met sulke prosesse. Klein veranderinge in omgewing kan lei tot produkte wat nie meer spesifikasies is nie en die vervaardigingslyn tot stilstand bring. Daar is gevalle waar 'n enkele vee op die optiese oppervlak met 'n skoon lap 'n produk aan die spesifikasies kan laat voldoen of die toets kan druip. Sommige gewilde glasmateriaal wat gebruik word, is saamgesmelte silika, kwarts, BK7. Ook die samestelling van sulke komponente vereis gespesialiseerde nis-ervaring. Soms word spesiale gom gebruik. Soms is 'n tegniek genaamd optiese kontak egter die beste keuse en behels geen materiaal tussen aangehegte optiese bril nie. Dit bestaan uit fisiese kontak met plat oppervlaktes om sonder gom aan mekaar te heg. In sommige gevalle word meganiese spasieerders, presisieglasstawe of -balle, klampe of bewerkte metaalkomponente gebruik om die optiese komponente op sekere afstande en met sekere geometriese oriëntasies na mekaar te monteer. Kom ons ondersoek sommige van ons gewilde tegnieke vir die vervaardiging van hoë-end optika. SLYP & LAPPING & POLIERING: Die growwe vorm van die optiese komponent word verkry deur 'n glasblanko te maal. Daarna word lap en polering uitgevoer deur die ruwe oppervlaktes van die optiese komponente te draai en te vryf teen gereedskap met gewenste oppervlakvorms. Slakke met klein skuurdeeltjies en vloeistof word tussen die optika en die vormgereedskap ingegooi. Die skuurdeeltjiegroottes in sulke slurries kan gekies word volgens die verlangde mate van platheid. Die afwykings van kritieke optiese oppervlaktes van gewenste vorms word uitgedruk in terme van golflengtes van die lig wat gebruik word. Ons hoë-presisie-optika het tiende van 'n golflengte (golflengte/10) toleransies of selfs strenger is moontlik. Behalwe oppervlakprofiel, word die kritieke oppervlaktes geskandeer en geëvalueer vir ander oppervlakkenmerke en defekte soos afmetings, skrape, skyfies, putte, spikkels ... ens. Die streng beheer van omgewingstoestande in die optiese vervaardigingsvloer en uitgebreide metrologie- en toetsvereistes met die nuutste toerusting maak dit 'n uitdagende tak van die industrie. • SEKONDÊRE PROSESSE IN GLASVERVAARDIGING: Weereens, ons is net beperk met jou verbeelding wanneer dit kom by sekondêre en afwerkingsprosesse van glas. Hier lys ons 'n paar van hulle: -Bedekkings op glas (opties, elektries, tribologies, termies, funksioneel, meganies...). As 'n voorbeeld kan ons oppervlak-eienskappe van glas verander sodat dit byvoorbeeld hitte weerkaats sodat dit die gebou se binnekant koel hou, of eenkant infrarooi absorberend maak deur nanotegnologie te gebruik. Dit help om die binnekant van geboue warm te hou omdat die buitenste oppervlaklaag glas die infrarooi straling binne die gebou sal absorbeer en dit na binne sal terugstraal. -Ets op glas - Toegepaste keramieketikettering (ACL) - Gravure -Vlam poleer - Chemiese polering - Verkleuring VERVAARDIGING VAN TEGNIESE KERAMIEK • STERFPERSING: Bestaan uit eenassige verdigting van korrelpoeiers wat in 'n matrys opgesluit is • WARMPERSING: Soortgelyk aan die pers maar met die byvoeging van temperatuur om verdigting te verbeter. Poeier of gekompakteerde voorvorm word in grafietmatrys geplaas en eenassige druk word toegepas terwyl die matrys by hoë temperature soos 2000 C gehou word. Temperature kan verskil afhangende van die tipe keramiekpoeier wat verwerk word. Vir ingewikkelde vorms en geometrieë kan ander daaropvolgende verwerking soos diamantslyp nodig wees. • ISOSTATIESE PERSING : Korrelpoeier of stanspers word in lugdigte houers geplaas en dan in 'n geslote drukhouer met vloeistof binne. Daarna word hulle gekompakteer deur die drukhouer se druk te verhoog. Die vloeistof binne die houer dra die drukkragte eenvormig oor die hele oppervlak van die lugdigte houer oor. Die materiaal word dus eenvormig gekompakteer en neem die vorm aan van sy buigsame houer en sy interne profiel en kenmerke. • WARM ISOSTATIESE PERSING : Soortgelyk aan isostatiese persing, maar benewens drukgas-atmosfeer, sinter ons die kompak by hoë temperatuur. Warm isostatiese pers lei tot bykomende verdigting en verhoogde sterkte. • SLIPGIETEN / DREINEERGIETEN: Ons vul die vorm met 'n suspensie van mikrometergrootte keramiekdeeltjies en draervloeistof. Hierdie mengsel word "glip" genoem. Die vorm het porieë en daarom word die vloeistof in die mengsel in die vorm gefiltreer. As gevolg hiervan word 'n gietvorm op die binne-oppervlaktes van die vorm gevorm. Na sintering kan die dele uit die vorm gehaal word. • BANDGOOI: Ons vervaardig keramiekbande deur keramiekflotte op plat bewegende draeroppervlaktes te giet. Die flodders bevat keramiekpoeiers gemeng met ander chemikalieë vir bind- en dradoeleindes. Soos die oplosmiddels verdamp, word digte en buigsame velle keramiek agtergelaat wat na wense gesny of gerol kan word. • EKSTRUSIEVORMING: Soos in ander ekstrusieprosesse, word 'n sagte mengsel van keramiekpoeier met bindmiddels en ander chemikalieë deur 'n matrys gevoer om sy deursneevorm te verkry en dan op verlangde lengtes gesny. Die proses word uitgevoer met koue of verhitte keramiekmengsels. • LAEDRUK INSPUITVORMING: Ons berei 'n mengsel van keramiekpoeier met bindmiddels en oplosmiddels voor en verhit dit tot 'n temperatuur waar dit maklik in die gereedskapholte gedruk en ingedruk kan word. Sodra die gietsiklus voltooi is, word die deel uitgewerp en die bindmiddel word afgebrand. Deur spuitgietwerk te gebruik, kan ons ingewikkelde onderdele teen hoë volumes ekonomies verkry. Gate wat 'n klein fraksie van 'n millimeter op 'n 10mm dik muur is, is moontlik, skroefdraad is moontlik sonder verdere bewerking, toleransies so nou as +/- 0.5% is moontlik en selfs laer wanneer onderdele gemasjineer word , wanddiktes in die orde van 0,5 mm tot 'n lengte van 12,5 mm is moontlik asook wanddiktes van 6,5 mm tot 'n lengte van 150 mm. • GROEN MAJERING: Deur dieselfde metaalbewerkingsgereedskap te gebruik, kan ons geperste keramiekmateriaal masjineer terwyl dit nog sag soos kryt is. Toleransies van +/- 1% is moontlik. Vir beter toleransies gebruik ons diamantslyp. • SINTERING of BRAND: Sintering maak volle verdigting moontlik. Beduidende krimping vind plaas op die groen kompakte dele, maar dit is nie 'n groot probleem nie aangesien ons hierdie dimensionele veranderinge in ag neem wanneer ons die onderdeel en gereedskap ontwerp. Poeierdeeltjies word aan mekaar gebind en porositeit wat deur die verdigtingsproses geïnduseer word, word in groot mate verwyder. • DIAMANTSLYP: Die wêreld se hardste materiaal "diamant" word gebruik om harde materiale soos keramiek te slyp en presisieonderdele word verkry. Toleransies in die mikrometerreeks en baie gladde oppervlaktes word bereik. As gevolg van die koste daarvan, oorweeg ons hierdie tegniek slegs wanneer ons dit regtig nodig het. • HERMETIESE SAMESTELLINGS is dié wat prakties gesproke geen uitruiling van materie, vaste stowwe, vloeistowwe of gasse tussen raakvlakke toelaat nie. Hermetiese verseëling is lugdig. Hermetiese elektroniese omhulsels is byvoorbeeld dié wat die sensitiewe binne-inhoud van 'n verpakte toestel ongedeerd hou deur vog, kontaminante of gasse. Niks is 100% hermeties nie, maar as ons van hermetisiteit praat, bedoel ons dit in praktiese terme, dat daar hermetisiteit is in die mate dat die lektempo so laag is dat die toestelle vir baie lang tye veilig is onder normale omgewingstoestande. Ons hermetiese samestellings bestaan uit metaal-, glas- en keramiekkomponente, metaal-keramiek, keramiek-metaal-keramiek, metaal-keramiek-metaal, metaal tot metaal, metaal-glas, metaal-glas-metaal, glas-metaal-glas, glas- metaal en glas tot glas en alle ander kombinasies van metaal-glas-keramiekbinding. Ons kan byvoorbeeld die keramiekkomponente met metaal bedek sodat hulle sterk aan ander komponente in die samestelling gebind kan word en uitstekende seëlvermoë het. Ons het die kundigheid om optiese vesels of deurvoere met metaal te bedek en dit aan die omhulsels te soldeer of te soldeer, so geen gasse gaan of lek in die omhulsels nie. Daarom word hulle gebruik vir die vervaardiging van elektroniese omhulsels om sensitiewe toestelle in te kap en hulle teen die buitenste atmosfeer te beskerm. Benewens hul uitstekende seëleienskappe, ander eienskappe soos die termiese uitsettingskoëffisiënt, vervormingsweerstand, nie-uitgassing aard, baie lang leeftyd, niegeleidende aard, termiese isolasie eienskappe, antistatiese aard ... ens. maak glas en keramiek materiaal die keuse vir sekere toepassings. Inligting oor ons fasiliteit wat keramiek-tot-metaal-toebehore vervaardig, hermetiese verseëling, vakuumdeurvoere, hoë en ultrahoë vakuum en vloeistofbeheerkomponente kan hier gevind word:Hermetiese komponente fabrieksbrosjure CLICK Product Finder-Locator Service VORIGE BLADSY
- Wire & Spring Forming, Shaping, Welding, Assembly of Wires, Coil, CNC
Wire & Spring Forming, Shaping, Welding, Assembly of Wires, Coil Compression Extension Torsion Flat Springs, Custom Wires, Helical Springs at AGS-TECH Inc. Draad- en veervorming Ons vervaardig persoonlike drade, draadsamestelling, drade gevorm in gewenste 2D- en 3D-vorms, draadnette, gaas, omhulsels, mandjie, heining, draadveer, platveer; torsie, kompressie, spanning, plat vere en meer. Ons prosesse is draad- en veervorming, draadtrek, vorming, buig, sweis, soldering, soldering, deurboor, smeer, boor, afkanting, slyp, inryg, bedek, viergly, gly vorming, wikkel, oprol, ontwrigting. Ons beveel aan dat jy hier klik om Laai ons skematiese illustrasies van draad- en veervormingsprosesse af deur AGS-TECH Inc. Hierdie aflaaibare lêer met foto's en sketse sal jou help om die inligting wat ons hieronder verskaf beter te verstaan. • DRAADTEKENING: Deur gebruik te maak van trekkragte strek ons die metaalvoorraad en trek dit deur 'n matrys om die deursnee te verminder en sy lengte te vergroot. Soms gebruik ons 'n reeks van dies. Ons is in staat om matryse te maak vir elke maat draad. Met materiaal met hoë treksterkte trek ons baie dun drade. Ons bied beide koue en warm gewerkte drade. • DRAADVORMING: 'n Rol gemete draad word gebuig en tot 'n nuttige produk gevorm. Ons het die vermoë om drade van alle meters te vorm, insluitend dun filamente sowel as dik drade soos dié wat as vere onder motoronderstel gebruik word. Toerusting wat ons vir draadvorming gebruik, is hand- en CNC-draadvormers, spoel-, kragperse, vierskuif-, multi-gly. Ons prosesse is trek, buig, reguit maak, plat, rek, sny, versteur, soldeer en sweis en soldeersel, monteer, oprol, swaai (of vlerk), deurboor, draadskroef, boor, afkanting, slyp, deklaag en oppervlakbehandelings. Ons moderne toerusting kan opgestel word om baie komplekse ontwerpe van enige vorm en streng toleransies te ontwikkel. Ons bied verskeie eindtipes agtige sferiese, gepunte of afgeskuinsde ente vir jou drade. Die meeste van ons draadvormprojekte het minimale tot geen gereedskapskoste nie. Voorbeeld omkeertye is gewoonlik dae. Veranderinge aan ontwerp/konfigurasie van draadvorms kan baie vinnig gemaak word. • VEERVORMING: AGS-TECH vervaardig 'n groot verskeidenheid vere, insluitend: -Wring / Dubbele Torsieveer - Spanning / drukveer -Konstante / veranderlike lente - Spoel- en heliese veer -Plat & Leaf Spring - Balanseer lente -Belleville Wasmasjien - Negator Spring -Progressiewe spoed kronkelveer - Golf lente -Voluut Lente - Tapered Springs - Lente ringe -Klok Springs - Knipsels Ons vervaardig vere van 'n verskeidenheid materiale en kan jou lei volgens jou toepassing. Mees algemene materiale is vlekvrye staal, chroom silikon, hoë-koolstof staal, olie-getemperde lae-koolstof, chroom vanadium, fosfor brons, titanium, berillium koper legering, hoë-temperatuur keramiek. Ons gebruik verskeie tegnieke in die vervaardiging van vere, insluitend CNC wikkeling, koue wikkeling, warm wikkeling, verharding, afwerking. Ander tegnieke wat reeds hierbo genoem onder draadvorming is ook algemeen in ons veervervaardigingsbedrywighede. • AFWERKINGSDIENSTE vir DRADE & VERE: Ons kan jou produkte op baie maniere afwerk, afhangende van jou keuse en behoeftes. Sommige algemene prosesse wat ons aanbied, is: verf, poeierbedekking, platering, vinieldoop, anodisering, stresverligting, hittebehandeling, skuimpen, tuimel, chromaat, elektrolose nikkel, passivering, gebakte emalje, plastiek , plasma skoonmaak. CLICK Product Finder-Locator Service VORIGE BLADSY
- Forging and Powdered Metallurgy, Die Forging, Heading, Hot Forging
Forging and Powdered Metallurgy, Die Forging, Heading, Hot Forging, Impression Die, Near Net Shape, Swaging, Metal Hobbing, Riveting, Coining from AGS-TECH Inc. Metaalsmee en poeiermetallurgie Die tipe METAAL SMEED-prosesse wat ons aanbied is warm en koue matrys, oop matrys en geslote matrys, indrukmatrijs en flitslose smeewerk, cogging, vollering, rand- en presisiesmee, byna-net-vorm, kop , smeewerk, ontwrigte smee, metaal smeer, druk & rol & radiaal & orbitaal & ring & isotermiese smee, smee, klinknagel, metaal bal smee, metaal deursteek, grootte, hoë energie tempo smee. Ons POEIER METALLURGIE en POEIERVERWERKINGStegnieke is poeierpers en sintering, impregnering, infiltrasie, warm en koue isostatiese pers, metaal spuitgiet, rol verdigting, poeier rol, poeier ekstrusie, los sintering, vonksintering, warm pers. Ons beveel aan dat jy hier klik om Laai ons skematiese illustrasies van smeeprosesse af deur AGS-TECH Inc. Laai ons skematiese illustrasies van poeiermetallurgieprosesse af deur AGS-TECH Inc. Hierdie aflaaibare lêers met foto's en sketse sal jou help om die inligting wat ons hieronder verskaf beter te verstaan. By metaalsmee word drukkragte toegepas en die materiaal word vervorm en die verlangde vorm word verkry. Die mees algemene gesmee materiaal in die industrie is yster en staal, maar talle ander soos aluminium, koper, titanium, magnesium word ook wyd gesmee. Gesmede metaalonderdele het verbeterde korrelstrukture bykomend tot verseëlde krake en geslote leë spasies, dus is die sterkte van dele wat deur hierdie proses verkry word, hoër. Smeedwerk produseer dele wat beduidend sterker vir hul gewig is as dele wat deur giet of bewerking gemaak word. Aangesien gesmede dele gevorm word deur die metaal in sy finale vorm te laat vloei, neem die metaal 'n rigtinggewende korrelstruktuur aan wat verantwoordelik is vir die voortreflike sterkte van die dele. Met ander woorde, onderdele wat deur smeeproses verkry word, toon beter meganiese eienskappe in vergelyking met eenvoudige gegote of gemasjineerde dele. Die gewig van metaalsmee kan wissel van klein liggewigonderdele tot honderdduisende ponde. Ons vervaardig smeewerk meestal vir meganies veeleisende toepassings waar hoë spanning toegepas word op onderdele soos motoronderdele, ratte, werkgereedskap, handgereedskap, turbine-asse, motorfietsrat. Omdat gereedskap- en opstelkoste relatief hoog is, beveel ons hierdie vervaardigingsproses slegs aan vir hoë volume produksie en vir lae volume maar hoë waarde kritieke komponente soos lugvaartlandingsgereedskap. Benewens die koste van gereedskap, kan die vervaardigingstye vir groot hoeveelhede gesmee onderdele langer wees in vergelyking met sommige eenvoudige gemasjineerde onderdele, maar die tegniek is van kardinale belang vir onderdele wat buitengewone sterkte vereis soos boute, moere, spesiale toepassing hegstukke, motor, vurkhyser, hyskraanonderdele. • WARMSTRYF- en KOUD-SMEDING: Warm-smeding, soos die naam aandui, word by hoë temperature uitgevoer, die rekbaarheid is dus hoog en sterkte van materiaal laag. Dit vergemaklik maklike vervorming en smee. Inteendeel, koue smee word by laer temperature uitgevoer en vereis hoër kragte wat lei tot vervorming verharding, beter oppervlak afwerking en akkuraatheid van die vervaardigde onderdele. • OPEN DIE en IMPRESSION STERF SMEDING: In oop matrys smee, beperk die matrys nie die materiaal wat saamgepers word nie, terwyl die holtes binne die matrys die holtes binne die matrys belemmer terwyl dit in die gewenste vorm gesmee word. UPSET FORGING of ook genoem UPSETTING, wat eintlik nie dieselfde is nie, maar 'n baie soortgelyke proses, is 'n oop matrysproses waar die werkstuk tussen twee plat matryse vasgedruk word en 'n drukkrag sy hoogte verminder. Soos die hoogte reduced is, neem die werkstukwydte toe. OPWEG, 'n omgekrapte smeeproses behels silindriese voorraad wat aan sy einde omgekrap word en sy deursnit plaaslik vergroot word. In kop word die voorraad deur die matrys gevoer, gesmee en dan in lengte gesny. Die operasie is in staat om vinnig groot hoeveelhede hegstukke te produseer. Meestal is dit 'n koue bewerking omdat dit gebruik word om spykerpunte, skroefpunte, moere en boute te maak waar die materiaal versterk moet word. Nog 'n oop matrysproses is COGGING, waar die werkstuk in 'n reeks stappe gesmee word, met elke stap wat lei tot samedrukking van die materiaal en die daaropvolgende beweging van die oop matrijs oor die lengte van die werkstuk. By elke stap word die dikte verminder en die lengte word met 'n klein hoeveelheid vergroot. Die proses lyk soos 'n senuweeagtige student wat heeltyd in klein stappe sy potlood byt. 'n Proses genaamd FULLERING is nog 'n oop smeemetode wat ons dikwels gebruik as 'n vroeëre stap om die materiaal in die werkstuk te versprei voordat ander metaal smeebewerkings plaasvind. Ons gebruik dit wanneer die werkstuk verskeie smee operasies vereis. In die operasie vervorm die matrys met konvekse oppervlaktes en veroorsaak dat metaal na beide kante uitvloei. 'n Soortgelyke proses as volmaak, EDGING aan die ander kant behels oop matrys met konkawe oppervlaktes om die werkstuk te vervorm. Omranding is ook 'n voorbereidingsproses vir daaropvolgende smeebewerkings, wat die materiaal van beide kante na 'n area in die middel laat vloei. IMPRESSION DIE FORGING of CLOSED DIE FORGING soos dit ook genoem word, gebruik 'n matrijs / gietvorm wat die materiaal saamdruk en die vloei daarvan in homself beperk. Die matrys sluit en die materiaal neem die vorm van die matrys / vormholte aan. PRESISIESMEE, 'n proses wat spesiale toerusting en vorm vereis, produseer dele met geen of baie min flits. Met ander woorde, die dele sal byna finale afmetings hê. In hierdie proses word 'n goed beheerde hoeveelheid materiaal versigtig in die vorm geplaas en geplaas. Ons gebruik hierdie metode vir komplekse vorms met dun snitte, klein toleransies en trekhoeke en wanneer die hoeveelhede groot genoeg is om die vorm en toerustingkoste te regverdig. • FLITLOOS smee: Die werkstuk word so in die matrys geplaas dat geen materiaal uit die holte kan vloei om flits te vorm nie. Geen ongewenste flitsknip is dus nodig nie. Dit is 'n presisie smeeproses en vereis dus noukeurige beheer van die hoeveelheid materiaal wat gebruik word. • METAAL SWAGING of RADIAAL SMEED: 'n Werkstuk word in die omtrek deur die matrys en gesmee. 'n Doorn kan ook gebruik word om die binnekant van die werkstuk geometrie te smee. In die smeerbewerking ontvang die werkstuk tipies verskeie houe per sekonde. Tipiese items wat deur smeer vervaardig word, is spitspuntgereedskap, tapse stawe, skroewedraaiers. • METAALPIERCING: Ons gebruik hierdie bewerking gereeld as 'n bykomende bewerking in die vervaardiging van onderdele. ’n Gat of holte word geskep met piercing op die werkstukoppervlak sonder om daardeur te breek. Let asseblief daarop dat deurboor anders is as boor wat 'n deurgat tot gevolg het. • HOBBING : 'n Pons met die verlangde geometrie word in die werkstuk ingedruk en skep 'n holte met die verlangde vorm. Ons noem hierdie punch 'n HOB. Die operasie behels hoë druk en word teen koue uitgevoer. Gevolglik word die materiaal koud bewerk en rekverhard. Daarom is hierdie proses baie geskik vir die vervaardiging van vorms, matrijs en holtes vir ander vervaardigingsprosesse. Sodra die kookplaat vervaardig is, kan 'n mens maklik baie identiese holtes vervaardig sonder dat dit nodig is om hulle een vir een te bewerk. • ROLSMEDE of ROLSVORMING: Twee opponerende rolle word gebruik om die metaaldeel te vorm. Die werkstuk word in die rolle ingevoer, die rolle draai en trek die werk in die gaping, die werk word dan deur die gegroefde gedeelte van die rolle gevoer en die drukkragte gee die materiaal sy gewenste vorm. Dit is nie 'n rolproses nie maar 'n smeeproses, want dit is 'n diskrete eerder as 'n deurlopende operasie. Die geometrie op die rolboorde smee die materiaal tot die vereiste vorm en geometrie. Dit word warm uitgevoer. Omdat dit 'n smeeproses is, produseer dit onderdele met uitstekende meganiese eienskappe en daarom gebruik ons dit vir vervaardiging van motoronderdele soos asse wat buitengewone uithouvermoë moet hê in moeilike werksomgewings. • ORBITAAL SMEE: Werkstuk word in 'n smeematrysholte geplaas en gesmee deur 'n boonste matrys wat in 'n wentelbaan beweeg soos dit om 'n skuins as draai. By elke omwenteling voltooi die boonste matrijs die drukkragte op die hele werkstuk uit. Deur hierdie omwentelinge 'n aantal keer te herhaal, word voldoende smee uitgevoer. Die voordele van hierdie vervaardigingstegniek is sy lae geraas werking en laer kragte wat nodig is. Met ander woorde met klein kragte kan 'n mens 'n swaar matrys om 'n as draai om groot druk toe te pas op 'n gedeelte van die werkstuk wat in kontak is met die matrys. Skyf- of koniese dele pas soms goed vir hierdie proses. • RINGSMEE: Ons gebruik gereeld om naatlose ringe te vervaardig. Vee word in lengte gesny, omgekrap en dan deurboor om 'n sentrale gat te skep. Dan word dit op 'n spil gesit en 'n smeematrys hamer dit van bo af terwyl die ring stadig gedraai word totdat gewenste afmetings verkry word. • KNALING: 'n Algemene proses om dele te verbind, begin met 'n reguit metaalstuk wat in voorafgemaakte gate deur die dele geplaas word. Daarna word die twee punte van die metaalstuk gesmee deur die las tussen 'n boonste en onderste matrys in te druk. • ONTWERP : Nog 'n gewilde proses wat deur meganiese pers uitgevoer word, wat groot kragte oor 'n kort afstand uitoefen. Die naam "coining" kom van die fyn besonderhede wat op die oppervlaktes van metaalmunte gesmee word. Dit is meestal 'n afwerkingsproses vir 'n produk waar fyn besonderhede op die oppervlaktes verkry word as gevolg van die groot krag wat die matrys uitoefen wat hierdie besonderhede na die werkstuk oordra. • METAAL BAL SMEE: Produkte soos kogellagers vereis hoë kwaliteit presies vervaardigde metaal balle. In een tegniek genaamd SKEW ROLLING, gebruik ons twee opponerende rolle wat voortdurend roteer terwyl die voorraad voortdurend in die rolle ingevoer word. Aan die een kant van die twee rolle word metaalbolletjies as die produk uitgestoot. 'n Tweede metode vir metaalbal smee is die gebruik van matrijs wat die materiaalvoorraad wat tussen hulle geplaas is, druk en die sferiese vorm van die vormholte neem. Dikwels vereis balle wat vervaardig word 'n paar bykomende stappe soos afwerking en poleer om 'n hoë kwaliteit produk te word. • ISTERMIESE SMEDING / WARMVOORSMEED: 'n Duur proses wat slegs uitgevoer word wanneer die voordeel/kostewaarde geregverdig is. 'n Warm werkproses waar die matrys verhit word tot ongeveer dieselfde temperatuur as die werkstuk. Aangesien beide matrijs en werk ongeveer dieselfde temperatuur is, is daar geen verkoeling nie en word die vloeieienskappe van die metaal verbeter. Die bewerking pas goed by superlegerings en materiale met minderwaardige smeebaarheid en materiale waarvan meganiese eienskappe is baie sensitief vir klein temperatuurgradiënte en veranderinge. • METAALGROOTTE: Dit is 'n koue afwerkingsproses. Materiaalvloei is onbeperk in alle rigtings met die uitsondering van die rigting waarin die krag toegepas word. Gevolglik word baie goeie oppervlakafwerking en akkurate afmetings verkry. • HOË ENERGIE SNEL SMEE: Die tegniek behels 'n boonste vorm wat aan die arm van 'n suier vasgemaak is wat vinnig gedruk word soos 'n brandstof-lugmengsel deur 'n vonkprop aan die brand gesteek word. Dit lyk soos die werking van suiers in 'n motorenjin. Die vorm tref die werkstuk baie vinnig en keer dan baie vinnig terug na sy oorspronklike posisie danksy die terugdruk. Die werk word binne 'n paar millisekondes gesmee en daarom is daar nie tyd vir die werk om af te koel nie. Dit is nuttig vir moeilik om te smee dele wat baie temperatuursensitiewe meganiese eienskappe het. Met ander woorde die proses is so vinnig dat die onderdeel deurgaans onder konstante temperatuur gevorm word en daar sal nie temperatuurgradiënte by die vorm/werkstuk-koppelvlakke wees nie. • In DIE FORGING word metaal tussen twee bypassende staalblokke met spesiale vorms daarin geslaan, wat dies genoem word. Wanneer die metaal tussen die matryse gehamer word, neem dit dieselfde vorm aan as die vorms in die matrys. Wanneer dit sy finale vorm bereik, word dit uitgehaal om af te koel. Hierdie proses produseer sterk dele wat van 'n presiese vorm is, maar vereis 'n groter belegging vir die gespesialiseerde matryse. Ontsteld smee vergroot die deursnee van 'n stuk metaal deur dit plat te maak. Dit word gewoonlik gebruik om klein dele te maak, veral om koppe op hegstukke soos boute en spykers te vorm. • POEIER METALLURGIE / POEIERVERWERKING : Soos die naam aandui, behels dit vervaardigingsprosesse om soliede dele van sekere geometrieë en vorms van poeiers te maak. As metaalpoeiers vir hierdie doel gebruik word, is dit die gebied van poeiermetallurgie en as nie-metaalpoeiers gebruik word, is dit poeierverwerking. Vaste dele word uit poeiers vervaardig deur te druk en te sinter. POEIERPERSING word gebruik om poeiers in gewenste vorms te kompakteer. Eerstens word die primêre materiaal fisies verpoeier, wat dit in baie klein individuele deeltjies verdeel. Poeiermengsel word in die matrijs gevul en 'n pons beweeg na die poeier en verdig dit in die verlangde vorm. Meestal by kamertemperatuur uitgevoer, met poeierpers word 'n soliede deel verkry en dit word groen kompakte genoem. Bindmiddels en smeermiddels word algemeen gebruik om kompakteerbaarheid te verbeter. Ons is in staat om poeierpers te vorm met behulp van hidrouliese perse met 'n paar duisend ton kapasiteit. Ons het ook dubbelaksieperse met opponerende bo- en onderponse sowel as veelvuldige aksieperse vir hoogs komplekse deelgeometrieë. Eenvormigheid wat 'n belangrike uitdaging vir baie poeiermetallurgie-/poeierverwerkingsaanlegte is, is geen groot probleem vir AGS-TECH nie as gevolg van ons uitgebreide ondervinding in die vervaardiging van sulke onderdele vir baie jare. Selfs met dikker dele waar eenvormigheid 'n uitdaging inhou, het ons daarin geslaag. As ons ons tot jou projek verbind, sal ons jou onderdele maak. As ons enige potensiële risiko's sien, sal ons jou inlig in vooraf. POEIERSINTER, wat die tweede stap is, behels die verhoging van temperatuur tot 'n sekere mate en die handhawing van die temperatuur op daardie vlak vir 'n sekere tyd sodat die poeierdeeltjies in die geperste deel saam kan bind. Dit lei tot baie sterker bindings en versterking van die werkstuk. Sintering vind naby die smelttemperatuur van die poeier plaas. Tydens sintering sal krimp plaasvind, materiaalsterkte, digtheid, rekbaarheid, termiese geleidingsvermoë, elektriese geleidingsvermoë word verhoog. Ons het wel bondel- en deurlopende oonde vir sintering. Een van ons vermoëns is om die vlak van porositeit van die dele wat ons vervaardig, aan te pas. Ons is byvoorbeeld in staat om metaalfilters te vervaardig deur die dele tot 'n mate poreus te hou. Deur 'n tegniek genaamd IMPREGNASIE te gebruik, vul ons die porieë in die metaal met 'n vloeistof soos olie. Ons vervaardig wel byvoorbeeld olie-geïmpregneerde laers wat self-smeer is. In die INFILTRASIE-proses vul ons 'n metaal se porieë met 'n ander metaal met 'n laer smeltpunt as die basismateriaal. Die mengsel word verhit tot 'n temperatuur tussen die smelttemperature van die twee metale. As gevolg hiervan kan 'n paar spesiale eienskappe verkry word. Ons doen ook gereeld sekondêre bewerkings soos bewerking en smee op poeiervervaardigde onderdele wanneer spesiale kenmerke of eienskappe verkry moet word of wanneer die onderdeel met minder prosesstappe vervaardig kan word. ISOSTATIESE PERSING: In hierdie proses word vloeistofdruk gebruik om die onderdeel te kompakteer. Metaalpoeiers word in 'n vorm geplaas wat van 'n verseëlde buigsame houer gemaak is. In isostatiese pers word druk van oraloor toegepas, in teenstelling met aksiale druk wat in konvensionele pers gesien word. Die voordele van isostatiese pers is eenvormige digtheid binne die deel, veral vir groter of dikker dele, voortreflike eienskappe. Die nadeel daarvan is lang siklustye en relatief lae meetkundige akkuraatheid. KOUE ISOSTATIESE PERSE word by kamertemperatuur uitgevoer en die buigsame vorm is gemaak van rubber, PVC of uretaan of soortgelyke materiale. Vloeistof wat gebruik word vir druk en verdigting is olie of water. Konvensionele sintering van die groen kompakte volg hierop. WARM ISOSTATIESE PERS word aan die ander kant by hoë temperature uitgevoer en die vormmateriaal is plaatmetaal of keramiek met 'n hoë genoeg smeltpunt wat die temperature weerstaan. Drukvloeistof is gewoonlik 'n inerte gas. Die pers- en sinterbewerkings word in een stap uitgevoer. Poreusheid word feitlik heeltemal uitgeskakel, 'n uniform grainstruktuur word verkry. Die voordeel van warm isostatiese pers is dat dit onderdele kan produseer wat vergelykbaar is met giet en smee gekombineer terwyl materiale wat nie geskik is vir giet en smee, moontlik gemaak word om te gebruik. Nadeel van warm isostatiese pers is die hoë siklustyd en dus koste. Dit is geskik vir kritieke dele van lae volume. METAAL spuitgiet: Baie geskikte proses vir die vervaardiging van komplekse dele met dun wande en gedetailleerde geometrieë. Die meeste geskik vir kleiner dele. Poeiers en polimeerbindmiddel word gemeng, verhit en in 'n vorm ingespuit. Die polimeerbindmiddel bedek die oppervlaktes van die poeierdeeltjies. Na giet, word die bindmiddel verwyder deur óf lae temperatuur verhitting óf opgelos met behulp van 'n oplosmiddel. ROLKOMPAKTASIE / POEIERROL: Poeders word gebruik om aaneenlopende stroke of vel te vervaardig. Poeier word vanaf 'n voerder gevoer en deur twee roterende rolle in vel of stroke saamgepers. Die operasie word koud uitgevoer. Die plaat word in 'n sinteroond ingedra. Die sinterproses kan 'n tweede keer herhaal word. POEIEREKSTRASIE: Onderdele met 'n groot lengte tot deursnee verhoudings word vervaardig deur 'n dun plaatmetaalhouer met poeier uit te druk. LOS SINTERING: Soos die naam aandui, is dit 'n druklose verdigting en sintermetode, geskik vir die vervaardiging van baie poreuse dele soos metaalfilters. Poeier word in die vormholte gevoer sonder om te verdig. LOS SINTERING: Soos die naam aandui, is dit 'n druklose verdigting en sintermetode, geskik vir die vervaardiging van baie poreuse dele soos metaalfilters. Poeier word in die vormholte gevoer sonder om te verdig. VONKSINTERING: Die poeier word in die vorm saamgepers deur twee opponerende pons en 'n hoëkrag elektriese stroom word op die pons toegedien en gaan deur die gekompakteerde poeier wat tussen hulle ingedruk is. Die hoë stroom brand oppervlakfilms van die poeierdeeltjies weg en sinter dit met die hitte wat gegenereer word. Die proses is vinnig omdat hitte nie van buite toegedien word nie, maar eerder van binne die vorm gegenereer word. WARMPERSING: Die poeiers word in 'n enkele stap gedruk en gesinter in 'n vorm wat die hoë temperature kan weerstaan. Soos die matrys verdig word, word die poeierhitte daarop toegepas. Goeie akkuraatheid en meganiese eienskappe wat deur hierdie metode verkry word, maak dit 'n aantreklike opsie. Selfs vuurvaste metale kan verwerk word deur vormmateriaal soos grafiet te gebruik. CLICK Product Finder-Locator Service VORIGE SPYSKAART
- Sheet Metal Forming Fabrication, Stamping, Punching, Deep Drawing, CNC
Sheet Metal Forming and Fabrication, Stamping, Punching, Bending, Progressive Die, Spot Welding, Deep Drawing, Metal Blanking and Slitting at AGS-TECH Inc. Stempels en plaatmetaalvervaardiging Ons bied plaatmetaal stempel, vorming, vorming, buig, pons, uitbrei, sny, gate, kerf, knibbel, skeer, persbewerking, vervaardiging, dieptrek deur gebruik te maak van enkelpons-/enkelslag-matryse sowel as progressiewe matryse en spin, rubbervorming en hidrovorming; plaatmetaal sny met waterstraal, plasma, laser, saag, vlam; plaatmetaalsamestelling met behulp van sweiswerk, puntsweiswerk; plaatmetaalbuis wat bult en buig; plaatmetaal oppervlakafwerking insluitend dip- of spuitverf, elektrostatiese poeierbedekking, anodisering, platering, sputtering en meer. Ons dienste wissel van vinnige plaatmetaalprototipering tot hoëvolume-vervaardiging. Ons beveel aan dat jy hier klik omLaai ons skematiese illustrasies van plaatmetaalvervaardiging en stempelprosesse af deur AGS-TECH Inc. Dit sal jou help om die inligting wat ons hieronder verskaf, beter te verstaan. • PLAATSNYE: Ons bied AFSNIJINGS en SKEIDINGS. Afsnypunte sny die plaatmetaal oor een paadjie op 'n slag en daar is basies geen vermorsing van materiaal nie, terwyl met skeidings die vorm nie presies genestel kan word nie en daarom word sekere hoeveelheid materiaal vermors. Een van ons gewildste prosesse is PONSEN, waar 'n stuk materiaal rond of ander vorm uit plaatmetaal uitgesny word. Die stuk wat uitgesny word, is afval. Nog 'n weergawe van pons is SLOTTING, waar reghoekige of langwerpige gate gepons word. BLANKING aan die ander kant is dieselfde proses as pons, met die onderskeid van die stuk wat uitgesny word, is die werk en word gehou. FYN BLANKING, 'n voortreflike weergawe van blanking, skep snitte met noue toleransies en reguit gladde kante en vereis nie sekondêre bewerkings vir perfeksie van die werkstuk nie. Nog 'n proses wat ons gereeld gebruik, is SLITTING, wat 'n skeerproses is waar plaatmetaal deur twee teenoorstaande sirkelvormige lemme in 'n reguit of geboë pad gesny word. Blikopener is 'n eenvoudige voorbeeld van die snyproses. Nog 'n gewilde proses vir ons is PERFORERING, waar baie gate rond of ander vorm in plaatmetaal in 'n sekere patroon gepons word. 'n Tipiese voorbeeld vir 'n geperforeerde produk is metaalfilters met baie gate vir vloeistowwe. In NOTCHING, nog 'n plaatmetaal snyproses, verwyder ons materiaal van 'n werkstuk, begin by die rand of elders en sny na binne totdat die verlangde vorm verkry is. Dit is 'n progressiewe proses waar elke bewerking nog 'n stuk verwyder totdat die verlangde kontoer verkry is. Vir klein produksielopies gebruik ons soms 'n relatief stadiger proses genaamd NIBBLING wat bestaan uit baie vinnige pons van oorvleuelende gate om 'n groter meer komplekse snit te maak. In PROGRESSIEWE SNYE gebruik ons 'n reeks verskillende bewerkings om 'n enkele snit of 'n sekere geometrie te verkry. Ten slotte help SKEER 'n sekondêre proses ons om rande van snitte wat reeds gemaak is, te verbeter. Dit word gebruik vir die afsny van die skyfies, growwe kante op plaatwerk. • BLAATBUIG : Behalwe sny, is buiging 'n noodsaaklike proses waarsonder ons nie die meeste produkte sou kon produseer nie. Meestal 'n koue werksoperasie, maar soms ook uitgevoer wanneer dit warm of warm is. Ons gebruik die meeste van die tyd matrys en pers vir hierdie operasie. In PROGRESSIEWE BUIG gebruik ons 'n reeks verskillende pons- en matrijsbewerkings om 'n enkele buiging of 'n sekere geometrie te verkry. AGS-TECH gebruik 'n verskeidenheid buigprosesse en maak die keuse na gelang van die werkstukmateriaal, sy grootte, dikte, gewenste grootte van buiging, radius, kromming en buighoek, ligging van buiging, ekonomie van werking, hoeveelhede wat vervaardig moet word ... ens. Ons gebruik V-BENDING waar 'n V-vormige pons die plaatmetaal in die V-vormige matrys dwing en dit buig. Goed vir beide baie skerp en stomp hoeke en tussenin, insluitend 90 grade. Deur gebruik te maak van afvee-matrye doen ons RANDBUIGING. Ons toerusting stel ons in staat om hoeke selfs groter as 90 grade te verkry. In randbuiging word die werkstuk tussen 'n drukkussing en die matrys ingeklem, die area vir buiging is op die matrysrand geleë en die res van die werkstuk word oor space gehou soos 'n vrykragbalk. Wanneer die pons op die cantilever-gedeelte inwerk, word dit oor die rand van die dobbelsteen gebuig. FLANGE is 'n randbuigproses wat 'n hoek van 90 grade tot gevolg het. Hoofdoelwitte van die operasie is die uitskakeling van skerp kante en die verkryging van geometriese oppervlaktes om die aansluiting van dele te vergemaklik. KRALERING, 'n ander algemene randbuigproses vorm 'n krul oor 'n deel se rand. SOMING aan die ander kant lei tot 'n rand van die laken wat heeltemal oor homself gebuig is. In SAMING word die rande van twee dele op mekaar gebuig en saamgevoeg. DUBBELNAAT daarenteen verskaf waterdigte en lugdigte plaatmetaalverbindings. Soortgelyk aan randbuiging, ontplooi 'n proses genaamd ROTARY BENDING 'n silinder met die verlangde hoek wat uitgesny is en dien as die pons. Soos die krag na die pons oorgedra word, sluit dit met die werkstuk. Die groef van die silinder gee die vrykraggedeelte die verlangde hoek. Die groef kan 'n hoek kleiner of groter as 90 grade hê. In AIR BENDING het ons nie die onderste matrijs nodig om 'n hoekige groef te hê nie. Die plaatmetaal word ondersteun deur twee oppervlaktes aan teenoorgestelde kante en op 'n sekere afstand. Die pons oefen dan 'n krag op die regte plek uit en buig die werkstuk. KANAALBUIG word uitgevoer met behulp van 'n kanaalvormige pons en matrijs, en U-BUIG word verkry met 'n U-vormige pons. OFFSET BENDING produseer afwykings op die plaatmetaal. ROLBUIG, 'n tegniek wat goed is vir dik werk en buig van groot stukke metaalplate, gebruik drie rolle om die plate tot gewenste krommings te voer en te buig. Rolle word so gerangskik dat die gewenste buiging van die werk verkry word. Die afstand en hoek tussen die rolle word beheer om die gewenste uitkoms te verkry. 'n Beweegbare rol maak dit moontlik om die kromming te beheer. BUISVORMING is nog 'n gewilde plaatmetaalbuigoperasie wat veelvuldige matryse behels. Buise word verkry na verskeie aksies. CORRUGATION word ook uitgevoer deur buigbewerkings. Basies is dit die simmetriese buiging met gereelde tussenposes oor 'n hele stuk plaatmetaal. Verskeie vorms kan gebruik word vir geriffel. Geriffelde plaatmetaal is meer rigied en het beter weerstand teen buiging en het dus toepassings in die konstruksiebedryf. BLAATROLVORMING, 'n aaneenlopende vervaardigingsproses word ontplooi om deursnee van 'n sekere geometrie met behulp van rolle te buig en die werk word in opeenvolgende stappe gebuig, met die finale rol wat die werk voltooi. In sommige gevalle word 'n enkele rol en in sommige gevalle 'n reeks rolle gebruik. • GEKOMBINEERDE PLAAT SNY- EN BUIGPROSESSE : Dit is die prosesse wat gelyktydig sny en buig. In PIERCING word 'n gat met 'n puntige pons geskep. Soos die pons die gat in die plaat verbreed, word die materiaal gelyktydig in 'n interne flens vir die gat gebuig. Die flens wat verkry word, kan belangrike funksies hê. Die LANSING-operasie aan die ander kant sny en buig die plaat om 'n verhoogde geometrie te skep. • METAALBUIS BULLING EN BUIG: In BULLING word 'n interne deel van 'n hol buis onder druk geplaas, wat veroorsaak dat die buis na buite bult. Aangesien die buis binne 'n matrys is, word die bultgeometrie deur die vorm van die matrys beheer. In STREKBUIG word 'n metaalbuis gestrek deur kragte parallel met die buis se as en buigkragte te gebruik om die buis oor 'n vormblok te trek. In DRAW BENDING, klem ons die buis naby sy einde vas aan 'n roterende vormblok wat die buis buig terwyl dit roteer. Laastens, in KOMPRESSIEBUIGING word die buis met krag aan 'n vaste vormblok vasgehou, en 'n matrys buig dit oor die vormblok. • DIEPTEKENING : In een van ons gewildste bewerkings word 'n pons, 'n bypassende dobbelsteen en 'n leë houer gebruik. Die plaatmetaalblanko word oor die matrysopening geplaas en die pons beweeg na die blanko wat deur die blankohouer gehou word. Sodra hulle in aanraking kom, dwing die pons die plaatmetaal in die matrysholte om die produk te vorm. Dieptrekbewerking lyk soos sny, maar die speling tussen die pons en matrijs verhoed egter dat die plaat gesny word. Nog 'n faktor wat verseker dat die plaat diep getrek en nie gesny is nie, is die afgeronde hoeke op die matrys en pons wat die skeer en sny verhoed. Om 'n groter omvang van dieptrek te bereik, word 'n HERTEKEN-proses ontplooi waar 'n daaropvolgende dieptrekking plaasvind op 'n deel wat reeds 'n dieptrekproses ondergaan het. In REVERSE HERTEKEN, word die diepgetekende deel omgedraai en in die teenoorgestelde rigting geteken. Diep tekening kan onreëlmatige gevormde voorwerpe verskaf soos koepelvormige, tapse of getrapte koppies, In reliëf gebruik ons 'n manlike en vroulike stempelpaar om die plaatmetaal met 'n ontwerp of skrif te beïndruk. • SPINNING : 'n Bewerking waar 'n plat of voorafgevormde werkstuk tussen 'n roterende deur en stertstok gehou word en 'n werktuig plaas gelokaliseerde druk op die werk toe dit geleidelik op die deurn beweeg. As gevolg hiervan word die werkstuk oor die deurn toegedraai en neem sy vorm aan. Ons gebruik hierdie tegniek as 'n alternatief vir dieptrek waar die hoeveelheid van 'n bestelling klein is, die dele groot is (deursnee tot 20 voet) en unieke kurwes het. Alhoewel die pryse per stuk oor die algemeen hoër is, is die opstelkoste vir CNC-spinbewerking laag in vergelyking met dieptrek. Inteendeel, dieptrek vereis hoë aanvanklike investering vir opstelling, maar die koste per stuk is laag wanneer 'n groot hoeveelheid onderdele vervaardig word. Nog 'n weergawe van hierdie proses is SHEAR SPINNING, waar daar ook metaalvloei binne die werkstuk is. Die metaalvloei sal die dikte van die werkstuk verminder soos die proses uitgevoer word. Nog 'n verwante proses is TUBE SPINNING, wat op silindiriese dele toegepas word. Ook in hierdie proses is daar metaalvloei binne die werkstuk. Die dikte word dus verminder en die buis se lengte word vergroot. Die instrument kan geskuif word om kenmerke aan die binnekant of buitekant van die buis te skep. • RUBBERVORMING VAN BLAAT : Rubber of poliuretaan materiaal word in 'n houer gesit en die werkstuk word op die oppervlak van die rubber geplaas. 'n Pons word dan op die werkstuk ingewerk en dwing dit in die rubber in. Aangesien die druk wat deur die rubber gegenereer word laag is, is die diepte van dele wat vervaardig word, beperk. Aangesien gereedskapskoste laag is, is die proses geskik vir lae hoeveelheid produksie. • HIDROVORMING: Soortgelyk aan rubbervorming, word plaatmetaalwerk in hierdie proses deur 'n pons in 'n vloeistof onder druk in 'n kamer gedruk. Die plaatmetaalwerk is tussen die pons en 'n rubberdiafragma ingeklem. Die diafragma omring die werkstuk heeltemal en die druk van die vloeistof dwing dit om op die pons te vorm. Baie dieptrekkings kan selfs dieper as in die dieptrekproses verkry word met hierdie tegniek. Ons vervaardig enkelpons-matryse sowel as progressiewe matryse, afhangende van jou deel. Enkelslag-stempels is 'n koste-effektiewe metode om groot hoeveelhede eenvoudige plaatmetaalonderdele soos wassers vinnig te vervaardig. Progressiewe matryse of die dieptrektegniek word gebruik vir die vervaardiging van meer komplekse geometrieë. Afhangende van jou geval, kan waterstraal-, laser- of plasmasnywerk gebruik word om jou plaatmetaalonderdele goedkoop, vinnig en akkuraat te vervaardig. Baie verskaffers het geen idee van hierdie alternatiewe tegnieke nie of het dit nie en daarom gaan hulle deur lang en duur maniere om stempels en gereedskap te maak wat net tyd en geld vir kliënte mors. As jy pasgemaakte plaatmetaal komponente soos omhulsels, elektroniese omhulsels ... ens so vinnig as binne dae benodig, kontak ons dan vir ons SNELLE PLAT METAL PROTOTIPING diens. CLICK Product Finder-Locator Service VORIGE SPYSKAART
- Plastic Rubber Metal Extrusions, Extrusion Dies, Aluminum Extruding
Plastic Rubber Metal Extrusions, Extrusion Dies, Aluminum Extruding, Pipe Tube Forming, Plastic Profiles, Metal Profiles Manufacturing, PVC at AGS-TECH Inc. Ekstrusies, Ekstrusieprodukte, Ekstrudate Ons gebruik die EXTRUSION proses om produkte met 'n vaste deursneeprofiel soos buise, pype en hitte-afdakke te vervaardig. Selfs al kan baie materiale geëxtrudeer word, is ons mees algemene ekstrusies gemaak van metaal, polimere / plastiek, keramiek verkry deur óf koue, warm of warm ekstrusie metode. Ons noem die geëxtrudeerde dele ekstrudate of ekstrudate indien meervoud. Sommige gespesialiseerde weergawes van die proses wat ons ook uitvoer, is oorkapping, koëkstrusie en saamgestelde ekstrusie. Ons beveel aan dat jy hier klik om Laai ons skematiese illustrasies van metaalkeramiek- en plastiek-ekstrusieprosesse af deur AGS-TECH Inc. Dit sal jou help om die inligting wat ons hieronder verskaf, beter te verstaan. In ekstrusie word materiaal wat geëkstrueer moet word deur 'n matrys gedruk of getrek wat die verlangde deursneeprofiel het. Die proses kan gebruik word om komplekse deursnee met uitstekende oppervlakafwerking te vervaardig en om op bros materiaal te werk. 'n Mens kan enige lengte onderdele vervaardig deur hierdie proses te gebruik. Om die prosesstappe te vereenvoudig: 1.) In warm of warm ekstrusies word die materiaal verhit en in 'n houer in die pers gelaai. Die materiaal word gedruk en uit die matrys gedruk. 2.) Geproduseerde ekstrudaat word gestrek vir reguit, hittebehandel of koud gewerk om die eienskappe daarvan te verbeter. Aan die ander kant vind COLD EXTRUSION plaas by ongeveer kamertemperatuur en het die voordele van minder goeie oksidasie-sterkte, hoë oksidasie-sterkte, hoë afwerkingsvermoë. WARM EKSTRUSIE word bo kamertemperatuur maar onder herkristallisasiepunt uitgevoer. Dit bied 'n kompromie en balans vir vereiste kragte, rekbaarheid en materiaal eienskappe en is dus die keuse vir sommige toepassings. HOT EXTRUSION vind bo die materiaal se herkristallisasietemperatuur plaas. Op hierdie manier is dit makliker om die materiaal deur die matrys te druk. Die koste van toerusting is egter hoog. Hoe meer kompleks 'n geëxtrudeerde profiel is, hoe duurder is die matrys (gereedskap) en hoe laer is die produksietempo. Die matrysdwarssnitte sowel as diktes het beperkings wat afhang van die materiaal wat geëxtrudeer moet word. Skerp hoeke in ekstrusie-matryse is altyd ongewens en moet vermy word, tensy dit nodig is. Volgens die materiaal wat geëxtrudeer word, bied ons: • METAL EXTRUSIONS : Mees algemene wat ons vervaardig is aluminium, koper, sink, koper, staal, titanium, magnesium • PLASTIEK EKSTRUSIE : Plastiek word gesmelt en tot 'n aaneenlopende profiel gevorm. Ons algemene verwerkte materiale is poliëtileen, nylon, polistireen, polivinielchloried, polipropileen, ABS-plastiek, polikarbonaat, akriel. Tipiese produkte wat ons vervaardig sluit in pype en buise, plastiekrame. In die proses word klein plastiekkraletjies / hars deur swaartekrag gevoer vanaf die bak in die vat van die ekstrusiemasjien. Dikwels meng ons ook kleurmiddels of ander bymiddels in die bak om die produk die vereiste spesifikasies en eienskappe te gee. Die materiaal wat die verhitte loop binnegaan, word deur die roterende skroef gedwing om die loop aan die einde te verlaat en deur die skermpak te beweeg vir die verwydering van kontaminante in die gesmelte plastiek. Nadat die skermpak verby is, gaan die plastiek in die ekstrusie-matrys. Die matrys gee die bewegende sagte plastiek sy profielvorm soos dit daardeur beweeg. Nou gaan die ekstrudate deur 'n waterbad vir afkoeling. Ander tegnieke wat AGS-TECH Inc. al vir baie jare gebruik, is: • PIPE & TUBING EXTRUSION : Plastiekpype en -buise word gevorm wanneer plastiek deur 'n ronde vormvorm geëkstrueer word en in 'n waterbad afgekoel word, dan in lengte gesny of opgerol/gespoel word. Helder of gekleurd, gestreep, enkel- of dubbelwand, buigsaam of styf, PE, PP, poliuretaan, PVC, nylon, PC, silikoon, viniel of anders, ons het dit alles. Ons het voorraadbuise sowel as die vermoë om volgens u spesifikasies te vervaardig. AGS-TECH vervaardig buise volgens FDA-, UL- en LE-vereistes vir mediese, elektriese en elektroniese, industriële en ander toepassings. • OVERJACKETING / OVER JACKETING EXTRUSION : Hierdie tegniek pas 'n buitenste laag plastiek op bestaande draad of kabel aan. Ons isolasiedrade word met hierdie metode vervaardig. • COEXTRUSION : Veelvuldige lae materiaal word gelyktydig geëxtrudeer. Die veelvuldige lae word deur verskeie ekstrueerders gelewer. Die verskillende laagdiktes kan aangepas word om aan klante se spesifikasies te voldoen. Hierdie proses maak dit moontlik om veelvuldige polimere te gebruik wat elk 'n ander funksionaliteit in die produk het. Gevolglik kan 'n mens 'n reeks eienskappe optimaliseer. • VERBONDE EKSTRUSIE: 'n Enkele of meervoudige polimere word met bymiddels gemeng om 'n plastiese verbinding te verkry. Ons dubbelskroef-ekstruders produseer saamgestelde ekstrusies. Ekstrusie-matryse is oor die algemeen goedkoop in vergelyking met metaalvorms. As jy baie meer as 'n paar duisend dollar betaal vir 'n klein of medium grootte ekstrusie-matrys wat aluminium uitdruk, betaal jy waarskynlik te veel. Ons is kundiges in die bepaling van watter tegniek die mees koste-effektiewe, vinnigste en mees geskikte vir jou toepassing is. Soms kan u baie kontant bespaar om 'n onderdeel uit te druk en dan te bewerk. Voordat jy 'n vaste besluit neem, vra ons eers ons mening. Ons het baie kliënte gehelp om die regte besluite te neem. Vir sommige wydgebruikte metaalekstrusies, kan jy ons brosjures en katalogusse aflaai deur op die gekleurde teks hieronder te klik. As dit 'n produk van die rak is wat aan jou vereistes voldoen, sal dit meer ekonomies wees. Laai ons mediese buis- en pyp-ekstruderingsvermoëns af Laai ons geëxtrudeerde heatsinks af • SEKONDÊRE VERVAARDIGING- EN VERVAARDIGINGSPROSESSE VIR EKSTRUSIES : Onder waardetoegevoegde prosesse wat ons vir geëxtrudeerde produkte bied, is: - Pasgemaakte buis- en pypbuiging, vorming en vorming, buisafsny, buiseindevorming, buisoprol, bewerking en afwerking, gatboor & deurboor en pons, - Pasgemaakte pyp-en-buissamestellings, buissamestelling, sweiswerk, soldering en soldering - Pasgemaakte ekstrusiebuiging, vorming en vorming -Skoonmaak, ontvet, beits, passivering, poleer, anodisering, platering, verf, hittebehandeling, uitgloeiing en verharding, merk, gravering en etikettering, persoonlike verpakking. CLICK Product Finder-Locator Service VORIGE BLADSY
- Casting and Machined Parts, CNC Manufacturing, Milling, Turning, Swiss
Casting and Machined Parts, CNC Manufacturing, Milling, Turning, Swiss Type Machining, Die Casting, Investment Casting, Lost Foam Cast Parts from AGS-TECH Inc. Giet en bewerking Ons pasgemaakte giet- en bewerkingstegnieke is verbruikbare en nie-vergooibare gietstukke, yster- en nie-ysterhoudende gietwerk, sand, matrijs, sentrifugale, deurlopende, keramiekvorm, belegging, verlore skuim, amper-netvorm, permanente vorm (gravitasiegietwerk), gips vorm (gipsgietwerk) en dopgietstukke, gemasjineerde onderdele vervaardig deur maal en draai met gebruik van konvensionele sowel as CNC-toerusting, Switserse tipe bewerking vir hoë deurset goedkoop klein presisieonderdele, skroefbewerking vir hegstukke, nie-konvensionele bewerking. Hou asseblief in gedagte dat ons, behalwe metale en metaallegerings, ook keramiek-, glas- en plastiekkomponente in sommige gevalle bewerk wanneer die vervaardiging van 'n vorm nie aanloklik of nie die opsie is nie. Die bewerking van polimeermateriale vereis die gespesialiseerde ervaring wat ons het as gevolg van die uitdaging wat plastiek en rubber bied as gevolg van hul sagtheid, nie-styfheid ... ens. Vir die bewerking van keramiek en glas, sien asseblief ons bladsy oor nie-konvensionele vervaardiging. AGS-TECH Inc. vervaardig en verskaf beide liggewig en swaar gietstukke. Ons verskaf metaalgietsels en gemasjineerde onderdele vir ketels, hitteruilers, motors, mikromotors, windturbines, voedselverpakkingstoerusting en meer. Ons beveel aan dat jy hier klik om Laai ons skematiese illustrasies van bewerking en gietprosesse af deur AGS-TECH Inc. Dit sal jou help om die inligting wat ons hieronder verskaf, beter te verstaan. Kom ons kyk in detail na sommige van die verskillende tegnieke wat ons aanbied: • VERBRUIKBARE VORMGIETEN: Hierdie breë kategorie verwys na metodes wat tydelike en nie-herbruikbare vorms behels. Voorbeelde is sand, gips, dop, belegging (ook genoem verlore-was) en gipsgieting. • SANDGOOI : 'n Proses waar sand as die vormmateriaal gebruik word. 'n Baie ou metode en steeds baie gewild in die mate dat die meeste metaalgietstukke wat vervaardig word deur hierdie tegniek gemaak word. Lae koste selfs by lae hoeveelheid produksie. Geskik vir die vervaardiging van klein en groot onderdele. Die tegniek kan gebruik word om onderdele binne dae of weke te vervaardig met baie min belegging. Die klam sand word met klei, bindmiddels of spesiale olies aan mekaar gebind. Sand word gewoonlik in vormbokse vervat en holte- en hekstelsel word geskep deur die sand rondom modelle te verdig. Die prosesse is: 1.) Plaas van die model in sand om die vorm te maak 2.) Inkorporering van model en sand in 'n hekstelsel 3.) Verwydering van model 4.) Vul van vormholte met gesmelte metaal 5.) Verkoeling van die metaal 6.) Breek die sandvorm en verwydering van die gietstuk • GIPSVORMGOOI : Soortgelyk aan sandgietwerk, en in plaas van sand word gips van paris as die vormmateriaal gebruik. Kort produksietydperke soos sandgieting en goedkoop. Goeie dimensionele toleransies en oppervlakafwerking. Die grootste nadeel daarvan is dat dit slegs met lae-smeltpuntmetale soos aluminium en sink gebruik kan word. • DOPVORMGOOI : Ook soortgelyk aan sandgietwerk. Vormholte verkry deur geharde dop van sand en termohardende harsbindmiddel in plaas van fles gevul met sand soos in die sandgietproses. Byna enige metaal wat geskik is om met sand gegiet te word, kan deur dopgietwerk gegiet word. Die proses kan opgesom word as: 1.) Vervaardiging van die dopvorm. Sand wat gebruik word, het 'n baie kleiner korrelgrootte in vergelyking met sand wat in sandgietwerk gebruik word. Die fyn sand word met termohardende hars gemeng. Die metaalpatroon is bedek met 'n skeidingsmiddel om die verwydering van die dop makliker te maak. Daarna word die metaalpatroon verhit en die sandmengsel word gepor of op die warm gietpatroon geblaas. ’n Dun dop vorm op die oppervlak van die patroon. Die dikte van hierdie dop kan aangepas word deur die tydsduur wat die sandharsmengsel in kontak is met die metaalpatroon te verander. Die los sand word dan verwyder met die dop bedekte patroon oor. 2.) Vervolgens word die dop en patroon in 'n oond verhit sodat die dop hard word. Nadat verharding voltooi is, word die dop uit die patroon gegooi met behulp van penne wat in die patroon ingebou is. 3.) Twee sulke skulpe word saamgevoeg deur vas te plak of vas te klamp en maak die volledige vorm op. Nou word die dopvorm in 'n houer geplaas waarin dit tydens die gietproses deur sand of metaalskoot ondersteun word. 4.) Nou kan die warm metaal in die dopvorm gegooi word. Voordele van dopgietwerk is produkte met baie goeie oppervlakafwerking, moontlikheid om komplekse dele met hoë dimensionele akkuraatheid te vervaardig, proses maklik om te outomatiseer, ekonomies vir groot volume produksie. Nadele is dat die vorms goeie ventilasie noodsaak as gevolg van gasse wat geskep word wanneer gesmelte metaal die bindmiddelchemikalieë in aanraking kom, die termohardende harse en metaalpatrone is duur. As gevolg van die koste van metaalpatrone, kan die tegniek dalk nie goed pas vir lae hoeveelhede produksielopies nie. • BELEGGINGSGIETEN (ook bekend as LOST-WAX CASTING): Ook 'n baie ou tegniek en geskik vir die vervaardiging van kwaliteit onderdele met hoë akkuraatheid, herhaalbaarheid, veelsydigheid en integriteit van baie metale, vuurvaste materiale en spesiale hoë werkverrigting legerings. Klein sowel as groot grootte dele kan vervaardig word. 'n Duur proses in vergelyking met sommige van die ander metodes, maar groot voordeel is die moontlikheid om onderdele met byna netto vorm, ingewikkelde kontoere en besonderhede te vervaardig. Die koste word dus ietwat geneutraliseer deur die uitskakeling van herbewerking en bewerking in sommige gevalle. Selfs al kan daar variasies wees, is hier 'n opsomming van die algemene beleggingsbepalingsproses: 1.) Skep van oorspronklike meesterpatroon van was of plastiek. Elke gietstuk benodig een patroon aangesien dit in die proses vernietig word. Vorm waaruit patrone vervaardig word, is ook nodig en die vorm word meestal gegiet of gemasjineer. Omdat die vorm nie oopgemaak hoef te word nie, kan komplekse gietwerk verkry word, baie waspatrone kan soos die takke van 'n boom verbind word en saam gegiet word, wat die vervaardiging van veelvuldige dele moontlik maak uit 'n enkele giet van die metaal of metaallegering. 2.) Vervolgens word die patroon gedoop of oorgegooi met 'n vuurvaste suspensie wat bestaan uit baie fynkorrelige silika, water, bindmiddels. Dit lei tot 'n keramieklaag oor die oppervlak van die patroon. Die vuurvaste laag op patroon word gelaat om droog te word en hard te word. Hierdie stap is waar die naam beleggingsgietwerk vandaan kom: Vuurvaste suspensie word oor die waspatroon belê. 3.) By hierdie stap word die verharde keramiekvorm onderstebo gedraai en verhit sodat die was smelt en uit die vorm giet. ’n Holte word agtergelaat vir die metaalgietwerk. 4.) Nadat die was uit is, word die keramiekvorm verhit tot selfs 'n hoër temperatuur wat lei tot versterking van die vorm. 5.) Metaal giet word in die warm vorm gegooi wat alle ingewikkelde afdelings vul. 6.) Gietwerk word toegelaat om te stol 7.) Uiteindelik word die keramiekvorm gebreek en vervaardigde dele word van die boom gesny. Hier is 'n skakel na Investment Casting Plant Brochure • VERDAMPINGSPATROON GIET : Die proses gebruik 'n patroon wat gemaak is van 'n materiaal soos polistireenskuim wat sal verdamp wanneer warm gesmelte metaal in die vorm gegooi word. Daar is twee tipes van hierdie proses: VERLORE KUIM GIETEN wat ongebonde sand gebruik en VOLVORMIGE GIETEN wat gebonde sand gebruik. Hier is die algemene prosesstappe: 1.) Vervaardig die patroon van 'n materiaal soos polistireen. Wanneer groot hoeveelhede vervaardig sal word, word die patroon gevorm. As deel 'n komplekse vorm het, moet verskeie dele van sulke skuimmateriaal aanmekaar geplak word om die patroon te vorm. Ons bedek die patroon dikwels met 'n vuurvaste verbinding om 'n goeie oppervlakafwerking op die gietstuk te skep. 2.) Die patroon word dan in vormsand gesit. 3.) Die gesmelte metaal word in die vorm gegooi, wat die skuimpatroon, dws polistireen in die meeste gevalle, verdamp soos dit deur die vormholte vloei. 4.) Die gesmelte metaal word in die sandvorm gelaat om hard te word. 5.) Nadat dit verhard is, verwyder ons die gietstuk. In sommige gevalle vereis die produk wat ons vervaardig 'n kern binne die patroon. In verdampingsgietwerk is dit nie nodig om 'n kern in die vormholte te plaas en vas te maak nie. Die tegniek is geskik vir die vervaardiging van baie komplekse geometrieë, dit kan maklik geoutomatiseer word vir hoë volume produksie, en daar is geen skeidingslyne in die gegote deel nie. Die basiese proses is eenvoudig en ekonomies om te implementeer. Vir groot volume produksie, aangesien 'n matrys of vorm nodig is om die patrone van polistireen te vervaardig, kan dit ietwat duur wees. • NIE-UITBREIDBARE VORMGIETEN: Hierdie breë kategorie verwys na metodes waar die vorm nie na elke produksiesiklus hervorm hoef te word nie. Voorbeelde is permanente, matrijs, deurlopende en sentrifugale giet. Herhaalbaarheid word verkry en dele kan as NABY NETVORM gekarakteriseer word. • PERMANENTE VORMGOOIE : Herbruikbare vorms gemaak van metaal word vir veelvuldige gietwerk gebruik. ’n Permanente vorm kan oor die algemeen vir tienduisende kere gebruik word voordat dit verslyt. Swaartekrag, gasdruk of vakuum word gewoonlik gebruik om die vorm te vul. Vorms (ook genoem matrijs) word gewoonlik gemaak van yster, staal, keramiek of ander metale. Die algemene proses is: 1.) Bewerk en skep die vorm. Dit is algemeen om die vorm te masjineer uit twee metaalblokke wat bymekaar pas en oop en toegemaak kan word. Beide die deelkenmerke sowel as die hekstelsel word gewoonlik in die gietvorm gemasjineer. 2.) Die interne vormoppervlaktes is bedek met 'n suspensie wat vuurvaste materiale insluit. Dit help om hittevloei te beheer en dien as 'n smeermiddel vir maklike verwydering van die gegote deel. 3.) Vervolgens word die permanente vormhelftes toegemaak en die vorm verhit. 4.) Gesmelte metaal word in vorm gegooi en laat stil word vir stolling. 5.) Voordat baie afkoeling plaasvind, verwyder ons die deel uit permanente vorm met uitwerpers wanneer vormhelftes oopgemaak word. Ons gebruik gereeld permanente gietvorm vir lae smeltpunt metale soos sink en aluminium. Vir staalgietstukke gebruik ons grafiet as vormmateriaal. Ons verkry soms komplekse geometrieë deur kerns binne permanente vorms te gebruik. Voordele van hierdie tegniek is gietstukke met goeie meganiese eienskappe wat verkry word deur vinnige verkoeling, eenvormigheid in eienskappe, goeie akkuraatheid en oppervlakafwerking, lae verwerpingstempo's, moontlikheid om die proses te outomatiseer en hoë volumes ekonomies te produseer. Nadele is hoë aanvanklike opstelkoste wat dit ongeskik maak vir lae volume bedrywighede, en beperkings op die grootte van die onderdele wat vervaardig word. • STERFGOOI: 'n Matrys word gemasjineer en gesmelte metaal word onder hoë druk in vormholtes ingedruk. Beide nie-ysterhoudende sowel as ysterhoudende metaal gietvorms is moontlik. Die proses is geskik vir groot hoeveelhede produksielopies van klein tot mediumgrootte dele met besonderhede, uiters dun mure, dimensionele konsekwentheid en goeie oppervlakafwerking. AGS-TECH Inc. is in staat om wanddiktes van so klein as 0,5 mm te vervaardig deur hierdie tegniek te gebruik. Soos in permanente gietvorm, moet die vorm uit twee helftes bestaan wat kan oop- en toemaak vir die verwydering van geproduseerde deel. 'n Gietvorm kan veelvuldige holtes hê om produksie van veelvuldige gietstukke met elke siklus moontlik te maak. Die gietvorms is baie swaar en baie groter as die onderdele wat hulle vervaardig, dus ook duur. Ons herstel en vervang verslete stempels gratis vir ons kliënte solank hulle hul onderdele by ons herbestel. Ons matryse het lang lewenstye in die reeks van honderdduisende siklusse. Hier is die basiese vereenvoudigde prosesstappe: 1.) Produksie van die vorm oor die algemeen van staal 2.) Vorm geïnstalleer op die gietmasjien 3.) Die suier dwing gesmelte metaal om in die matrysholtes te vloei en vul die ingewikkelde kenmerke en dun wande uit 4.) Nadat die vorm met die gesmelte metaal gevul is, word die gietstuk onder druk laat verhard 5.) Vorm word oopgemaak en gietstuk verwyder met behulp van uitwerppenne. 6.) Nou word die leë matrys weer gesmeer en geklem vir die volgende siklus. In die gietvorm gebruik ons gereeld insetvormwerk waar ons 'n bykomende deel in die vorm inkorporeer en die metaal daarom giet. Na stolling word hierdie dele deel van die gegote produk. Voordele van gietwerk is goeie meganiese eienskappe van die onderdele, moontlikheid van ingewikkelde kenmerke, fyn besonderhede en goeie oppervlakafwerking, hoë produksietempo's, maklike outomatisering. Nadele is: Nie baie geskik vir lae volume nie as gevolg van hoë matrys en toerustingkoste, beperkings in vorms wat gegiet kan word, klein ronde merke op gegote dele as gevolg van kontak van uitwerppenne, dun flits metaal wat by die skeilyn uitgedruk word, benodig vir vents langs die skeilyn tussen die matrys, noodsaaklikheid om vorm temperature laag te hou met behulp van water sirkulasie. • SENTRIFUGALE GOOI: Gesmelte metaal word in die middel van die roterende vorm by die rotasie-as gegooi. Sentrifugale kragte gooi die metaal na die omtrek en dit word laat stol soos die vorm aanhou draai. Beide horisontale en vertikale asrotasies kan gebruik word. Onderdele met ronde binneoppervlakke sowel as ander nie-ronde vorms kan gegiet word. Die proses kan opgesom word as: 1.) Gesmelte metaal word in sentrifugale vorm gegooi. Die metaal word dan na die buitenste mure gedwing as gevolg van spin van die vorm. 2.) Soos die vorm draai, verhard die metaalgietsel Sentrifugale gietwerk is 'n geskikte tegniek vir die vervaardiging van hol silindiriese dele soos pype, geen behoefte aan spruite, stygings en hekelemente nie, goeie oppervlakafwerking en gedetailleerde kenmerke, geen krimpprobleme, moontlikheid om lang pype met baie groot deursnee te vervaardig, hoë tempo produksievermoë . • DOORLOPENDE GIETEN ( STRANDGIETEN ) : Word gebruik om 'n aaneenlopende lengte metaal te giet. Basies word die gesmelte metaal in die tweedimensionele profiel van die vorm gegiet, maar die lengte daarvan is onbepaald. Nuwe gesmelte metaal word voortdurend in die vorm ingevoer soos die gietstuk afwaarts beweeg met die lengte wat mettertyd toeneem. Metale soos koper, staal, aluminium word in lang stringe gegiet deur die deurlopende gietproses te gebruik. Die proses kan verskeie konfigurasies hê, maar die algemene een kan vereenvoudig word soos: 1.) Gesmelte metaal word in 'n houer wat hoog bo die vorm geleë is gegooi teen goed berekende hoeveelhede en vloeitempo's en vloei deur die waterverkoelde vorm. Die metaalgietsel wat in die vorm gegooi word, stol tot 'n beginstaaf wat aan die onderkant van die vorm geplaas word. Hierdie aansitterstaaf gee die rollers aanvanklik iets om aan te gryp. 2.) Die lang metaaldraad word teen 'n konstante spoed deur rollers gedra. Die rollers verander ook die rigting van die vloei van metaaldraad van vertikaal na horisontaal. 3.) Nadat die deurlopende gietwerk 'n sekere horisontale afstand afgelê het, sny 'n fakkel of saag wat saam met die gietstuk beweeg dit vinnig tot verlangde lengtes. Deurlopende gietproses kan geïntegreer word met ROLSPROSES, waar die deurlopend gegote metaal direk in 'n walswerk ingevoer kan word om I-Beams, T-Beams ….ens. Deurlopende gietwerk lewer eenvormige eienskappe regdeur die produk, dit het 'n hoë stollingstempo, verminder koste as gevolg van baie lae verlies aan materiaal, bied 'n proses waar laai van metaal, giet, stolling, sny en gietverwydering alles in 'n deurlopende operasie plaasvind en dus lei tot hoë produktiwiteitsyfer en hoë kwaliteit. 'n Groot oorweging is egter die hoë aanvanklike belegging, opstelkoste en ruimtevereistes. • MAJERINGSDIENSTE: Ons bied drie-, vier- en vyf-as bewerking. Die tipe masjineringsprosesse wat ons gebruik, is DRAAI, FREES, BOORD, BORING, BREEK, SKAAF, SAAG, SLAP, LAPPING, POLIERING en NIE-TRADISIONELE MAJERING wat verder uitgebrei word onder 'n ander spyskaart van ons webwerf. Vir die meeste van ons vervaardiging gebruik ons CNC-masjiene. Vir sommige operasies pas konvensionele tegnieke egter beter en daarom maak ons ook daarop staat. Ons bewerkingsvermoëns bereik die hoogste vlak moontlik en sommige mees veeleisende onderdele word by 'n AS9100-gesertifiseerde aanleg vervaardig. Straalenjinlemme vereis hoogs gespesialiseerde vervaardigingservaring en die regte toerusting. Lugvaartbedryf het baie streng standaarde. Sommige komponente met komplekse geometriese strukture word die maklikste vervaardig deur vyf-as bewerking, wat slegs in sommige bewerkingsaanlegte, insluitend ons s'n, gevind word. Ons lugvaartgesertifiseerde aanleg het die nodige ondervinding om te voldoen aan uitgebreide dokumentasievereistes van die lugvaartbedryf. In DRAAI-bewerkings word 'n werkstuk geroteer en teen 'n snywerktuig beweeg. Vir hierdie proses word 'n masjien genaamd draaibank gebruik. In FRYS, het 'n masjien genaamd freesmasjien 'n roterende gereedskap om snykante teen 'n werkstuk te bring. BOOR bewerkings behels 'n roterende snyer met snykante wat gate maak wanneer dit met die werkstuk in aanraking kom. Boorperse, draaibanke of meulens word oor die algemeen gebruik. In BORING-bewerkings word 'n gereedskap met 'n enkele gebuig puntige punt in 'n growwe gat in 'n draaiende werkstuk geskuif om die gat effens te vergroot en akkuraatheid te verbeter. Dit word gebruik vir fyn afwerking doeleindes. BREUK behels 'n tandwerktuig om materiaal van 'n werkstuk te verwyder in een deurgang van die borsel (tandwerktuig). In lineêre borsing loop die bors lineêr teen 'n oppervlak van die werkstuk om die snit te bewerkstellig, terwyl in roterende breking die bors geroteer en in die werkstuk ingedruk word om 'n as simmetriese vorm te sny. SWISS TIPE MACHINING is een van ons waardevolle tegnieke wat ons gebruik vir hoë volume vervaardiging van klein hoë presisie onderdele. Met behulp van Switserse-tipe draaibank draai ons klein, komplekse, presisie-onderdele goedkoop. Anders as konvensionele draaibanke waar die werkstuk stil gehou word en gereedskap beweeg, word die werkstuk in Switserse tipe draaisentrums toegelaat om in die Z-as te beweeg en die werktuig is stilstaande. In Switserse tipe bewerking word die staafvoorraad in die masjien gehou en deur 'n geleidingsbus in die z-as gevorder, wat slegs die gedeelte wat gemasjineer moet word, blootstel. Op hierdie manier word 'n stywe greep verseker en akkuraatheid is baie hoog. Beskikbaarheid van lewendige gereedskap bied die geleentheid om te maal en te boor soos die materiaal van die leibus beweeg. Die Y-as van die Switserse-tipe toerusting bied volle maalvermoëns en bespaar baie tyd in vervaardiging. Verder het ons masjiene bore en boorgereedskap wat op die onderdeel werk wanneer dit in die subspil gehou word. Ons Switserse tipe bewerkingsvermoë gee ons 'n volledig outomatiese volledige bewerkingsgeleentheid in 'n enkele bewerking. Masjinering is een van die grootste segmente van AGS-TECH Inc. se besigheid. Ons gebruik dit óf as 'n primêre bewerking óf 'n sekondêre bewerking nadat 'n onderdeel gegiet of geëxtrudeer is sodat aan alle tekeningspesifikasies voldoen word. • OPPERVLAKAFAFWERKINGSDIENSTE: Ons bied 'n groot verskeidenheid van oppervlakbehandelings en oppervlakafwerking soos oppervlakkondisionering om adhesie te verbeter, afsetting van dun oksiedlaag om adhesie van coating te verbeter, sandblaas, chem-film, anodisering, nitrering, poeierbedekking, spuitbedekking , verskeie gevorderde metallisasie- en bedekkingstegnieke, insluitend sputtering, elektronstraal, verdamping, platering, harde bedekkings soos diamantagtige koolstof (DLC) of titaanbedekking vir boor- en snygereedskap. • PRODUKMERK- EN ETIKETTERINGSDIENSTE: Baie van ons kliënte benodig merk en etikettering, lasermerk, gravering op metaalonderdele. As u so 'n behoefte het, laat ons bespreek watter opsie die beste vir u sal wees. Hier is 'n paar van die algemeen gebruikte metaalgietprodukte. Aangesien dit van die rak af is, kan u op vormkoste bespaar indien enige van hierdie aan u vereistes voldoen: KLIK HIER OM ons 11-reeks gegote aluminium bokse van AGS-Electronics af te laai CLICK Product Finder-Locator Service VORIGE BLADSY
- Custom Manufactured Parts, Assemblies, Plastic Mold, Casting,Machining
Custom Manufactured Parts, Assemblies, Plastic Mold, Rubber Molding, Metal Casting, CNC Machining, Turning, Milling, Electrical Electronic Optical Assembly PCBA Pasgemaakte vervaardigde onderdele en samestellings en produkte Lees meer Plastiek- en rubbervorms en gietvorms Lees meer Giet en bewerking Lees meer Ekstrusies, geëxtrudeerde produkte Lees meer Stempels en plaatmetaalvervaardiging Lees meer Metaalsmee en poeiermetallurgie Lees meer Draad- en veervorming Lees meer Vorming en vorming van glas en keramiek Lees meer Byvoeging en vinnige vervaardiging Lees meer Saamgestelde en saamgestelde materiale vervaardiging Lees meer Verbind & Monteer & Bevestiging Prosesse Ons vervaardig onderdele en samestellings vir jou en bied die volgende vervaardigingsprosesse: • Plastiek- en rubbervorms en gevormde dele. Spuitgieten, termovorming, termohardende gietvorm, vakuumvorming, blaasvorm, rotasiegiet, gietvorm, insetvorm en ander. • Plastiek-, rubber- en metaalekstrusies • Yster- en nie-ysterhoudende gietstukke en gemasjineerde onderdele vervaardig deur maal- en draaitegnieke, Switserse tipe bewerking. • Poeiermetallurgie-onderdele • Metaal- en nie-metaalstempels, plaatmetaalvorming, gelaste plaatmetaalsamestellings • Koue en warm smee • Drade, gelaste draadsamestellings, draadvorming • Verskeie soorte vere, veervorming • Ratvervaardiging, ratkas, koppeling, wurm, spoedverminderaar, silinder, transmissiebande, transmissiekettings, transmissiekomponente • Pasgemaakte geharde en koeëlvaste glas wat aan NAVO en militêre standaarde voldoen • Balle, laers, katrolle en katrolsamestellings • Kleppe en pneumatiese komponente soos O-ring, wasser en seëls • Glas- en keramiekonderdele en samestellings, vakuumbestande en hermetiese komponente, metaal-keramiek en keramiek-keramiek binding. • Verskeie tipes meganiese, optomeganiese, elektromeganiese, opto-elektroniese samestellings. • Metaal-rubber, metaal-plastiek binding • Pyp en buis, pypvorming, buiging en pasgemaakte pypsamestellings, balgvervaardiging. • Veselglas vervaardiging • Sweis deur verskeie tegnieke soos puntsweis, lasersweis, MIG, TIG. Ultrasoniese sweiswerk vir plastiekonderdele. • Groot verskeidenheid oppervlakbehandelings en oppervlakafwerkings soos oppervlakkondisionering om adhesie te verbeter, afsetting van dun oksiedlaag om adhesie van bedekking te verbeter, sandblaas, chemiefilm, anodisering, nitrering, poeierbedekking, spuitbedekking, verskeie gevorderde metallisering en bedekkingstegnieke insluitend sputtering, elektronstraal, verdamping, platering, harde bedekkings soos diamant soos koolstof (DLC) of titanium vir sny- en boorgereedskap. • Merk en etikettering, lasermerk op metaalonderdele, drukwerk op plastiek- en rubberonderdele Laai brosjure af vir algemene meganiese ingenieursvoorwaardes wat deur ontwerpers en ingenieurs gebruik word Ons bou produkte volgens jou spesifieke spesifikasies en vereistes. Om u die beste gehalte, aflewering en pryse te bied, vervaardig ons produkte wêreldwyd in China, Indië, Taiwan, Filippyne, Suid-Korea, Maleisië, Sri Lanka, Turkye, VSA, Kanada, Duitsland, die Verenigde Koninkryk en Japan. Dit maak ons baie sterker en wêreldwyd meer mededingend as enige ander custom vervaardiger. Ons produkte word vervaardig in ISO9001:2000, QS9000, ISO14001, TS16949 gesertifiseerde omgewings en beskik oor CE, UL merk en voldoen aan ander industriestandaarde. Sodra ons vir jou projek aangestel is, kan ons sorg vir die hele vervaardiging, montering, toetsing, kwalifikasie, versending en doeane soos jy wil. As jy verkies, kan ons jou onderdele pak, pasgemaakte stelle bymekaarmaak, jou maatskappy se naam en handelsmerk druk en etiketteer en na jou kliënte stuur. Met ander woorde, ons kan ook jou pakhuis- en verspreidingsentrum wees indien verkies. Aangesien ons pakhuise naby groot seehawens geleë is, gee dit ons logistieke voordeel. Byvoorbeeld, wanneer jou produkte by 'n groot Amerikaanse seehawe aankom, kan ons dit direk na 'n nabygeleë pakhuis vervoer waar ons kan stoor, monteer, stelle maak, heretiketteer, druk, verpak volgens jou keuse en los stuur aan jou kliënte. Ons verskaf nie net produkte nie. Ons maatskappy werk aan pasgemaakte kontrakte waar ons na u webwerf kom, u projek ter plaatse evalueer en 'n projekvoorstel ontwikkel wat spesiaal vir u ontwerp is. Ons stuur dan ons ervare span om die projek te implementeer. Meer inligting oor ons ingenieurswerk kan gevind word op http://www.ags-engineering.com -Ons neem klein projekte sowel as groot projekte op industriële skaal. As 'n eerste stap kan ons jou per telefoon, telekonferensies of MSN-boodskapper met ons kundige spanlede verbind, sodat jy direk met 'n kenner kan kommunikeer, vrae kan vra en jou projek kan bespreek. Bel ons en indien nodig sal ons jou kom besoek. VORIGE BLADSY