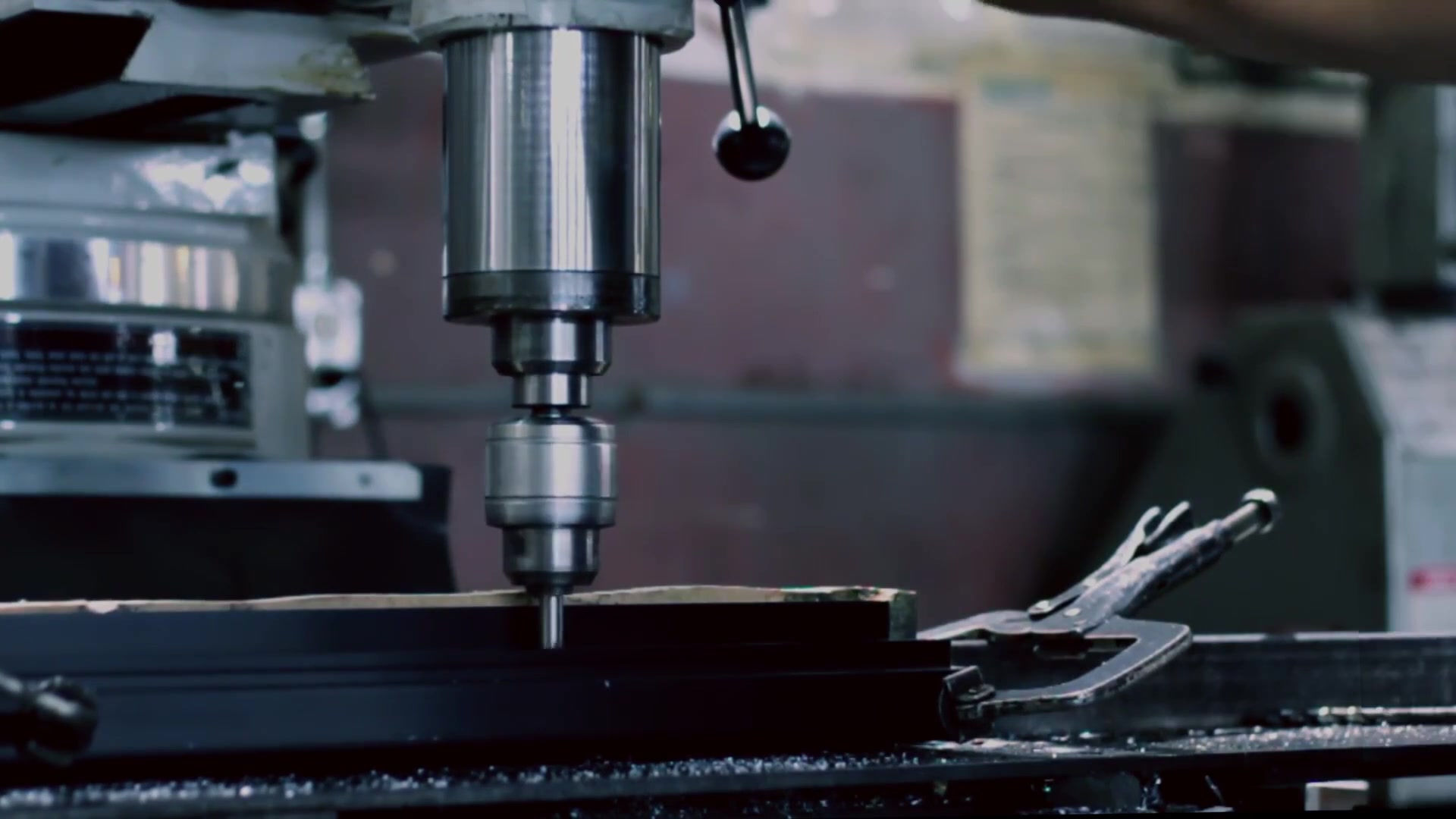
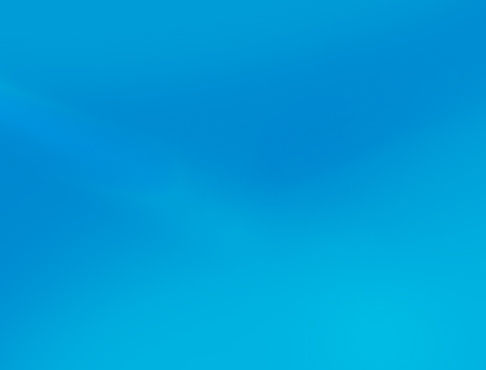
مُصنِّع مخصص عالمي ، مُدمج ، مُوحد ، شريك خارجي لمجموعة متنوعة من المنتجات والخدمات.
نحن المصدر الوحيد للتصنيع والتصنيع والهندسة والتوحيد والتكامل والاستعانة بمصادر خارجية للمنتجات والخدمات المصنعة حسب الطلب والجاهزة.
Choose your Language
-
التصنيع حسب الطلب
-
التصنيع بالعقود المحلية والعالمية
-
الاستعانة بمصادر خارجية التصنيع
-
المشتريات المحلية والعالمية
-
توحيد_ d04a07d8-9cd1-3239-9149-20813d6c673b_
-
التكامل الهندسي
-
خدمات هندسية
Search Results
تم العثور على 161 نتيجة مع بحث فارغ
- مكونات ناقل الحركة ، الأحزمة ، السلاسل ، محركات الكابلات ، البكرات
مكونات ناقل الحركة ، الأحزمة ، السلاسل ومحركات الكابلات ، التقليدية والمحززة أو المسننة ، المحرك الإيجابي ، البكرات تجميع الأحزمة والسلاسل ومحركات الكابلات تقدم شركة AGS-TECH Inc. مكونات نقل الطاقة بما في ذلك مجموعة الأحزمة والسلاسل ومحرك الكابلات. مع سنوات من التحسين ، أصبحت محركات المطاط والجلد وغيرها من الأحزمة أخف وزنا وأكثر إحكاما ، وقادرة على حمل أحمال أعلى بتكلفة أقل. وبالمثل ، فقد مرت محركات السلسلة الخاصة بنا بالكثير من التطوير بمرور الوقت وهي توفر لعملائنا العديد من المزايا. تتمثل بعض مزايا استخدام محركات السلسلة في مسافات مركز العمود غير المقيدة نسبيًا ، والاكتناز ، وسهولة التجميع ، والمرونة في التوتر دون الانزلاق أو الزحف ، والقدرة على العمل في بيئات ذات درجة حرارة عالية. تقدم محركات الكابلات أيضًا مزايا مثل البساطة في بعض التطبيقات مقارنة بأنواع أخرى من مكونات الإرسال. يتوفر كل من الحزام الجاهز والسلسلة ومحركات الكابلات بالإضافة إلى الإصدارات المصنعة والمجمعة حسب الطلب. يمكننا تصنيع مكونات النقل هذه بالحجم المناسب لتطبيقك ومن أنسب المواد. محركات الأحزمة والأحزمة: - أحزمة مسطحة تقليدية: أحزمة مسطحة عادية بدون أسنان أو أخاديد أو تسننات. توفر محركات الحزام المسطح المرونة ، وامتصاص الصدمات الجيد ، ونقل الطاقة الفعال بسرعات عالية ، ومقاومة التآكل ، والتكلفة المنخفضة. يمكن ربط الأحزمة أو توصيلها لصنع أحزمة أكبر. من المزايا الأخرى للأحزمة المسطحة التقليدية أنها رقيقة ولا تخضع لأحمال طرد مركزي عالية (يجعلها جيدة لعمليات عالية السرعة مع بكرات صغيرة). من ناحية أخرى ، فإنها تفرض أحمالًا عالية لأن الأحزمة المسطحة تتطلب توترًا عاليًا. يمكن أن تكون العيوب الأخرى لمحركات السيور المسطحة هي الانزلاق ، والتشغيل الصاخب ، وكفاءة أقل نسبيًا في سرعات التشغيل المنخفضة والمتوسطة. لدينا نوعان من الأحزمة التقليدية: الأحزمة المقواة وغير المقواة. الأحزمة المقواة لها عضو شد في هيكلها. الأحزمة المسطحة التقليدية متوفرة كجلد أو قماش أو حبل مطاطي أو مطاط أو بلاستيك غير مقوى أو قماش أو جلد مقوى. توفر الأحزمة الجلدية حياة طويلة ، ومرونة ، ومعامل احتكاك ممتاز ، وإصلاح سهل. ومع ذلك ، فإن الأحزمة الجلدية غالية الثمن نسبيًا ، وتحتاج إلى تضميدها وتنظيفها ، وقد تتقلص أو تتمدد حسب الجو. النسيج المطاطي أو الأحزمة السلكية مقاومة للرطوبة والأحماض والقلويات. تتكون الأحزمة القماشية المطاطية من طبقات من القطن أو البط الصناعي المشبع بالمطاط وهي الأكثر اقتصادا. تتكون أحزمة الحبال المطاطية من سلسلة من طبقات من الحبال المطاطية المشبعة. توفر أحزمة الحبال المطاطية قوة شد عالية وحجم وكتلة متواضعة. الأحزمة المطاطية أو البلاستيكية غير المقواة مناسبة لتطبيقات القيادة ذات المهام الخفيفة والسرعة المنخفضة. يمكن شد أحزمة المطاط والبلاستيك غير المقواة في مكانها فوق بكراتها. يمكن للأحزمة البلاستيكية غير المقواة أن تنقل طاقة أعلى مقارنة بالأحزمة المطاطية. تتكون الأحزمة الجلدية المقواة من قطعة بلاستيكية قابلة للشد محصورة بين الطبقات الجلدية العلوية والسفلية. أخيرًا ، قد تتكون الأحزمة القماشية الخاصة بنا من قطعة واحدة من القطن أو البط مطوية ومخيطة بصفوف من الغرز الطولية. الأحزمة القماشية قادرة على التعقب بشكل موحد وتعمل بسرعة عالية. - أحزمة مخددة أو مسننة (مثل أحزمة V): هذه أحزمة مسطحة أساسية تم تعديلها لتوفير مزايا نوع آخر من منتجات ناقل الحركة. هذه أحزمة مسطحة ذات جانب سفلي مضلع طوليًا. أحزمة Poly-V عبارة عن حزام مسطح مخدد أو مسنن طوليًا مع قسم شد وسلسلة من الأخاديد المجاورة على شكل V لأغراض التتبع والضغط. قدرة الطاقة تعتمد على عرض الحزام. V-belt هو العمود الفقري للصناعة ومتوفر في مجموعة متنوعة من الأحجام والأنواع القياسية لنقل أي قوة حمل تقريبًا. تعمل محركات V-belt بشكل جيد بين 1500 إلى 6000 قدم / دقيقة ، ومع ذلك ستعمل أحزمة V الضيقة حتى 10000 قدم / دقيقة. توفر محركات V-belt عمرًا طويلاً مثل 3 إلى 5 سنوات وتسمح بنسب سرعة كبيرة ، فهي سهلة التركيب والإزالة ، وتوفر تشغيلًا هادئًا ، وصيانة منخفضة ، وامتصاصًا جيدًا للصدمات بين سائق الحزام والأعمدة المدارة. عيب الأحزمة V هو انزلاقها وتسللها المؤكد ، وبالتالي قد لا تكون الحل الأفضل حيث تكون السرعات المتزامنة مطلوبة. لدينا أحزمة صناعية وسيارات وزراعية. أطوال قياسية مخزنة وكذلك أطوال مخصصة للأحزمة متوفرة. تتوفر جميع المقاطع العرضية القياسية للحزام على شكل V من المخزون. توجد جداول يمكنك من خلالها حساب معلمات غير معروفة مثل طول الحزام وقسم الحزام (العرض والسمك) بشرط أن تعرف بعض معلمات نظامك مثل القيادة وأقطار البكرة المدفوعة ومسافة المركز بين البكرات وسرعات دوران البكرات. يمكنك استخدام هذه الجداول أو تطلب منا اختيار حزام V المناسب لك . - أحزمة القيادة الموجبة (حزام التوقيت): هذه الأحزمة هي أيضًا من النوع المسطح مع سلسلة من الأسنان المتباعدة بشكل متساوٍ على المحيط الداخلي. تجمع أحزمة القيادة أو التوقيت الإيجابي بين مزايا الأحزمة المسطحة وخصائص القبضة الإيجابية للسلاسل والتروس. لا تكشف أحزمة القيادة الإيجابية عن أي انزلاق أو اختلافات في السرعة. مجموعة واسعة من نسب السرعة ممكنة. تحمل الأحمال منخفضة لأنها يمكن أن تعمل بتوتر منخفض. ومع ذلك فهي أكثر عرضة للاختلالات في البكرات. - البكرات والحزم والمحاور للأحزمة: تستخدم أنواع مختلفة من البكرات مع أحزمة دفع مسطحة ومضلعة (مسننة) وموجبة. نحن نصنعهم جميعًا. يتم تصنيع معظم بكرات الحزام المسطحة الخاصة بنا عن طريق صب الحديد ، ولكن الإصدارات الفولاذية متوفرة أيضًا في مجموعات مختلفة من الحواف والمحور. قد تحتوي بكراتنا ذات الحزام المسطح على محاور صلبة أو ذات قضبان أو منقسمة أو يمكننا تصنيعها حسب رغبتك. تتوفر الأحزمة المضلعة وذات الدفع الموجب في مجموعة متنوعة من الأحجام والعرض. يجب أن تكون بكرة واحدة على الأقل في محركات حزام التوقيت مشفهة لإبقاء الحزام على المحرك. بالنسبة لأنظمة القيادة ذات المركز الطويل ، فمن المستحسن أن تكون كلتا البكرتين مشفتين. الحزم عبارة عن عجلات محززة للبكرات ويتم تصنيعها بشكل عام عن طريق صب الحديد أو تشكيل الفولاذ أو صب البلاستيك. تشكيل الفولاذ هو عملية مناسبة لتصنيع الحزم الآلية والزراعية. نحن ننتج الحزم مع الأخاديد العادية والعميقة. تعتبر الحزم ذات الأخدود العميق مناسبة تمامًا عندما يدخل الحزام على شكل V في الحزم بزاوية ، كما هو الحال في محركات الأقراص ذات ربع دورة. كما أن الأخاديد العميقة مناسبة تمامًا لمحركات وتطبيقات العمود الرأسي حيث يمكن أن يمثل اهتزاز الأحزمة مشكلة. البكرات الوسيطة لدينا عبارة عن حزم محزومة أو بكرات مسطحة لا تخدم القدرة الميكانيكية الناقلة. تستخدم البكرات الوسيطة في الغالب لشد الأحزمة. - محركات الحزام الأحادية والمتعددة: تحتوي محركات الحزام الفردي على أخدود واحد بينما تحتوي محركات السيور المتعددة على أخاديد متعددة. بالنقر فوق النص الملون ذي الصلة أدناه ، يمكنك تنزيل كتالوجاتنا: - أحزمة نقل الطاقة (تشمل أحزمة V وأحزمة التوقيت وأحزمة Raw Edge وأحزمة ملفوفة وأحزمة خاصة) - سيور ناقلة - V- البكرات - توقيت البكرات سلاسل ومحركات السلاسل: تتميز سلاسل نقل الطاقة لدينا ببعض المزايا مثل مسافات مركز العمود غير المقيدة نسبيًا ، والتجميع السهل ، والاكتناز ، والمرونة تحت الشد دون الانزلاق أو الزحف ، والقدرة على التشغيل تحت درجات حرارة عالية. فيما يلي الأنواع الرئيسية لسلاسلنا: - السلاسل القابلة للفصل: سلاسلنا القابلة للفصل مصنوعة في مجموعة من الأحجام ، والميل والقوة المطلقة وعمومًا من الحديد أو الفولاذ القابل للطرق. تصنع السلاسل القابلة للطرق في مجموعة من الأحجام من 0.902 (23 مم) إلى 4.063 بوصة (103 مم) وقوة قصوى من 700 إلى 17000 رطل / بوصة مربعة. من ناحية أخرى ، فإن سلاسل الفولاذ القابلة للفصل الخاصة بنا مصنوعة بأحجام من 0.904 بوصة (23 مم) إلى حوالي 3.00 بوصة (76 مم) في الملعب ، مع قوة قصوى من 760 إلى 5000 رطل / بوصة مربعة. _cc781905-5cde-3194-bb3b- 136bad5cf58d_ - سلاسل Pintle: تُستخدم هذه السلاسل للأحمال الثقيلة والسرعات الأعلى قليلاً إلى حوالي 450 قدمًا / دقيقة (2.2 متر / ثانية). سلاسل Pintle مصنوعة من روابط مصبوبة فردية لها نهاية أسطوانية كاملة مستديرة مع أشرطة جانبية متوازنة. يتم ربط روابط السلسلة هذه بمسامير فولاذية. تتراوح هذه السلاسل في الملعب من حوالي 1.00 بوصة (25 مم) إلى 6.00 بوصة (150 مم) وقوى نهائية بين 3600 إلى 30.000 رطل / بوصة مربعة. - سلاسل الأوفست - الشريط الجانبي: هذه شائعة في سلاسل محركات آلات البناء. تعمل هذه السلاسل بسرعات تصل إلى 1000 قدم / دقيقة وتنقل الأحمال إلى حوالي 250 حصان. بشكل عام ، يحتوي كل رابط على قضيبين جانبيين ، جلبة واحدة ، بكرة واحدة ، دبوس واحد ، دبوس كوتر. - السلاسل الدوارة: وهي متوفرة في النغمات من 0.25 (6 مم) إلى 3.00 (75 مم) بوصة. تتراوح القوة القصوى لسلاسل البكرات أحادية العرض بين 925 إلى 130،000 رطل / بوصة مربعة. تتوفر إصدارات متعددة العرض من سلاسل البكرات وتنقل طاقة أكبر بسرعات أعلى. توفر سلاسل البكرات متعددة العرض أيضًا حركة أكثر سلاسة مع ضوضاء أقل. يتم تجميع سلاسل الأسطوانة من روابط الأسطوانة ووصلات الدبوس. تُستخدم دبابيس Cotter في سلاسل الأسطوانة القابلة للفصل. يتطلب تصميم محركات سلسلة الأسطوانة خبرة في الموضوع. في حين أن محركات الحزام تعتمد على السرعات الخطية ، فإن محركات السلسلة تعتمد على السرعة الدورانية للعجلة المسننة الأصغر ، والتي تكون في معظم التركيبات العضو المدفوع. إلى جانب تصنيفات القدرة الحصانية وسرعة الدوران ، يعتمد تصميم المحركات المتسلسلة على العديد من العوامل الأخرى. - سلاسل الملعب المزدوج: تشبه سلاسل الأسطوانة بشكل أساسي باستثناء أن طول الملعب يبلغ ضعف طوله. - سلاسل الأسنان المقلوبة (الصامتة): السلاسل عالية السرعة المستخدمة في الغالب للمحرك الرئيسي ومحركات الإقلاع الكهربائي. يمكن أن تنقل محركات سلسلة الأسنان المقلوبة طاقة تصل إلى 1200 حصان وتتكون من سلسلة من وصلات الأسنان ، يتم تجميعها بالتناوب مع أي من المسامير أو مجموعة من المكونات المشتركة. تحتوي سلسلة التوجيه المركزي على روابط إرشادية لإشراك الأخاديد في العجلة المسننة ، وتحتوي سلسلة التوجيه الجانبي على أدلة لإشراك جوانب العجلة المسننة. - سلاسل الخرزة أو المنزلق: تُستخدم هذه السلاسل لمحركات الأقراص ذات السرعة البطيئة وأيضًا في العمليات اليدوية. بالنقر فوق النص الملون ذي الصلة أدناه ، يمكنك تنزيل كتالوجاتنا: - سلاسل القيادة - سلاسل النقل - سلاسل نقل كبيرة - سلاسل أسطوانية من الستانلس ستيل - سلاسل الرفع - سلاسل الدراجات النارية - سلاسل الالات الزراعية - العجلة المسننة: تتوافق أسناننا القياسية مع معايير ANSI. العجلة المسننة للوحة مسننة ، مسننة بدون محور. يتم تدوير أسنان العجلة المسننة الصغيرة والمتوسطة الحجم الخاصة بنا من مخزون القضبان أو المطروقات أو يتم تصنيعها عن طريق لحام محور مخزون القضبان إلى لوحة مدلفنة على الساخن. يمكن لشركة AGS-TECH Inc. أن تزود المسننات المسننة من مصبوبات الحديد الرمادي والفولاذ المصبوب والمنشآت الملحومة ومسحوق المعادن الملبد والبلاستيك المصبوب أو المشكل آليًا. للتشغيل السلس بسرعات عالية ، من الضروري الاختيار الصحيح لحجم العجلة المسننة. تعد قيود المساحة بالطبع عاملاً لا يمكننا تجاهله عند اختيار ضرس. من المستحسن ألا تزيد نسبة السائق إلى العجلة المسننة عن 6: 1 ، وأن يكون التفاف السلسلة على السائق 120 درجة. يجب أيضًا اختيار مسافات المركز بين العجلة المسننة الأصغر والأكبر وأطوال السلسلة وشد السلسلة وفقًا لبعض الحسابات والإرشادات الهندسية الموصى بها وليس بشكل عشوائي. قم بتنزيل كتالوجاتنا بالنقر فوق النص الملون أدناه: - العجلة المسننة والعجلات المسننة - البطانات ناقل الحركة - اقتران سلسلة - أقفال السلسلة محركات الكابلات: هذه لها مزاياها على الأحزمة ومحركات السلسلة في بعض الحالات. يمكن أن تؤدي محركات الكبل نفس وظيفة الأحزمة وقد تكون أيضًا أبسط وأكثر اقتصادية في التنفيذ في بعض التطبيقات. على سبيل المثال ، تم تصميم سلسلة جديدة من محركات كبلات Synchromesh لسحب إيجابي لاستبدال الحبال التقليدية والكابلات البسيطة ومحركات الأقراص المسننة ، خاصة في المساحات الضيقة. تم تصميم محرك الكابلات الجديد لتوفير تحديد المواقع بدقة عالية في المعدات الإلكترونية مثل آلات النسخ ، والرسومات ، والآلات الكاتبة ، والطابعات ، ... إلخ. الميزة الرئيسية لمحرك الكبل الجديد هي قدرته على استخدامه في التكوينات ثلاثية الأبعاد السربنتينية التي تمكن تصاميم مصغرة للغاية. يمكن استخدام الكابلات المتزامنة مع شد أقل عند مقارنتها بالحبال وبالتالي تقليل استهلاك الطاقة. اتصل بـ AGS-TECH لطرح الأسئلة والآراء حول الأحزمة ، والسلاسل ومحركات الكابلات. CLICK Product Finder-Locator Service الصفحة السابقة
- النماذج الأولية السريعة ، التصنيع المكتبي ، التصنيع الإضافي ، FDM
النماذج الأولية السريعة ، التصنيع المكتبي ، التصنيع الإضافي ، الطباعة الحجرية المجسمة ، بولي جيت ، نمذجة الترسيب المنصهر ، التلبيد الانتقائي بالليزر ، FDM ، SLS التصنيع الإضافي والسريع في السنوات الأخيرة ، شهدنا زيادة في الطلب على التصنيع السريع أو PROTOTYPING السريع. قد تسمى هذه العملية أيضًا تصنيع سطح المكتب أو التصنيع الحر. في الأساس ، يتكون النموذج المادي الصلب للجزء مباشرة من رسم CAD ثلاثي الأبعاد. نستخدم مصطلح التصنيع الإضافي لهذه التقنيات المختلفة حيث نبني أجزاء في طبقات. باستخدام الأجهزة والبرامج المتكاملة التي يحركها الكمبيوتر ، نقوم بالتصنيع الإضافي. تقنيات النماذج الأولية والتصنيع لدينا هي الطباعة الحجرية ، والبولي جيت ، ونمذجة الترسيب المنصهر ، والغمر الانتقائي بالليزر ، وذوبان الحزمة الإلكترونية ، والطباعة ثلاثية الأبعاد ، والتصنيع المباشر ، والأدوات السريعة. نوصي بالضغط هنا لقم بتنزيل الرسوم التوضيحية التخطيطية الخاصة بنا لتصنيع المواد المضافة وعمليات التصنيع السريع بواسطة AGS-TECH Inc. سيساعدك هذا على فهم المعلومات التي نقدمها لك أدناه بشكل أفضل. توفر النماذج الأولية السريعة لنا: 1.) يتم عرض التصميم النظري للمنتج من زوايا مختلفة على الشاشة باستخدام نظام 3D / CAD. 2.) يتم تصنيع النماذج الأولية من المواد غير المعدنية والمعدنية ودراستها من الجوانب الوظيفية والتقنية والجمالية. 3.) يتم إنجاز نماذج أولية منخفضة التكلفة في وقت قصير جدًا. يمكن أن يشبه التصنيع الإضافي بناء رغيف الخبز عن طريق تكديس وربط الشرائح الفردية فوق بعضها البعض. بمعنى آخر ، يتم تصنيع المنتج شريحة بشريحة ، أو طبقة بطبقة ترسب على بعضها البعض. يمكن إنتاج معظم الأجزاء في غضون ساعات. هذه التقنية جيدة إذا كانت هناك حاجة إلى الأجزاء بسرعة كبيرة أو إذا كانت الكميات المطلوبة منخفضة وكان صنع القالب والأدوات باهظ التكلفة ويستغرق وقتًا طويلاً. ومع ذلك ، فإن تكلفة قطعة ما باهظة الثمن بسبب المواد الخام باهظة الثمن. • الطباعة الحجرية: تعتمد هذه التقنية ، التي يُشار إليها أيضًا باسم STL ، على معالجة البوليمر الضوئي السائل وتصلبه إلى شكل معين عن طريق تركيز شعاع الليزر عليه. يعمل الليزر على بلمرة البوليمر الضوئي وعلاجه. عن طريق مسح شعاع الليزر فوق البنفسجي وفقًا للشكل المبرمج على طول سطح خليط البوليمر الضوئي ، يتم إنتاج الجزء من الأسفل إلى الأعلى في شرائح فردية متتالية فوق بعضها البعض. يتكرر مسح بقعة الليزر عدة مرات لتحقيق الأشكال الهندسية المبرمجة في النظام. بعد تصنيع الجزء بالكامل ، يتم إزالته من المنصة وتنشيفه وتنظيفه بالموجات فوق الصوتية وباستخدام حمام كحول. بعد ذلك ، يتم تعريضه للإشعاع فوق البنفسجي لبضع ساعات للتأكد من أن البوليمر قد تمت معالجته وتصلبه بالكامل. لتلخيص العملية ، يتم التحكم في المنصة التي يتم غمسها في خليط فوتوبوليمر وشعاع ليزر UV وتحريكها عبر نظام تحكم مؤازر وفقًا لشكل الجزء المطلوب ويتم الحصول على الجزء عن طريق تصوير طبقة البوليمر بطبقة. بالطبع يتم تحديد الأبعاد القصوى للجزء المنتج بواسطة معدات الطباعة الحجرية المجسمة. • POLYJET: على غرار الطباعة النافثة للحبر ، لدينا في polyjet ثمانية رؤوس طباعة تودع فوتوبوليمر على صينية التصميم. يوضع الضوء فوق البنفسجي بجانب النفاثات على الفور يعالج ويقوي كل طبقة. يتم استخدام مادتين في بولي جيت. المادة الأولى لتصنيع النموذج الفعلي. المادة الثانية ، راتنج يشبه الهلام يستخدم للدعم. يتم ترسيب كلتا هاتين المادتين طبقة تلو الأخرى ويتم معالجتها في وقت واحد. بعد اكتمال النموذج ، تتم إزالة مادة الدعم بمحلول مائي. تشبه الراتنجات المستخدمة الطباعة الحجرية الحجرية (STL). تتميز البولي جيت بالمزايا التالية على الطباعة الحجرية الحجرية: 1.) لا حاجة لتنظيف الأجزاء. 2.) لا حاجة للمعالجة اللاحقة 3.) سماكة طبقة أصغر ممكنة وبالتالي نحصل على دقة أفضل ويمكننا تصنيع أجزاء دقيقة. • نمذجة الإيداع المنصهر: يُختصر أيضًا باسم FDM ، في هذه الطريقة يتحرك رأس الطارد المتحكم فيه بواسطة الروبوت في اتجاهين أساسيين فوق الطاولة. يتم خفض الكابل ورفعه حسب الحاجة. من فتحة قالب ساخن على الرأس ، يتم بثق خيوط لدائن حرارية وتوضع طبقة أولية على أساس رغوي. يتم تحقيق ذلك من خلال رأس الطارد الذي يتبع مسارًا محددًا مسبقًا. بعد الطبقة الأولية ، يتم خفض الجدول وتوضع الطبقات اللاحقة فوق بعضها البعض. في بعض الأحيان ، عند تصنيع جزء معقد ، هناك حاجة إلى هياكل داعمة بحيث يمكن أن يستمر الترسيب في اتجاهات معينة. في هذه الحالات ، يتم بثق مادة الدعم مع تباعد أقل كثافة للخيوط على طبقة بحيث تكون أضعف من مادة النموذج. يمكن لاحقًا إذابة أو قطع هياكل الدعم هذه بعد الانتهاء من الجزء. تحدد أبعاد قالب الطارد سمك الطبقات المبثوقة. تنتج عملية FDM أجزاء ذات أسطح متدرجة على مستويات خارجية مائلة. إذا كانت هذه الخشونة غير مقبولة ، فيمكن استخدام تلميع بالبخار الكيميائي أو أداة ساخنة لتنعيمها. حتى شمع التلميع متاح كمواد طلاء للتخلص من هذه الخطوات وتحقيق تفاوتات هندسية معقولة. • التغطيس الانتقائي بالليزر: يُشار إليه أيضًا باسم SLS ، وتستند العملية إلى تلبيد البوليمر أو السيراميك أو المساحيق المعدنية بشكل انتقائي في جسم ما. يحتوي الجزء السفلي من غرفة المعالجة على أسطوانتين: أسطوانة بناء جزئي وأسطوانة تغذية مسحوق. يتم خفض الأول بشكل تدريجي إلى حيث يتم تشكيل الجزء الملبد ويتم رفع الأخير بشكل تدريجي لتزويد المسحوق إلى أسطوانة البناء الجزئي من خلال آلية الأسطوانة. أولاً ، يتم ترسيب طبقة رقيقة من المسحوق في أسطوانة البناء الجزئي ، ثم يتم تركيز شعاع الليزر على تلك الطبقة ، وتتبع مقطع عرضي معين وذوبانه / تلبيده ، ثم يتم تجميده إلى مادة صلبة. المسحوق هو المناطق التي لم يصطدم بها شعاع الليزر وتبقى فضفاضة ولكنها لا تزال تدعم الجزء الصلب. ثم يتم ترسيب طبقة أخرى من المسحوق وتكرر العملية عدة مرات للحصول على الجزء. في النهاية ، يتم التخلص من جزيئات المسحوق السائب. يتم تنفيذ كل ذلك بواسطة كمبيوتر للتحكم في العمليات باستخدام الإرشادات التي تم إنشاؤها بواسطة برنامج CAD ثلاثي الأبعاد للجزء الذي يتم تصنيعه. يمكن ترسيب مواد مختلفة مثل البوليمرات (مثل ABS و PVC والبوليستر) والشمع والمعادن والسيراميك مع مواد رابطة البوليمر المناسبة. • ELECTRON-BEAM MELTING: على غرار التلبيد الانتقائي بالليزر ، ولكن باستخدام شعاع الإلكترون لصهر مساحيق التيتانيوم أو الكوبالت الكروم لعمل نماذج أولية في الفراغ. تم إجراء بعض التطورات لإجراء هذه العملية على الفولاذ المقاوم للصدأ والألمنيوم وسبائك النحاس. إذا كانت هناك حاجة إلى زيادة قوة الإجهاد للأجزاء المنتجة ، فإننا نستخدم الضغط المتوازنة الساخنة بعد تصنيع الأجزاء كعملية ثانوية. • الطباعة ثلاثية الأبعاد: يُشار إليها أيضًا بواسطة 3DP ، في هذه التقنية ، ترسب رأس الطباعة مادة رابطة غير عضوية على طبقة من مسحوق غير معدني أو مسحوق معدني. يتم خفض المكبس الذي يحمل طبقة المسحوق بشكل تدريجي وفي كل خطوة يتم ترسيب المادة الرابطة layer تلو الآخر ويتم دمجها بواسطة المادة الرابطة. مواد المسحوق المستخدمة عبارة عن مزيج من البوليمرات والألياف ورمل المسابك والمعادن. باستخدام رؤوس ربط مختلفة في وقت واحد ومجلدات ألوان مختلفة ، يمكننا الحصول على ألوان مختلفة. تشبه هذه العملية الطباعة النافثة للحبر ولكن بدلاً من الحصول على ورقة ملونة نحصل على كائن ثلاثي الأبعاد ملون. قد تكون الأجزاء المنتجة مسامية وبالتالي قد تتطلب تلبيد وتسرب المعادن لزيادة كثافتها وقوتها. سيؤدي التكلس إلى حرق الموثق ودمج مساحيق المعادن معًا. يمكن استخدام المعادن مثل الفولاذ المقاوم للصدأ والألمنيوم والتيتانيوم في صنع الأجزاء وكمواد تسلل نستخدم النحاس والبرونز بشكل شائع. يكمن جمال هذه التقنية في أنه حتى التجميعات المعقدة والمتحركة يمكن تصنيعها بسرعة كبيرة. على سبيل المثال ، مجموعة تروس ، يمكن صنع مفتاح ربط كأداة وسيكون به أجزاء متحركة ودوران جاهزة للاستخدام. يمكن تصنيع المكونات المختلفة للتجميع بألوان مختلفة وكل ذلك في لقطة واحدة. قم بتنزيل الكتيب الخاص بنا على:أساسيات الطباعة المعدنية ثلاثية الأبعاد • التصنيع المباشر والأدوات السريعة: إلى جانب تقييم التصميم واستكشاف الأخطاء وإصلاحها ، نستخدم نماذج أولية سريعة للتصنيع المباشر للمنتجات أو التطبيق المباشر في المنتجات. بمعنى آخر ، يمكن دمج النماذج الأولية السريعة في العمليات التقليدية لجعلها أفضل وأكثر قدرة على المنافسة. على سبيل المثال ، يمكن للنماذج الأولية السريعة إنتاج أنماط وقوالب. يمكن تجميع أنماط ذوبان وحرق البوليمر الناتج عن عمليات النماذج الأولية السريعة للاستثمار في الصب والاستثمار. مثال آخر يجب ذكره هو استخدام 3DP لإنتاج غلاف صب السيراميك واستخدامه في عمليات صب القشرة. حتى قوالب الحقن وإدخالات القوالب يمكن إنتاجها عن طريق النماذج الأولية السريعة ويمكن للمرء أن يوفر عدة أسابيع أو أشهر من الوقت اللازم لصنع القالب. من خلال تحليل ملف CAD للجزء المطلوب فقط ، يمكننا إنتاج هندسة الأداة باستخدام البرنامج. فيما يلي بعض طرق الأدوات السريعة الشائعة لدينا: RTV (تقسية درجة حرارة الغرفة) القوالب / صب اليوريثان: يمكن استخدام النماذج الأولية السريعة لعمل نمط الجزء المطلوب. ثم يتم طلاء هذا النموذج بعامل فراق ويتم سكب مطاط RTV السائل فوق النموذج لإنتاج أنصاف القالب. بعد ذلك ، يتم استخدام نصفي القالب لحقن قوالب اليوريثان السائل. عمر القالب قصير ، فقط مثل 0 أو 30 دورة ولكنها كافية لإنتاج دفعة صغيرة . ACES (Acetal Clear Epoxy Solid) قولبة الحقن: باستخدام تقنيات النماذج الأولية السريعة مثل الطباعة الحجرية الحجرية ، نقوم بإنتاج قوالب الحقن. هذه القوالب عبارة عن قشور ذات نهاية مفتوحة للسماح بالملء بمواد مثل الإيبوكسي أو الإيبوكسي المملوء بالألمنيوم أو المعادن. مرة أخرى ، يقتصر عمر القالب على عشرات أو مئات الأجزاء كحد أقصى . عملية الأدوات المعدنية بالرش: نستخدم نماذج أولية سريعة ونصنع نمطًا. نقوم برش سبائك الزنك والألمنيوم على سطح النموذج ونغلفها. يتم بعد ذلك وضع النموذج المطلي بالمعدن داخل دورق ويتم وضعه في إيبوكسي أو إيبوكسي مملوء بالألمنيوم. أخيرًا ، يتم إزالته ومن خلال إنتاج نصفين من هذا القالب نحصل على قالب كامل لقولبة الحقن. تتمتع هذه القوالب بعمر أطول ، وفي بعض الحالات اعتمادًا على المواد ودرجات الحرارة ، يمكنها إنتاج أجزاء بالآلاف. عملية كيلتول: يمكن أن تنتج هذه التقنية قوالب مع دورة حياة تتراوح بين 100،000 و 10 ملايين. باستخدام النماذج الأولية السريعة ، ننتج قالب RTV. يملأ القالب بعد ذلك بمزيج يتكون من مسحوق الصلب A6 ، كربيد التنجستن ، مادة رابطة البوليمر ويترك ليعالج. ثم يتم تسخين هذا القالب لإحراق البوليمر ودمج المساحيق المعدنية. الخطوة التالية هي تسرب النحاس لإنتاج القالب النهائي. إذا لزم الأمر ، يمكن إجراء عمليات ثانوية مثل المعالجة الآلية والتلميع على القالب للحصول على دقة أبعاد أفضل. CLICK Product Finder-Locator Service الصفحة السابقة
- المركبات ، تصنيع المواد المركبة ، الألياف المقواة
المركبات ، تصنيع المواد المركبة ، الجسيمات والألياف المقواة ، سيرميت ، السيراميك والمعدن المركب ، البوليمر المقوى بالألياف الزجاجية ، عملية التمدد صناعة المركبات والمواد المركبة تُعرف التركيبات أو المواد المركبة ببساطة بأنها مواد تتكون من مادتين أو عدة مواد لها خواص فيزيائية أو كيميائية مختلفة ، ولكن عند دمجها تصبح مادة مختلفة عن المواد المكونة لها. نحتاج إلى الإشارة إلى أن المواد المكونة تظل منفصلة ومتميزة في الهيكل. الهدف من تصنيع مادة مركبة هو الحصول على منتج أفضل من مكوناته ويجمع بين الميزات المرغوبة لكل مكون. كمثال؛ قد تكون القوة أو الوزن المنخفض أو السعر المنخفض هي الدافع وراء تصميم وإنتاج مركب. أنواع المركبات التي نقدمها هي مركبات مقواة بالجزيئات ، ومركبات مقواة بالألياف بما في ذلك مصفوفة سيراميك / مصفوفة بوليمر / مصفوفة معدنية / كربون-كربون / مركبات هجينة ، مركبات هيكلية ومصفوفة ومركبة ذات هيكل ساندويتش ومركبات متناهية الصغر. تقنيات التصنيع التي ننشرها في تصنيع المواد المركبة هي: Pultrusion ، عمليات إنتاج ما قبل التقديم ، وضع الألياف المتقدمة ، لف الشعيرات ، وضع الألياف المصممة خصيصًا ، عملية وضع رذاذ الألياف الزجاجية ، التفتت ، عملية lanxide ، z-pinning. تتكون العديد من المواد المركبة من مرحلتين ، المصفوفة ، وهي مستمرة وتحيط بالطور الآخر ؛ والمرحلة المشتتة التي تحيط بها المصفوفة. نوصي بالضغط هنا لقم بتنزيل الرسوم التوضيحية التخطيطية الخاصة بنا لتصنيع المواد المركبة والمواد المركبة بواسطة AGS-TECH Inc. سيساعدك هذا على فهم المعلومات التي نقدمها لك أدناه بشكل أفضل. • المركبات المقواة بالجزيئات: تتكون هذه الفئة من نوعين: المركبات ذات الجسيمات الكبيرة والمركبات المقواة بالتشتت. في النوع الأول ، لا يمكن معالجة تفاعلات مصفوفة الجسيمات على المستوى الذري أو الجزيئي. بدلا من ذلك فإن ميكانيكا الاستمرارية صالحة. من ناحية أخرى ، في المركبات المعززة بالتشتت ، تكون الجسيمات بشكل عام أصغر بكثير في عشرات النطاقات من النانومتر. مثال على مركب الجسيمات الكبيرة هو البوليمرات التي تمت إضافة مواد مالئة إليها. تعمل الحشوات على تحسين خصائص المادة وقد تستبدل بعض حجم البوليمر بمواد أكثر اقتصادا. تؤثر كسور الحجم في المرحلتين على سلوك المركب. تستخدم مركبات الجسيمات الكبيرة مع المعادن والبوليمرات والسيراميك. CERMETS هي أمثلة على مركبات السيراميك / المعدن. السيرمت الأكثر شيوعًا لدينا هو كربيد الأسمنت. يتكون من سيراميك كربيد حراري مثل جزيئات كربيد التنجستن في مصفوفة من معدن مثل الكوبالت أو النيكل. تستخدم مركبات الكربيد هذه على نطاق واسع كأدوات قطع للصلب المتصلب. جزيئات الكربيد الصلبة هي المسؤولة عن عملية القطع ويتم تعزيز صلابتها من خلال المصفوفة المعدنية المطيلة. وهكذا نحصل على مزايا كلتا المادتين في مركب واحد. مثال آخر شائع لمركب الجسيمات الكبير الذي نستخدمه هو جسيمات أسود الكربون الممزوجة بالمطاط المفلكن للحصول على مركب يتمتع بقوة شد عالية وصلابة ومقاومة للتمزق والتآكل. مثال على المركب المعزز بالتشتت هو المعادن والسبائك المعدنية المعززة والمتصلبة بالتشتت المنتظم للجزيئات الدقيقة من مادة صلبة وخاملة للغاية. عندما تتم إضافة رقائق أكسيد الألومنيوم الصغيرة جدًا إلى مصفوفة معدن الألمنيوم ، نحصل على مسحوق الألمنيوم الملبد الذي يتميز بقوة درجات الحرارة العالية. • المركبات المقواة بالألياف: هذه الفئة من المركبات هي في الواقع الأكثر أهمية. الهدف المراد تحقيقه هو القوة والصلابة العالية لكل وحدة وزن. يعد تكوين الألياف وطولها واتجاهها وتركيزها في هذه المركبات أمرًا بالغ الأهمية في تحديد خصائص وفائدة هذه المواد. هناك ثلاث مجموعات من الألياف التي نستخدمها: الشعيرات والألياف والأسلاك. الوايسكرز عبارة عن بلورات مفردة رفيعة جدًا وطويلة. هم من بين أقوى المواد. بعض الأمثلة على مواد الطولي هي الجرافيت ونتريد السيليكون وأكسيد الألومنيوم. FIBERS من ناحية أخرى تتكون معظمها من البوليمرات أو السيراميك وهي في حالة متعددة البلورات أو غير متبلورة. المجموعة الثالثة عبارة عن أسلاك رفيعة ذات أقطار كبيرة نسبيًا وتتكون بشكل متكرر من الفولاذ أو التنجستن. مثال على مركب مقوى بالأسلاك هو إطارات السيارات التي تحتوي على أسلاك فولاذية داخل المطاط. اعتمادًا على مادة المصفوفة ، لدينا المركبات التالية: مركبات مصفوفة البوليمر: وهي مصنوعة من راتينج البوليمر والألياف كمكون تقوية. تحتوي مجموعة فرعية تسمى مركبات البوليمر المقوى بالألياف الزجاجية (GFRP) على ألياف زجاجية مستمرة أو غير متصلة داخل مصفوفة بوليمر. يوفر الزجاج قوة عالية ، وهو اقتصادي ، ويسهل تصنيعه إلى ألياف ، كما أنه خامل كيميائيًا. العيوب هي محدودية صلابتها وصلابتها ، ودرجات حرارة الخدمة تصل فقط إلى 200 - 300 درجة مئوية. الألياف الزجاجية مناسبة لهيكل السيارات ومعدات النقل وأجسام المركبات البحرية وحاويات التخزين. وهي غير مناسبة للطيران ولا صناعة الجسور بسبب الصلابة المحدودة. المجموعة الفرعية الأخرى تسمى مركب البوليمر المقوى بألياف الكربون (CFRP). هنا ، الكربون هو مادة الألياف الخاصة بنا في مصفوفة البوليمر. يُعرف الكربون بمعامله النوعي العالي وقوته وقدرته على الحفاظ عليها في درجات حرارة عالية. يمكن أن توفر لنا ألياف الكربون وحدات شد قياسية ومتوسطة وعالية وفائقة الارتفاع. علاوة على ذلك ، توفر ألياف الكربون خصائص فيزيائية وميكانيكية متنوعة ، وبالتالي فهي مناسبة لمختلف التطبيقات الهندسية المصممة حسب الطلب. يمكن اعتبار مركبات CFRP لتصنيع المعدات الرياضية والترفيهية وأوعية الضغط والمكونات الهيكلية للطيران. ومع ذلك ، فإن مجموعة فرعية أخرى ، وهي مركبات البوليمر المقوى بألياف الأراميد هي أيضًا مواد ذات قوة عالية ومعاملية. نسب قوتهم إلى الوزن عالية بشكل ملحوظ. تُعرف ألياف الأراميد أيضًا بأسماء تجارية KEVLAR و NOMEX. في ظل التوتر ، فإنها تؤدي أداءً أفضل من مواد الألياف البوليمرية الأخرى ، لكنها ضعيفة في الانضغاط. ألياف الأراميد صلبة ، مقاومة للتأثيرات ، مقاومة الزحف والتعب ، مستقرة في درجات الحرارة العالية ، خاملة كيميائياً باستثناء الأحماض والقواعد القوية. تستخدم ألياف الأراميد على نطاق واسع في السلع الرياضية ، والسترات الواقية من الرصاص ، والإطارات ، والحبال ، وأغلفة كابلات الألياف البصرية. توجد مواد تقوية أخرى للألياف ولكنها تستخدم بدرجة أقل. هذه هي البورون وكربيد السيليكون وأكسيد الألومنيوم بشكل أساسي. من ناحية أخرى ، تعتبر مادة مصفوفة البوليمر مهمة أيضًا. يحدد درجة حرارة الخدمة القصوى للمركب لأن البوليمر لديه درجة حرارة انصهار وتدهور أقل بشكل عام. تستخدم البوليستر وإسترات الفينيل على نطاق واسع كمصفوفة البوليمر. تستخدم الراتنجات أيضًا ولها مقاومة ممتازة للرطوبة وخصائص ميكانيكية. على سبيل المثال ، يمكن استخدام راتنج البوليميد حتى 230 درجة مئوية . مركبات المصفوفة المعدنية: في هذه المواد نستخدم مصفوفة معدنية مطيلة ودرجات حرارة الخدمة أعلى بشكل عام من المكونات المكونة لها. عند مقارنتها بمركبات مصفوفة البوليمر ، يمكن أن يكون لها درجات حرارة تشغيل أعلى ، وتكون غير قابلة للاشتعال ، وقد يكون لها مقاومة تحلل أفضل ضد السوائل العضوية. ومع ذلك فهي أكثر تكلفة. مواد التعزيز مثل الشعيرات والجسيمات والألياف المستمرة والمتقطعة ؛ ومواد المصفوفة مثل النحاس والألومنيوم والمغنيسيوم والتيتانيوم والسبائك الفائقة يتم استخدامها بشكل شائع. التطبيقات النموذجية هي مكونات المحرك المصنوعة من مصفوفة من سبائك الألومنيوم المقواة بأكسيد الألومنيوم وألياف الكربون. مركبات المصفوفة الخزفية: تُعرف مواد السيراميك بموثوقيتها العالية في درجات الحرارة العالية. ومع ذلك فهي هشة للغاية ولها قيم منخفضة لمتانة الكسر. من خلال تضمين جزيئات أو ألياف أو شعيرات من السيراميك في مصفوفة أخرى ، يمكننا الحصول على مركبات ذات صلابة تكسير أعلى. تمنع هذه المواد المدمجة بشكل أساسي انتشار الشقوق داخل المصفوفة من خلال بعض الآليات مثل انحراف أطراف الكراك أو تشكيل الجسور عبر أوجه الشق. على سبيل المثال ، يتم استخدام الألومينا المقواة بشعيرات SiC كإدراج في أداة القطع لتصنيع السبائك المعدنية الصلبة. يمكن أن تكشف هذه عن أداء أفضل مقارنة بالكربيدات الأسمنتية. مركبات الكربون - الكربون: كل من التعزيز والمصفوفة من الكربون. لديهم معاملات شد عالية وقوة عند درجات حرارة عالية تزيد عن 2000 درجة مئوية ، ومقاومة الزحف ، وصلابة عالية للكسر ، ومعاملات تمدد حراري منخفضة ، وموصلات حرارية عالية. هذه الخصائص تجعلها مثالية للتطبيقات التي تتطلب مقاومة الصدمات الحرارية. ومع ذلك ، فإن ضعف مركبات الكربون والكربون هو ضعفها ضد الأكسدة في درجات الحرارة العالية. الأمثلة النموذجية للاستخدام هي قوالب الضغط الساخن وتصنيع مكونات محرك التوربينات المتقدمة . المركبات الهجينة: يتم خلط نوعين مختلفين أو أكثر من الألياف في مصفوفة واحدة. وبالتالي يمكن تصميم مادة جديدة بمزيج من الخصائص. مثال على ذلك عندما يتم دمج كل من ألياف الكربون والزجاج في راتينج بوليمري. توفر ألياف الكربون صلابة وقوة منخفضة الكثافة ولكنها غالية الثمن. الزجاج من ناحية أخرى غير مكلف ولكنه يفتقر إلى صلابة ألياف الكربون. المركب الهجين الزجاجي الكربوني أقوى وأكثر صرامة ويمكن تصنيعه بتكلفة أقل. معالجة التركيبات المقواة بالألياف: بالنسبة للبلاستيك المقوى بالألياف المستمر مع الألياف الموزعة بشكل موحد والموجهة في نفس الاتجاه ، نستخدم التقنيات التالية. النبض: يتم تصنيع قضبان وعوارض وأنابيب ذات أطوال مستمرة ومقاطع عرضية ثابتة. يتم تشريب حواف الألياف المستمرة براتنج التصلد بالحرارة ويتم سحبها من خلال قالب فولاذي لتشكيلها بالشكل المطلوب. بعد ذلك ، يمرون عبر قالب معالجة آلي دقيق للوصول إلى شكله النهائي. نظرًا لتسخين قالب المعالجة ، فإنه يعالج مصفوفة الراتنج. ساحبات سحب المواد من خلال القوالب. باستخدام النوى المجوفة المُدخلة ، يمكننا الحصول على أنابيب وأشكال هندسية مجوفة. طريقة pultrusion آلية وتوفر لنا معدلات إنتاج عالية. يمكن إنتاج أي طول للمنتج. عملية إنتاج ما قبل التحضير: التقوية الأولية عبارة عن تقوية مستمرة للألياف مشبعة مسبقًا براتنج بوليمر معالج جزئيًا. يستخدم على نطاق واسع للتطبيقات الهيكلية. تأتي المادة في شكل شريط ويتم شحنها كشريط. تصنعه الشركة المصنعة مباشرة وبشكل كامل دون الحاجة إلى إضافة أي راتنج. نظرًا لأن التقوية الأولية تخضع لتفاعلات المعالجة في درجات حرارة الغرفة ، يتم تخزينها عند درجة حرارة 0 مئوية أو درجات حرارة أقل. بعد الاستخدام ، يتم تخزين الأشرطة المتبقية مرة أخرى في درجات حرارة منخفضة. تستخدم راتنجات اللدائن الحرارية وراتنجات التصلد بالحرارة وتشيع ألياف تقوية الكربون والأراميد والزجاج. لاستخدام مواد التقوية المسبقة ، يتم أولاً إزالة ورق تغليف الحامل ثم يتم التصنيع عن طريق وضع شريط التقوية المسبق على سطح مزود بأدوات (عملية التجميع). يمكن وضع عدة طبقات للحصول على السماكات المرغوبة. الممارسة المتكررة هي تبديل اتجاه الألياف لإنتاج رقائق متقاطعة أو صفائح زاوية. أخيرًا يتم تطبيق الحرارة والضغط من أجل المعالجة. يتم استخدام كل من المعالجة اليدوية وكذلك العمليات الآلية لقطع مواد التقوية الأولية والتركيب. التفاف الملف: يتم وضع ألياف التعزيز المستمرة بدقة في نمط محدد مسبقًا لتتبع شكل مجوف وعادة ما يكون شكل دائري. تمر الألياف أولاً في حمام الراتنج ثم يتم لفها في مغزل بواسطة نظام آلي. بعد عدة مرات تكرار لف يتم الحصول على السماكات المرغوبة ويتم إجراء المعالجة إما في درجة حرارة الغرفة أو داخل الفرن. الآن تتم إزالة المغزل ويتم فك المنتج. يمكن أن يوفر لف الشعيرة نسبًا عالية جدًا من القوة إلى الوزن عن طريق لف الألياف بأنماط محيطية وحلزونية وقطبية. يتم تصنيع الأنابيب والخزانات والأغلفة باستخدام هذه التقنية . • التركيبات الهيكلية: تتكون هذه بشكل عام من مواد متجانسة ومركبة. لذلك يتم تحديد خصائص هذه من خلال المواد المكونة والتصميم الهندسي لعناصرها. فيما يلي الأنواع الرئيسية: التركيبات الصفيحية: هذه المواد الإنشائية مصنوعة من صفائح أو ألواح ثنائية الأبعاد ذات اتجاهات مفضلة عالية القوة. يتم تكديس الطبقات وتثبيتها معًا. من خلال تبديل الاتجاهات عالية القوة في المحورين المتعامدين ، نحصل على مركب له قوة عالية في كلا الاتجاهين في المستوى ثنائي الأبعاد. من خلال ضبط زوايا الطبقات ، يمكن للمرء أن يصنع مركبًا بقوة في الاتجاهات المفضلة. يتم تصنيع التزلج الحديث بهذه الطريقة . ألواح الساندويش: هذه المركبات الهيكلية خفيفة الوزن ولكنها تتمتع بصلابة وقوة عالية. تتكون الألواح العازلة من لوحين خارجيين مصنوعين من مادة صلبة وقوية مثل سبائك الألومنيوم أو البلاستيك المقوى بالألياف أو الفولاذ ونواة بين الألواح الخارجية. يجب أن يكون اللب خفيف الوزن ومعظم الوقت يكون له معامل مرونة منخفض. المواد الأساسية الشعبية هي الرغاوي البوليمرية الصلبة والخشب وأقراص العسل. تُستخدم الألواح العازلة على نطاق واسع في صناعة البناء كمواد تسقيف أو مواد أرضية أو حائط ، وكذلك في صناعات الطيران. • المركبات النانوية: تتكون هذه المواد الجديدة من جسيمات متناهية الصغر مدمجة في مصفوفة. باستخدام المركبات النانوية ، يمكننا تصنيع مواد مطاطية تمثل حواجز جيدة جدًا لاختراق الهواء مع الحفاظ على خصائصها المطاطية دون تغيير . CLICK Product Finder-Locator Service الصفحة السابقة
- عمليات الانضمام والتجميع والتثبيت ، اللحام ، اللحام بالنحاس ، اللحام
عمليات الربط والتجميع والتثبيت ، اللحام ، اللحام بالنحاس ، اللحام ، التلبيد ، الربط اللاصق ، تركيب الضغط ، عملية اللحام الموجي وإعادة التدفق ، فرن الشعلة عمليات الانضمام والتجميع والتثبيت ننضم إلى الأجزاء المصنعة الخاصة بك ونجمعها وربطها ونحولها إلى منتجات تامة الصنع أو نصف منتهية باستخدام اللحام ، والنسج ، والحديد ، والتشويش ، والترابط اللاصق ، والتثبيت ، والتثبيت بالضغط. بعض عمليات اللحام الأكثر شيوعًا لدينا هي القوس ، غاز الأكسجين ، المقاومة ، الإسقاط ، التماس ، الانزعاج ، الإيقاع ، الحالة الصلبة ، شعاع الإلكترون ، الليزر ، الحرارة ، اللحام التعريفي. عمليات اللحام بالنحاس الشائعة لدينا هي الشعلة ، والحث ، والأفران ، واللحام بالنحاس الغاطس. طرق اللحام لدينا هي الحديد ، اللوح الساخن ، الفرن ، الحث ، الغمس ، الموجة ، إعادة التدفق واللحام بالموجات فوق الصوتية. من أجل الترابط اللاصق ، نستخدم في كثير من الأحيان اللدائن الحرارية والتثبيت الحراري ، والإيبوكسي ، والفينولات ، والبولي يوريثين ، والسبائك اللاصقة ، بالإضافة إلى بعض المواد الكيميائية والأشرطة الأخرى. أخيرًا ، تتكون عمليات التثبيت لدينا من المسامير ، والبراغي ، والصواميل ، والمسامير ، والتثبيت ، والحسم ، والتثبيت ، والخياطة ، والتدبيس ، وتركيب الكبس. • اللحام: يتضمن اللحام ربط المواد عن طريق إذابة قطع العمل وإدخال مواد حشو ، والتي تنضم أيضًا إلى حوض اللحام المنصهر. عندما تبرد المنطقة ، نحصل على مفصل قوي. يتم تطبيق الضغط في بعض الحالات. على عكس اللحام ، تتضمن عمليات اللحام والنحاس فقط صهر مادة ذات نقطة انصهار أقل بين قطع العمل ، ولا تذوب قطع العمل. نوصي بالضغط هنا لقم بتنزيل الرسوم التوضيحية التخطيطية الخاصة بنا لعمليات اللحام بواسطة AGS-TECH Inc. سيساعدك هذا على فهم المعلومات التي نقدمها لك أدناه بشكل أفضل. في ARC WELDING ، نستخدم مصدر طاقة وإلكترود لإنشاء قوس كهربائي يذيب المعادن. نقطة اللحام محمية بغاز أو بخار أو مادة أخرى. هذه العملية شائعة في لحام قطع غيار السيارات والهياكل الفولاذية. في اللحام بالقوس المعدني الملحوم (SMAW) أو المعروف أيضًا باسم اللحام بالعصا ، يتم وضع عصا إلكترود بالقرب من المادة الأساسية ويتم إنشاء قوس كهربائي بينهما. يذوب قضيب القطب الكهربائي ويعمل كمواد حشو. يحتوي القطب أيضًا على تدفق يعمل كطبقة من الخبث ويطلق أبخرة تعمل بمثابة غاز التدريع. هذه تحمي منطقة اللحام من التلوث البيئي. لم يتم استخدام مواد مالئة أخرى. عيوب هذه العملية هي بطئها ، والحاجة إلى استبدال الأقطاب الكهربائية بشكل متكرر ، والحاجة إلى التخلص من الخبث المتبقي الناشئ عن التدفق. عدد من المعادن مثل الحديد والصلب والنيكل والألمنيوم والنحاس ... إلخ. يمكن أن تكون ملحومة. مزاياه هي أدواته غير المكلفة وسهولة الاستخدام. لحام القوس المعدني بالغاز (GMAW) المعروف أيضًا باسم الغاز الخامل المعدني (MIG) ، لدينا تغذية مستمرة لحشو سلك قطب كهربائي قابل للاستهلاك وغاز خامل أو خامل جزئيًا يتدفق حول السلك ضد التلوث البيئي لمنطقة اللحام. يمكن لحام الفولاذ والألمنيوم والمعادن غير الحديدية الأخرى. مزايا MIG هي سرعات لحام عالية ونوعية جيدة. تتمثل العيوب في معداتها المعقدة والتحديات التي تواجهها في البيئات الخارجية العاصفة لأننا يجب أن نحافظ على استقرار غاز التدريع حول منطقة اللحام. أحد أشكال GMAW هو اللحام القوسي ذو القلب المتدفق (FCAW) والذي يتكون من أنبوب معدني ناعم مملوء بمواد التدفق. أحيانًا يكون التدفق داخل الأنبوب كافيًا للحماية من التلوث البيئي. لحام القوس المغمور (SAW) على نطاق واسع عملية آلية ، تتضمن تغذية مستمرة للأسلاك وقوسًا يتم ضربه تحت طبقة من غطاء التدفق. معدلات الإنتاج وجودته عالية ، وخبث اللحام يسهل إزالته ، ولدينا بيئة عمل خالية من الدخان. العيب هو أنه لا يمكن استخدامه إلا في لحام parts في مواضع معينة. في اللحام بالقوس التنغستن بالغاز (GTAW) أو اللحام بالغاز الخامل بالتنغستن (TIG) ، نستخدم قطبًا كهربائيًا من التنغستن جنبًا إلى جنب مع حشو منفصل وغازات خاملة أو قريبة من الغازات الخاملة. كما نعلم فإن التنغستن لديه نقطة انصهار عالية وهو معدن مناسب جدًا لدرجات الحرارة العالية جدًا. لا يتم استهلاك التنغستن في TIG خلافًا للطرق الأخرى الموضحة أعلاه. تقنية لحام بطيئة ولكن عالية الجودة مفيدة على التقنيات الأخرى في لحام المواد الرقيقة. مناسب للعديد من المعادن. اللحام بالقوس البلازمي مشابه ولكنه يستخدم غاز البلازما لإنشاء القوس. يكون القوس في لحام القوس بالبلازما أكثر تركيزًا نسبيًا مقارنةً بـ GTAW ويمكن استخدامه لمجموعة أكبر من سماكة المعدن بسرعات أعلى بكثير. يمكن تطبيق لحام القوس والبلازما GTAW على نفس المواد أكثر أو أقل. OXY-FUEL / OXYFUEL WELDING يسمى أيضًا لحام أوكسي أسيتيلين ولحام الأكسجين واللحام بالغاز باستخدام وقود الغاز والأكسجين للحام. نظرًا لعدم استخدام الطاقة الكهربائية ، فهي محمولة ويمكن استخدامها في حالة عدم وجود كهرباء. باستخدام شعلة اللحام ، نقوم بتسخين القطع ومواد الحشو لإنتاج تجمع معدني منصهر مشترك. يمكن استخدام أنواع مختلفة من الوقود مثل الأسيتيلين ، والبنزين ، والهيدروجين ، والبروبان ، والبيوتان ... إلخ. في اللحام بالأكسجين ، نستخدم حاويتين ، واحدة للوقود والأخرى للأكسجين. يؤكسد الأكسجين الوقود (يحرقه). لحام المقاومة: يستفيد هذا النوع من اللحام من تسخين الجول وتتولد الحرارة في الموقع الذي يتم فيه تطبيق التيار الكهربائي لفترة معينة. يتم تمرير التيارات العالية من خلال المعدن. تتشكل برك من المعدن المنصهر في هذا الموقع. طرق اللحام بالمقاومة شائعة بسبب كفاءتها وإمكانية تلوث قليلة. ومع ذلك ، فإن العيوب هي أن تكاليف المعدات كبيرة نسبيًا والقيود المتأصلة في قطع العمل الرقيقة نسبيًا. اللحام البقعي هو أحد أنواع اللحام بالمقاومة. هنا ننضم إلى لوحين متداخلين أو أكثر أو قطع عمل باستخدام قطبين نحاسيين لربط الألواح ببعضها البعض وتمرير تيار عالي من خلالها. تسخن المادة الموجودة بين الأقطاب الكهربائية النحاسية ويتم إنشاء بركة منصهرة في ذلك الموقع. يتم بعد ذلك إيقاف التيار وتبريد أطراف القطب النحاسي موقع اللحام لأن الأقطاب الكهربائية يتم تبريدها بالماء. يعد تطبيق الكمية المناسبة من الحرارة على المادة والسمك المناسبين أمرًا أساسيًا لهذه التقنية ، لأنه إذا تم تطبيقه بشكل خاطئ ، فسيكون المفصل ضعيفًا. يتميز اللحام النقطي بمزايا عدم التسبب في أي تشوه كبير لقطع العمل ، وكفاءة الطاقة ، وسهولة التشغيل الآلي ومعدلات الإنتاج المتميزة ، وعدم الحاجة إلى أي مواد مالئة. العيب هو أنه نظرًا لأن اللحام يحدث في البقع بدلاً من تشكيل خط متواصل ، يمكن أن تكون القوة الإجمالية أقل نسبيًا مقارنة بطرق اللحام الأخرى. من ناحية أخرى ، ينتج SEAM WELDING اللحامات على الأسطح المتعرجة للمواد المماثلة. يمكن أن يكون التماس مفصلًا أو متداخلًا. يبدأ لحام اللحام من أحد الطرفين ويتحرك تدريجياً إلى الطرف الآخر. تستخدم هذه الطريقة أيضًا قطبين من النحاس لتطبيق الضغط والتيار على منطقة اللحام. تدور الأقطاب الكهربائية على شكل قرص مع اتصال مستمر على طول خط التماس وتصنع لحامًا مستمرًا. هنا أيضًا ، يتم تبريد الأقطاب الكهربائية بواسطة الماء. اللحامات قوية وموثوقة للغاية. طرق أخرى هي الإسقاط ، وتقنيات اللحام بالوميض والاضطراب. يختلف لحام SOLID-STATE قليلاً عن الطرق السابقة الموضحة أعلاه. يحدث الاندماج في درجات حرارة أقل من درجة حرارة انصهار المعادن المترابطة وبدون استخدام حشو المعادن. يمكن استخدام الضغط في بعض العمليات. طرق مختلفة هي لحام COEXTRUSION WELDING حيث يتم بثق المعادن غير المتشابهة من خلال نفس القالب ، لحام الضغط البارد حيث ننضم إلى السبائك اللينة أسفل نقاط الانصهار الخاصة بهم ، DIFFUSION WELDING تقنية بدون خطوط لحام مرئية ، لحام الانفجار للانضمام إلى المواد غير المتشابهة ، على سبيل المثال السبائك المقاومة للتآكل إلى الهيكلية الفولاذ ، اللحام النبضي الكهرومغناطيسي حيث نقوم بتسريع الأنابيب والألواح بالقوى الكهرومغناطيسية ، تشكيل اللحام الذي يتكون من تسخين المعادن إلى درجات حرارة عالية وطرقها معًا ، لحام الاحتكاك حيث يتم إجراء لحام احتكاك كافٍ ، لحام الاحتكاك الذي يتضمن دورانًا غير أداة قابلة للاستهلاك تعبر خط الوصلة ، لحام بالضغط الساخن حيث نضغط المعادن معًا في درجات حرارة مرتفعة أقل من درجة حرارة الانصهار في فراغ أو غازات خاملة ، عملية اللحام بالضغط ISOSTATIC الساخن ، عملية نقوم فيها بتطبيق الضغط باستخدام الغازات الخاملة داخل الوعاء ، ROLL WELDING حيث ننضم المواد غير المتشابهة عن طريق إجبارهم على الاختيار بين عجلتان دوارتان ، اللحام بالموجات فوق الصوتية حيث يتم لحام الصفائح المعدنية أو البلاستيكية الرقيقة باستخدام طاقة اهتزازية عالية التردد. عمليات اللحام الأخرى لدينا هي لحام شعاع الإلكترون مع اختراق عميق ومعالجة سريعة ولكن كونها طريقة باهظة الثمن نعتبرها لحالات خاصة ، اللحام بالكهرباء هو طريقة مناسبة للألواح السميكة الثقيلة وقطع العمل من الفولاذ فقط ، اللحام التعريفي حيث نستخدم الحث الكهرومغناطيسي و تسخين قطع العمل الموصلة كهربائياً أو المغناطيسية ، لحام شعاع الليزر أيضًا مع اختراق عميق ومعالجة سريعة ولكن طريقة باهظة الثمن ، اللحام الهجين بالليزر الذي يجمع LBW مع GMAW في نفس رأس اللحام وقادر على سد فجوات 2 مم بين الألواح ، يتضمن تفريغًا كهربائيًا متبوعًا بتزوير المواد بالضغط المطبق ، ولحام THERMIT الذي يتضمن تفاعلًا طاردًا للحرارة بين مساحيق أكسيد الحديد والألومنيوم. المواد مع الحرارة والضغط. نوصي بالضغط هنا لقم بتنزيل الرسوم التوضيحية التخطيطية الخاصة بنا لعمليات اللحام بالنحاس واللحام واللصق بواسطة AGS-TECH Inc سيساعدك هذا على فهم المعلومات التي نقدمها لك أدناه بشكل أفضل. • النحت: نجمع بين معدنين أو أكثر عن طريق تسخين معادن الحشو بينهما فوق نقاط الانصهار الخاصة بهم واستخدام الحركة الشعرية للانتشار. تشبه هذه العملية عملية اللحام ، لكن درجات الحرارة المستخدمة في إذابة الحشو تكون أعلى في اللحام بالنحاس. كما هو الحال في اللحام ، يحمي التدفق مادة الحشو من التلوث الجوي. بعد التبريد ، يتم ربط قطع العمل معًا. تتضمن العملية الخطوات الرئيسية التالية: التوافق الجيد والتخليص ، والتنظيف المناسب للمواد الأساسية ، والتثبيت المناسب ، واختيار التدفق المناسب والجو المناسب ، وتسخين التجميع وأخيراً تنظيف التجميع بالنحاس. بعض عمليات اللحام بالنحاس لدينا هي TORCH BRAZING ، وهي طريقة شائعة يتم تنفيذها يدويًا أو بطريقة آلية. إنها مناسبة لأوامر الإنتاج ذات الحجم المنخفض والحالات المتخصصة. يتم تطبيق الحرارة باستخدام ألسنة اللهب الغازية بالقرب من المفصل الذي يتم لحامه بالنحاس. تتطلب عملية صقل الأفران مهارة أقل للمشغل وهي عملية شبه آلية مناسبة للإنتاج الصناعي بكميات كبيرة. يعد كل من التحكم في درجة الحرارة والتحكم في الغلاف الجوي في الفرن من مزايا هذه التقنية ، لأن الأول يتيح لنا التحكم في دورات الحرارة والقضاء على التسخين الموضعي كما هو الحال في لحام اللحام بالنحاس ، والأخير يحمي الجزء من الأكسدة. باستخدام القفز ، نحن قادرون على تقليل تكاليف التصنيع إلى الحد الأدنى. تتمثل العيوب في ارتفاع استهلاك الطاقة وتكاليف المعدات واعتبارات التصميم الأكثر تحديًا. تحدث عملية صقل الفراغ في فرن الفراغ. يتم الحفاظ على اتساق درجة الحرارة ونحصل على مفاصل خالية من التدفق ونظيفة جدًا مع ضغوط متبقية قليلة جدًا. يمكن أن تحدث المعالجات الحرارية أثناء اللحام بالنحاس الفراغي ، بسبب الضغوط المتبقية المنخفضة الموجودة أثناء دورات التدفئة والتبريد البطيئة. العيب الرئيسي هو تكلفتها العالية لأن إنشاء بيئة فراغ عملية مكلفة. تقنية أخرى DIP BRAZING تنضم إلى الأجزاء المثبتة حيث يتم تطبيق مركب اللحام على أسطح التزاوج. بعد ذلك ، يتم غمس الأجزاء المعالجة في حمام من الملح المصهور مثل كلوريد الصوديوم (ملح الطعام) الذي يعمل كوسيط لنقل الحرارة وتدفق. يتم استبعاد الهواء وبالتالي لا يحدث تكوين للأكسيد. في عملية النحت التعريفي ، نقوم بربط المواد بمعدن حشو له نقطة انصهار أقل من المواد الأساسية. يخلق التيار المتردد من ملف الحث مجالًا كهرومغناطيسيًا يحث على تسخين الحث على المواد المغناطيسية الحديدية في الغالب. توفر الطريقة تسخينًا انتقائيًا ، ووصلات جيدة مع حشو يتدفق فقط في المناطق المرغوبة ، وأكسدة قليلة لعدم وجود لهب والتبريد سريع ، وتسخين سريع ، واتساق وملاءمة للتصنيع بكميات كبيرة. لتسريع عملياتنا ولضمان الاتساق ، نستخدم بشكل متكرر التشكيلات. يمكن العثور على معلومات عن منشأة اللحام الخاصة بنا لإنتاج وصلات من السيراميك إلى المعدن ، وختم محكم ، ومغذيات الفراغ ، ومكونات التحكم في السوائل والفراغ العالية والعالية للغاية هنا: كتيب مصنع اللحام بالنحاس • اللحام: في اللحام ليس لدينا انصهار لقطع العمل ، ولكن لدينا معدن حشو بنقطة انصهار أقل من الأجزاء الرابطة التي تتدفق إلى المفصل. يذوب معدن الحشو في اللحام عند درجة حرارة أقل من اللحام بالنحاس. نحن نستخدم سبائك خالية من الرصاص للحام ولدينا امتثال RoHS وللتطبيقات والمتطلبات المختلفة لدينا سبائك مختلفة ومناسبة مثل سبائك الفضة. يوفر لنا اللحام وصلات مانعة لتسرب الغاز والسائل. في SOFT SOLDERING ، يحتوي معدن الحشو الخاص بنا على درجة انصهار أقل من 400 درجة مئوية ، بينما في SILVER SOLDERING و BRAZING نحتاج إلى درجات حرارة أعلى. يستخدم اللحام الناعم درجات حرارة منخفضة ولكنه لا ينتج عنه وصلات قوية للتطبيقات الصعبة في درجات حرارة مرتفعة. من ناحية أخرى ، يتطلب لحام الفضة درجات حرارة عالية يوفرها الشعلة ويمنحنا وصلات قوية مناسبة لتطبيقات درجات الحرارة العالية. يتطلب اللحام بالنحاس أعلى درجات الحرارة وعادة ما يتم استخدام شعلة. نظرًا لأن مفاصل اللحام قوية جدًا ، فهي مرشحة جيدة لإصلاح الأجسام الحديدية الثقيلة. في خطوط التصنيع الخاصة بنا ، نستخدم خطوط اللحام اليدوي وكذلك خطوط اللحام الآلية. INDUCTION SOLDERING يستخدم تيار متردد عالي التردد في ملف نحاسي لتسهيل التسخين بالحث. يتم إحداث التيارات في الجزء الملحوم ونتيجة لذلك يتم توليد الحرارة عند المقاومة العالية joint. تعمل هذه الحرارة على إذابة معدن الحشو. يستخدم الجريان أيضًا. يعد اللحام التعريفي طريقة جيدة لحام الأسطوانات والأنابيب في عملية مستمرة عن طريق لف الملفات حولها. يعد لحام بعض المواد مثل الجرافيت والسيراميك أكثر صعوبة لأنه يتطلب طلاء قطع العمل بمعدن مناسب قبل اللحام. هذا يسهل الترابط البيني. نحن نقوم بلحام مثل هذه المواد خاصة لتطبيقات التغليف المحكم. نقوم بتصنيع لوحات الدوائر المطبوعة (PCB) بكميات كبيرة باستخدام WAVE SOLDERING في الغالب. فقط لكمية صغيرة من أغراض النماذج الأولية ، نستخدم اللحام اليدوي باستخدام مكواة اللحام. نحن نستخدم اللحام الموجي لكل من تجميعات ثنائي الفينيل متعدد الكلور (PCBA) عبر الفتحات وكذلك على السطح. يحافظ الغراء المؤقت على المكونات المتصلة بلوحة الدائرة ويتم وضع التجميع على ناقل ويتحرك عبر جهاز يحتوي على لحام منصهر. أولاً يتم تدفق ثنائي الفينيل متعدد الكلور ثم يدخل منطقة التسخين المسبق. اللحام المنصهر في مقلاة وله نمط من الموجات الواقفة على سطحه. عندما يتحرك ثنائي الفينيل متعدد الكلور فوق هذه الموجات ، فإن هذه الموجات تلامس الجزء السفلي من ثنائي الفينيل متعدد الكلور وتلتصق بوسادات اللحام. يبقى اللحام على المسامير والوسادات فقط وليس على ثنائي الفينيل متعدد الكلور نفسه. يجب التحكم جيدًا في الأمواج الموجودة في اللحام المصهور حتى لا يكون هناك تناثر ولا تلمس قمم الموجات المناطق غير المرغوب فيها من الألواح وتلوثها. في REFLOW SOLDERING ، نستخدم معجون لحام لزج لتوصيل المكونات الإلكترونية مؤقتًا باللوحات. ثم توضع الألواح في فرن إعادة التدفق مع التحكم في درجة الحرارة. هنا يذوب اللحام ويربط المكونات بشكل دائم. نحن نستخدم هذه التقنية لكل من المكونات المثبتة على السطح وكذلك للمكونات عبر الثقب. يعد التحكم المناسب في درجة الحرارة وضبط درجات حرارة الفرن أمرًا ضروريًا لتجنب تدمير المكونات الإلكترونية الموجودة على السبورة من خلال ارتفاع درجة حرارتها فوق حدود درجة الحرارة القصوى. في عملية اللحام بإعادة التدفق ، لدينا بالفعل عدة مناطق أو مراحل لكل منها ملف تعريف حراري مميز ، مثل خطوة التسخين المسبق وخطوة النقع الحراري وخطوات إعادة التدفق والتبريد. هذه الخطوات المختلفة ضرورية للحام بإعادة التدفق الخالي من التلف لتجمعات لوحات الدوائر المطبوعة (PCBA). ULTRASONIC SOLDERING هي تقنية أخرى شائعة الاستخدام ذات قدرات فريدة - يمكن استخدامها في لحام الزجاج والسيراميك والمواد غير المعدنية. على سبيل المثال ، تحتاج الألواح الكهروضوئية غير المعدنية إلى أقطاب كهربائية يمكن لصقها باستخدام هذه التقنية. في اللحام بالموجات فوق الصوتية ، نقوم بنشر طرف لحام ساخن ينبعث منه أيضًا اهتزازات فوق صوتية. تنتج هذه الاهتزازات فقاعات تجويف في واجهة الركيزة مع مادة اللحام المنصهرة. تعمل الطاقة المتفجرة للتجويف على تعديل سطح الأكسيد وإزالة الأوساخ والأكاسيد. خلال هذا الوقت يتم أيضًا تكوين طبقة سبيكة. يشتمل اللحام الموجود على سطح الترابط على الأكسجين ويتيح تكوين رابطة قوية مشتركة بين الزجاج واللحام. يمكن اعتبار DIP SOLDERING نسخة أبسط من اللحام الموجي المناسب للإنتاج على نطاق صغير فقط. يتم تطبيق تدفق التنظيف الأول كما هو الحال في العمليات الأخرى. يتم غمس مركبات ثنائي الفينيل متعدد الكلور ذات المكونات المركبة يدويًا أو بطريقة شبه آلية في خزان يحتوي على لحام منصهر. يلتصق اللحام المنصهر بالمناطق المعدنية المكشوفة غير المحمية بواسطة قناع اللحام على السبورة. المعدات بسيطة وغير مكلفة. • الربط اللاصق: هذه تقنية شائعة أخرى نستخدمها بشكل متكرر وتتضمن ربط الأسطح باستخدام الغراء أو الإيبوكسي أو العوامل البلاستيكية أو المواد الكيميائية الأخرى. يتم تحقيق الترابط إما عن طريق تبخير المذيب أو المعالجة الحرارية أو المعالجة بالأشعة فوق البنفسجية أو المعالجة بالضغط أو الانتظار لفترة معينة. يتم استخدام أنواع مختلفة من المواد اللاصقة عالية الأداء في خطوط الإنتاج الخاصة بنا. من خلال عمليات التطبيق والمعالجة المصممة هندسيًا بشكل صحيح ، يمكن أن ينتج عن الترابط اللاصق روابط ضغط منخفضة جدًا تكون قوية وموثوقة. يمكن أن تكون الروابط اللاصقة واقيًا جيدًا ضد العوامل البيئية مثل الرطوبة والملوثات والمواد المسببة للتآكل والاهتزاز ... إلخ. مزايا الترابط اللاصق هي: يمكن تطبيقها على المواد التي يصعب لحامها أو لحامها أو لحامها بالنحاس. كما يمكن أن يكون مفضلًا للمواد الحساسة للحرارة التي قد تتلف بسبب اللحام أو غيرها من عمليات درجات الحرارة المرتفعة. المزايا الأخرى للمواد اللاصقة هي إمكانية تطبيقها على الأسطح غير المنتظمة وزيادة وزن التجميع بكميات صغيرة جدًا عند مقارنتها بالطرق الأخرى. كما أن تغييرات الأبعاد في الأجزاء ضئيلة للغاية. تحتوي بعض المواد اللاصقة على خصائص مطابقة الفهرس ويمكن استخدامها بين المكونات الضوئية دون تقليل الضوء أو قوة الإشارة الضوئية بشكل كبير. من ناحية أخرى ، تتمثل العيوب في أوقات المعالجة الأطول والتي قد تبطئ خطوط التصنيع ومتطلبات التثبيت ومتطلبات تحضير السطح وصعوبة الفك عند الحاجة إلى إعادة العمل. تتضمن معظم عمليات الربط اللاصق لدينا الخطوات التالية: - معالجة السطح: إجراءات التنظيف الخاصة مثل تنظيف المياه منزوعة الأيونات وتنظيف الكحول وتنظيف البلازما أو الهالة شائعة. بعد التنظيف ، قد نضع معززات الالتصاق على الأسطح لضمان أفضل المفاصل الممكنة. - إصلاح الجزء: لكل من تطبيق المادة اللاصقة وكذلك للمعالجة ، نقوم بتصميم واستخدام تركيبات مخصصة. -التطبيق اللاصق: نستخدم في بعض الأحيان يدويًا ، وأحيانًا اعتمادًا على الأنظمة الآلية للحالة مثل الروبوتات والمحركات المؤازرة والمشغلات الخطية لتوصيل المواد اللاصقة إلى الموقع الصحيح ونستخدم موزعات لتسليمها بالحجم والكمية المناسبين. - المعالجة: اعتمادًا على المادة اللاصقة ، قد نستخدم التجفيف البسيط والمعالجة وكذلك المعالجة تحت مصابيح الأشعة فوق البنفسجية التي تعمل كمحفز أو معالجة بالحرارة في فرن أو باستخدام عناصر تسخين مقاومة مثبتة على أدوات التثبيت والتركيبات. نوصي بالضغط هنا لقم بتنزيل الرسوم التوضيحية التخطيطية الخاصة بنا لعمليات التثبيت بواسطة AGS-TECH Inc. سيساعدك هذا على فهم المعلومات التي نقدمها لك أدناه بشكل أفضل. • عمليات الربط: تنقسم عمليات الربط الميكانيكية الخاصة بنا إلى فئتين: المثبتات والمفاصل المتكاملة. من أمثلة السحابات التي نستخدمها البراغي ، والدبابيس ، والصواميل ، والبراغي ، والمسامير. أمثلة على المفاصل المتكاملة التي نستخدمها هي التركيبات المفاجئة والانكماشية والدرزات والتجعيد. باستخدام مجموعة متنوعة من طرق التثبيت ، نتأكد من أن وصلاتنا الميكانيكية قوية وموثوقة لسنوات عديدة من الاستخدام. تعد البراغي والمسامير من أكثر أدوات التثبيت شيوعًا لتثبيت الأشياء معًا وتحديد موضعها. البراغي والمسامير لدينا تلبي معايير ASME. يتم نشر أنواع مختلفة من البراغي والمسامير ، بما في ذلك مسامير الغطاء السداسي والمسامير السداسية ، ومسامير ومسامير التأخير ، والمسمار المزدوج ، ومسمار وتد ، ومسمار العين ، ومسمار المرآة ، ومسامير الصفائح المعدنية ، ومسامير الضبط الدقيقة ، والحفر الذاتي ، ومسامير التنصت الذاتية ، ومسامير تثبيت ، ومسامير مع غسالات مدمجة ، ... وأكثر من ذلك. لدينا أنواع مختلفة من رؤوس اللولب مثل الغاطسة ، القبة ، الدائرية ، ذات الحواف وأنواع مختلفة من محركات اللولب مثل الفتحة ، فيليبس ، مربع ، مقبس سداسي. من ناحية أخرى ، فإن A RIVET عبارة عن قفل ميكانيكي دائم يتكون من عمود أسطواني ناعم ورأس من جهة. بعد الإدخال ، يتم تشويه الطرف الآخر من البرشام ويتم توسيع قطره بحيث يظل في مكانه. بمعنى آخر ، قبل التثبيت ، يكون للمسمار رأس واحد وبعد التثبيت يكون له رأسان. نقوم بتركيب أنواع مختلفة من المسامير اعتمادًا على التطبيق والقوة وإمكانية الوصول والتكلفة مثل المسامير ذات الرأس الصلبة / الدائرية ، والهيكلية ، وشبه الأنبوبية ، والمعمية ، والأوسكار ، والمحرك ، والتدفق ، وقفل الاحتكاك ، والمسامير ذاتية الثقب. يمكن تفضيل التثبيت في الحالات التي يجب فيها تجنب تشوه الحرارة وتغير خواص المواد بسبب حرارة اللحام. يوفر التثبيت أيضًا وزنًا خفيفًا وقوة تحمل جيدة بشكل خاص ضد قوى القص. ضد أحمال الشد ولكن قد تكون البراغي والصواميل والمسامير أكثر ملاءمة. في عملية التطويق ، نستخدم الخرامة والقوالب الخاصة لتشكيل تعشيق ميكانيكي بين الصفائح المعدنية التي يتم ربطها. تقوم الخرامة بدفع طبقات الصفائح المعدنية إلى تجويف القالب وتؤدي إلى تكوين مفصل دائم. لا حاجة للتدفئة والتبريد في عملية الحسم وهي عملية تشغيل باردة. إنها عملية اقتصادية يمكن أن تحل محل اللحام النقطي في بعض الحالات. في PINNING ، نستخدم المسامير وهي عناصر الآلة المستخدمة لتأمين مواضع أجزاء الماكينة بالنسبة لبعضها البعض. الأنواع الرئيسية هي دبابيس clevis ، ودبوس cotter ، ودبوس زنبركي ، ودبابيس وتد ، ودبوس مقسم. في التدبيس ، نستخدم مسدسات التدبيس والمشابك وهي عبارة عن مشابك ذات شقين تستخدم لربط المواد أو ربطها. يتميز التدبيس بالمزايا التالية: اقتصادي وبسيط وسريع الاستخدام ، يمكن استخدام تاج الدبابيس لربط المواد ببعضها البعض ، ويمكن أن يسهل تاج الدعامة ربط قطعة مثل الكابل وتثبيتها على السطح دون ثقب أو ضارة ، سهلة الإزالة نسبيًا. يتم تنفيذ الضغط عن طريق دفع الأجزاء معًا والاحتكاك بينها يربط الأجزاء. يتم تجميع الأجزاء المناسبة للضغط التي تتكون من عمود كبير الحجم وثقب صغير الحجم بشكل عام بإحدى طريقتين: إما عن طريق تطبيق القوة أو الاستفادة من التمدد الحراري أو انكماش الأجزاء. عندما يتم تثبيت أداة الضغط عن طريق تطبيق القوة ، فإننا إما نستخدم مكبسًا هيدروليكيًا أو مكبسًا يدويًا. من ناحية أخرى ، عندما يتم تثبيت الضغط عن طريق التمدد الحراري ، فإننا نقوم بتسخين الأجزاء المغلفة وتجميعها في مكانها وهي ساخنة. عندما تبرد فإنها تتقلص وتعود إلى أبعادها الطبيعية. ينتج عن هذا نوبة صحفية جيدة. نسمي هذا بدلاً من ذلك SHRINK-FITTING. الطريقة الأخرى للقيام بذلك هي تبريد الأجزاء المغلفة قبل التجميع ثم تحريكها إلى أجزاء التزاوج. عندما يتم تسخين التجميع ، يتمددون ونحصل على نوبة محكمة. قد تكون هذه الطريقة الأخيرة مفضلة في الحالات التي يشكل فيها التسخين خطر تغيير خصائص المواد. التبريد أكثر أمانًا في تلك الحالات. المكونات والتركيبات الهوائية والهيدروليكية • الصمامات والمكونات الهيدروليكية والهوائية مثل الحلقة O ، والغسالة ، والأختام ، والحشية ، والحلقة ، والرقاقة. نظرًا لأن الصمامات والمكونات الهوائية تأتي بتنوع كبير ، فلا يمكننا سرد كل شيء هنا. اعتمادًا على البيئات الفيزيائية والكيميائية للتطبيق الخاص بك ، لدينا منتجات خاصة لك. يرجى تحديد التطبيق ونوع المكون والمواصفات والظروف البيئية مثل الضغط ودرجة الحرارة والسوائل أو الغازات التي ستكون على اتصال بصماماتك ومكوناتك الهوائية ؛ وسنختار المنتج الأنسب لك أو نصنعه خصيصًا لتطبيقك. CLICK Product Finder-Locator Service الصفحة السابقة
- عناصر الماكينة ، التروس ، محركات التروس ، المحامل ، المفاتيح ، المفاتيح
تصنيع عناصر الماكينة ، التروس ، محركات التروس ، المحامل ، المفاتيح ، المفاتيح ، الدبابيس ، الأعمدة ، الأختام ، السحابات ، القابض ، الكامات ، المتابعون ، الأحزمة ، الوصلات ، الأعمدة تصنيع عناصر الماكينة اقرأ أكثر تجميع الأحزمة والسلاسل ومحركات الكابلات اقرأ أكثر مجموعة التروس والعتاد اقرأ أكثر صناعة الوصلات والمحامل اقرأ أكثر صناعة المفاتيح والمفاتيح والدبابيس اقرأ أكثر صناعة الكاميرات والتابعين والروابط وعجلات السقاطة اقرأ أكثر صناعة الأعمدة اقرأ أكثر صناعة الأختام الميكانيكية اقرأ أكثر مجموعة القابض والفرامل اقرأ أكثر صناعة المشابك اقرأ أكثر تجميع الآلات البسيطة عناصر الماكينة هي مكونات أولية للآلة. تتكون هذه العناصر من ثلاثة أنواع أساسية: 1.) المكونات الهيكلية بما في ذلك أعضاء الإطار ، والمحامل ، والمحاور ، والخيوط ، والمثبتات ، والأختام ، ومواد التشحيم. 2.) آليات التحكم في الحركة بطرق مختلفة مثل قطارات التروس ، والحزام أو محركات السلسلة ، والوصلات ، وأنظمة الكامات والتابعين ، والمكابح والقوابض. 3.) مكونات التحكم مثل الأزرار والمفاتيح والمؤشرات وأجهزة الاستشعار والمحركات وأجهزة التحكم في الكمبيوتر. يتم توحيد معظم عناصر الماكينة التي نقدمها لك وفقًا للأحجام الشائعة ، ولكن تتوفر أيضًا عناصر الماكينة المخصصة لتطبيقاتك المتخصصة. يمكن أن يتم تخصيص عناصر الماكينة في التصميمات الحالية الموجودة في كتالوجاتنا القابلة للتنزيل أو في تصميمات جديدة تمامًا. يمكن تنفيذ النماذج الأولية وتصنيع عناصر الماكينة بمجرد الموافقة على التصميم من قبل الطرفين. إذا كانت عناصر الماكينة الجديدة بحاجة إلى التصميم والتصنيع ، فإما أن يرسل لنا عملاؤنا مخططاتهم الخاصة عبر البريد الإلكتروني ونراجعها للموافقة عليها ، أو يطلبون منا تصميم عناصر الماكينة لتطبيقهم. في الحالة الأخيرة ، نستخدم جميع المدخلات من عملائنا ونصمم عناصر الماكينة ونرسل المخططات النهائية لعملائنا للموافقة عليها. بمجرد الموافقة ، نقوم بإنتاج المواد الأولى ومن ثم تصنيع عناصر الماكينة وفقًا للتصميم النهائي. في أي مرحلة من مراحل هذا العمل ، في حالة أداء تصميم عنصر محدد للآلة بشكل غير مُرضٍ في المجال (وهو أمر نادر الحدوث) ، نقوم بمراجعة المشروع بأكمله وإجراء التعديلات بالاشتراك مع عملائنا حسب الحاجة. من ممارساتنا القياسية توقيع اتفاقيات عدم الإفشاء (NDA) مع عملائنا لتصميم عناصر الماكينة أو أي منتج آخر عند الحاجة أو الطلب. بمجرد أن يتم تصميم وتصنيع عناصر الماكينة لعميل معين حسب الطلب ، فإننا نخصص رمز منتج لها وننتجها ونبيعها فقط لعميلنا الذي يمتلك المنتج. نقوم بإعادة إنتاج عناصر الماكينة باستخدام الأدوات والقوالب والإجراءات المطورة عدة مرات حسب الحاجة وكلما أعاد عملائنا طلبها. بمعنى آخر ، بمجرد تصميم عنصر آلة مخصص وإنتاجه لك ، يتم حجز الملكية الفكرية وكذلك جميع الأدوات والقوالب وتخزينها إلى أجل غير مسمى من قبلنا لك وللمنتجات المستنسخة كما تريد. كما نقدم لعملائنا خدمات هندسية من خلال الجمع بين عناصر الماكينة بشكل خلاق في مكون أو تجميع يخدم تطبيقًا ويلبي أو يتجاوز توقعات عملائنا. المصانع التي تصنع عناصر الماكينة مؤهلة إما بشهادة ISO9001 أو QS9000 أو TS16949. بالإضافة إلى ذلك ، فإن معظم منتجاتنا تحمل علامة CE أو UL وتفي بالمعايير الدولية ذات الصلة مثل ISO و SAE و ASME و DIN. يرجى النقر فوق القوائم الفرعية للحصول على معلومات مفصلة حول عناصر أجهزتنا بما في ذلك: - الأحزمة والسلاسل ومحركات الكابلات - التروس ومحركات التروس - اقتران ومحامل - مفاتيح ومفاتيح ودبابيس - الكاميرات والوصلات - مهاوي - الأختام الميكانيكية - القابض الصناعي والفرامل - مهمات الربط - ماكينات بسيطة لقد قمنا بإعداد كتيب مرجعي لعملائنا ومصممي ومطوري المنتجات الجديدة بما في ذلك عناصر الماكينة. يمكنك التعرف على بعض المصطلحات الشائعة الاستخدام في تصميم مكونات الماكينة: قم بتنزيل كتيب عن مصطلحات الهندسة الميكانيكية الشائعة التي يستخدمها المصممون والمهندسون تجد عناصر الماكينات لدينا تطبيقات في مجموعة متنوعة من المجالات مثل الآلات الصناعية وأنظمة التشغيل الآلي ومعدات الاختبار والقياس ومعدات النقل وآلات البناء وعمليًا في أي مكان يمكنك التفكير فيه. تقوم شركة AGS-TECH بتطوير وتصنيع عناصر الماكينة من مواد مختلفة حسب التطبيق. يمكن أن تتراوح المواد المستخدمة لعناصر الماكينة من البلاستيك المقولب المستخدم في اللعب إلى الفولاذ المقوى والمغلف خصيصًا للآلات الصناعية. يستخدم المصممون لدينا أحدث البرامج الاحترافية وأدوات التصميم لتطوير عناصر الماكينة ، مع مراعاة التفاصيل مثل الزوايا في أسنان التروس ، والضغوط التي ينطوي عليها ، ومعدلات التآكل ... إلخ. يرجى التمرير عبر القوائم الفرعية الخاصة بنا وتنزيل الكتيبات والكتالوجات الخاصة بمنتجاتنا لمعرفة ما إذا كان يمكنك تحديد موقع عناصر الماكينة الجاهزة للتطبيق الخاص بك. إذا لم تتمكن من العثور على تطابق جيد لتطبيقك ، فيرجى إخبارنا وسنعمل معك لتطوير وتصنيع عناصر الماكينة التي تلبي احتياجاتك. إذا كنت مهتمًا في الغالب بقدراتنا الهندسية والبحثية والتطويرية بدلاً من قدرات التصنيع ، فنحن ندعوك لزيارة موقعنا على الويب http://www.ags-engineering.com حيث يمكنك العثور على مزيد من المعلومات التفصيلية حول التصميم وتطوير المنتجات وتطوير العمليات والخدمات الاستشارية الهندسية والمزيد CLICK Product Finder-Locator Service الصفحة السابقة
- صناعة الزجاج والسيراميك ، العبوات محكمة الغلق ، الأختام ، الترابط
تصنيع الزجاج والسيراميك ، الأختام والترابط المحكم للحزم ، الزجاج المضاد للرصاص ، قولبة النفخ ، الزجاج البصري ، الزجاج الموصل ، القولبة تشكيل وتشكيل الزجاج والسيراميك نوع تصنيع الزجاج الذي نقدمه هو زجاج الحاويات ، ونفخ الزجاج ، والألياف الزجاجية والأنابيب والقضبان ، والأواني الزجاجية المنزلية والصناعية ، والمصباح والمصابيح ، وصب الزجاج الدقيق ، والمكونات والتركيبات البصرية ، والزجاج المسطح والورق والعائم. نقوم بالتشكيل اليدوي وكذلك تشكيل الآلة. عمليات تصنيع السيراميك التقنية الشائعة لدينا هي الضغط بالقالب ، الضغط المتساوي ، الضغط المتساوي الساخن ، الضغط الساخن ، الصب المنزلق ، صب الشريط ، البثق ، التشكيل بالحقن ، المعالجة الخضراء ، التلبيد أو الحرق ، طحن الماس ، التجميعات المحكم. نوصي بالضغط هنا ل قم بتنزيل الرسوم التوضيحية التخطيطية الخاصة بنا لعمليات تشكيل وتشكيل الزجاج بواسطة AGS-TECH Inc. قم بتنزيل الرسوم التوضيحية التخطيطية الخاصة بنا لعمليات تصنيع السيراميك الفنية بواسطة AGS-TECH Inc. ستساعدك هذه الملفات القابلة للتنزيل مع الصور والرسومات على فهم المعلومات التي نقدمها لك أدناه بشكل أفضل. • تصنيع الحاويات الزجاجية: لدينا خطوط الضغط والنفخ الآلية وكذلك خطوط النفخ والنفخ للتصنيع. في عملية النفخ والنفخ ، نضع الكأس في قالب فارغ ونشكل العنق عن طريق تطبيق ضربة من الهواء المضغوط من الأعلى. بعد ذلك مباشرة ، يتم نفخ الهواء المضغوط مرة ثانية من الاتجاه الآخر عبر عنق الحاوية لتشكيل الشكل المسبق للزجاجة. يتم نقل هذا النموذج المسبق بعد ذلك إلى القالب الفعلي ، ويعاد تسخينه للتليين ويتم تطبيق الهواء المضغوط لإعطاء الشكل المسبق للحاوية النهائية. بشكل أكثر وضوحًا ، يتم ضغطه ودفعه مقابل جدران تجويف قالب النفخ لأخذ الشكل المطلوب. أخيرًا ، يتم نقل الحاوية الزجاجية المصنعة إلى فرن التلدين لإعادة التسخين اللاحقة وإزالة الضغوط الناتجة أثناء الصب ويتم تبريدها بطريقة محكومة. في طريقة الضغط والنفخ ، يتم وضع الكتل المنصهرة في قالب باريسون (قالب فارغ) ويتم ضغطها في شكل الباريسون (شكل فارغ). يتم بعد ذلك نقل الفراغات إلى قوالب النفخ ونفخها بطريقة مماثلة للعملية الموضحة أعلاه تحت عنوان "عملية النفخ والنفخ". الخطوات اللاحقة مثل التلدين وتخفيف الضغط متشابهة أو متشابهة. • نفخ الزجاج: لقد تم تصنيع منتجات الزجاج باستخدام النفخ اليدوي التقليدي وكذلك استخدام الهواء المضغوط مع المعدات الآلية. بالنسبة لبعض الطلبات ، يعد النفخ التقليدي ضروريًا ، مثل المشروعات التي تتضمن أعمالًا فنية على الزجاج ، أو المشروعات التي تتطلب عددًا أقل من الأجزاء ذات التفاوتات السائبة ، ومشروعات النماذج الأولية / التجريبية ... إلخ. يتضمن نفخ الزجاج التقليدي غمس أنبوب معدني مجوف في وعاء من الزجاج المصهور وتدوير الأنبوب لتجميع بعض كمية مادة الزجاج. يتم لف الزجاج الذي تم تجميعه على طرف الأنبوب على حديد مسطح ، ويتم تشكيله حسب الرغبة ، ويتم تمديده ، وإعادة تسخينه ، ويتم نفخه بالهواء. عندما تصبح جاهزة ، يتم إدخالها في قالب ويتم نفخ الهواء. تجويف القالب مبلل لتجنب ملامسة الزجاج للمعدن. يعمل فيلم الماء مثل الوسادة بينهما. النفخ اليدوي هو عملية بطيئة كثيفة العمالة ومناسبة فقط للنماذج الأولية أو العناصر ذات القيمة العالية ، وليست مناسبة للطلبات غير المكلفة لكل قطعة ذات الحجم الكبير. • تصنيع الأواني الزجاجية المنزلية والصناعية: باستخدام أنواع مختلفة من المواد الزجاجية ، يتم إنتاج مجموعة كبيرة ومتنوعة من الأواني الزجاجية. بعض الأكواب مقاومة للحرارة ومناسبة للأواني الزجاجية للمختبرات بينما بعضها جيد بما يكفي لتحمل غسالات الأطباق لعدة مرات ومناسب لصنع المنتجات المنزلية. باستخدام آلات Westlake ، يتم إنتاج عشرات الآلاف من قطع أكواب الشرب يوميًا. للتبسيط ، يتم جمع الزجاج المصهور عن طريق التفريغ وإدخاله في قوالب لعمل الأشكال المسبقة. ثم يتم نفخ الهواء في القوالب ، ثم يتم نقلها إلى قالب آخر ويتم نفخ الهواء مرة أخرى ويأخذ الزجاج شكله النهائي. كما هو الحال في النفخ اليدوي ، تظل هذه القوالب مبللة بالماء. التمدد الإضافي هو جزء من عملية التشطيب حيث يتم تشكيل الرقبة. الزجاج الزائد محترق. بعد ذلك ، تتبع عملية إعادة التسخين والتبريد التي يتم التحكم فيها الموضحة أعلاه. • الأنبوب الزجاجي وتشكيل القضبان: العمليات الرئيسية التي نستخدمها لتصنيع الأنابيب الزجاجية هي عمليات DANNER و VELLO. في عملية دانر ، يتدفق الزجاج من الفرن ويسقط على غلاف مائل مصنوع من مواد مقاومة للحرارة. يتم حمل الكم على عمود مجوف أو أنبوب نفخ. ثم يتم لف الزجاج حول الغلاف ويشكل طبقة ناعمة تتدفق أسفل الكم وفوق رأس العمود. في حالة تشكيل الأنبوب ، يتم نفخ الهواء عبر أنبوب نفخ ذي طرف مجوف ، وفي حالة تشكيل الأنبوب ، نستخدم أطرافًا صلبة على العمود. ثم يتم سحب الأنابيب أو القضبان فوق بكرات الحمل. يتم ضبط الأبعاد مثل سمك الجدار وقطر الأنابيب الزجاجية على القيم المرغوبة عن طريق تحديد قطر الغلاف ونفخ ضغط الهواء إلى القيمة المطلوبة ، وضبط درجة الحرارة ، ومعدل تدفق الزجاج وسرعة الرسم. من ناحية أخرى ، تتضمن عملية تصنيع الأنبوب الزجاجي Vello الزجاج الذي يخرج من الفرن إلى وعاء به مغزل أو جرس مجوف. ثم يمر الزجاج عبر الفراغ الهوائي بين المغزل والوعاء ويأخذ شكل الأنبوب. بعد ذلك ينتقل على بكرات إلى آلة سحب ويتم تبريده. في نهاية خط التبريد ، تتم عملية القطع والمعالجة النهائية. يمكن تعديل أبعاد الأنبوب تمامًا كما هو الحال في عملية Danner. عند مقارنة عملية Danner بعملية Vello ، يمكننا القول أن عملية Vello مناسبة بشكل أفضل للإنتاج بكميات كبيرة بينما قد تكون عملية Danner مناسبة بشكل أفضل لطلبات الأنابيب ذات الأحجام الصغيرة الدقيقة. • معالجة الصفيحة والزجاج المسطح والمسطّح: لدينا كميات كبيرة من الزجاج المسطح بسماكات تتراوح من سماكة subilimeter إلى عدة سنتيمترات. أكوابنا المسطحة شبه بصرية مثالية. نحن نقدم الزجاج بطلاء خاص مثل الطلاءات الضوئية ، حيث يتم استخدام تقنية ترسيب البخار الكيميائي لوضع الطلاءات مثل الطلاء المضاد للانعكاس أو طلاء المرآة. كما أن الطلاءات الموصلة الشفافة شائعة. تتوفر أيضًا الطلاءات المقاومة للماء أو المحبة للماء على الزجاج ، والطلاء الذي يجعل الزجاج التنظيف الذاتي. تعتبر الزجاجات المصقولة والمضادة للرصاص من العناصر الشائعة الأخرى. نقطع الزجاج بالشكل المطلوب بالتفاوتات المرغوبة. تتوفر عمليات ثانوية أخرى مثل التقويس أو ثني الزجاج المسطح. • صب الزجاج الدقيق: نستخدم هذه التقنية في الغالب لتصنيع مكونات بصرية دقيقة دون الحاجة إلى تقنيات أكثر تكلفة وتستغرق وقتًا طويلاً مثل الطحن واللف والتلميع. هذه التقنية ليست كافية دائمًا لصنع أفضل البصريات ، ولكن في بعض الحالات مثل المنتجات الاستهلاكية والكاميرات الرقمية والبصريات الطبية يمكن أن تكون خيارًا جيدًا أقل تكلفة للتصنيع بكميات كبيرة. كما أنه يتمتع بميزة على تقنيات تشكيل الزجاج الأخرى التي تتطلب أشكالًا هندسية معقدة ، كما هو الحال في حالة الأجسام الكروية. تتضمن العملية الأساسية تحميل الجانب السفلي من القالب مع الزجاج الفارغ ، وإخلاء غرفة العملية لإزالة الأكسجين ، والإغلاق القريب للقالب ، والتسخين السريع والمتساوي للحرارة للقالب والزجاج بضوء الأشعة تحت الحمراء ، وإغلاق المزيد من أنصاف القالب للضغط على الزجاج المخفف ببطء بطريقة مضبوطة إلى السماكة المطلوبة ، وأخيراً تبريد الزجاج وملء الحجرة بالنيتروجين وإزالة المنتج. التحكم الدقيق في درجة الحرارة ، مسافة إغلاق القالب ، قوة إغلاق القالب ، مطابقة معاملات تمدد القالب والمواد الزجاجية هي المفتاح في هذه العملية . • تصنيع المكونات والتجمعات الزجاجية الضوئية: إلى جانب قولبة الزجاج الدقيقة ، هناك عدد من العمليات القيمة التي نستخدمها لصنع مكونات وتجمعات بصرية عالية الجودة للتطبيقات الصعبة. يعتبر طحن ، ولف ، وتلميع الزجاج البصري في ملاط جلخ خاصة دقيقة فنًا وعلمًا لصنع العدسات البصرية ، والمنشورات ، والمسطحات وأكثر من ذلك. يتطلب تسطيح السطح والتموج والنعومة والأسطح البصرية الخالية من العيوب الكثير من الخبرة في مثل هذه العمليات. يمكن أن تؤدي التغييرات الصغيرة في البيئة إلى منتجات خارج المواصفات وإيقاف خط التصنيع. هناك حالات يمكن أن تؤدي فيها عملية مسح واحدة على السطح البصري بقطعة قماش نظيفة إلى جعل المنتج يلبي المواصفات أو يفشل في الاختبار. بعض المواد الزجاجية الشائعة المستخدمة هي السيليكا المنصهرة ، والكوارتز ، و BK7. كما يتطلب تجميع هذه المكونات خبرة متخصصة متخصصة. في بعض الأحيان يتم استخدام مواد لاصقة خاصة. ومع ذلك ، في بعض الأحيان تكون تقنية تسمى الاتصال البصري هي الخيار الأفضل ولا تتضمن أي مادة بين النظارات البصرية المرفقة. وهي تتكون من ملامسة الأسطح المسطحة جسديًا لتلتصق ببعضها البعض دون الغراء. في بعض الحالات ، تُستخدم المباعدات الميكانيكية أو قضبان أو كرات زجاجية دقيقة أو مشابك أو مكونات معدنية مُشكلة لتجميع المكونات الضوئية على مسافات معينة وبتوجهات هندسية معينة لبعضها البعض. دعونا نفحص بعض تقنياتنا الشائعة لتصنيع البصريات المتطورة. الطحن واللصق والتلميع: يتم الحصول على الشكل الخام للمكون البصري من خلال طحن الزجاج الفارغ. بعد ذلك يتم إجراء اللف والتلميع عن طريق تدوير وفرك الأسطح الخشنة للمكونات الضوئية مقابل الأدوات ذات الأشكال السطحية المرغوبة. يتم سكب الملاط مع جزيئات الكشط الصغيرة والسوائل بين البصريات وأدوات التشكيل. يمكن اختيار أحجام الجسيمات الكاشطة في مثل هذه الملاط وفقًا لدرجة التسطيح المطلوبة. يتم التعبير عن انحرافات الأسطح البصرية الحرجة عن الأشكال المرغوبة من حيث الأطوال الموجية للضوء المستخدم. تتمتع البصريات عالية الدقة الخاصة بنا بتفاوتات في الطول الموجي (الطول الموجي / 10) أو حتى تكون أكثر إحكامًا. إلى جانب المظهر الجانبي للسطح ، يتم مسح وتقييم الأسطح الحرجة بحثًا عن ميزات وعيوب السطح الأخرى مثل الأبعاد والخدوش والرقائق والحفر والبقع ... إلخ. إن التحكم الصارم في الظروف البيئية في أرضية التصنيع البصري ومتطلبات القياس والاختبار الشاملة بأحدث المعدات تجعل هذا فرعًا صعبًا للصناعة . • العمليات الثانوية في تصنيع الزجاج: مرة أخرى ، نحن مقيدون فقط بخيالك عندما يتعلق الأمر بالعمليات الثانوية والتشطيب للزجاج. هنا نسرد بعضًا منهم: - طلاءات على الزجاج (بصري ، كهربائي ، ترايبولوجي ، حراري ، وظيفي ، ميكانيكي ...). على سبيل المثال ، يمكننا تغيير خصائص سطح الزجاج مما يجعله على سبيل المثال يعكس الحرارة بحيث يحافظ على برودة التصميمات الداخلية للمبنى ، أو جعل أحد الجوانب يمتص الأشعة تحت الحمراء باستخدام تقنية النانو. يساعد هذا في الحفاظ على دفء المباني من الداخل لأن الطبقة الخارجية من الزجاج تمتص الأشعة تحت الحمراء داخل المبنى وتعود إلى الداخل. -الحفر on الزجاج - ملصقات السيراميك المطبقة (ACL) -نقش - تلميع اللهب - تلميع كيميائي -تلطيخ تصنيع السيراميك التقني • كبس القوالب: يتكون من ضغط أحادي المحور لمساحيق حبيبية محصورة في قالب • الضغط الساخن: يشبه الكبس بالقالب ولكن مع إضافة درجة الحرارة لتعزيز التكثيف. يتم وضع المسحوق أو التشكيل المضغوط في قالب الجرافيت ويتم تطبيق ضغط أحادي المحور بينما يتم الاحتفاظ بالقالب في درجات حرارة عالية مثل 2000 درجة مئوية يمكن أن تختلف درجات الحرارة اعتمادًا على نوع مسحوق السيراميك الذي تتم معالجته. بالنسبة للأشكال والهندسة المعقدة ، قد تكون هناك حاجة إلى معالجة أخرى لاحقة مثل طحن الماس. • الضغط الأيزوستاتي: يتم وضع المسحوق الحبيبي أو الكمادات المضغوطة بالقالب في حاويات محكمة الإغلاق ومن ثم في وعاء ضغط مغلق بداخله سائل. بعد ذلك يتم ضغطها عن طريق زيادة ضغط وعاء الضغط. يقوم السائل الموجود داخل الوعاء بنقل قوى الضغط بشكل موحد على كامل مساحة سطح الحاوية محكمة الإغلاق. وبالتالي يتم ضغط المواد بشكل موحد وتأخذ شكل الحاوية المرنة ومظهرها الداخلي وميزاتها. • الضغط الأيزوستاتي الساخن: على غرار الضغط المتساوي الساكن ، ولكن بالإضافة إلى الغلاف الجوي للغاز المضغوط ، نقوم بتلبيد المواد المضغوطة عند درجة حرارة عالية. ينتج عن الضغط المتساوي الساكن الساخن تكثيف إضافي وقوة متزايدة. • انزلاق الصب / صب الصب: نقوم بملء القالب بمعلق من جزيئات السيراميك بحجم ميكرومتر والسائل الحامل. هذا الخليط يسمى "زلة". القالب به مسام وبالتالي يتم ترشيح السائل الموجود في الخليط في القالب. نتيجة لذلك ، يتم تشكيل قالب على الأسطح الداخلية للقالب. بعد التلبيد ، يمكن إخراج الأجزاء من القالب. • صب الشريط: نقوم بتصنيع الأشرطة الخزفية عن طريق صب عجين السيراميك على الأسطح الحاملة المسطحة. تحتوي العجائن على مساحيق خزفية ممزوجة بمواد كيميائية أخرى لأغراض التجليد والحمل. مع تبخر المذيبات ، يتم ترك صفائح سيراميك كثيفة ومرنة يمكن قطعها أو دحرجتها حسب الرغبة. • تشكيل بالبثق: كما هو الحال في عمليات البثق الأخرى ، يتم تمرير خليط ناعم من مسحوق السيراميك مع مواد رابطة ومواد كيميائية أخرى عبر قالب للحصول على شكل المقطع العرضي ثم يتم قطعه بالأطوال المرغوبة. يتم تنفيذ العملية بمخاليط خزفية باردة أو ساخنة. • قوالب الحقن ذات الضغط المنخفض: نقوم بإعداد خليط من مسحوق السيراميك مع مواد رابطة ومذيبات ونسخنه إلى درجة حرارة حيث يمكن بسهولة الضغط عليه وإجباره على تجويف الأداة. بمجرد اكتمال دورة التشكيل ، يتم إخراج الجزء وحرق مادة الربط الكيميائية. باستخدام القولبة بالحقن ، يمكننا الحصول على أجزاء معقدة بكميات كبيرة اقتصاديًا. الثقوب t التي هي جزء صغير من المليمتر على جدار بسمك 10 مم ، الخيوط ممكنة بدون المعالجة الآلية ، والتفاوتات ضيقة بقدر +/- 0.5٪ ممكنة وحتى أقل عند تشكيل الأجزاء ، يمكن أن يتراوح سمك الجدار من 0.5 مم إلى 12.5 مم وكذلك سمك الجدار من 6.5 مم إلى 150 مم. • الآلات الخضراء: باستخدام نفس أدوات تصنيع المعادن ، يمكننا استخدام مواد السيراميك المضغوطة آليًا وهي لا تزال طرية مثل الطباشير. التسامح بنسبة +/- 1٪ ممكنة. لتحسين التحمل نستخدم الماس طحن. • الغرق أو الإطلاق: التلبيد يجعل التكثيف الكامل ممكنًا. يحدث انكماش كبير في الأجزاء المدمجة الخضراء ، لكن هذه ليست مشكلة كبيرة لأننا نأخذ في الاعتبار هذه التغييرات في الأبعاد عندما نصمم الجزء والأدوات. ترتبط جزيئات المسحوق ببعضها البعض وتتم إزالة المسامية الناتجة عن عملية الضغط إلى حد كبير .. • طحن الماس: يتم استخدام مادة "الماس" الأكثر صلابة في العالم لطحن المواد الصلبة مثل السيراميك والأجزاء الدقيقة. يتم تحقيق التفاوتات في نطاق الميكرومتر والأسطح الملساء للغاية. نظرًا لنفقاتها ، فإننا نأخذ هذه التقنية في الاعتبار فقط عندما نحتاج إليها حقًا. • التجمعات الهرمية هي تلك التي لا تسمح عمليًا بأي تبادل للمواد أو المواد الصلبة أو السوائل أو الغازات بين السطوح البينية. الختم المحكم محكم. على سبيل المثال ، العبوات الإلكترونية المغلقة هي تلك التي تحافظ على المحتويات الداخلية الحساسة للجهاز المعبأ دون أن تتضرر من الرطوبة أو الملوثات أو الغازات. لا يوجد شيء محكم بنسبة 100٪ ، ولكن عندما نتحدث عن الإحكام ، فإننا نعني أنه من الناحية العملية ، هناك إحكام إلى الحد الذي يكون فيه معدل التسرب منخفضًا جدًا بحيث تكون الأجهزة آمنة في ظل الظروف البيئية العادية لفترات طويلة جدًا. تتكون مجموعاتنا المحكم من المعدن والزجاج والسيراميك والمعدن والسيراميك والسيراميك والمعدن والسيراميك والمعدن والسيراميك والمعدن والمعدن والزجاج والمعادن والزجاج المعدني والزجاج المعدني والزجاج المعدن والزجاج إلى الزجاج وجميع التركيبات الأخرى من الروابط المعدنية والزجاجية والسيراميك. يمكننا على سبيل المثال طلاء مكونات السيراميك بالمعادن بحيث يمكن ربطها بقوة بالمكونات الأخرى في التجميع ولديها قدرة إحكام ممتازة. لدينا الدراية الفنية لطلاء الألياف الضوئية أو عمليات التغذية بالمعدن ولحامها أو لحامها بالنحاس في العبوات ، بحيث لا تمر الغازات أو تتسرب إلى العبوات. لذلك يتم استخدامها لتصنيع العبوات الإلكترونية لتغليف الأجهزة الحساسة وحمايتها من الغلاف الجوي الخارجي. إلى جانب خصائص الختم الممتازة ، هناك خصائص أخرى مثل معامل التمدد الحراري ، ومقاومة التشوه ، وطبيعة عدم إطلاق الغازات ، والعمر الطويل للغاية ، والطبيعة غير الموصلة ، وخصائص العزل الحراري ، والطبيعة المضادة للكهرباء الساكنة ... إلخ. جعل مواد الزجاج والسيراميك الاختيار لبعض التطبيقات. يمكن العثور على معلومات عن منشأتنا التي تنتج تركيبات من السيراميك إلى المعدن ، وختم محكم ، ومغذيات تفريغ الهواء ، ومكونات التحكم في السوائل والفراغ العالية والعالية للغاية هنا:كتيب مصنع المكونات المحكم CLICK Product Finder-Locator Service الصفحة السابقة
- تشكيل الأسلاك واليايات ، التشكيل ، اللحام ، تجميع الأسلاك ، الملف ، CNC
تشكيل الأسلاك والزنبركات وتشكيلها ولحامها وتجميع الأسلاك ونوابض تمديد ضغط الملف الملتوية والأسلاك المخصصة والينابيع الحلزونية في شركة AGS-TECH Inc. تشكيل الأسلاك واليايات نقوم بتصنيع الأسلاك المخصصة ، وتجميع الأسلاك ، والأسلاك المشكلة في الأشكال المرغوبة ثنائية وثلاثية الأبعاد ، وشبكات سلكية ، وشبكات ، ومرفقات ، وسلة ، وسياج ، وزنبرك سلكي ، ونوابض مسطحة ؛ الالتواء والضغط والتوتر والينابيع المسطحة وغير ذلك. عملياتنا هي تشكيل الأسلاك والربيع ، وسحب الأسلاك ، والتشكيل ، والانحناء ، واللحام ، والنحاس ، واللحام ، والثقب ، والتأرجح ، والحفر ، والشطب ، والطحن ، والخيوط ، والطلاء ، والشرائح الرباعية ، وتشكيل الشرائح ، واللف ، واللف ، والإزعاج. نوصي بالضغط هنا ل قم بتنزيل الرسوم التوضيحية التخطيطية الخاصة بنا لعمليات تشكيل الأسلاك والزنبرك بواسطة AGS-TECH Inc. سيساعدك هذا الملف القابل للتنزيل مع الصور والرسومات على فهم المعلومات التي نقدمها لك أدناه بشكل أفضل. • الرسم بالأسلاك: باستخدام قوى الشد ، نمد مخزون المعدن ونرسمه خلال قالب لتقليل القطر وزيادة طوله. في بعض الأحيان نستخدم سلسلة من القوالب. نحن قادرون على صنع قوالب لكل مقياس من الأسلاك. باستخدام مادة ذات قوة شد عالية ، نرسم أسلاكًا رفيعة جدًا. نحن نقدم كلاً من الأسلاك المشغولة على البارد والساخن. • تشكيل الأسلاك: يتم ثني لفة من الأسلاك المقاسة لتشكيل منتج مفيد. لدينا القدرة على تشكيل الأسلاك من جميع المقاييس ، بما في ذلك الخيوط الرفيعة وكذلك الأسلاك السميكة مثل تلك المستخدمة كزنبركات أسفل هيكل السيارة. المعدات التي نستخدمها لتشكيل الأسلاك هي أدوات تشكيل الأسلاك اليدوية و CNC ، والملفوف ، ومكابس الطاقة ، والشرائح الرباعية ، والشرائح المتعددة. عملياتنا هي الرسم ، والانحناء ، والاستقامة ، والتسطيح ، والتمديد ، والقطع ، والإزعاج ، واللحام واللحام والنحاس ، والتجميع ، واللف ، والتأرجح (أو الجناح) ، والثقب ، وخيوط الأسلاك ، والحفر ، والشطب ، والطحن ، والطلاء ، والمعالجات السطحية. يمكن إعداد أحدث المعدات لدينا لتطوير تصميمات معقدة للغاية من أي شكل وتحمل ضيق. نحن نقدم أنواع نهايات متنوعة مثل نهايات كروية أو مدببة أو مشطوبة للأسلاك الخاصة بك. معظم مشاريع تشكيل الأسلاك لدينا لها تكاليف أدوات من الحد الأدنى إلى الصفر. عادةً ما تكون أوقات الاستجابة للعينة أيامًا. يمكن إجراء التغييرات على تصميم / تكوين النماذج السلكية بسرعة كبيرة . • تشكيل الربيع: تقوم شركة AGS-TECH بتصنيع مجموعة كبيرة ومتنوعة من النوابض بما في ذلك: -التواء / زنبرك التواء مزدوج -زنبرك الشد / الضغط - زنبرك ثابت / متغير -لفائف ونابض حلزوني -زنبرك مسطح وأوراق -ربيع متوازن غسالة بيلفيل -الربيع الناجي - زنبرك ملف معدل التقدمي -موجة الربيع -فولوت سبرينج - نوابض مدببة -حلقات الربيع -الساعة الينابيع -دبابيس نقوم بتصنيع النوابض من مجموعة متنوعة من المواد ويمكننا إرشادك وفقًا للتطبيق الخاص بك. المواد الأكثر شيوعًا هي الفولاذ المقاوم للصدأ ، والسيليكون الكروم ، والفولاذ عالي الكربون ، والكربون المنخفض الزيت ، والكروم الفاناديوم ، والبرونز الفوسفوري ، والتيتانيوم ، وسبائك النحاس البريليوم ، والسيراميك عالي الحرارة. نحن نستخدم تقنيات مختلفة في تصنيع الزنبركات ، بما في ذلك اللف باستخدام الحاسب الآلي ، اللف البارد ، اللف الساخن ، التصلب ، التشطيب. التقنيات الأخرى المذكورة أعلاه تحت تشكيل الأسلاك شائعة أيضًا في عمليات تصنيع الزنبرك . • خدمات التشطيب للأسلاك والينابيع: يمكننا إنهاء منتجاتك بعدة طرق حسب اختيارك واحتياجاتك. بعض العمليات الشائعة التي نقدمها هي: الطلاء ، الطلاء بالمسحوق ، الطلاء ، غمس الفينيل ، الطلاء بأكسيد الألومنيوم ، تخفيف الضغط ، المعالجة الحرارية ، قلم الرصاص ، السقطة ، الكرومات ، النيكل عديم الكهرباء ، التخميل ، المينا المخبوزة ، طبقة بلاستيكية ، تنظيف البلازما. CLICK Product Finder-Locator Service الصفحة السابقة
- تصنيع تشكيل الصفائح المعدنية ، الختم ، التثقيب ، الرسم العميق ، CNC
تشكيل وتصنيع الصفائح المعدنية ، الختم ، التثقيب ، الثني ، القالب التدريجي ، اللحام النقطي ، الرسم العميق ، تقطيع المعادن والحز في شركة AGS-TECH Inc. أختام وتصنيع الصفائح المعدنية نحن نقدم ختم الصفائح المعدنية ، والتشكيل ، والتشكيل ، والانحناء ، واللكم ، والتقطيع ، والحز ، والتثقيب ، والتقطيع ، والقضم ، والحلاقة ، والضغط ، والتصنيع ، والرسم العميق باستخدام لكمة واحدة / ضربة واحدة للقوالب بالإضافة إلى القوالب التدريجية والغزل ، وتشكيل المطاط و تشكيل مائي. قطع الصفائح المعدنية باستخدام المياه النفاثة ، والبلازما ، والليزر ، والمنشار ، واللهب ؛ تجميع الصفائح المعدنية باستخدام اللحام واللحام النقطي ؛ انتفاخ وانحناء أنبوب الصفائح المعدنية ؛ تشطيب سطح الصفائح المعدنية بما في ذلك الطلاء بالغمس أو الرش والطلاء بالمسحوق الكهروستاتيكي والأنودة والطلاء والرش وأكثر من ذلك. تتراوح خدماتنا من النماذج الأولية السريعة للصفائح المعدنية إلى التصنيع بكميات كبيرة. نوصي بالضغط هنا لقم بتنزيل الرسوم التوضيحية التخطيطية الخاصة بنا لعمليات تصنيع الصفائح المعدنية وختمها بواسطة AGS-TECH Inc. سيساعدك هذا على فهم المعلومات التي نقدمها لك أدناه بشكل أفضل. • قطع الصفائح المعدنية: نحن نقدم قطع وأجزاء. تقطع القواطع الصفائح المعدنية على مسار واحد في كل مرة ولا يوجد أي إهدار للمواد بشكل أساسي ، بينما مع الفواصل لا يمكن تحديد الشكل بدقة وبالتالي يتم إهدار كمية معينة من المواد. واحدة من أكثر عملياتنا شيوعًا هي اللكم ، حيث يتم قطع قطعة من مادة مستديرة أو شكل آخر من الصفائح المعدنية. القطعة المقطوعة هي نفايات. نسخة أخرى من التثقيب هي الشق ، حيث يتم ثقب الثقوب المستطيلة أو المستطيلة. من ناحية أخرى ، فإن التفريغ هو نفس عملية التثقيب ، مع التمييز بين القطع التي يتم قطعها هو العمل والاحتفاظ به. FINE BLANKING ، وهو نسخة متفوقة من التقطيع ، يخلق جروحًا ذات تفاوتات قريبة وحواف ناعمة مستقيمة ولا يتطلب عمليات ثانوية لإتقان قطعة العمل. هناك عملية أخرى نستخدمها كثيرًا وهي الشق ، وهي عملية قص يتم فيها قطع الصفائح المعدنية بواسطة شفرتين دائريتين متعارضتين في مسار مستقيم أو منحني. فتاحة العلب هي مثال بسيط على عملية الحز. هناك طريقة أخرى مشهورة process بالنسبة لنا وهي PERFORATING ، حيث يتم ثقب العديد من الثقوب المستديرة أو الأشكال الأخرى في الصفائح المعدنية بنمط معين. مثال نموذجي للمنتج المثقوب هو المرشحات المعدنية التي تحتوي على العديد من الثقوب للسوائل. في عملية القطع ، وهي عملية أخرى لقطع الصفائح المعدنية ، نقوم بإزالة المواد من قطعة العمل ، بدءًا من الحافة أو في أي مكان آخر ونقطعها إلى الداخل حتى يتم الحصول على الشكل المطلوب. إنها عملية تقدمية حيث تزيل كل عملية قطعة أخرى حتى يتم الحصول على الكفاف المطلوب. بالنسبة لعمليات الإنتاج الصغيرة ، نستخدم أحيانًا عملية أبطأ نسبيًا تسمى NIBBLING والتي تتكون من العديد من اللكمات السريعة للثقوب المتداخلة لعمل قطع أكبر وأكثر تعقيدًا. في القطع التقدمي ، نستخدم سلسلة من العمليات المختلفة للحصول على قطع واحد أو هندسة معينة. أخيرًا ، يساعدنا حلق عملية ثانوية على تحسين حواف القطع التي تم إجراؤها بالفعل. يتم استخدامه لقطع الرقائق ، الحواف الخشنة في أعمال الصفائح المعدنية . • ثني الصفائح المعدنية: إلى جانب القطع ، يعتبر الثني عملية أساسية لن نتمكن من دونها من إنتاج معظم المنتجات. في الغالب عملية عمل بارد ولكن في بعض الأحيان يتم إجراؤها أيضًا عندما تكون دافئة أو ساخنة. نستخدم القوالب ونضغط معظم الوقت لهذه العملية. في الانحناء التدريجي ، نستخدم سلسلة من عمليات التثقيب والقوالب المختلفة للحصول على انحناء واحد أو هندسة معينة. تستخدم AGS-TECH مجموعة متنوعة من عمليات الانحناء وتقوم بالاختيار اعتمادًا على مادة قطعة العمل ، وحجمها ، وسمكها ، والحجم المطلوب للانحناء ، ونصف القطر ، والانحناء وزاوية الانحناء ، وموقع الانحناء ، واقتصاد التشغيل ، والكميات التي سيتم تصنيعها ... إلخ. نحن نستخدم V-BENDING حيث يفرض المثقاب على شكل V الصفائح المعدنية في القالب على شكل V وتثنيه. جيد لكل من الزوايا الحادة جدًا والمنفرجة وما بينهما ، بما في ذلك 90 درجة. باستخدام قوالب المسح نقوم بتنفيذ EDGE BENDING. تمكننا معداتنا من الحصول على زوايا أكبر من 90 درجة. في ثني الحافة ، يتم وضع قطعة العمل بين وسادة الضغط والقالب ، وتقع منطقة الانحناء على حافة القالب ويتم تثبيت بقية قطعة العمل فوق space like عارضة ناتئ. عندما تعمل المثقاب على جزء الكابول ، فإنها تنحني على حافة القالب. FLANGING هي عملية ثني حافة ينتج عنها زاوية 90 درجة. تتمثل الأهداف الرئيسية للعملية في التخلص من الحواف الحادة والحصول على أسطح هندسية لتسهيل الانضمام إلى الأجزاء. الشد ، عملية ثني حافة مشتركة أخرى تشكل تجعيدًا على حافة الجزء. من ناحية أخرى ، ينتج عن HEMMING حافة الورقة التي تنثني تمامًا على نفسها. في SEAMING ، تنحني حواف الجزأين على بعضها البعض وربطها. من ناحية أخرى ، يوفر الغمر المزدوج وصلات صفائح معدنية مانعة لتسرب الماء ومحكمة الإغلاق. على غرار ثني الحواف ، فإن عملية تسمى الانحناء الدوراني تنشر أسطوانة بالزاوية المرغوبة ويتم قطعها كثقب. عندما تنتقل القوة إلى الثقب ، فإنها تغلق بقطعة العمل. يعطي أخدود الأسطوانة الجزء الكابولي الزاوية المرغوبة. يمكن أن يكون للأخدود زاوية أصغر أو أكبر من 90 درجة. في AIR BENDING ، لا نحتاج إلى القالب السفلي للحصول على أخدود بزاوية. يتم دعم الصفائح المعدنية بواسطة t سطحين متقابلين وعلى مسافة معينة. ثم يطبق الثقب قوة في الموقع الصحيح ويثني قطعة العمل. يتم إجراء ثني القناة باستخدام ثقب على شكل قناة وقالب ، ويتم تحقيق U-BEND باستخدام ثقب على شكل حرف U. OFFSET BENDING تنتج تعويضات على الصفائح المعدنية. ثني الأسطوانة ، وهي تقنية جيدة للعمل السميك وثني القطع الكبيرة من الألواح المعدنية ، تستخدم ثلاث لفات لتغذية الألواح وثنيها إلى الانحناءات المرغوبة. يتم ترتيب القوائم بحيث يتم الحصول على الانحناء المطلوب للعمل. يتم التحكم في المسافة والزاوية بين الأسطوانات للحصول على النتيجة المرجوة. تجعل الأسطوانة المتحركة من الممكن التحكم في الانحناء. تشكيل الأنبوب هو عملية ثني صفائح معدنية شائعة أخرى تتضمن قوالب متعددة. يتم الحصول على الأنابيب بعد إجراءات متعددة. يتم إجراء الانحناء أيضًا عن طريق عمليات الانحناء. إنه الانحناء المتماثل على فترات منتظمة عبر قطعة كاملة من الصفائح المعدنية. يمكن استخدام أشكال مختلفة للتمويج. تعتبر الصفائح المعدنية المموجة أكثر صلابة ولديها مقاومة أفضل للثني وبالتالي لها تطبيقات في صناعة البناء. يتم نشر عملية تشكيل لفائف الصفائح المعدنية ، وهي عملية مستمرة manufacturing لثني المقاطع العرضية لهندسة معينة باستخدام لفات ويتم ثني العمل في خطوات متسلسلة ، مع استكمال لفة نهائية للعمل. في بعض الحالات ، يتم استخدام لفة واحدة وفي بعض الحالات سلسلة من القوائم. • عمليات تقطيع وانحناء الصفائح المعدنية المركبة: هذه هي العمليات التي تقطع وتثني في نفس الوقت. في PIERCING ، يتم إنشاء ثقب باستخدام لكمة مدببة. نظرًا لأن الثقب يوسع الفتحة الموجودة في الصفيحة ، تنثني المادة في نفس الوقت في شفة داخلية للفتحة. قد يكون للحافة التي تم الحصول عليها وظائف مهمة. تقوم عملية LANCING من ناحية أخرى بقص الورقة وثنيها لإنشاء شكل هندسي مرتفع . • انسداد وانحناء الأنبوب المعدني: في النفخ ، يتم ضغط بعض الأجزاء الداخلية من الأنبوب المجوف ، مما يتسبب في انتفاخ الأنبوب إلى الخارج. نظرًا لأن الأنبوب داخل قالب ، يتم التحكم في هندسة الانتفاخ من خلال شكل القالب. في عملية الانحناء الممتد ، يتم شد الأنبوب المعدني باستخدام قوى موازية لمحور الأنبوب وقوى الانحناء لسحب الأنبوب فوق كتلة الشكل. في الانحناء بالسحب ، نقوم بربط الأنبوب بالقرب من نهايته بكتلة شكل دوارة تثني الأنبوب أثناء الدوران. أخيرًا ، في الانحناء الضاغط ، يتم إمساك الأنبوب بالقوة إلى كتلة شكل ثابتة ، ويقوم القالب بثنيه فوق كتلة النموذج. • الرسم العميق: في واحدة من أكثر عملياتنا شيوعًا ، يتم استخدام لكمة ونرد مطابق وحامل فارغ. يتم وضع فراغ الصفائح المعدنية فوق فتحة القالب وتتحرك المثقاب نحو الفراغ الذي يحمله الحامل الفارغ. بمجرد أن يتلامسوا ، فإن الثقب يجبر الصفائح المعدنية في تجويف القالب لتشكيل المنتج. تشبه عملية السحب العميق القطع ، ولكن الفجوة بين الثقب والقالب تمنع قطع الصفيحة. هناك عامل آخر يؤكد أن الصفيحة مرسومة بعمق ولا تقطع وهي الزوايا الدائرية على القالب واللكمة التي تمنع القص والقطع. لتحقيق قدر أكبر من الرسم العميق ، يتم نشر عملية REDRAWING حيث يتم إجراء رسم عميق لاحق على جزء خضع بالفعل لعملية رسم عميق. في REVERSE REDRAWING ، يتم قلب الجزء المسحوب العميق ويتم رسمه في الاتجاه المعاكس. يمكن أن يوفر الرسم العميق أجسامًا غير منتظمة الشكل مثل أكواب مقببة أو مدببة أو متدرجة ، في EMBOSSING ، نستخدم زوجًا من الذكور والإناث لإبهار الصفائح المعدنية بتصميم أو نص. • SPINNING: عملية يتم فيها وضع قطعة عمل مسطحة أو مسبقة التشكيل بين مغزل دوار ومخزون ذيل وتطبق الأداة ضغطًا موضعيًا على العمل حيث تتحرك تدريجيًا لأعلى المغزل. نتيجة لذلك ، يتم لف قطعة العمل فوق المغزل وتأخذ شكلها. نستخدم هذه التقنية كبديل للرسم العميق حيث تكون كمية الطلب صغيرة والأجزاء كبيرة (بأقطار تصل إلى 20 قدمًا) ولها منحنيات فريدة. على الرغم من أن أسعار القطعة الواحدة أعلى بشكل عام ، فإن تكاليف الإعداد لعملية الغزل CNC منخفضة مقارنة بالسحب العميق. على العكس من ذلك ، يتطلب الرسم العميق استثمارًا أوليًا مرتفعًا للإعداد ، لكن تكاليف كل قطعة تكون منخفضة عند إنتاج كمية كبيرة من الأجزاء. إصدار آخر من هذه العملية هو SHEAR SPINNING ، حيث يوجد أيضًا تدفق معدني داخل قطعة العمل. سيقلل تدفق المعدن من سمك قطعة العمل أثناء تنفيذ العملية. عملية أخرى ذات صلة هي TUBE SPINNING ، والتي يتم تطبيقها على الأجزاء الأسطوانية. أيضًا في هذه العملية يوجد تدفق معدني داخل قطعة العمل. وبالتالي يتم تقليل السماكة وزيادة طول الأنبوب. يمكن نقل الأداة لإنشاء ميزات داخل الأنبوب أو خارجه . • تشكيل المطاط من الصفائح المعدنية: يتم وضع المطاط أو مادة البولي يوريثين في قالب حاوية وتوضع قطعة العمل على سطح المطاط. ثم يتم عمل لكمة على قطعة العمل وإجبارها على المطاط. نظرًا لأن الضغط الناتج عن المطاط منخفض ، فإن عمق الأجزاء المنتجة يكون محدودًا. نظرًا لأن تكاليف الأدوات منخفضة ، فإن العملية مناسبة للإنتاج بكميات منخفضة . • المعالجة المائية: على غرار تشكيل المطاط ، في هذه العملية يتم ضغط عمل الصفائح المعدنية بواسطة ثقب في سائل مضغوط داخل حجرة. يتم وضع أعمال الصفائح المعدنية بين المثقاب والغشاء المطاطي. يحيط الحجاب الحاجز بقطعة العمل تمامًا ويجبرها ضغط السائل على التشكل على الثقب. يمكن الحصول على رسومات عميقة جدًا حتى أكثر من عملية السحب العميق باستخدام هذه التقنية. نحن نصنع قوالب لكمة واحدة بالإضافة إلى قوالب متدرجة اعتمادًا على الجزء الخاص بك. تعتبر قوالب الختم أحادية السكتة طريقة فعالة من حيث التكلفة لإنتاج كميات كبيرة من أجزاء الصفائح المعدنية البسيطة مثل الغسالات بسرعة. تُستخدم القوالب التدريجية أو تقنية الرسم العميق لتصنيع أشكال هندسية أكثر تعقيدًا . اعتمادًا على حالتك ، يمكن استخدام تقنية Waterjet أو الليزر أو القطع بالبلازما لإنتاج أجزاء الصفائح المعدنية بسعر رخيص وسريع ودقيق. ليس لدى العديد من الموردين أي فكرة عن هذه التقنيات البديلة أو لا يمتلكونها ، وبالتالي فإنهم يمرون بطرق طويلة ومكلفة لصنع قوالب وأدوات لا تضيع سوى وقت ومال العملاء. إذا كنت بحاجة إلى مكونات صفائح معدنية مخصصة مثل العبوات والأغلفة الإلكترونية ... إلخ بأسرع ما يمكن في غضون أيام ، فاتصل بنا للحصول على خدمة RAPID SHEET METAL PROTOTYPING. CLICK Product Finder-Locator Service القائمة السابقة
- الحدادة والتعدين المسحوق ، التشكيل بالقالب ، العنوان ، التطريق الساخن
الحدادة والتعدين المسحوق ، التشكيل بالقالب ، العنوان ، التشكيل الساخن ، قالب الانطباع ، بالقرب من الشكل الصافي ، التأرجح ، التأرجح المعدني ، التثبيت ، النقش من شركة AGS-TECH Inc. تشكيل المعادن ومساحيق المعادن نوع عمليات التشكيل المعدني التي نقدمها هي القوالب الساخنة والباردة ، والقوالب المفتوحة والقوالب المغلقة ، والقوالب الانطباعية والمطروقات غير الومضية ، cogging ، ملء ، حواف ودقة تزوير ، شكل قريب من الشبكة ، عنوان ، التأرجح ، التزوير المقلوب ، التنقيط المعدني ، الكبس واللف والمطروقات الشعاعية والمدارية والحلقة والمتساوية ، النقش ، التثبيت ، تزوير الكرات المعدنية ، ثقب المعادن ، التحجيم ، تزوير معدل الطاقة العالي. إن تقنيات معالجة المعادن والمساحيق الخاصة بنا هي الضغط والتلبيد بالمسحوق ، والتشريب ، والتسلل ، والضغط المتساوي البارد والساخن ، وصب حقن المعادن ، وضغط الأسطوانة ، ولف المسحوق ، وبثق المسحوق ، والتلبيد السائب ، والتلبيد بالشرارة ، والضغط الساخن. نوصي بالضغط هنا ل قم بتنزيل الرسوم التوضيحية التخطيطية الخاصة بنا لعمليات تزوير بواسطة AGS-TECH Inc. قم بتنزيل الرسوم التوضيحية التخطيطية الخاصة بنا لعمليات تعدين المساحيق بواسطة AGS-TECH Inc. ستساعدك هذه الملفات القابلة للتنزيل مع الصور والرسومات على فهم المعلومات التي نقدمها لك أدناه بشكل أفضل. في تشكيل المعادن ، يتم تطبيق قوى الضغط وتشوه المادة والحصول على الشكل المطلوب. أكثر المواد المزورة شيوعًا في الصناعة هي الحديد والصلب ، ولكن العديد من المواد الأخرى مثل الألمنيوم والنحاس والتيتانيوم والمغنيسيوم يتم تزويرها أيضًا على نطاق واسع. الأجزاء المعدنية المطروقة لها هياكل حبيبية محسنة بالإضافة إلى الشقوق المغلقة والمساحات الفارغة المغلقة ، وبالتالي تكون قوة الأجزاء التي تم الحصول عليها من خلال هذه العملية أعلى. ينتج الحدادة أجزاء أقوى بشكل ملحوظ لوزنها من الأجزاء المصنوعة عن طريق الصب أو التشغيل الآلي. نظرًا لأن الأجزاء المطروقة تتشكل بجعل المعدن يتدفق إلى شكله النهائي ، يتخذ المعدن بنية حبيبية اتجاهية تمثل القوة الفائقة للأجزاء. بعبارة أخرى ، تكشف الأجزاء التي تم الحصول عليها من خلال عملية التطريق عن خصائص ميكانيكية أفضل مقارنة بأجزاء الصب البسيطة أو الأجزاء الآلية. يمكن أن يتراوح وزن المطروقات المعدنية من أجزاء صغيرة وخفيفة الوزن إلى مئات الآلاف من الجنيهات. نقوم بتصنيع المطروقات في الغالب للتطبيقات التي تتطلب متطلبات ميكانيكية حيث يتم تطبيق ضغوط عالية على أجزاء مثل قطع غيار السيارات والتروس وأدوات العمل والأدوات اليدوية وأعمدة التوربينات ومعدات الدراجات النارية. نظرًا لأن تكاليف الأدوات والإنشاء مرتفعة نسبيًا ، فإننا نوصي بعملية التصنيع هذه فقط للإنتاج بكميات كبيرة وللمكونات الحرجة ذات الحجم المنخفض ولكن ذات القيمة العالية مثل معدات الهبوط في الفضاء الجوي. إلى جانب تكلفة الأدوات ، يمكن أن تكون مهل التصنيع للأجزاء المزورة بكميات كبيرة أطول مقارنة ببعض الأجزاء الآلية البسيطة ، ولكن هذه التقنية ضرورية للأجزاء التي require قوة غير عادية مثل البراغي والصواميل والتطبيقات الخاصة السحابات ، السيارات ، الرافعة الشوكية ، أجزاء الرافعة. • التشكيل بالقالب الساخن والقوالب الباردة: تزوير القوالب الساخنة ، كما يوحي الاسم ، يتم في درجات حرارة عالية ، وبالتالي تكون الليونة عالية وقوة المادة منخفضة. هذا يسهل عملية التشويه والتزوير. على العكس من ذلك ، يتم إجراء عملية التشكيل بالقالب على البارد في درجات حرارة منخفضة وتتطلب قوى أعلى مما يؤدي إلى تصلب الإجهاد وإنهاء سطح أفضل ودقة للأجزاء المصنعة. • تشكيل القالب المفتوح وتكوين القالب المفتوح: في عملية التشكيل بالقالب المفتوح ، لا تقيد القوالب ضغط المادة ، بينما في قالب الانطباع ، يؤدي تشكيل التجاويف داخل القوالب إلى تقييد تدفق المواد أثناء تشكيلها بالشكل المطلوب. UPSET FORGING أو تسمى أيضًا UPSETTING ، وهي في الواقع ليست هي نفسها ولكنها عملية متشابهة جدًا ، هي عملية قالب مفتوح حيث يتم وضع قطعة العمل بين قطعتين منبسطتين وتقلل قوة الضغط من ارتفاعها. نظرًا لأن الارتفاع هو reduced ، يزداد عرض قطعة العمل. HEADING ، تتضمن عملية التشكيل المضطرب مخزونًا أسطوانيًا ينزعج في نهايته ويزداد المقطع العرضي محليًا. في العنوان ، يتم تغذية المخزون من خلال القالب ، ثم تزويره ثم تقطيعه إلى الطول. العملية قادرة على إنتاج كميات كبيرة من السحابات بسرعة. غالبًا ما تكون عملية تشغيل باردة لأنها تستخدم في صنع نهايات الأظافر ونهايات اللولب والصواميل والبراغي حيث تحتاج المادة إلى التعزيز. عملية القوالب المفتوحة الأخرى هي COGGING ، حيث يتم تشكيل قطعة العمل في سلسلة من الخطوات مع كل خطوة تؤدي إلى ضغط المادة والحركة اللاحقة للقالب المفتوح على طول قطعة العمل. في كل خطوة ، يتم تقليل السماكة وزيادة الطول بمقدار ضئيل. تشبه العملية طالبًا متوترًا يعض قلمه بخطوات صغيرة. عملية تسمى FULLERING هي طريقة أخرى للتزوير بالقالب المفتوح نقوم بنشرها غالبًا كخطوة سابقة لتوزيع المواد في قطعة العمل قبل إجراء عمليات تزوير المعادن الأخرى. نستخدمها عندما تتطلب قطعة العمل عدة عمليات تزوير operations. في العملية ، تموت مع تشوه الأسطح المحدبة وتسبب تدفق المعدن إلى كلا الجانبين. عملية مشابهة لعملية الحشو ، تتضمن EDGING من ناحية أخرى قالبًا مفتوحًا مع أسطح مقعرة لتشويه قطعة العمل. الشحذ أيضًا عملية تحضيرية لعمليات التشكيل اللاحقة تجعل تدفق المواد من كلا الجانبين إلى منطقة في المركز. يستخدم IMPRESSION DIE FORGING أو CLOSED DIE FORGING كما يطلق عليه أيضًا استخدام قالب / قالب يضغط على المادة ويحد من تدفقها داخل نفسه. يتم إغلاق القالب وتتخذ المادة شكل تجويف القالب / القالب. التشكيل الدقيق ، عملية تتطلب معدات خاصة وعفنًا ، ينتج أجزاء بدون وميض أو القليل جدًا من الفلاش. بمعنى آخر ، سيكون للأجزاء أبعاد نهائية تقريبًا. في هذه العملية ، يتم إدخال كمية من المواد التي يتم التحكم فيها جيدًا ووضعها داخل القالب. ننشر هذه الطريقة للأشكال المعقدة ذات المقاطع الرفيعة ، والتفاوتات الصغيرة وزوايا السحب وعندما تكون الكميات كبيرة بما يكفي لتبرير القالب وتكاليف المعدات. • التشكيل بدون وميض: يتم وضع قطعة العمل في القالب بطريقة لا يمكن لأي مادة أن تتدفق خارج التجويف لتشكيل وميض. وبالتالي لا حاجة إلى تشذيب غير مرغوب فيه باستخدام الفلاش. إنها عملية تزوير دقيقة وبالتالي تتطلب تحكمًا دقيقًا في كمية المواد المستخدمة . • النقش المعدني أو التزوير الشعاعي: يتم التصرف بشكل محيطي على قطعة العمل بالموت والتزوير. يمكن أيضًا استخدام مغزل لتشكيل هندسة قطع العمل الداخلية. في عملية التأرجح ، تتلقى قطعة العمل عادةً عدة ضربات في الثانية. العناصر النموذجية التي يتم إنتاجها عن طريق التأرجح هي أدوات ذات رأس مدبب ، وقضبان مدببة ، ومفكات براغي. • ثقب المعادن: نستخدم هذه العملية بشكل متكرر كعملية إضافية في تصنيع الأجزاء. يتم إنشاء ثقب أو تجويف مع ثقب على سطح قطعة العمل دون اختراقها. يرجى ملاحظة أن الثقب يختلف عن الثقب الذي ينتج عنه ثقب. • HOBBING: يتم الضغط على ثقب مع الهندسة المرغوبة في قطعة العمل ويخلق تجويفًا بالشكل المطلوب. نسمي هذا اللكمة HOB. تتضمن العملية ضغوطًا عالية ويتم إجراؤها في مكان بارد. ونتيجة لذلك ، فإن المادة تعمل على البارد وتصلب الإجهاد. لذلك هذه العملية مناسبة جدًا لتصنيع القوالب والقوالب والتجاويف لعمليات التصنيع الأخرى. بمجرد تصنيع الموقد ، يمكن بسهولة تصنيع العديد من التجاويف المتماثلة دون الحاجة إلى تصنيعها واحدة تلو الأخرى. • تشكيل الأسطوانة أو تشكيل الأسطوانة: يتم استخدام بكرتين متعارضتين لتشكيل الجزء المعدني. يتم إدخال قطعة العمل في البكرات ، وتدور البكرات وتسحب العمل إلى الفجوة ، ثم يتم تغذية العمل من خلال الجزء المحزز من البكرات وتعطي قوى الضغط المادة الشكل المطلوب. إنها ليست عملية دحرجة بل عملية تزوير ، لأنها عملية منفصلة وليست عملية مستمرة. إن الهندسة الموجودة على بساتين البكرات تصوغ المادة بالشكل والهندسة المطلوبين. يتم تنفيذ ساخنة. نظرًا لكونها عملية تطريق ، فإنها تنتج أجزاء ذات خصائص ميكانيكية متميزة ، وبالتالي نستخدمها لـ manufacturing أجزاء السيارات مثل الأعمدة التي تحتاج إلى تحمل غير عادي في بيئات العمل الشاقة. • التشكيل المداري: يتم وضع قطعة العمل في تجويف قالب بالطرق وتشكيله بواسطة قالب علوي ينتقل في مسار مداري حيث يدور على محور مائل. في كل ثورة ، يكمل القالب العلوي بذل قوى الضغط على قطعة العمل بأكملها. من خلال تكرار هذه الثورات عدة مرات ، يتم إجراء تزوير كافٍ. مزايا تقنية التصنيع هذه هي تشغيلها المنخفض الضوضاء والقوى المنخفضة المطلوبة. بعبارة أخرى ، باستخدام القوى الصغيرة ، يمكن للمرء أن يدور حول قالب ثقيل حول محور لتطبيق ضغوط كبيرة على جزء من قطعة العمل التي تلامس القالب. في بعض الأحيان تكون الأجزاء القرصية أو المخروطية الشكل مناسبة بشكل جيد لهذه العملية. • تشكيل الحلقات: نحن نستخدم بشكل متكرر لتصنيع الحلقات غير الملحومة. يتم قطع المخزون إلى الطول ، ثم تقلبه ثم ثقبه بالكامل لإنشاء ثقب مركزي. ثم يتم وضعها على مغزل ومطارقها من الأعلى حيث يتم تدوير الحلقة ببطء حتى يتم الحصول على الأبعاد المطلوبة. • التثبيت: عملية شائعة لربط الأجزاء ، تبدأ بقطعة معدنية مستقيمة يتم إدخالها في ثقوب مسبقة الصنع عبر الأجزاء. بعد ذلك يتم تشكيل طرفي القطعة المعدنية عن طريق الضغط على المفصل بين قالب علوي وسفلي. • التملك: عملية شائعة أخرى يتم تنفيذها بواسطة الضغط الميكانيكي ، حيث تمارس قوى كبيرة على مسافة قصيرة. يأتي اسم "سك" من التفاصيل الدقيقة التي تم تشكيلها على سطوح العملات المعدنية. إنها في الغالب عملية تشطيب لمنتج حيث يتم الحصول على تفاصيل دقيقة على الأسطح نتيجة للقوة الكبيرة المطبقة بواسطة القالب الذي ينقل هذه التفاصيل إلى قطعة العمل. • تشكيل الكرات المعدنية: منتجات مثل الكرات تتطلب كرات معدنية عالية الجودة مصنوعة بدقة. في تقنية واحدة تسمى SKEW ROLLING ، نستخدم أسطوانتين متعارضتين تدوران باستمرار حيث يتم تغذية المخزون باستمرار في البكرات. في أحد طرفي الأسطوانتين ، يتم إخراج الكرات المعدنية كمنتج. الطريقة الثانية للتزوير بالكرات المعدنية هي استخدام القالب الذي يضغط على مخزون المواد الموجود بينهما ويأخذ الشكل الكروي لتجويف القالب. في كثير من الأحيان ، تتطلب الكرات المنتجة بعض الخطوات الإضافية مثل الصقل والتلميع حتى تصبح منتجًا عالي الجودة. • التكوير النظيري / التشكيل الحراري: عملية مكلفة يتم إجراؤها فقط عندما تكون قيمة المنفعة / التكلفة مبررة. عملية تشغيل ساخنة حيث يتم تسخين القالب إلى نفس درجة حرارة قطعة العمل تقريبًا. نظرًا لأن كلا من الموت والعمل بنفس درجة الحرارة تقريبًا ، فلا يوجد تبريد ويتم تحسين خصائص تدفق المعدن. العملية مناسبة تمامًا للسبائك الفائقة والمواد ذات قابلية التسامح الرديئة والمواد التي الخصائص الميكانيكية حساسة للغاية لتدرجات وتغيرات درجات الحرارة الصغيرة . • تحجيم المعادن: إنها عملية تشطيب بارد. تدفق المواد غير مقيد في جميع الاتجاهات باستثناء الاتجاه الذي يتم تطبيق القوة فيه. نتيجة لذلك ، يتم الحصول على تشطيب جيد للسطح وأبعاد دقيقة. • HIGH ENERGY FORGING: تشتمل هذه التقنية على قالب علوي متصل بذراع مكبس يتم دفعه سريعًا كخليط وقود - هواء يشتعل بواسطة شمعة احتراق. إنه يشبه عمل المكابس في محرك السيارة. يضرب القالب قطعة العمل بسرعة كبيرة ثم يعود إلى موضعه الأصلي بسرعة كبيرة بفضل الضغط الخلفي. تم تشكيل العمل في غضون بضعة أجزاء من الثانية وبالتالي لا يوجد وقت ليبرد العمل. هذا مفيد للأجزاء التي يصعب تشكيلها والتي لها خصائص ميكانيكية حساسة لدرجة الحرارة. بمعنى آخر ، تكون العملية سريعة جدًا بحيث يتم تشكيل الجزء تحت درجة حرارة ثابتة طوال الوقت ولن يكون هناك تدرجات درجة حرارة في واجهات القالب / قطعة العمل . • في عملية التشكيل بالقوالب ، يتم ضرب المعدن بين كتلتين صلبتين متطابقتين بهما أشكال خاصة تسمى القوالب. عندما يتم دق المعدن بين القوالب ، فإنه يتخذ نفس شكل الأشكال الموجودة في القالب. عندما تصل إلى شكلها النهائي ، يتم إخراجها لتبرد. تنتج هذه العملية أجزاء قوية ذات شكل دقيق ، ولكنها تتطلب استثمارًا أكبر للقوالب المتخصصة. يزيد التزوير المضطرب قطر القطعة المعدنية بتسطيحها. يتم استخدامه بشكل عام في صنع الأجزاء الصغيرة ، خاصةً لتشكيل الرؤوس على السحابات مثل البراغي والمسامير. • تعدين المساحيق / معالجة المساحيق: كما يوحي الاسم ، فهي تتضمن عمليات تصنيع لصنع أجزاء صلبة من أشكال هندسية وأشكال معينة من المساحيق. إذا تم استخدام مساحيق المعادن لهذا الغرض ، فهو مجال تعدين المساحيق وإذا تم استخدام مساحيق غير معدنية ، فهذا يعني معالجة المسحوق. يتم إنتاج الأجزاء الصلبة من المساحيق بالضغط والتلبيد . يتم استخدام مسحوق الضغط لضغط المساحيق في الأشكال المرغوبة. أولاً ، يتم طحن المادة الأولية فيزيائيًا ، وتقسيمها إلى العديد من الجزيئات الفردية الصغيرة. يملأ خليط المسحوق في القالب وتتحرك المثقاب نحو المسحوق وتضغطه في الشكل المطلوب. يتم إجراؤه في الغالب في درجة حرارة الغرفة ، حيث يتم الحصول على مسحوق يضغط على جزء صلب ويسمى مضغوطًا خضراء. تستخدم مواد الربط ومواد التشحيم بشكل شائع لتعزيز قابلية الضغط. نحن قادرون على تشكيل مكبس المسحوق باستخدام مكابس هيدروليكية بقدرة عدة آلاف من الأطنان. لدينا أيضًا مكابس مزدوجة الحركة مع اللكمات العلوية والسفلية المتعارضة بالإضافة إلى مكابس الحركة المتعددة لأجزاء هندسية معقدة للغاية. التوحيد الذي يمثل تحديًا مهمًا للعديد من مصانع معالجة المساحيق / المساحيق ليس مشكلة كبيرة لـ AGS-TECH بسبب خبرتنا الواسعة في تصنيع هذه الأجزاء حسب الطلب لسنوات عديدة. لقد نجحنا حتى مع الأجزاء السميكة حيث يمثل التوحيد تحديًا. إذا التزمنا بمشروعك ، فسنصنع أجزائك. إذا رأينا أي مخاطر محتملة ، فسنبلغك بـ in مقدمًا. تنقع المساحيق ، وهي الخطوة الثانية ، تتضمن رفع درجة الحرارة إلى درجة معينة والحفاظ على درجة الحرارة عند هذا المستوى لفترة معينة بحيث يمكن لجزيئات المسحوق الموجودة في الجزء المضغوط أن تترابط معًا. ينتج عن هذا روابط أقوى بكثير وتقوية قطعة العمل. يحدث التلبيد بالقرب من درجة حرارة انصهار المسحوق. أثناء التلبيد يحدث الانكماش ، تزداد قوة المواد ، الكثافة ، الليونة ، التوصيل الحراري ، التوصيل الكهربائي. لدينا أفران دفعية ومستمرة للتلبيد. تتمثل إحدى قدراتنا في ضبط مستوى مسامية الأجزاء التي ننتجها. على سبيل المثال ، نحن قادرون على إنتاج مرشحات معدنية عن طريق الحفاظ على الأجزاء المسامية إلى حد ما . باستخدام تقنية تسمى IMPREGNATION ، نقوم بملء المسام في المعدن بسائل مثل الزيت. نحن ننتج على سبيل المثال محامل مشربة بالزيت تكون ذاتية التشحيم. في عملية التسريب ، نملأ مسام المعدن بمعدن آخر ذي درجة انصهار أقل من المادة الأساسية. يسخن الخليط إلى درجة حرارة بين درجات حرارة انصهار المعدنين. نتيجة لذلك يمكن الحصول على بعض الخصائص الخاصة. نقوم أيضًا بعمليات ثانوية بشكل متكرر مثل المعالجة الآلية والتزوير على الأجزاء المصنعة بالمسحوق عند الحاجة إلى الحصول على ميزات أو خصائص خاصة أو عندما يمكن تصنيع الجزء بخطوات معالجة أقل. الضغط الأيزوستاتي: في هذه العملية ، يتم استخدام ضغط السوائل لضغط الجزء. يتم وضع مساحيق المعادن في قالب مصنوع من حاوية مرنة محكمة الغلق. في الضغط المتساوي ، يتم تطبيق الضغط من كل مكان ، على عكس الضغط المحوري الذي يظهر في الضغط التقليدي. مزايا الضغط المتساوي هي كثافة موحدة داخل الجزء ، خاصة للأجزاء الأكبر أو السميكة ، وخصائص فائقة. عيبه هو أوقات الدورات الطويلة والدقة الهندسية المنخفضة نسبيًا. يتم إجراء الضغط الأيزوستاتي البارد في درجة حرارة الغرفة ويتم صنع القالب المرن من المطاط أو PVC أو اليوريثان أو مواد مماثلة. السائل المستخدم للضغط والضغط هو الزيت أو الماء. يتبع هذا التلبيد التقليدي للمضغوط الخضراء. من ناحية أخرى ، يتم إجراء الضغط الأيزوستاتي الساخن في درجات حرارة عالية وتكون مادة القالب عبارة عن صفائح معدنية أو سيراميك بنقطة انصهار عالية بما يكفي لمقاومة درجات الحرارة. عادة ما يكون سائل الضغط غاز خامل. يتم تنفيذ عمليات الضغط والتلبيد في خطوة واحدة. يتم التخلص من المسامية بشكل كامل تقريبًا ، يتم الحصول على هيكل موحد grain. تتمثل ميزة الضغط المتساوي الساكن في أنه يمكن أن ينتج أجزاء مماثلة للصب والتزوير معًا أثناء صنع المواد غير المناسبة للصب والتزوير الممكن استخدامها. من مساوئ الضغط المتساوي الساكن هو ارتفاع وقت الدورة وبالتالي التكلفة. إنها مناسبة للأجزاء الهامة ذات الحجم المنخفض. صب المعادن بالحقن: عملية مناسبة جدًا لإنتاج الأجزاء المعقدة بجدران رقيقة وهندسة مفصلة. الأنسب للأجزاء الأصغر. يتم خلط المساحيق والمواد اللاصقة للبوليمر ، وتسخينها وحقنها في قالب. تغلف مادة رابطة البوليمر أسطح جزيئات المسحوق. بعد التشكيل ، تتم إزالة المادة الرابطة إما عن طريق التسخين بدرجة حرارة منخفضة للمذابة باستخدام مذيب. انضغاط الأسطوانة / لف المسحوق: تستخدم المساحيق لإنتاج شرائح أو صفائح مستمرة. يتم تغذية المسحوق من وحدة التغذية وضغطه بواسطة بكرتين دوارتين في ورقة أو شرائح. يتم تنفيذ العملية على البارد. يتم نقل الصفيحة إلى فرن تلبيد. يمكن تكرار عملية التلبيد مرة ثانية. قذف المساحيق: يتم تصنيع الأجزاء ذات النسب الكبيرة من الطول إلى القطر عن طريق بثق وعاء معدني رفيع مع مسحوق. LOOSE SINTERING: كما يوحي الاسم ، إنها طريقة ضغط وتلبيد غير مضغوطة ، ومناسبة لإنتاج أجزاء مسامية للغاية مثل المرشحات المعدنية. يتم تغذية المسحوق في تجويف القالب بدون ضغط. LOOSE SINTERING: كما يوحي الاسم ، إنها طريقة ضغط وتلبيد غير مضغوطة ، ومناسبة لإنتاج أجزاء مسامية للغاية مثل المرشحات المعدنية. يتم تغذية المسحوق في تجويف القالب بدون ضغط. SPARK SINTERING: يتم ضغط المسحوق في القالب بواسطة مثقابين متعارضين ويتم تطبيق تيار كهربائي عالي الطاقة على الثقب ويمر عبر المسحوق المضغوط الموجود بينهما. يحرق التيار العالي الأغشية السطحية من جزيئات المسحوق ويخترقها بالحرارة المتولدة. العملية سريعة لأن الحرارة لا يتم تطبيقها من الخارج ولكن بدلاً من ذلك تتولد من داخل القالب. الضغط الساخن: يتم ضغط المساحيق وتلبيدها في خطوة واحدة في قالب يمكنه تحمل درجات الحرارة المرتفعة. عندما يضغط القالب يتم تطبيق حرارة المسحوق عليه. الدقة الجيدة والخصائص الميكانيكية التي تحققها هذه الطريقة تجعلها خيارًا جذابًا. حتى المعادن المقاومة للصهر يمكن معالجتها باستخدام مواد العفن مثل الجرافيت. CLICK Product Finder-Locator Service القائمة السابقة
- سحب المعادن من المطاط البلاستيكي ، قوالب البثق ، بثق الألمنيوم
سحب المعادن من المطاط البلاستيكي ، قوالب البثق ، بثق الألمنيوم ، تشكيل أنبوب الأنبوب ، المقاطع البلاستيكية ، تصنيع الملامح المعدنية ، PVC في AGS-TECH Inc. قذف ، منتجات مقذوفة ، بثق نستخدم the EXTRUSION process لتصنيع منتجات ذات مقطع عرضي ثابت مثل الأنابيب والأنابيب والمشتتات الحرارية. على الرغم من إمكانية بثق العديد من المواد ، إلا أن عمليات البثق الأكثر شيوعًا لدينا مصنوعة من المعدن والبوليمرات / البلاستيك والسيراميك التي يتم الحصول عليها إما بطريقة البثق الباردة أو الدافئة أو الساخنة. نسمي الأجزاء المبثوقة منبثقة أو منبثقة إذا كانت الجمع. بعض الإصدارات المتخصصة من العملية التي نقوم بها أيضًا هي overjackling ، والبثق المشترك ، والبثق المركب. نوصي بالنقر هنا إلى قم بتنزيل الرسوم التوضيحية التخطيطية الخاصة بنا لعمليات بثق المعادن من السيراميك والبلاستيك بواسطة AGS-TECH Inc. سيساعدك هذا على فهم المعلومات التي نقدمها لك أدناه بشكل أفضل. في مادة البثق التي يتم بثقها يتم دفعها أو سحبها من خلال قالب يحتوي على ملف المقطع العرضي المطلوب. يمكن استخدام هذه العملية لتصنيع مقاطع عرضية معقدة مع تشطيب سطح ممتاز والعمل على مواد هشة. يمكن للمرء أن ينتج أي طول للأجزاء باستخدام هذه العملية. لتبسيط خطوات العملية: 1.) في عمليات البثق الدافئة أو الساخنة ، يتم تسخين المادة وتحميلها في حاوية في المكبس. يتم ضغط المواد وإخراجها من القالب. 2.) يتم شد البثق المنتج لتقويمه أو معالجته بالحرارة أو العمل على البارد لتعزيز خصائصه. من ناحية أخرى COLD EXTRUSION t يتم وضعه في درجة حرارة الغرفة تقريبًا وله مزايا أكسدة أقل وقوة عالية وتحمل أقرب وإنهاء سطح جيد وثبات. يتم تنفيذ WARM EXTRUSION is فوق درجة حرارة الغرفة ولكن أقل من نقطة إعادة التبلور. إنه يوفر حلاً وسطًا وتوازنًا للقوى المطلوبة ، وخصائص الليونة والمواد ، وبالتالي فهو الاختيار لبعض التطبيقات. يتم وضع HOT EXTRUSION t فوق درجة حرارة إعادة بلورة المادة. بهذه الطريقة يكون من الأسهل دفع المادة خلال القالب. لكن تكلفة المعدات مرتفعة. كلما زاد تعقيد ملف التعريف المبثوق ، زادت تكلفة القالب (الأدوات) وكان معدل الإنتاج أقل. المقاطع العرضية للقالب وكذلك السماكات لها قيود تعتمد على المادة المراد بثقها. الزوايا الحادة في قوالب البثق غير مرغوب فيها دائمًا ويجب تجنبها ما لم يكن ذلك ضروريًا. وفقًا للمادة التي يتم بثقها ، نقدم: • METAL EXTRUSIONS : الأكثر شيوعًا التي ننتجها هي الألمنيوم والنحاس الأصفر والزنك والنحاس والفولاذ والتيتانيوم والمغنيسيوم • البلاستيك EXTRUSION : يتم صهر البلاستيك وتشكيله في شكل جانبي مستمر. موادنا الشائعة المعالجة هي البولي إيثيلين والنايلون والبوليسترين والبولي فينيل كلوريد والبولي بروبيلين والبلاستيك ABS والبولي كربونات والاكريليك. تشمل المنتجات النموذجية التي نصنعها الأنابيب والأنابيب والإطارات البلاستيكية. في هذه العملية ، يتم تغذية حبات / راتينج بلاستيكية صغيرة بالجاذبية من القادوس إلى برميل آلة البثق. في كثير من الأحيان نقوم أيضًا بخلط الملونات أو الإضافات الأخرى في القادوس لإعطاء المنتج المواصفات والخصائص المطلوبة. يتم إجبار المادة التي تدخل البرميل المسخن بواسطة المسمار الدوار على ترك البرميل في النهاية والتحرك عبر حزمة الشاشة لإزالة الملوثات في البلاستيك المصهور. بعد اجتياز عبوة الغربال ، يدخل البلاستيك في قالب البثق. يعطي القالب البلاستيك الناعم المتحرك شكله الجانبي أثناء مروره. الآن يمر البثق في حمام مائي للتبريد. التقنيات الأخرى التي تستخدمها شركة AGS-TECH Inc. لسنوات عديدة هي: • الأنابيب والأنابيب EXTRUSION : يتم تشكيل الأنابيب والأنابيب البلاستيكية عندما يتم بثق البلاستيك من خلال قالب تشكيل دائري ويتم تبريده في حمام مائي ، ثم يتم قصه للطول أو لفه / لفه. واضح أو ملون ، مخطط ، جدار واحد أو مزدوج ، مرن أو صلب ، PE ، PP ، بولي يوريثين ، بولي كلوريد الفينيل ، نايلون ، كمبيوتر شخصي ، سيليكون ، فينيل أو غير ذلك ، لدينا كل شيء. لدينا أنابيب مخزنة بالإضافة إلى القدرة على الإنتاج وفقًا لمواصفاتك. تقوم شركة AGS-TECH بتصنيع الأنابيب وفقًا لمتطلبات إدارة الأغذية والعقاقير (FDA) و UL و LE للتطبيقات الطبية والكهربائية والإلكترونية والصناعية وغيرها. • تجاوز جاكيتات / جاكيتات فوقية EXTRUSION : تطبق هذه التقنية طبقة خارجية من البلاستيك على السلك أو الكابل الموجود. يتم تصنيع أسلاك العزل الخاصة بنا بهذه الطريقة. • COEXTRUSION : يتم بثق طبقات متعددة من المواد في وقت واحد. يتم تسليم الطبقات المتعددة بواسطة أجهزة بثق متعددة. يمكن تعديل سماكات الطبقة المختلفة لتلبية مواصفات العملاء. تتيح هذه العملية استخدام بوليمرات متعددة لكل منها وظيفة مختلفة في المنتج. نتيجة لذلك ، يمكن للمرء تحسين مجموعة من الخصائص. • البثق المركب: يتم خلط بوليمرات مفردة أو متعددة مع إضافات للحصول على مركب بلاستيكي. تنتج آلات البثق المزدوجة اللولب مواد قذف مركبة. قوالب البثق رخيصة بشكل عام مقارنة بالقوالب المعدنية. إذا كنت تدفع أكثر بكثير من بضعة آلاف من الدولارات مقابل ألومنيوم صغير أو متوسط الحجم بقذف البثق ، فمن المحتمل أنك تدفع الكثير. نحن خبراء في تحديد التقنية الأكثر فعالية من حيث التكلفة والأسرع والأنسب لتطبيقك. في بعض الأحيان ، يمكن أن يوفر لك البثق ثم تصنيع جزء ما الكثير من المال. قبل اتخاذ قرار حازم ، اسألنا عن رأينا أولاً. لقد ساعدنا العديد من العملاء في اتخاذ القرارات الصحيحة. بالنسبة لبعض عمليات سحب المعادن المستخدمة على نطاق واسع ، يمكنك تنزيل الكتيبات والكتالوجات الخاصة بنا من خلال النقر على النص الملون أدناه. إذا كان منتجًا جاهزًا يلبي متطلباتك ، فسيكون أكثر اقتصادا. قم بتنزيل إمكانيات بثق الأنبوب والأنابيب الطبية الخاصة بنا قم بتنزيل أحواض الحرارة المبثوقة • عمليات التصنيع والتصنيع الثانوية للبثق : من بين العمليات ذات القيمة المضافة التي نقدمها للمنتجات المبثوقة: -أنبوب مخصص وثني الأنابيب ، والتشكيل والتشكيل ، وقطع الأنبوب ، وتشكيل نهاية الأنبوب ، ولف الأنبوب ، والتجهيز والتشطيب ، وحفر الثقب والثقب واللكم ، - تجميعات الأنابيب والأنابيب المخصصة ، التجميع الأنبوبي ، اللحام ، اللحام بالنحاس واللحام -مخصص البثق الانحناء والتشكيل والتشكيل - التنظيف ، إزالة الشحوم ، التخليل ، التخميل ، التلميع ، الأنودة ، الطلاء ، الطلاء ، المعالجة الحرارية ، التلدين والتصلب ، النقش والنقش ووضع العلامات ، التغليف المخصص. CLICK Product Finder-Locator Service الصفحة السابقة
- الصب وقطع الآلات ، التصنيع باستخدام الحاسب الآلي ، الطحن ، الخراطة ، الآلات السويسرية
أجزاء الصب والآلات ، التصنيع باستخدام الحاسب الآلي ، الطحن ، الخراطة ، التصنيع السويسري ، صب القوالب ، صب الاستثمار ، قطع الرغوة المفقودة من AGS-TECH Inc. الصب والتشغيل الآلي تقنيات الصب والآلات المخصصة لدينا هي المصبوبات القابلة للاستهلاك وغير القابلة للاستهلاك ، والصب الحديدية وغير الحديدية ، والرمل ، والقالب ، والطرد المركزي ، والمستمر ، والعفن الخزفي ، والاستثمار ، والرغوة المفقودة ، والشكل القريب من الشبكة ، والعفن الدائم (صب الجاذبية بالقالب) ، والجص قوالب (صب الجبس) ومسبوكات القشرة ، الأجزاء الآلية التي يتم إنتاجها عن طريق الطحن والخراطة باستخدام المعدات التقليدية وكذلك CNC ، والآلات من النوع السويسري للإنتاجية العالية للأجزاء الصغيرة الدقيقة غير المكلفة ، والتصنيع اللولبي للمثبتات ، والآلات غير التقليدية. يرجى أن تضع في اعتبارك أنه إلى جانب المعادن والسبائك المعدنية ، فإننا نصنع مكونات السيراميك والزجاج والبلاستيك أيضًا في بعض الحالات عندما يكون تصنيع قالب غير جذاب أو ليس خيارًا. يتطلب تصنيع مواد البوليمر الخبرة المتخصصة التي نمتلكها بسبب التحدي الذي يمثله البلاستيك والمطاط بسبب نعومتهما وعدم صلابتهما ... إلخ. لتصنيع السيراميك والزجاج ، يرجى الاطلاع على صفحتنا عن التصنيع غير التقليدي. تقوم شركة AGS-TECH Inc. بتصنيع وتوريد المسبوكات خفيفة الوزن وثقيلة على حد سواء. لقد قمنا بتوريد المسبوكات المعدنية والأجزاء الآلية للغلايات والمبادلات الحرارية والسيارات والمحركات الدقيقة وتوربينات الرياح ومعدات تغليف المواد الغذائية والمزيد. نوصي بالنقر هنا إلى قم بتنزيل الرسوم التوضيحية التخطيطية الخاصة بنا لعمليات التصنيع والسبك بواسطة AGS-TECH Inc. سيساعدك هذا على فهم المعلومات التي نقدمها لك أدناه بشكل أفضل. دعونا نلقي نظرة على بعض التقنيات المختلفة التي نقدمها بالتفصيل: • صب القالب القابل للاستهلاك: تشير هذه الفئة الواسعة إلى الطرق التي تتضمن قوالب مؤقتة وغير قابلة لإعادة الاستخدام. ومن الأمثلة على ذلك الرمل والجص والصدفة والاستثمار (وتسمى أيضًا الشمع المفقود) وصب الجبس. • صب الرمل: عملية يتم فيها استخدام الرمل كمواد للقولبة. طريقة قديمة جدًا ولا تزال شائعة جدًا لدرجة أن غالبية المسبوكات المعدنية التي يتم إنتاجها تتم بهذه التقنية. تكلفة منخفضة حتى في الإنتاج بكميات منخفضة. مناسبة لتصنيع الأجزاء الصغيرة والكبيرة. يمكن استخدام هذه التقنية لتصنيع الأجزاء في غضون أيام أو أسابيع باستثمارات قليلة جدًا. يتم ربط الرمل الرطب معًا باستخدام الطين أو المواد الرابطة أو الزيوت الخاصة. يتم احتواء الرمل بشكل عام في صناديق القوالب ويتم إنشاء نظام التجويف والبوابة عن طريق ضغط الرمل حول النماذج. العمليات هي: 1.) وضع النموذج في الرمل لعمل القالب 2.) دمج النموذج والرمل في نظام بوابات 3.) إزالة النموذج 4) ملء تجويف القالب بالمعدن المنصهر 5.) تبريد المعدن 6.) كسر قالب الرمل وإزالة الصب • صب الجص: على غرار صب الرمل ، وبدلاً من الرمل ، يتم استخدام جص باريس كمواد للقالب. فترات إنتاج قصيرة مثل صب الرمل وغير مكلفة. التحمل الجيد في الأبعاد وإنهاء السطح. عيبه الرئيسي هو أنه لا يمكن استخدامه إلا مع معادن ذات نقطة انصهار منخفضة مثل الألومنيوم والزنك. • صب قوالب القشرة: يشبه أيضًا صب الرمل. يتم الحصول على تجويف القالب عن طريق غلاف الرمل المتصلب وراتنج الراتينج المتصلب بالحرارة بدلاً من القارورة المملوءة بالرمل كما هو الحال في عملية صب الرمل. يمكن صب أي معدن مناسب للصب بالرمل تقريبًا عن طريق قولبة القشرة. يمكن تلخيص العملية على النحو التالي: 1.) تصنيع قالب الصدفة. الرمل المستخدم هو حجم حبيبات أصغر بكثير بالمقارنة مع الرمل المستخدم في صب الرمل. يتم خلط الرمل الناعم مع الراتنج بالحرارة. النموذج المعدني مطلي بعامل فراق لتسهيل إزالة الغلاف. بعد ذلك يتم تسخين النمط المعدني ويتم ثقب خليط الرمل أو نفخه على نمط الصب الساخن. تتشكل قشرة رقيقة على سطح النموذج. يمكن ضبط سماكة هذه القشرة عن طريق تغيير طول الفترة الزمنية التي يتلامس فيها خليط راتنج الرمل مع النمط المعدني. ثم تتم إزالة الرمل السائب مع بقاء النمط المغطى بالصدفة. 2.) بعد ذلك ، يتم تسخين القشرة والنمط في فرن حتى تتصلب القشرة. بعد اكتمال التصلب ، يتم إخراج الغلاف من النمط باستخدام دبابيس مدمجة في النموذج. 3) يتم تجميع اثنتين من هذه القذائف معًا عن طريق اللصق أو التثبيت وتشكيل القالب الكامل. الآن يتم إدخال قالب الصدفة في حاوية يتم دعمها بالرمل أو المعدن أثناء عملية الصب. 4.) الآن يمكن سكب المعدن الساخن في قالب الصدفة. مزايا صب القشرة هي منتجات ذات تشطيب سطحي جيد للغاية ، وإمكانية تصنيع أجزاء معقدة بدقة أبعاد عالية ، وعملية سهلة التشغيل الآلي ، واقتصادية للإنتاج بكميات كبيرة. العيوب هي أن القوالب تتطلب تهوية جيدة بسبب الغازات التي يتم تكوينها عندما يتلامس المعدن المنصهر مع المادة الكيميائية الرابطة ، وراتنجات التصلد بالحرارة والأنماط المعدنية باهظة الثمن. نظرًا لتكلفة الأنماط المعدنية ، قد لا تتناسب التقنية بشكل جيد مع عمليات الإنتاج ذات الكميات المنخفضة. • صب الاستثمار (المعروف أيضًا باسم صب الشمع المفقود): أيضًا تقنية قديمة جدًا ومناسبة لتصنيع أجزاء عالية الجودة بدقة عالية وقابلية تكرار وتنوع ونزاهة من العديد من المعادن والمواد المقاومة للحرارة والسبائك الخاصة عالية الأداء. يمكن إنتاج أجزاء صغيرة وكبيرة الحجم. عملية مكلفة عند مقارنتها ببعض الطرق الأخرى ، ولكن الميزة الرئيسية هي إمكانية إنتاج أجزاء ذات شكل قريب من الشبكة وخطوط وتفاصيل معقدة. لذلك يتم تعويض التكلفة إلى حد ما عن طريق التخلص من إعادة العمل والقطع في بعض الحالات. على الرغم من إمكانية وجود اختلافات ، فإليك ملخصًا لعملية اختيار الاستثمار العامة: 1.) إنشاء نموذج رئيسي أصلي من الشمع أو البلاستيك. يحتاج كل صب إلى نمط واحد حيث يتم تدميرها في العملية. هناك حاجة أيضًا إلى القالب الذي يتم تصنيع الأنماط منه ، وفي معظم الأحيان يتم صب القالب أو تشكيله. نظرًا لعدم الحاجة إلى فتح القالب ، يمكن تحقيق مصبوبات معقدة ، يمكن توصيل العديد من أنماط الشمع مثل أغصان الشجرة وصبها معًا ، مما يتيح إنتاج أجزاء متعددة من صب واحد للمعدن أو سبيكة معدنية. 2.) بعد ذلك ، يتم غمس النموذج أو سكبه باستخدام ملاط مقاوم للصهر يتكون من حبيبات السيليكا الدقيقة للغاية والماء والمواد اللاصقة. ينتج عن هذا طبقة خزفية فوق سطح النموذج. يُترك الغلاف المقاوم للصهر على النمط حتى يجف ويتصلب. هذه الخطوة هي المكان الذي يأتي منه اسم صب الاستثمار: يتم استثمار الملاط المقاوم للصهر على نمط الشمع. 3.) في هذه الخطوة ، يتم قلب قالب السيراميك المقوى رأسًا على عقب ويتم تسخينه بحيث يذوب الشمع ويصب خارج القالب. يتم ترك تجويف خلفه للصب المعدني. 4.) بعد إخراج الشمع ، يتم تسخين قالب السيراميك لدرجة حرارة أعلى مما يؤدي إلى تقوية القالب. 5.) يتم صب المعدن في القالب الساخن لملء جميع الأقسام المعقدة. 6.) يسمح الصب لتصلب 7.) أخيرًا تم كسر قالب السيراميك وقطع الأجزاء المصنعة من الشجرة. هنا رابط إلى كتيب الاستثمار في مصنع الصب • صب النمط التبخيري: تستخدم العملية نمطًا مصنوعًا من مادة مثل رغوة البوليسترين التي تتبخر عند سكب المعدن المنصهر الساخن في القالب. هناك نوعان من هذه العملية: LOST FOAM CASTING الذي يستخدم الرمل غير المرتبط و FULL MOLD CASTING الذي يستخدم الرمل المترابط. فيما يلي خطوات العملية العامة: 1.) تصنيع النموذج من مادة مثل البوليسترين. عندما يتم تصنيع كميات كبيرة ، يتم تشكيل النموذج. إذا كان للجزء شكل معقد ، فقد تحتاج عدة أقسام من مادة الرغوة هذه إلى الالتصاق معًا لتشكيل النموذج. غالبًا ما نغطي النموذج بمركب حراري لإنشاء تشطيب جيد للسطح على الصب. 2.) ثم يتم وضع النموذج في صب الرمل. 3.) يُسكب المعدن المنصهر في القالب ، ويبخر نمط الرغوة ، أي البوليسترين في معظم الحالات حيث يتدفق عبر تجويف القالب. 4.) يتم ترك المعدن المنصهر في قالب الرمل حتى يتصلب. 5.) بعد أن تصلب ، نقوم بإزالة الصب. في بعض الحالات ، يتطلب المنتج الذي نصنعه جوهرًا داخل النموذج. في عملية الصب بالتبخير ، ليست هناك حاجة لوضع قلب في تجويف القالب وتأمينه. هذه التقنية مناسبة لتصنيع الأشكال الهندسية المعقدة للغاية ، ويمكن تشغيلها آليًا بسهولة لإنتاج كميات كبيرة ، ولا توجد خطوط فاصلة في الجزء المصبوب. العملية الأساسية بسيطة واقتصادية التنفيذ. للإنتاج بكميات كبيرة ، نظرًا لأن هناك حاجة إلى قالب أو قالب لإنتاج الأنماط من البوليسترين ، فقد يكون هذا مكلفًا إلى حد ما. • صب القالب غير القابل للتوسيع: تشير هذه الفئة الواسعة إلى الطرق التي لا يحتاج فيها القالب إلى الإصلاح بعد كل دورة إنتاج. ومن الأمثلة الصب الدائم ، والقالب ، والمستمر ، والطرد المركزي. يتم الحصول على التكرار ويمكن وصف الأجزاء بأنها NEAR NET SHAPE. • الصب الدائم: قوالب قابلة لإعادة الاستخدام مصنوعة من المعدن تستخدم في المسبوكات المتعددة. يمكن استخدام القالب الدائم بشكل عام لعشرات الآلاف من المرات قبل أن يبلى. تستخدم الجاذبية أو ضغط الغاز أو الفراغ بشكل عام لملء القالب. تُصنع القوالب (وتسمى أيضًا القوالب) بشكل عام من الحديد أو الفولاذ أو السيراميك أو معادن أخرى. العملية العامة هي: 1.) آلة وإنشاء القالب. من الشائع تصنيع القالب من كتلتين معدنيتين يمكن فتحهما وإغلاقهما. يتم بشكل عام تشكيل كل من ميزات الجزء ونظام البوابة في قالب الصب. 2.) أسطح القالب الداخلية مطلية بملاط يحتوي على مواد مقاومة للحرارة. يساعد هذا في التحكم في تدفق الحرارة ويعمل كمواد تشحيم لسهولة إزالة الجزء المصبوب. 3.) بعد ذلك ، يتم إغلاق أنصاف القالب الدائم ويتم تسخين القالب. 4) يُسكب المعدن المنصهر في قالب ويترك حتى يصلب. 5.) قبل حدوث الكثير من التبريد ، نقوم بإزالة الجزء من القالب الدائم باستخدام قاذفات عند فتح نصفي القالب. كثيرًا ما نستخدم صب القالب الدائم للمعادن ذات نقطة الانصهار المنخفضة مثل الزنك والألمنيوم. للمسبوكات الفولاذية ، نستخدم الجرافيت كمادة العفن. نحصل أحيانًا على أشكال هندسية معقدة باستخدام النوى داخل قوالب دائمة. مزايا هذه التقنية هي المسبوكات ذات الخصائص الميكانيكية الجيدة التي يتم الحصول عليها من خلال التبريد السريع ، والتوحيد في الخصائص ، والدقة الجيدة وإنهاء السطح ، ومعدلات الرفض المنخفضة ، وإمكانية أتمتة العملية وإنتاج كميات كبيرة بشكل اقتصادي. تتمثل العيوب في ارتفاع تكاليف الإعداد الأولية مما يجعلها غير مناسبة لعمليات الحجم المنخفض والقيود المفروضة على حجم الأجزاء المصنعة. • صب القوالب: يتم تشكيل القالب ويتم دفع المعدن المنصهر تحت ضغط عالٍ إلى تجاويف القالب. كل من مصبوبات القوالب المعدنية غير الحديدية وكذلك المعدنية ممكنة. هذه العملية مناسبة لعمليات الإنتاج بكميات كبيرة من الأجزاء الصغيرة إلى المتوسطة الحجم مع التفاصيل والجدران الرقيقة للغاية والاتساق الأبعاد والتشطيب الجيد للسطح. AGS-TECH Inc. قادرة على تصنيع سماكة جدار صغيرة تصل إلى 0.5 مم باستخدام هذه التقنية. كما هو الحال في صب القالب الدائم ، يجب أن يتكون القالب من نصفين يمكن فتحهما وإغلاقهما لإزالة الجزء المنتج. قد يحتوي قالب الصب بالقالب على تجاويف متعددة لتمكين إنتاج مصبوبات متعددة مع كل دورة. تعتبر قوالب الصب بالقالب ثقيلة جدًا وأكبر بكثير من الأجزاء التي تنتجها ، وبالتالي فهي باهظة الثمن أيضًا. نقوم بإصلاح واستبدال القوالب البالية مجانًا لعملائنا طالما أنهم يعيدون طلب أجزائهم منا. يموت لدينا عمر طويل في نطاق عدة مئات الآلاف من الدورات. فيما يلي خطوات العملية المبسطة الأساسية: 1.) إنتاج القالب بشكل عام من الفولاذ 2.) قالب مثبت على آلة الصب بالقالب 3.) يقوم المكبس بإجبار المعدن المنصهر على التدفق في تجاويف القالب لملء الميزات المعقدة والجدران الرقيقة 4) بعد ملء القالب بالمعدن المنصهر ، يتم ترك الصب تحت الضغط 5.) يتم فتح القالب وإزالة الصب بمساعدة دبابيس القاذف. 6.) الآن يتم تشحيم القالب الفارغ مرة أخرى ويتم تثبيته للدورة التالية. في صب القوالب ، نستخدم بشكل متكرر قولبة إدراج حيث ندمج جزءًا إضافيًا في القالب ونصب المعدن حوله. بعد التصلب ، تصبح هذه الأجزاء جزءًا من منتج الصب. مزايا الصب بالقالب هي الخصائص الميكانيكية الجيدة للأجزاء ، وإمكانية الميزات المعقدة ، والتفاصيل الدقيقة والتشطيب الجيد للسطح ، ومعدلات الإنتاج العالية ، والتشغيل الآلي السهل. العيوب هي: ليست مناسبة جدًا للحجم المنخفض بسبب ارتفاع تكلفة القوالب والمعدات ، والقيود في الأشكال التي يمكن صبها ، وعلامات دائرية صغيرة على أجزاء المصبوب الناتجة عن ملامسة دبابيس القاذف ، وميض رقيق من المعدن مضغوط للخارج عند خط الفصل ، والحاجة بالنسبة للفتحات على طول الخط الفاصل بين القالب ، من الضروري الحفاظ على درجات حرارة العفن منخفضة باستخدام دوران المياه. • الصب المركزي: يتم سكب المعدن المنصهر في مركز القالب الدوار عند محور الدوران. تقوم قوى الطرد المركزي برمي المعدن باتجاه المحيط ويتركه ليتجمد بينما يستمر القالب في الدوران. يمكن استخدام كل من دوران المحور الأفقي والعمودي. يمكن صب الأجزاء ذات الأسطح الداخلية المستديرة بالإضافة إلى الأشكال الأخرى غير الدائرية. يمكن تلخيص العملية على النحو التالي: 1.) يتم سكب المعدن المنصهر في قالب طرد مركزي. ثم يتم دفع المعدن إلى الجدران الخارجية بسبب غزل القالب. 2) عندما يدور القالب ، يتماسك المعدن المصبوب الصب بالطرد المركزي هو تقنية مناسبة لإنتاج الأجزاء الأسطوانية المجوفة مثل الأنابيب ، ولا حاجة إلى المسامير ، والرافعات وعناصر البوابات ، والتشطيب الجيد للسطح والميزات التفصيلية ، وعدم وجود مشاكل في الانكماش ، وإمكانية إنتاج أنابيب طويلة بأقطار كبيرة جدًا ، وقدرة إنتاج عالية السرعة . • الصب المستمر (الصب المتواصل): يستخدم في صب المعدن بطول مستمر. في الأساس ، يتم صب المعدن المنصهر في شكل جانبي ثنائي الأبعاد للقالب ولكن طوله غير محدد. يتم إدخال المعدن المنصهر الجديد باستمرار في القالب حيث ينتقل المسبوك إلى أسفل مع زيادة طوله بمرور الوقت. يتم صب المعادن مثل النحاس والصلب والألمنيوم في خيوط طويلة باستخدام عملية الصب المستمر. قد تحتوي العملية على تكوينات مختلفة ولكن يمكن تبسيط الإعداد المشترك على النحو التالي: 1.) يُسكب المعدن المنصهر في وعاء يقع فوق القالب بكميات ومعدلات تدفق محسوبة جيدًا ويتدفق عبر القالب المبرد بالماء. يتم ترسيخ المعدن المصبوب في القالب إلى قضيب بداية يوضع في أسفل القالب. يعطي شريط البداية هذا البكرات شيئًا لتلتقطه في البداية. 2.) يتم نقل الخيط المعدني الطويل بواسطة بكرات بسرعة ثابتة. تقوم البكرات أيضًا بتغيير اتجاه تدفق الشريط المعدني من العمودي إلى الأفقي. 3) بعد انتقال الصب المستمر لمسافة أفقية معينة ، تقوم شعلة أو منشار يتحرك مع الصب بسرعة بقطعه إلى الأطوال المرغوبة. يمكن دمج عملية الصب المستمر مع عملية التدحرج ، حيث يمكن تغذية المعدن المصبوب بشكل مستمر مباشرة في مطحنة الدرفلة لإنتاج I-Beams و T-Beams ... إلخ. ينتج عن الصب المستمر خصائص موحدة في جميع أنحاء المنتج ، وله معدل تصلب عالٍ ، ويقلل من التكلفة بسبب الخسارة المنخفضة جدًا للمواد ، ويوفر عملية يتم فيها تحميل المعدن ، والسكب ، والتصلب ، والقطع ، وإزالة الصب في عملية مستمرة و مما أدى إلى ارتفاع معدل الإنتاجية والجودة العالية. ومع ذلك ، فإن الاعتبار الرئيسي هو الاستثمار الأولي المرتفع وتكاليف الإعداد ومتطلبات المساحة. • خدمات الآلات: نحن نقدم آلات من ثلاثة وأربعة وخمسة محاور. نوع عمليات التصنيع التي نستخدمها هي الخراطة ، والطحن ، والحفر ، والملل ، والخرس ، والتخطيط ، والصق ، والطحن ، واللبس ، والتلميع ، والآلات غير التقليدية التي تم تطويرها بشكل أكبر في قائمة مختلفة من موقعنا على الإنترنت. في معظم عمليات التصنيع لدينا ، نستخدم آلات CNC. ومع ذلك ، بالنسبة لبعض العمليات ، تعتبر التقنيات التقليدية مناسبة بشكل أفضل ، وبالتالي فإننا نعتمد عليها أيضًا. تصل قدرات التصنيع لدينا إلى أعلى مستوى ممكن ويتم تصنيع بعض الأجزاء الأكثر تطلبًا في مصنع معتمد من AS9100. تتطلب شفرات المحرك النفاث خبرة تصنيع عالية التخصص والمعدات المناسبة. صناعة الطيران لديها معايير صارمة للغاية. يتم تصنيع بعض المكونات ذات الهياكل الهندسية المعقدة بسهولة عن طريق تصنيع خمسة محاور ، والتي توجد فقط في بعض مصانع التصنيع بما في ذلك مصانعنا. يتمتع مصنعنا المعتمد في مجال الفضاء الجوي بالخبرة اللازمة للامتثال لمتطلبات التوثيق المكثفة لصناعة الطيران. في عمليات التقليب ، يتم تدوير قطعة العمل وتحريكها مقابل أداة القطع. لهذه العملية يتم استخدام آلة تسمى مخرطة. في MILLING ، آلة تسمى آلة الطحن لديها أداة دوارة لجلب حواف القطع لتحمل ضد قطعة العمل. تتضمن عمليات الحفر قاطعًا دوارًا بحواف قطع تنتج ثقوبًا عند ملامستها لقطعة العمل. تستخدم مكابس الحفر أو المخارط أو المطاحن بشكل عام. في عمليات التثقيب ، يتم نقل أداة ذات طرف مدبب منحني واحد إلى ثقب خشن في قطعة عمل دوارة لتوسيع الفتحة قليلاً وتحسين الدقة. يتم استخدامه لأغراض التشطيب الدقيق. الكشط يتضمن أداة مسننة لإزالة المواد من قطعة الشغل في مسار واحد من البروش (أداة مسننة). في التطرق الخطي ، يعمل التطرق خطيًا على سطح قطعة العمل للتأثير على القطع ، بينما في التطرق الدوار ، يتم تدوير البروش وضغطه في قطعة العمل لقطع شكل المحور المتماثل. تعد آلة النوع السويسري إحدى تقنياتنا القيمة التي نستخدمها لتصنيع كميات كبيرة من الأجزاء الصغيرة عالية الدقة. باستخدام مخرطة من النوع السويسري ، نقوم بتشغيل أجزاء صغيرة ومعقدة ودقيقة بشكل غير مكلف. على عكس المخارط التقليدية حيث تظل قطعة العمل ثابتة وتتحرك الأداة ، في مراكز الدوران من النوع السويسري ، يُسمح لقطعة العمل بالتحرك في المحور Z والأداة ثابتة. في المعالجة الآلية من النوع السويسري ، يتم الاحتفاظ بمخزون القضيب في الماكينة ويتقدم من خلال جلبة توجيهية في المحور z ، مما يؤدي فقط إلى تعريض الجزء المراد تشكيله. بهذه الطريقة يتم ضمان قبضة محكمة وتكون الدقة عالية جدًا. يوفر توفر الأدوات الحية فرصة للطحن والحفر مع تقدم المواد من جلبة التوجيه. يوفر المحور Y للمعدات من النوع السويسري إمكانات طحن كاملة ويوفر قدرًا كبيرًا من الوقت في التصنيع. علاوة على ذلك ، تحتوي أجهزتنا على مثاقب وأدوات مملة تعمل على الجزء عند الإمساك به في المغزل الفرعي. تمنحنا قدرة الخراطة من النوع السويسري لدينا فرصة تصنيع كاملة مؤتمتة بالكامل في عملية واحدة. يعد التصنيع من أكبر قطاعات أعمال شركة AGS-TECH. إما أن نستخدمها كعملية أولية أو عملية ثانوية بعد صب أو بثق جزء بحيث يتم استيفاء جميع مواصفات الرسم. • خدمات تشطيب الأسطح: نحن نقدم مجموعة واسعة من المعالجات السطحية وتشطيبات الأسطح مثل تكييف السطح لتعزيز الالتصاق ، وترسيب طبقة أكسيد رقيقة لتعزيز التصاق الطلاء ، وسفع الرمل ، والأغشية الكيميائية ، والأنودة ، والنترة ، وطلاء المسحوق ، والطلاء بالرش ، العديد من التقنيات المتقدمة للمعادن والطلاء بما في ذلك الرش ، شعاع الإلكترون ، التبخر ، الطلاء ، الطلاء الصلب مثل الماس مثل الكربون (DLC) أو طلاء التيتانيوم لأدوات الحفر والقطع. • خدمات توسيم المنتجات وتوسيمها: يطلب العديد من عملائنا وضع العلامات والتوسيم والنقش بالليزر والنقش على الأجزاء المعدنية. إذا كانت لديك أي حاجة من هذا القبيل ، دعنا نناقش الخيار الأفضل لك. فيما يلي بعض منتجات الصب المعدنية الشائعة الاستخدام. نظرًا لأن هذه المنتجات جاهزة ، يمكنك توفير تكاليف العفن في حالة تناسب أي منها مع متطلباتك: انقر هنا لتنزيل 11 سلسلة من علب الألمنيوم المصبوب من AGS-Electronics CLICK Product Finder-Locator Service الصفحة السابقة
- أجزاء مصنعة حسب الطلب ، تركيبات ، قوالب بلاستيكية ، صب ، تصنيع
الأجزاء المصنّعة حسب الطلب ، التجميعات ، قوالب البلاستيك ، قولبة المطاط ، صب المعادن ، التصنيع باستخدام الحاسب الآلي ، الخراطة ، الطحن ، التجميع البصري الإلكتروني الكهربائي الدوائر المطبوعة مجلس الجمعية قطع غيار مصنعة حسب الطلب التجميعات والمنتجات اقرأ أكثر قوالب وصب البلاستيك والمطاط اقرأ أكثر الصب والتشغيل الآلي اقرأ أكثر منتجات مقذوفة اقرأ أكثر أختام وتصنيع الصفائح المعدنية اقرأ أكثر تشكيل المعادن ومساحيق المعادن اقرأ أكثر تشكيل الأسلاك واليايات اقرأ أكثر تشكيل وتشكيل الزجاج والسيراميك اقرأ أكثر التصنيع الإضافي والسريع اقرأ أكثر صناعة المركبات والمواد المركبة اقرأ أكثر عمليات الانضمام والتجميع والتثبيت نحن ننتج الأجزاء والتركيبات من أجلك ونقدم لك عمليات التصنيع التالية: • قوالب وأجزاء مصبوبة من البلاستيك والمطاط. قولبة بالحقن ، تشكيل حراري ، قولبة بالحرارة ، تشكيل بالفراغ ، قولبة بالنفخ ، قولبة دورانية ، صب صب ، إدخال صب وغيرها. • سحب البلاستيك والمطاط والمعادن • المصبوبات الحديدية وغير الحديدية والأجزاء الآلية التي تنتجها تقنيات الطحن والخراطة ، وتصنيع آلي من النوع السويسري. • أجزاء مسحوق تعدين • أختام المعادن واللامعدنية وتشكيل الصفائح المعدنية وتركيبات الصفائح المعدنية الملحومة • الطرق الباردة والساخنة • الأسلاك وتجميعات الأسلاك الملحومة وتشكيل الأسلاك • أنواع مختلفة من النوابض ، تشكيل الزنبرك • تصنيع التروس ، علبة التروس ، أداة التوصيل ، الدودة ، مخفض السرعة ، الأسطوانة ، أحزمة النقل ، سلاسل النقل ، مكونات ناقل الحركة • زجاج مقسّى ومضاد للرصاص متوافق مع معايير الناتو والمعايير العسكرية • الكرات والمحامل والبكرات وتجميعات البكرات • الصمامات والمكونات الهوائية مثل الحلقة O والغسالة والسدادات • الأجزاء والتجمعات من الزجاج والسيراميك ، والمكونات المقاومة للفراغ والمحكم ، والسيراميك المعدني والسيراميك والسيراميك. • أنواع مختلفة من التركيبات الميكانيكية والبصرية والميكانيكية والكهروميكانيكية والبصرية الإلكترونية. • رابطة معدنية ـ مطاطية ـ معدنية ـ بلاستيكية • الأنابيب والأنابيب ، وتشكيل الأنابيب ، والانحناء وتجميعات الأنابيب المخصصة ، وتصنيع الخوار. • تصنيع الألياف الزجاجية • اللحام باستخدام تقنيات مختلفة مثل لحام البقعة واللحام بالليزر و MIG و TIG. لحام بالموجات فوق الصوتية للأجزاء البلاستيكية. • مجموعة كبيرة ومتنوعة من المعالجات السطحية والتشطيبات السطحية مثل تكييف السطح لتعزيز الالتصاق ، وترسيب طبقة أكسيد رقيقة لتعزيز التصاق الطلاء ، والسفع بالرمل ، والغشاء الكيميائي ، والأنودة ، والنترة ، وطلاء المسحوق ، والطلاء بالرش ، والعديد من تقنيات الطلاء والمعدن المتقدمة بما في ذلك الرش ، شعاع الإلكترون ، التبخر ، الطلاء ، الطلاء الصلب مثل الماس مثل الكربون (DLC) أو التيتانيوم لأدوات القطع والحفر. • الوسم والوسم ، النقش بالليزر على الأجزاء المعدنية ، الطباعة على الأجزاء البلاستيكية والمطاطية قم بتنزيل كتيب عن مصطلحات الهندسة الميكانيكية الشائعة التي يستخدمها المصممون والمهندسون نحن نصنع المنتجات وفقًا لمواصفاتك ومتطلباتك الخاصة. من أجل أن نقدم لك أفضل جودة وتسليم وأسعار ، نقوم بتصنيع المنتجات على مستوى العالم في الصين والهند وتايوان والفلبين وكوريا الجنوبية وماليزيا وسريلانكا وتركيا والولايات المتحدة الأمريكية وكندا وألمانيا والمملكة المتحدة واليابان. هذا يجعلنا أقوى بكثير وأكثر قدرة على المنافسة عالميًا من أي مخصص آخر manufacturer. يتم تصنيع منتجاتنا في بيئات معتمدة من ISO9001: 2000 ، QS9000 ، ISO14001 ، TS16949 وتمتلك علامة CE ، UL وتفي بمعايير الصناعة الأخرى. بمجرد تعييننا لمشروعك ، يمكننا الاهتمام بالتصنيع والتجميع والاختبار والتأهيل والشحن والجمارك بالكامل كما يحلو لك. إذا كنت تفضل ذلك ، يمكننا تخزين أجزائك وتجميع مجموعات مخصصة وطباعة وتسمية اسم الشركة والعلامة التجارية الخاصة بك وتوصيل الشحن إلى عملائك. بمعنى آخر ، يمكننا أن نكون مركز التخزين والتوزيع الخاص بك أيضًا إذا كنت تفضل ذلك. نظرًا لأن مستودعاتنا تقع بالقرب من الموانئ البحرية الرئيسية ، فإنها تمنحنا ميزة لوجستية. على سبيل المثال ، عندما تصل منتجاتك إلى ميناء بحري رئيسي بالولايات المتحدة الأمريكية ، يمكننا t نقلها مباشرة إلى مستودع قريب حيث يمكننا تخزينها وتجميعها وصنعها وإعادة تسميتها وطباعتها وحزمها وفقًا لاختيارك وإسقاطه. شحن إلى عملائك. نحن لا نورد المنتجات فقط. تعمل شركتنا على عقود مخصصة حيث نأتي إلى موقعك ، ونقوم بتقييم مشروعك في الموقع وتطوير اقتراح مشروع مخصص لك. ثم نرسل فريقنا المتمرس لتنفيذ المشروع. يمكن العثور على مزيد من المعلومات حول عملنا الهندسي على http://www.ags-engineering.com - نأخذ مشاريع صغيرة وكذلك مشاريع كبيرة على نطاق صناعي. كخطوة أولى ، يمكننا توصيلك إما عن طريق الهاتف أو المؤتمرات عن بعد أو MSN messenger بأعضاء فريق الخبراء لدينا ، حتى تتمكن من التواصل مباشرة مع أحد الخبراء وطرح الأسئلة ومناقشة مشروعك. اتصل بنا وسنأتي لزيارتك إذا لزم الأمر . الصفحة السابقة