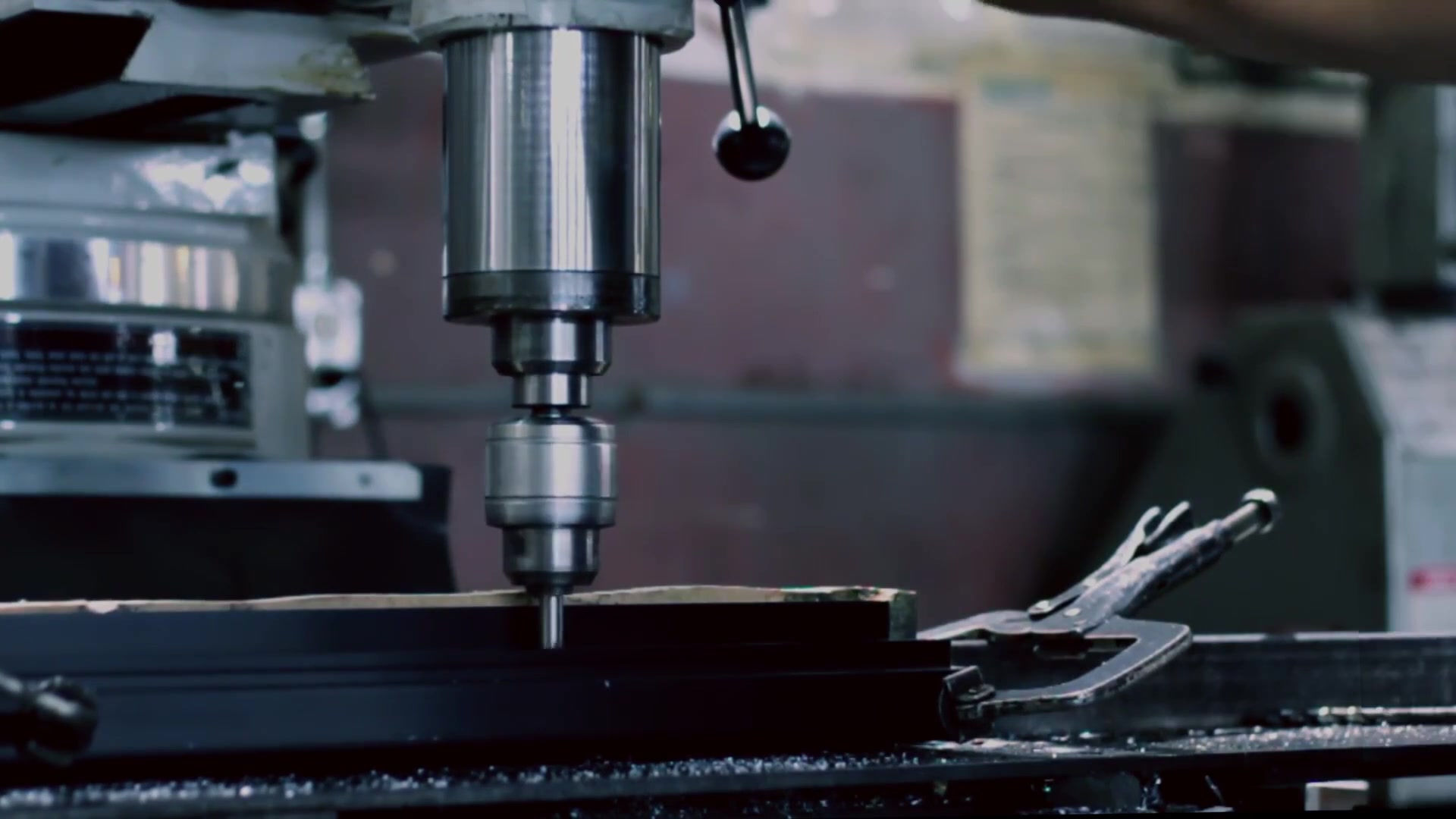
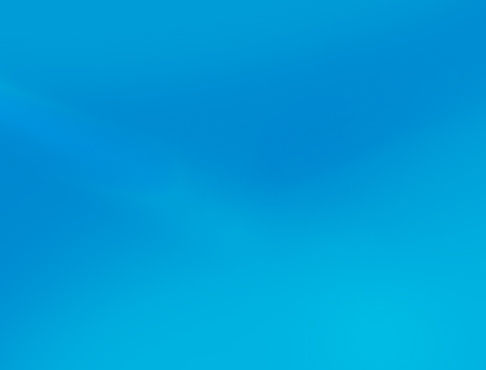
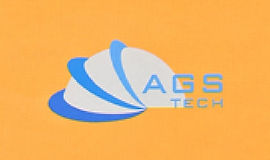
Глабальны індывідуальны вытворца, інтэгратар, кансалідатар, партнёр па аўтсорсінгу шырокага спектру прадуктаў і паслуг.
Мы ваша адзіная крыніца для вытворчасці, вырабу, праектавання, кансалідацыі, інтэграцыі, аўтсорсінгу вырабленых на заказ і гатовых прадуктаў і паслуг.
Выберыце мову
-
Вытворчасць на заказ
-
Унутраная і глабальная кантрактная вытворчасць
-
Аўтсорсінг вытворчасці
-
Унутраныя і сусветныя закупкі
-
Кансалідацыя
-
Інжынерная інтэграцыя
-
Інжынерныя паслугі
Сярод шматлікіх метадаў ЗЛУЧЭННЯ, якія мы выкарыстоўваем у вытворчасці, асаблівы акцэнт надаецца ЗВАРКІ, ПАЙКІ, ПАЯННЮ, КЛЕЮ і МАНТАЖНАЙ МЕХАНІЧНАЙ ЗБОРКЕ, таму што гэтыя метады шырока выкарыстоўваюцца ў такіх сферах, як вытворчасць герметычных зборак, вытворчасць высокатэхналагічных вырабаў і спецыялізаванае ўшчыльненне. Тут мы засяродзімся на больш спецыялізаваных аспектах гэтых метадаў злучэння, паколькі яны звязаны з вытворчасцю сучасных вырабаў і вузлоў.
ЗВАРКА ПЛАЎЛЕННЕМ: мы выкарыстоўваем цяпло для плаўлення і зліцця матэрыялаў. Цяпло падаецца электрычнасцю або пучкамі высокай энергіі. Тыпы зваркі плаўленнем, якія мы выкарыстоўваем, гэта кіслародная газавая зварка, дугавая зварка, зварка прамянём высокай энергіі.
ЦВЕРДАЦЕЛЬНАЯ ЗВАРКА: Мы злучаем дэталі без плаўлення і плаўлення. Нашы метады цвёрдацельнай зваркі - гэта халодная, ультрагукавая зварка, зварка супрацівам, трэннем, выбухам і дыфузійная зварка.
ПАЙКА І ПАЯННЕ: Яны выкарыстоўваюць прысадныя металы і даюць нам перавагу працы пры больш нізкіх тэмпературах, чым пры зварцы, такім чынам менш структурных пашкоджанняў вырабаў. Інфармацыю аб нашай паяльнай установцы, якая вырабляе фітынгі з керамікі да металу, герметычную герметызацыю, вакуумныя каналы, высокі і звышвысокі вакуум і кампаненты кантролю вадкасці можна знайсці тут:Брашура паяльнай фабрыкі
КЛЕЙ: з-за разнастайнасці клеяў, якія выкарыстоўваюцца ў прамысловасці, а таксама разнастайнасці прымянення, у нас ёсць спецыяльная старонка для гэтага. Каб перайсці на нашу старонку аб склейванні клеем, націсніце тут.
МАНТАЖНАЯ МЕХАНІЧНАЯ ЗБОРКА: мы выкарыстоўваем розныя крапежныя элементы, такія як балты, шрубы, гайкі, заклёпкі. Нашы зашпількі не абмяжоўваюцца стандартнымі зашпількамі. Мы праектуем, распрацоўваем і вырабляем спецыяльныя крапежныя элементы, якія вырабляюцца з нестандартных матэрыялаў, каб яны адпавядалі патрабаванням для спецыяльных прыкладанняў. Часам пажаданая электрычная або цеплавая неправоднасць, а часам - праводнасць. Для некаторых спецыяльных прыкладанняў кліенту могуць спатрэбіцца спецыяльныя крапежныя элементы, якія нельга зняць без разбурэння прадукту. Ёсць бясконцая колькасць ідэй і прыкладанняў. У нас ёсць усё для вас, калі не гатовае, мы можам хутка яго распрацаваць. Каб перайсці на нашу старонку па механічнай зборцы, націсніце тут. Давайце разгледзім нашы розныя метады злучэння больш падрабязна.
КІСЛАРОДНАЯ ГАЗОВАЯ ЗВАРКА (OFW): для атрымання зварачнага полымя мы выкарыстоўваем паліўны газ, змешаны з кіслародам. Калі мы выкарыстоўваем ацэтылен у якасці паліва і кіслароду, мы называем гэта кіслародна-ацэтыленавай газавай зваркай. У працэсе гарэння кіслароднага газу адбываюцца дзве хімічныя рэакцыі:
C2H2 + O2 ------» 2CO + H2 + Цяпл
2CO + H2 + 1,5 O2--------» 2 CO2 + H2O + Цяпло
Першая рэакцыя дысацыюе ацэтылен на вокіс вугляроду і вадарод, вырабляючы каля 33% ад агульнай колькасці вылучанага цяпла. Другі вышэйзгаданы працэс уяўляе сабой далейшае спальванне вадароду і вокісу вугляроду з выпрацоўкай каля 67% ад агульнай колькасці цяпла. Тэмпература ў полымі складае ад 1533 да 3573 Кельвінаў. Важны працэнт кіслароду ў газавай сумесі. Калі ўтрыманне кіслароду больш за палову, полымя становіцца акісляльнікам. Гэта непажадана для некаторых металаў, але пажадана для іншых. Прыкладам, калі акісляльнае полымя пажадана, з'яўляюцца сплавы на аснове медзі, таму што яна ўтварае пасіўны пласт на метале. З іншага боку, калі ўтрыманне кіслароду зніжаецца, поўнае згаранне немагчыма, і полымя становіцца аднаўленчым (науглероживающим) полымем. Тэмпературы ў аднаўленчым полымі ніжэйшыя, і таму ён прыдатны для такіх працэсаў, як пайка і пайка. Іншыя газы таксама з'яўляюцца патэнцыйным палівам, але яны маюць некаторыя недахопы ў параўнанні з ацэтыленам. Часам мы пастаўляем прысадныя металы ў зону зваркі ў выглядзе прысадных стрыжняў або дроту. Некаторыя з іх пакрытыя флюсам, каб запаволіць акісленне паверхняў і такім чынам абараніць расплаўлены метал. Дадатковым перавагай флюсу з'яўляецца выдаленне аксідаў і іншых рэчываў з зоны зваркі. Гэта прыводзіць да больш трывалай сувязі. Разнавіднасцю кіслароднай газавай зваркі з'яўляецца ГАЗОВАЯ ЗВАРКА ПАД ЦІСКАМ, пры якой два кампаненты награваюцца на мяжы з дапамогай кіслародна-ацэтыленавай газавай гарэлкі, і як толькі мяжа пачынае плавіцца, гарэлка выцягваецца і прыкладваецца восевая сіла, каб сціснуць дзве часткі разам пакуль інтэрфейс не зацвярдзее.
ДУГАВАЯ ЗВАРКА: мы выкарыстоўваем электрычную энергію для стварэння дугі паміж наканечнікам электрода і часткамі, якія зварваюцца. Крыніца харчавання можа быць пераменным або пастаянным токам, а электроды - расходнымі або нерасходнымі. Цеплаабмен пры дуговой зварцы можна выказаць наступным раўнаннем:
H / l = ex VI / v
Тут H - цеплаўкладанне, l - даўжыня зварнога шва, V і I - прыкладзеныя напружанне і ток, v - хуткасць зваркі і e - эфектыўнасць працэсу. Чым вышэй каэфіцыент эфектыўнасці "e", тым больш выгадна выкарыстоўваецца даступная энергія для плаўлення матэрыялу. Увод цяпла таксама можа быць выражаны як:
H = ux (аб'ём) = ux A xl
Тут u - удзельная энергія плаўлення, A - папярочны перасек шва, l - даўжыня шва. З двух ураўненняў вышэй мы можам атрымаць:
v = ex VI / u A
Разнавіднасцю дугавой зваркі з'яўляецца дугавая зварка ў экраніраваным метале (SMAW), якая складае каля 50% усіх прамысловых і тэхнічных зварачных працэсаў. ЭЛЕКТРАДУГАВАЯ ЗВАРКА (ЗВАРКА РУКАМ) выконваецца шляхам дакранання кончыкам электрода з пакрыццём да нарыхтоўкі і хуткага адвядзення яго на адлегласць, дастатковую для падтрымання дугі. Мы называем гэты працэс таксама зваркай, таму што электроды ўяўляюць сабой тонкія і доўгія палачкі. У працэсе зваркі наканечнік электрода плавіцца разам з пакрыццём і асноўным металам паблізу дугі. Сумесь асноўнага металу, металу электрода і рэчываў з пакрыцця электрода застывае ў зоне зваркі. Пакрыццё электрода раскісляе і забяспечвае ахоўны газ у вобласці шва, такім чынам абараняючы яго ад кіслароду ў навакольным асяроддзі. Таму працэс называюць дуговой зваркай у абароненым метале. Мы выкарыстоўваем ток ад 50 да 300 ампер і ўзровень магутнасці, як правіла, менш за 10 кВт для аптымальнай працы зваркі. Таксама важная палярнасць пастаяннага току (кірунак праходжання току). Прамая палярнасць, калі нарыхтоўка з'яўляецца станоўчай, а электрод - адмоўнай, з'яўляецца пераважнай пры зварцы ліставых металаў з-за яе невялікага правару, а таксама для злучэнняў з вельмі шырокімі зазорамі. Калі ў нас зваротная палярнасць, г.зн. электрод дадатны, а дэталь адмоўны, мы можам дамагчыся больш глыбокага праварвання шва. З дапамогай пераменнага току, паколькі мы маем пульсавалую дугу, мы можам зварваць тоўстыя секцыі, выкарыстоўваючы электроды вялікага дыяметра і максімальныя токі. Метад зваркі SMAW падыходзіць для нарыхтовак таўшчынёй ад 3 да 19 мм і нават больш з выкарыстаннем шматпраходных метадаў. Дзындра, якая ўтварылася на зварным шве, неабходна выдаліць з дапамогай драцяной шчоткі, каб у зоне зварнога шва не было карозіі і разрываў. Гэта, вядома, павялічвае кошт дуговой зваркі ў абароненым метале. Тым не менш SMAW з'яўляецца самым папулярным метадам зваркі ў прамысловасці і пры рамонце.
ЗВАРКА ПАД ФЛЮСАМ (ПІЛА): У гэтым працэсе мы абараняем зварную дугу з дапамогай грануляваных флюсавых матэрыялаў, такіх як вапна, дыяксід крэмнія, фларыд кальцыя, аксід марганца….і г.д. Грануляваны флюс падаецца ў зону зваркі самацёкам праз сопла. Флюс, які пакрывае расплаўленую зону зварнога шва, значна абараняе ад іскраў, дыму, ультрафіялетавага выпраменьвання і г.д. і дзейнічае як цеплаізалятар, дазваляючы цяплу пранікаць глыбока ў нарыхтоўку. Нерасплаўлены флюс аднаўляецца, апрацоўваецца і выкарыстоўваецца паўторна. Шпулька аголенага матэрыялу выкарыстоўваецца ў якасці электрода і падаецца праз трубку ў вобласць зварнога шва. Мы выкарыстоўваем ток ад 300 да 2000 ампер. Працэс зваркі пад флюсам (SAW) абмежаваны гарызантальным і плоскім становішчам і кругавымі зварнымі швамі, калі падчас зваркі магчыма паварот круглай канструкцыі (напрыклад, труб). Хуткасць можа дасягаць 5 м/мін. Працэс SAW падыходзіць для тоўстых пласцін і прыводзіць да атрымання высакаякасных, трывалых, пластычных і аднастайных зварных швоў. Прадукцыйнасць, гэта значыць колькасць зварнога матэрыялу, які наносіцца за гадзіну, у 4-10 разоў перавышае колькасць у параўнанні з працэсам SMAW.
Іншы працэс дуговой зваркі, а менавіта ГАЗОВАДУГАВАЯ ЗВАРКА МЕТАЛІЧНЫМ ГАЗАМ (GMAW) або альтэрнатыўна названая ЗВАРКА МЕТАЛІЧНЫМ ГАЗАМ (MIG), заснавана на тым, што вобласць зварнога шва абараняецца знешнімі крыніцамі газаў, такімі як гелій, аргон, вуглякіслы газ... і г.д. У метале электрода могуць быць дадатковыя раскісліцелі. Расплавляемая дрот падаецца праз сопла ў зону зваркі. Выраб з выкарыстаннем чорных, а таксама каляровых металаў ажыццяўляецца пры дапамозе газавай дугавой зваркі (GMAW). Прадукцыйнасць зваркі прыкладна ў 2 разы перавышае прадукцыйнасць працэсу SMAW. Выкарыстоўваецца аўтаматызаванае зварачнае абсталяванне. У гэтым працэсе метал пераносіцца адным з трох спосабаў: «Перанос распыленнем» прадугледжвае перанос некалькіх сотняў маленькіх кропель металу ў секунду ад электрода да зоны зваркі. З іншага боку, у «Глабулярным пераносе» выкарыстоўваюцца багатыя вуглякіслым газам газы, а шарыкі расплаўленага металу рухаюцца з дапамогай электрычнай дугі. Зварачныя токі высокія, пранікненне шва больш глыбокае, хуткасць зваркі большая, чым пры перадачы распыленнем. Такім чынам, шаравая перадача лепш падыходзіць для зваркі больш цяжкіх секцый. Нарэшце, пры метадзе «кароткага замыкання» наканечнік электрода датыкаецца з расплаўленай зварачнай ваннай, у выніку чаго метал з хуткасцю больш за 50 кропель у секунду пераносіцца асобнымі кроплямі. Разам з больш тонкім дротам выкарыстоўваюцца малыя токі і напружання. Выкарыстоўваная магутнасць каля 2 кВт і адносна нізкія тэмпературы, што робіць гэты метад прыдатным для тонкіх лістоў таўшчынёй менш за 6 мм.
Іншая разнавіднасць працэсу дугавой зваркі з парашком (FCAW) падобная на дугавую зварку газам, за выключэннем таго, што электрод - гэта трубка, напоўненая флюсам. Перавагі выкарыстання флюсовых электродаў з стрыжнем у тым, што яны ствараюць больш стабільную дугу, даюць магчымасць палепшыць ўласцівасці наплавляемых металаў, менш далікатны і гнуткі характар яго флюсу ў параўнанні са зваркай SMAW, палепшаныя контуры зваркі. Самаабароненыя электроды з стрыжнем утрымліваюць матэрыялы, якія абараняюць зону зваркі ад атмасферы. Мы выкарыстоўваем каля 20 кВт магутнасці. Як і працэс GMAW, працэс FCAW таксама дае магчымасць аўтаматызаваць працэсы бесперапыннай зваркі, і гэта эканамічна. Шляхам дадання розных сплаваў у стрыжань флюсу можна распрацаваць розныя хімічныя склады металу зварнога шва.
Пры электрагазавай зварцы (EGW) мы зварваем дэталі, размешчаныя край да краю. Яе часам яшчэ называюць Стыкавая зварка. Зварны метал змяшчаецца ў паражніну зварнога шва паміж дзвюма часткамі, якія трэба злучыць. Прастора агароджана дзвюма плацінамі з вадзяным астуджэннем, каб расплаўлены дзындра не выліваўся. Плаціны перамяшчаюцца ўверх механічнымі прывадамі. Калі нарыхтоўку можна круціць, мы можам выкарыстоўваць тэхніку электрагазавай зваркі і для кругавой зваркі труб. Электроды падаюцца праз трубаправод для падтрымання бесперапыннай дугі. Ток можа складаць каля 400 ампер або 750 ампер, а ўзровень магутнасці - каля 20 кВт. Інэртныя газы, якія паступаюць з парашковых электродаў або знешняй крыніцы, забяспечваюць экранаванне. Мы выкарыстоўваем электрагазавую зварку (EGW) для такіх металаў, як сталь, тытан… і г.д., таўшчынёй ад 12 мм да 75 мм. Тэхніка добра падыходзіць для вялікіх збудаванняў.
Тым не менш, у іншай тэхніцы, якая называецца ЭЛЕКТРАШЛАКОВАЯ ЗВАРКА (ESW), дуга запальваецца паміж электродам і дном нарыхтоўкі і дадаецца флюс. Калі расплаўлены дзындра даходзіць да кончыка электрода, дуга гасне. Энергія бесперапынна паступае праз электрычнае супраціўленне расплаўленага дзындры. Мы можам зварваць пліты таўшчынёй ад 50 мм да 900 мм і нават вышэй. Ток складае каля 600 ампер, а напружанне - ад 40 да 50 В. Хуткасць зваркі складае ад 12 да 36 мм/мін. Прымяненне аналагічна электрогазозварке.
Адзін з нашых працэсаў неплаўных электродаў, ГАЗАВАЛЬФРАМОВАЯ ДУГАВАЯ ЗВАРКА (GTAW), таксама вядомая як ЗВАРКА Ў ІНЭРТНЫМ ГАЗЕ ВАЛЬФРАМУ (TIG), прадугледжвае падачу прысадачнага металу з дапамогай дроту. Для шчыльных злучэнняў часам мы не выкарыстоўваем прысадкавы метал. У працэсе TIG мы не выкарыстоўваем флюс, але выкарыстоўваем аргон і гелій для экранавання. Вальфрам мае высокую тэмпературу плаўлення і не расходуецца ў працэсе зваркі TIG, таму можна падтрымліваць пастаянны ток, а таксама зазоры дугі. Узроўні магутнасці ад 8 да 20 кВт і ток 200 ампер (пастаяннага току) або 500 ампер (пераменнага току). Для алюмінія і магнію мы выкарыстоўваем пераменны ток для ачысткі аксідаў. Каб пазбегнуць забруджвання вальфрамавага электрода, мы пазбягаем яго кантакту з расплаўленымі металамі. Газавая дугавая зварка вальфрамам (GTAW) асабліва карысная для зваркі тонкіх металаў. Зварныя швы GTAW вельмі высокай якасці з добрай аздабленнем паверхні.
З-за больш высокага кошту газападобнага вадароду радзей выкарыстоўваецца метад зваркі ў атамным вадародзе (AHW), дзе мы генеруем дугу паміж двума вальфрамавымі электродамі ў ахоўнай атмасферы патоку вадароду. AHW таксама з'яўляецца працэсам зваркі неплавучым электродам. Двухатамны вадарод H2 распадаецца на атамную форму каля зварачнай дугі, дзе тэмпература перавышае 6273 кельвіна. Разбураючыся, ён паглынае вялікую колькасць цяпла ад дугі. Калі атамы вадароду трапляюць у зону зваркі, якая з'яўляецца адносна халоднай паверхняй, яны рэкамбінуюцца ў двухатамную форму і вылучаюць назапашанае цяпло. Энергію можна змяняць шляхам змены нарыхтоўкі на адлегласць дугі.
У іншым працэсе неплавучага электрода, ПЛАЗМЕННА-ДУГАВАЙ ЗВАРКІ (ПАВ), мы маем канцэнтраваную плазменную дугу, накіраваную да зоны зваркі. Тэмпература дасягае 33 273 Кельвінаў у PAW. Амаль роўная колькасць электронаў і іёнаў складае плазменны газ. Слабаточная пілотная дуга ініцыюе плазму, якая знаходзіцца паміж вальфрамавым электродам і адтулінай. Працоўны ток звычайна складае каля 100 ампер. Можна падаць прысадкавы метал. У плазменна-дугавой зварцы экранаванне ажыццяўляецца з дапамогай вонкавага экрануючага кольца і з выкарыстаннем такіх газаў, як аргон і гелій. Пры плазменна-дугавой зварцы дуга можа быць паміж электродам і нарыхтоўкай або паміж электродам і соплам. Гэты метад зваркі мае перавагі перад іншымі метадамі больш высокай канцэнтрацыі энергіі, больш глыбокай і вузкай магчымасці зваркі, лепшай стабільнасці дугі, больш высокай хуткасці зваркі да 1 метра/мін, меншага цеплавога скажэння. Як правіла, мы выкарыстоўваем плазменна-дугавую зварку для таўшчыні менш за 6 мм, а часам да 20 мм для алюмінія і тытана.
ЗВАРКА ВЫСОКАЙ ЭНЕРГІІ ПАМЯННЯМ: іншы тып метаду зваркі плаўленнем з электронна-прамянёвай зваркай (EBW) і лазернай зваркай (LBW) як два варыянты. Гэтыя метады ўяўляюць асаблівую каштоўнасць для нашай працы па вытворчасці высокатэхналагічнай прадукцыі. Пры электронна-прамянёвай зварцы высакахуткасныя электроны трапляюць на дэталь, і іх кінэтычная энергія ператвараецца ў цяпло. Вузкі пучок электронаў лёгка перамяшчаецца ў вакуумнай камеры. Як правіла, мы выкарыстоўваем высокі вакуум для зваркі электронным прамянём. Можна зварваць пліты таўшчынёй да 150 мм. Не патрэбныя ахоўныя газы, флюс або напаўняльнік. Электронна-прамянёвыя гарматы маюць магутнасць 100 кВт. Магчымыя глыбокія і вузкія зварныя швы з высокім каэфіцыентам бакоў да 30 і невялікімі зонамі тэрмічнага ўздзеяння. Хуткасць зваркі можа дасягаць 12 м/мін. Пры лазерна-прамянёвай зварцы ў якасці крыніцы цяпла выкарыстоўваюцца лазеры высокай магутнасці. Лазерныя прамяні памерам да 10 мікрон з высокай шчыльнасцю дазваляюць глыбока пранікаць у нарыхтоўку. Суадносіны глыбіні і шырыні дасягаюць 10 пры зварцы лазерным прамянём. Мы выкарыстоўваем як імпульсныя, так і бесперапынныя лазеры, прычым першыя прымяняюцца для тонкіх матэрыялаў, а другія ў асноўным для тоўстых нарыхтовак прыкладна да 25 мм. Ўзроўні магутнасці да 100 кВт. Зварка лазерным прамянём дрэнна падыходзіць для матэрыялаў, якія аптычна моцна адлюстроўваюць святло. У працэсе зваркі таксама могуць выкарыстоўвацца газы. Метад зваркі лазерным прамянём добра падыходзіць для аўтаматызацыі і вытворчасці вялікіх аб'ёмаў і можа забяспечваць хуткасць зваркі ад 2,5 м/мін да 80 м/мін. Адной з асноўных пераваг гэтай тэхнікі зваркі з'яўляецца доступ да месцаў, дзе нельга выкарыстоўваць іншыя метады. Лазерныя прамяні могуць лёгка перамяшчацца ў такія складаныя рэгіёны. Не патрабуецца вакууму, як пры электронна-прамянёвай зварцы. Зварныя швы добрай якасці і трываласці, нізкай усаджвання, нізкай скажэнні, нізкай сітаватасці можна атрымаць пры зварцы лазерным прамянём. Лазернымі прамянямі можна лёгка маніпуляваць і фармаваць іх з дапамогай валаконна-аптычных кабеляў. Тэхніка, такім чынам, добра падыходзіць для зваркі дакладных герметычных вузлоў, электронных пакетаў ... і г.д.
Давайце паглядзім на нашы метады зваркі цвёрдага цела. ХАЛОДНАЯ ЗВАРКА (CW) - гэта працэс, пры якім ціск замест цяпла ўжываецца з дапамогай штампаў або валкоў да злучаных частак. Пры халоднай зварцы хаця б адна з спалучаных частак павінна быць пластычнай. Найлепшыя вынікі дасягаюцца з двума падобнымі матэрыяламі. Калі два металу, якія трэба злучыць халоднай зваркай, неаднолькавыя, мы можам атрымаць слабыя і далікатныя злучэнні. Метад халоднай зваркі добра падыходзіць для мяккіх, пластычных і невялікіх нарыхтовак, такіх як электрычныя злучэнні, цеплаадчувальныя краю кантэйнераў, біметалічныя палоскі для тэрмастатаў і г.д. Адной з разнавіднасцяў халоднай зваркі з'яўляецца рулонная зварка (або рулонная зварка), дзе ціск аказваецца праз пару валкоў. Часам мы выконваем рулонную зварку пры павышаных тэмпературах для лепшай трываласці на паверхні паверхні.
Іншым працэсам зваркі цвёрдага цела, які мы выкарыстоўваем, з'яўляецца УЛЬТРАЗВУКОВАЯ ЗВАРКА (УСЗ), дзе нарыхтоўкі падвяргаюцца статычнай нармальнай сіле і вагальным напружанням зруху. Вагальныя напружання зруху прымяняюцца праз кончык пераўтваральніка. Ультрагукавая зварка разгортвае ваганні з частатой ад 10 да 75 кГц. У некаторых выпадках, такіх як зварка швоў, у якасці наканечніка выкарыстоўваецца верціцца зварачны дыск. Напружання зруху, прыкладзеныя да нарыхтовак, выклікаюць невялікія пластычныя дэфармацыі, разбураюць аксідныя пласты, забруджванні і прыводзяць да цвёрдацельнага злучэння. Тэмпература ультрагукавой зваркі значна ніжэйшая за тэмпературу плаўлення металаў, і плаўленне не адбываецца. Мы часта выкарыстоўваем працэс ультрагукавой зваркі (УСЗ) для неметалічных матэрыялаў, такіх як пластмасы. Аднак у тэрмапластах тэмпература дасягае тэмпературы плаўлення.
Іншая папулярная тэхніка, пры зварцы трэннем (FRW), цяпло выпрацоўваецца праз трэнне на стыку нарыхтовак, якія злучаюцца. Пры зварцы трэннем мы трымаем адну з нарыхтовак нерухомай, а іншую нарыхтоўку ўтрымліваем у прыстасаванні і круцім з пастаяннай хуткасцю. Затым нарыхтоўкі прыводзяцца ў кантакт пад дзеяннем восевай сілы. Хуткасць кручэння паверхні пры зварцы трэннем у некаторых выпадках можа дасягаць 900 м/мін. Пасля дастатковага паверхневага кантакту верціцца дэталь раптоўна спыняецца і восевая сіла павялічваецца. Зона зварнога шва - гэта звычайна вузкая вобласць. Тэхніка зваркі трэннем можа выкарыстоўвацца для злучэння суцэльных і трубчастых дэталяў з розных матэрыялаў. Некаторая ўспышка можа ўзнікнуць на стыку падзелу ў FRW, але гэтую ўспышку можна выдаліць шляхам другаснай апрацоўкі або шліфоўкі. Існуюць разнавіднасці працэсу зваркі трэннем. Напрыклад, "зварка трэннем па інэрцыі" ўключае махавік, кінетычная энергія кручэння якога выкарыстоўваецца для зваркі дэталяў. Зварка завершана, калі махавік спыняецца. Масу, якая верціцца, можна змяняць і, такім чынам, кінетычную энергію кручэння. Іншая разнавіднасць - гэта "лінейная фрыкцыйная зварка", дзе лінейны зваротна-паступальны рух накладваецца як мінімум на адзін з кампанентаў, якія злучаюцца. Пры лінейнай зварцы трэннем дэталі неабавязкова павінны быць круглымі, яны могуць мець прастакутную, квадратную або іншую форму. Частата можа быць у дзесятках Гц, амплітуда ў міліметровым дыяпазоне і ціск у дзесятках ці сотнях МПа. Нарэшце, "зварка трэннем з перамешваннем" некалькі адрозніваецца ад двух іншых, апісаных вышэй. У той час як пры зварцы трэннем па інэрцыі і лінейнай зварцы трэннем нагрэў межаў дасягаецца за кошт трэння дзвюх кантактуючых паверхняў, у метадзе зваркі трэннем з перамешваннем трэцяе цела трэцца аб дзве паверхні, якія злучаюцца. Які верціцца інструмент дыяметрам ад 5 да 6 мм ўводзяць у кантакт з суставам. Тэмпература можа павялічвацца да значэнняў ад 503 да 533 Кельвінаў. У шве адбываецца нагрэў, змешванне і перамешванне матэрыялу. Мы выкарыстоўваем зварку трэннем з перамешваннем для розных матэрыялаў, уключаючы алюміній, пластмасы і кампазіты. Зварныя швы аднастайныя і высокай якасці з мінімальнымі порамі. Пры зварцы трэннем з перамешваннем не ўтворыцца дым або пырскі, а працэс добра аўтаматызаваны.
ЗВАРКА СУПРАЦІЎЛЕННЕМ (RW): Цепла, неабходнае для зваркі, выпрацоўваецца электрычным супраціўленнем паміж дзвюма нарыхтоўкамі, якія злучаюцца. У кантактнай зварцы не выкарыстоўваюцца флюс, ахоўныя газы або расходныя электроды. Джоулевый нагрэў адбываецца пры зварцы супрацівам і можа быць выражаны як:
H = (Квадрат I) x R xtx K
H - гэта выдзяленне цяпла ў джоўлях (ват-секундах), I ток у амперах, R супраціўленне ў Омах, t - час у секундах, праз які цячэ ток. Каэфіцыент K меншы за 1 і ўяўляе долю энергіі, якая не губляецца ў выніку выпраменьвання і праводнасці. Ток у працэсах кантактнай зваркі можа дасягаць узроўняў да 100 000 А, але напружанне звычайна складае ад 0,5 да 10 Вольт. Электроды звычайна вырабляюцца з медных сплаваў. З дапамогай кантактнай зваркі можна злучаць як аднатыпныя, так і розныя матэрыялы. Для гэтага працэсу існуе некалькі варыянтаў: «Кропкавая зварка супрацівам» прадугледжвае кантакт двух супрацьлеглых круглых электродаў з паверхнямі злучэння двух лістоў унахлест. Ціск прыкладваецца да адключэння току. Зварны кавалак звычайна мае дыяметр да 10 мм. Супрацівная кропкавая зварка пакідае злёгку абескаляроўваюцца паглыбленні ў месцах зваркі. Кропкавая зварка - наша самая папулярная методыка супраціўляльнай зваркі. Розныя формы электродаў выкарыстоўваюцца ў кропкавай зварцы, каб дасягнуць складаных участкаў. Наша абсталяванне для кропкавай зваркі кіруецца ЧПУ і мае некалькі электродаў, якія можна выкарыстоўваць адначасова. Іншая разнавіднасць «зваркі швом супрацівам» выконваецца колавымі або ролікавымі электродамі, якія вырабляюць бесперапынную кропкавую зварку кожны раз, калі ток дасягае дастаткова высокага ўзроўню ў цыкле харчавання пераменнага току. Злучэнні, атрыманыя метадам супрацівнай зваркі, непранікальныя для вадкасці і газу. Хуткасць зваркі каля 1,5 м/мін з'яўляецца нармальнай для тонкіх лістоў. Можна ўжываць перарывісты ток, каб кропкавыя зварныя швы атрымліваліся праз жаданыя інтэрвалы ўздоўж шва. У «супраціўнай праекцыйнай зварцы» мы ціснем адзін або некалькі выступаў (ямачак) на адной з паверхняў нарыхтоўкі, якія зварваюцца. Гэтыя выступы могуць быць круглымі або авальнымі. Высокія лакалізаваныя тэмпературы дасягаюцца ў гэтых рэльефных плямах, якія ўступаюць у кантакт з спалучанай часткай. Электроды аказваюць ціск, каб сціснуць гэтыя выступы. Электроды пры супрацівнай зварцы маюць плоскія наканечнікі і ўяўляюць сабой медныя сплавы з вадзяным астуджэннем. Перавагай кантактнай зваркі з праекцыяй з'яўляецца наша здольнасць выконваць некалькі зварных швоў за адзін ход, што дазваляе падоўжыць тэрмін службы электрода, магчымасць зварваць лісты рознай таўшчыні, прыварваць гайкі і балты да лістоў. Недахопам кантактнай зваркі з'яўляюцца дадатковыя выдаткі на цісненне паглыбленняў. Яшчэ адна тэхніка, пры «зварцы імгненным» цяпло выпрацоўваецца ад дугі на канцах дзвюх нарыхтовак, калі яны пачынаюць кантактаваць. У якасці альтэрнатывы гэты метад можа разглядацца як дугавая зварка. Тэмпература на мяжы падзелу расце, і матэрыял размягчается. Прымяняецца восевая сіла, і ў размякчанай вобласці ўтвараецца зварной шво. Пасля завяршэння хуткай зваркі злучэнне можна апрацаваць для паляпшэння знешняга выгляду. Якасць зварнога шва, атрыманага пры зварцы вогнепластам, добрая. Ўзроўні магутнасці ад 10 да 1500 кВт. Тэхнічная зварка падыходзіць для злучэння ад краю да краю аднолькавых або розных металаў дыяметрам да 75 мм і лістоў таўшчынёй ад 0,2 мм да 25 мм. «Дугавая зварка шпілек» вельмі падобная на зварку агнём. Шпілька, такая як ніт або стрыжань з разьбой, служыць адным электродам пры злучэнні з нарыхтоўкай, напрыклад пласцінай. Для канцэнтрацыі вылучаемага цяпла, прадухілення акіслення і ўтрымання расплаўленага металу ў зоне зварнога шва вакол злучэння накладваецца аднаразовае керамічнае кольца. І, нарэшце, «ударная зварка» - іншы працэс зваркі супрацівам, у якім для падачы электрычнай энергіі выкарыстоўваецца кандэнсатар. Пры ўдарнай зварцы магутнасць разряжается на працягу мілісекунд вельмі хутка, у выніку чаго ў месцы злучэння ўзнікае моцнае лакалізаванае цяпло. Мы шырока выкарыстоўваем ударную зварку ў прамысловасці вытворчасці электронікі, дзе трэба пазбягаць нагрэву адчувальных электронных кампанентаў паблізу злучэння.
Тэхніка, якая называецца ЗВАРКА ВЫБУХАМ, прадугледжвае дэтанацыю пласта выбуховага рэчыва, які наносіцца на адну з дэталяў, якія злучаюцца. Вельмі высокі ціск, які аказваецца на нарыхтоўку, стварае турбулентную і хвалістую мяжу паверхні і адбываецца механічнае ўзаемазамыканне. Трываласць злучэння пры зварцы выбухам вельмі высокая. Зварка выбухам з'яўляецца добрым метадам плакіроўкі пласцін разнастайнымі металамі. Пасля ашалёўкі пліты можна раскачаць у больш тонкія профілі. Часам мы выкарыстоўваем зварку выбухам для пашырэння труб, каб яны шчыльна прылягалі да пласціны.
Наш апошні метад у галіне цвёрдацельнага злучэння - гэта ДЫФУЗІЙНАЯ ЗВАРКА або ДЫФУЗІЙНАЯ ЗВАРКА (DFW), у якой добрае злучэнне дасягаецца ў асноўным за кошт дыфузіі атамаў праз межы падзелу. Некаторая пластычная дэфармацыя на мяжы падзелу таксама спрыяе зварцы. Удзельныя тэмпературы складаюць каля 0,5 Tm, дзе Tm - гэта тэмпература плаўлення металу. Трываласць злучэння пры дыфузійнай зварцы залежыць ад ціску, тэмпературы, часу кантакту і чысціні кантактных паверхняў. Часам мы выкарыстоўваем прысадныя металы на мяжы падзелу. Цяпло і ціск патрабуюцца для дыфузійнага злучэння і забяспечваюцца электрычным супраціўленнем або печчу і грузамі, прэсам ці іншым чынам. З дапамогай дыфузійнай зваркі можна злучаць аднатыпныя і разнастайныя металы. Працэс адносна павольны з-за часу, які патрабуецца для міграцыі атамаў. DFW можа быць аўтаматызаваны і шырока выкарыстоўваецца ў вытворчасці складаных дэталяў для аэракасмічнай, электронікі, медыцынскай прамысловасці. Прадукцыя, якая вырабляецца, уключае артапедычныя імплантаты, датчыкі, элементы аэракасмічнай канструкцыі. Дыфузійнае склейванне можа спалучацца з СУПЕРПЛАСТЫЧНЫМ ФАРМАВАННЕМ для вырабу складаных канструкцый з ліставога металу. Выбраныя месцы на лістах спачатку змацоўваюцца дыфузіяй, а затым несвязанныя вобласці пашыраюцца ў форму з дапамогай ціску паветра. З дапамогай гэтай камбінацыі метадаў вырабляюцца аэракасмічныя канструкцыі з высокім стаўленнем калянасці да вагі. Камбінаваны працэс дыфузійнай зваркі і звышпластычнага фармавання памяншае колькасць неабходных дэталяў за кошт пазбаўляючы ад патрэбы ў крапежных элементах, у выніку чаго дэталі з нізкім узроўнем напружання і высокай дакладнасцю вырабляюцца эканамічна і з кароткім часам выканання.
ПАЙКА: Метады паяння і паяння ўключаюць больш нізкія тэмпературы, чым тыя, якія неабходныя для зваркі. Аднак тэмпература паяння вышэй, чым тэмпература паяння. Пры пайцы прысадкавы метал змяшчаецца паміж паверхнямі, якія злучаюцца, і тэмпература падымаецца да тэмпературы плаўлення прысадкавага матэрыялу вышэй за 723 кельвіна, але ніжэй тэмпературы плаўлення нарыхтовак. Расплаўлены метал запаўняе шчыльна прылеглую прастору паміж дэталямі. Астуджэнне і наступнае зацвярдзенне напойнага металу прыводзіць да моцных злучэнняў. Пры зварцы прыпоем прысадкавы метал наносіцца на злучэнне. Пры зварцы прыпоем выкарыстоўваецца значна больш прысадачнага металу ў параўнанні з прыпоем. Ацэтыленавая гарэлка з акісляльным полымем выкарыстоўваецца для нанясення прысадачнага металу пры зварцы прыпоем. Дзякуючы больш нізкім тэмпературам пры пайцы, праблемы ў зонах цеплавога ўздзеяння, такія як дэфармацыя і рэшткавыя напружання, менш. Чым меншы зазор пры пайцы, тым вышэй трываласць злучэння на зрух. Аднак максімальная трываласць на разрыў дасягаецца пры аптымальным зазоры (пікавае значэнне). Ніжэй і вышэй гэтага аптымальнага значэння трываласць на разрыў пры пайцы зніжаецца. Тыповыя зазоры пры пайцы могуць складаць ад 0,025 да 0,2 мм. Мы выкарыстоўваем разнастайныя матэрыялы для паяння рознай формы, такія як перфомы, парашок, кольцы, дрот, паласы…..і г.д. і можа вырабіць гэтыя выканання спецыяльна для вашага дызайну або геаметрыі прадукту. Мы таксама вызначаем утрыманне прыпойных матэрыялаў у залежнасці ад вашых асноўных матэрыялаў і прымянення. Мы часта выкарыстоўваем флюсы пры пайцы, каб выдаліць непажаданыя аксідныя слаі і прадухіліць акісленне. Каб пазбегнуць наступнай карозіі, флюсы звычайна выдаляюцца пасля аперацыі злучэння. AGS-TECH Inc. выкарыстоўвае розныя метады пайкі, у тым ліку:
- Пайка факелам
- Пячная пайка
- Індукцыйная пайка
- Супраціўная пайка
- Пайка акунаннем
- Інфрачырвоная пайка
- Дыфузійная пайка
- Прамень высокай энергіі
Нашы найбольш распаўсюджаныя прыклады паяных злучэнняў зроблены з разнародных металаў з добрай трываласцю, такіх як цвёрдасплаўныя свердзелы, устаўкі, оптаэлектронныя герметычныя пакеты, ушчыльняльнікі.
ПАЯННЕ: Гэта адзін з найбольш часта выкарыстоўваных метадаў, калі прыпой (прысадны метал) запаўняе злучэнне, як пры пайцы паміж шчыльна прылеглымі кампанентамі. Нашы прыпоі маюць тэмпературу плаўлення ніжэй за 723 кельвіна. Мы выкарыстоўваем ручную і аўтаматызаваную пайку ў вытворчых аперацыях. У параўнанні з пайкай тэмпература паяння ніжэй. Пайка не вельмі падыходзіць для прымянення пры высокай тэмпературы або высокай трываласці. Для паяння мы выкарыстоўваем бессвінцовыя прыпоі, а таксама алавяна-свінцовыя, алавяна-цынкавыя, свінцова-сярэбраныя, кадміева-сярэбраныя, цынкава-алюмініевыя сплавы і інш. У якасці флюсу пры пайцы выкарыстоўваюцца як неагрэсіўныя смалы, так і неарганічныя кіслоты і солі. Мы выкарыстоўваем спецыяльныя флюсы для паяння металаў з нізкай паяльнасць. У прыкладаннях, дзе мы павінны паяць керамічныя матэрыялы, шкло або графіт, мы спачатку пакрываем дэталі адпаведным металам для павышэння здольнасці да паяння. Нашы папулярныя метады паяння:
-Аплаўленне або пайка
-Хвалевая пайка
-Печная пайка
-Паяльная гарэлка
- Індукцыйная пайка
-Пайка жалеза
-Супраціў паяння
- Пайка апусканнем
-Ультрагукавая пайка
-Інфрачырвоная пайка
Ультрагукавая пайка дае нам унікальную перавагу, дзякуючы якой патрэба ў флюсах адпадае дзякуючы эфекту ультрагукавой кавітацыі, які выдаляе аксідныя плёнкі з злучаемых паверхняў. Пайка аплаўкай і хвалевай пайкай - гэта нашы выбітныя ў прамысловым плане метады для вытворчасці вялікіх аб'ёмаў электронікі, і таму іх варта растлумачыць больш падрабязна. Пры пайцы аплавленнем мы выкарыстоўваем паўцвёрдыя пасты, якія ўключаюць часціцы металічнага прыпоя. Паста наносіцца на стык з дапамогай прасейвання або трафарэта. У друкаваных поплатках (PCB) мы часта выкарыстоўваем гэтую тэхніку. Калі электрычныя кампаненты змяшчаюцца на гэтыя накладкі з пасты, павярхоўнае нацяжэнне падтрымлівае пакеты для павярхоўнага мантажу на адной лініі. Пасля размяшчэння кампанентаў мы награваем зборку ў печы, каб адбылася пайка аплавленнем. Падчас гэтага працэсу растваральнікі ў пасце выпараюцца, флюс у пасце актывуецца, кампаненты папярэдне награваюцца, часціцы прыпоя плавяцца і змочваюць злучэнне, і, нарэшце, зборка друкаванай платы павольна астуджаецца. Наша другая папулярная тэхніка для вытворчасці вялікіх аб'ёмаў друкаваных поплаткаў, а менавіта пайка хваляй, абапіраецца на тое, што расплаўленыя прыпоі змочваюць металічныя паверхні і ўтвараюць добрыя сувязі толькі тады, калі метал папярэдне нагрэты. Стаячая ламінарная хваля расплаўленага прыпою спачатку генеруецца помпай, а папярэдне нагрэтыя і нагрэтыя друкаваныя платы перамяшчаюцца па хвалі. Прыпой змочвае толькі адкрытыя металічныя паверхні, але не змочвае палімерныя пакеты мікрасхем і друкаваныя платы з палімерным пакрыццём. Высокая хуткасць бруі гарачай вады выдзімае лішкі прыпоя з злучэння і прадухіляе перамыканне паміж суседнімі провадамі. Пры хвалевай пайцы пакетаў для павярхоўнага мантажу мы спачатку прымацоўваем іх да друкаванай платы перад пайкай. Зноў выкарыстоўваецца скрынінг і трафарэт, але на гэты раз для эпаксіднай смалы. Пасля размяшчэння кампанентаў у правільным месцы эпаксідная смала зацвярдзее, дошкі пераварочваюцца і адбываецца пайка хваляй.