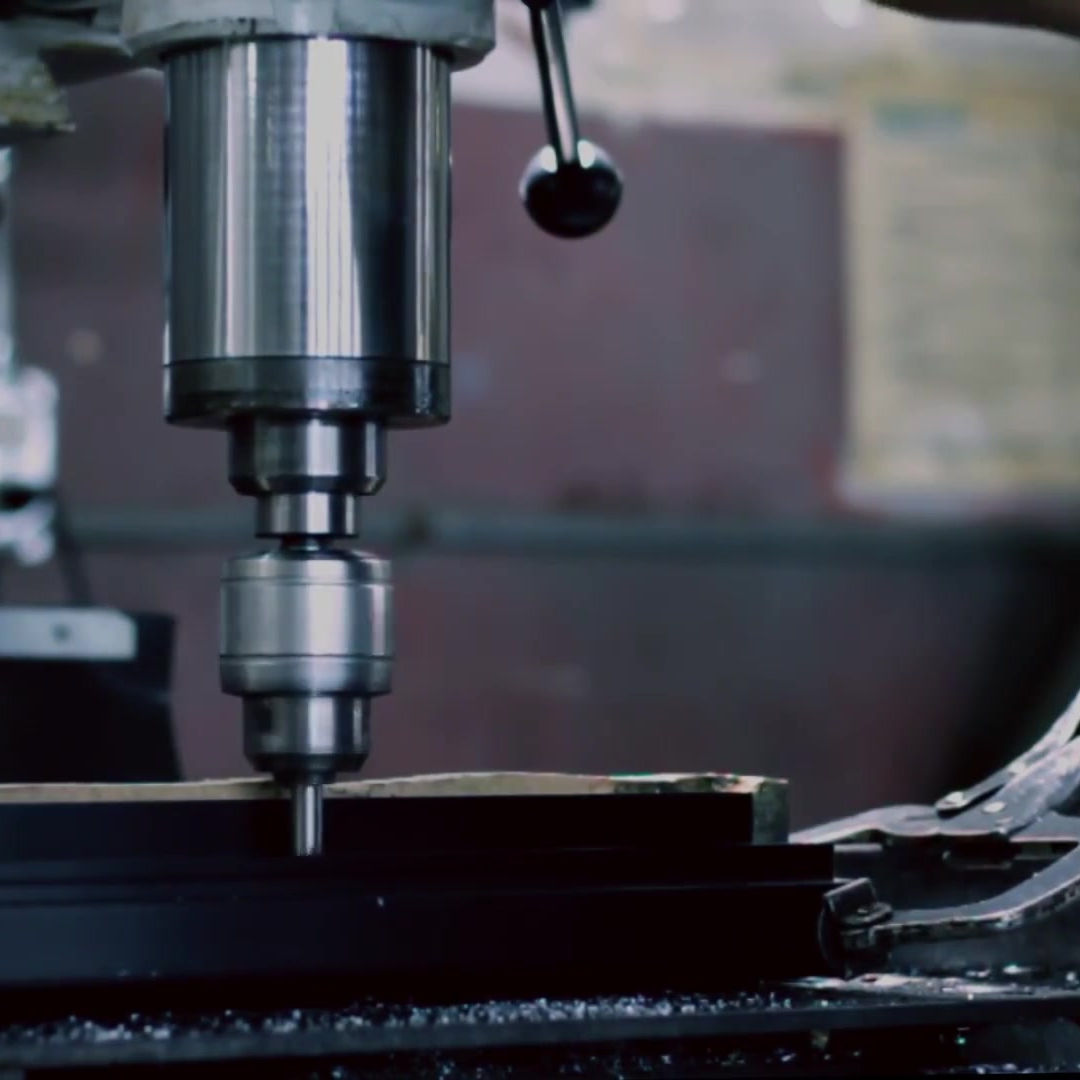
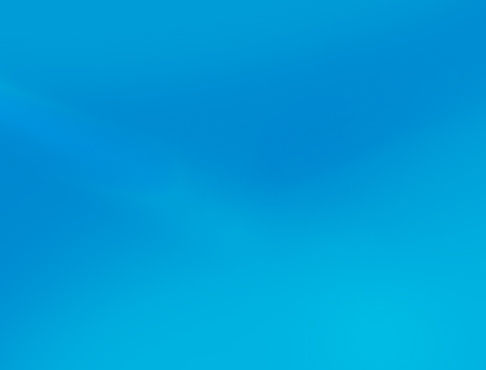
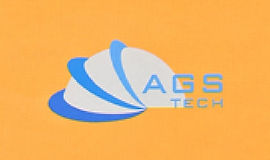
Глобален производител по поръчка, интегратор, консолидатор, аутсорсинг партньор за голямо разнообразие от продукти и услуги.
Ние сме вашият източник на едно гише за производство, производство, инженеринг, консолидация, интеграция, аутсорсинг на произведени по поръчка и готови продукти и услуги.
Изберете своя език
-
Производство по поръчка
-
Вътрешно и глобално договорно производство
-
Аутсорсинг на производство
-
Вътрешни и глобални доставки
-
Консолидация
-
Инженерна интеграция
-
Инженерни услуги
ELECTRICAL DISCHARGE MACHINING (EDM), also referred to as SPARK-EROSION or ELECTRODISCHARGE MACHINING, SPARK ERODING, DIE SINKING_cc781905-5cde-3194-bb3b -136bad5cf58d_or WIRE EROSION, is a NON-CONVENTIONAL MANUFACTURING process where erosion of metals takes place and desired shape is obtained using electrical discharges in the form на искри. Ние също така предлагаме някои разновидности на EDM, а именно NO-WEAR EDM, WIRE EDM (WEDM), EDM ШЛИФОВАНЕ (EDG), DIE-SINKING EDM, ЕЛЕКТРИЧЕСКО ФРЕЗОВАНЕ, micro-EDM, m-EDM_cc781905 -5cde-3194-bb3b-136bad5cf58d_and ЕЛЕКТРОХИМИЧНО-ИЗПЪЛНИТЕЛНО СМЪЛЧАНЕ (ECDG). Нашите EDM системи се състоят от оформени инструменти/електрод и детайла, свързани към DC захранвания и поставени в електрически непроводима диелектрична течност. След 1940 г. електроерозионната обработка се превърна в една от най-важните и популярни производствени технологии в производствените индустрии.
Когато разстоянието между двата електрода се намали, интензитетът на електрическото поле в обема между електродите става по-голям от силата на диелектрика в някои точки, който се скъсва, в крайна сметка образувайки мост за протичане на ток между двата електрода. Генерира се интензивна електрическа дъга, която причинява значително нагряване, което стопява част от детайла и част от инструменталния материал. В резултат на това материалът се отстранява и от двата електрода. В същото време диелектричната течност се нагрява бързо, което води до изпаряване на течността в междината на дъгата. След като токът спре или бъде спрян, топлината се отстранява от газовия мехур от околната диелектрична течност и мехурът кавитира (свива се). Ударната вълна, създадена от свиването на мехурчето и потока от диелектрична течност, отмиват остатъците от повърхността на детайла и увличат всеки разтопен материал на детайла в диелектричната течност. Скоростта на повторение за тези разряди е между 50 до 500 kHz, напрежения между 50 до 380 V и токове между 0,1 и 500 ампера. Нов течен диелектрик като минерални масла, керосин или дестилирана и дейонизирана вода обикновено се пренася в междуелектродния обем, отнасяйки твърдите частици (под формата на отломки) и изолационните свойства на диелектрика се възстановяват. След протичане на ток, потенциалната разлика между двата електрода се възстановява до това, което е била преди разрушаването, така че може да възникне нов пробив на течния диелектрик. Нашите модерни електроразрядни машини (EDM) предлагат цифрово контролирани движения и са оборудвани с помпи и филтриращи системи за диелектрични течности.
Електроерозионната обработка (EDM) е метод на обработка, използван главно за твърди метали или такива, които биха били много трудни за обработка с конвенционални техники. EDM обикновено работи с всякакви материали, които са електрически проводници, въпреки че са предложени и методи за обработка на изолационна керамика с EDM. Точката на топене и латентната топлина на топене са свойства, които определят обема на отстранения метал за едно изхвърляне. Колкото по-високи са тези стойности, толкова по-бавна е скоростта на отстраняване на материала. Тъй като процесът на обработка с електроразряд не включва никаква механична енергия, твърдостта, здравината и издръжливостта на детайла не влияят на скоростта на отстраняване. Честотата на разреждане или енергията на разреждане, напрежението и токът се променят, за да се контролира скоростта на отстраняване на материала. Скоростта на отстраняване на материала и грапавостта на повърхността се увеличават с увеличаване на плътността на тока и намаляване на честотата на искри. Можем да изрежем сложни контури или кухини в предварително закалена стомана с помощта на EDM без необходимост от термична обработка за тяхното омекотяване и повторно втвърдяване. Можем да използваме този метод с всеки метал или метални сплави като титан, хастелой, ковар и инконел. Приложенията на EDM процеса включват формоване на поликристални диамантени инструменти. EDM се счита за нетрадиционен или неконвенционален метод на обработка заедно с процеси като електрохимична обработка (ECM), рязане с водна струя (WJ, AWJ), лазерно рязане. От друга страна, конвенционалните методи на обработка включват струговане, фрезоване, шлайфане, пробиване и други процеси, чийто механизъм за отстраняване на материала се основава основно на механични сили. Електродите за електроерозионна обработка (EDM) са изработени от графит, месинг, мед и медно-волфрамова сплав. Възможни са диаметри на електродите до 0,1 мм. Тъй като износването на инструмента е нежелано явление, което влияе неблагоприятно на точността на размерите при EDM, ние се възползваме от процес, наречен NO-WEAR EDM, чрез обръщане на полярността и използване на медни инструменти за минимизиране на износването на инструмента.
Идеално казано, електроразрядната обработка (EDM) може да се счита за серия от разрушаване и възстановяване на диелектричната течност между електродите. В действителност обаче отстраняването на отломките от междуелектродната зона е почти винаги частично. Това води до това, че електрическите характеристики на диелектрика в междуелектродната зона са различни от техните номинални стойности и варират с времето. Междуелектродното разстояние (искрова междина) се регулира от алгоритмите за управление на конкретната използвана машина. За съжаление, искровата междина в EDM може понякога да бъде късо съединение от отломките. Системата за управление на електрода може да не успее да реагира достатъчно бързо, за да предотврати късо съединение на двата електрода (инструмент и детайл). Това нежелано късо съединение допринася за отстраняването на материала различно от идеалния случай. Отдаваме изключително значение на действието на промиване, за да възстановим изолационните свойства на диелектрика, така че токът винаги да се случва в точката на междуелектродната зона, като по този начин минимизираме възможността за нежелана промяна на формата (повреждане) на инструмента-електрод и детайл. За да се получи специфична геометрия, EDM инструментът се насочва по желаната траектория много близо до детайла, без да го докосва. Ние обръщаме изключително внимание на ефективността на контрола на движението при използване. По този начин се получават голям брой токови разряди / искри, като всеки допринася за отстраняването на материала както от инструмента, така и от детайла, където се образуват малки кратери. Размерът на кратерите е функция на технологичните параметри, зададени за конкретната работа и размерите могат да варират от наномащаб (като в случая на микро-EDM операции) до няколко стотици микрометра при груби условия. Тези малки кратери върху инструмента причиняват постепенна ерозия на електрода, наречена „износване на инструмента“. За да противодействаме на вредния ефект от износването върху геометрията на детайла, ние непрекъснато сменяме инструмента-електрод по време на обработка. Понякога постигаме това, като използваме непрекъснато сменяем проводник като електрод (този EDM процес се нарича още WIRE EDM ). Понякога използваме инструмента-електрод по такъв начин, че само малка част от него действително е ангажирана в процеса на обработка и тази част се променя редовно. Такъв е например случаят, когато се използва въртящ се диск като инструмент-електрод. Този процес се нарича EDM GRINDING. Друга техника, която прилагаме, се състои в използването на набор от електроди с различни размери и форми по време на една и съща EDM операция за компенсиране на износването. Наричаме тази техника с множество електроди и най-често се използва, когато електродът на инструмента възпроизвежда негативно желаната форма и се придвижва към заготовката в една посока, обикновено вертикалната посока (т.е. z-ос). Това наподобява потъването на инструмента в диелектричната течност, в която е потопен детайлът, и затова се нарича като DIE-SINKING EDM (понякога наричан_cc781905-5c 3194-bb3b-136bad5cf58d_CONVENTIONAL EDM or RAM EDM). Машините за тази операция се наричат SINKER EDM. Електродите за този тип EDM имат сложна форма. Ако крайната геометрия се получава с помощта на електрод с обикновено проста форма, движен в няколко посоки и също така подлежи на въртене, ние го наричаме EDM ФРЕЗОВАНЕ. Степента на износване е строго зависима от технологичните параметри, използвани в операцията (полярност, максимален ток, напрежение на отворена верига). Например в micro-EDM, известен също като m-EDM, тези параметри обикновено се задават на стойности, които генерират сериозно износване. Следователно износването е основен проблем в тази област, който минимизираме с помощта на натрупаното ни ноу-хау. Например, за да се сведе до минимум износването на графитните електроди, дигитален генератор, който може да се контролира в рамките на милисекунди, обръща полярността, когато настъпи електроерозия. Това води до ефект, подобен на галванопластиката, който непрекъснато отлага ерозирания графит обратно върху електрода. При друг метод, така наречената верига „Нулево износване“, ние свеждаме до минимум колко често започва и спира изхвърлянето, като го поддържаме възможно най-дълго време. Скоростта на отнемане на материала при електроерозионна обработка може да се оцени от:
MRR = 4 x 10 опит (4) x I x Tw опит (-1,23)
Тук MRR е в mm3/min, I е ток в ампери, Tw е точка на топене на детайла в K-273,15K. Експ означава експонента.
От друга страна, степента на износване Wt на електрода може да се получи от:
Wt = (1,1 x 10exp(11)) x I x Ttexp(-2,38)
Тук Wt е в mm3/min и Tt е точката на топене на материала на електрода в K-273.15K
И накрая, съотношението на износване на детайла към електрода R може да се получи от:
R = 2,25 x Trexp (-2,38)
Тук Tr е съотношението на точките на топене на детайла към електрода.
SINKER EDM :
Синкер EDM, наричан също като CAVITY TYPE EDM or EDM електрод, който се състои от поглъщащ се в течност и VOLUME електрод. Електродът и детайлът са свързани към захранване. Захранването генерира електрически потенциал между двете. Когато електродът се приближи до обработвания детайл, във флуида възниква диелектричен пробив, образувайки плазмен канал и прескача малка искра. Искрите обикновено падат една по една, тъй като е много малко вероятно различни места в междуелектродното пространство да имат идентични локални електрически характеристики, което би позволило възникването на искра във всички такива места едновременно. Стотици хиляди от тези искри възникват в произволни точки между електрода и детайла за секунда. Тъй като основният метал ерозира и искровата междина впоследствие се увеличава, електродът се спуска автоматично от нашата CNC машина, така че процесът да може да продължи без прекъсване. Нашето оборудване има контролни цикли, известни като „включено време“ и „изключено време“. Настройката за време на включване определя дължината или продължителността на искрата. По-дълго време на работа създава по-дълбока кухина за тази искра и всички последващи искри за този цикъл, създавайки по-грубо покритие на детайла и обратно. Времето на изключване е периодът от време, през който една искра се заменя с друга. По-дълго време на изключване позволява на диелектричната течност да измие през дюза, за да почисти ерозиралите отломки, като по този начин се избягва късо съединение. Тези настройки се настройват за микросекунди.
WIRE EDM :
In WIRE ELECTRICAL DISCHARGE MACHINING (WEDM), also called WIRE-CUT EDM or WIRE CUTTING, we feed a тънка едножилна метална тел от месинг през детайла, който е потопен в резервоар с диелектрична течност. Wire EDM е важен вариант на EDM. От време на време използваме EDM с телено рязане, за да изрязваме плочи с дебелина до 300 мм и да правим щанци, инструменти и матрици от твърди метали, които са трудни за обработка с други производствени методи. При този процес, който наподобява контурно рязане с лентов трион, телта, която непрекъснато се подава от макара, се държи между горния и долния диамантен водач. Водачите, контролирани от CNC, се движат в равнината x–y, а горният водач може също да се движи независимо по оста z–u–v, давайки възможност за изрязване на заострени и преходни форми (като кръг в долната част и квадрат в върха). Горният водач може да контролира движенията на осите в x–y–u–v–i–j–k–l–. Това позволява на WEDM да изрязва много сложни и деликатни форми. Средният прорез на нашето оборудване, който постига най-добри икономически разходи и време за обработка, е 0,335 mm при използване на Ø 0,25 месингова, медна или волфрамова тел. Въпреки това, горните и долните диамантени водачи на нашето CNC оборудване са с точност до около 0,004 mm и могат да имат път на рязане или прорез до 0,021 mm, като се използва тел Ø 0,02 mm. Така че са възможни наистина тесни кройки. Ширината на рязане е по-голяма от ширината на телта, тъй като искри възникват от страните на телта към детайла, причинявайки ерозия. Това „надрязване“ е необходимо, за много приложения то е предвидимо и следователно може да бъде компенсирано (в микро-EDM това не е често случаят). Макарите с тел са дълги — 8 кг макара с тел 0,25 мм е с дължина малко над 19 километра. Диаметърът на проводника може да бъде само 20 микрометра, а точността на геометрията е от порядъка на +/- 1 микрометър. Обикновено използваме жицата само веднъж и я рециклираме, защото е сравнително евтина. Той се движи с постоянна скорост от 0,15 до 9 m/min и по време на рязане се поддържа постоянен прорез (прорез). В процеса на EDM с телена обработка ние използваме вода като диелектрична течност, като контролираме нейното съпротивление и други електрически свойства с филтри и дейонизатори. Водата отмива отрязаните остатъци от зоната на рязане. Промиването е важен фактор при определяне на максималната скорост на подаване за дадена дебелина на материала и затова я поддържаме постоянна. Скоростта на рязане при EDM с тел се посочва от гледна точка на площта на напречното сечение, изрязана за единица време, като например 18 000 mm2/час за инструментална стомана D2 с дебелина 50 mm. Линейната скорост на рязане за този случай ще бъде 18 000/50 = 360 мм/час. Скоростта на отнемане на материал при телена електроерозия е:
MRR = Vf xhxb
Тук MRR е в mm3/min, Vf е скоростта на подаване на телта в детайла в mm/min, h е дебелината или височината в mm, а b е прорезът, който е:
b = dw + 2s
Тук dw е диаметърът на телта, а s е разстоянието между телта и детайла в mm.
Наред с по-строгите толеранси, нашите модерни многоосни EDM обработващи центрове за рязане на тел имат добавени функции като няколко глави за рязане на две части едновременно, контроли за предотвратяване на счупване на тел, функции за автоматично самонарязване в случай на скъсване на тел и програмирани стратегии за обработка за оптимизиране на работата, право и ъглово рязане.
Wire-EDM ни предлага ниски остатъчни напрежения, тъй като не изисква големи сили на рязане за отстраняване на материал. Когато енергията/мощността на импулс е относително ниска (както при довършителните операции), се очаква малка промяна в механичните свойства на материала поради ниските остатъчни напрежения.
ЕЛЕКТРОРАЗРЯДНО ШЛИФОВАНЕ (EDG) : Шлифовъчните колела не съдържат абразиви, изработени са от графит или месинг. Повтарящите се искри между въртящото се колело и детайла премахват материала от повърхностите на детайла. Скоростта на отнемане на материала е:
MRR = K x I
Тук MRR е в mm3/min, I е ток в ампери, а K е материалният фактор на детайла в mm3/A-min. Ние често използваме електроерозионно шлайфане, за да изрежем тесни прорези на компоненти. Понякога комбинираме процес EDG (Електроразрядно смилане) с процес ECG (Електрохимично смилане), при който материалът се отстранява чрез химическо действие, като електрическите разряди от графитното колело разрушават оксидния филм и се отмиват от електролита. Процесът се нарича ЕЛЕКТРОХИМИЧНО СМЪЛЧАНЕ С РАЗРЯД (ECDG). Въпреки че процесът ECDG консумира относително повече енергия, той е по-бърз процес от EDG. Ние предимно шлифоваме инструменти от твърд сплав, използвайки тази техника.
Приложения на електроерозионна обработка:
Производство на прототип:
Ние използваме EDM процеса при производство на матрици, инструменти и матрици, както и за производство на прототипи и производствени части, особено за космическата, автомобилната и електронната промишленост, в които производствените количества са сравнително ниски. При Sinker EDM електрод от графит, меден волфрам или чиста мед се обработва машинно в желаната (отрицателна) форма и се подава в детайла в края на вертикална шайба.
Изработка на щанци за монети:
За създаването на матрици за производство на бижута и значки чрез процеса на монетосечене (щамповане), позитивният шаблон може да бъде направен от стерлингово сребро, тъй като (при подходящи настройки на машината) шаблонът е значително ерозиран и се използва само веднъж. Получената отрицателна матрица след това се втвърдява и се използва в ударен чук за производство на щамповани плоскости от изрязани листови заготовки от бронз, сребро или златна сплав с ниска проба. За значки тези плоскости могат да бъдат допълнително оформени до извита повърхност от друга матрица. Този тип EDM обикновено се извършва потопен в диелектрик на маслена основа. Завършеният предмет може да бъде допълнително рафиниран чрез твърдо (стъкло) или меко (боя) емайлиране и/или галванично покритие с чисто злато или никел. По-меките материали като сребро могат да бъдат ръчно гравирани като усъвършенстване.
Пробиване на малки отвори:
На нашите EDM машини за телено рязане ние използваме EDM пробиване на малки дупки, за да направим проходен отвор в детайла, през който да прокараме телта за операцията EDM с телено рязане. Отделни EDM глави, специално за пробиване на малки дупки, са монтирани на нашите машини за рязане на тел, което позволява на големите закалени плочи да имат ерозирани готови части от тях, ако е необходимо и без предварително пробиване. Ние също използваме EDM с малки дупки за пробиване на редове от отвори в ръбовете на турбинните лопатки, използвани в реактивните двигатели. Потокът на газ през тези малки отвори позволява на двигателите да използват по-високи температури, отколкото е възможно иначе. Високотемпературните, много твърди, монокристални сплави, от които са направени тези остриета, правят конвенционалната обработка на тези отвори с високо аспектно съотношение изключително трудна и дори невъзможна. Други области на приложение на EDM с малки отвори е създаването на микроскопични отвори за компоненти на горивната система. Освен интегрираните EDM глави, ние внедряваме самостоятелни EDM машини за пробиване на малки отвори с оси x–y за обработка на слепи или проходни отвори. EDM пробиват дупки с дълъг месингов или меден тръбен електрод, който се върти в патронник с постоянен поток от дестилирана или дейонизирана вода, протичаща през електрода като промивно средство и диелектрик. Някои EDM машини за пробиване на малки отвори са в състояние да пробият 100 mm мека или дори закалена стомана за по-малко от 10 секунди. При тази операция на пробиване могат да се постигнат отвори между 0,3 mm и 6,1 mm.
Машинна обработка на метални дезинтегратори:
Разполагаме и със специални EDM машини за специфичната цел за отстраняване на счупени инструменти (свредла или метчици) от детайлите. Този процес се нарича „механична обработка с разпадане на метал“.
Предимства и недостатъци Електроерозионна обработка:
Предимствата на EDM включват обработка на:
- Сложни форми, които иначе биха били трудни за производство с конвенционални режещи инструменти
- Изключително твърд материал с много близки допуски
- Много малки детайли, при които конвенционалните режещи инструменти могат да повредят частта от прекомерно налягане на режещия инструмент.
- Няма пряк контакт между инструмента и обработвания детайл. Следователно деликатни участъци и слаби материали могат да бъдат обработвани без никакво изкривяване.
- Може да се получи добро покритие на повърхността.
- Лесно се пробиват много фини отвори.
Недостатъците на EDM включват:
- Бавната скорост на отстраняване на материала.
- Допълнителното време и разходи, използвани за създаване на електроди за бутална/потъваща EDM.
- Възпроизвеждането на остри ъгли върху детайла е трудно поради износване на електрода.
- Консумацията на енергия е висока.
- Образува се "Overcut".
- По време на обработка възниква прекомерно износване на инструмента.
- Електрически непроводимите материали могат да се обработват само със специфична настройка на процеса.