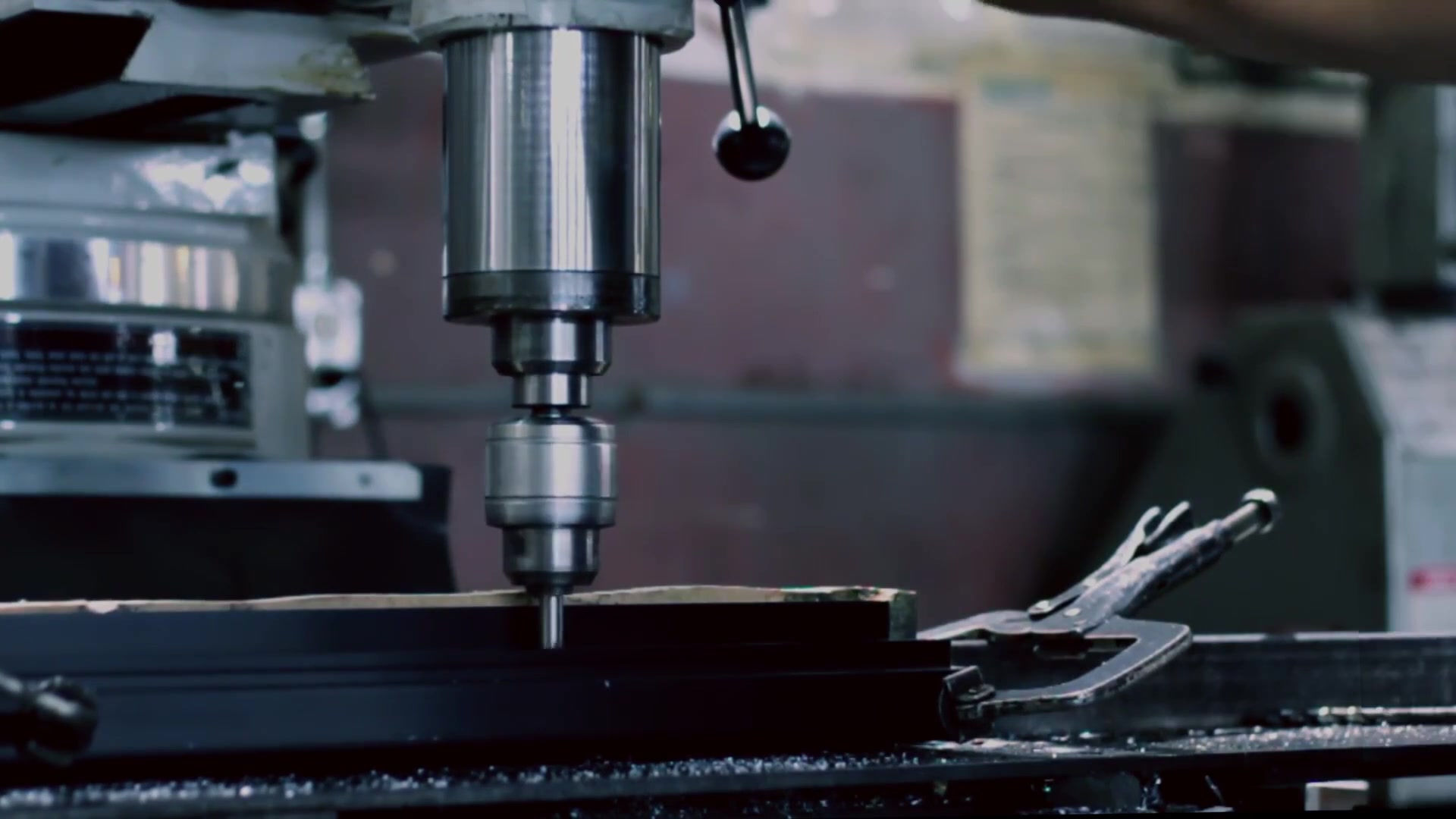
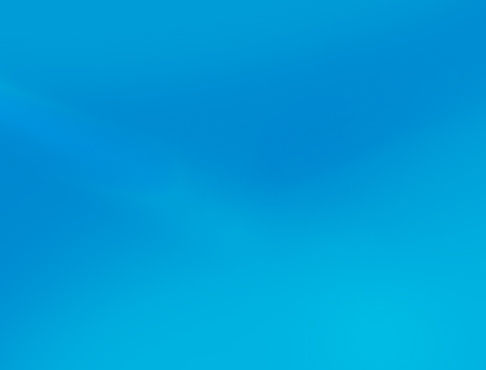
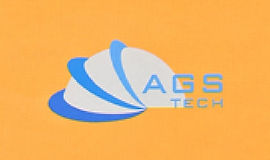
Глобален производител по поръчка, интегратор, консолидатор, аутсорсинг партньор за голямо разнообразие от продукти и услуги.
Ние сме вашият източник на едно гише за производство, производство, инженеринг, консолидация, интеграция, аутсорсинг на произведени по поръчка и готови продукти и услуги.
Изберете своя език
-
Производство по поръчка
-
Вътрешно и глобално договорно производство
-
Аутсорсинг на производство
-
Вътрешни и глобални доставки
-
Консолидация
-
Инженерна интеграция
-
Инженерни услуги
Ние съединяваме, сглобяваме и закрепваме вашите произведени части и ги превръщаме в завършени или полуготови продукти чрез ЗАВАРЯВАНЕ, СПОЯВАНЕ, ЗАПОЯВАНЕ, СПИТОЧАНЕ, СВЪРЗВАНЕ С ЛЕПИЛО, ЗАКРЕПВАНЕ, ПРЕСОВАНЕ. Някои от нашите най-популярни процеси на заваряване са дъгово заваряване, заваряване с кислородно гориво, съпротивление, проекция, шев, разместване, ударно заваряване, твърдо състояние, електронен лъч, лазерно, термитно, индукционно заваряване. Нашите популярни процеси на запояване са горелка, индукция, пещ и потапяне. Нашите методи за запояване са ютия, котлон, фурна, индукция, потапяне, вълна, претопяване и ултразвуково запояване. За адхезивно залепване ние често използваме термопласти и термореактивни, епоксиди, феноли, полиуретан, лепилни сплави, както и някои други химикали и ленти. И накрая, нашите процеси на закрепване се състоят от заковаване, завинтване, гайки и болтове, занитване, заклинване, закрепване, зашиване и телбод и пресоване.
• ЗАВАРЯВАНЕ: Заваряването включва свързване на материали чрез разтопяване на детайлите и въвеждане на добавъчни материали, които също се съединяват с разтопената заваръчна вана. Когато мястото се охлади, получаваме здрава фуга. В някои случаи се прилага натиск. За разлика от заваряването, операциите по спояване и запояване включват само топене на материал с по-ниска точка на топене между детайлите и детайлите не се топят. Препоръчваме ви да щракнете тук, заИЗТЕГЛЕТЕ нашите схематични илюстрации на заваръчни процеси от AGS-TECH Inc.
Това ще ви помогне да разберете по-добре информацията, която ви предоставяме по-долу.
При ДЪГОВО ЗАВАРЯВАНЕ ние използваме захранване и електрод, за да създадем електрическа дъга, която разтопява металите. Точката на заваряване е защитена със защитен газ или пара или друг материал. Този процес е популярен за заваряване на автомобилни части и стоманени конструкции. При електродъгово заваряване с метална дъга (SMAW) или известно още като заваряване с пръчка, електродна пръчка се доближава до основния материал и между тях се генерира електрическа дъга. Електродният прът се топи и действа като пълнежен материал. Електродът също така съдържа флюс, който действа като слой шлака и отделя пари, които действат като защитен газ. Те предпазват зоната на заваряване от замърсяване на околната среда. Не се използват други пълнители. Недостатъците на този процес са неговата бавност, необходимостта от честа смяна на електродите, необходимостта да се отстрани остатъчната шлака, произхождаща от флюса. Редица метали като желязо, стомана, никел, алуминий, мед… и др. Може да се заварява. Неговите предимства са евтините инструменти и лекотата на използване. Газово електродъгово заваряване (GMAW), известно също като метално-инертен газ (MIG), имаме непрекъснато подаване на консумативен пълнител за електродна тел и инертен или частично инертен газ, който тече около телта срещу замърсяване на околната среда на заваръчната област. Могат да се заваряват стомана, алуминий и други цветни метали. Предимствата на MIG са високите скорости на заваряване и доброто качество. Недостатъците са сложното му оборудване и предизвикателствата, с които се сблъскваме във ветровита външна среда, тъй като трябва да поддържаме стабилен защитния газ около зоната за заваряване. Разновидност на GMAW е дъгово заваряване с флюсова сърцевина (FCAW), което се състои от фина метална тръба, пълна с флюсови материали. Понякога потокът вътре в тръбата е достатъчен за защита от замърсяване на околната среда. Заваряването под флюс (SAW) е автоматизиран процес, който включва непрекъснато подаване на тел и дъга, която се запалва под слой покритие от флюс. Производствените нива и качество са високи, заваръчната шлака се отделя лесно и имаме работна среда без дим. Недостатъкът е, че може да се използва само за заваряване на части в определени позиции. При заваряване с волфрамова дъга (GTAW) или заваряване с волфрам и инертен газ (TIG) използваме волфрамов електрод заедно с отделен пълнител и инертни или почти инертни газове. Както знаем, волфрамът има висока точка на топене и е много подходящ метал за много високи температури. Волфрамът в TIG не се изразходва за разлика от другите методи, обяснени по-горе. Бавна, но висококачествена заваръчна техника с предимство пред другите техники за заваряване на тънки материали. Подходящ за много метали. Заваряването с плазмена дъга е подобно, но използва плазмен газ за създаване на дъга. Дъгата при плазмено-дъгово заваряване е относително по-концентрирана в сравнение с GTAW и може да се използва за по-широк диапазон от дебелини на метала при много по-високи скорости. GTAW и плазменодъгово заваряване могат да се прилагат към повече или по-малко еднакви материали.
ЗАВАРЯВАНЕ НА КИСЛОРОДНО ГОРИВО / КИСЛОРОДНО ГОРИВО, наричано още кислородно-ацетиленово заваряване, кислородно заваряване, газово заваряване се извършва с използване на газови горива и кислород за заваряване. Тъй като не се използва електричество, той е преносим и може да се използва там, където няма електричество. С помощта на заваръчна горелка ние нагряваме парчетата и пълнежния материал, за да произведем общ резервоар от разтопен метал. Могат да се използват различни горива като ацетилен, бензин, водород, пропан, бутан… и др. При заваряване с кислородно гориво използваме два контейнера, единият за горивото, а другият за кислорода. Кислородът окислява горивото (изгаря го).
СЪПРОТИВНО ЗАВАРЯВАНЕ: Този тип заваряване се възползва от нагряването с джаул и топлината се генерира на мястото, където се прилага електрически ток за определено време. Силни токове преминават през метала. На това място се образуват басейни от разтопен метал. Методите за електросъпротивително заваряване са популярни поради тяхната ефективност и малък потенциал за замърсяване. Недостатъците обаче са, че разходите за оборудване са относително значителни и присъщото ограничение до относително тънки детайли. ТОЧКОВОТО ЗАВАРЯВАНЕ е един от основните видове съпротивително заваряване. Тук съединяваме два или повече припокриващи се листа или детайли, като използваме два медни електрода, за да захванем листовете заедно и да прекараме силен ток през тях. Материалът между медните електроди се нагрява и на това място се генерира разтопен басейн. След това токът се спира и върховете на медните електроди охлаждат мястото на заварката, тъй като електродите се охлаждат с вода. Прилагането на точното количество топлина към правилния материал и дебелина е от ключово значение за тази техника, защото ако се приложи неправилно, фугата ще бъде слаба. Точковото заваряване има предимствата, че не причинява значителна деформация на детайлите, енергийна ефективност, лекота на автоматизация и изключителни производствени нива и не изисква никакви пълнители. Недостатъкът е, че тъй като заваряването се извършва на места, вместо да се образува непрекъснат шев, общата якост може да бъде относително по-ниска в сравнение с други методи на заваряване. ЗАВАРЯВАНЕТО НА ШЕВА, от друга страна, създава заварки на прилежащите повърхности на подобни материали. Шевът може да бъде челно или с припокриване. Заваряването на шевове започва от единия край и се придвижва постепенно към другия. Този метод също така използва два електрода от мед за прилагане на налягане и ток към заваръчната област. Електродите във формата на диск се въртят с постоянен контакт по линията на шева и правят непрекъсната заварка. И тук електродите се охлаждат с вода. Заварките са много здрави и надеждни. Други методи са техники за прожектиране, светкавично заваряване и заваряване с изместване.
ЗАВАРЯВАНЕТО В ТВЪРДО ТЪРДО ТЪРДО ТЯЛО е малко по-различно от предишните методи, обяснени по-горе. Коалесценцията се извършва при температури под температурата на топене на съединените метали и без използване на метален пълнител. В някои процеси може да се използва налягане. Различни методи са КОЕКСТРУЗИОННО ЗАВАРЯВАНЕ, при което различни метали се екструдират през една и съща матрица, СТУДЕНО ЗАВАРЯВАНЕ ПОД НАЛЯГАНЕ, при което съединяваме меки сплави под техните точки на топене, ДИФУЗИОННО ЗАВАРЯВАНЕ техника без видими заваръчни линии, ЕКСПЛОЗИОННО ЗАВАРЯВАНЕ за свързване на различни материали, напр. устойчиви на корозия сплави към структурни стомани, ЕЛЕКТРОМАГНИТНО ИМПУЛСНО ЗАВАРЯВАНЕ, при което ускоряваме тръби и листове чрез електромагнитни сили, КОВАЧЕСКО ЗАВАРЯВАНЕ, което се състои от нагряване на металите до високи температури и заковаването им заедно, ЗАВАРЯВАНЕ С ТЪРЕНИЕ, при което се извършва заваряване с достатъчно триене, ЗАВАРЯВАНЕ С ТЪРЕНИЕ, което включва въртящ се не- консумативен инструмент, пресичащ линията на съединението, ГОРЕЩО ЗАВАРЯВАНЕ ПОД НАЛЯГАНЕ, при което притискаме металите заедно при повишени температури под температурата на топене във вакуум или инертни газове, ГОРЕЩО ЗАВАРЯВАНЕ ПРЕДУ ИЗОСТАТИЧНО НАЛЯГАНЕ процес, при който прилагаме налягане с помощта на инертни газове вътре в съд, ЗАВАРЯВАНЕ НА РОЛКИ, при което съединяваме различни материали, като ги поставяте между тях две въртящи се колела, УЛТРАЗВУКОВО ЗАВАРЯВАНЕ, където тънки метални или пластмасови листове се заваряват с помощта на високочестотна вибрационна енергия.
Другите ни заваръчни процеси са ЕЛЕКТРОННО ЛЪЧЕВО ЗАВАРЯВАНЕ с дълбоко проникване и бърза обработка, но тъй като е скъп метод, считаме го за специални случаи, ЕЛЕКТРОШЛАКОВО ЗАВАРЯВАНЕ метод, подходящ само за тежки дебели плочи и детайли от стомана, ИНДУКЦИОННО ЗАВАРЯВАНЕ, при което използваме електромагнитна индукция и загряване на нашите електропроводими или феромагнитни детайли, ЗАВАРЯВАНЕ С ЛАЗЕРЕН ЛЪЧ също с дълбоко проникване и бърза обработка, но скъп метод, ЛАЗЕРНО ХИБРИДНО ЗАВАРЯВАНЕ, което комбинира LBW с GMAW в една и съща заваръчна глава и способно да преодолява празнини от 2 mm между плочите, УДАРНО ЗАВАРЯВАНЕ, което включва електрически разряд, последван от коване на материалите с приложен натиск, ТЕРМИТНО ЗАВАРЯВАНЕ, включващо екзотермична реакция между прахове от алуминий и железен оксид, ЕЛЕКТРОГАЗОВО ЗАВАРЯВАНЕ с консумативни електроди и използвано само със стомана във вертикално положение и накрая ДЪГОВО ЗАВАРЯВАНЕ НА ШПИЛКА за свързване на шпилка към основата материал с топлина и налягане.
Препоръчваме ви да щракнете тук, заИЗТЕГЛЕТЕ нашите схематични илюстрации на процеси на спояване, запояване и залепване от AGS-TECH Inc
Това ще ви помогне да разберете по-добре информацията, която ви предоставяме по-долу.
• ЗАПОЯВАНЕ: Свързваме два или повече метала чрез нагряване на добавъчни метали между тях над техните точки на топене и използване на капилярно действие за разпръскване. Процесът е подобен на запояване, но температурите, свързани с разтопяването на пълнителя, са по-високи при запояване. Както при заваряването, флюсът защитава пълнежния материал от атмосферно замърсяване. След охлаждане детайлите се съединяват. Процесът включва следните ключови стъпки: добро прилягане и хлабина, правилно почистване на основните материали, правилно фиксиране, правилен поток и избор на атмосфера, нагряване на сглобката и накрая почистване на запоената сглобка. Някои от нашите процеси на запояване са ЗАПОЯВАНЕ С ГОРЕЛ, популярен метод, извършван ръчно или по автоматизиран начин. Той е подходящ за малки производствени поръчки и специализирани случаи. Топлината се прилага с помощта на газови пламъци близо до съединението, което се споява. ЗАПОЯВАНЕТО В ПЕЩТА изисква по-малко умения на оператора и е полуавтоматичен процес, подходящ за промишлено масово производство. Както контролът на температурата, така и контролът на атмосферата в пещта са предимства на тази техника, тъй като първото ни позволява да имаме контролирани топлинни цикли и да елиминираме локалното нагряване, какъвто е случаят при запояване с горелка, а второто предпазва частта от окисляване. Използвайки jigging ние сме в състояние да намалим производствените разходи до минимум. Недостатъците са висока консумация на енергия, разходи за оборудване и по-предизвикателни съображения за проектиране. ВАКУУМНОТО ЗАПОЯВАНЕ се извършва във вакуумна пещ. Поддържа се еднородност на температурата и се получават много чисти съединения без флюс с много малко остатъчни напрежения. Топлинни обработки могат да се извършват по време на вакуумно спояване, поради ниските остатъчни напрежения, налични по време на бавни цикли на нагряване и охлаждане. Основният недостатък е високата му цена, тъй като създаването на вакуумна среда е скъп процес. Друга техника DIP BRAZING съединява неподвижни части, където спояващото съединение се нанася върху свързващите повърхности. След това фиксираните части се потапят във вана с разтопена сол като натриев хлорид (трапезна сол), която действа като топлопреносна среда и флюс. Въздухът е изключен и следователно не се образува оксид. При ИНДУКЦИОННОТО СПОЯВАНЕ ние съединяваме материали чрез добавъчен метал, който има по-ниска точка на топене от основните материали. Променливият ток от индукционната намотка създава електромагнитно поле, което индуцира индукционно нагряване на предимно железни магнитни материали. Методът осигурява селективно нагряване, добри фуги с пълнители, течащи само в желаните зони, малко окисление, тъй като няма пламъци и охлаждането е бързо, бързо нагряване, консистенция и пригодност за производство в голям обем. За да ускорим нашите процеси и да осигурим последователност, ние често използваме заготовки. Информация за нашето съоръжение за спояване, произвеждащо фитинги от керамика към метал, херметично запечатване, вакуумни канали, компоненти за висок и свръхвисок вакуум и контрол на течности може да бъде намерена тук: Брошура на завода за спояване
• ЗАПОЯВАНЕ: При запояването нямаме стапяне на детайлите, а допълнителен метал с по-ниска точка на топене от съединителните части, който се влива в съединението. Добавъчният метал при запояване се топи при по-ниска температура, отколкото при спояване. Ние използваме безоловни сплави за запояване и имаме съответствие с RoHS и за различни приложения и изисквания имаме различни и подходящи сплави като сребърна сплав. Запояването ни предлага съединения, които не пропускат газ и течности. При МЕКО ЗАПОЯВАНЕ нашият добавъчен метал има точка на топене под 400 градуса по Целзий, докато при СРЕБЪРНО ЗАПОЯВАНЕ и СПОЙКА се нуждаем от по-високи температури. Мекото запояване използва по-ниски температури, но не води до здрави съединения за взискателни приложения при повишени температури. Запояването със сребро, от друга страна, изисква високи температури, осигурени от горелката, и ни дава здрави съединения, подходящи за приложения при висока температура. Спояването изисква най-високи температури и обикновено се използва горелка. Тъй като спояващите фуги са много здрави, те са добри кандидати за ремонт на тежки железни предмети. В нашите производствени линии ние използваме както ръчно ръчно запояване, така и автоматизирани линии за запояване. ИНДУКЦИОННОТО ЗАПОЯВАНЕ използва високочестотен променлив ток в медна бобина, за да улесни индукционното нагряване. В запоената част се индуцират токове и в резултат се генерира топлина при високото съпротивление joint. Тази топлина разтопява добавъчния метал. Използва се и флюс. Индукционното запояване е добър метод за запояване на цилиндри и тръби в непрекъснат процес чрез увиване на намотките около тях. Запояването на някои материали като графит и керамика е по-трудно, защото изисква покритие на детайлите с подходящ метал преди запояване. Това улеснява междинното свързване. Ние запояваме такива материали специално за херметични опаковъчни приложения. Ние произвеждаме нашите печатни платки (PCB) в голям обем най-вече чрез ВЪЛНОВО ЗАПОЯВАНЕ. Само за малки количества с цел създаване на прототипи ние използваме ръчно запояване с помощта на поялник. Ние използваме вълново запояване както за сквозни отвори, така и за модули за печатни платки за повърхностен монтаж (PCBA). Временно лепило държи компонентите прикрепени към печатната платка и модулът се поставя върху конвейер и се движи през оборудване, което съдържа разтопена спойка. Първо печатната платка се флюсира и след това влиза в зоната за предварително нагряване. Разтопената спойка е в тиган и има шарка от стоящи вълни на повърхността си. Когато печатната платка се движи над тези вълни, тези вълни влизат в контакт с дъното на печатната платка и се придържат към подложките за запояване. Спойката остава само върху щифтове и подложки, а не върху самата печатна платка. Вълните в разтопената спойка трябва да бъдат добре контролирани, така че да няма пръски и върховете на вълните да не докосват и замърсяват нежелани зони на платките. При REFLOW SOLDERING ние използваме лепкава спояваща паста за временно закрепване на електронните компоненти към платките. След това плоскостите преминават през пещ за повторно оформяне с контрол на температурата. Тук спойката се топи и свързва компонентите трайно. Използваме тази техника както за компоненти за повърхностен монтаж, така и за компоненти с отвори. Правилният контрол на температурата и регулирането на температурите на фурната е от съществено значение, за да се избегне разрушаването на електронните компоненти на платката чрез прегряването им над техните максимални температурни граници. В процеса на запояване с преплавяне всъщност имаме няколко региона или етапа, всеки с различен термичен профил, като етап на предварително нагряване, етап на термично накисване, етап на преплавяне и охлаждане. Тези различни стъпки са от съществено значение за безвредно повторно запояване на печатни платки (PCBA). УЛТРАЗВУКОВОТО ЗАПОЯВАНЕ е друга често използвана техника с уникални възможности - може да се използва за запояване на стъкло, керамика и неметални материали. Например фотоволтаичните панели, които са неметални, се нуждаят от електроди, които могат да бъдат закрепени с помощта на тази техника. При ултразвуковото запояване ние използваме нагрят поялник, който също излъчва ултразвукови вибрации. Тези вибрации създават кавитационни мехурчета на границата на субстрата с разтопения спояващ материал. Имплозивната енергия на кавитацията модифицира повърхността на оксида и премахва мръсотията и оксидите. През това време се образува и слой от сплав. Спойката на повърхността на свързване включва кислород и позволява образуването на силна обща връзка между стъклото и спойката. ПОТАПЯВАНЕТО може да се разглежда като по-опростен вариант на вълново запояване, подходящ само за производство в малък мащаб. Първият почистващ флюс се прилага както при други процеси. ПХБ с монтирани компоненти се потапят ръчно или по полуавтоматичен начин в резервоар, съдържащ разтопен припой. Разтопеният припой полепва върху откритите метални зони, незащитени от маска за запояване на дъската. Оборудването е просто и евтино.
• СЛЕПВАНЕ С ЛЕПИЛО: Това е друга популярна техника, която често използваме и включва залепване на повърхности с помощта на лепила, епоксиди, пластмасови агенти или други химикали. Свързването се осъществява или чрез изпаряване на разтворителя, чрез втвърдяване чрез топлина, чрез втвърдяване чрез UV светлина, чрез втвърдяване под налягане или изчакване за определено време. В нашите производствени линии се използват различни високоефективни лепила. С правилно проектирани процеси на нанасяне и втвърдяване, свързването с лепило може да доведе до връзки с много ниско напрежение, които са здрави и надеждни. Адхезивните връзки могат да бъдат добри предпазители срещу фактори на околната среда като влага, замърсители, корозивни вещества, вибрации и др. Предимствата на адхезивното залепване са: могат да се прилагат към материали, които иначе биха били трудни за запояване, заваряване или спояване. Също така може да бъде за предпочитане за чувствителни на топлина материали, които биха били повредени от заваряване или други високотемпературни процеси. Други предимства на лепилата са, че могат да се нанасят върху повърхности с неправилна форма и увеличават теглото на сглобката с много много малки количества в сравнение с други методи. Също така промените в размерите на частите са много минимални. Някои лепила имат свойства за съвпадение на индекса и могат да се използват между оптични компоненти, без да намаляват значително силата на светлината или оптичния сигнал. Недостатъците от друга страна са по-дълги времена на втвърдяване, което може да забави производствените линии, изисквания за закрепване, изисквания за подготовка на повърхността и трудност при разглобяване, когато е необходима преработка. Повечето от нашите операции по залепване включват следните стъпки:
- Повърхностна обработка: Специални процедури за почистване като почистване с дейонизирана вода, почистване с алкохол, плазмено или коронно почистване са често срещани. След почистване можем да нанесем добавки за адхезия върху повърхностите, за да осигурим възможно най-добри фуги.
- Фиксиране на части: както за нанасяне на лепило, така и за втвърдяване ние проектираме и използваме персонализирани приспособления.
-Нанасяне на лепило: Понякога използваме ръчни, а понякога в зависимост от случая автоматизирани системи като роботика, серво мотори, линейни задвижващи механизми, за да доставяме лепилата на правилното място и използваме дозатори, за да ги доставяме в правилния обем и количество.
-Втвърдяване: В зависимост от лепилото, можем да използваме просто сушене и втвърдяване, както и втвърдяване под ултравиолетови светлини, които действат като катализатор или топлинно втвърдяване във фурна или с помощта на резистивни нагревателни елементи, монтирани на приспособления и приспособления.
Препоръчваме ви да щракнете тук, заИЗТЕГЛЕТЕ нашите схематични илюстрации на процеси на закрепване от AGS-TECH Inc.
Това ще ви помогне да разберете по-добре информацията, която ви предоставяме по-долу.
• ПРОЦЕСИ НА ЗАКРЕПВАНЕ: Нашите процеси на механично съединяване попадат в две категории: КРЕПЕЖИ и ИНТЕГРАЛНИ СЪЕДИНЕНИЯ. Примери за крепежни елементи, които използваме, са винтове, щифтове, гайки, болтове, нитове. Примери за интегрални съединения, които използваме, са щракване и свиване, шевове, гофрове. Използвайки различни методи за закрепване, ние гарантираме, че нашите механични съединения са здрави и надеждни за дълги години употреба. ВИНТОВЕТЕ и БОЛТОВЕТЕ са едни от най-често използваните крепежни елементи за задържане на предмети заедно и позициониране. Нашите винтове и болтове отговарят на стандартите ASME. Разполагат се различни видове винтове и болтове, включително винтове с шестостенна глава и шестостенни болтове, винтове и болтове за изоставане, винт с двоен край, винт за дюбел, винт за окото, винт за огледало, винт за ламарина, винт за фина настройка, самопробивни и самонарезни винтове , фиксиращ винт, винтове с вградени шайби,…и други. Разполагаме с различни типове винтови глави, като вдлъбнати, куполни, кръгли, фланцови глави и различни видове винтови задвижвания, като слот, кръстати, квадратни, шестограмни. RIVET от друга страна е постоянна механична закопчалка, състояща се от гладък цилиндричен вал и глава от една страна. След поставянето другият край на нита се деформира и диаметърът му се разширява, така че да остане на място. С други думи, преди монтажа нитът има една глава, а след монтажа има две. Монтираме различни видове нитове в зависимост от приложението, здравината, достъпността и цената, като нитове с твърда/кръгла глава, структурни, полутръбни, глухи, оскар, задвижващи, изравнени, фрикционни нитове, самопробивни нитове. Занитването може да бъде предпочитано в случаите, когато трябва да се избегне топлинна деформация и промяна в свойствата на материала поради топлината на заваряване. Занитването също предлага леко тегло и особено добра здравина и издръжливост срещу сили на срязване. Срещу натоварвания на опън обаче винтовете, гайките и болтовете може да са по-подходящи. В процеса на КЛИНЧУВАНЕ ние използваме специални щанци и матрици, за да образуваме механична връзка между съединяваните метални листове. Щансът избутва слоевете ламарина в кухината на матрицата и води до образуването на постоянна връзка. Не се изисква нагряване и охлаждане при клинчиране и това е процес на студена работа. Това е икономичен процес, който в някои случаи може да замени точковото заваряване. В ПИНИНГ използваме щифтове, които са машинни елементи, използвани за осигуряване на позиции на машинни части една спрямо друга. Основните типове са щифтове със скоба, шплинт, пружинен щифт, шплинт, и шплинт. В ТЕБЛОДА ние използваме пистолети за телбод и скоби, които са двузъби крепежни елементи, използвани за съединяване или свързване на материали. Телбодът има следните предимства: Икономичен, лесен и бърз за използване, короната на скобите може да се използва за свързване на материали, съединени една в друга, Короната на скобата може да улесни свързването на парче като кабел и закрепването му към повърхност без пробиване или повреждащо, относително лесно отстраняване. ПРЕСОВАНЕТО се извършва чрез натискане на части една в друга и триенето между тях закрепва частите. Притиснатите части, състоящи се от голям вал и малък отвор, обикновено се сглобяват по един от двата метода: или чрез прилагане на сила, или като се възползват от термичното разширение или свиване на частите. Когато пресов фитинг се установява чрез прилагане на сила, ние използваме или хидравлична преса, или ръчно задвижвана преса. От друга страна, когато пресоването се установява чрез термично разширение, ние нагряваме обгръщащите части и ги сглобяваме на мястото им, докато са горещи. Когато изстинат, те се свиват и се връщат към нормалните си размери. Това води до добро прилягане към пресата. Ние наричаме това алтернативно СВИВАНЕ. Другият начин да направите това е като охладите обвитите части преди сглобяването и след това ги плъзнете в техните свързващи части. Когато модулът се загрее, те се разширяват и се получава плътно прилягане. Последният метод може да бъде за предпочитане в случаите, когато нагряването крие риск от промяна на свойствата на материала. Охлаждането е по-безопасно в тези случаи.
Пневматични и хидравлични компоненти и възли
• Вентили, хидравлични и пневматични компоненти като О-пръстен, шайба, уплътнения, уплътнение, пръстен, подложка.
Тъй като клапаните и пневматичните компоненти се предлагат в голямо разнообразие, не можем да изброим всичко тук. В зависимост от физическата и химическата среда на вашето приложение, ние имаме специални продукти за вас. Моля, уточнете ни приложението, вида на компонента, спецификациите, условията на околната среда като налягане, температура, течности или газове, които ще бъдат в контакт с вашите клапани и пневматични компоненти; и ние ще изберем най-подходящия продукт за вас или ще го произведем специално за вашето приложение.