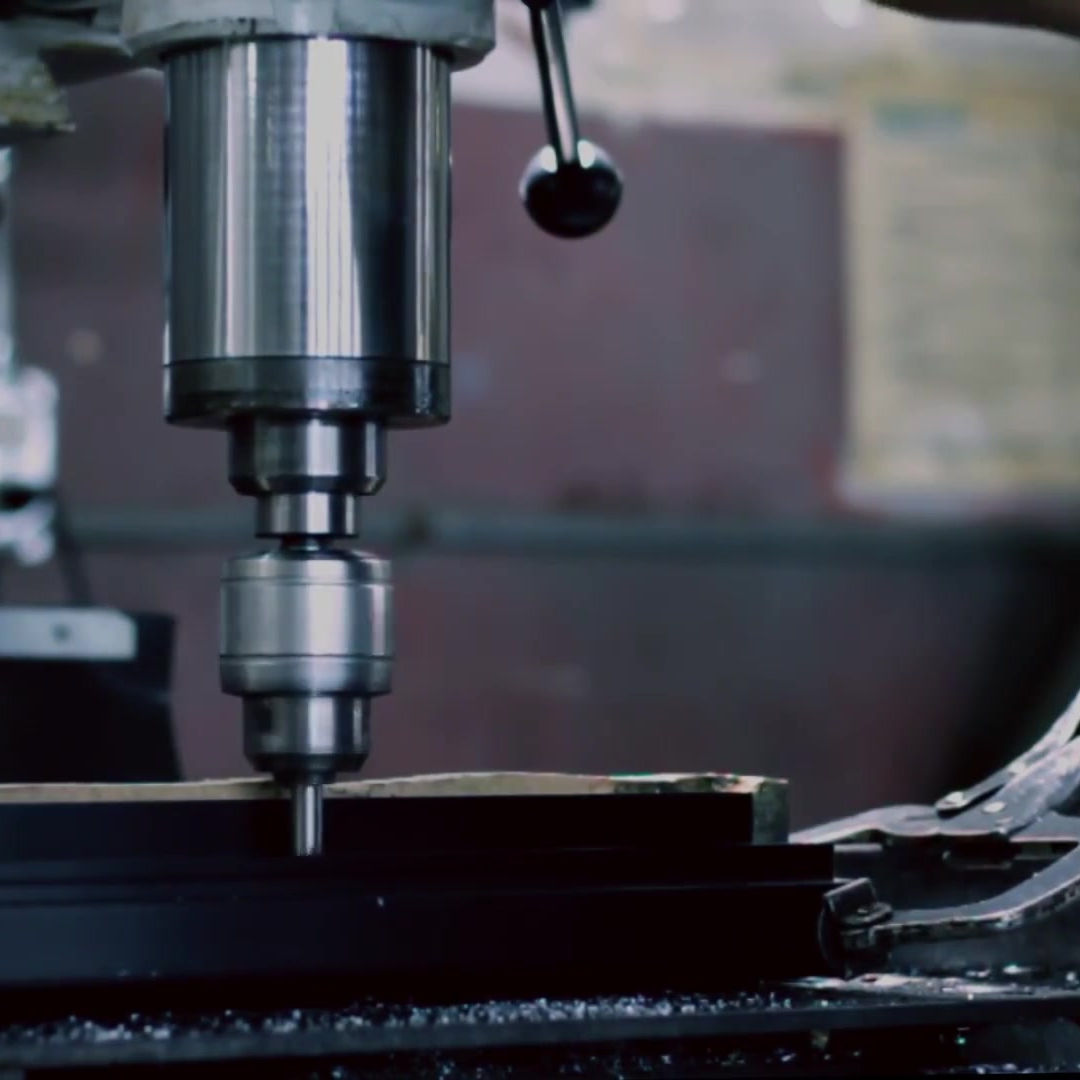
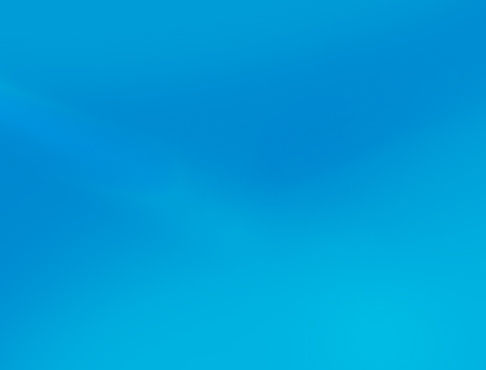
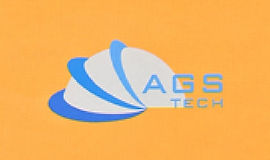
Глобален производител по поръчка, интегратор, консолидатор, аутсорсинг партньор за голямо разнообразие от продукти и услуги.
Ние сме вашият източник на едно гише за производство, производство, инженеринг, консолидация, интеграция, аутсорсинг на произведени по поръчка и готови продукти и услуги.
Изберете своя език
-
Производство по поръчка
-
Вътрешно и глобално договорно производство
-
Аутсорсинг на производство
-
Вътрешни и глобални доставки
-
Консолидация
-
Инженерна интеграция
-
Инженерни услуги
Search Results
164 резултата са намерени с празно търсене
- Transmission Components, Belts, Chains, Cable Drives, Pulleys,AGS-TECH
Transmission Components, Belts, Chains and Cable Drives, Conventional & Grooved or Serrated, Positive Drive, Pulleys Ремъци, вериги и кабелно задвижване AGS-TECH Inc. ви предлага компоненти за предаване на мощност, включително ремъци и вериги и кабелно задвижване. С години на усъвършенстване, нашите гумени, кожени и други ремъчни задвижвания станаха по-леки и по-компактни, способни да носят по-големи товари на по-ниска цена. По същия начин нашите верижни задвижвания са преминали през много развитие с течение на времето и предлагат на нашите клиенти няколко предимства. Някои предимства на използването на верижни задвижвания са техните сравнително неограничени централни разстояния на вала, компактност, лекота на сглобяване, еластичност при опън без приплъзване или пълзене, способност за работа в среда с висока температура. Нашите кабелни задвижвания също предлагат предимства като простота в някои приложения в сравнение с други видове трансмисионни компоненти. Предлагат се както стандартни ремъчни, верижни и кабелни задвижвания, така и изработени и сглобени по поръчка версии. Ние можем да произведем тези трансмисионни компоненти до правилния размер за вашето приложение и от най-подходящите материали. РЕМЪЦИ И РЕМЪЧНИ ЗАДВИЖАНИЯ: - Конвенционални плоски ремъци: Това са обикновени плоски ремъци без зъби, жлебове или назъбвания. Плоските ремъчни задвижвания предлагат гъвкавост, добро поглъщане на удари, ефективно предаване на мощността при високи скорости, устойчивост на абразия, ниска цена. Коланите могат да бъдат снаждани или свързани, за да се направят по-големи колани. Други предимства на конвенционалните плоски ремъци са, че са тънки, не са подложени на високи центробежни натоварвания (което ги прави добри за високоскоростни операции с малки ролки). От друга страна те налагат големи натоварвания на лагерите, тъй като плоските ремъци изискват голямо напрежение. Други недостатъци на плоските ремъчни задвижвания могат да бъдат приплъзване, шумна работа и относително по-ниска ефективност при ниски и умерени скорости на работа. Имаме два вида конвенционални ремъци: армирани и неармирани. Подсилените колани имат елемент на опън в структурата си. Конвенционалните плоски колани се предлагат като кожа, гумирана тъкан или шнур, неармирана гума или пластмаса, плат, подсилена кожа. Кожените колани предлагат дълъг живот, гъвкавост, отличен коефициент на триене, лесен ремонт. Кожените колани обаче са сравнително скъпи, изискват обработка и почистване на колана и в зависимост от атмосферата те могат да се свият или разтегнат. Коланите от гумирана тъкан или корда са устойчиви на влага, киселини и основи. Гумираните колани са съставени от памучни или синтетични пластове, импрегнирани с каучук и са най-икономичните. Гумираните кордови колани се състоят от поредица от пластове импрегнирани с гума корди. Гумираните кордови колани предлагат висока якост на опън и скромен размер и маса. Неподсилените гумени или пластмасови ремъци са подходящи за леки приложения с нискоскоростно задвижване. Неподсилените гумени и пластмасови колани могат да бъдат опънати на място върху техните макари. Пластмасовите неусилени ремъци могат да предават по-висока мощност в сравнение с гумените ремъци. Подсилените кожени колани се състоят от пластмасов елемент за опън, поставен между горния и долния слой на кожата. И накрая, нашите платнени колани могат да се състоят от едно парче памук или патица, сгънато и зашито с редове надлъжни шевове. Тъканните ремъци могат да се движат равномерно и да работят с висока скорост. - Назъбени или назъбени ремъци (като V-образни ремъци): Това са основни плоски ремъци, модифицирани да осигурят предимствата на друг тип трансмисионен продукт. Това са плоски колани с надлъжно оребрена долна страна. Poly-V ремъците са надлъжно набраздени или назъбени плоски ремъци със сечение на опън и серия от съседни V-образни канали за проследяване и компресия. Мощността зависи от ширината на лентата. V-ремъкът е работният кон на индустрията и се предлага в различни стандартизирани размери и типове за предаване на почти всяка мощност на натоварване. Задвижванията с клиновидни ремъци работят добре между 1500 до 6000 фута/мин, но тесните клиновидни ремъци ще работят до 10 000 фута/мин. Задвижванията с клиновидни ремъци предлагат дълъг живот от 3 до 5 години и позволяват големи съотношения на скоростта, те са лесни за инсталиране и демонтиране, предлагат тиха работа, ниска поддръжка, добро поглъщане на удари между задвижващия ремък и задвижваните валове. Недостатъкът на клиновите ремъци е тяхното известно приплъзване и пълзене и следователно те може да не са най-доброто решение, когато се изискват синхронни скорости. Разполагаме с индустриални, автомобилни и селскостопански ремъци. Предлагат се както стандартни дължини, така и дължини по избор на колани. Всички стандартни напречни сечения на клиновидни ремъци са налични от склад. Има таблици, в които можете да изчислите неизвестни параметри като дължина на ремъка, сечение на ремъка (ширина и дебелина), при условие че знаете някои параметри на вашата система, като диаметри на задвижващата и задвижваната ролка, централно разстояние между шайбите и скоростта на въртене на шайбите. Можете да използвате такива таблици или да ни помолите да изберем подходящия клинов ремък за вас. - Позитивни задвижващи ремъци (зъбен ремък): Тези ремъци също са плосък тип с поредица от равномерно разположени зъби по вътрешната обиколка. Позитивните задвижващи или зъбни ремъци комбинират предимствата на плоските ремъци с характеристиките на положителното сцепление на веригите и зъбните колела. Положителните задвижващи ремъци не показват приплъзване или промени в скоростта. Възможен е широк диапазон от съотношения на скоростта. Натоварванията на лагерите са ниски, защото могат да работят при ниско напрежение. Те обаче са по-податливи на несъосност в ролките. - Ролки, ролки, главини за ремъци: Използват се различни видове ремъци с плоски, оребрени (назъбени) и положителни задвижващи ремъци. Ние ги произвеждаме всички. Повечето от нашите макари с плосък ремък са направени чрез отливане на желязо, но стоманените версии също се предлагат в различни комбинации от джанти и главини. Нашите макари с плосък ремък могат да имат твърди главини, със спици или разделени главини или ние можем да произведем, както желаете. Оребрените и задвижващи ремъци се предлагат в различни размери и ширини на склад. Поне една ролка в задвижванията с ангренажен ремък трябва да бъде с фланец, за да поддържа ремъка върху задвижването. За задвижващи системи с дълъг център се препоръчва двете макари да са с фланец. Ролките са набраздени колела на макари и обикновено се произвеждат чрез чугунено леене, формоване на стомана или пластмасово формоване. Формоването на стомана е подходящ процес за производство на автомобилни и селскостопански снопове. Произвеждаме снопове с правилни и дълбоки канали. Ролките с дълбоки канали са много подходящи, когато клиновият ремък влиза в ролката под ъгъл, какъвто е случаят при четвърт оборотни задвижвания. Дълбоките канали също са много подходящи за задвижвания с вертикален вал и приложения, където вибрациите на ремъците могат да бъдат проблем. Нашите наклонени ролки са набраздени ролки или плоски ролки, които не служат за предаване на механична мощност. Наклонните ролки се използват най-вече за затягане на ремъци. - Единични и множество ремъчни задвижвания: Единичните ремъчни задвижвания имат един канал, докато множеството ремъчни задвижвания имат множество канали. Като щракнете върху съответния цветен текст по-долу, можете да изтеглите нашите каталози: - Ремъци за предаване на мощност (включва V-образни ремъци, ангренажни ремъци, ремъци с необработени ръбове, опаковани ремъци и специални ремъци) - Транспортни ленти - V-образни ролки - Синхронизиращи ролки ВЕРИГИ И ВЕРИЖНИ ЗАДВИЖАНИЯ: Нашите вериги за предаване на мощност имат някои предимства като относително неограничени разстояния между центровете на валовете, лесен монтаж, компактност, еластичност при опън без приплъзване или пълзене, способност за работа при високи температури. Ето основните видове наши вериги: - Разглобяеми вериги: Нашите разглобяеми вериги се произвеждат в различни размери, стъпка и крайна якост и обикновено от ковък чугун или стомана. Ковките вериги се произвеждат в диапазон от размери от 0,902 (23 мм) до 4,063 инча (103 мм) стъпка и крайна якост от 700 до 17 000 фунта/квадратен инч. Нашите разглобяеми стоманени вериги от друга страна са направени в размери от 0,904 инча (23 mm) до около 3,00 инча (76 mm) на стъпка, с максимална якост от 760 до 5000 lb/квадратен инч._cc781905-5cde-3194-bb3b- 136bad5cf58d_ - Вериги с щифтове: Тези вериги се използват за по-тежки товари и малко по-високи скорости до около 450 фута/мин (2,2 м/сек). Веригите за щифтове са направени от отделни ляти звена, които имат пълен кръгъл край на цевта с изместени странични ленти. Тези звена на веригата са съединени със стоманени щифтове. Стъпката на тези вериги варира от около 1,00 инча (25 мм) до 6,00 инча (150 мм) и максимална якост между 3600 до 30 000 фунта/квадратен инч. - Вериги с изместена странична греда: Те са популярни в задвижващите вериги на строителни машини. Тези вериги работят при скорости до 1000 ft/min и предават натоварване до около 250 к.с. Обикновено всяка връзка има две изместени странични греди, една втулка, една ролка, един щифт, шплента. - Ролкови вериги: Предлагат се на стъпки от 0,25 (6 mm) до 3,00 (75 mm) инча. Крайната якост на ролковите вериги с една ширина варира между 925 до 130 000 фунта/квадратен инч. Предлагат се версии на ролкови вериги с множество ширини и предават по-голяма мощност при по-високи скорости. Ролковите вериги с множество ширини също предлагат по-плавно действие с намален шум. Ролковите вериги се сглобяват от ролкови звена и щифтови звена. Шплинтите се използват в ролкови вериги с разглобяема версия. Проектирането на ролкови верижни задвижвания изисква експертни познания. Докато ремъчните задвижвания се основават на линейни скорости, верижните задвижвания се основават на скоростта на въртене на по-малкото зъбно колело, което в повечето инсталации е задвижваният елемент. Освен конските сили и скоростта на въртене, дизайнът на верижните задвижвания се основава на много други фактори. - Вериги с двойна стъпка: По принцип същите като ролковите вериги, с изключение на това, че стъпката е два пъти по-дълга. - Вериги с обърнати зъбци (Безшумни): Високоскоростни вериги, използвани най-вече за първични двигатели, задвижващи механизми. Верижните задвижвания с обърнати зъбци могат да предават мощности до 1200 к.с. и са съставени от поредица зъбни връзки, последователно сглобени с щифтове или комбинация от компоненти на съединението. Централната водеща верига има водещи връзки за захващане на канали в зъбното колело, а страничната водеща верига има водачи за захващане на страните на зъбното колело. - Перли или плъзгащи се вериги: Тези вериги се използват за задвижвания с ниска скорост, а също и при ръчни операции. Като щракнете върху съответния цветен текст по-долу, можете да изтеглите нашите каталози: - Задвижващи вериги - Транспортни вериги - Транспортни вериги с голяма стъпка - Ролкови вериги от неръждаема стомана - Подемни вериги - Вериги за мотоциклети - Вериги за селскостопански машини - Зъбни колела: Нашите стандартни зъбни колела отговарят на стандартите ANSI. Пластинчатите зъбни колела са плоски зъбни колела без главина. Нашите малки и средни зъбни колела на главина са струговани от прътов материал или изковки или са направени чрез заваряване на прътов материал към горещо валцована плоча. AGS-TECH Inc. може да достави зъбни колела, машинно изработени от чугунени отливки, лята стомана и заварени конструкции на главини, синтерован прах от метал, формовани или машинно обработени пластмаси. За безпроблемна работа при високи скорости, правилният избор на размера на зъбните колела е от съществено значение. Ограниченията на пространството, разбира се, са фактор, който не можем да пренебрегнем, когато избираме зъбно колело. Препоръчително е съотношението на задвижващите към задвижваните зъбни колела да бъде не повече от 6:1, а обвивката на веригата на задвижващия механизъм да е 120 градуса. Централните разстояния между по-малките и по-големите зъбни колела, дължините на веригата и напрежението на веригата също трябва да бъдат избрани според някои препоръчани инженерни изчисления и насоки, а не произволно. Изтеглете нашите каталози, като щракнете върху цветния текст по-долу: - Зъбни колела и пластинчати колела - Втулки на трансмисията - Верижен съединител - Верижни брави КАБЕЛИ: Те имат своите предимства пред ремъците и верижните задвижвания в някои случаи. Кабелните задвижвания могат да изпълняват същата функция като ремъците и може също да бъдат по-прости и по-икономични за изпълнение в някои приложения. Например, нова серия кабелни задвижвания Synchromesh са проектирани за положително сцепление, за да заменят конвенционалните въжета, прости кабели и зъбни задвижвания, особено в тесни пространства. Новото кабелно задвижване е проектирано да осигурява високо прецизно позициониране в електронно оборудване като копирни машини, плотери, пишещи машини, принтери и т.н. Ключова характеристика на новото кабелно задвижване е способността му да се използва в 3D серпентини конфигурации, които позволяват изключително миниатюрни дизайни. Синхронизираните кабели могат да се използват с по-малко напрежение в сравнение с въжетата, като по този начин се намалява консумацията на енергия. Свържете се с AGS-TECH за въпроси и мнение относно ремъци, верижни и кабелни задвижвания. CLICK Product Finder-Locator Service ПРЕДИШНА СТРАНИЦА
- Composites, Composite Materials Manufacturing, Fiber Reinforced
Composites, Composite Materials Manufacturing, Particle and Fiber Reinforced, Cermets, Ceramic & Metal Composite, Glass Fiber Reinforced Polymer, Lay-Up Process Производство на композитни материали и композитни материали Просто определени, КОМПОЗИТИТЕ или КОМПОЗИТНИТЕ МАТЕРИАЛИ са материали, състоящи се от два или множество материали с различни физични или химични свойства, но когато се комбинират, те стават материал, който е различен от съставните материали. Трябва да отбележим, че съставните материали остават отделни и различни в структурата. Целта при производството на композитен материал е да се получи продукт, който е по-добър от неговите съставки и съчетава желаните характеристики на всяка съставка. Като пример; силата, ниското тегло или по-ниската цена могат да бъдат мотиваторът зад проектирането и производството на композит. Типовете композити, които предлагаме, са композити, подсилени с частици, композити, подсилени с влакна, включително композити с керамична матрица / полимерна матрица / метална матрица / въглерод-въглерод / хибридни композити, структурни и ламинирани и сандвич-структурирани композити и нанокомпозити. Техниките за производство, които използваме в производството на композитни материали, са: пултрузия, производствени процеси на препрег, усъвършенствано поставяне на влакна, навиване на нишки, персонализирано поставяне на влакна, процес на нанасяне на фибростъкло със спрей, туфтинг, процес на ланксид, z-пининг. Много композитни материали са съставени от две фази, матрицата, която е непрекъсната и заобикаля другата фаза; и дисперсната фаза, която е заобиколена от матрицата. Препоръчваме ви да щракнете тук, заИЗТЕГЛЕТЕ нашите схематични илюстрации на композити и производство на композитни материали от AGS-TECH Inc. Това ще ви помогне да разберете по-добре информацията, която ви предоставяме по-долу. • КОМПОЗИТИ, ПОДДЪРНЕНИ С ЧАСТИЦИ: Тази категория се състои от два типа: композити с големи частици и композити, укрепени с дисперсия. В първия тип взаимодействията частица-матрица не могат да бъдат третирани на атомно или молекулярно ниво. Вместо това е валидна механиката на континуума. От друга страна, в дисперсно усилените композити частиците обикновено са много по-малки в диапазона от десетки нанометри. Пример за композит с големи частици са полимери, към които са добавени пълнители. Пълнителите подобряват свойствата на материала и могат да заменят част от обема на полимера с по-икономичен материал. Обемните фракции на двете фази влияят на поведението на композита. Композитите с големи частици се използват с метали, полимери и керамика. CERMETS са примери за керамични / метални композити. Нашият най-разпространен металокерамика е циментиран карбид. Състои се от огнеупорна карбидна керамика като частици от волфрамов карбид в матрица от метал като кобалт или никел. Тези карбидни композити се използват широко като режещи инструменти за закалена стомана. Твърдите карбидни частици са отговорни за действието на рязане и тяхната якост е подобрена от пластичната метална матрица. Така получаваме предимствата на двата материала в един композит. Друг често срещан пример за композит с големи частици, който използваме, са частици от сажди, смесени с вулканизиран каучук, за да се получи композит с висока якост на опън, издръжливост, устойчивост на разкъсване и абразия. Пример за дисперсно укрепен композит са метали и метални сплави, укрепени и закалени чрез равномерно разпръскване на фини частици от много твърд и инертен материал. Когато много малки люспи от алуминиев оксид се добавят към алуминиева метална матрица, ние получаваме синтерован алуминиев прах, който има повишена якост при висока температура. • КОМПОЗИТИ, ПОДДЪРНЕНИ С ВЛАКНА: Тази категория композити всъщност е най-важната. Целта, която трябва да се постигне, е висока якост и твърдост на единица тегло. Съставът на влакната, дължината, ориентацията и концентрацията в тези композити са от решаващо значение за определяне на свойствата и полезността на тези материали. Има три групи влакна, които използваме: мустаци, влакна и телове. WHISKERS са много тънки и дълги монокристали. Те са сред най-здравите материали. Някои примерни материали за мустаци са графит, силициев нитрид, алуминиев оксид. FIBERS от друга страна са предимно полимери или керамика и са в поликристално или аморфно състояние. Третата група са фини ЖИЛИ, които имат относително големи диаметри и се състоят често от стомана или волфрам. Пример за подсилен с тел композит са автомобилните гуми, които включват стоманена тел в гумата. В зависимост от материала на матрицата имаме следните композити: ПОЛИМЕРНО-МАТРИЧНИ КОМПОЗИТИ: Изработени са от полимерна смола и влакна като подсилваща съставка. Подгрупа от тях, наречени композити от подсилени със стъклени влакна полимери (GFRP), съдържат непрекъснати или прекъснати стъклени влакна в полимерна матрица. Стъклото предлага висока якост, икономично е, лесно се произвежда във влакна и е химически инертно. Недостатъците са тяхната ограничена твърдост и твърдост, работните температури са само до 200 – 300 градуса по Целзий. Фибростъклото е подходящо за каросерии на автомобили и транспортно оборудване, каросерии на морски превозни средства, контейнери за съхранение. Те не са подходящи за космическото производство или за създаване на мостове поради ограничена твърдост. Другата подгрупа се нарича композитен полимер, подсилен с въглеродни влакна (CFRP). Тук въглеродът е нашият влакнест материал в полимерната матрица. Въглеродът е известен със своя висок специфичен модул и якост и способността си да ги поддържа при високи температури. Въглеродните влакна могат да ни предложат стандартни, междинни, високи и свръхвисоки модули на опън. Освен това въглеродните влакна предлагат разнообразни физически и механични характеристики и следователно са подходящи за различни инженерни приложения по поръчка. CFRP композитите могат да се считат за производство на спортно и развлекателно оборудване, съдове под налягане и авиационни структурни компоненти. И все пак друга подгрупа, армираните с арамидни влакна полимерни композити също са материали с висока якост и модул. Техните съотношения на якост към тегло са изключително високи. Арамидните влакна са известни и с търговските имена KEVLAR и NOMEX. При напрежение те се представят по-добре от другите материали от полимерни влакна, но са слаби при натиск. Арамидните влакна са здрави, устойчиви на удар, пълзене и умора, стабилни при високи температури, химически инертни, освен срещу силни киселини и основи. Арамидните влакна се използват широко в спортни стоки, бронирани жилетки, гуми, въжета, обвивки на оптични кабели. Съществуват и други материали за армиране с влакна, но се използват в по-малка степен. Това са главно бор, силициев карбид, алуминиев оксид. Материалът на полимерната матрица от друга страна също е критичен. Той определя максималната работна температура на композита, тъй като полимерът обикновено има по-ниска температура на топене и разграждане. Полиестерите и виниловите естери се използват широко като полимерна матрица. Използват се и смоли, които имат отлична устойчивост на влага и механични свойства. Например полиимидната смола може да се използва до около 230 градуса по Целзий. КОМПОЗИТИ С МЕТАЛНА МАТРИЦА: В тези материали ние използваме пластична метална матрица и работните температури обикновено са по-високи от техните съставни компоненти. В сравнение с композитите с полимерна матрица, те могат да имат по-високи работни температури, да бъдат незапалими и може да имат по-добра устойчивост на разграждане срещу органични течности. Те обаче са по-скъпи. Подсилващи материали като нишки, частици, непрекъснати и прекъснати влакна; и масово се използват матрични материали като мед, алуминий, магнезий, титан, суперсплави. Примерни приложения са компоненти на двигателя, изработени от матрица от алуминиева сплав, подсилена с алуминиев оксид и въглеродни влакна. КЕРАМИЧНО-МАТРИЧНИ КОМПОЗИТИ: Керамичните материали са известни със своята изключително добра надеждност при високи температури. Те обаче са много крехки и имат ниски стойности за якост на счупване. Чрез вграждане на частици, влакна или мустаци от една керамика в матрицата на друга ние сме в състояние да постигнем композити с по-висока якост на счупване. Тези вградени материали основно възпрепятстват разпространението на пукнатини вътре в матрицата чрез някои механизми като отклоняване на върховете на пукнатините или образуване на мостове през повърхностите на пукнатините. Като пример, алуминиевият оксид, който е подсилен със SiC нишки, се използва като вложки за режещи инструменти за обработка на твърди метални сплави. Те могат да разкрият по-добри характеристики в сравнение с циментираните карбиди. ВЪГЛЕРОД-ВЪГЛЕРОДНИ КОМПОЗИТИ: Както армировката, така и матрицата са въглеродни. Те имат високи модули на опън и якост при високи температури над 2000 градуса по Целзий, устойчивост на пълзене, висока якост на счупване, ниски коефициенти на термично разширение, висока топлопроводимост. Тези свойства ги правят идеални за приложения, изискващи устойчивост на термичен удар. Слабостта на въглерод-въглеродните композити обаче е тяхната уязвимост срещу окисление при високи температури. Типични примери за използване са горещо пресовани форми, усъвършенствано производство на компоненти на турбинни двигатели. ХИБРИДНИ КОМПОЗИТИ: Два или повече различни вида влакна се смесват в една матрица. По този начин човек може да приспособи нов материал с комбинация от свойства. Пример е, когато както въглеродните, така и стъклените влакна са включени в полимерна смола. Въглеродните влакна осигуряват твърдост и здравина с ниска плътност, но са скъпи. Стъклото от друга страна е евтино, но му липсва твърдостта на въглеродните влакна. Стъкло-въглеродният хибриден композит е по-здрав и по-здрав и може да бъде произведен на по-ниска цена. ОБРАБОТКА НА КОМПОЗИТИ, ПОДДЪРНЕНИ С ВЛАКНА: За непрекъснати подсилени с влакна пластмаси с равномерно разпределени влакна, ориентирани в една и съща посока, ние използваме следните техники. PULTRUSION: Произвеждат се пръти, греди и тръби с непрекъснати дължини и постоянни напречни сечения. Ровингите с непрекъснати влакна се импрегнират с термореактивна смола и се изтеглят през стоманена матрица, за да се оформят предварително в желаната форма. След това те преминават през прецизно обработена матрица за втвърдяване, за да постигнат крайната си форма. Тъй като матрицата за втвърдяване се нагрява, тя втвърдява матрицата от смола. Тегличите изтеглят материала през матриците. Използвайки вложени кухи сърца, ние можем да получим тръби и кухи геометрии. Методът на пултрузия е автоматизиран и ни предлага висока производителност. Всякаква дължина на продукта е възможна за производство. ПРОИЗВОДСТВЕН ПРОЦЕС НА ПРЕДВАРИТЕЛНИ ПРЕПРЕГИ: Препрегът е армировка от непрекъснати влакна, предварително импрегнирана с частично втвърдена полимерна смола. Той се използва широко за структурни приложения. Материалът идва под формата на лента и се изпраща като лента. Производителят го формира директно и го втвърдява напълно, без да е необходимо да добавя смола. Тъй като препрегите претърпяват реакции на втвърдяване при стайна температура, те се съхраняват при 0 градуса по Целзий или по-ниски температури. След употреба останалите ленти се съхраняват обратно при ниски температури. Използват се термопластични и термореактивни смоли, а усилващите влакна от въглерод, арамид и стъкло са обичайни. За да използвате предварително импрегнирани материали, носещата хартия първо се отстранява и след това производството се извършва чрез полагане на предварително импрегнираната лента върху обработена с инструменти повърхност (процесът на поставяне). Няколко слоя могат да бъдат положени, за да се получат желаните дебелини. Честа практика е да се редува ориентацията на влакната, за да се получи ламинат с напречен или ъглов слой. Накрая се прилагат топлина и налягане за втвърдяване. Както ръчната обработка, така и автоматизираните процеси се използват за рязане на препреги и поставяне. НАМОТВАНЕ НА НИШКИ: Непрекъснатите подсилващи влакна са точно позиционирани в предварително определен модел, за да следват куха и обикновено кръгла форма. Влакната първо преминават през баня със смола и след това се навиват върху дорник от автоматизирана система. След няколко повторения на навиване се получават желаните дебелини и втвърдяването се извършва при стайна температура или в пещ. Сега дорникът се отстранява и продуктът се изважда от формата. Намотаването на нишките може да предложи много високи съотношения на якост към тегло чрез навиване на влакната в периферни, спирални и полярни модели. Тръби, резервоари, обвивки се произвеждат с помощта на тази техника. • СТРУКТУРНИ КОМПОЗИТИ: Обикновено те са съставени както от хомогенни, така и от композитни материали. Следователно свойствата им се определят от съставните материали и геометричния дизайн на елементите. Ето основните видове: ЛАМИНАРНИ КОМПОЗИТИ: Тези структурни материали са направени от двуизмерни листове или панели с предпочитани посоки с висока якост. Слоевете се подреждат и циментират заедно. Чрез редуване на посоките на висока якост в двете перпендикулярни оси, ние получаваме композит, който има висока якост и в двете посоки в двуизмерната равнина. Чрез регулиране на ъглите на слоевете може да се произведе композит със здравина в предпочитаните посоки. Модерните ски се произвеждат по този начин. САНДВИЧ ПАНЕЛИ: Тези структурни композитни материали са леки, но въпреки това имат висока твърдост и здравина. Сандвич панелите се състоят от два външни листа, изработени от твърд и здрав материал като алуминиеви сплави, подсилени с влакна пластмаси или стомана и сърцевина между външните листове. Сърцевината трябва да е лека и през повечето време да има нисък модул на еластичност. Популярни основни материали са твърда полимерна пяна, дърво и пчелни пити. Сандвич панелите се използват широко в строителната индустрия като покривен материал, под или стенен материал, а също и в космическата индустрия. • НАНОКОМПОЗИТИ: Тези нови материали се състоят от наноразмерни частици, вградени в матрица. Използвайки нанокомпозити, ние можем да произвеждаме каучукови материали, които са много добри бариери за проникване на въздух, като същевременно поддържат своите каучукови свойства непроменени. CLICK Product Finder-Locator Service ПРЕДИШНА СТРАНИЦА
- Joining & Assembly & Fastening Processes, Welding, Brazing, Soldering
Joining & Assembly & Fastening Processes, Welding, Brazing, Soldering, Sintering, Adhesive Bonding, Press Fitting, Wave and Reflow Solder Process, Torch Furnace Процеси на свързване, сглобяване и закрепване Ние съединяваме, сглобяваме и закрепваме вашите произведени части и ги превръщаме в завършени или полуготови продукти чрез ЗАВАРЯВАНЕ, СПОЯВАНЕ, ЗАПОЯВАНЕ, СПИТОЧАНЕ, СВЪРЗВАНЕ С ЛЕПИЛО, ЗАКРЕПВАНЕ, ПРЕСОВАНЕ. Някои от нашите най-популярни процеси на заваряване са дъгово заваряване, заваряване с кислородно гориво, съпротивление, проекция, шев, разместване, ударно заваряване, твърдо състояние, електронен лъч, лазерно, термитно, индукционно заваряване. Нашите популярни процеси на запояване са горелка, индукция, пещ и потапяне. Нашите методи за запояване са ютия, котлон, фурна, индукция, потапяне, вълна, претопяване и ултразвуково запояване. За адхезивно залепване ние често използваме термопласти и термореактивни, епоксиди, феноли, полиуретан, лепилни сплави, както и някои други химикали и ленти. И накрая, нашите процеси на закрепване се състоят от заковаване, завинтване, гайки и болтове, занитване, заклинване, закрепване, зашиване и телбод и пресоване. • ЗАВАРЯВАНЕ: Заваряването включва свързване на материали чрез разтопяване на детайлите и въвеждане на добавъчни материали, които също се съединяват с разтопената заваръчна вана. Когато мястото се охлади, получаваме здрава фуга. В някои случаи се прилага натиск. За разлика от заваряването, операциите по спояване и запояване включват само топене на материал с по-ниска точка на топене между детайлите и детайлите не се топят. Препоръчваме ви да щракнете тук, заИЗТЕГЛЕТЕ нашите схематични илюстрации на заваръчни процеси от AGS-TECH Inc. Това ще ви помогне да разберете по-добре информацията, която ви предоставяме по-долу. При ДЪГОВО ЗАВАРЯВАНЕ ние използваме захранване и електрод, за да създадем електрическа дъга, която разтопява металите. Точката на заваряване е защитена със защитен газ или пара или друг материал. Този процес е популярен за заваряване на автомобилни части и стоманени конструкции. При електродъгово заваряване с метална дъга (SMAW) или известно още като заваряване с пръчка, електродна пръчка се доближава до основния материал и между тях се генерира електрическа дъга. Електродният прът се топи и действа като пълнежен материал. Електродът също така съдържа флюс, който действа като слой шлака и отделя пари, които действат като защитен газ. Те предпазват зоната на заваряване от замърсяване на околната среда. Не се използват други пълнители. Недостатъците на този процес са неговата бавност, необходимостта от честа смяна на електродите, необходимостта да се отстрани остатъчната шлака, произхождаща от флюса. Редица метали като желязо, стомана, никел, алуминий, мед… и др. Може да се заварява. Неговите предимства са евтините инструменти и лекотата на използване. Газово електродъгово заваряване (GMAW), известно също като метално-инертен газ (MIG), имаме непрекъснато подаване на консумативен пълнител за електродна тел и инертен или частично инертен газ, който тече около телта срещу замърсяване на околната среда на заваръчната област. Могат да се заваряват стомана, алуминий и други цветни метали. Предимствата на MIG са високите скорости на заваряване и доброто качество. Недостатъците са сложното му оборудване и предизвикателствата, с които се сблъскваме във ветровита външна среда, тъй като трябва да поддържаме стабилен защитния газ около зоната за заваряване. Разновидност на GMAW е дъгово заваряване с флюсова сърцевина (FCAW), което се състои от фина метална тръба, пълна с флюсови материали. Понякога потокът вътре в тръбата е достатъчен за защита от замърсяване на околната среда. Заваряването под флюс (SAW) е автоматизиран процес, който включва непрекъснато подаване на тел и дъга, която се запалва под слой покритие от флюс. Производствените нива и качество са високи, заваръчната шлака се отделя лесно и имаме работна среда без дим. Недостатъкът е, че може да се използва само за заваряване на части в определени позиции. При заваряване с волфрамова дъга (GTAW) или заваряване с волфрам и инертен газ (TIG) използваме волфрамов електрод заедно с отделен пълнител и инертни или почти инертни газове. Както знаем, волфрамът има висока точка на топене и е много подходящ метал за много високи температури. Волфрамът в TIG не се изразходва за разлика от другите методи, обяснени по-горе. Бавна, но висококачествена заваръчна техника с предимство пред другите техники за заваряване на тънки материали. Подходящ за много метали. Заваряването с плазмена дъга е подобно, но използва плазмен газ за създаване на дъга. Дъгата при плазмено-дъгово заваряване е относително по-концентрирана в сравнение с GTAW и може да се използва за по-широк диапазон от дебелини на метала при много по-високи скорости. GTAW и плазменодъгово заваряване могат да се прилагат към повече или по-малко еднакви материали. ЗАВАРЯВАНЕ НА КИСЛОРОДНО ГОРИВО / КИСЛОРОДНО ГОРИВО, наричано още кислородно-ацетиленово заваряване, кислородно заваряване, газово заваряване се извършва с използване на газови горива и кислород за заваряване. Тъй като не се използва електричество, той е преносим и може да се използва там, където няма електричество. С помощта на заваръчна горелка ние нагряваме парчетата и пълнежния материал, за да произведем общ резервоар от разтопен метал. Могат да се използват различни горива като ацетилен, бензин, водород, пропан, бутан… и др. При заваряване с кислородно гориво използваме два контейнера, единият за горивото, а другият за кислорода. Кислородът окислява горивото (изгаря го). СЪПРОТИВНО ЗАВАРЯВАНЕ: Този тип заваряване се възползва от нагряването с джаул и топлината се генерира на мястото, където се прилага електрически ток за определено време. Силни токове преминават през метала. На това място се образуват басейни от разтопен метал. Методите за електросъпротивително заваряване са популярни поради тяхната ефективност и малък потенциал за замърсяване. Недостатъците обаче са, че разходите за оборудване са относително значителни и присъщото ограничение до относително тънки детайли. ТОЧКОВОТО ЗАВАРЯВАНЕ е един от основните видове съпротивително заваряване. Тук съединяваме два или повече припокриващи се листа или детайли, като използваме два медни електрода, за да захванем листовете заедно и да прекараме силен ток през тях. Материалът между медните електроди се нагрява и на това място се генерира разтопен басейн. След това токът се спира и върховете на медните електроди охлаждат мястото на заварката, тъй като електродите се охлаждат с вода. Прилагането на точното количество топлина към правилния материал и дебелина е от ключово значение за тази техника, защото ако се приложи неправилно, фугата ще бъде слаба. Точковото заваряване има предимствата, че не причинява значителна деформация на детайлите, енергийна ефективност, лекота на автоматизация и изключителни производствени нива и не изисква никакви пълнители. Недостатъкът е, че тъй като заваряването се извършва на места, вместо да се образува непрекъснат шев, общата якост може да бъде относително по-ниска в сравнение с други методи на заваряване. ЗАВАРЯВАНЕТО НА ШЕВА, от друга страна, създава заварки на прилежащите повърхности на подобни материали. Шевът може да бъде челно или с припокриване. Заваряването на шевове започва от единия край и се придвижва постепенно към другия. Този метод също така използва два електрода от мед за прилагане на налягане и ток към заваръчната област. Електродите във формата на диск се въртят с постоянен контакт по линията на шева и правят непрекъсната заварка. И тук електродите се охлаждат с вода. Заварките са много здрави и надеждни. Други методи са техники за прожектиране, светкавично заваряване и заваряване с изместване. ЗАВАРЯВАНЕТО В ТВЪРДО ТЪРДО ТЪРДО ТЯЛО е малко по-различно от предишните методи, обяснени по-горе. Коалесценцията се извършва при температури под температурата на топене на съединените метали и без използване на метален пълнител. В някои процеси може да се използва налягане. Различни методи са КОЕКСТРУЗИОННО ЗАВАРЯВАНЕ, при което различни метали се екструдират през една и съща матрица, СТУДЕНО ЗАВАРЯВАНЕ ПОД НАЛЯГАНЕ, при което съединяваме меки сплави под техните точки на топене, ДИФУЗИОННО ЗАВАРЯВАНЕ техника без видими заваръчни линии, ЕКСПЛОЗИОННО ЗАВАРЯВАНЕ за свързване на различни материали, напр. устойчиви на корозия сплави към структурни стомани, ЕЛЕКТРОМАГНИТНО ИМПУЛСНО ЗАВАРЯВАНЕ, при което ускоряваме тръби и листове чрез електромагнитни сили, КОВАЧЕСКО ЗАВАРЯВАНЕ, което се състои от нагряване на металите до високи температури и заковаването им заедно, ЗАВАРЯВАНЕ С ТЪРЕНИЕ, при което се извършва заваряване с достатъчно триене, ЗАВАРЯВАНЕ С ТЪРЕНИЕ, което включва въртящ се не- консумативен инструмент, пресичащ линията на съединението, ГОРЕЩО ЗАВАРЯВАНЕ ПОД НАЛЯГАНЕ, при което притискаме металите заедно при повишени температури под температурата на топене във вакуум или инертни газове, ГОРЕЩО ЗАВАРЯВАНЕ ПРЕДУ ИЗОСТАТИЧНО НАЛЯГАНЕ процес, при който прилагаме налягане с помощта на инертни газове вътре в съд, ЗАВАРЯВАНЕ НА РОЛКИ, при което съединяваме различни материали, като ги поставяте между тях две въртящи се колела, УЛТРАЗВУКОВО ЗАВАРЯВАНЕ, където тънки метални или пластмасови листове се заваряват с помощта на високочестотна вибрационна енергия. Другите ни заваръчни процеси са ЕЛЕКТРОННО ЛЪЧЕВО ЗАВАРЯВАНЕ с дълбоко проникване и бърза обработка, но тъй като е скъп метод, считаме го за специални случаи, ЕЛЕКТРОШЛАКОВО ЗАВАРЯВАНЕ метод, подходящ само за тежки дебели плочи и детайли от стомана, ИНДУКЦИОННО ЗАВАРЯВАНЕ, при което използваме електромагнитна индукция и загряване на нашите електропроводими или феромагнитни детайли, ЗАВАРЯВАНЕ С ЛАЗЕРЕН ЛЪЧ също с дълбоко проникване и бърза обработка, но скъп метод, ЛАЗЕРНО ХИБРИДНО ЗАВАРЯВАНЕ, което комбинира LBW с GMAW в една и съща заваръчна глава и способно да преодолява празнини от 2 mm между плочите, УДАРНО ЗАВАРЯВАНЕ, което включва електрически разряд, последван от коване на материалите с приложен натиск, ТЕРМИТНО ЗАВАРЯВАНЕ, включващо екзотермична реакция между прахове от алуминий и железен оксид, ЕЛЕКТРОГАЗОВО ЗАВАРЯВАНЕ с консумативни електроди и използвано само със стомана във вертикално положение и накрая ДЪГОВО ЗАВАРЯВАНЕ НА ШПИЛКА за свързване на шпилка към основата материал с топлина и налягане. Препоръчваме ви да щракнете тук, заИЗТЕГЛЕТЕ нашите схематични илюстрации на процеси на спояване, запояване и залепване от AGS-TECH Inc Това ще ви помогне да разберете по-добре информацията, която ви предоставяме по-долу. • ЗАПОЯВАНЕ: Свързваме два или повече метала чрез нагряване на добавъчни метали между тях над техните точки на топене и използване на капилярно действие за разпръскване. Процесът е подобен на запояване, но температурите, свързани с разтопяването на пълнителя, са по-високи при запояване. Както при заваряването, флюсът защитава пълнежния материал от атмосферно замърсяване. След охлаждане детайлите се съединяват. Процесът включва следните ключови стъпки: добро прилягане и хлабина, правилно почистване на основните материали, правилно фиксиране, правилен поток и избор на атмосфера, нагряване на сглобката и накрая почистване на запоената сглобка. Някои от нашите процеси на запояване са ЗАПОЯВАНЕ С ГОРЕЛ, популярен метод, извършван ръчно или по автоматизиран начин. Той е подходящ за малки производствени поръчки и специализирани случаи. Топлината се прилага с помощта на газови пламъци близо до съединението, което се споява. ЗАПОЯВАНЕТО В ПЕЩТА изисква по-малко умения на оператора и е полуавтоматичен процес, подходящ за промишлено масово производство. Както контролът на температурата, така и контролът на атмосферата в пещта са предимства на тази техника, тъй като първото ни позволява да имаме контролирани топлинни цикли и да елиминираме локалното нагряване, какъвто е случаят при запояване с горелка, а второто предпазва частта от окисляване. Използвайки jigging ние сме в състояние да намалим производствените разходи до минимум. Недостатъците са висока консумация на енергия, разходи за оборудване и по-предизвикателни съображения за проектиране. ВАКУУМНОТО ЗАПОЯВАНЕ се извършва във вакуумна пещ. Поддържа се еднородност на температурата и се получават много чисти съединения без флюс с много малко остатъчни напрежения. Топлинни обработки могат да се извършват по време на вакуумно спояване, поради ниските остатъчни напрежения, налични по време на бавни цикли на нагряване и охлаждане. Основният недостатък е високата му цена, тъй като създаването на вакуумна среда е скъп процес. Друга техника DIP BRAZING съединява неподвижни части, където спояващото съединение се нанася върху свързващите повърхности. След това фиксираните части се потапят във вана с разтопена сол като натриев хлорид (трапезна сол), която действа като топлопреносна среда и флюс. Въздухът е изключен и следователно не се образува оксид. При ИНДУКЦИОННОТО СПОЯВАНЕ ние съединяваме материали чрез добавъчен метал, който има по-ниска точка на топене от основните материали. Променливият ток от индукционната намотка създава електромагнитно поле, което индуцира индукционно нагряване на предимно железни магнитни материали. Методът осигурява селективно нагряване, добри фуги с пълнители, течащи само в желаните зони, малко окисление, тъй като няма пламъци и охлаждането е бързо, бързо нагряване, консистенция и пригодност за производство в голям обем. За да ускорим нашите процеси и да осигурим последователност, ние често използваме заготовки. Информация за нашето съоръжение за спояване, произвеждащо фитинги от керамика към метал, херметично запечатване, вакуумни канали, компоненти за висок и свръхвисок вакуум и контрол на течности може да бъде намерена тук: Брошура на завода за спояване • ЗАПОЯВАНЕ: При запояването нямаме стапяне на детайлите, а допълнителен метал с по-ниска точка на топене от съединителните части, който се влива в съединението. Добавъчният метал при запояване се топи при по-ниска температура, отколкото при спояване. Ние използваме безоловни сплави за запояване и имаме съответствие с RoHS и за различни приложения и изисквания имаме различни и подходящи сплави като сребърна сплав. Запояването ни предлага съединения, които не пропускат газ и течности. При МЕКО ЗАПОЯВАНЕ нашият добавъчен метал има точка на топене под 400 градуса по Целзий, докато при СРЕБЪРНО ЗАПОЯВАНЕ и СПОЙКА се нуждаем от по-високи температури. Мекото запояване използва по-ниски температури, но не води до здрави съединения за взискателни приложения при повишени температури. Запояването със сребро, от друга страна, изисква високи температури, осигурени от горелката, и ни дава здрави съединения, подходящи за приложения при висока температура. Спояването изисква най-високи температури и обикновено се използва горелка. Тъй като спояващите фуги са много здрави, те са добри кандидати за ремонт на тежки железни предмети. В нашите производствени линии ние използваме както ръчно ръчно запояване, така и автоматизирани линии за запояване. ИНДУКЦИОННОТО ЗАПОЯВАНЕ използва високочестотен променлив ток в медна бобина, за да улесни индукционното нагряване. В запоената част се индуцират токове и в резултат се генерира топлина при високото съпротивление joint. Тази топлина разтопява добавъчния метал. Използва се и флюс. Индукционното запояване е добър метод за запояване на цилиндри и тръби в непрекъснат процес чрез увиване на намотките около тях. Запояването на някои материали като графит и керамика е по-трудно, защото изисква покритие на детайлите с подходящ метал преди запояване. Това улеснява междинното свързване. Ние запояваме такива материали специално за херметични опаковъчни приложения. Ние произвеждаме нашите печатни платки (PCB) в голям обем най-вече чрез ВЪЛНОВО ЗАПОЯВАНЕ. Само за малки количества с цел създаване на прототипи ние използваме ръчно запояване с помощта на поялник. Ние използваме вълново запояване както за сквозни отвори, така и за модули за печатни платки за повърхностен монтаж (PCBA). Временно лепило държи компонентите прикрепени към печатната платка и модулът се поставя върху конвейер и се движи през оборудване, което съдържа разтопена спойка. Първо печатната платка се флюсира и след това влиза в зоната за предварително нагряване. Разтопената спойка е в тиган и има шарка от стоящи вълни на повърхността си. Когато печатната платка се движи над тези вълни, тези вълни влизат в контакт с дъното на печатната платка и се придържат към подложките за запояване. Спойката остава само върху щифтове и подложки, а не върху самата печатна платка. Вълните в разтопената спойка трябва да бъдат добре контролирани, така че да няма пръски и върховете на вълните да не докосват и замърсяват нежелани зони на платките. При REFLOW SOLDERING ние използваме лепкава спояваща паста за временно закрепване на електронните компоненти към платките. След това плоскостите преминават през пещ за повторно оформяне с контрол на температурата. Тук спойката се топи и свързва компонентите трайно. Използваме тази техника както за компоненти за повърхностен монтаж, така и за компоненти с отвори. Правилният контрол на температурата и регулирането на температурите на фурната е от съществено значение, за да се избегне разрушаването на електронните компоненти на платката чрез прегряването им над техните максимални температурни граници. В процеса на запояване с преплавяне всъщност имаме няколко региона или етапа, всеки с различен термичен профил, като етап на предварително нагряване, етап на термично накисване, етап на преплавяне и охлаждане. Тези различни стъпки са от съществено значение за безвредно повторно запояване на печатни платки (PCBA). УЛТРАЗВУКОВОТО ЗАПОЯВАНЕ е друга често използвана техника с уникални възможности - може да се използва за запояване на стъкло, керамика и неметални материали. Например фотоволтаичните панели, които са неметални, се нуждаят от електроди, които могат да бъдат закрепени с помощта на тази техника. При ултразвуковото запояване ние използваме нагрят поялник, който също излъчва ултразвукови вибрации. Тези вибрации създават кавитационни мехурчета на границата на субстрата с разтопения спояващ материал. Имплозивната енергия на кавитацията модифицира повърхността на оксида и премахва мръсотията и оксидите. През това време се образува и слой от сплав. Спойката на повърхността на свързване включва кислород и позволява образуването на силна обща връзка между стъклото и спойката. ПОТАПЯВАНЕТО може да се разглежда като по-опростен вариант на вълново запояване, подходящ само за производство в малък мащаб. Първият почистващ флюс се прилага както при други процеси. ПХБ с монтирани компоненти се потапят ръчно или по полуавтоматичен начин в резервоар, съдържащ разтопен припой. Разтопеният припой полепва върху откритите метални зони, незащитени от маска за запояване на дъската. Оборудването е просто и евтино. • СЛЕПВАНЕ С ЛЕПИЛО: Това е друга популярна техника, която често използваме и включва залепване на повърхности с помощта на лепила, епоксиди, пластмасови агенти или други химикали. Свързването се осъществява или чрез изпаряване на разтворителя, чрез втвърдяване чрез топлина, чрез втвърдяване чрез UV светлина, чрез втвърдяване под налягане или изчакване за определено време. В нашите производствени линии се използват различни високоефективни лепила. С правилно проектирани процеси на нанасяне и втвърдяване, свързването с лепило може да доведе до връзки с много ниско напрежение, които са здрави и надеждни. Адхезивните връзки могат да бъдат добри предпазители срещу фактори на околната среда като влага, замърсители, корозивни вещества, вибрации и др. Предимствата на адхезивното залепване са: могат да се прилагат към материали, които иначе биха били трудни за запояване, заваряване или спояване. Също така може да бъде за предпочитане за чувствителни на топлина материали, които биха били повредени от заваряване или други високотемпературни процеси. Други предимства на лепилата са, че могат да се нанасят върху повърхности с неправилна форма и увеличават теглото на сглобката с много много малки количества в сравнение с други методи. Също така промените в размерите на частите са много минимални. Някои лепила имат свойства за съвпадение на индекса и могат да се използват между оптични компоненти, без да намаляват значително силата на светлината или оптичния сигнал. Недостатъците от друга страна са по-дълги времена на втвърдяване, което може да забави производствените линии, изисквания за закрепване, изисквания за подготовка на повърхността и трудност при разглобяване, когато е необходима преработка. Повечето от нашите операции по залепване включват следните стъпки: - Повърхностна обработка: Специални процедури за почистване като почистване с дейонизирана вода, почистване с алкохол, плазмено или коронно почистване са често срещани. След почистване можем да нанесем добавки за адхезия върху повърхностите, за да осигурим възможно най-добри фуги. - Фиксиране на части: както за нанасяне на лепило, така и за втвърдяване ние проектираме и използваме персонализирани приспособления. -Нанасяне на лепило: Понякога използваме ръчни, а понякога в зависимост от случая автоматизирани системи като роботика, серво мотори, линейни задвижващи механизми, за да доставяме лепилата на правилното място и използваме дозатори, за да ги доставяме в правилния обем и количество. -Втвърдяване: В зависимост от лепилото, можем да използваме просто сушене и втвърдяване, както и втвърдяване под ултравиолетови светлини, които действат като катализатор или топлинно втвърдяване във фурна или с помощта на резистивни нагревателни елементи, монтирани на приспособления и приспособления. Препоръчваме ви да щракнете тук, заИЗТЕГЛЕТЕ нашите схематични илюстрации на процеси на закрепване от AGS-TECH Inc. Това ще ви помогне да разберете по-добре информацията, която ви предоставяме по-долу. • ПРОЦЕСИ НА ЗАКРЕПВАНЕ: Нашите процеси на механично съединяване попадат в две категории: КРЕПЕЖИ и ИНТЕГРАЛНИ СЪЕДИНЕНИЯ. Примери за крепежни елементи, които използваме, са винтове, щифтове, гайки, болтове, нитове. Примери за интегрални съединения, които използваме, са щракване и свиване, шевове, гофрове. Използвайки различни методи за закрепване, ние гарантираме, че нашите механични съединения са здрави и надеждни за дълги години употреба. ВИНТОВЕТЕ и БОЛТОВЕТЕ са едни от най-често използваните крепежни елементи за задържане на предмети заедно и позициониране. Нашите винтове и болтове отговарят на стандартите ASME. Разполагат се различни видове винтове и болтове, включително винтове с шестостенна глава и шестостенни болтове, винтове и болтове за изоставане, винт с двоен край, винт за дюбел, винт за окото, винт за огледало, винт за ламарина, винт за фина настройка, самопробивни и самонарезни винтове , фиксиращ винт, винтове с вградени шайби,…и други. Разполагаме с различни типове винтови глави, като вдлъбнати, куполни, кръгли, фланцови глави и различни видове винтови задвижвания, като слот, кръстати, квадратни, шестограмни. RIVET от друга страна е постоянна механична закопчалка, състояща се от гладък цилиндричен вал и глава от една страна. След поставянето другият край на нита се деформира и диаметърът му се разширява, така че да остане на място. С други думи, преди монтажа нитът има една глава, а след монтажа има две. Монтираме различни видове нитове в зависимост от приложението, здравината, достъпността и цената, като нитове с твърда/кръгла глава, структурни, полутръбни, глухи, оскар, задвижващи, изравнени, фрикционни нитове, самопробивни нитове. Занитването може да бъде предпочитано в случаите, когато трябва да се избегне топлинна деформация и промяна в свойствата на материала поради топлината на заваряване. Занитването също предлага леко тегло и особено добра здравина и издръжливост срещу сили на срязване. Срещу натоварвания на опън обаче винтовете, гайките и болтовете може да са по-подходящи. В процеса на КЛИНЧУВАНЕ ние използваме специални щанци и матрици, за да образуваме механична връзка между съединяваните метални листове. Щансът избутва слоевете ламарина в кухината на матрицата и води до образуването на постоянна връзка. Не се изисква нагряване и охлаждане при клинчиране и това е процес на студена работа. Това е икономичен процес, който в някои случаи може да замени точковото заваряване. В ПИНИНГ използваме щифтове, които са машинни елементи, използвани за осигуряване на позиции на машинни части една спрямо друга. Основните типове са щифтове със скоба, шплинт, пружинен щифт, шплинт, и шплинт. В ТЕБЛОДА ние използваме пистолети за телбод и скоби, които са двузъби крепежни елементи, използвани за съединяване или свързване на материали. Телбодът има следните предимства: Икономичен, лесен и бърз за използване, короната на скобите може да се използва за свързване на материали, съединени една в друга, Короната на скобата може да улесни свързването на парче като кабел и закрепването му към повърхност без пробиване или повреждащо, относително лесно отстраняване. ПРЕСОВАНЕТО се извършва чрез натискане на части една в друга и триенето между тях закрепва частите. Притиснатите части, състоящи се от голям вал и малък отвор, обикновено се сглобяват по един от двата метода: или чрез прилагане на сила, или като се възползват от термичното разширение или свиване на частите. Когато пресов фитинг се установява чрез прилагане на сила, ние използваме или хидравлична преса, или ръчно задвижвана преса. От друга страна, когато пресоването се установява чрез термично разширение, ние нагряваме обгръщащите части и ги сглобяваме на мястото им, докато са горещи. Когато изстинат, те се свиват и се връщат към нормалните си размери. Това води до добро прилягане към пресата. Ние наричаме това алтернативно СВИВАНЕ. Другият начин да направите това е като охладите обвитите части преди сглобяването и след това ги плъзнете в техните свързващи части. Когато модулът се загрее, те се разширяват и се получава плътно прилягане. Последният метод може да бъде за предпочитане в случаите, когато нагряването крие риск от промяна на свойствата на материала. Охлаждането е по-безопасно в тези случаи. Пневматични и хидравлични компоненти и възли • Вентили, хидравлични и пневматични компоненти като О-пръстен, шайба, уплътнения, уплътнение, пръстен, подложка. Тъй като клапаните и пневматичните компоненти се предлагат в голямо разнообразие, не можем да изброим всичко тук. В зависимост от физическата и химическата среда на вашето приложение, ние имаме специални продукти за вас. Моля, уточнете ни приложението, вида на компонента, спецификациите, условията на околната среда като налягане, температура, течности или газове, които ще бъдат в контакт с вашите клапани и пневматични компоненти; и ние ще изберем най-подходящия продукт за вас или ще го произведем специално за вашето приложение. CLICK Product Finder-Locator Service ПРЕДИШНА СТРАНИЦА
- Rapid Prototyping, Desktop Manufacturing, Additive Manufacturing, FDM
Rapid Prototyping, Desktop Manufacturing, Additive Manufacturing, Stereolithography, Polyjet, Fused Deposition Modeling, Selective Laser Sintering, FDM, SLS Адитивно и бързо производство През последните години наблюдаваме нарастване на търсенето на БЪРЗО ПРОИЗВОДСТВО или БЪРЗО ПРОТОТИПНО ИЗРАБОТВАНЕ. Този процес може да се нарича още ПРОИЗВОДСТВО НА НАСТОЛНИ КОМПЮТЪРИ или ПРОИЗВОДСТВО В СВОБОДНА ФОРМА. По принцип солиден физически модел на част се прави директно от триизмерен CAD чертеж. Използваме термина ДОБАВНО ПРОИЗВОДСТВО за тези различни техники, при които изграждаме части на слоеве. Използвайки интегриран компютърно управляван хардуер и софтуер, ние извършваме адитивно производство. Нашите техники за бързо създаване на прототипи и производство са СТЕРЕОЛИТОГРАФИЯ, ПОЛИСТРУЙНО МОДЕЛИРАНЕ, МОДЕЛИРАНЕ С ОТЛАГАНЕ, СЕЛЕКТИВНО ЛАЗЕРНО СИНТЕРОВАНЕ, ТОПЕНЕ НА ЕЛЕКТРОНЕН ЛЪЧ, ТРИИЗМЕРЕН ПЕЧАТ, ДИРЕКТНО ПРОИЗВОДСТВО, БЪРЗО ИНСТРУМЕНТИ. Препоръчваме ви да щракнете тук, заИЗТЕГЛЕТЕ нашите схематични илюстрации на адитивно производство и бързи производствени процеси от AGS-TECH Inc. Това ще ви помогне да разберете по-добре информацията, която ви предоставяме по-долу. Бързото прототипиране ни осигурява: 1.) Концептуалният дизайн на продукта се разглежда от различни ъгли на монитор с помощта на 3D / CAD система. 2.) Прототипите от неметални и метални материали се произвеждат и изучават от функционални, технически и естетически аспекти. 3.) Постига се прототипиране на ниска цена за много кратко време. Производството на добавки може да се наподоби на изграждането на един хляб чрез подреждане и залепване на отделни филийки един върху друг. С други думи, продуктът се произвежда парче по парче или слой по слой, наложен един върху друг. Повечето части могат да бъдат произведени в рамките на часове. Техниката е добра, ако частите са необходими много бързо или ако необходимите количества са малки и изработването на матрица и инструменти е твърде скъпо и отнема време. Въпреки това цената на една част е скъпа поради скъпите суровини. • СТЕРЕОЛИТОГРАФИЯ: Тази техника, също съкратено като STL, се основава на втвърдяване и втвърдяване на течен фотополимер в специфична форма чрез фокусиране на лазерен лъч върху него. Лазерът полимеризира фотополимера и го полимеризира. Чрез сканиране на UV лазерния лъч според програмираната форма по протежение на повърхността на фотополимерната смес детайлът се произвежда отдолу нагоре на отделни резени, каскадно разположени един върху друг. Сканирането на лазерното петно се повтаря многократно, за да се постигнат геометричните характеристики, програмирани в системата. След като частта е напълно произведена, тя се отстранява от платформата, попива се и се почиства ултразвуково и със спиртна баня. След това се излага на UV радиация за няколко часа, за да се увери, че полимерът е напълно втвърден и втвърден. За да обобщим процеса, платформа, която е потопена във фотополимерна смес и UV лазерен лъч се управляват и преместват през система за серво-контрол в съответствие с формата на желаната част и частта се получава чрез фотовтвърдяване на полимера слой по слой. Разбира се, максималните размери на произведения детайл се определят от стереолитографското оборудване. • POLYJET: Подобно на мастиленоструйния печат, при полиджета имаме осем печатащи глави, които отлагат фотополимер върху тавата за изграждане. Ултравиолетовата светлина, поставена до струите, веднага втвърдява и втвърдява всеки слой. В polyjet се използват два материала. Първият материал е за производството на същинския модел. Вторият материал, гелообразна смола, се използва за опора. И двата материала се отлагат слой по слой и едновременно се втвърдяват. След завършване на модела опорният материал се отстранява с воден разтвор. Използваните смоли са подобни на стереолитографията (STL). Полиджетът има следните предимства пред стереолитографията: 1.) Няма нужда от почистващи части. 2.) Няма нужда от последващо втвърдяване 3.) Възможни са по-малки дебелини на слоя и по този начин получаваме по-добра разделителна способност и можем да произвеждаме по-фини части. • МОДЕЛИРАНЕ НА ОТЛАГАНЕ НА СПОЙКА: Също съкратено като FDM, при този метод глава на екструдер, управлявана от робот, се движи в две основни посоки над маса. Кабелът се спуска и повдига според нуждите. От отвора на нагрята матрица на главата се екструдира термопластична нишка и начален слой се отлага върху основа от пяна. Това се постига от главата на екструдера, която следва предварително определена траектория. След първоначалния слой масата се спуска и следващите слоеве се нанасят един върху друг. Понякога при производството на сложна част са необходими поддържащи структури, така че отлагането да може да продължи в определени посоки. В тези случаи поддържащият материал се екструдира с по-малко плътно разстояние от нишки върху слой, така че да е по-слаб от моделния материал. Тези поддържащи структури могат по-късно да бъдат разтворени или отчупени след завършване на детайла. Размерите на матрицата на екструдера определят дебелината на екструдираните слоеве. Процесът FDM произвежда части със стъпаловидни повърхности върху наклонени външни равнини. Ако тази грапавост е неприемлива, може да се използва полиране с химическа пара или нагрят инструмент за изглаждане. Дори полираща вакса се предлага като материал за покритие, за да се елиминират тези стъпки и да се постигнат разумни геометрични толеранси. • СЕЛЕКТИВНО ЛАЗЕРНО СИНТЕРОВАНЕ: Означаван също като SLS, процесът се основава на синтероване на полимерни, керамични или метални прахове селективно в обект. Дъното на обработващата камера има два цилиндъра: цилиндър с частична конструкция и цилиндър за подаване на прах. Първият се спуска постепенно до мястото, където се оформя синтерованата част, а вторият се повдига постепенно, за да подаде прах към цилиндъра на частта чрез ролков механизъм. Първо тънък слой прах се отлага в цилиндъра на частта, след което лазерен лъч се фокусира върху този слой, проследявайки и стопявайки/спичайки определено напречно сечение, което след това се втвърдява отново в твърдо вещество. Пудрата е зони, които не са засегнати от лазерния лъч, остават рохкави, но все още поддържат твърдата част. След това се отлага друг слой прах и процесът се повтаря много пъти, за да се получи частта. Накрая насипните частици пудра се изтръскват. Всичко това се извършва от компютър за управление на процеса, като се използват инструкции, генерирани от 3D CAD програмата на детайла, който се произвежда. Могат да бъдат депозирани различни материали като полимери (като ABS, PVC, полиестер), восък, метали и керамика с подходящи полимерни свързващи вещества. • ЕЛЕКТРОНЕН ЛЪЧ МЕЛТИНГ: Подобно на селективното лазерно синтероване, но използвайки електронен лъч за стопяване на прахове от титан или кобалтов хром, за да се направят прототипи във вакуум. Бяха направени някои разработки за извършване на този процес върху неръждаеми стомани, алуминий и медни сплави. Ако трябва да се увеличи якостта на умора на произведените части, ние използваме горещо изостатично пресоване след производството на детайла като вторичен процес. • ТРИИЗМЕРЕН ПЕЧАТ: Означаван също с 3DP, при тази техника печатащата глава отлага неорганично свързващо вещество върху слой от неметален или метален прах. Буталото, носещо прахообразното легло, постепенно се спуска и на всяка стъпка свързващото вещество се отлага слой по слой и се стопява от свързващото вещество. Използваните прахообразни материали са полимерни смеси и влакна, леярски пясък, метали. Използвайки различни глави за класьори едновременно и различни цветове класьори, можем да получим различни цветове. Процесът е подобен на мастиленоструен печат, но вместо да получим цветен лист, ние получаваме цветен триизмерен обект. Произведените части може да са порести и следователно може да изискват синтероване и метална инфилтрация за увеличаване на плътността и здравината. Агломерирането ще изгори свързващото вещество и ще слее металните прахове заедно. Метали като неръждаема стомана, алуминий, титан могат да се използват за направата на частите, а като материали за инфилтрация обикновено използваме мед и бронз. Красотата на тази техника е, че дори сложни и движещи се възли могат да бъдат произведени много бързо. Например зъбно колело, гаечен ключ като инструмент може да бъде направен и ще има движещи се и въртящи се части, готови за използване. Различните компоненти на сглобката могат да бъдат произведени с различни цветове и всичко това наведнъж. Изтеглете нашата брошура на:Основи на 3D печат на метал • ДИРЕКТНО ПРОИЗВОДСТВО и БЪРЗО ИНСТРУМЕНТИ: Освен оценка на дизайна, отстраняване на неизправности, ние използваме бързо прототипиране за директно производство на продукти или директно приложение в продукти. С други думи, бързото прототипиране може да бъде включено в конвенционалните процеси, за да ги направи по-добри и по-конкурентоспособни. Например, бързото създаване на прототипи може да създаде модели и форми. Моделите на топящ се и горящ полимер, създаден чрез операции за бързо създаване на прототипи, могат да бъдат сглобени за леене по модели и инвестирани. Друг пример, който трябва да се спомене, е използването на 3DP за производство на керамична леярска черупка и използването на това за операции по леене на черупки. Дори шприцформите и формовъчните вложки могат да бъдат произведени чрез бързо създаване на прототипи и човек може да спести много седмици или месеци време за производство на матрици. Като анализираме само CAD файл на желаната част, можем да създадем геометрията на инструмента с помощта на софтуер. Ето някои от нашите популярни бързи методи за инструменти: RTV (вулканизиране при стайна температура) ФОРДОВАНЕ / УРЕТАНОВО ОТЛИВАНЕ: Използването на бързо прототипиране може да се използва за направата на модела на желаната част. След това този шаблон се покрива с разделителен агент и върху шаблона се излива течен RTV каучук, за да се получат половинките на формата. След това тези половини на формата се използват за шприцване на течни уретани. Животът на матрицата е кратък, само около 0 или 30 цикъла, но достатъчен за производство на малки партиди. ACES (Acetal Clear Epoxy Solid) ИНЖЕКТИРАНЕ: Използвайки техники за бързо създаване на прототипи като стереолитография, ние произвеждаме шприцформи. Тези форми са черупки с отворен край, за да позволят пълнене с материали като епоксидна смола, епоксидна смола с алуминиев пълнеж или метали. Отново животът на формата е ограничен до десетки или максимум стотици части. ПРОЦЕС НА ИНСТРУМЕНТАЛНА ИНСТРУМЕНТАЛНА ИНСТРУМЕНТАЦИЯ НА ПРЪСКАНЕ: Ние използваме бързо прототипиране и правим модел. Напръскваме цинково-алуминиева сплав върху повърхността на модела и го покриваме. След това моделът с метално покритие се поставя в колба и се запълва с епоксидна смола или епоксидна смола, напълнена с алуминий. Накрая се отстранява и чрез производството на две такива половини на матрицата се получава пълна форма за леене под налягане. Тези форми имат по-дълъг живот, в някои случаи в зависимост от материала и температурите могат да произвеждат хиляди части. ПРОЦЕС НА KEELTOOL: Тази техника може да произвежда форми с живот от 100 000 до 10 милиона цикъла. Използвайки бързо прототипиране, ние произвеждаме RTV матрица. След това матрицата се напълва със смес, състояща се от прах от инструментална стомана A6, волфрамов карбид, полимерно свързващо вещество и се оставя да се втвърди. След това тази форма се нагрява, за да се изгори полимерът и да се стопят металните прахове. Следващата стъпка е медна инфилтрация за производство на крайната форма. Ако е необходимо, вторични операции като механична обработка и полиране могат да бъдат извършени върху формата за по-добра точност на размерите. CLICK Product Finder-Locator Service ПРЕДИШНА СТРАНИЦА
- Machine Elements Manufacturing, Gears, Gear Drives, Bearings, Keys, Splines
Machine Elements Manufacturing, Gears, Gear Drives, Bearings, Keys, Splines, Pins, Shafts, Seals, Fasteners, Clutch, Cams, Followers, Belts, Couplings, Shafts Производство на машинни елементи Прочетете още Ремъци, вериги и кабелно задвижване Прочетете още Зъбни колела и зъбни колела Прочетете още Производство на съединители и лагери Прочетете още Производство на ключове, шлици и щифтове Прочетете още Производство на гърбици, последователи и връзки и храпови колела Прочетете още Производство на валове Прочетете още Производство на механични уплътнения Прочетете още Сглобка на съединителя и спирачката Прочетете още Крепежни елементи Производство Прочетете още Сглобяване на Simple Machines МАШИННИ ЕЛЕМЕНТИ са елементарни компоненти на машина. Тези елементи се състоят от три основни типа: 1.) Структурни компоненти, включително елементи на рамката, лагери, оси, шлици, крепежни елементи, уплътнения и смазочни материали. 2.) Механизми, контролиращи движението по различни начини, като зъбни предавки, ремъчни или верижни задвижвания, връзки, гърбични и следващи системи, спирачки и съединители. 3.) Компоненти за управление като бутони, превключватели, индикатори, сензори, задвижващи механизми и компютърни контролери. Повечето от машинните елементи, които ви предлагаме, са стандартизирани към общи размери, но машинни елементи, изработени по поръчка, също са налични за вашите специализирани приложения. Персонализирането на машинни елементи може да се извърши върху съществуващи дизайни, които са в нашите каталози за изтегляне, или върху чисто нови дизайни. Прототипирането и производството на машинни елементи могат да бъдат пренесени, след като проектът бъде одобрен от двете страни. Ако трябва да се проектират и произведат нови машинни елементи, нашите клиенти или ни изпращат по имейл свои собствени чертежи и ние ги преглеждаме за одобрение, или ни молят да проектираме машинни елементи за тяхното приложение. В последния случай ние използваме цялата информация от нашите клиенти и проектираме машинните елементи и изпращаме финализираните чертежи на нашите клиенти за одобрение. След одобрение произвеждаме първите артикули и впоследствие изработваме машинните елементи по окончателния проект. На всеки етап от тази работа, в случай че конкретен дизайн на машинен елемент се представи незадоволително на място (което е рядко), ние преглеждаме целия проект и правим промени съвместно с нашите клиенти, ако е необходимо. Наша стандартна практика е да подписваме споразумения за неразкриване на информация (NDA) с нашите клиенти за проектиране на машинни елементи или всеки друг продукт, когато това е необходимо или необходимо. След като машинните елементи за конкретен клиент са проектирани и произведени по поръчка, ние му присвояваме продуктов код и ги произвеждаме и продаваме само на нашия клиент, който притежава продукта. Ние възпроизвеждаме машинните елементи, като използваме разработените инструменти, форми и процедури толкова пъти, колкото е необходимо, и когато клиентът ни ги поръча отново. С други думи, след като персонализиран машинен елемент е проектиран и произведен за вас, интелектуалната собственост, както и всички инструменти и форми се запазват и съхраняват за неопределено време от нас за вас и продуктите се възпроизвеждат, както желаете. Ние също така предлагаме на нашите клиенти инженерни услуги чрез креативно комбиниране на машинни елементи в компонент или възел, който обслужва приложение и отговаря или надхвърля очакванията на нашите клиенти. Заводите, произвеждащи нашите машинни елементи, са квалифицирани по ISO9001, QS9000 или TS16949. В допълнение, повечето от нашите продукти имат маркировка CE или UL и отговарят на международни стандарти като ISO, SAE, ASME, DIN. Моля, щракнете върху подменютата, за да получите подробна информация за нашите машинни елементи, включително: - Ремъци, вериги и кабелни задвижвания - Зъбни колела и зъбни предавки - Съединители и лагери - Ключове, шлици и щифтове - Гърби и връзки - Валове - Механични уплътнения - Индустриален съединител и спирачка - Крепежни елементи - Прости машини Подготвихме референтна брошура за нашите клиенти, дизайнери и разработчици на нови продукти, включително машинни елементи. Можете да се запознаете с някои често използвани термини в проектирането на машинни компоненти: Изтеглете брошура за общи термини в машиностроенето, използвани от дизайнери и инженери Нашите машинни елементи намират приложение в различни области като промишлени машини, системи за автоматизация, тестово и метрологично оборудване, транспортно оборудване, строителни машини и практически навсякъде, за което се сетите. AGS-TECH разработва и произвежда машинни елементи от различни материали в зависимост от приложението. Материалите, използвани за машинни елементи, могат да варират от формовани пластмаси, използвани за играчки, до закалена и специално покрита стомана за индустриални машини. Нашите дизайнери използват най-съвременен професионален софтуер и инструменти за проектиране за разработване на машинни елементи, като вземат под внимание детайли като ъгли в зъбите на зъбните колела, включени напрежения, нива на износване ... и т.н. Моля, прегледайте нашите подменюта и изтеглете нашите продуктови брошури и каталози, за да видите дали можете да намерите готови машинни елементи за вашето приложение. Ако не можете да намерите подходящо за вашето приложение, моля, уведомете ни и ние ще работим с вас, за да разработим и произведем машинни елементи, които ще задоволят вашите нужди. Ако се интересувате най-вече от нашите инженерни и научноизследователски и развойни възможности, вместо от производствени възможности, тогава ви каним да посетите нашия уебсайт http://www.ags-engineering.com където можете да намерите по-подробна информация за нашия дизайн, разработване на продукти, разработване на процеси, инженерни консултантски услуги и други CLICK Product Finder-Locator Service ПРЕДИШНА СТРАНИЦА
- Glass and Ceramic Manufacturing, Hermetic Packages, Seals, Bonding
Glass and Ceramic Manufacturing, Hermetic Packages Seals and Bonding, Tempered Bulletproof Glass, Blow Moulding, Optical Grade Glass, Conductive Glass, Molding Формоване и оформяне на стъкло и керамика Типът производство на стъкло, което предлагаме, е контейнерно стъкло, издухване на стъкло, стъклени влакна и тръби и пръти, домакински и промишлени стъклария, лампи и крушки, прецизно формоване на стъкло, оптични компоненти и възли, плоско и листово и флоат стъкло. Извършваме както ръчно, така и машинно формоване. Нашите популярни производствени процеси за техническа керамика са щанцоване, изостатично пресоване, горещо изостатично пресоване, горещо пресоване, шликерно леене, леене на лента, екструдиране, леене под налягане, зелена обработка, синтероване или изпичане, диамантено шлайфане, херметични възли. Препоръчваме ви да щракнете тук, за ИЗТЕГЛЕТЕ нашите схематични илюстрации на процеси за формоване и оформяне на стъкло от AGS-TECH Inc. ИЗТЕГЛЕТЕ нашите схематични илюстрации на производствени процеси за техническа керамика от AGS-TECH Inc. Тези файлове за изтегляне със снимки и скици ще ви помогнат да разберете по-добре информацията, която ви предоставяме по-долу. • ПРОИЗВОДСТВО НА КОНТЕЙНЕРНО СТЪКЛО: Имаме автоматизирани линии за ПРЕСА И ИЗДУХВАНЕ, както и линии за ИЗДУХВАНЕ И ИЗДУХВАНЕ за производство. В процеса на издухване и издухване пускаме парче в празна форма и оформяме гърлото, като прилагаме удар със сгъстен въздух отгоре. Непосредствено след това сгъстеният въздух се издухва втори път от другата посока през гърлото на контейнера, за да се образува предварителната форма на бутилката. Тази предварителна форма след това се прехвърля в действителната форма, загрява се отново, за да омекне и се прилага сгъстен въздух, за да се придаде на предварителната форма окончателната форма на контейнер. По-ясно, той се поставя под налягане и се притиска към стените на кухината на формата за раздуване, за да заеме желаната форма. Накрая, произведеният стъклен контейнер се прехвърля в пещ за отгряване за последващо повторно нагряване и отстраняване на напреженията, получени по време на формоването, и се охлажда по контролиран начин. При метода на пресоване и издухване, разтопените частици се поставят във форма за запарване (празна форма) и се пресоват във формата за запарване (форма за заготовка). След това заготовките се прехвърлят във форми за издухване и се издухват подобно на процеса, описан по-горе в „Процес на издухване и издухване“. Последващите стъпки като отгряване и облекчаване на напрежението са подобни или същите. • ИЗДУХВАНЕ НА СТЪКЛО: Произвеждаме продукти от стъкло, използвайки конвенционално ръчно издухване, както и използвайки сгъстен въздух с автоматизирано оборудване. За някои поръчки е необходимо конвенционално издуване, като например проекти, включващи произведения на изкуството от стъкло, или проекти, които изискват по-малък брой части с разхлабени толеранси, прототипиране/демо проекти….и т.н. Конвенционалното издуване на стъкло включва потапяне на куха метална тръба в съд с разтопено стъкло и въртене на тръбата за събиране на известно количество от стъкления материал. Стъклото, събрано на върха на тръбата, се търкаля върху плоско желязо, оформя се по желание, удължава се, нагрява се отново и се продухва. Когато е готов, се поставя във форма и се пуска въздух. Кухината на формата е мокра, за да се избегне контакт на стъклото с метал. Водният филм действа като възглавница между тях. Ръчното издухване е трудоемък бавен процес и е подходящ само за създаване на прототипи или артикули с висока стойност, не е подходящ за евтини големи поръчки на бройка. • ПРОИЗВОДСТВО НА БИТОВА И ПРОМИШЛЕНА СТЪКЛАРИЯ: С помощта на различни видове стъклени материали се произвежда голямо разнообразие от стъклени изделия. Някои чаши са устойчиви на топлина и са подходящи за лабораторни стъклени съдове, докато някои са достатъчно добри, за да издържат многократно миене в съдомиялни машини и са подходящи за производство на домашни продукти. С помощта на машини на Westlake се произвеждат десетки хиляди чаши за пиене на ден. За да се опрости, стопеното стъкло се събира чрез вакуум и се вкарва във форми, за да се направят предварителните форми. След това във формите се вдухва въздух, те се прехвърлят в друга форма и отново се вдухва въздух и стъклото приема окончателната си форма. Подобно на ръчното издухване, тези форми се държат мокри с вода. По-нататъшното разтягане е част от довършителната операция, при която се оформя шийката. Излишното стъкло се изгаря. След това следва контролираният процес на повторно нагряване и охлаждане, описан по-горе. • ФОРМОВАНЕ НА СТЪКЛЕНИ ТРЪБИ И ПРЪТКИ: Основните процеси, които използваме за производство на стъклени тръби, са процесите DANNER и VELLO. В процеса на Данер стъклото от пещ тече и пада върху наклонена втулка, изработена от огнеупорни материали. Втулката се носи върху въртящ се кух вал или духалка. След това стъклото се увива около втулката и образува гладък слой, който тече надолу по втулката и върху върха на ствола. При формоване на тръби въздухът се издухва през вентилатор с кух връх, а при формоване на пръти използваме твърди накрайници на вала. След това тръбите или прътите се изтеглят върху носещи ролки. Размерите като дебелина на стената и диаметър на стъклените тръби се регулират до желаните стойности чрез задаване на диаметъра на втулката и въздушно налягане на продухване до желана стойност, регулиране на температурата, скоростта на потока на стъклото и скоростта на изтегляне. Процесът на производство на стъклена тръба Vello, от друга страна, включва стъкло, което излиза от пещ и се насочва към купа с кух дорник или камбана. След това стъклото преминава през въздушното пространство между дорника и купата и приема формата на тръба. След това преминава през ролки към машина за изтегляне и се охлажда. В края на охладителната линия се извършва рязане и крайна обработка. Размерите на тръбата могат да се регулират точно както в процеса на Danner. Когато сравняваме процеса Danner с Vello, можем да кажем, че процесът Vello е по-подходящ за производство на големи количества, докато процесът Danner може да е по-подходящ за прецизни поръчки на тръби с по-малък обем. • ОБРАБОТКА НА ЛИСТА И ПЛОСКО И ФЛОАТ СТЪКЛО: Разполагаме с големи количества плоско стъкло с дебелини, вариращи от субмилиметрови дебелини до няколко сантиметра. Нашите плоски стъкла са с почти оптично съвършенство. Ние предлагаме стъкла със специални покрития като оптични покрития, където се използва техника за химическо отлагане на пари за поставяне на покрития като антирефлексно или огледално покритие. Често се срещат и прозрачни проводими покрития. Предлагат се и хидрофобни или хидрофилни покрития върху стъкло, както и покритие, което прави стъклото самопочистващо се. Закалените, бронираните и ламинираните стъкла са други популярни артикули. Изрязваме стъкло в желана форма с желани толеранси. Налични са и други вторични операции като извиване или огъване на плоско стъкло. • ПРЕЦИЗНО ФОРМОВАНЕ НА СТЪКЛО: Използваме тази техника най-вече за производство на прецизни оптични компоненти без необходимост от по-скъпи и отнемащи време техники като шлайфане, прилепване и полиране. Тази техника не винаги е достатъчна, за да се направи най-доброто от най-добрата оптика, но в някои случаи като потребителски продукти, цифрови фотоапарати, медицинска оптика може да бъде по-евтин добър вариант за производство в голям обем. Също така има предимство пред другите техники за оформяне на стъкло, където се изискват сложни геометрии, като например в случая на асфери. Основният процес включва зареждане на долната страна на нашата форма със стъклената заготовка, евакуация на процесната камера за отстраняване на кислорода, близо до затваряне на формата, бързо и изотермично нагряване на матрицата и стъклото с инфрачервена светлина, по-нататъшно затваряне на половините на матрицата бавно и контролирано пресоване на омекотеното стъкло до желаната дебелина и накрая охлаждане на стъклото и пълнене на камерата с азот и отстраняване на продукта. Прецизният температурен контрол, разстоянието на затваряне на матрицата, силата на затваряне на матрицата, съответствието на коефициентите на разширение на матрицата и стъкления материал са ключови в този процес. • ПРОИЗВОДСТВО НА СТЪКЛЕНИ ОПТИЧНИ КОМПОНЕНТИ И ВЪЗЛОВИ: Освен прецизното формоване на стъкло, има редица ценни процеси, които използваме за изработване на висококачествени оптични компоненти и възли за взискателни приложения. Шлифоването, прилепването и полирането на оптични стъкла във фини специални абразивни суспензии е изкуство и наука за изработка на оптични лещи, призми, плоски и други. Плоскостта на повърхността, вълнообразността, гладкостта и оптичните повърхности без дефекти изискват много опит с такива процеси. Малки промени в околната среда могат да доведат до продукти извън спецификациите и спиране на производствената линия. Има случаи, при които едно избърсване на оптичната повърхност с чиста кърпа може да накара продукта да отговаря на спецификациите или да се провали на теста. Някои използвани популярни стъклени материали са разтопен силициев диоксид, кварц, BK7. Освен това сглобяването на такива компоненти изисква специализиран нишов опит. Понякога се използват специални лепила. Понякога обаче техника, наречена оптичен контакт, е най-добрият избор и не включва материал между прикрепените оптични стъкла. Състои се от физически контакт с плоски повърхности, за да се закрепят една към друга без лепило. В някои случаи се използват механични дистанционни елементи, прецизни стъклени пръчки или топки, скоби или обработени метални компоненти за сглобяване на оптичните компоненти на определени разстояния и с определени геометрични ориентации един спрямо друг. Нека разгледаме някои от нашите популярни техники за производство на оптика от висок клас. ШЛИФОВАНЕ & ЛЕПИРАНЕ & ПОЛИРАНЕ: Грубата форма на оптичния компонент се получава чрез шлайфане на стъклена заготовка. След това се извършва прилепване и полиране чрез въртене и триене на грапавите повърхности на оптичните компоненти срещу инструменти с желани повърхностни форми. Суспензии с малки абразивни частици и течност се изсипват между оптиката и оформящите инструменти. Размерите на абразивните частици в такива суспензии могат да бъдат избрани според желаната степен на плоскост. Отклоненията на критичните оптични повърхности от желаните форми се изразяват чрез дължини на вълните на използваната светлина. Нашата оптика с висока прецизност има допустими отклонения от една десета от дължината на вълната (дължина на вълната/10) или е възможно дори по-строго. Освен профила на повърхността, критичните повърхности се сканират и оценяват за други повърхностни характеристики и дефекти като размери, драскотини, чипове, вдлъбнатини, петна...и т.н. Строгият контрол на условията на околната среда в цеха за оптично производство и обширните изисквания за метрология и изпитване с най-съвременно оборудване правят този отрасъл предизвикателство. • ВТОРИЧНИ ПРОЦЕСИ В ПРОИЗВОДСТВОТО НА СТЪКЛО: Отново, ние сме ограничени само с вашето въображение, когато става дума за вторични и довършителни процеси на стъкло. Тук изброяваме някои от тях: -Покрития върху стъкло (оптични, електрически, трибологични, термични, функционални, механични...). Като пример можем да променим свойствата на повърхността на стъклото, правейки го например да отразява топлината, така че да поддържа интериора на сградата хладен, или да направим едната страна абсорбираща инфрачервените лъчи с помощта на нанотехнология. Това помага да се запази топлината във вътрешността на сградите, тъй като най-външният повърхностен слой стъкло ще абсорбира инфрачервеното лъчение вътре в сградата и ще го излъчва обратно навътре. -Офорт на стъкло -Приложено керамично етикетиране (ACL) -Гравиране - Пламъчно полиране - Химическо полиране -Оцветяване ПРОИЗВОДСТВО НА ТЕХНИЧЕСКА КЕРАМИКА • ПРЕСОВАНЕ НА МАТРИЦА: Състои се от едноосно уплътняване на гранулирани прахове, затворени в матрица • ГОРЕЩО ПРЕСОВАНЕ: Подобно на пресоването на матрицата, но с добавяне на температура за подобряване на уплътняването. Прах или пресована заготовка се поставя в графитна матрица и се прилага едноосно налягане, докато матрицата се поддържа при високи температури като 2000 C. Температурите могат да бъдат различни в зависимост от вида на керамичния прах, който се обработва. За сложни форми и геометрии може да е необходима друга последваща обработка, като диамантено шлайфане. • ИЗОСТАТИЧНО ПРЕСОВАНЕ: Гранулиран прах или пресовани пресовани пресовани се поставят в херметически затворени контейнери и след това в затворен съд под налягане с течност вътре. След това те се уплътняват чрез увеличаване на налягането в съда под налягане. Течността вътре в съда пренася равномерно силите на налягане върху цялата повърхност на херметически затворения контейнер. По този начин материалът се уплътнява равномерно и приема формата на своя гъвкав контейнер и неговия вътрешен профил и характеристики. • ГОРЕЩО ИЗОСТАТИЧНО ПРЕСОВАНЕ: Подобно на изостатичното пресоване, но в допълнение към газовата атмосфера под налягане, ние синтероваме компакта при висока температура. Горещото изостатично пресоване води до допълнително уплътняване и повишена якост. • Шликерно леене / дренажно леене: Напълваме матрицата със суспензия от керамични частици с микрометрови размери и носеща течност. Тази смес се нарича "приплъзване". Формата има пори и затова течността в сместа се филтрира във формата. В резултат на това се образува отливка върху вътрешните повърхности на формата. След синтероване частите могат да бъдат извадени от формата. • ЛЕЕНЕ НА ЛЕНТИ: Ние произвеждаме керамични ленти чрез леене на керамични суспензии върху плоски движещи се носещи повърхности. Суспензиите съдържат керамични прахове, смесени с други химикали за свързване и пренасяне. Тъй като разтворителите се изпаряват, остават плътни и гъвкави листове от керамика, които могат да бъдат нарязани или навити по желание. • ЕКСТРУЗИОННО ФОРМУВАНЕ: Както при други процеси на екструзия, мека смес от керамичен прах със свързващи вещества и други химикали преминава през матрица, за да придобие формата на напречното си сечение и след това се нарязва на желаните дължини. Процесът се извършва със студени или загряти керамични смеси. • ИНЖЕКТИРАНЕ ПОД НИСКО НАЛЯГАНЕ: Ние приготвяме смес от керамичен прах със свързващи вещества и разтворители и я загряваме до температура, при която може лесно да бъде пресована и принудена в кухината на инструмента. След като цикълът на формоване приключи, детайлът се изхвърля и свързващият химикал се изгаря. Използвайки леене под налягане, ние можем да получим сложни части в големи обеми икономично. Възможни са дупки , които са малка част от милиметър на стена с дебелина 10 mm, възможни са резби без допълнителна обработка, възможни са допуски до +/- 0,5% и дори по-ниски, когато частите се обработват , възможни са дебелини на стените от порядъка на 0,5 mm до дължина 12,5 mm, както и дебелини на стените от 6,5 mm до дължина 150 mm. • ЗЕЛЕНА МАШИННА ОБРАБОТКА: Използвайки същите инструменти за метална обработка, можем да обработваме пресовани керамични материали, докато те са все още меки като тебешир. Възможни са допустими отклонения от +/- 1%. За по-добри толеранси използваме диамантено шлайфане. • СИНТЕРОВАНЕ или ИЗПЕЧВАНЕ: Спечаването прави възможно пълното уплътняване. Появява се значително свиване на зелените компактни части, но това не е голям проблем, тъй като ние вземаме предвид тези промени в размерите, когато проектираме частта и инструменталната екипировка. Частиците на праха се свързват заедно и порьозността, предизвикана от процеса на уплътняване, се отстранява до голяма степен. • ДИАМАНТЕНО ШЛИФОВАНЕ: Най-твърдият материал в света „диамант“ се използва за шлайфане на твърди материали като керамика и се получават прецизни части. Постигат се толеранси в микрометровия диапазон и много гладки повърхности. Поради разходите си, ние обмисляме тази техника само когато наистина имаме нужда от нея. • ХЕРМЕТИЧНИ ВЪЗЛИ са тези, които на практика не позволяват обмен на материя, твърди вещества, течности или газове между интерфейсите. Херметичното запечатване е херметично. Например херметичните електронни кутии са тези, които пазят чувствителното вътрешно съдържание на опаковано устройство невредимо от влага, замърсители или газове. Нищо не е 100% херметично, но когато говорим за херметичност, имаме предвид, че на практика има херметичност до степента, в която степента на изтичане е толкова ниска, че устройствата са безопасни при нормални условия на околната среда за много дълго време. Нашите херметични възли се състоят от метални, стъклени и керамични компоненти, метал-керамика, керамика-метал-керамика, метал-керамика-метал, метал към метал, метал-стъкло, метал-стъкло-метал, стъкло-метал-стъкло, стъкло- метал и стъкло към стъкло и всички други комбинации на залепване метал-стъкло-керамика. Ние можем например да покрием керамичните компоненти с метално покритие, така че те да могат да бъдат здраво свързани с други компоненти в сглобката и да имат отлична способност за уплътняване. Имаме ноу-хауто за покриване на оптични влакна или захранващи канали с метал и запояването им или запояването им към корпусите, така че да не преминават или изтичат газове в корпусите. Поради това те се използват за производство на електронни кутии за капсулиране на чувствителни устройства и защитата им от външната атмосфера. Освен техните отлични характеристики на уплътняване, други свойства като коефициент на топлинно разширение, устойчивост на деформация, неотделяне на газове, много дълъг живот, непроводим характер, топлоизолационни свойства, антистатично естество... и т.н. правят стъклените и керамичните материали избор за определени приложения. Информация за нашето съоръжение, произвеждащо керамични към метални фитинги, херметично запечатване, вакуумни захранващи канали, висок и свръхвисок вакуум и компоненти за контрол на течности може да бъде намерена тук:Брошура на завода за херметични компоненти CLICK Product Finder-Locator Service ПРЕДИШНА СТРАНИЦА
- Wire & Spring Forming, Shaping, Welding, Assembly of Wires, Coil, CNC
Wire & Spring Forming, Shaping, Welding, Assembly of Wires, Coil Compression Extension Torsion Flat Springs, Custom Wires, Helical Springs at AGS-TECH Inc. Формоване на тел и пружина Произвеждаме телове по поръчка, монтаж на тел, телове, оформени в желани 2D и 3D форми, телени мрежи, мрежи, заграждения, кош, ограда, телена пружина, плоска пружина; усукване, натиск, опън, плоски пружини и др. Нашите процеси са формоване на тел и пружина, теглене на тел, оформяне, огъване, заваряване, спояване, запояване, пробиване, щанцоване, пробиване, скосяване, шлайфане, нарязване на резби, покритие, четириплъзгащо се формоване, навиване, навиване, разгъване. Препоръчваме ви да щракнете тук, за ИЗТЕГЛЕТЕ нашите схематични илюстрации на процеси за формоване на телове и пружини от AGS-TECH Inc. Този файл за изтегляне със снимки и скици ще ви помогне да разберете по-добре информацията, която ви предоставяме по-долу. • ИЗТЕГЛЯНЕ НА ТЕЛ: Използвайки сили на опън, ние разтягаме металния материал и го изтегляме през матрица, за да намалим диаметъра и да увеличим дължината му. Понякога използваме серия матрици. Ние сме в състояние да изработим матрици за всеки калибър на тел. Използвайки материал с висока якост на опън, изтегляме много тънки проводници. Предлагаме както студено, така и горещо обработени проводници. • ОФОРМЯВАНЕ НА ТЕЛ: Ролка премерена тел се огъва и оформя в полезен продукт. Имаме способността да формираме телове от всички габарити, включително тънки нишки, както и дебели телове като тези, използвани като пружини под автомобилни шасита. Оборудването, което използваме за формоване на тел, е ръчно и CNC формовъчно устройство за тел, машина за навиване, мощни преси, четири плъзгачи, много плъзгачи. Нашите процеси са теглене, огъване, изправяне, сплескване, разтягане, рязане, изкривяване, запояване и заваряване и спояване, сглобяване, навиване, навиване (или крило), пробиване, навиване на резби, пробиване, скосяване, шлайфане, покритие и повърхностни обработки. Нашето най-модерно оборудване може да бъде настроено за разработване на много сложни дизайни с всякаква форма и строги допуски. Ние предлагаме различни видове накрайници подобни на сферични, заострени или скосени накрайници за вашите проводници. Повечето от нашите проекти за формоване на тел имат минимални до нулеви разходи за инструменти. Примерните времена за изпълнение обикновено са дни. Промените в дизайна/конфигурацията на телените форми могат да бъдат направени много бързо. • ФОРМИРАНЕ НА ПРУЖИНИ: AGS-TECH произвежда голямо разнообразие от пружини, включително: -Торсионна / двойна торсионна пружина -Пружина за напрежение / компресия -Постоянна / променлива пружина - Спирална и спирална пружина -Плоска и листова пружина -Балансова пружина - Пералня Белвил -Отрицателна пролет - Спирална пружина с прогресивна скорост - Вълнова пролет - Спираловидна пружина - Заострени пружини - Пролетни пръстени - Часовникови пружини -Клипове Ние произвеждаме пружини от различни материали и можем да ви напътстваме според вашето приложение. Най-често срещаните материали са неръждаема стомана, хромиран силиций, високовъглеродна стомана, нисковъглеродна закалена в масло, хром ванадий, фосфорен бронз, титан, берилиево-медна сплав, високотемпературна керамика. Ние използваме различни техники в производството на пружини, включително CNC навиване, студено навиване, горещо навиване, закаляване, довършване. Други техники, вече споменати по-горе при формоване на тел, също са често срещани в нашите производствени операции на пружини. • ДОПЪЛНИТЕЛНИ УСЛУГИ за ТЕЛИ И ПРУЖИНИ: Ние можем да завършим вашите продукти по много начини в зависимост от вашия избор и нужди. Някои често срещани процеси, които предлагаме, са: боядисване, прахово боядисване, покритие, потапяне във винил, анодиране, облекчаване на напрежението, топлинна обработка, ударна обработка, барабанна обработка, хромиране, безелектрически никел, пасивиране, изпечен емайл, пластмасово покритие , плазмено почистване. CLICK Product Finder-Locator Service ПРЕДИШНА СТРАНИЦА
- Forging and Powdered Metallurgy, Die Forging, Heading, Hot Forging
Forging and Powdered Metallurgy, Die Forging, Heading, Hot Forging, Impression Die, Near Net Shape, Swaging, Metal Hobbing, Riveting, Coining from AGS-TECH Inc. Коване на метали и прахова металургия Типът процеси за МЕТАЛНО КОВАНЕ, които предлагаме, са гореща и студена матрица, отворена матрица и затворена матрица, матрица за отпечатване и изковки без флаш, cogging, запълване, кантиране и прецизно коване, почти мрежова форма, заглавие , щанцоване, изковаване, метално фрезоване, пресоване и валцуване, радиални и орбитални и пръстеновидни и изотермични изковки, монетосечене, занитване, коване на метални топки, пробиване на метал, оразмеряване, коване с висока енергийна скорост. Нашите техники за ПРАХОВА МЕТАЛУРГИЯ и ОБРАБОТКА НА ПРАХ са прахово пресоване и синтероване, импрегниране, инфилтрация, горещо и студено изостатично пресоване, леене под налягане на метал, уплътняване на руло, валцуване на прах, екструзия на прах, синтероване в насипно състояние, искрово синтероване, горещо пресоване. Препоръчваме ви да щракнете тук, за ИЗТЕГЛЕТЕ нашите схематични илюстрации на процеси на коване от AGS-TECH Inc. ИЗТЕГЛЕТЕ нашите схематични илюстрации на процеси в праховата металургия от AGS-TECH Inc. Тези файлове за изтегляне със снимки и скици ще ви помогнат да разберете по-добре информацията, която ви предоставяме по-долу. При коването на метал се прилагат сили на натиск и материалът се деформира и се получава желаната форма. Най-разпространените ковани материали в индустрията са желязо и стомана, но много други като алуминий, мед, титан, магнезий също са широко ковани. Кованите метални части имат подобрена зърнеста структура в допълнение към запечатаните пукнатини и затворените празни пространства, като по този начин здравината на частите, получени чрез този процес, е по-висока. Коването произвежда части, които са значително по-здрави за теглото си от частите, направени чрез леене или машинна обработка. Тъй като кованите части се оформят, като накарат метала да придобие крайната си форма, металът придобива насочена зърнеста структура, която отчита превъзходната здравина на частите. С други думи, частите, получени чрез процес на коване, показват по-добри механични свойства в сравнение с обикновените отлети или машинно обработени части. Теглото на металните изковки може да варира от малки леки части до стотици хиляди паунда. Ние произвеждаме изковки предимно за механично взискателни приложения, където се прилагат високи напрежения върху части като автомобилни части, зъбни колела, работни инструменти, ръчни инструменти, турбинни валове, мотоциклетни съоръжения. Тъй като разходите за инструментална екипировка и настройка са сравнително високи, ние препоръчваме този производствен процес само за голям обем производство и за малки обеми, но с висока стойност на критични компоненти, като например аерокосмически колесник. Освен разходите за инструментална екипировка, времето за производство на големи количества ковани части може да бъде по-дълго в сравнение с някои прости машинно обработени части, но техниката е от решаващо значение за части, които изискват изключителна здравина като болтове, гайки, специално приложение крепежни елементи, части за автомобили, мотокари, кранове. • ГОРЕЩО ЩАМПОВАНЕ и СТУДЕНО КОВАНЕ: Горещото щамповане, както подсказва името, се извършва при високи температури, следователно пластичността е висока, а якостта на материала ниска. Това улеснява лесното деформиране и коване. Напротив, студеното коване се извършва при по-ниски температури и изисква по-високи сили, което води до втвърдяване на деформация, по-добро покритие на повърхността и точност на произведените части. • ОТВОРЕНО КОВАНЕ НА МАТРИЦА и ОТПЕЧАНОВАНЕ НА МАТРИЦА: При коване с отворена матрица матриците не ограничават компресирания материал, докато при коване с отпечатъчна матрица кухините в матриците ограничават потока на материала, докато той се изковава в желаната форма. UPSET FORGING или наричан също UPSETTING, който всъщност не е същият, но много подобен процес, е процес на отворена матрица, при който детайлът е притиснат между две плоски матрици и силата на натиск намалява височината му. Тъй като височината е reduced, ширината на работния детайл се увеличава. HEADING, процесът на изковаване с изкривяване включва цилиндрична заготовка, която е извита в края си и нейното напречно сечение се увеличава локално. В заглавието материалът се подава през матрицата, изковава се и след това се нарязва на дължина. Операцията е способна да произвежда големи количества крепежни елементи бързо. Предимно това е операция за студена обработка, защото се използва за изработване на краища на пирони, краища на винтове, гайки и болтове, където материалът трябва да бъде укрепен. Друг процес на отворена матрица е COGGING, при който детайлът се кове в серия от стъпки, като всяка стъпка води до компресия на материала и последващото движение на отворената матрица по дължината на детайла. На всяка стъпка дебелината се намалява, а дължината се увеличава с малко. Процесът прилича на нервен ученик, който гризе молива си през цялото време на малки стъпки. Процесът, наречен FULLERING, е друг отворен метод за коване на матрици, който често използваме като по-ранна стъпка за разпределяне на материала в детайла, преди да се извършат други операции по коване на метал. Използваме го, когато детайлът изисква няколко forging operations. По време на операцията матрицата с изпъкнали повърхности се деформира и предизвиква изтичане на метал от двете страни. Подобен процес на фулиране, EDGING от друга страна включва отворена матрица с вдлъбнати повърхности за деформиране на обработвания детайл. Кантирането също е подготвителен процес за последващи операции по коване, което кара материала да тече от двете страни в зона в центъра. ОТПЕЧАТЪЧНО КОВАНЕ или ЗАТВОРЕНО КОВАНЕ, както се нарича, използва матрица/форма, която компресира материала и ограничава потока му вътре в себе си. Матрицата се затваря и материалът приема формата на кухината на матрицата/формата. ПРЕЦИЗНОТО КОВАНЕ, процес, изискващ специално оборудване и матрица, произвежда части без или с много малко пламване. С други думи, частите ще имат почти крайни размери. При този процес добре контролирано количество материал се вкарва внимателно и позиционира във формата. Ние използваме този метод за сложни форми с тънки профили, малки допуски и ъгли на наклон и когато количествата са достатъчно големи, за да оправдаят разходите за матрица и оборудване. • КОВАНЕ БЕЗ ФЛАШ: Заготовката се поставя в матрицата по такъв начин, че никакъв материал да не може да изтече от кухината, за да образува флаш. Следователно не е необходимо нежелано изрязване на светкавица. Това е процес на прецизно коване и следователно изисква строг контрол на количеството използван материал. • МЕТАЛНО ЩАБОВАНЕ или РАДИАЛНО КОВАНЕ: Заготовката се въздейства периферно от матрица и се изковава. Дорник може също да се използва за изковаване на вътрешната геометрия на работния детайл. При операцията по щамповане детайлът обикновено получава няколко удара в секунда. Типичните артикули, произведени чрез щанцоване, са инструменти със заострен връх, заострени пръти, отвертки. • ПРОБИВАНЕ НА МЕТАЛ: Използваме тази операция често като допълнителна операция при производството на части. Създава се дупка или кухина с пробиване върху повърхността на работния детайл, без да се пробие през нея. Моля, имайте предвид, че пробиването е различно от пробиването, което води до проходен отвор. • ФРЕЗОВАНЕ: Щанс с желаната геометрия се притиска в детайла и създава кухина с желаната форма. Ние наричаме този пунш HOB. Операцията включва високо налягане и се извършва на студено. В резултат на това материалът е студено обработен и закален. Следователно този процес е много подходящ за производство на форми, матрици и кухини за други производствени процеси. След като плочата е произведена, човек може лесно да произвежда много еднакви кухини, без да е необходимо да ги обработва една по една. • КОВАНЕ НА РОЛКИ или ФОРМОВАНЕ НА РОЛКИ: Използват се две противоположни ролки за оформяне на металната част. Работният детайл се подава в ролките, ролките се завъртат и издърпват детайла в процепа, след това детайлът се подава през набраздената част на ролките и силите на натиск придават на материала желаната форма. Това не е процес на валцуване, а процес на коване, защото е по-скоро дискретна, отколкото непрекъсната операция. Геометрията на горичките на ролките изковава материала до необходимата форма и геометрия. Изпълнява се горещо. Тъй като е процес на коване, той произвежда части с изключителни механични свойства и затова го използваме за производство на автомобилни части като валове, които трябва да имат изключителна издръжливост в тежки работни среди. • ОРБИТАЛНО КОВАНЕ: Заготовката се поставя в кухината на матрицата за коване и се изковава от горна матрица, която се движи по орбитална траектория, докато се върти около наклонена ос. При всяко завъртане горната матрица завършва упражняването на натиск върху целия детайл. Чрез повтаряне на тези обороти няколко пъти се извършва достатъчно коване. Предимствата на тази производствена техника са нейният нисък шум при работа и по-ниските необходими усилия. С други думи, с малки сили човек може да завърти тежка матрица около ос, за да приложи голям натиск върху част от обработвания детайл, който е в контакт с матрицата. Дискови или конусовидни части понякога са подходящи за този процес. • КОВАНЕ НА ПРЪСТЕН: Ние често използваме за производство на безшевни пръстени. Материалът се нарязва на дължина, разгъва се и след това се пробива докрай, за да се създаде централен отвор. След това се поставя върху дорник и ковашка матрица го изчуква отгоре, докато пръстенът се върти бавно, докато се получат желаните размери. • ЗАНИТОВВАНЕ: Общ процес за съединяване на части, започва с права метална част, вкарана в предварително направени отвори през частите. След това двата края на металната част се изковават чрез притискане на съединението между горната и долната матрица. • КОНЕНЕ: Друг популярен процес, извършван чрез механична преса, упражняваща големи сили на кратко разстояние. Името „сечене“ идва от фините детайли, които са изковани върху повърхностите на металните монети. Това е най-вече довършителен процес за продукт, при който се получават фини детайли върху повърхностите в резултат на голямата сила, приложена от матрицата, която пренася тези детайли върху обработвания детайл. • КОВАНЕ НА МЕТАЛНИ ТОПЧЕТА: Продукти като сачмени лагери изискват висококачествени прецизно произведени метални топки. В една техника, наречена КРИВО ВЪРТАЛЯНЕ, ние използваме две срещуположни ролки, които непрекъснато се въртят, докато материалът непрекъснато се подава в ролките. В единия край на двете ролки метални сфери се изхвърлят като продукт. Вторият метод за коване на метални топки е използването на матрица, която изстисква материалната маса, поставена между тях, приемайки сферичната форма на кухината на формата. Често произведените топки изискват някои допълнителни стъпки като довършителни работи и полиране, за да се превърнат в висококачествен продукт. • ИЗОТЕРМИЧНО КОВАНЕ / ГОРЕЩО КОВАНЕ: Скъп процес, извършван само когато съотношението полза/цена е оправдано. Процес на горещ работен процес, при който матрицата се нагрява до приблизително същата температура като детайла. Тъй като и матрицата, и работата са с приблизително еднаква температура, няма охлаждане и характеристиките на потока на метала са подобрени. Операцията е подходяща за супер сплави и материали с по-лоша ковакост и материали, чийто механичните свойства са много чувствителни към малки температурни градиенти и промени. • ОПРЕДЕЛЯНЕ НА МЕТАЛ: Това е студен довършителен процес. Материалният поток е неограничен във всички посоки с изключение на посоката, в която се прилага силата. В резултат на това се получава много добро покритие на повърхността и точни размери. • ВИСОКО ЕНЕРГИЙНО КОВАНЕ: Техниката включва горна форма, прикрепена към рамото на бутало, което се избутва бързо, докато гориво-въздушната смес се запалва от свещ. Наподобява работата на буталата в автомобилен двигател. Формата удря обработвания детайл много бързо и след това се връща в първоначалната си позиция много бързо благодарение на обратното налягане. Произведението се изковава за няколко милисекунди и следователно няма време за изстиване на произведението. Това е полезно за трудни за изковаване части, които имат много чувствителни към температурата механични свойства. С други думи, процесът е толкова бърз, че детайлът се формира при постоянна температура през цялото време и няма да има температурни градиенти на интерфейсите на матрицата/работния детайл. • При КОВАНЕТО, металът се набива между два съвпадащи стоманени блока със специални форми в тях, наречени матрици. Когато металът се изковава между матриците, той приема същата форма като формите в матрицата. Когато придобие окончателната си форма се изважда да се охлади. Този процес произвежда здрави части с прецизна форма, но изисква по-голяма инвестиция за специализираните матрици. Изкованото изковаване увеличава диаметъра на парче метал чрез сплескването му. Обикновено се използва за изработка на малки части, особено за оформяне на глави на крепежни елементи като болтове и пирони. • ПРАХОВА МЕТАЛУРГИЯ / ОБРАБОТКА НА ПРАХ: Както подсказва името, тя включва производствени процеси за изработване на твърди части с определени геометрии и форми от прахове. Ако за тази цел се използват метални прахове, това е сферата на праховата металургия, а ако се използват неметални прахове, това е прахова обработка. Твърдите части се произвеждат от прахове чрез пресоване и синтероване. ПРЕСОВАНЕТО НА ПРАХ се използва за уплътняване на прахове в желани форми. Първо, първичният материал е физически прахообразен, разделяйки го на много малки отделни частици. Праховата смес се напълва в матрицата и щанцата се придвижва към праха и го уплътнява в желаната форма. Най-често се извършва при стайна температура, при пресоване на прах се получава твърда част и се нарича зелен компакт. Свързващите вещества и лубрикантите обикновено се използват за подобряване на компактността. Ние сме способни да формоваме с прахова преса с помощта на хидравлични преси с капацитет няколко хиляди тона. Също така имаме преси с двойно действие с противоположни горни и долни щанци, както и преси с множество действия за изключително сложни геометрии на детайли. Уеднаквяването, което е важно предизвикателство за много предприятия за прахова металургия / прахова обработка, не е голям проблем за AGS-TECH поради нашия богат опит в производството на такива части по поръчка в продължение на много години. Дори и с по-дебели части, където еднаквостта представлява предизвикателство, ние успяхме. Ако се ангажираме с вашия проект, ние ще направим вашите части. Ако видим потенциални рискове, ще ви информираме in предварително. СИНТЕРОВАНЕТО НА ПРАХ, което е втората стъпка, включва повишаване на температурата до определена степен и поддържане на температурата на това ниво за определено време, така че частиците на праха в пресованата част да могат да се свържат заедно. Това води до много по-здрави връзки и укрепване на обработвания детайл. Агломерирането се извършва близо до температурата на топене на праха. По време на синтероването ще настъпи свиване, силата на материала, плътността, пластичността, топлопроводимостта, електрическата проводимост се увеличават. Разполагаме с периодични и непрекъснати пещи за синтероване. Една от възможностите ни е регулиране нивото на порьозност на детайлите, които произвеждаме. Например ние сме в състояние да произвеждаме метални филтри, като поддържаме частите порести до известна степен. Използвайки техника, наречена ИМПРЕГНАЦИЯ, ние запълваме порите в метала с течност като масло. Ние произвеждаме например импрегнирани с масло лагери, които са самосмазващи се. В процеса на ИНФИЛТРАЦИЯ ние запълваме порите на метала с друг метал с по-ниска точка на топене от основния материал. Сместа се нагрява до температура между температурите на топене на двата метала. В резултат на това могат да се получат някои специални свойства. Ние също така често извършваме вторични операции като машинна обработка и коване на части, произведени на прах, когато трябва да се получат специални характеристики или свойства или когато частта може да бъде произведена с по-малко стъпки на процеса. ИЗОСТАТИЧНО ПРЕСОВАНЕ: В този процес се използва налягане на течността за уплътняване на детайла. Металните прахове се поставят във форма, направена от запечатан гъвкав контейнер. При изостатичното пресоване налягането се прилага отвсякъде, за разлика от аксиалното налягане, наблюдавано при конвенционалното пресоване. Предимствата на изостатичното пресоване са еднаква плътност в частта, особено за по-големи или по-дебели части, превъзходни свойства. Неговият недостатък е дългите времена на цикъла и относително ниската геометрична точност. СТУДЕНОТО ИЗОСТАТИЧНО ПРЕСОВАНЕ се извършва при стайна температура и гъвкавата форма е изработена от гума, PVC или уретан или подобни материали. Течността, използвана за херметизиране и уплътняване, е масло или вода. Това следва конвенционалното синтероване на зелената преса. ГОРЕЩОТО ИЗОСТАТИЧНО ПРЕСОВАНЕ, от друга страна, се извършва при високи температури и материалът за формата е ламарина или керамика с достатъчно висока точка на топене, която издържа на температурите. Флуидът под налягане обикновено е инертен газ. Операциите по пресоване и синтероване се извършват на един етап. Порьозността е почти напълно елиминирана, получава се равномерна зърнеста структура. Предимството на горещото изостатично пресоване е, че може да произвежда части, сравними с комбинацията от леене и коване, като същевременно прави възможно използването на материали, които не са подходящи за леене и коване. Недостатък на горещото изостатично пресоване е неговото дълго време на цикъл и следователно цената. Подходящ е за критични части с малък обем. ИНЖЕКТИРАНЕ НА МЕТАЛ: Много подходящ процес за производство на сложни части с тънки стени и детайлна геометрия. Най-подходящ за по-малки части. Праховете и полимерното свързващо вещество се смесват, нагряват се и се инжектират във форма. Полимерното свързващо вещество покрива повърхностите на прахообразните частици. След формоване, свързващото вещество се отстранява чрез нагряване при ниска температура или чрез разтворител. УТЪПНЯВАНЕ НА РОЛКИ/ВАЛЦАНЕ НА ПРАХ: Праховете се използват за производство на непрекъснати ленти или листове. Прахът се подава от захранващо устройство и се уплътнява от две въртящи се ролки в лист или ленти. Операцията се извършва на студено. Листът се пренася в пещ за синтероване. Процесът на синтероване може да се повтори втори път. ЕКСТРУЗИЯ НА ПРАХ: Части с големи съотношения на дължина към диаметър се произвеждат чрез екструдиране на тънък метален контейнер с прах. РАЗХЛАБЕНО СИНТЕРОВАНЕ: Както подсказва името, това е метод за уплътняване и синтероване без налягане, подходящ за производство на много порести части като метални филтри. Прахът се подава в кухината на формата без уплътняване. РАЗХЛАБЕНО СИНТЕРОВАНЕ: Както подсказва името, това е метод за уплътняване и синтероване без налягане, подходящ за производство на много порести части като метални филтри. Прахът се подава в кухината на формата без уплътняване. ИСКРОВО СИНТЕРОВАНЕ: Прахът се компресира във формата от два противоположни щанца и електрически ток с голяма мощност се прилага към щанцата и преминава през компактния прах, поставен между тях. Силният ток изгаря повърхностните филми от прахообразните частици и ги синтерува с генерираната топлина. Процесът е бърз, защото топлината не се прилага отвън, а вместо това се генерира от матрицата. ГОРЕЩО ПРЕСОВАНЕ: Праховете се пресоват и синтероват в една стъпка във форма, която може да издържи на високи температури. Докато матрицата се уплътнява, топлината на праха се прилага към нея. Добрата точност и механични свойства, постигнати чрез този метод, го правят привлекателна опция. Дори огнеупорни метали могат да бъдат обработени с помощта на материали за формоване като графит. CLICK Product Finder-Locator Service ПРЕДИШНО МЕНЮ
- Sheet Metal Forming Fabrication, Stamping, Punching, Deep Drawing, CNC
Sheet Metal Forming and Fabrication, Stamping, Punching, Bending, Progressive Die, Spot Welding, Deep Drawing, Metal Blanking and Slitting at AGS-TECH Inc. Щамповки и производство на ламарина Ние предлагаме щамповане на ламарина, оформяне, формоване, огъване, щанцоване, изрязване, нарязване, перфориране, нарязване, изрязване, бръснене, пресоване, производство, дълбоко изтегляне с помощта на матрици с единичен удар / един удар, както и прогресивни матрици и предене, формоване на гума и хидроформиране; рязане на ламарина с водна струя, плазма, лазер, трион, пламък; монтаж на ламарина чрез заваряване, точково заваряване; издуване и огъване на ламаринени тръби; довършване на повърхността на ламарина, включително боядисване чрез потапяне или спрей, електростатично прахово покритие, анодиране, покритие, разпръскване и др. Нашите услуги варират от бързо създаване на прототипи от ламарина до производство на голям обем. Препоръчваме ви да щракнете тук, заИЗТЕГЛЕТЕ нашите схематични илюстрации на процеси за производство и щамповане на ламарина от AGS-TECH Inc. Това ще ви помогне да разберете по-добре информацията, която ви предоставяме по-долу. • РЯЗВАНЕ НА ЛАМАРИНА : Предлагаме ОТРЕЖИ и ОТРОЧКИ. Отрязванията режат ламарината по една пътека наведнъж и по същество няма загуба на материал, докато при разделянето формата не може да бъде поставена точно и следователно определено количество материал се губи. Един от нашите най-популярни процеси е щанцоване, при който парче материал с кръгла или друга форма се изрязва от ламарина. Изрязаното парче е отпадък. Друга разновидност на щанцоването е СЛОТИРАНЕТО, при което се пробиват правоъгълни или продълговати отвори. БЛАНКОВАНЕТО, от друга страна, е същият процес като щанцоването, като разликата е, че парчето, което се изрязва, е работата и се запазва. FINE BLANKING, превъзходна версия на изрязване, създава разрези с малки допуски и прави гладки ръбове и не изисква вторични операции за съвършенство на детайла. Друг процес, който често използваме, е НАРЯЗВАНЕ, което е процес на срязване, при който ламарина се нарязва от две срещуположни кръгли остриета по права или извита траектория. Отварачката за консерви е прост пример за процеса на рязане. Друг популярен за нас процес е ПЕРФОРАЦИЯТА, при която много кръгли или други дупки се пробиват в ламарина по определен модел. Типичен пример за перфориран продукт са металните филтри с много отвори за течности. При NOTCHING, друг процес на рязане на ламарина, ние отстраняваме материал от обработвания детайл, започвайки от ръба или другаде и изрязваме навътре, докато се получи желаната форма. Това е прогресивен процес, при който всяка операция премахва следващо парче, докато се получи желаният контур. За малки производствени тиражи понякога използваме сравнително по-бавен процес, наречен NIBBLING, който се състои от много бързи удари на припокриващи се дупки, за да се направи по-голям и сложен разрез. В ПРОГРЕСИВНОТО РЯЗАНЕ използваме серия от различни операции, за да получим единичен разрез или определена геометрия. И накрая, БРЪСНЕНЕ вторичен процес ни помага да подобрим краищата на вече направените порязвания. Използва се за отрязване на стърготини, груби ръбове на ламарина. • ОГЪВАНЕ НА ЛАМАРИНА: Освен рязането, огъването е основен процес, без който не бихме могли да произвеждаме повечето продукти. Предимно студена работна операция, но понякога се извършва и когато е топло или горещо. Ние използваме матрици и преса през повечето време за тази операция. В ПРОГРЕСИВНОТО ОГЪВАНЕ ние използваме поредица от различни операции на щанцоване и матрица, за да получим единично огъване или определена геометрия. AGS-TECH използва различни процеси на огъване и прави избора в зависимост от материала на детайла, неговия размер, дебелина, желан размер на огъване, радиус, кривина и ъгъл на огъване, местоположение на огъване, икономичност на работа, количества за производство... и т.н. Ние използваме V-ОБРАЗНО ОГЪВАНЕ, където V-образен поансон принуждава ламарината във V-образната матрица и го огъва. Добър както за много остри, така и за тъпи ъгли и между тях, включително 90 градуса. Използвайки матрици за избърсване, ние извършваме ОГЪВАНЕ НА РЪБОВЕ. Нашето оборудване ни позволява да получаваме ъгли дори по-големи от 90 градуса. При огъване на ръба детайлът е притиснат между притискаща подложка и матрицата, зоната за огъване се намира на ръба на матрицата, а останалата част от детайла се държи върху space като конзолна греда. Когато поансонът действа върху конзолната част, той се огъва над ръба на матрицата. FLANGING е процес на огъване на ръбове, водещ до ъгъл от 90 градуса. Основните цели на операцията са елиминиране на острите ръбове и получаване на геометрични повърхности за улесняване на съединяването на детайлите. BEADING, друг често срещан процес на огъване на ръбове, образува извивка върху ръба на детайла. ПОДГИВАНЕТО от друга страна води до ръб на листа, който е напълно огънат върху себе си. В SEAMING ръбовете на две части се огъват един върху друг и се съединяват. ДВОЙНОТО ШЕВОНЕ от друга страна осигурява водонепроницаеми и херметични съединения на ламарина. Подобно на огъването на ръба, процесът, наречен РОТАЦИОННО ОГЪВАНЕ, разгръща цилиндър с изрязан желания ъгъл и служи като щанца. Тъй като силата се предава на поансона, той се затваря с детайла. Жлебът на цилиндъра придава на конзолната част желания ъгъл. Жлебът може да има ъгъл по-малък или по-голям от 90 градуса. При AIR BENDING не е необходимо долната матрица да има жлеб под ъгъл. Ламарината се поддържа от две повърхности от противоположни страни и на определено разстояние. След това перфораторът прилага сила на правилното място и огъва детайла. ОКЪГВАНЕТО НА КАНАЛА се извършва с помощта на поансон с форма на канал и матрица, а U-ОГЪВАНЕ се постига с U-образен поансон. OFFSET BENDING създава отмествания върху ламарината. ОГЪВАНЕ НА РОЛКИ, техника, подходяща за дебела работа и огъване на големи парчета метални плочи, използва три ролки за подаване и огъване на плочите до желаната кривина. Ролките се подреждат така, че да се получи желаната чупка на произведението. Разстоянието и ъгълът между ролките се контролират, за да се получи желаният резултат. Подвижна ролка прави възможно контролирането на кривината. TUBE FORMING е друга популярна операция за огъване на ламарина, включваща множество матрици. Тръбите се получават след множество действия. ГОФРАНЕТО се извършва и чрез операции на огъване. По принцип това е симетрично огъване на равни интервали през цялото парче метален лист. За гофриране могат да се използват различни форми. Вълнообразната ламарина е по-твърда и има по-добра устойчивост на огъване и следователно намира приложение в строителната индустрия. ФОРМУВАНЕ НА РОЛКА НА ЛАМАРИНА, непрекъснат производствен процес се използва за огъване на напречни сечения с определена геометрия с помощта на ролки и работата се огъва на последователни стъпки, като последната ролка завършва работата. В някои случаи се използва една ролка, а в някои случаи серия от ролки. • КОМБИНИРАНИ ПРОЦЕСИ НА РЯЗАНЕ И ОГЪВАНЕ НА ЛАМАРИНА: Това са процеси, които режат и огъват едновременно. При ПИЪРСИНГА се създава дупка с помощта на остър перфоратор. Докато перфораторът разширява отвора в листа, материалът се огъва едновременно във вътрешен фланец за отвора. Полученият фланец може да има важни функции. Операцията LANCING от друга страна изрязва и огъва листа, за да създаде повдигната геометрия. • ИЗДУВАНЕ И ОГЪВЯНЕ НА МЕТАЛНА ТРЪБА: При ИЗДУВАНЕ вътрешната част на куха тръба е под налягане, което кара тръбата да се издува навън. Тъй като тръбата е вътре в матрица, геометрията на изпъкналостта се контролира от формата на матрицата. При ОГЪВАНЕ НА РАЗТЯГАНЕ метална тръба се разтяга с помощта на сили, успоредни на оста на тръбата, и сили на огъване, за да се изтегли тръбата върху блок на форма. При DRAW BENDING затягаме тръбата близо до нейния край към въртящ се формовъчен блок, който огъва тръбата, докато се върти. И накрая, при КОМПРЕСИОННО ОГЪВАНЕ тръбата се държи със сила към фиксиран блок и матрица я огъва върху блока на формата. • ДЪЛБОКО ИЗТЕГЛЯНЕ: В една от най-популярните ни операции се използват щанца, подходяща матрица и празен държач. Заготовката от ламарина се поставя върху отвора на матрицата и поансонът се придвижва към заготовката, задържана от държача на заготовката. След като влязат в контакт, поансонът принуждава ламарината да влезе в кухината на матрицата, за да оформи продукта. Операцията по дълбоко изтегляне наподобява рязане, но хлабината между поансона и матрицата предотвратява срязването на листа. Друг фактор, който гарантира, че листът е дълбоко изтеглен и не е нарязан, са заоблените ъгли на матрицата и поансона, които предотвратяват срязването и срязването. За постигане на по-голяма степен на дълбоко изтегляне се прилага процес на ПРЕЧЕРТАВАНЕ, при който се извършва последващо дълбоко изтегляне върху част, която вече е преминала процес на дълбоко изтегляне. При ОБРАТНО ПРЕЧЕРТАВАНЕ, дълбоко изтеглената част се обръща и изчертава в обратната посока. Дълбокото изтегляне може да осигури обекти с неправилна форма, като куполообразни, заострени или стъпаловидни чаши, При ЩАМПОВАНЕ ние използваме мъжка и женска двойка матрици, за да впечатлим металния лист с дизайн или надпис. • SPINNING : Операция, при която плосък или предварително формован детайл се държи между въртящ се дорник и опашка и инструментът прилага локализиран натиск върху детайла, докато постепенно се придвижва нагоре по дорника. В резултат на това детайлът се увива върху дорника и приема своята форма. Използваме тази техника като алтернатива на дълбокото изтегляне, където количеството на поръчката е малко, частите са големи (диаметър до 20 фута) и имат уникални криви. Въпреки че цените на бройка обикновено са по-високи, разходите за настройка на CNC предене са ниски в сравнение с дълбокото изтегляне. Напротив, дълбокото изтегляне изисква висока първоначална инвестиция за настройка, но разходите за парче са ниски, когато се произвежда голямо количество части. Друга версия на този процес е ПРЕДЕНИЕ НА СРЪЖА, при което също има метален поток в детайла. Металният поток ще намали дебелината на детайла, докато процесът се извършва. Още един свързан процес е ПРЕДЕНИЕ НА ТРЪБА, който се прилага върху цилиндрични части. Също така в този процес има метален поток в детайла. По този начин дебелината се намалява и дължината на тръбата се увеличава. Инструментът може да се мести, за да се създават елементи от вътрешната или външната страна на тръбата. • ФОРМОВАНЕ НА КАУЧУК НА ЛАМАРИНА: Каучукът или полиуретановият материал се поставят в контейнерна матрица и обработваният детайл се поставя върху повърхността на гумата. След това ударът се въздейства върху детайла и го притиска в гумата. Тъй като налягането, генерирано от гумата, е ниско, дълбочината на произведените части е ограничена. Тъй като разходите за инструменти са ниски, процесът е подходящ за производство в малки количества. • ХИДРОФОРМУВАНЕ: Подобно на формоването на каучук, при този процес ламаринените изделия се притискат от щанца в течност под налягане вътре в камера. Металната ламарина е притисната между щанцата и гумената диафрагма. Диафрагмата обхваща детайла изцяло и налягането на течността го принуждава да се оформи върху поансона. С тази техника могат да се получат много дълбоки чертежи, дори по-дълбоки, отколкото в процеса на дълбоко рисуване. Ние произвеждаме еднощанцови матрици, както и прогресивни матрици в зависимост от вашата част. Щампите за еднократно щамповане са рентабилен метод за бързо производство на големи количества прости части от ламарина, като например шайби. Прогресивните матрици или техниката на дълбоко изтегляне се използват за производство на по-сложни геометрии. В зависимост от вашия случай може да се използва водоструйно, лазерно или плазмено рязане, за да произведете вашите метални части евтино, бързо и точно. Много доставчици нямат представа за тези алтернативни техники или ги нямат и затова преминават през дълги и скъпи начини за изработка на матрици и инструменти, които само губят време и пари на клиентите. Ако се нуждаете от изработени по поръчка компоненти от ламарина, като кутии, електронни корпуси... и т.н. възможно най-бързо в рамките на дни, тогава се свържете с нас за нашата услуга БЪРЗО ИЗРАБОТВАНЕ НА ПРОТОТИПИ ОТ ЛАМАРИНА. CLICK Product Finder-Locator Service ПРЕДИШНО МЕНЮ
- Plastic Rubber Metal Extrusions, Extrusion Dies, Aluminum Extruding
Plastic Rubber Metal Extrusions, Extrusion Dies, Aluminum Extruding, Pipe Tube Forming, Plastic Profiles, Metal Profiles Manufacturing, PVC at AGS-TECH Inc. Екструзии, екструдирани продукти, екструдати Ние използваме EXTRUSION process за производство на продукти с фиксиран профил на напречното сечение, като тръби, тръби и радиатори. Въпреки че много материали могат да бъдат екструдирани, нашите най-често срещани екструдирания са изработени от метал, полимери / пластмаса, керамика, получени чрез студен, топъл или горещ метод на екструдиране. Ние наричаме екструдираните части екструдат или екструдати, ако е множествено число. Някои специализирани версии на процеса, които също изпълняваме, са покриване на кожух, коекструзия и комбинирана екструзия. Препоръчваме ви да щракнете тук, за да ИЗТЕГЛЕТЕ нашите схематични илюстрации на процеси за екструдиране на металокерамика и пластмаса от AGS-TECH Inc. Това ще ви помогне да разберете по-добре информацията, която ви предоставяме по-долу. При екструдиране материалът, който трябва да бъде екструдиран, се избутва или изтегля през матрица, която има желания профил на напречното сечение. Процесът може да се използва за производство на сложни напречни сечения с отлично покритие на повърхността и за работа с чуплив материал. Чрез този процес могат да се произвеждат части с всякаква дължина. За да опростите стъпките на процеса: 1.) При топло или горещо екструдиране материалът се нагрява и се зарежда в контейнер в пресата. Материалът се пресова и изтласква от матрицата. 2.) Произведеният екструдат се разтяга за изправяне, термично обработен или студено обработен за подобряване на свойствата му. От друга страна COLD EXTRUSION се извършва при около стайна температура и има предимствата на по-малко окисление, висока якост, по-малки толеранси, добро покритие на повърхността и устойчивост. WARM EXTRUSION се извършва над стайна температура, но под точката на рекристализация. Той предлага компромис и баланс за необходимите сили, пластичност и свойства на материала и следователно е изборът за някои приложения. HOT EXTRUSION се извършва над температурата на рекристализация на материала. По този начин е по-лесно да прокарате материала през матрицата. Но цената на оборудването е висока. Колкото по-сложен е екструдираният профил, толкова по-скъпа е матрицата (инструменталната екипировка) и толкова по-ниска е скоростта на производство. Напречните сечения на матрицата, както и дебелините имат ограничения, които зависят от материала, който ще се екструдира. Острите ъгли в матриците за екструдиране винаги са нежелателни и трябва да се избягват, освен ако не е необходимо. Според материала, който се екструдира предлагаме: • МЕТАЛНИ ЕКСТРУЗИИ : Най-често срещаните, които произвеждаме, са алуминий, месинг, цинк, мед, стомана, титан, магнезий • PLASTIC EXTRUSION : Пластмасата се разтопява и се оформя в непрекъснат профил. Нашите често обработвани материали са полиетилен, найлон, полистирен, поливинилхлорид, полипропилен, ABS пластмаса, поликарбонат, акрил. Типичните продукти, които произвеждаме, включват тръби и пластмасови рамки. В процеса малки пластмасови перли / смола се подават гравитачно от бункера в цевта на екструзионната машина. Често смесваме и оцветители или други добавки в бункера, за да придадем на продукта необходимите спецификации и свойства. Материалът, влизащ в нагрятия варел, се принуждава от въртящия се винт да напусне варела в края и да се движи през ситовата опаковка за отстраняване на замърсителите в разтопената пластмаса. След като премине ситовия пакет, пластмасата влиза в матрицата за екструдиране. Матрицата придава на движещата се мека пластмаса профилна форма, докато преминава през нея. Сега екструдатът преминава през водна баня за охлаждане. Други техники, които AGS-TECH Inc. използва от много години, са: • ЕКСТРУЗИЯ НА ТРЪБИ И ТРЪБИ : Пластмасовите тръби се формират, когато пластмасата се екструдира през кръгла формовъчна матрица и се охлажда във водна баня, след което се нарязва на дължина или се навива на рулони/навива. Прозрачни или цветни, на райета, с една или две стени, гъвкави или твърди, PE, PP, полиуретан, PVC, найлон, PC, силикон, винил или други, имаме всичко. Имаме заредени тръби, както и възможност за производство според вашите спецификации. AGS-TECH произвежда тръби според изискванията на FDA, UL и LE за медицински, електрически и електронни, индустриални и други приложения. • ПОКРИВАНЕ / ЕКСТРУЗИРАНЕ НА ОБКЛЮЧВАНЕ : Тази техника нанася външен слой от пластмаса върху съществуващ проводник или кабел. Нашите изолационни проводници се произвеждат по този метод. • COEXTRUSION : Множество слоеве материал се екструдират едновременно. Множеството слоеве се доставят от множество екструдери. Различните дебелини на слоя могат да се регулират, за да отговарят на спецификациите на клиента. Този процес прави възможно използването на множество полимери, всеки от които има различна функционалност в продукта. В резултат на това човек може да оптимизира набор от свойства. • ЕКСТРУЗИЯ НА СЪЕДИНЕНИЕ: Единичен или множество полимери се смесват с добавки, за да се получи пластмасово съединение. Нашите двушнекови екструдери произвеждат смесени екструдери. Екструзионните матрици обикновено са евтини в сравнение с металните форми. Ако плащате много повече от няколко хиляди долара за малка или средна екструдираща матрица за екструдиране на алуминий, вероятно плащате твърде много. Ние сме експерти в определянето коя техника е най-рентабилна, най-бърза и най-подходяща за вашето приложение. Понякога екструдирането и след това машинната обработка на част може да ви спести много пари. Преди да вземете твърдо решение, първо ни попитайте за нашето мнение. Помогнахме на много клиенти да вземат правилните решения. За някои широко използвани метални екструзии можете да изтеглите нашите брошури и каталози, като щракнете върху цветния текст по-долу. Ако това е готов продукт, който отговаря на вашите изисквания, той ще бъде по-икономичен. Изтеглете нашите възможности за екструдиране на медицински тръби Изтеглете нашите екструдирани радиатори • ПРОЦЕСИ ЗА ВТОРИЧНО ПРОИЗВОДСТВО И ПРОИЗВОДСТВО ЗА ЕКСТРУЗИИ : Сред процесите с добавена стойност, които предлагаме за екструдирани продукти, са: -Огъване, формоване и оформяне на тръби и тръби по поръчка, отрязване на тръби, оформяне на края на тръбите, навиване на тръби, машинна обработка и довършителни работи, пробиване на дупки и пробиване и щанцоване, - Сглобки на тръби и тръби по поръчка, тръбен монтаж, заваряване, спояване и запояване -Персонализирано екструзионно огъване, формоване и оформяне -Почистване, обезмасляване, ецване, пасивиране, полиране, анодиране, покритие, боядисване, топлинна обработка, отгряване и закаляване, маркиране, гравиране и етикетиране, опаковане по поръчка. CLICK Product Finder-Locator Service ПРЕДИШНА СТРАНИЦА
- Casting and Machined Parts, CNC Manufacturing, Milling, Turning, Swiss
Casting and Machined Parts, CNC Manufacturing, Milling, Turning, Swiss Type Machining, Die Casting, Investment Casting, Lost Foam Cast Parts from AGS-TECH Inc. Леене и машинна обработка Нашите персонализирани техники за леене и машинна обработка са отливки за еднократна употреба и отливки за еднократна употреба, отливки от черни и цветни метали, пясък, матрици, центробежни, непрекъснати, керамични форми, инвестиция, загубена пяна, почти мрежеста форма, постоянна форма (гравитационно леене под налягане), гипс матрици (гипсова отливка) и корпусни отливки, машинно обработени части, произведени чрез фрезоване и струговане с помощта на конвенционално, както и CNC оборудване, обработка от швейцарски тип за висока производителност, евтини малки прецизни части, обработка на винтове за крепежни елементи, неконвенционална обработка. Моля, имайте предвид, че освен метали и метални сплави, ние обработваме и керамични, стъклени и пластмасови компоненти в някои случаи, когато производството на матрица не е привлекателно или не е опция. Машинната обработка на полимерни материали изисква специализирания опит, който имаме, поради предизвикателството, което пластмасите и каучукът представляват поради тяхната мекота, липса на твърдост... и т.н. За механична обработка на керамика и стъкло, моля, вижте нашата страница за неконвенционална изработка. AGS-TECH Inc. произвежда и доставя както леки, така и тежки отливки. Ние доставяме метални отливки и машинни части за котли, топлообменници, автомобили, микромотори, вятърни турбини, оборудване за опаковане на храни и др. Препоръчваме ви да щракнете тук, за да ИЗТЕГЛЕТЕ нашите схематични илюстрации на процеси на обработка и леене от AGS-TECH Inc. Това ще ви помогне да разберете по-добре информацията, която ви предоставяме по-долу. Нека разгледаме подробно някои от различните техники, които предлагаме: • ОТЛИВАНЕ НА ИЗХОДНА ФОРМА: Тази широка категория се отнася за методи, които включват временни форми за еднократна употреба. Примери за това са пясък, гипс, черупки, облицовка (наричана също изгубен восък) и гипсова отливка. • ПЯСЪЧНО ЛЕЕНЕ: Процес, при който пясъкът се използва като материал за формовка. Много стар метод и все още много популярен до степен, че по-голямата част от произведените метални отливки са направени по тази техника. Ниска цена дори при ниско количество производство. Подходящ за производство на малки и големи части. Техниката може да се използва за производство на части в рамките на дни или седмици с много малко инвестиции. Влажният пясък се свързва с глина, свързващи вещества или специални масла. Пясъкът обикновено се съдържа във формовъчните кутии, а кухината и системата за врати се създават чрез уплътняване на пясъка около моделите. Процесите са: 1.) Поставяне на модела в пясък, за да се направи матрицата 2.) Включване на модел и пясък в стробна система 3.) Премахване на модел 4.) Запълване на кухината на формата с разтопен метал 5.) Охлаждане на метала 6.) Разчупване на пясъчната форма и отстраняване на отливката • ОТЛИВАНЕ НА ГИПСОВА ФОРМА: Подобно на леенето в пясък, но вместо пясък, като материал за матрица се използва парижки гипс. Кратки срокове за производство като леене в пясък и евтини. Добри толеранси на размерите и повърхностно покритие. Основният му недостатък е, че може да се използва само с метали с ниска точка на топене като алуминий и цинк. • ОТЛИВАНЕ НА ЧЕРЕПКИ: Също подобно на пясъчното леене. Кухина на формата, получена чрез втвърдена обвивка от пясък и свързващо вещество от термореактивна смола вместо колба, пълна с пясък, както при процеса на леене в пясък. Почти всеки метал, подходящ за отливане от пясък, може да бъде отлят чрез формоване на черупки. Процесът може да се обобщи като: 1.) Производство на корпусна форма. Използваният пясък е с много по-малък размер на зърното в сравнение с пясъка, използван при леене в пясък. Финият пясък се смесва с термореактивна смола. Металният шаблон е покрит с разделителен агент, за да се улесни отстраняването на черупката. След това металният модел се нагрява и пясъчната смес се поръсва или издухва върху горещия шаблон за отливане. На повърхността на шаблона се образува тънка черупка. Дебелината на тази обвивка може да се регулира чрез промяна на продължителността на времето, през което сместа от пясъчна смола е в контакт с металния шаблон. След това насипният пясък се отстранява, като остава шарката, покрита с черупки. 2.) След това черупката и шаблонът се загряват във фурна, така че черупката да се втвърди. След завършване на втвърдяването черупката се изважда от шаблона с помощта на щифтове, вградени в шаблона. 3.) Две такива черупки се сглобяват заедно чрез залепване или затягане и образуват пълната форма. Сега формата на черупката се вкарва в контейнер, в който се поддържа от пясък или метални изстрели по време на процеса на леене. 4.) Сега горещият метал може да се излее във формата за черупки. Предимствата на корпусното леене са продукти с много добра повърхностна обработка, възможност за производство на сложни детайли с висока точност на размерите, лесен за автоматизиране процес, икономичен за големи обеми на производство. Недостатъците са, че формите изискват добра вентилация поради газовете, които се образуват, когато разтопеният метал влезе в контакт със свързващия химикал, термореактивните смоли и металните шарки са скъпи. Поради цената на металните модели, техниката може да не е подходяща за производствени серии с малки количества. • ЛЕЕНЕ ПО ИНВЕСТИЦИОННИ МАТЕРИАЛИ (известно също като ЛЕЕНЕ НА ИЗГУБЕН ВОСАК): също много стара техника и подходяща за производство на качествени части с висока точност, повторяемост, гъвкавост и цялост от много метали, огнеупорни материали и специални сплави с висока производителност. Могат да се произвеждат както малки, така и големи части. Скъп процес в сравнение с някои от другите методи, но основно предимство е възможността да се произвеждат детайли с близка до мрежа форма, сложни контури и детайли. Така че цената донякъде се компенсира от елиминирането на преработката и обработката в някои случаи. Въпреки че може да има вариации, ето обобщение на общия процес на леене по инвестиция: 1.) Създаване на оригинален мастър модел от восък или пластмаса. Всяка отливка се нуждае от един модел, тъй като те се унищожават в процеса. Необходима е и матрица, от която се произвеждат моделите, като през повечето време матрицата се отлива или обработва машинно. Тъй като матрицата не трябва да се отваря, могат да се постигнат сложни отливки, много восъчни модели могат да бъдат свързани като клоните на дърво и излети заедно, като по този начин позволяват производството на множество части от едно изливане на метала или металната сплав. 2.) След това моделът се потапя или излива с огнеупорна суспензия, съставена от много фин зърнест силициев диоксид, вода, свързващи вещества. Това води до керамичен слой върху повърхността на шарката. Огнеупорното покритие върху шаблона се оставя да изсъхне и да се втвърди. От тази стъпка идва наименованието отливане по инвестиция: Огнеупорна суспензия се влага върху восъчната шарка. 3.) На тази стъпка втвърдената керамична форма се обръща с главата надолу и се нагрява, така че восъкът да се разтопи и да излее от формата. Остава кухина за металната отливка. 4.) След изтичане на восъка, керамичната форма се нагрява дори до по-висока температура, което води до укрепване на матрицата. 5.) Металната отливка се излива в горещата форма, запълвайки всички сложни секции. 6.) Отливката се оставя да се втвърди 7.) Накрая керамичната форма се счупва и произведените части се изрязват от дървото. Ето линк към брошурата на инсталацията за отливане по модели • ИЗПАРИТЕЛНО ОТЛИВАНЕ НА ШАБЛОН: Процесът използва модел, направен от материал като полистиролова пяна, която ще се изпари, когато горещ разтопен метал се излее във формата. Има два вида на този процес: ОТЛИВАНЕ НА ЗАГУБЕНА ПЯНА, при което се използва несвързан пясък и ОТЛИВАНЕ НА ПЪЛНА ФОРМА, при което се използва свързан пясък. Ето основните стъпки на процеса: 1.) Изработете модела от материал като полистирен. Когато ще се произвеждат големи количества, моделът се формова. Ако частта има сложна форма, може да се наложи няколко секции от такъв пенопласт да бъдат залепени заедно, за да се оформи шаблонът. Често покриваме модела с огнеупорна смес, за да създадем добро покритие на повърхността на отливката. 2.) След това моделът се поставя в пясък за формоване. 3.) Разтопеният метал се излива във формата, изпарявайки модела на пяната, т.е. полистиролът в повечето случаи, докато тече през кухината на формата. 4.) Разтопеният метал се оставя в пясъчната форма да се втвърди. 5.) След като се втвърди, махаме отливката. В някои случаи продуктът, който произвеждаме, изисква сърцевина в шаблона. При леене чрез изпаряване не е необходимо да се поставя и закрепва сърцевина в кухината на формата. Техниката е подходяща за производство на много сложни геометрии, може лесно да се автоматизира за голям обем производство и няма разделителни линии в отлятата част. Основният процес е прост и икономичен за изпълнение. За голям обем производство, тъй като е необходима матрица или матрица за производството на моделите от полистирен, това може да бъде донякъде скъпо. • НЕРАЗШИРЯВАЩА СЕ ОТЛИВКА НА ФОРМА: Тази широка категория се отнася до методи, при които не е необходимо матрицата да се реформира след всеки производствен цикъл. Примери за това са постоянното, щамповото, непрекъснатото и центробежното леене. Получава се повторяемост и частите могат да се характеризират като БЛИЗКА НЕТА ФОРМА. • ПОСТОЯННО ОТЛИВАНЕ НА ФОРМА: Многократно използваните форми, изработени от метал, се използват за множество отливки. Постоянната форма обикновено може да се използва десетки хиляди пъти, преди да се износи. Гравитацията, газовото налягане или вакуумът обикновено се използват за запълване на формата. Формите (наричани също матрици) обикновено са направени от желязо, стомана, керамика или други метали. Общият процес е: 1.) Обработете и създайте формата. Обичайно е формата да се обработва от два метални блока, които пасват заедно и могат да се отварят и затварят. И двете характеристики на частта, както и литниковата система обикновено се обработват машинно в леярската форма. 2.) Вътрешните повърхности на формата са покрити със суспензия, включваща огнеупорни материали. Това помага да се контролира топлинният поток и действа като смазка за лесно отстраняване на отлятата част. 3.) След това постоянните половини на формата се затварят и формата се нагрява. 4.) Разтопеният метал се излива във формата и се оставя да се втвърди. 5.) Преди да настъпи голямо охлаждане, ние изваждаме частта от постоянната форма с помощта на ежектори, когато половинките на матрицата се отварят. Ние често използваме трайно отливане за метали с ниска точка на топене като цинк и алуминий. За стоманени отливки използваме графит като материал за формовка. Понякога получаваме сложни геометрии, използвайки сърцевини в постоянни форми. Предимствата на тази техника са отливки с добри механични свойства, получени чрез бързо охлаждане, еднородност на свойствата, добра точност и повърхностна обработка, ниски проценти на брак, възможност за автоматизиране на процеса и икономично производство на големи обеми. Недостатъците са високите първоначални разходи за настройка, които го правят неподходящ за операции с малък обем, и ограниченията върху размера на произведените части. • ЛЕЕНЕ ПОД МАРШИНА: Щампата се обработва машинно и разтопеният метал се изтласква под високо налягане в кухините на формата. Възможни са отливки както от цветни, така и от черни метали. Процесът е подходящ за големи производствени серии на малки до средни по размер детайли, изключително тънки стени, последователност на размерите и добро покритие на повърхността. AGS-TECH Inc. е в състояние да произвежда дебелини на стени до 0,5 mm, използвайки тази техника. Подобно на постоянното отливане, формата трябва да се състои от две половини, които могат да се отварят и затварят за отстраняване на произведената част. Формата за леене под налягане може да има множество кухини, за да позволи производството на множество отливки с всеки цикъл. Формите за леене под налягане са много тежки и много по-големи от частите, които произвеждат, следователно също са скъпи. Ние ремонтираме и заменяме износените матрици безплатно за нашите клиенти, стига те да поръчат повторно своите части от нас. Нашите матрици имат дълъг живот в диапазона от няколкостотин хиляди цикъла. Ето основните опростени стъпки на процеса: 1.) Производство на формата обикновено от стомана 2.) Мухъл, инсталиран на машина за леене под налягане 3.) Буталото принуждава разтопения метал да тече в кухините на матрицата, запълвайки сложните елементи и тънките стени 4.) След напълване на формата с разтопен метал, отливката се оставя да се втвърди под налягане 5.) Формата се отваря и отливката се отстранява с помощта на ежекторни щифтове. 6.) Сега празната матрица се смазва отново и се затяга за следващия цикъл. При леенето под налягане често използваме формоване с вложки, при което вграждаме допълнителна част в матрицата и отливаме метала около нея. След втвърдяване тези части стават част от отлятия продукт. Предимствата на леенето под налягане са добри механични свойства на частите, възможност за сложни характеристики, фини детайли и добро покритие на повърхността, високи производствени нива, лесна автоматизация. Недостатъците са: Не е много подходящ за малък обем поради високата цена на матрицата и оборудването, ограничения във формите, които могат да бъдат отлети, малки кръгли следи върху отливките в резултат на контакт на ежекторни щифтове, тънък отблясък от метал, изстискан на линията на разделяне, необходимост за вентилационни отвори по линията на разделяне между матрицата, необходимостта да се поддържат ниски температури на формата чрез циркулация на водата. • ЦЕНТРОБЕЖНО ЛЕЕНЕ: Разтопеният метал се излива в центъра на въртящата се форма по оста на въртене. Центробежните сили изхвърлят метала към периферията и той се оставя да се втвърди, докато формата продължава да се върти. Могат да се използват както хоризонтални, така и вертикални завъртания на осите. Могат да се отливат части с кръгли вътрешни повърхности, както и други некръгли форми. Процесът може да се обобщи като: 1.) Разтопеният метал се излива в центробежна форма. След това металът се изтласква към външните стени поради въртене на формата. 2.) Когато формата се върти, металната отливка се втвърдява Центробежното леене е подходяща техника за производство на кухи цилиндрични части като тръби, няма нужда от канали, щрангове и литникови елементи, добро покритие на повърхността и детайлни характеристики, няма проблеми със свиването, възможност за производство на дълги тръби с много големи диаметри, производствена способност с висока скорост . • НЕПРЕКЪСНАТО ЛЕЕНЕ (СТРАНД КАСТИНГ): Използва се за леене на непрекъсната дължина на метал. По принцип разтопеният метал се излива в двуизмерен профил на формата, но дължината му е неопределена. Нов разтопен метал непрекъснато се подава във формата, докато отливката се движи надолу, като дължината й се увеличава с времето. Метали като мед, стомана, алуминий се отливат в дълги нишки чрез непрекъснат процес на леене. Процесът може да има различни конфигурации, но общата може да бъде опростена като: 1.) Разтопеният метал се излива в контейнер, разположен високо над матрицата, при добре изчислени количества и скорости на потока и протича през водно охлажданата форма. Металната отливка, излята във формата, се втвърдява до стартова лента, поставена на дъното на матрицата. Тази стартова лента дава на ролките нещо, за което да се хванат първоначално. 2.) Дългата метална нишка се носи от ролки с постоянна скорост. Ролките също променят посоката на потока на металната нишка от вертикална към хоризонтална. 3.) След като непрекъснатата отливка измине определено хоризонтално разстояние, горелка или трион, който се движи с отливката, бързо я нарязва на желаните дължини. Процесът на непрекъснато леене може да бъде интегриран с ПРОЦЕС НА ВАЛЦАВАНЕ, при който непрекъснато летият метал може да се подава директно във валцова мелница за производство на I-образни греди, T-образни греди….и т.н. Непрекъснатото леене създава еднакви свойства в целия продукт, има висока степен на втвърдяване, намалява разходите поради много ниска загуба на материал, предлага процес, при който зареждането на метал, изливането, втвърдяването, рязането и отстраняването на отливката се извършват в непрекъсната операция и което води до висока производителност и високо качество. Основно съображение обаче е високата първоначална инвестиция, разходите за настройка и изискванията за пространство. • МАШИННИ УСЛУГИ: Ние предлагаме три, четири и пет оси. Видовете обработващи процеси, които използваме, са СТРУГОВАНЕ, ФРЕЗОВАНЕ, ПРОБИВАНЕ, РАЗБОЧВАНЕ, ПРОБРАВАНЕ, РЕНДОСВАНЕ, РЯЗВАНЕ, ШЛИФОВАНЕ, ЛАПИТВАНЕ, ПОЛИРАНЕ и НЕТРАДИЦИОННА МАШИННА ОБРАБОТКА, която е допълнително разработена в друго меню на нашия уебсайт. За по-голямата част от нашето производство ние използваме машини с ЦПУ. За някои операции обаче конвенционалните техники са по-подходящи и затова разчитаме и на тях. Нашите възможности за обработка достигат възможно най-високото ниво и някои най-взискателни части се произвеждат в завод, сертифициран по AS9100. Лопатките на реактивните двигатели изискват високоспециализиран производствен опит и правилното оборудване. Аерокосмическата индустрия има много строги стандарти. Някои компоненти със сложни геометрични структури се произвеждат най-лесно чрез обработка с пет оси, която се среща само в някои заводи за обработка, включително нашия. Нашият аерокосмически сертифициран завод има необходимия опит, отговарящ на обширните изисквания за документация на аерокосмическата индустрия. При операциите СТРУГОВАНЕ детайлът се завърта и придвижва срещу режещ инструмент. За този процес се използва машина, наречена струг. При ФРЕЗОВАНЕ, машина, наречена фреза, има въртящ се инструмент, който привежда режещите ръбове към детайла. Операциите по ПРОБИВАНЕ включват въртящ се нож с режещи ръбове, който създава дупки при контакт с детайла. Обикновено се използват бормашини, стругове или мелници. При операциите BORING инструмент с един огънат заострен връх се премества в груб отвор във въртящ се детайл, за да се увеличи леко отворът и да се подобри точността. Използва се за фини довършителни цели. ПРОВИВАНЕТО включва назъбен инструмент за отстраняване на материал от детайла с едно преминаване на протягането (назъбен инструмент). При линейното протягане протягането се движи линейно по повърхността на детайла, за да се извърши разрезът, докато при ротационното протягане протягането се завърта и притиска в детайла, за да се изреже осесиметрична форма. SWISS TYPE MACHINING е една от нашите ценни техники, които използваме за производство на голям обем на малки детайли с висока точност. Използвайки струг от швейцарски тип, ние струговаме малки, сложни, прецизни детайли евтино. За разлика от конвенционалните стругове, при които детайлът се поддържа неподвижен, а инструментът се движи, в центровете за струговане от швейцарски тип детайлът може да се движи по Z-ос и инструментът е неподвижен. При машинна обработка от швейцарски тип прътът се държи в машината и се придвижва през водеща втулка по оста z, като се разкрива само частта, която ще се обработва. По този начин се осигурява плътен захват и точността е много висока. Наличието на живи инструменти предоставя възможност за фрезоване и пробиване, докато материалът напредва от направляващата втулка. Y-осата на оборудването от швейцарски тип осигурява пълни възможности за фрезоване и спестява много време в производството. Освен това нашите машини имат бормашини и пробиващи инструменти, които работят върху частта, когато се държи в подшпиндела. Нашата възможност за машинна обработка от швейцарски тип ни дава възможност за напълно автоматизирана цялостна обработка в една операция. Машинната обработка е един от най-големите сегменти на бизнеса на AGS-TECH Inc. Използваме го или като основна операция, или като вторична операция след отливане или екструдиране на част, така че да бъдат изпълнени всички спецификации на чертежа. • УСЛУГИ ЗА ОБРАБОТАВАНЕ НА ПОВЪРХНОСТИ: Ние предлагаме голямо разнообразие от повърхностни обработки и довършителни работи като повърхностно кондициониране за подобряване на адхезията, нанасяне на тънък оксиден слой за подобряване на адхезията на покритието, пясъкоструене, химичен филм, анодиране, азотиране, прахово покритие, покритие чрез пръскане , различни усъвършенствани техники за метализиране и нанасяне на покрития, включително разпрашване, електронен лъч, изпаряване, покритие, твърди покрития като диамант като въглерод (DLC) или титаниево покритие за пробивни и режещи инструменти. • УСЛУГИ ЗА МАРКИРАНЕ И ЕТИКЕТИРАНЕ НА ПРОДУКТИ: Много от нашите клиенти изискват маркиране и етикетиране, лазерно маркиране, гравиране върху метални части. Ако имате такава нужда, нека обсъдим кой вариант ще бъде най-добрият за вас. Ето някои от често използваните метални ляти продукти. Тъй като те са готови, можете да спестите от разходи за форми, в случай че някое от тях отговаря на вашите изисквания: КЛИКНЕТЕ ТУК, ЗА ДА ИЗТЕГЛИТЕ нашите 11 серии от ляти под налягане алуминиеви кутии от AGS-Electronics CLICK Product Finder-Locator Service ПРЕДИШНА СТРАНИЦА
- Custom Manufactured Parts, Assemblies, Plastic Mold, Casting,Machining
Custom Manufactured Parts, Assemblies, Plastic Mold, Rubber Molding, Metal Casting, CNC Machining, Turning, Milling, Electrical Electronic Optical Assembly PCBA Произведени по поръчка части & Ассембли и продукти Прочетете още Пластмасови и гумени форми и леене Прочетете още Леене и машинна обработка Прочетете още Екструзии, екструдирани продукти Прочетете още Щамповки и производство на ламарина Прочетете още Коване на метали и прахова металургия Прочетете още Формоване на тел и пружина Прочетете още Формоване и оформяне на стъкло и керамика Прочетете още Адитивно и бързо производство Прочетете още Производство на композитни материали и композитни материали Прочетете още Процеси на свързване, сглобяване и закрепване Ние произвеждаме части и възли за вас и предлагаме следните производствени процеси: • Пластмасови и гумени форми и формовани части. Инжекционно формоване, термоформоване, термореактивно формоване, вакуумно формоване, формоване чрез раздуване, ротационно формоване, формоване чрез изливане, формоване с вложки и други. • Пластмасови, гумени и метални екструзии • Отливки от черни и цветни метали и машинно обработени части, произведени чрез техники на фрезоване и струговане, обработка по швейцарски тип. • Части за прахова металургия • Метални и неметални щамповки, формоване на ламарина, заварени ламаринени възли • Студено и горещо коване • Телове, заварени комплекти от тел, формоване на тел • Различни видове пружини, оформяне на пружини • Производство на зъбни колела, скоростна кутия, съединител, червяк, редуктор, цилиндър, трансмисионни ремъци, трансмисионни вериги, трансмисионни компоненти • Специално закалено и бронирано стъкло, отговарящо на НАТО и военните стандарти • Сачми, лагери, ролки и ролки • Вентили и пневматични компоненти като О-пръстен, шайба и уплътнения • Стъклени и керамични детайли и възли, вакуумни и херметични компоненти, металокерамика и керамика-керамика. • Различни видове механични, оптомеханични, електромеханични, оптоелектронни възли. • Свързване метал-каучук, метал-пластмаса • Тръби и тръби, формоване на тръби, огъване и тръбни възли по поръчка, производство на сифони. • Производство на фибростъкло • Заваряване чрез различни техники като точково заваряване, лазерно заваряване, MIG, TIG. Ултразвуково заваряване на пластмасови детайли. • Голямо разнообразие от повърхностни обработки и повърхностни покрития като повърхностно кондициониране за подобряване на адхезията, нанасяне на тънък оксиден слой за подобряване на адхезията на покритието, пясъкоструене, химически филм, анодиране, азотиране, прахово покритие, покритие със спрей, различни усъвършенствани техники за метализиране и покритие включително разпрашване, електронен лъч, изпаряване, покритие, твърди покрития като диамантено-подобен въглерод (DLC) или титан за инструменти за рязане и пробиване. • Маркиране и етикетиране, лазерно маркиране върху метални части, печат върху пластмасови и гумени части Изтеглете брошура за общи термини в машиностроенето, използвани от дизайнери и инженери Ние създаваме продукти според вашите конкретни спецификации и изисквания. За да ви предложим най-доброто качество, доставка и цени, ние произвеждаме продукти в световен мащаб в Китай, Индия, Тайван, Филипините, Южна Корея, Малайзия, Шри Ланка, Турция, САЩ, Канада, Германия, Обединеното кралство и Япония. Това ни прави много по-силни и глобално по-конкурентоспособни от всеки друг персонализиран производител. Нашите продукти се произвеждат в сертифицирани среди по ISO9001:2000, QS9000, ISO14001, TS16949 и притежават маркировка CE, UL и отговарят на други индустриални стандарти. След като бъдем назначени за вашия проект, ние можем да се погрижим за цялото производство, монтаж, тестване, квалификация, доставка и митница, както желаете. Ако предпочитате, можем да складираме вашите части, да сглобим персонализирани комплекти, да отпечатаме и етикетираме името и марката на вашата компания и да изпратим до вашите клиенти. С други думи, ние можем да бъдем и ваш складов и дистрибуционен център, ако желаете. Тъй като нашите складове са разположени в близост до големи морски пристанища, това ни дава логистично предимство. Например, когато вашите продукти пристигнат в голямо пристанище на САЩ, ние можем да ги транспортираме директно до близкия склад, където можем да съхраняваме, сглобяваме, правим комплекти, преетикетираме, отпечатваме, опаковаме според вашия избор и оставяме изпращайте до вашите клиенти. Ние не само доставяме продукти. Нашата компания работи по договори по поръчка, при които идваме на вашия сайт, оценяваме вашия проект на място и разработваме предложение за проект, специално проектирано за вас. След това изпращаме наш опитен екип за изпълнение на проекта. Повече информация за нашата инженерна работа можете да намерите на http://www.ags-engineering.com -Поемаме малки проекти, както и големи проекти в индустриален мащаб. Като първа стъпка можем да ви свържем чрез телефон, телеконференция или MSN месинджър с членовете на нашия експертен екип, така че да можете да общувате директно с експерт, да задавате въпроси и да обсъждате проекта си. Обадете ни се и при нужда ще дойдем да ви посетим. ПРЕДИШНА СТРАНИЦА