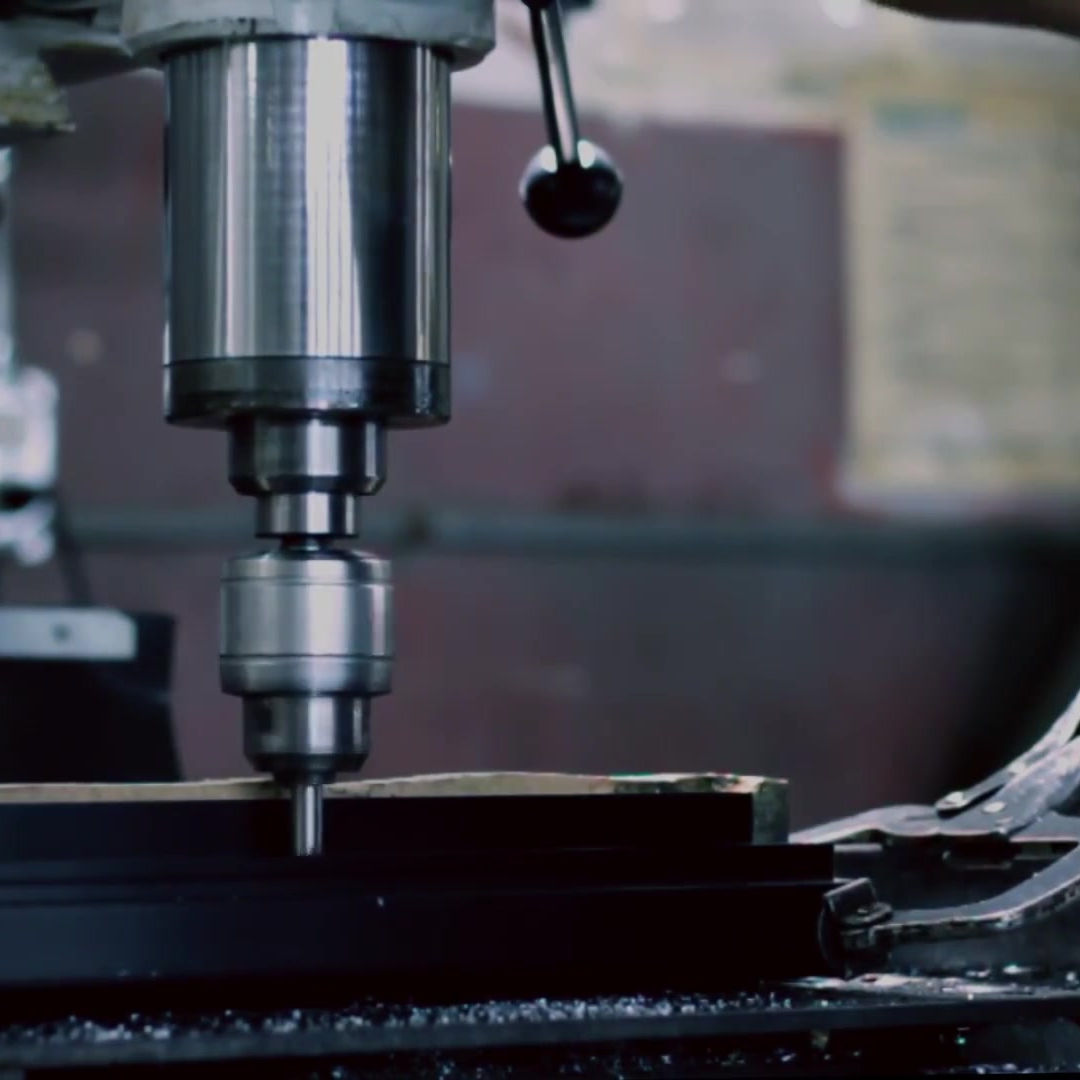
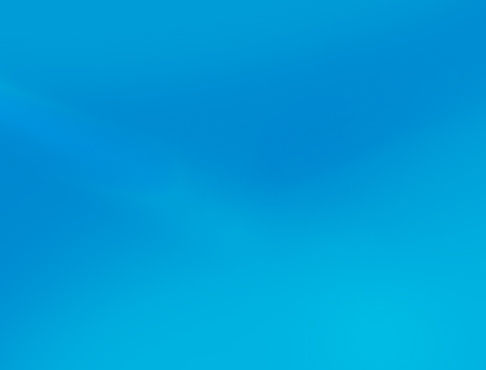
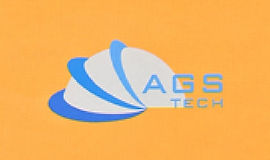
Глобален производител по поръчка, интегратор, консолидатор, аутсорсинг партньор за голямо разнообразие от продукти и услуги.
Ние сме вашият източник на едно гише за производство, производство, инженеринг, консолидация, интеграция, аутсорсинг на произведени по поръчка и готови продукти и услуги.
Изберете своя език
-
Производство по поръчка
-
Вътрешно и глобално договорно производство
-
Аутсорсинг на производство
-
Вътрешни и глобални доставки
-
Консолидация
-
Инженерна интеграция
-
Инженерни услуги
Search Results
164 резултата са намерени с празно търсене
- Fasteners including Anchors, Bolts, Nuts, Pin Fasteners, Rivets, Rods
Fasteners including Anchors, Bolts, Nuts, Pin Fasteners, Rivets, Rods, Screws, Sockets, Springs, Struts, Clamps, Washers, Weld Fasteners, Hangers from AGS-TECH Крепежни елементи Производство Ние произвеждаме FASTENERS под TS16949, система за управление на качеството ISO9001 съгласно международни стандарти като ASTM, SAE, ISO, DIN, MIL. Всички наши крепежни елементи се изпращат заедно със сертификати за материали и доклади от инспекции. Ние доставяме готови крепежни елементи, както и крепежни елементи, произведени по поръчка според вашите технически чертежи, в случай че имате нужда от нещо различно или специално. Ние предоставяме инженерни услуги при проектиране и разработване на специални крепежни елементи за вашите приложения. Някои основни видове крепежни елементи, които предлагаме са: • Анкери • Болтове • Хардуер • Нокти • Ядки • Закопчалки с щифтове • Нитове • Пръти • Винтове • Защитни крепежни елементи • Установителни винтове • Гнезда • Пружини • Подпори, скоби и закачалки • Шайби • Заварени крепежни елементи - КЛИКНЕТЕ ТУК, за да изтеглите каталог за нитови гайки, глухи нитове, гайки за вложки, найлонови контрагайки, заварени гайки, фланцови гайки - НАТИСНЕТЕ ТУК, за да изтеглите допълнителна информация-1 за нит гайки - НАТИСНЕТЕ ТУК, за да изтеглите допълнителна информация-2 за нит гайки - НАТИСНЕТЕ ТУК, за да изтеглите каталог с нашите титаниеви болтове и гайки - КЛИКНЕТЕ ТУК, за да изтеглите нашия каталог, съдържащ някои популярни готови крепежни елементи и хардуер, подходящи за електрониката и компютърната индустрия. Нашите КРЕПЕЖИ С РЕЗБА може да бъде с вътрешна резба, както и с външна резба и се предлага в различни форми, включително: - ISO метрична винтова резба - ACME - Американска национална винтова резба (инчови размери) - Единна национална винтова резба (инчови размери) - Червей - Квадрат - Кокалче - Подпора Нашите крепежни елементи с резба се предлагат с дясна и лява резба, както и с единична и много резба. За крепежни елементи се предлагат както инчови, така и метрични резби. За крепежни елементи с инчова резба се предлагат външни резби класове 1A, 2A и 3A, както и вътрешни резби класове 1B, 2B и 3B. Тези класове инчови резби се различават по количеството допустими отклонения и допустими отклонения. Класове 1A и 1B: Тези крепежни елементи осигуряват най-хлабавото прилягане при сглобяване. Използват се там, където е необходим лесен монтаж и демонтаж, като болтове за печка и други груби болтове и гайки. Класове 2A и 2B: Тези крепежни елементи са подходящи за обикновени търговски продукти и взаимозаменяеми части. Типични машинни винтове и крепежни елементи са примери. Класове 3A и 3B: Тези крепежни елементи са предназначени за изключително висококачествени търговски продукти, където се изисква плътно прилягане. Цената на крепежни елементи с резби в този клас е по-висока. За крепежни елементи с метрична резба предлагаме едра резба, фина резба и серия с постоянна стъпка. Серия с груба резба: Тази серия крепежни елементи е предназначена за използване в общи инженерни дейности и търговски приложения. Серия с фини резби: Тази серия крепежни елементи е за обща употреба, където е необходима по-фина резба от грубата. В сравнение с винта с груба резба, винтът с фина резба е по-здрав както на опън, така и на усукване и е по-малко вероятно да се разхлаби при вибрации. За стъпката на крепежните елементи и диаметъра на гребена разполагаме с редица степени на толеранс, както и позиции на толеранс. ТРУБНИ РЕЗБИ: Освен крепежни елементи, ние можем да обработим резби на тръби според обозначението, предоставено от вас. Не забравяйте да посочите размера на конеца във вашите технически чертежи за персонализирани тръби. ВЪЗЛИ С РЕЗБА: Ако ни предоставите монтажни чертежи с резба, ние можем да използваме нашите машини за изработване на крепежни елементи за обработка на вашите възли. Ако не сте запознати с представянето на винтови резби, ние можем да подготвим чертежите за вас. ИЗБОР НА КРЕПЕЖНИ ЕЛЕМЕНТИ: Изборът на продукт в идеалния случай трябва да започне на етапа на проектиране. Моля, определете целите на вашата работа по закрепване и се консултирайте с нас. Нашите експерти по крепежни елементи ще прегледат вашите цели и обстоятелства и ще препоръчат правилните крепежни елементи на най-добрата цена на място. За да се постигне максимална ефективност на машинния винт, е необходимо задълбочено познаване на свойствата както на винтовете, така и на закрепваните материали. Нашите експерти по крепежни елементи разполагат с тези знания, за да ви помогнат. Ще ни е необходима информация от вас, като натоварванията, които трябва да издържат винтовете и крепежните елементи, дали натоварването върху крепежните елементи и винтовете е на опън или срязване и дали закрепеният комплект ще бъде подложен на ударен удар или вибрации. В зависимост от всички тези и други фактори като лекота на сглобяване, цена… и т.н., ще ви бъдат предложени препоръчителният размер, здравина, форма на главата, тип резба на винтовете и крепежните елементи. Сред нашите най-разпространени крепежни елементи с резба са ВИНТОВЕ, БОЛТОВЕ и ШПИЛКИ. МАШИННИ ВИНТОВЕ: Тези крепежни елементи имат фина или груба резба и се предлагат с различни глави. Машинните винтове могат да се използват в резбовани отвори или с гайки. ВИНТОВЕ С КАПАЧКА: Това са крепежни елементи с резба, които свързват две или повече части, като преминават през отвор за хлабина в едната част и се завинтват в отвор с резба в другата. Винтовете с капачки също се предлагат с различни типове глави. ЗАХВАЩАЩИ ВИНТОВЕ: Тези крепежни елементи остават прикрепени към панела или основния материал дори когато свързващата част е освободена. Закрепващите винтове отговарят на военните изисквания, за да предотвратят загубата на винтове, за да позволят по-бързо сглобяване / разглобяване и да предотвратят повреда от падане на разхлабени винтове в движещи се части и електрически вериги. РЕЗБОВАЩИ ВИНТОВЕ: Тези крепежни елементи нарязват или образуват съвпадаща резба, когато се забиват в предварително оформени отвори. Самонарезните винтове позволяват бърз монтаж, тъй като не се използват гайки и се изисква достъп само от едната страна на съединението. Свързващата резба, произведена от самонарезния винт, приляга плътно към резбите на винта и не е необходима хлабина. Плътното прилягане обикновено държи винтовете стегнати, дори когато има вибрации. Самонарезните винтове имат специални върхове за пробиване и след това нарязване на собствени отвори. Не е необходимо пробиване или пробиване за самопробивни винтове. Самонарезните винтове се използват при отливки под налягане от стомана, алуминий (лят, екструдиран, валцуван или формован под налягане), чугун, изковки, пластмаси, подсилени пластмаси, импрегниран със смола шперплат и други материали. БОЛТОВЕ: Това са крепежни елементи с резба, които минават през хлабини в сглобени части и се навиват в гайките. ШПИЛКИ: Тези крепежни елементи са валове с резба в двата края и се използват в сглобки. Два основни вида шипове са шпилки с двоен край и непрекъснати шпилки. Що се отнася до другите крепежни елементи, важно е да се определи какъв вид качество и покритие (обшивка или покритие) е най-подходящо. ГАЙКИ: Налични са метрични гайки стил-1 и стил-2. Тези крепежни елементи обикновено се използват с болтове и шпилки. Популярни са шестостенните гайки, шестостенните гайки с фланец, шестостенните гайки. В рамките на тези групи също има вариации. ШАЙБИ: Тези крепежни елементи изпълняват много разнообразни функции в механично закрепени възли. Функциите на шайбите могат да бъдат да покриват голям отвор за хлабина, да дават по-добро лагеруване на гайките и повърхностите на винтовете, да разпределят натоварването върху по-големи площи, да служат като заключващи устройства за резбови крепежни елементи, да поддържат съпротивителното налягане на пружината, да предпазват повърхностите от повреждане, да осигуряват уплътнителна функция и много повече . Предлагат се много видове от тези крепежни елементи, като плоски шайби, конусовидни шайби, винтови пружинни шайби, типове зъбни ключалки, пружинни шайби, видове със специално предназначение… и т.н. SETSCREWS: Те се използват като полупостоянни крепежни елементи за задържане на яка, ролка или зъбно колело на вал срещу ротационни и транслационни сили. Тези крепежни елементи са основно устройства за компресия. Потребителите трябва да намерят най-добрата комбинация от форма, размер и стил на заострен винт, която осигурява необходимата сила на задържане. Установяващите винтове се категоризират според техния стил на главата и желания стил на върха. ЗАКЛЮЧВАЩИ ГАЙКИ: Тези крепежни елементи са гайки със специални вътрешни средства за захващане на крепежни елементи с резба за предотвратяване на завъртане. Можем да разглеждаме контрагайките основно като стандартни гайки, но с добавена заключваща функция. Контрагайките имат много много полезни области на приложение, включително тръбно закрепване, използване на контрагайки върху пружинни скоби, използване на контрагайки, когато монтажът е подложен на вибрационни или циклични движения, които могат да причинят разхлабване, за монтирани на пружина връзки, където гайката трябва да остане неподвижна или подлежи на регулиране . ЗАХВАЩАЩИ ИЛИ САМОЗАДЪРЖАЩИ ГАЙКИ: Този клас крепежни елементи осигурява трайно, здраво закрепване с множество резби върху тънки материали. Захващащите се или самозадържащите се гайки са особено добри, когато има слепи места и могат да се закрепят без да се повредят покритията. ВЛОЖКИ: Тези крепежни елементи са гайки със специална форма, предназначени да изпълняват функцията на отвор с резба в места на слепи или проходни отвори. Предлагат се различни видове като формовани вложки, самонарезни вложки, вложки с външна/вътрешна резба, вложки с пресовани вложки, вложки от тънък материал. УПЛЪТНЯВАЩИ КРЕПЕЖИ: Този клас крепежни елементи не само държат две или повече части заедно, но могат едновременно да предложат уплътнителна функция за газове и течности срещу изтичане. Ние предлагаме много видове уплътняващи крепежни елементи, както и проектирани по поръчка конструкции за уплътнени фуги. Някои популярни продукти са уплътнителни винтове, уплътнителни нитове, уплътнителни гайки и уплътнителни шайби. НИТОВЕ: Занитването е бърз, прост, универсален и икономичен метод за закрепване. Нитовете се считат за постоянни крепежни елементи за разлика от подвижните крепежни елементи като винтове и болтове. Описани просто, нитове са пластични метални щифтове, вкарани през отвори в две или повече части и имащи краища, оформени така, че да задържат частите сигурно. Тъй като нитовете са постоянни крепежни елементи, занитените части не могат да бъдат разглобени за поддръжка или подмяна, без да се избие нитът и да се монтира нов на място за повторно сглобяване. Наличните видове нитове са големи и малки нитове, нитове за аерокосмическа техника, глухи нитове. Както при всички крепежни елементи, които продаваме, ние помагаме на нашите клиенти в процеса на проектиране и избор на продукт. От типа нит, подходящ за вашето приложение, до скоростта на инсталиране, разходите на място, разстоянието, дължината, разстоянието до ръба и други, ние сме в състояние да ви помогнем в процеса на проектиране. Референтен код: OICASRET-GLOBAL, OICASTICDM CLICK Product Finder-Locator Service ПРЕДИШНА СТРАНИЦА
- Micromanufacturing, Nanomanufacturing, Mesomanufacturing AGS-TECH Inc.
Micromanufacturing, Nanomanufacturing, Mesomanufacturing - Electronic & Magnetic Optical & Coatings, Thin Film, Nanotubes, MEMS, Microscale Fabrication Производство в наномащаб, микромащаб и мезомащаб Прочетете още Our NANOMANUFACTURING, MICROMANUFACTURING and MESOMANUFACTURING processes can be categorized as: Повърхностни обработки и модификации Функционални покрития / Декоративни покрития / Тънък филм / дебел филм Наномащабно производство / Нанопроизводство Микромащабно производство / Микропроизводство / Микрообработка Мезомащабно производство / мезопроизводство Микроелектроника & Производство на полупроводници и производство Микрофлуидни устройства Manufacturing Производство на микрооптика Микро сглобяване и опаковане Мека литография Във всеки интелигентен продукт, проектиран днес, може да се вземе предвид елемент, който ще увеличи ефективността, гъвкавостта, ще намали консумацията на енергия, ще намали отпадъците, ще увеличи живота на продукта и по този начин ще бъде екологичен. За тази цел AGS-TECH се фокусира върху редица процеси и продукти, които могат да бъдат включени в устройства и оборудване за постигане на тези цели. Например low-friction FUNCTIONAL COATINGS може да намали консумацията на енергия. Някои други примери за функционални покрития са устойчиви на надраскване покрития, анти-wetting SURFACE TREATMENTS и покрития (хидрофобни), насърчаващи влагата, повърхностни обработки и покрития (хидрофилни) против гъбички диамантеноподобни въглеродни покрития за инструменти за рязане и писане, THIN FILЕлектронни покрития, тънкослойни магнитни покрития, многослойни оптични покрития. In NANOMANUFACTURING or NANOSCALE MANUFACTURING.метър, ние произвеждаме части с размери на дължина На практика това се отнася за производствени операции под микрометров мащаб. Нанопроизводството все още е в начален стадий в сравнение с микропроизводството, но тенденцията е в тази посока и нанопроизводството определено е много важно за близкото бъдеще. Някои приложения на нанопроизводството днес са въглеродните нанотръби като подсилващи влакна за композитни материали в рамки за велосипеди, бейзболни бухалки и тенис ракети. Въглеродните нанотръби, в зависимост от ориентацията на графита в нанотръбата, могат да действат като полупроводници или проводници. Въглеродните нанотръби имат много висока токопроводимост, 1000 пъти по-висока от среброто или медта. Друго приложение на нанопроизводството е нанофазната керамика. Използвайки наночастици в производството на керамични материали, ние можем едновременно да увеличим както здравината, така и пластичността на керамиката. Моля, щракнете върху подменюто за повече информация. MICROSCALE MANUFACTURING or MICROMANUFACTURING refers to our manufacturing and fabrication processes on a microscopic scale not visible to the naked eye. Термините микропроизводство, микроелектроника, микроелектромеханични системи не се ограничават до такива малки мащаби на дължина, а вместо това предполагат материална и производствена стратегия. В нашите микропроизводствени операции някои популярни техники, които използваме, са литография, мокро и сухо ецване, тънкослойно покритие. Широко разнообразие от сензори и задвижващи механизми, сонди, магнитни глави на твърди дискове, микроелектронни чипове, MEMS устройства като акселерометри и сензори за налягане между другото се произвеждат с помощта на такива микропроизводствени методи. По-подробна информация за тях ще намерите в подменютата. MESOSCALE MANUFACTURING or MESOMANUFACTURING refers to our processes for fabrication of miniature devices such as hearing aids, medical stents, medical valves, mechanical watches and extremely small двигатели. Мезомащабното производство припокрива както макро, така и микропроизводството. Миниатюрни стругове с двигател от 1,5 вата и размери 32 x 25 x 30,5 mm и тегло от 100 грама са произведени чрез мезомащабни производствени методи. Използвайки такива стругове, месингът се обработва до диаметър от 60 микрона и грапавост на повърхността от порядъка на микрон или два. Други подобни миниатюрни машинни инструменти, като фрезови машини и преси, също са били произведени чрез използване на мезопроизводство. In MICROELECTRONICS MANUFACTURING ние използваме същите техники като в микропроизводството. Нашите най-популярни субстрати са силиций, а други като галиев арсенид, индиев фосфид и германий също се използват. Филми/покрития от много видове и особено проводими и изолиращи тънкослойни покрития се използват при производството на микроелектронни устройства и вериги. Тези устройства обикновено се получават от многослойни. Изолационните слоеве обикновено се получават чрез окисление като SiO2. Добавките (както p, така и n) тип са често срещани и части от устройствата се легират, за да се променят техните електронни свойства и да се получат области от тип p и n. Използвайки литография като ултравиолетова, дълбока или екстремна ултравиолетова фотолитография или рентгенова, електронно-лъчева литография, ние прехвърляме геометрични модели, определящи устройствата от фотомаска/маска към повърхностите на субстрата. Тези литографски процеси се прилагат няколко пъти в микропроизводството на микроелектронни чипове, за да се постигнат необходимите структури в дизайна. Също така се извършват процеси на ецване, чрез които се отстраняват цели филми или определени участъци от филми или субстрат. Накратко, чрез използване на различни отлагане, ецване и множество литографски стъпки, ние получаваме многослойни структури върху поддържащите полупроводникови субстрати. След като пластините се обработят и върху тях се изработят много вериги, повтарящите се части се изрязват и се получават отделни матрици. След това всяка матрица се свързва с тел, опакова се и се тества и се превръща в търговски микроелектронен продукт. Някои повече подробности за производството на микроелектроника могат да бъдат намерени в нашето подменю, но темата е много обширна и затова ви препоръчваме да се свържете с нас, в случай че имате нужда от специфична за продукта информация или повече подробности. Нашите MICROFLUIDICS MANUFACTURING операции са насочени към производство на устройства и системи, в които се обработват малки обеми течности. Примери за микрофлуидни устройства са микро-задвижващи устройства, системи лаборатория върху чип, микротермични устройства, мастилено-струйни печатащи глави и др. В микрофлуидиката трябва да се справим с прецизния контрол и манипулиране на течности, ограничени до субмилиметрови области. Течностите се преместват, смесват, разделят и обработват. В микрофлуидните системи течностите се движат и контролират или активно с помощта на малки микропомпи и микроклапани и други подобни, или пасивно като се възползват от капилярните сили. При системите „лаборатория върху чип“ процесите, които обикновено се извършват в лаборатория, са миниатюризирани на един чип, за да се подобри ефективността и мобилността, както и да се намалят обемите на пробите и реагентите. Имаме способността да проектираме микрофлуидни устройства за вас и да предлагаме микрофлуидни прототипи и микропроизводство, персонализирани за вашите приложения. Друго обещаващо поле в микропроизводството е МИКРООПТИЧНО ПРОИЗВОДСТВО. Микрооптиката позволява манипулирането на светлината и управлението на фотони с микронни и субмикронни структури и компоненти. Микрооптиката ни позволява да свържем макроскопичния свят, в който живеем, с микроскопичния свят на опто- и наноелектронната обработка на данни. Микрооптичните компоненти и подсистеми намират широко приложение в следните области: Информационни технологии: В микродисплеи, микропроектори, оптично съхранение на данни, микрокамери, скенери, принтери, копирни машини… и др. Биомедицина: Минимално инвазивна/диагностика на място, наблюдение на лечението, сензори за микроизображение, ретинални импланти. Осветление: Системи, базирани на светодиоди и други ефективни източници на светлина Системи за безопасност и сигурност: Инфрачервени системи за нощно виждане за автомобилни приложения, оптични сензори за пръстови отпечатъци, скенери за ретината. Оптична комуникация и телекомуникация: във фотонни превключватели, пасивни оптични компоненти, оптични усилватели, мейнфрейм и системи за свързване на персонални компютри Интелигентни структури: В базирани на оптични влакна сензорни системи и много други Като най-разнообразен доставчик на инженерна интеграция, ние се гордеем с нашата способност да предоставим решение за почти всякакви нужди от консултации, инженеринг, обратно инженерство, бързо прототипиране, разработване на продукти, производство, производство и сглобяване. След микропроизводство на нашите компоненти много често трябва да продължим с MICRO ASSEMBLY & PACKAGING. Това включва процеси като закрепване на матрицата, свързване на проводници, свързване, херметично запечатване на опаковки, сондиране, тестване на опаковани продукти за екологична надеждност… и т.н. След микропроизводство на устройства върху матрица, ние прикрепяме матрицата към по-здрава основа, за да гарантираме надеждност. Често използваме специални епоксидни цименти или евтектични сплави за свързване на матрицата към нейната опаковка. След като чипът или матрицата се свържат със своя субстрат, ние го свързваме електрически към кабелите на пакета, като използваме жично свързване. Един метод е да се използват много тънки златни жици от кабелите на пакета към свързващи подложки, разположени около периметъра на матрицата. Накрая трябва да направим окончателното опаковане на свързаната верига. В зависимост от приложението и работната среда се предлагат различни стандартни и произведени по поръчка пакети за микропроизведени електронни, електрооптични и микроелектромеханични устройства. Друга техника за микропроизводство, която използваме, е SOFT LITHOGRAPHY, термин, използван за редица процеси за прехвърляне на шаблони. Във всички случаи е необходима основна матрица, която се изработва чрез стандартни литографски методи. Използвайки главната форма, ние произвеждаме еластомерен модел / печат. Един вариант на меката литография е „микроконтактен печат“. Еластомерният печат се покрива с мастило и се притиска към повърхността. Върховете на шаблона се допират до повърхността и се прехвърля тънък слой от около 1 монослой от мастилото. Този монослой от тънък слой действа като маска за селективно мокро ецване. Вторият вариант е „микротрансферно формоване“, при което вдлъбнатините на еластомерната форма се пълнят с течен полимерен прекурсор и се притискат към повърхността. След като полимерът се втвърди, ние отлепяме матрицата, оставяйки желания модел. И накрая, трета разновидност е „микроформоване в капиляри“, където шаблонът на еластомерния печат се състои от канали, които използват капилярни сили, за да вкарват течен полимер в печата от неговата страна. По принцип малко количество от течния полимер се поставя в близост до капилярните канали и капилярните сили издърпват течността в каналите. Излишният течен полимер се отстранява и полимерът вътре в каналите се оставя да се втвърди. Формата за печат се отлепя и изделието е готово. Можете да намерите повече подробности за нашите техники за микропроизводство с мека литография, като щракнете върху съответното подменю отстрани на тази страница. Ако се интересувате най-вече от нашите инженерни и научноизследователски и развойни възможности, вместо от производствени възможности, тогава ви каним да посетите и нашия инженерен уебсайт http://www.ags-engineering.com Прочетете още Прочетете още Прочетете още Прочетете още Прочетете още П рочетете още Прочетете още Прочетете още Прочетете още CLICK Product Finder-Locator Service ПРЕДИШНА СТРАНИЦА
- Microwave Components & Subassembly, Microwave Circuits, RF Transformer
Microwave Components - Subassembly - Microwave Circuits - RF Transformer - LNA - Mixer - Fixed Attenuator - AGS-TECH Производство и монтаж на микровълнови компоненти и системи Ние произвеждаме и доставяме: Микровълнова електроника, включително силициеви микровълнови диоди, диоди с точково докосване, диоди на Шотки, PIN диоди, варакторни диоди, диоди за стъпково възстановяване, микровълнови интегрални схеми, сплитери/комбинатори, миксери, насочени съединители, детектори, I/Q модулатори, филтри, фиксирани атенюатори, RF трансформатори, симулационни фазови регулатори, LNA, PA, превключватели, атенюатори и ограничители. Ние също така произвеждаме по поръчка възли и модули за микровълнова фурна според изискванията на потребителите. Моля, изтеглете нашите брошури за микровълнови компоненти и системи от връзките по-долу: RF и микровълнови компоненти Микровълнови вълноводи - Коаксиални компоненти - Милиметровълнови антени 5G - LTE 4G - LPWA 3G - 2G - GPS - GNSS - WLAN - BT - Комбо - Брошура за ISM антена Меки ферити - сърцевини - тороиди - продукти за потискане на EMI - RFID транспондери и брошура за аксесоари Изтеглете брошура за нашия ПРОГРАМА ЗА ДИЗАЙН ПАРТНЬОРСТВО Микровълните са електромагнитни вълни с дължина на вълната от 1 mm до 1 m или честоти между 0,3 GHz и 300 GHz. Микровълновият обхват включва ултрависока честота (UHF) (0,3–3 GHz), супер висока честота (SHF) (3– 30 GHz) и изключително високочестотни (EHF) (30–300 GHz) сигнали. Използване на микровълновата технология: КОМУНИКАЦИОННИ СИСТЕМИ: Преди изобретяването на технологията за предаване на оптични влакна, повечето телефонни разговори на дълги разстояния се извършваха чрез микровълнови връзки от точка до точка през сайтове като AT&T Long Lines. От началото на 50-те години на миналия век мултиплексирането с честотно разделяне се използва за изпращане на до 5400 телефонни канала на всеки микровълнов радиоканал, с до десет радиоканала, комбинирани в една антена за прескачане до следващия обект, който е на разстояние до 70 км . Безжичните LAN протоколи, като Bluetooth и спецификациите IEEE 802.11, също използват микровълни в 2,4 GHz ISM обхват, въпреки че 802.11a използва ISM обхват и U-NII честоти в 5 GHz обхват. Лицензирани услуги за безжичен интернет достъп на дълги разстояния (до около 25 км) могат да бъдат намерени в много страни в диапазона 3,5–4,0 GHz (но не и в САЩ). Столични мрежи: MAN протоколи, като WiMAX (Световна оперативна съвместимост за микровълнов достъп), базирани на спецификацията IEEE 802.16. Спецификацията IEEE 802.16 е проектирана да работи между 2 до 11 GHz честоти. Търговските реализации са в честотните диапазони 2,3 GHz, 2,5 GHz, 3,5 GHz и 5,8 GHz. Широкообластен мобилен широколентов безжичен достъп: MBWA протоколите, базирани на спецификации на стандарти като IEEE 802.20 или ATIS/ANSI HC-SDMA (напр. iBurst), са проектирани да работят между 1,6 и 2,3 GHz, за да осигурят мобилност и характеристики за проникване в сгради, подобни на мобилните телефони но с много по-голяма спектрална ефективност. Част от спектъра с по-ниска микровълнова честота се използва за кабелна телевизия и достъп до интернет по коаксиален кабел, както и за ефирна телевизия. Също така някои мобилни телефонни мрежи, като GSM, също използват по-ниски микровълнови честоти. Микровълновото радио се използва в радиоразпръскване и телекомуникационни предавания, тъй като поради късата им дължина на вълната силно насочените антени са по-малки и следователно по-практични, отколкото биха били при по-ниски честоти (по-дълги дължини на вълните). Освен това има по-голяма честотна лента в микровълновия спектър, отколкото в останалата част от радиоспектъра; използваемата честотна лента под 300 MHz е по-малка от 300 MHz, докато много GHz могат да се използват над 300 MHz. Обикновено микровълните се използват в телевизионните новини за предаване на сигнал от отдалечено място до телевизионна станция в специално оборудван микробус. Диапазоните C, X, Ka или Ku на микровълновия спектър се използват при работата на повечето сателитни комуникационни системи. Тези честоти позволяват голяма честотна лента, като същевременно избягват претъпканите UHF честоти и остават под атмосферното поглъщане на EHF честотите. Сателитната телевизия работи или в обхват C за традиционната фиксирана сателитна услуга с голяма чиния, или в обхват Ku за сателитно директно излъчване. Военните комуникационни системи работят предимно по X или Ku Band връзки, като Ka лентата се използва за Milstar. ДИСТАНЦИОННО СЪЗДАВАНЕ: Радарите използват радиация с микровълнова честота, за да открият обхвата, скоростта и други характеристики на отдалечени обекти. Радарите се използват широко за приложения, включително контрол на въздушното движение, навигация на кораби и контрол на ограниченията на скоростта. Освен ултразвукови устройства, понякога диодни осцилатори и вълноводи на Gunn се използват като детектори за движение за автоматични отварящи врати. Голяма част от радиоастрономията използва микровълнова технология. НАВИГАЦИОННИ СИСТЕМИ: Глобалните навигационни сателитни системи (GNSS), включително американската система за глобално позициониране (GPS), китайската Beidou и руската GLONASS, излъчват навигационни сигнали в различни честоти между около 1,2 GHz и 1,6 GHz. МОЩНОСТ: Микровълновата фурна пропуска (нейонизиращо) микровълново лъчение (с честота близо до 2,45 GHz) през храната, причинявайки диелектрично нагряване чрез абсорбиране на енергия във водата, мазнините и захарта, съдържащи се в храната. Микровълновите фурни станаха често срещани след разработването на евтини магнетрони с кухина. Микровълновото нагряване се използва широко в промишлени процеси за сушене и втвърдяване на продукти. Много техники за обработка на полупроводници използват микровълни за генериране на плазма за цели като реактивно йонно ецване (RIE) и усилено с плазма химическо отлагане на пари (PECVD). Микровълните могат да се използват за предаване на енергия на големи разстояния. НАСА работи през 70-те и началото на 80-те години на миналия век, за да проучи възможностите за използване на системи за слънчеви сателити (SPS) с големи слънчеви масиви, които биха излъчвали енергия надолу към земната повърхност чрез микровълни. Някои леки оръжия използват милиметрови вълни, за да нагреят тънък слой човешка кожа до непоносима температура, за да накарат набелязания човек да се отдалечи. Двусекунден изблик на 95 GHz фокусиран лъч загрява кожата до температура от 130 °F (54 °C) на дълбочина от 1/64 от инча (0,4 mm). Военновъздушните сили и морската пехота на Съединените щати използват този тип система за активен отказ. Ако се интересувате от инженерство и научноизследователска и развойна дейност, моля, посетете нашия инженерен сайт http://www.ags-engineering.com CLICK Product Finder-Locator Service ПРЕДИШНА СТРАНИЦА
- Microelectronics Manufacturing, Semiconductor Fabrication, Foundry, IC
Microelectronics Manufacturing, Semiconductor Fabrication - Foundry - FPGA - IC Assembly Packaging - AGS-TECH Inc. Производство и производство на микроелектроника и полупроводници Много от нашите техники и процеси за нанопроизводство, микропроизводство и мезопроизводство, обяснени в другите менюта, могат да се използват за MICROELECTRONICS MANUFACTURING too. Въпреки това, поради значението на микроелектрониката в нашите продукти, ние ще се концентрираме върху конкретните приложения на тези процеси тук. Процесите, свързани с микроелектрониката, също се наричат широко като SEMICONDUCTOR FABRICATION processes. Нашите услуги за проектиране и производство на полупроводниково инженерство включват: - FPGA дизайн, разработка и програмиране на платка - Микроелектронни леярски услуги: Проектиране, създаване на прототипи и производство, услуги на трети страни - Подготовка на полупроводникови пластини: Нарязване, обратно шлайфане, изтъняване, поставяне на мерна мрежа, сортиране на матрицата, избор и поставяне, проверка - Микроелектронен дизайн и изработка на опаковката: Както стандартен, така и персонализиран дизайн и изработка - Сглобяване и опаковане и тест на полупроводникови интегрални схеми: Свързване на матрици, проводници и чипове, капсулиране, сглобяване, маркиране и брандиране - Оловни рамки за полупроводникови устройства: Както стандартен, така и персонализиран дизайн и производство - Проектиране и изработка на радиатори за микроелектроника: както готови, така и персонализирани дизайн и изработка - Дизайн и изработка на сензори и задвижващи механизми: Както стандартен, така и персонализиран дизайн и изработка - Проектиране и производство на оптоелектронни и фотонни схеми Нека разгледаме по-подробно технологиите за производство и тестване на микроелектроника и полупроводници, за да можете да разберете по-добре услугите и продуктите, които предлагаме. Дизайн и разработка на FPGA платка и програмиране: Програмируемите на място гейт масиви (FPGA) са препрограмируеми силициеви чипове. Противно на процесорите, които намирате в персоналните компютри, програмирането на FPGA пренасочва самия чип, за да реализира функционалността на потребителя, вместо да изпълнява софтуерно приложение. Използвайки предварително изградени логически блокове и програмируеми ресурси за маршрутизиране, FPGA чиповете могат да бъдат конфигурирани да реализират персонализирана хардуерна функционалност без използване на макетна платка и поялник. Цифровите изчислителни задачи се изпълняват в софтуер и се компилират до конфигурационен файл или битов поток, който съдържа информация за това как компонентите трябва да бъдат свързани заедно. FPGA могат да се използват за прилагане на всяка логическа функция, която ASIC може да изпълнява и са напълно преконфигурируеми и могат да получат напълно различна „личност“ чрез прекомпилиране на различна конфигурация на верига. FPGA съчетават най-добрите части от специфични за приложения интегрални схеми (ASIC) и системи, базирани на процесори. Тези предимства включват следното: • По-бързи I/O времена за реакция и специализирана функционалност • Превишаване на изчислителната мощност на цифровите сигнални процесори (DSP) • Бързо създаване на прототипи и проверка без процеса на производство на персонализирани ASIC • Внедряване на персонализирана функционалност с надеждността на специален детерминистичен хардуер • Надграждане на място, което елиминира разходите за препроектиране и поддръжка по поръчка на ASIC FPGA осигуряват скорост и надеждност, без да изискват големи обеми, за да оправдаят големите предварителни разходи за персонализиран дизайн на ASIC. Препрограмируемият силикон също има същата гъвкавост като софтуер, работещ на системи, базирани на процесори, и не е ограничен от броя на наличните процесорни ядра. За разлика от процесорите, FPGA са наистина паралелни по природа, така че различните операции на обработка не трябва да се конкурират за едни и същи ресурси. Всяка независима задача за обработка е присвоена на специална секция на чипа и може да функционира автономно без влияние от други логически блокове. В резултат на това производителността на една част от приложението не се влияе, когато се добави повече обработка. Някои FPGA имат аналогови функции в допълнение към цифровите функции. Някои често срещани аналогови характеристики са програмируема скорост на нарастване и сила на задвижване на всеки изходен щифт, което позволява на инженера да зададе бавни скорости на леко натоварени щифтове, които иначе биха звънели или се свързвали неприемливо, и да зададе по-силни, по-бързи скорости на силно натоварени щифтове при висока скорост канали, които иначе биха работили твърде бавно. Друга относително често срещана аналогова характеристика са диференциалните компаратори на входни щифтове, проектирани да бъдат свързани към диференциални сигнални канали. Някои FPGA със смесен сигнал имат интегрирани периферни аналогово-цифрови преобразуватели (ADC) и цифрово-аналогови преобразуватели (DAC) с блокове за обработка на аналогов сигнал, които им позволяват да работят като система върху чип. Накратко, първите 5 предимства на FPGA чиповете са: 1. Добро представяне 2. Кратко време за пускане на пазара 3. Ниска цена 4. Висока надеждност 5. Възможност за дългосрочна поддръжка Добра производителност – Със своята способност за приспособяване към паралелна обработка, FPGA имат по-добра изчислителна мощност от процесорите за цифрови сигнали (DSP) и не изискват последователно изпълнение като DSP и могат да постигат повече за един такт. Контролирането на входове и изходи (I/O) на хардуерно ниво осигурява по-бързи времена за реакция и специализирана функционалност, за да отговаря точно на изискванията на приложението. Кратко време за пускане на пазара - FPGA предлагат гъвкавост и възможности за бързо създаване на прототипи и по този начин по-кратко време за пускане на пазара. Нашите клиенти могат да тестват идея или концепция и да я проверят в хардуера, без да преминават през дългия и скъп процес на производство на персонализиран ASIC дизайн. Можем да внедрим постепенни промени и да повторим дизайна на FPGA в рамките на часове вместо седмици. Предлага се и готов търговски хардуер с различни типове I/O, които вече са свързани към програмируем от потребителя FPGA чип. Нарастващата наличност на софтуерни инструменти от високо ниво предлага ценни IP ядра (предварително изградени функции) за разширен контрол и обработка на сигнали. Ниска цена – Еднократните инженерни разходи (NRE) за персонализирани дизайни на ASIC надвишават тези на базираните на FPGA хардуерни решения. Голямата първоначална инвестиция в ASIC може да бъде оправдана за OEM производителите, произвеждащи много чипове годишно, но много крайни потребители се нуждаят от персонализирана хардуерна функционалност за многото системи в процес на разработка. Нашата програмируема силициева FPGA ви предлага нещо без разходи за производство или дълги срокове за сглобяване. Системните изисквания често се променят с времето и разходите за извършване на постепенни промени в дизайна на FPGA са незначителни в сравнение с големите разходи за повторно завъртане на ASIC. Висока надеждност - Софтуерните инструменти осигуряват среда за програмиране, а FPGA схемите са истинска реализация на изпълнението на програмата. Системите, базирани на процесори, обикновено включват множество слоеве на абстракция, за да помогнат при планирането на задачи и да споделят ресурси между множество процеси. Слоят на драйвера контролира хардуерните ресурси, а операционната система управлява паметта и честотната лента на процесора. За всяко дадено процесорно ядро само една инструкция може да се изпълни в даден момент и системите, базирани на процесор, непрекъснато са изложени на риск критични за времето задачи да се изпреварват една друга. FPGA, не използват операционни системи, създават минимални проблеми с надеждността с истинското си паралелно изпълнение и детерминистичен хардуер, предназначен за всяка задача. Възможност за дългосрочна поддръжка - FPGA чиповете могат да се надграждат на място и не изискват време и разходи, свързани с препроектирането на ASIC. Цифровите комуникационни протоколи, например, имат спецификации, които могат да се променят с времето, а базираните на ASIC интерфейси могат да причинят предизвикателства при поддръжката и съвместимостта напред. Напротив, реконфигурируемите FPGA чипове могат да се справят с потенциално необходими бъдещи модификации. С напредването на продуктите и системите нашите клиенти могат да направят функционални подобрения, без да губят време за препроектиране на хардуера и модифициране на оформлението на платката. Леярски услуги за микроелектроника: Нашите леярски услуги за микроелектроника включват проектиране, създаване на прототипи и производство, услуги на трети страни. Ние предоставяме на нашите клиенти съдействие по време на целия цикъл на разработка на продукта - от поддръжка на дизайна до поддръжка на прототипи и производство на полупроводникови чипове. Нашата цел в услугите за поддръжка на проектиране е да позволим правилния подход за първи път за дизайни на полупроводникови устройства с цифрови, аналогови и смесени сигнали. Налични са например специфични инструменти за симулация на MEMS. Фабриките, които могат да работят с 6 и 8 инчови пластини за интегрирани CMOS и MEMS, са на ваше разположение. Ние предлагаме на нашите клиенти поддръжка за проектиране за всички основни платформи за автоматизация на електронното проектиране (EDA), като доставяме правилни модели, комплекти за проектиране на процеси (PDK), аналогови и цифрови библиотеки и поддръжка за проектиране за производство (DFM). Ние предлагаме две опции за създаване на прототипи за всички технологии: услугата Multi Product Wafer (MPW), при която няколко устройства се обработват паралелно на една пластина, и услугата Multi Level Mask (MLM) с четири нива на маска, начертани върху една и съща мрежа. Те са по-икономични от пълния комплект маски. Услугата MLM е много гъвкава в сравнение с фиксираните дати на услугата MPW. Компаниите могат да предпочетат аутсорсинг на полупроводникови продукти пред леярна за микроелектроника поради редица причини, включително необходимостта от втори източник, използване на вътрешни ресурси за други продукти и услуги, желание да се изгради фабрично и да се намали рискът и тежестта от управлението на фабрика за полупроводници… и т.н. AGS-TECH предлага процеси за производство на микроелектроника с отворена платформа, които могат да бъдат намалени за малки тиражи на пластини, както и за масово производство. При определени обстоятелства вашите съществуващи инструменти за производство на микроелектроника или MEMS или пълни комплекти инструменти могат да бъдат прехвърлени като изпратени инструменти или продадени инструменти от вашата фабрика в нашия фабричен сайт или вашите съществуващи микроелектроника и MEMS продукти могат да бъдат преработени с помощта на технологии за процес на отворена платформа и пренесени към процес, достъпен в нашата фабрика. Това е по-бързо и по-икономично от трансфер на технология по поръчка. При желание обаче съществуващите производствени процеси на микроелектроника/MEMS на клиента могат да бъдат прехвърлени. Подготовка на полупроводникови пластини: При желание от страна на клиентите, след като пластините са микропроизведени, ние извършваме нарязване, обратно шлайфане, изтъняване, поставяне на решетка, сортиране на матрицата, избор и поставяне, операции по проверка на полупроводникови пластини. Обработката на полупроводникови пластини включва метрология между различните етапи на обработка. Например, методите за изпитване на тънък слой, базирани на елипсометрия или рефлектометрия, се използват за строг контрол на дебелината на оксида на затвора, както и на дебелината, индекса на пречупване и коефициента на екстинкция на фоторезиста и други покрития. Използваме оборудване за тестване на полупроводникови пластини, за да проверим дали пластините не са били повредени от предишни стъпки на обработка до тестването. След като предните процеси са завършени, полупроводниковите микроелектронни устройства се подлагат на различни електрически тестове, за да се определи дали функционират правилно. Ние наричаме съотношението на микроелектронните устройства на пластината, за които е установено, че работят правилно, като „добив“. Тестването на микроелектронни чипове върху пластината се извършва с електронен тестер, който притиска малки сонди към полупроводниковия чип. Автоматизираната машина маркира всеки повреден микроелектронен чип с капка багрило. Данните от теста на вафли се записват в централна компютърна база данни и полупроводниковите чипове се сортират във виртуални контейнери според предварително определени тестови граници. Получените данни за групиране могат да бъдат изобразени на графика или регистрирани върху карта на вафла, за да се проследят производствените дефекти и да се маркират лоши чипове. Тази карта може да се използва и по време на сглобяване и опаковане на вафли. При окончателното тестване микроелектронните чипове се тестват отново след опаковането, тъй като свързващите проводници може да липсват или аналоговата производителност може да бъде променена от опаковката. След като полупроводниковата пластина бъде тествана, тя обикновено се намалява по дебелина, преди пластината да бъде набраздена и след това да се раздели на отделни матрици. Този процес се нарича разделяне на полупроводникови пластини. Използваме автоматизирани машини за вземане и поставяне, специално произведени за микроелектронната индустрия, за да сортираме добрите и лошите полупроводникови матрици. Опаковани са само добрите, немаркирани полупроводникови чипове. След това, в процеса на опаковане на микроелектроника от пластмаса или керамика, ние монтираме матрицата на полупроводника, свързваме подложките на матрицата към щифтовете на опаковката и запечатваме матрицата. Малки златни жици се използват за свързване на подложките към щифтовете с помощта на автоматизирани машини. Chip scale package (CSP) е друга технология за пакетиране на микроелектроника. Пластмасов двоен редов пакет (DIP), както повечето пакети, е многократно по-голям от действителния полупроводников матрица, поставен вътре, докато CSP чиповете са почти с размера на микроелектронната матрица; и CSP може да бъде конструиран за всяка матрица, преди полупроводниковата пластина да бъде нарязана на кубчета. Пакетираните микроелектронни чипове се тестват отново, за да се уверите, че не са повредени по време на опаковането и че процесът на свързване между матрицата и щифта е завършен правилно. С помощта на лазери след това гравираме имената и номерата на чиповете върху опаковката. Дизайн и производство на микроелектронни пакети: Ние предлагаме както стандартен, така и персонализиран дизайн и производство на микроелектронни пакети. Като част от тази услуга се извършва и моделиране и симулация на микроелектронни пакети. Моделирането и симулацията гарантират виртуално проектиране на експерименти (DoE) за постигане на оптимално решение, вместо тестване на пакети на място. Това намалява разходите и времето за производство, особено за разработване на нови продукти в микроелектрониката. Тази работа също така ни дава възможност да обясним на нашите клиенти как сглобяването, надеждността и тестването ще повлияят на техните микроелектронни продукти. Основната цел на микроелектронните опаковки е да се проектира електронна система, която ще удовлетвори изискванията за конкретно приложение на разумна цена. Поради многото налични опции за свързване и разполагане на микроелектронна система, изборът на технология за опаковане за дадено приложение се нуждае от експертна оценка. Критериите за избор на пакети за микроелектроника могат да включват някои от следните технологични драйвери: - Възможност за свързване -Доходност -Разходи - Свойства за разсейване на топлината - Електромагнитно екраниране - Механична издръжливост -Надеждност Тези съображения за проектиране на микроелектронни пакети засягат скоростта, функционалността, температурите на свързване, обема, теглото и др. Основната цел е да се избере най-рентабилната, но надеждна технология за взаимно свързване. Ние използваме усъвършенствани методи за анализ и софтуер за проектиране на пакети за микроелектроника. Микроелектронното опаковане се занимава с проектирането на методи за производство на взаимосвързани миниатюрни електронни системи и надеждността на тези системи. По-конкретно, опаковането на микроелектрониката включва маршрутизиране на сигнали, като същевременно се поддържа целостта на сигнала, разпределяне на земята и захранването към полупроводниковите интегрални схеми, разпръскване на разсейваната топлина, като същевременно се поддържа структурна и материална цялост, и защита на веригата от опасности за околната среда. Като цяло, методите за опаковане на микроелектронни интегрални схеми включват използването на PWB с конектори, които осигуряват входно-изходните данни в реалния свят на електронна верига. Традиционните подходи за опаковане на микроелектроника включват използването на единични опаковки. Основното предимство на пакета с един чип е възможността за пълно тестване на микроелектронната ИС преди свързването й към основния субстрат. Такива опаковани полупроводникови устройства са или монтирани през отвора, или повърхностно монтирани към PWB. Повърхностно монтираните микроелектронни пакети не изискват отвори за преминаване през цялата платка. Вместо това повърхностно монтираните микроелектронни компоненти могат да бъдат запоени към двете страни на PWB, което позволява по-висока плътност на веригата. Този подход се нарича технология за повърхностен монтаж (SMT). Добавянето на пакети в стил площен масив, като масиви с сферична решетка (BGA) и пакети с мащаб на чип (CSP), прави SMT конкурентноспособен с технологиите за опаковане на полупроводникова микроелектроника с най-висока плътност. По-новата технология за опаковане включва прикрепването на повече от едно полупроводниково устройство към субстрат за взаимно свързване с висока плътност, който след това се монтира в голям пакет, осигуряващ както I/O щифтове, така и защита на околната среда. Тази многочипова модулна (MCM) технология се характеризира допълнително с технологиите на субстрата, използвани за свързване на свързаните интегрални схеми. MCM-D представлява отложен тънък филм от метал и многослойни диелектрици. MCM-D субстратите имат най-високата плътност на окабеляването от всички MCM технологии благодарение на усъвършенстваните технологии за обработка на полупроводници. MCM-C се отнася до многослойни „керамични“ субстрати, изпечени от подредени редуващи се слоеве от екранирани метални мастила и неизпечени керамични листове. С помощта на MCM-C получаваме умерено плътен капацитет на окабеляване. MCM-L се отнася до многослойни субстрати, направени от подредени, метализирани PWB „ламинати“, които са индивидуално шарени и след това ламинирани. Преди беше технология за свързване с ниска плътност, но сега MCM-L бързо се доближава до плътността на технологиите за опаковане на микроелектроника MCM-C и MCM-D. Технологията за опаковане на микроелектроника с директно прикрепване на чип (DCA) или чип-на-борда (COB) включва монтиране на микроелектронните ИС директно към PWB. Пластмасов капсулант, който е "глобиран" върху голата IC и след това се втвърдява, осигурява защита на околната среда. Микроелектронните интегрални схеми могат да бъдат свързани помежду си към субстрата, като се използват или флип-чип, или методи за свързване с проводници. DCA технологията е особено икономична за системи, които са ограничени до 10 или по-малко полупроводникови ИС, тъй като по-големият брой чипове може да повлияе на производителността на системата и DCA модулите могат да бъдат трудни за преработка. Предимство, общо за опциите за опаковане на DCA и MCM, е премахването на нивото на взаимно свързване на пакета на полупроводникови IC, което позволява по-голяма близост (по-кратки закъснения при предаване на сигнала) и намалена индуктивност на проводника. Основният недостатък и на двата метода е трудността при закупуване на напълно тествани микроелектронни интегрални схеми. Други недостатъци на технологиите DCA и MCM-L включват лошо термично управление благодарение на ниската топлопроводимост на PWB ламинатите и слабия коефициент на топлинно разширение между матрицата на полупроводника и субстрата. Решаването на проблема с несъответствието на термичното разширение изисква междинен субстрат като молибден за матрица, свързана с тел, и епоксидна смола за запълване за матрица с обръщащ чип. Мултичиповият носещ модул (MCCM) съчетава всички положителни аспекти на DCA с MCM технологията. MCCM е просто малък MCM върху тънък метален носител, който може да бъде свързан или механично прикрепен към PWB. Металното дъно действа както като разсейвател на топлината, така и като междинно напрежение за MCM субстрата. MCCM има периферни проводници за свързване на проводници, запояване или свързване на пластини към PWB. Голите полупроводникови интегрални схеми са защитени с помощта на материал с топка. Когато се свържете с нас, ние ще обсъдим вашето приложение и изисквания, за да изберем най-добрата опция за опаковане на микроелектроника за вас. Сглобяване и опаковане и тестване на полупроводникови интегрални схеми: Като част от нашите услуги за производство на микроелектроника ние предлагаме свързване на матрици, проводници и чипове, капсулиране, сглобяване, маркиране и брандиране, тестване. За да функционира полупроводников чип или интегрирана микроелектронна схема, тя трябва да бъде свързана към системата, която ще управлява или ще й предоставя инструкции. Сглобяването на микроелектронни интегрални схеми осигурява връзките за захранване и трансфер на информация между чипа и системата. Това се постига чрез свързване на микроелектронния чип към пакет или директно свързване към PCB за тези функции. Връзките между чипа и пакета или печатната платка (PCB) се осъществяват чрез свързване на кабели, сглобяване на чипа чрез отвор или обръщане. Ние сме лидер в индустрията в намирането на микроелектронни IC опаковъчни решения, за да отговорим на сложните изисквания на безжичните и интернет пазарите. Ние предлагаме хиляди различни пакетни формати и размери, вариращи от традиционни IC пакети за микроелектроника с водещи рамки за монтиране през дупки и повърхностен монтаж, до най-новите решения за скала на чипове (CSP) и сферична решетка (BGA), необходими при приложения с голям брой пинове и висока плътност . Голямо разнообразие от пакети се предлагат от склад, включително CABGA (Chip Array BGA), CQFP, CTBGA (Chip Array Thin Core BGA), CVBGA (Very Thin Chip Array BGA), Flip Chip, LCC, LGA, MQFP, PBGA, PDIP, PLCC, PoP - Package on Package, PoP TMV - Through Mold Via, SOIC / SOJ, SSOP, TQFP, TSOP, WLP (Wafer Level Package)…..и др. Свързването на проводници с помощта на мед, сребро или злато е сред популярните в микроелектрониката. Медната (Cu) жица е била метод за свързване на силициеви полупроводникови матрици към клемите на пакета за микроелектроника. С неотдавнашното увеличение на цената на златен (Au) проводник, медният (Cu) проводник е привлекателен начин за управление на общите разходи за пакет в микроелектрониката. Той също така прилича на златна (Au) жица поради подобните си електрически свойства. Самоиндуктивността и собственият капацитет са почти еднакви за златен (Au) и меден (Cu) проводник, като медният (Cu) проводник има по-ниско съпротивление. В микроелектронни приложения, където съпротивлението, дължащо се на свързващия проводник, може да повлияе отрицателно на производителността на веригата, използването на меден (Cu) проводник може да предложи подобрение. Медни, медни с покритие от паладий (PCC) и сребърни (Ag) сплави се появиха като алтернативи на златните жици поради цената. Проводниците на основата на мед са евтини и имат ниско електрическо съпротивление. Твърдостта на медта обаче я прави трудна за използване в много приложения, като например тези с крехки структури на свързващи подложки. За тези приложения Ag-Alloy предлага свойства, подобни на тези на златото, докато цената му е подобна на тази на PCC. Жицата от Ag-Alloy е по-мека от PCC, което води до по-ниско пръскане на Al и по-малък риск от повреда на свързващата подложка. Ag-Alloy телта е най-добрият евтин заместител за приложения, които се нуждаят от щанцо-към-щанцо залепване, водопадно лепене, ултра фина стъпка на залепващата подложка и малки отвори за залепваща подложка, ултра ниска височина на примката. Ние предоставяме пълна гама от услуги за тестване на полупроводници, включително тестване на пластини, различни видове окончателно тестване, тестване на системно ниво, тестване на ленти и цялостни услуги в края на линията. Тестваме различни типове полупроводникови устройства във всички наши семейства пакети, включително радиочестоти, аналогови и смесени сигнали, цифрови, управление на мощността, памет и различни комбинации като ASIC, многочипови модули, система в пакет (SiP) и подредени 3D опаковки, сензори и MEMS устройства като акселерометри и сензори за налягане. Нашият тестов хардуер и контактно оборудване са подходящи за персонализиран размер на пакета SiP, двустранни контактни решения за пакет върху пакет (PoP), TMV PoP, гнезда FusionQuad, многоредова MicroLeadFrame, фина медна колона. Тестовото оборудване и тестовите подове са интегрирани с CIM / CAM инструменти, анализ на добивите и мониторинг на производителността, за да осигурят много висока ефективност от първия път. Ние предлагаме многобройни адаптивни тестови процеси за микроелектроника за нашите клиенти и предлагаме разпределени тестови потоци за SiP и други сложни монтажни потоци. AGS-TECH предоставя пълна гама от тестови консултации, развойна дейност и инженерингови услуги през целия ви жизнен цикъл на полупроводникови и микроелектронни продукти. Ние разбираме уникалните пазари и изисквания за тестване за SiP, автомобили, мрежи, игри, графики, компютри, RF / безжични. Процесите на производство на полупроводници изискват бързи и прецизно контролирани решения за маркиране. Скорости на маркиране над 1000 знака/секунда и дълбочини на проникване на материала под 25 микрона са често срещани в индустрията за полупроводникова микроелектроника, използваща модерни лазери. Ние сме способни да маркираме смеси за форми, вафли, керамика и други с минимално влагане на топлина и перфектна повторяемост. Използваме лазери с висока точност, за да маркираме и най-малките части без повреди. Оловни рамки за полупроводникови устройства: Възможни са както готови, така и персонализирани дизайн и производство. Оловните рамки се използват в процесите на сглобяване на полупроводникови устройства и по същество представляват тънки слоеве метал, които свързват окабеляването от малки електрически клеми на повърхността на полупроводниковата микроелектроника към големите вериги на електрически устройства и печатни платки. Оловните рамки се използват в почти всички пакети за полупроводникова микроелектроника. Повечето IC пакети за микроелектроника се правят чрез поставяне на полупроводниковия силициев чип върху оловна рамка, след това свързване на чипа с метални кабели на тази оловна рамка и впоследствие покриване на микроелектронния чип с пластмасов капак. Тази проста и относително евтина опаковка за микроелектроника все още е най-доброто решение за много приложения. Оловните рамки се произвеждат на дълги ленти, което позволява бързото им обработване на автоматизирани машини за сглобяване и обикновено се използват два производствени процеса: някакъв вид фотоецване и щамповане. В микроелектрониката дизайнът на водещата рамка често изисква персонализирани спецификации и характеристики, дизайни, които подобряват електрическите и термичните свойства и специфични изисквания за време на цикъл. Имаме задълбочен опит в производството на оловни рамки за микроелектроника за редица различни клиенти, използвайки лазерно фотоецване и щамповане. Проектиране и производство на радиатори за микроелектроника: както стандартни, така и персонализирани дизайн и производство. С увеличаването на разсейването на топлината от микроелектронните устройства и намаляването на общите форм-фактори, управлението на топлината става все по-важен елемент от дизайна на електронни продукти. Постоянността на производителността и продължителността на живота на електронното оборудване са обратно пропорционални на температурата на компонентите на оборудването. Връзката между надеждността и работната температура на типично силициево полупроводниково устройство показва, че намаляването на температурата съответства на експоненциално увеличение на надеждността и продължителността на живота на устройството. Следователно, дълъг живот и надеждна работа на компонент на полупроводниковата микроелектроника могат да бъдат постигнати чрез ефективно контролиране на работната температура на устройството в границите, определени от дизайнерите. Радиаторите са устройства, които подобряват разсейването на топлината от гореща повърхност, обикновено външния корпус на компонент, генериращ топлина, към по-хладна среда като въздух. За следващите дискусии се приема, че въздухът е охлаждащата течност. В повечето ситуации преносът на топлина през интерфейса между твърдата повърхност и охлаждащия въздух е най-малко ефективен в рамките на системата, а интерфейсът твърд въздух представлява най-голямата бариера за разсейване на топлината. Радиаторът намалява тази бариера главно чрез увеличаване на повърхността, която е в пряк контакт с охлаждащата течност. Това позволява да се разсейва повече топлина и/или понижава работната температура на полупроводниковото устройство. Основната цел на радиатора е да поддържа температурата на микроелектронното устройство под максимално допустимата температура, посочена от производителя на полупроводниковото устройство. Можем да класифицираме радиаторите по отношение на методите на производство и техните форми. Най-често срещаните видове радиатори с въздушно охлаждане включват: - Щамповани: Медни или алуминиеви ламарини се щамповат в желани форми. те се използват в традиционното въздушно охлаждане на електронни компоненти и предлагат икономично решение на топлинни проблеми с ниска плътност. Подходящи са за производство в голям обем. - Екструзия: Тези радиатори позволяват формирането на сложни двуизмерни форми, способни да разсейват големи топлинни натоварвания. Те могат да бъдат изрязани, обработени и добавени опции. Напречното рязане ще произведе многопосочни, правоъгълни радиатори с щифтови ребра, а включването на назъбени ребра подобрява производителността с приблизително 10 до 20%, но с по-бавна скорост на екструдиране. Ограниченията на екструзията, като например височината на ребрата до дебелината на ребрата, обикновено диктуват гъвкавостта на опциите за проектиране. Типично съотношение на височината на ребрата към процепа до 6 и минимална дебелина на ребрата от 1,3 мм са постижими със стандартни техники за екструдиране. Съотношение 10 към 1 и дебелина на перката от 0,8 инча могат да бъдат получени със специални характеристики на дизайна на матрицата. Въпреки това, тъй като съотношението на страните се увеличава, толерансът на екструдиране е компрометиран. - Свързани/изработени ребра: Повечето радиатори с въздушно охлаждане са с ограничена конвекция и общата топлинна ефективност на радиатора с въздушно охлаждане често може да бъде значително подобрена, ако по-голяма повърхност може да бъде изложена на въздушния поток. Тези високопроизводителни радиатори използват термично проводима епоксидна смола, напълнена с алуминий, за свързване на равнинни перки към набраздена екструдирана основна плоча. Този процес позволява много по-голямо съотношение на височината на ребрата към процепа от 20 до 40, което значително увеличава капацитета на охлаждане, без да увеличава нуждата от обем. - Отливки: Процесите на пясък, изгубен восък и леене под налягане за алуминий или мед/бронз се предлагат със или без вакуумна помощ. Ние използваме тази технология за производство на радиатори с щифтови ребра с висока плътност, които осигуряват максимална производителност при използване на импулсно охлаждане. - Сгънати перки: Вълнообразна ламарина от алуминий или мед увеличава повърхностната площ и обемната производителност. След това радиаторът се закрепва към основна плоча или директно към нагревателната повърхност чрез епоксидна смола или спояване. Не е подходящ за радиатори с висок профил поради наличността и ефективността на перките. Следователно, той позволява да се произвеждат високоефективни радиатори. При избора на подходящ радиатор, отговарящ на необходимите термични критерии за вашите микроелектронни приложения, ние трябва да проучим различни параметри, които влияят не само на самата производителност на радиатора, но и на цялостната производителност на системата. Изборът на конкретен тип радиатор в микроелектрониката зависи до голяма степен от топлинния бюджет, разрешен за радиатора и външните условия около радиатора. Никога няма една единствена стойност на топлинно съпротивление, присвоено на даден радиатор, тъй като топлинното съпротивление варира в зависимост от външните условия на охлаждане. Проектиране и производство на сензори и задвижващи механизми: Предлагат се както готови, така и персонализирани дизайн и производство. Ние предлагаме решения с готови за използване процеси за инерционни сензори, сензори за налягане и относително налягане и инфрачервени температурни сензори. Като използваме нашите IP блокове за акселерометри, инфрачервени сензори и сензори за налягане или прилагаме вашия дизайн според наличните спецификации и правила за проектиране, ние можем да ви доставим базирани на MEMS сензорни устройства в рамките на седмици. Освен MEMS могат да бъдат произведени и други видове сензорни и задвижващи структури. Проектиране и производство на оптоелектронни и фотонни схеми: Фотонна или оптична интегрална схема (PIC) е устройство, което интегрира множество фотонни функции. Може да се наподобява на електронни интегрални схеми в микроелектрониката. Основната разлика между двете е, че фотонната интегрална схема осигурява функционалност за информационни сигнали, наложени върху оптични дължини на вълните във видимия спектър или близо до инфрачервения 850 nm-1650 nm. Техниките за производство са подобни на тези, използвани в интегралните схеми на микроелектрониката, където фотолитографията се използва за моделиране на пластини за ецване и отлагане на материал. За разлика от полупроводниковата микроелектроника, където основното устройство е транзисторът, в оптоелектрониката няма едно доминиращо устройство. Фотонните чипове включват свързващи вълноводи с ниски загуби, разделители на мощност, оптични усилватели, оптични модулатори, филтри, лазери и детектори. Тези устройства изискват разнообразие от различни материали и техники за производство и затова е трудно да се реализират всички на един чип. Нашите приложения на фотонни интегрални схеми са главно в областта на оптичните комуникации, биомедицинските и фотонните изчисления. Някои примерни оптоелектронни продукти, които можем да проектираме и произведем за вас, са светодиоди (светлоизлъчващи диоди), диодни лазери, оптоелектронни приемници, фотодиоди, лазерни дистанционни модули, персонализирани лазерни модули и др. CLICK Product Finder-Locator Service ПРЕДИШНА СТРАНИЦА
- Thermal Infrared Test Equipment, Thermal Camera, Differential Scanning
Thermal Infrared Test Equipment, Thermal Camera, Differential Scanning Calorimeter, Thermo Gravimetric Analyzer, Thermo Mechanical Analyzer, Dynamic Mechanical Термично и инфрачервено тестово оборудване CLICK Product Finder-Locator Service Сред многото ОБОРУДВАНЕ ЗА ТЕРМИЧЕН АНАЛИЗ, ние фокусираме вниманието си върху популярните в индустрията, а именно ДИФЕРЕНЦИАЛНО СКАНИРАЩО КАЛОРИМЕТРИЯ ( DSC ), ТЕРМОТАНАЛИЧНА ТЕРМОГРАВИСНА -МЕХАНИЧЕН АНАЛИЗ (TMA), ДИЛАТОМЕТРИЯ, ДИНАМИЧЕН МЕХАНИЧЕН АНАЛИЗ (DMA), ДИФЕРЕНЦИАЛЕН ТЕРМИЧЕН АНАЛИЗ (DTA). Нашето ИНФРАЧЕРВЕНО ИЗПИТВАТЕЛНО ОБОРУДВАНЕ включва ТЕРМОВИЗИОННИ ИНСТРУМЕНТИ, ИНФРАЧЕРВЕНИ ТЕРМОГРАФИ, ИНФРАЧЕРВЕНИ КАМЕРИ. Някои приложения за нашите термовизионни инструменти са инспекция на електрически и механични системи, инспекция на електронни компоненти, щети от корозия и изтъняване на метал, откриване на дефекти. ДИФЕРЕНЦИАЛНИ СКАНИРАЩИ КАЛОРИМЕТРИ (DSC) : Техника, при която разликата в количеството топлина, необходимо за повишаване на температурата на проба и еталон, се измерва като функция на температурата. И пробата, и референтната температура се поддържат при почти една и съща температура по време на експеримента. Температурната програма за DSC анализ е установена така, че температурата на държача на пробата да нараства линейно като функция на времето. Референтната проба има добре дефиниран топлинен капацитет в диапазона от температури, които трябва да се сканират. DSC експериментите осигуряват като резултат крива на топлинния поток спрямо температурата или спрямо времето. Диференциалните сканиращи калориметри често се използват за изследване какво се случва с полимерите, когато се нагряват. Термичните преходи на полимер могат да бъдат изследвани с помощта на тази техника. Топлинните преходи са промени, които се извършват в полимера, когато се нагряват. Топенето на кристален полимер е пример. Стъкленият преход също е термичен преход. DSC термичният анализ се извършва за определяне на топлинните фазови промени, температурата на термично встъкляване (Tg), температурите на кристалната стопилка, ендотермичните ефекти, екзотермичните ефекти, термичната стабилност, стабилността на термичната формула, окислителната стабилност, феномените на прехода, структурите на твърдо състояние. DSC анализът определя Tg температурата на встъкляване, температурата, при която аморфните полимери или аморфната част от кристален полимер преминават от твърдо крехко състояние в меко гумено състояние, точка на топене, температура, при която се топи кристален полимер, Hm Погълната енергия (джаули /грам), количество енергия, което пробата абсорбира при топене, Tc точка на кристализация, температура, при която полимерът кристализира при нагряване или охлаждане, Hc освободена енергия (джаули/грам), количество енергия, което пробата освобождава при кристализация. Диференциалните сканиращи калориметри могат да се използват за определяне на термичните свойства на пластмаси, лепила, уплътнители, метални сплави, фармацевтични материали, восъци, храни, масла и смазочни материали и катализатори… и т.н. ДИФЕРЕНЦИАЛНИ ТЕРМИЧНИ АНАЛИЗАТОРИ (DTA): Алтернативна техника на DSC. При тази техника топлинният поток към пробата и референтната стойност остава същият вместо температурата. Когато пробата и еталонът се нагряват еднакво, фазовите промени и други топлинни процеси причиняват разлика в температурата между пробата и еталонната проба. DSC измерва енергията, необходима за поддържане на еталонната и пробата при една и съща температура, докато DTA измерва разликата в температурата между пробата и еталонната, когато и двете са подложени на една и съща топлина. Така че те са подобни техники. ТЕРМОМЕХАНИЧЕН АНАЛИЗАР (TMA) : TMA разкрива промяната в размерите на проба като функция от температурата. Човек може да разглежда ТМА като много чувствителен микрометър. TMA е устройство, което позволява прецизни измервания на позицията и може да бъде калибрирано спрямо известни стандарти. Система за контрол на температурата, състояща се от пещ, радиатор и термодвойка обгражда пробите. Кварцови, инварови или керамични приспособления задържат пробите по време на тестовете. Измерванията на TMA записват промени, причинени от промени в свободния обем на полимера. Промените в свободния обем са обемни промени в полимера, причинени от абсорбцията или освобождаването на топлина, свързана с тази промяна; загуба на твърдост; увеличен поток; или чрез промяна на времето за релаксация. Известно е, че свободният обем на полимера е свързан с вискоеластичността, стареенето, проникването на разтворители и свойствата на удар. Температурата на встъкляване Tg в полимер съответства на разширяването на свободния обем, което позволява по-голяма подвижност на веригата над този преход. Разглеждана като инфлексия или огъване в кривата на топлинно разширение, тази промяна в TMA може да се разглежда като обхващаща диапазон от температури. Температурата на встъкляване Tg се изчислява по съгласуван метод. Перфектното съответствие не се наблюдава веднага в стойността на Tg при сравняване на различни методи, но ако внимателно проучим съгласуваните методи за определяне на стойностите на Tg, тогава разбираме, че всъщност има добро съответствие. Освен абсолютната си стойност, ширината на Tg също е индикатор за промени в материала. TMA е сравнително проста техника за изпълнение. TMA често се използва за измерване на Tg на материали като силно омрежени термореактивни полимери, за които диференциалният сканиращ калориметър (DSC) е труден за използване. В допълнение към Tg, коефициентът на топлинно разширение (CTE) се получава от термомеханичен анализ. КТР се изчислява от линейните участъци на кривите на ТМА. Друг полезен резултат, който TMA може да ни предостави, е откриването на ориентацията на кристали или влакна. Композитните материали могат да имат три различни коефициента на термично разширение в посоките x, y и z. Чрез записване на CTE в посоки x, y и z може да се разбере в коя посока влакната или кристалите са предимно ориентирани. За измерване на обемното разширение на материала може да се използва техника, наречена DILATOMETRY . Пробата се потапя в течност като силициево масло или Al2O3 прах в дилатометъра, преминава през температурния цикъл и разширенията във всички посоки се преобразуват във вертикално движение, което се измерва от TMA. Съвременните термомеханични анализатори правят това лесно за потребителите. Ако се използва чиста течност, дилатометърът се пълни с тази течност вместо със силициево масло или алуминиев оксид. Използвайки диамантен TMA, потребителите могат да изпълняват криви на деформация на напрежението, експерименти за релаксация на напрежението, възстановяване при пълзене и сканиране на динамична механична температура. TMA е незаменимо тестово оборудване за индустрията и научните изследвания. ТЕРМОГРАВИМЕТРИЧНИ АНАЛИЗАТОРИ ( TGA ) : Термогравиметричният анализ е техника, при която масата на дадено вещество или образец се наблюдава като функция на температура или време. Пробата се подлага на програма с контролирана температура в контролирана атмосфера. TGA измерва теглото на пробата, докато тя се нагрява или охлажда в пещта. Инструментът TGA се състои от съд за проби, който се поддържа от прецизна везна. Този съд се намира в пещ и се нагрява или охлажда по време на теста. Масата на пробата се следи по време на изпитването. Средата на пробата се продухва с инертен или реактивен газ. Термогравиметричните анализатори могат да определят количествено загубата на вода, разтворител, пластификатор, декарбоксилиране, пиролиза, окисление, разлагане, тегловни % пълнежен материал и тегловни % пепел. В зависимост от случая информацията може да се получи при нагряване или охлаждане. Типична термична крива на TGA се показва отляво надясно. Ако термичната крива на TGA се спуска надолу, това показва загуба на тегло. Съвременните TGA са способни да провеждат изотермични експерименти. Понякога потребителят може да пожелае да използва реактивна проба прочистващи газове, като например кислород. Когато използвате кислород като продухващ газ, потребителят може да поиска да превключи газовете от азот към кислород по време на експеримента. Тази техника често се използва за идентифициране на процента въглерод в даден материал. Термогравиметричният анализатор може да се използва за сравняване на два подобни продукта, като инструмент за контрол на качеството, за да се гарантира, че продуктите отговарят на спецификациите на материалите, за да се гарантира, че продуктите отговарят на стандартите за безопасност, за определяне на съдържанието на въглерод, идентифициране на фалшиви продукти, за идентифициране на безопасни работни температури в различни газове, за подобряване на процесите на формулиране на продукта, за обратно инженерство на продукт. Накрая си струва да споменем, че са налични комбинации от TGA с GC/MS. GC е съкращение от газова хроматография, а MS е съкращение от масспектрометрия. ДИНАМИЧЕН МЕХАНИЧЕН АНАЛИЗАР (DMA) : Това е техника, при която малка синусоидална деформация се прилага върху образец с известна геометрия по цикличен начин. След това се изследва реакцията на материалите на стрес, температура, честота и други стойности. Пробата може да бъде подложена на контролирано напрежение или контролирано напрежение. При известно напрежение пробата ще се деформира в определена степен в зависимост от нейната коравина. DMA измерва коравина и затихване, те се отчитат като модул и тен делта. Тъй като прилагаме синусоидална сила, можем да изразим модула като синфазен компонент (модул на съхранение) и компонент извън фаза (модул на загуба). Модулът на съхранение, E' или G', е мярката за еластичното поведение на пробата. Съотношението на загубата към съхранението е тен делта и се нарича затихване. Счита се за мярка за разсейването на енергия от даден материал. Затихването варира в зависимост от състоянието на материала, неговата температура и честотата. DMA понякога се нарича DMTA стоящ за ДИНАМИЧЕН МЕХАНИЧЕН ТЕРМАЛИЧЕН АНАЛИЗ. Термомеханичният анализ прилага постоянна статична сила върху даден материал и записва промените в размерите на материала при промяна на температурата или времето. DMA, от друга страна, прилага осцилаторна сила при зададена честота към пробата и отчита промени в твърдостта и затихването. Данните за DMA ни предоставят информация за модула, докато данните за TMA ни дават коефициента на топлинно разширение. И двете техники откриват преходи, но DMA е много по-чувствителен. Стойностите на модула се променят с температурата и преходите в материалите могат да се видят като промени в E' или тен делта кривите. Това включва встъкляване, топене и други преходи, които се случват в стъкловидното или гумено плато, които са индикатори за фини промени в материала. ТЕРМОВИЗИОННИ ИНСТРУМЕНТИ, ИНФРАЧЕРВЕНИ ТЕРМОГРАФИ, ИНФРАЧЕРВЕНИ КАМЕРИ : Това са устройства, които формират изображение с помощта на инфрачервено лъчение. Стандартните ежедневни камери формират изображения, използвайки видима светлина в диапазона на дължината на вълната 450–750 нанометра. Инфрачервените камери обаче работят в инфрачервения диапазон на дължина на вълната до 14 000 nm. Като цяло, колкото по-висока е температурата на даден обект, толкова повече инфрачервено лъчение се излъчва като лъчение на черно тяло. Инфрачервените камери работят дори в пълна тъмнина. Изображенията от повечето инфрачервени камери имат един цветен канал, тъй като камерите обикновено използват сензор за изображения, който не различава различните дължини на вълната на инфрачервеното лъчение. За разграничаване на дължини на вълните сензорите за цветни изображения изискват сложна конструкция. В някои тестови инструменти тези монохроматични изображения се показват в псевдо цвят, където се използват промени в цвета, а не промени в интензитета, за да се покажат промените в сигнала. Най-ярките (най-топлите) части на изображенията обикновено са оцветени в бяло, междинните температури са оцветени в червено и жълто, а най-слабите (най-студените) части са оцветени в черно. Обикновено се показва скала до изображение с фалшив цвят, за да се свържат цветовете с температурите. Термичните камери имат значително по-ниска резолюция от тази на оптичните камери, със стойности от порядъка на 160 x 120 или 320 x 240 пиксела. По-скъпите инфрачервени камери могат да постигнат резолюция от 1280 x 1024 пиксела. Има две основни категории термографски камери: _CC781905-5CDE-3194-BB3B-136BAD5CF58D_COOLED Инфрачервен детектор на изображения Systems and_cc781905-5cde-3194cber------16cncuctns--sectons---16cncort5-sectons----1buctns----1furectns---1furectns---1furectns--sectons---1buct в. Охлаждаемите термографски камери имат детектори, поставени във вакуумно запечатан корпус и са криогенно охлаждани. Охлаждането е необходимо за работата на използваните полупроводникови материали. Без охлаждане тези сензори биха били наводнени от собствената си радиация. Охлаждаемите инфрачервени камери обаче са скъпи. Охлаждането изисква много енергия и отнема време, като изисква няколко минути време за охлаждане преди работа. Въпреки че охлаждащото устройство е обемисто и скъпо, охлажданите инфрачервени камери предлагат на потребителите превъзходно качество на изображението в сравнение с неохлажданите камери. По-добрата чувствителност на охлажданите камери позволява използването на обективи с по-високо фокусно разстояние. За охлаждане може да се използва бутилиран азот. Неохлажданите термични камери използват сензори, работещи при температура на околната среда, или сензори, стабилизирани при температура, близка до околната, като използват елементи за контрол на температурата. Неохлажданите инфрачервени сензори не се охлаждат до ниски температури и следователно не изискват обемисти и скъпи криогенни охладители. Тяхната разделителна способност и качество на изображението обаче е по-ниско в сравнение с охладените детектори. Термографските камери предлагат много възможности. Местата на прегряване са електропроводи, които могат да бъдат локализирани и ремонтирани. Могат да се наблюдават електрически вериги и необичайно горещи точки могат да показват проблеми като късо съединение. Тези камери също се използват широко в сгради и енергийни системи за локализиране на места, където има значителни топлинни загуби, така че да може да се обмисли по-добра топлоизолация в тези точки. Термовизионните инструменти служат като оборудване за безразрушителен тест. За подробности и друго подобно оборудване, моля, посетете нашия уебсайт за оборудване: http://www.sourceindustrialsupply.com ПРЕДИШНА СТРАНИЦА
- Laser Machining, LM, Laser Cutting, CO2 Laser Processing, Nd-YAG Cut
Laser Machining - LM - Laser Cutting - Custom Parts Manufacturing - CO2 Laser Processing - Nd-YAG - Cutting - Boring Лазерна обработка и рязане & LBM LASER CUTTING is a HIGH-ENERGY-BEAM MANUFACTURING technology that uses a laser to cut materials, and is typically used for industrial manufacturing applications. В ОБРАБОТКА С ЛАЗЕРЕН ЛЪЧ (LBM), лазерен източник фокусира оптичната енергия върху повърхността на детайла. Лазерното рязане насочва силно фокусирания изход с висока плътност на високомощен лазер чрез компютър към материала, който ще се реже. След това целевият материал се стопява, изгаря, изпарява или се издухва от струя газ, по контролиран начин, оставяйки ръб с висококачествено покритие на повърхността. Нашите промишлени лазерни ножове са подходящи за рязане на плоски листови материали, както и на структурни и тръбопроводни материали, метални и неметални детайли. Обикновено не се изисква вакуум при процесите на обработка и рязане с лазерен лъч. Има няколко типа лазери, използвани при лазерно рязане и производство. Импулсната или непрекъсната вълна CO2 LASER е подходяща за рязане, пробиване и гравиране. The NEODYMIUM (Nd) and neodymium yttrium-aluminum-garnet (Nd-YAG) LASERS are identical по стил и се различават само по приложение. Неодимовият Nd се използва за пробиване и където се изисква висока енергия, но малко повторение. Nd-YAG лазерът от друга страна се използва, когато се изисква много висока мощност и за пробиване и гравиране. Както CO2, така и Nd/Nd-YAG лазери могат да се използват за ЛАЗЕРНО ЗАВАРЯВАНЕ. Други лазери, които използваме в производството, включват Nd:GLASS, RUBY и EXCIMER. При обработката с лазерен лъч (LBM) следните параметри са важни: Коефициентът на отразяване и топлопроводимостта на повърхността на детайла и неговата специфична топлина и латентна топлина на топене и изпарение. Ефективността на процеса на обработка с лазерен лъч (LBM) се увеличава с намаляването на тези параметри. Дълбочината на рязане може да се изрази като: t ~ P / (vxd) Това означава, че дълбочината на рязане „t“ е пропорционална на входящата мощност P и обратно пропорционална на скоростта на рязане v и диаметъра на петното на лазерния лъч d. Повърхността, произведена с LBM, обикновено е грапава и има зона, засегната от топлина. ЛАЗЕРНО РЯЗАНЕ И ОБРАБОТКА С КАРБОНДИКСИД (CO2): CO2 лазерите с постоянен ток се изпомпват чрез пропускане на ток през газовата смес, докато RF възбудените CO2 лазери използват радиочестотна енергия за възбуждане. RF методът е сравнително нов и стана по-популярен. Дизайните с постоянен ток изискват електроди вътре в кухината и следователно могат да имат електродна ерозия и покритие от електроден материал върху оптиката. Напротив, RF резонаторите имат външни електроди и следователно не са склонни към тези проблеми. Ние използваме CO2 лазери при индустриално рязане на много материали като мека стомана, алуминий, неръждаема стомана, титан и пластмаси. YAG LASER CUTTING and MACHINING: Ние използваме YAG лазери за рязане и писане на метали и керамика. Лазерният генератор и външната оптика изискват охлаждане. Отпадната топлина се генерира и пренася от охлаждаща течност или директно във въздуха. Водата е обичайна охлаждаща течност, обикновено циркулираща през охладител или система за пренос на топлина. ЕКСИМЕРНО ЛАЗЕРНО РЯЗАНЕ и ОБРАБОТКА: Ексимерният лазер е вид лазер с дължини на вълните в ултравиолетовата област. Точната дължина на вълната зависи от използваните молекули. Например следните дължини на вълните са свързани с молекулите, показани в скоби: 193 nm (ArF), 248 nm (KrF), 308 nm (XeCl), 353 nm (XeF). Някои ексимерни лазери са регулируеми. Ексимерните лазери имат привлекателното свойство, че могат да премахват много фини слоеве от повърхностен материал без почти никакво нагряване или промяна на останалата част от материала. Следователно ексимерните лазери са много подходящи за прецизна микрообработка на органични материали като някои полимери и пластмаси. ЛАЗЕРНО РЯЗАНЕ С ГАЗ: Понякога използваме лазерни лъчи в комбинация с газов поток, като кислород, азот или аргон за рязане на тънки листови материали. Това се прави с помощта на a LASER-BEAM TORCH. За неръждаема стомана и алуминий ние използваме лазерно рязане под високо налягане с инертен газ и азот. Това води до ръбове без оксиди за подобряване на заваряемостта. Тези газови потоци също издухват разтопен и изпарен материал от повърхностите на детайлите. В a LASER MICROJET CUTTING имаме направляван с водна струя лазер, в който импулсен лазерен лъч се свързва с водна струя с ниско налягане. Използваме го за извършване на лазерно рязане, докато използваме водната струя за насочване на лазерния лъч, подобно на оптично влакно. Предимствата на лазерната микроструя са, че водата също премахва остатъците и охлажда материала, тя е по-бърза от традиционното „сухо“ лазерно рязане с по-високи скорости на рязане, паралелно рязане и възможност за многопосочно рязане. Ние използваме различни методи за рязане с помощта на лазери. Някои от методите са изпаряване, разтопяване и издухване, издухване с разтопяване и изгаряне, крекинг под термично напрежение, скрабиране, студено рязане и изгаряне, стабилизирано лазерно рязане. - Изпарително рязане: Фокусираният лъч нагрява повърхността на материала до точката на кипене и създава дупка. Дупката води до внезапно увеличаване на абсорбцията и бързо задълбочава дупката. Тъй като дупката се задълбочава и материалът кипи, генерираната пара разяжда разтопените стени, издухвайки материала навън и допълнително разширявайки дупката. Нетопими материали като дърво, въглерод и термореактивни пластмаси обикновено се режат по този метод. - Рязане с разтопяване и издухване: Ние използваме газ под високо налягане, за да издухаме разтопен материал от зоната на рязане, като намаляваме необходимата мощност. Материалът се нагрява до точката на топене и след това газова струя издухва разтопения материал от прореза. Това елиминира необходимостта от допълнително повишаване на температурата на материала. Ние режем метали с тази техника. - Напукване от термичен стрес: Крехките материали са чувствителни към термично счупване. Лъчът се фокусира върху повърхността, причинявайки локално нагряване и топлинно разширение. Това води до пукнатина, която след това може да бъде направлявана чрез преместване на гредата. Използваме тази техника при рязане на стъкло. - Стелт нарязване на силициеви пластини: Отделянето на микроелектронни чипове от силициеви пластини се извършва чрез процес на стелт нарязване, като се използва импулсен Nd:YAG лазер, дължината на вълната от 1064 nm е добре адаптирана към електронната забранена лента на силиций (1,11 eV или 1117 nm). Това е популярно при производството на полупроводникови устройства. - Реактивно рязане: Наричано също пламъчно рязане, тази техника може да бъде подобна на рязане с кислородна горелка, но с лазерен лъч като източник на запалване. Използваме това за рязане на въглеродна стомана с дебелина над 1 mm и дори много дебели стоманени плочи с малка мощност на лазера. ИМПУЛСНИ ЛАЗЕРИ ни осигуряват мощен изблик на енергия за кратък период от време и са много ефективни при някои процеси на лазерно рязане, като пробиване, или когато са необходими много малки отвори или много ниски скорости на рязане. Ако вместо това се използва постоянен лазерен лъч, топлината може да достигне точката на разтопяване на цялото обработвано парче. Нашите лазери имат способността да пулсират или режат CW (непрекъсната вълна) под NC (цифрово управление) програмно управление. Ние използваме ДВОЙНИ ИМПУЛСНИ ЛАЗЕРИ излъчване на поредица от импулсни двойки за подобряване на скоростта на отстраняване на материала и качеството на отвора. Първият импулс премахва материала от повърхността, а вторият импулс предотвратява залепването на изхвърления материал отстрани на отвора или среза. Допустимите отклонения и повърхностното покритие при лазерно рязане и машинна обработка са изключителни. Нашите модерни лазерни ножове имат точност на позициониране от около 10 микрометра и повторяемост от 5 микрометра. Стандартните грапавини Rz нарастват с дебелината на листа, но намаляват с лазерната мощност и скоростта на рязане. Процесите на лазерно рязане и машинна обработка са в състояние да постигнат близки допуски, често до 0,001 инча (0,025 mm). Геометрията на детайлите и механичните характеристики на нашите машини са оптимизирани за постигане на най-добри възможности за толеранс. Повърхностното покритие, което можем да получим чрез рязане с лазерен лъч, може да варира между 0,003 mm до 0,006 mm. Като цяло ние лесно постигаме отвори с диаметър 0,025 mm, а отвори с размери до 0,005 mm и съотношения между дълбочина и диаметър на отвора 50 към 1 са произведени в различни материали. Нашите най-прости и най-стандартни лазерни ножове ще режат метал от въглеродна стомана с дебелина 0,020–0,5 инча (0,51–13 mm) и лесно могат да бъдат до тридесет пъти по-бързи от стандартното рязане. Обработката с лазерен лъч се използва широко за пробиване и рязане на метали, неметали и композитни материали. Предимствата на лазерното рязане пред механичното рязане включват по-лесно захващане, чистота и намалено замърсяване на детайла (тъй като няма режещ ръб, както при традиционното фрезоване или струговане, който може да се замърси от материала или да замърси материала, т.е. натрупване). Абразивната природа на композитните материали може да ги направи трудни за машинна обработка чрез конвенционални методи, но лесни чрез лазерна обработка. Тъй като лазерният лъч не се износва по време на процеса, получената прецизност може да бъде по-добра. Тъй като лазерните системи имат малка зона, засегната от топлината, има и по-малък шанс за изкривяване на материала, който се реже. За някои материали лазерното рязане може да бъде единствената възможност. Процесите на рязане с лазерен лъч са гъвкави, а доставянето на оптичен лъч, простото закрепване, кратките времена за настройка, наличието на триизмерни CNC системи правят възможно лазерното рязане и машинната обработка да се конкурират успешно с други процеси за производство на ламарина, като щанцоване. Като се има предвид това, лазерната технология понякога може да се комбинира с технологиите за механично производство за подобрена обща ефективност. Лазерното рязане на ламарина има предимствата пред плазменото рязане, че е по-прецизно и използва по-малко енергия, но повечето индустриални лазери не могат да режат метал с по-голяма дебелина, отколкото плазмата. Лазерите, работещи с по-високи мощности като 6000 вата, се доближават до плазмените машини по способността си да режат дебели материали. Въпреки това капиталовите разходи за тези лазерни ножове с мощност 6000 вата са много по-високи от тези на машините за плазмено рязане, способни да режат дебели материали като стоманена плоча. Има и недостатъци на лазерното рязане и механична обработка. Лазерното рязане включва висока консумация на енергия. Ефективността на индустриалния лазер може да варира от 5% до 15%. Консумацията на енергия и ефективността на всеки конкретен лазер ще варира в зависимост от изходната мощност и работните параметри. Това ще зависи от вида на лазера и от това колко добре лазерът отговаря на работата, която извършвате. Количеството мощност на лазерно рязане, необходимо за конкретна задача, зависи от вида на материала, дебелината, използвания процес (реактивен/инертен) и желаната скорост на рязане. Максималната производителност при лазерно рязане и механична обработка е ограничена от редица фактори, включително лазерна мощност, тип процес (независимо дали е реактивен или инертен), свойства на материала и дебелина. In ЛАЗЕРНА АБЛАЦИЯ отстраняваме материал от твърда повърхност, като я облъчваме с лазерен лъч. При нисък лазерен поток материалът се нагрява от абсорбираната лазерна енергия и се изпарява или сублимира. При висок лазерен поток материалът обикновено се превръща в плазма. Високомощните лазери почистват голямо петно с един импулс. Лазерите с по-ниска мощност използват много малки импулси, които могат да бъдат сканирани в дадена област. При лазерната аблация премахваме материал с импулсен лазер или с лазерен лъч с непрекъсната вълна, ако интензитетът на лазера е достатъчно висок. Импулсните лазери могат да пробиват изключително малки, дълбоки отвори в много твърди материали. Много късите лазерни импулси премахват материала толкова бързо, че околният материал абсорбира много малко топлина, следователно лазерното пробиване може да се извършва върху деликатни или чувствителни към топлина материали. Лазерната енергия може да се абсорбира селективно от покритията, следователно CO2 и Nd:YAG импулсните лазери могат да се използват за почистване на повърхности, премахване на боя и покритие или подготовка на повърхности за боядисване, без да се повреди основната повърхност. We use LASER ENGRAVING and LASER MARKING to engrave or mark an object. Тези две техники всъщност са най-широко използваните приложения. Не се използват мастила, нито се включват части от инструменти, които влизат в контакт с гравираната повърхност и се износват, какъвто е случаят с традиционните методи за механично гравиране и маркиране. Материалите, специално проектирани за лазерно гравиране и маркиране, включват лазерно чувствителни полимери и специални нови метални сплави. Въпреки че оборудването за лазерно маркиране и гравиране е сравнително по-скъпо в сравнение с алтернативи като перфоратори, щифтове, стилуси, гравиращи печати… и т.н., те станаха по-популярни поради своята точност, възпроизводимост, гъвкавост, лекота на автоматизация и онлайн приложение в голямо разнообразие от производствени среди. И накрая, ние използваме лазерни лъчи за няколко други производствени операции: - ЛАЗЕРНО ЗАВАРЯВАНЕ - ЛАЗЕРНА ТОПЛИННА ОБРАБОТКА: Малкомащабна топлинна обработка на метали и керамика за модифициране на повърхностните им механични и трибологични свойства. - ЛАЗЕРНА ПОВЪРХНОСТНА ТРЕТИРАНЕ / МОДИФИКАЦИЯ: Лазерите се използват за почистване на повърхности, въвеждане на функционални групи, модифициране на повърхности в опит да се подобри адхезията преди нанасяне на покритие или процеси на свързване. CLICK Product Finder-Locator Service ПРЕДИШНА СТРАНИЦА
- Electron Beam Machining, EBM, E-Beam Machining & Cutting & Boring
Electron Beam Machining, EBM, E-Beam Machining & Cutting & Boring, Custom Manufacturing of Parts - AGS-TECH Inc. - NM - USA EBM обработка и обработка с електронен лъч В ЕЛЕКТРОННО-ЛЪЧОВА ОБРАБОТКА (EBM) имаме високоскоростни електрони, концентрирани в тесен лъч, който е насочен към обработвания детайл, създавайки топлина и изпарявайки материала. Така EBM е един вид HIGH-ENERGY-BEAM MACHINING техника. Електронно-лъчева обработка (EBM) може да се използва за много точно рязане или пробиване на различни метали. Повърхностното покритие е по-добро и ширината на прореза е по-тясна в сравнение с други процеси на термично рязане. Електронните лъчи в оборудването EBM-Machining се генерират в електронен лъчев пистолет. Приложенията на обработката с електронен лъч са подобни на тези на обработката с лазерен лъч, с изключение на това, че EBM изисква добър вакуум. По този начин тези два процеса се класифицират като електро-оптично-термични процеси. Заготовката, която ще се обработва с EBM процес, се намира под електронния лъч и се държи под вакуум. Електронно-лъчевите оръдия в нашите EBM машини също са снабдени с осветителни системи и телескопи за центриране на лъча спрямо детайла. Детайлът е монтиран на CNC маса, така че дупки с всякаква форма да могат да се обработват с помощта на CNC контрола и функцията за отклонение на лъча на пистолета. За да се постигне бързо изпаряване на материала, равнинната плътност на мощността в лъча трябва да бъде възможно най-висока. На мястото на удара могат да бъдат постигнати стойности до 10exp7 W/mm2. Електроните прехвърлят кинетичната си енергия в топлина в много малка площ и материалът, засегнат от лъча, се изпарява за много кратко време. Разтопеният материал в горната част на предната част се изтласква от зоната на рязане от високото налягане на парите в долните части. EBM оборудването е изградено подобно на машините за електронно лъчево заваряване. Електронно-лъчевите машини обикновено използват напрежение в диапазона от 50 до 200 kV, за да ускорят електроните до около 50 до 80% от скоростта на светлината (200 000 km/s). Магнитни лещи, чиято функция се основава на силите на Лоренц, се използват за фокусиране на електронния лъч към повърхността на детайла. С помощта на компютър електромагнитната отклоняваща система позиционира лъча според нуждите, така че да могат да се пробиват отвори с всякаква форма. С други думи, магнитните лещи в оборудването за електронно-лъчева обработка оформят лъча и намаляват отклонението. От друга страна, отворите позволяват само на конвергентните електрони да преминат и да уловят дивергентните електрони с ниска енергия от ръбовете. По този начин апертурата и магнитните лещи в EBM-Machines подобряват качеството на електронния лъч. Пистолетът в EBM се използва в импулсен режим. Дупките могат да се пробиват в тънки листове с помощта на един импулс. За по-дебели плочи обаче ще са необходими множество импулси. Обикновено се използват превключващи импулсни продължителности от 50 микросекунди до 15 милисекунди. За да се сведат до минимум сблъсъци на електрони с въздушни молекули, водещи до разсейване, и да се запази замърсяването до минимум, в EBM се използва вакуум. Вакуумът е труден и скъп за производство. Постигането на добър вакуум в големи обеми и камери е особено изискващо. Следователно EBM е най-подходящ за малки части, които се побират в компактни вакуумни камери с разумни размери. Нивото на вакуум в пистолета на EBM е от порядъка на 10EXP(-4) до 10EXP(-6) Torr. Взаимодействието на електронния лъч с обработвания детайл произвежда рентгенови лъчи, които представляват опасност за здравето и следователно добре обучен персонал трябва да работи с EBM оборудване. Най-общо казано, EBM-Machining се използва за рязане на отвори с диаметър от 0,001 инча (0,025 милиметра) и тесни канали от 0,001 инча в материали с дебелина до 0,250 инча (6,25 милиметра). Характерна дължина е диаметърът, върху който лъчът е активен. Електронният лъч в EBM може да има характерна дължина от десетки микрони до mm в зависимост от степента на фокусиране на лъча. Обикновено високоенергийният фокусиран електронен лъч се прави така, че да попадне върху детайла с размер на петна от 10 – 100 микрона. EBM може да осигури отвори с диаметри в диапазона от 100 микрона до 2 mm с дълбочина до 15 mm, т.е. със съотношение дълбочина/диаметър от около 10. В случай на разфокусирани електронни лъчи, плътността на мощността ще падне до 1 Ват/мм2. Въпреки това, в случай на фокусирани лъчи, плътността на мощността може да бъде увеличена до десетки kW/mm2. За сравнение, лазерните лъчи могат да бъдат фокусирани върху петно с размер от 10 – 100 микрона с плътност на мощността до 1 MW/mm2. Електрическият разряд обикновено осигурява най-висока плътност на мощността с по-малки размери на петна. Токът на лъча е пряко свързан с броя на наличните електрони в лъча. Токът на лъча при обработка с електронен лъч може да бъде нисък от 200 микроампера до 1 ампер. Увеличаването на тока на лъча на EBM и/или продължителността на импулса директно увеличава енергията на импулс. Ние използваме високоенергийни импулси над 100 J/импулс, за да обработваме по-големи отвори на по-дебели плочи. При нормални условия машинната обработка с EBM ни предлага предимството на продукти без грапавини. Параметрите на процеса, които пряко влияят върху характеристиките на обработка при електронно-лъчева обработка, са: • Ускорително напрежение • Ток на лъча • Продължителност на импулса • Енергия на импулс • Мощност на импулс • Ток на обектива • Размер на петна • Плътност на мощността Някои фантастични структури могат да бъдат получени и с помощта на електронно-лъчева обработка. Дупките могат да бъдат заострени по дълбочината или във формата на варел. Чрез фокусиране на лъча под повърхността могат да се получат обратни стеснения. Широка гама от материали като стомана, неръждаема стомана, титанови и никелови супер-сплави, алуминий, пластмаси, керамика могат да бъдат обработвани с помощта на обработка с електронни лъчи. Може да има термични щети, свързани с EBM. Въпреки това, засегнатата от топлината зона е тясна поради кратката продължителност на импулса в EBM. Зоните, засегнати от топлина, обикновено са около 20 до 30 микрона. Някои материали като алуминиеви и титанови сплави се обработват по-лесно в сравнение със стоманата. Освен това EBM машинната обработка не включва сили на рязане върху детайлите. Това позволява обработка на крехки и чупливи материали чрез EBM без значително затягане или закрепване, какъвто е случаят при техниките за механична обработка. Дупките могат да се пробиват и под много плитки ъгли като 20 до 30 градуса. Предимствата на Electron-Beam-Machining: EBM осигурява много високи скорости на пробиване, когато се пробиват малки отвори с високо аспектно съотношение. EBM може да обработва почти всеки материал, независимо от неговите механични свойства. Не се включват механични сили на рязане, като по този начин разходите за затягане, задържане и фиксиране са пренебрегнати, а крехките/чупливи материали могат да се обработват без проблеми. Зоните, засегнати от топлина в EBM, са малки поради късите импулси. EBM е в състояние да осигури всякаква форма на отвори с точност чрез използване на електромагнитни намотки за отклоняване на електронни лъчи и CNC маса. Недостатъците на електронно-лъчевата обработка: Оборудването е скъпо и работата и поддръжката на вакуумни системи изисква специализирани техници. EBM изисква значителни периоди на вакуумна помпа за постигане на необходимите ниски налягания. Въпреки че засегнатата от топлината зона е малка в EBM, образуването на преработен слой се случва често. Нашият дългогодишен опит и ноу-хау ни помага да се възползваме от това ценно оборудване в нашата производствена среда. CLICK Product Finder-Locator Service ПРЕДИШНА СТРАНИЦА
- Industrial Computers, Industrial PC, Rugged Computer, Janz Tec,Korenix
Industrial Computers - Industrial PC - Rugged Computer - Janz Tec - Korenix - AGS-TECH Inc. - New Mexico - USA Индустриален компютър Индустриалните компютри се използват най-вече за КОНТРОЛ НА ПРОЦЕСИ и/или НАБИРАНЕ НА ДАННИ. Понякога ИНДУСТРИАЛЕН компютър просто се използва като интерфейс към друг контролен компютър в среда за разпределена обработка. Персонализиран софтуер може да бъде написан за конкретно приложение или, ако е наличен, може да се използва готов пакет за осигуряване на основно ниво на програмиране. Сред предлаганите от нас марки индустриални компютри е JANZ TEC от Германия. Едно приложение може просто да изисква I/O, като например серийния порт, предоставен от дънната платка. В някои случаи се инсталират разширителни карти, за да осигурят аналогови и цифрови I/O, специфичен машинен интерфейс, разширени комуникационни портове и т.н., както се изисква от приложението. Индустриалните компютри предлагат характеристики, различни от потребителските компютри по отношение на надеждност, съвместимост, опции за разширение и дългосрочно снабдяване. Индустриалните компютри обикновено се произвеждат в по-малки обеми от домашните или офис компютрите. Популярна категория индустриални компютри е 19-ИНЧОВИЯТ РЕКМОУНТ ФОРМ ФАКТОР. Индустриалните компютри обикновено са по-скъпи от сравнимите компютри в офис стил с подобна производителност. ЕДНОПЛАТКОВИТЕ КОМПЮТРИ и ПЛАНИТЕ се използват предимно в индустриални компютърни системи. По-голямата част от индустриалните компютри обаче се произвеждат с ДЪННИ ПЛАТИ COTS. Конструкция и характеристики на индустриалните компютри: На практика всички индустриални компютри споделят основната философия на дизайна за осигуряване на контролирана среда за инсталираната електроника, за да оцелеят в суровите условия на производствения етаж. Самите електронни компоненти могат да бъдат избрани според способността им да издържат на по-високи и по-ниски работни температури от типичните търговски компоненти. - По-тежка и здрава метална конструкция в сравнение с типичния офис нездрав компютър - Фактор на формата на кутията, който включва възможност за монтиране в заобикалящата среда (като 19'' шкаф, стенен монтаж, панелен монтаж и т.н.) - Допълнително охлаждане с филтриране на въздуха - Алтернативни методи за охлаждане като използване на принудителен въздух, течност и/или проводимост - Запазване и поддръжка на разширителни карти - Подобрено филтриране и уплътнение на електромагнитни смущения (EMI). - Подобрена защита на околната среда като защита срещу прах, воден спрей или защита от потапяне и др. - Запечатани конектори MIL-SPEC или Circular-MIL - По-стабилни контроли и функции - По-висок клас захранване - 24 V захранване с по-ниска консумация, предназначено за използване с DC UPS - Контролиран достъп до контролите чрез използване на заключващи се врати - Контролиран достъп до I/O чрез използване на капаци за достъп - Включване на таймер за наблюдение за автоматично нулиране на системата в случай на блокиране на софтуера Изтеглете нашите ATOP ТЕХНОЛОГИИ compact продуктова брошура (Изтеглете продукта на ATOP Technologies List 2021) Изтеглете нашата брошура за компактни продукти на марката JANZ TEC Изтеглете нашата брошура за компактни продукти с марка KORENIX Изтеглете нашата марка DFI-ITOX Брошура за индустриални дънни платки Изтеглете нашата брошура за вградени едноплаткови компютри с марка DFI-ITOX Изтеглете нашата брошура за вградени контролери и DAQ на марката ICP DAS PAC За да изберете подходящ индустриален компютър за вашия проект, моля, посетете нашия магазин за индустриални компютри, като КЛИКНЕТЕ ТУК. Изтеглете брошура за нашия ПРОГРАМА ЗА ДИЗАЙН ПАРТНЬОРСТВО Някои от нашите популярни индустриални PC продукти от Janz Tec AG са: - ГЪВКАВИ 19'' СИСТЕМИ ЗА МОНТАЖ В СТАЛАЙЖИ: Областите на работа и изискванията за 19'' системи са много широки в индустрията. Можете да избирате между индустриална технология на основната платка и слот CPU технология с използването на пасивна задна платка. - СПЕСТЯВАЩИ ПРОСТРАНСТВО СИСТЕМИ ЗА МОНТАЖ НА СТЕНА: Нашата серия ENDEAVOUR са гъвкави индустриални компютри, включващи индустриални компоненти. Като стандарт се използват слот процесорни платки с технология за пасивна задна платка. Можете да изберете продукта, отговарящ на вашите изисквания, или можете да научите повече за отделните варианти на тази продуктова група, като се свържете с нас. Нашите индустриални компютри Janz Tec могат да се комбинират с конвенционални индустриални системи за управление или PLC контролери. CLICK Product Finder-Locator Service ПРЕДИШНА СТРАНИЦА
- Electromagnetic Components Manufacturing and Assembly, Selenoid
Electromagnetic Components Manufacturing and Assembly, Selenoid, Electromagnet, Transformer, Electric Motor, Generator, Meters, Indicators, Scales,Electric Fans Соленоиди и електромагнитни компоненти и възли Като персонализиран производител и инженерен интегратор, AGS-TECH може да ви предостави следните ЕЛЕКТРОМАГНИТНИ КОМПОНЕНТИ И АССЕМБЛИ: • Селеноид, електромагнит, трансформатор, електродвигател и генератор • Електромагнитни измервателни уреди, индикатори, везни, специално произведени за вашето измервателно устройство. • Електромагнитен сензор и изпълнителен механизъм • Електрически вентилатори и охладители с различни размери за електронни устройства и индустриални приложения • Монтаж на други сложни електромагнитни системи Щракнете тук, за да изтеглите брошура за нашите панелни измервателни уреди - OICASCHINT Меки ферити - сърцевини - тороиди - продукти за потискане на EMI - RFID транспондери и брошура за аксесоари Изтеглете брошура за нашия ПРОГРАМА ЗА ДИЗАЙН ПАРТНЬОРСТВО Ако се интересувате най-вече от нашите инженерни и научноизследователски и развойни възможности, вместо от производствени възможности, тогава ви каним да посетите нашия инженерен сайт http://www.ags-engineering.com CLICK Product Finder-Locator Service ПРЕДИШНА СТРАНИЦА
- Custom Electric Electronics Manufacturing, Lighting, Display, PCB,PCBA
Custom Electric Electronics Manufacturing, Lighting, Display, Touchscreen, Cable Assembly, PCB, PCBA, Wireless Devices, Wire Harness, Microwave Components Персонализирано електричество и електроника Производство на продукти Прочетете още Сглобяване и свързване на електрически и електронни кабели Прочетете още Производство и сглобяване на PCB & PCBA Прочетете още Производство и монтаж на електрически и енергийни компоненти и системи Прочетете още Производство и монтаж на RF и безжични устройства Прочетете още Производство и монтаж на микровълнови компоненти и системи Прочетете още Производство и монтаж на осветителни и осветителни системи Прочетете още Соленоиди и електромагнитни компоненти и възли Прочетете още Електрически и електронни компоненти и възли Прочетете още Производство и монтаж на дисплеи, сензорни екрани и монитори Прочетете още Производство и монтаж на автоматизирани и роботизирани системи Прочетете още Вградени системи и индустриални компютри и панелни компютри Прочетете още Индустриално тестово оборудване Ние предлагаме: • Персонализиран кабелен монтаж, PCB, дисплей и сензорен екран (като iPod), захранващи и енергийни компоненти, безжични, микровълнови, компоненти за управление на движението, осветителни продукти, електромагнитни и електронни компоненти. Ние създаваме продукти според вашите конкретни спецификации и изисквания. Нашите продукти се произвеждат в сертифицирани среди по ISO9001:2000, QS9000, ISO14001, TS16949 и притежават маркировка CE, UL и отговарят на други индустриални стандарти като IEEE, ANSI. След като бъдем назначени за вашия проект, ние сме в състояние да се погрижим за цялото производство, монтаж, тестване, квалификация, доставка и митници. Ако предпочитате, можем да складираме вашите части, да сглобим персонализирани комплекти, да отпечатаме и етикетираме името и марката на вашата компания и да ги изпратим до клиентите ви. С други думи, ние можем да бъдем вашият складов и дистрибуторски център, ако предпочитате това. Тъй като нашите складове са разположени в близост до големи морски пристанища, това ни дава логистично предимство. Например, когато вашите продукти пристигнат в голямо морско пристанище на САЩ, ние можем да ги транспортираме директно до близкия склад, където можем да съхраняваме, сглобяваме, правим комплекти, преетикетираме, отпечатваме, опаковаме според вашия избор и изпращаме до клиентите ви, ако желаете . Ние не само доставяме продукти. Нашата компания работи по договори по поръчка, при които идваме на вашия сайт, оценяваме вашия проект на място и разработваме предложение за проект, специално проектирано за вас. След това изпращаме наш опитен екип за изпълнение на проекта. Примерите за работа по договор включват инсталиране на слънчеви модули, вятърни генератори, LED осветление и енергоспестяващи системи за автоматизация във вашето промишлено съоръжение, за да намалите сметките си за енергия, инсталиране на фиброоптична система за откриване за откриване на повреди по вашите тръбопроводи или за откриване на потенциални нарушители, проникващи във вашия помещения. Поемаме малки проекти, както и големи проекти в индустриален мащаб. Като първа стъпка можем да ви свържем чрез телефон, телеконференция или MSN месинджър с членовете на нашия експертен екип, така че да можете да общувате директно с експерт, да задавате въпроси и да обсъждате вашия проект. При нужда ще дойдем да ви посетим. Ако имате нужда от някой от тези продукти или имате въпроси, моля, обадете ни се на +1-505-550-6501 или ни изпратете имейл на sales@agstech.net Ако се интересувате най-вече от нашите инженерни и научноизследователски и развойни възможности, вместо от производствени възможности, тогава ви каним да посетите нашия инженерен уебсайт http://www.ags-engineering.com CLICK Product Finder-Locator Service ПРЕДИШНА СТРАНИЦА
- Thickness Gauges, Ultrasonic Flaw Detector, Nondestructive Measurement
Thickness Gauges - Ultrasonic - Flaw Detector - Nondestructive Measurement of Thickness & Flaws from AGS-TECH Inc. - USA Дебеломери и детектори за измерване на дефекти AGS-TECH Inc. offers ULTRASONIC FLAW DETECTORS and a number of different THICKNESS GAUGES with different principles of operation. One of the popular types are the ULTRASONIC THICKNESS GAUGES ( also referred to as UTM ) which are measuring инструменти за НЕРАЗРУШИТЕЛЕН ТЕСТ & изследване на дебелината на материала с помощта на ултразвукови вълни. Another type is HALL EFFECT THICKNESS GAUGE ( also referred to as MAGNETIC BOTTLE THICKNESS GAUGE ). Уредите за измерване на дебелина с ефект на Хол предлагат предимството, че точността не се влияе от формата на пробите. A third common type of NON-DESTRUCTIVE TESTING ( NDT ) instruments are_cc781905-5cde-3194- bb3b-136bad5cf58d_EDDY ДЕБЕЛОТОКОВЕ. Уредите за измерване на дебелината на вихрови токове са електронни инструменти, които измерват промените в импеданса на намотка, предизвикваща вихрови токове, причинени от промени в дебелината на покритието. Те могат да се използват само ако електропроводимостта на покритието се различава значително от тази на основата. Все пак класически тип инструменти са ДИГИТАЛНИ ДЕБЕЛОМЕРИ. Те се предлагат в различни форми и възможности. Повечето от тях са сравнително евтини инструменти, които разчитат на контакт с две противоположни повърхности на образеца за измерване на дебелината. Някои от марковите дебеломери и ултразвукови дефектоскопи, които продаваме, са SADT, SINOAGE and_cc781905-5cde-3194-bb3b-136bad_MITE За да изтеглите брошурата за нашите ултразвукови дебеломери SADT, моля, КЛИКНЕТЕ ТУК. За да изтеглите каталог за нашата марка SADT метрологично и тестово оборудване, моля, КЛИКНЕТЕ ТУК. За да изтеглите брошурата за нашите многомодови ултразвукови дебеломери MITECH MT180 и MT190, моля, НАТИСНЕТЕ ТУК За да изтеглите брошурата за нашия ултразвуков дефектоскоп MITECH МОДЕЛ MFD620C, моля, щракнете тук. За да изтеглите таблицата за сравнение на продуктите за нашите дефектоскопи MITECH, моля, щракнете тук. УЛТРАЗВУКОВИ ДЕБЕЛОМЕРИ: Това, което прави ултразвуковите измервания толкова привлекателни, е способността им да измерват дебелината без необходимост от достъп до двете страни на тестовия образец. В търговската мрежа се предлагат различни версии на тези инструменти, като ултразвуков уред за измерване на дебелината на покритието, уред за дебелина на боята и цифров уред за измерване на дебелината. Могат да бъдат тествани различни материали, включително метали, керамика, стъкла и пластмаси. Инструментът измерва времето, необходимо на звуковите вълни да преминат от преобразувателя през материала до задния край на частта и след това времето, необходимо на отражението, за да се върне обратно до преобразувателя. От измереното време инструментът изчислява дебелината въз основа на скоростта на звука през образеца. Преобразувателните сензори обикновено са пиезоелектрични или EMAT. Налични са дебеломери както с предварително зададена честота, така и с някои с регулируеми честоти. Регулируемите позволяват проверка на по-широк спектър от материали. Типичните честоти на ултразвуковия измервател на дебелината са 5 mHz. Нашите дебеломери предлагат възможност за запазване на данни и извеждането им към устройства за регистриране на данни. Ултразвуковите дебеломери са безразрушителни тестери, те не изискват достъп до двете страни на тестовите образци, някои модели могат да се използват върху покрития и облицовки, могат да се получат точности под 0,1 mm, лесни за използване на полето и няма нужда за лабораторна среда. Някои недостатъци са изискването за калибриране за всеки материал, необходимостта от добър контакт с материала, което понякога изисква използването на специални свързващи гелове или вазелин на контактния интерфейс устройство/проба. Популярни области на приложение на преносими ултразвукови дебеломери са корабостроенето, строителната индустрия, тръбопроводите и производството на тръби, производството на контейнери и резервоари....и т.н. Техниците могат лесно да премахнат мръсотията и корозията от повърхностите и след това да нанесат свързващия гел и да притиснат сондата към метала, за да измерят дебелината. Уредите с ефект на Хол измерват само общата дебелина на стените, докато ултразвуковите уреди са в състояние да измерват отделни слоеве в многослойни пластмасови продукти. In HALL EFFECT THICKNESS GAUGES точността на измерване няма да бъде повлияна от формата на пробите. Тези устройства се основават на теорията за ефекта на Хол. За тестване стоманената топка се поставя от едната страна на пробата, а сондата от другата страна. Сензорът с ефект на Хол на сондата измерва разстоянието от върха на сондата до стоманената топка. Калкулаторът ще покаже действителните показания на дебелината. Както можете да си представите, този метод за неразрушителен тест предлага бързо измерване на дебелината на петна в зона, където се изисква точно измерване на ъгли, малки радиуси или сложни форми. При неразрушително изпитване измервателните уреди с ефект на Хол използват сонда, съдържаща силен постоянен магнит и полупроводник на Хол, свързан към верига за измерване на напрежение. Ако феромагнитна цел като стоманена топка с известна маса се постави в магнитното поле, тя огъва полето и това променя напрежението в сензора на Хол. Тъй като целта се отдалечава от магнита, магнитното поле и следователно напрежението на Хол се променят по предвидим начин. Изобразявайки тези промени, инструментът може да генерира калибровъчна крива, която сравнява измереното напрежение на Хол с разстоянието на целта от сондата. Информацията, въведена в инструмента по време на калибрирането, позволява на измервателния уред да създаде справочна таблица, на практика начертавайки крива на промените на напрежението. По време на измерванията уредът сверява измерените стойности спрямо справочната таблица и показва дебелината на цифров екран. Потребителите трябва само да въведат известни стойности по време на калибриране и да оставят измервателния уред да сравни и изчисли. Процесът на калибриране е автоматичен. Усъвършенстваните версии на оборудването предлагат показване на показанията на дебелината в реално време и автоматично улавят минималната дебелина. Дебеломери с ефект на Хол се използват широко в индустрията за пластмасови опаковки с възможност за бързо измерване, до 16 пъти в секунда и точност от около ±1%. Те могат да съхраняват хиляди показания за дебелина в паметта. Възможни са разделителни способности от 0,01 mm или 0,001 mm (еквивалентни на 0,001” или 0,0001”). ИЗМЕРИТЕЛИ ЗА ДЕБЕЛИНА ОТ ТИП ВЪРХОВ ТОК са електронни инструменти, които измерват вариациите в импеданса на намотка, предизвикваща вихров ток, причинени от вариации в дебелината на покритието. Те могат да се използват само ако електропроводимостта на покритието се различава значително от тази на основата. Техниките на вихрови токове могат да се използват за редица измервания на размерите. Способността да се извършват бързи измервания без необходимост от съединител или, в някои случаи дори без необходимост от повърхностен контакт, прави техниките на вихрови токове много полезни. Видовете измервания, които могат да бъдат направени, включват дебелина на тънък метален лист и фолио и на метални покрития върху метална и неметална подложка, размери на напречното сечение на цилиндрични тръби и пръти, дебелина на неметални покрития върху метални подложки. Едно приложение, при което техниката на вихрови токове обикновено се използва за измерване на дебелината на материала, е при откриването и характеризирането на корозионно увреждане и изтъняване на обшивките на самолети. Тестването с вихрови токове може да се използва за извършване на проверки на място или скенери могат да се използват за проверка на малки площи. Инспекцията с вихров ток има предимство пред ултразвука в това приложение, тъй като не е необходимо механично свързване, за да вкара енергията в структурата. Следователно, в многослойни зони на конструкцията, като снаждания в скута, вихровият ток често може да определи дали има корозионно изтъняване в заровените слоеве. Инспекцията с вихрови токове има предимство пред радиографията за това приложение, тъй като за извършване на инспекцията е необходим само едностранен достъп. За да получите парче радиографски филм върху задната страна на обшивката на самолета, може да се наложи демонтиране на вътрешно обзавеждане, панели и изолация, което може да бъде много скъпо и вредно. Техниките на вихрови токове се използват и за измерване на дебелината на горещи листове, ленти и фолио във валцови мелници. Важно приложение на измерването на дебелината на стената на тръбата е откриването и оценката на външна и вътрешна корозия. Вътрешни сонди трябва да се използват, когато външните повърхности не са достъпни, като например при изпитване на тръби, които са вкопани или поддържани от скоби. Постигнат е успех в измерването на вариациите в дебелината на феромагнитни метални тръби с техниката на дистанционно поле. Размерите на цилиндричните тръби и пръти могат да се измерват или с намотки с външен диаметър, или с намотки с вътрешен аксиален диаметър, което от двете е подходящо. Връзката между промяната в импеданса и промяната в диаметъра е доста постоянна, с изключение на много ниските честоти. Техниките на вихрови токове могат да определят промените в дебелината до около три процента от дебелината на кожата. Също така е възможно да се измерват дебелините на тънки слоеве метал върху метални субстрати, при условие че двата метала имат силно различна електрическа проводимост. Честотата трябва да бъде избрана така, че да има пълно проникване на вихров ток в слоя, но не и в самия субстрат. Методът се използва успешно и за измерване на дебелината на много тънки защитни покрития от феромагнитни метали (като хром и никел) върху неферомагнитни метални основи. От друга страна, дебелината на неметалните покрития върху метални субстрати може да се определи просто от ефекта на повдигане върху импеданса. Този метод се използва за измерване на дебелината на боя и пластмасови покрития. Покритието служи като разделител между сондата и проводящата повърхност. Тъй като разстоянието между сондата и проводящия основен метал се увеличава, силата на полето на вихровия ток намалява, тъй като по-малко от магнитното поле на сондата може да взаимодейства с основния метал. Дебелини между 0,5 и 25 µm могат да бъдат измерени с точност между 10% за по-ниски стойности и 4% за по-високи стойности. ЦИФРОВИ ДЕБЕЛОМЕРИ : Те разчитат на контакт с две противоположни повърхности на образеца за измерване на дебелината. Повечето цифрови дебеломери могат да превключват от метрично отчитане към отчитане в инчове. Те са ограничени в своите възможности, тъй като е необходим правилен контакт, за да се направят точни измервания. Те също така са по-склонни към грешка на оператора поради вариациите на разликите в обработката на образеца от потребител до потребител, както и големите разлики в свойствата на образеца като твърдост, еластичност… и т.н. Те обаче може да са достатъчни за някои приложения и цените им са по-ниски в сравнение с другите видове измерватели на дебелината. Марката MITUTOYO е добре позната със своите цифрови дебеломери. Our PORTABLE ULTRASONIC THICKNESS GAUGES from SADT are: Моделите SADT SA40 / SA40EZ / SA50 : SA40 / SA40EZ са миниатюрни ултразвукови дебеломери, които могат да измерват дебелината на стената и скоростта. Тези интелигентни измервателни уреди са проектирани да измерват дебелината както на метални, така и на неметални материали като стомана, алуминий, мед, месинг, сребро и т.н. Тези универсални модели могат лесно да бъдат оборудвани със сонди за ниска и висока честота, сонда за висока температура за взискателно приложение среди. Ултразвуковият дебеломер SA50 се управлява от микропроцесор и се основава на принципа на ултразвуково измерване. Той е способен да измерва дебелината и акустичната скорост на ултразвука, предаван през различни материали. SA50 е предназначен за измерване на дебелината на стандартни метални материали и метални материали, покрити с покритие. Изтеглете нашата продуктова брошура SADT от връзката по-горе, за да видите разликите в обхвата на измерване, разделителната способност, точността, капацитета на паметта и т.н. между тези три модела. SADT модели ST5900 / ST5900+ : Тези инструменти са миниатюрни ултразвукови дебеломери, които могат да измерват дебелини на стени. ST5900 има фиксирана скорост от 5900 m/s, която се използва само за измерване на дебелината на стената на стомана. От друга страна, моделът ST5900+ е в състояние да регулира скоростта между 1000~9990m/s, така че да може да измерва дебелината както на метални, така и на неметални материали като стомана, алуминий, месинг, сребро,…. и т.н. За подробности относно различни сонди, моля, изтеглете продуктова брошура от връзката по-горе. Our PORTABLE ULTRASONIC THICKNESS GAUGES from MITECH are: Многорежимен ултразвуков дебеломери MITECH MT180 / MT190 : Това са многомодови ултразвукови дебеломери, базирани на същите принципи на работа като SONAR. Инструментът може да измерва дебелината на различни материали с точност до 0,1/0,01 милиметра. Функцията за много режими на измервателния уред позволява на потребителя да превключва между импулсно-ехо режим (откриване на дефекти и вдлъбнатини) и ехо-ехо режим (филтриране на боята или дебелината на покритието). Мултирежим: режим Pulse-Echo и режим Echo-Echo. Моделите MITECH MT180 / MT190 са в състояние да извършват измервания на широка гама от материали, включително метали, пластмаса, керамика, композити, епоксиди, стъкло и други материали, провеждащи ултразвукови вълни. Предлагат се различни модели трансдюсери за специални приложения, като едрозърнести материали и среда с висока температура. Инструментите предлагат функция Probe-Zero, функция за калибриране на скоростта на звука, функция за двуточково калибриране, режим на една точка и режим на сканиране. Моделите MITECH MT180 / MT190 са способни на седем измервания в секунда в режим на една точка и шестнадесет в секунда в режим на сканиране. Те имат индикатор за състояние на свързване, опция за избор на метрична/имперска единица, индикатор за информация за батерията за оставащия капацитет на батерията, функция за автоматично заспиване и автоматично изключване за запазване на живота на батерията, допълнителен софтуер за обработка на данните от паметта на компютъра. За подробности относно различните сонди и преобразуватели, моля, изтеглете продуктовата брошура от връзката по-горе. УЛТРАЗВУКОВИ ДЕФЕКТОРИ : Съвременните версии са малки, преносими, базирани на микропроцесори инструменти, подходящи за използване в заводи и полета. Високочестотните звукови вълни се използват за откриване на скрити пукнатини, порьозност, кухини, дефекти и прекъсвания в твърди тела като керамика, пластмаса, метал, сплави… и др. Тези ултразвукови вълни се отразяват от или предават през такива дефекти в материала или продукта по предсказуеми начини и произвеждат отличителни модели на ехо. Ултразвуковите дефектоскопи са инструменти за безразрушителен тест (NDT тестване). Те са популярни при изпитване на заварени конструкции, конструкционни материали, производствени материали. По-голямата част от ултразвуковите дефектоскопи работят на честоти между 500 000 и 10 000 000 цикъла в секунда (500 KHz до 10 MHz), далеч над звуковите честоти, които ушите ни могат да открият. При ултразвуковото откриване на дефекти обикновено долната граница на откриване на малък дефект е половината дължина на вълната и всичко по-малко от това ще бъде невидимо за тестовия инструмент. Изразът, обобщаващ звукова вълна, е: Дължина на вълната = Скорост на звука / Честота Звуковите вълни в твърди тела показват различни начини на разпространение: - Надлъжната или компресионна вълна се характеризира с движение на частиците в същата посока като разпространението на вълната. С други думи, вълните се движат в резултат на компресии и разреждания в средата. - Срязваща/напречна вълна показва движение на частиците перпендикулярно на посоката на разпространение на вълната. - Повърхностната или Релеевата вълна има елиптично движение на частици и се движи по повърхността на материала, прониквайки на дълбочина приблизително една дължина на вълната. Сеизмичните вълни при земетресения също са вълни на Рейли. - Плочата или вълната на Lamb е сложен режим на вибрация, наблюдаван в тънки плочи, където дебелината на материала е по-малка от една дължина на вълната и вълната запълва цялото напречно сечение на средата. Звуковите вълни могат да се преобразуват от една форма в друга. Когато звукът преминава през материал и срещне граница на друг материал, част от енергията ще се отрази обратно, а част ще се предаде през него. Количеството отразена енергия или коефициентът на отражение е свързано с относителния акустичен импеданс на двата материала. Акустичният импеданс от своя страна е свойство на материала, дефинирано като плътност, умножена по скоростта на звука в даден материал. За два материала коефициентът на отражение като процент от инцидентното енергийно налягане е: R = (Z2 - Z1) / (Z2 + Z1) R = коефициент на отражение (напр. процент на отразената енергия) Z1 = акустичен импеданс на първия материал Z2 = акустичен импеданс на втория материал При ултразвуковото откриване на дефекти коефициентът на отражение се доближава до 100% за границите метал/въздух, което може да се тълкува като цялата звукова енергия, отразена от пукнатина или прекъсване по пътя на вълната. Това прави възможно ултразвуковото откриване на дефекти. Що се отнася до отражението и пречупването на звуковите вълни, ситуацията е подобна на тази при светлинните вълни. Звуковата енергия при ултразвукови честоти е силно насочена и звуковите лъчи, използвани за откриване на дефекти, са добре дефинирани. Когато звукът се отразява от граница, ъгълът на отражение е равен на ъгъла на падане. Звуков лъч, който удря повърхност при перпендикулярен наклон, ще се отрази право обратно. Звуковите вълни, които се предават от един материал на друг, се огъват в съответствие със закона за пречупването на Снел. Звуковите вълни, удрящи граница под ъгъл, ще бъдат огънати според формулата: Sin Ø1/Sin Ø2 = V1/V2 Ø1 = Ъгъл на падане в първия материал Ø2= Пречупен ъгъл във втори материал V1 = Скорост на звука в първия материал V2 = Скорост на звука във втория материал Преобразувателите на ултразвуковите дефектоскопи имат активен елемент, изработен от пиезоелектричен материал. Когато този елемент вибрира от входяща звукова вълна, той генерира електрически импулс. Когато се възбуди от електрически импулс с високо напрежение, той вибрира в определен спектър от честоти и генерира звукови вълни. Тъй като звуковата енергия при ултразвукови честоти не преминава ефективно през газове, се използва тънък слой свързващ гел между преобразувателя и тестовото парче. Ултразвуковите преобразуватели, използвани в приложения за откриване на дефекти, са: - Контактни преобразуватели: Те се използват в директен контакт с тестовото парче. Те изпращат звукова енергия перпендикулярно на повърхността и обикновено се използват за локализиране на кухини, порьозност, пукнатини, разслоения, успоредни на външната повърхност на част, както и за измерване на дебелината. - Преобразуватели на ъглови лъчи: Те се използват заедно с пластмасови или епоксидни клинове (ъглови греди) за въвеждане на срязващи вълни или надлъжни вълни в тестово парче под определен ъгъл по отношение на повърхността. Те са популярни при проверка на заваръчни шевове. - Преобразуватели на линия за забавяне: Те включват къс пластмасов вълновод или линия за забавяне между активния елемент и тестовото парче. Те се използват за подобряване на разделителната способност близо до повърхността. Те са подходящи за високотемпературно изпитване, при което линията на забавяне предпазва активния елемент от термично увреждане. - Потопяеми преобразуватели: Те са проектирани да свързват звукова енергия в изпитвания образец през воден стълб или водна баня. Те се използват в приложения за автоматизирано сканиране, а също и в ситуации, при които е необходим рязко фокусиран лъч за подобрено разрешаване на дефекти. - Преобразуватели с двоен елемент: Те използват отделни предавателни и приемни елементи в един комплект. Те често се използват в приложения, включващи грапави повърхности, едрозърнести материали, откриване на питинг или порьозност. Ултразвуковите детектори за дефекти генерират и показват ултразвукова форма на вълната, интерпретирана с помощта на софтуер за анализ, за да локализират дефекти в материалите и готовите продукти. Съвременните устройства включват излъчвател и приемник на ултразвукови импулси, хардуер и софтуер за улавяне и анализ на сигнала, дисплей с форма на вълната и модул за регистриране на данни. За стабилност и прецизност се използва цифрова обработка на сигнала. Секцията за излъчвател и приемник на импулси осигурява възбуждащ импулс за задвижване на трансдюсера и усилване и филтриране за връщащото се ехо. Амплитудата, формата и затихването на импулса могат да се контролират, за да се оптимизира работата на трансдюсера, а усилването и честотната лента на приемника могат да се регулират, за да се оптимизират съотношенията сигнал/шум. Усъвършенстваните версии на дефектоскопите улавят цифрово форма на вълната и след това извършват различни измервания и анализи върху нея. Часовник или таймер се използват за синхронизиране на импулсите на преобразувателя и осигуряване на калибриране на разстоянието. Обработката на сигнала генерира дисплей с формата на вълната, който показва амплитудата на сигнала спрямо времето на калибрирана скала, алгоритмите за цифрова обработка включват корекция на разстояние и амплитуда и тригонометрични изчисления за ъглови звукови пътища. Алармените портове наблюдават нивата на сигнала в избрани точки от вълновата поредица и сигнализират ехо от дефекти. Екраните с многоцветни дисплеи се калибрират в единици дълбочина или разстояние. Вътрешните регистратори на данни записват пълната форма на вълната и информация за настройка, свързана с всеки тест, информация като амплитуда на ехото, показания за дълбочина или разстояние, наличие или отсъствие на алармени условия. Ултразвуковото откриване на дефекти е основно сравнителна техника. Използвайки подходящи референтни стандарти заедно с познания за разпространението на звуковите вълни и общоприетите тестови процедури, обучен оператор идентифицира специфични ехо модели, съответстващи на ехото от добри части и от представителни дефекти. Ехото от тестван материал или продукт може след това да се сравни с моделите от тези стандарти за калибриране, за да се определи неговото състояние. Ехото, което предшества ехото в задната стена, предполага наличието на ламинарна пукнатина или празнина. Анализът на отразеното ехо разкрива дълбочината, размера и формата на структурата. В някои случаи тестването се извършва в режим на предаване. В такъв случай звуковата енергия се движи между два преобразувателя, разположени от противоположните страни на тестовия образец. Ако в звуковия път има голям дефект, лъчът ще бъде блокиран и звукът няма да достигне до приемника. Пукнатини и дефекти, перпендикулярни на повърхността на изпитвания образец или наклонени по отношение на тази повърхност, обикновено са невидими при техники за изпитване с прав лъч поради тяхната ориентация по отношение на звуковия лъч. В такива случаи, които са често срещани в заварени конструкции, се използват техники на ъглов лъч, като се използват или общи преобразувателни модули на ъглов лъч, или потопяеми преобразуватели, подравнени така, че да насочват звуковата енергия към изпитваната част под избран ъгъл. Тъй като ъгълът на падаща надлъжна вълна по отношение на повърхността се увеличава, нарастваща част от звуковата енергия се преобразува в срязваща вълна във втория материал. Ако ъгълът е достатъчно висок, цялата енергия във втория материал ще бъде под формата на срязващи вълни. Преносът на енергия е по-ефективен при ъгли на падане, които генерират срязващи вълни в стомана и подобни материали. В допълнение, разделителната способност на минималния размер на дефекта се подобрява чрез използването на срязващи вълни, тъй като при дадена честота дължината на вълната на срязваща вълна е приблизително 60% от дължината на вълната на сравнима надлъжна вълна. Ъгловият звуков лъч е силно чувствителен към пукнатини, перпендикулярни на далечната повърхност на тестовото парче, и след като отскочи от далечната страна, той е силно чувствителен към пукнатини, перпендикулярни на повърхността на свързване. Нашите ултразвукови дефектоскопи от SADT / SINOAGE са: Ултразвуков детектор за дефекти SADT SUD10 и SUD20 : SUD10 е преносим, базиран на микропроцесор инструмент, използван широко в производствените предприятия и на полето. SADT SUD10 е интелигентно цифрово устройство с нова EL дисплейна технология. SUD10 предлага почти всички функции на професионален инструмент за безразрушителен тест. Моделът SADT SUD20 има същите функции като SUD10, но е по-малък и по-лек. Ето някои характеристики на тези устройства: -Високоскоростно заснемане и много нисък шум -DAC, AVG, B сканиране -Твърд метален корпус (IP65) - Автоматизирано видео на процеса на тестване и игра - Висококонтрастно гледане на формата на вълната при ярка, пряка слънчева светлина, както и при пълна тъмнина. Лесно четене от всички ъгли. -Мощен компютърен софтуер и данни могат да бъдат експортирани в Excel -Автоматизирано калибриране на нула, отместване и/или скорост на датчика - Автоматично усилване, пиково задържане и пикови функции за памет - Автоматизирано показване на точното местоположение на дефекта (дълбочина d, ниво p, разстояние s, амплитуда, sz dB, Ø) -Автоматичен превключвател за три габарита (дълбочина d, ниво p, разстояние s) -Десет независими функции за настройка, всеки критерий може да бъде въведен свободно, може да работи на полето без тестов блок -Голяма памет от 300 A графика и 30 000 стойности на дебелината -A&B сканиране -RS232/USB порт, комуникацията с компютър е лесна -Вграденият софтуер може да се актуализира онлайн -Li батерия, непрекъсната работа до 8 часа -Функция за замразяване на дисплея -Автоматична степен на ехо -Ъгли и K-стойност -Функция за заключване и отключване на системните параметри -Пасивност и скрийнсейвъри - Електронен часовник календар - Настройка на две врати и алармена индикация За подробности изтеглете нашата брошура SADT / SINOAGE от връзката по-горе. Някои от нашите ултразвукови детектори от MITECH са: Преносим ултразвуков дефектоскоп MFD620C с цветен TFT LCD дисплей с висока разделителна способност. Цветът на фона и цветът на вълната могат да се избират според околната среда. LCD яркостта може да се настрои ръчно. Продължете да работите повече от 8 часа с високо производителен литиево-йонен батериен модул (с опция за литиево-йонна батерия с голям капацитет), лесно се разглобява и акумулаторният модул може да се зарежда независимо извън устройство. Той е лек и преносим, лесно се взема с една ръка; лесна работа; превъзхождащ надеждността гарантира дълъг живот. Обхват: 0~6000 mm (при скорост на стоманата); диапазон, избираем на фиксирани стъпки или непрекъснато променлив. Пулсатор: Пиково възбуждане с нисък, среден и висок избор на импулсна енергия. Честота на повторение на импулса: ръчно регулируема от 10 до 1000 Hz. Ширина на импулса: Регулируема в определен диапазон, за да съответства на различни сонди. Демпфиране: 200, 300, 400, 500, 600 по избор, за да отговарят на различна резолюция и нужди от чувствителност. Режим на работа на сондата: Единичен елемент, двоен елемент и чрез предаване; Приемник: Вземане на проби в реално време при висока скорост от 160MHz, достатъчно за запис на информация за дефекта. Коригиране: Положителна полувълна, отрицателна полувълна, пълна вълна и RF: DB стъпка: 0dB, 0.1 dB, 2dB, 6dB стойност на стъпка, както и режим на автоматично усилване Аларма: Аларма със звук и светлина Памет: Общо 1000 конфигурационни канала, всички работни параметри на инструмента плюс DAC/AVG кривата може да се съхранява; съхранените конфигурационни данни могат лесно да бъдат прегледани и извикани бърза, повторяема настройка на инструмента. Общо 1000 набора от данни съхраняват всички работещи инструменти параметри плюс A-сканиране. Всички конфигурационни канали и набори от данни могат да бъдат прехвърлени към Компютър през USB порт. Функции: Задържане на пик: Автоматично търси пиковата вълна вътре в гейта и я задържа на дисплея. Изчисляване на еквивалентен диаметър: намерете пиковото ехо и изчислете неговия еквивалент диаметър. Непрекъснат запис: Записвайте непрекъснато дисплея и го запазвайте в паметта вътре в инструмент. Локализация на дефекта: Локализирайте позицията на дефекта, включително разстоянието, дълбочината и неговата разстояние на равнинна проекция. Оразмеряване на дефекта: Изчислете размера на дефекта Оценка на дефекта: Оценете дефекта чрез ехо обвивка. DAC: Корекция на амплитудата на разстоянието AVG: Функция за крива на размера на усилването на разстоянието Измерване на пукнатини: Измерете и изчислете дълбочината на пукнатините B-Scan: Показване на напречното сечение на тестовия блок. Часовник в реално време: Часовник в реално време за следене на времето. Комуникация: USB2.0 високоскоростен комуникационен порт За подробности и друго подобно оборудване, моля, посетете нашия уебсайт за оборудване: http://www.sourceindustrialsupply.com CLICK Product Finder-Locator Service ПРЕДИШНА СТРАНИЦА
- Passive Optical Components, Splitter & Combiner, DWDM, Optical Switch
Passive Optical Components - Splitter - Combiner - DWDM - Optical Switch - MUX / DEMUX - Circulator - Waveguide - EDFA Производство и монтаж на пасивни оптични компоненти Ние доставяме ПАСИВЕН ОПТИЧЕН КОМПОНЕНТЕН МОНТАЖ, включително: • ФИБРЕНИ ОПТИЧНИ КОМУНИКАЦИОННИ УСТРОЙСТВА: Фиброоптични кранове, сплитери-комбинатори, фиксирани и променливи оптични атенюатори, оптичен превключвател, DWDM, MUX/DEMUX, EDFA, Раманови усилватели и други усилватели, циркулационни помпи, уравняващи усилватели, персонализирани модули за оптични влакна за телекомуникационни системи, оптични вълноводни устройства, корпуси за снаждане, CATV продукти. • ИНДУСТРИАЛЕН ОПТИЧЕН МОНТАЖ ОТ ВЛАКНА: Оптични модули за индустриални приложения (осветление, доставка на светлина или проверка на вътрешности на тръби, фиброскопи, ендоскопи...). • СВОБОДНО МЯСТО ПАСИВНИ ОПТИЧНИ КОМПОНЕНТИ и СГЛОБЯВАНЕ: Това са оптични компоненти, направени от специален клас стъкла и кристали с превъзходно предаване и отражение и други изключителни характеристики. Лещи, призми, разделители на лъчи, вълнови плочи, поляризатори, огледала, филтри ......и др. са сред тази категория. Можете да изтеглите нашите готови пасивни оптични компоненти и модули за свободно пространство от нашия каталог по-долу или да ни помолите за персонализирано проектиране и производство специално за вашето приложение. Сред пасивните оптични модули, разработени от нашите инженери, са: - Станция за тестване и рязане на поляризирани атенюатори. - Видеоендоскопи и фиброскопи за медицински приложения. Използваме специални техники и материали за свързване и закрепване за здрави, надеждни и дълготрайни сглобки. Дори при обширни циклични тестове на околната среда, като висока/ниска температура; висока влажност/ниска влажност нашите възли остават непокътнати и продължават да работят. Пасивните оптични компоненти и модули се превърнаха в стоки през последните години. Наистина няма нужда да плащате големи суми за тези компоненти. Свържете се с нас, за да се възползвате от нашите конкурентни цени за най-високото налично качество. Всички наши пасивни оптични компоненти и модули се произвеждат в заводи, сертифицирани по ISO9001 и TS16949, и отговарят на съответните международни стандарти като Telcordia за комуникационна оптика и UL, CE за индустриални оптични модули. Брошура за пасивни оптични компоненти и монтаж Брошура за оптични компоненти и монтаж на пасивно свободно пространство CLICK Product Finder-Locator Service ПРЕДИШНА СТРАНИЦА