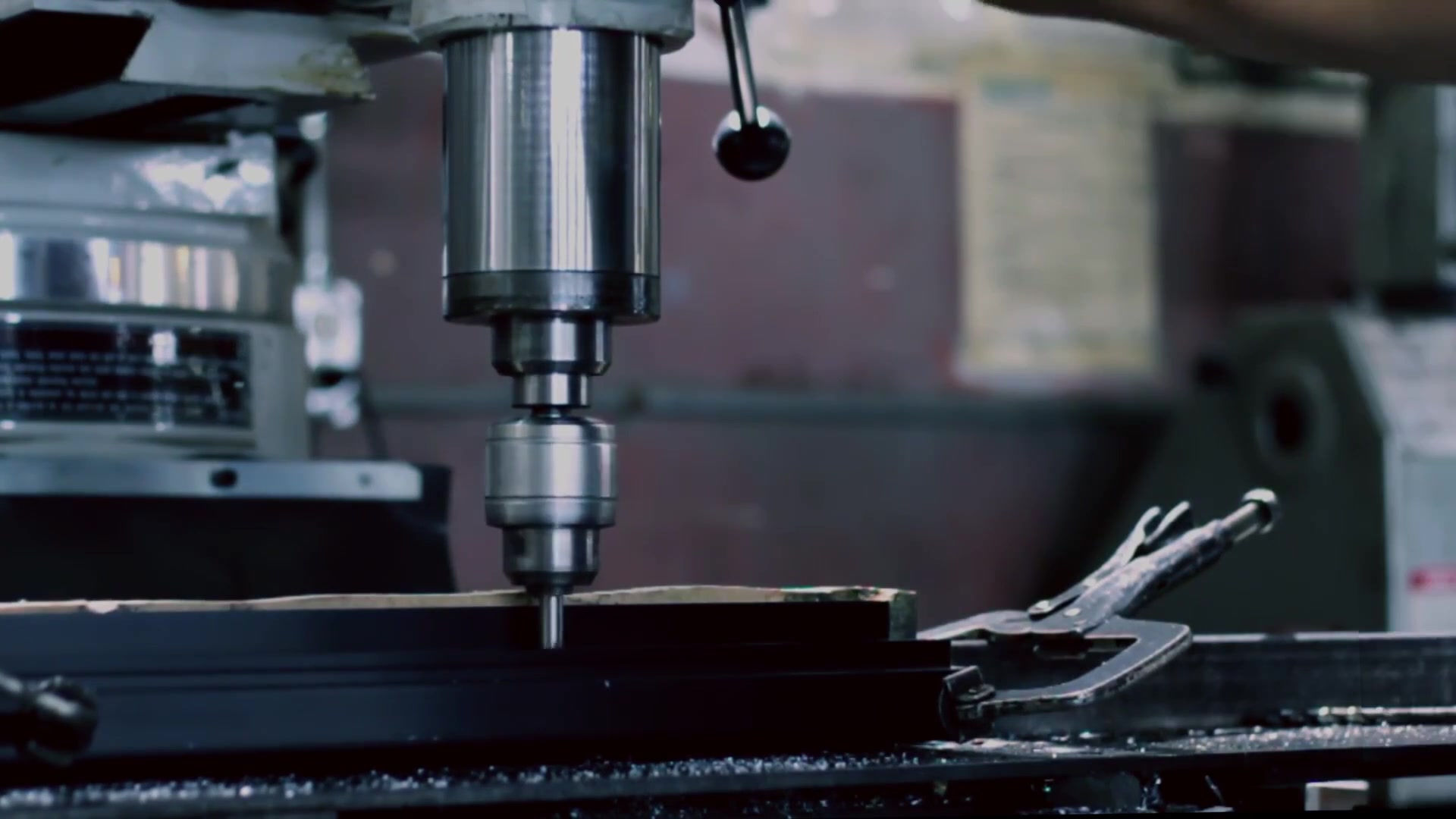
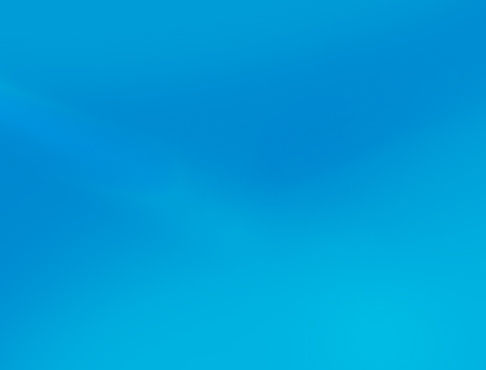
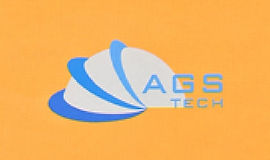
Глобален производител по поръчка, интегратор, консолидатор, аутсорсинг партньор за голямо разнообразие от продукти и услуги.
Ние сме вашият източник на едно гише за производство, производство, инженеринг, консолидация, интеграция, аутсорсинг на произведени по поръчка и готови продукти и услуги.
Изберете своя език
-
Производство по поръчка
-
Вътрешно и глобално договорно производство
-
Аутсорсинг на производство
-
Вътрешни и глобални доставки
-
Консолидация
-
Инженерна интеграция
-
Инженерни услуги
Повърхностите покриват всичко. Привлекателността и функциите, които материалните повърхности ни предоставят, са от изключително значение. Therefore SURFACE TREATMENT and SURFACE MODIFICATION are among our everyday industrial operations. Повърхностната обработка и модификация води до подобрени свойства на повърхността и може да се извърши или като крайна довършителна операция, или преди операция по нанасяне на покритие или свързване. Процесите на повърхностни обработки и модификация (наричани също като SURFACE ENGINEERING) , приспособяване на повърхностите на материалите и продуктите към:
- Контрол на триенето и износването
- Подобряване на устойчивостта на корозия
- Подобрява адхезията на последващи покрития или съединени части
- Промяна на физичните свойства на проводимостта, съпротивлението, повърхностната енергия и отражението
- Промяна на химичните свойства на повърхностите чрез въвеждане на функционални групи
- Промяна на размерите
- Променете външния вид, напр. цвят, грапавост… и т.н.
- Почистете и/или дезинфекцирайте повърхностите
Използвайки повърхностна обработка и модификация, функциите и експлоатационният живот на материалите могат да бъдат подобрени. Нашите общи методи за повърхностна обработка и модификация могат да бъдат разделени на две основни категории:
Повърхностна обработка и модификация, която обхваща повърхности:
Органични покрития: Органичните покрития нанасят бои, цименти, ламинати, разтопени прахове и лубриканти върху повърхностите на материалите.
Неорганични покрития: Нашите популярни неорганични покрития са галванопластика, автокаталитично покритие (безелектрически покрития), конверсионни покрития, термични спрейове, горещо потапяне, наваряване, топене в пещ, тънкослойни покрития като SiO2, SiN върху метал, стъкло, керамика и др. Повърхностната обработка и модификацията, включваща покрития, е обяснена подробно в съответното подменю, молящракнете тук Функционални покрития / Декоративни покрития / Тънък филм / Дебел филм
Повърхностна обработка и модификация, която променя повърхностите: Тук на тази страница ще се концентрираме върху тях. Не всички техники за повърхностна обработка и модифициране, които описваме по-долу, са в микро- или нано-мащаб, но въпреки това ще ги споменем накратко, тъй като основните цели и методи са сходни в значителна степен с тези, които са в мащаба на микропроизводството.
Закаляване: Селективно повърхностно закаляване чрез лазер, пламък, индукция и електронен лъч.
Високоенергийни лечения: Някои от нашите високоенергийни лечения включват йонна имплантация, лазерно остъкляване и синтез и обработка с електронен лъч.
Обработки с тънка дифузия: Процесите на тънка дифузия включват феритно-нитрокарбонизиране, бориране, други високотемпературни реакционни процеси като TiC, VC.
Обработки с тежка дифузия: Нашите процеси на тежка дифузия включват карбуризиране, азотиране и карбонитриране.
Специални повърхностни обработки: Специални обработки като криогенни, магнитни и звукови обработки засягат както повърхностите, така и насипните материали.
Процесите на селективно закаляване могат да се извършват чрез пламък, индукция, електронен лъч, лазерен лъч. Големите субстрати са дълбоко закалени чрез пламъчно закаляване. Индукционното закаляване от друга страна се използва за малки части. Лазерното закаляване и закаляването с електронен лъч понякога не се различават от тези при наваряване или обработка с висока енергия. Тези процеси на повърхностна обработка и модифициране са приложими само за стомани, които имат достатъчно съдържание на въглерод и сплав, за да позволят закаляване. Чугуни, въглеродни стомани, инструментални стомани и легирани стомани са подходящи за този метод на повърхностна обработка и модификация. Размерите на частите не се променят значително от тези втвърдяващи повърхностни обработки. Дълбочината на втвърдяване може да варира от 250 микрона до цялата дълбочина на сечението. Въпреки това, в случая с целия профил, профилът трябва да е тънък, по-малък от 25 mm (1 инч), или малък, тъй като процесите на втвърдяване изискват бързо охлаждане на материалите, понякога в рамките на секунда. Това е трудно постижимо при големи детайли и следователно при големи сечения могат да бъдат закалени само повърхностите. Като популярен процес на повърхностна обработка и модификация, ние закаляваме пружини, остриета за ножове и хирургически остриета сред много други продукти.
Високоенергийните процеси са сравнително нови методи за повърхностна обработка и модификация. Свойствата на повърхностите се променят без промяна на размерите. Нашите популярни процеси за повърхностна обработка с висока енергия са обработка с електронен лъч, йонна имплантация и обработка с лазерен лъч.
Обработка с електронен лъч: Обработката на повърхността с електронен лъч променя свойствата на повърхността чрез бързо нагряване и бързо охлаждане — от порядъка на 10Exp6 по Целзий/сек (10exp6 по Фаренхайт/сек) в много плитка област около 100 микрона близо до повърхността на материала. Обработката с електронен лъч може също да се използва при наваряване за получаване на повърхностни сплави.
Йонно имплантиране: Този метод за повърхностна обработка и модифициране използва електронен лъч или плазма за преобразуване на газови атоми в йони с достатъчна енергия и имплантиране/вмъкване на йоните в атомната решетка на субстрата, ускорено от магнитни бобини във вакуумна камера. Вакуумът улеснява йоните да се движат свободно в камерата. Несъответствието между имплантираните йони и повърхността на метала създава атомни дефекти, които втвърдяват повърхността.
Обработка с лазерен лъч: Подобно на обработката и модификацията на повърхността с електронен лъч, обработката с лазерен лъч променя свойствата на повърхността чрез бързо нагряване и бързо охлаждане в много плитка област близо до повърхността. Този метод на повърхностна обработка и модифициране може да се използва и при наваряване за производство на повърхностни сплави.
Ноу-хау в дозировките на имплантите и параметрите на лечение ни позволява да използваме тези високоенергийни техники за повърхностна обработка в нашите заводи за производство.
Тънки дифузионни повърхностни обработки:
Феритното нитровъглеродяване е процес на закаляване, който дифундира азот и въглерод в черни метали при подкритични температури. Температурата на обработка обикновено е 565 градуса по Целзий (1049 по Фаренхайт). При тази температура стоманите и другите железни сплави са все още във феритна фаза, което е предимство в сравнение с други процеси на закаляване, които се случват в аустенитната фаза. Процесът се използва за подобряване на:
• устойчивост на надраскване
•уморни свойства
•устойчивост на корозия
По време на процеса на втвърдяване се получава много малко изкривяване на формата благодарение на ниските температури на обработка.
Борирането е процесът, при който бор се въвежда в метал или сплав. Това е процес на повърхностно втвърдяване и модифициране, чрез който борните атоми се разпространяват в повърхността на метален компонент. В резултат на това повърхността съдържа метални бориди, като железни бориди и никелови бориди. В чисто състояние тези бориди имат изключително висока твърдост и устойчивост на износване. Борираните метални части са изключително устойчиви на износване и често ще издържат до пет пъти по-дълго от компонентите, третирани с конвенционална топлинна обработка като закаляване, карбуризиране, азотиране, нитрокарбюризиране или индукционно закаляване.
Тежка дифузионна повърхностна обработка и модификация: Ако съдържанието на въглерод е ниско (по-малко от 0,25% например), тогава можем да увеличим съдържанието на въглерод на повърхността за втвърдяване. Частта може да бъде термично обработена чрез охлаждане в течност или охладена в неподвижен въздух в зависимост от желаните свойства. Този метод ще позволи само локално втвърдяване на повърхността, но не и в сърцевината. Това понякога е много желателно, защото позволява твърда повърхност с добри свойства на износване, както при зъбните колела, но има здрава вътрешна сърцевина, която ще работи добре при натоварване от удар.
При една от техниките за повърхностна обработка и модифициране, а именно карбуризирането, ние добавяме въглерод към повърхността. Ние излагаме частта на атмосфера, богата на въглерод, при повишена температура и позволяваме дифузия да пренесе въглеродните атоми в стоманата. Дифузията ще се случи само ако стоманата има ниско съдържание на въглерод, тъй като дифузията работи на принципа на диференциала на концентрациите.
Пакетно карбуризиране: Частите се опаковат в среда с високо съдържание на въглерод като въглероден прах и се нагряват в пещ за 12 до 72 часа при 900 градуса по Целзий (1652 по Фаренхайт). При тези температури се произвежда CO газ, който е силен редуциращ агент. Реакцията на редукция протича на повърхността на стоманата, освобождавайки въглерод. След това въглеродът се разпространява в повърхността благодарение на високата температура. Въглеродът на повърхността е от 0,7% до 1,2% в зависимост от условията на процеса. Постигнатата твърдост е 60 - 65 RC. Дълбочината на карбуризираната кутия варира от около 0,1 mm до 1,5 mm. Карбуризирането на пакет изисква добър контрол на еднородността на температурата и постоянството при нагряване.
Газова карбуризация: При този вариант на повърхностна обработка газът въглероден оксид (CO) се подава към нагрята пещ и реакцията на редукция на отлагане на въглерод протича върху повърхността на частите. Този процес преодолява повечето от проблемите на карбуризирането на пакета. Едно притеснение обаче е безопасното задържане на CO газа.
Течно карбуризиране: Стоманените части се потапят в богата на въглерод вана.
Азотирането е повърхностна обработка и процес на модифициране, включващ дифузия на азот в повърхността на стоманата. Азотът образува нитриди с елементи като алуминий, хром и молибден. Частите са термично обработени и закалени преди азотиране. След това частите се почистват и нагряват в пещ в атмосфера на дисоцииран амоняк (съдържащ N и H) за 10 до 40 часа при 500-625 градуса по Целзий (932 - 1157 по Фаренхайт). Азотът дифундира в стоманата и образува нитридни сплави. Той прониква на дълбочина до 0,65 mm. Корпусът е много твърд и изкривяването е ниско. Тъй като корпусът е тънък, повърхностното шлайфане не се препоръчва и следователно обработката на повърхността с азотиране може да не е опция за повърхности с изисквания за много гладко покритие.
Процесът на повърхностна обработка и модифициране на карбонитриране е най-подходящ за нисковъглеродни легирани стомани. В процеса на карбонитриране и въглеродът, и азотът се разпространяват в повърхността. Частите се нагряват в атмосфера на въглеводород (като метан или пропан), смесен с амоняк (NH3). Казано по-просто, процесът е комбинация от карбуризиране и азотиране. Повърхностната обработка чрез карбонитриране се извършва при температури от 760 - 870 градуса по Целзий (1400 - 1598 по Фаренхайт), след което се охлажда в атмосфера на природен газ (без кислород). Процесът на карбонитриране не е подходящ за детайли с висока точност поради присъщите изкривявания. Постигнатата твърдост е подобна на карбуризирането (60 - 65 RC), но не толкова висока, колкото при азотирането (70 RC). Дълбочината на корпуса е между 0,1 и 0,75 мм. Корпусът е богат на нитриди, както и на мартензит. Необходимо е последващо темпериране, за да се намали чупливостта.
Специалните процеси за повърхностна обработка и модифициране са в ранен етап на развитие и тяхната ефективност все още не е доказана. Те са:
Криогенна обработка: Обикновено се прилага върху закалени стомани, бавно охладете субстрата до около -166 градуса по Целзий (-300 по Фаренхайт), за да увеличите плътността на материала и по този начин да увеличите устойчивостта на износване и стабилността на размерите.
Третиране с вибрации: Те имат за цел да облекчат топлинния стрес, натрупан при топлинна обработка чрез вибрации и да увеличат живота на износване.
Магнитно третиране: Те имат за цел да променят подреждането на атомите в материалите чрез магнитни полета и да се надяваме да подобрят живота на износване.
Ефективността на тези специални техники за повърхностна обработка и модификация все още предстои да бъде доказана. Също така тези три техники по-горе засягат насипния материал освен повърхностите.