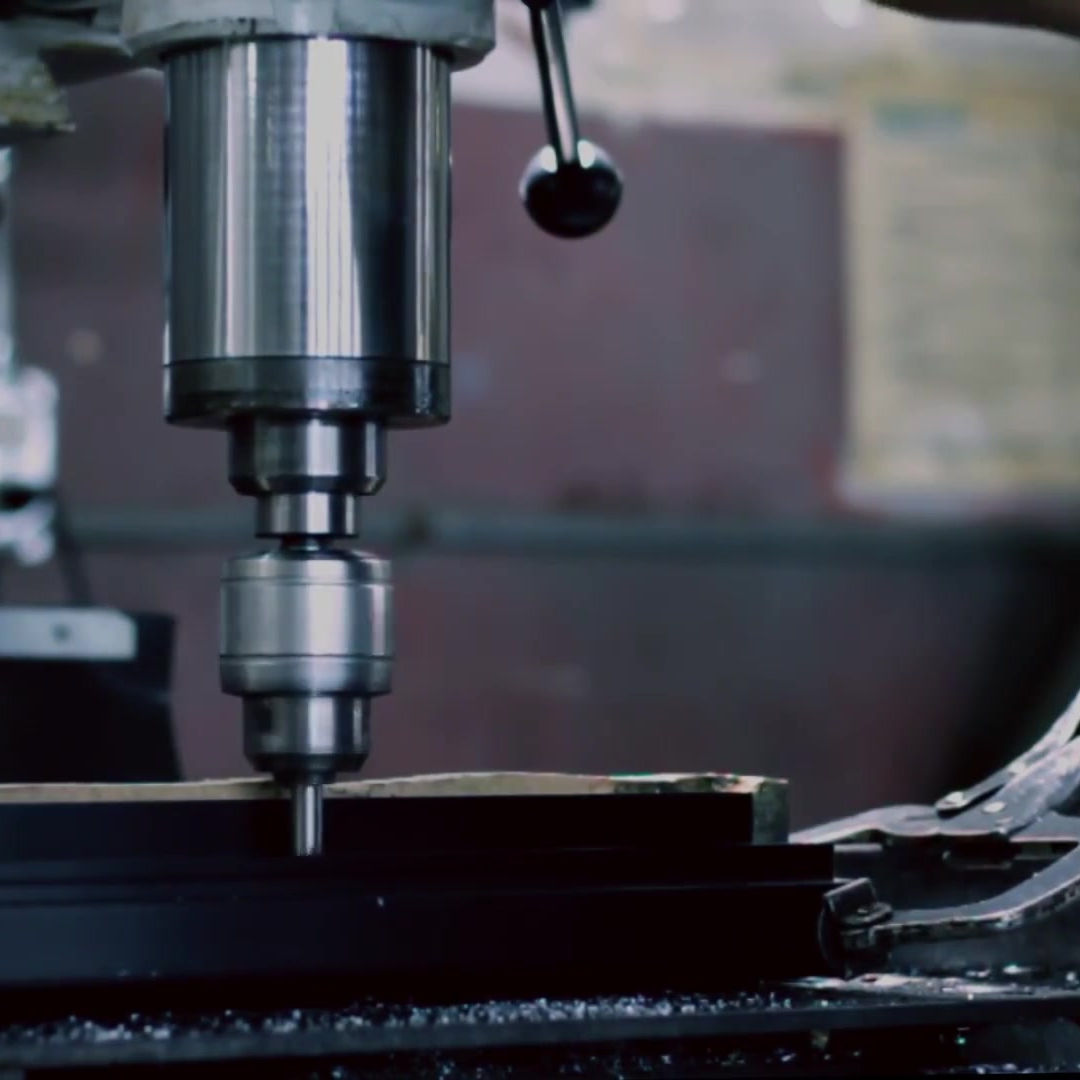
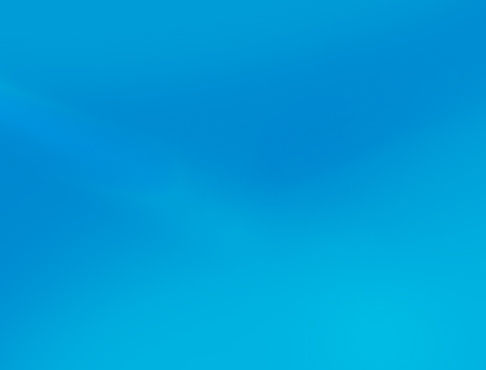
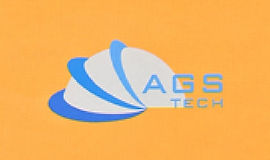
Global Custom Manufacturer, Integrator, Consolidator, Outsourcing Partner for a Wide Variety of Products & Services.
We are your one-stop source for manufacturing, fabrication, engineering, consolidation, integration, outsourcing of custom manufactured and off-shelf products & services. We also private label / white label your products with your brand name if you wish.
Choose your Language
-
Custom Manufacturing of Parts, Components, Assemblies, Finished Products, Machines and Industrial Equipment
-
Domestic & Global Contract Manufacturing
-
Manufacturing Outsourcing
-
Domestic, Global Procurement of Industrial Products
-
Private labeling / White Labeling your Products with your Brand Name
-
Product Finding & Locating Services
-
Global Design and Channel Partnership
-
Engineering Integration
-
Engineering Services
-
Global Consolidation, Warehousing, Logistics
Among the many JOINING techniques we deploy in manufacturing, special emphasis is given to WELDING, BRAZING, SOLDERING, ADHESIVE BONDING and CUSTOM MECHANICAL ASSEMBLY because these techniques are widely used in applications like manufacturing of hermetic assemblies, high-tech product manufacturing and specialized sealing. Here we will concentrate on the more specialized aspects of these joining techniques as they are related to manufacturing of advanced products and assemblies.
FUSION WELDING: We use heat to melt and coalesce materials. Heat is supplied by electricity or high-energy beams. The types of fusion welding we deploy are OXYFUEL GAS WELDING, ARC WELDING, HIGH-ENERGY-BEAM WELDING.
SOLID-STATE WELDING: We join parts without melting and fusion. Our solid-state welding methods are COLD, ULTRASONIC, RESISTANCE, FRICTION, EXPLOSION WELDING and DIFFUSION BONDING.
BRAZING & SOLDERING: They use filler metals and give us the advantage of working at lower temperatures than in welding, thus less structural damage to products. Information on our brazing facility producing ceramic to metal fittings, hermetic sealing, vacuum feedthroughs, high and ultrahigh vacuum and fluid control components can be found here: Brazing Factory Brochure
Brazing Machines (We private label these with your brand name and logo if you wish. This way you can promote your brand name when you resell these machines to your customers)
ADHESIVE BONDING: Because of the diversity of adhesives used in industry and also diversity of applications, we have a dedicated page for this. To go to our page about adhesive bonding, please click here.
CUSTOM MECHANICAL ASSEMBLY: We use a variety of fasteners such as bolts, screws, nuts, rivets. Our fasteners are not limited to standard off-shelf fasteners. We design, develop and manufacture specialty fasteners that are made from nonstandard materials so they can meet requirements for special applications. Sometimes electrical or heat non-conductivity is desired whereas sometimes conductivity. For some special applications, a customer may want special fasteners that cannot be removed without destroying the product. There are endless ideas and applications. We have it all for you, if not off-shelf we can quickly develop it. To go to our page on mechanical assembly, please click here. Let us examine our various joining techniques in more details.
OXYFUEL GAS WELDING (OFW): We use a fuel gas mixed with oxygen to produce the welding flame. When we use acetylene as the fuel and oxygen, we call it oxyacetylene gas welding. Two chemical reactions occur in the oxyfuel gas combustion process:
C2H2 + O2 ------» 2CO + H2 + Heat
2CO + H2 + 1.5 O2--------» 2 CO2 + H2O + Heat
The first reaction dissociates the acetylene into carbon monoxide and hydrogen while producing about 33% of the total heat generated. The second process above represents further combustion of the hydrogen and carbon monoxide while producing about 67% of the total heat. Temperatures in the flame are between 1533 to 3573 Kelvin. The oxygen percentage in the gas mixture is important. If the oxygen content is more than half, the flame becomes an oxidizing agent. This is undesirable for some metals but desirable for others. An example when oxidizing flame is desirable is copper-based alloys because it forms a passivation layer over the metal. On the other hand, when the oxygen content is reduced, full combustion is not possible and the flame becomes a reducing (carburizing) flame. The temperatures in a reducing flame are lower and therefore it is suitable for processes like soldering and brazing. Other gases are also potential fuels, but they have some disadvantages over acetylene. Occasionally we supply filler metals to the weld zone in the form of filler rods or wire. Some of them are coated with flux to retard oxidation of surfaces and thus protecting the molten metal. An additional benefit the flux gives us is the removal of oxides and other substances from the weld zone. This leads to stronger bonding. A variation of the oxyfuel gas welding is the PRESSURE GAS WELDING, where the two components are heated at their interface using oxyacetylene gas torch and once the interface starts to melt, the torch is withdrawn and an axial force is applied to press the two parts together until the interface is solidified.
ARC WELDING: We use electrical energy to produce an arc between the electrode tip and parts to be welded. The power supply can be AC or DC while the electrodes are either consumable or nonconsumable. Heat transfer in arc welding can be expressed by the following equation:
H / l = e x V I / v
Here H is the heat input, l is the weld length, V and I are the voltage and current applied, v is the welding speed and e is the process efficiency. The higher the efficiency “e” the more beneficially the available energy is used to melt the material. The heat input can also be expressed as :
H = u x (Volume) = u x A x l
Here u is the specific energy for melting, A the cross section of the weld and l the weld length. From the two equations above we can obtain:
v = e x V I / u A
A variation of arc welding is the SHIELDED METAL ARC WELDING (SMAW) which constitutes about 50% of all industrial and maintenance welding processes. ELECTRIC ARC WELDING (STICK WELDING) is performed by touching the tip of a coated electrode to the workpiece and quickly withdrawing it to a distance sufficient to maintain the arc. We call this process also stick-welding because the electrodes are thin and long sticks. During the welding process, the tip of the electrode melts along with its coating and the base metal in the vicinity of the arc. A mixture of the base metal, electrode metal and substances from the electrode coating solidify in the weld area. The coating of the electrode deoxidizes and provides a shielding gas in the weld region, thus protecting it from the oxygen in the environment. Therefore the process is referred to as shielded metal arc welding. We use currents between 50 and 300 Amperes and power levels generally less than 10 kW for optimum weld performance. Also of importance is the polarity of the DC current (direction of current flow). Straight polarity where the workpiece is positive and the electrode is negative is preferred in welding of sheet metals because of its shallow penetration and also for joints with very wide gaps. When we have reverse polarity, i.e. the electrode is positive and workpiece negative we can achieve deeper weld penetrations. With AC current, since we have pulsating arcs, we can weld thick sections using large diameter electrodes and maximum currents. The SMAW welding method is suitable for workpiece thicknesses of 3 to 19 mm and even more using multiple-pass techniques. The slag formed on top of the weld needs to be removed using a wire brush, so that there is no corrosion and failure at the weld area. This of course adds to the cost of shielded metal arc welding. Nevertheless the SMAW is the most popular welding technique in industry and repair work.
SUBMERGED ARC WELDING (SAW): In this process we shield the weld arc using granular flux materials like lime, silica, calcium floride, manganese oxide….etc. The granular flux is fed into the weld zone by gravity flow through a nozzle. The flux covering the molten weld zone significantly protects from sparks, fumes, UV radiation….etc and acts as a thermal insulator, thus letting heat penetrate deep into workpiece. The unfused flux is recovered, treated and reused. A coil of bare is used as electrode and fed through a tube to the area of weld. We use currents between 300 and 2000 Amperes. The submerged arc welding (SAW) process is limited to horizontal and flat positions and circular welds if rotation of the circular structure (such as pipes) is possible during welding. Speeds can reach 5 m/min. The SAW process is suitable for thick plates and results in high-quality, tough, ductile and uniform welds. The productivity, that is the amount of weld material deposited per hour is 4 to 10 times the amount as compared to the SMAW process.
Another arc welding process, namely the GAS METAL ARC WELDING (GMAW) or alternatively referred to as METAL INERT GAS WELDING (MIG) is based on the weld area being shielded by external sources of gases like helium, argon, carbon dioxide….etc. There may be additional deoxidizers present in the electrode metal. Consumable wire is fed through a nozzle into the weld zone. Fabrication involving bot ferrous as well as nonferrous metals is carried out using gas metal arc welding (GMAW). Welding productivity is about 2 times that of the SMAW process. Automated welding equipment is being used. Metal is transferred in one of three ways in this process: “Spray Transfer” involves transfer of several hundred small metal droplets per second from electrode to the weld area. In “Globular Transfer” on the other hand, carbon dioxide rich gases are used and globules of molten metal are propelled by the electric arc. Welding currents are high and weld penetration deeper, welding speed greater than in spray transfer. Thus the globular transfer is better for welding heavier sections. Finally, in the “Short Circuiting” method, the electrode tip touches the molten weld pool, short circuiting it as metal at rates over 50 droplets/second is transferred in individual droplets. Low currents and voltages are used along with thinner wire. Powers used are about 2 kW and temperatures relatively low, making this method suitable for thin sheets less than 6mm thickness.
Another variation the FLUX-CORED ARC WELDING (FCAW) process is similar to gas metal arc welding, except that the electrode is a tube filled with flux. The advantages of using cored-flux electrodes is that they produce more stable arcs, give us the opportunity to improve properties of weld metals, less brittle and flexible nature of its flux as compared to SMAW welding, improved welding contours. Self-shielded cored electrodes contain materials that shield the weld zone against the atmosphere. We use about 20 kW power. Like the GMAW process, the FCAW process also offers the opportunity to automate processes for continuous welding, and it is economical. Different weld metal chemistries can be developed by adding various alloys to the flux core.
In ELECTROGAS WELDING (EGW) we weld the pieces placed edge to edge. It is sometimes also called BUTT WELDING. Weld metal is put into a weld cavity between two pieces to be joined. The space is enclosed by two water-cooled dams to keep the molten slag from pouring out. The dams are moved up by mechanical drives. When workpiece can be rotated, we can use the electrogas welding technique for circumferential welding of pipes too. Electrodes are fed through a conduit to keep a continuous arc. Currents can be around 400Amperes or 750 Amperes and power levels around 20 kW. Inert gases originating from either a flux-cored electrode or external source provide shielding. We use the electrogas welding (EGW) for metals such as steels, titanium….etc with thicknesses from 12mm to 75mm. The technique is a good fit for large structures.
Yet, in another technique called ELECTROSLAG WELDING (ESW) the arc is ignited between the electrode and the bottom of the workpiece and flux is added. When molten slag reaches the electrode tip, the arc is extinguished. Energy is continuously supplied through the electrical resistance of the molten slag. We can weld plates with thicknesses between 50 mm and 900 mm and even higher. Currents are around 600 Ampere while voltages are between 40 – 50 V. The welding speeds are around 12 to 36 mm/min. Applications are similar to electrogas welding.
One of our nonconsumable electrode processes, the GAS TUNGSTEN ARC WELDING (GTAW) also known as TUNGSTEN INERT GAS WELDING (TIG) involves the supply of a filler metal by a wire. For closely-fit joints sometimes we do not use the filler metal. In the TIG process we do not use flux, but use argon and helium for shielding. Tungsten has a high melting point and is not consumed in the TIG welding process, therefore constant current as well as arc gaps can be maintained. Power levels are between 8 to 20 kW and currents at either 200 Ampere (DC) or 500 Ampere (AC). For aluminum and magnesium we use AC current for its oxide cleaning function. To avoid contamination of the tungsten electrode, we avoid its contact with molten metals. Gas Tungsten Arc Welding (GTAW) is especially useful for welding thin metals. GTAW welds are of very high quality with good surface finish.
Due to the higher cost of hydrogen gas, a less frequently used technique is ATOMIC HYDROGEN WELDING (AHW), where we generate an arc between two tungsten electrodes in a shielding atmosphere of flowing hydrogen gas. The AHW is also a nonconsumable electrode welding process. The diatomic hydrogen gas H2 breaks down into its atomic form near the welding arc where temperatures are over 6273 Kelvin. While breaking down, it absorbs large amount of heat from the arc. When the hydrogen atoms strike the weld zone which is a relatively cold surface, they recombine into diatomic form and release the stored heat. Energy can be varied by changing the workpiece to arc distance.
In another nonconsumable electrode process, PLASMA ARC WELDING (PAW) we have a concentrated plasma arc directed toward the weld zone. The temperatures reach 33,273 Kelvin in PAW. A nearly equal number of electrons and ions make up the plasma gas. A low-current pilot arc initiates the plasma which is between the tungsten electrode and orifice. Operating currents are generally around 100 Amperes. A filler metal may be fed. In plasma arc welding, shielding is accomplished by an outer shielding ring and using gases such as argon and helium. In plasma arc welding, the arc may be between the electrode and workpiece or between the electrode and nozzle. This welding technique has the advantages over other methods of higher energy concentration, deeper and narrower welding capability, better arc stability, higher welding speeds up to 1 meter/min, less thermal distortion. We generally use plasma arc welding for thicknesses less than 6 mm and sometimes up to 20 mm for aluminum and titanium.
HIGH-ENERGY-BEAM WELDING: Another type of fusion welding method with electron-beam welding (EBW) and laser welding (LBW) as two variants. These techniques are of particular value for our high-tech products manufacturing work. In electron-beam welding, high speed electrons strike the workpiece and their kinetic energy is converted to heat. The narrow beam of electrons travel easily in the vacuum chamber. Generally we use high vacuum in e-beam welding. Plates as thick as 150 mm can be welded. No shielding gases, flux or filler material is needed. Elecron beam guns have 100 kW capacities. Deep and narrow welds with high aspect ratios up to 30 and small heat-affected zones are possible. Welding speeds can reach 12 m/min. In laser-beam welding we use high-power lasers as the source of heat. Laser beams as small as 10 microns with high density enable deep penetration into the workpiece. Depth-to-width ratios as much as 10 is possible with laser-beam welding. We use both pulsed as well as continuous wave lasers, with the former in applications for thin materials and the latter mostly for thick workpieces up to about 25 mm. Power levels are up to 100 kW. The laser beam welding is not well suited for optically very reflective materials. Gases may also be used in the welding process. The laser beam welding method is well fit for automation & high volume manufacturing and can offer welding speeds between 2.5 m/min and 80 m/min. One major advantage this welding technique offers is access to areas where other techniques cannot be used. Laser beams can easily travel to such difficult regions. No vacuum as in electron-beam welding is needed. Welds with good quality & strength, low shrinkage, low distortion, low porosity can be obtained with laser beam welding. Laser beams can be easily manipulated and shaped using fiber optic cables. The technique is thus well suitable for welding of precision hermetic assemblies, electronic packages…etc.
Let us look at our SOLID STATE WELDING techniques. COLD WELDING (CW) is a process where pressure instead of heat is applied using dies or rolls to the parts that are mated. In cold welding, at least one of the mating parts needs to be ductile. Best results are obtained with two similar materials. If the two metals to be joined with cold welding are dissimilar, we may get weak and brittle joints. The cold welding method is well suited for soft, ductile and small workpieces such as electrical connections, heat sensitive container edges, bimetallic strips for thermostats…etc. One variation of cold welding is roll bonding (or roll welding), where the pressure is applied through a pair of rolls. Sometimes we perform roll welding at elevated temperatures for better interfacial strength.
Another solid state welding process we use is the ULTRASONIC WELDING (USW), where the workpieces are subjected to a static normal force and oscillating shearing stresses. The oscillating shearing stresses are applied through the tip of a transducer. Ultrasonic welding deploys oscillations with frequencies from 10 to 75 kHz. In some applications such as seam welding, we use a rotating welding disk as the tip. Shearing stresses applied to the workpieces cause small plastic deformations, break up oxide layers, contaminants and lead to solid state bonding. Temperatures involved in ultrasonic welding are way below melting point temperatures for metals and no fusion takes place. We frequently use the ultrasonic welding (USW) process for nonmetallic materials like plastics. In thermoplastics, the temperatures do reach melting points however.
Another popular technique, in FRICTION WELDING (FRW) the heat is generated through friction at the interface of the workpieces to be joined. In friction welding we keep one of the workpieces stationary while the other workpiece is held in a fixture and rotated at a constant speed. The workpieces are then brought into contact under an axial force. The surface speed of rotation in friction welding may reach 900m/min in some cases. After sufficient interfacial contact, the rotating workpiece is brought to a sudden stop and the axial force is increased. The weld zone is generally a narrow region. The friction welding technique can be used to join solid and tubular parts made of a variety of materials. Some flash may develop at the interface in FRW, but this flash can be removed by secondary machining or grinding. Variations of the friction welding process exist. For example “inertia friction welding” involves a flywheel whose rotational kinetic energy is used to weld the parts. The weld is complete when the flywheel comes to a stop. The rotating mass can be varied and thus the rotational kinetic energy. Another variation is “linear friction welding”, where linear reciprocating motion is imposed on at least one of the components to be joined. In linear friction welding parts do not have to be circular, they can be rectangular, square or of other shape. Frequencies can be in the tens of Hz, amplitudes in the millimeters range and pressures in the tens or hundreds of MPa. Finally “friction stir welding” is somewhat different than the other two explained above. Whereas in inertia friction welding and linear friction welding heating of interfaces is achieved through friction by rubbing two contacting surfaces, in the friction stir welding method a third body is rubbed against the two surfaces to be joined. A rotating tool of 5 to 6 mm diameter is brought into contact with the joint. The temperatures can increase to values between 503 to 533 Kelvin. Heating, mixing and stirring of the material in the joint takes place. We use the friction stir welding on a variety of materials including aluminum, plastics and composites. Welds are uniform and quality is high with minimum pores. No fumes or spatter are produced in friction stir welding and the process is well automated.
RESISTANCE WELDING (RW): The heat required for welding is produced by the electrical resistance between the two workpieces to be joined. No flux, shielding gases or consumable electrodes are used in resistance welding. Joule heating takes place in resistance welding and can be expressed as:
H = (Square I) x R x t x K
H is heat generated in joules (watt-seconds), I current in Amperes, R resistance in Ohms, t is the time in seconds the current flows through. The factor K is less than 1 and represents the fraction of energy that is not lost through radiation and conduction. Currents in resistance welding processes can reach levels as high as 100,000 A but voltages are typically 0.5 to 10 Volts. Electrodes are typically made of copper alloys. Both similar and dissimilar materials can be joined by resistance welding. Several variations exist for this process: “Resistance spot welding” involves two opposing round electrodes contacting the surfaces of the lap joint of the two sheets. Pressure is applied until current is turned off. The weld nugget is generally up to 10 mm in diameter. Resistance spot welding leaves slightly discolored indentation marks at weld spots. Spot welding is our most popular resistance welding technique. Various electrode shapes are used in spot welding in order to reach difficult areas. Our spot welding equipment is CNC controlled and has multiple electrodes that can be used simultaneously. Another variation “resistance seam welding” is carried out with wheel or roller electrodes that produce continuous spot welds whenever the current reaches a sufficiently high level in the AC power cycle. Joints produced by resistance seam welding are liquid and gas tight. Welding speeds of about 1.5 m/min are normal for thin sheets. One may apply intermittent currents so that spot welds are produced at desired intervals along the seam. In “resistance projection welding” we emboss one or more projections (dimples) on one of the workpiece surfaces to be welded. These projections may be round or oval. High localized temperatures are reached at these embossed spots that come into contact with the mating part. Electrodes exert pressure to compress these projections. Electrodes in resistance projection welding have flat tips and are water cooled copper alloys. The advantage of resistance projection welding is our ability to a number of welds in one stroke, thus the extended electrode life, capability to weld sheets of various thicknesses, capability to weld nuts and bolts to sheets. Disadvantage of resistance projection welding is the added cost of embossing the dimples. Yet another technique, in “flash welding” heat is generated from the arc at the ends of the two workpieces as they begin to make contact. This method may also alternatively considered arc welding. The temperature at the interface rises, and material softens. An axial force is applied and a weld is formed at the softened region. After the flash welding is complete, the joint can be machined for improved appearance. Weld quality obtained by flash welding is good. Power levels are 10 to 1500 kW. Flash welding is suitable for edge-to-edge joining of similar or dissimilar metals up to 75 mm diameter and sheets between 0.2 mm to 25 mm thickness. “Stud arc welding” is very similar to flash welding. The stud such as a bolt or threaded rod serves as one electrode while being joined to a workpiece such as a plate. To concentrate the generated heat, prevent oxidation and retain the molten metal in the weld zone, a disposable ceramic ring is placed around the joint. Finally “percussion welding” another resistance welding process, utilizes a capacitor to supply the electrical energy. In percussion welding the power is discharged within milliseconds of time very quickly developing high localized heat at the joint. We use percussion welding widely in the electronics manufacturing industry where heating of sensitive electronic components in the vicinity of the joint has to be avoided.
A technique called EXPLOSION WELDING involves detonation of a layer of explosive that is put over one of the workpieces to be joined. The very high pressure exerted on the workpiece produces a turbulent and wavy interface and mechanical interlocking takes place. Bond strengths in explosive welding are very high. Explosion welding is a good method for cladding of plates with dissimilar metals. After cladding, the plates may be rolled into thinner sections. Sometimes we use explosion welding for expanding tubes so that they get sealed tightly against the plate.
Our last method within the domain of solid state joining is DIFFUSION BONDING or DIFFUSION WELDING (DFW) in which a good joint is achieved mainly by diffusion of atoms across the interface. Some plastic deformation at the interface also contributes to the welding. Temperatures involved are around 0.5 Tm where Tm is melting temperature of the metal. Bond strength in diffusion welding depends on pressure, temperature, contact time and cleanliness of contacting surfaces. Sometimes we use filler metals at the interface. Heat and pressure are required in diffusion bonding and are supplied by electrical resistance or furnace and dead weights, press or else. Similar and dissimilar metals can be joined with diffusion welding. The process is relatively slow due to the time it takes for atoms to migrate. DFW can be automated and is widely used in the fabrication of complex parts for the aerospace, electronics, medical industries. Products manufactured include orthopedic implants, sensors, aerospace structural members. Diffusion bonding can be combined with SUPERPLASTIC FORMING to fabricate complex sheet metal structures. Selected locations on sheets are first diffusion bonded and then the unbonded regions are expanded into a mold using air pressure. Aerospace structures with high stiffness-to-weight ratios are manufactured using this combination of methods. The diffusion welding / superplastic forming combined process reduces the number of parts required by eliminating the need for fasteners, results in low-stress highly accurate parts economically and with short lead times.
BRAZING: The brazing and soldering techniques involve lower temperatures than those required for welding. Brazing temperatures are higher than soldering temperatures however. In brazing a filler metal is placed between the surfaces to be joined and temperatures are raised to the melting temperature of the filler material above 723 Kelvin but below the melting temperatures of the workpieces. The molten metal fills the closely fitting space between workpieces. Cooling and subsequent solidification of the filer metal results in strong joints. In braze welding the filler metal is deposited at the joint. Considerably more filler metal is used in braze welding compared to brazing. Oxyacetylene torch with oxidizing flame is used to deposit the filler metal in braze welding. Due to lower temperatures in brazing, problems at heat affected zones such as warping and residual stresses are less. The smaller the clearance gap in brazing the higher is the shear strength of the joint. Maximum tensile strength however is achieved at an optimum gap (a peak value). Below and above this optimum value, the tensile strength in brazing decreases. Typical clearances in brazing can be between 0.025 and 0.2 mm. We use a variety of brazing materials with different shapes such as performs, powder, rings, wire, strip…..etc. and can manufacture these performs specially for your design or product geometry. We do also determine the content of the brazing materials according to your base materials and application. We frequently use fluxes in brazing operations to remove unwanted oxide layers and prevent oxidation. To avoid subsequent corrosion, fluxes are generally removed after the joining operation. AGS-TECH Inc. uses various brazing methods, including:
- Torch Brazing
- Furnace Brazing
- Induction Brazing
- Resistance Brazing
- Dip Brazing
- Infrared Brazing
- Diffusion Brazing
- High Energy Beam
Our most common examples of brazed joints are made of dissimilar metals with good strength such as carbide drill bits, inserts, optoelectronic hermetic packages, seals.
SOLDERING : This is one of our most frequently used techniques where the solder (filler metal) fills the joint as in brazing between closely fitting components. Our solders have melting points below 723 Kelvin. We deploy both manual and automated soldering in manufacturing operations. Compared to brazing, soldering temperatures are lower. Soldering is not very suitable for high-temperature or high-strength applications. We use lead-free solders as well as tin-lead, tin-zinc, lead-silver, cadmium-silver, zinc-aluminum alloys besides others for soldering. Both noncorrosive resin-based as well as inorganic acids and salts are used as flux in soldering. We use special fluxes to solder metals with low solderability. In applications where we have to solder ceramic materials, glass or graphite, we first plate the parts with a suitable metal for increased solderability. Our popular soldering techniques are:
-Reflow or Paste Soldering
-Wave Soldering
-Furnace Soldering
-Torch Soldering
-Induction Soldering
-Iron Soldering
-Resistance Soldering
-Dip soldering
-Ultrasonic Soldering
-Infrared Soldering
Ultrasonic soldering offers us a unique advantage whereby the need for fluxes is eliminated due to ultrasonic cavitation effect which removes oxide films from the surfaces being joined. Reflow and Wave soldering are our industrially outstanding techniques for high volume manufacturing in electronics and therefore worth explaining in greater detail. In reflow soldering, we use semisolid pastes that include solder-metal particles. The paste is placed onto the joint using a screening or stenciling process. In printed circuit boards (PCB) we frequently use this technique. When electrical components are placed onto these pads from paste, the surface tension keeps the surface-mount packages aligned. After placing the components, we heat the assembly in a furnace so the reflow soldering takes place. During this process, the solvents in the paste evaporate, the flux in the paste is activated, the components are preheated, the solder particles are melted and wet the joint, and finally the PCB assembly is cooled slowly. Our second popular technique for high volume production of PCB boards, namely wave soldering relias on the fact that molten solders wet metal surfaces and form good bonds only when the metal is preheated. A standing laminar wave of molten solder is first generated by a pump and the preheated and prefluxed PCBs are conveyed over the wave. The solder wets only exposed metal surfaces but does not wet the IC polymer packages nor the polymer-coated circuit boards. A high-velocity of hot water jet blows excess solder from the joint and prevents bridging between adjacent leads. In wave soldering of surface-mount packages we first adhesively bond them to the circuit board before soldering. Again screening and stenciling is used but this time for epoxy. After the components are placed in their correct locations, the epoxy is cured, the boards are inverted and wave soldering takes place.