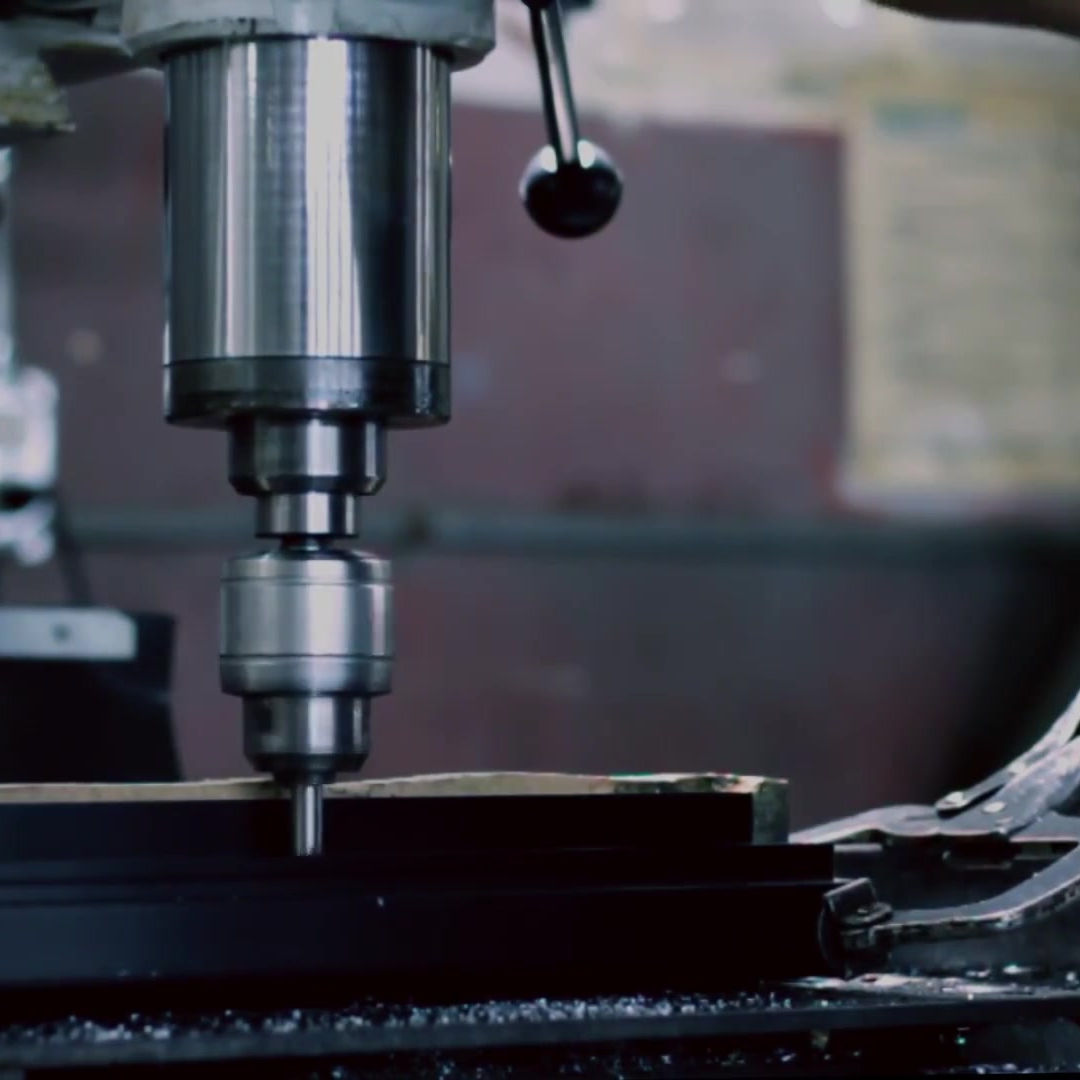
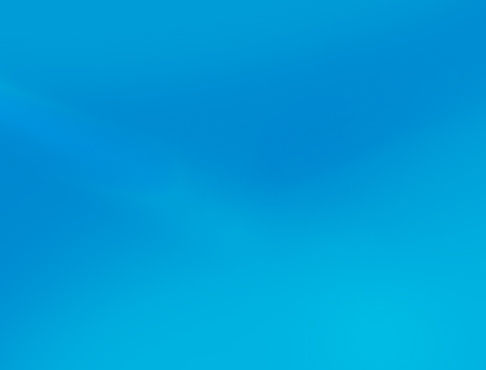
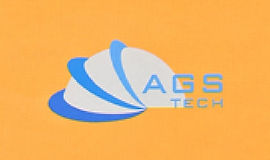
Globalni proizvođač po narudžbi, integrator, konsolidator, outsourcing partner za široku paletu proizvoda i usluga.
Mi smo vaš izvor na jednom mjestu za proizvodnju, proizvodnju, inženjering, konsolidaciju, integraciju, outsourcing prilagođenih proizvoda i usluga.
Odaberite svoj jezik
-
Custom Manufacturing
-
Domaća i globalna proizvodnja po ugovoru
-
Outsourcing proizvodnje
-
Domaće i globalne nabavke
-
Consolidation
-
Engineering Integration
-
Inženjerske usluge
Električna obrada za pražnjenje (EDM), također naziva i AS_CC781905-5CDE-3194-BB3B-136Bad5cf58d_spark-erosion or electrodisackectrodisackectrodiscycqureccycquecqurecquarcqurecqurecqurecqurecquarcycquargacquarcycquarcycquarcycque, die toning_cc781905-5cde-3194-bb3c -136bad5cf58d_or wire erozion, je A_CC781905-5CDE-3194-BB3B-136Bad5cf58d_non-konvencionalna proizvodnja process u kojem se odvija erozija metala i željeni oblik dobiva se pomoću električnih ispusta u obliku od iskri. Nudimo i neke varijante EDM-a, i to NO-WEAR EDM, WIRE EDM (WEDM), EDM BRUŠENJE (EDG), EDM-TUPANJE, EDM ELEKTRIČNO-PRAZNJENJE, ELEKTRIČNO-PRAZNJENO-MLODENJE, mc807 -5cde-3194-bb3b-136bad5cf58d_and ELEKTROHEMIJSKO BRUŠENJE (ECDG). Naši EDM sistemi se sastoje od oblikovanih alata/elektrode i radnog komada spojenih na DC izvore napajanja i umetnutih u električki neprovodni dielektrični fluid. Nakon 1940. godine obrada s električnim pražnjenjem postala je jedna od najvažnijih i najpopularnijih proizvodnih tehnologija u proizvodnoj industriji.
Kada se razmak između dvije elektrode smanji, intenzitet električnog polja u volumenu između elektroda postaje veći od jačine dielektrika u nekim točkama, koji se lomi, na kraju formirajući most za protok struje između dvije elektrode. Stvara se intenzivan električni luk koji uzrokuje značajno zagrijavanje da se otopi dio obratka i dio materijala za alat. Kao rezultat, materijal se uklanja s obje elektrode. U isto vrijeme, dielektrični fluid se brzo zagrijava, što rezultira isparavanjem tekućine u lučnom zazoru. Jednom kada struja prestane ili se zaustavi, toplina se uklanja iz mjehurića plina pomoću okolnog dielektričnog fluida i mjehur se kavitira (kolapsira). Udarni val stvoren kolapsom mjehurića i protokom dielektrične tekućine ispiraju ostatke s površine obratka i unose bilo koji rastopljeni materijal obratka u dielektrični fluid. Brzina ponavljanja za ova pražnjenja je između 50 do 500 kHz, napona između 50 i 380 V i struje između 0,1 i 500 Ampera. Novi tekući dielektrik kao što su mineralna ulja, kerozin ili destilovana i dejonizovana voda obično se prenosi u zapreminu između elektroda odvodeći čvrste čestice (u obliku krhotina) i vraćaju se izolaciona svojstva dielektrika. Nakon protoka struje, razlika potencijala između dvije elektrode se vraća na ono što je bila prije kvara, tako da može doći do novog proboja tekućeg dielektrika. Naše moderne mašine za električno pražnjenje (EDM) nude numerički kontrolisane pokrete i opremljene su pumpama i sistemima za filtriranje dielektričnih fluida.
Obrada električnim pražnjenjem (EDM) je metoda obrade koja se uglavnom koristi za tvrde metale ili one koje bi bilo vrlo teško obraditi konvencionalnim tehnikama. EDM tipično radi sa svim materijalima koji su električni provodnici, iako su također predložene metode za obradu izolacijske keramike sa EDM. Tačka topljenja i latentna toplina topljenja su svojstva koja određuju volumen metala uklonjenog po pražnjenju. Što su ove vrijednosti veće, to je sporija brzina uklanjanja materijala. Budući da proces obrade električnim pražnjenjem ne uključuje nikakvu mehaničku energiju, tvrdoća, čvrstoća i žilavost obratka ne utječu na brzinu skidanja. Frekvencija pražnjenja ili energija po pražnjenju, napon i struja se mijenjaju kako bi se kontrolirale brzine uklanjanja materijala. Brzina uklanjanja materijala i hrapavost površine se povećavaju sa povećanjem gustine struje i smanjenjem frekvencije iskre. Možemo izrezati zamršene konture ili šupljine u prethodno kaljenom čeliku koristeći EDM bez potrebe za termičkom obradom da bismo ih omekšali i ponovno očvrsnuli. Ovu metodu možemo koristiti sa bilo kojim metalom ili metalnim legurama kao što su titan, hastelloy, kovar i inkonel. Primjene EDM procesa uključuju oblikovanje polikristalnih dijamantskih alata. EDM se smatra netradicionalnom ili nekonvencionalnom metodom obrade zajedno sa procesima kao što su elektrohemijska obrada (ECM), rezanje vodenim mlazom (WJ, AWJ), lasersko rezanje. S druge strane, konvencionalne metode obrade uključuju tokarenje, glodanje, brušenje, bušenje i druge procese čiji se mehanizam uklanjanja materijala u osnovi zasniva na mehaničkim silama. Elektrode za mašinsku obradu sa električnim pražnjenjem (EDM) izrađuju se od grafita, mesinga, bakra i legure bakra i volframa. Mogući su prečnici elektroda do 0,1 mm. Budući da je trošenje alata neželjena pojava koja negativno utječe na točnost dimenzija u EDM-u, koristimo prednosti procesa koji se zove NO-WEAR EDM, mijenjanjem polariteta i korištenjem bakrenih alata kako bismo minimizirali habanje alata.
Idealno govoreći, obrada sa električnim pražnjenjem (EDM) se može smatrati nizom kvara i obnavljanja dielektrične tekućine između elektroda. U stvarnosti, međutim, uklanjanje ostataka iz područja između elektroda je gotovo uvijek djelomično. Ovo uzrokuje da se električna svojstva dielektrika u području između elektroda razlikuju od njihovih nominalnih vrijednosti i variraju s vremenom. Razmak između elektroda (iskrini razmak) se prilagođava kontrolnim algoritmima određene mašine koja se koristi. Varnični razmak u EDM-u nažalost ponekad može doći do kratkog spoja zbog krhotina. Kontrolni sistem elektrode možda neće reagovati dovoljno brzo da spreči kratki spoj dve elektrode (alata i radnog komada). Ovaj neželjeni kratki spoj doprinosi uklanjanju materijala drugačije od idealnog kućišta. Najveću važnost pridajemo akciji ispiranja kako bismo povratili izolacijska svojstva dielektrika tako da se struja uvijek javlja u tački međuelektrodnog područja, čime se na najmanju moguću mjeru svodi mogućnost neželjene promjene oblika (oštećenja) alatne elektrode. i radni komad. Da bi se dobila određena geometrija, EDM alat se vodi duž željene putanje vrlo blizu radnog predmeta bez dodirivanja. Najveću pažnju posvećujemo performansama kontrole kretanja u upotrebi. Na taj način dolazi do velikog broja strujnih pražnjenja/varnica, a svaki doprinosi uklanjanju materijala i sa alata i sa radnog predmeta, gdje se formiraju mali krateri. Veličina kratera je funkcija tehnoloških parametara postavljenih za konkretan posao, a dimenzije mogu biti u rasponu od nanoskala (kao što je u slučaju mikro-EDM operacija) do nekoliko stotina mikrometara u grubim uvjetima. Ovi mali krateri na alatu uzrokuju postupnu eroziju elektrode koja se naziva “habanje alata”. Kako bismo spriječili štetan učinak trošenja na geometriju obratka, kontinuirano zamjenjujemo elektrodu alata tokom operacije obrade. Ponekad to postižemo upotrebom žice koja se kontinuirano zamjenjuje kao elektroda (ovaj EDM proces se također naziva WIRE EDM ). Ponekad koristimo alat-elektrodu na način da je samo mali dio zapravo uključen u proces obrade i taj dio se redovno mijenja. To je, na primjer, slučaj kada se rotirajući disk koristi kao elektroda za alat. Ovaj proces se zove EDM BRUSENJE. Još jedna tehnika koju koristimo sastoji se od upotrebe seta elektroda različitih veličina i oblika tokom iste EDM operacije kako bi se kompenziralo trošenje. Ovu tehniku nazivamo višestrukim elektrodama i najčešće se koristi kada elektroda alata replicira u negativu željeni oblik i napreduje prema blanku u jednom smjeru, obično u vertikalnom smjeru (tj. z-osi). Ovo podsjeća na umivaonik alata u dielektričnu tekućinu u koju je obradak uronjen, pa se stoga naziva kao DIE-SINKING EDM_cc781905-5cde-3194-6bd_some-cde-3194-6bd55-5cde-3194-6b5d_cd-3194-6cf9d 3194-bb3b-136bad5cf58d_CONVENTIONAL EDM or RAM. Mašine za ovu operaciju se zovu SINKER EDM. Elektrode za ovu vrstu EDM imaju složene oblike. Ako se konačna geometrija dobije upotrebom obično jednostavnog oblika elektrode koja se pomiče u nekoliko smjerova i također je podložna rotaciji, nazivamo je EDM GLODANJE. Količina habanja striktno zavisi od tehnoloških parametara koji se koriste u radu (polaritet, maksimalna struja, napon otvorenog kola). Na primjer, in micro-EDM, također poznat kao m-EDM, ovi parametri se obično postavljaju na vrijednosti koje stvaraju habanje. Stoga je habanje glavni problem u toj oblasti koji minimiziramo koristeći naše akumulirano znanje. Na primjer, da bi se minimiziralo trošenje grafitnih elektroda, digitalni generator, kojim se može upravljati unutar milisekundi, obrće polaritet kako se elektro-erozija odvija. Ovo rezultira efektom sličnim galvanizaciji koja kontinuirano taloži erodirani grafit natrag na elektrodu. U drugoj metodi, takozvanom krugu ''Zero Wear'', minimiziramo koliko često pražnjenje počinje i prestaje, držeći ga uključenim što je duže moguće. Brzina skidanja materijala u mašinskoj obradi sa električnim pražnjenjem može se procijeniti iz:
MRR = 4 x 10 exp(4) x I x Tw exp (-1,23)
Ovdje je MRR u mm3/min, I je struja u Amperima, Tw je tačka topljenja obratka u K-273,15K. exp označava eksponent.
S druge strane, stopa habanja Wt elektrode može se dobiti iz:
Wt = ( 1,1 x 10exp(11) ) x I x Ttexp(-2,38)
Ovdje je Wt u mm3/min, a Tt je tačka topljenja materijala elektrode u K-273.15K
Konačno, omjer istrošenosti radnog predmeta i elektrode R može se dobiti iz:
R = 2,25 x Treexp(-2,38)
Ovdje je Tr omjer tačaka topljenja radnog predmeta i elektrode.
SINKER EDM :
Sinker EDM, koji se takođe naziva VRSTA ŠUPLJINE EDM or_cc781905-140d_or_cc781905-1000-136bad5cf58d_or_cc781905-1000-136bad5cf58d_or_cc781905-1000-1000-100000000000000000000000000000000000000000 Elektroda i radni komad su povezani na napajanje. Napajanje stvara električni potencijal između njih dvoje. Kako se elektroda približava radnom komadu, dolazi do proboja dielektrika u tekućini, formirajući plazma kanal, a mala iskra skače. Varnice obično pale jednu po jednu jer je malo vjerovatno da različite lokacije u međuelektrodnom prostoru imaju identične lokalne električne karakteristike koje bi omogućile da se iskra pojavi na svim takvim lokacijama istovremeno. Stotine hiljada ovih varnica se dešavaju na nasumične tačke između elektrode i radnog komada u sekundi. Kako osnovni metal erodira, a iskrište se nakon toga povećava, naša CNC mašina automatski spušta elektrodu tako da se proces može nastaviti bez prekida. Naša oprema ima kontrolne cikluse poznate kao "na vrijeme" i "isključeno vrijeme". Postavka vremena uključenja određuje dužinu ili trajanje iskre. Duže vrijeme proizvodi dublju šupljinu za tu iskru i sve naredne iskre za taj ciklus, stvarajući grublju završnu obradu na radnom komadu i obrnuto. Vrijeme isključenja je vremenski period u kojem se jedna iskra zamjenjuje drugom. Duže vrijeme mirovanja dozvoljava dielektričnoj tekućini da prođe kroz mlaznicu kako bi se očistili erodirani ostaci, čime se izbjegava kratki spoj. Ove postavke se podešavaju u mikro sekundama.
WIRE EDM :
In wire Električna obrada pražnjenja (Wedm), također nazvan wire-cut edm_cc781905-5cde-3194-bb3b-136bad5cf55d_or wire, hranimo a tanka jednožilna metalna žica od mesinga kroz radni komad, koji je potopljen u rezervoar dielektrične tekućine. Žičani EDM je važna varijacija EDM-a. Povremeno koristimo rezani EDM za rezanje ploča debljine do 300 mm i za izradu proboja, alata i kalupa od tvrdih metala koje je teško obraditi drugim proizvodnim metodama. U ovom procesu koji nalikuje konturnom rezanju tračnom testerom, žica, koja se stalno napaja sa kalema, drži se između gornje i donje dijamantske vodilice. CNC upravljane vodilice kreću se u ravnini x–y, a gornja vodilica se također može kretati nezavisno u z–u–v osi, što dovodi do mogućnosti rezanja konusnih i prelaznih oblika (kao što su krug na dnu i kvadrat na vrh). Gornja vodilica može kontrolirati pomicanje osi u x–y–u–v–i–j–k–l–. Ovo omogućava WEDM-u da reže veoma zamršene i delikatne oblike. Prosječan rez naše opreme koji postiže najbolju ekonomičnu cijenu i vrijeme obrade je 0,335 mm upotrebom mesingane, bakarne ili volframove žice Ø 0,25. Međutim, gornje i donje dijamantske vodilice naše CNC opreme su tačne do oko 0,004 mm i mogu imati putanju rezanja ili urez od samo 0,021 mm pomoću žice Ø 0,02 mm. Tako da su zaista uski rezovi mogući. Širina rezanja je veća od širine žice jer dolazi do iskrenja sa strana žice do radnog komada, što uzrokuje eroziju. Ovo ''presjecanje'' je neophodno, za mnoge aplikacije je predvidljivo i stoga se može nadoknaditi (u mikro-EDM-u to nije čest slučaj). Kalumi žice su dugi - kalem od 8 kg od žice od 0,25 mm dugačak je nešto više od 19 kilometara. Prečnik žice može biti čak 20 mikrometara, a preciznost geometrije je u blizini +/- 1 mikrometar. Obično koristimo žicu samo jednom i recikliramo je jer je relativno jeftina. Putuje konstantnom brzinom od 0,15 do 9 m/min i konstantan prorez (prorez) se održava tokom rezanja. U procesu rezanog EDM-a koristimo vodu kao dielektrični fluid, kontrolišući njegovu otpornost i druga električna svojstva pomoću filtera i dejonizatorskih jedinica. Voda ispire ostatke reza dalje od zone rezanja. Ispiranje je važan faktor u određivanju maksimalnog protoka za datu debljinu materijala i stoga ga održavamo dosljednim. Brzina rezanja u žičanoj EDM-u je izražena u smislu površine poprečnog presjeka rezanja u jedinici vremena, kao što je 18.000 mm2/h za alatni čelik D2 debljine 50 mm. Linearna brzina rezanja za ovaj slučaj bi bila 18.000/50 = 360 mm/h Brzina uklanjanja materijala u žičanoj EDM je:
MRR = Vf xhxb
Ovdje je MRR u mm3/min, Vf je brzina uvlačenja žice u radni komad u mm/min, h je debljina ili visina u mm, a b je prorez, što je:
b = dw + 2s
Ovdje je dw promjer žice, a s razmak između žice i obratka u mm.
Uz strože tolerancije, naši moderni višeosni EDM obradni centri za rezanje žice imaju dodane karakteristike kao što su više glava za rezanje dva dijela u isto vrijeme, kontrole za sprječavanje loma žice, funkcije automatskog samourezivanja u slučaju loma žice i programirane strategije obrade za optimizaciju rada, pravo i kutno sečenje.
Wire-EDM nudi niska zaostala naprezanja, jer ne zahtijeva velike sile rezanja za skidanje materijala. Kada je energija/snaga po impulsu relativno niska (kao u operacijama završne obrade), očekuje se mala promjena u mehaničkim svojstvima materijala zbog niskih zaostalih naprezanja.
ELEKTRIČNO BRUSENJE (EDG) : Brusilice ne sadrže abrazive, napravljene su od grafita ili mesinga. Ponavljajuće iskre između rotirajućeg točka i obratka uklanjaju materijal sa površina obratka. Brzina uklanjanja materijala je:
MRR = K x I
Ovdje je MRR u mm3/min, I je struja u Amperima, a K je faktor materijala obratka u mm3/A-min. Često koristimo električno brušenje za piljenje uskih proreza na komponentama. Ponekad kombinujemo EDG (Electrical-Discharge Grinding) proces s EKG (elektrohemijsko brušenje) proces gdje se materijal uklanja kemijskim djelovanjem, električna pražnjenja iz grafitnog kotača razbijaju oksidni film i ispiru ih elektrolit. Proces se zove ELEKTROHEMIJSKO BRUŠENJE (ECDG). Iako ECDG proces troši relativno više energije, to je brži proces od EDG. Alat od tvrdog metala uglavnom brusimo ovom tehnikom.
Primjena strojne obrade električnim pražnjenjem:
Proizvodnja prototipa:
EDM proces koristimo u izradi kalupa, alata i kalupa, kao i za izradu prototipova i proizvodnih dijelova, posebno za zrakoplovnu, automobilsku i elektroničku industriju u kojoj su količine proizvodnje relativno male. U Sinker EDM, elektroda od grafita, bakra i volframa ili čistog bakra se strojno obrađuje u željeni (negativni) oblik i ubacuje u radni komad na kraju vertikalnog rampa.
Izrada kalupa za kovanice:
Za izradu kalupa za izradu nakita i bedževa postupkom kovanog novca (žigosanja), pozitiv majstor se može izraditi od sterling srebra, budući da je (uz odgovarajuće strojne postavke) majstor značajno erodiran i koristi se samo jednom. Rezultirajuća negativna matrica se zatim stvrdne i koristi u čekiću za proizvodnju žigosanih ploča od izrezanih listova od bronze, srebra ili legure zlata niske otpornosti. Za značke, ovi ravni se mogu dalje oblikovati na zakrivljenu površinu pomoću druge matrice. Ovaj tip EDM se obično izvodi potopljen u dielektrik na bazi ulja. Gotovi predmet može se dodatno oplemeniti tvrdim (staklo) ili mekim (boja) emajliranjem i/ili galvaniziranim čistim zlatom ili niklom. Mekši materijali kao što je srebro mogu se ručno gravirati kao profinjenost.
Bušenje malih rupa:
Na našim EDM mašinama za sečenje žice koristimo EDM za bušenje malih rupa da napravimo prolaznu rupu u radnom komadu kroz koju provlačimo žicu za EDM operaciju sečenja žice. Odvojene EDM glave posebno za bušenje malih rupa montirane su na našim mašinama za sečenje žice koje omogućavaju velikim kaljenim pločama da se gotovi delovi erodiraju po potrebi i bez prethodnog bušenja. Također koristimo EDM za male rupe za bušenje nizova rupa na rubovima lopatica turbine koje se koriste u mlaznim motorima. Protok plina kroz ove male rupe omogućava motorima da koriste više temperature nego što je inače moguće. Visokotemperaturne, vrlo tvrde, monokristalne legure od kojih su napravljene ove oštrice čine konvencionalnu obradu ovih rupa sa visokim odnosom stranica izuzetno teškom, pa čak i nemogućem. Ostale oblasti primene za EDM malih rupa su stvaranje mikroskopskih otvora za komponente sistema goriva. Pored integrisanih EDM glava, postavljamo samostalne EDM mašine za bušenje malih rupa sa x–y osovinama na mašini za slijepe ili prolazne rupe. EDM buši rupe sa dugom elektrodom od mesinga ili bakra koja se rotira u steznoj glavi sa stalnim protokom destilovane ili dejonizovane vode koja teče kroz elektrodu kao sredstvo za ispiranje i dielektrik. Neki EDM-i za bušenje malih rupa mogu izbušiti 100 mm mekog ili čak kaljenog čelika za manje od 10 sekundi. Rupe između 0,3 mm i 6,1 mm mogu se postići ovom operacijom bušenja.
Obrada metala dezintegracijom:
Posedujemo i specijalne EDM mašine za specifične namene uklanjanja polomljenih alata (burgija ili slavina) sa radnih komada. Ovaj proces se naziva "mašinska obrada metala dezintegracijom".
Prednosti i nedostaci Mašinska obrada sa električnim pražnjenjem:
Prednosti EDM-a uključuju mašinsku obradu:
- Složeni oblici koje bi inače bilo teško proizvesti konvencionalnim alatima za rezanje
- Izuzetno tvrd materijal do vrlo bliskih tolerancija
- Vrlo mali radni komadi kod kojih konvencionalni alati za rezanje mogu oštetiti dio od prekomjernog pritiska reznog alata.
- Nema direktnog kontakta između alata i radnog komada. Stoga se osjetljivi dijelovi i slabi materijali mogu obraditi bez ikakvih izobličenja.
- Može se postići dobra završna obrada površine.
- Vrlo fine rupe se mogu lako izbušiti.
Nedostaci EDM-a uključuju:
- Spora brzina uklanjanja materijala.
- Dodatno vrijeme i trošak koji se koristi za izradu elektroda za ram/sinker EDM.
- Reprodukcija oštrih uglova na radnom komadu je otežana zbog trošenja elektroda.
- Potrošnja energije je velika.
- Formira se ''Presjek''.
- Tokom obrade dolazi do prekomernog trošenja alata.
- Električni neprovodni materijali mogu se obraditi samo uz specifičnu postavku procesa.