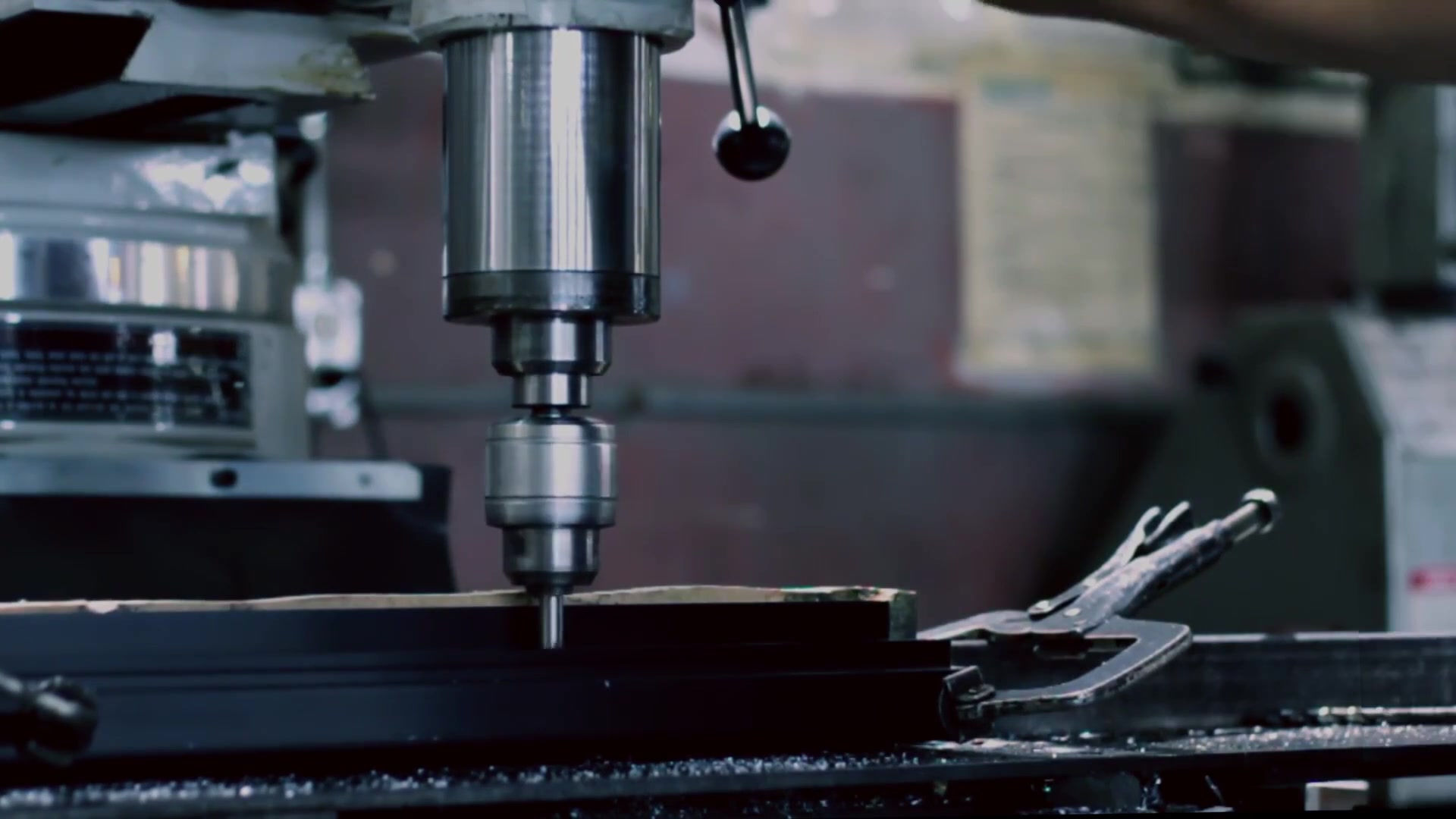
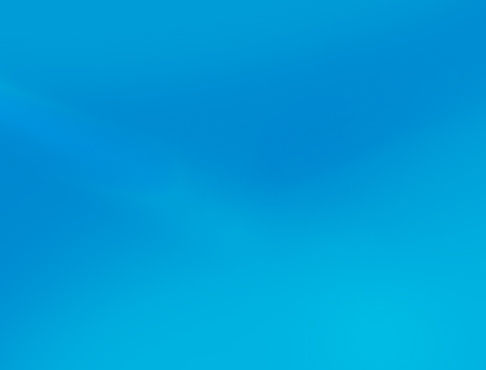
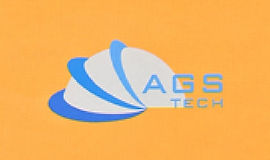
Globalni proizvođač po narudžbi, integrator, konsolidator, outsourcing partner za široku paletu proizvoda i usluga.
Mi smo vaš izvor na jednom mjestu za proizvodnju, proizvodnju, inženjering, konsolidaciju, integraciju, outsourcing prilagođenih proizvoda i usluga.
Odaberite svoj jezik
-
Custom Manufacturing
-
Domaća i globalna proizvodnja po ugovoru
-
Outsourcing proizvodnje
-
Domaće i globalne nabavke
-
Consolidation
-
Engineering Integration
-
Inženjerske usluge
Search Results
164 results found with an empty search
- Transmission Components, Belts, Chains, Cable Drives, Pulleys,AGS-TECH
Transmission Components, Belts, Chains and Cable Drives, Conventional & Grooved or Serrated, Positive Drive, Pulleys Remenje i lanci i sklop pogona kablova AGS-TECH Inc. nudi vam komponente za prijenos snage uključujući remenje i lance i sklop pogona kabela. Sa godinama usavršavanja, naši gumeni, kožni i drugi remenski pogoni postali su lakši i kompaktniji, sposobni da nose veća opterećenja po nižoj cijeni. Slično tome, naši lančani pogoni su prošli kroz dosta razvoja tokom vremena i našim kupcima nude nekoliko prednosti. Neke od prednosti korištenja lančanih pogona su relativno neograničene središnje udaljenosti osovine, kompaktnost, lakoća montaže, elastičnost pri zatezanju bez klizanja ili puzanja, sposobnost rada u okruženjima s visokim temperaturama. Naši kabelski pogoni također nude prednosti kao što je jednostavnost u nekim aplikacijama u odnosu na druge vrste komponenti prijenosa. Dostupni su i remeni, lančani i kabelski pogoni kao i prilagođene i sastavljene verzije. Ove komponente prijenosa možemo proizvesti do prave veličine za vašu primjenu i od najprikladnijih materijala. REMENOVI I POGONI: - Konvencionalni ravni pojasevi: Ovo su obični ravni pojasevi bez zubaca, žljebova ili nazubljenih. Pogoni s ravnim remenom nude fleksibilnost, dobru apsorpciju udara, efikasan prijenos snage pri velikim brzinama, otpornost na habanje, nisku cijenu. Pojasevi se mogu spojiti ili povezati kako bi se napravili veći pojasevi. Druge prednosti konvencionalnih ravnih kaiševa su da su tanke, nisu podložne velikim centrifugalnim opterećenjima (što ih čini dobrim za operacije velike brzine sa malim remenicama). S druge strane nameću velika nosiva opterećenja jer ravni kaiševi zahtijevaju visoku napetost. Drugi nedostaci pogona s ravnim remenom mogu biti klizanje, bučan rad i relativno niža efikasnost pri malim i umjerenim brzinama rada. Imamo dvije vrste konvencionalnih pojaseva: ojačane i neojačane. Ojačani pojasevi u svojoj strukturi imaju vlačni element. Konvencionalni ravni pojasevi su dostupni kao koža, gumirana tkanina ili gajtan, neojačana guma ili plastika, tkanina, ojačana koža. Kožni kaiševi nude dug vijek trajanja, fleksibilnost, odličan koeficijent trenja, laku popravku. Međutim, kožni kaiševi su relativno skupi, potrebno im je obvezivanje i čišćenje, a ovisno o atmosferi mogu se skupiti ili rastegnuti. Gumirani pojasevi od tkanine ili gajtana otporni su na vlagu, kiseline i lužine. Gumirani platneni pojasevi se sastoje od slojeva pamuka ili sintetičke patke impregnirane gumom i najekonomičniji su. Gumirani užad sastoje se od niza slojeva užadi impregniranih gumom. Gumirani kaiševi nude visoku vlačnu čvrstoću i skromnu veličinu i masu. Neojačani gumeni ili plastični kaiševi su prikladni za lagane, niske brzine pogona. Neojačani gumeni i plastični kaiševi mogu se navući na svoje mjesto preko remenica. Plastični neojačani pojasevi mogu prenijeti veću snagu u odnosu na gumene pojaseve. Ojačani kožni pojasevi sastoje se od plastičnog zateznog elementa u sendviču između gornjeg i donjeg sloja kože. Konačno, naši pojasevi od tkanine mogu se sastojati od jednog komada pamuka ili patke presavijenog i ušivenog nizovima uzdužnih šavova. Pojasevi od tkanine mogu da se ravnomerno prate i rade velikom brzinom. - Ožljebljeni ili nazubljeni kaiševi (kao što su klinasti remeni): Ovo su osnovni ravni kaiševi modificirani kako bi pružili prednosti drugog tipa proizvoda za prijenos. To su ravni pojasevi sa uzdužno rebrastom donjom stranom. Poly-V kaiševi su uzdužno užljebljeni ili nazubljeni ravni pojasevi sa vlačnim presjekom i nizom susjednih žljebova u obliku slova V za potrebe praćenja i kompresije. Kapacitet snage zavisi od širine trake. Klinasti remen je radni konj industrije i dostupan je u raznim standardiziranim veličinama i tipovima za prijenos gotovo svake snage opterećenja. Pogoni s klinastim remenom rade dobro između 1500 do 6000 ft/min, međutim uski klinasti remeni će raditi do 10,000 ft/min. Pogoni s klinastim remenom nude dug vijek trajanja od 3 do 5 godina i omogućavaju velike omjere brzine, lako se instaliraju i uklanjaju, nude tihi rad, nisko održavanje, dobru apsorpciju udara između pogonskog remena i pogonskih vratila. Nedostatak klinastih remena je njihovo izvjesno proklizavanje i puzanje i stoga možda nisu najbolje rješenje gdje su potrebne sinhrone brzine. Imamo industrijske, automobilske i poljoprivredne pojaseve. Dostupne su standardne dužine na zalihama, kao i prilagođene dužine pojaseva. Svi standardni poprečni presjeci klinastih remena dostupni su sa zaliha. Postoje tabele u kojima možete izračunati nepoznate parametre kao što su dužina remena, presek remena (širina i debljina) pod uslovom da znate neke parametre vašeg sistema kao što su prečnik pogonske i gonjene remenice, središnji razmak između remenica i brzine rotacije remenica. Možete koristiti takve tabele ili nas zamoliti da odaberemo pravi klinasti remen za vas. - Pozitivni pogonski remeni (Zupčasti remen): Ovi remeni su takođe ravnog tipa sa nizom ravnomerno raspoređenih zubaca na unutrašnjem obimu. Pozitivni pogonski ili zupčasti remeni kombinuju prednosti ravnih kaiševa sa karakteristikama pozitivnog prianjanja lanaca i zupčanika. Pozitivni pogonski remeni ne otkrivaju proklizavanje ili varijacije brzine. Moguć je širok raspon omjera brzina. Opterećenja ležajeva su mala jer mogu raditi pri niskom naponu. Međutim, oni su podložniji neusklađenosti remenica. - Remenice, snopovi, glavčine za remenje: Koriste se različite vrste remenica sa ravnim, rebrastim (nazubljenim) i pozitivnim pogonskim remenima. Sve ih proizvodimo. Većina naših ravnih remenica izrađena je od livenog gvožđa, ali su i čelične verzije dostupne u različitim kombinacijama naplataka i glavčine. Naše remenice sa ravnim remenom mogu imati pune, žbice ili podijeljene glavčine ili možemo proizvesti po vašoj želji. Rebrasti remeni i remeni sa pozitivnim pogonom dostupni su u različitim veličinama i širinama zaliha. Najmanje jedna remenica u pogonima sa razvodnim remenom mora biti prirubnica da bi remen ostao na pogonu. Za sisteme dugog središnjeg pogona, preporučuje se da obje remenice imaju prirubnicu. Noževi su kotači remenica s žljebovima i uglavnom se proizvode lijevanjem željeza, čeličnim oblikovanjem ili plastičnim oblikovanjem. Formiranje čelika je pogodan proces za proizvodnju automobilskih i poljoprivrednih snopova. Proizvodimo snopove sa pravilnim i dubokim žljebovima. Šipke s dubokim žljebovima su prikladne kada klinasti remen ulazi u snop pod uglom, kao što je slučaj u pogonima sa četvrtinom okreta. Duboki žljebovi su također pogodni za pogone s vertikalnim vratilom i primjene gdje vibracije kaiša mogu biti problem. Naše prazne remenice su žljebljene remenice ili ravne remenice koje ne služe za prijenos mehaničke snage. Produžne remenice se uglavnom koriste za zatezanje remena. - Jednostruki i višeremenski pogoni: Pogoni sa jednim remenom imaju jedan žljeb, dok višestruki remeni imaju više žljebova. Klikom na odgovarajući tekst u boji ispod možete preuzeti naše kataloge: - Remenje za prijenos snage (uključuje klinaste remenje, zupčaste remenje, remenje s sirovim rubom, omotane remenje i specijalne remenje) - Transportne trake - V-remenice - Razvodne remenice LANCI I LANČANI POGONI: Naši lanci za prijenos snage imaju neke prednosti kao što su relativno neograničeni razmaci osovina, laka montaža, kompaktnost, elastičnost pod zatezanjem bez klizanja ili puzanja, sposobnost rada na visokim temperaturama. Evo glavnih tipova naših lanaca: - Odvojivi lanci: Naši odvojivi lanci se izrađuju u različitim veličinama, nagibu i krajnjoj čvrstoći i općenito od kovanog željeza ili čelika. Savitljivi lanci se proizvode u rasponu veličina od 0,902 (23 mm) do 4,063 inča (103 mm) koraka i krajnje čvrstoće od 700 do 17,000 lb/kvadratnom inču. S druge strane, naši odvojivi čelični lanci izrađuju se u veličinama od 0,904 inča (23 mm) do oko 3,00 inča (76 mm) u nagibu, sa krajnjom čvrstoćom od 760 do 5000 lb/kvadratni inč._cc781905-5cde-3194-bb3b- 136bad5cf58d_ - Pintle lanci: Ovi lanci se koriste za veća opterećenja i malo veće brzine do oko 450 stopa/min (2,2 m/sec). Pintle lanci su napravljeni od pojedinačnih livenih karika sa punim, okruglim krajem cevi sa pomerenim bočnim šipkama. Ove karike lanca su međusobno povezane čeličnim klinovima. Ovi lanci su u rasponu od oko 1,00 inča (25 mm) do 6,00 inča (150 mm) i krajnje čvrstoće između 3600 do 30,000 lb/kvadratnom inču. - Offset-Sidebar lanci: Oni su popularni u pogonskim lancima građevinskih mašina. Ovi lanci rade pri brzinama do 1000 ft/min i prenose opterećenje do oko 250 KS. Općenito, svaka karika ima dvije pomaknute bočne šipke, jednu čahuru, jedan valjak, jedan klin, klin. - Valjčani lanci: Dostupni su u koracima od 0,25 (6 mm) do 3,00 (75 mm) inča. Konačna čvrstoća valjkastih lanaca jedne širine kreće se između 925 do 130.000 lb/kvadratnom inču. Dostupne su višeširinske verzije valjkastih lanaca i prenose veću snagu pri većim brzinama. Lanci višestrukih širina također nude uglađenije djelovanje uz smanjenu buku. Valjkasti lanci se sastavljaju od valjkastih karika i karika. U odvojivim verzijama kotrljajućih lanaca koriste se klinovi. Dizajn lančanih pogona zahtijeva stručnost. Dok se remenski prijenosi zasnivaju na linearnim brzinama, lančani prijenosi temelje se na brzini rotacije manjeg lančanika, koji je u većini instalacija pogonski element. Osim nominalnih konjskih snaga i brzine rotacije, dizajn lančanih pogona zasniva se na mnogim drugim faktorima. - Lanci sa dvostrukim korakom: U osnovi isti kao i lanci sa valjcima, osim što je korak dvostruko duži. - Lanci sa obrnutim zubima (tihi): Lanci velike brzine koji se koriste uglavnom za pogone sa glavnim motorom, pogonima za odvod snage. Pogoni sa obrnutim zupcima mogu prenositi snagu do 1200 KS i sastoje se od niza zupčastih karika, naizmjenično sastavljenih ili s klinovima ili kombinacijom spojnih komponenti. Lanac središnjeg vodiča ima karike za uključivanje u žljebove na lančaniku, a bočni lanac vodilice ima vodilice za spajanje sa strane lančanika. - Lanci sa perlama ili klizači: Ovi lanci se koriste za male brzine, kao i za ručne operacije. Klikom na odgovarajući tekst u boji ispod možete preuzeti naše kataloge: - Pogonski lanci - Transportni lanci - Transportni lanci velikog nagiba - Valjčani lanci od nerđajućeg čelika - Lanci za podizanje - Lanci za motocikle - Lanci poljoprivrednih mašina - Lančanici: Naši standardni lančanici su u skladu sa ANSI standardima. Pločasti lančanici su ravni lančanici bez glavčine. Naši mali i srednji lančanici glavčine se pretvaraju iz šipke ili otkovaka ili se izrađuju zavarivanjem glavčine šipke na toplo valjanu ploču. AGS-TECH Inc. može isporučiti lančanike mašinski obrađene od odlivaka od sivog gvožđa, livenog čelika i zavarenih konstrukcija glavčine, sinterovanog metala u prahu, livene ili mašinski obrađene plastike. Za nesmetan rad pri velikim brzinama, pravilan odabir veličine lančanika je bitan. Ograničenje prostora je naravno faktor koji ne možemo zanemariti pri odabiru lančanika. Preporučljivo je da odnos vozača i pogonskih lančanika ne bude veći od 6:1, a omotač lanca na vozaču je 120 stepeni. Središnji razmaci između manjih i većih lančanika, dužine lanca i napetost lanca također se moraju odabrati prema nekim preporučenim inženjerskim proračunima i smjernicama, a ne nasumično. Preuzmite naše kataloge klikom na tekst u boji ispod: - Lančanici i pločasti kotači - Čahuri mjenjača - Lanac spojnice - Lančane brave KABELSKI POGONSKI: Oni u nekim slučajevima imaju svoje prednosti u odnosu na kaišne i lančane pogone. Kabelski pogoni mogu ostvariti istu funkciju kao i kaiševi, a mogu biti jednostavniji i ekonomičniji za implementaciju u nekim aplikacijama. Na primjer, nova serija Synchromesh kabelskih pogona dizajnirana je za pozitivnu vuču kako bi zamijenila konvencionalna užad, jednostavne kablove i pogone zupčanika, posebno u uskim prostorima. Novi kablovski pogon je dizajniran da obezbedi visoko precizno pozicioniranje u elektronskoj opremi kao što su mašine za kopiranje, kateri, pisaće mašine, štampači,….. itd. Ključna karakteristika novog kablovskog pogona je njegova mogućnost korišćenja u 3D serpentinastim konfiguracijama koje omogućavaju izuzetno minijaturnih dizajna. Sinhroni kablovi se mogu koristiti sa nižom napetošću u poređenju sa užadima, čime se smanjuje potrošnja energije. Kontaktirajte AGS-TECH za pitanja i mišljenja o kaiševima, lančanim i kablovskim pogonima. CLICK Product Finder-Locator Service PRETHODNA STRANICA
- Rapid Prototyping, Desktop Manufacturing, Additive Manufacturing, FDM
Rapid Prototyping, Desktop Manufacturing, Additive Manufacturing, Stereolithography, Polyjet, Fused Deposition Modeling, Selective Laser Sintering, FDM, SLS Aditivna i brza proizvodnja Posljednjih godina bilježimo porast potražnje za BRZOM PROIZVODNJOM ili BRZOM PROTOTIPOM. Ovaj proces se takođe može nazvati PROIZVODNJA STOLA ili IZRADA U SLOBODNOM OBLIKU. U osnovi, čvrst fizički model dijela se pravi direktno iz trodimenzionalnog CAD crteža. Koristimo izraz ADITIVNA PROIZVODNJA za ove različite tehnike gdje gradimo dijelove u slojevima. Koristeći integrisani kompjuterski vođen hardver i softver vršimo aditivnu proizvodnju. Naše brze tehnike izrade prototipa i proizvodnje su STEREOLITOGRAFIJA, POLYJET, MODELIRANJE FUSED-DEPOSITION, SELEKTIVNO LASERSKO SINTERING, ELEKTRONSKE SNOPE TOPLJENJA, TRODIMENZIONALNA ŠTAMPA, DIREKTNA PROIZVODNJA, BRZI ALATI. Preporučujemo da kliknete ovdje zaPREUZMITE naše šematske ilustracije aditivne proizvodnje i brzih proizvodnih procesa od strane AGS-TECH Inc. Ovo će vam pomoći da bolje razumijete informacije koje vam pružamo u nastavku. Brza izrada prototipa nam omogućava: 1.) Idejni dizajn proizvoda se posmatra iz različitih uglova na monitoru koristeći 3D/CAD sistem. 2.) Prototipovi od nemetalnih i metalnih materijala se proizvode i proučavaju sa funkcionalnog, tehničkog i estetskog aspekta. 3.) Izrada prototipa niske cijene u vrlo kratkom vremenu je postignuta. Aditivna proizvodnja može ličiti na izradu vekne hleba slaganjem i lepljenjem pojedinačnih kriški jedna na drugu. Drugim riječima, proizvod se proizvodi krišku po krišku, ili sloj po sloj koji se nanosi jedan na drugi. Većina dijelova može se proizvesti u roku od nekoliko sati. Tehnika je dobra ako su dijelovi potrebni vrlo brzo ili ako su potrebne količine male, a izrada kalupa i alata je preskupa i oduzima vrijeme. Međutim, cijena dijela je skupa zbog skupih sirovina. • STEREOLITOGRAFIJA: Ova tehnika skraćeno STL, zasnovana je na očvršćavanju i stvrdnjavanju tečnog fotopolimera u određeni oblik fokusiranjem laserskog zraka na njega. Laser polimerizira fotopolimer i stvrdnjava ga. Skeniranjem UV laserskog snopa prema programiranom obliku duž površine fotopolimerne mješavine, dio se proizvodi odozdo prema gore u pojedinačnim kriškama raspoređenim jedna na drugu. Skeniranje laserske tačke se ponavlja mnogo puta kako bi se postigle geometrije programirane u sistemu. Nakon što je dio potpuno proizveden, skida se sa platforme, upija i čisti ultrazvučno i alkoholnom kupkom. Zatim se izlaže UV zračenju nekoliko sati kako bi se osiguralo da je polimer potpuno očvrsnuo i stvrdnuo. Da sumiramo proces, platforma koja je uronjena u mešavinu fotopolimera i UV laserski snop se kontrolišu i pokreću kroz servo-kontrolni sistem prema obliku željenog dela i deo se dobija fotoočvršćavanjem polimera sloj po sloj. Naravno, maksimalne dimenzije proizvedenog dijela su određene stereolitografskom opremom. • POLYJET : Slično inkjet štampi, u polyjet štampaču imamo osam glava za štampanje koje talože fotopolimer na ležište. Ultraljubičasto svjetlo postavljeno uz mlaznice odmah očvršćava i stvrdnjava svaki sloj. U polyjet-u se koriste dva materijala. Prvi materijal je za izradu stvarnog modela. Drugi materijal, smola nalik gelu, koristi se za potporu. Oba ova materijala se nanose sloj po sloj i istovremeno stvrdnjavaju. Nakon završetka modela, potporni materijal se uklanja vodenim rastvorom. Smole koje se koriste su slične stereolitografiji (STL). Polyjet ima sljedeće prednosti u odnosu na stereolitografiju: 1.) Nema potrebe za čišćenjem dijelova. 2.) Nema potrebe za postprocesnim očvršćavanjem 3.) Manje debljine sloja su moguće i na taj način dobijamo bolju rezoluciju i možemo proizvesti finije dijelove. • MODELIRANJE FUSED DEPOSITION MODELING : Takođe skraćeno kao FDM, u ovoj metodi glava ekstrudera upravljana robotom kreće se u dva glavna smjera preko stola. Kabel se po potrebi spušta i podiže. Iz otvora zagrijane matrice na glavi ekstrudira se termoplastični filament i početni sloj se nanosi na pjenastu podlogu. To se postiže pomoću glave ekstrudera koja prati unaprijed određenu putanju. Nakon početnog sloja, stol se spušta i naredni slojevi se nanose jedan na drugi. Ponekad su prilikom proizvodnje složenog dijela potrebne potporne strukture kako bi se taloženje moglo nastaviti u određenim smjerovima. U tim slučajevima, potporni materijal se ekstrudira s manje gustim razmakom filamenta na sloju tako da je slabiji od materijala modela. Ove potporne strukture mogu se kasnije rastvoriti ili odlomiti nakon završetka dela. Dimenzije matrice za ekstruder određuju debljinu ekstrudiranih slojeva. FDM proces proizvodi dijelove sa stepenastim površinama na kosim vanjskim ravnima. Ako je ova hrapavost neprihvatljiva, za zaglađivanje se može koristiti hemijsko poliranje parom ili zagrijani alat. Čak je i vosak za poliranje dostupan kao materijal za premazivanje kako bi se eliminisali ovi koraci i postigle razumne geometrijske tolerancije. • SELEKTIVNO LASERSKO SINTERING: Takođe označen kao SLS, proces se zasniva na sinterovanju polimera, keramičkih ili metalnih prahova selektivno u objekt. Dno komore za obradu ima dva cilindra: cilindar djelomične građe i cilindar za dovod praha. Prvi se postepeno spušta do mjesta gdje se formira sinterirani dio, a drugi se postepeno podiže kako bi doveo prah u cilindar za izradu dijelova kroz mehanizam valjka. Prvo se tanak sloj praha nanese u cilindar sa djelimično građenim, a zatim se laserski snop fokusira na taj sloj, prati i topi/sinteruje određeni poprečni presjek, koji se zatim ponovo učvršćuje u čvrstu supstancu. Puder je područja koja nisu pogođena laserskim snopom ostaju labavi, ali i dalje podržavaju čvrsti dio. Zatim se nanosi još jedan sloj praha i postupak se ponavlja više puta da bi se dobio dio. Na kraju se rastresite čestice praha. Sve ovo izvodi kompjuter za upravljanje procesom koristeći instrukcije koje generiše 3D CAD program za deo koji se proizvodi. Mogu se deponovati različiti materijali kao što su polimeri (kao što su ABS, PVC, poliester), vosak, metali i keramika sa odgovarajućim polimernim vezivom. • ELEKTRONSKI ZRAK TALJENJE : Slično selektivnom laserskom sinterovanju, ali korišćenjem elektronskog zraka za topljenje praha titanijuma ili kobalt hroma za pravljenje prototipova u vakuumu. Napravljeni su neki pomaci za izvođenje ovog procesa na nerđajućim čelicima, aluminijumu i legurama bakra. Ako je potrebno povećati otpornost na zamor proizvedenih dijelova, koristimo toplo izostatičko prešanje nakon proizvodnje dijela kao sekundarni proces. • TRODIMENZIONALNO ŠTAMPANJE: Takođe označeno sa 3DP, u ovoj tehnici glava za štampanje nanosi neorgansko vezivo na sloj bilo nemetalnog ili metalnog praha. Klip koji nosi sloj praha se postepeno spušta i u svakom koraku vezivo se taloži sloj po sloj i spaja vezivo. Praškasti materijali koji se koriste su mješavine polimera i vlakana, ljevački pijesak, metali. Koristeći različite glave veziva istovremeno i veziva različitih boja možemo dobiti različite boje. Proces je sličan inkjet štampi, ali umjesto da dobijemo obojeni list dobijamo obojeni trodimenzionalni objekat. Proizvedeni dijelovi mogu biti porozni i stoga mogu zahtijevati sinterovanje i infiltraciju metala kako bi se povećala njegova gustoća i čvrstoća. Sinterovanjem će sagorjeti vezivo i spojiti metalni prah zajedno. Metali kao što su nerđajući čelik, aluminij, titan se mogu koristiti za izradu dijelova, a kao infiltracijski materijali najčešće koristimo bakar i bronzu. Ljepota ove tehnike je u tome što se čak i komplikovani i pokretni sklopovi mogu proizvesti vrlo brzo. Na primjer, sklop zupčanika, ključ kao alat može se napraviti i imat će pokretne i okretne dijelove spremne za upotrebu. Različite komponente sklopa mogu se proizvesti u različitim bojama i sve u jednom trenutku. Preuzmite našu brošuru na:Osnove metalne 3D štampe • DIREKTNA PROIZVODNJA i BRZI ALATI: Osim procjene dizajna, rješavanja problema koristimo brzu izradu prototipa za direktnu proizvodnju proizvoda ili direktnu primjenu u proizvode. Drugim riječima, brza izrada prototipa može se ugraditi u konvencionalne procese kako bi bili bolji i konkurentniji. Na primjer, brza izrada prototipa može proizvesti uzorke i kalupe. Obrasci polimera koji se topi i sagorevaju stvoreni brzim operacijama izrade prototipa mogu se sastaviti za livenje i investirati. Još jedan primjer koji treba spomenuti je korištenje 3DP-a za proizvodnju ljuske za livenje keramike i korištenje za operacije livenja ljuske. Čak i kalupi za brizganje i umetci kalupa mogu se proizvesti brzim prototipom i može se uštedjeti mnogo sedmica ili mjeseci vremena izrade kalupa. Samo analizom CAD datoteke željenog dijela možemo proizvesti geometriju alata pomoću softvera. Evo nekih od naših popularnih brzih metoda alata: RTV (Vulkanizacija na sobnoj temperaturi) MOLDING / URETANO LIJEVANJE : Korištenje brze izrade prototipa može se koristiti za izradu uzorka željenog dijela. Zatim se ovaj uzorak premazuje sredstvom za razdvajanje i tečna RTV guma se sipa preko šare da bi se dobile polovice kalupa. Zatim se ove polovice kalupa koriste za brizganje tekućih uretana. Vek trajanja kalupa je kratak, samo 0 ili 30 ciklusa, ali dovoljno za proizvodnju u malim serijama. ACES (Acetal Clear Epoxy Solid) INJEKTIRANJE: Koristeći tehnike brze izrade prototipa kao što je stereolitografija, proizvodimo kalupe za brizganje. Ovi kalupi su školjke sa otvorenim krajem koji omogućavaju punjenje materijalima kao što su epoksid, epoksid punjen aluminijumom ili metali. Opet je vijek trajanja kalupa ograničen na desetine ili najviše stotine dijelova. PROCES OBRADE ALATA PRŠKANOM METALOM: Koristimo brzu izradu prototipa i pravimo šablon. Poprskamo leguru cink-aluminij na površinu uzorka i premažemo je. Uzorak sa metalnim premazom se zatim stavlja u bocu i preliva epoksidom ili aluminijumom punjenim epoksidom. Na kraju se uklanja i izradom dvije takve polovice kalupa dobijamo kompletan kalup za brizganje. Ovi kalupi imaju duži vijek trajanja, u nekim slučajevima u zavisnosti od materijala i temperature mogu proizvesti dijelove u hiljadama. KEELTOOL PROCES: Ova tehnika može proizvesti kalupe sa životnim ciklusom od 100.000 do 10 miliona. Koristeći brzu izradu prototipa proizvodimo RTV kalup. Kalup se zatim napuni mješavinom koja se sastoji od praha alatnog čelika A6, volframovog karbida, polimernog veziva i ostavi da se očvrsne. Ovaj kalup se zatim zagrijava kako bi polimer izgorio i metalni prah stopio. Sljedeći korak je infiltracija bakra za proizvodnju konačnog kalupa. Ako je potrebno, sekundarne operacije kao što su obrada i poliranje mogu se izvesti na kalupu za bolju točnost dimenzija. _cc781905-5cde-3194-bb3b-1358bad_ CLICK Product Finder-Locator Service PRETHODNA STRANICA
- Composites, Composite Materials Manufacturing, Fiber Reinforced
Composites, Composite Materials Manufacturing, Particle and Fiber Reinforced, Cermets, Ceramic & Metal Composite, Glass Fiber Reinforced Polymer, Lay-Up Process Composites & Composite Materials Manufacturing Jednostavno definirano, KOMPOZITI ili KOMPOZITNI MATERIJALI su materijali koji se sastoje od dva ili više materijala s različitim fizičkim ili kemijskim svojstvima, ali kada se spoje oni postaju materijal koji se razlikuje od sastavnih materijala. Moramo istaći da sastavni materijali ostaju odvojeni i različiti u strukturi. Cilj u proizvodnji kompozitnog materijala je dobiti proizvod koji je superiorniji od njegovih sastojaka i koji kombinuje željene karakteristike svakog sastojka. Kao primjer; snaga, mala težina ili niža cijena mogu biti motivator za dizajniranje i proizvodnju kompozita. Vrsta kompozita koje nudimo su kompoziti ojačani česticama, kompoziti ojačani vlaknima uključujući keramičko-matrične / polimer-matrice / metal-matrice / ugljik-ugljik / hibridne kompozite, strukturne i laminirane i sendvič strukturirane kompozite i nanokompozite. Tehnike proizvodnje koje koristimo u proizvodnji kompozitnih materijala su: pultruzija, procesi proizvodnje preprega, napredno postavljanje vlakana, namotavanje filamenta, prilagođeno postavljanje vlakana, proces polaganja raspršivanjem od stakloplastike, tafting, proces lanksida, z-pinovanje. Mnogi kompozitni materijali se sastoje od dvije faze, matrice, koja je kontinuirana i okružuje drugu fazu; i disperzovanu fazu koja je okružena matriksom. Preporučujemo da kliknete ovdje zaPREUZMITE naše šematske ilustracije proizvodnje kompozita i kompozitnih materijala od strane AGS-TECH Inc. Ovo će vam pomoći da bolje razumijete informacije koje vam pružamo u nastavku. • KOMPOZITI Ojačani česticama: Ova kategorija se sastoji od dva tipa: kompozita velikih čestica i kompozita ojačanih disperzijom. U prvom tipu, interakcije čestica-matrica ne mogu se tretirati na atomskom ili molekularnom nivou. Umjesto toga vrijedi mehanika kontinuuma. S druge strane, u kompozitima ojačanim disperzijom čestice su općenito mnogo manje u rasponima od desetina nanometara. Primjer kompozita velikih čestica su polimeri kojima su dodana punila. Punila poboljšavaju svojstva materijala i mogu zamijeniti dio volumena polimera ekonomičnijim materijalom. Zapreminski udjeli dvije faze utječu na ponašanje kompozita. Kompoziti velikih čestica koriste se s metalima, polimerima i keramikom. CERMETI su primjeri keramičkih/metalnih kompozita. Naš najčešći kermet je cementni karbid. Sastoji se od vatrostalne karbidne keramike kao što su čestice volframovog karbida u matrici metala poput kobalta ili nikla. Ovi karbidni kompoziti se široko koriste kao alati za rezanje kaljenog čelika. Tvrde čestice karbida su odgovorne za djelovanje rezanja, a njihova žilavost je poboljšana duktilnom metalnom matricom. Tako dobijamo prednosti oba materijala u jednom kompozitu. Još jedan uobičajeni primjer kompozita velikih čestica koji koristimo su čestice čađe pomiješane s vulkaniziranom gumom kako bi se dobio kompozit visoke vlačne čvrstoće, žilavosti, otpornosti na kidanje i habanje. Primjer disperzijski ojačanog kompozita su metali i legure metala ojačani i očvrsnuti ravnomjernom disperzijom finih čestica vrlo tvrdog i inertnog materijala. Kada se u aluminijumsku metalnu matricu dodaju vrlo male ljuspice aluminijum-oksida, dobijamo sinterovani aluminijumski prah koji ima povećanu čvrstoću pri visokim temperaturama. • KOMPOZITI Ojačani Vlaknima: Ova kategorija kompozita je u stvari najvažnija. Cilj koji treba postići je visoka čvrstoća i krutost po jedinici težine. Sastav vlakana, dužina, orijentacija i koncentracija u ovim kompozitima su kritični u određivanju svojstava i korisnosti ovih materijala. Postoje tri grupe vlakana koje koristimo: brkovi, vlakna i žice. BRKOVI su vrlo tanki i dugi monokristali. Oni su među najjačim materijalima. Neki primjeri materijala za brkove su grafit, silicijum nitrid, aluminijum oksid. VLAKNA s druge strane su uglavnom polimeri ili keramika i nalaze se u polikristalnom ili amorfnom stanju. Treća grupa su fine ŽICE koje imaju relativno velike prečnike i sastoje se često od čelika ili volframa. Primjer kompozita ojačanog žicom su automobilske gume koje sadrže čeličnu žicu unutar gume. U zavisnosti od materijala matrice, imamo sledeće kompozite: KOMPOZITI POLIMER-MATRICA: Napravljeni su od polimerne smole i vlakana kao sastojka za pojačanje. Podgrupa ovih koji se nazivaju polimerima ojačanim staklenim vlaknima (GFRP) kompoziti sadrže kontinuirana ili diskontinuirana staklena vlakna unutar polimerne matrice. Staklo nudi visoku čvrstoću, ekonomično je, lako se proizvodi u vlakna i hemijski je inertno. Nedostaci su njihova ograničena krutost i krutost, radne temperature su samo do 200 – 300 C. Fiberglas je pogodan za automobilske karoserije i transportnu opremu, karoserije brodskih vozila, kontejnere za skladištenje. Zbog ograničene krutosti nisu pogodni za vazduhoplovstvo niti za izradu mostova. Druga podgrupa se zove kompozit polimera ojačanog karbonskim vlaknima (CFRP). Ovdje je ugljik naš vlaknasti materijal u polimernoj matrici. Ugljik je poznat po svom visokom specifičnom modulu i čvrstoći i sposobnosti da ih održi na visokim temperaturama. Ugljična vlakna mogu nam ponuditi standardne, srednje, visoke i ultravisoke vlačne module. Nadalje, karbonska vlakna nude različite fizičke i mehaničke karakteristike i stoga su pogodna za različite inženjerske aplikacije po mjeri. CFRP kompoziti se mogu smatrati za proizvodnju sportske i rekreativne opreme, posuda pod pritiskom i strukturnih komponenti za vazduhoplovstvo. Ipak, druga podgrupa, polimerni kompoziti ojačani aramidnim vlaknima su također materijali visoke čvrstoće i modula. Njihov omjer snage i težine je izuzetno visok. Aramidna vlakna su poznata i pod trgovačkim nazivima KEVLAR i NOMEX. Pod zatezanjem se ponašaju bolje od ostalih materijala od polimernih vlakana, ali su slabi na kompresiju. Aramidna vlakna su čvrsta, otporna na udarce, otporna na puzanje i zamor, stabilna na visokim temperaturama, hemijski inertna osim na jake kiseline i baze. Aramidna vlakna se široko koriste u sportskoj robi, pancirima, gumama, užadima, omotima optičkih kablova. Postoje i drugi materijali za ojačanje vlaknima, ali se koriste u manjoj mjeri. To su uglavnom bor, silicijum karbid, aluminijum oksid. S druge strane, materijal polimerne matrice je također kritičan. On određuje maksimalnu temperaturu rada kompozita jer polimer općenito ima nižu temperaturu topljenja i razgradnje. Poliesteri i vinil estri se široko koriste kao polimerna matrica. Koriste se i smole koje imaju odličnu otpornost na vlagu i mehanička svojstva. Na primjer, poliimidna smola se može koristiti do oko 230 stepeni Celzijusa. KOMPOZITI METALNE MATRICE: U ovim materijalima koristimo duktilnu metalnu matricu i radne temperature su generalno više od njihovih sastavnih komponenti. U poređenju sa kompozitima polimer-matrix, oni mogu imati više radne temperature, biti nezapaljivi i mogu imati bolju otpornost na degradaciju prema organskim tekućinama. Međutim, oni su skuplji. Materijali za ojačanje kao što su brkovi, čestice, kontinuirana i diskontinuirana vlakna; i matrični materijali kao što su bakar, aluminijum, magnezijum, titanijum, superlegure se obično koriste. Primjer primjene su komponente motora napravljene od matrice od aluminijske legure ojačane aluminijumskim oksidom i ugljičnim vlaknima. KERAMIČKO-MATRIČNI KOMPOZITI: Keramički materijali su poznati po svojoj izuzetno dobroj pouzdanosti pri visokim temperaturama. Međutim, oni su vrlo krti i imaju niske vrijednosti žilavosti na lom. Ugrađivanjem čestica, vlakana ili brkova jedne keramike u matricu druge možemo postići kompozite veće žilavosti na lom. Ovi ugrađeni materijali u osnovi inhibiraju širenje pukotina unutar matrice nekim mehanizmima kao što su skretanje vrhova pukotine ili formiranje mostova preko lica pukotine. Na primjer, glinice koje su ojačane SiC brkovima koriste se kao umetci za rezne alate za obradu legura tvrdih metala. Oni mogu otkriti bolje performanse u usporedbi s cementiranim karbidima. KOMPOZITI UGLJENIK-UGLJENIK: I ojačanje kao i matrica su karbonski. Imaju visoke module zatezanja i čvrstoće na visokim temperaturama preko 2000 C, otpornost na puzanje, visoku žilavost loma, niske koeficijente termičkog širenja, visoku toplotnu provodljivost. Ova svojstva ih čine idealnim za aplikacije koje zahtijevaju otpornost na termalni udar. Slabost kompozita ugljik-ugljik je međutim njihova osjetljivost na oksidaciju na visokim temperaturama. Tipični primjeri upotrebe su kalupi za vruće prešanje, napredna proizvodnja komponenti turbinskih motora. HIBRIDNI KOMPOZITI: Dvije ili više različitih vrsta vlakana su pomiješane u jednoj matrici. Tako se može krojiti novi materijal s kombinacijom svojstava. Primjer je kada su i karbonska i staklena vlakna ugrađena u polimernu smolu. Ugljična vlakna pružaju krutost i čvrstoću niske gustine, ali su skupa. Staklo je s druge strane jeftino, ali mu nedostaje krutost karbonskih vlakana. Hibridni kompozit staklo-ugljik je jači i čvršći i može se proizvesti po nižoj cijeni. PRERADA KOMPOZITA Ojačanih vlaknima: Za kontinuiranu plastiku ojačanu vlaknima sa ravnomjerno raspoređenim vlaknima orijentiranim u istom smjeru koristimo sljedeće tehnike. PULTRUZIJA: Izrađuju se šipke, grede i cijevi kontinuiranih dužina i konstantnih poprečnih presjeka. Kontinuirani rovovi od vlakana su impregnirani termoreaktivnom smolom i provlače se kroz čeličnu matricu kako bi se preformirali u željeni oblik. Zatim prolaze kroz precizno obrađenu matricu za očvršćavanje kako bi postigli svoj konačni oblik. Pošto se matrica za sušenje zagreva, ona očvršćava matricu smole. Izvlakači provlače materijal kroz kalupe. Koristeći umetnute šuplje jezgre, u mogućnosti smo dobiti cijevi i šuplje geometrije. Metoda pultruzije je automatizirana i nudi nam visoke stope proizvodnje. Moguća je proizvodnja bilo koje dužine proizvoda. PROCES PROIZVODNJE PREPREG-a: Prepreg je armatura od kontinuiranih vlakana prethodno impregnirana djelomično očvrslom polimernom smolom. Široko se koristi za konstruktivne primjene. Materijal dolazi u obliku trake i isporučuje se kao traka. Proizvođač ga direktno oblikuje i potpuno stvrdnjava bez potrebe za dodavanjem bilo kakve smole. Pošto prepregi prolaze kroz reakcije očvršćavanja na sobnoj temperaturi, oni se čuvaju na 0 C ili nižim temperaturama. Nakon upotrebe preostale trake se pohranjuju na niskim temperaturama. Koriste se termoplastične i termoreaktivne smole, a česta su armaturna vlakna od ugljika, aramida i stakla. Da bi se koristili prepregovi, prvo se uklanja noseći papir, a zatim se izrada vrši polaganjem prepreg trake na obrađenu površinu (proces polaganja). Može se postaviti nekoliko slojeva kako bi se dobila željena debljina. Česta praksa je naizmjenična orijentacija vlakana kako bi se dobio poprečni ili kutni laminat. Na kraju se primjenjuju toplina i pritisak za sušenje. Za rezanje preprega i polaganje koriste se ručna obrada i automatizirani procesi. NAMOTAJ FILAMENTA: Kontinuirana ojačavajuća vlakna su precizno pozicionirana u unaprijed određenom uzorku kako bi pratili šuplji i obično ciklindični oblik. Vlakna prvo prolaze kroz kupku sa smolom, a zatim se automatizovanim sistemom namotaju na trn. Nakon nekoliko ponavljanja namotavanja dobijaju se željene debljine i sušenje se vrši na sobnoj temperaturi ili u pećnici. Sada se trn uklanja i proizvod se vadi iz kalupa. Namotavanje filamenta može ponuditi vrlo visoke omjere čvrstoće i težine namotavanjem vlakana u obodnim, spiralnim i polarnim obrascima. Cijevi, rezervoari, kućišta se proizvode ovom tehnikom. • STRUKTURNI KOMPOZITI: Generalno se sastoje od homogenih i kompozitnih materijala. Stoga su njihova svojstva određena sastavnim materijalima i geometrijskim dizajnom njegovih elemenata. Evo glavnih tipova: LAMINARNI KOMPOZITI: Ovi strukturni materijali su napravljeni od dvodimenzionalnih limova ili panela sa poželjnim pravcima visoke čvrstoće. Slojevi se slažu i cementiraju zajedno. Izmjenjivanjem smjerova visoke čvrstoće u dvije okomite ose, dobijamo kompozit koji ima visoku čvrstoću u oba smjera u dvodimenzionalnoj ravni. Podešavanjem uglova slojeva može se proizvesti kompozit sa čvrstoćom u željenim pravcima. Moderne skije se proizvode na ovaj način. SENDVIČ PANELI: Ovi strukturni kompoziti su lagani, ali ipak imaju visoku krutost i čvrstoću. Sendvič paneli se sastoje od dva vanjska lista napravljena od tvrdog i jakog materijala poput aluminijskih legura, plastike ojačane vlaknima ili čelika i jezgre između vanjskih listova. Jezgro treba da bude lagano i većinu vremena ima nizak modul elastičnosti. Popularni materijali za jezgro su krute polimerne pjene, drvo i saće. Sendvič paneli se široko koriste u građevinskoj industriji kao krovni materijal, pod ili zidni materijal, a također i u zrakoplovnoj industriji. • NANOKOMPOZITI : Ovi novi materijali se sastoje od čestica nano veličine ugrađenih u matricu. Koristeći nanokompozite možemo proizvesti gumene materijale koji predstavljaju vrlo dobre barijere za prodiranje zraka, a zadržavaju nepromijenjena svojstva gume. CLICK Product Finder-Locator Service PRETHODNA STRANICA
- Joining & Assembly & Fastening Processes, Welding, Brazing, Soldering
Joining & Assembly & Fastening Processes, Welding, Brazing, Soldering, Sintering, Adhesive Bonding, Press Fitting, Wave and Reflow Solder Process, Torch Furnace Procesi spajanja i montaže i pričvršćivanja Vaše proizvedene dijelove spajamo, sastavljamo i pričvršćujemo i pretvaramo u gotove ili poluproizvode pomoću ZAVARIVANJA, LEMLJENJA, LEMLJENJA, SINTERINGA, LEPLJENJA, PRIKVRĐIVANJA, PRESS FITTINGA. Neki od naših najpopularnijih procesa zavarivanja su lučno zavarivanje, gas oksigorivo, otpor, projekcija, šav, zavarivanje, udaranje, čvrsto stanje, elektronski snop, laser, termičko zavarivanje, indukcijsko zavarivanje. Naši popularni procesi lemljenja su baklje, indukcija, lemljenje u peći i potapanjem. Naše metode lemljenja su gvožđe, vruća ploča, pećnica, indukcija, potapanje, talasno lemljenje, reflow i ultrazvučno lemljenje. Za adhezivno lijepljenje često koristimo termoplaste i termovezne, epoksidne smole, fenole, poliuretan, ljepljive legure kao i neke druge kemikalije i trake. Konačno, naši procesi pričvršćivanja se sastoje od zakucavanja ekserima, zavrtanja, matica i vijaka, zakivanja, spajanja, pričvršćivanja, šivanja i heftanja i presovanja. • ZAVARIVANJE: Zavarivanje uključuje spajanje materijala topljenjem radnih komada i unošenjem materijala za punjenje, koji se takođe spajaju u rastopljeni zavareni bazen. Kada se područje ohladi, dobijamo čvrst spoj. U nekim slučajevima se primjenjuje pritisak. Za razliku od zavarivanja, operacije lemljenja i lemljenja uključuju samo topljenje materijala sa nižom tačkom topljenja između obradaka, a obradak se ne tope. Preporučujemo da kliknete ovdje zaPREUZMITE naše šematske ilustracije procesa zavarivanja od strane AGS-TECH Inc. Ovo će vam pomoći da bolje razumijete informacije koje vam pružamo u nastavku. U LUČNOM ZAVARIVANJU koristimo napajanje i elektrodu za stvaranje električnog luka koji topi metale. Mjesto zavarivanja je zaštićeno zaštitnim plinom ili parom ili drugim materijalom. Ovaj proces je popularan za zavarivanje automobilskih dijelova i čeličnih konstrukcija. Kod zavarivanja metala pod oklopljenim lukom (SMAW) ili također poznatog kao zavarivanje štapom, elektroda se približava osnovnom materijalu i između njih se stvara električni luk. Štap elektrode se topi i djeluje kao materijal za punjenje. Elektroda također sadrži fluks koji djeluje kao sloj šljake i ispušta pare koje djeluju kao zaštitni plin. Oni štite područje zavara od kontaminacije okoline. Ne koriste se nikakvi drugi punioci. Nedostaci ovog procesa su sporost, potreba za čestom zamjenom elektroda, potreba da se odvoji zaostala šljaka koja potiče od fluksa. Brojni metali kao što su gvožđe, čelik, nikl, aluminijum, bakar… itd. Može se zavariti. Njegove prednosti su jeftin alat i jednostavnost upotrebe. Zavarivanje elektrolučnim plinom (GMAW) također poznato kao metal-inertni plin (MIG), imamo kontinuirano punjenje potrošne elektrode za punjenje žice i inertnog ili djelomično inertnog plina koji struji oko žice protiv zagađenja okoline područja zavara. Mogu se zavariti čelik, aluminij i drugi obojeni metali. Prednosti MIG-a su velike brzine zavarivanja i dobar kvalitet. Nedostaci su njegova komplicirana oprema i izazovi s kojima se suočava u vjetrovitom vanjskom okruženju jer moramo održavati stabilan zaštitni plin oko područja zavarivanja. Varijacija GMAW-a je elektrolučno zavarivanje punjenom jezgrom (FCAW) koje se sastoji od fine metalne cijevi ispunjene fluksnim materijalima. Ponekad je fluks unutar cijevi dovoljan za zaštitu od kontaminacije okoline. Zavarivanje pod vodom (SAW) je široko automatizirani proces, uključuje kontinuirano dovođenje žice i luk koji se udara ispod sloja sloja fluksa. Stope proizvodnje i kvaliteta su visoki, šljaka zavarivanja se lako uklanja, a imamo radno okruženje bez dima. Nedostatak je što se može koristiti samo za zavarivanje dijelova u određenim pozicijama. Kod zavarivanja gasnim volframovim lukom (GTAW) ili zavarivanja inertnim volframom (TIG) koristimo volframovu elektrodu zajedno sa zasebnim punilom i inertnim ili blizu inertnim gasovima. Kao što znamo, volfram ima visoku tačku topljenja i veoma je pogodan metal za veoma visoke temperature. Volfram u TIG-u se ne troši suprotno drugim metodama objašnjenim gore. Spora, ali visokokvalitetna tehnika zavarivanja koja ima prednost u odnosu na druge tehnike zavarivanja tankih materijala. Pogodan za mnoge metale. Plazma-lučno zavarivanje je slično, ali koristi plazma plin za stvaranje luka. Luk u plazma lučnom zavarivanju je relativno koncentrisaniji u odnosu na GTAW i može se koristiti za širi raspon debljina metala pri mnogo većim brzinama. GTAW i plazma lučno zavarivanje mogu se primijeniti na manje-više iste materijale. ZAVARIVANJE OXY-FUEL/OKSIFUEL-om naziva se i oksiacetilensko zavarivanje, zavarivanje kisikom, plinsko zavarivanje se izvodi korištenjem plinskih goriva i kisika za zavarivanje. Budući da se ne koristi električna energija, prenosiv je i može se koristiti tamo gdje nema struje. Koristeći gorionik za zavarivanje zagrijavamo dijelove i materijal za punjenje kako bismo stvorili zajednički bazen rastopljenog metala. Mogu se koristiti različita goriva kao što su acetilen, benzin, vodonik, propan, butan…itd. Kod zavarivanja sa kisikom koristimo dva spremnika, jedan za gorivo, a drugi za kisik. Kiseonik oksidira gorivo (sagoreva ga). OTPORNO ZAVARIVANJE: Ova vrsta zavarivanja koristi prednost zagrijavanja u džulu i toplina se stvara na mjestu gdje se električna struja primjenjuje određeno vrijeme. Visoke struje prolaze kroz metal. Na ovoj lokaciji formiraju se bazeni rastopljenog metala. Metode otpornog zavarivanja su popularne zbog svoje efikasnosti, malog potencijala zagađenja. Međutim, nedostaci su relativno značajni troškovi opreme i inherentno ograničenje na relativno tanke radne komade. TAČKANO ZAVARIVANJE je jedna od glavnih vrsta otpornog zavarivanja. Ovdje spajamo dva ili više preklapajućih listova ili radnih komada korištenjem dvije bakrene elektrode da spojimo listove zajedno i propuštamo visoku struju kroz njih. Materijal između bakrenih elektroda se zagrijava i na tom mjestu se stvara rastopljeni bazen. Struja se tada zaustavlja i vrhovi bakrenih elektroda hlade mjesto zavara jer su elektrode hlađene vodom. Primjena prave količine topline na pravi materijal i debljinu ključna je za ovu tehniku, jer ako se pogrešno primjenjuje spoj će biti slab. Točkasto zavarivanje ima prednosti u tome što ne uzrokuje značajne deformacije obradaka, energetsku efikasnost, lakoću automatizacije i izvanredne stope proizvodnje, te ne zahtijeva nikakva punila. Nedostatak je u tome što se zavarivanje odvija na tačkama, a ne formira kontinuirani šav, ukupna čvrstoća može biti relativno niža u poređenju sa drugim metodama zavarivanja. S druge strane, SEAM WELDING proizvodi zavare na spojnim površinama sličnih materijala. Šav može biti čeoni ili preklopni spoj. Zavarivanje šavova počinje na jednom kraju i progresivno prelazi na drugi. Ova metoda također koristi dvije elektrode od bakra za primjenu pritiska i struje na područje zavara. Elektrode u obliku diska rotiraju se sa stalnim kontaktom duž linije šava i prave neprekidni zavar. I ovdje se elektrode hlade vodom. Zavari su vrlo jaki i pouzdani. Ostale metode su tehnike projekcije, fleš i zavarivanje. ZAVARIVANJE U ČVRSTVOM STANJU je malo drugačije od prethodnih metoda objašnjenih gore. Spajanje se odvija na temperaturama ispod temperature topljenja spojenih metala i bez upotrebe metalnog punila. Pritisak se može koristiti u nekim procesima. Različite metode su KOEKSTRUZIJSKO ZAVARIVANJE gdje se različiti metali istiskuju kroz istu matricu, ZAVARIVANJE NA HLADNI PRITISAK gdje spajamo meke legure ispod njihove tačke topljenja, DIFUZIJSKO ZAVARIVANJE tehnika bez vidljivih linija zavarivanja, EKSPLOZIJSKO ZAVARIVANJE za spajanje različitih materijala otpornih na koroziju, npr. čelika, ELEKTROMAGNETNO PULSNO ZAVARIVANJE gdje ubrzavamo cijevi i limove elektromagnetnim silama, KOVAČKO ZAVARIVANJE koje se sastoji od zagrijavanja metala na visoke temperature i njihovo čekiće zajedno, ZAVARIVANJE TRENJEM gdje se vrši dovoljno zavarivanje trenjem, ZAVARIVANJE TRENJEM KRETANJEM koje ne uključuje- potrošni alat koji prelazi liniju spoja, ZAVARIVANJE TOPLOM PRITISKOM gdje presujemo metale zajedno na povišenim temperaturama ispod temperature topljenja u vakuumu ili inertnim plinovima, VRUĆE IZOSTATIČKO ZAVARIVANJE PRITISKOM proces u kojem vršimo pritisak pomoću inertnih plinova unutar posude, VALJNO ZAVARIVANJE gdje spajamo različiti materijali gurajući ih između dva rotirajuća točka, ULTRAZVUČNO ZAVARIVANJE gdje se tanki metalni ili plastični limovi zavaruju korištenjem energije vibracija visoke frekvencije. Naši ostali procesi zavarivanja su ZAVARIVANJE ELEKTRONSKIM SNOPAMA sa dubokim prodiranjem i brzom obradom, ali kao skupa metoda koju smatramo za posebne slučajeve, ELEKTROSLAGNO ZAVARIVANJE je metoda pogodna samo za teške debele ploče i radne komade čelika, INDUKCIJSKO ZAVARIVANJE gdje koristimo elektromagnetnu indukciju i zagrijavaju naše električno vodljive ili feromagnetne obratke, LASERSKO ZVARIVANJE također sa dubokim prodiranjem i brzom obradom, ali skupom metodom, LASERSKO HIBRIDNO ZAVARIVANJE koje kombinuje LBW sa GMAW u istoj glavi za zavarivanje i sposobno da premosti praznine od 2 mm između ploča, UDARNO ZAVARIVANJE koje uključuje električno pražnjenje praćeno kovanjem materijala primijenjenim pritiskom, TERMIT ZAVARIVANJE koje uključuje egzotermnu reakciju između praha aluminijuma i željeznog oksida., ELEKTROGASNO ZAVARIVANJE sa potrošnim elektrodama koje se koristi samo sa čelikom u okomitom položaju, i konačno LUČNO ZAVARIVANJE STUDOVA za spajanje čepa na bazu materijal sa toplotom i pritiskom. Preporučujemo da kliknete ovdje zaPREUZMITE naše šematske ilustracije procesa lemljenja, lemljenja i lepljenja od strane AGS-TECH Inc. Ovo će vam pomoći da bolje razumijete informacije koje vam pružamo u nastavku. • LEMENJE: Spajamo dva ili više metala zagrijavanjem metala za punjenje između njih iznad njihovih tačaka topljenja i korištenjem kapilarnog djelovanja za širenje. Proces je sličan lemljenju, ali temperature koje su potrebne za topljenje punila su veće kod lemljenja. Kao i kod zavarivanja, fluks štiti materijal za punjenje od atmosferske kontaminacije. Nakon hlađenja obradak se spaja. Proces uključuje sljedeće ključne korake: Dobro pristajanje i zazor, pravilno čišćenje osnovnih materijala, pravilno pričvršćivanje, odgovarajući fluks i odabir atmosfere, zagrijavanje sklopa i konačno čišćenje lemljenog sklopa. Neki od naših procesa lemljenja su TORCH LEmljenje, popularna metoda koja se izvodi ručno ili na automatiziran način. Pogodan je za male količine proizvodnje i specijalizovane slučajeve. Toplota se primjenjuje pomoću plinskog plamena u blizini spoja koji se lemi. LEmljenje u peći zahtijeva manje vještine operatera i poluautomatski je proces pogodan za industrijsku masovnu proizvodnju. I kontrola temperature i kontrola atmosfere u peći su prednosti ove tehnike, jer prva nam omogućava da imamo kontrolisane toplotne cikluse i eliminišemo lokalno zagrevanje kao što je slučaj kod lemljenja gorionicima, a druga štiti deo od oksidacije. Koristeći jigging, u mogućnosti smo smanjiti troškove proizvodnje na minimum. Nedostaci su velika potrošnja energije, troškovi opreme i zahtjevnija razmatranja dizajna. VAKUUMNO LEMENJE se odvija u peći pod vakuumom. Ujednačenost temperature se održava i dobijamo vrlo čiste spojeve bez fluksa sa vrlo malim zaostalim naprezanjima. Toplinska obrada se može odvijati tokom vakuumskog lemljenja, zbog niskih zaostalih naprezanja prisutnih tokom sporih ciklusa grijanja i hlađenja. Glavni nedostatak je njegova visoka cijena jer je stvaranje vakuumskog okruženja skup proces. Još jedna tehnika DIP LEmljenje spaja učvršćene dijelove gdje se smjesa za lemljenje nanosi na površine koje se spajaju. Nakon toga, fixtured dijelovi se potapaju u kupku istopljene soli kao što je natrijum hlorid (kuhinjska so) koja djeluje kao medij za prijenos topline i fluks. Vazduh je isključen i stoga nema stvaranja oksida. Kod INDUKCIJSKOG LEMLJENJA spajamo materijale pomoću dodatnog metala koji ima nižu tačku topljenja od osnovnih materijala. Izmjenična struja iz indukcijskog svitka stvara elektromagnetno polje koje inducira indukcijsko zagrijavanje na uglavnom gvozdenim magnetskim materijalima. Metoda osigurava selektivno zagrijavanje, dobre spojeve sa punilima koja teku samo u željenim područjima, malo oksidacije jer nema plamena i hlađenje je brzo, brzo zagrijavanje, konzistenciju i pogodnost za proizvodnju velikih količina. Da bismo ubrzali naše procese i osigurali konzistentnost, često koristimo preforme. Informacije o našem postrojenju za lemljenje koje proizvodi spojeve od keramike do metala, hermetičko zaptivanje, vakuumske prolaze, komponente visokog i ultravisokog vakuuma i kontrole fluida možete pronaći ovdje:_cc781905_cc781905-136bad5cf58d_, možete pronaći ovdje:_cc781905-9c781906b35c781900b316b310b30b30b6b31b31b6b3b53cb3b3b3b3b3b3b3b3b3Brošura o fabrici lemljenja • LEMENJE : Kod lemljenja nemamo topljenje obradaka, već dodatni metal sa nižom tačkom topljenja od spojnih delova koji se uliva u spoj. Dodatni metal kod lemljenja se topi na nižoj temperaturi nego kod lemljenja. Koristimo legure bez olova za lemljenje i usklađenost sa RoHS, a za različite primjene i zahtjeve imamo različite i prikladne legure kao što je legura srebra. Lemljenje nam nudi spojeve koji su nepropusni za plin i tekućinu. Kod MEKOG LEMLJENJA, naš dodatni metal ima tačku topljenja ispod 400 C, dok su kod SREBRNOG LEMLJENJA i LEMLJENJA potrebne više temperature. Meko lemljenje koristi niže temperature, ali ne rezultira jakim spojevima za zahtjevne primjene na povišenim temperaturama. S druge strane, lemljenje srebrom zahtijeva visoke temperature koje osigurava gorionik i daje nam jake spojeve pogodne za primjenu na visokim temperaturama. Za lemljenje su potrebne najviše temperature i obično se koristi gorionik. Pošto su spojevi za lemljenje veoma jaki, dobri su kandidati za popravku teških gvozdenih predmeta. U našim proizvodnim linijama koristimo i ručno ručno lemljenje kao i automatizirane linije za lemljenje. INDUKCIJSKO LEMENJE koristi visokofrekventnu izmjeničnu struju u bakrenoj zavojnici kako bi se olakšalo indukcijsko zagrijavanje. U zalemljenom dijelu induciraju se struje i kao rezultat se stvara toplina na visokom otporu joint. Ova toplota topi dodatni metal. Također se koristi fluks. Indukcijsko lemljenje je dobra metoda za lemljenje cilindara i cijevi u kontinuiranom procesu omotavanjem zavojnica oko njih. Lemljenje nekih materijala kao što su grafit i keramika je teže jer zahtijeva obradak odgovarajućim metalom prije lemljenja. Ovo olakšava međufaznu vezu. Mi lemimo takve materijale posebno za primjenu u hermetičkom pakiranju. Naše štampane ploče (PCB) proizvodimo u velikom obimu uglavnom koristeći TALASNO LEMENJE. Samo za male količine prototipova koristimo ručno lemljenje pomoću lemilice. Koristimo talasno lemljenje i za sklopove PCB-a kroz otvore i za površinsku montažu (PCBA). Privremeni ljepilo drži komponente pričvršćene za ploču, a sklop se postavlja na transporter i kreće se kroz opremu koja sadrži rastopljeni lem. Prvo se PCB topi, a zatim ulazi u zonu predgrijavanja. Otopljeni lem se nalazi u posudi i na svojoj površini ima uzorak stajaćih valova. Kada se PCB kreće preko ovih valova, ovi valovi dodiruju dno PCB-a i lijepe se za jastučiće za lemljenje. Lem ostaje samo na pinovima i jastučićima, a ne na samoj PCB-u. Valovi u rastopljenom lemu moraju biti dobro kontrolirani kako ne bi došlo do prskanja, a vrhovi valova ne dodiruju i kontaminiraju neželjena područja ploča. U REFLOW SOLDERING, koristimo ljepljivu pastu za lemljenje da privremeno pričvrstimo elektronske komponente na ploče. Zatim se ploče prolaze kroz reflow peć sa kontrolom temperature. Ovdje se lem topi i trajno povezuje komponente. Ovu tehniku koristimo i za komponente za površinsku montažu kao i za komponente kroz rupe. Pravilna kontrola temperature i podešavanje temperature pećnice su od suštinskog značaja kako bi se izbjeglo uništavanje elektronskih komponenti na ploči pregrijavanjem iznad njihovih maksimalnih temperaturnih granica. U procesu ponovnog lemljenja imamo nekoliko regiona ili faza od kojih svaka ima poseban termalni profil, kao što su korak predgrijavanja, korak termičkog namakanja, koraci povratnog toka i koraci hlađenja. Ovi različiti koraci su neophodni za reflow bez oštećenja sklopova štampanih ploča (PCBA). ULTRAZVUČNO LEMENJE je još jedna često korišćena tehnika sa jedinstvenim mogućnostima- Može se koristiti za lemljenje stakla, keramike i nemetalnih materijala. Na primjer, fotonaponski paneli koji su nemetalni trebaju elektrode koje se mogu pričvrstiti ovom tehnikom. Kod ultrazvučnog lemljenja koristimo grijani vrh za lemljenje koji također emituje ultrazvučne vibracije. Ove vibracije stvaraju mjehuriće kavitacije na granici podloge sa rastopljenim materijalom za lemljenje. Implozivna energija kavitacije modificira površinu oksida i uklanja prljavštinu i okside. Za to vrijeme se formira i sloj legure. Lem na površini spajanja uključuje kisik i omogućava stvaranje snažne zajedničke veze između stakla i lema. DIP LEmljenje se može smatrati jednostavnijom verzijom talasnog lemljenja pogodnom samo za proizvodnju malih razmera. Prvo se nanosi fluks za čišćenje kao iu drugim procesima. PCB sa montiranim komponentama se ručno ili na poluautomatski način potapaju u rezervoar koji sadrži rastopljeni lem. Otopljeni lem se lijepi za izložena metalna područja nezaštićena maskom za lemljenje na ploči. Oprema je jednostavna i jeftina. • LEPLJENJE : Ovo je još jedna popularna tehnika koju često koristimo i uključuje lijepljenje površina pomoću ljepila, epoksida, plastičnih sredstava ili drugih hemikalija. Vezivanje se postiže ili isparavanjem rastvarača, termičkom polimerizacijom, polimerizacijom UV svjetlom, polimerizacijom pod pritiskom ili čekanjem određenog vremena. U našim proizvodnim linijama koriste se različita ljepila visokih performansi. Uz pravilno dizajnirane procese nanošenja i očvršćavanja, adhezivno spajanje može rezultirati vezama s vrlo malim naprezanjem koje su jake i pouzdane. Adhezivne veze mogu biti dobra zaštita od faktora okoline kao što su vlaga, zagađivači, korozivi, vibracije… itd. Prednosti lepljenja su: mogu se primeniti na materijale koje bi inače bilo teško zalemiti, zavariti ili zalemiti. Također može biti poželjno za materijale osjetljive na toplinu koji bi bili oštećeni zavarivanjem ili drugim procesima visoke temperature. Druge prednosti ljepila su što se mogu nanositi na površine nepravilnog oblika i povećavaju težinu sklopa za vrlo male količine u usporedbi s drugim metodama. Također, promjene dimenzija dijelova su vrlo minimalne. Neka ljepila imaju svojstva podudaranja indeksa i mogu se koristiti između optičkih komponenti bez značajnog smanjenja svjetlosti ili jačine optičkog signala. Nedostaci s druge strane su duže vrijeme očvršćavanja koje može usporiti proizvodne linije, zahtjeve za pričvršćivanje, zahtjeve za pripremu površine i poteškoće pri rastavljanju kada je potrebna ponovna obrada. Većina naših operacija lijepljenja uključuje sljedeće korake: -Površinska obrada: Uobičajeni su posebni postupci čišćenja kao što su čišćenje deioniziranom vodom, čišćenje alkoholom, plazma ili korona čišćenje. Nakon čišćenja možemo nanijeti sredstva za poboljšanje prianjanja na površine kako bismo osigurali najbolje moguće spojeve. -Učvršćivanje dijelova: Za primjenu ljepila kao i za očvršćavanje dizajniramo i koristimo prilagođene učvršćivače. -Primjena ljepila: Ponekad koristimo ručne, a ponekad ovisno o slučaju automatizirane sisteme kao što su robotika, servo motori, linearni aktuatori za isporuku ljepila na pravo mjesto i koristimo dozatore za isporuku u pravoj količini i količini. -Stvrdnjavanje: Ovisno o ljepilu, možemo koristiti jednostavno sušenje i očvršćavanje, kao i očvršćavanje pod UV svjetlima koja djeluju kao katalizator ili termička polimerizacija u pećnici ili korištenjem otpornih grijaćih elemenata postavljenih na držače i uređaje. Preporučujemo da kliknete ovdje zaPREUZMITE naše šematske ilustracije procesa pričvršćivanja od strane AGS-TECH Inc. Ovo će vam pomoći da bolje razumijete informacije koje vam pružamo u nastavku. • PROCESI PRIČVRŠĆIVANJA: Naši procesi mehaničkog spajanja spadaju u dvije kategorije: PRIKVAČI i INTEGRALNI SPOJOVI. Primjeri pričvršćivača koje koristimo su vijci, igle, matice, vijci, zakovice. Primjeri integralnih spojeva koje koristimo su uskočni i skupljajući spojevi, šavovi, nabori. Koristeći različite metode pričvršćivanja, osiguravamo da naši mehanički spojevi budu čvrsti i pouzdani za dugi niz godina upotrebe. VIJACI i VIJACI su neki od najčešće korišćenih spojnih elemenata za držanje objekata zajedno i pozicioniranje. Naši vijci i vijci ispunjavaju ASME standarde. Različiti tipovi vijaka i vijaka su raspoređeni uključujući šesterokutne vijke i vijke sa šestougaonim poklopcem, vijke i vijke sa zaostatkom, dvostrani vijak, vijak za tiple, vijak za oko, vijak za ogledalo, vijak za lim, vijak za fino podešavanje, vijke za samobušenje i samourezivanje , vijak za podešavanje, vijci sa ugrađenim podloškama,…i još mnogo toga. Imamo različite tipove glava zavrtnja kao što su upuštena, kupolasta, okrugla, sa prirubnicom i razne tipove vijaka kao što su utor, klinasti, kvadratni, šesterokutni nastavci. RIVET s druge strane je trajni mehanički zatvarač koji se sastoji od glatke cilindrične osovine i glave s jedne strane. Nakon umetanja, drugi kraj zakovice se deformiše i promjer joj se širi tako da ostaje na svom mjestu. Drugim riječima, prije ugradnje zakovica ima jednu glavu, a nakon ugradnje dvije. Ugrađujemo različite vrste zakovica ovisno o primjeni, čvrstoći, dostupnosti i cijeni, kao što su zakovice s punom/okruglom glavom, strukturalne, polucijevne, slijepe, oscar, pogonske, flush, frikcione zakovice, samoprobijajuće zakovice. Zakivanje se može dati prednost u slučajevima kada treba izbjeći toplotnu deformaciju i promjenu svojstava materijala zbog topline zavarivanja. Zakivanje također nudi malu težinu i posebno dobru snagu i izdržljivost protiv sila smicanja. Protiv vlačnih opterećenja, međutim, vijci, matice i vijci mogu biti prikladniji. U procesu CLINCHING koristimo specijalne probijače i kalupe za formiranje mehaničkog bloka između limova koji se spajaju. Probijanje gura slojeve lima u šupljinu kalupa i rezultira stvaranjem trajnog spoja. Kod klinča nije potrebno grijanje i hlađenje, a radi se o hladnom procesu. To je ekonomičan proces koji u nekim slučajevima može zamijeniti točkasto zavarivanje. U ZAKLJUČIVANJU koristimo klinove koji su mašinski elementi koji se koriste za osiguranje položaja dijelova mašine u odnosu jedan na drugi. Glavne vrste su klinovi, klinovi, opružni klinovi, klinovi, i klin. U HEFTOVANJU koristimo pištolje za klamanje i spajalice koje su dvokraki zatvarači koji se koriste za spajanje ili vezivanje materijala. Heftanje ima sljedeće prednosti: Ekonomično, jednostavno i brzo za korištenje, kruna spajalica se može koristiti za premošćivanje materijala spojenih zajedno, Kruna spajalice može olakšati premošćavanje komada poput kabla i pričvršćivanje na površinu bez bušenja ili štetno, relativno lako uklanjanje. PRESS FITTING se vrši guranjem delova zajedno i trenjem između njih se delovi pričvršćuju. Dijelovi za presovanje koji se sastoje od prevelike osovine i manje rupe općenito se sklapaju na jedan od dva načina: ili primjenom sile ili korištenjem prednosti toplinskog širenja ili kontrakcije dijelova. Kada se presa spojnica postavlja primjenom sile, koristimo ili hidrauličnu presu ili ručnu presu. S druge strane, kada je presovanje uspostavljeno termičkim širenjem, zagrijavamo dijelove omotača i montiramo ih na svoje mjesto dok su vrući. Kada se ohlade, skupljaju se i vraćaju se u normalne dimenzije. Ovo rezultira dobrim pristajanjem. Ovo alternativno nazivamo SKRUZIVANJEM. Drugi način za to je hlađenje omotanih dijelova prije sklapanja, a zatim ih gurnuti u dijelove koji se spajaju. Kada se sklop zagrije oni se šire i dobijamo čvrsto prianjanje. Ova potonja metoda može biti poželjnija u slučajevima kada zagrijavanje predstavlja rizik od promjene svojstava materijala. Hlađenje je u tim slučajevima sigurnije. Pneumatske i hidraulične komponente i sklopovi • Ventili, hidraulične i pneumatske komponente kao što su O-prsten, podloška, zaptivke, brtva, prsten, podloška. Budući da ventili i pneumatske komponente dolaze u velikom broju, ne možemo ovdje sve navesti. U zavisnosti od fizičkog i hemijskog okruženja vaše aplikacije, imamo posebne proizvode za vas. Molimo navedite nam aplikaciju, vrstu komponente, specifikacije, uslove okoline kao što su pritisak, temperatura, tečnosti ili gasovi koji će biti u kontaktu sa vašim ventilima i pneumatskim komponentama; a mi ćemo odabrati najprikladniji proizvod za vas ili ga proizvesti posebno za vašu primjenu. CLICK Product Finder-Locator Service PRETHODNA STRANICA
- Machine Elements Manufacturing, Gears, Gear Drives, Bearings, Keys, Splines
Machine Elements Manufacturing, Gears, Gear Drives, Bearings, Keys, Splines, Pins, Shafts, Seals, Fasteners, Clutch, Cams, Followers, Belts, Couplings, Shafts Proizvodnja mašinskih elemenata Čitaj više Remenje i lanci i sklop pogona kablova Čitaj više Zupčanici i sklop zupčanika Čitaj više Proizvodnja spojnica i ležajeva Čitaj više Keys & Splines & Pins Manufacturing Čitaj više Cams & Followers & Linkages & Ratchet Wheels Manufacturing Čitaj više Shafts Manufacturing Čitaj više Proizvodnja mehaničkih zaptivki Čitaj više Sklop kvačila i kočnice Čitaj više Fasteners Manufacturing Čitaj više Jednostavna montaža mašina MAŠINSKI ELEMENTI su elementarne komponente mašine. Ovi elementi se sastoje od tri osnovne vrste: 1.) Strukturne komponente uključujući elemente okvira, ležajeve, osovine, klinove, pričvršćivače, brtve i maziva. 2.) Mehanizmi koji kontrolišu kretanje na različite načine kao što su zupčanici, remeni ili lančani pogoni, karike, sistemi grebena i pratećih sistema, kočnice i kvačila. 3.) Komponente upravljanja kao što su dugmad, prekidači, indikatori, senzori, aktuatori i kompjuterski kontroleri. Većina mašinskih elemenata koje vam nudimo standardizovani su prema uobičajenim veličinama, ali su mašinski elementi napravljeni po meri dostupni i za vaše specijalizovane aplikacije. Prilagođavanje mašinskih elemenata može se izvršiti na postojećim dizajnima koji se nalaze u našim katalozima za preuzimanje ili na potpuno novim dizajnima. Izrada prototipa i proizvodnja mašinskih elemenata mogu se nastaviti nakon što obje strane odobre dizajn. Ako je potrebno dizajnirati i proizvesti nove mašinske elemente, naši kupci ili nam pošalju svoje vlastite nacrte i mi ih pregledamo za odobrenje ili traže od nas da dizajniramo mašinske elemente za njihovu primjenu. U potonjem slučaju koristimo sav input naših kupaca i dizajniramo elemente stroja i šaljemo finalizirane nacrte našim klijentima na odobrenje. Nakon odobrenja proizvodimo prve artikle, a zatim proizvodimo mašinske elemente prema konačnom dizajnu. U bilo kojoj fazi ovog posla, u slučaju da se pojedini mašinski element ne ponaša na zadovoljavajući način na terenu (što je retkost), pregledamo ceo projekat i zajedno sa našim klijentima vršimo izmene po potrebi. Naša standardna praksa je da potpisujemo ugovore o tajnosti podataka (NDA) sa našim klijentima za dizajn mašinskih elemenata ili bilo kojeg drugog proizvoda kad god je to potrebno ili potrebno. Nakon što su mašinski elementi za određenog kupca dizajnirani i proizvedeni po narudžbi, dodjeljujemo mu šifru proizvoda i proizvodimo ih i prodajemo samo našem kupcu koji posjeduje proizvod. Reproduciramo mašinske elemente koristeći razvijene alate, kalupe i postupke onoliko puta koliko je potrebno i kad god ih naš kupac ponovo naruči. Drugim riječima, nakon što je prilagođeni strojni element dizajniran i proizveden za vas, intelektualno vlasništvo, kao i sav alat i kalupi, mi rezerviramo i skladištimo na neodređeno vrijeme za vas i proizvode koji se reproduciraju kako želite. Našim klijentima nudimo i inženjerske usluge kreativnim kombinovanjem mašinskih elemenata u komponentu ili sklop koji služi aplikaciji i ispunjava ili prevazilazi očekivanja naših kupaca. Postrojenja za proizvodnju naših mašinskih elemenata su kvalifikovana prema ISO9001, QS9000 ili TS16949. Osim toga, većina naših proizvoda ima CE ili UL oznaku i ispunjava međunarodno relevantne standarde kao što su ISO, SAE, ASME, DIN. Molimo kliknite na podmenije da dobijete detaljne informacije o elementima naših mašina uključujući: - Kaiševi, lanci i kablovi - Zupčanici i zupčanici - Spojnice i ležajevi - Ključevi i zgibovi i igle - Kamere i veze - Osovine - Mehaničke brtve - Industrijsko kvačilo i kočnica - Pričvršćivači - Jednostavne mašine Pripremili smo referentnu brošuru za naše kupce, dizajnere i programere novih proizvoda uključujući mašinske elemente. Možete se upoznati s nekim uobičajenim terminima u dizajnu komponenti mašina: Preuzmite brošuru za uobičajene termine u mašinstvu koje koriste dizajneri i inženjeri Naši mašinski elementi nalaze primenu u raznim oblastima kao što su industrijske mašine, sistemi automatizacije, oprema za ispitivanje i metrologiju, transportna oprema, građevinske mašine i praktično svuda gde se možete setiti. AGS-TECH razvija i proizvodi mašinske elemente od različitih materijala u zavisnosti od primene. Materijali koji se koriste za elemente strojeva mogu se kretati od oblikovane plastike koja se koristi za igračke do čelika kaljenog i posebno obloženog čelika za industrijske strojeve. Naši dizajneri koriste vrhunski profesionalni softver i alate za dizajn za razvoj mašinskih elemenata, uzimajući u obzir detalje kao što su uglovi u zupcima zupčanika, uključena naprezanja, stope habanja….itd. Pomičite se kroz naše podizbornike i preuzmite naše brošure i kataloge proizvoda da vidite da li možete pronaći gotove strojne elemente za svoju primjenu. Ako ne možete pronaći dobar spoj za svoju aplikaciju, javite nam se i mi ćemo raditi s vama na razvoju i proizvodnji mašinskih elemenata koji će zadovoljiti vaše potrebe. Ako ste uglavnom zainteresirani za naše inženjerske i istraživačko-razvojne sposobnosti umjesto proizvodnih mogućnosti, pozivamo vas da posjetite našu web stranicu http://www.ags-engineering.com gdje možete pronaći detaljnije informacije o našem dizajnu, razvoju proizvoda, razvoju procesa, inženjerskim konsultantskim uslugama i još mnogo toga CLICK Product Finder-Locator Service PRETHODNA STRANICA
- Glass and Ceramic Manufacturing, Hermetic Packages, Seals, Bonding
Glass and Ceramic Manufacturing, Hermetic Packages Seals and Bonding, Tempered Bulletproof Glass, Blow Moulding, Optical Grade Glass, Conductive Glass, Molding Oblikovanje i oblikovanje stakla i keramike Vrste proizvodnje stakla koje nudimo su staklo za kontejnere, puhanje stakla, staklena vlakna i cijevi i šipka, staklo za domaćinstvo i industrijsko staklo, lampe i sijalice, precizne kalupe za staklo, optičke komponente i sklopovi, ravno i limeno i float staklo. Vršimo i ručno i mašinsko oblikovanje. Naši popularni proizvodni procesi tehničke keramike su presovanje, izostatičko prešanje, vruće izostatičko prešanje, vruće prešanje, livenje kliznim slojem, livenje trake, ekstruzija, injekcijsko prešanje, zelena obrada, sinterovanje ili pečenje, dijamantsko brušenje, hermetički sklopovi. Preporučujemo da kliknete ovdje za PREUZMITE naše šematske ilustracije procesa oblikovanja i oblikovanja stakla od strane AGS-TECH Inc. PREUZMITE naše šematske ilustracije tehničkih procesa proizvodnje keramike od strane AGS-TECH Inc. Ove datoteke sa fotografijama i skicama koje možete preuzeti pomoći će vam da bolje razumijete informacije koje vam pružamo u nastavku. • PROIZVODNJA KONTEJNERSKOG STAKLA: Posedujemo automatizovane PRESS AND BLOW kao i PUHANJE I DUVANJE linije za proizvodnju. U procesu duvanja i puhanja ubacimo gob u prazan kalup i formiramo vrat nanošenjem komprimovanog zraka odozgo. Odmah nakon toga, komprimirani zrak se upuhuje drugi put iz drugog smjera kroz vrat posude kako bi se formirao predforma boce. Ova predforma se zatim prenosi u stvarni kalup, ponovo se zagreva da bi omekšala i nanosi se komprimovani vazduh kako bi se predformi dao konačni oblik posude. Eksplicitnije rečeno, on je pod pritiskom i gurnut uza zidove šupljine kalupa za duvanje kako bi poprimio željeni oblik. Konačno, proizvedena staklena posuda se prenosi u peć za žarenje radi naknadnog ponovnog zagrijavanja i uklanjanja naprezanja nastalih tijekom oblikovanja i hladi se na kontrolirani način. U metodi presovanja i puhanja, rastopljeni komadići se stavljaju u parison kalup (prazni kalup) i presuju u parison oblik (prazni oblik). Praznine se zatim prenose u kalupe za puhanje i puhaju na sličan način kao što je gore opisano pod „Proces duvanja i puhanja“. Naknadni koraci poput žarenja i oslobađanja od naprezanja su slični ili isti. • PUHANJE STAKLA: Proizvodimo staklene proizvode koristeći konvencionalno ručno puhanje, kao i korištenje komprimovanog zraka sa automatiziranom opremom. Za neke narudžbe je potrebno konvencionalno puhanje, kao što su projekti koji uključuju umjetnička djela stakla, ili projekti koji zahtijevaju manji broj dijelova sa labavim tolerancijama, prototipovi/demo projekti….itd. Konvencionalno puhanje stakla uključuje uranjanje šuplje metalne cijevi u lonac od rastopljenog stakla i rotiranje cijevi za prikupljanje određene količine staklenog materijala. Staklo skupljeno na vrhu cijevi se valja na ravnom gvožđu, oblikuje po želji, izdužuje, ponovo zagreva i puhuje vazduhom. Kada je spreman, ubacuje se u kalup i uduvava vazduh. Šupljina kalupa je mokra kako bi se izbjegao kontakt stakla sa metalom. Vodeni film djeluje kao jastuk između njih. Ručno puhanje je radno intenzivan spor proces i pogodan je samo za izradu prototipa ili predmeta visoke vrijednosti, nije pogodan za jeftine narudžbe po komadu velike količine. • PROIZVODNJA DOMAĆEG I INDUSTRIJSKOG STAKLA : Koristeći različite vrste staklenog materijala proizvodi se veliki izbor staklenog posuđa. Neke čaše su otporne na toplinu i pogodne za laboratorijsko stakleno posuđe, dok su neke dovoljno dobre da izdrže više puta u perilici posuđa i pogodne su za izradu domaćih proizvoda. Koristeći Westlake mašine dnevno se proizvode desetine hiljada komada čaša za piće. Da pojednostavimo, rastopljeno staklo se skuplja vakuumom i ubacuje u kalupe za izradu pred-forma. Zatim se u kalupe uduvava vazduh, oni se prenose u drugi kalup i ponovo se uduvava vazduh i staklo poprima svoj konačni oblik. Kao i kod ručnog puhanja, ovi kalupi se drže vlažnim vodom. Dalje istezanje je dio završne operacije gdje se formira vrat. Višak stakla je izgoreo. Nakon toga slijedi kontrolirani proces ponovnog zagrijavanja i hlađenja opisan gore. • FORMIRANJE STAKLENE CIJEVI I ŠIPKE: Glavni procesi koje koristimo za proizvodnju staklenih cijevi su DANNER i VELLO procesi. U Dannerovom procesu staklo iz peći teče i pada na kosi rukavac od vatrostalnih materijala. Navlaka se nosi na rotirajućoj šupljoj osovini ili puhanju. Staklo se zatim omota oko rukava i formira glatki sloj koji teče niz rukav i preko vrha osovine. U slučaju oblikovanja cijevi, zrak se upuhuje kroz puhačku cijev sa šupljim vrhom, a kod oblikovanja šipke koristimo čvrste vrhove na osovini. Cijevi ili šipke se zatim prevlače preko nosećih valjaka. Dimenzije kao što su debljina stijenke i prečnik staklenih cijevi se podešavaju na željene vrijednosti postavljanjem prečnika čahure i pritiska zraka na željenu vrijednost, podešavanjem temperature, brzine protoka stakla i brzine izvlačenja. S druge strane, proces proizvodnje staklenih cijevi Vello uključuje staklo koje putuje iz peći u zdjelu sa šupljim trnom ili zvonom. Staklo zatim prolazi kroz zračni prostor između trna i posude i poprima oblik cijevi. Nakon toga putuje preko valjaka do mašine za izvlačenje i hladi se. Na kraju linije hlađenja vrši se rezanje i završna obrada. Dimenzije cijevi se mogu podesiti baš kao u Danner procesu. Kada upoređujemo Danner i Vello proces, možemo reći da je Vello proces bolje prikladan za proizvodnju velikih količina, dok Danner proces može bolje odgovarati za precizne narudžbe cijevi manjeg volumena. • OBRADA LISTOVA I RAVNOG & FLOAT STAKLA: Imamo velike količine ravnog stakla u debljinama od submilimetarske debljine do nekoliko centimetara. Naše ravne naočale su gotovo optičkog savršenstva. Nudimo staklo sa specijalnim premazima kao što su optički premazi, gdje se koristi tehnika hemijskog taloženja pare za nanošenje premaza kao što su antirefleksni ili zrcalni premazi. Uobičajeni su i transparentni provodljivi premazi. Dostupni su i hidrofobni ili hidrofilni premazi na staklu, te premazi koji čine staklo samočistivim. Kaljena, neprobojna i laminirana stakla još su popularni artikli. Staklo režemo u željeni oblik sa željenim tolerancijama. Dostupne su i druge sekundarne operacije kao što je savijanje ili savijanje ravnog stakla. • PRECIZNO MALJSTVO STAKLA: Koristimo ovu tehniku uglavnom za proizvodnju preciznih optičkih komponenti bez potrebe za skupljim i dugotrajnijim tehnikama kao što su brušenje, lepljenje i poliranje. Ova tehnika nije uvijek dovoljna za izradu najboljeg od najbolje optike, ali u nekim slučajevima kao što su proizvodi široke potrošnje, digitalni fotoaparati, medicinska optika može biti jeftinija dobra opcija za proizvodnju velikog obima. Također ima prednost u odnosu na druge tehnike oblikovanja stakla gdje su potrebne složene geometrije, kao što je slučaj sa asferama. Osnovni proces uključuje punjenje donje strane našeg kalupa staklenim blankom, evakuaciju procesne komore za uklanjanje kiseonika, skoro zatvaranje kalupa, brzo i izotermno zagrevanje kalupa i stakla infracrvenim svetlom, dalje zatvaranje polovica kalupa. da se omekšano staklo polako, kontrolisano pritisne do željene debljine, i na kraju hlađenje stakla i punjenje komore azotom i uklanjanje proizvoda. Precizna kontrola temperature, udaljenost za zatvaranje kalupa, sila zatvaranja kalupa, usklađivanje koeficijenata ekspanzije kalupa i staklenog materijala su ključni u ovom procesu. • PROIZVODNJA STAKLENIH OPTIČKIH KOMPONENTI I SKLOPOVA: Osim preciznog oblikovanja stakla, postoji niz vrijednih procesa koje koristimo za izradu visokokvalitetnih optičkih komponenti i sklopova za zahtjevne primjene. Brušenje, lepljenje i poliranje optičkih stakala u finim specijalnim abrazivnim rastvorima je umetnost i nauka za izradu optičkih sočiva, prizmi, ravnih površina i još mnogo toga. Ravnost površine, valovitost, glatkoća i optičke površine bez defekata zahtijevaju puno iskustva s takvim procesima. Male promjene u okruženju mogu rezultirati proizvodima izvan specifikacije i zaustaviti proizvodnu liniju. Postoje slučajevi u kojima jedno brisanje optičke površine čistom krpom može dovesti do toga da proizvod ispuni specifikacije ili da padne na testu. Neki popularni stakleni materijali koji se koriste su topljeni silicijum, kvarc, BK7. Također montaža takvih komponenti zahtijeva specijalizirano iskustvo u niši. Ponekad se koriste posebna ljepila. Međutim, ponekad je tehnika koja se zove optički kontakt najbolji izbor i ne uključuje materijal između pričvršćenih optičkih naočala. Sastoji se od fizičkih dodirivanja ravnih površina kako bi se pričvrstile jedna na drugu bez ljepila. U nekim slučajevima se koriste mehanički odstojnici, precizne staklene šipke ili kuglice, stege ili obrađene metalne komponente za sklapanje optičkih komponenti na određenim udaljenostima i sa određenim geometrijskim orijentacijama jedna prema drugoj. Hajde da ispitamo neke od naših popularnih tehnika za proizvodnju vrhunske optike. BRUŠENJE & LAPIRANJE & POLIRANJE: Grubi oblik optičke komponente dobija se brušenjem staklenog blanka. Nakon toga se vrši labavljenje i poliranje rotacijom i trljanjem grubih površina optičkih komponenti o alate željenog oblika površine. Između optike i alata za oblikovanje ulijevaju se kaša sa sitnim abrazivnim česticama i tekućinom. Veličina abrazivnih čestica u takvim suspenzijama može se odabrati prema željenom stepenu ravnosti. Odstupanja kritičnih optičkih površina od željenih oblika izražavaju se u valnim dužinama svjetlosti koja se koristi. Naša precizna optika ima desetinu valne dužine (valna dužina/10) tolerancije ili je moguće čak i manje. Osim površinskog profila, kritične površine se skeniraju i procjenjuju na druge karakteristike i nedostatke površine kao što su dimenzije, ogrebotine, strugotine, udubljenja, mrlje...itd. Stroga kontrola uslova okoline u optičkom proizvodnom podu i opsežni zahtjevi za mjeriteljstvo i testiranje sa najsavremenijom opremom čine ovu granu industrije izazovnom. • SEKUNDARNI PROCESI U PROIZVODNJI STAKLA: Opet smo ograničeni samo vašom maštom kada su u pitanju sekundarni i završni procesi stakla. Ovdje navodimo neke od njih: -Premazi na staklu (optički, električni, tribološki, termički, funkcionalni, mehanički...). Kao primjer možemo promijeniti svojstva površine stakla tako da ono, na primjer, reflektira toplinu kako bi unutrašnjost zgrade održavala hladnom, ili učiniti da jedna strana apsorbira infracrvene zrake pomoću nanotehnologije. Ovo pomaže u održavanju topline unutrašnjosti zgrada jer će vanjski površinski sloj stakla apsorbirati infracrveno zračenje unutar zgrade i zračiti ga natrag u unutrašnjost. -Etching na staklu -Primijenjeno keramičko označavanje (ACL) -Graviranje -Plamensko poliranje - Hemijsko poliranje -Mrljanje PROIZVODNJA TEHNIČKE KERAMIKE • PREŠANJE U MATERIJALO: Sastoji se od jednoosnog sabijanja granuliranih prahova zatvorenih u kalupu • VRUĆE PREŠANJE: Slično presovanju, ali sa dodatkom temperature radi povećanja gustoće. Prašak ili zbijena predforma stavlja se u grafitnu matricu i primjenjuje se jednoosni pritisak dok se matrica održava na visokim temperaturama kao što je 2000 C. Temperature mogu biti različite u zavisnosti od vrste keramičkog praha koji se obrađuje. Za komplikovane oblike i geometrije može biti potrebna druga naknadna obrada kao što je brušenje dijamanata. • IZOSTATIČKO PREŠANJE: granulirani prah ili komprimirani kompakti se stavljaju u hermetički zatvorene posude, a zatim u zatvorenu posudu pod pritiskom sa tečnošću unutra. Nakon toga se zbijaju povećanjem pritiska posude pod pritiskom. Tečnost unutar posude ravnomerno prenosi sile pritiska preko cele površine hermetičke posude. Materijal se na taj način ravnomjerno zbija i poprima oblik svog fleksibilnog spremnika i svog unutrašnjeg profila i karakteristika. • TOPLO IZOSTATIČKO PREŠANJE: Slično kao izostatičko presovanje, ali pored atmosfere gasa pod pritiskom, sinterujemo kompakt na visokoj temperaturi. Vruće izostatičko presovanje rezultira dodatnom zgušnjavanjem i povećanom čvrstoćom. • LIVANJE KLIZNOM / DRAIN LIJEVANJE : Kalup punimo suspenzijom mikrometarskih keramičkih čestica i tečnosti za nosač. Ova mješavina se naziva "slip". Kalup ima pore i stoga se tekućina iz smjese filtrira u kalup. Kao rezultat, na unutrašnjim površinama kalupa se formira odljevak. Nakon sinterovanja, dijelovi se mogu izvaditi iz kalupa. • LIJEVANJE TRAKA: Proizvodimo keramičke trake lijevanjem keramičkih suspenzija na ravne pokretne noseće površine. Mulj sadrži keramičke prahove pomiješane s drugim hemikalijama za vezivanje i nošenje. Kako rastvarači isparavaju, ostaju guste i fleksibilne ploče od keramike koje se mogu rezati ili valjati po želji. • EKSTRUZIJSKO FORMIRANJE: Kao iu drugim procesima ekstruzije, meka mješavina keramičkog praha sa vezivnim sredstvom i drugim hemikalijama prolazi kroz kalup da dobije oblik poprečnog presjeka, a zatim se reže na željene dužine. Proces se izvodi hladnim ili zagrijanim keramičkim mješavinama. • INJEKTIRANJE NISKIM PRITISKOM: Pripremamo mešavinu keramičkog praha sa vezivnim sredstvima i rastvaračima i zagrevamo je na temperaturu na kojoj se lako može pritisnuti i ugurati u šupljinu alata. Kada se ciklus oblikovanja završi, dio se izbacuje i hemikalija za vezivanje se spaljuje. Koristeći brizganje, možemo ekonomično dobiti složene dijelove u velikim količinama. Rupe koje su sićušni delić milimetra na zidu debljine 10 mm su moguće, navoji su mogući bez dalje obrade, tolerancije od +/- 0,5% su moguće i čak niže kada se delovi obrađuju , moguće su debljine zidova od 0,5 mm do dužine od 12,5 mm kao i debljine zidova od 6,5 mm do dužine od 150 mm. • ZELENA OBRADA: Koristeći iste alate za mašinsku obradu metala, možemo obraditi presovane keramičke materijale dok su još mekani poput krede. Moguća su odstupanja od +/- 1%. Za bolje tolerancije koristimo dijamantsko brušenje. • SINTERING ili PEČENJE: Sinterovanje omogućava potpuno zgušnjavanje. Na zelenim kompaktnim dijelovima dolazi do značajnog skupljanja, ali to nije veliki problem jer ove promjene dimenzija uzimamo u obzir kada dizajniramo dio i alat. Čestice praha su međusobno povezane i poroznost izazvana procesom zbijanja se u velikoj mjeri uklanja. • BRUŠENJE DIJAMANTA: Najtvrđi materijal na svijetu “dijamant” se koristi za mljevenje tvrdih materijala kao što je keramika i dobijaju se precizni dijelovi. Postižu se tolerancije u mikrometarskom opsegu i vrlo glatke površine. Zbog troškova, ovu tehniku razmatramo samo kada nam je zaista potrebna. • HERMETIČKI SKLOPOVI su oni koji praktično ne dozvoljavaju bilo kakvu razmenu materija, čvrstih materija, tečnosti ili gasova između interfejsa. Hermetičko zaptivanje je hermetičko. Na primjer, hermetička elektronska kućišta su ona koja čuvaju osjetljivi unutrašnji sadržaj upakovanog uređaja neoštećenim od vlage, zagađivača ili plinova. Ništa nije 100% hermetičko, ali kada govorimo o hermetičnosti, mislimo da u praksi, da postoji hermetičnost do te mere da je stopa curenja toliko niska da su uređaji bezbedni u normalnim uslovima okoline veoma dugo. Naši hermetički sklopovi se sastoje od metalnih, staklenih i keramičkih komponenti, metal-keramika, keramika-metal-keramika, metal-keramika-metal, metal na metal, metal-staklo, metal-staklo-metal, staklo-metal-staklo, staklo- metal i staklo na staklo i sve druge kombinacije spajanja metal-staklo-keramika. Na primjer, možemo premazati metalom keramičke komponente tako da mogu biti čvrsto vezane za druge komponente u sklopu i imaju odličnu sposobnost brtvljenja. Imamo znanje i iskustvo za oblaganje optičkih vlakana ili prolaza metalom i njihovo lemljenje ili lemljenje na kućišta, tako da plinovi ne prolaze ili ne propuštaju u kućišta. Stoga se koriste za proizvodnju elektronskih kućišta za kapsuliranje osjetljivih uređaja i zaštitu od vanjske atmosfere. Osim njihovih odličnih karakteristika zaptivanja, druga svojstva kao što su koeficijent toplinske ekspanzije, otpornost na deformacije, priroda ne ispuštanja plinova, vrlo dug vijek trajanja, neprovodna priroda, svojstva toplinske izolacije, antistatička priroda...itd. čine staklo i keramičke materijale izborom za određene primjene. Informacije o našem pogonu za proizvodnju spojeva od keramike do metala, hermetičkog zaptivanja, vakuumskih prolaza, visokog i ultravisokog vakuuma i komponenti za kontrolu fluida možete pronaći ovdje:Brošura tvornice hermetičkih komponenti CLICK Product Finder-Locator Service PRETHODNA STRANICA
- Wire & Spring Forming, Shaping, Welding, Assembly of Wires, Coil, CNC
Wire & Spring Forming, Shaping, Welding, Assembly of Wires, Coil Compression Extension Torsion Flat Springs, Custom Wires, Helical Springs at AGS-TECH Inc. Oblikovanje žice i opruge Izrađujemo žice po narudžbi, montažu žice, žice oblikovane u željene 2D i 3D oblike, žičane mreže, mreže, kućišta, korpe, ograde, žičane opruge, ravne opruge; torzija, kompresija, napetost, ravne opruge i još mnogo toga. Naši procesi su oblikovanje žice i opruga, izvlačenje žice, oblikovanje, savijanje, zavarivanje, lemljenje, lemljenje, bušenje, navijanje, bušenje, skošenje, brušenje, urezivanje navoja, premazivanje, četveroklizno, oblikovanje klizača, namotavanje, namotavanje, namještanje. Preporučujemo da kliknete ovdje za PREUZMITE naše šematske ilustracije procesa oblikovanja žice i opruga od strane AGS-TECH Inc. Ova datoteka sa fotografijama i skicama za preuzimanje pomoći će vam da bolje razumijete informacije koje vam pružamo u nastavku. • IZVLAČENJE ŽICE: Koristeći vlačne sile rastežemo metalni materijal i provlačimo ga kroz kalup kako bismo smanjili prečnik i povećali njegovu dužinu. Ponekad koristimo niz matrica. U mogućnosti smo da napravimo kalupe za svaki prečnik žice. Koristeći materijal visoke vlačne čvrstoće izvlačimo vrlo tanke žice. Nudimo i hladno i toplo obrađene žice. • FORMIRANJE ŽICE: Rola procijenjene žice se savija i oblikuje u koristan proizvod. Imamo mogućnost formiranja žica svih mjerača, uključujući tanke niti, kao i debele žice poput onih koje se koriste kao opruge ispod šasije automobila. Oprema koju koristimo za oblikovanje žice su ručne i CNC mašine za formiranje žice, namotač, elektro preše, četveroklizni, višeklizni. Naši procesi su izvlačenje, savijanje, ravnanje, ravnanje, istezanje, rezanje, narušavanje, lemljenje i zavarivanje i lemljenje, montaža, namotavanje, savijanje (ili krilo), bušenje, urezivanje žice, bušenje, skošenje, brušenje, premazivanje i površinska obrada. Naša najmodernija oprema može se postaviti za razvoj vrlo složenih dizajna bilo kojeg oblika i uskih tolerancija. Nudimo različite tipove krajeva like sferične, šiljaste ili zakošene krajeve za vaše žice. Većina naših projekata oblikovanja žice ima minimalne do nulte troškove alata. Vrijeme obrade uzorka je općenito dani. Promjene u dizajnu/konfiguraciji žičanih oblika mogu se izvršiti vrlo brzo. • FORMIRANJE OPRUGA: AGS-TECH proizvodi veliki izbor opruga uključujući: -Torziona / dvostruka torzijska opruga - Zatezna / kompresiona opruga -Konstantna / varijabilna opruga -Zavojnica i spiralna opruga -Flat & Leaf Spring -Balance Spring -Belleville Washer -Negator Spring -Progresivna zavojna opruga - Talasno proljeće -Volute Spring -Tapered Springs -Proljetno prstenje -Clock Springs -Klipovi Proizvodimo opruge od raznih materijala i možemo vas voditi prema vašoj primjeni. Najčešći materijali su nerđajući čelik, hrom silicij, visokougljični čelik, niskougljenični čelik kaljen u ulju, hrom vanadijum, fosforna bronza, titan, legura berilijum bakra, visokotemperaturna keramika. Koristimo različite tehnike u proizvodnji opruga, uključujući CNC namotavanje, hladno namotavanje, toplo namotavanje, kaljenje, doradu. Druge tehnike koje su već pomenute u okviru formiranja žice su takođe uobičajene u našim operacijama proizvodnje opruga. • ZAVRŠNE USLUGE ZA ŽICE I OPRUGE: Vaše proizvode možemo završiti na mnogo načina u zavisnosti od vašeg izbora i potreba. Neki uobičajeni procesi koje nudimo su: farbanje, premazivanje prahom, galvanizacija, potapanje vinila, eloksiranje, oslobađanje od stresa, toplinska obrada, brizganje, prevrtanje, kromat, bezelektrični nikl, plastika, pečeni emajl , plazma čišćenje. CLICK Product Finder-Locator Service PRETHODNA STRANICA
- Forging and Powdered Metallurgy, Die Forging, Heading, Hot Forging
Forging and Powdered Metallurgy, Die Forging, Heading, Hot Forging, Impression Die, Near Net Shape, Swaging, Metal Hobbing, Riveting, Coining from AGS-TECH Inc. Kovanje metala i metalurgija praha Tip procesa KOVANJA METALA koje nudimo su vruće i hladne matrice, otvorene i zatvorene kalupe, otiske i otkovci bez flešovanja, cogging, punjenje, ivica i precizno kovanje, oblik skoro mreže, , swaging, isturen kovanje, metal hobbing, press & roll & radijalno i orbitalno i prstenasto i izotermno kovanje, kovanje, zakivanje, kovanje metalnih kuglica, metalni piercing, dimenzioniranje, kovanje visoke energije. Naše tehnike METALURGIJE PRAŠKA i PRERADE PRAŠKA su presovanje i sinterovanje praha, impregnacija, infiltracija, toplo i hladno izostatičko prešanje, brizganje metala, sabijanje u rolama, valjanje praha, ekstruzija praha, sinterovanje u prahu, sinterovanje iskre, vruće prešanje. Preporučujemo da kliknete ovdje za PREUZMITE naše šematske ilustracije procesa kovanja od strane AGS-TECH Inc. PREUZMITE naše šematske ilustracije procesa metalurgije praha od strane AGS-TECH Inc. Ove datoteke sa fotografijama i skicama koje možete preuzeti pomoći će vam da bolje razumijete informacije koje vam pružamo u nastavku. Kod kovanja metala primjenjuju se tlačne sile i materijal se deformiše i dobija se željeni oblik. Najčešći kovani materijali u industriji su željezo i čelik, ali i brojni drugi kao što su aluminij, bakar, titan, magnezij također su široko rasprostranjeni. Kovani metalni delovi imaju poboljšanu zrnastu strukturu pored zapečaćenih pukotina i zatvorenih praznih prostora, pa je čvrstoća delova dobijenih ovim postupkom veća. Kovanjem se dobijaju delovi koji su značajno jači u odnosu na svoju težinu od delova napravljenih livenjem ili mašinskom obradom. Budući da se kovani dijelovi oblikuju tako što metal teče u svoj konačni oblik, metal poprima usmjerenu strukturu zrna koja objašnjava superiornu čvrstoću dijelova. Drugim riječima, dijelovi dobiveni postupkom kovanja pokazuju bolja mehanička svojstva u odnosu na jednostavne livene ili obrađene dijelove. Težina metalnih otkovaka može se kretati od malih lakih dijelova do stotina hiljada funti. Proizvodimo otkovke uglavnom za mehanički zahtjevne primjene gdje se primjenjuju velika naprezanja na dijelove kao što su dijelovi automobila, zupčanici, radni alati, ručni alati, osovine turbina, motocikli. Budući da su troškovi alata i podešavanja relativno visoki, ovaj proizvodni proces preporučujemo samo za proizvodnju velikog obima i za kritične komponente male količine, ali visoke vrijednosti kao što je stajni trap za zrakoplovstvo. Osim troškova alata, vrijeme proizvodnje velikih količina kovanih dijelova može biti duže u poređenju sa nekim jednostavnim strojno obrađenim dijelovima, ali tehnika je ključna za dijelove koji zahtijevaju izvanrednu čvrstoću kao što su vijci, matice, posebna primjena pričvršćivači, automobili, viljuškari, dijelovi za dizalice. • TOPLO KOVANJE I HLADNO KOVANJE: Vruće kovanje, kao što naziv govori, izvodi se na visokim temperaturama, stoga je duktilnost visoka, a čvrstoća materijala niska. To olakšava deformaciju i kovanje. Naprotiv, hladno kovanje se izvodi na nižim temperaturama i zahtijeva veće sile što rezultira stvrdnjavanjem deformacijom, boljom završnom obradom površine i preciznošću proizvedenih dijelova. • OTVORENO KOVANJE I UTISNO KOVANJE: Kod otvorenog kovanja, matrice ne ograničavaju materijal koji se sabija, dok kod kovanja otiskom kalupom šupljine unutar kalupa ograničavaju protok materijala dok se kovanje u željeni oblik. UPSET FORGING ili se još naziva UPSETTING, što zapravo nije isti već vrlo sličan proces, je otvoreni proces matrice gdje je radni komad u sendviču između dvije ravne kalupe i tlačna sila smanjuje njegovu visinu. Kako se visina smanjuje, širina radnog komada se povećava. HEADING, proces iskrivljenog kovanja uključuje cilindrični materijal koji je na svom kraju narušen i njegov poprečni presjek je povećan lokalno. U zaglavlju se kundak uvlači kroz kalup, kuje i zatim seče na dužinu. Operacija je u stanju da brzo proizvede velike količine zatvarača. Uglavnom se radi o hladnoj obradi jer se koristi za izradu krajeva eksera, krajeva vijaka, matica i vijaka gdje materijal treba ojačati. Drugi proces otvorene matrice je ZUBLJENJE, gdje se radni komad kuje u nizu koraka sa svakim korakom što rezultira kompresijom materijala i naknadnim kretanjem otvorene matrice duž dužine radnog komada. Na svakom koraku debljina se smanjuje, a dužina se malo povećava. Proces nalikuje nervoznom studentu koji u malim koracima grize olovku. Proces koji se zove FULLERING je još jedna metoda otvorenog kovanja koju često koristimo kao raniji korak za distribuciju materijala u radnom komadu prije nego što se dogode druge operacije kovanja metala. Koristimo ga kada radni komad zahtijeva nekoliko forging operacija. U radu se matrica sa konveksnim površinama deformira i uzrokuje istjecanje metala na obje strane. Sličan proces punjenja, KUTIRANJE s druge strane uključuje otvorenu matricu sa konkavnim površinama za deformaciju radnog komada. Ivica je također pripremni proces za naknadne operacije kovanja čini da materijal teče s obje strane u područje u sredini. IMPRESIJSKO KOVANJE ili ZATVORENO KOVANJE, kako ga još nazivaju, koristi matricu / kalup koji komprimira materijal i ograničava njegov protok unutar sebe. Matrica se zatvara i materijal poprima oblik šupljine kalupa. PRECIZNO KOVANJE, proces koji zahteva specijalnu opremu i kalup, proizvodi delove bez ili sa vrlo malo fleka. Drugim riječima, dijelovi će imati približne konačne dimenzije. U ovom procesu pažljivo se ubacuje dobro kontrolirana količina materijala i postavlja unutar kalupa. Ovu metodu primenjujemo za složene oblike sa tankim presecima, malim tolerancijama i uglovima promaja i kada su količine dovoljno velike da opravdaju troškove kalupa i opreme. • KOVANJE BEZ BLAGOVANJA: Radni komad se postavlja u kalup na takav način da nijedan materijal ne može da iscuri iz šupljine i formira fleš. Stoga nije potrebno neželjeno skraćivanje blica. To je precizan proces kovanja i stoga zahtijeva blisku kontrolu količine korištenog materijala. • KLUBANJE METALA ili RADIJALNO KOVANJE: Na radni komad se obodno djeluje matrica i kuje. Trn se takođe može koristiti za kovanje geometrije unutrašnjeg radnog komada. U operaciji zavijanja radni komad obično prima nekoliko udaraca u sekundi. Tipični predmeti koji se proizvode savijanjem su alati sa šiljastim vrhom, konusne šipke, odvijači. • PROBUŠANJE METALA: Ovu operaciju često koristimo kao dodatnu operaciju u proizvodnji dijelova. Probijanjem na površini radnog komada stvara se rupa ili šupljina bez probijanja. Imajte na umu da se bušenje razlikuje od bušenja koje rezultira prolaznom rupom. • HOBING : Proboj željene geometrije se utiskuje u radni komad i stvara šupljinu željenog oblika. Ovaj punch zovemo HOB. Operacija uključuje visoke pritiske i izvodi se na hladnom. Kao rezultat, materijal je hladno obrađen i stvrdnut deformacijom. Stoga je ovaj proces vrlo pogodan za proizvodnju kalupa, kalupa i šupljina za druge proizvodne procese. Jednom kada je ploča za kuhanje proizvedena, lako se može proizvesti mnogo identičnih šupljina bez potrebe da se obrađuju jednu po jednu. • KOVANJE VALJKAMA ili OBLIKOVANJE VALJKA: Dva suprotna valjaka se koriste za oblikovanje metalnog dijela. Radni komad se ubacuje u valjke, rolne se okreću i uvlače rad u zazor, rad se zatim uvlači kroz užljebljeni dio valjaka i tlačne sile daju materijalu željeni oblik. To nije proces valjanja već proces kovanja, jer je to diskretna, a ne kontinuirana operacija. Geometrija na rolnama kuje materijal do traženog oblika i geometrije. Izvodi se toplo. Budući da je proces kovanja, proizvodi dijelove sa izvanrednim mehaničkim svojstvima i stoga ga koristimo za proizvodnju automobilskih dijelova kao što su osovine koje moraju imati izuzetnu izdržljivost u teškim radnim okruženjima. • ORBITALNO KOVANJE: Radni komad se stavlja u šupljinu kalupa za kovanje i kuje pomoću gornje matrice koja putuje orbitalnom putanjom dok se okreće oko nagnute ose. Pri svakom okretu, gornja matrica završava djelovanjem tlačne sile na cijeli radni komad. Ponavljanjem ovih okretaja više puta, vrši se dovoljno kovanja. Prednosti ove proizvodne tehnike su niska razina buke i manje potrebne sile. Drugim riječima, uz male sile može se okretati teška matrica oko ose kako bi se izvršili veliki pritisci na dio radnog komada koji je u kontaktu s kalupom. Dijelovi u obliku diska ili konusnog oblika ponekad su dobri za ovaj proces. • KOVANJE PRSTENOVA: Često koristimo za proizvodnju bešavnih prstenova. Kućište se iseče na dužinu, izbode i zatim probuši do kraja kako bi se stvorila centralna rupa. Zatim se stavlja na trn i kovana matrica ga zabija odozgo dok se prsten polako okreće dok se ne dobiju željene dimenzije. • ZAKIVANJE: Uobičajen proces spajanja delova, počinje sa ravnim metalnim komadom umetnutim u prethodno napravljene rupe kroz delove. Nakon toga se dva kraja metalnog komada kovaju stiskanjem spoja između gornje i donje matrice. • KOVANJE: Još jedan popularan proces koji se izvodi mehaničkom presom, pri čemu se na kratkoj udaljenosti vrše velike sile. Naziv “kovanja” dolazi od finih detalja koji su iskovani na površinama metalnih kovanica. To je uglavnom proces završne obrade proizvoda gdje se fini detalji dobijaju na površinama kao rezultat velike sile koju primjenjuje matrica koja prenosi te detalje na radni komad. • KOVANJE METALNIH KUGLICA: Proizvodi kao što su kuglični ležajevi zahtevaju visokokvalitetne, precizno proizvedene metalne kuglice. U jednoj tehnici koja se zove ISKOSNO VALJANJE, koristimo dva suprotna valjka koja se neprekidno rotiraju dok se materijal kontinuirano ubacuje u rolne. Na jednom kraju dva valjka metalne sfere se izbacuju kao proizvod. Druga metoda za kovanje metalnih kuglica je korištenje kalupa koji istiskuju materijal postavljen između njih uzimajući sferni oblik šupljine kalupa. Često proizvedene kuglice zahtijevaju neke dodatne korake kao što su dorada i poliranje kako bi postale visokokvalitetan proizvod. • IZOTERMIČNO KOVANJE / TOPLO KOVANJE: Skup proces koji se izvodi samo kada je vrijednost koristi/troška opravdana. Proces vruće obrade u kojem se matrica zagrijava na približno istu temperaturu kao i radni komad. Budući da su i kalup i radna masa približno iste temperature, nema hlađenja i poboljšane su karakteristike protoka metala. Operacija je dobra za super legure i materijale sa lošijom sposobnošću kovanja i materijale čiji mehanička svojstva su vrlo osjetljiva na male temperaturne gradijente i promjene. • VELIČINA METALA: To je proces hladne završne obrade. Protok materijala je neograničen u svim smjerovima, osim u smjeru u kojem se primjenjuje sila. Kao rezultat, dobijaju se vrlo dobra završna obrada površine i točne dimenzije. • KOVANJE VISOKE ENERGIJE : Tehnika uključuje gornji kalup pričvršćen za krak klipa koji se brzo gura dok se mješavina goriva i zraka pali svjećicom. Podsjeća na rad klipova u motoru automobila. Kalup vrlo brzo udari u radni komad, a zatim se vrlo brzo vraća u prvobitni položaj zahvaljujući povratnom pritisku. Rad se kuje u roku od nekoliko milisekundi i stoga nema vremena da se rad ohladi. Ovo je korisno za dijelove koji se teško kovaju koji imaju mehanička svojstva vrlo osjetljiva na temperaturu. Drugim riječima, proces je toliko brz da se dio formira pod konstantnom temperaturom i neće biti temperaturnih gradijenta na sučeljima kalup/obradni komad. • U KOVANJU MATERIJALOM, metal se tuče između dva odgovarajuća čelična bloka sa posebnim oblicima u njima, koji se nazivaju kalupi. Kada se metal zabije između kalupa, on poprima isti oblik kao i oblici u kalupu. Kada dostigne konačni oblik, vadi se da se ohladi. Ovaj proces proizvodi jake dijelove koji su preciznog oblika, ali zahtijevaju veća ulaganja za specijalizirane kalupe. Uznemireno kovanje povećava prečnik komada metala tako što ga spljošti. Obično se koristi za izradu malih dijelova, posebno za formiranje glava na pričvršćivačima poput vijaka i eksera. • METALURGIJA PRAŠKA / PRERADA PRAŠKA: Kao što naziv govori, uključuje proizvodne procese za izradu čvrstih delova određene geometrije i oblika od praha. Ako se u tu svrhu koriste metalni prahovi, to je oblast metalurgije praha, a ako se koriste nemetalni prahovi, to je prerada praha. Čvrsti dijelovi se proizvode od praha presovanjem i sinterovanjem. POWDER PRESSING se koristi za kompaktiranje pudera u željene oblike. Prvo, primarni materijal se fizički usitnjava u prah, dijeleći ga na mnogo malih pojedinačnih čestica. Smjesa praha se puni u kalup i bušilica se kreće prema prahu i kompaktira ga u željeni oblik. Uglavnom se izvodi na sobnoj temperaturi, prešanjem praha dobija se čvrsti dio i naziva se zeleni kompakt. Veziva i maziva se obično koriste za poboljšanje kompaktabilnosti. Osposobljeni smo za prešanje praha pomoću hidrauličkih presa kapaciteta nekoliko hiljada tona. Takođe imamo prese sa dvostrukim dejstvom sa suprotnim gornjim i donjim udarcima, kao i višestruke prese za veoma složene geometrije delova. Ujednačenost koja je važan izazov za mnoge fabrike za metalurgiju praha / preradu praha nije veliki problem za AGS-TECH zbog našeg dugogodišnjeg iskustva u proizvodnji takvih delova po meri. Čak i sa debljim dijelovima gdje ujednačenost predstavlja izazov, uspjeli smo. Ako se posvetimo vašem projektu, mi ćemo napraviti vaše dijelove. Ako uočimo bilo kakve potencijalne rizike, obavijestit ćemo vas in unaprijed. SINTERIRANJE PRAŠKA, što je drugi korak, podrazumijeva podizanje temperature do određenog stepena i održavanje temperature na tom nivou određeno vrijeme kako bi se čestice praha u presovanom dijelu mogle međusobno povezati. To rezultira mnogo jačim vezama i jačanjem radnog komada. Sinterovanje se odvija blizu temperature topljenja praha. Tokom sinterovanja dolazi do skupljanja, povećava se čvrstoća materijala, gustina, duktilnost, toplotna provodljivost, električna provodljivost. Imamo serijske i kontinualne peći za sinterovanje. Jedna od naših mogućnosti je prilagođavanje nivoa poroznosti dijelova koje proizvodimo. Na primjer, u mogućnosti smo proizvesti metalne filtere držeći dijelove poroznima do određenog stepena. Koristeći tehniku koja se zove IMPREGNACIJA, punimo pore u metalu tekućinom kao što je ulje. Proizvodimo na primjer ležajeve impregnirane uljem koji su samopodmazujući. U procesu INFILTRACIJE ispunjavamo pore metala drugim metalom niže tačke topljenja od osnovnog materijala. Smjesa se zagrijava do temperature između temperatura topljenja dva metala. Kao rezultat, mogu se dobiti neka posebna svojstva. Također često izvodimo sekundarne operacije kao što su strojna obrada i kovanje na dijelovima proizvedenim u prahu kada je potrebno dobiti posebne karakteristike ili svojstva ili kada se dio može proizvesti s manje koraka procesa. IZOSTATIČKO PRESANJE: U ovom procesu se koristi pritisak tekućine za sabijanje dijela. Metalni prah se stavlja u kalup napravljen od zatvorene fleksibilne posude. Kod izostatičkog presovanja, pritisak se primenjuje sa svih strana, za razliku od aksijalnog pritiska koji se vidi kod konvencionalnog presovanja. Prednosti izostatičkog presovanja su ujednačena gustina unutar dela, posebno za veće ili deblje delove, vrhunska svojstva. Njegov nedostatak je dugo vrijeme ciklusa i relativno niska geometrijska preciznost. HLADNO IZOSTATIČKO PREŠANJE vrši se na sobnoj temperaturi, a fleksibilni kalup je izrađen od gume, PVC-a ili uretana ili sličnih materijala. Tečnost koja se koristi za pritisak i sabijanje je ulje ili voda. Nakon toga slijedi konvencionalno sinteriranje zelenog kompakta. VRUĆE IZOSTATIČKO PREŠANJE se s druge strane vrši na visokim temperaturama, a materijal kalupa je lim ili keramika sa dovoljno visokom tačkom topljenja koja je otporna na temperature. Fluid pod pritiskom je obično inertni gas. Operacije presovanja i sinterovanja izvode se u jednom koraku. Poroznost je skoro potpuno eliminisana, dobija se uniformna grain struktura. Prednost vrućeg izostatskog prešanja je u tome što može proizvesti dijelove koji se mogu usporediti s lijevanjem i kovanjem u kombinaciji, a istovremeno omogućava upotrebu materijala koji nisu pogodni za livenje i kovanje. Nedostatak vrućeg izostatskog prešanja je njegovo veliko vrijeme ciklusa, a time i cijena. Pogodan je za kritične dijelove male zapremine. brizganje metala : Veoma pogodan proces za proizvodnju složenih dijelova sa tankim zidovima i detaljnim geometrijama. Najprikladniji za manje dijelove. Praškovi i polimerno vezivo se miješaju, zagrijavaju i injektiraju u kalup. Polimerno vezivo oblaže površine čestica praha. Nakon oblikovanja, vezivo se uklanja ili zagrijavanjem na niskoj temperaturi ili otopljenim pomoću rastvarača. KOMPAKCIJA VALJKA / VALJANJE PRAŠKA: Prašci se koriste za proizvodnju kontinuiranih traka ili limova. Prah se napaja iz hranilice i sabija pomoću dva rotirajuća valjka u lim ili trake. Operacija se izvodi hladno. List se prenosi u peć za sinterovanje. Proces sinterovanja se može ponoviti drugi put. EKSTRUZIJA PRAŠKA: Dijelovi sa velikim odnosom dužine i prečnika se proizvode ekstrudiranjem tankog limenog kontejnera sa prahom. SINTERIRANJE: Kao što naziv govori, to je metoda sabijanja i sinterovanja bez pritiska, pogodna za proizvodnju vrlo poroznih dijelova kao što su metalni filteri. Prah se unosi u šupljinu kalupa bez sabijanja. SINTERIRANJE: Kao što naziv govori, to je metoda sabijanja i sinterovanja bez pritiska, pogodna za proizvodnju vrlo poroznih dijelova kao što su metalni filteri. Prah se unosi u šupljinu kalupa bez sabijanja. ISKRIČNO SINTERING: Prah se komprimira u kalupu pomoću dva suprotna udarca i električna struja velike snage se primjenjuje na bušilicu i prolazi kroz zbijeni prah smješten između njih. Visoka struja sagorijeva površinske filmove s čestica praha i sinteruje ih sa stvorenom toplinom. Proces je brz jer se toplina ne primjenjuje izvana, već se stvara unutar kalupa. TOPLO PREŠANJE: praškovi se presuju i sinteruju u jednom koraku u kalupu koji može da izdrži visoke temperature. Kako se matrica sabija, na nju se primjenjuje toplina praha. Dobra tačnost i mehanička svojstva postignuta ovom metodom čine je atraktivnom opcijom. Čak se i vatrostalni metali mogu obraditi korištenjem materijala za kalupe kao što je grafit. CLICK Product Finder-Locator Service PRETHODNI MENI
- Sheet Metal Forming Fabrication, Stamping, Punching, Deep Drawing, CNC
Sheet Metal Forming and Fabrication, Stamping, Punching, Bending, Progressive Die, Spot Welding, Deep Drawing, Metal Blanking and Slitting at AGS-TECH Inc. Štancanje i izrada limova Nudimo štancanje limova, oblikovanje, oblikovanje, savijanje, probijanje, izrezivanje, prorezivanje, perforiranje, urezivanje, grickanje, brijanje, presovanje, izradu, duboko izvlačenje pomoću jednostrukih / jednohodnih kalupa kao i progresivne kalupe i predenje, oblikovanje gume i hidroformiranje; rezanje lima vodenim mlazom, plazmom, laserom, pilom, plamenom; montaža lima zavarivanjem, tačkasto zavarivanje; ispupčenje i savijanje limene cijevi; završna obrada limova uključujući farbanje potapanjem ili sprejom, elektrostatičko nanošenje praha, eloksiranje, galvaniziranje, prskanje i još mnogo toga. Naše usluge se kreću od brze izrade prototipa limova do proizvodnje velikih količina. Preporučujemo da kliknete ovdje zaPREUZMITE naše šematske ilustracije procesa proizvodnje limova i štancanja od strane AGS-TECH Inc. Ovo će vam pomoći da bolje razumijete informacije koje vam pružamo u nastavku. • REZANJE LIMA : Nudimo REZE i DELOVE. Reznice režu lim po jednoj putanji i u osnovi nema otpada materijala, dok se kod odvajanja oblik ne može precizno ugnijezditi i samim tim se određena količina materijala gubi. Jedan od naših najpopularnijih procesa je PROBAVANJE, gdje se iz lima izrezuje komad materijala okruglog ili drugog oblika. Komad koji se iseče je otpad. Druga verzija probijanja je PROJEKANJE, gdje se probijaju pravokutne ili izdužene rupe. BLANKIRANJE je s druge strane isti proces kao i bušenje, s tim da je odlika komada koji se izrezuje je rad i koji se čuva. FINE BLANKING, superiorna verzija slepljivanja, stvara rezove sa bliskim tolerancijama i ravnim glatkim ivicama i ne zahteva sekundarne operacije za savršenstvo radnog komada. Drugi proces koji često koristimo je REZANJE, što je proces smicanja u kojem se lim seče sa dvije suprotne kružne oštrice na ravnoj ili zakrivljenoj putanji. Otvarač za konzerve je jednostavan primjer procesa rezanja. Još jedan popularan proces za nas je PERFORIRANJE, gdje se mnoge rupe okruglog ili drugog oblika probijaju u limu po određenom uzorku. Tipičan primjer za perforirani proizvod su metalni filteri s mnogo rupa za tekućine. U NOTCHING, još jednom procesu rezanja lima, uklanjamo materijal sa radnog komada, počevši od ruba ili negdje drugdje i režemo prema unutra dok se ne dobije željeni oblik. To je progresivan proces gdje se svakom operacijom uklanja još jedan komad dok se ne dobije željena kontura. Za male serije proizvodnje ponekad koristimo relativno sporiji proces koji se zove NIBBLING koji se sastoji od mnogih brzih probijanja rupa koje se preklapaju kako bi se napravio veći složeniji rez. U PROGRESIVNOM REZANJU koristimo niz različitih operacija da bismo dobili jedan rez ili određenu geometriju. Konačno, BRIJANJE, sekundarni proces nam pomaže da poboljšamo ivice već napravljenih rezova. Koristi se za rezanje strugotine, grubih ivica na limovima. • SAVIJANJE LIMA: Osim rezanja, savijanje je bitan proces bez kojeg ne bismo mogli proizvesti većinu proizvoda. Uglavnom rad na hladnom, ali se ponekad izvodi i kada je toplo ili vruće. Za ovu operaciju koristimo matrice i prešanje većinu vremena. U PROGRESIVNOM SAVIANJU koristimo seriju različitih operacija probijanja i kalupa da bismo dobili jedno savijanje ili određenu geometriju. AGS-TECH koristi različite procese savijanja i pravi izbor u zavisnosti od materijala obratka, njegove veličine, debljine, željene veličine savijanja, radijusa, zakrivljenosti i ugla savijanja, lokacije savijanja, ekonomičnosti rada, količina za proizvodnju… itd. Koristimo V-SAVIJANJE gdje proboj u obliku slova V gura lim u kalup u obliku slova V i savija ga. Dobro za vrlo oštre i tupe uglove i između njih, uključujući 90 stepeni. Koristeći matrice za brisanje izvodimo SAVIJANJE Ivica. Naša oprema nam omogućava da dobijemo uglove i veće od 90 stepeni. Kod savijanja rubova radni komad je u sendviču između tlačne ploče i kalupa, područje za savijanje se nalazi na rubu matrice, a ostatak radnog komada se drži preko space kao konzolna greda. Kada udarac djeluje na konzolni dio, on se savija preko ruba matrice. FLANGING je proces savijanja ivica koji rezultira uglom od 90 stepeni. Glavni ciljevi operacije su uklanjanje oštrih ivica i dobijanje geometrijskih površina radi lakšeg spajanja delova. BEADING, još jedan uobičajeni proces savijanja rubova formira uvojak preko ruba dijela. OŠIVANJE s druge strane rezultira s rubom čaršava koji je potpuno savijen na sebe. U ŠIVANJU se rubovi dva dijela savijaju jedan na drugi i spajaju. S druge strane, DVOSTRUKI SEAMING obezbeđuje vodonepropusne i hermetičke spojeve limova. Slično savijanju ivica, proces koji se zove ROTACIJSKO SAVIJANJE razvija cilindar sa željenim uglom izrezanim i služi kao proboj. Kako se sila prenosi na proboj, on se zatvara sa izratkom. Žljeb cilindra daje konzolnom dijelu željeni ugao. Žleb može imati ugao manji ili veći od 90 stepeni. U AIR BENDING, ne treba nam donja matrica da ima žljeb pod uglom. Lim je oslonjen na dvije površine na suprotnim stranama i na određenoj udaljenosti. Probijač tada primjenjuje silu na pravo mjesto i savija radni komad. SAVIJANJE KANALA se izvodi pomoću probijača i matrice u obliku kanala, a U-BEND se postiže probijanjem u obliku slova U. OFFSET BENDING proizvodi pomake na limu. ROLL BENDING, tehnika dobra za debele radove i savijanje velikih komada metalnih ploča, koristi tri valjka za povlačenje i savijanje ploča do željene zakrivljenosti. Rolne se poredaju tako da se dobije željeni zavoj rada. Udaljenost i ugao između valjaka se kontrolira kako bi se postigao željeni rezultat. Pokretna rolna omogućava kontrolu zakrivljenosti. FORMIRANJE CIJEVI je još jedna popularna operacija savijanja limova koja uključuje više kalupa. Cijevi se dobijaju nakon više radnji. KORUGACIJA se takođe izvodi operacijama savijanja. U osnovi je to simetrično savijanje u pravilnim intervalima preko cijelog komada lima. Za valovanje se mogu koristiti različiti oblici. Valoviti lim je čvršći i ima bolju otpornost na savijanje i stoga ima primjenu u građevinskoj industriji. FORMIRANJE VALJKA LIMA, kontinuirani proces proizvodnje koristi se za savijanje poprečnih presjeka određene geometrije pomoću valjaka i rad se savija u uzastopnim koracima, pri čemu finalna rola završava rad. U nekim slučajevima se koristi jedno rolo, au nekim slučajevima niz rolni. • KOMBINOVANI PROCESI REZANJA I SAVIJANJA LIMA: Ovo su procesi koji seku i savijaju u isto vreme. U PIERCING-u, rupa se stvara pomoću šiljastog bušilice. Kako bušilica širi rupu u listu, materijal se istovremeno savija u unutrašnju prirubnicu za rupu. Dobivena prirubnica može imati važne funkcije. Operacija LANCING s druge strane seče i savija list kako bi se stvorila podignuta geometrija. • IZPUBLJENJE I SAVIJANJE METALNE CIJEVI: U IZPUPĆENJU neki unutrašnji dio šuplje cijevi je pod pritiskom, što uzrokuje da cijev izboči prema van. Budući da je cijev unutar kalupa, geometrija ispupčenja kontrolira se oblikom kalupa. U STRETCH BENDING, metalna cijev se rasteže korištenjem sila paralelnih s osi cijevi i sila savijanja kako bi se cijev povukla preko bloka oplate. U DRAW BENDING, pričvrstimo cijev blizu njenog kraja za rotirajući blok forme koji savija cijev dok se okreće. Konačno, kod KOMPRESIJSKOG SAVIJANJA cijev se drži silom za fiksni blok forme, a matrica je savija preko bloka oplate. • DEEP DRAWING : U jednoj od naših najpopularnijih operacija, koristi se probijanje, odgovarajuća matrica i držač praznog materijala. Limeni supstanca se postavlja preko otvora matrice i bušilica se pomera prema blanku koji drži držač matrice. Kada dođu u kontakt, bušilica gura lim u šupljinu kalupa kako bi se formirao proizvod. Operacija dubokog izvlačenja nalikuje sečenju, međutim razmak između proboja i matrice sprečava da se list seče. Još jedan faktor koji osigurava da je list duboko izvučen i ne isječen su zaobljeni uglovi na matrici i bušilici koji sprječavaju smicanje i rezanje. Da bi se postigla veća veličina dubokog izvlačenja, primenjuje se proces REDRAWING gde se naknadno duboko izvlačenje odvija na delu koji je već prošao proces dubokog izvlačenja. Kod OBRNUTNOG PRECRTANJA, duboko nacrtani dio se preokreće i povlači u suprotnom smjeru. Duboko izvlačenje može pružiti objekte nepravilnog oblika kao što su kupolaste, sužene ili stepenaste čaše, U ULIVANJU koristimo par muških i ženskih matrica da utisnemo lim dizajnom ili ispisom. • SPINNING : Operacija u kojoj se ravan ili prethodno oblikovani radni komad drži između rotirajućeg trna i repa, a alat primjenjuje lokalizirani pritisak na rad dok se postepeno pomiče uz trn. Kao rezultat, radni komad se omotava preko trna i poprima svoj oblik. Koristimo ovu tehniku kao alternativu dubokom izvlačenju gde je količina narudžbe mala, delovi su veliki (prečnika do 20 stopa) i imaju jedinstvene krivine. Iako su cijene po komadu općenito veće, troškovi podešavanja za CNC predenje su niski u usporedbi s dubokim izvlačenjem. Naprotiv, duboko izvlačenje zahtijeva velika početna ulaganja za postavljanje, ali su troškovi po komadu niski kada se proizvodi velika količina dijelova. Druga verzija ovog procesa je SMIŽNO PREDENJE, gdje također postoji protok metala unutar radnog komada. Protok metala će smanjiti debljinu radnog komada kako se proces izvodi. Još jedan srodni proces je PREĐENJE CIJEVI, koje se primjenjuje na cilindrične dijelove. Takođe u ovom procesu postoji protok metala unutar radnog komada. Na taj način se smanjuje debljina i povećava dužina cijevi. Alat se može pomicati kako bi se stvorile karakteristike unutar ili izvan cijevi. • OBLIKOVANJE GUMA OD LIMA: Guma ili poliuretanski materijal se stavlja u kalup za kontejner i radni komad se postavlja na površinu gume. Proboj tada djeluje na radni komad i gura ga u gumu. Budući da je pritisak koji stvara guma nizak, dubina proizvedenih dijelova je ograničena. Budući da su troškovi alata niski, proces je pogodan za proizvodnju male količine. • HIDROFORMIRANJE: Slično oblikovanju gume, u ovom procesu lim se utiskuje udarcem u tečnost pod pritiskom unutar komore. Rad od lima je u sendviču između probijača i gumene membrane. Dijafragma u potpunosti okružuje radni predmet i pritisak fluida ga tjera da se formira na proboju. Ovom tehnikom mogu se postići vrlo duboki izvlačenje, čak i dublje nego u procesu dubokog izvlačenja. Izrađujemo matrice s jednim udarcem, kao i progesivne matrice ovisno o vašem dijelu. Matrice za jednokratno štancanje su isplativa metoda za brzu proizvodnju velikih količina jednostavnih dijelova od lima kao što su podloške. Progresivne matrice ili tehnika dubokog izvlačenja koriste se za proizvodnju složenijih geometrija. Ovisno o vašem slučaju, rezanje vodenim mlazom, laserom ili plazma sečenjem može se koristiti za jeftinu, brzu i preciznu proizvodnju vaših dijelova od lima. Mnogi dobavljači nemaju pojma o ovim alternativnim tehnikama ili ih nemaju i stoga prolaze kroz duge i skupe načine izrade kalupa i alata koji samo gube vrijeme i novac kupaca. Ako su vam potrebne komponente od lima izrađene po narudžbi kao što su kućišta, elektronska kućišta...itd što je brže moguće u roku od nekoliko dana, kontaktirajte nas za našu uslugu BRZOG PROTOTIPA LIMA. CLICK Product Finder-Locator Service PRETHODNI MENI
- Plastic Rubber Metal Extrusions, Extrusion Dies, Aluminum Extruding
Plastic Rubber Metal Extrusions, Extrusion Dies, Aluminum Extruding, Pipe Tube Forming, Plastic Profiles, Metal Profiles Manufacturing, PVC at AGS-TECH Inc. Ekstruzije, ekstrudirani proizvodi, ekstrudati Koristimo proces EXTRUSION process za proizvodnju proizvoda sa fiksnim profilom poprečnog presjeka kao što su cijevi, cijevi i toplinske cijevi Iako se mnogi materijali mogu ekstrudirati, naše najčešće ekstruzije su izrađene od metala, polimera/plastike, keramike dobivene metodom hladnog, toplog ili toplog ekstrudiranja. Ekstrudirane dijelove nazivamo ekstrudatom ili ekstrudatima u množini. Neke specijalizirane verzije procesa koje također izvodimo su prekrivanje, koekstruzija i ekstruzija spojeva. Preporučujemo da kliknete ovdje da PREUZMITE naše šematske ilustracije procesa ekstruzije metalne keramike i plastike od strane AGS-TECH Inc. Ovo će vam pomoći da bolje razumijete informacije koje vam pružamo u nastavku. U ekstruziji materijal koji se ekstrudira gura ili provlači kroz kalup koji ima željeni profil poprečnog presjeka. Proces se može koristiti za izradu složenih poprečnih presjeka sa odličnom završnom obradom površine i za rad na krhkom materijalu. Ovim postupkom možete proizvesti dijelove bilo koje dužine. Da pojednostavite korake procesa: 1.) U toplim ili toplim ekstruzijama materijal se zagrijava i ubacuje u kontejner u preši. Materijal se presuje i gura iz kalupa. 2.) Proizvedeni ekstrudat se rasteže za ravnanje, termički obrađuje ili hladno obrađuje radi poboljšanja njegovih svojstava. S druge strane COLD EXTRUSION odvija se na oko sobne temperature i ima prednosti visoke čvrstoće, bolje čvrstoće površine, dobre oksidacije, dobre oksidacije. TOPLO ISKLJUČIVANJE izvodi se iznad sobne temperature, ali ispod tačke rekristalizacije. Nudi kompromis i ravnotežu za potrebne sile, duktilnost i svojstva materijala i stoga je izbor za neke primjene. HOT EXTRUSION se odvija iznad temperature rekristalizacije materijala. Na ovaj način je lakše progurati materijal kroz kalup. Međutim, cijena opreme je visoka. Što je ekstrudirani profil složeniji, to je matrica (alat) skuplja i niža je stopa proizvodnje. Poprečni presjeci kalupa kao i debljine imaju ograničenja koja zavise od materijala koji se ekstrudira. Oštri uglovi u kalupima za ekstruziju su uvijek nepoželjni i treba ih izbjegavati osim ako je potrebno. Prema materijalu koji se ekstrudira nudimo: • METALNE EXTRUSIONS : Najčešći proizvodi koje proizvodimo su aluminijum, mesing, cink, bakar, čelik, titan, magnezijum • ISKLJUČIVANJE PLASTIKE : Plastika se topi i formira u kontinuirani profil. Naši uobičajeni materijali koji se obrađuju su polietilen, najlon, polistiren, polivinil hlorid, polipropilen, ABS plastika, polikarbonat, akril. Tipični proizvodi koje proizvodimo su cijevi i cijevi, plastični okviri. U tom procesu male plastične kuglice/smola se gravitacijom ubacuju iz lijevka u bačvu mašine za ekstruziju. Često također miješamo boje ili druge aditive u spremnik kako bismo dali proizvodu tražene specifikacije i svojstva. Materijal koji ulazi u zagrijanu cijev je prisiljen rotirajućim zavrtnjem da napusti cijev na kraju i da se kreće kroz sito za uklanjanje zagađivača u rastopljenoj plastici. Nakon prolaska kroz sito, plastika ulazi u kalup za ekstruziju. Matrica daje pokretnoj mekoj plastici njen profilni oblik dok prolazi kroz nju. Sada ekstrudat prolazi kroz vodeno kupatilo radi hlađenja. Ostale tehnike koje AGS-TECH Inc. koristi dugi niz godina su: • EKSTRUZIJA CIJEVI I CIJEVI : Plastične cijevi i cijevi se formiraju kada se plastika ekstrudira kroz kalup za okrugli oblik i ohladi u vodenom kupatilu, a zatim seče na dužinu ili se namota / namota na kalem. Prozirni ili obojeni, prugasti, jednostruki ili dvostruki, fleksibilni ili kruti, PE, PP, poliuretan, PVC, najlon, PC, silikon, vinil ili drugo, imamo sve. Imamo zalihe cijevi kao i mogućnost proizvodnje prema vašim specifikacijama. AGS-TECH proizvodi cijevi prema zahtjevima FDA, UL i LE za medicinske, električne i elektronske, industrijske i druge primjene. • PREKRIVANJE / PREKRIVANJE EXTRUSION : Ova tehnika nanosi spoljni sloj plastike na postojeću žicu ili kabl. Naše izolacijske žice se proizvode ovom metodom. • COEXTRUSION : Više slojeva materijala se istovremeno ekstrudira. Više slojeva se isporučuju pomoću više ekstrudera. Različite debljine slojeva mogu se podesiti kako bi zadovoljile specifikacije kupaca. Ovaj proces omogućava korištenje više polimera od kojih svaki ima različitu funkcionalnost u proizvodu. Kao rezultat, može se optimizirati niz svojstava. • EKSTRUZIJA JEDINJENJA: Jedan ili više polimera se miješaju sa aditivima kako bi se dobila plastična smjesa. Naši ekstruderi s dva vijka proizvode ekstruzije za mešanje. Ekstruzione kalupe su generalno jeftine u poređenju sa metalnim kalupima. Ako plaćate mnogo više od nekoliko hiljada dolara za malu ili srednju matricu za ekstrudiranje aluminijuma, verovatno plaćate previše. Mi smo stručnjaci u određivanju koja je tehnika najisplativija, najbrža i najprikladnija za vašu primjenu. Ponekad vam ekstrudiranje, a zatim strojna obrada dijela može uštedjeti mnogo novca. Prije donošenja čvrste odluke, prvo nas pitajte za mišljenje. Pomogli smo mnogim kupcima da donesu ispravne odluke. Za neke široko korištene metalne ekstruzije, možete preuzeti naše brošure i kataloge klikom na obojeni tekst ispod. Ako se radi o proizvodu koji ispunjava vaše zahtjeve, bit će ekonomičniji. Preuzmite naše mogućnosti ekstruzije medicinskih cijevi i cijevi Preuzmite naše ekstrudirane hladnjake • SEKUNDARNI PROCESI PROIZVODNJE I IZRADE ZA EKSTRUZIJE : Među procesima dodane vrijednosti koje nudimo za ekstrudirane proizvode su: -Savijanje cijevi i cijevi po narudžbi, oblikovanje i oblikovanje, odrezivanje cijevi, oblikovanje krajeva cijevi, namotavanje cijevi, obrada i završna obrada, bušenje i bušenje rupa i probijanje, -Sklop cijevi i cijevi po narudžbi, cijevni sklop, zavarivanje, lemljenje i lemljenje -Prilagođeno ekstruzijsko savijanje, oblikovanje i oblikovanje -Čišćenje, odmašćivanje, kiseljenje, pasiviranje, poliranje, eloksiranje, galvanizacija, farbanje, termička obrada, žarenje i stvrdnjavanje, označavanje, graviranje i etiketiranje, pakiranje po narudžbi. CLICK Product Finder-Locator Service PRETHODNA STRANICA
- Casting and Machined Parts, CNC Manufacturing, Milling, Turning, Swiss
Casting and Machined Parts, CNC Manufacturing, Milling, Turning, Swiss Type Machining, Die Casting, Investment Casting, Lost Foam Cast Parts from AGS-TECH Inc. Lijevanje i obrada Naše tehnike lijevanja i obrade po narudžbi su potrošni i nepotrošni odljevci, livenje gvožđa i obojenih gvožđa, lijevanje u pijesak, kalup za kalupe, centrifugalni, kontinuirani, keramički kalupi, ulaganje, izgubljena pjena, gotovo mrežni oblik, trajni kalup (lijevanje gravitacijskim tlakom), gips kalupi (gipsani odljevci) i odljevci školjki, obrađeni dijelovi proizvedeni glodanjem i struganjem koristeći konvencionalnu kao i CNC opremu, švicarski tip strojne obrade za visoku propusnost jeftinih malih preciznih dijelova, strojna obrada vijaka za pričvršćivače, nekonvencionalna obrada. Imajte na umu da osim metala i metalnih legura, obrađujemo i keramičke, staklene i plastične komponente kao iu nekim slučajevima kada proizvodnja kalupa nije privlačna ili nije opcija. Obrada polimernih materijala zahtijeva specijalizirano iskustvo koje imamo zbog izazova koje plastika i guma predstavljaju zbog njihove mekoće, ne-krutosti... itd. Za mašinsku obradu keramike i stakla, pogledajte našu stranicu o nekonvencionalnoj proizvodnji. AGS-TECH Inc. proizvodi i isporučuje lake i teške odljevke. Isporučujemo metalne odljevke i mašinske dijelove za kotlove, izmjenjivače topline, automobile, mikromotore, vjetroturbine, opremu za pakovanje hrane i drugo. Preporučujemo da kliknete ovdje da PREUZMITE naše šematske ilustracije procesa obrade i livenja od strane AGS-TECH Inc. Ovo će vam pomoći da bolje razumijete informacije koje vam pružamo u nastavku. Pogledajmo neke od različitih tehnika koje nudimo detaljno: • POTROŠNO LIJEVANJE U MALDU: Ova široka kategorija se odnosi na metode koje uključuju privremene kalupe koji se ne mogu višekratno koristiti. Primjeri su pijesak, gips, školjka, ulaganje (koji se također naziva izgubljeni vosak) i livenje gipsa. • LIJEVANJE PJESKOM: Proces u kojem se pijesak koristi kao materijal za kalup. Vrlo stara metoda i još uvijek vrlo popularna u mjeri u kojoj se većina metalnih odljevaka proizvodi ovom tehnikom. Niska cijena čak i pri maloj proizvodnji. Pogodno za proizvodnju malih i velikih dijelova. Tehnika se može koristiti za proizvodnju dijelova u roku od nekoliko dana ili sedmica uz vrlo malo ulaganja. Vlažni pijesak se spaja pomoću gline, veziva ili specijalnih ulja. Pijesak se uglavnom nalazi u kutijama za kalupe, a sistem šupljina i kapija se stvaraju sabijanjem pijeska oko modela. Procesi su: 1.) Stavljanje modela u pijesak za izradu kalupa 2.) Ugradnja modela i pijeska u sistem zalijevanja 3.) Uklanjanje modela 4.) Punjenje kalupne šupljine rastopljenim metalom 5.) Hlađenje metala 6.) Razbijanje peščanog kalupa i uklanjanje odlivaka • LIJEVANJE OD KALUPA : Slično livenju u pijesak, a umjesto pijeska, kao materijal kalupa koristi se pariški gips. Kratko vrijeme proizvodnje kao što je livenje u pijesak i jeftino. Dobre tolerancije dimenzija i obrada površine. Njegov glavni nedostatak je što se može koristiti samo sa metalima niske tačke topljenja kao što su aluminijum i cink. • LIJEVANJE OD LIJEKOVA OD LIJEKOVA : Također slično livenju u pijesak. Šupljina kalupa dobijena očvršćavanjem ljuske od pijeska i vezivom od termoreaktivne smole umjesto tikvice ispunjene pijeskom kao u procesu livenja u pijesak. Gotovo svaki metal pogodan za livenje u pijesku može se lijevati kalupljenjem školjke. Proces se može sažeti na sljedeći način: 1.) Izrada kalupa za školjke. Koristi se pijesak mnogo manje veličine u odnosu na pijesak koji se koristi za livenje u pijesak. Sitni pijesak se miješa sa termoreaktivnom smolom. Metalni uzorak je premazan sredstvom za razdvajanje radi lakšeg uklanjanja ljuske. Nakon toga se metalna šara zagrijava i mješavina pijeska se posipa ili puhuje na uzorak vrućeg livenja. Na površini uzorka formira se tanka ljuska. Debljina ove ljuske može se podesiti mijenjanjem dužine vremena u kojem je mješavina smole pijeska u kontaktu s metalnim uzorkom. Rastresiti pijesak se zatim uklanja sa preostalim uzorkom prekrivenim školjkom. 2.) Zatim se školjka i šara zagriju u pećnici tako da se školjka stvrdne. Nakon što je stvrdnjavanje završeno, školjka se izbacuje iz šare pomoću igala ugrađenih u uzorak. 3.) Dvije takve školjke se sklapaju zajedno lijepljenjem ili stezanjem i čine cijeli kalup. Sada se kalup za ljusku ubacuje u posudu u kojoj je poduprt pijeskom ili metalnom sačmom tokom procesa livenja. 4.) Sada se vrući metal može sipati u kalup. Prednosti livenja ljuske su proizvodi sa vrlo dobrom završnom obradom, mogućnost izrade složenih delova sa visokom dimenzionalnom preciznošću, proces lak za automatizaciju, ekonomičan za proizvodnju velikih količina. Nedostaci su što kalupi zahtijevaju dobru ventilaciju zbog plinova koji se stvaraju kada rastopljeni metal dođe u kontakt s vezivnom kemikalijom, termoreaktivne smole i metalni uzorci su skupi. Zbog cijene metalnih uzoraka, tehnika možda neće dobro odgovarati za male količine proizvodnje. • LIJEVANJE U INVESTICIJU (poznato i kao LOST VOSKA): Također vrlo stara tehnika i pogodna za proizvodnju kvalitetnih dijelova visoke preciznosti, ponovljivosti, svestranosti i integriteta od mnogih metala, vatrostalnih materijala i specijalnih legura visokih performansi. Mogu se proizvoditi mali kao i veliki dijelovi. Skup proces u poređenju sa nekim drugim metodama, ali glavna prednost je mogućnost proizvodnje delova sa skoro mrežastim oblikom, zamršenim konturama i detaljima. Dakle, trošak je donekle nadoknađen eliminacijom prerade i strojne obrade u nekim slučajevima. Iako mogu postojati varijacije, ovdje je sažetak općeg procesa investicionog livenja: 1.) Izrada originalnog master uzorka od voska ili plastike. Svaki odljevak treba jedan uzorak jer se oni uništavaju u procesu. Potreban je i kalup od kojeg se izrađuju uzorci, a najčešće se kalup lije ili mašinski obrađuje. Budući da se kalup ne mora otvarati, mogu se postići složeni odljevci, mnogi voštani uzorci se mogu povezati poput grana drveta i izliti zajedno, čime se omogućava proizvodnja više dijelova iz jednog izlivanja metala ili metalne legure. 2.) Zatim se uzorak umoči ili prelije vatrostalnom smjesom koja se sastoji od jako finog zrnastog silicijum dioksida, vode, veziva. To rezultira keramičkim slojem na površini uzorka. Vatrostalni premaz na uzorku ostavlja se da se osuši i stvrdne. Iz ovog koraka dolazi naziv livenje za ulaganje: Vatrostalna suspenzija se ulaže preko uzorka voska. 3.) U ovom koraku, očvrsli keramički kalup se okreće naopako i zagrijava tako da se vosak topi i izlije iz kalupa. Ostavljena je šupljina za odljevak metala. 4.) Nakon što se vosak ispusti, keramički kalup se zagrijava na još višu temperaturu što rezultira jačanjem kalupa. 5.) Metalni odljevak se sipa u vrući kalup ispunjavajući sve zamršene dijelove. 6.) Odlivanje je dozvoljeno da se stvrdne 7.) Konačno se keramički kalup razbije i proizvedeni dijelovi seku iz drveta. Ovdje je link do brošure postrojenja za livenje za ulaganje • LIJEVANJE ISPARIVANJEM UZORAKA: Proces koristi uzorak napravljen od materijala kao što je polistirenska pjena koja će ispariti kada se vrući rastopljeni metal ulije u kalup. Postoje dvije vrste ovog procesa: LOST PJENA koja koristi nevezani pijesak i FULL MOLD LIVE koje koristi vezani pijesak. Evo općih koraka procesa: 1.) Napravite uzorak od materijala kao što je polistiren. Kada će se proizvoditi velike količine, uzorak se oblikuje. Ako dio ima složen oblik, možda će biti potrebno nekoliko dijelova takvog pjenastog materijala zalijepiti zajedno kako bi se formirao uzorak. Često premažemo uzorak vatrostalnom smjesom kako bismo stvorili dobru završnu obradu na odljevku. 2.) Uzorak se zatim stavlja u pijesak za oblikovanje. 3.) Istopljeni metal se ulijeva u kalup, isparavajući pjenasti uzorak, odnosno polistiren u većini slučajeva dok teče kroz šupljinu kalupa. 4.) Istopljeni metal se ostavlja u pješčanom kalupu da se stvrdne. 5.) Nakon što se stvrdne, uklanjamo odljevak. U nekim slučajevima, proizvod koji proizvodimo zahtijeva jezgro unutar uzorka. Kod evaporativnog livenja, nema potrebe za postavljanjem i učvršćivanjem jezgra u šupljini kalupa. Tehnika je pogodna za izradu veoma složenih geometrija, lako se može automatizovati za proizvodnju velikog obima, a u livenom delu nema linija za razdvajanje. Osnovni proces je jednostavan i ekonomičan za implementaciju. Za proizvodnju velikih količina, budući da je za proizvodnju uzoraka od polistirena potrebna matrica ili kalup, to može biti skupo. • LIJEVANJE KOJI SE NE PROŠIRI: Ova široka kategorija se odnosi na metode kod kojih kalup ne mora biti reformisan nakon svakog proizvodnog ciklusa. Primjeri su trajno, tlačno, kontinuirano i centrifugalno lijevanje. Dobija se ponovljivost i dijelovi se mogu okarakterizirati kao BLIZU MREŽASTI OBLIK. • TRAJNO LIJEVANJE U MALDU: Kalupi za višekratnu upotrebu napravljeni od metala koriste se za višestruko livenje. Trajni kalup se općenito može koristiti desetine hiljada puta prije nego što se istroši. Gravitacija, pritisak plina ili vakuum se općenito koriste za punjenje kalupa. Kalupi (koji se nazivaju i kalupi) se uglavnom izrađuju od željeza, čelika, keramike ili drugih metala. Opšti proces je: 1.) Obradite mašinu i napravite kalup. Uobičajeno je da se kalup izrađuje od dva metalna bloka koji se uklapaju i mogu se otvarati i zatvarati. I karakteristike dijela kao i sistem zatvaranja se generalno mašinski obrađuju u kalupu za livenje. 2.) Unutrašnje površine kalupa su obložene kašom koja sadrži vatrostalne materijale. Ovo pomaže u kontroli protoka topline i djeluje kao mazivo za lako uklanjanje livenog dijela. 3.) Zatim se trajne polovice kalupa zatvaraju i kalup se zagrijava. 4.) Istopljeni metal se sipa u kalup i ostavi da se stvrdne. 5.) Prije punog hlađenja, uklanjamo dio iz trajnog kalupa pomoću ejektora kada se otvore polovice kalupa. Često koristimo trajno livenje u kalupe za metale niske tačke topljenja kao što su cink i aluminijum. Za čelične odljevke koristimo grafit kao materijal za kalupe. Ponekad dobijamo složene geometrije koristeći jezgre unutar trajnih kalupa. Prednosti ove tehnike su odlivci sa dobrim mehaničkim svojstvima dobijenim brzim hlađenjem, ujednačenost svojstava, dobra tačnost i obrada površine, niske stope odbijanja, mogućnost automatizacije procesa i ekonomična proizvodnja velikih količina. Nedostaci su visoki početni troškovi podešavanja koji ga čine neprikladnim za operacije male količine i ograničenja u veličini proizvedenih dijelova. • TURSKO LIJEVANJE: Mašina se obrađuje i rastopljeni metal se gura pod visokim pritiskom u šupljine kalupa. Mogući su livenje od obojenih kao i od crnih metala. Proces je pogodan za velike količine proizvodnje malih i srednjih dijelova sa detaljima, izuzetno tankim zidovima, konzistencijom dimenzija i dobrom završnom obradom površine. AGS-TECH Inc. je u stanju da proizvede zidove debljine od 0,5 mm koristeći ovu tehniku. Kao i kod trajnog livenja kalupa, kalup treba da se sastoji od dve polovine koje se mogu otvarati i zatvarati radi uklanjanja proizvedenog dela. Kalup za tlačno livenje može imati više šupljina koje omogućavaju proizvodnju više odlivaka u svakom ciklusu. Kalupi za tlačno livenje su veoma teški i mnogo veći od delova koje proizvode, stoga su i skupi. Za naše kupce besplatno popravljamo i zamjenjujemo dotrajale matrice sve dok kod nas naručuju svoje dijelove. Naše matrice imaju dug životni vek u rasponu od nekoliko stotina hiljada ciklusa. Evo osnovnih pojednostavljenih koraka procesa: 1.) Proizvodnja kalupa uglavnom od čelika 2.) Kalup instaliran na mašini za livenje pod pritiskom 3.) Klip tjera rastopljeni metal da teče u šupljinama kalupa ispunjavajući zamršene karakteristike i tanke zidove 4.) Nakon punjenja kalupa rastopljenim metalom, odljevak se ostavlja da se stvrdne pod pritiskom 5.) Kalup se otvara i odljevak uklanja uz pomoć klinova za izbacivanje. 6.) Sada se prazna matrica ponovo podmazuje i steže za sljedeći ciklus. Kod tlačnog livenja često koristimo umetnute kalupe gde u kalup ugrađujemo dodatni deo i oko njega izlivamo metal. Nakon skrućivanja, ovi dijelovi postaju dio livenog proizvoda. Prednosti tlačnog livenja su dobra mehanička svojstva delova, mogućnost složenih karakteristika, fini detalji i dobra završna obrada površine, visoka proizvodnja, laka automatizacija. Nedostaci su: Nije baš pogodan za male zapremine zbog visoke cijene matrice i opreme, ograničenja u oblicima koji se mogu izlivati, male okrugle mrlje na livenim dijelovima koje nastaju zbog kontakta klinova za izbacivanje, tanak bljesak metala istisnut na liniji razdvajanja, potreba za ventilacione otvore duž linije razdvajanja između kalupa, neophodnost održavanja niske temperature kalupa korišćenjem cirkulacije vode. • CENTRIFUGALNO LIVANJE: Rastopljeni metal se sipa u centar rotacionog kalupa na osi rotacije. Centrifugalne sile bacaju metal prema periferiji i ostavlja se da se stvrdne dok se kalup stalno rotira. Mogu se koristiti i horizontalne i vertikalne rotacije osi. Mogu se lijevati dijelovi sa okruglim unutrašnjim površinama, kao i drugi oblici koji nisu okrugli. Proces se može sažeti na sljedeći način: 1.) Istopljeni metal se sipa u centrifugalni kalup. Metal se zatim prisiljava na vanjske zidove zbog okretanja kalupa. 2.) Kako se kalup rotira, metalni odljevak se stvrdne Centrifugalno lijevanje je prikladna tehnika za proizvodnju šupljih cilindričnih dijelova kao što su cijevi, bez potrebe za izljevima, usponima i elementima za zatvaranje, dobra završna obrada površine i detaljne karakteristike, bez problema skupljanja, mogućnost proizvodnje dugih cijevi s vrlo velikim promjerima, mogućnost proizvodnje velike brzine . • KONTINUIRANO LJEVANJE ( LIJEVANJE U STROJIMA ) : Koristi se za livenje kontinuirane dužine metala. U osnovi, rastopljeni metal se lijeva u dvodimenzionalni profil kalupa, ali njegova dužina je neodređena. Novi rastopljeni metal se konstantno unosi u kalup dok odljevak putuje prema dolje, a njegova dužina se vremenom povećava. Metali kao što su bakar, čelik, aluminij se lijevaju u dugačke niti pomoću kontinuiranog procesa livenja. Proces može imati različite konfiguracije, ali uobičajena se može pojednostaviti na sljedeći način: 1.) Rastopljeni metal se sipa u posudu koja se nalazi visoko iznad kalupa pri dobro izračunatim količinama i brzinama protoka i teče kroz kalup hlađen vodom. Metalni odljevak izliven u kalup stvrdnjava se u startnu šipku postavljenu na dno kalupa. Ova startna šipka daje valjcima nešto za što se u početku mogu uhvatiti. 2.) Dugačak metalni pramen nosi se valjcima konstantnom brzinom. Valjci također mijenjaju smjer toka metalne niti iz vertikalnog u horizontalni. 3.) Nakon što kontinuirano livenje pređe određenu horizontalnu udaljenost, baklja ili testera koja se kreće zajedno sa odlivom brzo ga reže na željenu dužinu. Proces kontinuiranog livenja može se integrisati sa PROCESOM VALJANJA, gde se kontinuirano liveni metal može ubaciti direktno u valjaonicu za proizvodnju I-greda, T-greda….itd. Kontinuirano lijevanje daje ujednačena svojstva u cijelom proizvodu, ima visoku stopu očvršćavanja, smanjuje troškove zbog vrlo niskog gubitka materijala, nudi proces u kojem se utovar metala, izlijevanje, skrućivanje, rezanje i uklanjanje livenja odvijaju u kontinuiranom radu i što rezultira visokom stopom produktivnosti i visokim kvalitetom. Međutim, važno je uzeti u obzir visoke početne investicije, troškove postavljanja i potrebe za prostorom. • USLUGE MAŠINSKE OBRADE: Nudimo tri, četiri i petoosnu obradu. Vrste obradnih procesa koje koristimo su TOKARENJE, GLODANJE, BUŠENJE, BUŠENJE, PROČIVANJE, blanjanje, PILJENJE, BRUŠENJE, LAPIRANJE, POLIRANJE i NETRADICIONALNA MAŠINSKA OBRADA što je dalje razrađeno u drugom meniju naše web stranice. Za većinu naše proizvodnje koristimo CNC mašine. Međutim, za neke operacije se bolje uklapaju konvencionalne tehnike i stoga se oslanjamo i na njih. Naše mogućnosti obrade dostižu najviši mogući nivo, a neki najzahtjevniji dijelovi se proizvode u AS9100 certificiranoj fabrici. Lopatice mlaznog motora zahtijevaju visoko specijalizirano proizvodno iskustvo i odgovarajuću opremu. Vazdušna industrija ima veoma stroge standarde. Neke komponente složene geometrijske strukture najlakše se proizvedu obradom u pet osa, koja se nalazi samo u nekim postrojenjima za obradu, uključujući i našu. Naša fabrika sa sertifikatom o vazduhoplovstvu ima neophodno iskustvo u skladu sa zahtevima obimne dokumentacije vazduhoplovne industrije. U operacijama STUKANJA, radni komad se rotira i pomiče u odnosu na rezni alat. Za ovaj proces se koristi mašina koja se zove strug. U GLODANJI, mašina koja se zove glodalica ima rotirajući alat koji dovodi rezne ivice na radni komad. Operacije BUŠENJA uključuju rotirajući rezač sa reznim ivicama koji stvara rupe pri kontaktu sa obratkom. Uglavnom se koriste bušilice, strugovi ili glodalice. U operacijama BUŠIVANJA alat sa jednim savijenim šiljastim vrhom se pomera u grubu rupu u obrtnom komadu koji se okreće kako bi se malo povećala rupa i poboljšala preciznost. Koristi se za finu završnu obradu. PROČIVANJE uključuje nazubljeni alat za uklanjanje materijala sa radnog komada u jednom prolazu provlačenja (nazubljeni alat). Kod linearnog provlačenja, provlačenje se kreće linearno prema površini obratka kako bi se izvršilo rez, dok se kod rotacijskog provlačenja, provlačenje rotira i utiskuje u radni predmet kako bi se izrezao osno simetričan oblik. SWISS TYPE MACHINING je jedna od naših vrijednih tehnika koje koristimo za proizvodnju velikih količina malih dijelova visoke preciznosti. Koristeći strug švicarskog tipa, jeftino tokarimo male, složene, precizne dijelove. Za razliku od konvencionalnih strugova u kojima se radni komad drži nepomično, a alat se kreće, u centrima za struganje švajcarskog tipa, radnom komadu je dozvoljeno da se kreće po Z-osi i alat miruje. U mašinskoj obradi švajcarskog tipa, šipka se drži u mašini i napreduje kroz vodeću čahuru u z-osi, izlažući samo deo koji se obrađuje. Na ovaj način je osigurano čvrsto prianjanje i vrlo visoka preciznost. Dostupnost alata pod naponom pruža mogućnost glodanja i bušenja kako materijal napreduje iz vodeće čahure. Y-osa opreme švicarskog tipa pruža pune mogućnosti glodanja i štedi veliku količinu vremena u proizvodnji. Nadalje, naše mašine imaju bušilice i alate za bušenje koji rade na dijelu kada se drži u podvretenu. Naša sposobnost obrade švicarskog tipa daje nam potpuno automatiziranu potpunu mogućnost obrade u jednoj operaciji. Mašinska obrada je jedan od najvećih segmenata poslovanja AGS-TECH Inc. Koristimo ga ili kao primarnu operaciju ili kao sekundarnu operaciju nakon lijevanja ili ekstrudiranja dijela tako da su ispunjene sve specifikacije za crtanje. • USLUGE ZAVRŠNE ZAVRŠNE POVRŠINE: Nudimo širok izbor površinskih tretmana i završnih obrada kao što su kondicioniranje površine radi poboljšanja prianjanja, nanošenje tankog oksidnog sloja za poboljšanje prianjanja premaza, pjeskarenje, kemijski film, eloksiranje, nitriranje, premazivanje prahom, premazivanje sprejom , razne napredne tehnike metalizacije i premazivanja uključujući raspršivanje, elektronski snop, isparavanje, prevlačenje, tvrde premaze kao što su dijamantski ugljenik (DLC) ili titanijumski premaz za alate za bušenje i rezanje. • USLUGE OZNAČAVANJA I OZNAČAVANJA PROIZVODA: Mnogi naši kupci zahtijevaju označavanje i etiketiranje, lasersko obilježavanje, graviranje na metalnim dijelovima. Ako imate bilo kakvu takvu potrebu, dopustite nam da porazgovaramo koja opcija će biti najbolja za vas. Evo nekih od najčešće korištenih metalnih livenih proizvoda. S obzirom na to da su gotovi, možete uštedjeti na troškovima kalupa u slučaju da nešto od ovoga odgovara vašim zahtjevima: KLIKNITE OVDJE DA PREUZMETE naše kutije od livenog aluminijuma serije 11 od AGS-Electronics-a CLICK Product Finder-Locator Service PRETHODNA STRANICA
- Custom Manufactured Parts, Assemblies, Plastic Mold, Casting,Machining
Custom Manufactured Parts, Assemblies, Plastic Mold, Rubber Molding, Metal Casting, CNC Machining, Turning, Milling, Electrical Electronic Optical Assembly PCBA Custom Manufactured Parts & Assemblies & Products Čitaj više Plastični i gumeni kalupi i kalupi Čitaj više Lijevanje i obrada Čitaj više Ekstruzije, ekstrudirani proizvodi Čitaj više Štancanje i izrada limova Čitaj više Kovanje metala i metalurgija praha Čitaj više Oblikovanje žice i opruge Čitaj više Oblikovanje i oblikovanje stakla i keramike Čitaj više Aditivna i brza proizvodnja Čitaj više Composites & Composite Materials Manufacturing Čitaj više Procesi spajanja i montaže i pričvršćivanja Za Vas proizvodimo dijelove i sklopove i nudimo sljedeće proizvodne procese: • Plastični i gumeni kalupi i profilisani delovi. Injekciono prešanje, termoformiranje, termoreaktivno oblikovanje, vakumsko oblikovanje, puhanje, rotacijsko oblikovanje, livenje, livenje umetanjem i drugo. • Plastične, gumene i metalne ekstruzije • Odlivci od gvožđa i obojenih gvožđa i mašinski obrađeni delovi proizvedeni tehnikama glodanja i struganja, mašinska obrada švajcarskog tipa. • Delovi za metalurgiju praha • Štancanje metala i nemetala, oblikovanje lima, zavareni sklopovi lima • Hladno i toplo kovanje • Žice, sklopovi zavarene žice, oblikovanje žice • Razne vrste opruga, formiranje opruga • Proizvodnja zupčanika, mjenjač, spojnica, puž, reduktor brzine, cilindar, kaiševi prijenosa, lanci prijenosa, komponente prijenosa • Kaljeno i neprobojno staklo po narudžbi u skladu sa NATO i vojnim standardima • Kuglice, ležajevi, remenice i sklopovi remenica • Ventili i pneumatske komponente kao što su O-prsten, podloška i zaptivke • Stakleni i keramički dijelovi i sklopovi, vakum-otporne i hermetičke komponente, metal-keramika i keramičko-keramičko spajanje. • Razne vrste mehaničkih, optomehaničkih, elektromehaničkih, optoelektronskih sklopova. • Vezivanje metal-guma, metal-plastika • Cijevi i cijevi, oblikovanje cijevi, savijanje i cijevni sklopovi po narudžbi, proizvodnja mijeha. • Proizvodnja stakloplastike • Zavarivanje različitim tehnikama kao što su točkasto zavarivanje, lasersko zavarivanje, MIG, TIG. Ultrazvučno zavarivanje plastičnih delova. • Veliki izbor površinskih tretmana i završnih obrada kao što su kondicioniranje površine radi poboljšanja adhezije, nanošenje tankog oksidnog sloja za poboljšanje prianjanja premaza, pjeskarenje, kemijski film, eloksiranje, nitriranje, premazivanje prahom, premazivanje sprejom, razne napredne tehnike metalizacije i premazivanja uključujući raspršivanje, elektronski snop, isparavanje, oblaganje, tvrde premaze kao što su dijamantski ugljenik (DLC) ili titanijum za alate za rezanje i bušenje. • Obeležavanje i etiketiranje, lasersko obeležavanje na metalnim delovima, štampa na plastičnim i gumenim delovima Preuzmite brošuru za uobičajene termine u mašinstvu koje koriste dizajneri i inženjeri Proizvodimo proizvode prema vašim specifičnim specifikacijama i zahtjevima. Kako bismo vam ponudili najbolji kvalitet, isporuku i cijene, proizvodimo proizvode globalno u Kini, Indiji, Tajvanu, Filipinima, Južnoj Koreji, Maleziji, Šri Lanki, Turskoj, SAD-u, Kanadi, Njemačkoj, Velikoj Britaniji i Japanu. Ovo nas čini mnogo jačim i globalno konkurentnijim od bilo kojeg drugog custom proizvođača. Naši proizvodi se proizvode u okruženjima sa certifikatom ISO9001:2000, QS9000, ISO14001, TS16949 i posjeduju CE, UL oznaku i ispunjavaju druge industrijske standarde. Kada budemo imenovani za vaš projekat, možemo se pobrinuti za cjelokupnu proizvodnju, montažu, testiranje, kvalifikaciju, otpremu i carinu po vašoj želji. Ako želite, možemo skladištiti vaše dijelove, sastaviti prilagođene komplete, odštampati i označiti naziv vaše kompanije i brend i isporučiti vašim klijentima. Drugim riječima, po želji možemo biti i vaš centar za skladištenje i distribuciju. Budući da se naša skladišta nalaze u blizini velikih morskih luka, to nam daje logističku prednost. Na primjer, kada vaši proizvodi stignu u veliku pomorsku luku SAD-a, možemo ih prevoziti direktno u obližnje skladište gdje možemo skladištiti, sastavljati, praviti komplete, ponovo etiketirati, štampati, pakirati prema vašem izboru i isporučiti pošaljite svojim kupcima. Mi ne isporučujemo samo proizvode. Naša kompanija radi na ugovorima po narudžbi gdje dolazimo na vašu lokaciju, procjenjujemo vaš projekat na licu mjesta i razvijamo projektni prijedlog prilagođen vama. Zatim šaljemo naš iskusni tim da implementira projekat. Više informacija o našim inženjerskim radovima možete pronaći na http://www.ags-engineering.com -Mi preuzimamo male projekte kao i velike projekte u industrijskom obimu. Kao prvi korak, možemo vas povezati telefonom, telekonferencijom ili MSN messengerom sa članovima našeg stručnog tima, tako da možete direktno komunicirati sa stručnjakom, postavljati pitanja i razgovarati o svom projektu. Pozovite nas i ako je potrebno doći ćemo i posjetiti vas. PRETHODNA STRANICA