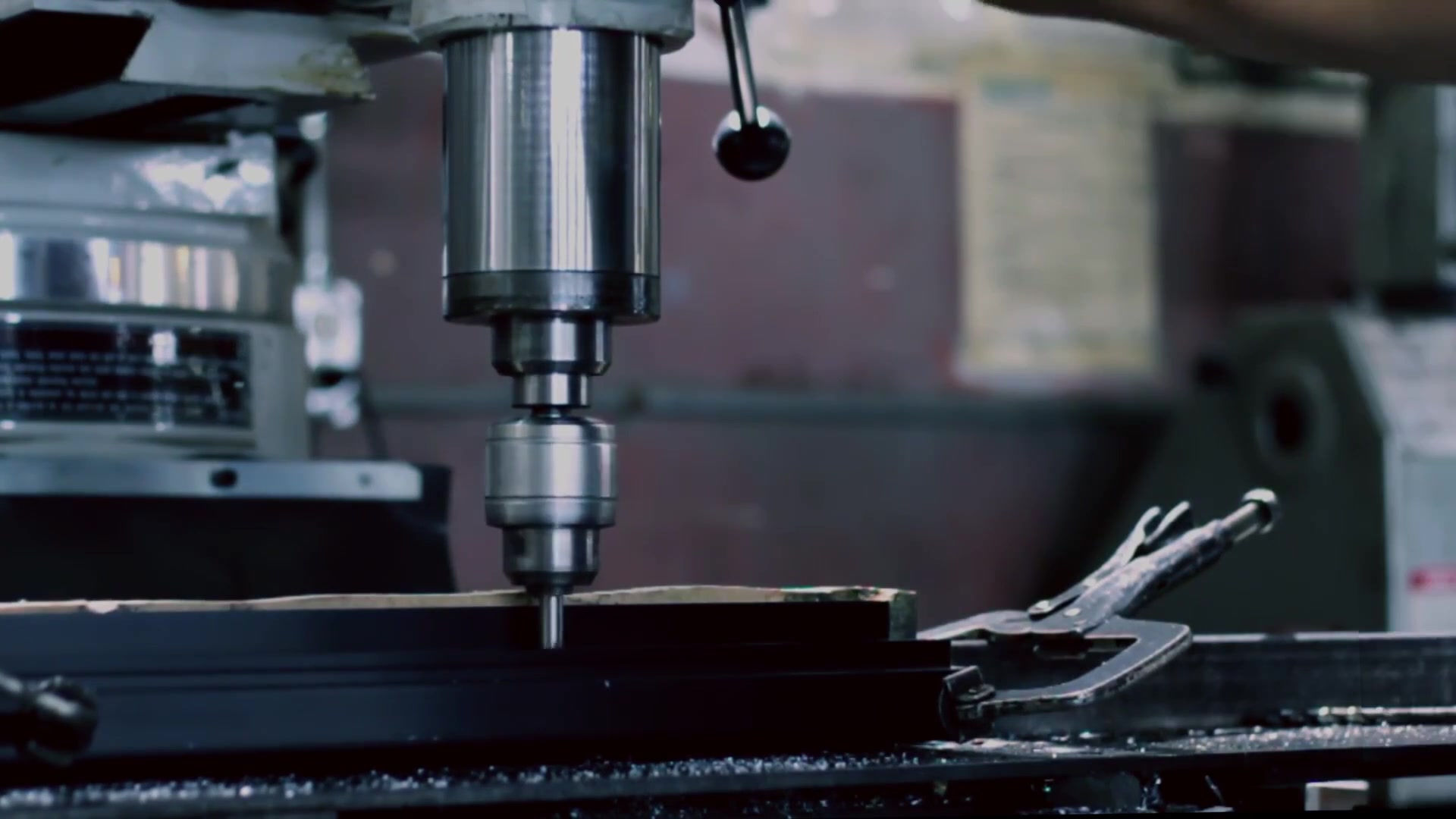
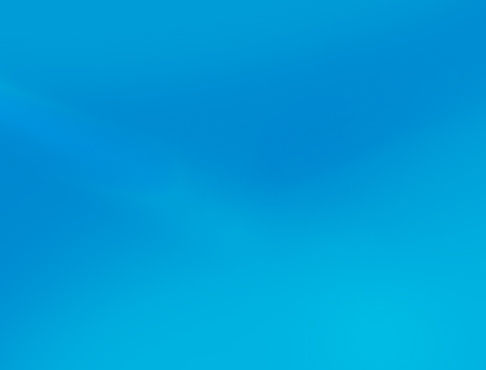
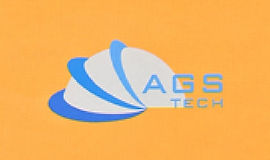
Fabricant global personalitzat, integrador, consolidador, soci d'externalització per a una àmplia varietat de productes i serveis.
Som la vostra font única per a la fabricació, fabricació, enginyeria, consolidació, integració, subcontractació de productes i serveis fabricats a mida i disponibles.
Trieu el vostre idioma
-
Fabricació personalitzada
-
Fabricació per contracte nacional i global
-
Outsourcing de fabricació
-
Adquisició nacional i global
-
Consolidació
-
Integració d'enginyeria
-
Serveis d'Enginyeria
ELECTRICAL DISCHARGE MACHINING (EDM), also referred to as SPARK-EROSION or ELECTRODISCHARGE MACHINING, SPARK ERODING, DIE SINKING_cc781905-5cde-3194-bb3b -136bad5cf58d_or WIRE EROSION, is a NON-CONVENTIONAL MANUFACTURING process where erosion of metals takes place and desired shape is obtained using electrical discharges in the form d'espurnes. També oferim algunes varietats de electroerosió, a saber NO-WEAR EDM, WIRE EDM (WEDM), EDM GRINDING (EDG), DIE-SINKING EDM, ELECTRICAL-DESCHARGE MILLING, micro-EDMcc7, -5cde-3194-bb3b-136bad5cf58d_and MOLTURA DE DESCÀRREGA ELECTROQUÍMICA (ECDG). Els nostres sistemes EDM consisteixen en eines/elèctrode amb forma i la peça connectada a fonts d'alimentació de CC i inserida en un fluid dielèctric no conductor elèctric. Després de 1940, el mecanitzat per descàrrega elèctrica s'ha convertit en una de les tecnologies de producció més importants i populars a les indústries manufactureres.
Quan es redueix la distància entre els dos elèctrodes, la intensitat del camp elèctric en el volum entre els elèctrodes esdevé més gran que la força del dielèctric en alguns punts, que es trenca, formant finalment un pont perquè el corrent flueixi entre els dos elèctrodes. Es genera un arc elèctric intens que provoca un escalfament important per fondre una part de la peça de treball i part del material de l'eina. Com a resultat, s'elimina material dels dos elèctrodes. Al mateix temps, el fluid dielèctric s'escalfa ràpidament, donant lloc a l'evaporació del fluid a l'espai d'arc. Un cop s'atura el flux de corrent o s'atura, la calor s'elimina de la bombolla de gas pel fluid dielèctric que l'envolta i la bombolla cavita (esfondra). L'ona de xoc creada pel col·lapse de la bombolla i el flux de fluid dielèctric treuen els residus de la superfície de la peça i arrossega qualsevol material fos de la peça al fluid dielèctric. La taxa de repetició d'aquestes descàrregues està entre 50 i 500 kHz, tensions entre 50 i 380 V i corrents entre 0,1 i 500 amperes. El nou dielèctric líquid, com ara olis minerals, querosè o aigua destil·lada i desionitzada, normalment es transporta al volum interelèctrode que s'emporta les partícules sòlides (en forma de deixalles) i es restableixen les propietats aïllants del dielèctric. Després d'un flux de corrent, la diferència de potencial entre els dos elèctrodes es restaura al que era abans de la ruptura, de manera que es pot produir una nova ruptura dielèctrica líquida. Les nostres modernes màquines de descàrrega elèctrica (EDM) ofereixen moviments controlats numèricament i estan equipades amb bombes i sistemes de filtratge dels fluids dielèctrics.
El mecanitzat per descàrrega elèctrica (EDM) és un mètode de mecanitzat utilitzat principalment per a metalls durs o aquells que serien molt difícils de mecanitzar amb tècniques convencionals. L'EDM funciona normalment amb qualsevol material que sigui conductor elèctric, tot i que també s'han proposat mètodes per mecanitzar ceràmiques aïllants amb EDM. El punt de fusió i la calor latent de fusió són propietats que determinen el volum de metall eliminat per descàrrega. Com més alts siguin aquests valors, més lenta serà la velocitat d'eliminació del material. Com que el procés de mecanitzat per descàrrega elèctrica no implica cap energia mecànica, la duresa, la resistència i la tenacitat de la peça no afecten la taxa d'eliminació. La freqüència de descàrrega o energia per descàrrega, la tensió i el corrent es varien per controlar les taxes d'eliminació de material. La taxa d'eliminació del material i la rugositat de la superfície augmenten amb l'augment de la densitat de corrent i la disminució de la freqüència d'espurna. Podem tallar contorns o cavitats complexos en acer pretemprat mitjançant EDM sense necessitat de tractament tèrmic per suavitzar-los i tornar-los a endurir. Podem utilitzar aquest mètode amb qualsevol metall o aliatge metàl·lic com el titani, l'hastelloy, el kovar i l'inconel. Les aplicacions del procés EDM inclouen la conformació d'eines de diamant policristalí. EDM es considera un mètode de mecanitzat no tradicional o no convencional juntament amb processos com el mecanitzat electroquímic (ECM), el tall per raig d'aigua (WJ, AWJ), el tall per làser. D'altra banda, els mètodes de mecanitzat convencionals inclouen tornejat, fresat, rectificat, trepat i altres processos el mecanisme d'eliminació de material dels quals es basa essencialment en forces mecàniques. Els elèctrodes per a mecanitzat de descàrrega elèctrica (EDM) estan fets d'aliatge de grafit, llautó, coure i coure-tungstè. Són possibles diàmetres d'elèctrodes de fins a 0,1 mm. Com que el desgast de les eines és un fenomen no desitjat que afecta negativament la precisió dimensional en EDM, aprofitem un procés anomenat NO-WEAR EDM, invertint la polaritat i utilitzant eines de coure per minimitzar el desgast de les eines.
Idealment parlant, el mecanitzat de descàrrega elèctrica (EDM) es pot considerar una sèrie d'avaria i restauració del líquid dielèctric entre els elèctrodes. En realitat, però, l'eliminació de les deixalles de la zona inter-elèctrodes és gairebé sempre parcial. Això fa que les propietats elèctriques del dielèctric a la zona dels interelèctrodes siguin diferents dels seus valors nominals i varien amb el temps. La distància entre elèctrodes, (espurna), s'ajusta mitjançant els algorismes de control de la màquina específica utilitzada. Malauradament, de vegades, el buit d'espurna en EDM es pot curtcircuitar pels residus. El sistema de control de l'elèctrode pot no reaccionar prou ràpidament per evitar que els dos elèctrodes (eina i peça de treball) es facin curtcircuits. Aquest curtcircuit no desitjat contribueix a l'eliminació de material de manera diferent del cas ideal. Donem la màxima importància a l'acció de rentat per tal de restaurar les propietats aïllants del dielèctric de manera que el corrent passi sempre en el punt de la zona inter-elèctrodes, minimitzant així la possibilitat de canvis de forma no desitjats (danys) de l'eina-elèctrode. i peça de treball. Per obtenir una geometria específica, l'eina EDM es guia pel camí desitjat molt a prop de la peça sense tocar-la, prestem la màxima atenció al rendiment del control de moviment en ús. D'aquesta manera, es produeixen un gran nombre de descàrregues/espurnes de corrent, i cadascuna contribueix a l'eliminació de material tant de l'eina com de la peça, on es formen petits cràters. La mida dels cràters és una funció dels paràmetres tecnològics establerts per a la feina específica i les dimensions poden anar des de la nanoescala (com en el cas de les operacions de micro-EDM) fins a uns centenars de micròmetres en condicions de desbast. Aquests petits cràters de l'eina provoquen una erosió gradual de l'elèctrode anomenada "desgast de l'eina". Per contrarestar l'efecte perjudicial del desgast sobre la geometria de la peça, substituïm contínuament l'eina-elèctrode durant una operació de mecanitzat. De vegades ho aconseguim utilitzant un cable substituït contínuament com a elèctrode (aquest procés EDM també s'anomena WIRE EDM ). De vegades, utilitzem l'eina-elèctrode de tal manera que només una petita part del mateix es dedica realment al procés de mecanitzat i aquesta part es canvia regularment. Aquest és, per exemple, el cas quan s'utilitza un disc giratori com a eina-elèctrode. Aquest procés s'anomena EDM GRINDING. Una altra tècnica que implementem consisteix a utilitzar un conjunt d'elèctrodes de diferents mides i formes durant la mateixa operació d'electroerosió per compensar el desgast. Anomenem aquesta tècnica d'elèctrodes múltiples, i s'utilitza més habitualment quan l'elèctrode de l'eina replica en negatiu la forma desitjada i s'avança cap al blanc en una sola direcció, normalment la direcció vertical (és a dir, l'eix z). Això s'assembla a l'aigüera de l'eina en el líquid dielèctric en el qual està immersa la peça de treball i, per tant, es coneix com a DIE-SINKING EDM_cc781905-5cde-3194-bb3b5cf1905-5cde-3194-bb3b5cf1905-136bad5cf58d_ 3194-bb3b-136bad5cf58d_CONVENTIONAL EDM or RAM EDM). Les màquines per a aquesta operació s'anomenen SINKER EDM. Els elèctrodes per a aquest tipus d'electroerosió tenen formes complexes. Si la geometria final s'obté utilitzant un elèctrode generalment de forma senzilla mogut en diverses direccions i també subjecte a rotacions, l'anomenem EDM MILLING. La quantitat de desgast depèn estrictament dels paràmetres tecnològics utilitzats en l'operació (polaritat, corrent màxima, tensió de circuit obert). Per exemple, in micro-EDM, també conegut com a m-EDM, aquests paràmetres solen establir-se en valors que generen un desgast greu. Per tant, el desgast és un problema important en aquesta àrea que minimitzem utilitzant el nostre coneixement acumulat. Per exemple, per minimitzar el desgast dels elèctrodes de grafit, un generador digital, controlable en mil·lisegons, inverteix la polaritat a mesura que es produeix l'electroerosió. Això dóna lloc a un efecte similar al galvanoplast que diposita contínuament el grafit erosionat a l'elèctrode. En un altre mètode, un circuit anomenat ''Zero Wear'' minimitzem la freqüència amb què s'inicia i s'atura la descàrrega, mantenint-la encesa el màxim de temps possible. La taxa d'eliminació de material en el mecanitzat de descàrrega elèctrica es pot estimar a partir de:
MRR = 4 x 10 exp(4) x I x Tw exp (-1,23)
Aquí MRR és en mm3/min, I és actual en amperes, Tw és el punt de fusió de la peça en K-273.15K. L'exp significa exponent.
D'altra banda, la taxa de desgast Wt de l'elèctrode es pot obtenir a partir de:
Pes = ( 1,1 x 10exp(11) ) x I x Ttexp (-2,38)
Aquí el pes està en mm3/min i Tt és el punt de fusió del material de l'elèctrode en K-273.15K
Finalment, la relació de desgast de la peça a l'elèctrode R es pot obtenir a partir de:
R = 2,25 x Trexp (-2,38)
Aquí Tr és la relació dels punts de fusió de la peça a l'elèctrode.
SINKER EDM :
Sinker EDM, també conegut com a CAVITY TYPE EDM or_cc781905-5cde-bad5cf58d_cavity TYPE EDM or_cc781905-5cde-bd5cf58d_o_cc781905-5cde-immersió líquida i submersió líquida, un treball de submersió i submersió líquida. L'elèctrode i la peça de treball estan connectats a una font d'alimentació. La font d'alimentació genera un potencial elèctric entre els dos. A mesura que l'elèctrode s'acosta a la peça de treball, es produeix una ruptura dielèctrica en el fluid, formant un canal de plasma i una petita espurna salta. Les espurnes solen colpejar una a la vegada perquè és molt poc probable que diferents ubicacions de l'espai interelèctrodes tinguin característiques elèctriques locals idèntiques que permetrien que es produeixi una espurna en totes aquestes ubicacions simultàniament. Centenars de milers d'aquestes espurnes es produeixen en punts aleatoris entre l'elèctrode i la peça per segon. A mesura que el metall base s'erosiona i la bretxa augmenta posteriorment, la nostra màquina CNC baixa automàticament l'elèctrode perquè el procés pugui continuar sense interrupcions. El nostre equip disposa de cicles de control coneguts com a ''on time'' i ''off time''. La configuració del temps d'encesa determina la durada o la durada de l'espurna. Un temps més llarg produeix una cavitat més profunda per a aquesta espurna i totes les espurnes posteriors per a aquest cicle, creant un acabat més rugós a la peça de treball i viceversa. El temps d'apagada és el període de temps que una espurna es substitueix per una altra. Un temps d'aturada més llarg permet que el fluid dielèctric s'enfili a través d'un broquet per netejar els residus erosionats, evitant així un curtcircuit. Aquests paràmetres s'ajusten en microsegons.
WIRE EDM :
In WIRE ELECTRICAL DISCHARGE MACHINING (WEDM), also called WIRE-CUT EDM or WIRE CUTTING, we feed a fil metàl·lic d'un sol fil de llautó a través de la peça de treball, que està submergida en un dipòsit de fluid dielèctric. EDM per fil és una variació important de l'EDM. De tant en tant fem servir l'erosió per electroerosió per filferro per tallar plaques de fins a 300 mm de gruix i per fer punxons, eines i matrius de metalls durs difícils de mecanitzar amb altres mètodes de fabricació. En aquest procés que s'assembla al tall de contorns amb una serra de cinta, el filferro, que s'alimenta constantment des d'una bobina, es manté entre les guies de diamant superior i inferior. Les guies controlades per CNC es mouen en el pla x–y i la guia superior també es pot moure de manera independent a l'eix z–u–v, donant lloc a la possibilitat de tallar formes afilades i de transició (com ara el cercle a la part inferior i el quadrat a la part inferior). la part superior). La guia superior pot controlar els moviments de l'eix en x–y–u–v–i–j–k–l–. Això permet al WEDM tallar formes molt complicades i delicades. El tall mitjà de tall dels nostres equips que aconsegueix el millor cost econòmic i temps de mecanitzat és de 0,335 mm utilitzant fil de llautó, coure o tungstè de Ø 0,25. No obstant això, les guies de diamant superior i inferior dels nostres equips CNC tenen una precisió d'uns 0,004 mm i poden tenir un recorregut de tall o un tall tan petit com 0,021 mm amb filferro de Ø 0,02 mm. Així que són possibles talls molt estrets. L'amplada de tall és més gran que l'amplada del cable perquè es produeix una espurna des dels costats del cable fins a la peça de treball, provocant l'erosió. Aquest ''sobretall'' és necessari, per a moltes aplicacions és previsible i, per tant, es pot compensar (en micro-EDM això no sol ser el cas). Les bobines de filferro són llargues: una bobina de 8 kg de filferro de 0,25 mm té una longitud de poc més de 19 quilòmetres. El diàmetre del cable pot ser tan petit com 20 micròmetres i la precisió de la geometria és al voltant de +/- 1 micròmetre. En general, fem servir el cable només una vegada i el reciclem perquè és relativament barat. Viatja a una velocitat constant de 0,15 a 9 m/min i es manté un tall constant (ranura) durant un tall. En el procés d'electroerosió per filferro utilitzem aigua com a fluid dielèctric, controlant la seva resistivitat i altres propietats elèctriques amb filtres i unitats desionitzadores. L'aigua elimina els residus tallats lluny de la zona de tall. El rentat és un factor important per determinar la velocitat d'alimentació màxima per a un gruix de material determinat i, per tant, el mantenim constant. La velocitat de tall en electroerosió per filferro s'indica en termes de l'àrea de la secció transversal tallada per unitat de temps, com ara 18.000 mm2/h per a acer d'eines D2 de 50 mm de gruix. La velocitat de tall lineal per a aquest cas seria de 18.000/50 = 360 mm/h. La taxa d'eliminació de material en electroerosió per filferro és:
MRR = Vf xhxb
Aquí MRR és en mm3/min, Vf és la velocitat d'alimentació del cable a la peça en mm/min, h és el gruix o l'alçada en mm i b és el tall, que és:
b = dw + 2s
Aquí dw és el diàmetre del cable i s és l'espai entre el cable i la peça en mm.
Juntament amb toleràncies més estrictes, els nostres moderns centres de mecanitzat de tall de filferro per electroerosió multieixos han afegit funcions com ara capçals múltiples per tallar dues peces alhora, controls per evitar el trencament del cable, funcions d'auto-roscat automàtic en cas de trencament de cable i programació. estratègies de mecanitzat per optimitzar el funcionament, les capacitats de tall recte i angular.
Wire-EDM ens ofereix baixes tensions residuals, perquè no requereix grans forces de tall per a l'eliminació de material. Quan l'energia/potència per pols és relativament baixa (com en les operacions d'acabat), s'espera un petit canvi en les propietats mecàniques d'un material a causa de les baixes tensions residuals.
MOLADOR DE DESCÀRREGA ELÈCTRICA (EDG) : Les moles no contenen abrasius, són de grafit o llautó. Les espurnes repetitives entre la roda giratòria i la peça de treball eliminen el material de les superfícies de la peça. La taxa d'eliminació de material és:
MRR = K x I
Aquí MRR és en mm3/min, I és el corrent en amperes i K és el factor de material de la peça en mm3/A-min. Sovint fem servir la mòlta de descàrrega elèctrica per serrar escletxes estretes als components. De vegades combinem el procés EDG (Electrical-Descharge Grinding) amb el procés ECG (Electrochemical Grinding) on el material s'elimina per acció química, les descàrregues elèctriques de la roda de grafit trenquen la pel·lícula d'òxid i s'eliminen per l'electròlit. El procés s'anomena MOLTURA DE DESCÀRREGA ELECTROQUÍMICA (ECDG). Tot i que el procés ECDG consumeix relativament més energia, és un procés més ràpid que l'EDG. Principalment triturem eines de carbur mitjançant aquesta tècnica.
Aplicacions del mecanitzat de descàrrega elèctrica:
Producció de prototips:
Utilitzem el procés EDM en la fabricació de motlles, eines i matrius, així com per a la fabricació de prototips i peces de producció, especialment per a les indústries aeroespacial, automòbil i electrònica en què les quantitats de producció són relativament baixes. A Sinker EDM, un elèctrode de grafit, tungstè de coure o coure pur es mecanitza en la forma desitjada (negativa) i s'introdueix a la peça de treball a l'extrem d'un ariet vertical.
Fabricació de matrius d'encunyació:
Per a la creació de matrius per a la producció de joies i insígnies mitjançant el procés d'encunyació (estampació), el mestre positiu es pot fer amb plata de llei, ja que (amb els ajustaments adequats de la màquina) el mestre s'erosiona significativament i només s'utilitza una vegada. La matriu negativa resultant s'endureix i s'utilitza en un martell de gota per produir plans estampats a partir de fulls en blanc retallats de bronze, plata o aliatge d'or de baixa resistència. Per a les insígnies, aquests plans es poden donar forma a una superfície corba amb un altre encuny. Aquest tipus d'electroerosió es realitza normalment submergit en un dielèctric a base d'oli. L'objecte acabat es pot refinar encara més mitjançant un esmalt dur (vidre) o suau (pintura) i/o galvanitzat amb or pur o níquel. Els materials més suaus com la plata es poden gravar a mà com a perfeccionament.
Perforació de petits forats:
A les nostres màquines d'electroerosió per tall de filferro, utilitzem l'electroerosió de forats petits per fer un forat passant en una peça de treball a través del qual enfilar el cable per a l'operació d'erosió de tall de filferro. A les nostres màquines de tall de filferro es munten capçals EDM separats específics per a la perforació de forats petits, que permeten que les plaques grans endurides s'erosionin les peces acabades segons sigui necessari i sense perforar prèviament. També fem servir EDM de forats petits per perforar files de forats a les vores de les pales de les turbines utilitzades en motors a reacció. El flux de gas a través d'aquests petits forats permet que els motors utilitzin temperatures més altes que les possibles. Els aliatges monocristalls d'alta temperatura i molt durs dels quals estan fetes aquestes fulles fa que el mecanitzat convencional d'aquests forats amb una relació d'aspecte elevada sigui extremadament difícil i fins i tot impossible. Altres àrees d'aplicació per a electroerosió per forats petits són crear orificis microscòpics per als components del sistema de combustible. A més dels capçals d'electroerosió integrats, despleguem màquines d'electroerosió de forats petits autònoms amb eixos x–y per mecanitzar forats cecs o passants. EDM perfora forats amb un elèctrode llarg de tub de llautó o coure que gira en un mandril amb un flux constant d'aigua destil·lada o desionitzada que flueix a través de l'elèctrode com a agent de neteja i dielèctric. Alguns EDM de perforació de forats petits són capaços de perforar 100 mm d'acer tou o fins i tot endurit en menys de 10 segons. En aquesta operació de perforació es poden aconseguir forats entre 0,3 mm i 6,1 mm.
Mecanitzat de desintegració de metalls:
També disposem de màquines d'electroerosió especials amb la finalitat específica d'eliminar eines trencades (broques o aixetes) de les peces de treball. Aquest procés s'anomena ''mecanitzat per desintegració de metalls''.
Avantatges i desavantatges Mecanitzat de descàrrega elèctrica:
Els avantatges de l'electroerosió inclouen el mecanitzat de:
- Formes complexes que, d'altra manera, serien difícils de produir amb eines de tall convencionals
- Material extremadament dur amb toleràncies molt estretes
- Peces de treball molt petites on les eines de tall convencionals poden danyar la peça per l'excés de pressió de l'eina de tall.
- No hi ha contacte directe entre l'eina i la peça de treball. Per tant, es poden mecanitzar seccions delicades i materials febles sense cap distorsió.
- Es pot obtenir un bon acabat superficial.
- Els forats molt fins es poden perforar fàcilment.
Els desavantatges de l'EDM inclouen:
- La velocitat lenta d'eliminació de material.
- El temps i el cost addicionals utilitzats per a la creació d'elèctrodes per a electroerosió ram/sinker.
- La reproducció de cantonades afilades a la peça és difícil a causa del desgast dels elèctrodes.
- El consum d'energia és elevat.
- Es forma ''Sobretalla''.
- Es produeix un desgast excessiu de l'eina durant el mecanitzat.
- Els materials elèctricament no conductors només es poden mecanitzar amb una configuració específica del procés.