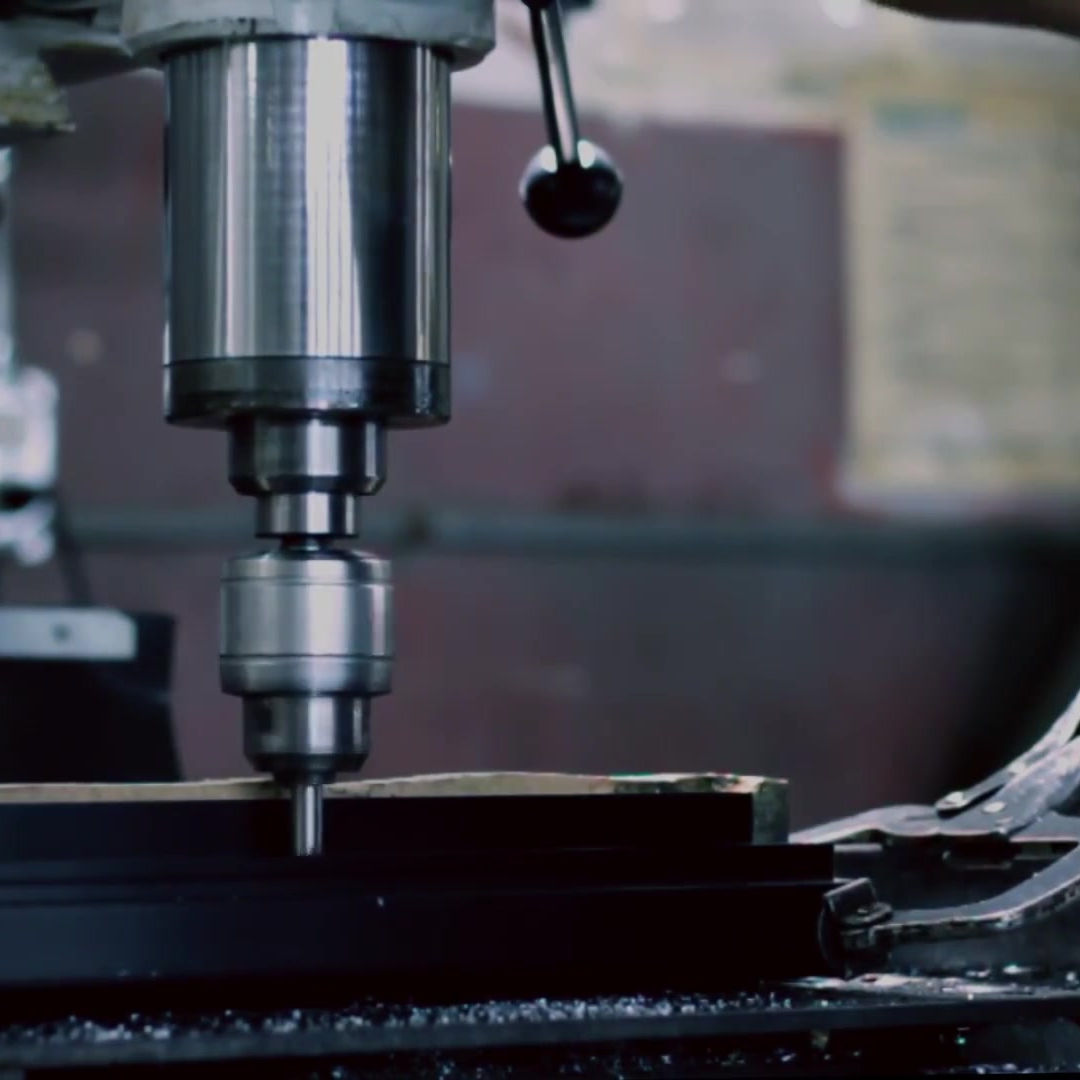
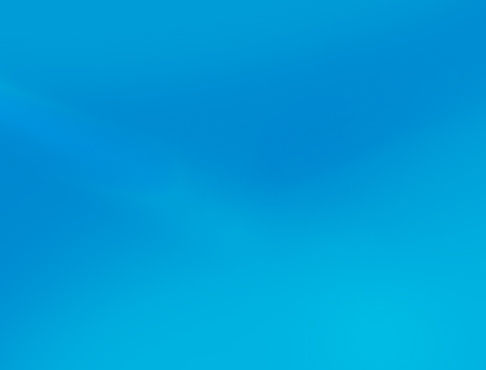
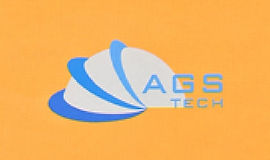
Fabricant global personalitzat, integrador, consolidador, soci d'externalització per a una àmplia varietat de productes i serveis.
Som la vostra font única per a la fabricació, fabricació, enginyeria, consolidació, integració, subcontractació de productes i serveis fabricats a mida i disponibles.
Trieu el vostre idioma
-
Fabricació personalitzada
-
Fabricació per contracte nacional i global
-
Outsourcing de fabricació
-
Adquisició nacional i global
-
Consolidació
-
Integració d'enginyeria
-
Serveis d'Enginyeria
Search Results
S'han trobat 164 resultats amb una cerca buida
- Transmission Components, Belts, Chains, Cable Drives, Pulleys,AGS-TECH
Transmission Components, Belts, Chains and Cable Drives, Conventional & Grooved or Serrated, Positive Drive, Pulleys Corretges i cadenes i conjunt d'accionament per cable AGS-TECH Inc. us ofereix components de transmissió d'energia, com ara corretges i cadenes i conjunts d'accionament per cable. Amb anys de perfeccionament, les nostres transmissió de cautxú, cuir i altres corretges s'han tornat més lleugers i compactes, capaços de transportar càrregues més altes a un cost més baix. De la mateixa manera, els nostres accionaments en cadena han passat per un gran desenvolupament al llarg del temps i ofereixen als nostres clients diversos avantatges. Alguns avantatges de l'ús d'accionaments per cadena són les distàncies del centre de l'eix relativament il·limitades, la compacitat, la facilitat de muntatge, l'elasticitat en tensió sense lliscament ni fluïdesa, la capacitat d'operar en entorns d'alta temperatura. Les nostres unitats de cable també ofereixen avantatges com ara la simplicitat en algunes aplicacions respecte a altres tipus de components de transmissió. Hi ha disponibles tant accionaments per corretja, cadenes i cables, com versions fabricades i muntades a mida. Podem fabricar aquests components de transmissió a la mida adequada per a la seva aplicació i amb els materials més adequats. CORREAS I TRANSMISSIONS PER CORREAS: - Cinturons plans convencionals: són cinturons plans llisos sense dents, ranures ni dentades. Les transmissió de corretja plana ofereixen flexibilitat, bona absorció de cops, transmissió eficient de potència a altes velocitats, resistència a l'abrasió i baix cost. Els cinturons es poden empalmar o connectar per fer cinturons més grans. Altres avantatges de les corretges planes convencionals són que són primes, no estan sotmeses a càrregues centrífugues elevades (les fa bones per a operacions d'alta velocitat amb politges petites). D'altra banda, imposen altes càrregues de suport perquè les corretges planes requereixen una tensió elevada. Altres desavantatges de les transmissió de corretja plana poden ser el lliscament, el funcionament sorollós i les eficiències relativament més baixes a velocitats de funcionament baixes i moderades. Disposem de dos tipus de cinturons convencionals: Reforçats i No Reforçats. Els cinturons reforçats tenen un element de tracció a la seva estructura. Els cinturons plans convencionals estan disponibles com a cuir, teixit de goma o cordó, cautxú no reforçat o plàstic, teixit, cuir reforçat. Els cinturons de cuir ofereixen una llarga vida útil, flexibilitat, excel·lent coeficient de fricció i fàcil reparació. No obstant això, els cinturons de cuir són relativament cars, necessiten vestir i netejar els cinturons i, depenent de l'atmosfera, poden encongir-se o estirar-se. Els cinturons de tela o cordó de goma són resistents a la humitat, l'àcid i els àlcalis. Els cinturons de teixit de goma estan formats per capes de cotó o ànec sintètic impregnats de cautxú i són els més econòmics. Els cinturons de cordó de goma consisteixen en una sèrie de capes de cordons impregnats de cautxú. Els cinturons de corda de goma ofereixen una gran resistència a la tracció i una mida i massa modestes. Els cinturons de plàstic o de cautxú no reforçats són aptes per a aplicacions d'accionament lleugeres i de baixa velocitat. Els cinturons de plàstic i de cautxú no reforçats es poden estirar al seu lloc sobre les seves politges. Els cinturons de plàstic no reforçats poden transmetre una potència més gran en comparació amb els cinturons de goma. Els cinturons de cuir reforçats consisteixen en un element de tracció de plàstic intercalat entre les capes superior i inferior de cuir. Finalment, els nostres cinturons de tela poden consistir en una sola peça de cotó o ànec plegada i cosida amb fileres de punts longitudinals. Els cinturons de tela poden fer un seguiment uniforme i funcionar a gran velocitat. - Corretges acanalats o serrats (com ara corretges en V): són corretges planes bàsiques modificades per oferir els avantatges d'un altre tipus de producte de transmissió. Es tracta de cinturons plans amb una part inferior acanalada longitudinalment. Els cinturons Poly-V són un cinturó pla acanalat longitudinalment o serrat amb secció de tracció i una sèrie de solcs en forma de V adjacents amb finalitats de seguiment i compressió. La capacitat de potència depèn de l'amplada del cinturó. El cinturó en V és el cavall de batalla de la indústria i està disponible en una varietat de mides i tipus estandarditzats per a la transmissió de gairebé qualsevol potència de càrrega. Els cinturons en V funcionen bé entre 1500 i 6000 peus/min, però els cinturons en V estrets funcionaran fins a 10.000 peus/min. Els accionaments per corretja en V ofereixen una llarga vida útil com ara de 3 a 5 anys i permeten grans ràtios de velocitat, són fàcils d'instal·lar i treure, ofereixen un funcionament silenciós, baix manteniment, bona absorció de cops entre el conductor de la corretja i els eixos impulsats. El desavantatge de les corretges en V és el seu cert lliscament i fluïdesa i, per tant, pot ser que no siguin la millor solució quan es requereixin velocitats sincròniques. Disposem de cinturons industrials, d'automoció i agrícoles. Hi ha disponibles longituds estàndard en estoc, així com longituds personalitzades de cinturons. Totes les seccions transversals estàndard de la corretja en V estan disponibles en estoc. Hi ha taules on podeu calcular paràmetres desconeguts com ara la longitud de la corretja, la secció de la corretja (amplada i gruix) sempre que conegueu alguns paràmetres del vostre sistema, com ara els diàmetres de la politja conduïda i conduïda, la distància entre les politges i les velocitats de rotació de les politges. Podeu utilitzar aquestes taules o demanar-nos que triem la corretja en V adequada per a vosaltres. - Corretges de transmissió positiva (cinturó de distribució): aquests cinturons també són de tipus pla amb una sèrie de dents uniformement espaiades a la circumferència interior. Les corretges de transmissió positiva o de distribució combinen els avantatges de les corretges planes amb les característiques d'adherència positiva de les cadenes i els engranatges. Les corretges de transmissió positives no mostren lliscament ni variacions de velocitat. És possible una àmplia gamma de relacions de velocitat. Les càrregues dels coixinets són baixes perquè poden funcionar a baixa tensió. Tanmateix, són més susceptibles a desalineaments a les politges. - Politges, polees, cubs per a corretges: s'utilitzen diferents tipus de politges amb corretges de transmissió planes, acanalades (dentades) i positives. Les fabriquem totes. La majoria de les nostres politges de cinturó planes es fabriquen amb fosa de ferro, però les versions d'acer també estan disponibles en diverses combinacions de llanta i cub. Les nostres politges de corretja plana poden tenir nuclis sòlids, de radis o dividits, o podem fabricar-los com desitgeu. Els cinturons acanalats i de transmissió positiva estan disponibles en una varietat de mides i amplades d'estoc. Almenys una politja en els accionaments de la corretja de distribució ha d'estar bridada per mantenir la corretja a la transmissió. Per als sistemes d'accionament central llarg, es recomana tenir les dues politges brides. Les polees són les rodes acanalades de les politges i generalment es fabriquen mitjançant fosa de ferro, conformació d'acer o modelat de plàstic. El conformat d'acer és un procés adequat per a la fabricació de polses d'automoció i agrícoles. Produïm garbes amb solcs regulars i profunds. Les polees de ranura profunda són molt adequades quan la corretja en V entra a la polea amb un angle, com és el cas dels accionaments de quart de volta. Les ranures profundes també són adequades per a accionaments d'eix vertical i aplicacions on la vibració de les corretges pot ser un problema. Les nostres politges locas són polees acanalades o politges planes que no serveixen per transmetre potència mecànica. Les politges tenses s'utilitzen principalment per tensar les corretges. - Transmissions de corretja simple i múltiples: les transmissió de corretja única tenen una sola ranura mentre que les transmissió de corretja múltiples tenen múltiples ranures. Si feu clic al text de color corresponent a continuació, podeu descarregar els nostres catàlegs: - Cinturons de transmissió de potència (inclou corretges en V, corretges de distribució, corretges de vora crua, corretges embolcallades i corretges especials) - Cintes transportadores - Politges en V - Politges de distribució CADENES I TRANSMISSIONS DE CADENA: Les nostres cadenes de transmissió de potència tenen alguns avantatges, com ara distàncies del centre de l'eix relativament il·limitades, fàcil muntatge, compacitat, elasticitat sota tensió sense lliscament ni fluïdesa, capacitat de funcionament a altes temperatures. Aquests són els principals tipus de les nostres cadenes: - Cadenes desmuntables: les nostres cadenes desmuntables es fabriquen en una varietat de mides, pas i resistència final i, generalment, amb ferro o acer mal·leable. Les cadenes mal·leables es fabriquen en un rang de mides des de 0,902 (23 mm) fins a 4,063 polzades (103 mm) de pas i una resistència màxima de 700 a 17.000 lliures/polzada quadrada. D'altra banda, les nostres cadenes d'acer desmuntables es fabriquen en mides des de 0,904 polzades (23 mm) fins a uns 3,00 polzades (76 mm) de pas, amb una resistència màxima de 760 a 5000 lliures/polzada quadrada._cc781905-5cde-3194-bb3b- 136bad5cf58d_ - Cadenes de pins: aquestes cadenes s'utilitzen per a càrregues més pesades i velocitats lleugerament superiors a uns 450 peus/min (2,2 m/s). Les cadenes de pins estan fetes d'enllaços de fosa individuals amb un extrem de canó rodó complet amb barres laterals desplaçades. Aquests enllaços de cadena s'acoblen amb agulles d'acer. Aquestes cadenes oscil·len en un pas d'aproximadament 1,00 polzades (25 mm) a 6,00 polzades (150 mm) i les forces últimes entre 3600 i 30.000 lliures/polzada quadrada. - Cadenes de barra lateral offset: són populars a les cadenes de transmissió de maquinària de construcció. Aquestes cadenes funcionen a velocitats de 1000 peus/min i transmeten càrregues a uns 250 CV. En general, cada enllaç té dues barres laterals desplaçades, un casquet, un corró, un passador, un passador. - Cadenes de rodets: estan disponibles en passos de 0,25 (6 mm) a 3,00 (75 mm) polzades. La força màxima de les cadenes de rodets d'amplada única oscil·la entre 925 i 130.000 lliures/polzada quadrada. Hi ha disponibles versions de cadenes de rodets d'amplada múltiple i transmeten una major potència a velocitats més altes. Les cadenes de rodets d'amplada múltiple també ofereixen una acció més suau amb un soroll reduït. Les cadenes de rodets es munten a partir d'enllaços de rodets i enllaços de passador. Els passadors s'utilitzen en les cadenes de rodets de la versió desmuntable. El disseny d'accionaments de cadena de rodets requereix experiència en la matèria. Mentre que els accionaments per corretja es basen en velocitats lineals, els accionaments per cadena es basen en la velocitat de rotació de la roda dentada més petita, que en la majoria de les instal·lacions és l'element impulsat. A més de la potència nominal i la velocitat de rotació, el disseny dels accionaments de cadena es basa en molts altres factors. - Cadenes de doble pas: bàsicament les mateixes que les cadenes de rodets, excepte que el pas és el doble de llarg. - Cadenes de dents invertides (silencioses): cadenes d'alta velocitat que s'utilitzen principalment per a accionaments de presa de força i motor principal. Els accionaments de cadena de dents invertides poden transmetre potències de fins a 1200 CV i estan formats per una sèrie d'enllaços de dents, muntats alternativament amb passadors o amb una combinació de components d'articulació. La cadena de guia central té enllaços de guia per enganxar les ranures a la roda dentada, i la cadena de guia lateral té guies per enganxar els costats de la roda dentada. - Bead or Slider Chains: Aquestes cadenes s'utilitzen per a unitats de velocitat lenta i també en operacions manuals. Si feu clic al text de color corresponent a continuació, podeu descarregar els nostres catàlegs: - Cadenes de conducció - Cadenes transportadores - Cadenes transportadores de pas gran - Cadenes de rodets d'acer inoxidable - Cadenes d'elevació - Cadenes de moto - Cadenes de Màquines Agrícoles - Pinyons: els nostres pinyons estàndard s'ajusten als estàndards ANSI. Els pinyons de la placa són pinyons plans i sense hubs. Els nostres pinyons de cub de mida petita i mitjana es tornen a partir d'estoc de barres o forjades o es fan mitjançant la soldadura d'un cub de barra a una placa laminada en calent. AGS-TECH Inc. pot subministrar rodes dentades mecanitzades a partir de peces de fosa de ferro gris, acer fos i construccions de cubs soldades, metall en pols sinteritzat, plàstics modelats o mecanitzats. Per a un funcionament suau a altes velocitats, és essencial la selecció adequada de la mida dels pinyons. Les limitacions d'espai són, per descomptat, un factor que no podem ignorar a l'hora d'escollir una roda dentada. Es recomana que la relació entre el conductor i els pinyons conduïts no sigui superior a 6:1 i l'embolcall de la cadena del conductor sigui de 120 graus. Les distàncies centrals entre els pinyons més petits i els més grans, les longituds de la cadena i la tensió de la cadena també s'han de triar d'acord amb alguns càlculs i directrius d'enginyeria recomanats i no de manera aleatòria. Descarrega els nostres catàlegs fent clic al text de color següent: - Pinyons i rodes de plat - Casquilles de transmissió - Acoblament de cadena - Panys de cadena TRANSMISSIONS PER CABLE: Aquests tenen els seus avantatges respecte a les corretges i les transmissió per cadena en alguns casos. Els accionaments per cable poden complir la mateixa funció que les corretges i també poden ser més senzills i econòmics d'implementar en algunes aplicacions. Per exemple, una nova sèrie d'accionaments per cable Synchromesh està dissenyada per a una tracció positiva per substituir cordes convencionals, cables simples i accionaments dentats, especialment en espais reduïts. La nova unitat de cable està dissenyada per proporcionar un posicionament d'alta precisió en equips electrònics com fotocopiadores, plotters, màquines d'escriure, impressores,... etc. Una característica clau de la nova unitat de cable és la seva capacitat d'utilitzar-se en configuracions serpentines 3D que permeten dissenys extremadament en miniatura. Els cables de sincronització es poden utilitzar amb menor tensió en comparació amb les cordes, reduint així el consum d'energia. Poseu-vos en contacte amb AGS-TECH per a preguntes i opinions sobre corretges, cadenes i transmissió per cable. CLICK Product Finder-Locator Service PÀGINA ANTERIOR
- Composites, Composite Materials Manufacturing, Fiber Reinforced
Composites, Composite Materials Manufacturing, Particle and Fiber Reinforced, Cermets, Ceramic & Metal Composite, Glass Fiber Reinforced Polymer, Lay-Up Process Fabricació de materials compostos i compostos En termes senzills, els COMPOSITS o MATERIALS COMPOSTS són materials formats per dos o múltiples materials amb propietats físiques o químiques diferents, però quan es combinen es converteixen en un material diferent dels materials que els constitueixen. Hem de destacar que els materials constitutius romanen separats i diferents en l'estructura. L'objectiu de la fabricació d'un material compost és obtenir un producte que sigui superior als seus components i que combini les característiques desitjades de cada constituent. Com un exemple; La força, el baix pes o el preu més baix poden ser el motivador darrere de dissenyar i produir un compost. El tipus de compostos que oferim són compostos reforçats amb partícules, composites reforçats amb fibra, incloent-hi composites de matriu ceràmica / matriu de polímer / matriu metàl·lica / carboni-carboni / híbrids, compostos estructurals i laminats i amb estructura sandvitx i nanocomposites. Les tècniques de fabricació que despleguem en la fabricació de materials compostos són: pultrusió, processos de producció de preimpregnats, col·locació avançada de fibres, bobinat de filaments, col·locació de fibres a mida, procés d'esprai de fibra de vidre, tufting, procés de lanxide, z-pinning. Molts materials compostos estan formats per dues fases, la matriu, que és contínua i envolta l'altra fase; i la fase dispersa que està envoltada per la matriu. Us recomanem que feu clic aquí perDESCARREGA les nostres il·lustracions esquemàtiques de la fabricació de materials compostos i compostos per AGS-TECH Inc. Això us ajudarà a entendre millor la informació que us oferim a continuació. • COMPOSTES REFORÇATS AMB PARTÍCULES : Aquesta categoria consta de dos tipus: Composites de partícules grans i compostos reforçats per dispersió. En el primer tipus, les interaccions partícula-matriu no es poden tractar a nivell atòmic o molecular. En canvi, la mecànica del continu és vàlida. D'altra banda, en els compostos reforçats per la dispersió les partícules són generalment molt més petites en els rangs de desenes de nanòmetres. Un exemple de compost de partícules grans són els polímers als quals s'han afegit farcits. Els farciments milloren les propietats del material i poden substituir part del volum del polímer per un material més econòmic. Les fraccions de volum de les dues fases influeixen en el comportament del compost. Els compostos de partícules grans s'utilitzen amb metalls, polímers i ceràmiques. Els CERMETS són exemples de compostos ceràmics/metalls. El nostre cermet més comú és el carbur cimentat. Consisteix en ceràmica de carbur refractari com ara partícules de carbur de tungstè en una matriu d'un metall com el cobalt o el níquel. Aquests compostos de carbur s'utilitzen àmpliament com a eines de tall per a acer endurit. Les partícules de carbur dur són les responsables de l'acció de tall i la seva duresa es veu millorada per la matriu metàl·lica dúctil. Així obtenim els avantatges d'ambdós materials en un sol compost. Un altre exemple comú d'un compost de partícules grans que fem servir són les partícules de negre de carboni barrejades amb cautxú vulcanitzat per obtenir un compost amb alta resistència a la tracció, duresa, resistència a l'esquinçament i a l'abrasió. Un exemple de composite reforçat per dispersió són els metalls i els aliatges metàl·lics reforçats i endurits per la dispersió uniforme de partícules fines d'un material molt dur i inert. Quan s'afegeixen flocs d'òxid d'alumini molt petits a la matriu metàl·lica d'alumini, obtenim pols d'alumini sinteritzat que té una resistència a alta temperatura millorada. • COMPOSTES REFORÇATS AMB FIBRAS: Aquesta categoria de composites és de fet la més important. L'objectiu a aconseguir és una alta resistència i rigidesa per unitat de pes. La composició, la longitud, l'orientació i la concentració de la fibra en aquests compostos són fonamentals per determinar les propietats i la utilitat d'aquests materials. Hi ha tres grups de fibres que utilitzem: bigotis, fibres i filferros. Els bigotis són monocristalls molt prims i llargs. Es troben entre els materials més forts. Alguns exemples de materials de bigotis són el grafit, el nitrur de silici i l'òxid d'alumini. FIBRES en canvi són majoritàriament polímers o ceràmiques i es troben en estat policristalí o amorf. El tercer grup són els filferros fins que tenen diàmetres relativament grans i estan formats sovint per acer o tungstè. Un exemple de composite reforçat amb filferro són els pneumàtics d'automòbils que incorporen filferro d'acer dins del cautxú. Depenent del material de la matriu, tenim els següents compostos: COMPOSITS DE MATRIU DE POLÍMERS: estan fets d'una resina de polímer i fibres com a ingredient de reforç. Un subgrup d'aquests anomenats composites de polímer reforçat amb fibra de vidre (GFRP) contenen fibres de vidre contínues o discontínues dins d'una matriu de polímer. El vidre ofereix una gran resistència, és econòmic, fàcil de fabricar en fibres i és químicament inert. Els desavantatges són la seva rigidesa i rigidesa limitades, les temperatures de servei són només de 200 a 300 graus centígrads. La fibra de vidre és adequada per a carrosseries d'automòbils i equips de transport, carrosseries de vehicles marins, contenidors d'emmagatzematge. No són aptes per a l'aeronàutica ni per a la fabricació de ponts a causa de la rigidesa limitada. L'altre subgrup s'anomena compost de polímer reforçat amb fibra de carboni (CFRP). Aquí, el carboni és el nostre material de fibra a la matriu del polímer. El carboni és conegut pel seu alt mòdul específic i força i la seva capacitat per mantenir-los a altes temperatures. Les fibres de carboni ens poden oferir mòduls de tracció estàndard, intermedis, alts i ultraalts. A més, les fibres de carboni ofereixen diverses característiques físiques i mecàniques i, per tant, són adequades per a diverses aplicacions d'enginyeria personalitzades. Els compostos CFRP es poden considerar per fabricar equips esportius i recreatius, recipients a pressió i components estructurals aeroespacials. No obstant això, un altre subgrup, els compostos polimèrics reforçats amb fibra d'aramida, també són materials d'alta resistència i mòdul. La seva relació força/pes és excepcionalment alta. Les fibres d'aramida també es coneixen amb els noms comercials KEVLAR i NOMEX. Sota tensió funcionen millor que altres materials de fibra polimèrica, però són febles en compressió. Les fibres d'aramida són resistents, resistents a l'impacte, resistents a la fluïdesa i a la fatiga, estables a altes temperatures, químicament inerts excepte contra àcids i bases forts. Les fibres d'aramida s'utilitzen àmpliament en articles esportius, armilles antibales, pneumàtics, cordes, cobertes de cable de fibra òptica. Existeixen altres materials de reforç de fibra, però s'utilitzen en menor grau. Aquests són principalment bor, carbur de silici i òxid d'alumini. D'altra banda, el material de la matriu polimèrica també és crític. Determina la temperatura màxima de servei del compost perquè el polímer té generalment una temperatura de fusió i degradació més baixa. Els polièsters i els èsters vinílics s'utilitzen àmpliament com a matriu polimèrica. També s'utilitzen resines que tenen una excel·lent resistència a la humitat i propietats mecàniques. Per exemple, la resina de poliimida es pot utilitzar fins a uns 230 graus centígrads. COMPOSITES DE MATRIU METÀLLICA: En aquests materials utilitzem una matriu metàl·lica dúctil i les temperatures de servei són generalment superiors a les dels seus components constitutius. En comparació amb els compostos de matriu de polímer, aquests poden tenir temperatures de funcionament més altes, ser no inflamables i poden tenir una millor resistència a la degradació contra els fluids orgànics. No obstant això, són més cars. Materials de reforç com ara bigotis, partícules, fibres contínues i discontínues; i materials de matriu com ara coure, alumini, magnesi, titani, superaliatges s'estan utilitzant habitualment. Exemples d'aplicacions són components del motor fets de matriu d'aliatge d'alumini reforçat amb òxid d'alumini i fibres de carboni. COMPOSITS DE MATRIX CERÀMICA: els materials ceràmics són coneguts per la seva fiabilitat a alta temperatura excepcionalment bona. No obstant això, són molt fràgils i tenen valors baixos de tenacitat a la fractura. Mitjançant la incrustació de partícules, fibres o bigotis d'una ceràmica a la matriu d'una altra, som capaços d'aconseguir compostos amb major duresa a la fractura. Aquests materials incrustats bàsicament inhibeixen la propagació de les esquerdes a l'interior de la matriu mitjançant alguns mecanismes com ara desviar les puntes de les esquerdes o formar ponts a través de les cares de les esquerdes. Com a exemple, les alúminas reforçades amb bigotis de SiC s'utilitzen com a inserts d'eines de tall per mecanitzar aliatges de metall dur. Aquests poden revelar millors rendiments en comparació amb els carburs cimentats. COMPOSITES CARBONI-CARBON: Tant el reforç com la matriu són de carboni. Tenen mòduls de tracció elevats i resistències a altes temperatures superiors a 2000 graus centígrads, resistència a la fluència, altes dureses a la fractura, baixos coeficients d'expansió tèrmica, altes conductivitats tèrmiques. Aquestes propietats els fan ideals per a aplicacions que requereixen resistència al xoc tèrmic. La debilitat dels compostos carboni-carboni és, però, la seva vulnerabilitat davant l'oxidació a altes temperatures. Exemples típics d'ús són motlles de premsat en calent, fabricació avançada de components de motor de turbina. COMPOSITES HÍBRIDES: Es barregen dos o més tipus diferents de fibres en una sola matriu. Així, es pot adaptar un material nou amb una combinació de propietats. Un exemple és quan s'incorporen tant fibres de carboni com de vidre a una resina polimèrica. Les fibres de carboni proporcionen rigidesa i resistència de baixa densitat, però són cares. El vidre, en canvi, és barat, però no té la rigidesa de les fibres de carboni. El compost híbrid vidre-carboni és més fort i resistent i es pot fabricar a un cost més baix. PROCESSAMENT DE COMPOSITS REFORÇATS AMB FIBRAS: Per a plàstics reforçats amb fibres continus amb fibres uniformement distribuïdes i orientades en la mateixa direcció, utilitzem les tècniques següents. PULTRUSIÓ: Es fabriquen varetes, bigues i tubs de longituds contínues i seccions transversals constants. Els rovings de fibra contínua s'impregnen amb una resina termoendurible i es treuen a través d'una matriu d'acer per preformar-los a la forma desitjada. A continuació, passen per una matriu de curat mecanitzat amb precisió per aconseguir la seva forma final. Com que la matriu de curat s'escalfa, cura la matriu de resina. Els extractors treuen el material a través de les matrius. Mitjançant nuclis buits inserits, podem obtenir tubs i geometries buides. El mètode de pultrusió està automatitzat i ens ofereix alts índexs de producció. Es pot produir qualsevol llargada de producte. PROCÉS DE PRODUCCIÓ PREPREG: Preimpreg és un reforç de fibra contínua preimpregnat amb una resina de polímer parcialment curada. S'utilitza àmpliament per a aplicacions estructurals. El material es presenta en forma de cinta i s'envia com a cinta. El fabricant l'emmotlla directament i el cura completament sense necessitat d'afegir cap resina. Com que els preimpregnats experimenten reaccions de curació a temperatura ambient, s'emmagatzemen a 0 graus centígrads o temperatures inferiors. Després de l'ús, les cintes restants es guarden a baixes temperatures. S'utilitzen resines termoplàstiques i termoestables i són habituals les fibres de reforç de carboni, aramida i vidre. Per utilitzar preimpregnats, primer s'elimina el paper de suport del portador i després es fa la fabricació col·locant la cinta preimpregnada sobre una superfície einada (procés de col·locació). Es poden col·locar diverses capes per obtenir els gruixos desitjats. La pràctica freqüent és alternar l'orientació de la fibra per produir un laminat de capes creuades o angulars. Finalment s'aplica calor i pressió per a la curació. Tant el processament manual com els processos automatitzats s'utilitzen per tallar preimpregnats i lay-up. BOBINACIÓ DE FILAMENTS: les fibres de reforç contínues es col·loquen amb precisió en un patró predeterminat per seguir una forma buida i normalment ciclíndir. Les fibres passen primer per un bany de resina i després s'enrotllen sobre un mandril mitjançant un sistema automatitzat. Després de diverses repeticions d'enrotllament s'obtenen els gruixos desitjats i el curat es realitza a temperatura ambient o dins d'un forn. Ara s'elimina el mandril i es desmolda el producte. L'enrotllament del filament pot oferir relacions força-pes molt elevades enrotllant les fibres en patrons circumferencials, helicoïdals i polars. Les canonades, els dipòsits i les carcasses es fabriquen amb aquesta tècnica. • COMPOSTES ESTRUCTURALS: Generalment estan formats per materials tant homogenis com compostos. Per tant, les propietats d'aquests estan determinades pels materials constitutius i el disseny geomètric dels seus elements. Aquests són els principals tipus: COMPOSITES LAMINARS: Aquests materials estructurals estan fets de làmines o panells bidimensionals amb direccions preferides d'alta resistència. Les capes s'apilen i s'hi cimenten. En alternar les direccions d'alta resistència en els dos eixos perpendiculars, obtenim un compost que té una gran resistència en ambdues direccions en el pla bidimensional. Ajustant els angles de les capes es pot fabricar un compost amb força en les direccions preferides. L'esquí modern es fa d'aquesta manera. PANELLS SANDWICH: aquests compostos estructurals són lleugers però tenen una gran rigidesa i resistència. Els panells sandvitx consisteixen en dues làmines exteriors fetes d'un material rígid i fort com ara aliatges d'alumini, plàstics reforçats amb fibra o acer i un nucli entre les làmines exteriors. El nucli ha de ser lleuger i la majoria de vegades tenir un mòdul d'elasticitat baix. Els materials bàsics populars són escumes polimèriques rígides, fusta i bresques. Els panells sandvitx s'utilitzen àmpliament a la indústria de la construcció com a material per a sostres, sòls o parets, i també a les indústries aeroespacials. • NANOCOMPOSITS : Aquests nous materials consisteixen en partícules nanomètriques incrustades en una matriu. Amb nanocomposites podem fabricar materials de cautxú que són molt bones barreres a la penetració de l'aire, mantenint les seves propietats de cautxú sense canvis. CLICK Product Finder-Locator Service PÀGINA ANTERIOR
- Joining & Assembly & Fastening Processes, Welding, Brazing, Soldering
Joining & Assembly & Fastening Processes, Welding, Brazing, Soldering, Sintering, Adhesive Bonding, Press Fitting, Wave and Reflow Solder Process, Torch Furnace Processos d'unió i muntatge i subjecció Ajuntem, muntem i subjectem les teves peces fabricades i les transformem en productes acabats o semielaborats mitjançant SOLDADURA, SOLDADURA, SINTERITZACIÓ, ENLLAÇOS ADHESIUS, FIXACIÓ, ENGANXAT A PREMSA. Alguns dels nostres processos de soldadura més populars són arc, gas d'oxicombustible, resistència, projecció, costura, alteració, percussió, estat sòlid, feix d'electrons, làser, tèrmita, soldadura per inducció. Els nostres processos de soldadura populars són la soldadura amb torxa, inducció, forn i soldadura per immersió. Els nostres mètodes de soldadura són ferro, placa calenta, forn, inducció, immersió, ona, reflux i soldadura per ultrasons. Per a l'enllaç adhesiu utilitzem sovint termoplàstics i termoestables, epoxis, fenòlics, poliuretà, aliatges adhesius, així com alguns altres productes químics i cintes. Finalment, els nostres processos de subjecció consisteixen en clavar, cargolar, femelles i cargols, reblar, enganxar, fixar, enganxar i grapar i encaixar amb premsa. • SOLDADURA: La soldadura consisteix en la unió de materials mitjançant la fusió de les peces de treball i la introducció de materials de farciment, que també s'uneixen a la piscina de soldadura fosa. Quan la zona es refreda, obtenim una junta forta. S'aplica pressió en alguns casos. Contràriament a la soldadura, les operacions de soldadura i soldadura impliquen només la fusió d'un material amb un punt de fusió més baix entre les peces de treball, i les peces de treball no es fonen. Us recomanem que feu clic aquí perDESCARREGA les nostres il·lustracions esquemàtiques de processos de soldadura per AGS-TECH Inc. Això us ajudarà a entendre millor la informació que us oferim a continuació. A la SOLDADURA D'ARC, fem servir una font d'alimentació i un elèctrode per crear un arc elèctric que fon els metalls. El punt de soldadura està protegit per un gas o vapor de protecció o un altre material. Aquest procés és popular per soldar peces d'automòbils i estructures d'acer. En la soldadura d'arc de metall protegit (SMAW) o també coneguda com a soldadura amb pal, s'acosta un pal d'elèctrode al material de base i es genera un arc elèctric entre ells. La vareta de l'elèctrode es fon i actua com a material de farciment. L'elèctrode també conté flux que actua com una capa d'escòria i desprèn vapors que actuen com a gas protector. Aquests protegeixen la zona de soldadura de la contaminació ambiental. No s'utilitzen altres farcits. Els inconvenients d'aquest procés són la seva lentitud, la necessitat de substituir els elèctrodes amb freqüència, la necessitat d'esborrar l'escòria residual originada pel flux. Diversos metalls com ara ferro, acer, níquel, alumini, coure... etc. Es pot soldar. Els seus avantatges són les seves eines econòmiques i la seva facilitat d'ús. Soldadura d'arc de metall amb gas (GMAW) també coneguda com a gas metall inert (MIG), tenim una alimentació contínua d'un farciment de filferro d'elèctrode consumible i un gas inert o parcialment inert que flueix al voltant del cable contra la contaminació ambiental de la regió de soldadura. Es poden soldar acer, alumini i altres metalls no fèrrics. Els avantatges del MIG són les altes velocitats de soldadura i la bona qualitat. Els inconvenients són els seus complicats equips i els reptes als quals s'enfronta en entorns exteriors ventosos perquè hem de mantenir estable el gas de protecció al voltant de la zona de soldadura. Una variació de GMAW és la soldadura per arc amb nucli de flux (FCAW) que consisteix en un tub de metall fi ple de materials de flux. De vegades, el flux dins del tub és suficient per protegir-se de la contaminació ambiental. La soldadura per arc submergit (SAW) és un procés àmpliament automatitzat, que implica l'alimentació contínua de filferro i l'arc que es produeix sota una capa de coberta de flux. Les taxes de producció i la qualitat són altes, l'escòria de soldadura es desprèn fàcilment i tenim un entorn de treball lliure de fum. El desavantatge és que només es pot utilitzar per soldar parts en determinades posicions. En la soldadura per arc de tungstè amb gas (GTAW) o la soldadura per gas tungstè inert (TIG) utilitzem un elèctrode de tungstè juntament amb un farciment separat i gasos inerts o gairebé inerts. Com sabem, el tungstè té un alt punt de fusió i és un metall molt adequat per a temperatures molt elevades. El tungstè en TIG no es consumeix al contrari dels altres mètodes explicats anteriorment. Una tècnica de soldadura lenta però d'alta qualitat avantatjosa respecte a altres tècniques en la soldadura de materials prims. Apte per a molts metalls. La soldadura per arc de plasma és similar, però utilitza gas de plasma per crear l'arc. L'arc de la soldadura per arc de plasma és relativament més concentrat en comparació amb GTAW i es pot utilitzar per a una gamma més àmplia de gruixos de metall a velocitats molt més altes. La soldadura per arc de plasma i GTAW es pot aplicar a més o menys els mateixos materials. SOLDADURA OXY-FUEL / OXYFUEL també anomenada soldadura oxiacetilè, soldadura oxi, la soldadura per gas es realitza utilitzant combustibles de gas i oxigen per a la soldadura. Com que no s'utilitza energia elèctrica, és portàtil i es pot utilitzar on no hi hagi electricitat. Amb una torxa de soldadura escalfem les peces i el material de farciment per produir una piscina de metall fos compartida. Es poden utilitzar diversos combustibles com acetilè, gasolina, hidrogen, propà, butà... etc. En la soldadura d'oxi-combustible fem servir dos recipients, un per al combustible i l'altre per a l'oxigen. L'oxigen oxida el combustible (el crema). SOLDADURA PER RESISTÈNCIA: Aquest tipus de soldadura aprofita l'escalfament de joule i es genera calor en el lloc on s'aplica corrent elèctric durant un temps determinat. A través del metall passen corrents elevades. En aquest lloc es formen piscines de metall fos. Els mètodes de soldadura per resistència són populars a causa de la seva eficiència i poc potencial de contaminació. Tanmateix, els desavantatges són que els costos de l'equip són relativament significatius i la limitació inherent a peces de treball relativament primes. LA SOLDADURA PER PUNTS és un tipus principal de soldadura per resistència. Aquí unim dues o més làmines o peces de treball superposades mitjançant l'ús de dos elèctrodes de coure per subjectar les làmines i fer passar un corrent elevat a través d'elles. El material entre els elèctrodes de coure s'escalfa i en aquest lloc es genera una piscina fosa. Aleshores s'atura el corrent i les puntes dels elèctrodes de coure refreden la ubicació de la soldadura perquè els elèctrodes es refreden per aigua. Aplicar la quantitat adequada de calor al material i al gruix adequats és clau per a aquesta tècnica, ja que si s'aplica malament la junta serà feble. La soldadura per punts té els avantatges de no provocar deformacions significatives a les peces, eficiència energètica, facilitat d'automatització i ritmes de producció excepcionals, i no requereix cap farcit. El desavantatge és que, com que la soldadura es realitza en punts en lloc de formar una costura contínua, la resistència general pot ser relativament menor en comparació amb altres mètodes de soldadura. D'altra banda, la SOLDADURA DE COSTURA produeix soldadures a les superfícies de contacte de materials similars. La costura pot ser a tope o solapada. La soldadura de costura comença per un extrem i es desplaça progressivament cap a l'altre. Aquest mètode també utilitza dos elèctrodes de coure per aplicar pressió i corrent a la regió de soldadura. Els elèctrodes en forma de disc giren amb contacte constant al llarg de la línia de costura i fan una soldadura contínua. Aquí també, els elèctrodes es refreden amb aigua. Les soldadures són molt fortes i fiables. Altres mètodes són les tècniques de soldadura de projecció, flaix i pertorbació. La soldadura d'estat sòlid és una mica diferent dels mètodes anteriors explicats anteriorment. La coalescència té lloc a temperatures inferiors a la temperatura de fusió dels metalls units i sense ús de farciment metàl·lic. La pressió es pot utilitzar en alguns processos. Diversos mètodes són la SOLDADURA PER COEXTRUSIÓ on s'extrudeixen metalls diferents a través de la mateixa matriu, la SOLDADURA PER PRESSIÓ FRIDA on unim aliatges tous per sota dels seus punts de fusió, la SOLDADURA PER DIFUSIÓ una tècnica sense línies de soldadura visibles, la SOLDADURA PER EXPLOSIÓ per unir materials diferents, per exemple, aliatges resistents a la corrosió a estructurals. acers, SOLDADURA ELECTROMAGNÈTICA PER POLLS on accelerem tubs i làmines per forces electromagnètiques, SOLDADURA DE FORJA que consisteix a escalfar els metalls a altes temperatures i martellejar-los entre si, SOLDADURA PER FRICCIÓ on es realitza amb suficient soldadura per fricció, SOLDADURA PER FRICCIÓ SISTIR que implica una rotació no rotativa. eina consumible que travessa la línia d'unió, SOLDADURA PER PRESSIÓ CALENTA on premem els metalls a temperatures elevades per sota de la temperatura de fusió en buit o gasos inerts, SOLDADURA PER PRESSIÓ ISOSTÀTICA EN CALENTA un procés on apliquem pressió utilitzant gasos inerts dins d'un recipient, SOLDADURA EN ROLL on ens unim. materials diferents forçant-los entre ells dues rodes giratòries, SOLDADURA ULTRASONICA on es solden fines làmines metàl·liques o de plàstic mitjançant energia vibratòria d'alta freqüència. Els nostres altres processos de soldadura són la SOLDADURA ELECTRÒNICA amb penetració profunda i processament ràpid, però al ser un mètode car ho considerem per a casos especials, SOLDADURA ELECTRÒNICA un mètode adequat per a plaques gruixudes i peces d'acer només, SOLDADURA PER INDUCCIÓ on utilitzem inducció electromagnètica i escalfar les nostres peces de treball elèctricament conductores o ferromagnètiques, SOLDADURA LÀSER FEAM també amb penetració profunda i processament ràpid però un mètode car, SOLDADURA LÀSER HÍBRIDA que combina LBW amb GMAW en el mateix capçal de soldadura i capaç de salvar buits de 2 mm entre plaques, SOLDADURA PER PERCUSSIÓ que implica una descàrrega elèctrica seguida de la forja dels materials amb pressió aplicada, SOLDADURA THERMIT que implica una reacció exotèrmica entre pols d'òxid d'alumini i ferro., SOLDADURA ELECTROGÀS amb elèctrodes consumibles i utilitzada només amb acer en posició vertical, i finalment SOLDADURA D'ARC PER A LA UNION DE PERNO a base. material amb calor i pressió. Us recomanem que feu clic aquí perDESCARREGA les nostres il·lustracions esquemàtiques dels processos de soldadura, soldadura i unió adhesiva per AGS-TECH Inc Això us ajudarà a entendre millor la informació que us oferim a continuació. • SOLDADURA: Unim dos o més metalls escalfant metalls d'aportació entre ells per sobre dels seus punts de fusió i utilitzant l'acció capil·lar per estendre's. El procés és similar a la soldadura, però les temperatures implicades per fondre el farciment són més altes en la soldadura. Igual que en la soldadura, el flux protegeix el material de farciment de la contaminació atmosfèrica. Després de refredar-se, les peces de treball s'uneixen. El procés inclou els següents passos clau: bon ajust i espai lliure, neteja adequada dels materials base, fixació adequada, selecció de flux i atmosfera adequada, escalfament del conjunt i, finalment, neteja del conjunt soldat. Alguns dels nostres processos de soldadura són la soldadura amb torxa, un mètode popular que es realitza manualment o de manera automatitzada. És adequat per a comandes de producció de baix volum i casos especialitzats. La calor s'aplica mitjançant flames de gas prop de la junta que s'està soldant. LA SOLDADURA AL FORN requereix menys habilitat de l'operador i és un procés semiautomàtic adequat per a la producció industrial en massa. Tant el control de la temperatura com el control de l'atmosfera al forn són avantatges d'aquesta tècnica, perquè la primera ens permet tenir cicles de calor controlats i eliminar l'escalfament local com és el cas de la soldadura amb soplet, i la segona protegeix la peça de l'oxidació. Mitjançant el jigging som capaços de reduir els costos de fabricació al mínim. Els desavantatges són un alt consum d'energia, els costos de l'equip i consideracions de disseny més difícils. La soldadura al buit es realitza en un forn de buit. Es manté la uniformitat de temperatura i obtenim juntes sense flux, molt netes i amb molt pocs esforços residuals. Els tractaments tèrmics poden tenir lloc durant la soldadura al buit, a causa de les baixes tensions residuals presents durant els cicles lents d'escalfament i refrigeració. El principal desavantatge és el seu alt cost perquè la creació d'un ambient de buit és un procés costós. Encara una altra tècnica DIP BRAZING uneix peces fixades on s'aplica un compost de soldadura a les superfícies d'acoblament. A continuació, les peces fixades fixtured es submergeixen en un bany d'una sal fosa com el clorur de sodi (sal de taula) que actua com a mitjà de transferència de calor i flux. S'exclou l'aire i, per tant, no es produeix cap formació d'òxids. A LA SOLDADURA PER INDUCCIÓ unim materials mitjançant un metall d'aportació que té un punt de fusió més baix que els materials base. El corrent altern de la bobina d'inducció crea un camp electromagnètic que indueix l'escalfament per inducció en materials magnètics majoritàriament ferrosos. El mètode proporciona un escalfament selectiu, bones juntes amb farcits que flueixen només a les zones desitjades, poca oxidació perquè no hi ha flames i el refredament és ràpid, escalfament ràpid, consistència i idoneïtat per a la fabricació de grans volums. Per agilitzar els nostres processos i garantir la coherència, utilitzem sovint preformes. La informació sobre la nostra instal·lació de soldadura que produeix accessoris de ceràmica a metall, segellat hermètic, passadors de buit, buit alt i ultraalt i components de control de fluids es pot trobar aquí:_cc781905-5cde-bb3b5936Fullet de la fàbrica de soldadura • SOLDADURA : En la soldadura no tenim la fusió de les peces de treball, sinó un metall d'aportació amb un punt de fusió més baix que les peces d'unió que desemboca a la unió. El metall d'aportació en la soldadura es fon a una temperatura més baixa que en la soldadura. Utilitzem aliatges sense plom per a la soldadura i complim amb RoHS i per a diferents aplicacions i requisits disposem d'aliatges diferents i adequats com l'aliatge de plata. La soldadura ens ofereix juntes estanques a gas i líquids. En SOLDADURA TOVA, el nostre metall d'aportació té un punt de fusió per sota dels 400 graus centígrads, mentre que en SOLDADURA i SOLDADURA DE PLATA necessitem temperatures més altes. La soldadura suau utilitza temperatures més baixes, però no produeix juntes fortes per a aplicacions exigents a temperatures elevades. D'altra banda, la soldadura de plata requereix altes temperatures proporcionades per la torxa i ens ofereix juntes fortes adequades per a aplicacions d'alta temperatura. La soldadura forta requereix les temperatures més altes i normalment s'utilitza una torxa. Com que les juntes de soldadura són molt fortes, són bons candidats per reparar objectes pesats de ferro. A les nostres línies de fabricació utilitzem tant soldadura manual manual com línies de soldadura automatitzades. SOLDADURA PER INDUCCIÓ utilitza corrent alterna d'alta freqüència en una bobina de coure per facilitar l'escalfament per inducció. S'indueixen corrents a la part soldada i, com a resultat, es genera calor a l'alta resistència joint. Aquesta calor fon el metall de farciment. També s'utilitza el flux. La soldadura per inducció és un bon mètode per soldar cilindres i canonades en un procés continu embolicant les bobines al seu voltant. Soldar alguns materials com el grafit i la ceràmica és més difícil perquè requereix el revestiment de les peces amb un metall adequat abans de la soldadura. Això facilita l'enllaç interfacial. Soldem aquests materials especialment per a aplicacions d'envasos hermètics. Fabriquem les nostres plaques de circuits impresos (PCB) en gran volum, principalment mitjançant la soldadura d'ones. Només per a una petita quantitat de propòsits de prototipatge utilitzem la soldadura manual amb ferro de soldadura. Utilitzem soldadura per ones tant per a forats passants com per a conjunts de PCB de muntatge superficial (PCBA). Una cola temporal manté els components units a la placa de circuits i el conjunt es col·loca en una cinta transportadora i es mou a través d'un equip que conté soldadura fosa. Primer el PCB es flueix i després entra a la zona de preescalfament. La soldadura fosa es troba en una paella i té un patró d'ones estacionàries a la seva superfície. Quan el PCB es mou sobre aquestes ones, aquestes ones es posen en contacte amb la part inferior del PCB i s'enganxen als coixinets de soldadura. La soldadura es manté només a les agulles i els coixinets i no a la pròpia PCB. Les ones de la soldadura fosa s'han de controlar bé perquè no hi hagi esquitxades i les onades no toquin i contaminin zones no desitjades de les plaques. A REFLOW SOLDERING, fem servir una pasta de soldadura enganxosa per connectar temporalment els components electrònics a les plaques. A continuació, les plaques es passen a través d'un forn de reflux amb control de temperatura. Aquí la soldadura es fon i connecta els components permanentment. Utilitzem aquesta tècnica tant per a components de muntatge superficial com per a components de forat passant. El control adequat de la temperatura i l'ajust de les temperatures del forn és essencial per evitar la destrucció dels components electrònics de la placa per sobreescalfament per sobre dels seus límits màxims de temperatura. En el procés de soldadura per reflux, en realitat tenim diverses regions o etapes cadascuna amb un perfil tèrmic diferent, com ara el pas de preescalfament, el pas de remull tèrmic, el reflux i els passos de refredament. Aquests diferents passos són essencials per a una soldadura de reflux sense danys dels conjunts de plaques de circuit imprès (PCBA). SOLDADURA ULTRASÒNICA és una altra tècnica d'ús freqüent amb capacitats úniques: es pot utilitzar per soldar vidre, ceràmica i materials no metàl·lics. Per exemple, els panells fotovoltaics que no són metàl·lics necessiten elèctrodes que es puguin col·locar mitjançant aquesta tècnica. En la soldadura per ultrasons, despleguem una punta de soldadura escalfada que també emet vibracions ultrasòniques. Aquestes vibracions produeixen bombolles de cavitació a la interfície del substrat amb el material de soldadura fos. L'energia implosiva de la cavitació modifica la superfície de l'òxid i elimina la brutícia i els òxids. Durant aquest temps també es forma una capa d'aliatge. La soldadura a la superfície d'unió incorpora oxigen i permet la formació d'un fort enllaç compartit entre el vidre i la soldadura. La soldadura per immersió es pot considerar com una versió més senzilla de la soldadura per ones adequada només per a la producció a petita escala. El primer flux de neteja s'aplica com en altres processos. Els PCB amb components muntats es submergeixen manualment o de manera semiautomatitzada en un dipòsit que conté soldadura fosa. La soldadura fosa s'adhereix a les zones metàl·liques exposades sense protecció per la màscara de soldadura a la placa. L'equip és senzill i econòmic. • ENLLAÇ ADHESIU: Aquesta és una altra tècnica popular que fem servir amb freqüència i consisteix en l'enllaç de superfícies mitjançant coles, epoxi, agents plàstics o altres productes químics. L'enllaç s'aconsegueix evaporant el dissolvent, per curat per calor, per curat per llum UV, per curat per pressió o esperant un temps determinat. A les nostres línies de producció s'utilitzen diverses coles d'alt rendiment. Amb processos d'aplicació i curat dissenyats correctament, la unió adhesiva pot donar lloc a enllaços de tensió molt baixes, forts i fiables. Els enllaços adhesius poden ser bons protectors contra factors ambientals com ara humitat, contaminants, corrosius, vibracions... etc. Els avantatges de la unió adhesiva són: es poden aplicar a materials que, d'altra manera, serien difícils de soldar, soldar o soldar. També pot ser preferible per a materials sensibles a la calor que es podrien danyar per soldadura o altres processos d'alta temperatura. Altres avantatges dels adhesius són que es poden aplicar a superfícies de forma irregular i augmentar el pes del muntatge en quantitats molt molt petites en comparació amb altres mètodes. També els canvis dimensionals en les peces són molt mínims. Algunes coles tenen propietats de concordança d'índexs i es poden utilitzar entre components òptics sense disminuir significativament la intensitat del senyal òptic o de llum. D'altra banda, els desavantatges són els temps de curat més llargs que poden alentir les línies de fabricació, els requisits de fixació, els requisits de preparació de la superfície i la dificultat de desmuntar quan es necessita una reelaboració. La majoria de les nostres operacions d'unió adhesiva inclouen els passos següents: - Tractament de superfícies: són habituals els procediments de neteja especials com la neteja amb aigua desionitzada, la neteja amb alcohol, la neteja amb plasma o corona. Després de la neteja podem aplicar promotors d'adhesió a les superfícies per assegurar les millors juntes possibles. - Fixació de peces: tant per a l'aplicació d'adhesius com per al curat dissenyem i utilitzem accessoris personalitzats. -Aplicació d'adhesius: De vegades utilitzem sistemes manuals, i de vegades segons el cas automatitzats com ara robòtica, servomotors, actuadors lineals per lliurar els adhesius a la ubicació correcta i fem servir dispensadors per lliurar-los al volum i quantitat adequats. - Curat: Depenent de l'adhesiu, podem utilitzar un assecat i curat senzill, així com el curat sota llums UV que actuen com a catalitzador o curat per calor en un forn o utilitzant elements calefactors resistius muntats en plantilles i accessoris. Us recomanem que feu clic aquí perDESCARREGA les nostres il·lustracions esquemàtiques dels processos de fixació d'AGS-TECH Inc. Això us ajudarà a entendre millor la informació que us oferim a continuació. • PROCESSOS DE FIXACIÓ: Els nostres processos d'unió mecànica es divideixen en dues categories: FIXACIONS i JUNTES INTEGRALS. Exemples de fixacions que fem servir són cargols, passadors, femelles, cargols, reblons. Exemples d'unions integrals que utilitzem són els ajustaments a pressió i retràctil, les costures i els encrespaments. Mitjançant una varietat de mètodes de fixació ens assegurem que les nostres juntes mecàniques siguin fortes i fiables durant molts anys d'ús. CARGOLS i CARGOLS són alguns dels elements de subjecció més utilitzats per subjectar objectes i col·locar-los. Els nostres cargols i cargols compleixen els estàndards ASME. Es despleguen diversos tipus de cargols i cargols, com ara cargols hexagonals i cargols hexagonals, cargols i cargols, cargols de doble extrem, cargol de tac, cargol d'ull, cargol de mirall, cargol de xapa, cargol d'ajustament fi, cargols autoperforants i autorroscants. , cargol de fixació, cargols amb volanderes incorporades,... i molt més. Tenim diversos tipus de capçal de cargol, com ara capçal avellanat, cúpula, rodó, amb brides i diversos tipus d'accionament de cargol, com ara ranura, Phillips, quadrat, hexagonal. Un RIVET, en canvi, és una fixació mecànica permanent que consisteix en un eix cilíndric llis i un cap d'una banda. Després de la inserció, l'altre extrem del rebló es deforma i el seu diàmetre s'amplia perquè es mantingui al seu lloc. És a dir, abans de la instal·lació un rebló té un cap i després de la instal·lació en té dos. Instal·lem diversos tipus de reblons en funció de l'aplicació, la força, l'accessibilitat i el cost, com ara reblons de capçal sòlid/rodonc, estructurals, semitubulars, cecs, oscar, drive, enrasat, bloqueig de fricció i autoperforants. El reblat es pot preferir en els casos en què s'ha d'evitar la deformació per calor i el canvi en les propietats del material a causa de la calor de la soldadura. El reblat també ofereix un pes lleuger i especialment una bona resistència i resistència davant les forces de cisalla. Contra les càrregues de tracció, però, els cargols, les femelles i els cargols poden ser més adequats. En el procés CLINCHING utilitzem punxons i matrius especials per formar un enclavament mecànic entre les xapes que s'uneixen. El punxó empeny les capes de xapa a la cavitat de la matriu i dóna lloc a la formació d'una unió permanent. No es requereix escalfament ni refrigeració en el clinching i és un procés de treball en fred. És un procés econòmic que pot substituir la soldadura per punts en alguns casos. A PINNING fem servir passadors que són elements de la màquina que s'utilitzen per assegurar les posicions de les peces de la màquina entre si. Els tipus principals són els passadors de la horma, el passador, el passador de molla, els passadors, i el passador dividit. A STAPLING utilitzem pistoles de grapat i grapes que són fixacions de dues puntes que s'utilitzen per unir o lligar materials. El grapat té els següents avantatges: econòmic, senzill i ràpid d'utilitzar, la corona de les grapes es pot utilitzar per unir materials entre si, la corona de la grapa pot facilitar un pont d'una peça com un cable i subjectar-la a una superfície sense punxar-la ni perforar-la. perjudicial, eliminació relativament fàcil. L'ajustament a premsa es realitza empènyer les peces juntes i la fricció entre elles subjecta les peces. Les peces d'ajustament a pressió que consisteixen en un eix sobredimensionat i un forat de mida inferior s'acoblen generalment per un dels dos mètodes: ja sigui aplicant força o aprofitant l'expansió o la contracció tèrmica de les peces. Quan s'estableix un accessori de premsa aplicant una força, fem servir una premsa hidràulica o una premsa manual. D'altra banda, quan s'estableix l'ajust a premsa per dilatació tèrmica, escalfem les peces d'envoltant i les muntem al seu lloc quan estiguin calentes. Quan es refreden es contrauen i tornen a les seves dimensions normals. Això resulta en un bon ajust de premsa. A això l'anomenem alternativament CONTACTE. L'altra manera de fer-ho és refredant les peces embolcallades abans del muntatge i després lliscar-les a les seves parts d'acoblament. Quan el conjunt s'escalfa s'expandeixen i obtenim un ajustament ajustat. Aquest últim mètode pot ser preferible en els casos en què l'escalfament comporta el risc de canviar les propietats del material. La refrigeració és més segura en aquests casos. Components i conjunts pneumàtics i hidràulics • Vàlvules, components hidràulics i pneumàtics com ara junta tòrica, rentadora, juntes, junta, anell, calçat. Atès que les vàlvules i components pneumàtics tenen una gran varietat, no podem enumerar-ho tot aquí. Depenent de l'entorn físic i químic de la seva aplicació, tenim productes especials per a vostè. Si us plau, especifiqueu-nos l'aplicació, tipus de component, especificacions, condicions ambientals com pressió, temperatura, líquids o gasos que estaran en contacte amb les vostres vàlvules i components pneumàtics; i triarem el producte més adequat per a tu o el fabricarem especialment per a la teva aplicació. CLICK Product Finder-Locator Service PÀGINA ANTERIOR
- Rapid Prototyping, Desktop Manufacturing, Additive Manufacturing, FDM
Rapid Prototyping, Desktop Manufacturing, Additive Manufacturing, Stereolithography, Polyjet, Fused Deposition Modeling, Selective Laser Sintering, FDM, SLS Fabricació additiva i ràpida En els darrers anys, hem vist un augment de la demanda de FABRICACIÓ RÀPIDA o PROTOTIPAT RÀPID. Aquest procés també es pot anomenar FABRICCIÓ D'ESCRIPTORI o FABRICACIÓN DE FORMA LLIURE. Bàsicament, un model físic sòlid d'una peça es fa directament a partir d'un dibuix CAD tridimensional. Utilitzem el terme FABRICACIÓ ADITIVA per a aquestes diferents tècniques on construïm peces en capes. Utilitzant maquinari i programari integrats impulsats per ordinador realitzem la fabricació additiva. Les nostres tècniques ràpides de prototipat i fabricació són ESTEREOLITOGRAFIA, POLYJET, MODELITZACIÓ DE DEPOSICIÓ FUSADA, SINTERITZACIÓ LÀSER SELECTIVA, FUSIÓ DE FIXES ELECTRONS, IMPRESSIÓ TRIDIMENSIONAL, FABRICACIÓ DIRECTA, UTILITZACIÓ RÀPIDA. Us recomanem que feu clic aquí perDESCARREGA les nostres il·lustracions esquemàtiques de la fabricació additiva i els processos de fabricació ràpida per AGS-TECH Inc. Això us ajudarà a entendre millor la informació que us oferim a continuació. El prototipat ràpid ens proporciona: 1.) El disseny conceptual del producte es visualitza des de diferents angles en un monitor mitjançant un sistema 3D/CAD. 2.) Es fabriquen i s'estudien prototips a partir de materials no metàl·lics i metàl·lics des dels aspectes funcionals, tècnics i estètics. 3.) S'aconsegueix un prototip de baix cost en molt poc temps. La fabricació additiva es pot semblar a la construcció d'una barra de pa apilant i unint llesques individuals una sobre l'altra. És a dir, el producte es fabrica llesca per rodanxa, o es diposita capa per capa una sobre l'altra. La majoria de peces es poden produir en hores. La tècnica és bona si es necessiten peces molt ràpidament o si les quantitats necessàries són baixes i fer un motlle i eines és massa car i requereix molt de temps. Tanmateix, el cost d'una peça és car a causa de les matèries primeres cares. • ESTEREOLITOGRAFIA : Aquesta tècnica també abreujada com STL, es basa en el curat i enduriment d'un fotopolímer líquid en una forma específica enfocant-hi un raig làser. El làser polimeritza el fotopolímer i el cura. Mitjançant l'escaneig del raig làser UV segons la forma programada al llarg de la superfície de la barreja de fotopolímers, la peça es produeix de baix a dalt en rodanxes individuals en cascada una sobre l'altra. L'escaneig del punt làser es repeteix moltes vegades per aconseguir les geometries programades al sistema. Després que la peça estigui completament fabricada, es retira de la plataforma, es borra i es neteja per ultrasons i amb bany d'alcohol. A continuació, s'exposa a la irradiació UV durant unes hores per assegurar-se que el polímer estigui completament curat i endurit. Per resumir el procés, una plataforma que es submergeix en una barreja de fotopolímers i un raig làser UV es controla i es mou a través d'un sistema de servocontrol segons la forma de la peça desitjada i la peça s'obté fotocurant el polímer capa per capa. Per descomptat, les dimensions màximes de la peça produïda estan determinades per l'equip d'estereolitografia. • POLYJET : semblant a la impressió d'injecció de tinta, en polyjet tenim vuit capçals d'impressió que dipositen fotopolímer a la safata de construcció. La llum ultraviolada col·locada al costat dels dolls cura i endureix immediatament cada capa. En polyjet s'utilitzen dos materials. El primer material és per a la fabricació del model real. El segon material, una resina semblant a un gel s'utilitza com a suport. Ambdós materials es dipositen capa per capa i es curen simultàniament. Un cop finalitzat el model, el material de suport s'elimina amb una solució aquosa. Les resines utilitzades són similars a la estereolitografia (STL). El polyjet té els següents avantatges respecte a l'estereolitografia: 1.) No cal netejar les peces. 2.) No cal curar postprocés 3.) Són possibles gruixos de capes més petits i així obtenim una millor resolució i podem fabricar peces més fines. • MODELITZACIÓ DE DEPOSICIÓ FUSADA: També abreujat com a FDM, en aquest mètode un capçal d'extrusora controlat per robot es mou en dues direccions principals sobre una taula. El cable es baixa i s'aixeca segons sigui necessari. Des de l'orifici d'una matriu escalfada al cap, s'extrudeix un filament termoplàstic i es diposita una capa inicial sobre una base d'escuma. Això s'aconsegueix mitjançant el capçal de l'extrusora que segueix un camí predeterminat. Després de la capa inicial, la taula es baixa i les capes posteriors es dipositen una sobre l'altra. De vegades, quan es fabriquen una peça complicada, es necessiten estructures de suport perquè la deposició pugui continuar en determinades direccions. En aquests casos, un material de suport s'extrudeix amb un espai de filament menys dens sobre una capa de manera que sigui més feble que el material del model. Aquestes estructures de suport es poden dissoldre o trencar posteriorment després de la finalització de la peça. Les dimensions de la matriu de l'extrusora determinen el gruix de les capes extruïdes. El procés FDM produeix peces amb superfícies esglaonades en plans exteriors oblics. Si aquesta rugositat és inacceptable, es pot utilitzar un poliment de vapor químic o una eina escalfada per suavitzar-los. Fins i tot hi ha disponible una cera de poliment com a material de recobriment per eliminar aquests passos i aconseguir toleràncies geomètriques raonables. • SINTERITZACIÓ LÀSER SELECTIVA: També denominat SLS, el procés es basa en la sinterització selectiva d'un polímer, pols ceràmiques o metàl·liques en un objecte. La part inferior de la cambra de processament té dos cilindres: un cilindre de construcció parcial i un cilindre d'alimentació de pols. El primer es baixa gradualment fins a on s'està formant la peça sinteritzada i el segon s'eleva gradualment per subministrar pols al cilindre de construcció de peces mitjançant un mecanisme de corró. Primer es diposita una fina capa de pols al cilindre de construcció parcial, després es centra un raig làser en aquesta capa, traçant i fonent/sinteritzant una secció transversal determinada, que després es torna a solidificar en un sòlid. La pols és que les zones que no són afectades pel raig làser es mantenen soltes, però encara suporten la part sòlida. Després es diposita una altra capa de pols i es repeteix el procés moltes vegades per obtenir la peça. Al final, es treuen les partícules de pols soltes. Tot això es realitza mitjançant un ordinador de control de processos mitjançant instruccions generades pel programa CAD 3D de la peça que s'està fabricant. Es poden dipositar diversos materials com polímers (com ABS, PVC, polièster), ceres, metalls i ceràmiques amb aglutinants de polímers adequats. • ELECTRON-BEAM MELTING : Similar a la sinterització làser selectiva, però utilitzant feix d'electrons per fondre pols de titani o crom cobalt per fer prototips al buit. S'han fet alguns desenvolupaments per realitzar aquest procés en acers inoxidables, alumini i aliatges de coure. Si cal augmentar la resistència a la fatiga de les peces produïdes, utilitzem la premsa isostàtica en calent posterior a la fabricació de peces com a procés secundari. • IMPRESSIÓ TRIDIMENSIONAL: També denotada per 3DP, en aquesta tècnica un capçal d'impressió diposita un aglutinant inorgànic sobre una capa de pols no metàl·lica o metàl·lica. Un pistó que porta el llit de pols es baixa gradualment i a cada pas es diposita l'aglutinant capa per capa i es fusiona per l'aglutinant. Els materials en pols utilitzats són barreges de polímers i fibres, sorra de fosa, metalls. Utilitzant diferents capçals d'enquadernador simultàniament i diferents aglutinants de colors podem obtenir diversos colors. El procés és semblant a la impressió d'injecció de tinta però en comptes d'obtenir una làmina de colors obtenim un objecte tridimensional de colors. Les peces produïdes poden ser poroses i per tant poden requerir sinterització i infiltració de metalls per augmentar la seva densitat i resistència. La sinterització cremarà l'aglutinant i fusionarà les pols metàl·liques. Metalls com l'acer inoxidable, l'alumini, el titani es poden utilitzar per fer les peces i com a materials d'infiltració utilitzem habitualment coure i bronze. La bellesa d'aquesta tècnica és que fins i tot conjunts complicats i mòbils es poden fabricar molt ràpidament. Per exemple, es pot fer un conjunt d'engranatges, una clau anglesa com a eina i tindrà peces mòbils i giratòries a punt per ser utilitzades. Els diferents components del conjunt es poden fabricar amb diferents colors i tot d'un sol cop. Descarrega el nostre fulletó a:Conceptes bàsics de la impressió 3D de metall • FABRICACIÓ DIRECTA i UTILITZACIÓ RÀPIDA: A més de l'avaluació del disseny i la resolució de problemes, utilitzem prototips ràpids per a la fabricació directa de productes o l'aplicació directa als productes. En altres paraules, el prototipat ràpid es pot incorporar als processos convencionals per fer-los millors i més competitius. Per exemple, el prototipat ràpid pot produir patrons i motlles. Els patrons d'un polímer de fusió i combustió creats per operacions de prototipat ràpid es poden muntar per a la fosa d'inversió i invertir. Un altre exemple a esmentar és utilitzar 3DP per produir carcassa de fosa de ceràmica i utilitzar-la per a operacions de fosa de closca. Fins i tot els motlles d'injecció i les insercions de motlles es poden produir mitjançant un prototipat ràpid i es poden estalviar moltes setmanes o mesos de temps de fabricació de motlles. Només analitzant un fitxer CAD de la peça desitjada, podem produir la geometria de l'eina mitjançant programari. Aquests són alguns dels nostres mètodes populars d'eines ràpides: RTV (Room-Temperature Vulcanizing) MOLDURA / COSTADA D'URETA: Es pot utilitzar el prototipat ràpid per fer el patró de la peça desitjada. A continuació, aquest patró es recobreix amb un agent de separació i s'aboca cautxú RTV líquid sobre el patró per produir les meitats del motlle. A continuació, aquestes meitats de motlle s'utilitzen per injecció d'uretans líquids. La vida útil del motlle és curta, només com 0 o 30 cicles, però suficient per a la producció de lots petits. ACES (Acetal Clear Epoxy Solid) MOLDETURA PER INJECCIÓ: Utilitzant tècniques de prototipat ràpid com l'estereolitografia, produïm motlles d'injecció. Aquests motlles són closques amb un extrem obert per permetre l'ompliment de materials com epoxi, epoxi farcit d'alumini o metalls. De nou, la vida útil del motlle es limita a desenes o centenars de peces com a màxim. PROCÉS D'EINES DE METÀLLIC POLVERIZAT: Utilitzem prototips ràpids i fem un patró. Ruixem un aliatge d'alumini-zinc a la superfície del patró i l'hi recobrim. A continuació, el patró amb el recobriment metàl·lic es col·loca dins d'un matràs i es posa en test amb un epoxi o farcit d'alumini. Finalment, es retira i produint dues meitats de motlle d'aquest tipus obtenim un motlle complet per a l'emmotllament per injecció. Aquests motlles tenen una vida útil més llarga, en alguns casos, segons el material i les temperatures, poden produir milers de peces. PROCÉS KEELTOOL: aquesta tècnica pot produir motlles amb 100.000 a 10 milions de cicles de vida. Utilitzant prototips ràpids produïm un motlle RTV. A continuació, s'omple el motlle amb una barreja que consisteix en pols d'acer per eines A6, carbur de tungstè, aglutinant de polímer i es deixa curar. A continuació, aquest motlle s'escalfa per cremar el polímer i fusionar les pols metàl·liques. El següent pas és la infiltració de coure per produir el motlle final. Si cal, es poden realitzar operacions secundàries com el mecanitzat i el polit al motlle per obtenir millors precisions dimensionals. CLICK Product Finder-Locator Service PÀGINA ANTERIOR
- Machine Elements Manufacturing, Gears, Gear Drives, Bearings, Keys, Splines
Machine Elements Manufacturing, Gears, Gear Drives, Bearings, Keys, Splines, Pins, Shafts, Seals, Fasteners, Clutch, Cams, Followers, Belts, Couplings, Shafts Fabricació d'elements de màquines Llegeix més Corretges i cadenes i conjunt d'accionament per cable Llegeix més Engranatges i conjunt d'accionament d'engranatges Llegeix més Fabricació d'acoblaments i coixinets Llegeix més Fabricació de claus i splines i passadors Llegeix més Lleves i seguidors i enllaços i fabricació de rodes de trinquet Llegeix més Fabricació d'eixos Llegeix més Fabricació de segells mecànics Llegeix més Conjunt d'embragatge i fre Llegeix més Fabricació de fixacions Llegeix més Muntatge de màquines senzilles ELS ELEMENTS DE LA MÀQUINA són components elementals d'una màquina. Aquests elements consten de tres tipus bàsics: 1.) Components estructurals, inclosos els membres del bastidor, els coixinets, els eixos, les estries, els elements de subjecció, els segells i els lubricants. 2.) Mecanismes que controlen el moviment de diverses maneres, com ara trens d'engranatges, transmissió per corretja o cadena, enllaços, sistemes de lleves i seguidors, frens i embragatges. 3.) Components de control com botons, interruptors, indicadors, sensors, actuadors i controladors d'ordinador. La majoria dels elements de la màquina que us oferim estan estandarditzats per a mides habituals, però també hi ha elements de màquina fets a mida per a les vostres aplicacions especialitzades. La personalització dels elements de la màquina es pot dur a terme en dissenys existents que es troben als nostres catàlegs descarregables o en dissenys nous. El prototipat i la fabricació d'elements de la màquina es poden dur a terme una vegada que el disseny sigui aprovat per ambdues parts. Si cal dissenyar i fabricar nous elements de la màquina, els nostres clients ens envien per correu electrònic els seus propis plànols i els revisem per a l'aprovació, o bé ens demanen que dissenyem elements de la màquina per a la seva aplicació. En aquest últim cas, utilitzem totes les aportacions dels nostres clients i dissenyem els elements de la màquina i enviem els plànols finalitzats als nostres clients per a la seva aprovació. Un cop aprovats, produïm primers articles i posteriorment fabriquem els elements de la màquina segons el disseny final. En qualsevol fase d'aquest treball, en cas que el disseny d'un element de màquina en particular funcioni de manera insatisfactòria al camp (cosa rara), revisem tot el projecte i fem les modificacions conjuntament amb els nostres clients segons sigui necessari. La nostra pràctica habitual és signar acords de confidencialitat (NDA) amb els nostres clients per al disseny d'elements de màquines o qualsevol altre producte sempre que sigui necessari o requerit. Un cop dissenyats i fabricats a mida els elements de la màquina per a un client en particular, li assignem un codi de producte i només els produïm i els venem al nostre client propietari del producte. Reproduïm els elements de la màquina utilitzant les eines, motlles i procediments desenvolupats tantes vegades com sigui necessari i sempre que el nostre client els reordena. És a dir, un cop dissenyat i produït un element de màquina personalitzat per a vostè, la propietat intel·lectual així com totes les eines i motlles es reserven i emmagatzemem indefinidament per a vostè i els productes reproduïts com desitgeu. També oferim als nostres clients serveis d'enginyeria combinant de manera creativa els elements de la màquina en un component o conjunt que serveixi per a una aplicació i compleix o supera les expectatives dels nostres clients. Les plantes que fabriquen els nostres elements de màquina estan qualificades per ISO9001, QS9000 o TS16949. A més, la majoria dels nostres productes tenen la marca CE o UL i compleixen estàndards internacionals rellevants com ISO, SAE, ASME, DIN. Feu clic als submenús per obtenir informació detallada sobre els elements de la nostra màquina, com ara: - Corretges, cadenes i transmissió per cable - Engranatges i accionaments - Acoblaments i coixinets - Tecles i Splines i pins - Càmeres i enllaços - Eixos - Segells mecànics - Embragatge i fre industrials - Subjeccions - Màquines simples Hem elaborat un fulletó de referència per als nostres clients, dissenyadors i desenvolupadors de nous productes, inclosos els elements de la màquina. Podeu familiaritzar-vos amb alguns termes d'ús habitual en el disseny de components de màquines: Baixeu el fulletó dels termes comuns d'enginyeria mecànica utilitzats per dissenyadors i enginyers Els nostres elements de màquines troben aplicacions en una varietat de camps com ara maquinària industrial, sistemes d'automatització, equips de prova i metrologia, equips de transport, màquines de construcció i pràcticament a qualsevol lloc que se us acudeixi. AGS-TECH desenvolupa i fabrica elements de màquines amb diferents materials segons l'aplicació. Els materials utilitzats per als elements de la màquina podrien anar des de plàstics modelats utilitzats per a joguines fins a acer endurit i recobert especialment per a maquinària industrial. Els nostres dissenyadors utilitzen programari professional d'última generació i eines de disseny per desenvolupar elements de la màquina, tenint en compte detalls com ara els angles de les dents de l'engranatge, les tensions implicades, les taxes de desgast... etc. Si us plau, desplaceu-vos pels nostres submenús i descarregueu els nostres fullets i catàlegs de productes per veure si podeu localitzar els elements de la màquina disponibles per a la vostra aplicació. Si no trobeu una bona combinació per a la vostra aplicació, feu-nos-ho saber i treballarem amb vosaltres per desenvolupar i fabricar elements de màquina que satisfan les vostres necessitats. Si esteu interessats principalment en les nostres capacitats d'enginyeria i recerca i desenvolupament en lloc de les capacitats de fabricació, us convidem a visitar el nostre lloc web http://www.ags-engineering.com on podeu trobar informació més detallada sobre el nostre disseny, desenvolupament de productes, desenvolupament de processos, serveis de consultoria d'enginyeria i molt més CLICK Product Finder-Locator Service PÀGINA ANTERIOR
- Glass and Ceramic Manufacturing, Hermetic Packages, Seals, Bonding
Glass and Ceramic Manufacturing, Hermetic Packages Seals and Bonding, Tempered Bulletproof Glass, Blow Moulding, Optical Grade Glass, Conductive Glass, Molding Formació i conformació de vidre i ceràmica El tipus de fabricació de vidre que oferim són vidre d'envasos, vidre bufat, fibra de vidre i tubs i varetes, vidre domèstic i industrial, làmpades i bombetes, modelat de precisió de vidre, components òptics i conjunts, vidre pla i làmina i flotat. Realitzem tant el conformat manual com el conformat a màquina. Els nostres populars processos de fabricació de ceràmica tècnica són el premsat en matriu, el premsat isostàtic, el premsat isostàtic en calent, el premsat en calent, la fosa antilliscant, la fosa de cinta, l'extrusió, l'emmotllament per injecció, el mecanitzat verd, la sinterització o la cocció, la mòlta de diamant, els muntatges hermètics. Us recomanem que feu clic aquí per DESCARREGA les nostres il·lustracions esquemàtiques dels processos de conformació i conformació de vidre d'AGS-TECH Inc. DESCARREGA les nostres il·lustracions esquemàtiques dels processos tècnics de fabricació de ceràmica per AGS-TECH Inc. Aquests fitxers descarregables amb fotos i esbossos us ajudaran a entendre millor la informació que us oferim a continuació. • FABRICACIÓ DE CONTENIDORS DE VIDRE: Disposem de línies automatitzades de PREMSA I SUPAT així com línies de SUPAT I SUPAT per a la fabricació. En el procés de bufat i bufat deixem caure un gob en un motlle en blanc i formem el coll aplicant un cop d'aire comprimit des de dalt. Immediatament després d'això, es bufa aire comprimit una segona vegada des de l'altra direcció a través del coll del recipient per formar la preforma de l'ampolla. A continuació, aquesta preforma es transfereix al motlle real, es torna a escalfar per suavitzar i s'aplica aire comprimit per donar a la preforma la seva forma final de recipient. Més explícitament, es pressuritza i s'empeny contra les parets de la cavitat del motlle de bufat per prendre la forma desitjada. Finalment, el recipient de vidre fabricat es trasllada a un forn de recuit per al seu posterior recalentament i eliminació de les tensions produïdes durant l'emmotllament i es refreda de manera controlada. En el mètode de premsa i bufat, les gobs foses es posen en un motlle parís (motlle en blanc) i es pressionen en forma de parís (forma en blanc). A continuació, els blancs es transfereixen a motlles de bufat i es bufen de manera similar al procés descrit anteriorment a "Procés de bufat i bufat". Els passos posteriors com el recuit i l'alleujament de tensió són similars o iguals. • BUFAT DE VIDRE: Hem estat fabricant productes de vidre amb bufat manual convencional així com amb aire comprimit amb equips automatitzats. Per a algunes comandes és necessari el bufat convencional, com ara projectes que impliquen obres d'art de vidre, o projectes que requereixen un nombre menor de peces amb toleràncies soltes, projectes de prototipatge/demo... etc. El bufat de vidre convencional consisteix a submergir una canonada de metall buida en una olla de vidre fos i fer girar la canonada per recollir una part del material de vidre. El vidre recollit a la punta de la canonada s'enrotlla sobre ferro pla, amb la forma desitjada, allargat, reescalfat i bufat amb aire. Quan estigui llest, s'introdueix en un motlle i es bufa aire. La cavitat del motlle està humida per evitar el contacte del vidre amb el metall. La pel·lícula d'aigua actua com un coixí entre ells. El bufat manual és un procés lent intensiu de mà d'obra i només apte per a la creació de prototips o articles d'alt valor, no apte per a comandes de gran volum per peça barates. • FABRICACIÓ DE VIDRERIA DOMÀSTICA I INDUSTRIAL: utilitzant diversos tipus de material de vidre s'està produint una gran varietat de vidre. Alguns gots són resistents a la calor i aptes per a la cristalleria de laboratori, mentre que alguns són prou bons per suportar els rentavaixelles moltes vegades i són aptes per fer productes domèstics. Amb les màquines de Westlake es produeixen desenes de milers de gots al dia. Per simplificar, el vidre fos es recull al buit i s'introdueix en motlles per fer les preformes. Després es bufa aire als motlles, aquests es traslladen a un altre motlle i es torna a bufar aire i el vidre pren la seva forma definitiva. Com en el bufat a mà, aquests motlles es mantenen humits amb aigua. L'estirament addicional forma part de l'operació d'acabat on s'està formant el coll. L'excés de vidre es crema. A continuació, es mostra el procés de reescalfament i refredament controlat descrit anteriorment. • FORMACIÓ DE TUBS DE VIDRE I VARILLA: Els principals processos que utilitzem per a la fabricació de tubs de vidre són els processos DANNER i VELLO. En el procés Danner, el vidre d'un forn flueix i cau sobre una màniga inclinada feta de materials refractaris. La màniga es porta sobre un eix buit giratori o una sobatana. A continuació, el vidre s'embolica al voltant de la màniga i forma una capa llisa que flueix per la màniga i sobre la punta de l'eix. En el cas de la conformació de tubs, l'aire es bufa a través d'una sabatana amb punta buida, i en el cas de la formació de varetes utilitzem puntes sòlides a l'eix. Aleshores, els tubs o barres s'arrosseguen sobre rodets de transport. Les dimensions com el gruix de la paret i el diàmetre dels tubs de vidre s'ajusten als valors desitjats configurant el diàmetre de la màniga i la pressió d'aire de bufat a un valor desitjat, ajustant la temperatura, la velocitat de flux del vidre i la velocitat d'estirament. El procés de fabricació del tub de vidre Vello, d'altra banda, implica el vidre que surt d'un forn i cap a un bol amb un mandril o campana buit. Aleshores, el vidre travessa l'espai d'aire entre el mandril i el bol i pren forma de tub. A continuació, viatja sobre rodets fins a una màquina de dibuix i es refreda. Al final de la línia de refrigeració es produeix el tall i el processament final. Les dimensions del tub es poden ajustar igual que en el procés Danner. Quan comparem el procés Danner amb el Vello, podem dir que el procés Vello s'adapta millor a la producció de grans quantitats, mentre que el procés Danner pot ser més adequat per a comandes precises de tubs de volum més petit. • PROCESSAMENT DE LLAMA I VIDRE PLA I FLOTAT: Disposem de grans quantitats de vidre pla en gruixos que van des de gruixos submilimètrics fins a diversos centímetres. Les nostres ulleres planes són d'una perfecció gairebé òptica. Oferim vidre amb recobriments especials com els recobriments òptics, on s'utilitza la tècnica de deposició química de vapor per posar recobriments com el recobriment antireflectant o mirall. També són habituals els recobriments conductors transparents. També hi ha recobriments hidrofòbics o hidròfils sobre vidre i recobriment que fa que el vidre s'autonetegi. Els vidres temperats, antibales i laminats són altres articles populars. Tallem el vidre a la forma desitjada amb les toleràncies desitjades. Hi ha altres operacions secundàries com corbar o doblegar el vidre pla. • MOLDETURA DE VIDRE DE PRECISIÓ: Utilitzem aquesta tècnica principalment per a la fabricació de components òptics de precisió sense la necessitat de tècniques més cares i que consumeixen molt de temps com el rectificat, el lligat i el polit. Aquesta tècnica no sempre és suficient per aprofitar al màxim les millors òptiques, però en alguns casos, com ara productes de consum, càmeres digitals, òptiques mèdiques, pot ser una bona opció menys costosa per a la fabricació de grans volums. També té un avantatge sobre les altres tècniques de conformació de vidre on es requereixen geometries complexes, com en el cas de les asferes. El procés bàsic consisteix a carregar la part inferior del nostre motlle amb el vidre en brut, evacuar la cambra de procés per a l'eliminació d'oxigen, prop del tancament del motlle, escalfament ràpid i isotèrmic de matriu i vidre amb llum infraroja, més tancament de les meitats del motlle. premsar el vidre suavitzat lentament de manera controlada fins al gruix desitjat, i finalment refredar el vidre i omplir la cambra amb nitrogen i eliminar el producte. El control precís de la temperatura, la distància de tancament del motlle, la força de tancament del motlle, la coincidència dels coeficients d'expansió del motlle i el material de vidre són clau en aquest procés. • FABRICACIÓ DE COMPONENTS I CONJUNTS ÒPTICS DE VIDRE: A més de l'emmotllament de precisió del vidre, hi ha una sèrie de processos valuosos que utilitzem per fabricar components òptics i conjunts d'alta qualitat per a aplicacions exigents. La mòlta, el polit i el poliment de vidres de grau òptic en purins abrasius especials és un art i una ciència per fabricar lents òptiques, prismes, plans i molt més. Les superfícies òptiques planes, ondulades, suaus i sense defectes requereixen molta experiència amb aquests processos. Petits canvis en l'entorn poden provocar productes fora de les especificacions i aturar la línia de fabricació. Hi ha casos en què una única tovallola a la superfície òptica amb un drap net pot fer que un producte compleixi les especificacions o falla la prova. Alguns materials de vidre populars utilitzats són sílice fosa, quars, BK7. També el muntatge d'aquests components requereix una experiència especialitzada en nínxols. De vegades s'utilitzen coles especials. No obstant això, de vegades una tècnica anomenada contacte òptic és la millor opció i no implica cap material entre les ulleres òptiques connectades. Consisteix en posar-se en contacte físicament amb superfícies planes per unir-se entre elles sense cola. En alguns casos, s'utilitzen separadors mecànics, varetes o boles de vidre de precisió, pinces o components metàl·lics mecanitzats per muntar els components òptics a determinades distàncies i amb determinades orientacions geomètriques entre si. Examinem algunes de les nostres tècniques populars per a la fabricació d'òptiques de gamma alta. MOLIT I LLAPET I POLIT: La forma rugosa del component òptic s'obté amb la mòlta d'un vidre en blanc. A continuació, es duu a terme el polit i el polit girant i fregant les superfícies rugoses dels components òptics contra eines amb les formes superficials desitjades. S'aboquen purins amb petites partícules abrasives i fluid entre l'òptica i les eines de conformació. Les mides de partícules abrasives en aquests purins es poden triar segons el grau de planitud desitjat. Les desviacions de les superfícies òptiques crítiques de les formes desitjades s'expressen en termes de longituds d'ona de la llum que s'utilitza. La nostra òptica d'alta precisió té toleràncies de dècims d'una longitud d'ona (longitud d'ona/10) o fins i tot és possible més ajustada. A més del perfil de la superfície, les superfícies crítiques s'escanegen i s'avaluen per a altres característiques de la superfície i defectes com ara dimensions, rascades, estelles, fosses, taques... etc. El control estricte de les condicions ambientals a la planta de fabricació òptica i els extensos requisits de metrologia i proves amb equips d'última generació fan d'aquesta una branca de la indústria desafiant. • PROCESSOS SECUNDARIS EN LA FABRICCIÓ DE VIDRE: De nou, només estem limitats amb la vostra imaginació quan es tracta de processos secundaris i d'acabat del vidre. A continuació enumerem alguns d'ells: -Recobriments sobre vidre (òptics, elèctrics, tribològics, tèrmics, funcionals, mecànics...). Com a exemple, podem alterar les propietats superficials del vidre fent que, per exemple, reflecteixi la calor de manera que mantingui fresc l'interior dels edificis, o fer que un costat absorbeixi l'infrarojo mitjançant la nanotecnologia. Això ajuda a mantenir calent l'interior dels edificis perquè la capa superficial de vidre més externa absorbirà la radiació infraroja dins de l'edifici i la radiarà cap a l'interior. -Gravat en vidre -Etiquetatge ceràmic aplicat (ACL) -Gravat - Polit amb flama - Polit químic -Tinció FABRICACIÓ DE CERÀMICA TÈCNICA • PREMSAT DE MATRIXES: Consisteix en la compactació uniaxial de pols granulars confinats en una matriu. • PREMSAT EN CALOR : semblant al premsat en matriu però amb l'addició de temperatura per millorar la densificació. La pols o la preforma compactada es col·loca a la matriu de grafit i s'aplica una pressió uniaxial mentre la matriu es manté a altes temperatures, com ara 2000 C. Les temperatures poden ser diferents segons el tipus de pols ceràmica que es processi. Per a formes i geometries complicades, poden ser necessaris altres processaments posteriors, com ara la mòlta de diamant. • PREMÉS ISOSTÀTIC: La pols granular o els compactes premsats en matriu es col·loquen en recipients hermètics i després en un recipient a pressió tancat amb líquid a l'interior. A continuació, es compacten augmentant la pressió del recipient a pressió. El líquid dins del recipient transfereix les forces de pressió uniformement sobre tota la superfície del recipient hermètic. Així, el material es compacta uniformement i pren la forma del seu recipient flexible i el seu perfil i característiques interiors. • PREMSAT ISOSTÀTICA EN CALOR : Similar al premsat isostàtic, però a més de l'atmosfera de gas a pressió, sinteritzem el compacte a alta temperatura. La pressió isostàtica en calent dóna com a resultat una densificació addicional i una major resistència. • FUNDACIÓ LLIBADA / COSTADA DE DRENAT: Omplim el motlle amb una suspensió de partícules ceràmiques de mida micromètrica i líquid portador. Aquesta mescla s'anomena "lliscament". El motlle té porus i per tant el líquid de la mescla es filtra al motlle. Com a resultat, es forma un motlle a les superfícies interiors del motlle. Després de la sinterització, les peces es poden treure del motlle. • FUNDACIÓ DE CINTES: Fabriquem cintes de ceràmica mitjançant la colada de purins de ceràmica sobre superfícies planes de suport mòbil. Els purins contenen pols ceràmiques barrejades amb altres productes químics amb finalitats d'unió i transport. A mesura que els dissolvents s'evaporen, es queden làmines denses i flexibles de ceràmica que es poden tallar o enrotllar segons es desitgi. • FORMACIÓ PER EXTRUSIÓ: Com en altres processos d'extrusió, una mescla suau de pols ceràmica amb aglutinants i altres productes químics es fa passar a través d'una matriu per adquirir la seva forma de secció transversal i després es talla a les longituds desitjades. El procés es realitza amb mescles ceràmiques fredes o escalfades. • MOLDETURA PER INYECCIÓ A BAIXA PRESSIÓ: Preparem una barreja de pols ceràmica amb aglutinants i dissolvents i l'escalfem a una temperatura que permeti pressionar i introduir fàcilment a la cavitat de l'eina. Un cop finalitzat el cicle d'emmotllament, la peça s'expulsa i el producte químic d'unió es crema. Mitjançant l'emmotllament per injecció, podem obtenir peces complexes a grans volums de manera econòmica. Els forats que són una petita fracció de mil·límetre en una paret de 10 mm de gruix són possibles, són possibles rosques sense mecanitzar més, són possibles toleràncies tan ajustades com +/- 0,5% i encara més baixes quan es mecanitzen les peces. , són possibles gruixos de paret de l'ordre de 0,5 mm a una longitud de 12,5 mm, així com gruixos de paret de 6,5 mm a una longitud de 150 mm. • MECANITZACIÓ VERDA: Utilitzant les mateixes eines de mecanitzat de metalls, podem mecanitzar materials ceràmics premsats mentre encara són tous com el guix. Són possibles toleràncies de +/- 1%. Per a millors toleràncies utilitzem la mòlta de diamant. • SINTERITZACIÓ o COC: La sinterització fa possible la densificació total. Es produeix una contracció important a les peces compactes verdes, però això no és un gran problema, ja que tenim en compte aquests canvis dimensionals quan dissenyem la peça i les eines. Les partícules de pols s'uneixen i la porositat induïda pel procés de compactació s'elimina en gran mesura. • MOLTURA DE DIAMANT: S'està utilitzant el material més dur del món “diamant” per moldre materials durs com la ceràmica i s'obtenen peces de precisió. S'estan aconseguint toleràncies en el rang del micròmetre i superfícies molt llises. A causa del seu cost, només considerem aquesta tècnica quan realment la necessitem. • ELS CONJUNTS HERMÈTICS són aquells que pràcticament no permeten cap intercanvi de matèria, sòlids, líquids o gasos entre interfícies. El segellat hermètic és hermètic. Per exemple, els tancaments electrònics hermètics són aquells que mantenen el contingut interior sensible d'un dispositiu envasat il·lès per la humitat, els contaminants o els gasos. Res és 100% hermètic, però quan parlem d'hermeticitat ens referim a que en termes pràctics, que hi ha hermeticitat en la mesura que la taxa de fuites és tan baixa que els dispositius són segurs en condicions ambientals normals durant molt de temps. Els nostres muntatges hermètics consisteixen en components de metall, vidre i ceràmica, metall-ceràmica, ceràmica-metall-ceràmica, metall-ceràmica-metall, metall a metall, metall-vidre, metall-vidre-metall, vidre-metall-vidre, vidre- metall i vidre a vidre i totes les altres combinacions d'unió metall-vidre-ceràmica. Podem, per exemple, revestir metàl·lics els components ceràmics perquè es puguin unir fortament a altres components del conjunt i tinguin una excel·lent capacitat de segellat. Tenim el know-how de revestir fibres òptiques o alimentacions amb metall i soldar-les o soldar-les als tancaments, de manera que no hi passin ni s'infiltran gasos als tancaments. Per tant, s'utilitzen per a la fabricació de tancaments electrònics per encapsular dispositius sensibles i protegir-los de l'atmosfera exterior. A més de les seves excel·lents característiques de segellat, altres propietats com el coeficient d'expansió tèrmica, la resistència a la deformació, la naturalesa sense desgasificació, la vida útil molt llarga, la naturalesa no conductora, les propietats d'aïllament tèrmic, la naturalesa antiestàtica... etc. fer que els materials de vidre i ceràmica siguin l'elecció per a determinades aplicacions. Podeu trobar informació sobre les nostres instal·lacions que produeixen accessoris de ceràmica a metall, segellat hermètic, passadors de buit, buit alt i ultraalt i components de control de fluids aquí:Fullet de fàbrica de components hermètics CLICK Product Finder-Locator Service PÀGINA ANTERIOR
- Wire & Spring Forming, Shaping, Welding, Assembly of Wires, Coil, CNC
Wire & Spring Forming, Shaping, Welding, Assembly of Wires, Coil Compression Extension Torsion Flat Springs, Custom Wires, Helical Springs at AGS-TECH Inc. Formació de filferro i molla Fabriquem cables personalitzats, muntatge de filferro, cables formats en les formes 2D i 3D desitjades, xarxes de filferro, malla, tancaments, cistella, tanca, molla de filferro, molla plana; torsió, compressió, tensió, molles planes i molt més. Els nostres processos són la conformació de filferro i molla, trefilatge, conformació, flexió, soldadura, soldadura forta, soldadura, perforació, estampació, perforació, xamfranat, rectificat, roscat, recobriment, lliscament, conformació de diapositives, enrotllament, enrotllament, enrotllament. Us recomanem que feu clic aquí per DESCARREGA les nostres il·lustracions esquemàtiques dels processos de formació de filferro i molles d'AGS-TECH Inc. Aquest fitxer descarregable amb fotos i esbossos us ajudarà a entendre millor la informació que us oferim a continuació. • TRIFAT: Utilitzant forces de tracció estirem el material metàl·lic i l'estirem a través d'un encuny per reduir-ne el diàmetre i augmentar-ne la longitud. De vegades fem servir una sèrie de matrius. Som capaços de fer matrius per a cada calibre de filferro. Utilitzant material d'alta resistència a la tracció dibuixem filferros molt prims. Oferim cables treballats en fred i en calent. • FORMACIÓ DE FILATGES: Es doblega un rotlle de filferro calibrat i es dóna forma en un producte útil. Tenim la capacitat de formar cables de tots els calibres, inclosos filaments prims i cables gruixuts com els que s'utilitzen com a molles sota el xassís d'automòbil. Els equips que utilitzem per a la conformació de filferro són formadors de filferro manuals i CNC, bobinador, premses de potència, quatre corredisses, multicorredissa. Els nostres processos són: estirar, doblegar, redreçar, aplanar, estirar, tallar, remuntar, soldar i soldar i soldar, muntatge, bobinat, estampat (o enrotllament), perforació, roscat de filferro, trepat, xamfranat, rectificat, recobriment i tractaments superficials. Els nostres equips d'última generació es poden configurar per desenvolupar dissenys molt complexos de qualsevol forma i toleràncies estrictes. Oferim diversos tipus d'extrems com els extrems esfèrics, punxeguts o xamfranats per als vostres cables. La majoria dels nostres projectes de conformació de filferro tenen costos d'eines mínims a zero. Els temps de lliurament de les mostres solen ser de dies. Els canvis en el disseny/configuració de les formes de cable es poden fer molt ràpidament. • FORMACIÓ DE MOLS: AGS-TECH fabrica una gran varietat de molles que inclouen: -Molla de torsió / doble torsió -Molla de tensió/compressió -Molla constant / variable -Molla helicoïdal i helicoïdal -Molla plana i de fulla - Balanç de primavera - Rentadora Belleville -Negator Spring -Molla helicoïdal de velocitat progressiva -Ona Primavera -Volute Spring -Molls cònics - Anells de primavera -Molles del rellotge -Clips Fabriquem molles amb una varietat de materials i us podem guiar segons la vostra aplicació. Els materials més comuns són acer inoxidable, silici cromat, acer d'alt carboni, baix carboni temperat a l'oli, crom vanadi, bronze fòsfor, titani, aliatge de coure beril·li, ceràmica d'alta temperatura. Utilitzem diverses tècniques en la fabricació de molles, com ara bobinat CNC, bobinat en fred, bobinat en calent, enduriment, acabat. Altres tècniques ja esmentades anteriorment a la formació de filferro també són habituals a les nostres operacions de fabricació de molles. • SERVEIS D'ACABAT DE FILLS I RESSOLS: Podem acabar els vostres productes de moltes maneres segons la vostra elecció i necessitats. Alguns dels processos habituals que oferim són: pintura, recobriment en pols, revestiment, immersió de vinil, anodització, alleujament de l'estrès, tractament tèrmic, granalla, cromat, níquel sense electros, passivació, esmalt al forn, plàstic recobert , neteja de plasma. CLICK Product Finder-Locator Service PÀGINA ANTERIOR
- Sheet Metal Forming Fabrication, Stamping, Punching, Deep Drawing, CNC
Sheet Metal Forming and Fabrication, Stamping, Punching, Bending, Progressive Die, Spot Welding, Deep Drawing, Metal Blanking and Slitting at AGS-TECH Inc. Estampació i fabricació de xapa Oferim estampació, conformació, conformació, plegat, punxonat, tallat, tallat, perforació, entallament, mossegada, afaitat, treball a premsa, fabricació, embutició profunda utilitzant matrius de punxó / traç únic, així com matrius progressius i filatura, conformació de cautxú i hidroconformat; tall de xapa mitjançant raig d'aigua, plasma, làser, serra, flama; muntatge de xapa mitjançant soldadura, soldadura per punts; tub de xapa abombat i doblegat; Acabat de superfícies de xapa metàl·lica que inclou pintura per immersió o aerosol, recobriment en pols electrostàtica, anodització, revestiment, pulverització i molt més. Els nostres serveis van des de la creació ràpida de prototips de xapa fins a la fabricació d'alt volum. Us recomanem que feu clic aquí perDESCARREGA les nostres il·lustracions esquemàtiques dels processos de fabricació i estampació de xapa per AGS-TECH Inc. Això us ajudarà a entendre millor la informació que us oferim a continuació. • TALLAT DE TXAPA: Oferim TALLATS i PARTIES. Els talls tallen la xapa d'un camí a la vegada i bàsicament no hi ha malbaratament de material, mentre que amb les separacions la forma no es pot encaixar amb precisió i, per tant, es malbarata certa quantitat de material. Un dels nostres processos més populars és el PUNTONAT, on es talla una peça de material rodona o d'una altra forma de xapa. La peça que es retalla és un residu. Una altra versió de perforació és SLOTTING, on es fan forats rectangulars o allargats. D'altra banda, l'estampació és el mateix procés que el punxonat, amb la distinció de la peça que es retalla és el treball i es manté. FINE BLANKING, una versió superior del blanking, crea talls amb toleràncies estretes i vores rectes i llises i no requereix operacions secundàries per a la perfecció de la peça. Un altre procés que utilitzem amb freqüència és el tallat, que és un procés de cisalla on la xapa és tallada per dues fulles circulars oposades en un camí recte o corbat. L'obrellauna és un exemple senzill del procés de tall. Un altre procés popular process per a nosaltres és PERFORAR, on molts forats rodons o d'una altra forma són perforats a la xapa amb un determinat patró. Un exemple típic d'un producte perforat són els filtres metàl·lics amb molts forats per a fluids. En NOTCHING, un altre procés de tall de xapa, retirem material d'una peça de treball, començant per la vora o en qualsevol altre lloc i tallem cap a dins fins a obtenir la forma desitjada. És un procés progressiu on cada operació treu una altra peça fins a obtenir el contorn desitjat. Per a petites sèries de producció, de vegades utilitzem un procés relativament més lent anomenat NIBBLING, que consisteix en molts cops ràpids de forats superposats per fer un tall més gran i complex. A TALL PROGRESSIU fem servir una sèrie d'operacions diferents per obtenir un sol tall o una geometria determinada. Finalment AFAITAR un procés secundari ens ajuda a millorar les vores dels talls que ja s'han fet. S'utilitza per tallar encenalls, vores aspres en treballs de xapa. • PLEGAT DE LA XAPA: A més del tall, el plegat és un procés essencial sense el qual no podríem produir la majoria de productes. Majoritàriament una operació de treball en fred, però de vegades també es realitza quan està calent o calent. Utilitzem matrius i premsa la major part del temps per a aquesta operació. En PROGRESSIVE BENDING utilitzem una sèrie d'operacions de punxó i matriu diferents per obtenir un sol corbat o una geometria determinada. AGS-TECH utilitza una varietat de processos de plegat i fa l'elecció en funció del material de la peça, la seva mida, gruix, mida desitjada de corba, radi, curvatura i angle de corbat, ubicació de corba, economia d'operació, quantitats a fabricar... etc. Utilitzem V-BENDING on un punxó en forma de V força la xapa a la matriu en forma de V i la doblega. Bo tant per a angles molt aguts com obtusos i intermedis, inclosos els 90 graus. Utilitzant matrius de neteja realitzem la flexió de vora. El nostre equip ens permet obtenir angles fins i tot superiors a 90 graus. En la flexió de la vora, la peça de treball s'intercala entre un coixinet de pressió i la matriu, l'àrea per a la flexió es troba a la vora de la matriu i la resta de la peça es manté sobre l'espai com una biga en voladís. Quan el punxó actua sobre la part del voladís, es doblega sobre la vora de la matriu. EL FANGING és un procés de flexió de vora que resulta en un angle de 90 graus. Els principals objectius de l'operació són l'eliminació de vores afilades i l'obtenció de superfícies geomètriques per facilitar la unió de peces. BEADING, un altre procés comú de flexió de vora forma un rínxol sobre la vora d'una peça. HMMING en canvi resulta amb una vora de la làmina que es doblega completament sobre si mateixa. A COSTURA, les vores de dues parts es dobleguen una sobre l'altra i s'uneixen. D'altra banda, la DOBLE COSTURA proporciona juntes de xapa estanques a l'aigua i a l'aire. De manera semblant a la flexió de vores, un procés anomenat ROTARY BENDING desplega un cilindre amb l'angle desitjat tallat i que serveix de punxó. A mesura que la força es transmet al punxó, aquest es tanca amb la peça. La ranura del cilindre dóna a la part del voladís l'angle desitjat. La ranura pot tenir un angle més petit o superior a 90 graus. En AIR BENDING, no necessitem que la matriu inferior tingui una ranura angulada. La xapa està suportada per dues superfícies a costats oposats i a una certa distància. Aleshores, el punxó aplica una força a la ubicació correcta i doblega la peça. El flexió del canal es realitza amb un punxó i matriu en forma de canal, i el flexió en U s'aconsegueix amb un punxó en forma d'U. OFFSET BENDING produeix desplaçaments a la xapa. ROLL BENDING, una tècnica bona per a treballs gruixuts i doblegat de grans peces de plaques metàl·liques, utilitza tres rotlles per alimentar i doblegar les plaques a les curvatures desitjades. Els rotlles es disposen de manera que s'obté la corba desitjada de l'obra. La distància i l'angle entre els rotlles es controla per obtenir el resultat desitjat. Un rotllo mòbil permet controlar la curvatura. TUBE FORMING és una altra operació popular de plegat de xapes que implica múltiples matrius. Els tubs s'obtenen després de múltiples accions. LA CORRUGACIÓ també es realitza mitjançant operacions de plegat. Bàsicament és la flexió simètrica a intervals regulars a través d'una peça sencera de xapa. Es poden utilitzar diverses formes per ondular. La xapa corrugada és més rígida i té una millor resistència a la flexió i, per tant, té aplicacions en la indústria de la construcció. SHET METAL ROLL FORMING, un procés continu manufacturing es desplega per doblegar seccions transversals d'una geometria determinada mitjançant rotlles i el treball es doblega en passos seqüencials, amb el rotlle final completant el treball. En alguns casos s'utilitza un sol rotllo i en alguns casos una sèrie de rotlles. • PROCESSOS COMBINATS DE TALL I PLEGAT DE LA XAPA: Són els processos que tallen i dobleguen al mateix temps. A PIERCING, es crea un forat amb un punxó punxegut. A mesura que el punxó amplia el forat de la làmina, el material es doblega simultàniament en una brida interna per al forat. La brida obtinguda pot tenir funcions importants. L'operació LANCING, en canvi, talla i doblega la làmina per crear una geometria elevada. • TUBO METÀL·LLIC PLUGAT I PLUGAT: En el TUBO METÀLLIC, una part interna d'un tub buit es pressuritza, fent que el tub s'abombi cap a l'exterior. Com que el tub està dins d'una matriu, la geometria de la protuberància està controlada per la forma de la matriu. En STRETCH BENDING, un tub metàl·lic s'estira utilitzant forces paral·leles a l'eix del tub i forces de flexió per estirar el tub sobre un bloc de forma. A DRAW BENDING, subjectem el tub prop del seu extrem a un bloc de forma giratòria que doblega el tub mentre gira. Finalment, en COMPRESSION BENDING, el tub es subjecta per força a un bloc de forma fixa i una matriu el doblega sobre el bloc de forma. • EMBUTICIÓ PROFUNDA: En una de les nostres operacions més populars, s'utilitza un punxó, un encuny a joc i un suport en blanc. El blanc de xapa metàl·lica es col·loca sobre l'obertura de la matriu i el punxó es mou cap al blanc subjecte pel suport de la matriu. Un cop entren en contacte, el punxó força la xapa a la cavitat de la matriu per formar el producte. L'operació d'embotició profunda s'assembla al tall, però l'espai lliure entre el punxó i la matriu evita que es talli la làmina. Un altre factor que garanteix que la làmina estigui embullada i no tallada són les cantonades arrodonides de la matriu i el punxó que impedeixen el tall i el tall. Per aconseguir una major magnitud de l'embotit profund, s'està desplegant un procés de REDRAWING on es realitza un posterior embutició profunda sobre una peça que ja ha estat sotmesa a un procés d'embotició profunda. En REDIBUIXAR INVERSA, la part profunda es gira i es dibuixa en la direcció oposada. El dibuix profund pot proporcionar objectes de forma irregular, com ara copes abovedades, afilades o esglaonades, A REFUAT fem servir un parell de matrius masculins i femenins per impressionar la xapa amb un disseny o guió. • SPINNING : operació en què una peça plana o preformada es manté entre un mandril giratori i una cua i una eina aplica una pressió localitzada a l'obra a mesura que es mou gradualment cap al mandril. Com a resultat, la peça de treball s'embolica sobre el mandril i pren la seva forma. Utilitzem aquesta tècnica com una alternativa a l'embutició profunda on la quantitat d'una comanda és petita, les peces són grans (diàmetres de fins a 20 peus) i tenen corbes úniques. Tot i que els preus per peça són generalment més alts, els costos de configuració per a l'operació de filatura CNC són baixos en comparació amb l'embotit profund. Al contrari, l'embotit requereix una inversió inicial elevada per a la seva instal·lació, però els costos per peça són baixos quan es produeixen grans quantitats de peces. Una altra versió d'aquest procés és el SHEAR SPINNING, on també hi ha flux metàl·lic dins de la peça. El flux metàl·lic reduirà el gruix de la peça a mesura que es realitza el procés. Un altre procés relacionat és el TUBE SPINNING, que s'aplica a peces cilíndriques. També en aquest procés hi ha flux metàl·lic dins de la peça de treball. Així es redueix el gruix i augmenta la longitud del tub. L'eina es pot moure per crear funcions a l'interior o a l'exterior del tub. • CONFORME DE CAUTXUTXA DE LLAMA: Es posa material de cautxú o poliuretà en una matriu de contenidor i la peça de treball es col·loca sobre la superfície de la goma. A continuació, s'actua un punxó sobre la peça de treball i la força a entrar en la goma. Com que la pressió generada pel cautxú és baixa, la profunditat de les peces produïdes és limitada. Com que els costos d'eines són baixos, el procés és adequat per a una producció en quantitats baixes. • HIDROFORMAT: De manera semblant a la conformació del cautxú, en aquest procés la xapa es pressiona mitjançant un punxó en un líquid a pressió dins d'una cambra. La xapa metàl·lica està intercalada entre el punxó i un diafragma de goma. El diafragma envolta la peça completament i la pressió del fluid l'obliga a formar-se al punxó. Amb aquesta tècnica es poden obtenir dibuixos molt profunds fins i tot més profunds que en el procés d'embutició. Fabriquem matrius d'un sol punxó així com matrius progressius segons la vostra peça. Les matrius d'estampació d'un sol curs són un mètode rendible per produir ràpidament grans quantitats de peces simples de xapa, com ara rentadores. Per a la fabricació de geometries més complexes s'utilitzen matrius progressius o la tècnica d'embotit profund. Segons el vostre cas, el tall per raig d'aigua, làser o plasma es pot utilitzar per produir les vostres peces de xapa de manera econòmica, ràpida i precisa. Molts proveïdors no tenen ni idea d'aquestes tècniques alternatives o no en tenen i, per tant, passen per maneres llargues i costoses de fabricar matrius i eines que només fan perdre temps i diners als clients. Si necessiteu components de xapa fabricats a mida, com ara tancaments, carcasses electròniques, etc. tan ràpid com en pocs dies, poseu-vos en contacte amb nosaltres per obtenir el nostre servei de PROTOTIP RÀPID DE TXAPA. CLICK Product Finder-Locator Service MENÚ ANTERIOR
- Forging and Powdered Metallurgy, Die Forging, Heading, Hot Forging
Forging and Powdered Metallurgy, Die Forging, Heading, Hot Forging, Impression Die, Near Net Shape, Swaging, Metal Hobbing, Riveting, Coining from AGS-TECH Inc. Forja de metalls i metal·lúrgia de pols El tipus de processos de FORJA DE METALLS que oferim són matriu en calent i en fred, matriu obert i tancat, matriu d'impressió i forja sense flaix, cogging, fullering, tall i forja de precisió, forma gairebé neta, encapçalament , estampat, forja desmuntada, fresat metàl·lic, premsa i rotllo i forja radial i orbital i anell i isotèrmic, encunyat, reblat, forja de boles metàl·liques, perforació de metall, dimensionament, forja d'alta velocitat energètica. Les nostres tècniques de METAL·LÚRGIA i PROCESSAT DE PÒLS són premsat i sinterització de pols, impregnació, infiltració, premsat isostàtic en fred i calent, emmotllament per injecció de metalls, compactació de bobines, laminació de pols, extrusió de pols, sinterització solta, sinterització per espurna, premsat en calent. Us recomanem que feu clic aquí per DESCARREGA les nostres il·lustracions esquemàtiques dels processos de forja d'AGS-TECH Inc. DESCARREGA les nostres il·lustracions esquemàtiques dels processos de metal·lúrgia de pols d'AGS-TECH Inc. Aquests fitxers descarregables amb fotos i esbossos us ajudaran a entendre millor la informació que us oferim a continuació. En la forja metàl·lica s'apliquen forces de compressió i el material es deforma i s'obté la forma desitjada. Els materials forjats més comuns a la indústria són el ferro i l'acer, però molts altres com l'alumini, coure, titani, magnesi també són àmpliament forjats. Les peces metàl·liques forjades tenen estructures de gra millorades a més d'esquerdes segellades i espais buits tancats, per la qual cosa la resistència de les peces obtingudes per aquest procés és més gran. La forja produeix peces que són significativament més resistents pel seu pes que les peces fetes per fosa o mecanitzat. Com que les peces forjades es formen fent que el metall flueixi en la seva forma final, el metall adquireix una estructura de gra direccional que explica la resistència superior de les peces. En altres paraules, les peces obtingudes per procés de forja revelen millors propietats mecàniques en comparació amb peces simples de fosa o mecanitzades. El pes de les peces forjades metàl·liques pot variar des de petites peces lleugeres fins a centenars de milers de lliures. Fabriquem peces forjades principalment per a aplicacions mecànicament exigents on s'apliquen tensions elevades a peces com peces d'automòbils, engranatges, eines de treball, eines manuals, eixos de turbines, engranatges de motocicletes. Com que els costos d'eines i de configuració són relativament elevats, recomanem aquest procés de fabricació només per a la producció de grans volums i per a components crítics de baix volum però d'alt valor, com ara el tren d'aterratge aeroespacial. A més del cost de les eines, els terminis de fabricació de peces forjades en gran quantitat poden ser més llargs en comparació amb algunes peces mecanitzades senzilles, però la tècnica és crucial per a peces que requereixen una força extraordinària com ara cargols, femelles, aplicacions especials. elements de subjecció, automoció, carretons elevadors, peces de grua. • FORJA EN TROQUELA EN CALOR i EN FRED: La forja en matriu en calent, com el seu nom indica, es realitza a altes temperatures, per tant la ductilitat és alta i la resistència del material baixa. Això facilita una fàcil deformació i forja. Al contrari, la forja amb matriu en fred es realitza a temperatures més baixes i requereix forces més elevades que es tradueixen en enduriment per deformació, millor acabat superficial i precisió de les peces fabricades. • FORJA DE MATRIUS OBERTS i D'IMPRESSIÓ: En la forja de matrius obertes, les matrius no limiten el material que s'està comprimint, mentre que en la forja de matrius d'impressió les cavitats dins dels matrius restringeixen el flux de material mentre es forja en la forma desitjada. FORJAT MOLTA o també anomenada MOLTATGE, que en realitat no és el mateix però un procés molt similar, és un procés de matriu obert on la peça de treball s'intercala entre dues matrius planes i una força de compressió redueix la seva alçada. A mesura que l'alçada és reduïda, l'amplada de la peça de treball augmenta. CAPÍTULA, un procés de forja revoltat implica un estoc cilíndric que es remunta al seu extrem i la seva secció transversal s'incrementa localment. A l'encapçalament, el material s'introdueix a través de la matriu, es forja i després es talla a la longitud. L'operació és capaç de produir grans quantitats de fixadors ràpidament. Majoritàriament és una operació de treball en fred perquè s'utilitza per fer puntes de claus, extrems de cargol, femelles i cargols on cal reforçar el material. Un altre procés de matriu obert és COGGING, on la peça de treball es forja en una sèrie de passos amb cada pas que resulta en la compressió del material i el posterior moviment de la matriu oberta al llarg de la peça de treball. A cada pas, el gruix es redueix i la longitud s'augmenta una petita quantitat. El procés s'assembla a un estudiant nerviós que mossegueix el llapis tot seguit a petits passos. Un procés anomenat FULLERING és un altre mètode de forja amb matriu obert que sovint implementem com a pas anterior per distribuir el material a la peça de treball abans que es facin altres operacions de forja de metall. L'utilitzem quan la peça de treball requereix diverses forja operations. En l'operació, la matriu amb superfícies convexes es deforme i fa que el metall flueixi cap a ambdós costats. D'altra banda, un procés similar al batut, el BORTS implica una matriu oberta amb superfícies còncaves per deformar la peça de treball. El tallat també és un procés preparatori per a les operacions de forja posteriors, fa que el material flueixi des dels dos costats cap a una zona del centre. LA FORJA DE TROQUES D'IMPRESIÓ o FORJA DE TROQUES TANCADAS, com també s'anomena, utilitza una matriu/motlle que comprimeix el material i restringeix el seu flux dins de si mateix. La matriu es tanca i el material pren la forma de la matriu / cavitat del motlle. LA FORJA DE PRECISIÓ, un procés que requereix equips i motlles especials, produeix peces sense o molt poc flaix. En altres paraules, les peces tindran unes dimensions gairebé finals. En aquest procés s'introdueix i col·loca amb cura una quantitat de material ben controlada dins del motlle. Despleguem aquest mètode per a formes complexes amb seccions primes, toleràncies petites i angles de tiratge i quan les quantitats són prou grans per justificar els costos de motlle i equip. • FORJA SIN FLASH: La peça de treball es col·loca a la matriu de manera que cap material pugui sortir de la cavitat per formar flaix. Per tant, no es necessita un retall de flaix no desitjat. És un procés de forja de precisió i, per tant, requereix un control estret de la quantitat de material utilitzat. • EMMUTACIÓ DE METALLS o FORJA RADIAL: Una peça de treball s'actua circumferencialment amb matriu i forja. També es pot utilitzar un mandril per forjar la geometria interior de la peça de treball. En l'operació d'estampació, la peça de treball normalment rep diversos cops per segon. Els articles típics produïts mitjançant l'estampació són eines de punta punxeguda, barres afilades i tornavís. • PIERCING METÀLLIC: Utilitzem aquesta operació amb freqüència com a operació addicional en la fabricació de peces. Es crea un forat o una cavitat amb una perforació a la superfície de la peça de treball sense trencar-la. Tingueu en compte que la perforació és diferent de la perforació, la qual cosa resulta en un forat passant. • HOBBING: Un punxó amb la geometria desitjada es pressiona a la peça de treball i crea una cavitat amb la forma desitjada. A aquest punx l'anomenem HOB. L'operació comporta altes pressions i es realitza en fred. Com a resultat, el material es treballa en fred i s'endureix. Per tant, aquest procés és molt adequat per a la fabricació de motlles, matrius i cavitats per a altres processos de fabricació. Un cop fabricada la placa, es poden fabricar fàcilment moltes cavitats idèntiques sense necessitat de mecanitzar-les una per una. • FORJATGE o CONFORMAT: S'utilitzen dos rotlles oposats per donar forma a la peça metàl·lica. La peça de treball s'introdueix als rotlles, els rotlles giren i estiren l'obra cap a l'espai, després la feina s'alimenta a través de la part acanalada dels rotlles i les forces de compressió donen al material la forma desitjada. No és un procés de laminació sinó un procés de forja, perquè és una operació discreta més que contínua. La geometria de les arbredes dels rotlles forja el material a la forma i geometria requerides. Es realitza en calent. Com que és un procés de forja produeix peces amb propietats mecàniques excel·lents i, per tant, l'utilitzem per fabricar peces d'automoció com ara eixos que necessiten tenir una resistència extraordinària en entorns de treball difícils. • FORJA ORBITAL : la peça de treball es posa en una cavitat de matriu de forja i es forja per una matriu superior que es desplaça en una trajectòria orbital mentre gira sobre un eix inclinat. A cada revolució, la matriu superior acaba exercint forces de compressió a tota la peça de treball. En repetir aquestes revolucions diverses vegades, es realitza una forja suficient. Els avantatges d'aquesta tècnica de fabricació són el seu funcionament baix soroll i les menors forces necessàries. En altres paraules, amb forces petites es pot girar una matriu pesada al voltant d'un eix per aplicar grans pressions sobre una secció de la peça de treball que està en contacte amb la matriu. De vegades, les peces en forma de disc o còniques són una bona opció per a aquest procés. • FORJA D'ANELLS: Utilitzem sovint per fabricar anells sense costures. L'estoc es talla a la llargada, es trenca i després es perfora per crear un forat central. A continuació, es posa sobre un mandril i una matriu de forja el martell des de dalt mentre l'anell es gira lentament fins a obtenir les dimensions desitjades. • REBALLAT: Un procés comú per unir peces, comença amb una peça metàl·lica recta introduïda en forats prefabricats a través de les peces. A continuació, els dos extrems de la peça metàl·lica es forgen apretant la unió entre una matriu superior i una inferior. • Encunyació : Un altre procés popular realitzat per premsa mecànica, exercint grans forces a poca distància. El nom "encunyar" prové dels petits detalls que es forgen a les superfícies de les monedes metàl·liques. Es tracta principalment d'un procés d'acabat d'un producte on s'obtenen detalls fins a les superfícies com a resultat de la gran força aplicada per la matriu que transfereix aquests detalls a la peça de treball. • FORJA DE BOLES DE METÀLLIC: Productes com els coixinets de boles requereixen boles metàl·liques d'alta qualitat fabricades amb precisió. En una tècnica anomenada SKEW ROLLING, fem servir dos rotlles oposats que giren contínuament a mesura que el material s'introdueix contínuament als rotllos. En un extrem dels dos rotlles s'expulsen esferes metàl·liques com a producte. Un segon mètode per a la forja de boles metàl·liques és l'ús de matrius que apreten el material col·locat entre ells prenent la forma esfèrica de la cavitat del motlle. Sovint, les boles produïdes requereixen alguns passos addicionals, com ara l'acabat i el poliment, per convertir-se en un producte d'alta qualitat. • FORJA ISOTÈRMICA / FORJA EN CALIENT: Un procés costós que només es realitza quan el valor benefici/cost està justificat. Un procés de treball en calent on la matriu s'escalfa a aproximadament la mateixa temperatura que la peça de treball. Com que tant la matriu com el treball tenen aproximadament la mateixa temperatura, no hi ha refrigeració i es milloren les característiques de flux del metall. L'operació s'adapta bé als súper aliatges i materials amb una forjabilitat inferior i materials els quals les propietats mecàniques són molt sensibles als petits gradients i canvis de temperatura. • CAMARAT METÀLLIC: És un procés d'acabat en fred. El flux de material no té restriccions en totes les direccions, a excepció de la direcció en què s'aplica la força. Com a resultat, s'aconsegueix un molt bon acabat superficial i unes dimensions precises. • FORJAT D'ALTA TASA ENERGÈTICA : La tècnica consisteix en un motlle superior unit al braç d'un pistó que s'empeny ràpidament a mesura que una barreja d'aire i combustible s'encén per una bugia. S'assembla al funcionament dels pistons en el motor d'un cotxe. El motlle colpeja la peça molt ràpidament i després torna a la seva posició original molt ràpid gràcies a la contrapressió. El treball es forja en pocs mil·lisegons i, per tant, no hi ha temps perquè el treball es refredi. Això és útil per a peces difícils de forjar que tenen propietats mecàniques molt sensibles a la temperatura. En altres paraules, el procés és tan ràpid que la peça es forma a temperatura constant i no hi haurà gradients de temperatura a les interfícies de motlle/peça de treball. • En la forja amb matriu, el metall es bat entre dos blocs d'acer coincidents amb formes especials, anomenats matrius. Quan el metall es martelleja entre els encunys, assumeix la mateixa forma que les formes de la matriu. Quan arriba a la seva forma definitiva, es treu perquè es refredi. Aquest procés produeix peces resistents que tenen una forma precisa, però requereix una inversió més gran per als matrius especialitzats. La forja alterada augmenta el diàmetre d'una peça de metall aplanant-la. Generalment s'utilitza per fer peces petites, especialment per formar capçals en elements de subjecció com perns i claus. • METAL·LÚRGIA DE POLLS / PROCESSAMENT DE POLLS: Com el seu nom indica, implica processos de fabricació per fer peces sòlides de determinades geometries i formes a partir de pols. Si s'utilitzen pols metàl·liques per a aquesta finalitat és l'àmbit de la pulvimetal·lúrgia i si s'utilitzen pols no metàl·liques és el processament de pols. Les peces sòlides es produeixen a partir de pols mitjançant premsat i sinterització. POWDER PRESSING s'utilitza per compactar les pols en les formes desitjades. En primer lloc, el material primari està físicament en pols, dividint-lo en moltes petites partícules individuals. La barreja de pols s'omple a la matriu i un punxó es mou cap a la pols i la compacta a la forma desitjada. Es realitza majoritàriament a temperatura ambient, amb premsat de pols s'obté una part sòlida i s'anomena compacta verda. Els aglutinants i els lubricants s'utilitzen habitualment per millorar la compactabilitat. Som capaços de formar pols mitjançant premses hidràuliques amb diversos milers de tones de capacitat. També tenim premses de doble acció amb punxons superior i inferior oposats, així com premses d'acció múltiple per a geometries de peces molt complexes. La uniformitat, que és un repte important per a moltes plantes de processament de pols / metal·lúrgia en pols, no és un gran problema per a AGS-TECH a causa de la nostra àmplia experiència en la fabricació personalitzada d'aquestes peces durant molts anys. Fins i tot amb parts més gruixudes on la uniformitat suposa un repte, ho hem aconseguit. Si ens comprometem amb el teu projecte, farem les teves peces. Si veiem algun risc potencial, us informarem a avanç. LA SINTERITZACIÓ DE PÒLS, que és el segon pas, implica l'augment de la temperatura fins a un cert grau i el manteniment de la temperatura a aquest nivell durant un temps determinat perquè les partícules de pols de la part premsada es puguin unir entre si. Això es tradueix en enllaços molt més forts i enfortiment de la peça de treball. La sinterització té lloc a prop de la temperatura de fusió de la pols. Durant la sinterització es produirà una contracció, augmentarà la resistència del material, la densitat, la ductilitat, la conductivitat tèrmica i la conductivitat elèctrica. Disposem de forns discontinus i continus per a la sinterització. Una de les nostres capacitats és ajustar el nivell de porositat de les peces que produïm. Per exemple, som capaços de produir filtres metàl·lics mantenint les peces poroses fins a cert punt. Mitjançant una tècnica anomenada IMPREGNACIÓ, omplim els porus del metall amb un fluid com l'oli. Produïm, per exemple, coixinets impregnats d'oli que són autolubricants. En el procés d'INFILTRACIÓ omplim els porus d'un metall amb un altre metall de punt de fusió més baix que el material base. La mescla s'escalfa a una temperatura entre les temperatures de fusió dels dos metalls. Com a resultat, es poden obtenir algunes propietats especials. També realitzem amb freqüència operacions secundàries com el mecanitzat i la forja de peces fabricades en pols quan cal obtenir característiques o propietats especials o quan la peça es pot fabricar amb menys passos de procés. PREMSAT ISOSTÀTIC: En aquest procés s'utilitza la pressió del fluid per compactar la peça. Les pols metàl·liques es col·loquen en un motlle fet d'un recipient flexible tancat. En el premsat isostàtic, la pressió s'aplica des de tot el voltant, al contrari de la pressió axial que es veu en el premsat convencional. Els avantatges de la premsa isostàtica són la densitat uniforme dins de la peça, especialment per a peces més grans o més gruixudes, propietats superiors. El seu desavantatge són els temps de cicle llargs i les precisions geomètriques relativament baixes. El PREMSAT ISOSTÀTIC EN FRED es realitza a temperatura ambient i el motlle flexible està fet de cautxú, PVC o uretà o materials similars. El fluid utilitzat per pressuritzar i compactar és l'oli o l'aigua. La sinterització convencional del compacte verd segueix això. D'altra banda, el PRENSAT ISOSTÀTIC EN CALOR es realitza a altes temperatures i el material del motlle és de xapa o ceràmica amb un punt de fusió prou alt que resisteixi les temperatures. El fluid a pressió sol ser un gas inert. Les operacions de premsat i sinterització es realitzen en un sol pas. La porositat s'elimina gairebé completament, s'obté una estructura uniform grain. L'avantatge de la premsa isostàtica en calent és que pot produir peces comparables a la fosa i la forja combinades alhora que permet utilitzar materials que no són adequats per a la fosa i la forja. El desavantatge de la premsa isostàtica en calent és el seu alt temps de cicle i, per tant, el seu cost. És adequat per a parts crítiques de baix volum. MOLDETURA PER INJECCIÓ DE METALLS: Procés molt adequat per a la producció de peces complexes amb parets primes i geometries detallades. El més adequat per a peces més petites. Les pols i l'aglutinant de polímer es barregen, s'escalfen i s'injecten en un motlle. L'aglutinant de polímer recobreix les superfícies de les partícules de pols. Després de l'emmotllament, l'aglutinant s'elimina mitjançant escalfament a baixa temperatura o dissolt mitjançant un dissolvent. COMPACTACIÓ DE ROTELLS / LAMINACIÓ DE PÒLS: Les pols s'utilitzen per produir tires o làmines contínues. La pols s'alimenta des d'un alimentador i es compacta mitjançant dos rotlles giratoris en làmines o tires. L'operació es realitza en fred. La làmina es porta a un forn de sinterització. El procés de sinterització es pot repetir una segona vegada. EXTRUSIÓ DE PÒLS: Les peces amb grans proporcions de longitud a diàmetre es fabriquen extruint un recipient de xapa fina amb pols. SINTERITZACIÓ SOLTA: Com el seu nom indica, és un mètode de compactació i sinterització sense pressió, adequat per produir peces molt poroses com ara filtres metàl·lics. La pols s'introdueix a la cavitat del motlle sense compactar-se. SINTERITZACIÓ SOLTA: Com el seu nom indica, és un mètode de compactació i sinterització sense pressió, adequat per produir peces molt poroses com ara filtres metàl·lics. La pols s'introdueix a la cavitat del motlle sense compactar-se. SINTERITZACIÓ SPARK: La pols es comprimeix al motlle mitjançant dos punxons oposats i s'aplica un corrent elèctric d'alta potència al punxó i passa a través de la pols compactada intercalada entre ells. L'elevat corrent crema les pel·lícules superficials de les partícules de pols i les sinteritza amb la calor generada. El procés és ràpid perquè la calor no s'aplica des de l'exterior sinó que es genera des de dins del motlle. PREMSAT EN CALOR: Les pols es premsen i sinteritzen en un sol pas en un motlle que suporta les altes temperatures. A mesura que la matriu es compacta, s'hi aplica calor en pols. Les bones precisions i propietats mecàniques aconseguides amb aquest mètode el converteixen en una opció atractiva. Fins i tot els metalls refractaris es poden processar utilitzant materials de motlle com el grafit. CLICK Product Finder-Locator Service MENÚ ANTERIOR
- Plastic Rubber Metal Extrusions, Extrusion Dies, Aluminum Extruding
Plastic Rubber Metal Extrusions, Extrusion Dies, Aluminum Extruding, Pipe Tube Forming, Plastic Profiles, Metal Profiles Manufacturing, PVC at AGS-TECH Inc. Extrusions, productes extrusats, extrusats Utilitzem el procés EXTRUSION process per fabricar productes amb un perfil de secció transversal fixa, com ara tubs, canonades i dissipadors de calor. Tot i que es poden extruir molts materials, les nostres extrusions més habituals són de metall, polímers/plàstics, ceràmica obtinguda pel mètode d'extrusió en fred, calent o calent. Les peces extruïdes les anomenem extrudes o extrudes si es plural. Algunes versions especialitzades del procés que també realitzem són la sobrecamisa, la coextrusió i l'extrusió composta. Us recomanem que feu clic aquí per DESCARREGA les nostres il·lustracions esquemàtiques dels processos d'extrusió de metalls, ceràmica i plàstic per AGS-TECH Inc. Això us ajudarà a entendre millor la informació que us oferim a continuació. En l'extrusió, el material que s'ha d'extruir és empès o estirat a través d'una matriu que té el perfil de secció transversal desitjat. El procés es pot utilitzar per fabricar seccions transversals complexes amb un acabat superficial excel·lent i per treballar material fràgil. Un pot produir peces de qualsevol longitud mitjançant aquest procés. Per simplificar els passos del procés: 1.) En extrusions calentes o calentes, el material s'escalfa i es carrega en un recipient a la premsa. El material es pressiona i s'empeny fora de la matriu. 2.) L'extrusat produït s'estira per allisar, es tracta tèrmicament o es treballa en fred per millorar les seves propietats. D'altra banda COLD EXTRUSION té lloc al voltant de la temperatura ambient i té els avantatges d'una menor oxidació, una alta resistència, una bona tolerància d'acabat i un acabat proper. WARM EXTRUSION es realitza per sobre de la temperatura ambient però per sota del punt de recristal·lització. Ofereix un compromís i un equilibri per a les forces requerides, la ductilitat i les propietats del material i, per tant, és l'elecció per a algunes aplicacions. HOT EXTRUSIÓ té lloc per sobre de la temperatura de recristal·lització del material. D'aquesta manera és més fàcil empènyer el material a través de la matriu. No obstant això, el cost de l'equip és elevat. Com més complex sigui un perfil extruït, més costós és la matriu (eines) i menor és la velocitat de producció. Les seccions transversals de la matriu així com els gruixos tenen limitacions que depenen del material a extruir. Les cantonades afilades en matrius d'extrusió sempre són indesitjables i s'han d'evitar tret que sigui necessari. Segons el material que s'està extruint, oferim: • EXTRUSIONS DE METAL : les més habituals que produïm són alumini, llautó, zinc, coure, acer, titani, magnesi • EXTRUSIÓ DE PLÀSTIC : El plàstic es fon i es forma en un perfil continu. Els nostres materials habituals processats són polietilè, niló, poliestirè, clorur de polivinil, polipropilè, plàstic ABS, policarbonat, acrílic. Els productes típics que fabriquem inclouen canonades i tubs, marcs de plàstic. En el procés, les petites perles de plàstic / resina s'alimenten per gravetat des de la tremuja al barril de la màquina d'extrusió. Sovint també barregem colorants o altres additius a la tremuja per donar al producte les especificacions i propietats requerides. El material que entra al barril escalfat és forçat pel cargol giratori a deixar el barril al final i moure's a través del paquet de pantalla per eliminar els contaminants del plàstic fos. Després de passar el paquet de pantalla, el plàstic entra a la matriu d'extrusió. La matriu dóna al plàstic tou en moviment la seva forma de perfil a mesura que passa. Ara l'extrudat passa per un bany maria per refredar-se. Altres tècniques que AGS-TECH Inc. ha estat utilitzant durant molts anys són: • EXTRUSIÓ DE TUBS I TUBS : Les canonades i tubs de plàstic es formen quan el plàstic s'extrudeix a través d'una matriu de conformació rodona i es refreda en un bany d'aigua, després es tallen a la longitud o s'enrotllen/enrotllen. Transparents o de colors, ratlles, parets simples o dobles, flexibles o rígides, PE, PP, poliuretà, PVC, niló, PC, silicona, vinil o bé, ho tenim tot. Tenim tubs en magatzem, així com la capacitat de produir segons les vostres especificacions. AGS-TECH fabrica tubs segons els requisits de la FDA, UL i LE per a aplicacions mèdiques, elèctriques i electròniques, industrials i altres. • EXTRUSIÓ DE OVERJAQUETING / OVER JACKETING : aquesta tècnica aplica una capa exterior de plàstic al cable o cable existent. Els nostres cables d'aïllament es fabriquen amb aquest mètode. • COEXTRUSION : S'extrudeixen simultàniament diverses capes de material. Les múltiples capes són lliurades per múltiples extrusores. Els diferents gruixos de capa es poden ajustar per satisfer les especificacions del client. Aquest procés permet utilitzar múltiples polímers cadascun amb una funcionalitat diferent en el producte. Com a resultat, es pot optimitzar una sèrie de propietats. • EXTRUSIÓ DE COMPOSTS: Es barregen un o diversos polímers amb additius per obtenir un compost plàstic. Les nostres extrusores de doble cargol produeixen extrusions de compostatge. Les matrius d'extrusió són generalment barates en comparació amb els motlles metàl·lics. Si pagueu molt més que uns quants milers de dòlars per una matriu d'extrusió d'alumini de mida petita o mitjana, probablement pagueu massa. Som experts a determinar quina tècnica és la més rendible, la més ràpida i la més adequada per a la vostra aplicació. De vegades, extrudir i mecanitzar una peça us pot estalviar molts diners. Abans de prendre una decisió ferma, demaneu-nos primer la nostra opinió. Hem ajudat a molts clients a prendre les decisions correctes. Per a algunes extrusions metàl·liques molt utilitzades, podeu descarregar els nostres fulletons i catàlegs fent clic al text de color següent. Si es tracta d'un producte comercial que compleix els vostres requisits, serà més econòmic. Descarregueu les nostres capacitats d'extrusió de tubs i canonades mèdiques Descarrega els nostres dissipadors de calor extruïts • PROCESSOS SECUNDARI DE FABRICCIÓ I FABRICCIÓ PER A EXTRUSSIONS : Entre els processos de valor afegit que oferim per als productes extrusats es troben: - Doblat personalitzat de tubs i canonades, conformació i conformació, tall de tubs, conformació d'extrems de tubs, bobinat de tubs, mecanitzat i acabat, perforació i perforació i perforació de forats, -Conjunts de tubs i tubs personalitzats, muntatge tubular, soldadura, soldadura i soldadura - Doblat, conformat i conformat per extrusió a mida -Neteja, desgreixatge, decapat, passivació, polit, anoditzat, xapat, pintura, tractament tèrmic, recuit i enduriment, marcatge, gravat i etiquetatge, embalatge personalitzat. CLICK Product Finder-Locator Service PÀGINA ANTERIOR
- Casting and Machined Parts, CNC Manufacturing, Milling, Turning, Swiss
Casting and Machined Parts, CNC Manufacturing, Milling, Turning, Swiss Type Machining, Die Casting, Investment Casting, Lost Foam Cast Parts from AGS-TECH Inc. Fosa i mecanitzat Les nostres tècniques de fosa i mecanitzat personalitzades són peces de fosa fungibles i no fungibles, fosa ferrosa i no ferrosa, sorra, matriu, centrífuga, motlle continu, ceràmic, inversió, escuma perduda, forma gairebé neta, motlle permanent (fosa per gravetat), guix. motlle (fosa de guix) i peces de fosa, peces mecanitzades produïdes per fresat i tornejat amb equips convencionals i CNC, mecanitzat de tipus suís per a peces petites de precisió d'alt rendiment, mecanitzat de cargols per a elements de fixació, mecanitzat no convencional. Tingueu en compte que, a més de metalls i aliatges metàl·lics, mecanitzem components ceràmics, de vidre i plàstics en alguns casos quan fabricar un motlle no és atractiu o no és l'opció. El mecanitzat de materials polimèrics requereix l'experiència especialitzada que tenim pel repte que presenten els plàstics i el cautxú per la seva suavitat, no rigidesa...etc. Per al mecanitzat de ceràmica i vidre, consulteu la nostra pàgina sobre Fabricació no convencional. AGS-TECH Inc. fabrica i subministra peces de fosa lleugeres i pesades. Hem estat subministrant peces de fosa metàl·lica i peces mecanitzades per a calderes, intercanviadors de calor, automòbils, micromotors, aerogeneradors, equips d'envasament d'aliments i molt més. Us recomanem que feu clic aquí per DESCARREGA les nostres il·lustracions esquemàtiques de processos de mecanitzat i fosa per AGS-TECH Inc. Això us ajudarà a entendre millor la informació que us oferim a continuació. Vegem en detall algunes de les diferents tècniques que oferim: • FUNDACIÓ DE MOTLLES EXPENDABLES: Aquesta àmplia categoria fa referència als mètodes que impliquen motlles temporals i no reutilitzables. En són exemples la sorra, el guix, la closca, la inversió (també anomenada cera perduda) i la fosa de guix. • FUNDACIÓ DE SORRA: Procés on s'utilitza la sorra com a material del motlle. Un mètode molt antic i encara molt popular en la mesura que la majoria de peces de fosa metàl·liques produïdes es fan amb aquesta tècnica. Baix cost fins i tot amb poca producció. Apte per a la fabricació de peces petites i grans. La tècnica es pot utilitzar per fabricar peces en dies o setmanes amb molt poca inversió. La sorra humida s'uneix amb argila, aglutinants o olis especials. La sorra generalment es troba a les caixes de motlles i el sistema de cavitats i porta es crea compactant la sorra al voltant dels models. Els processos són: 1.) Col·locació del model en sorra per fer el motlle 2.) Incorporació de model i sorra en un sistema de gating 3.) Eliminació del model 4.) Ompliment de la cavitat del motlle amb metall fos 5.) Refredament del metall 6.) Trencant el motlle de sorra i retirada de la fosa • FUNDACIÓ DE MOTLLES DE GUIX: De manera semblant a la fosa de sorra, i en lloc de sorra, s'utilitza guix de París com a material de motlle. Terminis de producció curts com la fosa de sorra i econòmics. Bones toleràncies dimensionals i acabat superficial. El seu principal desavantatge és que només es pot utilitzar amb metalls de baix punt de fusió com l'alumini i el zinc. • FUNDACIÓ DE MOTLLES DE SHELL : També semblant a la fosa en sorra. Cavitat del motlle obtingut per closca de sorra endurida i aglutinant de resina termoendurible en lloc d'un matràs ple de sorra com en el procés de fosa en sorra. Gairebé qualsevol metall apte per ser fos amb sorra es pot fer per modelat de closca. El procés es pot resumir en: 1.) Fabricació del motlle de closca. La sorra utilitzada té una mida de gra molt més petita en comparació amb la sorra utilitzada en la fosa de sorra. La sorra fina es barreja amb resina termoendurible. El patró metàl·lic està recobert amb un agent de separació per facilitar l'eliminació de la closca. A continuació, el patró de metall s'escalfa i la barreja de sorra s'escalfa o es bufa sobre el patró de fosa en calent. A la superfície del patró es forma una capa fina. El gruix d'aquesta closca es pot ajustar variant el temps que la barreja de resina de sorra està en contacte amb el patró metàl·lic. A continuació, s'elimina la sorra solta i queda el patró cobert de closca. 2.) A continuació, la closca i el patró s'escalfen al forn perquè la closca s'endureixi. Un cop finalitzat l'enduriment, la closca s'expulsa del patró mitjançant agulles incorporades al patró. 3.) Dues d'aquestes petxines s'ajunten enganxant o subjectant i formen el motlle complet. Ara el motlle de closca s'insereix en un recipient en el qual es recolza amb sorra o granalla metàl·lica durant el procés de fosa. 4.) Ara es pot abocar el metall calent al motlle de closca. Els avantatges de la fosa de closca són productes amb molt bon acabat superficial, possibilitat de fabricar peces complexes amb una gran precisió dimensional, procés fàcil d'automatitzar, econòmic per a una producció de grans volums. Els desavantatges són que els motlles necessiten una bona ventilació a causa dels gasos que es creen quan el metall fos entra en contacte amb el producte químic aglutinant, les resines termoestables i els patrons metàl·lics són cars. A causa del cost dels patrons metàl·lics, és possible que la tècnica no s'adapti bé a les sèries de producció de poca quantitat. • FUNDACIÓ PER INVERSIÓ (també coneguda com COSTÀ A CERA PERDIDA): tècnica també molt antiga i adequada per a la fabricació de peces de qualitat amb gran precisió, repetibilitat, versatilitat i integritat a partir de molts metalls, materials refractaris i aliatges especials d'alt rendiment. Es poden produir peces de mida petita i gran. Un procés car en comparació amb alguns dels altres mètodes, però el principal avantatge és la possibilitat de produir peces amb una forma gairebé neta, contorns complexos i detalls. Per tant, el cost es compensa una mica amb l'eliminació de reelaboració i mecanitzat en alguns casos. Tot i que hi pot haver variacions, aquí teniu un resum del procés general de càsting d'inversió: 1.) Creació de patró mestre original a partir de cera o plàstic. Cada fosa necessita un patró, ja que es destrueixen en el procés. També es necessita motlle a partir del qual es fabriquen els patrons i la majoria de les vegades el motlle és fos o mecanitzat. Com que no cal obrir el motlle, es poden aconseguir peces de fosa complexes, molts patrons de cera es poden connectar com les branques d'un arbre i abocar-los junts, permetent així la producció de múltiples peces a partir d'un sol abocament del metall o aliatge metàl·lic. 2.) A continuació, el patró es submergeix o s'aboca amb un purín refractari compost de sílice de gra molt fi, aigua i aglutinants. Això resulta en una capa de ceràmica sobre la superfície del patró. La capa refractària del patró es deixa assecar i endurir. Aquest pas és d'on prové el nom de fosa d'inversió: el purín refractari s'inverteix sobre el patró de cera. 3.) En aquest pas, el motlle de ceràmica endurida es capgira i s'escalfa perquè la cera es fongui i s'aboqui fora del motlle. Es deixa una cavitat per a la fosa metàl·lica. 4.) Després que la cera estigui fora, el motlle de ceràmica s'escalfa fins i tot a una temperatura més alta que resulta en l'enfortiment del motlle. 5.) La fosa de metall s'aboca al motlle calent omplint totes les seccions complexes. 6.) Es deixa solidificar la fosa 7.) Finalment es trenca el motlle de ceràmica i es tallen les peces fabricades de l'arbre. Aquí teniu un enllaç al fulletó de la planta de fosa d'inversió • FUNDACIÓ DE PATRÓ EVAPORATIU: El procés utilitza un patró fet d'un material com l'escuma de poliestirè que s'evapora quan s'aboca metall fos calent al motlle. Hi ha dos tipus d'aquest procés: FUNDACIÓ D'ESPUA PERDUDA que utilitza sorra sense lligar i FUNDACIÓ DE MOTLE COMPLET que utilitza sorra lligada. Aquests són els passos generals del procés: 1.) Fabricar el patró a partir d'un material com el poliestirè. Quan es fabricaran grans quantitats, el patró es modela. Si la part té una forma complexa, és possible que s'hagin d'adherir diverses seccions d'aquest material d'escuma per formar el patró. Sovint recobrim el patró amb un compost refractari per crear un bon acabat superficial a la fosa. 2.) A continuació, el patró es posa a la sorra de modelat. 3.) El metall fos s'aboca al motlle, evaporant el patró d'escuma, és a dir, el poliestirè en la majoria dels casos a mesura que flueix per la cavitat del motlle. 4.) El metall fos es deixa al motlle de sorra per endurir-se. 5.) Després que estigui endurit, traiem la fosa. En alguns casos, el producte que fabriquem requereix un nucli dins del patró. En la fosa evaporativa, no cal col·locar i assegurar un nucli a la cavitat del motlle. La tècnica és adequada per a la fabricació de geometries molt complexes, es pot automatitzar fàcilment per a la producció de grans volums i no hi ha línies de separació a la peça de fosa. El procés bàsic és senzill i econòmic d'implementar. Per a la producció de grans volums, ja que es necessita una matriu o motlle per produir els patrons a partir de poliestirè, això pot ser una mica costós. • FUNDACIÓ DE MOTLLES NO EXPANDABLES: Aquesta àmplia categoria fa referència als mètodes on no cal reformar el motlle després de cada cicle de producció. Alguns exemples són la colada permanent, en matriu, contínua i centrífuga. S'obté la repetibilitat i les peces es poden caracteritzar com a FORMA NETA PROP. • FUNDACIÓ DE MOTLLES PERMANENTS: Els motlles reutilitzables fets de metall s'utilitzen per a múltiples colades. Un motlle permanent es pot utilitzar generalment desenes de milers de vegades abans que es desgasti. La gravetat, la pressió del gas o el buit s'utilitzen generalment per omplir el motlle. Els motlles (també anomenats matrius) estan fets generalment de ferro, acer, ceràmica o altres metalls. El procés general és: 1.) Mecanitzar i crear el motlle. És habitual mecanitzar el motlle a partir de dos blocs metàl·lics que s'uneixen i es poden obrir i tancar. Tant les característiques de la peça com el sistema de tancament es mecanitza generalment al motlle de fosa. 2.) Les superfícies internes del motlle estan recobertes amb un purí que incorpora materials refractaris. Això ajuda a controlar el flux de calor i actua com a lubricant per a una fàcil eliminació de la peça de fosa. 3.) A continuació, es tanquen les meitats del motlle permanent i s'escalfa el motlle. 4.) El metall fos s'aboca al motlle i es deixa quiet per a la solidificació. 5.) Abans que es produeixi molt de refredament, retirem la peça del motlle permanent mitjançant expulsors quan s'obren les meitats del motlle. Sovint fem servir la fosa de motlle permanent per a metalls de baix punt de fusió com ara zinc i alumini. Per a peces de fosa d'acer, utilitzem grafit com a material de motlle. De vegades obtenim geometries complexes utilitzant nuclis dins de motlles permanents. Els avantatges d'aquesta tècnica són peces de fosa amb bones propietats mecàniques obtingudes per refredament ràpid, uniformitat de propietats, bona precisió i acabat superficial, baixes taxes de rebuig, possibilitat d'automatitzar el procés i produir grans volums econòmicament. Els desavantatges són els alts costos inicials de configuració que el fan inadequat per a operacions de baix volum i les limitacions de la mida de les peces fabricades. • FUNDACIÓ: Es mecanitza una matriu i el metall fos s'empeny a alta pressió a les cavitats del motlle. Són possibles tant peces de fosa de metalls no fèrrics com ferrosos. El procés és adequat per a sèries de producció en gran quantitat de peces de mida petita i mitjana amb detalls, parets extremadament primes, consistència dimensional i bon acabat superficial. AGS-TECH Inc. és capaç de fabricar gruixos de paret fins a 0,5 mm mitjançant aquesta tècnica. Igual que en la fosa de motlle permanent, el motlle ha de constar de dues meitats que es puguin obrir i tancar per eliminar la part produïda. Un motlle de fosa a pressió pot tenir múltiples cavitats per permetre la producció de múltiples peces de fosa amb cada cicle. Els motlles de fosa a pressió són molt pesats i molt més grans que les peces que produeixen, per tant també són cars. Reparem i substituïm matrius desgastats de manera gratuïta per als nostres clients, sempre que ens tornin a demanar les seves peces. Les nostres matrius tenen una llarga vida útil en el rang de diversos centenars de milers de cicles. Aquests són els passos bàsics del procés simplificat: 1.) Producció del motlle generalment a partir d'acer 2.) Motlle instal·lat a la màquina de fosa a pressió 3.) El pistó obliga el metall fos a fluir a les cavitats de la matriu omplint les característiques intricades i les parets primes 4.) Després d'omplir el motlle amb el metall fos, la fosa es deixa endurir a pressió 5.) S'obre el motlle i s'elimina la fosa amb l'ajuda de passadors d'expulsió. 6.) Ara es tornen a lubricar la matriu buida i es subjecten per al següent cicle. En la fosa a pressió, sovint fem servir el modelat d'inserció on incorporem una peça addicional al motlle i colem el metall al seu voltant. Després de la solidificació, aquestes peces passen a formar part del producte fos. Els avantatges de la fosa a pressió són bones propietats mecàniques de les peces, possibilitat de característiques complexes, detalls fins i bon acabat superficial, altes taxes de producció, fàcil automatització. Els desavantatges són: no molt adequat per a un volum baix a causa de l'elevat cost de la matriu i de l'equip, les limitacions en les formes que es poden colar, les petites marques rodones a les peces de fosa com a resultat del contacte de les agulles d'expulsió, el flaix prim de metall espremut a la línia de separació, la necessitat per a les ventilacions al llarg de la línia de separació entre la matriu, la necessitat de mantenir baixes les temperatures del motlle mitjançant la circulació d'aigua. • FUNDACIÓ CENTRÍFUGA: S'aboca metall fos al centre del motlle giratori en l'eix de rotació. Les forces centrífugues llancen el metall cap a la perifèria i es deixa solidificar a mesura que el motlle segueix girant. Es poden utilitzar tant rotacions d'eix horitzontal com vertical. Es poden colar peces amb superfícies interiors rodones i altres formes no rodones. El procés es pot resumir en: 1.) El metall fos s'aboca al motlle centrífug. A continuació, el metall és forçat a les parets exteriors a causa de la rotació del motlle. 2.) A mesura que el motlle gira, la fosa metàl·lica s'endureix La fosa centrífuga és una tècnica adequada per a la producció de peces cilíndriques buides com canonades, sense necessitat de becs, risers i elements de reixeta, bon acabat superficial i característiques detallades, sense problemes de contracció, possibilitat de produir tubs llargs amb diàmetres molt grans, capacitat de producció d'alta velocitat. . • FUSA CONTINUA ( STRAND CASTING ): S'utilitza per colar una longitud contínua de metall. Bàsicament, el metall fos es col·loca en un perfil bidimensional del motlle, però la seva longitud és indeterminada. El nou metall fos s'introdueix constantment al motlle a mesura que la fosa viatja cap avall i la seva longitud augmenta amb el temps. Els metalls com el coure, l'acer, l'alumini es colen en fils llargs mitjançant un procés de colada contínua. El procés pot tenir diverses configuracions, però la comuna es pot simplificar com: 1.) El metall fos s'aboca en un recipient situat molt per sobre del motlle en quantitats i cabals ben calculats i flueix a través del motlle refrigerat per aigua. La fosa metàl·lica abocada al motlle es solidifica en una barra d'inici col·locada a la part inferior del motlle. Aquesta barra d'arrencada dóna als rodets alguna cosa per agafar-se inicialment. 2.) El fil metàl·lic llarg és portat per corrons a velocitat constant. Els corrons també canvien la direcció del flux del fil metàl·lic de vertical a horitzontal. 3.) Després que la colada contínua hagi recorregut una certa distància horitzontal, una torxa o una serra que es mou amb la fosa la talla ràpidament a les longituds desitjades. El procés de colada contínua es pot integrar amb el PROCÉS DE LAMINAT, on el metall de fosa contínua es pot alimentar directament a un laminador per produir bigues en I, bigues en T... etc. La colada contínua produeix propietats uniformes en tot el producte, té una alta taxa de solidificació, redueix el cost a causa de la molt baixa pèrdua de material, ofereix un procés on la càrrega de metall, l'abocament, la solidificació, el tall i l'eliminació de la fosa tenen lloc en una operació contínua i D'aquesta manera, s'aconsegueix una alta productivitat i una alta qualitat. Tanmateix, una consideració important és l'elevada inversió inicial, els costos de configuració i els requisits d'espai. • SERVEIS DE MECANITZACIÓ: Oferim mecanitzats de tres, quatre i cinc eixos. El tipus de processos de mecanitzat que utilitzem són TORNEJAT, FRESAT, PERFORAT, MANDRADO, BROCAT, REPELLAT, SERRAT, MOLIT, LAPET, POLIT i MECANISAT NO TRADICIONAL que s'elabora en un menú diferent de la nostra web. Per a la major part de la nostra fabricació, utilitzem màquines CNC. Tanmateix, per a algunes operacions les tècniques convencionals s'ajusten millor i, per tant, també confiem en elles. Les nostres capacitats de mecanitzat assoleixen el nivell més alt possible i algunes peces més exigents es fabriquen en una planta certificada AS9100. Les pales dels motors a reacció requereixen una experiència de fabricació altament especialitzada i l'equip adequat. La indústria aeroespacial té estàndards molt estrictes. Alguns components amb estructures geomètriques complexes es fabriquen més fàcilment mitjançant el mecanitzat de cinc eixos, que només es troba en algunes plantes de mecanitzat, inclosa la nostra. La nostra planta certificada aeroespacial compta amb l'experiència necessària complint amb els exigències de documentació extens de la indústria aeroespacial. En les operacions de TORNET, una peça es gira i es mou contra una eina de tall. Per a aquest procés s'utilitza una màquina anomenada torn. A MILLING, una màquina anomenada fresadora té una eina giratòria per portar les vores de tall contra una peça de treball. Les operacions de PERFORAT impliquen un tallador giratori amb vores de tall que produeix forats en contacte amb la peça de treball. Generalment s'utilitzen perforadores, torns o molins. En les operacions d'ABORRING, una eina amb una sola punta de punta doblegada es mou a un forat rugós d'una peça de treball girant per ampliar lleugerament el forat i millorar la precisió. S'utilitza per a un acabat fi. EL BROCHAT consisteix en una eina dentada per treure material d'una peça en una passada de la brotxa (eina dentada). En la brotxa lineal, la brotxa s'executa linealment contra una superfície de la peça de treball per efectuar el tall, mentre que en la brotxa rotativa, la brotxa es gira i es pressiona a la peça per tallar una forma simètrica d'eix. SWISS TYPE MACHINING és una de les nostres valuoses tècniques que utilitzem per a la fabricació de grans volums de peces petites d'alta precisió. Utilitzant un torn de tipus suís tornem peces petites, complexes i de precisió de manera econòmica. A diferència dels torns convencionals on la peça es manté estacionària i l'eina es mou, en els centres de tornejat de tipus suís, la peça es pot moure en l'eix Z i l'eina està estacionària. En el mecanitzat de tipus suís, el material de la barra es manté a la màquina i s'avança a través d'un casquet guia a l'eix z, deixant al descobert només la porció a mecanitzar. D'aquesta manera s'assegura una adherència ferma i la precisió és molt alta. La disponibilitat d'eines actives ofereix l'oportunitat de fresar i perforar a mesura que el material avança des del casquet guia. L'eix Y de l'equip de tipus suís ofereix capacitats completes de fresat i estalvia una gran quantitat de temps en la fabricació. A més, les nostres màquines disposen de trepants i eines de mandrinar que operen sobre la peça quan es subjecta al subeix. La nostra capacitat de mecanitzat de tipus suís ens ofereix una oportunitat de mecanitzat complet totalment automatitzat en una sola operació. El mecanitzat és un dels segments més grans del negoci d'AGS-TECH Inc. L'utilitzem com a operació primària o secundària després de la fosa o extrusió d'una peça perquè es compleixin totes les especificacions de dibuix. • SERVEIS D'ACABAT DE SUPERFÍCIES: Oferim una gran varietat de tractaments superficials i acabats de superfícies, com ara condicionament de superfícies per millorar l'adhesió, dipòsit de capa fina d'òxid per millorar l'adhesió del recobriment, sorra, pel·lícula química, anodització, nitruració, recobriment en pols, recobriment en polvorització. , diverses tècniques avançades de metal·lització i recobriment, com ara sputtering, feix d'electrons, evaporació, revestiment, recobriments durs com el diamant com el carboni (DLC) o el recobriment de titani per a eines de perforació i tall. • SERVEIS DE MARCAT I ETIQUETATGE DE PRODUCTES: Molts dels nostres clients requereixen marcatge i etiquetatge, marcatge làser, gravat en peces metàl·liques. Si teniu alguna necessitat d'aquest tipus, deixeu-nos discutir quina opció serà la millor per a vosaltres. Aquests són alguns dels productes de fosa metàl·lica d'ús habitual. Com que no estan disponibles, podeu estalviar en costos de motlle en cas que algun d'aquests s'adapti als vostres requisits: FEU CLIC AQUÍ PER DESCARREGAR les nostres caixes d'alumini fosa de la sèrie 11 d'AGS-Electronics CLICK Product Finder-Locator Service PÀGINA ANTERIOR
- Custom Manufactured Parts, Assemblies, Plastic Mold, Casting,Machining
Custom Manufactured Parts, Assemblies, Plastic Mold, Rubber Molding, Metal Casting, CNC Machining, Turning, Milling, Electrical Electronic Optical Assembly PCBA Peces i conjunts i productes fabricats a mida Llegeix més Motlles i motlles de plàstic i cautxú Llegeix més Fosa i mecanitzat Llegeix més Extrusions, Productes extrusats Llegeix més Estampació i fabricació de xapa Llegeix més Forja de metalls i metal·lúrgia de pols Llegeix més Formació de filferro i molla Llegeix més Formació i conformació de vidre i ceràmica Llegeix més Fabricació additiva i ràpida Llegeix més Fabricació de materials compostos i compostos Llegeix més Processos d'unió i muntatge i subjecció Produïm peces i conjunts per a vostè i oferim els següents processos de fabricació: • Motlles de plàstic i cautxú i peces modelades. Emmotllament per injecció, termoconformat, modelat termoestabl, modelat al buit, modelat per bufat, modelat rotacional, modelat per abocament, modelat per inserció i altres. • Extrusions de plàstic, cautxú i metall • Colades ferrosos i no fèrrics i peces mecanitzades produïdes per tècniques de fresat i tornejat, mecanitzat de tipus suís. • Peces de pulvimetal·lúrgia • Estampacions metàl·liques i no metàl·liques, conformació de xapa, conjunts de xapa soldada • Forja en fred i calent • Filferros, conjunts de filferro soldat, conformació de filferro • Diversos tipus de molles, formant molles • Fabricació d'engranatges, caixa de canvis, acoblament, cuc, reductor de velocitat, cilindre, corretges de transmissió, cadenes de transmissió, components de transmissió • Vidre temperat a mida i antibales conforme a les normes de l'OTAN i militars • Boles, coixinets, politges i conjunts de politges • Vàlvules i components pneumàtics com ara O-ring, rentadora i segells • Peces i conjunts de vidre i ceràmica, components hermètics i estancs al buit, unió metall-ceràmica i ceràmica-ceràmica. • Diversos tipus de conjunts mecànics, optomecànics, electromecànics, optoelectrònics. • Unió metall-cautxú, metall-plàstic • Tubs i tubs, conformació de tubs, plegat i conjunts de tubs personalitzats, fabricació de manxes. • Fabricació de fibra de vidre • Soldadura mitjançant diverses tècniques com ara soldadura per punts, soldadura làser, MIG, TIG. Soldadura per ultrasons per a peces de plàstic. • Gran varietat de tractaments superficials i acabats superficials, com ara condicionament de superfícies per millorar l'adhesió, dipòsit de capa fina d'òxid per millorar l'adhesió del recobriment, sorra, pel·lícula química, anodització, nitruració, recobriment en pols, recobriment per polvorització, diverses tècniques avançades de metal·lització i recobriment. incloent-hi la polsadora, el feix d'electrons, l'evaporació, el revestiment, els recobriments durs com el diamant com el carboni (DLC) o el titani per a eines de tall i perforació. • Marcat i etiquetatge, marcatge làser sobre peces metàl·liques, impressió sobre peces de plàstic i cautxú Baixeu el fulletó dels termes comuns d'enginyeria mecànica utilitzats per dissenyadors i enginyers Construïm productes segons les vostres especificacions i requisits particulars. Per oferir-vos la millor qualitat, lliurament i preus, fabriquem productes a nivell mundial a la Xina, Índia, Taiwan, Filipines, Corea del Sud, Malàisia, Sri Lanka, Turquia, EUA, Canadà, Alemanya, Regne Unit i Japó. Això ens fa molt més forts i competitius a nivell mundial que qualsevol altre custom manufacturer. Els nostres productes es fabriquen en entorns certificats ISO9001:2000, QS9000, ISO14001, TS16949 i tenen la marca CE, UL i compleixen altres estàndards de la indústria. Un cop designats per al vostre projecte, ens podem encarregar de tota la fabricació, muntatge, proves, qualificació, enviament i duanes com vulgueu. Si ho prefereixes, podem emmagatzemar les teves peces, muntar kits personalitzats, imprimir i etiquetar el nom i la marca de la teva empresa i enviar-los als teus clients. En altres paraules, també podem ser el vostre centre d'emmagatzematge i distribució si ho preferiu. Com que els nostres magatzems estan situats a prop dels principals ports marítims, ens proporciona un avantatge logístic. Per exemple, quan els vostres productes arriben a un port marítim important dels EUA, podem transportar-los directament a un magatzem proper on podem emmagatzemar, muntar, fabricar kits, reetiquetar, imprimir, empaquetar segons la vostra elecció i deixar-los anar. envia als teus clients. No només subministrem productes. La nostra empresa treballa amb contractes personalitzats on arribem al vostre lloc, avaluem el vostre projecte in situ i desenvolupem una proposta de projecte dissenyada a mida per a vosaltres. Aleshores enviem el nostre equip experimentat per implementar el projecte. Podeu trobar més informació sobre el nostre treball d'enginyeria a http://www.ags-engineering.com -Acceptem projectes petits i grans a escala industrial. Com a primer pas, et podem connectar per telèfon, teleconferència o MSN Messenger amb els membres del nostre equip d'experts, perquè puguis comunicar-te directament amb un expert, fer preguntes i discutir el teu projecte. Truca'ns i si cal et vindrem a visitar. PÀGINA ANTERIOR