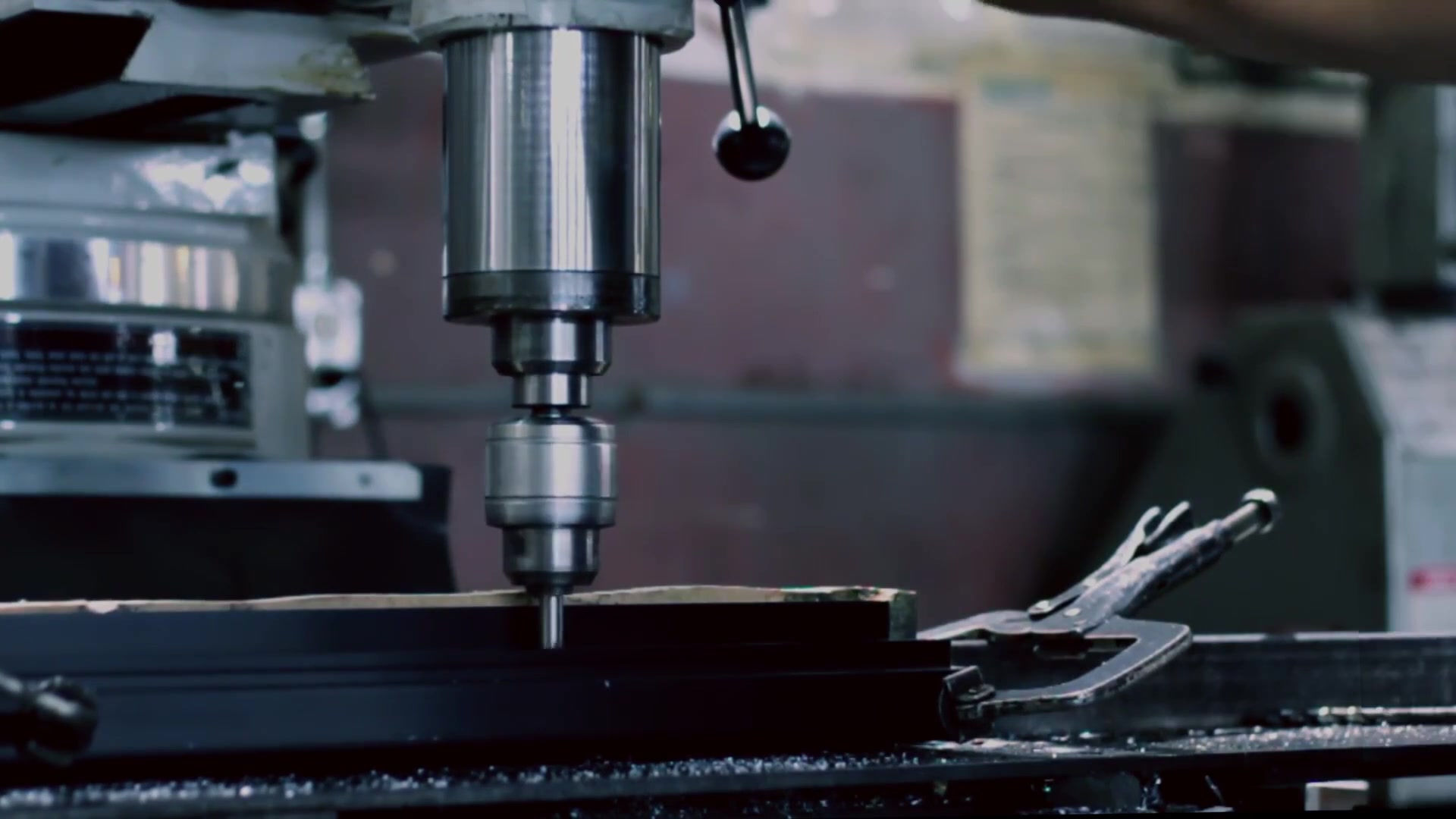
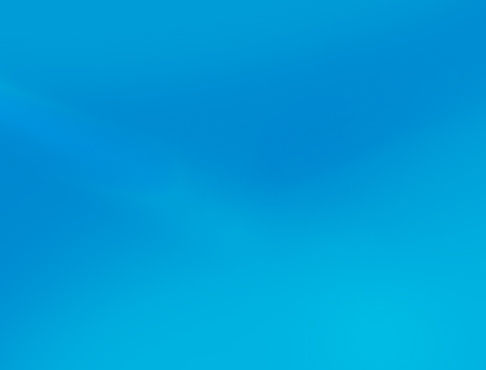
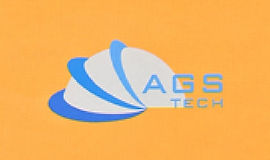
Global Custom Manufacturer, Integrator, Consolidator, Outsourcing Partner for a Wide Variety of Products & Services.
We are your one-stop source for manufacturing, fabrication, engineering, consolidation, integration, outsourcing of custom manufactured and off-shelf products & services. We also private label / white label your products with your brand name if you wish.
Choose your Language
-
Custom Manufacturing of Parts, Components, Assemblies, Finished Products, Machines and Industrial Equipment
-
Domestic & Global Contract Manufacturing
-
Manufacturing Outsourcing
-
Domestic, Global Procurement of Industrial Products
-
Private labeling / White Labeling your Products with your Brand Name
-
Product Finding & Locating Services
-
Global Design and Channel Partnership
-
Engineering Integration
-
Engineering Services
-
Global Consolidation, Warehousing, Logistics
Our custom casting and machining techniques are expendable and non-expendable castings, ferrous and nonferrous casting, sand, die, centrifugal, continuous, ceramic mold, investment, lost foam, near-net-shape, permanent mold (gravity die casting), plaster mold (plaster casting) and shell castings, machined parts produced by milling and turning using conventional as well as CNC equipment, swiss type machining for high throughput inexpensive small precision parts, screw machining for fasteners, non-conventional machining. Please keep in mind that besides metals and metal alloys, we machine ceramic, glass and plastic components as well in some cases when manufacturing a mould is not appealing or not the option. Machining of polymer materials requires the specialized experience we have because of the challenge plastics and rubber presents due to their softness, non-rigidity...etc. For machining of ceramic and glass, please see our page on Non-Conventional Fabrication. AGS-TECH Inc. manufactures and supplies both lightweight and heavy castings. We have been supplying metal castings and machined parts for boilers, heat exchangers, automobiles, micromotors, wind turbines, food packaging equipment and more. We recommend that you click here to DOWNLOAD our Schematic Illustrations of Machining and Casting Processes by AGS-TECH Inc.
This will help you better understand the information we are providing you below. Let’s look at some of the various techniques we offer in detail:
• EXPENDABLE MOLD CASTING : This broad category refers to methods that involve temporary and non-reusable molds. Examples are sand, plaster, shell, investment (also called lost-wax) and plaster casting.
• SAND CASTING : A process where sand is used as the mold material. A very old method and still very popular to the extent that the majority of metal castings produced are made by this technique . Low cost even at low quantity production. Suitable for small and large parts manufacturing. The technique can be used to manufacture parts within days or weeks with very little investment. The moist sand is bonded together using clay, binders or special oils. Sand is generally contained in mold boxes and cavity & gate system are created by compacting the sand around models. The processes are:
1.) Placing of the model in sand to make the mold
2.) Incorporation of model and sand in a gating system
3.) Removal of model
4.) Filling of mold cavity with molten metal
5.) Cooling of the metal
6.) Breaking the sand mold and removal of the casting
• PLASTER MOLD CASTING : Similar to sand casting, and instead of sand, plaster of paris is being used as the mold material. Short production lead times like sand casting and inexpensive. Good dimensional tolerances and surface finish. Its major disadvantage is that it can only be used with low melting point metals like aluminum and zinc.
• SHELL MOLD CASTING : Also similar to sand casting. Mold cavity obtained by hardened shell of sand and thermosetting resin binder instead of flask filled with sand as in sand casting process. Almost any metal suitable to be cast by sand can be cast by shell molding. The process can be summarized as:
1.) Manufacturing of the shell mold. Sand used is of a much smaller grain size when compared to sand used in sand casting. The fine sand is mixed with thermosetting resin. The metal pattern is coated with a parting agent to make removal of the shell easier. Thereafter the metal pattern is heated and the sand mixture is pored or blown onto the hot casting pattern. A thin shell forms on the surface of the pattern. The thickness of this shell can be adjusted by varying the length of time the sand resin mixture is in contact with the metal pattern. The loose sand is then removed with the shell covered pattern remaining.
2.) Next, the shell and pattern are heated in an oven so that the shell hardens. After hardening is complete, the shell is ejected from pattern using pins built into the pattern.
3.) Two such shells are assembled together by gluing or clamping and make up the complete mold. Now the shell mold is inserted into a container in which it is supported by sand or metal shot during the casting process.
4.) Now the hot metal can be poured into the shell mold.
Advantages of shell casting are products with very good surface finish, possibility of manufacturing complex parts with high dimensional accuracy, process easy to automate, economical for large volume production.
Disadvantages are the molds necessitate good ventilation because of gases that are created when molten metal contacts the binder chemical, the thermosetting resins and metal patterns are expensive. Due to the cost of metal patterns, the technique may not suit well for low quantity production runs.
• INVESTMENT CASTING ( also known as LOST-WAX CASTING ): Also a very old technique and suitable for manufacturing quality parts with high accuracy, repeatability, versatility and integrity from many metals, refractory materials and special high performance alloys. Small as well as large sized parts can be produced. An expensive process when compared to some of the other methods, but major advantage is the possibility to produce parts with near net shape, intricate contours and details. So the cost is somewhat offset by the elimination of rework and machining in some cases. Even though there can be variations, here is a summary of the general investment casting process:
1.) Creation of original master pattern from wax or plastic. Each casting needs one pattern as these are destroyed in the process. Mold from which patterns are manufactured is also needed and most of the time the mold is cast or machined. Because the mold does not need to be opened, complex castings can be achieved, many wax patterns can be connected like the branches of a tree and poured together, thus enabling production of multiple parts from a single pouring of the metal or metal alloy.
2.) Next, the pattern is dipped or poured over with a refractory slurry composed of very fine grained silica, water, binders. This results in a ceramic layer over the surface of the pattern. The refractory coat on pattern is left to dry and harden. This step is where the name investment casting comes from: Refractory slurry is invested over the wax pattern.
3.) At this step, the hardened ceramic mould is turned upside down and heated so that the wax melts and pours out of the mould. A cavity is left behind for the metal casting.
4.) After the wax is out, the ceramic mold is heated to even a higher temperature which results in strengthening of the mold.
5.) Metal casting is poured into the hot mold filling all intricate sections.
6.) Casting is allowed to solidify
7.) Finally the ceramic mould is broken and manufactured parts are cut from the tree.
Here is a link to Investment Casting Plant Brochure
• EVAPORATIVE PATTERN CASTING : The process uses a pattern made from a material such as polystyrene foam that will evaporate when hot molten metal is poured into the mold. There are two types of this process: LOST FOAM CASTING which uses unbonded sand and FULL MOLD CASTING which uses bonded sand. Here are the general process steps:
1.) Manufacture the pattern from a material such as polystyrene. When large quantities will be manufactured, the pattern is molded. If part has a complex shape, several sections of such foam material may need to be adhered together to form the pattern. We often coat the pattern with a refractory compound to create a good surface finish on the casting.
2.) The pattern is then put into molding sand.
3.) The molten metal is poured into the mould, evaporating the foam pattern, i.e. polystyrene in most cases as it flows through the mold cavity.
4.) The molten metal is left in the sand mold to harden.
5.) After it is hardened, we remove the casting.
In some cases, the product we manufacture requires a core within the pattern. In evaporative casting, there is no need to place and secure a core in the mold cavity. The technique is suitable for manufacturing of very complex geometries, it can be easily automated for high volume production, and there are no parting lines in the cast part. The basic process is simple and economical to implement. For large volume production, since a die or mold is needed to produce the patterns from polystyrene, this may be somewhat costly.
• NON-EXPANDABLE MOLD CASTING : This broad category refers to methods where the mold does not need to be reformed after each production cycle. Examples are permanent, die, continuous and centrifugal casting. Repeatability is obtained and parts can be characterized as NEAR NET SHAPE.
• PERMANENT MOLD CASTING : Reusable molds made from metal are used for multiple castings. A permanent mold can generally be used for tens of thousands of times before it wears out. Gravity, gass pressure or vacuum are generally used to fill the mould. Molds (also called die) is generally made of iron, steel, ceramic or other metals. The general process is:
1.) Machine and create the mould. It is common to machine the mold out of two metal blocks that fit together and can be opened and closed. Both the part features as well as the gating system is generally machined into the casting mould.
2.) The internal mold surfaces are coated with a slurry incorporating refractory materials. This helps to control heat flow and acts as a lubricant for easy removal of the cast part.
3.) Next, the permanent mold halves are closed and the mold is heated.
4.) Molten metal is poured into mould and let still for solidification.
5.) Before much cooling occurs, we remove the part from permanent mold using ejectors when mold halves are opened.
We frequently use permanent mold casting for low melting point metals such as zinc and aluminum. For steel castings, we use graphite as mold material. We sometimes obtain complex geometries using cores within permanent molds. Advantages of this technique are castings with good mechanical properties obtained by rapid cooling, uniformity in properties, good accuracy and surface finish, low reject rates, possibility of automating the process and producing high volumes economically. Disadvantages are high initial setup costs which make it unsuitable for low volume operations, and limitations on the size of the parts manufactured.
• DIE CASTING : A die is machined and molten metal is pushed under high pressure into mold cavities. Both nonferrous as well as ferrous metal die castings are possible. The process is suitable for high quantity production runs of small to medium sized parts with details, extremely thin walls, dimensional consistency and good surface finish. AGS-TECH Inc. is capable to manufacture wall thicknesses as small as 0.5 mm using this technique. Like in permanent mold casting, the mold needs to consist of two halves that can open and close for removal of part produced. A die casting mold may have multiple cavities to enable production of multiple castings with each cycle. Die casting molds are very heavy and much larger than the parts they produce, therefore also expensive. We repair and replace worn out dies free of charge for our customers as long as they reorder their parts from us. Our dies have long lifetimes in the several hundred thousand cycles range.
Here are the basic simplified process steps:
1.) Production of the mold generally from steel
2.) Mold installed on die casting machine
3.) The piston forces molten metal to flow in the die cavities filling out the intricate features and thin walls
4.) After filling the mold with the molten metal, the casting is let hardened under pressure
5.) Mold is opened and casting removed with the help of ejector pins.
6.) Now the empty die are lubricated again and are clamped for the next cycle.
In die casting, we frequently use insert molding where we incorporate an additional part into the mold and cast the metal around it. After solidification, these parts become part of the cast product. Advantages of die casting are good mechanical properties of the parts, possibility of intricate features, fine details and good surface finish, high production rates, easy automation. Disadvantages are: Not very suitable for low volume because of high die and equipment cost, limitations in shapes that can be cast, small round marks on cast parts resulting from contact of ejector pins, thin flash of metal squeezed out at the parting line, need for vents along the parting line between the die, necessity to keep mold temperatures low using water circulation.
• CENTRIFUGAL CASTING : Molten metal is poured into the center of the rotating mold at the axis of rotation. Centrifugal forces throw the metal towards the periphery and it is let to solidify as the mold keeps rotating. Both horizontal and vertical axis rotations can be used. Parts with round inner surfaces as well as other non-round shapes can be cast. The process can be summarized as:
1.) Molten metal is poured into centrifugal mould. The metal is then forced to the outer walls due to spinning of the mold.
2.) As the mold rotates, the metal casting hardens
Centrifugal casting is a suitable technique for production of hollow cylindirical parts like pipes, no need for sprues, risers and gating elements, good surface finish and detailed features, no shrinkage issues, possibility to produce long pipes with very large diameters, high rate production capability.
• CONTINUOUS CASTING ( STRAND CASTING ) : Used to cast a continuous length of metal. Basically the molten metal is cast into two dimensional profile of the mold but its length is indeterminate. New molten metal is constantly fed into the mould as the casting travels downward with its length increasing with time. Metals such as copper, steel, aluminum are cast into long strands using continuous casting process. The process may have various configurations but the common one can be simplified as:
1.) Molten metal is poured into a container located high above the mold at well calculated amounts and flow rates and flows through the water cooled mold. The metal casting poured into the mould solidifies to a starter bar placed at the bottom of the mold. This starter bar gives the rollers something to grab onto initially.
2.) The long metal strand is carried by rollers at a constant speed. The rollers also change the direction of the flow of metal strand from vertical to horizontal.
3.) After the continuous casting has travelled a certain horizontal distance, a torch or saw that moves with the casting quickly cuts it to desired lengths.
Continuous casting process can be integrated with ROLLING PROCESS, where the continuously cast metal can be fed directly into a rolling mill to produce I-Beams, T-Beams….etc. Continuous casting produces uniform properties throughout the product, it has a high solidification rate, reduces cost due to very low loss of material, offers a process where loading of metal, pouring, solidification, cutting and casting removal all take place in a continuous operation and thus resulting in high productivity rate and high quality. A major consideration is however the high initial investment, setup costs and space requirements.
• MACHINING SERVICES : We offer three, four and five - axis machining. The type of machining processes we use are TURNING, MILLING, DRILLING, BORING, BROACHING, PLANING, SAWING, GRINDING, LAPPING, POLISHING and NON-TRADITIONAL MACHINING which is further elaborated under a different menu of our website. For most of our manufacturing, we use CNC machines. However for some operations conventional techniques are a better fit and therefore we rely on them as well. Our machining capabilities reach the highest level possible and some most demanding parts are manufactured at an AS9100 certified plant. Jet engine blades require highly specialized manufacturing experience and the right equipment. Aerospace industry has very strict standards. Some components with complex geometrical structures are most easily manufactured by five axis machining, which is found only in some machining plants including ours. Our aerospace certified plant has the necessary experience complying to extensive documentation requirement of the aerospace industry.
In TURNING operations, a workpiece is rotated and moved against a cutting tool. For this process a machine called lathe is being used.
In MILLING, a machine called milling machine has a rotating tool to bring cutting edges to bear against a workpiece.
DRILLING operations involve a rotating cutter with cutting edges that produces holes upon contact with the workpiece. Drill presses, lathes or mills are generally used.
In BORING operations a tool with a single bent pointed tip is moved into a rough hole in a spinning workpiece to slightly enlarge the hole and improve accuracy. It is used for fine finishing purposes.
BROACHING involves a toothed tool to remove material from a workpiece in one pass of the broach (toothed tool). In linear broaching, the broach runs linearly against a surface of the workpiece to effect the cut, whereas in rotary broaching, the broach is rotated and pressed into the workpiece to cut an axis symmetric shape.
SWISS TYPE MACHINING is one of our valuable techniques we use for high volume manufacturing of small high precision parts. Using Swiss-type lathe we turn small, complex, precision parts inexpensively. Unlike conventional lathes where the workpiece is kept stationary and tool moving, in Swiss-type turning centers, the workpiece is allowed to move in the Z-axis and the tool is stationary. In Swiss-type machining, the bar stock is held in the machine and advanced through a guide bushing in the z-axis, only exposing the portion to be machined. This way a tight grip is ensured and accuracy is very high. Availability of live tools provide the opportunity to mill and drill as the material advances from the guide bushing. The Y-axis of the Swiss-type equipment provides full milling capabilities and saves great amount of time in manufacturing. Furthermore, our machines have drills and boring tools that operate on the part when it is held in the sub spindle. Our Swiss-Type machining capability gives us a fully automated complete machining opportunity in a single operation.
Machining is one of the largest segments of AGS-TECH Inc. business. We either use it as a primary operation or a secondary operation after casting or extruding a part so that all drawing specifications are met.
• SURFACE FINISHING SERVICES : We offer a vast variety of surface treatments and surface finishing such as surface conditioning to enhance adhesion, depositing thin oxide layer to enhance adhesion of coating, sand blasting, chem-film, anodizing, nitriding, powder coating, spray coating, various advanced metallization and coating techniques including sputtering, electron beam, evaporation, plating, hard coatings such as diamond like carbon (DLC) or titanium coating for drilling and cutting tools.
• PRODUCT MARKING & LABELING SERVICES : Many of our customers require marking and labeling, laser marking, engraving on metal parts. If you have any such need, let us discuss which option will be the best for you.
Here are some of commonly used metal cast products. Since these are off-the-shelf, you can save on mould costs in case any of these fits your requirements:
CLICK HERE TO DOWNLOAD our 11 Series Die-cast Aluminium Boxes from AGS-Electronics