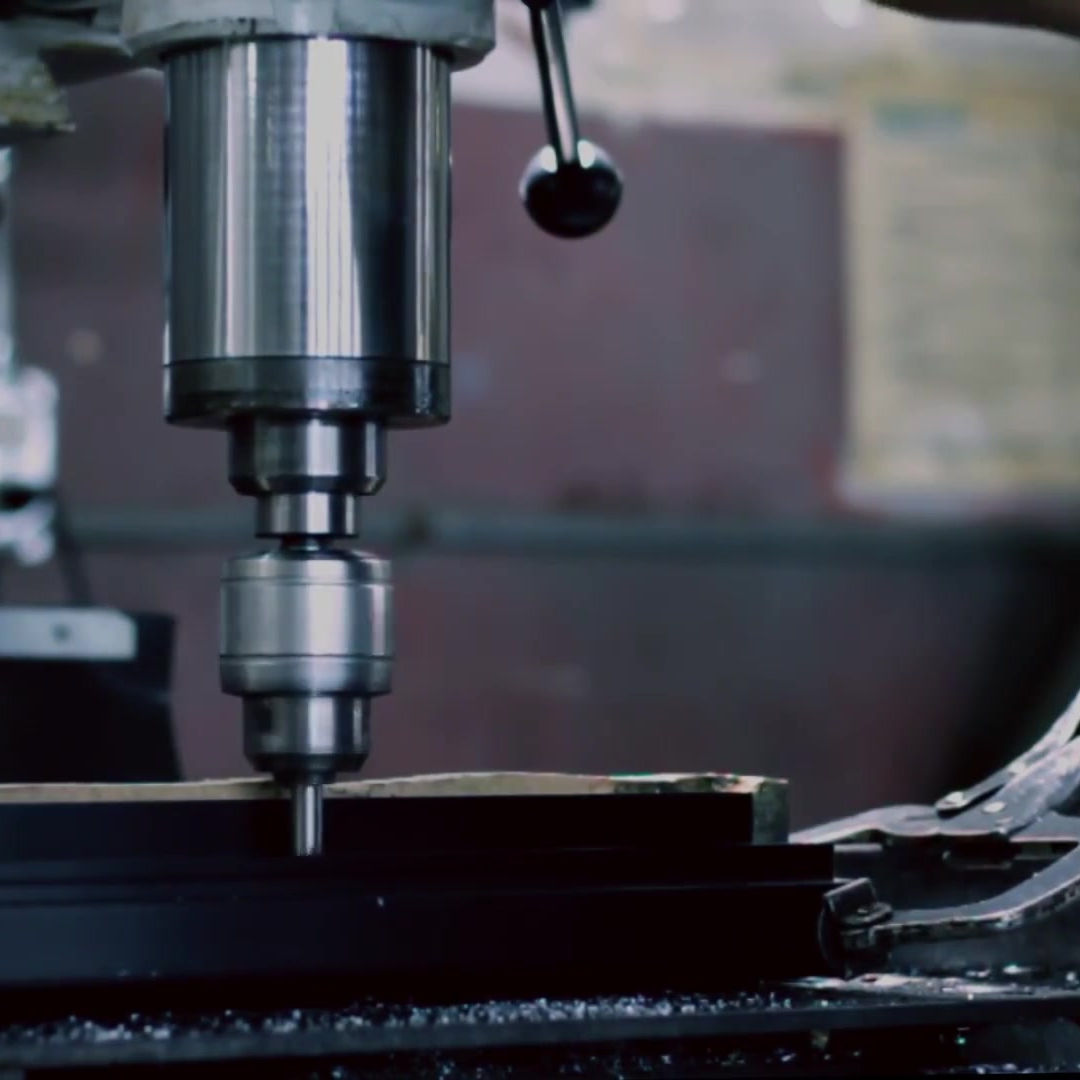
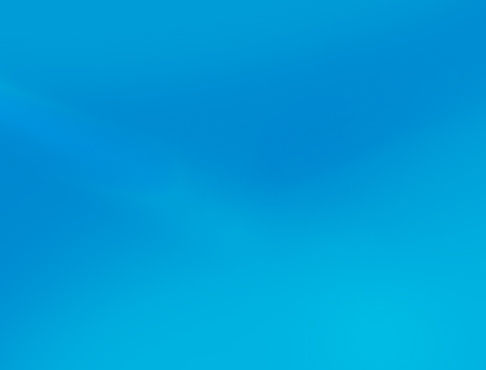
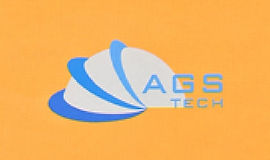
Global Custom Manufacturer, Integrator, Consolidator, Outsourcing Partner for a Wide Variety of Products & Services.
We are your one-stop source for manufacturing, fabrication, engineering, consolidation, integration, outsourcing of custom manufactured and off-shelf products & services. We also private label / white label your products with your brand name if you wish.
Choose your Language
-
Custom Manufacturing of Parts, Components, Assemblies, Finished Products, Machines and Industrial Equipment
-
Domestic & Global Contract Manufacturing
-
Manufacturing Outsourcing
-
Domestic, Global Procurement of Industrial Products
-
Private labeling / White Labeling your Products with your Brand Name
-
Product Finding & Locating Services
-
Global Design and Channel Partnership
-
Engineering Integration
-
Engineering Services
-
Global Consolidation, Warehousing, Logistics
We offer off-the-shelf and custom manufactured COMPRESSORS, PUMPS and MOTORS for PNEUMATIC, HYDRAULIC and VACUUM APPLICATIONS. You can choose the products you need in our downloadable brochures or if you are unsure, you may describe us your needs and applications and we can offer you the suitable compressors, pumps and pneumatic & hydraulic motors. For some of our compressors, pumps and motors we are capable of making modifications and custom manufacture them to your applications.
PNEUMATIC COMPRESSORS: Also called gas compressors, these are mechanical devices that increase the pressure of a gas by reducing its volume. Compressors supply air to a pneumatic system. An air compressor is a specific type of gas compressor. Compressors are similar to pumps, they both increase the pressure on a fluid and can transport the fluid through a pipe. Since gases are compressible, the compressor also reduces the volume of a gas. Liquids are relatively incompressible; while some can be compressed. The main action of a pump is to pressurize and transport liquids. Both piston and rotary screw version pneumatic compressors are available in many versions and suitable for any production activity. Mobile compressors, low- or high-pressure compressors, on-frame / vessel-mounted compressors: They are designed to meet intermittent compressed air demands. Our belt driven compressors are designed to deliver more air and higher pressures to increase the number of possible applications. Some of our belt driven two stage piston compressors have pre-installed and tank-mounted dryers. The silent range of pneumatic compressors are especially attractive for applications in closed areas or when many units need to be used. The small and compact yet powerful screw compressors are also among our popular products. The rotors of our pneumatic compressors are mounted on high quality low wear bearings. Pneumatic Variable Speed (CPVS) compressors allow users to save operating costs when the application does not require the compressors full capacity. Air-cooled compressors are designed for heavy duty installations and harsh conditions. Compressors can be categorized as:
- Positive Type Displacement Compressors: These compressors operate by opening up a cavity to draw in air, and then make the cavity smaller to expel compressed air. Three designs of positive displacement compressors are common in industry: First one are the Reciprocating Compressors (single stage and two stage). As the crankshaft rotates, it causes the piston to reciprocate, alternately drawing in atmospheric air and pushing out compressed air. Piston compressors are popular in small and medium commercial applications. A single-stage compressor has only one piston connected to a crankshaft and can pressures up to 150 psi. On the other hand, two-stage compressors have two pistons of different sizes. The larger piston is called the first stage and the smaller one the second stage. Two-stage compressors can generate pressures higher than 150 psi. The second type are the Rotary Vane Compressors which have a rotor mounted off center to the housing. As the rotor spins, the vanes extend and retract to keep contact with the housing. At the inlet, the chambers between vanes increase in volume and create a vacuum to pull in the atmospheric air. When the chambers reach the outlet, their volume decreases. The air is compressed before being exhausted into the receiver tank. Rotary vane compressors produce up to 150 psi pressure. Lastly Rotary Screw Compressors have two shafts with the air seal-off contours that look similar to a screw. Air entering from the top on one end of the rotary screw compressors is exhausted out at the other end. At the location where the air enters the compressors, the volume of the chambers between the contours is large. As the screws turn and mesh, the volume of the chambers decreases and causes the air to be compressed before being exhausted into the receiver tank.
- Non-Positive Type Displacement Compressors: These compressors operate by using an impeller to increase the velocity of the air. As the air enters into a diffuser, its pressure increases before the air goes into a receiver tank. Centrifugal compressors are an example. Multistage centrifugal compressor designs can generate high pressures by feeding the outlet air of a preceding stage to the inlet of the next stage.
HYDRAULIC COMPRESSORS: Similar to pneumatic compressors, these are mechanical devices that increase the pressure of a liquid by reducing its volume. Hydraulic compressors are usually divided into four major groups: Piston Compressors, Rotary Vane Compressors, Rotary Screw Compressors and Gear Compressors. Rotary vane-models include also a cooled lubrication system, oil separator, relief valve on the air intake and automatic rotation speed valve. Rotary vane-models are the most suitable for installation on different excavators, mining and other machines.
PNEUMATIC PUMPS: AGS-TECH Inc. offers a wide variety of Diaphragm Pumps and Piston Pumps for pneumatic applications. Piston pumps and Plunger Pumps are reciprocating pumps that use a plunger or piston to move media through a cylindrical chamber. The plunger or piston is actuated by a steam powered, pneumatic, hydraulic, or electric drive. Piston and plunger pumps are also called high viscosity pumps. Diaphragm pumps are positive displacement pumps in which the reciprocating piston is separated from the solution by a flexible diaphragm. This flexible membrane allows fluid movement. These pumps can handle many different types of fluids, even those with some solid material. Compressed air driven piston pumps use large area air-driven piston connected to small-area hydraulic piston, to convert compressed air into hydraulic power. Our pumps are designed to provide an economical, compact and portable source of hydraulic pressure. To size the right pump for your application contact us.
HYDRAULIC PUMPS: A hydraulic pump is a mechanical source of power that converts mechanical power into hydraulic energy (i.e. flow, pressure). Hydraulic pumps are used in hydraulic drive systems. They can be hydrostatic or hydrodynamic. Hydraulic pumps generate flow with enough power to overcome pressure induced by the load at the pump outlet. Hydraulic pumps in operation create a vacuum at the pump inlet, forcing liquid from the reservoir into the inlet line to the pump and by mechanical action delivering this liquid to the pump outlet and forcing it into the hydraulic system. Hydrostatic pumps are positive displacement pumps while hydrodynamic pumps can be fixed displacement pumps, in which the displacement (flow through the pump per rotation of the pump) cannot be adjusted, or variable displacement pumps, which have a more complicated construction that allows the displacement to be adjusted. Hydrostatic pumps are of various types and work on the principle of Pascal's law. It states that the increase in pressure at one point of the enclosed liquid in equilibrium is transmitted equally to all other points of the liquid, unless the effect of gravity is neglected. A pump produces liquid movement or flow, and does not generate pressure. Pumps produce the flow necessary for the development of pressure which is a function of resistance to fluid flow in the system. As an example, the pressure of the fluid at the pump outlet is zero for a pump not connected to a system or load. On the other hand, for a pump delivering into a system, the pressure will rise only to the level necessary to overcome the resistance of the load. All pumps may be classified as either positive-displacement or non-positive-displacement. The majority of pumps used in hydraulic systems are positive-displacement. A Non-Positive-Displacement Pump produces a continuous flow. However, since it does not provide a positive internal seal against slippage, its output varies considerably as the pressure varies. Examples of non-positive-displacement pumps are centrifugal and propeller pumps. If the output port of a non-positive-displacement pump were blocked off, the pressure would rise, and output would decrease to zero. Although the pumping element would continue moving, flow would stop because of the slippage inside the pump. On the other hand, in aPositive-Displacement Pump, slippage is negligible compared to the pump's volumetric output flow. If the output port were plugged, pressure would increase instantaneously to the point that the pump's pumping elements or the pump’s case would fail, or the pump's prime mover would stall. A positive-displacement pump is one that displaces or delivers the same amount of liquid with each rotating cycle of the pumping element. Constant delivery during each cycle is possible because of the close-tolerance fit between the pumping elements and the pump case. This means, the amount of liquid that slips past the pumping element in a positive-displacement pump is minimal and negligible compared to the theoretical maximum possible delivery. In positive-displacement pumps the delivery per cycle remains almost constant, regardless of changes in pressure against which the pump is working. If fluid slippage is substantial, this means the pump is not operating properly and should be repaired or replaced. Positive-displacement pumps can be of either fixed or variable displacement type. The output of a fixed displacement pump remains constant at a given pump speed during each pumping cycle. The output of a variable displacement pump can be changed by altering the geometry of the displacement chamber. The term Hydrostatic is used for positive-displacement pumps and Hydrodynamic is used for non-positive-displacement pumps. Hydrostatic meaning that the pump converts mechanical energy to hydraulic energy with comparatively small quantity and velocity of liquid. On the other hand, in a hydrodynamic pump, liquid velocity and movement are large and output pressure depends on the velocity at which the liquid is made to flow. Here are the commercially available hydraulic pumps:
- Reciprocating pumps: As the piston extends, the partial vacuum created in the pump chamber draws some liquid from the reservoir through the inlet check valve into the chamber. The partial vacuum helps seat the outlet check valve firmly. The volume of liquid drawn into the chamber is known because of the geometry of the pump case. As the piston retracts, the inlet check valve reseats, closing the valve, and the force of the piston unseats the outlet check valve, forcing liquid out of the pump and into the system.
- Rotary pumps (external-gear pumps, lobe pump, screw pump, internal-gear pumps, vane pumps): In a rotary-type pump, rotary motion carries the liquid from the pump inlet to the pump outlet. Rotary pumps are usually classified according to the type of element that transmits the liquid.
- Piston pumps (axial-piston pumps, inline-piston pumps, bent-axis pumps, radial-piston pumps, plunger pumps): The piston pump is a rotary unit which uses the principle of the reciprocating pump to produce fluid flow. Instead of using a single piston, these pumps have many piston-cylinder combinations. Part of the pump mechanism rotates about a drive shaft to generate the reciprocating motions, which draw fluid into each cylinder and then expels it, producing flow. Plunger pumps are somewhat similar to rotary piston pumps, in that pumping is the result of pistons reciprocating in cylinder bores. However, the cylinders are fixed in these pumps. Cylinders do not rotate around the drive shaft. Pistons may be reciprocated by a crankshaft, by eccentrics on a shaft, or by a wobble plate.
VACUUM PUMPS: A vacuum pump is a device that removes gas molecules from a sealed volume in order to leave behind a partial vacuum. The mechanics of the pump design inherently dictate the pressure range at which the pump is able to operate. The vacuum industry recognizes the following pressure regimes:
Coarse Vacuum: 760 - 1 Torr
Rough Vacuum: 1 Torr – 10exp-3 Torr
High Vacuum: 10exp-4 – 10exp-8 Torr
Ultra High Vacuum: 10exp-9 – 10exp-12 Torr
The transition from atmospheric pressure to the bottom of the UHV range (approx. 1 x 10exp-12 Torr) is a dynamic range of about 10exp+15 and beyond the capabilities of any single pump. Indeed, to get to any pressure below 10exp-4 Torr requires more than one pump.
- Positive displacement pumps: These expand a cavity, seal, exhaust and repeat it.
- Momentum transfer pumps (molecular pumps): These use high speed liquids or blades to knock gasses around.
- Entrapment pumps (cryopumps): Create solids or adsorbed gases .
In vacuum systems roughing pumps are used from atmospheric pressure down to rough vacuum (0.1 Pa, 1X10exp-3 Torr). Roughing pumps are necessary because turbo pumps have trouble starting from atmospheric pressure. Usually Rotary Vane Pumps are used for roughing. They may have oil or not.
After roughing, if lower pressures (better vacuum) are needed, Turbomolecular Pumps are useful. Gas molecules interact with spinning blades and are preferentially forced downward. High vacuum (10exp-6 Pa) requires rotation of 20,000 to 90,000 revolutions per minute. Turbomolecular pumps generally work between 10exp-3 and 10exp-7 Torr Turbomolecular pumps are ineffective before gas is in “molecular flow”.
PNEUMATIC MOTORS: Pneumatic motors, also called compressed air engines are types of motors which do mechanical work by expanding compressed air. Pneumatic motors generally convert the compressed air energy to mechanical work through either linear or rotary motion. Linear motion can come from a diaphragm or piston actuator, while rotary motion can come from either a vane type air motor, piston air motor, air turbine or gear type motor. Pneumatic motors have found widespread use in the hand-held tool industry for impact wrenches, pulse tools, screwdrivers, nut runners, drills, grinders, sanders, …etc, dentistry, medicine and a wide range of industrial applications. There are several advantages of pneumatic motors over electric tools. Pneumatic motors offer greater power density because a smaller pneumatic motor can provide the same amount of power as a larger electric motor. Pneumatic motors do not require an auxiliary speed controller which adds to their compactness, they generate less heat, and can be used in more volatile atmospheres because they do not require electric power, nor do they create sparks. They can be loaded to stop with full torque without damage.
Please click on highlighted text below to download our product brochures:
- Oil-Less Mini Air Compressors
- YC Series Hydraulic Gear Pumps (Motors)
- Medium and Medium-High Pressure Hydraulic Vane Pumps
- Caterpillar Series Hydraulic Pumps
- Komatsu Series Hydraulic Pumps
- Vickers Series Hydraulic Vane Pumps and Motors - Vickers Series Valves
- YC-Rexroth Series Variable Displacement Piston Pumps-Hydraulic Valves-Multiple Valves