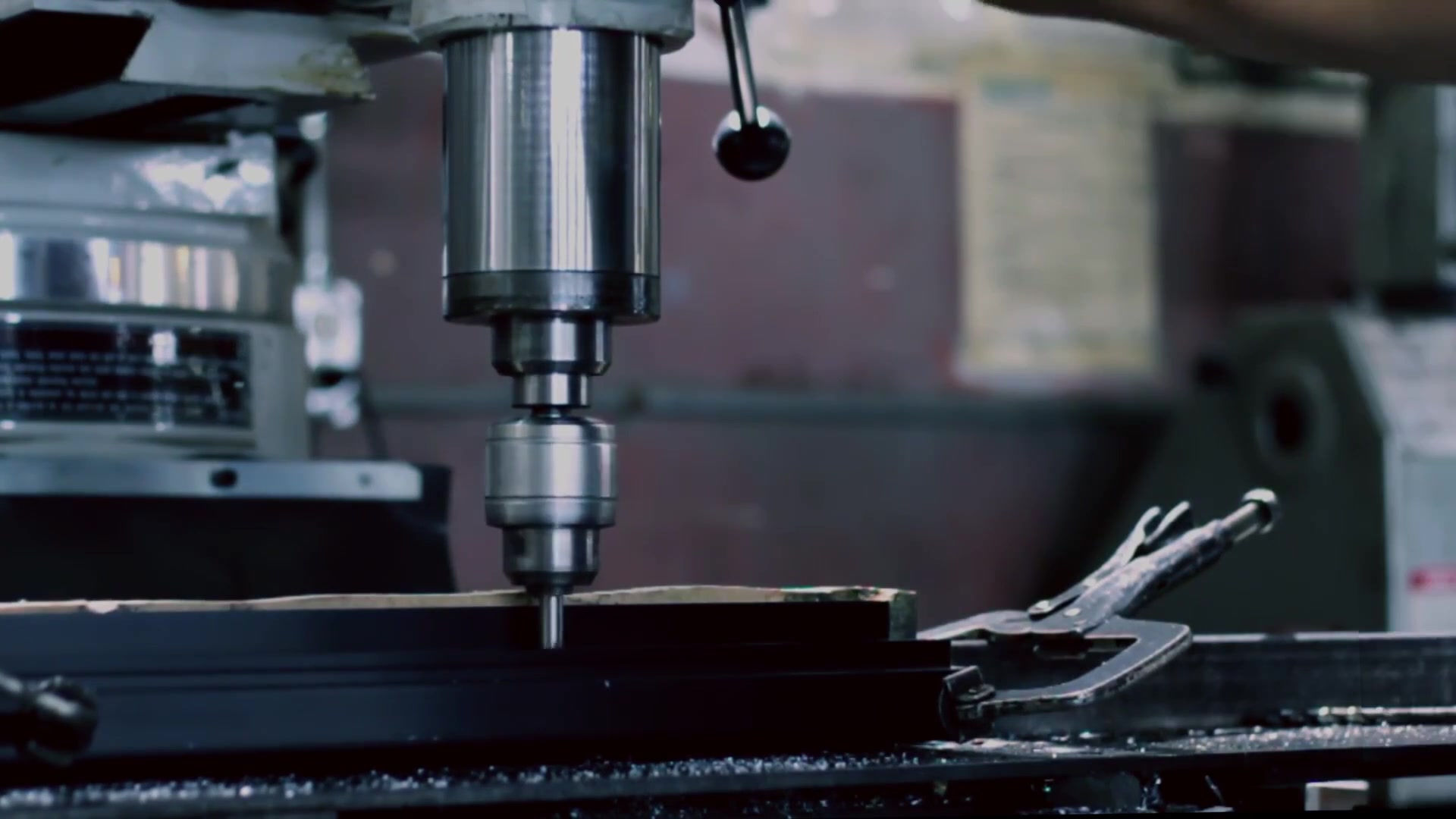
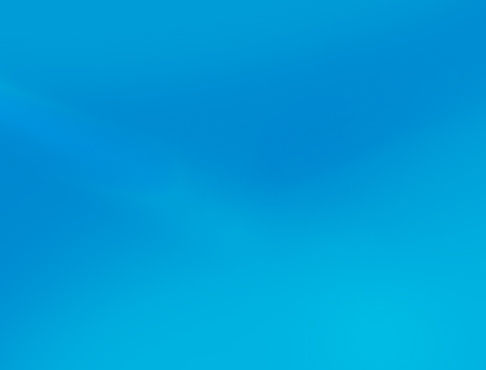
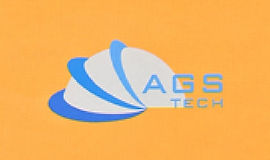
Globální zakázkový výrobce, integrátor, konsolidátor, partner pro outsourcing pro širokou škálu produktů a služeb.
Jsme vaším komplexním zdrojem pro výrobu, výrobu, inženýrství, konsolidaci, integraci, outsourcing zakázkově vyráběných i volně prodejných produktů a služeb.
Choose your Language
-
Zakázková výroba
-
Domácí a globální smluvní výroba
-
Outsourcing výroby
-
Domácí a globální zadávání zakázek
-
Konsolidace
-
Engineering Integration
-
Inženýrské služby
Mezi mnoha technikami SPOJOVÁNÍ, které používáme ve výrobě, je zvláštní důraz kladen na SVAŘOVÁNÍ, PÁJENÍ, PÁJENÍ, LEPENÍ a MECHANICKÁ MONTÁŽ NA MÍRU, protože tyto techniky jsou široce používány v aplikacích, jako je výroba hermetických sestav, výroba high-tech produktů a specializované těsnění. Zde se zaměříme na specializovanější aspekty těchto spojovacích technik, protože souvisí s výrobou pokročilých produktů a sestav.
FUSION WELDING: Používáme teplo k tavení a spojování materiálů. Teplo je dodáváno elektřinou nebo vysokoenergetickými paprsky. Typy tavného svařování, které nasazujeme, jsou PLYNOVÉ SVAŘOVÁNÍ, OBLOUKOVÉ SVAŘOVÁNÍ, VYSOKOENERGETICKÉ SVAŘOVÁNÍ.
SVAŘOVÁNÍ V PEVNÉM STAVU: Spojujeme díly bez tavení a tavení. Naše metody svařování v pevné fázi jsou SVAŘOVÁNÍ ZA STUDENA, ULTRAZVUK, ODPORU, TŘENÍ, EXPLOZNÍ SVAŘOVÁNÍ a DIFUZNÍ SVAŘOVÁNÍ.
PÁJENÍ A PÁJENÍ: Používají přídavné kovy a dávají nám výhodu práce při nižších teplotách než při svařování, čímž dochází k menšímu poškození struktury výrobků. Informace o našem pájecím zařízení vyrábějícím armatury z keramiky na kov, hermetické těsnění, vakuové průchodky, komponenty pro řízení vysokého a ultravysokého vakua a kapaliny naleznete zde:Brožura továrny na pájení
LEPENÍ LEPIDLA: Kvůli rozmanitosti lepidel používaných v průmyslu a také rozmanitosti aplikací máme pro toto vyhrazenou stránku. Chcete-li přejít na naši stránku o lepení, klikněte prosím zde.
MECHANICKÁ MONTÁŽ NA MÍRU: Používáme různé spojovací prvky, jako jsou šrouby, šrouby, matice, nýty. Naše spojovací prvky nejsou omezeny na standardní standardní spojovací prvky. Navrhujeme, vyvíjíme a vyrábíme speciální spojovací prvky, které jsou vyrobeny z nestandardních materiálů tak, aby splňovaly požadavky pro speciální aplikace. Někdy je požadována elektrická nebo tepelná nevodivost, zatímco někdy vodivost. Pro některé speciální aplikace může zákazník chtít speciální spojovací prvky, které nelze odstranit bez zničení produktu. Nápadů a aplikací je nekonečně mnoho. Máme to všechno pro vás, pokud to není hotové, můžeme to rychle vyvinout. Chcete-li přejít na naši stránku o mechanické montáži, klikněte prosím zde. Podívejme se na naše různé techniky spojování podrobněji.
SVAŘOVÁNÍ OXYFUEL GAS (OFW): K vytvoření svařovacího plamene používáme topný plyn smíchaný s kyslíkem. Když používáme acetylen jako palivo a kyslík, nazýváme to svařování kyslíkem a acetylenem. V procesu spalování kyslíku a paliva probíhají dvě chemické reakce:
C2H2 + O2 ------» 2CO + H2 + Teplo
2CO + H2 + 1,5 O2--------» 2 CO2 + H2O + teplo
První reakce rozkládá acetylen na oxid uhelnatý a vodík, přičemž produkuje asi 33 % celkového generovaného tepla. Druhý výše uvedený proces představuje další spalování vodíku a oxidu uhelnatého při produkci asi 67 % celkového tepla. Teploty v plameni se pohybují mezi 1533 až 3573 Kelviny. Procento kyslíku ve směsi plynů je důležité. Pokud je obsah kyslíku více než poloviční, stává se plamen oxidačním činidlem. To je pro některé kovy nežádoucí, ale pro jiné žádoucí. Příkladem, kdy je žádoucí oxidační plamen, jsou slitiny na bázi mědi, protože tvoří pasivační vrstvu na kovu. Na druhou stranu při snížení obsahu kyslíku není možné plné hoření a plamen se stává redukčním (karburačním) plamenem. Teploty v redukčním plameni jsou nižší, a proto je vhodný pro procesy jako pájení a pájení. Jiné plyny jsou také potenciální paliva, ale mají některé nevýhody oproti acetylenu. Příležitostně dodáváme přídavné kovy do svarové zóny ve formě přídavných tyčí nebo drátu. Některé z nich jsou potaženy tavidlem ke zpomalení oxidace povrchů a tím k ochraně roztaveného kovu. Další výhodou, kterou nám tavidlo poskytuje, je odstranění oxidů a dalších látek ze svarové zóny. To vede k silnějšímu spojení. Variantou svařování kyslíko-palivovým plynem je TLAKOVÉ PLYNOVÉ SVAŘOVÁNÍ, kde se dvě součásti na svém rozhraní zahřívají pomocí kyslíkoacetylenového plynového hořáku a jakmile se rozhraní začne tavit, hořák se stáhne a použije se axiální síla, aby se obě části stlačily k sobě. dokud rozhraní neztuhne.
OBLOUKOVÉ SVAŘOVÁNÍ: K vytvoření oblouku mezi špičkou elektrody a svařovanými díly používáme elektrickou energii. Napájecí zdroj může být střídavý nebo stejnosměrný, zatímco elektrody jsou buď spotřební nebo nespotřebovatelné. Přenos tepla při obloukovém svařování lze vyjádřit následující rovnicí:
H / l = ex VI / v
Zde H je tepelný příkon, l je délka svaru, V a I jsou použité napětí a proud, v je rychlost svařování a e je účinnost procesu. Čím vyšší je účinnost „e“, tím výhodnější je využití dostupné energie k roztavení materiálu. Tepelný příkon lze také vyjádřit jako:
H = ux (objem) = ux A xl
Zde u je měrná energie pro tavení, A průřez svaru a l délka svaru. Ze dvou výše uvedených rovnic můžeme získat:
v = ex VI / u A
Variantou obloukového svařování je SHIELDED METAL ARC WELDING (SMAW), které tvoří asi 50 % všech průmyslových a údržbových svařovacích procesů. SVAŘOVÁNÍ ELEKTRICKÝM OBLOUKEM (STICK WELDING) se provádí dotykem špičky potažené elektrody s obrobkem a jejím rychlým odtažením do vzdálenosti dostatečné k udržení oblouku. Tento proces nazýváme také svařováním tyčí, protože elektrody jsou tenké a dlouhé tyčinky. Během procesu svařování se hrot elektrody roztaví spolu s jejím povlakem a základním kovem v blízkosti oblouku. Směs základního kovu, elektrodového kovu a látek z elektrodového povlaku tuhne v oblasti svaru. Povlak elektrody dezoxiduje a poskytuje ochranný plyn v oblasti svaru, čímž ji chrání před kyslíkem z okolního prostředí. Proto se tento proces nazývá obloukové svařování v ochranné atmosféře. Pro optimální výkon svařování používáme proudy mezi 50 a 300 ampéry a úrovně výkonu obecně nižší než 10 kW. Důležitá je také polarita stejnosměrného proudu (směr toku proudu). Přímá polarita, kde je obrobek kladný a elektroda záporná, je preferována při svařování plechů pro její mělký průvar a také pro spoje s velmi širokými spárami. Když máme obrácenou polaritu, tj. elektroda je kladná a obrobek záporná, můžeme dosáhnout hlubších průvarů svaru. Se střídavým proudem, protože máme pulzující oblouky, můžeme svařovat tlusté profily pomocí elektrod s velkým průměrem a maximálními proudy. Metoda svařování SMAW je vhodná pro obrobky o tloušťce 3 až 19 mm a ještě více pomocí víceprůchodových technik. Struska vytvořená na povrchu svaru musí být odstraněna pomocí drátěného kartáče, aby nedocházelo ke korozi a porušení v oblasti svaru. To samozřejmě zvyšuje náklady na obloukové svařování kovů v ochranné atmosféře. Přesto je SMAW nejoblíbenější svařovací technikou v průmyslu a opravách.
SVAŘOVÁNÍ PONOŘENÝM OBLOUKEM (PILA): V tomto procesu stíníme svarový oblouk použitím materiálů zrnitého tavidla, jako je vápno, oxid křemičitý, fluorid vápenatý, oxid manganu….atd. Granulované tavidlo je přiváděno do svarové zóny gravitačním tokem přes trysku. Tavidlo pokrývající zónu roztaveného svaru výrazně chrání před jiskrami, výpary, UV zářením atd. a působí jako tepelný izolant, čímž umožňuje pronikání tepla hluboko do obrobku. Netavené tavidlo se získá, zpracuje a znovu použije. Jako elektroda se používá holá cívka, která se přivádí trubicí do oblasti svaru. Používáme proudy mezi 300 a 2000 ampéry. Proces svařování pod tavidlem (SAW) je omezen na horizontální a ploché polohy a kruhové svary, pokud je během svařování možná rotace kruhové konstrukce (jako jsou trubky). Rychlosti mohou dosáhnout 5 m/min. Proces SAW je vhodný pro tlusté plechy a výsledkem jsou vysoce kvalitní, houževnaté, tažné a stejnoměrné svary. Produktivita, tj. množství svarového materiálu naneseného za hodinu, je 4 až 10násobné množství ve srovnání s procesem SMAW.
Další proces obloukového svařování, jmenovitě GAS METAL ARC WELDING (GMAW) nebo alternativně označovaný jako METAL INERT GAS WELDING (MIG) je založen na odstínění oblasti svaru vnějšími zdroji plynů, jako je helium, argon, oxid uhličitý….atd. V kovu elektrody mohou být přítomny další deoxidanty. Tavný drát je přiváděn tryskou do svarové zóny. Výroba zahrnující železné i neželezné kovy se provádí pomocí plynového obloukového svařování kovů (GMAW). Produktivita svařování je asi dvakrát vyšší než u procesu SMAW. Používá se automatizované svařovací zařízení. Kov se v tomto procesu přenáší jedním ze tří způsobů: „Přenos sprejem“ zahrnuje přenos několika stovek malých kapiček kovu za sekundu z elektrody do oblasti svaru. Na druhé straně při „Globular Transfer“ se používají plyny bohaté na oxid uhličitý a kuličky roztaveného kovu jsou poháněny elektrickým obloukem. Svařovací proudy jsou vysoké a svar proniká hlouběji, rychlost svařování je vyšší než při přenosu sprejem. Kulový přenos je tedy lepší pro svařování těžších profilů. A konečně, u metody „Short Circuiting“ se hrot elektrody dotkne roztavené svarové lázně a zkratuje ji, protože kov je přenášen rychlostí přes 50 kapek/s v jednotlivých kapkách. Spolu s tenčím drátem se používají nízké proudy a napětí. Používané výkony jsou asi 2 kW a teploty jsou relativně nízké, díky čemuž je tato metoda vhodná pro tenké plechy o tloušťce menší než 6 mm.
Další varianta procesu FLUX-CORED ARC WELDING (FCAW) je podobný obloukovému svařování plynovým kovovým obloukem, kromě toho, že elektrodou je trubice naplněná tavidlem. Výhodou použití elektrod s jádrovým tokem je, že produkují stabilnější oblouky, dávají nám možnost zlepšit vlastnosti svarových kovů, méně křehký a pružný charakter jeho toku ve srovnání se svařováním SMAW, zlepšené obrysy svařování. Elektrody s vlastním stíněním obsahují materiály, které stíní zónu svaru proti atmosféře. Používáme výkon cca 20 kW. Stejně jako proces GMAW nabízí proces FCAW také možnost automatizovat procesy pro kontinuální svařování a je ekonomický. Různé chemické složení svarových kovů lze vyvinout přidáním různých slitin do jádra tavidla.
V ELEKTROGASOVÉM SVAŘOVÁNÍ (EGW) svařujeme kusy umístěné hranou na hranu. Někdy se mu také říká SVAŘOVÁNÍ NA TUPA. Svarový kov se vloží do svarové dutiny mezi dva spojované kusy. Prostor je uzavřen dvěma vodou chlazenými hrázemi, aby se roztavená struska nevylévala ven. Přehrady se pohybují nahoru mechanickými pohony. Když lze obrobek otáčet, můžeme použít techniku elektroplynového svařování i pro obvodové svařování trubek. Elektrody jsou vedeny potrubím pro udržení nepřetržitého oblouku. Proudy mohou být kolem 400 ampér nebo 750 ampér a úrovně výkonu kolem 20 kW. Inertní plyny pocházející buď z elektrody s tokem nebo externího zdroje poskytují stínění. Elektroplynové svařování (EGW) používáme pro kovy jako jsou oceli, titan….atd o tloušťkách od 12 mm do 75 mm. Tato technika je vhodná pro velké konstrukce.
V jiné technice zvané ELEKTROSLAGOVÉ SVAŘOVÁNÍ (ESW) se oblouk zapálí mezi elektrodou a dnem obrobku a přidá se tavidlo. Když roztavená struska dosáhne špičky elektrody, oblouk zhasne. Energie je nepřetržitě dodávána prostřednictvím elektrického odporu roztavené strusky. Dokážeme svařit plechy o tloušťkách od 50 mm do 900 mm i větší. Proudy se pohybují kolem 600 A, zatímco napětí se pohybují mezi 40 – 50 V. Rychlosti svařování se pohybují kolem 12 až 36 mm/min. Aplikace jsou podobné elektroplynovému svařování.
Jeden z našich nekonzumovatelných elektrodových procesů, GAS TUNGSTEN ARC WELDING (GTAW), také známý jako TUNGSTEN INERT GAS WELDING (TIG), zahrnuje dodávání přídavného kovu drátem. Pro těsné spoje někdy nepoužíváme přídavný kov. V procesu TIG nepoužíváme tavidlo, ale pro stínění používáme argon a helium. Wolfram má vysoký bod tání a při svařování TIG se nespotřebovává, proto lze udržovat konstantní proud i mezery mezi oblouky. Úrovně výkonu jsou mezi 8 až 20 kW a proudy buď 200 Ampér (DC) nebo 500 Ampér (AC). Pro hliník a hořčík používáme střídavý proud pro jeho funkci čištění oxidů. Aby nedošlo ke kontaminaci wolframové elektrody, vyhýbáme se jejímu kontaktu s roztavenými kovy. Gas Tungsten Arc Welding (GTAW) je zvláště užitečné pro svařování tenkých kovů. Svary GTAW jsou velmi kvalitní s dobrou povrchovou úpravou.
Vzhledem k vyšší ceně plynného vodíku je méně často používanou technikou ATOMIC HYDROGEN WELDING (AHW), kdy generujeme oblouk mezi dvěma wolframovými elektrodami v ochranné atmosféře proudícího plynného vodíku. AHW je také proces svařování elektrodou bez spotřebního materiálu. Dvouatomový vodíkový plyn H2 se rozkládá na atomární formu v blízkosti svařovacího oblouku, kde jsou teploty vyšší než 6273 Kelvinů. Při lámání absorbuje velké množství tepla z oblouku. Když atomy vodíku narazí na svarovou zónu, která je relativně chladným povrchem, rekombinují se do dvouatomové formy a uvolňují uložené teplo. Energii lze měnit změnou vzdálenosti obrobku na oblouk.
V dalším procesu s nespotřebitelnými elektrodami, PLASMA ARC WELDING (PAW), máme koncentrovaný plazmový oblouk nasměrovaný do svarové zóny. Teploty dosahují 33 273 Kelvinů v PAW. Téměř stejný počet elektronů a iontů tvoří plazmový plyn. Nízkoproudý pilotní oblouk iniciuje plazmu, která je mezi wolframovou elektrodou a otvorem. Provozní proudy jsou obecně kolem 100 ampérů. Může být přiváděn přídavný kov. Při svařování plazmovým obloukem je stínění dosaženo vnějším stínícím kroužkem a pomocí plynů, jako je argon a helium. Při svařování plazmovým obloukem může být oblouk mezi elektrodou a obrobkem nebo mezi elektrodou a tryskou. Tato svařovací technika má oproti jiným metodám výhody vyšší koncentrace energie, hlubší a užší svařovací schopnost, lepší stabilita oblouku, vyšší rychlosti svařování až 1 metr/min, menší tepelné zkreslení. Plazmové obloukové svařování obecně používáme pro tloušťky menší než 6 mm a někdy až 20 mm pro hliník a titan.
VYSOKOENERGETICKÉ SVAŘOVÁNÍ: Další typ metody tavného svařování se svařováním elektronovým paprskem (EBW) a laserovým svařováním (LBW) ve dvou variantách. Tyto techniky mají zvláštní hodnotu pro naši práci při výrobě high-tech produktů. Při svařování elektronovým paprskem dopadají vysokorychlostní elektrony na obrobek a jejich kinetická energie se přeměňuje na teplo. Úzký paprsek elektronů se snadno pohybuje ve vakuové komoře. Obecně používáme při svařování elektronovým paprskem vysoké vakuum. Lze svařovat plechy o tloušťce až 150 mm. Nejsou potřeba žádné ochranné plyny, tavidla ani výplňový materiál. Elektronové paprskové zbraně mají kapacitu 100 kW. Jsou možné hluboké a úzké svary s vysokým poměrem stran až 30 a malými tepelně ovlivněnými zónami. Rychlost svařování může dosáhnout 12 m/min. Při svařování laserovým paprskem používáme jako zdroj tepla vysokovýkonné lasery. Laserové paprsky o velikosti pouhých 10 mikronů s vysokou hustotou umožňují hluboký průnik do obrobku. Při svařování laserovým paprskem je možný poměr hloubky k šířce až 10. Používáme jak pulzní, tak i kontinuální lasery, přičemž první v aplikacích pro tenké materiály a druhý většinou pro tlusté obrobky do cca 25 mm. Výkony jsou až 100 kW. Svařování laserovým paprskem není vhodné pro opticky velmi reflexní materiály. Plyny mohou být také použity v procesu svařování. Metoda svařování laserovým paprskem je vhodná pro automatizaci a velkoobjemovou výrobu a může nabídnout rychlosti svařování mezi 2,5 m/min a 80 m/min. Jednou z hlavních výhod této svařovací techniky je přístup do oblastí, kde nelze použít jiné techniky. Laserové paprsky mohou snadno cestovat do takto obtížných oblastí. Není potřeba žádné vakuum jako při svařování elektronovým paprskem. Svařováním laserovým paprskem lze dosáhnout svarů s dobrou kvalitou a pevností, nízkým smršťováním, nízkým zkreslením a nízkou porézností. Laserové paprsky lze snadno manipulovat a tvarovat pomocí optických kabelů. Technika je tak vhodná pro svařování přesných hermetických sestav, elektronických obalů atd.
Podívejme se na naše techniky PEVNÉ SVAŘOVÁNÍ. SVAŘOVÁNÍ ZA STUDENA (CW) je proces, při kterém je na spojované díly aplikován tlak místo tepla pomocí matric nebo válců. Při svařování za studena musí být alespoň jedna z protilehlých částí tažná. Nejlepších výsledků se dosáhne se dvěma podobnými materiály. Pokud jsou dva kovy, které mají být spojeny studeným svařováním, odlišné, můžeme získat slabé a křehké spoje. Metoda svařování za studena je vhodná pro měkké, tvárné a malé obrobky, jako jsou elektrické spoje, okraje nádob citlivých na teplo, bimetalové pásy pro termostaty atd. Jednou z variant studeného svařování je spojování válců (nebo svařování válců), kde je tlak aplikován přes pár válců. Někdy provádíme svařování válců při zvýšených teplotách pro lepší pevnost na rozhraní.
Dalším procesem svařování v pevné fázi, který používáme, je ULTRASONIC WELDING (USW), kde jsou obrobky vystaveny statické normálové síle a oscilačnímu namáhání ve smyku. Oscilační smyková napětí jsou aplikována přes hrot převodníku. Ultrazvukové svařování využívá oscilace s frekvencí od 10 do 75 kHz. V některých aplikacích, jako je švové svařování, používáme jako hrot rotující svařovací kotouč. Smyková napětí působící na obrobky způsobují malé plastické deformace, rozrušují oxidové vrstvy, nečistoty a vedou k pevnému spojení. Teploty používané při ultrazvukovém svařování jsou hluboko pod teplotami bodu tání kovů a nedochází k žádné fúzi. U nekovových materiálů, jako jsou plasty, často používáme proces ultrazvukového svařování (USW). V termoplastech však teploty dosahují bodů tání.
Další oblíbenou technikou je při FRICTION WELDING (FRW) teplo generované třením na rozhraní spojovaných obrobků. Při třecím svařování udržujeme jeden z obrobků nehybný, zatímco druhý obrobek je držen v přípravku a otáčí se konstantní rychlostí. Obrobky se pak přivedou do kontaktu pod axiální silou. Povrchová rychlost rotace při třecím svařování může v některých případech dosáhnout 900 m/min. Po dostatečném mezifázovém kontaktu se rotující obrobek náhle zastaví a axiální síla se zvýší. Svarová zóna je obecně úzká oblast. Technika třecího svařování může být použita pro spojování pevných a trubkových dílů vyrobených z různých materiálů. Některé záblesky se mohou vyvinout na rozhraní ve FRW, ale tyto záblesky lze odstranit sekundárním obráběním nebo broušením. Existují různé varianty procesu třecího svařování. Například „setrvačné třecí svařování“ zahrnuje setrvačník, jehož rotační kinetická energie se využívá ke svařování dílů. Svar je dokončen, když se setrvačník zastaví. Rotující hmota se může měnit a tím i rotační kinetická energie. Další variantou je „lineární třecí svařování“, kde je na alespoň jednu ze spojovaných součástí vyvíjen lineární vratný pohyb. Při lineárním svařování třením části nemusí být kruhové, mohou být obdélníkové, čtvercové nebo jiného tvaru. Frekvence se mohou pohybovat v desítkách Hz, amplitudy v rozsahu milimetrů a tlaky v desítkách nebo stovkách MPa. Konečně „třecí svařování s mícháním“ je poněkud odlišné od ostatních dvou vysvětlených výše. Zatímco při setrvačném třecím svařování a lineárním třecím svařování se ohřev rozhraní dosahuje třením třením dvou kontaktních ploch, při metodě třecího třecího svařování se třetí těleso otírá o dva spojované plochy. Ke spoji se přivede rotující nástroj o průměru 5 až 6 mm. Teploty se mohou zvýšit na hodnoty mezi 503 až 533 Kelviny. Dochází k zahřívání, míchání a míchání hmoty ve spoji. Svařování třením promícháváme na různé materiály včetně hliníku, plastů a kompozitů. Svary jsou jednotné a kvalita je vysoká s minimem pórů. Při frikčním svařování nevznikají žádné výpary ani rozstřiky a proces je dobře automatizován.
ODPOROVÉ SVAŘOVÁNÍ (RW): Teplo potřebné pro svařování vzniká elektrickým odporem mezi dvěma spojovanými díly. Při odporovém svařování se nepoužívá žádné tavidlo, ochranné plyny ani spotřební elektrody. Joulový ohřev probíhá při odporovém svařování a lze jej vyjádřit jako:
H = (čtverec I) x R xtx K
H je teplo generované v joulech (wattsekundách), proud I v ampérech, odpor R v ohmech, t je doba v sekundách, kterou proud protéká. Faktor K je menší než 1 a představuje část energie, která se neztrácí zářením a vedením. Proudy v procesech odporového svařování mohou dosáhnout úrovně až 100 000 A, ale napětí jsou obvykle 0,5 až 10 voltů. Elektrody jsou obvykle vyrobeny ze slitin mědi. Odporovým svařováním lze spojovat podobné i rozdílné materiály. Pro tento proces existuje několik variant: „Odporové bodové svařování“ zahrnuje dvě protilehlé kulaté elektrody, které se dotýkají povrchů přeplátovaného spoje dvou plechů. Tlak je aplikován, dokud se proud nevypne. Svarový nuget má obecně průměr do 10 mm. Odporové bodové svařování zanechává v místech svaru lehce zabarvené vtisky. Bodové svařování je naše nejoblíbenější technika odporového svařování. Při bodovém svařování se používají různé tvary elektrod, aby se dosáhlo obtížných oblastí. Naše zařízení pro bodové svařování je řízeno CNC a má více elektrod, které lze používat současně. Další varianta „odporového švového svařování“ se provádí pomocí kolových nebo válečkových elektrod, které vytvářejí kontinuální bodové svary, kdykoli proud dosáhne dostatečně vysoké úrovně v cyklu střídavého proudu. Spoje vyrobené odporovým švovým svařováním jsou kapalinotěsné a plynotěsné. Rychlost svařování kolem 1,5 m/min je u tenkých plechů normální. Je možné aplikovat přerušované proudy, takže bodové svary jsou vytvářeny v požadovaných intervalech podél švu. Při „odporovém projekčním svařování“ vyrazíme jeden nebo více výstupků (důlků) na jeden z povrchů obrobku, který se má svařit. Tyto výstupky mohou být kulaté nebo oválné. Na těchto vyražených místech, která přicházejí do kontaktu s protilehlou částí, je dosahováno vysokých lokalizovaných teplot. Elektrody vyvíjejí tlak, aby tyto výstupky stlačily. Elektrody pro odporové projekční svařování mají ploché hroty a jsou vodou chlazené slitiny mědi. Výhodou odporového projekčního svařování je naše schopnost provést řadu svarů jedním zdvihem, tím prodloužená životnost elektrod, schopnost svařovat plechy různých tlouštěk, schopnost navařovat matice a šrouby na plechy. Nevýhodou odporového projekčního svařování jsou dodatečné náklady na ražení důlků. Ještě další technika, při „bleskovém svařování“, se teplo generuje z oblouku na koncích dvou obrobků, když se začnou dotýkat. Tato metoda může také alternativně uvažovat o obloukovém svařování. Teplota na rozhraní stoupá a materiál měkne. Aplikuje se axiální síla a ve změkčené oblasti se vytvoří svar. Po dokončení bleskového svařování může být spoj opracován pro lepší vzhled. Kvalita svaru dosažená bleskovým svařováním je dobrá. Výkonové úrovně jsou 10 až 1500 kW. Bleskové svařování je vhodné pro spojování podobných nebo odlišných kovů do průměru 75 mm a plechů o tloušťce od 0,2 mm do 25 mm. „Svařování pod obloukem“ je velmi podobné bleskovému svařování. Čep, jako je šroub nebo závitová tyč, slouží jako jedna elektroda, zatímco je připojen k obrobku, jako je deska. Pro koncentraci generovaného tepla, zabránění oxidaci a udržení roztaveného kovu v zóně svaru je kolem spoje umístěn keramický kroužek na jedno použití. Konečně „příklepové svařování“ další proces odporového svařování, který využívá kondenzátor k dodávání elektrické energie. Při příklepovém svařování se energie vybíjí během milisekund velmi rychle a ve spoji se vyvíjí vysoké lokalizované teplo. Příklepové svařování široce používáme v průmyslu výroby elektroniky, kde je třeba se vyhnout zahřívání citlivých elektronických součástek v blízkosti spoje.
Technika zvaná EXPLOSION WELDING zahrnuje detonaci vrstvy výbušniny, která se nanese na jeden ze spojovaných obrobků. Velmi vysoký tlak vyvíjený na obrobek vytváří turbulentní a zvlněné rozhraní a dochází k mechanickému spojení. Pevnost spoje při výbušném svařování je velmi vysoká. Výbušné svařování je dobrou metodou pro opláštění plechů různými kovy. Po opláštění mohou být desky válcovány na tenčí části. Někdy používáme výbuchové svařování pro roztažení trubek tak, aby byly těsně utěsněny k desce.
Naší poslední metodou v oblasti spojování v pevné fázi je DIFFUSION BONDING nebo DIFFUSION WELDING (DFW), při které je dobrého spoje dosaženo především difúzí atomů přes rozhraní. Ke svařování přispívá i určitá plastická deformace na rozhraní. Teploty se pohybují kolem 0,5 Tm, kde Tm je teplota tání kovu. Pevnost spoje při difuzním svařování závisí na tlaku, teplotě, době kontaktu a čistotě stykových ploch. Někdy na rozhraní používáme přídavné kovy. Teplo a tlak jsou vyžadovány při difúzním spojování a jsou dodávány elektrickým odporem nebo pecí a závažím, lisem nebo jiným způsobem. Podobné a rozdílné kovy lze spojovat difúzním svařováním. Proces je relativně pomalý kvůli době, kterou atomy potřebují k migraci. DFW lze automatizovat a je široce používán při výrobě složitých dílů pro letecký, elektronický a lékařský průmysl. Vyráběné produkty zahrnují ortopedické implantáty, senzory, letecké konstrukční prvky. Difuzní lepení lze kombinovat se SUPERPLASTICKÝM TVÁŘENÍM pro výrobu složitých plechových konstrukcí. Vybraná místa na listech jsou nejprve difúzně spojena a poté jsou nespojené oblasti expandovány do formy pomocí tlaku vzduchu. Pomocí této kombinace metod jsou vyráběny letecké konstrukce s vysokým poměrem tuhosti k hmotnosti. Kombinovaný proces difúzního svařování/superplastického tvarování snižuje počet požadovaných dílů tím, že eliminuje potřebu spojovacích prvků, výsledkem jsou vysoce přesné díly s nízkým namáháním, ekonomicky as krátkými dodacími lhůtami.
PÁJENÍ: Techniky pájení a pájení zahrnují nižší teploty, než jsou teploty potřebné pro svařování. Teploty pájení jsou však vyšší než teploty pájení. Při pájení se mezi spojované povrchy umístí přídavný kov a teploty se zvýší na teplotu tavení přídavného materiálu nad 723 Kelvinů, ale pod teploty tavení obrobků. Roztavený kov vyplňuje těsně přiléhající prostor mezi obrobky. Ochlazením a následným ztuhnutím kovu pilníku vznikají pevné spoje. Při pájení natvrdo se přídavný kov ukládá ve spoji. Při pájení natvrdo se ve srovnání s pájením používá podstatně více přídavného kovu. Kyslíkoacetylenový hořák s oxidačním plamenem se používá k nanášení přídavného kovu při pájení natvrdo. Díky nižším teplotám při pájení jsou problémy v tepelně ovlivněných oblastech, jako je deformace a zbytková napětí, menší. Čím menší je vůle při pájení, tím vyšší je pevnost spoje ve smyku. Maximální pevnosti v tahu je však dosaženo při optimální mezeře (špičková hodnota). Pod a nad touto optimální hodnotou se pevnost v tahu při pájení snižuje. Typické vůle při pájení mohou být mezi 0,025 a 0,2 mm. Používáme různé pájecí materiály různých tvarů, jako jsou výlisky, prášek, kroužky, dráty, pásy…..atd. a dokáže vyrobit tyto prvky speciálně pro váš návrh nebo geometrii produktu. Také určujeme obsah pájecích materiálů podle vašich základních materiálů a použití. Často používáme tavidla při pájecích operacích, abychom odstranili nežádoucí vrstvy oxidu a zabránili oxidaci. Aby se předešlo následné korozi, tavidla se obvykle po operaci spojování odstraní. AGS-TECH Inc. používá různé metody pájení, včetně:
- Pájení hořákem
- Pájení v peci
- Indukční pájení
- Odporové pájení
- Pájení ponorem
- Infračervené pájení
- Difúzní pájení
- Vysokoenergetický paprsek
Naše nejběžnější příklady pájených spojů jsou vyrobeny z různých kovů s dobrou pevností, jako jsou tvrdokovové vrtáky, vložky, optoelektronické hermetické obaly, těsnění.
PÁJENÍ: Toto je jedna z našich nejčastěji používaných technik, kdy pájka (výplňový kov) vyplňuje spoj jako při pájení mezi těsně lícujícími součástmi. Naše pájky mají bod tání nižší než 723 Kelvinů. Ve výrobních provozech nasazujeme ruční i automatické pájení. Ve srovnání s pájením jsou teploty pájení nižší. Pájení není příliš vhodné pro vysokoteplotní nebo vysokopevnostní aplikace. K pájení používáme mj. bezolovnaté pájky, slitiny cín-olovo, cín-zinek, olovo-stříbro, kadmium-stříbro, zinek-hliník. Jako tavidlo při pájení se používají jak nekorozivní pryskyřice, tak anorganické kyseliny a soli. K pájení kovů s nízkou pájitelností používáme speciální tavidla. V aplikacích, kde musíme pájet keramické materiály, sklo nebo grafit, díly nejprve pokovujeme vhodným kovem pro zvýšenou pájitelnost. Naše oblíbené techniky pájení jsou:
- Přetavení nebo pájení pastou
- Pájení vlnou
-Pájení v peci
-Pájení hořákem
- Indukční pájení
-Pájení železa
- Odporové pájení
- Pájení ponorem
- Ultrazvukové pájení
- Infračervené pájení
Ultrazvukové pájení nám nabízí jedinečnou výhodu, kdy je eliminována potřeba tavidel díky ultrazvukovému kavitačnímu efektu, který odstraňuje oxidové filmy ze spojovaných povrchů. Přetavení a pájení vlnou jsou naše průmyslově vynikající techniky pro velkoobjemovou výrobu v elektronice, a proto stojí za to je podrobněji vysvětlit. Při pájení přetavením používáme polotuhé pasty, které obsahují částice pájky. Pasta se nanáší na spoj pomocí prosévání nebo šablonování. V deskách plošných spojů (PCB) tuto techniku často používáme. Když jsou elektrické součástky umístěny na tyto podložky z pasty, povrchové napětí udržuje obaly pro povrchovou montáž zarovnané. Po umístění součástek ohřejeme sestavu v peci, aby došlo k přetavení. Během tohoto procesu se odpaří rozpouštědla v pastě, aktivuje se tavidlo v pastě, součástky se předehřejí, částice pájky se roztaví a smáčejí spoj a nakonec se sestava DPS pomalu ochladí. Naše druhá oblíbená technika pro velkoobjemovou výrobu desek plošných spojů, jmenovitě pájení vlnou, spočívá v tom, že roztavené pájky smáčejí kovové povrchy a vytvářejí dobré spoje pouze tehdy, když je kov předehřátý. Stojatá laminární vlna roztavené pájky je nejprve generována čerpadlem a předehřáté a předem natavené PCB jsou dopravovány přes tuto vlnu. Pájka smáčí pouze exponované kovové povrchy, ale nesmáčí obaly IC polymeru ani desky plošných spojů potažené polymerem. Vysokorychlostní proud horké vody vyfoukne přebytečnou pájku ze spoje a zabrání přemostění mezi sousedními vodiči. Při vlnovém pájení obalů pro povrchovou montáž je před pájením nejprve přilepíme k desce plošných spojů. Opět se používá stínění a šablonování, ale tentokrát pro epoxid. Po umístění součástek na správné místo se epoxid vytvrdí, desky se obrátí a dojde k pájení vlnou.