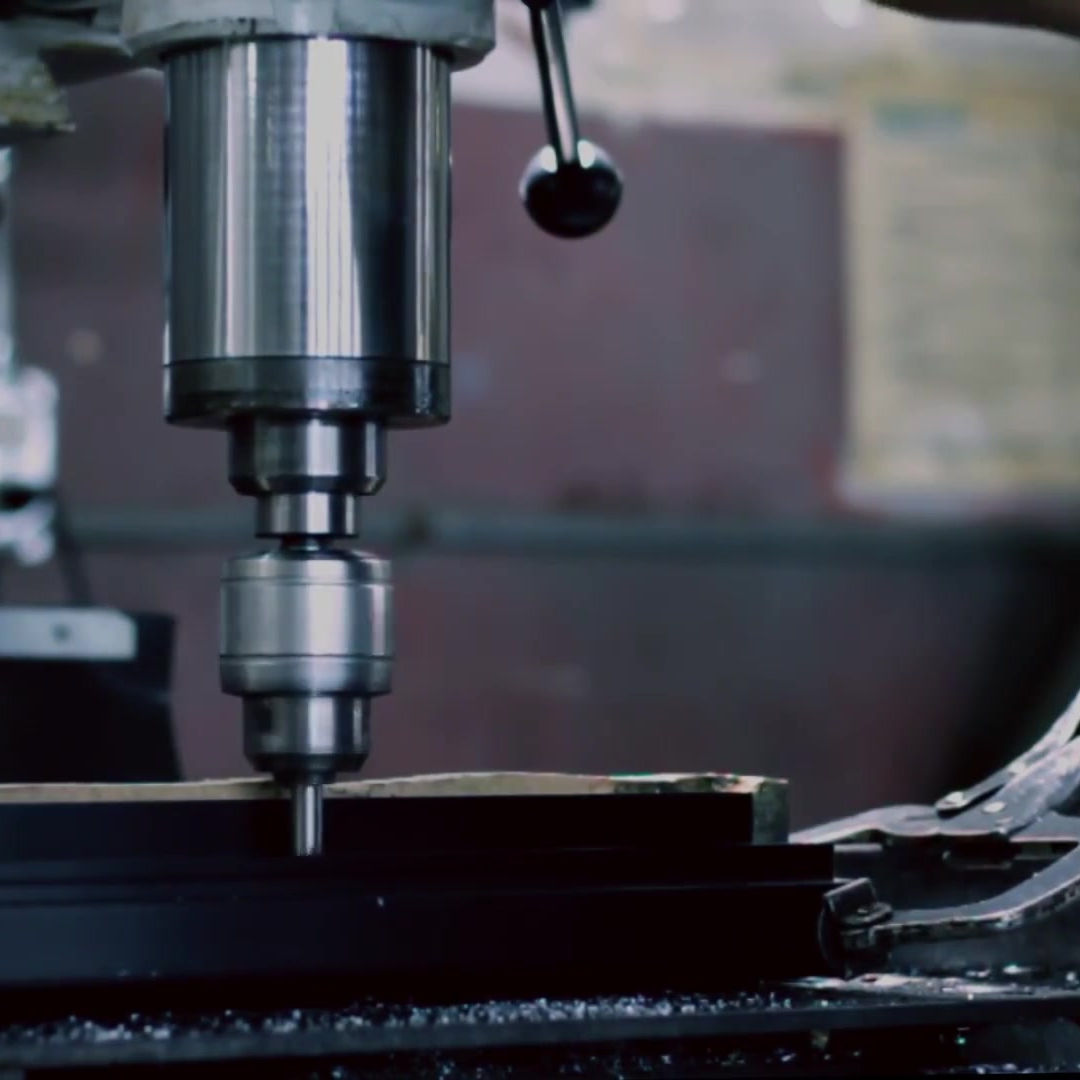
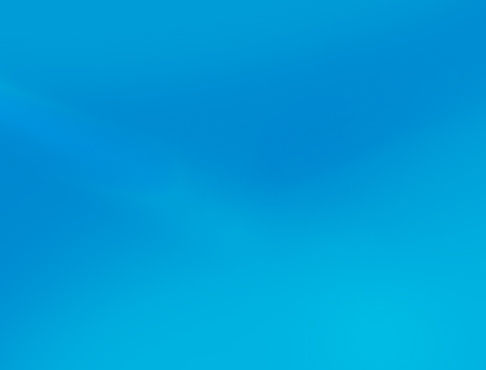
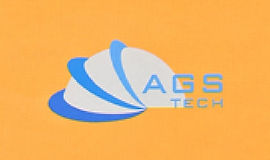
Globální zakázkový výrobce, integrátor, konsolidátor, partner pro outsourcing pro širokou škálu produktů a služeb.
Jsme vaším komplexním zdrojem pro výrobu, výrobu, inženýrství, konsolidaci, integraci, outsourcing zakázkově vyráběných i volně prodejných produktů a služeb.
Choose your Language
-
Zakázková výroba
-
Domácí a globální smluvní výroba
-
Outsourcing výroby
-
Domácí a globální zadávání zakázek
-
Konsolidace
-
Engineering Integration
-
Inženýrské služby
ELECTRICAL DISCHARGE MACHINING (EDM), also referred to as SPARK-EROSION or ELECTRODISCHARGE MACHINING, SPARK ERODING, DIE SINKING_cc781905-5cde-3194-bb3b -136bad5cf58d_or WIRE EROSION, is a NON-CONVENTIONAL MANUFACTURING process where erosion of metals takes place and desired shape is obtained using electrical discharges in the form jisker. Nabízíme také některé druhy EDM, jmenovitě NO-WEAR EDM, DRÁTOVÉ EDM (WEDM), EDM GRINDING (EDG), DIE-DIE-SNKING EDM, ELEKTRICKÉ VYBITÍ FRÉZOVÁNÍ, micro-EDM_790 m, micro-EDM_790 -5cde-3194-bb3b-136bad5cf58d_and ELEKTROCHEMICKÉ-VYPOJOVACÍ BROUŠENÍ (ECDG). Naše EDM systémy se skládají z tvarovaných nástrojů/elektrod a obrobku připojeného ke stejnosměrnému napájení a vloženého do elektricky nevodivé dielektrické kapaliny. Po roce 1940 se elektroerozivní obrábění stalo jednou z nejdůležitějších a nejoblíbenějších výrobních technologií ve zpracovatelském průmyslu.
Když se vzdálenost mezi dvěma elektrodami zmenší, intenzita elektrického pole v objemu mezi elektrodami se v některých bodech stane větší než síla dielektrika, které se zlomí a případně vytvoří můstek pro proudění mezi dvěma elektrodami. Vzniká intenzivní elektrický oblouk, který způsobí značné zahřátí k roztavení části obrobku a části nástrojového materiálu. Výsledkem je odstranění materiálu z obou elektrod. Současně se dielektrická kapalina rychle zahřívá, což má za následek odpařování kapaliny v obloukové mezeře. Jakmile se tok proudu zastaví nebo je zastaven, teplo je z plynové bubliny odstraněno okolní dielektrickou kapalinou a bublina kavituje (zkolabuje). Rázová vlna vytvořená zhroucením bubliny a proudem dielektrické tekutiny spláchne úlomky z povrchu obrobku a strhne jakýkoli roztavený materiál obrobku do dielektrické tekutiny. Opakovací frekvence těchto výbojů se pohybuje mezi 50 až 500 kHz, napětí mezi 50 a 380 V a proudy mezi 0,1 a 500 ampéry. Nové kapalné dielektrikum, jako jsou minerální oleje, petrolej nebo destilovaná a deionizovaná voda, je obvykle dopravováno do mezielektrodového objemu, který odnáší pevné částice (ve formě úlomků) a izolační vlastnosti dielektrika jsou obnoveny. Po průtoku proudu se potenciálový rozdíl mezi dvěma elektrodami obnoví na to, co byl před průrazem, takže může dojít k novému průrazu kapalného dielektrika. Naše moderní elektroerozivní stroje (EDM) nabízejí numericky řízené pohyby a jsou vybaveny čerpadly a filtračními systémy pro dielektrické kapaliny.
Elektroerozivní obrábění (EDM) je metoda obrábění používaná hlavně pro tvrdé kovy nebo ty, které by bylo velmi obtížné obrábět konvenčními technikami. Elektroerozivní obrábění typicky pracuje s libovolnými materiály, které jsou elektrickými vodiči, i když byly také navrženy způsoby obrábění izolační keramiky pomocí EDM. Teplota tání a latentní teplo tání jsou vlastnosti, které určují objem kovu odstraněného na jeden výboj. Čím vyšší jsou tyto hodnoty, tím pomalejší je rychlost úběru materiálu. Protože proces obrábění elektrickým výbojem nezahrnuje žádnou mechanickou energii, tvrdost, pevnost a houževnatost obrobku neovlivňuje rychlost úběru. Frekvence výboje nebo energie na výboj, napětí a proud se mění, aby se řídily rychlosti úběru materiálu. Rychlost úběru materiálu a drsnost povrchu se zvyšují s rostoucí hustotou proudu a klesající frekvencí jisker. Můžeme řezat složité obrysy nebo dutiny v předtvrzené oceli pomocí EDM bez nutnosti tepelného zpracování k jejich změknutí a opětovnému vytvrzení. Tuto metodu můžeme použít s jakýmkoliv kovem nebo kovovými slitinami, jako je titan, hastelloy, kovar a inconel. Aplikace procesu EDM zahrnují tvarování nástrojů z polykrystalického diamantu. EDM je považováno za netradiční nebo nekonvenční metodu obrábění spolu s procesy jako je elektrochemické obrábění (ECM), řezání vodním paprskem (WJ, AWJ), řezání laserem. Na druhé straně konvenční způsoby obrábění zahrnují soustružení, frézování, broušení, vrtání a další procesy, jejichž mechanismus úběru materiálu je v podstatě založen na mechanických silách. Elektrody pro elektroerozivní obrábění (EDM) jsou vyrobeny z grafitu, mosazi, mědi a slitiny mědi a wolframu. Jsou možné průměry elektrod až do 0,1 mm. Protože opotřebení nástroje je nežádoucím jevem, který nepříznivě ovlivňuje rozměrovou přesnost v EDM, využíváme proces nazvaný NO-WEAR EDM, a to obrácením polarity a použitím měděných nástrojů k minimalizaci opotřebení nástroje.
V ideálním případě lze elektroerozivní obrábění (EDM) považovat za sérii rozpadů a obnovení dielektrické kapaliny mezi elektrodami. Ve skutečnosti je však odstranění úlomků z mezielektrodové oblasti téměř vždy částečné. To způsobuje, že elektrické vlastnosti dielektrika v oblasti mezi elektrodami se liší od jejich jmenovitých hodnot a mění se s časem. Mezielektrodová vzdálenost (jiskřiště) je nastavena řídicími algoritmy konkrétního použitého stroje. Jiskřiště v EDM může být bohužel někdy zkratováno úlomky. Řídicí systém elektrody nemusí reagovat dostatečně rychle, aby zabránil zkratu dvou elektrod (nástroje a obrobku). Tento nechtěný zkrat přispívá k odstranění materiálu jinak než v ideálním případě. Největší důraz klademe na proplachovací činnost, abychom obnovili izolační vlastnosti dielektrika tak, aby proud probíhal vždy v místě mezielektrodové oblasti, čímž se minimalizuje možnost nežádoucí změny tvaru (poškození) nástrojové elektrody. a obrobek. Pro získání specifické geometrie je nástroj EDM veden po požadované dráze velmi blízko obrobku, aniž by se ho dotýkal. Maximální pozornost věnujeme výkonu řízení pohybu při použití. Tímto způsobem dochází k velkému počtu proudových výbojů / jisker a každý přispívá k odstranění materiálu z nástroje i obrobku, kde se tvoří malé krátery. Velikost kráterů je funkcí technologických parametrů nastavených pro konkrétní zakázku a rozměry se mohou pohybovat od nanoměřítek (jako v případě mikro-EDM operací) až po několik stovek mikrometrů v podmínkách hrubování. Tyto malé krátery na nástroji způsobují postupnou erozi elektrody nazývanou „opotřebení nástroje“. Abychom zabránili škodlivému vlivu opotřebení na geometrii obrobku, průběžně vyměňujeme nástrojovou elektrodu během obrábění. Někdy toho dosáhneme použitím průběžně nahrazovaného drátu jako elektrody (tento EDM proces se také nazývá WIRE EDM ). Někdy používáme nástrojovou elektrodu tak, že jen její malá část je skutečně zapojena do procesu obrábění a tato část je pravidelně obměňována. To je například případ použití rotačního disku jako nástrojové elektrody. Tento proces se nazývá EDM GRINDING. Ještě další technika, kterou používáme, spočívá v použití sady elektrod s různými velikostmi a tvary během stejné operace EDM pro kompenzaci opotřebení. Nazýváme tuto techniku s více elektrodami a nejčastěji se používá, když nástrojová elektroda kopíruje negativně požadovaný tvar a postupuje směrem k polotovaru v jediném směru, obvykle ve vertikálním směru (tj. osy z). To se podobá ponoření nástroje do dielektrické kapaliny, ve které je obrobek ponořen, a proto je označován jako DIE-SINKING EDM_cc781905-5cde-3194-bb5csd8136 3194-bb3b-136bad5cf58d_CONVENTIONAL EDM or RAM EDM). Stroje pro tuto operaci se nazývají SINKER EDM. Elektrody pro tento typ EDM mají složité tvary. Pokud je konečná geometrie získána pomocí elektrody obvykle jednoduchého tvaru, která se pohybuje v několika směrech a zároveň podléhá rotaci, nazýváme ji EDM MILLING. Velikost opotřebení je striktně závislá na technologických parametrech použitých v provozu (polarita, maximální proud, napětí naprázdno). Například in micro-EDM, také známý jako m-EDM, jsou tyto parametry obvykle nastaveny na hodnoty, které generují silné opotřebení. Proto je opotřebení hlavním problémem v této oblasti, kterou minimalizujeme pomocí našeho nashromážděného know-how. Například, aby se minimalizovalo opotřebení grafitových elektrod, digitální generátor, ovladatelný během milisekund, obrací polaritu, když dochází k elektroerozi. To má za následek efekt podobný galvanickému pokovování, kdy se erodovaný grafit kontinuálně ukládá zpět na elektrodu. V jiné metodě, tzv. ''Zero Wear'' okruhu minimalizujeme, jak často začíná a zastavuje výboj, a udržujeme jej tak dlouho, jak je to možné. Rychlost úběru materiálu při obrábění elektrickým výbojem lze odhadnout z:
MRR = 4 x 10 exp(4) x I x Tw exp (-1,23)
Zde je MRR v mm3/min, I je proud v ampérech, Tw je bod tání obrobku v K-273,15K. Exp znamená exponent.
Na druhou stranu, rychlost opotřebení Wt elektrody lze získat z:
Hmot. = ( 1,1 x 10exp(11) ) x I x Ttexp(-2,38)
Zde je Wt v mm3/min a Tt je bod tání materiálu elektrody v K-273,15K
Nakonec poměr opotřebení obrobku k elektrodě R lze získat z:
R = 2,25 x Trexp (-2,38)
Zde Tr je poměr bodů tání obrobku k elektrodě.
SINKER EDM :
Sinker EDM, také označovaný jako CAVITY TYP EDM or_cc781905-95cde-leanse skládá z elektrody a subculfDM781905-VOL35cde-in. Elektroda a obrobek jsou připojeny k napájecímu zdroji. Napájecí zdroj vytváří mezi nimi elektrický potenciál. Když se elektroda přiblíží k obrobku, dojde v tekutině k dielektrickému průrazu, který vytvoří plazmový kanál a přeskakuje malá jiskra. Jiskry obvykle udeří jedna po druhé, protože je vysoce nepravděpodobné, že by různá místa v mezielektrodovém prostoru měla identické místní elektrické charakteristiky, které by umožnily vznik jiskry ve všech takových místech současně. V náhodných bodech mezi elektrodou a obrobkem dochází za sekundu ke stovkám tisíc těchto jisker. Jak základní kov eroduje a jiskřiště se následně zvětšuje, elektroda je automaticky spuštěna naším CNC strojem, takže proces může pokračovat bez přerušení. Naše zařízení má kontrolní cykly známé jako ''čas zapnutí'' a ''čas vypnutí''. Nastavení doby zapnutí určuje délku nebo trvání jiskry. Delší doba provozu vytváří hlubší dutinu pro tuto jiskru a všechny následující jiskry pro tento cyklus, což vytváří hrubší povrch na obrobku a naopak. Doba vypnutí je doba, po kterou je jedna jiskra nahrazena jinou. Delší doba vypnutí umožňuje dielektrické kapalině propláchnout tryskou, aby se vyčistily erodované nečistoty, čímž se zabrání zkratu. Tato nastavení se upravují během mikrosekund.
WIRE EDM :
In WIRE ELECTRICAL DISCHARGE MACHINING (WEDM), also called WIRE-CUT EDM or WIRE CUTTING, we feed a tenký jednopramenný kovový drát z mosazi skrz obrobek, který je ponořen v nádrži s dielektrickou kapalinou. Drátové EDM je důležitou variantou EDM. Příležitostně používáme elektroerozivní elektroerozivní řezání pro řezání plechů o tloušťce až 300 mm a pro výrobu razníků, nástrojů a zápustek z tvrdých kovů, které se obtížně obrábějí jinými výrobními metodami. V tomto procesu, který se podobá obrysovému řezání pásovou pilou, je drát, který je neustále přiváděn z cívky, držen mezi horním a spodním diamantovým vedením. CNC řízená vodítka se pohybují v rovině x–y a horní vodítko se také může pohybovat nezávisle v ose z–u–v, což umožňuje řezat zužující se a přecházející tvary (jako je kruh na spodní straně a čtverec na vrchol). Horní vedení může ovládat pohyby os v x–y–u–v–i–j–k–l–. To umožňuje WEDM řezat velmi složité a jemné tvary. Průměrná řezná spára našeho zařízení, která dosahuje nejlepších ekonomických nákladů a doby obrábění, je 0,335 mm při použití mosazného, měděného nebo wolframového drátu Ø 0,25. Horní a spodní diamantová vodítka našeho CNC zařízení jsou však přesné na přibližně 0,004 mm a mohou mít řeznou dráhu nebo zářez až 0,021 mm při použití drátu Ø 0,02 mm. Jsou tedy možné opravdu úzké střihy. Šířka řezu je větší než šířka drátu, protože ze stran drátu k obrobku dochází k jiskření, což způsobuje erozi. Tento „overcut“ je nezbytný, pro mnoho aplikací je předvídatelný, a proto může být kompenzován (v mikro-EDM tomu tak často není). Cívky drátu jsou dlouhé – 8 kg cívka 0,25 mm drátu má na délku něco málo přes 19 kilometrů. Průměr drátu může být až 20 mikrometrů a přesnost geometrie je v blízkosti +/- 1 mikrometr. Drát obecně používáme pouze jednou a recyklujeme ho, protože je relativně levný. Pohybuje se konstantní rychlostí 0,15 až 9 m/min a během řezu je udržována konstantní řezná spára (drážka). V procesu elektroerozivního řezání drátem používáme vodu jako dielektrickou kapalinu, která řídí její odpor a další elektrické vlastnosti pomocí filtrů a deionizačních jednotek. Voda spláchne řezané nečistoty z oblasti řezu. Proplachování je důležitým faktorem při stanovení maximální rychlosti posuvu pro danou tloušťku materiálu, a proto jej udržujeme konzistentní. Řezná rychlost v drátovém EDM se udává jako plocha průřezu řezu za jednotku času, např. 18 000 mm2/h pro nástrojovou ocel D2 o tloušťce 50 mm. Lineární řezná rychlost by v tomto případě byla 18 000/50 = 360 mm/h Rychlost úběru materiálu při EDM drátu je:
MRR = Vf xhxb
Zde je MRR v mm3/min, Vf je rychlost posuvu drátu do obrobku v mm/min, h je tloušťka nebo výška v mm a b je řez, což je:
b = dw + 2 s
Zde dw je průměr drátu a s je mezera mezi drátem a obrobkem v mm.
Spolu s užšími tolerancemi mají naše moderní víceosá obráběcí centra pro řezání drátem EDM přidané funkce, jako jsou vícehlavy pro řezání dvou dílů současně, ovládací prvky pro zamezení přetržení drátu, funkce automatického samořezání v případě přetržení drátu a programování strategie obrábění pro optimalizaci provozu, možnosti přímého a úhlového řezání.
Wire-EDM nám nabízí nízká zbytková napětí, protože nevyžaduje vysoké řezné síly pro úběr materiálu. Když je energie/výkon na puls relativně nízký (jako při dokončovacích operacích), očekává se malá změna mechanických vlastností materiálu kvůli nízkým zbytkovým napětím.
BROUŠENÍ ELEKTRICKÝM VÝBĚREM (EDG) : Brusné kotouče neobsahují abraziva, jsou vyrobeny z grafitu nebo mosazi. Opakující se jiskry mezi rotujícím kolem a obrobkem odstraňují materiál z povrchu obrobku. Rychlost úběru materiálu je:
MRR = K x I
Zde je MRR v mm3/min, I je proud v ampérech a K je faktor materiálu obrobku v mm3/A-min. K řezání úzkých štěrbin na součástech často používáme broušení elektrickým výbojem. Někdy kombinujeme proces EDG (Electrical-Discharge Grinding) s procesem ECG (Electrochemical Grinding), kdy je materiál odstraněn chemickým působením, elektrické výboje z grafitového kotouče rozbijí oxidový film a odplaví elektrolytem. Proces se nazývá ELECTROCHEMICAL-DISCHARGE GRINDING (ECDG). Přestože proces ECDG spotřebovává relativně více energie, je rychlejší než proces EDG. Touto technikou brousíme převážně tvrdokovové nástroje.
Aplikace elektroerozivního obrábění:
Výroba prototypu:
EDM proces používáme při výrobě forem, nástrojů a zápustek, stejně jako při výrobě prototypů a výrobních dílů, zejména pro letecký, automobilový a elektronický průmysl, kde jsou objemy výroby relativně nízké. V Sinker EDM se grafitová, měděná, wolframová nebo čistá měděná elektroda opracovává do požadovaného (negativního) tvaru a přivádí se do obrobku na konci svislého pístu.
Výroba ražení mincí:
Pro výrobu razidel pro výrobu šperků a odznaků procesem ražby (ražby) může být pozitivní matrice vyrobena z mincovního stříbra, protože (při vhodném nastavení stroje) je matrice značně erodována a je použita pouze jednou. Výsledná negativní matrice je poté vytvrzena a použita v kladívku k výrobě lisovaných ploch z vyříznutých plechových polotovarů z bronzu, stříbra nebo slitiny zlata s nízkou věrohodností. U odznaků mohou být tyto plošky dále tvarovány do zakřiveného povrchu jinou matricí. Tento typ EDM se obvykle provádí ponořený v dielektriku na bázi oleje. Hotový předmět může být dále zušlechťován tvrdým (sklo) nebo měkkým (barva) smaltováním a/nebo galvanicky pokovován čistým zlatem nebo niklem. Měkčí materiály, jako je stříbro, mohou být ručně vyryty jako zdokonalení.
Vrtání malých otvorů:
Na našich elektroerozivních strojích pro drátové řezání používáme elektroerozivní elektroerozivní vrtání malých otvorů k vytvoření průchozího otvoru v obrobku, kterým provlékneme drát pro operaci drátového řezání. Samostatné EDM hlavy speciálně pro vrtání malých otvorů jsou namontovány na našich drátových řezacích strojích, které umožňují, aby z velkých kalených plechů byly podle potřeby a bez předvrtání erodovány hotové díly. EDM s malými otvory také používáme k vrtání řad otvorů do okrajů lopatek turbín používaných v proudových motorech. Proudění plynu těmito malými otvory umožňuje motorům používat vyšší teploty, než je jinak možné. Vysokoteplotní, velmi tvrdé, monokrystalické slitiny, ze kterých jsou čepele vyrobeny, činí konvenční obrábění těchto otvorů s vysokým poměrem stran extrémně obtížné a dokonce nemožné. Další oblastí použití pro elektroerozivní obrábění malých otvorů je vytváření mikroskopických otvorů pro součásti palivového systému. Kromě integrovaných EDM hlav nasazujeme samostatné EDM stroje na vrtání malých otvorů s osami x–y pro obrábění slepých nebo průchozích otvorů. Elektroerozivní vrtání otvorů pomocí dlouhé mosazné nebo měděné trubkové elektrody, která se otáčí ve sklíčidle s konstantním průtokem destilované nebo deionizované vody protékající elektrodou jako proplachovací činidlo a dielektrikum. Některé elektroerozivní nástroje pro vrtání malých otvorů jsou schopny provrtat 100 mm měkké nebo dokonce kalené oceli za méně než 10 sekund. Při tomto vrtání lze dosáhnout otvorů mezi 0,3 mm a 6,1 mm.
Obrábění s dezintegrací kovů:
Máme také speciální EDM stroje pro specifické účely odstraňování zlomených nástrojů (vrtáků nebo závitníků) z obrobků. Tento proces se nazývá ''rozmělňovací obrábění''.
Výhody a nevýhody elektroerozivního obrábění:
Mezi výhody EDM patří obrábění:
- Složité tvary, které by bylo jinak obtížné vyrobit běžnými řeznými nástroji
- Extrémně tvrdý materiál s velmi úzkými tolerancemi
- Velmi malé obrobky, kde běžné řezné nástroje mohou součást poškodit nadměrným tlakem řezného nástroje.
- Neexistuje žádný přímý kontakt mezi nástrojem a obrobkem. Jemné profily a slabé materiály lze tedy obrábět bez jakéhokoli zkreslení.
- Lze dosáhnout dobré povrchové úpravy.
- Velmi jemné otvory lze snadno vyvrtat.
Nevýhody EDM zahrnují:
- Pomalá rychlost úběru materiálu.
- Dodatečný čas a náklady vynaložené na vytvoření elektrod pro elektroerozivní elektroerozivní hloubení.
- Reprodukce ostrých rohů na obrobku je obtížná kvůli opotřebení elektrody.
- Spotřeba energie je vysoká.
- Vytvoří se ''Overcut''.
- Při obrábění dochází k nadměrnému opotřebení nástroje.
- Elektricky nevodivé materiály lze obrábět pouze se specifickým nastavením procesu.