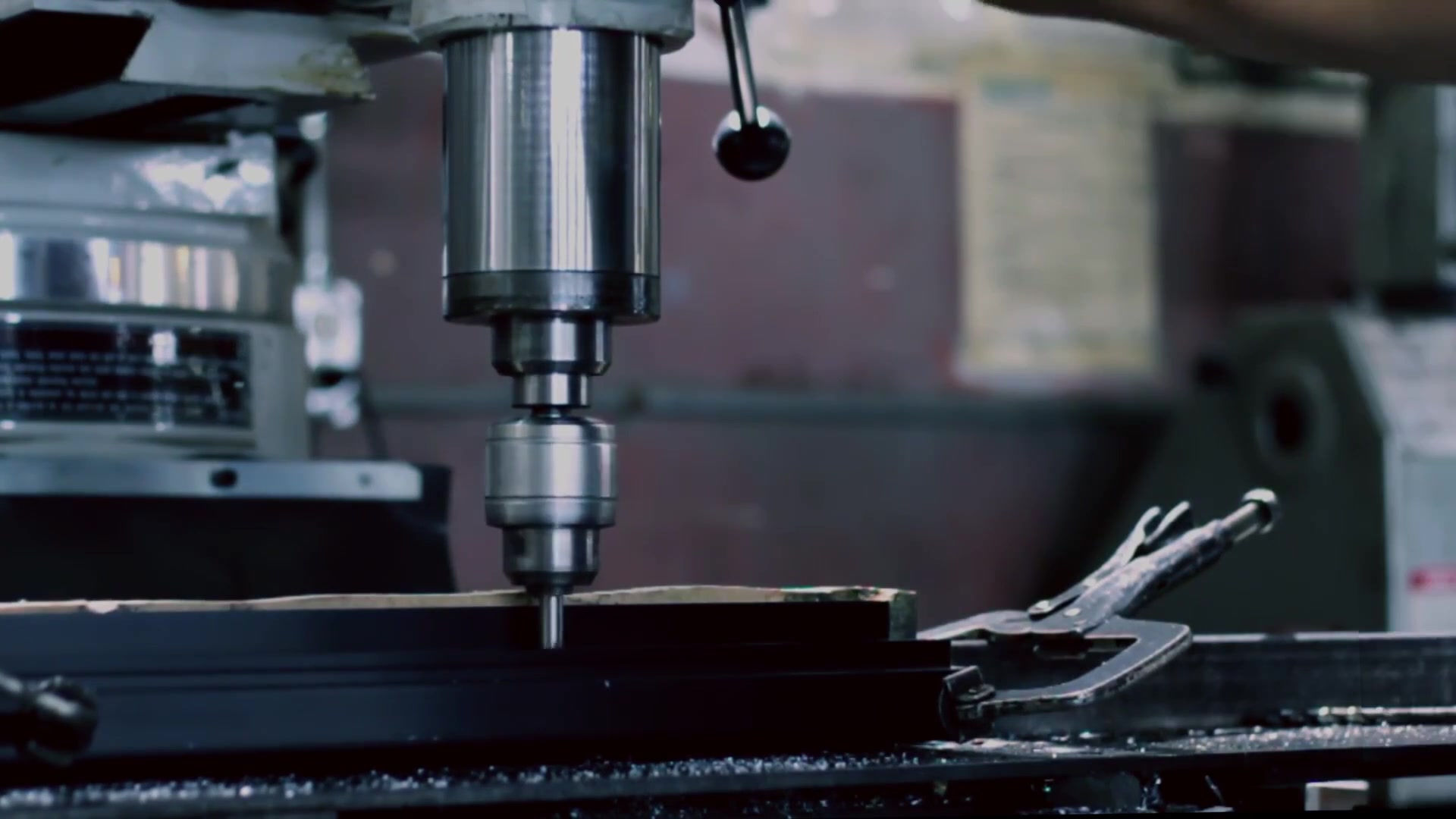
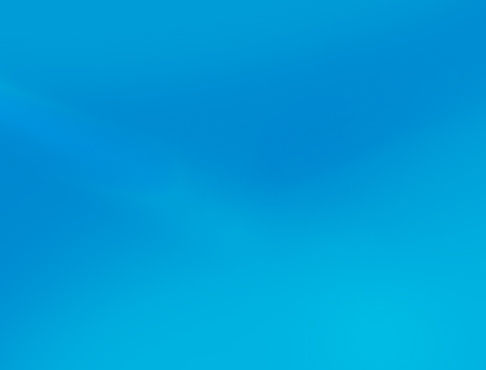
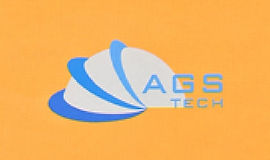
Globální zakázkový výrobce, integrátor, konsolidátor, partner pro outsourcing pro širokou škálu produktů a služeb.
Jsme vaším komplexním zdrojem pro výrobu, výrobu, inženýrství, konsolidaci, integraci, outsourcing zakázkově vyráběných i volně prodejných produktů a služeb.
Choose your Language
-
Zakázková výroba
-
Domácí a globální smluvní výroba
-
Outsourcing výroby
-
Domácí a globální zadávání zakázek
-
Konsolidace
-
Engineering Integration
-
Inženýrské služby
Typy výroby skla, které nabízíme, jsou obalové sklo, foukané sklo, skleněné vlákno a trubky a tyče, domácí a průmyslové sklo, lampy a žárovky, přesné lisování skla, optické komponenty a sestavy, ploché a tabulové a plavené sklo. Provádíme ruční tvarování i strojní tvarování.
Naše oblíbené výrobní procesy technické keramiky jsou lisování, izostatické lisování, izostatické lisování za horka, lisování za tepla, lití do licí pásky, páskové lití, vytlačování, vstřikování, surové obrábění, slinování nebo vypalování, diamantové broušení, hermetické sestavy.
Doporučujeme kliknout sem
STÁHNĚTE SI naše schematické ilustrace procesů tvarování a tvarování skla od AGS-TECH Inc.
STÁHNĚTE SI naše schématická vyobrazení technických procesů výroby keramiky od AGS-TECH Inc.
Tyto soubory ke stažení s fotografiemi a nákresy vám pomohou lépe porozumět informacím, které vám poskytujeme níže.
• VÝROBA OBALOVÉHO SKLA: Pro výrobu jsme zautomatizovali linky PRESS AND FLOW a také FLOW AND BLOW. V procesu vyfukování a vyfukování vpustíme dávku do přední formy a vytvarujeme hrdlo foukáním stlačeného vzduchu shora. Bezprostředně poté je stlačený vzduch vháněn podruhé z druhého směru hrdlem nádoby, aby se vytvořil předtvar láhve. Tento předvýrobek se poté přenese do skutečné formy, znovu se zahřeje, aby změkl, a aplikuje se stlačený vzduch, aby předvýrobek získal konečný tvar nádoby. Přesněji řečeno, je natlakován a tlačen proti stěnám dutiny konečné formy, aby získal požadovaný tvar. Nakonec se vyrobený skleněný obal přemístí do žíhací pece k následnému ohřátí a odstranění pnutí vzniklých během tvarování a kontrolovaným způsobem se ochladí. Při metodě lisování a vyfukování jsou roztavené kapky dány do předlisku (předlisku) a lisovány do předlisku (tvar předlisku). Polotovary jsou poté přeneseny do vyfukovacích forem a vyfukovány podobně jako proces popsaný výše v části „Proces vyfukování a vyfukování“. Následné kroky jako žíhání a uvolnění napětí jsou podobné nebo stejné.
• FUKÁNÍ SKLA : Vyrábíme skleněné výrobky pomocí konvenčního ručního foukání i pomocí stlačeného vzduchu s automatickým zařízením. Pro některé zakázky je nutné konvenční foukání, jako jsou projekty zahrnující sklářské umělecké práce nebo projekty, které vyžadují menší počet dílů s volnými tolerancemi, prototypování / demo projekty….atd. Konvenční foukání skla zahrnuje ponoření duté kovové trubky do hrnce s roztaveným sklem a otáčení trubky pro zachycení určitého množství skleněného materiálu. Sklo shromážděné na špičce dýmky se naválcuje na ploché železo, tvaruje se podle potřeby, prodlužuje se, znovu se zahřívá a fouká vzduchem. Když je připraven, vloží se do formy a fouká vzduch. Dutina formy je mokrá, aby se zabránilo kontaktu skla s kovem. Vodní film mezi nimi působí jako polštář. Ruční foukání je pracný pomalý proces a je vhodný pouze pro prototypování nebo položky vysoké hodnoty, není vhodný pro levné velkoobjemové objednávky za kus.
• VÝROBA DOMÁCÍHO A PRŮMYSLOVÉHO SKLA: S použitím různých typů skleněného materiálu se vyrábí velké množství různých druhů skla. Některé sklenice jsou odolné vůči teplu a jsou vhodné pro laboratorní sklo, zatímco některé jsou dostatečně dobré na to, aby mnohokrát vydržely v myčkách nádobí a jsou vhodné pro výrobu domácích produktů. Na strojích Westlake se denně vyrobí desítky tisíc kusů nápojového skla. Pro zjednodušení se roztavené sklo shromažďuje vakuem a vkládá se do forem, aby se vyrobily předlisky. Poté je do forem vháněn vzduch, tyto jsou přemístěny do jiné formy a opět je vháněn vzduch a sklo získá svůj konečný tvar. Stejně jako při ručním foukání jsou tyto formy udržovány vlhké vodou. Další protahování je součástí dokončovací operace, kde se tvoří krk. Přebytečné sklo je spáleno. Poté následuje výše popsaný proces řízeného opětovného ohřevu a chlazení.
• TVÁŘENÍ SKLENĚNÝCH TRUBEK A TYČÍ: Hlavní procesy, které používáme pro výrobu skleněných trubic, jsou procesy DANNER a VELLO. V Dannerově procesu sklo z pece teče a padá na nakloněnou manžetu vyrobenou ze žáruvzdorných materiálů. Objímka je nesena na otočné duté hřídeli nebo foukačce. Sklo se pak obalí kolem pouzdra a vytvoří hladkou vrstvu stékající po pouzdru a přes špičku dříku. V případě tvarování trubek je vzduch vháněn foukačkou s dutým hrotem a v případě tvarování tyčí používáme pevné hroty na hřídel. Trubky nebo tyče jsou pak taženy přes nosné válečky. Rozměry, jako je tloušťka stěny a průměr skleněných trubic, se upravují na požadované hodnoty nastavením průměru objímky a foukáním tlaku vzduchu na požadovanou hodnotu, nastavením teploty, rychlosti proudění skla a rychlosti tažení. Proces výroby skleněných trubic Vello na druhé straně zahrnuje sklo, které putuje z pece do misky s dutým trnem nebo zvonem. Sklo pak prochází vzduchovým prostorem mezi trnem a miskou a získává tvar trubice. Poté putuje přes válce do tažného stroje a ochladí se. Na konci chladicí linky probíhá řezání a konečné zpracování. Rozměry trubky lze upravit stejně jako v procesu Danner. Když porovnáme proces Danner a Vello, můžeme říci, že proces Vello je vhodnější pro výrobu velkého množství, zatímco proces Danner může být vhodnější pro přesné objednávky menších objemů trubek.
• ZPRACOVÁNÍ TABULÍ A PLOCHÉHO A PLOVACÍHO SKLA: Máme velké množství plochého skla v tloušťkách od submilimetrových až po několik centimetrů. Naše ploché brýle jsou téměř optické dokonalosti. Nabízíme skla se speciálními povlaky, jako jsou optické povlaky, kde se používá technika chemického napařování k nanášení povlaků, jako je antireflexní nebo zrcadlový povlak. Běžné jsou také průhledné vodivé povlaky. K dispozici jsou také hydrofobní nebo hydrofilní povlaky na skle a povlak, který zajišťuje samočištění skla. Dalším oblíbeným zbožím jsou tvrzená, neprůstřelná a vrstvená skla. Sklo nařežeme do požadovaného tvaru s požadovanými tolerancemi. K dispozici jsou další sekundární operace, jako je zakřivení nebo ohýbání plochého skla.
• PŘESNÉ LIŠOVÁNÍ SKLA: Tuto techniku používáme většinou pro výrobu přesných optických komponentů bez potřeby nákladnějších a časově náročných technik, jako je broušení, lapování a leštění. Tato technika není vždy dostatečná pro výrobu nejlepší optiky, ale v některých případech, jako jsou spotřební výrobky, digitální fotoaparáty, lékařská optika, může být levnější a dobrou volbou pro velkoobjemovou výrobu. Také má výhodu oproti jiným technikám tvarování skla, kde jsou vyžadovány složité geometrie, jako v případě asfér. Základní proces zahrnuje plnění spodní strany naší formy skleněným polotovarem, evakuaci procesní komory pro odstranění kyslíku, blízké uzavření formy, rychlý a izotermický ohřev formy a skla infračerveným světlem, další uzavření polovin formy pomalé lisování měkčeného skla kontrolovaným způsobem na požadovanou tloušťku a nakonec ochlazení skla a naplnění komory dusíkem a odstranění produktu. Přesná regulace teploty, vzdálenost uzavření formy, síla uzavření formy, přizpůsobení koeficientů roztažnosti formy a skleněného materiálu jsou v tomto procesu klíčové.
• VÝROBA SKLENĚNÝCH OPTICKÝCH KOMPONENTŮ A SESTAV : Kromě přesného lisování skla existuje řada cenných procesů, které používáme pro výrobu vysoce kvalitních optických komponent a sestav pro náročné aplikace. Broušení, lapování a leštění optických skel v jemných speciálních brusných kaších je umění a věda pro výrobu optických čoček, hranolů, ploch a dalších. Plochost povrchu, zvlnění, hladkost a optické povrchy bez defektů vyžadují mnoho zkušeností s takovými procesy. Malé změny v prostředí mohou vést k tomu, že produkty nesplňují specifikace a zastavit výrobní linku. Existují případy, kdy jediné setření optického povrchu čistým hadříkem může způsobit, že výrobek splňuje specifikace nebo neprojde testem. Některé populární skleněné materiály jsou tavený oxid křemičitý, křemen, BK7. Také montáž takových komponent vyžaduje specializované specializované zkušenosti. Někdy se používají speciální lepidla. Někdy je však nejlepší volbou technika nazývaná optický kontakt, která nezahrnuje žádný materiál mezi připojenými optickými skly. Skládá se z fyzického kontaktu plochých povrchů, které se k sobě připojí bez lepidla. V některých případech se k sestavení optických součástí v určitých vzdálenostech a s určitými vzájemnými geometrickými orientacemi používají mechanické rozpěrky, přesné skleněné tyčinky nebo kuličky, svorky nebo obrobené kovové součásti. Podívejme se na některé z našich oblíbených technik výroby špičkové optiky.
BRUŠENÍ A LAPOVÁNÍ A LEŠTĚNÍ: Hrubý tvar optické součásti se získá broušením skleněného polotovaru. Poté se provádí lapování a leštění otáčením a otíráním hrubých povrchů optických součástí o nástroje s požadovanými tvary povrchu. Mezi optiku a tvarovací nástroje se nalévají kaše s drobnými abrazivními částicemi a kapalinou. Velikosti abrazivních částic v takových suspenzích lze zvolit podle požadovaného stupně rovinnosti. Odchylky kritických optických povrchů od požadovaných tvarů jsou vyjádřeny pomocí vlnových délek použitého světla. Naše vysoce přesná optika má desetinovou toleranci vlnové délky (vlnová délka/10) nebo je možná ještě těsnější. Kromě profilu povrchu jsou kritické povrchy skenovány a vyhodnocovány na další povrchové vlastnosti a vady, jako jsou rozměry, škrábance, třísky, důlky, skvrny...atd. Přísná kontrola podmínek prostředí v optické výrobě a rozsáhlé požadavky na metrologii a testování s nejmodernějším vybavením z něj činí náročné průmyslové odvětví.
• SEKUNDÁRNÍ PROCESY VE VÝROBĚ SKLA: Opět jsme omezeni pouze vaší představivostí, pokud jde o sekundární a dokončovací procesy skla. Zde uvádíme některé z nich:
-Povlaky na skle (optické, elektrické, tribologické, tepelné, funkční, mechanické...). Jako příklad můžeme změnit povrchové vlastnosti skla tak, aby například odráželo teplo, aby udržovalo interiéry v budovách chladné, nebo jednostranně pohlcují infračervené záření pomocí nanotechnologie. To pomáhá udržovat vnitřek budov v teple, protože vnější povrchová vrstva skla absorbuje infračervené záření uvnitř budovy a vyzařuje je zpět dovnitř.
- Leptání on sklo
- Aplikované keramické značení (ACL)
-Rytina
-Leštění plamenem
- Chemické leštění
- Barvení
VÝROBA TECHNICKÉ KERAMIKY
• LIŠOVÁNÍ V ZÁSOBNÍKU : Skládá se z jednoosého lisování granulovaných prášků uzavřených v matrici
• LISOVÁNÍ ZA HORKA: Podobné lisování, ale s přidáním teploty pro zvýšení zhuštění. Prášek nebo zhutněný předlisek se umístí do grafitové matrice a aplikuje se jednoosý tlak, zatímco matrice se udržuje při vysokých teplotách, jako je 2000 C. Teploty se mohou lišit v závislosti na typu zpracovávaného keramického prášku. U komplikovaných tvarů a geometrií může být zapotřebí další následné zpracování, jako je broušení diamantem.
• IZSTATICKÉ LISOVÁNÍ: Granulovaný prášek nebo lisované výlisky se umístí do vzduchotěsných nádob a poté do uzavřené tlakové nádoby s kapalinou uvnitř. Poté se zhutňují zvýšením tlaku v tlakové nádobě. Kapalina uvnitř nádoby přenáší tlakové síly rovnoměrně po celé ploše vzduchotěsné nádoby. Materiál je tak stejnoměrně zhutněn a získává tvar své flexibilní nádoby a jejího vnitřního profilu a vlastností.
• IZostatické lisování za tepla : Podobně jako u izostatického lisování, ale kromě atmosféry stlačeného plynu slinujeme výlisky při vysoké teplotě. Izostatické lisování za tepla má za následek dodatečné zhuštění a zvýšenou pevnost.
• LITÍ SLIP / DRAIN CASTING : Formu naplníme suspenzí mikrometrových keramických částic a nosnou kapalinou. Tato směs se nazývá „skluz“. Forma má póry a proto se kapalina ve směsi filtruje do formy. V důsledku toho se na vnitřních plochách formy vytvoří odlitek. Po slinování lze díly vyjmout z formy.
• ODLÉVÁNÍ PÁSKY: Vyrábíme keramické pásky odléváním keramických kaší na rovné pohyblivé povrchy nosiče. Kaše obsahují keramické prášky smíchané s jinými chemikáliemi pro účely spojování a přenášení. Když se rozpouštědla vypařují, zůstávají husté a pružné keramické desky, které lze řezat nebo válcovat podle potřeby.
• VYTVÁŘENÍ VYTLAČOVÁNÍM: Stejně jako v jiných procesech vytlačování prochází měkká směs keramického prášku s pojivy a dalšími chemikáliemi matricí, aby získala tvar příčného řezu, a poté se řeže na požadované délky. Proces se provádí studenými nebo zahřátými keramickými směsmi.
• NÍZKOTLAKÉ VSTŘIKOVÁNÍ: Připravíme směs keramického prášku s pojivy a rozpouštědly a zahřejeme ji na teplotu, kterou lze snadno vtlačit a vytlačit do dutiny nástroje. Jakmile je lisovací cyklus dokončen, díl se vysune a pojivo se spálí. Pomocí vstřikování můžeme ekonomicky získat složité díly ve velkých objemech. Jsou možné otvory , které jsou nepatrným zlomkem milimetru na stěně o tloušťce 10 mm, závity jsou možné bez dalšího obrábění, tolerance až +/- 0,5 % jsou možné a ještě nižší při obrábění dílů jsou možné tloušťky stěn v řádu od 0,5 mm do délky 12,5 mm, stejně jako tloušťky stěny od 6,5 mm do délky 150 mm.
• ZELENÉ OBRÁBĚNÍ : Pomocí stejných nástrojů na obrábění kovů můžeme obrábět lisované keramické materiály, dokud jsou stále měkké jako křída. Jsou možné tolerance +/- 1 %. Pro lepší tolerance používáme diamantové broušení.
• SINTROVÁNÍ nebo VYPALOVÁNÍ: Slinování umožňuje plné zhuštění. Na zelených kompaktních dílech dochází k výraznému smrštění, ale to není velký problém, protože tyto rozměrové změny bereme v úvahu při návrhu dílu a nástroje. Částice prášku jsou spojeny dohromady a pórovitost způsobená procesem zhutňování je do značné míry odstraněna.
• BRUŠENÍ DIAMANTŮ: Nejtvrdší materiál na světě „diamant“ se používá k broušení tvrdých materiálů, jako je keramika, a získává se přesné díly. Dosahuje se tolerancí v řádu mikrometrů a velmi hladkých povrchů. Vzhledem k její náročnosti uvažujeme o této technice pouze tehdy, když ji opravdu potřebujeme.
• HERMETICKÉ SESTAVY jsou takové, které prakticky neumožňují výměnu látek, pevných látek, kapalin nebo plynů mezi rozhraními. Hermetické těsnění je vzduchotěsné. Například hermetické elektronické kryty jsou takové, které udržují citlivý vnitřní obsah zabaleného zařízení bez poškození vlhkostí, nečistotami nebo plyny. Nic není 100% hermetické, ale když mluvíme o hermetičnosti, máme na mysli to, že v praxi existuje hermetika do té míry, že míra úniku je tak nízká, že zařízení jsou za normálních podmínek prostředí bezpečná po velmi dlouhou dobu. Naše hermetické sestavy se skládají z kovových, skleněných a keramických komponentů, kov-keramika, keramika-kov-keramika, kovokeramika-kov, kov na kov, kov-sklo, kov-sklo-kov, sklo-kov-sklo, sklo- kov a sklo na sklo a všechny další kombinace spojů kov-sklo-keramika. Můžeme například pokovovat keramické součásti, aby mohly být pevně spojeny s ostatními součástmi v sestavě a měly vynikající těsnící schopnost. Máme know-how v oblasti potahování optických vláken nebo průchodek kovem a jejich připájení nebo pájení natvrdo na kryty, takže do krytů neprocházejí ani neunikají žádné plyny. Proto se používají k výrobě elektronických krytů pro zapouzdření citlivých zařízení a jejich ochranu před vnější atmosférou. Kromě vynikajících těsnících vlastností mají i další vlastnosti, jako je koeficient tepelné roztažnosti, odolnost proti deformaci, bezodplyňování, velmi dlouhá životnost, nevodivost, tepelně izolační vlastnosti, antistatická povaha...atd. učinit ze skla a keramiky volbu pro určité aplikace. Informace o naší provozovně, která vyrábí armatury z keramiky na kov, hermetické těsnění, vakuové průchodky, komponenty pro řízení vysokého a ultravysokého vakua a kapalin naleznete zde:Brožura továrny na hermetické komponenty