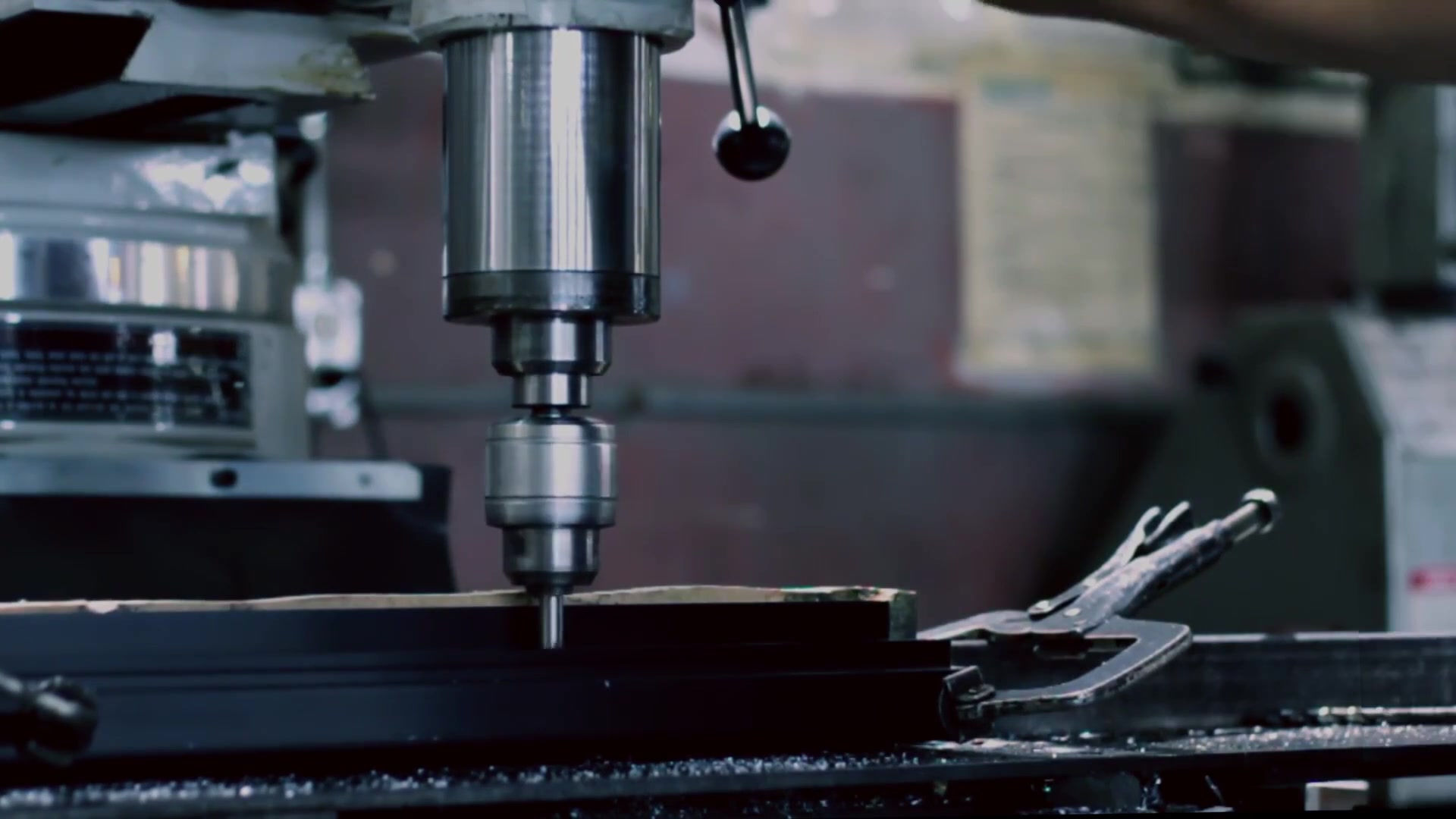
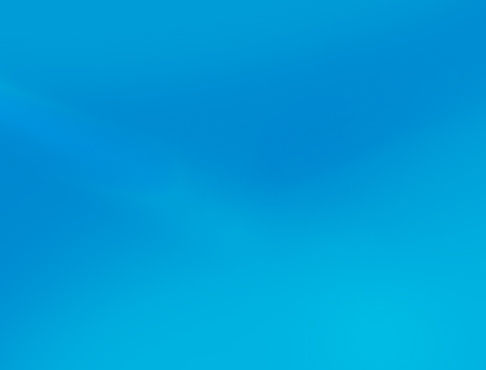
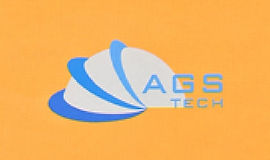
Globální zakázkový výrobce, integrátor, konsolidátor, partner pro outsourcing pro širokou škálu produktů a služeb.
Jsme vaším komplexním zdrojem pro výrobu, výrobu, inženýrství, konsolidaci, integraci, outsourcing zakázkově vyráběných i volně prodejných produktů a služeb.
Choose your Language
-
Zakázková výroba
-
Domácí a globální smluvní výroba
-
Outsourcing výroby
-
Domácí a globální zadávání zakázek
-
Konsolidace
-
Engineering Integration
-
Inženýrské služby
Vaše vyrobené díly spojíme, smontujeme a upevníme a přeměníme na hotové nebo polotovary pomocí SVAŘOVÁNÍ, PÁJENÍ, PÁJENÍ, SPÉKÁNÍ, LEPENÍ, UPEVŇOVÁNÍ, LISKOVÁNÍ. Některé z našich nejoblíbenějších svařovacích procesů jsou obloukové, kyslíko-palivové, odporové, projekční, svarové, pěchovací, perkusní, pevné, elektronové, laserové, termitové, indukční svařování. Naše oblíbené pájecí procesy jsou pájení hořákem, indukce, pece a ponorem. Naše metody pájení jsou železo, plotýnka, trouba, indukce, ponor, vlna, přetavení a ultrazvukové pájení. Pro lepení často používáme termoplasty a termosety, epoxidy, fenoly, polyuretany, lepicí slitiny a také některé další chemikálie a pásky. Nakonec naše upevňovací procesy sestávají z hřebíků, šroubování, matic a šroubů, nýtování, sevření, sešívání, sešívání a sešívání a lisování.
• SVAŘOVÁNÍ: Svařování zahrnuje spojování materiálů tavením obrobků a zaváděním přídavných materiálů, které také spojují roztavenou svarovou lázeň. Když se oblast ochladí, získáme pevný spoj. V některých případech je aplikován tlak. Na rozdíl od svařování zahrnují operace pájení natvrdo pouze tavení materiálu s nižším bodem tavení mezi obrobky a obrobky se netaví. Doporučujeme kliknout semSTÁHNĚTE SI naše schématická vyobrazení svařovacích procesů od AGS-TECH Inc.
To vám pomůže lépe porozumět informacím, které vám poskytujeme níže.
Při OBLOUKOVÉM SVAŘOVÁNÍ používáme napájecí zdroj a elektrodu k vytvoření elektrického oblouku, který taví kovy. Svařovaný bod je chráněn ochranným plynem nebo párou nebo jiným materiálem. Tento proces je oblíbený pro svařování automobilových dílů a ocelových konstrukcí. Při obloukovém svařování obaleným kovem (SMAW) nebo také známém jako svařování tyčí se tyč elektrody přiblíží k základnímu materiálu a mezi nimi se vytvoří elektrický oblouk. Tyč elektrody se taví a působí jako výplňový materiál. Elektroda také obsahuje tavidlo, které působí jako vrstva strusky a vydává páry, které působí jako ochranný plyn. Ty chrání oblast svaru před kontaminací prostředí. Žádná jiná plniva se nepoužívají. Nevýhodou tohoto procesu je jeho pomalost, nutnost časté výměny elektrod, nutnost odštípávání zbytkové strusky pocházející z tavidla. Řada kovů, jako je železo, ocel, nikl, hliník, měď atd. Lze svařit. Jeho výhodou jsou levné nástroje a snadné použití. Plynové obloukové svařování kovů (GMAW), známé také jako kov-inertní plyn (MIG), máme kontinuální přívod tavné elektrodové výplně drátu a inertního nebo částečně inertního plynu, který proudí kolem drátu proti znečištění oblasti svaru prostředím. Lze svařovat ocel, hliník a další neželezné kovy. Výhodou MIG je vysoká rychlost svařování a dobrá kvalita. Nevýhodou je komplikované vybavení a problémy, kterým čelíme ve větrném venkovním prostředí, protože musíme udržovat ochranný plyn kolem svařovací oblasti stabilní. Variantou GMAW je obloukové svařování s tavidlem (FCAW), které se skládá z jemné kovové trubky naplněné tavidlem. Někdy je tavidlo uvnitř trubky dostatečné pro ochranu před kontaminací životního prostředí. Svařování pod tavidlem (SAW) je široce automatizovaný proces, který zahrnuje kontinuální podávání drátu a oblouk, který je zapálen pod vrstvou tavidla. Rychlost výroby a kvalita jsou vysoké, struska ze svařování se snadno odstraňuje a máme nekuřácké pracovní prostředí. Nevýhodou je, že jej lze použít pouze pro svařování dílů parts v určitých polohách. Při obloukovém svařování plynovým wolframem (GTAW) nebo svařování wolframem v inertním plynu (TIG) používáme wolframovou elektrodu spolu se samostatnou výplní a inertními nebo téměř inertními plyny. Jak víme, wolfram má vysokou teplotu tání a je to velmi vhodný kov pro velmi vysoké teploty. Wolfram se při TIG nespotřebovává na rozdíl od jiných metod vysvětlených výše. Pomalá, ale vysoce kvalitní svařovací technika výhodná oproti jiným technikám při svařování tenkých materiálů. Vhodné pro mnoho kovů. Svařování plazmovým obloukem je podobné, ale k vytvoření oblouku používá plazmový plyn. Oblouk při svařování plazmovým obloukem je relativně koncentrovanější ve srovnání s GTAW a může být použit pro širší rozsah tlouštěk kovu při mnohem vyšších rychlostech. GTAW a plazmové obloukové svařování lze aplikovat na víceméně stejné materiály.
OXY-FUEL / OXYFUEL WELDING také nazývané svařování kyslíkem a acetylenem, svařování kyslíkem, svařování plynem se provádí pomocí plynných paliv a kyslíku pro svařování. Protože se nepoužívá žádná elektrická energie, je přenosný a lze jej použít tam, kde není elektřina. Pomocí svařovacího hořáku ohříváme kusy a přídavný materiál, abychom vytvořili společnou lázeň roztaveného kovu. Lze použít různá paliva, jako je acetylén, benzín, vodík, propan, butan atd. Při kyslíko-palivovém svařování používáme dvě nádoby, jednu na palivo a druhou na kyslík. Kyslík okysličuje palivo (spaluje ho).
ODPOROVÉ SVAŘOVÁNÍ: Tento typ svařování využívá joulového ohřevu a teplo vzniká v místě, kde je po určitou dobu aplikován elektrický proud. Kovem procházejí vysoké proudy. Na tomto místě se tvoří kaluže roztaveného kovu. Metody odporového svařování jsou oblíbené pro svou účinnost, malý potenciál znečištění. Nevýhodou však jsou relativně značné náklady na vybavení a vlastní omezení na relativně tenké obrobky. BODOVÉ SVAŘOVÁNÍ je jedním z hlavních typů odporového svařování. Zde spojujeme dva nebo více překrývajících se plechů nebo obrobků pomocí dvou měděných elektrod, které sevřou plechy k sobě a prochází jimi vysoký proud. Materiál mezi měděnými elektrodami se zahřívá a v tomto místě se vytváří roztavená lázeň. Proud se poté zastaví a hroty měděných elektrod ochlazují místo svaru, protože elektrody jsou chlazeny vodou. Aplikace správného množství tepla na správný materiál a tloušťku je pro tuto techniku klíčová, protože při nesprávné aplikaci bude spoj slabý. Bodové svařování má výhody v tom, že nezpůsobuje žádné významné deformace obrobků, energetickou účinnost, snadnou automatizaci a vynikající rychlost výroby a nevyžaduje žádná plniva. Nevýhodou je, že vzhledem k tomu, že svařování probíhá bodově, spíše než tvoří souvislý šev, může být celková pevnost relativně nižší ve srovnání s jinými způsoby svařování. ŠVOVÉ SVAŘOVÁNÍ na druhé straně vytváří svary na lícujících površích podobných materiálů. Šev může být natupo nebo překryt. Svarové svařování začíná na jednom konci a postupně se přesouvá na druhý. Tato metoda také používá dvě elektrody z mědi k aplikaci tlaku a proudu na oblast svaru. Kotoučové elektrody rotují s konstantním kontaktem podél linie švu a vytvářejí souvislý svar. I zde jsou elektrody chlazeny vodou. Svary jsou velmi pevné a spolehlivé. Dalšími metodami jsou projekční, zábleskové a přerušované svařovací techniky.
SVAŘOVÁNÍ V PEVNÉM STAVU je trochu jiné než předchozí metody vysvětlené výše. Koalescence probíhá při teplotách pod teplotou tání spojených kovů a bez použití kovového plniva. V některých procesech lze použít tlak. Různé metody jsou KOEXTRUZNÍ SVAŘOVÁNÍ, kde jsou rozdílné kovy vytlačovány stejnou matricí, SVAŘOVÁNÍ TLAKEM STUDENA, kde spojujeme měkké slitiny pod jejich teplotou tání, DIFFUSION WELDING technika bez viditelných svarových linií, EXPLOZNÍ SVAŘOVÁNÍ pro spojování odlišných materiálů, např. korozi odolných slitin ke konstrukčním oceli, ELEKTROMAGNETICKÉ PULZNÍ SVAŘOVÁNÍ, kde urychlujeme trubky a plechy elektromagnetickými silami, KOVACÍ SVAŘOVÁNÍ, které spočívá v zahřátí kovů na vysoké teploty a jejich srážení k sobě, TŘECÍ SVAŘOVÁNÍ kde se provádí dostatečné třecí svařování, TŘECÍ SVAŘOVÁNÍ, které zahrnuje rotační ne spotřební nástroj procházející spojovou linkou, HORKOVÉ TLAKOVÉ SVAŘOVÁNÍ, kde lisujeme kovy k sobě při zvýšených teplotách pod teplotou tavení ve vakuu nebo v inertních plynech, HORKÁ IZOSTATICKÁ TLAKOVÁ SVAŘOVÁNÍ proces, kdy aplikujeme tlak pomocí inertních plynů uvnitř nádoby, ROLOVÉ SVAŘOVÁNÍ, kde spojujeme nepodobné materiály tím, že je vnucujeme mezi sebe dvě rotující kola, ULTRAZVUKOVÉ SVAŘOVÁNÍ, kde jsou svařovány tenké kovové nebo plastové plechy pomocí vysokofrekvenční vibrační energie.
Další naše svařovací procesy jsou SVAŘOVÁNÍ ELEKTRONOVÝM PAPRSKEM s hlubokým průvarem a rychlým zpracováním, ale jako nákladnou metodu ji považujeme pro speciální případy, ELEKTROSLAGOVÉ SVAŘOVÁNÍ metodu vhodnou pouze pro těžké tlusté plechy a obrobky z oceli, INDUKČNÍ SVAŘOVÁNÍ, kde využíváme elektromagnetickou indukci a ohřívejte naše elektricky vodivé nebo feromagnetické obrobky, SVAŘOVÁNÍ LASEROVÝM PAPRSKEM také s hlubokou penetrací a rychlým zpracováním, ale nákladnou metodou, LASEROVÉ HYBRIDNÍ SVAŘOVÁNÍ, které kombinuje LBW s GMAW ve stejné svařovací hlavě a schopné přemostit mezery 2 mm mezi deskami, SVAŘOVÁNÍ NÁBOJE, které zahrnuje elektrický výboj s následným kováním materiálů aplikovaným tlakem, THERMIT WELDING zahrnující exotermickou reakci mezi prášky oxidu hliníku a železa, ELEKTROPLYNOVÉ SVAŘOVÁNÍ s tavnými elektrodami a používá se pouze s ocelí ve vertikální poloze a nakonec STUD ARC WELDING pro spojení trnu se základnou materiál s teplem a tlakem.
Doporučujeme kliknout semSTÁHNĚTE SI naše schématické ilustrace procesů pájení, pájení a lepení od AGS-TECH Inc
To vám pomůže lépe porozumět informacím, které vám poskytujeme níže.
• PÁJENÍ: Spojujeme dva nebo více kovů tak, že se mezi nimi zahřejí přídavné kovy nad jejich bod tání a pomocí kapilárního účinku se rozšíří. Proces je podobný pájení, ale teploty spojené s roztavením plniva jsou vyšší při pájení. Podobně jako při svařování tavidlo chrání přídavný materiál před atmosférickou kontaminací. Po ochlazení se obrobky spojí dohromady. Proces zahrnuje následující klíčové kroky: Dobré lícování a vůle, správné čištění základních materiálů, správné upevnění, správný výběr tavidla a atmosféry, ohřev sestavy a nakonec čištění pájené sestavy. Některé z našich procesů pájení jsou PÁJENÍ S PÁČKEM, oblíbená metoda prováděná ručně nebo automatizovaně. Je vhodný pro zakázky s malým objemem výroby a specializované případy. Teplo je aplikováno pomocí plynových plamenů v blízkosti pájeného spoje. PÁJENÍ V PECÍ vyžaduje méně dovedností operátora a je to poloautomatický proces vhodný pro průmyslovou hromadnou výrobu. Jak regulace teploty, tak regulace atmosféry v peci jsou výhodami této techniky, protože první umožňuje mít řízené tepelné cykly a eliminovat lokální ohřev, jako je tomu u pájení hořákem, a druhá chrání součást před oxidací. Pomocí jiggingu jsme schopni snížit výrobní náklady na minimum. Nevýhodou je vysoká spotřeba energie, náklady na vybavení a náročnější konstrukční úvahy. VAKUOVÉ PÁJENÍ probíhá ve vakuové peci. Rovnoměrnost teploty je zachována a získáváme velmi čisté spoje bez tavidel s velmi malým zbytkovým napětím. Tepelné zpracování může probíhat během vakuového pájení, kvůli nízkým zbytkovým napětím přítomným během pomalých cyklů ohřevu a chlazení. Hlavní nevýhodou je jeho vysoká cena, protože vytvoření vakuového prostředí je nákladný proces. Ještě další technika DIP BRAZING spojuje upevněné díly, kde se na styčné povrchy aplikuje pájecí směs. Poté jsou díly fixtured ponořeny do lázně roztavené soli, jako je chlorid sodný (kuchyňská sůl), která působí jako teplosměnné médium a tavidlo. Vzduch je vyloučen, a proto nedochází k tvorbě oxidů. Při INDUKČNÍM PÁJENÍ spojujeme materiály přídavným kovem, který má nižší bod tání než základní materiály. Střídavý proud z indukční cívky vytváří elektromagnetické pole, které indukuje indukční ohřev na převážně železných magnetických materiálech. Metoda poskytuje selektivní ohřev, dobré spoje s plnidly tekoucími pouze v požadovaných oblastech, malou oxidaci, protože nejsou přítomny plameny a chlazení je rychlé, rychlý ohřev, konzistenci a vhodnost pro velkosériovou výrobu. Abychom urychlili naše procesy a zajistili konzistenci, často používáme předlisky. Informace o našem pájecím zařízení vyrábějícím armatury z keramiky na kov, hermetické těsnění, vakuové průchodky, komponenty pro řízení vysokého a ultravysokého vakua a kapaliny naleznete zde:_cc781905-5cde-3194-bb3b_536Brožura továrny na pájení
• PÁJENÍ : Při pájení nedochází k tavení obrobků, ale přídavného kovu s nižším bodem tavení než mají spojované části, které zatékají do spoje. Přídavný kov se při pájení taví při nižší teplotě než při pájení. Pro pájení používáme bezolovnaté slitiny a splňují RoHS a pro různé aplikace a požadavky máme různé a vhodné slitiny, jako je slitina stříbra. Pájení nám nabízí spoje, které jsou plynotěsné a kapalinotěsné. Při MĚKKÉM PÁJENÍ má náš přídavný kov bod tání pod 400 stupňů Celsia, zatímco při PÁJENÍ STŘÍBREM a PÁJENÍ natvrdo potřebujeme vyšší teploty. Měkké pájení využívá nižší teploty, ale nevede k pevným spojům pro náročné aplikace při zvýšených teplotách. Stříbrné pájení na druhé straně vyžaduje vysoké teploty poskytované hořákem a poskytuje nám pevné spoje vhodné pro vysokoteplotní aplikace. Pájení vyžaduje nejvyšší teploty a obvykle se používá hořák. Protože jsou pájené spoje velmi pevné, jsou dobrými kandidáty pro opravy těžkých železných předmětů. V našich výrobních linkách používáme jak ruční ruční pájení, tak i automatizované pájecí linky. INDUCTION PÁJENÍ používá vysokofrekvenční střídavý proud v měděné cívce pro usnadnění indukčního ohřevu. V pájené části se indukují proudy a v důsledku toho vzniká teplo na vysokém odporu joint. Toto teplo roztaví přídavný kov. Používá se také tavidlo. Indukční pájení je dobrou metodou pro pájení válců a trubek v nepřetržitém procesu tak, že se kolem nich obalí cívky. Pájení některých materiálů, jako je grafit a keramika, je obtížnější, protože vyžaduje pokovení obrobků před pájením vhodným kovem. To usnadňuje mezifázové propojení. Takové materiály pájeme zejména pro aplikace hermetické obaly. Naše desky plošných spojů (PCB) vyrábíme ve velkém množství převážně pomocí VLNOVÉHO PÁJENÍ. Pouze pro malé množství prototypových účelů používáme ruční pájení pomocí páječky. Pájení vlnou používáme jak pro průchozí, tak pro povrchovou montáž PCB sestav (PCBA). Dočasné lepidlo udržuje součásti připojené k desce s obvody a sestava je umístěna na dopravníku a pohybuje se skrz zařízení, které obsahuje roztavenou pájku. Nejprve je deska plošných spojů natavena a poté vstoupí do zóny předehřívání. Roztavená pájka je v pánvi a má na svém povrchu vzor stojatých vln. Když se deska plošných spojů pohybuje přes tyto vlny, tyto vlny se dotýkají spodní části desky plošných spojů a přilnou k pájecím ploškám. Pájka zůstává pouze na kolících a ploškách a ne na samotné desce plošných spojů. Vlny v roztavené pájce musí být dobře řízeny, aby nedocházelo k rozstřikování a horní části vln se nedotýkaly a nekontaminovaly nežádoucí místa desek. V REFLOW SOLDERING používáme lepivou pájecí pastu k dočasnému připevnění elektronických součástek k deskám. Poté se desky vloží do reflow pece s regulací teploty. Zde se pájka roztaví a trvale spojí součástky. Tuto techniku používáme jak pro komponenty pro povrchovou montáž, tak pro komponenty s průchozími otvory. Správná regulace teploty a nastavení teplot pece je nezbytné, aby se zabránilo zničení elektronických součástek na desce jejich přehřátím nad jejich maximální teplotní limity. V procesu pájení přetavením máme ve skutečnosti několik oblastí nebo stupňů, z nichž každý má odlišný tepelný profil, jako je krok předehřívání, krok tepelného namáčení, kroky přetavování a chlazení. Tyto různé kroky jsou nezbytné pro pájení bez poškození přetavením sestav desek s plošnými spoji (PCBA). ULTRAZVUKOVÉ PÁJENÍ je další často používaná technika s jedinečnými schopnostmi - lze ji použít k pájení skla, keramiky a nekovových materiálů. Například fotovoltaické panely, které jsou nekovové, potřebují elektrody, které lze připevnit pomocí této techniky. Při ultrazvukovém pájení nasazujeme vyhřívaný pájecí hrot, který také vydává ultrazvukové vibrace. Tyto vibrace vytvářejí kavitační bubliny na rozhraní substrátu s roztaveným pájkovým materiálem. Implozivní energie kavitace upravuje povrch oxidu a odstraňuje nečistoty a oxidy. Během této doby se také vytvoří vrstva slitiny. Pájka na spojovacím povrchu obsahuje kyslík a umožňuje vytvoření silné sdílené vazby mezi sklem a pájkou. PÁJENÍ MÁČEM lze považovat za jednodušší verzi vlnového pájení vhodnou pouze pro malosériovou výrobu. Jako u jiných procesů se aplikuje první čistící tavidlo. Desky plošných spojů s osazenými součástkami jsou ručně nebo poloautomaticky ponořeny do nádrže obsahující roztavenou pájku. Roztavená pájka ulpívá na odkrytých kovových plochách nechráněných pájecí maskou na desce. Zařízení je jednoduché a levné.
• LEPENÍ: Toto je další oblíbená technika, kterou často používáme a zahrnuje lepení povrchů pomocí lepidel, epoxidů, plastů nebo jiných chemikálií. Lepení se provádí buď odpařením rozpouštědla, tepelným vytvrzením, vytvrzením UV světlem, tlakovým vytvrzením nebo čekáním po určitou dobu. V našich výrobních linkách se používají různá vysoce výkonná lepidla. Při správně navržených procesech aplikace a vytvrzování může lepení vést k spojům s velmi nízkým napětím, které jsou pevné a spolehlivé. Lepené spoje mohou být dobrou ochranou proti faktorům prostředí, jako je vlhkost, nečistoty, korozivní látky, vibrace atd. Výhody lepení jsou: lze je aplikovat na materiály, které by se jinak těžko pájely, svařovaly nebo pájely. Také může být výhodnější pro materiály citlivé na teplo, které by byly poškozeny svařováním nebo jinými vysokoteplotními procesy. Další výhodou lepidel je, že mohou být aplikovány na nepravidelně tvarované povrchy a ve srovnání s jinými metodami zvyšují hmotnost sestavy o velmi malé množství. Také rozměrové změny dílů jsou velmi minimální. Některá lepidla mají vlastnosti přizpůsobení indexu a lze je použít mezi optickými součástmi bez výrazného snížení intenzity světla nebo optického signálu. Nevýhody na druhé straně jsou delší doby vytvrzování, které mohou zpomalit výrobní linky, požadavky na upevnění, požadavky na přípravu povrchu a potíže s demontáží v případě potřeby přepracování. Většina našich operací lepení zahrnuje následující kroky:
-Povrchová úprava: Běžné jsou speciální čisticí postupy, jako je čištění deionizovanou vodou, čištění alkoholem, plazmové nebo korónové čištění. Po očištění můžeme na povrchy nanést promotory přilnavosti, abychom zajistili co nejlepší spoje.
-Upevnění dílů: Jak pro aplikaci lepidla, tak pro vytvrzování navrhujeme a používáme vlastní přípravky.
-Aplikace lepidla: Někdy používáme ruční a někdy v závislosti na případu automatizované systémy, jako je robotika, servomotory, lineární pohony k dodání lepidla na správné místo a používáme dávkovače k dodání ve správném objemu a množství.
-Vytvrzování: V závislosti na lepidle můžeme použít jednoduché sušení a vytvrzování, stejně jako vytvrzování pod UV světlem, které funguje jako katalyzátor, nebo vytvrzování teplem v peci nebo pomocí odporových topných prvků namontovaných na přípravcích a upínacích přípravcích.
Doporučujeme kliknout semSTÁHNĚTE SI naše schématická vyobrazení upevňovacích procesů od AGS-TECH Inc.
To vám pomůže lépe porozumět informacím, které vám poskytujeme níže.
• SPOJOVACÍ PROCESY: Naše mechanické spojovací procesy spadají do dvou hlavních kategorií: SPOJOVACÍ PRVKY a INTEGRÁLNÍ SPOJKY. Příklady spojovacích prvků, které používáme, jsou šrouby, kolíky, matice, šrouby, nýty. Příklady integrálních spojů, které používáme, jsou nacvakávací a smršťovací spoje, švy, lemování. Pomocí různých způsobů upevnění zajišťujeme, že naše mechanické spoje jsou pevné a spolehlivé po mnoho let používání. ŠROUBY a ŠROUBY jsou některé z nejběžněji používaných spojovacích prvků pro držení předmětů pohromadě a jejich umístění. Naše šrouby a šrouby splňují normy ASME. Používají se různé typy šroubů a šroubů, včetně šroubů se šestihrannou hlavou a šroubů s šestihrannou hlavou, pozdržených šroubů a šroubů, dvoukoncových šroubů, šroubů s hmoždinkami, šroubů s okem, zrcadlových šroubů, šroubů do plechu, šroubů pro jemné nastavení, samořezných a samořezných šroubů , stavěcí šroub, šrouby s vestavěnými podložkami,…a další. Máme různé typy hlav šroubů, jako jsou zápustné, kopulovité, kulaté, přírubové hlavy a různé typy šroubů, jako jsou drážkové, křížové, čtyřhranné, šestihranné. RIVET na druhé straně je trvalý mechanický spojovací prvek sestávající z hladké válcové násady a hlavy na jedné straně. Po vložení se druhý konec nýtu zdeformuje a jeho průměr se roztáhne tak, aby zůstal na místě. Jinými slovy, před instalací má nýt jednu hlavu a po instalaci dvě. Instalujeme různé typy nýtů v závislosti na aplikaci, síle, přístupnosti a ceně, jako jsou nýty s pevnou/kulatou hlavou, konstrukční, polotrubkové, slepé, oscarové, hnací, zapuštěné, třecí nýty, samořezné nýty. Nýtování lze upřednostnit v případech, kdy je třeba zabránit tepelné deformaci a změně vlastností materiálu vlivem svařovacího tepla. Nýtování nabízí také nízkou hmotnost a především dobrou pevnost a odolnost vůči střižným silám. Proti tahovým zatížením však mohou být vhodnější šrouby, matice a šrouby. V procesu CLINCHING používáme speciální razníky a matrice k vytvoření mechanického spojení mezi spojovanými plechy. Razník tlačí vrstvy plechu do dutiny zápustky a výsledkem je vytvoření trvalého spoje. Clinchování nevyžaduje žádné zahřívání ani chlazení a jedná se o proces zpracování za studena. Je to ekonomický proces, který může v některých případech nahradit bodové svařování. V PINNING používáme čepy, což jsou strojní prvky sloužící k zajištění poloh strojních součástí vůči sobě. Hlavní typy jsou vidlicové kolíky, závlačky, pružinové kolíky, kolíky, a závlačka. V SEŠÍVÁNÍ používáme sešívací pistole a sponky, což jsou dvouhrotové spojovací prvky používané ke spojování nebo spojování materiálů. Sešívání má následující výhody: Ekonomické, jednoduché a rychlé použití, korunku sponek lze použít k přemostění materiálů spojených dohromady, Koruna sponek může usnadnit přemostění kusu, jako je kabel a jeho upevnění k povrchu bez proražení nebo poškození, relativně snadné odstranění. LISKOVÁNÍ se provádí přitlačením dílů k sobě a tření mezi nimi díly spojí. Lisované díly skládající se z nadrozměrného hřídele a poddimenzovaného otvoru se obecně montují jedním ze dvou způsobů: Buď použitím síly, nebo využitím tepelné roztažnosti nebo smrštění dílů. Když je lisovací tvarovka vytvořena působením síly, použijeme buď hydraulický lis, nebo ručně ovládaný lis. Na druhou stranu, když je lisovaná tvarovka ustavena tepelnou roztažností, zahřejeme obalové díly a za tepla je smontujeme na své místo. Když vychladnou, smrští se a vrátí se do svých normálních rozměrů. Výsledkem je dobré lisování. Alternativně tomu říkáme SHRINK-FITTING. Dalším způsobem, jak toho dosáhnout, je ochlazení obalovaných dílů před montáží a jejich následné zasunutí do příslušných dílů. Když se sestava zahřeje, roztáhnou se a získáme pevné usazení. Tato druhá metoda může být výhodnější v případech, kdy ohřev představuje riziko změny vlastností materiálu. Chlazení je v těchto případech bezpečnější.
Pneumatické a hydraulické komponenty a sestavy
• Ventily, hydraulické a pneumatické komponenty jako O-kroužek, podložka, těsnění, těsnění, kroužek, podložka.
Vzhledem k tomu, že ventily a pneumatické komponenty jsou k dispozici ve velkém množství, nemůžeme zde vyjmenovat vše. V závislosti na fyzikálním a chemickém prostředí vaší aplikace pro vás máme speciální produkty. Upřesněte nám prosím aplikaci, typ součásti, specifikace, podmínky prostředí, jako je tlak, teplota, kapaliny nebo plyny, které budou v kontaktu s vašimi ventily a pneumatickými součástmi; a vybereme pro vás nejvhodnější produkt nebo jej vyrobíme speciálně pro vaši aplikaci.