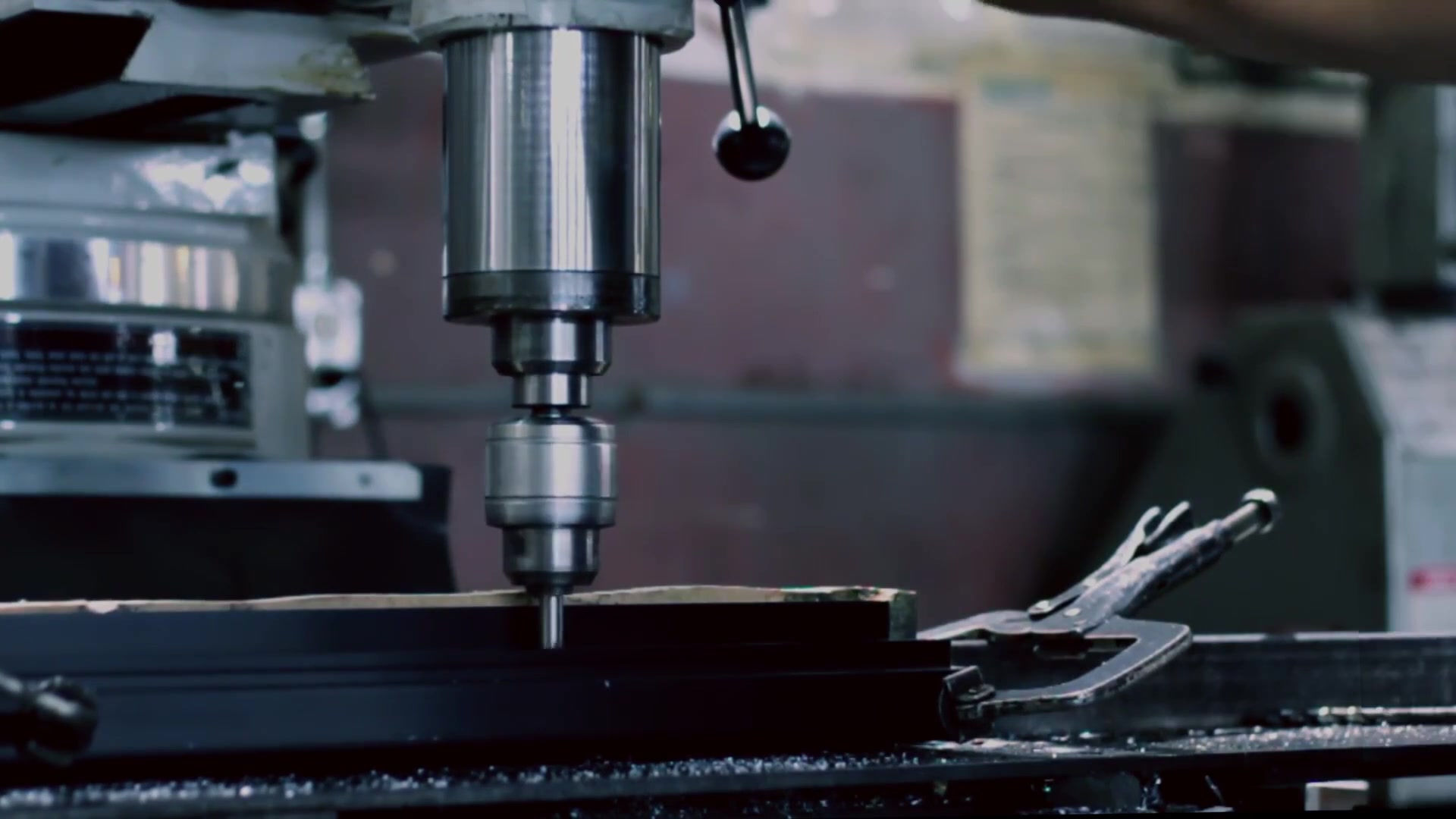
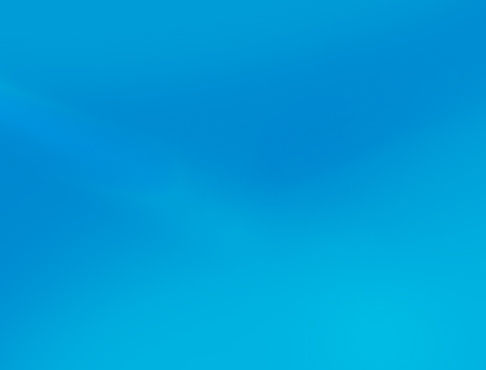
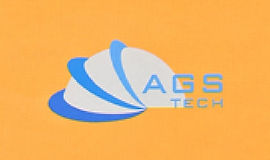
Globální zakázkový výrobce, integrátor, konsolidátor, partner pro outsourcing pro širokou škálu produktů a služeb.
Jsme vaším komplexním zdrojem pro výrobu, výrobu, inženýrství, konsolidaci, integraci, outsourcing zakázkově vyráběných i volně prodejných produktů a služeb.
Choose your Language
-
Zakázková výroba
-
Domácí a globální smluvní výroba
-
Outsourcing výroby
-
Domácí a globální zadávání zakázek
-
Konsolidace
-
Engineering Integration
-
Inženýrské služby
Search Results
Bylo nalezeno 164 výsledků u prázdného vyhledávání
- Transmission Components, Belts, Chains, Cable Drives, Pulleys,AGS-TECH
Transmission Components, Belts, Chains and Cable Drives, Conventional & Grooved or Serrated, Positive Drive, Pulleys Sestava řemenů a řetězů a kabelového pohonu AGS-TECH Inc. vám nabízí komponenty pro přenos síly včetně řemenů a řetězů a sestavy pohonu lanek. S léty zdokonalování se naše pryžové, kožené a další řemenové pohony staly lehčími a kompaktnějšími, schopné přenášet vyšší zatížení při nižších nákladech. Stejně tak naše řetězové pohony prošly postupem času velkým vývojem a našim zákazníkům nabízejí několik výhod. Některé výhody použití řetězových pohonů jsou jejich relativně neomezené osové vzdálenosti hřídele, kompaktnost, snadná montáž, elasticita v tahu bez prokluzu nebo tečení, schopnost pracovat v prostředí s vysokou teplotou. Naše kabelové pohony také nabízejí výhody, jako je jednoduchost v některých aplikacích oproti jiným typům komponent převodovky. K dispozici jsou jak standardní řemenové, řetězové a kabelové pohony, tak i zakázkově vyrobené a sestavené verze. Můžeme vyrobit tyto komponenty převodovky ve správné velikosti pro vaši aplikaci a z nejvhodnějších materiálů. ŘEMENY A ŘEMENOVÉ POHONY: - Konvenční ploché řemeny: Jedná se o hladké ploché řemeny bez zubů, drážek nebo zoubků. Pohony s plochým řemenem nabízejí flexibilitu, dobré tlumení nárazů, účinný přenos síly při vysokých rychlostech, odolnost proti oděru, nízkou cenu. Pásy lze spojovat nebo spojovat a vytvářet tak větší pásy. Další výhodou běžných plochých řemenů je, že jsou tenké, nepodléhají vysokému odstředivému zatížení (vhodné pro vysokorychlostní operace s malými řemenicemi). Na druhou stranu kladou vysoké zatížení ložisek, protože ploché řemeny vyžadují vysoké napětí. Dalšími nevýhodami plochých řemenových pohonů může být prokluzování, hlučný provoz a relativně nižší účinnost při nízkých a středních rychlostech provozu. Máme dva typy konvenčních pásů: vyztužené a nevyztužené. Vyztužené pásy mají ve své struktuře tahový prvek. Běžné ploché řemeny jsou k dispozici jako kůže, pogumovaná tkanina nebo šňůra, nevyztužená pryž nebo plast, tkanina, zesílená kůže. Kožené řemeny nabízí dlouhou životnost, pružnost, výborný koeficient tření, snadnou opravu. Kožené opasky jsou však relativně drahé, vyžadují úpravu a čištění opasku a v závislosti na atmosféře se mohou smrštit nebo natáhnout. Pogumované textilní nebo kordové pásy jsou odolné vůči vlhkosti, kyselinám a zásadám. Pogumované textilní pásy jsou vyrobeny z vrstev bavlny nebo syntetické kachny impregnované pryží a jsou nejekonomičtější. Pogumované kordové pásy se skládají z řady vrstev kaučukem impregnovaných kordů. Pogumované kordové pásy nabízejí vysokou pevnost v tahu a skromné rozměry a hmotnost. Nevyztužené pryžové nebo plastové řemeny jsou vhodné pro nenáročné aplikace s nízkými otáčkami. Nevyztužené pryžové a plastové pásy lze natáhnout na jejich místo přes jejich kladky. Plastové nevyztužené řemeny mohou přenášet vyšší výkon ve srovnání s pryžovými řemeny. Vyztužené kožené opasky se skládají z plastového tahového prvku vloženého mezi koženou horní a spodní vrstvu. Nakonec mohou naše látkové pásy sestávat z jednoho kusu bavlny nebo kachny složeného a sešitého řadami podélných stehů. Látkové pásy jsou schopny stejnoměrně sledovat a pracovat vysokou rychlostí. - Drážkované nebo ozubené řemeny (jako jsou klínové řemeny): Jedná se o základní ploché řemeny upravené tak, aby poskytovaly výhody jiného typu převodového produktu. Jedná se o ploché pásy s podélně žebrovanou spodní stranou. Poly-V řemeny jsou podélně rýhované nebo zoubkované ploché řemeny s tažnou částí a řadou sousedních drážek ve tvaru V pro účely sledování a stlačení. Výkon závisí na šířce pásu. Klínové řemeny jsou tahounem průmyslu a jsou k dispozici v různých standardizovaných velikostech a typech pro přenos téměř jakékoli zátěže. Pohony klínovými řemeny fungují dobře mezi 1500 až 6000 stop/min, avšak úzké klínové řemeny budou fungovat až do 10 000 stop/min. Pohony s klínovým řemenem nabízejí dlouhou životnost, např. 3 až 5 let a umožňují velké rychlostní poměry, snadno se instalují a demontují, nabízejí tichý provoz, nízké nároky na údržbu, dobré tlumení rázů mezi hnacím řemenem a hnanými hřídeli. Nevýhodou klínových řemenů je jejich určitý prokluz a dotvarování, a proto nemusí být nejlepším řešením tam, kde jsou vyžadovány synchronní otáčky. Máme průmyslové, automobilové a zemědělské řemeny. K dispozici jsou skladové standardní délky i zakázkové délky řemenů. Všechny standardní průřezy klínových řemenů jsou dostupné ze skladu. Existují tabulky, kde můžete vypočítat neznámé parametry, jako je délka řemene, sekce řemenu (šířka a tloušťka), pokud znáte některé parametry vašeho systému, jako jsou průměry hnacích a hnaných řemenic, středová vzdálenost mezi řemenicemi a rychlosti otáčení řemenic. Můžete použít takové tabulky nebo nás požádat, abychom pro vás vybrali ten správný klínový řemen. - Pozitivní hnací řemeny (rozvodový řemen): Tyto řemeny jsou také plochého typu s řadou rovnoměrně rozmístěných zubů na vnitřním obvodu. Pozitivní hnací nebo rozvodové řemeny kombinují výhody plochých řemenů s pozitivním záběrem řetězů a ozubených kol. Pozitivní hnací řemeny nevykazují žádné prokluzování nebo kolísání rychlosti. Je možný široký rozsah rychlostních poměrů. Zatížení ložisek je nízké, protože mohou pracovat při nízkém napětí. Jsou však náchylnější k nesouososti řemenic. - Řemenice, kladky, náboje pro řemeny: Používají se různé typy řemenic s plochými, žebrovanými (zubatými) a pozitivními hnacími řemeny. Všechny je vyrábíme. Většina našich plochých řemenic je vyrobena litím ze železa, ale ocelové verze jsou k dispozici také v různých kombinacích ráfků a nábojů. Naše řemenice s plochým řemenem mohou mít pevné, paprskové nebo dělené náboje nebo je můžeme vyrobit podle vašeho přání. Žebrované řemeny a řemeny s pozitivním pohonem jsou k dispozici v různých velikostech a šířkách. Alespoň jedna řemenice v pohonech s rozvodovým řemenem musí být opatřena přírubou, aby řemen na pohonu zůstal. U systémů s dlouhým středovým pohonem se doporučuje mít obě řemenice s přírubou. Kladky jsou drážkovaná kola řemenic a jsou obecně vyráběny litím železa, tvářením oceli nebo lisováním plastů. Tváření oceli je vhodný proces pro výrobu automobilových a zemědělských kladek. Vyrábíme kladky s pravidelnými a hlubokými drážkami. Kladky s hlubokou drážkou jsou vhodné, když klínový řemen vstupuje do kladky pod úhlem, jako je tomu u čtvrtotáčkových pohonů. Hluboké drážky jsou také vhodné pro pohony s vertikálními hřídeli a aplikace, kde mohou být problémem vibrace řemenů. Naše napínací kladky jsou drážkované kladky nebo ploché kladky, které neslouží k přenosu mechanické síly. Napínací kladky se používají převážně pro napínání řemenů. - Pohony s jedním a více řemeny: Pohony s jedním řemenem mají jednu drážku, zatímco více řemenové pohony mají více drážek. Kliknutím na příslušný barevný text níže si můžete stáhnout naše katalogy: - Řemeny pro přenos síly (zahrnuje klínové řemeny, rozvodové řemeny, řemeny s hrubými okraji, obalené řemeny a speciální řemeny) - Dopravní pásy - V-kladky - Rozvodové řemenice ŘETĚZY A ŘETĚZOVÉ POHONY: Naše řetězy pro přenos síly mají některé výhody, jako jsou relativně neomezené osové vzdálenosti hřídele, snadná montáž, kompaktnost, pružnost v tahu bez prokluzu nebo tečení, schopnost provozu za vysokých teplot. Zde jsou hlavní typy našich řetězů: - Odnímatelné řetězy: Naše odnímatelné řetězy jsou vyráběny v různých velikostech, roztečí a maximální pevnosti a obecně z kujného železa nebo oceli. Kujné řetězy jsou vyráběny v řadě velikostí od 0,902 (23 mm) do 4,063 palce (103 mm) rozteče a maximální pevnosti od 700 do 17 000 lb/čtvereční palec. Naše odnímatelné ocelové řetězy jsou na druhé straně vyráběny ve velikostech od 0,904 palce (23 mm) do asi 3,00 palce (76 mm) v rozteči, s maximální pevností od 760 do 5000 lb/čtvereční palec._cc781905-5cde-3194-bb3b- 136bad5cf58d_ - Jehlové řetězy: Tyto řetězy se používají pro větší zatížení a mírně vyšší rychlosti do asi 450 stop/min (2,2 m/s). Jetové řetězy jsou vyrobeny z jednotlivých litých článků s plným kulatým koncem hlavně s odsazenými bočnicemi. Tyto články řetězu jsou propojeny s ocelovými čepy. Tyto řetězy se pohybují v rozteči od asi 1,00 palce (25 mm) do 6,00 palce (150 mm) a maximální pevnosti mezi 3600 až 30 000 lb/palec čtvereční. - Řetězy s offsetovou boční lištou: Jsou oblíbené u hnacích řetězů stavebních strojů. Tyto řetězy pracují při rychlostech do 1000 stop/min a přenášejí zatížení na přibližně 250 hp. Obecně má každý článek dvě odsazené boční lišty, jedno pouzdro, jeden válec, jeden čep, závlačku. - Válečkové řetězy: Jsou k dispozici v roztečích od 0,25 (6 mm) do 3,00 (75 mm) palce. Maximální pevnost válečkových řetězů s jednou šířkou se pohybuje mezi 925 až 130 000 lb/čtvereční palec. K dispozici jsou verze válečkových řetězů s více šířkami a přenášejí větší výkon při vyšších rychlostech. Válečkové řetězy s více šířkami také nabízejí hladší chod se sníženou hlučností. Válečkové řetězy jsou sestaveny z válečkových a čepových článků. Závlačky se používají u válečkových řetězů odnímatelné verze. Konstrukce válečkových řetězových pohonů vyžaduje odbornou způsobilost. Zatímco řemenové pohony jsou založeny na lineárních rychlostech, řetězové pohony jsou založeny na rychlosti otáčení menšího řetězového kola, které je ve většině instalací hnaným členem. Kromě jmenovitého výkonu a rychlosti otáčení je konstrukce řetězových pohonů založena na mnoha dalších faktorech. - Dvojité řetězy: V podstatě stejné jako válečkové řetězy s tím rozdílem, že rozteč je dvakrát delší. - Řetězy s obráceným ozubením (tiché): Vysokorychlostní řetězy používané většinou pro pohony s hnacím hřídelem a vývodovým hřídelem. Pohony s obráceným ozubeným řetězem mohou přenášet výkon až 1200 hp a jsou tvořeny řadou ozubených článků, střídavě sestavených buď s čepy, nebo kombinací součástí kloubu. Středový vodicí řetěz má vodicí články pro zasunutí do drážek v ozubeném kole a boční vodicí řetěz má vodítka pro zapojení do stran ozubeného kola. - Korálkové nebo posuvné řetězy: Tyto řetězy se používají pro pomalé jízdy a také pro ruční operace. Kliknutím na příslušný barevný text níže si můžete stáhnout naše katalogy: - Hnací řetězy - Dopravníkové řetězy - Dopravníkové řetězy s velkým roztečím - Válečkové řetězy z nerezové oceli - Zvedací řetězy - Motocyklové řetězy - Řetězy zemědělských strojů - Řetězová kola: Naše standardní ozubená kola odpovídají normám ANSI. Talířová ozubená kola jsou plochá ozubená kola bez náboje. Naše malá a středně velká řetězová kola jsou soustružena z tyčového materiálu nebo výkovků nebo jsou vyrobena přivařením náboje tyčového materiálu k plechu válcovaném za tepla. AGS-TECH Inc. může dodat řetězová kola obrobená z odlitků ze šedé litiny, ocelolitiny a svařovaných konstrukcí nábojů, slinutých práškových kovů, lisovaných nebo obráběných plastů. Pro hladký chod při vysokých rychlostech je nezbytný správný výběr velikosti řetězových kol. Prostorové omezení je samozřejmě faktor, který nemůžeme při výběru řetězového kola ignorovat. Doporučuje se, aby poměr unašeče k hnaným řetězovým kolům nebyl větší než 6:1 a navinutí řetězu na unašeči bylo 120 stupňů. Středové vzdálenosti mezi menšími a většími řetězovými koly, délky řetězu a napnutí řetězu musí být také zvoleny podle některých doporučených technických výpočtů a pokynů a nikoli náhodně. Stáhněte si naše katalogy kliknutím na barevný text níže: - Řetězová kola a talířová kola - Převodová pouzdra - Řetězová spojka - Zámky řetězu LANOVÉ POHONY: Tyto mají v některých případech své výhody oproti řemenovým a řetězovým pohonům. Kabelové pohony mohou plnit stejnou funkci jako řemeny a v některých aplikacích mohou být také jednodušší a ekonomičtější. Například nová řada Synchromesh Cable Drives je navržena pro pozitivní trakci, aby nahradila konvenční lana, jednoduchá lana a ozubené pohony, zejména ve stísněných prostorech. Nový kabelový pohon je navržen tak, aby poskytoval vysoce přesné polohování v elektronických zařízeních, jako jsou kopírky, plotry, psací stroje, tiskárny,….. atd. Klíčovou vlastností nového kabelového pohonu je jeho schopnost použití ve 3D hadovitých konfiguracích, které umožňují extrémně miniaturní designy. Synchromované kabely lze použít s nižším napětím ve srovnání s lany, čímž se snižuje spotřeba energie. Pro dotazy a názory na řemeny, řetězové a lanové pohony kontaktujte AGS-TECH. CLICK Product Finder-Locator Service PŘEDCHOZÍ STRÁNKA
- Rapid Prototyping, Desktop Manufacturing, Additive Manufacturing, FDM
Rapid Prototyping, Desktop Manufacturing, Additive Manufacturing, Stereolithography, Polyjet, Fused Deposition Modeling, Selective Laser Sintering, FDM, SLS Aditivní a rychlá výroba V posledních letech zaznamenáváme nárůst poptávky po RAPID MANUFACTURING nebo RAPID PROTOTYPING. Tento proces může být také nazýván DESKTOP MANUFACTURING nebo FREE-FORM FABRICATION. V zásadě je pevný fyzický model součásti vyroben přímo z trojrozměrného výkresu CAD. Pro tyto různé techniky, kdy stavíme díly ve vrstvách, používáme termín ADITIVNÍ VÝROBA. Pomocí integrovaného počítačem řízeného hardwaru a softwaru provádíme aditivní výrobu. Naše rychlé prototypování a výrobní techniky jsou STEREOLITOGRAFIE, POLYJET, FUSED-DEPOZIČNÍ MODELOVÁNÍ, SELEKTIVNÍ LASEROVÉ SINTROVÁNÍ, TAVENÍ ELEKTRONOVÝM PAPRSKEM, TROJROZMĚRNÝ TISK, PŘÍMÁ VÝROBA, RYCHLÉ NÁSTROJE. Doporučujeme kliknout semSTÁHNĚTE SI naše schematické ilustrace aditivní výroby a rychlých výrobních procesů od AGS-TECH Inc. To vám pomůže lépe porozumět informacím, které vám poskytujeme níže. Rapid prototyping nám poskytuje: 1.) Koncepční návrh produktu je nahlížen z různých úhlů na monitor pomocí 3D / CAD systému. 2.) Prototypy z nekovových a kovových materiálů jsou vyráběny a studovány z funkčního, technického a estetického hlediska. 3.) Nízkonákladové prototypování je provedeno ve velmi krátké době. Aditivní výroba se může podobat stavbě bochníku chleba stohováním a lepením jednotlivých plátků na sebe. Jinými slovy, produkt se vyrábí plátek po plátku nebo vrstva po vrstvě nanesená jedna na druhou. Většinu dílů lze vyrobit během několika hodin. Tato technika je dobrá, pokud jsou díly potřeba velmi rychle nebo pokud jsou potřebná množství malá a výroba formy a nástrojů je příliš drahá a časově náročná. Náklady na součást jsou však drahé kvůli drahým surovinám. • STEREOLITOGRAFIE : Tato technika označovaná také jako STL je založena na vytvrzování a vytvrzování kapalného fotopolymeru do specifického tvaru zaostřením laserového paprsku na něj. Laser polymerizuje fotopolymer a vytvrzuje jej. Skenováním UV laserového paprsku podle naprogramovaného tvaru podél povrchu směsi fotopolymerů je díl vyráběn zdola nahoru v jednotlivých řezech kaskádovitě na sebe. Skenování laserového bodu se mnohokrát opakuje, aby se dosáhlo geometrií naprogramovaných v systému. Poté, co je díl kompletně vyroben, sejme se z platformy, odsaje a vyčistí ultrazvukem a lihovou lázní. Poté se na několik hodin vystaví UV záření, aby se zajistilo úplné vytvrzení a vytvrzení polymeru. Abychom shrnuli proces, platforma, která je ponořena do směsi fotopolymeru a UV laserový paprsek jsou řízeny a pohybovány přes servořídicí systém podle tvaru požadovaného dílu a díl je získán fotovytvrzením polymerní vrstvy po vrstvě. Maximální rozměry vyráběného dílu jsou samozřejmě určeny stereolitografickým zařízením. • POLYJET: Podobně jako u inkoustového tisku máme v polyjetu osm tiskových hlav, které ukládají fotopolymer na sestavovací zásobník. Ultrafialové světlo umístěné vedle trysek okamžitě vytvrzuje a vytvrzuje každou vrstvu. V polyjetu se používají dva materiály. První materiál je pro výrobu skutečného modelu. Druhý materiál, gelovitá pryskyřice, se používá jako podpora. Oba tyto materiály se nanášejí vrstvu po vrstvě a současně vytvrzují. Po dokončení modelu se nosný materiál odstraní vodným roztokem. Použité pryskyřice jsou podobné stereolitografii (STL). Polyjet má oproti stereolitografii následující výhody: 1.) Není potřeba čištění dílů. 2.) Není potřeba vytvrzování po procesu 3.) Menší tloušťky vrstvy jsou možné a tím získáváme lepší rozlišení a můžeme vyrábět jemnější díly. • FUSED DEPOSITION MODELING: Také zkráceně FDM, v této metodě se robotem řízená extruderová hlava pohybuje nad stolem ve dvou hlavních směrech. Kabel se spouští a zvedá podle potřeby. Z otvoru vyhřívané matrice na hlavě se vytlačuje termoplastické vlákno a na pěnový základ se nanese počáteční vrstva. Toho je dosaženo vytlačovací hlavou, která sleduje předem stanovenou dráhu. Po počáteční vrstvě se stůl spustí a další vrstvy se ukládají na sebe. Někdy jsou při výrobě komplikovaného dílu potřeba podpůrné konstrukce, aby nanášení mohlo pokračovat v určitých směrech. V těchto případech je nosný materiál vytlačován s menší hustotou rozmístění filamentů na vrstvě, takže je slabší než modelový materiál. Tyto nosné konstrukce lze později po dokončení dílu rozpustit nebo odlomit. Rozměry vytlačovací hubice určují tloušťku vytlačovaných vrstev. Proces FDM vytváří díly se stupňovitými povrchy na šikmých vnějších rovinách. Pokud je tato drsnost nepřijatelná, lze je vyhladit chemickým leštěním par nebo vyhřívaným nástrojem. Dokonce i leštící vosk je k dispozici jako nátěrový materiál, který eliminuje tyto kroky a dosahuje přiměřených geometrických tolerancí. • SELEKTIVNÍ LASEROVÉ SPÍNÁNÍ: Také označované jako SLS, proces je založen na slinování polymerních, keramických nebo kovových prášků selektivně do předmětu. Spodní část zpracovací komory má dva válce: válec s částečnou konstrukcí a válec pro podávání prášku. První jmenovaný je postupně spouštěn do místa, kde se tvoří slinutá část, a druhý je postupně zvednut, aby přiváděl prášek do válce pro částečnou konstrukci prostřednictvím válečkového mechanismu. Nejprve se nanese tenká vrstva prášku ve válci pro částečnou stavbu, poté se na tuto vrstvu zaostří laserový paprsek, nakreslí a roztaví/slinuje konkrétní průřez, který pak znovu ztuhne na pevnou látku. Prášek jsou oblasti, které nejsou zasaženy laserovým paprskem, zůstávají volné, ale stále podporují pevnou část. Poté se nanese další vrstva prášku a proces se mnohokrát opakuje, aby se získal díl. Na konci se setřesou volné částice prášku. To vše provádí procesní řídicí počítač pomocí instrukcí generovaných 3D CAD programem vyráběného dílu. Lze nanášet různé materiály, jako jsou polymery (jako ABS, PVC, polyester), vosk, kovy a keramika s vhodnými polymerními pojivy. • ELECTRON-BEAM MELTING : Podobné jako selektivní laserové slinování, ale s použitím elektronového paprsku k roztavení titanu nebo kobalt-chromových prášků k výrobě prototypů ve vakuu. Pro provádění tohoto procesu na nerezových ocelích, hliníku a slitinách mědi došlo k určitému vývoji. Pokud je třeba zvýšit únavovou pevnost vyráběných dílů, používáme jako sekundární proces po výrobě dílu izostatické lisování za tepla. • TROJROZMĚRNÝ TISK: Také označovaný jako 3DP, v této technice tisková hlava nanáší anorganické pojivo na vrstvu buď nekovového nebo kovového prášku. Píst nesoucí práškové lože je postupně spouštěn a v každém kroku je pojivo nanášeno vrstva po vrstvě a taveno pojivem. Používanými práškovými materiály jsou polymerní směsi a vlákna, slévárenský písek, kovy. Použitím různých hlav pojiva současně a různých barevných pojiv můžeme získat různé barvy. Proces je podobný inkoustovému tisku, ale místo získání barevného listu získáme barevný trojrozměrný objekt. Vyrobené díly mohou být porézní, a proto mohou vyžadovat slinování a infiltraci kovu ke zvýšení jejich hustoty a pevnosti. Slinování spálí pojivo a spojí kovové prášky dohromady. K výrobě dílů lze použít kovy jako nerez, hliník, titan a jako infiltrační materiály běžně používáme měď a bronz. Krása této techniky spočívá v tom, že i složité a pohyblivé sestavy lze vyrobit velmi rychle. Například lze vyrobit ozubenou sestavu, klíč jako nástroj a bude mít pohyblivé a otáčecí části připravené k použití. Různé součásti sestavy lze vyrobit v různých barvách a to vše najednou. Stáhněte si naši brožuru na:Základy 3D tisku kovů • PŘÍMÁ VÝROBA a RYCHLÉ NÁSTROJE: Kromě hodnocení návrhu, řešení problémů používáme rychlé prototypování pro přímou výrobu produktů nebo přímou aplikaci do produktů. Jinými slovy, rychlé prototypování lze začlenit do konvenčních procesů, aby byly lepší a konkurenceschopnější. Například rychlé prototypování může vytvářet vzory a formy. Vzory tavícího se a hořícího polymeru vytvořené operacemi rychlého prototypování lze sestavit pro vytavitelné lití a zatavit. Dalším příkladem, který je třeba zmínit, je použití 3DP k výrobě keramické odlévací skořepiny a její použití pro operace odlévání skořepin. Dokonce i vstřikovací formy a vložky do forem lze vyrábět rychlým prototypováním a lze ušetřit mnoho týdnů nebo měsíců doby výroby forem. Pouze analýzou CAD souboru požadovaného dílu můžeme vytvořit geometrii nástroje pomocí softwaru. Zde jsou některé z našich oblíbených metod rychlého obrábění: RTV (Vulkanizace při pokojové teplotě) LISOVÁNÍ / URETANOVÉ ODLITÍ: Pomocí rychlého prototypování lze vytvořit vzor požadovaného dílu. Poté se tento vzor potáhne separačním prostředkem a na vzor se nalije tekutá RTV pryž, aby se vytvořily poloviny formy. Dále se tyto poloviny formy použijí pro vstřikování kapalných uretanů. Životnost formy je krátká, jen jako 0 nebo 30 cyklů, ale dostačující pro výrobu malých sérií. ACES (Acetal Clear Epoxy Solid) VSTŘIKOVÁNÍ: Pomocí technik rychlého prototypování, jako je stereolitografie, vyrábíme vstřikovací formy. Tyto formy jsou skořepiny s otevřeným koncem, které umožňují plnění materiály, jako je epoxid, epoxid plněný hliníkem nebo kovy. Životnost formy je opět omezena na desítky nebo maximálně stovky dílů. PROCES STŘÍKANÝCH KOVOVÝCH NÁSTROJŮ: Používáme rychlé prototypování a vyrábíme vzor. Na povrch vzoru nastříkáme slitinu zinku a hliníku a natřeme. Vzor s kovovým povlakem se pak umístí do baňky a zalije se epoxidem nebo epoxidem plněným hliníkem. Nakonec se odstraní a vyrobením dvou takových polovin formy získáme kompletní formu pro vstřikování. Tyto formy mají delší životnost, v některých případech v závislosti na materiálu a teplotách mohou vyrábět díly v tisících. PROCES KEELTOOL: Tato technika může vyrábět formy s životností 100 000 až 10 milionů cyklů. Pomocí rychlého prototypování vyrábíme formu RTV. Forma se poté naplní směsí skládající se z prášku nástrojové oceli A6, karbidu wolframu, polymerního pojiva a nechá se vytvrdit. Tato forma se poté zahřeje, aby se polymer spálil a kovové prášky se roztavily. Dalším krokem je infiltrace mědi za účelem výroby konečné formy. V případě potřeby lze na formě provádět sekundární operace, jako je obrábění a leštění pro lepší rozměrovou přesnost. _cc781905-5cde-3194-bb3b-136d_5c CLICK Product Finder-Locator Service PŘEDCHOZÍ STRÁNKA
- Composites, Composite Materials Manufacturing, Fiber Reinforced
Composites, Composite Materials Manufacturing, Particle and Fiber Reinforced, Cermets, Ceramic & Metal Composite, Glass Fiber Reinforced Polymer, Lay-Up Process Výroba kompozitů a kompozitních materiálů Jednoduše definováno, KOMPOZITY nebo KOMPOZITNÍ MATERIÁLY jsou materiály sestávající ze dvou nebo více materiálů s různými fyzikálními nebo chemickými vlastnostmi, ale když se zkombinují, stanou se materiálem, který se liší od základních materiálů. Musíme zdůraznit, že základní materiály zůstávají ve struktuře oddělené a odlišné. Cílem při výrobě kompozitního materiálu je získat produkt, který je lepší než jeho složky a kombinuje požadované vlastnosti každé složky. Jako příklad; síla, nízká hmotnost nebo nižší cena mohou být motivací při navrhování a výrobě kompozitu. Typy kompozitů, které nabízíme, jsou kompozity vyztužené částicemi, kompozity vyztužené vlákny včetně kompozitů s keramickou matricí / polymerovou matricí / kovovou matricí / uhlík-uhlík / hybridní kompozity, strukturní a laminované a sendvičové kompozity a nanokompozity. Výrobní techniky, které používáme při výrobě kompozitních materiálů, jsou: Pultruze, výrobní procesy prepregu, pokročilé umístění vláken, navíjení filamentů, navíjení vláken na míru, proces nanášení skleněných vláken sprejem, všívání, lanxide proces, z-pinning. Mnoho kompozitních materiálů se skládá ze dvou fází, matrice, která je spojitá a obklopuje druhou fázi; a dispergovanou fázi, která je obklopena matricí. Doporučujeme kliknout semSTÁHNĚTE SI naše schématická vyobrazení výroby kompozitů a kompozitních materiálů společností AGS-TECH Inc. To vám pomůže lépe porozumět informacím, které vám poskytujeme níže. • KOMPOZITY VYZTUŽENÉ ČÁSTICEMI: Tato kategorie se skládá ze dvou typů: kompozity s velkými částicemi a kompozity zesílené disperzí. U prvního typu nelze interakce mezi částicí a matricí řešit na atomové nebo molekulární úrovni. Místo toho platí mechanika kontinua. Na druhou stranu v disperzně zpevněných kompozitech jsou částice obecně mnohem menší v řádech desítek nanometrů. Příkladem kompozitu s velkými částicemi jsou polymery, do kterých byla přidána plniva. Plniva zlepšují vlastnosti materiálu a mohou nahradit část objemu polymeru ekonomičtějším materiálem. Objemové podíly dvou fází ovlivňují chování kompozitu. Kompozity s velkými částicemi se používají s kovy, polymery a keramikou. CERMETY jsou příklady keramických / kovových kompozitů. Náš nejběžnější cermet je slinutý karbid. Skládá se ze žáruvzdorné karbidové keramiky, jako jsou částice karbidu wolframu v matrici z kovu, jako je kobalt nebo nikl. Tyto karbidové kompozity jsou široce používány jako řezné nástroje pro kalenou ocel. Tvrdé karbidové částice jsou zodpovědné za řezný účinek a jejich houževnatost je zvýšena tažnou kovovou matricí. Získáváme tak výhody obou materiálů v jediném kompozitu. Dalším běžným příkladem kompozitu s velkými částicemi, který používáme, jsou částice sazí smíchané s vulkanizovanou pryží za účelem získání kompozitu s vysokou pevností v tahu, houževnatostí, odolností proti roztržení a oděru. Příkladem disperzně zpevněného kompozitu jsou kovy a kovové slitiny zpevněné a vytvrzené rovnoměrnou disperzí jemných částic velmi tvrdého a inertního materiálu. Když se do hliníkové kovové matrice přidají velmi malé vločky oxidu hlinitého, získáme slinutý hliníkový prášek, který má zvýšenou pevnost při vysokých teplotách. • KOMPOZITY VYZTUŽENÉ VLÁKNY: Tato kategorie kompozitů je ve skutečnosti nejdůležitější. Cílem je dosáhnout vysoké pevnosti a tuhosti na jednotku hmotnosti. Složení vláken, délka, orientace a koncentrace v těchto kompozitech jsou rozhodující pro určení vlastností a užitečnosti těchto materiálů. Existují tři skupiny vláken, která používáme: whiskery, vlákna a dráty. WHISKERS jsou velmi tenké a dlouhé monokrystaly. Patří mezi nejpevnější materiály. Některé příklady materiálů s vousy jsou grafit, nitrid křemíku, oxid hlinitý. FIBERS na druhé straně jsou většinou polymery nebo keramika a jsou v polykrystalickém nebo amorfním stavu. Třetí skupinou jsou jemné DRÁTY, které mají relativně velké průměry a sestávají často z oceli nebo wolframu. Příkladem drátem vyztuženého kompozitu jsou pneumatiky automobilů, které obsahují ocelový drát uvnitř pryže. V závislosti na materiálu matrice máme následující kompozity: KOMPOZITY POLYMER-MATRIX: Jsou vyrobeny z polymerní pryskyřice a vláken jako výztužné složky. Podskupina těchto kompozitů s názvem Glass Fibre-Reinforced Polymer (GFRP) obsahuje spojitá nebo nespojitá skleněná vlákna v polymerní matrici. Sklo nabízí vysokou pevnost, je ekonomické, snadno se zpracovává na vlákna a je chemicky inertní. Nevýhodou je jejich omezená tuhost a tuhost, provozní teploty pouze do 200 – 300 stupňů Celsia. Sklolaminát je vhodný pro automobilové karoserie a dopravní zařízení, karoserie námořních vozidel, skladovací kontejnery. Kvůli omezené tuhosti nejsou vhodné pro letectví ani výrobu mostů. Druhá podskupina se nazývá kompozit polymeru vyztužený uhlíkovými vlákny (CFRP). Zde je uhlík naším vláknitým materiálem v polymerní matrici. Uhlík je známý svým vysokým specifickým modulem a pevností a schopností udržovat je při vysokých teplotách. Uhlíková vlákna nám mohou nabídnout standardní, střední, vysoké a ultravysoké moduly v tahu. Kromě toho uhlíková vlákna nabízejí různé fyzikální a mechanické vlastnosti, a proto jsou vhodná pro různé zakázkové inženýrské aplikace. Kompozity CFRP lze považovat za výrobu sportovních a rekreačních zařízení, tlakových nádob a konstrukčních součástí leteckého průmyslu. Další podskupina, polymerní kompozity vyztužené aramidovými vlákny, jsou také materiály s vysokou pevností a modulem. Jejich poměr pevnosti k hmotnosti je mimořádně vysoký. Aramidová vlákna jsou známá také pod obchodními názvy KEVLAR a NOMEX. Pod napětím fungují lépe než jiné materiály z polymerních vláken, ale jsou slabé v tlaku. Aramidová vlákna jsou houževnatá, odolná proti nárazu, tečení a únavě, stabilní při vysokých teplotách, chemicky inertní s výjimkou silných kyselin a zásad. Aramidová vlákna jsou široce používána ve sportovních potřebách, neprůstřelných vestách, pneumatikách, lanech, pláštích kabelů z optických vláken. Existují i jiné materiály pro vyztužení vláken, ale používají se v menší míře. Jedná se především o bór, karbid křemíku, oxid hlinitý. Materiál polymerní matrice je na druhé straně také kritický. Určuje maximální provozní teplotu kompozitu, protože polymer má obecně nižší teplotu tání a degradace. Polyestery a vinylestery jsou široce používány jako polymerní matrice. Používají se také pryskyřice, které mají vynikající odolnost proti vlhkosti a mechanické vlastnosti. Například polyimidovou pryskyřici lze použít až do teploty asi 230 stupňů Celsia. KOMPOZITY KOVOVÉ MATRICE: V těchto materiálech používáme tažnou kovovou matrici a provozní teploty jsou obecně vyšší než u jejich složek. Ve srovnání s kompozity s polymerní matricí mohou mít vyšší provozní teploty, být nehořlavé a mohou mít lepší odolnost proti degradaci vůči organickým tekutinám. Jsou však dražší. Výztužné materiály, jako jsou whiskery, částice, kontinuální a nespojitá vlákna; a běžně se používají matricové materiály, jako je měď, hliník, hořčík, titan, superslitiny. Příkladem použití jsou součásti motoru vyrobené z matrice z hliníkové slitiny vyztužené oxidem hliníku a uhlíkovými vlákny. KOMPOZITY KERAMIC-MATRIX: Keramické materiály jsou známé svou mimořádně dobrou spolehlivostí při vysokých teplotách. Jsou však velmi křehké a mají nízké hodnoty lomové houževnatosti. Zapuštěním částic, vláken nebo whiskerů jedné keramiky do matrice druhé jsme schopni dosáhnout kompozitů s vyšší lomovou houževnatostí. Tyto vložené materiály v podstatě zabraňují šíření trhlin uvnitř matrice některými mechanismy, jako je vychylování špiček trhlin nebo vytváření můstků přes čela trhlin. Například aluminy, které jsou vyztuženy SiC whiskery, se používají jako břitové destičky pro obrábění tvrdokovových slitin. Ty mohou odhalit lepší výkony ve srovnání se slinutými karbidy. KOMPOZITY UHLÍK-UHLÍK: Výztuha i matrice jsou uhlíkové. Mají vysoké moduly tahu a pevnosti při vysokých teplotách nad 2000 stupňů Celsia, odolnost proti tečení, vysokou lomovou houževnatost, nízké koeficienty tepelné roztažnosti, vysokou tepelnou vodivost. Tyto vlastnosti je činí ideálními pro aplikace vyžadující odolnost proti tepelným šokům. Slabinou uhlík-uhlíkových kompozitů je však jejich zranitelnost vůči oxidaci při vysokých teplotách. Typickými příklady použití jsou formy pro lisování za tepla, pokročilá výroba součástí turbínových motorů. HYBRIDNÍ KOMPOZITY: Dva nebo více různých typů vláken jsou smíchány v jedné matrici. Dá se tak ušít na míru nový materiál s kombinací vlastností. Příkladem je, když jsou do polymerní pryskyřice zabudována uhlíková i skleněná vlákna. Uhlíková vlákna poskytují tuhost a pevnost s nízkou hustotou, ale jsou drahá. Sklo je na druhé straně levné, ale postrádá tuhost uhlíkových vláken. Hybridní kompozit sklo-uhlík je pevnější a houževnatější a lze jej vyrábět s nižšími náklady. ZPRACOVÁNÍ KOMPOZITŮ VYZTUŽENÝCH VLÁKNY: Pro kontinuální plasty vyztužené vlákny s rovnoměrně rozmístěnými vlákny orientovanými ve stejném směru používáme následující techniky. PULTRUSION: Vyrábí se tyče, nosníky a trubky spojitých délek a konstantních průřezů. Nepřetržité prameny vláken jsou impregnovány termosetovou pryskyřicí a protahovány ocelovou matricí, aby se předtvarovaly do požadovaného tvaru. Dále procházejí přesně obrobenou vytvrzovací matricí, aby dosáhly konečného tvaru. Protože se vytvrzovací forma zahřívá, vytvrzuje pryskyřičnou matrici. Stahováky protahují materiál přes matrice. Pomocí vložených dutých jader jsme schopni získat trubky a duté geometrie. Metoda pultruze je automatizovaná a nabízí nám vysokou produktivitu. Je možné vyrobit libovolnou délku produktu. PROCES VÝROBY PREPREG: Prepreg je výztuž z nekonečných vláken předem impregnovaná částečně vytvrzenou polymerní pryskyřicí. Je široce používán pro konstrukční aplikace. Materiál je dodáván ve formě pásky a je dodáván jako páska. Výrobce jej přímo formuje a plně vytvrzuje bez nutnosti přidávat jakoukoliv pryskyřici. Protože prepregy podléhají vytvrzovacím reakcím při pokojové teplotě, skladují se při 0 °C nebo nižších teplotách. Po použití jsou zbývající pásky uloženy zpět při nízkých teplotách. Používají se termoplastické a termosetové pryskyřice a běžná jsou výztužná vlákna z uhlíku, aramidu a skla. Pro použití prepregů se nejprve odstraní nosný podkladový papír a poté se provede výroba položením prepregové pásky na upravený povrch (proces kladení). Pro dosažení požadované tloušťky lze položit několik vrstev. Častou praxí je střídat orientaci vláken za účelem vytvoření vrstveného nebo šikmého laminátu. Nakonec se pro vytvrzení aplikuje teplo a tlak. Pro řezání prepregů a kladení se používá ruční zpracování i automatizované procesy. NAVÍJENÍ FILAMENTU: Souvislá výztužná vlákna jsou přesně umístěna v předem určeném vzoru, aby sledovala dutý a obvykle cyklický tvar. Vlákna nejprve projdou pryskyřičnou lázní a poté jsou automatizovaným systémem navinuta na trn. Po několika opakováních navíjení se získají požadované tloušťky a vytvrzování se provádí buď při pokojové teplotě nebo v peci. Nyní je trn odstraněn a výrobek je vyjmut z formy. Vinutí vlákna může nabídnout velmi vysoké poměry pevnosti k hmotnosti navíjením vláken v obvodových, spirálových a polárních vzorech. Trubky, nádrže, pláště jsou vyráběny touto technikou. • KONSTRUKČNÍ KOMPOZITY: Obvykle se skládají z homogenních i kompozitních materiálů. Vlastnosti těchto prvků jsou proto určovány materiálem a geometrickým designem jejich prvků. Zde jsou hlavní typy: LAMINÁRNÍ KOMPOZITY: Tyto konstrukční materiály jsou vyrobeny z dvourozměrných plechů nebo panelů s preferovanými směry vysoké pevnosti. Vrstvy jsou naskládány a slepeny dohromady. Střídáním vysokopevnostních směrů ve dvou kolmých osách získáme kompozit, který má vysokou pevnost v obou směrech ve dvourozměrné rovině. Nastavením úhlů vrstev lze vyrobit kompozit s pevností ve výhodných směrech. Moderní lyže se vyrábí tímto způsobem. SANDWICH PANELY: Tyto strukturální kompozity jsou lehké, ale přesto mají vysokou tuhost a pevnost. Sendvičové panely se skládají ze dvou vnějších plechů vyrobených z tuhého a pevného materiálu, jako jsou hliníkové slitiny, vlákny vyztužené plasty nebo ocel, a jádro mezi vnějšími plechy. Jádro musí být lehké a většinou musí mít nízký modul pružnosti. Populárními materiály jádra jsou tuhé polymerní pěny, dřevo a voštiny. Sendvičové panely jsou široce používány ve stavebnictví jako střešní materiál, podlahový nebo stěnový materiál a také v leteckém průmyslu. • NANOKOMPOZITY : Tyto nové materiály se skládají z částic o velikosti nanočástic uložených v matrici. Pomocí nanokompozitů můžeme vyrábět pryžové materiály, které velmi dobře brání pronikání vzduchu při zachování jejich pryžových vlastností beze změny. CLICK Product Finder-Locator Service PŘEDCHOZÍ STRÁNKA
- Joining & Assembly & Fastening Processes, Welding, Brazing, Soldering
Joining & Assembly & Fastening Processes, Welding, Brazing, Soldering, Sintering, Adhesive Bonding, Press Fitting, Wave and Reflow Solder Process, Torch Furnace Procesy spojování a montáže a upevňování Vaše vyrobené díly spojíme, smontujeme a upevníme a přeměníme na hotové nebo polotovary pomocí SVAŘOVÁNÍ, PÁJENÍ, PÁJENÍ, SPÉKÁNÍ, LEPENÍ, UPEVŇOVÁNÍ, LISKOVÁNÍ. Některé z našich nejoblíbenějších svařovacích procesů jsou obloukové, kyslíko-palivové, odporové, projekční, svarové, pěchovací, perkusní, pevné, elektronové, laserové, termitové, indukční svařování. Naše oblíbené pájecí procesy jsou pájení hořákem, indukce, pece a ponorem. Naše metody pájení jsou železo, plotýnka, trouba, indukce, ponor, vlna, přetavení a ultrazvukové pájení. Pro lepení často používáme termoplasty a termosety, epoxidy, fenoly, polyuretany, lepicí slitiny a také některé další chemikálie a pásky. Nakonec naše upevňovací procesy sestávají z hřebíků, šroubování, matic a šroubů, nýtování, sevření, sešívání, sešívání a sešívání a lisování. • SVAŘOVÁNÍ: Svařování zahrnuje spojování materiálů tavením obrobků a zaváděním přídavných materiálů, které také spojují roztavenou svarovou lázeň. Když se oblast ochladí, získáme pevný spoj. V některých případech je aplikován tlak. Na rozdíl od svařování zahrnují operace pájení natvrdo pouze tavení materiálu s nižším bodem tavení mezi obrobky a obrobky se netaví. Doporučujeme kliknout semSTÁHNĚTE SI naše schématická vyobrazení svařovacích procesů od AGS-TECH Inc. To vám pomůže lépe porozumět informacím, které vám poskytujeme níže. Při OBLOUKOVÉM SVAŘOVÁNÍ používáme napájecí zdroj a elektrodu k vytvoření elektrického oblouku, který taví kovy. Svařovaný bod je chráněn ochranným plynem nebo párou nebo jiným materiálem. Tento proces je oblíbený pro svařování automobilových dílů a ocelových konstrukcí. Při obloukovém svařování obaleným kovem (SMAW) nebo také známém jako svařování tyčí se tyč elektrody přiblíží k základnímu materiálu a mezi nimi se vytvoří elektrický oblouk. Tyč elektrody se taví a působí jako výplňový materiál. Elektroda také obsahuje tavidlo, které působí jako vrstva strusky a vydává páry, které působí jako ochranný plyn. Ty chrání oblast svaru před kontaminací prostředí. Žádná jiná plniva se nepoužívají. Nevýhodou tohoto procesu je jeho pomalost, nutnost časté výměny elektrod, nutnost odštípávání zbytkové strusky pocházející z tavidla. Řada kovů, jako je železo, ocel, nikl, hliník, měď atd. Lze svařit. Jeho výhodou jsou levné nástroje a snadné použití. Plynové obloukové svařování kovů (GMAW), známé také jako kov-inertní plyn (MIG), máme kontinuální přívod tavné elektrodové výplně drátu a inertního nebo částečně inertního plynu, který proudí kolem drátu proti znečištění oblasti svaru prostředím. Lze svařovat ocel, hliník a další neželezné kovy. Výhodou MIG je vysoká rychlost svařování a dobrá kvalita. Nevýhodou je komplikované vybavení a problémy, kterým čelíme ve větrném venkovním prostředí, protože musíme udržovat ochranný plyn kolem svařovací oblasti stabilní. Variantou GMAW je obloukové svařování s tavidlem (FCAW), které se skládá z jemné kovové trubky naplněné tavidlem. Někdy je tavidlo uvnitř trubky dostatečné pro ochranu před kontaminací životního prostředí. Svařování pod tavidlem (SAW) je široce automatizovaný proces, který zahrnuje kontinuální podávání drátu a oblouk, který je zapálen pod vrstvou tavidla. Rychlost výroby a kvalita jsou vysoké, struska ze svařování se snadno odstraňuje a máme nekuřácké pracovní prostředí. Nevýhodou je, že jej lze použít pouze pro svařování dílů parts v určitých polohách. Při obloukovém svařování plynovým wolframem (GTAW) nebo svařování wolframem v inertním plynu (TIG) používáme wolframovou elektrodu spolu se samostatnou výplní a inertními nebo téměř inertními plyny. Jak víme, wolfram má vysokou teplotu tání a je to velmi vhodný kov pro velmi vysoké teploty. Wolfram se při TIG nespotřebovává na rozdíl od jiných metod vysvětlených výše. Pomalá, ale vysoce kvalitní svařovací technika výhodná oproti jiným technikám při svařování tenkých materiálů. Vhodné pro mnoho kovů. Svařování plazmovým obloukem je podobné, ale k vytvoření oblouku používá plazmový plyn. Oblouk při svařování plazmovým obloukem je relativně koncentrovanější ve srovnání s GTAW a může být použit pro širší rozsah tlouštěk kovu při mnohem vyšších rychlostech. GTAW a plazmové obloukové svařování lze aplikovat na víceméně stejné materiály. OXY-FUEL / OXYFUEL WELDING také nazývané svařování kyslíkem a acetylenem, svařování kyslíkem, svařování plynem se provádí pomocí plynných paliv a kyslíku pro svařování. Protože se nepoužívá žádná elektrická energie, je přenosný a lze jej použít tam, kde není elektřina. Pomocí svařovacího hořáku ohříváme kusy a přídavný materiál, abychom vytvořili společnou lázeň roztaveného kovu. Lze použít různá paliva, jako je acetylén, benzín, vodík, propan, butan atd. Při kyslíko-palivovém svařování používáme dvě nádoby, jednu na palivo a druhou na kyslík. Kyslík okysličuje palivo (spaluje ho). ODPOROVÉ SVAŘOVÁNÍ: Tento typ svařování využívá joulového ohřevu a teplo vzniká v místě, kde je po určitou dobu aplikován elektrický proud. Kovem procházejí vysoké proudy. Na tomto místě se tvoří kaluže roztaveného kovu. Metody odporového svařování jsou oblíbené pro svou účinnost, malý potenciál znečištění. Nevýhodou však jsou relativně značné náklady na vybavení a vlastní omezení na relativně tenké obrobky. BODOVÉ SVAŘOVÁNÍ je jedním z hlavních typů odporového svařování. Zde spojujeme dva nebo více překrývajících se plechů nebo obrobků pomocí dvou měděných elektrod, které sevřou plechy k sobě a prochází jimi vysoký proud. Materiál mezi měděnými elektrodami se zahřívá a v tomto místě se vytváří roztavená lázeň. Proud se poté zastaví a hroty měděných elektrod ochlazují místo svaru, protože elektrody jsou chlazeny vodou. Aplikace správného množství tepla na správný materiál a tloušťku je pro tuto techniku klíčová, protože při nesprávné aplikaci bude spoj slabý. Bodové svařování má výhody v tom, že nezpůsobuje žádné významné deformace obrobků, energetickou účinnost, snadnou automatizaci a vynikající rychlost výroby a nevyžaduje žádná plniva. Nevýhodou je, že vzhledem k tomu, že svařování probíhá bodově, spíše než tvoří souvislý šev, může být celková pevnost relativně nižší ve srovnání s jinými způsoby svařování. ŠVOVÉ SVAŘOVÁNÍ na druhé straně vytváří svary na lícujících površích podobných materiálů. Šev může být natupo nebo překryt. Svarové svařování začíná na jednom konci a postupně se přesouvá na druhý. Tato metoda také používá dvě elektrody z mědi k aplikaci tlaku a proudu na oblast svaru. Kotoučové elektrody rotují s konstantním kontaktem podél linie švu a vytvářejí souvislý svar. I zde jsou elektrody chlazeny vodou. Svary jsou velmi pevné a spolehlivé. Dalšími metodami jsou projekční, zábleskové a přerušované svařovací techniky. SVAŘOVÁNÍ V PEVNÉM STAVU je trochu jiné než předchozí metody vysvětlené výše. Koalescence probíhá při teplotách pod teplotou tání spojených kovů a bez použití kovového plniva. V některých procesech lze použít tlak. Různé metody jsou KOEXTRUZNÍ SVAŘOVÁNÍ, kde jsou rozdílné kovy vytlačovány stejnou matricí, SVAŘOVÁNÍ TLAKEM STUDENA, kde spojujeme měkké slitiny pod jejich teplotou tání, DIFFUSION WELDING technika bez viditelných svarových linií, EXPLOZNÍ SVAŘOVÁNÍ pro spojování odlišných materiálů, např. korozi odolných slitin ke konstrukčním oceli, ELEKTROMAGNETICKÉ PULZNÍ SVAŘOVÁNÍ, kde urychlujeme trubky a plechy elektromagnetickými silami, KOVACÍ SVAŘOVÁNÍ, které spočívá v zahřátí kovů na vysoké teploty a jejich srážení k sobě, TŘECÍ SVAŘOVÁNÍ kde se provádí dostatečné třecí svařování, TŘECÍ SVAŘOVÁNÍ, které zahrnuje rotační ne spotřební nástroj procházející spojovou linkou, HORKOVÉ TLAKOVÉ SVAŘOVÁNÍ, kde lisujeme kovy k sobě při zvýšených teplotách pod teplotou tavení ve vakuu nebo v inertních plynech, HORKÁ IZOSTATICKÁ TLAKOVÁ SVAŘOVÁNÍ proces, kdy aplikujeme tlak pomocí inertních plynů uvnitř nádoby, ROLOVÉ SVAŘOVÁNÍ, kde spojujeme nepodobné materiály tím, že je vnucujeme mezi sebe dvě rotující kola, ULTRAZVUKOVÉ SVAŘOVÁNÍ, kde jsou svařovány tenké kovové nebo plastové plechy pomocí vysokofrekvenční vibrační energie. Další naše svařovací procesy jsou SVAŘOVÁNÍ ELEKTRONOVÝM PAPRSKEM s hlubokým průvarem a rychlým zpracováním, ale jako nákladnou metodu ji považujeme pro speciální případy, ELEKTROSLAGOVÉ SVAŘOVÁNÍ metodu vhodnou pouze pro těžké tlusté plechy a obrobky z oceli, INDUKČNÍ SVAŘOVÁNÍ, kde využíváme elektromagnetickou indukci a ohřívejte naše elektricky vodivé nebo feromagnetické obrobky, SVAŘOVÁNÍ LASEROVÝM PAPRSKEM také s hlubokou penetrací a rychlým zpracováním, ale nákladnou metodou, LASEROVÉ HYBRIDNÍ SVAŘOVÁNÍ, které kombinuje LBW s GMAW ve stejné svařovací hlavě a schopné přemostit mezery 2 mm mezi deskami, SVAŘOVÁNÍ NÁBOJE, které zahrnuje elektrický výboj s následným kováním materiálů aplikovaným tlakem, THERMIT WELDING zahrnující exotermickou reakci mezi prášky oxidu hliníku a železa, ELEKTROPLYNOVÉ SVAŘOVÁNÍ s tavnými elektrodami a používá se pouze s ocelí ve vertikální poloze a nakonec STUD ARC WELDING pro spojení trnu se základnou materiál s teplem a tlakem. Doporučujeme kliknout semSTÁHNĚTE SI naše schématické ilustrace procesů pájení, pájení a lepení od AGS-TECH Inc To vám pomůže lépe porozumět informacím, které vám poskytujeme níže. • PÁJENÍ: Spojujeme dva nebo více kovů tak, že se mezi nimi zahřejí přídavné kovy nad jejich bod tání a pomocí kapilárního účinku se rozšíří. Proces je podobný pájení, ale teploty spojené s roztavením plniva jsou vyšší při pájení. Podobně jako při svařování tavidlo chrání přídavný materiál před atmosférickou kontaminací. Po ochlazení se obrobky spojí dohromady. Proces zahrnuje následující klíčové kroky: Dobré lícování a vůle, správné čištění základních materiálů, správné upevnění, správný výběr tavidla a atmosféry, ohřev sestavy a nakonec čištění pájené sestavy. Některé z našich procesů pájení jsou PÁJENÍ S PÁČKEM, oblíbená metoda prováděná ručně nebo automatizovaně. Je vhodný pro zakázky s malým objemem výroby a specializované případy. Teplo je aplikováno pomocí plynových plamenů v blízkosti pájeného spoje. PÁJENÍ V PECÍ vyžaduje méně dovedností operátora a je to poloautomatický proces vhodný pro průmyslovou hromadnou výrobu. Jak regulace teploty, tak regulace atmosféry v peci jsou výhodami této techniky, protože první umožňuje mít řízené tepelné cykly a eliminovat lokální ohřev, jako je tomu u pájení hořákem, a druhá chrání součást před oxidací. Pomocí jiggingu jsme schopni snížit výrobní náklady na minimum. Nevýhodou je vysoká spotřeba energie, náklady na vybavení a náročnější konstrukční úvahy. VAKUOVÉ PÁJENÍ probíhá ve vakuové peci. Rovnoměrnost teploty je zachována a získáváme velmi čisté spoje bez tavidel s velmi malým zbytkovým napětím. Tepelné zpracování může probíhat během vakuového pájení, kvůli nízkým zbytkovým napětím přítomným během pomalých cyklů ohřevu a chlazení. Hlavní nevýhodou je jeho vysoká cena, protože vytvoření vakuového prostředí je nákladný proces. Ještě další technika DIP BRAZING spojuje upevněné díly, kde se na styčné povrchy aplikuje pájecí směs. Poté jsou díly fixtured ponořeny do lázně roztavené soli, jako je chlorid sodný (kuchyňská sůl), která působí jako teplosměnné médium a tavidlo. Vzduch je vyloučen, a proto nedochází k tvorbě oxidů. Při INDUKČNÍM PÁJENÍ spojujeme materiály přídavným kovem, který má nižší bod tání než základní materiály. Střídavý proud z indukční cívky vytváří elektromagnetické pole, které indukuje indukční ohřev na převážně železných magnetických materiálech. Metoda poskytuje selektivní ohřev, dobré spoje s plnidly tekoucími pouze v požadovaných oblastech, malou oxidaci, protože nejsou přítomny plameny a chlazení je rychlé, rychlý ohřev, konzistenci a vhodnost pro velkosériovou výrobu. Abychom urychlili naše procesy a zajistili konzistenci, často používáme předlisky. Informace o našem pájecím zařízení vyrábějícím armatury z keramiky na kov, hermetické těsnění, vakuové průchodky, komponenty pro řízení vysokého a ultravysokého vakua a kapaliny naleznete zde:_cc781905-5cde-3194-bb3b_536Brožura továrny na pájení • PÁJENÍ : Při pájení nedochází k tavení obrobků, ale přídavného kovu s nižším bodem tavení než mají spojované části, které zatékají do spoje. Přídavný kov se při pájení taví při nižší teplotě než při pájení. Pro pájení používáme bezolovnaté slitiny a splňují RoHS a pro různé aplikace a požadavky máme různé a vhodné slitiny, jako je slitina stříbra. Pájení nám nabízí spoje, které jsou plynotěsné a kapalinotěsné. Při MĚKKÉM PÁJENÍ má náš přídavný kov bod tání pod 400 stupňů Celsia, zatímco při PÁJENÍ STŘÍBREM a PÁJENÍ natvrdo potřebujeme vyšší teploty. Měkké pájení využívá nižší teploty, ale nevede k pevným spojům pro náročné aplikace při zvýšených teplotách. Stříbrné pájení na druhé straně vyžaduje vysoké teploty poskytované hořákem a poskytuje nám pevné spoje vhodné pro vysokoteplotní aplikace. Pájení vyžaduje nejvyšší teploty a obvykle se používá hořák. Protože jsou pájené spoje velmi pevné, jsou dobrými kandidáty pro opravy těžkých železných předmětů. V našich výrobních linkách používáme jak ruční ruční pájení, tak i automatizované pájecí linky. INDUCTION PÁJENÍ používá vysokofrekvenční střídavý proud v měděné cívce pro usnadnění indukčního ohřevu. V pájené části se indukují proudy a v důsledku toho vzniká teplo na vysokém odporu joint. Toto teplo roztaví přídavný kov. Používá se také tavidlo. Indukční pájení je dobrou metodou pro pájení válců a trubek v nepřetržitém procesu tak, že se kolem nich obalí cívky. Pájení některých materiálů, jako je grafit a keramika, je obtížnější, protože vyžaduje pokovení obrobků před pájením vhodným kovem. To usnadňuje mezifázové propojení. Takové materiály pájeme zejména pro aplikace hermetické obaly. Naše desky plošných spojů (PCB) vyrábíme ve velkém množství převážně pomocí VLNOVÉHO PÁJENÍ. Pouze pro malé množství prototypových účelů používáme ruční pájení pomocí páječky. Pájení vlnou používáme jak pro průchozí, tak pro povrchovou montáž PCB sestav (PCBA). Dočasné lepidlo udržuje součásti připojené k desce s obvody a sestava je umístěna na dopravníku a pohybuje se skrz zařízení, které obsahuje roztavenou pájku. Nejprve je deska plošných spojů natavena a poté vstoupí do zóny předehřívání. Roztavená pájka je v pánvi a má na svém povrchu vzor stojatých vln. Když se deska plošných spojů pohybuje přes tyto vlny, tyto vlny se dotýkají spodní části desky plošných spojů a přilnou k pájecím ploškám. Pájka zůstává pouze na kolících a ploškách a ne na samotné desce plošných spojů. Vlny v roztavené pájce musí být dobře řízeny, aby nedocházelo k rozstřikování a horní části vln se nedotýkaly a nekontaminovaly nežádoucí místa desek. V REFLOW SOLDERING používáme lepivou pájecí pastu k dočasnému připevnění elektronických součástek k deskám. Poté se desky vloží do reflow pece s regulací teploty. Zde se pájka roztaví a trvale spojí součástky. Tuto techniku používáme jak pro komponenty pro povrchovou montáž, tak pro komponenty s průchozími otvory. Správná regulace teploty a nastavení teplot pece je nezbytné, aby se zabránilo zničení elektronických součástek na desce jejich přehřátím nad jejich maximální teplotní limity. V procesu pájení přetavením máme ve skutečnosti několik oblastí nebo stupňů, z nichž každý má odlišný tepelný profil, jako je krok předehřívání, krok tepelného namáčení, kroky přetavování a chlazení. Tyto různé kroky jsou nezbytné pro pájení bez poškození přetavením sestav desek s plošnými spoji (PCBA). ULTRAZVUKOVÉ PÁJENÍ je další často používaná technika s jedinečnými schopnostmi - lze ji použít k pájení skla, keramiky a nekovových materiálů. Například fotovoltaické panely, které jsou nekovové, potřebují elektrody, které lze připevnit pomocí této techniky. Při ultrazvukovém pájení nasazujeme vyhřívaný pájecí hrot, který také vydává ultrazvukové vibrace. Tyto vibrace vytvářejí kavitační bubliny na rozhraní substrátu s roztaveným pájkovým materiálem. Implozivní energie kavitace upravuje povrch oxidu a odstraňuje nečistoty a oxidy. Během této doby se také vytvoří vrstva slitiny. Pájka na spojovacím povrchu obsahuje kyslík a umožňuje vytvoření silné sdílené vazby mezi sklem a pájkou. PÁJENÍ MÁČEM lze považovat za jednodušší verzi vlnového pájení vhodnou pouze pro malosériovou výrobu. Jako u jiných procesů se aplikuje první čistící tavidlo. Desky plošných spojů s osazenými součástkami jsou ručně nebo poloautomaticky ponořeny do nádrže obsahující roztavenou pájku. Roztavená pájka ulpívá na odkrytých kovových plochách nechráněných pájecí maskou na desce. Zařízení je jednoduché a levné. • LEPENÍ: Toto je další oblíbená technika, kterou často používáme a zahrnuje lepení povrchů pomocí lepidel, epoxidů, plastů nebo jiných chemikálií. Lepení se provádí buď odpařením rozpouštědla, tepelným vytvrzením, vytvrzením UV světlem, tlakovým vytvrzením nebo čekáním po určitou dobu. V našich výrobních linkách se používají různá vysoce výkonná lepidla. Při správně navržených procesech aplikace a vytvrzování může lepení vést k spojům s velmi nízkým napětím, které jsou pevné a spolehlivé. Lepené spoje mohou být dobrou ochranou proti faktorům prostředí, jako je vlhkost, nečistoty, korozivní látky, vibrace atd. Výhody lepení jsou: lze je aplikovat na materiály, které by se jinak těžko pájely, svařovaly nebo pájely. Také může být výhodnější pro materiály citlivé na teplo, které by byly poškozeny svařováním nebo jinými vysokoteplotními procesy. Další výhodou lepidel je, že mohou být aplikovány na nepravidelně tvarované povrchy a ve srovnání s jinými metodami zvyšují hmotnost sestavy o velmi malé množství. Také rozměrové změny dílů jsou velmi minimální. Některá lepidla mají vlastnosti přizpůsobení indexu a lze je použít mezi optickými součástmi bez výrazného snížení intenzity světla nebo optického signálu. Nevýhody na druhé straně jsou delší doby vytvrzování, které mohou zpomalit výrobní linky, požadavky na upevnění, požadavky na přípravu povrchu a potíže s demontáží v případě potřeby přepracování. Většina našich operací lepení zahrnuje následující kroky: -Povrchová úprava: Běžné jsou speciální čisticí postupy, jako je čištění deionizovanou vodou, čištění alkoholem, plazmové nebo korónové čištění. Po očištění můžeme na povrchy nanést promotory přilnavosti, abychom zajistili co nejlepší spoje. -Upevnění dílů: Jak pro aplikaci lepidla, tak pro vytvrzování navrhujeme a používáme vlastní přípravky. -Aplikace lepidla: Někdy používáme ruční a někdy v závislosti na případu automatizované systémy, jako je robotika, servomotory, lineární pohony k dodání lepidla na správné místo a používáme dávkovače k dodání ve správném objemu a množství. -Vytvrzování: V závislosti na lepidle můžeme použít jednoduché sušení a vytvrzování, stejně jako vytvrzování pod UV světlem, které funguje jako katalyzátor, nebo vytvrzování teplem v peci nebo pomocí odporových topných prvků namontovaných na přípravcích a upínacích přípravcích. Doporučujeme kliknout semSTÁHNĚTE SI naše schématická vyobrazení upevňovacích procesů od AGS-TECH Inc. To vám pomůže lépe porozumět informacím, které vám poskytujeme níže. • SPOJOVACÍ PROCESY: Naše mechanické spojovací procesy spadají do dvou hlavních kategorií: SPOJOVACÍ PRVKY a INTEGRÁLNÍ SPOJKY. Příklady spojovacích prvků, které používáme, jsou šrouby, kolíky, matice, šrouby, nýty. Příklady integrálních spojů, které používáme, jsou nacvakávací a smršťovací spoje, švy, lemování. Pomocí různých způsobů upevnění zajišťujeme, že naše mechanické spoje jsou pevné a spolehlivé po mnoho let používání. ŠROUBY a ŠROUBY jsou některé z nejběžněji používaných spojovacích prvků pro držení předmětů pohromadě a jejich umístění. Naše šrouby a šrouby splňují normy ASME. Používají se různé typy šroubů a šroubů, včetně šroubů se šestihrannou hlavou a šroubů s šestihrannou hlavou, pozdržených šroubů a šroubů, dvoukoncových šroubů, šroubů s hmoždinkami, šroubů s okem, zrcadlových šroubů, šroubů do plechu, šroubů pro jemné nastavení, samořezných a samořezných šroubů , stavěcí šroub, šrouby s vestavěnými podložkami,…a další. Máme různé typy hlav šroubů, jako jsou zápustné, kopulovité, kulaté, přírubové hlavy a různé typy šroubů, jako jsou drážkové, křížové, čtyřhranné, šestihranné. RIVET na druhé straně je trvalý mechanický spojovací prvek sestávající z hladké válcové násady a hlavy na jedné straně. Po vložení se druhý konec nýtu zdeformuje a jeho průměr se roztáhne tak, aby zůstal na místě. Jinými slovy, před instalací má nýt jednu hlavu a po instalaci dvě. Instalujeme různé typy nýtů v závislosti na aplikaci, síle, přístupnosti a ceně, jako jsou nýty s pevnou/kulatou hlavou, konstrukční, polotrubkové, slepé, oscarové, hnací, zapuštěné, třecí nýty, samořezné nýty. Nýtování lze upřednostnit v případech, kdy je třeba zabránit tepelné deformaci a změně vlastností materiálu vlivem svařovacího tepla. Nýtování nabízí také nízkou hmotnost a především dobrou pevnost a odolnost vůči střižným silám. Proti tahovým zatížením však mohou být vhodnější šrouby, matice a šrouby. V procesu CLINCHING používáme speciální razníky a matrice k vytvoření mechanického spojení mezi spojovanými plechy. Razník tlačí vrstvy plechu do dutiny zápustky a výsledkem je vytvoření trvalého spoje. Clinchování nevyžaduje žádné zahřívání ani chlazení a jedná se o proces zpracování za studena. Je to ekonomický proces, který může v některých případech nahradit bodové svařování. V PINNING používáme čepy, což jsou strojní prvky sloužící k zajištění poloh strojních součástí vůči sobě. Hlavní typy jsou vidlicové kolíky, závlačky, pružinové kolíky, kolíky, a závlačka. V SEŠÍVÁNÍ používáme sešívací pistole a sponky, což jsou dvouhrotové spojovací prvky používané ke spojování nebo spojování materiálů. Sešívání má následující výhody: Ekonomické, jednoduché a rychlé použití, korunku sponek lze použít k přemostění materiálů spojených dohromady, Koruna sponek může usnadnit přemostění kusu, jako je kabel a jeho upevnění k povrchu bez proražení nebo poškození, relativně snadné odstranění. LISKOVÁNÍ se provádí přitlačením dílů k sobě a tření mezi nimi díly spojí. Lisované díly skládající se z nadrozměrného hřídele a poddimenzovaného otvoru se obecně montují jedním ze dvou způsobů: Buď použitím síly, nebo využitím tepelné roztažnosti nebo smrštění dílů. Když je lisovací tvarovka vytvořena působením síly, použijeme buď hydraulický lis, nebo ručně ovládaný lis. Na druhou stranu, když je lisovaná tvarovka ustavena tepelnou roztažností, zahřejeme obalové díly a za tepla je smontujeme na své místo. Když vychladnou, smrští se a vrátí se do svých normálních rozměrů. Výsledkem je dobré lisování. Alternativně tomu říkáme SHRINK-FITTING. Dalším způsobem, jak toho dosáhnout, je ochlazení obalovaných dílů před montáží a jejich následné zasunutí do příslušných dílů. Když se sestava zahřeje, roztáhnou se a získáme pevné usazení. Tato druhá metoda může být výhodnější v případech, kdy ohřev představuje riziko změny vlastností materiálu. Chlazení je v těchto případech bezpečnější. Pneumatické a hydraulické komponenty a sestavy • Ventily, hydraulické a pneumatické komponenty jako O-kroužek, podložka, těsnění, těsnění, kroužek, podložka. Vzhledem k tomu, že ventily a pneumatické komponenty jsou k dispozici ve velkém množství, nemůžeme zde vyjmenovat vše. V závislosti na fyzikálním a chemickém prostředí vaší aplikace pro vás máme speciální produkty. Upřesněte nám prosím aplikaci, typ součásti, specifikace, podmínky prostředí, jako je tlak, teplota, kapaliny nebo plyny, které budou v kontaktu s vašimi ventily a pneumatickými součástmi; a vybereme pro vás nejvhodnější produkt nebo jej vyrobíme speciálně pro vaši aplikaci. CLICK Product Finder-Locator Service PŘEDCHOZÍ STRÁNKA
- Machine Elements Manufacturing, Gears, Gear Drives, Bearings, Keys, Splines
Machine Elements Manufacturing, Gears, Gear Drives, Bearings, Keys, Splines, Pins, Shafts, Seals, Fasteners, Clutch, Cams, Followers, Belts, Couplings, Shafts Výroba strojních prvků Přečtěte si více Sestava řemenů a řetězů a kabelového pohonu Přečtěte si více Sestava ozubených kol a ozubených kol Přečtěte si více Výroba spojek a ložisek Přečtěte si více Výroba klíčů a drážek a kolíků Přečtěte si více Výroba vaček a kladek a spojek a ráčnových kol Přečtěte si více Výroba hřídelí Přečtěte si více Výroba mechanických ucpávek Přečtěte si více Sestava spojky a brzdy Přečtěte si více Výroba spojovacího materiálu Přečtěte si více Montáž jednoduchých strojů PRVKY STROJE jsou základní součásti stroje. Tyto prvky se skládají ze tří základních typů: 1.) Konstrukční součásti včetně prvků rámu, ložisek, náprav, drážkování, upevňovacích prvků, těsnění a maziv. 2.) Mechanismy řídící pohyb různými způsoby, jako jsou ozubená soukolí, řemenové nebo řetězové pohony, táhla, vačkové a kladkové systémy, brzdy a spojky. 3.) Ovládací prvky, jako jsou tlačítka, spínače, indikátory, senzory, akční členy a počítačové ovladače. Většina strojních prvků, které vám nabízíme, je standardizována na běžné velikosti, ale pro vaše specializované aplikace jsou k dispozici i strojní prvky na míru. Přizpůsobení strojních prvků může probíhat na stávajících konstrukcích, které jsou v našich katalozích ke stažení, nebo na zcela nových konstrukcích. Prototypování a výroba strojních prvků může pokračovat po schválení návrhu oběma stranami. Pokud je třeba navrhnout a vyrobit nové strojní prvky, naši zákazníci nám buď pošle e-mail se svými vlastními plány a my je zkontrolujeme ke schválení, nebo nás požádají o návrh strojních prvků pro jejich aplikaci. V druhém případě využíváme veškeré podněty od našich zákazníků a navrhujeme strojní prvky a posíláme hotové plány našim klientům ke schválení. Po schválení vyrobíme první výrobky a následně vyrobíme strojní prvky podle finálního návrhu. V jakékoli fázi této práce, v případě, že konkrétní návrh strojního prvku funguje v terénu neuspokojivě (což je vzácné), zkontrolujeme celý projekt a společně s našimi klienty provedeme úpravy podle potřeby. Naší standardní praxí je podepisovat smlouvy o mlčenlivosti (NDA) s našimi zákazníky pro návrh strojních prvků nebo jakéhokoli jiného produktu, kdykoli je to potřeba nebo požadováno. Jakmile jsou strojní prvky pro konkrétního zákazníka navrženy a vyrobeny na zakázku, přiřadíme jim kód produktu a pouze je vyrobíme a prodáme našemu zákazníkovi, který produkt vlastní. Strojní prvky reprodukujeme pomocí vyvinutých nástrojů, forem a postupů tolikrát, kolikrát je potřeba a kdykoli si je zákazník objedná. Jinými slovy, jakmile je pro vás navržen a vyroben vlastní strojní prvek, duševní vlastnictví, stejně jako veškeré nástroje a formy jsou námi vyhrazeny a na dobu neurčitou skladovány pro vás a produkty reprodukované podle vašeho přání. Našim klientům také nabízíme inženýrské služby kreativním kombinováním strojních prvků do součásti nebo sestavy, která slouží aplikaci a splňuje nebo překračuje očekávání našich zákazníků. Závody vyrábějící naše strojní prvky jsou kvalifikovány buď podle ISO9001, QS9000 nebo TS16949. Většina našich výrobků má navíc značku CE nebo UL a splňuje mezinárodně relevantní normy, jako jsou ISO, SAE, ASME, DIN. Kliknutím na podnabídky získáte podrobné informace o našich strojních prvcích včetně: - Řemeny, řetězy a kabelové pohony - Ozubená kola a ozubené převody - Spojky a ložiska - Klíče a drážky a kolíky - Vačky a vazby - Hřídele - Mechanické těsnění - Průmyslová spojka a brzda - Spojovací materiál - Jednoduché stroje Pro naše zákazníky, konstruktéry a vývojáře nových produktů včetně strojních prvků jsme připravili referenční brožuru. Můžete se seznámit s některými běžně používanými pojmy v konstrukci strojních součástí: Stáhněte si brožuru s obecnými pojmy strojního inženýrství, které používají konstruktéři a inženýři Naše strojní prvky nacházejí uplatnění v různých oblastech, jako jsou průmyslové stroje, automatizační systémy, zkušební a metrologická zařízení, dopravní zařízení, stavební stroje a prakticky kdekoli, na co si vzpomenete. AGS-TECH vyvíjí a vyrábí strojní prvky z různých materiálů v závislosti na aplikaci. Materiály používané pro strojní prvky mohou sahat od lisovaných plastů používaných pro hračky až po povrchově tvrzenou a speciálně potaženou ocel pro průmyslové stroje. Naši konstruktéři používají nejmodernější profesionální software a konstrukční nástroje pro vývoj strojních prvků, přičemž berou v úvahu detaily, jako jsou úhly v zubech ozubených kol, související napětí, rychlost opotřebení….atd. Procházejte prosím naše podnabídky a stáhněte si naše produktové brožury a katalogy, abyste zjistili, zda můžete najít standardní součásti stroje pro vaši aplikaci. Pokud nemůžete najít vhodnou shodu pro vaši aplikaci, dejte nám prosím vědět a my s vámi budeme spolupracovat na vývoji a výrobě strojních prvků, které budou splňovat vaše potřeby. Pokud vás zajímají především naše inženýrské a výzkumné a vývojové kapacity místo výrobních kapacit, pak vás zveme k návštěvě naší webové stránky http://www.ags-engineering.com kde můžete najít podrobnější informace o našem designu, vývoji produktů, vývoji procesů, inženýrských konzultačních službách a další CLICK Product Finder-Locator Service PŘEDCHOZÍ STRÁNKA
- Glass and Ceramic Manufacturing, Hermetic Packages, Seals, Bonding
Glass and Ceramic Manufacturing, Hermetic Packages Seals and Bonding, Tempered Bulletproof Glass, Blow Moulding, Optical Grade Glass, Conductive Glass, Molding Tvarování a tvarování skla a keramiky Typy výroby skla, které nabízíme, jsou obalové sklo, foukané sklo, skleněné vlákno a trubky a tyče, domácí a průmyslové sklo, lampy a žárovky, přesné lisování skla, optické komponenty a sestavy, ploché a tabulové a plavené sklo. Provádíme ruční tvarování i strojní tvarování. Naše oblíbené výrobní procesy technické keramiky jsou lisování, izostatické lisování, izostatické lisování za horka, lisování za tepla, lití do licí pásky, páskové lití, vytlačování, vstřikování, surové obrábění, slinování nebo vypalování, diamantové broušení, hermetické sestavy. Doporučujeme kliknout sem STÁHNĚTE SI naše schematické ilustrace procesů tvarování a tvarování skla od AGS-TECH Inc. STÁHNĚTE SI naše schématická vyobrazení technických procesů výroby keramiky od AGS-TECH Inc. Tyto soubory ke stažení s fotografiemi a nákresy vám pomohou lépe porozumět informacím, které vám poskytujeme níže. • VÝROBA OBALOVÉHO SKLA: Pro výrobu jsme zautomatizovali linky PRESS AND FLOW a také FLOW AND BLOW. V procesu vyfukování a vyfukování vpustíme dávku do přední formy a vytvarujeme hrdlo foukáním stlačeného vzduchu shora. Bezprostředně poté je stlačený vzduch vháněn podruhé z druhého směru hrdlem nádoby, aby se vytvořil předtvar láhve. Tento předvýrobek se poté přenese do skutečné formy, znovu se zahřeje, aby změkl, a aplikuje se stlačený vzduch, aby předvýrobek získal konečný tvar nádoby. Přesněji řečeno, je natlakován a tlačen proti stěnám dutiny konečné formy, aby získal požadovaný tvar. Nakonec se vyrobený skleněný obal přemístí do žíhací pece k následnému ohřátí a odstranění pnutí vzniklých během tvarování a kontrolovaným způsobem se ochladí. Při metodě lisování a vyfukování jsou roztavené kapky dány do předlisku (předlisku) a lisovány do předlisku (tvar předlisku). Polotovary jsou poté přeneseny do vyfukovacích forem a vyfukovány podobně jako proces popsaný výše v části „Proces vyfukování a vyfukování“. Následné kroky jako žíhání a uvolnění napětí jsou podobné nebo stejné. • FUKÁNÍ SKLA : Vyrábíme skleněné výrobky pomocí konvenčního ručního foukání i pomocí stlačeného vzduchu s automatickým zařízením. Pro některé zakázky je nutné konvenční foukání, jako jsou projekty zahrnující sklářské umělecké práce nebo projekty, které vyžadují menší počet dílů s volnými tolerancemi, prototypování / demo projekty….atd. Konvenční foukání skla zahrnuje ponoření duté kovové trubky do hrnce s roztaveným sklem a otáčení trubky pro zachycení určitého množství skleněného materiálu. Sklo shromážděné na špičce dýmky se naválcuje na ploché železo, tvaruje se podle potřeby, prodlužuje se, znovu se zahřívá a fouká vzduchem. Když je připraven, vloží se do formy a fouká vzduch. Dutina formy je mokrá, aby se zabránilo kontaktu skla s kovem. Vodní film mezi nimi působí jako polštář. Ruční foukání je pracný pomalý proces a je vhodný pouze pro prototypování nebo položky vysoké hodnoty, není vhodný pro levné velkoobjemové objednávky za kus. • VÝROBA DOMÁCÍHO A PRŮMYSLOVÉHO SKLA: S použitím různých typů skleněného materiálu se vyrábí velké množství různých druhů skla. Některé sklenice jsou odolné vůči teplu a jsou vhodné pro laboratorní sklo, zatímco některé jsou dostatečně dobré na to, aby mnohokrát vydržely v myčkách nádobí a jsou vhodné pro výrobu domácích produktů. Na strojích Westlake se denně vyrobí desítky tisíc kusů nápojového skla. Pro zjednodušení se roztavené sklo shromažďuje vakuem a vkládá se do forem, aby se vyrobily předlisky. Poté je do forem vháněn vzduch, tyto jsou přemístěny do jiné formy a opět je vháněn vzduch a sklo získá svůj konečný tvar. Stejně jako při ručním foukání jsou tyto formy udržovány vlhké vodou. Další protahování je součástí dokončovací operace, kde se tvoří krk. Přebytečné sklo je spáleno. Poté následuje výše popsaný proces řízeného opětovného ohřevu a chlazení. • TVÁŘENÍ SKLENĚNÝCH TRUBEK A TYČÍ: Hlavní procesy, které používáme pro výrobu skleněných trubic, jsou procesy DANNER a VELLO. V Dannerově procesu sklo z pece teče a padá na nakloněnou manžetu vyrobenou ze žáruvzdorných materiálů. Objímka je nesena na otočné duté hřídeli nebo foukačce. Sklo se pak obalí kolem pouzdra a vytvoří hladkou vrstvu stékající po pouzdru a přes špičku dříku. V případě tvarování trubek je vzduch vháněn foukačkou s dutým hrotem a v případě tvarování tyčí používáme pevné hroty na hřídel. Trubky nebo tyče jsou pak taženy přes nosné válečky. Rozměry, jako je tloušťka stěny a průměr skleněných trubic, se upravují na požadované hodnoty nastavením průměru objímky a foukáním tlaku vzduchu na požadovanou hodnotu, nastavením teploty, rychlosti proudění skla a rychlosti tažení. Proces výroby skleněných trubic Vello na druhé straně zahrnuje sklo, které putuje z pece do misky s dutým trnem nebo zvonem. Sklo pak prochází vzduchovým prostorem mezi trnem a miskou a získává tvar trubice. Poté putuje přes válce do tažného stroje a ochladí se. Na konci chladicí linky probíhá řezání a konečné zpracování. Rozměry trubky lze upravit stejně jako v procesu Danner. Když porovnáme proces Danner a Vello, můžeme říci, že proces Vello je vhodnější pro výrobu velkého množství, zatímco proces Danner může být vhodnější pro přesné objednávky menších objemů trubek. • ZPRACOVÁNÍ TABULÍ A PLOCHÉHO A PLOVACÍHO SKLA: Máme velké množství plochého skla v tloušťkách od submilimetrových až po několik centimetrů. Naše ploché brýle jsou téměř optické dokonalosti. Nabízíme skla se speciálními povlaky, jako jsou optické povlaky, kde se používá technika chemického napařování k nanášení povlaků, jako je antireflexní nebo zrcadlový povlak. Běžné jsou také průhledné vodivé povlaky. K dispozici jsou také hydrofobní nebo hydrofilní povlaky na skle a povlak, který zajišťuje samočištění skla. Dalším oblíbeným zbožím jsou tvrzená, neprůstřelná a vrstvená skla. Sklo nařežeme do požadovaného tvaru s požadovanými tolerancemi. K dispozici jsou další sekundární operace, jako je zakřivení nebo ohýbání plochého skla. • PŘESNÉ LIŠOVÁNÍ SKLA: Tuto techniku používáme většinou pro výrobu přesných optických komponentů bez potřeby nákladnějších a časově náročných technik, jako je broušení, lapování a leštění. Tato technika není vždy dostatečná pro výrobu nejlepší optiky, ale v některých případech, jako jsou spotřební výrobky, digitální fotoaparáty, lékařská optika, může být levnější a dobrou volbou pro velkoobjemovou výrobu. Také má výhodu oproti jiným technikám tvarování skla, kde jsou vyžadovány složité geometrie, jako v případě asfér. Základní proces zahrnuje plnění spodní strany naší formy skleněným polotovarem, evakuaci procesní komory pro odstranění kyslíku, blízké uzavření formy, rychlý a izotermický ohřev formy a skla infračerveným světlem, další uzavření polovin formy pomalé lisování měkčeného skla kontrolovaným způsobem na požadovanou tloušťku a nakonec ochlazení skla a naplnění komory dusíkem a odstranění produktu. Přesná regulace teploty, vzdálenost uzavření formy, síla uzavření formy, přizpůsobení koeficientů roztažnosti formy a skleněného materiálu jsou v tomto procesu klíčové. • VÝROBA SKLENĚNÝCH OPTICKÝCH KOMPONENTŮ A SESTAV : Kromě přesného lisování skla existuje řada cenných procesů, které používáme pro výrobu vysoce kvalitních optických komponent a sestav pro náročné aplikace. Broušení, lapování a leštění optických skel v jemných speciálních brusných kaších je umění a věda pro výrobu optických čoček, hranolů, ploch a dalších. Plochost povrchu, zvlnění, hladkost a optické povrchy bez defektů vyžadují mnoho zkušeností s takovými procesy. Malé změny v prostředí mohou vést k tomu, že produkty nesplňují specifikace a zastavit výrobní linku. Existují případy, kdy jediné setření optického povrchu čistým hadříkem může způsobit, že výrobek splňuje specifikace nebo neprojde testem. Některé populární skleněné materiály jsou tavený oxid křemičitý, křemen, BK7. Také montáž takových komponent vyžaduje specializované specializované zkušenosti. Někdy se používají speciální lepidla. Někdy je však nejlepší volbou technika nazývaná optický kontakt, která nezahrnuje žádný materiál mezi připojenými optickými skly. Skládá se z fyzického kontaktu plochých povrchů, které se k sobě připojí bez lepidla. V některých případech se k sestavení optických součástí v určitých vzdálenostech a s určitými vzájemnými geometrickými orientacemi používají mechanické rozpěrky, přesné skleněné tyčinky nebo kuličky, svorky nebo obrobené kovové součásti. Podívejme se na některé z našich oblíbených technik výroby špičkové optiky. BRUŠENÍ A LAPOVÁNÍ A LEŠTĚNÍ: Hrubý tvar optické součásti se získá broušením skleněného polotovaru. Poté se provádí lapování a leštění otáčením a otíráním hrubých povrchů optických součástí o nástroje s požadovanými tvary povrchu. Mezi optiku a tvarovací nástroje se nalévají kaše s drobnými abrazivními částicemi a kapalinou. Velikosti abrazivních částic v takových suspenzích lze zvolit podle požadovaného stupně rovinnosti. Odchylky kritických optických povrchů od požadovaných tvarů jsou vyjádřeny pomocí vlnových délek použitého světla. Naše vysoce přesná optika má desetinovou toleranci vlnové délky (vlnová délka/10) nebo je možná ještě těsnější. Kromě profilu povrchu jsou kritické povrchy skenovány a vyhodnocovány na další povrchové vlastnosti a vady, jako jsou rozměry, škrábance, třísky, důlky, skvrny...atd. Přísná kontrola podmínek prostředí v optické výrobě a rozsáhlé požadavky na metrologii a testování s nejmodernějším vybavením z něj činí náročné průmyslové odvětví. • SEKUNDÁRNÍ PROCESY VE VÝROBĚ SKLA: Opět jsme omezeni pouze vaší představivostí, pokud jde o sekundární a dokončovací procesy skla. Zde uvádíme některé z nich: -Povlaky na skle (optické, elektrické, tribologické, tepelné, funkční, mechanické...). Jako příklad můžeme změnit povrchové vlastnosti skla tak, aby například odráželo teplo, aby udržovalo interiéry v budovách chladné, nebo jednostranně pohlcují infračervené záření pomocí nanotechnologie. To pomáhá udržovat vnitřek budov v teple, protože vnější povrchová vrstva skla absorbuje infračervené záření uvnitř budovy a vyzařuje je zpět dovnitř. - Leptání on sklo - Aplikované keramické značení (ACL) -Rytina -Leštění plamenem - Chemické leštění - Barvení VÝROBA TECHNICKÉ KERAMIKY • LIŠOVÁNÍ V ZÁSOBNÍKU : Skládá se z jednoosého lisování granulovaných prášků uzavřených v matrici • LISOVÁNÍ ZA HORKA: Podobné lisování, ale s přidáním teploty pro zvýšení zhuštění. Prášek nebo zhutněný předlisek se umístí do grafitové matrice a aplikuje se jednoosý tlak, zatímco matrice se udržuje při vysokých teplotách, jako je 2000 C. Teploty se mohou lišit v závislosti na typu zpracovávaného keramického prášku. U komplikovaných tvarů a geometrií může být zapotřebí další následné zpracování, jako je broušení diamantem. • IZSTATICKÉ LISOVÁNÍ: Granulovaný prášek nebo lisované výlisky se umístí do vzduchotěsných nádob a poté do uzavřené tlakové nádoby s kapalinou uvnitř. Poté se zhutňují zvýšením tlaku v tlakové nádobě. Kapalina uvnitř nádoby přenáší tlakové síly rovnoměrně po celé ploše vzduchotěsné nádoby. Materiál je tak stejnoměrně zhutněn a získává tvar své flexibilní nádoby a jejího vnitřního profilu a vlastností. • IZostatické lisování za tepla : Podobně jako u izostatického lisování, ale kromě atmosféry stlačeného plynu slinujeme výlisky při vysoké teplotě. Izostatické lisování za tepla má za následek dodatečné zhuštění a zvýšenou pevnost. • LITÍ SLIP / DRAIN CASTING : Formu naplníme suspenzí mikrometrových keramických částic a nosnou kapalinou. Tato směs se nazývá „skluz“. Forma má póry a proto se kapalina ve směsi filtruje do formy. V důsledku toho se na vnitřních plochách formy vytvoří odlitek. Po slinování lze díly vyjmout z formy. • ODLÉVÁNÍ PÁSKY: Vyrábíme keramické pásky odléváním keramických kaší na rovné pohyblivé povrchy nosiče. Kaše obsahují keramické prášky smíchané s jinými chemikáliemi pro účely spojování a přenášení. Když se rozpouštědla vypařují, zůstávají husté a pružné keramické desky, které lze řezat nebo válcovat podle potřeby. • VYTVÁŘENÍ VYTLAČOVÁNÍM: Stejně jako v jiných procesech vytlačování prochází měkká směs keramického prášku s pojivy a dalšími chemikáliemi matricí, aby získala tvar příčného řezu, a poté se řeže na požadované délky. Proces se provádí studenými nebo zahřátými keramickými směsmi. • NÍZKOTLAKÉ VSTŘIKOVÁNÍ: Připravíme směs keramického prášku s pojivy a rozpouštědly a zahřejeme ji na teplotu, kterou lze snadno vtlačit a vytlačit do dutiny nástroje. Jakmile je lisovací cyklus dokončen, díl se vysune a pojivo se spálí. Pomocí vstřikování můžeme ekonomicky získat složité díly ve velkých objemech. Jsou možné otvory , které jsou nepatrným zlomkem milimetru na stěně o tloušťce 10 mm, závity jsou možné bez dalšího obrábění, tolerance až +/- 0,5 % jsou možné a ještě nižší při obrábění dílů jsou možné tloušťky stěn v řádu od 0,5 mm do délky 12,5 mm, stejně jako tloušťky stěny od 6,5 mm do délky 150 mm. • ZELENÉ OBRÁBĚNÍ : Pomocí stejných nástrojů na obrábění kovů můžeme obrábět lisované keramické materiály, dokud jsou stále měkké jako křída. Jsou možné tolerance +/- 1 %. Pro lepší tolerance používáme diamantové broušení. • SINTROVÁNÍ nebo VYPALOVÁNÍ: Slinování umožňuje plné zhuštění. Na zelených kompaktních dílech dochází k výraznému smrštění, ale to není velký problém, protože tyto rozměrové změny bereme v úvahu při návrhu dílu a nástroje. Částice prášku jsou spojeny dohromady a pórovitost způsobená procesem zhutňování je do značné míry odstraněna. • BRUŠENÍ DIAMANTŮ: Nejtvrdší materiál na světě „diamant“ se používá k broušení tvrdých materiálů, jako je keramika, a získává se přesné díly. Dosahuje se tolerancí v řádu mikrometrů a velmi hladkých povrchů. Vzhledem k její náročnosti uvažujeme o této technice pouze tehdy, když ji opravdu potřebujeme. • HERMETICKÉ SESTAVY jsou takové, které prakticky neumožňují výměnu látek, pevných látek, kapalin nebo plynů mezi rozhraními. Hermetické těsnění je vzduchotěsné. Například hermetické elektronické kryty jsou takové, které udržují citlivý vnitřní obsah zabaleného zařízení bez poškození vlhkostí, nečistotami nebo plyny. Nic není 100% hermetické, ale když mluvíme o hermetičnosti, máme na mysli to, že v praxi existuje hermetika do té míry, že míra úniku je tak nízká, že zařízení jsou za normálních podmínek prostředí bezpečná po velmi dlouhou dobu. Naše hermetické sestavy se skládají z kovových, skleněných a keramických komponentů, kov-keramika, keramika-kov-keramika, kovokeramika-kov, kov na kov, kov-sklo, kov-sklo-kov, sklo-kov-sklo, sklo- kov a sklo na sklo a všechny další kombinace spojů kov-sklo-keramika. Můžeme například pokovovat keramické součásti, aby mohly být pevně spojeny s ostatními součástmi v sestavě a měly vynikající těsnící schopnost. Máme know-how v oblasti potahování optických vláken nebo průchodek kovem a jejich připájení nebo pájení natvrdo na kryty, takže do krytů neprocházejí ani neunikají žádné plyny. Proto se používají k výrobě elektronických krytů pro zapouzdření citlivých zařízení a jejich ochranu před vnější atmosférou. Kromě vynikajících těsnících vlastností mají i další vlastnosti, jako je koeficient tepelné roztažnosti, odolnost proti deformaci, bezodplyňování, velmi dlouhá životnost, nevodivost, tepelně izolační vlastnosti, antistatická povaha...atd. učinit ze skla a keramiky volbu pro určité aplikace. Informace o naší provozovně, která vyrábí armatury z keramiky na kov, hermetické těsnění, vakuové průchodky, komponenty pro řízení vysokého a ultravysokého vakua a kapalin naleznete zde:Brožura továrny na hermetické komponenty CLICK Product Finder-Locator Service PŘEDCHOZÍ STRÁNKA
- Wire & Spring Forming, Shaping, Welding, Assembly of Wires, Coil, CNC
Wire & Spring Forming, Shaping, Welding, Assembly of Wires, Coil Compression Extension Torsion Flat Springs, Custom Wires, Helical Springs at AGS-TECH Inc. Tváření drátů a pružin Vyrábíme dráty na zakázku, drátěné montáže, dráty tvarované do požadovaných 2D a 3D tvarů, drátěné sítě, pletiva, ohrádky, košík, plot, drátěná pružina, plochá pružina; torzní, kompresní, tahové, ploché pružiny a další. Naše procesy jsou tvarování drátu a pružin, tažení drátu, tvarování, ohýbání, svařování, pájení natvrdo, pájení, děrování, kování, vrtání, srážení hran, broušení, závitování, povlakování, čtyřskluzové tvarování, navíjení, navíjení, pěchování. Doporučujeme kliknout sem STÁHNĚTE SI naše schematické ilustrace procesů tváření drátů a pružin od AGS-TECH Inc. Tento soubor ke stažení s fotografiemi a nákresy vám pomůže lépe porozumět informacím, které vám poskytujeme níže. • TAŽENÍ DRÁTU: Pomocí tahových sil natahujeme kovový polotovar a protahujeme ho průvlakem, abychom zmenšili průměr a zvětšili jeho délku. Někdy používáme řadu matric. Jsme schopni vyrobit matrice pro každou tloušťku drátu. Pomocí materiálu s vysokou pevností v tahu kreslíme velmi tenké dráty. Nabízíme dráty opracované za studena i za tepla. • TVÁŘENÍ DRÁTU: Role kalibrovaného drátu se ohne a vytvaruje do užitečného produktu. Jsme schopni tvořit dráty ze všech tloušťek, včetně tenkých vláken i silných drátů, jako jsou ty, které se používají jako pružiny pod podvozky automobilů. Zařízení, která používáme pro tvarování drátu, jsou ruční a CNC tvarovače drátu, navíječka, silové lisy, čtyřsuňky, vícesaně. Naše procesy jsou tažení, ohýbání, rovnání, zploštění, natahování, řezání, pěchování, pájení a svařování a pájení, montáž, navíjení, pěchování (nebo křidélkování), děrování, závitování drátu, vrtání, srážení hran, broušení, povlakování a povrchové úpravy. Naše nejmodernější zařízení lze nastavit tak, aby vyvíjelo velmi složité návrhy jakéhokoli tvaru a úzkých tolerancí. Nabízíme různé typy koncovek jako kulové, špičaté nebo zkosené konce pro vaše dráty. Většina našich projektů tvarování drátu má minimální až nulové náklady na nástroje. Vzorové doby obratu jsou obvykle dny. Změny v designu/konfiguraci drátěných forem lze provést velmi rychle. • TVÁŘENÍ PRUŽIN: AGS-TECH vyrábí širokou škálu pružin včetně: -Torzní / Dvojitá torzní pružina -Tažná / tlačná pružina - Konstantní / variabilní pružina - Spirálová a spirálová pružina -Plochá a listová pružina -Bilance Spring - Belleville Washer - Negator Spring - Vinutá pružina s progresivní rychlostí -Vlnová pružina -Volute Spring - Kuželové pružiny - Pružinové prsteny -Clock Springs -Klipy Vyrábíme pružiny z různých materiálů a můžeme vás vést podle vaší aplikace. Nejběžnějšími materiály jsou nerezová ocel, chromový křemík, vysoce uhlíková ocel, v oleji temperovaná nízkouhlíková, chromvanad, fosforový bronz, titan, slitina berylia a mědi, vysokoteplotní keramika. Při výrobě pružin používáme různé techniky, včetně CNC navíjení, navíjení za studena, navíjení za tepla, kalení, dokončování. Další techniky již zmíněné výše pod tvarováním drátu jsou také běžné v našich operacích výroby pružin. • DOKONČOVACÍ SLUŽBY PRO DRÁTY & PRUŽINY: Vaše výrobky můžeme dokončit mnoha způsoby v závislosti na vašem výběru a potřebách. Některé běžné procesy, které nabízíme, jsou: lakování, práškové lakování, pokovování, máčení vinylu, eloxování, odlehčení pnutí, tepelné zpracování, brokování, bubnování, chromátování, electroless nikl, pasivace, vypalovaný smalt, plastový povlak , čištění plazmou. CLICK Product Finder-Locator Service PŘEDCHOZÍ STRÁNKA
- Sheet Metal Forming Fabrication, Stamping, Punching, Deep Drawing, CNC
Sheet Metal Forming and Fabrication, Stamping, Punching, Bending, Progressive Die, Spot Welding, Deep Drawing, Metal Blanking and Slitting at AGS-TECH Inc. Lisování a výroba plechů Nabízíme lisování plechů, tvarování, tváření, ohýbání, děrování, vysekávání, prořezávání, děrování, vrubování, vysekávání, stříhání, lisování, výrobu, hluboké tažení pomocí raznic/jednotahů, dále postupové raznice a zvlákňování, tvarování pryže a hydroforming; řezání plechů vodním paprskem, plazmou, laserem, pilou, plamenem; montáž plechů pomocí svařování, bodové svařování; vyboulení a ohýbání plechových trubek; povrchová úprava plechů včetně lakování ponorem nebo stříkáním, elektrostatické práškové lakování, eloxování, pokovování, naprašování a další. Naše služby sahají od rychlého prototypování plechů až po velkosériovou výrobu. Doporučujeme kliknout semSTÁHNĚTE SI naše schematické ilustrace procesů výroby a lisování plechů od AGS-TECH Inc. To vám pomůže lépe porozumět informacím, které vám poskytujeme níže. • ŘEZÁNÍ PLECHŮ : Nabízíme ŘEZÁNÍ a DĚLENÍ. Odřezky řežou plech po jedné dráze a v podstatě nedochází k žádnému plýtvání materiálem, kdežto u upichování nelze tvar přesně usadit a tím dochází k plýtvání určitého množství materiálu. Jedním z našich nejoblíbenějších procesů je VYDĚROVÁNÍ, kdy se z plechu vystřihne kus materiálu kulatého nebo jiného tvaru. Vyříznutý kus je odpad. Další verzí děrování je DRÁŽKOVÁNÍ, kdy se děrují obdélníkové nebo podlouhlé otvory. BLANKING na druhé straně je stejný proces jako děrování, s rozlišením vyřezávaného kusu je práce a je zachována. FINE BLANKING, špičková verze blankingu, vytváří řezy s úzkými tolerancemi a rovnými hladkými hranami a nevyžaduje sekundární operace pro dokonalost obrobku. Dalším procesem, který často používáme, je ŘEZÁNÍ, což je proces stříhání, kdy se plech řeže dvěma protilehlými kruhovými čepelemi v přímé nebo zakřivené dráze. Otvírák na konzervy je jednoduchým příkladem procesu řezání. Dalším oblíbeným procesem pro nás je DĚROVÁNÍ, kde je do plechu vyraženo mnoho otvorů kulatého nebo jiného tvaru v určitém vzoru. Typickým příkladem pro perforovaný výrobek jsou kovové filtry s mnoha otvory pro tekutiny. V NOTCHING, dalším procesu řezání plechu, odebíráme materiál z obrobku, počínaje od okraje nebo jinde a řežeme dovnitř, dokud nezískáme požadovaný tvar. Jedná se o progresivní proces, kdy každá operace odstraňuje další kus, dokud není získán požadovaný obrys. U malých výrobních sérií někdy používáme relativně pomalejší proces zvaný NIBBLING, který se skládá z mnoha rychlých děrování překrývajících se otvorů pro vytvoření většího a složitějšího řezu. V PROGRESIVNÍM ŘEZÁNÍ používáme řadu různých operací k získání jednoho řezu nebo určité geometrie. Sekundární proces HOLENÍ nám nakonec pomůže zlepšit hrany řezů, které již byly provedeny. Používá se k odřezávání třísek, hrubování hran na plechu. • OHÝBÁNÍ PLECHŮ: Kromě řezání je ohýbání nezbytným procesem, bez kterého bychom nebyli schopni vyrobit většinu výrobků. Většinou se jedná o práci za studena, ale někdy se také provádí za tepla nebo za tepla. Většinu času pro tuto operaci používáme matrice a lis. V PROGRESIVNÍM OHÝBÁNÍ používáme řadu různých operací razníku a matrice, abychom získali jeden ohyb nebo určitou geometrii. AGS-TECH používá různé ohýbací procesy a vybírá v závislosti na materiálu obrobku, jeho velikosti, tloušťce, požadované velikosti ohybu, poloměru, zakřivení a úhlu ohybu, umístění ohybu, ekonomice provozu, vyráběném množství… atd. Používáme V-BENDING, kde razník ve tvaru V zatlačí plech do matrice ve tvaru V a ohne jej. Dobré pro velmi ostré i tupé úhly a mezi nimi, včetně 90 stupňů. Pomocí stíracích forem provádíme OHÝBÁNÍ HRAN. Naše zařízení nám umožňuje získat úhly i větší než 90 stupňů. Při ohýbání okraje je obrobek vložen mezi přítlačnou podložku a matrici, oblast pro ohýbání je umístěna na okraji matrice a zbytek obrobku je držen nad space jako konzolový nosník. Když razník působí na konzolovou část, je ohnut přes okraj matrice. FLANGING je proces ohýbání hran, jehož výsledkem je úhel 90 stupňů. Hlavním cílem operace je odstranění ostrých hran a získání geometrických povrchů pro usnadnění spojování dílů. BEADING, další běžný proces ohýbání hran vytváří zvlnění přes hranu součásti. LEMOVÁNÍ na druhé straně vede k okraji listu, který je zcela ohnutý přes sebe. V SEAMING jsou okraje dvou dílů ohnuty na sebe a spojeny. DOUBLE SEAMING na druhé straně poskytuje vodotěsné a vzduchotěsné spoje plechů. Podobně jako u ohýbání hran, proces nazvaný OTOČNÉ OHYBOVÁNÍ rozvine válec s požadovaným úhlem vyříznutí a slouží jako razník. Jak je síla přenášena na razník, uzavírá se s obrobkem. Drážka válce dává konzolové části požadovaný úhel. Drážka může mít úhel menší nebo větší než 90 stupňů. Při VZDUCHOVÉM OHÝBÁNÍ nepotřebujeme, aby spodní matrice měla lomenou drážku. Plech je podepřen dvěma plochami na protilehlých stranách a v určité vzdálenosti. Razník pak působí silou ve správném místě a ohýbá obrobek. OHYB KANÁLU se provádí pomocí razníku a matrice ve tvaru kanálu a U-BEND se dosahuje razníkem ve tvaru U. OFFSET BENDING vytváří ofsety na plechu. ROLL BENDING, technika vhodná pro tlustou práci a ohýbání velkých kusů kovových plátů, používá tři válce k podávání a ohýbání plátů do požadovaného zakřivení. Role jsou uspořádány tak, aby bylo dosaženo požadovaného ohybu díla. Vzdálenost a úhel mezi válci jsou řízeny pro dosažení požadovaného výsledku. Pohyblivý válec umožňuje ovládat zakřivení. TVÁŘENÍ TRUBEK je další oblíbená operace ohýbání plechu zahrnující více zápustek. Zkumavky se získávají po několika akcích. Zvlnění se provádí také ohýbáním. V podstatě jde o symetrické ohýbání v pravidelných intervalech přes celý kus plechu. Pro zvlnění lze použít různé tvary. Vlnitý plech je tužší a má lepší odolnost proti ohybu, a proto má uplatnění ve stavebnictví. TVÁŘENÍ PLECHŮ, kontinuální manufacturing proces se používá k ohýbání příčných řezů určité geometrie pomocí válců a práce je ohýbána v sekvenčních krocích, přičemž finální role dokončuje práci. V některých případech se používá jedna role a v některých případech série rolí. • KOMBINOVANÉ PROCESY ŘEZÁNÍ A OHÝBÁNÍ PLECHŮ: Jedná se o procesy, které řežou a ohýbají současně. V PIERCINGU se díra vytvoří pomocí špičatého razníku. Jak průbojník rozšiřuje otvor v plechu, materiál je současně ohýbán do vnitřní příruby pro otvor. Získaná příruba může mít důležité funkce. Operace LNCING na druhé straně řeže a ohýbá plech, aby vytvořila zvýšenou geometrii. • VYDOUČENÍ A OHÝBÁNÍ KOVOVÉ TRUBKY: Při VYDUŠENÍ je některá vnitřní část duté trubky pod tlakem, což způsobuje vyboulení trubky směrem ven. Protože je trubka uvnitř matrice, geometrie vyboulení je řízena tvarem matrice. Při STRETCH BENDING se kovová trubka natahuje pomocí sil rovnoběžných s osou trubky a ohybových sil, aby se trubka přetáhla přes tvarový blok. Při DRAW BENDING upínáme trubku blízko jejího konce k otočnému tvarovému bloku, který trubku při otáčení ohýbá. A konečně, při KOMPRESNÍM OHYBOVÁNÍ je trubka držena silou k pevnému tvarovému bloku a matrice ji ohýbá přes tvarovací blok. • HLUBOKÉ TAŽENÍ: V jedné z našich nejoblíbenějších operací se používá razník, odpovídající matrice a držák polotovaru. Plechový polotovar je umístěn nad otvorem matrice a razník se pohybuje směrem k polotovaru drženému držákem polotovaru. Jakmile se dostanou do kontaktu, razník tlačí plech do dutiny formy, aby se vytvořil produkt. Hluboké tažení se podobá řezání, avšak vůle mezi razníkem a matricí brání řezání plechu. Dalším faktorem, který zajišťuje hluboké tažení plechu a neřezání, jsou zaoblené rohy na matrici a razníku, které brání stříhání a řezání. Pro dosažení větší velikosti hlubokého tažení je nasazen proces PŘEKRESLOVÁNÍ, kdy následné hluboké tažení probíhá na součásti, která již prošla procesem hlubokého tažení. V REVERSE REDRAWING je hluboce tažená součást převrácena a nakreslena v opačném směru. Hluboké tažení může poskytnout předměty nepravidelného tvaru, jako jsou kupolovité, zkosené nebo stupňovité poháry, Při EMBOSSOVÁNÍ používáme dvojici samčích a samičích matric, abychom plechu vtiskli design nebo písmo. • SPINNING : Operace, při které je plochý nebo předtvarovaný obrobek držen mezi rotujícím trnem a koníkem a nástroj vyvíjí lokalizovaný tlak na obrobek, jak se postupně posouvá nahoru po trnu. Výsledkem je, že obrobek se obalí přes trn a získá jeho tvar. Tuto techniku používáme jako alternativu k hlubokému tažení, kde je množství zakázky malé, díly jsou velké (průměry až 20 stop) a mají jedinečné křivky. I když jsou ceny za kus obecně vyšší, náklady na seřízení CNC spřádání jsou ve srovnání s hlubokým tažením nízké. Naopak hluboké tažení vyžaduje vysokou počáteční investici na nastavení, ale náklady na kus jsou nízké, když se vyrábí velké množství dílů. Další verzí tohoto procesu je SHEAR SPINNING, kde také dochází k toku kovu uvnitř obrobku. Tok kovu sníží tloušťku obrobku, jak se proces provádí. Dalším souvisejícím procesem je TUBE SPINNING, který se aplikuje na válcové díly. Také v tomto procesu dochází k toku kovu uvnitř obrobku. Tím se zmenší tloušťka a zvětší se délka trubky. Nástroj lze přesunout a vytvořit prvky na vnitřní nebo vnější straně trubky. • TVÁŘENÍ PRYŽOVÉHO PLECHU: Pryžový nebo polyuretanový materiál se vloží do nádobky a obrobek se položí na povrch pryže. Poté se na obrobek působí razníkem a vtlačí jej do pryže. Protože tlak generovaný pryží je nízký, hloubka vyráběných dílů je omezená. Vzhledem k tomu, že náklady na nástroje jsou nízké, je tento proces vhodný pro výrobu malého množství. • HYDROFORMOVÁNÍ: Podobně jako u tváření pryže je v tomto procesu plech lisován razníkem do stlačené kapaliny uvnitř komory. Plech je vložen mezi razník a pryžovou membránu. Membrána zcela obklopuje obrobek a tlak kapaliny jej nutí k vytvoření na razníku. Pomocí této techniky lze dosáhnout velmi hlubokého tažení ještě hlouběji než v procesu hlubokého tažení. Vyrábíme jednoděrové raznice i postupové raznice v závislosti na vašem dílu. Jednorázové raznice jsou nákladově efektivní metodou pro rychlou výrobu velkého množství jednoduchých plechových dílů, jako jsou podložky. Pro výrobu složitějších geometrií se používají postupové matrice nebo technika hlubokého tažení. V závislosti na vašem případě lze použít řezání vodním paprskem, laserem nebo plazmou k výrobě vašich plechových dílů levně, rychle a přesně. Mnoho dodavatelů o těchto alternativních technikách nemá ani ponětí, a proto procházejí zdlouhavými a drahými způsoby výroby zápustek a nástrojů, které pouze plýtvají časem a penězi zákazníků. Pokud požadujete zakázkové plechové komponenty, jako jsou kryty, elektronická pouzdra atd. tak rychle jako do několika dnů, kontaktujte nás pro naši službu RAPID SHEET METAL PROTOTYPING. CLICK Product Finder-Locator Service PŘEDCHOZÍ MENU
- Forging and Powdered Metallurgy, Die Forging, Heading, Hot Forging
Forging and Powdered Metallurgy, Die Forging, Heading, Hot Forging, Impression Die, Near Net Shape, Swaging, Metal Hobbing, Riveting, Coining from AGS-TECH Inc. Kování kovů a prášková metalurgie Typy procesů KOVÁNÍ KOVU, které nabízíme, jsou zápustka za tepla a za studena, otevřená zápustka a uzavřená zápustka, otiskovací zápustka a bezvýkovkové výkovky, cogging, válcování, lemování a přesné kování, tvar blízký síti, záhlaví , kování, pěchované kování, kovové odvalovací frézy, lisovací a válečkové & radiální & orbitální & prstencové & izotermické výkovky, ražení mincí, nýtování, kování kovových koulí, děrování kovů, klížení, vysokoenergetické kování. Naše techniky PRÁŠKOVÉ METALURGIE a PRÁŠKOVÉHO ZPRACOVÁNÍ jsou práškové lisování a slinování, impregnace, infiltrace, izostatické lisování za tepla a za studena, vstřikování kovů, zhutňování válcováním, válcování prášku, vytlačování prášku, volné slinování, jiskrové slinování, lisování za tepla. Doporučujeme kliknout sem STÁHNĚTE SI naše schématické ilustrace kovacích procesů od AGS-TECH Inc. STÁHNĚTE SI naše schématické ilustrace procesů práškové metalurgie od AGS-TECH Inc. Tyto soubory ke stažení s fotografiemi a nákresy vám pomohou lépe porozumět informacím, které vám poskytujeme níže. Při kování kovu se uplatňují tlakové síly a materiál se deformuje a získá se požadovaný tvar. Nejběžnějšími kovanými materiály v průmyslu jsou železo a ocel, ale hojně se kují i četné další, jako je hliník, měď, titan, hořčík. Kované kovové díly mají kromě utěsněných trhlin a uzavřených prázdných prostor zlepšenou strukturu zrna, takže pevnost dílů získaných tímto procesem je vyšší. Kováním se vyrábějí díly, které jsou výrazně pevnější vzhledem ke své hmotnosti než díly vyrobené litím nebo obráběním. Vzhledem k tomu, že kované díly jsou tvarovány tak, že kov teče do svého konečného tvaru, získává kov směrově zrnitou strukturu, která odpovídá za vynikající pevnost dílů. Jinými slovy, díly získané kovacím procesem vykazují lepší mechanické vlastnosti ve srovnání s jednoduchými litými nebo obráběnými díly. Hmotnost kovových výkovků se může pohybovat od malých lehkých dílů až po stovky tisíc liber. Vyrábíme výkovky převážně pro mechanicky náročné aplikace, kde je vyvíjeno vysoké namáhání dílů, jako jsou automobilové díly, ozubená kola, pracovní nástroje, ruční nářadí, hřídele turbín, motocyklové převody. Protože náklady na nástroje a nastavení jsou relativně vysoké, doporučujeme tento výrobní proces pouze pro velkoobjemovou výrobu a pro nízkoobjemové, ale vysoce hodnotné kritické součásti, jako jsou letecké přistávací zařízení. Kromě nákladů na nástroje mohou být výrobní doby pro velké množství kovaných dílů delší ve srovnání s některými jednoduchými obráběnými díly, ale tato technika je zásadní pro díly, které vyžadují mimořádnou pevnost, jako jsou šrouby, matice, speciální aplikace spojovací materiál, automobilový průmysl, vysokozdvižné vozíky, díly jeřábů. • KOVÁNÍ ZA TEPLA a STUDENA : Kování za tepla, jak název napovídá, se provádí při vysokých teplotách, tažnost je proto vysoká a pevnost materiálu nízká. To umožňuje snadnou deformaci a kování. Naopak zápustkové kování za studena se provádí při nižších teplotách a vyžaduje vyšší síly, což má za následek deformační zpevnění, lepší povrchovou úpravu a přesnost vyráběných dílů. • OTEVŘENÉ ZÁPLATY a KOVÁNÍ V TLAKU: Při volném kování zápustky neomezují materiál, který je stlačován, zatímco při kování v zápustce omezují dutiny v zápustkách tok materiálu při jeho kování do požadovaného tvaru. UPET FORGING nebo také nazývané UPSETTING, což ve skutečnosti není stejný, ale velmi podobný proces, je proces s otevřenou matricí, kde je obrobek vložen mezi dvě ploché matrice a tlaková síla snižuje jeho výšku. Když je výška reduced, šířka obrobku se zvětšuje. HLAVA, proces pěchovaného kování zahrnuje válcový materiál, který je na svém konci pěchován a jeho průřez se lokálně zvětšuje. V záhlaví je materiál veden přes zápustku, kován a poté nařezán na délku. Provoz je schopen rychle vyrábět velké množství spojovacích prvků. Většinou se jedná o operaci tváření za studena, protože se používá k výrobě konců hřebíků, konců šroubů, matic a šroubů, kde je třeba materiál zpevnit. Dalším procesem otevřené formy je COGGING, kde je obrobek kován v sérii kroků, přičemž každý krok vede ke stlačení materiálu a následnému pohybu otevřeného nástroje po délce obrobku. V každém kroku se tloušťka zmenšuje a délka se o malé množství zvětšuje. Tento proces připomíná nervózního studenta, který si celou dobu po malých krocích okusuje tužku. Proces zvaný FULLERING je další metodou kování v otevřeném zápustce, kterou často používáme jako dřívější krok k distribuci materiálu v obrobku před tím, než proběhnou další operace kování kovu. Používáme jej, když obrobek vyžaduje několik operací kování operations. Při operaci se matrice s konvexními plochami deformuje a způsobuje vytékání kovu na obě strany. Podobný proces jako válcování, na druhé straně EDGING zahrnuje otevřenou matrici s konkávními povrchy k deformaci obrobku. Okrajování je také přípravným procesem pro následné operace kování, díky nimž materiál proudí z obou stran do oblasti ve středu. KOVÁNÍ V TISKU nebo UZAVŘENÉ ZÁPLOVNÉ KOVÁNÍ, jak se tomu také říká, používá zápustku / formu, která stlačuje materiál a omezuje jeho tok v sobě. Forma se uzavře a materiál převezme tvar dutiny formy / formy. PŘESNÉ KOVÁNÍ, proces vyžadující speciální vybavení a formy, vyrábí díly bez nebo jen s velmi malým zábleskem. Jinými slovy, díly budou mít téměř konečné rozměry. V tomto procesu se pečlivě vloží a umístí dovnitř formy dobře kontrolované množství materiálu. Tuto metodu používáme pro složité tvary s tenkými průřezy, malými tolerancemi a úhly úkosu a když jsou množství dostatečně velká, aby ospravedlnila náklady na formu a vybavení. • BEZPROBLÉKOVÉ KOVÁNÍ: Obrobek je umístěn v zápustce tak, aby z dutiny nemohl vytékat žádný materiál, který by vytvořil výron. Není tedy potřeba žádné nežádoucí oříznutí blesku. Jedná se o přesný proces kování, a proto vyžaduje pečlivou kontrolu množství použitého materiálu. • KOVÁNÍ KOVU nebo RADIÁLNÍ KOVÁNÍ: Na obrobek se po obvodu působí zápustkou a kuje se. K vykování vnitřní geometrie obrobku lze také použít trn. Při operaci pěchování obrobek typicky přijímá několik zdvihů za sekundu. Typickými položkami vyráběnými pěchováním jsou špičaté nástroje, kuželové tyče, šroubováky. • DĚROVÁNÍ KOVU: Tuto operaci často používáme jako doplňkovou operaci při výrobě dílů. Otvor nebo dutina se vytvoří děrováním na povrchu obrobku, aniž by se prorazil. Vezměte prosím na vědomí, že děrování je něco jiného než vrtání, jehož výsledkem je průchozí otvor. • HOBBING : Razník s požadovanou geometrií se zatlačí do obrobku a vytvoří dutinu požadovaného tvaru. Tomuto razníku říkáme HOB. Operace zahrnuje vysoké tlaky a provádí se za studena. Výsledkem je, že materiál je opracován za studena a deformován. Proto je tento proces velmi vhodný pro výrobu forem, zápustek a dutin pro jiné výrobní procesy. Jakmile je varná deska vyrobena, lze snadno vyrobit mnoho stejných dutin, aniž by bylo nutné je jednu po druhé obrábět. • KOVÁNÍ VÁLCE nebo TVÁŘENÍ VÁLCE: K tvarování kovové součásti se používají dva protilehlé válce. Obrobek je přiváděn do válců, válce se otáčejí a vtahují obrobek do mezery, obrobek je pak veden drážkovanou částí válců a tlakové síly dávají materiálu požadovaný tvar. Nejedná se o proces válcování, ale o proces kování, protože je to spíše diskrétní než kontinuální operace. Geometrie na drážkách válců vykovává materiál do požadovaného tvaru a geometrie. Provádí se za tepla. Protože se jedná o proces kování, vyrábí díly s vynikajícími mechanickými vlastnostmi, a proto jej používáme pro výrobu automobilových dílů, jako jsou hřídele, které potřebují mít mimořádnou odolnost v náročných pracovních prostředích. • ORBITÁLNÍ KOVÁNÍ: Obrobek je vložen do dutiny kovací zápustky a vykován horní zápustkou, která se pohybuje po orbitální dráze, když se otáčí na nakloněné ose. Při každé otáčce horní matrice dokončuje vyvíjení tlakových sil na celý obrobek. Několikanásobným opakováním těchto otáček se provede dostatečné kování. Výhodou této výrobní techniky je její nízká hlučnost a menší potřeba síly. Jinými slovy s malými silami lze otáčet těžkou matricí kolem osy a vyvíjet velké tlaky na část obrobku, která je v kontaktu s matricí. Pro tento proces se někdy hodí kotoučové nebo kónické tvarované díly. • KOVÁNÍ KROUŽKŮ: Často používáme k výrobě bezešvých kroužků. Pažba je nařezána na požadovanou délku, převrácena a poté proražena až do konce, aby se vytvořil středový otvor. Poté se nasadí na trn a kovací zápustka jej zatluče shora, zatímco se prstenec pomalu otáčí, dokud se nedosáhne požadovaných rozměrů. • NÝTOVÁNÍ: Běžný proces spojování dílů začíná přímým kovovým kusem vloženým do předem připravených otvorů skrz díly. Poté jsou dva konce kovového kusu vykovány stlačením spoje mezi horní a spodní zápustkou. • RAŽENÍ : Další oblíbený proces prováděný mechanickým lisem, vyvíjejícím velké síly na krátkou vzdálenost. Název „coining“ pochází z jemných detailů, které jsou kované na povrchu kovových mincí. Jedná se většinou o dokončovací proces produktu, kde se jemné detaily získávají na površích v důsledku velké síly vyvíjené matricí, která tyto detaily přenáší na obrobek. • KOVÁNÍ KOVOVÝCH KULIČEK : Výrobky jako kuličková ložiska vyžadují vysoce kvalitní precizně vyrobené kovové kuličky. V jedné technice zvané SKEW ROLLING používáme dva protilehlé válce, které se kontinuálně otáčejí, jak je materiál kontinuálně přiváděn do válců. Na jednom konci dvou válců jsou kovové kuličky vyhazovány jako produkt. Druhým způsobem kování kovových koulí je použití zápustky, která stlačuje materiál uložený mezi nimi, přičemž má kulový tvar dutiny formy. Vyrobené koule často vyžadují některé další kroky, jako je konečná úprava a leštění, aby se staly vysoce kvalitním produktem. • IZOTERMICKÉ KOVÁNÍ / KOVÁNÍ V ZÁJEMCE: Nákladný proces prováděný pouze tehdy, je-li opodstatněná hodnota přínosu / nákladů. Proces zpracování za tepla, při kterém se matrice zahřeje na přibližně stejnou teplotu jako obrobek. Protože jak zápustka, tak obrobek mají přibližně stejnou teplotu, nedochází k žádnému ochlazování a zlepšuje se tokové vlastnosti kovu. Operace je vhodná pro superslitiny a materiály s horší kujností a materiály, jejichž mechanické vlastnosti jsou velmi citlivé na malé teplotní gradienty a změny. • VELIKOSTI KOVŮ: Jedná se o proces konečné úpravy za studena. Tok materiálu je neomezený ve všech směrech s výjimkou směru, ve kterém působí síla. Výsledkem je velmi dobrá povrchová úprava a přesné rozměry. • KOVÁNÍ S VYSOKOU ENERGIÍ: Tato technika zahrnuje horní formu připevněnou k ramenu pístu, která je rychle tlačena, když se směs paliva a vzduchu zapaluje zapalovací svíčkou. Připomíná činnost pístů v motoru automobilu. Forma velmi rychle narazí na obrobek a díky protitlaku se velmi rychle vrátí do původní polohy. Dílo je vykováno během několika milisekund, a proto není čas na vychladnutí díla. To je užitečné pro těžko kovatelné součásti, které mají mechanické vlastnosti velmi citlivé na teplotu. Jinými slovy, proces je tak rychlý, že se díl tvoří za konstantní teploty a na rozhraní formy/obrobku nebudou žádné teplotní gradienty. • Při ZÁPORNÉM KOVÁNÍ se kov tluče mezi dva odpovídající ocelové bloky se speciálními tvary, které se nazývají zápustky. Když je kov vtlačen mezi matrice, získá stejný tvar jako tvary v matrici. Když dosáhne konečného tvaru, vyjme se, aby vychladl. Tento proces produkuje pevné díly, které mají přesný tvar, ale vyžadují větší investice do specializovaných zápustek. Píchané kování zvětšuje průměr kusu kovu jeho zploštěním. Obecně se používá k výrobě malých dílů, zejména k vytváření hlav na spojovacích prvcích, jako jsou šrouby a hřebíky. • PRÁŠKOVÁ METALURGIE / PRÁŠKOVÉ ZPRACOVÁNÍ: Jak název napovídá, zahrnuje výrobní procesy pro výrobu pevných dílů určitých geometrií a tvarů z prášků. Pokud se pro tento účel používají kovové prášky, jedná se o oblast práškové metalurgie a pokud se používají nekovové prášky, jedná se o práškové zpracování. Pevné díly se vyrábějí z prášků lisováním a slinováním. POWDER PRESSING se používá k lisování prášků do požadovaných tvarů. Za prvé, primární materiál je fyzikálně práškový, čímž se rozděluje na mnoho malých jednotlivých částic. Prášková směs se plní do formy a razník se pohybuje směrem k prášku a lisuje jej do požadovaného tvaru. Většinou se provádí při pokojové teplotě, lisováním prášku se získá pevný díl, kterému se říká zelený výlisek. Pojiva a lubrikanty se běžně používají ke zlepšení stlačitelnosti. Jsme schopni práškové lisování na hydraulických lisech o kapacitě několika tisíc tun. Máme také dvojčinné lisy s protilehlými horními a spodními razníky a také vícečinné lisy pro vysoce složité geometrie součástí. Uniformita, která je důležitou výzvou pro mnoho závodů práškové metalurgie / zpracování prášku, není pro AGS-TECH žádný velký problém, protože máme dlouholeté zkušenosti se zakázkovou výrobou takových dílů. Uspěli jsme i u silnějších dílů, kde jednotnost představuje výzvu. Pokud se zavážeme k vašemu projektu, vyrobíme vaše díly. Pokud uvidíme nějaká potenciální rizika, budeme vás informovat in záloha. SPÍNÁNÍ PRÁŠKU, což je druhý krok, zahrnuje zvýšení teploty na určitý stupeň a udržování teploty na této úrovni po určitou dobu, aby se částice prášku ve výlisku mohly spojit. To má za následek mnohem pevnější vazby a zpevnění obrobku. Slinování probíhá blízko teplotě tání prášku. Během slinování dojde ke smrštění, zvýší se pevnost materiálu, hustota, tažnost, tepelná vodivost a elektrická vodivost. Máme vsádkové a průběžné pece pro slinování. Jednou z našich schopností je úprava úrovně poréznosti dílů, které vyrábíme. Například jsme schopni vyrábět kovové filtry tak, že díly do určité míry udržíme porézní. Pomocí techniky zvané IMPREGNACE vyplníme póry v kovu tekutinou, jako je olej. Vyrábíme například ložiska impregnovaná olejem, která jsou samomazná. V procesu INFILTRACE plníme póry kovu jiným kovem s nižší teplotou tání, než má základní materiál. Směs se zahřeje na teplotu mezi teplotami tání obou kovů. V důsledku toho lze získat některé speciální vlastnosti. Často také provádíme sekundární operace, jako je obrábění a kování na práškově vyrobených dílech, když je třeba získat speciální vlastnosti nebo vlastnosti nebo když lze díl vyrobit s menším počtem procesních kroků. IZSTATICKÉ LIŠOVÁNÍ: V tomto procesu se ke zhutnění součásti používá tlak tekutiny. Kovové prášky jsou umístěny ve formě vyrobené z uzavřené flexibilní nádoby. Při izostatickém lisování je tlak aplikován ze všech stran, na rozdíl od axiálního tlaku pozorovaného u konvenčního lisování. Výhodou izostatického lisování je rovnoměrná hustota v dílu, zvláště u větších nebo silnějších dílů, vynikající vlastnosti. Jeho nevýhodou jsou dlouhé doby cyklu a relativně malá geometrická přesnost. IZOSTATICKÉ LISKOVÁNÍ ZA STUDENA se provádí při pokojové teplotě a pružná forma je vyrobena z pryže, PVC nebo uretanu nebo podobných materiálů. Kapalina používaná pro tlakování a zhutňování je olej nebo voda. Následuje konvenční slinování zeleného výlisku. IZOSTATICKÉ LIŠOVÁNÍ ZA HORKA se naproti tomu provádí při vysokých teplotách a materiál formy je plech nebo keramika s dostatečně vysokým bodem tání, který teplotám odolává. Tlaková kapalina je obvykle inertní plyn. Operace lisování a slinování se provádějí v jednom kroku. Pórovitost je téměř úplně eliminována, je získána uniformní grain struktura. Výhodou izostatického lisování za tepla je, že lze vyrábět díly srovnatelné s litím a kováním v kombinaci, přičemž lze použít materiály, které nejsou vhodné pro lití a kování. Nevýhodou izostatického lisování za tepla je jeho dlouhá doba cyklu a tím i cena. Je vhodný pro kritické části s nízkou hlasitostí. VSTŘIKOVÁNÍ KOVŮ: Velmi vhodný proces pro výrobu složitých dílů s tenkými stěnami a detailní geometrií. Nejvhodnější pro menší díly. Prášky a polymerní pojivo se smíchají, zahřejí a vstříknou do formy. Polymerní pojivo pokrývá povrchy částic prášku. Po formování se pojivo odstraní buď nízkoteplotním zahříváním, nebo rozpuštěním za použití rozpouštědla. HUTNĚNÍ VÁLCE / VÁLCOVÁNÍ PRÁŠKU : Prášky se používají k výrobě souvislých pásů nebo plechů. Prášek je podáván z podavače a zhutňován dvěma rotujícími válci do archů nebo pásů. Operace se provádí za studena. Plech je dopraven do slinovací pece. Proces slinování lze opakovat podruhé. VYTLAČOVÁNÍ PRÁŠKU: Díly s velkými poměry délky k průměru se vyrábějí vytlačováním tenké plechové nádoby s práškem. VOLNÉ SINTROVÁNÍ: Jak již název napovídá, jedná se o beztlakou metodu zhutňování a slinování, vhodnou pro výrobu velmi porézních dílů, jako jsou kovové filtry. Prášek je přiváděn do dutiny formy bez zhutňování. VOLNÉ SINTROVÁNÍ: Jak již název napovídá, jedná se o beztlakou metodu zhutňování a slinování, vhodnou pro výrobu velmi porézních dílů, jako jsou kovové filtry. Prášek je přiváděn do dutiny formy bez zhutňování. JISKROVÉ SPÍNÁNÍ: Prášek je stlačen ve formě dvěma protilehlými razníky a na razník je přiveden elektrický proud o vysokém výkonu a prochází zhutněným práškem vloženým mezi ně. Vysoký proud spálí povrchové filmy z částic prášku a spéká je vzniklým teplem. Proces je rychlý, protože teplo není aplikováno zvenčí, ale je generováno zevnitř formy. LISOVÁNÍ ZA HORKA: Prášky se lisují a slinují v jediném kroku ve formě, která odolá vysokým teplotám. Když se forma zhutňuje, je na ni aplikováno práškové teplo. Dobrá přesnost a mechanické vlastnosti dosažené touto metodou z ní činí atraktivní volbu. Dokonce i žáruvzdorné kovy mohou být zpracovány použitím formovacích materiálů, jako je grafit. CLICK Product Finder-Locator Service PŘEDCHOZÍ MENU
- Plastic Rubber Metal Extrusions, Extrusion Dies, Aluminum Extruding
Plastic Rubber Metal Extrusions, Extrusion Dies, Aluminum Extruding, Pipe Tube Forming, Plastic Profiles, Metal Profiles Manufacturing, PVC at AGS-TECH Inc. Extruze, extrudované výrobky, extrudáty Proces EXTRUSION process používáme k výrobě produktů s pevným profilem průřezu, jako jsou trubky, trubky a chladiče. I když lze vytlačovat mnoho materiálů, naše nejběžnější vytlačované materiály jsou vyrobeny z kovu, polymerů / plastů, keramiky získané metodou vytlačování za studena, za tepla nebo za tepla. Vytlačené části nazýváme vytlačit nebo vytlačit, pokud je množné číslo. Některé specializované verze procesu, který také provádíme, jsou opláštění, koextruze a kombinované vytlačování. Doporučujeme, abyste klikli sem na STÁHNĚTE SI naše schématická ilustrace procesů vytlačování kovů, keramiky a plastů od AGS-TECH Inc. To vám pomůže lépe porozumět informacím, které vám poskytujeme níže. Při vytlačování se materiál, který má být vytlačován, protlačuje nebo protahuje skrz matrici, která má požadovaný profil průřezu. Proces lze použít k výrobě složitých průřezů s vynikající povrchovou úpravou a k opracování křehkého materiálu. Pomocí tohoto procesu lze vyrábět díly libovolné délky. Pro zjednodušení kroků procesu: 1.) Při vytlačování za tepla nebo za tepla se materiál ohřeje a vloží do kontejneru v lisu. Materiál je lisován a vytlačován z matrice. 2.) Vyrobený extrudát je tažen pro rovnání, tepelně zpracován nebo opracován za studena pro zlepšení jeho vlastností. Na druhou stranu COLD EXTRUSION probíhá při teplotě kolem pokojové teploty a má výhody nižší oxidace, vysoká pevnost povrchu a konečná úprava. WARM EXTRUSION se provádí nad pokojovou teplotou, ale pod bodem rekrystalizace. Nabízí kompromis a rovnováhu pro požadované síly, tažnost a vlastnosti materiálu, a proto je volbou pro některé aplikace. HOT EXTRUSION probíhá nad teplotou rekrystalizace materiálu. Tímto způsobem je snadnější protlačit materiál skrz matrici. Náklady na vybavení jsou však vysoké. Čím složitější je vytlačovaný profil, tím dražší je matrice (nástroj) a tím nižší je rychlost výroby. Průřezy matrice stejně jako tloušťky mají omezení, která závisí na materiálu, který má být vytlačován. Ostré rohy ve vytlačovacích nástrojích jsou vždy nežádoucí a je třeba se jim vyhnout, pokud to není nutné. Podle materiálu, který je vytlačován, nabízíme: • METAL EXTRUSIONS : Nejčastěji vyrábíme hliník, mosaz, zinek, měď, ocel, titan, hořčík • VYTLAČOVÁNÍ PLASTU : Plast se roztaví a vytvaruje do souvislého profilu. Naše běžně zpracovávané materiály jsou polyethylen, nylon, polystyren, polyvinylchlorid, polypropylen, ABS plast, polykarbonát, akryl. Mezi typické produkty, které vyrábíme, patří trubky a trubky, plastové rámy. V procesu jsou malé plastové kuličky / pryskyřice gravitačně přiváděny z násypky do válce vytlačovacího stroje. Často do násypky také přimícháváme barviva nebo jiné přísady, abychom dodali produktu požadované specifikace a vlastnosti. Materiál vstupující do vyhřívaného barelu je nucen rotujícím šnekem opustit hlaveň na konci a pohybovat se skrz síto pro odstranění kontaminantů v roztaveném plastu. Po průchodu sítem vstupuje plast do vytlačovací hubice. Forma dává pohyblivému měkkému plastu při průchodu tvar profilu. Nyní extrudát prochází vodní lázní za účelem chlazení. Další techniky, které AGS-TECH Inc. používá již mnoho let, jsou: • VYTLAČOVÁNÍ POTRUBÍ A TUBING : Plastové trubky a trubky se formují, když se plast vytlačuje přes kulatou tvarovací matrici a ochladí se ve vodní lázni, poté se řeže na délku nebo se svíjí/navíjí. Čiré nebo barevné, pruhované, jednoduché nebo dvoustěnné, flexibilní nebo tuhé, PE, PP, polyuretan, PVC, nylon, PC, silikon, vinyl nebo jinak, to vše máme. Máme skladované trubky a také schopnost vyrábět podle vašich specifikací. AGS-TECH vyrábí hadičky podle požadavků FDA, UL a LE pro lékařské, elektrické a elektronické, průmyslové a další aplikace. • OVERJACKETING / OVER JACKETING EXTRUSION : Tato technika aplikuje vnější vrstvu plastu na stávající drát nebo kabel. Naše izolační dráty jsou vyráběny touto metodou. • COEXTRUSION : Současně je vytlačováno více vrstev materiálu. Více vrstev je dodáváno více extrudéry. Různé tloušťky vrstvy lze upravit podle požadavků zákazníka. Tento proces umožňuje použít více polymerů, z nichž každý má v produktu odlišnou funkčnost. V důsledku toho lze optimalizovat řadu vlastností. • EXTRUZE KOMPOZICE: Jeden nebo více polymerů se smísí s přísadami, aby se získala plastická směs. Naše dvoušnekové extrudery produkují směšovací výlisky. Vytlačovací nástroje jsou obecně levné ve srovnání s kovovými formami. Pokud platíte mnohem více než několik tisíc dolarů za malou nebo střední vytlačovací matrici vytlačující hliník, pravděpodobně platíte příliš mnoho. Jsme experti na určení, která technika je pro vaši aplikaci nejefektivnější, nejrychlejší a nejvhodnější. Někdy vám vytlačení a následné opracování součásti může ušetřit spoustu peněz. Než učiníte pevné rozhodnutí, zeptejte se nás nejprve na náš názor. Pomohli jsme mnoha zákazníkům učinit správná rozhodnutí. Pro některé široce používané kovové výlisky si můžete stáhnout naše brožury a katalogy kliknutím na barevný text níže. Pokud se jedná o standardní produkt splňující vaše požadavky, bude to ekonomičtější. Stáhněte si naše možnosti vytlačování lékařských trubek a trubek Stáhněte si naše extrudované chladiče • SEKUNDÁRNÍ VÝROBNÍ A VÝROBNÍ PROCESY PRO VYTLAČOVÁNÍ : Mezi procesy s přidanou hodnotou, které nabízíme pro extrudované produkty, patří: -Zakázkové ohýbání, tvarování a tvarování trubek a trubek, odřezávání trubek, tvarování konců trubek, navíjení trubek, obrábění a dokončovací práce, vrtání a děrování a děrování, -Zakázkové sestavy trubek a trubek, trubková montáž, svařování, pájení a pájení -Zakázkové vytlačování ohýbání, tváření a tvarování -Čištění, odmašťování, moření, pasivace, leštění, eloxování, pokovování, lakování, tepelné zpracování, žíhání a kalení, značení, rytí a etiketování, zakázkové balení. CLICK Product Finder-Locator Service PŘEDCHOZÍ STRÁNKA
- Casting and Machined Parts, CNC Manufacturing, Milling, Turning, Swiss
Casting and Machined Parts, CNC Manufacturing, Milling, Turning, Swiss Type Machining, Die Casting, Investment Casting, Lost Foam Cast Parts from AGS-TECH Inc. Odlévání a obrábění Naše zakázkové odlévací a obráběcí techniky jsou spotřební a nestárnoucí odlitky, železné a neželezné lití, písek, zápustka, odstředivá, kontinuální, keramická forma, zatavovací, ztracená pěna, téměř síťový tvar, trvalá forma (gravitační lití), sádra formy (sádrové odlévání) a skořepinové odlitky, obráběné díly vyráběné frézováním a soustružením na konvenčních i CNC zařízeních, obrábění švýcarským typem pro vysoce výkonné levné malé přesné díly, šroubové obrábění spojovacích prvků, nekonvenční obrábění. Mějte prosím na paměti, že kromě kovů a kovových slitin obrábíme také keramické, skleněné a plastové součásti v některých případech, kdy výroba formy není přitažlivá nebo není možná. Obrábění polymerních materiálů vyžaduje specializované zkušenosti, které máme kvůli výzvě, kterou plasty a pryž představují kvůli jejich měkkosti, netuhosti...atd. Pro obrábění keramiky a skla se podívejte na naši stránku Nekonvenční výroba. AGS-TECH Inc. vyrábí a dodává lehké i těžké odlitky. Dodáváme kovové odlitky a obráběné díly pro kotle, výměníky tepla, automobily, mikromotory, větrné turbíny, zařízení na balení potravin a další. Doporučujeme, abyste klikli sem na STÁHNĚTE SI naše schematické ilustrace procesů obrábění a odlévání od AGS-TECH Inc. To vám pomůže lépe porozumět informacím, které vám poskytujeme níže. Podívejme se podrobně na některé z různých technik, které nabízíme: • EXPENDABLE ODLIVOVÁNÍ: Tato široká kategorie se týká metod, které zahrnují dočasné a neopakovaně použitelné formy. Příklady jsou písek, sádra, skořápka, zatmelovací (také nazývaný ztracený vosk) a sádrový odlitek. • LITÍ DO PÍSKU: Proces, kde se jako materiál formy používá písek. Velmi stará metoda a stále velmi oblíbená do té míry, že většina vyráběných kovových odlitků je vyrobena touto technikou. Nízké náklady i při výrobě malého množství. Vhodné pro výrobu malých i velkých dílů. Technika může být použita k výrobě dílů během dnů nebo týdnů s velmi malými investicemi. Vlhký písek se spojuje pomocí jílu, pojiv nebo speciálních olejů. Písek je obecně obsažen ve formovacích boxech a systém dutin a vrátek je vytvořen zhutněním písku kolem modelů. Procesy jsou: 1.) Uložení modelu do písku pro výrobu formy 2.) Začlenění modelu a písku do vtokového systému 3.) Odstranění modelu 4.) Vyplnění dutiny formy roztaveným kovem 5.) Chlazení kovu 6.) Rozbití pískové formy a vyjmutí odlitku • LITÍ DO SÁDROVÝCH FOREM: Podobně jako lití do písku a místo písku se jako materiál formy používá pařížská sádra. Krátké dodací lhůty výroby, jako je lití do písku a levné. Dobré rozměrové tolerance a povrchová úprava. Jeho hlavní nevýhodou je, že jej lze použít pouze s kovy s nízkým bodem tání, jako je hliník a zinek. • LITÍ KOŘEPIN: Také podobné lití do písku. Dutina formy získaná vytvrzeným pláštěm z písku a pojivem z termosetové pryskyřice namísto baňky naplněné pískem jako při procesu lití do písku. Téměř každý kov vhodný pro lití do písku lze odlévat skořepinovým litím. Proces lze shrnout takto: 1.) Výroba skořepinové formy. Použitý písek má mnohem menší zrnitost ve srovnání s pískem používaným při lití do písku. Jemný písek se smíchá s termosetovou pryskyřicí. Kovový vzor je potažen separačním činidlem pro snadnější odstranění skořepiny. Poté se kovový model zahřeje a písková směs se nanese na horký model odlévání nebo se na něj nafoukne. Na povrchu vzoru se vytvoří tenká skořápka. Tloušťku této skořepiny lze upravit změnou doby, po kterou je směs pískové pryskyřice v kontaktu s kovovým vzorem. Volný písek se poté odstraní a zůstane vzor pokrytý skořápkou. 2.) Dále se skořápka a vzor zahřejí v troubě, aby skořápka ztvrdla. Po dokončení vytvrzení se skořepina vysune ze vzoru pomocí kolíků zabudovaných do vzoru. 3.) Dvě takové skořepiny se spojí dohromady slepením nebo sevřením a tvoří kompletní formu. Nyní je skořepinová forma vložena do nádoby, ve které je během procesu odlévání podepřena pískem nebo kovovými broky. 4.) Nyní lze horký kov nalít do skořepinové formy. Předností skořepinového odlévání jsou výrobky s velmi dobrou povrchovou úpravou, možnost výroby složitých dílů s vysokou rozměrovou přesností, proces snadno automatizovatelný, ekonomický pro velkosériovou výrobu. Nevýhody jsou, že formy vyžadují dobré větrání, protože plyny vznikají při kontaktu roztaveného kovu s pojivem, termosetové pryskyřice a kovové vzory jsou drahé. Vzhledem k nákladům na kovové vzory nemusí tato technika dobře vyhovovat pro malé výrobní série. • INVESTIČNÍ LITÍ (také známé jako LOST-WAX CASTING): Také velmi stará technika a vhodná pro výrobu kvalitních dílů s vysokou přesností, opakovatelností, všestranností a integritou z mnoha kovů, žáruvzdorných materiálů a speciálních vysoce výkonných slitin. Lze vyrábět díly malých i velkých rozměrů. Nákladný proces ve srovnání s některými jinými metodami, ale hlavní výhodou je možnost vyrábět díly s téměř čistým tvarem, složitými obrysy a detaily. Náklady jsou tedy poněkud kompenzovány eliminací předělávek a obrábění v některých případech. I když mohou existovat odchylky, zde je shrnutí obecného procesu lití na investiční lití: 1.) Vytvoření originálního vzoru z vosku nebo plastu. Každý odlitek potřebuje jeden vzor, protože tyto jsou během procesu zničeny. Forma, ze které se vyrábí vzory, je také potřeba a většinou se forma odlévá nebo obrábí. Protože se forma nemusí otevírat, lze docílit složitých odlitků, mnoho voskových vzorů lze spojovat jako větve stromu a slévat dohromady, což umožňuje výrobu více dílů z jednoho odlití kovu nebo kovové slitiny. 2.) Dále se model ponoří nebo přelije žáruvzdornou kaší složenou z velmi jemnozrnného oxidu křemičitého, vody, pojiv. Výsledkem je keramická vrstva na povrchu vzoru. Žáruvzdorná vrstva na vzoru se nechá zaschnout a vytvrdit. Od tohoto kroku pochází název vytavovací lití: Žáruvzdorná kaše se zalije přes voskový vzor. 3.) V tomto kroku se vytvrzená keramická forma obrátí dnem vzhůru a zahřeje se, aby se vosk roztavil a vylil z formy. Pro kovový odlitek je ponechána dutina. 4.) Po vypuštění vosku se keramická forma zahřeje na ještě vyšší teplotu, což má za následek zpevnění formy. 5.) Kovový odlitek se nalije do horké formy vyplňující všechny složité sekce. 6.) Odlitek se nechá ztuhnout 7.) Nakonec se keramická forma rozbije a vyrobené díly se vyříznou ze stromu. Zde je odkaz na brožuru investičního lití • ODPAŘOVACÍ ODLÉVÁNÍ VZORU: Proces využívá vzor vyrobený z materiálu, jako je polystyrenová pěna, který se odpaří, když je horký roztavený kov nalit do formy. Existují dva typy tohoto procesu: LOST FOAM CASTING, který používá nespojený písek, a FULL MOLD CASTING, který používá pojený písek. Zde jsou obecné kroky procesu: 1.) Vyrobte vzor z materiálu jako je polystyren. Když se bude vyrábět velké množství, vzor se lisuje. Pokud má část složitý tvar, může být nutné k vytvoření vzoru slepit několik částí takového pěnového materiálu. Vzor často potahujeme žáruvzdornou hmotou, abychom vytvořili dobrou povrchovou úpravu odlitku. 2.) Vzor se pak vloží do formovacího písku. 3.) Roztavený kov se nalévá do formy, přičemž se odpařuje pěnový vzor, tj. ve většině případů polystyren, když protéká dutinou formy. 4.) Roztavený kov se nechá v pískové formě ztvrdnout. 5.) Po vytvrdnutí odlitek sejmeme. V některých případech produkt, který vyrábíme, vyžaduje jádro uvnitř vzoru. Při odpařovacím lití není potřeba umísťovat a zajišťovat jádro v dutině formy. Technika je vhodná pro výrobu velmi složitých geometrií, lze ji snadno automatizovat pro velkosériovou výrobu a v odlitku nejsou žádné dělicí linky. Základní proces je jednoduchý a ekonomický. Pro velkoobjemovou výrobu, protože k výrobě vzorů z polystyrenu je zapotřebí raznice nebo forma, to může být poněkud nákladné. • LITÍ NEEXPANDOVATELNÝCH FOREM: Tato široká kategorie se vztahuje k metodám, kde formu není třeba reformovat po každém výrobním cyklu. Příkladem je trvalé lití, lití v zápustce, kontinuální a odstředivé lití. Je dosaženo opakovatelnosti a díly lze charakterizovat jako NEAR NET HAPE. • TRVALÉ ODLITÍ FOREM: Opakovaně použitelné formy vyrobené z kovu se používají pro vícenásobné odlévání. Trvalou formu lze obecně použít desítky tisíckrát, než se opotřebuje. K plnění formy se obecně používá gravitace, tlak plynu nebo vakuum. Formy (také nazývané matrice) jsou obecně vyrobeny ze železa, oceli, keramiky nebo jiných kovů. Obecný proces je: 1.) Obrobte a vytvořte formu. Je běžné obrábět formu ze dvou kovových bloků, které do sebe zapadají a lze je otevírat a zavírat. Jak prvky součásti, tak i vtokový systém jsou obecně obrobeny do licí formy. 2.) Vnitřní povrchy formy jsou potaženy kaší obsahující žáruvzdorné materiály. To pomáhá řídit tepelný tok a působí jako mazivo pro snadné odstranění odlitku. 3.) Dále se poloviny trvalé formy uzavřou a forma se zahřeje. 4.) Roztavený kov se nalije do formy a nechá se ještě ztuhnout. 5.) Než dojde k velkému ochlazení, vyjmeme díl z trvalé formy pomocí vyhazovačů při otevření polovin formy. Často používáme trvalé lití do forem pro kovy s nízkým bodem tání, jako je zinek a hliník. Pro ocelové odlitky používáme jako formovací materiál grafit. Někdy získáváme složité geometrie pomocí jader v trvalých formách. Výhodou této techniky jsou odlitky s dobrými mechanickými vlastnostmi získanými rychlým ochlazením, rovnoměrnost vlastností, dobrá přesnost a povrchová úprava, nízká zmetkovitost, možnost automatizace procesu a ekonomická výroba velkých objemů. Nevýhodou jsou vysoké počáteční náklady na nastavení, které jej činí nevhodným pro operace s malým objemem, a omezení velikosti vyráběných dílů. • LITÍ POD TLAKU: Forma je obrobena a roztavený kov je vtlačován pod vysokým tlakem do dutin formy. Jsou možné tlakové odlitky z neželezných i železných kovů. Proces je vhodný pro velkosériovou výrobu malých až středně velkých dílů s detaily, extrémně tenkými stěnami, rozměrovou stálostí a dobrou povrchovou úpravou. AGS-TECH Inc. je schopna touto technikou vyrábět stěny o tloušťce 0,5 mm. Stejně jako u trvalého lití do formy musí forma sestávat ze dvou polovin, které se mohou otevírat a zavírat pro odstranění vyrobeného dílu. Forma pro tlakové lití může mít více dutin pro umožnění výroby více odlitků v každém cyklu. Formy na tlakové lití jsou velmi těžké a mnohem větší než díly, které vyrábějí, a proto jsou také drahé. Opravujeme a vyměňujeme opotřebované raznice zdarma pro naše zákazníky, pokud si u nás objednají své díly. Naše matrice mají dlouhou životnost v rozsahu několika set tisíc cyklů. Zde jsou základní zjednodušené procesní kroky: 1.) Výroba formy obecně z oceli 2.) Forma nainstalovaná na tlakovém licím stroji 3.) Píst nutí roztavený kov proudit v dutinách matrice a vyplňovat tak složité prvky a tenké stěny 4.) Po naplnění formy roztaveným kovem se odlitek nechá pod tlakem vytvrdit 5.) Forma se otevře a odlitek se vyjme pomocí vyhazovacích kolíků. 6.) Nyní se prázdná matrice znovu namaže a upne pro další cyklus. Při tlakovém lití často používáme vložkové lití, kdy do formy zabudujeme další díl a odléváme kov kolem něj. Po ztuhnutí se tyto díly stávají součástí odlévaného výrobku. Předností tlakového lití jsou dobré mechanické vlastnosti dílů, možnost složitých prvků, jemné detaily a dobrá povrchová úprava, vysoká produktivita, snadná automatizace. Nevýhody jsou: Nepříliš vhodné pro malý objem kvůli vysokým nákladům na matrici a vybavení, omezení tvarů, které lze odlévat, malé kulaté stopy na odlévaných dílech v důsledku kontaktu vyhazovacích kolíků, tenký záblesk kovu vytlačený na dělicí čáře, potřeba pro průduchy podél dělicí čáry mezi matricí nutnost udržovat nízké teploty formy pomocí cirkulace vody. • ODSTŘEDIVÉ LITÍ: Roztavený kov se nalévá do středu rotující formy v ose rotace. Odstředivé síly vrhají kov směrem k periferii a ten se nechá ztuhnout, když se forma stále otáčí. Lze použít horizontální i vertikální rotaci os. Lze odlévat díly s kulatými vnitřními plochami i jiné nekulaté tvary. Proces lze shrnout takto: 1.) Roztavený kov se nalije do odstředivé formy. Kov je pak vytlačován k vnějším stěnám v důsledku rotace formy. 2.) Jak se forma otáčí, kovový odlitek tvrdne Odstředivé lití je vhodná technika pro výrobu dutých válcových dílů, jako jsou trubky, není potřeba vtoků, nálitků a vtokových prvků, dobrá povrchová úprava a detailní vlastnosti, žádné problémy se smršťováním, možnost výroby dlouhých trubek s velmi velkými průměry, vysoká rychlost výroby . • KONTINUÁLNÍ ODLITÍ ( LINUTÍ STRAND ): Používá se k odlévání plynulé délky kovu. V zásadě je roztavený kov odléván do dvourozměrného profilu formy, ale jeho délka je neurčitá. Nový roztavený kov je neustále přiváděn do formy, jak se odlitek pohybuje směrem dolů a jeho délka se s časem zvětšuje. Kovy jako měď, ocel, hliník se odlévají do dlouhých pramenů pomocí procesu kontinuálního lití. Proces může mít různé konfigurace, ale tu společnou lze zjednodušit jako: 1.) Roztavený kov se nalévá do nádoby umístěné vysoko nad formou v dobře vypočítaných množstvích a průtokech a protéká vodou chlazenou formou. Kovový odlitek nalitý do formy tuhne na startovací tyč umístěnou na dně formy. Tato startovací lišta dává válečkům něco, čeho se mohou zpočátku chytit. 2.) Dlouhý kovový pramen je unášen válečky konstantní rychlostí. Válce také mění směr toku kovového pásu z vertikálního na horizontální. 3.) Poté, co plynulý odlitek urazí určitou vodorovnou vzdálenost, hořák nebo pila, která se pohybuje s odlitkem, jej rychle nařeže na požadované délky. Proces kontinuálního lití může být integrován s ROLLING PROCESS, kde kontinuálně litý kov může být přiváděn přímo do válcovací stolice pro výrobu I-nosníků, T-nosníků….atd. Kontinuální lití vytváří jednotné vlastnosti v celém výrobku, má vysokou rychlost tuhnutí, snižuje náklady díky velmi nízkým ztrátám materiálu, nabízí proces, kde nakládání kovu, lití, tuhnutí, řezání a odebírání odlitků probíhá v nepřetržitém provozu a výsledkem je vysoká produktivita a vysoká kvalita. Hlavním hlediskem je však vysoká počáteční investice, náklady na instalaci a prostorové nároky. • OBRÁBĚCÍ SLUŽBY : Nabízíme tří, čtyř a pětiosé obrábění. Typy obráběcích procesů, které používáme, jsou SOUSTRUŽENÍ, FRÉZOVÁNÍ, VRTÁNÍ, VYVRTÁVÁNÍ, PROTAHOVÁNÍ, HOBLOVÁNÍ, PILOVÁNÍ, BRUŠENÍ, LAPOVÁNÍ, LEŠTĚNÍ a NETRADIČNÍ OBRÁBĚNÍ, které je dále rozvedeno v jiné nabídce našeho webu. Pro většinu naší výroby používáme CNC stroje. Pro některé operace jsou však konvenční techniky vhodnější, a proto na ně také spoléháme. Naše obráběcí schopnosti dosahují nejvyšší možné úrovně a některé nejnáročnější díly jsou vyráběny v závodě s certifikací AS9100. Lopatky proudových motorů vyžadují vysoce specializované výrobní zkušenosti a správné vybavení. Letecký průmysl má velmi přísné normy. Některé součásti se složitou geometrickou strukturou se nejsnáze vyrábějí pětiosým obráběním, které se vyskytuje pouze v některých obráběcích provozech včetně naší. Náš závod s certifikací pro letectví a kosmonautiku má potřebné zkušenosti v souladu s požadavky rozsáhlé dokumentace leteckého průmyslu. Při operacích SOUSTRUŽENÍ se obrobek otáčí a pohybuje proti řeznému nástroji. K tomuto procesu se používá stroj zvaný soustruh. Při FRÉZOVÁNÍ má stroj zvaný frézka rotační nástroj, který přivádí řezné hrany k dosednutí na obrobek. VRTÁNÍ zahrnuje rotační frézu s břity, která vytváří otvory při kontaktu s obrobkem. Obvykle se používají vrtací lisy, soustruhy nebo frézy. Při operacích VYVRTÁVÁNÍ se nástroj s jednou ohnutou špičatou špičkou přesune do hrubé díry v otáčejícím se obrobku, aby se díra mírně zvětšila a zlepšila se přesnost. Používá se pro jemné dokončovací účely. PROTAHOVÁNÍ zahrnuje ozubený nástroj k odstranění materiálu z obrobku v jednom průchodu protahovačem (ozubený nástroj). Při lineárním protahování běží protahovač lineárně proti povrchu obrobku, aby se provedl řez, zatímco u rotačního protahování se protahovač otáčí a vtlačuje do obrobku, aby vyřízl osově symetrický tvar. SWISS TYPE MACHINING je jednou z našich cenných technik, kterou používáme pro velkoobjemovou výrobu malých vysoce přesných dílů. Na soustruhu švýcarského typu levně soustružíme malé, složité a přesné díly. Na rozdíl od konvenčních soustruhů, kde je obrobek držen v klidu a nástroj se pohybuje, v soustružnických centrech švýcarského typu se obrobek může pohybovat v ose Z a nástroj je nehybný. Při obrábění švýcarského typu je tyčový materiál držen ve stroji a posouvá se přes vodicí pouzdro v ose z, čímž se pouze obnaží obráběná část. Tímto způsobem je zajištěno pevné uchopení a přesnost je velmi vysoká. Dostupnost nástrojů pod napětím poskytuje příležitost frézovat a vrtat, když materiál postupuje z vodícího pouzdra. Osa Y zařízení švýcarského typu poskytuje plné možnosti frézování a šetří velké množství času při výrobě. Kromě toho naše stroje mají vrtáky a vyvrtávací nástroje, které pracují na součásti, když je držena v pomocném vřetenu. Naše obráběcí schopnost švýcarského typu nám dává možnost plně automatizovaného kompletního obrábění v jediné operaci. Obrábění je jedním z největších segmentů podnikání AGS-TECH Inc. Buď ji používáme jako primární operaci nebo sekundární operaci po odlití nebo vytlačení součásti tak, aby byly splněny všechny specifikace výkresu. • SLUŽBY POVRCHOVÉ ÚPRAVY: Nabízíme širokou škálu povrchových úprav a povrchových úprav, jako je úprava povrchu pro zvýšení adheze, nanášení tenké oxidové vrstvy pro zvýšení přilnavosti nátěru, pískování, chemický film, eloxování, nitridace, práškové lakování, lakování stříkáním , různé pokročilé techniky pokovování a povlakování včetně naprašování, elektronového paprsku, napařování, pokovování, tvrdých povlaků, jako je diamant jako uhlík (DLC) nebo titanový povlak pro vrtací a řezné nástroje. • SLUŽBY ZNAČENÍ A OZNAČOVÁNÍ VÝROBKŮ: Mnoho našich zákazníků vyžaduje značení a štítkování, laserové značení, gravírování na kovové části. Pokud máte nějakou takovou potřebu, nechte nás prodiskutovat, která možnost bude pro vás nejlepší. Zde jsou některé běžně používané kovové lité výrobky. Vzhledem k tomu, že jsou běžně dostupné, můžete ušetřit na nákladech na formy, pokud některá z nich vyhovuje vašim požadavkům: KLIKNĚTE ZDE A STAŽTE SI našich 11 hliníkových boxů řady 11 od AGS-Electronics CLICK Product Finder-Locator Service PŘEDCHOZÍ STRÁNKA
- Custom Manufactured Parts, Assemblies, Plastic Mold, Casting,Machining
Custom Manufactured Parts, Assemblies, Plastic Mold, Rubber Molding, Metal Casting, CNC Machining, Turning, Milling, Electrical Electronic Optical Assembly PCBA Zakázkově vyráběné díly & Sestavy a produkty Přečtěte si více Plastové a pryžové formy a lisování Přečtěte si více Odlévání a obrábění Přečtěte si více Extruze, extrudované výrobky Přečtěte si více Lisování a výroba plechů Přečtěte si více Kování kovů a prášková metalurgie Přečtěte si více Tváření drátů a pružin Přečtěte si více Tvarování a tvarování skla a keramiky Přečtěte si více Aditivní a rychlá výroba Přečtěte si více Výroba kompozitů a kompozitních materiálů Přečtěte si více Procesy spojování a montáže a upevňování Vyrábíme pro vás díly a sestavy a nabízíme následující výrobní procesy: • Plastové a pryžové formy a lisované díly. Vstřikování, tvarování za tepla, tvarování termosetem, vakuové tvarování, vyfukování, rotační tvarování, lité tvarování, tvarování vložek a další. • Plastové, pryžové a kovové výlisky • Železné a neželezné odlitky a obráběné díly vyráběné technikou frézování a soustružení, obráběním švýcarským typem. • Díly z práškové metalurgie • Kovové a nekovové výlisky, tváření plechů, svařované plechové sestavy • Kování za studena a za tepla • Dráty, svařované sestavy drátu, tvarování drátu • Různé typy pružin, tvarování pružin • Výroba ozubení, převodovky, spojky, šneku, reduktoru rychlosti, válce, převodových řemenů, převodových řetězů, převodových komponent • Zakázkové tvrzené a neprůstřelné sklo v souladu s NATO a vojenskými standardy • Kuličky, ložiska, řemenice a sestavy řemenic • Ventily a pneumatické komponenty, jako jsou O-kroužky, podložky a těsnění • Skleněné a keramické díly a sestavy, vakuově odolné a hermetické komponenty, kovokeramické a keramicko-keramické lepení. • Různé typy mechanických, optomechanických, elektromechanických, optoelektronických sestav. • Spojení kov-pryž, kov-plast • Trubky a trubky, tvarování trubek, ohýbání a zakázkové sestavy trubek, výroba měchů. • Výroba skelných vláken • Svařování pomocí různých technik, jako je bodové svařování, laserové svařování, MIG, TIG. Ultrazvukové svařování plastových dílů. • Široká škála povrchových úprav a povrchových úprav, jako je úprava povrchu pro zvýšení adheze, nanášení tenké oxidové vrstvy pro zvýšení adheze povlaku, pískování, chemický film, eloxování, nitridace, práškové lakování, stříkání, různé pokročilé metalizační a lakovací techniky včetně naprašování, elektronového paprsku, napařování, pokovování, tvrdých povlaků, jako je diamant jako uhlík (DLC) nebo titan pro řezné a vrtací nástroje. • Značení a etiketování, laserové značení na kovové díly, tisk na plastové a pryžové díly Stáhněte si brožuru s obecnými pojmy strojního inženýrství, které používají konstruktéři a inženýři Vyrábíme produkty podle vašich konkrétních specifikací a požadavků. Abychom vám mohli nabídnout nejlepší kvalitu, dodávky a ceny, vyrábíme produkty po celém světě v Číně, Indii, Tchaj-wanu, Filipínách, Jižní Koreji, Malajsii, Srí Lance, Turecku, USA, Kanadě, Německu, Velké Británii a Japonsku. To nás dělá mnohem silnějšími a globálně konkurenceschopnějšími než kterýkoli jiný custom manufacturer. Naše produkty jsou vyráběny v certifikovaných prostředích ISO9001:2000, QS9000, ISO14001, TS16949 a mají značku CE, UL a splňují další průmyslové normy. Jakmile jsme jmenováni pro váš projekt, můžeme se postarat o celou výrobu, montáž, testování, kvalifikaci, expedici a clo, jak si budete přát. Pokud chcete, můžeme skladovat vaše díly, sestavovat vlastní sady, vytisknout a označit název a značku vaší společnosti a poslat zásilku vašim zákazníkům. Jinými slovy, můžeme být také vaším skladovým a distribučním centrem, pokud chcete. Vzhledem k tomu, že naše sklady se nacházejí v blízkosti hlavních námořních přístavů, poskytuje nám to logistickou výhodu. Když například vaše produkty dorazí do velkého námořního přístavu v USA, můžeme je dopravit přímo do nedalekého skladu, kde je můžeme uložit, sestavit, vyrobit sady, přelepit, vytisknout, zabalit podle vašeho výběru a shodit odeslat vašim zákazníkům. Nedodáváme pouze produkty. Naše společnost pracuje na zakázkách na zakázku, kdy přijedeme k vám, zhodnotíme váš projekt na místě a vypracujeme návrh projektu na míru. K realizaci projektu pak vyšleme náš zkušený tým. Více informací o naší inženýrské činnosti naleznete na http://www.ags-engineering.com -Bereme malé projekty i velké projekty v průmyslovém měřítku. Jako první krok vás můžeme spojit buď telefonicky, telekonferencí nebo MSN messenger s členy našeho expertního týmu, takže můžete komunikovat přímo s odborníkem, klást otázky a diskutovat o svém projektu. Zavolejte nám a v případě potřeby vás přijedeme navštívit. PŘEDCHOZÍ STRÁNKA