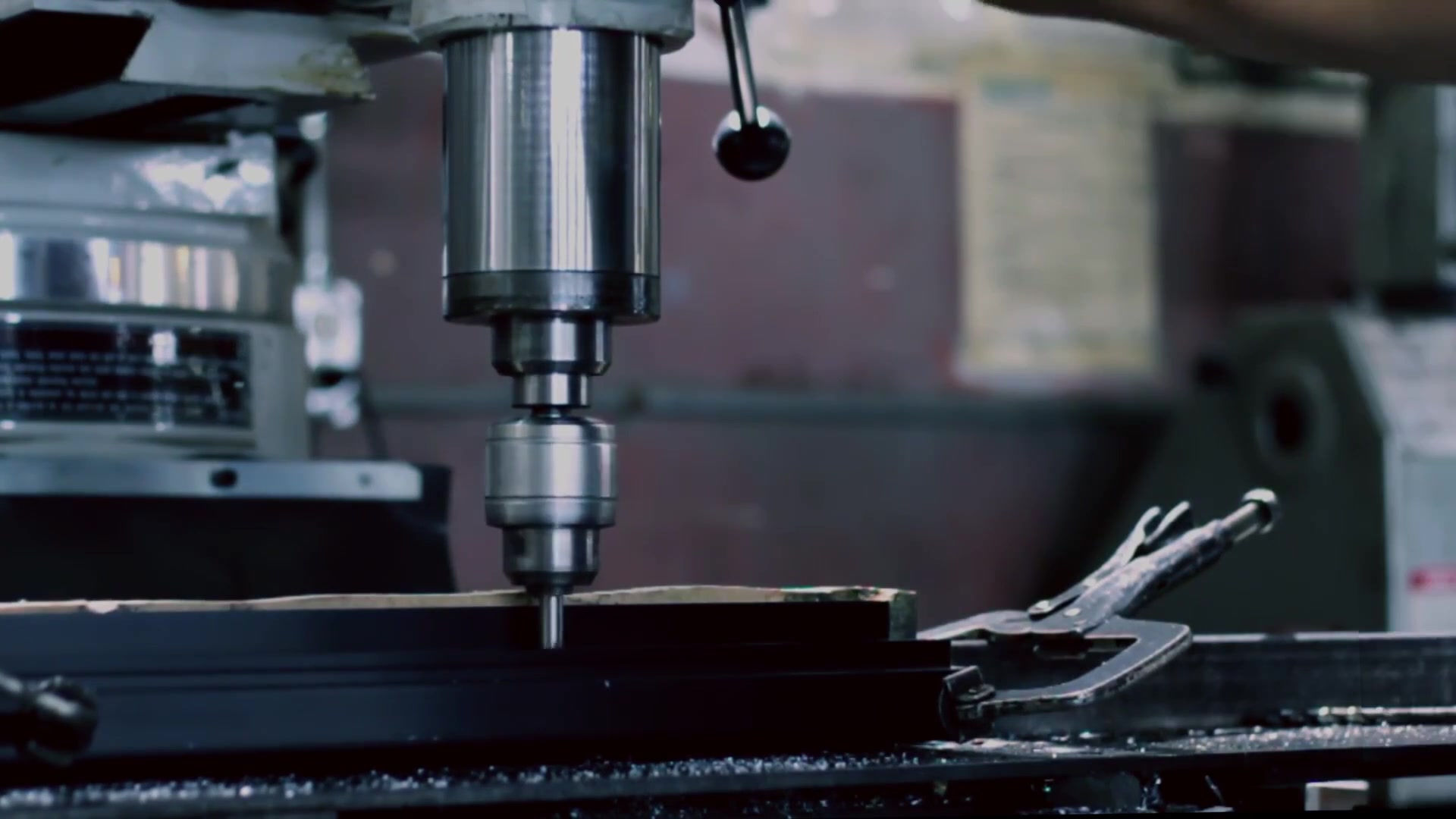
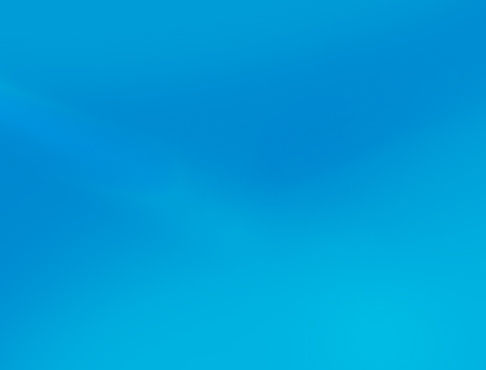
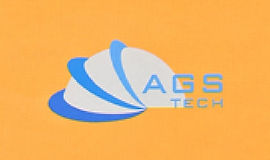
Global Custom Manufacturer, Integrator, Consolidator, Outsourcing Partner for en bred vifte af produkter og tjenester.
Vi er din one-stop-kilde til fremstilling, fremstilling, konstruktion, konsolidering, integration, outsourcing af specialfremstillede og hyldeprodukter og -tjenester.
Vælg dit sprog
-
Brugerdefineret fremstilling
-
Indenlandsk og global kontraktfremstilling
-
Outsourcing af produktion
-
Indenlandske og globale indkøb
-
Consolidation
-
Engineering Integration
-
Ingeniørtjenester
Blandt de mange JOINING-teknikker, vi anvender i fremstillingen, lægges der særlig vægt på SVEJSNING, SLODNING, LØDNING, KLÆBENDE LÆBNING og BRUGERDEFINERET MEKANISK MONTERING, fordi disse teknikker er meget udbredt i applikationer som fremstilling af hermetiske samlinger, højteknologisk produktfremstilling og specialiseret forsegling. Her vil vi koncentrere os om de mere specialiserede aspekter af disse sammenføjningsteknikker, da de er relateret til fremstilling af avancerede produkter og samlinger.
FUSIONSVEJSNING: Vi bruger varme til at smelte og samle materialer. Varme tilføres af el eller højenergistråler. De typer fusionssvejsning, vi anvender, er OXYFUEL GAS-SVEJSNING, BUESVEJSNING, HØJENERGISVEJSNING.
SVEJSNING I SOLID-STATE: Vi samler dele uden smeltning og sammensmeltning. Vores solid-state svejsemetoder er KOLDE, ULTRALYD, MODSTAND, FRIKTION, EKSPLOSIONSSVEJSNING og DIFFUSIONSKLÆBNING.
LØDNING OG LODNING: De bruger tilsætningsmetaller og giver os fordelen ved at arbejde ved lavere temperaturer end ved svejsning, og dermed mindre strukturelle skader på produkterne. Oplysninger om vores loddeanlæg, der producerer keramiske til metalfittings, hermetisk tætning, vakuumgennemføringer, høj- og ultrahøjvakuum- og væskekontrolkomponenter kan findes her:Lodningsfabriksbrochure
Klæbemidler: På grund af mangfoldigheden af klæbemidler, der bruges i industrien og også mangfoldigheden af applikationer, har vi en dedikeret side til dette. For at gå til vores side om limning, klik venligst her.
BRUGERDEFINERET MEKANISK MONTERING: Vi bruger en række forskellige fastgørelsesmidler såsom bolte, skruer, møtrikker, nitter. Vores fastgørelseselementer er ikke begrænset til standard hyldebefæstelser. Vi designer, udvikler og fremstiller specialbefæstelser, der er lavet af ikke-standardmaterialer, så de kan opfylde kravene til specielle anvendelser. Nogle gange ønskes elektrisk eller varme ikke-ledningsevne, mens nogle gange ledningsevne. Til nogle specielle applikationer kan en kunde ønske specielle fastgørelseselementer, som ikke kan fjernes uden at ødelægge produktet. Der er uendelige ideer og applikationer. Vi har det hele til dig, hvis ikke hyldevare kan vi hurtigt udvikle det. For at gå til vores side om mekanisk montage, klik venligst her. Lad os undersøge vores forskellige sammenføjningsteknikker mere detaljeret.
OXYFUEL GAS WELDING (OFW): Vi bruger en brændstofgas blandet med oxygen til at producere svejseflammen. Når vi bruger acetylen som brændstof og ilt, kalder vi det oxyacetylengassvejsning. To kemiske reaktioner forekommer i oxyfuel gasforbrændingsprocessen:
C2H2 + O2 ------» 2CO + H2 + Varme
2CO + H2 + 1,5 O2--------» 2 CO2 + H2O + Varme
Den første reaktion dissocierer acetylen til kulilte og brint, mens den producerer omkring 33% af den samlede varme, der genereres. Den anden proces ovenfor repræsenterer yderligere forbrænding af brint og carbonmonoxid, mens den producerer omkring 67% af den samlede varme. Temperaturer i flammen er mellem 1533 og 3573 Kelvin. Iltprocenten i gasblandingen er vigtig. Hvis iltindholdet er mere end det halve, bliver flammen et oxidationsmiddel. Dette er uønsket for nogle metaller, men ønskværdigt for andre. Et eksempel, hvor oxiderende flamme er ønskeligt, er kobberbaserede legeringer, fordi det danner et passiveringslag over metallet. På den anden side, når iltindholdet reduceres, er fuld forbrænding ikke mulig, og flammen bliver en reducerende (karburerende) flamme. Temperaturerne i en reducerende flamme er lavere, og derfor er den velegnet til processer som lodning og slaglodning. Andre gasser er også potentielle brændstoffer, men de har nogle ulemper i forhold til acetylen. Lejlighedsvis leverer vi fyldmetaller til svejsezonen i form af fyldstænger eller tråd. Nogle af dem er belagt med flusmiddel for at forsinke oxidation af overflader og dermed beskytte det smeltede metal. En yderligere fordel, fluxen giver os, er fjernelse af oxider og andre stoffer fra svejsezonen. Dette fører til stærkere binding. En variation af oxyfuel gassvejsningen er TRYKGASSVEJSNING, hvor de to komponenter opvarmes ved deres grænseflade ved hjælp af oxyacetylen gasbrænder, og når grænsefladen begynder at smelte, trækkes brænderen tilbage, og en aksial kraft påføres for at presse de to dele sammen indtil grænsefladen er størknet.
BUESVEJSNING: Vi bruger elektrisk energi til at producere en bue mellem elektrodespidsen og dele, der skal svejses. Strømforsyningen kan være AC eller DC, mens elektroderne enten kan forbruges eller ikke kan forbruges. Varmeoverførsel ved buesvejsning kan udtrykkes ved følgende ligning:
H/l = ex VI/v
Her er H varmetilførslen, l er svejselængden, V og I er den påførte spænding og strøm, v er svejsehastigheden og e er proceseffektiviteten. Jo højere effektivitet "e" jo mere fordelagtigt bruges den tilgængelige energi til at smelte materialet. Varmetilførslen kan også udtrykkes som:
H = ux (volumen) = ux A xl
Her er u den specifikke energi for smeltning, A tværsnittet af svejsningen og l svejselængden. Fra de to ovenstående ligninger kan vi få:
v = ex VI / u A
En variant af lysbuesvejsning er SHIELDED METAL RC WELDING (SMAW), som udgør omkring 50 % af alle industrielle og vedligeholdelsesmæssige svejseprocesser. ELEKTRISK BUESVEJSNING (STIKSVEJSNING) udføres ved at røre spidsen af en belagt elektrode til emnet og hurtigt trække det tilbage til en tilstrækkelig afstand til at opretholde lysbuen. Vi kalder denne proces også stavsvejsning, fordi elektroderne er tynde og lange stifter. Under svejseprocessen smelter spidsen af elektroden sammen med dens belægning og basismetallet i nærheden af buen. En blanding af basismetallet, elektrodemetallet og stoffer fra elektrodebelægningen størkner i svejseområdet. Belægningen af elektroden deoxiderer og giver en beskyttelsesgas i svejseområdet, hvilket beskytter den mod ilten i miljøet. Derfor omtales processen som skærmet metalbuesvejsning. Vi bruger strømme mellem 50 og 300 Ampere og effektniveauer generelt mindre end 10 kW for optimal svejseydelse. Også af betydning er polariteten af DC-strømmen (strømstrømmens retning). Lige polaritet, hvor emnet er positivt, og elektroden er negativ, foretrækkes ved svejsning af metalplader på grund af dens overfladiske gennemtrængning og også for samlinger med meget store mellemrum. Når vi har omvendt polaritet, dvs. elektroden er positiv og emnet negativ, kan vi opnå dybere svejsegennemføringer. Med vekselstrøm, da vi har pulserende buer, kan vi svejse tykke sektioner ved hjælp af elektroder med stor diameter og maksimal strøm. SMAW-svejsemetoden er velegnet til emnetykkelser på 3 til 19 mm og endnu mere ved brug af multiple-pass-teknikker. Slaggen, der dannes oven på svejsningen, skal fjernes med en stålbørste, så der ikke opstår korrosion og svigt i svejseområdet. Dette øger naturligvis omkostningerne ved skærmet metalbuesvejsning. Ikke desto mindre er SMAW den mest populære svejseteknik inden for industri og reparationsarbejde.
DYKKET BUESVEJSNING (SAV): I denne proces afskærmer vi svejsebuen ved hjælp af granulære flusmaterialer som kalk, silica, calciumflorid, manganoxid….osv. Det granulære flusmiddel føres ind i svejsezonen ved tyngdekraftstrøm gennem en dyse. Fluxen, der dækker den smeltede svejsezone, beskytter væsentligt mod gnister, dampe, UV-stråling osv. og fungerer som en termisk isolator og lader således varme trænge dybt ind i emnet. Den ufusionerede flux genvindes, behandles og genbruges. En spole af blottet bruges som elektrode og føres gennem et rør til svejseområdet. Vi bruger strømme mellem 300 og 2000 Ampere. Den nedsænkede buesvejseproces (SAW) er begrænset til vandrette og flade positioner og cirkulære svejsninger, hvis rotation af den cirkulære struktur (såsom rør) er mulig under svejsning. Hastigheden kan nå 5 m/min. SAW-processen er velegnet til tykke plader og resulterer i højkvalitets, seje, duktile og ensartede svejsninger. Produktiviteten, det vil sige mængden af aflejret svejsemateriale pr. time, er 4 til 10 gange mængden sammenlignet med SMAW-processen.
En anden buesvejseproces, nemlig GAS METAL ARRC WELDING (GMAW) eller alternativt benævnt METAL INERT GAS WELDING (MIG) er baseret på, at svejseområdet er afskærmet af eksterne gaskilder som helium, argon, kuldioxid….osv. Der kan være yderligere deoxidationsmidler til stede i elektrodemetallet. Forbrugstråd føres gennem en dyse ind i svejsezonen. Fremstilling, der involverer både jernholdige og ikke-jernholdige metaller, udføres ved hjælp af gasmetalbuesvejsning (GMAW). Svejseproduktiviteten er omkring 2 gange større end SMAW-processen. Der anvendes automatisk svejseudstyr. Metal overføres på en af tre måder i denne proces: "Spray Transfer" involverer overførsel af flere hundrede små metaldråber pr. sekund fra elektrode til svejseområdet. I "Globular Transfer" på den anden side bruges kuldioxidrige gasser, og kugler af smeltet metal drives frem af den elektriske lysbue. Svejsestrømmene er høje og svejsegennemtrængningen dybere, svejsehastigheden er større end ved sprøjteoverførsel. Den kugleformede overføring er således bedre til svejsning af tungere sektioner. Til sidst, i "Short Circuiting"-metoden, rører elektrodespidsen det smeltede svejsebad og kortslutter det, da metal med hastigheder på over 50 dråber/sekund overføres i individuelle dråber. Lave strømme og spændinger bruges sammen med tyndere ledning. Den anvendte effekt er omkring 2 kW og temperaturerne relativt lave, hvilket gør denne metode velegnet til tynde plader med en tykkelse på mindre end 6 mm.
En anden variation af FLUX-CORED ARC WELDING (FCAW)-processen ligner gasmetalbuesvejsning, bortset fra at elektroden er et rør fyldt med flux. Fordelene ved at bruge kerne-flux-elektroder er, at de producerer mere stabile buer, giver os mulighed for at forbedre egenskaberne af svejsemetaller, mindre skør og fleksibel karakter af dets flux sammenlignet med SMAW-svejsning, forbedrede svejsekonturer. Selvafskærmede elektroder med kerne indeholder materialer, der skærmer svejsezonen mod atmosfæren. Vi bruger omkring 20 kW strøm. Ligesom GMAW-processen giver FCAW-processen også mulighed for at automatisere processer til kontinuerlig svejsning, og det er økonomisk. Forskellige svejsemetalkemier kan udvikles ved at tilføje forskellige legeringer til fluxkernen.
I ELECTROGAS WELDING (EGW) svejser vi de anbragte stykker kant i kant. Det kaldes nogle gange også STUMSSVEJSNING. Svejsemetal anbringes i et svejsehulrum mellem to stykker, der skal sammenføjes. Rummet er omsluttet af to vandkølede dæmninger for at forhindre den smeltede slagge i at vælte ud. Dæmningerne flyttes op af mekaniske drev. Når emnet kan roteres, kan vi også bruge elektrogassvejseteknikken til periferisk svejsning af rør. Elektroder føres gennem en ledning for at holde en kontinuerlig bue. Strømmen kan være omkring 400 Ampere eller 750 Ampere og effektniveauer omkring 20 kW. Inerte gasser, der stammer fra enten en flux-kerneelektrode eller ekstern kilde, giver afskærmning. Vi bruger elektrogassvejsning (EGW) til metaller som stål, titanium ... osv. med tykkelser fra 12 mm til 75 mm. Teknikken passer godt til store strukturer.
Men i en anden teknik kaldet ELECTROSLAG WELDING (ESW) antændes lysbuen mellem elektroden og bunden af emnet, og der tilføjes flux. Når smeltet slagge når elektrodespidsen, slukkes lysbuen. Energi tilføres kontinuerligt gennem den smeltede slagges elektriske modstand. Vi kan svejse plader med tykkelser mellem 50 mm og 900 mm og endnu højere. Strømmen er omkring 600 Ampere, mens spændingerne er mellem 40 – 50 V. Svejsehastighederne er omkring 12 til 36 mm/min. Anvendelser ligner elektrogassvejsning.
En af vores ikke-forbrugelige elektrodeprocesser, GAS TUNGSTEN ARC WELDING (GTAW), også kendt som TUNGSTEN INERT GAS WELDING (TIG), involverer tilførsel af et fyldmetal via en ledning. Til tætsiddende samlinger bruger vi nogle gange ikke spartelmetallet. I TIG-processen bruger vi ikke flux, men bruger argon og helium til afskærmning. Wolfram har et højt smeltepunkt og forbruges ikke i TIG-svejseprocessen, derfor kan konstant strøm såvel som lysbuespalter opretholdes. Effektniveauer er mellem 8 og 20 kW og strømstyrker ved enten 200 Ampere (DC) eller 500 Ampere (AC). Til aluminium og magnesium bruger vi AC-strøm til dets oxidrensningsfunktion. For at undgå forurening af wolframelektroden undgår vi dens kontakt med smeltede metaller. Gas Tungsten Arc Welding (GTAW) er især nyttig til svejsning af tynde metaller. GTAW svejsninger er af meget høj kvalitet med god overfladefinish.
På grund af de højere omkostninger ved brintgas er en mindre hyppigt anvendt teknik ATOMIC HYDROGEN WELDING (AHW), hvor vi genererer en bue mellem to wolframelektroder i en afskærmende atmosfære af strømmende brintgas. AHW er også en ikke-forbrugbar elektrodesvejseproces. Den diatomiske hydrogengas H2 nedbrydes til sin atomare form nær svejsebuen, hvor temperaturen er over 6273 Kelvin. Mens den nedbrydes, absorberer den store mængder varme fra lysbuen. Når brintatomerne rammer svejsezonen, som er en relativt kold overflade, rekombinerer de til diatomisk form og frigiver den lagrede varme. Energi kan varieres ved at ændre emnet til bueafstand.
I en anden ikke-forbrugelig elektrodeproces, PLASMA BUESVEJSNING (PAW), har vi en koncentreret plasmabue rettet mod svejsezonen. Temperaturerne når 33.273 Kelvin i PAW. Et næsten lige så stort antal elektroner og ioner udgør plasmagassen. En lavstrøms pilotbue initierer plasmaet, som er mellem wolframelektroden og åbningen. Driftsstrømmene er generelt omkring 100 Ampere. Et fyldmetal kan tilføres. Ved plasmabuesvejsning udføres afskærmning af en ydre afskærmningsring og ved hjælp af gasser som argon og helium. Ved plasmabuesvejsning kan lysbuen være mellem elektroden og emnet eller mellem elektroden og dysen. Denne svejseteknik har fordelene i forhold til andre metoder med højere energikoncentration, dybere og smallere svejseevne, bedre buestabilitet, højere svejsehastigheder op til 1 meter/min, mindre termisk forvrængning. Vi bruger generelt plasmabuesvejsning til tykkelser mindre end 6 mm og nogle gange op til 20 mm til aluminium og titanium.
HØJENERGISVEJSNING: En anden type fusionssvejsemetode med elektronstrålesvejsning (EBW) og lasersvejsning (LBW) som to varianter. Disse teknikker er af særlig værdi for vores højteknologiske produktfremstillingsarbejde. Ved elektronstrålesvejsning rammer højhastighedselektroner arbejdsemnet, og deres kinetiske energi omdannes til varme. Den smalle stråle af elektroner bevæger sig let i vakuumkammeret. Generelt bruger vi højvakuum ved e-beam svejsning. Plader så tykke som 150 mm kan svejses. Ingen beskyttelsesgasser, flux eller fyldmateriale er nødvendige. Elektronstrålekanoner har en kapacitet på 100 kW. Dybe og smalle svejsninger med høje aspektforhold op til 30 og små varmepåvirkede zoner er mulige. Svejsehastigheder kan nå 12 m/min. Ved laserstrålesvejsning bruger vi højeffektlasere som varmekilde. Laserstråler så små som 10 mikron med høj densitet muliggør dyb penetrering i arbejdsemnet. Dybde-til-bredde-forhold så meget som 10 er muligt med laserstrålesvejsning. Vi bruger både pulserende og kontinuerlige lasere, hvor førstnævnte anvendes til tynde materialer og sidstnævnte mest til tykke emner op til ca. 25 mm. Effektniveauer er op til 100 kW. Laserstrålesvejsningen er ikke velegnet til optisk meget reflekterende materialer. Gasser kan også bruges i svejseprocessen. Laserstrålesvejsemetoden er velegnet til automatisering og højvolumenfremstilling og kan tilbyde svejsehastigheder mellem 2,5 m/min og 80 m/min. En stor fordel ved denne svejseteknik er adgang til områder, hvor andre teknikker ikke kan bruges. Laserstråler kan nemt rejse til sådanne vanskelige områder. Der er ikke behov for vakuum som ved elektronstrålesvejsning. Svejsninger med god kvalitet og styrke, lavt krympning, lav forvrængning, lav porøsitet kan opnås med laserstrålesvejsning. Laserstråler kan let manipuleres og formes ved hjælp af fiberoptiske kabler. Teknikken er således velegnet til svejsning af præcisionshermetiske samlinger, elektroniske pakker...osv.
Lad os se på vores SOLID STATE SVEJSEteknikker. KOLDSVEJSNING (CW) er en proces, hvor tryk i stedet for varme påføres ved hjælp af matricer eller valser til de dele, der parres. Ved koldsvejsning skal mindst en af de sammenpassende dele være duktil. De bedste resultater opnås med to lignende materialer. Hvis de to metaller, der skal sammenføjes med koldsvejsning, er forskellige, kan vi få svage og sprøde samlinger. Koldsvejsemetoden er velegnet til bløde, duktile og små emner såsom elektriske forbindelser, varmefølsomme beholderkanter, bimetalliske strimler til termostater...osv. En variant af koldsvejsning er rullebinding (eller rullesvejsning), hvor trykket påføres gennem et par ruller. Nogle gange udfører vi rullesvejsning ved forhøjede temperaturer for bedre grænsefladestyrke.
En anden solid state svejseproces, vi anvender, er ULTRASONIC WELDING (USW), hvor emnerne udsættes for en statisk normalkraft og oscillerende forskydningsspændinger. De oscillerende forskydningsspændinger påføres gennem spidsen af en transducer. Ultralydssvejsning anvender oscillationer med frekvenser fra 10 til 75 kHz. I nogle applikationer, såsom sømsvejsning, bruger vi en roterende svejseskive som spids. Forskydningsspændinger påført emnerne forårsager små plastiske deformationer, opbryder oxidlag, forurenende stoffer og fører til faststofbinding. Temperaturer involveret i ultralydssvejsning er langt under smeltepunktstemperaturer for metaller, og ingen fusion finder sted. Vi bruger ofte ultralydssvejseprocessen (USW) til ikke-metalliske materialer som plast. I termoplast når temperaturerne dog smeltepunkter.
En anden populær teknik, i FRICTION WELDING (FRW) genereres varmen gennem friktion ved grænsefladen mellem de emner, der skal sammenføjes. Ved friktionssvejsning holder vi et af emnerne stationært, mens det andet emne holdes i en fikstur og roteres med konstant hastighed. Arbejdsemnerne bringes derefter i kontakt under en aksial kraft. Overfladerotationshastigheden ved friktionssvejsning kan i nogle tilfælde nå 900 m/min. Efter tilstrækkelig grænsefladekontakt bringes det roterende emne til et pludseligt stop, og den aksiale kraft øges. Svejsezonen er generelt et smalt område. Friktionssvejseteknikken kan bruges til at forbinde solide og rørformede dele lavet af en række forskellige materialer. Nogle blitz kan udvikle sig ved grænsefladen i FRW, men denne flash kan fjernes ved sekundær bearbejdning eller slibning. Variationer af friktionssvejseprocessen findes. For eksempel involverer "inerti friktionssvejsning" et svinghjul, hvis rotationskinetiske energi bruges til at svejse delene. Svejsningen er færdig, når svinghjulet stopper. Den roterende masse kan varieres og dermed den roterende kinetiske energi. En anden variation er "lineær friktionssvejsning", hvor lineær frem- og tilbagegående bevægelse pålægges mindst en af de komponenter, der skal sammenføjes. Ved lineær friktionssvejsning behøver dele ikke at være cirkulære, de kan være rektangulære, kvadratiske eller af anden form. Frekvenser kan være i tiere af Hz, amplituder i millimeterområdet og tryk i tiere eller hundreder af MPa. Endelig er "friction stir welding" noget anderledes end de to andre forklaret ovenfor. Mens der ved inertifriktionssvejsning og lineær friktionssvejsning opnås opvarmning af grænseflader gennem friktion ved at gnide to kontaktflader, ved friktionsomrøringssvejsning gnides et tredje legeme mod de to overflader, der skal forbindes. Et roterende værktøj med en diameter på 5 til 6 mm bringes i kontakt med samlingen. Temperaturerne kan stige til værdier mellem 503 og 533 Kelvin. Opvarmning, blanding og omrøring af materialet i fugen foregår. Vi bruger friktionsrørsvejsning på en række forskellige materialer, herunder aluminium, plast og kompositter. Svejsninger er ensartede og kvaliteten er høj med minimale porer. Der produceres ingen dampe eller sprøjt ved friktionsrørsvejsning, og processen er velautomatiseret.
MODSTANDSVEJSNING (RW): Den varme, der kræves til svejsning, produceres af den elektriske modstand mellem de to emner, der skal sammenføjes. Ingen flux, beskyttelsesgasser eller forbrugselektroder anvendes til modstandssvejsning. Joule-opvarmning foregår ved modstandssvejsning og kan udtrykkes som:
H = (Kvadrat I) x R xtx K
H er varme genereret i joule (watt-sekunder), I strøm i ampere, R modstand i ohm, t er tiden i sekunder strømmen løber igennem. Faktoren K er mindre end 1 og repræsenterer den del af energi, der ikke går tabt gennem stråling og ledning. Strømme i modstandssvejseprocesser kan nå niveauer så høje som 100.000 A, men spændingerne er typisk 0,5 til 10 volt. Elektroder er typisk lavet af kobberlegeringer. Både lignende og uens materialer kan sammenføjes ved modstandssvejsning. Der findes adskillige variationer for denne proces: "Modstandspunktsvejsning" involverer to modstående runde elektroder, der kommer i kontakt med overfladerne af overlapningssamlingen på de to plader. Der påføres tryk, indtil strømmen afbrydes. Svejseklumpen er generelt op til 10 mm i diameter. Modstandspunktsvejsning efterlader let misfarvede fordybningsmærker ved svejsepunkter. Punktsvejsning er vores mest populære modstandssvejseteknik. Forskellige elektrodeformer bruges til punktsvejsning for at nå vanskelige områder. Vores punktsvejseudstyr er CNC-styret og har flere elektroder, der kan bruges samtidigt. En anden variation "modstandssømsvejsning" udføres med hjul- eller rulleelektroder, der producerer kontinuerlige punktsvejsninger, når strømmen når et tilstrækkeligt højt niveau i vekselstrømscyklussen. Samlinger fremstillet ved modstandssømsvejsning er væske- og gastætte. Svejsehastigheder på ca. 1,5 m/min er normale for tynde plader. Man kan anvende intermitterende strømme, således at der frembringes punktsvejsninger med ønskede intervaller langs sømmen. Ved "modstandsprojektionssvejsning" præger vi en eller flere fremspring (fordybninger) på en af emnets overflader, der skal svejses. Disse fremspring kan være runde eller ovale. Høje lokaliserede temperaturer nås ved disse prægede pletter, der kommer i kontakt med parringsdelen. Elektroder udøver tryk for at komprimere disse fremspring. Elektroder i modstandsprojektionssvejsning har flade spidser og er vandkølede kobberlegeringer. Fordelen ved modstandsprojektionssvejsning er vores evne til at svejse flere svejsninger i et slag, således den forlængede elektrodelevetid, evnen til at svejse plader af forskellige tykkelser, evnen til at svejse møtrikker og bolte til plader. Ulempen ved modstandsprojektionssvejsning er de ekstra omkostninger ved at præge fordybningerne. Endnu en teknik, i "flash-svejsning" genereres varme fra buen i enderne af de to emner, når de begynder at få kontakt. Denne metode kan også alternativt betragtes som buesvejsning. Temperaturen ved grænsefladen stiger, og materialet blødgøres. En aksial kraft påføres, og der dannes en svejsning i det blødgjorte område. Når lynsvejsningen er færdig, kan samlingen bearbejdes for at få et forbedret udseende. Svejsekvalitet opnået ved lynsvejsning er god. Effektniveauer er 10 til 1500 kW. Lynsvejsning er velegnet til kant-til-kant sammenføjning af lignende eller uens metaller op til 75 mm diameter og plader mellem 0,2 mm til 25 mm tykkelse. "Stud arc welding" ligner meget lynsvejsning. Tappen, såsom en bolt eller gevindstang, tjener som én elektrode, mens den forbindes med et emne, såsom en plade. For at koncentrere den genererede varme, forhindre oxidation og fastholde det smeltede metal i svejsezonen, placeres en keramisk engangsring rundt om samlingen. Endelig "percussion svejsning" en anden modstand svejsning proces, bruger en kondensator til at levere den elektriske energi. Ved slagsvejsning aflades kraften i løbet af millisekunder meget hurtigt og udvikler høj lokaliseret varme ved samlingen. Vi anvender slagsvejsning i vid udstrækning i den elektroniske fremstillingsindustri, hvor opvarmning af følsomme elektroniske komponenter i nærheden af samlingen skal undgås.
En teknik kaldet EKSPLOSIONSSVEJSNING involverer detonation af et lag sprængstof, der lægges over et af emnerne, der skal sammenføjes. Det meget høje tryk, der udøves på emnet, giver en turbulent og bølget grænseflade, og mekanisk sammenlåsning finder sted. Vedhæftningsstyrkerne ved eksplosiv svejsning er meget høje. Eksplosionssvejsning er en god metode til beklædning af plader med uens metaller. Efter beklædning kan pladerne rulles i tyndere sektioner. Nogle gange bruger vi eksplosionssvejsning til at udvide rør, så de bliver tætnet tæt mod pladen.
Vores sidste metode inden for domænet faststofsammenføjning er DIFFUSION BONDING eller DIFFUSION WELDING (DFW), hvor en god samling opnås hovedsageligt ved diffusion af atomer over grænsefladen. En vis plastisk deformation ved grænsefladen bidrager også til svejsningen. De involverede temperaturer er omkring 0,5 Tm, hvor Tm er metallets smeltetemperatur. Vedhæftningsstyrken ved diffusionssvejsning afhænger af tryk, temperatur, kontakttid og renhed af kontaktflader. Nogle gange bruger vi fyldmetaller ved grænsefladen. Varme og tryk er påkrævet i diffusionsbinding og leveres af elektrisk modstand eller ovn og dødvægte, presse eller andet. Lignende og uens metaller kan sammenføjes med diffusionssvejsning. Processen er relativt langsom på grund af den tid, det tager for atomer at migrere. DFW kan automatiseres og bruges i vid udstrækning til fremstilling af komplekse dele til rumfarts-, elektronik- og medicinske industrier. Produkter, der fremstilles, omfatter ortopædiske implantater, sensorer, strukturelle dele til rumfart. Diffusionsbinding kan kombineres med SUPERPLASTISK FORMNING for at fremstille komplekse metalpladestrukturer. Udvalgte steder på plader diffusionsbindes først, og derefter udvides de ubundne områder til en form ved hjælp af lufttryk. Luftfartsstrukturer med høje stivhed-til-vægt-forhold fremstilles ved hjælp af denne kombination af metoder. Den kombinerede diffusionssvejsning/superplastiske formningsproces reducerer antallet af dele, der kræves ved at eliminere behovet for fastgørelseselementer, hvilket resulterer i lavspænding og meget nøjagtige dele økonomisk og med korte gennemløbstider.
LODNING: Lodning og loddeteknikker involverer lavere temperaturer end dem, der kræves til svejsning. Dog er loddetemperaturerne højere end loddetemperaturerne. Ved slaglodning anbringes et fyldmetal mellem overfladerne, der skal sammenføjes, og temperaturerne hæves til smeltetemperaturen for fyldmaterialet over 723 Kelvin, men under emnernes smeltetemperatur. Det smeltede metal fylder det tætsiddende mellemrum mellem emnerne. Afkøling og efterfølgende størkning af filtermetallet resulterer i stærke samlinger. Ved loddesvejsning aflejres tilsatsmetallet ved samlingen. Der bruges betydeligt mere spartelmetal ved lodningssvejsning sammenlignet med lodning. Oxyacetylenbrænder med oxiderende flamme bruges til at afsætte fyldmetallet ved loddesvejsning. På grund af lavere temperaturer ved lodning er problemerne i de varmepåvirkede zoner, såsom vridning og resterende spændinger, mindre. Jo mindre frigangsmellemrum der er ved lodning, desto højere er samlingens forskydningsstyrke. Maksimal trækstyrke opnås dog ved et optimalt mellemrum (en spidsværdi). Under og over denne optimale værdi falder trækstyrken ved slaglodning. Typiske afstande ved slaglodning kan være mellem 0,025 og 0,2 mm. Vi bruger en række loddematerialer med forskellige former, såsom performs, pulver, ringe, wire, strip...osv. og kan fremstille disse udfører specielt til dit design eller produktgeometri. Vi bestemmer også indholdet af loddematerialerne i henhold til dine grundmaterialer og anvendelse. Vi bruger ofte flusmidler i loddeoperationer for at fjerne uønskede oxidlag og forhindre oxidation. For at undgå efterfølgende korrosion fjernes flusmidler generelt efter sammenføjningen. AGS-TECH Inc. anvender forskellige slaglodningsmetoder, herunder:
- Fakkellodning
- Ovnslodning
- Induktionslodning
- Modstandslodning
- Dyplodning
- Infrarød lodning
- Diffusionslodning
- Højenergistråle
Vores mest almindelige eksempler på loddesamlinger er lavet af forskellige metaller med god styrke, såsom hårdmetalbor, skær, optoelektroniske hermetiske pakker, tætninger.
LODNING : Dette er en af vores mest anvendte teknikker, hvor loddemetal (fyldmetal) fylder samlingen som ved lodning mellem tætsluttende komponenter. Vores lodninger har smeltepunkter under 723 Kelvin. Vi anvender både manuel og automatiseret lodning i fremstillingsoperationer. Sammenlignet med lodning er loddetemperaturerne lavere. Lodning er ikke særlig velegnet til applikationer med høj temperatur eller høj styrke. Vi anvender blyfri lodninger samt tin-bly, tin-zink, bly-sølv, cadmium-sølv, zink-aluminium legeringer foruden andre til lodning. Både ikke-ætsende harpiksbaserede såvel som uorganiske syrer og salte bruges som flusmiddel ved lodning. Vi bruger specielle flusmidler til at lodde metaller med lav loddeevne. I applikationer, hvor vi skal lodde keramiske materialer, glas eller grafit, beklæder vi først delene med et passende metal for øget loddeevne. Vores populære loddeteknikker er:
-Reflow eller Paste Lodning
- Bølgelodning
- Ovnslodning
- Brænderlodning
-Induktionslodning
- Jern lodning
- Modstandslodning
- Dyplodning
- Ultralyd lodning
- Infrarød lodning
Ultralydslodning giver os en unik fordel, hvorved behovet for flusmidler elimineres på grund af ultralydskavitationseffekten, som fjerner oxidfilm fra overfladerne, der sammenføjes. Reflow og Wave lodning er vores industrielt fremragende teknikker til højvolumen fremstilling i elektronik og derfor værd at forklare mere detaljeret. Ved reflowlodning bruger vi halvfaste pastaer, der indeholder loddemetalpartikler. Pastaen anbringes på samlingen ved hjælp af en screenings- eller stencileringsproces. I printkort (PCB) bruger vi ofte denne teknik. Når elektriske komponenter placeres på disse puder fra pasta, holder overfladespændingen de overflademonterede pakker på linje. Efter at have placeret komponenterne opvarmer vi samlingen i en ovn, så reflow-lodningen finder sted. Under denne proces fordamper opløsningsmidlerne i pastaen, fluxen i pastaen aktiveres, komponenterne forvarmes, loddepartiklerne smeltes og fugter samlingen, og til sidst afkøles PCB-samlingen langsomt. Vores anden populære teknik til højvolumen produktion af printplader, nemlig bølgelodning er afhængig af, at smeltede lodninger våder metaloverflader og kun danner gode bindinger, når metallet er forvarmet. En stående laminær bølge af smeltet loddemetal genereres først af en pumpe, og de forvarmede og præfluxede PCB'er føres hen over bølgen. Loddemetal fugter kun udsatte metaloverflader, men befugter ikke IC-polymerpakkerne eller de polymerbelagte printkort. En høj hastighed af varmtvandsstråle blæser overskydende loddegods fra samlingen og forhindrer brodannelse mellem tilstødende ledninger. Ved bølgelodning af overflademonterede pakker limer vi dem først klæbende til printkortet før lodning. Igen bruges screening og stenciling, men denne gang til epoxy. Efter at komponenterne er placeret på de rigtige steder, er epoxyen hærdet, pladerne vendes om og bølgelodning finder sted.