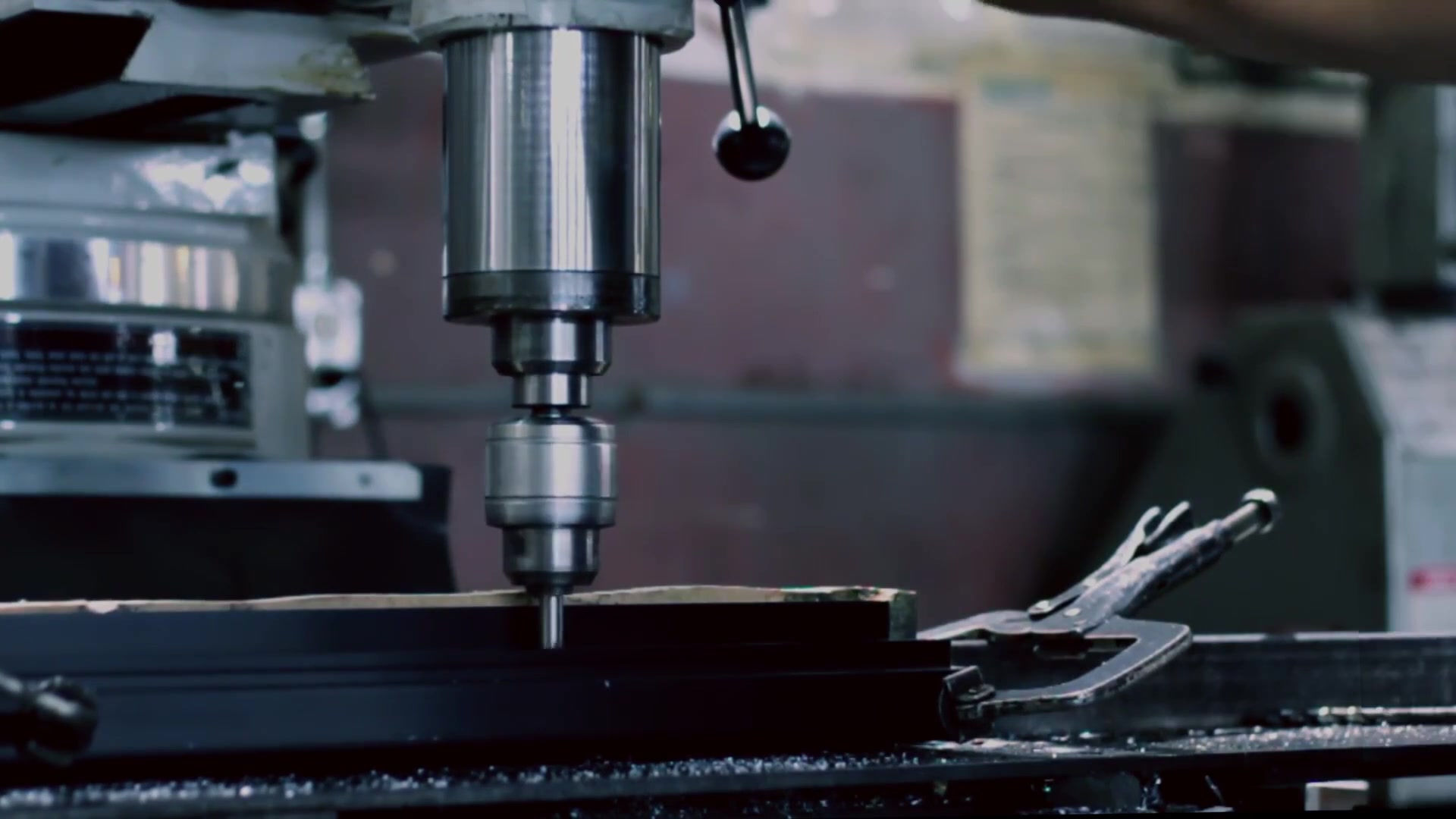
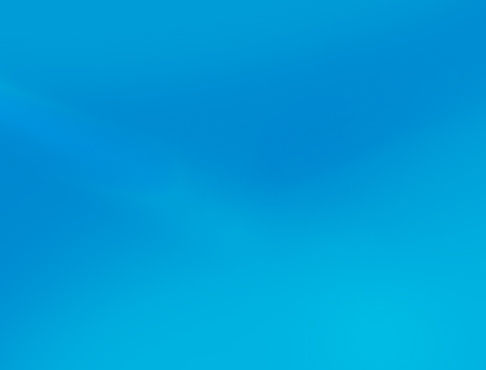
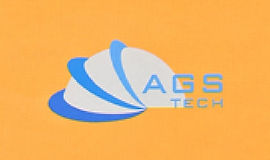
Global Custom Manufacturer, Integrator, Consolidator, Outsourcing Partner for en bred vifte af produkter og tjenester.
Vi er din one-stop-kilde til fremstilling, fremstilling, konstruktion, konsolidering, integration, outsourcing af specialfremstillede og hyldeprodukter og -tjenester.
Vælg dit sprog
-
Brugerdefineret fremstilling
-
Indenlandsk og global kontraktfremstilling
-
Outsourcing af produktion
-
Indenlandske og globale indkøb
-
Consolidation
-
Engineering Integration
-
Ingeniørtjenester
ELECTRICAL DISCHARGE MACHINING (EDM), also referred to as SPARK-EROSION or ELECTRODISCHARGE MACHINING, SPARK ERODING, DIE SINKING_cc781905-5cde-3194-bb3b -136bad5cf58d_or WIRE EROSION, is a NON-CONVENTIONAL MANUFACTURING process where erosion of metals takes place and desired shape is obtained using electrical discharges in the form af gnister. Vi tilbyder også nogle varianter af EDM, nemlig NO-WEAR EDM, WIRE EDM (WEDM), EDM GRINDING (EDG), DIE-SINKING EDM, ELECTRICAL-UDLADSFRÆSNING, m-19EDM5 -5cde-3194-bb3b-136bad5cf58d_and ELEKTROKEMISK-UDLEDNING SLIBNING (ECDG). Vores EDM-systemer består af formede værktøjer/elektrode og emnet forbundet til DC-strømforsyninger og indsat i en elektrisk ikke-ledende dielektrisk væske. Efter 1940 er elektrisk afladningsbearbejdning blevet en af de vigtigste og mest populære produktionsteknologier i fremstillingsindustrien.
Når afstanden mellem de to elektroder reduceres, bliver intensiteten af det elektriske felt i rumfanget mellem elektroderne større end styrken af dielektrikumet i nogle punkter, som går i stykker og til sidst danner en bro for strøm til at flyde mellem de to elektroder. En intens elektrisk lysbue genereres, der forårsager betydelig opvarmning til at smelte en del af emnet og noget af værktøjsmaterialet. Som et resultat fjernes materiale fra begge elektroder. Samtidig opvarmes den dielektriske væske hurtigt, hvilket resulterer i fordampning af væsken i buespalten. Når strømmen stopper, eller den er stoppet, fjernes varme fra gasboblen af den omgivende dielektriske væske, og boblen kaviterer (kollapser). Chokbølgen skabt af boblens kollaps og strømmen af dielektrisk væske skyller snavs ud af emnets overflade og fører alt smeltet emnemateriale ind i den dielektriske væske. Gentagelseshastigheden for disse udladninger er mellem 50 og 500 kHz, spændinger mellem 50 og 380 V og strømme mellem 0,1 og 500 Ampere. Nyt flydende dielektrikum, såsom mineralolier, petroleum eller destilleret og deioniseret vand, føres sædvanligvis ind i inter-elektrodevolumenet og transporterer de faste partikler væk (i form af snavs), og dielektriskets isolerende egenskaber genoprettes. Efter en strømstrøm genoprettes potentialforskellen mellem de to elektroder til, hvad den var før sammenbruddet, så der kan opstå et nyt væskedielektrisk nedbrud. Vores moderne elektriske udladningsmaskiner (EDM) tilbyder numerisk styrede bevægelser og er udstyret med pumper og filtreringssystemer til de dielektriske væsker.
Electrical discharge machining (EDM) er en bearbejdningsmetode, der hovedsageligt anvendes til hårde metaller eller dem, der ville være meget vanskelige at bearbejde med konventionelle teknikker. EDM fungerer typisk med alle materialer, der er elektriske ledere, selvom metoder til bearbejdning af isolerende keramik med EDM også er blevet foreslået. Smeltepunktet og latent smeltevarme er egenskaber, der bestemmer mængden af fjernet metal pr. udledning. Jo højere disse værdier er, jo langsommere er materialefjernelseshastigheden. Fordi den elektriske afladningsbearbejdningsproces ikke involverer nogen mekanisk energi, påvirker hårdheden, styrken og sejheden af emnet ikke fjernelseshastigheden. Afladningsfrekvens eller energi pr. udladning, spændingen og strømmen varieres for at kontrollere materialefjernelseshastigheden. Hastighed for materialefjernelse og overfladeruhed stiger med stigende strømtæthed og faldende gnistfrekvens. Vi kan skære indviklede konturer eller hulrum i forhærdet stål ved hjælp af EDM uden behov for varmebehandling for at blødgøre og genhærde dem. Vi kan bruge denne metode med ethvert metal eller metallegeringer som titanium, hastelloy, kovar og inconel. Anvendelser af EDM-processen omfatter formning af polykrystallinske diamantværktøjer. EDM betragtes som en ikke-traditionel eller ikke-konventionel bearbejdningsmetode sammen med processer som elektrokemisk bearbejdning (ECM), vandstråleskæring (WJ, AWJ), laserskæring. På den anden side omfatter de konventionelle bearbejdningsmetoder drejning, fræsning, slibning, boring og andre processer, hvis materialefjernelsesmekanisme i det væsentlige er baseret på mekaniske kræfter. Elektroder til elektrisk udladningsbearbejdning (EDM) er lavet af grafit, messing, kobber og kobber-wolframlegering. Elektrodediametre ned til 0,1 mm er mulige. Da værktøjsslid er et uønsket fænomen, der negativt påvirker dimensionsnøjagtigheden i EDM, drager vi fordel af en proces kaldet NO-WEAR EDM, ved at vende polariteten og bruge kobberværktøj til at minimere værktøjsslid.
Ideelt set kan den elektriske udladningsbearbejdning (EDM) betragtes som en række nedbrud og genoprettelse af den dielektriske væske mellem elektroderne. I virkeligheden er fjernelsen af snavset fra interelektrodeområdet dog næsten altid delvist. Dette bevirker, at de elektriske egenskaber af dielektrikumet i inter-elektrodeområdet er forskellige fra deres nominelle værdier og varierer med tiden. Afstanden mellem elektroderne, (gnistgab), justeres af kontrolalgoritmerne for den specifikke maskine, der anvendes. Gnistgabet i EDM kan desværre nogle gange kortsluttes af affaldet. Elektrodens styresystem reagerer muligvis ikke hurtigt nok til at forhindre de to elektroder (værktøj og emne) i at kortslutte. Denne uønskede kortslutning bidrager til materialefjernelse anderledes end den ideelle sag. Vi lægger stor vægt på skyllehandlinger for at genoprette dielektrikumets isolerende egenskaber, så strømmen altid sker i spidsen af interelektrodeområdet, og derved minimerer muligheden for uønsket formændring (beskadigelse) af værktøjselektroden og arbejdsemne. For at opnå en specifik geometri føres EDM-værktøjet langs den ønskede bane meget tæt på emnet uden at røre det. Vi er yderst opmærksomme på udførelsen af bevægelseskontrol under brug. På denne måde sker der et stort antal strømudladninger/gnister, og hver især bidrager til at fjerne materiale fra både værktøj og emne, hvor der dannes små kratere. Kraternes størrelse er en funktion af de teknologiske parametre, der er indstillet til det specifikke job, og dimensionerne kan variere fra nanoskalaen (som f.eks. i tilfælde af mikro-EDM-operationer) til nogle hundrede mikrometer under skrubningsforhold. Disse små kratere på værktøjet forårsager gradvis erosion af elektroden kaldet "værktøjsslid". For at modvirke slidets skadelige effekt på emnets geometri udskifter vi løbende værktøjselektroden under en bearbejdning. Nogle gange opnår vi dette ved at bruge en kontinuerligt udskiftet ledning som elektrode (denne EDM-proces kaldes også WIRE EDM ). Nogle gange bruger vi værktøjselektroden på en sådan måde, at kun en lille del af den faktisk er involveret i bearbejdningsprocessen, og denne del ændres regelmæssigt. Dette er for eksempel tilfældet, når man bruger en roterende skive som værktøjselektrode. Denne proces kaldes EDM GRINDING. Endnu en teknik, vi anvender, består i at bruge et sæt elektroder med forskellige størrelser og former under den samme EDM-operation for at kompensere for slid. Vi kalder denne teknik med flere elektroder og er mest almindeligt anvendt, når værktøjselektroden gentager den ønskede form negativt og føres frem mod emnet i en enkelt retning, normalt den lodrette retning (dvs. z-aksen). Dette minder om værktøjets synke ned i den dielektriske væske, som emnet er nedsænket i, og derfor omtales det som DIE-SINKING EDM_cc781905-5cde-3194-6bad_5b-1ccde-15cde-15cde-15cde-5cde-5cde-5cde-3194-6bad_5b-7cc-15cde 3194-bb3b-136bad5cf58d_CONVENTIONAL EDM or RAM EDM). Maskinerne til denne operation hedder SINKER EDM. Elektroderne til denne type EDM har komplekse former. Hvis den endelige geometri opnås ved hjælp af en sædvanligvis simpel formet elektrode, der bevæges langs flere retninger og også er genstand for rotationer, kalder vi det EDM Fræsning. Mængden af slid er strengt afhængig af de teknologiske parametre, der anvendes i operationen (polaritet, maksimal strøm, åben kredsløbsspænding). For eksempel, in micro-EDM, også kendt som m-EDM, er disse parametre normalt indstillet til værdier, som genererer alvorligt slid. Derfor er slid et stort problem på det område, som vi minimerer ved at bruge vores oparbejdede knowhow. For eksempel for at minimere slid på grafitelektroder, vender en digital generator, der kan kontrolleres inden for millisekunder, polariteten, når elektroerosion finder sted. Dette resulterer i en effekt svarende til galvanisering, der kontinuerligt afsætter den eroderede grafit tilbage på elektroden. I en anden metode, et såkaldt ''Zero Wear''-kredsløb, minimerer vi, hvor ofte udledningen starter og stopper, og holder den tændt så længe som muligt. Materialefjernelseshastigheden ved elektrisk afladningsbearbejdning kan estimeres ud fra:
MRR = 4 x 10 exp(4) x I x Tw exp (-1,23)
Her er MRR i mm3/min, I er strøm i Ampere, Tw er emnets smeltepunkt i K-273,15K. Exp står for eksponent.
På den anden side kan elektrodens slidhastighed Wt fås fra:
Wt = ( 1,1 x 10exp(11) ) x I x Ttexp(-2,38)
Her er Wt i mm3/min og Tt er smeltepunktet for elektrodematerialet i K-273.15K
Endelig kan slidforholdet mellem emnet og elektrode R fås fra:
R = 2,25 x Trexp(-2,38)
Her er Tr forholdet mellem smeltepunkter for emne og elektrode.
SINKER EDM :
Sinker EDM, også benævnt CAVITY TYPE EDM or_cc781905-5cde-5cde, elektricitet i anc. Elektroden og emnet er forbundet til en strømforsyning. Strømforsyningen genererer et elektrisk potentiale mellem de to. Når elektroden nærmer sig arbejdsemnet, sker dielektrisk nedbrydning i væsken, der danner en plasmakanal, og en lille gnist springer. Gnisterne slår normalt én ad gangen, fordi det er højst usandsynligt, at forskellige steder i inter-elektroderummet har identiske lokale elektriske karakteristika, som ville gøre det muligt for en gnist at opstå på alle sådanne steder samtidigt. Hundredtusindvis af disse gnister sker på tilfældige punkter mellem elektroden og emnet pr. sekund. Efterhånden som basismetallet eroderer, og gnistgabet efterfølgende øges, sænkes elektroden automatisk af vores CNC-maskine, så processen kan fortsætte uafbrudt. Vores udstyr har kontrolcyklusser kendt som ''on time'' og ''off time''. Indstillingen for tændt tid bestemmer gnistens længde eller varighed. En længere tid giver et dybere hulrum for den gnist og alle efterfølgende gnister for den cyklus, hvilket skaber en mere ru finish på emnet og omvendt. Sluk-tiden er den periode, hvor en gnist erstattes af en anden. En længere afbrydelsestid tillader den dielektriske væske at skylle gennem en dyse for at rense det eroderede affald og derved undgå en kortslutning. Disse indstillinger justeres i mikrosekunder.
WIRE EDM :
In WIRE ELECTRICAL DISCHARGE MACHINING (WEDM), also called WIRE-CUT EDM or WIRE CUTTING, we feed a tynd enkeltstrenget metaltråd af messing gennem emnet, som er nedsænket i en tank med dielektrisk væske. Wire EDM er en vigtig variation af EDM. Vi bruger lejlighedsvis wire-cut EDM til at skære plader så tykke som 300 mm og til at lave stanser, værktøj og matricer af hårde metaller, som er svære at bearbejde med andre fremstillingsmetoder. I denne proces, der ligner konturskæring med en båndsav, holdes tråden, som konstant føres fra en spole, mellem øvre og nedre diamantstyr. De CNC-styrede guider bevæger sig i x–y-planet, og den øvre guide kan også bevæge sig uafhængigt i z–u–v-aksen, hvilket giver anledning til muligheden for at skære tilspidsede og overgangsformer (såsom cirkel på bunden og firkantet ved toppen). Den øverste guide kan styre aksebevægelser i x–y–u–v–i–j–k–l–. Dette gør det muligt for WEDM at skære meget indviklede og sarte former. Det gennemsnitlige skæresnit på vores udstyr, der opnår de bedste økonomiske omkostninger og bearbejdningstid, er 0,335 mm ved brug af Ø 0,25 messing-, kobber- eller wolframtråd. Imidlertid er de øvre og nedre diamantføringer på vores CNC-udstyr nøjagtige til omkring 0,004 mm og kan have en skærebane eller snit så lille som 0,021 mm ved brug af Ø 0,02 mm tråd. Så virkelig smalle snit er mulige. Skærebredden er større end trådens bredde, fordi der opstår gnister fra siderne af tråden til emnet, hvilket forårsager erosion. Denne ''overcut'' er nødvendig, for mange applikationer er den forudsigelig og kan derfor kompenseres for (i mikro-EDM er dette ikke ofte tilfældet). Trådspolerne er lange — en 8 kg spole på 0,25 mm tråd er godt 19 kilometer lang. Tråddiameteren kan være så lille som 20 mikrometer, og geometripræcisionen er i nærheden af +/- 1 mikrometer. Vi bruger generelt kun ledningen én gang og genbruger den, fordi den er relativt billig. Den bevæger sig med en konstant hastighed på 0,15 til 9 m/min, og en konstant skæring (slids) opretholdes under et snit. I den trådskårne EDM-proces bruger vi vand som den dielektriske væske, og kontrollerer dens resistivitet og andre elektriske egenskaber med filtre og deionisatorenheder. Vandet skyller det afskårne affald væk fra skærezonen. Skylning er en vigtig faktor for at bestemme den maksimale fremføringshastighed for en given materialetykkelse, og derfor holder vi den konsistent. Skærehastighed i wire EDM er angivet i tværsnitsarealet skåret pr. tidsenhed, såsom 18.000 mm2/time for 50 mm tykt D2 værktøjsstål. Den lineære skærehastighed for dette tilfælde ville være 18.000/50 = 360 mm/time. Materialefjernelseshastigheden i wire EDM er:
MRR = Vf xhxb
Her er MRR i mm3/min, Vf er trådens fremføringshastighed til emnet i mm/min, h er tykkelse eller højde i mm, og b er snittet, som er:
b = dw + 2s
Her er dw tråddiameter og s er afstand mellem tråd og emne i mm.
Sammen med snævrere tolerancer har vores moderne fleraksede EDM-trådskærende bearbejdningscentre tilføjet funktioner såsom multihoveder til at skære to dele på samme tid, kontroller til at forhindre ledningsbrud, automatiske selvskærende funktioner i tilfælde af ledningsbrud og programmeret bearbejdningsstrategier for at optimere driften, lige og vinkelskæring.
Wire-EDM giver os lave restspændinger, fordi det ikke kræver høje skærekræfter for at fjerne materiale. Når energien/effekten pr. impuls er relativt lav (som ved efterbehandlingsoperationer), forventes en lille ændring i et materiales mekaniske egenskaber på grund af lave restspændinger.
ELEKTRISK UDSLIPNING (EDG) : Slibeskiverne indeholder ikke slibemidler, de er lavet af grafit eller messing. Gentagne gnister mellem det roterende hjul og emnet fjerner materiale fra emnets overflader. Materialefjernelseshastigheden er:
MRR = K x I
Her er MRR i mm3/min, I er strøm i Ampere, og K er emnematerialefaktor i mm3/A-min. Vi bruger ofte elektrisk afladningsslibning til at save smalle slidser på komponenter. Vi kombinerer nogle gange EDG (Electrical-Discharge Grinding) proces med EKG (Electrochemical Grinding) proces, hvor materiale fjernes ved kemisk påvirkning, idet de elektriske udladninger fra grafithjulet bryder oxidfilmen op og vaskes væk af elektrolytten. Processen kaldes ELECTROCHEMICAL-DISCHARGE GRINDING (ECDG). Selvom ECGD-processen bruger relativt mere strøm, er den en hurtigere proces end EDG. Vi sliber for det meste hårdmetalværktøj ved hjælp af denne teknik.
Anvendelser af elektrisk afladningsbearbejdning:
Prototype produktion:
Vi bruger EDM-processen til fremstilling af støbeforme, værktøjs- og matricefremstilling samt til fremstilling af prototyper og produktionsdele, især til rumfarts-, bil- og elektronikindustrien, hvor produktionsmængderne er relativt lave. I Sinker EDM bearbejdes en grafit-, kobber-wolfram- eller ren kobberelektrode til den ønskede (negative) form og føres ind i emnet på enden af en lodret stødstang.
Fremstilling af mønter:
Til fremstilling af matricer til fremstilling af smykker og badges ved mønt- (stempling)-processen, kan den positive master være lavet af sterling sølv, da (med passende maskinindstillinger) masteren er betydeligt eroderet og kun bruges én gang. Den resulterende negative matrice hærdes derefter og bruges i en dråbehammer til at fremstille udstemplede plader fra udskårne arkemner af bronze, sølv eller lavfast guldlegering. For badges kan disse flade flader formes yderligere til en buet overflade af en anden matrice. Denne type EDM udføres normalt nedsænket i et oliebaseret dielektrikum. Den færdige genstand kan forfines yderligere ved hård (glas) eller blød (maling) emaljering og/eller galvaniseret med rent guld eller nikkel. Blødere materialer såsom sølv kan håndgraveres som en raffinement.
Boring af små huller:
På vores wirecut EDM-maskiner bruger vi småhulsboring EDM til at lave et gennemgående hul i et emne, hvorigennem vi kan tråde wiren til wirecut EDM-operationen. Separate EDM-hoveder specielt til småhulsboring er monteret på vores wirecut-maskiner, som gør det muligt for store hærdede plader at få eroderet færdige dele fra dem efter behov og uden forboring. Vi bruger også EDM med små huller til at bore rækker af huller i kanterne på turbinevinger, der bruges i jetmotorer. Gasstrømmen gennem disse små huller gør det muligt for motorerne at bruge højere temperaturer end ellers muligt. De højtemperatur-, meget hårde, enkeltkrystallegeringer, som disse klinger er lavet af, gør konventionel bearbejdning af disse huller med højt billedformat ekstremt vanskelig og endda umulig. Andre anvendelsesområder for EDM med små huller er at skabe mikroskopiske åbninger til brændstofsystemkomponenter. Udover de integrerede EDM-hoveder implementerer vi selvstændige småhulsbore-EDM-maskiner med x-y-akser til at bearbejde blinde eller gennemgående huller. EDM borer huller med en lang messing- eller kobberrørelektrode, der roterer i en borepatron med en konstant strøm af destilleret eller deioniseret vand, der strømmer gennem elektroden som skyllemiddel og dielektrikum. Nogle EDM'er til boring af små huller er i stand til at bore gennem 100 mm blødt eller endda hærdet stål på mindre end 10 sekunder. Huller mellem 0,3 mm og 6,1 mm kan opnås ved denne boreoperation.
Metaldesintegrationsbearbejdning:
Vi har også specielle EDM-maskiner til det specifikke formål at fjerne ødelagt værktøj (bor eller haner) fra arbejdsemner. Denne proces kaldes ''bearbejdning af metaldesintegration''.
Fordele og ulemper Elektrisk afladningsbearbejdning:
Fordele ved EDM omfatter bearbejdning af:
- Komplekse former, som ellers ville være svære at fremstille med konventionelle skæreværktøjer
- Ekstremt hårdt materiale til meget tætte tolerancer
- Meget små arbejdsemner, hvor konventionelle skæreværktøjer kan beskadige delen på grund af for meget skæreværktøjstryk.
- Der er ingen direkte kontakt mellem værktøj og arbejdsemne. Derfor kan sarte sektioner og svage materialer bearbejdes uden nogen form for forvrængning.
- En god overfladefinish kan opnås.
- Meget fine huller kan nemt bores.
Ulemper ved EDM omfatter:
- Den langsomme hastighed af materialefjernelse.
- Den ekstra tid og omkostninger, der bruges til at skabe elektroder til ram/synker EDM.
- Det er vanskeligt at gengive skarpe hjørner på emnet på grund af elektrodeslid.
- Strømforbruget er højt.
- ''Overcut'' dannes.
- Der opstår for stort værktøjsslid under bearbejdning.
- Elektrisk ikke-ledende materialer kan kun bearbejdes med specifik opsætning af processen.