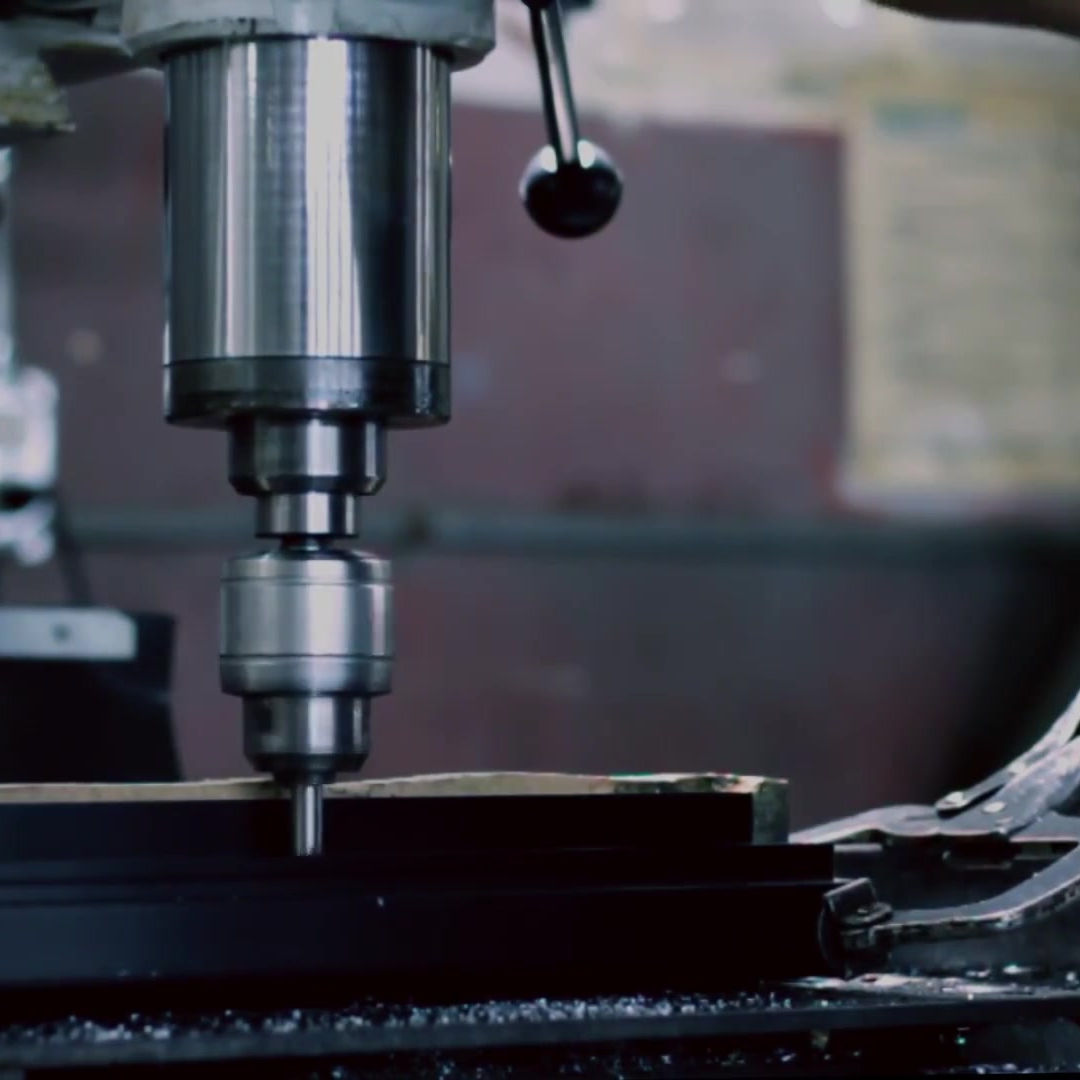
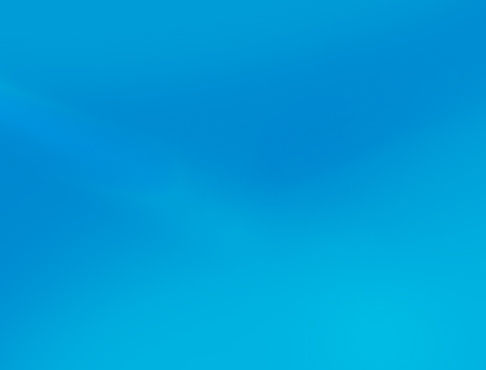
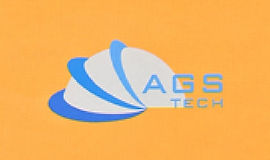
Global Custom Manufacturer, Integrator, Consolidator, Outsourcing Partner for en bred vifte af produkter og tjenester.
Vi er din one-stop-kilde til fremstilling, fremstilling, konstruktion, konsolidering, integration, outsourcing af specialfremstillede og hyldeprodukter og -tjenester.
Vælg dit sprog
-
Brugerdefineret fremstilling
-
Indenlandsk og global kontraktfremstilling
-
Outsourcing af produktion
-
Indenlandske og globale indkøb
-
Consolidation
-
Engineering Integration
-
Ingeniørtjenester
Search Results
164 resultater fundet med en tom søgning
- Transmission Components, Belts, Chains, Cable Drives, Pulleys,AGS-TECH
Transmission Components, Belts, Chains and Cable Drives, Conventional & Grooved or Serrated, Positive Drive, Pulleys Bælte & kæder & kabeltræk AGS-TECH Inc. tilbyder dig kraftoverførselskomponenter, herunder bælter & kæder & kabeltræk. Med mange års raffinement er vores gummi-, læder- og andre remdrev blevet lettere og mere kompakte, der er i stand til at bære større belastninger til lavere omkostninger. På samme måde har vores kædedrev gennemgået meget udvikling gennem tiden, og de tilbyder vores kunder flere fordele. Nogle fordele ved at bruge kædedrev er deres relativt ubegrænsede akselcenterafstande, kompakthed, lette montering, elasticitet i spændingen uden at glide eller krybe, evne til at arbejde i højtemperaturmiljøer. Vores kabeldrev tilbyder også fordele såsom enkelhed i nogle applikationer i forhold til andre typer transmissionskomponenter. Både hyldebælte, kæde- og kabeldrev samt specialfremstillede og monterede versioner er tilgængelige. Vi kan fremstille disse transmissionskomponenter til den rigtige størrelse til din applikation og af de bedst egnede materialer. BÆMME- OG BÆLTEDREV: - Konventionelle flade bælter: Disse er almindelige flade bælter uden tænder, riller eller takker. Fladremsdrev tilbyder fleksibilitet, god stødabsorbering, effektiv kraftoverførsel ved høje hastigheder, slidstyrke, lave omkostninger. Bælter kan splejses eller forbindes for at lave større bælter. Andre fordele ved konventionelle flade remme er, at de er tynde, de er ikke udsat for høje centrifugalbelastninger (gør dem gode til højhastighedsoperationer med små remskiver). På den anden side påfører de høje bærende belastninger, fordi flade remme kræver høj spænding. Andre ulemper ved fladremsdrev kan være glidning, støjende drift og relativt lavere effektivitet ved lave og moderate driftshastigheder. Vi har to typer konventionelle bælter: Forstærkede og ikke-forstærkede. Forstærkede bælter har et trækelement i deres struktur. Konventionelle flade bælter fås som læder, gummieret stof eller snor, ikke-forstærket gummi eller plastik, stof, forstærket læder. Læderbælter giver lang levetid, fleksibilitet, fremragende friktionskoefficient, nem reparation. Men læderbælter er relativt dyre, har brug for bæltebeklædning og rengøring, og afhængigt af atmosfæren kan de krympe eller strække sig. Gummibelagte stof- eller snorbælter er modstandsdygtige over for fugt, syre og baser. Gummierede stofbælter er lavet af lag af bomuld eller syntetisk and imprægneret med gummi og er de mest økonomiske. Gummierede snorebånd består af en række lag af gummiimprægnerede snore. Gummierede snorebånd giver høj trækstyrke og beskeden størrelse og masse. Ikke-forstærkede gummi- eller plastremme er velegnede til lette kørselsopgaver med lav hastighed. Ikke-forstærkede gummi- og plastremme kan strækkes på plads over deres remskiver. Ikke-forstærkede plastremme kan overføre større kraft sammenlignet med gummibælter. Forstærkede læderbælter består af et trækelement af plastik, der er klemt mellem læderets top- og bundlag. Endelig kan vores stofbælter bestå af et enkelt stykke bomuld eller and foldet og syet med rækker af langsgående sting. Stofbælter er i stand til at spore ensartet og fungerer ved høj hastighed. - Rillede eller takkede bælter (såsom kileremme): Disse er grundlæggende flade remme, der er modificeret for at give fordelene ved en anden type transmissionsprodukt. Disse er flade bælter med en langsgående ribbet underside. Poly-V-remme er langsgående rillede eller takkede fladrem med træksektion og en række tilstødende V-formede riller til sporings- og kompressionsformål. Effektkapacitet afhænger af båndbredden. Kilerem er industriens arbejdshest og fås i en række standardiserede størrelser og typer til transmission af næsten enhver belastningskraft. Kileremsdrev fungerer godt mellem 1500 til 6000 ft/min, men smalle kileremme vil køre op til 10.000 ft/min. Kileremsdrev giver lang levetid, såsom 3 til 5 år og tillader store hastighedsforhold, de er nemme at installere og fjerne, tilbyder stille drift, lav vedligeholdelse, god stødabsorbering mellem remtrækker og drevne aksler. Ulempen med kileremme er deres sikre glidning og krybning, og derfor er de måske ikke den bedste løsning, hvor synkrone hastigheder er påkrævet. Vi har industri-, bil- og landbrugsbælter. Lagerførte standardlængder samt tilpassede længder af bælter er tilgængelige. Alle standard kileremstværsnit fås fra lager. Der er tabeller, hvor du kan beregne ukendte parametre såsom remlængde, remsektion (bredde og tykkelse), forudsat at du kender nogle parametre for dit system, såsom drivende og drevne remskivediametre, centerafstand mellem remskiver og remskivernes omdrejningshastigheder. Du kan bruge sådanne tabeller eller bede os om at vælge den rigtige kilerem til dig. - Positive drivremme (tandrem): Disse remme er også flad type med en række jævnt fordelte tænder på den indvendige omkreds. Positive driv- eller tandremme kombinerer fordelene ved flade remme med de positive grebsegenskaber ved kæder og gear. Positive drivremme viser ingen glidning eller hastighedsvariationer. Et bredt udvalg af hastighedsforhold er muligt. Lejebelastningerne er lave, fordi de kan fungere ved lav spænding. De er dog mere modtagelige for skævheder i remskiver. - Remskiver, skiver, nav til remme: Forskellige typer remskiver bruges med flade, ribbede (siret) og positive drivremme. Vi fremstiller dem alle. De fleste af vores flade remskiver er lavet af støbning af jern, men stålversioner fås også i forskellige fælg- og navkombinationer. Vores fladremskiver kan have solide, eger eller splitnav, eller vi kan fremstille som du ønsker. Ribbede og positive drivremme er tilgængelige i en række lagerstørrelser og -bredder. Mindst én remskive i tandremsdrev skal flanges for at holde remmen på drevet. For lange center-drivsystemer anbefales det at have begge remskiver med flange. Skiver er de rillede hjul på remskiver og er generelt fremstillet ved jernstøbning, stålformning eller plaststøbning. Stålformning er velegnet proces til fremstilling af bil- og landbrugsskiver. Vi producerer skiver med regelmæssige og dybe riller. Skiver med dybe riller er velegnede, når kilerem kommer ind i skiven i en vinkel, som det er tilfældet ved kvartsvingsdrev. Dybe riller er også velegnede til drev med lodret aksel og applikationer, hvor vibrationer af remme kan være et problem. Vores remskiver er rillede skiver eller flade remskiver, der ikke tjener til at overføre mekanisk kraft. Mellemremskiver bruges mest til at stramme remme. - Enkelt og flere remdrev: Enkelt remdrev har en enkelt rille, mens flere remdrev har flere riller. Ved at klikke på den relevante farvede tekst nedenfor kan du downloade vores kataloger: - Krafttransmissionsremme (inkluderer kileremme, tandremme, rå kantremme, indviklede remme og specialremme) - Transportbånd - V-remskiver - Tandremskiver KÆDER OG KÆDEDRIV: Vores kraftoverførselskæder har nogle fordele, såsom relativt ubegrænsede akselafstande, nem montering, kompakthed, elasticitet under spænding uden glid eller krybning, funktionsevne under høje temperaturer. Her er de vigtigste typer af vores kæder: - Aftagelige kæder: Vores aftagelige kæder er lavet i en række størrelser, stigning og ultimativ styrke og generelt af smidbart jern eller stål. Smidbare kæder er lavet i en række størrelser fra 0,902 (23 mm) til 4,063 tommer (103 mm) pitch og ultimativ styrke fra 700 til 17.000 lb/square inch. Vores aftagelige stålkæder er på den anden side lavet i størrelser fra 0,904 tommer (23 mm) til omkring 3,00 tommer (76 mm) i stigning, med ultimativ styrke fra 760 til 5000 lb/square inch._cc781905-5cde-3194-bb3b- 136bad5cf58d_ - Pintle Chains: Disse kæder bruges til tungere belastninger og lidt højere hastigheder til omkring 450 fod/min (2,2 m/sek.). Pintle kæder er lavet af individuelle støbte led med fuld, rund ende med forskudte sidebjælker. Disse kædeled er sammenkoblet med stålstifter. Disse kæder varierer i stigning fra omkring 1,00 tommer (25 mm) til 6,00 tommer (150 mm) og ultimative styrker mellem 3600 til 30.000 lb/square inch. - Forskudte sidestangskæder: Disse er populære i drivkæder til entreprenørmaskiner. Disse kæder arbejder ved hastigheder op til 1000 ft/min og overfører belastninger til omkring 250 hk. Generelt har hvert led to forskudte sidestænger, en bøsning, en rulle, en stift, en splittap. - Rullekæder: De fås i stigninger fra 0,25 (6 mm) til 3,00 (75 mm) tommer. Den ultimative styrke af enkelt-bredde rullekæder spænder mellem 925 til 130.000 lb/square tomme. Rullekæder i flere bredder er tilgængelige og overfører større kraft ved højere hastigheder. Rullekæder med flere bredder giver også en mere jævn handling med reduceret støj. Rullekæder er samlet af rulleled og stiftled. Splinter bruges i aftagelige versioner af rullekæder. Designet af rullekædedrev kræver fagekspertise. Hvor remdrev er baseret på lineære hastigheder, er kædedrev baseret på rotationshastigheden af det mindre kædehjul, som i de fleste installationer er det drevne element. Udover antal hestekræfter og omdrejningshastighed er designet af kædedrev baseret på mange andre faktorer. - Double-Pitch Chains: Grundlæggende det samme som rullekæder, bortset fra at stigningen er dobbelt så lang. - Inverterede tandkæder (stille): Højhastighedskæder, der mest bruges til drivkraft, kraftudtag. Omvendte tandkædedrev kan overføre kræfter op til 1200 hk og består af en række tandled, der skiftevis er samlet med enten stifter eller en kombination af ledkomponenter. Center-guide-kæden har styreled til at gå i indgreb med riller i tandhjulet, og side-guide-kæden har guider til at gå i indgreb med siderne af tandhjulet. - Perle- eller glidekæder: Disse kæder bruges til drev med langsom hastighed og også til manuelle operationer. Ved at klikke på den relevante farvede tekst nedenfor kan du downloade vores kataloger: - Drivkæder - Transportbånd - Store transportbåndskæder - Rullekæder i rustfrit stål - Løftekæder - Motorcykelkæder - Landbrugsmaskinkæder - Tandhjul: Vores standard kædehjul overholder ANSI-standarder. Pladekædehjul er flade, navløse kædehjul. Vores små og mellemstore navhjul drejes fra stang eller smedning eller fremstilles ved at svejse et stangnav til en varmvalset plade. AGS-TECH Inc. kan levere kædehjul bearbejdet af gråjernsstøbegods, støbt stål og svejste navkonstruktioner, sintret pulvermetal, støbt eller bearbejdet plast. For jævn drift ved høje hastigheder er korrekt valg af størrelse af kædehjul afgørende. Pladsbegrænsninger er naturligvis en faktor, vi ikke kan ignorere, når vi vælger et kædehjul. Det anbefales, at forholdet mellem driver og drevne tandhjul ikke bør være mere end 6:1, og kædeviklingen på driveren er 120 grader. Centerafstande mellem de mindre og større tandhjul, kædelængder og kædespænding skal også vælges i henhold til nogle anbefalede tekniske beregninger & retningslinjer og ikke tilfældigt. Download vores kataloger ved at klikke på den farvede tekst nedenfor: - Tandhjul og pladehjul - Transmissionsbøsninger - Kædekobling - Kædelåse KABELDRÆVNINGER: Disse har deres fordele i forhold til remme og kædetræk i nogle tilfælde. Kabeldrev kan udføre den samme funktion som remme og kan også være enklere og mere økonomisk at implementere i nogle applikationer. For eksempel er en ny serie af Synchromesh kabeldrev designet til positiv trækkraft til at erstatte konventionelle reb, simple kabler og tanddrev, især på trange steder. Det nye kabeldrev er designet til at give højpræcisionspositionering i elektronisk udstyr såsom kopimaskiner, plottere, skrivemaskiner, printere osv. Et nøgletræk ved det nye kabeldrev er dets evne til at blive brugt i 3D-serpentinkonfigurationer, der muliggør ekstremt miniature designs. Synchromesh kabler kan bruges med lavere spænding sammenlignet med reb, hvilket reducerer strømforbruget. Kontakt AGS-TECH for spørgsmål og mening om remme, kæde og kabeltræk. CLICK Product Finder-Locator Service FORRIGE SIDE
- Joining & Assembly & Fastening Processes, Welding, Brazing, Soldering
Joining & Assembly & Fastening Processes, Welding, Brazing, Soldering, Sintering, Adhesive Bonding, Press Fitting, Wave and Reflow Solder Process, Torch Furnace Sammenføjning & montering & fastgørelsesprocesser Vi samler, samler og fastgør dine fremstillede dele og forvandler dem til færdige eller halvfabrikata ved hjælp af SVEJSNING, SLODNING, LODNING, SINTERING, KLÆBNING, FASTSÆTNING, PRESSMASNING. Nogle af vores mest populære svejseprocesser er lysbue, oxyfuel gas, modstand, projektion, søm, stød, percussion, solid state, elektronstråle, laser, termit, induktionssvejsning. Vores populære loddeprocesser er brænder-, induktions-, ovn- og dyppelodning. Vores lodningsmetoder er jern, varmeplade, ovn, induktion, dip, wave, reflow og ultralydslodning. Til klæbende limning bruger vi ofte termoplast og termohærdende, epoxy, phenoler, polyurethan, klæbende legeringer samt nogle andre kemikalier og tape. Endelig består vores fastgørelsesprocesser af sømning, skruning, møtrikker og bolte, nitning, clinching, pinning, syning & hæftning og prespasning. • SVEJSNING: Svejsning involverer sammenføjning af materialer ved at smelte emnerne og indføre fyldmaterialer, som også forbinder det smeltede svejsebad. Når området afkøles, opnår vi en stærk fuge. Der påføres pres i nogle tilfælde. I modsætning til svejsning involverer lodning og loddeoperationer kun smeltning af et materiale med lavere smeltepunkt mellem emnerne, og emner smelter ikke. Vi anbefaler, at du klikker her for atDOWNLOAD vores skematiske illustrationer af svejseprocesser af AGS-TECH Inc. Dette vil hjælpe dig med bedre at forstå de oplysninger, vi giver dig nedenfor. I ARRC WELDING bruger vi en strømforsyning og en elektrode til at skabe en elektrisk lysbue, der smelter metallerne. Svejsepunktet er beskyttet af en beskyttelsesgas eller damp eller andet materiale. Denne proces er populær til svejsning af autodele og stålkonstruktioner. Ved shelled metal arc welding (SMAW) eller også kendt som stavsvejsning, bringes en elektrodepind tæt på grundmaterialet, og der dannes en elektrisk lysbue mellem dem. Elektrodestangen smelter og fungerer som fyldmateriale. Elektroden indeholder også flux, der fungerer som et slaggelag og afgiver dampe, der fungerer som beskyttelsesgassen. Disse beskytter svejseområdet mod miljøforurening. Der bruges ingen andre fyldstoffer. Ulemperne ved denne proces er dens langsomhed, behovet for at udskifte elektroder hyppigt, behovet for at spåne den resterende slagge, der stammer fra flux, væk. En række metaller såsom jern, stål, nikkel, aluminium, kobber...osv. Kan svejses. Dens fordele er dets billige værktøjer og brugervenlighed. Gasmetalbuesvejsning (GMAW) også kendt som metal-inert gas (MIG), vi har kontinuerlig tilførsel af et forbrugsbart elektrodetrådfyldstof og en inert eller delvist inert gas, der strømmer rundt om tråden mod miljømæssig forurening af svejseområdet. Stål, aluminium og andre ikke-jernholdige metaller kan svejses. Fordelene ved MIG er høje svejsehastigheder og god kvalitet. Ulemperne er dets komplicerede udstyr og udfordringer i blæsende udendørs miljøer, fordi vi skal holde beskyttelsesgassen omkring svejseområdet stabil. En variant af GMAW er flux-coreed arc welding (FCAW), som består af et fint metalrør fyldt med fluxmaterialer. Nogle gange er fluxen inde i røret tilstrækkelig til beskyttelse mod miljøforurening. Submerged Arc Welding (SAW) er i vid udstrækning en automatiseret proces, der involverer kontinuerlig trådfremføring og lysbue, der slås under et lag af fluxdæksel. Produktionshastigheden og kvaliteten er høj, svejseslagger slipper let af, og vi har et røgfrit arbejdsmiljø. Ulempen er, at den kun kan bruges til at svejse parts i bestemte positioner. Ved gaswolframbuesvejsning (GTAW) eller wolfram-inert gassvejsning (TIG) bruger vi en wolframelektrode sammen med et separat fyldstof og inerte eller næsten inerte gasser. Som vi ved har wolfram et højt smeltepunkt, og det er et meget velegnet metal til meget høje temperaturer. Tungsten i TIG indtages ikke i modsætning til de andre metoder forklaret ovenfor. En langsom, men en højkvalitets svejseteknik fordelagtig i forhold til andre teknikker til svejsning af tynde materialer. Velegnet til mange metaller. Plasmabuesvejsning ligner, men bruger plasmagas til at skabe lysbuen. Lysbuen ved plasmabuesvejsning er relativt mere koncentreret sammenlignet med GTAW og kan bruges til et bredere udvalg af metaltykkelser ved meget højere hastigheder. GTAW- og plasmabuesvejsning kan anvendes på mere eller mindre de samme materialer. OXY-FUEL / OXYFUEL WELDING også kaldet oxyacetylensvejsning, oxysvejsning, gassvejsning udføres ved hjælp af gasbrændstoffer og ilt til svejsning. Da der ikke bruges strøm, er den bærbar og kan bruges, hvor der ikke er strøm. Ved hjælp af en svejsebrænder opvarmer vi stykkerne og fyldmaterialet for at producere en fælles pool af smeltet metal. Forskellige brændstoffer kan bruges såsom acetylen, benzin, brint, propan, butan ... osv. Ved oxy-fuel svejsning bruger vi to beholdere, en til brændstoffet og den anden til ilt. Ilten oxiderer brændstoffet (forbrænder det). MODSTANDSVEJSNING: Denne type svejsning udnytter joule-opvarmning, og varme genereres på det sted, hvor der tilføres elektrisk strøm i en vis tid. Høje strømme føres gennem metallet. Puljer af smeltet metal dannes på dette sted. Modstandssvejsemetoder er populære på grund af deres effektivitet, lille forureningspotentiale. Ulemperne er imidlertid, at udstyrsomkostningerne er relativt betydelige og den iboende begrænsning til relativt tynde arbejdsemner. PUNTSVEJSNING er en hovedtype af modstandssvejsning. Her forbinder vi to eller flere overlappende plader eller arbejdsemner ved at bruge to kobberelektroder til at klemme pladerne sammen og føre en høj strøm gennem dem. Materialet mellem kobberelektroderne opvarmes, og der dannes en smeltet pool på det sted. Strømmen stoppes derefter, og kobberelektrodespidserne afkøler svejsestedet, fordi elektroderne er vandkølede. At påføre den rigtige mængde varme til det rigtige materiale og tykkelse er nøglen til denne teknik, for hvis den påføres forkert, vil samlingen være svag. Punktsvejsning har den fordel, at den ikke forårsager nogen væsentlig deformation af emner, energieffektivitet, let automatisering og fremragende produktionshastigheder og ikke kræver nogen fyldstoffer. Ulempen er, at da svejsning finder sted på steder i stedet for at danne en kontinuerlig søm, kan den samlede styrke være relativt lavere sammenlignet med andre svejsemetoder. SØMSVEJSNING på den anden side producerer svejsninger på de falsende overflader af lignende materialer. Sømmen kan være numse eller overlappende samling. Sømsvejsning starter i den ene ende og bevæger sig gradvist til den anden. Denne metode bruger også to elektroder fra kobber til at påføre tryk og strøm til svejseområdet. De skiveformede elektroder roterer med konstant kontakt langs sømlinjen og laver en kontinuerlig svejsning. Også her afkøles elektroder af vand. Svejsningerne er meget stærke og pålidelige. Andre metoder er projektion, flash og forstyrrede svejseteknikker. SVEJSNING i fast tilstand er en smule anderledes end de foregående metoder, der er forklaret ovenfor. Koalescens finder sted ved temperaturer under smeltetemperaturen for de sammenføjede metaller og uden brug af metalfyldstof. Tryk kan bruges i nogle processer. Forskellige metoder er COEKTRUSIONSVEJSNING, hvor uens metaller ekstruderes gennem den samme matrice, KOLDTRYKSVEJSNING, hvor vi samler bløde legeringer under deres smeltepunkter, DIFFUSIONSVEJSNING en teknik uden synlige svejselinjer, EKSPLOSIONSSVEJSNING til sammenføjning af forskellige materialer, f.eks. korrosionsbestandige legeringer stål, ELEKTROMAGNETISK PULSVEJSNING, hvor vi accelererer rør og plader ved elektromagnetiske kræfter, SMEDESVEJSNING, der består i at opvarme metallerne til høje temperaturer og hamre dem sammen, FRIKTIONS-SVEJSNING, hvor der med tilstrækkelig friktionssvejsning udføres, FRIKTIONS-STØRSVEJSNING, der involverer en roterende ikke- forbrugsværktøj, der krydser samlingslinjen, VARMTRYKSVEJSNING, hvor vi presser metaller sammen ved forhøjede temperaturer under smeltetemperaturen i vakuum eller inerte gasser, VARMT ISOSTATISK TRYKSVEJSNING en proces, hvor vi påfører tryk ved hjælp af inaktive gasser inde i en beholder, RULLESVEJSNING, hvor vi samler uens materialer ved at tvinge dem imellem to roterende hjul, ULTRALYDSVEJSNING hvor tynde metal- eller plastplader svejses ved hjælp af højfrekvent vibrationsenergi. Vores andre svejseprocesser er ELEKTRONSVEJSNING med dyb indtrængning og hurtig bearbejdning, men da vi er en dyr metode, betragter vi det i specielle tilfælde, ELEKTROSLAG-SVEJSNING en metode, der kun er egnet til tunge tykke plader og emner af stål, INDUKTIONSVEJSNING, hvor vi anvender elektromagnetisk induktion og opvarme vores elektrisk ledende eller ferromagnetiske emner, LASERSTRALSVEJSNING også med dyb indtrængning og hurtig bearbejdning, men en dyr metode, LASER HYBRID-SVEJSNING, der kombinerer LBW med GMAW i samme svejsehoved og er i stand til at bygge bro mellem plader på 2 mm, PERKUSSIONSVEJSNING, der involverer en elektrisk udladning efterfulgt af smedning af materialerne med påført tryk, THERMIT-SVEJSNING, der involverer eksoterm reaktion mellem aluminium- og jernoxidpulvere., ELEKTROGAS-SVEJSNING med forbrugselektroder og kun brugt med stål i lodret position, og til sidst STUDBUUSVEJSNING til sammenføjning af tap til bund. materiale med varme og tryk. Vi anbefaler, at du klikker her for atDOWNLOAD vores skematiske illustrationer af lodning, lodning og klæbemiddelprocesser af AGS-TECH Inc. Dette vil hjælpe dig med bedre at forstå de oplysninger, vi giver dig nedenfor. • LØDNING : Vi forbinder to eller flere metaller ved at opvarme fyldmetaller imellem dem over deres smeltepunkter og bruge kapillærvirkning til at sprede sig. Processen ligner lodning, men de involverede temperaturer for at smelte fyldstoffet er højere ved lodning. Ligesom ved svejsning beskytter flux fyldmaterialet mod atmosfærisk forurening. Efter afkøling sammenføjes emnerne. Processen involverer følgende nøgletrin: God pasform og frigang, korrekt rengøring af basismaterialer, korrekt fastgørelse, korrekt valg af flux og atmosfære, opvarmning af samlingen og endelig rengøring af loddet samling. Nogle af vores slaglodningsprocesser er TORCH BRAZING, en populær metode, der udføres manuelt eller på en automatiseret måde. Den er velegnet til lave produktionsordrer og specialiserede sager. Varme tilføres ved hjælp af gasflammer i nærheden af samlingen, der loddes. OVNSLODNING kræver mindre operatørfærdighed og er en halvautomatisk proces, der er velegnet til industriel masseproduktion. Både temperaturstyring og styring af atmosfæren i ovnen er fordele ved denne teknik, fordi førstnævnte gør det muligt for os at have kontrollerede varmecyklusser og eliminere lokal opvarmning, som det er tilfældet ved brænderlodning, og sidstnævnte beskytter delen mod oxidation. Ved at bruge jigging er vi i stand til at reducere produktionsomkostningerne til et minimum. Ulemperne er højt strømforbrug, udstyrsomkostninger og mere udfordrende designovervejelser. VAKUUMSLODNING foregår i en ovn af vakuum. Temperaturens ensartethed bibeholdes, og vi opnår fluxfrie, meget rene fuger med meget få restspændinger. Varmebehandlinger kan finde sted under vakuumlodning på grund af de lave restspændinger, der er til stede under langsomme opvarmnings- og afkølingscyklusser. Den største ulempe er dens høje omkostninger, fordi skabelsen af et vakuummiljø er en dyr proces. Endnu en anden teknik DIP-LODNING forbinder fastmonterede dele, hvor loddemasse påføres på parrende overflader. Derefter dyppes de faste dele i et bad med et smeltet salt såsom natriumchlorid (bordsalt), der fungerer som et varmeoverførselsmedium og flusmiddel. Luft er udelukket, og derfor finder der ingen oxiddannelse sted. I INDUKTIONSLODNING samler vi materialer med et fyldmetal, der har et lavere smeltepunkt end basismaterialerne. Vekselstrømmen fra induktionsspolen skaber et elektromagnetisk felt, som inducerer induktionsopvarmning på for det meste jernholdige magnetiske materialer. Metoden giver selektiv opvarmning, gode samlinger med fyldstoffer, der kun flyder i ønskede områder, lille oxidation, fordi der ikke er flammer til stede, og afkøling er hurtig, hurtig opvarmning, konsistens og egnethed til fremstilling af store mængder. For at fremskynde vores processer og for at sikre ensartethed bruger vi ofte præforme. Oplysninger om vores loddeanlæg, der producerer keramiske til metalfittings, hermetisk forsegling, vakuumgennemføringer, høj- og ultrahøjvakuum- og væskekontrolkomponenter kan findes her:_cc781905-156-5cde_cc781905-916-5cde_cc781905-916-5cdeLodningsfabriksbrochure • LODNING : Ved lodning har vi ikke smeltning af emnerne, men et fyldmetal med et lavere smeltepunkt end de sammenføjningsdele, der flyder ind i samlingen. Fyldmetallet ved lodning smelter ved lavere temperatur end ved lodning. Vi bruger blyfri legeringer til lodning og har RoHS-overensstemmelse og til forskellige anvendelser og krav har vi forskellige og egnede legeringer såsom sølvlegering. Lodning giver os samlinger, der er gas- og væsketætte. I BLØD LØDNING har vores fyldmetal et smeltepunkt under 400 Celsius, hvorimod vi ved SØLVLODNING og LODNING har brug for højere temperaturer. Blød lodning bruger lavere temperaturer, men resulterer ikke i stærke samlinger til krævende applikationer ved høje temperaturer. Sølvlodning på den anden side kræver høje temperaturer leveret af brænderen og giver os stærke samlinger, der er egnede til højtemperaturapplikationer. Lodning kræver de højeste temperaturer, og der bruges normalt en brænder. Da loddesamlinger er meget stærke, er de gode kandidater til at reparere tunge jerngenstande. I vores produktionslinjer bruger vi både manuel håndlodning samt automatiserede loddelinjer. INDUKTIONSLODNING bruger højfrekvent vekselstrøm i en kobberspole for at lette induktionsopvarmning. Strømme induceres i den loddede del, og som følge heraf genereres varme ved den høje modstand joint. Denne varme smelter fyldmetallet. Flux bruges også. Induktionslodning er en god metode til at lodde cyclindere og rør i en kontinuerlig proces ved at vikle spolerne omkring dem. Lodning af nogle materialer såsom grafit og keramik er vanskeligere, fordi det kræver plettering af emnerne med et passende metal før lodning. Dette letter grænsefladebinding. Vi lodder sådanne materialer især til hermetiske emballageapplikationer. Vi fremstiller vores printkort (PCB) i høj volumen, for det meste ved hjælp af BØLGELODNING. Kun til små mængder af prototypeformål bruger vi håndlodning med loddekolbe. Vi bruger bølgelodning til både gennemgående huller såvel som overflademonterede PCB-samlinger (PCBA). En midlertidig lim holder komponenterne fastgjort til printpladen, og samlingen placeres på en transportør og bevæger sig gennem et udstyr, der indeholder smeltet loddemetal. Først fluxes PCB'en og går derefter ind i forvarmningszonen. Det smeltede loddemiddel er i en gryde og har et mønster af stående bølger på overfladen. Når printet bevæger sig over disse bølger, kommer disse bølger i kontakt med bunden af printet og klæber til loddepuderne. Loddet bliver kun på stifter og puder og ikke på selve printkortet. Bølgerne i det smeltede loddemateriale skal være godt kontrolleret, så der ikke er sprøjt, og bølgetoppene ikke rører ved og forurener uønskede områder af pladerne. I REFLOW SOLDERING bruger vi en klæbrig loddepasta til midlertidigt at fastgøre de elektroniske komponenter til pladerne. Herefter sættes pladerne gennem en reflowovn med temperaturkontrol. Her smelter loddet og forbinder komponenterne permanent. Vi bruger denne teknik til både overflademonteringskomponenter såvel som til gennemgående hulkomponenter. Korrekt temperaturkontrol og justering af ovntemperaturer er afgørende for at undgå ødelæggelse af elektroniske komponenter på kortet ved at overophede dem over deres maksimale temperaturgrænser. I processen med reflow-lodning har vi faktisk flere regioner eller trin, hver med en særskilt termisk profil, såsom forvarmningstrin, termisk iblødsætningstrin, reflow og afkølingstrin. Disse forskellige trin er afgørende for en skadesfri reflow-lodning af printkortsamlinger (PCBA). ULTRALYDSLODNING er en anden hyppigt brugt teknik med unikke egenskaber- Den kan bruges til at lodde glas, keramiske og ikke-metalliske materialer. For eksempel fotovoltaiske paneler, som er ikke-metalliske, har brug for elektroder, som kan fastgøres ved hjælp af denne teknik. Ved ultralydslodning anvender vi en opvarmet loddespids, der også udsender ultralydsvibrationer. Disse vibrationer producerer kavitationsbobler ved grænsefladen mellem substratet og det smeltede loddemateriale. Den implosive energi fra kavitation modificerer oxidoverfladen og fjerner snavs og oxider. I løbet af denne tid dannes der også et legeringslag. Loddet på bindingsoverfladen inkorporerer ilt og muliggør dannelsen af en stærk fælles binding mellem glasset og loddemetal. DIPLODNING kan betragtes som en enklere version af bølgelodning, der kun er egnet til produktion i mindre skala. Første renseflux påføres som i andre processer. PCB'er med monterede komponenter dyppes manuelt eller på en semi-automatisk måde i en tank indeholdende smeltet lod. Det smeltede loddemiddel klæber til de udsatte metalliske områder ubeskyttet af loddemaske på brættet. Udstyret er enkelt og billigt. • KLÆBENDE KLÆBNING: Dette er en anden populær teknik, vi ofte bruger, og den involverer limning af overflader ved hjælp af lim, epoxy, plastikmidler eller andre kemikalier. Binding opnås ved enten at fordampe opløsningsmidlet, ved varmehærdning, ved UV-lyshærdning, ved trykhærdning eller afventning i en vis tid. Forskellige højtydende lime bruges i vores produktionslinjer. Med korrekt konstruerede påførings- og hærdningsprocesser kan klæbemiddelbinding resultere i meget lave spændingsbindinger, der er stærke og pålidelige. Klæbemidler kan være gode beskyttere mod miljøfaktorer som fugt, forurenende stoffer, ætsende, vibrationer...osv. Fordele ved klæbende limning er: de kan påføres materialer, der ellers ville være svære at lodde, svejse eller lodde. Det kan også være at foretrække for varmefølsomme materialer, der ville blive beskadiget ved svejsning eller andre højtemperaturprocesser. Andre fordele ved klæbemidler er, at de kan påføres uregelmæssigt formede overflader og øger samlingsvægten med meget meget små mængder sammenlignet med andre metoder. Også dimensionsændringer i dele er meget minimale. Nogle lime har indeksmatchende egenskaber og kan bruges mellem optiske komponenter uden at reducere lyset eller den optiske signalstyrke væsentligt. Ulemperne på den anden side er længere hærdetider, som kan forsinke fremstillingslinjerne, krav til fastgørelse, krav til overfladeforberedelse og vanskeligheder ved at skille ad, når der er behov for efterbearbejdning. De fleste af vores adhæsive liming operationer involverer følgende trin: -Overfladebehandling: Særlige rengøringsprocedurer såsom deioniseret vandrensning, alkoholrensning, plasma- eller coronarensning er almindelige. Efter rengøring kan vi påføre vedhæftningsfremmende midler på overfladerne for at sikre de bedst mulige samlinger. -Delmontering: Til både klæbemiddelpåføring såvel som til hærdning designer og bruger vi tilpassede armaturer. -Klæbemiddelanvendelse: Vi bruger nogle gange manuelle, og nogle gange afhængigt af sagen, automatiserede systemer såsom robotter, servomotorer, lineære aktuatorer til at levere klæbemidlerne til det rigtige sted, og vi bruger dispensere til at levere det i den rigtige volumen og mængde. -Hærdning: Afhængigt af klæbemidlet kan vi bruge simpel tørring og hærdning samt hærdning under UV-lys, der fungerer som katalysator eller varmehærdning i en ovn eller ved hjælp af resistive varmeelementer monteret på jigs og armaturer. Vi anbefaler, at du klikker her for atDOWNLOAD vores skematiske illustrationer af fastgørelsesprocesser af AGS-TECH Inc. Dette vil hjælpe dig med bedre at forstå de oplysninger, vi giver dig nedenfor. • FASTGØRELSESPROCESSER: Vores mekaniske sammenføjningsprocesser falder i to kategorier: FASTNINGSMIDLER og INTEGRALE SAMLINGER. Eksempler på fastgørelsesmidler vi bruger er skruer, stifter, møtrikker, bolte, nitter. Eksempler på integrerede samlinger, vi bruger, er snap- og krympepasninger, sømme, krympninger. Ved at bruge en række forskellige fastgørelsesmetoder sikrer vi, at vores mekaniske samlinger er stærke og pålidelige til mange års brug. SKRUER og BOLTE er nogle af de mest almindeligt anvendte fastgørelsesanordninger til at holde genstande sammen og positionere. Vores skruer og bolte opfylder ASME-standarder. Forskellige typer skruer og bolte er installeret, herunder sekskantskruer og sekskantskruer, lagskruer og bolte, dobbeltskruer, dyvelskruer, øjeskruer, spejlskruer, metalpladeskruer, finjusteringsskruer, selvborende og selvskærende skruer , sætskrue, skruer med indbyggede spændeskiver,...og mere. Vi har forskellige skruehovedertyper såsom forsænket, kuppel, rundt, flangehoved og forskellige skruetræktyper såsom slot, phillips, firkantet, sekskantet fatning. En RIVET på den anden side er et permanent mekanisk fastgørelseselement bestående af et glat cylindrisk skaft og et hoved på den ene side. Efter indsættelse deformeres den anden ende af nitten, og dens diameter udvides, så den bliver på plads. Med andre ord, før installationen har en nitte et hoved, og efter installationen har den to. Vi installerer forskellige typer nitter afhængigt af anvendelse, styrke, tilgængelighed og omkostninger, såsom solide/runde nitter, strukturelle, semi-tubulære, blinde, oscar, drive, flush, friktionslåse, selvgennemborende nitter. Nitning kan foretrækkes i tilfælde, hvor varmedeformation og ændringer i materialeegenskaber på grund af svejsevarme skal undgås. Nitning giver også let vægt og især god styrke og udholdenhed mod forskydningskræfter. Mod trækbelastninger kan skruer, møtrikker og bolte dog være mere egnede. I CLINCHING-processen bruger vi specielle stanser og matricer til at danne en mekanisk sammenlåsning mellem metalplader, der samles. Stansen skubber lagene af metal ind i matricehulrummet og resulterer i dannelsen af en permanent samling. Ingen opvarmning og ingen køling er påkrævet i clinching, og det er en kold arbejdsproces. Det er en økonomisk proces, der i nogle tilfælde kan erstatte punktsvejsning. I PINNING bruger vi stifter, som er maskinelementer, der bruges til at sikre positioner af maskindele i forhold til hinanden. Vigtigste typer er gaffelstifter, splinter, fjederstift, dyvelstifter, og splitstift. I STAPLING bruger vi hæftepistoler og hæfteklammer, som er to-benede fastgørelseselementer, der bruges til at sammenføje eller binde materialer. Hæftning har følgende fordele: Økonomisk, enkel og hurtig at bruge, hæfteklammernes krone kan bruges til at bygge bro over materialer, der er stødt sammen, Kronen på hæfteklammer kan lette at bygge bro over et stykke som et kabel og fastgøre det til en overflade uden at punktere eller beskadigende, forholdsvis nem fjernelse. PRESSMONTERING udføres ved at skubbe dele sammen og friktionen mellem dem fastgør delene. Presspasningsdele, der består af et overdimensioneret skaft og et underdimensioneret hul, samles generelt ved en af to metoder: Enten ved at påføre kraft eller udnytte termisk udvidelse eller sammentrækning af delene. Når en presfitting etableres ved at påføre en kraft, bruger vi enten en hydraulisk presse eller en håndbetjent presse. På den anden side, når presfitting etableres ved termisk ekspansion, opvarmer vi de omsluttende dele og samler dem på deres plads, mens de er varme. Når de afkøles, trækker de sig sammen og vender tilbage til deres normale dimensioner. Dette resulterer i en god prespasning. Dette kalder vi alternativt SHRINK-FITTING. Den anden måde at gøre dette på er ved at afkøle de omsluttede dele før montering og derefter skubbe dem ind i deres parringsdele. Når samlingen varmer op, udvider de sig, og vi opnår en tæt pasform. Sidstnævnte metode kan være at foretrække i tilfælde, hvor opvarmning udgør en risiko for at ændre materialeegenskaber. Køling er mere sikker i disse tilfælde. Pneumatiske og hydrauliske komponenter og samlinger • Ventiler, hydrauliske og pneumatiske komponenter såsom O-ring, skive, tætninger, pakning, ring, mellemlæg. Da ventiler og pneumatiske komponenter findes i et stort udvalg, kan vi ikke liste alt her. Afhængigt af de fysiske og kemiske miljøer i din applikation, har vi specielle produkter til dig. Angiv venligst anvendelse, type komponent, specifikationer, miljøforhold såsom tryk, temperatur, væsker eller gasser, der vil være i kontakt med dine ventiler og pneumatiske komponenter; og vi vil vælge det mest passende produkt til dig eller fremstille det specielt til din applikation. CLICK Product Finder-Locator Service FORRIGE SIDE
- Rapid Prototyping, Desktop Manufacturing, Additive Manufacturing, FDM
Rapid Prototyping, Desktop Manufacturing, Additive Manufacturing, Stereolithography, Polyjet, Fused Deposition Modeling, Selective Laser Sintering, FDM, SLS Additiv og hurtig fremstilling I de senere år har vi set en stigning i efterspørgslen efter RAPID MANUFACTURING eller RAPID PROTOTYPING. Denne proces kan også kaldes DESKTOP FREMSTILLING eller FRITFORM FABRIKATION. Grundlæggende er en solid fysisk model af en del lavet direkte fra en tredimensionel CAD-tegning. Vi bruger betegnelsen ADDITIVE MANUFACTURING om disse forskellige teknikker, hvor vi bygger dele i lag. Ved hjælp af integreret computerdrevet hardware og software udfører vi additiv fremstilling. Vores hurtige prototyping og fremstillingsteknikker er STEREOLITHOGRAFI, POLYJET, FUSED-DEPOSITION MODELING, SELECTIVE LASER SINTERING, ELEKTRONBEAM SMELTING, TRE-DIMENSIONAL PRINTING, DIREKTE FREMSTILLING, HURTIG VÆRKTØJ. Vi anbefaler, at du klikker her for atDOWNLOAD vores skematiske illustrationer af additiv fremstilling og hurtige fremstillingsprocesser af AGS-TECH Inc. Dette vil hjælpe dig med bedre at forstå de oplysninger, vi giver dig nedenfor. Hurtig prototyping giver os: 1.) Det konceptuelle produktdesign ses fra forskellige vinkler på en skærm ved hjælp af et 3D/CAD-system. 2.) Prototyper af ikke-metalliske og metalliske materialer fremstilles og studeres ud fra funktionelle, tekniske og æstetiske aspekter. 3.) Lavpris prototyping på meget kort tid er opnået. Additiv fremstilling kan ligne konstruktionen af et brød ved at stable og lime individuelle skiver oven på hinanden. Med andre ord fremstilles produktet skive for skive, eller lag for lag aflejret på hinanden. De fleste dele kan produceres på få timer. Teknikken er god, hvis der er behov for dele meget hurtigt, eller hvis mængden er lav, og det er for dyrt og tidskrævende at lave en form og værktøj. Men prisen på en del er dyr på grund af de dyre råvarer. • STEREOLITHOGRAFI: Denne teknik også forkortet som STL, er baseret på hærdning og hærdning af en flydende fotopolymer til en bestemt form ved at fokusere en laserstråle på den. Laseren polymeriserer fotopolymeren og hærder den. Ved at scanne UV-laserstrålen i henhold til den programmerede form langs overfladen af fotopolymerblandingen fremstilles delen nedefra og op i individuelle skiver kaskade oven på hinanden. Scanningen af laserpunktet gentages mange gange for at opnå de geometrier, der er programmeret ind i systemet. Efter at delen er fuldstændig fremstillet, fjernes den fra platformen, duppes og renses ultralyd og med alkoholbad. Derefter udsættes den for UV-bestråling i et par timer for at sikre, at polymeren er fuldstændig hærdet og hærdet. For at opsummere processen styres en platform, der dyppes i en fotopolymerblanding og en UV-laserstråle, gennem et servokontrolsystem i henhold til formen på den ønskede del, og delen opnås ved at fotohærde polymeren lag for lag. Naturligvis bestemmes de maksimale dimensioner af den producerede del af stereolitografiudstyret. • POLYJET: I lighed med inkjet-print har vi i polyjet otte printhoveder, der afsætter fotopolymer på byggebakken. Ultraviolet lys placeret ved siden af dyserne hærder og hærder straks hvert lag. Der bruges to materialer i polyjet. Det første materiale er til fremstilling af den faktiske model. Det andet materiale, en gel-lignende harpiks, bruges til støtte. Begge disse materialer aflejres lag for lag og hærdes samtidigt. Efter færdiggørelsen af modellen fjernes støttematerialet med en vandig opløsning. Anvendte harpikser ligner stereolitografi (STL). Polyjet har følgende fordele i forhold til stereolitografi: 1.) Intet behov for at rense dele. 2.) Intet behov for efterproceshærdning 3.) Mindre lagtykkelser er mulige og dermed får vi bedre opløsning og kan fremstille finere dele. • FUSED DEPOSITION MODELING: Også forkortet som FDM, i denne metode bevæger et robotstyret ekstruderhoved sig i to principielle retninger over et bord. Kablet sænkes og hæves efter behov. Fra åbningen af en opvarmet matrice på hovedet ekstruderes et termoplastisk filament, og et indledende lag afsættes på et skumfundament. Dette opnås ved hjælp af ekstruderhovedet, der følger en forudbestemt bane. Efter det indledende lag sænkes bordet, og efterfølgende lag lægges oven på hinanden. Nogle gange, når man fremstiller en kompliceret del, er der behov for støttestrukturer, så aflejringen kan fortsætte i bestemte retninger. I disse tilfælde ekstruderes et bæremateriale med en mindre tæt afstand af filament på et lag, så det er svagere end modelmaterialet. Disse støttestrukturer kan senere opløses eller brydes af efter færdiggørelsen af delen. Ekstrudermatricedimensionerne bestemmer tykkelsen af de ekstruderede lag. FDM-processen producerer dele med trinformede overflader på skrå udvendige planer. Hvis denne ruhed er uacceptabel, kan kemisk damppolering eller et opvarmet værktøj bruges til at udglatte disse. Selv en poleringsvoks er tilgængelig som et belægningsmateriale for at eliminere disse trin og opnå rimelige geometriske tolerancer. • SELEKTIV LASER SINTERING: Også betegnet som SLS, er processen baseret på sintring af en polymer, keramik eller metallisk pulver selektivt ind i en genstand. Bunden af forarbejdningskammeret har to cylindre: En delbygget cylinder og en pulverfødecylinder. Førstnævnte sænkes trinvist til det sted, hvor den sintrede del bliver dannet, og sidstnævnte hæves trinvist for at tilføre pulver til den delbyggede cylinder gennem en rullemekanisme. Først aflejres et tyndt lag pulver i den delbyggede cylinder, derefter fokuseres en laserstråle på dette lag, der sporer og smelter/sintrer et bestemt tværsnit, som derefter størkner til et fast stof. Pulveret er områder, der ikke rammes af laserstrålen, forbliver løse, men understøtter stadig den faste del. Derefter afsættes endnu et lag pulver, og processen gentages mange gange for at opnå delen. Til sidst rystes de løse pulverpartikler af. Alle disse udføres af en proceskontrolcomputer ved hjælp af instruktioner genereret af 3D CAD-programmet for den del, der fremstilles. Forskellige materialer såsom polymerer (såsom ABS, PVC, polyester), voks, metaller og keramik med passende polymerbindemidler kan aflejres. • ELECTRON-BEAM MELTING : Svarende til selektiv lasersintring, men ved at bruge elektronstråle til at smelte titanium- eller koboltkrompulver til fremstilling af prototyper i vakuum. Der er foretaget nogle udviklinger for at udføre denne proces på rustfrit stål, aluminium og kobberlegeringer. Hvis udmattelsesstyrken af de producerede dele skal øges, anvender vi varm isostatisk presning efter delfremstillingen som en sekundær proces. • TRE-DIMENSIONEL UDSKRIVNING: Også betegnet med 3DP, i denne teknik afsætter et printhoved et uorganisk bindemiddel på et lag af enten ikke-metallisk eller metallisk pulver. Et stempel, der bærer pulverlejet, sænkes trinvist, og ved hvert trin aflejres bindemidlet lag for lag og smeltes sammen af bindemidlet. Anvendte pulvermaterialer er polymerblandinger og fibre, støbesand, metaller. Ved at bruge forskellige bindehoveder samtidigt og forskellige farvebindere kan vi få forskellige farver. Processen ligner inkjet-print, men i stedet for at opnå et farvet ark får vi et farvet tredimensionelt objekt. De fremstillede dele kan være porøse og kan derfor kræve sintring og metalinfiltration for at øge dens densitet og styrke. Sintring vil brænde bindemidlet af og smelte metalpulverne sammen. Metaller såsom rustfrit stål, aluminium, titanium kan bruges til at fremstille delene, og som infiltrationsmaterialer bruger vi almindeligvis kobber og bronze. Skønheden ved denne teknik er, at selv komplicerede og bevægelige enheder kan fremstilles meget hurtigt. For eksempel kan en tandhjulssamling, en skruenøgle som værktøj fremstilles og vil have bevægelige og drejende dele klar til brug. Forskellige komponenter i samlingen kan fremstilles med forskellige farver og alt i ét skud. Download vores brochure på:Grundlæggende om 3D-udskrivning af metal • DIREKTE FREMSTILLING og HURTIG VÆRKTØJ: Udover designevaluering, fejlfinding bruger vi hurtig prototyping til direkte fremstilling af produkter eller direkte anvendelse i produkter. Med andre ord kan rapid prototyping inkorporeres i konventionelle processer for at gøre dem bedre og mere konkurrencedygtige. For eksempel kan hurtig prototyping producere mønstre og forme. Mønstre af en smeltende og brændende polymer skabt ved hurtige prototypeoperationer kan samles til investeringsstøbning og investeres. Et andet eksempel at nævne er at bruge 3DP til at producere keramisk støbeskal og bruge det til skalstøbeoperationer. Selv sprøjtestøbeforme og formindsatser kan fremstilles ved hurtig prototyping, og man kan spare mange uger eller måneders leveringstid for formfremstilling. Ved kun at analysere en CAD-fil af den ønskede del, kan vi producere værktøjsgeometrien ved hjælp af software. Her er nogle af vores populære hurtige værktøjsmetoder: RTV (Room-Temperature Vulcanizing) STØBNING / URETHAN STØBNING: Brug af hurtig prototyping kan bruges til at lave mønsteret af den ønskede del. Derefter belægges dette mønster med et skillemiddel, og flydende RTV-gummi hældes over mønsteret for at fremstille formhalvdelene. Dernæst bruges disse formhalvdele til at sprøjtestøbe flydende urethaner. Formens levetid er kort, kun som 0 eller 30 cyklusser, men nok til produktion af små partier. ACES (Acetal Clear Epoxy Solid) SPRØJTESTØBNING: Ved hjælp af hurtige prototypeteknikker såsom stereolitografi producerer vi sprøjtestøbeforme. Disse forme er skaller med en åben ende for at tillade fyldning med materialer som epoxy, aluminiumfyldt epoxy eller metaller. Igen er formens levetid begrænset til tiere eller maksimalt hundredvis af dele. SPRAYET METAL VÆRKTØJSPROCES: Vi bruger hurtig prototyping og laver et mønster. Vi sprøjter en zink-aluminiumslegering på mønsteroverfladen og belægger den. Mønsteret med metalbelægningen placeres derefter inde i en kolbe og indkapsles med en epoxy- eller aluminiumfyldt epoxy. Til sidst fjernes den og ved at fremstille to sådanne formhalvdele får vi en komplet form til sprøjtestøbning. Disse forme har længere levetid, i nogle tilfælde afhængigt af materiale og temperaturer kan de producere dele i tusindvis. KEELTOOL PROCES: Denne teknik kan producere forme med 100.000 til 10 millioner cyklusliv. Ved hjælp af rapid prototyping producerer vi en RTV form. Formen fyldes derefter med en blanding bestående af A6 værktøjsstålpulver, wolframcarbid, polymerbindemiddel og lader hærde. Denne form opvarmes derefter for at få polymeren brændt af og metalpulverne til at smelte sammen. Det næste trin er kobberinfiltration for at producere den endelige form. Om nødvendigt kan sekundære operationer såsom bearbejdning og polering udføres på formen for bedre dimensionsnøjagtigheder. _cc781905-5cde-3194-bb3b-136dbad_5cf58 CLICK Product Finder-Locator Service FORRIGE SIDE
- Composites, Composite Materials Manufacturing, Fiber Reinforced
Composites, Composite Materials Manufacturing, Particle and Fiber Reinforced, Cermets, Ceramic & Metal Composite, Glass Fiber Reinforced Polymer, Lay-Up Process Fremstilling af kompositter og kompositmaterialer Simpelt defineret er KOMPOSITTER eller KOMPOSITMATERIALER materialer, der består af to eller flere materialer med forskellige fysiske eller kemiske egenskaber, men når de kombineres, bliver de til et materiale, der er anderledes end de indgående materialer. Vi skal påpege, at de indgående materialer forbliver adskilte og adskilte i strukturen. Målet med at fremstille et kompositmateriale er at opnå et produkt, der er overlegent end dets bestanddele og kombinerer hver enkelt bestanddels ønskede egenskaber. Som et eksempel; styrke, lav vægt eller lavere pris kan være motivatoren bag at designe og producere en komposit. Den type kompositmaterialer, vi tilbyder, er partikelforstærkede kompositter, fiberforstærkede kompositter inklusive keramisk-matrix / polymer-matrix / metal-matrix / carbon-carbon / hybrid-kompositter, strukturelle & laminerede & sandwich-strukturerede kompositter og nanokompositter. De fremstillingsteknikker, vi anvender i fremstilling af kompositmaterialer, er: Pultrusion, prepreg-produktionsprocesser, avanceret fiberplacering, filamentvikling, skræddersyet fiberplacering, glasfiberspray-oplægningsproces, tufting, lanxidproces, z-pinning. Mange kompositmaterialer består af to faser, matrixen, som er kontinuerlig og omgiver den anden fase; og den dispergerede fase, som er omgivet af matrixen. Vi anbefaler, at du klikker her for atDOWNLOAD vores skematiske illustrationer af kompositmaterialer og kompositmaterialefremstilling af AGS-TECH Inc. Dette vil hjælpe dig med bedre at forstå de oplysninger, vi giver dig nedenfor. • PARTIKEL-FORSTERKTE KOMPOSITTER: Denne kategori består af to typer: kompositter med store partikler og dispersionsforstærkede kompositter. I den førstnævnte type kan partikel-matrix-interaktioner ikke behandles på atom- eller molekylært niveau. I stedet er kontinuummekanik gyldig. På den anden side er partikler i dispersionsforstærkede kompositter generelt meget mindre i intervaller på 10 nanometer. Et eksempel på komposit med store partikler er polymerer, hvortil der er tilsat fyldstoffer. Fyldstofferne forbedrer materialets egenskaber og kan erstatte noget af polymervolumenet med et mere økonomisk materiale. Volumenfraktionerne af de to faser påvirker kompositmaterialets opførsel. Store partikelkompositter bruges sammen med metaller, polymerer og keramik. CERMETS er eksempler på keramik/metalkompositter. Vores mest almindelige cermet er hårdmetal. Den består af ildfast carbidkeramik såsom wolframcarbidpartikler i en matrix af et metal såsom kobolt eller nikkel. Disse hårdmetalkompositter er meget udbredt som skærende værktøjer til hærdet stål. De hårde karbidpartikler er ansvarlige for skærevirkningen, og deres sejhed forstærkes af den duktile metalmatrix. Således opnår vi fordelene ved begge materialer i en enkelt komposit. Et andet almindeligt eksempel på en komposit med store partikler, vi bruger, er carbon black-partikler blandet med vulkaniseret gummi for at opnå en komposit med høj trækstyrke, sejhed, rive- og slidstyrke. Et eksempel på en dispersionsforstærket komposit er metaller og metallegeringer styrket og hærdet ved ensartet spredning af fine partikler af et meget hårdt og inert materiale. Når meget små aluminiumoxidflager tilsættes til aluminiummetalmatrix, opnår vi sintret aluminiumspulver, som har en forbedret højtemperaturstyrke. • FIBERFORSTERKTE KOMPOSITTER: Denne kategori af kompositter er faktisk den vigtigste. Målet at opnå er høj styrke og stivhed pr. vægtenhed. Fibersammensætningen, længden, orienteringen og koncentrationen i disse kompositter er afgørende for at bestemme egenskaberne og anvendeligheden af disse materialer. Der er tre grupper af fibre, vi bruger: knurhår, fibre og tråde. WHISKERS er meget tynde og lange enkeltkrystaller. De er blandt de stærkeste materialer. Nogle eksempler på whiskermaterialer er grafit, siliciumnitrid, aluminiumoxid. FIBERS på den anden side er for det meste polymerer eller keramik og er i polykrystallinsk eller amorf tilstand. Den tredje gruppe er fine TRÅDE, der har relativt store diametre og ofte består af stål eller wolfram. Et eksempel på trådforstærket komposit er bildæk, der indeholder ståltråd inde i gummi. Afhængigt af matrixmaterialet har vi følgende kompositter: POLYMER-MATRIX-KOMPOSITTER: Disse er lavet af en polymerharpiks og fibre som forstærkningsingrediens. En undergruppe af disse kaldet Glass Fiber-Reinforced Polymer (GFRP) Composites indeholder kontinuerlige eller diskontinuerlige glasfibre i en polymermatrix. Glas giver høj styrke, det er økonomisk, let at fremstille til fibre og er kemisk inert. Ulemperne er deres begrænsede stivhed og stivhed, idet driftstemperaturer kun er op til 200 – 300 Celsius. Glasfiber er velegnet til bilkarosserier og transportudstyr, karosserier til marinekøretøjer, opbevaringsbeholdere. De er ikke egnede til rumfart eller brofremstilling på grund af begrænset stivhed. Den anden undergruppe kaldes Carbon Fiber-Reinforced Polymer (CFRP) Composite. Her er kulstof vores fibermateriale i polymermatrixen. Carbon er kendt for sit høje specifikke modul og styrke og dets evne til at opretholde disse ved høje temperaturer. Kulfibre kan tilbyde os standard-, mellem-, høj- og ultrahøj trækstyrkemoduler. Desuden tilbyder kulfibre forskellige fysiske og mekaniske egenskaber og er derfor velegnet til forskellige skræddersyede tekniske applikationer. CFRP-kompositter kan betragtes som fremstilling af sports- og fritidsudstyr, trykbeholdere og strukturelle komponenter til rumfart. Endnu en anden undergruppe, Aramid Fiber-Reinforced Polymer Composites, er også materialer med høj styrke og modulus. Deres styrke/vægt-forhold er enestående høje. Aramidfibre er også kendt under handelsnavnene KEVLAR og NOMEX. Under spænding klarer de sig bedre end andre polymere fibermaterialer, men de er svage i kompression. Aramidfibre er seje, slagfaste, krybe- og træthedsbestandige, stabile ved høje temperaturer, kemisk inerte undtagen mod stærke syrer og baser. Aramidfibre er meget udbredt i sportsartikler, skudsikre veste, dæk, reb, fiberoptiske kabelkapper. Andre fiberforstærkningsmaterialer findes, men bruges i mindre grad. Disse er hovedsageligt bor, siliciumcarbid, aluminiumoxid. Polymermatrixmaterialet er på den anden side også kritisk. Det bestemmer den maksimale driftstemperatur for kompositten, fordi polymeren generelt har en lavere smelte- og nedbrydningstemperatur. Polyestere og vinylestere er meget udbredt som polymermatrix. Harpikser bruges også, og de har fremragende fugtbestandighed og mekaniske egenskaber. For eksempel kan polyimidharpiks bruges op til omkring 230 grader Celcius. METAL-MATRIX-KOMPOSITTER: I disse materialer bruger vi en duktil metalmatrix, og driftstemperaturerne er generelt højere end deres bestanddele. Sammenlignet med polymer-matrix-kompositter kan disse have højere driftstemperaturer, være ikke-brændbare og kan have bedre nedbrydningsmodstand mod organiske væsker. Men de er dyrere. Forstærkningsmaterialer såsom whiskers, partikler, kontinuerlige og diskontinuerlige fibre; og matrixmaterialer såsom kobber, aluminium, magnesium, titanium, superlegeringer er almindeligt anvendt. Eksempler på anvendelser er motorkomponenter lavet af aluminiumslegeringsmatrix forstærket med aluminiumoxid og kulfibre. KERAMISK-MATRIX-KOMPOSITTER: Keramiske materialer er kendt for deres fremragende høje temperaturpålidelighed. De er dog meget skøre og har lave værdier for brudsejhed. Ved at indlejre partikler, fibre eller whiskers af én keramik i matrixen af en anden er vi i stand til at opnå kompositter med højere brudsejhed. Disse indlejrede materialer hæmmer dybest set revneudbredelse inde i matrixen ved nogle mekanismer, såsom afbøjning af revnespidserne eller dannelse af broer hen over revneflader. Som et eksempel bruges alumina, der er forstærket med SiC whiskers, som skærende værktøjsindsatser til bearbejdning af hårdmetallegeringer. Disse kan afsløre bedre ydeevne sammenlignet med cementerede carbider. KUL-KUL-KOMPOSITTER: Både forstærkningen og matrixen er carbon. De har høje trækmoduler og styrker ved høje temperaturer over 2000 Celsius, krybemodstand, høj brudsejhed, lave termiske udvidelseskoefficienter, høje termiske ledningsevner. Disse egenskaber gør dem ideelle til applikationer, der kræver modstand mod termisk stød. Svagheden ved carbon-carbon-kompositter er imidlertid dens sårbarhed over for oxidation ved høje temperaturer. Typiske eksempler på brug er varmpressende forme, avanceret fremstilling af turbinemotorkomponenter. HYBRIDKOMPOSITTER: To eller flere forskellige typer fibre blandes i en enkelt matrix. Man kan således skræddersy et nyt materiale med en kombination af egenskaber. Et eksempel er, når både kul- og glasfibre er inkorporeret i en polymerharpiks. Kulfibre giver stivhed og styrke med lav densitet, men er dyre. Glasset er på den anden side billigt, men mangler kulfibernes stivhed. Glas-carbon-hybridkompositten er stærkere og sejere og kan fremstilles til en lavere pris. BEHANDLING AF FIBERFORSTERKTE KOMPOSITTER: Til kontinuerlig fiberarmeret plast med ensartet fordelte fibre orienteret i samme retning bruger vi følgende teknikker. PULTRUSION: Stænger, bjælker og rør af kontinuerlige længder og konstante tværsnit fremstilles. Kontinuerlige fiberrovings er imprægneret med en termohærdende harpiks og trækkes gennem en stålmatrice for at præforme dem til en ønsket form. Derefter passerer de gennem en præcisionsbearbejdet hærdningsmatrice for at opnå sin endelige form. Da hærdningsmatricen opvarmes, hærder den harpiksmatricen. Aftrækkere trækker materialet gennem matricerne. Ved hjælp af indsatte hule kerner er vi i stand til at opnå rør og hule geometrier. Pultrusionsmetoden er automatiseret og giver os høje produktionshastigheder. Enhver længde af produktet er muligt at producere. PREPREG PRODUKTIONSPROCES: Prepreg er en kontinuerlig fiberarmering præimprægneret med en delvis hærdet polymerharpiks. Det er meget udbredt til strukturelle applikationer. Materialet kommer i tapeform og sendes som tape. Producenten støber det direkte og hærder det fuldstændigt uden behov for at tilføje harpiks. Da prepregs undergår hærdningsreaktioner ved stuetemperatur, opbevares de ved 0 grader Celsius eller lavere temperaturer. Efter brug opbevares de resterende bånd tilbage ved lave temperaturer. Der anvendes termoplastiske og termohærdende harpikser, og forstærkningsfibre af kulstof, aramid og glas er almindelige. For at bruge prepregs fjernes først bærepapiret, og derefter udføres fremstillingen ved at lægge prepreg-tapen på en bearbejdet overflade (oplægningsprocessen). Der kan lægges flere lag op for at opnå den ønskede tykkelse. Hyppig praksis er at skifte fiberorienteringen for at fremstille et tværlags- eller vinkellagslaminat. Til sidst påføres varme og tryk til hærdning. Både håndbearbejdning og automatiserede processer bruges til at skære prepregs og lay-up. FILAMENTVIKLING: Kontinuerlige forstærkende fibre er nøjagtigt placeret i et forudbestemt mønster for at følge en hul og sædvanligvis cyklindirisk form. Fibrene går først gennem et harpiksbad og vikles derefter på en dorn ved hjælp af et automatiseret system. Efter flere viklingsgentagelser opnås de ønskede tykkelser, og hærdningen udføres enten ved stuetemperatur eller inde i en ovn. Nu fjernes dornen, og produktet tages ud af formen. Filamentvikling kan tilbyde meget høje styrke-til-vægt-forhold ved at vikle fibrene i periferiske, spiralformede og polære mønstre. Rør, tanke, huse er fremstillet ved hjælp af denne teknik. • STRUKTURELLE KOMPOSITTER: Generelt består disse af både homogene og kompositmaterialer. Derfor er disses egenskaber bestemt af de indgående materialer og dens geometriske udformning. Her er de vigtigste typer: LAMINÆRE KOMPOSITTER: Disse strukturelle materialer er lavet af todimensionelle plader eller paneler med foretrukne højstyrkeretninger. Lag stables og cementeres sammen. Ved at veksle højstyrkeretningerne i de to vinkelrette akser opnår vi en komposit, der har højstyrke i begge retninger i det todimensionelle plan. Ved at justere vinklerne på lagene kan man fremstille en komposit med styrke i de foretrukne retninger. Moderne ski er fremstillet på denne måde. SANDWICH-PANELER: Disse strukturelle kompositmaterialer er lette, men har alligevel høj stivhed og styrke. Sandwichpaneler består af to ydre plader lavet af et stift og stærkt materiale som aluminiumslegeringer, fiberforstærket plast eller stål og en kerne mellem yderpladerne. Kernen skal være let og det meste af tiden have et lavt elasticitetsmodul. Populære kernematerialer er stive polymerskum, træ og honningkager. Sandwichpaneler er meget udbredt i byggebranchen som tagmateriale, gulv- eller vægmateriale, og også i flyindustrien. • NANOKOMPOSITTER: Disse nye materialer består af partikler i nanostørrelse indlejret i en matrix. Ved hjælp af nanokompositter kan vi fremstille gummimaterialer, der er meget gode barrierer for luftgennemtrængning, mens de bibeholder deres gummiegenskaber uændrede. CLICK Product Finder-Locator Service FORRIGE SIDE
- Machine Elements Manufacturing, Gears, Gear Drives, Bearings, Keys, Splines
Machine Elements Manufacturing, Gears, Gear Drives, Bearings, Keys, Splines, Pins, Shafts, Seals, Fasteners, Clutch, Cams, Followers, Belts, Couplings, Shafts Fremstilling af maskinelementer Læs mere Bælte & kæder & kabeltræk Læs mere Gear & Gear Drive Samling Læs mere Fremstilling af koblinger og lejer Læs mere Fremstilling af nøgler og splines og stifter Læs mere Knaster & følgere & koblinger & skraldehjulsfremstilling Læs mere Fremstilling af aksler Læs mere Fremstilling af mekaniske tætninger Læs mere Koblings- og bremsesamling Læs mere Fremstilling af befæstelser Læs mere Enkel maskinsamling MACHINE ELEMENTS er elementære komponenter i en maskine. Disse elementer består af tre grundlæggende typer: 1.) Strukturelle komponenter, herunder rammeelementer, lejer, aksler, splines, fastgørelseselementer, tætninger og smøremidler. 2.) Mekanismer, der styrer bevægelse på forskellige måder, såsom gear, rem- eller kædetræk, koblinger, knast- og følgesystemer, bremser og koblinger. 3.) Kontrolkomponenter som knapper, kontakter, indikatorer, sensorer, aktuatorer og computercontrollere. De fleste af de maskinelementer, vi tilbyder dig, er standardiserede til almindelige størrelser, men specialfremstillede maskinelementer er også tilgængelige til dine specialiserede applikationer. Tilpasning af maskinelementer kan foregå på eksisterende designs, der er i vores downloadbare kataloger eller på helt nye designs. Prototyping og fremstilling af maskinelementer kan videreføres, når et design er godkendt af begge parter. Hvis nye maskinelementer skal designes og fremstilles, e-mailer vores kunder os enten deres egne tegninger, og vi gennemgår dem til godkendelse, eller de beder os om at designe maskinelementer til deres anvendelse. I sidstnævnte tilfælde bruger vi alle input fra vores kunder og designer maskinelementerne og sender de færdige tegninger til vores kunder til godkendelse. Når vi er godkendt, producerer vi de første artikler og fremstiller efterfølgende maskinelementerne efter det endelige design. På et hvilket som helst trin i dette arbejde, i tilfælde af at et bestemt maskinelementdesign fungerer utilfredsstillende i marken (hvilket er sjældent), gennemgår vi hele projektet og foretager ændringer i fællesskab med vores kunder efter behov. Det er vores standardpraksis at underskrive fortrolighedsaftaler (NDA) med vores kunder om design af maskinelementer eller ethvert andet produkt, når det er nødvendigt eller påkrævet. Når maskinelementer til en bestemt kunde er specialdesignet og fremstillet, tildeler vi en produktkode til den og producerer og sælger dem kun til vores kunde, der ejer produktet. Vi reproducerer maskinelementerne ved hjælp af de udviklede værktøjer, forme og procedurer så mange gange som nødvendigt, og når vores kunde genbestiller dem. Med andre ord, når først et brugerdefineret maskinelement er designet og produceret til dig, bliver den intellektuelle ejendomsret såvel som alt værktøj og forme reserveret og lagerført på ubestemt tid af os til dig og produkterne gengivet som du ønsker. Vi tilbyder også vores kunder ingeniørtjenester ved kreativt at kombinere maskinelementer til en komponent eller samling, der tjener en applikation og opfylder eller overgår vores kunders forventninger. Anlæg, der fremstiller vores maskinelementer, er kvalificeret af enten ISO9001, QS9000 eller TS16949. Derudover har de fleste af vores produkter CE- eller UL-mærke og opfylder internationalt relevante standarder som ISO, SAE, ASME, DIN. Klik venligst på undermenuer for at få detaljeret information om vores maskinelementer, herunder: - Remme, kæder og kabeltræk - Gear og Gear Drives - Koblinger og lejer - Nøgler & Splines & stifter - Knaster og koblinger - Skafter - Mekaniske tætninger - Industriel kobling og bremse - Befæstelser - Simple maskiner Vi har udarbejdet en referencebrochure til vores kunder, designere og udviklere af nye produkter inklusive maskinelementer. Du kan gøre dig bekendt med nogle almindeligt anvendte termer i maskinkomponentdesign: Download brochure for almindelige maskintekniske termer, der bruges af designere og ingeniører Vores maskinelementer finder anvendelse inden for en række forskellige områder såsom industrimaskiner, automationssystemer, test- og metrologiudstyr, transportudstyr, entreprenørmaskiner og praktisk talt hvor som helst du kan tænke dig. AGS-TECH udvikler og fremstiller maskinelementer af forskellige materialer afhængig af anvendelse. Materialer, der bruges til maskinelementer, kan variere fra støbt plast, der bruges til legetøj, til kassehærdet og specialbelagt stål til industrimaskiner. Vores designere bruger avanceret professionel software og designværktøjer til at udvikle maskinelementer, idet de tager hensyn til detaljer såsom vinkler i tandhjulstænder, involverede spændinger, slidhastigheder...osv. Rul venligst gennem vores undermenuer og download vores produktbrochurer og kataloger for at se, om du kan finde hyldevareelementer til din applikation. Hvis du ikke kan finde et godt match til din applikation, så lad os det vide, og vi vil sammen med dig udvikle og fremstille maskinelementer, der opfylder dine behov. Hvis du mest er interesseret i vores ingeniør- og forsknings- og udviklingskapaciteter i stedet for produktionskapaciteter, så inviterer vi dig til at besøge vores website http://www.ags-engineering.com hvor du kan finde mere detaljeret information om vores design, produktudvikling, procesudvikling, ingeniørrådgivning og mere CLICK Product Finder-Locator Service FORRIGE SIDE
- Glass and Ceramic Manufacturing, Hermetic Packages, Seals, Bonding
Glass and Ceramic Manufacturing, Hermetic Packages Seals and Bonding, Tempered Bulletproof Glass, Blow Moulding, Optical Grade Glass, Conductive Glass, Molding Formning og formning af glas og keramik Den type glasfremstilling, vi tilbyder, er beholderglas, glasblæsning, glasfiber & rør & stang, husholdnings- og industriglas, lampe og pære, præcisionsglasstøbning, optiske komponenter og samlinger, fladt & plade & floatglas. Vi udfører både håndformning såvel som maskinformning. Vores populære tekniske keramiske fremstillingsprocesser er formpresning, isostatisk presning, varm isostatisk presning, varmpresning, slipstøbning, tapestøbning, ekstrudering, sprøjtestøbning, grøn bearbejdning, sintring eller brænding, diamantslibning, hermetiske samlinger. Vi anbefaler, at du klikker her for at DOWNLOAD vores skematiske illustrationer af glasformnings- og formgivningsprocesser af AGS-TECH Inc. DOWNLOAD vores skematiske illustrationer af tekniske keramiske fremstillingsprocesser af AGS-TECH Inc. Disse downloadbare filer med fotos og skitser hjælper dig med bedre at forstå de oplysninger, vi giver dig nedenfor. • FREMSTILLING AF CONTAINERGLAS: Vi har automatiserede PRESS AND BLOW samt BLOW AND BLOW linjer til fremstilling. I blæse- og blæseprocessen taber vi en gob i en blank form og danner halsen ved at påføre et trykluftslag fra toppen. Umiddelbart efter dette blæses trykluft endnu en gang fra den anden retning gennem beholderhalsen for at danne flaskens præform. Denne præform overføres derefter til den faktiske form, genopvarmes for at blødgøre, og trykluft påføres for at give præformen dens endelige beholderform. Mere eksplicit sættes den under tryk og skubbes mod væggene i blæseformens hulrum for at få dens ønskede form. Til sidst overføres den fremstillede glasbeholder til en udglødningsovn til efterfølgende genopvarmning og fjernelse af spændinger frembragt under støbningen og afkøles på en kontrolleret måde. I presse- og blæsemetoden anbringes smeltede gobs i en formeform (emneform) og presses ind i formen (emneform). Emnerne overføres derefter til blæseforme og blæses i lighed med processen beskrevet ovenfor under "Blæse- og blæseproces". Efterfølgende trin som udglødning og stressaflastning er ens eller de samme. • GLAS PUBLÆSNING: Vi har fremstillet glasprodukter ved hjælp af konventionel håndblæsning samt brug af trykluft med automatiseret udstyr. For nogle ordrer er konventionel blæsning nødvendig, såsom projekter, der involverer glaskunst, eller projekter, der kræver et mindre antal dele med løse tolerancer, prototyping/demoprojekter….osv. Konventionel glasblæsning involverer dypning af et hult metalrør i en gryde af smeltet glas og rotation af røret for at opsamle en vis mængde af glasmaterialet. Glasset opsamlet på spidsen af røret rulles på fladjern, formes efter ønske, forlænges, genopvarmes og luftblæses. Når den er klar, sættes den i en form, og der blæses luft. Formhulrummet er vådt for at undgå kontakt mellem glasset og metal. Vandfilmen fungerer som en pude mellem dem. Manuel blæsning er en arbejdskrævende langsom proces og kun egnet til prototyper eller genstande af høj værdi, ikke egnet til billige ordrer i store mængder pr. styk. • FREMSTILLING AF HUS- OG INDUSTRIEL GLASVARER: Ved at bruge forskellige typer glasmateriale produceres en lang række glasvarer. Nogle glas er varmebestandige og velegnede til laboratorieglas, hvorimod nogle er gode nok til at tåle opvaskemaskiner i mange gange og er egnede til fremstilling af husholdningsprodukter. Ved hjælp af Westlake-maskiner bliver der produceret titusindvis af stykker drikkeglas om dagen. For at forenkle opsamles smeltet glas ved vakuum og indsættes i forme for at lave præformene. Derefter blæses luft ind i formene, disse overføres til en anden form og luft blæses igen og glasset får sin endelige form. Som ved håndblæsning holdes disse forme våde med vand. Yderligere strækning er en del af efterbehandlingen, hvor halsen bliver dannet. Overskydende glas brændes af. Derefter følger den kontrollerede genopvarmnings- og afkølingsproces beskrevet ovenfor. • FORMNING AF GLAS RØR OG STANG: De vigtigste processer, vi bruger til fremstilling af glasrør, er DANNER- og VELLO-processerne. I Danner-processen flyder glas fra en ovn og falder ned på en skrå muffe lavet af ildfaste materialer. Muffen bæres på en roterende hul aksel eller blæserør. Glasset vikles derefter rundt om ærmet og danner et glat lag, der flyder ned ad ærmet og over spidsen af skaftet. Ved rørformning blæses luft gennem et blæserør med hul spids, og ved stavformning bruger vi solide spidser på akslen. Rørene eller stængerne trækkes derefter over bæreruller. Dimensionerne som vægtykkelse og diameter af glasrørene justeres til ønskede værdier ved at indstille diameteren af muffen og blæse lufttrykket til en ønsket værdi, justere temperaturen, glassets flowhastighed og trækkehastigheden. Vello glasrørs fremstillingsprocessen involverer på den anden side glas, der rejser ud af en ovn og ind i en skål med en hul dorn eller klokke. Glasset går derefter gennem luftrummet mellem dornen og skålen og får form som et rør. Derefter kører den over ruller til en tegnemaskine og afkøles. Ved afslutningen af kølelinjen sker skæring og slutbehandling. Rørdimensionerne kan justeres ligesom i Danner-processen. Når vi sammenligner Danner- og Vello-processen, kan vi sige, at Vello-processen passer bedre til produktion af store mængder, mens Danner-processen måske passer bedre til præcise rørordrer med mindre volumen. • BEHANDLING AF PLADER & FLAD & FLOAT GLAS: Vi har store mængder fladt glas i tykkelser lige fra submilimeter tykkelser til flere centimeter. Vores flade briller er af næsten optisk perfektion. Vi tilbyder glas med specielle belægninger såsom optiske belægninger, hvor der anvendes kemisk dampaflejringsteknik til at lægge belægninger såsom antirefleks eller spejlbelægning. Også transparente ledende belægninger er almindelige. Også tilgængelige er hydrofobe eller hydrofile belægninger på glas og belægning, der gør glas selvrensende. Hærdede, skudsikre og laminerede glas er endnu andre populære genstande. Vi skærer glas i ønsket form med ønskede tolerancer. Andre sekundære operationer såsom buning eller bøjning af fladt glas er tilgængelige. • PRÆCISIONSGLASSTØBNING: Vi bruger mest denne teknik til fremstilling af optiske præcisionskomponenter uden behov for dyrere og tidskrævende teknikker som slibning, lapning og polering. Denne teknik er ikke altid tilstrækkelig til at få det bedste ud af den bedste optik, men i nogle tilfælde som forbrugerprodukter, digitale kameraer, medicinsk optik kan det være en billigere god mulighed for højvolumen fremstilling. Det har også en fordel i forhold til de andre glasformningsteknikker, hvor komplekse geometrier er påkrævet, såsom i tilfælde af asfærer. Den grundlæggende proces involverer fyldning af undersiden af vores form med glasemnet, evakuering af proceskammeret til iltfjernelse, nær lukning af formen, hurtig og isotermisk opvarmning af matrice og glas med infrarødt lys, yderligere lukning af formhalvdelene at presse det blødgjorte glas langsomt på en kontrolleret måde til den ønskede tykkelse, og til sidst afkøling af glasset og fyldning af kammeret med nitrogen og fjernelse af produktet. Præcis temperaturkontrol, formens lukkeafstand, formens lukkekraft, matchning af udvidelseskoefficienterne for formen og glasmaterialet er nøglen i denne proces. • FREMSTILLING AF OPTISKE KOMPONENTER OG SAMLINGER AF GLAS: Udover præcisionsglasstøbning er der en række værdifulde processer, vi bruger til at fremstille optiske komponenter og samlinger af høj kvalitet til krævende applikationer. Slibning, lapning og polering af glas af optisk kvalitet i fine specielle slibende slam er en kunst og videnskab til fremstilling af optiske linser, prismer, flade linser og mere. Overfladeplanhed, bølgethed, glathed og fejlfri optiske overflader kræver masser af erfaring med sådanne processer. Små ændringer i miljøet kan resultere i produkter uden for specifikationerne og bringe produktionslinjen til at stoppe. Der er tilfælde, hvor en enkelt aftørring på den optiske overflade med en ren klud kan få et produkt til at leve op til specifikationerne eller bestå testen. Nogle populære glasmaterialer, der anvendes, er smeltet silica, kvarts, BK7. Også montering af sådanne komponenter kræver specialiseret nicheerfaring. Nogle gange bruges specielle lime. Men nogle gange er en teknik kaldet optisk kontakt det bedste valg og involverer intet materiale mellem påsatte optiske briller. Den består af fysisk kontakt med flade overflader for at fastgøres til hinanden uden lim. I nogle tilfælde bruges mekaniske afstandsstykker, præcisionsglasstænger eller -kugler, klemmer eller bearbejdede metalkomponenter til at samle de optiske komponenter i visse afstande og med visse geometriske orienteringer til hinanden. Lad os undersøge nogle af vores populære teknikker til fremstilling af high-end optik. SLIBNING & LAPPING & POLIERING: Den ru form af den optiske komponent opnås ved slibning af et glasemne. Derefter udføres lapning og polering ved at rotere og gnide de ru overflader af de optiske komponenter mod værktøjer med ønskede overfladeformer. Slam med bittesmå slibende partikler og væske hældes ind mellem optikken og formværktøjerne. Slibemiddelpartikelstørrelserne i sådanne opslæmninger kan vælges i overensstemmelse med den ønskede fladhedsgrad. Afvigelserne af kritiske optiske overflader fra ønskede former udtrykkes i form af bølgelængder af det lys, der anvendes. Vores højpræcisionsoptik har en tiendedel af en bølgelængde (bølgelængde/10) tolerancer eller endnu snævrere er muligt. Udover overfladeprofil scannes og evalueres de kritiske overflader for andre overfladeegenskaber og defekter såsom dimensioner, ridser, afslag, gruber, pletter...osv. Den stramme styring af miljøforhold i det optiske produktionsgulv og omfattende metrologi- og testkrav med avanceret udstyr gør dette til en udfordrende branche. • SEKUNDÆRE PROCESSER I GLASFREMSTILLING: Igen er vi kun begrænset med din fantasi, når det kommer til sekundære og efterbehandlingsprocesser af glas. Her lister vi nogle af dem: -Belægninger på glas (optisk, elektrisk, tribologisk, termisk, funktionel, mekanisk...). Som et eksempel kan vi ændre glasets overfladeegenskaber, så det for eksempel reflekterer varme, så det holder bygningsinteriøret køligt, eller gøre den ene side infrarød absorberende ved hjælp af nanoteknologi. Dette hjælper med at holde bygningernes indre varme, fordi det yderste overfladelag af glas vil absorbere den infrarøde stråling inde i bygningen og udstråle den tilbage til indersiden. -Etching on glas -Anvendt keramisk mærkning (ACL) - Gravering - Flammepolering -Kemisk polering - Farvning FREMSTILLING AF TEKNISK KERAMIK • PRÆSNING : Består af enakset komprimering af granuleret pulver indesluttet i en matrice • VARMPRESSNING: Svarer til formpresning, men med tilføjelse af temperatur for at øge fortætningen. Pulver eller komprimeret præform anbringes i grafitmatrice, og uniaksialt tryk påføres, mens matricen holdes ved høje temperaturer såsom 2000 C. Temperaturer kan være forskellige afhængigt af typen af keramisk pulver, der behandles. For komplicerede former og geometrier kan anden efterfølgende bearbejdning såsom diamantslibning være nødvendig. • ISOSTATISK PRESSNING: Granulært pulver eller formpressede komprimeringer anbringes i lufttætte beholdere og derefter i en lukket trykbeholder med væske indeni. Derefter komprimeres de ved at øge trykbeholderens tryk. Væsken inde i beholderen overfører trykkræfterne ensartet over hele overfladen af den lufttætte beholder. Materialet komprimeres således ensartet og tager form af sin fleksible beholder og dens indvendige profil og funktioner. • VARMT ISOSTATISK PRESSNING: Svarende til isostatisk presning, men ud over tryksat gasatmosfære sintrer vi kompakten ved høj temperatur. Varm isostatisk presning resulterer i yderligere fortætning og øget styrke. • SLIPSTØBNING / DÆNSTØBNING: Vi fylder formen med en suspension af mikrometerstore keramiske partikler og bærervæske. Denne blanding kaldes "slip". Formen har porer og derfor filtreres væsken i blandingen ned i formen. Som følge heraf dannes en afstøbning på formens indre overflader. Efter sintring kan delene tages ud af formen. • BÅNDSTØBNING: Vi fremstiller keramiske bånd ved at støbe keramiske slam på flade, bevægelige bæreflader. Opslæmningerne indeholder keramiske pulvere blandet med andre kemikalier til binding og transport. Da opløsningsmidlerne fordamper, efterlades tætte og fleksible keramikplader, som kan skæres eller rulles efter ønske. • EKSTRUSIONSFORMNING: Som i andre ekstruderingsprocesser føres en blød blanding af keramisk pulver med bindemidler og andre kemikalier gennem en matrice for at opnå dens tværsnitsform og skæres derefter i de ønskede længder. Processen udføres med kolde eller opvarmede keramiske blandinger. • LAVTRYKSPRØJTESTØBNING: Vi forbereder en blanding af keramisk pulver med bindemidler og opløsningsmidler og opvarmer det til en temperatur, hvor det nemt kan presses og presses ind i værktøjshulrummet. Når støbecyklussen er afsluttet, udstødes delen, og det bindende kemikalie brændes af. Ved hjælp af sprøjtestøbning kan vi opnå indviklede dele ved høje volumener økonomisk. Huller der er en lille brøkdel af en millimeter på en 10 mm tyk væg er mulige, gevind er muligt uden yderligere bearbejdning, tolerancer så snævre som +/- 0,5 % er mulige og endnu lavere, når dele er bearbejdet , vægtykkelser i størrelsesordenen 0,5 mm til en længde på 12,5 mm er mulige samt vægtykkelser på 6,5 mm til en længde på 150 mm. • GRØN BEARBEJDNING: Ved hjælp af de samme metalbearbejdningsværktøjer kan vi bearbejde pressede keramiske materialer, mens de stadig er bløde som kridt. Tolerancer på +/- 1 % er mulige. For bedre tolerancer bruger vi diamantslibning. • SINTERING eller BRYDNING: Sintring muliggør fuld fortætning. Der sker et betydeligt svind på de grønne kompaktdele, men dette er ikke et stort problem, da vi tager højde for disse dimensionsændringer, når vi designer delen og værktøjet. Pulverpartikler bindes sammen, og porøsitet induceret af komprimeringsprocessen fjernes i høj grad. • DIAMANTSLIBNING: Verdens hårdeste materiale "diamant" bliver brugt til at slibe hårde materialer som keramik, og der opnås præcisionsdele. Der opnås tolerancer i mikrometerområdet og meget glatte overflader. På grund af dens omkostninger overvejer vi kun denne teknik, når vi virkelig har brug for den. • HERMETISKE ENHEDER er dem, der praktisk talt ikke tillader nogen udveksling af stof, faste stoffer, væsker eller gasser mellem grænseflader. Hermetisk forsegling er lufttæt. For eksempel er hermetiske elektroniske kabinetter dem, der holder det følsomme indre indhold af en emballeret enhed uskadt af fugt, forurenende stoffer eller gasser. Intet er 100% hermetisk, men når vi taler om hermeticitet, mener vi i praksis, at der er hermeticitet i det omfang, at lækageraten er så lav, at apparaterne er sikre under normale miljøforhold i meget lang tid. Vores hermetiske samlinger består af metal, glas og keramiske komponenter, metal-keramik, keramik-metal-keramik, metal-keramik-metal, metal til metal, metal-glas, metal-glas-metal, glas-metal-glas, glas- metal og glas til glas og alle andre kombinationer af metal-glas-keramisk limning. Vi kan for eksempel metalcoate de keramiske komponenter, så de kan bindes stærkt til andre komponenter i samlingen og har fremragende tætningsevne. Vi har knowhow til at belægge optiske fibre eller gennemføringer med metal og lodde eller lodde dem til kabinetterne, så ingen gasser passerer eller siver ind i kabinetterne. Derfor bruges de til fremstilling af elektroniske kabinetter til at indkapsle følsomme enheder og beskytte dem mod den ydre atmosfære. Udover deres fremragende tætningsegenskaber, andre egenskaber såsom den termiske udvidelseskoefficient, deformationsmodstand, ikke-afgasning karakter, meget lang levetid, ikke-ledende karakter, termiske isoleringsegenskaber, antistatisk natur...osv. gør glas og keramiske materialer til valget til visse anvendelser. Oplysninger om vores anlæg, der producerer keramiske til metalfittings, hermetisk forsegling, vakuumgennemføringer, høj- og ultrahøjvakuum- og væskekontrolkomponenter kan findes her:Hermetic Components Factory Brochure CLICK Product Finder-Locator Service FORRIGE SIDE
- Wire & Spring Forming, Shaping, Welding, Assembly of Wires, Coil, CNC
Wire & Spring Forming, Shaping, Welding, Assembly of Wires, Coil Compression Extension Torsion Flat Springs, Custom Wires, Helical Springs at AGS-TECH Inc. Tråd- og fjederformning Vi fremstiller brugerdefinerede ledninger, trådsamling, ledninger formet til ønskede 2D- og 3D-former, trådnet, mesh, kabinetter, kurv, hegn, trådfjeder, flad fjeder; vridning, kompression, spænding, flade fjedre og mere. Vores processer er tråd- og fjederformning, trådtrækning, formning, bukning, svejsning, lodning, lodning, gennemboring, sænkning, boring, affasning, slibning, gevindskæring, belægning, fourslide, glideformning, vikling, oprulning, oprulning. Vi anbefaler, at du klikker her for at DOWNLOAD vores skematiske illustrationer af tråd- og fjederformningsprocesser af AGS-TECH Inc. Denne downloadbare fil med fotos og skitser hjælper dig med bedre at forstå de oplysninger, vi giver dig nedenfor. • TRÅDNING: Ved hjælp af trækkræfter strækker vi metalmaterialet og trækker det gennem en matrice for at reducere diameteren og øge dets længde. Nogle gange bruger vi en række matricer. Vi er i stand til at lave matricer til alle tråde. Ved at bruge materiale med høj trækstyrke trækker vi meget tynde tråde. Vi tilbyder både kold- og varmbearbejdede ledninger. • TRÅDLÆSNING: En rulle af trådtråd bøjes og formes til et nyttigt produkt. Vi har evnen til at danne ledninger fra alle målere, inklusive tynde filamenter såvel som tykke ledninger som dem, der bruges som fjedre under bilchassis. Udstyr, vi bruger til trådformning, er manuelle og CNC-tråddannere, coiler, kraftpresser, fourslide, multi-slide. Vores processer er tegning, bukning, udretning, udfladning, strækning, skæring, opstilling, lodning & svejsning & slaglodning, samling, oprulning, sænkning (eller vingning), gennemboring, trådskæring, boring, affasning, slibning, coating og overfladebehandlinger. Vores state-of-the-art udstyr kan sættes op til at udvikle meget komplekse designs af enhver form og snævre tolerancer. Vi tilbyder forskellige endetyper lignende sfæriske, spidse eller affasede ender til dine ledninger. De fleste af vores trådformningsprojekter har minimale til nul værktøjsomkostninger. Eksempler på behandlingstiderne er generelt dage. Ændringer i design/konfiguration af trådforme kan foretages meget hurtigt. • FJEDERFORMNING: AGS-TECH fremstiller et stort udvalg af fjedre, herunder: -Torsion / Dobbelt torsionsfjeder -Spænding/kompressionsfjeder -Konstant / Variabel Fjeder -Spiral- og spiralfjeder -Flat & Leaf Spring -Balance forår - Belleville vaskemaskine -Negator fjeder -Skruefjeder med progressiv hastighed - Bølgeforår -Volut Spring - Tilspidsede fjedre -Forårsringe - Urfjedre - Klip Vi fremstiller fjedre af en række forskellige materialer og kan vejlede dig efter din applikation. De mest almindelige materialer er rustfrit stål, krom silicium, højkulstofstål, oliehærdet lavkulstof, kromvanadium, fosforbronze, titanium, berylliumkobberlegering, højtemperaturkeramik. Vi anvender forskellige teknikker til fremstilling af fjedre, herunder CNC-spolning, koldvikling, varmvikling, hærdning, efterbehandling. Andre teknikker, der allerede er nævnt ovenfor under trådformning, er også almindelige i vores fjederfremstillingsoperationer. • EFTERBEHANDLING TIL LEDNINGER OG FJEDRE: Vi kan færdiggøre dine produkter på mange måder afhængigt af dit valg og behov. Nogle almindelige processer, vi tilbyder, er: maling, pulverlakering, plettering, vinyldypning, anodisering, stressaflastning, varmebehandling, shot peen, tumbling, kromat, elektrofri nikkel, passivering, bagt emalje, plastikcoat , plasmarensning. CLICK Product Finder-Locator Service FORRIGE SIDE
- Sheet Metal Forming Fabrication, Stamping, Punching, Deep Drawing, CNC
Sheet Metal Forming and Fabrication, Stamping, Punching, Bending, Progressive Die, Spot Welding, Deep Drawing, Metal Blanking and Slitting at AGS-TECH Inc. Stempler og metalpladefremstilling Vi tilbyder stempling, formning, formning, bukning, stansning, blanking, slidsning, perforering, indhak, nibbling, barbering, presbearbejdning, fremstilling, dybtrækning ved hjælp af enkelt stanse-/enkeltslagsmatricer samt progressive matricer og spinding, gummiformning og hydroformning; metalskæring ved hjælp af vandstråle, plasma, laser, sav, flamme; metalplade ved hjælp af svejsning, punktsvejsning; metalpladerør udbuling og bøjning; overfladebehandling af metalplader inklusive dyppe- eller spraymaling, elektrostatisk pulverbelægning, anodisering, plettering, sputtering og mere. Vores ydelser spænder fra hurtig fremstilling af metalpladeprototyper til højvolumenfremstilling. Vi anbefaler, at du klikker her for atDOWNLOAD vores skematiske illustrationer af metalpladefremstilling og stemplingsprocesser af AGS-TECH Inc. Dette vil hjælpe dig med bedre at forstå de oplysninger, vi giver dig nedenfor. • PLADSkæring: Vi tilbyder AFSKÆRINGER og AFSKÆRINGER. Afskæringer skærer pladen over en vej ad gangen, og der er stort set intet spild af materiale, hvorimod formen ikke kan nestles præcist ved afskæringer, og derfor går en vis mængde materiale til spilde. En af vores mest populære processer er PUNCHING, hvor et stykke materiale rund eller anden form skæres ud af metalplade. Det stykke, der skæres ud, er affald. En anden version af udstansning er SLOTTING, hvor der udstanses rektangulære eller aflange huller. BLANKNING på den anden side er den samme proces som stansning, med forskellen på det stykke, der skæres ud, er arbejdet og bevares. FINE BLANKING, en overlegen version af blanking, skaber snit med tætte tolerancer og lige glatte kanter og kræver ikke sekundære operationer for perfektion af arbejdsemnet. En anden proces, vi ofte bruger, er SLITTING, som er en skæreproces, hvor metalplade skæres af to modstående cirkulære klinger i en lige eller buet bane. Dåseåbner er et simpelt eksempel på opskæringsprocessen. En anden populær proces for os er PERFORERING, hvor mange huller runde eller anden form er udstanset i metalplade i et bestemt mønster. Et typisk eksempel på et perforeret produkt er metalfiltre med mange huller til væsker. I NOTCHING, en anden pladeskæringsproces, fjerner vi materiale fra et arbejdsemne, startende ved kanten eller andre steder og skærer indad, indtil den ønskede form er opnået. Det er en progressiv proces, hvor hver operation fjerner endnu et stykke, indtil den ønskede kontur er opnået. Til små produktionsserier bruger vi nogle gange en relativt langsommere proces kaldet NIBBLING, som består af mange hurtige udstansninger af overlappende huller for at lave et større og mere komplekst snit. I PROGRESSIVE CUTTING bruger vi en række forskellige operationer for at opnå et enkelt snit eller en bestemt geometri. Endelig hjælper SHAVING en sekundær proces os med at forbedre kanter af snit, der allerede er lavet. Den bruges til at skære spånerne af, ru kanter på metalplader. • BUKNING AF PLADER: Udover skæring er bukning en væsentlig proces, uden hvilken vi ikke ville være i stand til at fremstille de fleste produkter. For det meste en kold arbejdsoperation, men nogle gange også udført, når den er varm eller varm. Vi bruger matricer og presser det meste af tiden til denne operation. I PROGRESSIVE BENDING bruger vi en række forskellige stanse- og matriceoperationer for at opnå en enkelt bøjning eller en bestemt geometri. AGS-TECH anvender en række forskellige bukkeprocesser og træffer valget afhængigt af emnematerialet, dets størrelse, tykkelse, ønsket størrelse af bøjning, radius, krumning og bøjningsvinkel, bøjningsplacering, driftsøkonomi, mængder, der skal fremstilles... etc. Vi bruger V-BENDING, hvor en V-formet stanse tvinger metalpladen ind i den V-formede matrice og bøjer den. God til både meget spidse og stumpe vinkler og derimellem, inklusive 90 grader. Ved hjælp af aftørringsmatricer udfører vi KANTBUJNING. Vores udstyr gør det muligt for os at opnå vinkler endnu større end 90 grader. Ved kantbøjning er emnet klemt mellem en trykpude og matricen, området til bøjning er placeret på matricekanten, og resten af emnet holdes over space som en udkraget bjælke. Når stansen virker på udkragningsdelen, bøjes den over kanten af matricen. FLANGING er en kantbukningsproces, der resulterer i en 90 graders vinkel. Hovedmålene med operationen er eliminering af skarpe kanter og opnåelse af geometriske overflader for at lette sammenføjningen af dele. BEADING, en anden almindelig kantbøjningsproces danner en krølle over en dels kant. HEMNING på den anden side resulterer med en kant af arket, der er bøjet helt om på sig selv. I SØMNING bukkes kanterne af to dele om på hinanden og samles. DOBBELTSØMNING giver derimod vandtætte og lufttætte pladesamlinger. I lighed med kantbøjning anvender en proces kaldet ROTARY BENDING en cylinder med den ønskede vinkel udskåret og tjener som stempel. Når kraften overføres til stansen, lukkes den med emnet. Cylinderens rille giver udkragningsdelen den ønskede vinkel. Rillen kan have en vinkel mindre eller større end 90 grader. I AIR BENDING behøver vi ikke den nederste dyse for at have en vinklet rille. Metalpladen er understøttet af to overflader på modsatte sider og i en vis afstand. Stansen påfører derefter en kraft på det rigtige sted og bøjer emnet. KANALBØJNING udføres ved hjælp af en kanalformet stanse og matrice, og U-BØJNING opnås med en U-formet stanse. OFFSET BENDING producerer forskydninger på pladen. RULLEBØJNING, en teknik, der er god til tykt arbejde og bukning af store stykker metalplader, bruger tre ruller til at fremføre og bukke pladerne til de ønskede krumninger. Ruller er arrangeret, så den ønskede bøjning af arbejdet opnås. Afstanden og vinklen mellem rullerne styres for at opnå det ønskede resultat. En bevægelig rulle gør det muligt at kontrollere krumningen. RØRFORMNING er en anden populær pladebøjningsoperation, der involverer flere matricer. Rør opnås efter flere handlinger. KORRUGERING udføres også ved bøjningsoperationer. Grundlæggende er det den symmetriske bøjning med jævne mellemrum hen over et helt stykke metalplade. Forskellige former kan bruges til korrugering. Bølgeplader er mere stive og har bedre modstandsdygtighed mod bøjning og har derfor anvendelse i byggebranchen. PLADERULLEFORMNING, en kontinuerlig fremstillingsproces anvendes til at bukke tværsnit af en bestemt geometri ved hjælp af ruller, og arbejdet bukkes i sekventielle trin, hvor den sidste valse afslutter arbejdet. I nogle tilfælde anvendes en enkelt rulle og i nogle tilfælde en række ruller. • KOMBINEREDE PLADESKÆRINGS- OG BUKNINGSPROCESSER : Det er de processer, der skærer og bøjer på samme tid. I PIERCING skabes et hul ved hjælp af et spidst stempel. Når stansen udvider hullet i arket, bøjes materialet samtidigt til en indvendig flange til hullet. Den opnåede flange kan have vigtige funktioner. LANCER-operationen på den anden side skærer og bøjer arket for at skabe en hævet geometri. • BULGING OG BØJNING AF METALRØR: Ved BULGING sættes en indre del af et hult rør under tryk, hvilket får røret til at bule udad. Da røret er inde i en matrice, styres bulgeometrien af formen på formen. Ved STRETCH BENDING strækkes et metalrør ved hjælp af kræfter parallelt med rørets akse og bøjningskræfter for at trække røret over en formblok. I DRAW BENDING klemmer vi røret nær dets ende til en roterende formblok, der bøjer røret, mens det roterer. Til sidst, i KOMPRESSIONSBØJNING, holdes røret med kraft til en fast formblok, og en matrice bøjer det over formblokken. • DYBETEGNING : I en af vores mest populære operationer bruges en stanse, en matchende matrice og en blankholder. Pladeemnet placeres over matriceåbningen, og stansen bevæger sig mod det emne, som fastholdes af emneholderen. Når de kommer i kontakt, tvinger stansen metalpladen ind i matricehulrummet for at danne produktet. Dybtrækningsoperationen ligner skæring, men mellemrummet mellem stansen og matricen forhindrer arket i at blive skåret. En anden faktor, der sikrer, at arket er dybttrukket og ikke skåret, er de afrundede hjørner på matricen og stansen, som forhindrer klipning og skæring. For at opnå en større omfang af dybtrækning, bliver der implementeret en REDRAWING-proces, hvor en efterfølgende dybtrækning finder sted på en del, der allerede har gennemgået en dybtegningsproces. I REVERSE REDRAWING vendes den dybtrukne del om og tegnes i den modsatte retning. Dyb tegning kan give uregelmæssigt formede genstande såsom kuppelformede, tilspidsede eller trinformede kopper, I PRÆGNING bruger vi et han- og hunformepar til at imponere metalpladen med et design eller skrift. • SPINNING : En operation, hvor et fladt eller præformet emne holdes mellem en roterende dorn og halestamme, og et værktøj udøver lokalt tryk på arbejdet, mens det gradvist bevæger sig op ad dornen. Som et resultat vikles emnet over dornen og tager sin form. Vi bruger denne teknik som et alternativ til dybtegning, hvor mængden af en ordre er lille, delene er store (diametre op til 20 fod) og har unikke kurver. Selvom priserne pr. styk generelt er højere, er opsætningsomkostningerne for CNC-spinding lave sammenlignet med dybtrækning. Tværtimod kræver dybtrækning en høj initial investering for opsætning, men omkostningerne pr. styk er lave, når der produceres store mængder dele. En anden version af denne proces er SHEAR SPINNING, hvor der også er metalflow inde i emnet. Metalstrømmen vil reducere tykkelsen af emnet, efterhånden som processen udføres. Endnu en anden relateret proces er TUBE SPINNING, som anvendes på cylindiriske dele. Også i denne proces er der metalstrøm inde i emnet. Tykkelsen reduceres dermed og rørets længde øges. Værktøjet kan flyttes for at skabe funktioner på indersiden eller ydersiden af røret. • GUMMIFORMNING AF PLAD: Gummi eller polyurethanmateriale anbringes i en beholderform, og emnet placeres på gummiets overflade. Et stempel bliver derefter påvirket af arbejdsemnet og tvinger det ind i gummiet. Da trykket genereret af gummiet er lavt, er dybden af de producerede dele begrænset. Da værktøjsomkostningerne er lave, er processen velegnet til produktion af små mængder. • HYDROFORMNING: I lighed med gummiformning, bliver plademetal i denne proces presset med et stempel ind i en væske under tryk inde i et kammer. Metalpladen er klemt ind mellem stansen og en gummimembran. Membranen omgiver emnet fuldstændigt, og væsketrykket tvinger det til at dannes på stansen. Meget dybe tegninger kan opnås med denne teknik, endnu dybere end i dybtegningsprocessen. Vi fremstiller enkelt-punch dies såvel som progressive dies afhængigt af din del. Enkeltslagspresseforme er en omkostningseffektiv metode til hurtigt at producere store mængder af simple metalpladedele, såsom skiver. Progressive matricer eller dybtegningsteknikken bruges til at fremstille mere komplekse geometrier. Afhængigt af dit tilfælde kan vandstråle-, laser- eller plasmaskæring bruges til at producere dine metalpladedele billigt, hurtigt og præcist. Mange leverandører har ingen idé om disse alternative teknikker eller har ikke det, og derfor gennemgår de lange og dyre måder at fremstille matricer og værktøjer, der kun spilder kundernes tid og penge. Hvis du har brug for specialbyggede metalpladekomponenter såsom kabinetter, elektroniske huse ... osv. så hurtigt som inden for få dage, så kontakt os for vores RAPID SHEET METAL PROTOTYPING-service. CLICK Product Finder-Locator Service FORRIGE MENU
- Forging and Powdered Metallurgy, Die Forging, Heading, Hot Forging
Forging and Powdered Metallurgy, Die Forging, Heading, Hot Forging, Impression Die, Near Net Shape, Swaging, Metal Hobbing, Riveting, Coining from AGS-TECH Inc. Metalsmedning og pulvermetallurgi Den type METALSMEDEprocesser, vi tilbyder, er varm og kold matrice, åben matrice og lukket matrice, aftryksmatrice & flashless smedning, cogging, fuldering, kant- og præcisionssmedning, næsten-net-form, heading , smedning, forstyrret smedning, metalsmedning, tryk og rul & radial & orbital & ring & isotermisk smedning, prægning, nitning, metalkuglesmedning, metalgennemboring, dimensionering, smedning med høj energihastighed. Vores POWDER METALLURGY og POWDER PROCESSION teknikker er pulverpresning og sintring, imprægnering, infiltration, varm og kold isostatisk presning, metalsprøjtestøbning, valsekomprimering, pulvervalsning, pulverekstrudering, løs sintring, gnistsintring, varmpresning. Vi anbefaler, at du klikker her for at DOWNLOAD vores skematiske illustrationer af smedeprocesser af AGS-TECH Inc. DOWNLOAD vores skematiske illustrationer af pulvermetallurgiprocesser af AGS-TECH Inc. Disse downloadbare filer med fotos og skitser hjælper dig med bedre at forstå de oplysninger, vi giver dig nedenfor. Ved metalsmedning påføres trykkræfter og materialet deformeres og den ønskede form opnås. De mest almindelige smedede materialer i industrien er jern og stål, men adskillige andre såsom aluminium, kobber, titanium, magnesium er også meget smedet. Smedede metaldele har forbedrede kornstrukturer ud over forseglede revner og lukkede tomme rum, så styrken af dele opnået ved denne proces er højere. Smedning producerer dele, der er signifikant stærkere for deres vægt end dele fremstillet ved støbning eller bearbejdning. Da smedede dele formes ved at få metallet til at flyde ind i dets endelige form, antager metallet en retningsbestemt kornstruktur, der tegner sig for delenes overlegne styrke. Med andre ord, dele opnået ved smedning afslører bedre mekaniske egenskaber sammenlignet med simple støbte eller bearbejdede dele. Vægten af metalsmedninger kan variere fra små letvægtsdele til hundredtusindvis af pund. Vi fremstiller smedegods for det meste til mekanisk krævende applikationer, hvor der påføres høje belastninger på dele som autodele, gear, arbejdsværktøj, håndværktøj, turbineaksler, motorcykel gear. Fordi værktøjs- og opsætningsomkostninger er relativt høje, anbefaler vi kun denne fremstillingsproces til højvolumenproduktion og til lavvolumen, men høj værdi kritiske komponenter såsom flylandingsstel. Udover omkostninger til værktøj kan fremstillingstiden for store mængder smedede dele være længere sammenlignet med nogle simple bearbejdede dele, men teknikken er afgørende for dele, der kræver ekstraordinær styrke såsom bolte, møtrikker, speciel anvendelse fastgørelsesanordninger, biler, gaffeltruck, krandele. • VARM- og KOLDSMEDE : Varmsmedning, som navnet antyder, udføres ved høje temperaturer, derfor er duktiliteten høj og materialets styrke lav. Dette letter let deformation og smedning. Tværtimod udføres koldsmedning ved lavere temperaturer og kræver højere kræfter, hvilket resulterer i strækhærdning, bedre overfladefinish og nøjagtighed af de fremstillede dele. • ÅBEN MATrice- og IMPRESSION-SMEDE: Ved åben matricesmedning begrænser matricerne ikke materialet, der komprimeres, hvorimod hulrummene inde i matricerne begrænser materialestrømmen, mens det smedes til den ønskede form. UPSET FORGING eller også kaldet UPSETTING, som faktisk ikke er den samme, men en meget lignende proces, er en åben matriceproces, hvor arbejdsemnet klemmes mellem to flade matricer, og en trykkraft reducerer dets højde. Da højden er reduceret, øges arbejdsemnets bredde. HEADING, en forstyrret smedningsproces involverer cylindrisk papir, der er stødt for enden, og dets tværsnit øges lokalt. I heading føres papiret gennem matricen, smedet og derefter skåret i længden. Operationen er i stand til hurtigt at producere store mængder fastgørelseselementer. For det meste er det en koldbearbejdning, fordi den bruges til at lave søm, skrueender, møtrikker og bolte, hvor materialet skal forstærkes. En anden åben matriceproces er COGGING, hvor arbejdsemnet smedes i en række trin, hvor hvert trin resulterer i komprimering af materialet og den efterfølgende bevægelse af den åbne matrice langs arbejdsemnets længde. Ved hvert trin reduceres tykkelsen, og længden øges med en lille mængde. Processen ligner en nervøs elev, der hele tiden bider sin blyant i små trin. En proces kaldet FULLERING er en anden åben formsmedningsmetode, som vi ofte anvender som et tidligere trin for at fordele materialet i arbejdsemnet, før andre metalsmedningsoperationer finder sted. Vi bruger det, når emnet kræver flere smedning operationer. Under operationen deformeres matrice med konvekse overflader og forårsager metalstrømning ud til begge sider. En lignende proces som fyldning, EDGING involverer på den anden side åben matrice med konkave overflader til at deformere arbejdsemnet. Kantning er også en forberedelsesproces til efterfølgende smedeoperationer, der får materialet til at flyde fra begge sider ind i et område i midten. IMPRESSION DIE FORGING eller CLOSED DIE FORGING som det også kaldes bruger en dyse/støbeform, der komprimerer materialet og begrænser dets flow i sig selv. Matricen lukker, og materialet tager form af formen / formhulrummet. PRECISION FORGING, en proces, der kræver specielt udstyr og forme, producerer dele med ingen eller meget lidt flash. Med andre ord vil delene have næsten endelige dimensioner. I denne proces bliver en velkontrolleret mængde materiale omhyggeligt indsat og placeret inde i formen. Vi anvender denne metode til komplekse former med tynde sektioner, små tolerancer og trækvinkler, og når mængderne er store nok til at retfærdiggøre omkostningerne til form og udstyr. • FLAMMELØS SMEDE: Arbejdsemnet placeres i matricen på en sådan måde, at intet materiale kan flyde ud af hulrummet og danne flash. Der er således ikke behov for uønsket flashtrimning. Det er en præcisionssmedningsproces og kræver derfor nøje kontrol med mængden af anvendt materiale. • METALSVEJDNING eller RADIALSMEDE: Et arbejdsemne påvirkes i omkredsen af matrice og smedet. En dorn kan lige så godt bruges til at smede den indvendige emnegeometri. I sænkeoperationen modtager arbejdsemnet typisk flere slag pr. sekund. Typiske genstande fremstillet ved sænkning er spidsværktøjer, koniske stænger, skruetrækkere. • METALPIERCING: Vi bruger denne operation ofte som en ekstra operation ved fremstilling af dele. Et hul eller hulrum skabes med piercing på arbejdsemnets overflade uden at bryde igennem det. Bemærk venligst, at piercing er anderledes end boring, hvilket resulterer i et gennemgående hul. • HOBBING : Et stempel med den ønskede geometri presses ind i arbejdsemnet og skaber et hulrum med den ønskede form. Vi kalder denne punch en HOB. Operationen involverer høje tryk og udføres ved kulde. Som et resultat er materialet koldbearbejdet og strækhærdet. Derfor er denne proces meget velegnet til fremstilling af forme, forme og hulrum til andre fremstillingsprocesser. Når først kogepladen er fremstillet, kan man nemt fremstille mange identiske hulrum uden at skulle bearbejde dem én efter én. • RULLESMEDE eller RULLEFORMNING: To modstående ruller bruges til at forme metaldelen. Arbejdsemnet føres ind i rullerne, rullerne drejer og trækker værket ind i mellemrummet, værket føres derefter gennem den rillede del af rullerne, og trykkræfterne giver materialet dens ønskede form. Det er ikke en rullende proces, men en smedeproces, fordi det er en diskret snarere end en kontinuerlig operation. Geometrien på rullerillerne smeder materialet til den ønskede form og geometri. Det udføres varmt. Da det er en smedeproces, producerer det dele med enestående mekaniske egenskaber, og derfor bruger vi det til fremstilling af autodele såsom aksler, der skal have ekstraordinær udholdenhed i hårde arbejdsmiljøer. • ORBITAL SMEDE: Arbejdsemnet anbringes i et smedningsmatricehulrum og smedet af en øvre matrice, der bevæger sig i en kredsløbsbane, mens den drejer om en skrå akse. Ved hver omdrejning afslutter den øvre matrice at udøve trykkræfter på hele arbejdsemnet. Ved at gentage disse omdrejninger et antal gange udføres tilstrækkelig smedning. Fordelene ved denne fremstillingsteknik er dens lave støjdrift og lavere nødvendige kræfter. Med andre ord kan man med små kræfter dreje en tung matrice om en akse for at påføre store tryk på en del af arbejdsemnet, der er i kontakt med matricen. Skive eller konisk formede dele passer nogle gange godt til denne proces. • RINGSMEDE: Vi bruger ofte til fremstilling af sømløse ringe. Stock skæres i længden, forstyrres og derefter gennembores hele vejen igennem for at skabe et centralt hul. Derefter sættes den på en dorn, og en smedematrice hamrer den fra oven, mens ringen langsomt roteres, indtil de ønskede dimensioner er opnået. • NITNING: En almindelig proces til sammenføjning af dele, starter med et lige metalstykke indsat i forfremstillede huller gennem delene. Derefter smedes de to ender af metalstykket ved at klemme sammenføjningen mellem en øvre og nedre matrice. • MØNTNING: En anden populær proces udført ved mekanisk presse, der udøver store kræfter over en kort afstand. Navnet "coining" kommer fra de fine detaljer, der er smedet på overfladerne af metalmønter. Det er mest en efterbehandlingsproces for et produkt, hvor der opnås fine detaljer på overfladerne som følge af den store kraft, der påføres af matricen, der overfører disse detaljer til emnet. • METALKUGLESMEDE: Produkter såsom kuglelejer kræver præcist fremstillede metalkugler af høj kvalitet. I en teknik kaldet SKEW ROLLING, bruger vi to modsatrettede ruller, der kontinuerligt roterer, mens papiret kontinuerligt føres ind i rullerne. I den ene ende af de to ruller udstødes metalkugler som produkt. En anden metode til smedning af metalkugler er at bruge matrice, der klemmer materialet, der er placeret mellem dem, og tager den sfæriske form af formhulrummet. Ofte kræver producerede bolde nogle ekstra trin, såsom efterbehandling og polering, for at blive et produkt af høj kvalitet. • ISOTHERMAL SMEDE / VARM SMEDE: En dyr proces, der kun udføres, når fordelen/omkostningsværdien er berettiget. En varm arbejdsproces, hvor matricen opvarmes til omtrent samme temperatur som emnet. Da både matrice og arbejde har omtrent samme temperatur, er der ingen afkøling, og metallets strømningsegenskaber forbedres. Betjeningen passer godt til superlegeringer og materialer med ringere smedbarhed og materialer, hvis mekaniske egenskaber er meget følsomme over for små temperaturgradienter og ændringer. • METALFORMAT: Det er en kold efterbehandlingsproces. Materialestrømmen er ubegrænset i alle retninger med undtagelse af retningen, hvori kraften påføres. Som et resultat opnås en meget god overfladefinish og nøjagtige dimensioner. • HIGH ENERGY RATE SMEDE: Teknikken involverer en øvre form fastgjort til armen af et stempel, som hurtigt skubbes, når en brændstof-luftblanding antændes af et tændrør. Det ligner driften af stempler i en bilmotor. Formen rammer arbejdsemnet meget hurtigt og vender derefter meget hurtigt tilbage til sin oprindelige position takket være modtrykket. Værket er smedet i løbet af få millisekunder, og derfor er der ikke tid til, at arbejdet køles ned. Dette er nyttigt til svære at smede dele, der har meget temperaturfølsomme mekaniske egenskaber. Med andre ord er processen så hurtig, at delen formes under konstant temperatur hele vejen igennem, og der vil ikke være temperaturgradienter ved støbeform/arbejdsemne-grænseflader. • I DIE FORGING slås metal mellem to matchende stålblokke med specielle former i, kaldet matricer. Når metallet hamres mellem matricerne, antager det samme form som formerne i matricen. Når den når sin endelige form, tages den ud til afkøling. Denne proces producerer stærke dele, der har en præcis form, men kræver en større investering for de specialiserede matricer. Forstyrret smedning øger diameteren af et stykke metal ved at gøre det fladt. Det bruges generelt til at lave små dele, især til at danne hoveder på fastgørelseselementer som bolte og søm. • PULVERMETALLURGI / PULVERBEHANDLING: Som navnet antyder, involverer det fremstillingsprocesser til fremstilling af faste dele af visse geometrier og former ud fra pulvere. Hvis metalpulvere bruges til dette formål, er det pulvermetallurgiens område, og hvis ikke-metalpulvere anvendes, er det pulverforarbejdning. Faste dele fremstilles af pulver ved presning og sintring. POWDER PRESSING bruges til at komprimere pulvere til de ønskede former. For det første er det primære materiale fysisk pulveriseret, idet det opdeles i mange små individuelle partikler. Pulverblandingen fyldes i formen, og et stempel bevæger sig mod pulveret og komprimerer det til den ønskede form. For det meste udført ved stuetemperatur, med pulverpresning opnås en fast del, og den kaldes grøn kompakt. Bindemidler og smøremidler bruges almindeligvis til at øge komprimeringsevnen. Vi er i stand til at pulverpresse ved hjælp af hydrauliske presser med flere tusinde tons kapacitet. Vi har også dobbeltvirkende presser med modsatrettede top- og bundstanser samt multi-action presser til meget komplekse emnegeometrier. Ensartethed, som er en vigtig udfordring for mange pulvermetallurgi-/pulverforarbejdningsanlæg, er ikke noget stort problem for AGS-TECH på grund af vores omfattende erfaring med specialfremstilling af sådanne dele i mange år. Selv med tykkere dele, hvor ensartethed udgør en udfordring, er vi lykkedes. Hvis vi forpligter os til dit projekt, laver vi dine dele. Hvis vi ser nogen potentielle risici, vil vi informere dig in advance. POWDER SINTERING, som er det andet trin, involverer hævning af temperaturen til en vis grad og opretholdelse af temperaturen på dette niveau i en vis tid, så pulverpartiklerne i den pressede del kan binde sammen. Dette resulterer i meget stærkere bindinger og styrkelse af arbejdsemnet. Sintring foregår tæt på pulverets smeltetemperatur. Under sintring vil der forekomme krympning, materialestyrke, tæthed, duktilitet, termisk ledningsevne, elektrisk ledningsevne øges. Vi har batch- og kontinuerlige ovne til sintring. En af vores muligheder er at justere porøsitetsniveauet for de dele, vi producerer. For eksempel er vi i stand til at producere metalfiltre ved at holde delene porøse til en vis grad. Ved hjælp af en teknik kaldet IMPREGNERING fylder vi porerne i metallet med en væske som olie. Vi producerer f.eks. olieimprægnerede lejer, der er selvsmørende. I INFILTRATIONsprocessen fylder vi et metals porer med et andet metal med lavere smeltepunkt end basismaterialet. Blandingen opvarmes til en temperatur mellem smeltetemperaturerne for de to metaller. Som et resultat kan nogle specielle egenskaber opnås. Vi udfører også hyppigt sekundære operationer såsom bearbejdning og smedning på pulverfremstillede dele, når særlige funktioner eller egenskaber skal opnås, eller når delen kan fremstilles med færre procestrin. ISOSTATISK PRESSNING: I denne proces bruges væsketryk til at komprimere delen. Metalpulvere anbringes i en form lavet af en forseglet fleksibel beholder. Ved isostatisk presning påføres tryk hele vejen rundt, i modsætning til det aksiale tryk, der ses ved konventionel presning. Fordelene ved isostatisk presning er ensartet tæthed i delen, især for større eller tykkere dele, overlegne egenskaber. Dens ulempe er lange cyklustider og relativt lav geometrisk nøjagtighed. KOLD ISOSTATISK PRESSNING udføres ved stuetemperatur, og den fleksible form er lavet af gummi, PVC eller urethan eller lignende materialer. Væske, der anvendes til tryk og komprimering, er olie eller vand. Konventionel sintring af den grønne kompakt følger dette. VARMT ISOSTATISK PRESSNING udføres derimod ved høje temperaturer, og formmaterialet er metalplade eller keramik med højt nok smeltepunkt til at modstå temperaturerne. Trykvæske er normalt en inert gas. Presse- og sintringsoperationerne udføres i ét trin. Porøsiteten er næsten fuldstændig elimineret, en uniform kornstruktur opnås. Fordelen ved varm isostatisk presning er, at den kan producere dele, der kan sammenlignes med støbning og smedning kombineret, samtidig med at materialer, der ikke er egnet til støbning og smedning, kan anvendes. Ulempen ved varm isostatisk presning er dens høje cyklustid og derfor omkostninger. Den er velegnet til kritiske dele med lav volumen. METALSPRØJTESTØBNING: Meget velegnet proces til fremstilling af komplekse dele med tynde vægge og detaljerede geometrier. Mest velegnet til mindre dele. Pulvere og polymerbindemiddel blandes, opvarmes og sprøjtes ind i en form. Polymerbindemidlet dækker overfladerne af pulverpartiklerne. Efter støbning fjernes bindemidlet enten ved lav temperatur opvarmning eller opløst ved hjælp af et opløsningsmiddel. RULLEKOMPAKTERING / PULVERRULNING: Pulvere bruges til at fremstille kontinuerlige strimler eller ark. Pulver tilføres fra en føder og komprimeres af to roterende ruller til ark eller strimler. Operationen udføres koldt. Arket føres ind i en sintringsovn. Sintringsprocessen kan gentages en anden gang. PULVEREKSTRUSION: Dele med store længde-/diameterforhold fremstilles ved at ekstrudere en tynd metalbeholder med pulver. LØS SINTERING: Som navnet antyder, er det en trykløs komprimerings- og sintringsmetode, velegnet til fremstilling af meget porøse dele såsom metalfiltre. Pulver føres ind i formhulrummet uden at komprimere. LØS SINTERING: Som navnet antyder, er det en trykløs komprimerings- og sintringsmetode, velegnet til fremstilling af meget porøse dele såsom metalfiltre. Pulver føres ind i formhulrummet uden at komprimere. GNISTSINTERING: Pulveret komprimeres i formen af to modstående stempel, og en højeffekt elektrisk strøm påføres stansen og passerer gennem det komprimerede pulver, der er klemt ind imellem dem. Den høje strøm brænder overfladefilm væk fra pulverpartiklerne og sinter dem med den genererede varme. Processen er hurtig, fordi varme ikke tilføres udefra, men i stedet genereres inde fra formen. VARMPRESSNING : Pulverne presses og sintres i et enkelt trin i en form, der kan modstå de høje temperaturer. Efterhånden som matricen komprimeres, påføres pulvervarmen den. Gode nøjagtigheder og mekaniske egenskaber opnået ved denne metode gør det til en attraktiv mulighed. Selv ildfaste metaller kan behandles ved at bruge formmaterialer såsom grafit. CLICK Product Finder-Locator Service FORRIGE MENU
- Plastic Rubber Metal Extrusions, Extrusion Dies, Aluminum Extruding
Plastic Rubber Metal Extrusions, Extrusion Dies, Aluminum Extruding, Pipe Tube Forming, Plastic Profiles, Metal Profiles Manufacturing, PVC at AGS-TECH Inc. Ekstruderinger, ekstruderede produkter, ekstrudater Vi bruger EXTRUSION processen til at fremstille produkter med en fast tværsnitsprofil såsom rør, rør og køleplader. Selvom mange materialer kan ekstruderes, er vores mest almindelige ekstruderinger lavet af metal, polymerer/plastik, keramik fremstillet ved enten kold, varm eller varm ekstruderingsmetode. Vi kalder de ekstruderede dele for ekstrudat eller ekstrudater, hvis flertallet. Nogle specialiserede versioner af den proces, vi også udfører, er overkapping, coekstrudering og sammensat ekstrudering. Vi anbefaler, at du klikker her for at DOWNLOAD vores skematiske illustrationer af metalkeramiske og plastiske ekstruderingsprocesser af AGS-TECH Inc. Dette vil hjælpe dig med bedre at forstå de oplysninger, vi giver dig nedenfor. I ekstrudering skubbes eller trækkes materiale, der skal ekstruderes, gennem en matrice, der har den ønskede tværsnitsprofil. Processen kan bruges til at fremstille komplekse tværsnit med fremragende overfladefinish og til at arbejde på skørt materiale. Man kan fremstille enhver længde af dele ved hjælp af denne proces. For at forenkle procestrinene: 1.) I varme eller varme ekstruderinger opvarmes materialet og fyldes i en beholder i pressen. Materialet presses og skubbes ud af matricen. 2.) Produceret ekstrudat er strakt til glatning, varmebehandlet eller koldbearbejdet for at forbedre dets egenskaber. På den anden side finder COLD EXTRUSION sted ved omkring stuetemperatur og har fordelene ved mindre god overfladefinish, mindre god overfladefinish, høj oxidationsevne og høj overfladefinish. VARM EKSTRUSION udføres over stuetemperatur, men under omkrystallisationspunktet. Det giver et kompromis og balance for nødvendige kræfter, duktilitet og materialeegenskaber og er derfor valget til nogle applikationer. HOT EXTRUSION finder sted over materialets omkrystallisationstemperatur. På denne måde er det lettere at skubbe materialet gennem matricen. Udstyrets omkostninger er dog høje. Jo mere kompleks en ekstruderet profil er, jo dyrere er matricen (værktøj) og jo lavere er produktionshastigheden. Matricetværsnittene såvel som tykkelserne har begrænsninger, der afhænger af det materiale, der skal ekstruderes. Skarpe hjørner i ekstruderingsmatricer er altid uønskede og bør undgås, medmindre det er nødvendigt. Afhængigt af det materiale, der ekstruderes, tilbyder vi: • METAL EXTRUSIONS : De mest almindelige, vi producerer, er aluminium, messing, zink, kobber, stål, titanium, magnesium • PLASTEKTRUSION : Plast smeltes og formes til en kontinuerlig profil. Vores almindelige forarbejdede materialer er polyethylen, nylon, polystyren, polyvinylchlorid, polypropylen, ABS-plast, polycarbonat, akryl. Typiske produkter, vi fremstiller, omfatter rør og slanger, plastrammer. I processen tilføres små plastikperler/harpiks tyngdekraften fra tragten til tønden på ekstruderingsmaskinen. Ofte blander vi også farvestoffer eller andre tilsætningsstoffer i tragten for at give produktet de nødvendige specifikationer og egenskaber. Materialet, der kommer ind i den opvarmede tønde, tvinges af den roterende skrue til at forlade tønden for enden og bevæge sig gennem skærmpakken for at fjerne forurenende stoffer i den smeltede plast. Efter at have passeret skærmpakken kommer plastikken ind i ekstruderingsdysen. Matricen giver den bevægelige bløde plast sin profilform, når den passerer igennem. Nu går ekstrudatet gennem et vandbad til afkøling. Andre teknikker AGS-TECH Inc. har brugt i mange år er: • RØR- OG RØREKTRUSION : Plastrør og -rør dannes, når plast ekstruderes gennem en rund formstøbning og afkøles i et vandbad, hvorefter de skæres i længden eller rulles/spoles. Klar eller farvet, stribet, enkelt- eller dobbeltvæg, fleksibel eller stiv, PE, PP, polyurethan, PVC, nylon, PC, silikone, vinyl eller andet, vi har det hele. Vi har lagerførte rør samt evnen til at producere i henhold til dine specifikationer. AGS-TECH fremstiller slanger til FDA, UL og LE krav til medicinske, elektriske og elektroniske, industrielle og andre applikationer. • OVERJACKETING / OVER JACKETING EXTRUSION : Denne teknik påfører et ydre lag af plastik på eksisterende ledning eller kabel. Vores isoleringsledninger er fremstillet med denne metode. • COEXTRUSION : Flere lag materiale ekstruderes samtidigt. De flere lag leveres af flere ekstrudere. De forskellige lagtykkelser kan justeres efter kundens specifikationer. Denne proces gør det muligt at anvende flere polymerer, der hver har en forskellig funktionalitet i produktet. Som et resultat kan man optimere en række egenskaber. • FORBUNDET EKSTRUSION: En enkelt eller flere polymerer blandes med additiver for at opnå en plastikforbindelse. Vores dobbeltskrueekstrudere producerer sammensatte ekstruderinger. Ekstrusionsmatricer er generelt billige sammenlignet med metalforme. Hvis du betaler meget mere end et par tusinde dollars for en lille eller mellemstor ekstruderingsmatrice, der ekstruderer aluminium, betaler du sandsynligvis for meget. Vi er eksperter i at afgøre, hvilken teknik der er den mest omkostningseffektive, hurtigste og bedst egnede til din applikation. Nogle gange kan ekstrudering og derefter bearbejdning af en del spare dig for mange penge. Inden du træffer en bestemt beslutning, så spørg os om vores mening først. Vi har hjulpet mange kunder med at træffe de rigtige beslutninger. For nogle udbredte metalekstruderinger kan du downloade vores brochurer og kataloger ved at klikke på den farvede tekst nedenfor. Hvis det er et hyldeprodukt, der opfylder dine krav, vil det være mere økonomisk. Download vores medicinske slange- og rørekstruderingsfunktioner Download vores ekstruderede køleplader • SEKUNDÆRE FREMSTILLINGS- OG FABRIKATIONSPROCESSER FOR EKSTRUSIONER : Blandt værdiskabende processer, vi tilbyder til ekstruderede produkter, er: - Brugerdefineret rør- og rørbøjning, formning og formning, rørafskæring, rørendeformning, rørspoling, bearbejdning og efterbehandling, hulboring og gennemboring og stansning, -Tilpassede rør- og rørsamlinger, rørmontage, svejsning, lodning og lodning - Brugerdefineret ekstruderingsbøjning, formning og formning -Rengøring, affedtning, bejdsning, passivering, polering, anodisering, plettering, maling, varmebehandling, udglødning og hærdning, mærkning, gravering og etikettering, specialindpakning. CLICK Product Finder-Locator Service FORRIGE SIDE
- Casting and Machined Parts, CNC Manufacturing, Milling, Turning, Swiss
Casting and Machined Parts, CNC Manufacturing, Milling, Turning, Swiss Type Machining, Die Casting, Investment Casting, Lost Foam Cast Parts from AGS-TECH Inc. Støbning og bearbejdning Vores specialfremstillede støbe- og bearbejdningsteknikker er forbrugs- og ikke-forbrugbare støbegods, jernholdig og ikke-jernholdig støbning, sand, matrice, centrifugal, kontinuerlig, keramisk form, investering, tabt skum, næsten-net-form, permanent form (gravitation trykstøbning), gips støbeforme (gipsstøbning) og skalstøbning, bearbejdede dele fremstillet ved fræsning og drejning ved brug af konventionelt såvel som CNC-udstyr, bearbejdning af schweizisk type til højkapacitets- og billige små præcisionsdele, skruebearbejdning til fastgørelseselementer, ikke-konventionel bearbejdning. Vær opmærksom på, at udover metaller og metallegeringer, bearbejder vi keramik-, glas- og plastkomponenter også i nogle tilfælde, når fremstillingen af en form ikke er tiltalende eller ikke er muligheden. Bearbejdning af polymermaterialer kræver den specialiserede erfaring, vi har på grund af den udfordring, plast og gummi giver på grund af deres blødhed, ikke-stivhed...osv. For bearbejdning af keramik og glas, se venligst vores side om ikke-konventionel fremstilling. AGS-TECH Inc. fremstiller og leverer både lette og tunge støbegods. Vi har leveret metalstøbegods og bearbejdede dele til kedler, varmevekslere, biler, mikromotorer, vindmøller, madpakkeudstyr og meget mere. Vi anbefaler, at du klikker her for at DOWNLOAD vores skematiske illustrationer af bearbejdnings- og støbeprocesser af AGS-TECH Inc. Dette vil hjælpe dig med bedre at forstå de oplysninger, vi giver dig nedenfor. Lad os se nærmere på nogle af de forskellige teknikker, vi tilbyder: • FORBRUGSTØBNING: Denne brede kategori refererer til metoder, der involverer midlertidige og ikke-genanvendelige forme. Eksempler er sand, gips, skal, investering (også kaldet lost-wax) og gipsstøbning. • SANDSTØBNING: En proces, hvor sand bruges som formmateriale. En meget gammel metode og stadig meget populær i det omfang, at størstedelen af metalstøbegods er fremstillet ved denne teknik. Lave omkostninger selv ved lave mængder produktion. Velegnet til fremstilling af små og store dele. Teknikken kan bruges til at fremstille dele inden for dage eller uger med meget lidt investering. Det fugtige sand bindes sammen med ler, bindemidler eller specialolier. Sand er generelt indeholdt i formkasser, og hulrums- og portsystem skabes ved at komprimere sandet omkring modeller. Processerne er: 1.) Anbringelse af modellen i sand for at lave formen 2.) Indbygning af model og sand i et portsystem 3.) Fjernelse af model 4.) Fyldning af formhulrum med smeltet metal 5.) Køling af metallet 6.) Brydning af sandformen og fjernelse af støbningen • GIPSSTØBNING: I lighed med sandstøbning, og i stedet for sand, bruges gips som formmateriale. Korte produktionstider som sandstøbning og billig. Gode dimensionstolerancer og overfladefinish. Dens største ulempe er, at den kun kan bruges med metaller med lavt smeltepunkt som aluminium og zink. • SKALSTØBNING: Ligner også til sandstøbning. Formhule opnået ved en hærdet skal af sand og termohærdende harpiksbindemiddel i stedet for en kolbe fyldt med sand som i sandstøbeprocessen. Næsten ethvert metal, der er egnet til at blive støbt med sand, kan støbes ved skalstøbning. Processen kan opsummeres som: 1.) Fremstilling af skalformen. Det anvendte sand har en meget mindre kornstørrelse sammenlignet med sand, der bruges til sandstøbning. Det fine sand blandes med termohærdende harpiks. Metalmønsteret er belagt med et skillemiddel for at gøre det nemmere at fjerne skallen. Derefter opvarmes metalmønsteret, og sandblandingen poreres eller blæses på det varme støbemønster. En tynd skal dannes på overfladen af mønsteret. Tykkelsen af denne skal kan justeres ved at variere, hvor lang tid sandharpiksblandingen er i kontakt med metalmønsteret. Det løse sand fjernes derefter med det skaldækkede mønster tilbage. 2.) Dernæst varmes skallen og mønsteret i en ovn, så skallen stivner. Efter hærdning er fuldført, skydes skallen ud af mønsteret ved hjælp af stifter indbygget i mønsteret. 3.) To sådanne skaller samles sammen ved limning eller fastspænding og udgør den komplette form. Nu lægges skalformen ind i en beholder, hvori den under støbeprocessen understøttes af sand eller metalskud. 4.) Nu kan det varme metal hældes i skalformen. Fordele ved skalstøbning er produkter med meget god overfladefinish, mulighed for fremstilling af komplekse dele med høj dimensionel nøjagtighed, proces let at automatisere, økonomisk til produktion af store mængder. Ulemperne er, at formene kræver god ventilation på grund af gasser, der dannes, når smeltet metal kommer i kontakt med bindemiddelkemikaliet, de termohærdende harpikser og metalmønstre er dyre. På grund af omkostningerne ved metalmønstre egner teknikken sig muligvis ikke godt til små produktionskørsler. • INVESTERINGSSTØBNING (også kendt som LOST-WAX CASTING): Også en meget gammel teknik og velegnet til fremstilling af kvalitetsdele med høj nøjagtighed, repeterbarhed, alsidighed og integritet fra mange metaller, ildfaste materialer og specielle højtydende legeringer. Små såvel som store dele kan fremstilles. En dyr proces sammenlignet med nogle af de andre metoder, men en stor fordel er muligheden for at producere dele med næsten netform, indviklede konturer og detaljer. Så omkostningerne er noget opvejet af eliminering af efterbearbejdning og bearbejdning i nogle tilfælde. Selvom der kan være variationer, er her en oversigt over den generelle investeringscastingproces: 1.) Oprettelse af originalt mastermønster fra voks eller plastik. Hver støbning har brug for et mønster, da disse ødelægges i processen. Form, hvorfra der fremstilles mønstre, er også nødvendig, og det meste af tiden er formen støbt eller bearbejdet. Fordi formen ikke skal åbnes, kan komplekse støbninger opnås, mange voksmønstre kan forbindes som grenene af et træ og hældes sammen, hvilket muliggør produktion af flere dele fra en enkelt udstøbning af metallet eller metallegeringen. 2.) Dernæst dyppes eller hældes mønsteret over med en ildfast opslæmning sammensat af meget finkornet silica, vand, bindemidler. Dette resulterer i et keramisk lag over overfladen af mønsteret. Det ildfaste lag på mønster efterlades til at tørre og hærde. Dette trin er, hvor navnet investeringsstøbning kommer fra: Ildfast gylle lægges over voksmønsteret. 3.) På dette trin vendes den hærdede keramiske form på hovedet og varmes op, så voksen smelter og hælder ud af formen. Der efterlades et hulrum til metalstøbningen. 4.) Efter at voksen er ude, opvarmes den keramiske form til endnu en højere temperatur, hvilket resulterer i forstærkning af formen. 5.) Metalstøbning hældes i den varme form, der fylder alle indviklede sektioner. 6.) Støbning får lov til at størkne 7.) Til sidst knækkes den keramiske form og fremstillede dele skæres fra træet. Her er et link til Investment Casting Plant Brochure • FORdampningsmønsterstøbning: Processen bruger et mønster lavet af et materiale såsom polystyrenskum, der vil fordampe, når varmt smeltet metal hældes i formen. Der er to typer af denne proces: LOST FOAM CASTING, som bruger ubundet sand, og FULL MOLD CASTING, der bruger bundet sand. Her er de generelle procestrin: 1.) Fremstil mønsteret af et materiale såsom polystyren. Når der skal fremstilles store mængder, støbes mønsteret. Hvis en del har en kompleks form, skal flere sektioner af et sådant skummateriale muligvis klæbes sammen for at danne mønsteret. Vi belægger ofte mønsteret med en ildfast masse for at skabe en god overfladefinish på støbningen. 2.) Mønsteret lægges derefter i formsand. 3.) Det smeltede metal hældes i formen, hvorved skummønsteret, dvs. polystyren i de fleste tilfælde, fordamper, når det strømmer gennem formhulen. 4.) Det smeltede metal efterlades i sandformen for at hærde. 5.) Efter at det er hærdet, fjerner vi støbningen. I nogle tilfælde kræver det produkt, vi fremstiller, en kerne i mønsteret. Ved fordampningsstøbning er det ikke nødvendigt at placere og sikre en kerne i formhulrummet. Teknikken er velegnet til fremstilling af meget komplekse geometrier, den kan let automatiseres til højvolumen produktion, og der er ingen skillelinjer i den støbte del. Den grundlæggende proces er enkel og økonomisk at implementere. For produktion af store mængder, da en matrice eller form er nødvendig for at fremstille mønstrene fra polystyren, kan dette være noget dyrt. • IKKE-EKSPANDERBAR FORMSTØBNING: Denne brede kategori refererer til metoder, hvor formen ikke skal reformeres efter hver produktionscyklus. Eksempler er permanent, matrice, kontinuerlig og centrifugalstøbning. Repeterbarhed opnås, og dele kan karakteriseres som NEAR NET SHAPE. • PERMANENT STØBNING : Genanvendelige forme fremstillet af metal bruges til flere støbninger. En permanent form kan generelt bruges i titusindvis af gange, før den bliver slidt. Tyngdekraft, gastryk eller vakuum bruges generelt til at fylde formen. Forme (også kaldet matrice) er generelt lavet af jern, stål, keramik eller andre metaller. Den generelle proces er: 1.) Bearbejd og lav formen. Det er almindeligt at bearbejde formen af to metalblokke, der passer sammen og kan åbnes og lukkes. Både delens funktioner såvel som portsystemet er generelt bearbejdet i støbeformen. 2.) De indvendige formoverflader er belagt med en opslæmning, der indeholder ildfaste materialer. Dette hjælper med at kontrollere varmestrømmen og fungerer som et smøremiddel for nem fjernelse af den støbte del. 3.) Dernæst lukkes de permanente formhalvdele, og formen opvarmes. 4.) Smeltet metal hældes i form og lades stille til størkning. 5.) Inden der sker meget afkøling, fjerner vi delen fra den permanente form ved hjælp af ejektorer, når formhalvdelene åbnes. Vi bruger ofte permanent formstøbning til lavsmeltende metaller som zink og aluminium. Til stålstøbegods bruger vi grafit som formmateriale. Nogle gange opnår vi komplekse geometrier ved hjælp af kerner i permanente forme. Fordele ved denne teknik er støbegods med gode mekaniske egenskaber opnået ved hurtig afkøling, ensartet egenskaber, god nøjagtighed og overfladefinish, lave afvisningsprocenter, mulighed for at automatisere processen og producere høje volumener økonomisk. Ulemperne er høje initiale opsætningsomkostninger, som gør den uegnet til lavvolumenoperationer, og begrænsninger på størrelsen af de fremstillede dele. • DISTØBNING: En matrice bearbejdes, og smeltet metal skubbes under højt tryk ind i formhulrum. Både ikke-jernholdige såvel som jernholdige trykstøbninger er mulige. Processen er velegnet til produktion af store mængder af små til mellemstore dele med detaljer, ekstremt tynde vægge, dimensionskonsistens og god overfladefinish. AGS-TECH Inc. er i stand til at fremstille vægtykkelser helt ned til 0,5 mm ved hjælp af denne teknik. Ligesom ved permanent formstøbning skal formen bestå af to halvdele, der kan åbne og lukke for at fjerne den producerede del. En trykstøbeform kan have flere hulrum for at muliggøre produktion af flere støbegods med hver cyklus. Trykstøbeforme er meget tunge og meget større end de dele, de producerer, og derfor også dyre. Vi reparerer og udskifter slidte matricer gratis for vores kunder, så længe de genbestiller deres dele hos os. Vores matricer har lang levetid i flere hundrede tusinde cyklusser. Her er de grundlæggende forenklede procestrin: 1.) Fremstilling af formen generelt af stål 2.) Form installeret på trykstøbemaskine 3.) Stemplet tvinger smeltet metal til at flyde i matricehulrummene og udfylder de indviklede funktioner og tynde vægge 4.) Efter fyldning af formen med det smeltede metal, lades støbegodset hærde under tryk 5.) Form åbnes og støbning fjernes ved hjælp af udkasterstifter. 6.) Nu smøres den tomme matrice igen og spændes fast til næste cyklus. Ved trykstøbning bruger vi hyppigt indsatsstøbning, hvor vi indarbejder en ekstra del i formen og støber metallet rundt om den. Efter størkning bliver disse dele en del af det støbte produkt. Fordele ved trykstøbning er delenes gode mekaniske egenskaber, mulighed for indviklede funktioner, fine detaljer og god overfladefinish, høje produktionshastigheder, nem automatisering. Ulemper er: Ikke særlig velegnet til lav volumen på grund af høje matrice- og udstyrsomkostninger, begrænsninger i forme, der kan støbes, små runde mærker på støbte dele som følge af kontakt med udkasterstifter, tynde metalglimt presset ud ved skillelinjen, behov for udluftninger langs skillelinjen mellem formen, nødvendigheden af at holde formtemperaturerne lave ved hjælp af vandcirkulation. • CENTRIFUGALSTØBNING: Smeltet metal hældes ind i midten af den roterende form ved rotationsaksen. Centrifugalkræfter kaster metallet mod periferien, og det lades størkne, mens formen bliver ved med at rotere. Både vandrette og lodrette akserotationer kan anvendes. Der kan støbes dele med runde indvendige overflader samt andre ikke-runde former. Processen kan opsummeres som: 1.) Smeltet metal hældes i centrifugalform. Metallet tvinges derefter til ydervæggene på grund af spinding af formen. 2.) Når formen roterer, hærder metalstøbningen Centrifugalstøbning er en velegnet teknik til produktion af hule cylindiriske dele som rør, intet behov for indløb, stigrør og portelementer, god overfladefinish og detaljerede funktioner, ingen krympningsproblemer, mulighed for at producere lange rør med meget store diametre, høj produktionskapacitet . • KONTINUERLIG STØBNING ( STRANDSTØBNING ): Bruges til at støbe en kontinuerlig længde af metal. Grundlæggende er det smeltede metal støbt ind i en todimensionel profil af formen, men dens længde er ubestemt. Nyt smeltet metal tilføres konstant i formen, efterhånden som støbegodset bevæger sig nedad med dets længde stigende med tiden. Metaller som kobber, stål, aluminium støbes til lange tråde ved hjælp af kontinuerlig støbeproces. Processen kan have forskellige konfigurationer, men den almindelige kan forenkles som: 1.) Smeltet metal hældes i en beholder placeret højt over støbeformen ved velberegnet mængder og strømningshastigheder og strømmer gennem den vandkølede støbeform. Metalstøbningen, der hældes i formen, størkner til en startstang placeret i bunden af formen. Denne startstang giver rullerne noget at tage fat i i starten. 2.) Den lange metalstreng bæres af ruller med konstant hastighed. Rullerne ændrer også retningen af strømmen af metalstreng fra lodret til vandret. 3.) Efter den kontinuerlige støbning har tilbagelagt en vis vandret afstand, skærer en brænder eller sav, der bevæger sig med støbningen, den hurtigt til de ønskede længder. Kontinuerlig støbeproces kan integreres med ROLLING PROCESS, hvor det kontinuerligt støbte metal kan føres direkte ind i et valseværk for at producere I-Beams, T-Beams….osv. Kontinuerlig støbning giver ensartede egenskaber i hele produktet, det har en høj størkningshastighed, reducerer omkostninger på grund af meget lavt materialetab, tilbyder en proces, hvor læsning af metal, støbning, størkning, skæring og støbefjernelse alt sammen foregår i en kontinuerlig drift og hvilket resulterer i høj produktivitet og høj kvalitet. En vigtig overvejelse er dog den høje initialinvestering, opsætningsomkostninger og pladsbehov. • BEARBEJDNINGSSERVICE: Vi tilbyder tre-, fire- og femakset bearbejdning. Den type bearbejdningsprocesser, vi bruger, er DREJNING, FRÆSNING, BORING, BORING, BRINGNING, HØVNING, SAVNING, SLIBNING, LAPPING, POLIERING og IKKE-TRADITIONEL BEARBEJDNING, som er yderligere uddybet under en anden menu på vores hjemmeside. Til det meste af vores produktion bruger vi CNC-maskiner. Men til nogle operationer passer konventionelle teknikker bedre, og derfor stoler vi også på dem. Vores bearbejdningsevner når det højest mulige niveau, og nogle af de mest krævende dele er fremstillet på et AS9100-certificeret anlæg. Jetmotorvinger kræver højt specialiseret fremstillingserfaring og det rigtige udstyr. Luftfartsindustrien har meget strenge standarder. Nogle komponenter med komplekse geometriske strukturer fremstilles nemmest ved femakset bearbejdning, som kun findes i nogle bearbejdningsanlæg, inklusive vores. Vores rumfartscertificerede anlæg har den nødvendige erfaring med at overholde omfattende dokumentationskrav fra luftfartsindustrien. Ved DREJE-operationer roteres et emne og bevæges mod et skæreværktøj. Til denne proces bruges en maskine kaldet drejebænk. I FRÆSNING har en maskine kaldet fræsemaskine et roterende værktøj til at bringe skærekanter til at ligge an mod et emne. BORING involverer en roterende fræser med skærekanter, der producerer huller ved kontakt med emnet. Borepresser, drejebænke eller møller anvendes generelt. Ved BORING-operationer flyttes et værktøj med en enkelt bøjet spids spids ind i et groft hul i et roterende emne for at forstørre hullet lidt og forbedre nøjagtigheden. Det bruges til fine efterbehandlingsformål. BRACHING involverer et fortandet værktøj til at fjerne materiale fra et emne i en gang af brochen (tandværktøj). Ved lineær brobning løber brochen lineært mod en overflade af emnet for at udføre snittet, hvorimod ved roterende brochning roteres brochen og presses ind i arbejdsemnet for at skære en aksesymmetrisk form. SWISS TYPE MACHINING er en af vores værdifulde teknikker, vi bruger til fremstilling af små højpræcisionsdele i store mængder. Ved at bruge drejebænk af schweizisk type drejer vi små, komplekse præcisionsdele billigt. I modsætning til konventionelle drejebænke, hvor emnet holdes stationært og værktøj i bevægelse, i drejecentre af schweizisk type, tillades emnet at bevæge sig i Z-aksen, og værktøjet er stationært. Ved bearbejdning af schweizisk type holdes stangen i maskinen og føres frem gennem en styrebøsning i z-aksen, hvilket blot blotlægger den del, der skal bearbejdes. På denne måde sikres et stramt greb, og nøjagtigheden er meget høj. Tilgængeligheden af levende værktøjer giver mulighed for at fræse og bore, efterhånden som materialet kommer frem fra styrebøsningen. Y-aksen i det schweiziske udstyr giver fuld fræsekapacitet og sparer meget tid i fremstillingen. Ydermere har vores maskiner bor og boreværktøj, der opererer på delen, når den holdes i underspindelen. Vores bearbejdningskapacitet af schweizisk type giver os en fuldautomatisk komplet bearbejdningsmulighed i en enkelt operation. Bearbejdning er et af de største segmenter af AGS-TECH Inc. forretning. Vi bruger det enten som en primær operation eller en sekundær operation efter støbning eller ekstrudering af en del, så alle tegningsspecifikationer overholdes. • OVERFLADEBEHANDLING: Vi tilbyder en bred vifte af overfladebehandlinger og overfladebehandling, såsom overfladebehandling for at forbedre vedhæftningen, aflejring af tyndt oxidlag for at forbedre vedhæftningen af belægningen, sandblæsning, kemisk film, anodisering, nitrering, pulverlakering, spraybelægning , forskellige avancerede metalliserings- og belægningsteknikker, herunder sputtering, elektronstråle, fordampning, plettering, hårde belægninger såsom diamantlignende kulstof (DLC) eller titaniumbelægning til bore- og skæreværktøjer. • PRODUKTMÆRKNING & ETIKETTERING: Mange af vores kunder kræver mærkning og mærkning, lasermærkning, gravering på metaldele. Hvis du har et sådant behov, så lad os diskutere, hvilken løsning der vil være den bedste for dig. Her er nogle af de mest brugte metalstøbte produkter. Da disse er hyldevare, kan du spare på formomkostningerne, hvis nogen af disse passer til dine krav: KLIK HER FOR AT DOWNLOAD vores 11 serie trykstøbte aluminiumskasser fra AGS-Electronics CLICK Product Finder-Locator Service FORRIGE SIDE
- Custom Manufactured Parts, Assemblies, Plastic Mold, Casting,Machining
Custom Manufactured Parts, Assemblies, Plastic Mold, Rubber Molding, Metal Casting, CNC Machining, Turning, Milling, Electrical Electronic Optical Assembly PCBA Specialfremstillede dele og samlinger og produkter Læs mere Plast- og gummiforme og støbning Læs mere Støbning og bearbejdning Læs mere Ekstruderinger, ekstruderede produkter Læs mere Stempler og metalpladefremstilling Læs mere Metalsmedning og pulvermetallurgi Læs mere Tråd- og fjederformning Læs mere Formning og formning af glas og keramik Læs mere Additiv og hurtig fremstilling Læs mere Fremstilling af kompositter og kompositmaterialer Læs mere Sammenføjning & montering & fastgørelsesprocesser Vi producerer dele og samlinger til dig og tilbyder følgende fremstillingsprocesser: • Plast- og gummiforme og støbte dele. Sprøjtestøbning, termoformning, termohærdende støbning, vakuumformning, blæsestøbning, rotationsstøbning, hældestøbning, indsatsstøbning og andre. • Ekstruderinger af plast, gummi og metal • Jernholdige og ikke-jernholdige støbegods og bearbejdede dele fremstillet ved fræse- og drejeteknikker, bearbejdning af schweizisk type. • Pulvermetallurgiske dele • Metal- og ikke-metalprægninger, metalpladeformning, svejste metalpladesamlinger • Kold og varm smedning • Tråde, svejsede trådsamlinger, trådformning • Forskellige typer fjedre, fjederformning • Gearfremstilling, gearkasse, kobling, snekke, hastighedsdæmper, cylinder, transmissionsremme, transmissionskæder, transmissionskomponenter • Skræddersyet hærdet og skudsikkert glas i overensstemmelse med NATO og militære standarder • Kugler, lejer, remskiver og remskiver • Ventiler og pneumatiske komponenter såsom O-ring, skive og tætninger • Glas og keramiske dele og samlinger, vakuumtætte og hermetiske komponenter, metal-keramik og keramik-keramik limning. • Forskellige typer af mekaniske, optomekaniske, elektromekaniske, optoelektroniske samlinger. • Metal-gummi, metal-plastik-binding • Rør og rør, rørformning, bukning og tilpassede rørsamlinger, bælgfremstilling. • Glasfiberfremstilling • Svejsning med forskellige teknikker såsom punktsvejsning, lasersvejsning, MIG, TIG. Ultralydssvejsning til plastdele. • Stort udvalg af overfladebehandlinger og overfladefinisher såsom overfladekonditionering for at forbedre vedhæftning, aflejring af tyndt oxidlag for at forbedre vedhæftning af belægning, sandblæsning, kemisk film, anodisering, nitrering, pulverlakering, spraybelægning, forskellige avancerede metalliserings- og belægningsteknikker inklusive sputtering, elektronstråle, fordampning, plettering, hårde belægninger såsom diamantlignende kulstof (DLC) eller titanium til skære- og boreværktøjer. • Mærkning og mærkning, lasermærkning på metaldele, print på plast- og gummidele Download brochure for almindelige maskintekniske termer, der bruges af designere og ingeniører Vi bygger produkter efter dine særlige specifikationer og krav. For at kunne tilbyde dig den bedste kvalitet, levering og priser fremstiller vi produkter globalt i Kina, Indien, Taiwan, Filippinerne, Sydkorea, Malaysia, Sri Lanka, Tyrkiet, USA, Canada, Tyskland, Storbritannien og Japan. Dette gør os meget stærkere og globalt mere konkurrencedygtige end nogen anden custom producent. Vores produkter er fremstillet i ISO9001:2000, QS9000, ISO14001, TS16949 certificerede miljøer og har CE, UL mærke og opfylder andre industristandarder. Når vi er udpeget til dit projekt, kan vi tage os af hele fremstilling, montage, test, kvalificering, forsendelse & told som du ønsker. Hvis du foretrækker det, kan vi oplagre dine dele, samle brugerdefinerede sæt, udskrive og mærke dit firmanavn og mærke og sende fragt til dine kunder. Med andre ord kan vi også være dit lager- og distributionscenter, hvis det foretrækkes. Da vores lagre er placeret i nærheden af større havne, giver det os logistiske fordele. For eksempel, når dine produkter ankommer til en større USA-havn, kan vi transportere det direkte til et nærliggende lager, hvor vi kan opbevare, samle, lave sæt, ommærke, printe, pakke efter dit valg og slippe. sende til dine kunder. Vi leverer ikke kun produkter. Vores virksomhed arbejder på tilpassede kontrakter, hvor vi kommer til dit websted, evaluerer dit projekt på stedet og udvikler et projektforslag, der er skræddersyet til dig. Vi sender derefter vores erfarne team til at gennemføre projektet. Mere information om vores ingeniørarbejde kan findes på http://www.ags-engineering.com -Vi tager små projekter såvel som store projekter i industriel skala. Som et første skridt kan vi forbinde dig enten via telefon, telekonference eller MSN messenger til vores ekspertteammedlemmer, så du kan kommunikere direkte til en ekspert, stille spørgsmål og diskutere dit projekt. Ring til os, og hvis nødvendigt kommer vi og besøger dig. FORRIGE SIDE