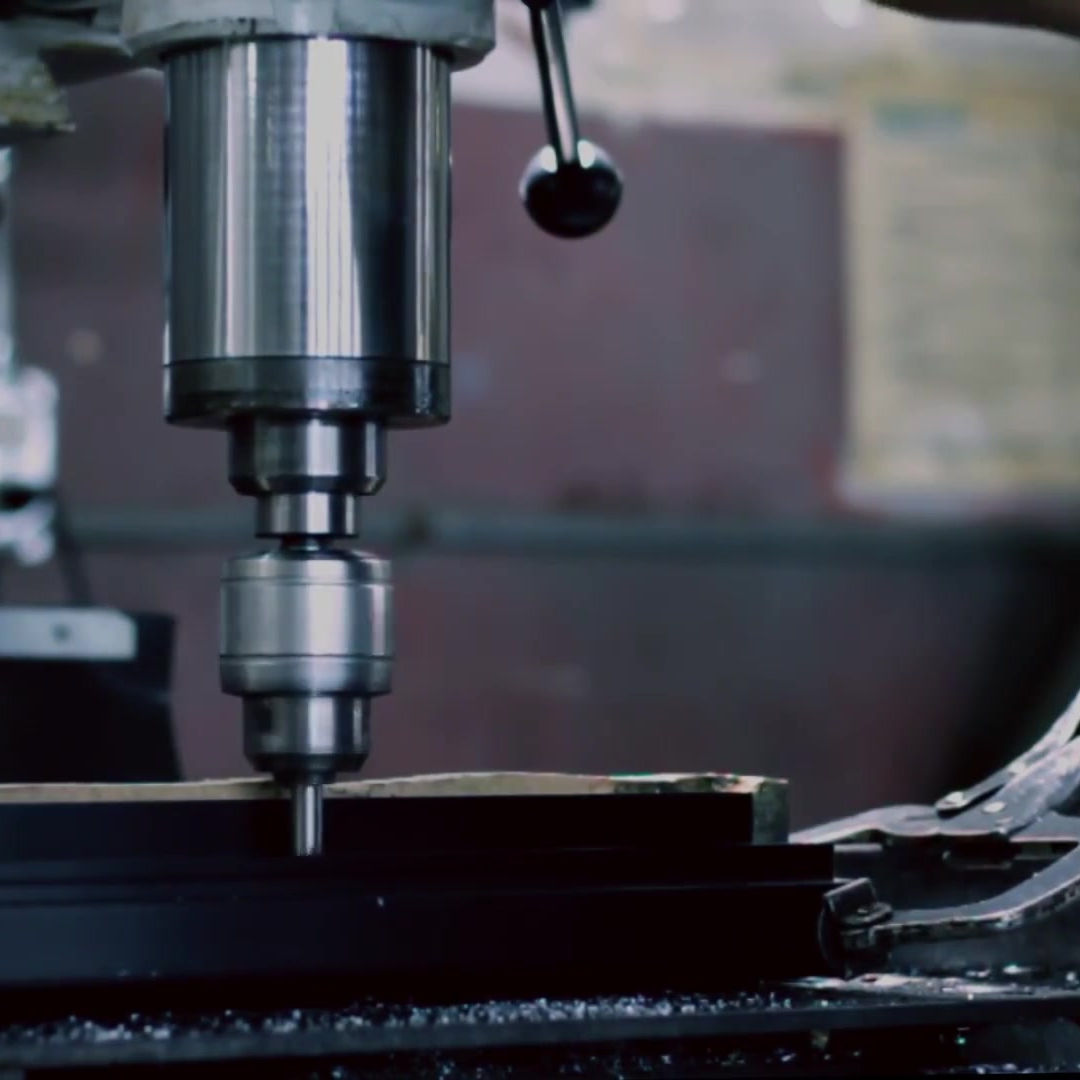
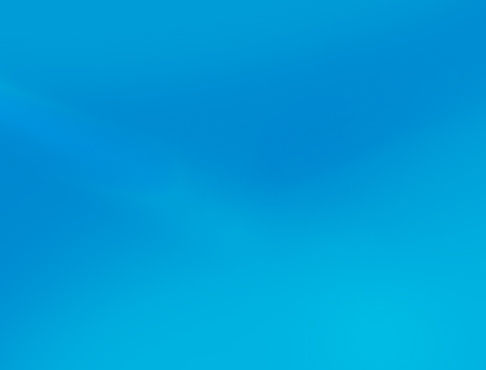
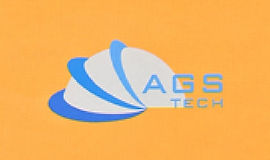
Global Custom Manufacturer, Integrator, Consolidator, Outsourcing Partner for a Wide Variety of Products & Services.
We are your one-stop source for manufacturing, fabrication, engineering, consolidation, integration, outsourcing of custom manufactured and off-shelf products & services. We also private label / white label your products with your brand name if you wish.
Choose your Language
-
Custom Manufacturing of Parts, Components, Assemblies, Finished Products, Machines and Industrial Equipment
-
Domestic & Global Contract Manufacturing
-
Manufacturing Outsourcing
-
Domestic, Global Procurement of Industrial Products
-
Private labeling / White Labeling your Products with your Brand Name
-
Product Finding & Locating Services
-
Global Design and Channel Partnership
-
Engineering Integration
-
Engineering Services
-
Global Consolidation, Warehousing, Logistics
Some of the valuable NON-CONVENTIONAL MANUFACTURING processes AGS-TECH Inc offers are ELECTROCHEMICAL MACHINING (ECM), SHAPED-TUBE ELECTROLYTIC MACHINING (STEM), PULSED ELECTROCHEMICAL MACHINING (PECM), ELECTROCHEMICAL GRINDING (ECG), HYBRID MACHINING PROCESSES.
ELECTROCHEMICAL MACHINING (ECM) is a non-conventional manufacturing technique where metal is removed by an electrochemical process. ECM is typically a mass production technique, used for machining extremely hard materials and materials that are difficult to machine using the conventional manufacturing methods. Electrochemical-machining systems we use for production are numerically controlled machining centers with high production rates, flexibility, perfect control of dimensional tolerances. Electrochemical machining is capable of cutting small and odd-shaped angles, intricate contours or cavities in hard and exotic metals like titanium aluminides, Inconel, Waspaloy, and high nickel, cobalt, and rhenium alloys. Both external and internal geometries can be machined. Modifications of the electrochemical machining process are used for operations like turning, facing, slotting, trepanning, profiling where the electrode becomes the cutting tool. The metal removal rate is only a function of ion exchange rate and is not affected by the strength, hardness or toughness of the workpiece. Unfortunately the method of electrochemical machining (ECM) is limited to electrically conductive materials. Another important point to consider deploying the ECM technique is to compare the mechanical properties of the produced parts with those produced by other machining methods.
ECM removes material instead of adding it and therefore is sometimes referred to as ''reverse electroplating''. It resembles in some ways to electrical discharge machining (EDM) in that a high current is passed between an electrode and the part, through an electrolytic material removal process having a negatively charged electrode (cathode), a conductive fluid (electrolyte), and a conductive workpiece (anode). The electrolyte acts as the current carrier and is a highly conductive inorganic salt solution like sodium chloride mixed and dissolved in water or sodium nitrate. The advantage of ECM is that there is no tool wear. The ECM cutting tool is guided along the desired path close to the work but without touching the piece. Unlike EDM, however, no sparks are created. High metal removal rates and mirror surface finishes are possible with ECM, with no thermal or mechanical stresses being transferred to the part. ECM does not cause any thermal damage to the part and since there are no tool forces there is no distortion to the part and no tool wear, as would be the case with typical machining operations. In electrochemical machining cavity produced is the female mating image of the tool.
In the ECM process, a cathode tool is moved into an anode workpiece. The shaped tool is generally made of copper, brass, bronze or stainless steel. The pressurized electrolyte is pumped at a high rate at a set temperature through the passages in the tool to the area being cut. The feed rate is the same as the rate of ''liquification'' of the material, and the electrolyte movement in the tool-workpiece gap washes metal ions away from the workpiece anode before they have a chance to plate onto the cathode tool. The gap between the tool and the workpiece varies between 80-800 micrometers and the DC power supply in the range 5 – 25 V maintains current densities between 1.5 – 8 A/mm2 of active machined surface. As electrons cross the gap, material from the workpiece is dissolved, as the tool forms the desired shape in the workpiece. The electrolytic fluid carries away the metal hydroxide formed during this process. Commercial electrochemical machines with current capacities between 5A and 40,000A are available. The material removal rate in electrochemical machining can be expressed as:
MRR = C x I x n
Here MRR=mm3/min, I=current in amperes, n=current efficiency, C=a material constant in mm3/A-min. The constant C depends on valence for pure materials. The higher the valence, the lower is its value. For most metals it is in between 1 and 2.
If Ao denotes the uniform cross-sectional area being electrochemically machined in mm2, the feed rate f in mm/min can be expressed as:
F = MRR / Ao
Feed rate f is the speed the electrode is penetrating the workpiece.
In the past there were problems of poor dimensional accuracy and environmentally polluting waste from electrochemical machining operations. These have largely been overcome.
Some of the applications of electrochemical machining of high-strength materials are:
- Die-Sinking operations. Die-sinking is machining forging – die cavities.
- Drilling a jet engine turbine blades, jet-engine parts and nozzles.
- Multiple small holes drilling. The electrochemical machining process leaves a burr-free surface.
- Steam turbine blades can be machined within close limits.
- For deburring of surfaces. In deburring, ECM removes metal projections left from the machining processes and so dulls sharp edges. Electrochemical machining process is fast and often more convenient than the conventional methods of deburring by hand or non-traditional machining processes.
SHAPED-TUBE ELECTROLYTIC MACHINING (STEM) is a version of electrochemical machining process we use for drilling small diameter deep holes. A titanium tube is used as the tool which is coated with an electrically insulating resin to prevent the removal of material from other regions like the lateral faces of the hole and tube. We can drill hole sizes of 0.5 mm with depth-to-diameter ratios of 300:1
PULSED ELECTROCHEMICAL MACHINING (PECM): We use very high pulsed current densities in the order of 100 A/cm2. By using pulsed currents we eliminate the need for high electrolyte flow rates which poses limitations for the ECM method in mold and die fabrication. Pulsed electrochemical machining improves fatigue life and eliminates the recast layer left by the electrical discharge machining (EDM) technique on mold and die surfaces.
In ELECTROCHEMICAL GRINDING (ECG) we combine the conventional grinding operation with electrochemical machining. The grinding wheel is a rotating cathode with abrasive particles of diamond or aluminum oxide that are metal bonded. The current densities range between 1 and 3 A/mm2. Similar to ECM, an electrolyte such as sodium nitrate flows and the metal removal in electrochemical grinding is dominated by the electrolytic action. Less than 5% of metal removal is by abrasive action of the wheel. The ECG technique is well suited for carbides and high-strength alloys, but not so much of a fit for die-sinking or mould making because the grinder may not easily access deep cavities. The material removal rate in electrochemical grinding can be expressed as:
MRR = G I / d F
Here MRR is in mm3/min, G is mass in grams, I is current in amperes, d is density in g/mm3 and F is Faraday’s constant (96,485 Coulombs/mole). The speed of penetration of the grinding wheel into workpiece can be expressed as:
Vs = (G / d F) x (E / g Kp) x K
Here Vs is in mm3/min, E is cell voltage in volts, g is wheel to workpiece gap in mm, Kp is coefficient of loss and K is electrolyte conductivity. The advantage of the electrochemical grinding method over conventional grinding is less wheel wear because less than 5% of the metal removal is by abrasive action of the wheel.
There are similarities between EDM and ECM:
1. The tool and workpiece are separated by a very small gap without a contact in between them.
2. Both tool and material must be conductors of electricity.
3. Both techniques need high capital investment. Modern CNC machines are used
4. Both methods consume lots of electric power.
5. A conductive fluid is used as a medium between the tool and the work piece for ECM and a dielectric fluid for EDM.
6. The tool is fed continuously towards the workpiece to maintain a constant gap between them (EDM may incorporate intermittent or cyclic, typically partial, tool withdrawal).
HYBRID MACHINING PROCESSES: We frequently take advantage of the benefits of hybrid machining processes where two or more different processes such as ECM, EDM….etc. are used in combination. This gives us the opportunity to overcome the shortcomings of one process by the other, and benefit from the advantages of each process.