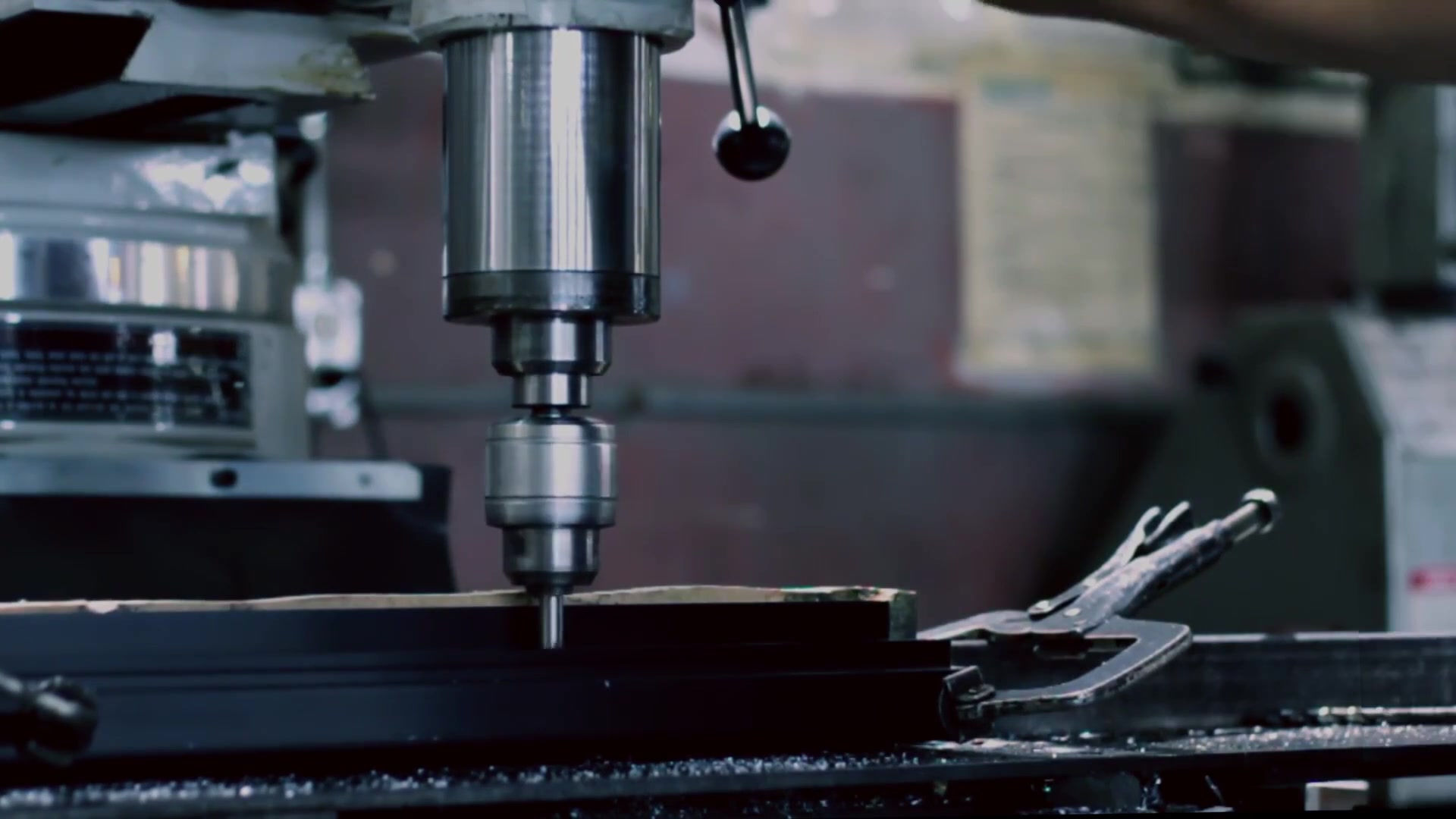
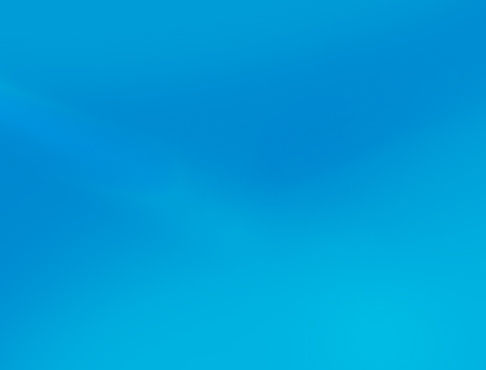
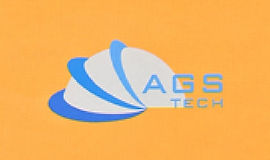
Παγκόσμιος Custom Manufacturer, Integrator, Consolidator, Outsourcing Partner για μια μεγάλη ποικιλία προϊόντων και υπηρεσιών.
Είμαστε η μοναδική σας πηγή για την κατασκευή, την κατασκευή, τη μηχανική, την ενοποίηση, την ενοποίηση, την εξωτερική ανάθεση προϊόντων και υπηρεσιών που κατασκευάζονται κατά παραγγελία και εκτός ραφιού.
Επιλέξτε τη γλώσσα σας
-
Προσαρμοσμένη Κατασκευή
-
Εγχώρια & Παγκόσμια Συμβολαιακή Κατασκευή
-
Εξωτερική ανάθεση της παραγωγής
-
Εγχώριες & Παγκόσμια Προμήθειες
-
Consolidation
-
Engineering Integration
-
Υπηρεσίες Μηχανικών
Search Results
Βρέθηκαν 164 αποτελέσματα με κενή αναζήτηση
- Transmission Components, Belts, Chains, Cable Drives, Pulleys,AGS-TECH
Transmission Components, Belts, Chains and Cable Drives, Conventional & Grooved or Serrated, Positive Drive, Pulleys Ιμάντες & αλυσίδες & Συγκρότημα κίνησης καλωδίων Η AGS-TECH Inc. σας προσφέρει εξαρτήματα μετάδοσης ισχύος, όπως Ζώνες & Αλυσίδες & Συγκρότημα κίνησης καλωδίων. Με χρόνια τελειοποίησης, οι ιμάντες μας από καουτσούκ, δέρμα και άλλους ιμάντες έχουν γίνει ελαφρύτεροι και πιο συμπαγείς, ικανοί να μεταφέρουν υψηλότερα φορτία με χαμηλότερο κόστος. Ομοίως, οι αλυσίδες μας έχουν εξελιχθεί πολύ με την πάροδο του χρόνου και προσφέρουν στους πελάτες μας πολλά πλεονεκτήματα. Μερικά πλεονεκτήματα της χρήσης αλυσίδων μετάδοσης κίνησης είναι οι σχετικά απεριόριστες αποστάσεις στο κέντρο του άξονα, η συμπαγής, η ευκολία συναρμολόγησης, η ελαστικότητα στην τάση χωρίς ολίσθηση ή ερπυσμός, η ικανότητα λειτουργίας σε περιβάλλοντα υψηλής θερμοκρασίας. Οι μονάδες καλωδίων μας προσφέρουν επίσης πλεονεκτήματα όπως η απλότητα σε ορισμένες εφαρμογές έναντι άλλων τύπων εξαρτημάτων μετάδοσης. Διατίθενται τόσο ιμάντας εκτός ραφιού, κινητήρες αλυσίδας και καλωδίων, καθώς και προσαρμοσμένες κατασκευασμένες και συναρμολογημένες εκδόσεις. Μπορούμε να κατασκευάσουμε αυτά τα εξαρτήματα μετάδοσης στο σωστό μέγεθος για την εφαρμογή σας και από τα πιο κατάλληλα υλικά. BELTS & BELT DRIVES: - Συμβατικές επίπεδες ζώνες: Πρόκειται για απλές επίπεδες ζώνες χωρίς δόντια, αυλακώσεις ή οδοντώσεις. Οι επίπεδοι ιμάντες κίνησης προσφέρουν ευελιξία, καλή απορρόφηση κραδασμών, αποτελεσματική μετάδοση ισχύος σε υψηλές ταχύτητες, αντοχή στην τριβή, χαμηλό κόστος. Οι ζώνες μπορούν να συνδεθούν ή να συνδεθούν για να φτιάξουν μεγαλύτερες ζώνες. Άλλα πλεονεκτήματα των συμβατικών επίπεδων ιμάντων είναι ότι είναι λεπτές, δεν υπόκεινται σε υψηλά φυγόκεντρα φορτία (τους καθιστά κατάλληλους για λειτουργίες υψηλής ταχύτητας με μικρές τροχαλίες). Από την άλλη πλευρά επιβάλλουν υψηλά φέροντα φορτία επειδή οι επίπεδες ζώνες απαιτούν υψηλή τάση. Άλλα μειονεκτήματα των επίπεδων ιμάντων μετάδοσης κίνησης μπορεί να είναι η ολίσθηση, η θορυβώδης λειτουργία και η σχετικά χαμηλότερη απόδοση σε χαμηλές και μέτριες ταχύτητες λειτουργίας. Έχουμε δύο τύπους συμβατικών ζωνών: Ενισχυμένους και Μη Ενισχυμένους. Οι ενισχυμένοι ιμάντες έχουν ένα ελαστικό μέλος στη δομή τους. Οι συμβατικές επίπεδες ζώνες είναι διαθέσιμες ως δέρμα, ύφασμα ή κορδόνι από καουτσούκ, μη ενισχυμένο καουτσούκ ή πλαστικό, ύφασμα, ενισχυμένο δέρμα. Οι δερμάτινες ζώνες προσφέρουν μεγάλη διάρκεια ζωής, ευελιξία, εξαιρετικό συντελεστή τριβής, εύκολη επισκευή. Ωστόσο, οι δερμάτινες ζώνες είναι σχετικά ακριβές, χρειάζονται ντύσιμο και καθάρισμα και ανάλογα με την ατμόσφαιρα μπορεί να συρρικνωθούν ή να τεντωθούν. Οι ζώνες από ελαστικό ύφασμα ή κορδόνι είναι ανθεκτικές στην υγρασία, τα οξέα και τα αλκάλια. Οι υφασμάτινες ζώνες από καουτσούκ αποτελούνται από στρώματα βαμβακιού ή συνθετικής πάπιας εμποτισμένες με καουτσούκ και είναι οι πιο οικονομικές. Οι ζώνες από καουτσούκ αποτελούνται από μια σειρά από στρώσεις κορδονιών εμποτισμένων με καουτσούκ. Οι ζώνες καλωδίων από καουτσούκ προσφέρουν υψηλή αντοχή σε εφελκυσμό και μέτριο μέγεθος και μάζα. Οι μη ενισχυμένοι ιμάντες από καουτσούκ ή πλαστικοί είναι κατάλληλοι για εφαρμογές ελαφριάς χρήσης και χαμηλής ταχύτητας. Οι μη ενισχυμένοι ιμάντες από καουτσούκ και πλαστικές μπορούν να τεντωθούν στη θέση τους πάνω από τις τροχαλίες τους. Οι πλαστικοί μη ενισχυμένοι ιμάντες μπορούν να μεταδώσουν μεγαλύτερη ισχύ σε σύγκριση με τους ιμάντες από καουτσούκ. Οι ενισχυμένες δερμάτινες ζώνες αποτελούνται από ένα πλαστικό εφελκυστικό μέλος που βρίσκεται μεταξύ των δερμάτινων στρωμάτων επάνω και κάτω. Τέλος, οι υφασμάτινες ζώνες μας μπορεί να αποτελούνται από ένα μόνο κομμάτι βαμβάκι ή πάπιας διπλωμένο και ραμμένο με σειρές διαμήκεις βελονιές. Οι υφασμάτινες ζώνες μπορούν να παρακολουθούν ομοιόμορφα και να λειτουργούν με υψηλή ταχύτητα. - Ιμάντες με αυλακώσεις ή οδοντώσεις (όπως οι ιμάντες V): Πρόκειται για βασικούς επίπεδους ιμάντες που τροποποιήθηκαν για να παρέχουν τα πλεονεκτήματα ενός άλλου τύπου προϊόντος μετάδοσης. Πρόκειται για επίπεδες ζώνες με διαμήκη ραβδωτή κάτω πλευρά. Οι ιμάντες Poly-V είναι διαμήκης αυλακωμένος ή οδοντωτός επίπεδος ιμάντας με τμήμα εφελκυσμού και μια σειρά από παρακείμενες αυλακώσεις σε σχήμα V για σκοπούς παρακολούθησης και συμπίεσης. Η χωρητικότητα ισχύος εξαρτάται από το πλάτος του ιμάντα. Ο ιμάντας V είναι ο βασικός άξονας της βιομηχανίας και διατίθεται σε μια ποικιλία τυποποιημένων μεγεθών και τύπων για μετάδοση σχεδόν οποιασδήποτε ισχύος φορτίου. Οι ιμάντες V λειτουργούν καλά μεταξύ 1500 και 6000 πόδια/λεπτό, ωστόσο οι στενοί ιμάντες θα λειτουργούν έως και 10.000 πόδια/λεπτό. Οι μηχανισμοί κίνησης ιμάντα V προσφέρουν μεγάλη διάρκεια ζωής, όπως 3 έως 5 χρόνια και επιτρέπουν μεγάλες αναλογίες ταχύτητας, είναι εύκολο να εγκατασταθούν και να αφαιρεθούν, προσφέρουν αθόρυβη λειτουργία, χαμηλή συντήρηση, καλή απορρόφηση κραδασμών μεταξύ του οδηγού ιμάντα και των κινητήριων αξόνων. Το μειονέκτημα των ιμάντων V είναι η βέβαιη ολίσθηση και ερπυσμός τους και επομένως μπορεί να μην είναι η καλύτερη λύση όπου απαιτούνται σύγχρονες ταχύτητες. Διαθέτουμε βιομηχανικές, αυτοκινητοβιομηχανίες και αγροτικές ζώνες. Διατίθενται κανονικά μήκη καθώς και προσαρμοσμένα μήκη ζωνών. Όλες οι τυπικές διατομές ιμάντα V διατίθενται από το απόθεμα. Υπάρχουν πίνακες στους οποίους μπορείτε να υπολογίσετε άγνωστες παραμέτρους όπως μήκος ιμάντα, διατομή ιμάντα (πλάτος & πάχος) υπό την προϋπόθεση ότι γνωρίζετε ορισμένες παραμέτρους του συστήματός σας όπως οι διάμετροι τροχαλίας κίνησης και κίνησης, η κεντρική απόσταση μεταξύ των τροχαλιών και οι ταχύτητες περιστροφής των τροχαλιών. Μπορείτε να χρησιμοποιήσετε τέτοιους πίνακες ή να μας ζητήσετε να επιλέξουμε τον κατάλληλο ιμάντα V για εσάς. - Θετικοί ιμάντες μετάδοσης κίνησης (ιμάντας χρονισμού): Αυτοί οι ιμάντες είναι επίσης επίπεδοι με μια σειρά από ομοιόμορφα τοποθετημένα δόντια στην εσωτερική περιφέρεια. Οι θετικοί ιμάντες μετάδοσης κίνησης ή χρονισμού συνδυάζουν τα πλεονεκτήματα των επίπεδων ιμάντων με τα χαρακτηριστικά θετικής πρόσφυσης των αλυσίδων και των γραναζιών. Οι θετικοί ιμάντες κίνησης δεν αποκαλύπτουν ολίσθηση ή διακυμάνσεις ταχύτητας. Είναι δυνατό ένα ευρύ φάσμα αναλογιών ταχύτητας. Τα φέροντα φορτία είναι χαμηλά επειδή μπορούν να λειτουργήσουν με χαμηλή τάση. Ωστόσο, είναι πιο ευαίσθητα σε κακές ευθυγραμμίσεις στις τροχαλίες. - Τροχαλίες, τροχαλίες, πλήμνες για ιμάντες: Διαφορετικοί τύποι τροχαλιών χρησιμοποιούνται με επίπεδους, ραβδωτούς (οδοντωτούς) και θετικούς ιμάντες κίνησης. Τα κατασκευάζουμε όλα. Οι περισσότερες από τις επίπεδες τροχαλίες μας με ιμάντα κατασκευάζονται από χύτευση σιδήρου, αλλά οι εκδόσεις από χάλυβα είναι επίσης διαθέσιμες σε διάφορους συνδυασμούς στεφάνης και πλήμνης. Οι τροχαλίες μας με επίπεδο ιμάντα μπορεί να έχουν συμπαγείς, ακτινωτές ή σπαστές πλήμνες ή μπορούμε να τις κατασκευάσουμε όπως εσείς επιθυμείτε. Οι ιμάντες με ραβδώσεις και θετική κίνηση διατίθενται σε διάφορα μεγέθη και πλάτη στοκ. Τουλάχιστον μία τροχαλία στους μηχανισμούς μετάδοσης κίνησης ιμάντα χρονισμού πρέπει να είναι φλαντζωτή για να διατηρείται ο ιμάντας στον κινητήρα. Για μεγάλα συστήματα κεντρικής μετάδοσης κίνησης, συνιστάται να έχετε και τις δύο τροχαλίες με φλάντζα. Τα στάχυα είναι οι αυλακωτοί τροχοί των τροχαλιών και γενικά κατασκευάζονται με χύτευση σιδήρου, χάλυβα ή πλαστική χύτευση. Η μορφοποίηση χάλυβα είναι κατάλληλη διαδικασία για την κατασκευή τροχαλιών αυτοκινήτων και γεωργικών προϊόντων. Παράγουμε στάχυα με κανονικές και βαθιές αυλακώσεις. Οι τροχαλίες με βαθιές αυλακώσεις είναι κατάλληλες όταν ο ιμάντας V εισέρχεται στην τροχαλία υπό γωνία, όπως συμβαίνει στις μηχανές κίνησης τετάρτων. Οι βαθιές αυλακώσεις είναι επίσης κατάλληλες για μετάδοση κίνησης κάθετου άξονα και εφαρμογές όπου η δόνηση των ιμάντων μπορεί να είναι πρόβλημα. Οι αδρανείς τροχαλίες μας είναι αυλακωτές τροχαλίες ή επίπεδες τροχαλίες που δεν εξυπηρετούν τη μετάδοση μηχανικής ισχύος. Οι τροχαλίες ρελαντί χρησιμοποιούνται κυρίως για το σφίξιμο των ζωνών. - Μονοί και πολλαπλοί ιμάντες κίνησης: Οι μηχανισμοί κίνησης με έναν ιμάντα έχουν ένα μόνο αυλάκι ενώ οι πολλαπλοί ιμάντες κίνησης έχουν πολλαπλές αυλακώσεις. Κάνοντας κλικ στο σχετικό έγχρωμο κείμενο παρακάτω μπορείτε να κατεβάσετε τους καταλόγους μας: - Ζώνες μετάδοσης ισχύος (περιλαμβάνονται ιμάντες V, ιμάντες χρονισμού, ιμάντες ακατέργαστων άκρων, τυλιγμένοι ιμάντες και ειδικοί ιμάντες) - Μεταφορικές Ιμάντες - Τροχαλίες V - Τροχαλίες χρονισμού ΑΛΥΣΙΔΕΣ & ΑΛΥΣΙΔΕΣ: Οι αλυσίδες μας μετάδοσης ισχύος έχουν ορισμένα πλεονεκτήματα, όπως σχετικά απεριόριστες αποστάσεις στο κέντρο του άξονα, εύκολη συναρμολόγηση, συμπαγή, ελαστικότητα υπό τάση χωρίς ολίσθηση ή ερπυσμό, ικανότητα λειτουργίας σε υψηλές θερμοκρασίες. Εδώ είναι οι κύριοι τύποι των αλυσίδων μας: - Αποσπώμενες αλυσίδες: Οι αποσπώμενες αλυσίδες μας κατασκευάζονται σε μια σειρά μεγεθών, βήματος και απόλυτης αντοχής και γενικά από ελατό σίδηρο ή χάλυβα. Οι εύπλαστες αλυσίδες κατασκευάζονται σε μια σειρά μεγεθών από 0,902 (23 mm) έως 4,063 ίντσες (103 mm) βήμα και τελική αντοχή από 700 έως 17.000 λίβρες/τετραγωνική ίντσα. Οι αποσπώμενες χαλύβδινες αλυσίδες μας από την άλλη πλευρά κατασκευάζονται σε μεγέθη από 0,904 ίντσες (23 mm) έως περίπου 3,00 ίντσες (76 mm) σε βήμα, με απόλυτη αντοχή από 760 έως 5000 λίβρες/τετραγωνική ίντσα._cc781905-5cde-3194-bb3- 136bad5cf58d_ - Αλυσίδες Pintle: Αυτές οι αλυσίδες χρησιμοποιούνται για βαρύτερα φορτία και ελαφρώς υψηλότερες ταχύτητες σε περίπου 450 πόδια/λεπτό (2,2 m/sec). Οι αλυσίδες pintle είναι κατασκευασμένες από μεμονωμένους χυτούς συνδέσμους που έχουν πλήρες, στρογγυλό άκρο κάννης με πλευρικές ράβδους μετατόπισης. Αυτοί οι σύνδεσμοι αλυσίδας συνδέονται με χαλύβδινους πείρους. Αυτές οι αλυσίδες κυμαίνονται στο βήμα από περίπου 1,00 ίντσα (25 mm) έως 6,00 ίντσες (150 mm) και τελικές αντοχές μεταξύ 3600 και 30.000 λίβρες/τετραγωνική ίντσα. - Αλυσίδες Offset-Sidebar: Είναι δημοφιλείς σε αλυσίδες μετάδοσης κίνησης μηχανημάτων κατασκευής. Αυτές οι αλυσίδες λειτουργούν με ταχύτητες έως 1000 πόδια/λεπτό και μεταδίδουν φορτία σε περίπου 250 ίππους. Γενικά, κάθε σύνδεσμος έχει δύο πλευρικές ράβδους μετατόπισης, έναν δακτύλιο, έναν κύλινδρο, έναν πείρο, έναν πείρο κοτσαδόρου. - Αλυσίδες κυλίνδρων: Διατίθενται σε γήπεδα από 0,25 (6 mm) έως 3,00 (75 mm) ίντσες. Η απόλυτη αντοχή των αλυσίδων κυλίνδρων μονού πλάτους κυμαίνεται μεταξύ 925 και 130.000 λίβρες/τετραγωνική ίντσα. Υπάρχουν διαθέσιμες εκδόσεις πολλαπλού πλάτους αλυσίδων κυλίνδρων και μεταδίδουν μεγαλύτερη ισχύ σε υψηλότερες ταχύτητες. Οι αλυσίδες κυλίνδρων πολλαπλού πλάτους προσφέρουν επίσης πιο ομαλή δράση με μειωμένο θόρυβο. Οι αλυσίδες κυλίνδρων συναρμολογούνται από συνδέσμους κυλίνδρων και συνδέσμους πείρων. Οι καρφίτσες Cotter χρησιμοποιούνται σε αποσπώμενες αλυσίδες κυλίνδρων έκδοσης. Ο σχεδιασμός των μηχανισμών κίνησης αλυσίδας κυλίνδρων απαιτεί εξειδίκευση στο θέμα. Ενώ οι ιμάντες κίνησης βασίζονται σε γραμμικές ταχύτητες, οι μηχανισμοί μετάδοσης κίνησης αλυσίδας βασίζονται στην ταχύτητα περιστροφής του μικρότερου οδοντωτού τροχού, ο οποίος στις περισσότερες εγκαταστάσεις είναι το κινούμενο μέλος. Εκτός από τις βαθμολογίες ιπποδύναμης και την ταχύτητα περιστροφής, η σχεδίαση των αλυσίδων μετάδοσης κίνησης βασίζεται σε πολλούς άλλους παράγοντες. - Αλυσίδες διπλού βήματος: Βασικά το ίδιο με τις αλυσίδες κυλίνδρων εκτός από το ότι το βήμα είναι διπλάσιο. - Αντεστραμμένες οδοντωτές (αθόρυβες) αλυσίδες: Αλυσίδες υψηλής ταχύτητας που χρησιμοποιούνται ως επί το πλείστον για κινητήρες κινητήριας δύναμης, μηχανές απογείωσης. Οι ανεστραμμένες οδοντώσεις αλυσίδας δοντιών μπορούν να μεταδώσουν ισχύ έως και 1200 ίππους και αποτελούνται από μια σειρά οδοντωτών συνδέσμων, εναλλάξ συναρμολογημένων είτε με ακίδες είτε με συνδυασμό εξαρτημάτων αρθρώσεων. Η αλυσίδα του κέντρου-οδηγού έχει συνδέσμους-οδηγούς για την εμπλοκή των αυλακώσεων στον οδοντωτό τροχό και η πλευρική αλυσίδα-οδηγός έχει οδηγούς για την εμπλοκή των πλευρών του οδοντωτού τροχού. - Αλυσίδες με σφαιρίδια ή ολισθητήρες: Αυτές οι αλυσίδες χρησιμοποιούνται για κινήσεις αργής ταχύτητας και επίσης σε χειροκίνητες λειτουργίες. Κάνοντας κλικ στο σχετικό έγχρωμο κείμενο παρακάτω μπορείτε να κατεβάσετε τους καταλόγους μας: - Αλυσίδες οδήγησης - Μεταφορικές Αλυσίδες - Αλυσίδες Μεταφορέων Μεγάλης Βήμας - Αλυσίδες κυλίνδρων από ανοξείδωτο χάλυβα - Αλυσίδες ανύψωσης - Αλυσίδες μοτοσυκλετών - Αλυσίδες Γεωργικών Μηχανών - Γρανάζια: Τα στάνταρ γρανάζια μας συμμορφώνονται με τα πρότυπα ANSI. Οι οδοντωτοί τροχοί πλάκας είναι επίπεδοι, χωρίς κύβους. Οι μικρού και μεσαίου μεγέθους οδοντωτοί τροχοί πλήμνης μας μετατρέπονται από υλικό ράβδου ή σφυρηλάτηση ή κατασκευάζονται με συγκόλληση μιας πλήμνης ράβδου σε μια πλάκα θερμής έλασης. Η AGS-TECH Inc. μπορεί να προμηθεύει οδοντωτούς τροχούς κατεργασμένους από χύτευση γκρίζου σιδήρου, χυτοσίδηρο και συγκολλημένες κατασκευές πλήμνης, συντηγμένο μέταλλο σε σκόνη, χυτευμένα ή επεξεργασμένα πλαστικά. Για ομαλή λειτουργία σε υψηλές ταχύτητες, η σωστή επιλογή του μεγέθους των αλυσοτροχών είναι απαραίτητη. Οι περιορισμοί χώρου είναι φυσικά ένας παράγοντας που δεν μπορούμε να αγνοήσουμε όταν επιλέγουμε ένα γρανάζι. Συνιστάται η αναλογία οδηγού προς κινούμενους αλυσοτροχούς να μην είναι μεγαλύτερη από 6:1 και το περιτύλιγμα της αλυσίδας στον οδηγό να είναι 120 μοίρες. Οι κεντρικές αποστάσεις μεταξύ των μικρότερων και μεγαλύτερων γραναζιών, τα μήκη της αλυσίδας και η τάση της αλυσίδας πρέπει επίσης να επιλέγονται σύμφωνα με ορισμένους συνιστώμενους υπολογισμούς και οδηγίες μηχανικής και όχι τυχαία. Κατεβάστε τους καταλόγους μας κάνοντας κλικ στο έγχρωμο κείμενο παρακάτω: - Γρανάζια και Ρόδες - Δοχεία μετάδοσης - Σύζευξη αλυσίδας - Κλειδαριές με αλυσίδα ΚΙΝΗΤΟΠΟΙΗΣΕΙΣ ΚΑΛΩΔΙΩΝ: Αυτά έχουν τα πλεονεκτήματά τους έναντι των ιμάντων και των μηχανισμών κίνησης αλυσίδας σε ορισμένες περιπτώσεις. Οι ηλεκτροκινητήρες καλωδίων μπορούν να επιτελέσουν την ίδια λειτουργία με τους ιμάντες και μπορεί επίσης να είναι απλούστερες και πιο οικονομικές στην εφαρμογή σε ορισμένες εφαρμογές. Για παράδειγμα, μια νέα σειρά οδηγών καλωδίων Synchromesh έχει σχεδιαστεί για θετική πρόσφυση για να αντικαταστήσει τα συμβατικά σχοινιά, τα απλά καλώδια και τους οδοντωτούς οδηγούς, ειδικά σε στενούς χώρους. Η νέα μονάδα καλωδίου έχει σχεδιαστεί για να παρέχει τοποθέτηση υψηλής ακρίβειας σε ηλεκτρονικό εξοπλισμό όπως φωτοαντιγραφικά μηχανήματα, plotters, γραφομηχανές, εκτυπωτές,….. κ.λπ. εξαιρετικά μικροσκοπικά σχέδια. Τα καλώδια Synchromesh μπορούν να χρησιμοποιηθούν με χαμηλότερη τάση σε σύγκριση με τα σχοινιά, μειώνοντας έτσι την κατανάλωση ενέργειας. Επικοινωνήστε με την AGS-TECH για ερωτήσεις και γνώμη σχετικά με ιμάντες, αλυσίδες και συρματόσχοινα. CLICK Product Finder-Locator Service ΠΡΟΗΓΟΥΜΕΝΗ ΣΕΛΙΔΑ
- Joining & Assembly & Fastening Processes, Welding, Brazing, Soldering
Joining & Assembly & Fastening Processes, Welding, Brazing, Soldering, Sintering, Adhesive Bonding, Press Fitting, Wave and Reflow Solder Process, Torch Furnace Διαδικασίες Σύνδεσης & Συναρμολόγησης & Στερέωσης Ενώνουμε, συναρμολογούμε και στερεώνουμε τα κατασκευασμένα εξαρτήματά σας και τα μετατρέπουμε σε έτοιμα ή ημικατεργασμένα προϊόντα χρησιμοποιώντας ΣΥΓΚΟΛΛΗΣΗ, BRAZING, SOLDERING, SINTERING, KOLLING BONDING, FESTENING, PESS FITTING. Μερικές από τις πιο δημοφιλείς διαδικασίες συγκόλλησης είναι τόξο, οξυκαύσιμο αέριο, αντίσταση, προβολή, ραφή, ανατροπή, κρούση, στερεά κατάσταση, δέσμη ηλεκτρονίων, λέιζερ, θερμίτης, επαγωγική συγκόλληση. Οι δημοφιλείς διεργασίες συγκόλλησης είναι η δάδα, η επαγωγή, η συγκόλληση σε φούρνο και η βύθιση. Οι μέθοδοι συγκόλλησης μας είναι η συγκόλληση σιδήρου, θερμής πλάκας, φούρνος, επαγωγής, εμβάπτισης, κύματος, επαναροής και συγκόλλησης με υπερήχους. Για συγκόλληση κόλλας χρησιμοποιούμε συχνά θερμοπλαστικά και θερμοσκληρυντικά, εποξικά, φαινολικά, πολυουρεθάνη, κράματα κόλλας καθώς και κάποια άλλα χημικά και ταινίες. Τέλος, οι διαδικασίες στερέωσης μας αποτελούνται από κάρφωμα, βίδωμα, παξιμάδια και μπουλόνια, πριτσίνωμα, στερέωση, καρφίτσωμα, ραφή & συρραφή και προσαρμογή με πίεση. • ΣΥΓΚΟΛΛΗΣΗ: Η συγκόλληση περιλαμβάνει την ένωση υλικών με τήξη των τεμαχίων εργασίας και εισαγωγή υλικών πλήρωσης, τα οποία ενώνουν επίσης τη δεξαμενή λειωμένης συγκόλλησης. Όταν η περιοχή κρυώσει, αποκτάμε μια δυνατή άρθρωση. Σε ορισμένες περιπτώσεις εφαρμόζεται πίεση. Σε αντίθεση με τη συγκόλληση, οι εργασίες συγκόλλησης και συγκόλλησης περιλαμβάνουν μόνο την τήξη ενός υλικού με χαμηλότερο σημείο τήξης μεταξύ των τεμαχίων εργασίας και τα τεμάχια εργασίας δεν λιώνουν. Σας συνιστούμε να κάνετε κλικ εδώ για ναΚΑΤΕΒΑΣΤΕ τις Σχηματικές απεικονίσεις των Διαδικασιών Συγκόλλησης από την AGS-TECH Inc. Αυτό θα σας βοηθήσει να κατανοήσετε καλύτερα τις πληροφορίες που σας παρέχουμε παρακάτω. Στη ΣΥΓΚΟΛΛΗΣΗ ΤΞΟΥ, χρησιμοποιούμε τροφοδοτικό και ηλεκτρόδιο για να δημιουργήσουμε ένα ηλεκτρικό τόξο που λιώνει τα μέταλλα. Το σημείο συγκόλλησης προστατεύεται από προστατευτικό αέριο ή ατμό ή άλλο υλικό. Αυτή η διαδικασία είναι δημοφιλής για τη συγκόλληση εξαρτημάτων αυτοκινήτων και χαλύβδινων κατασκευών. Στη συγκόλληση με θωρακισμένο μέταλλο τόξου (SMAW) ή επίσης γνωστή ως συγκόλληση με ραβδί, ένα ραβδί ηλεκτροδίου φέρεται κοντά στο υλικό βάσης και δημιουργείται ένα ηλεκτρικό τόξο μεταξύ τους. Η ράβδος του ηλεκτροδίου λιώνει και λειτουργεί ως υλικό πλήρωσης. Το ηλεκτρόδιο περιέχει επίσης ροή που λειτουργεί ως στρώμα σκωρίας και εκπέμπει ατμούς που λειτουργούν ως προστατευτικό αέριο. Αυτά προστατεύουν την περιοχή συγκόλλησης από περιβαλλοντική μόλυνση. Δεν χρησιμοποιούνται άλλα πληρωτικά. Τα μειονεκτήματα αυτής της διαδικασίας είναι η βραδύτητα της, η ανάγκη για συχνή αντικατάσταση ηλεκτροδίων, η ανάγκη απομάκρυνσης της υπολειμματικής σκωρίας που προέρχεται από τη ροή. Μια σειρά από μέταλλα όπως ο σίδηρος, ο χάλυβας, το νικέλιο, το αλουμίνιο, ο χαλκός κ.λπ. Μπορεί να συγκολληθεί. Τα πλεονεκτήματά του είναι τα φθηνά εργαλεία και η ευκολία χρήσης. Η συγκόλληση με τόξο μετάλλου αερίου (GMAW) γνωστή και ως μεταλλικό αδρανές αέριο (MIG), έχουμε συνεχή τροφοδοσία ενός αναλώσιμου ηλεκτροδίου πλήρωσης σύρματος και ενός αδρανούς ή μερικώς αδρανούς αερίου που ρέει γύρω από το σύρμα έναντι της περιβαλλοντικής μόλυνσης της περιοχής συγκόλλησης. Ο χάλυβας, το αλουμίνιο και άλλα μη σιδηρούχα μέταλλα μπορούν να συγκολληθούν. Τα πλεονεκτήματα της MIG είναι οι υψηλές ταχύτητες συγκόλλησης και η καλή ποιότητα. Τα μειονεκτήματα είναι ο περίπλοκος εξοπλισμός και οι προκλήσεις που αντιμετωπίζει σε υπαίθρια περιβάλλοντα με θυελλώδεις ανέμους, επειδή πρέπει να διατηρήσουμε σταθερό το προστατευτικό αέριο γύρω από την περιοχή συγκόλλησης. Μια παραλλαγή του GMAW είναι η συγκόλληση τόξου με πυρήνα ροής (FCAW) που αποτελείται από έναν λεπτό μεταλλικό σωλήνα γεμάτο με υλικά ροής. Μερικές φορές η ροή στο εσωτερικό του σωλήνα είναι επαρκής για προστασία από τη μόλυνση του περιβάλλοντος. Η συγκόλληση με υποβρύχιο τόξο (SAW) είναι ευρέως μια αυτοματοποιημένη διαδικασία, που περιλαμβάνει συνεχή τροφοδοσία σύρματος και τόξο που χτυπιέται κάτω από ένα στρώμα καλύμματος ροής. Τα ποσοστά παραγωγής και η ποιότητα είναι υψηλά, η σκωρία συγκόλλησης αφαιρείται εύκολα και έχουμε ένα περιβάλλον εργασίας χωρίς καπνό. Το μειονέκτημα είναι ότι μπορεί να χρησιμοποιηθεί μόνο για τη συγκόλληση εξαρτημάτων parts σε ορισμένες θέσεις. Στη συγκόλληση τόξου με αέριο βολφραμίου (GTAW) ή στη συγκόλληση με αδρανή αέριο βολφραμίου (TIG) χρησιμοποιούμε ένα ηλεκτρόδιο βολφραμίου μαζί με ένα ξεχωριστό πληρωτικό και αδρανή ή σχεδόν αδρανή αέρια. Όπως γνωρίζουμε το βολφράμιο έχει υψηλό σημείο τήξης και είναι ένα πολύ κατάλληλο μέταλλο για πολύ υψηλές θερμοκρασίες. Το βολφράμιο στο TIG δεν καταναλώνεται σε αντίθεση με τις άλλες μεθόδους που εξηγήθηκαν παραπάνω. Μια αργή αλλά υψηλής ποιότητας τεχνική συγκόλλησης πλεονεκτική έναντι άλλων τεχνικών συγκόλλησης λεπτών υλικών. Κατάλληλο για πολλά μέταλλα. Η συγκόλληση με τόξο πλάσματος είναι παρόμοια, αλλά χρησιμοποιεί αέριο πλάσματος για τη δημιουργία του τόξου. Το τόξο στη συγκόλληση τόξου πλάσματος είναι σχετικά πιο συγκεντρωμένο σε σύγκριση με το GTAW και μπορεί να χρησιμοποιηθεί για ένα ευρύτερο φάσμα πάχους μετάλλων σε πολύ υψηλότερες ταχύτητες. Το GTAW και η συγκόλληση με τόξο πλάσματος μπορούν να εφαρμοστούν σε λίγο πολύ τα ίδια υλικά. ΣΥΓΚΟΛΛΗΣΗ ΟΞΥ-ΚΑΥΣΙΜΟΥ/ΟΞΥΚΑΥΣΙΜΟΥ που ονομάζεται επίσης συγκόλληση με οξυακετυλένιο, συγκόλληση με οξυγόνο, η συγκόλληση αερίου πραγματοποιείται με τη χρήση καυσίμων αερίου και οξυγόνου για συγκόλληση. Δεδομένου ότι δεν χρησιμοποιείται ηλεκτρική ενέργεια, είναι φορητό και μπορεί να χρησιμοποιηθεί όπου δεν υπάρχει ηλεκτρικό ρεύμα. Χρησιμοποιώντας ένα φακό συγκόλλησης θερμαίνουμε τα τεμάχια και το υλικό πλήρωσης για να δημιουργήσουμε μια κοινή πισίνα λιωμένου μετάλλου. Μπορούν να χρησιμοποιηθούν διάφορα καύσιμα όπως ακετυλένιο, βενζίνη, υδρογόνο, προπάνιο, βουτάνιο κ.λπ. Στη συγκόλληση με οξυγόνο χρησιμοποιούμε δύο δοχεία, το ένα για το καύσιμο και το άλλο για το οξυγόνο. Το οξυγόνο οξειδώνει το καύσιμο (το καίει). ΣΥΓΚΟΛΛΗΣΗ ΑΝΤΙΣΤΑΣΗΣ: Αυτός ο τύπος συγκόλλησης εκμεταλλεύεται τη θέρμανση joule και παράγεται θερμότητα στη θέση όπου εφαρμόζεται ηλεκτρικό ρεύμα για ορισμένο χρόνο. Μέσα από το μέταλλο διέρχονται υψηλά ρεύματα. Σε αυτή τη θέση σχηματίζονται δεξαμενές λιωμένου μετάλλου. Οι μέθοδοι συγκόλλησης με αντίσταση είναι δημοφιλείς λόγω της αποτελεσματικότητάς τους, του μικρού δυναμικού ρύπανσης. Ωστόσο, τα μειονεκτήματα είναι ότι το κόστος του εξοπλισμού είναι σχετικά σημαντικό και ο εγγενής περιορισμός στα σχετικά λεπτά τεμάχια εργασίας. Η ΣΗΜΕΙΑΚΗ ΣΥΓΚΟΛΛΗΣΗ είναι ένας σημαντικός τύπος συγκόλλησης με αντίσταση. Εδώ ενώνουμε δύο ή περισσότερα επικαλυπτόμενα φύλλα ή τεμάχια εργασίας χρησιμοποιώντας δύο χάλκινα ηλεκτρόδια για να σφίξουμε τα φύλλα μεταξύ τους και να περάσουμε ένα υψηλό ρεύμα μέσα από αυτά. Το υλικό μεταξύ των ηλεκτροδίων χαλκού θερμαίνεται και δημιουργείται μια λιωμένη λίμνη σε αυτή τη θέση. Στη συνέχεια, το ρεύμα διακόπτεται και οι άκρες των ηλεκτροδίων χαλκού ψύχουν τη θέση συγκόλλησης επειδή τα ηλεκτρόδια ψύχονται με νερό. Η εφαρμογή της σωστής ποσότητας θερμότητας στο σωστό υλικό και πάχος είναι το κλειδί για αυτήν την τεχνική, γιατί εάν εφαρμοστεί λανθασμένα η ένωση θα είναι αδύναμη. Η σημειακή συγκόλληση έχει τα πλεονεκτήματα ότι δεν προκαλεί σημαντική παραμόρφωση στα τεμάχια εργασίας, ενεργειακή απόδοση, ευκολία αυτοματισμού και εξαιρετικούς ρυθμούς παραγωγής και δεν απαιτεί πληρωτικά. Το μειονέκτημα είναι ότι εφόσον η συγκόλληση λαμβάνει χώρα σε σημεία αντί να σχηματίζει μια συνεχή ραφή, η συνολική αντοχή μπορεί να είναι σχετικά χαμηλότερη σε σύγκριση με άλλες μεθόδους συγκόλλησης. Η SEAM WELDING από την άλλη πλευρά παράγει συγκολλήσεις στις επιφάνειες στεγανοποίησης παρόμοιων υλικών. Η ραφή μπορεί να είναι πισινή ή επικαλυπτόμενη άρθρωση. Η συγκόλληση με ραφές ξεκινά από το ένα άκρο και προχωρά προοδευτικά στο άλλο. Αυτή η μέθοδος χρησιμοποιεί επίσης δύο ηλεκτρόδια από χαλκό για την εφαρμογή πίεσης και ρεύματος στην περιοχή συγκόλλησης. Τα ηλεκτρόδια σε σχήμα δίσκου περιστρέφονται με συνεχή επαφή κατά μήκος της γραμμής ραφής και κάνουν μια συνεχή συγκόλληση. Και εδώ, τα ηλεκτρόδια ψύχονται με νερό. Οι συγκολλήσεις είναι πολύ ισχυρές και αξιόπιστες. Άλλες μέθοδοι είναι οι τεχνικές συγκόλλησης προβολής, φλας και ανατροπής. Η ΣΥΓΚΟΛΛΗΣΗ ΣΤΕΡΕΑΣ ΚΑΤΑΣΤΑΣΗΣ είναι λίγο διαφορετική από τις προηγούμενες μεθόδους που εξηγήθηκαν παραπάνω. Η συνένωση λαμβάνει χώρα σε θερμοκρασίες κάτω από τη θερμοκρασία τήξης των ενωμένων μετάλλων και χωρίς χρήση μεταλλικού πληρωτικού. Η πίεση μπορεί να χρησιμοποιηθεί σε ορισμένες διαδικασίες. Διάφορες μέθοδοι είναι η ΣΥΓΚΟΛΛΗΣΗ ΣΥΝΕΞΩΘΗΣΗΣ όπου ανόμοια μέταλλα εξωθούνται μέσω της ίδιας μήτρας, η ΣΥΓΚΟΛΛΗΣΗ ΨΥΧΡΗΣ ΠΙΕΣΗΣ όπου ενώνουμε μαλακά κράματα κάτω από τα σημεία τήξης τους, η ΣΥΓΚΟΛΛΗΣΗ ΔΙΑΧΥΣΗΣ μια τεχνική χωρίς ορατές γραμμές συγκόλλησης, η ΕΚΡΗΚΤΙΚΗ ΣΥΓΚΟΛΛΗΣΗ για την ένωση ανόμοιων υλικών σε όλα τα υλικά, π.χ. χάλυβες, ΣΥΓΚΟΛΛΗΣΗ ΗΛΕΚΤΡΟΜΑΓΝΗΤΙΚΟΥ ΠΑΛΜΟΥ όπου επιταχύνουμε σωλήνες και φύλλα με ηλεκτρομαγνητικές δυνάμεις, ΣΦΗΡΗΤΙΚΟΣΥΓΚΟΛΛΗΣΗ που συνίσταται στη θέρμανση των μετάλλων σε υψηλές θερμοκρασίες και στη σφυρηλάτηση τους μεταξύ τους, ΣΥΓΚΟΛΛΗΣΗ ΜΕ ΤΡΙΒΗ όπου εκτελείται συγκόλληση με επαρκή τριβή, ΣΥΓΚΟΛΛΗΣΗ ΜΕ ΑΝΑΔΕΙΞΗ με τριβή που περιλαμβάνει αναλώσιμο εργαλείο που διασχίζει τη γραμμή άρθρωσης, ΣΥΓΚΟΛΛΗΣΗ ΘΕΡΜΗΣ ΠΙΕΣΗΣ όπου πιέζουμε μέταλλα μεταξύ τους σε υψηλές θερμοκρασίες κάτω από τη θερμοκρασία τήξης στο κενό ή αδρανή αέρια, ΣΥΓΚΟΛΛΗΣΗ ΘΕΡΜΗΣ ΙΣΟΣΤΑΤΙΚΗΣ ΠΙΕΣΗΣ μια διαδικασία όπου ασκούμε πίεση χρησιμοποιώντας αδρανή αέρια μέσα σε ένα δοχείο, ΣΥΓΚΟΛΛΗΣΗ ROLL όπου ενώνουμε ανόμοια υλικά πιέζοντάς τα μεταξύ τους δύο περιστρεφόμενοι τροχοί, ΣΥΓΚΟΛΛΗΣΗ ΥΠΕΡΗΧΩΝ όπου συγκολλούνται λεπτά μεταλλικά ή πλαστικά φύλλα χρησιμοποιώντας δονητική ενέργεια υψηλής συχνότητας. Οι άλλες διεργασίες συγκόλλησης μας είναι η ΣΥΓΚΟΛΛΗΣΗ ΔΟΚΩΝ ΗΛΕΚΤΡΟΝΙΟΥ με βαθιά διείσδυση και γρήγορη επεξεργασία αλλά είναι μια ακριβή μέθοδος που τη θεωρούμε για ειδικές περιπτώσεις, η ΗΛΕΚΤΡΟΣΚΟΛΛΗΣΗ μια μέθοδος κατάλληλη μόνο για βαριές χοντρές πλάκες και τεμάχια χάλυβα, η ΕΠΑΓΩΓΙΚΗ ΣΥΓΚΟΛΛΗΣΗ όπου χρησιμοποιούμε ηλεκτρομαγνητική επαγωγή και θερμαίνουμε τα ηλεκτρικά αγώγιμα ή σιδηρομαγνητικά τεμάχιά μας, ΣΥΓΚΟΛΛΗΣΗ ΔΕΣΜΩΝ LASER επίσης με βαθιά διείσδυση και γρήγορη επεξεργασία αλλά ακριβή μέθοδο, ΥΒΡΙΔΙΚΗ ΣΥΓΚΟΛΛΗΣΗ LASER που συνδυάζει LBW με GMAW στην ίδια κεφαλή συγκόλλησης και ικανή να γεφυρώσει κενά 2 mm μεταξύ των πλακών, ΣΥΓΚΟΛΛΗΣΗ ΚΡΟΥΣΗΣ περιλαμβάνει ηλεκτρική εκκένωση που ακολουθείται από σφυρηλάτηση των υλικών με ασκούμενη πίεση, ΣΥΓΚΟΛΛΗΣΗ THERMIT που περιλαμβάνει εξώθερμη αντίδραση μεταξύ σκονών αλουμινίου και οξειδίου σιδήρου., ΣΥΓΚΟΛΛΗΣΗ ΗΛΕΚΤΡΟΑΕΡΙΟΥ με αναλώσιμα ηλεκτρόδια και χρησιμοποιείται μόνο με χάλυβα σε κατακόρυφη θέση, και τέλος ΣΥΓΚΟΛΛΗΣΗ ΤΟΞΟΥ STUD για ένωση καρφιού με βάση υλικό με θερμότητα και πίεση. Σας συνιστούμε να κάνετε κλικ εδώ για ναΚΑΤΕΒΑΣΤΕ τις Σχηματικές μας απεικονίσεις των διεργασιών συγκόλλησης, συγκόλλησης και συγκόλλησης από την AGS-TECH Inc Αυτό θα σας βοηθήσει να κατανοήσετε καλύτερα τις πληροφορίες που σας παρέχουμε παρακάτω. • BRAZING : Ενώνουμε δύο ή περισσότερα μέταλλα θερμαίνοντας μέταλλα πλήρωσης μεταξύ τους πάνω από τα σημεία τήξης τους και χρησιμοποιώντας τριχοειδή δράση για να απλώσουμε. Η διαδικασία είναι παρόμοια με τη συγκόλληση, αλλά οι θερμοκρασίες που απαιτούνται για την τήξη του πληρωτικού είναι υψηλότερες στη συγκόλληση. Όπως και στη συγκόλληση, η ροή προστατεύει το υλικό πλήρωσης από την ατμοσφαιρική μόλυνση. Μετά την ψύξη τα τεμάχια εργασίας ενώνονται μεταξύ τους. Η διαδικασία περιλαμβάνει τα ακόλουθα βασικά βήματα: Καλή εφαρμογή και διάκενο, σωστός καθαρισμός των βασικών υλικών, σωστή στερέωση, σωστή επιλογή ροής και ατμόσφαιρας, θέρμανση του συγκροτήματος και, τέλος, καθαρισμός του συγκολλημένου συγκροτήματος. Μερικές από τις διεργασίες συγκόλλησης είναι η TORCH BRAZING, μια δημοφιλής μέθοδος που πραγματοποιείται με το χέρι ή με αυτοματοποιημένο τρόπο. Είναι κατάλληλο για παραγγελίες παραγωγής χαμηλού όγκου και εξειδικευμένες θήκες. Η θερμότητα εφαρμόζεται χρησιμοποιώντας φλόγες αερίου κοντά στην άρθρωση που συγκολλάται. Η BRAZING FURNACE απαιτεί λιγότερη ικανότητα χειριστή και είναι μια ημιαυτόματη διαδικασία κατάλληλη για βιομηχανική μαζική παραγωγή. Τόσο ο έλεγχος της θερμοκρασίας όσο και ο έλεγχος της ατμόσφαιρας στον κλίβανο είναι πλεονεκτήματα αυτής της τεχνικής, επειδή η πρώτη μας επιτρέπει να έχουμε ελεγχόμενους κύκλους θερμότητας και να εξαλείφουμε την τοπική θέρμανση όπως συμβαίνει στη συγκόλληση με πυρσό και η δεύτερη προστατεύει το μέρος από την οξείδωση. Χρησιμοποιώντας το jigging είμαστε σε θέση να μειώσουμε το κόστος κατασκευής στο ελάχιστο. Τα μειονεκτήματα είναι η υψηλή κατανάλωση ενέργειας, το κόστος εξοπλισμού και πιο δύσκολα σχεδιαστικά ζητήματα. ΚΕΝΟ Η BRAZING πραγματοποιείται σε κλίβανο κενού. Διατηρείται η ομοιομορφία θερμοκρασίας και λαμβάνουμε αρμούς χωρίς ροή, πολύ καθαρούς με πολύ μικρές υπολειμματικές τάσεις. Οι θερμικές επεξεργασίες μπορούν να πραγματοποιηθούν κατά τη συγκόλληση υπό κενό, λόγω των χαμηλών υπολειμματικών τάσεων που υπάρχουν κατά τους αργούς κύκλους θέρμανσης και ψύξης. Το σημαντικότερο μειονέκτημα είναι το υψηλό κόστος του γιατί η δημιουργία περιβάλλοντος κενού είναι μια δαπανηρή διαδικασία. Μια άλλη τεχνική με το DIP BRAZING ενώνει σταθερά μέρη όπου η ένωση συγκόλλησης εφαρμόζεται σε ζευγαρωμένες επιφάνειες. Στη συνέχεια, τα σταθεροποιημένα μέρη βυθίζονται σε ένα λουτρό λιωμένου άλατος όπως το χλωριούχο νάτριο (επιτραπέζιο αλάτι) το οποίο δρα ως μέσο μεταφοράς θερμότητας και ροή. Ο αέρας αποκλείεται και επομένως δεν λαμβάνει χώρα σχηματισμός οξειδίου. Στο INDUCTION BRAZING ενώνουμε υλικά με μέταλλο πλήρωσης που έχει χαμηλότερο σημείο τήξης από τα βασικά υλικά. Το εναλλασσόμενο ρεύμα από το πηνίο επαγωγής δημιουργεί ένα ηλεκτρομαγνητικό πεδίο που προκαλεί επαγωγική θέρμανση σε κυρίως σιδηρούχα μαγνητικά υλικά. Η μέθοδος παρέχει επιλεκτική θέρμανση, καλούς αρμούς με πληρωτικά που ρέουν μόνο στις επιθυμητές περιοχές, μικρή οξείδωση επειδή δεν υπάρχουν φλόγες και η ψύξη είναι γρήγορη, γρήγορη θέρμανση, συνοχή και καταλληλότητα για παραγωγή μεγάλου όγκου. Για να επιταχύνουμε τις διαδικασίες μας και να διασφαλίσουμε τη συνέπεια, χρησιμοποιούμε συχνά προδιαμορφώματα. Πληροφορίες σχετικά με τις εγκαταστάσεις συγκόλλησης που παράγουν εξαρτήματα από κεραμικό σε μέταλλο, ερμητική σφράγιση, τροφοδοσίες κενού, εξαρτήματα ελέγχου υψηλού και εξαιρετικά υψηλού κενού και ρευστού μπορείτε να βρείτε εδώ:_cc781905-31-5cΜπροσούρα Brazing Factory • ΚΟΛΛΗΣΗ : Στη συγκόλληση δεν έχουμε τήξη των τεμαχίων, αλλά πληρωτικό μέταλλο με χαμηλότερο σημείο τήξης από τα εξαρτήματα ένωσης που ρέει στον σύνδεσμο. Το μέταλλο πλήρωσης στη συγκόλληση λιώνει σε χαμηλότερη θερμοκρασία από ότι στη συγκόλληση. Χρησιμοποιούμε κράματα χωρίς μόλυβδο για συγκόλληση και έχουμε συμμόρφωση με RoHS και για διαφορετικές εφαρμογές και απαιτήσεις έχουμε διαφορετικά και κατάλληλα κράματα όπως κράμα αργύρου. Η συγκόλληση μας προσφέρει αρμούς που είναι στεγανοί στα αέρια και στα υγρά. Στην μαλακή συγκόλληση, το μέταλλο πλήρωσης έχει σημείο τήξης κάτω από 400 Κελσίου, ενώ στην ΑΣΗΜΕΝΙΑ ΣΥΓΚΟΛΛΗΣΗ και BRAZING χρειαζόμαστε υψηλότερες θερμοκρασίες. Η μαλακή συγκόλληση χρησιμοποιεί χαμηλότερες θερμοκρασίες, αλλά δεν οδηγεί σε ισχυρούς αρμούς για απαιτητικές εφαρμογές σε υψηλές θερμοκρασίες. Η συγκόλληση με ασήμι από την άλλη, απαιτεί υψηλές θερμοκρασίες που παρέχονται από τον φακό και μας δίνει ισχυρούς αρμούς κατάλληλους για εφαρμογές υψηλής θερμοκρασίας. Η συγκόλληση απαιτεί τις υψηλότερες θερμοκρασίες και συνήθως χρησιμοποιείται φακός. Δεδομένου ότι οι σύνδεσμοι συγκόλλησης είναι πολύ ισχυροί, είναι καλοί υποψήφιοι για την επισκευή βαρέων σιδερένιων αντικειμένων. Στις γραμμές παραγωγής μας χρησιμοποιούμε τόσο χειροκίνητη συγκόλληση όσο και αυτοματοποιημένες γραμμές συγκόλλησης. Η INDUCTION SOLDERING χρησιμοποιεί ρεύμα εναλλασσόμενου ρεύματος υψηλής συχνότητας σε ένα πηνίο χαλκού για να διευκολύνει την επαγωγική θέρμανση. Τα ρεύματα προκαλούνται στο συγκολλημένο τμήμα και ως αποτέλεσμα δημιουργείται θερμότητα στην υψηλή αντίσταση joint. Αυτή η θερμότητα λιώνει το μέταλλο πλήρωσης. Χρησιμοποιείται επίσης Flux. Η επαγωγική συγκόλληση είναι μια καλή μέθοδος για τη συγκόλληση κυλίνδρων και σωλήνων σε συνεχή διαδικασία τυλίγοντας τα πηνία γύρω τους. Η συγκόλληση ορισμένων υλικών όπως ο γραφίτης και τα κεραμικά είναι πιο δύσκολη γιατί απαιτεί την επιμετάλλωση των τεμαχίων με κατάλληλο μέταλλο πριν από τη συγκόλληση. Αυτό διευκολύνει τη διεπιφανειακή συγκόλληση. Συγκολλάμε τέτοια υλικά ειδικά για εφαρμογές ερμητικής συσκευασίας. Κατασκευάζουμε τις πλακέτες τυπωμένων κυκλωμάτων μας (PCB) σε μεγάλο όγκο, κυρίως χρησιμοποιώντας ΚΥΜΑΤΟΚΟΛΗΣΗ. Μόνο για μικρές ποσότητες πρωτοτύπων χρησιμοποιούμε συγκόλληση με το χέρι χρησιμοποιώντας κολλητήρι. Χρησιμοποιούμε συγκόλληση με κύμα τόσο για διαμπερείς οπές όσο και για επιφανειακά συγκροτήματα PCB (PCBA). Μια προσωρινή κόλλα κρατά τα εξαρτήματα προσαρτημένα στην πλακέτα κυκλώματος και το συγκρότημα τοποθετείται σε έναν μεταφορέα και μετακινείται μέσα από έναν εξοπλισμό που περιέχει τηγμένη συγκόλληση. Πρώτα το PCB ρέει και μετά εισέρχεται στη ζώνη προθέρμανσης. Η λιωμένη κόλληση βρίσκεται σε ένα ταψί και έχει ένα σχέδιο στάσιμων κυμάτων στην επιφάνειά της. Όταν το PCB κινείται πάνω από αυτά τα κύματα, αυτά τα κύματα έρχονται σε επαφή με το κάτω μέρος του PCB και κολλάνε στα μαξιλαράκια συγκόλλησης. Η συγκόλληση μένει μόνο σε καρφίτσες και τακάκια και όχι στο ίδιο το PCB. Τα κύματα στη λιωμένη κόλληση πρέπει να ελέγχονται καλά, ώστε να μην υπάρχει πιτσίλισμα και οι κορυφές κυμάτων να μην αγγίζουν και να μολύνουν ανεπιθύμητες περιοχές των σανίδων. Στο REFLOW SOLDERING, χρησιμοποιούμε μια κολλώδη πάστα συγκόλλησης για να συνδέσουμε προσωρινά τα ηλεκτρονικά εξαρτήματα στις πλακέτες. Στη συνέχεια, οι σανίδες περνούν μέσα από έναν φούρνο επαναροής με έλεγχο θερμοκρασίας. Εδώ η συγκόλληση λιώνει και συνδέει μόνιμα τα εξαρτήματα. Χρησιμοποιούμε αυτήν την τεχνική τόσο για εξαρτήματα επιφανειακής στήριξης όσο και για εξαρτήματα διαμπερούς οπής. Ο σωστός έλεγχος θερμοκρασίας και η προσαρμογή των θερμοκρασιών του φούρνου είναι ουσιαστικής σημασίας για την αποφυγή καταστροφής ηλεκτρονικών εξαρτημάτων στην πλακέτα με την υπερθέρμανση τους πάνω από τα μέγιστα όρια θερμοκρασίας. Στη διαδικασία της συγκόλλησης με επαναροή έχουμε στην πραγματικότητα πολλές περιοχές ή στάδια το καθένα με ένα ξεχωριστό θερμικό προφίλ, όπως το βήμα προθέρμανσης, το στάδιο θερμικής διαβροχής, τα βήματα επαναροής και ψύξης. Αυτά τα διαφορετικά βήματα είναι απαραίτητα για μια συγκόλληση χωρίς ζημιά με επαναροή των συγκροτημάτων πλακέτας τυπωμένου κυκλώματος (PCBA). Η ΚΟΛΛΗΣΗ ΥΠΕΡΗΧΩΝ είναι μια άλλη συχνά χρησιμοποιούμενη τεχνική με μοναδικές δυνατότητες- Μπορεί να χρησιμοποιηθεί για τη συγκόλληση γυαλιού, κεραμικών και μη μεταλλικών υλικών. Για παράδειγμα, τα φωτοβολταϊκά πάνελ που είναι μη μεταλλικά χρειάζονται ηλεκτρόδια που μπορούν να τοποθετηθούν χρησιμοποιώντας αυτή την τεχνική. Στη συγκόλληση με υπερήχους, αναπτύσσουμε ένα θερμαινόμενο άκρο συγκόλλησης που εκπέμπει επίσης υπερηχητικούς κραδασμούς. Αυτές οι δονήσεις παράγουν φυσαλίδες σπηλαίωσης στη διεπαφή του υποστρώματος με το λιωμένο υλικό συγκόλλησης. Η εκρηκτική ενέργεια της σπηλαίωσης τροποποιεί την επιφάνεια του οξειδίου και απομακρύνει τη βρωμιά και τα οξείδια. Κατά τη διάρκεια αυτής της περιόδου σχηματίζεται επίσης ένα στρώμα κράματος. Η συγκόλληση στην επιφάνεια συγκόλλησης ενσωματώνει οξυγόνο και επιτρέπει το σχηματισμό ενός ισχυρού κοινόχρηστου δεσμού μεταξύ του γυαλιού και της συγκόλλησης. Το DIP SOLDERING μπορεί να θεωρηθεί ως μια απλούστερη εκδοχή της συγκόλλησης με κύμα κατάλληλη μόνο για παραγωγή μικρής κλίμακας. Η πρώτη ροή καθαρισμού εφαρμόζεται όπως και σε άλλες διαδικασίες. Τα PCB με τοποθετημένα εξαρτήματα βυθίζονται χειροκίνητα ή με ημιαυτόματο τρόπο σε μια δεξαμενή που περιέχει τηγμένη συγκόλληση. Η λιωμένη κόλληση κολλάει στις εκτεθειμένες μεταλλικές περιοχές χωρίς να προστατεύεται από τη μάσκα συγκόλλησης στην πλακέτα. Ο εξοπλισμός είναι απλός και φθηνός. • ΚΟΛΛΗΣΗ: Αυτή είναι μια άλλη δημοφιλής τεχνική που χρησιμοποιούμε συχνά και περιλαμβάνει συγκόλληση επιφανειών χρησιμοποιώντας κόλλες, εποξειδικά, πλαστικά μέσα ή άλλα χημικά. Η συγκόλληση επιτυγχάνεται είτε με εξάτμιση του διαλύτη, με θερμική σκλήρυνση, με σκλήρυνση με υπεριώδη ακτινοβολία, με σκλήρυνση υπό πίεση ή αναμονή για ορισμένο χρόνο. Στις γραμμές παραγωγής μας χρησιμοποιούνται διάφορες κόλλες υψηλής απόδοσης. Με σωστά σχεδιασμένες διαδικασίες εφαρμογής και σκλήρυνσης, η συγκόλληση με κόλλα μπορεί να οδηγήσει σε δεσμούς πολύ χαμηλής τάσης που είναι ισχυροί και αξιόπιστοι. Οι αυτοκόλλητες δεσμοί μπορούν να είναι καλά προστατευτικά έναντι περιβαλλοντικών παραγόντων όπως υγρασία, ρύπους, διαβρωτικά, κραδασμούς… κ.λπ. Τα πλεονεκτήματα της συγκόλλησης με κόλλα είναι: μπορούν να εφαρμοστούν σε υλικά που διαφορετικά θα ήταν δύσκολο να συγκολληθούν, να συγκολληθούν ή να συγκολληθούν. Επίσης, μπορεί να είναι προτιμότερο για ευαίσθητα στη θερμότητα υλικά που θα μπορούσαν να καταστραφούν από συγκόλληση ή άλλες διεργασίες υψηλής θερμοκρασίας. Άλλα πλεονεκτήματα των συγκολλητικών είναι ότι μπορούν να εφαρμοστούν σε επιφάνειες ακανόνιστου σχήματος και αυξάνουν το βάρος συναρμολόγησης κατά πολύ πολύ μικρές ποσότητες σε σύγκριση με άλλες μεθόδους. Επίσης, οι αλλαγές διαστάσεων στα μέρη είναι πολύ ελάχιστες. Ορισμένες κόλλες έχουν ιδιότητες αντιστοίχισης δείκτη και μπορούν να χρησιμοποιηθούν μεταξύ των οπτικών εξαρτημάτων χωρίς να μειώνεται σημαντικά το φως ή η ισχύς του οπτικού σήματος. Τα μειονεκτήματα από την άλλη πλευρά είναι οι μεγαλύτεροι χρόνοι σκλήρυνσης που μπορεί να επιβραδύνουν τις γραμμές κατασκευής, τις απαιτήσεις στερέωσης, τις απαιτήσεις προετοιμασίας της επιφάνειας και τη δυσκολία αποσυναρμολόγησης όταν απαιτείται εκ νέου επεξεργασία. Οι περισσότερες από τις εργασίες συγκόλλησης κόλλας περιλαμβάνουν τα ακόλουθα βήματα: -Επεξεργασία επιφάνειας: Ειδικές διαδικασίες καθαρισμού, όπως καθαρισμός απιονισμένου νερού, καθαρισμός με οινόπνευμα, καθαρισμός πλάσματος ή κορώνας είναι συνήθεις. Μετά τον καθαρισμό, μπορούμε να εφαρμόσουμε ενισχυτικά πρόσφυσης στις επιφάνειες για να εξασφαλίσουμε τους καλύτερους δυνατούς αρμούς. -Στερέωση εξαρτημάτων: Τόσο για εφαρμογή κόλλας όσο και για σκλήρυνση σχεδιάζουμε και χρησιμοποιούμε προσαρμοσμένα φωτιστικά. -Εφαρμογή κόλλας: Μερικές φορές χρησιμοποιούμε χειροκίνητα και μερικές φορές ανάλογα με την περίπτωση αυτοματοποιημένα συστήματα όπως ρομποτική, σερβοκινητήρες, γραμμικοί ενεργοποιητές για να παραδίδουμε τις κόλλες στη σωστή θέση και χρησιμοποιούμε διανομείς για να τις παραδίδουμε στο σωστό όγκο και ποσότητα. -Στερέωση: Ανάλογα με την κόλλα, μπορούμε να χρησιμοποιήσουμε απλό στέγνωμα και σκλήρυνση, καθώς και σκλήρυνση κάτω από λάμπες UV που λειτουργούν ως καταλύτης ή θερμική σκλήρυνση σε φούρνο ή χρησιμοποιώντας θερμαντικά στοιχεία αντίστασης τοποθετημένα σε εξαρτήματα και εξαρτήματα. Σας συνιστούμε να κάνετε κλικ εδώ για ναΚΑΤΕΒΑΣΤΕ τις Σχηματικές μας απεικονίσεις των Διαδικασιών Στερέωσης από την AGS-TECH Inc. Αυτό θα σας βοηθήσει να κατανοήσετε καλύτερα τις πληροφορίες που σας παρέχουμε παρακάτω. • ΔΙΑΔΙΚΑΣΙΕΣ ΣΤΕΡΕΩΣΗΣ: Οι μηχανικές διαδικασίες συνδέσεως που διαθέτουμε εμπίπτουν σε δύο κατηγορίες: ΣΦΕΣΤΕΡΕΣ και ΟΛΟΚΛΗΡΩΜΕΝΕΣ ΑΡΘΡΩΣΕΙΣ. Παραδείγματα συνδετήρων που χρησιμοποιούμε είναι βίδες, καρφίτσες, παξιμάδια, μπουλόνια, πριτσίνια. Παραδείγματα ενσωματωμένων αρμών που χρησιμοποιούμε είναι κουμπωτά και συρρίκνωση, ραφές, πτυχώσεις. Χρησιμοποιώντας μια ποικιλία μεθόδων στερέωσης διασφαλίζουμε ότι οι μηχανικοί μας σύνδεσμοι είναι ισχυροί και αξιόπιστοι για πολλά χρόνια χρήσης. Οι ΒΙΔΕΣ και οι ΜΠΟΥΛΕΣ είναι μερικοί από τους πιο συχνά χρησιμοποιούμενους συνδετήρες για τη συγκράτηση και την τοποθέτηση αντικειμένων. Οι βίδες και τα μπουλόνια μας πληρούν τα πρότυπα ASME. Χρησιμοποιούνται διάφοροι τύποι βιδών και μπουλονιών, συμπεριλαμβανομένων εξαγωνικών βιδών και εξαγωνικών μπουλονιών, βιδών και μπουλονιών με υστέρηση, βίδα διπλού άκρου, βίδα βελόνας, βίδα με μάτι, βίδα καθρέφτη, βίδα από λαμαρίνα, βίδα λεπτής ρύθμισης, βίδες με αυτοδιάτρηση και αυτοκόλλητες βίδες , βίδα ρύθμισης, βίδες με ενσωματωμένες ροδέλες,…και πολλά άλλα. Διαθέτουμε διάφορους τύπους κεφαλής βιδών όπως κεφαλή βύθισης, θόλος, στρογγυλή, φλαντζωτή κεφαλή και διάφορους τύπους βιδωτών όπως σχισμή, φίλιπς, τετράγωνη, εξάγωνη υποδοχή. Ένα RIVET από την άλλη πλευρά είναι ένας μόνιμος μηχανικός συνδετήρας που αποτελείται από έναν λείο κυλινδρικό άξονα και μια κεφαλή αφενός. Μετά την εισαγωγή, το άλλο άκρο του πριτσίνι παραμορφώνεται και η διάμετρός του διευρύνεται ώστε να παραμείνει στη θέση του. Με άλλα λόγια, πριν την τοποθέτηση ένα πριτσίνι έχει μια κεφαλή και μετά την τοποθέτηση έχει δύο. Τοποθετούμε διάφορους τύπους πριτσίνια ανάλογα με την εφαρμογή, την αντοχή, την προσβασιμότητα και το κόστος όπως πριτσίνια συμπαγούς/στρογγυλής κεφαλής, δομικά, ημισωληνωτά, τυφλά, oscar, drive, flush, triction-lock, self-diercing πριτσίνια. Το πριτσίνωμα μπορεί να προτιμηθεί σε περιπτώσεις όπου πρέπει να αποφευχθεί η θερμική παραμόρφωση και η αλλαγή στις ιδιότητες του υλικού λόγω της θερμότητας συγκόλλησης. Το πριτσίνωμα προσφέρει επίσης μικρό βάρος και ιδιαίτερα καλή αντοχή και αντοχή στις δυνάμεις διάτμησης. Ενάντια σε φορτία εφελκυσμού, ωστόσο οι βίδες, τα παξιμάδια και τα μπουλόνια μπορεί να είναι πιο κατάλληλα. Στη διαδικασία CLINCHING χρησιμοποιούμε ειδική διάτρηση και μήτρες για να σχηματίσουμε μια μηχανική ασφάλιση μεταξύ των λαμαρινών που ενώνονται. Η διάτρηση σπρώχνει τα στρώματα της λαμαρίνας στην κοιλότητα της μήτρας και έχει ως αποτέλεσμα το σχηματισμό μιας μόνιμης άρθρωσης. Δεν απαιτείται θέρμανση και ψύξη στο σφίξιμο και είναι μια ψυχρή διαδικασία εργασίας. Είναι μια οικονομική διαδικασία που μπορεί να αντικαταστήσει τη σημειακή συγκόλληση σε ορισμένες περιπτώσεις. Στο PINNING χρησιμοποιούμε καρφίτσες που είναι στοιχεία μηχανής που χρησιμοποιούνται για τη στερέωση θέσεων εξαρτημάτων μηχανής μεταξύ τους. Οι κύριοι τύποι είναι οι ακίδες clevis, οι καρφίτσες με ελατηριωτό πείρο, οι καρφίτσες με πείρο, και σπαστός. Στο STAPLING χρησιμοποιούμε πιστόλια συρραφής και συνδετήρες που είναι συνδετήρες δύο οδόντων που χρησιμοποιούνται για την ένωση ή τη σύνδεση υλικών. Το συρραπτικό έχει τα ακόλουθα πλεονεκτήματα: Οικονομικό, απλό και γρήγορο στη χρήση, η κορώνα των συνδετήρων μπορεί να χρησιμοποιηθεί για τη γεφύρωση υλικών ενωμένα μεταξύ τους, Η κορώνα του συρραπτικού μπορεί να διευκολύνει τη γεφύρωση ενός κομματιού όπως ένα καλώδιο και τη στερέωσή του σε μια επιφάνεια χωρίς τρύπημα ή επιβλαβής, σχετικά εύκολη αφαίρεση. Η PRESS FITTING εκτελείται πιέζοντας εξαρτήματα μεταξύ τους και η τριβή μεταξύ τους στερεώνει τα εξαρτήματα. Τα εξαρτήματα προσαρμογής με πίεση που αποτελούνται από έναν υπερμεγέθη άξονα και μια οπή μικρού μεγέθους συναρμολογούνται γενικά με μία από τις δύο μεθόδους: Είτε εφαρμόζοντας δύναμη είτε εκμεταλλευόμενοι τη θερμική διαστολή ή συστολή των εξαρτημάτων. Όταν ένα εξάρτημα πρέσας δημιουργείται με την εφαρμογή δύναμης, χρησιμοποιούμε είτε μια υδραυλική πρέσα είτε μια χειροκίνητη πρέσα. Από την άλλη πλευρά, όταν η εφαρμογή πρέσας γίνεται με θερμική διαστολή, θερμαίνουμε τα περιβλήματα και τα συναρμολογούμε στη θέση τους όσο είναι ζεστά. Όταν κρυώσουν συστέλλονται και επανέρχονται στις κανονικές τους διαστάσεις. Αυτό έχει ως αποτέλεσμα καλή εφαρμογή στην πρέσα. Αυτό το ονομάζουμε εναλλακτικά ΣΥΡΛΙΚΝΩΣΗ-FITTING. Ο άλλος τρόπος για να το κάνετε αυτό είναι να ψύχετε τα περιβλημένα μέρη πριν από τη συναρμολόγηση και στη συνέχεια να τα σύρετε στα ζευγαρώματά τους. Όταν ζεσταθεί το συγκρότημα διαστέλλονται και έχουμε μια σφιχτή εφαρμογή. Αυτή η τελευταία μέθοδος μπορεί να είναι προτιμότερη σε περιπτώσεις όπου η θέρμανση ενέχει τον κίνδυνο αλλαγής των ιδιοτήτων του υλικού. Η ψύξη είναι ασφαλέστερη σε αυτές τις περιπτώσεις. Πνευματικά & Υδραυλικά Εξαρτήματα και Συγκροτήματα • Βαλβίδες, υδραυλικά και πνευματικά εξαρτήματα όπως δακτύλιος Ο, ροδέλα, στεγανοποιήσεις, φλάντζα, δακτύλιος, στεφάνη. Δεδομένου ότι οι βαλβίδες και τα πνευματικά εξαρτήματα διατίθενται σε μεγάλη ποικιλία, δεν μπορούμε να τα αναφέρουμε όλα εδώ. Ανάλογα με το φυσικό και χημικό περιβάλλον της εφαρμογής σας, έχουμε ειδικά προϊόντα για εσάς. Προσδιορίστε μας την εφαρμογή, τον τύπο του εξαρτήματος, τις προδιαγραφές, τις περιβαλλοντικές συνθήκες, όπως πίεση, θερμοκρασία, υγρά ή αέρια που θα έρθουν σε επαφή με τις βαλβίδες και τα πνευματικά εξαρτήματά σας. και θα επιλέξουμε το πιο κατάλληλο προϊόν για εσάς ή θα το κατασκευάσουμε ειδικά για την εφαρμογή σας. CLICK Product Finder-Locator Service ΠΡΟΗΓΟΥΜΕΝΗ ΣΕΛΙΔΑ
- Rapid Prototyping, Desktop Manufacturing, Additive Manufacturing, FDM
Rapid Prototyping, Desktop Manufacturing, Additive Manufacturing, Stereolithography, Polyjet, Fused Deposition Modeling, Selective Laser Sintering, FDM, SLS Προσθετική και Ταχεία Παραγωγή Τα τελευταία χρόνια παρατηρούμε αύξηση της ζήτησης για ΤΑΧΕΙΑ ΚΑΤΑΣΚΕΥΗ ή ΓΡΗΓΟΡΗ ΠΡΟΤΥΠΟΠΟΙΗΣΗ. Αυτή η διαδικασία μπορεί να ονομάζεται επίσης ΚΑΤΑΣΚΕΥΗ ΕΠΙΦΑΝΕΙΑΣ ή ΚΑΤΑΣΚΕΥΗ ΕΛΕΥΘΕΡΗΣ ΜΟΡΦΗΣ. Βασικά ένα συμπαγές φυσικό μοντέλο ενός εξαρτήματος κατασκευάζεται απευθείας από ένα τρισδιάστατο σχέδιο CAD. Χρησιμοποιούμε τον όρο ΠΡΟΣΘΕΤΙΚΗ ΠΑΡΑΓΩΓΗ για αυτές τις διάφορες τεχνικές όπου κατασκευάζουμε εξαρτήματα σε στρώματα. Χρησιμοποιώντας ενσωματωμένο υλικό και λογισμικό που βασίζεται σε υπολογιστή, εκτελούμε την κατασκευή προσθέτων. Οι τεχνικές ταχείας δημιουργίας πρωτοτύπων και κατασκευής μας είναι η ΣΤΕΡΕΟΛΙΘΟΓΡΑΦΙΑ, η ΠΟΛΥΖΕΤ, η ΜΟΝΤΕΛΟΓΡΑΦΙΑ ΜΕ ΕΝΠΟΘΕΣΗ, η ΕΠΙΛΕΚΤΙΚΗ ΣΥΝΤΗΞΗΣΗ ΜΕ ΛΑΖΕΡ, η ΤΗΚΩΣΗ ΔΕΣΜΩΝ ΗΛΕΚΤΡΟΝΙΩΝ, η ΤΡΙΣΔΙΑΣΤΑΤΙΚΗ ΕΚΤΥΠΩΣΗ, η ΑΜΕΣΗ ΚΑΤΑΣΚΕΥΗ ΚΑΤΑΣΚΕΥΑΣΤΙΚΗ,. Σας συνιστούμε να κάνετε κλικ εδώ για ναΚΑΤΕΒΑΣΤΕ τις Σχηματικές μας απεικονίσεις των Διαδικασιών Κατασκευής Πρόσθετων και Ταχείας Κατασκευής από την AGS-TECH Inc. Αυτό θα σας βοηθήσει να κατανοήσετε καλύτερα τις πληροφορίες που σας παρέχουμε παρακάτω. Η γρήγορη δημιουργία πρωτοτύπων μας παρέχει: 1.) Ο εννοιολογικός σχεδιασμός του προϊόντος προβάλλεται από διαφορετικές οπτικές γωνίες σε μια οθόνη χρησιμοποιώντας ένα σύστημα 3D / CAD. 2.) Πρωτότυπα από μη μεταλλικά και μεταλλικά υλικά κατασκευάζονται και μελετώνται από λειτουργικές, τεχνικές και αισθητικές πτυχές. 3.) Η κατασκευή πρωτοτύπων χαμηλού κόστους σε πολύ σύντομο χρονικό διάστημα ολοκληρώνεται. Η παραγωγή προσθέτων μπορεί να μοιάζει με την κατασκευή ενός καρβέλι ψωμιού στοιβάζοντας και κολλώντας μεμονωμένες φέτες τη μία πάνω στην άλλη. Με άλλα λόγια, το προϊόν κατασκευάζεται φέτα-φέτα ή στρώμα-στρώμα εναποτίθεται το ένα πάνω στο άλλο. Τα περισσότερα εξαρτήματα μπορούν να παραχθούν μέσα σε λίγες ώρες. Η τεχνική είναι καλή εάν τα εξαρτήματα χρειάζονται πολύ γρήγορα ή αν οι ποσότητες που χρειάζονται είναι μικρές και η κατασκευή καλουπιού και εργαλείων είναι πολύ δαπανηρή και απαιτεί χρόνο. Ωστόσο, το κόστος ενός ανταλλακτικού είναι ακριβό λόγω των ακριβών πρώτων υλών. • ΣΤΕΡΕΟΛΙΘΟΓΡΑΦΙΑ : Αυτή η τεχνική που επίσης συντομογραφείται ως STL, βασίζεται στη σκλήρυνση και σκλήρυνση ενός υγρού φωτοπολυμερούς σε ένα συγκεκριμένο σχήμα εστιάζοντας σε αυτό μια δέσμη λέιζερ. Το λέιζερ πολυμερίζει το φωτοπολυμερές και το πολυμερίζει. Με σάρωση της δέσμης λέιζερ υπεριώδους ακτινοβολίας σύμφωνα με το προγραμματισμένο σχήμα κατά μήκος της επιφάνειας του μείγματος φωτοπολυμερούς, το εξάρτημα παράγεται από κάτω προς τα πάνω σε μεμονωμένες φέτες σε καταρράκτη η μία πάνω στην άλλη. Η σάρωση του σημείου λέιζερ επαναλαμβάνεται πολλές φορές για να επιτευχθούν οι γεωμετρίες που έχουν προγραμματιστεί στο σύστημα. Αφού κατασκευαστεί πλήρως το εξάρτημα, αφαιρείται από την πλατφόρμα, στυπώνεται και καθαρίζεται με υπερήχους και με λουτρό αλκοόλης. Στη συνέχεια, εκτίθεται σε ακτινοβολία UV για μερικές ώρες για να βεβαιωθεί ότι το πολυμερές έχει σκληρυνθεί πλήρως και σκληρυνθεί. Για να συνοψίσουμε τη διαδικασία, μια πλατφόρμα που βυθίζεται σε ένα μείγμα φωτοπολυμερούς και μια δέσμη λέιζερ υπεριώδους ακτινοβολίας ελέγχονται και μετακινούνται μέσω ενός συστήματος σερβοελέγχου σύμφωνα με το σχήμα του επιθυμητού εξαρτήματος και το τμήμα λαμβάνεται με φωτοπολυμερισμό του πολυμερούς στρώματος. Φυσικά οι μέγιστες διαστάσεις του παραγόμενου εξαρτήματος καθορίζονται από τον εξοπλισμό στερεολιθογραφίας. • POLYJET : Παρόμοια με την εκτύπωση inkjet, στο polyjet έχουμε οκτώ κεφαλές εκτύπωσης που εναποθέτουν φωτοπολυμερές στον δίσκο κατασκευής. Το υπεριώδες φως που τοποθετείται δίπλα στους πίδακες σκληραίνει αμέσως και σκληραίνει κάθε στρώμα. Δύο υλικά χρησιμοποιούνται στο polyjet. Το πρώτο υλικό είναι για την κατασκευή του πραγματικού μοντέλου. Το δεύτερο υλικό, μια ρητίνη που μοιάζει με γέλη χρησιμοποιείται για στήριξη. Και τα δύο αυτά υλικά εναποτίθενται στρώση προς στρώση και ωριμάζουν ταυτόχρονα. Μετά την ολοκλήρωση του μοντέλου, το υλικό στήριξης αφαιρείται με υδατικό διάλυμα. Οι ρητίνες που χρησιμοποιούνται είναι παρόμοιες με τη στερεολιθογραφία (STL). Το polyjet έχει τα ακόλουθα πλεονεκτήματα έναντι της στερεολιθογραφίας: 1.) Δεν χρειάζεται καθαρισμός εξαρτημάτων. 2.) Δεν χρειάζεται σκλήρυνση μετά τη διαδικασία 3.) Είναι δυνατά μικρότερα πάχη στρώσης και έτσι έχουμε καλύτερη ανάλυση και μπορούμε να κατασκευάσουμε λεπτότερα μέρη. • ΜΟΝΤΕΛΟΠΟΙΗΣΗ ΕΝΤΑΣΗΣ : Επίσης συντομογραφία FDM, σε αυτή τη μέθοδο μια κεφαλή εξώθησης ελεγχόμενη από ρομπότ κινείται σε δύο βασικές κατευθύνσεις πάνω από ένα τραπέζι. Το καλώδιο χαμηλώνει και ανυψώνεται όπως χρειάζεται. Από το στόμιο μιας θερμαινόμενης μήτρας στην κεφαλή, εξωθείται ένα θερμοπλαστικό νήμα και ένα αρχικό στρώμα εναποτίθεται σε μια βάση αφρού. Αυτό επιτυγχάνεται από την κεφαλή του εξωθητή που ακολουθεί μια προκαθορισμένη διαδρομή. Μετά την αρχική στρώση, το τραπέζι χαμηλώνεται και τα επόμενα στρώματα εναποτίθενται το ένα πάνω στο άλλο. Μερικές φορές κατά την κατασκευή ενός περίπλοκου εξαρτήματος, χρειάζονται δομές στήριξης ώστε η εναπόθεση να μπορεί να συνεχιστεί προς ορισμένες κατευθύνσεις. Σε αυτές τις περιπτώσεις, ένα υλικό στήριξης εξωθείται με μια λιγότερο πυκνή απόσταση του νήματος σε ένα στρώμα έτσι ώστε να είναι πιο αδύναμο από το υλικό του μοντέλου. Αυτές οι δομές στήριξης μπορούν αργότερα να διαλυθούν ή να αποκοπούν μετά την ολοκλήρωση του εξαρτήματος. Οι διαστάσεις της μήτρας εξώθησης καθορίζουν το πάχος των εξωθημένων στρωμάτων. Η διαδικασία FDM παράγει εξαρτήματα με κλιμακωτές επιφάνειες σε λοξά εξωτερικά επίπεδα. Εάν αυτή η τραχύτητα είναι απαράδεκτη, μπορεί να χρησιμοποιηθεί χημική στίλβωση με ατμό ή ένα θερμαινόμενο εργαλείο για την εξομάλυνσή τους. Ακόμη και ένα κερί στίλβωσης είναι διαθέσιμο ως υλικό επίστρωσης για την εξάλειψη αυτών των βημάτων και την επίτευξη λογικών γεωμετρικών ανοχών. • SELECTIVE LASER SINTERING : Συμβολίζεται επίσης ως SLS, η διαδικασία βασίζεται στην πυροσυσσωμάτωση ενός πολυμερούς, κεραμικής ή μεταλλικής σκόνης επιλεκτικά σε ένα αντικείμενο. Ο πυθμένας του θαλάμου επεξεργασίας έχει δύο κυλίνδρους: έναν κύλινδρο μερικής κατασκευής και έναν κύλινδρο τροφοδοσίας σκόνης. Το πρώτο χαμηλώνει σταδιακά στο σημείο όπου σχηματίζεται το συντηγμένο τμήμα και το δεύτερο ανυψώνεται σταδιακά για να τροφοδοτήσει σκόνη στον κύλινδρο μερικής κατασκευής μέσω ενός μηχανισμού κυλίνδρου. Πρώτα ένα λεπτό στρώμα σκόνης εναποτίθεται στον κύλινδρο μερικής κατασκευής, στη συνέχεια μια δέσμη λέιζερ εστιάζει σε αυτό το στρώμα, ανιχνεύοντας και λιώνοντας / συντήκοντας μια συγκεκριμένη διατομή, η οποία στη συνέχεια στερεοποιείται ξανά σε στερεό. Η σκόνη είναι περιοχές που δεν χτυπιούνται από τη δέσμη λέιζερ παραμένουν χαλαρές αλλά εξακολουθούν να υποστηρίζουν το συμπαγές τμήμα. Στη συνέχεια εναποτίθεται άλλη μια στρώση σκόνης και η διαδικασία επαναλαμβάνεται πολλές φορές για να ληφθεί το εξάρτημα. Στο τέλος, τα χαλαρά σωματίδια σκόνης ανακινούνται. Όλα αυτά εκτελούνται από έναν υπολογιστή ελέγχου διεργασίας χρησιμοποιώντας οδηγίες που δημιουργούνται από το πρόγραμμα 3D CAD του κατασκευασμένου εξαρτήματος. Μπορούν να εναποτεθούν διάφορα υλικά όπως πολυμερή (όπως ABS, PVC, πολυεστέρας), κερί, μέταλλα και κεραμικά με κατάλληλα συνδετικά πολυμερών. • ELECTRON-BEAM MELTING : Παρόμοια με την επιλεκτική πυροσυσσωμάτωση λέιζερ, αλλά με χρήση δέσμης ηλεκτρονίων για την τήξη σκονών τιτανίου ή χρωμίου κοβαλτίου για την κατασκευή πρωτοτύπων στο κενό. Έχουν γίνει κάποιες εξελίξεις για την εκτέλεση αυτής της διαδικασίας σε ανοξείδωτους χάλυβες, αλουμίνιο και κράματα χαλκού. Εάν πρέπει να αυξηθεί η αντοχή σε κόπωση των παραγόμενων εξαρτημάτων, χρησιμοποιούμε θερμή ισοστατική συμπίεση μετά την κατασκευή εξαρτημάτων ως δευτερεύουσα διαδικασία. • ΤΡΙΣΔΙΑΣΤΑΤΙΚΗ ΕΚΤΥΠΩΣΗ: Υποδηλώνεται επίσης με 3DP, σε αυτήν την τεχνική μια κεφαλή εκτύπωσης εναποθέτει ένα ανόργανο συνδετικό σε ένα στρώμα είτε μη μεταλλικής είτε μεταλλικής σκόνης. Ένα έμβολο που φέρει την κλίνη σκόνης χαμηλώνεται σταδιακά και σε κάθε βήμα το συνδετικό εναποτίθεται στρώμα ανά στρώμα και συντήκεται από το συνδετικό. Τα υλικά σκόνης που χρησιμοποιούνται είναι μείγματα πολυμερών και ινών, άμμος χυτηρίου, μέταλλα. Χρησιμοποιώντας ταυτόχρονα διαφορετικές κεφαλές συνδετήρων και διαφορετικούς χρωματικούς συνδετήρες μπορούμε να αποκτήσουμε διάφορα χρώματα. Η διαδικασία είναι παρόμοια με την εκτύπωση inkjet, αλλά αντί να λάβουμε ένα έγχρωμο φύλλο, λαμβάνουμε ένα έγχρωμο τρισδιάστατο αντικείμενο. Τα παραγόμενα μέρη μπορεί να είναι πορώδη και επομένως μπορεί να απαιτούν πυροσυσσωμάτωση και διείσδυση μετάλλου για να αυξηθεί η πυκνότητα και η αντοχή του. Η πυροσυσσωμάτωση θα κάψει το συνδετικό υλικό και θα λιώσει τις μεταλλικές σκόνες μαζί. Μέταλλα όπως ανοξείδωτος χάλυβας, αλουμίνιο, τιτάνιο μπορούν να χρησιμοποιηθούν για την κατασκευή των εξαρτημάτων και ως υλικά διήθησης χρησιμοποιούμε συνήθως χαλκό και μπρούτζο. Η ομορφιά αυτής της τεχνικής είναι ότι ακόμη και πολύπλοκα και κινούμενα συγκροτήματα μπορούν να κατασκευαστούν πολύ γρήγορα. Για παράδειγμα, ένα συγκρότημα γραναζιών, ένα κλειδί ως εργαλείο μπορεί να κατασκευαστεί και θα έχει κινούμενα και περιστρεφόμενα μέρη έτοιμα για χρήση. Διαφορετικά εξαρτήματα του συγκροτήματος μπορούν να κατασκευαστούν με διαφορετικά χρώματα και όλα σε μία λήψη. Κατεβάστε το φυλλάδιό μας για:Βασικά στοιχεία τρισδιάστατης εκτύπωσης μετάλλων • ΑΜΕΣΗ ΚΑΤΑΣΚΕΥΗ και ΤΑΧΕΙΑ ΕΡΓΑΛΕΙΑ: Εκτός από την αξιολόγηση σχεδιασμού, την αντιμετώπιση προβλημάτων, χρησιμοποιούμε ταχεία δημιουργία πρωτοτύπων για άμεση κατασκευή προϊόντων ή άμεση εφαρμογή σε προϊόντα. Με άλλα λόγια, η ταχεία δημιουργία πρωτοτύπων μπορεί να ενσωματωθεί σε συμβατικές διαδικασίες για να γίνουν καλύτερες και πιο ανταγωνιστικές. Για παράδειγμα, η ταχεία δημιουργία πρωτοτύπων μπορεί να παράγει σχέδια και καλούπια. Μοτίβα ενός πολυμερούς τήξης και καύσης που δημιουργούνται από γρήγορες εργασίες δημιουργίας πρωτοτύπων μπορούν να συναρμολογηθούν για χύτευση επενδύσεων και να επενδυθούν. Ένα άλλο παράδειγμα που πρέπει να αναφέρουμε είναι η χρήση 3DP για την παραγωγή κεραμικού κελύφους χύτευσης και χρήση αυτού για εργασίες χύτευσης κελύφους. Ακόμη και τα καλούπια έγχυσης και τα ένθετα καλουπιών μπορούν να παραχθούν με γρήγορη δημιουργία πρωτοτύπων και μπορεί κανείς να εξοικονομήσει χρόνο παράδοσης για πολλές εβδομάδες ή μήνες. Αναλύοντας μόνο ένα αρχείο CAD του επιθυμητού τμήματος, μπορούμε να παράγουμε τη γεωμετρία του εργαλείου χρησιμοποιώντας λογισμικό. Ακολουθούν μερικές από τις δημοφιλείς μεθόδους ταχείας επεξεργασίας εργαλείων: RTV (Βουλκανισμός σε θερμοκρασία δωματίου) ΧΥΤΟΥΣ / ΧΥΤΩΣΗ ΟΥΡΕΘΑΝΗΣ : Η χρήση ταχείας πρωτοτυποποίησης μπορεί να χρησιμοποιηθεί για την κατασκευή του σχεδίου του επιθυμητού εξαρτήματος. Στη συνέχεια, αυτό το σχέδιο επικαλύπτεται με ένα διαχωριστικό και υγρό καουτσούκ RTV χύνεται πάνω από το σχέδιο για να παραχθούν τα μισά καλούπια. Στη συνέχεια, αυτά τα μισά καλούπια χρησιμοποιούνται για την έγχυση υγρών ουρεθανών καλουπιών. Η διάρκεια ζωής του καλουπιού είναι μικρή, μόνο σαν 0 ή 30 κύκλοι, αλλά αρκετή για παραγωγή μικρής παρτίδας. ACES (Acetal Clear Epoxy Solid) INJECTION MOLDING : Χρησιμοποιώντας τεχνικές ταχείας δημιουργίας πρωτοτύπων όπως η στερεολιθογραφία, παράγουμε καλούπια έγχυσης. Αυτά τα καλούπια είναι κελύφη με ανοιχτό άκρο για να επιτρέπεται η πλήρωση με υλικά όπως εποξειδικά, εποξειδικά γεμισμένα με αλουμίνιο ή μέταλλα. Και πάλι η διάρκεια ζωής του καλουπιού περιορίζεται σε δεκάδες ή το μέγιστο εκατοντάδες μέρη. ΔΙΑΔΙΚΑΣΙΑ ΕΡΓΑΛΕΙΩΣΗΣ ΜΕ ΨΕΚΑΣΜΕΝΟ ΜΕΤΑΛΛΟ: Χρησιμοποιούμε γρήγορη δημιουργία πρωτοτύπων και φτιάχνουμε μοτίβο. Ψεκάζουμε ένα κράμα ψευδαργύρου-αλουμινίου στην επιφάνεια του σχεδίου και το ντύνουμε. Το μοτίβο με τη μεταλλική επίστρωση τοποθετείται στη συνέχεια μέσα σε μια φιάλη και τοποθετείται σε γλάστρα με εποξειδικό ή γεμισμένο με αλουμίνιο εποξειδικό. Τέλος, αφαιρείται και δημιουργώντας δύο τέτοια μισά καλούπια παίρνουμε ένα πλήρες καλούπι για χύτευση με έγχυση. Αυτά τα καλούπια έχουν μεγαλύτερη διάρκεια ζωής, σε ορισμένες περιπτώσεις ανάλογα με το υλικό και τις θερμοκρασίες μπορούν να παράγουν εξαρτήματα σε χιλιάδες. ΔΙΑΔΙΚΑΣΙΑ KEELTOOL: Αυτή η τεχνική μπορεί να παράγει καλούπια με 100.000 έως 10 εκατομμύρια κύκλους ζωής. Χρησιμοποιώντας ταχεία δημιουργία πρωτοτύπων, παράγουμε ένα καλούπι RTV. Στη συνέχεια, το καλούπι γεμίζεται με ένα μείγμα που αποτελείται από σκόνη χάλυβα εργαλείων Α6, καρβίδιο βολφραμίου, συνδετικό πολυμερούς και αφήνεται να σκληρυνθεί. Αυτό το καλούπι στη συνέχεια θερμαίνεται για να καεί το πολυμερές και να λιώσουν οι μεταλλικές σκόνες. Το επόμενο βήμα είναι η διείσδυση χαλκού για την παραγωγή του τελικού καλουπιού. Εάν χρειάζεται, μπορούν να εκτελεστούν δευτερεύουσες εργασίες όπως μηχανική κατεργασία και στίλβωση στο καλούπι για καλύτερες διαστάσεις. _cc781905-5cde-3194-bb3b-136bad_cf5 CLICK Product Finder-Locator Service ΠΡΟΗΓΟΥΜΕΝΗ ΣΕΛΙΔΑ
- Composites, Composite Materials Manufacturing, Fiber Reinforced
Composites, Composite Materials Manufacturing, Particle and Fiber Reinforced, Cermets, Ceramic & Metal Composite, Glass Fiber Reinforced Polymer, Lay-Up Process Βιομηχανία Σύνθετων Υλικών και Σύνθετων Υλικών Με απλά λόγια, τα ΣΥΝΘΕΤΑ ή ΣΥΝΘΕΤΑ ΥΛΙΚΑ είναι υλικά που αποτελούνται από δύο ή πολλαπλά υλικά με διαφορετικές φυσικές ή χημικές ιδιότητες, αλλά όταν συνδυάζονται γίνονται ένα υλικό διαφορετικό από τα συστατικά υλικά. Πρέπει να επισημάνουμε ότι τα συστατικά παραμένουν ξεχωριστά και διακριτά στη δομή. Ο στόχος στην κατασκευή ενός σύνθετου υλικού είναι να ληφθεί ένα προϊόν που να είναι ανώτερο από τα συστατικά του και να συνδυάζει τα επιθυμητά χαρακτηριστικά κάθε συστατικού. Ως παράδειγμα? Η αντοχή, το χαμηλό βάρος ή η χαμηλότερη τιμή μπορεί να είναι το κίνητρο πίσω από το σχεδιασμό και την παραγωγή ενός σύνθετου υλικού. Ο τύπος των σύνθετων υλικών που προσφέρουμε είναι σύνθετα υλικά ενισχυμένα με σωματίδια, σύνθετα σύνθετα ενισχυμένα με ίνες, συμπεριλαμβανομένων σύνθετων υλικών κεραμικής μήτρας / πολυμερούς μήτρας / μήτρας μετάλλου / άνθρακα-άνθρακα / υβριδικών σύνθετων, δομικών & ελασματοποιημένων σύνθετων δομών και σάντουιτς και νανοσύνθετων. Οι τεχνικές κατασκευής που εφαρμόζουμε στην κατασκευή σύνθετων υλικών είναι: Pultrusion, διεργασίες παραγωγής προεμποτισμού, προηγμένη τοποθέτηση ινών, περιέλιξη νήματος, προσαρμοσμένη τοποθέτηση ινών, διαδικασία τοποθέτησης ψεκασμού υαλοβάμβακα, θυσάνιση, διαδικασία lanxide, z-pinning. Πολλά σύνθετα υλικά αποτελούνται από δύο φάσεις, τη μήτρα, η οποία είναι συνεχής και περιβάλλει την άλλη φάση. και η διεσπαρμένη φάση που περιβάλλεται από τη μήτρα. Σας συνιστούμε να κάνετε κλικ εδώ για ναΚΑΤΕΒΑΣΤΕ τις Σχηματικές μας απεικονίσεις Σύνθετων και Σύνθετων Υλικών Κατασκευής από την AGS-TECH Inc. Αυτό θα σας βοηθήσει να κατανοήσετε καλύτερα τις πληροφορίες που σας παρέχουμε παρακάτω. • ΣΥΝΘΕΤΑ ΕΝΙΣΧΥΜΕΝΑ ΜΕ ΣΩΜΑΤΙΔΙΑ: Αυτή η κατηγορία αποτελείται από δύο τύπους: Σύνθετα με μεγάλα σωματίδια και σύνθετα υλικά ενισχυμένα με διασπορά. Στον πρώτο τύπο, οι αλληλεπιδράσεις σωματιδίων-μήτρας δεν μπορούν να αντιμετωπιστούν σε ατομικό ή μοριακό επίπεδο. Αντίθετα, ισχύει η μηχανική συνέχειας. Από την άλλη πλευρά, στα ενισχυμένα με διασπορά σύνθετα σωματίδια είναι γενικά πολύ μικρότερα σε εύρος δεκάδων νανομέτρων. Ένα παράδειγμα σύνθετου υλικού μεγάλων σωματιδίων είναι τα πολυμερή στα οποία έχουν προστεθεί πληρωτικά. Τα πληρωτικά βελτιώνουν τις ιδιότητες του υλικού και μπορεί να αντικαταστήσουν μέρος του όγκου του πολυμερούς με ένα πιο οικονομικό υλικό. Τα κλάσματα όγκου των δύο φάσεων επηρεάζουν τη συμπεριφορά του σύνθετου υλικού. Τα σύνθετα υλικά μεγάλων σωματιδίων χρησιμοποιούνται με μέταλλα, πολυμερή και κεραμικά. Τα CERMETS είναι παραδείγματα σύνθετων κεραμικών / μετάλλων. Το πιο συνηθισμένο κεραμικό μας είναι το καρβίδιο με τσιμέντο. Αποτελείται από πυρίμαχο κεραμικό καρβιδίου όπως σωματίδια καρβιδίου βολφραμίου σε μήτρα μετάλλου όπως το κοβάλτιο ή το νικέλιο. Αυτά τα σύνθετα καρβιδίου χρησιμοποιούνται ευρέως ως εργαλεία κοπής για σκληρυμένο χάλυβα. Τα σωματίδια σκληρού καρβιδίου είναι υπεύθυνα για τη δράση κοπής και η σκληρότητά τους ενισχύεται από την όλκιμο μεταλλική μήτρα. Έτσι αποκτάμε τα πλεονεκτήματα και των δύο υλικών σε ένα μόνο σύνθετο. Ένα άλλο συνηθισμένο παράδειγμα σύνθετου υλικού μεγάλων σωματιδίων που χρησιμοποιούμε είναι τα σωματίδια αιθάλης που αναμιγνύονται με βουλκανισμένο καουτσούκ για να ληφθεί ένα σύνθετο υλικό με υψηλή αντοχή σε εφελκυσμό, σκληρότητα, αντοχή σε σχίσιμο και τριβή. Ένα παράδειγμα σύνθετου υλικού ενισχυμένου με διασπορά είναι μέταλλα και κράματα μετάλλων που ενισχύονται και σκληρύνονται από την ομοιόμορφη διασπορά λεπτών σωματιδίων ενός πολύ σκληρού και αδρανούς υλικού. Όταν προστίθενται πολύ μικρές νιφάδες οξειδίου του αλουμινίου στη μεταλλική μήτρα αλουμινίου, λαμβάνουμε πυροσυσσωματωμένη σκόνη αλουμινίου που έχει ενισχυμένη αντοχή σε υψηλή θερμοκρασία. • ΣΥΝΘΕΤΑ ΕΝΙΣΧΥΜΕΝΑ ΜΕ ΙΝΕΣ: Αυτή η κατηγορία σύνθετων υλικών είναι στην πραγματικότητα η πιο σημαντική. Ο στόχος που πρέπει να επιτευχθεί είναι η υψηλή αντοχή και ακαμψία ανά μονάδα βάρους. Η σύνθεση, το μήκος, ο προσανατολισμός και η συγκέντρωση των ινών σε αυτά τα σύνθετα υλικά είναι κρίσιμα για τον προσδιορισμό των ιδιοτήτων και της χρησιμότητας αυτών των υλικών. Υπάρχουν τρεις ομάδες ινών που χρησιμοποιούμε: μουστάκια, ίνες και σύρματα. Τα μουστάκια είναι πολύ λεπτά και μακριά μονοκρύσταλλα. Είναι από τα πιο δυνατά υλικά. Μερικά παραδείγματα υλικών μουστάκι είναι ο γραφίτης, το νιτρίδιο του πυριτίου, το οξείδιο του αλουμινίου. Οι FIBERS από την άλλη πλευρά είναι κυρίως πολυμερή ή κεραμικά και βρίσκονται σε πολυκρυσταλλική ή άμορφη κατάσταση. Η τρίτη ομάδα είναι τα λεπτά ΣΥΡΜΑΤΑ που έχουν σχετικά μεγάλες διαμέτρους και αποτελούνται συχνά από χάλυβα ή βολφράμιο. Ένα παράδειγμα σύνθετου ενισχυμένου με σύρμα είναι τα ελαστικά αυτοκινήτων που ενσωματώνουν χαλύβδινο σύρμα μέσα σε καουτσούκ. Ανάλογα με το υλικό της μήτρας, έχουμε τα ακόλουθα σύνθετα: ΣΥΝΘΕΤΑ ΠΟΛΥΜΕΡΗ-ΜΕΤΡΙΞ: Κατασκευάζονται από πολυμερή ρητίνη και ίνες ως ενισχυτικό συστατικό. Μια υποομάδα αυτών που ονομάζονται Σύνθετα Πολυμερή Ενισχυμένα με Ίνες Γυαλιού (GFRP) περιέχουν συνεχείς ή ασυνεχείς ίνες γυαλιού μέσα σε μια πολυμερή μήτρα. Το γυαλί προσφέρει υψηλή αντοχή, είναι οικονομικό, εύκολο στην κατασκευή ινών και είναι χημικά αδρανές. Τα μειονεκτήματα είναι η περιορισμένη ακαμψία και ακαμψία τους, καθώς οι θερμοκρασίες σέρβις είναι μόνο μέχρι 200 – 300 Κελσίου. Το Fiberglass είναι κατάλληλο για αμαξώματα και εξοπλισμό μεταφοράς αυτοκινήτων, αμαξώματα θαλάσσιων οχημάτων, δοχεία αποθήκευσης. Δεν είναι κατάλληλα για αεροδιαστημική ή κατασκευή γεφυρών λόγω περιορισμένης ακαμψίας. Η άλλη υποομάδα ονομάζεται σύνθετο πολυμερές ενισχυμένο με ίνες άνθρακα (CFRP). Εδώ, ο άνθρακας είναι το ινώδες υλικό μας στη μήτρα του πολυμερούς. Ο άνθρακας είναι γνωστός για το υψηλό ειδικό μέτρο και την αντοχή του και την ικανότητά του να τα διατηρεί σε υψηλές θερμοκρασίες. Οι ίνες άνθρακα μπορούν να μας προσφέρουν στάνταρ, ενδιάμεσους, υψηλούς και υπερυψηλούς συντελεστές εφελκυσμού. Επιπλέον, οι ίνες άνθρακα προσφέρουν ποικίλα φυσικά και μηχανικά χαρακτηριστικά και επομένως είναι κατάλληλα για διάφορες προσαρμοσμένες εφαρμογές μηχανικής. Τα σύνθετα υλικά CFRP μπορούν να θεωρηθούν ότι κατασκευάζουν αθλητικό και ψυχαγωγικό εξοπλισμό, δοχεία πίεσης και δομικά στοιχεία της αεροδιαστημικής. Ωστόσο, μια άλλη υποομάδα, τα σύνθετα πολυμερή ενισχυμένα με ίνες Aramid είναι επίσης υλικά υψηλής αντοχής και συντελεστή μέτρησης. Οι αναλογίες αντοχής προς βάρος τους είναι εξαιρετικά υψηλές. Οι ίνες αραμιδίου είναι επίσης γνωστές με τις εμπορικές ονομασίες KEVLAR και NOMEX. Υπό τάνυση αποδίδουν καλύτερα από άλλα υλικά πολυμερών ινών, αλλά είναι αδύναμα στη συμπίεση. Οι ίνες αραμιδίου είναι σκληρές, ανθεκτικές στην κρούση, ανθεκτικές σε ερπυσμό και κόπωση, σταθερές σε υψηλές θερμοκρασίες, χημικά αδρανείς εκτός από ισχυρά οξέα και βάσεις. Οι ίνες αραμιδίου χρησιμοποιούνται ευρέως σε αθλητικά είδη, αλεξίσφαιρα γιλέκα, ελαστικά, σχοινιά, καλύμματα καλωδίων οπτικών ινών. Υπάρχουν και άλλα υλικά ενίσχυσης ινών, αλλά χρησιμοποιούνται σε μικρότερο βαθμό. Αυτά είναι κυρίως το βόριο, το καρβίδιο του πυριτίου, το οξείδιο του αργιλίου. Το υλικό πολυμερούς μήτρας από την άλλη πλευρά είναι επίσης κρίσιμο. Καθορίζει τη μέγιστη θερμοκρασία λειτουργίας του σύνθετου υλικού επειδή το πολυμερές έχει γενικά χαμηλότερη θερμοκρασία τήξης και αποδόμησης. Οι πολυεστέρες και οι βινυλεστέρες χρησιμοποιούνται ευρέως ως πολυμερής μήτρα. Χρησιμοποιούνται επίσης ρητίνες και έχουν εξαιρετική αντοχή στην υγρασία και μηχανικές ιδιότητες. Για παράδειγμα, η ρητίνη πολυιμιδίου μπορεί να χρησιμοποιηθεί μέχρι περίπου 230 βαθμούς Κελσίου. ΣΥΝΘΕΤΑ ΜΕΤΑΛΛΩΝ-ΜΗΤΡΩΝ: Σε αυτά τα υλικά χρησιμοποιούμε όλκιμο μεταλλικό πλέγμα και οι θερμοκρασίες συντήρησης είναι γενικά υψηλότερες από τα συστατικά τους. Σε σύγκριση με τα σύνθετα υλικά πολυμερούς μήτρας, αυτά μπορεί να έχουν υψηλότερες θερμοκρασίες λειτουργίας, να είναι άφλεκτα και μπορεί να έχουν καλύτερη αντοχή στην αποικοδόμηση έναντι οργανικών ρευστών. Ωστόσο είναι πιο ακριβά. Υλικά ενίσχυσης όπως μουστάκια, σωματίδια, συνεχείς και ασυνεχείς ίνες. και υλικά μήτρας όπως χαλκός, αλουμίνιο, μαγνήσιο, τιτάνιο, υπερκράματα χρησιμοποιούνται συνήθως. Παραδείγματα εφαρμογών είναι εξαρτήματα κινητήρα κατασκευασμένα από μήτρα κράματος αλουμινίου ενισχυμένη με οξείδιο αλουμινίου και ίνες άνθρακα. ΣΥΝΘΕΤΑ ΚΕΡΑΜΙΚΩΝ ΜΗΤΡΩΝ: Τα κεραμικά υλικά είναι γνωστά για την εξαιρετικά καλή αξιοπιστία τους σε υψηλές θερμοκρασίες. Ωστόσο, είναι πολύ εύθραυστα και έχουν χαμηλές τιμές αντοχής σε θραύση. Ενσωματώνοντας σωματίδια, ίνες ή μουστάκια ενός κεραμικού στη μήτρα ενός άλλου, είμαστε σε θέση να επιτύχουμε σύνθετα υλικά με υψηλότερη αντοχή στη θραύση. Αυτά τα ενσωματωμένα υλικά αναστέλλουν βασικά τη διάδοση ρωγμών μέσα στη μήτρα με ορισμένους μηχανισμούς όπως η εκτροπή των άκρων των ρωγμών ή ο σχηματισμός γεφυρών στις επιφάνειες των ρωγμών. Για παράδειγμα, οι αλουμίνες που είναι ενισχυμένες με μουστάκια SiC χρησιμοποιούνται ως ένθετα κοπτικών εργαλείων για την κατεργασία σκληρών κραμάτων μετάλλων. Αυτά μπορούν να αποκαλύψουν καλύτερες επιδόσεις σε σύγκριση με τα καρβίδια με τσιμέντο. ΣΥΝΘΕΤΑ ΑΝΘΡΑΚΑ-ΑΝΘΡΑΚΑ: Τόσο ο οπλισμός όσο και η μήτρα είναι άνθρακας. Έχουν υψηλά συντελεστές εφελκυσμού και αντοχές σε υψηλές θερμοκρασίες άνω των 2000 Κελσίου, αντοχή σε ερπυσμό, υψηλές σκληρότητες θραύσης, χαμηλούς συντελεστές θερμικής διαστολής, υψηλή θερμική αγωγιμότητα. Αυτές οι ιδιότητες τα καθιστούν ιδανικά για εφαρμογές που απαιτούν αντοχή σε θερμικό σοκ. Ωστόσο, η αδυναμία των σύνθετων υλικών άνθρακα-άνθρακα είναι η ευαισθησία τους έναντι της οξείδωσης σε υψηλές θερμοκρασίες. Τυπικά παραδείγματα χρήσης είναι καλούπια θερμής πίεσης, προηγμένη κατασκευή εξαρτημάτων κινητήρα στροβίλου. ΥΒΡΙΔΙΚΑ ΣΥΝΘΕΤΑ : Δύο ή περισσότεροι διαφορετικοί τύποι ινών αναμειγνύονται σε μια ενιαία μήτρα. Μπορεί κανείς έτσι να προσαρμόσει ένα νέο υλικό με συνδυασμό ιδιοτήτων. Ένα παράδειγμα είναι όταν τόσο οι ίνες άνθρακα όσο και οι ίνες γυαλιού ενσωματώνονται σε μια πολυμερή ρητίνη. Οι ίνες άνθρακα παρέχουν ακαμψία και αντοχή χαμηλής πυκνότητας αλλά είναι ακριβές. Το γυαλί από την άλλη είναι φθηνό αλλά δεν έχει την ακαμψία των ινών άνθρακα. Το υβριδικό σύνθετο γυαλί-άνθρακα είναι ισχυρότερο και πιο σκληρό και μπορεί να κατασκευαστεί με χαμηλότερο κόστος. ΕΠΕΞΕΡΓΑΣΙΑ ΣΥΝΘΕΤΩΝ ΕΝΙΣΧΥΜΕΝΩΝ ΜΕ ΙΝΕΣ : Για συνεχή πλαστικά ενισχυμένα με ίνες με ομοιόμορφα κατανεμημένες ίνες προσανατολισμένες προς την ίδια κατεύθυνση χρησιμοποιούμε τις ακόλουθες τεχνικές. PULTRUSION: Κατασκευάζονται ράβδοι, δοκοί και σωλήνες συνεχών μηκών και σταθερών διατομών. Οι συνεχείς περιστροφές ινών εμποτίζονται με μια θερμοσκληρυνόμενη ρητίνη και έλκονται μέσω μιας μήτρας χάλυβα για να προδιαμορφωθούν στο επιθυμητό σχήμα. Στη συνέχεια, περνούν μέσα από μια μήτρα ωρίμανσης επεξεργασμένης ακριβείας για να αποκτήσουν το τελικό της σχήμα. Εφόσον η μήτρα ωρίμανσης θερμαίνεται, σκληραίνει τη μήτρα της ρητίνης. Οι εξολκείς τραβούν το υλικό μέσα από τις μήτρες. Χρησιμοποιώντας εισαγόμενους κοίλους πυρήνες, μπορούμε να αποκτήσουμε σωλήνες και κοίλες γεωμετρίες. Η μέθοδος pultrusion είναι αυτοματοποιημένη και μας προσφέρει υψηλούς ρυθμούς παραγωγής. Είναι δυνατό να παραχθεί οποιοδήποτε μήκος προϊόντος. ΔΙΑΔΙΚΑΣΙΑ ΠΑΡΑΓΩΓΗΣ PREPREG: Το Prepreg είναι μια ενίσχυση συνεχών ινών προεμποτισμένη με μια μερικώς σκληρυμένη πολυμερή ρητίνη. Χρησιμοποιείται ευρέως για δομικές εφαρμογές. Το υλικό έρχεται σε μορφή ταινίας και αποστέλλεται ως ταινία. Ο κατασκευαστής το καλουπώνει απευθείας και το πολυμερίζει πλήρως χωρίς να χρειάζεται να προσθέσει ρητίνη. Δεδομένου ότι τα προεμποτίσματα υφίστανται αντιδράσεις ωρίμανσης σε θερμοκρασίες δωματίου, αποθηκεύονται σε θερμοκρασίες 0 C ή χαμηλότερες. Μετά τη χρήση, οι υπόλοιπες ταινίες αποθηκεύονται ξανά σε χαμηλές θερμοκρασίες. Χρησιμοποιούνται θερμοπλαστικές και θερμοσκληρυνόμενες ρητίνες και κοινές είναι οι ενισχυτικές ίνες άνθρακα, αραμιδίου και γυαλιού. Για τη χρήση προεμποτισμάτων, αφαιρείται πρώτα το χαρτί στήριξης φορέα και στη συνέχεια η κατασκευή πραγματοποιείται με την τοποθέτηση της ταινίας προεμποτισμού σε μια εργαλειοθήκη (διαδικασία τοποθέτησης). Μπορούν να τοποθετηθούν πολλές πτυχές για να ληφθούν τα επιθυμητά πάχη. Συχνή πρακτική είναι να εναλλάσσετε τον προσανατολισμό της ίνας για να δημιουργήσετε ένα πολυστρωματικό υλικό με σταυρωτά ή γωνιακά φύλλα. Τέλος εφαρμόζεται θερμότητα και πίεση για σκλήρυνση. Τόσο η χειροκίνητη επεξεργασία όσο και οι αυτοματοποιημένες διεργασίες χρησιμοποιούνται για την κοπή προεμποτισμού και το lay-up. ΤΥΛΙΣΗ ΝΗΜΑΤΟΣ: Οι συνεχείς ενισχυτικές ίνες τοποθετούνται με ακρίβεια σε ένα προκαθορισμένο σχέδιο ώστε να ακολουθούν ένα κοίλο και συνήθως κυκλινδρικό σχήμα. Οι ίνες περνούν πρώτα από ένα λουτρό ρητίνης και στη συνέχεια τυλίγονται σε έναν άξονα με ένα αυτοματοποιημένο σύστημα. Μετά από αρκετές επαναλήψεις περιέλιξης επιτυγχάνονται τα επιθυμητά πάχη και η σκλήρυνση πραγματοποιείται είτε σε θερμοκρασία δωματίου είτε μέσα σε φούρνο. Τώρα αφαιρείται ο άξονας και το προϊόν ξεκαλουπώνεται. Η περιέλιξη του νήματος μπορεί να προσφέρει πολύ υψηλές αναλογίες αντοχής προς βάρος τυλίγοντας τις ίνες σε περιφερειακά, ελικοειδή και πολικά σχέδια. Οι σωλήνες, οι δεξαμενές, τα περιβλήματα κατασκευάζονται με αυτήν την τεχνική. • ΔΟΜΙΚΑ ΣΥΝΘΕΤΑ : Γενικά αποτελούνται από ομοιογενή και σύνθετα υλικά. Επομένως οι ιδιότητες αυτών καθορίζονται από τα συστατικά υλικά και τη γεωμετρική σχεδίαση των στοιχείων του. Εδώ είναι οι κύριοι τύποι: LAMINAR COMPOSITES : Αυτά τα δομικά υλικά είναι κατασκευασμένα από δισδιάστατα φύλλα ή πάνελ με προτιμώμενες κατευθύνσεις υψηλής αντοχής. Τα στρώματα στοιβάζονται και τσιμεντώνονται μεταξύ τους. Εναλλάσσοντας τις διευθύνσεις υψηλής αντοχής στους δύο κάθετους άξονες, παίρνουμε ένα σύνθετο που έχει υψηλή αντοχή και στις δύο κατευθύνσεις στο δισδιάστατο επίπεδο. Ρυθμίζοντας τις γωνίες των στρωμάτων μπορεί κανείς να κατασκευάσει ένα σύνθετο υλικό με αντοχή στις προτιμώμενες κατευθύνσεις. Το σύγχρονο σκι κατασκευάζεται με αυτόν τον τρόπο. ΠΑΝΕΛ ΣΑΝΤΟΥΙΤΣ: Αυτά τα δομικά σύνθετα είναι ελαφριά αλλά έχουν όμως υψηλή ακαμψία και αντοχή. Τα πάνελ σάντουιτς αποτελούνται από δύο εξωτερικά φύλλα κατασκευασμένα από άκαμπτο και ισχυρό υλικό όπως κράματα αλουμινίου, πλαστικά ενισχυμένα με ίνες ή χάλυβας και έναν πυρήνα ανάμεσα στα εξωτερικά φύλλα. Ο πυρήνας πρέπει να είναι ελαφρύς και τις περισσότερες φορές να έχει χαμηλό συντελεστή ελαστικότητας. Δημοφιλή υλικά πυρήνα είναι οι άκαμπτοι πολυμερικοί αφροί, το ξύλο και οι κηρήθρες. Τα πάνελ σάντουιτς χρησιμοποιούνται ευρέως στον κατασκευαστικό κλάδο ως υλικό στέγης, υλικό δαπέδου ή τοίχου, καθώς και στην αεροδιαστημική βιομηχανία. • ΝΑΝΟΣΥΝΘΕΤΑ : Αυτά τα νέα υλικά αποτελούνται από σωματίδια νανομεγέθους ενσωματωμένα σε μια μήτρα. Χρησιμοποιώντας νανοσύνθετα υλικά μπορούμε να κατασκευάσουμε ελαστικά υλικά που είναι πολύ καλά εμπόδια στη διείσδυση του αέρα, διατηρώντας παράλληλα αμετάβλητες τις ιδιότητες του καουτσούκ. CLICK Product Finder-Locator Service ΠΡΟΗΓΟΥΜΕΝΗ ΣΕΛΙΔΑ
- Machine Elements Manufacturing, Gears, Gear Drives, Bearings, Keys, Splines
Machine Elements Manufacturing, Gears, Gear Drives, Bearings, Keys, Splines, Pins, Shafts, Seals, Fasteners, Clutch, Cams, Followers, Belts, Couplings, Shafts Κατασκευή στοιχείων μηχανών Διαβάστε περισσότερα Ιμάντες & αλυσίδες & Συγκρότημα κίνησης καλωδίων Διαβάστε περισσότερα Συγκρότημα Gears & Gear Driver Διαβάστε περισσότερα Κατασκευή συνδέσμων & ρουλεμάν Διαβάστε περισσότερα Βιομηχανία κλειδιών & σφηνών & καρφιτσών Διαβάστε περισσότερα Κατασκευή κάμερας & ακολούθων & συνδέσμων & τροχών καστάνιας Διαβάστε περισσότερα Κατασκευή αξόνων Διαβάστε περισσότερα Κατασκευή μηχανικών σφραγίδων Διαβάστε περισσότερα Συναρμολόγηση συμπλέκτη & φρένων Διαβάστε περισσότερα Κατασκευή συνδετήρων Διαβάστε περισσότερα Συναρμολόγηση απλών μηχανών MACHINE ELEMENTS είναι στοιχειώδη στοιχεία μιας μηχανής. Αυτά τα στοιχεία αποτελούνται από τρεις βασικούς τύπους: 1.) Δομικά εξαρτήματα συμπεριλαμβανομένων των μελών πλαισίου, των ρουλεμάν, των αξόνων, των σφηνών, των συνδετήρων, των σφραγίδων και των λιπαντικών. 2.) Μηχανισμοί που ελέγχουν την κίνηση με διάφορους τρόπους, όπως συρμούς ταχυτήτων, ιμάντα ή αλυσίδες, συνδέσεις, συστήματα έκκεντρου και ακολούθων, φρένα και συμπλέκτες. 3.) Έλεγχος στοιχείων όπως κουμπιά, διακόπτες, ενδείξεις, αισθητήρες, ενεργοποιητές και ελεγκτές υπολογιστών. Τα περισσότερα από τα στοιχεία μηχανής που σας προσφέρουμε είναι τυποποιημένα σε κοινά μεγέθη, αλλά τα ειδικά κατασκευασμένα στοιχεία μηχανής είναι επίσης διαθέσιμα για τις εξειδικευμένες εφαρμογές σας. Η προσαρμογή των στοιχείων μηχανής μπορεί να πραγματοποιηθεί σε υπάρχοντα σχέδια που βρίσκονται στους καταλόγους μας με δυνατότητα λήψης ή σε ολοκαίνουργια σχέδια. Η δημιουργία πρωτοτύπων και η κατασκευή στοιχείων μηχανής μπορεί να συνεχιστεί μόλις εγκριθεί ένα σχέδιο και από τα δύο μέρη. Εάν πρέπει να σχεδιαστούν και να κατασκευαστούν νέα στοιχεία μηχανής, οι πελάτες μας είτε μας στέλνουν με email τα δικά τους σχεδιαγράμματα και τα εξετάζουμε για έγκριση ή μας ζητούν να σχεδιάσουμε στοιχεία μηχανής για την εφαρμογή τους. Στην τελευταία περίπτωση χρησιμοποιούμε όλα τα στοιχεία από τους πελάτες μας και σχεδιάζουμε τα στοιχεία του μηχανήματος και αποστέλλουμε τα τελικά σχέδια στους πελάτες μας για έγκριση. Μόλις εγκριθεί, παράγουμε τα πρώτα προϊόντα και στη συνέχεια κατασκευάζουμε τα στοιχεία του μηχανήματος σύμφωνα με τον τελικό σχεδιασμό. Σε οποιοδήποτε στάδιο αυτής της εργασίας, σε περίπτωση που ένα συγκεκριμένο σχέδιο στοιχείου μηχανής δεν αποδώσει ικανοποιητικά στο πεδίο (κάτι που είναι σπάνιο), εξετάζουμε ολόκληρο το έργο και κάνουμε αλλαγές από κοινού με τους πελάτες μας, όπως απαιτείται. Αποτελεί συνήθη πρακτική μας να υπογράφουμε συμφωνίες μη αποκάλυψης (NDA) με τους πελάτες μας για το σχεδιασμό στοιχείων μηχανής ή οποιουδήποτε άλλου προϊόντος όποτε χρειάζεται ή απαιτείται. Μόλις σχεδιαστούν και κατασκευαστούν κατά παραγγελία τα στοιχεία μηχανής για έναν συγκεκριμένο πελάτη, του εκχωρούμε έναν κωδικό προϊόντος και τα παράγουμε και τα πουλάμε μόνο στον πελάτη μας στον οποίο ανήκει το προϊόν. Αναπαράγουμε τα στοιχεία του μηχανήματος χρησιμοποιώντας τα αναπτυγμένα εργαλεία, τα καλούπια και τις διαδικασίες όσες φορές χρειάζεται και όποτε ο πελάτης μας τα ξαναπαραγγείλει. Με άλλα λόγια, μόλις σχεδιαστεί και παραχθεί ένα προσαρμοσμένο στοιχείο μηχανής για εσάς, η πνευματική ιδιοκτησία καθώς και όλα τα εργαλεία και τα καλούπια δεσμεύονται και αποθηκεύονται επ' αόριστον από εμάς για εσάς και τα προϊόντα που αναπαράγονται όπως θέλετε. Προσφέρουμε επίσης στους πελάτες μας υπηρεσίες μηχανικής συνδυάζοντας δημιουργικά στοιχεία μηχανής σε ένα εξάρτημα ή συγκρότημα που εξυπηρετεί μια εφαρμογή και ανταποκρίνεται ή υπερβαίνει τις προσδοκίες των πελατών μας. Τα εργοστάσια που κατασκευάζουν τα στοιχεία του μηχανήματος μας έχουν πιστοποιηθεί είτε με ISO9001, QS9000 ή TS16949. Επιπλέον, τα περισσότερα από τα προϊόντα μας έχουν σήμα CE ή UL και πληρούν τα διεθνή σχετικά πρότυπα όπως ISO, SAE, ASME, DIN. Κάντε κλικ στα υπομενού για να λάβετε λεπτομερείς πληροφορίες σχετικά με τα στοιχεία του μηχανήματος μας, όπως: - Ζώνες, αλυσίδες και μηχανισμοί καλωδίων - Gears και Gear Drives - Συνδέσεις & Ρουλεμάν - Κλειδιά & Splines & καρφίτσες - Κάμερες & Συνδέσεις - Άξονες - Μηχανικές σφραγίδες - Βιομηχανικός συμπλέκτης & φρένο - Συνδετήρες - Απλές μηχανές Έχουμε ετοιμάσει ένα φυλλάδιο αναφοράς για τους πελάτες μας, τους σχεδιαστές και τους προγραμματιστές νέων προϊόντων, συμπεριλαμβανομένων στοιχείων μηχανής. Μπορείτε να εξοικειωθείτε με ορισμένους όρους που χρησιμοποιούνται συνήθως στο σχεδιασμό εξαρτημάτων μηχανής: Κατεβάστε το φυλλάδιο για τους Κοινούς Όρους Μηχανολόγων Μηχανικών που χρησιμοποιούνται από Σχεδιαστές και Μηχανικούς Τα μηχανήματα μας βρίσκουν εφαρμογές σε διάφορους τομείς όπως βιομηχανικά μηχανήματα, συστήματα αυτοματισμού, εξοπλισμός δοκιμών και μετρολογίας, εξοπλισμός μεταφοράς, μηχανές κατασκευής και σχεδόν οπουδήποτε μπορείτε να σκεφτείτε. Η AGS-TECH αναπτύσσει και κατασκευάζει στοιχεία μηχανής από διάφορα υλικά ανάλογα με την εφαρμογή. Τα υλικά που χρησιμοποιούνται για τα στοιχεία της μηχανής μπορεί να κυμαίνονται από χυτευμένα πλαστικά που χρησιμοποιούνται για παιχνίδια έως σκληρυμένο και ειδικά επικαλυμμένο χάλυβα για βιομηχανικά μηχανήματα. Οι σχεδιαστές μας χρησιμοποιούν επαγγελματικό λογισμικό τελευταίας τεχνολογίας και εργαλεία σχεδίασης για την ανάπτυξη στοιχείων μηχανής, λαμβάνοντας υπόψη λεπτομέρειες όπως γωνίες στα δόντια του γραναζιού, καταπονήσεις, ποσοστά φθοράς... κ.λπ. Κάντε κύλιση στα υπομενού μας και κατεβάστε τα φυλλάδια και τους καταλόγους των προϊόντων μας για να δείτε εάν μπορείτε να εντοπίσετε στοιχεία μηχανής εκτός ραφιού για την εφαρμογή σας. Εάν δεν μπορείτε να βρείτε ένα καλό ταίρι για την αίτησή σας, ενημερώστε μας και θα συνεργαστούμε μαζί σας για την ανάπτυξη και την κατασκευή στοιχείων μηχανής που θα ικανοποιούν τις ανάγκες σας. Εάν ενδιαφέρεστε κυρίως για τις δυνατότητες μηχανικής και έρευνας και ανάπτυξης αντί για τις δυνατότητες παραγωγής, τότε σας προσκαλούμε να επισκεφτείτε τον ιστότοπό μας http://www.ags-engineering.com όπου μπορείτε να βρείτε πιο λεπτομερείς πληροφορίες σχετικά με το σχεδιασμό, την ανάπτυξη προϊόντων, την ανάπτυξη διαδικασιών, τις συμβουλευτικές υπηρεσίες μηχανικής και άλλα CLICK Product Finder-Locator Service ΠΡΟΗΓΟΥΜΕΝΗ ΣΕΛΙΔΑ
- Glass and Ceramic Manufacturing, Hermetic Packages, Seals, Bonding
Glass and Ceramic Manufacturing, Hermetic Packages Seals and Bonding, Tempered Bulletproof Glass, Blow Moulding, Optical Grade Glass, Conductive Glass, Molding Μορφοποίηση & Διαμόρφωση Γυαλιού & Κεραμικού Ο τύπος κατασκευής γυαλιού που προσφέρουμε είναι γυαλί δοχείων, εμφύσηση γυαλιού, ίνες και σωλήνες και ράβδοι υάλου, οικιακά και βιομηχανικά γυάλινα σκεύη, λαμπτήρες και λαμπτήρες, χύτευση γυαλιού ακριβείας, οπτικά εξαρτήματα και συγκροτήματα, επίπεδοι υαλοπίνακες και υαλοπίνακες. Εκτελούμε τόσο τη μορφοποίηση με το χέρι όσο και τη διαμόρφωση μηχανών. Οι δημοφιλείς τεχνικές μας διαδικασίες κατασκευής κεραμικών είναι η συμπίεση, η ισοστατική συμπίεση, η θερμή ισοστατική συμπίεση, η θερμή συμπίεση, η χύτευση με ολίσθηση, η χύτευση ταινίας, η εξώθηση, η χύτευση με έγχυση, η πράσινη κατεργασία, η πυροσυσσωμάτωση ή το ψήσιμο, η λείανση διαμαντιών, τα ερμητικά συγκροτήματα. Σας συνιστούμε να κάνετε κλικ εδώ για να ΚΑΤΕΒΑΣΤΕ τις Σχηματικές απεικονίσεις Διαδικασιών Μορφοποίησης και Διαμόρφωσης Γυαλιού από την AGS-TECH Inc. ΚΑΤΕΒΑΣΤΕ τις Σχηματικές μας απεικονίσεις των Τεχνικών Διαδικασιών Κατασκευής Κεραμικών από την AGS-TECH Inc. Αυτά τα αρχεία με δυνατότητα λήψης με φωτογραφίες και σκίτσα θα σας βοηθήσουν να κατανοήσετε καλύτερα τις πληροφορίες που σας παρέχουμε παρακάτω. • ΚΑΤΑΣΚΕΥΗ ΓΥΑΛΙΩΝ ΔΟΧΕΙΩΝ: Διαθέτουμε αυτοματοποιημένες γραμμές PRESS AND BLOW καθώς και γραμμές BLOW AND BLOW για κατασκευή. Στη διαδικασία του φυσήματος και του φυσήματος ρίχνουμε μια σβούρα σε κενή φόρμα και σχηματίζουμε το λαιμό εφαρμόζοντας ένα χτύπημα πεπιεσμένου αέρα από την κορυφή. Αμέσως μετά από αυτό, ο πεπιεσμένος αέρας διοχετεύεται για δεύτερη φορά από την άλλη κατεύθυνση μέσω του λαιμού του δοχείου για να σχηματίσει την προ-μορφή της φιάλης. Αυτή η προ-φόρμα στη συνέχεια μεταφέρεται στο πραγματικό καλούπι, ξαναθερμαίνεται για να μαλακώσει και εφαρμόζεται συμπιεσμένος αέρας για να δώσει στην προ-φόρμα το τελικό της σχήμα δοχείου. Πιο συγκεκριμένα, πιέζεται και πιέζεται στα τοιχώματα της κοιλότητας του καλουπιού εμφύσησης για να πάρει το επιθυμητό σχήμα. Τέλος, το κατασκευασμένο γυάλινο δοχείο μεταφέρεται σε φούρνο ανόπτησης για επακόλουθη επαναθέρμανση και αφαίρεση των τάσεων που παράγονται κατά τη χύτευση και ψύχεται με ελεγχόμενο τρόπο. Στη μέθοδο της πρέσας και εμφύσησης, οι λιωμένοι σβώλοι τοποθετούνται σε ένα καλούπι parison (κενό καλούπι) και συμπιέζονται στο σχήμα parison (κενό σχήμα). Τα κενά στη συνέχεια μεταφέρονται σε καλούπια εμφύσησης και φυσούνται παρόμοια με τη διαδικασία που περιγράφεται παραπάνω στην ενότητα «Διαδικασία εμφύσησης και φυσήματος». Τα επόμενα βήματα όπως η ανόπτηση και η ανακούφιση από το στρες είναι παρόμοια ή ίδια. • ΦΥΣΗΣΗ ΓΥΑΛΙΟΥ: Κατασκευάζουμε προϊόντα γυαλιού χρησιμοποιώντας συμβατικό φύσημα με το χέρι καθώς και χρησιμοποιώντας πεπιεσμένο αέρα με αυτοματοποιημένο εξοπλισμό. Για ορισμένες παραγγελίες είναι απαραίτητο το συμβατικό φύσημα, όπως έργα που περιλαμβάνουν έργα τέχνης από γυαλί ή έργα που απαιτούν μικρότερο αριθμό εξαρτημάτων με χαλαρές ανοχές, πρωτότυπα / έργα επίδειξης… κ.λπ. Το συμβατικό φύσημα γυαλιού περιλαμβάνει τη βύθιση ενός κοίλου μεταλλικού σωλήνα σε ένα δοχείο με λιωμένο γυαλί και την περιστροφή του σωλήνα για τη συλλογή κάποιας ποσότητας του γυάλινου υλικού. Το γυαλί που συλλέγεται στην άκρη του σωλήνα τυλίγεται σε επίπεδο σίδερο, διαμορφώνεται όπως επιθυμείτε, επιμηκύνεται, θερμαίνεται ξανά και διοχετεύεται αέρας. Όταν είναι έτοιμο, μπαίνει σε καλούπι και φυσάται αέρας. Η κοιλότητα του καλουπιού είναι υγρή για να αποφευχθεί η επαφή του γυαλιού με το μέταλλο. Η μεμβράνη νερού λειτουργεί σαν μαξιλάρι ανάμεσά τους. Το χειροκίνητο φύσημα είναι μια αργή διαδικασία εντατικής εργασίας και είναι κατάλληλη μόνο για πρωτότυπα ή αντικείμενα υψηλής αξίας, δεν είναι κατάλληλη για φθηνές ανά τεμάχιο παραγγελίες μεγάλου όγκου. • ΚΑΤΑΣΚΕΥΗ ΟΙΚΙΑΚΩΝ & ΒΙΟΜΗΧΑΝΙΚΩΝ ΥΑΛΙΚΩΝ : Χρησιμοποιώντας διάφορα είδη γυαλιού παράγεται μεγάλη ποικιλία γυαλικών. Ορισμένα ποτήρια είναι ανθεκτικά στη θερμότητα και κατάλληλα για εργαστηριακά γυάλινα σκεύη, ενώ μερικά είναι αρκετά καλά για να αντέχουν στο πλυντήριο πιάτων πολλές φορές και είναι κατάλληλα για την κατασκευή οικιακών προϊόντων. Χρησιμοποιώντας μηχανές Westlake παράγονται δεκάδες χιλιάδες κομμάτια ποτηριών την ημέρα. Για απλοποίηση, το λιωμένο γυαλί συλλέγεται με κενό και εισάγεται σε καλούπια για να γίνουν οι προ-μορφές. Στη συνέχεια διοχετεύεται αέρας στα καλούπια, αυτά μεταφέρονται σε άλλο καλούπι και φυσάται ξανά αέρας και το ποτήρι παίρνει την τελική του μορφή. Όπως και στο φύσημα με το χέρι, αυτά τα καλούπια διατηρούνται υγρά με νερό. Το περαιτέρω τέντωμα είναι μέρος της διαδικασίας φινιρίσματος όπου σχηματίζεται ο λαιμός. Το περίσσιο γυαλί έχει καεί. Στη συνέχεια ακολουθεί η ελεγχόμενη διαδικασία επαναθέρμανσης και ψύξης που περιγράφεται παραπάνω. • ΔΙΑΜΟΡΦΩΣΗ ΓΥΑΛΙΝΩΝ ΣΩΛΗΝΩΝ & ΡΑΒΔΩΝ: Οι κύριες διαδικασίες που χρησιμοποιούμε για την κατασκευή γυάλινων σωλήνων είναι οι διεργασίες DANNER και VELLO. Στη διαδικασία Danner, το γυαλί από έναν κλίβανο ρέει και πέφτει σε ένα κεκλιμένο χιτώνιο κατασκευασμένο από πυρίμαχα υλικά. Το χιτώνιο φέρεται σε περιστρεφόμενο κοίλο άξονα ή σωλήνα φυσητήρα. Στη συνέχεια, το γυαλί τυλίγεται γύρω από το χιτώνιο και σχηματίζει ένα λείο στρώμα που ρέει κάτω από το χιτώνιο και πάνω από την άκρη του άξονα. Στην περίπτωση σχηματισμού σωλήνων, ο αέρας διοχετεύεται μέσω ενός φυσητήρα με κοίλο άκρο, και στην περίπτωση σχηματισμού ράβδων χρησιμοποιούμε συμπαγείς άκρες στον άξονα. Στη συνέχεια, οι σωλήνες ή οι ράβδοι σύρονται πάνω από κυλίνδρους μεταφοράς. Οι διαστάσεις όπως το πάχος του τοιχώματος και η διάμετρος των γυάλινων σωλήνων προσαρμόζονται στις επιθυμητές τιμές ρυθμίζοντας τη διάμετρο του χιτωνίου και φυσώντας την πίεση αέρα σε μια επιθυμητή τιμή, ρυθμίζοντας τη θερμοκρασία, τον ρυθμό ροής του γυαλιού και την ταχύτητα έλξης. Η διαδικασία κατασκευής γυάλινων σωλήνων Vello από την άλλη πλευρά περιλαμβάνει γυαλί που ταξιδεύει έξω από έναν κλίβανο και σε ένα μπολ με ένα κοίλο μανδρέλι ή κουδούνι. Στη συνέχεια, το ποτήρι περνά μέσα από τον χώρο αέρα μεταξύ του μανδρελιού και του μπολ και παίρνει το σχήμα ενός σωλήνα. Στη συνέχεια ταξιδεύει πάνω από κυλίνδρους σε μια μηχανή σχεδίασης και ψύχεται. Στο τέλος της γραμμής ψύξης γίνεται η κοπή και η τελική επεξεργασία. Οι διαστάσεις του σωλήνα μπορούν να ρυθμιστούν όπως ακριβώς στη διαδικασία Danner. Όταν συγκρίνουμε τη διαδικασία Danner με Vello, μπορούμε να πούμε ότι η διαδικασία Vello είναι καλύτερη για παραγωγή μεγάλης ποσότητας, ενώ η διαδικασία Danner μπορεί να ταιριάζει καλύτερα για ακριβείς παραγγελίες σωλήνων μικρότερου όγκου. • ΕΠΕΞΕΡΓΑΣΙΑ ΦΥΛΑΚΩΝ & ΕΠΙΠΕΔΩΝ & FLOAT GLASS : Διαθέτουμε μεγάλες ποσότητες επίπεδων υαλοπινάκων σε πάχη που κυμαίνονται από πάχη υποχιλιοστών έως αρκετά εκατοστά. Τα επίπεδα γυαλιά μας είναι σχεδόν οπτικής τελειότητας. Προσφέρουμε γυαλί με ειδικές επικαλύψεις όπως οπτικές επιστρώσεις, όπου χρησιμοποιείται η τεχνική χημικής εναπόθεσης ατμού για την τοποθέτηση επικαλύψεων όπως αντιανακλαστική ή κατοπτρική επίστρωση. Επίσης διαφανείς αγώγιμες επικαλύψεις είναι κοινές. Διατίθενται επίσης υδρόφοβες ή υδρόφιλες επικαλύψεις σε γυαλί και επικάλυψη που κάνει το γυαλί αυτοκαθαριζόμενο. Τα σκληρυμένα, αλεξίσφαιρα και πλαστικοποιημένα γυαλιά είναι ακόμα άλλα δημοφιλή αντικείμενα. Κόβουμε το γυαλί στο επιθυμητό σχήμα με τις επιθυμητές ανοχές. Άλλες δευτερεύουσες λειτουργίες, όπως καμπύλωση ή κάμψη επίπεδου γυαλιού είναι διαθέσιμες. • ΧΥΤΩΣΗ ΓΥΑΛΙΩΝ ΑΚΡΙΒΕΙΑΣ: Χρησιμοποιούμε αυτή την τεχνική κυρίως για την κατασκευή οπτικών εξαρτημάτων ακριβείας χωρίς την ανάγκη για πιο ακριβές και χρονοβόρες τεχνικές όπως λείανση, λείανση και στίλβωση. Αυτή η τεχνική δεν είναι πάντα αρκετή για την καλύτερη δυνατή απόδοση των καλύτερων οπτικών, αλλά σε ορισμένες περιπτώσεις, όπως καταναλωτικά προϊόντα, ψηφιακές φωτογραφικές μηχανές, ιατρικά οπτικά, μπορεί να είναι μια λιγότερο δαπανηρή καλή επιλογή για κατασκευή μεγάλου όγκου. Επίσης έχει ένα πλεονέκτημα έναντι των άλλων τεχνικών σχηματισμού γυαλιού όπου απαιτούνται πολύπλοκες γεωμετρίες, όπως στην περίπτωση των ασφαίρων. Η βασική διαδικασία περιλαμβάνει φόρτωση της κάτω πλευράς του καλουπιού μας με το τυφλό γυαλί, εκκένωση του θαλάμου επεξεργασίας για αφαίρεση οξυγόνου, κοντά στο κλείσιμο του καλουπιού, γρήγορη και ισοθερμική θέρμανση καλουπιού και γυαλιού με υπέρυθρο φως, περαιτέρω κλείσιμο των μισών του καλουπιού για να πιέσετε αργά το μαλακωμένο γυαλί με ελεγχόμενο τρόπο στο επιθυμητό πάχος και τέλος ψύξη του γυαλιού και πλήρωση του θαλάμου με άζωτο και αφαίρεση του προϊόντος. Ο ακριβής έλεγχος θερμοκρασίας, η απόσταση κλεισίματος του καλουπιού, η δύναμη κλεισίματος του καλουπιού, η αντιστοίχιση των συντελεστών διαστολής του καλουπιού και του υλικού γυαλιού είναι βασικά σε αυτή τη διαδικασία. • ΚΑΤΑΣΚΕΥΗ ΟΠΤΙΚΩΝ ΣΤΟΙΧΕΙΩΝ ΚΑΙ ΣΥΝΑΡΜΟΛΟΓΗΣΕΩΝ ΓΥΑΛΙΩΝ: Εκτός από τη χύτευση γυαλιού ακριβείας, υπάρχει μια σειρά από πολύτιμες διαδικασίες που χρησιμοποιούμε για την κατασκευή οπτικών εξαρτημάτων και συγκροτημάτων υψηλής ποιότητας για απαιτητικές εφαρμογές. Το τρίψιμο, το τύλιγμα και το γυάλισμα γυαλιών οπτικής ποιότητας σε λεπτούς ειδικούς λειαντικούς πολτούς είναι μια τέχνη και επιστήμη για την κατασκευή οπτικών φακών, πρισμάτων, επιπέδων και άλλων. Οι επιφάνειες επιπεδότητας, κυματισμού, ομαλότητας και χωρίς ελαττώματα οπτικών επιφανειών απαιτούν μεγάλη εμπειρία σε τέτοιες διαδικασίες. Μικρές αλλαγές στο περιβάλλον μπορεί να οδηγήσουν σε προϊόντα εκτός προδιαγραφών και να σταματήσουν τη γραμμή παραγωγής. Υπάρχουν περιπτώσεις όπου ένα μόνο σκούπισμα στην οπτική επιφάνεια με ένα καθαρό πανί μπορεί να κάνει ένα προϊόν να πληροί τις προδιαγραφές ή να αποτύχει στη δοκιμή. Μερικά δημοφιλή υλικά γυαλιού που χρησιμοποιούνται είναι λιωμένο πυρίτιο, χαλαζίας, BK7. Επίσης, η συναρμολόγηση τέτοιων εξαρτημάτων απαιτεί εξειδικευμένη εμπειρία. Μερικές φορές χρησιμοποιούνται ειδικές κόλλες. Ωστόσο, μερικές φορές μια τεχνική που ονομάζεται οπτική επαφή είναι η καλύτερη επιλογή και δεν περιλαμβάνει υλικό ανάμεσα στα προσαρτημένα οπτικά γυαλιά. Αποτελείται από επίπεδες επιφάνειες που έρχονται σε φυσική επαφή για να συνδέονται μεταξύ τους χωρίς κόλλα. Σε ορισμένες περιπτώσεις, χρησιμοποιούνται μηχανικοί αποστάτες, γυάλινες ράβδοι ή μπάλες ακριβείας, σφιγκτήρες ή κατεργασμένα μεταλλικά εξαρτήματα για τη συναρμολόγηση των οπτικών εξαρτημάτων σε ορισμένες αποστάσεις και με συγκεκριμένους γεωμετρικούς προσανατολισμούς μεταξύ τους. Ας εξετάσουμε μερικές από τις δημοφιλείς τεχνικές μας για την κατασκευή οπτικών υψηλών προδιαγραφών. ΛΕΙΣΜΑ & ΤΕΙΡΩΣΗ & ΓΥΑΛΙΣΜΑ : Το τραχύ σχήμα του οπτικού εξαρτήματος αποκτάται με λείανση ενός τεμαχίου γυαλιού. Στη συνέχεια, το τύλιγμα και η στίλβωση πραγματοποιούνται περιστρέφοντας και τρίβοντας τις τραχιές επιφάνειες των οπτικών εξαρτημάτων πάνω σε εργαλεία με επιθυμητά σχήματα επιφάνειας. Μεταξύ των οπτικών και των εργαλείων διαμόρφωσης χύνονται πολτές με μικροσκοπικά λειαντικά σωματίδια και υγρό. Τα μεγέθη λειαντικών σωματιδίων σε τέτοιους πολτούς μπορούν να επιλεγούν σύμφωνα με τον επιθυμητό βαθμό επιπεδότητας. Οι αποκλίσεις των κρίσιμων οπτικών επιφανειών από τα επιθυμητά σχήματα εκφράζονται ως προς τα μήκη κύματος του φωτός που χρησιμοποιείται. Τα οπτικά μας υψηλής ακρίβειας έχουν ανοχές δέκατου μήκους κύματος (μήκος κύματος/10) ή ακόμα πιο αυστηρή είναι δυνατή. Εκτός από το προφίλ της επιφάνειας, οι κρίσιμες επιφάνειες σαρώνονται και αξιολογούνται για άλλα χαρακτηριστικά και ελαττώματα επιφάνειας όπως διαστάσεις, γρατσουνιές, τσιπς, κοιλώματα, κηλίδες κ.λπ. Ο αυστηρός έλεγχος των περιβαλλοντικών συνθηκών στο δάπεδο κατασκευής οπτικών και οι εκτεταμένες απαιτήσεις μετρολογίας και δοκιμών με εξοπλισμό τελευταίας τεχνολογίας καθιστούν αυτόν τον κλάδο πρόκλησης της βιομηχανίας. • ΔΕΥΤΕΡΟΓΕΝΕΣ ΔΙΕΡΓΑΣΙΕΣ ΣΤΗΝ ΚΑΤΑΣΚΕΥΗ ΓΥΑΛΙΟΥ: Και πάλι, περιοριζόμαστε μόνο με τη φαντασία σας όταν πρόκειται για δευτερεύουσες και φινιριστικές διεργασίες γυαλιού. Παραθέτουμε μερικά από αυτά: -Επιστρώσεις σε γυαλί (οπτικά, ηλεκτρικά, τριβολογικά, θερμικά, λειτουργικά, μηχανικά...). Ως παράδειγμα, μπορούμε να αλλάξουμε τις επιφανειακές ιδιότητες του γυαλιού κάνοντάς το, για παράδειγμα, να αντανακλά τη θερμότητα, ώστε να διατηρεί δροσερό το εσωτερικό του κτιρίου ή να κάνει τη μία πλευρά να απορροφά το υπέρυθρο χρησιμοποιώντας τη νανοτεχνολογία. Αυτό βοηθά να διατηρείται ζεστό το εσωτερικό των κτιρίων, επειδή το εξωτερικό επιφανειακό στρώμα γυαλιού απορροφά την υπέρυθρη ακτινοβολία μέσα στο κτίριο και την εκπέμπει πίσω στο εσωτερικό. -Χαλκογραφία σε γυαλί -Εφαρμοσμένη κεραμική ετικέτα (ACL) -Χαρακτική -Γυάλισμα με φλόγα -Χημική στίλβωση -Χρώση ΚΑΤΑΣΚΕΥΗ ΤΕΧΝΙΚΗΣ ΚΕΡΑΜΙΚΗΣ • DIE PRESSING : Αποτελείται από μονοαξονική συμπίεση κοκκωδών σκονών που περιορίζονται σε μια μήτρα • HOT PRESSING : Παρόμοια με την συμπίεση μήτρας αλλά με προσθήκη θερμοκρασίας για ενίσχυση της πύκνωσης. Η σκόνη ή το συμπιεσμένο πρόπλασμα τοποθετείται σε καλούπι γραφίτη και εφαρμόζεται μονοαξονική πίεση ενώ η μήτρα διατηρείται σε υψηλές θερμοκρασίες όπως 2000 C. Οι θερμοκρασίες μπορεί να διαφέρουν ανάλογα με τον τύπο της κεραμικής σκόνης που επεξεργάζεται. Για περίπλοκα σχήματα και γεωμετρίες μπορεί να χρειαστεί άλλη μεταγενέστερη επεξεργασία, όπως λείανση διαμαντιών. • ΙΣΟΣΤΑΤΙΚΗ ΠΙΕΣΗ : Κοκκώδη κόκκους ή συμπιεσμένα με μήτρα συμπιεσμένα δοχεία τοποθετούνται σε αεροστεγή δοχεία και στη συνέχεια σε κλειστό δοχείο πίεσης με υγρό μέσα. Στη συνέχεια συμπιέζονται αυξάνοντας την πίεση του δοχείου πίεσης. Το υγρό μέσα στο δοχείο μεταφέρει τις δυνάμεις πίεσης ομοιόμορφα σε ολόκληρη την επιφάνεια του αεροστεγούς δοχείου. Το υλικό συμπιέζεται έτσι ομοιόμορφα και παίρνει το σχήμα του εύκαμπτου δοχείου και το εσωτερικό του προφίλ και χαρακτηριστικά. • ΖΕΣΤΗ ΙΣΟΣΤΑΤΙΚΗ ΠΙΕΣΗ : Παρόμοια με την ισοστατική συμπίεση, αλλά εκτός από ατμόσφαιρα πεπιεσμένου αερίου, πυροσυσσωματώνουμε το συμπαγές σε υψηλή θερμοκρασία. Η θερμή ισοστατική πίεση έχει ως αποτέλεσμα πρόσθετη πύκνωση και αυξημένη αντοχή. • SLIP CASTING / DRAIN CASTING : Γεμίζουμε το καλούπι με εναιώρημα από κεραμικά σωματίδια μεγέθους μικρομέτρου και υγρό φορέα. Αυτό το μείγμα ονομάζεται «ολίσθηση». Το καλούπι έχει πόρους και επομένως το υγρό του μείγματος φιλτράρεται μέσα στο καλούπι. Ως αποτέλεσμα, στις εσωτερικές επιφάνειες του καλουπιού σχηματίζεται γύψος. Μετά την πυροσυσσωμάτωση, τα μέρη μπορούν να αφαιρεθούν από το καλούπι. • ΧΥΤΩΣΗ ΤΑΙΝΙΑΣ: Κατασκευάζουμε κεραμικές ταινίες χυτεύοντας κεραμικούς πολτούς σε επίπεδες κινούμενες επιφάνειες φορέα. Οι πολτές περιέχουν κεραμικές σκόνες αναμεμειγμένες με άλλες χημικές ουσίες για σκοπούς δέσμευσης και μεταφοράς. Καθώς οι διαλύτες εξατμίζονται, αφήνονται πίσω πυκνά και εύκαμπτα φύλλα κεραμικού τα οποία μπορούν να κοπούν ή να τυλιχτούν κατά βούληση. • ΣΧΗΜΑΤΙΣΜΟΣ ΔΙΕΛΛΑΣΗΣ: Όπως και σε άλλες διεργασίες εξώθησης, ένα μαλακό μείγμα κεραμικής σκόνης με συνδετικά και άλλες χημικές ουσίες περνά μέσα από μια μήτρα για να αποκτήσει το σχήμα της διατομής του και στη συνέχεια κόβεται στα επιθυμητά μήκη. Η διαδικασία πραγματοποιείται με κρύα ή θερμαινόμενα κεραμικά μείγματα. • ΧΥΤΩΣΗ ΕΓΧΥΣΗΣ ΧΑΜΗΛΗΣ ΠΙΕΣΗΣ : Ετοιμάζουμε ένα μείγμα κεραμικής σκόνης με συνδετικά και διαλύτες και το θερμαίνουμε σε θερμοκρασία που να μπορεί εύκολα να πιεστεί και να ωθηθεί στην κοιλότητα του εργαλείου. Μόλις ολοκληρωθεί ο κύκλος καλουπώματος, το εξάρτημα εκτοξεύεται και η συνδετική χημική ουσία καίγεται. Χρησιμοποιώντας χύτευση με έγχυση, μπορούμε να αποκτήσουμε πολύπλοκα εξαρτήματα σε υψηλούς όγκους οικονομικά. Τρύπες που είναι ένα μικρό κλάσμα του χιλιοστού σε τοίχο πάχους 10 mm είναι δυνατές, σπειρώματα είναι δυνατά χωρίς περαιτέρω κατεργασία, ανοχές τόσο σφιχτές όσο +/- 0,5% είναι δυνατές όταν τα εξαρτήματα είναι δυνατά , είναι δυνατά πάχη τοιχώματος της τάξης από 0,5 mm έως μήκος 12,5 mm καθώς και πάχη τοιχώματος από 6,5 mm έως μήκος 150 mm. • ΠΡΑΣΙΝΗ ΜΗΧΑΝΙΚΗ : Χρησιμοποιώντας τα ίδια εργαλεία μηχανικής κατεργασίας μετάλλων, μπορούμε να επεξεργαστούμε πεπιεσμένα κεραμικά υλικά ενώ είναι ακόμα μαλακά σαν κιμωλία. Είναι δυνατές ανοχές +/- 1%. Για καλύτερες ανοχές χρησιμοποιούμε λείανση διαμαντιών. • ΣΥΝΤΗΡΗΣΗ ή ΠΥΡΩΣΗ: Η πυροσυσσωμάτωση καθιστά δυνατή την πλήρη συμπύκνωση. Σημαντική συρρίκνωση παρουσιάζεται στα πράσινα συμπαγή μέρη, αλλά αυτό δεν είναι μεγάλο πρόβλημα αφού λαμβάνουμε υπόψη αυτές τις αλλαγές διαστάσεων όταν σχεδιάζουμε το εξάρτημα και τα εργαλεία. Τα σωματίδια σκόνης συνδέονται μεταξύ τους και το πορώδες που προκαλείται από τη διαδικασία συμπίεσης αφαιρείται σε μεγάλο βαθμό. • ΛΕΙΣΜΑ ΜΕ ΔΙΑΜΑΝΤΙ: Το σκληρότερο υλικό στον κόσμο «διαμάντι» χρησιμοποιείται για την άλεση σκληρών υλικών όπως κεραμικά και λαμβάνονται εξαρτήματα ακριβείας. Επιτυγχάνονται ανοχές στο εύρος των μικρομέτρων και πολύ λείες επιφάνειες. Λόγω του κόστους της, εξετάζουμε αυτήν την τεχνική μόνο όταν τη χρειαζόμαστε πραγματικά. • ΕΡΜΗΤΙΚΕΣ ΣΥΝΑΡΜΟΛΟΓΗΣΕΙΣ είναι εκείνες που πρακτικά δεν επιτρέπουν καμία ανταλλαγή ύλης, στερεών, υγρών ή αερίων μεταξύ διεπαφών. Η ερμητική σφράγιση είναι αεροστεγής. Για παράδειγμα, τα ερμητικά ηλεκτρονικά περιβλήματα είναι εκείνα που διατηρούν το ευαίσθητο εσωτερικό περιεχόμενο μιας συσκευασμένης συσκευής άθικτο από υγρασία, ρύπους ή αέρια. Τίποτα δεν είναι 100% ερμητικό, αλλά όταν μιλάμε για ερμητικότητα εννοούμε ότι πρακτικά υπάρχει ερμητικότητα σε βαθμό που ο ρυθμός διαρροής είναι τόσο χαμηλός που οι συσκευές είναι ασφαλείς υπό κανονικές περιβαλλοντικές συνθήκες για πολύ μεγάλο χρονικό διάστημα. Τα ερμητικά μας συγκροτήματα αποτελούνται από μέταλλο, γυαλί και κεραμικά εξαρτήματα, μέταλλο-κεραμικό, κεραμικό-μέταλλο-κεραμικό, μέταλλο-κεραμικό-μέταλλο, μέταλλο σε μέταλλο, μέταλλο-γυαλί, μέταλλο-γυαλί-μέταλλο, γυαλί-μέταλλο-γυαλί, γυαλί- μέταλλο και γυαλί με γυαλί και όλους τους άλλους συνδυασμούς συγκόλλησης μετάλλου-γυαλιού-κεραμικού. Μπορούμε, για παράδειγμα, να επικαλύψουμε μεταλλικά τα κεραμικά εξαρτήματα ώστε να μπορούν να συνδεθούν ισχυρά με άλλα εξαρτήματα της συναρμολόγησης και να έχουν εξαιρετική ικανότητα σφράγισης. Διαθέτουμε την τεχνογνωσία να επικαλύπτουμε τις οπτικές ίνες ή τις διόδους τροφοδοσίας με μέταλλο και να τις κολλάμε ή να κολλάμε στα περιβλήματα, έτσι ώστε να μην περνούν ή να διαρρεύσουν αέρια στα περιβλήματα. Ως εκ τούτου, χρησιμοποιούνται για την κατασκευή ηλεκτρονικών περιβλημάτων για την ενθυλάκωση ευαίσθητων συσκευών και την προστασία τους από την εξωτερική ατμόσφαιρα. Εκτός από τα εξαιρετικά χαρακτηριστικά σφράγισής τους, άλλες ιδιότητες όπως ο συντελεστής θερμικής διαστολής, η αντίσταση στην παραμόρφωση, η φύση χωρίς αέρια, η πολύ μεγάλη διάρκεια ζωής, η μη αγώγιμη φύση, οι θερμομονωτικές ιδιότητες, η αντιστατική φύση κ.λπ. κάνουν γυαλί και κεραμικά υλικά την επιλογή για ορισμένες εφαρμογές. Πληροφορίες για τις εγκαταστάσεις μας που παράγουν εξαρτήματα από κεραμικό σε μέταλλο, ερμητική σφράγιση, τροφοδοσίες κενού, εξαρτήματα ελέγχου υψηλού και εξαιρετικά υψηλού κενού και υγρών μπορείτε να βρείτε εδώ:Μπροσούρα Hermetic Components Factory CLICK Product Finder-Locator Service ΠΡΟΗΓΟΥΜΕΝΗ ΣΕΛΙΔΑ
- Wire & Spring Forming, Shaping, Welding, Assembly of Wires, Coil, CNC
Wire & Spring Forming, Shaping, Welding, Assembly of Wires, Coil Compression Extension Torsion Flat Springs, Custom Wires, Helical Springs at AGS-TECH Inc. Μορφοποίηση σύρματος & ελατηρίου Κατασκευάζουμε προσαρμοσμένα σύρματα, συναρμολόγηση σύρματος, σύρματα διαμορφωμένα σε επιθυμητά σχήματα 2D και 3D, συρμάτινα δίχτυα, πλέγμα, περιβλήματα, καλάθι, φράχτη, συρμάτινο ελατήριο, επίπεδο ελατήριο. στρέψη, συμπίεση, τάση, επίπεδα ελατήρια και άλλα. Οι διεργασίες μας είναι η διαμόρφωση σύρματος και ελατηρίου, το τράβηγμα σύρματος, η διαμόρφωση, η κάμψη, η συγκόλληση, η συγκόλληση, η συγκόλληση, η διάτρηση, η αιώρηση, το τρύπημα, η λοξοτομή, η λείανση, το σπείρωμα, η επίστρωση, η τετραολίσθηση, η διαμόρφωση ολίσθησης, η περιέλιξη, η περιέλιξη, η ανατροπή. Σας συνιστούμε να κάνετε κλικ εδώ για να ΚΑΤΕΒΑΣΤΕ τις Σχηματικές απεικονίσεις των Διαδικασιών Σχηματισμού Σύρματος και Ελατηρίου από την AGS-TECH Inc. Αυτό το αρχείο με δυνατότητα λήψης με φωτογραφίες και σκίτσα θα σας βοηθήσει να κατανοήσετε καλύτερα τις πληροφορίες που σας παρέχουμε παρακάτω. • ΣΧΕΔΙΟ ΣΥΡΜΑΤΟΣ : Χρησιμοποιώντας δυνάμεις εφελκυσμού τεντώνουμε το μεταλλικό κοντάκι και το τραβάμε μέσα από μια μήτρα για να μειωθεί η διάμετρος και να αυξηθεί το μήκος του. Μερικές φορές χρησιμοποιούμε μια σειρά από μήτρες. Είμαστε σε θέση να φτιάξουμε μήτρες για κάθε μετρητή σύρματος. Χρησιμοποιώντας υλικό υψηλής αντοχής σε εφελκυσμό τραβάμε πολύ λεπτά σύρματα. Προσφέρουμε και κρύα και ζεστά κατεργασμένα καλώδια. • ΣΧΗΜΑΤΙΣΜΟΣ ΣΥΡΜΑΤΟΣ : Ένα ρολό σύρματος με μετρητή λυγίζει και διαμορφώνεται σε ένα χρήσιμο προϊόν. Έχουμε τη δυνατότητα να σχηματίζουμε σύρματα από όλους τους μετρητές, συμπεριλαμβανομένων λεπτών νημάτων καθώς και χοντρά σύρματα όπως αυτά που χρησιμοποιούνται ως ελατήρια κάτω από το σασί του αυτοκινήτου. Ο εξοπλισμός που χρησιμοποιούμε για τη διαμόρφωση σύρματος είναι χειροκίνητοι και CNC διαμορφωτές σύρματος, πηνίο, πρέσες ισχύος, τετράπλευροι, πολλαπλοί ολισθητήρες. Οι διαδικασίες μας είναι το τράβηγμα, η κάμψη, το ίσιωμα, το ίσιωμα, το τέντωμα, η κοπή, η ανατροπή, η συγκόλληση και η συγκόλληση και η συγκόλληση, η συναρμολόγηση, η περιέλιξη, η περιτύλιξη (ή το φτερό), η διάτρηση, το σπείρωμα σύρματος, η διάτρηση, η λοξοτομή, η λείανση, η επίστρωση και οι επιφανειακές επεξεργασίες. Ο υπερσύγχρονος εξοπλισμός μας μπορεί να ρυθμιστεί ώστε να αναπτύσσει πολύ περίπλοκα σχέδια οποιουδήποτε σχήματος και αυστηρών ανοχών. Προσφέρουμε διάφορους τύπους άκρων όπως σφαιρικά, μυτερά ή λοξότμητα άκρα για τα καλώδιά σας. Τα περισσότερα από τα έργα μας για τη διαμόρφωση συρμάτων έχουν ελάχιστο έως μηδενικό κόστος εργαλείων. Οι χρόνοι ολοκλήρωσης του δείγματος είναι γενικά ημέρες. Οι αλλαγές στη σχεδίαση/διαμόρφωση των καλωδίων μπορούν να γίνουν πολύ γρήγορα. • SPRING FORMING : Η AGS-TECH κατασκευάζει μια μεγάλη ποικιλία ελατηρίων που περιλαμβάνουν: -Στρέψη / Διπλό Ελατήριο Στρέψης -Ελατήριο τάσης / συμπίεσης -Σταθερό / Μεταβλητό Ελατήριο -Σπειροειδής & Ελικοειδής Ελατήριο -Flat & Leaf Spring -Ελατήριο ισορροπίας - Πλυντήριο Belleville -Άνοιξη αρνητή -Ελατήριο προοδευτικού ρυθμού - Άνοιξη κυμάτων -Volute Spring -Τα κωνικά ελατήρια -Δαχτυλίδια άνοιξης -Ρολόι ελατήρια -Κλιπ Κατασκευάζουμε ελατήρια από ποικιλία υλικών και μπορούμε να σας καθοδηγήσουμε ανάλογα με την εφαρμογή σας. Τα πιο κοινά υλικά είναι ο ανοξείδωτος χάλυβας, το χρώμιο πυρίτιο, ο χάλυβας υψηλής περιεκτικότητας σε άνθρακα, το λιπαντικό με χαμηλή περιεκτικότητα σε άνθρακα, το χρώμιο βανάδιο, ο φώσφορος μπρούτζος, το τιτάνιο, το κράμα χαλκού βηρυλλίου, το κεραμικό υψηλής θερμοκρασίας. Χρησιμοποιούμε διάφορες τεχνικές στην κατασκευή ελατηρίων, όπως περιέλιξη CNC, ψυχρή περιέλιξη, θερμή περιέλιξη, σκλήρυνση, φινίρισμα. Άλλες τεχνικές που έχουν ήδη αναφερθεί παραπάνω για τη διαμόρφωση σύρματος είναι επίσης κοινές στις εργασίες κατασκευής ελατηρίων μας. • ΥΠΗΡΕΣΙΕΣ ΦΙΝΙΡΙΣΜΑΤΟΣ ΣΥΡΜΑΤΩΝ & ΕΛΑΤΗΡΙΩΝ: Μπορούμε να ολοκληρώσουμε τα προϊόντα σας με πολλούς τρόπους ανάλογα με την επιλογή και τις ανάγκες σας. Μερικές κοινές διαδικασίες που προσφέρουμε είναι: βαφή, επίστρωση σε σκόνη, επιμετάλλωση, εμβάπτιση βινυλίου, ανοδίωση, ανακούφιση από το στρες, θερμική επεξεργασία, shot peen, tumble, chromate, electroless nickel, e passivation, cobaked , καθαρισμός πλάσματος. CLICK Product Finder-Locator Service ΠΡΟΗΓΟΥΜΕΝΗ ΣΕΛΙΔΑ
- Sheet Metal Forming Fabrication, Stamping, Punching, Deep Drawing, CNC
Sheet Metal Forming and Fabrication, Stamping, Punching, Bending, Progressive Die, Spot Welding, Deep Drawing, Metal Blanking and Slitting at AGS-TECH Inc. Σφραγίδες & Κατασκευή Λαμαρινών Προσφέρουμε σφράγιση λαμαρίνας, μορφοποίηση, μορφοποίηση, κάμψη, διάτρηση, τύφλωση, σχίσιμο, διάτρηση, εγκοπή, τσιμπήματα, ξύρισμα, κατεργασία με πίεση, κατασκευή, βαθιά σχεδίαση χρησιμοποιώντας μήτρες μονής διάτρησης / μονής διαδρομής καθώς και προοδευτικές μήτρες και στύψιμο, διαμόρφωση από καουτσούκ και υδροδιαμόρφωση; κοπή λαμαρίνας με πίδακα νερού, πλάσμα, λέιζερ, πριόνι, φλόγα. Συγκρότημα λαμαρίνας με συγκόλληση, συγκόλληση σημείου. λαμαρίνα σωλήνας διόγκωση και κάμψη? Φινίρισμα επιφανειών λαμαρίνας, συμπεριλαμβανομένης της βαφής με εμβάπτιση ή με ψεκασμό, ηλεκτροστατική βαφή πούδρας, ανοδίωση, επιμετάλλωση, ψεκασμό και άλλα. Οι υπηρεσίες μας κυμαίνονται από την ταχεία κατασκευή πρωτοτύπων λαμαρίνας έως την κατασκευή μεγάλου όγκου. Σας συνιστούμε να κάνετε κλικ εδώ για ναΚΑΤΕΒΑΣΤΕ τις Σχηματικές μας απεικονίσεις των Διαδικασιών Κατασκευής και Σφράγισης Λαμαρινών από την AGS-TECH Inc. Αυτό θα σας βοηθήσει να κατανοήσετε καλύτερα τις πληροφορίες που σας παρέχουμε παρακάτω. • ΚΟΠΗ ΛΑΜΑΡΙΝΑΣ : Προσφέρουμε ΚΟΦΕΣ και ΧΩΡΙΣΤΙΚΑ. Τα κοψίματα κόβουν τη λαμαρίνα σε ένα μονοπάτι τη φορά και ουσιαστικά δεν υπάρχει σπατάλη υλικού, ενώ με χωρίσματα το σχήμα δεν μπορεί να φωλιαστεί με ακρίβεια και επομένως μια συγκεκριμένη ποσότητα υλικού σπαταλιέται. Μία από τις πιο δημοφιλείς διαδικασίες μας είναι το PUNCHING, όπου ένα κομμάτι υλικού στρογγυλό ή άλλο σχήμα κόβεται από λαμαρίνα. Το κομμάτι που κόβεται είναι απόβλητο. Μια άλλη εκδοχή της διάτρησης είναι το SLOTTING, όπου ανοίγονται ορθογώνιες ή επιμήκεις τρύπες. Το BLANKING από την άλλη είναι η ίδια διαδικασία με το punching, με τη διάκριση του κομματιού που κόβεται είναι το έργο και διατηρείται. Το FINE BLANKING, μια ανώτερη έκδοση του τυφλού, δημιουργεί κοψίματα με κοντινές ανοχές και ίσιες λείες άκρες και δεν απαιτεί δευτερεύουσες εργασίες για την τελειοποίηση του τεμαχίου εργασίας. Μια άλλη διαδικασία που χρησιμοποιούμε συχνά είναι το SLITTING, η οποία είναι μια διαδικασία διάτμησης όπου η λαμαρίνα κόβεται από δύο αντίθετες κυκλικές λεπίδες σε ευθεία ή καμπύλη διαδρομή. Το ανοιχτήρι κονσερβών είναι ένα απλό παράδειγμα της διαδικασίας κοπής. Μια άλλη δημοφιλής process για εμάς είναι η ΔΙΑΡΥΣΗ, όπου πολλές τρύπες στρογγυλές ή άλλου σχήματος ανοίγονται σε λαμαρίνα με ένα συγκεκριμένο σχέδιο. Χαρακτηριστικό παράδειγμα για ένα διάτρητο προϊόν είναι τα μεταλλικά φίλτρα με πολλές οπές για υγρά. Στο NOTCHING, μια άλλη διαδικασία κοπής λαμαρίνας, αφαιρούμε υλικό από ένα τεμάχιο εργασίας, ξεκινώντας από την άκρη ή αλλού και κόβουμε προς τα μέσα μέχρι να πάρουμε το επιθυμητό σχήμα. Είναι μια προοδευτική διαδικασία όπου κάθε επέμβαση αφαιρεί ένα άλλο κομμάτι μέχρι να επιτευχθεί το επιθυμητό περίγραμμα. Για μικρές σειρές παραγωγής χρησιμοποιούμε μερικές φορές μια σχετικά πιο αργή διαδικασία που ονομάζεται NIBBLING, η οποία αποτελείται από πολλές γρήγορες διατρήσεις επικαλυπτόμενων οπών για να κάνουμε μια μεγαλύτερη, πιο περίπλοκη κοπή. Στην ΠΡΟΟΔΕΥΤΙΚΗ ΚΟΠΗ χρησιμοποιούμε μια σειρά διαφορετικών πράξεων για να αποκτήσουμε ένα μόνο κόψιμο ή μια συγκεκριμένη γεωμετρία. Τέλος, το ξύρισμα μιας δευτερεύουσας διαδικασίας μας βοηθά να βελτιώσουμε τις άκρες των κοπών που έχουν ήδη γίνει. Χρησιμοποιείται για το κόψιμο των τσιπς, τις τραχιές άκρες στη λαμαρίνα. • ΚΑΜΨΗ ΛΑΜΑΡΙΝΩΝ : Εκτός από την κοπή, η κάμψη είναι μια βασική διαδικασία χωρίς την οποία δεν θα μπορούσαμε να παράγουμε τα περισσότερα προϊόντα. Κυρίως μια λειτουργία ψυχρής εργασίας, αλλά μερικές φορές εκτελείται επίσης όταν είναι ζεστό ή ζεστό. Χρησιμοποιούμε μήτρες και πατάμε τις περισσότερες φορές για αυτή τη λειτουργία. Στην ΠΡΟΟΔΕΥΤΙΚΗ ΚΑΜΨΗ χρησιμοποιούμε μια σειρά διαφορετικών λειτουργιών διάτρησης και μήτρας για να επιτύχουμε μια μόνο κάμψη ή μια συγκεκριμένη γεωμετρία. Η AGS-TECH χρησιμοποιεί μια ποικιλία διαδικασιών κάμψης και επιλέγει ανάλογα με το υλικό του τεμαχίου εργασίας, το μέγεθος, το πάχος του, το επιθυμητό μέγεθος κάμψης, την ακτίνα, την καμπυλότητα και τη γωνία κάμψης, τη θέση της κάμψης, την οικονομία λειτουργίας, τις ποσότητες που πρόκειται να κατασκευαστούν… και τα λοιπά. Χρησιμοποιούμε V-BENDING όπου μια διάτρηση σε σχήμα V πιέζει τη λαμαρίνα στη μήτρα σχήματος V και την λυγίζει. Καλό τόσο για πολύ οξείες όσο και για αμβλείες γωνίες και ενδιάμεσα, συμπεριλαμβανομένων των 90 μοιρών. Χρησιμοποιώντας μήτρες σκουπίσματος εκτελούμε EDGE BENDING. Ο εξοπλισμός μας μας δίνει τη δυνατότητα να αποκτήσουμε γωνίες ακόμη μεγαλύτερες από 90 μοίρες. Στην κάμψη ακμών το τεμάχιο εργασίας τοποθετείται ανάμεσα σε ένα υπόθεμα πίεσης και τη μήτρα, η περιοχή για την κάμψη βρίσκεται στην άκρη της μήτρας και το υπόλοιπο τεμάχιο εργασίας συγκρατείται πάνω από space όπως μια δοκός προβόλου. Όταν η διάτρηση ενεργεί στο τμήμα του προβόλου, κάμπτεται πάνω από την άκρη της μήτρας. Το FLANGING είναι μια διαδικασία κάμψης άκρων που οδηγεί σε γωνία 90 μοιρών. Κύριοι στόχοι της λειτουργίας είναι η εξάλειψη των αιχμηρών άκρων και η λήψη γεωμετρικών επιφανειών για τη διευκόλυνση της ένωσης των εξαρτημάτων. Η ΧΑΝΤΡΑ, μια άλλη κοινή διαδικασία κάμψης άκρων σχηματίζει μια μπούκλα πάνω από την άκρη ενός εξαρτήματος. Το HEMMING από την άλλη πλευρά έχει ως αποτέλεσμα μια άκρη του φύλλου που είναι τελείως λυγισμένη πάνω του. Στο SEAMING, οι άκρες δύο τμημάτων κάμπτονται το ένα πάνω στο άλλο και ενώνονται. Το DOUBLE SEAMING από την άλλη πλευρά παρέχει στεγανές και αεροστεγείς ενώσεις λαμαρίνας. Παρόμοια με την κάμψη άκρων, μια διαδικασία που ονομάζεται ROTARY BENDING αναπτύσσει έναν κύλινδρο με την επιθυμητή γωνία κομμένη και χρησιμεύει ως διάτρηση. Καθώς η δύναμη μεταδίδεται στη διάτρηση, κλείνει με το τεμάχιο εργασίας. Η αυλάκωση του κυλίνδρου δίνει στο τμήμα προβόλου την επιθυμητή γωνία. Το αυλάκι μπορεί να έχει γωνία μικρότερη ή μεγαλύτερη από 90 μοίρες. Στο AIR BENDING δεν χρειαζόμαστε την κάτω μήτρα για να έχουμε γωνιακή αυλάκωση. Η λαμαρίνα υποστηρίζεται από δύο επιφάνειες σε αντίθετες πλευρές και σε συγκεκριμένη απόσταση. Στη συνέχεια, η διάτρηση ασκεί μια δύναμη στη σωστή θέση και λυγίζει το τεμάχιο εργασίας. Η ΚΑΜΨΗ ΚΑΝΑΛΙΟΥ εκτελείται με διάτρηση και μήτρα σχήματος καναλιού και το U-BEND επιτυγχάνεται με διάτρηση σε σχήμα U. Το OFFSET BENDING παράγει μετατοπίσεις στη λαμαρίνα. Το ROLL BENDING, μια τεχνική καλή για χοντρή εργασία και κάμψη μεγάλων κομματιών μεταλλικών πλακών, χρησιμοποιεί τρία ρολά για να τροφοδοτήσει και να κάμψει τις πλάκες στις επιθυμητές καμπυλότητες. Τα ρολά είναι διατεταγμένα έτσι ώστε να επιτυγχάνεται η επιθυμητή κάμψη της εργασίας. Η απόσταση και η γωνία μεταξύ των κυλίνδρων ελέγχονται για να επιτευχθεί το επιθυμητό αποτέλεσμα. Ένα κινητό ρολό καθιστά δυνατό τον έλεγχο της καμπυλότητας. Το TUBE FORMING είναι μια άλλη δημοφιλής εργασία κάμψης λαμαρίνας που περιλαμβάνει πολλαπλές μήτρες. Οι σωλήνες λαμβάνονται μετά από πολλαπλές ενέργειες. Η ΔΙΑΤΡΟΦΗ πραγματοποιείται επίσης με εργασίες κάμψης. Βασικά είναι η συμμετρική κάμψη σε τακτά χρονικά διαστήματα σε ένα ολόκληρο κομμάτι λαμαρίνας. Μπορούν να χρησιμοποιηθούν διάφορα σχήματα για αυλάκωση. Η κυματοειδές λαμαρίνα είναι πιο άκαμπτη και έχει καλύτερη αντοχή στην κάμψη και επομένως έχει εφαρμογές στον κατασκευαστικό κλάδο. ΔΙΑΜΟΡΦΩΣΗ ΡΟΛΟΥ ΦΥΛΑΚΗΣ, μια διαδικασία συνεχούς manufacturing αναπτύσσεται για την κάμψη των διατομών μιας συγκεκριμένης γεωμετρίας με χρήση κυλίνδρων και η εργασία κάμπτεται σε διαδοχικά βήματα, με το τελικό ρολό εργασίας να ολοκληρώνεται. Σε ορισμένες περιπτώσεις χρησιμοποιείται ένα μόνο ρολό και σε ορισμένες περιπτώσεις μια σειρά από ρολά. • ΣΥΝΔΥΑΣΜΕΝΕΣ ΔΙΑΔΙΚΑΣΙΕΣ ΚΟΠΗΣ & ΚΥΨΗΣ ΛΑΜΑΡΙΝΑΣ : Είναι οι διαδικασίες που κόβουν και λυγίζουν ταυτόχρονα. Στο PIERCING, δημιουργείται μια τρύπα χρησιμοποιώντας μια μυτερή διάτρηση. Καθώς η διάτρηση ανοίγει την οπή στο φύλλο, το υλικό κάμπτεται ταυτόχρονα σε μια εσωτερική φλάντζα για την οπή. Η φλάντζα που λαμβάνεται μπορεί να έχει σημαντικές λειτουργίες. Η λειτουργία LANCING από την άλλη πλευρά κόβει και λυγίζει το φύλλο για να δημιουργήσει μια ανυψωμένη γεωμετρία. • ΦΥΣΜΑ ΚΑΙ ΚΑΜΨΗ ΜΕΤΑΛΛΙΚΟΥ ΣΩΛΗΝΑ : Στο BUGGING κάποιο εσωτερικό μέρος ενός κοίλου σωλήνα υφίσταται πίεση, προκαλώντας διόγκωση του σωλήνα προς τα έξω. Δεδομένου ότι ο σωλήνας βρίσκεται μέσα σε μια μήτρα, η γεωμετρία της διόγκωσης ελέγχεται από το σχήμα της μήτρας. Στο STRETCH BENDING, ένας μεταλλικός σωλήνας τεντώνεται χρησιμοποιώντας δυνάμεις παράλληλες προς τον άξονα του σωλήνα και δυνάμεις κάμψης για να τραβήξει τον σωλήνα πάνω από ένα μπλοκ μορφής. Στο DRAW BENDING, σφίγγουμε τον σωλήνα κοντά στο άκρο του σε ένα μπλοκ περιστρεφόμενης μορφής που λυγίζει τον σωλήνα ενώ περιστρέφεται. Τέλος, στην ΚΑΜΨΗ ΣΥΜΠΙΕΣΗΣ ο σωλήνας συγκρατείται με δύναμη σε ένα μπλοκ σταθερής μορφής και μια μήτρα τον λυγίζει πάνω από το μπλοκ φόρμας. • ΒΑΘΙΟ ΣΧΕΔΙΟ: Σε μια από τις πιο δημοφιλείς εργασίες μας, χρησιμοποιείται μια γροθιά, μια ταιριαστή μήτρα και μια θήκη κενού. Το ακατέργαστο φύλλο μετάλλου τοποθετείται πάνω από το άνοιγμα της μήτρας και η διάτρηση κινείται προς το ακατέργαστο τεμάχιο που συγκρατείται από τη θήκη του τυφλού. Μόλις έρθουν σε επαφή, η διάτρηση πιέζει τη λαμαρίνα μέσα στην κοιλότητα της μήτρας για να σχηματίσει το προϊόν. Η λειτουργία βαθιάς έλξης μοιάζει με την κοπή, ωστόσο το διάκενο μεταξύ της διάτρησης και της μήτρας εμποδίζει την κοπή του φύλλου. Ένας άλλος παράγοντας που διασφαλίζει ότι το φύλλο είναι βαθιά τραβηγμένο και μη κομμένο είναι οι στρογγυλεμένες γωνίες στη μήτρα και η διάτρηση που εμποδίζει το κούρεμα και το κόψιμο. Για να επιτευχθεί μεγαλύτερο μέγεθος βαθιάς σχεδίασης, αναπτύσσεται μια διαδικασία ΕΠΑΝΑΣΧΕΩΣΗΣ όπου λαμβάνει χώρα ένα επόμενο βαθύ σχέδιο σε ένα τμήμα που έχει ήδη υποβληθεί σε διαδικασία βαθιάς σχεδίασης. Στην ΑΝΤΙΣΤΡΟΦΗ ΕΠΑΝΑΣΧΕΩΣΗ, το βαθύ τραβηγμένο τμήμα αναποδογυρίζεται και τραβιέται προς την αντίθετη κατεύθυνση. Το βαθύ σχέδιο μπορεί να παρέχει αντικείμενα ακανόνιστου σχήματος, όπως κούπες με θόλο, κωνικό ή βαθμιδωτό, Στο EMBOSSING χρησιμοποιούμε ένα ζεύγος αρσενικής και θηλυκής μήτρας για να εντυπωσιάσουμε τη λαμαρίνα με σχέδιο ή σενάριο. • SPINNING : Μια λειτουργία κατά την οποία ένα επίπεδο ή προσχηματισμένο τεμάχιο εργασίας συγκρατείται μεταξύ ενός περιστρεφόμενου άξονα και του ουρανού και ένα εργαλείο ασκεί τοπική πίεση στο έργο καθώς κινείται σταδιακά προς τα πάνω στον άξονα. Ως αποτέλεσμα, το τεμάχιο εργασίας τυλίγεται πάνω από το μανδρέλι και παίρνει το σχήμα του. Χρησιμοποιούμε αυτήν την τεχνική ως εναλλακτική στο βαθύ σχέδιο όπου η ποσότητα μιας παραγγελίας είναι μικρή, τα μέρη είναι μεγάλα (διάμετροι έως 20 πόδια) και έχουν μοναδικές καμπύλες. Παρόλο που οι τιμές ανά τεμάχιο είναι γενικά υψηλότερες, το κόστος εγκατάστασης για τη λειτουργία στυψίματος CNC είναι χαμηλό σε σύγκριση με το βαθύ τράβηγμα. Αντίθετα, το βαθύ σχέδιο απαιτεί υψηλή αρχική επένδυση για την εγκατάσταση, αλλά το κόστος ανά τεμάχιο είναι χαμηλό όταν παράγεται μεγάλη ποσότητα εξαρτημάτων. Μια άλλη εκδοχή αυτής της διαδικασίας είναι το SHEAR SPINNING, όπου υπάρχει επίσης ροή μετάλλου μέσα στο τεμάχιο εργασίας. Η ροή μετάλλου θα μειώσει το πάχος του τεμαχίου εργασίας καθώς εκτελείται η διαδικασία. Μια άλλη σχετική διαδικασία είναι το TUBE SPINNING, το οποίο εφαρμόζεται σε κυλινδρικά μέρη. Επίσης σε αυτή τη διαδικασία υπάρχει ροή μετάλλου μέσα στο τεμάχιο εργασίας. Το πάχος μειώνεται έτσι και το μήκος του σωλήνα αυξάνεται. Το εργαλείο μπορεί να μετακινηθεί για να δημιουργήσει χαρακτηριστικά στο εσωτερικό ή στο εξωτερικό του σωλήνα. • ΔΙΑΜΟΡΦΩΣΗ ΛΑΣΟΥΧΟΥ ΛΑΜΑΡΙΝΟΥ : Το υλικό από καουτσούκ ή πολυουρεθάνη τοποθετείται σε μήτρα δοχείου και το τεμάχιο εργασίας τοποθετείται στην επιφάνεια του καουτσούκ. Στη συνέχεια, ασκείται μια διάτρηση πάνω στο τεμάχιο εργασίας και το πιέζει μέσα στο λάστιχο. Δεδομένου ότι η πίεση που δημιουργείται από το καουτσούκ είναι χαμηλή, το βάθος των παραγόμενων εξαρτημάτων είναι περιορισμένο. Δεδομένου ότι το κόστος εργαλείων είναι χαμηλό, η διαδικασία είναι κατάλληλη για παραγωγή χαμηλής ποσότητας. • ΥΔΡΟΔΙΑΜΟΡΦΩΣΗ: Παρόμοια με τη μορφοποίηση από καουτσούκ, σε αυτή τη διαδικασία η λαμαρίνα πιέζεται με διάτρηση σε υγρό υπό πίεση μέσα σε ένα θάλαμο. Η λαμαρίνα τοποθετείται ανάμεσα στη διάτρηση και ένα ελαστικό διάφραγμα. Το διάφραγμα περιβάλλει πλήρως το τεμάχιο εργασίας και η πίεση του υγρού το αναγκάζει να σχηματιστεί στη διάτρηση. Με αυτήν την τεχνική μπορούν να επιτευχθούν πολύ βαθιές τραβήξεις ακόμα πιο βαθιά από ό,τι στη διαδικασία σχεδίασης σε βάθος. Κατασκευάζουμε μήτρες μονής διάτρησης καθώς και προοδευτικές μήτρες ανάλογα με τη δική σας πλευρά. Οι μήτρες σφράγισης μιας διαδρομής είναι μια οικονομικά αποδοτική μέθοδος για την γρήγορη παραγωγή μεγάλων ποσοτήτων απλών μεταλλικών εξαρτημάτων όπως ροδέλες. Οι προοδευτικές μήτρες ή η τεχνική βαθιάς σχεδίασης χρησιμοποιούνται για την κατασκευή πιο σύνθετων γεωμετριών. Ανάλογα με την περίπτωσή σας, η κοπή νερού, λέιζερ ή πλάσματος μπορεί να χρησιμοποιηθεί για την παραγωγή λαμαρίνας σας φθηνά, γρήγορα και με ακρίβεια. Πολλοί προμηθευτές δεν έχουν ιδέα για αυτές τις εναλλακτικές τεχνικές ή δεν τις έχουν και επομένως περνούν από μακροχρόνιους και δαπανηρούς τρόπους κατασκευής μήτρων και εργαλείων που σπαταλούν μόνο χρόνο και χρήμα στους πελάτες. Εάν χρειάζεστε ειδικά κατασκευασμένα εξαρτήματα λαμαρίνας, όπως περιβλήματα, ηλεκτρονικά περιβλήματα... κ.λπ. τόσο γρήγορα όσο εντός ημερών, τότε επικοινωνήστε μαζί μας για την υπηρεσία ΤΑΧΕΙΑΣ ΠΡΩΤΟΤΥΠΩΣΗΣ ΛΑΜΑΡΙΝΩΝ. CLICK Product Finder-Locator Service ΠΡΟΗΓΟΥΜΕΝΟ ΜΕΝΟΥ
- Forging and Powdered Metallurgy, Die Forging, Heading, Hot Forging
Forging and Powdered Metallurgy, Die Forging, Heading, Hot Forging, Impression Die, Near Net Shape, Swaging, Metal Hobbing, Riveting, Coining from AGS-TECH Inc. Σφυρηλάτηση Μετάλλων & Μεταλλουργία Σκόνης Ο τύπος των διαδικασιών ΣΦΥΡΗΤΗΣΗΣ ΜΕΤΑΛΛΩΝ που προσφέρουμε είναι θερμή και κρύα μήτρα, ανοιχτή μήτρα και κλειστή μήτρα, σφυρηλάτηση αποτύπωσης και σφυρηλάτηση χωρίς λάμψη, cogging, fullering, μπορντούρα και σφυρηλάτηση ακριβείας, σχεδόν διχτυωτή , σφυρηλάτηση, σφυρηλάτηση ανατρεπόμενης σφυρηλάτησης, κολάρο μετάλλου, σφυρηλάτηση με πρέσα & roll & ακτινικά & τροχιακά & δακτυλιοειδείς & ισοθερμικές σφυρηλάτες, νομισματοκοπία, πριτσίνωμα, σφυρηλάτηση μεταλλικών σφαιρών, διάτρηση μετάλλων, διαστασιολόγηση, σφυρηλάτηση υψηλής ενεργειακής απόδοσης. Οι τεχνικές μας ΜΕΤΑΛΛΟΥΡΓΙΑΣ ΚΟΝΗΣ και ΕΠΕΞΕΡΓΑΣΙΑΣ ΚΟΝΗΣ είναι η συμπίεση και πυροσυσσωμάτωση σε σκόνη, ο εμποτισμός, η διήθηση, η θερμή και ψυχρή ισοστατική συμπίεση, η χύτευση με έγχυση μετάλλων, η συμπίεση σε ρολό, η έλαση σκόνης, η εξώθηση σκόνης, η χαλαρή πυροσυσσωμάτωση, η πυροσυσσωμάτωση με σπινθήρα, η θερμή έκθλιψη. Σας συνιστούμε να κάνετε κλικ εδώ για να ΚΑΤΕΒΑΣΤΕ τις Σχηματικές μας απεικονίσεις των Διαδικασιών Σφυρηλάτησης από την AGS-TECH Inc. ΚΑΤΕΒΑΣΤΕ τις Σχηματικές μας απεικονίσεις των Διαδικασιών Μεταλλουργίας Σκόνης από την AGS-TECH Inc. Αυτά τα αρχεία με δυνατότητα λήψης με φωτογραφίες και σκίτσα θα σας βοηθήσουν να κατανοήσετε καλύτερα τις πληροφορίες που σας παρέχουμε παρακάτω. Στη σφυρηλάτηση μετάλλων εφαρμόζονται συμπιεστικές δυνάμεις και παραμορφώνεται το υλικό και αποκτάται το επιθυμητό σχήμα. Τα πιο κοινά σφυρήλατα υλικά στη βιομηχανία είναι ο σίδηρος και ο χάλυβας, αλλά πολλά άλλα όπως το αλουμίνιο, ο χαλκός, το τιτάνιο, το μαγνήσιο είναι επίσης ευρέως σφυρηλατημένα. Τα σφυρήλατα μεταλλικά μέρη έχουν βελτιωμένες δομές κόκκων εκτός από σφραγισμένες ρωγμές και κλειστούς κενούς χώρους, επομένως η αντοχή των εξαρτημάτων που λαμβάνεται με αυτή τη διαδικασία είναι μεγαλύτερη. Η σφυρηλάτηση παράγει εξαρτήματα που είναι σημαντικά ισχυρότερα για το βάρος τους από τα μέρη που κατασκευάζονται με χύτευση ή μηχανική κατεργασία. Δεδομένου ότι τα σφυρήλατα μέρη διαμορφώνονται κάνοντας το μέταλλο να ρέει στο τελικό του σχήμα, το μέταλλο αποκτά μια κατευθυντική δομή κόκκων που αντιπροσωπεύει την ανώτερη αντοχή των εξαρτημάτων. Με άλλα λόγια, τα μέρη που λαμβάνονται με τη διαδικασία σφυρηλάτησης αποκαλύπτουν καλύτερες μηχανικές ιδιότητες σε σύγκριση με τα απλά χυτά ή κατεργασμένα εξαρτήματα. Το βάρος των μεταλλικών σφυρηλάτησης μπορεί να κυμαίνεται από μικρά ελαφριά εξαρτήματα έως εκατοντάδες χιλιάδες λίβρες. Κατασκευάζουμε σφυρήλατα κυρίως για μηχανικά απαιτητικές εφαρμογές όπου ασκούνται υψηλές καταπονήσεις σε μέρη όπως ανταλλακτικά αυτοκινήτων, γρανάζια, εργαλεία εργασίας, εργαλεία χειρός, άξονες τουρμπίνας, εργαλεία μοτοσικλετών. Επειδή το κόστος εργαλείων και εγκατάστασης είναι σχετικά υψηλά, συνιστούμε αυτήν τη διαδικασία κατασκευής μόνο για παραγωγή μεγάλου όγκου και για κρίσιμα εξαρτήματα χαμηλού όγκου αλλά υψηλής αξίας, όπως εξοπλισμός προσγείωσης αεροδιαστημικής. Εκτός από το κόστος εργαλείων, οι χρόνοι κατασκευής για σφυρήλατα εξαρτήματα μεγάλης ποσότητας μπορεί να είναι μεγαλύτεροι σε σύγκριση με ορισμένα απλά κατεργασμένα εξαρτήματα, αλλά η τεχνική είναι ζωτικής σημασίας για εξαρτήματα που απαιτούν εξαιρετική αντοχή, όπως μπουλόνια, παξιμάδια, ειδική εφαρμογή, συνδετήρες, ανταλλακτικά αυτοκινήτων, περονοφόρων, γερανών. • ΣΦΥΡΗΤΟΠΟΙΗΣΗ ΘΕΡΜΗΣ ΜΗΧΑΝΗΣ και ΣΦΥΡΥΔΡΩΣΗΣ ΨΥΧΡΗΣ ΜΗΧΑΝΗΣ: Η σφυρηλάτηση με θερμή μήτρα, όπως υποδηλώνει το όνομα, πραγματοποιείται σε υψηλές θερμοκρασίες, επομένως η ολκιμότητα είναι υψηλή και η αντοχή του υλικού χαμηλή. Αυτό διευκολύνει την εύκολη παραμόρφωση και σφυρηλάτηση. Αντίθετα, η σφυρηλάτηση ψυχρής μήτρας πραγματοποιείται σε χαμηλότερες θερμοκρασίες και απαιτεί υψηλότερες δυνάμεις που έχουν ως αποτέλεσμα τη σκλήρυνση της τάσης, το καλύτερο φινίρισμα της επιφάνειας και την ακρίβεια των κατασκευασμένων εξαρτημάτων. • ΑΝΟΙΧΤΗ ΜΕΤΡΗΤΗ ΚΑΙ ΣΦΥΡΗΤΗΡΙΑ ΜΕΤΡΗΣΗΣ ΑΠΟΣΠΑΣΗΣ: Στην σφυρηλάτηση ανοιχτής μήτρας, οι μήτρες δεν περιορίζουν το υλικό που συμπιέζεται, ενώ στη σφυρηλάτηση με μήτρα αποτύπωσης οι κοιλότητες μέσα στις μήτρες περιορίζουν τη ροή του υλικού ενώ σφυρηλατείται στο επιθυμητό σχήμα. Το UPSET FORGING ή ονομάζεται επίσης UPSETTING, το οποίο στην πραγματικότητα δεν είναι το ίδιο αλλά μια πολύ παρόμοια διαδικασία, είναι μια διαδικασία ανοιχτής μήτρας όπου το τεμάχιο εργασίας τοποθετείται ανάμεσα σε δύο επίπεδες μήτρες και μια δύναμη συμπίεσης μειώνει το ύψος του. Καθώς το ύψος είναι reduced, το πλάτος του τεμαχίου εργασίας αυξάνεται. HEADING, μια διαδικασία σφυρηλάτησης με ανατροπή περιλαμβάνει κυλινδρικό κοντάκι που ανατρέπεται στο άκρο του και η διατομή του αυξάνεται τοπικά. Στην επικεφαλίδα το απόθεμα τροφοδοτείται μέσω της μήτρας, σφυρηλατείται και στη συνέχεια κόβεται σε μήκος. Η λειτουργία είναι ικανή να παράγει γρήγορα μεγάλες ποσότητες συνδετήρων. Κυρίως είναι μια εργασία ψυχρής επεξεργασίας επειδή χρησιμοποιείται για την κατασκευή άκρων καρφιών, βιδών, παξιμαδιών και μπουλονιών όπου το υλικό πρέπει να ενισχυθεί. Μια άλλη διαδικασία ανοικτής μήτρας είναι το COGGING, όπου το τεμάχιο εργασίας σφυρηλατείται σε μια σειρά βημάτων με κάθε βήμα να έχει ως αποτέλεσμα τη συμπίεση του υλικού και την επακόλουθη κίνηση της ανοιχτής μήτρας κατά μήκος του τεμαχίου εργασίας. Σε κάθε βήμα, το πάχος μειώνεται και το μήκος αυξάνεται κατά ένα μικρό ποσό. Η διαδικασία μοιάζει με νευρικό μαθητή που δαγκώνει το μολύβι του όλη την ώρα με μικρά βήματα. Μια διαδικασία που ονομάζεται FULLERING είναι μια άλλη μέθοδος σφυρηλάτησης ανοιχτής μήτρας που συχνά αναπτύσσουμε ως προηγούμενο βήμα για τη διανομή του υλικού στο τεμάχιο εργασίας πριν πραγματοποιηθούν άλλες εργασίες σφυρηλάτησης μετάλλων. Το χρησιμοποιούμε όταν το τεμάχιο εργασίας απαιτεί πολλές εργασίες forging operations. Κατά τη λειτουργία, μήτρα με κυρτές επιφάνειες παραμορφώνονται και προκαλούν ροή μετάλλου και στις δύο πλευρές. Μια παρόμοια διαδικασία με το γέμισμα, το EDGING από την άλλη πλευρά περιλαμβάνει ανοιχτή μήτρα με κοίλες επιφάνειες για παραμόρφωση του τεμαχίου εργασίας. Το χείλος είναι επίσης μια προπαρασκευαστική διαδικασία για επακόλουθες εργασίες σφυρηλάτησης κάνει το υλικό να ρέει και από τις δύο πλευρές σε μια περιοχή στο κέντρο. IMPRESSION DIE FORGING ή CLOSED DIE FORGING όπως ονομάζεται επίσης χρησιμοποιεί μια μήτρα / καλούπι που συμπιέζει το υλικό και περιορίζει τη ροή του μέσα του. Η μήτρα κλείνει και το υλικό παίρνει το σχήμα της κοιλότητας της μήτρας/καλουπιού. Η ΣΦΥΡΗΤΗΡΙΑ ΑΚΡΙΒΕΙΑΣ, μια διαδικασία που απαιτεί ειδικό εξοπλισμό και καλούπι, παράγει εξαρτήματα χωρίς ή πολύ λίγο φλας. Με άλλα λόγια, τα μέρη θα έχουν σχεδόν τελικές διαστάσεις. Σε αυτή τη διαδικασία μια καλά ελεγχόμενη ποσότητα υλικού εισάγεται προσεκτικά και τοποθετείται μέσα στο καλούπι. Χρησιμοποιούμε αυτή τη μέθοδο για πολύπλοκα σχήματα με λεπτές τομές, μικρές ανοχές και γωνίες ρεύματος και όταν οι ποσότητες είναι αρκετά μεγάλες ώστε να δικαιολογούν το κόστος του καλουπιού και του εξοπλισμού. • ΣΦΥΡΗΤΗΡΙΑ χωρίς λάμψη: Το τεμάχιο εργασίας τοποθετείται στη μήτρα με τέτοιο τρόπο ώστε κανένα υλικό να μην μπορεί να ρέει έξω από την κοιλότητα για να σχηματίσει φλας. Επομένως, δεν απαιτείται ανεπιθύμητο κόψιμο φλας. Είναι μια διαδικασία σφυρηλάτησης ακριβείας και επομένως απαιτεί στενό έλεγχο της ποσότητας του υλικού που χρησιμοποιείται. • ΜΕΤΑΛΛΙΚΗ ΣΦΥΡΗΤΗΡΙΑ ή ΑΚΤΙΝΙΚΗ ΣΦΥΡΗΤΟΠΟΙΗΣΗ: Ένα τεμάχιο εργασίας επεξεργάζεται περιφερειακά με μήτρα και σφυρηλατείται. Ένας άξονας μπορεί επίσης να χρησιμοποιηθεί για τη διαμόρφωση της γεωμετρίας του εσωτερικού τεμαχίου εργασίας. Στη λειτουργία αιώρησης το τεμάχιο εργασίας λαμβάνει τυπικά αρκετές πινελιές ανά δευτερόλεπτο. Τυπικά αντικείμενα που παράγονται με αιώρηση είναι εργαλεία με αιχμηρά άκρα, κωνικές ράβδοι, κατσαβίδια. • ΤΡΑΠΗΜΑ ΜΕΤΑΛΛΟΥ: Χρησιμοποιούμε αυτή τη λειτουργία συχνά ως πρόσθετη λειτουργία στην κατασκευή εξαρτημάτων. Μια οπή ή κοιλότητα δημιουργείται με τρύπημα στην επιφάνεια του τεμαχίου εργασίας χωρίς να τη σπάσει. Λάβετε υπόψη ότι το τρύπημα είναι διαφορετικό από το τρύπημα που οδηγεί σε μια διαμπερή οπή. • HOBBING : Μια διάτρηση με την επιθυμητή γεωμετρία πιέζεται στο τεμάχιο εργασίας και δημιουργεί μια κοιλότητα με το επιθυμητό σχήμα. Αυτή τη διάτρηση ονομάζουμε ΕΣΤΙΑ. Η επέμβαση περιλαμβάνει υψηλές πιέσεις και πραγματοποιείται σε κρύο. Ως αποτέλεσμα, το υλικό υποβάλλεται σε ψυχρή κατεργασία και σκληρύνει με στέλεχος. Επομένως, αυτή η διαδικασία είναι πολύ κατάλληλη για την κατασκευή καλουπιών, καλουπιών και κοιλοτήτων για άλλες διαδικασίες παραγωγής. Μόλις κατασκευαστεί η εστία, μπορεί κανείς εύκολα να κατασκευάσει πολλές πανομοιότυπες κοιλότητες χωρίς να χρειάζεται να τις επεξεργαστεί μία προς μία. • ΣΦΥΡΗΤΟΠΟΙΗΣΗ ΡΟΛΟΥ ή ΣΧΗΜΑΤΙΣΜΟΣ ΡΟΛΟΥ : Χρησιμοποιούνται δύο αντίθετα ρολά για τη διαμόρφωση του μεταλλικού τμήματος. Το τεμάχιο εργασίας τροφοδοτείται στους κυλίνδρους, οι κύλινδροι γυρίζουν και τραβούν το έργο στο διάκενο, το έργο στη συνέχεια τροφοδοτείται μέσω του αυλακωμένου τμήματος των κυλίνδρων και οι δυνάμεις συμπίεσης δίνουν στο υλικό το επιθυμητό σχήμα. Δεν είναι μια διαδικασία έλασης αλλά μια διαδικασία σφυρηλάτησης, επειδή είναι μια διακριτή και όχι μια συνεχής λειτουργία. Η γεωμετρία στα άλση με ρολά σφυρηλατεί το υλικό στο επιθυμητό σχήμα και γεωμετρία. Εκτελείται ζεστό. Επειδή είναι μια διαδικασία σφυρηλάτησης παράγει εξαρτήματα με εξαιρετικές μηχανικές ιδιότητες και ως εκ τούτου το χρησιμοποιούμε για manufacturing ανταλλακτικών αυτοκινήτων όπως άξονες που πρέπει να έχουν εξαιρετική αντοχή σε σκληρά περιβάλλοντα εργασίας. • ΚΟΧΙΑΚΗ ΣΦΥΡΗΤΗΡΙΑ : Το τεμάχιο εργασίας τοποθετείται σε μια κοιλότητα μήτρας σφυρηλάτησης και σφυρηλατείται από μια άνω μήτρα που ταξιδεύει σε τροχιακή διαδρομή καθώς περιστρέφεται σε κεκλιμένο άξονα. Σε κάθε περιστροφή, η άνω μήτρα ολοκληρώνει την άσκηση συμπιεστικών δυνάμεων σε ολόκληρο το τεμάχιο εργασίας. Επαναλαμβάνοντας αυτές τις περιστροφές πολλές φορές, εκτελείται επαρκής σφυρηλάτηση. Τα πλεονεκτήματα αυτής της τεχνικής κατασκευής είναι η λειτουργία χαμηλού θορύβου και οι χαμηλότερες δυνάμεις που απαιτούνται. Με άλλα λόγια, με μικρές δυνάμεις μπορεί κανείς να περιστρέφει μια βαριά μήτρα γύρω από έναν άξονα για να ασκήσει μεγάλες πιέσεις σε ένα τμήμα του τεμαχίου εργασίας που βρίσκεται σε επαφή με τη μήτρα. Τα εξαρτήματα σε σχήμα δίσκου ή κωνικού σχήματος ταιριάζουν μερικές φορές σε αυτή τη διαδικασία. • ΣΦΥΡΗΤΗΡΙΑ ΔΑΧΤΥΛΙΩΝ: Χρησιμοποιούμε συχνά για την κατασκευή δακτυλίων χωρίς ραφή. Το απόθεμα κόβεται σε μήκος, ανατρέπεται και στη συνέχεια τρυπιέται μέχρι το τέλος για να δημιουργηθεί μια κεντρική τρύπα. Στη συνέχεια, τοποθετείται σε ένα μανδρέλι και μια μήτρα σφυρηλάτησης το σφυρίζει από πάνω καθώς ο δακτύλιος περιστρέφεται αργά μέχρι να ληφθούν οι επιθυμητές διαστάσεις. • ΠΑΡΤΙΝΩΣΗ: Μια κοινή διαδικασία για την ένωση εξαρτημάτων, ξεκινά με ένα ίσιο μεταλλικό κομμάτι που εισάγεται σε προκατασκευασμένες τρύπες μέσα από τα μέρη. Στη συνέχεια, τα δύο άκρα του μεταλλικού τεμαχίου σφυρηλατούνται με συμπίεση της άρθρωσης μεταξύ μιας άνω και κάτω μήτρας. • ΝΟΜΙΣΜΑ : Μια άλλη δημοφιλής διαδικασία που πραγματοποιείται με μηχανική πρέσα, ασκώντας μεγάλες δυνάμεις σε μικρή απόσταση. Το όνομα «coining» προέρχεται από τις λεπτές λεπτομέρειες που σφυρηλατούνται στις επιφάνειες των μεταλλικών νομισμάτων. Είναι κυρίως μια διαδικασία φινιρίσματος για ένα προϊόν όπου λαμβάνονται λεπτές λεπτομέρειες στις επιφάνειες ως αποτέλεσμα της μεγάλης δύναμης που ασκείται από τη μήτρα που μεταφέρει αυτές τις λεπτομέρειες στο τεμάχιο εργασίας. • ΣΦΥΡΗΤΟΠΟΙΗΣΗ ΜΕΤΑΛΛΙΚΗΣ ΣΦΑΛΑΣ: Προϊόντα όπως τα ρουλεμάν απαιτούν υψηλής ποιότητας μεταλλικές σφαίρες με ακρίβεια. Σε μια τεχνική που ονομάζεται SKEW ROLLING, χρησιμοποιούμε δύο αντίθετους κυλίνδρους που περιστρέφονται συνεχώς καθώς το κοντάκι τροφοδοτείται συνεχώς στους κυλίνδρους. Στο ένα άκρο των δύο κυλίνδρων εκτοξεύονται μεταλλικές σφαίρες ως προϊόν. Μια δεύτερη μέθοδος για σφυρηλάτηση μεταλλικών σφαιρών είναι η χρήση μήτρας που συμπιέζει το υλικό υλικού που τοποθετείται μεταξύ τους παίρνοντας το σφαιρικό σχήμα της κοιλότητας του καλουπιού. Συχνά οι μπάλες που παράγονται απαιτούν ορισμένα πρόσθετα βήματα, όπως φινίρισμα και γυάλισμα, προκειμένου να γίνουν προϊόν υψηλής ποιότητας. • ΙΣΟΘΕΡΜΙΚΗ ΣΦΥΡΗΤΟΠΟΙΗΣΗ / ΣΦΥΡΗΤΟΠΟΙΗΣΗ ΘΕΡΜΗΣ ΜΗΧΑΝΗΣ: Μια δαπανηρή διαδικασία που εκτελείται μόνο όταν δικαιολογείται το όφελος / η αξία κόστους. Μια θερμή διαδικασία εργασίας όπου η μήτρα θερμαίνεται περίπου στην ίδια θερμοκρασία με το τεμάχιο εργασίας. Δεδομένου ότι τόσο η μήτρα όσο και η εργασία έχουν περίπου την ίδια θερμοκρασία, δεν υπάρχει ψύξη και τα χαρακτηριστικά ροής του μετάλλου βελτιώνονται. Η λειτουργία είναι κατάλληλη για σούπερ κράματα και υλικά με κατώτερη σφυρηλάτηση και υλικά των οποίων οι μηχανικές ιδιότητες είναι πολύ ευαίσθητες σε μικρές διαβαθμίσεις θερμοκρασίας και αλλαγές. • ΜΕΓΕΘΟΣ ΜΕΤΑΛΛΟΥ : Είναι μια κρύα διαδικασία φινιρίσματος. Η ροή του υλικού είναι απεριόριστη προς όλες τις κατευθύνσεις, με εξαίρεση την κατεύθυνση στην οποία εφαρμόζεται η δύναμη. Ως αποτέλεσμα, επιτυγχάνεται πολύ καλό φινίρισμα επιφάνειας και ακριβείς διαστάσεις. • ΣΦΥΡΗΤΟΠΟΙΗΣΗ ΥΨΗΛΟΥ ΡΥΘΜΟΥ ΕΝΕΡΓΕΙΑΣ: Η τεχνική περιλαμβάνει ένα άνω καλούπι προσαρτημένο στον βραχίονα ενός εμβόλου που ωθείται γρήγορα καθώς ένα μείγμα καυσίμου-αέρα αναφλέγεται από ένα μπουζί. Μοιάζει με τη λειτουργία των εμβόλων σε έναν κινητήρα αυτοκινήτου. Το καλούπι χτυπά το τεμάχιο εργασίας πολύ γρήγορα και στη συνέχεια επιστρέφει στην αρχική του θέση πολύ γρήγορα χάρη στην αντίθλιψη. Το έργο σφυρηλατείται μέσα σε λίγα χιλιοστά του δευτερολέπτου και επομένως δεν υπάρχει χρόνος για να κρυώσει το έργο. Αυτό είναι χρήσιμο για δύσκολα σφυρηλατούμενα εξαρτήματα που έχουν πολύ ευαίσθητες στη θερμοκρασία μηχανικές ιδιότητες. Με άλλα λόγια, η διαδικασία είναι τόσο γρήγορη που το εξάρτημα σχηματίζεται υπό σταθερή θερμοκρασία καθ' όλη τη διάρκεια και δεν θα υπάρχουν κλίσεις θερμοκρασίας στις διεπαφές καλουπιού/τεμαχίου εργασίας. • Στο DIE FORGING, το μέταλλο χτυπιέται ανάμεσα σε δύο ταιριαστούς χαλύβδινους όγκους με ειδικά σχήματα, που ονομάζονται μήτρες. Όταν το μέταλλο σφυρηλατηθεί ανάμεσα στις μήτρες, παίρνει το ίδιο σχήμα με τα σχήματα στη μήτρα. Όταν φτάσει στο τελικό του σχήμα, το βγάζουμε για να κρυώσει. Αυτή η διαδικασία παράγει ισχυρά εξαρτήματα που έχουν ακριβές σχήμα, αλλά απαιτεί μεγαλύτερη επένδυση για τις εξειδικευμένες μήτρες. Η ανατρεπτική σφυρηλάτηση αυξάνει τη διάμετρο ενός κομματιού μετάλλου ισοπεδώνοντάς το. Χρησιμοποιείται γενικά για την κατασκευή μικρών εξαρτημάτων, ειδικά για το σχηματισμό κεφαλών σε συνδετήρες όπως μπουλόνια και καρφιά. • ΜΕΤΑΛΛΟΥΡΓΙΑ ΚΟΝΙΩΝ / ΕΠΕΞΕΡΓΑΣΙΑ ΚΟΝΙΩΝ : Όπως υποδηλώνει το όνομα, περιλαμβάνει διαδικασίες κατασκευής για την κατασκευή στερεών μερών ορισμένων γεωμετριών και σχημάτων από σκόνες. Εάν χρησιμοποιούνται μεταλλικές σκόνες για το σκοπό αυτό, είναι το βασίλειο της μεταλλουργίας σκόνης και εάν χρησιμοποιούνται μη μεταλλικές σκόνες είναι η επεξεργασία σκόνης. Τα στερεά μέρη παράγονται από σκόνες με συμπίεση και πυροσυσσωμάτωση. Το POWDER PRESSING χρησιμοποιείται για τη συμπίεση σκόνης σε επιθυμητά σχήματα. Πρώτον, το πρωτογενές υλικό κονιοποιείται φυσικά, χωρίζοντάς το σε πολλά μικρά μεμονωμένα σωματίδια. Το μείγμα σκόνης γεμίζεται στη μήτρα και μια γροθιά κινείται προς τη σκόνη και τη συμπυκνώνει στο επιθυμητό σχήμα. Κυρίως εκτελείται σε θερμοκρασία δωματίου, με συμπίεση σκόνης λαμβάνεται ένα στερεό μέρος και ονομάζεται πράσινο συμπαγές. Τα συνδετικά και τα λιπαντικά χρησιμοποιούνται συνήθως για την ενίσχυση της συμπαγοποίησης. Είμαστε σε θέση να σχηματίσουμε πρέσα σκόνης χρησιμοποιώντας υδραυλικές πρέσες χωρητικότητας αρκετών χιλιάδων τόνων. Επίσης διαθέτουμε πρέσες διπλής δράσης με αντίθετες διατρήσεις πάνω και κάτω καθώς και πρέσες πολλαπλής δράσης για εξαιρετικά πολύπλοκες γεωμετρίες εξαρτημάτων. Η ομοιομορφία, η οποία αποτελεί σημαντική πρόκληση για πολλές μονάδες μεταλλουργίας σκόνης / επεξεργασίας σκόνης δεν αποτελεί μεγάλο πρόβλημα για την AGS-TECH λόγω της εκτεταμένης εμπειρίας μας στην προσαρμοσμένη κατασκευή τέτοιων εξαρτημάτων για πολλά χρόνια. Ακόμα και με πιο χοντρά μέρη όπου η ομοιομορφία αποτελεί πρόκληση, τα καταφέραμε. Εάν δεσμευτούμε για το έργο σας, θα φτιάξουμε τα μέρη σας. Εάν δούμε πιθανούς κινδύνους, θα σας ενημερώσουμε in advance. Η ΣΥΝΤΗΡΗΣΗ ΣΚΟΝΗΣ, που είναι το δεύτερο βήμα, περιλαμβάνει την αύξηση της θερμοκρασίας σε έναν ορισμένο βαθμό και τη διατήρηση της θερμοκρασίας σε αυτό το επίπεδο για ορισμένο χρόνο, έτσι ώστε τα σωματίδια σκόνης στο συμπιεσμένο μέρος να μπορούν να συνδεθούν μεταξύ τους. Αυτό έχει ως αποτέλεσμα πολύ ισχυρότερους δεσμούς και ενίσχυση του τεμαχίου εργασίας. Η πυροσυσσωμάτωση λαμβάνει χώρα κοντά στη θερμοκρασία τήξης της σκόνης. Κατά τη διάρκεια της πυροσυσσωμάτωσης θα συμβεί συρρίκνωση, η αντοχή του υλικού, η πυκνότητα, η ολκιμότητα, η θερμική αγωγιμότητα, η ηλεκτρική αγωγιμότητα αυξάνονται. Διαθέτουμε φούρνους συνεχούς και παρτίδας για πυροσυσσωμάτωση. Μία από τις δυνατότητές μας είναι η προσαρμογή του επιπέδου πορώδους των εξαρτημάτων που παράγουμε. Για παράδειγμα, μπορούμε να παράγουμε μεταλλικά φίλτρα διατηρώντας τα μέρη πορώδη σε κάποιο βαθμό. Χρησιμοποιώντας μια τεχνική που ονομάζεται ΕΜΠΟΤΙΣΜΟΣ, γεμίζουμε τους πόρους του μετάλλου με ένα υγρό όπως το λάδι. Παράγουμε, για παράδειγμα, ρουλεμάν εμποτισμένα με λάδι που είναι αυτολιπαινόμενα. Στη διαδικασία INFILTRATION γεμίζουμε τους πόρους ενός μετάλλου με άλλο μέταλλο χαμηλότερου σημείου τήξης από το υλικό βάσης. Το μίγμα θερμαίνεται σε θερμοκρασία μεταξύ των θερμοκρασιών τήξης των δύο μετάλλων. Ως αποτέλεσμα, μπορούν να αποκτηθούν ορισμένες ειδικές ιδιότητες. Εκτελούμε επίσης συχνά δευτερεύουσες εργασίες, όπως μηχανική κατεργασία και σφυρηλάτηση σε εξαρτήματα που κατασκευάζονται σε σκόνη, όταν πρέπει να αποκτηθούν ειδικά χαρακτηριστικά ή ιδιότητες ή όταν το εξάρτημα μπορεί να κατασκευαστεί με λιγότερα βήματα διαδικασίας. ΙΣΟΣΤΑΤΙΚΗ ΠΙΕΣΗ : Σε αυτή τη διαδικασία χρησιμοποιείται πίεση υγρού για τη συμπίεση του εξαρτήματος. Οι μεταλλικές σκόνες τοποθετούνται σε καλούπι κατασκευασμένο από σφραγισμένο εύκαμπτο δοχείο. Στην ισοστατική πίεση, η πίεση εφαρμόζεται από παντού, σε αντίθεση με την αξονική πίεση που παρατηρείται στη συμβατική πίεση. Τα πλεονεκτήματα της ισοστατικής συμπίεσης είναι η ομοιόμορφη πυκνότητα εντός του εξαρτήματος, ειδικά για μεγαλύτερα ή παχύτερα μέρη, ανώτερες ιδιότητες. Το μειονέκτημά του είναι οι μεγάλοι χρόνοι κύκλου και οι σχετικά μικρές γεωμετρικές ακρίβειες. Η ΨΥΧΡΗ ΙΣΟΣΤΑΤΙΚΗ ΠΙΕΣΗ πραγματοποιείται σε θερμοκρασία δωματίου και το εύκαμπτο καλούπι είναι κατασκευασμένο από καουτσούκ, PVC ή ουρεθάνη ή παρόμοια υλικά. Το υγρό που χρησιμοποιείται για συμπίεση και συμπίεση είναι λάδι ή νερό. Ακολουθεί η συμβατική πυροσυσσωμάτωση του πράσινου συμπαγούς. Η HOT ISOSTATIC PRESSING από την άλλη πλευρά πραγματοποιείται σε υψηλές θερμοκρασίες και το υλικό καλουπιού είναι λαμαρίνα ή κεραμικό με αρκετά υψηλό σημείο τήξης που αντέχει στις θερμοκρασίες. Το υγρό υπό πίεση είναι συνήθως ένα αδρανές αέριο. Οι εργασίες συμπίεσης και πυροσυσσωμάτωσης εκτελούνται σε ένα βήμα. Το πορώδες εξαλείφεται σχεδόν πλήρως, λαμβάνεται μια δομή ομοιόμορφου grain. Το πλεονέκτημα της θερμής ισοστατικής συμπίεσης είναι ότι μπορεί να παράγει εξαρτήματα συγκρίσιμα με τη χύτευση και τη σφυρηλάτηση σε συνδυασμό ενώ καθιστά δυνατή τη χρήση υλικών που δεν είναι κατάλληλα για χύτευση και σφυρηλάτηση. Το μειονέκτημα της θερμής ισοστατικής συμπίεσης είναι ο υψηλός χρόνος κύκλου και συνεπώς το κόστος. Είναι κατάλληλο για κρίσιμα μέρη χαμηλού όγκου. METAL INJECTION MOLDING : Πολύ κατάλληλη διαδικασία για την παραγωγή σύνθετων εξαρτημάτων με λεπτά τοιχώματα και λεπτομερείς γεωμετρίες. Καταλληλότερο για μικρότερα εξαρτήματα. Οι σκόνες και το πολυμερές συνδετικό αναμειγνύονται, θερμαίνονται και εγχέονται σε καλούπι. Το πολυμερές συνδετικό επικαλύπτει τις επιφάνειες των σωματιδίων σκόνης. Μετά τη χύτευση, το συνδετικό αφαιρείται είτε με θέρμανση σε χαμηλή θερμοκρασία του διαλυμένου με χρήση διαλύτη. ΣΥΜΠΙΕΣΗ ΡΟΛΟΥ / ΡΟΛΟ ΣΚΟΝΗΣ : Οι πούδρες χρησιμοποιούνται για την παραγωγή συνεχών λωρίδων ή φύλλων. Η σκόνη τροφοδοτείται από έναν τροφοδότη και συμπιέζεται με δύο περιστρεφόμενους κυλίνδρους σε φύλλο ή λωρίδες. Η επέμβαση γίνεται κρύα. Το φύλλο μεταφέρεται σε κλίβανο πυροσυσσωμάτωσης. Η διαδικασία πυροσυσσωμάτωσης μπορεί να επαναληφθεί για δεύτερη φορά. ΔΙΕΛΛΑΣΗ ΣΚΟΝΗΣ: Τα εξαρτήματα με μεγάλες αναλογίες μήκους προς διάμετρο κατασκευάζονται με εξώθηση ενός λεπτού μεταλλικού δοχείου με σκόνη. ΧΑΛΑΡΗ ΣΥΝΤΗΡΗΣΗ: Όπως υποδηλώνει το όνομα, είναι μια μέθοδος συμπύκνωσης και πυροσυσσωμάτωσης χωρίς πίεση, κατάλληλη για την παραγωγή πολύ πορωδών εξαρτημάτων όπως μεταλλικά φίλτρα. Η σκόνη τροφοδοτείται στην κοιλότητα του καλουπιού χωρίς συμπίεση. ΧΑΛΑΡΗ ΣΥΝΤΗΡΗΣΗ: Όπως υποδηλώνει το όνομα, είναι μια μέθοδος συμπύκνωσης και πυροσυσσωμάτωσης χωρίς πίεση, κατάλληλη για την παραγωγή πολύ πορωδών εξαρτημάτων όπως μεταλλικά φίλτρα. Η σκόνη τροφοδοτείται στην κοιλότητα του καλουπιού χωρίς συμπίεση. SPARK SINTERING : Η σκόνη συμπιέζεται στο καλούπι με δύο αντίθετες διατρήσεις και ένα ηλεκτρικό ρεύμα υψηλής ισχύος εφαρμόζεται στη διάτρηση και περνά μέσα από τη συμπιεσμένη σκόνη που βρίσκεται ανάμεσα τους. Το υψηλό ρεύμα καίει τα επιφανειακά φιλμ από τα σωματίδια της σκόνης και τα πυροσυσσωματώνει με τη θερμότητα που παράγεται. Η διαδικασία είναι γρήγορη γιατί η θερμότητα δεν εφαρμόζεται από το εξωτερικό, αλλά αντίθετα παράγεται μέσα από το καλούπι. HOT PRESSING : Οι σκόνες συμπιέζονται και πυροσυσσωματώνονται σε ένα μόνο βήμα σε ένα καλούπι που αντέχει στις υψηλές θερμοκρασίες. Καθώς η μήτρα συμπυκνώνεται, η θερμότητα της σκόνης εφαρμόζεται σε αυτήν. Οι καλές ακρίβειες και οι μηχανικές ιδιότητες που επιτυγχάνονται με αυτή τη μέθοδο την καθιστούν ελκυστική επιλογή. Ακόμη και τα πυρίμαχα μέταλλα μπορούν να υποστούν επεξεργασία χρησιμοποιώντας υλικά καλουπιού όπως ο γραφίτης. CLICK Product Finder-Locator Service ΠΡΟΗΓΟΥΜΕΝΟ ΜΕΝΟΥ
- Plastic Rubber Metal Extrusions, Extrusion Dies, Aluminum Extruding
Plastic Rubber Metal Extrusions, Extrusion Dies, Aluminum Extruding, Pipe Tube Forming, Plastic Profiles, Metal Profiles Manufacturing, PVC at AGS-TECH Inc. Εξωθήσεις, Εξωθημένα Προϊόντα, Εξωθήσεις Χρησιμοποιούμε το EXTRUSION process για την κατασκευή προϊόντων με σταθερή διατομή όπως σωλήνες θερμότητας, σωλήνες και σωλήνες. Παρόλο που πολλά υλικά μπορούν να εξωθηθούν, οι πιο κοινές μας εξωθήσεις είναι κατασκευασμένες από μέταλλο, πολυμερή / πλαστικό, κεραμικό που λαμβάνεται είτε με ψυχρή, θερμή ή θερμή μέθοδο εξώθησης. Τα εξωθημένα μέρη ονομάζουμε εξώθηση ή εξώθηση αν είναι πληθυντικά. Ορισμένες εξειδικευμένες εκδοχές της διαδικασίας που εκτελούμε επίσης είναι η υπερκάλυψη, η συνεξώθηση και η εξώθηση σύνθετων. Σας συνιστούμε να κάνετε κλικ εδώ για να ΚΑΤΕΒΑΣΤΕ τις Σχηματικές μας απεικονίσεις διεργασιών εξώθησης μεταλλοκεραμικών και πλαστικών από την AGS-TECH Inc. Αυτό θα σας βοηθήσει να κατανοήσετε καλύτερα τις πληροφορίες που σας παρέχουμε παρακάτω. Στην εξώθηση το προς εξώθηση υλικό ωθείται ή τραβιέται μέσα από μια μήτρα που έχει το επιθυμητό προφίλ διατομής. Η διαδικασία μπορεί να χρησιμοποιηθεί για την κατασκευή πολύπλοκων διατομών με εξαιρετικό φινίρισμα επιφάνειας και για εργασία σε εύθραυστο υλικό. Κάποιος μπορεί να παράγει οποιοδήποτε μήκος εξαρτημάτων χρησιμοποιώντας αυτή τη διαδικασία. Για να απλοποιήσετε τα βήματα της διαδικασίας: 1.) Σε θερμές ή θερμές εξωθήσεις το υλικό θερμαίνεται και φορτώνεται σε δοχείο στην πρέσα. Το υλικό πιέζεται και ωθείται έξω από τη μήτρα. 2.) Το παραγόμενο εξώθημα τεντώνεται για ίσιωμα, θερμική επεξεργασία ή ψυχρή επεξεργασία για ενίσχυση των ιδιοτήτων του. Από την άλλη πλευρά COLD EXTRUSION λαμβάνει χώρα περίπου σε θερμοκρασία δωματίου και έχει τα πλεονεκτήματα της λιγότερης οξείδωσης, της καλύτερης οξείδωσης και της υψηλής αντοχής. WARM EXTRUSION εκτελείται πάνω από τη θερμοκρασία δωματίου αλλά κάτω από το σημείο ανακρυστάλλωσης. Προσφέρει συμβιβασμό και ισορροπία για τις απαιτούμενες δυνάμεις, την ολκιμότητα και τις ιδιότητες του υλικού και επομένως είναι η επιλογή για ορισμένες εφαρμογές. HOT EXTRUSION λαμβάνει χώρα πάνω από τη θερμοκρασία ανακρυστάλλωσης του υλικού. Με αυτόν τον τρόπο είναι ευκολότερο να σπρώξετε το υλικό μέσα από τη μήτρα. Ωστόσο, το κόστος του εξοπλισμού είναι υψηλό. Όσο πιο περίπλοκο είναι ένα εξωθημένο προφίλ, τόσο πιο δαπανηρή είναι η μήτρα (εργαλείο) και τόσο χαμηλότερος είναι ο ρυθμός παραγωγής. Οι διατομές της μήτρας καθώς και τα πάχη έχουν περιορισμούς που εξαρτώνται από το υλικό που πρόκειται να εξωθηθεί. Οι αιχμηρές γωνίες στις μήτρες εξώθησης είναι πάντα ανεπιθύμητες και πρέπει να αποφεύγονται εκτός εάν είναι απαραίτητο. Σύμφωνα με το υλικό που εξωθείται, προσφέρουμε: • METAL EXTRUSIONS : Τα πιο κοινά που παράγουμε είναι αλουμίνιο, ορείχαλκος, ψευδάργυρος, χαλκός, χάλυβας, τιτάνιο, μαγνήσιο • PLASTIC EXTRUSION : Το πλαστικό τήκεται και σχηματίζεται σε συνεχές προφίλ. Τα κοινά μας υλικά που επεξεργαζόμαστε είναι πολυαιθυλένιο, νάιλον, πολυστυρένιο, πολυβινυλοχλωρίδιο, πολυπροπυλένιο, πλαστικό ABS, πολυανθρακικό, ακρυλικό. Τα τυπικά προϊόντα που κατασκευάζουμε περιλαμβάνουν σωλήνες και σωλήνες, πλαστικά κουφώματα. Στη διαδικασία μικρές πλαστικές χάντρες / ρητίνη τροφοδοτούνται με βαρύτητα από τη χοάνη στο βαρέλι της μηχανής εξώθησης. Συχνά αναμιγνύουμε επίσης χρωστικές ή άλλα πρόσθετα σε χοάνη για να δώσουμε στο προϊόν τις απαιτούμενες προδιαγραφές και ιδιότητες. Το υλικό που εισέρχεται στο θερμαινόμενο βαρέλι αναγκάζεται από την περιστρεφόμενη βίδα να εγκαταλείψει την κάννη στο άκρο και να μετακινηθεί μέσα από το πακέτο οθόνης για την απομάκρυνση των ρύπων στο λιωμένο πλαστικό. Αφού περάσει το πακέτο οθόνης, το πλαστικό εισέρχεται στη μήτρα εξώθησης. Η μήτρα δίνει στο κινούμενο μαλακό πλαστικό το σχήμα προφίλ του καθώς περνά μέσα από αυτό. Τώρα το προϊόν εξώθησης περνά μέσα από ένα λουτρό νερού για ψύξη. Άλλες τεχνικές που χρησιμοποιεί η AGS-TECH Inc. εδώ και πολλά χρόνια είναι: • PIPE & TUBING EXTRUSION : Οι πλαστικοί σωλήνες και σωλήνες σχηματίζονται όταν το πλαστικό εξωθείται μέσω μιας στρογγυλής μήτρας διαμόρφωσης και ψύχεται σε ένα λουτρό νερού και στη συνέχεια κόβεται σε μήκος ή περιτυλίσσεται / περιτυλίσσεται. Διαφανές ή έγχρωμο, ριγέ, μονό ή διπλό τοίχωμα, εύκαμπτο ή άκαμπτο, PE, PP, πολυουρεθάνη, PVC, νάιλον, PC, σιλικόνη, βινύλιο ή αλλιώς, τα έχουμε όλα. Διαθέτουμε σωλήνες καθώς και τη δυνατότητα παραγωγής σύμφωνα με τις προδιαγραφές σας. Η AGS-TECH κατασκευάζει σωληνώσεις σύμφωνα με τις απαιτήσεις των FDA, UL και LE για ιατρικές, ηλεκτρικές και ηλεκτρονικές, βιομηχανικές και άλλες εφαρμογές. • OVER JACKETING / OVER JACKETING EXTRUSION : Αυτή η τεχνική εφαρμόζει ένα εξωτερικό στρώμα πλαστικού σε υπάρχον σύρμα ή καλώδιο. Τα καλώδια μόνωσης μας κατασκευάζονται με αυτή τη μέθοδο. • COEXTRUSION : Πολλαπλές στρώσεις υλικού εξωθούνται ταυτόχρονα. Τα πολλαπλά στρώματα παραδίδονται από πολλαπλούς εξωθητές. Τα διάφορα πάχη στρώσης μπορούν να ρυθμιστούν ώστε να πληρούν τις προδιαγραφές του πελάτη. Αυτή η διαδικασία καθιστά δυνατή τη χρήση πολλαπλών πολυμερών που το καθένα έχει διαφορετική λειτουργικότητα στο προϊόν. Ως αποτέλεσμα, μπορεί κανείς να βελτιστοποιήσει μια σειρά ιδιοτήτων. • ΕΞΕΛΑΣΗ ΕΝΩΣΗΣ: Ένα μόνο ή πολλαπλά πολυμερή αναμιγνύονται με πρόσθετα για να ληφθεί μια πλαστική ένωση. Οι εξωθητές διπλού κοχλία μας παράγουν εξωθήσεις σύνθεσης. Οι μήτρες εξώθησης είναι γενικά φθηνές σε σύγκριση με τα μεταλλικά καλούπια. Εάν πληρώνετε πολύ περισσότερα από μερικές χιλιάδες δολάρια για μια μικρού ή μεσαίου μεγέθους μήτρα εξώθησης αλουμινίου, πιθανότατα πληρώνετε πάρα πολλά. Είμαστε ειδικοί στον καθορισμό της τεχνικής που είναι η πιο οικονομική, η ταχύτερη και η καταλληλότερη για την εφαρμογή σας. Μερικές φορές η εξώθηση και στη συνέχεια η κατεργασία ενός εξαρτήματος μπορεί να σας εξοικονομήσει πολλά μετρητά. Πριν πάρετε μια σταθερή απόφαση, ρωτήστε μας πρώτα τη γνώμη μας. Έχουμε βοηθήσει πολλούς πελάτες να λάβουν τις σωστές αποφάσεις. Για ορισμένες ευρέως χρησιμοποιούμενες εξωθήσεις μετάλλων, μπορείτε να κατεβάσετε τα φυλλάδια και τους καταλόγους μας κάνοντας κλικ στο έγχρωμο κείμενο παρακάτω. Εάν πρόκειται για προϊόν εκτός ραφιού που ανταποκρίνεται στις απαιτήσεις σας, θα είναι πιο οικονομικό. Κατεβάστε τις δυνατότητες εξώθησης ιατρικών σωλήνων και σωλήνων Κατεβάστε τις εξωθημένες ψύκτες μας • ΔΙΑΔΙΚΑΣΙΕΣ ΔΕΥΤΕΡΕΥΟΥΣΗΣ ΚΑΤΑΣΚΕΥΗΣ & ΚΑΤΑΣΚΕΥΗΣ ΓΙΑ ΕΞΩΛΕΣ : Μεταξύ των διαδικασιών προστιθέμενης αξίας που προσφέρουμε για προϊόντα εξέλασης είναι: - Προσαρμοσμένη κάμψη σωλήνων και σωλήνων, διαμόρφωση και διαμόρφωση, αποκοπή σωλήνα, διαμόρφωση άκρου σωλήνα, περιέλιξη σωλήνων, μηχανική κατεργασία και φινίρισμα, διάτρηση οπών & διάτρηση & διάτρηση, -Προσαρμοσμένα συγκροτήματα σωλήνων και σωλήνων, σωληνοειδές συγκρότημα, συγκόλληση, συγκόλληση και συγκόλληση -Προσαρμοσμένη κάμψη, διαμόρφωση και διαμόρφωση με εξώθηση -Καθαρισμός, απολίπανση, παστοποίηση, παθητικοποίηση, στίλβωση, ανοδίωση, επιμετάλλωση, βαφή, θερμική επεξεργασία, ανόπτηση και σκλήρυνση, σήμανση, χάραξη και επισήμανση, συσκευασία κατά παραγγελία. CLICK Product Finder-Locator Service ΠΡΟΗΓΟΥΜΕΝΗ ΣΕΛΙΔΑ
- Casting and Machined Parts, CNC Manufacturing, Milling, Turning, Swiss
Casting and Machined Parts, CNC Manufacturing, Milling, Turning, Swiss Type Machining, Die Casting, Investment Casting, Lost Foam Cast Parts from AGS-TECH Inc. Χύτευση και Μηχανική Οι προσαρμοσμένες τεχνικές χύτευσης και κατεργασίας μας είναι αναλώσιμα και μη αναλώσιμα χύτευση, σιδηρούχα και μη σιδηρούχα χύτευση, άμμος, μήτρα, φυγόκεντρος, συνεχής, κεραμικό καλούπι, επένδυση, χαμένος αφρός, σχεδόν δίχτυ, μόνιμο καλούπι (χύτευση με βαρύτητα), γύψος καλούπια (χύτευση γύψου) και κελύφους, κατεργασμένα εξαρτήματα που παράγονται με φρεζάρισμα και τόρνευση με χρήση συμβατικού καθώς και εξοπλισμού CNC, μηχανουργική κατεργασία ελβετικού τύπου για φθηνά μικρά εξαρτήματα ακριβείας υψηλής απόδοσης, κατεργασία με κοχλία για συνδετήρες, μη συμβατική μηχανική κατεργασία. Λάβετε υπόψη ότι εκτός από μέταλλα και κράματα μετάλλων, επεξεργαζόμαστε κεραμικά, γυάλινα και πλαστικά εξαρτήματα, καθώς και σε ορισμένες περιπτώσεις, όταν η κατασκευή ενός καλουπιού δεν είναι ελκυστική ή δεν είναι η επιλογή. Η κατεργασία πολυμερών υλικών απαιτεί την εξειδικευμένη εμπειρία που έχουμε λόγω της πρόκλησης που παρουσιάζουν τα πλαστικά και το καουτσούκ λόγω της απαλότητας, της μη ακαμψίας τους... κ.λπ. Για κατεργασία κεραμικών και γυαλιού, δείτε τη σελίδα μας στη Μη Συμβατική Κατασκευή. Η AGS-TECH Inc. κατασκευάζει και προμηθεύει τόσο ελαφριά όσο και βαριά χυτά. Προμηθεύουμε μεταλλικά χυτά και κατεργασμένα εξαρτήματα για λέβητες, εναλλάκτες θερμότητας, αυτοκίνητα, μικροκινητήρες, ανεμογεννήτριες, εξοπλισμό συσκευασίας τροφίμων και άλλα. Σας συνιστούμε να κάνετε κλικ εδώ για να ΚΑΤΕΒΑΣΤΕ τις Σχηματικές μας απεικονίσεις Διαδικασιών Μηχανικής και Χύτευσης από την AGS-TECH Inc. Αυτό θα σας βοηθήσει να κατανοήσετε καλύτερα τις πληροφορίες που σας παρέχουμε παρακάτω. Ας δούμε μερικές από τις διάφορες τεχνικές που προσφέρουμε αναλυτικά: • ΧΥΤΟΠΟΙΗΣΗ ΑΝΑΛΩΣΙΜΟΥ ΜΟΥΛΟΥΠΙΟΥ: Αυτή η ευρεία κατηγορία αναφέρεται σε μεθόδους που περιλαμβάνουν προσωρινά και μη επαναχρησιμοποιήσιμα καλούπια. Παραδείγματα είναι η άμμος, ο σοβάς, το κέλυφος, η επένδυση (ονομάζεται επίσης χαμένο κερί) και η χύτευση γύψου. • ΧΥΤΕΥΣΗ ΑΜΜΟΥ: Μια διαδικασία όπου η άμμος χρησιμοποιείται ως υλικό καλουπιού. Μια πολύ παλιά μέθοδος και εξακολουθεί να είναι πολύ δημοφιλής στο βαθμό που η πλειονότητα των μεταλλικών χυτών που παράγονται γίνονται με αυτήν την τεχνική. Χαμηλό κόστος ακόμα και σε χαμηλή ποσότητα παραγωγής. Κατάλληλο για την κατασκευή μικρών και μεγάλων ανταλλακτικών. Η τεχνική μπορεί να χρησιμοποιηθεί για την κατασκευή εξαρτημάτων εντός ημερών ή εβδομάδων με πολύ μικρή επένδυση. Η υγρή άμμος συγκολλάται μεταξύ τους χρησιμοποιώντας πηλό, συνδετικά ή ειδικά έλαια. Η άμμος περιέχεται γενικά στα κουτιά καλουπιών και το σύστημα κοιλότητας και πύλης δημιουργείται με τη συμπίεση της άμμου γύρω από τα μοντέλα. Οι διαδικασίες είναι: 1.) Τοποθέτηση του μοντέλου σε άμμο για την κατασκευή του καλουπιού 2.) Ενσωμάτωση μακέτας και άμμου σε σύστημα πυλών 3.) Αφαίρεση μοντέλου 4.) Γέμισμα της κοιλότητας του καλουπιού με λιωμένο μέταλλο 5.) Ψύξη του μετάλλου 6.) Σπάσιμο του καλουπιού άμμου και αφαίρεση του καλουπιού • ΧΥΤΩΣΗ ΜΟΥΧΟΥΡΙΟΥ ΓΥΨΟΥ: Παρόμοια με τη χύτευση με άμμο, και αντί για άμμο, χρησιμοποιείται σοβάς του Παρισιού ως υλικό καλουπιού. Μικροί χρόνοι παραγωγής όπως χύτευση με άμμο και φθηνός. Καλές ανοχές διαστάσεων και φινίρισμα επιφάνειας. Το κύριο μειονέκτημά του είναι ότι μπορεί να χρησιμοποιηθεί μόνο με μέταλλα χαμηλού σημείου τήξης όπως το αλουμίνιο και ο ψευδάργυρος. • SHELL MOULD CASTING : Επίσης παρόμοιο με τη χύτευση με άμμο. Κοιλότητα καλουπιού που λαμβάνεται από σκληρυμένο κέλυφος άμμου και συνδετικό θερμοσκληρυνόμενης ρητίνης αντί για φιάλη γεμάτη με άμμο όπως στη διαδικασία χύτευσης με άμμο. Σχεδόν κάθε μέταλλο κατάλληλο για χύτευση με άμμο μπορεί να χυτευθεί με χύτευση κελύφους. Η διαδικασία μπορεί να συνοψιστεί ως εξής: 1.) Κατασκευή του καλουπιού κελύφους. Η χρησιμοποιούμενη άμμος έχει πολύ μικρότερο μέγεθος κόκκου σε σύγκριση με την άμμο που χρησιμοποιείται στη χύτευση με άμμο. Η λεπτή άμμος αναμιγνύεται με θερμοσκληρυνόμενη ρητίνη. Το μεταλλικό σχέδιο είναι επικαλυμμένο με διαχωριστικό για να διευκολύνει την αφαίρεση του κελύφους. Στη συνέχεια, το μεταλλικό σχέδιο θερμαίνεται και το μίγμα άμμου τρυπάται ή εμφυσείται στο καυτό σχέδιο χύτευσης. Ένα λεπτό κέλυφος σχηματίζεται στην επιφάνεια του σχεδίου. Το πάχος αυτού του κελύφους μπορεί να ρυθμιστεί μεταβάλλοντας το χρονικό διάστημα που το μείγμα ρητίνης άμμου έρχεται σε επαφή με το μεταλλικό σχέδιο. Στη συνέχεια αφαιρείται η χαλαρή άμμος με το μοτίβο που καλύπτεται από το κέλυφος να παραμένει. 2.) Στη συνέχεια, το κέλυφος και το σχέδιο θερμαίνονται σε φούρνο, έτσι ώστε το κέλυφος να σκληρύνει. Αφού ολοκληρωθεί η σκλήρυνση, το κέλυφος εκτινάσσεται από το σχέδιο χρησιμοποιώντας καρφίτσες ενσωματωμένες στο σχέδιο. 3.) Δύο τέτοια κοχύλια συναρμολογούνται μεταξύ τους με κόλληση ή σύσφιξη και συνθέτουν ολόκληρο το καλούπι. Τώρα το καλούπι του κελύφους εισάγεται σε ένα δοχείο στο οποίο υποστηρίζεται από άμμο ή μέταλλο κατά τη διαδικασία χύτευσης. 4.) Τώρα το καυτό μέταλλο μπορεί να χυθεί στο καλούπι του κελύφους. Πλεονεκτήματα της χύτευσης κελύφους είναι προϊόντα με πολύ καλό φινίρισμα επιφάνειας, δυνατότητα κατασκευής σύνθετων εξαρτημάτων με υψηλή ακρίβεια διαστάσεων, διαδικασία εύκολη στην αυτοματοποίηση, οικονομική για παραγωγή μεγάλου όγκου. Τα μειονεκτήματα είναι ότι τα καλούπια απαιτούν καλό αερισμό λόγω των αερίων που δημιουργούνται όταν το λιωμένο μέταλλο έρχεται σε επαφή με το συνδετικό χημικό, οι θερμοσκληρυνόμενες ρητίνες και τα μεταλλικά σχέδια είναι ακριβά. Λόγω του κόστους των μεταλλικών μοτίβων, η τεχνική μπορεί να μην ταιριάζει καλά για μικρές ποσότητες παραγωγής. • INVESTMENT CASTING (γνωστό και ως LOST-WAX CASTING): Επίσης πολύ παλιά τεχνική και κατάλληλη για την κατασκευή ποιοτικών εξαρτημάτων με υψηλή ακρίβεια, επαναληψιμότητα, ευελιξία και ακεραιότητα από πολλά μέταλλα, πυρίμαχα υλικά και ειδικά κράματα υψηλής απόδοσης. Μπορούν να παραχθούν ανταλλακτικά μικρού αλλά και μεγάλου μεγέθους. Μια δαπανηρή διαδικασία σε σύγκριση με ορισμένες από τις άλλες μεθόδους, αλλά σημαντικό πλεονέκτημα είναι η δυνατότητα παραγωγής εξαρτημάτων με σχεδόν δίχτυ σχήμα, περίπλοκα περιγράμματα και λεπτομέρειες. Έτσι το κόστος αντισταθμίζεται κάπως από την εξάλειψη της επανεπεξεργασίας και της κατεργασίας σε ορισμένες περιπτώσεις. Παρόλο που μπορεί να υπάρχουν παραλλαγές, εδώ είναι μια περίληψη της γενικής διαδικασίας χύτευσης επενδύσεων: 1.) Δημιουργία πρωτότυπου κύριου σχεδίου από κερί ή πλαστικό. Κάθε casting χρειάζεται ένα μοτίβο καθώς καταστρέφονται στη διαδικασία. Χρειάζεται επίσης καλούπι από το οποίο κατασκευάζονται τα σχέδια και τις περισσότερες φορές το καλούπι χυτεύεται ή υποβάλλεται σε μηχανική επεξεργασία. Επειδή το καλούπι δεν χρειάζεται να ανοίξει, μπορούν να επιτευχθούν πολύπλοκα χυτά, πολλά σχέδια κεριού μπορούν να συνδεθούν όπως τα κλαδιά ενός δέντρου και να χυθούν μαζί, επιτρέποντας έτσι την παραγωγή πολλαπλών εξαρτημάτων από μια μόνο έκχυση του μετάλλου ή του κράματος μετάλλου. 2.) Στη συνέχεια, το σχέδιο βυθίζεται ή χύνεται με πυρίμαχο εναιώρημα που αποτελείται από πολύ λεπτόκοκκο πυρίτιο, νερό, συνδετικά. Αυτό έχει ως αποτέλεσμα ένα κεραμικό στρώμα πάνω από την επιφάνεια του σχεδίου. Η πυρίμαχη επίστρωση στο σχέδιο αφήνεται να στεγνώσει και να σκληρύνει. Αυτό το βήμα είναι από όπου προέρχεται το όνομα επένδυση χύτευσης: Ο πυρίμαχος πολτός επενδύεται πάνω από το σχέδιο κεριού. 3.) Σε αυτό το βήμα, το σκληρυμένο κεραμικό καλούπι αναποδογυρίζεται και θερμαίνεται έτσι ώστε το κερί να λιώσει και να χυθεί έξω από το καλούπι. Μια κοιλότητα αφήνεται πίσω για τη χύτευση μετάλλων. 4.) Αφού βγει το κερί, το κεραμικό καλούπι θερμαίνεται σε ακόμη υψηλότερη θερμοκρασία που έχει ως αποτέλεσμα την ενίσχυση του καλουπιού. 5.) Η χύτευση μετάλλου χύνεται στο ζεστό καλούπι γεμίζοντας όλα τα περίπλοκα τμήματα. 6.) Η χύτευση επιτρέπεται να στερεοποιηθεί 7.) Τέλος το κεραμικό καλούπι σπάει και τα κατασκευασμένα μέρη κόβονται από το δέντρο. Εδώ είναι ένας σύνδεσμος για το φυλλάδιο Investment Casting Plant • ΧΥΤΩΣΗ ΕΞΑΤΜΙΣΤΙΚΟΥ ΣΧΕΔΙΟΥ: Η διαδικασία χρησιμοποιεί ένα μοτίβο κατασκευασμένο από υλικό όπως αφρό πολυστυρενίου που θα εξατμιστεί όταν χυθεί καυτό λιωμένο μέταλλο στο καλούπι. Υπάρχουν δύο τύποι αυτής της διαδικασίας: LOST FOAM CASTING που χρησιμοποιεί μη συνδεδεμένη άμμο και FULL MOULD CASTING που χρησιμοποιεί συγκολλημένη άμμο. Ακολουθούν τα γενικά βήματα της διαδικασίας: 1.) Κατασκευάστε το σχέδιο από ένα υλικό όπως το πολυστυρένιο. Όταν θα κατασκευαστούν μεγάλες ποσότητες, το σχέδιο χυτεύεται. Εάν το τμήμα έχει πολύπλοκο σχήμα, πολλά τμήματα αυτού του αφρώδους υλικού μπορεί να χρειαστεί να κολληθούν μεταξύ τους για να σχηματίσουν το σχέδιο. Συχνά επικαλύπτουμε το σχέδιο με μια πυρίμαχη ένωση για να δημιουργήσουμε ένα καλό φινίρισμα επιφάνειας στο χυτό. 2.) Το σχέδιο τοποθετείται στη συνέχεια σε άμμο χύτευσης. 3.) Το λιωμένο μέταλλο χύνεται στο καλούπι, εξατμίζοντας το σχέδιο αφρού, δηλαδή το πολυστυρένιο στις περισσότερες περιπτώσεις καθώς ρέει μέσα από την κοιλότητα του καλουπιού. 4.) Το λιωμένο μέταλλο αφήνεται στο καλούπι άμμου για να σκληρύνει. 5.) Αφού σκληρύνει, αφαιρούμε το casting. Σε ορισμένες περιπτώσεις, το προϊόν που κατασκευάζουμε απαιτεί έναν πυρήνα εντός του σχεδίου. Στη χύτευση με εξάτμιση, δεν χρειάζεται να τοποθετηθεί και να στερεωθεί ένας πυρήνας στην κοιλότητα του καλουπιού. Η τεχνική είναι κατάλληλη για την κατασκευή πολύ σύνθετων γεωμετριών, μπορεί εύκολα να αυτοματοποιηθεί για παραγωγή μεγάλου όγκου και δεν υπάρχουν διαχωριστικές γραμμές στο χυτό μέρος. Η βασική διαδικασία είναι απλή και οικονομική στην εφαρμογή. Για παραγωγή μεγάλου όγκου, καθώς απαιτείται μήτρα ή καλούπι για την παραγωγή των σχεδίων από πολυστυρένιο, αυτό μπορεί να είναι κάπως δαπανηρό. • ΧΥΤΟΠΟΙΗΣΗ ΜΟΥΧΟΥΛΙΟΥ ΜΗ ΕΠΕΚΤΑΣΗ : Αυτή η ευρεία κατηγορία αναφέρεται σε μεθόδους όπου το καλούπι δεν χρειάζεται να αναμορφωθεί μετά από κάθε κύκλο παραγωγής. Παραδείγματα είναι η μόνιμη, η μήτρα, η συνεχής και η φυγοκεντρική χύτευση. Επιτυγχάνεται επαναληψιμότητα και τα εξαρτήματα μπορούν να χαρακτηριστούν ως ΣΧΗΜΑ ΚΟΝΤΑ ΔΙΧΤΥΟΥ. • ΜΟΝΙΜΗ ΧΥΤΩΣΗ ΜΟΥΡΟΥΧΩΝ: Επαναχρησιμοποιήσιμα καλούπια κατασκευασμένα από μέταλλο χρησιμοποιούνται για πολλαπλές χύτευση. Ένα μόνιμο καλούπι μπορεί γενικά να χρησιμοποιηθεί για δεκάδες χιλιάδες φορές πριν φθαρεί. Η βαρύτητα, η πίεση αερίου ή το κενό χρησιμοποιούνται γενικά για την πλήρωση του καλουπιού. Τα καλούπια (ονομάζονται επίσης καλούπια) είναι γενικά κατασκευασμένα από σίδηρο, χάλυβα, κεραμικό ή άλλα μέταλλα. Η γενική διαδικασία είναι: 1.) Επεξεργαστείτε και δημιουργήστε το καλούπι. Είναι σύνηθες να κατεργάζεται το καλούπι από δύο μεταλλικά τεμάχια που ταιριάζουν μεταξύ τους και μπορούν να ανοιγοκλείνουν. Τόσο τα χαρακτηριστικά του εξαρτήματος όσο και το σύστημα πύλης γενικά επεξεργάζονται μηχανικά στο καλούπι χύτευσης. 2.) Οι εσωτερικές επιφάνειες καλουπιού επικαλύπτονται με πολτό που ενσωματώνει πυρίμαχα υλικά. Αυτό βοηθά στον έλεγχο της ροής θερμότητας και λειτουργεί ως λιπαντικό για την εύκολη αφαίρεση του χυτού μέρους. 3.) Στη συνέχεια, τα μισά μόνιμα καλούπια κλείνουν και το καλούπι θερμαίνεται. 4.) Το λιωμένο μέταλλο χύνεται στο καλούπι και το αφήνουμε να στερεοποιηθεί. 5.) Πριν από πολύ ψύξη, αφαιρούμε το εξάρτημα από το μόνιμο καλούπι χρησιμοποιώντας εκτοξευτές όταν ανοίγουν τα μισά καλούπια. Χρησιμοποιούμε συχνά μόνιμη χύτευση καλουπιών για μέταλλα χαμηλού σημείου τήξης όπως ο ψευδάργυρος και το αλουμίνιο. Για τα χυτά χάλυβα, χρησιμοποιούμε γραφίτη ως υλικό καλουπιού. Μερικές φορές λαμβάνουμε πολύπλοκες γεωμετρίες χρησιμοποιώντας πυρήνες μέσα σε μόνιμα καλούπια. Πλεονεκτήματα αυτής της τεχνικής είναι χύτευση με καλές μηχανικές ιδιότητες που επιτυγχάνονται με γρήγορη ψύξη, ομοιομορφία στις ιδιότητες, καλή ακρίβεια και φινίρισμα επιφάνειας, χαμηλά ποσοστά απόρριψης, δυνατότητα αυτοματοποίησης της διαδικασίας και οικονομική παραγωγή υψηλών όγκων. Τα μειονεκτήματα είναι το υψηλό κόστος αρχικής εγκατάστασης που το καθιστά ακατάλληλο για λειτουργίες χαμηλού όγκου και οι περιορισμοί στο μέγεθος των εξαρτημάτων που κατασκευάζονται. • ΧΥΤΟΠΟΙΗΣΗ : Μια μήτρα υποβάλλεται σε μηχανική επεξεργασία και το λιωμένο μέταλλο ωθείται υπό υψηλή πίεση στις κοιλότητες του καλουπιού. Είναι δυνατή η χύτευση τόσο μη σιδηρούχων όσο και σιδηρούχων μετάλλων. Η διαδικασία είναι κατάλληλη για μεγάλες ποσότητες παραγωγής εξαρτημάτων μικρού έως μεσαίου μεγέθους με λεπτομέρειες, εξαιρετικά λεπτά τοιχώματα, συνοχή διαστάσεων και καλό φινίρισμα επιφάνειας. Η AGS-TECH Inc. είναι σε θέση να κατασκευάζει πάχη τοιχωμάτων τόσο μικρά όσο 0,5 mm χρησιμοποιώντας αυτήν την τεχνική. Όπως και στη μόνιμη χύτευση καλουπιού, το καλούπι πρέπει να αποτελείται από δύο μισά που μπορούν να ανοίγουν και να κλείνουν για την αφαίρεση του παραγόμενου τμήματος. Ένα καλούπι χύτευσης μπορεί να έχει πολλαπλές κοιλότητες για να επιτρέπει την παραγωγή πολλαπλών χυτών σε κάθε κύκλο. Τα καλούπια χύτευσης είναι πολύ βαριά και πολύ μεγαλύτερα από τα εξαρτήματα που παράγουν, επομένως και ακριβά. Επισκευάζουμε και αντικαθιστούμε τις φθαρμένες μήτρες δωρεάν για τους πελάτες μας, αρκεί να παραγγείλουν εκ νέου τα ανταλλακτικά τους από εμάς. Οι μήτρες μας έχουν μεγάλη διάρκεια ζωής στην περιοχή αρκετών εκατοντάδων χιλιάδων κύκλων. Ακολουθούν τα βασικά απλοποιημένα βήματα της διαδικασίας: 1.) Παραγωγή του καλουπιού γενικά από χάλυβα 2.) Καλούπι εγκατεστημένο στη μηχανή χύτευσης 3.) Το έμβολο αναγκάζει το λιωμένο μέταλλο να ρέει στις κοιλότητες της μήτρας γεμίζοντας τα περίπλοκα χαρακτηριστικά και τα λεπτά τοιχώματα 4.) Μετά την πλήρωση του καλουπιού με το λιωμένο μέταλλο, η χύτευση αφήνεται να σκληρύνει υπό πίεση 5.) Το καλούπι ανοίγει και το χύτευμα αφαιρείται με τη βοήθεια ακίδων εκτίναξης. 6.) Τώρα η άδεια μήτρα λιπαίνεται ξανά και σφίγγεται για τον επόμενο κύκλο. Στη χύτευση, χρησιμοποιούμε συχνά χύτευση με ένθετα όπου ενσωματώνουμε ένα επιπλέον μέρος στο καλούπι και ρίχνουμε το μέταλλο γύρω του. Μετά τη στερεοποίηση, αυτά τα μέρη γίνονται μέρος του χυτού προϊόντος. Τα πλεονεκτήματα της χύτευσης είναι καλές μηχανικές ιδιότητες των εξαρτημάτων, δυνατότητα περίπλοκων χαρακτηριστικών, λεπτές λεπτομέρειες και καλό φινίρισμα επιφάνειας, υψηλοί ρυθμοί παραγωγής, εύκολος αυτοματισμός. Τα μειονεκτήματα είναι: Δεν είναι πολύ κατάλληλο για χαμηλό όγκο λόγω υψηλού κόστους μήτρας και εξοπλισμού, περιορισμοί στα σχήματα που μπορούν να χυτευτούν, μικρά στρογγυλά σημάδια στα χυτά μέρη που προκύπτουν από την επαφή των ακίδων του εκτοξευτήρα, λεπτή λάμψη μετάλλου που συμπιέζεται στη γραμμή διαχωρισμού, ανάγκη για αεραγωγούς κατά μήκος της γραμμής διαχωρισμού μεταξύ της μήτρας, είναι ανάγκη να διατηρούνται χαμηλές οι θερμοκρασίες του καλουπιού χρησιμοποιώντας την κυκλοφορία του νερού. • ΦΥΓΟΚΕΝΤΡΙΚΗ ΧΥΤΩΣΗ : Το λιωμένο μέταλλο χύνεται στο κέντρο του περιστρεφόμενου καλουπιού στον άξονα περιστροφής. Οι φυγόκεντρες δυνάμεις ρίχνουν το μέταλλο προς την περιφέρεια και αφήνεται να στερεοποιηθεί καθώς το καλούπι συνεχίζει να περιστρέφεται. Μπορούν να χρησιμοποιηθούν περιστροφές τόσο οριζόντιου όσο και κατακόρυφου άξονα. Μπορούν να χυθούν μέρη με στρογγυλές εσωτερικές επιφάνειες καθώς και άλλα μη στρογγυλά σχήματα. Η διαδικασία μπορεί να συνοψιστεί ως εξής: 1.) Το λιωμένο μέταλλο χύνεται σε φυγοκεντρικό καλούπι. Το μέταλλο στη συνέχεια πιέζεται στα εξωτερικά τοιχώματα λόγω της περιστροφής του καλουπιού. 2.) Καθώς το καλούπι περιστρέφεται, η μεταλλική χύτευση σκληραίνει Η φυγόκεντρη χύτευση είναι μια κατάλληλη τεχνική για την παραγωγή κοίλων κυλινδρικών εξαρτημάτων όπως σωλήνες, δεν χρειάζονται σπιράλ, ανυψωτικά στοιχεία και στοιχεία πύλης, καλό φινίρισμα επιφάνειας και λεπτομερή χαρακτηριστικά, χωρίς προβλήματα συρρίκνωσης, δυνατότητα παραγωγής μακριών σωλήνων με πολύ μεγάλες διαμέτρους, δυνατότητα παραγωγής υψηλής ταχύτητας . • ΣΥΝΕΧΗΣ ΧΥΤΩΣΗ ( ΣΧΗΜΑ ΧΥΤΟΥ ) : Χρησιμοποιείται για τη χύτευση συνεχούς μήκους μετάλλου. Βασικά το λιωμένο μέταλλο χυτεύεται στο δισδιάστατο προφίλ του καλουπιού αλλά το μήκος του είναι απροσδιόριστο. Νέο λιωμένο μέταλλο τροφοδοτείται συνεχώς στο καλούπι καθώς το χύτευμα ταξιδεύει προς τα κάτω με το μήκος του να αυξάνεται με το χρόνο. Μέταλλα όπως ο χαλκός, ο χάλυβας, το αλουμίνιο χυτεύονται σε μακριά νήματα χρησιμοποιώντας τη διαδικασία συνεχούς χύτευσης. Η διαδικασία μπορεί να έχει διάφορες διαμορφώσεις, αλλά η κοινή μπορεί να απλοποιηθεί ως εξής: 1.) Το λιωμένο μέταλλο χύνεται σε ένα δοχείο που βρίσκεται ψηλά πάνω από το καλούπι σε καλά υπολογισμένες ποσότητες και ρυθμούς ροής και ρέει μέσα από το υδρόψυκτο καλούπι. Το μεταλλικό καλούπι που χύνεται στο καλούπι στερεοποιείται σε μια ράβδο εκκίνησης που τοποθετείται στο κάτω μέρος του καλουπιού. Αυτή η μπάρα εκκίνησης δίνει στους κυλίνδρους κάτι να πιάσουν αρχικά. 2.) Ο μακρύς μεταλλικός κλώνος μεταφέρεται από κυλίνδρους με σταθερή ταχύτητα. Οι κύλινδροι αλλάζουν επίσης την κατεύθυνση της ροής του μεταλλικού κλώνου από κάθετη σε οριζόντια. 3.) Αφού η συνεχής χύτευση έχει διανύσει μια ορισμένη οριζόντια απόσταση, ένας φακός ή πριόνι που κινείται με τη χύτευση το κόβει γρήγορα στα επιθυμητά μήκη. Η διαδικασία συνεχούς χύτευσης μπορεί να ενσωματωθεί με το ROLLING PROCESS, όπου το συνεχώς χυτευμένο μέταλλο μπορεί να τροφοδοτηθεί απευθείας σε ένα ελασματουργείο για την παραγωγή I-Beams, T-Beams… κ.λπ. Η συνεχής χύτευση παράγει ομοιόμορφες ιδιότητες σε όλο το προϊόν, έχει υψηλό ρυθμό στερεοποίησης, μειώνει το κόστος λόγω πολύ χαμηλής απώλειας υλικού, προσφέρει μια διαδικασία όπου η φόρτωση μετάλλου, η έκχυση, η στερεοποίηση, η κοπή και η αφαίρεση χύτευσης πραγματοποιούνται όλα σε συνεχή λειτουργία και με αποτέλεσμα υψηλό ποσοστό παραγωγικότητας και υψηλή ποιότητα. Ένα σημαντικό στοιχείο είναι ωστόσο η υψηλή αρχική επένδυση, το κόστος εγκατάστασης και οι απαιτήσεις χώρου. • ΥΠΗΡΕΣΙΕΣ ΜΗΧΑΝΙΚΗΣ: Προσφέρουμε μηχανουργική κατεργασία τριών, τεσσάρων και πέντε αξόνων. Ο τύπος των διεργασιών μηχανικής κατεργασίας που χρησιμοποιούμε είναι ΤΟΡΝΗΣΗ, ΦΡΕΕΖΟΜΕΝΗ, ΔΙΑΤΡΗΣΗ, ΔΙΑΤΡΗΣΗ, ΠΛΑΝΙΣΜΑ, ΠΡΙΟΝΙΜΟ, ΛΕΞΗ, ΛΕΙΤΩΣΗ, ΓΥΑΛΙΣΜΑ και ΜΗ ΠΑΡΑΔΟΣΙΑΚΗ ΜΗΧΑΝΙΚΗ, η οποία αναλύεται περαιτέρω σε διαφορετικό μενού του ιστότοπού μας. Για το μεγαλύτερο μέρος της κατασκευής μας, χρησιμοποιούμε μηχανές CNC. Ωστόσο, για ορισμένες λειτουργίες οι συμβατικές τεχνικές ταιριάζουν καλύτερα και επομένως βασιζόμαστε και σε αυτές. Οι ικανότητές μας σε μηχανουργική κατεργασία φτάνουν στο υψηλότερο δυνατό επίπεδο και ορισμένα πιο απαιτητικά εξαρτήματα κατασκευάζονται σε εργοστάσιο με πιστοποίηση AS9100. Τα πτερύγια κινητήρων αεριωθούμενων απαιτούν εξαιρετικά εξειδικευμένη εμπειρία κατασκευής και τον κατάλληλο εξοπλισμό. Η αεροδιαστημική βιομηχανία έχει πολύ αυστηρά πρότυπα. Ορισμένα εξαρτήματα με πολύπλοκες γεωμετρικές δομές κατασκευάζονται πιο εύκολα με μηχανική κατεργασία πέντε αξόνων, η οποία βρίσκεται μόνο σε ορισμένες μονάδες κατεργασίας, συμπεριλαμβανομένης της δικής μας. Το εργοστάσιό μας με πιστοποίηση αεροδιαστημικής διαθέτει την απαραίτητη πείρα σύμφωνα με τις εκτενείς απαιτήσεις τεκμηρίωσης της αεροδιαστημικής βιομηχανίας. Κατά τις εργασίες ΣΤΡΟΦΗΣ, ένα τεμάχιο εργασίας περιστρέφεται και μετακινείται πάνω σε ένα εργαλείο κοπής. Για αυτή τη διαδικασία χρησιμοποιείται ένα μηχάνημα που ονομάζεται τόρνος. Στο FILLING, ένα μηχάνημα που ονομάζεται φρέζα έχει ένα περιστρεφόμενο εργαλείο για να φέρει τις κοπτικές άκρες σε ένα τεμάχιο εργασίας. Οι εργασίες γεώτρησης περιλαμβάνουν έναν περιστρεφόμενο κόφτη με κοπτικές άκρες που δημιουργεί τρύπες κατά την επαφή με το τεμάχιο εργασίας. Γενικά χρησιμοποιούνται πρέσες, τόρνοι ή μύλοι. Στις λειτουργίες BORING ένα εργαλείο με ένα μόνο λυγισμένο μυτερό άκρο μετακινείται σε μια τραχιά οπή σε ένα περιστρεφόμενο τεμάχιο εργασίας για να μεγεθύνει ελαφρώς την οπή και να βελτιώσει την ακρίβεια. Χρησιμοποιείται για λεπτούς σκοπούς φινιρίσματος. Το BROACHING περιλαμβάνει ένα οδοντωτό εργαλείο για την αφαίρεση υλικού από ένα τεμάχιο εργασίας με ένα πέρασμα του αυλακιού (οδοντωτό εργαλείο). Στη γραμμική διάνοιξη, η αυλάκωση τρέχει γραμμικά πάνω σε μια επιφάνεια του τεμαχίου εργασίας για να πραγματοποιήσει την κοπή, ενώ στην περιστροφική διάνοιξη, η αυλάκωση περιστρέφεται και πιέζεται στο τεμάχιο εργασίας για να κόψει ένα συμμετρικό σχήμα άξονα. Η ΜΗΧΑΝΗΣΗ ΕΛΒΕΤΙΚΟΥ ΤΥΠΟΥ είναι μια από τις πολύτιμες τεχνικές μας που χρησιμοποιούμε για την κατασκευή μικρών εξαρτημάτων υψηλής ακρίβειας μεγάλου όγκου. Χρησιμοποιώντας ελβετικού τόρνου γυρίζουμε μικρά, πολύπλοκα, ακριβείας εξαρτήματα φθηνά. Σε αντίθεση με τους συμβατικούς τόρνους όπου το τεμάχιο εργασίας παραμένει ακίνητο και το εργαλείο κινείται, σε ελβετικού τύπου κέντρα στροφής, το τεμάχιο εργασίας επιτρέπεται να κινείται στον άξονα Z και το εργαλείο είναι ακίνητο. Στη μηχανική κατεργασία ελβετικού τύπου, το κοντάκι της ράβδου συγκρατείται στη μηχανή και προωθείται μέσω ενός δακτυλίου οδηγού στον άξονα z, εκθέτοντας μόνο το τμήμα που πρόκειται να κατεργαστεί. Με αυτόν τον τρόπο εξασφαλίζεται σφιχτό κράτημα και η ακρίβεια είναι πολύ υψηλή. Η διαθεσιμότητα ενεργών εργαλείων παρέχει την ευκαιρία για φρεζάρισμα και διάτρηση καθώς το υλικό προχωρά από τον δακτύλιο οδηγό. Ο άξονας Υ του εξοπλισμού ελβετικού τύπου παρέχει πλήρεις δυνατότητες φρεζαρίσματος και εξοικονομεί μεγάλο χρόνο στην κατασκευή. Επιπλέον, τα μηχανήματα μας διαθέτουν τρυπάνια και εργαλεία διάτρησης που λειτουργούν στο εξάρτημα όταν κρατιέται στον δευτερεύοντα άξονα. Η ικανότητα κατεργασίας Ελβετικού Τύπου μας δίνει μια πλήρως αυτοματοποιημένη ευκαιρία πλήρους μηχανικής κατεργασίας σε μία μόνο λειτουργία. Η μηχανική κατεργασία είναι ένας από τους μεγαλύτερους κλάδους της AGS-TECH Inc. Το χρησιμοποιούμε είτε ως κύρια λειτουργία είτε ως δευτερεύουσα λειτουργία μετά τη χύτευση ή την εξώθηση ενός εξαρτήματος έτσι ώστε να πληρούνται όλες οι προδιαγραφές σχεδίασης. • ΥΠΗΡΕΣΙΕΣ ΦΙΝΙΡΙΣΜΑΤΟΣ ΕΠΙΦΑΝΕΙΑΣ: Προσφέρουμε μια μεγάλη ποικιλία επιφανειακών επεξεργασιών και φινιρίσματος επιφανειών, όπως ρύθμιση επιφανειών για ενίσχυση της πρόσφυσης, εναπόθεση λεπτού στρώματος οξειδίου για ενίσχυση της πρόσφυσης της επίστρωσης, αμμοβολή, χημική μεμβράνη, ανοδίωση, νιτρίωση, βαφή πούδρας, επίστρωση ψεκασμού , διάφορες προηγμένες τεχνικές επιμετάλλωσης και επίστρωσης, συμπεριλαμβανομένης της διασκορπισμού, της δέσμης ηλεκτρονίων, της εξάτμισης, της επιμετάλλωσης, των σκληρών επικαλύψεων όπως ο άνθρακας με διαμάντι (DLC) ή η επίστρωση τιτανίου για εργαλεία διάτρησης και κοπής. • ΥΠΗΡΕΣΙΕΣ ΣΗΜΑΝΣΗΣ & ΕΠΙΣΗΜΑΝΣΗΣ ΠΡΟΪΟΝΤΩΝ: Πολλοί από τους πελάτες μας απαιτούν σήμανση και σήμανση, σήμανση με λέιζερ, χάραξη σε μεταλλικά μέρη. Εάν έχετε οποιαδήποτε τέτοια ανάγκη, αφήστε μας να συζητήσουμε ποια επιλογή θα είναι η καλύτερη για εσάς. Εδώ είναι μερικά από τα προϊόντα που χρησιμοποιούνται συνήθως από χυτό μέταλλο. Δεδομένου ότι αυτά δεν είναι διαθέσιμα στο ράφι, μπορείτε να εξοικονομήσετε κόστος καλουπιού σε περίπτωση που κάποιο από αυτά ταιριάζει στις απαιτήσεις σας: ΚΑΝΤΕ ΚΛΙΚ ΕΔΩ ΓΙΑ ΝΑ ΚΑΤΕΒΑΣΕΤΕ τα κουτιά αλουμινίου της σειράς 11 από χυτό αλουμίνιο από την AGS-Electronics CLICK Product Finder-Locator Service ΠΡΟΗΓΟΥΜΕΝΗ ΣΕΛΙΔΑ
- Custom Manufactured Parts, Assemblies, Plastic Mold, Casting,Machining
Custom Manufactured Parts, Assemblies, Plastic Mold, Rubber Molding, Metal Casting, CNC Machining, Turning, Milling, Electrical Electronic Optical Assembly PCBA Εξατομικευμένα Ανταλλακτικά & Συναρμολογήσεις & Προϊόντα Διαβάστε περισσότερα Καλούπια και καλούπια πλαστικών & καουτσούκ Διαβάστε περισσότερα Χύτευση και Μηχανική Διαβάστε περισσότερα Διέλαση, Εξωθημένα Προϊόντα Διαβάστε περισσότερα Σφραγίδες & Κατασκευή Λαμαρινών Διαβάστε περισσότερα Σφυρηλάτηση Μετάλλων & Μεταλλουργία Σκόνης Διαβάστε περισσότερα Μορφοποίηση σύρματος & ελατηρίου Διαβάστε περισσότερα Μορφοποίηση & Διαμόρφωση Γυαλιού & Κεραμικού Διαβάστε περισσότερα Προσθετική και Ταχεία Παραγωγή Διαβάστε περισσότερα Βιομηχανία Σύνθετων Υλικών και Σύνθετων Υλικών Διαβάστε περισσότερα Διαδικασίες Σύνδεσης & Συναρμολόγησης & Στερέωσης Παράγουμε εξαρτήματα και συγκροτήματα για εσάς και προσφέρουμε τις ακόλουθες διαδικασίες κατασκευής: • Καλούπια από πλαστικό και καουτσούκ και χυτά μέρη. Χύτευση με έγχυση, θερμοδιαμόρφωση, θερμοσκληρυνόμενη χύτευση, διαμόρφωση υπό κενό, χύτευση με εμφύσηση, περιστροφική χύτευση, χύτευση με χύτευση, χύτευση με ένθετα και άλλα. • Εξωθήσεις πλαστικών, καουτσούκ και μετάλλων • Σιδηρούχα και μη σιδηρούχα χυτά και μηχανικά κατεργασμένα εξαρτήματα που παράγονται με τεχνικές φρεζαρίσματος και τόρνευσης, μηχανουργική κατεργασία ελβετικού τύπου. • Μέρη μεταλλουργίας πούδρας • Σφραγίδες μετάλλων και μη μετάλλων, μορφοποίηση λαμαρίνας, συγκολλημένα συγκροτήματα λαμαρίνας • Ψυχρή και θερμή σφυρηλάτηση • Σύρματα, συγκροτήματα συγκολλημένων συρμάτων, διαμόρφωση σύρματος • Διάφοροι τύποι ελατηρίων, ελατήριο forming • Κατασκευή γραναζιών, κιβώτιο ταχυτήτων, ζεύξη, σκουλήκι, μειωτήρας ταχύτητας, κύλινδρος, ιμάντες μετάδοσης, αλυσίδες μετάδοσης, εξαρτήματα μετάδοσης • Προσαρμοσμένο σκληρυμένο και αλεξίσφαιρο γυαλί συμβατό με τα πρότυπα του NATO και των στρατιωτικών προτύπων • Μπάλες, ρουλεμάν, τροχαλίες και συγκροτήματα τροχαλιών • Βαλβίδες και πνευματικά εξαρτήματα όπως δακτύλιος Ο, ροδέλα και στεγανοποιήσεις • Γυάλινα και κεραμικά εξαρτήματα και συγκροτήματα, αδιάβροχα και ερμητικά εξαρτήματα, συγκόλληση μετάλλου-κεραμικού και κεραμικού-κεραμικού. • Διάφοροι τύποι μηχανικών, οπτομηχανικών, ηλεκτρομηχανικών, οπτοηλεκτρονικών συγκροτημάτων. • Μέταλλο-καουτσούκ, μέταλλο-πλαστικό bonding • Συγκροτήματα σωλήνων και σωλήνων, διαμόρφωση σωλήνων, κάμψη και προσαρμοσμένες συναρμολογήσεις σωλήνων, κατασκευή φούτερ. • Κατασκευή υαλοβάμβακα • Συγκόλληση με χρήση διαφόρων τεχνικών όπως σημειακή συγκόλληση, συγκόλληση με laser, MIG, TIG. Συγκόλληση με υπερήχους για πλαστικά μέρη. • Μεγάλη ποικιλία επιφανειακών επεξεργασιών και επιφανειακών φινιρισμάτων, όπως ρύθμιση επιφανειών για ενίσχυση της πρόσφυσης, εναπόθεση λεπτού στρώματος οξειδίου για ενίσχυση της πρόσφυσης της επίστρωσης, αμμοβολή, χημική μεμβράνη, ανοδίωση, νίτρωση, επίστρωση σκόνης, επίστρωση με ψεκασμό, διάφορες προηγμένες τεχνικές επιμετάλλωσης και επίστρωσης συμπεριλαμβανομένης της διασκορπισμού, της δέσμης ηλεκτρονίων, της εξάτμισης, της επιμετάλλωσης, των σκληρών επικαλύψεων όπως ο άνθρακας με διαμάντια (DLC) ή το τιτάνιο για εργαλεία κοπής και διάτρησης. • Σήμανση και επισήμανση, σήμανση με λέιζερ σε μεταλλικά μέρη, εκτύπωση σε πλαστικά και ελαστικά μέρη Κατεβάστε το φυλλάδιο για τους Κοινούς Όρους Μηχανολόγων Μηχανικών που χρησιμοποιούνται από Σχεδιαστές και Μηχανικούς Κατασκευάζουμε προϊόντα σύμφωνα με τις ιδιαίτερες προδιαγραφές και απαιτήσεις σας. Προκειμένου να σας προσφέρουμε την καλύτερη ποιότητα, παράδοση και τιμές, κατασκευάζουμε προϊόντα παγκοσμίως σε Κίνα, Ινδία, Ταϊβάν, Φιλιππίνες, Νότια Κορέα, Μαλαισία, Σρι Λάνκα, Τουρκία, ΗΠΑ, Καναδά, Γερμανία, Ηνωμένο Βασίλειο και Ιαπωνία. Αυτό μας κάνει πολύ πιο δυνατούς και παγκοσμίως πιο ανταγωνιστικούς από οποιονδήποτε άλλο custom manufacturer. Τα προϊόντα μας κατασκευάζονται σε περιβάλλοντα με πιστοποίηση ISO9001:2000, QS9000, ISO14001, TS16949 και διαθέτουν σήμα CE, UL και πληρούν άλλα βιομηχανικά πρότυπα. Μόλις διοριστούμε για το έργο σας, μπορούμε να φροντίσουμε για ολόκληρη την κατασκευή, συναρμολόγηση, δοκιμή, πιστοποίηση, αποστολή και τελωνείο όπως εσείς επιθυμείτε. Εάν προτιμάτε, μπορούμε να αποθηκεύσουμε τα ανταλλακτικά σας, να συναρμολογήσουμε προσαρμοσμένα κιτ, να εκτυπώσουμε και να επισημάνουμε το όνομα και την επωνυμία της εταιρείας σας και να αποστείλουμε στους πελάτες σας. Με άλλα λόγια, μπορούμε να είμαστε και το κέντρο αποθήκευσης και διανομής σας εάν το προτιμάτε. Δεδομένου ότι οι αποθήκες μας βρίσκονται κοντά σε μεγάλα θαλάσσια λιμάνια, μας δίνει υλικοτεχνικό πλεονέκτημα. Για παράδειγμα, όταν τα προϊόντα σας φτάνουν σε ένα σημαντικό λιμάνι των ΗΠΑ, μπορούμε μεταφέρουμε απευθείας σε μια κοντινή αποθήκη όπου μπορούμε να αποθηκεύσουμε, να συναρμολογήσουμε, να φτιάξουμε κιτ, να επαναλάβουμε ετικέτα, να εκτυπώσουμε, να συσκευάσουμε σύμφωνα με την επιλογή σας και να αποθέσουμε αποστολή στους πελάτες σας. Δεν προμηθεύουμε μόνο προϊόντα. Η εταιρεία μας εργάζεται σε προσαρμοσμένες συμβάσεις όπου ερχόμαστε στον ιστότοπό σας, αξιολογούμε το έργο σας επί τόπου και αναπτύσσουμε μια πρόταση έργου προσαρμοσμένης σχεδιασμένης για εσάς. Στη συνέχεια στέλνουμε την έμπειρη ομάδα μας για την υλοποίηση του έργου. Περισσότερες πληροφορίες σχετικά με τις μηχανολογικές εργασίες μας μπορείτε να βρείτε στο http://www.ags-engineering.com -Αναλαμβάνουμε μικρά έργα καθώς και μεγάλα έργα σε βιομηχανική κλίμακα. Ως πρώτο βήμα, μπορούμε να σας συνδέσουμε είτε μέσω τηλεφώνου, είτε μέσω τηλεδιάσκεψης είτε μέσω MSN messenger με τα μέλη της ομάδας ειδικών μας, ώστε να μπορείτε να επικοινωνήσετε απευθείας με έναν ειδικό, να κάνετε ερωτήσεις και να συζητήσετε το έργο σας. Καλέστε μας και αν χρειαστεί θα έρθουμε και θα σας επισκεφτούμε. ΠΡΟΗΓΟΥΜΕΝΗ ΣΕΛΙΔΑ