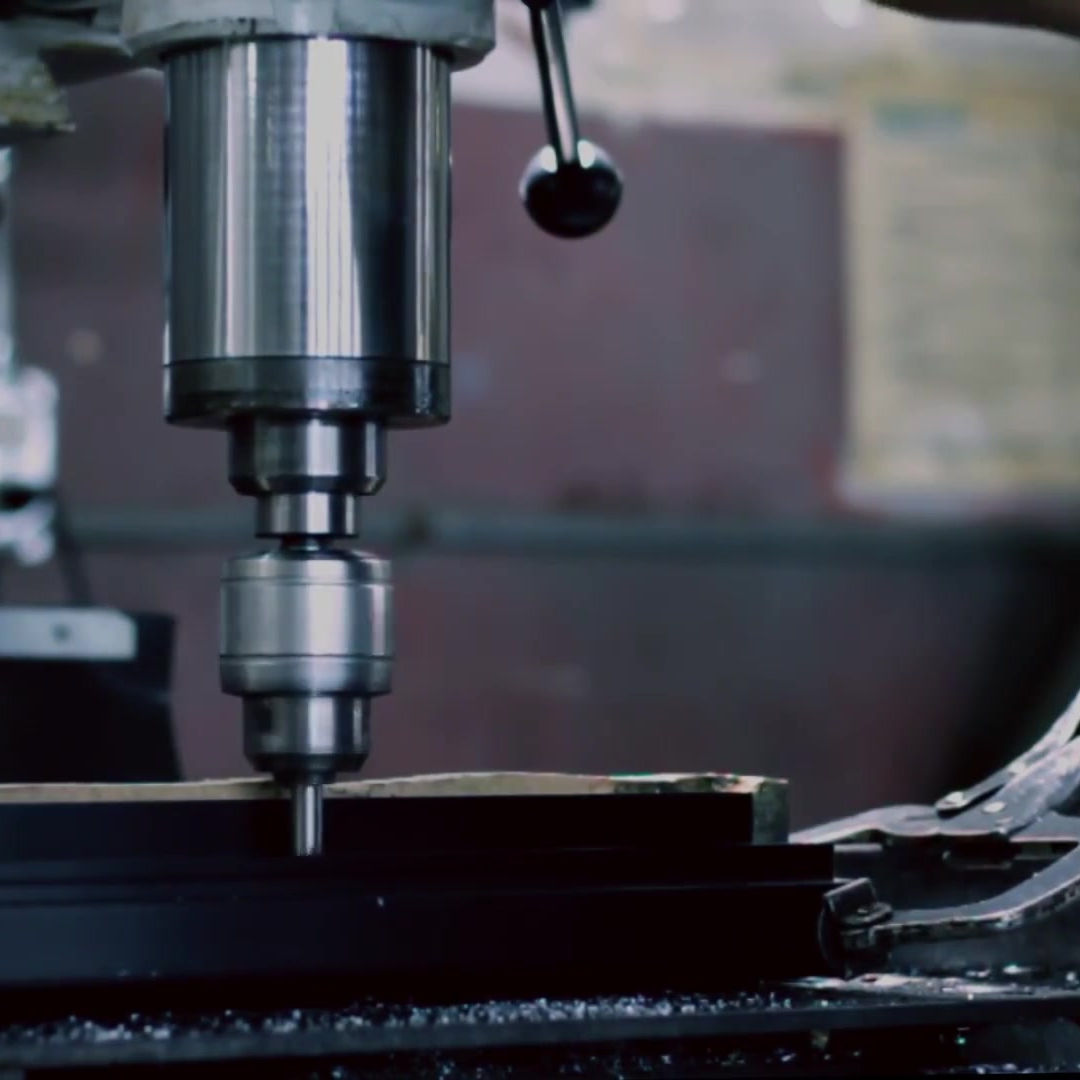
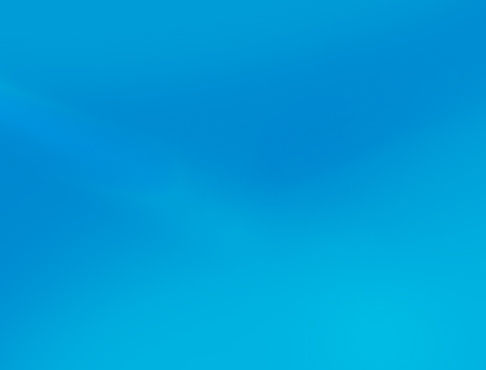
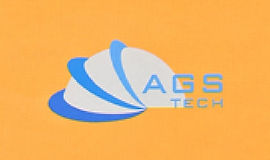
Fabricante personalizado global, integrador, consolidador, socio de subcontratación para una amplia variedad de productos y servicios.
Somos su fuente única para la fabricación, la fabricación, la ingeniería, la consolidación, la integración y la subcontratación de productos y servicios fabricados a medida y listos para usar.
Choose your Language
-
Fabricación personalizada
-
Fabricación por contrato nacional y mundial
-
Subcontratación de fabricación
-
Adquisiciones nacionales y globales
-
Consolidación
-
Integración de ingeniería
-
Servicios de Ingenieria
En los últimos años, hemos visto un aumento en la demanda de FABRICACIÓN RÁPIDA o PROTOTIPO RÁPIDO. Este proceso también puede llamarse FABRICACIÓN DE ESCRITORIO o FABRICACIÓN DE FORMA LIBRE. Básicamente, un modelo físico sólido de una pieza se crea directamente a partir de un dibujo CAD tridimensional. Usamos el término FABRICACIÓN ADITIVA para estas diversas técnicas en las que construimos piezas en capas. Mediante el uso de hardware y software integrados controlados por computadora, realizamos la fabricación aditiva. Nuestras técnicas de fabricación y prototipado rápido son ESTEREOLITOGRAFÍA, POLYJET, MODELADO POR DEPOSICIÓN FUNDIDA, SINTERIZACIÓN SELECTIVA POR LÁSER, FUSIÓN POR HAZ DE ELECTRONES, IMPRESIÓN TRIDIMENSIONAL, FABRICACIÓN DIRECTA, UTILLAJE RÁPIDO. Le recomendamos que haga clic aquí paraDESCARGUE nuestras ilustraciones esquemáticas de los procesos de fabricación aditiva y fabricación rápida de AGS-TECH Inc.
Esto lo ayudará a comprender mejor la información que le brindamos a continuación.
La creación rápida de prototipos nos proporciona: 1.) El diseño conceptual del producto se ve desde diferentes ángulos en un monitor usando un sistema 3D/CAD. 2.) Se fabrican prototipos de materiales no metálicos y metálicos y se estudian desde aspectos funcionales, técnicos y estéticos. 3.) Se logra la creación de prototipos de bajo costo en muy poco tiempo. La fabricación aditiva se puede asemejar a la construcción de una hogaza de pan apilando y uniendo rebanadas individuales una encima de la otra. En otras palabras, el producto se fabrica rebanada por rebanada, o capa por capa depositada una sobre otra. La mayoría de las piezas se pueden producir en cuestión de horas. La técnica es buena si las piezas se necesitan muy rápidamente o si las cantidades necesarias son bajas y la fabricación de un molde y herramientas es demasiado costosa y requiere mucho tiempo. Sin embargo, el costo de una pieza es alto debido a las costosas materias primas.
• ESTEREOLITOGRAFÍA: Esta técnica, también abreviada como STL, se basa en el curado y endurecimiento de un fotopolímero líquido en una forma específica al enfocar un rayo láser sobre él. El láser polimeriza el fotopolímero y lo cura. Al escanear el rayo láser UV de acuerdo con la forma programada a lo largo de la superficie de la mezcla de fotopolímero, la pieza se produce de abajo hacia arriba en rebanadas individuales en cascada una encima de la otra. El escaneo del punto láser se repite muchas veces para lograr las geometrías programadas en el sistema. Una vez que la pieza está completamente fabricada, se retira de la plataforma, se seca y se limpia con ultrasonidos y baño de alcohol. Luego, se expone a la radiación ultravioleta durante algunas horas para asegurarse de que el polímero esté completamente curado y endurecido. Para resumir el proceso, una plataforma que se sumerge en una mezcla de fotopolímeros y un rayo láser UV se controlan y mueven a través de un sistema de servocontrol de acuerdo con la forma de la pieza deseada y la pieza se obtiene fotocurando el polímero capa por capa. Por supuesto, las dimensiones máximas de la pieza producida están determinadas por el equipo de estereolitografía.
• POLYJET: similar a la impresión de inyección de tinta, en Polyjet tenemos ocho cabezales de impresión que depositan fotopolímero en la bandeja de construcción. La luz ultravioleta colocada junto a los chorros cura y endurece inmediatamente cada capa. Se utilizan dos materiales en polyjet. El primer material es para la fabricación del modelo real. El segundo material, una resina similar a un gel, se utiliza como soporte. Ambos materiales se depositan capa por capa y se curan simultáneamente. Después de completar el modelo, el material de soporte se elimina con una solución acuosa. Las resinas utilizadas son similares a las de la estereolitografía (STL). El polyjet tiene las siguientes ventajas sobre la estereolitografía: 1.) No es necesario limpiar las piezas. 2.) No es necesario un curado posterior al proceso. 3.) Son posibles espesores de capa más pequeños y, por lo tanto, obtenemos una mejor resolución y podemos fabricar piezas más finas.
• MODELADO DE DEPÓSITO FUNDIDO: También abreviado como FDM, en este método un cabezal extrusor controlado por robot se mueve en dos direcciones principales sobre una mesa. El cable se baja y se eleva según sea necesario. Desde el orificio de un troquel calentado en la cabeza, se extruye un filamento termoplástico y se deposita una capa inicial sobre una base de espuma. Esto se logra mediante el cabezal del extrusor que sigue un camino predeterminado. Después de la capa inicial, la mesa se baja y las capas posteriores se depositan una encima de la otra. A veces, cuando se fabrica una pieza complicada, se necesitan estructuras de soporte para que la deposición pueda continuar en ciertas direcciones. En estos casos, se extruye un material de soporte con un espaciado de filamentos menos denso en una capa, de modo que es más débil que el material del modelo. Estas estructuras de soporte pueden disolverse o romperse después de la finalización de la pieza. Las dimensiones de la matriz del extrusor determinan el grosor de las capas extruidas. El proceso FDM produce piezas con superficies escalonadas en planos exteriores oblicuos. Si esta aspereza es inaceptable, se puede usar un pulido con vapor químico o una herramienta caliente para suavizarlas. Incluso una cera de pulido está disponible como material de recubrimiento para eliminar estos pasos y lograr tolerancias geométricas razonables.
• SINTERIZACIÓN SELECTIVA POR LÁSER: También denominado SLS, el proceso se basa en la sinterización selectiva de un polímero, cerámica o polvos metálicos en un objeto. La parte inferior de la cámara de procesamiento tiene dos cilindros: un cilindro de construcción parcial y un cilindro de alimentación de polvo. El primero se baja progresivamente hasta donde se está formando la pieza sinterizada y el último se eleva progresivamente para suministrar polvo al cilindro de construcción parcial a través de un mecanismo de rodillos. Primero se deposita una capa delgada de polvo en el cilindro de construcción parcial, luego se enfoca un rayo láser en esa capa, rastreando y derritiendo/sinterizando una sección transversal particular, que luego se vuelve a solidificar en un sólido. El polvo es áreas que no son golpeadas por el rayo láser permanecen sueltas pero aún soportan la parte sólida. Luego se deposita otra capa de polvo y se repite el proceso muchas veces hasta obtener la pieza. Al final, las partículas de polvo sueltas se sacuden. Todo ello lo realiza un ordenador de control de procesos mediante instrucciones generadas por el programa CAD 3D de la pieza que se fabrica. Se pueden depositar diversos materiales como polímeros (como ABS, PVC, poliéster), cera, metales y cerámica con aglutinantes poliméricos apropiados.
• RAYO DE ELECTRONES MELTING : Similar a la sinterización selectiva por láser, pero usando un haz de electrones para fundir polvos de titanio o cobalto-cromo para hacer prototipos en vacío. Se han realizado algunos desarrollos para realizar este proceso en aceros inoxidables, aluminio y aleaciones de cobre. Si es necesario aumentar la resistencia a la fatiga de las piezas producidas, utilizamos el prensado isostático en caliente posterior a la fabricación de la pieza como proceso secundario.
• IMPRESIÓN TRIDIMENSIONAL: También denominada 3DP, en esta técnica un cabezal de impresión deposita un aglutinante inorgánico sobre una capa de polvo no metálico o metálico. Un pistón que transporta el lecho de polvo se baja gradualmente y en cada paso el aglutinante se deposita capa por capa y se fusiona con el aglutinante. Los materiales en polvo utilizados son mezclas de polímeros y fibras, arena de fundición, metales. Utilizando diferentes cabezales aglutinantes simultáneamente y aglutinantes de diferentes colores podemos obtener varios colores. El proceso es similar a la impresión por chorro de tinta pero en lugar de obtener una hoja coloreada obtenemos un objeto tridimensional coloreado. Las piezas producidas pueden ser porosas y, por lo tanto, pueden requerir sinterización e infiltración de metal para aumentar su densidad y resistencia. La sinterización quemará el aglutinante y fusionará los polvos metálicos. Los metales como el acero inoxidable, el aluminio y el titanio se pueden usar para fabricar las piezas y, como materiales de infiltración, comúnmente usamos cobre y bronce. La belleza de esta técnica es que incluso los ensamblajes complicados y móviles se pueden fabricar muy rápidamente. Por ejemplo, se puede fabricar un conjunto de engranajes, una llave inglesa como herramienta y tendrá partes móviles y giratorias listas para usar. Se pueden fabricar diferentes componentes del conjunto con diferentes colores y todo de una sola vez. Descargue nuestro folleto en:Fundamentos de la impresión 3D en metal
• FABRICACIÓN DIRECTA y HERRAMIENTAS RÁPIDAS: Además de la evaluación del diseño, la resolución de problemas utilizamos la creación rápida de prototipos para la fabricación directa de productos o la aplicación directa en los productos. En otras palabras, la creación rápida de prototipos se puede incorporar a los procesos convencionales para hacerlos mejores y más competitivos. Por ejemplo, la creación rápida de prototipos puede producir patrones y moldes. Los patrones de un polímero fundido y quemado creados por operaciones de creación rápida de prototipos se pueden ensamblar para fundición de inversión e invertir. Otro ejemplo a mencionar es el uso de 3DP para producir carcasas de fundición de cerámica y usarlas para operaciones de fundición de carcasas. Incluso los moldes de inyección y los insertos de moldes se pueden producir mediante prototipos rápidos y se pueden ahorrar muchas semanas o meses de tiempo de preparación de moldes. Con solo analizar un archivo CAD de la pieza deseada, podemos producir la geometría de la herramienta mediante software. Estos son algunos de nuestros populares métodos de herramientas rápidas:
RTV (Vulcanización a temperatura ambiente) MOLDEADO / FUNDICIÓN DE URETANO: El uso de prototipos rápidos se puede utilizar para hacer el patrón de la pieza deseada. Luego, este patrón se recubre con un agente separador y se vierte caucho RTV líquido sobre el patrón para producir las mitades del molde. A continuación, estas mitades de molde se utilizan para moldear por inyección uretanos líquidos. La vida útil del molde es corta, solo 0 o 30 ciclos, pero suficiente para la producción de lotes pequeños.
MOLDEO POR INYECCIÓN ACES (Acetal Clear Epoxy Solid): Utilizando técnicas de creación rápida de prototipos como la estereolitografía, producimos moldes de inyección. Estos moldes son carcasas con un extremo abierto para permitir el llenado con materiales como epoxi, epoxi con carga de aluminio o metales. Una vez más, la vida útil del molde está limitada a decenas o un máximo de cientos de piezas.
PROCESO DE HERRAMIENTAS DE METAL PULVERIZADO: Utilizamos prototipado rápido y hacemos un patrón. Rociamos una aleación de zinc-aluminio sobre la superficie del patrón y la recubrimos. Luego, el patrón con el revestimiento de metal se coloca dentro de un matraz y se encapsula con epoxi o epoxi con relleno de aluminio. Finalmente, se retira y al producir dos mitades de este tipo de molde obtenemos un molde completo para moldeo por inyección. Estos moldes tienen una vida más larga, en algunos casos, dependiendo del material y las temperaturas, pueden producir piezas por miles.
PROCESO KEELTOOL: Esta técnica puede producir moldes con 100.000 a 10 millones de ciclos de vida. Usando prototipos rápidos producimos un molde RTV. El molde se llena a continuación con una mezcla que consta de polvo de acero para herramientas A6, carburo de tungsteno, aglutinante de polímero y se deja curar. Luego, este molde se calienta para quemar el polímero y fusionar los polvos metálicos. El siguiente paso es la infiltración de cobre para producir el molde final. Si es necesario, se pueden realizar operaciones secundarias como el mecanizado y el pulido en el molde para obtener mejores precisiones dimensionales.