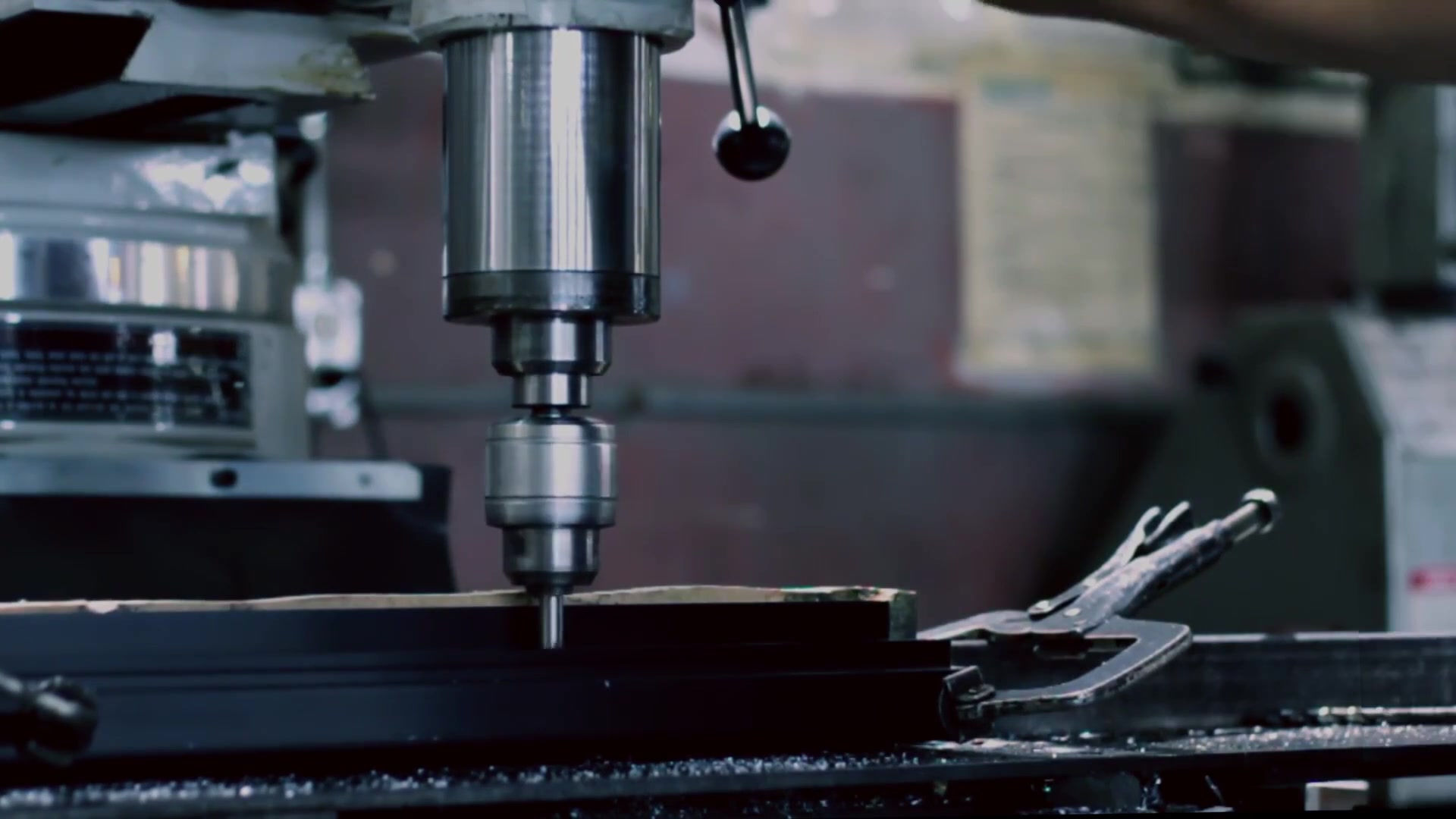
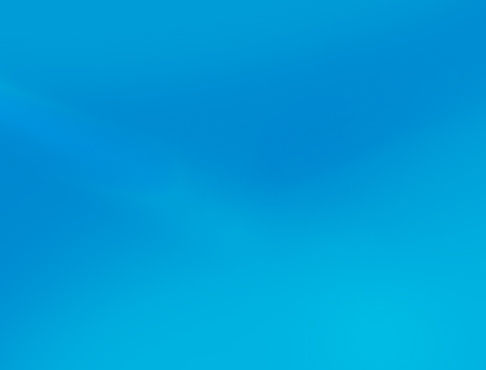
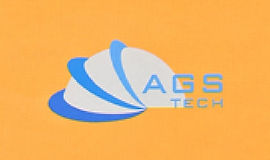
تولید کننده سفارشی جهانی، یکپارچه ساز، تثبیت کننده، شریک برون سپاری برای طیف گسترده ای از محصولات و خدمات.
ما منبع اصلی شما برای تولید، ساخت، مهندسی، ادغام، ادغام، برون سپاری محصولات و خدمات تولید شده سفارشی و خارج از قفسه هستیم.
زبان خود را انتخاب کنید
-
ساخت سفارشی
-
ساخت قرارداد داخلی و جهانی
-
برون سپاری تولید
-
تدارکات داخلی و جهانی
-
Consolidation
-
ادغام مهندسی
-
خدمات مهندسی
در میان بسیاری از تکنیکهای JOINING که ما در ساخت به کار میبریم، تأکید ویژهای به جوشکاری، لحیم کاری، لحیم کاری، چسباندن چسب و مونتاژ مکانیکی سفارشی داده میشود، زیرا این تکنیکها به طور گسترده در کاربردهایی مانند ساخت مجموعههای هرمتیک، ساخت قطعات با فناوری پیشرفته و محصولات تخصصی استفاده میشوند. در اینجا ما بر جنبههای تخصصیتر این تکنیکهای اتصال تمرکز میکنیم، زیرا مربوط به تولید محصولات و مجموعههای پیشرفته است.
جوشکاری فیوژن: از گرما برای ذوب و ادغام مواد استفاده می کنیم. گرما از طریق برق یا پرتوهای پر انرژی تامین می شود. انواع جوشکاری ذوبی که ما به کار می بریم جوشکاری با گاز اکسیژن، جوش قوس الکتریکی، جوشکاری پرتو با انرژی بالا می باشد.
جوش حالت جامد: قطعات را بدون ذوب و همجوشی به هم وصل می کنیم. روش های جوشکاری حالت جامد ما عبارتند از: سرد، اولتراسونیک، مقاومت، اصطکاک، جوشکاری انفجاری و پیوند انتشار.
لحیم کاری و لحیم کاری: آنها از فلزات پرکننده استفاده می کنند و به ما مزیت کار در دماهای پایین تر از جوشکاری را می دهند، بنابراین آسیب ساختاری کمتری به محصولات وارد می شود. اطلاعات مربوط به تاسیسات لحیم کاری ما برای تولید اتصالات سرامیکی به فلز، آب بندی هرمتیک، ورودی خلاء، خلاء بالا و فوق العاده بالا و اجزای کنترل سیال را می توانید در اینجا بیابید:بروشور Brazing Factory
چسباندن چسب: به دلیل تنوع چسب های مورد استفاده در صنعت و همچنین کاربردهای متنوع، ما یک صفحه اختصاصی برای این کار داریم. برای رفتن به صفحه ما در مورد چسبندگی، لطفا اینجا را کلیک کنید.
مونتاژ مکانیکی سفارشی: ما از انواع اتصال دهنده ها مانند پیچ، پیچ، مهره، پرچ استفاده می کنیم. اتصال دهنده های ما به بست های استاندارد خارج از قفسه محدود نمی شوند. ما بست های تخصصی را طراحی، توسعه و تولید می کنیم که از مواد غیر استاندارد ساخته شده اند تا بتوانند الزامات کاربردهای ویژه را برآورده کنند. گاهی اوقات نارسانایی الکتریکی یا گرمایی مورد نظر است در حالی که گاهی اوقات رسانایی. برای برخی از کاربردهای خاص، مشتری ممکن است بست های خاصی را بخواهد که بدون از بین بردن محصول قابل برداشتن نباشند. ایده ها و کاربردهای بی پایانی وجود دارد. ما همه چیز را برای شما داریم، اگر خارج از قفسه نباشد، می توانیم به سرعت آن را توسعه دهیم. برای رفتن به صفحه ما در مورد مونتاژ مکانیکی، لطفا اینجا را کلیک کنید. اجازه دهید تکنیک های مختلف اتصال خود را با جزئیات بیشتر بررسی کنیم.
جوشکاری با گاز اکسیژن (OFW): برای تولید شعله جوش از گاز سوختی مخلوط با اکسیژن استفاده می کنیم. هنگامی که از استیلن به عنوان سوخت و اکسیژن استفاده می کنیم، آن را جوشکاری با گاز اکسی استیلن می نامیم. دو واکنش شیمیایی در فرآیند احتراق گاز اکسیسوخت رخ میدهد:
C2H2 + O2 ------» 2CO + H2 + حرارت
2CO + H2 + 1.5 O2--------» 2 CO2 + H2O + گرما
اولین واکنش استیلن را به مونوکسید کربن و هیدروژن تجزیه می کند در حالی که حدود 33 درصد از کل گرمای تولید شده را تولید می کند. فرآیند دوم در بالا نشان دهنده احتراق بیشتر هیدروژن و مونوکسید کربن در حالی که حدود 67٪ از کل گرما را تولید می کند. دمای شعله بین 1533 تا 3573 کلوین است. درصد اکسیژن در مخلوط گاز مهم است. اگر میزان اکسیژن بیش از نصف باشد، شعله به یک عامل اکسید کننده تبدیل می شود. این برای برخی فلزات نامطلوب اما برای برخی دیگر مطلوب است. به عنوان مثال هنگامی که شعله اکسید کننده مطلوب است آلیاژهای مبتنی بر مس هستند زیرا یک لایه غیرفعال بر روی فلز تشکیل می دهند. از طرف دیگر، زمانی که میزان اکسیژن کاهش می یابد، احتراق کامل امکان پذیر نیست و شعله تبدیل به یک شعله کاهنده (کربور کننده) می شود. دما در شعله کاهنده کمتر است و بنابراین برای فرآیندهایی مانند لحیم کاری و لحیم کاری مناسب است. گازهای دیگر نیز سوخت های بالقوه ای هستند، اما نسبت به استیلن دارای معایبی هستند. گاهی اوقات فلزات پرکننده را به صورت میله پرکننده یا سیم به ناحیه جوش عرضه می کنیم. برخی از آنها با شار پوشش داده می شوند تا اکسیداسیون سطوح را به تاخیر بیاندازند و در نتیجه از فلز مذاب محافظت کنند. یک مزیت اضافی که شار به ما می دهد حذف اکسیدها و سایر مواد از ناحیه جوش است. این منجر به پیوند قوی تر می شود. یکی از انواع جوشکاری گاز اکسیژن، جوشکاری با گاز فشار است، که در آن دو جزء در محل مشترک خود با استفاده از مشعل گاز اکسی استیلن گرم می شوند و هنگامی که رابط شروع به ذوب شدن کرد، مشعل خارج می شود و نیروی محوری برای فشار دادن دو قسمت به هم اعمال می شود. تا زمانی که رابط جامد شود.
جوش قوس الکتریکی: ما از انرژی الکتریکی برای ایجاد قوس بین نوک الکترود و قطعاتی که قرار است جوش داده شوند استفاده می کنیم. منبع تغذیه می تواند AC یا DC باشد در حالی که الکترودها مصرفی یا غیر مصرفی هستند. انتقال حرارت در جوشکاری قوس الکتریکی را می توان با رابطه زیر بیان کرد:
H / l = ex VI / v
در اینجا H ورودی گرما، l طول جوش، V و I ولتاژ و جریان اعمال شده، v سرعت جوش و e راندمان فرآیند است. هر چه راندمان "e" بیشتر باشد، انرژی موجود برای ذوب مواد به طور مفیدتری استفاده می شود. گرمای ورودی را می توان به صورت زیر نیز بیان کرد:
H = ux (حجم) = ux A xl
در اینجا u انرژی ویژه برای ذوب، A مقطع جوش و l طول جوش است. از دو معادله بالا به دست می آید:
v = سابق VI / u A
یکی از انواع جوشکاری قوس الکتریکی، جوشکاری قوس فلزی محافظ (SMAW) است که حدود 50 درصد از تمام فرآیندهای جوشکاری صنعتی و تعمیر و نگهداری را تشکیل می دهد. جوشکاری قوس الکتریکی (جوشکاری چوبی) با لمس نوک یک الکترود پوشش داده شده به قطعه کار و بیرون کشیدن سریع آن به فاصله کافی برای حفظ قوس انجام می شود. ما به این فرآیند جوشکاری چسب می گوییم زیرا الکترودها میله های نازک و بلندی هستند. در طول فرآیند جوشکاری، نوک الکترود به همراه پوشش آن و فلز پایه در مجاورت قوس ذوب می شود. مخلوطی از فلز پایه، فلز الکترود و مواد از پوشش الکترود در ناحیه جوش جامد می شود. پوشش الکترود اکسیده می شود و یک گاز محافظ در ناحیه جوش ایجاد می کند، بنابراین از اکسیژن موجود در محیط محافظت می کند. بنابراین این فرآیند به عنوان جوشکاری قوس فلزی محافظ نامیده می شود. ما از جریان های بین 50 تا 300 آمپر و سطوح توان معمولاً کمتر از 10 کیلو وات برای عملکرد بهینه جوش استفاده می کنیم. همچنین قطبیت جریان DC (جهت جریان جریان) اهمیت دارد. قطبیت مستقیم در جایی که قطعه کار مثبت و الکترود منفی است در جوشکاری ورق های فلزی به دلیل نفوذ کم آن و همچنین برای اتصالات با شکاف های بسیار گسترده ترجیح داده می شود. وقتی قطبیت معکوس داریم، یعنی الکترود مثبت و قطعه کار منفی است، میتوانیم به نفوذ جوش عمیقتری برسیم. با جریان AC، از آنجایی که قوسهای ضربانی داریم، میتوانیم با استفاده از الکترودهای با قطر بزرگ و حداکثر جریان، بخشهای ضخیم را جوش دهیم. روش جوشکاری SMAW برای ضخامت های قطعه کار 3 تا 19 میلی متر و حتی بیشتر با استفاده از تکنیک های چند پاس مناسب است. سرباره تشکیل شده در بالای جوش باید با استفاده از برس سیمی حذف شود تا در محل جوش خوردگی و شکست ایجاد نشود. این البته به هزینه جوشکاری قوس فلزی محافظ می افزاید. با این وجود SMAW محبوب ترین روش جوشکاری در صنعت و تعمیرات است.
جوشکاری با قوس غوطهور (SAW): در این فرآیند با استفاده از مواد شار دانهای مانند آهک، سیلیس، فلورید کلسیم، اکسید منگنز و غیره از قوس جوش محافظت میکنیم. شار دانه ای توسط جریان گرانشی از طریق یک نازل به ناحیه جوش وارد می شود. شار پوشش دهنده منطقه جوش مذاب به طور قابل توجهی از جرقه، دود، اشعه ماوراء بنفش و غیره محافظت می کند و به عنوان یک عایق حرارتی عمل می کند، بنابراین اجازه می دهد گرما به اعماق قطعه کار نفوذ کند. شار ذوب نشده بازیابی، درمان و استفاده مجدد می شود. یک سیم پیچ لخت به عنوان الکترود استفاده می شود و از طریق یک لوله به ناحیه جوش تغذیه می شود. ما از جریان های بین 300 تا 2000 آمپر استفاده می کنیم. اگر چرخش ساختار دایره ای (مانند لوله ها) در حین جوشکاری امکان پذیر باشد، فرآیند جوشکاری قوس زیردریایی (SAW) به موقعیت های افقی و مسطح و جوش های دایره ای محدود می شود. سرعت می تواند به 5 متر در دقیقه برسد. فرآیند SAW برای صفحات ضخیم مناسب است و منجر به جوش های با کیفیت، سخت، انعطاف پذیر و یکنواخت می شود. بهره وری، یعنی مقدار مواد جوشی که در ساعت رسوب می کند، 4 تا 10 برابر مقدار در مقایسه با فرآیند SMAW است.
یکی دیگر از فرآیندهای جوشکاری قوس الکتریکی، یعنی جوشکاری قوس فلزی با گاز (GMAW) یا به طور جایگزین به عنوان جوشکاری با گاز بیاثر فلزی (MIG) نامیده میشود، بر این اساس است که ناحیه جوش توسط منابع خارجی گازهایی مانند هلیوم، آرگون، دی اکسید کربن و غیره محافظت میشود. ممکن است اکسید زدای اضافی در فلز الکترود وجود داشته باشد. سیم مصرفی از طریق یک نازل به ناحیه جوش وارد می شود. ساخت فلزات آهنی و غیر آهنی با استفاده از جوشکاری قوس فلزی گازی (GMAW) انجام می شود. بهره وری جوش حدود 2 برابر فرآیند SMAW است. از تجهیزات جوشکاری خودکار استفاده می شود. فلز به یکی از سه روش در این فرآیند منتقل می شود: "انتقال اسپری" شامل انتقال چند صد قطره کوچک فلزی در ثانیه از الکترود به ناحیه جوش است. از سوی دیگر، در «انتقال گلوبولار» از گازهای غنی از دی اکسید کربن استفاده می شود و گلبول های فلز مذاب توسط قوس الکتریکی به پیش می روند. جریان جوشکاری زیاد است و نفوذ جوش عمیق تر است و سرعت جوشکاری بیشتر از انتقال اسپری است. بنابراین انتقال کروی برای جوشکاری مقاطع سنگین تر بهتر است. در نهایت، در روش «مدار کوتاه»، نوک الکترود حوضچه جوش مذاب را لمس میکند و آن را به عنوان فلز با سرعت بیش از 50 قطره در ثانیه در قطرات جداگانه منتقل میکند. جریان و ولتاژ کم همراه با سیم نازک تر استفاده می شود. توان های مورد استفاده در حدود 2 کیلو وات و دماهای نسبتاً پایین است که این روش را برای ورق های نازک با ضخامت کمتر از 6 میلی متر مناسب می کند.
یکی دیگر از تغییرات فرآیند جوشکاری قوس الکتریکی با هسته FLUX (FCAW) شبیه به جوشکاری قوس فلزی با گاز است، با این تفاوت که الکترود یک لوله پر از شار است. مزایای استفاده از الکترودهای شار هستهای این است که قوسهای پایدارتری تولید میکنند، این فرصت را به ما میدهند تا خواص فلزات جوش را بهبود بخشیم، ماهیت شکننده و انعطافپذیر کمتر شار آن در مقایسه با جوشکاری SMAW، بهبود خطوط جوش را به ما میدهند. الکترودهای هسته خود محافظ حاوی موادی هستند که از ناحیه جوش در برابر جو محافظت می کنند. ما حدود 20 کیلو وات برق مصرف می کنیم. مانند فرآیند GMAW، فرآیند FCAW نیز فرصتی را برای خودکارسازی فرآیندها برای جوشکاری پیوسته ارائه می دهد و مقرون به صرفه است. با افزودن آلیاژهای مختلف به هسته شار، می توان شیمی های مختلف فلز جوش را توسعه داد.
در جوش الکتروگاز (EGW) قطعات قرار داده شده لبه به لبه را جوش می دهیم. گاهی اوقات به آن جوش لب به لب نیز گفته می شود. فلز جوش در یک حفره جوش بین دو قطعه قرار می گیرد تا به هم متصل شوند. این فضا توسط دو سد خنک کننده با آب محصور شده است تا سرباره مذاب به بیرون نریزد. سدها توسط درایوهای مکانیکی به سمت بالا حرکت می کنند. هنگامی که قطعه کار می تواند چرخانده شود، می توانیم از تکنیک جوش الکتروگاز برای جوشکاری محیطی لوله ها نیز استفاده کنیم. الکترودها از طریق یک مجرا تغذیه می شوند تا یک قوس پیوسته را حفظ کنند. جریان می تواند حدود 400 آمپر یا 750 آمپر و سطوح توان حدود 20 کیلو وات باشد. گازهای خنثی که از یک الکترود هسته شار یا منبع خارجی منشأ می گیرند، محافظی را ایجاد می کنند. ما از جوش الکتروگاز (EGW) برای فلزاتی مانند فولاد، تیتانیوم و غیره با ضخامت های 12 تا 75 میلی متر استفاده می کنیم. این تکنیک برای سازه های بزرگ مناسب است.
با این حال، در روش دیگری به نام جوشکاری الکتریکی (ESW) قوس بین الکترود و پایین قطعه کار مشتعل شده و شار اضافه میشود. هنگامی که سرباره مذاب به نوک الکترود می رسد، قوس خاموش می شود. انرژی به طور مداوم از طریق مقاومت الکتریکی سرباره مذاب تامین می شود. ما می توانیم صفحات با ضخامت های بین 50 میلی متر تا 900 میلی متر و حتی بالاتر را جوش دهیم. جریان حدود 600 آمپر و ولتاژ بین 40 تا 50 ولت است. سرعت جوشکاری حدود 12 تا 36 میلی متر در دقیقه است. کاربردها مشابه جوشکاری با گاز است.
یکی از فرآیندهای الکترود غیر مصرفی ما، جوشکاری با قوس تنگستن گاز (GTAW) که به عنوان جوشکاری گاز بیاثر تنگستن (TIG) نیز شناخته میشود، شامل تامین یک فلز پرکننده توسط یک سیم است. برای اتصالات نزدیک، گاهی اوقات از فلز پرکننده استفاده نمی کنیم. در فرآیند TIG ما از فلاکس استفاده نمی کنیم، بلکه از آرگون و هلیوم برای محافظت استفاده می کنیم. تنگستن نقطه ذوب بالایی دارد و در فرآیند جوشکاری TIG مصرف نمی شود، بنابراین جریان ثابت و همچنین شکاف قوس را می توان حفظ کرد. سطوح توان بین 8 تا 20 کیلو وات و جریان در 200 آمپر (DC) یا 500 آمپر (AC) است. برای آلومینیوم و منیزیم از جریان AC برای عملکرد تمیز کردن اکسید آن استفاده می کنیم. برای جلوگیری از آلودگی الکترود تنگستن، از تماس آن با فلزات مذاب جلوگیری می کنیم. جوشکاری قوسی تنگستن گازی (GTAW) به ویژه برای جوشکاری فلزات نازک مفید است. جوش های GTAW کیفیت بسیار بالایی دارند و سطح خوبی دارند.
با توجه به هزینه بالاتر گاز هیدروژن، روشی که کمتر مورد استفاده قرار می گیرد، جوشکاری هیدروژن اتمی (AHW) است، که در آن یک قوس بین دو الکترود تنگستن در یک اتمسفر محافظ از گاز هیدروژن جریان ایجاد می کنیم. AHW همچنین یک فرآیند جوشکاری الکترود غیر مصرفی است. گاز هیدروژن دو اتمی H2 به شکل اتمی خود در نزدیکی قوس جوشکاری تجزیه می شود که دمای آن بیش از 6273 کلوین است. در حین شکستن، مقدار زیادی گرما را از قوس جذب می کند. هنگامی که اتم های هیدروژن به ناحیه جوش که یک سطح نسبتا سرد است برخورد می کنند، دوباره به شکل دو اتمی ترکیب می شوند و گرمای ذخیره شده را آزاد می کنند. انرژی را می توان با تغییر قطعه کار به فاصله قوس تغییر داد.
در یکی دیگر از فرآیندهای الکترود غیر مصرفی، جوشکاری قوس پلاسما (PAW) یک قوس پلاسمایی متمرکز داریم که به سمت ناحیه جوش هدایت می شود. دما در PAW به 33273 کلوین می رسد. تعداد تقریباً مساوی الکترون و یون گاز پلاسما را تشکیل می دهند. یک قوس پایلوت جریان کم، پلاسمایی را که بین الکترود تنگستن و روزنه قرار دارد، آغاز میکند. جریان عملیاتی معمولاً حدود 100 آمپر است. ممکن است یک فلز پرکننده تغذیه شود. در جوشکاری قوس پلاسما، محافظ توسط یک حلقه محافظ بیرونی و با استفاده از گازهایی مانند آرگون و هلیوم انجام می شود. در جوشکاری قوس پلاسما، قوس ممکن است بین الکترود و قطعه کار یا بین الکترود و نازل باشد. این روش جوشکاری دارای مزایایی نسبت به سایر روشهای تمرکز انرژی بالاتر، قابلیت جوشکاری عمیقتر و باریکتر، پایداری بهتر قوس، سرعت جوشکاری بالاتر تا 1 متر در دقیقه، اعوجاج حرارتی کمتر است. ما معمولاً از جوش قوس پلاسما برای ضخامت های کمتر از 6 میلی متر و گاهی تا 20 میلی متر برای آلومینیوم و تیتانیوم استفاده می کنیم.
جوشکاری پرتو انرژی بالا: نوع دیگری از روش جوشکاری ذوبی با جوشکاری با پرتو الکترونی (EBW) و جوشکاری لیزری (LBW) به عنوان دو نوع. این تکنیک ها برای کار تولید محصولات با فناوری پیشرفته ما از ارزش خاصی برخوردار هستند. در جوشکاری با پرتو الکترونی، الکترون های با سرعت بالا به قطعه کار برخورد می کنند و انرژی جنبشی آنها به گرما تبدیل می شود. پرتو باریک الکترون به راحتی در محفظه خلاء حرکت می کند. به طور کلی در جوشکاری پرتو الکترونیکی از خلاء بالا استفاده می کنیم. صفحات به ضخامت 150 میلی متر را می توان جوش داد. هیچ گاز محافظ، شار یا مواد پرکننده مورد نیاز نیست. تفنگ های پرتو الکترون دارای ظرفیت 100 کیلووات هستند. جوش های عمیق و باریک با نسبت های بالا تا 30 و مناطق کوچک متاثر از حرارت امکان پذیر است. سرعت جوش می تواند به 12 متر در دقیقه برسد. در جوشکاری با پرتو لیزر از لیزرهای پرقدرت به عنوان منبع حرارت استفاده می کنیم. پرتوهای لیزر به کوچکی 10 میکرون با چگالی بالا امکان نفوذ عمیق به قطعه کار را فراهم می کند. نسبت عمق به عرض تا 10 با جوشکاری پرتو لیزر امکان پذیر است. ما هم از لیزرهای پالسی و هم از لیزرهای موج پیوسته استفاده می کنیم که اولی در کاربردهای مواد نازک و دومی بیشتر برای قطعات کار ضخیم تا حدود 25 میلی متر است. سطوح قدرت تا 100 کیلو وات است. جوشکاری پرتو لیزر برای مواد بسیار بازتابنده نوری مناسب نیست. همچنین ممکن است از گازها در فرآیند جوشکاری استفاده شود. روش جوشکاری پرتو لیزر برای اتوماسیون و تولید با حجم بالا مناسب است و می تواند سرعت جوش بین 2.5 متر در دقیقه تا 80 متر در دقیقه را ارائه دهد. یکی از مزیت های اصلی این روش جوشکاری دسترسی به مناطقی است که نمی توان از تکنیک های دیگر استفاده کرد. پرتوهای لیزر به راحتی می توانند به چنین مناطق سختی سفر کنند. مانند جوشکاری با پرتو الکترونی به خلاء نیاز نیست. جوش هایی با کیفیت و استحکام خوب، انقباض کم، اعوجاج کم، تخلخل کم را می توان با جوش پرتو لیزر به دست آورد. پرتوهای لیزر را می توان به راحتی با استفاده از کابل های فیبر نوری دستکاری و شکل داد. بنابراین این تکنیک برای جوشکاری مجموعه های دقیق هرمتیک، بسته های الکترونیکی و غیره مناسب است.
بیایید به تکنیک های جوشکاری حالت جامد خود نگاه کنیم. جوش سرد (CW) فرآیندی است که در آن فشار به جای گرما با استفاده از قالب ها یا رول ها به قطعات جفت شده اعمال می شود. در جوش سرد، حداقل یکی از قطعات جفت شده باید شکل پذیر باشد. بهترین نتایج با دو ماده مشابه به دست می آید. اگر دو فلزی که باید با جوش سرد به هم وصل شوند متفاوت باشند، ممکن است اتصالات ضعیف و شکننده داشته باشیم. روش جوش سرد برای قطعات کار نرم، انعطاف پذیر و کوچک مانند اتصالات الکتریکی، لبه های ظروف حساس به حرارت، نوارهای دو فلزی برای ترموستات ها و غیره مناسب است. یکی از انواع جوش سرد، باندینگ رول (یا جوشکاری رول) است که در آن فشار از طریق یک جفت رول اعمال می شود. گاهی اوقات برای استحکام سطحی بهتر، جوشکاری رول را در دماهای بالا انجام می دهیم.
یکی دیگر از فرآیندهای جوشکاری حالت جامد که ما از آن استفاده می کنیم، جوشکاری اولتراسونیک (USW) است، که در آن قطعات کار تحت یک نیروی عادی ساکن و تنش های برشی نوسانی قرار می گیرند. تنش های برشی نوسانی از طریق نوک مبدل اعمال می شود. جوشکاری اولتراسونیک نوسانات را با فرکانس های 10 تا 75 کیلوهرتز مستقر می کند. در برخی از کاربردها مانند جوشکاری درز، از دیسک جوش دوار به عنوان نوک استفاده می کنیم. تنش های برشی اعمال شده بر روی قطعه کار باعث تغییر شکل های پلاستیکی کوچک، شکستن لایه های اکسیدی، آلاینده ها و منجر به اتصال حالت جامد می شود. دماهای درگیر در جوشکاری اولتراسونیک بسیار کمتر از دمای نقطه ذوب فلزات است و هیچ گداختی صورت نمی گیرد. ما اغلب از فرآیند جوشکاری اولتراسونیک (USW) برای مواد غیرفلزی مانند پلاستیک استفاده می کنیم. در ترموپلاستیک ها، دما به نقطه ذوب می رسد.
یکی دیگر از روش های رایج، در جوشکاری اصطکاکی (FRW) گرما از طریق اصطکاک در سطح مشترک قطعات کار که قرار است به یکدیگر متصل شوند، تولید می شود. در جوشکاری اصطکاکی یکی از قطعات کار را ثابت نگه می داریم در حالی که قطعه کار دیگر در یک فیکسچر نگه داشته شده و با سرعت ثابت می چرخد. سپس قطعات کار تحت یک نیروی محوری در تماس قرار می گیرند. سرعت چرخش سطحی در جوشکاری اصطکاکی ممکن است در برخی موارد به 900 متر در دقیقه برسد. پس از تماس سطحی کافی، قطعه کار چرخان به طور ناگهانی متوقف می شود و نیروی محوری افزایش می یابد. ناحیه جوش عموماً یک ناحیه باریک است. از روش جوشکاری اصطکاکی می توان برای اتصال قطعات جامد و لوله ای ساخته شده از انواع مواد استفاده کرد. ممکن است مقداری فلاش در رابط در FRW ایجاد شود، اما این فلاش را می توان با ماشینکاری یا آسیاب ثانویه حذف کرد. تغییراتی در فرآیند جوشکاری اصطکاکی وجود دارد. به عنوان مثال "جوشکاری اصطکاکی اینرسی" شامل یک چرخ طیار است که انرژی جنبشی دورانی آن برای جوش دادن قطعات استفاده می شود. هنگامی که فلایویل متوقف می شود، جوش کامل می شود. جرم دوار را می توان تغییر داد و بنابراین انرژی جنبشی چرخشی را می توان تغییر داد. تغییر دیگر "جوشکاری اصطکاکی خطی" است، که در آن حرکت رفت و برگشتی خطی بر حداقل یکی از اجزایی که باید به یکدیگر متصل شوند تحمیل می شود. در جوشکاری اصطکاکی خطی لازم نیست قطعات دایره ای باشند، می توانند مستطیل، مربع و یا به شکل های دیگر باشند. فرکانس ها می توانند در ده ها هرتز، دامنه ها در محدوده میلی متر و فشارها در ده ها یا صدها مگاپاسکال باشند. در نهایت "جوشکاری اصطکاکی اغتشاشی" تا حدودی با دو مورد دیگر که در بالا توضیح داده شد متفاوت است. در حالی که در جوشکاری اصطکاکی اینرسی و جوشکاری اصطکاکی خطی گرمایش رابط ها از طریق اصطکاک با مالش دو سطح تماس حاصل می شود، در روش جوشکاری اصطکاکی اغتشاشی بدنه سوم به دو سطحی که قرار است به هم متصل شوند مالش می شود. ابزار چرخشی به قطر 5 تا 6 میلی متر با اتصال تماس می گیرد. دما می تواند به مقادیر بین 503 تا 533 کلوین افزایش یابد. حرارت دادن، اختلاط و هم زدن مواد در محل اتصال صورت می گیرد. ما از جوش اصطکاکی اغتشاشی بر روی انواع مواد از جمله آلومینیوم، پلاستیک و کامپوزیت استفاده می کنیم. جوش ها یکنواخت و کیفیت بالا با حداقل منافذ است. در جوشکاری اصطکاکی اغتشاشی دود یا پاشش تولید نمی شود و این فرآیند به خوبی خودکار است.
جوش مقاومتی (RW): گرمای مورد نیاز برای جوشکاری از مقاومت الکتریکی بین دو قطعه کار که باید به هم متصل شوند تولید می شود. در جوشکاری مقاومتی از شار، گاز محافظ یا الکترود مصرفی استفاده نمی شود. گرمایش ژول در جوشکاری مقاومتی صورت می گیرد و می تواند به صورت زیر بیان شود:
H = (مربع I) x R xtx K
H گرمای تولید شده بر حسب ژول (وات-ثانیه)، جریان I بر حسب آمپر، مقاومت R بر حسب اهم، t زمان بر حسب ثانیه است که جریان از آن عبور می کند. ضریب K کمتر از 1 است و نشان دهنده کسری از انرژی است که از طریق تشعشع و رسانایی از بین نمی رود. جریان در فرآیندهای جوشکاری مقاومتی می تواند به سطوحی تا 100000 A برسد اما ولتاژها معمولاً 0.5 تا 10 ولت هستند. الکترودها معمولاً از آلیاژهای مس ساخته می شوند. مواد مشابه و غیر مشابه را می توان با جوشکاری مقاومتی به یکدیگر متصل کرد. چندین تغییر برای این فرآیند وجود دارد: "جوشکاری نقطه ای مقاومتی" شامل دو الکترود گرد متضاد است که با سطوح مفصل لبه دو ورق تماس می گیرند. فشار اعمال می شود تا زمانی که جریان خاموش شود. قطر قطعه جوش به طور کلی تا 10 میلی متر است. جوشکاری نقطهای مقاومتی، علائم فرورفتگی کمی تغییر رنگ در نقاط جوش ایجاد میکند. جوش نقطه ای محبوب ترین روش جوشکاری مقاومتی ما است. از اشکال مختلف الکترود در جوشکاری نقطه ای برای رسیدن به مناطق دشوار استفاده می شود. تجهیزات جوش نقطه ای ما با کنترل CNC هستند و دارای چندین الکترود هستند که می توانند به طور همزمان استفاده شوند. یکی دیگر از تغییرات "جوشکاری درز مقاومتی" با الکترودهای چرخ یا غلتکی انجام می شود که هر زمان که جریان به سطح کافی در چرخه برق AC برسد، جوش های نقطه ای پیوسته ایجاد می کند. اتصالات تولید شده توسط جوشکاری درز مقاومتی مایع و گاز محکم هستند. سرعت جوش حدود 1.5 متر در دقیقه برای ورق های نازک طبیعی است. می توان جریان های متناوب را اعمال کرد تا جوش های نقطه ای در فواصل دلخواه در امتداد درز تولید شوند. در "جوشکاری طرح مقاومتی" یک یا چند برجستگی (گودی) را روی یکی از سطوح قطعه کار برای جوشکاری برجسته می کنیم. این برجستگی ها ممکن است گرد یا بیضی شکل باشند. در این نقاط برجسته که در تماس با قسمت جفت گیری قرار می گیرند، دمای محلی بالا حاصل می شود. الکترودها برای فشرده سازی این برجستگی ها فشار وارد می کنند. الکترودها در جوشکاری طرح مقاومتی دارای نوک مسطح هستند و از آلیاژهای مسی هستند که آب خنک می شوند. مزیت جوشکاری پروجکشن مقاومتی توانایی ما در چندین جوش در یک زمان است، بنابراین عمر الکترود طولانی تر، قابلیت جوش دادن ورق های با ضخامت های مختلف، قابلیت جوش مهره ها و پیچ ها به ورق ها است. نقطه ضعف جوشکاری برجستگی مقاومتی، هزینه اضافی برجسته کردن گودی ها است. روش دیگر، در "جوشکاری فلاش" گرما از قوس انتهایی دو قطعه کار هنگام شروع تماس تولید می شود. این روش ممکن است به طور متناوب جوشکاری قوس الکتریکی را نیز در نظر بگیرد. دما در سطح مشترک افزایش می یابد و مواد نرم می شوند. یک نیروی محوری اعمال می شود و یک جوش در ناحیه نرم شده تشکیل می شود. پس از اتمام جوشکاری فلاش، اتصال را می توان برای بهبود ظاهر ماشینکاری کرد. کیفیت جوش حاصل از جوشکاری فلاش خوب است. سطوح توان 10 تا 1500 کیلو وات است. جوشکاری فلاش برای اتصال لبه به لبه فلزات مشابه یا غیر مشابه تا قطر 75 میلی متر و ورق هایی با ضخامت 0.2 میلی متر تا 25 میلی متر مناسب است. "جوشکاری با قوس گل میخ" بسیار شبیه به جوشکاری فلاش است. گل میخ مانند پیچ یا میله رزوه ای به عنوان یک الکترود عمل می کند در حالی که به قطعه کار مانند صفحه متصل می شود. برای تمرکز گرمای تولید شده، جلوگیری از اکسیداسیون و حفظ فلز مذاب در ناحیه جوش، یک حلقه سرامیکی یکبار مصرف در اطراف محل اتصال قرار می گیرد. در نهایت "جوشکاری ضربه ای" یکی دیگر از فرآیندهای جوشکاری مقاومتی، از یک خازن برای تامین انرژی الکتریکی استفاده می کند. در جوشکاری کوبه ای، نیرو در چند میلی ثانیه زمان بسیار سریع تخلیه می شود و گرمای موضعی بالایی در محل اتصال ایجاد می کند. ما از جوش ضربه ای به طور گسترده در صنعت تولید الکترونیک استفاده می کنیم که در آن از گرم کردن قطعات الکترونیکی حساس در مجاورت اتصال باید اجتناب شود.
تکنیکی به نام جوشکاری انفجاری شامل انفجار لایه ای از مواد منفجره است که روی یکی از قطعات کار قرار می گیرد که باید به یکدیگر متصل شوند. فشار بسیار بالایی که بر روی قطعه کار وارد می شود، یک رابط متلاطم و موجی ایجاد می کند و در هم قفل شدن مکانیکی صورت می گیرد. استحکام باند در جوشکاری انفجاری بسیار بالاست. جوش انفجاری روش خوبی برای روکش کردن صفحات با فلزات غیر مشابه است. پس از روکش فلزی، صفحات ممکن است به بخش های نازک تر تبدیل شوند. گاهی اوقات برای انبساط لوله ها از جوش انفجاری استفاده می کنیم تا محکم به صفحه ببندند.
آخرین روش ما در حوزه اتصال حالت جامد، پیوند انتشار یا جوش انتشار (DFW) است که در آن یک اتصال خوب عمدتاً با انتشار اتم ها در سطح مشترک حاصل می شود. مقداری تغییر شکل پلاستیک در سطح مشترک نیز به جوشکاری کمک می کند. دماهای درگیر حدود 0.5 Tm است که Tm دمای ذوب فلز است. استحکام باند در جوشکاری دیفیوژن به فشار، دما، زمان تماس و تمیزی سطوح در تماس بستگی دارد. گاهی اوقات ما از فلزات پرکننده در رابط استفاده می کنیم. گرما و فشار در پیوند انتشار مورد نیاز است و توسط مقاومت الکتریکی یا کوره و وزنه های مرده، پرس یا موارد دیگر تامین می شود. فلزات مشابه و غیر مشابه را می توان با جوشکاری انتشاری به هم وصل کرد. این فرآیند به دلیل زمانی که طول می کشد تا اتم ها مهاجرت کنند، نسبتا کند است. DFW می تواند خودکار باشد و به طور گسترده در ساخت قطعات پیچیده برای صنایع هوافضا، الکترونیک و پزشکی استفاده می شود. محصولات تولید شده شامل ایمپلنت های ارتوپدی، حسگرها، اعضای ساختاری هوافضا است. پیوند انتشار را می توان با SUPERPLASTIC FORMING ترکیب کرد تا سازه های فلزی پیچیده بسازد. مکانهای انتخابی روی ورقها ابتدا با پیوند پخش میشوند و سپس نواحی بدون پیوند با استفاده از فشار هوا در قالب گسترش مییابند. سازه های هوافضا با نسبت سختی به وزن بالا با استفاده از این ترکیب از روش ها ساخته می شوند. فرآیند ترکیبی جوشکاری انتشار / شکلدهی فوقپلاستیک با حذف نیاز به اتصال دهندهها، تعداد قطعات مورد نیاز را کاهش میدهد و به قطعات با تنش بسیار دقیق و اقتصادی و با زمانهای کوتاه منجر میشود.
لحیم کاری: تکنیک های لحیم کاری و لحیم کاری شامل دماهای کمتری نسبت به دمای مورد نیاز برای جوشکاری است. با این حال، دمای لحیم کاری بالاتر از دمای لحیم کاری است. در لحیم کاری، یک فلز پرکننده بین سطوحی که قرار است به هم متصل شوند قرار میگیرد و دماها تا دمای ذوب ماده پرکننده بالاتر از 723 کلوین اما کمتر از دمای ذوب قطعات کار افزایش مییابد. فلز مذاب فضای نزدیک بین قطعات کار را پر می کند. خنک شدن و انجماد متعاقب آن فلز فیلر منجر به اتصالات قوی می شود. در جوشکاری برنج، فلز پرکننده در محل اتصال رسوب میکند. در مقایسه با لحیم کاری، فلز پرکننده به میزان قابل توجهی در جوشکاری بریز استفاده می شود. از مشعل اکسی استیلن با شعله اکسید کننده برای رسوب فلز پرکننده در جوشکاری برنج استفاده می شود. به دلیل دماهای پایین تر در لحیم کاری، مشکلات در مناطق متاثر از گرما مانند تاب خوردگی و تنش های پسماند کمتر است. هر چه فاصله فاصله در لحیم کاری کمتر باشد، استحکام برشی اتصال بیشتر است. با این حال حداکثر استحکام کششی در شکاف بهینه (مقدار اوج) به دست می آید. در زیر و بالاتر از این مقدار بهینه، استحکام کششی در لحیم کاری کاهش می یابد. فاصله های معمول در لحیم کاری می تواند بین 0.025 و 0.2 میلی متر باشد. ما از انواع مواد لحیم کاری با اشکال مختلف مانند اجرا، پودر، حلقه، سیم، نوار و ... استفاده می کنیم. و می تواند این کارها را به خصوص برای طراحی یا هندسه محصول شما تولید کند. ما همچنین محتوای مواد لحیم کاری را با توجه به مواد پایه و کاربرد شما تعیین می کنیم. ما اغلب از شارها در عملیات لحیم کاری برای حذف لایه های اکسید ناخواسته و جلوگیری از اکسیداسیون استفاده می کنیم. برای جلوگیری از خوردگی بعدی، شارها معمولاً پس از عملیات اتصال حذف می شوند. شرکت AGS-TECH از روش های مختلف لحیم کاری استفاده می کند، از جمله:
- لحیم کاری مشعل
- لحیم کاری کوره
- لحیم کاری القایی
- لحیم کاری مقاومتی
- لحیم کاری شیب دار
- لحیم کاری مادون قرمز
- لحیم کاری نفوذی
- پرتو انرژی بالا
رایج ترین نمونه های ما از اتصالات لحیم کاری شده از فلزات غیر مشابه با استحکام خوب مانند مته های کاربید، درج ها، بسته های هرمتیک نوری الکترونیکی، مهر و موم ساخته شده اند.
لحیم کاری: این یکی از تکنیک های متداول ما است که در آن لحیم کاری (فلز پرکننده) محل اتصال را مانند لحیم کاری بین اجزای نزدیک پر می کند. لحیم کاری های ما دارای نقطه ذوب زیر 723 کلوین هستند. ما از لحیم کاری دستی و خودکار در عملیات تولید استفاده می کنیم. در مقایسه با لحیم کاری، دمای لحیم کاری کمتر است. لحیم کاری برای کاربردهای با دمای بالا یا مقاومت بالا چندان مناسب نیست. ما از لحیم کاری های بدون سرب و همچنین آلیاژهای قلع سرب، قلع روی، سرب-نقره، کادمیوم-نقره، روی-آلومینیوم علاوه بر سایر آلیاژهای لحیم کاری استفاده می کنیم. هم اسیدها و نمک های غیر خورنده بر پایه رزین و هم غیر آلی به عنوان شار در لحیم کاری استفاده می شوند. برای لحیم کاری فلزات با لحیم کاری کم از شارهای مخصوص استفاده می کنیم. در کاربردهایی که باید مواد سرامیکی، شیشه یا گرافیت را لحیم کاری کنیم، ابتدا قطعات را با فلزی مناسب برای افزایش قابلیت لحیم کاری آبکاری می کنیم. تکنیک های لحیم کاری محبوب ما عبارتند از:
-Reflow یا Paste Soldering
- لحیم کاری موجی
- لحیم کاری کوره ای
-لحیم کاری مشعل
- لحیم کاری القایی
-لحیم کاری آهن
لحیم کاری مقاومتی
- لحیم کاری غوطه ور
-لحیم کاری اولتراسونیک
- لحیم کاری مادون قرمز
لحیم کاری اولتراسونیک یک مزیت منحصر به فرد را به ما ارائه می دهد که به موجب آن نیاز به شار به دلیل اثر کاویتاسیون اولتراسونیک که لایه های اکسیدی را از سطوح متصل می کند حذف می شود. لحیم کاری مجدد و موجی تکنیک های برجسته صنعتی ما برای تولید با حجم بالا در الکترونیک هستند و بنابراین ارزش توضیح با جزئیات بیشتری را دارند. در لحیم کاری مجدد از خمیرهای نیمه جامد استفاده می کنیم که شامل ذرات لحیم-فلز است. خمیر با استفاده از فرآیند غربالگری یا شابلون روی مفصل قرار می گیرد. در بردهای مدار چاپی (PCB) ما اغلب از این تکنیک استفاده می کنیم. هنگامی که اجزای الکتریکی از خمیر روی این پدها قرار می گیرند، کشش سطحی بسته های نصب شده روی سطح را در یک راستا نگه می دارد. پس از قرار دادن قطعات، مجموعه را در یک کوره گرم می کنیم تا لحیم کاری مجدد انجام شود. در طی این فرآیند، حلالهای خمیر تبخیر میشوند، شار در خمیر فعال میشود، اجزا از قبل گرم میشوند، ذرات لحیم کاری ذوب میشوند و محل اتصال خیس میشوند و در نهایت مجموعه PCB به آرامی خنک میشود. دومین تکنیک محبوب ما برای تولید بردهای PCB با حجم بالا، یعنی لحیم کاری موجی به این واقعیت متکی است که لحیم کاری مذاب سطوح فلزی را مرطوب می کند و پیوندهای خوبی را تنها زمانی که فلز از قبل گرم شده است تشکیل می دهد. یک موج آرام ثابت از لحیم مذاب ابتدا توسط یک پمپ تولید میشود و PCBهای پیشگرمشده و پیشفلاکس شده روی موج منتقل میشوند. لحیم کاری فقط سطوح فلزی در معرض دید را خیس می کند اما بسته های پلیمری آی سی و تخته مدارهای پوشش داده شده با پلیمر را خیس نمی کند. جت آب گرم با سرعت بالا، لحیم اضافی را از محل اتصال می دمد و از پل زدن بین سیم های مجاور جلوگیری می کند. در لحیم کاری موجی پکیج های روی سطح، ابتدا آنها را قبل از لحیم کاری به صورت چسب به صفحه مدار می چسبانیم. باز هم از غربالگری و شابلون استفاده می شود اما این بار برای اپوکسی. پس از قرار دادن قطعات در محل صحیح خود، اپوکسی پخته می شود، تخته ها معکوس می شوند و لحیم کاری موجی انجام می شود.