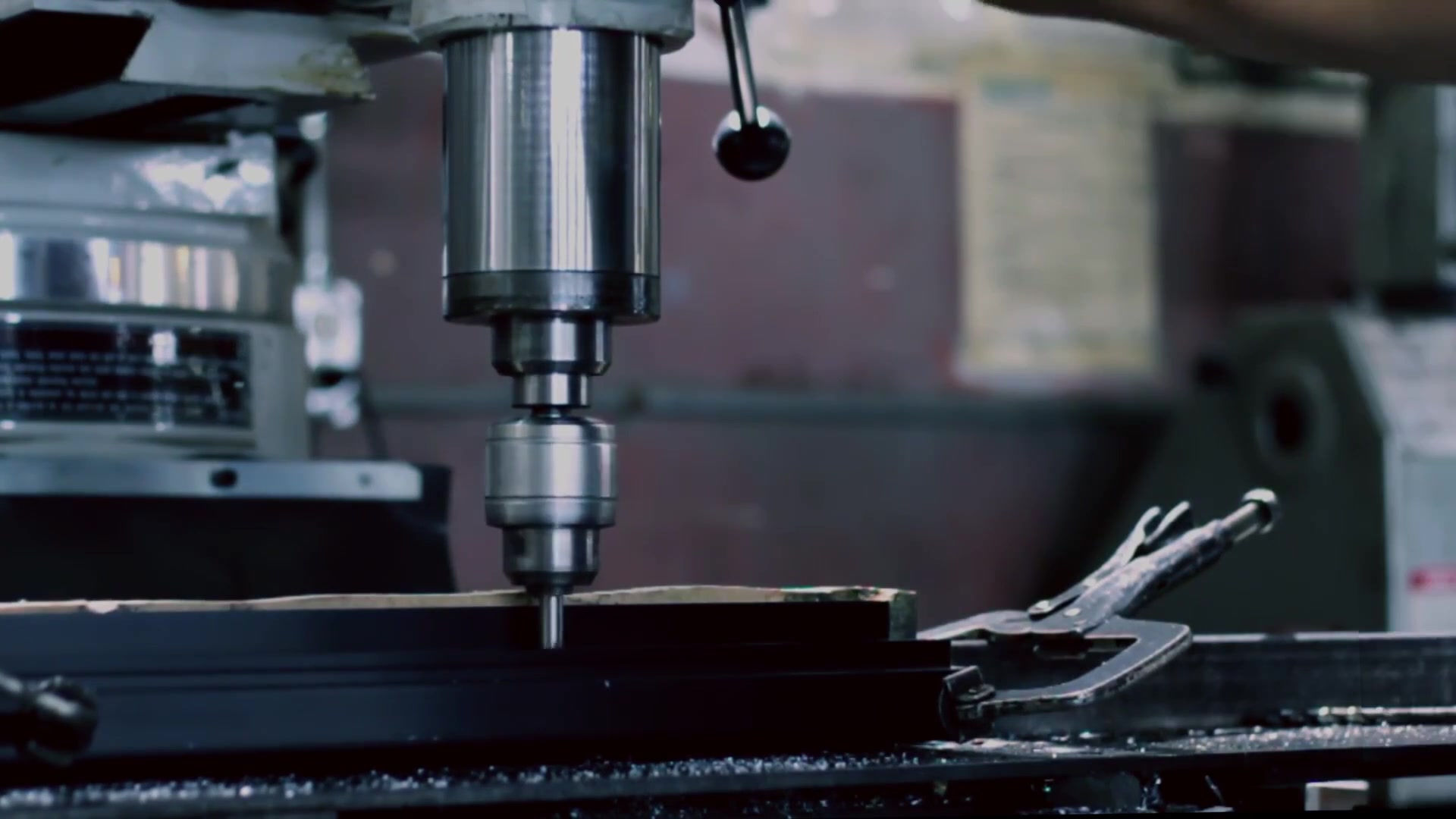
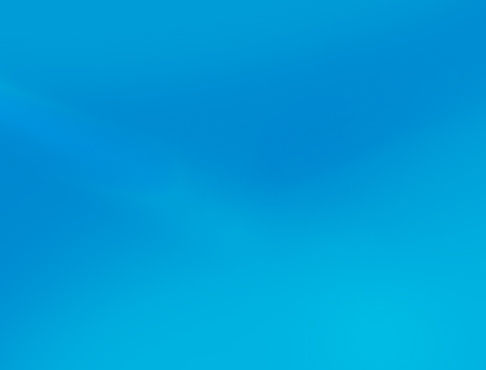
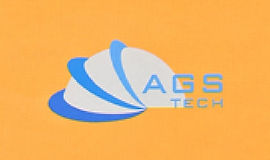
تولید کننده سفارشی جهانی، یکپارچه ساز، تثبیت کننده، شریک برون سپاری برای طیف گسترده ای از محصولات و خدمات.
ما منبع اصلی شما برای تولید، ساخت، مهندسی، ادغام، ادغام، برون سپاری محصولات و خدمات تولید شده سفارشی و خارج از قفسه هستیم.
زبان خود را انتخاب کنید
-
ساخت سفارشی
-
ساخت قرارداد داخلی و جهانی
-
برون سپاری تولید
-
تدارکات داخلی و جهانی
-
Consolidation
-
ادغام مهندسی
-
خدمات مهندسی
روش های ریخته گری و ماشینکاری سفارشی ما عبارتند از ریخته گری های مصرفی و غیر قابل مصرف، ریخته گری آهنی و غیر آهنی، شن و ماسه، قالب، گریز از مرکز، پیوسته، قالب سرامیکی، سرمایه گذاری، فوم گم شده، شکل نزدیک به شبکه، قالب دائمی (ریخته گری گرانشی)، گچ قالب (ریخته گری گچ) و پوسته، قطعات ماشینکاری شده تولید شده توسط آسیاب و تراشکاری با استفاده از تجهیزات معمولی و همچنین CNC، ماشینکاری نوع سوئیسی برای قطعات دقیق ارزان قیمت با توان بالا، ماشینکاری پیچ برای اتصال دهنده ها، ماشینکاری غیر متعارف. لطفاً در نظر داشته باشید که علاوه بر فلزات و آلیاژهای فلزی، در برخی موارد که ساخت قالب جذاب نیست یا گزینه مناسبی نیست، قطعات سرامیکی، شیشه و پلاستیک را نیز ماشین می کنیم. ماشینکاری مواد پلیمری به دلیل چالشی که پلاستیک و لاستیک به دلیل نرمی، عدم سفتی و غیره دارند، به تجربه تخصصی ما نیاز دارد. برای ماشینکاری سرامیک و شیشه، لطفا به صفحه ما در مورد ساخت غیر متعارف مراجعه کنید. شرکت AGS-TECH هر دو ریخته گری سبک و سنگین را تولید و عرضه می کند. ما قطعات ریخته گری فلز و قطعات ماشینکاری شده برای دیگهای بخار، مبدل های حرارتی، خودروها، میکروموتورها، توربین های بادی، تجهیزات بسته بندی مواد غذایی و موارد دیگر را تامین می کنیم. توصیه می کنیم اینجا را کلیک کنید تا دانلود تصاویر شماتیک فرآیندهای ماشینکاری و ریخته گری توسط AGS-TECH Inc.
این به شما کمک می کند تا اطلاعاتی را که در زیر به شما ارائه می کنیم را بهتر درک کنید. بیایید به برخی از تکنیک های مختلفی که ارائه می دهیم با جزئیات نگاه کنیم:
• ریخته گری قالب مصرفی: این دسته بندی گسترده به روش هایی اشاره دارد که شامل قالب های موقت و غیرقابل استفاده مجدد است. به عنوان مثال می توان به ماسه، گچ، پوسته، سرمایه گذاری (که به آن موم گم شده نیز گفته می شود) و ریخته گری گچ اشاره کرد.
• ریخته گری شن و ماسه: فرآیندی که در آن از ماسه به عنوان ماده قالب استفاده می شود. روشی بسیار قدیمی و همچنان بسیار پرطرفدار تا جایی که اکثر ریخته گری های فلزی تولید شده با این تکنیک ساخته می شوند. هزینه کم حتی در تولید کم. مناسب برای ساخت قطعات کوچک و بزرگ از این تکنیک می توان برای ساخت قطعات در عرض چند روز یا چند هفته با سرمایه گذاری بسیار کم استفاده کرد. شن و ماسه مرطوب با استفاده از خاک رس، چسب یا روغن های مخصوص به یکدیگر متصل می شوند. شن و ماسه به طور کلی در جعبه های قالب وجود دارد و سیستم حفره و دروازه با فشرده سازی ماسه در اطراف مدل ها ایجاد می شود. فرآیندها عبارتند از:
1.) قرار دادن مدل در ماسه برای ساخت قالب
2.) ادغام مدل و ماسه در یک سیستم دروازه
3.) حذف مدل
4. پر کردن حفره قالب با فلز مذاب
5.) خنک کردن فلز
6. شکستن قالب ماسه و برداشتن قالب
• ریخته گری قالب گچی: مشابه ریخته گری شن و ماسه و به جای ماسه از گچ پاری به عنوان ماده قالب استفاده می شود. زمان تولید کوتاه مانند ریخته گری شن و ماسه و ارزان. تحمل ابعادی خوب و پرداخت سطحی. عیب اصلی آن این است که فقط با فلزات با نقطه ذوب پایین مانند آلومینیوم و روی قابل استفاده است.
• SHELL MOLD CASTING : همچنین شبیه ریخته گری شن و ماسه است. حفره قالب از پوسته سخت شده ماسه و چسب رزین ترموست به جای فلاسک پر شده با ماسه مانند فرآیند ریخته گری ماسه به دست می آید. تقریباً هر فلزی که برای ریختهگری با ماسه مناسب باشد، میتواند با قالبگیری پوستهای ریختهگری شود. فرآیند را می توان به صورت زیر خلاصه کرد:
1.) ساخت قالب پوسته. شن و ماسه مورد استفاده در مقایسه با شن و ماسه مورد استفاده در ریخته گری شن و ماسه، اندازه دانه بسیار کوچکتری دارد. ماسه ریز با رزین ترموست مخلوط می شود. الگوی فلزی با یک عامل جداکننده پوشانده شده است تا برداشتن پوسته آسانتر شود. پس از آن الگوی فلزی حرارت داده می شود و مخلوط ماسه منفذ شده یا روی الگوی ریخته گری داغ دمیده می شود. یک پوسته نازک روی سطح الگو تشکیل می شود. ضخامت این پوسته را می توان با تغییر مدت زمان تماس مخلوط رزین ماسه با الگوی فلزی تنظیم کرد. سپس شن و ماسه شل با الگوی پوشیده شده با پوسته باقی مانده برداشته می شود.
2.) سپس پوسته و الگو را در فر گرم می کنند تا پوسته سفت شود. پس از اتمام سخت شدن، پوسته با استفاده از پین های تعبیه شده در الگو از الگو خارج می شود.
3.) دو پوسته از این دست با چسباندن یا گیره به هم مونتاژ می شوند و قالب کامل را می سازند. اکنون قالب پوسته در ظرفی قرار می گیرد که در طی فرآیند ریخته گری توسط ماسه یا گلوله فلزی پشتیبانی می شود.
4.) حالا فلز داغ را می توان در قالب پوسته ریخت.
مزایای ریخته گری پوسته محصولاتی با سطح بسیار خوب، امکان ساخت قطعات پیچیده با دقت ابعادی بالا، فرآیند آسان برای خودکارسازی، مقرون به صرفه بودن برای تولید حجم زیاد است.
معایب این است که قالب ها به تهویه مناسب نیاز دارند زیرا گازهایی که هنگام تماس فلز مذاب با ماده شیمیایی بایندر ایجاد می شوند، رزین های ترموست و الگوهای فلزی گران هستند. با توجه به هزینه الگوهای فلزی، این تکنیک ممکن است برای دوره های تولید با مقدار کم مناسب نباشد.
• ریخته گری سرمایه گذاری (همچنین به نام ریخته گری موم گمشده): همچنین یک تکنیک بسیار قدیمی و مناسب برای ساخت قطعات با کیفیت با دقت، تکرارپذیری، تطبیق پذیری و یکپارچگی از بسیاری از فلزات، مواد نسوز و آلیاژهای خاص با کارایی بالا می باشد. قطعات کوچک و بزرگ را می توان تولید کرد. در مقایسه با برخی از روشهای دیگر فرآیندی گرانقیمت است، اما مزیت اصلی امکان تولید قطعات با شکل شبکه، خطوط پیچیده و جزئیات است. بنابراین هزینه تا حدودی با حذف دوباره کاری و ماشینکاری در برخی موارد جبران می شود. حتی اگر ممکن است تغییراتی وجود داشته باشد، در اینجا خلاصه ای از فرآیند کلی ریخته گری سرمایه گذاری آمده است:
1.) ایجاد الگوی اصلی اصلی از موم یا پلاستیک. هر ریخته گری به یک الگو نیاز دارد زیرا در این فرآیند از بین می روند. قالبی که از آن الگوها ساخته می شود نیز مورد نیاز است و بیشتر اوقات قالب ریخته گری یا ماشین کاری می شود. از آنجایی که قالب نیازی به باز کردن ندارد، می توان به ریخته گری های پیچیده دست یافت، بسیاری از الگوهای مومی را می توان مانند شاخه های یک درخت به هم متصل کرد و با هم ریخت، بنابراین امکان تولید چندین قسمت از یک بار ریختن فلز یا آلیاژ فلز را فراهم کرد.
2.) در مرحله بعد، الگو را با دوغاب نسوز متشکل از سیلیس دانه ریز، آب، چسباننده آغشته کرده یا می ریزند. این باعث ایجاد یک لایه سرامیکی بر روی سطح الگو می شود. روکش نسوز روی الگو را گذاشته تا خشک و سفت شود. این مرحله جایی است که نام ریخته گری سرمایه گذاری از آن گرفته شده است: دوغاب نسوز روی الگوی موم ریخته می شود.
3.) در این مرحله قالب سرامیکی سخت شده را زیر و رو کرده و حرارت می دهند تا موم ذوب شده و از قالب بریزد. یک حفره برای ریخته گری فلز باقی مانده است.
4.) پس از خارج شدن موم، قالب سرامیکی حتی تا دمای بالاتری گرم می شود که منجر به تقویت قالب می شود.
5.) ریخته گری فلز در قالب داغ ریخته می شود و تمام بخش های پیچیده را پر می کند.
6.) ریخته گری مجاز است تا جامد شود
7. در نهایت قالب سرامیکی شکسته شده و قطعات ساخته شده از درخت جدا می شود.
در اینجا پیوندی به بروشور کارخانه ریخته گری سرمایه گذاری شده است
ریخته گری الگوی تبخیری: این فرآیند از الگویی ساخته شده از موادی مانند فوم پلی استایرن استفاده می کند که وقتی فلز مذاب داغ در قالب ریخته می شود تبخیر می شود. دو نوع از این فرآیند وجود دارد: LOST FOAM CASTING که از ماسه بدون پیوند استفاده می کند و FULL MOLD CASTING که از ماسه چسبانده شده استفاده می کند. در اینجا مراحل کلی فرآیند آمده است:
1.) الگو را از موادی مانند پلی استایرن بسازید. هنگامی که مقادیر زیادی تولید می شود، الگوی قالب گیری می شود. اگر قطعه شکل پیچیده ای داشته باشد، ممکن است لازم باشد چندین بخش از چنین مواد فومی به هم بچسبند تا الگو را تشکیل دهند. ما اغلب الگو را با یک ترکیب نسوز می پوشانیم تا سطح خوبی روی ریخته گری ایجاد کنیم.
2.) سپس الگو را در ماسه قالب گیری قرار می دهیم.
3.) فلز مذاب در قالب ریخته می شود و الگوی فوم تبخیر می شود، یعنی پلی استایرن در بیشتر موارد در حفره قالب جریان می یابد.
4.) فلز مذاب در قالب ماسه گذاشته می شود تا سفت شود.
5.) پس از سفت شدن، قالب را جدا می کنیم.
در برخی موارد، محصولی که ما تولید می کنیم به یک هسته درون الگو نیاز دارد. در ریخته گری تبخیری، نیازی به قرار دادن و محکم کردن هسته در حفره قالب نیست. این تکنیک برای ساخت هندسه های بسیار پیچیده مناسب است، می توان آن را به راحتی برای تولید با حجم بالا خودکار کرد و هیچ خط جدایی در قسمت ریخته گری وجود ندارد. اجرای فرآیند اصلی ساده و مقرون به صرفه است. برای تولید حجم زیاد، از آنجایی که برای تولید الگوها از پلی استایرن به قالب یا قالب نیاز است، ممکن است تا حدودی هزینه بر باشد.
• ریخته گری قالب غیر قابل انبساط: این دسته بندی گسترده به روش هایی اشاره دارد که در آن قالب پس از هر چرخه تولید نیازی به اصلاح ندارد. به عنوان مثال می توان به ریخته گری دائمی، قالبی، پیوسته و گریز از مرکز اشاره کرد. تکرار پذیری به دست می آید و قطعات را می توان به شکل NEAR NET SHAPE مشخص کرد.
• ریخته گری قالب دائمی: قالب های قابل استفاده مجدد ساخته شده از فلز برای ریخته گری های متعدد استفاده می شود. یک قالب دائمی به طور کلی می تواند ده ها هزار بار قبل از فرسوده شدن استفاده شود. گرانش، فشار گاز یا خلاء به طور کلی برای پر کردن قالب استفاده می شود. قالب ها (که قالب نیز نامیده می شود) عموماً از آهن، فولاد، سرامیک یا فلزات دیگر ساخته می شوند. روند کلی این است:
1.) ماشین و قالب را ایجاد کنید. معمول است که قالب را از دو بلوک فلزی که در کنار هم قرار می گیرند و می توانند باز و بسته شوند، ماشین کاری کنند. هم ویژگی های قطعه و هم سیستم دروازه به طور کلی در قالب ریخته گری ماشینکاری می شود.
2.) سطوح داخلی قالب با دوغاب حاوی مواد نسوز پوشانده شده است. این به کنترل جریان گرما کمک می کند و به عنوان روان کننده برای حذف آسان قسمت ریختگی عمل می کند.
3.) در مرحله بعد، نیمه های قالب دائمی بسته شده و قالب گرم می شود.
4.) فلز مذاب در قالب ریخته می شود و برای انجماد می گذارند.
5.) قبل از اینکه خیلی خنک شود، وقتی نیمه های قالب باز می شوند، قطعه را با استفاده از اجکتورها از قالب دائمی خارج می کنیم.
ما اغلب از ریخته گری قالب دائمی برای فلزات با نقطه ذوب پایین مانند روی و آلومینیوم استفاده می کنیم. برای ریخته گری فولاد، ما از گرافیت به عنوان مواد قالب استفاده می کنیم. ما گاهی اوقات هندسه های پیچیده ای را با استفاده از هسته های درون قالب های دائمی به دست می آوریم. از مزایای این روش می توان به ریخته گری هایی با خواص مکانیکی خوب به دست آمده از خنک سازی سریع، یکنواختی در خواص، دقت و پرداخت سطحی خوب، نرخ رد پایین، امکان خودکارسازی فرآیند و تولید حجم های بالا از نظر اقتصادی اشاره کرد. معایب آن هزینه های بالای راه اندازی اولیه است که آن را برای عملیات با حجم کم نامناسب می کند و محدودیت در اندازه قطعات تولید شده.
ریخته گری: قالب ماشینکاری می شود و فلز مذاب تحت فشار بالا به داخل حفره های قالب رانده می شود. ریخته گری فلزات آهنی و غیر آهنی امکان پذیر است. این فرآیند برای تولید مقادیر زیاد قطعات کوچک تا متوسط با جزئیات، دیوارههای بسیار نازک، سازگاری ابعادی و سطح خوب مناسب است. شرکت AGS-TECH قادر است با استفاده از این تکنیک، ضخامت دیوارهای کوچک تا 0.5 میلی متر را تولید کند. مانند ریختهگری قالب دائمی، قالب باید از دو نیمه تشکیل شده باشد که میتوانند برای برداشتن قطعه تولید شده باز و بسته شوند. یک قالب دایکاست ممکن است حفره های متعددی داشته باشد تا امکان تولید چند ریخته گری در هر چرخه را فراهم کند. قالب های دایکاست بسیار سنگین و بسیار بزرگتر از قطعاتی هستند که تولید می کنند، بنابراین گران هستند. ما قالب های فرسوده را به صورت رایگان برای مشتریان خود تعمیر و تعویض می کنیم تا زمانی که آنها قطعات خود را از ما سفارش دهند. قالب های ما عمر طولانی در محدوده چند صد هزار چرخه دارند.
در اینجا مراحل اولیه فرآیند ساده آمده است:
1.) تولید قالب به طور کلی از فولاد
2.) قالب نصب شده روی دستگاه ریخته گری
3.) پیستون فلز مذاب را مجبور می کند تا در حفره های قالب جریان یابد و ویژگی های پیچیده و دیواره های نازک را پر می کند.
4.) پس از پر کردن قالب با فلز مذاب، قالب ریخته گری تحت فشار سفت می شود
5.) قالب باز می شود و ریخته گری با کمک پین های اجکتور خارج می شود.
6.) حالا قالب خالی دوباره روغن کاری می شود و برای چرخه بعدی گیره می شود.
در دایکاست، ما اغلب از قالبگیری درج استفاده میکنیم که در آن قسمت اضافی را در قالب قرار میدهیم و فلز را در اطراف آن میریزیم. این قطعات پس از انجماد بخشی از محصول ریخته گری می شوند. از مزایای دایکاست می توان به خواص مکانیکی خوب قطعات، امکان ویژگی های پیچیده، جزئیات ظریف و سطح خوب، نرخ تولید بالا، اتوماسیون آسان اشاره کرد. معایب آن عبارتند از: برای حجم کم خیلی مناسب نیست به دلیل قالب و هزینه تجهیزات بالا، محدودیت در شکل های ریخته گری، علائم گرد کوچک روی قطعات ریخته گری ناشی از تماس پین های اجکتور، فلاش نازک فلز فشرده شده در خط جداسازی، نیاز برای منافذ در امتداد خط جدایی بین قالب، باید دمای قالب را با استفاده از گردش آب پایین نگه داشت.
ریخته گری گریز از مرکز: فلز مذاب در محور چرخش در مرکز قالب دوار ریخته می شود. نیروهای گریز از مرکز، فلز را به سمت حاشیه پرتاب می کنند و در حالی که قالب به چرخش خود ادامه می دهد، اجازه می دهد تا جامد شود. می توان از چرخش محور افقی و عمودی استفاده کرد. می توان قطعاتی با سطوح داخلی گرد و سایر اشکال غیر گرد ریخته گری کرد. فرآیند را می توان به صورت زیر خلاصه کرد:
1.) فلز مذاب در قالب گریز از مرکز ریخته می شود. سپس فلز به دلیل چرخاندن قالب به دیواره های بیرونی منتقل می شود.
2.) با چرخش قالب، ریخته گری فلز سخت می شود
ریخته گری سانتریفیوژ روشی مناسب برای تولید قطعات استوانه ای توخالی مانند لوله، عدم نیاز به اسپرو، رایزر و المان های دروازه ای، روکش سطحی خوب و ویژگی های دقیق، بدون مشکل انقباض، امکان تولید لوله های بلند با قطر بسیار زیاد، قابلیت تولید با سرعت بالا. .
• ريخته گري پيوسته ( ريخته گري رشته اي ): براي ريخته گري به طول پيوسته از فلز استفاده مي شود. اساساً فلز مذاب در پروفیل دو بعدی قالب ریخته می شود اما طول آن نامشخص است. فلز مذاب جدید به طور مداوم به داخل قالب وارد می شود، زیرا قالب ریخته گری به سمت پایین حرکت می کند و طول آن با گذشت زمان افزایش می یابد. فلزاتی مانند مس، فولاد، آلومینیوم با استفاده از فرآیند ریختهگری پیوسته به رشتههای بلند ریخته میشوند. این فرآیند ممکن است پیکربندی های مختلفی داشته باشد، اما یکی از موارد رایج را می توان به صورت زیر ساده کرد:
1.) فلز مذاب در ظرفی که در بالای قالب قرار دارد با مقادیر و سرعت جریان خوب محاسبه شده ریخته می شود و از طریق قالب خنک شده با آب جریان می یابد. ریختهگری فلزی که در قالب ریخته میشود به یک میله شروع که در پایین قالب قرار میگیرد جامد میشود. این نوار شروع به غلتکها چیزی میدهد که در ابتدا روی آن چنگ بزنند.
2.) رشته فلزی بلند توسط غلتک ها با سرعت ثابت حمل می شود. همچنین غلتک ها جهت جریان رشته فلزی را از عمودی به افقی تغییر می دهند.
3.) پس از اینکه ریخته گری پیوسته یک مسافت افقی مشخص را طی کرد، مشعل یا اره ای که همراه با ریخته گری حرکت می کند به سرعت آن را به طول های دلخواه برش می دهد.
فرآیند ریختهگری پیوسته را میتوان با فرآیند نورد ادغام کرد، جایی که فلز ریختهگریشده بهطور پیوسته میتواند مستقیماً به یک آسیاب نورد برای تولید تیرهای I، تیرهای T... و غیره وارد شود. ریختهگری پیوسته خواص یکنواختی را در سراسر محصول ایجاد میکند، نرخ انجماد بالایی دارد، هزینه را به دلیل از دست دادن بسیار کم مواد کاهش میدهد، فرآیندی را ارائه میدهد که در آن بارگذاری فلز، ریختن، انجماد، برش و حذف ریختهگری همه در یک عملیات مداوم انجام میشود و بنابراین منجر به بهره وری بالا و کیفیت بالا می شود. با این حال، یک مورد مهم سرمایه گذاری اولیه بالا، هزینه های راه اندازی و فضای مورد نیاز است.
• خدمات ماشینکاری: ما ماشینکاری سه، چهار و پنج محوره را ارائه می دهیم. نوع فرآیندهای ماشینکاری که ما استفاده می کنیم عبارتند از: تراشکاری، فرزکاری، حفاری، حفاری، بریچ کردن، اره کردن، اره کردن، آسیاب کردن، لپینگ، پرداخت و ماشینکاری غیر سنتی که در منوی متفاوتی از وب سایت ما توضیح داده شده است. برای بیشتر تولیدات خود، از ماشین های CNC استفاده می کنیم. با این حال، برای برخی از عملیات، تکنیکهای مرسوم مناسبتر هستند و بنابراین ما نیز بر آنها تکیه میکنیم. قابلیتهای ماشینکاری ما به بالاترین سطح ممکن میرسد و برخی از قطعات سختگیرانه در کارخانه دارای گواهینامه AS9100 تولید میشوند. تیغه های موتور جت به تجربه ساخت بسیار تخصصی و تجهیزات مناسب نیاز دارند. صنعت هوافضا استانداردهای بسیار سختگیرانه ای دارد. برخی از قطعات با ساختارهای هندسی پیچیده به آسانی توسط ماشینکاری پنج محوری ساخته می شوند که فقط در برخی از کارخانه های ماشینکاری از جمله ما یافت می شود. کارخانه دارای گواهینامه هوافضا ما تجربه لازم را در مطابقت با الزامات مستندات گسترده صنعت هوافضا دارد.
در عملیات TURNING، یک قطعه کار چرخانده شده و در برابر یک ابزار برش حرکت می کند. برای این فرآیند از ماشینی به نام تراش استفاده می شود.
در آسیاب، ماشینی به نام ماشین فرز دارای ابزار چرخشی است تا لبه های برش را در برابر قطعه کار قرار دهد.
عملیات حفاری شامل یک برش چرخان با لبه های برش است که در تماس با قطعه کار سوراخ هایی ایجاد می کند. معمولاً از پرس مته، ماشین تراش یا آسیاب استفاده می شود.
در عملیات BORING یک ابزار با یک نوک نوک خمیده منفرد به سوراخ ناهموار در یک قطعه کار چرخان منتقل می شود تا سوراخ را کمی بزرگ کرده و دقت را بهبود بخشد. برای اهداف تکمیلی خوب استفاده می شود.
BROACHING شامل یک ابزار دندانه دار برای حذف مواد از قطعه کار در یک گذر از براچ (ابزار دندانه دار) است. در بروشینگ خطی، بروشک به صورت خطی روی سطح قطعه کار می رود تا برش را ایجاد کند، در حالی که در بروشینگ چرخشی، بروشک چرخانده شده و به قطعه کار فشار داده می شود تا یک شکل متقارن محور را برش دهد.
ماشینکاری نوع سوئیس یکی از تکنیک های ارزشمند ما است که برای تولید قطعات کوچک با دقت بالا از آن استفاده می کنیم. با استفاده از تراش نوع سوئیسی، قطعات کوچک، پیچیده و دقیق را ارزان میکنیم. برخلاف ماشین های تراش معمولی که قطعه کار ثابت نگه داشته می شود و ابزار در حال حرکت است، در مراکز تراشکاری نوع سوئیسی، قطعه کار مجاز است در محور Z حرکت کند و ابزار ثابت است. در ماشینکاری نوع سوئیسی، استوک میله در دستگاه نگه داشته میشود و از طریق یک بوش راهنما در محور z پیش میرود و تنها قسمتی را که قرار است ماشینکاری شود، نمایان میکند. به این ترتیب گرفتن محکم تضمین می شود و دقت بسیار بالا است. در دسترس بودن ابزارهای زنده، فرصتی برای آسیاب و حفاری با پیشروی مواد از بوش راهنما فراهم می کند. محور Y تجهیزات نوع سوئیسی قابلیت فرز کامل را فراهم می کند و باعث صرفه جویی در زمان زیادی در ساخت می شود. علاوه بر این، ماشینهای ما دارای متهها و ابزارهای حفاری هستند که در هنگام نگهداشتن آن در اسپیندل فرعی روی آن کار میکنند. قابلیت ماشینکاری نوع سوئیس ما یک فرصت ماشینکاری کاملاً خودکار را در یک عملیات واحد به ما می دهد.
ماشینکاری یکی از بزرگترین بخش های تجارت AGS-TECH Inc. ما از آن به عنوان عملیات اولیه یا عملیات ثانویه پس از ریخته گری یا اکسترود کردن یک قطعه استفاده می کنیم تا تمام مشخصات نقشه رعایت شود.
خدمات تکمیل سطح: ما طیف گسترده ای از عملیات سطح و پرداخت سطح را ارائه می دهیم، مانند حالت دهنده سطح برای افزایش چسبندگی، رسوب لایه نازک اکسید برای افزایش چسبندگی پوشش، سند بلاست، فیلم شیمیایی، آنودایز، نیترید، پوشش پودری، پوشش اسپری انواع متالیزاسیون و تکنیک های پوشش دهی پیشرفته از جمله کندوپاش، پرتو الکترونی، تبخیر، آبکاری، پوشش های سخت مانند الماس مانند کربن (DLC) یا پوشش تیتانیوم برای ابزارهای حفاری و برش.
• خدمات علامت گذاری و برچسب گذاری محصول: بسیاری از مشتریان ما به علامت گذاری و برچسب گذاری، علامت گذاری لیزری، حکاکی روی قطعات فلزی نیاز دارند. اگر چنین نیازی دارید، اجازه دهید در مورد اینکه کدام گزینه برای شما بهترین است صحبت کنیم.
در اینجا برخی از محصولات ریخته گری فلزی رایج مورد استفاده قرار می گیرند. از آنجایی که اینها خارج از قفسه هستند، در صورتی که هر یک از این موارد با نیازهای شما مطابقت داشته باشد، می توانید در هزینه های قالب صرفه جویی کنید:
برای دانلود جعبه های آلومینیومی دایکاست سری 11 ما از AGS-Electronics اینجا را کلیک کنید