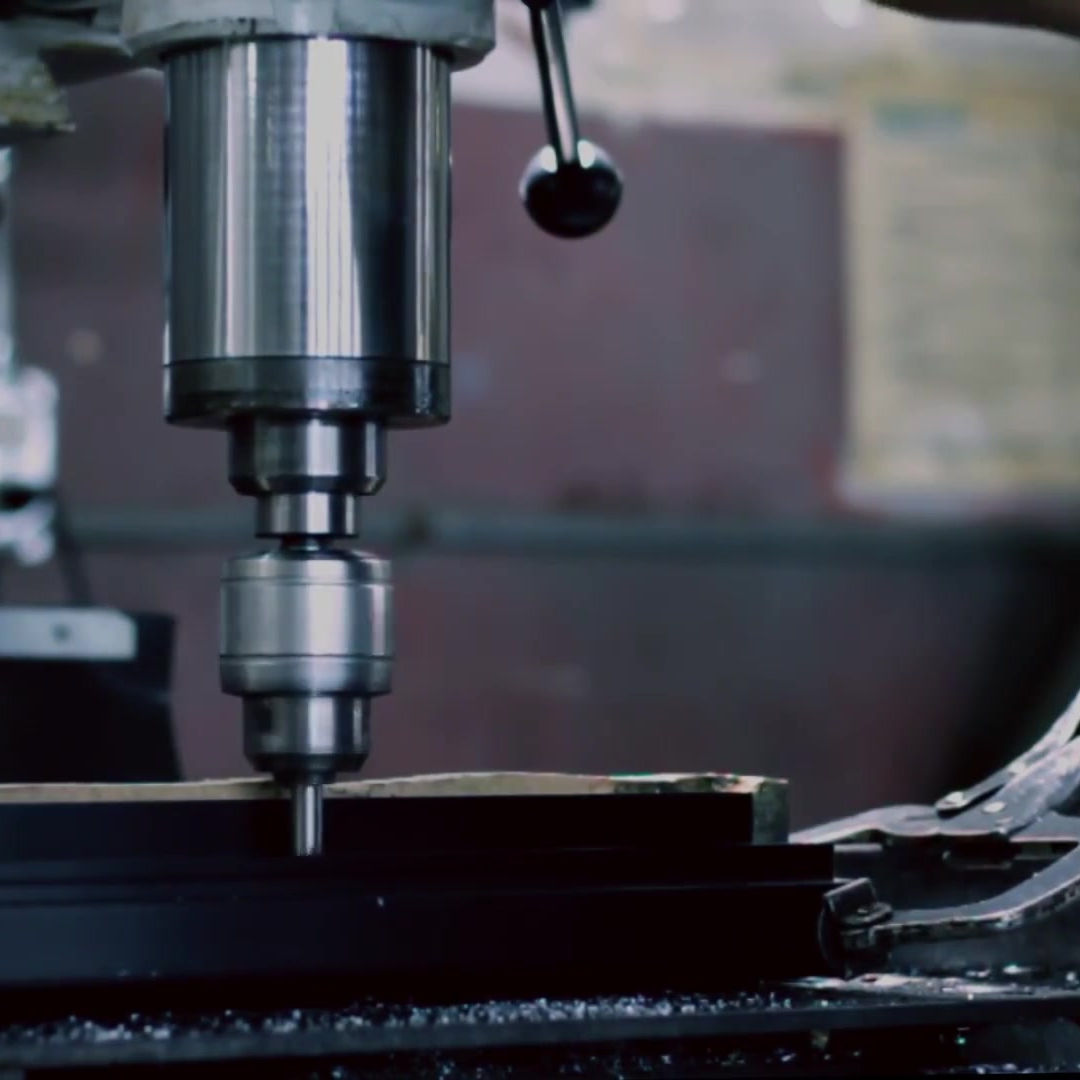
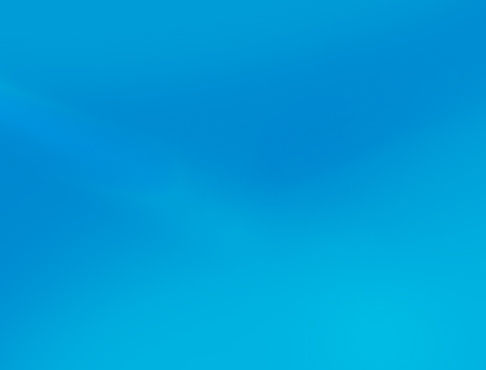
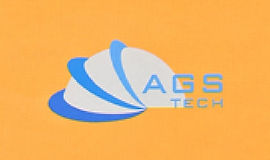
تولید کننده سفارشی جهانی، یکپارچه ساز، تثبیت کننده، شریک برون سپاری برای طیف گسترده ای از محصولات و خدمات.
ما منبع اصلی شما برای تولید، ساخت، مهندسی، ادغام، ادغام، برون سپاری محصولات و خدمات تولید شده سفارشی و خارج از قفسه هستیم.
زبان خود را انتخاب کنید
-
ساخت سفارشی
-
ساخت قرارداد داخلی و جهانی
-
برون سپاری تولید
-
تدارکات داخلی و جهانی
-
Consolidation
-
ادغام مهندسی
-
خدمات مهندسی
به طور ساده، کامپوزیت ها یا مواد مرکب، موادی هستند که از دو یا چند ماده با خواص فیزیکی یا شیمیایی متفاوت تشکیل شده اند، اما وقتی با هم ترکیب شوند، به ماده ای متفاوت از مواد تشکیل دهنده تبدیل می شوند. لازم به ذکر است که مواد تشکیل دهنده در ساختار مجزا و متمایز می مانند. هدف در ساخت یک ماده کامپوزیت، به دست آوردن محصولی است که نسبت به اجزای تشکیل دهنده آن برتری داشته باشد و ویژگی های مورد نظر هر یک از اجزا را ترکیب کند. به عنوان مثال؛ استحکام، وزن کم یا قیمت کمتر ممکن است انگیزه طراحی و تولید کامپوزیت باشد. نوع کامپوزیت های ما کامپوزیت های تقویت شده با ذرات، کامپوزیت های تقویت شده با الیاف شامل ماتریس سرامیکی / زمینه پلیمری / زمینه فلزی / کربن- کربن / کامپوزیت های هیبریدی، کامپوزیت های ساختاری و چند لایه و ساختار ساندویچی و نانوکامپوزیت ها می باشد.
تکنیک های ساختی که ما در تولید مواد کامپوزیت به کار می بریم عبارتند از: Pultrusion، فرآیندهای تولید پیش آغشته، قرار دادن الیاف پیشرفته، سیم پیچی رشته، قرار دادن فیبر متناسب، فرآیند چیدمان اسپری فایبر گلاس، تافتینگ، فرآیند لانکساید، پین زدن z.
بسیاری از مواد کامپوزیتی از دو فاز تشکیل شده اند، ماتریس که پیوسته است و فاز دیگر را احاطه می کند. و فاز پراکنده که توسط ماتریس احاطه شده است.
توصیه می کنیم اینجا را کلیک کنیددانلود تصاویر شماتیک ما از کامپوزیت ها و مواد کامپوزیت ساخت توسط AGS-TECH Inc.
این به شما کمک می کند اطلاعاتی را که در زیر به شما ارائه می دهیم بهتر درک کنید.
• کامپوزیت های تقویت شده با ذرات: این دسته از دو نوع تشکیل شده است: کامپوزیت های با ذرات بزرگ و کامپوزیت های تقویت شده با پراکندگی. در نوع اول، فعل و انفعالات ذره-ماتریس را نمی توان در سطح اتمی یا مولکولی بررسی کرد. در عوض مکانیک پیوسته معتبر است. از سوی دیگر، در کامپوزیت های تقویت شده با پراکندگی، ذرات به طور کلی در محدوده ده ها نانومتری بسیار کوچکتر هستند. نمونه ای از کامپوزیت ذرات بزرگ، پلیمرهایی است که به آنها پرکننده ها اضافه شده است. پرکننده ها خواص مواد را بهبود می بخشند و ممکن است مقداری از حجم پلیمر را با مواد مقرون به صرفه تری جایگزین کنند. کسر حجمی دو فاز بر رفتار کامپوزیت تأثیر می گذارد. کامپوزیت های ذرات بزرگ با فلزات، پلیمرها و سرامیک ها استفاده می شود. CERMETS نمونه هایی از کامپوزیت های سرامیکی / فلزی هستند. رایج ترین سرمت ما کاربید سیمانی است. از سرامیک کاربید نسوز مانند ذرات کاربید تنگستن در زمینه فلزی مانند کبالت یا نیکل تشکیل شده است. این کامپوزیت های کاربید به طور گسترده ای به عنوان ابزار برش برای فولاد سخت شده استفاده می شود. ذرات کاربید سخت مسئول عمل برش هستند و چقرمگی آنها توسط ماتریس فلزی انعطاف پذیر افزایش می یابد. بنابراین ما مزایای هر دو ماده را در یک کامپوزیت به دست می آوریم. نمونه رایج دیگری از کامپوزیت ذرات بزرگ که ما استفاده می کنیم ذرات کربن سیاه است که با لاستیک ولکانیزه مخلوط شده اند تا کامپوزیتی با استحکام کششی، چقرمگی، پارگی و مقاومت سایشی بالا به دست آید. نمونهای از کامپوزیتهای تقویتشده با پراکندگی، فلزات و آلیاژهای فلزی است که توسط پراکندگی یکنواخت ذرات ریز یک ماده بسیار سخت و خنثی تقویت و سخت شدهاند. هنگامی که تکه های بسیار کوچک اکسید آلومینیوم به ماتریس فلز آلومینیوم اضافه می شود، پودر آلومینیوم متخلخل را به دست می آوریم که استحکام بالایی در دمای بالا دارد.
• کامپوزیت های تقویت شده با الیاف: این دسته از کامپوزیت ها در واقع مهم ترین هستند. هدف دستیابی به استحکام و سفتی بالا در واحد وزن است. ترکیب الیاف، طول، جهت گیری و غلظت در این کامپوزیت ها در تعیین خواص و سودمندی این مواد حیاتی است. ما از سه گروه الیاف استفاده می کنیم: سبیل، الیاف و سیم. WHISKERS تک بلورهای بسیار نازک و بلندی هستند. آنها از قوی ترین مواد هستند. برخی از مواد سبیل مانند گرافیت، نیترید سیلیکون، اکسید آلومینیوم هستند. FIBERS از طرف دیگر بیشتر پلیمرها یا سرامیک ها هستند و در حالت پلی کریستالی یا آمورف هستند. گروه سوم سیمهای ظریفی هستند که قطر نسبتاً زیادی دارند و اغلب از فولاد یا تنگستن تشکیل شدهاند. نمونه ای از کامپوزیت های تقویت شده با سیم، لاستیک های اتومبیل است که از سیم فولادی در داخل لاستیک استفاده می کند. بسته به ماده ماتریس، کامپوزیت های زیر را داریم:
کامپوزیت های ماتریس پلیمری: این کامپوزیت ها از رزین پلیمری و الیاف به عنوان ماده تقویت کننده ساخته شده اند. زیرگروهی از این کامپوزیتهای پلیمر تقویتشده با الیاف شیشه (GFRP) حاوی الیاف شیشهای پیوسته یا ناپیوسته در یک ماتریس پلیمری است. شیشه استحکام بالایی دارد، مقرون به صرفه است، به راحتی در الیاف ساخته می شود و از نظر شیمیایی بی اثر است. معایب آن سختی و سفتی محدود آنهاست، دمای سرویس فقط تا 200 تا 300 درجه سانتیگراد است. فایبرگلاس برای بدنه خودرو و تجهیزات حمل و نقل، بدنه وسایل نقلیه دریایی، ظروف ذخیره سازی مناسب است. به دلیل سفتی محدود برای هوافضا یا پل سازی مناسب نیستند. زیرگروه دیگر کامپوزیت پلیمر تقویت شده با فیبر کربن (CFRP) نام دارد. در اینجا، کربن ماده فیبری ما در ماتریس پلیمری است. کربن به دلیل مدول و استحکام ویژه بالا و توانایی آن در حفظ این مدول ها در دماهای بالا شناخته شده است. الیاف کربن می توانند مدول های کششی استاندارد، متوسط، بالا و فوق العاده را به ما ارائه دهند. علاوه بر این، الیاف کربن ویژگی های فیزیکی و مکانیکی متنوعی را ارائه می دهند و بنابراین برای کاربردهای مهندسی سفارشی مختلف مناسب هستند. کامپوزیت های CFRP را می توان برای ساخت تجهیزات ورزشی و تفریحی، مخازن تحت فشار و اجزای ساختاری هوافضا در نظر گرفت. با این حال، یک زیر گروه دیگر، کامپوزیت های پلیمری تقویت شده با الیاف آرامید نیز موادی با استحکام و مدول بالا هستند. نسبت استحکام به وزن آنها به طور فوق العاده بالا است. الیاف آرامید با نام های تجاری KEVLAR و NOMEX نیز شناخته می شوند. تحت کشش، عملکرد بهتری نسبت به سایر مواد الیاف پلیمری دارند، اما در فشار ضعیف هستند. الیاف آرامید سخت، مقاوم در برابر ضربه، مقاوم در برابر خزش و خستگی، پایدار در دماهای بالا، بی اثر شیمیایی به جز در برابر اسیدها و بازهای قوی هستند. الیاف آرامید به طور گسترده ای در کالاهای ورزشی، جلیقه های ضد گلوله، لاستیک ها، طناب ها، پوشش های کابل فیبر نوری استفاده می شود. مواد تقویت کننده الیاف دیگری وجود دارند اما به میزان کمتری استفاده می شوند. اینها عمدتاً بور، کاربید سیلیکون، اکسید آلومینیوم هستند. از طرف دیگر مواد ماتریس پلیمری نیز حیاتی است. حداکثر دمای سرویس کامپوزیت را تعیین می کند زیرا پلیمر معمولا دمای ذوب و تخریب کمتری دارد. پلی استرها و وینیل استرها به طور گسترده ای به عنوان ماتریس پلیمری استفاده می شوند. رزین ها نیز مورد استفاده قرار می گیرند و دارای مقاومت در برابر رطوبت و خواص مکانیکی عالی هستند. به عنوان مثال رزین پلی آمید را می توان تا حدود 230 درجه سانتیگراد استفاده کرد.
کامپوزیت های ماتریس فلزی: در این مواد از ماتریس فلزی انعطاف پذیر استفاده می شود و دمای سرویس به طور کلی بالاتر از اجزای تشکیل دهنده آنها است. در مقایسه با کامپوزیت های زمینه پلیمری، این کامپوزیت ها می توانند دمای عملیاتی بالاتری داشته باشند، غیر قابل اشتعال باشند و ممکن است مقاومت بهتری در برابر تخریب در برابر سیالات آلی داشته باشند. با این حال آنها گران تر هستند. مواد تقویت کننده مانند سبیل، ذرات، الیاف پیوسته و ناپیوسته؛ و مواد ماتریسی مانند مس، آلومینیوم، منیزیم، تیتانیوم، سوپرآلیاژها معمولا استفاده می شوند. به عنوان مثال، اجزای موتور ساخته شده از ماتریس آلیاژ آلومینیوم تقویت شده با اکسید آلومینیوم و الیاف کربن هستند.
کامپوزیت های ماتریس سرامیکی: مواد سرامیکی به دلیل قابلیت اطمینان فوق العاده خوب در دمای بالا شناخته شده اند. با این حال، آنها بسیار شکننده هستند و دارای مقادیر پایینی برای چقرمگی شکست هستند. با قرار دادن ذرات، الیاف یا سبیل های یک سرامیک در ماتریس سرامیک دیگر، می توانیم به کامپوزیت هایی با چقرمگی شکست بالاتر دست یابیم. این مواد جاسازی شده اساساً با مکانیسم هایی مانند انحراف نوک ترک یا ایجاد پل در سطح ترک ها، از انتشار ترک در داخل ماتریس جلوگیری می کنند. به عنوان مثال، آلومیناهایی که با سبیل های SiC تقویت شده اند به عنوان درج ابزار برش برای ماشینکاری آلیاژهای فلزات سخت استفاده می شوند. اینها می توانند عملکرد بهتری را در مقایسه با کاربیدهای سیمانی نشان دهند.
کامپوزیت های کربن-کربن: هم تقویت کننده و هم ماتریس کربن هستند. آنها دارای مدول کششی بالا و استحکام در دماهای بالا بیش از 2000 درجه سانتیگراد، مقاومت در برابر خزش، چقرمگی شکست بالا، ضرایب انبساط حرارتی پایین، رسانایی حرارتی بالا هستند. این ویژگی ها آنها را برای کاربردهایی که نیاز به مقاومت در برابر شوک حرارتی دارند ایده آل می کند. اما ضعف کامپوزیت های کربن-کربن آسیب پذیری آن در برابر اکسیداسیون در دماهای بالا است. نمونههای معمول استفاده عبارتند از قالبهای پرس گرم، ساخت اجزای موتور توربین پیشرفته.
کامپوزیت های هیبرید: دو یا چند نوع الیاف مختلف در یک ماتریس مخلوط می شوند. بنابراین می توان یک ماده جدید با ترکیبی از ویژگی ها طراحی کرد. یک مثال زمانی است که هر دو الیاف کربن و شیشه در یک رزین پلیمری ادغام می شوند. الیاف کربن سفتی و استحکام با چگالی کم را ارائه می دهند اما گران هستند. از طرف دیگر شیشه ارزان است اما فاقد سفتی الیاف کربن است. کامپوزیت هیبریدی شیشه-کربن قوی تر و محکم تر است و می توان آن را با هزینه کمتری تولید کرد.
پردازش کامپوزیت های تقویت شده با الیاف: برای پلاستیک های تقویت شده با الیاف پیوسته با الیاف توزیع شده یکنواخت که در جهت یکسانی قرار دارند، از تکنیک های زیر استفاده می کنیم.
PULTRUSION: میله ها، تیرها و لوله های با طول پیوسته و مقطع ثابت ساخته می شوند. رووینگ های الیاف پیوسته با یک رزین ترموست آغشته شده و از طریق قالب فولادی کشیده می شوند تا به شکل دلخواه پیش بروند. در مرحله بعد، آنها از یک قالب پخت ماشینکاری شده دقیق عبور می کنند تا به شکل نهایی آن برسند. از آنجایی که قالب کیور گرم می شود، ماتریس رزین را پخت می کند. کشنده ها مواد را از میان قالب ها می کشند. با استفاده از هسته های توخالی وارد شده، می توانیم لوله ها و هندسه های توخالی را بدست آوریم. روش pultrusion خودکار است و نرخ تولید بالایی را به ما ارائه می دهد. تولید هر طول محصول امکان پذیر است.
فرآیند تولید پیش پره: Prepreg یک تقویت کننده الیاف پیوسته است که با یک رزین پلیمری نیمه پخته شده از قبل آغشته شده است. به طور گسترده ای برای کاربردهای ساختاری استفاده می شود. این مواد به صورت نوار عرضه می شود و به صورت نوار ارسال می شود. سازنده مستقیماً آن را قالب می زند و بدون نیاز به افزودن هیچ رزینی آن را کاملاً پخت می کند. از آنجایی که پیش آغشتهها در دمای اتاق تحت واکنشهای پخت قرار میگیرند، در دمای 0 سانتیگراد یا پایینتر نگهداری میشوند. پس از استفاده، نوارهای باقیمانده در دمای پایین ذخیره می شوند. از رزین های ترموپلاستیک و ترموست استفاده می شود و الیاف تقویت کننده کربن، آرامید و شیشه رایج است. برای استفاده از پیش آغشتهسازیها، ابتدا کاغذ پشتی حامل برداشته میشود و سپس با گذاشتن نوار پیشآبسازی روی سطح ابزار (فرایند لایهآپ) ساخت انجام میشود. برای به دست آوردن ضخامت های مورد نظر ممکن است چندین لایه چیده شود. تمرین متداول این است که جهت الیاف را به طور متناوب تغییر دهید تا یک لایه لایه متقاطع یا زاویه دار ایجاد شود. در نهایت حرارت و فشار برای پخت اعمال می شود. هر دو پردازش دستی و همچنین فرآیندهای خودکار برای برش پیش آغشتهسازیها و lay-up استفاده میشوند.
سیم پیچی رشته: الیاف تقویت کننده پیوسته به طور دقیق در یک الگوی از پیش تعیین شده قرار می گیرند تا از شکل توخالی و معمولاً دایره ای شکل پیروی کنند. الیاف ابتدا از یک حمام رزین عبور می کنند و سپس توسط یک سیستم خودکار روی سنبه پیچ می شوند. پس از چندین بار تکرار سیم پیچی ضخامت های مورد نظر به دست می آید و عمل آوری یا در دمای اتاق و یا در داخل کوره انجام می شود. اکنون سنبه برداشته شده و محصول قالب گیری می شود. سیم پیچی رشته می تواند با پیچاندن الیاف در الگوهای محیطی، مارپیچ و قطبی نسبت مقاومت به وزن بسیار بالایی را ارائه دهد. لوله ها، مخازن، پوشش ها با استفاده از این تکنیک ساخته می شوند.
• کامپوزیت های ساختاری: عموماً از مواد همگن و کامپوزیت ساخته شده اند. بنابراین خواص اینها توسط مواد تشکیل دهنده و طراحی هندسی عناصر آن تعیین می شود. در اینجا انواع عمده وجود دارد:
کامپوزیت های LAMINAR: این مواد ساختاری از صفحات یا پانل های دو بعدی با جهت های ترجیحی با مقاومت بالا ساخته می شوند. لایه ها روی هم چیده شده و سیمانی می شوند. با تناوب جهات با استحکام بالا در دو محور عمود بر هم، کامپوزیتی به دست میآوریم که در صفحه دوبعدی در هر دو جهت استحکام بالایی دارد. با تنظیم زوایای لایه ها می توان یک کامپوزیت با استحکام در جهت های دلخواه ساخت. اسکی مدرن به این روش تولید می شود.
پانل های ساندویچ: این کامپوزیت های ساختاری سبک وزن هستند اما در عین حال دارای سفتی و استحکام بالایی هستند. ساندویچ پانل از دو ورق بیرونی ساخته شده از مواد سفت و محکم مانند آلیاژهای آلومینیوم، پلاستیک های تقویت شده با الیاف یا فولاد و یک هسته در بین ورق های بیرونی تشکیل شده است. هسته باید سبک باشد و بیشتر اوقات مدول الاستیسیته پایینی داشته باشد. مواد اصلی محبوب فوم های پلیمری سفت و سخت، چوب و لانه زنبوری هستند. ساندویچ پانل به طور گسترده در صنعت ساختمان به عنوان مصالح سقف، مصالح کف یا دیوار و همچنین در صنایع هوافضا استفاده می شود.
• نانوکامپوزیت ها: این مواد جدید از ذرات ذرات با اندازه نانو تشکیل شده اند که در یک ماتریس جاسازی شده اند. با استفاده از نانوکامپوزیت ها می توانیم مواد لاستیکی بسازیم که مانع بسیار خوبی برای نفوذ هوا هستند و در عین حال خواص لاستیکی خود را بدون تغییر حفظ می کنند.