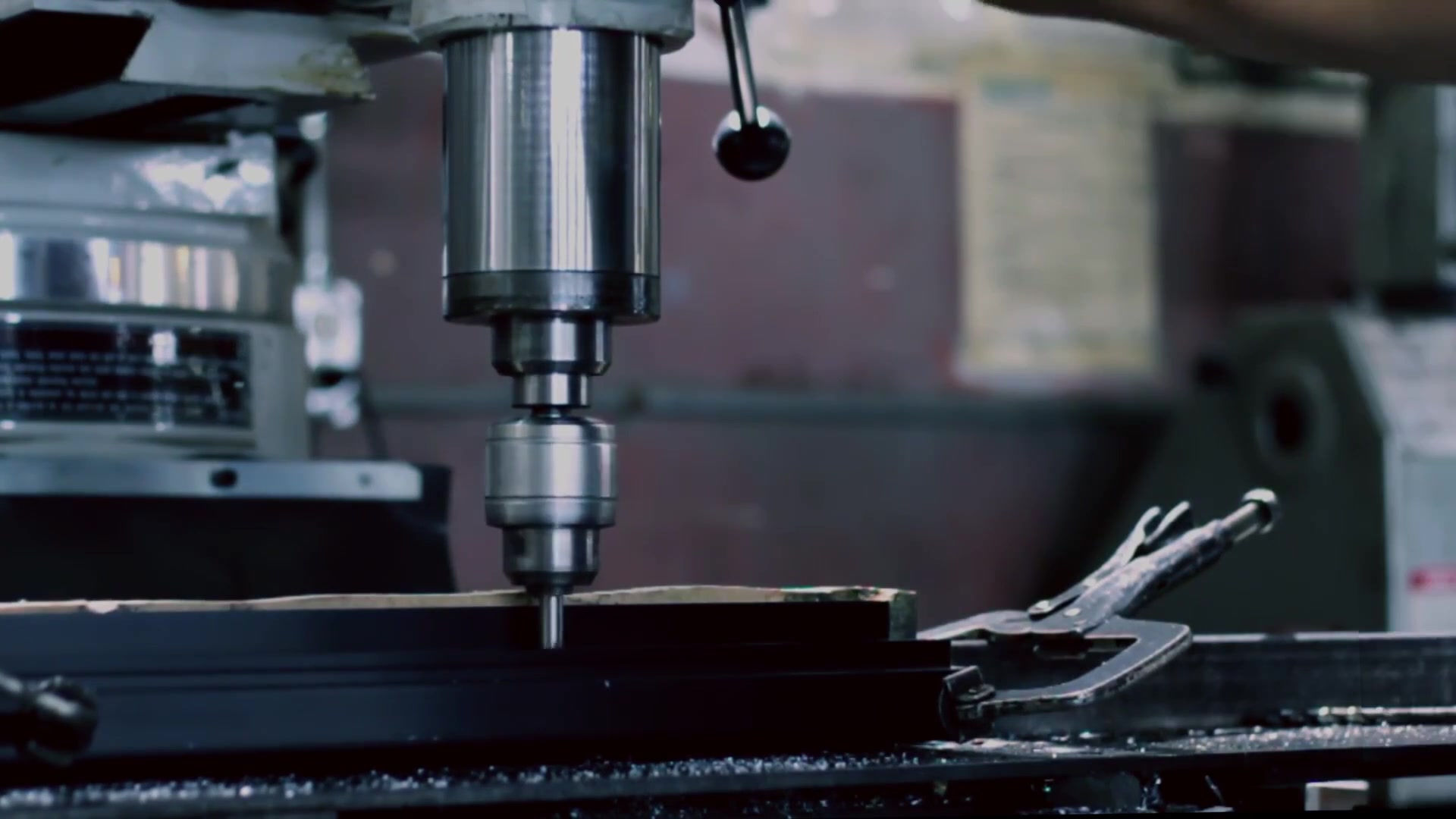
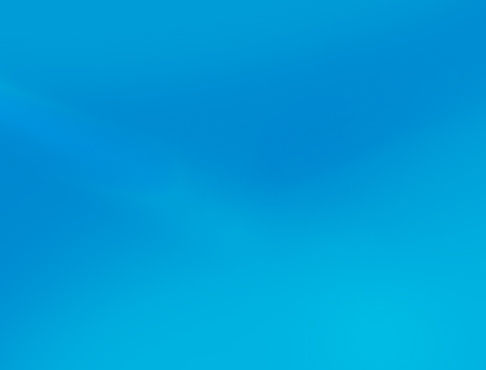
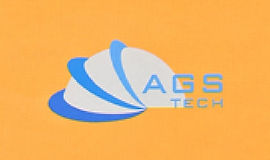
تولید کننده سفارشی جهانی، یکپارچه ساز، تثبیت کننده، شریک برون سپاری برای طیف گسترده ای از محصولات و خدمات.
ما منبع اصلی شما برای تولید، ساخت، مهندسی، ادغام، ادغام، برون سپاری محصولات و خدمات تولید شده سفارشی و خارج از قفسه هستیم.
زبان خود را انتخاب کنید
-
ساخت سفارشی
-
ساخت قرارداد داخلی و جهانی
-
برون سپاری تولید
-
تدارکات داخلی و جهانی
-
Consolidation
-
ادغام مهندسی
-
خدمات مهندسی
ELECTRICAL DISCHARGE MACHINING (EDM), also referred to as SPARK-EROSION or ELECTRODISCHARGE MACHINING, SPARK ERODING, DIE SINKING_cc781905-5cde-3194-bb3b -136bad5cf58d_or WIRE EROSION, is a NON-CONVENTIONAL MANUFACTURING process where erosion of metals takes place and desired shape is obtained using electrical discharges in the form از جرقه ها ما همچنین انواعی از EDM را ارائه می دهیم، به نام های NO-WEAR EDM، WIRE EDM (WEDM)، EDM GriNDING (EDG)، EDM DIE-SINKING، ELECTRICAL-DISCHARGE-MCCED-MILLING, ELECTRICAL-DISCHARGE-Mcc58, -5cde-3194-bb3b-136bad5cf58d_and سوز کردن الکتروشیمیایی-تخلیه (ECDG). سیستمهای EDM ما شامل ابزار/الکترود شکلدار و قطعه کار متصل به منبع تغذیه DC و وارد شده در یک سیال دیالکتریک نارسانای الکتریکی است. پس از سال 1940، ماشینکاری تخلیه الکتریکی به یکی از مهمترین و محبوبترین فناوریهای تولید در صنایع تولیدی تبدیل شد.
هنگامی که فاصله بین دو الکترود کاهش می یابد، شدت میدان الکتریکی در حجم بین الکترودها در برخی نقاط از قدرت دی الکتریک بیشتر می شود که شکسته می شود و در نهایت پلی برای عبور جریان بین دو الکترود ایجاد می کند. یک قوس الکتریکی شدید ایجاد می شود که باعث می شود حرارت قابل توجهی بخشی از قطعه کار و برخی از مواد ابزار را ذوب کند. در نتیجه، مواد از هر دو الکترود حذف می شود. در عین حال، سیال دی الکتریک به سرعت گرم می شود و در نتیجه سیال در شکاف قوس تبخیر می شود. هنگامی که جریان قطع می شود یا متوقف می شود، گرما توسط سیال دی الکتریک اطراف از حباب گاز خارج می شود و حباب حفره می کند (جمع می شود). موج ضربه ای ایجاد شده در اثر فروپاشی حباب و جریان سیال دی الکتریک، زباله ها را از سطح قطعه کار خارج می کند و هر ماده مذاب قطعه کار را به داخل سیال دی الکتریک می کشاند. نرخ تکرار برای این تخلیه ها بین 50 تا 500 کیلوهرتز، ولتاژ بین 50 تا 380 ولت و جریان بین 0.1 تا 500 آمپر است. دیالکتریک مایع جدید مانند روغنهای معدنی، نفت سفید یا آب مقطر و دییونیزه معمولاً به داخل حجم بین الکترود منتقل میشود و ذرات جامد (به شکل زباله) را میبرد و ویژگیهای عایق دیالکتریک بازسازی میشود. پس از یک جریان جریان، اختلاف پتانسیل بین دو الکترود به آنچه قبل از شکست بود بازگردانده می شود، بنابراین یک شکست دی الکتریک مایع جدید می تواند رخ دهد. ماشین های تخلیه الکتریکی مدرن ما (EDM) حرکات کنترل شده عددی را ارائه می دهند و مجهز به پمپ ها و سیستم های فیلتر برای سیالات دی الکتریک هستند.
ماشینکاری تخلیه الکتریکی (EDM) یک روش ماشینکاری است که عمدتاً برای فلزات سخت یا فلزاتی که ماشینکاری با تکنیکهای معمولی بسیار دشوار است، استفاده میشود. EDM معمولا با هر ماده ای که رسانای الکتریکی است کار می کند، اگرچه روش هایی برای ماشینکاری سرامیک های عایق با EDM نیز پیشنهاد شده است. نقطه ذوب و گرمای نهان ذوب خواصی هستند که حجم فلز حذف شده در هر تخلیه را تعیین می کنند. هر چه این مقادیر بالاتر باشد، سرعت حذف مواد کندتر می شود. از آنجایی که فرآیند ماشینکاری تخلیه الکتریکی شامل هیچ انرژی مکانیکی نمی شود، سختی، استحکام و چقرمگی قطعه کار بر میزان حذف تأثیر نمی گذارد. فرکانس تخلیه یا انرژی در هر تخلیه، ولتاژ و جریان برای کنترل نرخ حذف مواد تغییر می کند. سرعت حذف مواد و زبری سطح با افزایش چگالی جریان و کاهش فرکانس جرقه افزایش می یابد. میتوانیم خطوط یا حفرههای پیچیده را در فولاد از پیش سخت شده با استفاده از EDM بدون نیاز به عملیات حرارتی برای نرم کردن و سختشدن مجدد آنها برش دهیم. ما می توانیم از این روش برای هر فلز یا آلیاژ فلزی مانند تیتانیوم، hastelloy، kovar و inconel استفاده کنیم. کاربردهای فرآیند EDM شامل شکل دادن به ابزارهای الماس پلی کریستالی است. EDM یک روش ماشینکاری غیر سنتی یا غیر متعارف به همراه فرآیندهایی مانند ماشینکاری الکتروشیمیایی (ECM)، برش با جت آب (WJ، AWJ)، برش لیزری در نظر گرفته می شود. از سوی دیگر روشهای ماشینکاری مرسوم شامل تراشکاری، آسیاب، سنگزنی، حفاری و سایر فرآیندهایی است که مکانیسم حذف مواد اساساً بر اساس نیروهای مکانیکی است. الکترودهای مخصوص ماشینکاری تخلیه الکتریکی (EDM) از گرافیت، برنج، مس و آلیاژ مس- تنگستن ساخته می شوند. قطر الکترود تا 0.1 میلی متر امکان پذیر است. از آنجایی که سایش ابزار یک پدیده نامطلوب است که بر دقت ابعادی در EDM تأثیر منفی میگذارد، ما از فرآیندی به نام NO-WEAR EDM با معکوس کردن قطبیت و استفاده از ابزار مسی برای به حداقل رساندن سایش ابزار استفاده میکنیم.
در حالت ایدهآل، ماشینکاری تخلیه الکتریکی (EDM) را میتوان مجموعهای از شکستن و بازیابی مایع دی الکتریک بین الکترودها در نظر گرفت. اما در واقعیت، حذف زباله از ناحیه بین الکترود تقریباً همیشه جزئی است. این باعث می شود که ویژگی های الکتریکی دی الکتریک در ناحیه بین الکترودها با مقادیر اسمی آنها متفاوت باشد و با زمان تغییر کند. فاصله بین الکترود، (شکاف جرقه)، توسط الگوریتم های کنترل ماشین خاص مورد استفاده تنظیم می شود. متأسفانه گاهی اوقات شکاف جرقه در EDM می تواند توسط زباله ها اتصال کوتاه پیدا کند. سیستم کنترل الکترود ممکن است به اندازه کافی سریع واکنش نشان ندهد تا از اتصال کوتاه دو الکترود (ابزار و قطعه کار) جلوگیری کند. این اتصال کوتاه ناخواسته به حذف مواد متفاوت از حالت ایده آل کمک می کند. ما برای بازگرداندن خواص عایق دی الکتریک به عمل شستشو بسیار اهمیت می دهیم تا جریان همیشه در نقطه بین الکترود اتفاق بیفتد و در نتیجه احتمال تغییر شکل ناخواسته (آسیب) ابزار-الکترود را به حداقل برسانیم. و قطعه کار برای به دست آوردن یک هندسه خاص، ابزار EDM در امتداد مسیر مورد نظر بسیار نزدیک به قطعه کار بدون دست زدن به آن هدایت می شود، ما نهایت توجه را به عملکرد کنترل حرکت در استفاده می کنیم. به این ترتیب، تعداد زیادی تخلیه / جرقه جریان رخ می دهد، و هر کدام به حذف مواد از ابزار و قطعه کار، که در آن دهانه های کوچک تشکیل می شود، کمک می کند. اندازه دهانه ها تابعی از پارامترهای تکنولوژیکی تعیین شده برای کار خاص است و ابعاد ممکن است از مقیاس نانو (مانند عملیات میکرو EDM) تا حدود صدها میکرومتر در شرایط ناهموار متغیر باشد. این دهانه های کوچک روی ابزار باعث فرسایش تدریجی الکترود به نام "سایش ابزار" می شود. برای خنثی کردن اثر مضر سایش بر روی هندسه قطعه کار، ما به طور مداوم الکترود ابزار را در طول عملیات ماشینکاری تعویض می کنیم. گاهی اوقات ما با استفاده از یک سیم به طور مداوم جایگزین شده به عنوان الکترود به این امر دست مییابیم (این فرآیند EDM همچنین نامیده میشود WIRE EDM ). گاهی اوقات ما از ابزار-الکترود به گونه ای استفاده می کنیم که تنها بخش کوچکی از آن در واقع درگیر فرآیند ماشینکاری می شود و این قسمت به طور منظم تغییر می کند. به عنوان مثال، این مورد در هنگام استفاده از یک دیسک چرخان به عنوان یک ابزار-الکترود است. این فرآیند EDM GRINDING نامیده می شود. روش دیگری که ما به کار میگیریم شامل استفاده از مجموعهای از الکترودها با اندازهها و شکلهای مختلف در طول یک عملیات EDM برای جبران سایش است. ما این تکنیک الکترود چندگانه را مینامیم و معمولاً زمانی استفاده میشود که الکترود ابزار به شکل منفی شکل دلخواه را تکرار میکند و به سمت قسمت خالی در امتداد یک جهت، معمولاً جهت عمودی (یعنی محور z) پیش میرود. این شبیه به سینک ابزار در مایع دی الکتریک است که قطعه کار در آن غوطه ور شده است، و بنابراین به آن با عنوان DIE-SINKING EDM_cc781905-5cde-3194-bb3_5-5cde-3194-bb3b-136bad5cf58d_DIE-SINKING گفته می شود. 3194-bb3b-136bad5cf58d_CONVENTIONAL EDM or RA). ماشین های این عملیات به نام های SINKER EDM هستند. الکترودهای این نوع EDM اشکال پیچیده ای دارند. اگر هندسه نهایی با استفاده از یک الکترود معمولی ساده شکل گرفته شود که در امتداد چندین جهت حرکت می کند و همچنین در معرض چرخش است، آن را می گوییم EDM MILLING. مقدار سایش به شدت به پارامترهای تکنولوژیکی مورد استفاده در عملیات (قطبیت، حداکثر جریان، ولتاژ مدار باز) بستگی دارد. به عنوان مثال، in micro-EDM، که با نام m-EDM نیز شناخته می شود، این پارامترها معمولاً در مقادیری تنظیم می شوند که سایش شدید ایجاد می کنند. بنابراین، سایش یک مشکل عمده در آن زمینه است که ما با استفاده از دانش انباشته خود آن را به حداقل می رسانیم. به عنوان مثال برای به حداقل رساندن سایش الکترودهای گرافیتی، یک ژنراتور دیجیتالی که در عرض میلی ثانیه قابل کنترل است، قطبیت را با وقوع فرسایش الکتریکی معکوس می کند. این منجر به اثری مشابه آبکاری الکتریکی می شود که به طور مداوم گرافیت فرسایش یافته را بر روی الکترود رسوب می دهد. در روشی دیگر، مداری که اصطلاحاً «سایش صفر» نامیده میشود، تعداد دفعات شروع و توقف تخلیه را به حداقل میرسانیم و آن را برای مدت طولانی روشن نگه میداریم. سرعت حذف مواد در ماشینکاری تخلیه الکتریکی را می توان از موارد زیر تخمین زد:
MRR = 4 x 10 exp(4) x I x Tw exp (-1.23)
در اینجا MRR بر حسب mm3/min است، I بر حسب آمپر جریان دارد، Tw نقطه ذوب قطعه کار در K-273.15K است. exp مخفف exponent است.
از طرف دیگر، میزان سایش Wt الکترود را می توان از موارد زیر بدست آورد:
Wt = ( 1.1 x 10 exp (11) ) x I x Ttexp (-2.38)
در اینجا Wt بر حسب mm3/min است و Tt نقطه ذوب ماده الکترود در K-273.15K است.
در نهایت، نسبت سایش قطعه کار به الکترود R را می توان از موارد زیر بدست آورد:
R = 2.25 x Trexp (-2.38)
در اینجا Tr نسبت نقاط ذوب قطعه کار به الکترود است.
SINKER EDM :
Sinker EDM، که به نامهای CAVITY TYPE EDM or_cc781905-31905-136bad5cf58d_or_cc781905-31905-136، EDM ادغام شده است. الکترود و قطعه کار به منبع تغذیه متصل می شوند. منبع تغذیه یک پتانسیل الکتریکی بین این دو تولید می کند. با نزدیک شدن الکترود به قطعه کار، تجزیه دی الکتریک در سیال رخ می دهد و یک کانال پلاسما تشکیل می دهد و یک جرقه کوچک می پرد. جرقهها معمولاً یکی یکی زده میشوند، زیرا بعید است که مکانهای مختلف در فضای بین الکترود ویژگیهای الکتریکی محلی یکسانی داشته باشند که باعث میشود جرقه در همه مکانها به طور همزمان رخ دهد. صدها هزار مورد از این جرقه ها در نقاط تصادفی بین الکترود و قطعه کار در هر ثانیه اتفاق می افتد. با فرسایش فلز پایه، و متعاقباً شکاف جرقه افزایش می یابد، الکترود به طور خودکار توسط دستگاه CNC ما پایین می آید تا فرآیند بتواند بدون وقفه ادامه یابد. تجهیزات ما دارای چرخه های کنترلی هستند که به عنوان "به موقع" و "زمان خاموش" شناخته می شوند. تنظیم زمان، طول یا مدت جرقه را تعیین می کند. زمان طولانیتر، حفره عمیقتری برای آن جرقه و تمام جرقههای بعدی برای آن چرخه ایجاد میکند و سطح خشنتری روی قطعه کار ایجاد میکند و بالعکس. زمان خاموشی دوره زمانی است که یک جرقه با جرقه دیگری جایگزین می شود. زمان خاموش شدن طولانی تر به سیال دی الکتریک اجازه می دهد تا از یک نازل برای تمیز کردن زباله های فرسوده شده عبور کند و در نتیجه از اتصال کوتاه جلوگیری شود. این تنظیمات در میکرو ثانیه تنظیم می شوند.
WIRE EDM :
In WIRE ELECTRICAL DISCHARGE MACHINING (WEDM), also called WIRE-CUT EDM or WIRE CUTTING, we feed a سیم فلزی نازک تک رشته ای از برنج از طریق قطعه کار، که در مخزن سیال دی الکتریک غوطه ور است. Wire EDM یکی از انواع مهم EDM است. ما گهگاه از EDM سیمبرش برای برش صفحات به ضخامت 300 میلیمتر و ساخت پانچها، ابزارها و قالبها از فلزات سخت استفاده میکنیم که ماشینکاری با روشهای دیگر تولید دشوار است. در این فرآیند که شبیه برش کانتور با اره نواری است، سیمی که دائماً از یک قرقره تغذیه می شود، بین راهنماهای الماس بالایی و پایینی نگه داشته می شود. راهنماهای کنترلشده با CNC در صفحه x–y حرکت میکنند و راهنمای بالایی نیز میتواند بهطور مستقل در محور z–u–v حرکت کند و توانایی برش اشکال مخروطی و انتقالی (مانند دایره در پایین و مربع در بالاترین). راهنمای بالایی می تواند حرکات محور را در x–y–u–v–i–j–k–l– کنترل کند. این به WEDM اجازه می دهد تا اشکال بسیار پیچیده و ظریف را برش دهد. متوسط برش تجهیزات ما که بهترین هزینه اقتصادی و زمان ماشینکاری را به دست می آورد 0.335 میلی متر با استفاده از برنج Ø 0.25، مس یا سیم تنگستن است. با این حال، راهنماهای الماسی بالایی و پایینی تجهیزات CNC ما دقتی در حدود 0.004 میلی متر دارند و می توانند با استفاده از سیم Ø 0.02 میلی متر، مسیر برش یا قفسه ای به کوچکی 0.021 میلی متر داشته باشند. بنابراین برش های بسیار باریک امکان پذیر است. عرض برش بیشتر از عرض سیم است زیرا جرقه از طرفین سیم به قطعه کار ایجاد می شود و باعث فرسایش می شود. این "اضافه برش" ضروری است، برای بسیاری از برنامه ها قابل پیش بینی است و بنابراین می توان آن را جبران کرد (در میکرو EDM اغلب اینطور نیست). قرقره های سیم بلند هستند - یک قرقره 8 کیلوگرمی از سیم 0.25 میلی متری کمی بیش از 19 کیلومتر طول دارد. قطر سیم می تواند به کوچکی 20 میکرومتر باشد و دقت هندسی آن در مجاورت +/- 1 میکرومتر است. ما معمولاً فقط یک بار از سیم استفاده می کنیم و آن را بازیافت می کنیم زیرا نسبتاً ارزان است. با سرعت ثابت 0.15 تا 9 متر در دقیقه حرکت میکند و در طول برش، یک شکاف (شکاف) ثابت حفظ میشود. در فرآیند EDM با سیم برش، از آب به عنوان سیال دی الکتریک استفاده می کنیم و مقاومت آن و سایر خواص الکتریکی آن را با فیلترها و واحدهای دی یونیزر کنترل می کنیم. آب زباله های بریده شده را از منطقه برش دور می کند. فلاشینگ یک عامل مهم در تعیین حداکثر نرخ تغذیه برای یک ضخامت ماده معین است و بنابراین ما آن را ثابت نگه می داریم. سرعت برش در سیم EDM بر حسب سطح مقطع برش در واحد زمان بیان می شود، مانند 18000 میلی متر مربع در ساعت برای فولاد ابزار D2 ضخامت 50 میلی متر. سرعت برش خطی برای این مورد 18000/50 = 360mm/hr خواهد بود. نرخ حذف مواد در سیم EDM برابر است با:
MRR = Vf xhxb
در اینجا MRR بر حسب mm3/min است، Vf نرخ تغذیه سیم به قطعه کار بر حسب میلیمتر در دقیقه، h ضخامت یا ارتفاع بر حسب میلیمتر، و b بهعنوان کرف است که:
b = dw + 2s
در اینجا dw قطر سیم و s شکاف بین سیم و قطعه کار بر حسب میلی متر است.
در کنار تلورانسهای سختتر، مراکز ماشینکاری سیمبرش چند محوره EDM ما ویژگیهایی مانند چند سر برای برش دو قسمت به طور همزمان، کنترلهایی برای جلوگیری از شکستن سیم، ویژگیهای خود رزوهای خودکار در صورت شکستن سیم و برنامهریزی شده را اضافه کردهاند. استراتژی های ماشینکاری برای بهینه سازی عملیات، قابلیت های برش مستقیم و زاویه ای.
Wire-EDM تنش های پسماند کمی را به ما ارائه می دهد، زیرا برای حذف مواد به نیروهای برش زیادی نیاز ندارد. هنگامی که انرژی/قدرت هر پالس نسبتاً کم باشد (مانند عملیات تکمیلی)، به دلیل تنشهای پسماند کم، تغییر کمی در خواص مکانیکی یک ماده انتظار میرود.
سنگ زنی تخلیه الکتریکی (EDG) : چرخ های سنگ زنی حاوی مواد ساینده نیستند، آنها از گرافیت یا برنج ساخته شده اند. جرقه های مکرر بین چرخ دوار و قطعه کار، مواد را از سطوح قطعه کار حذف می کند. نرخ حذف مواد:
MRR = K x I
در اینجا MRR بر حسب mm3/min، I بر حسب آمپر جریان دارد و K ضریب ماده قطعه کار بر حسب mm3/A-min است. ما اغلب از سنگ زنی با تخلیه الکتریکی برای اره کردن شکاف های باریک روی قطعات استفاده می کنیم. ما گاهی اوقات فرآیند EDG (سوز کردن تخلیه الکتریکی) را با فرآیند ECG (سنگزنی الکتروشیمیایی) ترکیب میکنیم که در آن مواد با عمل شیمیایی حذف میشوند، تخلیههای الکتریکی از چرخ گرافیت فیلم اکسید را میشکند و توسط الکترولیت شسته میشود. این فرآیند ELECTROCHEMICAL-DISCHARGE GriNDING (ECDG) نامیده می شود. اگرچه فرآیند ECDG انرژی نسبتاً بیشتری مصرف میکند، این فرآیند سریعتر از EDG است. ما بیشتر ابزار کاربید را با استفاده از این تکنیک آسیاب می کنیم.
کاربردهای ماشینکاری تخلیه الکتریکی:
تولید نمونه اولیه:
ما از فرآیند EDM در ساخت قالب، ساخت ابزار و قالب، و همچنین برای ساخت نمونه اولیه و قطعات تولید، به ویژه برای صنایع هوافضا، خودرو و الکترونیک استفاده می کنیم که در آن مقدار تولید نسبتاً کم است. در Sinker EDM، یک گرافیت، تنگستن مس یا الکترود مس خالص به شکل دلخواه (منفی) ماشینکاری می شود و در انتهای یک قوچ عمودی به قطعه کار وارد می شود.
ساخت قالب سکه:
برای ایجاد قالبهایی برای تولید جواهرات و نشانها با فرآیند ضرب سکه (مهر زدن)، ممکن است ماتریس مثبت از نقره استرلینگ ساخته شود، زیرا (با تنظیمات ماشین مناسب) استاد به طور قابل توجهی فرسایش یافته و فقط یک بار استفاده میشود. قالب منفی حاصل سخت می شود و در یک چکش قطره ای برای تولید تخت های مهر و موم شده از ورقه های برش خورده برنز، نقره، یا آلیاژ طلای کم مقاومت استفاده می شود. برای نشان ها، این تخت ها ممکن است توسط قالب دیگری به یک سطح منحنی شکل داده شوند. این نوع EDM معمولا به صورت غوطه ور در دی الکتریک مبتنی بر روغن انجام می شود. شی تمام شده ممکن است بیشتر با میناکاری سخت (شیشه ای) یا نرم (رنگ) و/یا با طلای خالص یا نیکل آبکاری شود. مواد نرم تری مانند نقره ممکن است به عنوان یک اصلاح با دست حکاکی شوند.
حفاری سوراخ های کوچک:
در دستگاههای EDM سیمبرش، از EDM حفاری سوراخ کوچک برای ایجاد سوراخی در قطعه کار استفاده میکنیم تا سیم را برای عملیات EDM سیم برش رزوه بکشیم. سرهای EDM جداگانه مخصوص حفاری سوراخ های کوچک بر روی دستگاه های سیم برش ما نصب می شوند که به صفحات سخت شده بزرگ اجازه می دهد تا در صورت نیاز و بدون پیش حفاری، قطعات تمام شده از آنها ساییده شوند. ما همچنین از EDM سوراخ کوچک برای سوراخ کردن ردیفهایی از سوراخها در لبههای پرههای توربین مورد استفاده در موتورهای جت استفاده میکنیم. جریان گاز از طریق این سوراخ های کوچک به موتورها اجازه می دهد تا از دماهای بالاتری نسبت به موارد دیگر استفاده کنند. آلیاژهای تک کریستالی با دمای بالا، بسیار سخت و بسیار سخت که این تیغه ها از آن ساخته شده اند، ماشینکاری معمولی این سوراخ ها را با نسبت تصویر بالا بسیار دشوار و حتی غیرممکن می کند. سایر زمینه های کاربردی برای EDM سوراخ کوچک ایجاد روزنه های میکروسکوپی برای اجزای سیستم سوخت است. علاوه بر سرهای EDM یکپارچه، ما دستگاههای EDM حفاری سوراخ کوچک مستقل را با محورهای x-y برای کور کردن ماشینها یا سوراخها به کار میگیریم. EDM سوراخ هایی را با یک الکترود لوله برنجی یا مسی دراز ایجاد می کند که در یک چاک با جریان ثابتی از آب مقطر یا یونیزه شده در الکترود به عنوان یک عامل شستشو و دی الکتریک می چرخد. برخی از EDM های حفاری با سوراخ کوچک می توانند 100 میلی متر فولاد نرم یا حتی سخت شده را در کمتر از 10 ثانیه سوراخ کنند. در این عملیات حفاری می توان سوراخ هایی بین 0.3 میلی متر تا 6.1 میلی متر ایجاد کرد.
ماشینکاری تجزیه فلز:
ما همچنین ماشینهای مخصوص EDM را برای حذف ابزارهای شکسته (مته یا شیر آلات) از قطعات کار داریم. این فرآیند "ماشینکاری تجزیه فلز" نامیده می شود.
مزایا و معایب ماشینکاری تخلیه الکتریکی:
از مزایای EDM می توان به ماشینکاری موارد زیر اشاره کرد:
- اشکال پیچیده ای که در غیر این صورت تولید آنها با ابزارهای برش معمولی دشوار خواهد بود
- مواد بسیار سخت تا تلورانس های بسیار نزدیک
- قطعات کار بسیار کوچک که ابزارهای برش معمولی ممکن است در اثر فشار اضافی ابزار برش به قطعه آسیب برسانند.
- هیچ تماس مستقیمی بین ابزار و قطعه کار وجود ندارد. بنابراین مقاطع ظریف و مواد ضعیف را می توان بدون هیچ گونه اعوجاج ماشین کاری کرد.
- یک سطح خوب می توان به دست آورد.
- سوراخ های بسیار ریز را می توان به راحتی سوراخ کرد.
معایب EDM عبارتند از:
- سرعت کند حذف مواد.
- زمان و هزینه اضافی مورد استفاده برای ایجاد الکترود برای ram/sinker EDM.
- بازتولید گوشه های تیز روی قطعه کار به دلیل سایش الکترود مشکل است.
- مصرف برق بالاست.
- "Overcut" تشکیل می شود.
- سایش بیش از حد ابزار در حین ماشین کاری رخ می دهد.
- مواد غیر رسانای الکتریکی را می توان تنها با تنظیم خاصی از فرآیند ماشین کاری کرد.