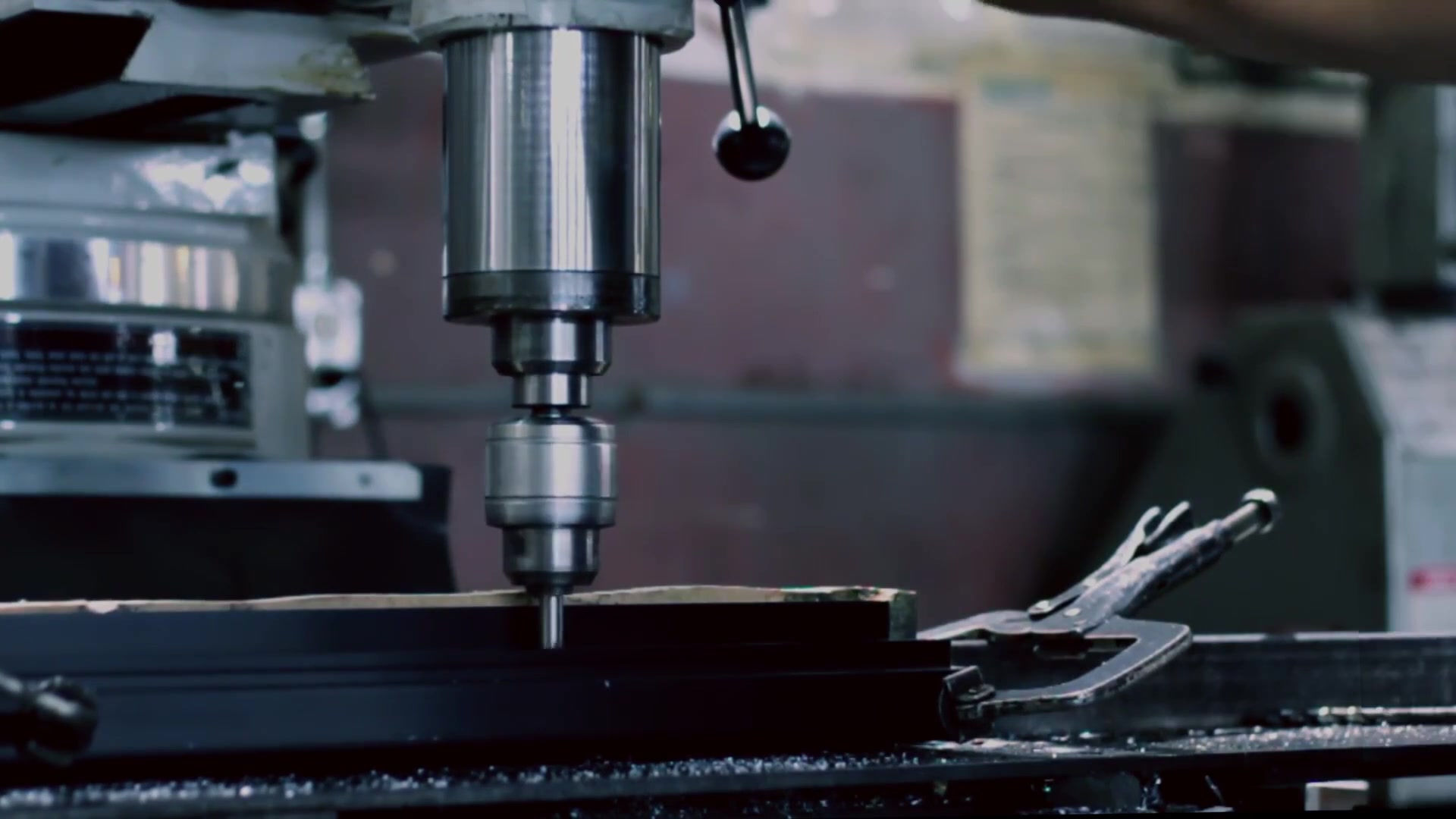
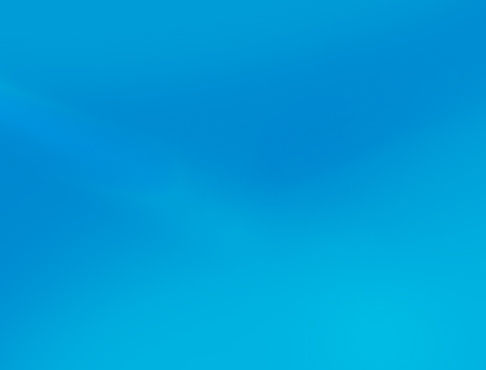
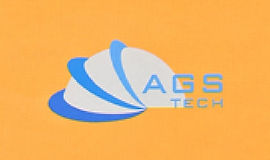
تولید کننده سفارشی جهانی، یکپارچه ساز، تثبیت کننده، شریک برون سپاری برای طیف گسترده ای از محصولات و خدمات.
ما منبع اصلی شما برای تولید، ساخت، مهندسی، ادغام، ادغام، برون سپاری محصولات و خدمات تولید شده سفارشی و خارج از قفسه هستیم.
زبان خود را انتخاب کنید
-
ساخت سفارشی
-
ساخت قرارداد داخلی و جهانی
-
برون سپاری تولید
-
تدارکات داخلی و جهانی
-
Consolidation
-
ادغام مهندسی
-
خدمات مهندسی
ما قطعات تولیدی شما را به هم متصل، مونتاژ و محکم می کنیم و با استفاده از جوش، لحیم کاری، لحیم کاری، زینترینگ، چسباندن، چسباندن، اتصالات پرس به محصولات نهایی یا نیمه تمام تبدیل می کنیم. برخی از محبوب ترین فرآیندهای جوشکاری ما عبارتند از: قوس الکتریکی، گاز اکسیژن، مقاومت، برآمدگی، درز، ناراحتی، ضربه ای، حالت جامد، پرتو الکترونی، لیزر، ترمیت، جوش القایی. فرآیندهای لحیم کاری محبوب ما عبارتند از: مشعل، القایی، کوره و لحیم کاری. روش های لحیم کاری ما عبارتند از لحیم کاری آهن، صفحه داغ، اجاق، القایی، شیب، موج، جریان مجدد و لحیم کاری اولتراسونیک. برای چسباندن چسب، ما اغلب از ترموپلاستیک ها و گرمانرم، اپوکسی ها، فنولیک ها، پلی اورتان، آلیاژهای چسب و همچنین برخی مواد شیمیایی و نوارهای دیگر استفاده می کنیم. در نهایت فرآیندهای چفت و بست ما شامل میخ زدن، پیچ کردن، مهره و پیچ و مهره، پرچ کردن، گیره زدن، سنجاق کردن، دوخت و منگنه کردن و اتصال پرس است.
• جوشکاری: جوشکاری شامل اتصال مواد با ذوب قطعات کار و وارد کردن مواد پرکننده است که به حوضچه جوش مذاب نیز می پیوندد. وقتی ناحیه سرد شد، یک مفصل قوی بدست می آوریم. فشار در برخی موارد اعمال می شود. بر خلاف جوشکاری، عملیات لحیم کاری و لحیم کاری فقط شامل ذوب ماده ای با نقطه ذوب پایین تر بین قطعات کار می شود و قطعات کار ذوب نمی شوند. توصیه می کنیم اینجا را کلیک کنیددانلود تصاویر شماتیک فرآیندهای جوشکاری توسط AGS-TECH Inc.
این به شما کمک می کند اطلاعاتی را که در زیر به شما ارائه می دهیم بهتر درک کنید.
در جوشکاری قوس الکتریکی از یک منبع تغذیه و یک الکترود برای ایجاد قوس الکتریکی استفاده می کنیم که فلزات را ذوب می کند. نقطه جوش توسط یک گاز محافظ یا بخار یا مواد دیگر محافظت می شود. این فرآیند برای جوشکاری قطعات خودرو و سازه های فولادی رایج است. در جوشکاری قوس فلزی پوسته دار (SMAW) یا به عنوان جوشکاری چوبی نیز شناخته می شود، یک چوب الکترود به مواد پایه نزدیک می شود و یک قوس الکتریکی بین آنها ایجاد می شود. میله الکترود ذوب می شود و به عنوان ماده پرکننده عمل می کند. الکترود همچنین حاوی شار است که به عنوان لایه ای از سرباره عمل می کند و بخاراتی را منتشر می کند که به عنوان گاز محافظ عمل می کند. اینها ناحیه جوش را از آلودگی محیطی محافظت می کنند. هیچ پرکننده دیگری استفاده نمی شود. معایب این فرآیند کند بودن آن، نیاز به تعویض مکرر الکترودها، نیاز به جدا کردن سرباره باقیمانده ناشی از شار است. تعدادی از فلزات مانند آهن، فولاد، نیکل، آلومینیوم، مس و... قابل جوشکاری است. از مزایای آن می توان به ابزارهای ارزان قیمت و سهولت استفاده آن اشاره کرد. جوشکاری قوس فلزی گازی (GMAW) همچنین به عنوان گاز بیاثر فلزی (MIG) شناخته میشود، ما تغذیه مداوم یک پرکننده سیم الکترود مصرفی و یک گاز بیاثر یا تا حدی بیاثر داریم که در برابر آلودگی محیطی ناحیه جوش در اطراف سیم جریان دارد. فولاد، آلومینیوم و سایر فلزات غیر آهنی را می توان جوش داد. از مزایای MIG سرعت جوش بالا و کیفیت خوب است. معایب آن تجهیزات پیچیده و چالشهایی است که در محیطهای بادی در فضای باز با آن مواجه میشوند، زیرا ما باید گاز محافظ اطراف ناحیه جوش را پایدار نگه داریم. یکی از انواع GMAW جوش قوس الکتریکی با هسته شار (FCAW) است که از یک لوله فلزی ظریف پر از مواد شار تشکیل شده است. گاهی اوقات شار داخل لوله برای محافظت در برابر آلودگی محیطی کافی است. جوشکاری قوس زیردریایی (SAW) به طور گسترده یک فرآیند خودکار است که شامل تغذیه مداوم سیم و قوس می شود که در زیر لایه ای از پوشش شار زده می شود. نرخ تولید و کیفیت بالا است، سرباره جوش به راحتی جدا می شود و ما یک محیط کار بدون دود داریم. نقطه ضعف آن این است که فقط می توان از آن برای جوش دادن قطعات _cc781905-5cde-3194-bb3b-136bad5cf58d در موقعیت های خاص استفاده کرد. در جوشکاری قوسی تنگستن گاز (GTAW) یا جوشکاری تنگستن با گاز بی اثر (TIG) از الکترود تنگستن به همراه پرکننده جداگانه و گازهای بی اثر یا نزدیک به بی اثر استفاده می کنیم. همانطور که می دانیم تنگستن نقطه ذوب بالایی دارد و فلزی بسیار مناسب برای دماهای بسیار بالا می باشد. تنگستن در TIG بر خلاف روش های دیگر توضیح داده شده در بالا مصرف نمی شود. یک تکنیک جوش آهسته اما با کیفیت بالا نسبت به سایر تکنیک ها در جوشکاری مواد نازک مزیت دارد. مناسب برای بسیاری از فلزات جوشکاری قوس پلاسما مشابه است اما از گاز پلاسما برای ایجاد قوس استفاده می کند. قوس در جوشکاری قوس پلاسما در مقایسه با GTAW نسبتاً متمرکزتر است و می تواند برای طیف وسیع تری از ضخامت های فلزی با سرعت های بسیار بالاتر استفاده شود. GTAW و جوشکاری قوس پلاسما را می توان برای مواد کم و بیش مشابه اعمال کرد.
OXY-FUEL / OXYFUEL WELDING همچنین به نام جوش اکسی استیلن، جوش اکسی، جوشکاری گاز با استفاده از سوخت گاز و اکسیژن برای جوشکاری انجام می شود. از آنجایی که از برق استفاده نمی شود، قابل حمل است و در جاهایی که برق وجود ندارد می توان از آن استفاده کرد. با استفاده از یک مشعل جوشکاری، قطعات و مواد پرکننده را برای تولید یک حوضچه فلز مذاب مشترک گرم می کنیم. می توان از سوخت های مختلفی مانند استیلن، بنزین، هیدروژن، پروپان، بوتان و ... استفاده کرد. در جوشکاری با سوخت اکسیژن از دو ظرف یکی برای سوخت و دیگری برای اکسیژن استفاده می کنیم. اکسیژن سوخت را اکسید می کند (آن را می سوزاند).
جوش مقاومتی: این نوع جوش از گرمایش ژول بهره می برد و در محلی که جریان الکتریکی برای مدت معینی اعمال می شود گرما ایجاد می شود. جریان های زیادی از فلز عبور می کنند. حوضچه هایی از فلز مذاب در این مکان تشکیل می شود. روشهای جوشکاری مقاومتی به دلیل کارایی و پتانسیل آلودگی کم محبوب هستند. با این حال معایب هزینه تجهیزات نسبتاً قابل توجه و محدودیت ذاتی برای قطعات کار نسبتاً نازک است. جوش نقطه ای یکی از انواع عمده جوشکاری مقاومتی است. در اینجا با استفاده از دو الکترود مسی دو یا چند ورق یا قطعه کار روی هم قرار گرفته اند تا ورق ها را به هم بچسبانیم و جریان بالایی را از آنها عبور دهیم. ماده بین الکترودهای مسی گرم می شود و یک حوضچه مذاب در آن مکان ایجاد می شود. سپس جریان قطع می شود و نوک الکترودهای مسی محل جوش را خنک می کنند زیرا الکترودها با آب خنک می شوند. اعمال مقدار مناسب گرما به مواد و ضخامت مناسب برای این تکنیک کلیدی است، زیرا در صورت اعمال اشتباه، اتصال ضعیف می شود. جوشکاری نقطه ای از مزایای عدم تغییر شکل قابل توجهی در قطعه کار، بهره وری انرژی، سهولت اتوماسیون و نرخ تولید فوق العاده و عدم نیاز به پرکننده است. نقطه ضعف این است که از آنجایی که جوشکاری به جای ایجاد یک درز پیوسته در نقاطی انجام می شود، استحکام کلی می تواند نسبت به سایر روش های جوشکاری نسبتاً کمتر باشد. از طرف دیگر، درز جوش، جوش هایی را در سطوح فایری مواد مشابه ایجاد می کند. درز می تواند لب به لب یا مفصل همپوشانی باشد. جوشکاری درز از یک انتها شروع می شود و به تدریج به سمت دیگر حرکت می کند. این روش همچنین از دو الکترود مس برای اعمال فشار و جریان به ناحیه جوش استفاده می کند. الکترودهای دیسکی شکل با تماس ثابت در امتداد خط درز می چرخند و یک جوش پیوسته ایجاد می کنند. در اینجا نیز الکترودها با آب خنک می شوند. جوش ها بسیار قوی و قابل اعتماد هستند. روشهای دیگر عبارتند از تکنیکهای جوشکاری برآمدگی، فلاشی و جوشی.
جوش حالت جامد با روش های قبلی که در بالا توضیح داده شد کمی متفاوت است. ادغام در دماهای کمتر از دمای ذوب فلزات متصل شده و بدون استفاده از پرکننده فلزی صورت می گیرد. ممکن است در برخی فرآیندها از فشار استفاده شود. روشهای مختلف عبارتند از: جوشکاری همزمان که در آن فلزات غیرمشابه از طریق یک قالب اکسترود میشوند، جوشکاری با فشار سرد که در آن آلیاژهای نرم را در زیر نقطه ذوب آنها به هم میپیوندیم، جوشکاری انتشاری یک تکنیک بدون خطوط جوش قابل مشاهده، جوش انفجاری برای اتصال مجدد آلیاژهای غیر مشابه به مواد آلیاژی غیر مشابه، فولادها، جوشکاری با پالس الکترومغناطیسی که در آن لوله ها و ورق ها را توسط نیروهای الکترومغناطیسی تسریع می کنیم، جوش فورج که شامل حرارت دادن فلزات تا دمای بالا و کوبیدن آنها به یکدیگر است، جوش اصطکاکی که در آن جوشکاری اصطکاکی کافی انجام می شود، جوشکاری اصطکاکی اغتشاشی که شامل جوشکاری غیر اصطکاکی می شود. ابزار مصرفی که از خط اتصال عبور می کند، جوشکاری با فشار داغ که در آن فلزات را در دماهای بالا زیر دمای ذوب در خلاء یا گازهای بی اثر فشار می دهیم، جوشکاری فشار ایزواستاتیک داغ فرآیندی است که در آن فشار را با استفاده از گازهای بی اثر در داخل ظرف اعمال می کنیم، جوشکاری غلتکی در جایی که می پیوندیم. مواد غیر مشابه با فشار دادن آنها بین دو چرخ دوار، جوش اولتراسونیک که در آن ورق های فلزی یا پلاستیکی نازک با استفاده از انرژی ارتعاشی فرکانس بالا جوش داده می شود.
سایر فرآیندهای جوشکاری ما عبارتند از: جوشکاری با پرتو الکترونی با نفوذ عمیق و پردازش سریع، اما به عنوان روشی پرهزینه، آن را برای موارد خاص در نظر می گیریم، جوش الکترولاسگ روشی مناسب فقط برای صفحات ضخیم سنگین و قطعات فولادی، جوش القایی که در آن از القای الکترومغناطیسی استفاده می کنیم. قطعه کار رسانای الکتریکی یا فرومغناطیسی ما را گرم کنیم، جوش پرتو لیزر نیز با نفوذ عمیق و پردازش سریع اما روشی گران قیمت، جوش هیبریدی لیزری که LBW را با GMAW در همان سر جوش ترکیب می کند و قادر به پر کردن شکاف های 2 میلی متری بین صفحات است، جوش ضربه ای که شامل تخلیه الکتریکی به دنبال آهنگری مواد با فشار اعمال شده، جوش حرارتی حرارتی شامل واکنش گرمازا بین پودرهای آلومینیوم و اکسید آهن، جوش الکتروگاز با الکترودهای مصرفی و فقط با فولاد در حالت عمودی مورد استفاده قرار می گیرد، و در نهایت جوشکاری قوس میخ برای اتصال گل میخ به پایه. مواد با گرما و فشار
توصیه می کنیم اینجا را کلیک کنیددانلود تصاویر شماتیک ما از فرآیندهای لحیم کاری، لحیم کاری و چسبندگی توسط AGS-TECH Inc.
این به شما کمک می کند اطلاعاتی را که در زیر به شما ارائه می دهیم بهتر درک کنید.
• لحیم کاری: ما دو یا چند فلز را با حرارت دادن فلزات پرکننده در بین آنها بالای نقطه ذوب آنها و با استفاده از عمل مویرگی برای پخش به هم وصل می کنیم. فرآیند مشابه لحیم کاری است اما دمای ذوب پرکننده در لحیم کاری بالاتر است. مانند جوشکاری، شار از مواد پرکننده در برابر آلودگی جوی محافظت می کند. پس از خنک شدن، قطعات کار به هم متصل می شوند. این فرآیند شامل مراحل کلیدی زیر است: تناسب و ترخیص خوب، تمیز کردن مناسب مواد پایه، نصب مناسب، انتخاب شار و جو مناسب، گرم کردن مجموعه و در نهایت تمیز کردن مجموعه لحیم کاری شده. برخی از فرآیندهای لحیم کاری ما عبارتند از TORCH BRAZING، یک روش محبوب که به صورت دستی یا به صورت خودکار انجام می شود. برای سفارشات تولید کم حجم و موارد تخصصی مناسب است. گرما با استفاده از شعله های گاز در نزدیکی محل لحیم کاری اعمال می شود. لحیم کاری کوره به مهارت کمتر اپراتور نیاز دارد و یک فرآیند نیمه اتوماتیک مناسب برای تولید انبوه صنعتی است. هم کنترل دما و هم کنترل اتمسفر در کوره از مزایای این روش است، زیرا اولی ما را قادر می سازد چرخه های حرارتی کنترل شده داشته باشیم و گرمایش موضعی را حذف کنیم، همانطور که در لحیم کاری مشعل وجود دارد، و دومی از قطعه در برابر اکسیداسیون محافظت می کند. با استفاده از جیگینگ میتوانیم هزینههای تولید را به حداقل برسانیم. معایب مصرف انرژی بالا، هزینه تجهیزات و ملاحظات چالش برانگیزتر طراحی است. لحیم کاری خلاء در یک کوره خلاء صورت می گیرد. یکنواختی دما حفظ می شود و اتصالات بدون شار و بسیار تمیز با تنش های پسماند بسیار کم به دست می آید. عملیات حرارتی میتواند در خلاء لحیم کاری انجام شود، زیرا تنشهای پسماند کم در چرخههای گرمایش و سرمایش آهسته وجود دارد. عیب اصلی آن هزینه بالای آن است زیرا ایجاد محیط خلاء یک فرآیند گران است. با این حال، روش دیگری DIP BRAZING، قطعات ثابتی را که در آن ترکیب لحیم کاری به سطوح جفت اعمال می شود، متصل می کند. سپس قطعات ثابت در حمام نمک مذاب مانند کلرید سدیم (نمک خوراکی) غوطه ور می شوند که به عنوان یک واسطه انتقال حرارت و شار عمل می کند. هوا حذف می شود و بنابراین هیچ اکسیدی تشکیل نمی شود. در لحیم کاری القایی ما مواد را توسط یک فلز پرکننده که نقطه ذوب کمتری نسبت به مواد پایه دارد به هم وصل می کنیم. جریان متناوب از سیم پیچ القایی یک میدان الکترومغناطیسی ایجاد می کند که گرمایش القایی را بر روی مواد مغناطیسی عمدتا آهنی القا می کند. این روش گرمایش انتخابی، اتصالات خوب با پرکنندههایی که فقط در نواحی مورد نظر جریان دارند، اکسیداسیون کم به دلیل عدم وجود شعله و سرد شدن سریع، گرمایش سریع، قوام و مناسب بودن برای تولید با حجم بالا را فراهم میکند. برای سرعت بخشیدن به فرآیندهای خود و اطمینان از ثبات، ما اغلب از پریفرم ها استفاده می کنیم. اطلاعات مربوط به تاسیسات لحیم کاری ما برای تولید اتصالات سرامیکی به فلز، آب بندی هرمتیک، ورودی خلاء، خلاء بالا و فوق العاده بالا و اجزای کنترل سیال را می توانید در اینجا بیابید:_cc781905-3005-00-00-00-00-00-00بروشور Brazing Factory
• لحیم کاری: در لحیم کاری ذوب قطعات کار نداریم، بلکه یک فلز پرکننده با نقطه ذوب کمتر از قطعات اتصال دهنده که به داخل محل اتصال می ریزد، نداریم. فلز پرکننده در لحیم کاری در دمای پایین تری نسبت به لحیم کاری ذوب می شود. ما از آلیاژهای بدون سرب برای لحیم کاری استفاده می کنیم و دارای انطباق RoHS هستیم و برای کاربردها و نیازهای مختلف آلیاژهای مختلف و مناسب مانند آلیاژ نقره داریم. لحیم کاری مفاصلی را به ما ارائه می دهد که ضد گاز و مایع هستند. در لحیم کاری نرم، فلز پرکننده ما دارای نقطه ذوب زیر 400 درجه سانتیگراد است، در حالی که در لحیم کاری نقره و لحیم کاری به دمای بالاتری نیاز داریم. لحیم کاری نرم از دماهای پایین تری استفاده می کند اما منجر به اتصالات قوی برای کاربردهای سخت در دماهای بالا نمی شود. از طرف دیگر، لحیم کاری نقره به دماهای بالایی که توسط مشعل ارائه می شود نیاز دارد و اتصالات قوی مناسب برای کاربردهای دمای بالا را به ما می دهد. لحیم کاری به بالاترین درجه حرارت نیاز دارد و معمولاً از مشعل استفاده می شود. از آنجایی که اتصالات لحیم کاری بسیار قوی هستند، کاندیدای مناسبی برای تعمیر اجسام آهنی سنگین هستند. در خطوط تولید ما از لحیم کاری دستی و همچنین خطوط لحیم کاری خودکار استفاده می کنیم. INDUCTION SOLDERING از جریان AC با فرکانس بالا در یک سیم پیچ مسی برای تسهیل گرمایش القایی استفاده می کند. جریان در قسمت لحیم شده القا می شود و در نتیجه گرما در مقاومت بالا joint ایجاد می شود. این گرما فلز پرکننده را ذوب می کند. Flux نیز استفاده می شود. لحیم کاری القایی روش خوبی برای لحیم کاری سیکلندرها و لوله ها در یک فرآیند مداوم با پیچاندن سیم پیچ ها به دور آنها می باشد. لحیم کاری برخی از مواد مانند گرافیت و سرامیک دشوارتر است زیرا نیاز به آبکاری قطعات کار با فلز مناسب قبل از لحیم کاری دارد. این اتصال سطحی را تسهیل می کند. ما چنین موادی را به ویژه برای کاربردهای بسته بندی هرمتیک لحیم کاری انجام می دهیم. ما تخته های مدار چاپی (PCB) خود را در حجم بالا عمدتاً با استفاده از لحیم کاری موج تولید می کنیم. فقط برای مقادیر کمی از اهداف نمونه سازی ما از لحیم کاری دستی با استفاده از آهن لحیم کاری استفاده می کنیم. ما از لحیم کاری موجی هم برای مجموعه های PCB از طریق سوراخ و هم برای نصب روی سطح (PCBA) استفاده می کنیم. یک چسب موقت اجزا را به برد مدار متصل نگه می دارد و مجموعه روی یک نوار نقاله قرار می گیرد و از طریق تجهیزاتی که حاوی لحیم مذاب است حرکت می کند. ابتدا PCB فلکس شده و سپس وارد منطقه پیش گرمایش می شود. لحیم مذاب در تابه است و روی سطح آن دارای الگوی امواج ایستاده است. هنگامی که PCB روی این امواج حرکت می کند، این امواج با پایین PCB تماس می گیرند و به پدهای لحیم کاری می چسبند. لحیم کاری فقط روی پین ها و لنت ها می ماند و روی خود PCB نمی ماند. امواج در لحیم مذاب باید به خوبی کنترل شوند تا پاشیده نشود و نواحی ناخواسته تخته ها را لمس نکرده و آلوده نکنند. در REFLOW SOLDERING از خمیر لحیم چسبنده برای اتصال موقت قطعات الکترونیکی به بردها استفاده می کنیم. سپس تخته ها را با کنترل دما از طریق کوره جریان مجدد قرار می دهند. در اینجا لحیم کاری ذوب می شود و قطعات به طور دائم به هم متصل می شوند. ما از این تکنیک برای اجزای نصب سطحی و همچنین برای اجزای سوراخ دار استفاده می کنیم. کنترل دمای مناسب و تنظیم دمای فر برای جلوگیری از تخریب قطعات الکترونیکی روی برد با گرم کردن بیش از حد آنها بیش از حداکثر دمای آنها ضروری است. در فرآیند لحیم کاری مجدد، ما در واقع چندین ناحیه یا مراحل داریم که هر کدام دارای مشخصات حرارتی مشخصی هستند، مانند مرحله پیش گرم کردن، مرحله خیساندن حرارتی، مراحل جریان مجدد و خنک کننده. این مراحل مختلف برای لحیم کاری بدون آسیب در مجموعه های برد مدار چاپی (PCBA) ضروری است. ULTRASONIC SOLDERING یکی دیگر از تکنیک های پرکاربرد با قابلیت های منحصر به فرد است- می توان از آن برای لحیم کاری شیشه، سرامیک و مواد غیرفلزی استفاده کرد. به عنوان مثال پانل های فتوولتائیک که غیرفلزی هستند به الکترودهایی نیاز دارند که می توانند با استفاده از این تکنیک چسبانده شوند. در لحیم کاری اولتراسونیک، ما یک نوک لحیم کاری گرم شده را مستقر می کنیم که ارتعاشات اولتراسونیک را نیز منتشر می کند. این ارتعاشات حبابهای حفرهای را در سطح مشترک زیرلایه با مواد لحیم مذاب ایجاد میکنند. انرژی انفجاری کاویتاسیون سطح اکسید را اصلاح می کند و کثیفی و اکسیدها را از بین می برد. در این مدت یک لایه آلیاژی نیز تشکیل می شود. لحیم کاری در سطح اتصال دارای اکسیژن است و باعث ایجاد یک پیوند مشترک قوی بین شیشه و لحیم می شود. DIP SOLDERING را می توان به عنوان یک نسخه ساده تر از لحیم کاری موجی مناسب برای تولید در مقیاس کوچک در نظر گرفت. اولین شار تمیز کردن مانند سایر فرآیندها اعمال می شود. PCB ها با قطعات نصب شده به صورت دستی یا به صورت نیمه خودکار در یک مخزن حاوی لحیم مذاب فرو می روند. لحیم مذاب به نواحی فلزی در معرض دید می چسبد که توسط ماسک لحیم روی تخته محافظت نشده است. تجهیزات ساده و ارزان هستند.
• چسباندن چسب: این روش محبوب دیگری است که ما اغلب از آن استفاده می کنیم و شامل چسباندن سطوح با استفاده از چسب، اپوکسی، مواد پلاستیکی یا سایر مواد شیمیایی است. پیوند با تبخیر حلال، پخت با حرارت، پخت در نور UV، پخت تحت فشار یا انتظار برای مدت زمان معین انجام می شود. چسب های مختلف با کارایی بالا در خطوط تولید ما استفاده می شود. با کاربرد و فرآیندهای پخت به درستی مهندسی شده، اتصال چسب می تواند منجر به اتصالات با تنش بسیار کم شود که قوی و قابل اعتماد هستند. باندهای چسب می توانند محافظ خوبی در برابر عوامل محیطی مانند رطوبت، آلاینده ها، خورنده ها، لرزش و ... باشند. مزایای اتصال چسب عبارتند از: آنها را می توان روی موادی اعمال کرد که در غیر این صورت لحیم کاری، جوشکاری یا لحیم کاری سخت است. همچنین می تواند برای مواد حساس به حرارت که در اثر جوشکاری یا سایر فرآیندهای دمای بالا آسیب می بینند، ترجیح داده شود. از دیگر مزایای چسب ها این است که می توان آنها را روی سطوح نامنظم اعمال کرد و در مقایسه با روش های دیگر، وزن مونتاژ را به مقدار بسیار کمی افزایش داد. همچنین تغییرات ابعادی در قطعات بسیار کم است. برخی از چسب ها دارای خواص تطبیق شاخص هستند و می توانند در بین اجزای نوری بدون کاهش قابل توجه نور یا قدرت سیگنال نوری استفاده شوند. از سوی دیگر معایب زمان پخت طولانی تر است که ممکن است خطوط تولید را کند کند، الزامات اتصال، الزامات آماده سازی سطح و مشکل در جداسازی قطعات در صورت نیاز به کار مجدد. اکثر عملیات چسباندن چسب ما شامل مراحل زیر است:
-تصفیه سطح: روشهای تمیز کردن ویژه مانند تمیز کردن آب دیونیزه، تمیز کردن الکل، تمیز کردن پلاسما یا کرونا رایج هستند. پس از تمیز کردن، ممکن است برای اطمینان از بهترین اتصالات ممکن، تقویت کننده های چسبندگی را روی سطوح اعمال کنیم.
-تثبیت قطعات: هم برای کاربرد چسب و هم برای پخت، وسایل سفارشی را طراحی و استفاده می کنیم.
-کاربرد چسب: گاهی اوقات از سیستم های دستی و گاهی بسته به مورد از سیستم های خودکار مانند رباتیک، سروموتورها، محرک های خطی برای تحویل چسب ها در محل مناسب استفاده می کنیم و برای تحویل آن در حجم و مقدار مناسب از دیسپنسر استفاده می کنیم.
- پخت: بسته به نوع چسب، ممکن است از خشک کردن و پخت ساده و همچنین پخت در زیر نورهای ماوراء بنفش استفاده کنیم که به عنوان کاتالیزور یا پخت حرارتی در اجاق عمل می کنند یا با استفاده از عناصر گرمایش مقاومتی نصب شده بر روی جیگ ها و فیکسچرها.
توصیه می کنیم اینجا را کلیک کنیددانلود تصاویر شماتیک ما از فرآیندهای بستن توسط AGS-TECH Inc.
این به شما کمک می کند اطلاعاتی را که در زیر به شما ارائه می دهیم بهتر درک کنید.
• فرآیندهای چفت و بست: فرآیندهای اتصال مکانیکی ما به دو دسته تقسیم می شوند: اتصال دهنده ها و اتصالات انتگرال. نمونه هایی از اتصال دهنده هایی که ما استفاده می کنیم عبارتند از پیچ، پین، مهره، پیچ و مهره، پرچ. نمونههایی از اتصالات یکپارچه که ما استفاده میکنیم عبارتند از اتصالات محکم و کوچک، درزها، چینخوردگیها. با استفاده از انواع روشهای بست، مطمئن میشویم که اتصالات مکانیکی ما برای سالها استفاده قوی و قابل اعتماد هستند. پیچها و پیچها از رایجترین بستها برای نگهداشتن اجسام در کنار هم و قرار دادن آنها هستند. پیچ ها و پیچ های ما مطابق با استانداردهای ASME هستند. انواع مختلفی از پیچ ها و پیچ ها از جمله پیچ ها و پیچ های شش گوش، پیچ ها و پیچ ها، پیچ های دو سر، پیچ رولپلاک، پیچ چشمی، پیچ آینه ای، پیچ ورق فلزی، پیچ تنظیم ریز، پیچ های خوددریل و پیچ های خودکاری استفاده می شوند. ، پیچ تنظیم ، پیچ با واشر داخلی و ... و موارد دیگر. ما انواع مختلفی از سر پیچ مانند سرپیچ، گنبدی، گرد، سر فلنجی و انواع مختلف پیچ درایو مانند شکاف، فیلیپس، مربع، سوکت شش گوش داریم. از طرف دیگر یک RIVET یک بست مکانیکی دائمی است که از یک محور استوانه ای صاف و یک سر تشکیل شده است. پس از وارد کردن، انتهای دیگر پرچ تغییر شکل داده و قطر آن به گونه ای منبسط می شود که در جای خود باقی بماند. به عبارت دیگر پرچ قبل از نصب یک سر و بعد از نصب دو سر دارد. ما انواع مختلفی از پرچ ها را بسته به کاربرد، استحکام، دسترسی و هزینه نصب می کنیم، مانند پرچ های سر جامد/گرد، ساختاری، نیمه لوله ای، کور، اسکار، درایو، فلاش، قفل اصطکاکی، پرچ های خود سوراخ شونده. در مواردی که باید از تغییر شکل حرارتی و تغییر خواص مواد به دلیل گرمای جوشکاری اجتناب شود، می توان پرچ را ترجیح داد. پرچ نیز وزن سبک و به ویژه استحکام و استقامت خوبی در برابر نیروهای برشی ارائه می دهد. در برابر بارهای کششی، پیچ ها، مهره ها و پیچ ها ممکن است مناسب تر باشند. در فرآیند CLINCHING از پانچ و قالب های مخصوص برای ایجاد یک قفل مکانیکی بین ورق های فلزی در حال اتصال استفاده می کنیم. پانچ لایه های ورق فلز را به داخل حفره قالب می راند و منجر به تشکیل یک مفصل دائمی می شود. در کلینچ کردن نیازی به گرمایش و سرمایش نیست و این یک فرآیند سرد است. این یک فرآیند اقتصادی است که می تواند در برخی موارد جایگزین جوش نقطه ای شود. در PINNING ما از پین هایی استفاده می کنیم که عناصر ماشینی هستند که برای ایمن کردن موقعیت قطعات ماشین نسبت به یکدیگر استفاده می شوند. انواع اصلی آن عبارتند از: پینهای کلویس، سنجاق چوبی، سنجاق فنری، پینهای رولپلاک، و پین اسپلیت. در STAPLING ما از تفنگ های منگنه و منگنه استفاده می کنیم که بست های دو شاخه ای هستند که برای اتصال یا اتصال مواد استفاده می شوند. منگنه دارای مزایای زیر است: مقرون به صرفه بودن، استفاده آسان و سریع، تاج منگنه را می توان برای پل زدن مواد به هم چسبیده به هم استفاده کرد، تاج منگنه می تواند پل زدن یک قطعه مانند کابل و چسباندن آن را به یک سطح بدون سوراخ یا سوراخ کردن آسان کند. آسیب رسان، حذف نسبتا آسان. پرس فیتینگ با فشار دادن قطعات به هم و اصطکاک بین آنها قطعات را محکم می کند. قطعات پرس مناسب متشکل از یک محور بزرگ و یک سوراخ کم اندازه معمولاً با یکی از دو روش مونتاژ می شوند: یا با اعمال نیرو یا استفاده از انبساط یا انقباض حرارتی قطعات. وقتی اتصالات پرس با اعمال نیرو ایجاد می شود، یا از پرس هیدرولیک یا پرس دستی استفاده می کنیم. از طرف دیگر هنگامی که اتصالات پرس با انبساط حرارتی برقرار می شود، قطعات پوششی را گرم کرده و در حالی که گرم هستند در جای خود مونتاژ می کنیم. وقتی سرد می شوند منقبض می شوند و به ابعاد طبیعی خود باز می گردند. این باعث تناسب پرس خوب می شود. ما به این روش SHRINK-FITTING می گوییم. راه دیگر انجام این کار این است که قسمت های بسته بندی شده را قبل از مونتاژ سرد کنید و سپس آنها را به قسمت های جفت خود بکشید. هنگامی که مجموعه گرم می شود، آنها منبسط می شوند و ما یک تناسب محکم به دست می آوریم. این روش دوم ممکن است در مواردی که گرمایش خطر تغییر خواص مواد را به همراه دارد ارجح باشد. خنک کردن در آن موارد ایمن تر است.
قطعات و مجموعه های پنوماتیک و هیدرولیک
• سوپاپ ها، قطعات هیدرولیک و پنوماتیک مانند O-ring، واشر، آب بندی، واشر، رینگ، شیم.
از آنجایی که شیرها و اجزای پنوماتیکی تنوع زیادی دارند، نمیتوانیم همه چیز را در اینجا فهرست کنیم. بسته به محیط های فیزیکی و شیمیایی برنامه شما، ما محصولات ویژه ای برای شما داریم. لطفاً کاربرد، نوع قطعه، مشخصات، شرایط محیطی مانند فشار، دما، مایعات یا گازهایی که با شیرها و اجزای پنوماتیک شما در تماس هستند را برای ما مشخص کنید. و ما مناسب ترین محصول را برای شما انتخاب می کنیم یا آن را به طور خاص برای کاربرد شما تولید می کنیم.