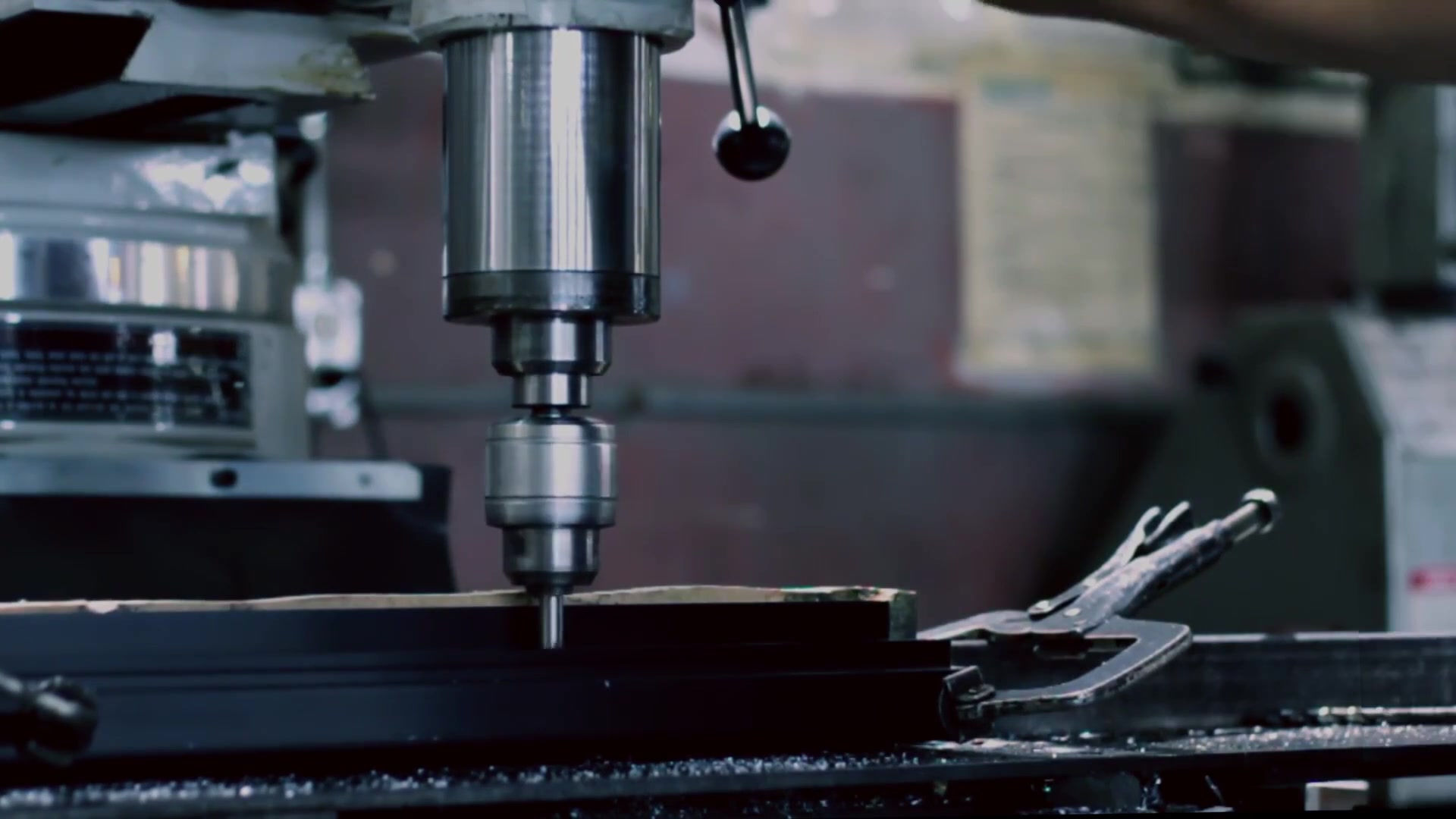
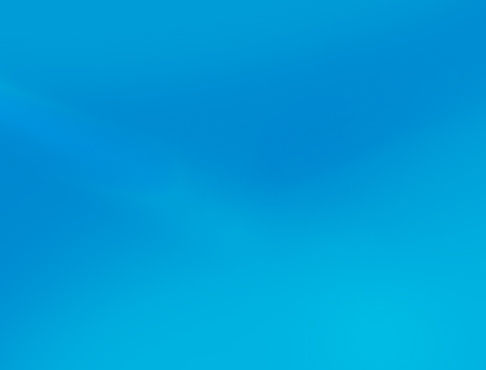
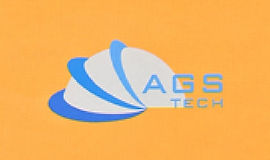
تولید کننده سفارشی جهانی، یکپارچه ساز، تثبیت کننده، شریک برون سپاری برای طیف گسترده ای از محصولات و خدمات.
ما منبع اصلی شما برای تولید، ساخت، مهندسی، ادغام، ادغام، برون سپاری محصولات و خدمات تولید شده سفارشی و خارج از قفسه هستیم.
زبان خود را انتخاب کنید
-
ساخت سفارشی
-
ساخت قرارداد داخلی و جهانی
-
برون سپاری تولید
-
تدارکات داخلی و جهانی
-
Consolidation
-
ادغام مهندسی
-
خدمات مهندسی
Search Results
164 results found with an empty search
- Transmission Components, Belts, Chains, Cable Drives, Pulleys,AGS-TECH
Transmission Components, Belts, Chains and Cable Drives, Conventional & Grooved or Serrated, Positive Drive, Pulleys تسمه و زنجیر و مونتاژ کابل درایو شرکت AGS-TECH به شما قطعات انتقال نیرو از جمله تسمه و زنجیر و مونتاژ کابل درایو را ارائه می دهد. با سالها اصلاح، محرکهای لاستیک، چرم و سایر تسمههای ما سبکتر و فشردهتر شدهاند و قادر به حمل بارهای بالاتر با هزینه کمتر هستند. به طور مشابه، درایوهای زنجیره ای ما در طول زمان توسعه زیادی را پشت سر گذاشته اند و مزایای متعددی را به مشتریان ما ارائه می دهند. برخی از مزایای استفاده از درایوهای زنجیره ای، فواصل نسبتاً نامحدود مرکز شفت، فشرده بودن، سهولت در مونتاژ، کشش در کشش بدون لغزش یا خزش، توانایی کار در محیط های با دمای بالا است. درایوهای کابل ما همچنین مزایایی مانند سادگی در برخی کاربردها نسبت به سایر انواع اجزای انتقال ارائه می دهند. هر دو تسمه خارج از قفسه، درایوهای زنجیره ای و کابل و همچنین نسخه های سفارشی ساخته شده و مونتاژ شده در دسترس هستند. ما می توانیم این اجزای انتقال را در اندازه مناسب برای کاربرد شما و از مناسب ترین مواد تولید کنیم. تسمه و درایوهای تسمه: - تسمه های مسطح معمولی: تسمه های مسطح ساده و بدون دندانه، شیار یا دندانه هستند. درایوهای تسمه مسطح انعطاف پذیری، جذب ضربه خوب، انتقال توان کارآمد در سرعت های بالا، مقاومت در برابر سایش و هزینه کم را ارائه می دهند. تسمه ها را می توان به هم متصل کرد یا به هم وصل کرد تا کمربندهای بزرگتر بسازند. از دیگر مزایای تسمه های تخت معمولی نازک بودن آنهاست، آنها در معرض بارهای گریز از مرکز بالا نیستند (آنها را برای عملیات با سرعت بالا با قرقره های کوچک مناسب می کند). از طرف دیگر آنها بارهای باربری بالایی را تحمیل می کنند زیرا تسمه های تخت نیاز به کشش بالایی دارند. از دیگر معایب درایوهای تسمه تخت می توان به لیز خوردن، عملکرد پر سر و صدا و راندمان نسبتاً پایین در سرعت های کم و متوسط کارکرد اشاره کرد. ما دو نوع تسمه معمولی داریم: تقویت شده و غیر تقویت شده. تسمه های تقویت شده دارای یک عضو کششی در ساختار خود هستند. کمربندهای تخت معمولی به صورت چرم، پارچه یا بند ناف لاستیکی، لاستیک یا پلاستیک تقویت نشده، پارچه، چرم تقویت شده در دسترس هستند. کمربندهای چرمی عمر طولانی، انعطاف پذیری، ضریب اصطکاک عالی، تعمیر آسان را ارائه می دهند. با این حال کمربندهای چرمی نسبتاً گران هستند، نیاز به پانسمان و تمیز کردن کمربند دارند و بسته به جو ممکن است منقبض یا کشیده شوند. تسمه های پارچه ای لاستیکی یا بند ناف در برابر رطوبت، اسید و مواد قلیایی مقاوم هستند. کمربندهای پارچه ای لاستیکی از لایه های پنبه ای یا اردک مصنوعی آغشته به لاستیک ساخته شده اند و مقرون به صرفه ترین هستند. تسمههای بند ناف لاستیکی از مجموعهای از طنابهای آغشته به لاستیکی تشکیل شدهاند. تسمه های طناب لاستیکی دارای استحکام کششی بالا و اندازه و جرم متوسطی هستند. تسمه های لاستیکی یا پلاستیکی غیر تقویت شده برای کاربردهای سبک و با سرعت کم مناسب هستند. تسمه های لاستیکی و پلاستیکی غیر تقویت شده را می توان روی قرقره های آنها در جای خود کشید. تسمه های پلاستیکی غیر تقویت شده می توانند در مقایسه با تسمه های لاستیکی قدرت بیشتری را انتقال دهند. کمربندهای چرمی تقویتشده از یک عضو کششی پلاستیکی تشکیل شدهاند که بین لایههای بالا و پایین چرم قرار گرفته است. در نهایت، کمربندهای پارچهای ما ممکن است شامل یک تکه پنبه یا اردک باشد که با ردیفهایی از بخیههای طولی تا شده و دوخته شده است. تسمه های پارچه ای قادر به ردیابی یکنواخت و عملکرد با سرعت بالا هستند. - تسمههای شیاردار یا دندانهدار (مانند تسمههای V): اینها تسمههای تخت اولیه هستند که برای ارائه مزایای نوع دیگری از محصولات انتقال اصلاح شدهاند. اینها کمربندهای مسطح با قسمت زیرین آجدار طولی هستند. تسمه های Poly-V یک تسمه صاف طولی شیاردار یا دندانه دار با بخش کششی و یک سری شیارهای V شکل مجاور برای اهداف ردیابی و فشرده سازی هستند. ظرفیت توان به عرض تسمه بستگی دارد. تسمه V شکل کار صنعت است و در انواع اندازه ها و انواع استاندارد برای انتقال تقریباً هر بار قدرت موجود است. درایوهای تسمه V به خوبی بین 1500 تا 6000 فوت در دقیقه کار می کنند، اما تسمه های باریک تا 10000 فوت در دقیقه کار می کنند. درایوهای تسمه V عمر طولانی مانند 3 تا 5 سال را ارائه می دهند و نسبت سرعت زیادی را امکان پذیر می کنند، نصب و برداشتن آنها آسان است، عملکرد بی صدا، تعمیر و نگهداری کم، جذب ضربه خوب بین درایور تسمه و محورهای محرک ارائه می شود. نقطه ضعف تسمه های V در لغزش و خزش مشخص آنها است و بنابراین ممکن است بهترین راه حل برای سرعت های سنکرون نباشند. تسمه های صنعتی، خودرویی و کشاورزی داریم. طول های استاندارد و همچنین طول های سفارشی کمربند موجود است. تمام مقاطع عرضی تسمه V شکل استاندارد در انبار موجود است. جداول وجود دارد که می توانید پارامترهای ناشناخته مانند طول تسمه، بخش تسمه (عرض و ضخامت) را محاسبه کنید، البته به شرطی که برخی از پارامترهای سیستم خود مانند قطر قرقره رانده و محرک، فاصله مرکزی بین قرقره ها و سرعت چرخش قرقره ها را بدانید. می توانید از چنین جداول استفاده کنید یا از ما بخواهید که کمربند V شکل مناسب شما را انتخاب کنیم. - تسمه های محرک مثبت (تسمه تایم): این تسمه ها نیز از نوع مسطح با یک سری دندانه های مساوی در محیط داخلی هستند. تسمه های درایو یا تایم مثبت مزایای تسمه های تخت را با ویژگی های چسبندگی مثبت زنجیر و چرخ دنده ها ترکیب می کند. تسمه های محرک مثبت هیچ لغزشی یا تغییرات سرعت را نشان نمی دهند. طیف گسترده ای از نسبت های سرعت ممکن است. بارهای تحمل کم هستند زیرا می توانند در کشش کم کار کنند. با این حال، آنها بیشتر در معرض ناهماهنگی در قرقره ها هستند. - قرقره ها، قرقره ها، هاب برای تسمه: انواع مختلف قرقره ها با تسمه های محرک مسطح، آجدار (آجدار) و مثبت استفاده می شود. ما همه آنها را تولید می کنیم. اکثر قرقره های تسمه مسطح ما از ریخته گری آهن ساخته می شوند، اما نسخه های فولادی نیز در ترکیب های مختلف رینگ و توپی موجود هستند. قرقره های تسمه مسطح ما ممکن است توپی های جامد، پره ای یا شکاف دار داشته باشند یا می توانیم به دلخواه شما را بسازیم. تسمه های آجدار و مثبت در اندازه ها و عرض های مختلف موجود است. حداقل یک قرقره در درایوهای تسمه تایم باید فلنج زده شود تا تسمه روی درایو بماند. برای سیستم های محرک مرکزی طولانی، توصیه می شود هر دو قرقره فلنج دار باشند. قرقره ها چرخ های شیاردار قرقره ها هستند و عموماً با ریخته گری آهن، قالب گیری فولاد یا قالب گیری پلاستیک ساخته می شوند. شکل دهی فولادی فرآیند مناسبی برای ساخت شیارهای خودرویی و کشاورزی است. شیارهایی با شیارهای منظم و عمیق تولید می کنیم. شیارهای شیار عمیق زمانی مناسب هستند که تسمه V شکل با زاویه وارد شیار می شود، مانند درایوهای یک چهارم دور. شیارهای عمیق نیز برای درایوهای شافت عمودی و کاربردهایی که لرزش تسمه ها می تواند مشکل ساز باشد، مناسب هستند. قرقره های بیکار ما قرقره های شیاردار یا قرقره های مسطحی هستند که برای انتقال نیروی مکانیکی عمل نمی کنند. قرقره های هرزگرد بیشتر برای سفت کردن تسمه ها استفاده می شود. - درایوهای تک تسمه ای و چندگانه: درایوهای تک تسمه دارای یک شیار هستند در حالی که درایوهای تسمه چندگانه دارای شیارهای متعدد هستند. با کلیک بر روی متن رنگی مربوطه در زیر می توانید کاتالوگ های ما را دانلود کنید: - تسمه های انتقال نیرو (شامل تسمه های V-Timing، تسمه های لبه خام، تسمه های پیچیده و تسمه های تخصصی) - تسمه های نقاله - قرقره های V - قرقره های زمان بندی زنجیر و درایوهای زنجیر: زنجیرهای انتقال قدرت ما دارای مزایایی مانند فواصل نسبتاً نامحدود مرکز شفت، مونتاژ آسان، فشرده بودن، قابلیت ارتجاعی تحت کشش بدون لغزش یا خزش، توانایی عملکرد در دمای بالا هستند. در اینجا انواع اصلی زنجیر ما آمده است: - زنجیر جداشدنی: زنجیرهای جداشدنی ما در طیف وسیعی از اندازه ها، گام و استحکام نهایی و به طور کلی از آهن یا فولاد چکش خوار ساخته می شوند. زنجیرهای چکش خوار در محدوده ای از اندازه های 0.902 (23 میلی متر) تا 4.063 اینچ (103 میلی متر) گام و استحکام نهایی از 700 تا 17000 پوند بر اینچ مربع ساخته می شوند. از سوی دیگر، زنجیرهای فولادی جداشدنی ما در اندازههای 0.904 اینچ (23 میلیمتر) تا حدود 3.00 اینچ (76 میلیمتر) با استحکام نهایی از 760 تا 5000 پوند بر اینچ مربع ساخته میشوند._cc781905-5cde-3194-bb3b- 136bad5cf58d_ - زنجیر Pintle: این زنجیر برای بارهای سنگین تر و سرعت کمی بالاتر تا حدود 450 فوت در دقیقه (2.2 متر بر ثانیه) استفاده می شود. زنجیرهای پینتل از پیوندهای ریختهگری جداگانه ساخته شدهاند که انتهای بشکهای گرد و کامل با میلههای جانبی افست دارند. این پیوندهای زنجیره ای با پین های فولادی به هم متصل می شوند. این زنجیرها دارای گامی از حدود 1.00 اینچ (25 میلی متر) تا 6.00 اینچ (150 میلی متر) و قدرت نهایی بین 3600 تا 30000 پوند بر اینچ مربع هستند. - زنجیر نوار کناری افست: اینها در زنجیره های محرک ماشین آلات ساختمانی محبوب هستند. این زنجیرها با سرعت 1000 فوت در دقیقه کار می کنند و بارها را تا حدود 250 اسب بخار انتقال می دهند. به طور کلی هر پیوند دارای دو میله جانبی افست، یک بوش، یک غلتک، یک پین، یک پین چوبی است. - زنجیر غلتکی: آنها در گام های 0.25 (6 میلی متر) تا 3.00 (75 میلی متر) اینچ موجود هستند. استحکام نهایی زنجیرهای غلتکی تک عرض بین 925 تا 130000 پوند بر اینچ مربع است. نسخههای عرض چندگانه زنجیر غلتکی در دسترس هستند و قدرت بیشتری را در سرعتهای بالاتر منتقل میکنند. زنجیرهای غلتکی با عرض چندگانه نیز عملکرد نرم تری را با کاهش نویز ارائه می دهند. زنجیرهای غلتکی از پیوندهای غلتکی و پیوندهای پین مونتاژ می شوند. پین های کاتر در زنجیره های غلتکی نسخه جداشونده استفاده می شود. طراحی درایوهای زنجیره ای غلتکی نیاز به تخصص موضوعی دارد. در حالی که درایوهای تسمه بر اساس سرعت های خطی هستند، درایوهای زنجیره ای بر اساس سرعت چرخش چرخ دنده کوچکتر است که در اکثر تاسیسات عضو محرکه است. علاوه بر رتبه بندی اسب بخار و سرعت چرخش، طراحی درایوهای زنجیره ای بر اساس بسیاری از عوامل دیگر است. - زنجیر دو گام: اساساً مانند زنجیرهای غلتکی است با این تفاوت که طول گام دو برابر است. - زنجیر دندان معکوس (بی صدا): زنجیر با سرعت بالا که بیشتر برای درایوهای پرایم موور، برق-تیک آف استفاده می شود. درایوهای زنجیر دندان معکوس می توانند قدرتی تا 1200 اسب بخار را انتقال دهند و از یک سری پیوندهای دندانی تشکیل شده اند که به طور متناوب با پین ها یا ترکیبی از اجزای مفصلی مونتاژ می شوند. زنجیر راهنمای مرکزی دارای پیوندهای راهنما برای درگیر کردن شیارها در چرخ دنده است و زنجیره راهنمای جانبی دارای راهنماهایی برای درگیر کردن دو طرف چرخ دنده است. - زنجیر مهره ای یا اسلایدر: این زنجیر برای درایوهای با سرعت کم و همچنین در عملیات دستی استفاده می شود. با کلیک بر روی متن رنگی مربوطه در زیر می توانید کاتالوگ های ما را دانلود کنید: - زنجیر چرخ رانندگی - زنجیر نقاله - زنجیر نوار نقاله گام بزرگ - زنجیر غلتکی از جنس استنلس استیل - زنجیر بالابر - زنجیر موتور سیکلت - زنجیر ماشین های کشاورزی - چرخ دنده ها: چرخ دنده های استاندارد ما مطابق با استانداردهای ANSI هستند. چرخدندههای صفحهای، چرخدندههای تخت و بدون توپ هستند. چرخ دنده های توپی کوچک و متوسط ما از استوک میله یا آهنگری تبدیل می شوند یا با جوش دادن توپی میله به یک صفحه نورد گرم ساخته می شوند. شرکت AGS-TECH می تواند چرخ دنده های ماشینکاری شده از ریخته گری آهن خاکستری، فولاد ریخته گری و سازه های توپی جوش داده شده، فلز پودر متخلخل، پلاستیک های قالب گیری شده یا ماشینکاری شده را تامین کند. برای عملکرد روان در سرعت های بالا، انتخاب مناسب اندازه چرخ دنده ها ضروری است. البته محدودیت فضا عاملی است که نمی توانیم هنگام انتخاب چرخ دنده از آن چشم پوشی کنیم. توصیه میشود که نسبت چرخدندههای راننده به چرخدنده نباید بیشتر از 6:1 باشد و روکش زنجیر روی راننده 120 درجه باشد. فواصل مرکزی بین چرخ دنده های کوچکتر و بزرگتر، طول زنجیر و کشش زنجیر نیز باید طبق برخی از محاسبات و دستورالعمل های مهندسی توصیه شده و نه به صورت تصادفی انتخاب شوند. کاتالوگ های ما را با کلیک بر روی متن رنگی زیر دانلود کنید: - چرخ دنده و صفحه - بوش های انتقال - کوپلینگ زنجیری - قفل های زنجیره ای درایوهای کابل: اینها در برخی موارد مزایای خود را نسبت به تسمه ها و درایوهای زنجیره ای دارند. درایوهای کابل می توانند همان عملکرد تسمه ها را انجام دهند و همچنین ممکن است برای پیاده سازی در برخی از برنامه ها ساده تر و اقتصادی تر باشند. به عنوان مثال، سری جدیدی از درایوهای کابل Synchromesh برای کشش مثبت طراحی شده اند تا جایگزین طناب های معمولی، کابل های ساده و درایوهای چرخ دنده، به ویژه در فضاهای تنگ شوند. درایو کابل جدید برای ارائه موقعیتیابی با دقت بالا در تجهیزات الکترونیکی مانند ماشینهای کپی، پلاتر، ماشینهای تحریر، چاپگرها و .... طراحی شده است. یکی از ویژگیهای کلیدی درایو کابلی جدید، توانایی آن در استفاده در پیکربندیهای مارپیچ سه بعدی است که امکان استفاده از آن را فراهم میکند. طرح های بسیار مینیاتوری کابل های Synchromesh را می توان با کشش کمتری در مقایسه با طناب ها استفاده کرد، بنابراین مصرف برق را کاهش می دهد. برای سوالات و نظر در مورد تسمه، زنجیر و کابل درایو با AGS-TECH تماس بگیرید. CLICK Product Finder-Locator Service صفحه قبلی
- Rapid Prototyping, Desktop Manufacturing, Additive Manufacturing, FDM
Rapid Prototyping, Desktop Manufacturing, Additive Manufacturing, Stereolithography, Polyjet, Fused Deposition Modeling, Selective Laser Sintering, FDM, SLS افزایشی و ساخت سریع در سال های اخیر شاهد افزایش تقاضا برای تولید سریع یا نمونه سازی سریع بوده ایم. این فرآیند ممکن است ساخت دسکتاپ یا ساخت فرم آزاد نیز نامیده شود. اساساً یک مدل فیزیکی جامد از یک قطعه مستقیماً از یک نقشه سه بعدی CAD ساخته می شود. ما از اصطلاح تولید افزودنی برای این تکنیک های مختلف استفاده می کنیم که در آن قطعات را به صورت لایه ای می سازیم. با استفاده از سختافزار و نرمافزار کامپیوتری یکپارچه، تولید افزودنی را انجام میدهیم. تکنیکهای نمونهسازی و ساخت سریع ما عبارتند از: استریولیتوگرافی، پلی جت، مدلسازی رسوب ذوب شده، تف جوشی لیزری انتخابی، ذوب پرتو الکترونی، چاپ سه بعدی، ساخت ماشینسازی مستقیم، ساخت مستقیم. توصیه می کنیم اینجا را کلیک کنیدتصاویر شماتیک ما از تولید افزودنی و فرآیندهای تولید سریع توسط AGS-TECH Inc. را دانلود کنید این به شما کمک می کند اطلاعاتی را که در زیر به شما ارائه می دهیم بهتر درک کنید. نمونه سازی سریع به ما ارائه می دهد: 1.) طرح مفهومی محصول از زوایای مختلف بر روی یک مانیتور با استفاده از یک سیستم 3D / CAD مشاهده می شود. 2.) نمونه های اولیه از مواد غیر فلزی و فلزی از جنبه های کاربردی، فنی و زیبایی شناسی ساخته و مورد مطالعه قرار می گیرند. 3.) نمونه سازی کم هزینه در زمان بسیار کوتاه انجام می شود. تولید افزودنی را می توان با ساختن یک قرص نان با چیدن و چسباندن تکه های تکی روی هم شبیه کرد. به عبارت دیگر، محصول به صورت تکه تکه تولید می شود یا لایه به لایه بر روی یکدیگر قرار می گیرد. اکثر قطعات را می توان در عرض چند ساعت تولید کرد. اگر قطعات خیلی سریع مورد نیاز باشد یا اگر مقادیر مورد نیاز کم باشد و ساخت قالب و ابزار بسیار گران و زمان بر باشد، این تکنیک خوب است. با این حال هزینه یک قطعه به دلیل گران بودن مواد اولیه گران است. • استریولیتوگرافی: این تکنیک که به اختصار STL نیز نامیده می شود، مبتنی بر پخت و سخت شدن یک فوتوپلیمر مایع به شکلی خاص با متمرکز کردن پرتو لیزر بر روی آن است. لیزر فوتوپلیمر را پلیمریزه کرده و آن را درمان می کند. با اسکن اشعه لیزر UV بر اساس شکل برنامه ریزی شده در امتداد سطح مخلوط فوتوپلیمر، قطعه از پایین به بالا در برش های جداگانه که روی هم قرار گرفته اند تولید می شود. اسکن نقطه لیزری بارها تکرار می شود تا به هندسه های برنامه ریزی شده در سیستم دست یابد. پس از ساخت کامل قطعه، آن را از روی پلت فرم جدا کرده و به صورت اولتراسونیک و با حمام الکلی تمیز می کنند. سپس برای چند ساعت در معرض تابش اشعه ماوراء بنفش قرار می گیرد تا مطمئن شود که پلیمر کاملا پخته و سخت شده است. به طور خلاصه، یک پلت فرم که در مخلوط فوتوپلیمر فرو میرود و یک پرتو لیزر UV از طریق یک سیستم کنترل سروو با توجه به شکل قطعه مورد نظر هدایت میشود و با فتوکور کردن لایه به لایه پلیمر به دست میآید. البته حداکثر ابعاد قطعه تولید شده توسط تجهیزات استریولیتوگرافی تعیین می شود. • POLYJET: مشابه چاپ جوهرافشان، در پلی جت ما هشت هد چاپ داریم که فوتوپلیمر را روی سینی ساخت قرار می دهد. نور ماوراء بنفش که در کنار جت ها قرار می گیرد بلافاصله هر لایه را خشک و سخت می کند. در پلی جت از دو ماده استفاده می شود. اولین ماده برای ساخت مدل واقعی است. ماده دوم، رزین ژل مانند برای پشتیبانی استفاده می شود. هر دوی این مواد لایه به لایه رسوب کرده و به طور همزمان پخته می شوند. پس از اتمام مدل، مواد نگهدارنده با محلول آبی حذف می شود. رزین های مورد استفاده مشابه استریولیتوگرافی (STL) هستند. پلی جت دارای مزایای زیر نسبت به استریولیتوگرافی است: 1.) عدم نیاز به تمیز کردن قطعات. 2.) عدم نیاز به پخت پس از فرآیند 3.) ضخامت لایه های کوچکتر امکان پذیر است و بنابراین وضوح بهتری بدست می آوریم و می توانیم قطعات ظریف تری تولید کنیم. • FUSED DEPOSITION MODELING: همچنین به اختصار FDM نامیده می شود، در این روش سر اکسترودر کنترل شده توسط ربات در دو جهت اصلی روی یک میز حرکت می کند. کابل در صورت نیاز پایین و بلند می شود. از دهانه یک قالب گرم شده روی سر، یک رشته ترموپلاستیک اکسترود می شود و یک لایه اولیه روی یک پایه فوم قرار می گیرد. این کار توسط سر اکسترودر که یک مسیر از پیش تعیین شده را دنبال می کند، انجام می شود. پس از لایه اولیه، جدول پایین آمده و لایه های بعدی روی هم قرار می گیرند. گاهی اوقات هنگام ساخت یک قطعه پیچیده، ساختارهای پشتیبانی مورد نیاز است تا رسوب گذاری در جهات خاصی ادامه یابد. در این موارد، یک ماده نگهدارنده با فاصله کمتر متراکم از رشته بر روی یک لایه اکسترود می شود تا از ماده مدل ضعیف تر باشد. این سازه های نگهدارنده بعداً می توانند پس از اتمام قطعه منحل یا شکسته شوند. ابعاد قالب اکسترودر ضخامت لایه های اکسترود شده را تعیین می کند. فرآیند FDM قطعاتی را با سطوح پلکانی روی سطوح خارجی مورب تولید می کند. اگر این زبری غیرقابل قبول باشد، می توان از پولیش شیمیایی بخار یا ابزار گرم شده برای صاف کردن آنها استفاده کرد. حتی یک موم پولیش به عنوان ماده پوششی برای حذف این مراحل و دستیابی به تحمل هندسی معقول در دسترس است. • تف جوشی لیزری انتخابی: همچنین به عنوان SLS مشخص می شود، این فرآیند بر اساس تف جوشی یک پلیمر، سرامیک یا پودرهای فلزی به صورت انتخابی در یک جسم است. پایین محفظه پردازش دارای دو سیلندر است: یک استوانه نیمه ساخت و یک سیلندر تغذیه پودر. اولی به صورت تدریجی تا جایی که قسمت متخلخل در حال تشکیل است پایین می آید و دومی به صورت تدریجی بالا می رود تا از طریق مکانیزم غلتکی پودر به سیلندر قطعه ساز عرضه شود. ابتدا یک لایه نازک از پودر در استوانه قسمت ساخته می شود، سپس یک پرتو لیزر بر روی آن لایه متمرکز می شود و یک مقطع خاص را ردیابی و ذوب / تف جوشی می کند، که سپس دوباره به حالت جامد تبدیل می شود. پودر قسمت هایی است که توسط پرتو لیزر مورد اصابت قرار نمی گیرند، شل باقی می مانند اما همچنان قسمت جامد را پشتیبانی می کنند. سپس لایه دیگری از پودر ریخته می شود و این فرآیند بارها تکرار می شود تا قطعه به دست آید. در پایان، ذرات پودر شل تکان داده می شود. همه اینها توسط یک کامپیوتر کنترل فرآیند با استفاده از دستورالعمل های تولید شده توسط برنامه 3D CAD قطعه در حال ساخت انجام می شود. مواد مختلفی مانند پلیمرها (مانند ABS، PVC، پلی استر)، موم، فلزات و سرامیک ها با چسب های پلیمری مناسب می توانند رسوب داده شوند. • ELECTRON-BEAM MELTING: شبیه به تف جوشی لیزری انتخابی، اما با استفاده از پرتو الکترونی برای ذوب تیتانیوم یا پودرهای کروم کبالت برای ساخت نمونه های اولیه در خلاء. برخی از پیشرفت ها برای انجام این فرآیند بر روی فولادهای زنگ نزن، آلومینیوم و آلیاژهای مس انجام شده است. در صورت نیاز به افزایش استحکام خستگی قطعات تولید شده، از پرس ایزواستاتیک داغ متعاقب ساخت قطعه به عنوان فرآیند ثانویه استفاده می کنیم. • چاپ سه بعدی: همچنین با 3DP نشان داده می شود، در این روش یک هد چاپ یک چسب معدنی را روی لایه ای از پودر غیرفلزی یا فلزی قرار می دهد. پیستونی که بستر پودر را حمل می کند به صورت تدریجی پایین می آید و در هر مرحله بایندر لایه به صورت لایه رسوب می کند و توسط بایندر ذوب می شود. مواد پودری مورد استفاده عبارتند از مخلوط پلیمرها و الیاف، ماسه ریخته گری، فلزات. با استفاده از سر کلاسورهای مختلف به طور همزمان و کلاسورهای رنگی مختلف می توانیم رنگ های متنوعی را بدست آوریم. فرآیند مشابه چاپ جوهر افشان است، اما به جای به دست آوردن یک صفحه رنگی، یک شی سه بعدی رنگی به دست می آوریم. قطعات تولید شده ممکن است متخلخل باشند و بنابراین ممکن است نیاز به تف جوشی و نفوذ فلز برای افزایش چگالی و استحکام آن داشته باشند. تف جوشی باعث سوختن بایندر و ذوب پودرهای فلزی با هم می شود. فلزاتی مانند فولاد ضد زنگ، آلومینیوم، تیتانیوم را می توان برای ساخت قطعات استفاده کرد و معمولاً به عنوان مواد نفوذی از مس و برنز استفاده می کنیم. زیبایی این تکنیک این است که حتی مجموعه های پیچیده و متحرک را می توان خیلی سریع ساخت. به عنوان مثال یک مجموعه چرخ دنده، یک آچار به عنوان ابزار می تواند ساخته شود و دارای قطعات متحرک و چرخشی آماده استفاده باشد. اجزای مختلف مجموعه را می توان با رنگ های مختلف و همه در یک شات تولید کرد. دانلود بروشور ما در:اصول چاپ سه بعدی فلزی • ساخت مستقیم و ابزار سریع: علاوه بر ارزیابی طراحی، عیب یابی، ما از نمونه سازی سریع برای تولید مستقیم محصولات یا کاربرد مستقیم در محصولات استفاده می کنیم. به عبارت دیگر، نمونه سازی سریع می تواند در فرآیندهای مرسوم گنجانده شود تا آنها را بهتر و رقابتی تر کند. به عنوان مثال، نمونه سازی سریع می تواند الگوها و قالب ها را تولید کند. الگوهای یک پلیمر ذوب و سوزان که توسط عملیات نمونه سازی سریع ایجاد می شود را می توان برای ریخته گری سرمایه گذاری و سرمایه گذاری کرد. مثال دیگری که باید ذکر شود استفاده از 3DP برای تولید پوسته ریخته گری سرامیک و استفاده از آن برای عملیات ریخته گری پوسته است. حتی قالبهای تزریق و درجهای قالب را میتوان با نمونهسازی سریع تولید کرد و میتوان هفتهها یا ماهها در زمان تولید قالب صرفهجویی کرد. تنها با آنالیز یک فایل CAD از قسمت مورد نظر، می توانیم هندسه ابزار را با استفاده از نرم افزار تولید کنیم. در اینجا برخی از روش های محبوب ابزار سریع ما آورده شده است: RTV (ولکانیزاسیون در دمای اتاق) قالب گیری / ریخته گری اورتان: با استفاده از نمونه سازی سریع می توان برای ساخت الگوی قطعه مورد نظر استفاده کرد. سپس این الگو با یک عامل جداکننده پوشانده می شود و لاستیک RTV مایع روی الگو ریخته می شود تا نیمه های قالب تولید شود. در مرحله بعد، از این نیمه های قالب برای تزریق یورتان های مایع قالب استفاده می شود. عمر قالب کوتاه است، فقط مانند 0 یا 30 چرخه، اما برای تولید دسته ای کوچک کافی است. ACES (جامد اپوکسی شفاف استال) قالبگیری تزریقی: با استفاده از تکنیکهای نمونهسازی سریع مانند استریولیتوگرافی، قالبهای تزریقی تولید میکنیم. این قالب ها پوسته هایی با انتهای باز هستند تا امکان پر شدن با موادی مانند اپوکسی، اپوکسی پر شده با آلومینیوم یا فلزات را فراهم کنند. باز هم عمر قالب به ده ها یا حداکثر صدها قطعه محدود شده است. فرآیند ابزارآلات فلزی پاشیده شده: ما از نمونه سازی سریع استفاده می کنیم و یک الگو می سازیم. روی سطح الگو یک آلیاژ روی-آلومینیوم می پاشیم و روی آن را می پوشانیم. سپس الگوی با پوشش فلزی در داخل یک فلاسک قرار می گیرد و با اپوکسی یا اپوکسی پر شده با آلومینیوم در گلدان قرار می گیرد. در نهایت برداشته می شود و با تولید دو نیمه قالب یک قالب کامل برای قالب گیری تزریقی به دست می آوریم. این قالب ها عمر طولانی تری دارند، در برخی موارد بسته به مواد و دما می توانند هزاران قطعه تولید کنند. فرآیند KEELTOOL: این تکنیک می تواند قالب هایی با عمر چرخه 100000 تا 10 میلیون تولید کند. با استفاده از نمونه سازی سریع، ما یک قالب RTV تولید می کنیم. سپس قالب با مخلوطی متشکل از پودر فولاد ابزار A6، کاربید تنگستن، بایندر پلیمری پر می شود و اجازه می دهیم تا خشک شود. سپس این قالب گرم می شود تا پلیمر بسوزد و پودرهای فلزی ذوب شوند. مرحله بعدی نفوذ مس برای تولید قالب نهایی است. در صورت نیاز می توان عملیات ثانویه مانند ماشینکاری و پرداخت را برای دقت ابعادی بهتر روی قالب انجام داد. _cc781905-5cde-3194-bb3b-136bad_5cf58 CLICK Product Finder-Locator Service صفحه قبلی
- Composites, Composite Materials Manufacturing, Fiber Reinforced
Composites, Composite Materials Manufacturing, Particle and Fiber Reinforced, Cermets, Ceramic & Metal Composite, Glass Fiber Reinforced Polymer, Lay-Up Process تولید کامپوزیت و مواد کامپوزیت به طور ساده، کامپوزیت ها یا مواد مرکب، موادی هستند که از دو یا چند ماده با خواص فیزیکی یا شیمیایی متفاوت تشکیل شده اند، اما وقتی با هم ترکیب شوند، به ماده ای متفاوت از مواد تشکیل دهنده تبدیل می شوند. لازم به ذکر است که مواد تشکیل دهنده در ساختار مجزا و متمایز می مانند. هدف در ساخت یک ماده کامپوزیت، به دست آوردن محصولی است که نسبت به اجزای تشکیل دهنده آن برتری داشته باشد و ویژگی های مورد نظر هر یک از اجزا را ترکیب کند. به عنوان مثال؛ استحکام، وزن کم یا قیمت کمتر ممکن است انگیزه طراحی و تولید کامپوزیت باشد. نوع کامپوزیت های ما کامپوزیت های تقویت شده با ذرات، کامپوزیت های تقویت شده با الیاف شامل ماتریس سرامیکی / زمینه پلیمری / زمینه فلزی / کربن- کربن / کامپوزیت های هیبریدی، کامپوزیت های ساختاری و چند لایه و ساختار ساندویچی و نانوکامپوزیت ها می باشد. تکنیک های ساختی که ما در تولید مواد کامپوزیت به کار می بریم عبارتند از: Pultrusion، فرآیندهای تولید پیش آغشته، قرار دادن الیاف پیشرفته، سیم پیچی رشته، قرار دادن فیبر متناسب، فرآیند چیدمان اسپری فایبر گلاس، تافتینگ، فرآیند لانکساید، پین زدن z. بسیاری از مواد کامپوزیتی از دو فاز تشکیل شده اند، ماتریس که پیوسته است و فاز دیگر را احاطه می کند. و فاز پراکنده که توسط ماتریس احاطه شده است. توصیه می کنیم اینجا را کلیک کنیددانلود تصاویر شماتیک ما از کامپوزیت ها و مواد کامپوزیت ساخت توسط AGS-TECH Inc. این به شما کمک می کند اطلاعاتی را که در زیر به شما ارائه می دهیم بهتر درک کنید. • کامپوزیت های تقویت شده با ذرات: این دسته از دو نوع تشکیل شده است: کامپوزیت های با ذرات بزرگ و کامپوزیت های تقویت شده با پراکندگی. در نوع اول، فعل و انفعالات ذره-ماتریس را نمی توان در سطح اتمی یا مولکولی بررسی کرد. در عوض مکانیک پیوسته معتبر است. از سوی دیگر، در کامپوزیت های تقویت شده با پراکندگی، ذرات به طور کلی در محدوده ده ها نانومتری بسیار کوچکتر هستند. نمونه ای از کامپوزیت ذرات بزرگ، پلیمرهایی است که به آنها پرکننده ها اضافه شده است. پرکننده ها خواص مواد را بهبود می بخشند و ممکن است مقداری از حجم پلیمر را با مواد مقرون به صرفه تری جایگزین کنند. کسر حجمی دو فاز بر رفتار کامپوزیت تأثیر می گذارد. کامپوزیت های ذرات بزرگ با فلزات، پلیمرها و سرامیک ها استفاده می شود. CERMETS نمونه هایی از کامپوزیت های سرامیکی / فلزی هستند. رایج ترین سرمت ما کاربید سیمانی است. از سرامیک کاربید نسوز مانند ذرات کاربید تنگستن در زمینه فلزی مانند کبالت یا نیکل تشکیل شده است. این کامپوزیت های کاربید به طور گسترده ای به عنوان ابزار برش برای فولاد سخت شده استفاده می شود. ذرات کاربید سخت مسئول عمل برش هستند و چقرمگی آنها توسط ماتریس فلزی انعطاف پذیر افزایش می یابد. بنابراین ما مزایای هر دو ماده را در یک کامپوزیت به دست می آوریم. نمونه رایج دیگری از کامپوزیت ذرات بزرگ که ما استفاده می کنیم ذرات کربن سیاه است که با لاستیک ولکانیزه مخلوط شده اند تا کامپوزیتی با استحکام کششی، چقرمگی، پارگی و مقاومت سایشی بالا به دست آید. نمونهای از کامپوزیتهای تقویتشده با پراکندگی، فلزات و آلیاژهای فلزی است که توسط پراکندگی یکنواخت ذرات ریز یک ماده بسیار سخت و خنثی تقویت و سخت شدهاند. هنگامی که تکه های بسیار کوچک اکسید آلومینیوم به ماتریس فلز آلومینیوم اضافه می شود، پودر آلومینیوم متخلخل را به دست می آوریم که استحکام بالایی در دمای بالا دارد. • کامپوزیت های تقویت شده با الیاف: این دسته از کامپوزیت ها در واقع مهم ترین هستند. هدف دستیابی به استحکام و سفتی بالا در واحد وزن است. ترکیب الیاف، طول، جهت گیری و غلظت در این کامپوزیت ها در تعیین خواص و سودمندی این مواد حیاتی است. ما از سه گروه الیاف استفاده می کنیم: سبیل، الیاف و سیم. WHISKERS تک بلورهای بسیار نازک و بلندی هستند. آنها از قوی ترین مواد هستند. برخی از مواد سبیل مانند گرافیت، نیترید سیلیکون، اکسید آلومینیوم هستند. FIBERS از طرف دیگر بیشتر پلیمرها یا سرامیک ها هستند و در حالت پلی کریستالی یا آمورف هستند. گروه سوم سیمهای ظریفی هستند که قطر نسبتاً زیادی دارند و اغلب از فولاد یا تنگستن تشکیل شدهاند. نمونه ای از کامپوزیت های تقویت شده با سیم، لاستیک های اتومبیل است که از سیم فولادی در داخل لاستیک استفاده می کند. بسته به ماده ماتریس، کامپوزیت های زیر را داریم: کامپوزیت های ماتریس پلیمری: این کامپوزیت ها از رزین پلیمری و الیاف به عنوان ماده تقویت کننده ساخته شده اند. زیرگروهی از این کامپوزیتهای پلیمر تقویتشده با الیاف شیشه (GFRP) حاوی الیاف شیشهای پیوسته یا ناپیوسته در یک ماتریس پلیمری است. شیشه استحکام بالایی دارد، مقرون به صرفه است، به راحتی در الیاف ساخته می شود و از نظر شیمیایی بی اثر است. معایب آن سختی و سفتی محدود آنهاست، دمای سرویس فقط تا 200 تا 300 درجه سانتیگراد است. فایبرگلاس برای بدنه خودرو و تجهیزات حمل و نقل، بدنه وسایل نقلیه دریایی، ظروف ذخیره سازی مناسب است. به دلیل سفتی محدود برای هوافضا یا پل سازی مناسب نیستند. زیرگروه دیگر کامپوزیت پلیمر تقویت شده با فیبر کربن (CFRP) نام دارد. در اینجا، کربن ماده فیبری ما در ماتریس پلیمری است. کربن به دلیل مدول و استحکام ویژه بالا و توانایی آن در حفظ این مدول ها در دماهای بالا شناخته شده است. الیاف کربن می توانند مدول های کششی استاندارد، متوسط، بالا و فوق العاده را به ما ارائه دهند. علاوه بر این، الیاف کربن ویژگی های فیزیکی و مکانیکی متنوعی را ارائه می دهند و بنابراین برای کاربردهای مهندسی سفارشی مختلف مناسب هستند. کامپوزیت های CFRP را می توان برای ساخت تجهیزات ورزشی و تفریحی، مخازن تحت فشار و اجزای ساختاری هوافضا در نظر گرفت. با این حال، یک زیر گروه دیگر، کامپوزیت های پلیمری تقویت شده با الیاف آرامید نیز موادی با استحکام و مدول بالا هستند. نسبت استحکام به وزن آنها به طور فوق العاده بالا است. الیاف آرامید با نام های تجاری KEVLAR و NOMEX نیز شناخته می شوند. تحت کشش، عملکرد بهتری نسبت به سایر مواد الیاف پلیمری دارند، اما در فشار ضعیف هستند. الیاف آرامید سخت، مقاوم در برابر ضربه، مقاوم در برابر خزش و خستگی، پایدار در دماهای بالا، بی اثر شیمیایی به جز در برابر اسیدها و بازهای قوی هستند. الیاف آرامید به طور گسترده ای در کالاهای ورزشی، جلیقه های ضد گلوله، لاستیک ها، طناب ها، پوشش های کابل فیبر نوری استفاده می شود. مواد تقویت کننده الیاف دیگری وجود دارند اما به میزان کمتری استفاده می شوند. اینها عمدتاً بور، کاربید سیلیکون، اکسید آلومینیوم هستند. از طرف دیگر مواد ماتریس پلیمری نیز حیاتی است. حداکثر دمای سرویس کامپوزیت را تعیین می کند زیرا پلیمر معمولا دمای ذوب و تخریب کمتری دارد. پلی استرها و وینیل استرها به طور گسترده ای به عنوان ماتریس پلیمری استفاده می شوند. رزین ها نیز مورد استفاده قرار می گیرند و دارای مقاومت در برابر رطوبت و خواص مکانیکی عالی هستند. به عنوان مثال رزین پلی آمید را می توان تا حدود 230 درجه سانتیگراد استفاده کرد. کامپوزیت های ماتریس فلزی: در این مواد از ماتریس فلزی انعطاف پذیر استفاده می شود و دمای سرویس به طور کلی بالاتر از اجزای تشکیل دهنده آنها است. در مقایسه با کامپوزیت های زمینه پلیمری، این کامپوزیت ها می توانند دمای عملیاتی بالاتری داشته باشند، غیر قابل اشتعال باشند و ممکن است مقاومت بهتری در برابر تخریب در برابر سیالات آلی داشته باشند. با این حال آنها گران تر هستند. مواد تقویت کننده مانند سبیل، ذرات، الیاف پیوسته و ناپیوسته؛ و مواد ماتریسی مانند مس، آلومینیوم، منیزیم، تیتانیوم، سوپرآلیاژها معمولا استفاده می شوند. به عنوان مثال، اجزای موتور ساخته شده از ماتریس آلیاژ آلومینیوم تقویت شده با اکسید آلومینیوم و الیاف کربن هستند. کامپوزیت های ماتریس سرامیکی: مواد سرامیکی به دلیل قابلیت اطمینان فوق العاده خوب در دمای بالا شناخته شده اند. با این حال، آنها بسیار شکننده هستند و دارای مقادیر پایینی برای چقرمگی شکست هستند. با قرار دادن ذرات، الیاف یا سبیل های یک سرامیک در ماتریس سرامیک دیگر، می توانیم به کامپوزیت هایی با چقرمگی شکست بالاتر دست یابیم. این مواد جاسازی شده اساساً با مکانیسم هایی مانند انحراف نوک ترک یا ایجاد پل در سطح ترک ها، از انتشار ترک در داخل ماتریس جلوگیری می کنند. به عنوان مثال، آلومیناهایی که با سبیل های SiC تقویت شده اند به عنوان درج ابزار برش برای ماشینکاری آلیاژهای فلزات سخت استفاده می شوند. اینها می توانند عملکرد بهتری را در مقایسه با کاربیدهای سیمانی نشان دهند. کامپوزیت های کربن-کربن: هم تقویت کننده و هم ماتریس کربن هستند. آنها دارای مدول کششی بالا و استحکام در دماهای بالا بیش از 2000 درجه سانتیگراد، مقاومت در برابر خزش، چقرمگی شکست بالا، ضرایب انبساط حرارتی پایین، رسانایی حرارتی بالا هستند. این ویژگی ها آنها را برای کاربردهایی که نیاز به مقاومت در برابر شوک حرارتی دارند ایده آل می کند. اما ضعف کامپوزیت های کربن-کربن آسیب پذیری آن در برابر اکسیداسیون در دماهای بالا است. نمونههای معمول استفاده عبارتند از قالبهای پرس گرم، ساخت اجزای موتور توربین پیشرفته. کامپوزیت های هیبرید: دو یا چند نوع الیاف مختلف در یک ماتریس مخلوط می شوند. بنابراین می توان یک ماده جدید با ترکیبی از ویژگی ها طراحی کرد. یک مثال زمانی است که هر دو الیاف کربن و شیشه در یک رزین پلیمری ادغام می شوند. الیاف کربن سفتی و استحکام با چگالی کم را ارائه می دهند اما گران هستند. از طرف دیگر شیشه ارزان است اما فاقد سفتی الیاف کربن است. کامپوزیت هیبریدی شیشه-کربن قوی تر و محکم تر است و می توان آن را با هزینه کمتری تولید کرد. پردازش کامپوزیت های تقویت شده با الیاف: برای پلاستیک های تقویت شده با الیاف پیوسته با الیاف توزیع شده یکنواخت که در جهت یکسانی قرار دارند، از تکنیک های زیر استفاده می کنیم. PULTRUSION: میله ها، تیرها و لوله های با طول پیوسته و مقطع ثابت ساخته می شوند. رووینگ های الیاف پیوسته با یک رزین ترموست آغشته شده و از طریق قالب فولادی کشیده می شوند تا به شکل دلخواه پیش بروند. در مرحله بعد، آنها از یک قالب پخت ماشینکاری شده دقیق عبور می کنند تا به شکل نهایی آن برسند. از آنجایی که قالب کیور گرم می شود، ماتریس رزین را پخت می کند. کشنده ها مواد را از میان قالب ها می کشند. با استفاده از هسته های توخالی وارد شده، می توانیم لوله ها و هندسه های توخالی را بدست آوریم. روش pultrusion خودکار است و نرخ تولید بالایی را به ما ارائه می دهد. تولید هر طول محصول امکان پذیر است. فرآیند تولید پیش پره: Prepreg یک تقویت کننده الیاف پیوسته است که با یک رزین پلیمری نیمه پخته شده از قبل آغشته شده است. به طور گسترده ای برای کاربردهای ساختاری استفاده می شود. این مواد به صورت نوار عرضه می شود و به صورت نوار ارسال می شود. سازنده مستقیماً آن را قالب می زند و بدون نیاز به افزودن هیچ رزینی آن را کاملاً پخت می کند. از آنجایی که پیش آغشتهها در دمای اتاق تحت واکنشهای پخت قرار میگیرند، در دمای 0 سانتیگراد یا پایینتر نگهداری میشوند. پس از استفاده، نوارهای باقیمانده در دمای پایین ذخیره می شوند. از رزین های ترموپلاستیک و ترموست استفاده می شود و الیاف تقویت کننده کربن، آرامید و شیشه رایج است. برای استفاده از پیش آغشتهسازیها، ابتدا کاغذ پشتی حامل برداشته میشود و سپس با گذاشتن نوار پیشآبسازی روی سطح ابزار (فرایند لایهآپ) ساخت انجام میشود. برای به دست آوردن ضخامت های مورد نظر ممکن است چندین لایه چیده شود. تمرین متداول این است که جهت الیاف را به طور متناوب تغییر دهید تا یک لایه لایه متقاطع یا زاویه دار ایجاد شود. در نهایت حرارت و فشار برای پخت اعمال می شود. هر دو پردازش دستی و همچنین فرآیندهای خودکار برای برش پیش آغشتهسازیها و lay-up استفاده میشوند. سیم پیچی رشته: الیاف تقویت کننده پیوسته به طور دقیق در یک الگوی از پیش تعیین شده قرار می گیرند تا از شکل توخالی و معمولاً دایره ای شکل پیروی کنند. الیاف ابتدا از یک حمام رزین عبور می کنند و سپس توسط یک سیستم خودکار روی سنبه پیچ می شوند. پس از چندین بار تکرار سیم پیچی ضخامت های مورد نظر به دست می آید و عمل آوری یا در دمای اتاق و یا در داخل کوره انجام می شود. اکنون سنبه برداشته شده و محصول قالب گیری می شود. سیم پیچی رشته می تواند با پیچاندن الیاف در الگوهای محیطی، مارپیچ و قطبی نسبت مقاومت به وزن بسیار بالایی را ارائه دهد. لوله ها، مخازن، پوشش ها با استفاده از این تکنیک ساخته می شوند. • کامپوزیت های ساختاری: عموماً از مواد همگن و کامپوزیت ساخته شده اند. بنابراین خواص اینها توسط مواد تشکیل دهنده و طراحی هندسی عناصر آن تعیین می شود. در اینجا انواع عمده وجود دارد: کامپوزیت های LAMINAR: این مواد ساختاری از صفحات یا پانل های دو بعدی با جهت های ترجیحی با مقاومت بالا ساخته می شوند. لایه ها روی هم چیده شده و سیمانی می شوند. با تناوب جهات با استحکام بالا در دو محور عمود بر هم، کامپوزیتی به دست میآوریم که در صفحه دوبعدی در هر دو جهت استحکام بالایی دارد. با تنظیم زوایای لایه ها می توان یک کامپوزیت با استحکام در جهت های دلخواه ساخت. اسکی مدرن به این روش تولید می شود. پانل های ساندویچ: این کامپوزیت های ساختاری سبک وزن هستند اما در عین حال دارای سفتی و استحکام بالایی هستند. ساندویچ پانل از دو ورق بیرونی ساخته شده از مواد سفت و محکم مانند آلیاژهای آلومینیوم، پلاستیک های تقویت شده با الیاف یا فولاد و یک هسته در بین ورق های بیرونی تشکیل شده است. هسته باید سبک باشد و بیشتر اوقات مدول الاستیسیته پایینی داشته باشد. مواد اصلی محبوب فوم های پلیمری سفت و سخت، چوب و لانه زنبوری هستند. ساندویچ پانل به طور گسترده در صنعت ساختمان به عنوان مصالح سقف، مصالح کف یا دیوار و همچنین در صنایع هوافضا استفاده می شود. • نانوکامپوزیت ها: این مواد جدید از ذرات ذرات با اندازه نانو تشکیل شده اند که در یک ماتریس جاسازی شده اند. با استفاده از نانوکامپوزیت ها می توانیم مواد لاستیکی بسازیم که مانع بسیار خوبی برای نفوذ هوا هستند و در عین حال خواص لاستیکی خود را بدون تغییر حفظ می کنند. CLICK Product Finder-Locator Service صفحه قبلی
- Machine Elements Manufacturing, Gears, Gear Drives, Bearings, Keys, Splines
Machine Elements Manufacturing, Gears, Gear Drives, Bearings, Keys, Splines, Pins, Shafts, Seals, Fasteners, Clutch, Cams, Followers, Belts, Couplings, Shafts تولید المان های ماشینی ادامه مطلب تسمه و زنجیر و مونتاژ کابل درایو ادامه مطلب مجموعه چرخ دنده ها و چرخ دنده ها ادامه مطلب تولید کوپلینگ و بلبرینگ ادامه مطلب ساخت کلید و اسپلاین و پین ادامه مطلب تولید دوربینها و فالوورها و پیوندها و چرخهای ضامن دار ادامه مطلب تولید شفت ادامه مطلب تولید مهر و موم مکانیکی ادامه مطلب مجموعه کلاچ و ترمز ادامه مطلب تولید بست ادامه مطلب مونتاژ ماشین های ساده MACHINE ELEMENTS اجزای اولیه یک ماشین هستند. این عناصر از سه نوع اساسی تشکیل شده اند: 1.) اجزای ساختاری شامل اعضای قاب، یاتاقان ها، محورها، اسپلاین ها، بست ها، مهر و موم ها و روان کننده ها. 2.) مکانیسم های کنترل کننده حرکت به روش های مختلف مانند قطار دنده، تسمه یا زنجیر درایو، اتصالات، سیستم های بادامک و پیرو، ترمز و کلاچ. 3.) اجزایی مانند دکمه ها، سوئیچ ها، نشانگرها، حسگرها، محرک ها و کنترل کننده های کامپیوتر را کنترل کنید. اکثر عناصر ماشینی که ما به شما پیشنهاد می کنیم در اندازه های معمولی استاندارد شده اند، اما عناصر ماشینی سفارشی نیز برای کاربردهای تخصصی شما موجود است. سفارشیسازی عناصر ماشینی میتواند روی طرحهای موجود که در کاتالوگهای قابل دانلود ما هستند یا روی طرحهای کاملاً جدید انجام شود. نمونه سازی و ساخت عناصر ماشین می تواند به محض تایید طرح توسط هر دو طرف ادامه یابد. اگر المانهای ماشین جدید نیاز به طراحی و ساخت داشته باشند، مشتریان ما طرحهای خود را برای ما ایمیل میکنند و ما آنها را برای تایید بررسی میکنیم، یا از ما میخواهند عناصر ماشین را برای کاربردشان طراحی کنیم. در مورد دوم، ما از تمام ورودی های مشتریان خود استفاده می کنیم و عناصر ماشین را طراحی می کنیم و نقشه های نهایی را برای تایید به مشتریان خود ارسال می کنیم. پس از تأیید، ما اولین مقالات را تولید می کنیم و متعاقباً عناصر دستگاه را مطابق طراحی نهایی تولید می کنیم. در هر مرحله از این کار، در صورتی که یک طراحی المان ماشینی خاص در زمینه عملکرد نامطلوب داشته باشد (که نادر است)، کل پروژه را بررسی می کنیم و به طور مشترک با مشتریان خود در صورت نیاز تغییراتی را انجام می دهیم. امضای قراردادهای عدم افشا (NDA) با مشتریان خود برای طراحی عناصر ماشین یا هر محصول دیگری در صورت نیاز یا نیاز، رویه استاندارد ما است. هنگامی که عناصر ماشین برای یک مشتری خاص به صورت سفارشی طراحی و ساخته می شوند، ما یک کد محصول را به آن اختصاص می دهیم و آنها را فقط به مشتری خود که مالک محصول است تولید و می فروشیم. ما عناصر ماشین را با استفاده از ابزارها، قالبها و روشهای توسعهیافته، هر چند بار که لازم است و هر زمان که مشتری دوباره آنها را سفارش دهد، تکثیر میکنیم. به عبارت دیگر، هنگامی که یک عنصر ماشین سفارشی برای شما طراحی و تولید شد، مالکیت معنوی و همچنین تمامی ابزار و قالبها توسط ما بهطور نامحدود برای شما محفوظ و ذخیره میشود و محصولات بهصورت دلخواه بازتولید میشوند. ما همچنین با ترکیب خلاقانه عناصر ماشین در یک جزء یا مجموعه ای که به یک برنامه کاربردی خدمت می کند و انتظارات مشتریان ما را برآورده می کند یا فراتر می رود، خدمات مهندسی را به مشتریان خود ارائه می دهیم. کارخانههایی که عناصر ماشین ما را میسازند دارای شرایط ISO9001، QS9000 یا TS16949 هستند. علاوه بر این، اکثر محصولات ما دارای علامت CE یا UL هستند و استانداردهای بین المللی مرتبط مانند ISO، SAE، ASME، DIN را برآورده می کنند. لطفاً روی منوهای فرعی کلیک کنید تا اطلاعات دقیقی در مورد عناصر دستگاه ما از جمله: - تسمه، زنجیر و کابل درایو - چرخ دنده ها و درایوهای دنده - کوپلینگ و بلبرینگ - کلیدها و Splines و پین ها - دوربینها و پیوندها - شفت ها - مهر و موم مکانیکی - کلاچ و ترمز صنعتی - اتصال دهنده ها - ماشین های ساده ما یک بروشور مرجع برای مشتریان، طراحان و توسعه دهندگان محصولات جدید از جمله عناصر ماشین آماده کرده ایم. شما می توانید با برخی از اصطلاحات رایج در طراحی اجزای ماشین آشنا شوید: دانلود بروشور اصطلاحات رایج مهندسی مکانیک مورد استفاده طراحان و مهندسان عناصر ماشینی ما در زمینه های مختلفی مانند ماشین آلات صنعتی، سیستم های اتوماسیون، تجهیزات تست و اندازه گیری، تجهیزات حمل و نقل، ماشین آلات ساختمانی و عملاً در هر جایی که فکرش را بکنید کاربرد دارد. AGS-TECH المان های ماشین را از مواد مختلف بسته به کاربرد توسعه و تولید می کند. مواد مورد استفاده برای عناصر ماشین میتواند از پلاستیکهای قالبگیری شده برای اسباببازیها گرفته تا فولاد سختشده و روکششده مخصوص ماشینآلات صنعتی متغیر باشد. طراحان ما از جدیدترین نرمافزارهای حرفهای و ابزارهای طراحی برای توسعه عناصر ماشین، با در نظر گرفتن جزئیاتی مانند زوایای دندانههای چرخ دنده، تنشهای وارده، نرخ سایش و غیره استفاده میکنند. لطفاً در زیر منوهای ما ورق بزنید و بروشورها و کاتالوگ های محصولات ما را دانلود کنید تا ببینید آیا می توانید عناصر دستگاه خارج از قفسه را برای برنامه خود پیدا کنید. اگر نمی توانید مطابقت خوبی برای برنامه خود پیدا کنید، لطفاً به ما اطلاع دهید و ما با شما برای توسعه و ساخت عناصر ماشینی که نیازهای شما را برآورده می کند، همکاری خواهیم کرد. اگر بیشتر به توانایی های مهندسی و تحقیق و توسعه ما به جای قابلیت های تولید علاقه مند هستید، از شما دعوت می کنیم از وب سایت ما دیدن کنید http://www.ags-engineering.com که در آن می توانید اطلاعات دقیق تری درباره طراحی، توسعه محصول، توسعه فرآیند، خدمات مشاوره مهندسی و موارد دیگر پیدا کنید. CLICK Product Finder-Locator Service صفحه قبلی
- Joining & Assembly & Fastening Processes, Welding, Brazing, Soldering
Joining & Assembly & Fastening Processes, Welding, Brazing, Soldering, Sintering, Adhesive Bonding, Press Fitting, Wave and Reflow Solder Process, Torch Furnace فرآیندهای اتصال و مونتاژ و چسباندن ما قطعات تولیدی شما را به هم متصل، مونتاژ و محکم می کنیم و با استفاده از جوش، لحیم کاری، لحیم کاری، زینترینگ، چسباندن، چسباندن، اتصالات پرس به محصولات نهایی یا نیمه تمام تبدیل می کنیم. برخی از محبوب ترین فرآیندهای جوشکاری ما عبارتند از: قوس الکتریکی، گاز اکسیژن، مقاومت، برآمدگی، درز، ناراحتی، ضربه ای، حالت جامد، پرتو الکترونی، لیزر، ترمیت، جوش القایی. فرآیندهای لحیم کاری محبوب ما عبارتند از: مشعل، القایی، کوره و لحیم کاری. روش های لحیم کاری ما عبارتند از لحیم کاری آهن، صفحه داغ، اجاق، القایی، شیب، موج، جریان مجدد و لحیم کاری اولتراسونیک. برای چسباندن چسب، ما اغلب از ترموپلاستیک ها و گرمانرم، اپوکسی ها، فنولیک ها، پلی اورتان، آلیاژهای چسب و همچنین برخی مواد شیمیایی و نوارهای دیگر استفاده می کنیم. در نهایت فرآیندهای چفت و بست ما شامل میخ زدن، پیچ کردن، مهره و پیچ و مهره، پرچ کردن، گیره زدن، سنجاق کردن، دوخت و منگنه کردن و اتصال پرس است. • جوشکاری: جوشکاری شامل اتصال مواد با ذوب قطعات کار و وارد کردن مواد پرکننده است که به حوضچه جوش مذاب نیز می پیوندد. وقتی ناحیه سرد شد، یک مفصل قوی بدست می آوریم. فشار در برخی موارد اعمال می شود. بر خلاف جوشکاری، عملیات لحیم کاری و لحیم کاری فقط شامل ذوب ماده ای با نقطه ذوب پایین تر بین قطعات کار می شود و قطعات کار ذوب نمی شوند. توصیه می کنیم اینجا را کلیک کنیددانلود تصاویر شماتیک فرآیندهای جوشکاری توسط AGS-TECH Inc. این به شما کمک می کند اطلاعاتی را که در زیر به شما ارائه می دهیم بهتر درک کنید. در جوشکاری قوس الکتریکی از یک منبع تغذیه و یک الکترود برای ایجاد قوس الکتریکی استفاده می کنیم که فلزات را ذوب می کند. نقطه جوش توسط یک گاز محافظ یا بخار یا مواد دیگر محافظت می شود. این فرآیند برای جوشکاری قطعات خودرو و سازه های فولادی رایج است. در جوشکاری قوس فلزی پوسته دار (SMAW) یا به عنوان جوشکاری چوبی نیز شناخته می شود، یک چوب الکترود به مواد پایه نزدیک می شود و یک قوس الکتریکی بین آنها ایجاد می شود. میله الکترود ذوب می شود و به عنوان ماده پرکننده عمل می کند. الکترود همچنین حاوی شار است که به عنوان لایه ای از سرباره عمل می کند و بخاراتی را منتشر می کند که به عنوان گاز محافظ عمل می کند. اینها ناحیه جوش را از آلودگی محیطی محافظت می کنند. هیچ پرکننده دیگری استفاده نمی شود. معایب این فرآیند کند بودن آن، نیاز به تعویض مکرر الکترودها، نیاز به جدا کردن سرباره باقیمانده ناشی از شار است. تعدادی از فلزات مانند آهن، فولاد، نیکل، آلومینیوم، مس و... قابل جوشکاری است. از مزایای آن می توان به ابزارهای ارزان قیمت و سهولت استفاده آن اشاره کرد. جوشکاری قوس فلزی گازی (GMAW) همچنین به عنوان گاز بیاثر فلزی (MIG) شناخته میشود، ما تغذیه مداوم یک پرکننده سیم الکترود مصرفی و یک گاز بیاثر یا تا حدی بیاثر داریم که در برابر آلودگی محیطی ناحیه جوش در اطراف سیم جریان دارد. فولاد، آلومینیوم و سایر فلزات غیر آهنی را می توان جوش داد. از مزایای MIG سرعت جوش بالا و کیفیت خوب است. معایب آن تجهیزات پیچیده و چالشهایی است که در محیطهای بادی در فضای باز با آن مواجه میشوند، زیرا ما باید گاز محافظ اطراف ناحیه جوش را پایدار نگه داریم. یکی از انواع GMAW جوش قوس الکتریکی با هسته شار (FCAW) است که از یک لوله فلزی ظریف پر از مواد شار تشکیل شده است. گاهی اوقات شار داخل لوله برای محافظت در برابر آلودگی محیطی کافی است. جوشکاری قوس زیردریایی (SAW) به طور گسترده یک فرآیند خودکار است که شامل تغذیه مداوم سیم و قوس می شود که در زیر لایه ای از پوشش شار زده می شود. نرخ تولید و کیفیت بالا است، سرباره جوش به راحتی جدا می شود و ما یک محیط کار بدون دود داریم. نقطه ضعف آن این است که فقط می توان از آن برای جوش دادن قطعات _cc781905-5cde-3194-bb3b-136bad5cf58d در موقعیت های خاص استفاده کرد. در جوشکاری قوسی تنگستن گاز (GTAW) یا جوشکاری تنگستن با گاز بی اثر (TIG) از الکترود تنگستن به همراه پرکننده جداگانه و گازهای بی اثر یا نزدیک به بی اثر استفاده می کنیم. همانطور که می دانیم تنگستن نقطه ذوب بالایی دارد و فلزی بسیار مناسب برای دماهای بسیار بالا می باشد. تنگستن در TIG بر خلاف روش های دیگر توضیح داده شده در بالا مصرف نمی شود. یک تکنیک جوش آهسته اما با کیفیت بالا نسبت به سایر تکنیک ها در جوشکاری مواد نازک مزیت دارد. مناسب برای بسیاری از فلزات جوشکاری قوس پلاسما مشابه است اما از گاز پلاسما برای ایجاد قوس استفاده می کند. قوس در جوشکاری قوس پلاسما در مقایسه با GTAW نسبتاً متمرکزتر است و می تواند برای طیف وسیع تری از ضخامت های فلزی با سرعت های بسیار بالاتر استفاده شود. GTAW و جوشکاری قوس پلاسما را می توان برای مواد کم و بیش مشابه اعمال کرد. OXY-FUEL / OXYFUEL WELDING همچنین به نام جوش اکسی استیلن، جوش اکسی، جوشکاری گاز با استفاده از سوخت گاز و اکسیژن برای جوشکاری انجام می شود. از آنجایی که از برق استفاده نمی شود، قابل حمل است و در جاهایی که برق وجود ندارد می توان از آن استفاده کرد. با استفاده از یک مشعل جوشکاری، قطعات و مواد پرکننده را برای تولید یک حوضچه فلز مذاب مشترک گرم می کنیم. می توان از سوخت های مختلفی مانند استیلن، بنزین، هیدروژن، پروپان، بوتان و ... استفاده کرد. در جوشکاری با سوخت اکسیژن از دو ظرف یکی برای سوخت و دیگری برای اکسیژن استفاده می کنیم. اکسیژن سوخت را اکسید می کند (آن را می سوزاند). جوش مقاومتی: این نوع جوش از گرمایش ژول بهره می برد و در محلی که جریان الکتریکی برای مدت معینی اعمال می شود گرما ایجاد می شود. جریان های زیادی از فلز عبور می کنند. حوضچه هایی از فلز مذاب در این مکان تشکیل می شود. روشهای جوشکاری مقاومتی به دلیل کارایی و پتانسیل آلودگی کم محبوب هستند. با این حال معایب هزینه تجهیزات نسبتاً قابل توجه و محدودیت ذاتی برای قطعات کار نسبتاً نازک است. جوش نقطه ای یکی از انواع عمده جوشکاری مقاومتی است. در اینجا با استفاده از دو الکترود مسی دو یا چند ورق یا قطعه کار روی هم قرار گرفته اند تا ورق ها را به هم بچسبانیم و جریان بالایی را از آنها عبور دهیم. ماده بین الکترودهای مسی گرم می شود و یک حوضچه مذاب در آن مکان ایجاد می شود. سپس جریان قطع می شود و نوک الکترودهای مسی محل جوش را خنک می کنند زیرا الکترودها با آب خنک می شوند. اعمال مقدار مناسب گرما به مواد و ضخامت مناسب برای این تکنیک کلیدی است، زیرا در صورت اعمال اشتباه، اتصال ضعیف می شود. جوشکاری نقطه ای از مزایای عدم تغییر شکل قابل توجهی در قطعه کار، بهره وری انرژی، سهولت اتوماسیون و نرخ تولید فوق العاده و عدم نیاز به پرکننده است. نقطه ضعف این است که از آنجایی که جوشکاری به جای ایجاد یک درز پیوسته در نقاطی انجام می شود، استحکام کلی می تواند نسبت به سایر روش های جوشکاری نسبتاً کمتر باشد. از طرف دیگر، درز جوش، جوش هایی را در سطوح فایری مواد مشابه ایجاد می کند. درز می تواند لب به لب یا مفصل همپوشانی باشد. جوشکاری درز از یک انتها شروع می شود و به تدریج به سمت دیگر حرکت می کند. این روش همچنین از دو الکترود مس برای اعمال فشار و جریان به ناحیه جوش استفاده می کند. الکترودهای دیسکی شکل با تماس ثابت در امتداد خط درز می چرخند و یک جوش پیوسته ایجاد می کنند. در اینجا نیز الکترودها با آب خنک می شوند. جوش ها بسیار قوی و قابل اعتماد هستند. روشهای دیگر عبارتند از تکنیکهای جوشکاری برآمدگی، فلاشی و جوشی. جوش حالت جامد با روش های قبلی که در بالا توضیح داده شد کمی متفاوت است. ادغام در دماهای کمتر از دمای ذوب فلزات متصل شده و بدون استفاده از پرکننده فلزی صورت می گیرد. ممکن است در برخی فرآیندها از فشار استفاده شود. روشهای مختلف عبارتند از: جوشکاری همزمان که در آن فلزات غیرمشابه از طریق یک قالب اکسترود میشوند، جوشکاری با فشار سرد که در آن آلیاژهای نرم را در زیر نقطه ذوب آنها به هم میپیوندیم، جوشکاری انتشاری یک تکنیک بدون خطوط جوش قابل مشاهده، جوش انفجاری برای اتصال مجدد آلیاژهای غیر مشابه به مواد آلیاژی غیر مشابه، فولادها، جوشکاری با پالس الکترومغناطیسی که در آن لوله ها و ورق ها را توسط نیروهای الکترومغناطیسی تسریع می کنیم، جوش فورج که شامل حرارت دادن فلزات تا دمای بالا و کوبیدن آنها به یکدیگر است، جوش اصطکاکی که در آن جوشکاری اصطکاکی کافی انجام می شود، جوشکاری اصطکاکی اغتشاشی که شامل جوشکاری غیر اصطکاکی می شود. ابزار مصرفی که از خط اتصال عبور می کند، جوشکاری با فشار داغ که در آن فلزات را در دماهای بالا زیر دمای ذوب در خلاء یا گازهای بی اثر فشار می دهیم، جوشکاری فشار ایزواستاتیک داغ فرآیندی است که در آن فشار را با استفاده از گازهای بی اثر در داخل ظرف اعمال می کنیم، جوشکاری غلتکی در جایی که می پیوندیم. مواد غیر مشابه با فشار دادن آنها بین دو چرخ دوار، جوش اولتراسونیک که در آن ورق های فلزی یا پلاستیکی نازک با استفاده از انرژی ارتعاشی فرکانس بالا جوش داده می شود. سایر فرآیندهای جوشکاری ما عبارتند از: جوشکاری با پرتو الکترونی با نفوذ عمیق و پردازش سریع، اما به عنوان روشی پرهزینه، آن را برای موارد خاص در نظر می گیریم، جوش الکترولاسگ روشی مناسب فقط برای صفحات ضخیم سنگین و قطعات فولادی، جوش القایی که در آن از القای الکترومغناطیسی استفاده می کنیم. قطعه کار رسانای الکتریکی یا فرومغناطیسی ما را گرم کنیم، جوش پرتو لیزر نیز با نفوذ عمیق و پردازش سریع اما روشی گران قیمت، جوش هیبریدی لیزری که LBW را با GMAW در همان سر جوش ترکیب می کند و قادر به پر کردن شکاف های 2 میلی متری بین صفحات است، جوش ضربه ای که شامل تخلیه الکتریکی به دنبال آهنگری مواد با فشار اعمال شده، جوش حرارتی حرارتی شامل واکنش گرمازا بین پودرهای آلومینیوم و اکسید آهن، جوش الکتروگاز با الکترودهای مصرفی و فقط با فولاد در حالت عمودی مورد استفاده قرار می گیرد، و در نهایت جوشکاری قوس میخ برای اتصال گل میخ به پایه. مواد با گرما و فشار توصیه می کنیم اینجا را کلیک کنیددانلود تصاویر شماتیک ما از فرآیندهای لحیم کاری، لحیم کاری و چسبندگی توسط AGS-TECH Inc. این به شما کمک می کند اطلاعاتی را که در زیر به شما ارائه می دهیم بهتر درک کنید. • لحیم کاری: ما دو یا چند فلز را با حرارت دادن فلزات پرکننده در بین آنها بالای نقطه ذوب آنها و با استفاده از عمل مویرگی برای پخش به هم وصل می کنیم. فرآیند مشابه لحیم کاری است اما دمای ذوب پرکننده در لحیم کاری بالاتر است. مانند جوشکاری، شار از مواد پرکننده در برابر آلودگی جوی محافظت می کند. پس از خنک شدن، قطعات کار به هم متصل می شوند. این فرآیند شامل مراحل کلیدی زیر است: تناسب و ترخیص خوب، تمیز کردن مناسب مواد پایه، نصب مناسب، انتخاب شار و جو مناسب، گرم کردن مجموعه و در نهایت تمیز کردن مجموعه لحیم کاری شده. برخی از فرآیندهای لحیم کاری ما عبارتند از TORCH BRAZING، یک روش محبوب که به صورت دستی یا به صورت خودکار انجام می شود. برای سفارشات تولید کم حجم و موارد تخصصی مناسب است. گرما با استفاده از شعله های گاز در نزدیکی محل لحیم کاری اعمال می شود. لحیم کاری کوره به مهارت کمتر اپراتور نیاز دارد و یک فرآیند نیمه اتوماتیک مناسب برای تولید انبوه صنعتی است. هم کنترل دما و هم کنترل اتمسفر در کوره از مزایای این روش است، زیرا اولی ما را قادر می سازد چرخه های حرارتی کنترل شده داشته باشیم و گرمایش موضعی را حذف کنیم، همانطور که در لحیم کاری مشعل وجود دارد، و دومی از قطعه در برابر اکسیداسیون محافظت می کند. با استفاده از جیگینگ میتوانیم هزینههای تولید را به حداقل برسانیم. معایب مصرف انرژی بالا، هزینه تجهیزات و ملاحظات چالش برانگیزتر طراحی است. لحیم کاری خلاء در یک کوره خلاء صورت می گیرد. یکنواختی دما حفظ می شود و اتصالات بدون شار و بسیار تمیز با تنش های پسماند بسیار کم به دست می آید. عملیات حرارتی میتواند در خلاء لحیم کاری انجام شود، زیرا تنشهای پسماند کم در چرخههای گرمایش و سرمایش آهسته وجود دارد. عیب اصلی آن هزینه بالای آن است زیرا ایجاد محیط خلاء یک فرآیند گران است. با این حال، روش دیگری DIP BRAZING، قطعات ثابتی را که در آن ترکیب لحیم کاری به سطوح جفت اعمال می شود، متصل می کند. سپس قطعات ثابت در حمام نمک مذاب مانند کلرید سدیم (نمک خوراکی) غوطه ور می شوند که به عنوان یک واسطه انتقال حرارت و شار عمل می کند. هوا حذف می شود و بنابراین هیچ اکسیدی تشکیل نمی شود. در لحیم کاری القایی ما مواد را توسط یک فلز پرکننده که نقطه ذوب کمتری نسبت به مواد پایه دارد به هم وصل می کنیم. جریان متناوب از سیم پیچ القایی یک میدان الکترومغناطیسی ایجاد می کند که گرمایش القایی را بر روی مواد مغناطیسی عمدتا آهنی القا می کند. این روش گرمایش انتخابی، اتصالات خوب با پرکنندههایی که فقط در نواحی مورد نظر جریان دارند، اکسیداسیون کم به دلیل عدم وجود شعله و سرد شدن سریع، گرمایش سریع، قوام و مناسب بودن برای تولید با حجم بالا را فراهم میکند. برای سرعت بخشیدن به فرآیندهای خود و اطمینان از ثبات، ما اغلب از پریفرم ها استفاده می کنیم. اطلاعات مربوط به تاسیسات لحیم کاری ما برای تولید اتصالات سرامیکی به فلز، آب بندی هرمتیک، ورودی خلاء، خلاء بالا و فوق العاده بالا و اجزای کنترل سیال را می توانید در اینجا بیابید:_cc781905-3005-00-00-00-00-00-00بروشور Brazing Factory • لحیم کاری: در لحیم کاری ذوب قطعات کار نداریم، بلکه یک فلز پرکننده با نقطه ذوب کمتر از قطعات اتصال دهنده که به داخل محل اتصال می ریزد، نداریم. فلز پرکننده در لحیم کاری در دمای پایین تری نسبت به لحیم کاری ذوب می شود. ما از آلیاژهای بدون سرب برای لحیم کاری استفاده می کنیم و دارای انطباق RoHS هستیم و برای کاربردها و نیازهای مختلف آلیاژهای مختلف و مناسب مانند آلیاژ نقره داریم. لحیم کاری مفاصلی را به ما ارائه می دهد که ضد گاز و مایع هستند. در لحیم کاری نرم، فلز پرکننده ما دارای نقطه ذوب زیر 400 درجه سانتیگراد است، در حالی که در لحیم کاری نقره و لحیم کاری به دمای بالاتری نیاز داریم. لحیم کاری نرم از دماهای پایین تری استفاده می کند اما منجر به اتصالات قوی برای کاربردهای سخت در دماهای بالا نمی شود. از طرف دیگر، لحیم کاری نقره به دماهای بالایی که توسط مشعل ارائه می شود نیاز دارد و اتصالات قوی مناسب برای کاربردهای دمای بالا را به ما می دهد. لحیم کاری به بالاترین درجه حرارت نیاز دارد و معمولاً از مشعل استفاده می شود. از آنجایی که اتصالات لحیم کاری بسیار قوی هستند، کاندیدای مناسبی برای تعمیر اجسام آهنی سنگین هستند. در خطوط تولید ما از لحیم کاری دستی و همچنین خطوط لحیم کاری خودکار استفاده می کنیم. INDUCTION SOLDERING از جریان AC با فرکانس بالا در یک سیم پیچ مسی برای تسهیل گرمایش القایی استفاده می کند. جریان در قسمت لحیم شده القا می شود و در نتیجه گرما در مقاومت بالا joint ایجاد می شود. این گرما فلز پرکننده را ذوب می کند. Flux نیز استفاده می شود. لحیم کاری القایی روش خوبی برای لحیم کاری سیکلندرها و لوله ها در یک فرآیند مداوم با پیچاندن سیم پیچ ها به دور آنها می باشد. لحیم کاری برخی از مواد مانند گرافیت و سرامیک دشوارتر است زیرا نیاز به آبکاری قطعات کار با فلز مناسب قبل از لحیم کاری دارد. این اتصال سطحی را تسهیل می کند. ما چنین موادی را به ویژه برای کاربردهای بسته بندی هرمتیک لحیم کاری انجام می دهیم. ما تخته های مدار چاپی (PCB) خود را در حجم بالا عمدتاً با استفاده از لحیم کاری موج تولید می کنیم. فقط برای مقادیر کمی از اهداف نمونه سازی ما از لحیم کاری دستی با استفاده از آهن لحیم کاری استفاده می کنیم. ما از لحیم کاری موجی هم برای مجموعه های PCB از طریق سوراخ و هم برای نصب روی سطح (PCBA) استفاده می کنیم. یک چسب موقت اجزا را به برد مدار متصل نگه می دارد و مجموعه روی یک نوار نقاله قرار می گیرد و از طریق تجهیزاتی که حاوی لحیم مذاب است حرکت می کند. ابتدا PCB فلکس شده و سپس وارد منطقه پیش گرمایش می شود. لحیم مذاب در تابه است و روی سطح آن دارای الگوی امواج ایستاده است. هنگامی که PCB روی این امواج حرکت می کند، این امواج با پایین PCB تماس می گیرند و به پدهای لحیم کاری می چسبند. لحیم کاری فقط روی پین ها و لنت ها می ماند و روی خود PCB نمی ماند. امواج در لحیم مذاب باید به خوبی کنترل شوند تا پاشیده نشود و نواحی ناخواسته تخته ها را لمس نکرده و آلوده نکنند. در REFLOW SOLDERING از خمیر لحیم چسبنده برای اتصال موقت قطعات الکترونیکی به بردها استفاده می کنیم. سپس تخته ها را با کنترل دما از طریق کوره جریان مجدد قرار می دهند. در اینجا لحیم کاری ذوب می شود و قطعات به طور دائم به هم متصل می شوند. ما از این تکنیک برای اجزای نصب سطحی و همچنین برای اجزای سوراخ دار استفاده می کنیم. کنترل دمای مناسب و تنظیم دمای فر برای جلوگیری از تخریب قطعات الکترونیکی روی برد با گرم کردن بیش از حد آنها بیش از حداکثر دمای آنها ضروری است. در فرآیند لحیم کاری مجدد، ما در واقع چندین ناحیه یا مراحل داریم که هر کدام دارای مشخصات حرارتی مشخصی هستند، مانند مرحله پیش گرم کردن، مرحله خیساندن حرارتی، مراحل جریان مجدد و خنک کننده. این مراحل مختلف برای لحیم کاری بدون آسیب در مجموعه های برد مدار چاپی (PCBA) ضروری است. ULTRASONIC SOLDERING یکی دیگر از تکنیک های پرکاربرد با قابلیت های منحصر به فرد است- می توان از آن برای لحیم کاری شیشه، سرامیک و مواد غیرفلزی استفاده کرد. به عنوان مثال پانل های فتوولتائیک که غیرفلزی هستند به الکترودهایی نیاز دارند که می توانند با استفاده از این تکنیک چسبانده شوند. در لحیم کاری اولتراسونیک، ما یک نوک لحیم کاری گرم شده را مستقر می کنیم که ارتعاشات اولتراسونیک را نیز منتشر می کند. این ارتعاشات حبابهای حفرهای را در سطح مشترک زیرلایه با مواد لحیم مذاب ایجاد میکنند. انرژی انفجاری کاویتاسیون سطح اکسید را اصلاح می کند و کثیفی و اکسیدها را از بین می برد. در این مدت یک لایه آلیاژی نیز تشکیل می شود. لحیم کاری در سطح اتصال دارای اکسیژن است و باعث ایجاد یک پیوند مشترک قوی بین شیشه و لحیم می شود. DIP SOLDERING را می توان به عنوان یک نسخه ساده تر از لحیم کاری موجی مناسب برای تولید در مقیاس کوچک در نظر گرفت. اولین شار تمیز کردن مانند سایر فرآیندها اعمال می شود. PCB ها با قطعات نصب شده به صورت دستی یا به صورت نیمه خودکار در یک مخزن حاوی لحیم مذاب فرو می روند. لحیم مذاب به نواحی فلزی در معرض دید می چسبد که توسط ماسک لحیم روی تخته محافظت نشده است. تجهیزات ساده و ارزان هستند. • چسباندن چسب: این روش محبوب دیگری است که ما اغلب از آن استفاده می کنیم و شامل چسباندن سطوح با استفاده از چسب، اپوکسی، مواد پلاستیکی یا سایر مواد شیمیایی است. پیوند با تبخیر حلال، پخت با حرارت، پخت در نور UV، پخت تحت فشار یا انتظار برای مدت زمان معین انجام می شود. چسب های مختلف با کارایی بالا در خطوط تولید ما استفاده می شود. با کاربرد و فرآیندهای پخت به درستی مهندسی شده، اتصال چسب می تواند منجر به اتصالات با تنش بسیار کم شود که قوی و قابل اعتماد هستند. باندهای چسب می توانند محافظ خوبی در برابر عوامل محیطی مانند رطوبت، آلاینده ها، خورنده ها، لرزش و ... باشند. مزایای اتصال چسب عبارتند از: آنها را می توان روی موادی اعمال کرد که در غیر این صورت لحیم کاری، جوشکاری یا لحیم کاری سخت است. همچنین می تواند برای مواد حساس به حرارت که در اثر جوشکاری یا سایر فرآیندهای دمای بالا آسیب می بینند، ترجیح داده شود. از دیگر مزایای چسب ها این است که می توان آنها را روی سطوح نامنظم اعمال کرد و در مقایسه با روش های دیگر، وزن مونتاژ را به مقدار بسیار کمی افزایش داد. همچنین تغییرات ابعادی در قطعات بسیار کم است. برخی از چسب ها دارای خواص تطبیق شاخص هستند و می توانند در بین اجزای نوری بدون کاهش قابل توجه نور یا قدرت سیگنال نوری استفاده شوند. از سوی دیگر معایب زمان پخت طولانی تر است که ممکن است خطوط تولید را کند کند، الزامات اتصال، الزامات آماده سازی سطح و مشکل در جداسازی قطعات در صورت نیاز به کار مجدد. اکثر عملیات چسباندن چسب ما شامل مراحل زیر است: -تصفیه سطح: روشهای تمیز کردن ویژه مانند تمیز کردن آب دیونیزه، تمیز کردن الکل، تمیز کردن پلاسما یا کرونا رایج هستند. پس از تمیز کردن، ممکن است برای اطمینان از بهترین اتصالات ممکن، تقویت کننده های چسبندگی را روی سطوح اعمال کنیم. -تثبیت قطعات: هم برای کاربرد چسب و هم برای پخت، وسایل سفارشی را طراحی و استفاده می کنیم. -کاربرد چسب: گاهی اوقات از سیستم های دستی و گاهی بسته به مورد از سیستم های خودکار مانند رباتیک، سروموتورها، محرک های خطی برای تحویل چسب ها در محل مناسب استفاده می کنیم و برای تحویل آن در حجم و مقدار مناسب از دیسپنسر استفاده می کنیم. - پخت: بسته به نوع چسب، ممکن است از خشک کردن و پخت ساده و همچنین پخت در زیر نورهای ماوراء بنفش استفاده کنیم که به عنوان کاتالیزور یا پخت حرارتی در اجاق عمل می کنند یا با استفاده از عناصر گرمایش مقاومتی نصب شده بر روی جیگ ها و فیکسچرها. توصیه می کنیم اینجا را کلیک کنیددانلود تصاویر شماتیک ما از فرآیندهای بستن توسط AGS-TECH Inc. این به شما کمک می کند اطلاعاتی را که در زیر به شما ارائه می دهیم بهتر درک کنید. • فرآیندهای چفت و بست: فرآیندهای اتصال مکانیکی ما به دو دسته تقسیم می شوند: اتصال دهنده ها و اتصالات انتگرال. نمونه هایی از اتصال دهنده هایی که ما استفاده می کنیم عبارتند از پیچ، پین، مهره، پیچ و مهره، پرچ. نمونههایی از اتصالات یکپارچه که ما استفاده میکنیم عبارتند از اتصالات محکم و کوچک، درزها، چینخوردگیها. با استفاده از انواع روشهای بست، مطمئن میشویم که اتصالات مکانیکی ما برای سالها استفاده قوی و قابل اعتماد هستند. پیچها و پیچها از رایجترین بستها برای نگهداشتن اجسام در کنار هم و قرار دادن آنها هستند. پیچ ها و پیچ های ما مطابق با استانداردهای ASME هستند. انواع مختلفی از پیچ ها و پیچ ها از جمله پیچ ها و پیچ های شش گوش، پیچ ها و پیچ ها، پیچ های دو سر، پیچ رولپلاک، پیچ چشمی، پیچ آینه ای، پیچ ورق فلزی، پیچ تنظیم ریز، پیچ های خوددریل و پیچ های خودکاری استفاده می شوند. ، پیچ تنظیم ، پیچ با واشر داخلی و ... و موارد دیگر. ما انواع مختلفی از سر پیچ مانند سرپیچ، گنبدی، گرد، سر فلنجی و انواع مختلف پیچ درایو مانند شکاف، فیلیپس، مربع، سوکت شش گوش داریم. از طرف دیگر یک RIVET یک بست مکانیکی دائمی است که از یک محور استوانه ای صاف و یک سر تشکیل شده است. پس از وارد کردن، انتهای دیگر پرچ تغییر شکل داده و قطر آن به گونه ای منبسط می شود که در جای خود باقی بماند. به عبارت دیگر پرچ قبل از نصب یک سر و بعد از نصب دو سر دارد. ما انواع مختلفی از پرچ ها را بسته به کاربرد، استحکام، دسترسی و هزینه نصب می کنیم، مانند پرچ های سر جامد/گرد، ساختاری، نیمه لوله ای، کور، اسکار، درایو، فلاش، قفل اصطکاکی، پرچ های خود سوراخ شونده. در مواردی که باید از تغییر شکل حرارتی و تغییر خواص مواد به دلیل گرمای جوشکاری اجتناب شود، می توان پرچ را ترجیح داد. پرچ نیز وزن سبک و به ویژه استحکام و استقامت خوبی در برابر نیروهای برشی ارائه می دهد. در برابر بارهای کششی، پیچ ها، مهره ها و پیچ ها ممکن است مناسب تر باشند. در فرآیند CLINCHING از پانچ و قالب های مخصوص برای ایجاد یک قفل مکانیکی بین ورق های فلزی در حال اتصال استفاده می کنیم. پانچ لایه های ورق فلز را به داخل حفره قالب می راند و منجر به تشکیل یک مفصل دائمی می شود. در کلینچ کردن نیازی به گرمایش و سرمایش نیست و این یک فرآیند سرد است. این یک فرآیند اقتصادی است که می تواند در برخی موارد جایگزین جوش نقطه ای شود. در PINNING ما از پین هایی استفاده می کنیم که عناصر ماشینی هستند که برای ایمن کردن موقعیت قطعات ماشین نسبت به یکدیگر استفاده می شوند. انواع اصلی آن عبارتند از: پینهای کلویس، سنجاق چوبی، سنجاق فنری، پینهای رولپلاک، و پین اسپلیت. در STAPLING ما از تفنگ های منگنه و منگنه استفاده می کنیم که بست های دو شاخه ای هستند که برای اتصال یا اتصال مواد استفاده می شوند. منگنه دارای مزایای زیر است: مقرون به صرفه بودن، استفاده آسان و سریع، تاج منگنه را می توان برای پل زدن مواد به هم چسبیده به هم استفاده کرد، تاج منگنه می تواند پل زدن یک قطعه مانند کابل و چسباندن آن را به یک سطح بدون سوراخ یا سوراخ کردن آسان کند. آسیب رسان، حذف نسبتا آسان. پرس فیتینگ با فشار دادن قطعات به هم و اصطکاک بین آنها قطعات را محکم می کند. قطعات پرس مناسب متشکل از یک محور بزرگ و یک سوراخ کم اندازه معمولاً با یکی از دو روش مونتاژ می شوند: یا با اعمال نیرو یا استفاده از انبساط یا انقباض حرارتی قطعات. وقتی اتصالات پرس با اعمال نیرو ایجاد می شود، یا از پرس هیدرولیک یا پرس دستی استفاده می کنیم. از طرف دیگر هنگامی که اتصالات پرس با انبساط حرارتی برقرار می شود، قطعات پوششی را گرم کرده و در حالی که گرم هستند در جای خود مونتاژ می کنیم. وقتی سرد می شوند منقبض می شوند و به ابعاد طبیعی خود باز می گردند. این باعث تناسب پرس خوب می شود. ما به این روش SHRINK-FITTING می گوییم. راه دیگر انجام این کار این است که قسمت های بسته بندی شده را قبل از مونتاژ سرد کنید و سپس آنها را به قسمت های جفت خود بکشید. هنگامی که مجموعه گرم می شود، آنها منبسط می شوند و ما یک تناسب محکم به دست می آوریم. این روش دوم ممکن است در مواردی که گرمایش خطر تغییر خواص مواد را به همراه دارد ارجح باشد. خنک کردن در آن موارد ایمن تر است. قطعات و مجموعه های پنوماتیک و هیدرولیک • سوپاپ ها، قطعات هیدرولیک و پنوماتیک مانند O-ring، واشر، آب بندی، واشر، رینگ، شیم. از آنجایی که شیرها و اجزای پنوماتیکی تنوع زیادی دارند، نمیتوانیم همه چیز را در اینجا فهرست کنیم. بسته به محیط های فیزیکی و شیمیایی برنامه شما، ما محصولات ویژه ای برای شما داریم. لطفاً کاربرد، نوع قطعه، مشخصات، شرایط محیطی مانند فشار، دما، مایعات یا گازهایی که با شیرها و اجزای پنوماتیک شما در تماس هستند را برای ما مشخص کنید. و ما مناسب ترین محصول را برای شما انتخاب می کنیم یا آن را به طور خاص برای کاربرد شما تولید می کنیم. CLICK Product Finder-Locator Service صفحه قبلی
- Glass and Ceramic Manufacturing, Hermetic Packages, Seals, Bonding
Glass and Ceramic Manufacturing, Hermetic Packages Seals and Bonding, Tempered Bulletproof Glass, Blow Moulding, Optical Grade Glass, Conductive Glass, Molding شکل دهی و شکل دهی شیشه و سرامیک نوع تولید شیشه ای که ما ارائه می دهیم عبارتند از: شیشه کانتینری، دمیدن شیشه، الیاف و لوله و میله شیشه، ظروف شیشه ای خانگی و صنعتی، لامپ و لامپ، قالب گیری شیشه ای دقیق، قطعات و مجموعه های نوری، شیشه های تخت و ورق و فلوت. ما هم فرمینگ با دست و هم فرمینگ ماشین را انجام می دهیم. فرآیندهای محبوب فنی تولید سرامیک ما عبارتند از پرس قالب، پرس ایزواستاتیک، پرس گرم ایزواستاتیک، پرس گرم، ریختهگری لغزشی، ریختهگری نوار، اکستروژن، قالبگیری تزریقی، ماشینکاری سبز، تف جوشی یا پخت، سنگزنی الماس، مجموعههای هرمتیک. توصیه می کنیم اینجا را کلیک کنید دانلود تصاویر شماتیک فرآیندهای شکل دهی و شکل دهی شیشه توسط AGS-TECH Inc. دانلود تصاویر شماتیک ما از فرآیندهای فنی تولید سرامیک توسط AGS-TECH Inc. این فایلهای دانلودی به همراه عکسها و طرحها به شما در درک بهتر اطلاعاتی که در زیر در اختیار شما قرار میدهیم کمک میکنند. • تولید شیشه ظروف: ما خطوط پرس و دمش خودکار و همچنین خطوط دمنده و دمنده را برای تولید داریم. در فرآیند دمیدن و دمیدن، یک گوب را در قالب خالی می اندازیم و با ضربه ای از هوای فشرده از بالا، گردن را تشکیل می دهیم. بلافاصله پس از این، هوای فشرده برای بار دوم از جهت دیگر از طریق گردن ظرف دمیده می شود تا پیش فرم بطری را تشکیل دهد. سپس این پیشفرم به قالب واقعی منتقل میشود، مجدداً گرم میشود تا نرم شود و هوای فشرده اعمال میشود تا شکل ظرف نهایی به پیشفرم بدهد. به طور واضح تر، تحت فشار قرار می گیرد و به دیواره های حفره قالب دمنده فشار داده می شود تا شکل دلخواه خود را بگیرد. در نهایت، ظرف شیشهای تولید شده برای گرم کردن مجدد و حذف تنشهای حاصل از قالبگیری به یک کوره بازپخت منتقل میشود و به صورت کنترلشده سرد میشود. در روش پرس و دم، گودهای مذاب را در قالب پاریسون (قالب خالی) قرار داده و به شکل پاریسون (شکل خالی) فشار می دهند. سپس مواد خالی به قالبهای دمنده منتقل میشوند و مانند فرآیندی که در بالا در قسمت «فرآیند دمیدن و دمیدن» توضیح داده شد، دمیده میشوند. مراحل بعدی مانند بازپخت و کاهش استرس مشابه یا مشابه هستند. • دمیدن شیشه: ما محصولات شیشه ای را با استفاده از دمیدن دستی معمولی و همچنین با استفاده از هوای فشرده با تجهیزات خودکار تولید کرده ایم. برای برخی از سفارشات، دمیدن معمولی ضروری است، مانند پروژههایی که شامل کارهای هنری شیشهای هستند، یا پروژههایی که به تعداد قطعات کمتری با تلورانسهای ضعیف نیاز دارند، پروژههای نمونهسازی/دمو... و غیره. دمیدن شیشه معمولی شامل فرو بردن یک لوله فلزی توخالی در یک گلدان شیشه مذاب و چرخاندن لوله برای جمع آوری مقداری از مواد شیشه است. شیشه جمعآوریشده در نوک لوله بر روی آهن مسطح، به شکل دلخواه، کشیده، دوباره گرم شده و هوا دمیده میشود. پس از آماده شدن، داخل قالب گذاشته و هوا دمیده می شود. حفره قالب مرطوب است تا از تماس شیشه با فلز جلوگیری شود. فیلم آب مانند یک بالشتک بین آنها عمل می کند. دمیدن دستی یک فرآیند آهسته کار فشرده است و فقط برای نمونه سازی یا اقلام با ارزش بالا مناسب است و برای سفارشات ارزان قیمت در هر قطعه مناسب نیست. • ساخت ظروف شیشه ای خانگی و صنعتی: با استفاده از انواع مواد شیشه ای انواع زیادی ظروف شیشه ای تولید می شود. برخی از لیوان ها مقاوم در برابر حرارت هستند و برای ظروف آزمایشگاهی مناسب هستند، در حالی که برخی از آنها به اندازه کافی برای مقاومت در برابر ماشین های ظرفشویی برای چندین بار خوب هستند و برای ساخت محصولات داخلی مناسب هستند. با استفاده از دستگاه های Westlake روزانه ده ها هزار قطعه لیوان نوشیدنی تولید می شود. برای سادهتر شدن، شیشه مذاب با خلاء جمعآوری میشود و برای ساختن پیشفرمها در قالب قرار میگیرد. سپس هوا به داخل قالب ها دمیده می شود، این ها به قالب دیگری منتقل می شوند و دوباره هوا دمیده می شود و شیشه شکل نهایی خود را به خود می گیرد. مانند دمیدن دستی، این قالب ها با آب مرطوب نگه داشته می شوند. کشش بیشتر بخشی از عملیات تکمیلی است که در آن گردن در حال شکل گیری است. شیشه اضافی سوخته است. پس از آن فرآیند گرمایش و سرمایش مجدد کنترل شده که در بالا توضیح داده شد به شرح زیر است. • شکل دهی لوله و میله شیشه ای: فرآیندهای اصلی که ما برای ساخت لوله های شیشه ای استفاده می کنیم، فرآیندهای DANNER و VELLO هستند. در فرآیند دانر، شیشه از یک کوره جریان می یابد و روی یک آستین شیبدار ساخته شده از مواد نسوز می افتد. آستین بر روی یک محور توخالی چرخان یا لوله دمنده حمل می شود. سپس شیشه به دور آستین پیچیده می شود و یک لایه صاف تشکیل می دهد که به سمت پایین آستین و روی نوک میل جریان می یابد. در حالت تیوبفرمینگ، هوا از طریق لوله دمنده با نوک توخالی دمیده میشود و در شکلگیری میلهای از نوکهای جامد روی شفت استفاده میکنیم. سپس لوله ها یا میله ها روی غلتک های حامل کشیده می شوند. ابعادی مانند ضخامت دیواره و قطر لوله های شیشه ای با تنظیم قطر آستین و دمیدن فشار هوا به مقدار دلخواه، تنظیم دما، سرعت جریان شیشه و سرعت کشیدن به مقادیر دلخواه تنظیم می شود. از طرف دیگر، فرآیند تولید لوله شیشهای Vello شامل شیشهای است که از کوره بیرون میرود و به کاسهای با سنبه یا زنگ توخالی وارد میشود. سپس شیشه از فضای هوایی بین سنبه و کاسه عبور می کند و شکل لوله ای به خود می گیرد. سپس از روی غلتک ها به ماشین کشش می رود و خنک می شود. در انتهای خط خنک کننده برش و پردازش نهایی انجام می شود. ابعاد لوله را می توان درست مانند فرآیند Danner تنظیم کرد. هنگام مقایسه فرآیند Danner با Vello، میتوان گفت که فرآیند Vello برای تولید مقادیر زیاد مناسبتر است، در حالی که فرآیند Danner ممکن است برای سفارشات لولههای با حجم کوچکتر مناسبتر باشد. فرآوری شیشههای شیت و تخت و فلوت: ما مقادیر زیادی شیشههای مسطح در ضخامتهای متفاوت از ضخامتهای زیر میلیمتری تا چندین سانتیمتر داریم. عینک های تخت ما تقریباً از نظر نوری کامل هستند. ما شیشه ای را با پوشش های خاص مانند پوشش های نوری ارائه می دهیم که در آن از روش رسوب بخار شیمیایی برای قرار دادن پوشش هایی مانند پوشش ضد انعکاس یا آینه استفاده می شود. همچنین پوشش های رسانای شفاف رایج هستند. همچنین پوششهای آبگریز یا آبدوست روی شیشه و پوششی که شیشه را خود تمیز میکند نیز موجود است. عینک های سکوریت، ضد گلوله و لمینت از دیگر اقلام محبوب هستند. شیشه را با تلورانس های دلخواه به شکل دلخواه برش می دهیم. سایر عملیات ثانویه مانند خم کردن یا خم کردن شیشه تخت در دسترس هستند. قالب گیری شیشه ای دقیق: ما از این تکنیک بیشتر برای ساخت قطعات نوری دقیق بدون نیاز به تکنیک های گران تر و زمان برتر مانند سنگ زنی، لایه برداری و پرداخت استفاده می کنیم. این تکنیک همیشه برای ساخت بهترین اپتیک کافی نیست، اما در برخی موارد مانند محصولات مصرفی، دوربینهای دیجیتال، اپتیکهای پزشکی میتواند گزینه ارزانتری برای تولید با حجم بالا باشد. همچنین نسبت به دیگر تکنیک های شکل دهی شیشه که در آن هندسه های پیچیده مورد نیاز است، مانند در مورد قیر، مزیت دارد. فرآیند اصلی شامل بارگذاری قسمت پایینی قالب با شیشه خالی، تخلیه محفظه فرآیند برای حذف اکسیژن، نزدیک شدن به بسته شدن قالب، گرم کردن سریع و همدما قالب و شیشه با نور مادون قرمز، بسته شدن بیشتر نیمه های قالب است. شیشه نرم شده را به آرامی و به صورت کنترل شده به ضخامت مورد نظر فشار دهید و در نهایت شیشه خنک شود و محفظه با نیتروژن پر شود و محصول خارج شود. کنترل دقیق دما، فاصله بسته شدن قالب، نیروی بسته شدن قالب، تطبیق ضرایب انبساط قالب و مواد شیشه ای در این فرآیند کلیدی هستند. • ساخت قطعات و مجموعه های نوری شیشه ای: علاوه بر قالب گیری شیشه ای دقیق، تعدادی از فرآیندهای ارزشمندی وجود دارد که ما برای ساخت قطعات و مجموعه های نوری با کیفیت بالا برای کاربردهای سخت استفاده می کنیم. سنگ زنی، روکش و صیقل دادن شیشه های درجه نوری در دوغاب های ساینده خاص، یک هنر و علم برای ساخت لنزهای نوری، منشور، تخت و غیره است. صافی سطح، موج دار بودن، صافی و سطوح نوری بدون نقص نیاز به تجربه زیادی با چنین فرآیندهایی دارد. تغییرات کوچک در محیط می تواند منجر به خارج شدن محصولات با مشخصات فنی شود و خط تولید را متوقف کند. مواردی وجود دارد که تنها یک پاک کردن روی سطح نوری با یک پارچه تمیز می تواند باعث شود که یک محصول با مشخصات مطابقت داشته باشد یا در تست شکست بخورد. برخی از مواد محبوب شیشه ای مورد استفاده عبارتند از: سیلیس ذوب شده، کوارتز، BK7. همچنین مونتاژ چنین قطعاتی نیاز به تجربه تخصصی در طاقچه دارد. گاهی اوقات از چسب های مخصوص استفاده می شود. با این حال، گاهی اوقات تکنیکی به نام تماس نوری بهترین انتخاب است و شامل هیچ ماده ای در بین شیشه های نوری متصل نیست. این شامل تماس فیزیکی با سطوح صاف برای اتصال بدون چسب به یکدیگر است. در برخی موارد از اسپیسرهای مکانیکی، میلهها یا گلولههای شیشهای دقیق، گیرهها یا اجزای فلزی ماشینکاری شده برای مونتاژ اجزای نوری در فواصل معین و با جهتگیریهای هندسی خاص به یکدیگر استفاده میشود. اجازه دهید برخی از تکنیک های محبوب خود را برای ساخت اپتیک های پیشرفته بررسی کنیم. سنگ زنی و لپینگ و صیقل دادن: شکل خشن قطعه نوری با آسیاب کردن یک شیشه خالی به دست می آید. سپس با چرخاندن و مالش سطوح ناصاف اجزای نوری بر روی ابزارهایی با شکل های سطحی دلخواه، لایه برداری و پرداخت انجام می شود. دوغاب هایی با ذرات ساینده ریز و سیال در بین اپتیک و ابزارهای شکل دهنده ریخته می شوند. اندازه ذرات ساینده در این گونه دوغاب ها را می توان با توجه به درجه صافی مورد نظر انتخاب کرد. انحراف سطوح نوری بحرانی از اشکال مورد نظر بر حسب طول موج نور مورد استفاده بیان می شود. اپتیک با دقت بالا ما دارای یک دهم طول موج (Wavelength/10) تلورانس یا حتی بیشتر از آن ممکن است. علاوه بر پروفیل سطح، سطوح بحرانی اسکن می شوند و از نظر سایر ویژگی ها و عیوب سطح مانند ابعاد، خراش ها، براده ها، حفره ها، لکه ها و غیره ارزیابی می شوند. کنترل شدید شرایط محیطی در کف تولید نوری و الزامات اندازه گیری و آزمایش گسترده با تجهیزات پیشرفته این صنعت را به یک شاخه چالش برانگیز از صنعت تبدیل کرده است. • فرآیندهای ثانویه در تولید شیشه: باز هم، ما فقط در مورد فرآیندهای ثانویه و تکمیلی شیشه به تخیل شما محدود می شویم. در اینجا تعدادی از آنها را فهرست می کنیم: -پوشش روی شیشه (نوری، الکتریکی، تریبولوژیکی، حرارتی، عملکردی، مکانیکی...). به عنوان مثال میتوانیم ویژگیهای سطحی شیشه را تغییر دهیم و بهعنوان مثال، گرما را منعکس کنیم تا فضای داخلی ساختمان خنک بماند، یا با استفاده از فناوری نانو، یک طرف مادون قرمز را جذب کند. این به گرم نگه داشتن داخل ساختمان ها کمک می کند زیرا بیرونی ترین لایه سطحی شیشه اشعه مادون قرمز را در داخل ساختمان جذب می کند و آن را به داخل بازتاب می دهد. -اچینگ روی شیشه -برچسب سرامیکی کاربردی (ACL) -حکاکی - پرداخت شعله ای - پولیش شیمیایی -رنگآمیزی ساخت سرامیک های فنی • پرس دای: شامل فشرده سازی تک محوری پودرهای دانه ای محصور در قالب است. • پرس گرم: شبیه پرس قالب است اما با افزودن دما برای افزایش تراکم. پودر یا پریفرم فشرده در قالب گرافیتی قرار می گیرد و فشار تک محوری اعمال می شود در حالی که قالب در دماهای بالا مانند 2000 درجه سانتیگراد نگهداری می شود. دماها بسته به نوع پودر سرامیکی در حال پردازش می تواند متفاوت باشد. برای شکلها و هندسههای پیچیده، ممکن است به پردازشهای بعدی دیگر مانند آسیاب الماس نیاز باشد. • پرس ایزواستاتیک: پودرهای گرانول یا مواد فشرده قالبی در ظروف دربسته قرار می گیرند و سپس در یک ظرف تحت فشار بسته با مایع داخل آن قرار می گیرند. سپس با افزایش فشار مخزن تحت فشار فشرده می شوند. مایع داخل ظرف، نیروهای فشار را به طور یکنواخت در کل سطح ظرف محفوظ منتقل می کند. بنابراین مواد به طور یکنواخت فشرده می شوند و شکل ظرف انعطاف پذیر و مشخصات داخلی و ویژگی های آن را به خود می گیرند. • پرس ایزواستاتیک گرم: مشابه پرس ایزواستاتیک است، اما علاوه بر اتمسفر گاز تحت فشار، ما فشرده را در دمای بالا تف جوشی می کنیم. پرس ایزواستاتیک داغ منجر به تراکم بیشتر و افزایش استحکام می شود. • ریخته گری لغزنده / ریخته گری تخلیه: قالب را با سوسپانسیونی از ذرات سرامیکی به اندازه میکرومتر و مایع حامل پر می کنیم. این مخلوط "لغزش" نامیده می شود. قالب دارای منافذ است و بنابراین مایع موجود در مخلوط به داخل قالب فیلتر می شود. در نتیجه روی سطوح داخلی قالب قالبی تشکیل می شود. پس از پخت می توان قطعات را از قالب خارج کرد. • ریخته گری نواری: ما نوارهای سرامیکی را با ریخته گری دوغاب های سرامیکی بر روی سطوح حامل متحرک مسطح تولید می کنیم. دوغاب ها حاوی پودرهای سرامیکی مخلوط با سایر مواد شیمیایی برای مقاصد اتصال و حمل هستند. همانطور که حلال ها تبخیر می شوند ورقه های متراکم و انعطاف پذیر سرامیکی باقی می مانند که می توانند به دلخواه بریده یا نورد شوند. • شکل دهی اکستروژن: مانند سایر فرآیندهای اکستروژن، مخلوط نرم پودر سرامیک با بایندرها و سایر مواد شیمیایی از داخل قالب عبور داده می شود تا شکل مقطع خود را به دست آورد و سپس در طول های دلخواه برش داده می شود. این فرآیند با مخلوط های سرامیکی سرد یا گرم شده انجام می شود. قالب گیری تزریقی با فشار کم: مخلوطی از پودر سرامیک را با چسب ها و حلال ها تهیه می کنیم و آن را تا دمایی گرم می کنیم که بتوان آن را به راحتی فشار داد و به داخل حفره ابزار وارد کرد. هنگامی که چرخه قالب گیری کامل شد، قطعه خارج می شود و ماده شیمیایی اتصال سوزانده می شود. با استفاده از قالبگیری تزریقی، میتوانیم قطعات پیچیده را در حجمهای بالا از نظر اقتصادی بدست آوریم. سوراخها که کسری کوچک از میلیمتر بر روی دیواری با ضخامت 10 میلیمتر هستند، امکانپذیر است، رزوهها بدون ماشینکاری دیگر امکانپذیر است، تلرانسهایی تا حد سختی تا 0.5% +/- ممکن است زمانی که قطعات ماشین کاری شوند، حتی کمتر ضخامت دیوار از 0.5 میلی متر تا طول 12.5 میلی متر و همچنین ضخامت دیوار 6.5 میلی متر تا طول 150 میلی متر امکان پذیر است. • ماشینکاری سبز: با استفاده از همان ابزارهای ماشینکاری فلزی، می توانیم مواد سرامیکی فشرده را در حالی که هنوز مانند گچ نرم هستند، ماشین کنیم. تحمل +/- 1٪ امکان پذیر است. برای تحمل بهتر از آسیاب الماس استفاده می کنیم. زینترینگ یا پخت: زینترینگ، متراکم شدن کامل را ممکن می سازد. انقباض قابل توجهی در قسمت های فشرده سبز رخ می دهد، اما این مشکل بزرگی نیست زیرا ما این تغییرات ابعادی را هنگام طراحی قطعه و ابزار در نظر می گیریم. ذرات پودر به یکدیگر متصل می شوند و تخلخل ناشی از فرآیند تراکم تا حد زیادی از بین می رود. • سنگ زنی الماس: سخت ترین ماده جهان "الماس" برای آسیاب کردن مواد سخت مانند سرامیک و قطعات دقیق به دست می آید. تلورانس ها در محدوده میکرومتر و سطوح بسیار صاف به دست می آیند. با توجه به هزینه ای که دارد، ما این تکنیک را تنها زمانی در نظر می گیریم که واقعاً به آن نیاز داشته باشیم. • مجموعه های HERMETIC آنهایی هستند که عملاً اجازه تبادل ماده، جامد، مایع یا گاز را بین سطوح مشترک نمی دهند. آب بندی هرمتیک هوادار است. به عنوان مثال محفظه های الکترونیکی هرمتیک آنهایی هستند که محتویات داخلی حساس یک دستگاه بسته بندی شده را از رطوبت، آلاینده ها یا گازها در امان نگه می دارند. هیچ چیز 100% هرمتیک نیست، اما وقتی از هرمسیتی صحبت می کنیم، منظورمان این است که از نظر عملی، هرمتیکی وجود دارد تا جایی که میزان نشتی آنقدر کم است که دستگاه ها در شرایط محیطی عادی برای مدت زمان طولانی ایمن هستند. مجموعه های هرمتیک ما شامل اجزای فلزی، شیشه ای و سرامیکی، فلز-سرامیک، سرامیک-فلز-سرامیک، فلز-سرامیک-فلز، فلز به فلز، فلز-شیشه، فلز-شیشه-فلز، شیشه-فلز-شیشه، شیشه- فلز و شیشه به شیشه و سایر ترکیبات اتصال فلز-شیشه-سرامیک. به عنوان مثال، میتوانیم اجزای سرامیکی را پوشش فلزی بپوشانیم تا بتوانند به شدت به اجزای دیگر در مجموعه متصل شوند و قابلیت آببندی عالی داشته باشند. ما دانش پوشش دادن فیبرهای نوری یا ورودی ها را با فلز و لحیم کاری یا لحیم کاری آنها به محفظه ها داریم، بنابراین هیچ گازی به داخل محفظه ها عبور نمی کند یا نشت نمی کند. بنابراین از آنها برای ساخت محفظه های الکترونیکی برای محصور کردن دستگاه های حساس و محافظت از آنها در برابر جو بیرونی استفاده می شود. علاوه بر ویژگیهای آببندی عالی، ویژگیهای دیگری مانند ضریب انبساط حرارتی، مقاومت در برابر تغییر شکل، ماهیت عدم خروج گاز، طول عمر بسیار طولانی، ماهیت نارسانا، خواص عایق حرارتی، طبیعت ضد الکتریسیته ساکن... مواد شیشه ای و سرامیکی را برای کاربردهای خاص انتخاب کنید. اطلاعات مربوط به تاسیسات ما برای تولید اتصالات سرامیکی به فلز، آب بندی هرمتیک، ورودی خلاء، اجزای کنترل خلاء و سیال بالا و فوق العاده بالا را می توانید در اینجا بیابید:بروشور Hermetic Components Factory CLICK Product Finder-Locator Service صفحه قبلی
- Wire & Spring Forming, Shaping, Welding, Assembly of Wires, Coil, CNC
Wire & Spring Forming, Shaping, Welding, Assembly of Wires, Coil Compression Extension Torsion Flat Springs, Custom Wires, Helical Springs at AGS-TECH Inc. شکل دهی سیم و فنر ما سیم های سفارشی، مونتاژ سیم، سیم هایی که به شکل های دو بعدی و سه بعدی دلخواه شکل می گیرند، شبکه های سیمی، مش، محفظه ها، سبد، حصار، فنر سیمی، فنر مسطح تولید می کنیم. پیچش، فشرده سازی، کشش، فنرهای صاف و موارد دیگر. فرآیندهای ما عبارتند از شکل دهی سیم و فنر، سیم کشی، شکل دهی، خمش، جوشکاری، لحیم کاری، لحیم کاری، سوراخ کردن، تاب دادن، سوراخ کردن، پخ زدن، سنگ زنی، رزوه کاری، پوشش دهی، چهار لغزنده، شکل دهی اسلاید، سیم پیچی، سیم پیچی، برهم زدن. توصیه می کنیم اینجا را کلیک کنید تصاویر شماتیک ما از فرآیندهای شکل دهی سیم و فنر توسط AGS-TECH Inc. این فایل قابل دانلود با عکس و طرح به شما کمک می کند تا اطلاعاتی را که در زیر در اختیار شما قرار می دهیم بهتر درک کنید. • سیم کشی: با استفاده از نیروهای کششی، استوک فلزی را کشیده و از طریق قالب می کشیم تا قطر آن کاهش یافته و طول آن افزایش یابد. گاهی از یک سری قالب استفاده می کنیم. ما قادریم برای هر گیج سیم قالب بسازیم. با استفاده از مواد با استحکام کششی بالا سیم های بسیار نازکی می کشیم. ما سیم های سرد و گرم را ارائه می دهیم. • شکل دهی سیم: رول سیم اندازه گیری شده خم شده و به یک محصول مفید تبدیل می شود. ما قابلیت تشکیل سیم از تمامی گیج ها از جمله رشته های نازک و همچنین سیم های ضخیم مانند فنرهای زیر شاسی خودرو را داریم. تجهیزاتی که ما برای شکلدهی سیم استفاده میکنیم، سیمسازهای دستی و CNC، کویل، پرسهای برقی، چهارسرلاید، چند لغزنده هستند. فرآیندهای ما کشیدن، خم کردن، صاف کردن، مسطح کردن، کشش، برش، برهم زدن، لحیم کاری و جوشکاری و لحیم کاری، مونتاژ، سیم پیچی، پیچاندن (یا بال زدن)، سوراخ کردن، رزوه کشی، سوراخ کردن، پخ زدن، سنگ زنی، پوشش دهی و عملیات سطحی است. تجهیزات پیشرفته ما را می توان به گونه ای تنظیم کرد که طرح های بسیار پیچیده با هر شکل و تلورانس های دقیق ایجاد کند. ما انواع مختلف انتهایی مانند انتهای کروی، نوک تیز یا پخ را برای سیم های شما پیشنهاد می کنیم. اکثر پروژه های سیم سازی ما حداقل تا صفر هزینه ابزارآلات دارند. زمان چرخش نمونه به طور کلی روز است. تغییرات در طراحی/پیکربندی فرم های سیم را می توان خیلی سریع انجام داد. • SPRING FORMING: AGS-TECH انواع زیادی از فنرها را تولید می کند از جمله: -پیچ خوردگی / دو فنر پیچشی فنر کششی / فشاری فنر ثابت / متغیر سیم پیچ و فنر حلزونی فنر تخت و برگ -تعادل فنر - واشر بللویل -بهار نفیگر فنر پیچشی با نرخ پیشرونده -بهار موج -Volute Spring چشمه های مخروطی حلقه های بهار چشمه های ساعت -کلیپ های ما فنرها را از مواد مختلف تولید می کنیم و می توانیم با توجه به کاربرد شما شما را راهنمایی کنیم. متداول ترین مواد عبارتند از فولاد ضد زنگ، کروم سیلیکون، فولاد پر کربن، کم کربن با حرارت روغن، کروم وانادیوم، برنز فسفر، تیتانیوم، آلیاژ مس بریلیم، سرامیک با دمای بالا. ما در ساخت فنرها از تکنیک های مختلفی از جمله سیم پیچی CNC، سیم پیچی سرد، سیم پیچی گرم، سخت کاری، تکمیل استفاده می کنیم. سایر تکنیکهایی که قبلاً در بالا ذکر شد تحت شکلدهی سیم نیز در عملیات تولید فنر ما رایج هستند. • خدمات تکمیلی سیم ها و فنرها: بسته به انتخاب و نیاز شما می توانیم محصولات شما را به طرق مختلف تکمیل کنیم. برخی از فرآیندهای رایجی که ما ارائه می دهیم عبارتند از: رنگ آمیزی، پوشش پودری، آبکاری، غوطه ور شدن وینیل، آنودایز کردن، کاهش استرس، عملیات حرارتی، شات پین، غلتش، کرومات، نیکل بدون الکترود، غیرفعال سازی، پخته شدن پلاستیک , تمیز کردن پلاسما. CLICK Product Finder-Locator Service صفحه قبلی
- Sheet Metal Forming Fabrication, Stamping, Punching, Deep Drawing, CNC
Sheet Metal Forming and Fabrication, Stamping, Punching, Bending, Progressive Die, Spot Welding, Deep Drawing, Metal Blanking and Slitting at AGS-TECH Inc. مهر زنی و ساخت ورق فلز ما مهر زنی ورق فلزی، شکل دهی، شکل دهی، خم شدن، پانچ کردن، خالی کردن، بریدن، سوراخ کردن، بریدگی، نوک زدن، تراشیدن، پرس کاری، ساخت، کشیدن عمیق با استفاده از قالب های تک پانچ / تک ضربه ای و همچنین قالب های پیشرونده و ریسندگی، شکل دهی لاستیکی و هیدروفرمینگ؛ برش ورق فلزی با استفاده از جت آب، پلاسما، لیزر، اره، شعله؛ مونتاژ ورق فلزی با استفاده از جوشکاری، جوشکاری نقطه ای؛ برآمدگی و خم شدن لوله ورق فلزی؛ تکمیل سطوح ورق فلزی شامل رنگ آمیزی غوطه ور یا اسپری، پوشش پودری الکترواستاتیک، آنودایز، آبکاری، کندوپاش و موارد دیگر. خدمات ما از نمونه سازی سریع ورق فلزی تا تولید با حجم بالا را شامل می شود. توصیه می کنیم اینجا را کلیک کنیددانلود تصاویر شماتیک ما از فرآیندهای ساخت ورق فلز و مهر زنی توسط AGS-TECH Inc. این به شما کمک می کند تا اطلاعاتی را که در زیر به شما ارائه می کنیم را بهتر درک کنید. • برش ورق فلزی: ما برش و جداکننده را ارائه می دهیم. برشها ورقهای فلزی را در یک مسیر برش میدهند و اساساً هیچ اتلاف موادی وجود ندارد، در حالی که با جدا کردن شکل نمیتوان دقیقاً در جای خود قرار داد و بنابراین مقدار مشخصی از مواد هدر میرود. یکی از پرطرفدارترین فرآیندهای ما PUNCHING است که در آن قطعه ای گرد یا شکل دیگر از ورق فلز بریده می شود. قطعه ای که بریده می شود زباله است. نوع دیگری از پانچ SLOTTING است که در آن سوراخ های مستطیلی یا کشیده سوراخ می شود. از طرف دیگر بلنکینگ همان فرآیند پانچ است، با تمایز قطعه بریده شده کار است و حفظ می شود. FINE BLANKING، نسخه برتر بلنکینگ، برش هایی با تلورانس نزدیک و لبه های صاف مستقیم ایجاد می کند و برای کامل شدن قطعه کار نیازی به عملیات ثانویه ندارد. فرآیند دیگری که ما اغلب از آن استفاده می کنیم، SLITTING است، که یک فرآیند برشی است که در آن ورق فلز توسط دو تیغه مدور مخالف در یک مسیر مستقیم یا منحنی بریده می شود. درب بازکن یک نمونه ساده از فرآیند شکاف است. یکی دیگر از فرآیندهای محبوب_cc781905-5cde-3194-bb3b-136bad5cf58d برای ما، PERFORATING است، که در آن بسیاری از سوراخهای گرد یا شکل دیگر در ورق فلز با الگوی خاصی سوراخ میشوند. یک مثال معمولی برای یک محصول سوراخ شده فیلترهای فلزی با سوراخ های زیادی برای سیالات است. در NOTCHING، یکی دیگر از فرآیندهای برش ورق فلز، مواد را از یک قطعه کار، با شروع از لبه یا جای دیگر جدا می کنیم و به سمت داخل برش می دهیم تا شکل دلخواه به دست آید. این یک فرآیند پیشرونده است که در آن هر عملیات قطعه دیگری را حذف می کند تا زمانی که کانتور مورد نظر به دست آید. برای دورههای تولید کوچک، ما گاهی از یک فرآیند نسبتاً کندتر به نام NIBBLING استفاده میکنیم که شامل سوراخهای سریع بسیاری از سوراخهای روی هم میشود تا برش پیچیدهتر بزرگتری ایجاد کند. در برش پیشرونده از یک سری عملیات مختلف برای به دست آوردن یک برش منفرد یا یک هندسه خاص استفاده می کنیم. در نهایت تراشیدن یک فرآیند ثانویه به ما کمک میکند تا لبههای برشهایی را که قبلاً ایجاد شدهاند، بهبود دهیم. برای برش براده ها، لبه های زبر روی ورق فلز استفاده می شود. خم کردن ورق فلز: علاوه بر برش، خم کردن یک فرآیند ضروری است که بدون آن ما قادر به تولید اکثر محصولات نخواهیم بود. عمدتاً یک عملیات سرد است، اما گاهی اوقات در زمان گرم یا گرم نیز انجام می شود. ما برای این عملیات از قالب ها و پرس استفاده می کنیم. در خم شدن پیشرونده از یک سری عملیات پانچ و قالب مختلف برای به دست آوردن یک خم یا هندسه خاص استفاده می کنیم. AGS-TECH از انواع فرآیندهای خمشی استفاده می کند و بسته به مواد قطعه کار، اندازه، ضخامت، اندازه مورد نظر خم، شعاع، انحنا و زاویه خم، محل خم، صرفه جویی در عملکرد، مقادیر مورد نیاز، انتخاب می کند. و غیره. ما از V-BENDING استفاده می کنیم که در آن یک پانچ V شکل ورق فلز را وارد قالب V شکل می کند و آن را خم می کند. هم برای زوایای بسیار حاد و هم برای زوایای مبهم و هم برای زوایای بین 90 درجه خوب است. با استفاده از قالب های پاک کن، EDGE BENDING را انجام می دهیم. تجهیزات ما ما را قادر می سازد زوایایی حتی بزرگتر از 90 درجه بدست آوریم. در خم شدن لبه قطعه کار بین یک پد فشار و قالب قرار می گیرد، ناحیه خمش روی لبه قالب قرار می گیرد و بقیه قطعه کار روی space مانند یک تیر کنسول نگه داشته می شود. هنگامی که پانچ روی قسمت کنسول عمل می کند، روی لبه قالب خم می شود. FLANGING یک فرآیند خمشی لبه است که منجر به زاویه 90 درجه می شود. اهداف اصلی عملیات حذف لبه های تیز و به دست آوردن سطوح هندسی برای سهولت در اتصال قطعات می باشد. BEADING، یکی دیگر از فرآیندهای معمول خم شدن لبه، یک حلقه را روی لبه یک قطعه تشکیل می دهد. از طرف دیگر HEMMING باعث ایجاد لبه ای از ورق می شود که کاملاً روی خود خم شده است. در SEAMING لبه های دو قسمت روی هم خم شده و به هم متصل می شوند. از طرف دیگر SEAMING دوبل اتصالات ورق فلزی ضد آب و هوا را فراهم می کند. مشابه خم شدن لبه، فرآیندی به نام خمش چرخشی استوانه ای را با زاویه دلخواه به کار می گیرد و به عنوان پانچ عمل می کند. همانطور که نیرو به پانچ منتقل می شود، با قطعه کار بسته می شود. شیار سیلندر به قسمت کنسول زاویه مورد نظر می دهد. شیار می تواند زاویه ای کوچکتر یا بزرگتر از 90 درجه داشته باشد. در AIR BENDING برای داشتن شیار زاویه دار نیازی به قالب پایینی نداریم. ورق فلز توسط دو سطح در طرف مقابل و در فاصله معینی پشتیبانی می شود. سپس پانچ نیرویی را در محل مناسب اعمال می کند و قطعه کار را خم می کند. CHANNEL BENDING با استفاده از پانچ و قالب کانالی شکل انجام می شود و U-BEND با پانچ U شکل به دست می آید. OFFSET BENDING باعث ایجاد انحراف روی ورق فلز می شود. ROLL BENDING، تکنیکی است که برای کار ضخیم و خم کردن قطعات بزرگ صفحات فلزی مناسب است، از سه رول برای تغذیه و خم کردن صفحات تا انحنای دلخواه استفاده می کند. رول ها طوری چیده می شوند که خم دلخواه کار حاصل شود. فاصله و زاویه بین رول ها برای به دست آوردن نتیجه مطلوب کنترل می شود. یک رول متحرک کنترل انحنا را امکان پذیر می کند. TUBE FORMING یکی دیگر از عملیات خمشی رایج ورق فلزی است که شامل قالب های متعدد است. لوله ها پس از چندین عمل به دست می آیند. CORRUGATION نیز توسط عملیات خمشی انجام می شود. اساساً این خمش متقارن در فواصل منظم در سراسر یک قطعه ورق فلز است. از اشکال مختلف می توان برای راه راه استفاده کرد. ورق فلزی راه راه سفت تر است و مقاومت بهتری در برابر خمش دارد و به همین دلیل در صنعت ساختمان سازی کاربرد دارد. شکل دهی رول ورق فلزی، یک فرآیند تولید Continuous manufacturing برای خم کردن مقاطع عرضی یک هندسه خاص با استفاده از رول ها استفاده می شود و کار در مراحل متوالی خم می شود، با رول نهایی کار خم می شود. در برخی موارد از یک رول و در برخی موارد یک سری رول استفاده می شود. فرآیندهای ترکیبی برش و خمش ورق فلز: اینها فرآیندهایی هستند که همزمان برش و خم می شوند. در سوراخ کردن، یک سوراخ با استفاده از پانچ نوک تیز ایجاد می شود. همانطور که پانچ سوراخ ورق را باز می کند، مواد به طور همزمان به یک فلنج داخلی برای سوراخ خم می شوند. فلنج به دست آمده ممکن است عملکردهای مهمی داشته باشد. از طرف دیگر عملیات LANCING ورق را برش داده و خم می کند تا هندسه ای برجسته ایجاد کند. • برآمدگی و خم شدن لوله فلزی: در برآمدگی بخشی از قسمت داخلی لوله توخالی تحت فشار قرار می گیرد و باعث برآمدگی لوله به سمت بیرون می شود. از آنجایی که لوله درون یک قالب قرار دارد، هندسه برآمدگی توسط شکل قالب کنترل می شود. در SRETCH BENDING، یک لوله فلزی با استفاده از نیروهای موازی با محور لوله و نیروهای خمشی برای کشیدن لوله بر روی یک بلوک شکل کشیده میشود. در DRAW BENDING، لوله را نزدیک انتهای آن به یک بلوک چرخشی میبندیم که در حین چرخش لوله را خم میکند. در نهایت، در خمش فشرده سازی، لوله با فشار به یک بلوک فرم ثابت نگه داشته می شود و یک قالب آن را روی بلوک فرم خم می کند. • DEEP DRAWING: در یکی از پرطرفدارترین عملیات ما، از پانچ، یک قالب مطابق و یک نگهدارنده خالی استفاده می شود. ورق فلزی خالی روی دهانه قالب قرار می گیرد و پانچ به سمت قسمت خالی نگه داشته شده توسط نگهدارنده بلانک حرکت می کند. پس از تماس آنها، پانچ ورق فلزی را به داخل حفره قالب وارد می کند تا محصول را تشکیل دهد. عملیات کشش عمیق شبیه برش است، اما فاصله بین پانچ و قالب مانع از برش ورق می شود. عامل دیگری که تضمین می کند ورق عمیق کشیده شده و بریده نمی شود، گوشه های گرد روی قالب و پانچ است که از برش و برش جلوگیری می کند. برای دستیابی به بزرگی بیشتر ترسیم عمیق، یک فرآیند REDRAWING در حال گسترش است که در آن یک ترسیم عمیق بعدی روی قسمتی انجام می شود که قبلاً یک فرآیند ترسیم عمیق را پشت سر گذاشته است. در REVERSE REDRAWING قسمت عمیق کشیده شده برعکس شده و در جهت مخالف کشیده می شود. طراحی عمیق می تواند اشیایی با شکل نامنظم مانند فنجان های گنبدی، مخروطی یا پلکانی ارائه دهد. • SPINNING: عملیاتی که در آن یک قطعه کار مسطح یا از پیش ساخته شده بین سنبه چرخان و استوک دم نگه داشته می شود و ابزاری فشار موضعی به کار وارد می کند که به تدریج از سنبه بالا می رود. در نتیجه قطعه کار روی سنبه پیچیده می شود و شکل خود را به خود می گیرد. ما از این تکنیک به عنوان جایگزینی برای ترسیم عمیق استفاده می کنیم که در آن مقدار سفارش کم است، قطعات بزرگ هستند (قطر تا 20 فوت) و منحنی های منحصر به فردی دارند. حتی اگر قیمت هر قطعه به طور کلی بالاتر است، هزینه های راه اندازی برای عملیات چرخش CNC در مقایسه با کشش عمیق پایین است. برعکس، کشش عمیق نیاز به سرمایهگذاری اولیه بالایی برای راهاندازی دارد، اما هزینههای هر قطعه زمانی که مقدار بالایی از قطعات تولید میشود، پایین است. نسخه دیگری از این فرآیند SHEAR SPINNING است که در آن جریان فلز در قطعه کار نیز وجود دارد. جریان فلز ضخامت قطعه کار را در حین انجام فرآیند کاهش می دهد. یکی دیگر از فرآیندهای مرتبط، TUBE SPINNING است که روی قطعات استوانهای اعمال میشود. همچنین در این فرآیند جریان فلز در داخل قطعه کار وجود دارد. بنابراین ضخامت کاهش می یابد و طول لوله افزایش می یابد. ابزار را می توان برای ایجاد ویژگی هایی در داخل یا خارج لوله جابجا کرد. • شکل دهی لاستیکی ورق فلزی: مواد لاستیکی یا پلی اورتان را در قالب ظرف قرار داده و قطعه کار را روی سطح لاستیک قرار می دهند. سپس یک پانچ روی قطعه کار وارد می شود و آن را به داخل لاستیک وارد می کند. از آنجایی که فشار تولید شده توسط لاستیک کم است، عمق قطعات تولید شده محدود است. از آنجایی که هزینههای ابزارآلات کم است، این فرآیند برای تولید در مقادیر کم مناسب است. • HYDROFORMING: مشابه شکل دهی لاستیک، در این فرآیند ورق فلز توسط یک پانچ به یک مایع تحت فشار در داخل یک محفظه فشرده می شود. ورق فلزی بین پانچ و دیافراگم لاستیکی قرار می گیرد. دیافراگم قطعه کار را به طور کامل احاطه کرده و فشار سیال آن را مجبور می کند تا روی پانچ شکل بگیرد. با این تکنیک می توان كشش های بسیار عمیقی را حتی عمیق تر از فرآیند ترسیم عمیق بدست آورد. ما قالب های تک پانچ و همچنین قالب های پیشرو را بسته به قسمت شما تولید می کنیم. قالب های مهر زنی یک زمانه یک روش مقرون به صرفه برای تولید سریع مقادیر زیاد قطعات ورق فلزی ساده مانند واشر است. قالب های پیشرونده یا تکنیک ترسیم عمیق برای ساخت هندسه های پیچیده تر استفاده می شود. بسته به مورد شما، می توان از واترجت، لیزر یا برش پلاسما برای تولید قطعات ورق فلزی شما ارزان، سریع و دقیق استفاده کرد. بسیاری از تامین کنندگان هیچ ایده ای در مورد این تکنیک های جایگزین ندارند یا آن را ندارند و به همین دلیل از راه های طولانی و گران قیمت ساخت قالب ها و ابزارهایی استفاده می کنند که فقط وقت و هزینه مشتریان را هدر می دهد. اگر به قطعات سفارشی ورق فلزی مانند محفظه ها، محفظه های الکترونیکی ... و غیره به سرعت در عرض چند روز نیاز دارید، برای خدمات نمونه سازی سریع ورق فلزی ما با ما تماس بگیرید. CLICK Product Finder-Locator Service منوی قبلی
- Forging and Powdered Metallurgy, Die Forging, Heading, Hot Forging
Forging and Powdered Metallurgy, Die Forging, Heading, Hot Forging, Impression Die, Near Net Shape, Swaging, Metal Hobbing, Riveting, Coining from AGS-TECH Inc. آهنگری فلزات و متالورژی پودر نوع فرآیندهای آهنگری فلزی که ما ارائه می دهیم عبارتند از قالب سرد و گرم، قالب باز و قالب بسته، قالب قالب گیری و آهنگری بدون فلاش، cogging، فولرینگ، لبه گذاری و آهنگری دقیق، شکل دهی نزدیک به شبکه. ، تاب دادن، آهنگری ناراحت کننده، سوراخکاری فلزی، پرس و رول و آهنگری شعاعی و مداری و حلقه ای و همدما، سکه زنی، پرچ کردن، آهنگری گلوله ای فلزی، سوراخ کردن فلز، اندازه، آهنگری با نرخ انرژی بالا. متالورژی پودر و تکنیک های پردازش پودر ما عبارتند از پرس و تف جوشی پودر، اشباع، نفوذ، پرس ایزواستاتیک گرم و سرد، قالب گیری تزریق فلز، فشرده سازی رول، نورد پودر، اکستروژن پودر، تف جوشی شل، تف جوشی جرقه ای، پرس گرم. توصیه می کنیم اینجا را کلیک کنید دانلود تصاویر شماتیک ما از فرآیندهای آهنگری توسط AGS-TECH Inc. دانلود تصاویر شماتیک ما از فرآیندهای متالورژی پودر توسط AGS-TECH Inc. این فایلهای دانلودی به همراه عکسها و طرحها به شما در درک بهتر اطلاعاتی که در زیر در اختیار شما قرار میدهیم کمک میکنند. در آهنگری فلزات نیروهای فشاری وارد می شود و ماده تغییر شکل داده و شکل مورد نظر به دست می آید. متداول ترین مواد آهنگری در صنعت آهن و فولاد هستند، اما بسیاری از مواد دیگر مانند آلومینیوم، مس، تیتانیوم، منیزیم نیز به طور گسترده آهنگری می شوند. قطعات فلزی آهنگری علاوه بر ترک های مهر و موم شده و فضاهای خالی بسته، ساختار دانه را بهبود بخشیده اند، بنابراین استحکام قطعات به دست آمده از این فرآیند بیشتر است. آهنگری قطعاتی را تولید میکند که بهطور قابلتوجهی نسبت به قطعاتی که با ریختهگری یا ماشینکاری ساخته میشوند، قویتر هستند. از آنجایی که قطعات آهنگری با ایجاد جریان فلز به شکل نهایی خود شکل میگیرند، فلز ساختار دانهای جهتدار به خود میگیرد که استحکام برتر قطعات را به خود اختصاص میدهد. به عبارت دیگر، قطعات بهدستآمده از فرآیند آهنگری، خواص مکانیکی بهتری را در مقایسه با قطعات ساده ریختهگری یا ماشینکاری شده نشان میدهند. وزن آهنگرهای فلزی می تواند از قطعات سبک وزن کوچک تا صدها هزار پوند متغیر باشد. ما آهنگرها را بیشتر برای کاربردهای مکانیکی میسازیم که در آن تنشهای زیاد بر روی قطعاتی مانند قطعات خودرو، چرخ دندهها، ابزار کار، ابزار دستی، شفت توربین، چرخ دنده موتور سیکلت اعمال میشود. از آنجایی که هزینههای ابزارآلات و راهاندازی نسبتاً زیاد است، ما این فرآیند تولید را فقط برای تولید با حجم بالا و برای قطعات مهم با حجم کم اما با ارزش بالا مانند ارابه فرود هوافضا توصیه میکنیم. علاوه بر هزینه ابزار، زمان تولید قطعات آهنگری با مقادیر زیاد می تواند در مقایسه با برخی از قطعات ماشینکاری ساده طولانی تر باشد، اما این تکنیک برای قطعاتی که نیازمند استحکام فوق العاده ای مانند پیچ و مهره، مهره، کاربرد ویژه بسیار مهم است. بست، خودرو، لیفتراک، قطعات جرثقیل. • قالب داغ و قالب سرد: آهنگری قالب داغ، همانطور که از نامش پیداست در دماهای بالا انجام می شود، بنابراین شکل پذیری بالا و استحکام مواد کم است. این تغییر شکل و آهنگری آسان را تسهیل می کند. برعکس، فورج قالب سرد در دماهای پایینتر انجام میشود و به نیروهای بیشتری نیاز دارد که منجر به سخت شدن کرنش، سطح بهتر و دقت قطعات تولید شده میشود. قالب باز و قالب گیری قالب: در آهنگری قالب باز، قالب ها مواد فشرده شده را محدود نمی کنند، در حالی که در قالب قالب گیری، حفره های درون قالب ها جریان مواد را در حالی که به شکل دلخواه آهنگری می کنند، محدود می کنند. UPSET FORGING یا UPSETTING نیز نامیده می شود، که در واقع یکسان نیست اما یک فرآیند بسیار مشابه است، یک فرآیند قالب باز است که در آن قطعه کار بین دو قالب تخت قرار می گیرد و نیروی فشاری ارتفاع آن را کاهش می دهد. با کاهش ارتفاع، عرض قطعه کار افزایش می یابد. HEADING، یک فرآیند آهنگری آشفته شامل استوانهای است که در انتهای خود به هم ریخته و سطح مقطع آن به صورت موضعی افزایش مییابد. در هد، استوک از طریق قالب تغذیه می شود، آهنگری می شود و سپس به طول بریده می شود. این عملیات قادر است مقادیر بالایی از اتصال دهنده ها را به سرعت تولید کند. عمدتاً یک عملیات سرد کار است زیرا برای ساخت انتهای میخ، انتهای پیچ، مهره و پیچ و مهره در جایی که مواد نیاز به تقویت دارند استفاده می شود. یکی دیگر از فرآیندهای قالب باز COGGING است که در آن قطعه کار در یک سری مراحل آهنگری می شود که در هر مرحله منجر به فشرده سازی مواد و حرکت بعدی قالب باز در طول قطعه کار می شود. در هر مرحله ضخامت کاهش می یابد و طول به مقدار کمی افزایش می یابد. این فرآیند شبیه یک دانش آموز عصبی است که مداد خود را در تمام مراحل کوچک گاز می گیرد. فرآیندی به نام FULLERING یکی دیگر از روش های آهنگری قالب باز است که ما اغلب به عنوان مرحله اولیه برای توزیع مواد در قطعه کار قبل از انجام سایر عملیات آهنگری فلز به کار می بریم. زمانی از آن استفاده می کنیم که قطعه کار نیاز به چندین عملیات فورج داشته باشد. در این عملیات، قالب با سطوح محدب تغییر شکل داده و باعث جریان فلز به دو طرف می شود. از طرف دیگر، EDGING فرآیندی مشابه با پر کردن، شامل قالب باز با سطوح مقعر برای تغییر شکل قطعه کار است. لبهبندی همچنین یک فرآیند آمادهسازی برای عملیات آهنگری بعدی است که باعث میشود مواد از هر دو طرف به یک ناحیه در مرکز جریان یابد. IMPRESSION DIE FORGING یا CLOSED DIE FORGING همانطور که به آن نیز گفته می شود از قالب / قالبی استفاده می کند که مواد را فشرده می کند و جریان آن را در داخل خود محدود می کند. قالب بسته می شود و مواد به شکل حفره قالب / قالب می گیرند. آهنگری دقیق، فرآیندی که به تجهیزات و قالب خاصی نیاز دارد، قطعاتی را بدون فلاش یا بسیار کم تولید می کند. به عبارت دیگر قطعات تقریباً ابعاد نهایی خواهند داشت. در این فرآیند مقداری از مواد به خوبی کنترل شده با دقت وارد شده و در داخل قالب قرار می گیرد. ما این روش را برای اشکال پیچیده با مقاطع نازک، تلورانس های کوچک و زوایای کشش و زمانی که مقادیر به اندازه کافی بزرگ هستند تا هزینه های قالب و تجهیزات را توجیه کنند، به کار می بریم. • آهنگری بدون فلاش: قطعه کار به گونه ای در قالب قرار می گیرد که هیچ ماده ای نتواند از حفره خارج شود و فلاش را تشکیل دهد. بنابراین نیازی به برش ناخواسته فلاش نیست. این یک فرآیند آهنگری دقیق است و بنابراین نیاز به کنترل دقیق مقدار مواد مورد استفاده دارد. • آهنگری فلزی یا آهنگری شعاعی: یک قطعه کار به صورت محیطی توسط قالب و آهنگری بر روی آن اثر می گذارد. همچنین می توان از سنبه برای جعل هندسه قطعه کار داخلی استفاده کرد. در عملیات swaging قطعه کار معمولاً چندین ضربه در ثانیه دریافت می کند. اقلام معمولی که توسط چرخاندن تولید می شوند عبارتند از ابزارهای نوک تیز، میله های مخروطی، پیچ گوشتی ها. • سوراخ کردن فلز: ما اغلب از این عملیات به عنوان یک عملیات اضافی در ساخت قطعات استفاده می کنیم. یک سوراخ یا حفره با سوراخ کردن روی سطح قطعه کار بدون شکستن آن ایجاد می شود. لطفاً توجه داشته باشید که سوراخ کردن با سوراخ کردن متفاوت است که منجر به ایجاد سوراخ می شود. • HOBBING : پانچ با هندسه دلخواه در قطعه کار فشرده شده و حفره ای به شکل دلخواه ایجاد می کند. ما به این پانچ HOB می گوییم. این عملیات شامل فشارهای بالا است و در سرما انجام می شود. در نتیجه مواد سرد کار شده و با کرنش سخت می شوند. بنابراین این فرآیند برای ساخت قالب، قالب و حفره برای سایر فرآیندهای تولید بسیار مناسب است. هنگامی که اجاق گاز ساخته شد، می توان به راحتی بسیاری از حفره های یکسان را بدون نیاز به ماشینکاری تک تک آنها ساخت. • ROLL FORGING یا ROLL FORMING : دو رول متضاد برای شکل دادن به قسمت فلزی استفاده می شود. قطعه کار وارد رول ها می شود، رول ها می چرخند و کار را به داخل شکاف می کشند، سپس کار از طریق قسمت شیاردار رول ها وارد می شود و نیروهای فشاری شکل دلخواه را به مواد می دهند. این یک فرآیند نورد نیست، بلکه یک فرآیند آهنگری است، زیرا یک عملیات گسسته و نه پیوسته است. هندسه روی نخلستان های رول، مواد را به شکل و هندسه مورد نیاز جعل می کند. گرم اجرا می شود. به دلیل اینکه یک فرآیند آهنگری است، قطعاتی با خواص مکانیکی برجسته تولید می کند و بنابراین از آن برای ساخت قطعات خودرو مانند شفت هایی که نیاز به استقامت فوق العاده در محیط های کاری سخت دارند استفاده می کنیم. • آهنگری مداری: قطعه کار در یک حفره قالب آهنگری قرار داده می شود و توسط قالب بالایی که در یک مسیر مداری حرکت می کند و در یک محور شیبدار می چرخد، آهنگری می شود. در هر چرخش، قالب بالایی اعمال نیروهای فشاری را به کل قطعه کار تکمیل می کند. با تکرار چند بار این چرخش ها آهنگری کافی انجام می شود. از مزایای این روش ساخت می توان به عملکرد کم صدا و نیروهای کمتر مورد نیاز آن اشاره کرد. به عبارت دیگر با نیروهای کم می توان یک قالب سنگین را حول یک محور چرخاند تا فشارهای زیادی بر روی قسمتی از قطعه کار که در تماس با قالب است اعمال شود. قطعات دیسکی یا مخروطی شکل گاهی اوقات برای این فرآیند مناسب هستند. • آهنگری حلقه: ما اغلب برای تولید حلقه های بدون درز استفاده می کنیم. استوک به طول بریده می شود، ناراحت می شود و سپس تا انتها سوراخ می شود تا یک سوراخ مرکزی ایجاد شود. سپس روی سنبه قرار میگیرد و قالب آهنگری آن را از بالا میکوبد و حلقه به آرامی میچرخد تا ابعاد دلخواه به دست آید. پرچ کردن: یک فرآیند معمول برای اتصال قطعات، با یک قطعه فلزی مستقیم که در سوراخ های از پیش ساخته شده از طریق قطعات وارد می شود، شروع می شود. سپس دو سر قطعه فلزی با فشردن محل اتصال بین قالب بالایی و پایینی آهنگری می شود. • سکه گذاری: یکی دیگر از فرآیندهای رایج که توسط پرس مکانیکی انجام می شود و نیروهای زیادی را در فاصله کوتاهی اعمال می کند. نام سکهسازی از جزئیات ظریفی که بر روی سطوح سکههای فلزی جعل میشود، گرفته میشود. این عمدتاً یک فرآیند تکمیلی برای محصولی است که در آن جزئیات ظریف بر روی سطوح در نتیجه نیروی زیاد اعمال شده توسط قالب که این جزئیات را به قطعه کار منتقل می کند، به دست می آید. • آهنگری گلوله ای فلزی: محصولاتی مانند بلبرینگ ها به توپ های فلزی با کیفیت بالا نیاز دارند. در یک تکنیک به نام SKEW ROLLING، از دو رول متضاد استفاده میکنیم که بهطور پیوسته در حال چرخش استوک به طور مداوم به رولها میچرخند. در یک انتهای دو رول، کره های فلزی به عنوان محصول خارج می شوند. روش دوم برای آهنگری گلوله ای فلزی استفاده از قالبی است که مواد موجود در بین آنها را فشرده می کند و شکل کروی حفره قالب را می گیرد. اغلب اوقات توپ های تولید شده برای تبدیل شدن به یک محصول با کیفیت به مراحل اضافی مانند تکمیل و پرداخت نیاز دارند. • آهنگری ایزوترمال / آهنگری قالب داغ: یک فرآیند گران قیمت که تنها زمانی انجام می شود که سود / ارزش هزینه توجیه شده باشد. یک فرآیند کار داغ که در آن قالب تا دمایی برابر با قطعه کار گرم می شود. از آنجایی که دمای قالب و کار تقریباً یکسان است، خنک کننده وجود ندارد و ویژگی های جریان فلز بهبود می یابد. این عملیات برای سوپر آلیاژها و مواد با قابلیت جعل پذیری پایین و موادی که مناسب است خواص مکانیکی به شیب و تغییرات دما بسیار حساس است. • اندازه فلز: این یک فرآیند تکمیل سرد است. جریان مواد در تمام جهات به استثنای جهتی که نیرو در آن اعمال می شود، نامحدود است. در نتیجه سطح بسیار خوب و ابعاد دقیق به دست می آید. • آهنگری با نرخ انرژی بالا: این تکنیک شامل قالب بالایی متصل به بازوی پیستون است که با مشتعل شدن مخلوط سوخت و هوا توسط یک شمع به سرعت هل داده می شود. این شبیه عملکرد پیستون در موتور ماشین است. قالب خیلی سریع به قطعه کار برخورد می کند و سپس به لطف فشار برگشتی خیلی سریع به موقعیت اولیه خود باز می گردد. کار در عرض چند میلی ثانیه فورج می شود و بنابراین زمانی برای خنک شدن کار وجود ندارد. این برای قطعات سخت آهنگری که دارای خواص مکانیکی بسیار حساس به دما هستند مفید است. به عبارت دیگر فرآیند آنقدر سریع است که قطعه تحت دمای ثابت در سرتاسر شکل میگیرد و شیب دما در رابطهای قالب/قطعه کار وجود نخواهد داشت. • در DIE FORGING، فلز بین دو بلوک فولادی منطبق با اشکال خاص در آنها که قالب نامیده می شود، کوبیده می شود. هنگامی که فلز بین قالب ها کوبیده می شود، شکلی مشابه شکل های موجود در قالب به خود می گیرد. وقتی به شکل نهایی رسید بیرون می آورند تا خنک شود. این فرآیند قطعات محکمی را تولید می کند که شکل دقیقی دارند، اما نیاز به سرمایه گذاری بیشتر برای قالب های تخصصی دارد. آهنگری ناراحت کننده قطر یک قطعه فلز را با صاف کردن آن افزایش می دهد. به طور کلی برای ساخت قطعات کوچک، به ویژه برای ایجاد سر بر روی اتصال دهنده ها مانند پیچ و مهره استفاده می شود. • متالورژی پودر / پردازش پودر: همانطور که از نام آن پیداست، شامل فرآیندهای ساخت برای ساخت قطعات جامد هندسه ها و اشکال خاص از پودر است. اگر از پودرهای فلزی برای این منظور استفاده شود، حوزه متالورژی پودر و اگر از پودرهای غیر فلزی استفاده شود، فرآوری پودر است. قطعات جامد از پودرها با پرس و تف جوشی تولید می شوند. پودر پرس برای فشرده سازی پودرها به شکل دلخواه استفاده می شود. ابتدا، ماده اولیه به صورت فیزیکی پودر می شود و آن را به بسیاری از ذرات کوچک جداگانه تقسیم می کند. مخلوط پودر داخل قالب پر می شود و پانچ به سمت پودر حرکت می کند و آن را به شکل دلخواه فشرده می کند. بیشتر در دمای اتاق انجام می شود که با پرس پودر یک قسمت جامد به دست می آید و به آن فشرده سبز می گویند. چسب ها و روان کننده ها معمولا برای افزایش تراکم پذیری استفاده می شوند. ما قادر به شکل دهی پرس پودری با استفاده از پرس های هیدرولیک با ظرفیت چند هزار تن هستیم. همچنین ما پرس های دوتایی با پانچ های بالا و پایین مخالف و همچنین پرس های چندگانه برای هندسه های بسیار پیچیده قطعات داریم. یکنواختی که یک چالش مهم برای بسیاری از کارخانه های متالورژی پودر / فرآوری پودر است، مشکل بزرگی برای AGS-TECH به دلیل تجربه گسترده ما در تولید سفارشی چنین قطعاتی برای سال ها نیست. حتی با قطعات ضخیم تر که یکنواختی یک چالش است، ما موفق شده ایم. اگر ما به پروژه شما متعهد باشیم، قطعات شما را خواهیم ساخت. در صورت مشاهده هرگونه خطر احتمالی، به شما اطلاع خواهیم داد in advance. زینترینگ پودری که مرحله دوم است، شامل افزایش دما تا حد معینی و حفظ دما در آن سطح برای مدت معینی است تا ذرات پودر در قسمت فشرده شده بتوانند به یکدیگر بچسبند. این منجر به پیوندهای بسیار قوی تر و استحکام قطعه کار می شود. تف جوشی نزدیک به دمای ذوب پودر انجام می شود. در طول پخت، انقباض رخ می دهد، استحکام مواد، چگالی، شکل پذیری، هدایت حرارتی، هدایت الکتریکی افزایش می یابد. ما کوره های دسته ای و پیوسته برای پخت داریم. یکی از قابلیت های ما تنظیم سطح تخلخل قطعاتی است که تولید می کنیم. به عنوان مثال، ما قادر به تولید فیلترهای فلزی با متخلخل نگه داشتن قطعات تا حدی هستیم. با استفاده از تکنیکی به نام IMPREGNATION، منافذ فلز را با مایعی مانند روغن پر می کنیم. ما به عنوان مثال یاتاقان های آغشته به روغن تولید می کنیم که خود روان کننده هستند. در فرآیند INFILTRATION، منافذ یک فلز را با فلز دیگری با نقطه ذوب پایینتر از ماده پایه پر میکنیم. مخلوط تا دمای بین دمای ذوب دو فلز گرم می شود. در نتیجه می توان برخی از خواص ویژه را به دست آورد. ما همچنین اغلب عملیات ثانویه مانند ماشینکاری و آهنگری را بر روی قطعات تولید شده پودر انجام می دهیم، زمانی که باید ویژگی ها یا ویژگی های خاصی را به دست آورد یا زمانی که قطعه را می توان با مراحل فرآیند کمتری تولید کرد. پرس ایزواستاتیک: در این فرآیند از فشار سیال برای فشرده سازی قطعه استفاده می شود. پودرهای فلزی در یک قالب ساخته شده از یک ظرف انعطاف پذیر در بسته قرار می گیرند. در پرس ایزواستاتیک، بر خلاف فشار محوری که در پرس معمولی دیده می شود، فشار از اطراف اعمال می شود. از مزایای پرس ایزواستاتیک، چگالی یکنواخت درون قطعه، به ویژه برای قطعات بزرگتر یا ضخیم تر، خواص برتر است. نقطه ضعف آن زمان چرخه طولانی و دقت هندسی نسبتا کم است. پرس ایزواستاتیک سرد در دمای اتاق انجام می شود و قالب انعطاف پذیر از لاستیک، PVC یا یورتان یا مواد مشابه ساخته شده است. سیال مورد استفاده برای فشار دادن و فشرده سازی روغن یا آب است. تف جوشی معمولی فشرده سبز به دنبال این است. از طرف دیگر فشار ایزواستاتیک گرم در دماهای بالا انجام می شود و مواد قالب از ورق فلز یا سرامیک با نقطه ذوب به اندازه کافی بالا است که در برابر دما مقاومت می کند. سیال تحت فشار معمولاً یک گاز بی اثر است. عملیات پرس و تف جوشی در یک مرحله انجام می شود. تخلخل تقریباً به طور کامل حذف شده است، یک ساختار uniform grain به دست می آید. مزیت پرس ایزواستاتیک گرم این است که می تواند قطعاتی قابل مقایسه با ترکیب ریخته گری و آهنگری تولید کند و در عین حال موادی را که برای ریخته گری و آهنگری مناسب نیستند قابل استفاده باشد. نقطه ضعف پرس ایزواستاتیک گرم زمان چرخه بالا و در نتیجه هزینه آن است. برای قسمت های بحرانی با حجم کم مناسب است. قالبگیری تزریقی فلز: فرآیندی بسیار مناسب برای تولید قطعات پیچیده با دیوارههای نازک و هندسههای دقیق. مناسب ترین برای قطعات کوچکتر. پودرها و بایندر پلیمری مخلوط، حرارت داده شده و به قالب تزریق می شوند. بایندر پلیمری سطوح ذرات پودر را می پوشاند. پس از قالب گیری، بایندر با حرارت دادن در دمای پایین محلول با استفاده از یک حلال حذف می شود. فشرده سازی رول / نورد پودری: از پودرها برای تولید نوارها یا ورق های پیوسته استفاده می شود. پودر از یک فیدر تغذیه می شود و توسط دو رول چرخان به صورت ورق یا نوار فشرده می شود. عملیات به صورت سرد انجام می شود. ورق به داخل کوره تف جوشی حمل می شود. فرآیند پخت ممکن است برای بار دوم تکرار شود. اکستروژن پودری: قطعات با نسبت طول به قطر زیاد با اکسترود کردن یک ظرف ورق فلزی نازک با پودر ساخته می شوند. تف جوشی شل: همانطور که از نام آن پیداست، روشی بدون فشار و بدون فشار است که برای تولید قطعات بسیار متخلخل مانند فیلترهای فلزی مناسب است. پودر بدون فشرده شدن به داخل حفره قالب وارد می شود. تف جوشی شل: همانطور که از نام آن پیداست، روشی بدون فشار و بدون فشار است که برای تولید قطعات بسیار متخلخل مانند فیلترهای فلزی مناسب است. پودر بدون فشرده شدن به داخل حفره قالب وارد می شود. SPARK SINTERING : پودر توسط دو پانچ مخالف در قالب فشرده می شود و جریان الکتریکی با قدرت بالا به پانچ وارد می شود و از پودر فشرده که در بین آنها قرار گرفته است عبور می کند. جریان بالا، لایههای سطحی را از ذرات پودر میسوزاند و آنها را با گرمای تولید شده متخلخل میکند. این فرآیند سریع است زیرا گرما از خارج اعمال نمی شود بلکه از داخل قالب تولید می شود. پرس گرم: پودرها در یک مرحله در قالبی که می تواند در برابر درجه حرارت بالا مقاومت کند، فشرده و پخته می شوند. همانطور که قالب فشرده می شود، گرمای پودر به آن اعمال می شود. دقت و خواص مکانیکی خوب به دست آمده توسط این روش، آن را به گزینه ای جذاب تبدیل می کند. حتی فلزات نسوز را می توان با استفاده از مواد قالب مانند گرافیت پردازش کرد. CLICK Product Finder-Locator Service منوی قبلی
- Plastic Rubber Metal Extrusions, Extrusion Dies, Aluminum Extruding
Plastic Rubber Metal Extrusions, Extrusion Dies, Aluminum Extruding, Pipe Tube Forming, Plastic Profiles, Metal Profiles Manufacturing, PVC at AGS-TECH Inc. اکستروژن، محصولات اکسترود شده، اکسترودات ما از فرآیند EXTRUSION process برای تولید محصولات با سطح مقطع ثابت مانند لوله های حرارتی، لوله ها و لوله ها استفاده می کنیم. حتی اگر بسیاری از مواد را می توان اکسترود کرد، رایج ترین اکستروژن های ما از فلز، پلیمرها / پلاستیک، سرامیک به دست آمده با روش اکستروژن سرد، گرم یا گرم ساخته شده است. قطعات اکسترود شده را اکسترود یا اکسترودات در صورت جمع می نامیم. برخی از نسخههای تخصصی فرآیندی که ما نیز انجام میدهیم عبارتند از پوشش بیش از حد، کواکستروژن و اکستروژن مرکب. توصیه می کنیم اینجا را کلیک کنید تا دانلود تصاویر شماتیک ما از فرآیندهای اکستروژن فلز سرامیک و پلاستیک توسط AGS-TECH Inc. این به شما کمک می کند تا اطلاعاتی را که در زیر به شما ارائه می کنیم را بهتر درک کنید. در اکستروژن، موادی که قرار است اکسترود شوند، از طریق قالبی که دارای سطح مقطع مطلوب است، رانده یا کشیده میشود. این فرآیند را می توان برای ساخت مقاطع پیچیده با سطح عالی و برای کار بر روی مواد شکننده استفاده کرد. با استفاده از این فرآیند می توان هر طولی از قطعات را تولید کرد. برای ساده کردن مراحل فرآیند: 1.) در اکستروژن های گرم یا گرم، مواد گرم شده و در یک ظرف در پرس قرار می گیرند. مواد فشرده شده و از قالب بیرون رانده می شوند. 2.) اکسترود تولید شده برای صاف کردن، عملیات حرارتی یا سرد کار می شود تا خواص آن افزایش یابد. از طرف دیگر COLD EXTRUSION در دمای اتاق اتفاق میافتد و دارای مزایای اکسیداسیون کمتر، استحکام کمتر به سطح، استحکام بیشتر، اکسیداسیون بالا و پایان پذیری است. WARM EXTRUSION بالاتر از دمای اتاق اما زیر نقطه تبلور مجدد انجام می شود. این یک سازش و تعادل برای نیروهای مورد نیاز، شکل پذیری و خواص مواد ارائه می دهد و بنابراین برای برخی از کاربردها گزینه مناسبی است. HOT EXTRUSION بالاتر از دمای تبلور مجدد ماده اتفاق می افتد. به این ترتیب عبور مواد از درون قالب راحت تر است. با این حال هزینه تجهیزات بالا است. هرچه یک پروفیل اکسترود شده پیچیده تر باشد، قالب (ابزار) پرهزینه تر و نرخ تولید کمتر است. مقاطع قالب و همچنین ضخامت ها دارای محدودیت هایی هستند که به ماده ای که باید اکسترود شود بستگی دارد. گوشه های تیز در قالب های اکستروژن همیشه نامطلوب هستند و مگر در موارد ضروری باید از آنها اجتناب کرد. با توجه به موادی که اکسترود می شود، پیشنهاد می کنیم: • METAL EXTRUSIONS : رایج ترین مواردی که ما تولید می کنیم عبارتند از آلومینیوم، برنج، روی، مس، فولاد، تیتانیوم، منیزیم • PLASTIC EXTRUSION : پلاستیک ذوب شده و به شکل پروفیل پیوسته در می آید. مواد رایج پردازش شده ما پلی اتیلن، نایلون، پلی استایرن، پلی وینیل کلرید، پلی پروپیلن، پلاستیک ABS، پلی کربنات، اکریلیک است. محصولات معمولی که ما تولید می کنیم شامل لوله ها و لوله ها، قاب های پلاستیکی است. در این فرآیند دانههای پلاستیکی کوچک / رزین با نیروی جاذبه از قیف به بشکه دستگاه اکستروژن تغذیه میشود. ما اغلب رنگها یا سایر افزودنیها را در قیف مخلوط میکنیم تا مشخصات و خواص لازم را به محصول بدهیم. مواد وارد شده به بشکه گرم شده توسط پیچ چرخان مجبور می شوند تا در انتها از بشکه خارج شده و برای حذف آلاینده های پلاستیک مذاب از روی بسته صفحه حرکت کنند. پس از عبور از بسته صفحه نمایش، پلاستیک وارد قالب اکستروژن می شود. قالب به پلاستیک نرم متحرک شکل پروفیل خود را در هنگام عبور می دهد. اکنون اکسترود برای خنک شدن از حمام آب عبور می کند. تکنیک های دیگری که شرکت AGS-TECH برای سال ها از آن استفاده می کند عبارتند از: • PIPE & TUBING EXTRUSION : لولهها و لولههای پلاستیکی زمانی تشکیل میشوند که پلاستیک از طریق یک قالب گرد اکسترود شده و در یک حمام آب سرد شود، سپس به طول برش داده شود یا کلاف یا قرقره شود. شفاف یا رنگی، راه راه، تک یا دو جداره، انعطاف پذیر یا سفت، PE، PP، پلی اورتان، پی وی سی، نایلون، PC، سیلیکون، وینیل یا موارد دیگر، همه اینها را داریم. ما لوله ها و همچنین قابلیت تولید مطابق با مشخصات شما را داریم. AGS-TECH لوله هایی مطابق با الزامات FDA، UL و LE برای کاربردهای پزشکی، الکتریکی و الکترونیکی، صنعتی و سایر کاربردها تولید می کند. • OVERJACKETING / OVER JACKETING EXTRUSION : این تکنیک یک لایه پلاستیکی خارجی را روی سیم یا کابل موجود اعمال می کند. سیم های عایق ما با این روش تولید می شوند. • COEXTRUSION : چندین لایه از مواد به طور همزمان اکسترود می شوند. لایه های متعدد توسط اکسترودرهای متعدد تحویل داده می شوند. ضخامت لایه های مختلف را می توان برای مطابقت با مشخصات مشتری تنظیم کرد. این فرآیند امکان استفاده از چندین پلیمر را فراهم می کند که هر کدام عملکرد متفاوتی در محصول دارند. در نتیجه، می توان طیف وسیعی از خواص را بهینه کرد. • اکستروژن ترکیبی: یک پلیمر منفرد یا چندگانه با مواد افزودنی مخلوط می شوند تا یک ترکیب پلاستیکی به دست آید. اکسترودرهای دو مارپیچ ما اکستروژن های ترکیبی تولید می کنند. قالب های اکستروژن در مقایسه با قالب های فلزی معمولاً ارزان هستند. اگر برای یک دای اکستروژن آلومینیومی سایز کوچک یا متوسط بیش از چند هزار دلار می پردازید، احتمالاً هزینه زیادی می پردازید. ما در تعیین اینکه کدام تکنیک برای کاربرد شما مقرون به صرفه ترین، سریع ترین و مناسب ترین است، متخصص هستیم. گاهی اوقات اکسترود کردن و سپس ماشینکاری یک قطعه می تواند پول نقد زیادی را برای شما ذخیره کند. قبل از تصمیم قطعی، ابتدا نظر ما را بپرسید. ما به بسیاری از مشتریان کمک کرده ایم تا تصمیمات درستی بگیرند. برای برخی از اکستروژن های فلزی پرکاربرد، می توانید بروشورها و کاتالوگ های ما را با کلیک بر روی متن رنگی زیر دانلود کنید. اگر محصولی خارج از قفسه باشد که نیازهای شما را برآورده می کند، مقرون به صرفه تر خواهد بود. قابلیت های اکستروژن لوله و لوله پزشکی ما را دانلود کنید هیت سینک های اکسترود شده ما را دانلود کنید • فرآیندهای ساخت و ساز ثانویه برای EXTRUSIONS : از جمله فرآیندهای ارزش افزوده ای که ما برای محصولات اکسترود شده ارائه می کنیم عبارتند از: -خمش سفارشی لوله و لوله، شکل دهی و شکل دهی، قطع لوله، شکل دهی انتهای لوله، سیم پیچی لوله، ماشین کاری و تکمیل، سوراخ کاری و سوراخ کردن و پانچ کردن، - مجموعه های سفارشی لوله و لوله، مونتاژ لوله، جوش، لحیم کاری و لحیم کاری -خمش، شکل دهی و شکل دهی اکستروژن سفارشی - تمیز کردن، چربی زدایی، ترشی کردن، غیرفعال کردن، پرداخت، آنودایز کردن، آبکاری، رنگ آمیزی، عملیات حرارتی، بازپخت و سخت شدن، علامت گذاری، حکاکی و برچسب زدن، بسته بندی سفارشی. CLICK Product Finder-Locator Service صفحه قبلی
- Casting and Machined Parts, CNC Manufacturing, Milling, Turning, Swiss
Casting and Machined Parts, CNC Manufacturing, Milling, Turning, Swiss Type Machining, Die Casting, Investment Casting, Lost Foam Cast Parts from AGS-TECH Inc. ریخته گری و ماشینکاری روش های ریخته گری و ماشینکاری سفارشی ما عبارتند از ریخته گری های مصرفی و غیر قابل مصرف، ریخته گری آهنی و غیر آهنی، شن و ماسه، قالب، گریز از مرکز، پیوسته، قالب سرامیکی، سرمایه گذاری، فوم گم شده، شکل نزدیک به شبکه، قالب دائمی (ریخته گری گرانشی)، گچ قالب (ریخته گری گچ) و پوسته، قطعات ماشینکاری شده تولید شده توسط آسیاب و تراشکاری با استفاده از تجهیزات معمولی و همچنین CNC، ماشینکاری نوع سوئیسی برای قطعات دقیق ارزان قیمت با توان بالا، ماشینکاری پیچ برای اتصال دهنده ها، ماشینکاری غیر متعارف. لطفاً در نظر داشته باشید که علاوه بر فلزات و آلیاژهای فلزی، در برخی موارد که ساخت قالب جذاب نیست یا گزینه مناسبی نیست، قطعات سرامیکی، شیشه و پلاستیک را نیز ماشین می کنیم. ماشینکاری مواد پلیمری به دلیل چالشی که پلاستیک و لاستیک به دلیل نرمی، عدم سفتی و غیره دارند، به تجربه تخصصی ما نیاز دارد. برای ماشینکاری سرامیک و شیشه، لطفا به صفحه ما در مورد ساخت غیر متعارف مراجعه کنید. شرکت AGS-TECH هر دو ریخته گری سبک و سنگین را تولید و عرضه می کند. ما قطعات ریخته گری فلز و قطعات ماشینکاری شده برای دیگهای بخار، مبدل های حرارتی، خودروها، میکروموتورها، توربین های بادی، تجهیزات بسته بندی مواد غذایی و موارد دیگر را تامین می کنیم. توصیه می کنیم اینجا را کلیک کنید تا دانلود تصاویر شماتیک فرآیندهای ماشینکاری و ریخته گری توسط AGS-TECH Inc. این به شما کمک می کند تا اطلاعاتی را که در زیر به شما ارائه می کنیم را بهتر درک کنید. بیایید به برخی از تکنیک های مختلفی که ارائه می دهیم با جزئیات نگاه کنیم: • ریخته گری قالب مصرفی: این دسته بندی گسترده به روش هایی اشاره دارد که شامل قالب های موقت و غیرقابل استفاده مجدد است. به عنوان مثال می توان به ماسه، گچ، پوسته، سرمایه گذاری (که به آن موم گم شده نیز گفته می شود) و ریخته گری گچ اشاره کرد. • ریخته گری شن و ماسه: فرآیندی که در آن از ماسه به عنوان ماده قالب استفاده می شود. روشی بسیار قدیمی و همچنان بسیار پرطرفدار تا جایی که اکثر ریخته گری های فلزی تولید شده با این تکنیک ساخته می شوند. هزینه کم حتی در تولید کم. مناسب برای ساخت قطعات کوچک و بزرگ از این تکنیک می توان برای ساخت قطعات در عرض چند روز یا چند هفته با سرمایه گذاری بسیار کم استفاده کرد. شن و ماسه مرطوب با استفاده از خاک رس، چسب یا روغن های مخصوص به یکدیگر متصل می شوند. شن و ماسه به طور کلی در جعبه های قالب وجود دارد و سیستم حفره و دروازه با فشرده سازی ماسه در اطراف مدل ها ایجاد می شود. فرآیندها عبارتند از: 1.) قرار دادن مدل در ماسه برای ساخت قالب 2.) ادغام مدل و ماسه در یک سیستم دروازه 3.) حذف مدل 4. پر کردن حفره قالب با فلز مذاب 5.) خنک کردن فلز 6. شکستن قالب ماسه و برداشتن قالب • ریخته گری قالب گچی: مشابه ریخته گری شن و ماسه و به جای ماسه از گچ پاری به عنوان ماده قالب استفاده می شود. زمان تولید کوتاه مانند ریخته گری شن و ماسه و ارزان. تحمل ابعادی خوب و پرداخت سطحی. عیب اصلی آن این است که فقط با فلزات با نقطه ذوب پایین مانند آلومینیوم و روی قابل استفاده است. • SHELL MOLD CASTING : همچنین شبیه ریخته گری شن و ماسه است. حفره قالب از پوسته سخت شده ماسه و چسب رزین ترموست به جای فلاسک پر شده با ماسه مانند فرآیند ریخته گری ماسه به دست می آید. تقریباً هر فلزی که برای ریختهگری با ماسه مناسب باشد، میتواند با قالبگیری پوستهای ریختهگری شود. فرآیند را می توان به صورت زیر خلاصه کرد: 1.) ساخت قالب پوسته. شن و ماسه مورد استفاده در مقایسه با شن و ماسه مورد استفاده در ریخته گری شن و ماسه، اندازه دانه بسیار کوچکتری دارد. ماسه ریز با رزین ترموست مخلوط می شود. الگوی فلزی با یک عامل جداکننده پوشانده شده است تا برداشتن پوسته آسانتر شود. پس از آن الگوی فلزی حرارت داده می شود و مخلوط ماسه منفذ شده یا روی الگوی ریخته گری داغ دمیده می شود. یک پوسته نازک روی سطح الگو تشکیل می شود. ضخامت این پوسته را می توان با تغییر مدت زمان تماس مخلوط رزین ماسه با الگوی فلزی تنظیم کرد. سپس شن و ماسه شل با الگوی پوشیده شده با پوسته باقی مانده برداشته می شود. 2.) سپس پوسته و الگو را در فر گرم می کنند تا پوسته سفت شود. پس از اتمام سخت شدن، پوسته با استفاده از پین های تعبیه شده در الگو از الگو خارج می شود. 3.) دو پوسته از این دست با چسباندن یا گیره به هم مونتاژ می شوند و قالب کامل را می سازند. اکنون قالب پوسته در ظرفی قرار می گیرد که در طی فرآیند ریخته گری توسط ماسه یا گلوله فلزی پشتیبانی می شود. 4.) حالا فلز داغ را می توان در قالب پوسته ریخت. مزایای ریخته گری پوسته محصولاتی با سطح بسیار خوب، امکان ساخت قطعات پیچیده با دقت ابعادی بالا، فرآیند آسان برای خودکارسازی، مقرون به صرفه بودن برای تولید حجم زیاد است. معایب این است که قالب ها به تهویه مناسب نیاز دارند زیرا گازهایی که هنگام تماس فلز مذاب با ماده شیمیایی بایندر ایجاد می شوند، رزین های ترموست و الگوهای فلزی گران هستند. با توجه به هزینه الگوهای فلزی، این تکنیک ممکن است برای دوره های تولید با مقدار کم مناسب نباشد. • ریخته گری سرمایه گذاری (همچنین به نام ریخته گری موم گمشده): همچنین یک تکنیک بسیار قدیمی و مناسب برای ساخت قطعات با کیفیت با دقت، تکرارپذیری، تطبیق پذیری و یکپارچگی از بسیاری از فلزات، مواد نسوز و آلیاژهای خاص با کارایی بالا می باشد. قطعات کوچک و بزرگ را می توان تولید کرد. در مقایسه با برخی از روشهای دیگر فرآیندی گرانقیمت است، اما مزیت اصلی امکان تولید قطعات با شکل شبکه، خطوط پیچیده و جزئیات است. بنابراین هزینه تا حدودی با حذف دوباره کاری و ماشینکاری در برخی موارد جبران می شود. حتی اگر ممکن است تغییراتی وجود داشته باشد، در اینجا خلاصه ای از فرآیند کلی ریخته گری سرمایه گذاری آمده است: 1.) ایجاد الگوی اصلی اصلی از موم یا پلاستیک. هر ریخته گری به یک الگو نیاز دارد زیرا در این فرآیند از بین می روند. قالبی که از آن الگوها ساخته می شود نیز مورد نیاز است و بیشتر اوقات قالب ریخته گری یا ماشین کاری می شود. از آنجایی که قالب نیازی به باز کردن ندارد، می توان به ریخته گری های پیچیده دست یافت، بسیاری از الگوهای مومی را می توان مانند شاخه های یک درخت به هم متصل کرد و با هم ریخت، بنابراین امکان تولید چندین قسمت از یک بار ریختن فلز یا آلیاژ فلز را فراهم کرد. 2.) در مرحله بعد، الگو را با دوغاب نسوز متشکل از سیلیس دانه ریز، آب، چسباننده آغشته کرده یا می ریزند. این باعث ایجاد یک لایه سرامیکی بر روی سطح الگو می شود. روکش نسوز روی الگو را گذاشته تا خشک و سفت شود. این مرحله جایی است که نام ریخته گری سرمایه گذاری از آن گرفته شده است: دوغاب نسوز روی الگوی موم ریخته می شود. 3.) در این مرحله قالب سرامیکی سخت شده را زیر و رو کرده و حرارت می دهند تا موم ذوب شده و از قالب بریزد. یک حفره برای ریخته گری فلز باقی مانده است. 4.) پس از خارج شدن موم، قالب سرامیکی حتی تا دمای بالاتری گرم می شود که منجر به تقویت قالب می شود. 5.) ریخته گری فلز در قالب داغ ریخته می شود و تمام بخش های پیچیده را پر می کند. 6.) ریخته گری مجاز است تا جامد شود 7. در نهایت قالب سرامیکی شکسته شده و قطعات ساخته شده از درخت جدا می شود. در اینجا پیوندی به بروشور کارخانه ریخته گری سرمایه گذاری شده است ریخته گری الگوی تبخیری: این فرآیند از الگویی ساخته شده از موادی مانند فوم پلی استایرن استفاده می کند که وقتی فلز مذاب داغ در قالب ریخته می شود تبخیر می شود. دو نوع از این فرآیند وجود دارد: LOST FOAM CASTING که از ماسه بدون پیوند استفاده می کند و FULL MOLD CASTING که از ماسه چسبانده شده استفاده می کند. در اینجا مراحل کلی فرآیند آمده است: 1.) الگو را از موادی مانند پلی استایرن بسازید. هنگامی که مقادیر زیادی تولید می شود، الگوی قالب گیری می شود. اگر قطعه شکل پیچیده ای داشته باشد، ممکن است لازم باشد چندین بخش از چنین مواد فومی به هم بچسبند تا الگو را تشکیل دهند. ما اغلب الگو را با یک ترکیب نسوز می پوشانیم تا سطح خوبی روی ریخته گری ایجاد کنیم. 2.) سپس الگو را در ماسه قالب گیری قرار می دهیم. 3.) فلز مذاب در قالب ریخته می شود و الگوی فوم تبخیر می شود، یعنی پلی استایرن در بیشتر موارد در حفره قالب جریان می یابد. 4.) فلز مذاب در قالب ماسه گذاشته می شود تا سفت شود. 5.) پس از سفت شدن، قالب را جدا می کنیم. در برخی موارد، محصولی که ما تولید می کنیم به یک هسته درون الگو نیاز دارد. در ریخته گری تبخیری، نیازی به قرار دادن و محکم کردن هسته در حفره قالب نیست. این تکنیک برای ساخت هندسه های بسیار پیچیده مناسب است، می توان آن را به راحتی برای تولید با حجم بالا خودکار کرد و هیچ خط جدایی در قسمت ریخته گری وجود ندارد. اجرای فرآیند اصلی ساده و مقرون به صرفه است. برای تولید حجم زیاد، از آنجایی که برای تولید الگوها از پلی استایرن به قالب یا قالب نیاز است، ممکن است تا حدودی هزینه بر باشد. • ریخته گری قالب غیر قابل انبساط: این دسته بندی گسترده به روش هایی اشاره دارد که در آن قالب پس از هر چرخه تولید نیازی به اصلاح ندارد. به عنوان مثال می توان به ریخته گری دائمی، قالبی، پیوسته و گریز از مرکز اشاره کرد. تکرار پذیری به دست می آید و قطعات را می توان به شکل NEAR NET SHAPE مشخص کرد. • ریخته گری قالب دائمی: قالب های قابل استفاده مجدد ساخته شده از فلز برای ریخته گری های متعدد استفاده می شود. یک قالب دائمی به طور کلی می تواند ده ها هزار بار قبل از فرسوده شدن استفاده شود. گرانش، فشار گاز یا خلاء به طور کلی برای پر کردن قالب استفاده می شود. قالب ها (که قالب نیز نامیده می شود) عموماً از آهن، فولاد، سرامیک یا فلزات دیگر ساخته می شوند. روند کلی این است: 1.) ماشین و قالب را ایجاد کنید. معمول است که قالب را از دو بلوک فلزی که در کنار هم قرار می گیرند و می توانند باز و بسته شوند، ماشین کاری کنند. هم ویژگی های قطعه و هم سیستم دروازه به طور کلی در قالب ریخته گری ماشینکاری می شود. 2.) سطوح داخلی قالب با دوغاب حاوی مواد نسوز پوشانده شده است. این به کنترل جریان گرما کمک می کند و به عنوان روان کننده برای حذف آسان قسمت ریختگی عمل می کند. 3.) در مرحله بعد، نیمه های قالب دائمی بسته شده و قالب گرم می شود. 4.) فلز مذاب در قالب ریخته می شود و برای انجماد می گذارند. 5.) قبل از اینکه خیلی خنک شود، وقتی نیمه های قالب باز می شوند، قطعه را با استفاده از اجکتورها از قالب دائمی خارج می کنیم. ما اغلب از ریخته گری قالب دائمی برای فلزات با نقطه ذوب پایین مانند روی و آلومینیوم استفاده می کنیم. برای ریخته گری فولاد، ما از گرافیت به عنوان مواد قالب استفاده می کنیم. ما گاهی اوقات هندسه های پیچیده ای را با استفاده از هسته های درون قالب های دائمی به دست می آوریم. از مزایای این روش می توان به ریخته گری هایی با خواص مکانیکی خوب به دست آمده از خنک سازی سریع، یکنواختی در خواص، دقت و پرداخت سطحی خوب، نرخ رد پایین، امکان خودکارسازی فرآیند و تولید حجم های بالا از نظر اقتصادی اشاره کرد. معایب آن هزینه های بالای راه اندازی اولیه است که آن را برای عملیات با حجم کم نامناسب می کند و محدودیت در اندازه قطعات تولید شده. ریخته گری: قالب ماشینکاری می شود و فلز مذاب تحت فشار بالا به داخل حفره های قالب رانده می شود. ریخته گری فلزات آهنی و غیر آهنی امکان پذیر است. این فرآیند برای تولید مقادیر زیاد قطعات کوچک تا متوسط با جزئیات، دیوارههای بسیار نازک، سازگاری ابعادی و سطح خوب مناسب است. شرکت AGS-TECH قادر است با استفاده از این تکنیک، ضخامت دیوارهای کوچک تا 0.5 میلی متر را تولید کند. مانند ریختهگری قالب دائمی، قالب باید از دو نیمه تشکیل شده باشد که میتوانند برای برداشتن قطعه تولید شده باز و بسته شوند. یک قالب دایکاست ممکن است حفره های متعددی داشته باشد تا امکان تولید چند ریخته گری در هر چرخه را فراهم کند. قالب های دایکاست بسیار سنگین و بسیار بزرگتر از قطعاتی هستند که تولید می کنند، بنابراین گران هستند. ما قالب های فرسوده را به صورت رایگان برای مشتریان خود تعمیر و تعویض می کنیم تا زمانی که آنها قطعات خود را از ما سفارش دهند. قالب های ما عمر طولانی در محدوده چند صد هزار چرخه دارند. در اینجا مراحل اولیه فرآیند ساده آمده است: 1.) تولید قالب به طور کلی از فولاد 2.) قالب نصب شده روی دستگاه ریخته گری 3.) پیستون فلز مذاب را مجبور می کند تا در حفره های قالب جریان یابد و ویژگی های پیچیده و دیواره های نازک را پر می کند. 4.) پس از پر کردن قالب با فلز مذاب، قالب ریخته گری تحت فشار سفت می شود 5.) قالب باز می شود و ریخته گری با کمک پین های اجکتور خارج می شود. 6.) حالا قالب خالی دوباره روغن کاری می شود و برای چرخه بعدی گیره می شود. در دایکاست، ما اغلب از قالبگیری درج استفاده میکنیم که در آن قسمت اضافی را در قالب قرار میدهیم و فلز را در اطراف آن میریزیم. این قطعات پس از انجماد بخشی از محصول ریخته گری می شوند. از مزایای دایکاست می توان به خواص مکانیکی خوب قطعات، امکان ویژگی های پیچیده، جزئیات ظریف و سطح خوب، نرخ تولید بالا، اتوماسیون آسان اشاره کرد. معایب آن عبارتند از: برای حجم کم خیلی مناسب نیست به دلیل قالب و هزینه تجهیزات بالا، محدودیت در شکل های ریخته گری، علائم گرد کوچک روی قطعات ریخته گری ناشی از تماس پین های اجکتور، فلاش نازک فلز فشرده شده در خط جداسازی، نیاز برای منافذ در امتداد خط جدایی بین قالب، باید دمای قالب را با استفاده از گردش آب پایین نگه داشت. ریخته گری گریز از مرکز: فلز مذاب در محور چرخش در مرکز قالب دوار ریخته می شود. نیروهای گریز از مرکز، فلز را به سمت حاشیه پرتاب می کنند و در حالی که قالب به چرخش خود ادامه می دهد، اجازه می دهد تا جامد شود. می توان از چرخش محور افقی و عمودی استفاده کرد. می توان قطعاتی با سطوح داخلی گرد و سایر اشکال غیر گرد ریخته گری کرد. فرآیند را می توان به صورت زیر خلاصه کرد: 1.) فلز مذاب در قالب گریز از مرکز ریخته می شود. سپس فلز به دلیل چرخاندن قالب به دیواره های بیرونی منتقل می شود. 2.) با چرخش قالب، ریخته گری فلز سخت می شود ریخته گری سانتریفیوژ روشی مناسب برای تولید قطعات استوانه ای توخالی مانند لوله، عدم نیاز به اسپرو، رایزر و المان های دروازه ای، روکش سطحی خوب و ویژگی های دقیق، بدون مشکل انقباض، امکان تولید لوله های بلند با قطر بسیار زیاد، قابلیت تولید با سرعت بالا. . • ريخته گري پيوسته ( ريخته گري رشته اي ): براي ريخته گري به طول پيوسته از فلز استفاده مي شود. اساساً فلز مذاب در پروفیل دو بعدی قالب ریخته می شود اما طول آن نامشخص است. فلز مذاب جدید به طور مداوم به داخل قالب وارد می شود، زیرا قالب ریخته گری به سمت پایین حرکت می کند و طول آن با گذشت زمان افزایش می یابد. فلزاتی مانند مس، فولاد، آلومینیوم با استفاده از فرآیند ریختهگری پیوسته به رشتههای بلند ریخته میشوند. این فرآیند ممکن است پیکربندی های مختلفی داشته باشد، اما یکی از موارد رایج را می توان به صورت زیر ساده کرد: 1.) فلز مذاب در ظرفی که در بالای قالب قرار دارد با مقادیر و سرعت جریان خوب محاسبه شده ریخته می شود و از طریق قالب خنک شده با آب جریان می یابد. ریختهگری فلزی که در قالب ریخته میشود به یک میله شروع که در پایین قالب قرار میگیرد جامد میشود. این نوار شروع به غلتکها چیزی میدهد که در ابتدا روی آن چنگ بزنند. 2.) رشته فلزی بلند توسط غلتک ها با سرعت ثابت حمل می شود. همچنین غلتک ها جهت جریان رشته فلزی را از عمودی به افقی تغییر می دهند. 3.) پس از اینکه ریخته گری پیوسته یک مسافت افقی مشخص را طی کرد، مشعل یا اره ای که همراه با ریخته گری حرکت می کند به سرعت آن را به طول های دلخواه برش می دهد. فرآیند ریختهگری پیوسته را میتوان با فرآیند نورد ادغام کرد، جایی که فلز ریختهگریشده بهطور پیوسته میتواند مستقیماً به یک آسیاب نورد برای تولید تیرهای I، تیرهای T... و غیره وارد شود. ریختهگری پیوسته خواص یکنواختی را در سراسر محصول ایجاد میکند، نرخ انجماد بالایی دارد، هزینه را به دلیل از دست دادن بسیار کم مواد کاهش میدهد، فرآیندی را ارائه میدهد که در آن بارگذاری فلز، ریختن، انجماد، برش و حذف ریختهگری همه در یک عملیات مداوم انجام میشود و بنابراین منجر به بهره وری بالا و کیفیت بالا می شود. با این حال، یک مورد مهم سرمایه گذاری اولیه بالا، هزینه های راه اندازی و فضای مورد نیاز است. • خدمات ماشینکاری: ما ماشینکاری سه، چهار و پنج محوره را ارائه می دهیم. نوع فرآیندهای ماشینکاری که ما استفاده می کنیم عبارتند از: تراشکاری، فرزکاری، حفاری، حفاری، بریچ کردن، اره کردن، اره کردن، آسیاب کردن، لپینگ، پرداخت و ماشینکاری غیر سنتی که در منوی متفاوتی از وب سایت ما توضیح داده شده است. برای بیشتر تولیدات خود، از ماشین های CNC استفاده می کنیم. با این حال، برای برخی از عملیات، تکنیکهای مرسوم مناسبتر هستند و بنابراین ما نیز بر آنها تکیه میکنیم. قابلیتهای ماشینکاری ما به بالاترین سطح ممکن میرسد و برخی از قطعات سختگیرانه در کارخانه دارای گواهینامه AS9100 تولید میشوند. تیغه های موتور جت به تجربه ساخت بسیار تخصصی و تجهیزات مناسب نیاز دارند. صنعت هوافضا استانداردهای بسیار سختگیرانه ای دارد. برخی از قطعات با ساختارهای هندسی پیچیده به آسانی توسط ماشینکاری پنج محوری ساخته می شوند که فقط در برخی از کارخانه های ماشینکاری از جمله ما یافت می شود. کارخانه دارای گواهینامه هوافضا ما تجربه لازم را در مطابقت با الزامات مستندات گسترده صنعت هوافضا دارد. در عملیات TURNING، یک قطعه کار چرخانده شده و در برابر یک ابزار برش حرکت می کند. برای این فرآیند از ماشینی به نام تراش استفاده می شود. در آسیاب، ماشینی به نام ماشین فرز دارای ابزار چرخشی است تا لبه های برش را در برابر قطعه کار قرار دهد. عملیات حفاری شامل یک برش چرخان با لبه های برش است که در تماس با قطعه کار سوراخ هایی ایجاد می کند. معمولاً از پرس مته، ماشین تراش یا آسیاب استفاده می شود. در عملیات BORING یک ابزار با یک نوک نوک خمیده منفرد به سوراخ ناهموار در یک قطعه کار چرخان منتقل می شود تا سوراخ را کمی بزرگ کرده و دقت را بهبود بخشد. برای اهداف تکمیلی خوب استفاده می شود. BROACHING شامل یک ابزار دندانه دار برای حذف مواد از قطعه کار در یک گذر از براچ (ابزار دندانه دار) است. در بروشینگ خطی، بروشک به صورت خطی روی سطح قطعه کار می رود تا برش را ایجاد کند، در حالی که در بروشینگ چرخشی، بروشک چرخانده شده و به قطعه کار فشار داده می شود تا یک شکل متقارن محور را برش دهد. ماشینکاری نوع سوئیس یکی از تکنیک های ارزشمند ما است که برای تولید قطعات کوچک با دقت بالا از آن استفاده می کنیم. با استفاده از تراش نوع سوئیسی، قطعات کوچک، پیچیده و دقیق را ارزان میکنیم. برخلاف ماشین های تراش معمولی که قطعه کار ثابت نگه داشته می شود و ابزار در حال حرکت است، در مراکز تراشکاری نوع سوئیسی، قطعه کار مجاز است در محور Z حرکت کند و ابزار ثابت است. در ماشینکاری نوع سوئیسی، استوک میله در دستگاه نگه داشته میشود و از طریق یک بوش راهنما در محور z پیش میرود و تنها قسمتی را که قرار است ماشینکاری شود، نمایان میکند. به این ترتیب گرفتن محکم تضمین می شود و دقت بسیار بالا است. در دسترس بودن ابزارهای زنده، فرصتی برای آسیاب و حفاری با پیشروی مواد از بوش راهنما فراهم می کند. محور Y تجهیزات نوع سوئیسی قابلیت فرز کامل را فراهم می کند و باعث صرفه جویی در زمان زیادی در ساخت می شود. علاوه بر این، ماشینهای ما دارای متهها و ابزارهای حفاری هستند که در هنگام نگهداشتن آن در اسپیندل فرعی روی آن کار میکنند. قابلیت ماشینکاری نوع سوئیس ما یک فرصت ماشینکاری کاملاً خودکار را در یک عملیات واحد به ما می دهد. ماشینکاری یکی از بزرگترین بخش های تجارت AGS-TECH Inc. ما از آن به عنوان عملیات اولیه یا عملیات ثانویه پس از ریخته گری یا اکسترود کردن یک قطعه استفاده می کنیم تا تمام مشخصات نقشه رعایت شود. خدمات تکمیل سطح: ما طیف گسترده ای از عملیات سطح و پرداخت سطح را ارائه می دهیم، مانند حالت دهنده سطح برای افزایش چسبندگی، رسوب لایه نازک اکسید برای افزایش چسبندگی پوشش، سند بلاست، فیلم شیمیایی، آنودایز، نیترید، پوشش پودری، پوشش اسپری انواع متالیزاسیون و تکنیک های پوشش دهی پیشرفته از جمله کندوپاش، پرتو الکترونی، تبخیر، آبکاری، پوشش های سخت مانند الماس مانند کربن (DLC) یا پوشش تیتانیوم برای ابزارهای حفاری و برش. • خدمات علامت گذاری و برچسب گذاری محصول: بسیاری از مشتریان ما به علامت گذاری و برچسب گذاری، علامت گذاری لیزری، حکاکی روی قطعات فلزی نیاز دارند. اگر چنین نیازی دارید، اجازه دهید در مورد اینکه کدام گزینه برای شما بهترین است صحبت کنیم. در اینجا برخی از محصولات ریخته گری فلزی رایج مورد استفاده قرار می گیرند. از آنجایی که اینها خارج از قفسه هستند، در صورتی که هر یک از این موارد با نیازهای شما مطابقت داشته باشد، می توانید در هزینه های قالب صرفه جویی کنید: برای دانلود جعبه های آلومینیومی دایکاست سری 11 ما از AGS-Electronics اینجا را کلیک کنید CLICK Product Finder-Locator Service صفحه قبلی
- Custom Manufactured Parts, Assemblies, Plastic Mold, Casting,Machining
Custom Manufactured Parts, Assemblies, Plastic Mold, Rubber Molding, Metal Casting, CNC Machining, Turning, Milling, Electrical Electronic Optical Assembly PCBA قطعات و مجموعه ها و محصولات سفارشی ساخته شده ادامه مطلب قالب ها و قالب های پلاستیکی و لاستیکی ادامه مطلب ریخته گری و ماشینکاری ادامه مطلب اکستروژن، محصولات اکسترود شده ادامه مطلب مهر زنی و ساخت ورق فلز ادامه مطلب آهنگری فلزات و متالورژی پودر ادامه مطلب شکل دهی سیم و فنر ادامه مطلب شکل دهی و شکل دهی شیشه و سرامیک ادامه مطلب افزایشی و ساخت سریع ادامه مطلب تولید کامپوزیت و مواد کامپوزیت ادامه مطلب فرآیندهای اتصال و مونتاژ و چسباندن ما قطعات و مجموعه ها را برای شما تولید می کنیم و فرآیندهای تولید زیر را ارائه می دهیم: • قالب های پلاستیکی و لاستیکی و قطعات قالب گیری شده. قالبگیری تزریقی، ترموفرمینگ، قالبگیری ترموست، شکلدهی خلاء، قالبگیری دمشی، قالبگیری چرخشی، قالبگیری ریختنی، قالبگیری درج و غیره. • اکستروژن پلاستیک، لاستیک و فلز • قطعات ریخته گری آهنی و غیر آهنی و قطعات ماشینکاری شده تولید شده با تکنیک های آسیاب و تراشکاری، ماشینکاری از نوع سوئیسی. • قطعات متالورژی پودر • مهر زنی فلزی و غیرفلزی، شکل دهی ورق فلزی، مجموعه های فلزی جوش داده شده • آهنگری سرد و گرم • سیم ها، مجموعه های سیم جوش داده شده، شکل دهی سیم • انواع فنر فنر فرمینگ • ساخت دنده، گیربکس، کوپلینگ، کرم، کاهنده سرعت، سیلندر، تسمه انتقال، زنجیر انتقال، اجزای انتقال • شیشه های سفارشی و ضد گلوله مطابق با استانداردهای ناتو و نظامی • توپ، یاتاقان، قرقره و مجموعه قرقره • شیرها و اجزای پنوماتیکی مانند O-ring، واشر و آب بندی • قطعات و مجموعه های شیشه ای و سرامیکی، اجزای ضد خلاء و هرمتیک، اتصالات فلز-سرامیک و سرامیک-سرامیک. • انواع مجموعه های مکانیکی، اپتومکانیکی، الکترومکانیکی، اپتوالکترونیک. • اتصال فلز-لاستیک، فلز-پلاستیک • لوله و لوله، شکل دهی لوله، خمش و مجموعه لوله های سفارشی، ساخت زیر. • تولید فایبرگلاس • جوشکاری با استفاده از تکنیک های مختلف مانند جوش نقطه ای، جوش لیزری، MIG، TIG. جوشکاری اولتراسونیک برای قطعات پلاستیکی. • طیف گسترده ای از عملیات سطح و پرداخت های سطحی مانند تهویه سطح برای افزایش چسبندگی، رسوب لایه نازک اکسید برای افزایش چسبندگی پوشش، سند بلاست، فیلم شیمیایی، آنودایز، نیتریدینگ، پوشش پودری، پوشش اسپری، انواع متالیزاسیون پیشرفته و تکنیک های پوشش دهی از جمله کندوپاش، پرتو الکترونی، تبخیر، آبکاری، پوشش های سخت مانند الماس مانند کربن (DLC) یا تیتانیوم برای ابزارهای برش و حفاری. • علامت گذاری و لیبل گذاری، علامت گذاری لیزری روی قطعات فلزی، چاپ روی قطعات پلاستیکی و لاستیکی دانلود بروشور اصطلاحات رایج مهندسی مکانیک مورد استفاده طراحان و مهندسان ما محصولات را با توجه به مشخصات و نیازهای خاص شما می سازیم. به منظور ارائه بهترین کیفیت، تحویل و قیمت به شما، ما محصولاتی را در سراسر جهان در چین، هند، تایوان، فیلیپین، کره جنوبی، مالزی، سریلانکا، ترکیه، ایالات متحده آمریکا، کانادا، آلمان، بریتانیا و ژاپن تولید می کنیم. این ما را بسیار قوی تر و در سطح جهانی رقابتی تر از هر custom manufacturer دیگر می کند. محصولات ما در محیطهای دارای گواهی ISO9001:2000، QS9000، ISO14001، TS16949 تولید میشوند و دارای علامت CE، UL و مطابق با سایر استانداردهای صنعت هستند. هنگامی که ما برای پروژه شما منصوب شدیم، می توانیم کل تولید، مونتاژ، آزمایش، صلاحیت، حمل و نقل و گمرک را همانطور که می خواهید انجام دهیم. اگر ترجیح می دهید، ما می توانیم قطعات شما را انبار کنیم، کیت های سفارشی را جمع آوری کنیم، نام و برند شرکت شما را چاپ و برچسب گذاری کنیم و به مشتریان شما ارسال کنیم. به عبارت دیگر در صورت تمایل می توانیم مرکز انبارداری و توزیع شما نیز باشیم. از آنجایی که انبارهای ما در نزدیکی بنادر دریایی اصلی قرار دارند، مزیت لجستیکی به ما می دهد. به عنوان مثال، هنگامی که محصولات شما به یک بندر بزرگ ایالات متحده می رسد، ما می توانیم آن را مستقیماً به یک انبار نزدیک منتقل کنیم، جایی که می توانیم ذخیره، مونتاژ، کیت ها، برچسب گذاری مجدد، چاپ، بسته بندی بر اساس انتخاب شما و رها کردن آن ها برای مشتریان خود ارسال کنید ما نه تنها محصولات را عرضه می کنیم. شرکت ما روی قراردادهای سفارشی کار می کند که در آن ما به سایت شما می آییم، پروژه شما را در محل ارزیابی می کنیم و یک پیشنهاد پروژه سفارشی طراحی شده برای شما ایجاد می کنیم. سپس تیم مجرب خود را برای اجرای پروژه می فرستیم. اطلاعات بیشتر در مورد کارهای مهندسی ما را می توانید در اینجا بیابید http://www.ags-engineering.com -ما پروژه های کوچک و همچنین پروژه های بزرگ را در مقیاس صنعتی می گیریم. به عنوان اولین قدم، ما می توانیم شما را از طریق تلفن، کنفرانس راه دور یا پیام رسان MSN به اعضای تیم متخصص خود متصل کنیم، بنابراین شما می توانید مستقیماً با یک متخصص ارتباط برقرار کنید، سؤال بپرسید و در مورد پروژه خود بحث کنید. با ما تماس بگیرید و در صورت نیاز به شما مراجعه کنیم. صفحه قبلی