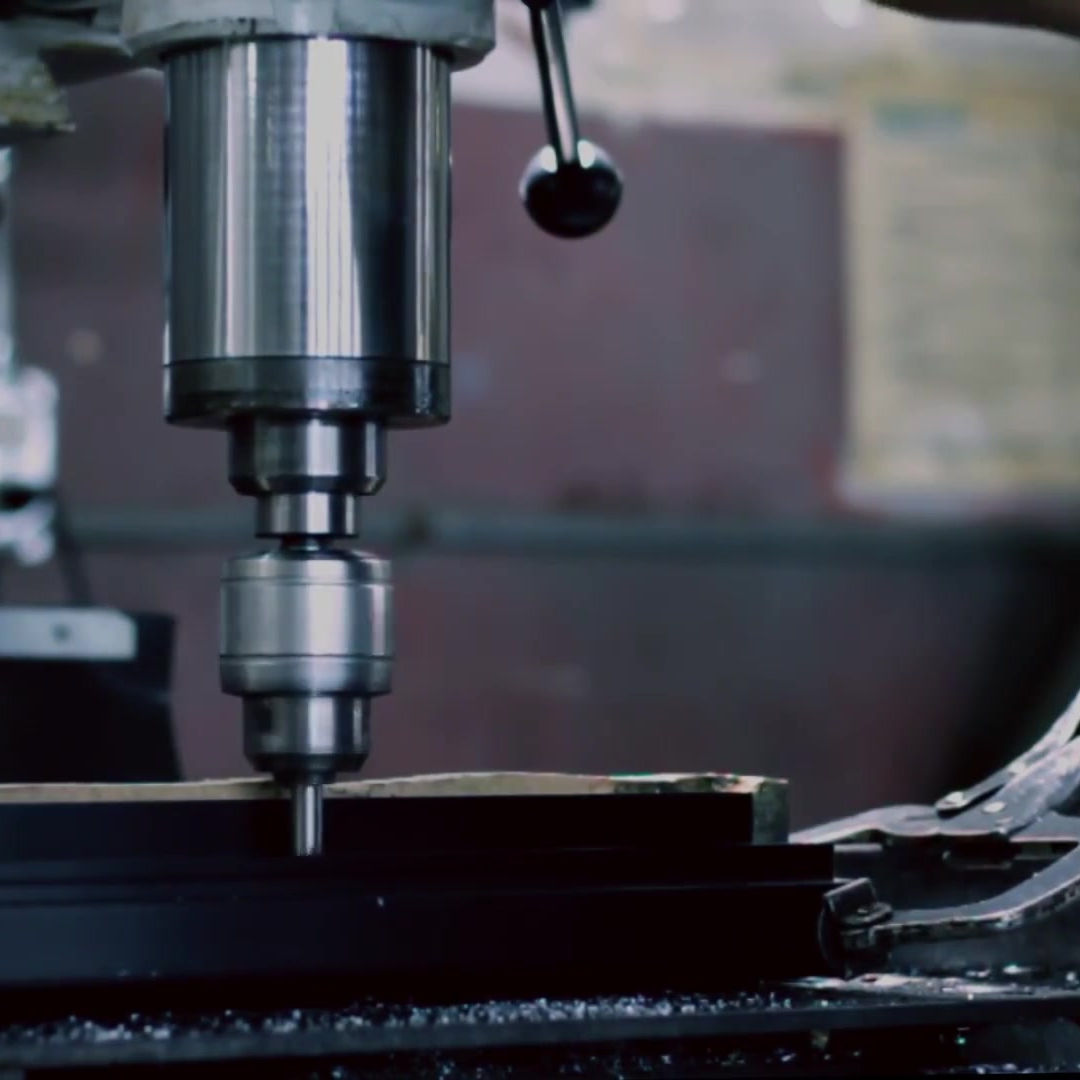
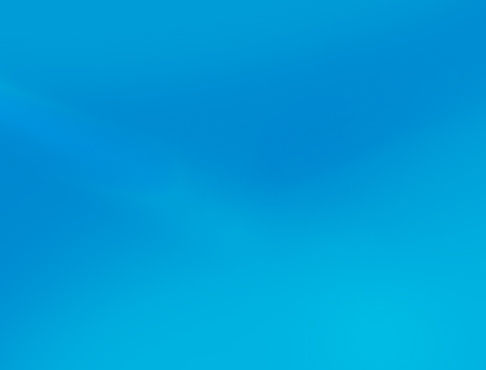
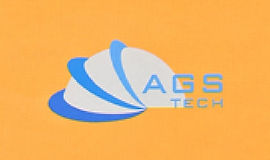
Maailmanlaajuinen räätälöity valmistaja, integraattori, yhdistäjä, ulkoistuskumppani laajalle valikoimalle tuotteita ja palveluita.
Olemme keskitetty lähde räätälöityjen ja valmiiden tuotteiden ja palvelujen valmistukseen, valmistukseen, suunnitteluun, konsolidointiin, integrointiin ja ulkoistamiseen.
Valitse kielesi
-
Räätälöity valmistus
-
Kotimainen ja kansainvälinen sopimusvalmistus
-
Valmistuksen ulkoistaminen
-
Kotimaiset ja maailmanlaajuiset hankinnat
-
Consolidation
-
Tekninen integrointi
-
Suunnittelupalvelut
Monien valmistuksessa käyttämiemme JOINING-tekniikoiden joukossa erityistä huomiota kiinnitetään HITSAUS-, JUOTTAMINEN, JUOTTAMINEN, LIIMASIDOTUS ja MUKAUTETTU MEKAANINEN ASENNUS, koska näitä tekniikoita käytetään laajalti sellaisissa sovelluksissa kuin hermeettisten kokoonpanojen valmistus, korkean teknologian tuotteiden valmistus ja erikoissaumaus. Tässä keskitymme näiden liitostekniikoiden erikoisempiin näkökohtiin, koska ne liittyvät edistyneiden tuotteiden ja kokoonpanojen valmistukseen.
FUSION HITSAUS: Käytämme lämpöä materiaalien sulattamiseen ja yhdistämiseen. Lämpö toimitetaan sähköllä tai suurenergiasäteillä. Käyttämämme sulatushitsaustyypit ovat OXYFUEL-GAASHITSUS, KAARIHITSaus, SUURIENERGIASÄHITSAUS.
KIINTEÄTILAHITSaus: Yhdistämme osat ilman sulatusta ja sulattamista. Puolijohdehitsausmenetelmämme ovat KYLMÄ-, ULTRAÄÄNI-, KESTÄVÄ-, KITKA-, RÄJÄHDYSHITSAUS ja DIFFUUSIOSIIDOS.
JUOTTAMINEN: Ne käyttävät täyteainemetalleja ja antavat meille edun työskennellä alhaisemmissa lämpötiloissa kuin hitsauksessa, mikä vähentää tuotteiden rakenteellisia vaurioita. Tietoja juotoslaitoksestamme, joka tuottaa keraamisia metalliliittimiä, hermeettistä tiivistystä, tyhjiöläpivientiä, korkea- ja ultrakorkeaa tyhjiö- ja nesteenohjauskomponentteja löytyy täältä:Juotostehtaan esite
LIIMASIDOTUS: Teollisuudessa käytettävien liimojen ja käyttökohteiden moninaisuuden vuoksi meillä on tätä varten oma sivu. Siirry liimaussivullemme napsauttamalla tätä.
MUKAUTETTU MEKAANINEN ASENNUS: Käytämme erilaisia kiinnikkeitä, kuten pultteja, ruuveja, muttereita, niittejä. Kiinnikkeemme eivät rajoitu tavallisiin off-shelf-kiinnittimiin. Suunnittelemme, kehitämme ja valmistamme erikoiskiinnittimiä, jotka on valmistettu epätyypillisistä materiaaleista, jotta ne täyttävät erikoissovellusten vaatimukset. Joskus halutaan sähkön tai lämmön johtamattomuus, kun taas joskus johtavuus. Joissakin erikoissovelluksissa asiakas saattaa haluta erityisiä kiinnikkeitä, joita ei voida poistaa tuhoamatta tuotetta. Ideoita ja sovelluksia on loputtomasti. Meillä on kaikki sinulle, jos ei valmiina, voimme kehittää sen nopeasti. Siirry mekaanista kokoonpanoa käsittelevälle sivullemme napsauttamalla tätä. Tutustutaanpa erilaisiin liitostekniikoihimme tarkemmin.
OXYFUEL GAS WELDING (OFW): Käytämme hapella sekoitettua polttokaasua hitsausliekin tuottamiseen. Kun käytämme asetyleeniä polttoaineena ja hapena, kutsumme sitä oksiasetyleenikaasuhitsaukseksi. Happikaasun palamisprosessissa tapahtuu kaksi kemiallista reaktiota:
C2H2 + O2 ------» 2CO + H2 + Lämpö
2CO + H2 + 1,5 O2--------» 2 CO2 + H2O + lämpö
Ensimmäinen reaktio hajottaa asetyleenin hiilimonoksidiksi ja vedyksi ja tuottaa noin 33 % syntyneestä kokonaislämmöstä. Toinen yllä oleva prosessi edustaa vedyn ja hiilimonoksidin lisäpolttoa samalla kun tuotetaan noin 67 % kokonaislämmöstä. Liekin lämpötilat ovat välillä 1533-3573 Kelvin. Happiprosentti kaasuseoksessa on tärkeä. Jos happipitoisuus on yli puolet, liekistä tulee hapettava aine. Tämä ei ole toivottavaa joillekin metalleille, mutta toivottavaa toisille. Esimerkki, kun hapettava liekki on toivottavaa, ovat kuparipohjaiset seokset, koska ne muodostavat passivoivan kerroksen metallin päälle. Toisaalta, kun happipitoisuutta vähennetään, täysi palaminen ei ole mahdollista ja liekki muuttuu pelkistäväksi (hiilettäväksi) liekiksi. Pelkistävän liekin lämpötilat ovat alhaisemmat ja siksi se soveltuu prosesseihin, kuten juottamiseen ja juottamiseen. Myös muut kaasut ovat mahdollisia polttoaineita, mutta niillä on joitain haittoja asetyleeniin verrattuna. Ajoittain toimitamme hitsausalueelle lisäainemetalleja täytetankojen tai lankojen muodossa. Jotkut niistä on päällystetty juoksuttimella pintojen hapettumisen hidastamiseksi ja siten sulan metallin suojaamiseksi. Fluxin lisäetu on oksidien ja muiden aineiden poistaminen hitsausalueelta. Tämä johtaa vahvempaan sidokseen. Eräs muunnelma happikaasuhitsauksesta on PAINEKAASUHITSAUS, jossa kahta komponenttia lämmitetään rajapinnallaan oksiasetyleenikaasupolttimella ja kun rajapinta alkaa sulaa, poltin vedetään pois ja kohdistetaan aksiaalinen voima puristamaan kaksi osaa yhteen. kunnes käyttöliittymä on jähmettynyt.
KAARIHITSaus: Käytämme sähköenergiaa kaaren tuottamiseen elektrodin kärjen ja hitsattavien osien välille. Virtalähde voi olla AC tai DC, kun taas elektrodit ovat joko kuluvia tai ei-kuluvia. Lämmönsiirto kaarihitsauksessa voidaan ilmaista seuraavalla yhtälöllä:
H / l = ex VI / v
Tässä H on lämmönsyöttö, l on hitsin pituus, V ja I ovat käytetty jännite ja virta, v on hitsausnopeus ja e on prosessin tehokkuus. Mitä korkeampi hyötysuhde "e", sitä edullisemmin käytettävissä oleva energia käytetään materiaalin sulattamiseen. Lämmöntuotto voidaan ilmaista myös seuraavasti:
H = ux (tilavuus) = ux A xl
Tässä u on sulamisen ominaisenergia, A hitsin poikkileikkaus ja l hitsin pituus. Kahdesta yllä olevasta yhtälöstä voimme saada:
v = ex VI / u A
Valokaarihitsauksen muunnelma on SHIELDED METAL ARC WELDING (SMAW), joka muodostaa noin 50 % kaikista teollisuus- ja kunnossapitohitsausprosesseista. SÄHKÖKÄRIHITSaus (PUIKKOHITSAUS) suoritetaan koskettamalla pinnoitetun elektrodin kärkeä työkappaleeseen ja vetämällä se nopeasti ulos kaaren ylläpitämiseen riittävälle etäisyydelle. Kutsumme tätä prosessia myös puikkohitsaukseksi, koska elektrodit ovat ohuita ja pitkiä puikkoja. Hitsausprosessin aikana elektrodin kärki sulaa pinnoitteensa ja perusmetallin kanssa kaaren läheisyydessä. Seos perusmetallista, elektrodimetallista ja elektrodin pinnoitteesta peräisin olevista aineista jähmettyy hitsausalueella. Elektrodin pinnoite poistaa hapettumista ja muodostaa suojakaasun hitsausalueelle, mikä suojaa sitä ympäristön hapelta. Siksi prosessia kutsutaan suojatuksi metallikaarihitsaukseksi. Käytämme 50-300 ampeerin virtoja ja yleensä alle 10 kW tehotasoja optimaalisen hitsaustehon saavuttamiseksi. Tärkeää on myös tasavirran polariteetti (virran suunta). Suora napaisuus, jossa työkappale on positiivinen ja elektrodi negatiivinen, on edullinen ohutlevyjen hitsauksessa sen matalan tunkeutumisen vuoksi ja myös liitoksissa, joissa on erittäin suuria rakoja. Kun meillä on käänteinen napaisuus, eli elektrodi on positiivinen ja työkappale negatiivinen, voimme saavuttaa syvempiä hitsausläpivientejä. Vaihtovirralla, koska meillä on sykkiviä kaaria, voimme hitsata paksuja osia käyttämällä suurihalkaisijaisia elektrodeja ja maksimivirtoja. SMAW-hitsausmenetelmä soveltuu työkappaleiden paksuuksille 3-19 mm ja jopa suuremmille monikierrostekniikoilla. Hitsin päälle muodostunut kuona on poistettava teräsharjalla, jotta hitsauskohdassa ei tapahdu korroosiota ja vaurioita. Tämä tietysti lisää suojatun metallin kaarihitsauksen kustannuksia. Siitä huolimatta SMAW on suosituin hitsaustekniikka teollisuudessa ja korjaustöissä.
UPOTETTU KAARIHITSaus (SAH): Tässä prosessissa suojaamme hitsauskaaren käyttämällä rakeisia juoksutemateriaaleja, kuten kalkkia, piidioksidia, kalsiumfluoridia, mangaanioksidia jne. Rakeinen juoksute syötetään hitsausalueelle painovoimavirralla suuttimen läpi. Sulan hitsausvyöhykkeen peittävä juoksute suojaa merkittävästi kipinöiltä, höyryiltä, UV-säteilyltä jne. ja toimii lämmöneristeenä, jolloin lämpö pääsee tunkeutumaan syvälle työkappaleeseen. Sulautumaton juoksute otetaan talteen, käsitellään ja käytetään uudelleen. Paljaskelaa käytetään elektrodina ja se syötetään putken kautta hitsausalueelle. Käytämme 300-2000 ampeerin virtoja. Submerged kaarihitsaus (SAW) -prosessi on rajoitettu vaaka- ja tasaisiin asentoihin ja pyöreisiin hitseihin, jos pyöreän rakenteen (kuten putkien) pyöriminen on mahdollista hitsauksen aikana. Nopeudet voivat olla 5 m/min. SAW-prosessi soveltuu paksuille levyille ja tuottaa laadukkaita, sitkeitä, sitkeitä ja tasaisia hitsejä. Tuottavuus eli tunnissa levitettävän hitsausmateriaalin määrä on 4-10 kertaa SMAW-prosessiin verrattuna.
Toinen kaarihitsausprosessi, nimittäin GAS METAL ARC WELDING (GMAW) tai vaihtoehtoisesti METAL INERT GAS WELDING (MIG) -hitsaus perustuu siihen, että hitsausalue suojataan ulkoisilta kaasulähteiltä, kuten helium, argon, hiilidioksidi jne. Elektrodimetallissa voi olla muita hapettumisenestoaineita. Kulutuslanka syötetään suuttimen kautta hitsausalueelle. Valmistus, jossa käytetään sekä rauta- että ei-rautametalleja, suoritetaan kaasumetallikaarihitsauksella (GMAW). Hitsauksen tuottavuus on noin 2 kertaa SMAW-prosessiin verrattuna. Käytössä on automatisoitu hitsauslaitteisto. Metalli siirretään tässä prosessissa jollakin kolmesta tavasta: "Spray Transfer" tarkoittaa useiden satojen pienten metallipisaroiden siirtämistä sekunnissa elektrodilta hitsausalueelle. "Globulaarisessa siirrossa" sitä vastoin käytetään hiilidioksidipitoisia kaasuja ja sulan metallin palloja ajaa valokaari. Hitsausvirrat ovat suuria ja hitsin tunkeutuminen syvemmälle, hitsausnopeus suurempi kuin ruiskusiirrossa. Siten pallomainen siirto on parempi raskaampien osien hitsaukseen. Lopuksi "oikosulku"-menetelmässä elektrodin kärki koskettaa sulaa hitsausallasta ja oikosulkee sen, kun metallia siirtyy yksittäisissä pisaroissa yli 50 pisaraa sekunnissa. Pieniä virtoja ja jännitteitä käytetään ohuemman johdon ohella. Käytetyt tehot ovat noin 2 kW ja lämpötilat suhteellisen alhaiset, joten tämä menetelmä sopii ohuille levyille, joiden paksuus on alle 6 mm.
Toinen muunnelma FLUX-CORED ARC WELDING (FCAW) -prosessista on samanlainen kuin kaasumetallikaarihitsaus, paitsi että elektrodi on juoksutuksella täytetty putki. Hydraulielektrodien käytön etuna on, että ne tuottavat vakaampia kaaria, antavat meille mahdollisuuden parantaa hitsausmetallien ominaisuuksia, vähemmän haurautta ja joustavuutta SMAW-hitsaukseen verrattuna, paremmat hitsausääriviivat. Itsesuojatut ydinelektrodit sisältävät materiaaleja, jotka suojaavat hitsausaluetta ilmakehältä. Käytämme noin 20 kW tehoa. Kuten GMAW-prosessi, myös FCAW-prosessi tarjoaa mahdollisuuden automatisoida jatkuvan hitsauksen prosesseja, ja se on taloudellinen. Erilaisia hitsausmetallien kemiallisia yhdisteitä voidaan kehittää lisäämällä erilaisia metalliseoksia sulatusytimeen.
ELECTROGAS WELDING (EGW) hitsaa kappaleet reunasta reunaan. Sitä kutsutaan joskus myös BUTT WELDING. Hitsausmetalli asetetaan hitsausonteloon kahden liitettävän kappaleen väliin. Tilaa ympäröi kaksi vesijäähdytteistä patoa, jotka estävät sulan kuonan valumisen ulos. Patoja nostetaan ylös mekaanisilla käyttövoimalla. Kun työkappaletta voidaan pyörittää, voimme käyttää sähkökaasuhitsaustekniikkaa myös putkien kehähitsaukseen. Elektrodit syötetään putken läpi jatkuvan kaaren pitämiseksi. Virrat voivat olla noin 400 ampeeria tai 750 ampeeria ja tehotasot noin 20 kW. Inertit kaasut, jotka ovat peräisin joko täyteelektrodista tai ulkoisesta lähteestä, tarjoavat suojan. Käytämme sähkökaasuhitsausta (EGW) metalleille, kuten teräksille, titaanille jne., joiden paksuus on 12-75 mm. Tekniikka sopii hyvin suuriin rakenteisiin.
Kuitenkin toisessa tekniikassa nimeltä ELECTROSLAG WELDING (ESW) kaari sytytetään elektrodin ja työkappaleen pohjan välissä ja lisätään sulatetta. Kun sula kuona saavuttaa elektrodin kärjen, kaari sammuu. Energiaa syötetään jatkuvasti sulan kuonan sähkövastuksen kautta. Voimme hitsata levyjä, joiden paksuus on 50 mm - 900 mm ja jopa suurempi. Virrat ovat noin 600 ampeeria ja jännitteet 40 - 50 V. Hitsausnopeudet ovat noin 12 - 36 mm/min. Käyttökohteet ovat samanlaisia kuin sähkökaasuhitsaus.
Yksi non-sumable elektrodiprosesseistamme, GAS TUNGSTEN ARC WELDING (GTAW), joka tunnetaan myös nimellä TUNGSTEN INERT GAS WELDING (TIG), sisältää täytemetallin syöttämisen langalla. Tiiviin saumoihin emme joskus käytä täytemetallia. TIG-prosessissa emme käytä sulatetta, vaan käytämme argonia ja heliumia suojaukseen. Volframilla on korkea sulamispiste, eikä sitä kuluteta TIG-hitsausprosessissa, joten vakiovirta ja kaarivälit voidaan säilyttää. Tehotasot ovat 8-20 kW ja virrat joko 200 ampeeria (DC) tai 500 ampeeria (AC). Alumiinille ja magnesiumille käytämme vaihtovirtaa sen oksidipuhdistustoimintoon. Välttääksemme volframielektrodin kontaminoitumisen, vältämme sen kosketusta sulan metallin kanssa. Gas Tungsten Arc Welding (GTAW) on erityisen hyödyllinen ohuiden metallien hitsaukseen. GTAW-hitsaukset ovat erittäin korkealaatuisia ja hyvällä pintakäsittelyllä.
Vetykaasun kalliimman hinnan vuoksi harvemmin käytetty tekniikka on ATOMIC HYDROGEN WELDING (AHW), jossa muodostetaan kaari kahden volframielektrodin väliin virtaavan vetykaasun suojaavassa ilmakehässä. AHW on myös ei-kuluva puikkohitsausprosessi. Kaksiatominen vetykaasu H2 hajoaa atomimuotoonsa lähellä hitsauskaarta, jossa lämpötilat ovat yli 6273 Kelviniä. Hajotessaan se imee suuren määrän lämpöä kaaresta. Kun vetyatomit osuvat hitsausalueeseen, joka on suhteellisen kylmä pinta, ne yhdistyvät uudelleen kaksiatomiseen muotoon ja vapauttavat varastoitunutta lämpöä. Energiaa voidaan vaihdella muuttamalla työkappaleen kaarietäisyys.
Toisessa ei-kuluvassa elektrodiprosessissa, PLASMA ARC WELDING (PAW), meillä on keskitetty plasmakaari, joka on suunnattu kohti hitsausaluetta. Lämpötila saavuttaa 33 273 Kelviniä PAW:ssa. Plasmakaasun muodostaa lähes yhtä suuri määrä elektroneja ja ioneja. Pienvirran pilottikaari käynnistää plasman, joka on volframielektrodin ja aukon välissä. Käyttövirrat ovat yleensä noin 100 ampeeria. Täytemetallia voidaan syöttää. Plasmakaarihitsauksessa suojaus suoritetaan ulomman suojarenkaan avulla ja käyttämällä kaasuja, kuten argonia ja heliumia. Plasmakaarihitsauksessa kaari voi olla elektrodin ja työkappaleen tai elektrodin ja suuttimen välissä. Tällä hitsaustekniikalla on etuja muihin menetelmiin verrattuna korkeampi energiapitoisuus, syvempi ja kapeampi hitsauskyky, parempi valokaaren vakaus, korkeammat hitsausnopeudet jopa 1 metriin/min, vähemmän lämpöä. Käytämme plasmakaarihitsausta yleensä alle 6 mm:n ja joskus jopa 20 mm:n paksuisille alumiinille ja titaanille.
SUURIENERGIASSÄTEHITSaus: Toinen sulatushitsausmenetelmä, jossa on elektronisuihkuhitsaus (EBW) ja laserhitsaus (LBW) kahtena muunnelmana. Nämä tekniikat ovat erityisen arvokkaita korkean teknologian tuotteidemme valmistustyössä. Elektronisuihkuhitsauksessa nopeat elektronit iskevät työkappaleeseen ja niiden liike-energia muuttuu lämmöksi. Kapea elektronisäde kulkee helposti tyhjiökammiossa. Yleensä käytämme suurtyhjiötä sähköpalkkihitsauksessa. Levyt, joiden paksuus on 150 mm, voidaan hitsata. Suojakaasuja, juoksutetta tai täyteainetta ei tarvita. Elektronisuihkupistoolien teho on 100 kW. Syvät ja kapeat hitsaukset korkeilla, jopa 30:n sivusuhteilla ja pienet lämpövaikutusvyöhykkeet ovat mahdollisia. Hitsausnopeudet voivat olla 12 m/min. Lasersädehitsauksessa käytämme lämmönlähteenä suuritehoisia lasereita. Jo 10 mikronin suuret lasersäteet ja korkea tiheys mahdollistavat syvän tunkeutumisen työkappaleeseen. Syvyys-leveyssuhde on jopa 10 mahdollista lasersädehitsauksella. Käytämme sekä pulssi- että jatkuvaa aaltolasereita, joista ensimmäinen soveltuu ohuille materiaaleille ja jälkimmäinen enimmäkseen noin 25 mm paksuille työkappaleille. Tehot ovat jopa 100 kW. Lasersädehitsaus ei sovellu optisesti hyvin heijastaville materiaaleille. Kaasuja voidaan käyttää myös hitsausprosessissa. Lasersädehitsausmenetelmä sopii hyvin automaatioon ja suurien volyymien valmistukseen ja voi tarjota hitsausnopeudet välillä 2,5 m/min - 80 m/min. Yksi tämän hitsaustekniikan suuri etu on pääsy alueille, joissa muita tekniikoita ei voida käyttää. Lasersäteet voivat kulkea helposti tällaisille vaikeille alueille. Tyhjiötä ei tarvita kuten elektronisuihkuhitsauksessa. Lasersädehitsauksella voidaan saada hitsejä, joilla on hyvä laatu ja lujuus, alhainen kutistuminen, pieni vääristymä ja pieni huokoisuus. Lasersäteitä voidaan helposti käsitellä ja muotoilla valokuitukaapeleilla. Tekniikka soveltuu siis hyvin hermeettisten tarkkuuskokoonpanojen, elektroniikkapakettien jne. hitsaukseen.
Katsotaanpa SOLID STATE -HITSaustekniikoitamme. COLD WELDING (CW) on prosessi, jossa painetta kohdistetaan lämmön sijasta meistien tai telojen avulla liitettäviin osiin. Kylmähitsauksessa vähintään yhden liitososista on oltava sitkeä. Parhaat tulokset saadaan kahdella samankaltaisella materiaalilla. Jos kylmähitsauksella liitettävät metallit ovat erilaisia, liitokset voivat olla heikkoja ja hauraita. Kylmähitsausmenetelmä soveltuu hyvin pehmeille, sitkeille ja pienille työkappaleille, kuten sähköliitännät, lämpöherkät säiliön reunat, bimetallilistat termostaatteihin jne. Kylmähitsauksen eräs muunnelma on telaliitos (tai telahitsaus), jossa paine kohdistetaan telaparin kautta. Joskus teemme telahitsausta korkeissa lämpötiloissa paremman rajapinnan lujuuden saavuttamiseksi.
Toinen käyttämämme puolijohdehitsausprosessi on ULTRASONIC WELDING (USW), jossa työkappaleisiin kohdistuu staattinen normaalivoima ja värähtelevät leikkausjännitykset. Värähtelevät leikkausjännitykset kohdistetaan anturin kärjen kautta. Ultraäänihitsaus käyttää värähtelyjä taajuuksilla 10 - 75 kHz. Joissakin sovelluksissa, kuten saumahitsauksessa, käytämme pyörivää hitsauskiekkoa kärjenä. Työkappaleisiin kohdistuvat leikkausjännitykset aiheuttavat pieniä plastisia muodonmuutoksia, hajottavat oksidikerroksia, epäpuhtauksia ja johtavat kiinteään olomuotoon. Ultraäänihitsaukseen liittyvät lämpötilat ovat reilusti metallien sulamispistelämpötilojen alapuolella, eikä fuusiota tapahdu. Käytämme usein ultraäänihitsausprosessia (USW) ei-metallisten materiaalien, kuten muovien, käsittelyyn. Kestomuoveissa lämpötilat saavuttavat kuitenkin sulamispisteitä.
Toinen suosittu tekniikka, KITKAHITSAUKSESSA (FRW) lämpö syntyy kitkan kautta liitettävien työkappaleiden rajapinnassa. Kitkahitsauksessa pidämme yhden työkappaleen paikallaan, kun taas toista työkappaletta pidetään kiinnikkeessä ja pyöritetään vakionopeudella. Työkappaleet saatetaan sitten kosketukseen aksiaalisen voiman alaisena. Kitkahitsauksessa pinnan pyörimisnopeus voi joissain tapauksissa olla jopa 900 m/min. Riittävän rajapinnan kosketuksen jälkeen pyörivä työkappale pysäytetään äkillisesti ja aksiaalivoimaa lisätään. Hitsausalue on yleensä kapea alue. Kitkahitsaustekniikkaa voidaan käyttää eri materiaaleista valmistettujen kiinteiden ja putkimaisten osien liittämiseen. FRW:n liitännässä saattaa kehittyä salamaa, mutta tämä salama voidaan poistaa toissijaisella työstyksellä tai hiomalla. Kitkahitsausprosessissa on muunnelmia. Esimerkiksi "hitauskitkahitsaukseen" liittyy vauhtipyörä, jonka pyörimiskineettistä energiaa käytetään osien hitsaukseen. Hitsaus on valmis, kun vauhtipyörä pysähtyy. Pyörivää massaa ja siten pyörimiskineettistä energiaa voidaan vaihdella. Toinen muunnelma on "lineaarinen kitkahitsaus", jossa lineaarinen edestakainen liike kohdistetaan ainakin yhteen liitettävistä komponenteista. Lineaarisessa kitkahitsauksessa osien ei tarvitse olla pyöreitä, ne voivat olla suorakaiteen, neliön tai muun muotoisia. Taajuudet voivat olla kymmenissä hertseissä, amplitudit millimetreissä ja paineet kymmenissä tai satoissa MPa. Lopuksi "kitkasekoitushitsaus" on jonkin verran erilainen kuin kaksi muuta edellä selostettua. Kun inertiakitkahitsauksessa ja lineaarisessa kitkahitsauksessa rajapintojen kuumennus saadaan aikaan kitkan avulla hankaamalla kahta kosketuspintaa, kun kitkasekoitushitsausmenetelmässä kolmatta kappaletta hierotaan kahta liitettävää pintaa vasten. Pyörivä työkalu, jonka halkaisija on 5-6 mm, saatetaan kosketukseen liitoksen kanssa. Lämpötilat voivat nousta 503-533 Kelvinin arvoihin. Saumassa materiaalia kuumennetaan, sekoitetaan ja sekoitetaan. Käytämme kitkasekoitushitsausta erilaisiin materiaaleihin, kuten alumiiniin, muoviin ja komposiitteihin. Hitsaukset ovat tasalaatuisia ja korkealaatuisia minimaalisilla huokosilla. Kitkasekoitushitsauksessa ei synny höyryjä tai roiskeita ja prosessi on hyvin automatisoitu.
VASTUSHITSaus (RW): Hitsaukseen tarvittava lämpö syntyy kahden liitettävän työkappaleen välisestä sähkövastuksesta. Vastushitsauksessa ei käytetä juoksutetta, suojakaasuja tai kuluvia elektrodeja. Joule-lämmitys tapahtuu vastushitsauksessa ja se voidaan ilmaista seuraavasti:
H = (neliö I) x R xtx K
H on lämpöä jouleina (wattisekunteina), I virta ampeereina, R vastus ohmeina, t on virran läpikulkuaika sekunteina. Tekijä K on pienempi kuin 1 ja edustaa energian osaa, joka ei häviä säteilyn ja johtumisen kautta. Vastushitsausprosessien virrat voivat saavuttaa jopa 100 000 A, mutta jännitteet ovat tyypillisesti 0,5 - 10 volttia. Elektrodit on tyypillisesti valmistettu kupariseoksista. Sekä samanlaisia että erilaisia materiaaleja voidaan liittää vastushitsauksella. Tälle prosessille on olemassa useita muunnelmia: "Resistenssipistehitsaus" sisältää kaksi vastakkaista pyöreää elektrodia, jotka koskettavat kahden levyn nivelliitoksen pintoja. Painetta käytetään, kunnes virta katkaistaan. Hitsauskimpale on yleensä halkaisijaltaan enintään 10 mm. Resistanssipistehitsaus jättää hieman värjäytyneitä painumisjälkiä hitsauskohtiin. Pistehitsaus on suosituin vastushitsaustekniikkamme. Pistehitsauksessa käytetään erilaisia elektrodimuotoja vaikeiden alueiden saavuttamiseksi. Pistehitsauslaitteistomme on CNC-ohjattu ja siinä on useita elektrodeja, joita voidaan käyttää samanaikaisesti. Toinen muunnelma "vastussaumahitsaus" suoritetaan pyörä- tai rullaelektrodeilla, jotka tuottavat jatkuvia pistehitsauksia aina, kun virta saavuttaa riittävän korkean tason vaihtovirtakierrossa. Vastussaumahitsauksella valmistetut saumat ovat neste- ja kaasutiiviitä. Noin 1,5 m/min hitsausnopeudet ovat normaalit ohuille levyille. Voidaan käyttää katkonaisia virtoja niin, että pistehitsaukset muodostuvat halutuin väliajoin pitkin saumaa. "Resistenssiprojektiohitsauksessa" kohokuvioitamme yhden tai useamman ulokkeen (kuoppauksen) yhdelle hitsattavalle työkappaleen pinnalle. Nämä ulokkeet voivat olla pyöreitä tai soikeita. Korkeat paikalliset lämpötilat saavutetaan näissä kohokuvioiduissa kohdissa, jotka joutuvat kosketuksiin liitososan kanssa. Elektrodit kohdistavat painetta puristaakseen nämä ulokkeet. Resistanssiprojektiohitsauksessa elektrodeilla on litteät kärjet ja ne ovat vesijäähdytteisiä kupariseoksia. Vastusprojektiohitsauksen etuna on kykymme tehdä useita hitsejä yhdellä iskulla, jolloin elektrodin pidempi käyttöikä, kyky hitsata eripaksuisia levyjä, kyky hitsata muttereita ja pultteja levyihin. Vastusprojektiohitsauksen haittana on kuoppien kohokuvioinnin lisäkustannukset. Vielä toinen tekniikka, "flashhitsauksessa" lämpöä syntyy valokaaresta kahden työkappaleen päissä, kun ne alkavat koskettaa. Tätä menetelmää voidaan vaihtoehtoisesti harkita myös kaarihitsaukseksi. Lämpötila rajapinnalla nousee ja materiaali pehmenee. Aksiaalinen voima kohdistetaan ja hitsaus muodostetaan pehmennetylle alueelle. Kun flash-hitsaus on valmis, liitos voidaan työstää ulkonäön parantamiseksi. Flash-hitsauksella saatu hitsin laatu on hyvä. Tehot ovat 10-1500 kW. Flash-hitsaus soveltuu samanlaisten tai erilaisten metallien, joiden halkaisija on enintään 75 mm, ja levyjen, joiden paksuus on 0,2 mm - 25 mm, liittämiseen reunasta reunaan. "Kaarihitsaus" on hyvin samanlainen kuin flash-hitsaus. Nasta, kuten pultti tai kierretanko, toimii yhtenä elektrodina, kun se liitetään työkappaleeseen, kuten levyyn. Syntyneen lämmön keskittämiseksi, hapettumisen estämiseksi ja sulan metallin pitämiseksi hitsausalueella, liitoksen ympärille asetetaan kertakäyttöinen keraaminen rengas. Lopuksi "iskuhitsaus" toinen vastushitsausprosessi käyttää kondensaattoria sähköenergian syöttämiseen. Iskuhitsauksessa teho purkautuu millisekuntien sisällä erittäin nopeasti kehittäen liitokseen korkeaa paikallista lämpöä. Käytämme iskuhitsausta laajasti elektroniikkateollisuudessa, jossa herkkien elektronisten komponenttien kuumenemista liitoksen läheisyydessä on vältettävä.
RÄJÄHDYSHITSAUKSeksi kutsuttu tekniikka sisältää räjähdysainekerroksen räjäyttämisen, joka asetetaan yhden liitettävän työkappaleen päälle. Työkappaleeseen kohdistettu erittäin korkea paine tuottaa turbulentin ja aaltoilevan rajapinnan ja tapahtuu mekaaninen lukitus. Räjähdysainehitsauksessa sidoslujuudet ovat erittäin korkeat. Räjähdyshitsaus on hyvä menetelmä levyjen päällystämiseen erilaisilla metalleilla. Päällystyksen jälkeen levyt voidaan rullata ohuempiin osiin. Joskus käytämme räjähdyshitsausta putkien laajentamiseen, jotta ne tiivistyvät tiiviisti levyä vasten.
Viimeinen menetelmämme solid-state-liitoksen alueella on DIFFUSION BONDING tai DIFFUSION WELDING (DFW), jossa hyvä liitos saavutetaan pääasiassa atomien diffuusiolla rajapinnan poikki. Myös rajapinnan plastinen muodonmuutos vaikuttaa hitsaukseen. Lämpötilat ovat noin 0,5 Tm, jossa Tm on metallin sulamislämpötila. Diffuusiohitsauksen sidoslujuus riippuu paineesta, lämpötilasta, kosketusajasta ja kosketuspintojen puhtaudesta. Joskus käytämme rajapinnassa täytemetalleja. Lämpöä ja painetta tarvitaan diffuusioliitokseen ja ne tuotetaan sähkövastuksen tai uunin ja kuolleiden painojen, puristimen tai muun avulla. Samanlaisia ja erilaisia metalleja voidaan liittää diffuusiohitsauksella. Prosessi on suhteellisen hidas johtuen ajasta, joka kestää atomien siirtymiseen. DFW voidaan automatisoida ja sitä käytetään laajalti monimutkaisten osien valmistuksessa ilmailu-, elektroniikka- ja lääketeollisuudelle. Valmistettuja tuotteita ovat ortopediset implantit, anturit, ilmailun rakenneosat. Diffuusioliimaus voidaan yhdistää SUPERPLASTIC FORINGIN kanssa monimutkaisten metallilevyrakenteiden valmistamiseksi. Arkkien valitut kohdat diffuusioliimataan ensin ja sitten sitoutumattomat alueet laajennetaan muottiin ilmanpaineella. Tällä menetelmäyhdistelmällä valmistetaan ilmailu- ja avaruusrakenteita, joilla on korkea jäykkyys-painosuhde. Diffuusiohitsauksen/superplastisen muovauksen yhdistetty prosessi vähentää tarvittavien osien määrää eliminoimalla kiinnikkeiden tarpeen, tuottaa alhaisen jännityksen erittäin tarkkoja osia taloudellisesti ja lyhyillä toimitusajoilla.
JUOTOS: Juotos- ja juotostekniikat sisältävät alhaisempia lämpötiloja kuin hitsaukseen vaaditaan. Juotoslämpötilat ovat kuitenkin korkeampia kuin juotoslämpötilat. Juottamisessa liitettävän pinnan väliin sijoitetaan täytemetallia ja lämpötilat nostetaan täyteaineen sulamislämpötilaan yli 723 Kelvinin, mutta työkappaleiden sulamislämpötilojen alapuolelle. Sula metalli täyttää tiiviisti sopivan tilan työkappaleiden välillä. Viilametallin jäähtyminen ja myöhempi jähmettyminen johtavat vahvoihin liitoksiin. Juotoshitsauksessa täytemetalli kerrostuu liitokseen. Juotoshitsauksessa käytetään huomattavasti enemmän lisäainemetallia kuin juottamisessa. Oksiasetyleenipoltinta, jossa on hapettava liekki, käytetään lisäainemetallin kerrostamiseen juotoshitsauksessa. Alhaisten juotoslämpötilojen vuoksi lämmön vaikutuksilla esiintyvät ongelmat, kuten vääntyminen ja jäännösjännitykset, ovat pienemmät. Mitä pienempi välysrako juotuksessa on, sitä suurempi on liitoksen leikkauslujuus. Suurin vetolujuus saavutetaan kuitenkin optimaalisella välillä (huippuarvo). Tämän optimiarvon ala- ja yläpuolella juottamisen vetolujuus pienenee. Tyypilliset juotosvälykset voivat olla välillä 0,025 - 0,2 mm. Käytämme erilaisia juotosmateriaaleja, joilla on eri muotoja, kuten jauheita, renkaita, lankaa, nauhaa jne. ja voi valmistaa näitä suorituksia erityisesti suunnitteluasi tai tuotteen geometriaa varten. Määrittelemme myös juotosmateriaalien sisällön perusmateriaalien ja käyttötarkoituksen mukaan. Käytämme juotuksissa usein juoksutetta ei-toivottujen oksidikerrosten poistamiseksi ja hapettumisen estämiseksi. Myöhemmän korroosion välttämiseksi sulatteet poistetaan yleensä liittämisen jälkeen. AGS-TECH Inc. käyttää erilaisia juotosmenetelmiä, mukaan lukien:
- Polttimen juottaminen
- Uunin juottaminen
- Induktiojuotto
- Vastusjuotto
- Kastojuotto
- Infrapunajuotto
- Diffuusiojuotto
- High Energy Beam
Yleisimmät juotetut liitosesimerkit on valmistettu erilaisista metalleista, joilla on hyvä lujuus, kuten kovametalliporanterät, terät, optoelektroniset hermeettiset paketit, tiivisteet.
JUOTTAMINEN: Tämä on yksi useimmin käytetyistä tekniikoistamme, jossa juotos (täytemetalli) täyttää liitoksen, kuten juotettaessa tiiviisti yhteensopivien komponenttien välillä. Juotteidemme sulamispisteet ovat alle 723 Kelviniä. Käytämme tuotannossa sekä manuaalista että automatisoitua juottamista. Juottoon verrattuna juotoslämpötilat ovat alhaisemmat. Juottaminen ei ole kovin sopivaa korkeisiin lämpötiloihin tai lujuuteen. Käytämme juottamiseen muiden lisäksi lyijytöntä juotetta sekä tina-lyijyä, tina-sinkkiä, lyijy-hopeaa, kadmium-hopeaa, sinkki-alumiiniseoksia. Juotoksen juoksutteena käytetään sekä ei-syövyttäviä hartsipohjaisia että epäorgaanisia happoja ja suoloja. Käytämme erikoisjuotetta huonon juotettavuuden omaavien metallien juottamiseen. Sovelluksissa, joissa joudumme juottamaan keraamisia materiaaleja, lasia tai grafiittia, pinnoitamme osat ensin sopivalla metallilla juotettavuuden parantamiseksi. Suosittuja juotostekniikoitamme ovat:
- Reflow tai Paste Juotos
- Aaltojuotto
- Uunin juottaminen
- Taskulamppujen juottaminen
- Induktiojuotto
- Rautajuotos
- Vastusjuotto
- Kastojuotto
- Ultraäänijuotto
- Infrapuna juottaminen
Ultraäänijuottaminen tarjoaa meille ainutlaatuisen edun, jossa sulatteiden tarve jää pois ultraäänikavitaatiovaikutuksesta, joka poistaa oksidikalvot liitettäviltä pinnoilta. Reflow- ja Wave-juotto ovat teollisesti erinomaisia tekniikoitamme elektroniikan suurien volyymien valmistukseen ja siksi niitä kannattaa selittää tarkemmin. Reflow-juotuksessa käytämme puolikiinteitä pastoja, jotka sisältävät juotosmetallihiukkasia. Tahna asetetaan sauman päälle seulonta- tai leikkaamisprosessilla. Käytämme tätä tekniikkaa usein painetuissa piirilevyissä (PCB). Kun sähkökomponentit asetetaan näille tahnatyynyille, pintajännitys pitää pinta-asennuspakkaukset kohdakkain. Komponenttien sijoittamisen jälkeen lämmitämme kokoonpanon uunissa, jolloin reflow-juotto tapahtuu. Tämän prosessin aikana tahnassa olevat liuottimet haihtuvat, tahnassa oleva juoksutusaine aktivoituu, komponentit esilämmitetään, juotoshiukkaset sulatetaan ja kostutetaan liitos, ja lopuksi PCB-kokoonpano jäähdytetään hitaasti. Toinen suosittu tekniikkamme PCB-levyjen suurien volyymien valmistukseen, nimittäin aaltojuotto perustuu siihen tosiasiaan, että sula juotos kastelee metallipintoja ja muodostaa hyvät sidokset vain, kun metalli on esilämmitetty. Ensin pumppu tuottaa sulan juotteen seisovan laminaarisen aallon ja esilämmitetyt ja esifluksoidut PCB:t kuljetetaan aallon yli. Juotos kastelee vain paljaat metallipinnat, mutta ei kastele IC-polymeeripakkauksia eikä polymeeripinnoitettuja piirilevyjä. Suurinopeuksinen kuumavesisuihku puhaltaa ylimääräisen juotteen liitoksesta ja estää siltojen muodostumisen vierekkäisten johtimien välillä. Pinta-asennuspakkausten aaltojuotuksessa ne liimataan ensin piirilevyyn ennen juottamista. Jälleen käytetään seulontaa ja stencilointia, mutta tällä kertaa epoksille. Kun komponentit on asetettu oikeille paikoilleen, epoksi kovettuu, levyt käännetään ylösalaisin ja aaltojuotto tapahtuu.