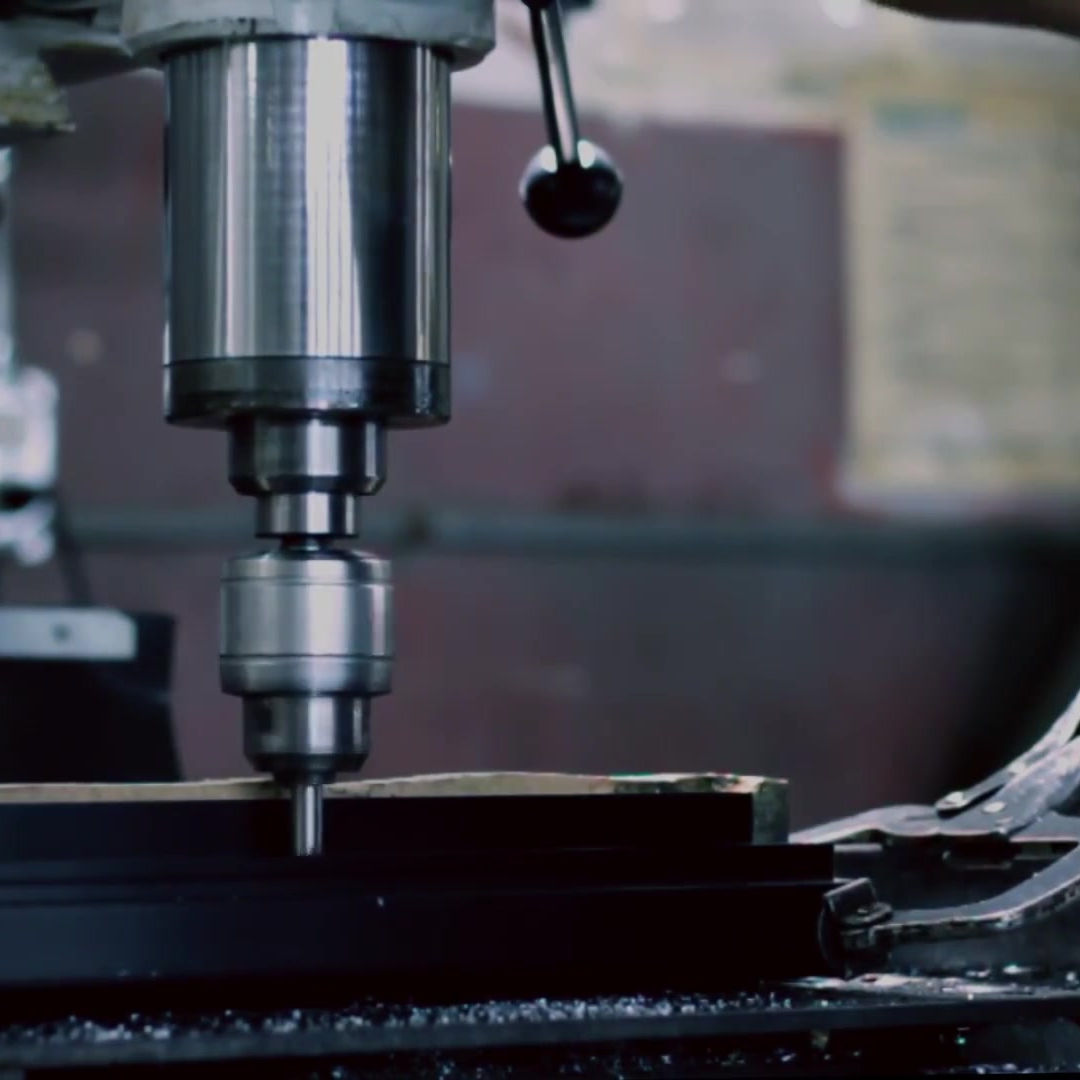
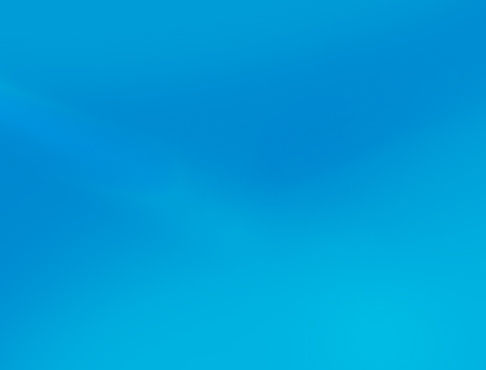
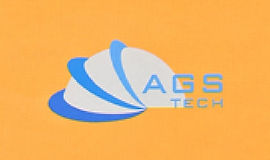
Maailmanlaajuinen räätälöity valmistaja, integraattori, yhdistäjä, ulkoistuskumppani laajalle valikoimalle tuotteita ja palveluita.
Olemme keskitetty lähde räätälöityjen ja valmiiden tuotteiden ja palvelujen valmistukseen, valmistukseen, suunnitteluun, konsolidointiin, integrointiin ja ulkoistamiseen.
Valitse kielesi
-
Räätälöity valmistus
-
Kotimainen ja kansainvälinen sopimusvalmistus
-
Valmistuksen ulkoistaminen
-
Kotimaiset ja maailmanlaajuiset hankinnat
-
Consolidation
-
Tekninen integrointi
-
Suunnittelupalvelut
ELECTRICAL DISCHARGE MACHINING (EDM), also referred to as SPARK-EROSION or ELECTRODISCHARGE MACHINING, SPARK ERODING, DIE SINKING_cc781905-5cde-3194-bb3b -136bad5cf58d_or WIRE EROSION, is a NON-CONVENTIONAL MANUFACTURING process where erosion of metals takes place and desired shape is obtained using electrical discharges in the form kipinöistä. Tarjoamme myös joitain EDM-lajikkeita, nimittäin NO-WEAR EDM, WIRE EDM (WEDM), EDM-HIOMAUS (EDG), uppoava EDM, SÄHKÖPURKKAUSJYRSINTÄ, m-10-0Mccm_8 -5cde-3194-bb3b-136bad5cf58d_and SÄHKÖKEMIALLINEN PURKAUSHIOMAUS (ECDG). EDM-järjestelmämme koostuvat muotoilluista työkaluista/elektrodeista ja työkappaleesta, jotka on liitetty tasavirtalähteisiin ja asetettu sähköä johtamattomaan dielektriseen nesteeseen. Vuoden 1940 jälkeen sähköpurkaustyöstyksestä on tullut yksi valmistusteollisuuden tärkeimmistä ja suosituimmista tuotantotekniikoista.
Kun kahden elektrodin välistä etäisyyttä pienennetään, sähkökentän intensiteetti elektrodien välisessä tilavuudessa kasvaa joissakin kohdissa eristeen vahvuutta suuremmiksi, mikä rikkoutuu muodostaen lopulta sillan virran kulkemiselle kahden elektrodin välillä. Syntyy voimakas sähkökaari, joka aiheuttaa huomattavan kuumenemisen sulattaakseen osan työkappaleesta ja osan työkalumateriaalista. Tämän seurauksena materiaali poistetaan molemmista elektrodeista. Samanaikaisesti dielektrinen neste kuumenee nopeasti, mikä johtaa nesteen haihtumiseen kaarivälissä. Kun virran virtaus pysähtyy tai se pysähtyy, ympäröivä dielektrinen neste poistaa lämpöä kaasukuplasta ja kupla kavitoituu (lupautuu). Kuplan romahtamisen ja dielektrisen nesteen virtauksen aiheuttama iskuaalto huuhtelee roskat työkappaleen pinnasta ja kuljettaa kaiken sulaneen työkappaleen materiaalin dielektriseen nesteeseen. Näiden purkausten toistotaajuus on 50 - 500 kHz, jännitteet 50 - 380 V ja virrat 0,1 - 500 ampeeria. Uusi nestemäinen dielektrinen aine, kuten mineraaliöljyt, kerosiini tai tislattu ja deionisoitu vesi, johdetaan yleensä elektrodien väliseen tilavuuteen kuljettaen pois kiinteät hiukkaset (jätteen muodossa) ja eristeen eristävät ominaisuudet palautetaan. Virran virtauksen jälkeen kahden elektrodin välinen potentiaaliero palautuu siihen, mikä se oli ennen hajoamista, joten uusi nestedielektrinen hajoaminen voi tapahtua. Nykyaikaiset sähköpurkauskoneemme (EDM) tarjoavat numeerisesti ohjattuja liikkeitä, ja ne on varustettu pumpuilla ja suodatusjärjestelmillä dielektrisille nesteille.
Sähköpurkauskoneistus (EDM) on koneistusmenetelmä, jota käytetään pääasiassa koville metalleille tai sellaisille, joita olisi erittäin vaikea työstää tavanomaisilla tekniikoilla. EDM toimii tyypillisesti kaikkien materiaalien kanssa, jotka ovat sähköjohtimia, vaikka menetelmiä eristävän keramiikan työstämiseksi EDM:llä on myös ehdotettu. Sulamispiste ja sulamislämpö ovat ominaisuuksia, jotka määräävät poistetun metallin määrän purkausta kohti. Mitä korkeammat nämä arvot, sitä hitaampi materiaalin poistonopeus. Koska sähköpurkaustyöstöprosessi ei sisällä mekaanista energiaa, työkappaleen kovuus, lujuus ja sitkeys eivät vaikuta poistonopeuteen. Purkaustaajuutta tai energiaa purkausta kohti, jännitettä ja virtaa muutetaan materiaalinpoistonopeuden ohjaamiseksi. Materiaalin poistonopeus ja pinnan karheus lisääntyvät virrantiheyden kasvaessa ja kipinöiden taajuuden pienentyessä. Voimme leikata monimutkaisia muotoja tai onteloita esikarkaistusta teräksestä EDM:llä ilman, että niiden pehmentämiseksi ja uudelleen kovettamiseksi tarvitaan lämpökäsittelyä. Voimme käyttää tätä menetelmää minkä tahansa metallin tai metalliseosten, kuten titaanin, hastelloyn, kovarin ja inconelin, kanssa. EDM-prosessin sovelluksiin kuuluu monikiteisten timanttityökalujen muotoilu. EDM:ä pidetään ei-perinteisenä tai ei-tavanomaisena koneistusmenetelmänä yhdessä prosessien, kuten sähkökemiallisen koneistuksen (ECM), vesisuihkuleikkauksen (WJ, AWJ) ja laserleikkauksen kanssa. Toisaalta tavanomaisia työstömenetelmiä ovat sorvaus, jyrsintä, hionta, poraus ja muut prosessit, joiden materiaalinpoistomekanismi perustuu olennaisesti mekaanisiin voimiin. Sähköpurkauskoneistukseen (EDM) tarkoitetut elektrodit on valmistettu grafiitista, messingistä, kuparista ja kupari-volframiseoksesta. Elektrodien halkaisijat jopa 0,1 mm ovat mahdollisia. Koska työkalun kuluminen on ei-toivottu ilmiö, joka vaikuttaa haitallisesti EDM:n mittatarkkuuteen, hyödynnämme prosessia nimeltä NO-WEAR EDM vaihtamalla napaisuutta ja käyttämällä kuparityökaluja työkalun kulumisen minimoimiseksi.
Ihannetapauksessa sähköpurkauskoneistusta (EDM) voidaan pitää sarjana elektrodien välisen dielektrisen nesteen hajoamista ja palauttamista. Todellisuudessa roskien poisto elektrodien väliseltä alueelta on kuitenkin lähes aina osittainen. Tämä aiheuttaa sen, että eristeen sähköiset ominaisuudet elektrodien välisellä alueella eroavat niiden nimellisarvoista ja vaihtelevat ajan myötä. Elektrodien välinen etäisyys (kipinäväli) säädetään tietyn käytetyn koneen ohjausalgoritmeilla. EDM:n kipinäväli voi valitettavasti joskus joutua oikosulkuun roskien takia. Elektrodin ohjausjärjestelmä ei ehkä reagoi tarpeeksi nopeasti estääkseen kahta elektrodia (työkalu ja työkappale) oikosulusta. Tämä ei-toivottu oikosulku edistää materiaalin poistoa eri tavalla kuin ihannetapauksessa. Kiinnitämme äärimmäisen tärkeänä huuhtelua, jotta eristeen eristävät ominaisuudet palautetaan niin, että virta tapahtuu aina elektrodien välisen alueen kohdassa, mikä minimoi työkaluelektrodin ei-toivotun muodonmuutoksen (vaurion) mahdollisuuden. ja työkappale. Tietyn geometrian saavuttamiseksi EDM-työkalu ohjataan haluttua reittiä pitkin hyvin lähelle työkappaletta koskematta siihen. Kiinnitämme erityistä huomiota liikkeenohjauksen suorituskykyyn käytössä. Tällä tavalla tapahtuu suuri määrä virtapurkauksia / kipinöitä, ja jokainen edistää materiaalin poistamista sekä työkalusta että työkappaleesta, jossa muodostuu pieniä kraattereita. Kraatterien koko on funktio kulloiseenkin työhön asetettujen teknisten parametrien funktiona, ja mitat voivat vaihdella nanomittakaavasta (kuten mikro-EDM-operaatioissa) useisiin satoihin mikrometreihin rouhintaolosuhteissa. Nämä pienet kraatterit työkalussa aiheuttavat elektrodin asteittaista eroosiota, jota kutsutaan "työkalun kulumiseksi". Työkappaleen geometriaan kohdistuvan kulumisen haitallisen vaikutuksen estämiseksi vaihdamme jatkuvasti työkaluelektrodia koneistuksen aikana. Joskus saavutamme tämän käyttämällä jatkuvasti vaihdettua lankaa elektrodina (tätä EDM-prosessia kutsutaan myös nimellä WIRE EDM ). Joskus käytämme työkaluelektrodia siten, että vain pieni osa siitä on todella mukana työstössä ja tätä osaa vaihdetaan säännöllisesti. Näin on esimerkiksi käytettäessä pyörivää kiekkoa työkaluelektrodina. Tätä prosessia kutsutaan nimellä EDM HIOMAUS. Vielä toinen käyttämämme tekniikka koostuu erikokoisten ja -muotoisten elektrodien käyttämisestä saman EDM-operaation aikana kulumisen kompensoimiseksi. Kutsumme tätä usean elektrodin tekniikkaa, ja sitä käytetään yleisimmin, kun työkaluelektrodi toistaa negatiivisesti halutun muodon ja etenee kohti aihiota yhtä suuntaa, yleensä pystysuuntaa (eli z-akselia) pitkin. Tämä muistuttaa työkalun uppoamista dielektriseen nesteeseen, johon työkappale on upotettu, ja siksi sitä kutsutaan nimellä DIE-SINKING EDM_cc781905-5cde-5ccome-9ccsd(5ccome-5ccba3b_bcde-3194-5ccba3 3194-bb3b-136bad5cf58d_CONVENTIONAL EDM or RAM). Tämän toiminnon koneet ovat nimeltään SINKER EDM. Tämän tyyppisen EDM:n elektrodeilla on monimutkaiset muodot. Jos lopullinen geometria saadaan käyttämällä tavallisesti yksinkertaisen muotoista elektrodia, jota liikutetaan useaan suuntaan ja joka on myös kiertojen alainen, kutsutaan sitä EDM JYRSINTÄ. Kulumisen määrä riippuu tiukasti toiminnassa käytetyistä teknisistä parametreista (napaisuus, maksimivirta, avoimen piirin jännite). Esimerkiksi in micro-EDM, joka tunnetaan myös nimellä m-EDM, nämä parametrit asetetaan yleensä arvoihin, jotka aiheuttavat voimakasta kulumista. Siksi kuluminen on tällä alueella suuri ongelma, jonka minimoimme kertyneen osaamisemme avulla. Esimerkiksi grafiittielektrodien kulumisen minimoimiseksi digitaalinen generaattori, jota voidaan ohjata millisekunneissa, kääntää napaisuuden, kun sähköeroosiota tapahtuu. Tämä johtaa sähköpinnoituksen kaltaiseen vaikutukseen, jossa kulunut grafiitti laskeutuu jatkuvasti takaisin elektrodille. Toisessa menetelmässä, ns. "Zero Wear" -piirissä, minimoimme purkauksen alkamis- ja lopputiheyden pitäen sitä päällä mahdollisimman pitkään. Purkauskoneistuksen materiaalinpoistonopeus voidaan arvioida seuraavasti:
MRR = 4 x 10 exp(4) x I x Tw exp (-1,23)
Tässä MRR on yksikössä mm3/min, I on virta ampeerina, Tw on työkappaleen sulamispiste K-273.15K. exp tarkoittaa eksponenttia.
Toisaalta elektrodin kulumisnopeus Wt voidaan saada seuraavista:
Wt = ( 1,1 x 10exp(11) ) x I x Ttexp(-2,38)
Tässä Wt on mm3/min ja Tt on elektrodimateriaalin sulamispiste K-273.15K
Lopuksi työkappaleen kulumissuhde elektrodiin R voidaan saada seuraavista:
R = 2,25 x Trex (-2,38)
Tässä Tr on työkappaleen ja elektrodin sulamispisteiden suhde.
SINKER EDM :
Sinker EDM, jota kutsutaan myös nimellä CAVITY TYPE EDM_cc781905-5cde-3194-bb3b-136bad5cf58d. Elektrodi ja työkappale on kytketty virtalähteeseen. Virtalähde synnyttää sähköpotentiaalin näiden kahden välille. Kun elektrodi lähestyy työkappaletta, nesteessä tapahtuu dielektrinen hajoaminen, joka muodostaa plasmakanavan ja pieni kipinä hyppää. Kipinät iskevät yleensä yksi kerrallaan, koska on erittäin epätodennäköistä, että elektrodien välisen tilan eri paikoissa on samat paikalliset sähköiset ominaisuudet, jotka mahdollistaisivat kipinän esiintymisen kaikissa tällaisissa paikoissa samanaikaisesti. Satoja tuhansia näitä kipinöitä tapahtuu satunnaisissa kohdissa elektrodin ja työkappaleen välillä sekunnissa. Kun perusmetalli kuluu ja kipinäväli kasvaa, CNC-koneemme laskee elektrodin automaattisesti alas, jotta prosessi voi jatkua keskeytyksettä. Laitteissamme on ohjausjaksot, jotka tunnetaan nimellä "on time" ja "off time". Päällä-aika-asetus määrittää kipinän pituuden tai keston. Pidempi käyttöaika tuottaa syvemmän ontelon kyseiselle kipinälle ja kaikki myöhemmät kipinät kyseiselle jaksolle, luoden työkappaleeseen karkeamman pinnan ja päinvastoin. Poiskytkentäaika on aika, jolloin yksi kipinä korvataan toisella. Pidempi sammutusaika sallii dielektrisen nesteen huuhtoutua suuttimen läpi eroonneen roskan puhdistamiseksi, mikä välttää oikosulun. Nämä asetukset säädetään mikrosekunneissa.
WIRE EDM :
In WIRE ELECTRICAL DISCHARGE MACHINING (WEDM), also called WIRE-CUT EDM or WIRE CUTTING, we feed a ohut yksisäikeinen messinkilanka työkappaleen läpi, joka upotetaan dielektrisen nesteen säiliöön. Wire EDM on tärkeä muunnelma EDM:stä. Käytämme satunnaisesti lankaleikattua EDM:ää jopa 300 mm:n paksuisten levyjen leikkaamiseen sekä meistien, työkalujen ja meistien valmistamiseen kovista metalleista, joita on vaikea työstää muilla valmistusmenetelmillä. Tässä vannesahalla ääriviivojen leikkaamista muistuttavassa prosessissa lanka, jota syötetään jatkuvasti kelalta, pidetään ylemmän ja alemman timanttiohjaimen välissä. CNC-ohjatut ohjaimet liikkuvat x–y-tasossa ja yläohjain voi myös liikkua itsenäisesti z–u–v-akselilla, mikä mahdollistaa kapenevien ja siirtyvien muotojen leikkaamisen (kuten ympyrän pohjassa ja neliön huippu). Yläohjain voi ohjata akselin liikkeitä x–y–u–v–i–j–k–l–. Tämän ansiosta WEDM voi leikata erittäin monimutkaisia ja herkkiä muotoja. Laitteidemme keskimääräinen leikkausura, jolla saavutetaan edullisimmat kustannukset ja työstöaika, on 0,335 mm Ø 0,25 messinki-, kupari- tai volframilangalla. CNC-laitteemme ylemmän ja alemman timanttiohjaimen tarkkuus on kuitenkin noin 0,004 mm, ja niiden leikkausrata tai uurre voi olla jopa 0,021 mm käyttämällä Ø 0,02 mm:n lankaa. Joten todella kapeat leikkaukset ovat mahdollisia. Leikkausleveys on suurempi kuin langan leveys, koska langan sivuilta syntyy kipinöitä työkappaleeseen, mikä aiheuttaa eroosiota. Tämä "ylileikkaus" on välttämätön, monissa sovelluksissa se on ennustettavissa ja siksi se voidaan kompensoida (mikro-EDM:ssä näin ei usein ole). Lankakelat ovat pitkiä – 8 kg painava 0,25 mm lankakela on hieman yli 19 kilometriä pitkä. Langan halkaisija voi olla jopa 20 mikrometriä ja geometrian tarkkuus on +/- 1 mikrometrin luokkaa. Käytämme lankaa yleensä vain kerran ja kierrätämme sen, koska se on suhteellisen edullista. Se kulkee vakionopeudella 0,15 - 9 m/min ja tasainen ura (ura) säilyy leikkauksen aikana. Lankaleikatussa EDM-prosessissa käytämme vettä dielektrisenä nesteenä ja säätelemme sen ominaisvastusta ja muita sähköisiä ominaisuuksia suodattimilla ja ioninpoistoyksiköillä. Vesi huuhtelee leikatut roskat pois leikkausalueelta. Huuhtelu on tärkeä tekijä määritettäessä enimmäissyöttönopeutta tietylle materiaalipaksuudelle, ja siksi pidämme sen yhtenäisenä. Leikkausnopeus langan EDM:ssä ilmaistaan poikkileikkauspinta-alana aikayksikköä kohti, esim. 18 000 mm2/h 50 mm paksulle D2-työkaluteräkselle. Lineaarinen leikkausnopeus tässä tapauksessa olisi 18 000/50 = 360 mm/h. Materiaalin poistonopeus langan EDM:ssä on:
MRR = Vf xhxb
Tässä MRR on mm3/min, Vf on langan syöttönopeus työkappaleeseen mm/min, h on paksuus tai korkeus millimetreinä ja b on ura, joka on:
b = dw + 2s
Tässä dw on langan halkaisija ja s on langan ja työkappaleen välinen rako millimetreinä.
Tiukempien toleranssien ohella modernit moniakseliset EDM-langankatkaisutyöstökeskuksemme ovat lisänneet ominaisuuksia, kuten usean pään kahden osan leikkaamiseen samanaikaisesti, ohjaimet langan katkeamisen estämiseksi, automaattiset itsekierteitysominaisuudet langan katkeamisen varalta ja ohjelmoidut koneistusstrategiat toiminnan optimoimiseksi, suoran ja kulman leikkausominaisuudet.
Wire-EDM tarjoaa meille alhaiset jäännösjännitykset, koska se ei vaadi suuria leikkausvoimia materiaalin poistamiseen. Kun energia/teho pulssia kohden on suhteellisen alhainen (kuten viimeistelyoperaatioissa), materiaalin mekaanisissa ominaisuuksissa odotetaan vain vähän muutosta alhaisten jäännösjännitysten vuoksi.
SÄHKÖPURKKAUSHIOMA (EDG) : Hiomalaikat eivät sisällä hankausaineita, ne on valmistettu grafiitista tai messingistä. Toistuvat kipinät pyörivän pyörän ja työkappaleen välillä poistavat materiaalia työkappaleen pinnoilta. Materiaalin poistonopeus on:
MRR = K x I
Tässä MRR on yksikössä mm3/min, I on virta ampeereina ja K on työkappaleen materiaalitekijä mm3/A-min. Käytämme usein purkaushiontaa kapeiden rakojen sahaamiseen komponentteihin. Joskus yhdistämme EDG (Electrical-Discharge Grinding) -prosessin EKG (Electrochemical Grinding) -prosessiin, jossa materiaali poistetaan kemiallisen toiminnan avulla, jolloin grafiittipyörän sähköpurkaukset rikkovat oksidikalvon ja elektrolyytit huuhtoutuvat pois. Prosessi on nimeltään ELECTROCHEMICAL-DISCHARGE GINDING (ECDG). Vaikka ECDG-prosessi kuluttaa suhteellisesti enemmän tehoa, se on nopeampi prosessi kuin EDG. Hiomme pääasiassa kovametallityökaluja tällä tekniikalla.
Sähköpurkauskoneistuksen sovellukset:
Prototyyppien tuotanto:
Käytämme EDM-prosessia muottien valmistuksessa, työkalujen ja muottien valmistuksessa sekä prototyyppien ja tuotantoosien valmistuksessa erityisesti ilmailu-, auto- ja elektroniikkateollisuudessa, joissa tuotantomäärät ovat suhteellisen pieniä. Sinker EDM:ssä grafiitti-, kuparivolframi- tai puhdaskuparielektrodi koneistetaan haluttuun (negatiiviseen) muotoon ja syötetään työkappaleeseen pystysylinterin päässä.
Kolikkomuotin valmistus:
Korujen ja rintamerkkien valmistukseen kolikoiden (leimaus) menetelmällä valmistamista varten positiivinen mestari voidaan valmistaa sterlinghopeasta, koska (asianmukaisilla koneasetuksilla) mestari kuluu merkittävästi ja sitä käytetään vain kerran. Tuloksena oleva negatiivisuulake kovetetaan sitten ja sitä käytetään pudotusvasarassa leimattujen litteiden valmistukseen pronssista, hopeasta tai heikosti kestävästä kultaseoksesta tehdyistä levyaihioista. Merkkejä varten nämä tasot voidaan edelleen muotoilla kaarevaksi pinnalle toisella meistillä. Tämän tyyppinen EDM suoritetaan yleensä öljypohjaiseen dielektriseen aineeseen upotettuna. Valmis esine voidaan edelleen jalostaa kovalla (lasi) tai pehmeällä (maali) emalointilla ja/tai galvanoida puhtaalla kullalla tai nikkelillä. Pehmeämmät materiaalit, kuten hopea, voidaan kaivertaa käsin tarkennukseksi.
Pienten reikien poraus:
Lankaleikatuissa EDM-koneissamme käytämme pientä reiänporausta EDM:ään tehdäksemme läpimenevän reiän työkappaleeseen, jonka läpi pujotetaan lanka lankaleikattua EDM-toimintoa varten. Erilliset EDM-päät erityisesti pienten reikien poraukseen on asennettu lankaleikkauskoneihimme, jotka mahdollistavat suurten karkaistujen levyjen valmiiden osien irrotuksen tarpeen mukaan ja ilman esiporausta. Käytämme myös pienireikäistä EDM:ää poraamaan reikärivejä suihkumoottoreissa käytettävien turbiinien siipien reunoihin. Kaasuvirtaus näiden pienten reikien läpi mahdollistaa moottoreiden käyttää korkeampia lämpötiloja kuin muuten olisi mahdollista. Nämä terät on valmistettu korkeissa lämpötiloissa erittäin kovista yksikidelejeeringeistä, jotka tekevät näiden korkean kuvasuhteen omaavien reikien perinteisen koneistuksen erittäin vaikeaksi ja jopa mahdottomaksi. Muita pienireikäisen EDM:n käyttökohteita ovat mikroskooppisten aukkojen luominen polttoainejärjestelmän komponenteille. Integroitujen EDM-päiden lisäksi käytämme erillisiä pienten reikien EDM-koneita, joissa on x-y-akseli, työstämään sokeita tai läpimeneviä reikiä. EDM poraa reikiä pitkällä messinki- tai kupariputkielektrodilla, joka pyörii istukassa, jolloin elektrodin läpi virtaa jatkuvasti tislattua tai deionisoitua vettä huuhteluaineena ja eristeenä. Jotkut pienireikäiset EDM:t pystyvät poraamaan 100 mm pehmeän tai jopa karkaistun teräksen läpi alle 10 sekunnissa. Tällä porauksella saadaan aikaan 0,3–6,1 mm:n reikiä.
Metallin hajoamistyöstö:
Meillä on myös erityisiä EDM-koneita, jotka on tarkoitettu rikkoutuneiden työkalujen (poranterät tai tapit) poistamiseen työkappaleista. Tätä prosessia kutsutaan "metallin hajotustyöstöksi".
Sähköpurkauskoneistuksen edut ja haitat:
EDM:n etuja ovat mm.
- Monimutkaisia muotoja, joita muuten olisi vaikea tuottaa perinteisillä leikkaustyökaluilla
- Erittäin kovaa materiaalia erittäin pieniin toleransseihin
- Erittäin pienet työkappaleet, joissa tavanomaiset leikkuutyökalut voivat vahingoittaa osaa leikkaustyökalun liiallisesta paineesta.
- Työkalun ja työkappaleen välillä ei ole suoraa kosketusta. Siksi herkät osat ja heikot materiaalit voidaan työstää ilman vääristymiä.
- Hyvä pintakäsittely saadaan aikaan.
- Erittäin hienot reiät voidaan porata helposti.
EDM:n haittoja ovat mm.
- Hidas materiaalin poistonopeus.
- Ylimääräinen aika ja kustannukset, joita käytetään elektrodien luomiseen ram/sinkker EDM:lle.
- Terävien kulmien toistaminen työkappaleeseen on vaikeaa elektrodien kulumisen vuoksi.
– Virrankulutus on korkea.
- "Overcut" muodostuu.
- Työstön aikana esiintyy työkalujen liiallista kulumista.
- Sähköä johtamattomia materiaaleja voidaan työstää vain tietyllä prosessin asetuksella.