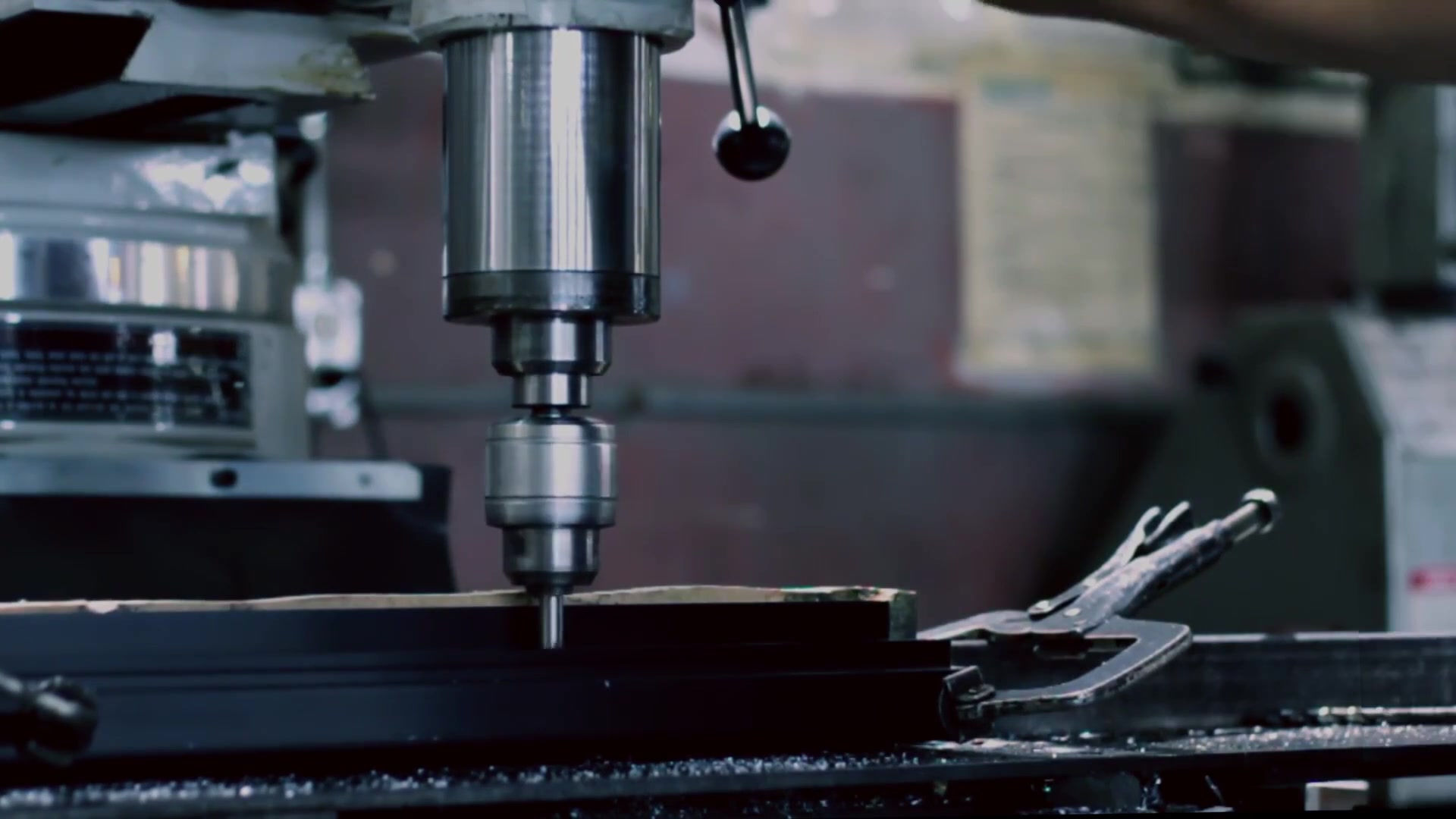
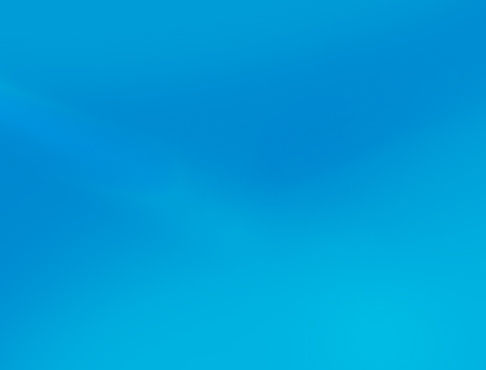
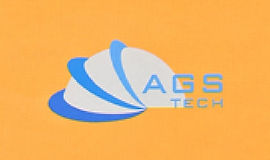
Maailmanlaajuinen räätälöity valmistaja, integraattori, yhdistäjä, ulkoistuskumppani laajalle valikoimalle tuotteita ja palveluita.
Olemme keskitetty lähde räätälöityjen ja valmiiden tuotteiden ja palvelujen valmistukseen, valmistukseen, suunnitteluun, konsolidointiin, integrointiin ja ulkoistamiseen.
Valitse kielesi
-
Räätälöity valmistus
-
Kotimainen ja kansainvälinen sopimusvalmistus
-
Valmistuksen ulkoistaminen
-
Kotimaiset ja maailmanlaajuiset hankinnat
-
Consolidation
-
Tekninen integrointi
-
Suunnittelupalvelut
Search Results
164 tulosta löytyi tyhjällä haulla
- Industrial Leather Products, USA, AGS-TECH Inc.
Industrial leather products including honing and sharpening belts, leather transmission belts, sewing machine leather treadle belt, leather tool organizers and holders, leather gun holsters, leather steering wheel covers and more. Teollisuuden nahkatuotteet Valmistettuja teollisuusnahkatuotteita ovat: - Nahan hionta- ja teroitusvyöt - Nahkaiset vaihteistohihnat - Ompelukone Nahkainen poljinvyö - Nahkaisten työkalujen järjestäjät ja pidikkeet - Nahkaiset asekotelot Nahka on luonnontuote, jolla on erinomaiset ominaisuudet, jotka tekevät siitä hyvän istuvuuden moniin käyttötarkoituksiin. Teollisuusnahkahihnoja käytetään voimansiirroissa, ompelukoneen nahkaisina polvihihnoina sekä metalliterien kiinnittämiseen, kiinnittämiseen, hiomiseen ja teroittamiseen mm. Esitteissämme lueteltujen teollisuusnahkahihnojen lisäksi voidaan valmistaa myös loputtomia vöitä ja erikoispituuksia/leveyksiä. Teollisuusnahan käyttökohteet sisältävät Litteä nahkahihna voimansiirtoon ja pyöreä nahkahihna teollisuusompelukoneisiin. Industrial leather is one of the oldest types of manufactured products. Our Vegetable Tanned Industrial leathers are pit tanned for useita kuukausia ja runsaasti öljyseoksella peitetty ja voideltu antaakseen sen lopullisen lujuuden. Kromiteollisuusnahojamme voidaan valmistaa eri tavoin for moulding. We offer a chrome-retanned leather manufactured to withstand very high temperatures and they can be used for hydraulic applications_cc781905-5cde- are ed, jolla on poikkeukselliset hankausominaisuudet. Erilaisia Shore-kovuuksia on saatavana. 7_d1369cf58d_1363699c0d_1363699c0d_136b3694c0d_136bad5cf58c Teollisille nahkatuotteille on olemassa monia muita sovelluksia, mukaan lukien puettavat työkalujen järjestelyt, työkalunpitimet, nahkalangat, ohjauspyörän suojukset jne. Olemme täällä auttaaksemme sinua projekteissasi. Suunnitelma, luonnos, valokuva tai näyte voi auttaa meitä ymmärtämään tuotetarpeesi. Voimme joko valmistaa teollisuusnahkatuotteen suunnitelmasi mukaan tai voimme auttaa sinua suunnittelutyössäsi ja kun olet hyväksynyt lopullisen suunnittelun, voimme valmistaa tuotteen sinulle. Koska toimitamme suuren valikoiman teollisuusnahkatuotteita joilla eri mitat, sovellukset ja materiaalilaadut; on mahdotonta luetella niitä kaikkia tähän. Suosittelemme lähettämään sähköpostia tai soittamaan meille, jotta voimme päättää, mikä tuote sopii sinulle parhaiten. Kun otat meihin yhteyttä, muista ilmoittaa meille: - Hakemuksesi teollisuusnahkatuotteisiin - Haluttu ja tarvittava materiaaliluokka - Mitat - Suorittaa loppuun - Pakkausvaatimukset - Merkintävaatimukset - Määrä EDELLINEN SIVU
- Surface Treatment and Modification - Surface Engineering - Hardening
Surface Treatment and Modification - Surface Engineering - Hardening - Plasma - Laser - Ion Implantation - Electron Beam Processing at AGS-TECH Pintakäsittelyt ja muokkaukset Pinnat peittävät kaiken. Materiaalipintojen viehätys ja toiminnot ovat meille äärimmäisen tärkeitä. Therefore SURFACE TREATMENT and SURFACE MODIFICATION are among our everyday industrial operations. Pintakäsittely ja modifiointi parantavat pinnan ominaisuuksia, ja ne voidaan suorittaa joko lopullisena viimeistelynä tai ennen päällystystä tai liittämistä. Pintakäsittely- ja muokkausprosessit (kutsutaan myös nimellä PINNATUNNITELU) , räätälöidä materiaalien ja tuotteiden pinnat: - Hallitse kitkaa ja kulumista - Parantaa korroosionkestävyyttä - Parantaa myöhempien pinnoitteiden tai liitettyjen osien tarttuvuutta - Muuttaa fysikaalisia ominaisuuksia johtavuutta, ominaisvastusta, pintaenergiaa ja heijastusta - Muuttaa pintojen kemiallisia ominaisuuksia ottamalla käyttöön funktionaalisia ryhmiä - Muuta mittoja - Muuta ulkonäköä, esim. väriä, karheutta jne. - Puhdista ja/tai desinfioi pinnat Pintakäsittelyn ja modifioinnin avulla materiaalien toimintoja ja käyttöikää voidaan parantaa. Yleiset pintakäsittely- ja muokkausmenetelmämme voidaan jakaa kahteen pääluokkaan: Pintakäsittely ja pinnat kattavat muutokset: Orgaaniset pinnoitteet: Orgaaniset pinnoitteet levittävät maaleja, sementtejä, laminaatteja, sulatettuja jauheita ja voiteluaineita materiaalien pinnoille. Epäorgaaniset pinnoitteet: Suosittuja epäorgaanisia pinnoitteitamme ovat galvanointi, autokatalyyttinen pinnoitus (sähköttömät pinnoitteet), muunnospinnoitteet, lämpösuihkeet, kuumakasto, kovapinnoitus, uunisulatus, ohutkalvopinnoitteet, kuten SiO2, SiN metallille, lasille, keramiikalle jne. Pintakäsittelyä ja pinnoitteita sisältäviä muokkauksia selitetään yksityiskohtaisesti vastaavassa alavalikossa, kiitosklikkaa tästä Funktionaaliset pinnoitteet / Koristepinnoitteet / Ohutkalvo / Paksukalvo Pintakäsittely ja pintoja muuttava modifiointi: Tällä sivulla keskitymme näihin. Kaikki alla kuvailemamme pintakäsittely- ja muunnostekniikat eivät ole mikro- tai nanomittakaavaisia, mutta mainitaan niistä kuitenkin lyhyesti, koska perustavoitteet ja -menetelmät ovat olennaisesti samanlaisia kuin mikrovalmistusmittakaavassa. Kovetus: Selektiivinen pintakarkaisu laserilla, liekillä, induktiolla ja elektronisuihkulla. Korkean energian hoidot: Jotkut korkean energian hoidoistamme sisältävät ioni-istutuksen, laserlasituksen ja -fuusion sekä elektronisädekäsittelyn. Ohut diffuusiokäsittelyt: Ohuet diffuusioprosessit sisältävät ferriittisen nitrohiiletyksen, boronisoinnin ja muut korkean lämpötilan reaktioprosessit, kuten TiC, VC. Voimakkaat diffuusiokäsittelyt: Raskaisiin diffuusioprosesseihimme kuuluvat hiiletys, nitridointi ja hiiletys. Erikoispintakäsittelyt: Erikoiskäsittelyt, kuten kryogeeniset, magneettiset ja äänikäsittelyt, vaikuttavat sekä pintoihin että bulkkimateriaaleihin. Selektiiviset kovetusprosessit voidaan suorittaa liekillä, induktiolla, elektronisäteellä tai lasersäteellä. Suuret alustat syväkarkaistaan liekkikarkaisulla. Induktiokarkaisua sitä vastoin käytetään pienille osille. Laser- ja elektronisuihkukarkaisua ei toisinaan eroteta pinnoitteissa tai korkean energian käsittelyissä olevista. Näitä pintakäsittely- ja modifiointiprosesseja voidaan soveltaa vain teräksiin, joissa on riittävä hiili- ja seosainepitoisuus karkaisukarkaisun mahdollistamiseksi. Valuraudat, hiiliteräkset, työkaluteräkset ja seosteräkset sopivat tähän pintakäsittely- ja muokkausmenetelmään. Nämä kovettuvat pintakäsittelyt eivät muuta osien mittoja merkittävästi. Kovettumissyvyys voi vaihdella 250 mikronista koko leikkaussyvyyteen. Kuitenkin koko profiilin tapauksessa osan tulee olla ohut, alle 25 mm (1 tuuma) tai pieni, koska karkaisuprosessit vaativat materiaalien nopean jäähdytyksen, joskus sekunnissa. Tämä on vaikea saavuttaa suurissa työkappaleissa, ja siksi suurissa osissa vain pinnat voidaan karkaista. Suosittuna pintakäsittely- ja muokkausprosessina kovetamme jousia, veitsen teriä ja kirurgisia teriä monien muiden tuotteiden joukossa. Korkean energian prosessit ovat suhteellisen uusia pintakäsittely- ja modifiointimenetelmiä. Pintojen ominaisuudet muuttuvat mittoja muuttamatta. Suosittuja korkean energian pintakäsittelyprosessejamme ovat elektronisuihkukäsittely, ioni-istutus ja lasersädekäsittely. Elektronisuihkukäsittely: Elektronisuihkupintakäsittely muuttaa pinnan ominaisuuksia nopealla kuumennuksella ja nopealla jäähdytyksellä – luokkaa 10Exp6 Celsius-astetta/s (10exp6 Fahrenheit/s) erittäin matalalla alueella noin 100 mikronia lähellä materiaalin pintaa. Elektronisuihkukäsittelyä voidaan käyttää myös kovetuksessa pintaseosten valmistukseen. Ioni-istutus: Tämä pintakäsittely- ja muokkausmenetelmä käyttää elektronisuihkua tai plasmaa muuttamaan kaasuatomit ioneiksi, joilla on riittävä energia, ja istuttamaan/lisäämään ionit substraatin atomihilaan tyhjiökammiossa olevien magneettikäämien kiihdytettynä. Tyhjiö helpottaa ionien vapaata liikkumista kammiossa. Implantoitujen ionien ja metallin pinnan välinen epäsuhta aiheuttaa atomivirheitä, jotka kovettavat pintaa. Lasersädekäsittely: Kuten elektronisäteen pintakäsittely ja modifiointi, lasersädekäsittely muuttaa pinnan ominaisuuksia nopealla lämmityksellä ja jäähdytyksellä hyvin matalalla alueella lähellä pintaa. Tätä pintakäsittely- ja muokkausmenetelmää voidaan käyttää myös kovetuksessa pintaseosten valmistukseen. Implanttien annostelu- ja käsittelyparametrejen osaaminen mahdollistaa näiden korkeaenergiaisten pintakäsittelytekniikoiden käytön tuotantolaitoksissamme. Ohut diffuusiopintakäsittelyt: Ferriittinen nitrohiiletys on kotelon karkaisuprosessi, joka diffundoi typpeä ja hiiltä rautamealleihin alikriittisissä lämpötiloissa. Käsittelylämpötila on yleensä 565 Celsius-astetta (1049 Fahrenheit). Tässä lämpötilassa teräkset ja muut rautaseokset ovat edelleen ferriittisessä faasissa, mikä on edullista verrattuna muihin austeniittisessa faasissa tapahtuviin kotelon karkaisuprosesseihin. Prosessia käytetään parantamaan: •hankauskestävyys •väsymisominaisuudet •korroosionkestävyys Alhaisten käsittelylämpötilojen ansiosta kovettumisprosessin aikana esiintyy hyvin vähän muotovääristymiä. Boronisointi on prosessi, jossa boori lisätään metalliin tai seokseen. Se on pinnan karkaisu- ja modifiointiprosessi, jolla booriatomit diffundoidaan metallikomponentin pintaan. Tämän seurauksena pinta sisältää metalliborideja, kuten rautaborideja ja nikkeliborideja. Puhtaassa tilassaan näillä borideilla on erittäin korkea kovuus ja kulutuskestävyys. Boronoidut metalliosat ovat erittäin kulutusta kestäviä ja kestävät usein jopa viisi kertaa pidempään kuin komponentit, jotka on käsitelty tavanomaisilla lämpökäsittelyillä, kuten karkaisulla, hiiletyksellä, nitrauksella, nitrohiilellä tai induktiokarkaisulla. Raskas diffuusiopintakäsittely ja modifiointi: Jos hiilipitoisuus on alhainen (alle 0,25 % esim.), voimme lisätä pinnan hiilipitoisuutta kovettumista varten. Osa voidaan joko lämpökäsitellä jäähdyttämällä nesteessä tai jäähdyttää tyynessä ilmassa haluttujen ominaisuuksien mukaan. Tämä menetelmä sallii paikallisen kovettumisen vain pinnalla, mutta ei ytimessä. Tämä on joskus erittäin toivottavaa, koska se mahdollistaa kovan pinnan, jolla on hyvät kulutusominaisuudet, kuten hammaspyörissä, mutta siinä on sitkeä sisäydin, joka toimii hyvin iskukuormituksessa. Yhdessä pintakäsittely- ja muokkaustekniikoissa, nimittäin hiiletyksessä, lisäämme pintaan hiiltä. Altistamme osan hiilipitoiselle ilmakehälle korotetussa lämpötilassa ja sallimme diffuusion siirtää hiiliatomit teräkseen. Diffuusio tapahtuu vain, jos teräksen hiilipitoisuus on alhainen, koska diffuusio toimii pitoisuuksien eroperiaatteella. Pakkauksen hiiletys: Osat pakataan hiilipitoiseen väliaineeseen, kuten hiilijauheeseen, ja niitä kuumennetaan uunissa 12–72 tuntia 900 asteen (1652 Fahrenheitin) lämpötilassa. Näissä lämpötiloissa muodostuu CO-kaasua, joka on vahva pelkistävä aine. Pelkistysreaktio tapahtuu teräksen pinnalla vapauttaen hiiltä. Hiili leviää sitten pintaan korkean lämpötilan ansiosta. Pinnan hiiltä on 0,7–1,2 % prosessiolosuhteista riippuen. Saavutettu kovuus on 60 - 65 RC. Hiiltyneen kotelon syvyys vaihtelee noin 0,1 mm - 1,5 mm. Pakkauksen hiiletys vaatii hyvää lämpötilan tasaisuuden ja lämmityksen johdonmukaisuuden hallintaa. Kaasuhiiletys: Tässä pintakäsittelyversiossa hiilimonoksidi (CO) -kaasua syötetään lämmitettyyn uuniin ja hiilen laskeuman pelkistysreaktio tapahtuu osien pinnalla. Tämä prosessi ratkaisee suurimman osan pakkauksen hiilettämiseen liittyvistä ongelmista. Yksi huolenaihe on kuitenkin CO-kaasun turvallinen eristäminen. Nestehiiletys: Teräsosat upotetaan sulaan hiilipitoiseen kylpyyn. Nitraus on pintakäsittely- ja modifiointiprosessi, jossa typen diffuusio teräksen pintaan. Typpi muodostaa nitridejä elementtien, kuten alumiinin, kromin ja molybdeenin, kanssa. Osat on lämpökäsitelty ja karkaistu ennen nitrausta. Sen jälkeen osat puhdistetaan ja kuumennetaan uunissa dissosioituneen ammoniakin (sisältää N ja H) ilmakehässä 10-40 tuntia 500-625 Celsius-asteessa (932-1157 Fahrenheit). Typpi diffundoituu teräkseen ja muodostaa nitridiseoksia. Tämä tunkeutuu jopa 0,65 mm:n syvyyteen. Kotelo on erittäin kova ja vääristymät vähäiset. Koska kotelo on ohut, pintahiontaa ei suositella, joten nitrauspintakäsittely ei välttämättä ole vaihtoehto pinnoille, joilla on erittäin tasainen viimeistelyvaatimus. Hiiletyspintakäsittely- ja modifiointiprosessi soveltuu parhaiten vähähiiliselle seosteräkselle. Hiilenpoistoprosessissa sekä hiiltä että typpeä levitetään pintaan. Osat kuumennetaan hiilivedyn (kuten metaani tai propaani) ilmakehässä, johon on sekoitettu ammoniakkia (NH3). Yksinkertaisesti sanottuna prosessi on sekoitus hiiletystä ja typpitystä. Hiiletyspintakäsittely suoritetaan 760 - 870 Celsius-asteen (1400 - 1598 Fahrenheit) lämpötiloissa. Sitten se sammutetaan maakaasuatmosfäärissä (happivapaassa). Hiilitriding-prosessi ei sovellu erittäin tarkkoihin osiin luontaisten vääristymien vuoksi. Saavutettu kovuus on samanlainen kuin hiiletys (60 - 65 RC), mutta ei niin korkea kuin nitraus (70 RC). Kotelon syvyys on 0,1-0,75 mm. Kotelossa on runsaasti nitridejä sekä martensiittia. Myöhempi karkaisu on tarpeen haurauden vähentämiseksi. Erityiset pintakäsittely- ja modifiointiprosessit ovat kehitysvaiheessa ja niiden tehokkuutta ei ole vielä todistettu. He ovat: Kryogeeninen käsittely: Levitetään yleensä karkaistuille teräksille, jäähdytä alusta hitaasti noin -166 Celsius-asteeseen (-300 Fahrenheit) lisätäksesi materiaalin tiheyttä ja siten lisätäksesi kulutuskestävyyttä ja mittojen vakautta. Tärinäkäsittely: Näiden tarkoituksena on lievittää lämpökäsittelyissä tärinän aiheuttamaa lämpörasitusta ja lisätä käyttöikää. Magneettinen käsittely: Näiden tarkoituksena on muuttaa materiaalien atomien kokoonpanoa magneettikenttien kautta ja toivottavasti parantaa käyttöikää. Näiden erityisten pintakäsittely- ja muokkaustekniikoiden tehokkuus on vielä todistamatta. Myös nämä kolme yllä olevaa tekniikkaa vaikuttavat pintojen lisäksi bulkkimateriaaliin. CLICK Product Finder-Locator Service EDELLINEN SIVU
- Industrial & Specialty & Functional Textiles, Hydrophobic - Hydrophillic Textile Materials, Flame Resistant, Antibasterial, Antifungal, Antistatic Fabrics, Filtering Cloths, Biocompatible Fabric
Industrial & Specialty & Functional Textiles, Hydrophobic - Hydrophillic Textile Materials, Flame Resistant Textiles, Antibasterial, Antifungal, Antistatic, UC Protective Fabrics, Filtering Clothes, Textiles for Surgery, Biocompatible Fabric Teollisuus- ja erikoistekstiilit ja toiminnalliset tekstiilit Meitä kiinnostavat vain erikois- ja toiminnalliset tekstiilit ja kankaat ja niistä tehdyt tuotteet, jotka palvelevat tiettyä käyttötarkoitusta. Nämä ovat arvokkaita teknisiä tekstiilejä, joita joskus kutsutaan myös teknisiksi tekstiileiksi ja kankaiksi. Kudottuja sekä kuitukangaskankaita ja kankaita on saatavana useisiin sovelluksiin. Alla on luettelo tärkeimmistä teollisuus-, erikois- ja toiminnallisista tekstiileistä, jotka kuuluvat tuotekehitys- ja valmistusalueeseemme. Olemme valmiita työskentelemään kanssasi suunnittelemaan, kehittämään ja valmistamaan tuotteitasi: Hydrofobiset (vettä hylkivät) ja hydrofiiliset (vettä imevät) tekstiilimateriaalit Tekstiilit ja kankaat, jotka ovat poikkeuksellisen lujia, kestävyys ja kestävyys vaikeissa ympäristöolosuhteissa (kuten luodinkestävä, korkean lämmönkestävä, matalan lämpötilan kestävä, tulenkestävä, inertti tai kestää syövyttäviä nesteitä ja kaasuja, muodostus….) Antibakteeriset ja antifungaaliset tekstiilit ja kankaat UV-suoja Sähköä johtavat ja johtamattomat tekstiilit ja kankaat Antistaattiset kankaat ESD-hallintaan jne. Tekstiilit ja kankaat, joilla on erityisiä optisia ominaisuuksia ja tehosteita (fluoresoiva… jne.) Tekstiilit, kankaat ja kankaat erityisillä suodatusominaisuuksilla, suodattimien valmistus Teollisuustekstiilit, kuten kanavakankaat, välivuoraukset, vahvikkeet, voimansiirtohihnat, kumivahvikkeet (kuljetinhihnat, painopeitot, narut), tekstiilit nauhoille ja hioma-aineille. Tekstiilit autoteollisuudelle (letkut, vyöt, turvatyynyt, välilevyt, renkaat) Tekstiilit rakentamiseen, rakennus- ja infrastruktuurituotteisiin (betonikangas, geokalvot ja kankaan sisäputki) Monikäyttöiset yhdistelmätekstiilit, joissa on eri kerrokset tai komponentit eri tarkoituksiin. Tekstiilit, jotka on valmistettu aktiivihiilestä infusion on polyesterikuiduista, tarjoavat puuvillan käsituntuman, hajunpoiston, kosteuden hallinnan ja UV-suojan. Muotomuistipolymeereistä valmistetut tekstiilit Tekstiilit kirurgiaan ja kirurgisiin implantteihin, bioyhteensopivat kankaat Huomaa, että suunnittelemme, suunnittelemme ja valmistamme tuotteita tarpeidesi ja määritystesi mukaan. Voimme joko valmistaa tuotteita toiveidesi mukaan tai halutessasi auttaa sinua oikeiden materiaalien valinnassa ja tuotteen suunnittelussa. EDELLINEN SIVU
- Plasma Machining, HF Plasma Cutting, Plasma Gouging, CNC, Arc Welding
Plasma Machining - HF Plasma Cutting - Plasma Gouging - CNC - Plasma Arc Welding - PAW - GTAW - AGS-TECH Inc. - New Mexico Plasmakoneistus ja -leikkaus We use the PLASMA CUTTING and PLASMA MACHINING processes to cut and machine steel, aluminum, metals and other materials of eri paksuisia plasmapolttimen avulla. Plasmaleikkauksessa (kutsutaan myös joskus PLASMA-ARC CUTTING) inerttiä kaasua tai paineilmaa puhalletaan suurella nopeudella ulos suuttimesta ja samanaikaisesti muodostuu sähkökaari tämän kaasun läpi suuttimesta. pinta leikataan, jolloin osa kaasusta muuttuu plasmaksi. Yksinkertaistaen plasmaa voidaan kuvata aineen neljänneksi tilaksi. Aineen kolme tilaa ovat kiinteä, nestemäinen ja kaasu. Yleisessä esimerkissä, vedessä, nämä kolme tilaa ovat jää, vesi ja höyry. Ero näiden tilojen välillä liittyy niiden energiatasoihin. Kun lisäämme energiaa lämmön muodossa jäähän, se sulaa ja muodostaa vettä. Kun lisäämme energiaa, vesi höyrystyy höyryn muodossa. Lisäämällä enemmän energiaa höyryyn nämä kaasut ionisoituvat. Tämä ionisaatioprosessi saa kaasun sähköä johtavaksi. Kutsumme tätä sähköä johtavaa, ionisoitua kaasua "plasmaksi". Plasma on erittäin kuumaa ja sulattaa leikattavan metallin ja puhaltaa samalla sulan metallin pois leikkauksesta. Käytämme plasmaa ohuiden ja paksujen, rauta- ja ei-rautapitoisten materiaalien leikkaamiseen. Kädessä pidettävät taskulamppumme pystyvät yleensä leikkaamaan jopa 2 tuuman paksuista teräslevyä, ja vahvemmat tietokoneohjatut taskulamput voivat leikata terästä jopa 6 tuumaa paksuksi. Plasmaleikkurit tuottavat erittäin kuuman ja paikallisen kartion leikkaamiseen, joten ne soveltuvat erittäin hyvin kaarevien ja kulmien muotoisten metallilevyjen leikkaamiseen. Plasmakaarileikkauksessa syntyvät lämpötilat ovat erittäin korkeita ja noin 9673 Kelviniä happiplasmapolttimessa. Tämä tarjoaa meille nopean prosessin, pienen uurreleveyden ja hyvän pintakäsittelyn. Volframielektrodeja käyttävissä järjestelmissämme plasma on inerttiä, muodostuu joko argonista, argon-H2:sta tai typpikaasuista. Käytämme kuitenkin joskus myös hapettavia kaasuja, kuten ilmaa tai happea, ja niissä järjestelmissä elektrodi on kuparia hafniumin kanssa. Ilmaplasmapolttimen etuna on, että se käyttää ilmaa kalliiden kaasujen sijaan, mikä saattaa vähentää koneistuksen kokonaiskustannuksia. Meidän HF-TYYPPI PLASMALEIKKAUS koneemme käyttävät korkeataajuista valokaaren kipinöintipäätä ja ionisoivaa ilmaa. HF-plasmaleikkuremme eivät vaadi polttimen olevan kosketuksissa työkappaleen materiaaliin alussa, ja ne soveltuvat sovelluksiin, joihin kuuluu TIETOKONEEN NUMEROSÄÄTÖ (CNC)_cc781905-5cbtd5cbbt8d. Muut valmistajat käyttävät primitiivisiä koneita, jotka vaativat kärjen kosketuksen perusmetallin kanssa käynnistyäkseen ja sitten tapahtuu rakoerottelu. Nämä alkeellisemmat plasmaleikkurit ovat alttiimpia kosketuskärkien ja suojan vaurioille käynnistyksen yhteydessä. Meidän PILOT-ARC TYYPPI PLASMA koneemme käyttävät kaksivaiheista prosessia plasman tuottamiseen ilman tarvetta. Ensimmäisessä vaiheessa käytetään korkeajännitteistä, matalavirtapiiriä alustamaan erittäin pieni korkean intensiteetin kipinä polttimen rungossa, jolloin syntyy pieni plasmakaasutasku. Tätä kutsutaan pilottikaareksi. Ohjauskaaressa on sähköinen paluupolku polttimen päähän. Ohjauskaari säilyy ja säilytetään, kunnes se tuodaan työkappaleen lähelle. Siellä pilottikaari sytyttää pääplasmaleikkauskaaren. Plasmakaaret ovat erittäin kuumia ja ovat alueella 25 000 °C = 45 000 °F. Perinteisempi menetelmä, jota käytämme myös, on OXYFUEL-GAS CUTTING (OFC) ch, jossa käytämme hitsauksessa. Toimintaa käytetään teräksen, valuraudan ja valuteräksen leikkaamiseen. Leikkauksen periaate happikaasuleikkauksessa perustuu teräksen hapettumiseen, palamiseen ja sulamiseen. Happikaasuleikkauksen teräleveydet ovat noin 1,5-10 mm. Plasmakaariprosessi on nähty vaihtoehtona happipolttoaineprosessille. Plasmakaariprosessi eroaa happipolttoaineprosessista siinä, että se toimii sulattamalla metallia kaarella, kun taas happipolttoaineprosessissa happi hapettaa metallin ja eksotermisen reaktion lämpö sulattaa metallin. Siksi, toisin kuin happipolttoaineprosessia, plasmaprosessia voidaan soveltaa metallien leikkaamiseen, jotka muodostavat tulenkestäviä oksideja, kuten ruostumaton teräs, alumiini ja ei-rautametalliseokset. PLASMA GOUGING plasmaleikkauksen kaltainen prosessi suoritetaan tyypillisesti samoilla laitteilla kuin plasmaleikkaus. Materiaalin leikkaamisen sijaan plasmatalttauksessa käytetään erilaista poltinkokoonpanoa. Polttimen suutin ja kaasuhajotin ovat yleensä erilaisia, ja polttimen ja työkappaleen välinen etäisyys säilyy pidempään metallin puhaltamista varten. Plasmatalttausta voidaan käyttää erilaisissa sovelluksissa, mukaan lukien hitsin poistaminen uudelleenkäsittelyä varten. Jotkut plasmaleikkureistamme on sisäänrakennettu CNC-pöytään. CNC-pöydissä on tietokone, joka ohjaa polttimen päätä puhtaiden terävien leikkausten tuottamiseksi. Nykyaikaiset CNC-plasmalaitteistomme pystyvät leikkaamaan paksuja materiaaleja moniakselisesti ja mahdollistavat monimutkaiset hitsaussaumat, jotka muuten eivät ole mahdollisia. Plasmakaarileikkurimme ovat pitkälle automatisoituja ohjelmoitavien ohjainten avulla. Ohuemmille materiaaleille suosittelemme laserleikkausta plasmaleikkauksen sijaan, lähinnä laserleikkurimme erinomaisten reiänleikkauskykyjen vuoksi. Käytämme myös pystysuuntaisia CNC-plasmaleikkauskoneita, jotka tarjoavat meille pienemmän jalanjäljen, suuremman joustavuuden, paremman turvallisuuden ja nopeamman toiminnan. Plasmaleikkausreunan laatu on samanlainen kuin happipolttoaineleikkausprosesseilla saavutettava. Kuitenkin, koska plasmaprosessi leikkaa sulattamalla, tyypillinen piirre on suurempi sulamisaste kohti metallin yläosaa, mikä johtaa yläreunan pyöristymiseen, huonoon reunan neliömäisyyteen tai viistoon leikatussa reunassa. Käytämme uusia plasmapolttimien malleja pienemmällä suuttimella ja ohuemmalla plasmakaarilla parantamaan kaaren supistumista ja tuottamaan tasaisemman lämmityksen leikkauksen ylä- ja alaosassa. Tämä mahdollistaa lähes laserin tarkkuuden plasmaleikkauksilla ja koneistetuilla reunoilla. Meidän KORKEAN TOLERANSSIN PLASMAKAARLEIKKAUS (HTPAC) järjestelmämme toimivat erittäin vaativan plasman kanssa. Plasman fokusointi saavutetaan pakottamalla hapen tuottama plasma pyörimään, kun se tulee plasman aukkoon, ja toissijainen kaasuvirtaus ruiskutetaan plasmasuuttimen jälkeen. Meillä on erillinen magneettikenttä ympärillämme kaaria. Tämä stabiloi plasmasuihkun ylläpitämällä pyörivän kaasun aiheuttamaa pyörimistä. Yhdistämällä tarkan CNC-ohjauksen näihin pienempiin ja ohuempiin polttimiin pystymme valmistamaan osia, jotka vaativat vain vähän tai ei ollenkaan viimeistelyä. Plasmatyöstössä materiaalin poistonopeus on paljon korkeampi kuin sähköpurkauskoneistuksessa (EDM) ja lasersädekoneistuksessa (LBM), ja osia voidaan työstää hyvällä toistettavuudella. PLASMAKAARIHITSAUS (PAW) on kaasuvolframikaarihitsauksen (GTAW) kaltainen prosessi. Sähkökaari muodostuu yleensä sintratusta volframista valmistetun elektrodin ja työkappaleen väliin. Keskeinen ero GTAW:ssa on, että PAW:ssa asettamalla elektrodi polttimen runkoon plasmakaari voidaan erottaa suojakaasuverhosta. Plasma pakotetaan sitten hienoreikäisen kuparisuuttimen läpi, joka supistaa kaaria ja plasmaa, joka poistuu aukosta suurilla nopeuksilla ja lämpötiloissa, jotka lähestyvät 20 000 °C. Plasmakaarihitsaus on edistysaskel GTAW-prosessiin verrattuna. PAW-hitsausprosessissa käytetään kulumatonta volframielektrodia ja kaaria, joka on puristettu hienoreikäisen kuparisuuttimen läpi. PAW:lla voidaan liittää kaikki metallit ja metalliseokset, jotka ovat hitsattavissa GTAW:lla. Useat PAW-prosessin perusmuunnelmat ovat mahdollisia muuttamalla virtaa, plasmakaasun virtausnopeutta ja aukon halkaisijaa, mukaan lukien: Mikroplasma (< 15 ampeeria) Sulamistila (15–400 ampeeria) Avaimenreikätila (>100 ampeeria) Plasmakaarihitsauksessa (PAW) saamme suuremman energiapitoisuuden GTAW:hen verrattuna. Syvä ja kapea tunkeutuminen on saavutettavissa, maksimi syvyys on 12-18 mm (0,47-0,71 tuumaa) materiaalista riippuen. Suurempi kaaren vakaus mahdollistaa paljon pidemmän kaaren pituuden (stand-off) ja paljon suuremman toleranssin kaaren pituuden muutoksille. Haittapuolena kuitenkin PAW vaatii suhteellisen kalliita ja monimutkaisia laitteita verrattuna GTAW:hen. Myös polttimen huolto on kriittistä ja haastavampaa. Muita PAW:n haittoja ovat: Hitsaustoimenpiteet ovat yleensä monimutkaisempia ja vähemmän sietäviä sovitusten jne. vaihteluille. Käyttäjän taidot vaaditaan hieman enemmän kuin GTAW:ssa. Aukon vaihto on tarpeen. CLICK Product Finder-Locator Service EDELLINEN SIVU
- Camera Systems & Components, Optic Scanner, Optical Readers, CCD
Camera Systems - Components - Optic Scanner - Optical Readers - Imaging System - CCD - Optomechanical Systems - IR Cameras Räätälöityjen kamerajärjestelmien valmistus ja kokoonpano AGS-TECH tarjoaa: • Kamerajärjestelmät, kamerakomponentit ja mukautetut kamerakokoonpanot • Mittatilaustyönä suunnitellut ja valmistetut optiset skannerit, lukijat, optiset turvatuotekokoonpanot. • Tarkkuusoptiset, optomekaaniset ja sähköoptiset kokoonpanot, joissa on integroitu kuvantamis- ja ei-kuvausoptiikka, LED-valaistus, kuituoptiikka ja CCD-kamerat • Optisten suunnittelijoidemme kehittämiä tuotteita ovat: - Omni-suuntainen periskooppi ja kamera valvonta- ja turvallisuussovelluksiin. 360 x 60º näkökenttä korkearesoluutioinen kuva, ei vaadi ompeleita. - Laajakulmainen sisäontelovideokamera - Erittäin ohut 0,6 mm halkaisijaltaan joustava videoendoskooppi. Kaikki lääketieteelliset videoliittimet sopivat tavallisten endoskooppiokulaarien päälle ja ovat täysin suljettuja ja liotettavia. Lääketieteelliset endoskooppi- ja kamerajärjestelmämme ovat osoitteessa: http://www.agsmedical.com - Videokamera ja liitin puolijäykkää endoskooppia varten - Eye-Q Videoprobe. Kosketukseton zoom-videoanturi koordinaattimittauskoneille. - Optinen spektrografi & IR-kuvausjärjestelmä (OSIRIS) ODIN-satelliittia varten. Insinöörimme työskentelivät lentoyksikön kokoonpanon, kohdistuksen, integroinnin ja testauksen parissa. - Tuulenkuvausinterferometri (WINDII) NASA:n yläilmakehän tutkimussatelliittiin (UARS). Insinöörimme konsultoivat kokoonpanoa, integrointia ja testausta. WINDII:n suorituskyky ja käyttöikä ylittivät huomattavasti suunnittelutavoitteet ja -vaatimukset. Sovelluksestasi riippuen määritämme kamerasovelluksesi vaatimat mitat, pikselimäärän, resoluution ja aallonpituusherkkyyden. Voimme rakentaa sinulle infrapuna-, näkyvä- ja muille aallonpituuksille sopivia järjestelmiä. Ota yhteyttä jo tänään saadaksesi lisätietoja. Lataa esite meille SUUNNITTELUKUMPPANUUSOHJELMA Varmista myös, että lataat kattavan sähkö- ja elektroniikkakomponenttiluettelomme valmiita tuotteita varten KLIKKAAMALLA TÄSTÄ. CLICK Product Finder-Locator Service EDELLINEN SIVU
- Embedded Systems, Embedded Computer, Industrial Computers, Janz Tec
Embedded Systems - Embedded Computer - Industrial Computers - Janz Tec - Korenix - AGS-TECH Inc. - New Mexico - USA Sulautetut järjestelmät ja tietokoneet SULAUTETTU JÄRJESTELMÄ on tietokonejärjestelmä, joka on suunniteltu erityisiä ohjaustoimintoja varten suuremmassa järjestelmässä, usein reaaliaikaisilla laskentarajoitteilla. Se on upotettu osaksi kokonaista laitetta, joka sisältää usein laitteistoa ja mekaanisia osia. Sitä vastoin yleiskäyttöinen tietokone, kuten henkilökohtainen tietokone (PC), on suunniteltu joustavaksi ja vastaamaan monenlaisiin loppukäyttäjien tarpeisiin. Sulautetun järjestelmän arkkitehtuuri on suunnattu tavalliselle PC:lle, jolloin EMBEDDED PC koostuu vain niistä komponenteista, joita se todella tarvitsee kyseiseen sovellukseen. Sulautetut järjestelmät ohjaavat monia nykyään yleisesti käytössä olevia laitteita. Tarjoamme sinulle SULAUTETTUJEN TIETOKONEIDEN joukossa ATOP TECHNOLOGIES, JANZ TEC, KORENIX TECHNOLOGY, DFI-ITOX ja muita tuotemalleja. Sulautetut tietokoneemme ovat kestäviä ja luotettavia järjestelmiä teolliseen käyttöön, jossa seisokit voivat olla tuhoisia. Ne ovat energiatehokkaita, erittäin joustavia käytössä, modulaarisesti rakennettuja, kompakteja, tehokkaita kuin täydellinen tietokone, ilman tuuletinta ja meluttomia. Sulautetuilla tietokoneillamme on erinomainen lämpötilan, tiiviyden, iskun ja tärinänkestävyys ankarissa ympäristöissä, ja niitä käytetään laajalti kone- ja tehdasrakentamisessa, voima- ja energialaitoksissa, liikenne- ja kuljetusteollisuudessa, lääketieteessä, biolääketieteessä, bioinstrumenteissa, autoteollisuudessa, armeijassa, kaivosteollisuudessa, laivastossa. , merenkulku, ilmailu ja paljon muuta. Lataa kompakti ATOP TECHNOLOGIES -tuoteesitteemme (Lataa ATOP Technologies -tuote List 2021) Lataa JANZ TEC -mallin kompakti tuoteesitteemme Lataa KORENIX-mallin kompakti tuoteesitteemme Lataa DFI-ITOX-mallin sulautettujen järjestelmien esite Lataa DFI-ITOX-mallin sulautetut yksilevytietokoneet -esite Lataa DFI-ITOX-mallin tietokonemoduulien esitteemme Lataa ICP DAS -mallin PACs Embedded Controllers & DAQ -esite Siirry teollisuustietokonekauppaamme KLIKKAAMALLA TÄSTÄ. Tässä on muutamia suosituimpia tarjoamiamme sulautettuja tietokoneita: Sulautettu PC Intel ATOM Technology Z510/530 Tuulettimeton sulautettu PC Sulautettu PC-järjestelmä Freescale i.MX515:llä Kestävät sulautetut PC-järjestelmät Modulaariset sulautetut PC-järjestelmät HMI-järjestelmät ja tuulettimettomat teollisuusnäytöt Muista aina, että AGS-TECH Inc. on vakiintunut ENGINEERING INTEGRAATTORI ja MUKAUTETTU VALMISTAJA. Siksi, jos tarvitset jotain mittatilaustyötä valmistettua, kerro siitä meille, niin tarjoamme sinulle avaimet käteen -ratkaisun, joka vie palapelin pöydältäsi ja helpottaa työtäsi. Lataa esite meille SUUNNITTELUKUMPPANUUSOHJELMA Esittelemme sinulle lyhyesti kumppaneitamme, jotka rakentavat näitä sulautettuja tietokoneita: JANZ TEC AG: Janz Tec AG on ollut johtava elektroniikkakokoonpanojen ja kokonaisten teollisuuden tietokonejärjestelmien valmistaja vuodesta 1982 lähtien. Yritys kehittää sulautettuja laskentatuotteita, teollisuustietokoneita ja teollisia viestintälaitteita asiakkaiden tarpeiden mukaan. Kaikki JANZ TEC -tuotteet valmistetaan yksinomaan Saksassa korkeimmalla laadulla. Yli 30 vuoden kokemuksella markkinoilla Janz Tec AG pystyy vastaamaan asiakkaiden yksilöllisiin tarpeisiin – tämä alkaa konseptivaiheesta ja jatkuu komponenttien kehittämisen ja tuotannon kautta toimitukseen saakka. Janz Tec AG asettaa standardit sulautetun tietojenkäsittelyn, teollisen PC:n, teollisen viestinnän ja mukautetun suunnittelun aloilla. Janz Tec AG:n työntekijät suunnittelevat, kehittävät ja valmistavat sulautettuja tietokonekomponentteja ja järjestelmiä maailmanlaajuisten standardien pohjalta, jotka on mukautettu yksilöllisesti asiakkaan erityisvaatimuksiin. Janz Tecin sulautettujen tietokoneiden lisäetuina ovat pitkäaikainen saatavuus ja paras mahdollinen laatu sekä optimaalinen hinta-suorituskykysuhde. Janz Tec sulautettuja tietokoneita käytetään aina, kun niille asetettujen vaatimusten vuoksi tarvitaan erittäin kestäviä ja luotettavia järjestelmiä. Modulaarisesti rakennetut ja kompaktit Janz Tec teollisuustietokoneet ovat vähän huoltoa vaativia, energiatehokkaita ja erittäin joustavia. Janz Tecin sulautettujen järjestelmien tietokonearkkitehtuuri on suunnattu tavalliselle PC:lle, jolloin sulautettu PC koostuu vain niistä komponenteista, joita se todella tarvitsee kyseiseen sovellukseen. Tämä mahdollistaa täysin itsenäisen käytön ympäristöissä, joissa palvelu muutoin olisi erittäin kallista. Huolimatta siitä, että ne ovat sulautettuja tietokoneita, monet Janz Tec -tuotteet ovat niin tehokkaita, että ne voivat korvata täydellisen tietokoneen. Janz Tec -merkkisten sulautettujen tietokoneiden etuja ovat toiminta ilman tuuletinta ja vähäinen huolto. Janz Tecin sulautettuja tietokoneita käytetään kone- ja laitosrakentamisessa, sähkön ja energian tuotannossa, kuljetuksissa ja liikenteessä, lääketieteellisessä tekniikassa, autoteollisuudessa, tuotanto- ja valmistustekniikassa ja monissa muissa teollisissa sovelluksissa. Prosessorit, jotka ovat yhä tehokkaampia, mahdollistavat Janz Tecin sulautetun PC:n käytön silloinkin, kun näiden toimialojen erityisen monimutkaiset vaatimukset kohtaavat. Eräs etu tässä on monille kehittäjille tuttu laitteistoympäristö ja sopivien ohjelmistokehitysympäristöjen saatavuus. Janz Tec AG on hankkinut tarvittavaa kokemusta omien sulautettujen tietokonejärjestelmiensä kehittämisestä, joita voidaan tarvittaessa mukauttaa asiakkaan tarpeisiin. Janz Tec -suunnittelijat sulautetun tietojenkäsittelyn alalla keskittyvät sovellukseen ja asiakkaan yksilöllisiin tarpeisiin sopivaan optimaaliseen ratkaisuun. Janz Tec AG:n tavoitteena on aina ollut tarjota järjestelmien korkea laatu, vankka muotoilu pitkäaikaiseen käyttöön ja poikkeukselliset hinta-suorituskykysuhteet. Nykyaikaiset sulautetuissa tietokonejärjestelmissä käytettävät prosessorit ovat Freescale Intel Core i3/i5/i7, i.MX5x ja Intel Atom, Intel Celeron ja Core2Duo. Lisäksi Janz Tec teollisuustietokoneissa ei ole vain vakioliitäntöjä, kuten ethernet, USB ja RS 232, vaan myös CANbus-liitäntä on käyttäjän käytettävissä. Janz Tec sulautettu PC on usein ilman tuuletinta, ja siksi sitä voidaan käyttää CompactFlash-median kanssa useimmissa tapauksissa, joten se on huoltovapaa. CLICK Product Finder-Locator Service EDELLINEN SIVU
- Optical Displays, Screen, Monitors Manufacturing - AGS-TECH Inc.
Optical Displays, Screen, Monitors, Touch Panel Manufacturing Optisten näyttöjen, näyttöjen, näyttöjen valmistus ja kokoonpano Lataa esite meille SUUNNITTELUKUMPPANUUSOHJELMA CLICK Product Finder-Locator Service EDELLINEN SIVU
- Microelectronics Manufacturing, Semiconductor Fabrication, Foundry, IC
Microelectronics Manufacturing, Semiconductor Fabrication - Foundry - FPGA - IC Assembly Packaging - AGS-TECH Inc. Mikroelektroniikka ja puolijohteiden valmistus ja valmistus Monia nanovalmistus-, mikrovalmistus- ja mesovalmistustekniikoitamme ja -prosessejamme, jotka on kuvattu muissa valikoissa, voidaan käyttää for MICROELECTRONICS MANUFACTURING_cc781905-14f-6bbd. Mikroelektroniikan merkityksen vuoksi tuotteissamme keskitymme kuitenkin tässä näiden prosessien aihekohtaisiin sovelluksiin. Mikroelektroniikkaan liittyviä prosesseja kutsutaan laajalti myös nimellä SEMICONDUCTOR FABRICATION processes. Puolijohdesuunnittelu- ja valmistuspalveluihimme kuuluvat: - FPGA-kortin suunnittelu, kehitys ja ohjelmointi - Mikroelektroniikkavalimopalvelut: Suunnittelu, prototyyppien valmistus ja valmistus, kolmannen osapuolen palvelut - Puolijohdekiekkojen valmistus: Kuutioiminen, taustahionta, ohentaminen, ristikon sijoittaminen, muotin lajittelu, poiminta ja sijoittaminen, tarkastus - Mikroelektroninen pakkaussuunnittelu ja valmistus: Sekä valmiina että räätälöitynä suunnittelu ja valmistus - Puolijohdepiirin kokoonpano ja pakkaus ja testaus: Muotti-, lanka- ja siruliitos, kapselointi, kokoonpano, merkintä ja brändäys - Puolijohdelaitteiden lyijykehykset: Sekä valmiina että räätälöitynä suunnittelu ja valmistus - Mikroelektroniikkaan tarkoitettujen jäähdytyslevyjen suunnittelu ja valmistus: Sekä valmiina että räätälöitynä suunnittelu ja valmistus - Anturien ja toimilaitteen suunnittelu ja valmistus: Sekä valmiina että räätälöitynä suunnittelu ja valmistus - Optoelektronisten ja fotonisten piirien suunnittelu ja valmistus Tutustutaanpa tarkemmin mikroelektroniikan ja puolijohteiden valmistus- ja testaustekniikoihin, jotta ymmärrät paremmin tarjoamiamme palveluita ja tuotteita. FPGA-levyjen suunnittelu ja kehittäminen sekä ohjelmointi: Kenttäohjelmoitavat porttiryhmät (FPGA:t) ovat uudelleen ohjelmoitavia piisiruja. Toisin kuin henkilökohtaisissa tietokoneissa esiintyvät prosessorit, FPGA:n ohjelmointi ohjaa itse sirun uudelleen toteuttamaan käyttäjän toimintoja ohjelmistosovelluksen käyttämisen sijaan. Käyttämällä valmiita logiikkalohkoja ja ohjelmoitavia reititysresursseja, FPGA-sirut voidaan konfiguroida toteuttamaan mukautettuja laitteistotoimintoja ilman koeppilevyä ja juotoskolvia. Digitaaliset laskentatehtävät suoritetaan ohjelmistossa ja käännetään konfiguraatiotiedostoksi tai bittivirtaan, joka sisältää tietoa komponenttien kytkemisestä yhteen. FPGA:ita voidaan käyttää toteuttamaan mitä tahansa loogista toimintoa, jonka ASIC voisi suorittaa, ja ne ovat täysin uudelleenkonfiguroitavissa, ja niille voidaan antaa täysin erilainen "persoonallisuus" kääntämällä uudelleen eri piirikokoonpano. FPGA:t yhdistävät sovelluskohtaisten integroitujen piirien (ASIC) ja prosessoripohjaisten järjestelmien parhaat puolet. Näitä etuja ovat seuraavat: • Nopeammat I/O-vasteajat ja erikoistoiminnot • Digitaalisten signaaliprosessorien (DSP) laskentatehon ylittäminen • Nopea prototyyppien luominen ja todentaminen ilman mukautetun ASIC:n valmistusprosessia • Räätälöityjen toimintojen käyttöönotto deterministisen laitteiston luotettavuudella • Kentällä päivitettävissä, mikä eliminoi mukautetun ASIC-uudelleensuunnittelun ja -huollon kustannukset FPGA:t tarjoavat nopeutta ja luotettavuutta ilman suuria volyymeja, jotka oikeuttavat mukautetun ASIC-suunnittelun suuret ennakkokustannukset. Uudelleenohjelmoitavalla piillä on myös sama joustavuus kuin prosessoripohjaisissa järjestelmissä toimivissa ohjelmistoissa, eikä sitä rajoita käytettävissä olevien prosessointiytimien määrä. Toisin kuin prosessorit, FPGA:t ovat luonteeltaan todella rinnakkaisia, joten eri käsittelytoimintojen ei tarvitse kilpailla samoista resursseista. Jokainen itsenäinen prosessointitehtävä on osoitettu sirun omistetulle osalle, ja se voi toimia itsenäisesti ilman muiden logiikkalohkojen vaikutusta. Tämän seurauksena yhden sovelluksen osan suorituskyky ei vaikuta, jos lisää käsittelyä lisätään. Joissakin FPGA:issa on digitaalisten toimintojen lisäksi analogisia ominaisuuksia. Joitakin yleisiä analogisia ominaisuuksia ovat ohjelmoitava kääntönopeus ja taajuusmuuttajan voimakkuus jokaisessa lähtönastassa, jolloin insinööri voi asettaa hitaita nopeuksia kevyesti kuormitetuille nastille, jotka muuten soisivat tai pariutuisivat luvattomasti, ja voi asettaa vahvempia ja nopeampia nopeuksia raskaasti kuormitetuille nastille suurissa nopeuksissa. kanavia, jotka muuten toimisivat liian hitaasti. Toinen suhteellisen yleinen analoginen ominaisuus on differentiaaliset komparaattorit tulonastoissa, jotka on suunniteltu kytkettäväksi differentiaalisiin signalointikanaviin. Joissakin sekasignaalin FPGA:issa on integroidut oheislaitteet analogia-digitaalimuuntimet (ADC) ja digitaali-analogimuuntimet (DAC) ja analogiset signaalinkäsittelylohkot, joiden avulla ne voivat toimia sirulla. Lyhyesti sanottuna FPGA-sirujen viisi parasta etua ovat: 1. Hyvä suorituskyky 2. Lyhyt aika markkinoille 3. Alhaiset kustannukset 4. Korkea luotettavuus 5. Pitkäaikainen huoltokyky Hyvä suorituskyky – FPGA-prosessoreilla on parempi laskentateho kuin digitaalisilla signaaliprosessoreilla (DSP), eivätkä ne vaadi peräkkäistä suoritusta DSP:inä ja voivat saavuttaa enemmän kellojaksoa kohden. Tulojen ja lähtöjen (I/O) ohjaus laitteistotasolla tarjoaa nopeammat vasteajat ja erikoistoiminnot, jotka vastaavat tarkasti sovellusvaatimuksia. Lyhyt markkinoilletuloaika – FPGA:t tarjoavat joustavuutta ja nopeat prototyyppiominaisuudet ja siten lyhyemmän markkinoille tulon. Asiakkaamme voivat testata ideaa tai konseptia ja varmistaa sen laitteistossa ilman pitkää ja kallista räätälöidyn ASIC-suunnittelun valmistusprosessia. Voimme toteuttaa vaiheittaisia muutoksia ja iteroida FPGA-suunnittelua tunneissa viikkojen sijaan. Kaupallisia valmiita laitteita on saatavana myös erilaisilla I/O-tyypeillä, jotka on jo liitetty käyttäjän ohjelmoitavaan FPGA-siruun. Korkean tason ohjelmistotyökalujen kasvava saatavuus tarjoaa arvokkaita IP-ytimiä (esirakennettuja toimintoja) edistyneeseen ohjaukseen ja signaalinkäsittelyyn. Alhaiset kustannukset – Mukautettujen ASIC-mallien kertaluonteiset suunnittelukustannukset (NRE) ylittävät FPGA-pohjaisten laitteistoratkaisujen kustannukset. Suuri alkuinvestointi ASIC-järjestelmiin voi olla perusteltua OEM-valmistajille, jotka tuottavat useita siruja vuodessa, mutta monet loppukäyttäjät tarvitsevat mukautettuja laitteistotoimintoja moniin kehitteillä oleviin järjestelmiin. Ohjelmoitava silikoni-FPGA tarjoaa sinulle jotain ilman valmistuskustannuksia tai pitkiä kokoonpanon toimitusaikoja. Järjestelmävaatimukset muuttuvat usein ajan myötä, ja FPGA-rakenteiden asteittaisten muutosten kustannukset ovat mitättömät verrattuna ASIC:n uudelleenpyörityksen suuriin kustannuksiin. Korkea luotettavuus – Ohjelmistotyökalut tarjoavat ohjelmointiympäristön, ja FPGA-piirit ovat todellisen ohjelman suorittamisen toteutus. Prosessoripohjaisissa järjestelmissä on yleensä useita abstraktiokerroksia, jotka helpottavat tehtävien ajoittamista ja resurssien jakamista useiden prosessien kesken. Ohjainkerros hallitsee laitteistoresursseja ja käyttöjärjestelmä muistia ja prosessorin kaistanleveyttä. Jokaisella prosessoriytimellä vain yksi käsky voidaan suorittaa kerrallaan, ja prosessoripohjaiset järjestelmät ovat jatkuvasti vaarassa aikakriittisten tehtävien ennaltaehkäisystä toisensa. FPGA:t, jotka eivät käytä käyttöjärjestelmiä, aiheuttavat vähimmäisluotettavuusongelmia niiden todellisen rinnakkaissuorituksen ja jokaiseen tehtävään omistetun deterministisen laitteiston vuoksi. Pitkän aikavälin huoltokyky – FPGA-sirut ovat päivitettävissä kentällä, eivätkä ne vaadi ASIC:n uudelleensuunnitteluun liittyvää aikaa ja kustannuksia. Esimerkiksi digitaalisten viestintäprotokollien spesifikaatiot voivat muuttua ajan myötä, ja ASIC-pohjaiset rajapinnat voivat aiheuttaa ylläpito- ja yhteensopivuushaasteita. Päinvastoin, uudelleenkonfiguroitavat FPGA-sirut voivat pysyä mahdollisten tulevien muutosten mukana. Kun tuotteet ja järjestelmät kehittyvät, asiakkaamme voivat tehdä toiminnallisia parannuksia kuluttamatta aikaa laitteiston uudelleensuunnitteluun ja levyasettelujen muokkaamiseen. Mikroelektroniikan valimopalvelut: Mikroelektroniikan valimopalvelut sisältävät suunnittelun, prototyyppien valmistuksen ja valmistuksen sekä kolmannen osapuolen palvelut. Tarjoamme asiakkaillemme apua koko tuotekehityssyklin ajan suunnittelutuesta puolijohdesirujen prototyyppien ja valmistustukeen. Tavoitteenamme suunnittelun tukipalveluissa on mahdollistaa ensimmäistä kertaa oikea lähestymistapa puolijohdelaitteiden digitaaliseen, analogiseen ja sekasignaalisuunnitteluun. Saatavilla on esimerkiksi MEMS-kohtaisia simulointityökaluja. Fabit, jotka pystyvät käsittelemään 6 ja 8 tuuman kiekkoja integroitua CMOS- ja MEMS-järjestelmää varten, ovat palveluksessasi. Tarjoamme asiakkaillemme suunnittelutukea kaikille tärkeimmille elektronisen suunnittelun automaation (EDA) alustoille, toimittamalla oikeat mallit, prosessisuunnittelusarjat (PDK), analogiset ja digitaaliset kirjastot sekä suunnittelutukea valmistukseen (DFM). Tarjoamme kaksi prototyyppivaihtoehtoa kaikille teknologioille: Multi Product Wafer (MPW) -palvelun, jossa useita laitteita käsitellään rinnakkain yhdellä kiekolla, ja Multi Level Mask (MLM) -palvelun, jossa on neljä maskitasoa piirrettynä samalle ristikkolle. Nämä ovat taloudellisempia kuin koko maskisarja. MLM-palvelu on erittäin joustava verrattuna MPW-palvelun kiinteisiin päivämääriin. Yritykset voivat mieluummin ulkoistaa puolijohdetuotteet mikroelektroniikan valimolle useista syistä, mukaan lukien toisen lähteen tarve, sisäisten resurssien käyttäminen muihin tuotteisiin ja palveluihin, halukkuus tarttua ja vähentää puolijohdetehtaan pyörittämisen riskiä ja taakkaa jne. AGS-TECH tarjoaa avoimen alustan mikroelektroniikan valmistusprosesseja, jotka voidaan skaalata pieniin kiekkosarjoihin sekä massatuotantoon. Tietyissä olosuhteissa olemassa olevat mikroelektroniikka- tai MEMS-valmistustyökalut tai täydelliset työkalusarjat voidaan siirtää toimitetuina työkaluina tai myydään työkaluina tehtaaltasi tehtaallemme, tai olemassa olevat mikroelektroniikka- ja MEMS-tuotteesi voidaan suunnitella uudelleen käyttämällä avoimen alustan prosessiteknologioita ja siirtää prosessi, joka on saatavilla tehtaallamme. Tämä on nopeampaa ja taloudellisempaa kuin mukautettu teknologian siirto. Haluttaessa voidaan kuitenkin siirtää asiakkaan olemassa olevia mikroelektroniikan / MEMS-valmistusprosesseja. Puolijohdekiekkojen valmistus: Asiakkaiden halutessaan puolijohdekiekkojen mikromuokkauksen jälkeen suoritamme kuutioinnit, taustahionnat, ohennukset, ristikkosijoittelut, stanssauslajittelut, poiminta ja sijoittelut, puolijohdekiekkojen tarkastustoimenpiteet. Puolijohdekiekkojen käsittely sisältää metrologian eri käsittelyvaiheiden välillä. Esimerkiksi ellipsometriaan tai reflektometriaan perustuvilla ohutkalvotestausmenetelmillä kontrolloidaan tiukasti hilaoksidin paksuutta sekä fotoresistin ja muiden pinnoitteiden paksuutta, taitekerrointa ja ekstinktiokerrointa. Käytämme puolijohdekiekkojen testauslaitteita varmistaaksemme, että kiekot eivät ole vaurioituneet aikaisemmissa prosessointivaiheissa testaukseen asti. Kun etupään prosessit on saatu päätökseen, puolijohdemikroelektronisille laitteille tehdään erilaisia sähkötestejä sen määrittämiseksi, toimivatko ne kunnolla. Viittaamme "tuottoksi" mikroelektroniikan osuuteen kiekossa, joka on todettu toimivan oikein. Mikroelektroniikan sirujen testaus kiekolla suoritetaan elektronisella testerillä, joka puristaa pieniä antureita puolijohdesirua vasten. Automaattinen kone merkitsee jokaisen huonon mikroelektroniikkasirun väriainepisaralla. Kiekkotestitiedot kirjataan keskustietokantaan ja puolijohdesirut lajitellaan virtuaalilokeroihin ennalta määrättyjen testirajojen mukaan. Tuloksena oleva binning-data voidaan piirtää tai kirjata lokiin kiekkokartalle valmistusvirheiden jäljittämiseksi ja huonojen sirujen merkitsemiseksi. Tätä karttaa voidaan käyttää myös kiekkojen kokoamisessa ja pakkaamisessa. Lopputestauksessa mikroelektroniikan sirut testataan uudelleen pakkauksen jälkeen, koska liitosjohdot saattavat puuttua tai pakkauksen analoginen suorituskyky saattaa muuttua. Kun puolijohdekiekko on testattu, sen paksuutta tyypillisesti pienennetään ennen kuin kiekko uurretaan ja jaetaan sitten yksittäisiksi muottiksi. Tätä prosessia kutsutaan puolijohdekiekkojen kuutioiksi. Käytämme erityisesti mikroelektroniikkateollisuudelle valmistettuja automaattisia poimintakoneita hyvien ja huonojen puolijohdemuottien selvittämiseen. Vain hyvät, merkitsemättömät puolijohdesirut pakataan. Seuraavaksi mikroelektroniikan muovi- tai keramiikkapakkausprosessissa asennamme puolijohdesuulakkeen, yhdistämme muottityynyt pakkauksessa oleviin nastoihin ja suljemme suulakkeen. Pieniä kultajohtoja käytetään tyynyjen yhdistämiseen nastoihin automatisoitujen koneiden avulla. Chip scale pakkaus (CSP) on toinen mikroelektroniikan pakkaustekniikka. Muovinen dual in-line -pakkaus (DIP), kuten useimmat paketit, on useita kertoja suurempi kuin varsinainen puolijohdesuula, joka on sijoitettu sen sisään, kun taas CSP-sirut ovat lähes mikroelektroniikan muottikokoisia; ja CSP voidaan rakentaa kullekin suulakkeelle ennen kuin puolijohdekiekko pilkotaan. Pakatut mikroelektroniikkasirut testataan uudelleen sen varmistamiseksi, että ne eivät vaurioidu pakkaamisen aikana ja että die-to-pin-liitäntäprosessi on suoritettu oikein. Lasereiden avulla etsaamme sitten sirujen nimet ja numerot pakkaukseen. Mikroelektroniikkapakettien suunnittelu ja valmistus: Tarjoamme sekä valmiita että räätälöityjä mikroelektroniikkapakkausten suunnittelua ja valmistusta. Osana tätä palvelua tehdään myös mikroelektroniikkapakettien mallintamista ja simulointia. Mallintaminen ja simulointi varmistaa virtuaalisen kokeiden suunnittelun (DoE) optimaalisen ratkaisun saavuttamiseksi pakettien testaamisen sijaan kentällä. Tämä vähentää kustannuksia ja tuotantoaikaa erityisesti mikroelektroniikan uusien tuotteiden kehittämisessä. Tämä työ antaa meille myös mahdollisuuden selittää asiakkaillemme, miten kokoonpano, luotettavuus ja testaus vaikuttavat heidän mikroelektroniikkatuotteisiinsa. Mikroelektroniikan pakkausten ensisijaisena tavoitteena on suunnitella elektroninen järjestelmä, joka täyttää tietyn sovelluksen vaatimukset kohtuullisin kustannuksin. Koska käytettävissä on monia vaihtoehtoja mikroelektroniikan yhteenliittämiseen ja sijoittamiseen, pakkaustekniikan valinta tiettyä sovellusta varten vaatii asiantuntija-arvion. Mikroelektroniikkapakettien valintakriteerit voivat sisältää joitain seuraavista teknologia-ajureista: -Johdotettavuus -Tuotto -Kustannus -Lämmönpoistoominaisuudet -Sähkömagneettisen suojauksen suorituskyky - Mekaaninen sitkeys -Luotettavuus Nämä mikroelektroniikkapakettien suunnittelunäkökohdat vaikuttavat nopeuteen, toimivuuteen, liitoslämpötiloihin, tilavuuteen, painoon ja muihin. Ensisijainen tavoite on valita kustannustehokkain mutta luotettava yhteenliittämistekniikka. Käytämme kehittyneitä analyysimenetelmiä ja ohjelmistoja mikroelektroniikan pakettien suunnittelussa. Mikroelektroniikan pakkaukset käsittelevät toisiinsa kytkettyjen pienoiselektroniikkajärjestelmien valmistusmenetelmien suunnittelua ja näiden järjestelmien luotettavuutta. Tarkemmin sanottuna mikroelektroniikan pakkaus sisältää signaalien reitittämisen samalla kun signaalin eheys säilyy, maan ja virran jakaminen integroituihin puolijohdepiireihin, hajotetun lämmön hajottaminen samalla kun säilytetään rakenteellinen ja materiaalien eheys sekä piirin suojaaminen ympäristövaaroilta. Yleensä menetelmät mikroelektroniikan IC:iden pakkaamiseksi sisältävät PWB:n käytön liittimillä, jotka tarjoavat todelliset I/O:t elektroniikkapiirille. Perinteisissä mikroelektroniikan pakkausmenetelmissä käytetään yksittäispakkauksia. Yksisiruisen paketin tärkein etu on kyky testata mikroelektroniikan IC täysin ennen sen yhdistämistä alla olevaan substraattiin. Tällaiset pakatut puolijohdelaitteet asennetaan PWB:hen joko reiän läpi tai pinta-asennus. Pinta-asennettavat mikroelektroniikkapaketit eivät vaadi läpivientireikiä koko levyn läpi. Sen sijaan pinta-asennetut mikroelektroniikan komponentit voidaan juottaa PWB:n molemmille puolille, mikä mahdollistaa suuremman piiritiheyden. Tätä lähestymistapaa kutsutaan pinta-asennustekniikaksi (SMT). Aluematriisityyppisten pakettien, kuten BGA- ja sirumittakaavapakettien (CSP) lisääminen tekee SMT:stä kilpailukykyisen tiheimpien puolijohdemikroelektroniikan pakkaustekniikoiden kanssa. Uudempi pakkaustekniikka käsittää useamman kuin yhden puolijohdelaitteen kiinnittämisen suuritiheyksiselle liitäntäalustalle, joka sitten asennetaan suureen pakkaukseen, mikä tarjoaa sekä I/O-nastat että ympäristönsuojelun. Tälle MCM (multichip module) -tekniikalle on lisäksi tunnusomaista substraattiteknologiat, joita käytetään liitettävien IC:ien yhdistämiseen. MCM-D edustaa kerrostettua ohutkalvometallia ja dielektrisiä monikerroksia. MCM-D-substraateilla on kaikkien MCM-tekniikoiden korkeimmat johdotustiheydet kehittyneiden puolijohdekäsittelytekniikoiden ansiosta. MCM-C viittaa monikerroksisiin "keraamisiin" substraatteihin, jotka poltetaan pinotuista vuorotellen seulottujen metallimusteiden ja polttamattomien keraamisten levyjen kerroksista. MCM-C:tä käyttämällä saadaan kohtalaisen tiheä kytkentäkapasiteetti. MCM-L viittaa monikerroksisiin substraatteihin, jotka on valmistettu pinotuista metalloiduista PWB-"laminaateista", jotka on kuvioitu yksilöllisesti ja sitten laminoitu. Se oli aiemmin pienitiheyksinen liitäntätekniikka, mutta nyt MCM-L lähestyy nopeasti MCM-C- ja MCM-D-mikroelektroniikan pakkaustekniikoiden tiheyttä. Suora siruliitos (DCA) tai chip-on-board (COB) mikroelektroniikan pakkaustekniikka sisältää mikroelektroniikan IC:iden asentamisen suoraan PWB:hen. Muovinen kapselointiaine, joka "pallotetaan" paljaan IC:n päälle ja sitten kovetetaan, suojaa ympäristöä. Mikroelektroniikan IC:t voidaan liittää alustaan joko flip-chip- tai lankaliitosmenetelmillä. DCA-tekniikka on erityisen taloudellinen järjestelmissä, joissa on enintään 10 puolijohde-IC:tä, koska suurempi määrä siruja voi vaikuttaa järjestelmän tehoon ja DCA-kokoonpanoja voi olla vaikea muokata uudelleen. Sekä DCA- että MCM-pakkausvaihtoehdoille yhteinen etu on puolijohde-IC-paketin liitäntätason eliminointi, mikä mahdollistaa läheisyyden (lyhyemmät signaalin lähetysviiveet) ja pienentyneen johdininduktanssin. Molempien menetelmien ensisijainen haittapuoli on vaikeus ostaa täysin testattuja mikroelektroniikan piirilevyjä. Muita DCA- ja MCM-L-tekniikoiden haittoja ovat huono lämmönhallinta, joka johtuu PWB-laminaattien alhaisesta lämmönjohtavuudesta ja huonosta lämpölaajenemiskertoimesta puolijohdesuulakkeen ja alustan välillä. Lämpölaajenemisen yhteensopimattomuusongelman ratkaiseminen vaatii välialustan, kuten molybdeenin lankaliitossuuttimeen ja alatäyteepoksia flip-chip-suuttimeen. Multichip carrier module (MCCM) yhdistää kaikki DCA:n positiiviset puolet MCM-tekniikkaan. MCCM on yksinkertaisesti pieni MCM ohuella metallikannattimella, joka voidaan liittää tai kiinnittää mekaanisesti PWB:hen. Metallipohja toimii sekä lämmönpoistajana että jännityksen väliaineena MCM-substraatille. MCCM:ssä on oheisjohdot johtimien liittämistä, juottamista tai kielekeliittämistä varten PWB:hen. Paljaat puolijohdepiirit on suojattu glob-top-materiaalilla. Kun otat meihin yhteyttä, keskustelemme hakemuksestasi ja vaatimuksistasi valitaksemme sinulle parhaan mikroelektroniikan pakkausvaihtoehdon. Semiconductor IC Assembly & Packaging & Test: Osana mikroelektroniikan valmistuspalveluitamme tarjoamme stanssauksen, lankojen ja sirujen liittämistä, kapselointia, kokoonpanoa, merkintää ja brändäystä sekä testausta. Jotta puolijohdesiru tai integroitu mikroelektroniikkapiiri toimisi, se on liitettävä järjestelmään, jota se ohjaa tai antaa ohjeita. Microelectronics IC -kokoonpano tarjoaa kytkennät tehon ja tiedon siirtoon sirun ja järjestelmän välillä. Tämä saavutetaan yhdistämällä mikroelektroniikkasiru pakkaukseen tai suoraan piirilevyyn näitä toimintoja varten. Sirun ja pakkauksen tai painetun piirilevyn (PCB) väliset liitännät tehdään lankaliitoksen, läpireiän tai flip chip -kokoonpanon kautta. Olemme alan johtavia mikroelektroniikan IC-pakkausratkaisuja, jotka vastaavat langattoman ja internetin markkinoiden monimutkaisiin vaatimuksiin. Tarjoamme tuhansia erilaisia pakkausmuotoja ja -kokoja perinteisistä lyijykehyksen mikroelektroniikan IC-paketteista läpireikä- ja pinta-asennusta varten uusimpiin sirumittakaava- (CSP) ja BGA-ratkaisuihin, joita tarvitaan korkean nastamäärän ja suuren tiheyden sovelluksissa. . Varastossa on saatavilla laaja valikoima paketteja, mukaan lukien CABGA (Chip Array BGA), CQFP, CTBGA (Chip Array Thin Core BGA), CVBGA (Very Thin Chip Array BGA), Flip Chip, LCC, LGA, MQFP, PBGA, PDIP, PLCC, PoP - Package on Package, PoP TMV - Muotin kautta, SOIC / SOJ, SSOP, TQFP, TSOP, WLP (Wafer Level Package) jne. Johtojen liittäminen kuparilla, hopealla tai kullalla on suosittuja mikroelektroniikassa. Kuparilanka (Cu) on ollut tapa liittää piipuolijohdesuulakkeet mikroelektroniikkapaketin liittimiin. Kultalangan (Au) hinta on viime aikoina noussut, joten kuparilanka (Cu) on houkutteleva tapa hallita pakettien kokonaiskustannuksia mikroelektroniikan alalla. Se muistuttaa myös kultalankaa (Au) samanlaisten sähköisten ominaisuuksiensa vuoksi. Itseinduktanssi ja omakapasitanssi ovat lähes samat kulta- (Au) ja kuparilangalla (Cu), kun kuparilangalla (Cu) on pienempi resistanssi. Mikroelektroniikan sovelluksissa, joissa sidoslangan aiheuttama vastus voi vaikuttaa negatiivisesti piirin suorituskykyyn, kuparilangan (Cu) käyttö voi tarjota parannusta. Kuparista, palladiumilla päällystetystä kuparista (PCC) ja hopeaseoksesta (Ag) valmistettuja lankoja on noussut vaihtoehtoina kultasidoslangoille kustannusten vuoksi. Kuparipohjaiset johdot ovat halpoja ja niillä on alhainen sähkövastus. Kuparin kovuus vaikeuttaa kuitenkin sen käyttöä monissa sovelluksissa, kuten sellaisissa, joissa on hauraita sidostyynyrakenteita. Näihin sovelluksiin Ag-Alloy tarjoaa kullan ominaisuuksien kaltaisia ominaisuuksia, kun taas sen hinta on samanlainen kuin PCC:n. Ag-seoslanka on pehmeämpi kuin PCC, mikä johtaa alhaisempaan Al-Splash-pitoisuuteen ja pienempi liimatyynyn vaurioitumisriski. Ag-seoslanka on paras edullinen korvaaja sovelluksiin, jotka tarvitsevat die-to-die-sidontaa, vesiputoussidontaa, erittäin hienoa sidostyynyn jakoa ja pieniä liitostyynyn aukkoja, erittäin matalaa silmukan korkeutta. Tarjoamme täydellisen valikoiman puolijohteiden testauspalveluita, mukaan lukien kiekkojen testaus, erityyppiset lopputestaukset, järjestelmätason testaukset, liuskatestaukset ja täydelliset päätepalvelut. Testaamme erilaisia puolijohdelaitteita kaikissa pakettiperheissämme, mukaan lukien radiotaajuus, analoginen ja sekasignaali, digitaalinen, virranhallinta, muisti ja erilaiset yhdistelmät, kuten ASIC, monisiruiset moduulit, System-in-Package (SiP) ja pinottu 3D-pakkaus, anturit ja MEMS-laitteet, kuten kiihtyvyysmittarit ja paineanturit. Testauslaitteistomme ja kosketuslaitteistomme sopivat mukautettuun pakkauskokoon SiP, kaksipuolisiin kosketusratkaisuihin Package on Package (PoP), TMV PoP, FusionQuad-liitännät, monirivinen MicroLeadFrame, Fine-Pitch Copper Pillar. Testauslaitteet ja testilattiat on integroitu CIM/CAM-työkaluihin, tuottoanalyysiin ja suorituskyvyn seurantaan, jotta saadaan erittäin korkea hyötysuhde ensimmäistä kertaa. Tarjoamme asiakkaillemme lukuisia mukautuvia mikroelektroniikan testausprosesseja ja hajautettuja testivirtoja SiP:lle ja muille monimutkaisille kokoonpanovirroille. AGS-TECH tarjoaa täyden valikoiman testikonsultointi-, kehitys- ja suunnittelupalveluita puolijohde- ja mikroelektroniikkatuotteesi koko elinkaaren ajalta. Ymmärrämme SiP:n, autojen, verkkojen, pelien, grafiikan, tietojenkäsittelyn, RF/langattomien laitteiden ainutlaatuiset markkinat ja testausvaatimukset. Puolijohteiden valmistusprosessit vaativat nopeita ja tarkasti ohjattuja merkintäratkaisuja. Yli 1000 merkin sekunnissa merkintänopeudet ja alle 25 mikronin materiaalin tunkeutumissyvyys ovat yleisiä puolijohdemikroelektroniikkateollisuudessa, jossa käytetään edistyneitä lasereita. Pystymme merkitsemään muottiyhdisteitä, kiekkoja, keramiikkaa ja paljon muuta minimaalisella lämmönkulutuksella ja täydellisellä toistettavuudella. Käytämme lasereita erittäin tarkasti merkitsemään pienimmätkin osat ilman vaurioita. Johtokehykset puolijohdelaitteille: Sekä valmiina että mukautettuna suunnittelu ja valmistus ovat mahdollisia. Lyijykehyksiä käytetään puolijohdelaitteiden kokoonpanoprosesseissa, ja ne ovat pääosin ohuita metallikerroksia, jotka yhdistävät johdot pienistä puolijohdemikroelektroniikan pinnalla olevista sähköliittimistä sähkölaitteiden ja piirilevyjen laajamittaiseen piiriin. Lyijykehyksiä käytetään lähes kaikissa puolijohdemikroelektroniikan pakkauksissa. Useimmat mikroelektroniikan IC-paketit valmistetaan asettamalla puolijohdesiru lyijykehyksen päälle, liittämällä siru sitten johtokehyksen metallijohtimiin ja peittämällä mikroelektroniikan siru muovikuorella. Tämä yksinkertainen ja suhteellisen edullinen mikroelektroniikan pakkaus on edelleen paras ratkaisu moniin sovelluksiin. Lyijykehykset valmistetaan pitkinä nauhoina, mikä mahdollistaa niiden nopean prosessoinnin automatisoiduilla kokoonpanokoneilla ja yleensä käytetään kahta valmistusprosessia: jonkinlaista valokuvaetsausta ja leimaamista. Mikroelektroniikan lyijyrunkojen suunnittelussa vaaditaan usein räätälöityjä spesifikaatioita ja ominaisuuksia, sähköisiä ja lämpöominaisuuksia parantavia malleja sekä erityisiä sykliaikavaatimuksia. Meillä on syvällinen kokemus mikroelektroniikan lyijykehysten valmistuksesta useille eri asiakkaille laseravusteisesta valoetsauksesta ja leimaamisesta. Jäähdytyslevyjen suunnittelu ja valmistus mikroelektroniikkaan: Sekä valmiina että räätälöitynä suunnittelu ja valmistus. Mikroelektroniikan laitteista peräisin olevan lämmön haihtumisen lisääntyessä ja yleisten muototekijöiden pienentyessä lämmönhallinnasta tulee entistä tärkeämpi elementti elektroniikkatuotteiden suunnittelussa. Elektronisten laitteiden suorituskyvyn ja käyttöiän johdonmukaisuus ovat käänteisessä suhteessa laitteen komponenttien lämpötilaan. Tyypillisen piipuolijohdelaitteen luotettavuuden ja käyttölämpötilan välinen suhde osoittaa, että lämpötilan lasku vastaa laitteen luotettavuuden ja käyttöiän eksponentiaalista kasvua. Siksi puolijohdemikroelektroniikkakomponentin pitkä käyttöikä ja luotettava suorituskyky voidaan saavuttaa ohjaamalla tehokkaasti laitteen käyttölämpötilaa suunnittelijoiden asettamissa rajoissa. Jäähdytyselementit ovat laitteita, jotka tehostavat lämmön poistumista kuumalta pinnalta, yleensä lämpöä tuottavan komponentin ulkokuoresta, viileämpään ympäristöön, kuten ilmaan. Seuraavissa keskusteluissa ilman oletetaan olevan jäähdytysneste. Useimmissa tilanteissa lämmönsiirto kiinteän pinnan ja jäähdytysnesteilman välisen rajapinnan yli on vähiten tehokasta järjestelmässä, ja kiinteän ilman välinen rajapinta on suurin este lämmönpoistolle. Jäähdytyselementti alentaa tätä estettä lähinnä lisäämällä pinta-alaa, joka on suorassa kosketuksessa jäähdytysnesteen kanssa. Tämä mahdollistaa suuremman lämmön haihtumisen ja/tai alentaa puolijohdelaitteen käyttölämpötilaa. Jäähdytyslevyn ensisijainen tarkoitus on pitää mikroelektroniikan laitteen lämpötila puolijohdelaitteen valmistajan määrittämän suurimman sallitun lämpötilan alapuolella. Voimme luokitella jäähdytyslevyt valmistusmenetelmien ja niiden muotojen perusteella. Yleisimmät ilmajäähdytteisten jäähdytyslevyjen tyypit ovat: - Meistot: Kupari- tai alumiinilevyt meistetään haluttuun muotoon. niitä käytetään elektronisten komponenttien perinteisessä ilmajäähdytyksessä ja ne tarjoavat taloudellisen ratkaisun matalatiheyksisiin lämpöongelmiin. Ne soveltuvat suurien volyymien tuotantoon. - Ekstruusio: Nämä jäähdytyselementit mahdollistavat monimutkaisten kaksiulotteisten muotojen muodostumisen, jotka pystyvät haihduttamaan suuria lämpökuormia. Niitä voidaan leikata, työstää ja lisätä lisävarusteita. Poikittaisleikkaus tuottaa monisuuntaisia, suorakaiteen muotoisia tapin jäähdytyselementtejä, ja sahalaitaisten ripojen käyttö parantaa suorituskykyä noin 10-20 %, mutta hitaammin pursotusnopeudella. Pursotusrajat, kuten evän korkeus rakoon, sanelevat yleensä suunnitteluvaihtoehtojen joustavuuden. Tyypillinen evän korkeus-rako-kuvasuhde jopa 6 ja evän vähimmäispaksuus 1,3 mm voidaan saavuttaa tavallisilla suulakepuristustekniikoilla. Kuvasuhde 10:1 ja evän paksuus 0,8″ voidaan saavuttaa erityisillä muotin suunnitteluominaisuuksilla. Kuitenkin, kun kuvasuhde kasvaa, ekstruusiotoleranssi vaarantuu. - Liimatut/valmistetut rivat: Useimmissa ilmajäähdytteisissä jäähdytyselementeissä on konvektio rajoitettu, ja ilmajäähdytetyn jäähdytyslevyn yleistä lämpötehoa voidaan usein parantaa merkittävästi, jos enemmän pinta-alaa voidaan altistaa ilmavirralle. Nämä korkean suorituskyvyn jäähdytyslevyt käyttävät lämpöä johtavaa alumiinitäytteistä epoksia liittääkseen tasomaiset rivat uritettuun ekstruusiopohjalevyyn. Tämä prosessi mahdollistaa paljon suuremman evän korkeus-rako-kuvasuhteen 20-40, mikä lisää merkittävästi jäähdytyskapasiteettia lisäämättä tilavuuden tarvetta. - Valukappaleet: Hiekka-, vaha- ja painevaluprosessit alumiinille tai kuparille/pronssille ovat saatavilla tyhjiöavulla tai ilman. Käytämme tätä tekniikkaa korkeatiheyksisten pin eväjäähdytyslevyjen valmistukseen, jotka tarjoavat maksimaalisen suorituskyvyn käytettäessä törmäysjäähdytystä. - Taitetut rivat: Alumiinista tai kuparista valmistettu aallotettu metallilevy lisää pinta-alaa ja tilavuutta. Jäähdytyselementti kiinnitetään sitten joko pohjalevyyn tai suoraan lämmityspintaan epoksilla tai juottamalla. Se ei sovellu korkean profiilin jäähdytyslevyihin saatavuuden ja lamellitehokkuuden vuoksi. Siksi se mahdollistaa korkean suorituskyvyn jäähdytyslevyjen valmistamisen. Valittaessa sopivaa jäähdytyselementtiä, joka täyttää mikroelektroniikan sovelluksillesi vaaditut lämpökriteerit, meidän on tutkittava useita parametreja, jotka eivät vaikuta pelkästään jäähdytyselementin suorituskykyyn vaan myös järjestelmän yleiseen suorituskykyyn. Tietyn tyyppisen jäähdytyselementin valinta mikroelektroniikassa riippuu suurelta osin jäähdytyslevylle sallitusta lämpöbudjetista ja jäähdytyselementtiä ympäröivistä ulkoisista olosuhteista. Tietylle jäähdytyselementille ei ole koskaan määritetty yhtä lämpöresistanssin arvoa, koska lämpövastus vaihtelee ulkoisten jäähdytysolosuhteiden mukaan. Anturin ja toimilaitteen suunnittelu ja valmistus: Saatavilla on sekä valmiita että mukautettuja suunnittelu ja valmistus. Tarjoamme ratkaisuja käyttövalmiilla prosesseilla inertia-antureille, paine- ja suhteellisille paineantureille sekä IR-lämpötila-antureille. Käyttämällä IP-lohkojamme kiihtyvyysantureille, IR- ja paineantureille tai soveltamalla suunnitteluasi saatavilla olevien spesifikaatioiden ja suunnittelusääntöjen mukaan, voimme toimittaa MEMS-pohjaiset anturilaitteet sinulle viikkojen kuluessa. MEMS:n lisäksi voidaan valmistaa muun tyyppisiä anturi- ja toimilaiterakenteita. Optoelektronisten ja fotonisten piirien suunnittelu ja valmistus: Fotoni- tai optinen integroitu piiri (PIC) on laite, joka yhdistää useita fotonitoimintoja. Sitä voidaan muistuttaa mikroelektroniikan elektronisia integroituja piirejä. Suurin ero näiden kahden välillä on se, että integroitu fotoninen piiri tarjoaa toiminnallisuuden informaatiosignaaleille, jotka asetetaan optisille aallonpituuksille näkyvässä spektrissä tai lähellä infrapunaa 850 nm-1650 nm. Valmistustekniikat ovat samanlaisia kuin mikroelektroniikan integroiduissa piireissä, joissa fotolitografiaa käytetään kiekkojen kuvioimiseen etsausta ja materiaalin kerrostamista varten. Toisin kuin puolijohdemikroelektroniikassa, jossa ensisijainen laite on transistori, optoelektroniikassa ei ole yhtä hallitsevaa laitetta. Fotonisia siruja ovat pienihäviöiset aaltoputket, tehonjakajat, optiset vahvistimet, optiset modulaattorit, suodattimet, laserit ja ilmaisimet. Nämä laitteet vaativat useita erilaisia materiaaleja ja valmistustekniikoita, ja siksi niitä kaikkia on vaikea toteuttaa yhdellä sirulla. Fotonisten integroitujen piirien sovelluksemme ovat pääasiassa kuituoptisen viestinnän, biolääketieteen ja fotonisen laskennan aloilla. Joitakin esimerkkejä optoelektronisista tuotteista, joita voimme suunnitella ja valmistaa sinulle, ovat LEDit (Light Emitting Diodes), diodilaserit, optoelektroniset vastaanottimet, valodiodit, laseretäisyysmoduulit, räätälöidyt lasermoduulit ja paljon muuta. CLICK Product Finder-Locator Service EDELLINEN SIVU