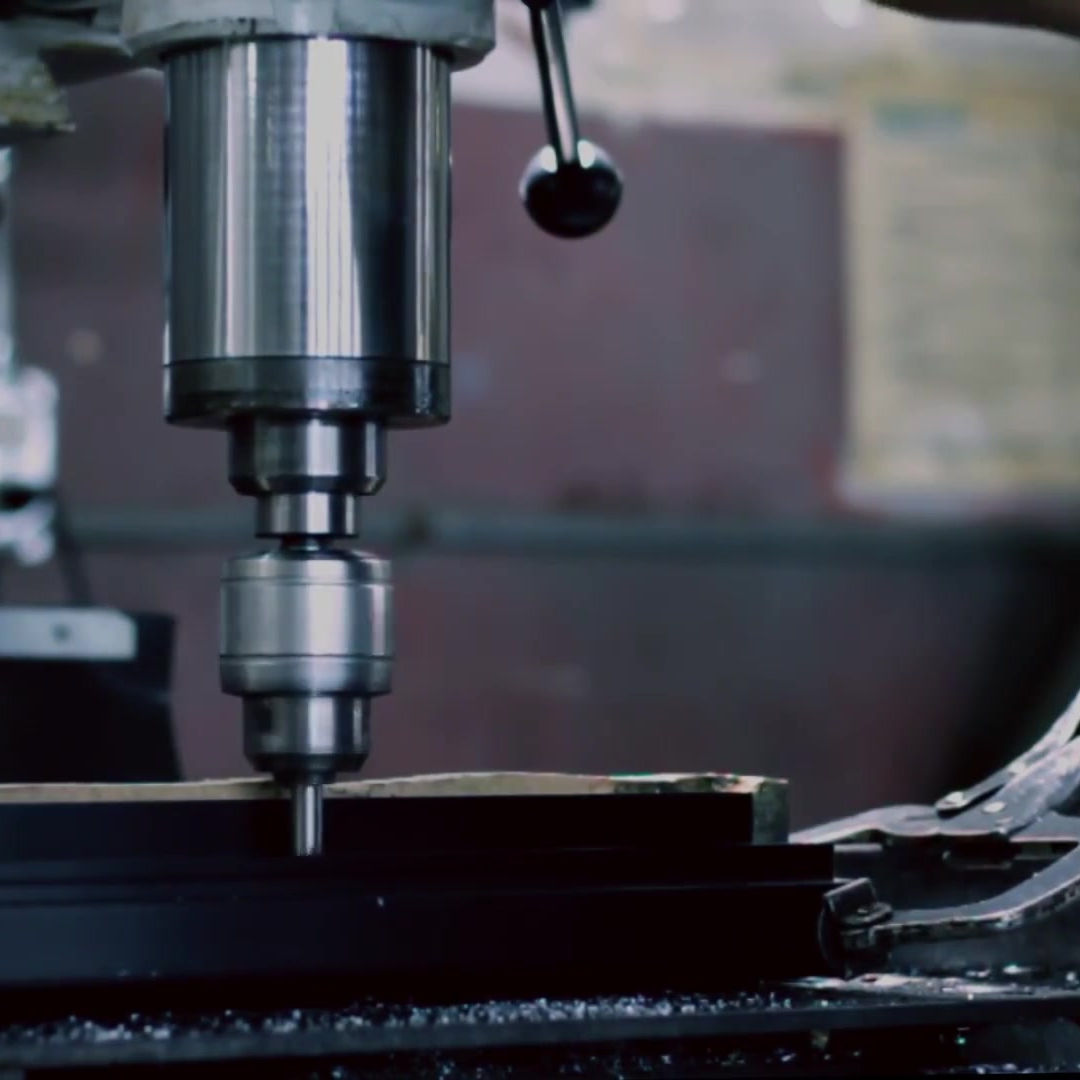
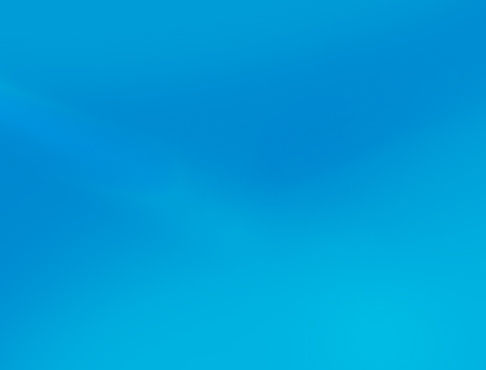
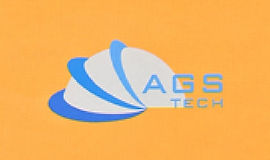
Maailmanlaajuinen räätälöity valmistaja, integraattori, yhdistäjä, ulkoistuskumppani laajalle valikoimalle tuotteita ja palveluita.
Olemme keskitetty lähde räätälöityjen ja valmiiden tuotteiden ja palvelujen valmistukseen, valmistukseen, suunnitteluun, konsolidointiin, integrointiin ja ulkoistamiseen.
Valitse kielesi
-
Räätälöity valmistus
-
Kotimainen ja kansainvälinen sopimusvalmistus
-
Valmistuksen ulkoistaminen
-
Kotimaiset ja maailmanlaajuiset hankinnat
-
Consolidation
-
Tekninen integrointi
-
Suunnittelupalvelut
Search Results
164 tulosta löytyi tyhjällä haulla
- Transmission Components, Belts, Chains, Cable Drives, Pulleys,AGS-TECH
Transmission Components, Belts, Chains and Cable Drives, Conventional & Grooved or Serrated, Positive Drive, Pulleys Hihnat ja ketjut ja kaapelin käyttökokoonpano AGS-TECH Inc. tarjoaa sinulle voimansiirtokomponentteja, mukaan lukien hihnat ja ketjut sekä kaapelin käyttökokoonpano. Vuosien jalostuksen myötä kumi-, nahka- ja muut hihnakäyttömme ovat tulleet kevyemmiksi ja kompakteiksi, ja ne pystyvät kantamaan suurempia kuormia pienemmillä kustannuksilla. Samoin ketjukäyttömme ovat käyneet läpi paljon kehitystä ajan mittaan ja tarjoavat asiakkaillemme useita etuja. Ketjukäyttöjen käytön etuja ovat niiden suhteellisen rajoittamattomat akselin keskietäisyydet, tiiviys, helppo asentaa, kireys joustavuus ilman liukumista tai virumista, kyky toimia korkeissa lämpötiloissa. Kaapelikäyttömme tarjoavat myös etuja, kuten yksinkertaisuuden joissakin sovelluksissa muihin siirtokomponentteihin verrattuna. Saatavilla on sekä valmiita hihna-, ketju- ja kaapelikäyttöjä että mittatilaustyönä valmistettuja ja koottuja versioita. Voimme valmistaa nämä voimansiirtokomponentit käyttötarkoitukseesi sopivan kokoisiksi ja sopivimmista materiaaleista. HIHNAT JA HIHNAVETOT: - Perinteiset litteät hihnat: Nämä ovat tavallisia litteitä hihnoja, joissa ei ole hampaita, uria tai hammastuksia. Litteät hihnakäytöt tarjoavat joustavuutta, hyvän iskunvaimennuksen, tehokkaan voimansiirron suurilla nopeuksilla, kulutuskestävyyden ja alhaiset kustannukset. Hihnoja voidaan jatkossa jakaa tai liittää suurempien hihnojen muodostamiseksi. Perinteisten litteiden hihnojen muita etuja ovat ne ovat ohuet, ne eivät ole alttiina suurille keskipakokuormituksille (tekee niistä sopivia suuriin nopeuksiin pienillä hihnapyörillä). Toisaalta ne aiheuttavat suuria laakerikuormia, koska litteät hihnat vaativat suurta jännitystä. Muita litteän hihnakäytön haittoja voivat olla liukuminen, meluisa toiminta ja suhteellisen alhaisempi hyötysuhde alhaisilla ja kohtalaisilla käyttönopeuksilla. Meillä on kahden tyyppisiä perinteisiä hihnoja: vahvistettu ja vahvistamaton. Vahvistettujen hihnojen rakenteessa on vetoelin. Perinteisiä litteitä vyöitä on saatavana nahkana, kumitettuna kankaana tai naruna, vahvistamattomana kumina tai muovina, kankaana, vahvistettuna nahana. Nahkahihnat tarjoavat pitkän käyttöiän, joustavuuden, erinomaisen kitkakertoimen ja helpon korjauksen. Nahkavyöt ovat kuitenkin suhteellisen kalliita, vaativat vyön pukemista ja puhdistusta, ja ne voivat kutistua tai venyä ilmasta riippuen. Kumipäällysteiset kangas- tai naruhihnat kestävät kosteutta, happoa ja emäksiä. Kumikankaiset vyöt koostuvat puuvilla- tai synteettisistä kumilla kyllästetyistä kerroksista ja ovat taloudellisimpia. Kumipäällysteiset naruhihnat koostuvat sarjasta kumilla kyllästettyjä johtoja. Kumipäällysteiset nauhahihnat tarjoavat suuren vetolujuuden ja vaatimattoman koon ja massan. Vahvistamattomat kumi- tai muovihihnat sopivat kevyisiin, hitaisiin käyttökohteisiin. Vahvistamattomat kumi- ja muovihihnat voidaan venyttää paikoilleen niiden hihnapyörien päälle. Muoviset vahvistamattomat hihnat voivat siirtää suurempaa tehoa kuin kumihihnat. Vahvistetut nahkavyöt koostuvat muovisesta vetoelementistä, joka on välissä nahkaisen ylä- ja alakerroksen välissä. Lopuksi kangasvyömme voivat koostua yhdestä puuvilla- tai ankkapalasta, joka on taitettu ja ommeltu pitkittäisompeleilla. Kangashihnat seuraavat tasaisesti ja toimivat suurella nopeudella. - Uritetut tai hammastetut hihnat (kuten kiilahihnat): Nämä ovat litteitä perushihnoja, jotka on muunnettu tarjoamaan toisen tyyppisten voimansiirtotuotteiden edut. Nämä ovat litteitä vöitä, joissa on pitkittäin uurrettu alapuoli. Poly-V-hihnat ovat pitkittäin uritettuja tai sahalaitaisia litteitä hihnoja, joissa on vetolujuus ja sarja vierekkäisiä V-muotoisia uria seuranta- ja puristustarkoituksiin. Tehokapasiteetti riippuu hihnan leveydestä. Kiilahihna on teollisuuden työhevonen, ja niitä on saatavana useissa standardoiduissa kokoissa ja tyypeissä lähes minkä tahansa kuormitusvoiman siirtoon. Kiilahihnakäytöt toimivat hyvin välillä 1500-6000 jalkaa/min, mutta kapeat kiilahihnat toimivat jopa 10 000 jalkaa/min. Kiilahihnakäytöt tarjoavat pitkän käyttöiän, kuten 3–5 vuotta, ja mahdollistavat suuret nopeussuhteet, ne on helppo asentaa ja irrottaa, ne tarjoavat hiljaisen toiminnan, vähän huoltoa, hyvän iskunvaimennuksen hihnan ohjaimen ja vetoakselien välillä. Kiilahihnojen haittana on niiden tietty luisto ja ryömintä, joten ne eivät välttämättä ole paras ratkaisu, kun vaaditaan synkronisia nopeuksia. Meillä on teollisuus-, auto- ja maataloushihnoja. Saatavilla on vakiopituuksia sekä mukautettuja hihnojen pituuksia. Kaikki vakiokiilahihnapoikkileikkaukset ovat saatavilla varastosta. On taulukoita, joissa voit laskea tuntemattomia parametreja, kuten hihnan pituuden, hihnan poikkileikkauksen (leveys ja paksuus) edellyttäen, että tiedät joitain järjestelmäsi parametreja, kuten käyttö- ja vetopyörän halkaisijat, hihnapyörien keskietäisyys ja hihnapyörien pyörimisnopeudet. Voit käyttää tällaisia pöytiä tai pyytää meitä valitsemaan sinulle oikean kiilahihnan. - Positiiviset käyttöhihnat (jakohihna): Nämä hihnat ovat myös litteitä, ja niiden sisäkehällä on sarja tasaisin välein olevia hampaita. Positiivisissa veto- tai jakohihnoissa yhdistyvät litteiden hihnojen edut ketjujen ja vaihteiden positiiviseen pito-ominaisuuksiin. Positiiviset käyttöhihnat eivät paljasta luistoa tai nopeusvaihteluita. Laaja valikoima nopeussuhteita on mahdollista. Laakereiden kuormitukset ovat pieniä, koska ne voivat toimia alhaisella jännityksellä. Ne ovat kuitenkin herkempiä hihnapyörien kohdistusvirheille. - Hihnapyörät, hihnapyörät, hihnojen navat: Erityyppisiä hihnapyöriä käytetään litteillä, uurteisilla (hammastettuilla) ja positiivisilla käyttöhihnoilla. Valmistamme ne kaikki. Suurin osa lattahihnapyöristämme on valmistettu rautaa valamalla, mutta teräsversioita on saatavana myös erilaisina vanne- ja napayhdistelminä. Litteähihnapyörissämme voi olla kiinteät, puolaiset tai halkaistut navat tai voimme valmistaa toiveidesi mukaan. Uri- ja vetohihnat ovat saatavilla useissa eri kokoisina ja -leveyksinä. Vähintään yksi hihnapyörä jakohihnakäytöissä on oltava laipallinen, jotta hihna pysyy vetokäytössä. Pitkissä keskikäyttöjärjestelmissä on suositeltavaa, että molemmat hihnapyörät ovat laipallisia. Pyörät ovat hihnapyörien uritettuja pyöriä, ja ne valmistetaan yleensä rautavalulla, teräsmuovauksella tai muovivalulla. Teräksen muovaus on sopiva prosessi auto- ja maatalouspyörien valmistukseen. Valmistamme pyörät, joissa on säännölliset ja syvät urit. Syväuraiset pyörät sopivat hyvin, kun kiilahihna tulee pyörään kulmassa, kuten neljänneskierroskäytöissä. Syvät urat sopivat hyvin myös pystyakselikäyttöihin ja sovelluksiin, joissa hihnojen tärinä voi olla ongelma. Tyhjäpyörämme ovat uritettuja tai litteitä hihnapyöriä, jotka eivät siirrä mekaanista voimaa. Tyhjäpyöriä käytetään enimmäkseen hihnojen kiristykseen. - Yksi- ja useat hihnakäytöt: Yksittäisissä hihnakäytöissä on yksi ura, kun taas useissa hihnakäytöissä on useita uria. Napsauta alla olevaa värillistä tekstiä, voit ladata luettelomme: - Voimansiirtohihnat (sisältää kiilahihnat, jakohihnat, raakareunahihnat, kierretyt hihnat ja erikoishihnat) - Kuljetinhihnat - V-hihnapyörät - Ajoituspyörät KETJUT JA KETJUAJAT: Voimansiirtoketjuillamme on joitain etuja, kuten suhteellisen rajoittamattomat akselin keskietäisyydet, helppo kokoaminen, tiiviys, kireys joustavuus ilman liukumista tai virumista, toimintakyky korkeissa lämpötiloissa. Tässä ovat tärkeimmät ketjujemme tyypit: - Irrotettavat ketjut: Irrotettavat ketjumme on valmistettu eri kokoisina, jako- ja enimmäislujuksina ja yleensä tempervaluradasta tai teräksestä. Muokattavia ketjuja valmistetaan eri kokoisina 0,902 (23 mm) ja 4,063 tuuman (103 mm) väliltä ja lopullinen lujuus 700 - 17 000 lb/neliötuuma. Irrotettavat teräsketjumme ovat sitä vastoin valmistettuja 0,904 tuuman (23 mm) ja noin 3,00 tuuman (76 mm) väliltä, ja niiden enimmäislujuus on 760 - 5000 lb/neliötuuma._cc781905-5cde-3194-bb3b- 136bad5cf58d_ - Pintle-ketjut: Näitä ketjuja käytetään raskaammille kuormille ja hieman suuremmille nopeuksille noin 450 jalkaan/min (2,2 m/s). Nastaketjut on valmistettu yksittäisistä valetuista lenkeistä, joissa on täysi, pyöreä piippupää ja sivupalkit. Nämä ketjun lenkit on kytketty terästappeihin. Näiden ketjujen jako on noin 1,00 tuumasta (25 mm) 6,00 tuumaan (150 mm) ja lopullinen lujuus välillä 3600 - 30 000 lb/neliötuuma. - Offset-sivupalkkiketjut: Nämä ovat suosittuja rakennuskoneiden käyttöketjuissa. Nämä ketjut toimivat 1000 ft/min nopeuksilla ja siirtävät kuormia noin 250 hv. Yleensä jokaisessa lenkissä on kaksi sivupalkkia, yksi holkki, yksi rulla, yksi tappi, sokka. - Rullaketjut: Niitä on saatavana 0,25 (6 mm) - 3,00 (75 mm) tuuman jakovälillä. Yksileveisten rullaketjujen lopullinen lujuus vaihtelee välillä 925 - 130 000 lb/neliötuuma. Rullaketjuista on saatavana useita leveitä versioita, jotka siirtävät enemmän tehoa suuremmilla nopeuksilla. Monileveiset rullaketjut tarjoavat myös pehmeämmän toiminnan ja vähentävät melua. Rullaketjut kootaan rullalenkeistä ja tappilenkkeistä. Irrotettavan version rullaketjuissa käytetään sokkoja. Rullaketjukäyttöjen suunnittelu vaatii aineosaamista. Hihnakäytöt perustuvat lineaarisiin nopeuksiin, kun taas ketjukäytöt pienemmän ketjupyörän pyörimisnopeuteen, joka on useimmissa asennuksissa käyttöelin. Ketjukäyttöjen suunnittelu perustuu hevosvoimien ja pyörimisnopeuden lisäksi moniin muihin tekijöihin. - Kaksinkertaiset ketjut: Pohjimmiltaan samat kuin rullaketjut, paitsi että jako on kaksi kertaa pidempi. - Käänteiset hammasketjut (hiljaiset): Nopeat ketjut, joita käytetään enimmäkseen voimanotto- ja voimanottokäytöissä. Käänteiset hammasketjukäytöt voivat siirtää jopa 1 200 hv:n tehoa, ja ne koostuvat sarjasta hammaslenkkejä, jotka on koottu vuorotellen joko tapeilla tai nivelkomponenttien yhdistelmällä. Keskiohjainketjussa on ohjauslenkit ketjupyörän uriin kytkemiseksi, ja sivuohjainketjussa on ohjaimet ketjupyörän sivuille kytkemiseksi. - Helmi- tai liukuketjut: Näitä ketjuja käytetään hitaissa nopeuksissa ja myös manuaalisissa toimissa. Napsauta alla olevaa värillistä tekstiä, voit ladata luettelomme: - Ajoketjut - Kuljetinketjut - Suuret kuljetinketjut - Rullaketjut ruostumattomasta teräksestä - Nostoketjut - Moottoripyörän ketjut - Maatalouskoneketjut - Rattaat: Vakioketjupyörämme ovat ANSI-standardien mukaisia. Levyrattaat ovat litteitä, napattomia ketjupyöriä. Pienet ja keskikokoiset napapyörämme sorvataan tankomateriaalista tai takoista tai valmistetaan hitsaamalla tanko-napa kuumavalssatuksi levyksi. AGS-TECH Inc. voi toimittaa harmaarautavaluista koneistettuja hammasrattaita, valuteräs- ja hitsattuja naparakenteita, sintrattua jauhemetallia, muovattua tai koneistettua muovia. Sujuvan toiminnan takaamiseksi suurilla nopeuksilla ketjupyörien oikea koon valinta on välttämätöntä. Tilarajoitukset ovat tietysti tekijä, jota emme voi jättää huomiotta hammaspyörää valittaessa. On suositeltavaa, että vetopyörän ja käytettävien ketjupyörien suhde on korkeintaan 6:1 ja ketjun kääre kuljettajassa on 120 astetta. Myös pienempien ja suurempien ketjupyörien keskietäisyydet, ketjun pituudet ja ketjun kireys on valittava joidenkin suositeltujen teknisten laskelmien ja ohjeiden mukaan, ei satunnaisesti. Lataa luettelomme napsauttamalla alla olevaa värillistä tekstiä: - Rattaat ja levypyörät - Vaihteiston holkit - Ketjun kytkentä - Ketjun lukot KAAPELIAJO: Niillä on joissakin tapauksissa etunsa hihnoihin ja ketjukäyttöihin verrattuna. Kaapelikäytöt voivat suorittaa saman toiminnon kuin hihnat, ja ne voivat myös olla yksinkertaisempia ja taloudellisempia toteuttaa joissakin sovelluksissa. Esimerkiksi uusi Synchromesh Cable Drive -sarja on suunniteltu positiiviseen vetovoimaan korvaamaan perinteiset köydet, yksinkertaiset kaapelit ja hammaspyöräkäytöt erityisesti ahtaissa tiloissa. Uusi kaapeliasema on suunniteltu tarjoamaan erittäin tarkka paikannus elektronisissa laitteissa, kuten kopiokoneissa, piirtureissa, kirjoituskoneissa, tulostimissa jne. Uuden kaapeliaseman keskeinen ominaisuus on sen kyky käyttää 3D-käärmekokoonpanoissa, mikä mahdollistaa erittäin miniatyyri kuvioita. Synkromikaapeleita voidaan käyttää köysiin verrattuna pienemmällä jännityksellä, mikä vähentää virrankulutusta. Ota yhteyttä AGS-TECHiin saadaksesi kysymyksiä ja mielipiteitä hihnoista, ketju- ja kaapelikäytöistä. CLICK Product Finder-Locator Service EDELLINEN SIVU
- Rapid Prototyping, Desktop Manufacturing, Additive Manufacturing, FDM
Rapid Prototyping, Desktop Manufacturing, Additive Manufacturing, Stereolithography, Polyjet, Fused Deposition Modeling, Selective Laser Sintering, FDM, SLS Lisäaine ja nopea valmistus Viime vuosina olemme nähneet RAPID MANUFACTURINGin tai RAPID PROTOTYPINGin kysynnän lisääntyneen. Tätä prosessia voidaan kutsua myös PÖYTÄVALMISTUKSEKSI tai VAPAAN MUODOSSA VALMISTUKSEKSI. Periaatteessa osan kiinteä fyysinen malli tehdään suoraan kolmiulotteisesta CAD-piirustuksesta. Käytämme termiä ADDITIVE MANUFACTURING näille erilaisille tekniikoille, joissa rakennamme osia kerroksittain. Käytämme integroitua tietokoneohjattua laitteistoa ja ohjelmistoa. Nopeat prototyyppi- ja valmistustekniikkamme ovat STEREOLITOGRAFIA, POLYJET, SULAITETTU MALLINNUS, VALIKKOINEN LASERSINTRAUS, ELEKTRONISÄDESULATUS, KOLMIULOTTEINEN TULOSTUS, SUORA VALMISTUS, NOPEA TYÖKALU. Suosittelemme, että napsautat tätäLATAA AGS-TECH Inc:n lisäainevalmistuksen ja nopeiden valmistusprosessien kaavamaiset kuvamme. Tämä auttaa sinua ymmärtämään paremmin alla toimittamiamme tietoja. Nopea prototyyppien luominen tarjoaa meille: 1.) Konseptuaalista tuotesuunnittelua tarkastellaan eri näkökulmista näytöllä 3D/CAD-järjestelmän avulla. 2.) Prototyyppejä ei-metallisista ja metallisista materiaaleista valmistetaan ja tutkitaan toiminnallisista, teknisistä ja esteettisistä näkökohdista. 3.) Edullinen prototyyppien valmistus hyvin lyhyessä ajassa on suoritettu. Additiivinen valmistus voidaan muistuttaa leivän rakentamista pinoamalla ja liimaamalla yksittäisiä viipaleita päällekkäin. Toisin sanoen tuote valmistetaan viipaleelta tai kerros kerrokselta kerrostettuna toistensa päälle. Suurin osa osista voidaan valmistaa muutamassa tunnissa. Tekniikka on hyvä, jos osia tarvitaan hyvin nopeasti tai jos tarvittavat määrät ovat pieniä ja muotin ja työkalujen valmistaminen on liian kallista ja aikaa vievää. Osan hinta on kuitenkin kallis kalliiden raaka-aineiden vuoksi. • STEREOLITOGRAFIA: Tämä tekniikka, josta käytetään myös lyhennettä STL, perustuu nestemäisen fotopolymeerin kovettamiseen ja kovettamiseen tiettyyn muotoon kohdistamalla siihen lasersäde. Laser polymeroi fotopolymeerin ja kovettaa sen. Pyyhkäisemällä UV-lasersäde ohjelmoidun muodon mukaan pitkin fotopolymeeriseoksen pintaa, osa tuotetaan alhaalta ylöspäin yksittäisinä siivuina, jotka on kaskadoitu päällekkäin. Laserpisteen skannaus toistetaan monta kertaa järjestelmään ohjelmoitujen geometrioiden saavuttamiseksi. Kun osa on täysin valmistettu, se poistetaan alustalta, kuivataan ja puhdistetaan ultraäänellä ja alkoholihauteella. Seuraavaksi se altistetaan UV-säteilylle muutaman tunnin ajan varmistaakseen, että polymeeri on täysin kovettunut ja kovettunut. Yhteenvetona voidaan todeta, että fotopolymeeriseokseen upotettua alustaa ja UV-lasersädettä ohjataan ja siirretään servo-ohjausjärjestelmän läpi halutun osan muodon mukaan ja osa saadaan valokovettamalla polymeeri kerros kerrokselta. Tietysti valmistettavan osan maksimimitat määräytyvät stereolitografialaitteistolla. • POLYJET: Samoin kuin mustesuihkutulostuksessa, polyjetissä meillä on kahdeksan tulostuspäätä, jotka levittävät fotopolymeeriä rakennusalustalle. Suihkujen viereen sijoitettu ultraviolettivalo kovettaa ja kovettaa välittömästi jokaisen kerroksen. Polyjetissä käytetään kahta materiaalia. Ensimmäinen materiaali on varsinaisen mallin valmistukseen. Toista materiaalia, geelimäistä hartsia, käytetään tukena. Molemmat materiaalit kerrostetaan kerros kerrokselta ja kovetetaan samanaikaisesti. Mallin valmistumisen jälkeen tukimateriaali poistetaan vesiliuoksella. Käytetyt hartsit ovat samanlaisia kuin stereolitografia (STL). Polyjetillä on seuraavat edut stereolitografiaan verrattuna: 1.) Ei tarvetta puhdistaa osia. 2.) Ei tarvetta jälkikäsittelyyn 3.) Pienemmät kerrospaksuudet ovat mahdollisia ja näin saadaan parempi resoluutio ja voidaan valmistaa hienompia osia. • FUSED DEPOSITION MALLING: Myös lyhennettynä FDM, tässä menetelmässä robottiohjattu ekstruuderin pää liikkuu kahteen periaatteelliseen suuntaan pöydän yli. Kaapeli lasketaan ja nostetaan tarpeen mukaan. Päässä olevan kuumennetun muotin aukosta ekstrudoidaan termoplastinen filamentti ja ensimmäinen kerros kerrostetaan vaahtomuovipohjalle. Tämä saadaan aikaan ekstruuderin päällä, joka seuraa ennalta määrättyä reittiä. Ensimmäisen kerroksen jälkeen pöytä lasketaan alas ja seuraavat kerrokset asetetaan päällekkäin. Joskus monimutkaisen osan valmistuksessa tarvitaan tukirakenteita, jotta kerrostaminen voi jatkua tiettyihin suuntiin. Näissä tapauksissa tukimateriaali ekstrudoidaan pienemmällä filamenttivälillä kerrokselle niin, että se on mallimateriaalia heikompi. Nämä tukirakenteet voidaan myöhemmin purkaa tai rikkoa osan valmistuttua. Ekstruuderin suuttimen mitat määräävät ekstrudoitujen kerrosten paksuuden. FDM-prosessi tuottaa osia, joissa on porrastetut pinnat vinoilla ulkotasoilla. Jos tämä karheus ei ole hyväksyttävää, voidaan käyttää kemiallista höyrykiillotusta tai kuumennettua työkalua näiden tasoittamiseen. Päällystysmateriaalina on saatavana jopa kiillotusvaha näiden vaiheiden poistamiseksi ja kohtuullisten geometristen toleranssien saavuttamiseksi. • SELECTIVE LASER SINTERING: Tunnetaan myös nimellä SLS, prosessi perustuu polymeerin, keraamisten tai metallijauheiden sintraamiseen valikoivasti esineeseen. Käsittelykammion pohjassa on kaksi sylinteriä: osarakenteinen sylinteri ja jauheen syöttösylinteri. Ensin mainittua lasketaan asteittain sinne, missä sintrattu osa muodostuu, ja jälkimmäistä nostetaan asteittain jauheen syöttämiseksi osarakennesylinteriin rullamekanismin kautta. Ensin ohut kerros jauhetta kerrostetaan osarakennesylinteriin, sitten lasersäde kohdistetaan kyseiseen kerrokseen jäljittäen ja sulattaen/sintraten tietyn poikkileikkauksen, joka sitten kiinteytyy uudelleen kiinteäksi aineeksi. Jauhe on alueita, joihin lasersäde ei osu, jää löysäksi, mutta tukee silti kiinteää osaa. Sitten kerrostetaan toinen jauhekerros ja prosessi toistetaan monta kertaa osan saamiseksi. Lopussa irtonaiset jauhehiukkaset ravistetaan pois. Kaikki nämä suoritetaan prosessinohjaustietokoneella valmistettavan osan 3D CAD -ohjelman luomien ohjeiden avulla. Erilaisia materiaaleja, kuten polymeerejä (kuten ABS, PVC, polyesteri), vahaa, metalleja ja keramiikkaa sopivilla polymeerisideaineilla voidaan kerrostaa. • ELECTRON-BEAM SULATUS: Samanlainen kuin selektiivinen lasersintraus, mutta käyttää elektronisuihkua titaani- tai kobolttikromijauheiden sulattamiseen prototyyppien valmistamiseksi tyhjiössä. Jotkut kehitystyöt on tehty tämän prosessin suorittamiseksi ruostumattomille teräksille, alumiinille ja kupariseoksille. Jos valmistettujen osien väsymislujuutta on lisättävä, käytämme toissijaisena prosessina osien valmistuksen jälkeistä kuumaisostaattista puristusta. • KOLMIULOTTEINEN TULOSTUS: Merkitään myös 3DP:llä, tässä tekniikassa tulostuspää tallentaa epäorgaanisen sideaineen joko ei-metallisen tai metallisen jauheen pinnalle. Jauhepetiä kantava mäntä lasketaan asteittain ja jokaisessa vaiheessa sideaine kerrostetaan kerros kerrokselta ja sulatetaan sideaineella. Jauhemateriaaleina käytetään polymeeriseoksia ja kuituja, valimohiekkaa, metalleja. Käyttämällä eri sidontapäitä samanaikaisesti ja eri värisiä sideaineita saamme erilaisia värejä. Prosessi on samanlainen kuin mustesuihkutulostus, mutta värillisen arkin sijaan saamme värillisen kolmiulotteisen esineen. Valmistetut osat voivat olla huokoisia ja siksi voivat vaatia sintrausta ja metallin tunkeutumista sen tiheyden ja lujuuden lisäämiseksi. Sintraus polttaa sideaineen pois ja sulattaa metallijauheet yhteen. Metalleja, kuten ruostumatonta terästä, alumiinia, titaania, voidaan käyttää osien valmistukseen ja tunkeutumismateriaaleina käytämme yleisesti kuparia ja pronssia. Tämän tekniikan kauneus on, että jopa monimutkaiset ja liikkuvat kokoonpanot voidaan valmistaa erittäin nopeasti. Voidaan valmistaa esimerkiksi hammaspyöräasennelma, jakoavain työkaluksi ja siinä on liikkuvat ja kääntyvät osat käyttövalmiina. Kokoonpanon eri osia voidaan valmistaa eri väreillä ja kaikki yhdellä kertaa. Lataa esitteemme:Metallin 3D-tulostuksen perusteet • SUORA VALMISTUS ja NOPEA TYÖKALU: Suunnittelun arvioinnin ja vianetsinnän lisäksi käytämme nopeaa prototyyppiä tuotteiden suoraan valmistukseen tai suoraan tuotteisiin. Toisin sanoen nopea prototyyppien valmistus voidaan sisällyttää perinteisiin prosesseihin, jotta niistä tulee parempia ja kilpailukykyisempiä. Esimerkiksi nopea prototyyppien valmistus voi tuottaa kuvioita ja muotteja. Nopeilla prototyypeillä luotuja sulavan ja palavan polymeerin kuvioita voidaan koota investointivalua varten ja investoida. Toinen mainittava esimerkki on 3DP:n käyttäminen keraamisen valukuoren valmistukseen ja sen käyttämiseen vaipan valutoimintoihin. Jopa ruiskumuotteja ja muottien sisäosia voidaan valmistaa nopealla prototyyppityöllä, jolloin voidaan säästää useita viikkoja tai kuukausia muottien valmistuksessa. Analysoimalla vain halutun kappaleen CAD-tiedosto, voimme tuottaa työkalun geometrian ohjelmiston avulla. Tässä on joitain suosittuja nopeat työkalut: RTV (Room-Temperature Vulcanizing) MUOTTAMINEN / URETAANIN VALU: Pikaprototyyppien avulla voidaan tehdä halutun osan kuvio. Sitten tämä kuvio päällystetään irrotusaineella ja nestemäinen RTV-kumi kaadetaan kuvion päälle muotin puolikkaiden valmistamiseksi. Seuraavaksi näitä muotin puolikkaita käytetään nestemäisten uretaanien ruiskupuristukseen. Muotin käyttöikä on lyhyt, vain noin 0 tai 30 sykliä, mutta riittää pienten erien tuotantoon. ACES (Acetal Clear Epoxy Solid) ruiskupuristus: Tuotamme ruiskumuotteja käyttämällä nopeita prototyyppitekniikoita, kuten stereolitografiaa. Nämä muotit ovat kuoria, joissa on avoin pää, jotta ne voidaan täyttää sellaisilla materiaaleilla kuin epoksi, alumiinitäytteinen epoksi tai metalleja. Muotin käyttöikä on jälleen rajoitettu kymmeniin tai enintään satoihin osiin. RUISKETUN METALLIN TYÖKALUPROSESSI: Käytämme nopeaa prototyyppiä ja teemme kuvioita. Suihkutamme kuviopinnalle sinkki-alumiiniseosta ja pinnoitamme sen. Metallipinnoitettu kuvio asetetaan sitten pullon sisään ja täytetään epoksilla tai alumiinilla täytetyllä epoksilla. Lopuksi se poistetaan ja valmistamalla kaksi tällaista muotin puolikasta saadaan täydellinen muotti ruiskuvalua varten. Näiden muottien käyttöikä on pidempi, ja joissakin tapauksissa materiaalista ja lämpötiloista riippuen niistä voidaan valmistaa tuhansia osia. KEELTOOL-PROSESSI: Tällä tekniikalla voidaan tuottaa muotteja, joiden käyttöikä on 100 000-10 miljoonaa. Nopeaa prototyyppiä käyttämällä valmistamme RTV-muotin. Muotti täytetään seuraavaksi seoksella, joka koostuu A6-työkaluteräsjauheesta, volframikarbidista, polymeerisideaineesta ja annetaan kovettua. Tämä muotti kuumennetaan sitten polymeerin polttamiseksi pois ja metallijauheiden sulattamiseksi. Seuraava vaihe on kuparin tunkeutuminen lopullisen muotin valmistamiseksi. Tarvittaessa muotille voidaan suorittaa toissijaisia toimenpiteitä, kuten koneistus ja kiillotus paremman mittatarkkuuden saavuttamiseksi. _cc781905-5cde-3194-bb3b-136bad_cf58bad CLICK Product Finder-Locator Service EDELLINEN SIVU
- Joining & Assembly & Fastening Processes, Welding, Brazing, Soldering
Joining & Assembly & Fastening Processes, Welding, Brazing, Soldering, Sintering, Adhesive Bonding, Press Fitting, Wave and Reflow Solder Process, Torch Furnace Liitos- ja kokoonpano- ja kiinnitysprosessit Yhdistämme, koomme ja kiinnitämme valmistamasi osat ja teemme niistä valmiita tai puolivalmiita tuotteita HITSAUKSEN, JUOTTAMIN, JUOTTAMISEN, SINTRAUKSEN, LIIMASTAMISEN, KIINNITYKSEN, PURISTUSSOITTAMISEN avulla. Jotkut suosituimmista hitsausprosesseistamme ovat kaari-, happikaasu-, vastus-, projektio-, sauma-, isku-, isku-, solid-state-, elektronisuihku-, laser-, lämpö-, induktiohitsaus-. Suosittuja juotosprosessejamme ovat poltin-, induktio-, uuni- ja upotusjuotto. Juotosmenetelmämme ovat rauta-, keittolevy-, uuni-, induktio-, dip-, aalto-, reflow- ja ultraäänijuotto. Liimaukseen käytämme usein kestomuoveja ja lämpökovettuvia, epoksideja, fenoleja, polyuretaania, liimaseoksia sekä joitain muita kemikaaleja ja teippejä. Lopuksi kiinnitysprosessimme koostuvat naulaamisesta, ruuvaamisesta, muttereista ja pulteista, niittauksesta, puristamisesta, kiinnityksestä, ompelemisesta ja nidonnasta sekä puristussovituksesta. • HITSAUS: Hitsaukseen liittyy materiaalien liittäminen sulattamalla työkappaleet ja lisäämällä täyteaineita, jotka myös liitetään sulaan hitsausaltaaseen. Kun alue jäähtyy, saadaan vahva liitos. Joissakin tapauksissa käytetään painetta. Päinvastoin kuin hitsauksessa, kovajuotos- ja juotostoiminnot sisältävät vain matalamman sulamispisteen omaavan materiaalin sulamisen työkappaleiden välissä, eivätkä työkappaleet sula. Suosittelemme, että napsautat tätäLATAA AGS-TECH Inc:n hitsausprosessien kaavamaiset kuvamme. Tämä auttaa sinua ymmärtämään paremmin alla toimittamiamme tietoja. KAARIHITSAUKSESSA luomme sähkökaaren, joka sulattaa metallit, virtalähteen ja elektrodin avulla. Hitsauskohta on suojattu suojakaasulla tai höyryllä tai muulla materiaalilla. Tämä prosessi on suosittu autonosien ja teräsrakenteiden hitsauksessa. Suojatussa metallikaarihitsauksessa (SMAW) tai puikkohitsauksessa elektrodipuikko tuodaan lähelle perusmateriaalia ja niiden väliin syntyy sähkökaari. Elektroditanko sulaa ja toimii täyteaineena. Elektrodi sisältää myös sulatetta, joka toimii kuonakerroksena ja vapauttaa höyryjä, jotka toimivat suojakaasuna. Nämä suojaavat hitsausaluetta ympäristön saastumiselta. Muita täyteaineita ei käytetä. Tämän prosessin haittoja ovat sen hitaus, tarve vaihtaa elektrodeja usein, tarve hakea pois juoksutuksesta peräisin oleva jäännöskuona. Useita metalleja, kuten rauta, teräs, nikkeli, alumiini, kupari jne. Voidaan hitsata. Sen etuja ovat edulliset työkalut ja helppokäyttöisyys. Kaasumetallikaarihitsaus (GMAW), joka tunnetaan myös nimellä metalliinertti kaasu (MIG), syötämme jatkuvasti kuluvaa elektrodilangan täyteainetta ja inerttiä tai osittain inerttiä kaasua, joka virtaa langan ympärillä hitsausalueen ympäristön saastumiselta. Teräs, alumiini ja muut ei-rautametallit voidaan hitsata. MIG:n etuja ovat korkeat hitsausnopeudet ja hyvä laatu. Haittoja ovat sen monimutkaiset varusteet ja tuulisissa ulkoilmaympäristöissä kohtaamat haasteet, koska joudumme pitämään hitsausalueen ympärillä oleva suojakaasu vakaana. GMAW:n muunnelma on täytehitsaus (FCAW), joka koostuu hienosta metalliputkesta, joka on täytetty juoksuteaineilla. Joskus putken sisällä oleva virtaus riittää suojaamaan ympäristön saastumiselta. Submerged Arc Welding (SAW) on laajalti automatisoitu prosessi, joka sisältää jatkuvan langansyötön ja valokaaren, joka lyödään sulatussuojakerroksen alle. Tuotantonopeudet ja laatu ovat korkeat, hitsauskuona irtoaa helposti ja meillä on savuton työympäristö. Haittapuolena on, että sillä voidaan hitsata vain osia tietyissä asennoissa. Kaasukaarihitsauksessa (GTAW) tai volframi-inertissä kaasuhitsauksessa (TIG) käytämme volframielektrodia yhdessä erillisen täyteaineen ja inerttien tai lähes inerttien kaasujen kanssa. Kuten tiedämme, volframilla on korkea sulamispiste ja se on erittäin sopiva metalli erittäin korkeisiin lämpötiloihin. TIG:ssä olevaa volframia ei kuluteta toisin kuin muut edellä selostetut menetelmät. Hidas mutta laadukas hitsaustekniikka, joka on muita ohuiden materiaalien hitsaustekniikoita parempi. Sopii useille metalleille. Plasmakaarihitsaus on samanlainen, mutta käyttää plasmakaasua kaaren luomiseen. Plasmakaarihitsauksen kaari on suhteellisen keskittyneempi verrattuna GTAW:hen, ja sitä voidaan käyttää useammille metallipaksuuksille paljon suuremmilla nopeuksilla. GTAW- ja plasmakaarihitsausta voidaan soveltaa enemmän tai vähemmän samoihin materiaaleihin. OXY-FUEL / OXYFUEL WELDING kutsutaan myös oksiasetyleenihitsaukseksi, oksihitsaukseksi, kaasuhitsaus suoritetaan käyttämällä kaasupolttoaineita ja happea hitsaukseen. Koska sähköä ei käytetä, se on kannettava ja sitä voidaan käyttää siellä, missä ei ole sähköä. Hitsauspolttimella lämmitämme kappaleet ja täytemateriaalin, jolloin syntyy yhteinen sulametalliallas. Voidaan käyttää erilaisia polttoaineita, kuten asetyleeniä, bensiiniä, vetyä, propaania, butaania jne. Happipolttoainehitsauksessa käytämme kahta säiliötä, joista toinen polttoaineelle ja toinen hapelle. Happi hapettaa polttoaineen (polttaa sen). VASTUSHITSaus: Tämän tyyppinen hitsaus hyödyntää joule-lämmitystä ja lämpöä syntyy paikassa, jossa sähkövirtaa syötetään tietyn ajan. Suuret virrat kulkevat metallin läpi. Tähän kohtaan muodostuu sulan metallin altaat. Vastushitsausmenetelmät ovat suosittuja tehokkuutensa ja vähäisen saastepotentiaalinsa vuoksi. Haittoja ovat kuitenkin laitekustannukset, jotka ovat suhteellisen merkittäviä, ja luontainen rajoitus suhteellisen ohuisiin työkappaleisiin. PISTÄHITSaus on yksi tärkeimmistä vastushitsauksen tyypeistä. Tässä yhdistämme kaksi tai useampia päällekkäisiä levyjä tai työkappaleita käyttämällä kahta kuparielektrodia kiinnittämään levyt yhteen ja ohjaamaan niiden läpi suuri virta. Kuparielektrodien välissä oleva materiaali lämpenee ja siihen kohtaan muodostuu sulaallas. Tämän jälkeen virta pysäytetään ja kuparipuikkokärjet jäähdyttävät hitsauskohtaa, koska elektrodit ovat vesijäähdytteisiä. Oikea määrä lämpöä oikeaan materiaaliin ja oikeaan paksuuteen on avainasemassa tässä tekniikassa, koska väärin käytettynä sauma on heikko. Pistehitsauksen etuna on se, että se ei aiheuta merkittäviä muodonmuutoksia työkappaleisiin, energiatehokkuus, automaation helppous ja erinomaiset tuotantonopeudet, eikä se vaadi täyteaineita. Haittapuolena on, että koska hitsaus tapahtuu pisteissä yhtenäisen sauman muodostamisen sijaan, kokonaislujuus voi olla suhteellisen alhaisempi verrattuna muihin hitsausmenetelmiin. SEAM WELDING puolestaan tuottaa hitsejä samanlaisten materiaalien vastakkaisiin pintoihin. Sauma voi olla päittäis- tai limityssauma. Saumahitsaus alkaa toisesta päästä ja siirtyy asteittain toiseen. Tämä menetelmä käyttää myös kahta kuparista valmistettua elektrodia paineen ja virran kohdistamiseksi hitsausalueelle. Kiekon muotoiset elektrodit pyörivät jatkuvalla kosketuksella saumalinjaa pitkin ja muodostavat jatkuvan hitsin. Myös tässä elektrodit jäähdytetään vedellä. Hitsaukset ovat erittäin vahvoja ja luotettavia. Muita menetelmiä ovat projisointi-, välähdys- ja upset-hitsaustekniikat. SOLID-STATE HITSAUS on hieman erilainen kuin edellä selostetut menetelmät. Yhdistäminen tapahtuu lämpötiloissa, jotka ovat liitettyjen metallien sulamislämpötilan alapuolella ja ilman metallitäyteainetta. Painetta voidaan käyttää joissakin prosesseissa. Erilaisia menetelmiä ovat RÄJÄHDYSHITSaus, jossa erilaisia metalleja puristetaan saman suuttimen läpi, KYLMÄPAINEHITSAUS, jossa liitetään pehmeät metalliseokset niiden sulamispisteiden alapuolelle, DIFFUUSIOHITSaus tekniikka, jossa ei ole näkyviä hitsausviivoja, RÄJÄHDYSHITSaus erilaisten rakenteellisten materiaalien liittämiseen, esim. korroosionkestävä. teräkset, SÄHKÖMAGNEETTINEN PULKSIHITSaus, jossa kiihdyttämme putkia ja levyjä sähkömagneettisilla voimilla, TAKOHITSaus, joka koostuu metallien kuumentamisesta korkeisiin lämpötiloihin ja vasaroimiseen yhteen, KITKAHITSAUS, jossa suoritetaan riittävällä kitkahitsauksella, KITKAHITSAUS, johon liittyy pyörivä ei-hitsaus kulutustyökalu, joka kulkee liitoslinjan läpi, KUUPAINEHITSaus, jossa puristamme metalleja yhteen korotetuissa lämpötiloissa, jotka ovat sulamislämpötilan alapuolella tyhjiössä tai inertissä kaasussa, KUUMISAATTINEN PAINEHITSaus prosessi, jossa kohdistamme painetta käyttämällä inerttejä kaasuja astian sisällä, TELLAHITSaus, jossa liitämme erilaisia materiaaleja pakottamalla ne väliin kaksi pyörivää pyörää, ULTRAÄÄNIHITSaus, jossa ohuita metalli- tai muovilevyjä hitsataan korkeataajuisella värähtelyenergialla. Muita hitsausprosessejamme ovat ELEKTRONISÄHITSAUS syvällä tunkeutumisella ja nopealla käsittelyllä, mutta kalliina menetelmänä pidämme sitä erikoistapauksissa, SÄHKÖLEKKIHITSaus vain raskaille paksuille levyille ja terästyökappaleille soveltuva menetelmä, INDUKTIOHITSaus, jossa käytämme sähkömagneettista induktiota ja lämmitä sähköä johtavia tai ferromagneettisia työkappaleitamme, LASERSÄDEHITSaus myös syvällä tunkeutumisella ja nopealla käsittelyllä, mutta kallis menetelmä, LASERHYBRIDIHITSaus, joka yhdistää LBW:n ja GMAW:n samassa hitsauspäässä ja pystyy yhdistämään 2 mm:n raot levyjen välillä sisältää sähköpurkauksen, jota seuraa materiaalien takominen käytetyllä paineella, LÄMPÖHITSaus, johon liittyy eksoterminen reaktio alumiinin ja rautaoksidijauheiden välillä, SÄHKÖKAASHITSaus kuluvilla elektrodeilla ja käytetään vain teräksen ollessa pystyasennossa, ja lopuksi KAARIHITSaus nastan liittämiseen alustaan. materiaalia lämmön ja paineen kanssa. Suosittelemme, että napsautat tätäLATAA AGS-TECH Inc:n kaaviomaiset kuvamme juotos-, juotos- ja liimausprosesseista Tämä auttaa sinua ymmärtämään paremmin alla toimittamiamme tietoja. • JUOTO: Yhdistämme kaksi tai useampia metallia kuumentamalla täytemetallia niiden välissä niiden sulamispisteiden yläpuolelle ja käyttämällä kapillaaritoimintaa levittämiseen. Prosessi on samanlainen kuin juottaminen, mutta juottamiseen liittyvät lämpötilat täyteaineen sulamiseen ovat korkeammat. Kuten hitsauksessa, juoksutusaine suojaa täyteainetta ilman epäpuhtauksilta. Jäähtymisen jälkeen työkappaleet liitetään yhteen. Prosessi sisältää seuraavat avainvaiheet: Hyvä istuvuus ja välys, perusmateriaalien asianmukainen puhdistus, oikea kiinnitys, oikea juoksutteen ja ilmakehän valinta, kokoonpanon lämmitys ja lopuksi juotetun kokoonpanon puhdistus. Jotkut juotosprosesseistamme ovat TORCH BRAZING, suosittu menetelmä, joka suoritetaan manuaalisesti tai automaattisesti. Se soveltuu pienikokoisiin tuotantotilauksiin ja erikoistapauksiin. Lämpö levitetään kaasuliekeillä juotettavan liitoksen lähellä. UUNIJUOTTAMINEN vaatii vähemmän operaattorin taitoja ja on puoliautomaattinen prosessi, joka soveltuu teolliseen massatuotantoon. Sekä lämpötilan säätö että uunin ilmakehän säätö ovat tämän tekniikan etuja, koska edellinen mahdollistaa kontrolloidun lämpökierron ja paikallisen kuumenemisen eliminoimisen, kuten polttimen juottamisessa, ja jälkimmäinen suojaa osaa hapettumiselta. Jiggiä käyttämällä pystymme alentamaan valmistuskustannukset minimiin. Haittoja ovat korkea virrankulutus, laitekustannukset ja haastavammat suunnittelunäkökohdat. Tyhjiöjuotto tapahtuu tyhjiöuunissa. Lämpötilan tasaisuus säilyy ja saamme vuoteettomat, erittäin puhtaat liitokset hyvin pienillä jäännösjännityksillä. Lämpökäsittelyt voivat tapahtua tyhjiökoottamisen aikana hitaiden lämmitys- ja jäähdytysjaksojen aikana esiintyvien alhaisten jäännösjännitysten vuoksi. Suurin haittapuoli on sen korkea hinta, koska tyhjiöympäristön luominen on kallis prosessi. Vielä toinen tekniikka DIP BRAZING liittää kiinnitetyt osat, joissa juotosmassaa levitetään yhteenliittyville pinnoille. Sen jälkeen kiinnitetyt osat kastetaan sulan suolan, kuten natriumkloridin (pöytäsuola) kylpyyn, joka toimii lämmönsiirtoaineena ja juoksutena. Ilma on poissuljettu, joten oksideja ei muodostu. INDUKTIOJUOTTAMISESSA yhdistämme materiaalit täytemetallilla, jonka sulamispiste on alhaisempi kuin perusmateriaaleissa. Induktiokäämin vaihtovirta muodostaa sähkömagneettisen kentän, joka indusoi induktiokuumennusta enimmäkseen rautapitoisissa magneettisissa materiaaleissa. Menetelmä tarjoaa selektiivisen lämmityksen, hyvät saumat täyteaineilla, jotka virtaavat vain halutuille alueille, vähän hapettumista, koska liekkejä ei ole läsnä ja jäähdytys on nopeaa, nopeaa lämpenemistä, konsistenssia ja soveltuvuutta suurien volyymien valmistukseen. Nopeuttaaksemme prosessejamme ja varmistaaksemme johdonmukaisuuden käytämme usein esimuotteja. Tietoja juotoslaitoksestamme, joka tuottaa keraamista metalliin liittimiä, hermeettistä tiivistystä, tyhjiöläpivientiä, korkea- ja ultrakorkeaa tyhjiö- ja nesteenohjauskomponentteja löytyy täältä:_cc781905-31-14cdebbbad8Juotostehtaan esite • JUOTTAMINEN: Juottamisessa meillä ei ole työkappaleiden sulamista, vaan liitokseen virtaava täytemetalli, jonka sulamispiste on alempi kuin liitososilla. Juotoksen täytemetalli sulaa alhaisemmassa lämpötilassa kuin juotettaessa. Käytämme juottamiseen lyijyttömät metalliseokset ja niillä on RoHS-yhteensopivuus ja erilaisiin käyttötarkoituksiin ja vaatimuksiin meillä on erilaisia ja sopivia metalliseoksia, kuten hopeaseos. Juotos tarjoaa meille kaasu- ja nestetiiviitä liitoksia. PEHMEÄJUOTOKSESSA täytemetallimme sulamispiste on alle 400 Celsiusastetta, kun taas HOPEANJUOTTAMISESSA ja JUOTOKSESSA tarvitsemme korkeampia lämpötiloja. Pehmeäjuotos käyttää alhaisempia lämpötiloja, mutta ei johda vahvoihin liitoksiin vaativiin sovelluksiin korkeissa lämpötiloissa. Toisaalta hopeajuotto vaatii polttimen tarjoamia korkeita lämpötiloja ja antaa meille vahvoja liitoksia, jotka sopivat korkeisiin lämpötiloihin. Juottaminen vaatii korkeimpia lämpötiloja ja yleensä käytetään poltinta. Koska juotosliitokset ovat erittäin vahvoja, ne ovat hyviä ehdokkaita raskaiden rautaesineiden korjaamiseen. Valmistuslinjoillamme käytämme sekä manuaalista käsijuottamista että automatisoituja juotoslinjoja. INDUCTION SOLDERING käyttää suurtaajuista vaihtovirtaa kuparikelassa induktiolämmityksen helpottamiseksi. Juotososaan indusoituu virtoja ja sen seurauksena lämpöä syntyy korkearesistanssissa liitoksessa. Tämä lämpö sulattaa täytemetallin. Fluxia käytetään myös. Induktiojuotto on hyvä menetelmä sylinterien ja putkien juottamiseen jatkuvassa prosessissa käärimällä kelat niiden ympärille. Joidenkin materiaalien, kuten grafiitin ja keramiikan, juottaminen on vaikeampaa, koska se vaatii työkappaleiden pinnoittamista sopivalla metallilla ennen juottamista. Tämä helpottaa rajapintojen liittämistä. Juotamme tällaisia materiaaleja erityisesti hermeettisiin pakkaussovelluksiin. Valmistamme painettuja piirilevyjämme (PCB) suuria määriä enimmäkseen aaltojootuksella. Vain pienissä prototyyppimäärissä käytämme juotoskolvia käsin juottamista. Käytämme aaltojuottamista sekä läpimeneviin että pinta-asennettaviin piirilevykokoonpanoihin (PCBA). Väliaikainen liima pitää komponentit kiinni piirilevyssä ja kokoonpano asetetaan kuljettimelle ja liikkuu sulaa juotetta sisältävän laitteen läpi. Ensin piirilevy sulatetaan ja menee sitten esilämmitysalueelle. Sula juote on kattilassa ja sen pinnalla on seisovien aaltojen kuvio. Kun piirilevy liikkuu näiden aaltojen yli, nämä aallot koskettavat piirilevyn pohjaa ja tarttuvat juotostyynyihin. Juotos pysyy vain nastoissa ja tyynyissä, ei itse piirilevyssä. Sulan juotteen aallot on hallittava hyvin, jotta roiskeita ei tapahdu ja aallonpäät eivät kosketa ja saastuttaa levyjen ei-toivottuja alueita. REFLOW SOLDERING:ssä käytämme tahmeaa juotospastaa elektronisten komponenttien väliaikaiseen kiinnittämiseen levyihin. Sitten levyt laitetaan reflow-uunin läpi lämpötilan säätöön. Täällä juote sulaa ja yhdistää komponentit pysyvästi. Käytämme tätä tekniikkaa sekä pinta-asennuskomponentteihin että läpireikään asennettaviin komponentteihin. Asianmukainen lämpötilan säätö ja uunin lämpötilojen säätö on välttämätöntä, jotta vältetään levyn elektronisten komponenttien tuhoutuminen ylikuumenemalla ne yli maksimilämpötilarajojen. Uudelleenvirtausjuottamisen prosessissa meillä on itse asiassa useita alueita tai vaiheita, joilla kullakin on erillinen lämpöprofiili, kuten esilämmitysvaihe, lämpöliotusvaihe, sulatus- ja jäähdytysvaiheet. Nämä eri vaiheet ovat välttämättömiä painettujen piirilevykokoonpanojen (PCBA) vaurioitumattomaan uudelleenvirtausjuottoon. ULTRASONIC JUOTTAMINEN on toinen usein käytetty tekniikka, jolla on ainutlaatuiset ominaisuudet. Sitä voidaan käyttää lasin, keraamisten ja ei-metallisten materiaalien juottamiseen. Esimerkiksi aurinkosähköpaneelit, jotka ovat ei-metallisia, tarvitsevat elektrodeja, jotka voidaan kiinnittää tällä tekniikalla. Ultraäänijuotuksessa käytämme lämmitettyä juotoskärkeä, joka lähettää myös ultraäänivärähtelyä. Nämä värähtelyt tuottavat kavitaatiokuplia substraatin ja sulan juotosmateriaalin rajapinnalle. Kavitaation räjähtävä energia muokkaa oksidipintaa ja poistaa likaa ja oksideja. Tänä aikana muodostuu myös seoskerros. Liimauspinnan juote sisältää happea ja mahdollistaa vahvan jaetun sidoksen muodostumisen lasin ja juotteen välille. DIP JUOTTAMISTA voidaan pitää yksinkertaisempi versio aaltojuotuksesta, joka soveltuu vain pienimuotoiseen tuotantoon. Ensimmäinen puhdistusfluksi levitetään kuten muissakin prosesseissa. PCB-levyt, joissa on asennettuja komponentteja, upotetaan manuaalisesti tai puoliautomaattisesti säiliöön, joka sisältää sulaa juotetta. Sula juote tarttuu paljaisiin metallisiin alueisiin, joita ei suojaa levyllä oleva juotosmaski. Laite on yksinkertainen ja edullinen. • LIIMAUS: Tämä on toinen suosittu tekniikka, jota käytämme usein, ja se sisältää pintojen liimauksen liimalla, epokseilla, muoviaineilla tai muilla kemikaaleilla. Kiinnitys suoritetaan joko haihduttamalla liuotin, lämpökovettamalla, UV-valokovetuksella, painekovetuksella tai odottamalla tietty aika. Tuotantolinjoillamme käytetään erilaisia korkean suorituskyvyn liimoja. Oikein suunnitelluilla levitys- ja kovetusprosesseilla liimaus voi johtaa erittäin alhaisiin jännityssidoksiin, jotka ovat vahvoja ja luotettavia. Liimat voivat suojata hyvin ympäristötekijöiltä, kuten kosteudelta, epäpuhtauksilta, syövyttäviltä aineilta, tärinältä jne. Liimausliimauksen edut ovat: niitä voidaan käyttää materiaaleihin, joita muuten olisi vaikea juottaa, hitsata tai juottaa. Se voi myös olla parempi lämpöherkille materiaaleille, jotka voivat vaurioitua hitsauksen tai muiden korkean lämpötilan prosessien seurauksena. Muita liimojen etuja ovat, että niitä voidaan levittää epäsäännöllisen muotoisille pinnoille ja ne lisäävät kokoonpanon painoa hyvin pienillä määrillä muihin menetelmiin verrattuna. Myös osien mittamuutokset ovat hyvin vähäisiä. Joillakin liimoilla on indeksinsovitusominaisuudet, ja niitä voidaan käyttää optisten komponenttien välissä heikentämättä merkittävästi valon tai optisen signaalin voimakkuutta. Toisaalta haitat ovat pidemmät kovettumisajat, jotka voivat hidastaa valmistuslinjoja, kiinnitysvaatimuksia, pinnan esikäsittelyvaatimuksia ja purkamisvaikeus, kun tarvitaan uudelleenkäsittelyä. Suurin osa liimaustoimenpiteistämme sisältää seuraavat vaiheet: -Pintakäsittely: Erikoispuhdistustoimenpiteet, kuten deionisoidun veden puhdistus, alkoholipuhdistus, plasma- tai koronapuhdistus ovat yleisiä. Puhdistuksen jälkeen voimme levittää pinnoille tarttumista edistäviä aineita parhaan mahdollisen sauman varmistamiseksi. -Osien kiinnitys: Suunnittelemme ja käytämme räätälöityjä kiinnikkeitä sekä liimakäyttöön että kovettumiseen. -Liimasovellus: Käytämme toisinaan manuaalisia ja joskus tapauksesta riippuen automatisoituja järjestelmiä, kuten robotiikkaa, servomoottoreita, lineaarisia toimilaitteita liima-aineiden toimittamiseksi oikeaan paikkaan ja annostelijoilla toimitamme ne oikeaan määrään ja määrään. -Kovettuminen: Liimasta riippuen voimme käyttää yksinkertaista kuivausta ja kovettumista sekä kovetusta UV-valoissa, jotka toimivat katalysaattorina tai lämpökovetuksella uunissa tai käyttämällä jigeihin ja kiinnikkeisiin asennettuja resistiivisiä lämmityselementtejä. Suosittelemme, että napsautat tätäLATAA AGS-TECH Inc:n kaaviomaiset kuvamme kiinnitysprosesseista. Tämä auttaa sinua ymmärtämään paremmin alla toimittamiamme tietoja. • KIINNITYSPROSESSIT: Mekaaniset liitosprosessimme jakautuvat kahteen nauhaluokkaan: KIINNITTIMET ja INTEGRAALILIITOKSET. Esimerkkejä käyttämistämme kiinnikkeistä ovat ruuvit, tapit, mutterit, pultit, niitit. Esimerkkejä käyttämistämme yhtenäisistä liitoksista ovat napsautus- ja kutistusliitokset, saumat, puristusliitokset. Erilaisten kiinnitysmenetelmien avulla varmistamme, että mekaaniset liitosemme ovat vahvoja ja luotettavia monien vuosien käyttöön. RUUVIT ja PULTIT ovat yleisimmin käytettyjä kiinnikkeitä esineiden pitämiseen yhdessä ja asennossa. Ruuvit ja pultit täyttävät ASME-standardit. Käytetään monenlaisia ruuveja ja pultteja, mukaan lukien kuusiokantaruuvit ja kuusiopultit, viiveruuvit ja pultit, kaksipäiset ruuvit, tappiruuvit, silmukkaruuvit, peiliruuvit, metallilevyruuvit, hienosäätöruuvit, itseporaavat ja itseporautuvat ruuvit , säätöruuvi, ruuvit sisäänrakennetuilla aluslevyillä ja paljon muuta. Meillä on erilaisia ruuvin päätyyppejä, kuten upotettu, kupu, pyöreä, laipallinen kanta ja erilaisia ruuvikäyttötyyppejä, kuten ura, risteys, neliö, kuusiokanta. RIVET toisaalta on pysyvä mekaaninen kiinnike, joka koostuu sileästä sylinterimäisestä akselista ja toisaalta päästä. Asennuksen jälkeen niitin toinen pää vääntyy ja sen halkaisija laajenee niin, että se pysyy paikallaan. Toisin sanoen ennen asennusta niitissä on yksi pää ja asennuksen jälkeen kaksi. Asennamme erilaisia niitit sovelluksesta, lujuudesta, saavutettavuudesta ja hinnasta riippuen, kuten kiinteät/pyöreäpäiset niitit, rakenteelliset, puoliputkimaiset, sokeat, oscar-, veto-, taso-, kitkalukko-, itselävistävät niitit. Niittausta voidaan suosia tapauksissa, joissa hitsauslämmöstä johtuvia lämpömuodonmuutoksia ja materiaaliominaisuuksien muutoksia on vältettävä. Niittaus tarjoaa myös kevyen painon ja erityisen hyvän lujuuden ja kestävyyden leikkausvoimia vastaan. Vetokuormitusta vastaan ruuvit, mutterit ja pultit voivat kuitenkin olla sopivampia. CLINCHING-prosessissa käytämme erityistä meistiä ja meistiä, jotka muodostavat mekaanisen lukituksen liitettävien metallilevyjen välille. Lävistin työntää metallilevykerrokset muotinonteloon ja johtaa pysyvän liitoksen muodostumiseen. Puristamisessa ei tarvita lämmitystä eikä jäähdytystä, ja se on kylmätyöstöprosessi. Se on taloudellinen prosessi, joka voi joissain tapauksissa korvata pistehitsauksen. PINNING:ssä käytämme tappeja, jotka ovat koneen elementtejä, joilla varmistetaan koneenosien asennot toisiinsa nähden. Tärkeimmät tyypit ovat haarukkatapit, sokkat, jousitapit, vaarnatapit, ja halkotapit. SIDOTAESSA käytämme nidontapistooleja ja niittejä, jotka ovat kaksihaaraisia kiinnikkeitä, joita käytetään materiaalien liittämiseen tai sitomiseen. Nidontalla on seuraavat edut: Taloudellinen, yksinkertainen ja nopea käyttää, niittien kruunulla voidaan sillata yhteen liitettyjä materiaaleja, Niitin kruunu voi helpottaa kappaleen silloittamista kaapelin tapaan ja kiinnittämistä pintaan ilman puhkaisua tai vaurioittava, suhteellisen helppo poistaa. PRESS FITTING suoritetaan työntämällä osia yhteen ja niiden välinen kitka kiinnittää osat. Puristussovitusosat, jotka koostuvat ylisuuresta akselista ja alimitoista reiästä, kootaan yleensä kahdella tavalla: Joko käyttämällä voimaa tai hyödyntämällä osien lämpölaajenemista tai supistumista. Kun puristusliitos muodostetaan voimaa käyttämällä, käytämme joko hydraulipuristinta tai käsikäyttöistä puristinta. Toisaalta kun puristusliitos muodostetaan lämpölaajenemisen avulla, lämmitämme ympäröivät osat ja kokoamme ne paikoilleen kuumana. Jäähtyessään ne supistuvat ja palaavat normaaleihin mittoihinsa. Näin saadaan hyvä puristussovitus. Kutsumme tätä vaihtoehtoisesti SHRINK-FITTING:ksi. Toinen tapa tehdä tämä on jäähdyttää vaipalliset osat ennen kokoamista ja liu'uttamalla ne sitten yhteensopiviin osiinsa. Kun kokoonpano lämpenee, ne laajenevat ja saamme tiukan istuvuuden. Tämä jälkimmäinen menetelmä voi olla parempi tapauksissa, joissa lämmitys aiheuttaa riskin materiaalin ominaisuuksien muuttumisesta. Jäähdytys on näissä tapauksissa turvallisempaa. Pneumaattiset ja hydrauliset komponentit ja kokoonpanot • Venttiilit, hydrauliset ja pneumaattiset komponentit, kuten O-rengas, aluslevy, tiivisteet, tiiviste, rengas, välilevy. Koska venttiilejä ja pneumaattisia komponentteja on laaja valikoima, emme voi luetella kaikkea tässä. Sovelluksesi fysikaalisista ja kemiallisista ympäristöistä riippuen meillä on sinulle erikoistuotteita. Ilmoita meille sovellus, komponentin tyyppi, tekniset tiedot, ympäristöolosuhteet, kuten paine, lämpötila, nesteet tai kaasut, jotka joutuvat kosketuksiin venttiileidesi ja pneumaattisten komponenttien kanssa. ja valitsemme sinulle sopivimman tuotteen tai valmistamme sen erityisesti käyttötarkoitustasi varten. CLICK Product Finder-Locator Service EDELLINEN SIVU
- Composites, Composite Materials Manufacturing, Fiber Reinforced
Composites, Composite Materials Manufacturing, Particle and Fiber Reinforced, Cermets, Ceramic & Metal Composite, Glass Fiber Reinforced Polymer, Lay-Up Process Komposiittien ja komposiittimateriaalien valmistus Yksinkertaisesti määriteltynä, KOMPOSIITTIT tai KOMPOSIITTIMATERIAALIT ovat materiaaleja, jotka koostuvat kahdesta tai useammasta materiaalista, joilla on erilaiset fysikaaliset tai kemialliset ominaisuudet, mutta yhdistettyinä niistä tulee eri materiaalia kuin ainesosien materiaalit. Meidän on huomautettava, että rakennemateriaalit pysyvät erillisinä ja erottuvina rakenteessa. Komposiittimateriaalin valmistuksen tavoitteena on saada aineosaan parempi tuote, jossa yhdistyvät kunkin ainesosan halutut ominaisuudet. Esimerkiksi; lujuus, alhainen paino tai alempi hinta voivat olla motivaattorina komposiitin suunnittelussa ja valmistuksessa. Tarjoamamme komposiitit ovat hiukkasvahvistetut komposiitit, kuituvahvisteiset komposiitit mukaan lukien keraaminen matriisi / polymeerimatriisi / metallimatriisi / hiili-hiili / hybridikomposiitit, rakenne- ja laminoidut ja sandwich-rakenteiset komposiitit ja nanokomposiitit. Komposiittimateriaalien valmistuksessa käyttämämme valmistustekniikat ovat: Pultruusio, prepreg-tuotantoprosessit, edistynyt kuidun sijoittelu, filamenttien käämitys, räätälöity kuidun sijoitus, lasikuitujen ruiskutusprosessi, tuftaus, lanoksidiprosessi, z-kiinnitys. Monet komposiittimateriaalit koostuvat kahdesta faasista, matriisista, joka on jatkuva ja ympäröi toista vaihetta; ja dispergoitu faasi, jota matriisi ympäröi. Suosittelemme, että napsautat tätäLATAA AGS-TECH Inc.:n komposiittien ja komposiittimateriaalien valmistuksen kaavamaiset kuvamme. Tämä auttaa sinua ymmärtämään paremmin alla toimittamiamme tietoja. • HIUKSELLA VAHVISTETUT KOMPOSIITTIT: Tämä luokka koostuu kahdesta tyypistä: suurihiukkasiset komposiitit ja dispersiovahvistetut komposiitit. Edellisessä tyypissä hiukkas-matriisivuorovaikutuksia ei voida käsitellä atomi- tai molekyylitasolla. Sen sijaan jatkuvuusmekaniikka on voimassa. Toisaalta dispersiovahvistetuissa komposiiteissa hiukkaset ovat yleensä paljon pienempiä kymmenien nanometrien alueella. Esimerkki suurhiukkaskomposiitista on polymeerit, joihin on lisätty täyteaineita. Täyteaineet parantavat materiaalin ominaisuuksia ja voivat korvata osan polymeeritilavuudesta edullisemmalla materiaalilla. Kahden faasin tilavuusosuudet vaikuttavat komposiitin käyttäytymiseen. Suurhiukkaskomposiitteja käytetään metallien, polymeerien ja keramiikan kanssa. CERMETS ovat esimerkkejä keraami-/metallikomposiiteista. Yleisin kermettimme on kovametalli. Se koostuu tulenkestävästä karbidikeramiikasta, kuten volframikarbidihiukkasista metallin, kuten koboltin tai nikkelin, matriisissa. Näitä kovametallikomposiitteja käytetään laajalti karkaistun teräksen leikkaustyökaluina. Kovat kovametallihiukkaset vastaavat leikkaustoiminnasta ja niiden sitkeyttä parantaa sitkeä metallimatriisi. Näin saamme molempien materiaalien edut yhdessä komposiitissa. Toinen yleinen esimerkki käyttämämme suurihiukkaskomposiitista on hiilimustahiukkaset, jotka on sekoitettu vulkanoidun kumin kanssa, jotta saadaan komposiitti, jolla on korkea vetolujuus, sitkeys, repeämis- ja kulutuskestävyys. Esimerkki dispersiovahvistetusta komposiitista on metallit ja metalliseokset, jotka on vahvistettu ja kovetettu erittäin kovan ja inertin materiaalin pienten hiukkasten tasaisella dispersiolla. Kun alumiinimetallimatriisiin lisätään hyvin pieniä alumiinioksidihiutaleita, saadaan sintrattua alumiinijauhetta, jolla on parannettu lujuus korkeissa lämpötiloissa. • KUITUVAHVISTETUT KOMPOSIITTIT: Tämä komposiittien luokka on itse asiassa tärkein. Tavoitteena on korkea lujuus ja jäykkyys painoyksikköä kohden. Kuitukoostumus, pituus, suuntaus ja pitoisuus näissä komposiiteissa ovat kriittisiä näiden materiaalien ominaisuuksien ja käyttökelpoisuuden määrittämisessä. Käytämme kolmea kuituryhmää: viikset, kuidut ja langat. WHISKERS ovat erittäin ohuita ja pitkiä yksikiteitä. Ne ovat vahvimpia materiaaleja. Eräitä esimerkkejä viiksimateriaaleista ovat grafiitti, piinitridi, alumiinioksidi. FIBERS toisaalta ovat enimmäkseen polymeerejä tai keraamisia materiaaleja ja ovat monikiteisessä tai amorfisessa tilassa. Kolmas ryhmä ovat hienot JOHDOT, joilla on suhteellisen suuri halkaisija ja jotka koostuvat usein teräksestä tai volframista. Esimerkki lankavahvisteisesta komposiitista ovat autonrenkaat, joissa on teräslankaa kumin sisällä. Matriisimateriaalista riippuen meillä on seuraavat komposiitit: POLYMERI-MATRIISIKOMPOSIIITIT: Nämä on valmistettu polymeerihartsista ja kuiduista vahvistusaineena. Näiden GFRP-komposiiteiksi kutsuttu alaryhmä sisältää jatkuvia tai epäjatkuvia lasikuituja polymeerimatriisissa. Lasilla on korkea lujuus, se on taloudellinen, helppo valmistaa kuiduiksi ja on kemiallisesti inerttiä. Haittoja ovat niiden rajallinen jäykkyys ja jäykkyys, käyttölämpötilat ovat vain 200 – 300 astetta. Lasikuitu soveltuu autojen koriin ja kuljetusvälineisiin, meriajoneuvojen koriin, varastosäiliöihin. Ne eivät sovellu ilmailu- tai siltojen valmistukseen rajoitetun jäykkyyden vuoksi. Toinen alaryhmä on nimeltään Carbon Fiber-Reforced Polymer (CFRP) -komposiitti. Tässä hiili on kuitumateriaalimme polymeerimatriisissa. Hiili tunnetaan korkeasta ominaismoduulistaan ja lujuudestaan sekä kyvystään ylläpitää niitä korkeissa lämpötiloissa. Hiilikuidut voivat tarjota meille vakio-, keski-, korkea- ja ultrakorkeat vetomoduulit. Lisäksi hiilikuidut tarjoavat erilaisia fyysisiä ja mekaanisia ominaisuuksia ja sopivat siksi erilaisiin räätälöityihin suunnittelusovelluksiin. CFRP-komposiitteja voidaan harkita urheilu- ja vapaa-ajan laitteiden, paineastioiden ja ilmailun rakennekomponenttien valmistuksessa. Kuitenkin toinen alaryhmä, Aramid Fiber-Reforced Polymer Composites, ovat myös erittäin lujia ja moduulirakenteita materiaaleja. Niiden lujuus-painosuhde on erittäin korkea. Aramidikuidut tunnetaan myös kauppanimillä KEVLAR ja NOMEX. Jännityksessä ne toimivat paremmin kuin muut polymeerikuitumateriaalit, mutta ne ovat heikkoja puristuksessa. Aramidikuidut ovat sitkeitä, iskunkestäviä, virumisen ja väsymisen kestäviä, kestäviä korkeissa lämpötiloissa, kemiallisesti inerttejä paitsi vahvoja happoja ja emäksiä vastaan. Aramidikuituja käytetään laajalti urheiluvälineissä, luodinkestävissä liiveissä, renkaissa, köysissä ja valokaapelin vaippaissa. Muita kuitulujitemateriaaleja on olemassa, mutta niitä käytetään vähemmän. Nämä ovat boori, piikarbidi ja alumiinioksidi pääasiassa. Toisaalta polymeerimatriisimateriaali on myös kriittinen. Se määrittää komposiitin maksimikäyttölämpötilan, koska polymeerillä on yleensä alhaisempi sulamis- ja hajoamislämpötila. Polyestereitä ja vinyyliestereitä käytetään laajalti polymeerimatriisina. Myös hartseja käytetään ja niillä on erinomaiset kosteudenkestävyys ja mekaaniset ominaisuudet. Esimerkiksi polyimidihartsia voidaan käyttää noin 230 Celsius-asteeseen asti. METALLI-MATRIISIKOMPOSIIITIT: Näissä materiaaleissa käytämme sitkeää metallimatriisia ja käyttölämpötilat ovat yleensä korkeampia kuin niiden komponentit. Polymeeri-matriisikomposiitteihin verrattuna näillä voi olla korkeammat käyttölämpötilat, ne voivat olla syttymättömiä ja niillä voi olla parempi hajoamiskestävyys orgaanisia nesteitä vastaan. Ne ovat kuitenkin kalliimpia. Vahvistusmateriaalit, kuten viikset, hiukkaset, jatkuvat ja epäjatkuvat kuidut; ja matriisimateriaaleja, kuten kuparia, alumiinia, magnesiumia, titaania, superseoksia käytetään yleisesti. Esimerkkisovelluksia ovat moottorin komponentit, jotka on valmistettu alumiinioksidilla ja hiilikuiduilla vahvistetusta alumiiniseoksesta. KERAAMINEN-MATRIISIKOMPOSIIITIT: Keraamiset materiaalit tunnetaan erinomaisesta korkeiden lämpötilojen luotettavuudestaan. Ne ovat kuitenkin erittäin hauraita ja niillä on alhaiset murtolujuusarvot. Upottamalla yhden keramiikan hiukkasia, kuituja tai viiksiä toisen matriisiin pystymme saavuttamaan komposiitteja, joilla on suurempi murtolujuus. Nämä upotetut materiaalit estävät pohjimmiltaan halkeamien leviämistä matriisin sisällä joidenkin mekanismien avulla, kuten taivuttamalla halkeaman kärkiä tai muodostamalla siltoja halkeamien pintojen yli. Esimerkiksi alumiinioksidia, jotka on vahvistettu piikarbidiviskeillä, käytetään leikkaustyökaluna kovametalliseosten työstöön. Nämä voivat paljastaa paremman suorituskyvyn verrattuna sementoituihin karbideihin. HIILI-HIILIKOMPOSIIITIT: Sekä vahvistus että matriisi ovat hiiltä. Niillä on korkea vetomoduuli ja lujuus korkeissa yli 2000 asteen lämpötiloissa, virumisvastus, korkea murtolujuus, alhaiset lämpölaajenemiskertoimet, korkea lämmönjohtavuus. Nämä ominaisuudet tekevät niistä ihanteellisia käyttökohteisiin, jotka vaativat lämpöiskun kestävyyttä. Hiili-hiili-komposiittien heikkous on kuitenkin niiden haavoittuvuus hapettumista vastaan korkeissa lämpötiloissa. Tyypillisiä käyttöesimerkkejä ovat kuumapuristusmuotit, edistynyt turbiinimoottorikomponenttien valmistus. HYBRIDIKOMOSIITTIT: Kaksi tai useampia erityyppisiä kuituja sekoitetaan yhteen matriisiin. Näin voidaan räätälöidä uusi materiaali ominaisuuksien yhdistelmällä. Esimerkki on, kun sekä hiili- että lasikuituja sisällytetään polymeerihartsiin. Hiilikuidut tarjoavat alhaisen tiheyden jäykkyyttä ja lujuutta, mutta ovat kalliita. Lasi on toisaalta edullinen, mutta siitä puuttuu hiilikuitujen jäykkyys. Lasi-hiilihybridikomposiitti on vahvempi ja sitkeämpi ja sitä voidaan valmistaa halvemmalla. KUITUVAHVISTEISTEN KOMPOSIITTIEN KÄSITTELY: Jatkuvalle kuituvahvisteiselle muoville, jossa kuidut ovat tasaisesti jakautuneet samaan suuntaan, käytämme seuraavia tekniikoita. PULTRUSIO: Valmistetaan jatkuvan pituisia ja vakiopoikkileikkauksia olevia tankoja, palkkeja ja putkia. Jatkuvat kuitukankaat kyllästetään lämpökovettuvalla hartsilla ja vedetään teräsmuotin läpi, jotta ne muotoutuvat haluttuun muotoon. Seuraavaksi ne kulkevat tarkasti koneistetun kovettumissuuttimen läpi lopullisen muotonsa saavuttamiseksi. Koska kovettumissuutin kuumennetaan, se kovettaa hartsimatriisin. Vetimet vetävät materiaalin muottien läpi. Asennettujen onttojen ytimien avulla pystymme saamaan putkia ja onttoja geometrioita. Pultruusiomenetelmä on automatisoitu ja tarjoaa meille korkeat tuotantonopeudet. Minkä tahansa pituisia tuotteita on mahdollista valmistaa. PREPREG-TUOTANTOPROSESSI: Prepreg on jatkuvakuituinen lujite, joka on esikyllästetty osittain kovettuneella polymeerihartsilla. Sitä käytetään laajalti rakenteellisissa sovelluksissa. Materiaali toimitetaan teipin muodossa ja toimitetaan nauhana. Valmistaja muotoilee sen suoraan ja kovettaa sen täysin ilman hartsin lisäämistä. Koska prepregit käyvät läpi kovettumisreaktiot huoneenlämmössä, niitä säilytetään 0 Celsius-asteen tai sitä alhaisemmissa lämpötiloissa. Käytön jälkeen jäljellä olevat teipit säilytetään alhaisissa lämpötiloissa. Termoplastisia ja lämpökovettuvia hartseja käytetään ja hiili-, aramid- ja lasivahvistuskuidut ovat yleisiä. Prepregien käyttämiseksi alustan taustapaperi poistetaan ensin ja sitten valmistus suoritetaan asettamalla prepreg-teippi työkalutetulle pinnalle (ladontaprosessi). Voidaan asettaa useita kerroksia halutun paksuuden saavuttamiseksi. Usein käytäntö on vaihtaa kuitujen suuntausta risti- tai kulmakerroslaminaatin valmistamiseksi. Lopuksi kovetetaan lämpöä ja painetta. Prepreg- ja lay-up-leikkauksessa käytetään sekä käsinkäsittelyä että automatisoituja prosesseja. FILAMENTIN KÄÄMINEN: Jatkuvat lujitekuidut sijoitetaan tarkasti ennalta määrättyyn kuvioon noudattamaan onttoa ja tavallisesti syklinpyöreän muotoa. Kuidut menevät ensin hartsikylvyn läpi ja sitten ne kääritään tuurnalle automatisoidulla järjestelmällä. Useiden kelauskertojen jälkeen saadaan halutut paksuudet ja kovetus suoritetaan joko huoneenlämmössä tai uunissa. Nyt kara irrotetaan ja tuote puretaan. Filamenttikäämitys voi tarjota erittäin korkeat lujuus-painosuhteet kelaamalla kuidut kehämäisesti, kierteisesti ja polaarisesti. Putket, säiliöt ja kotelot valmistetaan tällä tekniikalla. • RAKENNEKOMPOSIITTIT: Yleensä nämä koostuvat sekä homogeenisista että komposiittimateriaaleista. Siksi niiden ominaisuudet määräytyvät niiden elementtien materiaalien ja geometrisen rakenteen perusteella. Tässä ovat tärkeimmät tyypit: LAMINAARIKOMPOSIITTIT: Nämä rakennemateriaalit on valmistettu kaksiulotteisista levyistä tai paneeleista, joilla on suositeltavat lujat. Kerrokset pinotaan ja liimataan yhteen. Vuorottelemalla lujuussuuntia kahdella kohtisuoralla akselilla saadaan komposiitti, jolla on suuri lujuus molempiin suuntiin kaksiulotteisessa tasossa. Kerrosten kulmia säätämällä voidaan valmistaa komposiitti, jolla on lujuus haluttuihin suuntiin. Nykyaikaiset suksit valmistetaan tällä tavalla. SANDWICH-PANEELIT: Nämä rakennekomposiitit ovat kevyitä, mutta silti niillä on korkea jäykkyys ja lujuus. Sandwich-paneelit koostuvat kahdesta ulkolevystä, jotka on valmistettu jäykästä ja vahvasta materiaalista, kuten alumiiniseoksista, kuituvahvisteisesta muovista tai teräksestä, ja ytimestä ulkolevyjen välissä. Ytimen tulee olla kevyt, ja suurimman osan ajasta sillä on oltava alhainen kimmokerroin. Suosittuja ydinmateriaaleja ovat jäykät polymeerivaahdot, puu ja kennot. Sandwich-paneeleja käytetään laajalti rakennusteollisuudessa kattomateriaalina, lattia- tai seinämateriaalina sekä myös ilmailuteollisuudessa. • NANOKOMPOSIITTIT: Nämä uudet materiaalit koostuvat nanokokoisista hiukkashiukkasista, jotka on upotettu matriisiin. Nanokomposiiteilla voimme valmistaa kumimateriaaleja, jotka estävät erittäin hyvin ilman tunkeutumisen ja säilyttävät kumin ominaisuudet ennallaan. CLICK Product Finder-Locator Service EDELLINEN SIVU
- Machine Elements Manufacturing, Gears, Gear Drives, Bearings, Keys, Splines
Machine Elements Manufacturing, Gears, Gear Drives, Bearings, Keys, Splines, Pins, Shafts, Seals, Fasteners, Clutch, Cams, Followers, Belts, Couplings, Shafts Koneelementtien valmistus Lue lisää Hihnat ja ketjut ja kaapelin käyttökokoonpano Lue lisää Gears & Gear Drive Assembly Lue lisää Kytkimien ja laakerien valmistus Lue lisää Avainten ja nastajen valmistus Lue lisää Kamerat & seuraajat & kytkimet & räikkäpyörien valmistus Lue lisää Akselien valmistus Lue lisää Mekaanisten tiivisteiden valmistus Lue lisää Kytkin ja jarru kokoonpano Lue lisää Kiinnittimien valmistus Lue lisää Yksinkertaisten koneiden kokoonpano MACHINE ELEMENTS ovat koneen peruskomponentteja. Nämä elementit koostuvat kolmesta perustyypistä: 1.) Rakenneosat, mukaan lukien runko-osat, laakerit, akselit, urit, kiinnikkeet, tiivisteet ja voiteluaineet. 2.) Mekanismit, jotka ohjaavat liikettä eri tavoin, kuten hammaspyörät, hihna- tai ketjukäytöt, vivustot, nokka- ja seuraajajärjestelmät, jarrut ja kytkimet. 3.) Ohjauskomponentit, kuten painikkeet, kytkimet, ilmaisimet, anturit, toimilaitteet ja tietokoneohjaimet. Suurin osa tarjoamistamme koneelementeistä on standardoitu yleisiin kokoihin, mutta erikoissovelluksiin on saatavilla myös mittatilaustyönä valmistettuja koneelementtejä. Koneelementtien räätälöinti voi tapahtua ladattavissa luetteloissamme olevilla olemassa olevilla malleilla tai aivan uusilla malleilla. Koneelementtien prototyyppien valmistus ja valmistus voidaan viedä eteenpäin, kun molemmat osapuolet ovat hyväksyneet suunnittelun. Jos uusia koneen elementtejä on suunniteltava ja valmistettava, asiakkaamme joko lähettävät meille sähköpostilla omat piirustuksensa ja tarkistamme ne hyväksyttäviksi, tai he pyytävät meitä suunnittelemaan koneenelementtejä heidän sovelluksiinsa. Jälkimmäisessä tapauksessa käytämme kaikkia asiakkaidemme panoksia ja suunnittelemme koneen elementit ja lähetämme valmiit piirustukset asiakkaillemme hyväksyttäväksi. Hyväksynnän jälkeen valmistamme ensimmäiset tuotteet ja valmistamme sen jälkeen koneen elementit lopullisen suunnittelun mukaan. Työn missä tahansa vaiheessa, mikäli jokin koneen elementtisuunnittelu toimii epätyydyttävästi kentällä (mikä on harvinaista), käymme läpi koko projektin ja teemme tarvittaessa muutoksia yhdessä asiakkaidemme kanssa. Vakiokäytäntömme on allekirjoittaa salassapitosopimukset (NDA) asiakkaidemme kanssa koneenelementtien tai minkä tahansa muun tuotteen suunnittelusta aina, kun sitä tarvitaan tai vaaditaan. Kun tietyn asiakkaan koneelementit on suunniteltu ja valmistettu mittatilaustyönä, annamme sille tuotekoodin ja valmistamme ja myymme ne vain asiakkaallemme, joka omistaa tuotteen. Toistamme koneen elementit kehitetyillä työkaluilla, muotteilla ja menetelmillä niin monta kertaa kuin tarvitaan ja aina kun asiakkaamme tilaa ne uudelleen. Toisin sanoen, kun räätälöity koneelementti on suunniteltu ja valmistettu puolestasi, me varaamme ja varastoimme määräämättömäksi ajaksi henkisen omaisuuden sekä kaikki työkalut ja muotit sinulle ja tuotteet toistetaan haluamallasi tavalla. Tarjoamme asiakkaillemme myös suunnittelupalveluita yhdistämällä luovasti koneen elementit komponentiksi tai kokoonpanoksi, joka palvelee sovellusta ja täyttää tai ylittää asiakkaidemme odotukset. Koneelementtejämme valmistavat tehtaat ovat joko ISO9001-, QS9000- tai TS16949-sertifioituja. Lisäksi suurimmalla osalla tuotteistamme on CE- tai UL-merkintä ja ne täyttävät kansainvälisesti merkitykselliset standardit, kuten ISO, SAE, ASME, DIN. Napsauta alavalikoita saadaksesi yksityiskohtaisia tietoja koneen osistamme, mukaan lukien: - Hihnat, ketjut ja kaapelikäytöt - Vaihteet ja vaihteistot - Kytkimet ja laakerit - Avaimet & Splines & tapit - Kamerat ja linkit - Akselit - Mekaaniset tiivisteet - Teollinen kytkin ja jarru - Kiinnikkeet - Yksinkertaiset koneet Olemme laatineet referenssiesitteen asiakkaillemme, uusien tuotteiden suunnittelijoille ja kehittäjille, mukaan lukien koneelementit. Voit tutustua joihinkin konekomponenttien suunnittelussa yleisesti käytettyihin termeihin: Lataa esite suunnittelijoiden ja insinöörien käyttämistä yleisistä konetekniikan termeistä Koneelementteillemme löytyy käyttökohteita monilla eri aloilla, kuten teollisuuskoneissa, automaatiojärjestelmissä, testaus- ja metrologisissa laitteissa, kuljetusvälineissä, rakennuskoneissa ja käytännössä kaikkialla. AGS-TECH kehittää ja valmistaa koneenelementtejä eri materiaaleista sovelluksesta riippuen. Koneen elementeissä käytettävät materiaalit voivat vaihdella leluissa käytettävästä muovatusta muovista kotelokarkaistuun ja erikoispäällystettyyn teräkseen teollisuuskoneissa. Suunnittelijamme käyttävät uusinta ammattiohjelmistoa ja suunnittelutyökaluja koneenelementtien kehittämiseen ottaen huomioon yksityiskohdat, kuten hammaspyörien kulmat, rasitukset, kulumisasteet jne. Selaa alivalikoitamme ja lataa tuoteesitteemme ja luettelomme nähdäksesi, voitko löytää valmiita koneen osia sovellukseesi. Jos et löydä sovelluksellesi sopivaa vastinetta, ilmoita siitä meille, niin kehitämme ja valmistamme kanssasi tarpeitasi vastaavia koneelementtejä. Jos olet lähinnä kiinnostunut suunnittelu- ja tutkimus- ja kehitysmahdollisuuksistamme valmistuskyvyn sijaan, kutsumme sinut vierailemaan verkkosivustollamme http://www.ags-engineering.com josta löydät tarkempaa tietoa suunnittelusta, tuotekehityksestä, prosessikehityksestä, suunnittelukonsultointipalveluistamme ja muista CLICK Product Finder-Locator Service EDELLINEN SIVU
- Glass and Ceramic Manufacturing, Hermetic Packages, Seals, Bonding
Glass and Ceramic Manufacturing, Hermetic Packages Seals and Bonding, Tempered Bulletproof Glass, Blow Moulding, Optical Grade Glass, Conductive Glass, Molding Lasin ja keramiikan muotoilu ja muotoilu Tarjoamamme lasinvalmistustyypit ovat konttilasi, lasinpuhallus, lasikuitu & letkut & tangot, kotitalous- ja teollisuuslasiesineet, lamppu ja polttimo, tarkkuuslasin muovaus, optiset komponentit ja kokoonpanot, taso- ja arkki- ja floatlasi. Suoritamme sekä käsin että konemuovauksen. Suosittuja teknisiä keramiikan valmistusprosessejamme ovat stanssaus, isostaattipuristus, kuumaisostaattinen puristus, kuumapuristus, liukuvalu, nauhavalu, suulakepuristus, ruiskuvalu, raakakoneistus, sintraus tai poltto, timanttihionta, hermeettiset kokoonpanot. Suosittelemme, että napsautat tätä LATAA AGS-TECH Inc:n kaaviomaiset kuvamme lasinmuodostus- ja muotoiluprosesseista. LATAA AGS-TECH Inc:n teknisten keramiikan valmistusprosessien kaavamaiset kuvamme. Nämä ladattavat tiedostot, joissa on valokuvia ja luonnoksia, auttavat sinua ymmärtämään paremmin alla tarjoamamme tiedot. • SÄILIÖLASIN VALMISTUS: Meillä on automatisoitu PURISTUS JA PUHAUS sekä PUHAUS- JA PUHALLUSlinjat valmistusta varten. Puhallus- ja puhallusprosessissa pudotamme pölyn tyhjään muottiin ja muodostamme kaulan puhaltamalla paineilmaa ylhäältä. Välittömästi tämän jälkeen paineilmaa puhalletaan toisen kerran toisesta suunnasta säiliön kaulan läpi pullon esimuodon muodostamiseksi. Tämä esimuoto siirretään sitten varsinaiseen muottiin, lämmitetään uudelleen pehmentämään ja paineilmaa käytetään antamaan esimuodolle sen lopullinen säiliömuoto. Tarkemmin sanottuna se paineistetaan ja työnnetään puhallusmuotin ontelon seinämiä vasten saadakseen halutun muotonsa. Lopuksi valmistettu lasiastia siirretään hehkutusuuniin myöhempää uudelleenkuumennusta ja valun aikana syntyneiden jännitysten poistamista varten ja jäähdytetään kontrolloidusti. Puristus- ja puhallusmenetelmässä sulat pakkaukset laitetaan aihiomuottiin (aihiomuotti) ja puristetaan aihion muotoon (aihiomuoto). Aihiot siirretään sitten puhallusmuotteihin ja puhalletaan samalla tavalla kuin edellä kohdassa "Puhallus- ja puhallusprosessi" kuvattu prosessi. Myöhemmät vaiheet, kuten hehkutus ja stressinpoisto, ovat samanlaisia tai samoja. • LASINPUHALLUS: Olemme valmistaneet lasituotteita tavanomaisella käsipuhalluksella sekä paineilmalla automatisoiduilla laitteilla. Joillekin tilauksille tavanomainen puhallus on välttämätöntä, kuten projektit, joissa on lasitaideteoksia tai projektit, jotka vaativat pienempiä osia löysällä toleranssilla, prototyyppi/demoprojektit jne. Perinteisessä lasinpuhalluksessa ontto metalliputki upotetaan sulaan lasiastiaan ja putkea pyöritetään jonkin määrän lasimateriaalia keräämiseksi. Putken kärkeen kerätty lasi rullataan tasaiselle raudalle, muotoillaan halutulla tavalla, pidennetään, kuumennetaan uudelleen ja puhalletaan ilmalla. Kun se on valmis, se työnnetään muottiin ja puhalletaan ilmaa. Muotin ontelo on märkä, jotta vältetään lasin kosketus metalliin. Vesikalvo toimii tyynynä niiden välillä. Manuaalinen puhallus on työvoimavaltainen hidas prosessi ja se soveltuu vain prototyyppien tai arvokkaiden esineiden valmistukseen, ei sovellu halvoille kappalekohtaisille suurille tilauksille. • KOTIMAISTEN JA TEOLLISUUDEN LASITAVAROIDEN VALMISTUS: Erityyppisten lasimateriaalien avulla valmistetaan laaja valikoima lasitavaroita. Jotkut lasit ovat lämmönkestäviä ja soveltuvat laboratoriolaseihin, kun taas toiset kestävät astianpesukoneen monta kertaa ja soveltuvat kotimaisten tuotteiden valmistukseen. Westlaken koneilla valmistetaan kymmeniä tuhansia juomalaseja päivässä. Yksinkertaistaaksemme sulaa lasia kerätään tyhjiöllä ja työnnetään muotteihin esimuotojen valmistamiseksi. Sitten muotteihin puhalletaan ilmaa, nämä siirretään toiseen muottiin ja puhalletaan ilmaa uudelleen ja lasi saa lopullisen muotonsa. Kuten käsipuhalluksessa, nämä muotit pidetään veden märkinä. Lisävenyttely on osa viimeistelyä, jossa kaula muodostetaan. Ylimääräinen lasi palaa pois. Sen jälkeen seuraa yllä kuvattu ohjattu uudelleenlämmitys- ja jäähdytysprosessi. • LASIPUTKEN JA TAUVOMUOTOS: Pääprosessit, joita käytämme lasiputkien valmistuksessa, ovat DANNER- ja VELLO-prosessit. Danner-prosessissa uunin lasi virtaa ja putoaa kaltevalle, tulenkestävästä materiaalista tehdylle holkille. Holkki on pyörivässä ontossa akselissa tai puhallusputkessa. Lasi kääritään sitten holkin ympärille ja muodostaa sileän kerroksen, joka virtaa alas holkkia pitkin ja varren kärjen yli. Putkimuovauksessa ilmaa puhalletaan onttokärkisen puhallusputken läpi ja sauvamuovauksessa akselissa käytetään kiinteitä kärkiä. Putket tai tangot vedetään sitten kantotelojen yli. Lasiputkien mitat, kuten seinämän paksuus ja halkaisija, säädetään haluttuihin arvoihin asettamalla holkin halkaisija ja puhallusilmanpaine haluttuun arvoon, säätämällä lämpötilaa, lasin virtausnopeutta ja vetonopeutta. Vellon lasiputken valmistusprosessi puolestaan sisältää lasia, joka kulkee uunista ulos kulhoon, jossa on ontto kara tai kello. Lasi kulkee sitten karan ja kulhon välisen ilmatilan läpi ja ottaa putken muodon. Sen jälkeen se kulkee rullien yli vetokoneelle ja jäähtyy. Jäähdytyslinjan lopussa tapahtuu leikkaus ja loppukäsittely. Putken mittoja voidaan säätää kuten Danner-prosessissa. Verrattaessa Danner- ja Vello-prosessia voidaan sanoa, että Vello-prosessi sopii paremmin suuriin tuotantomääriin, kun taas Danner-prosessi voi sopia paremmin tarkkoihin pienempien volyymien putkitilauksiin. • LEVY- JA TASOLASIN KÄSITTELY: Meillä on suuria määriä tasolasia, joiden paksuus vaihtelee submilimetreistä useisiin senttimetreihin. Tasolasimme ovat lähes optisesti täydellisiä. Tarjoamme lasia erikoispinnoitteilla, kuten optisilla pinnoitteilla, joissa käytetään kemiallista höyrypinnoitustekniikkaa pinnoitteiden, kuten heijastuksenesto- tai peilipinnoitteen, levittämiseen. Myös läpinäkyvät johtavat pinnoitteet ovat yleisiä. Saatavilla on myös hydrofobisia tai hydrofiilisiä pinnoitteita lasille sekä pinnoitteita, jotka tekevät lasista itsepuhdistuvan. Karkaistut, luodinkestävät ja laminoidut lasit ovat vielä muita suosittuja tuotteita. Leikkaamme lasin haluttuun muotoon halutuilla toleransseilla. Muita toissijaisia toimintoja, kuten tasolasin taivutus tai taivutus, on saatavana. • TARKKUUSLASIN MUOLI: Käytämme tätä tekniikkaa enimmäkseen tarkkuusoptisten komponenttien valmistukseen ilman kalliimpia ja aikaa vieviä tekniikoita, kuten hiontaa, hiontaa ja kiillotusta. Tämä tekniikka ei aina riitä parhaan optiikan tuottamiseen, mutta joissain tapauksissa, kuten kuluttajatuotteissa, digikameroissa, lääketieteellisessä optiikassa, se voi olla halvempi hyvä vaihtoehto suuren volyymin valmistukseen. Sillä on myös etu verrattuna muihin lasinmuodostustekniikoihin, joissa vaaditaan monimutkaisia geometrioita, kuten asfäärien tapauksessa. Perusprosessi sisältää muottimme alapuolen lataamisen lasiaihiolla, prosessikammion tyhjennyksen hapenpoistoon, muotin lähes sulkemisen, muotin ja lasin nopean ja isotermisen kuumennuksen infrapunavalolla, muotin puoliskojen sulkemisen edelleen pehmennetyn lasin puristaminen hitaasti hallitusti haluttuun paksuuteen ja lopuksi lasin jäähdytys ja kammion täyttäminen typellä ja tuotteen poistaminen. Tarkka lämpötilan säätö, muotin sulkemisetäisyys, muotin sulkemisvoima, muotin ja lasimateriaalin laajenemiskertoimien yhteensovittaminen ovat avainasemassa tässä prosessissa. • OPTISTEN LASIKOMPONENTTIEN JA KOKOONPANOJEN VALMISTUS: Tarkkuuslasin muovauksen lisäksi käytämme lukuisia arvokkaita prosesseja korkealaatuisten optisten komponenttien ja kokoonpanojen valmistukseen vaativiin sovelluksiin. Optisten lasien hionta, hionta ja kiillotus hienoissa erikoishiomalietteissä on taidetta ja tiedettä optisten linssien, prismien, litteiden ja muiden valmistuksessa. Pinnan tasaisuus, aaltoilu, sileys ja virheetön optinen pinta vaatii paljon kokemusta tällaisista prosesseista. Pienet muutokset ympäristössä voivat johtaa spesifikaatioiden ulkopuolisiin tuotteisiin ja pysäyttää valmistuslinjan. Joissakin tapauksissa tuote voi täyttää vaatimukset tai epäonnistua testissä yhdellä pyyhkeellä optisella pinnalla puhtaalla liinalla. Jotkut käytetyt suositut lasimateriaalit ovat sulatettu piidioksidi, kvartsi, BK7. Myös tällaisten komponenttien kokoaminen vaatii erikoisalan kokemusta. Joskus käytetään erityisiä liimoja. Joskus optiseksi kosketukseksi kutsuttu tekniikka on kuitenkin paras valinta, eikä siinä ole materiaalia kiinnitettyjen optisten lasien välissä. Se koostuu fyysisesti koskettavista tasaisista pinnoista kiinnittämiseksi toisiinsa ilman liimaa. Joissakin tapauksissa käytetään mekaanisia välikappaleita, tarkkuuslasitankoja tai -palloja, puristimia tai koneistettuja metallikomponentteja optisten komponenttien kokoamiseen tietyin välimatkoin ja tietyillä geometrisilla suuntauksilla toisiinsa nähden. Tarkastellaanpa joitain suosittuja tekniikoitamme huippuluokan optiikan valmistukseen. HIOMAUS & LIPOTUS & KIOLOTUS: Optisen komponentin karkea muoto saadaan hiomalla lasiaihiota. Tämän jälkeen suoritetaan läppäys ja kiillotus pyörittämällä ja hankaamalla optisten komponenttien karkeita pintoja halutun muotoisia työkaluja vasten. Pieniä hankaavia hiukkasia ja nestettä sisältäviä lietteitä kaadetaan optiikan ja muotoilutyökalujen väliin. Tällaisten lietteiden hiomahiukkaskoot voidaan valita halutun tasaisuusasteen mukaan. Kriittisten optisten pintojen poikkeamat halutuista muodoista ilmaistaan käytettävän valon aallonpituuksina. Tarkkuusoptiikallamme on kymmenesosan aallonpituuden (Wavelength/10) toleranssit tai jopa tiukemmat ovat mahdollisia. Pintaprofiilin lisäksi kriittiset pinnat skannataan ja arvioidaan muiden pinnan ominaisuuksien ja vikojen, kuten mittojen, naarmujen, lastujen, kuoppien, pilkkujen jne. varalta. Optisen valmistuskerroksen ympäristöolosuhteiden tiukka hallinta sekä kattavat metrologian ja testausvaatimukset huippuluokan laitteistoilla tekevät tästä haastavan teollisuudenalan. • LASIN VALMISTEEN TOISIJAISET PROSESSIT: Jälleen kerran, meillä on vain mielikuvituksesi rajallinen lasin toissijaisten ja viimeistelyprosessien suhteen. Tässä listataan joitain niistä: -Lasin pinnoitteet (optiset, sähköiset, tribologiset, lämpö-, toiminnalliset, mekaaniset...). Esimerkkinä voidaan muuttaa lasin pintaominaisuuksia niin, että se heijastaa esimerkiksi lämpöä niin, että se pitää rakennuksen sisätilat viileänä, tai saada toinen puoli infrapunaa absorboivaksi nanoteknologian avulla. Tämä auttaa pitämään rakennusten sisäpuolen lämpimänä, koska lasin uloin pintakerros absorboi infrapunasäteilyä rakennuksen sisällä ja säteilee sitä takaisin sisälle. -etsaus on lasi - Applied Ceramic Labeling (ACL) -Kaiverrus - Liekkikiillotus -Kemiallinen kiillotus - Värjäys TEKNISEN KERAMIKAN VALMISTUS • MUOTTEEN PURISTUS: Koostuu rakeisten jauheiden yksiakselisesta tiivistämisestä suulakkeessa • KUUMAPURISTUS: Samanlainen kuin stanssaus, mutta lämpötilan lisääminen tiivistymisen parantamiseksi. Jauhe tai tiivistetty aihio asetetaan grafiittisuuttimeen ja kohdistetaan yksiakselinen paine, samalla kun muotti pidetään korkeissa lämpötiloissa, kuten 2000 C. Lämpötilat voivat vaihdella riippuen käsiteltävän keraamisen jauheen tyypistä. Monimutkaisia muotoja ja geometrioita varten voidaan tarvita muuta jatkokäsittelyä, kuten timanttihionta. • ISOSTAATTINEN PURISTUS: Rakeiset jauhe- tai puristetut puristetut tiivisteet asetetaan ilmatiiviisiin säiliöihin ja sitten suljettuun paineastiaan, jossa on nestettä. Sen jälkeen ne tiivistetään lisäämällä paineastian painetta. Astian sisällä oleva neste siirtää painevoimat tasaisesti ilmatiiviin säiliön koko pinta-alalla. Materiaali tiivistyy siten tasaisesti ja ottaa joustavan säiliönsä muodon ja sen sisäprofiilin ja ominaisuudet. • ISOSTAATTINEN KUUMAPURISTUS: Samanlainen kuin isostaattinen puristus, mutta paineistetun kaasuilmakehän lisäksi sintraamme kompaktin korkeassa lämpötilassa. Kuumaisostaattinen puristus lisää tiivistymistä ja lisää lujuutta. • LIIKKUVALU / TIETOVALLU: Täytämme muotin mikrometrin kokoisten keraamisten hiukkasten ja kantajanesteen suspensiolla. Tätä seosta kutsutaan "liukumiseksi". Muotissa on huokoset ja siksi seoksessa oleva neste suodatetaan muottiin. Tämän seurauksena muotin sisäpinnoille muodostuu valu. Sintrauksen jälkeen osat voidaan ottaa pois muotista. • TEIPPUVALUMINEN: Valmistamme keraamisia nauhoja valamalla keraamisia lietteitä tasaisille liikkuville alustapinnoille. Lietteet sisältävät keraamisia jauheita sekoitettuna muihin kemikaaleihin sitomista ja kantamista varten. Liuottimien haihtuessa jäljelle jää tiheitä ja taipuisia keramiikkalevyjä, joita voidaan leikata tai rullata halutessaan. • EKRUUSIOMUOKKAUS: Kuten muissakin suulakepuristusprosesseissa, pehmeä keraamisen jauheen seos sideaineiden ja muiden kemikaalien kanssa johdetaan muotin läpi poikkileikkauksen muotoon ja leikataan sitten haluttuihin pituuksiin. Prosessi suoritetaan kylmillä tai lämmitetyillä keraamiseoksilla. • MATALAPAINERUiskupuristus: Valmistamme keraamisen jauheen seoksen sideaineiden ja liuottimien kanssa ja kuumennamme sen lämpötilaan, jossa se voidaan helposti puristaa ja pakottaa työkaluonteloon. Kun muovausjakso on valmis, osa työnnetään ulos ja sideaine poltetaan pois. Ruiskuvalua käyttämällä voimme saada monimutkaisia osia suurilla määrillä taloudellisesti. Reiät jotka ovat millimetrin pieni murto-osa 10 mm paksussa seinässä ovat mahdollisia, kierteet ovat mahdollisia ilman jatkotyöstöä, toleranssit jopa +/- 0,5 % ovat mahdollisia ja jopa pienempiä osia koneistettaessa , seinäpaksuudet luokkaa 0,5 mm - 12,5 mm ovat mahdollisia sekä seinämäpaksuudet 6,5 mm - 150 mm. • VIHREÄ TYÖSTÖ: Samoja metallintyöstötyökaluja käyttämällä voimme työstää puristettuja keraamisia materiaaleja, kun ne ovat vielä pehmeitä kuin liitu. +/- 1 % toleranssit ovat mahdollisia. Paremman toleranssin saavuttamiseksi käytämme timanttihiontaa. • Sintraus tai POLTTO: Sintraus mahdollistaa täyden tiivistymisen. Vihreissä kompakteissa osissa tapahtuu merkittävää kutistumista, mutta tämä ei ole suuri ongelma, koska otamme nämä mittamuutokset huomioon osaa ja työkaluja suunniteltaessa. Jauhehiukkaset sitoutuvat toisiinsa ja tiivistysprosessin aiheuttama huokoisuus poistuu suurelta osin. • TIMANTTIHIONTA: Maailman kovinta materiaalia "timanttia" käytetään kovien materiaalien, kuten keramiikan, hiomiseen ja saadaan tarkkuusosia. Mikrometrialueen toleranssit ja erittäin sileät pinnat saavutetaan. Kustannusten vuoksi harkitsemme tätä tekniikkaa vain silloin, kun todella tarvitsemme sitä. • HERMEETTISET KOKOONPANOT ovat sellaisia, jotka eivät käytännössä salli aineiden, kiinteiden aineiden, nesteiden tai kaasujen vaihtoa rajapintojen välillä. Hermeettinen tiiviste on ilmatiivis. Esimerkiksi hermeettiset elektroniikkakotelot ovat sellaisia, jotka pitävät pakatun laitteen herkän sisäsisällön vahingoittumattomana kosteudesta, epäpuhtauksista tai kaasuista. Mikään ei ole 100 % hermeettistä, mutta kun puhumme hermeettisyydestä, tarkoitamme käytännössä sitä, että hermeettisyys on siinä määrin, että vuotonopeus on niin alhainen, että laitteet ovat turvallisia normaaleissa ympäristöolosuhteissa hyvin pitkiä aikoja. Hermeettiset kokoonpanomme koostuvat metalli-, lasi- ja keraamikomponenteista, metalli-keramiikka, keramiikka-metalli-keramiikka, metalli-keramiikka-metalli, metallista metalliin, metalli-lasi, metalli-lasi-metalli, lasi-metalli-lasi, lasi- metalli ja lasi lasiin ja kaikki muut metalli-lasi-keramiikkasidoksen yhdistelmät. Voimme esimerkiksi metallipinnoittaa keraamiset komponentit niin, että ne voivat sitoutua vahvasti muihin kokoonpanon komponentteihin ja niillä on erinomainen tiivistyskyky. Meillä on tietotaito optisten kuitujen tai läpivientien päällystämisestä metallilla ja niiden juottamisesta koteloihin, jotta koteloihin ei pääse tai vuoda kaasuja. Siksi niitä käytetään elektronisten koteloiden valmistukseen herkkien laitteiden kapseloimiseksi ja suojaamiseksi ulkoilmalta. Erinomaisten tiivistysominaisuuksiensa lisäksi muita ominaisuuksia, kuten lämpölaajenemiskerroin, muodonmuutoskestävyys, ei-kaasupäästö, erittäin pitkä käyttöikä, johtamaton luonne, lämmöneristysominaisuudet, antistaattinen luonne jne. tehdä lasista ja keraamisista materiaaleista valinta tiettyihin sovelluksiin. Tietoja laitoksestamme, joka valmistaa keraamisia metalliliittimiä, hermeettistä tiivistystä, tyhjiöläpivientiä, korkea- ja ultrakorkea tyhjiö- ja nesteenohjauskomponentteja löytyy täältä:Hermetic Components Factory -esite CLICK Product Finder-Locator Service EDELLINEN SIVU
- Wire & Spring Forming, Shaping, Welding, Assembly of Wires, Coil, CNC
Wire & Spring Forming, Shaping, Welding, Assembly of Wires, Coil Compression Extension Torsion Flat Springs, Custom Wires, Helical Springs at AGS-TECH Inc. Langan ja jousimuodostus Valmistamme räätälöityjä lankoja, lankakokoonpanoa, haluttuun 2D- ja 3D-muotoon muotoiltuja lankoja, lankaverkkoja, verkkoja, koteloita, koria, aitaa, lankajousia, tasojousia; vääntö, puristus, jännitys, litteät jouset ja paljon muuta. Prosessejamme ovat lanka- ja jousimuovaus, langanveto, muotoilu, taivutus, hitsaus, juotto, juottaminen, lävistys, taivutus, poraus, viisto, hionta, kierteitys, pinnoitus, neliliuku, liukumuovaus, käämitys, kelaus, irrotus. Suosittelemme, että napsautat tätä LATAA AGS-TECH Inc:n kaaviomaiset kuvamme lanka- ja jousimuovausprosesseista. Tämä ladattava tiedosto, joka sisältää valokuvia ja luonnoksia, auttaa sinua ymmärtämään paremmin alla tarjoamamme tiedot. • LANGARIN VETO: Vetovoimalla venytetään metallimassaa ja vedetään se muotin läpi halkaisijan pienentämiseksi ja sen pituuden lisäämiseksi. Joskus käytämme sarjaa meistiä. Pystymme valmistamaan muotit jokaiselle langalle. Käyttämällä materiaalia, jolla on suuri vetolujuus, vedämme erittäin ohuita lankoja. Tarjoamme sekä kylmä- että kuumatyöstettyjä lankoja. • LANGAN MUOSTO: Rulla mitattua lankaa taivutetaan ja muotoillaan hyödylliseksi tuotteeksi. Pystymme muodostamaan johtoja kaikista mittareista, mukaan lukien ohuet filamentit sekä paksut langat, kuten jousina auton alustan alla. Laitteita, joita käytämme langanmuovaukseen, ovat manuaaliset ja CNC-langanmuodostajat, kelaus, tehopuristimet, neliliukumäki, moniliukumäki. Prosessejamme ovat vetäminen, taivutus, oikaisu, tasoitus, venytys, leikkaus, jyrsintä, juottaminen ja hitsaus, kokoaminen, kelaus, siivetys (tai siivetys), lävistys, langan pujotus, poraus, viisto, hionta, pinnoitus ja pintakäsittelyt. Huippuluokan laitteistomme voidaan asentaa kehittämään erittäin monimutkaisia malleja minkä tahansa muotoisina ja tiukoina toleransseina. Tarjoamme erilaisia johtotyyppejä kuin pallomaisia, teräviä tai viistettyjä päitä. Useimmissa langanmuovausprojekteissamme on minimaaliset työkalukustannukset nollaan. Näytteiden käsittelyajat ovat yleensä päiviä. Muutokset lankamuotojen suunnitteluun/konfiguraatioon voidaan tehdä erittäin nopeasti. • JOUSIEN MUOTO: AGS-TECH valmistaa laajan valikoiman jousia, mukaan lukien: - Vääntö / Double Torsion -jousi - Kiristys/puristusjousi -Vakio/muuttuva jousi -Kierre ja kierrejousi - Tasainen ja lehtijousi - Tasapainotusjousi -Bellevillen pesukone -Negator Spring -Progressiivinen kierrejousi - Aaltokevät -Volute Spring -Kartiojouset - Kevätsormukset -Kellojouset - Leikkeet Valmistamme jousia useista eri materiaaleista ja voimme opastaa sinua sovelluksesi mukaan. Yleisimmät materiaalit ovat ruostumaton teräs, kromipii, korkeahiilinen teräs, öljykarkaistu vähähiilinen, kromivanadiini, fosforipronssi, titaani, berylliumkupariseos, korkean lämpötilan keramiikka. Käytämme jousien valmistuksessa erilaisia tekniikoita, mukaan lukien CNC-kelaus, kylmäkäämitys, kuumakäämitys, karkaisu, viimeistely. Myös muut edellä langanmuovauksen yhteydessä mainitut tekniikat ovat yleisiä jousivalmistuksessamme. • JOHTOJEN JA JOUSIEN VIIMEISTELYPALVELUT: Voimme viimeistellä tuotteesi monella tavalla valinnastasi ja tarpeistasi riippuen. Joitakin yleisiä tarjoamiamme prosesseja ovat: maalaus, jauhemaalaus, pinnoitus, vinyylin kasto, anodisointi, jännityksenpoisto, lämpökäsittely, haulilasi, rumpu, kromaatti, elektroton nikkeli, passivointi, paistettu emali, muovipinnoite , plasmapuhdistus. CLICK Product Finder-Locator Service EDELLINEN SIVU
- Forging and Powdered Metallurgy, Die Forging, Heading, Hot Forging
Forging and Powdered Metallurgy, Die Forging, Heading, Hot Forging, Impression Die, Near Net Shape, Swaging, Metal Hobbing, Riveting, Coining from AGS-TECH Inc. Metallin taonta ja jauhemetallurgia Tarjoamamme METALLITAKOON prosessityypit ovat kuuma- ja kylmämuotti, avoimet ja suljetut muotti, painatusmuotti ja salamattomat taotut, cogging, täytös, särmäys ja tarkkuustaonta, lähes verkkomuotoinen muoto. , takominen, taonta, metallin takominen, puristus- ja rullatako- ja säteittäinen sekä orbitaali- ja rengas- ja isoterminen takominen, metallin lyönti, niittaus, metallipallon taonta, metallin lävistys, mitoitus, korkean energian taonta. JAUHEMETALLURIA- ja JAUHEJÄSITTELYtekniikoitamme ovat jauhepuristus ja sintraus, kyllästäminen, tunkeutuminen, kuuma- ja kylmäisostaattinen puristus, metallin ruiskupuristus, telapuristus, jauhevalssaus, jauheekstruusio, irtosintraus, kipinäsintraus, kuumapuristus. Suosittelemme, että napsautat tätä LATAA AGS-TECH Inc.:n taontaprosessien kaavamaiset kuvat. LATAA AGS-TECH Inc:n kaaviomaiset kuvamme jauhemetallurgiaprosesseista. Nämä ladattavat tiedostot, joissa on valokuvia ja luonnoksia, auttavat sinua ymmärtämään paremmin alla tarjoamamme tiedot. Metallin takomisessa kohdistetaan puristusvoimia ja materiaalia muutetaan ja haluttu muoto saadaan aikaan. Teollisuuden yleisimmät taotut materiaalit ovat rauta ja teräs, mutta myös lukuisia muita, kuten alumiinia, kuparia, titaania ja magnesiumia, takotaan laajalti. Taotuissa metalliosissa on tiivistettyjen halkeamien ja suljettujen tyhjien tilojen lisäksi parannetut rakerakenteet, joten tällä menetelmällä saatujen osien lujuus on suurempi. Takomalla saadaan osia, jotka ovat painoonsa nähden huomattavasti vahvempia kuin valamalla tai koneistamalla tehdyt osat. Koska taotut osat muotoillaan saattamalla metalli virtaamaan lopulliseen muotoonsa, metalli saa suunnatun raerakenteen, joka vastaa osien ylivoimaista lujuutta. Toisin sanoen taontaprosessilla saadut osat paljastavat paremmat mekaaniset ominaisuudet kuin yksinkertaiset valetut tai koneistetut osat. Metallitakkojen paino voi vaihdella pienistä kevyistä osista satoihin tuhansiin kiloihin. Valmistamme takeita pääosin mekaanisesti vaativiin sovelluksiin, joissa kohdistuu suuria rasituksia osiin, kuten autonosiin, vaihteisiin, työvälineisiin, käsityökaluihin, turbiinien akseliin, moottoripyörien varusteisiin. Koska työkalu- ja asennuskustannukset ovat suhteellisen korkeat, suosittelemme tätä valmistusprosessia vain suuren volyymin tuotantoon ja pienimääräisille mutta arvokkaille kriittisille komponenteille, kuten ilmailutelineille. Työkalukustannusten lisäksi suurten taotujen osien valmistuksen läpimenoajat voivat olla pidempiä verrattuna joihinkin yksinkertaisiin koneistettuihin osiin, mutta tekniikka on ratkaisevan tärkeä osille, jotka vaativat poikkeuksellista lujuutta, kuten pultit, mutterit, erikoiskäyttö kiinnikkeet, autot, trukit, nosturin osat. • HOT DIE ja COLD DIE TAKOUS : Kuumamuottistaonta, kuten nimestä voi päätellä, suoritetaan korkeissa lämpötiloissa, joten sitkeys on korkea ja materiaalin lujuus alhainen. Tämä helpottaa muodonmuutosta ja taontaa. Päinvastoin, kylmämuottitaonta suoritetaan alhaisemmissa lämpötiloissa ja vaatii suurempia voimia, mikä johtaa jännityskovettumiseen, parempaan pintakäsittelyyn ja valmistettujen osien tarkkuuteen. • OPEN DIE ja IMRESSION DIET TAKOUS: Avoimessa takomisessa muotit eivät rajoita puristettavaa materiaalia, kun taas painatusmuotissa muottien sisällä olevat ontelot rajoittavat materiaalin virtausta, kun se taotaan haluttuun muotoon. UPSET FORGING tai kutsutaan myös UPSETTING, joka ei itse asiassa ole sama, mutta hyvin samanlainen prosessi, on avoin muottiprosessi, jossa työkappale asetetaan kahden litteän muotin väliin ja puristusvoima alentaa sen korkeutta. Kun korkeutta on pienennetty, työkappaleen leveys kasvaa. HEADING, taontaprosessissa on sylinterimäinen massa, joka on murtunut päässä ja sen poikkileikkausta kasvatetaan paikallisesti. Otsikossa massa syötetään muotin läpi, taotaan ja leikataan sitten pituuteen. Toiminta pystyy tuottamaan nopeasti suuria määriä kiinnikkeitä. Useimmiten se on kylmätyöstö, koska siitä valmistetaan naulapäitä, ruuvinpäitä, muttereita ja pultteja, joissa materiaalia on vahvistettava. Toinen avoin muottiprosessi on COGGING, jossa työkappale taotaan sarjassa vaiheissa, jolloin jokainen vaihe johtaa materiaalin puristumiseen ja sitä seuraavaan avoimen muotin liikkeeseen työkappaleen pituudella. Jokaisessa vaiheessa paksuus pienenee ja pituus kasvaa pienellä määrällä. Prosessi muistuttaa hermostunutta opiskelijaa, joka puree kynää koko ajan pienin askelin. FULLERING-niminen prosessi on toinen avoin taontamenetelmä, jota käytämme usein aikaisemmassa vaiheessa materiaalin jakamiseksi työkappaleeseen ennen muita metallin taontatoimintoja. Käytämme sitä, kun työkappale vaatii useita taonta operaatioita. Toiminnassa kuperapintainen meisti vääntyy ja aiheuttaa metallin virtauksen ulos molemmille puolille. Samanlainen prosessi kuin fullering, EDGING toisaalta sisältää avoimen muotin koverilla pinnoilla työkappaleen vääntämiseksi. Särmäys myös valmisteleva prosessi myöhempiä taontatoimenpiteitä varten saa materiaalin virtaamaan molemmilta puolilta keskellä olevalle alueelle. JÄLKEMUOTTAMUOTO tai SULJETTU MUOTTISTAKOUS, kuten sitä myös kutsutaan, käyttää muottia/muottia, joka puristaa materiaalia ja rajoittaa sen virtausta itsessään. Suulake sulkeutuu ja materiaali ottaa muotin/muotin onkalon muodon. PRECISION FORGING, erikoislaitteita ja muottia vaativa prosessi, tuottaa osia ilman tai erittäin vähän välähdystä. Toisin sanoen osilla on lähes lopulliset mitat. Tässä prosessissa hyvin kontrolloitu määrä materiaalia työnnetään huolellisesti sisään ja sijoitetaan muotin sisään. Käytämme tätä menetelmää monimutkaisille muodoille, joissa on ohuet poikkileikkaukset, pienet toleranssit ja vetokulmat ja kun määrät ovat riittävän suuria oikeuttamaan muottien ja laitekustannusten. • FLASHLES TAKOUS : Työkappale asetetaan suulakkeeseen siten, että mitään materiaalia ei voi virrata ulos ontelosta muodostamaan välähdystä. Ei-toivottua salamaleikkausta ei siis tarvita. Se on tarkkuustaontaprosessi ja vaatii siksi käytetyn materiaalin määrän tarkkaa hallintaa. • METALLIN SWAGING tai SÄTEITÄ TAKOUS: Työkappaleeseen kohdistuu kehän suuntainen vaikutus meistillä ja taottu. Karaa voidaan käyttää myös työkappaleen sisägeometrian takomiseen. Huuhtelutoiminnossa työkappale saa tyypillisesti useita iskuja sekunnissa. Tyypillisiä swaging-tuotteita ovat teräväkärkiset työkalut, kartiotangot ja ruuvitaltat. • METALLI Lävistys: Käytämme tätä toimintoa usein lisätoimenpiteenä osien valmistuksessa. Työkappaleen pintaan tehdään reikä tai onkalo lävistyksellä murtamatta sitä läpi. Huomaa, että lävistys on eri asia kuin poraus, joka johtaa läpireikään. • HOBBING: Halutun geometrian meisti painetaan työkappaleeseen ja muodostaa halutun muotoisen ontelon. Kutsumme tätä lävistystä keittolevyksi. Toimintoon liittyy korkeita paineita ja se suoritetaan kylmässä. Tämän seurauksena materiaali on kylmämuokattu ja rasituskarkaistu. Siksi tämä prosessi soveltuu erittäin hyvin muottien, muottien ja onteloiden valmistukseen muita valmistusprosesseja varten. Kun liesi on valmistettu, voidaan helposti valmistaa useita identtisiä onteloita ilman, että niitä tarvitsee työstää yksitellen. • RULLATAKOINTI tai RULLAMUOKKAUS: Metalliosan muotoilemiseen käytetään kahta vastakkaista rullaa. Työkappale syötetään rullille, telat kääntyvät ja vetävät työn rakoon, sitten työ syötetään telojen uritetun osan läpi ja puristusvoimat antavat materiaalille halutun muodon. Se ei ole valssausprosessi vaan taontaprosessi, koska se on pikemminkin erillinen kuin jatkuva toiminta. Rullaurien geometria takoo materiaalin haluttuun muotoon ja geometriaan. Se suoritetaan kuumana. Koska se on taontaprosessi, se tuottaa osia, joilla on erinomaiset mekaaniset ominaisuudet, ja siksi käytämme sitä auton osien, kuten akseleiden, valmistukseen, joiden on oltava poikkeuksellisen kestäviä vaikeissa työympäristöissä. • ORBITAL TAKOUS: Työkappale asetetaan taontamuottionteloon ja taotaan ylemmällä muotilla, joka kulkee kiertoradalla sen pyöriessä kaltevalla akselilla. Jokaisella kierroksella ylempi muotti suorittaa loppuun puristusvoimien kohdistamisen koko työkappaleeseen. Toistamalla nämä kierrokset useita kertoja saadaan aikaan riittävä taonta. Tämän valmistustekniikan etuja ovat sen hiljainen toiminta ja pienemmät tarvittavat voimat. Toisin sanoen pienillä voimilla voidaan pyörittää raskasta meistiä akselin ympäri suuren paineen kohdistamiseksi työkappaleen osaan, joka on kosketuksessa muotin kanssa. Levy- tai kartiomaiset osat sopivat joskus hyvin tähän prosessiin. • RENKAUSTAKOUS: Käytämme usein saumattomien renkaiden valmistukseen. Kangas leikataan pituudeltaan, sekaisin ja lävistetään sitten koko matkan läpi keskireiän luomiseksi. Sitten se asetetaan karan päälle ja taontamuotti vasaroi sitä ylhäältä samalla kun rengasta pyöritetään hitaasti, kunnes halutut mitat ovat saavutettu. • NIITTAMINEN: Yleinen prosessi osien liittämiseksi, alkaa suoralla metallikappaleella, joka työnnetään valmiiksi tehtyihin reikiin osien läpi. Tämän jälkeen metallikappaleen kaksi päätä taotaan puristamalla ylemmän ja alemman muotin välinen liitos. • LÄHTÖ: Toinen suosittu prosessi, joka suoritetaan mekaanisella puristimella, joka kohdistaa suuria voimia lyhyellä matkalla. Kolikoiden nimi tulee hienoista yksityiskohdista, jotka on taottu metallikolikoiden pinnoille. Se on enimmäkseen tuotteen viimeistelyprosessi, jossa pinnoille saadaan hienoja yksityiskohtia työkappaleeseen siirtävän muotin suuren voiman seurauksena. • METALLIKUULALAAKERI: Tuotteet, kuten kuulalaakerit, vaativat korkealaatuisia tarkasti valmistettuja metallikuulia. Yhdessä tekniikassa, nimeltä SKEW ROLLING, käytämme kahta vastakkaista rullaa, jotka pyörivät jatkuvasti, kun massaa syötetään jatkuvasti rullille. Kahden telan toisesta päästä työntyy ulos tuotteena metallipalloja. Toinen menetelmä metallipallon takomiseen on käyttää muottia, joka puristaa niiden väliin asetettua materiaalia ottamalla muottipesän pallomaisen muodon. Usein valmistetut pallot vaativat joitain lisävaiheita, kuten viimeistelyä ja kiillotusta, jotta niistä tulee korkealaatuisia tuotteita. • ISTERMINEN TAKOUS / KUUMUOTTAMINEN: Kallis prosessi, joka suoritetaan vain, kun hyöty/kustannusarvo on perusteltu. Kuuma työstöprosessi, jossa muotti kuumennetaan suunnilleen samaan lämpötilaan kuin työkappale. Koska sekä suutin että työ ovat suunnilleen samassa lämpötilassa, jäähdytystä ei tapahdu ja metallin virtausominaisuudet paranevat. Toiminta sopii hyvin superseoksille ja materiaaleille, joiden muokattavuus on huono, ja materiaaleille, joiden mekaaniset ominaisuudet ovat erittäin herkkiä pienille lämpötilagradienteille ja muutoksille. • METALLILOITOINTI: Se on kylmäviimeistelyprosessi. Materiaalivirtaus on rajoittamaton kaikkiin suuntiin, lukuun ottamatta suuntaa, johon voima kohdistuu. Tuloksena saadaan erittäin hyvä pintakäsittely ja tarkat mitat. • KORKEAN ENERGIAN NOPEUSTAKOUS: Tekniikassa on männän varteen kiinnitetty ylämuotti, jota työnnetään nopeasti, kun polttoaine-ilmaseos syttyy sytytystulpalla. Se muistuttaa mäntien toimintaa auton moottorissa. Muotti osuu työkappaleeseen erittäin nopeasti ja palaa sitten takaisin alkuperäiseen asentoonsa erittäin nopeasti vastapaineen ansiosta. Teos takotaan muutamassa millisekunnissa, joten teokselle ei ole aikaa jäähtyä. Tämä on hyödyllistä vaikeasti taotettaville osille, joilla on erittäin lämpötilaherkkiä mekaanisia ominaisuuksia. Toisin sanoen prosessi on niin nopea, että kappale muodostetaan tasaisessa lämpötilassa koko ajan eikä muotin/työkappaleen rajapinnoissa ole lämpötilagradientteja. • DIE FORGING:ssa metalli lyödään kahden yhteensopivan teräspalan väliin, joissa on erityismuotoja, joita kutsutaan meistiksi. Kun metalli vasaroi muottien väliin, se saa saman muodon kuin muotissa olevat muodot. Kun se saavuttaa lopullisen muotonsa, se otetaan ulos jäähtymään. Tämä prosessi tuottaa vahvoja osia, jotka ovat tarkan muotoisia, mutta vaativat suuremman investoinnin erikoissuulakkeisiin. Järkyttynyt taonta lisää metallikappaleen halkaisijaa litistämällä sitä. Sitä käytetään yleensä pienten osien valmistukseen, erityisesti päiden muodostamiseen kiinnittimiin, kuten pultteihin ja nauloihin. • JAUHEMETALLURGIA / JAUHEIDEN KÄSITTELY: Kuten nimestä voi päätellä, se sisältää valmistusprosesseja tietyn geometrian ja muotoisten kiinteiden osien valmistamiseksi jauheista. Jos metallijauheita käytetään tähän tarkoitukseen, se on jauhemetallurgian alaa ja jos käytetään ei-metallijauheita, se on jauhekäsittelyä. Kiinteät osat valmistetaan jauheista puristamalla ja sintraamalla. POWDER PRESSING:iä käytetään jauheiden puristamiseen haluttuun muotoon. Ensin primaarimateriaali jauhetaan fyysisesti ja jakaa sen moniin pieniin yksittäisiin hiukkasiin. Jauheseos täytetään suulakkeeseen ja meisti liikkuu kohti jauhetta ja tiivistää sen haluttuun muotoon. Useimmiten suoritetaan huoneenlämmössä, jauhepuristamalla saadaan kiinteä osa ja sitä kutsutaan vihreäksi kompaktiksi. Sideaineita ja voiteluaineita käytetään yleisesti parantamaan tiiviyttävyyttä. Pystymme jauhepuristimeen useiden tuhansien tonnin kapasiteetin hydraulipuristimilla. Meillä on myös kaksitoimiset puristimet, joissa on vastakkaiset ylä- ja alalävistykset, sekä monitoimipuristimet erittäin monimutkaisiin kappalegeometrioihin. Tasaisuus, joka on tärkeä haaste monille jauhemetallurgia-/jauhekäsittelylaitoksille, ei ole suuri ongelma AGS-TECH:lle, koska meillä on laaja kokemus tällaisten osien räätälöimisestä useiden vuosien ajan. Olemme onnistuneet myös paksummilla osilla, joissa tasaisuus on haaste. Jos sitoudumme projektiisi, teemme osasi. Jos havaitsemme mahdollisia riskejä, ilmoitamme sinulle in advance. JAUHESINTRAUS, joka on toinen vaihe, käsittää lämpötilan nostamisen tiettyyn asteeseen ja lämpötilan pitämisen tällä tasolla tietyn ajan, jotta puristetussa osassa olevat jauhehiukkaset voivat sitoutua toisiinsa. Tämä johtaa paljon vahvempiin sidoksiin ja työkappaleen vahvistumiseen. Sintraus tapahtuu lähellä jauheen sulamislämpötilaa. Sintrauksen aikana tapahtuu kutistumista, materiaalin lujuus, tiheys, sitkeys, lämmönjohtavuus ja sähkönjohtavuus lisääntyvät. Meillä on panos- ja jatkuvatoimisia uuneja sintraukseen. Yksi kyvyistämme on valmistamiemme osien huokoisuuden säätö. Pystymme valmistamaan esimerkiksi metallisuodattimia pitämällä osat jossain määrin huokoisina. IMPREGNATION-nimisellä tekniikalla täytämme metallin huokoset nesteellä, kuten öljyllä. Valmistamme esimerkiksi öljykyllästettyjä laakereita, jotka ovat itsevoitelevia. INFILTRATION-prosessissa täytämme metallin huokoset toisella metallilla, jonka sulamispiste on alhaisempi kuin perusmateriaali. Seos kuumennetaan lämpötilaan, joka on kahden metallin sulamislämpötilojen välillä. Tämän seurauksena voidaan saavuttaa joitain erikoisominaisuuksia. Suoritamme myös usein toissijaisia toimenpiteitä, kuten koneistusta ja taontaa jauhevalmisteisille osille, kun tarvitaan erityispiirteitä tai -ominaisuuksia tai kun osa voidaan valmistaa pienemmillä prosessivaiheilla. ISOSTAATTINEN PURISTUS: Tässä prosessissa nestepainetta käytetään osan tiivistämiseen. Metallijauheet asetetaan suljetusta joustavasta astiasta valmistettuun muottiin. Isostaattisessa puristuksessa painetta kohdistetaan joka puolelta, toisin kuin tavanomaisessa puristuksessa havaitaan aksiaalipaine. Isostaattisen puristuksen etuja ovat tasainen tiheys kappaleen sisällä, erityisesti suurempien tai paksumpien osien kohdalla, erinomaiset ominaisuudet. Sen haittana ovat pitkät sykliajat ja suhteellisen alhainen geometrinen tarkkuus. KYLMÄISOSTAATTINEN PURISTUS suoritetaan huoneenlämmössä ja joustava muotti on valmistettu kumista, PVC:stä tai uretaanista tai vastaavista materiaaleista. Paineistamiseen ja tiivistämiseen käytettävä neste on öljyä tai vettä. Vihreän kompaktin perinteinen sintraus seuraa tätä. KUUMAISOSTAATTINEN PURISTUS sen sijaan suoritetaan korkeissa lämpötiloissa ja muotin materiaali on peltiä tai keramiikkaa, jolla on riittävän korkea sulamispiste, joka kestää lämpötiloja. Paineneste on yleensä inerttiä kaasua. Puristus- ja sintraustoimenpiteet suoritetaan yhdessä vaiheessa. Huokoisuus eliminoituu lähes kokonaan, saadaan yhtenäinen raerakenne. Kuumaisostaattisen puristuksen etuna on, että sillä voidaan valmistaa valun ja takomisen yhdistelmiin verrattavia osia, jolloin voidaan käyttää materiaaleja, jotka eivät sovellu valuun ja takomiseen. Kuumaisostaattisen puristuksen haittana on sen pitkä sykliaika ja siten hinta. Se sopii kriittisiin osiin, joiden äänenvoimakkuus on pieni. METALLIRUiskupuristus: Erittäin sopiva prosessi monimutkaisten ohuiden seinämien ja yksityiskohtaisten geometristen osien valmistukseen. Sopii parhaiten pienempiin osiin. Jauheet ja polymeerisideaine sekoitetaan, kuumennetaan ja ruiskutetaan muottiin. Polymeerisideaine pinnoittaa jauhehiukkasten pinnat. Muotin jälkeen sideaine poistetaan joko kuumentamalla matalassa lämpötilassa tai liuottamalla liuotinta käyttämällä. TELLAN TIIVISTYS / JAUHEEN VALSSITUS: Jauheita käytetään jatkuvien nauhojen tai levyjen valmistukseen. Jauhe syötetään syöttölaitteesta ja puristetaan kahdella pyörivällä telalla levyiksi tai nauhoiksi. Toimenpide suoritetaan kylmänä. Levy viedään sintrausuuniin. Sintrausprosessi voidaan toistaa toisen kerran. JAUHEEKRUUSIO: Osat, joilla on suuri pituus-halkaisijasuhde, valmistetaan suulakepuristamalla ohut metallilevysäiliö jauheella. LÖÖRÄSINTRAUS: Kuten nimestä voi päätellä, se on paineeton tiivistys- ja sintrausmenetelmä, joka soveltuu erittäin huokoisten osien, kuten metallisuodattimien, valmistukseen. Jauhe syötetään muotin onteloon tiivistämättä. LÖÖRÄSINTRAUS: Kuten nimestä voi päätellä, se on paineeton tiivistys- ja sintrausmenetelmä, joka soveltuu erittäin huokoisten osien, kuten metallisuodattimien, valmistukseen. Jauhe syötetään muotin onteloon tiivistämättä. KIPKISIINTROINTI: Jauhe puristetaan muotissa kahdella vastakkaisella lävistimellä ja lävistimeen kohdistetaan suuritehoinen sähkövirta, joka kulkee niiden välissä olevan puristetun jauheen läpi. Suuri virta polttaa pois pintakalvot jauhehiukkasista ja sintraa ne syntyvän lämmön mukana. Prosessi on nopea, koska lämpöä ei syötetä ulkopuolelta, vaan se syntyy muotin sisältä. KUUMAPURISTUS: Jauheet puristetaan ja sintrataan yhdessä vaiheessa muotissa, joka kestää korkeita lämpötiloja. Kun suulake tiivistyy, siihen kohdistetaan jauhelämpö. Tällä menetelmällä saavutettu hyvä tarkkuus ja mekaaniset ominaisuudet tekevät siitä houkuttelevan vaihtoehdon. Myös tulenkestäviä metalleja voidaan työstää käyttämällä muottimateriaaleja, kuten grafiittia. CLICK Product Finder-Locator Service EDELLINEN VALIKKO
- Sheet Metal Forming Fabrication, Stamping, Punching, Deep Drawing, CNC
Sheet Metal Forming and Fabrication, Stamping, Punching, Bending, Progressive Die, Spot Welding, Deep Drawing, Metal Blanking and Slitting at AGS-TECH Inc. Meistot ja ohutlevyjen valmistus Tarjoamme ohutlevyn leimaamista, muotoilua, muotoilua, taivutusta, lävistystä, aihiota, halkaisua, rei'itystä, loveamista, näppäilyä, parranajoa, puristustyöstöä, valmistusta, syvävetoa yhdellä lävistyksellä/yksiiskuisella meistillä sekä progressiivisia meistijä ja kehruua, kumin muotoilua ja hydroforming; ohutlevyn leikkaus vesisuihkulla, plasmalla, laserilla, sahalla, liekillä; metallilevyjen kokoonpano hitsauksella, pistehitsaus; ohutlevyputkien pullistuminen ja taivutus; ohutlevypintojen viimeistely, mukaan lukien kasto- tai ruiskumaalaus, sähköstaattinen jauhemaalaus, anodisointi, pinnoitus, sputterointi ja paljon muuta. Palvelumme vaihtelevat nopeasta peltiprototyyppien valmistuksesta suurien volyymien valmistukseen. Suosittelemme, että napsautat tätäLATAA AGS-TECH Inc:n kaavamaiset kuvamme ohutlevyn valmistus- ja leimausprosesseista. Tämä auttaa sinua ymmärtämään paremmin alla tarjoamamme tiedot. • PELVIEN LEIKKAUS: Tarjoamme LEIKKAUKSET ja VÄRIT. Leikkaukset katkaisevat peltiä polku kerrallaan eikä materiaalia periaatteessa mene hukkaan, kun taas väliseinillä muotoa ei voida sovittaa tarkasti sisään ja siksi tietty määrä materiaalia menee hukkaan. Yksi suosituimmista prosesseistamme on LEITÄMINEN, jossa metallilevystä leikataan pyöreä tai muun muotoinen materiaalipala. Pois leikattu pala on jätettä. Toinen versio lävistyksestä on SLOTTING, jossa tehdään suorakaiteen muotoisia tai pitkänomaisia reikiä. Tyhjennys on toisaalta sama prosessi kuin lävistys, ja leikattavan kappaleen ero on työ ja se säilytetään. FINE BLANKING, ylivoimainen aihion versio, tekee leikkauksia tiukoilla toleransseilla ja suorilla sileillä reunoilla eikä vaadi toissijaisia toimenpiteitä työkappaleen täydellisyyden saavuttamiseksi. Toinen usein käyttämämme prosessi on SLITTING, joka on leikkausprosessi, jossa metallilevyä leikataan kahdella vastakkaisella pyöreällä terällä suoraa tai kaarevaa reittiä pitkin. Tölkinavaaja on yksinkertainen esimerkki leikkausprosessista. Toinen meille suosittu prosessi on PERFORAATIO, jossa metallilevyyn tehdään useita pyöreitä tai muun muotoisia reikiä tietyllä kuviolla. Tyypillinen esimerkki rei'itetystä tuotteesta ovat metallisuodattimet, joissa on useita reikiä nesteitä varten. NOTCHING:ssa, toisessa pellinleikkausprosessissa, poistamme materiaalia työkappaleesta alkaen reunasta tai muualta ja leikkaamme sisäänpäin, kunnes haluttu muoto saadaan. Se on progressiivinen prosessi, jossa jokainen toimenpide poistaa toisen kappaleen, kunnes haluttu ääriviiva on saavutettu. Pienissä tuotantosarjoissa käytämme joskus suhteellisen hitaampaa prosessia nimeltä NIBBLING, joka koostuu useista nopeista päällekkäisten reikien rei'istämisestä suuremman, monimutkaisemman leikkauksen tekemiseksi. PROGRESSIIVINEN LEIKKAUS käytämme sarjaa erilaisia operaatioita yksittäisen leikkauksen tai tietyn geometrian aikaansaamiseksi. Lopuksi SHAVING toissijainen prosessi auttaa meitä parantamaan jo tehtyjen leikkausten reunoja. Sitä käytetään lastujen, karkeiden reunojen leikkaamiseen peltitöissä. • PELTTIEN TAIVUTUS: Leikkauksen lisäksi taivutus on olennainen prosessi, jota ilman emme pystyisi valmistamaan useimpia tuotteita. Useimmiten kylmätyöskentely, mutta joskus myös lämpimänä tai kuumana. Käytämme meistejä ja puristamista suurimman osan ajasta tähän operaatioon. PROGRESSIVE BENDING:ssä käytämme sarjaa erilaisia lävistys- ja meistioperaatioita yhden taivutuksen tai tietyn geometrian saavuttamiseksi. AGS-TECH käyttää erilaisia taivutusprosesseja ja tekee valinnan työkappaleen materiaalin, sen koon, paksuuden, halutun taivutuskoon, säteen, kaarevuuden ja taivutuskulman, taivutuksen sijainnin, toiminnan taloudellisuuden, valmistettavien määrien mukaan... jne. Käytämme V-TAIVUTTAMISTA, jossa V-muotoinen meisti pakottaa metallilevyn V-muotoiseen muottiin ja taivuttaa sitä. Sopii sekä erittäin teräville että tylpäille kulmille ja niiden väliin, mukaan lukien 90 astetta. Suoritamme REUNAN TAIVUTUKSEN käyttämällä pyyhkimismuovia. Laitteillamme pystymme saavuttamaan jopa 90 astetta suurempia kulmia. Reunataivutuksessa työkappale asetetaan puristustyynyn ja muotin väliin, taivutusalue sijaitsee muotin reunassa ja loput työkappaleesta pidetään space kuin ulokepalkki. Kun meisti vaikuttaa ulokeosaan, se taivutetaan muotin reunan yli. FLANGING on reunan taivutusprosessi, joka johtaa 90 asteen kulmaan. Toiminnan päätavoitteena on terävien reunojen eliminointi ja geometristen pintojen saaminen osien liittämistä helpottamaan. BEADING, toinen yleinen reunan taivutusprosessi muodostaa kiharan osan reunan yli. HEMMING puolestaan johtaa siihen, että arkin reuna on taivutettu kokonaan itsensä päälle. SAUMAUKSESSA kahden osan reunat taivutetaan päällekkäin ja liitetään yhteen. DOUBLE SAUMING puolestaan tarjoaa vesitiiviit ja ilmatiiviit metallilevyliitokset. Samoin kuin reunataivutus, ROTARY BENDING -niminen prosessi ottaa käyttöön sylinterin, josta on leikattu haluttu kulma ja joka toimii lävistimenä. Kun voima välittyy meistiin, se sulkeutuu työkappaleen mukana. Sylinterin ura antaa ulokeosalle halutun kulman. Uran kulma voi olla pienempi tai suurempi kuin 90 astetta. AIR BENDING:ssä emme tarvitse alemmassa muotissa kulmassa olevaa uraa. Peltiä tukee kaksi pintaa vastakkaisilla puolilla ja tietyn etäisyyden päässä. Lävistin kohdistaa sitten voiman oikeaan kohtaan ja taivuttaa työkappaletta. CHANNEL BENDING suoritetaan kanavan muotoisella meistillä ja U-BEND U-muotoisella meistillä. OFFSET BENDING tuottaa offsetit peltiin. ROLL BENDING, tekniikka, joka sopii paksuun työskentelyyn ja suurten metallilevypalojen taivutukseen, syöttää ja taivuttaa levyt haluttuihin kaareviin kolmella telalla. Rullat järjestetään siten, että työn haluttu taivutus saavutetaan. Telojen välistä etäisyyttä ja kulmaa säädetään halutun lopputuloksen saavuttamiseksi. Siirrettävä tela mahdollistaa kaarevuuden hallinnan. TUBE FORMING on toinen suosittu metallilevyn taivutusoperaatio, johon liittyy useita muotteja. Putket saadaan useiden toimien jälkeen. ALOITTELU suoritetaan myös taivutusoperaatioilla. Pohjimmiltaan se on symmetristä taivutusta säännöllisin väliajoin koko levypalan yli. Aallottamiseen voidaan käyttää erilaisia muotoja. Aaltopahvilevy on jäykempi ja kestää paremmin taivutusta, joten sillä on käyttöä rakennusteollisuudessa. METALLIRULLAMUOKKAUS, jatkuva valmistusprosessi, jossa taivutetaan tietyn geometrian poikkileikkauksia telojen avulla ja työ taivutetaan peräkkäin, jolloin lopullinen tela suorittaa työn. Joissakin tapauksissa käytetään yhtä rullaa ja joissakin tapauksissa sarjaa rullia. • YHDISTETYT LEIKKAUS- JA TAIVUTUSPROSESSIT: Nämä ovat prosesseja, jotka leikkaavat ja taivuttavat samanaikaisesti. PIERCING:ssä reikä luodaan terävällä lyönnillä. Kun meisti leventää levyssä olevaa reikää, materiaali taivutetaan samanaikaisesti reiän sisälaipaksi. Saadulla laipalla voi olla tärkeitä tehtäviä. LANCE-toiminto puolestaan leikkaa ja taivuttaa arkkia luodakseen kohotetun geometrian. • METALLIPUTKUN PÖÖRISTYMINEN JA TAIVUTTAMINEN: PUHJOITUKSESSA jokin onton putken sisäosa paineistetaan, jolloin putki pullistuu ulospäin. Koska putki on muotin sisällä, pullistumageometriaa säätelee muotin muoto. STRETCH BENDING:ssä metalliputkea venytetään käyttämällä putken akselin suuntaisia voimia ja taivutusvoimia putken vetämiseksi muotokappaleen yli. DRAW BENDING -toiminnossa kiinnitämme putken läheltä sen päätä pyörivään muotokappaleeseen, joka taivuttaa putkea pyöriessään. Lopuksi, PURISTUSTAIVUTUKSESSA putki pidetään voimalla kiinteään muotokappaleeseen, ja muotti taivuttaa sen muotokappaleen päälle. • SYVÄPIIRTO: Yhdessä suosituimmista operaatioistamme käytetään meistiä, vastaavaa meistiä ja aihion pidikettä. Peltiaihio asetetaan muotin aukon päälle ja meisti liikkuu kohti aihion pidikkeen pitämää aihiota. Kun ne joutuvat kosketuksiin, meisti pakottaa metallilevyn muottipesään tuotteen muodostamiseksi. Syvävetotoiminto muistuttaa leikkaamista, mutta meistin ja muotin välinen välys estää arkin leikkaamisen. Toinen tekijä, joka varmistaa, että arkki on syvävedetty eikä leikattu, ovat pyöreät kulmat suuttimessa ja lävistimessä, jotka estävät leikkaamisen ja leikkaamisen. Suuremman syvävedon saavuttamiseksi otetaan käyttöön REDRAWING-prosessi, jossa myöhempi syväveto tehdään osalle, joka on jo läpikäynyt syvävetoprosessin. REVERSE REDRAWING -toiminnossa syvävedetty osa käännetään ympäri ja piirretään vastakkaiseen suuntaan. Syväveto voi tarjota epäsäännöllisen muotoisia esineitä, kuten kupuisia, kartiomaisia tai porrastettuja kuppeja, Kohokuviointissa käytämme uros- ja naarasmuottiparia tehdäksemme vaikutuksen metallilevyyn kuviolla tai käsikirjoituksella. • SPINNING : Toiminto, jossa tasaista tai esimuotoiltua työkappaletta pidetään pyörivän tuurnan ja takakappaleen välissä ja työkalu kohdistaa työhön paikallista painetta, kun se liikkuu vähitellen tuurnaa ylöspäin. Tämän seurauksena työkappale kääritään karan päälle ja saa muotonsa. Käytämme tätä tekniikkaa vaihtoehtona syvävetolle, jossa tilausmäärä on pieni, osat ovat suuria (halkaisija jopa 20 jalkaa) ja niissä on ainutlaatuiset kaarevat. Vaikka kappalehinnat ovat yleensä korkeammat, CNC-kehruuoperaation asennuskustannukset ovat alhaiset syvävetoon verrattuna. Päinvastoin, syväveto vaatii suuria alkuinvestointeja asennukseen, mutta kappalekohtaiset kustannukset ovat alhaiset, kun osia valmistetaan suuria määriä. Toinen versio tästä prosessista on SHEAR SPINNING, jossa myös metalli virtaa työkappaleen sisällä. Metallivirtaus vähentää työkappaleen paksuutta prosessin aikana. Vielä toinen asiaan liittyvä prosessi on TUBE SPINNING, jota levitetään lieriömäisille osille. Myös tässä prosessissa metalli virtaa työkappaleen sisällä. Näin paksuus pienenee ja putken pituus kasvaa. Työkalua voidaan liikuttamalla luoda ominaisuuksia putken sisä- tai ulkopuolelle. • OHJELMAN KUMIN MUOTOS: Kumi- tai polyuretaanimateriaali laitetaan säiliösuuttimeen ja työkappale asetetaan kumin pinnalle. Sitten työkappaleeseen kohdistetaan lyönti, joka pakottaa sen kumiin. Koska kumin synnyttämä paine on alhainen, valmistettujen osien syvyys on rajoitettu. Koska työkalukustannukset ovat alhaiset, prosessi soveltuu pienikokoiseen tuotantoon. • HYDROMUOTUS: Kumin muovauksen tapaan tässä prosessissa metallilevyt puristetaan meistin avulla paineistettuun nesteeseen kammion sisällä. Peltityö on kerrostettu lävistimen ja kumikalvon väliin. Kalvo ympäröi työkappaleen kokonaan ja nesteen paine pakottaa sen muodostumaan meistiin. Tällä tekniikalla voidaan saada erittäin syväveto jopa syvemmälle kuin syvävetoprosessissa. Valmistamme sekä yksilävistyksiä että progressiivisia muotteja osastasi riippuen. Yksitahtiset leimausmuotit ovat kustannustehokas tapa valmistaa nopeasti suuria määriä yksinkertaisia metallilevyosia, kuten aluslevyjä. Progressiivisia meistiä tai syvävetotekniikkaa käytetään monimutkaisempien geometrioiden valmistukseen. Tapauksestasi riippuen voidaan käyttää vesisuihku-, laser- tai plasmaleikkausta metallilevyosien valmistukseen edullisesti, nopeasti ja tarkasti. Monilla toimittajilla ei ole aavistustakaan näistä vaihtoehtoisista tekniikoista tai heillä ei ole niitä, ja siksi he käyvät läpi pitkiä ja kalliita tapoja valmistaa meistiä ja työkaluja, jotka vain tuhlaavat asiakkaiden aikaa ja rahaa. Jos tarvitset räätälöityjä metallilevykomponentteja, kuten koteloita, elektroniikkakoteloita... jne. niin nopeasti kuin muutamassa päivässä, ota meihin yhteyttä saadaksesi RAPID PLETTIN PROTOTYPING -palvelumme. CLICK Product Finder-Locator Service EDELLINEN VALIKKO
- Plastic Rubber Metal Extrusions, Extrusion Dies, Aluminum Extruding
Plastic Rubber Metal Extrusions, Extrusion Dies, Aluminum Extruding, Pipe Tube Forming, Plastic Profiles, Metal Profiles Manufacturing, PVC at AGS-TECH Inc. Suulakepuristukset, suulakepuristetut tuotteet, ekstrudaatit Käytämme EXTRUSION prosessia valmistaaksemme tuotteita, joilla on kiinteä poikkileikkausprofiili, kuten putkia, putkia ja lämpönieluja. Vaikka monia materiaaleja voidaan suulakepuristaa, yleisimmät ekstruusiomme on valmistettu metallista, polymeereistä/muovista, keramiikasta, joka saadaan joko kylmä-, lämmin- tai kuumapuristusmenetelmällä. Kutsumme suulakepuristettuja osia suulakepuristeiksi tai suulakepuristeiksi, jos ne ovat monikkoa. Jotkut myös suorittamamme prosessin erikoisversiot ovat päällystys, koekstruusio ja yhdistelmäekstruusio. Suosittelemme, että napsautat tätä LATAA AGS-TECH Inc:n kaavamaiset kuvamme metallikeraami- ja muoviekstruusioprosesseista. Tämä auttaa sinua ymmärtämään paremmin alla tarjoamamme tiedot. Ekstruusiossa suulakepuristettava materiaali työnnetään tai vedetään muotin läpi, jolla on haluttu poikkileikkausprofiili. Prosessilla voidaan valmistaa monimutkaisia poikkileikkauksia erinomaisella pinnalla ja työstää hauraita materiaaleja. Tällä prosessilla voidaan valmistaa minkä tahansa pituisia osia. Prosessin vaiheiden yksinkertaistamiseksi: 1.) Lämpimissä tai kuumassa suulakepuristuksessa materiaali kuumennetaan ja ladataan puristimessa olevaan säiliöön. Materiaali puristetaan ja työnnetään ulos muotista. 2.) Valmistettu ekstrudaatti venytetään suoristusta varten, lämpökäsitellään tai kylmätyöstetään sen ominaisuuksien parantamiseksi. Toisaalta COLD EXTRUSION tapahtuu huoneenlämmössä, ja sen etuna on: pinnan lujuus, korkea viimeistely, vähemmän hapettumista. WARM EXTRUSION suoritetaan huoneenlämpötilan yläpuolella, mutta uudelleenkiteytyspisteen alapuolella. Se tarjoaa kompromissin ja tasapainon vaadituille voimille, sitkeydelle ja materiaalin ominaisuuksille ja on siksi valinta joihinkin sovelluksiin. HOT EXTRUSION tapahtuu materiaalin uudelleenkiteytyslämpötilan yläpuolella. Näin materiaalia on helpompi työntää muotin läpi. Laitteiden hinta on kuitenkin korkea. Mitä monimutkaisempi suulakepuristettu profiili on, sitä kalliimpi on suulake (työkalut) ja sitä pienempi on tuotantonopeus. Suulakkeen poikkileikkauksilla ja paksuuksilla on rajoituksia, jotka riippuvat ekstrudoitavasta materiaalista. Suulakepuristussuutinten terävät kulmat ovat aina ei-toivottuja ja niitä tulee välttää, ellei se ole välttämätöntä. Suulakepuristettavan materiaalin mukaan tarjoamme: • METAL EXTRUSIONS : Yleisimmät valmistamamme tuotteet ovat alumiini, messinki, sinkki, kupari, teräs, titaani, magnesium • MUOVIN EXTRUSION : Muovi sulatetaan ja muotoillaan jatkuvaksi profiiliksi. Yleisimmät materiaalimme ovat polyeteeni, nylon, polystyreeni, polyvinyylikloridi, polypropeeni, ABS-muovi, polykarbonaatti, akryyli. Tyypillisiä valmistamiamme tuotteita ovat putket ja letkut, muovikehykset. Prosessissa pieniä muovihelmiä / hartsia syötetään painovoimalla suppilosta suulakepuristuskoneen tynnyriin. Sekoitamme usein myös väriaineita tai muita lisäaineita suppiloon saadaksemme tuotteelle vaaditut spesifikaatiot ja ominaisuudet. Pyörivä ruuvi pakottaa lämmitettyyn tynnyriin tulevan materiaalin poistumaan tynnyristä sen päässä ja liikkumaan seulapaketin läpi sulassa muovissa olevien epäpuhtauksien poistamiseksi. Seulapakkauksen ohitettuaan muovi menee suulakepuristussuuttimeen. Suulake antaa liikkuvalle pehmeälle muoville profiilimuodon sen kulkiessaan läpi. Nyt ekstrudaatti menee vesihauteen läpi jäähdytystä varten. Muita tekniikoita, joita AGS-TECH Inc. on käyttänyt useiden vuosien ajan, ovat: • PIPE & TUBING EXTRUSION : Muoviputket muodostuvat, kun muovi ekstrudoidaan pyöreän muotoilusuuttimen läpi ja jäähdytetään vesihauteessa, sitten leikataan pituuteen tai kelataan/kelataan. Kirkas tai värillinen, raidallinen, yksi- tai kaksiseinäinen, joustava tai jäykkä, PE, PP, polyuretaani, PVC, nailon, PC, silikoni, vinyyli tai muuten, meillä on kaikki. Meillä on varastossa putkia sekä valmiudet tuottaa toiveidesi mukaan. AGS-TECH valmistaa putkia FDA-, UL- ja LE-vaatimusten mukaisesti lääketieteellisiin, sähköisiin ja elektronisiin, teollisiin ja muihin sovelluksiin. • YLIVAIPKO / YLIVAIPKO EXTRUSION : Tämä tekniikka levittää muovisen ulomman kerroksen olemassa olevaan johtoon tai kaapeliin. Eristysjohdomme valmistetaan tällä menetelmällä. • COEXTRUSION : Useita materiaalikerroksia ekstrudoidaan samanaikaisesti. Useat kerrokset toimitetaan useilla ekstruudereilla. Eri kerrospaksuudet voidaan säätää asiakkaan toiveiden mukaan. Tämä prosessi mahdollistaa useiden polymeerien käytön, joilla kullakin on erilainen toiminnallisuus tuotteessa. Tämän seurauksena voidaan optimoida useita ominaisuuksia. • YHDISTEKRUUSIO: Yksi tai useampi polymeeri sekoitetaan lisäaineiden kanssa muoviyhdisteen saamiseksi. Kaksoisruuviekstruuderimme tuottavat seospuristeja. Suulakepuristusmuotit ovat yleensä edullisia metallimuotteihin verrattuna. Jos maksat paljon enemmän kuin muutama tuhat dollaria pienestä tai keskikokoisesta suulakepuristussuuttimesta, joka puristaa alumiinia, maksat todennäköisesti liikaa. Olemme asiantuntijoita määrittämään, mikä tekniikka on kustannustehokkain, nopein ja sopivin sovellukseesi. Joskus osan suulakepuristaminen ja sitten koneistus voi säästää paljon rahaa. Ennen kuin teet varman päätöksen, kysy meiltä ensin mielipiteemme. Olemme auttaneet monia asiakkaita tekemään oikeita päätöksiä. Joitakin laajalti käytettyjä metallipursotuksia varten voit ladata esitteemme ja luettelomme napsauttamalla alla olevaa värillistä tekstiä. Jos se on tarpeidesi mukainen valmis tuote, se on taloudellisempi. Lataa lääketieteelliset putket ja putkien suulakepuristusominaisuudet Lataa ekstrudoidut jäähdytyslevymme • EXTRUSIONS TOISIJAISET VALMISTUS- JA VALMISTUSPROSESSIT: Suulakepuristetuille tuotteille tarjoamiamme lisäarvoprosesseja ovat: -Räätälöity putkien ja putken taivutus, muotoilu ja muotoilu, putken katkaisu, putken päiden muotoilu, putken kelaus, koneistus ja viimeistely, reikien poraus ja lävistys ja lävistys, -Räätälöidyt putki- ja putkikokoonpanot, putkikokoonpanot, hitsaus, juotto ja juottaminen -Räätälöity ekstruusiotaivutus, muotoilu ja muotoilu -Puhdistus, rasvanpoisto, peittaus, passivointi, kiillotus, anodisointi, pinnoitus, maalaus, lämpökäsittely, hehkutus ja kovetus, merkintä, kaiverrus ja etiketöinti, tilauspakkaus. CLICK Product Finder-Locator Service EDELLINEN SIVU
- Casting and Machined Parts, CNC Manufacturing, Milling, Turning, Swiss
Casting and Machined Parts, CNC Manufacturing, Milling, Turning, Swiss Type Machining, Die Casting, Investment Casting, Lost Foam Cast Parts from AGS-TECH Inc. Valu ja koneistus Räätälöidyt valu- ja koneistustekniikkamme ovat kulutus- ja ei-kuluvat valut, rauta- ja ei-rautametallivalut, hiekka-, muotti-, keskipako-, jatkuva-, keraaminen muotti, investointi, kadonnut vaahto, lähes verkkomuoto, pysyvä muotti (painovoimavalu), kipsi muotit (kipsivalu) ja vaippavalut, koneistetut osat, jotka valmistetaan jyrsinnällä ja sorvauksella tavanomaisilla sekä CNC-laitteilla, sveitsiläinen koneistus korkean suorituskyvyn halpoja pieniä tarkkuusosia varten, ruuvityöstö kiinnikkeille, ei-perinteinen koneistus. Muista, että metallien ja metalliseosten lisäksi koneistamme myös keraamisia, lasi- ja muovikomponentteja joissain tapauksissa, kun muotin valmistus ei ole houkuttelevaa tai vaihtoehto. Polymeerimateriaalien työstö vaatii erikoiskokemusta, joka meillä on, koska muovit ja kumi asettavat haasteeseen pehmeyden, jäykkyyden jne. vuoksi. Katso lisätietoja keramiikan ja lasin koneistamisesta sivultamme Ei-perinteinen valmistus. AGS-TECH Inc. valmistaa ja toimittaa sekä kevyitä että raskaita valukappaleita. Olemme toimittaneet metallivaluja ja koneistettuja osia kattiloihin, lämmönvaihtimiin, autoihin, mikromoottoreihin, tuuliturbiineihin, elintarvikepakkauslaitteisiin ja muihin. Suosittelemme, että napsautat tätä LATAA AGS-TECH Inc:n kaaviomaiset kuvaukset koneistus- ja valuprosesseista. Tämä auttaa sinua ymmärtämään paremmin alla tarjoamamme tiedot. Katsotaanpa joitain tarjoamistamme erilaisista tekniikoista yksityiskohtaisesti: • KÄYTETTÄVÄN MUOTTIEN VALU: Tämä laaja luokka viittaa menetelmiin, joissa käytetään väliaikaisia ja kertakäyttöisiä muotteja. Esimerkkejä ovat hiekka, kipsi, kuori, investointi (kutsutaan myös kadonneeksi vahaksi) ja kipsivalu. • HIEKAN VALU: Prosessi, jossa hiekkaa käytetään muottimateriaalina. Hyvin vanha menetelmä ja edelleen erittäin suosittu siinä määrin, että suurin osa valmistetuista metallivaluista on valmistettu tällä tekniikalla. Alhaiset kustannukset jopa pienillä tuotantomäärillä. Soveltuu pienten ja suurten osien valmistukseen. Tekniikalla voidaan valmistaa osia muutamassa päivässä tai viikossa hyvin pienin investoinnein. Kostea hiekka liimataan yhteen käyttämällä savea, sideaineita tai erikoisöljyjä. Hiekka sisältyy yleensä muottilaatikoihin ja ontelo- ja porttijärjestelmät luodaan tiivistämällä hiekkaa mallien ympärille. Prosessit ovat: 1.) Mallin asettaminen hiekkaan muotin valmistamiseksi 2.) Mallin ja hiekan liittäminen porttijärjestelmään 3.) Mallin poistaminen 4.) Muotin ontelon täyttö sulalla metallilla 5.) Metallin jäähdytys 6.) Hiekkamuotin rikkominen ja valukappaleen poistaminen • KIPSIMUOTTIVALUN : Hiekan sijasta muottimateriaalina käytetään kipsiä. Lyhyet tuotannon läpimenoajat kuten hiekkavalu ja edullinen. Hyvät mittatoleranssit ja pintakäsittely. Sen suurin haitta on, että sitä voidaan käyttää vain alhaisen sulamispisteen metallien, kuten alumiinin ja sinkin, kanssa. • SHELL MUOTTAVALU: Samanlainen kuin hiekkavalu. Muotin onkalo saadaan karkaistulla hiekkakuorella ja lämpökovettuvalla hartsisideaineella hiekalla täytetyn pullon sijaan kuten hiekkavaluprosessissa. Melkein mikä tahansa hiekkavalattavaksi sopiva metalli voidaan valaa kuorivalulla. Prosessi voidaan tiivistää seuraavasti: 1.) Kuorimuotin valmistus. Käytetty hiekka on paljon pienempää raekokoa verrattuna hiekkavalussa käytettävään hiekkaan. Hieno hiekka sekoitetaan lämpökovettuvan hartsin kanssa. Metallikuvio on päällystetty irrotusaineella kuoren poistamisen helpottamiseksi. Tämän jälkeen metallikuvio kuumennetaan ja hiekkaseos huokotetaan tai puhalletaan kuumavalukuvion päälle. Kuvion pintaan muodostuu ohut kuori. Tämän kuoren paksuutta voidaan säätää vaihtelemalla aikaa, jonka hiekkahartsiseos on kosketuksissa metallikuvion kanssa. Irtonainen hiekka poistetaan sitten kuoren peittämän kuvion jälkeen. 2.) Seuraavaksi kuori ja kuvio kuumennetaan uunissa niin, että kuori kovettuu. Kun kovettuminen on valmis, kuori irrotetaan kuviosta käyttämällä kuvioon sisäänrakennettuja tappeja. 3.) Kaksi tällaista kuorta kootaan yhteen liimaamalla tai puristamalla, ja ne muodostavat täydellisen muotin. Nyt vaippamuotti työnnetään säiliöön, jossa se on tuettu hiekalla tai metallikuulilla valuprosessin aikana. 4.) Nyt kuuma metalli voidaan kaataa kuori muottiin. Vaippavalun etuja ovat tuotteet, joissa on erittäin hyvä pintakäsittely, mahdollisuus valmistaa monimutkaisia osia suurella mittatarkkuudella, prosessi on helppo automatisoida, taloudellinen suuriin tuotantomääriin. Haittapuolena on, että muotit edellyttävät hyvää ilmanvaihtoa kaasujen vuoksi, joita syntyy sulan metallin kosketuksessa sideainekemikaaliin, lämpökovettuvat hartsit ja metallikuviot ovat kalliita. Metallikuvioiden hinnasta johtuen tekniikka ei välttämättä sovellu pieniin tuotantomääriin. • INVESTOINNUSVALUN (tunnetaan myös nimellä LOST-WAX CASTING): Myös hyvin vanha tekniikka ja soveltuu laadukkaiden osien valmistukseen suurella tarkkuudella, toistettavuudella, monipuolisuudella ja eheydellä monista metalleista, tulenkestävistä materiaaleista ja erityisistä korkean suorituskyvyn metalliseoksista. Voidaan valmistaa niin pieniä kuin suuriakin osia. Kallis prosessi verrattuna joihinkin muihin menetelmiin, mutta suuri etu on mahdollisuus valmistaa osia, joilla on lähes verkkomuoto, monimutkaiset ääriviivat ja yksityiskohdat. Joten kustannuksia kompensoi jossain tapauksissa uudelleentyöstön ja koneistuksen poistaminen. Vaikka vaihteluita voi olla, tässä on yhteenveto yleisestä sijoitusprosessista: 1.) Alkuperäisen mestarikuvion luominen vahasta tai muovista. Jokainen valu tarvitsee yhden kuvion, koska ne tuhoutuvat prosessissa. Myös muottia, josta kuvioita valmistetaan, tarvitaan ja useimmiten muotti valetaan tai koneistetaan. Koska muottia ei tarvitse avata, voidaan saavuttaa monimutkaisia valukappaleita, monia vahakuvioita voidaan yhdistää kuten puun oksia ja kaataa yhteen, mikä mahdollistaa useiden osien valmistamisen yhdestä metallin tai metalliseoksen kaatamisesta. 2.) Seuraavaksi kuvio kastetaan tai kaadetaan tulenkestävällä lietteellä, joka koostuu erittäin hienorakeisesta piidioksidista, vedestä ja sideaineista. Tämä johtaa keraamiseen kerrokseen kuvion pinnalle. Kuvion tulenkestävä pinnoite jätetään kuivumaan ja kovettumaan. Tästä vaiheesta tulee nimi investointivalu: Tulenkestävä liete sijoitetaan vahakuvion päälle. 3.) Tässä vaiheessa kovettunut keraaminen muotti käännetään ylösalaisin ja kuumennetaan niin, että vaha sulaa ja valuu ulos muotista. Jäljelle jätetään onkalo metallivalua varten. 4.) Kun vaha on poistunut, keraaminen muotti kuumennetaan vielä korkeampaan lämpötilaan, mikä johtaa muotin vahvistumiseen. 5.) Metallivalu kaadetaan kuumaan muottiin täyttäen kaikki monimutkaiset osat. 6.) Valun annetaan jähmettyä 7.) Lopuksi keraaminen muotti rikotaan ja valmistetut osat leikataan puusta. Tässä on linkki Investment Casting Plant -esitteeseen • HAISUUSKUVIOINNIN VALU: Prosessissa käytetään kuviota, joka on valmistettu materiaalista, kuten polystyreenivaahdosta, joka haihtuu, kun kuumaa sulaa metallia kaadetaan muottiin. Tätä prosessia on kahta tyyppiä: LOST FOAM CASTING, jossa käytetään sitomatonta hiekkaa, ja FULL MOLD CASTING, jossa käytetään sidottua hiekkaa. Tässä ovat yleiset prosessin vaiheet: 1.) Valmista kuvio materiaalista, kuten polystyreenistä. Kun valmistetaan suuria määriä, kuvio muovataan. Jos osalla on monimutkainen muoto, useita tällaisen vaahtomateriaalin osia on ehkä liitettävä yhteen kuvion muodostamiseksi. Usein pinnoitamme kuvion tulenkestävällä seoksella hyvän pinnan viimeistelyn aikaansaamiseksi. 2.) Kuvio laitetaan sitten muovaushiekkaan. 3.) Sula metalli kaadetaan muottiin haihduttamalla vaahtomuovikuvio eli polystyreeni useimmissa tapauksissa sen virratessa muotin ontelon läpi. 4.) Sula metalli jätetään hiekkamuottiin kovettumaan. 5.) Kun se on kovettunut, poistamme valukappaleen. Joissakin tapauksissa valmistamamme tuote vaatii ytimen kuviossa. Haihdutusvalussa ydintä ei tarvitse asettaa ja kiinnittää muottipesään. Tekniikka soveltuu erittäin monimutkaisten geometrioiden valmistukseen, se on helposti automatisoitavissa suuria volyymeja varten, eikä valuosassa ole jakolinjoja. Perusprosessi on yksinkertainen ja taloudellinen toteuttaa. Suuren volyymin tuotannossa, koska kuvioiden valmistamiseksi polystyreenistä tarvitaan muotti tai muotti, tämä voi olla jonkin verran kallista. • EI LAAJENNETTUVA MUOTTIEN VALU: Tämä laaja luokka viittaa menetelmiin, joissa muottia ei tarvitse uudistaa jokaisen tuotantosyklin jälkeen. Esimerkkejä ovat kesto-, paine-, jatkuva- ja keskipakovalu. Toistettavuus saavutetaan ja osat voidaan luonnehtia LÄHELLÄ VERKKOMUOKSI. • PYSYVÄ MUOTTAVALU: Metallista valmistettuja uudelleenkäytettäviä muotteja käytetään useisiin valuihin. Pysyvää muottia voidaan yleensä käyttää kymmeniä tuhansia kertoja ennen kuin se kuluu loppuun. Muotin täyttämiseen käytetään yleensä painovoimaa, kaasun painetta tai tyhjiötä. Muotit (kutsutaan myös suulakkeiksi) on yleensä valmistettu raudasta, teräksestä, keraamisesta tai muista metalleista. Yleinen prosessi on: 1.) Kone ja luo muotti. On tavallista työstää muotti kahdesta metallikappaleesta, jotka sopivat yhteen ja voidaan avata ja sulkea. Sekä osien ominaisuudet että porttijärjestelmä koneistetaan yleensä valumuottiin. 2.) Sisäiset muotin pinnat on päällystetty lietteellä, joka sisältää tulenkestäviä materiaaleja. Tämä auttaa säätelemään lämmön virtausta ja toimii voiteluaineena, joka helpottaa valuosan irrottamista. 3.) Seuraavaksi pysyvät muotin puolikkaat suljetaan ja muotti kuumennetaan. 4.) Sula metalli kaadetaan muottiin ja annetaan rauhassa jähmettyä. 5.) Ennen kuin paljon jäähtymistä tapahtuu, poistamme osan pysyvästä muotista ejektoreilla, kun muotin puolikkaat avataan. Käytämme usein pysyvää muottivalua matalan sulamispisteen metalleille, kuten sinkille ja alumiinille. Teräsvaluissa käytämme muottimateriaalina grafiittia. Joskus saamme monimutkaisia geometrioita käyttämällä kestäviä muotteja sisältäviä ytimiä. Tämän tekniikan etuja ovat valut, joilla on hyvät mekaaniset ominaisuudet, jotka saadaan nopealla jäähdytyksellä, ominaisuuksien tasaisuus, hyvä tarkkuus ja pinnan viimeistely, alhaiset hylkäysnopeudet, mahdollisuus automatisoida prosessi ja tuottaa suuria määriä taloudellisesti. Haittoja ovat korkeat alkuasennuskustannukset, jotka tekevät siitä sopimattomaksi pienikokoisiin toimintoihin, ja valmistettujen osien koon rajoitukset. • SULAVALUS: Muotti työstetään ja sula metalli työnnetään korkealla paineella muotin onteloihin. Sekä ei-rautametallien että rautametallien painevalut ovat mahdollisia. Prosessi soveltuu suurten määrien tuotantosarjoihin pienistä ja keskikokoisista osista, joissa on yksityiskohdat, erittäin ohuet seinät, mittojen tasaisuus ja hyvä pintakäsittely. AGS-TECH Inc. pystyy valmistamaan tällä tekniikalla jopa 0,5 mm:n seinämän paksuuksia. Kuten pysyvässä muottivalussa, muotin tulee koostua kahdesta puolikkaasta, jotka voivat avautua ja sulkeutua valmistetun osan poistamiseksi. Painevalumuotissa voi olla useita onteloita, jotta voidaan tuottaa useita valukappaleita kullakin syklillä. Painevalumuotit ovat erittäin raskaita ja paljon suurempia kuin niiden valmistamat osat, joten myös kalliita. Korjaamme ja vaihdamme kuluneet muotit asiakkaillemme maksutta niin kauan kuin he tilaavat osansa meiltä. Suulakkeillamme on pitkä käyttöikä useiden satojen tuhansien syklien alueella. Tässä on yksinkertaistetun prosessin perusvaiheet: 1.) Muotin valmistus yleensä teräksestä 2.) Muotti asennettu painevalukoneeseen 3.) Mäntä pakottaa sulan metallin virtaamaan suulakkeen onteloissa täyttäen monimutkaiset piirteet ja ohuet seinät 4.) Kun muotti on täytetty sulalla metallilla, valukappaleen annetaan kovettua paineen alaisena 5.) Muotti avataan ja valu poistetaan ejektorin tappien avulla. 6.) Nyt tyhjät suuttimet voidellaan uudelleen ja ne kiinnitetään seuraavaa sykliä varten. Painevalussa käytämme usein puristusmuovausta, jossa lisäämme muottiin lisäosan ja valetaan metalli sen ympärille. Kiinteytymisen jälkeen näistä osista tulee osa valutuotetta. Painevalun etuja ovat osien hyvät mekaaniset ominaisuudet, monimutkaisten ominaisuuksien mahdollisuus, hienot yksityiskohdat ja hyvä pintakäsittely, korkeat tuotantonopeudet, helppo automatisointi. Haitat ovat: Ei kovin sopiva pieneen tilavuuteen korkeiden muotti- ja laitekustannusten vuoksi, valaettavien muotojen rajoitukset, pienet pyöreät jäljet valuosissa, jotka johtuvat ejektorin tappien kosketuksesta, ohut metallin välähdys irtoamislinjasta, tarve suuttimen välisen jakolinjan tuuletusaukkojen osalta tarve pitää muotin lämpötilat alhaisina käyttämällä veden kiertoa. • KESKIPAKOVALUN : Sula metalli kaadetaan pyörivän muotin keskelle pyörimisakselin kohdalta. Keskipakovoimat heittävät metallin reunaa kohti ja sen annetaan jähmettyä muotin pyöriessä. Voidaan käyttää sekä vaaka- että pystyakselin kiertoa. Osat, joissa on pyöreä sisäpinta, sekä muita ei-pyöreitä muotoja voidaan valaa. Prosessi voidaan tiivistää seuraavasti: 1.) Sula metalli kaadetaan keskipakomuottiin. Sitten metalli pakotetaan ulkoseiniin muotin pyörimisen vuoksi. 2.) Kun muotti pyörii, metallivalu kovettuu Keskipakovalu on sopiva tekniikka onttojen sylinterimäisten osien, kuten putkien, valmistukseen, ei tarvita putkia, nousuputkia ja porttielementtejä, hyvä pinnan viimeistely ja yksityiskohtaiset ominaisuudet, ei kutistumisongelmia, mahdollisuus valmistaa pitkiä putkia, joilla on erittäin suuri halkaisija, korkea tuotantokapasiteetti . • JATKUVA VALU ( STRAND CASTING ): Käytetään jatkuvan metallin valumiseen. Periaatteessa sula metalli valetaan muotin kaksiulotteiseen profiiliin, mutta sen pituus on määrittelemätön. Uutta sulaa metallia syötetään jatkuvasti muottiin, kun valu kulkee alaspäin pituuden kasvaessa ajan myötä. Metallit, kuten kupari, teräs ja alumiini, valetaan pitkiksi säikeiksi jatkuvalla valuprosessilla. Prosessilla voi olla useita konfiguraatioita, mutta yleinen voidaan yksinkertaistaa seuraavasti: 1.) Sula metalli kaadetaan korkealla muotin yläpuolella olevaan astiaan hyvin lasketuilla määrillä ja virtausnopeuksilla ja virtaa vesijäähdytetyn muotin läpi. Muottiin kaadettu metallivalu jähmettyy muotin pohjalle sijoitetuksi starttitankoon. Tämä aloitustanko antaa teloille jotain tarttua aluksi. 2.) Rullat kantavat pitkää metallinauhaa tasaisella nopeudella. Telat muuttavat myös metallisäikeen virtaussuuntaa pystysuorasta vaakasuoraan. 3.) Kun jatkuva valu on kulkenut tietyn vaakamatkan, valun mukana liikkuva taskulamppu tai saha leikkaa sen nopeasti haluttuihin pituuksiin. Jatkuva valuprosessi voidaan integroida ROLLING PROCESSiin, jossa jatkuvasti valettu metalli voidaan syöttää suoraan valssaamolle I-palkkien, T-palkkien jne. valmistamiseksi. Jatkuva valu tuottaa yhtenäiset ominaisuudet koko tuotteelle, sillä on korkea jähmettymisnopeus, se alentaa kustannuksia erittäin alhaisen materiaalihäviön vuoksi, tarjoaa prosessin, jossa metallin kuormaus, kaataminen, jähmettyminen, leikkaus ja valun poisto tapahtuvat jatkuvassa toiminnassa ja tuloksena on korkea tuottavuus ja korkea laatu. Tärkeä näkökohta on kuitenkin korkea alkuinvestointi, asennuskustannukset ja tilantarve. • TYÖSTÖPALVELUT: Tarjoamme kolmen, neljän ja viiden akselin koneistusta. Käyttämämme työstöprosesseja ovat SORVAUS, JYRSINTÄ, PORAUS, PORAUS, AVENEMINEN, HÖYLÄYS, SAHAUS, HIOMAUS, LIPOTUS, KIOLTO ja EI-PERINTEINEN TYÖSTÖ, jota käsitellään tarkemmin verkkosivustomme eri valikoissa. Käytämme suurimmassa osassa tuotannostamme CNC-koneita. Kuitenkin joihinkin operaatioihin perinteiset tekniikat sopivat paremmin ja siksi luotamme myös niihin. Koneistuskykymme saavuttavat korkeimman mahdollisen tason ja jotkin vaativimmat osat valmistetaan AS9100-sertifioidussa tehtaassa. Suihkumoottorien siivet vaativat erittäin erikoistuneen valmistuskokemuksen ja oikean laitteiston. Ilmailuteollisuudella on erittäin tiukat standardit. Jotkut komponentit, joilla on monimutkainen geometrinen rakenne, on helpoimmin valmistaa viisiakselisella työstyksellä, jota löytyy vain joistakin koneistuslaitoksista, mukaan lukien meidän. Ilmailu-sertifioidulla tehtaallamme on tarvittava kokemus ilmailuteollisuuden laajan dokumentointivaatimuksen mukaisesti. KORVAUStoiminnoissa työkappaletta pyöritetään ja liikutetaan leikkaustyökalua vasten. Tätä prosessia varten käytetään konetta nimeltä sorvi. JYRSINTÄ koneessa, jota kutsutaan jyrsintäkoneeksi, on pyörivä työkalu, joka tuo leikkuureunat vasten työkappaletta. PORAUStoiminnot sisältävät pyörivän leikkurin, jossa on leikkuureunat, jotka muodostavat reikiä joutuessaan kosketuksiin työkappaleen kanssa. Yleensä käytetään poranpuristimia, sorveja tai myllyjä. PORAUSoperaatioissa työkalu, jossa on yksi taivutettu teräväkärkinen kärki, siirretään pyörivän työkappaleen karkeaan reikään, mikä suurentaa hieman reikää ja parantaa tarkkuutta. Sitä käytetään hienoja viimeistelytarkoituksiin. AVENNUS tarkoittaa hammastettua työkalua materiaalin poistamiseksi työkappaleesta yhdellä avennuksella (hammastyökalu). Lineaarisessa avennuksessa avennin kulkee lineaarisesti työkappaleen pintaa vasten leikkauksen aikaansaamiseksi, kun taas kiertoavennuksen yhteydessä avennin pyöritetään ja puristetaan työkappaleeseen akselisymmetrisen muodon leikkaamiseksi. SWISS TYPE MACHINING on yksi arvokkaista tekniikoistamme, joita käytämme pienten erittäin tarkkojen osien suuren volyymin valmistukseen. Sveitsiläisen sorvin avulla sorvaamme pieniä, monimutkaisia, tarkkoja osia edullisesti. Toisin kuin perinteiset sorvit, joissa työkappale pidetään paikallaan ja työkalu liikkuu, sveitsiläisissä sorvauskeskuksissa työkappaleen annetaan liikkua Z-akselilla ja työkalu on paikallaan. Sveitsin tyyppisessä koneistuksessa tankovarasto pidetään koneessa ja viedään eteenpäin z-akselin ohjausholkin kautta, jolloin vain koneistettava osa tulee näkyviin. Näin varmistetaan tiukka pito ja tarkkuus on erittäin korkea. Jännitteisten työkalujen saatavuus tarjoaa mahdollisuuden jyrsimiseen ja poraamiseen materiaalin edetessä ohjausholkista. Sveitsin tyyppisten laitteiden Y-akseli tarjoaa täyden jyrsintäkyvyn ja säästää huomattavasti valmistusaikaa. Lisäksi koneissamme on porat ja poraustyökalut, jotka toimivat osalla, kun sitä pidetään alakarassa. Swiss-Type-työstökykymme antaa meille täysin automatisoidun täydellisen koneistuksen yhdessä työvaiheessa. Koneistus on yksi AGS-TECH Inc:n liiketoiminnan suurimmista segmenteistä. Käytämme sitä joko ensisijaisena tai toissijaisena toimenpiteenä osan valun tai suulakepuristamisen jälkeen, jotta kaikki piirustusvaatimukset täyttyvät. • PINNAN VIIMEISTELYPALVELUT: Tarjoamme laajan valikoiman pintakäsittelyjä ja pintakäsittelyjä, kuten pintakäsittelyä tarttuvuuden parantamiseksi, ohuen oksidikerroksen levittämistä pinnoitteen tarttuvuuden parantamiseksi, hiekkapuhallus, kemiallinen kalvo, anodisointi, nitraus, jauhemaalaus, ruiskupinnoitus , erilaisia edistyneitä metallointi- ja pinnoitustekniikoita, mukaan lukien sputterointi, elektronisuihku, haihdutus, pinnoitus, kovat pinnoitteet, kuten timantin kaltainen hiili (DLC) tai titaanipinnoite poraus- ja leikkaustyökaluihin. • TUOTTEIDEN MERKINTÄ- JA MERKINNÄT PALVELUT: Monet asiakkaamme tarvitsevat merkintöjä ja etiketöintejä, lasermerkintöjä ja kaiverruksia metalliosiin. Jos sinulla on tällainen tarve, keskustelemme siitä, mikä vaihtoehto on sinulle paras. Tässä on joitain yleisesti käytettyjä metallivalutuotteita. Koska nämä ovat valmiita, voit säästää muottikustannuksissa, jos jokin näistä sopii tarpeisiisi: NAPSAUTA TÄSTÄ LATAAksesi AGS-Electronicsin 11-sarjan painevaletut alumiinilaatikot CLICK Product Finder-Locator Service EDELLINEN SIVU
- Custom Manufactured Parts, Assemblies, Plastic Mold, Casting,Machining
Custom Manufactured Parts, Assemblies, Plastic Mold, Rubber Molding, Metal Casting, CNC Machining, Turning, Milling, Electrical Electronic Optical Assembly PCBA Mittatilaustyönä valmistetut osat ja kokoonpanot ja tuotteet Lue lisää Muoviset ja kumiset muotit ja valu Lue lisää Valu ja koneistus Lue lisää Ekstruusio, suulakepuristetut tuotteet Lue lisää Meistot ja ohutlevyjen valmistus Lue lisää Metallin taonta ja jauhemetallurgia Lue lisää Langan ja jousimuodostus Lue lisää Lasin ja keramiikan muotoilu ja muotoilu Lue lisää Lisäaine ja nopea valmistus Lue lisää Komposiittien ja komposiittimateriaalien valmistus Lue lisää Liitos- ja kokoonpano- ja kiinnitysprosessit Tuotamme sinulle osia ja kokoonpanoja ja tarjoamme seuraavat valmistusprosessit: • Muovi- ja kumimuotit ja valetut osat. Ruiskupuristus, lämpömuovaus, lämpökovettuva muovaus, tyhjiömuovaus, puhallusmuovaus, rotaatiomuovaus, valumuovaus, terämuovaus ja muut. • Muovi-, kumi- ja metallipuristukset • Jyrsintä- ja sorvaustekniikoilla valmistetut rauta- ja ei-rautametallivalut ja koneistetut osat, sveitsiläinen koneistus. • Jauhemetallurgiset osat • Metallien ja ei-metallisten meistot, ohutlevyjen muovaus, hitsatut peltikokoonpanot • Kylmä ja kuuma taonta • Johdot, hitsauslankakokoonpanot, langanmuovaus • Erityyppiset jouset, jousimuodostus • Vaihteistovalmistus, vaihteisto, kytkin, mato, nopeudenrajoitin, sylinteri, voimansiirtohihnat, voimansiirtoketjut, voimansiirtokomponentit • Räätälöity karkaistu ja luodinkestävä lasi, joka on NATO- ja sotilasstandardien mukainen • Kuulat, laakerit, hihnapyörät ja hihnapyöräkokoonpanot • Venttiilit ja pneumaattiset komponentit, kuten O-rengas, aluslevy ja tiivisteet • Lasi- ja keraamiset osat ja kokoonpanot, tyhjiön kestävät ja hermeettiset komponentit, metalli-keramiikka ja keramiikka-keraamiliitos. • Erityyppiset mekaaniset, optomekaaniset, sähkömekaaniset, optoelektroniset kokoonpanot. • Metalli-kumi, metalli-muovi liimaus • Putket ja putket, putkien muotoilu, taivutus ja räätälöidyt putkikokoonpanot, palkeiden valmistus. • Lasikuidun valmistus • Hitsaus eri tekniikoilla, kuten pistehitsaus, laserhitsaus, MIG, TIG. Ultraäänihitsaus muoviosille. • Laaja valikoima pintakäsittelyjä ja pintakäsittelyjä, kuten pintakäsittely tarttuvuuden parantamiseksi, ohuen oksidikerroksen kerrostaminen pinnoitteen tarttuvuuden parantamiseksi, hiekkapuhallus, kemiallinen kalvo, anodisointi, nitraus, jauhemaalaus, ruiskupinnoitus, erilaiset edistyneet metallointi- ja pinnoitustekniikat mukaan lukien sputterointi, elektronisuihku, haihdutus, pinnoitus, kovat pinnoitteet, kuten timantin kaltainen hiili (DLC) tai titaani leikkaus- ja poraustyökaluihin. • Merkintä ja etiketöinti, lasermerkintä metalliosiin, painatus muovi- ja kumiosiin Lataa esite suunnittelijoiden ja insinöörien käyttämistä yleisistä konetekniikan termeistä Rakennamme tuotteita erityisten eritelmien ja vaatimusten mukaan. Voidaksemme tarjota sinulle parasta laatua, toimitusta ja hintoja, valmistamme tuotteita maailmanlaajuisesti Kiinassa, Intiassa, Taiwanissa, Filippiineillä, Etelä-Koreassa, Malesiassa, Sri Lankassa, Turkissa, Yhdysvalloissa, Kanadassa, Saksassa, Isossa-Britanniassa ja Japanissa. Tämä tekee meistä paljon vahvempia ja maailmanlaajuisesti kilpailukykyisempiä kuin mikään muu custom manufacturer. Tuotteemme valmistetaan ISO9001:2000, QS9000, ISO14001, TS16949 sertifioiduissa ympäristöissä ja niillä on CE-, UL-merkki ja muut alan standardit. Kun meidät on nimetty projektiisi, voimme hoitaa koko valmistuksen, kokoonpanon, testauksen, pätevyyden, toimituksen ja tullin haluamallasi tavalla. Halutessasi voimme varastoida osasi, koota räätälöityjä sarjoja, tulostaa ja merkitä yrityksesi nimen ja tuotemerkin sekä toimittaa lähetyksen asiakkaillesi. Toisin sanoen voimme halutessasi olla myös varasto- ja jakelukeskuksesi. Koska varastomme sijaitsevat lähellä suuria merisatamia, se antaa meille logistista etua. Esimerkiksi kun tuotteesi saapuvat suureen USA:n satamaan, voimme kuljettaa ne suoraan läheiseen varastoon, jossa voimme varastoida, koota, tehdä sarjat, etiketöidä, tulostaa, pakata valintasi mukaan ja pudottaa. lähettää asiakkaillesi. Emme vain toimita tuotteita. Yrityksemme työskentelee räätälöityjen sopimusten mukaisesti, jolloin tulemme paikan päälle, arvioimme projektisi paikan päällä ja kehitämme sinulle räätälöidyn projektiehdotuksen. Lähetämme sitten kokeneen tiimimme toteuttamaan projektin. Lisätietoa suunnittelutyöstämme löydät osoitteesta http://www.ags-engineering.com -Otamme vastaan pieniä projekteja sekä suuria teollisen mittakaavan projekteja. Ensimmäisenä askeleena voimme yhdistää sinut joko puhelimitse, puhelinneuvottelulla tai MSN-messengerillä asiantuntijatiimiimme, jotta voit olla yhteydessä suoraan asiantuntijaan, esittää kysymyksiä ja keskustella projektistasi. Soita meille, niin tulemme tarvittaessa käymään. EDELLINEN SIVU