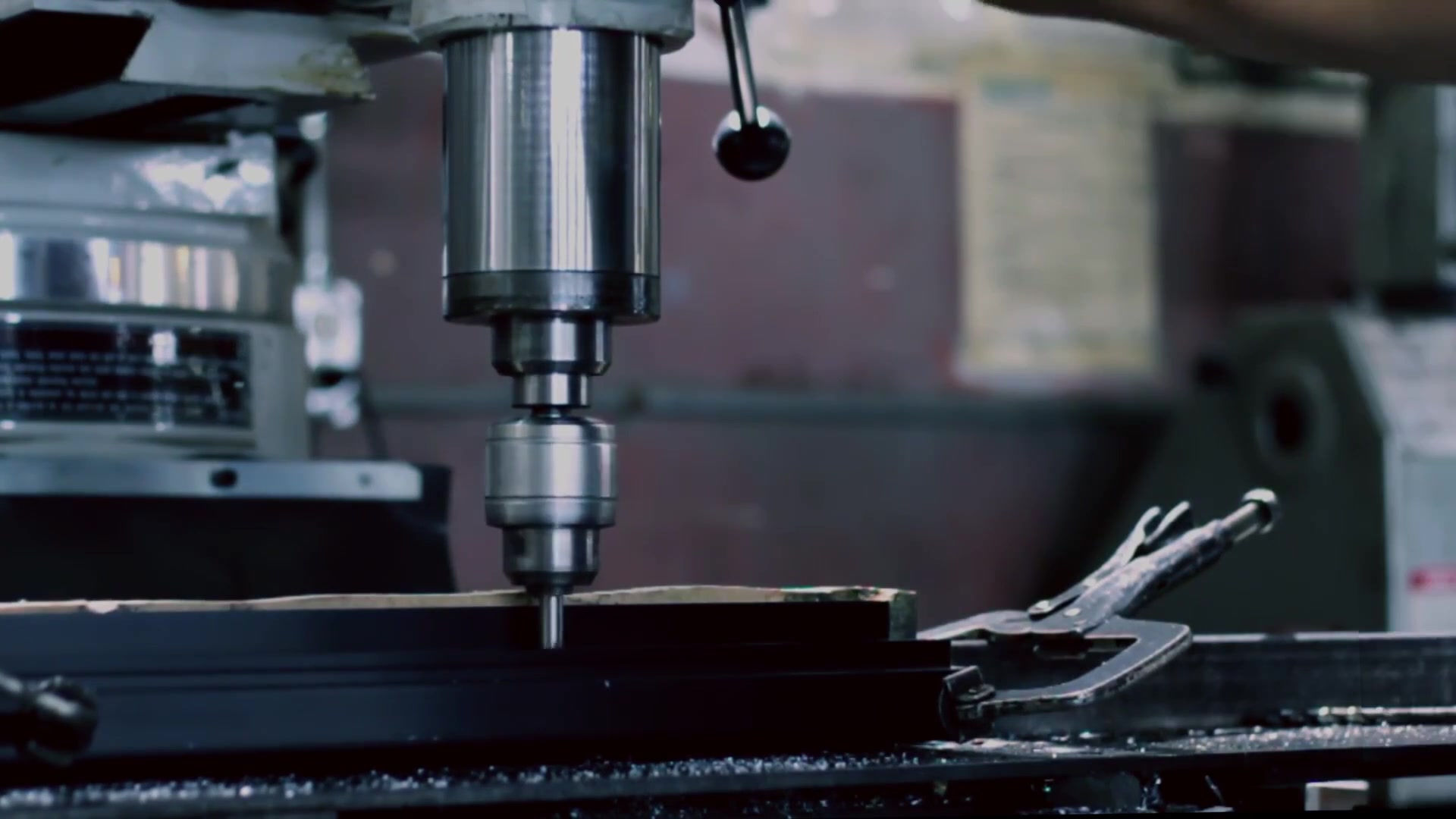
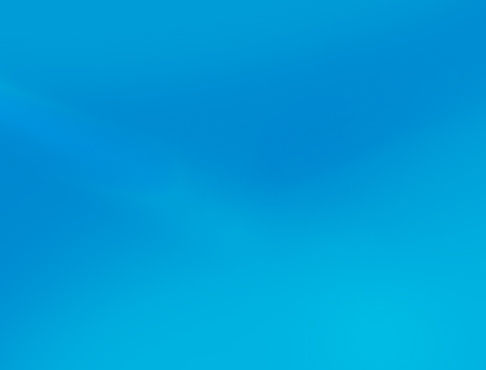
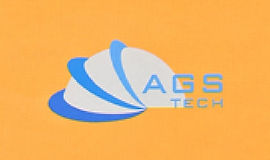
Fabricant mondial sur mesure, intégrateur, consolidateur, partenaire d'externalisation pour une grande variété de produits et services.
Nous sommes votre source unique pour la fabrication, la fabrication, l'ingénierie, la consolidation, l'intégration, l'externalisation de produits et services fabriqués sur mesure et prêts à l'emploi.
Choisissez votre langue
-
Fabrication sur mesure
-
Fabrication sous contrat nationale et mondiale
-
Sous-traitance de fabrication
-
Approvisionnement national et mondial
-
Consolidation
-
Intégration d'ingénierie
-
Services d'ingénierie
ELECTRICAL DISCHARGE MACHINING (EDM), also referred to as SPARK-EROSION or ELECTRODISCHARGE MACHINING, SPARK ERODING, DIE SINKING_cc781905-5cde-3194-bb3b -136bad5cf58d_ou WIRE EROSION, est un NON-CONVENTIONAL MANUFACTURING NON-CONVENTIONAL MANUFACTURING_cc781905-5cde-3194-bb3b-136bad5cf58d où la décharge électrique prend la forme souhaitée des métaux et où la décharge électrique prend la forme souhaitée des métaux. d'étincelles. Nous proposons également certaines variétés d'EDM, à savoir NO-WEAR EDM, WIRE EDM (WEDM), EDM GRINDING (EDG), DIE-SINKING EDM, ELECTRICAL-DISCHARGE MILLING, micro-EDM, m-EDM_cc781905 -5cde-3194-bb3b-136bad5cf58d_and RECTIFICATION PAR DÉCHARGE ÉLECTROCHIMIQUE (ECDG). Nos systèmes EDM se composent d'outils/d'électrodes façonnés et de la pièce à usiner connectés à des alimentations en courant continu et insérés dans un fluide diélectrique électriquement non conducteur. Après 1940, l'usinage par décharge électrique est devenu l'une des technologies de production les plus importantes et les plus populaires dans les industries manufacturières.
Lorsque la distance entre les deux électrodes est réduite, l'intensité du champ électrique dans le volume entre les électrodes devient supérieure à la force du diélectrique en certains points, qui se rompt, formant finalement un pont pour que le courant circule entre les deux électrodes. Un arc électrique intense est généré provoquant un échauffement important pour faire fondre une partie de la pièce et une partie du matériau d'outillage. En conséquence, le matériau est retiré des deux électrodes. En même temps, le fluide diélectrique est chauffé rapidement, ce qui entraîne l'évaporation du fluide dans l'espace d'arc. Une fois que le flux de courant s'arrête ou qu'il est arrêté, la chaleur est évacuée de la bulle de gaz par le fluide diélectrique environnant et la bulle cavite (s'effondre). L'onde de choc créée par l'effondrement de la bulle et l'écoulement du fluide diélectrique chasse les débris de la surface de la pièce et entraîne tout matériau fondu de la pièce dans le fluide diélectrique. Les taux de répétition de ces décharges sont compris entre 50 et 500 kHz, les tensions entre 50 et 380 V et les courants entre 0,1 et 500 Ampères. Un nouveau diélectrique liquide tel que des huiles minérales, du kérosène ou de l'eau distillée et désionisée est généralement acheminé dans le volume inter-électrodes emportant les particules solides (sous forme de débris) et les propriétés isolantes du diélectrique sont restaurées. Après un passage de courant, la différence de potentiel entre les deux électrodes est restaurée à ce qu'elle était avant le claquage, de sorte qu'un nouveau claquage diélectrique liquide peut se produire. Nos machines d'électroérosion (EDM) modernes offrent des mouvements à commande numérique et sont équipées de pompes et de systèmes de filtrage des fluides diélectriques.
L'usinage par décharge électrique (EDM) est une méthode d'usinage principalement utilisée pour les métaux durs ou ceux qui seraient très difficiles à usiner avec les techniques conventionnelles. L'EDM fonctionne généralement avec tous les matériaux qui sont des conducteurs électriques, bien que des méthodes d'usinage de céramiques isolantes avec EDM aient également été proposées. Le point de fusion et la chaleur latente de fusion sont des propriétés qui déterminent le volume de métal retiré par décharge. Plus ces valeurs sont élevées, plus le taux d'enlèvement de matière est lent. Étant donné que le processus d'usinage par décharge électrique n'implique aucune énergie mécanique, la dureté, la résistance et la ténacité de la pièce n'affectent pas le taux d'enlèvement. La fréquence de décharge ou l'énergie par décharge, la tension et le courant sont variés pour contrôler les taux d'enlèvement de matière. Le taux d'enlèvement de matière et la rugosité de surface augmentent avec l'augmentation de la densité de courant et la diminution de la fréquence des étincelles. Nous pouvons découper des contours complexes ou des cavités dans de l'acier pré-trempé à l'aide de l'EDM sans avoir besoin de traitement thermique pour les adoucir et les durcir à nouveau. Nous pouvons utiliser cette méthode avec n'importe quel métal ou alliage métallique comme le titane, l'hastelloy, le kovar et l'inconel. Les applications du procédé EDM comprennent le façonnage d'outils en diamant polycristallin. L'EDM est considérée comme une méthode d'usinage non traditionnelle ou non conventionnelle avec des procédés tels que l'usinage électrochimique (ECM), la découpe au jet d'eau (WJ, AWJ), la découpe au laser. D'autre part, les méthodes d'usinage conventionnelles comprennent le tournage, le fraisage, la rectification, le perçage et d'autres processus dont le mécanisme d'enlèvement de matière est essentiellement basé sur des forces mécaniques. Les électrodes pour l'usinage par électroérosion (EDM) sont en graphite, laiton, cuivre et alliage cuivre-tungstène. Des diamètres d'électrode jusqu'à 0,1 mm sont possibles. Étant donné que l'usure de l'outil est un phénomène indésirable qui affecte négativement la précision dimensionnelle dans l'EDM, nous profitons d'un processus appelé NO-WEAR EDM, en inversant la polarité et en utilisant des outils en cuivre pour minimiser l'usure de l'outil.
Idéalement parlant, l'usinage par décharge électrique (EDM) peut être considéré comme une série de claquage et de restauration du liquide diélectrique entre les électrodes. En réalité cependant, l'évacuation des débris de la zone inter-électrodes est presque toujours partielle. Il en résulte que les propriétés électriques du diélectrique dans la zone inter-électrodes sont différentes de leurs valeurs nominales et varient dans le temps. La distance inter-électrodes (éclateur) est ajustée par les algorithmes de contrôle de la machine spécifique utilisée. L'éclateur dans l'EDM peut malheureusement parfois être court-circuité par les débris. Le système de contrôle de l'électrode peut ne pas réagir assez rapidement pour empêcher les deux électrodes (outil et pièce) de se court-circuiter. Ce court-circuit indésirable contribue à un enlèvement de matière différent du cas idéal. Nous accordons la plus haute importance à l'action de rinçage afin de restaurer les propriétés isolantes du diélectrique afin que le courant passe toujours au point de la zone inter-électrodes, minimisant ainsi la possibilité d'un changement de forme indésirable (endommagement) de l'outil-électrode et pièce à usiner. Pour obtenir une géométrie spécifique, l'outil EDM est guidé le long de la trajectoire souhaitée très près de la pièce sans la toucher. Nous accordons la plus grande attention aux performances du contrôle de mouvement en cours d'utilisation. De cette façon, un grand nombre de décharges/étincelles de courant ont lieu, et chacune contribue à l'enlèvement de matière à la fois de l'outil et de la pièce, où de petits cratères se forment. La taille des cratères est fonction des paramètres technologiques définis pour le travail spécifique à accomplir et les dimensions peuvent aller de l'échelle nanométrique (comme dans le cas des opérations de micro-EDM) à quelques centaines de micromètres dans des conditions d'ébauche. Ces petits cratères sur l'outil provoquent une érosion progressive de l'électrode appelée « usure de l'outil ». Pour contrer l'effet néfaste de l'usure sur la géométrie de la pièce, nous remplaçons en permanence l'électrode-outil au cours d'une opération d'usinage. Parfois, nous y parvenons en utilisant un fil remplacé en permanence comme électrode (ce processus EDM est également appelé WIRE EDM ). Parfois, nous utilisons l'électrode-outil de telle manière que seule une petite partie de celle-ci est réellement engagée dans le processus d'usinage et cette partie est changée régulièrement. C'est par exemple le cas lorsqu'on utilise un disque rotatif comme électrode-outil. Ce processus est appelé EDM GRINDING. Une autre technique encore que nous déployons consiste à utiliser un jeu d'électrodes de tailles et de formes différentes lors d'une même opération d'électroérosion pour compenser l'usure. Nous appelons cette technique à électrodes multiples, et est le plus souvent utilisée lorsque l'électrode de l'outil reproduit en négatif la forme souhaitée et est avancée vers l'ébauche le long d'une seule direction, généralement la direction verticale (c'est-à-dire l'axe z). Cela ressemble à l'évier de l'outil dans le liquide diélectrique dans lequel la pièce est immergée, et par conséquent, il est appelé DIE-SINKING EDM (parfois appelé_cc781905-5cde- 3194-bb3b-136bad5cf58d_CONVENTIONNEL EDM ou RAM EDM). Les machines pour cette opération sont appelées SINKER EDM. Les électrodes pour ce type d'EDM ont des formes complexes. Si la géométrie finale est obtenue à l'aide d'une électrode de forme généralement simple déplacée dans plusieurs directions et soumise également à des rotations, nous l'appelons it EDM MILLING. La quantité d'usure dépend strictement des paramètres technologiques utilisés dans l'opération (polarité, courant maximum, tension en circuit ouvert). Par exemple, in micro-EDM, également appelé m-EDM, ces paramètres sont généralement réglés à des valeurs qui génèrent une usure importante. L'usure est donc un problème majeur dans ce domaine que nous minimisons grâce à notre savoir-faire accumulé. Par exemple, pour minimiser l'usure des électrodes en graphite, un générateur numérique, contrôlable en quelques millisecondes, inverse la polarité lors de l'électro-érosion. Il en résulte un effet similaire à la galvanoplastie qui dépose en continu le graphite érodé sur l'électrode. Dans une autre méthode, un circuit dit '' Zero Wear '', nous minimisons la fréquence de démarrage et d'arrêt de la décharge, en la maintenant allumée aussi longtemps que possible. Le taux d'enlèvement de matière dans l'usinage par électroérosion peut être estimé à partir de :
MRR = 4 x 10 exp(4) x I x Tw exp (-1,23)
Ici, MRR est en mm3/min, I est le courant en ampères, Tw est le point de fusion de la pièce en K-273,15K. L'exp signifie exposant.
D'autre part, le taux d'usure Wt de l'électrode peut être obtenu à partir de :
Poids = ( 1,1 x 10exp(11) ) x I x Ttexp(-2,38)
Ici Wt est en mm3/min et Tt est le point de fusion du matériau d'électrode en K-273.15K
Enfin, le taux d'usure de la pièce à usiner sur l'électrode R peut être obtenu à partir de :
R = 2,25 x Trexp(-2,38)
Ici, Tr est le rapport des points de fusion de la pièce à usiner à l'électrode.
PLOMB EDM :
EDM à encastrer, également appelé CAVITY TYPE EDM or VOLUME EDM, le liquide se compose d'une électrode et d'une pièce isolante submergées. L'électrode et la pièce sont connectées à une alimentation électrique. L'alimentation génère un potentiel électrique entre les deux. Lorsque l'électrode s'approche de la pièce, une rupture diélectrique se produit dans le fluide, formant un canal de plasma, et une petite étincelle saute. Les étincelles frappent généralement une à la fois car il est hautement improbable que différents emplacements dans l'espace inter-électrodes aient des caractéristiques électriques locales identiques qui permettraient à une étincelle de se produire simultanément dans tous ces emplacements. Des centaines de milliers de ces étincelles se produisent à des points aléatoires entre l'électrode et la pièce à usiner par seconde. Au fur et à mesure que le métal de base s'érode et que l'éclateur augmente par la suite, l'électrode est automatiquement abaissée par notre machine CNC afin que le processus puisse se poursuivre sans interruption. Nos équipements ont des cycles de contrôle appelés ''on time'' et ''off time''. Le réglage de l'heure détermine la longueur ou la durée de l'étincelle. Un temps plus long produit une cavité plus profonde pour cette étincelle et toutes les étincelles suivantes pour ce cycle, créant une finition plus rugueuse sur la pièce et vice versa. Le temps d'arrêt est la période de temps pendant laquelle une étincelle est remplacée par une autre. Un temps d'arrêt plus long permet au fluide diélectrique de rincer à travers une buse pour nettoyer les débris érodés, évitant ainsi un court-circuit. Ces paramètres sont ajustés en micro secondes.
FIL EDM :
In WIRE ELECTRICAL DISCHARGE MACHINING (WEDM), also called WIRE-CUT EDM or WIRE CUTTING, we feed a fin fil métallique monobrin en laiton à travers la pièce, qui est immergé dans un réservoir de fluide diélectrique. L'EDM à fil est une variante importante de l'EDM. Nous utilisons occasionnellement l'électroérosion à fil pour couper des plaques jusqu'à 300 mm d'épaisseur et pour fabriquer des poinçons, des outils et des matrices à partir de métaux durs difficiles à usiner avec d'autres méthodes de fabrication. Dans ce processus qui ressemble à la coupe de contour avec une scie à ruban, le fil, qui est constamment alimenté à partir d'une bobine, est maintenu entre des guides diamantés supérieur et inférieur. Les guides commandés par CNC se déplacent dans le plan x-y et le guide supérieur peut également se déplacer indépendamment dans l'axe z-u-v, donnant lieu à la possibilité de couper des formes coniques et de transition (telles que le cercle en bas et le carré à haut). Le guide supérieur peut contrôler les mouvements des axes en x–y–u–v–i–j–k–l–. Cela permet au WEDM de découper des formes très complexes et délicates. Le trait de coupe moyen de nos équipements qui permettent d'obtenir le meilleur coût économique et le meilleur temps d'usinage est de 0,335 mm en utilisant du fil Ø 0,25 en laiton, cuivre ou tungstène. Cependant, les guides diamantés supérieurs et inférieurs de notre équipement CNC sont précis à environ 0,004 mm et peuvent avoir un chemin de coupe ou un trait de coupe aussi petit que 0,021 mm en utilisant un fil de Ø 0,02 mm. Des coupes vraiment étroites sont donc possibles. La largeur de coupe est supérieure à la largeur du fil car des étincelles se produisent des côtés du fil vers la pièce, provoquant une érosion. Ce ''overcut'' est nécessaire, pour de nombreuses applications il est prévisible et peut donc être compensé (en micro-EDM ce n'est pas souvent le cas). Les bobines de fil sont longues : une bobine de 8 kg de fil de 0,25 mm fait un peu plus de 19 kilomètres de long. Le diamètre du fil peut être aussi petit que 20 micromètres et la précision de la géométrie est de l'ordre de +/- 1 micromètre. Nous n'utilisons généralement le fil qu'une seule fois et le recyclons car il est relativement peu coûteux. Il se déplace à une vitesse constante de 0,15 à 9 m/min et une saignée (fente) constante est maintenue pendant une coupe. Dans le processus d'électroérosion à fil, nous utilisons l'eau comme fluide diélectrique, contrôlant sa résistivité et d'autres propriétés électriques avec des filtres et des unités de désionisation. L'eau évacue les débris coupés de la zone de coupe. Le rinçage est un facteur important dans la détermination de la vitesse d'alimentation maximale pour une épaisseur de matériau donnée et nous la gardons donc cohérente. La vitesse de coupe dans l'électroérosion à fil est exprimée en termes de section transversale coupée par unité de temps, par exemple 18 000 mm2/h pour un acier à outils D2 de 50 mm d'épaisseur. La vitesse de coupe linéaire dans ce cas serait de 18 000/50 = 360 mm/h. Le taux d'enlèvement de matière dans l'électroérosion à fil est :
MRR = Vf xhxb
Ici MRR est en mm3/min, Vf est la vitesse d'alimentation du fil dans la pièce en mm/min, h est l'épaisseur ou la hauteur en mm, et b est le trait de coupe, qui est :
b = dw + 2s
Ici, dw est le diamètre du fil et s est l'écart entre le fil et la pièce en mm.
Outre des tolérances plus strictes, nos centres d'usinage de coupe de fil EDM multi-axes modernes ont ajouté des fonctionnalités telles que plusieurs têtes pour couper deux pièces en même temps, des commandes pour prévenir la rupture de fil, des fonctions d'auto-filetage automatique en cas de rupture de fil et programmé stratégies d'usinage pour optimiser l'opération, les capacités de coupe droite et angulaire.
Wire-EDM nous offre de faibles contraintes résiduelles, car il ne nécessite pas d'efforts de coupe élevés pour l'enlèvement de matière. Lorsque l'énergie/puissance par impulsion est relativement faible (comme dans les opérations de finition), on s'attend à peu de changement dans les propriétés mécaniques d'un matériau en raison des faibles contraintes résiduelles.
MEULAGE PAR ÉLECTRO-ÉLECTROCUTION (EDG) : Les meules ne contiennent pas d'abrasifs, elles sont en graphite ou en laiton. Des étincelles répétitives entre la meule en rotation et la pièce enlèvent de la matière des surfaces de la pièce. Le taux d'enlèvement de matière est de :
MRR = K x I
Ici, MRR est en mm3/min, I est le courant en ampères et K est le facteur de matériau de la pièce en mm3/A-min. Nous utilisons fréquemment le meulage par décharge électrique pour scier des fentes étroites sur les composants. Nous combinons parfois le processus EDG (Electrical-Discharge Grinding) avec le processus ECG (Electrochemical Grinding) où la matière est éliminée par action chimique, les décharges électriques de la roue en graphite brisant le film d'oxyde et emportées par l'électrolyte. Le processus est appelé ELECTROCHEMICAL-DISCHARGE GRINDING (ECDG). Même si le processus ECDG consomme relativement plus d'énergie, il s'agit d'un processus plus rapide que l'EDG. Nous meulons principalement des outils en carbure avec cette technique.
Applications de l'usinage par électroérosion :
Fabrication de prototypes :
Nous utilisons le procédé EDM dans la fabrication de moules, la fabrication d'outils et de matrices, ainsi que pour la fabrication de prototypes et de pièces de production, en particulier pour les industries aérospatiale, automobile et électronique dans lesquelles les quantités de production sont relativement faibles. Dans Sinker EDM, une électrode en graphite, en tungstène de cuivre ou en cuivre pur est usinée dans la forme (négative) souhaitée et introduite dans la pièce à usiner à l'extrémité d'un vérin vertical.
Fabrication de matrices de monnaie :
Pour la création de matrices pour la production de bijoux et de badges par le processus de frappe (estampage), le maître positif peut être en argent sterling, car (avec les réglages appropriés de la machine) le maître est considérablement érodé et n'est utilisé qu'une seule fois. La matrice négative résultante est ensuite durcie et utilisée dans un marteau-pilon pour produire des méplats estampés à partir d'ébauches de feuilles découpées en bronze, en argent ou en alliage d'or à faible épreuve. Pour les badges, ces plats peuvent être en outre façonnés en une surface incurvée par une autre matrice. Ce type d'EDM est généralement réalisé immergé dans un diélectrique à base d'huile. L'objet fini peut être encore affiné par un émaillage dur (verre) ou doux (peinture) et/ou électroplaqué avec de l'or pur ou du nickel. Des matériaux plus tendres tels que l'argent peuvent être gravés à la main comme raffinement.
Perçage de petits trous :
Sur nos machines d'électroérosion à fil, nous utilisons l'électroérosion par perçage de petits trous pour faire un trou traversant dans une pièce à travers laquelle passer le fil pour l'opération d'électroérosion à fil. Des têtes d'électroérosion séparées spécialement conçues pour le perçage de petits trous sont montées sur nos machines à découper au fil, ce qui permet d'éroder des pièces finies sur de grandes plaques trempées selon les besoins et sans pré-perçage. Nous utilisons également l'EDM à petits trous pour percer des rangées de trous dans les bords des aubes de turbine utilisées dans les moteurs à réaction. Le flux de gaz à travers ces petits trous permet aux moteurs d'utiliser des températures plus élevées que ce qui serait autrement possible. Les alliages monocristallins à haute température et très durs dont ces lames sont constituées rendent l'usinage conventionnel de ces trous avec un rapport d'aspect élevé extrêmement difficile, voire impossible. D'autres domaines d'application pour l'EDM à petit trou consistent à créer des orifices microscopiques pour les composants du système de carburant. Outre les têtes EDM intégrées, nous déployons des machines EDM de perçage de petits trous autonomes avec axes x-y pour usiner des trous borgnes ou débouchants. L'EDM perce des trous avec une longue électrode en tube de laiton ou de cuivre qui tourne dans un mandrin avec un flux constant d'eau distillée ou déminéralisée traversant l'électrode en tant qu'agent de rinçage et diélectrique. Certaines machines d'électroérosion pour petits trous sont capables de percer 100 mm d'acier doux ou même trempé en moins de 10 secondes. Des trous entre 0,3 mm et 6,1 mm peuvent être obtenus dans cette opération de perçage.
Usinage par désintégration des métaux :
Nous avons également des machines EDM spéciales dans le but spécifique de retirer les outils cassés (forets ou tarauds) des pièces à usiner. Ce procédé est appelé ''usinage par désintégration des métaux''.
Avantages et inconvénients de l'usinage par électroérosion :
Les avantages de l'EDM incluent l'usinage de :
- Formes complexes qui seraient autrement difficiles à produire avec des outils de coupe conventionnels
- Matériau extrêmement dur avec des tolérances très étroites
- Très petites pièces où les outils de coupe conventionnels peuvent endommager la pièce à cause d'une pression excessive de l'outil de coupe.
- Il n'y a pas de contact direct entre l'outil et la pièce à usiner. Par conséquent, les sections délicates et les matériaux fragiles peuvent être usinés sans aucune distorsion.
- Une bonne finition de surface peut être obtenue.
- Des trous très fins peuvent être facilement percés.
Les inconvénients de l'EDM incluent :
- La lenteur de l'enlèvement de matière.
- Le temps et les coûts supplémentaires utilisés pour créer des électrodes pour l'EDM à piston/plongeur.
- La reproduction d'angles vifs sur la pièce est difficile en raison de l'usure des électrodes.
- La consommation électrique est élevée.
- ''Overcut'' est formé.
- Une usure excessive de l'outil se produit pendant l'usinage.
- Les matériaux électriquement non conducteurs ne peuvent être usinés qu'avec une configuration spécifique du processus.