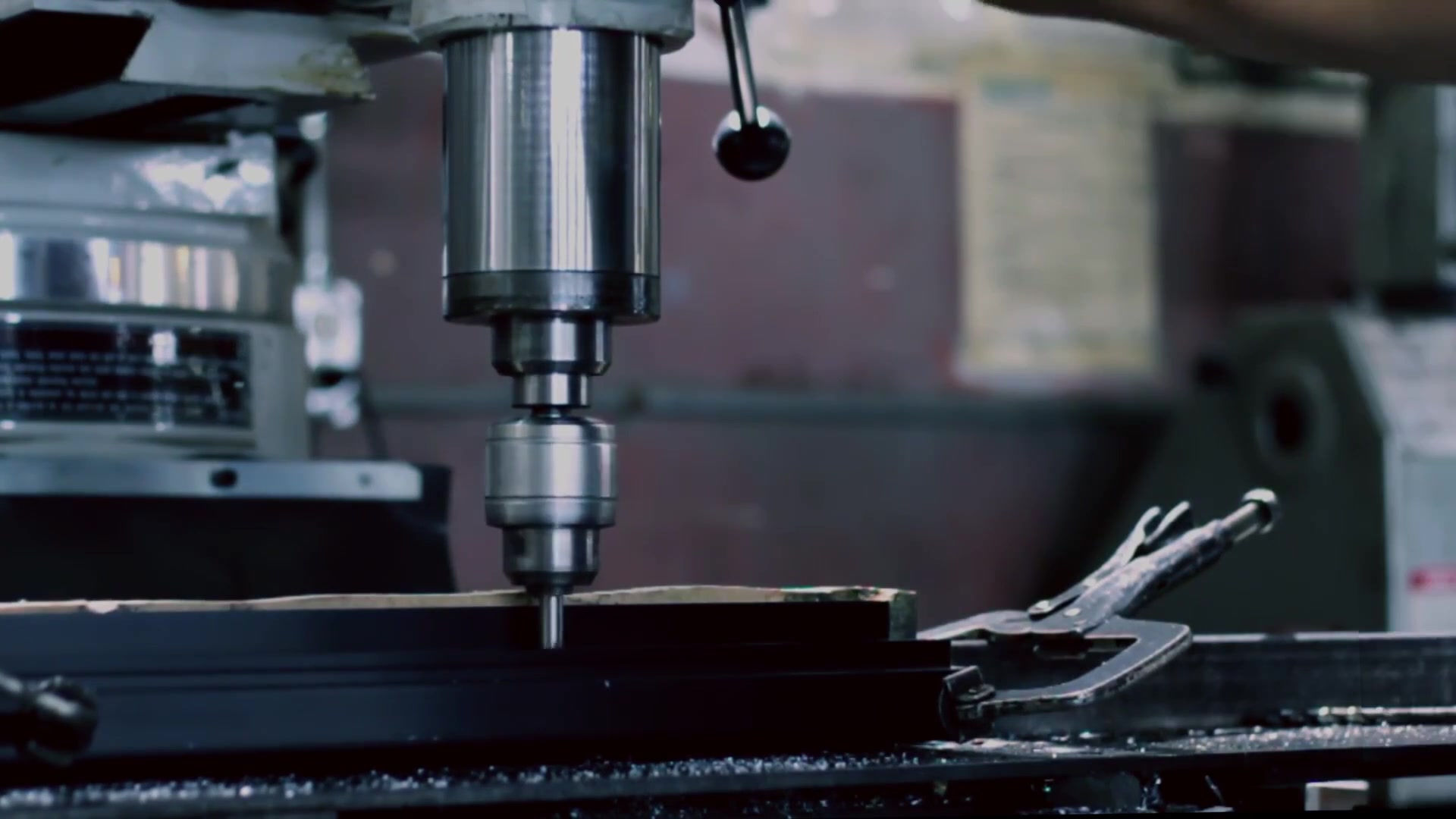
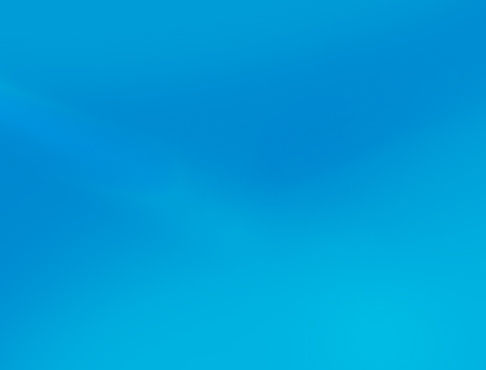
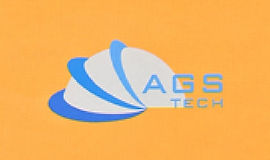
Fabricant mondial sur mesure, intégrateur, consolidateur, partenaire d'externalisation pour une grande variété de produits et services.
Nous sommes votre source unique pour la fabrication, la fabrication, l'ingénierie, la consolidation, l'intégration, l'externalisation de produits et services fabriqués sur mesure et prêts à l'emploi.
Choisissez votre langue
-
Fabrication sur mesure
-
Fabrication sous contrat nationale et mondiale
-
Sous-traitance de fabrication
-
Approvisionnement national et mondial
-
Consolidation
-
Intégration d'ingénierie
-
Services d'ingénierie
Search Results
161 résultats trouvés avec une recherche vide
- Composants de transmission, courroies, chaînes, entraînements par câble, poulies, AGS-TECH
Composants de transmission, courroies, chaînes et entraînements par câble, conventionnels et rainurés ou dentelés, entraînement positif, poulies Courroies et chaînes et assemblage d'entraînement par câble AGS-TECH Inc. vous offre des composants de transmission de puissance, y compris des courroies et des chaînes et un ensemble d'entraînement par câble. Avec des années de raffinement, nos courroies en caoutchouc, en cuir et autres sont devenues plus légères et plus compactes, capables de supporter des charges plus élevées à moindre coût. De même, nos transmissions par chaîne ont beaucoup évolué au fil du temps et offrent à nos clients plusieurs avantages. Certains avantages de l'utilisation d'entraînements par chaîne sont leurs entraxes d'arbre relativement illimités, leur compacité, leur facilité de montage, leur élasticité en tension sans glissement ni fluage, leur capacité à fonctionner dans des environnements à haute température. Nos entraînements par câble offrent également des avantages tels que la simplicité dans certaines applications par rapport à d'autres types de composants de transmission. Des entraînements par courroie, chaîne et câble prêts à l'emploi ainsi que des versions fabriquées et assemblées sur mesure sont disponibles. Nous pouvons fabriquer ces composants de transmission à la bonne taille pour votre application et à partir des matériaux les plus appropriés. COURROIES ET COURROIES : - Courroies plates conventionnelles : Ce sont des courroies plates simples sans dents, rainures ou dentelures. Les entraînements par courroie plate offrent une flexibilité, une bonne absorption des chocs, une transmission de puissance efficace à haute vitesse, une résistance à l'abrasion et un faible coût. Les ceintures peuvent être épissées ou connectées pour créer des ceintures plus grandes. Les autres avantages des courroies plates conventionnelles sont qu'elles sont minces, qu'elles ne sont pas soumises à des charges centrifuges élevées (ce qui les rend idéales pour les opérations à grande vitesse avec de petites poulies). D'autre part, ils imposent des charges élevées sur les roulements car les courroies plates nécessitent une tension élevée. D'autres inconvénients des entraînements par courroie plate peuvent être le glissement, le fonctionnement bruyant et des rendements relativement inférieurs à des vitesses de fonctionnement faibles et modérées. Nous avons deux types de courroies conventionnelles : renforcées et non renforcées. Les courroies renforcées ont un élément de traction dans leur structure. Les courroies plates conventionnelles sont disponibles en cuir, en tissu caoutchouté ou en corde, en caoutchouc ou en plastique non renforcé, en tissu, en cuir renforcé. Les ceintures en cuir offrent une longue durée de vie, une flexibilité, un excellent coefficient de frottement et une réparation facile. Cependant, les ceintures en cuir sont relativement chères, nécessitent un habillage et un nettoyage de la ceinture et, selon l'atmosphère, elles peuvent rétrécir ou s'étirer. Les ceintures en tissu caoutchouté ou en corde résistent à l'humidité, aux acides et aux alcalis. Les bandes en tissu caoutchouté sont constituées de nappes de coton ou de canard synthétique imprégnées de caoutchouc et sont les plus économiques. Les ceintures à cordes caoutchoutées consistent en une série de nappes de cordes imprégnées de caoutchouc. Les courroies à cordon caoutchouté offrent une résistance élevée à la traction et une taille et une masse modestes. Les courroies en caoutchouc ou en plastique non renforcées conviennent aux applications d'entraînement légères et à basse vitesse. Les courroies en caoutchouc et en plastique non renforcées peuvent être tendues en place sur leurs poulies. Les courroies en plastique non renforcées peuvent transmettre une puissance plus élevée que les courroies en caoutchouc. Les ceintures en cuir renforcées consistent en un élément de traction en plastique pris en sandwich entre les couches supérieure et inférieure en cuir. Enfin, nos ceintures en tissu peuvent être constituées d'une seule pièce de coton ou de canard pliée et cousue avec des rangées de points longitudinaux. Les courroies en tissu sont capables de suivre uniformément et de fonctionner à grande vitesse. - Courroies rainurées ou dentelées (telles que les courroies trapézoïdales) : il s'agit de courroies plates de base modifiées pour offrir les avantages d'un autre type de produit de transmission. Ce sont des courroies plates avec une face inférieure nervurée longitudinalement. Les courroies Poly-V sont des courroies plates rainurées longitudinalement ou dentelées avec une section de traction et une série de rainures adjacentes en forme de V à des fins de suivi et de compression. La capacité de puissance dépend de la largeur de la bande. La courroie trapézoïdale est le cheval de bataille de l'industrie et est disponible dans une variété de tailles et de types standardisés pour la transmission de presque toutes les puissances de charge. Les entraînements par courroie trapézoïdale fonctionnent bien entre 1 500 et 6 000 pi/min, mais les courroies trapézoïdales étroites fonctionneront jusqu'à 10 000 pi/min. Les entraînements par courroie trapézoïdale offrent une longue durée de vie de 3 à 5 ans et permettent de grands rapports de vitesse, ils sont faciles à installer et à retirer, offrent un fonctionnement silencieux, peu d'entretien, une bonne absorption des chocs entre l'entraînement de la courroie et les arbres entraînés. L'inconvénient des courroies trapézoïdales est leur certain glissement et fluage et, par conséquent, elles peuvent ne pas être la meilleure solution lorsque des vitesses synchrones sont requises. Nous avons des courroies industrielles, automobiles et agricoles. Des longueurs standard en stock ainsi que des longueurs personnalisées de courroies sont disponibles. Toutes les sections de courroie trapézoïdale standard sont disponibles en stock. Il existe des tableaux où vous pouvez calculer des paramètres inconnus tels que la longueur de la courroie, la section de la courroie (largeur et épaisseur) à condition que vous connaissiez certains paramètres de votre système tels que les diamètres des poulies motrices et entraînées, l'entraxe entre les poulies et les vitesses de rotation des poulies. Vous pouvez utiliser ces tableaux ou nous demander de choisir la courroie trapézoïdale qui vous convient. - Courroies d'entraînement positif (courroie de distribution) : ces courroies sont également de type plat avec une série de dents régulièrement espacées sur la circonférence intérieure. Les courroies à entraînement positif ou dentées combinent les avantages des courroies plates avec les caractéristiques d'adhérence positive des chaînes et des engrenages. Les courroies d'entraînement positives ne révèlent aucun patinage ou variation de vitesse. Une large gamme de rapports de vitesse est possible. Les charges des roulements sont faibles car ils peuvent fonctionner à basse tension. Ils sont cependant plus sensibles aux désalignements dans les poulies. - Poulies, réas, moyeux pour courroies : Différents types de poulies sont utilisés avec des courroies plates, striées (crantées) et à entraînement positif. Nous les fabriquons tous. La plupart de nos poulies à courroie plate sont fabriquées par moulage de fonte, mais des versions en acier sont également disponibles dans diverses combinaisons de jantes et de moyeux. Nos poulies à courroie plate peuvent avoir des moyeux pleins, à rayons ou fendus ou nous pouvons fabriquer comme vous le souhaitez. Les courroies striées et à entraînement positif sont disponibles dans une variété de tailles et de largeurs de stock. Au moins une poulie dans les entraînements par courroie de distribution doit être bridée pour maintenir la courroie sur l'entraînement. Pour les systèmes à entraînement central long, il est recommandé d'avoir les deux poulies bridées. Les réas sont les roues rainurées des poulies et sont généralement fabriqués par moulage de fonte, formage d'acier ou moulage de plastique. Le formage de l'acier est un processus approprié pour fabriquer des poulies automobiles et agricoles. Nous réalisons des réas à gorges régulières et profondes. Les poulies à gorge profonde conviennent bien lorsque la courroie trapézoïdale pénètre dans la poulie sous un angle, comme c'est le cas dans les entraînements quart de tour. Les rainures profondes sont également bien adaptées aux entraînements à arbre vertical et aux applications où la vibration des courroies peut être un problème. Nos poulies folles sont des poulies à gorge ou des poulies plates qui ne servent pas à transmettre la puissance mécanique. Les poulies folles sont principalement utilisées pour serrer les courroies. - Entraînements à courroie unique et multiples : les entraînements à courroie unique ont une seule rainure, tandis que les entraînements à courroie multiple ont plusieurs rainures. En cliquant sur le texte de couleur correspondant ci-dessous, vous pouvez télécharger nos catalogues : - Courroies de transmission de puissance (comprend les courroies trapézoïdales, les courroies de distribution, les courroies à bords bruts, les courroies enveloppées et les courroies spécialisées) - Bandes transporteuses - Poulies en V - Poulies synchrones CHAÎNES ET TRANSMISSIONS PAR CHAÎNE : Nos chaînes de transmission de puissance présentent certains avantages tels que des entraxes d'arbres relativement libres, un montage facile, une compacité, une élasticité sous tension sans glissement ni fluage, une capacité de fonctionnement à des températures élevées. Voici les principaux types de nos chaînes : - Chaînes amovibles : nos chaînes amovibles sont fabriquées dans une gamme de tailles, de pas et de résistance ultime et généralement en fonte ou en acier malléable. Les chaînes malléables sont fabriquées dans une gamme de tailles allant de 0,902 (23 mm) à 4,063 pouces (103 mm) de pas et de résistance ultime de 700 à 17 000 lb/pouce carré. Nos chaînes en acier amovibles, d'autre part, sont fabriquées dans des tailles allant de 0,904 pouce (23 mm) à environ 3,00 pouces (76 mm) de pas, avec une résistance ultime de 760 à 5 000 lb/pouce carré._cc781905-5cde-3194-bb3b- 136bad5cf58d_ - Chaînes d'attelage : Ces chaînes sont utilisées pour des charges plus lourdes et des vitesses légèrement supérieures à environ 450 pieds/min (2,2 m/sec). Les chaînes d'attelage sont constituées de maillons moulés individuels ayant une extrémité de barillet pleine et ronde avec des barres latérales décalées. Ces maillons de chaîne sont couplés avec des broches en acier. Ces chaînes ont un pas allant d'environ 1,00 pouce (25 mm) à 6,00 pouces (150 mm) et des résistances ultimes entre 3 600 et 30 000 lb/pouce carré. - Chaînes à barre latérale décalée : elles sont populaires dans les chaînes d'entraînement des engins de chantier. Ces chaînes fonctionnent à des vitesses allant jusqu'à 1000 pieds/min et transmettent des charges d'environ 250 ch. Généralement, chaque lien a deux barres latérales décalées, une douille, un rouleau, une goupille, une goupille fendue. - Chaînes à rouleaux : elles sont disponibles dans des pas de 0,25 (6 mm) à 3,00 (75 mm) pouces. La résistance ultime des chaînes à rouleaux simple largeur varie entre 925 et 130 000 lb/pouce carré. Des versions à plusieurs largeurs de chaînes à rouleaux sont disponibles et transmettent une plus grande puissance à des vitesses plus élevées. Les chaînes à rouleaux à largeurs multiples offrent également une action plus douce avec un bruit réduit. Les chaînes à rouleaux sont assemblées à partir de maillons à rouleaux et de maillons à broches. Les goupilles fendues sont utilisées dans les chaînes à rouleaux en version détachable. La conception des entraînements par chaîne à rouleaux nécessite une expertise en la matière. Alors que les entraînements par courroie sont basés sur des vitesses linéaires, les entraînements par chaîne sont basés sur la vitesse de rotation du plus petit pignon, qui est dans la plupart des installations l'élément entraîné. Outre les puissances nominales et la vitesse de rotation, la conception des entraînements par chaîne est basée sur de nombreux autres facteurs. - Chaînes à pas double : Fondamentalement identiques aux chaînes à rouleaux, sauf que le pas est deux fois plus long. - Chaînes à dents inversées (silencieuses) : chaînes à grande vitesse utilisées principalement pour les moteurs principaux et les prises de force. Les entraînements à chaîne à dents inversées peuvent transmettre des puissances allant jusqu'à 1200 ch et sont constitués d'une série de maillons dentés, alternativement assemblés avec des broches ou une combinaison de composants d'articulation. La chaîne de guidage central a des maillons de guidage pour engager les rainures dans le pignon, et la chaîne de guidage latéral a des guides pour engager les côtés du pignon. - Chaînes à billes ou coulissantes : ces chaînes sont utilisées pour les entraînements à vitesse lente et également dans les opérations manuelles. En cliquant sur le texte de couleur correspondant ci-dessous, vous pouvez télécharger nos catalogues : - Chaînes d'entraînement - Chaînes de transport - Chaînes de convoyeur à grand pas - Chaînes à rouleaux en acier inoxydable - Chaînes de levage - Chaînes de moto - Chaînes de machines agricoles - Pignons : Nos pignons standard sont conformes aux normes ANSI. Les pignons à plaque sont des pignons plats sans moyeu. Nos pignons de moyeu de petite et moyenne taille sont tournés à partir de barres ou de pièces forgées ou fabriqués en soudant un moyeu en barres à une plaque laminée à chaud. AGS-TECH Inc. peut fournir des pignons usinés à partir de pièces moulées en fonte grise, d'acier moulé et de constructions de moyeu soudé, de poudre de métal frittée, de plastique moulé ou usiné. Pour un fonctionnement en douceur à des vitesses élevées, une sélection appropriée de la taille des pignons est essentielle. Les limitations d'espace sont bien sûr un facteur que nous ne pouvons pas ignorer lors du choix d'un pignon. Il est recommandé que le rapport entre l'entraînement et les pignons entraînés ne dépasse pas 6:1 et que l'enroulement de la chaîne sur l'entraînement soit de 120 degrés. Les distances centrales entre les pignons plus petits et plus grands, les longueurs de chaîne et la tension de la chaîne doivent également être choisies en fonction de certains calculs et directives d'ingénierie recommandés et non au hasard. Téléchargez nos catalogues en cliquant sur le texte coloré ci-dessous : - Pignons et roues de plaque - Bagues de transmission - Accouplement à chaîne - Antivols à chaîne ENTRAÎNEMENTS PAR CÂBLE : Ceux-ci ont leurs avantages par rapport aux courroies et aux entraînements par chaîne dans certains cas. Les entraînements par câble peuvent accomplir la même fonction que les courroies et peuvent également être plus simples et plus économiques à mettre en œuvre dans certaines applications. Par exemple, une nouvelle série d'entraînements par câble Synchromesh est conçue pour une traction positive afin de remplacer les câbles conventionnels, les câbles simples et les entraînements à crémaillère, en particulier dans les espaces restreints. Le nouveau câble d'entraînement est conçu pour fournir un positionnement de haute précision dans les équipements électroniques tels que les photocopieurs, les traceurs, les machines à écrire, les imprimantes, etc. Une caractéristique clé du nouveau câble d'entraînement est sa capacité à être utilisé dans des configurations serpentines 3D qui permettent conceptions extrêmement miniatures. Les câbles Synchromesh peuvent être utilisés avec une tension plus faible par rapport aux cordes, réduisant ainsi la consommation d'énergie. Contactez AGS-TECH pour des questions et avis sur les entraînements par courroies, chaînes et câbles. CLICK Product Finder-Locator Service PAGE PRÉCÉDENTE
- Composites, fabrication de matériaux composites, renforcés de fibres
Composites, fabrication de matériaux composites, renforcés de particules et de fibres, cermets, composite céramique et métallique, polymère renforcé de fibre de verre, procédé de stratification Fabrication de composites et de matériaux composites Simplement définis, les COMPOSITES ou les MATÉRIAUX COMPOSITES sont des matériaux constitués de deux ou plusieurs matériaux ayant des propriétés physiques ou chimiques différentes, mais lorsqu'ils sont combinés, ils deviennent un matériau différent des matériaux constitutifs. Précisons que les matériaux constitutifs restent séparés et distincts dans la structure. Le but de la fabrication d'un matériau composite est d'obtenir un produit supérieur à ses constituants et combinant les caractéristiques souhaitées de chacun des constituants. Par exemple; la résistance, le faible poids ou le prix inférieur peuvent être la motivation derrière la conception et la production d'un composite. Les types de composites que nous proposons sont les composites renforcés de particules, les composites renforcés de fibres, y compris les composites à matrice céramique / à matrice polymère / à matrice métallique / carbone-carbone / hybrides, les composites structuraux, stratifiés et structurés en sandwich et les nanocomposites. Les techniques de fabrication que nous déployons dans la fabrication de matériaux composites sont : la pultrusion, les processus de production de préimprégnés, le placement avancé de fibres, l'enroulement filamentaire, le placement de fibres sur mesure, le processus de stratification par pulvérisation de fibre de verre, le tuftage, le processus de lanxide, le z-pinning. De nombreux matériaux composites sont constitués de deux phases, la matrice, qui est continue et entoure l'autre phase ; et la phase dispersée qui est entourée par la matrice. Nous vous recommandons de cliquer ici pourTÉLÉCHARGEZ nos illustrations schématiques de la fabrication de composites et de matériaux composites par AGS-TECH Inc. Cela vous aidera à mieux comprendre les informations que nous vous fournissons ci-dessous. • COMPOSITES RENFORCÉS PAR DES PARTICULES : Cette catégorie comprend deux types : les composites à grosses particules et les composites renforcés par dispersion. Dans le premier type, les interactions particule-matrice ne peuvent pas être traitées au niveau atomique ou moléculaire. Au lieu de cela, la mécanique du continuum est valide. D'autre part, dans les composites renforcés par dispersion, les particules sont généralement beaucoup plus petites dans des plages de dizaines de nanomètres. Un exemple de composite à grosses particules est celui des polymères auxquels des charges ont été ajoutées. Les charges améliorent les propriétés du matériau et peuvent remplacer une partie du volume de polymère par un matériau plus économique. Les fractions volumiques des deux phases influencent le comportement du composite. Les composites à grosses particules sont utilisés avec des métaux, des polymères et des céramiques. Les CERMETS sont des exemples de composites céramique/métal. Notre cermet le plus courant est le carbure cémenté. Il est constitué d'une céramique de carbure réfractaire telle que des particules de carbure de tungstène dans une matrice d'un métal tel que le cobalt ou le nickel. Ces composites de carbure sont largement utilisés comme outils de coupe pour l'acier trempé. Les particules de carbure dur sont responsables de l'action de coupe et leur ténacité est renforcée par la matrice métallique ductile. Ainsi, nous obtenons les avantages des deux matériaux dans un seul composite. Un autre exemple courant de composite à grosses particules que nous utilisons est celui des particules de noir de carbone mélangées à du caoutchouc vulcanisé pour obtenir un composite à haute résistance à la traction, à la ténacité, à la déchirure et à l'abrasion. Un exemple de composite renforcé par dispersion est constitué par les métaux et alliages métalliques renforcés et durcis par la dispersion uniforme de fines particules d'un matériau très dur et inerte. Lorsque de très petits flocons d'oxyde d'aluminium sont ajoutés à la matrice métallique d'aluminium, nous obtenons une poudre d'aluminium frittée qui a une résistance à haute température améliorée. • COMPOSITES RENFORCÉS DE FIBRES : Cette catégorie de composites est en fait la plus importante. L'objectif à atteindre est une résistance et une rigidité élevées par unité de poids. La composition, la longueur, l'orientation et la concentration des fibres dans ces composites sont essentielles pour déterminer les propriétés et l'utilité de ces matériaux. Il existe trois groupes de fibres que nous utilisons : les moustaches, les fibres et les fils. Les WHISKERS sont des monocristaux très fins et longs. Ils font partie des matériaux les plus résistants. Certains exemples de matériaux de trichites sont le graphite, le nitrure de silicium, l'oxyde d'aluminium. Les FIBERS en revanche sont majoritairement des polymères ou des céramiques et sont à l'état polycristallin ou amorphe. Le troisième groupe comprend les FILS fins qui ont des diamètres relativement grands et sont souvent constitués d'acier ou de tungstène. Un exemple de composite renforcé de fil est celui des pneus de voiture qui incorporent du fil d'acier à l'intérieur du caoutchouc. Selon le matériau de la matrice, nous avons les composites suivants : COMPOSITES POLYMER-MATRIX : Ils sont constitués d'une résine polymère et de fibres comme ingrédient de renforcement. Un sous-groupe de ces composites appelés polymères renforcés de fibres de verre (GFRP) contient des fibres de verre continues ou discontinues dans une matrice polymère. Le verre offre une résistance élevée, il est économique, facile à transformer en fibres et chimiquement inerte. Les inconvénients sont leur rigidité et leur rigidité limitées, les températures de service n'étant que de 200 à 300 degrés centigrades. La fibre de verre convient aux carrosseries automobiles et aux équipements de transport, aux carrosseries de véhicules marins, aux conteneurs de stockage. Ils ne conviennent pas à l'aérospatiale ni à la fabrication de ponts en raison de leur rigidité limitée. L'autre sous-groupe est appelé composite de polymère renforcé de fibre de carbone (CFRP). Ici, le carbone est notre matériau fibreux dans la matrice polymère. Le carbone est connu pour son module spécifique et sa résistance élevés et sa capacité à les maintenir à des températures élevées. Les fibres de carbone peuvent nous offrir des modules de traction standard, intermédiaires, élevés et ultra-élevés. De plus, les fibres de carbone offrent diverses caractéristiques physiques et mécaniques et conviennent donc à diverses applications d'ingénierie personnalisées. Les composites CFRP peuvent être envisagés pour fabriquer des équipements sportifs et récréatifs, des récipients sous pression et des composants structurels aérospatiaux. Pourtant, un autre sous-groupe, les composites polymères renforcés de fibres d'aramide, sont également des matériaux à haute résistance et module. Leurs rapports résistance/poids sont remarquablement élevés. Les fibres d'aramide sont également connues sous les noms commerciaux KEVLAR et NOMEX. Sous tension, ils fonctionnent mieux que d'autres matériaux en fibres polymères, mais ils sont faibles en compression. Les fibres d'aramide sont résistantes, résistantes aux chocs, au fluage et à la fatigue, stables à des températures élevées, chimiquement inertes sauf contre les acides et les bases forts. Les fibres d'aramide sont largement utilisées dans les articles de sport, les gilets pare-balles, les pneus, les cordes, les gaines de câbles à fibres optiques. D'autres matériaux de renforcement fibreux existent mais sont moins utilisés. Ce sont le bore, le carbure de silicium, l'oxyde d'aluminium principalement. Le matériau de la matrice polymère, d'autre part, est également critique. Elle détermine la température maximale de service du composite car le polymère a généralement une température de fusion et de dégradation plus faible. Les polyesters et les esters vinyliques sont largement utilisés comme matrice polymère. Des résines sont également utilisées et elles ont une excellente résistance à l'humidité et des propriétés mécaniques. Par exemple, la résine polyimide peut être utilisée jusqu'à environ 230 degrés Celsius. COMPOSITES MÉTALLIQUES : Dans ces matériaux on utilise une matrice métallique ductile et les températures de service sont généralement plus élevées que leurs composants constitutifs. Par rapport aux composites à matrice polymère, ceux-ci peuvent avoir des températures de fonctionnement plus élevées, être ininflammables et peuvent avoir une meilleure résistance à la dégradation contre les fluides organiques. Cependant ils sont plus chers. Les matériaux de renforcement tels que les trichites, les particules, les fibres continues et discontinues ; et des matériaux de matrice tels que le cuivre, l'aluminium, le magnésium, le titane, les superalliages sont couramment utilisés. Des exemples d'applications sont les composants de moteur constitués d'une matrice en alliage d'aluminium renforcée d'oxyde d'aluminium et de fibres de carbone. COMPOSITES CÉRAMIQUES À MATRICE : Les matériaux céramiques sont connus pour leur excellente fiabilité à haute température. Cependant, ils sont très fragiles et ont de faibles valeurs de ténacité à la rupture. En incorporant des particules, des fibres ou des trichites d'une céramique dans la matrice d'une autre, nous sommes en mesure d'obtenir des composites avec des ténacités à la rupture plus élevées. Ces matériaux intégrés inhibent essentiellement la propagation des fissures à l'intérieur de la matrice par certains mécanismes tels que la déviation des extrémités des fissures ou la formation de ponts sur les faces des fissures. A titre d'exemple, les alumines renforcées de trichites de SiC sont utilisées comme inserts d'outils de coupe pour l'usinage d'alliages de métaux durs. Ceux-ci peuvent révéler de meilleures performances par rapport aux carbures cémentés. COMPOSITES CARBONE-CARBONE : Le renfort ainsi que la matrice sont en carbone. Ils ont des modules de traction élevés et des résistances à des températures élevées supérieures à 2000 degrés centigrades, une résistance au fluage, des ténacités à la rupture élevées, de faibles coefficients de dilatation thermique, des conductivités thermiques élevées. Ces propriétés les rendent idéales pour les applications nécessitant une résistance aux chocs thermiques. La faiblesse des composites carbone-carbone est cependant leur vulnérabilité à l'oxydation à haute température. Des exemples typiques d'utilisation sont les moules de pressage à chaud, la fabrication de composants de moteurs à turbine avancés. COMPOSITES HYBRIDES : Deux ou plusieurs types de fibres différentes sont mélangés dans une seule matrice. On peut ainsi adapter un nouveau matériau avec une combinaison de propriétés. Un exemple est lorsque des fibres de carbone et de verre sont incorporées dans une résine polymère. Les fibres de carbone offrent une rigidité et une résistance à faible densité mais sont coûteuses. Le verre, quant à lui, est peu coûteux mais n'a pas la rigidité des fibres de carbone. Le composite hybride verre-carbone est plus solide et plus résistant et peut être fabriqué à moindre coût. TRAITEMENT DES COMPOSITES RENFORCÉS DE FIBRES : Pour les plastiques renforcés de fibres continues avec des fibres uniformément réparties orientées dans la même direction, nous utilisons les techniques suivantes. PULTRUSION : Des tiges, des poutres et des tubes de longueurs continues et de sections constantes sont fabriqués. Les mèches de fibres continues sont imprégnées d'une résine thermodurcissable et sont tirées à travers une filière en acier pour les préformer à la forme souhaitée. Ensuite, ils passent à travers une matrice de durcissement usinée avec précision pour atteindre sa forme finale. Puisque la matrice de durcissement est chauffée, elle durcit la matrice de résine. Les extracteurs tirent le matériau à travers les matrices. En utilisant des noyaux creux insérés, nous sommes en mesure d'obtenir des tubes et des géométries creuses. La méthode de pultrusion est automatisée et nous offre des cadences de production élevées. N'importe quelle longueur de produit est possible de produire. PROCÉDÉ DE PRODUCTION DE PREPREG : Le préimprégné est un renfort en fibres continues préimprégné d'une résine polymère partiellement polymérisée. Il est largement utilisé pour les applications structurelles. Le matériel se présente sous forme de bande et est expédié sous forme de bande. Le fabricant le moule directement et le durcit complètement sans qu'il soit nécessaire d'ajouter de la résine. Étant donné que les préimprégnés subissent des réactions de durcissement à température ambiante, ils sont stockés à 0 centigrade ou à des températures inférieures. Après utilisation, les bandes restantes sont stockées à basse température. Des résines thermoplastiques et thermodurcissables sont utilisées et les fibres de renfort de carbone, d'aramide et de verre sont courantes. Pour utiliser des préimprégnés, le papier de support du support est d'abord retiré, puis la fabrication est réalisée en posant le ruban préimprégné sur une surface usinée (le processus de superposition). Plusieurs plis peuvent être superposés pour obtenir les épaisseurs souhaitées. Une pratique fréquente consiste à alterner l'orientation des fibres pour produire un stratifié à plis croisés ou à plis angulaires. Enfin, la chaleur et la pression sont appliquées pour le durcissement. Le traitement manuel ainsi que les processus automatisés sont utilisés pour couper les préimprégnés et la superposition. ENROULEMENT FILAMENTAIRE : Les fibres de renforcement continues sont positionnées avec précision selon un motif prédéterminé pour suivre une forme creuse et généralement cyclindrique. Les fibres passent d'abord dans un bain de résine puis sont enroulées sur un mandrin par un système automatisé. Après plusieurs répétitions d'enroulement, les épaisseurs souhaitées sont obtenues et le durcissement est effectué soit à température ambiante, soit à l'intérieur d'un four. Maintenant, le mandrin est retiré et le produit est démoulé. L'enroulement filamentaire peut offrir des rapports résistance/poids très élevés en enroulant les fibres selon des motifs circonférentiels, hélicoïdaux et polaires. Tuyaux, réservoirs, carters sont fabriqués selon cette technique. • COMPOSITES STRUCTURELS : Généralement, ils sont constitués à la fois de matériaux homogènes et composites. Par conséquent, les propriétés de ceux-ci sont déterminées par les matériaux constitutifs et la conception géométrique de ses éléments. Voici les principaux types : COMPOSITES LAMINAIRES : Ces matériaux structuraux sont constitués de feuilles ou de panneaux bidimensionnels avec des directions privilégiées à haute résistance. Les couches sont empilées et cimentées ensemble. En alternant les directions de haute résistance dans les deux axes perpendiculaires, nous obtenons un composite qui a une haute résistance dans les deux directions dans le plan bidimensionnel. En ajustant les angles des couches, on peut fabriquer un composite résistant dans les directions préférées. Le ski moderne est fabriqué de cette façon. PANNEAUX SANDWICH : Ces composites structuraux sont légers mais ont une rigidité et une résistance élevées. Les panneaux sandwich se composent de deux feuilles extérieures faites d'un matériau rigide et solide comme les alliages d'aluminium, les plastiques renforcés de fibres ou l'acier et un noyau entre les feuilles extérieures. Le noyau doit être léger et la plupart du temps avoir un faible module d'élasticité. Les matériaux de base populaires sont les mousses polymères rigides, le bois et les nids d'abeilles. Les panneaux sandwich sont largement utilisés dans l'industrie de la construction comme matériau de toiture, de sol ou de mur, ainsi que dans les industries aérospatiales. • NANOCOMPOSITES : Ces nouveaux matériaux sont constitués de particules nanométriques enchâssées dans une matrice. En utilisant des nanocomposites, nous pouvons fabriquer des matériaux en caoutchouc qui sont de très bonnes barrières à la pénétration de l'air tout en conservant leurs propriétés de caoutchouc inchangées. CLICK Product Finder-Locator Service PAGE PRÉCÉDENTE
- Processus d'assemblage et d'assemblage et de fixation, soudage, brasage
Processus d'assemblage et d'assemblage et de fixation, soudage, brasage, frittage, collage, ajustement à la presse, processus de soudure à la vague et par refusion, four à chalumeau Processus d'assemblage, d'assemblage et de fixation Nous assemblons, assemblons et fixons vos pièces manufacturées et les transformons en produits finis ou semi-finis par SOUDURE, BRASAGE, BRASAGE, FRITTAGE, COLLAGE, FIXATION, EMBOUTISSAGE. Certains de nos procédés de soudage les plus populaires sont l'arc, le gaz oxycombustible, la résistance, la projection, la couture, le renversement, la percussion, l'état solide, le faisceau d'électrons, le laser, le thermit, le soudage par induction. Nos procédés de brasage populaires sont le brasage au chalumeau, par induction, au four et par trempage. Nos méthodes de soudure sont le fer, la plaque chauffante, le four, l'induction, l'immersion, la vague, la refusion et la soudure par ultrasons. Pour le collage, nous utilisons fréquemment des thermoplastiques et des thermodurcissables, des époxydes, des phénoliques, du polyuréthane, des alliages adhésifs ainsi que d'autres produits chimiques et rubans. Enfin, nos procédés de fixation consistent en clouage, vissage, boulonnerie, rivetage, clinchage, goupillage, couture & agrafage et emmanchement à la presse. • SOUDAGE : Le soudage consiste à assembler des matériaux en faisant fondre les pièces et en introduisant des matériaux d'apport, qui rejoignent également le bain de soudure en fusion. Lorsque la zone se refroidit, on obtient un joint solide. La pression est appliquée dans certains cas. Contrairement au soudage, les opérations de brasage et de brasage impliquent uniquement la fusion d'un matériau à point de fusion inférieur entre les pièces, et les pièces ne fondent pas. Nous vous recommandons de cliquer ici pourTÉLÉCHARGEZ nos illustrations schématiques des procédés de soudage par AGS-TECH Inc. Cela vous aidera à mieux comprendre les informations que nous vous fournissons ci-dessous. En SOUDAGE À L'ARC, nous utilisons une source d'alimentation et une électrode pour créer un arc électrique qui fait fondre les métaux. Le point de soudage est protégé par un gaz ou une vapeur de protection ou un autre matériau. Ce processus est populaire pour le soudage de pièces automobiles et de structures en acier. Dans le soudage à l'arc sous protection (SMAW) ou également connu sous le nom de soudage à la baguette, une baguette d'électrode est rapprochée du matériau de base et un arc électrique est généré entre eux. La tige d'électrode fond et sert de matériau de remplissage. L'électrode contient également un flux qui agit comme une couche de laitier et dégage des vapeurs qui agissent comme gaz de protection. Ceux-ci protègent la zone de soudure de la contamination environnementale. Aucune autre charge n'est utilisée. Les inconvénients de ce procédé sont sa lenteur, la nécessité de remplacer fréquemment les électrodes, la nécessité d'éliminer les scories résiduelles provenant du flux. Un certain nombre de métaux tels que le fer, l'acier, le nickel, l'aluminium, le cuivre…etc. Peut être soudé. Ses avantages sont ses outils peu coûteux et sa facilité d'utilisation. Soudage à l'arc sous gaz métal (GMAW) également connu sous le nom de gaz inerte métal (MIG), nous avons une alimentation continue d'un fil d'apport d'électrode consommable et d'un gaz inerte ou partiellement inerte qui circule autour du fil contre la contamination environnementale de la région de soudure. L'acier, l'aluminium et d'autres métaux non ferreux peuvent être soudés. Les avantages du MIG sont des vitesses de soudage élevées et une bonne qualité. Les inconvénients sont son équipement compliqué et les défis rencontrés dans les environnements extérieurs venteux car nous devons maintenir stable le gaz de protection autour de la zone de soudage. Une variante du GMAW est le soudage à l'arc avec fil fourré (FCAW) qui consiste en un tube métallique fin rempli de matériaux de flux. Parfois, le flux à l'intérieur du tube est suffisant pour la protection contre la contamination de l'environnement. Le soudage à l'arc submergé (SAW) est un processus largement automatisé, qui implique une alimentation continue du fil et un arc qui est amorcé sous une couche de couverture de flux. Les taux de production et la qualité sont élevés, les scories de soudage se détachent facilement et nous avons un environnement de travail sans fumée. L'inconvénient est qu'il ne peut être utilisé que pour souder des parts dans certaines positions. Dans le soudage à l'arc au tungstène au gaz (GTAW) ou le soudage au tungstène sous gaz inerte (TIG), nous utilisons une électrode de tungstène avec une charge séparée et des gaz inertes ou presque inertes. Comme nous le savons, le tungstène a un point de fusion élevé et c'est un métal très approprié pour les températures très élevées. Le Tungstène en TIG n'est pas consommé contrairement aux autres méthodes expliquées ci-dessus. Une technique de soudage lente mais de haute qualité avantageuse par rapport aux autres techniques de soudage de matériaux minces. Convient à de nombreux métaux. Le soudage à l'arc plasma est similaire mais utilise du gaz plasma pour créer l'arc. L'arc dans le soudage à l'arc plasma est relativement plus concentré par rapport au GTAW et peut être utilisé pour une plus large gamme d'épaisseurs de métal à des vitesses beaucoup plus élevées. Le soudage GTAW et le soudage à l'arc plasma peuvent être appliqués à plus ou moins les mêmes matériaux. SOUDAGE OXY-COMBUSTIBLE / OXYCOMBUSTIBLE également appelé soudage oxyacétylénique, soudage oxy, le soudage au gaz est réalisé en utilisant des combustibles gazeux et de l'oxygène pour le soudage. Comme aucune alimentation électrique n'est utilisée, il est portable et peut être utilisé là où il n'y a pas d'électricité. À l'aide d'une torche de soudage, nous chauffons les pièces et le matériau d'apport pour produire un bain de métal en fusion partagé. Différents carburants peuvent être utilisés tels que l'acétylène, l'essence, l'hydrogène, le propane, le butane…etc. Dans le soudage oxy-combustible, nous utilisons deux conteneurs, l'un pour le combustible et l'autre pour l'oxygène. L'oxygène oxyde le carburant (le brûle). SOUDAGE PAR RÉSISTANCE : Ce type de soudage tire parti du chauffage Joule et de la chaleur est générée à l'endroit où le courant électrique est appliqué pendant un certain temps. Des courants élevés traversent le métal. Des flaques de métal en fusion se forment à cet endroit. Les méthodes de soudage par résistance sont populaires en raison de leur efficacité et de leur faible potentiel de pollution. Cependant, les inconvénients sont les coûts d'équipement relativement importants et la limitation inhérente à des pièces relativement minces. LE SOUDAGE PAR POINTS est un type majeur de soudage par résistance. Ici, nous joignons deux ou plusieurs feuilles ou pièces qui se chevauchent en utilisant deux électrodes en cuivre pour serrer les feuilles ensemble et faire passer un courant élevé à travers elles. Le matériau entre les électrodes de cuivre chauffe et un bain de fusion est généré à cet endroit. Le courant est alors arrêté et les pointes des électrodes en cuivre refroidissent l'emplacement de la soudure car les électrodes sont refroidies à l'eau. L'application de la bonne quantité de chaleur au bon matériau et à la bonne épaisseur est essentielle pour cette technique, car si elle est mal appliquée, le joint sera faible. Le soudage par points présente les avantages de ne provoquer aucune déformation significative des pièces, d'efficacité énergétique, de facilité d'automatisation et de taux de production exceptionnels, et de ne nécessiter aucun matériau de remplissage. L'inconvénient est que, puisque le soudage a lieu par points plutôt que de former un joint continu, la résistance globale peut être relativement inférieure par rapport aux autres méthodes de soudage. Le SOUDAGE PAR JOINT, d'autre part, produit des soudures sur les surfaces de contact de matériaux similaires. La couture peut être bout à bout ou chevauchement. Le soudage à la molette commence à une extrémité et se déplace progressivement vers l'autre. Cette méthode utilise également deux électrodes en cuivre pour appliquer une pression et un courant à la région de soudure. Les électrodes en forme de disque tournent avec un contact constant le long de la ligne de couture et réalisent une soudure continue. Ici aussi, les électrodes sont refroidies par de l'eau. Les soudures sont très solides et fiables. D'autres méthodes sont les techniques de soudage par projection, flash et refoulement. Le SOUDAGE À L'ÉTAT SOLIDE est un peu différent des méthodes précédentes expliquées ci-dessus. La coalescence a lieu à des températures inférieures à la température de fusion des métaux assemblés et sans utilisation de charge métallique. La pression peut être utilisée dans certains procédés. Diverses méthodes sont le SOUDAGE PAR COEXTRUSION où des métaux dissemblables sont extrudés à travers la même filière, le SOUDAGE PAR PRESSION A FROID où nous assemblons des alliages souples en dessous de leurs points de fusion, le SOUDAGE PAR DIFFUSION une technique sans lignes de soudure visibles, le SOUDAGE PAR EXPLOSION pour assembler des matériaux dissemblables, par exemple des alliages résistants à la corrosion à des structures aciers, SOUDAGE ÉLECTROMAGNÉTIQUE PAR IMPULSIONS où l'on accélère tubes et tôles par des forces électromagnétiques, SOUDAGE PAR FORGE qui consiste à chauffer les métaux à haute température et les marteler ensemble, SOUDAGE PAR FRICTION où l'on effectue un soudage par friction suffisant, SOUDAGE PAR FRICTION STIR qui implique un non- outil consommable traversant la ligne de joint, SOUDAGE À LA PRESSION À CHAUD où nous pressons les métaux ensemble à des températures élevées inférieures à la température de fusion dans le vide ou les gaz inertes, SOUDAGE À LA PRESSION ISOSTATIQUE À CHAUD un processus où nous appliquons une pression à l'aide de gaz inertes à l'intérieur d'un récipient, SOUDAGE AU ROULEAU où nous joignons matériaux dissemblables en les forçant entre deux roues rotatives, SOUDURE ULTRASONIQUE où de fines feuilles de métal ou de plastique sont soudées en utilisant une énergie vibratoire à haute fréquence. Nos autres procédés de soudage sont le SOUDAGE PAR FAISCEAU D'ÉLECTRONS avec une pénétration profonde et un traitement rapide, mais étant une méthode coûteuse, nous la considérons pour des cas particuliers, le SOUDAGE ÉLECTRONIQUE une méthode adaptée aux plaques épaisses lourdes et aux pièces en acier uniquement, le SOUDAGE PAR INDUCTION où nous utilisons l'induction électromagnétique et chauffer nos pièces électriquement conductrices ou ferromagnétiques, SOUDAGE PAR FAISCEAU LASER également avec une pénétration profonde et un traitement rapide mais une méthode coûteuse, SOUDAGE HYBRIDE LASER qui combine LBW avec GMAW dans la même tête de soudage et capable de combler des espaces de 2 mm entre les plaques, SOUDAGE PAR PERCUSSION qui implique une décharge électrique suivie du forgeage des matériaux avec une pression appliquée, SOUDAGE THERMIT impliquant une réaction exothermique entre les poudres d'aluminium et d'oxyde de fer., SOUDAGE ELECTROGAZ avec des électrodes consommables et utilisé uniquement avec de l'acier en position verticale, et enfin SOUDAGE À L'ARC DE GOUJONS pour joindre le goujon à la base matériau avec chaleur et pression. Nous vous recommandons de cliquer ici pourTÉLÉCHARGEZ nos illustrations schématiques des processus de brasage, de soudage et de collage par AGS-TECH Inc Cela vous aidera à mieux comprendre les informations que nous vous fournissons ci-dessous. • BRASAGE : Nous joignons deux ou plusieurs métaux en chauffant les métaux d'apport entre eux au-dessus de leurs points de fusion et en utilisant l'action capillaire pour se répandre. Le processus est similaire au brasage, mais les températures impliquées pour faire fondre la charge sont plus élevées lors du brasage. Comme en soudage, le flux protège le matériau d'apport de la contamination atmosphérique. Après refroidissement, les pièces sont assemblées. Le processus implique les étapes clés suivantes : un bon ajustement et un bon dégagement, un nettoyage approprié des matériaux de base, une fixation appropriée, une sélection appropriée du flux et de l'atmosphère, le chauffage de l'assemblage et enfin le nettoyage de l'assemblage brasé. Certains de nos processus de brasage sont le BRASAGE AU CHALUMEAU, une méthode populaire réalisée manuellement ou de manière automatisée. Il convient aux commandes de production à faible volume et aux cas spécialisés. La chaleur est appliquée à l'aide de flammes de gaz près du joint à braser. Le BRASAGE AU FOUR nécessite moins de compétences de l'opérateur et est un processus semi-automatique adapté à la production industrielle de masse. Le contrôle de la température et le contrôle de l'atmosphère dans le four sont des avantages de cette technique, car le premier permet d'avoir des cycles thermiques contrôlés et d'éliminer les échauffements locaux comme c'est le cas dans le brasage au chalumeau, et le second protège la pièce de l'oxydation. En utilisant le jigging, nous sommes capables de réduire les coûts de fabrication au minimum. Les inconvénients sont une consommation d'énergie élevée, des coûts d'équipement et des considérations de conception plus difficiles. LE BRASAGE SOUS VIDE a lieu dans un four sous vide. L'uniformité de la température est maintenue et nous obtenons des joints sans flux, très propres avec très peu de contraintes résiduelles. Des traitements thermiques peuvent avoir lieu lors du brasage sous vide, en raison des faibles contraintes résiduelles présentes lors des cycles lents de chauffage et de refroidissement. L'inconvénient majeur est son coût élevé car la création d'un environnement sous vide est un processus coûteux. Encore une autre technique DIP BRAZING joint les pièces fixées où le composé de brasage est appliqué sur les surfaces de contact. Par la suite, les pièces fixtured sont plongées dans un bain de sel fondu tel que le chlorure de sodium (sel de table) qui agit comme fluide caloporteur et fondant. L'air est exclu et donc aucune formation d'oxyde n'a lieu. Dans le BRASAGE PAR INDUCTION, nous assemblons des matériaux par un métal d'apport qui a un point de fusion inférieur à celui des matériaux de base. Le courant alternatif de la bobine d'induction crée un champ électromagnétique qui induit un chauffage par induction sur des matériaux magnétiques principalement ferreux. La méthode fournit un chauffage sélectif, de bons joints avec des charges ne circulant que dans les zones souhaitées, peu d'oxydation car aucune flamme n'est présente et le refroidissement est rapide, un chauffage rapide, une consistance et une aptitude à la fabrication à grand volume. Pour accélérer nos processus et assurer la cohérence, nous utilisons fréquemment des préformes. Des informations sur notre installation de brasage produisant des raccords céramique-métal, des joints hermétiques, des traversées de vide, des composants de contrôle des fluides et des vides poussés et ultra-poussés peuvent être trouvées ici : Brochure de l'usine de brasage • SOUDAGE : Dans le brasage, nous n'avons pas de fusion des pièces, mais un métal d'apport avec un point de fusion plus bas que les pièces d'assemblage qui coule dans le joint. Le métal d'apport dans le brasage fond à une température plus basse que dans le brasage. Nous utilisons des alliages sans plomb pour le brasage et sommes conformes à RoHS. Pour différentes applications et exigences, nous avons des alliages différents et appropriés tels que l'alliage d'argent. La soudure nous offre des joints étanches aux gaz et aux liquides. En SOFT SOLDERING, notre métal d'apport a un point de fusion inférieur à 400 degrés centigrades, alors qu'en SILVER SOLDERING et BRAZING, nous avons besoin de températures plus élevées. Le brasage tendre utilise des températures plus basses mais ne produit pas de joints solides pour les applications exigeantes à des températures élevées. La soudure à l'argent, d'autre part, nécessite des températures élevées fournies par la torche et nous donne des joints solides adaptés aux applications à haute température. Le brasage nécessite les températures les plus élevées et une torche est généralement utilisée. Comme les joints de brasage sont très résistants, ils sont de bons candidats pour la réparation d'objets en fer lourds. Dans nos lignes de fabrication, nous utilisons à la fois la soudure manuelle manuelle et des lignes de soudure automatisées. INDUCTION SOLDERING utilise un courant alternatif haute fréquence dans une bobine de cuivre pour faciliter le chauffage par induction. Des courants sont induits dans la partie soudée et, par conséquent, de la chaleur est générée au niveau de la haute résistance joint. Cette chaleur fait fondre le métal d'apport. Le flux est également utilisé. Le soudage par induction est une bonne méthode pour souder des cylindres et des tuyaux dans un processus continu en enroulant les bobines autour d'eux. Le soudage de certains matériaux tels que le graphite et la céramique est plus difficile car il nécessite le placage des pièces avec un métal approprié avant le soudage. Cela facilite la liaison interfaciale. Nous soudons ces matériaux en particulier pour les applications d'emballage hermétiques. Nous fabriquons nos cartes de circuits imprimés (PCB) en grande quantité en utilisant principalement la SOUDURE À LA VAGUE. Seulement pour une petite quantité à des fins de prototypage, nous utilisons le soudage manuel à l'aide d'un fer à souder. Nous utilisons le soudage à la vague pour les assemblages de circuits imprimés traversants et à montage en surface (PCBA). Une colle temporaire maintient les composants attachés à la carte de circuit imprimé et l'ensemble est placé sur un convoyeur et se déplace dans un équipement contenant de la soudure fondue. Le PCB est d'abord fluxé puis entre dans la zone de préchauffage. La soudure fondue est dans une casserole et présente un motif d'ondes stationnaires sur sa surface. Lorsque le PCB se déplace sur ces ondes, ces ondes entrent en contact avec le bas du PCB et collent aux pastilles de soudure. La soudure reste uniquement sur les broches et les pastilles et non sur le circuit imprimé lui-même. Les vagues dans la soudure fondue doivent être bien contrôlées afin qu'il n'y ait pas d'éclaboussures et que les sommets des vagues ne touchent pas et ne contaminent pas les zones indésirables des cartes. Dans REFLOW SOLDERING, nous utilisons une pâte à souder collante pour fixer temporairement les composants électroniques aux cartes. Ensuite, les planches sont passées dans un four de refusion avec contrôle de température. Ici, la soudure fond et connecte les composants de manière permanente. Nous utilisons cette technique pour les composants montés en surface ainsi que pour les composants traversants. Un bon contrôle de la température et un réglage des températures du four sont essentiels pour éviter la destruction des composants électroniques sur la carte en les surchauffant au-dessus de leurs limites de température maximales. Dans le processus de brasage par refusion, nous avons en fait plusieurs régions ou étapes chacune avec un profil thermique distinct, comme l'étape de préchauffage, l'étape de trempage thermique, les étapes de refusion et de refroidissement. Ces différentes étapes sont essentielles pour une soudure par refusion sans dommage des assemblages de cartes de circuits imprimés (PCBA). LA SOUDURE PAR ULTRASONS est une autre technique fréquemment utilisée avec des capacités uniques. Elle peut être utilisée pour souder du verre, de la céramique et des matériaux non métalliques. Par exemple, les panneaux photovoltaïques non métalliques nécessitent des électrodes qui peuvent être fixées selon cette technique. Dans le soudage par ultrasons, nous déployons une panne à souder chauffée qui émet également des vibrations ultrasonores. Ces vibrations produisent des bulles de cavitation à l'interface du substrat avec le matériau de soudure fondu. L'énergie implosive de cavitation modifie la surface d'oxyde et élimine la saleté et les oxydes. Pendant ce temps, une couche d'alliage se forme également. La soudure à la surface de liaison incorpore de l'oxygène et permet la formation d'une forte liaison partagée entre le verre et la soudure. Le SOUDAGE PAR IMMERSION peut être considéré comme une version plus simple du brasage à la vague adaptée uniquement à une production à petite échelle. Le premier flux de nettoyage est appliqué comme dans les autres processus. Les PCB avec des composants montés sont plongés manuellement ou de manière semi-automatisée dans un réservoir contenant de la soudure fondue. La soudure fondue adhère aux zones métalliques exposées non protégées par un masque de soudure sur la carte. L'équipement est simple et peu coûteux. • COLLAGE ADHÉSIF : Il s'agit d'une autre technique populaire que nous utilisons fréquemment et qui implique le collage de surfaces à l'aide de colles, d'époxydes, d'agents plastiques ou d'autres produits chimiques. Le collage est réalisé soit par évaporation du solvant, par durcissement à la chaleur, par durcissement à la lumière UV, par durcissement sous pression ou en attendant un certain temps. Différentes colles hautes performances sont utilisées dans nos lignes de production. Avec des processus d'application et de durcissement correctement conçus, le collage peut entraîner des liaisons à très faible contrainte qui sont solides et fiables. Les liaisons adhésives peuvent être de bons protecteurs contre les facteurs environnementaux tels que l'humidité, les contaminants, les corrosifs, les vibrations, etc. Les avantages du collage adhésif sont les suivants : ils peuvent être appliqués sur des matériaux qui seraient autrement difficiles à souder, souder ou braser. Il peut également être préférable pour les matériaux sensibles à la chaleur qui seraient endommagés par le soudage ou d'autres processus à haute température. Les autres avantages des adhésifs sont qu'ils peuvent être appliqués sur des surfaces de forme irrégulière et augmenter le poids de l'assemblage de très très petites quantités par rapport à d'autres méthodes. De plus, les changements dimensionnels des pièces sont très minimes. Certaines colles ont des propriétés d'adaptation d'indice et peuvent être utilisées entre des composants optiques sans diminuer de manière significative l'intensité de la lumière ou du signal optique. Les inconvénients, d'autre part, sont des temps de durcissement plus longs qui peuvent ralentir les lignes de fabrication, les exigences de montage, les exigences de préparation de surface et la difficulté à démonter lorsqu'une reprise est nécessaire. La plupart de nos opérations de collage impliquent les étapes suivantes : -Traitement de surface : des procédures de nettoyage spéciales telles que le nettoyage à l'eau déminéralisée, le nettoyage à l'alcool, le nettoyage au plasma ou corona sont courantes. Après le nettoyage, nous pouvons appliquer des promoteurs d'adhérence sur les surfaces pour assurer les meilleurs joints possibles. - Fixation des pièces : pour l'application d'adhésif ainsi que pour le durcissement, nous concevons et utilisons des fixations personnalisées. -Application d'adhésif : nous utilisons parfois des systèmes manuels et parfois, selon le cas, des systèmes automatisés tels que la robotique, des servomoteurs, des actionneurs linéaires pour livrer les adhésifs au bon endroit et nous utilisons des distributeurs pour le livrer au bon volume et en bonne quantité. -Durcissement : selon l'adhésif, nous pouvons utiliser un séchage et un durcissement simples ainsi qu'un durcissement sous des lampes UV qui agissent comme catalyseur ou un durcissement thermique dans un four ou à l'aide d'éléments chauffants résistifs montés sur des gabarits et des fixations. Nous vous recommandons de cliquer ici pourTÉLÉCHARGEZ nos illustrations schématiques des processus de fixation par AGS-TECH Inc. Cela vous aidera à mieux comprendre les informations que nous vous fournissons ci-dessous. • PROCÉDÉS DE FIXATION : Nos procédés d'assemblage mécanique se répartissent en deux catégories de brad : FIXATIONS et JOINTS INTÉGRÉS. Des exemples de fixations que nous utilisons sont des vis, des goupilles, des écrous, des boulons, des rivets. Des exemples de joints intégraux que nous utilisons sont les ajustements par encliquetage et rétraction, les coutures, les sertissages. En utilisant une variété de méthodes de fixation, nous nous assurons que nos joints mécaniques sont solides et fiables pendant de nombreuses années d'utilisation. Les VIS et les BOULONS sont parmi les fixations les plus couramment utilisées pour maintenir et positionner des objets ensemble. Nos vis et boulons répondent aux normes ASME. Différents types de vis et de boulons sont déployés, y compris des vis à tête hexagonale et des boulons hexagonaux, des tirefonds et des boulons, des vis à double extrémité, des vis à goujon, des vis à œil, des vis à miroir, des vis à tôle, des vis de réglage fin, des vis autoperceuses et autotaraudeuses , vis de réglage, vis avec rondelles intégrées,… et plus encore. Nous avons différents types de têtes de vis telles que tête fraisée, dôme, ronde, tête à bride et divers types d'entraînement de vis tels que fente, phillips, carré, douille hexagonale. Un RIVET d'autre part est une fixation mécanique permanente constituée d'une tige cylindrique lisse et d'une tête d'une part. Après insertion, l'autre extrémité du rivet est déformée et son diamètre est agrandi pour qu'il reste en place. En d'autres termes, avant l'installation, un rivet a une tête et après l'installation, il en a deux. Nous installons différents types de rivets en fonction de l'application, de la résistance, de l'accessibilité et du coût tels que les rivets à tête pleine/ronde, les rivets structuraux, semi-tubulaires, aveugles, oscar, d'entraînement, affleurants, à friction, auto-perforants. Le rivetage peut être préféré dans les cas où la déformation thermique et la modification des propriétés du matériau dues à la chaleur de soudage doivent être évitées. Le rivetage offre également un poids léger et surtout une bonne résistance et endurance contre les forces de cisaillement. Contre les charges de traction, les vis, les écrous et les boulons peuvent cependant être plus appropriés. Dans le processus de CLINCHING, nous utilisons des poinçons et des matrices spéciaux pour former un verrouillage mécanique entre les tôles à assembler. Le poinçon pousse les couches de tôle dans la cavité de la matrice et entraîne la formation d'un joint permanent. Aucun chauffage ni refroidissement n'est nécessaire lors du clinchage et il s'agit d'un processus de travail à froid. C'est un procédé économique qui peut remplacer le soudage par points dans certains cas. Dans PINNING, nous utilisons des broches qui sont des éléments de machine utilisés pour sécuriser les positions des pièces de machine les unes par rapport aux autres. Les principaux types sont les goupilles de chape, les goupilles fendues, les goupilles élastiques, les goupilles cylindriques, et les goupilles fendues. Dans STAPLING, nous utilisons des agrafeuses et des agrafes qui sont des attaches à deux dents utilisées pour joindre ou lier des matériaux. L'agrafage présente les avantages suivants : Économique, simple et rapide à utiliser, la couronne des agrafes peut être utilisée pour ponter des matériaux aboutés, La couronne de l'agrafe peut faciliter le pontage d'une pièce comme un câble et la fixer à une surface sans perforer ni dommageable, retrait relativement facile. Le PRESS FITTING est réalisé en poussant les pièces ensemble et le frottement entre elles fixe les pièces. Les pièces à ajustement serré composées d'un arbre surdimensionné et d'un trou sous-dimensionné sont généralement assemblées par l'une des deux méthodes suivantes : soit en appliquant une force, soit en tirant parti de la dilatation ou de la contraction thermique des pièces. Lorsqu'un emmanchement est établi en appliquant une force, nous utilisons soit une presse hydraulique, soit une presse manuelle. Par contre lorsque l'emmanchement est réalisé par dilatation thermique on chauffe les pièces enveloppantes et on les assemble à chaud à leur place. Lorsqu'elles refroidissent, elles se contractent et reprennent leurs dimensions normales. Il en résulte un bon ajustement serré. Nous appelons cela alternativement SHRINK-FITTING. L'autre façon de procéder consiste à refroidir les pièces enveloppées avant l'assemblage, puis à les faire glisser dans leurs pièces d'accouplement. Lorsque l'ensemble s'échauffe ils se dilatent et on obtient un ajustement serré. Cette dernière méthode peut être préférable dans les cas où le chauffage présente le risque de modifier les propriétés du matériau. Le refroidissement est plus sûr dans ces cas. Composants et assemblages pneumatiques et hydrauliques • Vannes, composants hydrauliques et pneumatiques tels que joint torique, rondelle, joints, garniture, bague, cale. Étant donné que les vannes et les composants pneumatiques sont très variés, nous ne pouvons pas tout énumérer ici. Selon les environnements physiques et chimiques de votre application, nous avons des produits spéciaux pour vous. Veuillez nous préciser l'application, le type de composant, les spécifications, les conditions environnementales telles que la pression, la température, les liquides ou les gaz qui seront en contact avec vos vannes et composants pneumatiques ; et nous choisirons le produit le plus approprié pour vous ou le fabriquerons spécialement pour votre application. CLICK Product Finder-Locator Service PAGE PRÉCÉDENTE
- Fabrication d'éléments de machine, engrenages, entraînements par engrenages, roulements, clés, cannelures, goupilles, arbres, joints, attaches, embrayage, cames, suiveurs, courroies, accouplements
Fabrication d'éléments de machine, engrenages, entraînements par engrenages, roulements, clés, cannelures, goupilles, arbres, joints, attaches, embrayage, cames, suiveurs, courroies, accouplements, arbres Fabrication d'éléments de machines Lire la suite Courroies et chaînes et assemblage d'entraînement par câble Lire la suite Engrenages et ensemble d'entraînement par engrenages Lire la suite Fabrication d'accouplements et de roulements Lire la suite Fabrication de clés, de cannelures et de goupilles Lire la suite Fabrication de cames et de suiveurs et de liaisons et de roues à rochet Lire la suite Fabrication d'arbres Lire la suite Fabrication de garnitures mécaniques Lire la suite Ensemble d'embrayage et de frein Lire la suite Fabrication de fixations Lire la suite Assemblage de machines simples MACHINE ELEMENTS sont des composants élémentaires d'une machine. Ces éléments se composent de trois types de base : 1.) Composants structurels, y compris les éléments de châssis, les roulements, les essieux, les cannelures, les fixations, les joints et les lubrifiants. 2.) Mécanismes contrôlant le mouvement de diverses manières, tels que les trains d'engrenages, les entraînements par courroie ou chaîne, les liaisons, les systèmes de came et de suiveur, les freins et les embrayages. 3.) Contrôlez les composants tels que les boutons, les interrupteurs, les indicateurs, les capteurs, les actionneurs et les contrôleurs d'ordinateur. La plupart des éléments de machine que nous vous proposons sont standardisés à des tailles courantes, mais des éléments de machine sur mesure sont également disponibles pour vos applications spécialisées. La personnalisation des éléments de la machine peut avoir lieu sur des conceptions existantes qui se trouvent dans nos catalogues téléchargeables ou sur de toutes nouvelles conceptions. Le prototypage et la fabrication des éléments de la machine peuvent être poursuivis une fois la conception approuvée par les deux parties. Si de nouveaux éléments de machine doivent être conçus et fabriqués, nos clients nous envoient leurs propres plans par e-mail et nous les examinons pour approbation, ou ils nous demandent de concevoir des éléments de machine pour leur application. Dans ce dernier cas, nous utilisons toutes les contributions de nos clients et concevons les éléments de la machine et envoyons les plans finalisés à nos clients pour approbation. Une fois approuvés, nous produisons les premiers articles et fabriquons ensuite les éléments de la machine selon la conception finale. À n'importe quelle étape de ce travail, dans le cas où une conception particulière d'un élément de machine ne fonctionne pas de manière satisfaisante sur le terrain (ce qui est rare), nous examinons l'ensemble du projet et apportons des modifications conjointement avec nos clients si nécessaire. Il est de notre pratique courante de signer des accords de non-divulgation (NDA) avec nos clients pour la conception d'éléments de machine ou de tout autre produit chaque fois que cela est nécessaire ou requis. Une fois que les éléments de la machine pour un client particulier sont conçus et fabriqués sur mesure, nous lui attribuons un code de produit et ne les produisons et ne les vendons qu'à notre client qui possède le produit. Nous reproduisons les éléments de la machine en utilisant les outils, moules et procédés développés autant de fois que nécessaire et chaque fois que notre client les commande à nouveau. En d'autres termes, une fois qu'un élément de machine sur mesure est conçu et produit pour vous, la propriété intellectuelle ainsi que tous les outillages et moules sont réservés et stockés indéfiniment par nous pour vous et les produits reproduits comme vous le souhaitez. Nous proposons également à nos clients des services d'ingénierie en combinant de manière créative des éléments de machine dans un composant ou un assemblage qui sert une application et répond ou dépasse les attentes de nos clients. Les usines fabriquant nos éléments de machine sont qualifiées par ISO9001, QS9000 ou TS16949. De plus, la plupart de nos produits portent le marquage CE ou UL et répondent aux normes internationales pertinentes telles que ISO, SAE, ASME, DIN. Veuillez cliquer sur les sous-menus pour obtenir des informations détaillées sur nos éléments de machine, notamment : - Courroies, chaînes et entraînements par câble - Engrenages et engrenages - Accouplements et roulements - Clés et cannelures et broches - Cames et liaisons - Arbres - Garnitures mécaniques - Embrayage et frein industriels - Attaches - Machines simples Nous avons préparé une brochure de référence pour nos clients, concepteurs et développeurs de nouveaux produits comprenant des éléments de machine. Vous pouvez vous familiariser avec certains termes couramment utilisés dans la conception de composants de machines : Téléchargez la brochure sur les termes courants en génie mécanique utilisés par les concepteurs et les ingénieurs Nos éléments de machine trouvent des applications dans une variété de domaines tels que les machines industrielles, les systèmes d'automatisation, les équipements de test et de métrologie, les équipements de transport, les machines de construction et pratiquement partout où vous pouvez penser. AGS-TECH développe et fabrique des éléments de machine à partir de divers matériaux en fonction de l'application. Les matériaux utilisés pour les éléments de machine peuvent aller des plastiques moulés utilisés pour les jouets à l'acier cémenté et spécialement revêtu pour les machines industrielles. Nos concepteurs utilisent des logiciels professionnels et des outils de conception de pointe pour développer des éléments de machine, en tenant compte de détails tels que les angles dans les dents des engrenages, les contraintes impliquées, les taux d'usure… etc. Veuillez faire défiler nos sous-menus et télécharger nos brochures et catalogues de produits pour voir si vous pouvez trouver des éléments de machine prêts à l'emploi pour votre application. Si vous ne trouvez pas une bonne correspondance pour votre application, veuillez nous en informer et nous travaillerons avec vous pour développer et fabriquer des éléments de machine qui répondront à vos besoins. Si vous êtes principalement intéressé par nos capacités d'ingénierie et de recherche et développement plutôt que par nos capacités de fabrication, nous vous invitons à visiter notre site Web http://www.ags-engineering.com où vous pouvez trouver des informations plus détaillées sur nos services de conception, de développement de produits, de développement de processus, de conseil en ingénierie, etc. CLICK Product Finder-Locator Service PAGE PRÉCÉDENTE
- Prototypage rapide, fabrication de bureau, fabrication additive, FDM
Prototypage rapide, Fabrication de bureau, Fabrication additive, Stéréolithographie, Polyjet, Modélisation par dépôt de fil fondu, Frittage sélectif par laser, FDM, SLS Fabrication additive et rapide Ces dernières années, nous avons constaté une augmentation de la demande de FABRICATION RAPIDE ou de PROTOTYPAGE RAPIDE. Ce processus peut également être appelé FABRICATION DESKTOP ou FABRICATION DE FORME LIBRE. Fondamentalement, un modèle physique solide d'une pièce est réalisé directement à partir d'un dessin CAO en trois dimensions. Nous utilisons le terme FABRICATION ADDITIVE pour ces différentes techniques où nous construisons des pièces en couches. En utilisant du matériel informatique et des logiciels intégrés, nous effectuons la fabrication additive. Nos techniques de prototypage rapide et de fabrication sont la STÉRÉOLITHOGRAPHIE, le POLYJET, le MODÉLISATION PAR DÉPÔT FONDU, LE FRITTAGE SÉLECTIF AU LASER, LA FUSION PAR FAISCEAU D'ÉLECTRONS, L'IMPRESSION TRIDIMENSIONNELLE, LA FABRICATION DIRECTE, L'OUTILLAGE RAPIDE. Nous vous recommandons de cliquer ici pourTÉLÉCHARGEZ nos illustrations schématiques des processus de fabrication additive et de fabrication rapide par AGS-TECH Inc. Cela vous aidera à mieux comprendre les informations que nous vous fournissons ci-dessous. Le prototypage rapide nous fournit : 1.) La conception conceptuelle du produit est visualisée sous différents angles sur un moniteur à l'aide d'un système 3D/CAO. 2.) Des prototypes à partir de matériaux non métalliques et métalliques sont fabriqués et étudiés d'un point de vue fonctionnel, technique et esthétique. 3.) Un prototypage à faible coût en très peu de temps est réalisé. La fabrication additive peut ressembler à la construction d'une miche de pain en empilant et en collant des tranches individuelles les unes sur les autres. En d'autres termes, le produit est fabriqué tranche par tranche, ou couche par couche déposée les unes sur les autres. La plupart des pièces peuvent être produites en quelques heures. La technique est bonne si les pièces sont nécessaires très rapidement ou si les quantités nécessaires sont faibles et que la fabrication d'un moule et d'un outillage est trop coûteuse et prend du temps. Cependant le coût d'une pièce est cher en raison des matières premières chères. • STÉRÉOLITHOGRAPHIE : Cette technique également abrégée en STL, est basée sur le durcissement et le durcissement d'un photopolymère liquide en une forme spécifique en focalisant un faisceau laser dessus. Le laser polymérise le photopolymère et le durcit. En balayant le faisceau laser UV selon la forme programmée le long de la surface du mélange photopolymère, la pièce est produite de bas en haut en tranches individuelles en cascade les unes sur les autres. Le balayage du spot laser est répété plusieurs fois pour obtenir les géométries programmées dans le système. Une fois la pièce entièrement fabriquée, elle est retirée de la plate-forme, essuyée et nettoyée par ultrasons et avec un bain d'alcool. Ensuite, il est exposé à une irradiation UV pendant quelques heures pour s'assurer que le polymère est complètement durci et durci. Pour résumer le processus, une plate-forme qui est plongée dans un mélange de photopolymères et un faisceau laser UV sont contrôlés et déplacés à travers un système d'asservissement en fonction de la forme de la pièce souhaitée et la pièce est obtenue en photodurcissant le polymère couche par couche. Bien entendu, les dimensions maximales de la pièce produite sont déterminées par l'équipement de stéréolithographie. • POLYJET : Semblable à l'impression à jet d'encre, dans le polyjet, nous avons huit têtes d'impression qui déposent le photopolymère sur le plateau de fabrication. La lumière ultraviolette placée le long des jets polymérise et durcit immédiatement chaque couche. Deux matériaux sont utilisés dans le polyjet. Le premier matériau est destiné à la fabrication du modèle réel. Le deuxième matériau, une résine de type gel, est utilisé comme support. Ces deux matériaux sont déposés couche par couche et polymérisés simultanément. Après l'achèvement du modèle, le matériau de support est retiré avec une solution aqueuse. Les résines utilisées sont similaires à la stéréolithographie (STL). Le polyjet présente les avantages suivants par rapport à la stéréolithographie : 1.) Pas besoin de nettoyer les pièces. 2.) Pas besoin de durcissement post-traitement 3.) Des épaisseurs de couche plus petites sont possibles et nous obtenons ainsi une meilleure résolution et pouvons fabriquer des pièces plus fines. • MODÉLISATION DE DÉPÔT FUSÉ : Également abrégé en FDM, dans cette méthode, une tête d'extrudeuse contrôlée par un robot se déplace dans deux directions principales sur une table. Le câble est abaissé et relevé au besoin. A partir de l'orifice d'une filière chauffée sur la tête, un filament thermoplastique est extrudé et une couche initiale est déposée sur une base en mousse. Ceci est accompli par la tête d'extrusion qui suit un chemin prédéterminé. Après la couche initiale, la table est abaissée et les couches suivantes sont déposées les unes sur les autres. Parfois, lors de la fabrication d'une pièce compliquée, des structures de support sont nécessaires pour que le dépôt puisse se poursuivre dans certaines directions. Dans ces cas, un matériau de support est extrudé avec un espacement moins dense de filaments sur une couche de sorte qu'il est plus faible que le matériau modèle. Ces structures de support peuvent ensuite être dissoutes ou rompues après l'achèvement de la pièce. Les dimensions de la filière de l'extrudeuse déterminent l'épaisseur des couches extrudées. Le procédé FDM produit des pièces avec des surfaces étagées sur des plans extérieurs obliques. Si cette rugosité est inacceptable, un polissage chimique à la vapeur ou un outil chauffé peuvent être utilisés pour les lisser. Même une cire de polissage est disponible comme matériau de revêtement pour éliminer ces étapes et atteindre des tolérances géométriques raisonnables. • FRITTAGE SÉLECTIF AU LASER : Egalement appelé SLS, le procédé est basé sur le frittage sélectif d'un polymère, de poudres céramiques ou métalliques dans un objet. Le fond de la chambre de traitement comporte deux cylindres : un cylindre de fabrication partielle et un cylindre d'alimentation en poudre. Le premier est abaissé par incréments jusqu'à l'endroit où la pièce frittée est en cours de formation et le second est relevé par incréments pour fournir de la poudre au cylindre de fabrication de pièces par l'intermédiaire d'un mécanisme à rouleaux. Une fine couche de poudre est d'abord déposée dans le cylindre de fabrication partielle, puis un faisceau laser est focalisé sur cette couche, traçant et fondant/frittant une section transversale particulière, qui se resolidifie ensuite en un solide. La poudre est les zones qui ne sont pas touchées par le faisceau laser restent lâches mais supportent toujours la partie solide. Ensuite, une autre couche de poudre est déposée et le processus répété plusieurs fois pour obtenir la pièce. À la fin, les particules de poudre libre sont secouées. Tous ces éléments sont exécutés par un ordinateur de contrôle de processus à l'aide d'instructions générées par le programme de CAO 3D de la pièce en cours de fabrication. Divers matériaux tels que les polymères (tels que l'ABS, le PVC, le polyester), la cire, les métaux et les céramiques avec des liants polymères appropriés peuvent être déposés. • ELECTRON-BEAM MELTING : Semblable au frittage sélectif par laser, mais utilisant un faisceau d'électrons pour fondre des poudres de titane ou de chrome-cobalt pour fabriquer des prototypes sous vide. Certains développements ont été réalisés pour réaliser ce procédé sur les aciers inoxydables, l'aluminium et les alliages de cuivre. Si la résistance à la fatigue des pièces produites doit être augmentée, nous utilisons le pressage isostatique à chaud après la fabrication de la pièce comme processus secondaire. • IMPRESSION TRIDIMENSIONNELLE : Egalement désignée par 3DP, dans cette technique une tête d'impression dépose un liant inorganique sur une couche de poudre non métallique ou métallique. Un piston portant le lit de poudre est progressivement abaissé et à chaque étape le liant est déposé couche par couche et fondu par le liant. Les matériaux en poudre utilisés sont des mélanges de polymères et des fibres, du sable de fonderie, des métaux. En utilisant simultanément différentes têtes de reliure et des liants de couleurs différentes, nous pouvons obtenir différentes couleurs. Le processus est similaire à l'impression à jet d'encre mais au lieu d'obtenir une feuille colorée, nous obtenons un objet tridimensionnel coloré. Les pièces produites peuvent être poreuses et peuvent donc nécessiter un frittage et une infiltration de métal pour augmenter sa densité et sa résistance. Le frittage brûlera le liant et fusionnera les poudres métalliques. Des métaux tels que l'acier inoxydable, l'aluminium, le titane peuvent être utilisés pour fabriquer les pièces et comme matériaux d'infiltration, nous utilisons couramment le cuivre et le bronze. La beauté de cette technique est que même des assemblages compliqués et mobiles peuvent être fabriqués très rapidement. Par exemple, un engrenage, une clé en tant qu'outil peut être fabriqué et aura des pièces mobiles et tournantes prêtes à être utilisées. Différents composants de l'ensemble peuvent être fabriqués avec différentes couleurs et le tout en une seule fois. Téléchargez notre brochure sur :Les bases de l'impression 3D métal • FABRICATION DIRECTE et OUTILLAGE RAPIDE : outre l'évaluation de la conception, le dépannage, nous utilisons le prototypage rapide pour la fabrication directe des produits ou l'application directe dans les produits. En d'autres termes, le prototypage rapide peut être intégré aux processus conventionnels pour les rendre meilleurs et plus compétitifs. Par exemple, le prototypage rapide peut produire des modèles et des moules. Des modèles d'un polymère en fusion et en combustion créés par des opérations de prototypage rapide peuvent être assemblés pour un moulage à modèle perdu et revêtus. Un autre exemple à mentionner est l'utilisation de 3DP pour produire une coque de coulée en céramique et l'utiliser pour les opérations de coulée de coque. Même les moules à injection et les inserts de moule peuvent être produits par prototypage rapide et on peut économiser plusieurs semaines ou mois de délai de fabrication de moules. En analysant uniquement un fichier CAO de la pièce souhaitée, nous pouvons produire la géométrie de l'outil à l'aide d'un logiciel. Voici quelques-unes de nos méthodes d'outillage rapide populaires : MOULAGE RTV (Room-Temperature Vulcanizing) / COULAGE URETHANE : L'utilisation du prototypage rapide permet de réaliser le patronage de la pièce souhaitée. Ensuite, ce modèle est enduit d'un agent de séparation et du caoutchouc RTV liquide est versé sur le modèle pour produire les moitiés de moule. Ensuite, ces demi-moules sont utilisés pour mouler par injection des uréthanes liquides. La durée de vie du moule est courte, seulement comme 0 ou 30 cycles mais suffisante pour la production de petits lots. MOULAGE PAR INJECTION ACES (Acetal Clear Epoxy Solid) : Grâce à des techniques de prototypage rapide telles que la stéréolithographie, nous réalisons des moules à injection. Ces moules sont des coques avec une extrémité ouverte pour permettre le remplissage avec des matériaux tels que l'époxy, l'époxy chargé aluminium ou les métaux. Encore une fois, la durée de vie du moule est limitée à des dizaines ou des centaines de pièces maximum. PROCÉDÉ D'OUTILLAGE EN MÉTAL PROJETÉ : Nous utilisons un prototypage rapide et réalisons un modèle. Nous pulvérisons un alliage zinc-aluminium sur la surface du motif et l'enduisons. Le motif avec le revêtement métallique est ensuite placé à l'intérieur d'un flacon et mis en pot avec un époxy ou un époxy rempli d'aluminium. Enfin, il est retiré et en produisant deux de ces demi-moules, nous obtenons un moule complet pour le moulage par injection. Ces moules ont une durée de vie plus longue, dans certains cas, en fonction du matériau et des températures, ils peuvent produire des milliers de pièces. PROCÉDÉ KEELTOOL : Cette technique peut produire des moules avec 100 000 à 10 millions de cycles de vie. Grâce au prototypage rapide, nous produisons un moule RTV. Le moule est ensuite rempli d'un mélange constitué de poudre d'acier à outils A6, de carbure de tungstène, de liant polymère et laissé durcir. Ce moule est ensuite chauffé pour brûler le polymère et fusionner les poudres métalliques. L'étape suivante est l'infiltration de cuivre pour produire le moule final. Si nécessaire, des opérations secondaires telles que l'usinage et le polissage peuvent être effectuées sur le moule pour de meilleures précisions dimensionnelles. CLICK Product Finder-Locator Service PAGE PRÉCÉDENTE
- Fabrication de verre et de céramique, emballages hermétiques, joints, collage
Fabrication de verre et de céramique, Joints et collage d'emballages hermétiques, Verre trempé pare-balles, Moulage par soufflage, Verre de qualité optique, Verre conducteur, Moulage Formage et façonnage du verre et de la céramique Les types de fabrication de verre que nous proposons sont le verre de récipient, le soufflage de verre, la fibre de verre, les tubes et les tiges, la verrerie domestique et industrielle, les lampes et les ampoules, le moulage de précision du verre, les composants et assemblages optiques, le verre plat, le verre plat et le verre flotté. Nous effectuons à la fois le formage à la main et le formage à la machine. Nos procédés de fabrication de céramiques techniques populaires sont le pressage, le pressage isostatique, le pressage isostatique à chaud, le pressage à chaud, le coulage en barbotine, le coulage en bande, l'extrusion, le moulage par injection, l'usinage vert, le frittage ou la cuisson, le meulage au diamant, les assemblages hermétiques. Nous vous recommandons de cliquer ici pour TÉLÉCHARGEZ nos illustrations schématiques des processus de formage et de façonnage du verre par AGS-TECH Inc. TÉLÉCHARGEZ nos illustrations schématiques des procédés de fabrication de céramique technique par AGS-TECH Inc. Ces fichiers téléchargeables avec photos et croquis vous aideront à mieux comprendre les informations que nous vous fournissons ci-dessous. • FABRICATION DE VERRE D'EMBALLAGE : Nous disposons de lignes automatisées PRESS AND BLOW ainsi que BLOW AND BLOW pour la fabrication. Dans le processus de soufflage et de soufflage, nous déposons une paraison dans un moule vierge et formons le col en appliquant un coup d'air comprimé par le haut. Immédiatement après cela, de l'air comprimé est soufflé une seconde fois depuis l'autre direction à travers le goulot du récipient pour former la préforme de la bouteille. Cette préforme est ensuite transférée dans le moule réel, réchauffée pour ramollir et de l'air comprimé est appliqué pour donner à la préforme sa forme finale de récipient. Plus explicitement, il est pressurisé et poussé contre les parois de la cavité du moule de soufflage pour prendre sa forme souhaitée. Enfin, le récipient en verre fabriqué est transféré dans un four de recuit pour un réchauffage ultérieur et l'élimination des contraintes produites lors du moulage et est refroidi de manière contrôlée. Dans la méthode de pressage et de soufflage, les paraisons fondues sont placées dans un moule à paraison (moule vierge) et pressées en forme de paraison (forme vierge). Les ébauches sont ensuite transférées dans des moules de soufflage et soufflées de la même manière que le processus décrit ci-dessus sous «Processus de soufflage et de soufflage». Les étapes suivantes comme le recuit et le soulagement des contraintes sont similaires ou identiques. • SOUFFLAGE DU VERRE : Nous fabriquons des produits en verre en utilisant le soufflage à la main conventionnel ainsi qu'en utilisant de l'air comprimé avec des équipements automatisés. Pour certaines commandes, un soufflage conventionnel est nécessaire, comme les projets impliquant des œuvres d'art en verre, ou des projets qui nécessitent un plus petit nombre de pièces avec des tolérances lâches, des projets de prototypage / démo… etc. Le soufflage de verre conventionnel implique le trempage d'un tuyau métallique creux dans un pot de verre fondu et la rotation du tuyau pour recueillir une certaine quantité de matériau de verre. Le verre recueilli sur le bout de la pipe est roulé sur du fer plat, façonné à volonté, allongé, réchauffé et soufflé à l'air. Lorsqu'il est prêt, il est inséré dans un moule et de l'air est soufflé. La cavité du moule est humide pour éviter le contact du verre avec le métal. Le film d'eau agit comme un coussin entre eux. Le soufflage manuel est un processus lent à forte intensité de main-d'œuvre et ne convient qu'au prototypage ou aux articles de grande valeur, ne convient pas aux commandes bon marché à volume élevé par pièce. • FABRICATION DE VERRERIE DOMESTIQUE ET INDUSTRIELLE : En utilisant différents types de matériaux en verre, une grande variété de verrerie est produite. Certains verres sont résistants à la chaleur et conviennent à la verrerie de laboratoire, tandis que d'autres sont suffisamment bons pour résister plusieurs fois au lave-vaisselle et conviennent à la fabrication de produits domestiques. À l'aide des machines Westlake, des dizaines de milliers de verres à boire sont produits chaque jour. Pour simplifier, le verre en fusion est collecté sous vide et inséré dans des moules pour fabriquer les préformes. Ensuite, de l'air est insufflé dans les moules, ceux-ci sont transférés dans un autre moule et de l'air est soufflé à nouveau et le verre prend sa forme définitive. Comme pour le soufflage à la main, ces moules sont maintenus humides avec de l'eau. Un étirement supplémentaire fait partie de l'opération de finition où le col est formé. L'excédent de verre est brûlé. Ensuite, le processus de réchauffage et de refroidissement contrôlés décrit ci-dessus suit. • FORMAGE DE TUBE & BARRE DE VERRE : Les principaux procédés que nous utilisons pour la fabrication des tubes de verre sont les procédés DANNER et VELLO. Dans le procédé Danner, le verre d'un four s'écoule et tombe sur un manchon incliné en matériaux réfractaires. Le manchon est porté sur un arbre creux rotatif ou chalumeau. Le verre est ensuite enroulé autour du manchon et forme une couche lisse coulant le long du manchon et sur la pointe de la tige. Dans le cas de la formation de tubes, l'air est soufflé à travers un chalumeau à pointe creuse, et dans le cas de la formation de tiges, nous utilisons des pointes pleines sur l'arbre. Les tubes ou tiges sont ensuite tirés sur des rouleaux porteurs. Les dimensions telles que l'épaisseur de paroi et le diamètre des tubes de verre sont ajustées aux valeurs souhaitées en réglant le diamètre du manchon et en soufflant la pression d'air à une valeur souhaitée, en ajustant la température, le débit de verre et la vitesse d'étirage. Le processus de fabrication du tube de verre Vello, quant à lui, implique du verre qui sort d'un four et dans un bol avec un mandrin creux ou une cloche. Le verre traverse alors l'espace d'air entre le mandrin et le bol et prend la forme d'un tube. Ensuite, il se déplace sur des rouleaux jusqu'à une machine d'étirage et est refroidi. À la fin de la ligne de refroidissement, la coupe et le traitement final ont lieu. Les dimensions du tube peuvent être ajustées comme dans le procédé Danner. En comparant le processus Danner à Vello, nous pouvons dire que le processus Vello convient mieux à la production en grande quantité, tandis que le processus Danner peut être mieux adapté aux commandes précises de tubes de plus petit volume. • TRAITEMENT DES FEUILLES & VERRE PLAT & FLOAT : Nous disposons de grandes quantités de verre plat dans des épaisseurs allant du submillimétrique à plusieurs centimètres. Nos verres plats sont d'une perfection presque optique. Nous proposons du verre avec des revêtements spéciaux tels que les revêtements optiques, où la technique de dépôt chimique en phase vapeur est utilisée pour mettre des revêtements tels que l'antireflet ou le revêtement miroir. Les revêtements conducteurs transparents sont également courants. Sont également disponibles des revêtements hydrophobes ou hydrophiles sur le verre et des revêtements qui rendent le verre autonettoyant. Les verres trempés, pare-balles et feuilletés sont d'autres articles populaires. Nous coupons le verre dans la forme souhaitée avec les tolérances souhaitées. D'autres opérations secondaires comme le cintrage ou le cintrage du verre plat sont possibles. • MOULAGE DE PRÉCISION DU VERRE : Nous utilisons cette technique principalement pour fabriquer des composants optiques de précision sans avoir besoin de techniques plus coûteuses et chronophages comme le meulage, le rodage et le polissage. Cette technique n'est pas toujours suffisante pour tirer le meilleur parti des meilleures optiques, mais dans certains cas, comme les produits de consommation, les appareils photo numériques, l'optique médicale, elle peut être une bonne option moins coûteuse pour la fabrication à grand volume. Il présente également un avantage par rapport aux autres techniques de formage du verre où des géométries complexes sont requises, comme dans le cas des asphères. Le processus de base implique le chargement de la face inférieure de notre moule avec l'ébauche de verre, l'évacuation de la chambre de traitement pour l'élimination de l'oxygène, la fermeture proche du moule, le chauffage rapide et isotherme de la matrice et du verre avec une lumière infrarouge, une fermeture supplémentaire des moitiés de moule presser le verre ramolli lentement de façon contrôlée jusqu'à l'épaisseur désirée, et enfin refroidissement du verre et remplissage de la chambre avec de l'azote et élimination du produit. Le contrôle précis de la température, la distance de fermeture du moule, la force de fermeture du moule, l'adaptation des coefficients de dilatation du moule et du verre sont essentiels dans ce processus. • FABRICATION DE COMPOSANTS ET D'ASSEMBLAGES OPTIQUES EN VERRE : outre le moulage de précision du verre, nous utilisons un certain nombre de procédés précieux pour fabriquer des composants et des assemblages optiques de haute qualité pour des applications exigeantes. Le meulage, le rodage et le polissage de verres de qualité optique dans de fines suspensions abrasives spéciales sont un art et une science pour la fabrication de lentilles optiques, de prismes, de plats et plus encore. La planéité de surface, l'ondulation, le lissé et les surfaces optiques sans défaut nécessitent une grande expérience de ces processus. De petits changements dans l'environnement peuvent entraîner des produits hors spécifications et entraîner l'arrêt de la chaîne de fabrication. Il existe des cas où un simple essuyage sur la surface optique avec un chiffon propre peut rendre un produit conforme aux spécifications ou échouer au test. Certains matériaux de verre populaires utilisés sont la silice fondue, le quartz, le BK7. De plus, l'assemblage de tels composants nécessite une expérience de niche spécialisée. Parfois, des colles spéciales sont utilisées. Cependant, une technique appelée mise en contact optique est parfois le meilleur choix et n'implique aucun matériau entre les verres optiques attachés. Il consiste à mettre physiquement en contact des surfaces planes pour les attacher les unes aux autres sans colle. Dans certains cas, des entretoises mécaniques, des tiges ou billes de verre de précision, des pinces ou des composants métalliques usinés sont utilisés pour assembler les composants optiques à certaines distances et avec certaines orientations géométriques les uns par rapport aux autres. Examinons certaines de nos techniques populaires de fabrication d'optiques haut de gamme. MEULAGE & RODAGE & POLISSAGE : La forme brute du composant optique est obtenue par meulage d'une ébauche de verre. Ensuite, le rodage et le polissage sont effectués en faisant tourner et en frottant les surfaces rugueuses des composants optiques contre des outils avec des formes de surface souhaitées. Des boues contenant de minuscules particules abrasives et du liquide sont versées entre l'optique et les outils de mise en forme. Les tailles de particules abrasives dans de telles suspensions peuvent être choisies en fonction du degré de planéité souhaité. Les écarts des surfaces optiques critiques par rapport aux formes souhaitées sont exprimés en termes de longueurs d'onde de la lumière utilisée. Nos optiques de haute précision ont des tolérances d'un dixième de longueur d'onde (longueur d'onde/10) ou même plus sont possibles. Outre le profil de surface, les surfaces critiques sont numérisées et évaluées pour d'autres caractéristiques et défauts de surface tels que les dimensions, les rayures, les éclats, les piqûres, les taches, etc. Le contrôle strict des conditions environnementales dans l'atelier de fabrication optique et les exigences de métrologie et de test étendues avec des équipements de pointe en font une branche de l'industrie difficile. • PROCESSUS SECONDAIRES DANS LA FABRICATION DU VERRE : Encore une fois, nous ne sommes limités que par votre imagination lorsqu'il s'agit de processus secondaires et de finition du verre. Nous en énumérons ici quelques-uns : -Revêtements sur verre (optique, électrique, tribologique, thermique, fonctionnel, mécanique...). Par exemple, nous pouvons modifier les propriétés de surface du verre en le faisant par exemple réfléchir la chaleur afin qu'il garde les intérieurs des bâtiments frais, ou faire en sorte qu'un côté absorbe l'infrarouge à l'aide de la nanotechnologie. Cela permet de garder l'intérieur des bâtiments au chaud, car la couche de verre la plus externe absorbe le rayonnement infrarouge à l'intérieur du bâtiment et le renvoie vers l'intérieur. -Gravure sur verre -Étiquetage céramique appliqué (ACL) -Gravure -Polissage à la flamme -Polissage chimique -La coloration FABRICATION DE CÉRAMIQUES TECHNIQUES • DIE PRESSING : Consiste en un compactage uniaxial de poudres granulaires confinées dans une filière • PRESSAGE A CHAUD : Semblable au pressage à chaud mais avec l'ajout de température pour améliorer la densification. La poudre ou la préforme compactée est placée dans une matrice en graphite et une pression uniaxiale est appliquée tandis que la matrice est maintenue à des températures élevées telles que 2000 C. Les températures peuvent être différentes selon le type de poudre céramique en cours de traitement. Pour les formes et géométries compliquées, d'autres traitements ultérieurs tels que le meulage au diamant peuvent être nécessaires. • PRESSAGE ISOSTATIQUE : La poudre granulaire ou les compacts pressés sont placés dans des conteneurs hermétiques puis dans un récipient sous pression fermé avec du liquide à l'intérieur. Ensuite, ils sont compactés en augmentant la pression du récipient sous pression. Le liquide à l'intérieur du récipient transmet les forces de pression uniformément sur toute la surface du récipient hermétique. Le matériau est ainsi compacté uniformément et prend la forme de son contenant souple et de son profil et de ses caractéristiques internes. • PRESSAGE ISOSTATIQUE A CHAUD : Similaire au pressage isostatique, mais en plus de l'atmosphère gazeuse sous pression, nous frittons le compact à haute température. Le pressage isostatique à chaud entraîne une densification supplémentaire et une résistance accrue. • SLIP CASTING / DRAIN CASTING : Nous remplissons le moule avec une suspension de particules céramiques de taille micrométrique et de liquide porteur. Ce mélange est appelé « barbotine ». Le moule a des pores et donc le liquide du mélange est filtré dans le moule. En conséquence, un moulage est formé sur les surfaces intérieures du moule. Après frittage, les pièces peuvent être sorties du moule. • MOULAGE DE RUBAN : Nous fabriquons des rubans céramiques en coulant des boues céramiques sur des surfaces planes porteuses en mouvement. Les bouillies contiennent des poudres céramiques mélangées à d'autres produits chimiques à des fins de liaison et de transport. Au fur et à mesure que les solvants s'évaporent, il reste des feuilles de céramique denses et flexibles qui peuvent être coupées ou roulées à volonté. • FORMAGE PAR EXTRUSION : Comme dans d'autres processus d'extrusion, un mélange mou de poudre céramique avec des liants et d'autres produits chimiques est passé à travers une filière pour acquérir sa forme en coupe transversale et est ensuite coupé aux longueurs désirées. Le processus est effectué avec des mélanges céramiques froids ou chauffés. • MOULAGE PAR INJECTION BASSE PRESSION : Nous préparons un mélange de poudre céramique avec des liants et des solvants et le chauffons à une température où il peut être facilement pressé et forcé dans la cavité de l'outil. Une fois le cycle de moulage terminé, la pièce est éjectée et le liant chimique est brûlé. En utilisant le moulage par injection, nous pouvons obtenir des pièces complexes à des volumes élevés de manière économique. Des trous qui sont une infime fraction de millimètre sur une paroi de 10 mm d'épaisseur sont possibles, des filetages sont possibles sans autre usinage, des tolérances aussi serrées que +/- 0,5% sont possibles et même inférieures lorsque les pièces sont usinées , des épaisseurs de paroi de l'ordre de 0,5 mm à une longueur de 12,5 mm sont possibles ainsi que des épaisseurs de paroi de 6,5 mm à une longueur de 150 mm. • USINAGE VERT : Avec les mêmes outils d'usinage des métaux, nous pouvons usiner les céramiques pressées alors qu'elles sont encore tendres comme de la craie. Des tolérances de +/- 1% sont possibles. Pour de meilleures tolérances, nous utilisons une rectification au diamant. • FRITTAGE ou CUISSON : Le frittage permet une densification complète. Un retrait important se produit sur les pièces compactes vertes, mais ce n'est pas un gros problème puisque nous prenons en compte ces changements dimensionnels lorsque nous concevons la pièce et l'outillage. Les particules de poudre sont liées ensemble et la porosité induite par le processus de compactage est supprimée dans une large mesure. • BROYAGE AU DIAMANT : Le matériau le plus dur au monde, le « diamant », est utilisé pour broyer des matériaux durs comme la céramique et des pièces de précision sont obtenues. Des tolérances de l'ordre du micromètre et des surfaces très lisses sont atteintes. En raison de son coût, nous n'envisageons cette technique que lorsque nous en avons vraiment besoin. • LES ENSEMBLES HERMÉTIQUES sont ceux qui ne permettent pratiquement aucun échange de matière, solide, liquide ou gazeux entre les interfaces. Le scellement hermétique est étanche à l'air. Par exemple, les boîtiers électroniques hermétiques sont ceux qui maintiennent le contenu intérieur sensible d'un appareil emballé à l'abri de l'humidité, des contaminants ou des gaz. Rien n'est hermétique à 100%, mais quand on parle d'herméticité on veut dire qu'en termes pratiques, il y a herméticité dans la mesure où le taux de fuite est si faible que les appareils sont sûrs dans des conditions environnementales normales pendant de très longues durées. Nos assemblages hermétiques sont constitués de composants métal, verre et céramique, métal-céramique, céramique-métal-céramique, métal-céramique-métal, métal sur métal, métal-verre, métal-verre-métal, verre-métal-verre, verre- métal et verre sur verre et toutes les autres combinaisons de collage métal-verre-céramique. Nous pouvons par exemple revêtir de métal les composants en céramique afin qu'ils puissent être fortement liés aux autres composants de l'assemblage et avoir une excellente capacité d'étanchéité. Nous avons le savoir-faire pour revêtir les fibres optiques ou les traversées de métal et les souder ou les braser aux boîtiers, afin qu'aucun gaz ne passe ou ne fuie dans les boîtiers. Ils sont donc utilisés pour fabriquer des boîtiers électroniques pour encapsuler des appareils sensibles et les protéger de l'atmosphère extérieure. Outre leurs excellentes caractéristiques d'étanchéité, d'autres propriétés telles que le coefficient de dilatation thermique, la résistance à la déformation, la nature non dégazante, la très longue durée de vie, la nature non conductrice, les propriétés d'isolation thermique, la nature antistatique... etc. faire du verre et des matériaux céramiques le choix pour certaines applications. Des informations sur notre usine de production de raccords céramique-métal, d'étanchéité hermétique, de traversées de vide, de composants de contrôle des fluides et des vides poussés et ultra-poussés peuvent être trouvées ici :Brochure de l'usine de composants hermétiques CLICK Product Finder-Locator Service PAGE PRÉCÉDENTE
- Formage de fils et de ressorts, façonnage, soudage, assemblage de fils, bobines, CNC
Formage de fils et de ressorts, façonnage, soudage, assemblage de fils, ressorts plats de torsion d'extension de compression de bobine, fils sur mesure, ressorts hélicoïdaux chez AGS-TECH Inc. Formage de fils et de ressorts Nous fabriquons des fils personnalisés, des assemblages de fils, des fils formés dans les formes 2D et 3D souhaitées, des filets métalliques, des treillis, des enceintes, des paniers, des clôtures, des ressorts métalliques, des ressorts plats ; torsion, compression, tension, ressorts plats et plus encore. Nos processus sont le formage de fils et de ressorts, le tréfilage, le façonnage, le pliage, le soudage, le brasage, le perçage, le sertissage, le perçage, le chanfreinage, le meulage, le filetage, le revêtement, le fourslide, le formage de glissières, l'enroulement, l'enroulement, le refoulement. Nous vous recommandons de cliquer ici pour TÉLÉCHARGEZ nos illustrations schématiques des processus de formage de fils et de ressorts par AGS-TECH Inc. Ce fichier téléchargeable avec photos et croquis vous aidera à mieux comprendre les informations que nous vous fournissons ci-dessous. • TRÉFICAGE : En utilisant des forces de traction, nous étirons le stock de métal et le tirons à travers une filière pour réduire le diamètre et augmenter sa longueur. Parfois, nous utilisons une série de matrices. Nous sommes capables de fabriquer des matrices pour chaque calibre de fil. En utilisant un matériau à haute résistance à la traction, nous étirons des fils très fins. Nous proposons des fils travaillés à froid et à chaud. • FORMAGE DU FIL : Un rouleau de fil calibré est plié et façonné en un produit utile. Nous avons la capacité de former des fils de tous les calibres, y compris des filaments minces ainsi que des fils épais tels que ceux utilisés comme ressorts sous les châssis d'automobiles. Les équipements que nous utilisons pour le formage de fil sont des formeuses de fil manuelles et CNC, des bobineuses, des presses électriques, des fourslide, des multi-coulisses. Nos processus sont l'étirage, le pliage, le dressage, l'aplatissement, l'étirement, la coupe, le refoulement, le soudage et le soudage et le brasage, l'assemblage, le bobinage, l'emboutissage (ou l'ailette), le perçage, le filetage de fil, le perçage, le chanfreinage, le meulage, le revêtement et les traitements de surface. Notre équipement de pointe peut être configuré pour développer des conceptions très complexes de n'importe quelle forme et avec des tolérances serrées. Nous proposons différents types d'extrémités like extrémités sphériques, pointues ou chanfreinées pour vos fils. La plupart de nos projets de formage de fil ont des coûts d'outillage minimes à nuls. Les délais d'exécution des échantillons sont généralement de jours. Les modifications de conception/configuration des formes de fil peuvent être apportées très rapidement. • FORMAGE DES RESSORTS : AGS-TECH fabrique une grande variété de ressorts dont : -Ressort de torsion/double torsion -Ressort de tension/compression -Ressort constant/variable -Ressort hélicoïdal et hélicoïdal -Ressort plat et à lames -Ressort d'équilibre -Laveuse Belleville -Ressort négatif -Ressort hélicoïdal à taux progressif -Vague Ressort -Ressort Volute -Ressorts coniques -Anneaux à ressort -Ressorts d'horloge -Clips Nous fabriquons des ressorts à partir d'une variété de matériaux et pouvons vous guider selon votre application. Les matériaux les plus courants sont l'acier inoxydable, le chrome-silicium, l'acier à haute teneur en carbone, l'huile à faible teneur en carbone, le chrome vanadium, le bronze phosphoreux, le titane, l'alliage de cuivre au béryllium, la céramique haute température. Nous utilisons diverses techniques dans la fabrication des ressorts, notamment le bobinage CNC, le bobinage à froid, le bobinage à chaud, la trempe, la finition. D'autres techniques déjà mentionnées ci-dessus sous la forme de fil sont également courantes dans nos opérations de fabrication de ressorts. • SERVICES DE FINITION pour FILS & RESSORTS : Nous pouvons finir vos produits de plusieurs manières selon votre choix et vos besoins. Certains processus courants que nous proposons sont : peinture, revêtement en poudre, placage, trempage de vinyle, anodisation, soulagement des contraintes, traitement thermique, grenaillage, culbutage, chromate, nickel autocatalytique, passivation, émail cuit, revêtement plastique , nettoyage au plasma. CLICK Product Finder-Locator Service PAGE PRÉCÉDENTE
- Fabrication de formage de tôle, emboutissage, poinçonnage, emboutissage profond, CNC
Formage et fabrication de tôle, emboutissage, poinçonnage, pliage, matrice progressive, soudage par points, emboutissage profond, découpe et refendage de métal chez AGS-TECH Inc. Estampage et fabrication de tôles Nous proposons l'emboutissage, le façonnage, le formage, le pliage, le poinçonnage, le découpage, le refendage, la perforation, l'encochage, le grignotage, le rasage, le travail à la presse, la fabrication, l'emboutissage profond à l'aide de matrices à poinçonnage unique / à un seul coup ainsi que les matrices progressives et le repoussage, le formage du caoutchouc et hydroformage; découpe de tôles au jet d'eau, plasma, laser, scie, flamme; assemblage de tôles par soudage, soudage par points; renflement et flexion des tubes en tôle ; finition de surface de tôle, y compris la peinture par trempage ou par pulvérisation, le revêtement en poudre électrostatique, l'anodisation, le placage, la pulvérisation et plus encore. Nos services vont du prototypage rapide de tôlerie à la fabrication à grand volume. Nous vous recommandons de cliquer ici pourTÉLÉCHARGEZ nos illustrations schématiques des processus de fabrication et d'emboutissage de tôle par AGS-TECH Inc. Cela vous aidera à mieux comprendre les informations que nous vous fournissons ci-dessous. • DÉCOUPE DE TÔLE : Nous proposons des TRONÇONS et des DÉCOUPES. Les coupures coupent la tôle sur un chemin à la fois et il n'y a fondamentalement aucun gaspillage de matériau, alors qu'avec les séparations, la forme ne peut pas être nichée avec précision et donc une certaine quantité de matériau est gaspillée. L'un de nos processus les plus populaires est le POINÇONNAGE, où un morceau de matériau rond ou d'une autre forme est découpé dans une tôle. Le morceau qui est découpé est un déchet. Une autre version du poinçonnage est le SLOTTING, où des trous rectangulaires ou allongés sont poinçonnés. Le BLANKING, quant à lui, est le même processus que le poinçonnage, à la différence que la pièce découpée est le travail et est conservée. FINE BLANKING, une version supérieure du découpage, crée des coupes avec des tolérances étroites et des bords lisses et droits et ne nécessite pas d'opérations secondaires pour la perfection de la pièce. Un autre processus que nous utilisons fréquemment est le SLITTING, qui est un processus de cisaillement où la tôle est coupée par deux lames circulaires opposées dans un chemin droit ou courbe. L'ouvre-boîte est un exemple simple du processus de refendage. Un autre processus populaire pour nous est la PERFORATION, où de nombreux trous ronds ou d'une autre forme sont percés dans la tôle selon un certain motif. Un exemple typique de produit perforé est celui des filtres métalliques avec de nombreux trous pour les fluides. Dans NOTCHING, un autre processus de découpe de tôle, nous enlevons de la matière d'une pièce à usiner, en commençant par le bord ou ailleurs et coupons vers l'intérieur jusqu'à l'obtention de la forme souhaitée. C'est un processus progressif où chaque opération enlève une autre pièce jusqu'à ce que le contour désiré soit obtenu. Pour les petites séries de production, nous utilisons parfois un processus relativement plus lent appelé GRIGNOTAGE qui consiste en de nombreux poinçons rapides de trous qui se chevauchent pour faire une coupe plus grande et plus complexe. Dans la COUPE PROGRESSIVE, nous utilisons une série d'opérations différentes pour obtenir une seule coupe ou une certaine géométrie. Enfin LE RASAGE un processus secondaire nous aide à améliorer les bords des coupes qui ont déjà été faites. Il est utilisé pour couper les copeaux, les bords rugueux sur la tôlerie. • PLIAGE DE LA TÔLE : Outre la découpe, le pliage est un processus essentiel sans lequel nous ne serions pas en mesure de réaliser la plupart des produits. Principalement une opération de travail à froid, mais parfois également effectuée à chaud ou à chaud. Nous utilisons des matrices et pressons la plupart du temps pour cette opération. Dans le PLIAGE PROGRESSIF, nous utilisons une série d'opérations différentes de poinçonnage et de matriçage pour obtenir un seul pli ou une certaine géométrie. AGS-TECH utilise une variété de procédés de pliage et fait le choix en fonction de la matière de la pièce, sa taille, son épaisseur, la taille de pliage souhaitée, le rayon, la courbure et l'angle de pliage, l'emplacement du pliage, l'économie de fonctionnement, les quantités à fabriquer... etc. Nous utilisons V-BENDING où un poinçon en forme de V force la tôle dans la matrice en forme de V et la plie. Bon pour les angles très aigus et obtus et entre les deux, y compris 90 degrés. À l'aide de matrices d'essuyage, nous effectuons EDGE BENDING. Notre équipement nous permet d'obtenir des angles encore plus grands que 90 degrés. Dans le pliage des bords, la pièce est prise en sandwich entre un tampon de pression et la matrice, la zone de pliage est située sur le bord de la matrice et le reste de la pièce est maintenu au-dessus de space comme une poutre en porte-à-faux. Lorsque le poinçon agit sur la partie en porte-à-faux, il est plié sur le bord de la matrice. BRIDE est un processus de cintrage des bords résultant en un angle de 90 degrés. Les principaux objectifs de l'opération sont l'élimination des arêtes vives et l'obtention de surfaces géométriques pour faciliter l'assemblage des pièces. BEADING, un autre processus de pliage de bord commun forme une boucle sur le bord d'une pièce. L'OURLET, quant à lui, se traduit par un bord de la feuille complètement replié sur lui-même. Dans SEAMING, les bords de deux pièces sont pliés l'un sur l'autre et joints. DOUBLE SEAMING, quant à lui, permet d'obtenir des joints de tôle étanches à l'eau et à l'air. Semblable à la flexion des bords, un processus appelé ROTARY BENDING déploie un cylindre avec l'angle souhaité découpé et servant de poinçon. Lorsque la force est transmise au poinçon, il se ferme avec la pièce. La rainure du cylindre donne à la partie en porte-à-faux l'angle souhaité. La rainure peut avoir un angle inférieur ou supérieur à 90 degrés. En AIR BENDING, nous n'avons pas besoin que la matrice inférieure ait une rainure inclinée. La tôle est supportée par deux surfaces sur des côtés opposés et à une certaine distance. Le poinçon applique alors une force au bon endroit et plie la pièce. CHANNEL BENDING est réalisé à l'aide d'un poinçon et d'une matrice en forme de canal, et U-BEND est réalisé avec un poinçon en forme de U. OFFSET BENDING produit des décalages sur la tôle. ROLL BENDING, une technique idéale pour les travaux épais et le pliage de gros morceaux de plaques de métal, utilise trois rouleaux pour alimenter et plier les plaques aux courbures souhaitées. Les rouleaux sont disposés de manière à obtenir le pli souhaité du travail. La distance et l'angle entre les rouleaux sont contrôlés pour obtenir le résultat souhaité. Un rouleau mobile permet de contrôler la courbure. Le TUBE FORMING est une autre opération populaire de pliage de tôle impliquant plusieurs matrices. Les tubes sont obtenus après plusieurs actions. L'ONDULATION est également réalisée par des opérations de pliage. Fondamentalement, il s'agit de la flexion symétrique à intervalles réguliers sur toute une pièce de tôle. Différentes formes peuvent être utilisées pour l'ondulation. La tôle ondulée est plus rigide et a une meilleure résistance à la flexion et a donc des applications dans l'industrie de la construction. FORMAGE DE ROULEAUX DE TÔLE, un processus de fabrication continu est déployé pour plier des sections transversales d'une certaine géométrie à l'aide de rouleaux et le travail est plié en étapes séquentielles, le rouleau final complétant le travail. Dans certains cas, un seul rouleau et dans certains cas une série de rouleaux sont utilisés. • PROCÉDÉS COMBINÉS DE COUPE ET DE PLIAGE DE LA TÔLE : Ce sont les processus qui coupent et plient en même temps. En PIERCING, un trou est créé à l'aide d'un poinçon pointu. Au fur et à mesure que le poinçon élargit le trou dans la feuille, le matériau est plié simultanément dans une bride interne pour le trou. La bride obtenue peut avoir des fonctions importantes. L'opération LANCING, quant à elle, coupe et plie la tôle pour créer une géométrie en relief. • RENFORCEMENT ET PLIAGE DU TUBE MÉTALLIQUE : Lors du RENFORCEMENT, une partie interne d'un tube creux est mise sous pression, provoquant le renflement du tube vers l'extérieur. Puisque le tube est à l'intérieur d'une matrice, la géométrie du renflement est contrôlée par la forme de la matrice. Dans STRETCH BENDING, un tube métallique est étiré en utilisant des forces parallèles à l'axe du tube et des forces de flexion pour tirer le tube sur un bloc de forme. Dans DRAW BENDING, nous serrons le tube près de son extrémité sur un bloc de forme rotatif qui plie le tube tout en tournant. Enfin, dans le CINTRAGE PAR COMPRESSION, le tube est maintenu par la force sur un bloc de forme fixe, et une matrice le plie sur le bloc de forme. • EMBOUTISSAGE PROFOND : Dans l'une de nos opérations les plus populaires, un poinçon, une matrice assortie et un serre-flan sont utilisés. Le flan de tôle est placé sur l'ouverture de la matrice et le poinçon se déplace vers le flan maintenu par le serre-flan. Une fois qu'ils entrent en contact, le poinçon force la tôle dans la cavité de la matrice pour former le produit. L'opération d'emboutissage profond ressemble à la coupe, mais le jeu entre le poinçon et la matrice empêche la tôle d'être coupée. Un autre facteur assurant que la feuille est emboutie et non coupée sont les coins arrondis de la matrice et du poinçon qui empêchent le cisaillement et la coupe. Pour obtenir une plus grande ampleur d'emboutissage profond, un processus de REDRAWING est déployé où un emboutissage profond ultérieur a lieu sur une pièce qui a déjà subi un processus d'emboutissage profond. Dans REVERSE REDRAWING, la partie emboutie est retournée et dessinée dans la direction opposée. L'emboutissage profond peut fournir des objets de forme irrégulière tels que des gobelets bombés, coniques ou étagés, En EMBOSSAGE, nous utilisons une paire de matrices mâle et femelle pour imprimer la tôle avec un dessin ou un script. • SPINNING : opération au cours de laquelle une pièce plate ou préformée est maintenue entre un mandrin en rotation et une contre-poupée et un outil applique une pression localisée sur la pièce à mesure qu'elle remonte progressivement le mandrin. En conséquence, la pièce est enroulée sur le mandrin et prend sa forme. Nous utilisons cette technique comme alternative à l'emboutissage profond lorsque la quantité d'une commande est petite, les pièces sont grandes (diamètres jusqu'à 20 pieds) et ont des courbes uniques. Même si les prix par pièce sont généralement plus élevés, les coûts d'installation pour l'opération de filage CNC sont faibles par rapport à l'emboutissage profond. Au contraire, l'emboutissage profond nécessite un investissement initial élevé pour la configuration, mais les coûts par pièce sont faibles lorsqu'une grande quantité de pièces est produite. Une autre version de ce processus est SHEAR SPINNING, où il y a également un flux de métal dans la pièce. Le flux de métal réduira l'épaisseur de la pièce au fur et à mesure de l'exécution du processus. Encore un autre procédé connexe est le TUBE SPINNING, qui est appliqué sur des pièces cylindriques. Dans ce processus également, il y a un flux de métal dans la pièce. L'épaisseur est ainsi réduite et la longueur du tube est augmentée. L'outil peut être déplacé pour créer des éléments à l'intérieur ou à l'extérieur du tube. • FORMAGE EN CAOUTCHOUC DE LA TÔLE : Le matériau en caoutchouc ou en polyuréthane est placé dans une matrice de conteneur et la pièce à usiner est placée sur la surface du caoutchouc. Un coup de poing est ensuite appliqué sur la pièce à usiner et la force dans le caoutchouc. La pression générée par la gomme étant faible, la profondeur des pièces produites est limitée. Les coûts d'outillage étant faibles, le procédé convient à une production en petite quantité. • HYDROFORMAGE : Semblable au formage du caoutchouc, dans ce procédé, la tôle est pressée par un poinçon dans un liquide sous pression à l'intérieur d'une chambre. La tôlerie est prise en sandwich entre le poinçon et un diaphragme en caoutchouc. Le diaphragme entoure complètement la pièce et la pression du fluide l'oblige à se former sur le poinçon. Des tirages très profonds encore plus profonds que dans le processus d'emboutissage profond peuvent être obtenus avec cette technique. Nous fabriquons des matrices mono-poinçon ainsi que des matrices progressives selon votre pièce. Les matrices d'estampage à course unique sont une méthode rentable pour produire rapidement de grandes quantités de pièces en tôle simples telles que des rondelles. Les matrices progressives ou la technique d'emboutissage profond sont utilisées pour la fabrication de géométries plus complexes. Selon votre cas, la découpe jet d'eau, laser ou plasma permet de réaliser vos pièces de tôlerie à peu de frais, rapidement et avec précision. De nombreux fournisseurs n'ont aucune idée de ces techniques alternatives ou ne les ont pas et, par conséquent, ils passent par des moyens longs et coûteux de fabriquer des matrices et des outils qui ne font que perdre du temps et de l'argent aux clients. Si vous avez besoin de composants en tôle sur mesure tels que des boîtiers, des boîtiers électroniques, etc. en quelques jours, contactez-nous pour notre service de PROTOTYPAGE RAPIDE DE LA TÔLE. CLICK Product Finder-Locator Service MENU PRÉCÉDENT
- Forgeage et métallurgie des poudres, Matriçage, Frappe, Forgeage à chaud
Forgeage et métallurgie des poudres, forgeage, tête, forgeage à chaud, matrice d'impression, forme proche du filet, emboutissage, taillage du métal, rivetage, frappe d'AGS-TECH Inc. Forgeage des métaux et métallurgie des poudres Les types de procédés de FORGEAGE DES MÉTAL que nous proposons sont les matrices à chaud et à froid, les matrices ouvertes et les matrices fermées, les matrices d'impression et les pièces forgées sans bavure, cogging, foulage, délignage et forgeage de précision, forme proche du filet, en-tête , emboutissage, forgeage bouleversé, taillage de métaux, presse et roulis et forgeages radiaux et orbitaux et annulaires et isothermes, frappe, rivetage, forgeage de boules métalliques, perçage de métaux, dimensionnement, forgeage à haut taux d'énergie. Nos techniques de MÉTALLURGIE DES POUDRE et de TRAITEMENT DES POUDRE sont le pressage et le frittage des poudres, l'imprégnation, l'infiltration, le pressage isostatique à chaud et à froid, le moulage par injection de métal, le compactage au rouleau, le laminage des poudres, l'extrusion des poudres, le frittage libre, le frittage par étincelle, le pressage à chaud. Nous vous recommandons de cliquer ici pour TÉLÉCHARGEZ nos illustrations schématiques des processus de forgeage par AGS-TECH Inc. TÉLÉCHARGEZ nos illustrations schématiques des procédés de métallurgie des poudres par AGS-TECH Inc. Ces fichiers téléchargeables avec photos et croquis vous aideront à mieux comprendre les informations que nous vous fournissons ci-dessous. Dans le forgeage des métaux, des forces de compression sont appliquées et le matériau est déformé et la forme souhaitée est obtenue. Les matériaux forgés les plus courants dans l'industrie sont le fer et l'acier, mais de nombreux autres tels que l'aluminium, le cuivre, le titane, le magnésium sont également largement forgés. Les pièces métalliques forgées ont des structures de grain améliorées en plus des fissures scellées et des espaces vides fermés, ainsi la résistance des pièces obtenues par ce procédé est plus élevée. Le forgeage produit des pièces qui sont significativement plus résistantes pour leur poids que les pièces fabriquées par moulage ou usinage. Étant donné que les pièces forgées sont façonnées en faisant couler le métal dans sa forme finale, le métal prend une structure de grain directionnelle qui explique la résistance supérieure des pièces. En d'autres termes, les pièces obtenues par forgeage présentent de meilleures propriétés mécaniques par rapport à de simples pièces coulées ou usinées. Le poids des pièces forgées en métal peut aller de petites pièces légères à des centaines de milliers de livres. Nous fabriquons des pièces forgées principalement pour des applications mécaniquement exigeantes où des contraintes élevées sont appliquées sur des pièces telles que des pièces automobiles, des engrenages, des outils de travail, des outils à main, des arbres de turbine, des engrenages de moto. Étant donné que les coûts d'outillage et d'installation sont relativement élevés, nous recommandons ce processus de fabrication uniquement pour la production à volume élevé et pour les composants critiques à faible volume mais de grande valeur tels que les trains d'atterrissage aérospatiaux. Outre le coût de l'outillage, les délais de fabrication des pièces forgées en grande quantité peuvent être plus longs par rapport à certaines pièces usinées simples, mais la technique est cruciale pour les pièces qui nécessitent une résistance extraordinaire telles que les boulons, les écrous, les applications spéciales. fixations, automobile, chariot élévateur, pièces de grue. • MATRICE A CHAUD et MATRICE A FROID : La matriçage à chaud, comme son nom l'indique s'effectue à haute température, la ductilité est donc élevée et la résistance du matériau faible. Cela facilite la déformation et le forgeage. Au contraire, le forgeage à froid est effectué à des températures plus basses et nécessite des forces plus élevées, ce qui se traduit par un écrouissage, une meilleure finition de surface et une précision des pièces fabriquées. • MATRICE OUVERTE et MATRICE D'IMPRESSION : Dans le forgeage à matrice ouverte, les matrices ne limitent pas le matériau à comprimer, tandis que dans le forgeage à matrice d'impression, les cavités à l'intérieur des matrices limitent le flux de matériau pendant qu'il est forgé dans la forme souhaitée. FORGAGE UPSET ou également appelé UPSETTING, qui n'est en fait pas le même mais un processus très similaire, est un processus à matrice ouverte où la pièce est prise en sandwich entre deux matrices plates et une force de compression réduit sa hauteur. Lorsque la hauteur est réduite, la largeur de la pièce augmente. HEADING, un procédé de forgeage refoulé implique une matière cylindrique qui est refoulée à son extrémité et dont la section est augmentée localement. Dans le titre, le stock est introduit dans la matrice, forgé puis coupé à longueur. L'opération est capable de produire rapidement de grandes quantités de fixations. Il s'agit principalement d'une opération de travail à froid car elle est utilisée pour fabriquer des bouts de clous, des bouts de vis, des écrous et des boulons là où le matériau doit être renforcé. Un autre processus de matrice ouverte est COGGING, où la pièce est forgée en une série d'étapes, chaque étape entraînant une compression du matériau et le mouvement ultérieur de la matrice ouverte sur la longueur de la pièce. A chaque étape, l'épaisseur est réduite et la longueur est légèrement augmentée. Le processus ressemble à un étudiant nerveux mordant son crayon tout le long à petits pas. Un processus appelé FULLERING est une autre méthode de forgeage à matrice ouverte que nous déployons souvent comme une étape antérieure pour répartir le matériau dans la pièce à usiner avant que d'autres opérations de forgeage du métal n'aient lieu. Nous l'utilisons lorsque la pièce nécessite plusieurs forging operations. Lors de l'opération, les matrices à surfaces convexes se déforment et provoquent l'écoulement du métal des deux côtés. Processus similaire au foulage, le BORDURE, d'autre part, implique une matrice ouverte avec des surfaces concaves pour déformer la pièce à usiner. Le délignage est également un processus préparatoire pour les opérations de forgeage ultérieures qui fait que le matériau s'écoule des deux côtés dans une zone au centre. Le FORGEAGE PAR IMPRESSION ou MATRICE FERMÉE, comme on l'appelle aussi, utilise une matrice / un moule qui comprime le matériau et limite son écoulement à l'intérieur de lui-même. La matrice se referme et la matière prend la forme de la cavité matrice/moule. LA FORGE DE PRÉCISION, procédé nécessitant un outillage et un moule particuliers, produit des pièces sans ou très peu de bavures. En d'autres termes, les pièces auront des dimensions quasi finales. Dans ce processus, une quantité bien contrôlée de matériau est soigneusement insérée et positionnée à l'intérieur du moule. Nous déployons cette méthode pour des formes complexes avec des sections minces, de faibles tolérances et angles de dépouille et lorsque les quantités sont suffisamment importantes pour justifier les coûts du moule et de l'équipement. • FORGEAGE SANS FLASH : La pièce est placée dans la matrice de manière à ce qu'aucune matière ne puisse s'écouler hors de la cavité pour former des bavures. Aucun ajustement de flash indésirable n'est donc nécessaire. Il s'agit d'un processus de forgeage de précision et nécessite donc un contrôle étroit de la quantité de matière utilisée. • MÉTALLAGE OU FORGEAGE RADIAL : Une pièce est sollicitée circonférentiellement par une matrice et forgée. Un mandrin peut également être utilisé pour forger la géométrie intérieure de la pièce à usiner. Lors de l'opération d'emboutissage, la pièce à usiner reçoit généralement plusieurs coups par seconde. Les articles typiques produits par emboutissage sont les outils à bout pointu, les barres coniques, les tournevis. • PERÇAGE DES MÉTAUX : Nous utilisons fréquemment cette opération comme opération complémentaire dans la fabrication des pièces. Un trou ou une cavité est créé en perçant sur la surface de la pièce sans la percer. Veuillez noter que le perçage est différent du perçage qui se traduit par un trou traversant. • TAILLE-TAILLE : Un poinçon avec la géométrie souhaitée est pressé dans la pièce à usiner et crée une cavité avec la forme souhaitée. Nous appelons ce coup de poing un HOB. L'opération implique des pressions élevées et s'effectue à froid. En conséquence, le matériau est travaillé à froid et écroui. Par conséquent, ce procédé convient parfaitement à la fabrication de moules, de matrices et de cavités pour d'autres procédés de fabrication. Une fois la table de cuisson fabriquée, on peut facilement fabriquer de nombreuses cavités identiques sans avoir besoin de les usiner une par une. • ROLL FORGING ou ROLL FORMING : Deux cylindres opposés sont utilisés pour façonner la pièce métallique. La pièce est introduite dans les rouleaux, les rouleaux tournent et tirent le travail dans l'espace, le travail est ensuite alimenté à travers la partie rainurée des rouleaux et les forces de compression donnent au matériau la forme souhaitée. Il ne s'agit pas d'un processus de laminage mais d'un processus de forgeage, car il s'agit d'une opération discrète plutôt que continue. La géométrie des rainures des rouleaux forge le matériau à la forme et à la géométrie requises. Elle est réalisée à chaud. En raison de son processus de forgeage, il produit des pièces aux propriétés mécaniques exceptionnelles et nous l'utilisons donc pour fabrication de pièces automobiles telles que des arbres qui doivent avoir une endurance extraordinaire dans des environnements de travail difficiles. • FORGE ORBITALE : La pièce à usiner est placée dans une cavité de matrice de forgeage et forgée par une matrice supérieure qui se déplace dans une trajectoire orbitale lorsqu'elle tourne sur un axe incliné. A chaque révolution, la matrice supérieure achève d'exercer des forces de compression sur l'ensemble de la pièce à usiner. En répétant ces révolutions un certain nombre de fois, un forgeage suffisant est effectué. Les avantages de cette technique de fabrication sont son fonctionnement peu bruyant et la réduction des efforts nécessaires. En d'autres termes, avec de petites forces, on peut faire tourner une matrice lourde autour d'un axe pour appliquer de grandes pressions sur une section de la pièce qui est en contact avec la matrice. Les pièces en forme de disque ou de forme conique conviennent parfois bien à ce processus. • RING FORGING : Nous utilisons fréquemment pour fabriquer des anneaux sans soudure. Le stock est coupé à longueur, bouleversé puis percé de part en part pour créer un trou central. Ensuite, il est placé sur un mandrin et une matrice de forgeage le martèle par le haut pendant que l'anneau tourne lentement jusqu'à ce que les dimensions souhaitées soient obtenues. • RIVETAGE : Un processus courant pour assembler des pièces commence par une pièce métallique droite insérée dans des trous préfabriqués à travers les pièces. Ensuite, les deux extrémités de la pièce métallique sont forgées en serrant le joint entre une matrice supérieure et inférieure. • MONNAIE : Autre procédé populaire réalisé par presse mécanique, exerçant des forces importantes sur une courte distance. Le nom "coining" vient des détails fins qui sont forgés sur les surfaces des pièces de monnaie en métal. Il s'agit principalement d'un processus de finition pour un produit où des détails fins sont obtenus sur les surfaces en raison de la grande force appliquée par la matrice qui transfère ces détails à la pièce à usiner. • FORGE DE BILLES MÉTALLIQUES : Les produits tels que les roulements à billes nécessitent des billes métalliques de haute qualité fabriquées avec précision. Dans une technique appelée SKEW ROLLING, nous utilisons deux rouleaux opposés qui tournent en continu lorsque le stock est alimenté en continu dans les rouleaux. À une extrémité des deux rouleaux, des sphères métalliques sont éjectées en tant que produit. Une deuxième méthode de forgeage de billes de métal consiste à utiliser des matrices qui pressent le stock de matériau placé entre elles en prenant la forme sphérique de la cavité du moule. Souvent, les balles produites nécessitent des étapes supplémentaires telles que la finition et le polissage afin de devenir un produit de haute qualité. • FORGEAGE ISOTHERME / MATRICE A CHAUD : Un procédé coûteux réalisé uniquement lorsque le rapport bénéfice/coût est justifié. Un processus de travail à chaud où la matrice est chauffée à peu près à la même température que la pièce à usiner. Étant donné que la matrice et le travail sont à peu près à la même température, il n'y a pas de refroidissement et les caractéristiques d'écoulement du métal sont améliorées. L'opération convient bien aux super alliages et aux matériaux à forgeabilité inférieure et aux matériaux dont les propriétés mécaniques sont très sensibles aux petits gradients et changements de température. • CALIBRE MÉTALLIQUE : C'est un procédé de finition à froid. Le flux de matière est illimité dans toutes les directions à l'exception de la direction dans laquelle la force est appliquée. On obtient ainsi un très bon état de surface et des cotes précises. • FORGAGE À HAUTE ÉNERGIE : La technique consiste en un moule supérieur fixé au bras d'un piston qui est poussé rapidement au fur et à mesure qu'un mélange air-carburant est enflammé par une bougie d'allumage. Cela ressemble au fonctionnement des pistons dans un moteur de voiture. Le moule frappe très rapidement la pièce à usiner, puis revient très rapidement à sa position d'origine grâce à la contre-pression. Le travail est forgé en quelques millisecondes et il n'y a donc pas de temps pour que le travail se refroidisse. Ceci est utile pour les pièces difficiles à forger qui ont des propriétés mécaniques très sensibles à la température. En d'autres termes, le processus est si rapide que la pièce est formée à température constante et qu'il n'y aura pas de gradients de température aux interfaces moule/pièce. • Dans DIE FORGING, le métal est battu entre deux blocs d'acier assortis avec des formes spéciales, appelées matrices. Lorsque le métal est martelé entre les matrices, il prend la même forme que les formes de la matrice. Lorsqu'il atteint sa forme définitive, il est sorti pour refroidir. Ce processus produit des pièces solides qui ont une forme précise, mais nécessite un investissement plus important pour les matrices spécialisées. Le forgeage bouleversé augmente le diamètre d'une pièce de métal en l'aplatissant. Il est généralement utilisé pour fabriquer de petites pièces, en particulier pour former des têtes sur des fixations comme des boulons et des clous. • MÉTALLURGIE DES POUDRE / TRAITEMENT DES POUDRE : Comme son nom l'indique, il s'agit de procédés de fabrication permettant de réaliser des pièces solides de certaines géométries et formes à partir de poudres. Si des poudres métalliques sont utilisées à cette fin, c'est le domaine de la métallurgie des poudres et si des poudres non métalliques sont utilisées, c'est le traitement des poudres. Les pièces solides sont produites à partir de poudres par pressage et frittage. Le POWDER PRESSING est utilisé pour compacter les poudres dans les formes souhaitées. Tout d'abord, le matériau primaire est physiquement réduit en poudre, ce qui le divise en plusieurs petites particules individuelles. Le mélange de poudre est versé dans la matrice et un poinçon se déplace vers la poudre et la compacte dans la forme souhaitée. Réalisé principalement à température ambiante, avec le pressage de poudre, on obtient une partie solide et on l'appelle compact vert. Les liants et les lubrifiants sont couramment utilisés pour améliorer la compactabilité. Nous sommes capables de presser les poudres à l'aide de presses hydrauliques de plusieurs milliers de tonnes de capacité. Nous avons également des presses à double action avec des poinçons supérieurs et inférieurs opposés ainsi que des presses à actions multiples pour des géométries de pièces très complexes. L'uniformité qui est un défi important pour de nombreuses usines de métallurgie des poudres / de traitement des poudres n'est pas un gros problème pour AGS-TECH en raison de notre vaste expérience dans la fabrication sur mesure de telles pièces depuis de nombreuses années. Même avec des pièces plus épaisses où l'uniformité pose un défi, nous avons réussi. Si nous nous engageons dans votre projet, nous fabriquerons vos pièces. Si nous voyons des risques potentiels, nous vous en informerons in avance. LE FRITTAGE DE POUDRE, qui est la deuxième étape, implique l'élévation de la température à un certain degré et le maintien de la température à ce niveau pendant un certain temps afin que les particules de poudre dans la partie pressée puissent se lier. Il en résulte des liaisons beaucoup plus fortes et un renforcement de la pièce à usiner. Le frittage a lieu à proximité de la température de fusion de la poudre. Pendant le frittage, un retrait se produit, la résistance du matériau, la densité, la ductilité, la conductivité thermique et la conductivité électrique sont augmentées. Nous avons des fours discontinus et continus pour le frittage. L'une de nos capacités est d'ajuster le niveau de porosité des pièces que nous produisons. Par exemple, nous sommes en mesure de produire des filtres métalliques en gardant les pièces poreuses dans une certaine mesure. En utilisant une technique appelée IMPREGNATION, nous remplissons les pores du métal avec un fluide tel que de l'huile. Nous produisons par exemple des roulements imprégnés d'huile qui sont autolubrifiants. Dans le processus d'INFILTRATION, nous remplissons les pores d'un métal avec un autre métal dont le point de fusion est inférieur à celui du matériau de base. Le mélange est chauffé à une température située entre les températures de fusion des deux métaux. En conséquence, certaines propriétés spéciales peuvent être obtenues. Nous effectuons également fréquemment des opérations secondaires telles que l'usinage et le forgeage de pièces fabriquées en poudre lorsque des caractéristiques ou des propriétés spéciales doivent être obtenues ou lorsque la pièce peut être fabriquée avec moins d'étapes de processus. PRESSAGE ISOSTATIQUE : Dans ce processus, la pression du fluide est utilisée pour compacter la pièce. Les poudres métalliques sont placées dans un moule constitué d'un récipient souple étanche. Dans le pressage isostatique, la pression est appliquée de partout, contrairement à la pression axiale observée dans le pressage conventionnel. Les avantages du pressage isostatique sont une densité uniforme dans la pièce, en particulier pour les pièces plus grandes ou plus épaisses, des propriétés supérieures. Son inconvénient est des temps de cycle longs et des précisions géométriques relativement faibles. Le PRESSAGE ISOSTATIQUE À FROID est réalisé à température ambiante et le moule flexible est en caoutchouc, PVC ou uréthane ou matériaux similaires. Le fluide utilisé pour la pressurisation et le compactage est de l'huile ou de l'eau. Le frittage conventionnel du compact cru suit cela. Le pressage isostatique à chaud, quant à lui, est effectué à haute température et le matériau du moule est une tôle ou une céramique avec un point de fusion suffisamment élevé pour résister aux températures. Le fluide de pressurisation est généralement un gaz inerte. Les opérations de pressage et de frittage sont réalisées en une seule étape. La porosité est presque complètement éliminée, une structure uniform grain est obtenue. L'avantage du pressage isostatique à chaud est qu'il permet de produire des pièces comparables au moulage et au forgeage combinés tout en rendant possible l'utilisation de matériaux qui ne conviennent pas au moulage et au forgeage. L'inconvénient du pressage isostatique à chaud est son temps de cycle élevé et donc son coût. Il convient aux pièces critiques de faible volume. MOULAGE PAR INJECTION MÉTALLIQUE : Procédé très adapté à la réalisation de pièces complexes à parois fines et aux géométries détaillées. Convient le mieux aux petites pièces. Les poudres et le liant polymère sont mélangés, chauffés et injectés dans un moule. Le liant polymère recouvre les surfaces des particules de poudre. Après moulage, le liant est éliminé soit par chauffage à basse température soit dissous à l'aide d'un solvant. COMPACTAGE AU ROULEAU / LAMINAGE EN POUDRE : Les poudres sont utilisées pour produire des bandes ou des feuilles continues. La poudre est alimentée à partir d'un alimentateur et compactée par deux rouleaux rotatifs en feuilles ou en bandes. L'opération est réalisée à froid. La tôle est amenée dans un four de frittage. Le processus de frittage peut être répété une deuxième fois. EXTRUSION DE POUDRE : Les pièces avec des rapports longueur/diamètre importants sont fabriquées en extrudant un récipient en tôle mince avec de la poudre. FRITTAGE LIBRE : Comme son nom l'indique, il s'agit d'une méthode de compactage et de frittage sans pression, adaptée à la production de pièces très poreuses telles que des filtres métalliques. La poudre est introduite dans la cavité du moule sans compactage. FRITTAGE LIBRE : Comme son nom l'indique, il s'agit d'une méthode de compactage et de frittage sans pression, adaptée à la production de pièces très poreuses telles que des filtres métalliques. La poudre est introduite dans la cavité du moule sans compactage. SPARK SINTERING : La poudre est comprimée dans le moule par deux poinçons opposés et un courant électrique de forte puissance est appliqué au poinçon et traverse la poudre compactée prise en sandwich entre eux. Le courant élevé brûle les films de surface des particules de poudre et les fritte avec la chaleur générée. Le processus est rapide car la chaleur n'est pas appliquée de l'extérieur, mais plutôt générée à l'intérieur du moule. PRESSAGE A CHAUD : Les poudres sont pressées et frittées en une seule étape dans un moule résistant aux hautes températures. Au fur et à mesure que la matrice se compacte, la chaleur de la poudre lui est appliquée. Les bonnes précisions et propriétés mécaniques obtenues par cette méthode en font une option intéressante. Même les métaux réfractaires peuvent être traités en utilisant des matériaux de moulage tels que le graphite. CLICK Product Finder-Locator Service MENU PRÉCÉDENT
- Extrusions plastique caoutchouc métal, matrices d'extrusion, extrusion d'aluminium
Extrusions plastique caoutchouc métal, matrices d'extrusion, extrusion d'aluminium, formage de tubes, profilés en plastique, fabrication de profilés métalliques, PVC chez AGS-TECH Inc. Extrusions, Produits extrudés, Extrudés Nous utilisons le procédé EXTRUSION pour fabriquer des produits avec un profil de section fixe tels que des tubes, des tuyaux et des dissipateurs thermiques. Même si de nombreux matériaux peuvent être extrudés, nos extrusions les plus courantes sont en métal, polymères / plastique, céramique obtenus par une méthode d'extrusion à froid, à chaud ou à chaud. Nous appelons les pièces extrudées extrudées ou extrudées si pluriel. Certaines versions spécialisées du processus que nous réalisons également sont le surchemisage, la coextrusion et l'extrusion composée. Nous vous recommandons de cliquer ici pour TÉLÉCHARGEZ nos illustrations schématiques des procédés d'extrusion métal céramique et plastique par AGS-TECH Inc. Cela vous aidera à mieux comprendre les informations que nous vous fournissons ci-dessous. Dans l'extrusion, le matériau à extruder est poussé ou tiré à travers une filière qui a le profil de section souhaité. Le procédé peut être utilisé pour fabriquer des sections transversales complexes avec un excellent état de surface et pour travailler sur des matériaux fragiles. On peut produire n'importe quelle longueur de pièces en utilisant ce procédé. Pour simplifier les étapes du processus : 1.) Dans les extrusions chaudes ou chaudes, le matériau est chauffé et chargé dans un récipient dans la presse. Le matériau est pressé et poussé hors de la matrice. 2.) L'extrudat produit est étiré pour le redressage, traité thermiquement ou travaillé à froid pour améliorer ses propriétés. D'autre part COLD EXTRUSION a lieu autour de la température ambiante et présente les avantages d'une moindre oxydation, d'une résistance élevée, de tolérances plus étroites, d'une bonne finition de surface et de solidité. L'EXTRUSION CHAUDE est effectuée au-dessus de la température ambiante mais en dessous du point de recristallisation. Il offre un compromis et un équilibre pour les forces requises, la ductilité et les propriétés des matériaux et est donc le choix pour certaines applications. L'EXTRUSION A CHAUD a lieu au-dessus de la température de recristallisation du matériau. De cette façon, il est plus facile de pousser le matériau à travers la matrice. Cependant, le coût de l'équipement est élevé. Plus un profilé extrudé est complexe, plus la filière (outillage) est coûteuse et plus la cadence de production est faible. Les sections de filière ainsi que les épaisseurs ont des limitations qui dépendent du matériau à extruder. Les angles vifs des filières d'extrusion sont toujours indésirables et doivent être évités sauf si nécessaire. Selon le matériau extrudé, nous proposons : • EXTRUSION MÉTALLIQUE : les plus courants que nous produisons sont l'aluminium, le laiton, le zinc, le cuivre, l'acier, le titane, le magnésium • EXTRUSION PLASTIQUE : le plastique est fondu et formé en un profil continu. Nos matériaux communs traités sont le polyéthylène, le nylon, le polystyrène, le chlorure de polyvinyle, le polypropylène, le plastique ABS, le polycarbonate, l'acrylique. Les produits typiques que nous fabriquons comprennent des tuyaux et des tubes, des cadres en plastique. Dans le processus, de petites billes de plastique/résine sont alimentées par gravité de la trémie dans le baril de la machine d'extrusion. Fréquemment, nous mélangeons également des colorants ou d'autres additifs dans la trémie pour donner au produit les spécifications et propriétés requises. Le matériau entrant dans le baril chauffé est forcé par la vis rotative à quitter le baril à la fin et à se déplacer à travers le tamis pour éliminer les contaminants dans le plastique fondu. Après avoir passé le tamis, le plastique entre dans la filière d'extrusion. La matrice donne au plastique souple en mouvement sa forme de profil lors de son passage. Maintenant, l'extrudat passe dans un bain-marie pour le refroidissement. Les autres techniques qu'AGS-TECH Inc. utilise depuis de nombreuses années sont : • EXTRUSION DE TUYAUX ET TUBES : les tuyaux et tubes en plastique sont formés lorsque le plastique est extrudé à travers une filière de façonnage ronde et refroidi dans un bain d'eau, puis coupé à la longueur ou enroulé/enroulé. Transparent ou coloré, rayé, simple ou double paroi, souple ou rigide, PE, PP, polyuréthane, PVC, nylon, PC, silicone, vinyle ou autre, nous avons de tout. Nous avons des tubes stockés ainsi que la capacité de produire selon vos spécifications. AGS-TECH fabrique des tubes conformes aux exigences FDA, UL et LE pour les applications médicales, électriques et électroniques, industrielles et autres. • OVERJACKETING / OVERJACKETING EXTRUSION : Cette technique applique une couche extérieure de plastique sur le fil ou le câble existant. Nos fils isolants sont fabriqués avec cette méthode. • COEXTRUSION : plusieurs couches de matériau sont extrudées simultanément. Les multiples couches sont délivrées par plusieurs extrudeuses. Les différentes épaisseurs de couche peuvent être ajustées pour répondre aux spécifications du client. Ce procédé permet d'utiliser plusieurs polymères ayant chacun une fonctionnalité différente dans le produit. En conséquence, on peut optimiser une gamme de propriétés. • EXTRUSION COMPOSÉE : Un ou plusieurs polymères sont mélangés avec des additifs pour obtenir un composé plastique. Nos extrudeuses à double vis produisent des extrusions de mélange. Les matrices d'extrusion sont généralement peu coûteuses par rapport aux moules métalliques. Si vous payez beaucoup plus que quelques milliers de dollars pour une filière d'extrusion d'aluminium de petite ou moyenne taille, vous payez probablement trop cher. Nous sommes des experts pour déterminer quelle technique est la plus rentable, la plus rapide et la plus adaptée à votre application. Parfois, l'extrusion puis l'usinage d'une pièce peuvent vous faire économiser beaucoup d'argent. Avant de prendre une décision ferme, demandez-nous d'abord notre avis. Nous avons aidé de nombreux clients à prendre les bonnes décisions. Pour certaines extrusions métalliques largement utilisées, vous pouvez télécharger nos brochures et catalogues en cliquant sur le texte en couleur ci-dessous. S'il s'agit d'un produit standard répondant à vos exigences, il sera plus économique. Téléchargez nos capacités d'extrusion de tubes et tuyaux médicaux Téléchargez nos dissipateurs de chaleur extrudés • PROCÉDÉS SECONDAIRES DE FABRICATION ET DE FABRICATION POUR EXTRUSIONS : Parmi les processus à valeur ajoutée que nous proposons pour les produits extrudés, citons : -Cintrage, formage et mise en forme de tubes et de tuyaux sur mesure, découpe de tubes, formage d'extrémités de tubes, enroulement de tubes, usinage et finition, perçage, perçage et poinçonnage de trous, -Assemblages de tuyaux et de tubes sur mesure, assemblage tubulaire, soudage, brasage et brasage -Cintrage, formage et mise en forme par extrusion sur mesure -Nettoyage, dégraissage, décapage, passivation, polissage, anodisation, placage, peinture, traitement thermique, recuit et durcissement, marquage, gravure et étiquetage, emballage personnalisé. CLICK Product Finder-Locator Service PAGE PRÉCÉDENTE
- Fonderie et pièces usinées, Fabrication CNC, Fraisage, Tournage, Suisse
Pièces moulées et usinées, fabrication CNC, fraisage, tournage, usinage de type suisse, moulage sous pression, moulage à modèle perdu, pièces moulées en mousse perdue d'AGS-TECH Inc. Fonderie et Usinage Nos techniques de coulée et d'usinage sur mesure sont les pièces coulées consommables et non consommables, la coulée ferreuse et non ferreuse, le sable, la matrice, la centrifugeuse, la continue, le moule en céramique, l'investissement, la mousse perdue, la forme quasi nette, le moule permanent (moulage sous pression par gravité), le plâtre moules (fonderie de plâtre) et coquilles, pièces usinées réalisées par fraisage et tournage avec des équipements conventionnels et à commande numérique, usinage de type suisse pour petites pièces de précision peu coûteuses à haut débit, décolletage pour la visserie, usinage non conventionnel. Veuillez garder à l'esprit qu'en plus des métaux et des alliages métalliques, nous usinons également des composants en céramique, en verre et en plastique dans certains cas lorsque la fabrication d'un moule n'est pas attrayante ou n'est pas l'option. L'usinage de matériaux polymères nécessite l'expérience spécialisée que nous avons en raison du défi que présentent les plastiques et le caoutchouc en raison de leur souplesse, de leur non-rigidité...etc. Pour l'usinage de la céramique et du verre, veuillez consulter notre page sur la fabrication non conventionnelle. AGS-TECH Inc. fabrique et fournit des pièces moulées légères et lourdes. Nous fournissons des pièces moulées en métal et des pièces usinées pour les chaudières, les échangeurs de chaleur, les automobiles, les micromoteurs, les éoliennes, les équipements d'emballage alimentaire et plus encore. Nous vous recommandons de cliquer ici pour TÉLÉCHARGEZ nos illustrations schématiques des processus d'usinage et de moulage par AGS-TECH Inc. Cela vous aidera à mieux comprendre les informations que nous vous fournissons ci-dessous. Examinons en détail certaines des différentes techniques que nous proposons : • MOULAGE CONSOMMABLE : Cette large catégorie fait référence aux méthodes qui impliquent des moules temporaires et non réutilisables. Les exemples sont le sable, le plâtre, la coquille, l'investissement (également appelé cire perdue) et le moulage en plâtre. • MOULAGE AU SABLE : Un processus où le sable est utilisé comme matériau de moulage. Une méthode très ancienne et toujours très populaire dans la mesure où la majorité des pièces moulées en métal produites sont réalisées par cette technique. Faible coût même à faible quantité de production. Convient pour la fabrication de petites et grandes pièces. La technique peut être utilisée pour fabriquer des pièces en quelques jours ou semaines avec très peu d'investissement. Le sable humide est lié à l'aide d'argile, de liants ou d'huiles spéciales. Le sable est généralement contenu dans les moules et le système de cavité et de porte est créé en compactant le sable autour des modèles. Les processus sont : 1.) Mise en place du modèle dans le sable pour faire le moule 2.) Incorporation du modèle et du sable dans un système de gating 3.) Suppression du modèle 4.) Remplissage de la cavité du moule avec du métal en fusion 5.) Refroidissement du métal 6.) Casser le moule en sable et retirer le moulage • MOULAGE EN PLÂTRE : Similaire au moulage au sable, et au lieu du sable, le plâtre de Paris est utilisé comme matériau de moulage. Délais de production courts comme le moulage au sable et peu coûteux. Bonnes tolérances dimensionnelles et finition de surface. Son inconvénient majeur est qu'il ne peut être utilisé qu'avec des métaux à bas point de fusion comme l'aluminium et le zinc. • MOULAGE EN COQUILLE : Semblable également au moulage au sable. Cavité de moule obtenue par une coquille durcie de sable et de liant de résine thermodurcissable au lieu d'un flacon rempli de sable comme dans le processus de moulage au sable. Presque tous les métaux aptes à être coulés au sable peuvent être coulés par moulage en coquille. Le processus peut être résumé comme suit : 1.) Fabrication du moule carapace. Le sable utilisé est d'une granulométrie beaucoup plus petite par rapport au sable utilisé dans le moulage au sable. Le sable fin est mélangé à de la résine thermodurcissable. Le motif métallique est recouvert d'un agent de séparation pour faciliter le retrait de la coque. Ensuite, le modèle métallique est chauffé et le mélange de sable est poreux ou soufflé sur le modèle de moulage à chaud. Une fine coquille se forme à la surface du motif. L'épaisseur de cette coque peut être ajustée en faisant varier la durée de contact du mélange sable-résine avec le motif métallique. Le sable meuble est ensuite retiré avec le motif recouvert de coquille restant. 2.) Ensuite, la coque et le motif sont chauffés dans un four afin que la coque durcisse. Une fois le durcissement terminé, la coque est éjectée du modèle à l'aide de broches intégrées au modèle. 3.) Deux de ces coquilles sont assemblées par collage ou serrage et constituent le moule complet. Maintenant, le moule carapace est inséré dans un récipient dans lequel il est soutenu par du sable ou de la grenaille de métal pendant le processus de coulée. 4.) Maintenant, le métal chaud peut être versé dans le moule en coquille. Les avantages de la fonderie coquille sont des produits avec un très bon état de surface, la possibilité de fabriquer des pièces complexes avec une grande précision dimensionnelle, un processus facile à automatiser, économique pour une production en grand volume. Les inconvénients sont que les moules nécessitent une bonne ventilation en raison des gaz qui sont créés lorsque le métal en fusion entre en contact avec le liant chimique, les résines thermodurcissables et les modèles métalliques sont coûteux. En raison du coût des modèles métalliques, la technique peut ne pas convenir aux cycles de production en petite quantité. • INVESTMENT CASTING (également connu sous le nom de LOST-WAX CASTING) : également une technique très ancienne et adaptée à la fabrication de pièces de qualité avec une grande précision, répétabilité, polyvalence et intégrité à partir de nombreux métaux, matériaux réfractaires et alliages spéciaux à hautes performances. Des pièces de petite comme de grande taille peuvent être produites. Un processus coûteux par rapport à certaines des autres méthodes, mais le principal avantage est la possibilité de produire des pièces avec une forme presque nette, des contours et des détails complexes. Ainsi, le coût est quelque peu compensé par l'élimination des retouches et de l'usinage dans certains cas. Même s'il peut y avoir des variations, voici un résumé du processus général de moulage de précision : 1.) Création d'un modèle maître original à partir de cire ou de plastique. Chaque moulage a besoin d'un motif car ceux-ci sont détruits au cours du processus. Le moule à partir duquel les modèles sont fabriqués est également nécessaire et la plupart du temps, le moule est coulé ou usiné. Parce que le moule n'a pas besoin d'être ouvert, des moulages complexes peuvent être réalisés, de nombreux modèles de cire peuvent être connectés comme les branches d'un arbre et coulés ensemble, permettant ainsi la production de plusieurs pièces à partir d'un seul coulage du métal ou de l'alliage métallique. 2.) Ensuite, le modèle est trempé ou versé avec une suspension réfractaire composée de silice à grains très fins, d'eau et de liants. Il en résulte une couche de céramique sur la surface du motif. La couche réfractaire sur modèle est laissée sécher et durcir. Cette étape est à l'origine du nom de la coulée de précision : une suspension réfractaire est investie sur le modèle en cire. 3.) À cette étape, le moule en céramique durcie est retourné et chauffé afin que la cire fonde et se déverse du moule. Une cavité est laissée pour la coulée du métal. 4.) Une fois la cire sortie, le moule en céramique est chauffé à une température encore plus élevée, ce qui renforce le moule. 5.) La coulée de métal est coulée dans le moule chaud remplissant toutes les sections complexes. 6.) Le moulage est autorisé à se solidifier 7.) Enfin, le moule en céramique est cassé et les pièces fabriquées sont coupées de l'arbre. Voici un lien vers la brochure de l'usine de moulage de précision • MOULAGE PAR MOTIF PAR ÉVAPORATION : Le procédé utilise un modèle fabriqué à partir d'un matériau tel que la mousse de polystyrène qui s'évapore lorsque du métal fondu chaud est versé dans le moule. Il existe deux types de ce procédé : LOST FOAM CASTING qui utilise du sable non lié et FULL MOLD CASTING qui utilise du sable lié. Voici les étapes générales du processus : 1.) Fabriquez le motif à partir d'un matériau tel que le polystyrène. Lorsque de grandes quantités seront fabriquées, le modèle est moulé. Si la pièce a une forme complexe, plusieurs sections d'un tel matériau en mousse peuvent devoir être collées ensemble pour former le motif. Nous enduisons souvent le modèle avec un composé réfractaire pour créer une bonne finition de surface sur le moulage. 2.) Le motif est ensuite placé dans du sable de moulage. 3.) Le métal en fusion est versé dans le moule, évaporant le motif en mousse, c'est-à-dire le polystyrène dans la plupart des cas lorsqu'il s'écoule à travers la cavité du moule. 4.) Le métal fondu est laissé dans le moule en sable pour durcir. 5.) Après durcissement, nous retirons le moulage. Dans certains cas, le produit que nous fabriquons nécessite un noyau dans le modèle. Dans la coulée par évaporation, il n'est pas nécessaire de placer et de fixer un noyau dans la cavité du moule. La technique convient à la fabrication de géométries très complexes, elle peut être facilement automatisée pour une production à grand volume et il n'y a pas de lignes de séparation dans la pièce moulée. Le procédé de base est simple et économique à mettre en oeuvre. Pour une production en grand volume, puisqu'une matrice ou un moule est nécessaire pour produire les motifs en polystyrène, cela peut être quelque peu coûteux. • MOULAGE NON EXPANSIBLE : Cette large catégorie fait référence aux méthodes où le moule n'a pas besoin d'être reformé après chaque cycle de production. Des exemples sont la coulée permanente, en matrice, continue et centrifuge. La répétabilité est obtenue et les pièces peuvent être caractérisées comme NEAR NET SHAPE. • COULÉE EN MOULE PERMANENT : Des moules réutilisables en métal sont utilisés pour les coulées multiples. Un moule permanent peut généralement être utilisé des dizaines de milliers de fois avant de s'user. La gravité, la pression de gaz ou le vide sont généralement utilisés pour remplir le moule. Les moules (également appelés moules) sont généralement en fer, en acier, en céramique ou en d'autres métaux. Le processus général est le suivant : 1.) Usiner et créer le moule. Il est courant d'usiner le moule à partir de deux blocs métalliques qui s'emboîtent et peuvent être ouverts et fermés. Les caractéristiques de la pièce ainsi que le système de porte sont généralement usinés dans le moule de coulée. 2.) Les surfaces internes du moule sont recouvertes d'une suspension incorporant des matériaux réfractaires. Cela aide à contrôler le flux de chaleur et agit comme un lubrifiant pour un retrait facile de la pièce moulée. 3.) Ensuite, les moitiés de moule permanentes sont fermées et le moule est chauffé. 4.) Le métal en fusion est versé dans le moule et laissé immobile pour la solidification. 5.) Avant que le refroidissement ne se produise, nous retirons la pièce du moule permanent à l'aide d'éjecteurs lorsque les moitiés de moule sont ouvertes. Nous utilisons fréquemment la coulée en moule permanent pour les métaux à bas point de fusion tels que le zinc et l'aluminium. Pour les pièces moulées en acier, nous utilisons du graphite comme matériau de moule. Nous obtenons parfois des géométries complexes en utilisant des noyaux dans des moules permanents. Les avantages de cette technique sont des pièces moulées avec de bonnes propriétés mécaniques obtenues par un refroidissement rapide, une uniformité des propriétés, une bonne précision et un bon état de surface, de faibles taux de rebut, la possibilité d'automatiser le processus et de produire de gros volumes de manière économique. Les inconvénients sont les coûts d'installation initiaux élevés qui le rendent inadapté aux opérations à faible volume et les limitations de la taille des pièces fabriquées. • MOULAGE SOUS PRESSION : Une matrice est usinée et le métal en fusion est poussé sous haute pression dans les cavités du moule. Les moulages sous pression de métaux non ferreux et ferreux sont possibles. Le procédé convient aux grandes séries de production de pièces de petite à moyenne taille avec des détails, des parois extrêmement minces, une cohérence dimensionnelle et une bonne finition de surface. AGS-TECH Inc. est capable de fabriquer des épaisseurs de paroi aussi petites que 0,5 mm en utilisant cette technique. Comme dans la coulée en moule permanent, le moule doit être composé de deux moitiés qui peuvent s'ouvrir et se fermer pour retirer la pièce produite. Un moule de coulée sous pression peut avoir plusieurs cavités pour permettre la production de plusieurs pièces moulées à chaque cycle. Les moules de coulée sous pression sont très lourds et beaucoup plus grands que les pièces qu'ils produisent, donc également coûteux. Nous réparons et remplaçons gratuitement les matrices usées pour nos clients tant qu'ils commandent à nouveau leurs pièces chez nous. Nos matrices ont de longues durées de vie dans la gamme de plusieurs centaines de milliers de cycles. Voici les étapes de base du processus simplifié : 1.) Fabrication du moule généralement en acier 2.) Moule installé sur la machine de coulée sous pression 3.) Le piston force le métal en fusion à s'écouler dans les cavités de la matrice en remplissant les caractéristiques complexes et les parois minces 4.) Après avoir rempli le moule avec le métal en fusion, le moulage est laissé durcir sous pression 5.) Le moule est ouvert et le moulage retiré à l'aide d'éjecteurs. 6.) Maintenant, les moules vides sont à nouveau lubrifiés et serrés pour le cycle suivant. Dans le moulage sous pression, nous utilisons fréquemment le moulage par insertion où nous incorporons une pièce supplémentaire dans le moule et coulons le métal autour de celui-ci. Après solidification, ces pièces font partie du produit coulé. Les avantages du moulage sous pression sont de bonnes propriétés mécaniques des pièces, la possibilité de caractéristiques complexes, des détails fins et une bonne finition de surface, des taux de production élevés, une automatisation facile. Les inconvénients sont : Pas très adapté aux faibles volumes en raison du coût élevé de la matrice et de l'équipement, limitations des formes pouvant être moulées, petites marques rondes sur les pièces coulées résultant du contact des broches d'éjecteur, mince éclat de métal expulsé au niveau de la ligne de séparation, besoin pour les évents le long de la ligne de séparation entre la matrice, nécessité de maintenir des températures de moule basses en utilisant la circulation d'eau. • COULÉE CENTRIFUGE : Le métal en fusion est coulé au centre du moule rotatif au niveau de l'axe de rotation. Les forces centrifuges projettent le métal vers la périphérie et le laissent se solidifier tandis que le moule continue de tourner. Les rotations horizontales et verticales peuvent être utilisées. Les pièces avec des surfaces intérieures rondes ainsi que d'autres formes non rondes peuvent être coulées. Le processus peut être résumé comme suit : 1.) Le métal en fusion est versé dans un moule centrifuge. Le métal est ensuite forcé vers les parois extérieures en raison de la rotation du moule. 2.) Au fur et à mesure que le moule tourne, la coulée de métal durcit La coulée centrifuge est une technique appropriée pour la production de pièces cylindriques creuses telles que des tuyaux, pas besoin de tiges de coulée, de colonnes montantes et d'éléments d'injection, bon état de surface et caractéristiques détaillées, pas de problèmes de retrait, possibilité de produire de longs tuyaux avec de très grands diamètres, capacité de production à haut débit . • COULÉE CONTINUE ( STRAND CASTING ) : Utilisée pour couler une longueur continue de métal. Fondamentalement, le métal en fusion est coulé dans le profil bidimensionnel du moule, mais sa longueur est indéterminée. Du nouveau métal en fusion est constamment introduit dans le moule au fur et à mesure que la coulée se déplace vers le bas, sa longueur augmentant avec le temps. Les métaux tels que le cuivre, l'acier, l'aluminium sont coulés en longs brins à l'aide d'un procédé de coulée continue. Le processus peut avoir différentes configurations, mais la plus courante peut être simplifiée comme suit : 1.) Le métal fondu est versé dans un récipient situé au-dessus du moule à des quantités et des débits bien calculés et s'écoule à travers le moule refroidi à l'eau. La coulée de métal coulée dans le moule se solidifie en une barre de démarrage placée au fond du moule. Cette barre de démarrage donne aux rouleaux quelque chose à saisir au départ. 2.) Le long toron métallique est transporté par des rouleaux à vitesse constante. Les rouleaux modifient également la direction du flux de torons métalliques de la verticale à l'horizontale. 3.) Une fois que la coulée continue a parcouru une certaine distance horizontale, une torche ou une scie qui se déplace avec la coulée la coupe rapidement aux longueurs souhaitées. Le processus de coulée continue peut être intégré au PROCESSUS DE LAMINAGE, où le métal coulé en continu peut être introduit directement dans un laminoir pour produire des poutres en I, des poutres en T… etc. La coulée continue produit des propriétés uniformes dans tout le produit, elle a un taux de solidification élevé, réduit les coûts grâce à une très faible perte de matière, offre un processus où le chargement du métal, le coulage, la solidification, la coupe et l'enlèvement de la coulée se déroulent tous en une opération continue et résultant ainsi en un taux de productivité élevé et une qualité élevée. Une considération majeure est cependant l'investissement initial élevé, les coûts d'installation et les besoins en espace. • SERVICES D'USINAGE : Nous proposons des usinages trois, quatre et cinq axes. Les types de processus d'usinage que nous utilisons sont le TOURNAGE, le FRAISAGE, le PERÇAGE, l'ALÉSAGE, le BROCHAGE, le RABOTAGE, le SCIAGE, le MEULAGE, le RODAGE, le POLISSAGE et l'USINAGE NON TRADITIONNEL qui est développé dans un menu différent de notre site Web. Pour la plupart de nos fabrications, nous utilisons des machines CNC. Cependant, pour certaines opérations, les techniques conventionnelles conviennent mieux et nous nous appuyons donc également sur elles. Nos capacités d'usinage atteignent le plus haut niveau possible et certaines pièces les plus exigeantes sont fabriquées dans une usine certifiée AS9100. Les aubes de moteur à réaction nécessitent une expérience de fabrication hautement spécialisée et le bon équipement. L'industrie aérospatiale a des normes très strictes. Certains composants aux structures géométriques complexes sont plus facilement fabriqués par usinage cinq axes, que l'on ne trouve que dans certaines usines d'usinage dont la nôtre. Notre usine certifiée aérospatiale possède l'expérience nécessaire pour se conformer aux exigences de documentation étendues de l'industrie aérospatiale. Dans les opérations de TOURNAGE, une pièce est tournée et déplacée contre un outil de coupe. Pour ce processus, une machine appelée tour est utilisée. En FRAISAGE, une machine appelée fraiseuse dispose d'un outil rotatif pour amener les arêtes de coupe en appui contre une pièce. Les opérations de PERÇAGE impliquent une fraise rotative avec des arêtes de coupe qui produisent des trous au contact de la pièce. Des perceuses à colonne, des tours ou des broyeurs sont généralement utilisés. Dans les opérations d'alésage, un outil avec une seule pointe pointue pliée est déplacé dans un trou rugueux dans une pièce en rotation pour agrandir légèrement le trou et améliorer la précision. Il est utilisé à des fins de finition fine. Le BROCHAGE implique un outil denté pour enlever le matériau d'une pièce en un seul passage de la broche (outil denté). Dans le brochage linéaire, la broche passe linéairement contre une surface de la pièce pour effectuer la coupe, tandis que dans le brochage rotatif, la broche est tournée et enfoncée dans la pièce pour couper une forme symétrique d'axe. L'USINAGE DE TYPE SUISSE est l'une de nos précieuses techniques que nous utilisons pour la fabrication en grand volume de petites pièces de haute précision. À l'aide d'un tour de type suisse, nous tournons de petites pièces complexes de précision à peu de frais. Contrairement aux tours conventionnels où la pièce est maintenue immobile et l'outil en mouvement, dans les centres de tournage de type suisse, la pièce est autorisée à se déplacer dans l'axe Z et l'outil est immobile. Dans l'usinage de type suisse, la barre est maintenue dans la machine et avancée à travers une douille de guidage dans l'axe z, n'exposant que la partie à usiner. De cette façon, une prise ferme est assurée et la précision est très élevée. La disponibilité d'outils motorisés offre la possibilité de fraiser et de percer au fur et à mesure que le matériau avance de la douille de guidage. L'axe Y de l'équipement de type suisse offre des capacités de fraisage complètes et permet de gagner beaucoup de temps dans la fabrication. De plus, nos machines sont équipées de perceuses et d'outils d'alésage qui agissent sur la pièce lorsqu'elle est maintenue dans la contre-broche. Notre capacité d'usinage de type suisse nous offre une possibilité d'usinage complet entièrement automatisé en une seule opération. L'usinage est l'un des plus grands segments d'activité d'AGS-TECH Inc. Nous l'utilisons soit comme opération primaire, soit comme opération secondaire après la coulée ou l'extrusion d'une pièce afin que toutes les spécifications de dessin soient respectées. • SERVICES DE FINITION DE SURFACE : Nous offrons une grande variété de traitements de surface et de finition de surface tels que le conditionnement de surface pour améliorer l'adhérence, le dépôt d'une fine couche d'oxyde pour améliorer l'adhérence du revêtement, le sablage, le film chimique, l'anodisation, la nitruration, le revêtement en poudre, le revêtement par pulvérisation , diverses techniques avancées de métallisation et de revêtement, notamment la pulvérisation, le faisceau d'électrons, l'évaporation, le placage, les revêtements durs tels que le diamant comme le carbone (DLC) ou le revêtement de titane pour les outils de forage et de coupe. • SERVICES DE MARQUAGE ET D'ÉTIQUETAGE DE PRODUITS : Beaucoup de nos clients ont besoin de marquage et d'étiquetage, marquage laser, gravure sur pièces métalliques. Si vous avez un tel besoin, laissez-nous discuter de l'option qui vous conviendra le mieux. Voici quelques-uns des produits de fonte de métal couramment utilisés. Étant donné qu'ils sont prêts à l'emploi, vous pouvez économiser sur les coûts de moules au cas où l'un d'entre eux répondrait à vos besoins : CLIQUEZ ICI POUR TÉLÉCHARGER nos boîtiers en aluminium moulé sous pression de la série 11 d'AGS-Electronics CLICK Product Finder-Locator Service PAGE PRÉCÉDENTE
- Pièces fabriquées sur mesure, assemblages, moules en plastique, moulage, usinage
Pièces fabriquées sur mesure, Assemblages, Moule plastique, Moulage de caoutchouc, Fonderie de métal, Usinage CNC, Tournage, Fraisage, Assemblage électrique électronique optique PCBA Pièces, assemblages et produits fabriqués sur mesure Lire la suite Moules et moulures en plastique et en caoutchouc Lire la suite Fonderie et Usinage Lire la suite Extrusions, produits extrudés Lire la suite Estampage et fabrication de tôles Lire la suite Forgeage des métaux et métallurgie des poudres Lire la suite Formage de fils et de ressorts Lire la suite Formage et façonnage du verre et de la céramique Lire la suite Fabrication additive et rapide Lire la suite Fabrication de composites et de matériaux composites Lire la suite Processus d'assemblage, d'assemblage et de fixation Nous produisons pour vous des pièces et des assemblages et proposons les procédés de fabrication suivants : • Moules et pièces moulées en plastique et en caoutchouc. Moulage par injection, thermoformage, moulage thermodurcissable, formage sous vide, moulage par soufflage, rotomoulage, moulage par coulée, moulage par insertion et autres. • Extrusions de plastique, de caoutchouc et de métal • Pièces moulées ferreuses et non ferreuses et pièces usinées produites par des techniques de fraisage et de tournage, usinage de type suisse. • Pièces de métallurgie des poudres • Pièces embouties métalliques et non métalliques, formage de tôles, assemblages de tôles soudées • Forgeage à froid et à chaud • Fils, assemblages de fils soudés, formage de fils • Différents types de ressorts, formant ressort • Fabrication d'engrenages, boîte de vitesses, accouplement, vis sans fin, réducteur de vitesse, cylindre, courroies de transmission, chaînes de transmission, composants de transmission • Verre trempé et pare-balles personnalisé conforme aux normes OTAN et militaires • Billes, roulements, poulies et assemblages de poulies • Vannes et composants pneumatiques tels que joint torique, rondelle et joints • Pièces et assemblages en verre et céramique, composants étanches au vide et hermétiques, collage métal-céramique et céramique-céramique. • Différents types d'ensembles mécaniques, optomécaniques, électromécaniques, optoélectroniques. • Liaison métal-caoutchouc, métal-plastique • Tuyaux et tubes, formage de tuyaux, cintrage et assemblages de tuyaux sur mesure, fabrication de soufflets. • Fabrication de fibre de verre • Soudage utilisant diverses techniques telles que le soudage par points, le soudage laser, MIG, TIG. Soudage par ultrasons pour pièces en plastique. • Grande variété de traitements de surface et de finitions de surface tels que le conditionnement de surface pour améliorer l'adhérence, le dépôt d'une fine couche d'oxyde pour améliorer l'adhérence du revêtement, le sablage, le film chimique, l'anodisation, la nitruration, le revêtement en poudre, le revêtement par pulvérisation, diverses techniques avancées de métallisation et de revêtement y compris la pulvérisation, le faisceau d'électrons, l'évaporation, le placage, les revêtements durs tels que le diamant comme le carbone (DLC) ou le titane pour les outils de coupe et de forage. • Marquage et étiquetage, marquage laser sur pièces métalliques, impression sur pièces plastiques et caoutchouc Téléchargez la brochure sur les termes courants en génie mécanique utilisés par les concepteurs et les ingénieurs Nous construisons des produits selon vos spécifications et exigences particulières. Afin de vous offrir la meilleure qualité, livraison et prix, nous fabriquons des produits dans le monde entier en Chine, en Inde, à Taïwan, aux Philippines, en Corée du Sud, en Malaisie, au Sri Lanka, en Turquie, aux États-Unis, au Canada, en Allemagne, au Royaume-Uni et au Japon. Cela nous rend beaucoup plus forts et globalement plus compétitifs que tout autre custom manufacturer. Nos produits sont fabriqués dans des environnements certifiés ISO9001:2000, QS9000, ISO14001, TS16949 et possèdent la marque CE, UL et répondent à d'autres normes de l'industrie. Une fois que nous sommes mandatés pour votre projet, nous pouvons prendre en charge l'ensemble de la fabrication, de l'assemblage, des tests, de la qualification, de l'expédition et des douanes comme vous le souhaitez. Si vous préférez, nous pouvons entreposer vos pièces, assembler des kits personnalisés, imprimer et étiqueter le nom et la marque de votre entreprise et expédier directement à vos clients. En d'autres termes, nous pouvons également être votre centre d'entreposage et de distribution si vous le souhaitez. Étant donné que nos entrepôts sont situés à proximité des principaux ports maritimes, cela nous donne un avantage logistique. Par exemple, lorsque vos produits arrivent dans un grand port maritime américain, nous pouvons les transporter directement vers un entrepôt à proximité où nous pouvons stocker, assembler, fabriquer des kits, réétiqueter, imprimer, emballer selon votre choix et déposer livrer à vos clients. Nous ne fournissons pas seulement des produits. Notre entreprise travaille sur des contrats personnalisés où nous nous rendons sur votre site, évaluons votre projet sur place et développons une proposition de projet conçue sur mesure pour vous. Nous envoyons ensuite notre équipe expérimentée pour mettre en œuvre le projet. Vous trouverez plus d'informations sur nos travaux d'ingénierie sur http://www.ags-engineering.com -Nous prenons aussi bien les petits projets que les grands projets à l'échelle industrielle. Dans un premier temps, nous pouvons vous connecter soit par téléphone, téléconférence ou messagerie MSN aux membres de notre équipe d'experts, afin que vous puissiez communiquer directement avec un expert, poser des questions et discuter de votre projet. Appelez-nous et si besoin nous viendrons vous rendre visite. PAGE PRÉCÉDENTE