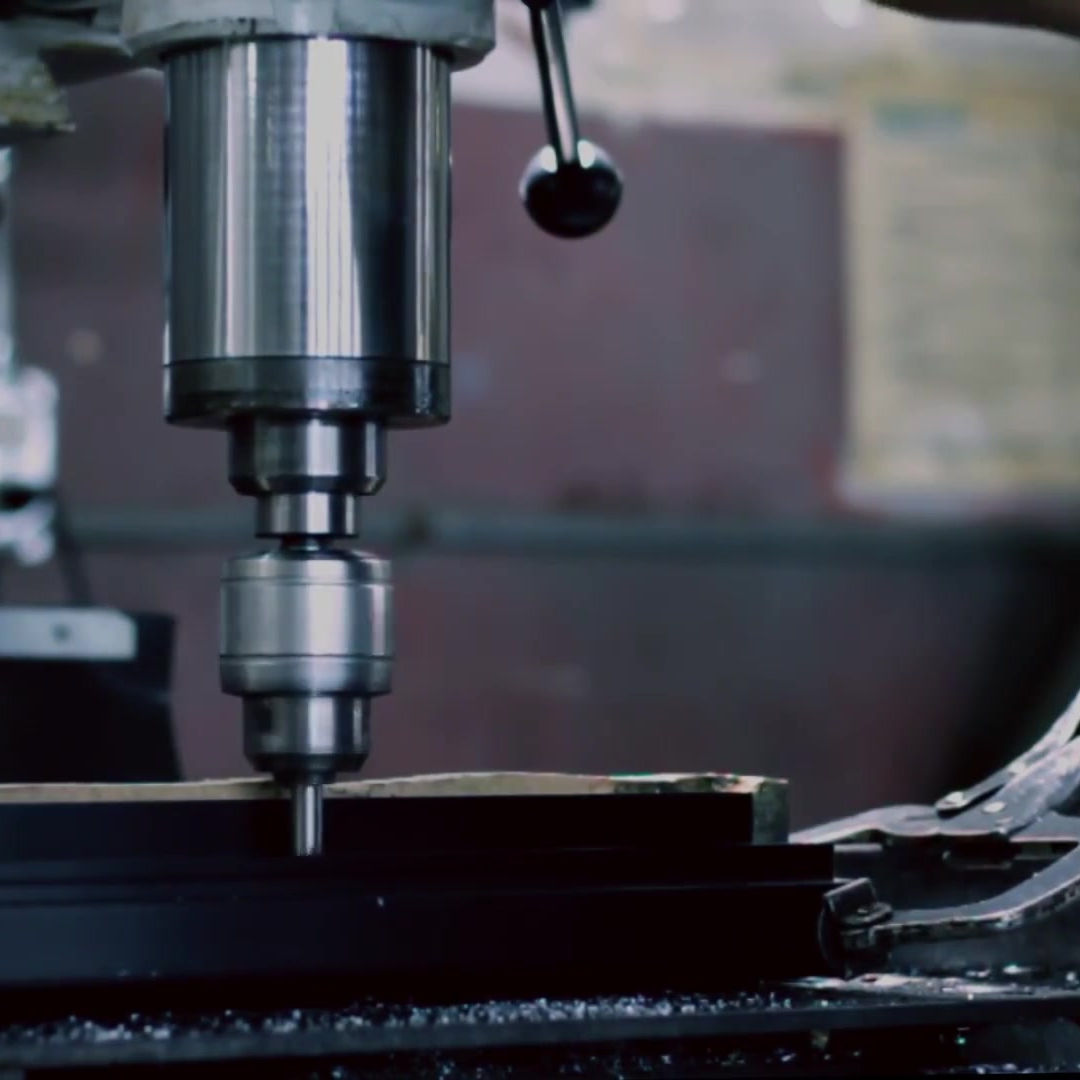
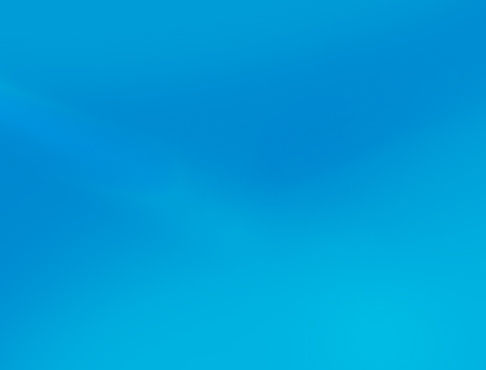
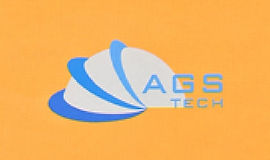
Fabricante global personalizado, integrador, consolidador, socio de outsourcing para unha ampla variedade de produtos e servizos.
Somos a súa fonte única para a fabricación, fabricación, enxeñaría, consolidación, integración e subcontratación de produtos e servizos fabricados a medida e dispoñibles.
Escolla o seu idioma
-
Fabricación personalizada
-
Fabricación por contrato nacional e global
-
Outsourcing de Manufactura
-
Compras domésticas e globais
-
Consolidación
-
Integración de enxeñería
-
Servizos de Enxeñaría
ELECTRICAL DISCHARGE MACHINING (EDM), also referred to as SPARK-EROSION or ELECTRODISCHARGE MACHINING, SPARK ERODING, DIE SINKING_cc781905-5cde-3194-bb3b -136bad5cf58d_or WIRE EROSION, is a NON-CONVENTIONAL MANUFACTURING process where erosion of metals takes place and desired shape is obtained using electrical discharges in the form de chispas. Tamén ofrecemos algunhas variedades de electroerosión, a saber, NO-WEAR EDM, WIRE EDM (WEDM), EDM GRINDING (EDG), DIE-SINKING EDM, ELECTRICAL-DISCHARGE MILLING, micro-EDMcc78190_5, -5cde-3194-bb3b-136bad5cf58d_and TRITURADO POR DESCARGA ELECTROQUÍMICA (ECDG). Os nosos sistemas EDM consisten en ferramentas/electrodos conformados e a peza de traballo conectada a fontes de alimentación de CC e inserida nun fluído dieléctrico non condutor. Despois de 1940, o mecanizado de descarga eléctrica converteuse nunha das tecnoloxías de produción máis importantes e populares nas industrias manufactureras.
Cando se reduce a distancia entre os dous eléctrodos, a intensidade do campo eléctrico no volume entre os electrodos faise maior que a forza do dieléctrico nalgúns puntos, que se rompe, formando finalmente unha ponte para que a corrente fluya entre os dous electrodos. Xérase un intenso arco eléctrico que provoca un importante quecemento para fundir unha parte da peza de traballo e parte do material da ferramenta. Como resultado, o material é eliminado de ambos os electrodos. Ao mesmo tempo, o fluído dieléctrico quéntase rapidamente, o que provoca a evaporación do fluído no espazo do arco. Unha vez que o fluxo de corrente se detén ou se detén, a calor é eliminada da burbulla de gas polo fluído dieléctrico circundante e a burbulla cavita (colapso). A onda de choque creada polo colapso da burbulla e o fluxo de fluído dieléctrico expulsan os restos da superficie da peza de traballo e arrastran calquera material fundido da peza ao fluído dieléctrico. A taxa de repetición destas descargas está entre 50 e 500 kHz, tensións entre 50 e 380 V e correntes entre 0,1 e 500 Amperios. O novo dieléctrico líquido, como aceites minerais, queroseno ou auga destilada e desionizada, adoita transportarse ao volume entre electrodos levando as partículas sólidas (en forma de restos) e restablecen as propiedades illantes do dieléctrico. Despois dun fluxo de corrente, a diferenza de potencial entre os dous electrodos restablece ao que era antes da avaría, polo que pode ocorrer unha nova avaría dieléctrica líquida. As nosas modernas máquinas de descarga eléctrica (EDM) ofrecen movementos controlados numéricos e están equipadas con bombas e sistemas de filtrado dos fluídos dieléctricos.
O mecanizado por descarga eléctrica (EDM) é un método de mecanizado utilizado principalmente para metais duros ou aqueles que serían moi difíciles de mecanizar con técnicas convencionais. A electroerosión normalmente funciona con calquera material que sexa condutor eléctrico, aínda que tamén se propuxeron métodos para mecanizar cerámicas illantes con electroerosión. O punto de fusión e a calor latente de fusión son propiedades que determinan o volume de metal eliminado por descarga. Canto máis altos sexan estes valores, menor será a taxa de eliminación do material. Debido a que o proceso de mecanizado por descarga eléctrica non implica ningunha enerxía mecánica, a dureza, resistencia e tenacidade da peza non afectan á taxa de eliminación. A frecuencia de descarga ou enerxía por descarga, a tensión e a corrente varíanse para controlar as taxas de eliminación de material. A taxa de eliminación do material e a rugosidade da superficie aumentan co aumento da densidade de corrente e a diminución da frecuencia de faíscas. Podemos cortar contornos ou cavidades complicados en aceiro pre-endurecido mediante electroerosión sen necesidade de tratamento térmico para suavizar e volver a endurecer. Podemos usar este método con calquera metal ou aliaxe metálica como titanio, hastelloy, kovar e inconel. As aplicacións do proceso de electroerosión inclúen a conformación de ferramentas de diamante policristalino. EDM considérase un método de mecanizado non tradicional ou non convencional xunto con procesos como o mecanizado electroquímico (ECM), o corte por chorro de auga (WJ, AWJ), o corte con láser. Por outra banda, os métodos de mecanizado convencionais inclúen torneado, fresado, rectificado, perforación e outros procesos cuxo mecanismo de eliminación de material baséase esencialmente en forzas mecánicas. Os electrodos para mecanizado por descarga eléctrica (EDM) están feitos de grafito, latón, cobre e aliaxe de cobre-tungsteno. Son posibles diámetros de electrodos de ata 0,1 mm. Dado que o desgaste da ferramenta é un fenómeno non desexado que afecta negativamente á precisión dimensional na electroerosión, aproveitamos un proceso chamado NO-WEAR EDM, invertendo a polaridade e utilizando ferramentas de cobre para minimizar o desgaste da ferramenta.
Idealmente falando, o mecanizado de descarga eléctrica (EDM) pode considerarse unha serie de ruptura e restauración do líquido dieléctrico entre os electrodos. En realidade, con todo, a eliminación dos restos da zona entre electrodos é case sempre parcial. Isto fai que as propiedades eléctricas do dieléctrico na zona entre electrodos sexan diferentes dos seus valores nominais e varíen co tempo. A distancia inter-electrodos, (gapa de chispa), axústase polos algoritmos de control da máquina específica utilizada. Desafortunadamente, a fenda de chispa en EDM pode ser curtocircuitada polos restos. É posible que o sistema de control do eléctrodo non reaccione con suficiente rapidez para evitar que os dous electrodos (ferramenta e peza) se produzan un curtocircuíto. Este curtocircuíto non desexado contribúe á eliminación de material de forma diferente ao caso ideal. Prestamos a máxima importancia á acción de lavado para restablecer as propiedades illantes do dieléctrico para que a corrente se produza sempre no punto da zona inter-electrodo, minimizando así a posibilidade de cambios non desexados de forma (danos) da ferramenta-electrodo. e peza de traballo. Para obter unha xeometría específica, a ferramenta EDM é guiada polo camiño desexado moi preto da peza de traballo sen tocala, Prestamos a máxima atención ao rendemento do control de movemento en uso. Deste xeito, prodúcense un gran número de descargas / chispas de corrente, e cada unha contribúe á eliminación de material tanto da ferramenta como da peza de traballo, onde se forman pequenos cráteres. O tamaño dos cráteres é unha función dos parámetros tecnolóxicos establecidos para o traballo específico a que se refire e as dimensións poden variar desde a nanoescala (como no caso das operacións de microEDM) ata algúns centos de micrómetros en condicións de desbaste. Estes pequenos cráteres na ferramenta provocan unha erosión gradual do electrodo chamado "desgaste da ferramenta". Para contrarrestar o efecto prexudicial do desgaste na xeometría da peza substitúese continuamente o electrodo da ferramenta durante unha operación de mecanizado. Ás veces conseguimos isto usando un fío continuamente substituído como electrodo (este proceso de electroerosión tamén se chama WIRE EDM ). Ás veces usamos a ferramenta-electrodo de tal xeito que só unha pequena parte del está realmente implicada no proceso de mecanizado e esta parte cámbiase regularmente. Este é, por exemplo, o caso cando se usa un disco xiratorio como electrodo de ferramenta. Este proceso chámase EDM GRINDING. Outra técnica que implementamos consiste en utilizar un conxunto de electrodos con diferentes tamaños e formas durante a mesma operación de electroerosión para compensar o desgaste. Chamamos a esta técnica de electrodos múltiples, e úsase máis habitualmente cando o electrodo da ferramenta replica en negativo a forma desexada e avanza cara ao branco ao longo dunha única dirección, normalmente a dirección vertical (é dicir, o eixe z). Isto aseméllase ao sumidoiro da ferramenta no líquido dieléctrico no que está inmersa a peza de traballo e, polo tanto, denomínase DIE-SINKING EDM_cc781905-5cde-3194-bb3b5cf5805-5cde-3194 3194-bb3b-136bad5cf58d_CONVENTIONAL EDM or RAM EDM). As máquinas para esta operación chámanse SINKER EDM. Os electrodos para este tipo de electroerosión teñen formas complexas. Se a xeometría final se obtén mediante un electrodo de forma xeralmente simple movido en varias direccións e tamén está suxeito a rotacións, chamámoslle EDM MILLING. A cantidade de desgaste depende estritamente dos parámetros tecnolóxicos utilizados na operación (polaridade, corrente máxima, tensión de circuíto aberto). Por exemplo, in micro-EDM, tamén coñecido como m-EDM, estes parámetros adoitan establecerse en valores que xeran un desgaste severo. Polo tanto, o desgaste é un problema importante nesa área que minimizamos utilizando o noso coñecemento acumulado. Por exemplo, para minimizar o desgaste dos electrodos de grafito, un xerador dixital, controlable en milisegundos, inverte a polaridade a medida que se produce a electroerosión. Isto dá como resultado un efecto similar ao galvanoplastia que deposita continuamente o grafito erosionado de volta no electrodo. Noutro método, un circuíto denominado ''Zero Wear'', minimizamos a frecuencia con que se inicia e se detén a descarga, mantendo acendida o maior tempo posible. A taxa de eliminación de material no mecanizado con descarga eléctrica pódese estimar a partir de:
MRR = 4 x 10 exp(4) x I x Tw exp (-1,23)
Aquí MRR está en mm3/min, I é a corrente en Amperios, Tw é o punto de fusión da peza en K-273.15K. Exp significa expoñente.
Por outra banda, a taxa de desgaste Wt do electrodo pódese obter a partir de:
Peso = ( 1,1 x 10exp(11) ) x I x Ttexp(-2,38)
Aquí Wt está en mm3/min e Tt é o punto de fusión do material do electrodo en K-273.15K
Finalmente, a relación de desgaste da peza de traballo respecto ao electrodo R pódese obter a partir de:
R = 2,25 x Trexp (-2,38)
Aquí Tr é a relación entre os puntos de fusión da peza a traballar co electrodo.
SINKER EDM :
Sinker EDM, tamén coñecido como CAVITY TYPE EDM or_cc781905-5cde-bad5cf58d_cavity TYPE EDM or_cc781905-5cde-bad5cf58d_emersión e submersión de líquidos e pezas de submersión e submersión de líquidos e 3cf1905-5cde-emersión e pezas de electroerosión. O electrodo e a peza de traballo están conectados a unha fonte de alimentación. A fonte de alimentación xera un potencial eléctrico entre ambos. A medida que o electrodo se achega á peza de traballo, prodúcese a ruptura dieléctrica no fluído, formando unha canle de plasma e salta unha pequena chispa. As faíscas adoitan caer unha a unha porque é moi improbable que diferentes localizacións do espazo entre electrodos teñan idénticas características eléctricas locais que permitan que unha faísca se produza en todas esas localizacións simultaneamente. Centos de miles destas faíscas ocorren en puntos aleatorios entre o electrodo e a peza por segundo. A medida que o metal base se erosiona e a fenda de chispa aumenta posteriormente, o electrodo baixa automaticamente pola nosa máquina CNC para que o proceso poida continuar sen interrupcións. O noso equipo dispón de ciclos de control coñecidos como ''on time'' e ''off time''. A configuración de tempo de activación determina a duración ou a duración da faísca. Un tempo máis longo produce unha cavidade máis profunda para esa faísca e todas as faíscas posteriores para ese ciclo, creando un acabado máis rugoso na peza de traballo e viceversa. O tempo de apagado é o período de tempo que unha chispa é substituída por outra. Un tempo de apagado máis longo permite que o fluído dieléctrico pase a través dunha boquilla para limpar os restos erosionados, evitando así un curtocircuíto. Estes axustes axústanse en microsegundos.
WIRE EDM :
In WIRE ELECTRICAL DISCHARGE MACHINING (WEDM), also called WIRE-CUT EDM or WIRE CUTTING, we feed a fío metálico fino dun só fío de latón a través da peza de traballo, que está mergullada nun tanque de fluído dieléctrico. Wire EDM é unha variación importante da EDM. Ocasionalmente usamos electroerosión con fío para cortar placas de ata 300 mm de grosor e para fabricar punzóns, ferramentas e matrices a partir de metais duros que son difíciles de mecanizar con outros métodos de fabricación. Neste proceso, que se asemella ao corte de contornos cunha serra de cinta, o fío, que se alimenta constantemente dunha bobina, mantéñense entre as guías de diamante superior e inferior. As guías controladas por CNC móvense no plano x–y e a guía superior tamén pode moverse de forma independente no eixe z–u–v, dando lugar á capacidade de cortar formas cónicas e de transición (como círculo na parte inferior e cadrado no a parte superior). A guía superior pode controlar os movementos do eixe en x–y–u–v–i–j–k–l–. Isto permite que o WEDM corte formas moi complicadas e delicadas. O corte medio de corte dos nosos equipos que consegue o mellor custo económico e tempo de mecanizado é de 0,335 mm utilizando fío de latón, cobre ou wolframio de Ø 0,25. Non obstante, as guías de diamante superior e inferior dos nosos equipos CNC teñen unha precisión de aproximadamente 0,004 mm e poden ter unha traxectoria de corte ou un corte de tan pequeno como 0,021 mm utilizando un fío de 0,02 mm de Ø. Polo tanto, os cortes moi estreitos son posibles. O ancho de corte é maior que o ancho do fío porque prodúcese chispa desde os lados do fío ata a peza de traballo, causando erosión. Este ''sobrecorte'' é necesario, para moitas aplicacións é previsible e, polo tanto, pódese compensar (no micro-EDM non adoita ser o caso). As bobinas de fío son longas: unha bobina de 8 kg de fío de 0,25 mm ten algo máis de 19 quilómetros de lonxitude. O diámetro do fío pode ser tan pequeno como 20 micrómetros e a precisión xeométrica é de aproximadamente +/- 1 micrómetro. Xeralmente usamos o fío só unha vez e reciclámolo porque é relativamente barato. Viaxa a unha velocidade constante de 0,15 a 9 m/min e mantense unha ranura (ranura) constante durante o corte. No proceso de electroerosión por fío utilizamos auga como fluído dieléctrico, controlando a súa resistividade e outras propiedades eléctricas con filtros e unidades desionizadoras. A auga elimina os restos cortados fóra da zona de corte. O lavado é un factor importante para determinar a taxa de alimentación máxima para un determinado espesor de material e, polo tanto, mantemos consistente. A velocidade de corte na electroerosión por fío indícase en termos da área de sección transversal cortada por unidade de tempo, como 18.000 mm2/h para o aceiro para ferramentas D2 de 50 mm de espesor. A velocidade de corte lineal para este caso sería 18.000/50 = 360 mm/h. A taxa de eliminación de material na electroerosión por fío é:
MRR = Vf xhxb
Aquí MRR está en mm3/min, Vf é a velocidade de avance do fío na peza de traballo en mm/min, h é o grosor ou altura en mm e b é o corte, que é:
b = dw + 2s
Aquí dw é o diámetro do fío e s é a distancia entre o fío e a peza en mm.
Xunto con tolerancias máis estritas, os nosos modernos centros de mecanizado de corte de fíos por electroerosión de eixes múltiples engadiron funcións como cabezas múltiples para cortar dúas pezas ao mesmo tempo, controis para evitar a rotura do fío, funcións automáticas de rosca automática en caso de rotura de fíos e funcións programadas. estratexias de mecanizado para optimizar o funcionamento, as capacidades de corte recto e angular.
Wire-EDM ofrécenos baixas tensións residuais, porque non precisa de altas forzas de corte para a eliminación de material. Cando a enerxía/potencia por pulso é relativamente baixa (como nas operacións de acabado), espérase un pequeno cambio nas propiedades mecánicas dun material debido ás baixas tensións residuais.
MOLIADORA DE DESCARGA ELÉCTRICA (EDG) : As moas non conteñen abrasivos, son de grafito ou latón. As faíscas repetitivas entre a roda xiratoria e a peza de traballo eliminan o material das superficies da peza. A taxa de eliminación do material é:
MRR = K x I
Aquí MRR está en mm3/min, I é a corrente en amperes e K é o factor de material da peza en mm3/A-min. Adoitamos usar o rectificado de descarga eléctrica para cortar fendas estreitas nos compoñentes. Algunhas veces combinamos o proceso EDG (Electrical-Discharge Grinding) co proceso ECG (Electrochemical Grinding) no que o material é eliminado por acción química, as descargas eléctricas da roda de grafito rompen a película de óxido e lavadas polo electrólito. O proceso chámase MOLIADO POR DESCARGA ELECTROQUÍMICA (ECDG). Aínda que o proceso ECDG consume relativamente máis enerxía, é un proceso máis rápido que o EDG. Amolamos principalmente ferramentas de carburo usando esta técnica.
Aplicacións do mecanizado de descarga eléctrica:
Produción de prototipos:
Usamos o proceso de electroerosión na fabricación de moldes, ferramentas e matrices, así como para facer prototipos e pezas de produción, especialmente para as industrias aeroespacial, automotriz e electrónica nas que as cantidades de produción son relativamente baixas. En Sinker EDM, un electrodo de grafito, tungsteno de cobre ou cobre puro é mecanizado na forma desexada (negativa) e introdúcese na peza de traballo no extremo dun pistón vertical.
Fabricación de troqueles de moeda:
Para a creación de matrices para a produción de xoias e insignias mediante o proceso de acuñación (estampación), o master positivo pode estar feito de prata esterlina, xa que (con axustes de máquina adecuados) o master está significativamente erosionado e úsase só unha vez. A matriz negativa resultante endurece e úsase nun martelo para producir planos estampados a partir de follas en branco recortadas de aliaxe de bronce, prata ou ouro de baixa resistencia. Para os distintivos, estes pisos poden ter unha forma adicional nunha superficie curva mediante outro troquel. Este tipo de electroerosión adoita realizarse mergullada nun dieléctrico a base de aceite. O obxecto acabado pódese refinar aínda máis mediante esmaltado duro (vidro) ou brando (pintura) e/ou galvanoplastia con ouro puro ou níquel. Os materiais máis suaves, como a prata, poden ser gravados a man como un refinamento.
Perforación de pequenos buratos:
Nas nosas máquinas de electroerosión con fío, usamos electroerosión con perforación de pequenos buratos para facer un burato pasante nunha peza de traballo a través do cal pasar o fío para a operación de electroerosión con fío. Nas nosas máquinas cortadoras de fío están montadas cabezas EDM separadas específicamente para perforacións de pequenos buratos, o que permite que as placas endurecidas grandes poidan erosionar as pezas acabadas delas segundo sexa necesario e sen perforación previa. Tamén usamos EDM de pequenos buratos para perforar filas de buratos nos bordos das palas das turbinas utilizadas nos motores a reacción. O fluxo de gas a través destes pequenos orificios permite que os motores usen temperaturas máis altas do posible. As aliaxes monocristais de alta temperatura e moi duras das que están feitas estas láminas fai que o mecanizado convencional destes buratos cunha relación de aspecto elevada sexa extremadamente difícil e mesmo imposible. Outras áreas de aplicación para EDM de pequenos buratos son a creación de orificios microscópicos para os compoñentes do sistema de combustible. Ademais dos cabezales de electroerosión integrados, implantamos máquinas de electroerosión de pequenos buratos autónomos con eixes x–y para mecanizar buratos cegos ou pasantes. EDM perfora orificios cun electrodo longo de tubo de latón ou cobre que xira nun portabrocas cun fluxo constante de auga destilada ou desionizada que flúe polo eléctrodo como axente de lavado e dieléctrico. Algúns EDM de perforación de pequenos buratos son capaces de perforar 100 mm de aceiro brando ou incluso endurecido en menos de 10 segundos. Nesta operación de perforación pódense conseguir buratos entre 0,3 mm e 6,1 mm.
Mecanizado de desintegración de metais:
Tamén contamos con máquinas de electroerosión especiais para o propósito específico de eliminar ferramentas rotas (brocas ou machos) das pezas de traballo. Este proceso denomínase ''mecanizado de desintegración de metal''.
Vantaxes e inconvenientes Mecanizado de descarga eléctrica:
As vantaxes da electroerosión inclúen o mecanizado de:
- Formas complexas que doutro xeito serían difíciles de producir con ferramentas de corte convencionais
- Material extremadamente duro con tolerancias moi estreitas
- Pezas de traballo moi pequenas onde as ferramentas de corte convencionais poden danar a peza por exceso de presión da ferramenta de corte.
- Non hai contacto directo entre a ferramenta e a peza de traballo. Polo tanto, as seccións delicadas e os materiais débiles pódense mecanizar sen ningunha distorsión.
- Pódese obter un bo acabado superficial.
- Os buratos moi finos pódense perforar facilmente.
As desvantaxes da EDM inclúen:
- A baixa taxa de eliminación do material.
- O tempo e o custo adicionais utilizados para crear electrodos para electroerosión ram/sinker.
- Reproducir cantos afiados na peza de traballo é difícil debido ao desgaste dos electrodos.
- O consumo de enerxía é elevado.
- Fórmase ''Sobrecorte''.
- Durante o mecanizado prodúcese un desgaste excesivo da ferramenta.
- Os materiais eléctricamente non condutores só se poden mecanizar cunha configuración específica do proceso.