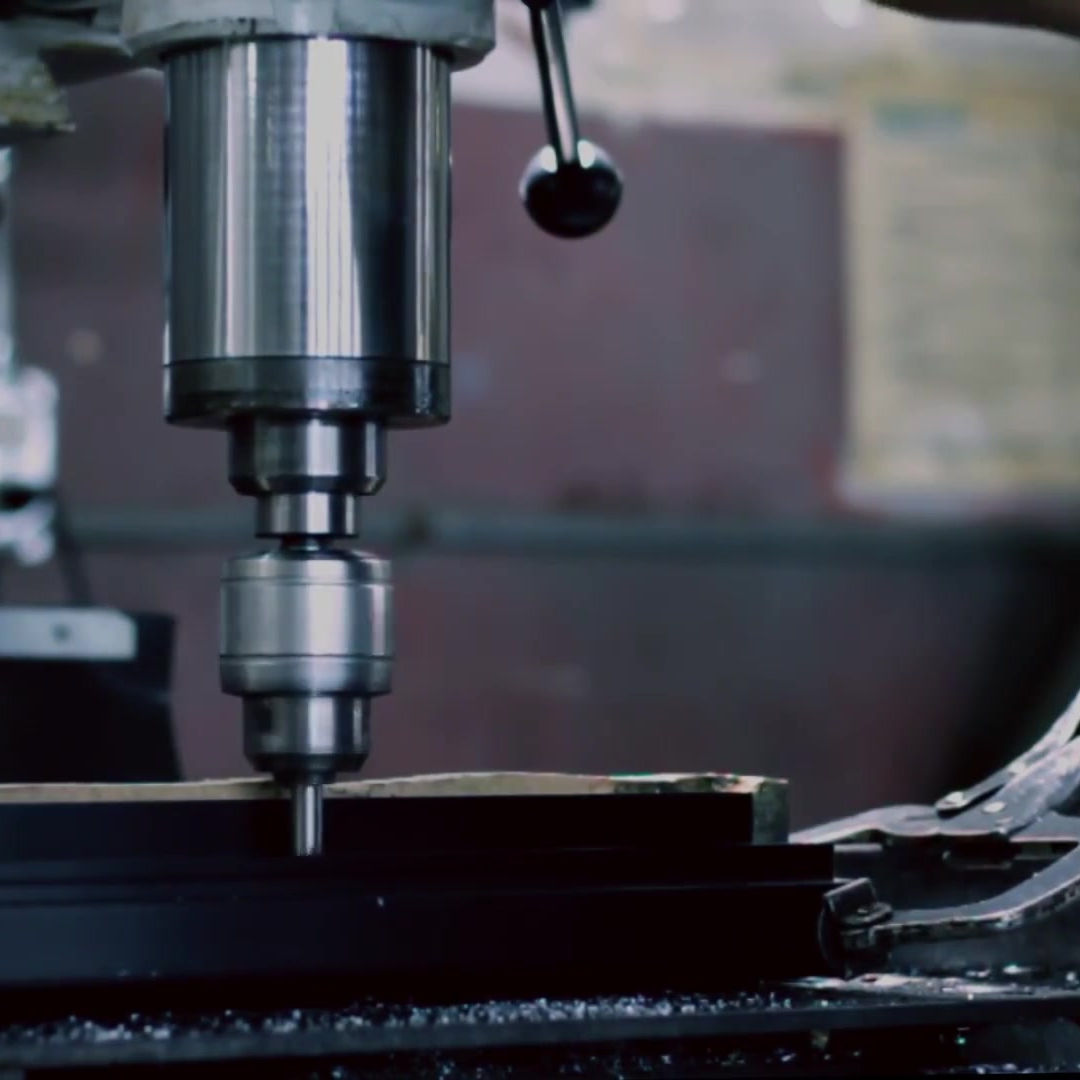
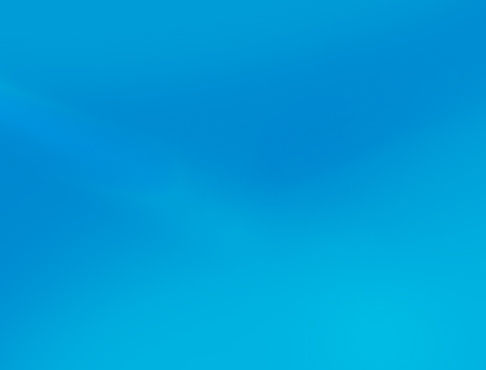
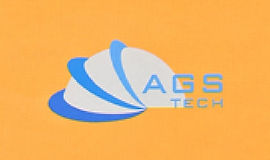
Fabricante global personalizado, integrador, consolidador, socio de outsourcing para unha ampla variedade de produtos e servizos.
Somos a súa fonte única para a fabricación, fabricación, enxeñaría, consolidación, integración e subcontratación de produtos e servizos fabricados a medida e dispoñibles.
Escolla o seu idioma
-
Fabricación personalizada
-
Fabricación por contrato nacional e global
-
Outsourcing de Manufactura
-
Compras domésticas e globais
-
Consolidación
-
Integración de enxeñería
-
Servizos de Enxeñaría
Search Results
164 results found with an empty search
- Transmission Components, Belts, Chains, Cable Drives, Pulleys,AGS-TECH
Transmission Components, Belts, Chains and Cable Drives, Conventional & Grooved or Serrated, Positive Drive, Pulleys Correas e cadeas e conxunto de transmisión por cable AGS-TECH Inc. ofrécelle compoñentes de transmisión de enerxía, incluíndo correas e cadeas e conxunto de transmisión de cables. Con anos de perfeccionamento, as nosas transmisións de caucho, coiro e outras correas fixéronse máis lixeiras e compactas, capaces de soportar cargas máis elevadas a un custo inferior. Do mesmo xeito, as nosas unidades de cadea pasaron por moito desenvolvemento ao longo do tempo e ofrecen aos nosos clientes varias vantaxes. Algunhas vantaxes do uso de transmisións en cadea son as súas distancias entre os eixos relativamente sen restricións, a compacidade, a facilidade de montaxe, a elasticidade en tensión sen escorregar ou fluír, a capacidade de operar en ambientes de alta temperatura. As nosas unidades de cable tamén ofrecen vantaxes como a simplicidade nalgunhas aplicacións fronte a outros tipos de compoñentes de transmisión. Están dispoñibles tanto cintas, cadeas e transmisións por cable, como versións fabricadas e montadas a medida. Podemos fabricar estes compoñentes de transmisión co tamaño adecuado para a súa aplicación e cos materiais máis axeitados. CORREAS E TRANSMISIÓNS DE CORREA: - Correas planas convencionais: son cintas planas lisas sen dentes, ranuras ou dentaduras. As transmisións de correa plana ofrecen flexibilidade, boa absorción de impactos, transmisión de enerxía eficiente a altas velocidades, resistencia á abrasión e baixo custo. Os cintos pódense empalmar ou conectar para facer cintas máis grandes. Outras vantaxes das correas planas convencionais son que son delgadas, non están sometidas a altas cargas centrífugas (fainas boas para operacións de alta velocidade con poleas pequenas). Por outra banda, impoñen altas cargas de soporte porque as correas planas requiren unha tensión elevada. Outras desvantaxes das transmisións por correa plana poden ser o deslizamento, o funcionamento ruidoso e eficiencias relativamente inferiores a velocidades de operación baixas e moderadas. Temos dous tipos de correas convencionais: Reforzadas e Non Reforzadas. As correas reforzadas teñen un elemento tensor na súa estrutura. Os cintos planos convencionais están dispoñibles como coiro, tecido de goma ou cordón, caucho non reforzado ou plástico, tecido, coiro reforzado. Os cintos de coiro ofrecen longa vida útil, flexibilidade, excelente coeficiente de fricción e fácil reparación. Non obstante, os cintos de coiro son relativamente caros, necesitan vestir e limpar o cinto e, dependendo da atmosfera, poden encollerse ou estirarse. Os cintos de tecido de goma ou cordón son resistentes á humidade, ao ácido e aos álcalis. Os cintos de tecido de goma están formados por capas de algodón ou de pato sintético impregnados de caucho e son os máis económicos. Os cintos de cordón de goma consisten nunha serie de capas de cordóns impregnados de caucho. As correas de cordón de goma ofrecen unha alta resistencia á tracción e un tamaño e masa modestos. As correas de plástico ou de goma non reforzadas son aptas para aplicacións de accionamento lixeiros e de baixa velocidade. As correas de plástico e goma non reforzadas pódense estirar no seu lugar sobre as súas poleas. Os cintos de plástico non reforzados poden transmitir unha maior potencia en comparación cos cintos de goma. Os cintos de coiro reforzados consisten nun elemento de tracción de plástico intercalado entre as capas superior e inferior de coiro. Finalmente, os nosos cintos de tea poden consistir nunha única peza de algodón ou pato dobrada e cosida con filas de puntos lonxitudinais. Os cintos de tecido poden realizar un seguimento uniforme e funcionar a alta velocidade. - Correas acanaladas ou dentadas (como as correas trapezoidales): son correas planas básicas modificadas para proporcionar as vantaxes doutro tipo de produto de transmisión. Trátase de cintos planos cunha parte inferior nervada lonxitudinalmente. Os cintos Poly-V son cintos planos con ranuras lonxitudinais ou dentadas con sección de tracción e unha serie de sucos adxacentes en forma de V para fins de seguimento e compresión. A capacidade de potencia depende do ancho do cinto. A correa en V é o cabalo de batalla da industria e está dispoñible nunha variedade de tamaños e tipos estandarizados para a transmisión de case calquera potencia de carga. As transmisións por correa trapezoidal funcionan ben entre 1500 e 6000 pés/min, pero as correas trapezoidales estreitas funcionarán ata 10.000 pés/min. As transmisións por correa trapezoidal ofrecen unha longa vida útil, como de 3 a 5 anos e permiten grandes relacións de velocidade, son fáciles de instalar e quitar, ofrecen un funcionamento silencioso, baixo mantemento, unha boa absorción de impactos entre o condutor da correa e os eixes impulsados. A desvantaxe das correas trapezoidales é o seu certo deslizamento e fluencia e, polo tanto, poden non ser a mellor solución onde se requiren velocidades síncronas. Temos correas industriais, automoción e agrícolas. Están dispoñibles lonxitudes estándar almacenadas, así como lonxitudes personalizadas de cintos. Todas as seccións transversais de correa trapezoidal estándar están dispoñibles en stock. Existen táboas nas que pode calcular parámetros descoñecidos como a lonxitude da correa, a sección da correa (ancho e grosor) sempre que coñeza algúns parámetros do seu sistema, como os diámetros das poleas impulsoras e conducidas, a distancia entre centros e as velocidades de rotación das poleas. Podes utilizar esas táboas ou pedirnos que elixamos a correa trapezoidal adecuada para ti. - Correas de transmisión positiva (correa de distribución): Estas correas tamén son de tipo plano cunha serie de dentes uniformemente espazados na circunferencia interior. As correas de transmisión ou distribución positivas combinan as vantaxes das correas planas coas características de agarre positivo das cadeas e engrenaxes. As correas de transmisión positivas non revelan deslizamentos nin variacións de velocidade. É posible unha ampla gama de relacións de velocidade. As cargas dos rodamentos son baixas porque poden funcionar a baixa tensión. Non obstante, son máis susceptibles a desalineacións nas poleas. - Poleas, poleas, bujes para correas: utilízanse diferentes tipos de poleas con correas de transmisión planas, estriadas (dentadas) e positivas. Nós os fabricamos todos. A maioría das nosas poleas de correa plana están feitas por fundición de ferro, pero tamén están dispoñibles versións de aceiro en varias combinacións de llanta e cubo. As nosas poleas de correa plana poden ter cubos sólidos, con radios ou divididos, ou podemos fabricar como desexes. As correas estriadas e de transmisión positiva están dispoñibles nunha variedade de tamaños e anchos. Polo menos unha polea nas transmisións por correa de distribución debe estar bridada para manter a correa na transmisión. Para sistemas de transmisión central longa, recoméndase ter as dúas poleas con bridas. As poleas son as rodas acanaladas das poleas e fanse xeralmente mediante fundición de ferro, conformación de aceiro ou moldeado de plástico. A conformación de aceiro é un proceso axeitado para fabricar poleas de automóbiles e agrícolas. Producimos poleas con sucos regulares e profundos. As poleas de ranura profunda son moi adecuadas cando a correa trapezoidal entra na polea en ángulo, como é o caso dos accionamentos de cuarto de volta. As ranuras profundas tamén son moi adecuadas para accionamentos de eixe vertical e aplicacións onde a vibración das correas pode ser un problema. As nosas poleas locas son poleas acanaladas ou poleas planas que non serven para transmitir potencia mecánica. As poleas locas úsanse principalmente para tensar as correas. - Transmisións por correa simple e múltiple: as transmisións por correa única teñen unha única ranura mentres que as transmisións por correa múltiples teñen varias ranuras. Premendo no texto de cores correspondente a continuación podes descargar os nosos catálogos: - Correas de transmisión de potencia (inclúe correas trapezoidales, correas de distribución, correas de borde bruto, correas envoltas e correas especiais) - Cintas Transportadoras - Poleas en V - Poleas de distribución CADEAS E TRANSMISIÓNS DE CADEA: As nosas cadeas de transmisión de potencia teñen algunhas vantaxes, como distancias entre os eixos relativamente sen restricións, fácil montaxe, compacidade, elasticidade baixo tensión sen escorregar ou fluír, capacidade de operación a altas temperaturas. Estes son os principais tipos das nosas cadeas: - Cadenas desmontables: as nosas cadeas desmontables están feitas nunha variedade de tamaños, paso e resistencia máxima e, en xeral, de ferro maleable ou aceiro. As cadeas maleables fanse nun rango de tamaños de 0,902 (23 mm) a 4,063 polgadas (103 mm) de paso e unha resistencia máxima de 700 a 17.000 lb/polgada cadrada. Pola súa banda, as nosas cadeas de aceiro desmontables están fabricadas en tamaños de 0,904 polgadas (23 mm) a aproximadamente 3,00 polgadas (76 mm) de paso, cunha resistencia máxima de 760 a 5000 lb/polgada cadrada._cc781905-5cde-3194-bb3b- 136bad5cf58d_ - Cadenas de pinza: estas cadeas úsanse para cargas máis pesadas e velocidades lixeiramente superiores a uns 2,2 m/s (450 pés/min). As cadeas de pinza están feitas de eslabóns individuais de fundición que teñen un extremo de barril redondo completo con barras laterais compensadas. Estes elos da cadea están acoplados con pasadores de aceiro. Estas cadeas varían de paso de aproximadamente 1,00 polgadas (25 mm) a 6,00 polgadas (150 mm) e as forzas máximas entre 3600 e 30,000 lb/polgada cadrada. - Cadenas de barra lateral compensada: son populares nas cadeas de transmisión de maquinaria de construción. Estas cadeas funcionan a velocidades de ata 1000 pés/min e transmiten cargas a uns 250 hp. Xeralmente, cada enlace ten dúas barras laterais desplazadas, un casco, un rolo, un pasador, un pasador de chaveta. - Cadenas de rolos: están dispoñibles en pasos de 0,25 (6 mm) a 3,00 (75 mm) polgadas. A forza máxima das cadeas de rolos de ancho único varía entre 925 e 130.000 lb/polgada cadrada. Existen versións de cadeas de rolos de ancho múltiple que transmiten maior potencia a velocidades máis altas. As cadeas de rolos de ancho múltiple tamén ofrecen unha acción máis suave cun ruído reducido. As cadeas de rolos están montadas a partir de elos de rolos e elos de pasadores. Os pasadores utilízanse nas cadeas de rolos versión desmontable. O deseño das unidades de cadea de rolos require coñecementos especializados na materia. Mentres que as transmisións por correa baséanse en velocidades lineais, as transmisións por cadea baséanse na velocidade de rotación do piñón máis pequeno, que na maioría das instalacións é o membro impulsado. Ademais dos cabalos de potencia e da velocidade de rotación, o deseño das transmisións en cadea baséase en moitos outros factores. - Cadenas de dobre paso: basicamente o mesmo que as cadeas de rolos, excepto que o paso é o dobre. - Cadenas de dentes invertidos (silenciosas): cadeas de alta velocidade que se usan principalmente para motores primarios e unidades de toma de forza. As transmisións por cadea de dentes invertidos poden transmitir potencias de ata 1200 hp e están formadas por unha serie de elos de dentes, ensamblados alternativamente con pasadores ou unha combinación de compoñentes de unión. A cadea de guía central ten elos guía para enganchar rañuras no piñón, e a cadea de guía lateral ten guías para enganchar os lados do piñón. - Cadenas de contas ou deslizantes: estas cadeas úsanse para unidades de velocidade lenta e tamén en operacións manuais. Premendo no texto de cores correspondente a continuación podes descargar os nosos catálogos: - Cadenas de Conducción - Cadenas transportadoras - Cadenas transportadoras de paso grande - Cadenas de rolos de aceiro inoxidable - Cadenas de elevación - Cadenas de motos - Cadeas de Máquinas Agrícolas - Piñóns: os nosos piñóns estándar cumpre cos estándares ANSI. Os piñóns da placa son piñóns planos e sen cubo. Os nosos piñóns de cubo de tamaño pequeno e mediano están transformados a partir de barras ou forxados ou fabricados soldando un cubo de barras a unha placa laminada en quente. AGS-TECH Inc. pode proporcionar rodas dentadas mecanizadas a partir de fundicións de ferro gris, aceiro fundido e construcións de cubos soldados, po de metal sinterizado, plásticos moldeados ou mecanizados. Para un funcionamento suave a altas velocidades, é esencial unha selección adecuada do tamaño dos piñóns. As limitacións de espazo son, por suposto, un factor que non podemos ignorar ao elixir un piñón. Recoméndase que a relación entre o condutor e as ruedas dentadas conducidas non sexa superior a 6:1 e a envoltura da cadea do condutor sexa de 120 graos. As distancias centrais entre os piñóns máis pequenos e maiores, a lonxitude da cadea e a tensión da cadea tamén se deben escoller de acordo con algúns cálculos e directrices de enxeñería recomendados e non ao azar. Descarga os nosos catálogos premendo no texto en cor a continuación: - Rodas dentadas e placas - Casquillos de transmisión - Acoplamento de cadea - Pechaduras de cadea TRANSMISIÓNS POR CABLES: Teñen nalgúns casos as súas vantaxes sobre as correas e as transmisións por cadea. Os cables de transmisión poden realizar a mesma función que as correas e tamén poden ser máis sinxelos e económicos de implementar nalgunhas aplicacións. Por exemplo, unha nova serie de unidades de cable Synchromesh están deseñadas para unha tracción positiva para substituír as cordas convencionais, os cables simples e as unidades de engranaxe, especialmente en espazos reducidos. A nova unidade de cable está deseñada para proporcionar un posicionamento de alta precisión en equipos electrónicos como copiadoras, plotters, máquinas de escribir, impresoras,... etc. Unha característica fundamental da nova unidade de cable é a súa capacidade de utilizarse en configuracións serpentinas 3D que permiten deseños extremadamente en miniatura. Os cables sincronizados pódense usar con menor tensión en comparación coas cordas, reducindo así o consumo de enerxía. Póñase en contacto con AGS-TECH para preguntas e opinións sobre correas, cadeas e transmisións por cable. CLICK Product Finder-Locator Service PÁXINA ANTERIOR
- Composites, Composite Materials Manufacturing, Fiber Reinforced
Composites, Composite Materials Manufacturing, Particle and Fiber Reinforced, Cermets, Ceramic & Metal Composite, Glass Fiber Reinforced Polymer, Lay-Up Process Fabricación de materiais compostos e compostos Simplemente definidos, os MATERIAIS COMPOSTOS ou MATERIAIS COMPOSTOS son materiais formados por dous ou varios materiais con propiedades físicas ou químicas diferentes, pero cando se combinan convértense nun material diferente aos materiais constituíntes. Debemos sinalar que os materiais constituíntes permanecen separados e distintos na estrutura. O obxectivo na fabricación dun material composto é obter un produto que sexa superior aos seus compoñentes e combine as características desexadas de cada constituínte. Como exemplo; a forza, o baixo peso ou o prezo máis baixo pode ser o motivador detrás do deseño e produción dun composto. O tipo de compostos que ofrecemos son compostos reforzados con partículas, compostos reforzados con fibra, incluíndo compostos de matriz cerámica / matriz de polímero / matriz metálica / carbono-carbono / compostos híbridos, compostos estruturais e laminados e estruturados en sandwich e nanocomposites. As técnicas de fabricación que implantamos na fabricación de materiais compostos son: pultrusión, procesos de produción de preimpregnados, colocación avanzada de fibras, enrolamento de filamentos, colocación de fibras a medida, proceso de pulverización de fibra de vidro, tufting, proceso de lanxide, z-pinning. Moitos materiais compostos están formados por dúas fases, a matriz, que é continua e rodea á outra fase; e a fase dispersa que está rodeada pola matriz. Recomendamos que faga clic aquí paraDESCARGA as nosas ilustracións esquemáticas da fabricación de materiais compostos e compostos por AGS-TECH Inc. Isto axudarache a comprender mellor a información que che proporcionamos a continuación. • COMPOSTOS REFORZADO CON PARTÍCULAS: Esta categoría consta de dous tipos: Compostos de partículas grandes e compostos reforzados por dispersión. No primeiro tipo, as interaccións partícula-matriz non se poden tratar a nivel atómico ou molecular. En cambio, a mecánica do continuo é válida. Por outra banda, nos compostos reforzados pola dispersión as partículas son xeralmente moito máis pequenas nas decenas de rangos de nanómetros. Un exemplo de composto de partículas grandes son os polímeros aos que se engadiron cargas. Os recheos melloran as propiedades do material e poden substituír parte do volume do polímero por un material máis económico. As fraccións de volume das dúas fases inflúen no comportamento do composto. Os compostos de partículas grandes úsanse con metais, polímeros e cerámicas. Os CERMETS son exemplos de compostos cerámicos/metálicos. O noso cermet máis común é o carburo cementado. Consiste en cerámica de carburo refractario como partículas de carburo de tungsteno nunha matriz de metal como cobalto ou níquel. Estes compostos de carburo úsanse amplamente como ferramentas de corte para aceiro endurecido. As partículas de carburo duro son as responsables da acción de corte e a súa dureza é mellorada pola matriz metálica dúctil. Así obtemos as vantaxes de ambos materiais nun único composto. Outro exemplo común dun composto de partículas grandes que usamos son as partículas de negro de carbón mesturadas con caucho vulcanizado para obter un composto con alta resistencia á tracción, tenacidade, rasgadura e resistencia á abrasión. Un exemplo de composto reforzado pola dispersión son os metais e as aliaxes metálicas reforzadas e endurecidas pola dispersión uniforme de partículas finas dun material moi duro e inerte. Cando se engaden escamas moi pequenas de óxido de aluminio á matriz metálica de aluminio, obtemos un po de aluminio sinterizado que ten unha resistencia mellorada ás altas temperaturas. • COMPOSTOS REFORZADOS CON FIBRAS : esta categoría de compostos é de feito a máis importante. O obxectivo a acadar é a alta resistencia e rixidez por unidade de peso. A composición, lonxitude, orientación e concentración da fibra nestes compostos é fundamental para determinar as propiedades e a utilidade destes materiais. Usamos tres grupos de fibras: bigotes, fibras e fíos. Os bigotes son monocristais moi finos e longos. Están entre os materiais máis resistentes. Algúns exemplos de materiais de bigotes son o grafito, o nitruro de silicio e o óxido de aluminio. FIBRAS pola súa banda son na súa maioría polímeros ou cerámicos e están en estado policristalino ou amorfo. O terceiro grupo son os fíos finos que teñen diámetros relativamente grandes e constan frecuentemente de aceiro ou volframio. Un exemplo de composto reforzado con fío son os pneumáticos de automóbiles que incorporan fío de aceiro dentro da goma. Dependendo do material da matriz, temos os seguintes compostos: COMPOSTOS DE MATRIZ POLÍMERA: están feitos de resina polimérica e fibras como ingrediente de reforzo. Un subgrupo destes chamados compostos de polímero reforzado con fibra de vidro (GFRP) conteñen fibras de vidro continuas ou discontinuas dentro dunha matriz de polímero. O vidro ofrece unha alta resistencia, é económico, fácil de fabricar en fibras e é quimicamente inerte. As desvantaxes son a súa limitada rixidez e rixidez, sendo as temperaturas de servizo só de 200 a 300 graos centígrados. A fibra de vidro é adecuada para carrocerías de automóbiles e equipos de transporte, carrocerías de vehículos mariños, recipientes de almacenamento. Non son axeitados para a fabricación de pontes nin para a industria aeroespacial debido á limitada rixidez. O outro subgrupo chámase composto de polímero reforzado con fibra de carbono (CFRP). Aquí, o carbono é o noso material de fibra na matriz polimérica. O carbono é coñecido polo seu alto módulo específico e resistencia e a súa capacidade para mantelos a altas temperaturas. As fibras de carbono poden ofrecernos módulos de tracción estándar, intermedios, altos e ultraaltos. Ademais, as fibras de carbono ofrecen diversas características físicas e mecánicas e, polo tanto, son adecuadas para varias aplicacións de enxeñería personalizadas. Os compostos CFRP pódense considerar para fabricar equipos deportivos e recreativos, recipientes a presión e compoñentes estruturais aeroespaciais. Porén, outro subgrupo, os compostos de polímero reforzado con fibra de aramida, tamén son materiais de alta resistencia e módulo. As súas relacións entre peso e forza son moi altas. As fibras de aramida tamén son coñecidas polos nomes comerciais KEVLAR e NOMEX. Baixo tensión funcionan mellor que outros materiais de fibra polimérica, pero son débiles en compresión. As fibras de aramida son resistentes, resistentes aos impactos, á fluencia e á fatiga, estables a altas temperaturas, químicamente inertes excepto contra ácidos e bases fortes. As fibras de aramida son amplamente utilizadas en artigos deportivos, chalecos antibalas, pneumáticos, cordas, fundas de cables de fibra óptica. Existen outros materiais de reforzo de fibra pero utilízanse en menor medida. Estes son principalmente boro, carburo de silicio e óxido de aluminio. Por outra banda, o material da matriz polimérica tamén é crítico. Determina a temperatura máxima de servizo do composto porque o polímero ten xeralmente unha temperatura de fusión e degradación máis baixa. Os poliésteres e os ésteres vinílicos úsanse amplamente como matriz polimérica. Tamén se utilizan resinas que teñen unha excelente resistencia á humidade e propiedades mecánicas. Por exemplo, a resina de poliimida pódese usar ata uns 230 graos centígrados. COMPOSITOS DE MATRIZ METÁLICA: Nestes materiais utilizamos unha matriz metálica dúctil e as temperaturas de servizo son xeralmente superiores ás dos seus compoñentes. En comparación cos compostos de matriz de polímero, estes poden ter temperaturas de funcionamento máis altas, ser non inflamables e poden ter unha mellor resistencia á degradación contra os fluídos orgánicos. Sen embargo son máis caros. Materiais de reforzo como bigotes, partículas, fibras continuas e discontinuas; e os materiais de matriz como cobre, aluminio, magnesio, titanio, superaliaxes están sendo habitualmente utilizados. Exemplos de aplicacións son os compoñentes do motor feitos de matriz de aliaxe de aluminio reforzada con óxido de aluminio e fibras de carbono. COMPOSITOS DE MATRIZ CERÁMICA: os materiais cerámicos son coñecidos pola súa excelente fiabilidade a altas temperaturas. Non obstante, son moi fráxiles e teñen valores baixos de tenacidade á fractura. Ao incorporar partículas, fibras ou bigotes dunha cerámica na matriz doutra podemos conseguir compostos con maior dureza á fractura. Estes materiais incrustados inhiben basicamente a propagación da greta no interior da matriz mediante algúns mecanismos como desviar as puntas da greta ou formar pontes a través das caras da greta. Como exemplo, as alúminas reforzadas con bigotes de SiC úsanse como insertos de ferramentas de corte para mecanizar aliaxes de metal duro. Estes poden revelar mellores rendementos en comparación cos carburos cementados. COMPOSITOS CARBONO-CARBONO: Tanto o reforzo como a matriz son de carbono. Teñen altos módulos de tracción e resistencias a altas temperaturas superiores a 2000 centígrados, resistencia á fluencia, altas durezas á fractura, baixos coeficientes de expansión térmica, altas condutividades térmicas. Estas propiedades fan que sexan ideais para aplicacións que requiren resistencia ao choque térmico. Non obstante, a debilidade dos compostos carbono-carbono é a súa vulnerabilidade fronte á oxidación a altas temperaturas. Exemplos típicos de uso son moldes de prensado en quente, fabricación avanzada de compoñentes de motores de turbina. COMPOSITOS HÍBRIDOS: mestúranse dous ou máis tipos diferentes de fibras nunha única matriz. Así, pódese adaptar un novo material cunha combinación de propiedades. Un exemplo é cando se incorporan fibras de carbono e de vidro nunha resina polimérica. As fibras de carbono proporcionan rixidez e resistencia de baixa densidade, pero son caras. O vidro, por outra banda, é barato pero carece da rixidez das fibras de carbono. O composto híbrido vidro-carbono é máis resistente e resistente e pódese fabricar a un custo máis baixo. PROCESAMIENTO DE COMPOSTOS REFORZADOS CON FIBRAS: Para plásticos reforzados con fibras continuos con fibras uniformemente distribuídas e orientadas na mesma dirección, utilizamos as seguintes técnicas. PULTRUSIÓN: fabrícanse varillas, vigas e tubos de lonxitudes continuas e seccións transversais constantes. Os rovings de fibra continua están impregnados cunha resina termoendurecible e pasan a través dunha matriz de aceiro para preformalos coa forma desexada. A continuación, pasan por unha matriz de curado mecanizada de precisión para acadar a súa forma final. Dado que a matriz de curado se quenta, cura a matriz de resina. Os tiradores atraen o material a través das matrices. Usando núcleos ocos inseridos, podemos obter tubos e xeometrías ocas. O método de pultrusión está automatizado e ofrécenos altas taxas de produción. É posible producir calquera lonxitude de produto. PROCESO DE PRODUCIÓN DE PREPREGADO: Prepreg é un reforzo de fibra continua preimpregnado cunha resina polimérica parcialmente curada. É amplamente utilizado para aplicacións estruturais. O material vén en forma de cinta e envíase como unha cinta. O fabricante o moldea directamente e cúrao por completo sen necesidade de engadir ningunha resina. Dado que os preimpregnados sofren reaccións de curado a temperatura ambiente, almacénanse a temperaturas de 0 graos centígrados ou inferiores. Despois do uso, as cintas restantes almacénanse de novo a baixas temperaturas. Empréganse resinas termoplásticas e termoendurecibles e son habituais as fibras de reforzo de carbono, aramida e vidro. Para usar preimpregnados, primeiro elimínase o papel de soporte do soporte e despois a fabricación realízase colocando a cinta preimpregnada sobre unha superficie labrada (proceso de colocación). Pódense colocar varias capas para obter os espesores desexados. A práctica frecuente é alternar a orientación da fibra para producir un laminado de capas cruzadas ou angulares. Finalmente aplícanse calor e presión para o curado. Tanto o procesamento manual como os procesos automatizados úsanse para cortar preimpregnados e lay-up. ENROBACIÓN DE FILAMENTOS: as fibras de reforzo continuas colócanse con precisión nun patrón predeterminado para seguir unha forma oca e xeralmente ciclíndica. As fibras pasan primeiro por un baño de resina e despois enrólanse nun mandril mediante un sistema automatizado. Despois de varias repeticións de bobinado obtéñense os espesores desexados e o curado realízase a temperatura ambiente ou dentro dun forno. Agora quítase o mandril e desmoldase o produto. O enrolamento do filamento pode ofrecer relacións resistencia/peso moi altas ao enrolar as fibras en patróns circunferenciais, helicoidais e polares. Con esta técnica fabrícanse tubos, tanques e envolturas. • COMPOSTOS ESTRUTURAIS: Xeralmente están formados por materiais tanto homoxéneos como compostos. Polo tanto, as propiedades destes están determinadas polos materiais constituíntes e o deseño xeométrico dos seus elementos. Aquí están os principais tipos: COMPOSITOS LAMINARES: Estes materiais estruturais están feitos de láminas ou paneis bidimensionais con direccións preferentes de alta resistencia. As capas apílanse e cíñense entre si. Ao alternar as direccións de alta resistencia nos dous eixes perpendiculares, obtemos un composto que ten alta resistencia en ambas direccións no plano bidimensional. Axustando os ángulos das capas pódese fabricar un composto con resistencia nas direccións preferidas. O esquí moderno faise deste xeito. PANEIS SANDWICH: Estes compostos estruturais son lixeiros, pero teñen unha elevada rixidez e resistencia. Os paneis sándwich consisten en dúas follas exteriores feitas dun material ríxido e forte como aliaxes de aluminio, plásticos reforzados con fibra ou aceiro e un núcleo entre as follas exteriores. O núcleo debe ser lixeiro e a maioría das veces ter un baixo módulo de elasticidade. Os materiais básicos populares son as escumas poliméricas ríxidas, a madeira e os panales. Os paneis sándwich son amplamente utilizados na industria da construción como material para cubertas, pisos ou paredes, e tamén nas industrias aeroespaciales. • NANOCOMPOSITOS : Estes novos materiais consisten en partículas de nanopartículas incrustadas nunha matriz. Usando nanocompostos podemos fabricar materiais de caucho que son moi boas barreiras para a penetración do aire mantendo as súas propiedades de caucho sen cambios. CLICK Product Finder-Locator Service PÁXINA ANTERIOR
- Machine Elements Manufacturing, Gears, Gear Drives, Bearings, Keys, Splines
Machine Elements Manufacturing, Gears, Gear Drives, Bearings, Keys, Splines, Pins, Shafts, Seals, Fasteners, Clutch, Cams, Followers, Belts, Couplings, Shafts Fabricación de elementos de máquinas Le máis Correas e cadeas e conxunto de transmisión por cable Le máis Engrenaxes e conxunto de transmisión de engrenaxes Le máis Fabricación de acoplamentos e rodamentos Le máis Fabricación de chaves e estrías e pasadores Le máis Fabricación de levas e seguidores e enlaces e rodas de trinquete Le máis Fabricación de Eixos Le máis Fabricación de selos mecánicos Le máis Conxunto de embrague e freo Le máis Fabricación de Suxeidores Le máis Montaxe de máquinas simples ELEMENTOS DA MÁQUINA son compoñentes elementais dunha máquina. Estes elementos constan de tres tipos básicos: 1.) Compoñentes estruturais, incluíndo membros do cadro, rodamentos, eixes, estrías, fixadores, selos e lubricantes. 2.) Mecanismos que controlan o movemento de varias maneiras, como trens de engrenaxes, transmisións por correa ou cadea, enlaces, sistemas de levas e seguidores, freos e embragues. 3.) Compoñentes de control como botóns, interruptores, indicadores, sensores, actuadores e controladores de ordenador. A maioría dos elementos da máquina que lle ofrecemos están estandarizados para tamaños comúns, pero tamén están dispoñibles elementos de máquina feitos a medida para as súas aplicacións especializadas. A personalización dos elementos da máquina pode realizarse en deseños existentes que están nos nosos catálogos descargables ou en deseños novos. A creación de prototipos e a fabricación de elementos da máquina pódese levar adiante unha vez que o deseño sexa aprobado por ambas as partes. Se hai que deseñar e fabricar novos elementos da máquina, os nosos clientes envíannos un correo electrónico os seus propios planos e revisámolos para a súa aprobación, ou ben pídennos que deseñamos elementos da máquina para a súa aplicación. Neste último caso utilizamos todas as entradas dos nosos clientes e deseñamos os elementos da máquina e enviamos os planos finalizados aos nosos clientes para a súa aprobación. Unha vez aprobado, producimos primeiros artigos e posteriormente fabricamos os elementos da máquina segundo o deseño final. En calquera fase deste traballo, no caso de que o deseño dun elemento da máquina en particular funcione de forma insatisfactoria no campo (o que é raro), revisamos todo o proxecto e realizamos as modificacións conxuntamente cos nosos clientes segundo sexa necesario. A nosa práctica estándar é asinar acordos de non divulgación (NDA) cos nosos clientes para o deseño de elementos da máquina ou calquera outro produto sempre que sexa necesario ou necesario. Unha vez que os elementos da máquina para un cliente concreto están deseñados e fabricados a medida, asignámoslle un código de produto e só os producimos e vendemos ao noso cliente propietario do produto. Reproducimos os elementos da máquina utilizando as ferramentas, moldes e procedementos desenvolvidos tantas veces como sexa necesario e sempre que o noso cliente os reordena. Noutras palabras, unha vez que se deseña e produce un elemento de máquina personalizado para ti, a propiedade intelectual, así como todas as ferramentas e moldes, reservamos e almacenamos indefinidamente para ti e os produtos reproducidos como queiras. Tamén ofrecemos aos nosos clientes servizos de enxeñería combinando creativamente elementos da máquina nun compoñente ou conxunto que serve para unha aplicación e que satisfaga ou supere as expectativas dos nosos clientes. As plantas que fabrican os nosos elementos de máquina están cualificadas por ISO9001, QS9000 ou TS16949. Ademais, a maioría dos nosos produtos teñen marca CE ou UL e cumpren estándares internacionalmente relevantes como ISO, SAE, ASME, DIN. Faga clic nos submenús para obter información detallada sobre os elementos da nosa máquina, incluíndo: - Correas, cadeas e transmisión por cable - Engrenaxes e transmisións - Acoplamentos e rodamentos - Chaves e Splines e pinos - Cámaras e enlaces - Eixos - Selos mecánicos - Embrague e freo industrial - Fixadores - Máquinas simples Elaboramos un folleto de referencia para os nosos clientes, deseñadores e desenvolvedores de novos produtos, incluíndo elementos de máquinas. Pode familiarizarse con algúns termos de uso común no deseño de compoñentes de máquinas: Descarga o folleto dos termos comúns de enxeñaría mecánica empregados por deseñadores e enxeñeiros Os nosos elementos de máquinas atopan aplicacións en diversos campos, como maquinaria industrial, sistemas de automatización, equipos de proba e metroloxía, equipos de transporte, máquinas de construción e practicamente en calquera lugar que se ocorra. AGS-TECH desenvolve e fabrica elementos de máquinas a partir de diversos materiais dependendo da aplicación. Os materiais utilizados para os elementos da máquina poden ir desde plásticos moldeados usados para xoguetes ata aceiro endurecido e revestido especialmente para maquinaria industrial. Os nosos deseñadores usan software e ferramentas de deseño profesionais de última xeración para desenvolver elementos da máquina, tendo en conta detalles como os ángulos dos dentes das engrenaxes, as tensións implicadas, as taxas de desgaste, etc. Desprácese polos nosos submenús e descargue os nosos folletos e catálogos de produtos para ver se pode localizar elementos de máquinas dispoñibles para a súa aplicación. Se non pode atopar unha boa correspondencia para a súa aplicación, infórmenos e traballaremos con vostede para desenvolver e fabricar elementos de máquina que satisfagan as súas necesidades. Se estás principalmente interesado nas nosas capacidades de enxeñería e investigación e desenvolvemento en lugar das capacidades de fabricación, invitámosche a visitar o noso sitio web http://www.ags-engineering.com onde podes atopar información máis detallada sobre o noso deseño, desenvolvemento de produtos, desenvolvemento de procesos, servizos de consultoría de enxeñería e moito máis CLICK Product Finder-Locator Service PÁXINA ANTERIOR
- Joining & Assembly & Fastening Processes, Welding, Brazing, Soldering
Joining & Assembly & Fastening Processes, Welding, Brazing, Soldering, Sintering, Adhesive Bonding, Press Fitting, Wave and Reflow Solder Process, Torch Furnace Procesos de unión e montaxe e fixación Unimos, montamos e suxeitamos as súas pezas manufacturadas e convertémolas en produtos acabados ou semielaborados mediante SOLDADURA, SOLDADURA, SINTERIZACIÓN, ENGOLADO ADHESIVO, FIXACIÓN, EMPRUNTADO. Algúns dos nosos procesos de soldadura máis populares son arco, gas oxicombustible, resistencia, proxección, costura, alteración, percusión, estado sólido, feixe de electróns, láser, termita, soldadura por indución. Os nosos procesos de soldadura máis populares son o soplete, a indución, o forno e a soldadura por inmersión. Os nosos métodos de soldadura son ferro, placa quente, forno, indución, inmersión, onda, refluxo e soldadura por ultrasóns. Para a unión adhesiva usamos con frecuencia termoplásticos e termoestables, epoxi, fenólicos, poliuretano, aliaxes adhesivas, así como algúns outros produtos químicos e cintas. Finalmente, os nosos procesos de suxeición consisten en cravar, aparafusar, porcas e parafusos, remachar, enganchar, enganchar, pegar e grapar e encaixar a prensa. • SOLDADURA: A soldadura consiste na unión de materiais mediante a fusión das pezas de traballo e a introdución de materiais de recheo, que tamén se unen ao baño de soldadura fundido. Cando a zona arrefría, obtemos unha xunta forte. Nalgúns casos aplícase presión. Ao contrario da soldadura, as operacións de soldadura e soldadura só implican a fusión dun material con menor punto de fusión entre as pezas de traballo, e as pezas non se funden. Recomendamos que faga clic aquí paraDESCARGA as nosas ilustracións esquemáticas de procesos de soldadura de AGS-TECH Inc. Isto axudarache a comprender mellor a información que che proporcionamos a continuación. En SOLDADURA POR ARCO, utilizamos unha fonte de alimentación e un electrodo para crear un arco eléctrico que funde os metais. O punto de soldadura está protexido por un gas ou vapor de protección ou outro material. Este proceso é popular para soldar pezas de automóbiles e estruturas de aceiro. Na soldadura por arco metálico protexido (SMAW) ou tamén coñecida como soldadura por varilla, achégase unha varilla de electrodo ao material base e xérase un arco eléctrico entre eles. A varilla do electrodo funde e actúa como material de recheo. O electrodo tamén contén fluxo que actúa como unha capa de escoura e desprende vapores que actúan como gas protector. Estes protexen a zona de soldadura da contaminación ambiental. Non se están a utilizar outros recheos. As desvantaxes deste proceso son a súa lentitude, a necesidade de substituír os electrodos con frecuencia, a necesidade de descascarar as escouras residuais orixinadas polo fluxo. Varios metais como ferro, aceiro, níquel, aluminio, cobre, etc. Pódese soldar. As súas vantaxes son as súas ferramentas económicas e a facilidade de uso. Soldadura por arco metálico con gas (GMAW) tamén coñecida como gas metal-inerte (MIG), temos a alimentación continua dun recheo de fío de electrodo consumible e un gas inerte ou parcialmente inerte que flúe ao redor do fío contra a contaminación ambiental da rexión de soldadura. Pódense soldar aceiro, aluminio e outros metais non férreos. As vantaxes do MIG son as altas velocidades de soldadura e a boa calidade. As desvantaxes son os seus complicados equipos e os retos aos que se enfrontan en ambientes exteriores ventosos porque temos que manter estable o gas protector ao redor da zona de soldadura. Unha variación de GMAW é a soldadura por arco con núcleo de fluxo (FCAW) que consiste nun tubo de metal fino cheo de materiais fundentes. Ás veces, o fluxo dentro do tubo é suficiente para protexerse da contaminación ambiental. A soldadura por arco mergullado (SAW) é un proceso amplamente automatizado, que implica unha alimentación continua do fío e un arco que se produce baixo unha capa de cuberta de fluxo. As taxas de produción e a calidade son altas, a escoria de soldadura despréndese facilmente e temos un ambiente de traballo libre de fume. A desvantaxe é que só se pode usar para soldar parts en determinadas posicións. Na soldadura por arco de tungsteno con gas (GTAW) ou soldadura con gas tungsteno-inerte (TIG) usamos un electrodo de tungsteno xunto cun recheo separado e gases inertes ou case inertes. Como sabemos, o volframio ten un alto punto de fusión e é un metal moi axeitado para temperaturas moi altas. O volframio en TIG non se consume ao contrario dos outros métodos explicados anteriormente. Unha técnica de soldadura lenta pero de alta calidade vantaxosa sobre outras técnicas na soldadura de materiais finos. Adecuado para moitos metais. A soldadura por arco de plasma é similar pero usa gas plasma para crear o arco. O arco na soldadura por arco de plasma é relativamente máis concentrado en comparación co GTAW e pódese usar para unha gama máis ampla de espesores de metal a velocidades moito máis altas. A soldadura por arco de plasma e GTAW pódese aplicar a máis ou menos os mesmos materiais. A SOLDADURA OXY-FUEL / OXYFUEL tamén chamada soldadura de oxiacetileno, a soldadura de oxi, a soldadura de gas realízase utilizando combustibles de gas e osíxeno para soldar. Dado que non se utiliza enerxía eléctrica é portátil e pódese usar onde non hai electricidade. Usando un soplete quentamos as pezas e o material de recheo para producir unha piscina de metal fundido compartido. Pódense empregar varios combustibles como acetileno, gasolina, hidróxeno, propano, butano, etc. Na soldadura de oxicombustibles empregamos dous recipientes, un para o combustible e outro para osíxeno. O osíxeno oxida o combustible (queimao). SOLDADURA POR RESISTENCIA: Este tipo de soldadura aproveita o quecemento en joule e xérase calor no lugar onde se aplica corrente eléctrica durante un tempo determinado. Polo metal pásanse correntes elevadas. Neste lugar fórmanse piscinas de metal fundido. Os métodos de soldadura por resistencia son populares debido á súa eficiencia, pouco potencial de contaminación. Non obstante, as desvantaxes son que os custos dos equipos son relativamente importantes e a limitación inherente a pezas de traballo relativamente delgadas. A SOLDADURA POR PUNTOS é un dos principais tipos de soldadura por resistencia. Aquí unimos dúas ou máis follas ou pezas de traballo superpostas usando dous electrodos de cobre para unir as follas e facer pasar unha corrente elevada a través delas. O material entre os electrodos de cobre quéntase e nese lugar xérase unha piscina fundida. A corrente detense entón e as puntas dos electrodos de cobre arrefrían a localización da soldadura porque os electrodos están arrefriados por auga. Aplicar a cantidade correcta de calor ao material e grosor correctos é fundamental para esta técnica, xa que se se aplica incorrectamente a unión será débil. A soldadura por puntos ten as vantaxes de non provocar deformacións significativas nas pezas de traballo, eficiencia enerxética, facilidade de automatización e excelentes taxas de produción e non require ningún recheo. A desvantaxe é que, dado que a soldadura ten lugar en puntos en lugar de formar unha costura continua, a resistencia global pode ser relativamente menor en comparación con outros métodos de soldadura. A SOLDADURA DE COSTURA, pola súa banda, produce soldaduras nas superficies de contacto de materiais similares. A costura pode ser a tope ou solapada. A soldadura de costura comeza nun extremo e vaise progresivamente cara ao outro. Este método tamén usa dous electrodos de cobre para aplicar presión e corrente á rexión de soldadura. Os electrodos en forma de disco xiran con contacto constante ao longo da liña de costura e fan unha soldadura continua. Aquí tamén, os electrodos son arrefriados por auga. As soldaduras son moi fortes e fiables. Outros métodos son as técnicas de soldadura por proxección, flash e revolto. A SOLDADURA EN ESTADO SÓLIDO é un pouco diferente dos métodos anteriores explicados anteriormente. A coalescencia ten lugar a temperaturas inferiores á temperatura de fusión dos metais unidos e sen uso de recheo metálico. A presión pódese utilizar nalgúns procesos. Varios métodos son a SOLDADURA POR COEXTRUSIÓN na que se extruyen metais diferentes a través da mesma matriz, a SOLDADURA A PRESIÓN FRÍA onde unimos aliaxes brandas por debaixo dos seus puntos de fusión, a SOLDADURA POR DIFUSIÓN unha técnica sen liñas de soldadura visibles, a SOLDADURA POR EXPLOSIÓN para unir materiais diferentes, por exemplo, aliaxes resistentes á corrosión a estruturas. aceiros, SOLDADURA POR IMPULSO ELECTROMAGNÉTICO onde aceleramos tubos e chapas por forzas electromagnéticas, SOLDADURA DE FORXA que consiste en quentar os metais a altas temperaturas e martelalos entre si, SOLDADURA POR FRCCIÓN onde se realiza coa suficiente soldadura por rozamento, SOLDADURA POR FRICCIÓN SISTIR que implica un ferramenta consumible que atravesa a liña de unión, SOLDADURA POR PRESIÓN CALENTE onde presionamos os metais xuntos a temperaturas elevadas por debaixo da temperatura de fusión no baleiro ou gases inertes, SOLDADURA POR PRESIÓN ISOSTÁTICA CALENTE un proceso no que aplicamos presión mediante gases inertes no interior dun recipiente, SOLDADURA POR RODOLO onde unimos materiais diferentes forzándoos entre eles dúas rodas xiratorias, SOLDADURA ULTRASONICA onde se sueldan láminas finas de metal ou plástico mediante enerxía vibratoria de alta frecuencia. Outros dos nosos procesos de soldadura son a SOLDADURA POR FIXES ELECTRÓNICOS con penetración profunda e procesamento rápido, pero sendo un método caro considerámolo para casos especiais, SOLDADURA ELECTROSALGADA un método axeitado para placas de grosor e pezas de aceiro só, SOLDADURA POR INDUCCIÓN onde utilizamos indución electromagnética e quentar as nosas pezas eléctricamente condutoras ou ferromagnéticas, SOLDADURA LÁSER tamén cunha penetración profunda e procesamento rápido pero un método caro, SOLDADURA LÁSER HÍBRIDA que combina LBW con GMAW no mesmo cabezal de soldadura e capaz de salvar ocos de 2 mm entre placas, SOLDADURA POR PERCUSIÓN que implica unha descarga eléctrica seguida de forxa dos materiais coa presión aplicada, SOLDADURA TÉRMICA que implica reacción exotérmica entre po de aluminio e óxido de ferro., SOLDADURA ELECTROGÁS con electrodos consumibles e empregada só con aceiro en posición vertical, e finalmente SOLDADURA POR ARCO DE PERNOS para a unión de pernos a base. material con calor e presión. Recomendamos que faga clic aquí paraDESCARGA as nosas ilustracións esquemáticas dos procesos de soldadura, soldadura e unión adhesiva de AGS-TECH Inc Isto axudarache a comprender mellor a información que che proporcionamos a continuación. • SOLDADURA: Unimos dous ou máis metais quentando metais de recheo entre eles por encima dos seus puntos de fusión e empregando a acción capilar para estenderse. O proceso é similar á soldadura, pero as temperaturas implicadas para fundir o recheo son máis altas na soldadura. Do mesmo xeito que na soldadura, o fluxo protexe o material de recheo da contaminación atmosférica. Despois do arrefriamento, as pezas únense entre si. O proceso implica os seguintes pasos clave: bo axuste e separación, limpeza adecuada dos materiais de base, fixación adecuada, selección adecuada do fluxo e da atmosfera, quecemento do conxunto e finalmente a limpeza do conxunto soldado. Algúns dos nosos procesos de soldadura son o SOPORTE CON TORCH, un método popular que se realiza manualmente ou de forma automatizada. É axeitado para pedidos de produción de baixo volume e casos especializados. A calor aplícase usando chamas de gas preto da unión que se está soldando. A SOLDADURA A FORNO require menos habilidade do operador e é un proceso semiautomático axeitado para a produción industrial en masa. Tanto o control da temperatura como o control da atmosfera no forno son vantaxes desta técnica, porque a primeira permite ter ciclos de calor controlados e eliminar o quecemento local como é o caso da soldadura con soplete, e a segunda protexe a peza da oxidación. Usando jigging somos capaces de reducir os custos de fabricación ao mínimo. As desvantaxes son o alto consumo de enerxía, os custos dos equipos e consideracións de deseño máis desafiantes. A SOLDADURA A VALO realízase nun forno de baleiro. Mantense a uniformidade da temperatura e obtemos unións sen fluxo, moi limpas e con moi poucos esforzos residuais. Os tratamentos térmicos poden realizarse durante a soldadura ao baleiro, debido ás baixas tensións residuais presentes durante os ciclos lentos de quecemento e arrefriamento. A principal desvantaxe é o seu alto custo porque a creación dun ambiente de baleiro é un proceso caro. Outra técnica de soldadura por inmersión une pezas fixas onde se aplica o composto de soldadura ás superficies de acoplamento. Despois, as pezas fixtured son mergulladas nun baño dun sal fundido como o cloruro de sodio (sal de mesa) que actúa como medio de transferencia de calor e fluxo. O aire está excluído e, polo tanto, non se produce formación de óxidos. En SOLDADURA POR INDUCIÓN unimos materiais mediante un metal de recheo que ten un punto de fusión máis baixo que os materiais de base. A corrente alterna da bobina de indución crea un campo electromagnético que induce quecemento por indución en materiais magnéticos principalmente férreos. O método proporciona quecemento selectivo, boas xuntas con recheos que só flúen nas áreas desexadas, pouca oxidación porque non hai chamas e o arrefriamento é rápido, quentamento rápido, consistencia e idoneidade para a fabricación de gran volume. Para axilizar os nosos procesos e garantir a coherencia, utilizamos con frecuencia preformas. A información sobre as nosas instalacións de soldadura que producen accesorios de cerámica a metal, selado hermético, pasaxes ao baleiro, baleiro alto e ultraalto e compoñentes de control de fluídos pódese atopar aquí:_cc781905-5cde-bb31905-5cde-bb31984Folleto de Brazing Factory • SOLDADURA : Na soldadura non temos fusión das pezas de traballo, senón un metal de aporte cun punto de fusión inferior ao das pezas de unión que desemboca na unión. O metal de recheo na soldadura funde a temperatura máis baixa que na soldadura. Usamos aliaxes sen chumbo para soldar e cumprimos RoHS e para diferentes aplicacións e requisitos temos aliaxes diferentes e adecuadas, como a aliaxe de prata. A soldadura ofrécenos unións estancas a gases e líquidos. En SOLDADURA BLANDA, o noso metal de recheo ten un punto de fusión inferior a 400 centígrados, mentres que en SOLDADURA DE PRATA e SOLDADURA necesitamos temperaturas máis altas. A soldadura suave usa temperaturas máis baixas pero non resulta en xuntas fortes para aplicacións esixentes a temperaturas elevadas. A soldadura de prata, por outra banda, require altas temperaturas proporcionadas polo facho e dános unións fortes e adecuadas para aplicacións a altas temperaturas. A soldadura esixe as temperaturas máis altas e normalmente úsase un facho. Dado que as xuntas de soldadura son moi fortes, son un bo candidato para reparar obxectos pesados de ferro. Nas nosas liñas de fabricación utilizamos tanto soldadura manual manual como liñas de soldadura automatizadas. A SOLDADURA POR INDUCCIÓN utiliza corrente alterna de alta frecuencia nunha bobina de cobre para facilitar o quecemento por indución. Indúcense correntes na parte soldada e, como resultado, xérase calor na alta resistencia joint. Esta calor derrete o metal de recheo. Tamén se usa fluxo. A soldadura por indución é un bo método para soldar cilindros e tubos nun proceso continuo envolvendo as bobinas ao seu redor. Soldar algúns materiais como grafito e cerámica é máis difícil porque require o revestimento das pezas cun metal adecuado antes da soldadura. Isto facilita a unión interfacial. Soldamos estes materiais especialmente para aplicacións de envases herméticos. Fabricamos as nosas placas de circuíto impreso (PCB) en gran volume, principalmente mediante SOLDADURA DE ONDA. Só para pequenas cantidades de prototipos utilizamos soldadura manual mediante soldador. Usamos soldadura por ondas tanto para conxuntos de PCB de montaxe en superficie (PCBA) como de orificios pasantes. Unha cola temporal mantén os compoñentes unidos á placa de circuíto e o conxunto colócase nun transportador e móvese a través dun equipo que contén soldadura fundida. Primeiro o PCB é fluxo e despois entra na zona de prequecemento. A soldadura fundida está nunha tixola e ten un patrón de ondas estacionarias na súa superficie. Cando o PCB se move sobre estas ondas, estas ondas entran en contacto coa parte inferior do PCB e adhírense ás almofadas de soldadura. A soldadura permanece só en pins e almofadas e non na propia PCB. As ondas na soldadura fundida teñen que estar ben controladas para que non haxa salpicaduras e as partes superiores das ondas non toquen e contaminen áreas non desexadas das placas. En REFLOW SOLDERING, usamos unha pasta de soldadura pegajosa para unir temporalmente os compoñentes electrónicos ás placas. A continuación, as táboas pasan por un forno de refluxo con control de temperatura. Aquí a soldadura se funde e conecta os compoñentes de forma permanente. Usamos esta técnica tanto para compoñentes de montaxe en superficie como para compoñentes de orificios pasantes. O control adecuado da temperatura e o axuste das temperaturas do forno é fundamental para evitar a destrución dos compoñentes electrónicos da placa por sobrequentamento por encima dos seus límites máximos de temperatura. No proceso de soldadura por refluxo, en realidade temos varias rexións ou etapas cada unha cun perfil térmico distinto, como o paso de prequecemento, o paso de remollo térmico, os pasos de refluxo e de arrefriamento. Estes diferentes pasos son esenciais para unha soldadura por refluxo sen danos dos conxuntos de placas de circuíto impreso (PCBA). A SOLDADURA POR ULTRASONS é outra técnica de uso frecuente con capacidades únicas: pódese usar para soldar vidro, cerámica e materiais non metálicos. Por exemplo, os paneis fotovoltaicos que non son metálicos necesitan electrodos que se poidan colocar mediante esta técnica. Na soldadura por ultrasóns, implantamos unha punta de soldadura quente que tamén emite vibracións ultrasónicas. Estas vibracións producen burbullas de cavitación na interface do substrato co material de soldadura fundido. A enerxía implosiva da cavitación modifica a superficie do óxido e elimina a sucidade e os óxidos. Durante este tempo tamén se forma unha capa de aliaxe. A soldadura na superficie de unión incorpora osíxeno e permite a formación dunha forte unión compartida entre o vidro e a soldadura. A SOLDADURA POR INMERSIÓN pode considerarse como unha versión máis sinxela da soldadura por onda adecuada só para a produción a pequena escala. O primeiro fluxo de limpeza aplícase como noutros procesos. Os PCB con compoñentes montados son mergullados manualmente ou de forma semiautomatizada nun tanque que contén soldadura fundida. A soldadura fundida adhírese ás áreas metálicas expostas sen protección pola máscara de soldadura no taboleiro. O equipo é sinxelo e barato. • ENLACE ADHESIVO: Esta é outra técnica popular que utilizamos con frecuencia e consiste na unión de superficies mediante colas, epoxi, axentes plásticos ou outros produtos químicos. A unión realízase mediante a evaporación do disolvente, o curado térmico, o curado por luz UV, o curado a presión ou agardando un tempo determinado. Nas nosas liñas de produción utilízanse varias colas de alto rendemento. Cuns procesos de aplicación e curado debidamente deseñados, a unión adhesiva pode producir unións de tensión moi baixa, fortes e fiables. As unións adhesivas poden ser bos protectores contra factores ambientais como humidade, contaminantes, corrosivos, vibracións, etc. As vantaxes da unión adhesiva son: pódense aplicar a materiais que doutro xeito serían difíciles de soldar, soldar ou soldar. Tamén pode ser preferible para materiais sensibles á calor que serían danados pola soldadura ou outros procesos de alta temperatura. Outras vantaxes dos adhesivos son que poden aplicarse a superficies de forma irregular e aumentar o peso da montaxe en cantidades moi moi pequenas en comparación con outros métodos. Tamén os cambios dimensionais nas pezas son moi mínimos. Algunhas colas teñen propiedades de coincidencia de índices e pódense usar entre compoñentes ópticos sen diminuír significativamente a intensidade do sinal de luz ou óptico. As desvantaxes, por outra banda, son os tempos de curado máis longos que poden ralentizar as liñas de fabricación, os requisitos de fixación, os requisitos de preparación da superficie e a dificultade para desmontar cando se precisa un retraballo. A maioría das nosas operacións de unión adhesiva implican os seguintes pasos: -Tratamento de superficies: son habituais procedementos especiais de limpeza como a limpeza con auga desionizada, a limpeza con alcohol, a limpeza de plasma ou de coroa. Despois da limpeza podemos aplicar promotores de adherencia nas superficies para asegurar as mellores unións posibles. -Fijación de pezas: tanto para a aplicación de adhesivo como para o curado, deseñamos e utilizamos accesorios personalizados. -Aplicación de adhesivos: ás veces utilizamos sistemas manuais, e outras segundo o caso, automatizados como robótica, servomotores, actuadores lineais para entregar os adhesivos no lugar correcto e utilizamos dispensadores para entregalos no volume e cantidade adecuados. -Curamento: dependendo do adhesivo, podemos utilizar o secado e o curado sinxelos, así como o curado baixo luces UV que actúan como catalizador ou curado térmico nun forno ou mediante elementos calefactores resistivos montados en plantillas e accesorios. Recomendamos que faga clic aquí paraDESCARGA as nosas ilustracións esquemáticas dos procesos de fixación de AGS-TECH Inc. Isto axudarache a comprender mellor a información que che proporcionamos a continuación. • PROCESOS DE FIXACIÓN: Os nosos procesos de unión mecánica divídense en dúas categorías: FIXADORS e UNIDADES INTEGRALES. Exemplos de elementos de fixación que usamos son parafusos, pasadores, porcas, parafusos, remaches. Exemplos de xuntas integrais que usamos son os encaixes, as costuras e os engastes. Usando unha variedade de métodos de fixación, asegurámonos de que as nosas unións mecánicas sexan fortes e fiables durante moitos anos de uso. OS PARAFUSOS e os parafusos son algúns dos elementos de fixación máis utilizados para suxeitar e colocar obxectos. Os nosos parafusos e parafusos cumpren as normas ASME. Implíganse varios tipos de parafusos e parafusos, incluíndo parafusos hexagonales e parafusos hexagonales, parafusos e parafusos, parafusos de dobre punta, parafuso de espiga, parafuso de ollo, parafuso de espello, parafuso de chapa, parafuso de axuste fino, parafusos autoperforantes e autorroscantes. , parafuso de fixación, parafusos con arandelas incorporadas,... e moito máis. Temos varios tipos de cabeza de parafuso, como cabeza avellanada, cúpula, redonda, con brida e varios tipos de unidades de parafuso, como ranura, Phillips, cadrada, hexagonal. Pola súa banda, un RIVET é un elemento de fixación mecánico permanente que consiste nun eixe cilíndrico liso e unha cabeza por unha banda. Despois da inserción, o outro extremo do remache defórmase e o seu diámetro se expande para que quede no seu lugar. Noutras palabras, antes da instalación un remache ten unha cabeza e despois da instalación ten dúas. Instalamos varios tipos de remaches dependendo da aplicación, resistencia, accesibilidade e custo, como remaches de cabeza sólida/redondo, estruturais, semitubulares, cegos, oscar, drive, enrasados, de bloqueo por fricción, autoperforantes. O remache pode ser preferido nos casos en que se debe evitar a deformación térmica e o cambio nas propiedades do material debido á calor de soldadura. O remachado tamén ofrece un peso lixeiro e especialmente unha boa resistencia e resistencia contra as forzas de corte. Contra as cargas de tracción, non obstante, os parafusos, porcas e parafusos poden ser máis axeitados. No proceso de CLINCHING utilizamos punzóns e matrices especiais para formar un enclavamiento mecánico entre as chapas que se unen. O punzón empurra as capas de chapa na cavidade da matriz e resulta na formación dunha unión permanente. Non se require ningún quentamento nin arrefriamento no clinch e é un proceso de traballo en frío. É un proceso económico que pode substituír a soldadura por puntos nalgúns casos. En PINNING usamos pasadores que son elementos da máquina que se utilizan para asegurar posicións das pezas da máquina entre si. Os principais tipos son pasadores de horquilla, pasadores de chaveta, pasadores de resorte, pasadores de pasadores, e pasadores divididos. En STAPLING utilizamos pistolas de grapado e grapas que son fixadores de dúas puntas que se usan para unir ou unir materiais. O grapado ten as seguintes vantaxes: Económico, sinxelo e rápido de usar, a coroa das grapas pódese usar para unir materiais unidos entre si, A coroa da grapa pode facilitar a ponte dunha peza como un cable e suxeitala a unha superficie sen perforar ou prexudicial, eliminación relativamente fácil. O MONTADO A PRENSA realízase empuxando pezas xuntas e a fricción entre elas fixa as pezas. As pezas axustadas a presión que consisten nun eixe sobredimensionado e un burato de tamaño inferior ensamblan xeralmente por un dos dous métodos: ben aplicando forza ou aproveitando a expansión ou contracción térmica das pezas. Cando se establece un accesorio de prensa aplicando unha forza, utilizamos unha prensa hidráulica ou unha prensa manual. Por outra banda, cando se establece o encaixe a prensa por expansión térmica, quentamos as pezas envolventes e montamos no seu lugar estando quentes. Cando se arrefrían contraen e volven ás súas dimensións normais. Isto dá como resultado un bo axuste de prensa. Chamámoslle a isto alternativamente SHRINK-FITTING. A outra forma de facelo é arrefriando as pezas envolventes antes da montaxe e despois deslizándoas nas súas partes de acoplamento. Cando se quenta o conxunto expándense e conseguimos un axuste axustado. Este último método pode ser preferible nos casos en que o quecemento supón o risco de alterar as propiedades do material. O arrefriamento é máis seguro neses casos. Compoñentes e conxuntos pneumáticos e hidráulicos • Válvulas, compoñentes hidráulicos e pneumáticos como junta tórica, arandela, xuntas, xunta, anel, cuña. Dado que as válvulas e os compoñentes pneumáticos veñen nunha gran variedade, non podemos enumerar todo aquí. Dependendo do ambiente físico e químico da súa aplicación, temos produtos especiais para vostede. Especifíquenos a aplicación, o tipo de compoñente, as especificacións, as condicións ambientais como presión, temperatura, líquidos ou gases que estarán en contacto coas súas válvulas e compoñentes pneumáticos; e escolleremos o produto máis axeitado para ti ou fabricarémolo especialmente para a túa aplicación. CLICK Product Finder-Locator Service PÁXINA ANTERIOR
- Rapid Prototyping, Desktop Manufacturing, Additive Manufacturing, FDM
Rapid Prototyping, Desktop Manufacturing, Additive Manufacturing, Stereolithography, Polyjet, Fused Deposition Modeling, Selective Laser Sintering, FDM, SLS Fabricación aditiva e rápida Nos últimos anos observamos un aumento da demanda de FABRICACIÓN RÁPIDA ou PROTOTIPADO RÁPIDO. Este proceso tamén pode denominarse FABRICACIÓN DE ESCRITORIO ou FABRICACIÓN DE FORMA LIBRE. Basicamente, un modelo físico sólido dunha peza faise directamente a partir dun debuxo CAD tridimensional. Usamos o termo FABRICACIÓN ADITIVA para estas diversas técnicas nas que construímos pezas en capas. Usando hardware e software integrados por ordenador realizamos a fabricación aditiva. As nosas técnicas rápidas de prototipado e fabricación son ESTEREOLITOGRAFÍA, POLYJET, MODELADO POR DEPOSICIÓN FUSIÓN, SINTERIZACIÓN LÁSER SELECTIVA, FUSIÓN POR FAIS DE ELECTRÓNS, IMPRESIÓN TRIDIMENSIONAL, FABRICACIÓN DIRECTA, UTILIZACIÓN RÁPIDA. Recomendamos que faga clic aquí paraDESCARGA as nosas ilustracións esquemáticas de fabricación aditiva e procesos de fabricación rápida de AGS-TECH Inc. Isto axudarache a comprender mellor a información que che proporcionamos a continuación. O prototipado rápido ofrécenos: 1.) O deseño conceptual do produto é visto desde diferentes ángulos nun monitor mediante un sistema 3D/CAD. 2.) Realízanse e estúdanse prototipos a partir de materiais non metálicos e metálicos desde os aspectos funcionais, técnicos e estéticos. 3.) Realízase un prototipado de baixo custo en moi pouco tempo. A fabricación aditiva pode asemellarse á construción dunha barra de pan ao apilar e unir rebandas individuais unhas encima das outras. Noutras palabras, o produto é fabricado porción por porción, ou capa por capa depositada unha sobre outra. A maioría das pezas pódense producir en horas. A técnica é boa se as pezas son necesarias moi rapidamente ou se as cantidades necesarias son poucas e facer un molde e ferramentas é demasiado caro e leva moito tempo. Non obstante, o custo dunha peza é caro debido ao custo das materias primas. • ESTEREOLITOGRAFÍA : Esta técnica tamén abreviada como STL, baséase no curado e endurecemento dun fotopolímero líquido nunha forma específica enfocando un raio láser nel. O láser polimeriza o fotopolímero e cúrao. Ao escanear o raio láser UV segundo a forma programada ao longo da superficie da mestura de fotopolímeros, a peza prodúcese de abaixo cara arriba en franxas individuais colocadas en cascada unhas sobre outras. A exploración do punto láser repítese moitas veces para conseguir as xeometrías programadas no sistema. Despois de que a peza estea completamente fabricada, elimínase da plataforma, límpase e límpase por ultrasóns e cun baño de alcohol. A continuación, exponse á irradiación UV durante unhas horas para asegurarse de que o polímero estea completamente curado e endurecido. Para resumir o proceso, unha plataforma que se mergulla nunha mestura de fotopolímeros e un raio láser UV son controladas e trasladadas a través dun sistema de servocontrol segundo a forma da peza desexada e a peza obtense mediante o fotocurado do polímero capa por capa. Por suposto que as dimensións máximas da peza producida veñen determinadas polo equipo de estereolitografía. • POLYJET : Similar á impresión inkjet, en polyjet temos oito cabezales de impresión que depositan fotopolímero na bandexa de construción. A luz ultravioleta colocada xunto aos chorros cura e endurece inmediatamente cada capa. En polyjet utilízanse dous materiais. O primeiro material é para a fabricación do modelo real. O segundo material, unha resina tipo xel úsase como soporte. Estes dous materiais son depositados capa por capa e simultaneamente curados. Despois de completar o modelo, o material de soporte elimínase cunha solución acuosa. As resinas utilizadas son similares á estereolitografía (STL). O polyjet ten as seguintes vantaxes fronte á estereolitografía: 1.) Non é necesario limpar pezas. 2.) Non hai necesidade de curado posterior ao proceso. 3.) Son posibles grosores de capa máis pequenos e así obtemos unha mellor resolución e podemos fabricar pezas máis finas. • MODELADO POR DEPOSICIÓN FUSIÓN: Tamén abreviado como FDM, neste método un cabezal de extrusión controlado por robot móvese en dúas direccións principais sobre unha mesa. O cable báixase e levántase segundo sexa necesario. Desde o orificio dunha matriz quentada na cabeza, extrúese un filamento termoplástico e deposita unha capa inicial sobre unha base de escuma. Isto conséguese polo cabezal da extrusora que segue un camiño predeterminado. Despois da capa inicial, a mesa redúcese e as capas posteriores deposítanse unhas sobre outras. Ás veces, cando se fabrica unha peza complicada, son necesarias estruturas de soporte para que a deposición poida continuar en certas direccións. Nestes casos, extrúese un material de soporte cunha separación de filamentos menos densa nunha capa para que sexa máis débil que o material do modelo. Estas estruturas de soporte poden posteriormente disolverse ou romperse despois da finalización da peza. As dimensións da matriz de extrusión determinan o espesor das capas extruidas. O proceso FDM produce pezas con superficies escalonadas en planos exteriores oblicuos. Se esta rugosidade é inaceptable, pódese usar pulido con vapor químico ou unha ferramenta quente para suavizar. Incluso unha cera de pulido está dispoñible como material de revestimento para eliminar estes pasos e acadar tolerancias xeométricas razoables. • SINTERIZACIÓN LÁSER SELECTIVA: Tamén denotada como SLS, o proceso baséase na sinterización dun polímero, po cerámico ou metálico de forma selectiva nun obxecto. A parte inferior da cámara de procesamento ten dous cilindros: un cilindro de construción parcial e un cilindro de alimentación en po. O primeiro redúcese gradualmente ata onde se está formando a parte sinterizada e o segundo elévase gradualmente para subministrar po ao cilindro de construción da peza a través dun mecanismo de rolos. Primeiro deposítase unha fina capa de po no cilindro de construción parcial, despois céntrase un raio láser nesa capa, trazando e fundindo/sinterizando unha sección transversal particular, que despois se solidifica nun sólido. O po é que as áreas que non son afectadas polo raio láser permanecen soltas pero aínda soportan a parte sólida. Despois deposítase outra capa de po e repítese o proceso moitas veces para obter a peza. Ao final, as partículas de po soltas son sacudidas. Todo isto realízase mediante un ordenador de control de procesos mediante instrucións xeradas polo programa CAD 3D da peza que se está a fabricar. Pódense depositar diversos materiais como polímeros (como ABS, PVC, poliéster), cera, metais e cerámicas con aglutinantes poliméricos axeitados. • ELECTRON-BEAM MELTING : Similar á sinterización selectiva con láser, pero usando feixe de electróns para fundir po de titanio ou cromo cobalto para facer prototipos ao baleiro. Realizáronse algúns desenvolvementos para realizar este proceso en aceiros inoxidables, aluminio e aliaxes de cobre. Se é preciso aumentar a resistencia á fatiga das pezas producidas, utilizamos prensa isostática en quente posterior á fabricación da peza como proceso secundario. • IMPRESIÓN TRIDIMENSIONAL: tamén denotada por 3DP, nesta técnica un cabezal de impresión deposita un aglutinante inorgánico sobre unha capa de po non metálico ou metálico. Un pistón que leva o leito de po redúcese gradualmente e en cada paso deposítase o aglutinante capa por capa e fundido polo aglutinante. Os materiais en po utilizados son mesturas de polímeros e fibras, area de fundición, metais. Usando simultáneamente diferentes cabezas de aglutinante e aglutinantes de diferentes cores podemos obter varias cores. O proceso é similar á impresión con chorro de tinta pero en lugar de obter unha folla de cores obtemos un obxecto tridimensional de cores. As pezas producidas poden ser porosas e, polo tanto, poden requirir sinterización e infiltración de metal para aumentar a súa densidade e resistencia. A sinterización queimará o aglutinante e fundirá os pos metálicos. Para facer as pezas pódense usar metais como o aceiro inoxidable, o aluminio ou o titanio e, como materiais de infiltración, utilizamos habitualmente cobre e bronce. A beleza desta técnica é que ata os conxuntos complicados e en movemento poden fabricarse moi rapidamente. Por exemplo, pódese facer un conxunto de engrenaxes, unha chave como ferramenta e terá pezas móbiles e xiratorias listas para ser utilizadas. Pódense fabricar diferentes compoñentes do conxunto con diferentes cores e todo nun só tiro. Descarga o noso folleto en:Fundamentos de impresión 3D de metal • FABRICACIÓN DIRECTA e FERRAMENTAS RÁPIDAS: Ademais da avaliación do deseño e da resolución de problemas, utilizamos prototipado rápido para a fabricación directa de produtos ou a aplicación directa en produtos. Noutras palabras, o prototipado rápido pódese incorporar aos procesos convencionais para facelos mellores e máis competitivos. Por exemplo, a creación de prototipos rápidos pode producir patróns e moldes. Os patróns dun polímero de fusión e combustión creados mediante operacións de prototipado rápido pódense montar para a fundición de investimento e investilos. Outro exemplo a mencionar é o uso de 3DP para producir shell de fundición de cerámica e úsao para operacións de fundición de shell. Incluso os moldes de inxección e as insercións de moldes pódense producir mediante prototipado rápido e pódense aforrar moitas semanas ou meses de tempo de fabricación de moldes. Ao analizar só un ficheiro CAD da peza desexada, podemos producir a xeometría da ferramenta mediante software. Estes son algúns dos nosos métodos populares de ferramentas rápidas: RTV (Room-Temperature Vulcanizing) MOLDEADO / FUNDACIÓN DE URETANO: Pódese usar prototipado rápido para facer o patrón da peza desexada. A continuación, este patrón está revestido cun axente de separación e bótase goma RTV líquida sobre o patrón para producir as metades do molde. A continuación, estas metades do molde úsanse para inxectar uretanos líquidos. A vida útil do molde é curta, só como 0 ou 30 ciclos, pero suficiente para a produción de lotes pequenos. ACES (Acetal Clear Epoxy Solid) MOLDEADO POR INXECCIÓN: Usando técnicas de prototipado rápido como estereolitografía, producimos moldes de inxección. Estes moldes son cunchas cun extremo aberto para permitir o recheo de materiais como epoxi, epoxi recheo de aluminio ou metais. De novo, a vida útil do molde está limitada a decenas ou centos de pezas como máximo. PROCESO DE UTILIZACIÓN METÁLICA PULVERIZADA: Utilizamos prototipado rápido e facemos un patrón. Pulverizamos unha aliaxe de cinc-aluminio na superficie do patrón e recubrimos. O patrón co revestimento metálico colócase entón dentro dun matraz e envasado cun epoxi ou recheo de aluminio. Finalmente, elimínase e producindo dúas metades destes moldes obtemos un molde completo para o moldeo por inxección. Estes moldes teñen unha vida útil máis longa, nalgúns casos dependendo do material e das temperaturas poden producir pezas por milleiros. PROCESO KEELTOOL: Esta técnica pode producir moldes con ciclos de vida de 100.000 a 10 millóns. Usando prototipos rápidos producimos un molde RTV. O molde énchese a continuación cunha mestura formada por po de aceiro para ferramentas A6, carburo de tungsteno, aglutinante de polímero e déixase curar. Este molde quéntase entón para que o polímero se queime e os pos metálicos se fusionen. O seguinte paso é a infiltración de cobre para producir o molde final. Se é necesario, pódense realizar operacións secundarias como mecanizado e pulido no molde para obter mellores precisións dimensionales. CLICK Product Finder-Locator Service PÁXINA ANTERIOR
- Glass and Ceramic Manufacturing, Hermetic Packages, Seals, Bonding
Glass and Ceramic Manufacturing, Hermetic Packages Seals and Bonding, Tempered Bulletproof Glass, Blow Moulding, Optical Grade Glass, Conductive Glass, Molding Formación e conformación de vidro e cerámica O tipo de fabricación de vidro que ofrecemos son vidro de envases, soplado de vidro, fibra de vidro e tubos e varilla, vidro doméstico e industrial, lámpadas e lámpadas, molduras de vidro de precisión, compoñentes e conxuntos ópticos, vidro plano e de folla e flotado. Realizamos tanto o conformado manual como a máquina. Os nosos populares procesos de fabricación de cerámica técnica son o prensado con troquel, o prensado isostático, o prensado isostático en quente, o prensado en quente, a fundición deslizante, a fundición de cinta, a extrusión, o moldeo por inxección, o mecanizado en verde, a sinterización ou cocción, o rectificado de diamante, as montaxes herméticas. Recomendamos que faga clic aquí para DESCARGA as nosas ilustracións esquemáticas dos procesos de conformación e conformación de vidro de AGS-TECH Inc. DESCARGA as nosas ilustracións esquemáticas dos procesos técnicos de fabricación de cerámica de AGS-TECH Inc. Estes ficheiros descargables con fotos e esbozos axudaranche a comprender mellor a información que che proporcionamos a continuación. • FABRICACIÓN DE VIDRO DE CONTENEDOR: Contamos con liñas automatizadas de PRENSA E SOPLO e SOPLO E SOPLO para a súa fabricación. No proceso de golpe e soplado botamos un gob nun molde en branco e formamos o pescozo aplicando un golpe de aire comprimido desde arriba. Inmediatamente despois disto, inflárase aire comprimido unha segunda vez dende a outra dirección a través do pescozo do recipiente para formar a preforma da botella. A continuación, esta preforma transfírese ao molde real, quenta de novo para suavizar e aplícase aire comprimido para darlle á preforma a súa forma final de recipiente. Máis explícitamente, presúrase e empúxase contra as paredes da cavidade do molde de soplado para tomar a forma desexada. Finalmente, o recipiente de vidro fabricado trasládase a un forno de recocido para o seu posterior recalentamento e eliminación das tensións producidas durante o moldeado e arrefríase de forma controlada. No método de prensa e soplado, os gobs fundidos colócanse nun molde parison (molde en branco) e preséntanse na forma de parison (forma en branco). A continuación, os espazos en branco son transferidos a moldes de soplado e soplados de xeito similar ao proceso descrito anteriormente en "Proceso de soplado e soplado". Os pasos posteriores como o recocido e o alivio de tensión son similares ou iguais. • SOPLADO DE VIDRO: estivemos fabricando produtos de vidro mediante o soplado manual convencional, así como utilizando aire comprimido con equipos automatizados. Para algúns pedidos é necesario o soplado convencional, como proxectos que impliquen obras de arte en vidro ou proxectos que requiren un número menor de pezas con tolerancias soltas, proxectos de prototipado/demo... etc. O soplado de vidro convencional implica mergullar un tubo metálico oco nunha pota de vidro fundido e facer xirar o tubo para recoller algunha cantidade de material de vidro. O vidro recollido na punta do tubo enróllase sobre ferro plano, da forma que se desexa, alargado, quentado de novo e soplado con aire. Cando estea listo, métese nun molde e bótase aire. A cavidade do molde está húmida para evitar o contacto do vidro co metal. A película de auga actúa como un coxín entre eles. O soplado manual é un proceso lento que require moito traballo e só é apto para prototipos ou artigos de alto valor, non é adecuado para pedidos de gran volume por peza barato. • FABRICACIÓN DE VIDRO DOMÉSTICO E INDUSTRIAL: utilizando varios tipos de material de vidro estase producindo unha gran variedade de vidro. Algúns vasos son resistentes á calor e axeitados para vidro de laboratorio, mentres que outros son o suficientemente bos para soportar moitas veces os lavalouzas e son aptos para facer produtos domésticos. Usando máquinas Westlake estanse producindo decenas de miles de pezas de vasos ao día. Para simplificar, recóllese o vidro fundido ao baleiro e insírese en moldes para facer as preformas. Despois infórmase aire nos moldes, estes trasládanse a outro molde e bótase de novo aire e o vidro toma a súa forma definitiva. Como no soplado manual, estes moldes mantéñense mollados con auga. O estiramento adicional forma parte da operación de acabado onde se está formando o pescozo. O exceso de vidro está queimado. A continuación, o proceso controlado de requecemento e arrefriamento descrito anteriormente. • FORMACIÓN DE TUBO DE VIDRO E VARILLA: Os principais procesos que utilizamos para a fabricación de tubos de vidro son os procesos DANNER e VELLO. No proceso Danner, o vidro dun forno flúe e cae sobre unha manga inclinada feita de materiais refractarios. A manga lévase sobre un eixe oco ou soplete xiratorio. A continuación, o vidro envólvese ao redor da manga e forma unha capa suave que flúe pola manga e sobre a punta do eixe. No caso do conformado de tubos, o aire é soprado por un soplete con punta oca, e no caso do conformado de varillas utilizamos puntas sólidas no eixe. A continuación, os tubos ou varillas pasan sobre os rolos de transporte. As dimensións como o espesor da parede e o diámetro dos tubos de vidro axústanse aos valores desexados configurando o diámetro da manga e insuflando presión de aire ao valor desexado, axustando a temperatura, a taxa de fluxo do vidro e a velocidade de extracción. O proceso de fabricación do tubo de vidro Vello, por outra banda, implica o vidro que sae dun forno a unha cunca cun mandril oco ou campá. O vidro atravesa entón o espazo de aire entre o mandril e a cunca e toma forma de tubo. Despois, viaxa sobre rolos ata unha máquina de debuxo e arrefríase. Ao final da liña de refrixeración prodúcese o corte e o procesamento final. As dimensións do tubo pódense axustar igual que no proceso Danner. Ao comparar o proceso Danner con Vello, podemos dicir que o proceso Vello é máis adecuado para a produción de grandes cantidades, mentres que o proceso Danner pode ser un mellor para pedidos precisos de tubos de menor volume. • PROCESAMIENTO DE LÁMINAS E VIDRO PLANO E FLOTADOR: Dispoñemos de grandes cantidades de vidro plano en espesores que van desde espesores submilimétricos ata varios centímetros. As nosas lentes planas son dunha perfección case óptica. Ofrecemos vidro con revestimentos especiais como revestimentos ópticos, onde se utiliza a técnica de deposición química de vapor para poñer revestimentos como revestimentos antirreflectantes ou espellos. Tamén son comúns os revestimentos condutores transparentes. Tamén están dispoñibles os revestimentos hidrófobos ou hidrófilos sobre o vidro e un revestimento que fai que o vidro se autolimpe. Os lentes temperados, antibalas e laminados son outros elementos populares. Cortamos o vidro na forma desexada coas tolerancias desexadas. Existen outras operacións secundarias como curvar ou dobrar o vidro plano. • MOLDEADO DE VIDRO DE PRECISIÓN: utilizamos esta técnica principalmente para fabricar compoñentes ópticos de precisión sen necesidade de técnicas máis caras e que consumen moito tempo, como esmerilado, lapeado e pulido. Esta técnica non sempre é suficiente para sacar o máximo proveito das mellores ópticas, pero nalgúns casos, como produtos de consumo, cámaras dixitais, ópticas médicas, pode ser unha boa opción menos custosa para a fabricación de gran volume. Tamén ten vantaxe sobre as outras técnicas de conformación de vidro onde se requiren xeometrías complexas, como no caso das asferas. O proceso básico consiste na carga da parte inferior do noso molde co branco de vidro, a evacuación da cámara de proceso para a eliminación de osíxeno, preto do peche do molde, o quecemento rápido e isotérmico da matriz e do vidro con luz infravermella, o peche adicional das metades do molde. presionar lentamente o vidro amolecido de forma controlada ata o espesor desexado, e finalmente arrefriar o vidro e encher a cámara con nitróxeno e eliminar o produto. O control preciso da temperatura, a distancia de peche do molde, a forza de peche do molde, a coincidencia dos coeficientes de expansión do molde e do material de vidro son fundamentais neste proceso. • FABRICACIÓN DE COMPOÑENTES E CONXUNTOS ÓPTICOS DE VIDRO: Ademais do moldeado de precisión de vidro, utilizamos unha serie de procesos valiosos para fabricar compoñentes e conxuntos ópticos de alta calidade para aplicacións esixentes. Moer, lapear e pulir lentes de calidade óptica en lechadas abrasivas especiais finas é unha arte e ciencia para facer lentes ópticas, prismas, planos e moito máis. A planitude da superficie, a ondulación, a suavidade e as superficies ópticas sen defectos requiren moita experiencia con estes procesos. Pequenos cambios no ambiente poden producir produtos fóra das especificacións e deter a liña de fabricación. Hai casos nos que unha soa limpeza na superficie óptica cun pano limpo pode facer que un produto cumpra as especificacións ou falla a proba. Algúns materiais de vidro populares utilizados son sílice fundida, cuarzo, BK7. Tamén a montaxe de tales compoñentes require unha experiencia especializada en nichos. Ás veces úsanse colas especiais. Non obstante, ás veces unha técnica chamada contacto óptico é a mellor opción e non implica ningún material entre as lentes ópticas adxuntas. Consiste en poñer en contacto fisicamente superficies planas para unilas entre si sen pegar. Nalgúns casos, para ensamblar os compoñentes ópticos a determinadas distancias e con certas orientacións xeométricas, nalgúns casos, están a utilizarse separadores mecánicos, varillas ou bolas de vidro de precisión, abrazaderas ou compoñentes metálicos mecanizados. Imos examinar algunhas das nosas técnicas populares para fabricar ópticas de gama alta. TRITURADO E LAPEADO E PULIDO: A forma rugosa do compoñente óptico obtense co moenda dun branco de vidro. Despois, o lapeado e o pulido realízanse xirando e fregando as superficies rugosas dos compoñentes ópticos contra ferramentas coas formas de superficie desexadas. Entre a óptica e as ferramentas de conformación están a verterse puríns con pequenas partículas abrasivas e fluídos. Os tamaños de partículas abrasivas en tales suspensións pódense escoller segundo o grao de planitude desexado. As desviacións das superficies ópticas críticas das formas desexadas exprésanse en termos de lonxitudes de onda da luz que se utiliza. A nosa óptica de alta precisión ten tolerancias de décimas de lonxitude de onda (Lonxitude de onda/10) ou é posible aínda máis axustado. Ademais do perfil da superficie, as superficies críticas son dixitalizadas e avalíanse para outras características e defectos da superficie, como dimensións, arañazos, astillas, pozos, manchas... etc. O estricto control das condicións ambientais na planta de fabricación de ópticas e os extensos requisitos de metroloxía e probas con equipos de última xeración fan desta industria unha rama desafiante. • PROCESOS SECUNDARIOS NA FABRICACIÓN DE VIDRO: De novo, só estamos limitados coa túa imaxinación cando se trata de procesos secundarios e de acabado do vidro. Aquí enumeramos algúns deles: -Recubrimentos sobre vidro (ópticos, eléctricos, tribolóxicos, térmicos, funcionais, mecánicos...). Por exemplo, podemos alterar as propiedades da superficie do vidro facendo que, por exemplo, reflicta a calor para manter frescos os interiores dos edificios, ou facer que un lado absorba os infravermellos mediante a nanotecnoloxía. Isto axuda a manter quente o interior dos edificios porque a capa superficial máis externa de vidro absorberá a radiación infravermella dentro do edificio e irradiala de volta ao interior. -Grabado en vidro - Etiquetado cerámico aplicado (ACL) - Gravado -Pulido á chama -Pulido químico -A mancha FABRICACIÓN DE CERÁMICA TÉCNICA • PRESENTACIÓN DE TROQUELAS: Consiste na compactación uniaxial de polvos granulares confinados nunha matriz. • PRENSADO EN CALENTE: Similar ao prensado con troquel pero con adición de temperatura para mellorar a densificación. O po ou a preforma compactada colócase nunha matriz de grafito e aplícase presión uniaxial mentres a matriz se mantén a altas temperaturas, como 2000 C. As temperaturas poden ser diferentes dependendo do tipo de po cerámico que se procese. Para formas e xeometrías complicadas poden ser necesarios outros procesamentos posteriores, como a moenda con diamante. • PRENSA ISOSTÁTICA: Pos granulares ou compactos prensados con troquel colócanse en recipientes herméticos e despois nun recipiente a presión pechado con líquido no interior. Despois son compactados aumentando a presión do recipiente a presión. O líquido no interior do recipiente transfire as forzas de presión uniformemente sobre toda a superficie do recipiente hermético. O material compáctase así uniformemente e toma a forma do seu recipiente flexible e do seu perfil e características internas. • PRENSADO ISOSTÁTICO EN CALENTE: Similar ao prensado isostático, pero ademais da atmosfera de gas presurizado, sinterizamos o compacto a alta temperatura. O prensado isostático en quente dá como resultado unha densificación adicional e unha maior resistencia. • FUNDACIÓN POR DESLIZACIÓN / FUNDACIÓN POR DRENADO: Enchemos o molde cunha suspensión de partículas cerámicas de tamaño micrómetro e líquido portador. Esta mestura chámase "deslizamento". O molde ten poros e, polo tanto, o líquido da mestura fíltrase no molde. Como resultado, fórmase un molde nas superficies internas do molde. Despois da sinterización, as pezas pódense sacar do molde. • FUNDACIÓN DE CINTAS: Fabricamos cintas cerámicas fundindo pastas cerámicas sobre superficies planas móbiles. Os puríns conteñen pos cerámicos mesturados con outros produtos químicos para fins de unión e transporte. A medida que se evaporan os disolventes quedan láminas densas e flexibles de cerámica que se poden cortar ou enrolar como se desexe. • FORMACIÓN POR EXTRUSIÓN: Como noutros procesos de extrusión, unha mestura suave de po cerámico con aglutinantes e outros produtos químicos pásase a través dunha matriz para adquirir a súa forma de sección transversal e despois córtase na lonxitude desexada. O proceso realízase con mesturas cerámicas frías ou quentadas. • MOLDEADO POR INXECCIÓN A BAIXA PRESIÓN: Preparamos unha mestura de po cerámico con aglutinantes e disolventes e quentamos a unha temperatura onde poida ser facilmente presionado e forzado na cavidade da ferramenta. Unha vez que se completa o ciclo de moldeo, a peza é expulsada e o produto químico aglutinante é queimado. Usando o moldeado por inxección, podemos obter pezas complicadas en grandes volumes de forma económica. Son posibles orificios que son unha pequena fracción de milímetro nunha parede de 10 mm de espesor, pódense roscar sen máis mecanizado, tolerancias tan axustadas como +/- 0,5 % e aínda máis baixas cando se mecanizan pezas. , son posibles espesores de parede da orde de 0,5 mm a unha lonxitude de 12,5 mm, así como grosores de parede de 6,5 mm a unha lonxitude de 150 mm. • MECANIZADO VERDE : Usando as mesmas ferramentas de mecanizado de metais, podemos mecanizar materiais cerámicos prensados mentres estean aínda brandos como o giz. Son posibles tolerancias de +/- 1%. Para mellores tolerancias usamos moenda de diamante. • SINTERIZACIÓN ou COCCIÓN: A sinterización permite a densificación total. Prodúcese unha contracción significativa nas pezas compactas verdes, pero este non é un gran problema xa que temos en conta estes cambios dimensionais cando deseñamos a peza e as ferramentas. As partículas de po únense entre si e elimínase en gran medida a porosidade inducida polo proceso de compactación. • MOLIENDA DE DIAMANTE: o “diamante” do material máis duro do mundo está a ser usado para moer materiais duros como cerámica e obtéñense pezas de precisión. Estase a conseguir tolerancias no rango micrométrico e superficies moi lisas. Debido ao seu custo, só consideramos esta técnica cando realmente a necesitamos. • OS CONXUNTOS HERMÉTICOS son aqueles que practicamente non permiten ningún intercambio de materia, sólidos, líquidos ou gases entre interfaces. O selado hermético é hermético. Por exemplo, as caixas electrónicas herméticas son aquelas que manteñen o sensible contido interior dun dispositivo embalado ileso pola humidade, os contaminantes ou os gases. Nada é 100% hermético, pero cando falamos de hermeticidade queremos dicir que, en termos prácticos, que hai hermeticidade na medida en que a taxa de fuga é tan baixa que os dispositivos están seguros en condicións ambientais normais durante moito tempo. Os nosos conxuntos herméticos consisten en compoñentes de metal, vidro e cerámica, metal-cerámica, cerámica-metal-cerámica, metal-cerámica-metal, metal a metal, metal-vidro, metal-vidro-metal, vidro-metal-vidro, vidro. metal e vidro a vidro e todas as outras combinacións de unión metal-vidro-cerámica. Podemos, por exemplo, recubrir de metal os compoñentes cerámicos para que poidan unirse fortemente a outros compoñentes do conxunto e ter unha excelente capacidade de selado. Temos o know-how de revestir fibras ópticas ou pasadores con metal e soldalas ou soldalas aos recintos, para que non pasen nin se filtren gases aos recintos. Polo tanto, utilízanse para a fabricación de caixas electrónicas para encapsular dispositivos sensibles e protexelos da atmosfera exterior. Ademais das súas excelentes características de selado, outras propiedades como o coeficiente de expansión térmica, resistencia á deformación, natureza sen desgasificación, vida útil moi longa, natureza non condutora, propiedades de illamento térmico, natureza antiestática... etc. facer que os materiais de vidro e cerámica sexan a elección para determinadas aplicacións. A información sobre as nosas instalacións que producen accesorios de cerámica a metal, selado hermético, pasadores de baleiro, baleiro alto e ultraalto e compoñentes de control de fluídos pódese atopar aquí:Folleto da fábrica de compoñentes herméticos CLICK Product Finder-Locator Service PÁXINA ANTERIOR
- Wire & Spring Forming, Shaping, Welding, Assembly of Wires, Coil, CNC
Wire & Spring Forming, Shaping, Welding, Assembly of Wires, Coil Compression Extension Torsion Flat Springs, Custom Wires, Helical Springs at AGS-TECH Inc. Formación de fíos e resortes Nós fabricamos fíos personalizados, montaxe de fíos, fíos formados en formas 2D e 3D desexadas, redes de arame, mallas, recintos, cesta, cerca, resorte de arame, resorte plano; torsión, compresión, tensión, resortes planos e moito máis. Os nosos procesos son a formación de arame e resorte, trefilado, conformación, dobrado, soldadura, soldadura, perforación, estampación, perforación, achaflanado, rectificado, roscado, revestimento, fourslide, conformación de diapositivas, bobinado, bobinado, revolta. Recomendamos que faga clic aquí para DESCARGA as nosas ilustracións esquemáticas dos procesos de formación de fíos e resortes de AGS-TECH Inc. Este ficheiro descargable con fotos e bosquexos axudarache a comprender mellor a información que che ofrecemos a continuación. • TREFADO: Mediante forzas de tracción estiramos o material metálico e pasámolo a través dunha matriz para reducir o diámetro e aumentar a súa lonxitude. Ás veces usamos unha serie de matrices. Somos capaces de facer matrices para cada calibre de fío. Usando material de alta resistencia á tracción trazamos fíos moi finos. Ofrecemos fíos traballados en frío e en quente. • FORMACIÓN DE ARAMES: un rolo de arame calibre dóbrase e dáse forma nun produto útil. Temos a capacidade de formar fíos de todos os calibres, incluídos filamentos finos e fíos grosos, como os usados como resortes baixo o chasis do automóbil. Os equipos que usamos para a formación de fíos son formadores de fíos manuais e CNC, bobinadores, prensas eléctricas, fourslide, multi-slide. Os nosos procesos son debuxo, dobrado, alisado, aplanado, estirado, corte, revolta, soldadura e soldadura, montaxe, bobinado, estampación (ou alado), perforación, roscado de fío, perforación, achaflanado, rectificado, revestimento e tratamentos de superficie. O noso equipo de última xeración pódese configurar para desenvolver deseños moi complexos de calquera forma e tolerancias estreitas. Ofrecemos varios tipos de extremos como extremos esféricos, puntiagudos ou achaflanados para os seus cables. A maioría dos nosos proxectos de formación de fíos teñen custos de ferramentas mínimos ou cero. Os tempos de entrega das mostras son xeralmente de días. Os cambios no deseño/configuración dos formularios de cable pódense facer moi rapidamente. • FORMACIÓN DE RESORTES: AGS-TECH fabrica unha gran variedade de resortes, incluíndo: - Resorte de torsión/doble torsión -Resorte de tensión/compresión - Resorte constante / variable - Resorte helicoidal e helicoidal -Soporte plano e de ballesta - Primavera de equilibrio -Lavadora Belleville - Primavera Negator -Resorte helicoidal de velocidade progresiva -Onda primavera -Volute Spring - Resortes cónicos - Aneis de primavera - Resortes do reloxo -Clips Fabricamos resortes a partir dunha variedade de materiais e podemos guiarte segundo a túa aplicación. Os materiais máis comúns son o aceiro inoxidable, o silicio cromado, o aceiro con alto contido de carbono, o aceite de baixo carbono, o cromo vanadio, o bronce fósforo, o titanio, a aliaxe de cobre berilio e a cerámica de alta temperatura. Usamos diversas técnicas na fabricación de resortes, incluíndo bobinado CNC, bobinado en frío, bobinado en quente, endurecemento, acabado. Outras técnicas xa mencionadas anteriormente baixo a formación de fíos tamén son comúns nas nosas operacións de fabricación de resortes. • SERVIZOS DE ACABADO DE FAIMES E RESORTES: Podemos rematar os seus produtos de moitas formas dependendo da súa elección e necesidades. Algúns procesos comúns que ofrecemos son: pintura, recubrimento en po, galvanoplastia, inmersión en vinilo, anodizado, alivio de tensión, tratamento térmico, granalla, cromado, níquel sen electricidade, pasivación, esmalte cocido, plástico cocido. , limpeza de plasma. CLICK Product Finder-Locator Service PÁXINA ANTERIOR
- Sheet Metal Forming Fabrication, Stamping, Punching, Deep Drawing, CNC
Sheet Metal Forming and Fabrication, Stamping, Punching, Bending, Progressive Die, Spot Welding, Deep Drawing, Metal Blanking and Slitting at AGS-TECH Inc. Estampación e fabricación de chapas Ofrecemos estampación, conformación, conformación, dobrado, perforación, corte, corte, perforación, entallado, picado, afeitado, prensado, fabricación, embutición profunda mediante troqueles de punzón único/trazo único, así como troqueles progresivos e fiado, conformación de caucho e hidroformación; corte de chapa mediante chorro de auga, plasma, láser, serra, chama; montaxe de chapa mediante soldadura, soldadura por puntos; tubo de chapa abombada e dobrada; Acabado de superficie de chapa metálica, incluíndo pintura por inmersión ou pulverización, revestimento en po electrostático, anodizado, revestimento, pulverización e moito máis. Os nosos servizos van desde a creación rápida de prototipos de chapa ata a fabricación de gran volume. Recomendamos que faga clic aquí paraDESCARGA as nosas ilustracións esquemáticas dos procesos de fabricación e estampación de chapa metálica de AGS-TECH Inc. Isto axudarache a comprender mellor a información que che proporcionamos a continuación. • CORTE DE CHAPA : Ofrecemos CORTE e PARTIDA. Os cortes cortan a chapa nun camiño á vez e basicamente non hai desperdicio de material, mentres que coas separacións a forma non se pode axustar con precisión e, polo tanto, desperdicia certa cantidade de material. Un dos nosos procesos máis populares é o PERFORADO, onde se corta unha peza de material redonda ou doutra forma da chapa. A peza que se recorta é un desperdicio. Outra versión de perforación é o RANURADO, onde se perforan buratos rectangulares ou alongados. O BORDO pola súa banda é o mesmo proceso que o punzonado, coa distinción da peza que se recorta é o traballo e se mantén. FINE BLANKING, unha versión superior do blanking, crea cortes con tolerancias estreitas e bordos rectos e lisos e non require operacións secundarias para a perfección da peza. Outro proceso que usamos con frecuencia é o CORTE, que é un proceso de cizalla no que se corta a chapa mediante dúas láminas circulares opostas nun camiño recto ou curvo. O abrelatas é un exemplo sinxelo do proceso de corte. Outro popular process para nós é PERFORACIÓN, onde moitos buracos redondos ou doutra forma son perforados na chapa nun determinado patrón. Un exemplo típico dun produto perforado son os filtros metálicos con moitos orificios para fluídos. En NOTCHING, outro proceso de corte de chapa, retiramos material dunha peza de traballo, comezando polo bordo ou noutro lugar e cortamos cara a dentro ata obter a forma desexada. É un proceso progresivo onde cada operación elimina outra peza ata conseguir o contorno desexado. Para pequenas tiradas de produción ás veces usamos un proceso relativamente máis lento chamado NIBBLING, que consiste en moitos golpes rápidos de buracos superpostos para facer un corte máis grande e complexo. En CORTE PROGRESIVO utilizamos unha serie de operacións diferentes para obter un único corte ou unha xeometría determinada. Finalmente RAPETAR un proceso secundario axúdanos a mellorar os bordos dos cortes xa realizados. Úsase para cortar as virutas, as beiras rugosas en traballos de chapa. • PLEGADO DA CHAPA: Ademais do corte, o dobrado é un proceso esencial sen o cal non poderiamos producir a maioría dos produtos. Principalmente unha operación de traballo en frío, pero ás veces tamén se realiza cando está quente ou quente. Usamos matrices e prensas a maior parte do tempo para esta operación. En PROGRESSIVE BENDING utilizamos unha serie de operacións de punzonado e troquelado diferentes para obter unha única curva ou unha xeometría determinada. AGS-TECH utiliza unha variedade de procesos de curvatura e elixe dependendo do material da peza, o seu tamaño, grosor, tamaño de curvatura desexado, raio, curvatura e ángulo de curvatura, localización da curva, economía de operación, cantidades a fabricar... etc. Utilizamos V-BENDING onde un punzón en forma de V forza a chapa a entrar na matriz en forma de V e dóbraa. Bo tanto para ángulos moi agudos como obtusos e intermedios, incluíndo 90 graos. Usando troqueles de limpeza realizamos o DOBADO DE BORDES. Os nosos equipos permítennos obter ángulos aínda maiores de 90 graos. No dobrado de bordos, a peza de traballo está encaixada entre unha almofada de presión e a matriz, a área de dobrado sitúase no bordo da troquela e o resto da peza de traballo suxeitase sobre o espazo como unha viga en voladizo. Cando o punzón actúa sobre a parte en voladizo, está dobrado sobre o bordo da matriz. O FANGING é un proceso de dobrado de bordos que resulta nun ángulo de 90 graos. Os principais obxectivos da operación son a eliminación de arestas cortantes e a obtención de superficies xeométricas para facilitar a unión de pezas. BEADING, outro proceso común de dobrado de bordos forma un rizo sobre o bordo dunha peza. O DOBLADO pola contra resulta cun bordo da folla que está completamente dobrado sobre si mesma. En COSTURA, os bordos de dúas partes están dobrados un sobre outro e unidos. A DOBRE COSTURA, pola súa banda, proporciona xuntas de chapa estancas e estancas. Semellante ao dobrado de bordos, un proceso chamado ROTARY BENDING desprega un cilindro co ángulo desexado cortado e que serve como punzón. A medida que a forza se transmite ao punzón, péchase coa peza de traballo. A ranura do cilindro dálle á parte en voladizo o ángulo desexado. O suco pode ter un ángulo menor ou maior que 90 graos. En AIR BENDING, non necesitamos que a matriz inferior teña unha ranura en ángulo. A chapa está apoiada por dúas superficies en lados opostos e a certa distancia. A continuación, o punzón aplica unha forza no lugar correcto e dobra a peza. O CHANNEL BEND realízase mediante un punzón e unha matriz en forma de canle, e o U-BEND conséguese cun punzón en forma de U. OFFSET BENDING produce compensacións na chapa. ROLL BENDING, unha técnica boa para traballos grosos e dobrado de grandes pezas de placas metálicas, utiliza tres rolos para alimentar e dobrar as placas ata as curvaturas desexadas. Os rolos están dispostos de xeito que se obteña a curva desexada do traballo. Contrólase a distancia e o ángulo entre os rolos para obter o resultado desexado. Un rolo móbil permite controlar a curvatura. TUBE FORMING é outra operación popular de dobrado de chapas metálicas que implica múltiples matrices. Os tubos obtéñense despois de varias accións. A CORRUGACIÓN tamén se realiza mediante operacións de dobrado. Basicamente é a flexión simétrica a intervalos regulares a través dunha peza enteira de chapa. Pódense usar varias formas para ondular. A chapa ondulada é máis ríxida e ten unha mellor resistencia á flexión e, polo tanto, ten aplicacións na industria da construción. O PROCESO DE FABRICACIÓN DE CHAPA METÁLICA, úsase un proceso continuo fabricación para dobrar seccións transversais dunha determinada xeometría mediante rolos e o traballo cóbrase en pasos secuenciais, co rolo final rematando o traballo. Nalgúns casos emprégase un só rolo e nalgúns casos unha serie de rolos. • PROCESOS COMBINADOS DE CORTE E DOBLADO DE CHAPA: Son os procesos que cortan e dobran ao mesmo tempo. En PIERCING, créase un burato usando un punzón puntiagudo. A medida que o punzón amplía o burato na folla, o material dóbrase simultaneamente nunha brida interna para o burato. A brida obtida pode ter funcións importantes. A operación LANCING, pola súa banda, corta e dobra a folla para crear unha xeometría elevada. • TUBO METÁLICO Abombado e dobrado: no TUBO METÁLICO se presuriza algunha parte interna dun tubo oco, o que fai que o tubo se abombe cara ao exterior. Dado que o tubo está dentro dunha matriz, a xeometría da protuberancia está controlada pola forma da matriz. En STRETCH BENDING, un tubo metálico estrésase usando forzas paralelas ao eixe do tubo e forzas de flexión para tirar o tubo sobre un bloque de forma. En Draw BENDING, sujetamos o tubo preto do seu extremo a un bloque de forma xiratoria que dobra o tubo mentres xira. Por último, en COMPRESIÓN BENDING o tubo suxeitase por forza a un bloque de forma fixa, e unha matriz dóbrao sobre o bloque de forma. • DEBUXO PROFUNDO: nunha das nosas operacións máis populares, utilízase un punzón, un troquel a xogo e un soporte en branco. O branco de chapa metálica colócase sobre a abertura da matriz e o punzón móvese cara ao branco que suxeita o soporte da matriz. Unha vez que entran en contacto, o punzón forza a chapa a entrar na cavidade da matriz para formar o produto. A operación de embutición profunda aseméllase ao corte, pero o espazo libre entre o punzón e a matriz impide que a folla sexa cortada. Outro factor que asegura que a folla estea profundamente embutida e non cortada son as esquinas redondeadas da matriz e do punzón que evitan o corte e o corte. Para acadar unha maior magnitude de embutición profunda, estase a despregar un proceso de REDEBUXO onde se realiza un posterior embutido profundo sobre unha peza que xa foi sometida a un proceso de embutición profunda. En REDEBUXO INVERSO, a parte embutida profunda é volteada e debuxada na dirección oposta. O embutido profundo pode proporcionar obxectos de forma irregular, como copas abovedadas, cónicas ou escalonadas. • SPINNING : operación na que se suxeita unha peza plana ou preformada entre un mandril rotativo e un material de cola e unha ferramenta aplica presión localizada ao traballo mentres avanza gradualmente polo mandril. Como resultado, a peza de traballo envólvese sobre o mandril e toma a súa forma. Usamos esta técnica como alternativa á embutición profunda onde a cantidade dun pedido é pequena, as pezas son grandes (diámetros de ata 20 pés) e teñen curvas únicas. Aínda que os prezos por peza son xeralmente máis altos, os custos de configuración para a operación de fiación CNC son baixos en comparación coa embutición profunda. Pola contra, a embutición profunda require un alto investimento inicial para a súa instalación, pero os custos por peza son baixos cando se producen grandes cantidades de pezas. Outra versión deste proceso é o SHEAR SPINNING, onde tamén hai fluxo de metal dentro da peza. O fluxo de metal reducirá o grosor da peza a medida que se realiza o proceso. Outro proceso relacionado é o TUBE SPINNING, que se aplica a pezas cilíndricas. Tamén neste proceso hai un fluxo de metal dentro da peza. Redúcese así o espesor e aumenta a lonxitude do tubo. A ferramenta pódese mover para crear funcións no interior ou no exterior do tubo. • CONFORMACIÓN DE GOMA DA CHAPA: Encóntrase material de caucho ou poliuretano nunha matriz de recipiente e colócase a peza sobre a superficie da goma. A continuación actúase un puñetazo sobre a peza de traballo e fórzaa contra a goma. Dado que a presión xerada pola goma é baixa, a profundidade das pezas producidas é limitada. Dado que os custos de ferramentas son baixos, o proceso é axeitado para a produción en cantidades baixas. • HIDROFORMADO: Similar ao conformado de caucho, neste proceso a chapa metálica é presionada por un punzón nun líquido a presión dentro dunha cámara. A chapa metálica está encaixada entre o punzón e un diafragma de goma. O diafragma rodea completamente a peza de traballo e a presión do fluído obrígaa a formarse no punzón. Con esta técnica pódense obter debuxos moi profundos aínda máis profundos que no proceso de embutición profunda. Fabricamos troqueles de punzón único así como troqueles progresivos dependendo da súa parte. As matrices de estampación dun só golpe son un método rendible para producir rapidamente grandes cantidades de pezas simples de chapa, como arandelas. Os troqueles progresivos ou a técnica de embutición profunda úsanse para fabricar xeometrías máis complexas. Segundo o seu caso, pódese utilizar o corte por chorro de auga, láser ou plasma para producir as súas pezas de chapa de forma económica, rápida e precisa. Moitos provedores non teñen idea destas técnicas alternativas ou non as teñen e, polo tanto, pasan por formas longas e caras de facer matrices e ferramentas que só fan perder tempo e diñeiro aos clientes. Se necesitas compoñentes de chapa construídos a medida, como carcasas, carcasas electrónicas... etc tan rápido como nuns días, ponte en contacto connosco para obter o noso servizo de PROTOTIPADO RÁPIDO DE CHAPA. CLICK Product Finder-Locator Service MENÚ ANTERIOR
- Forging and Powdered Metallurgy, Die Forging, Heading, Hot Forging
Forging and Powdered Metallurgy, Die Forging, Heading, Hot Forging, Impression Die, Near Net Shape, Swaging, Metal Hobbing, Riveting, Coining from AGS-TECH Inc. Forxa de metais e pulvimetalurxia O tipo de procesos de FORXADO DE METAL que ofrecemos son troqueles en quente e frío, troqueles abertos e pechados, troqueles de impresión e forxa sen flash, cogging, bateado, forxa de cantos e de precisión, forma case en rede, encabezado. , estampado, forxado revolto, fresado metálico, prensa e rolo e forxa radial e orbital e anular e isotérmica, acuñación, remachado, forxa de bolas metálicas, perforación de metal, encolado, forxa de alta taxa de enerxía. As nosas técnicas de METALURXÍA e PROCESADO DE POLOS son o prensado e sinterización de po, a impregnación, a infiltración, o prensado isostático en quente e en frío, o moldeado por inxección de metal, a compactación por bobina, o laminado en po, a extrusión de po, a sinterización solta, a sinterización con chispa, o prensado en quente. Recomendamos que faga clic aquí para DESCARGA as nosas ilustracións esquemáticas de procesos de forxa de AGS-TECH Inc. DESCARGA as nosas ilustracións esquemáticas de procesos de metalurxia de po de AGS-TECH Inc. Estes ficheiros descargables con fotos e esbozos axudaranche a comprender mellor a información que che proporcionamos a continuación. Na forxa metálica aplícanse forzas de compresión e o material defórmase e obtense a forma desexada. Os materiais forxados máis comúns na industria son o ferro e o aceiro, pero moitos outros como o aluminio, o cobre, o titanio e o magnesio tamén están moi forxados. As pezas metálicas forxadas teñen estruturas de gran melloradas ademais de fendas seladas e espazos baleiros pechados, polo que a resistencia das pezas obtidas por este proceso é maior. A forxa produce pezas que son significativamente máis resistentes polo seu peso que as pezas feitas por fundición ou mecanizado. Dado que as pezas forxadas se conforman facendo fluír o metal na súa forma final, o metal adquire unha estrutura de gran direccional que explica a resistencia superior das pezas. Noutras palabras, as pezas obtidas por proceso de forxa revelan mellores propiedades mecánicas en comparación coas pezas simples fundidas ou mecanizadas. O peso das forxas metálicas pode variar desde pequenas pezas lixeiras ata centos de miles de libras. Fabricamos pezas forxadas principalmente para aplicacións mecánicamente esixentes onde se aplican grandes esforzos a pezas como pezas de automóbiles, engrenaxes, ferramentas de traballo, ferramentas manuais, eixes de turbinas, engrenaxes de motocicletas. Debido a que os custos de ferramentas e configuración son relativamente altos, recomendamos este proceso de fabricación só para a produción de gran volume e para compoñentes críticos de baixo volume pero de alto valor, como o tren de aterraxe aeroespacial. Ademais do custo de ferramentas, os prazos de fabricación de pezas forxadas en gran cantidade poden ser máis longos en comparación con algunhas pezas simples mecanizadas, pero a técnica é crucial para pezas que requiren unha resistencia extraordinaria, como parafusos, porcas, aplicacións especiais. elementos de fixación, automoción, carretillas elevadoras, pezas de guindastre. • FORXADO EN QUEnte e FRÍO: A forxa en quente, como o seu nome indica, realízase a altas temperaturas, polo que a ductilidade é alta e a resistencia do material baixa. Isto facilita a fácil deformación e forxa. Pola contra, a forxa en frío realízase a temperaturas máis baixas e require forzas máis elevadas, o que se traduce nun endurecemento por deformación, un mellor acabado superficial e unha precisión das pezas fabricadas. • FORXADO DE MATRICES ABERTAS e IMPRESIÓN: Na forxa de matrices abertas, as matrices non limitan o material que se está a comprimir, mentres que na forxa de matrices de impresión as cavidades dentro dos troqueles restrinxen o fluxo de material mentres se forxa na forma desexada. A FORXA TURBINA ou tamén chamada TORTURA, que en realidade non é o mesmo pero un proceso moi similar, é un proceso de matriz aberto onde a peza de traballo queda encaixada entre dúas matrices planas e unha forza de compresión reduce a súa altura. A medida que a altura é reduced, o ancho da peza de traballo aumenta. RUTA, un proceso de forxado revolto implica un stock cilíndrico que está revolto no seu extremo e a súa sección transversal aumenta localmente. No encabezado, o material é alimentado a través da matriz, forxado e despois cortado ao longo. A operación é capaz de producir grandes cantidades de fixadores rapidamente. Principalmente é unha operación de traballo en frío porque se usa para facer puntas de cravos, parafusos, porcas e parafusos onde hai que reforzar o material. Outro proceso de matriz aberto é o COGGING, onde a peza de traballo se forxa nunha serie de pasos con cada paso que resulta na compresión do material e o posterior movemento da matriz aberta ao longo da lonxitude da peza. En cada paso, o grosor redúcese e a lonxitude aumenta nunha pequena cantidade. O proceso semella un estudante nervioso que morde o seu lapis todo o tempo en pequenos pasos. Un proceso chamado FULLERING é outro método de forxa con matriz aberta que adoitamos implementar como un paso anterior para distribuír o material na peza de traballo antes de que teñan lugar outras operacións de forxa metálica. Utilizámolo cando a peza de traballo require varias operacións de forxa operations. Na operación, morrer con superficies convexas defórmanse e provocan que o metal salga a ambos os dous lados. Un proceso similar ao batanado, o BORDO, por outra banda, implica unha matriz aberta con superficies cóncavas para deformar a peza de traballo. O bordado tamén é un proceso preparatorio para as operacións de forxa posteriores fai que o material flúe desde ambos lados cara a unha zona no centro. FORXADO POR TROQUELA DE IMPRESIÓN ou FORXADO TROQUELADO PECHADO, como tamén se chama, utiliza un troquel/molde que comprime o material e restrinxe o seu fluxo dentro de si mesmo. A matriz péchase e o material toma a forma da cavidade da matriz/molde. A FORXA DE PRECISIÓN, un proceso que require equipos e moldes especiais, produce pezas sen ou con moi pouco flash. Noutras palabras, as pezas terán dimensións case finais. Neste proceso insírese coidadosamente unha cantidade de material ben controlada e colócase dentro do molde. Implementamos este método para formas complexas con seccións finas, pequenas tolerancias e ángulos de calado e cando as cantidades son o suficientemente grandes como para xustificar os custos do molde e do equipamento. • FORXADO SIN FLASH: A peza de traballo colócase na matriz de forma que ningún material poida saír da cavidade para formar flash. Polo tanto, non é necesario un recorte de flash non desexado. É un proceso de forxa de precisión e, polo tanto, require un estreito control da cantidade de material empregado. • FORXADO METÁLICO ou FORXADO RADIAL: Unha peza de traballo é actuada circunferencialmente por matriz e forxada. Tamén se pode usar un mandril para forxar a xeometría da peza interior. Na operación de estampación, a peza de traballo normalmente recibe varios golpes por segundo. Os elementos típicos producidos por estampación son ferramentas de punta puntiaguda, barras cónicas, desaparafusadores. • PERFORACIÓN METÁLICA : Utilizamos esta operación con frecuencia como operación adicional na fabricación de pezas. Créase un buraco ou cavidade cunha perforación na superficie da peza de traballo sen atravesala. Teña en conta que a perforación é diferente da perforación, o que resulta nun orificio pasante. • FRESCADO : un punzón coa xeometría desexada preséntase na peza de traballo e crea unha cavidade coa forma desexada. Chamámoslle a este punzón un HOB. A operación implica altas presións e realízase en frío. Como resultado, o material é traballado en frío e endurecido. Polo tanto, este proceso é moi axeitado para a fabricación de moldes, matrices e cavidades para outros procesos de fabricación. Unha vez fabricada a placa, pódese fabricar facilmente moitas cavidades idénticas sen necesidade de mecanizarlas unha por unha. • FORXADO DE ROLLOS ou CONFORMADO DE ROLLOS : Para dar forma á peza metálica empréganse dous rolos opostos. A peza de traballo introdúcese nos rolos, os rolos xiran e tiran do traballo cara á fenda, despois o traballo pasa pola parte acanalada dos rolos e as forzas de compresión dan ao material a forma desexada. Non é un proceso de laminación senón un proceso de forxa, porque é unha operación discreta máis que continua. A xeometría dos soutos de rolos forxa o material coa forma e xeometría requiridas. Realízase en quente. Por ser un proceso de forxa produce pezas con propiedades mecánicas sobresalientes e, polo tanto, usámola para fabricación de pezas de automóbiles como eixes que precisan ter unha resistencia extraordinaria en ambientes de traballo difíciles. • FORXA ORBITAL : a peza de traballo colócase nunha cavidade da matriz de forxa e fórxase mediante unha matriz superior que se despraza nun camiño orbital mentres xira sobre un eixe inclinado. En cada revolución, a matriz superior completa exercendo forzas de compresión a toda a peza de traballo. Ao repetir estas revolucións varias veces, realízase unha forxa suficiente. As vantaxes desta técnica de fabricación son o seu funcionamento baixo ruído e as menores forzas necesarias. Noutras palabras, con pequenas forzas pódese facer xirar unha matriz pesada arredor dun eixe para aplicar grandes presións sobre unha sección da peza de traballo que está en contacto coa matriz. Ás veces, as pezas con forma de disco ou cónica son boas para este proceso. • FORXADO DE ANEIS: Usamos frecuentemente para fabricar aneis sen costura. O material córtase ao longo, córtase e despois perforase ata o final para crear un burato central. Despois colócase nun mandril e un troquel de forxa martelo desde arriba mentres o anel vai xirando lentamente ata obter as dimensións desexadas. • REMACHADO: Proceso común para unir pezas, comeza cunha peza metálica recta introducida en orificios prefabricados a través das pezas. Despois fórxanse os dous extremos da peza metálica apretando a unión entre unha matriz superior e inferior. • ACUÑADO: Outro proceso popular realizado por prensa mecánica, exercendo grandes forzas a pouca distancia. O nome "coining" provén dos finos detalles que se forxan nas superficies das moedas metálicas. Principalmente é un proceso de acabado dun produto onde se obteñen detalles finos nas superficies como resultado da gran forza aplicada pola matriz que transfire estes detalles á peza de traballo. • FORXADO DE BOLAS METÁLICAS: produtos como os rodamentos de bolas requiren bolas de metal de alta calidade fabricadas con precisión. Nunha técnica chamada SKEW ROLLING, usamos dous rolos opostos que xiran continuamente mentres o stock está a ser alimentado continuamente nos rolos. Nun extremo dos dous rolos expulsan esferas metálicas como produto. Un segundo método para forxar bolas metálicas é o uso de matrices que apertan o material colocado entre elas tomando a forma esférica da cavidade do molde. Moitas veces, as bólas producidas requiren algúns pasos adicionais como o acabado e o pulido para converterse nun produto de alta calidade. • FORXADO ISOTÉRMICO / FORXADO EN CALENTE : Un proceso caro que se realiza só cando o valor beneficio/custo está xustificado. Proceso de traballo en quente onde a matriz se quenta ata aproximadamente a mesma temperatura que a peza de traballo. Dado que tanto a matriz como o traballo teñen aproximadamente a mesma temperatura, non hai arrefriamento e mellóranse as características de fluxo do metal. A operación é unha boa opción para superaliaxes e materiais con forxabilidade inferior e materiais cuxo as propiedades mecánicas son moi sensibles a pequenos gradientes de temperatura e cambios. • ENCALADO DE METAL : É un proceso de acabado en frío. O fluxo de material non está restrinxido en todas as direccións con excepción da dirección na que se aplica a forza. Como resultado, obtense moi bo acabado superficial e dimensións precisas. • FORXADO DE ALTA ENERXÍA: A técnica consiste nun molde superior unido ao brazo dun pistón que se empurra rapidamente mentres unha mestura de aire-combustible se acende mediante unha bujía. Semella o funcionamento dos pistóns nun motor de coche. O molde golpea a peza moi rápido e despois volve á súa posición orixinal moi rápido grazas á contrapresión. O traballo fórxase nuns poucos milisegundos e, polo tanto, non hai tempo para que o traballo se arrefríe. Isto é útil para pezas difíciles de forxar que teñen propiedades mecánicas moi sensibles á temperatura. Noutras palabras, o proceso é tan rápido que a peza fórmase a temperatura constante e non haberá gradientes de temperatura nas interfaces de molde/peça de traballo. • Na forxa de troqueles, o metal é batido entre dous bloques de aceiro coincidentes con formas especiais, chamados troqueles. Cando o metal é martelado entre as matrices, asume a mesma forma que as formas da matriz. Cando alcanza a súa forma definitiva, sácase para arrefriar. Este proceso produce pezas fortes que teñen unha forma precisa, pero requiren un maior investimento para as matrices especializadas. A forxa alterada aumenta o diámetro dunha peza de metal ao aplanala. Úsase xeralmente para facer pezas pequenas, especialmente para formar cabezas en elementos de fixación como parafusos e cravos. • METALURXÍA DE POLOS / PROCESAMIENTO DE POLOS : como o seu nome indica, implica procesos de fabricación para facer pezas sólidas de determinadas xeometrías e formas a partir de po. Se se usan po metálicos para este fin é o ámbito da pulvimetalurxia e se se usan po non metálico é o procesamento de po. As pezas sólidas prodúcense a partir de po mediante prensado e sinterización. POWDER PRESSING úsase para compactar os po nas formas desexadas. En primeiro lugar, o material primario está fisicamente en po, dividíndoo en moitas pequenas partículas individuais. A mestura de po énchese na matriz e un punzón móvese cara ao po e compáctao na forma desexada. Realízase maioritariamente a temperatura ambiente, co prensado en po obtense unha parte sólida e chámase compacto verde. Os aglutinantes e lubricantes úsanse habitualmente para mellorar a compactabilidade. Somos capaces de prensar en po mediante prensas hidráulicas con varios miles de toneladas de capacidade. Tamén temos prensas de dobre acción con punzóns superiores e inferiores opostos, así como prensas de accións múltiples para xeometrías de pezas moi complexas. A uniformidade, que é un reto importante para moitas plantas de procesamento de po/metalurxia en po, non é un gran problema para AGS-TECH debido á nosa ampla experiencia na fabricación personalizada deste tipo de pezas durante moitos anos. Incluso con partes máis grosas onde a uniformidade supón un reto, conseguimos. Se nos comprometemos co teu proxecto, faremos as túas pezas. Se observamos algún risco potencial, informarémosche en avance. A SINTERIZACIÓN EN PO, que é o segundo paso, implica o aumento da temperatura ata certo grao e o mantemento da temperatura a ese nivel durante un tempo determinado para que as partículas de po na parte prensada poidan unirse entre si. Isto resulta en vínculos moito máis fortes e fortalecemento da peza de traballo. A sinterización ten lugar preto da temperatura de fusión do po. Durante a sinterización ocorrerá a contracción, aumenta a resistencia do material, a densidade, a ductilidade, a condutividade térmica e a condutividade eléctrica. Contamos con fornos discontinuos e continuos para sinterización. Unha das nosas capacidades é axustar o nivel de porosidade das pezas que producimos. Por exemplo, podemos producir filtros metálicos mantendo as pezas porosas ata certo punto. Mediante unha técnica chamada IMPREGNACIÓN, enchemos os poros do metal cun fluído como o aceite. Producimos, por exemplo, rodamentos impregnados de aceite que son autolubricantes. No proceso de INFILTRACIÓN enchemos os poros dun metal con outro metal de menor punto de fusión que o material base. A mestura quéntase a unha temperatura entre as temperaturas de fusión dos dous metais. Como resultado pódense obter algunhas propiedades especiais. Tamén realizamos frecuentemente operacións secundarias, como mecanizado e forxa de pezas fabricadas en po, cando se necesitan características ou propiedades especiais ou cando a peza se pode fabricar con menos pasos de proceso. PRENSADO ISOSTÁTICO: Neste proceso estase empregando a presión do fluído para compactar a peza. Os po metálicos colócanse nun molde feito dun recipiente flexible pechado. No prensado isostático, a presión aplícase desde todo o contorno, contrariamente á presión axial que se observa no prensado convencional. As vantaxes do prensado isostático son a densidade uniforme dentro da peza, especialmente para pezas máis grandes ou grosas, propiedades superiores. A súa desvantaxe son os tempos de ciclo longos e as precisións xeométricas relativamente baixas. O PRENSADO ISOSTÁTICO EN FRÍO realízase a temperatura ambiente e o molde flexible está feito de caucho, PVC ou uretano ou materiais similares. O fluído utilizado para presurizar e compactar é aceite ou auga. A sinterización convencional do compacto verde segue isto. O PRENSADO ISOSTÁTICO EN CALENTE, pola súa banda, realízase a altas temperaturas e o material do molde é chapa ou cerámica cun punto de fusión suficientemente alto que resista as temperaturas. O fluído presurizador adoita ser un gas inerte. As operacións de prensado e sinterización realízanse nun só paso. Elimínase case por completo a porosidade, obtense unha estrutura uniform grain. A vantaxe do prensado isostático en quente é que pode producir pezas comparables á fundición e á forxa combinadas ao tempo que se poden utilizar materiais que non son axeitados para a fundición e a forxa. A desvantaxe da prensa isostática en quente é o seu alto tempo de ciclo e polo tanto custo. É adecuado para pezas críticas de baixo volume. MOLDEADO POR INXECCIÓN DE METÁIS: Proceso moi axeitado para a produción de pezas complexas con paredes finas e xeometrías detalladas. O máis axeitado para pezas máis pequenas. Os po e o aglutinante de polímero mestúranse, quéntanse e inxéctanse nun molde. O aglutinante de polímero recubre as superficies das partículas de po. Despois do moldeado, o aglutinante elimínase mediante quecemento a baixa temperatura ou disolto mediante un disolvente. COMPACTACIÓN DE ROLOS / LAMINACIÓN DE POLOS: Os po úsanse para producir tiras ou follas continuas. O po é alimentado desde un alimentador e compactado por dous rolos xiratorios en follas ou tiras. A operación realízase en frío. A folla lévase a un forno de sinterización. O proceso de sinterización pódese repetir unha segunda vez. EXTRUSIÓN DE POL: As pezas con grandes relacións entre lonxitude e diámetro fanse extrusionando un recipiente de chapa fina con po. SINTERIZACIÓN FLOXA : Como o seu nome indica, é un método de compactación e sinterización sen presión, axeitado para producir pezas moi porosas como filtros metálicos. O po introdúcese na cavidade do molde sen compactar. SINTERIZACIÓN FLOXA : Como o seu nome indica, é un método de compactación e sinterización sen presión, axeitado para producir pezas moi porosas como filtros metálicos. O po introdúcese na cavidade do molde sen compactar. SINTERIZACIÓN DE SPARK: O po comprímese no molde mediante dous punzóns opostos e aplícase unha corrente eléctrica de alta potencia ao punzón e pasa polo po compactado encaixado entre eles. A alta corrente queima as películas superficiais das partículas de po e sinterizas coa calor xerada. O proceso é rápido porque a calor non se aplica desde fóra senón que se xera dende dentro do molde. PRENSADO EN CALENTE: Os polvos son prensados e sinterizados nun só paso nun molde que resiste as altas temperaturas. A medida que a matriz se compacta, aplícaselle calor en po. As boas precisións e propiedades mecánicas acadadas por este método fan que sexa unha opción atractiva. Mesmo os metais refractarios poden procesarse utilizando materiais de molde como o grafito. CLICK Product Finder-Locator Service MENÚ ANTERIOR
- Plastic Rubber Metal Extrusions, Extrusion Dies, Aluminum Extruding
Plastic Rubber Metal Extrusions, Extrusion Dies, Aluminum Extruding, Pipe Tube Forming, Plastic Profiles, Metal Profiles Manufacturing, PVC at AGS-TECH Inc. Extrusións, produtos extruídos, extruídos Usamos o proceso EXTRUSION process para fabricar produtos cun perfil de sección transversal fixa, como tubos, tubos e disipadores de calor. Aínda que se poden extruir moitos materiais, as nosas extrusións máis comúns son de metal, polímeros/plásticos, cerámicas obtidas por métodos de extrusión en frío, quente ou quente. Denominamos extrusión ás pezas extruídas ou extruídas en plural. Algunhas versións especializadas do proceso que tamén realizamos son a sobrecamisa, a coextrusión e a extrusión composta. Recomendámosche que fagas clic aquí para DESCARGA as nosas ilustracións esquemáticas dos procesos de extrusión de metal, cerámica e plástico de AGS-TECH Inc. Isto axudarache a comprender mellor a información que che proporcionamos a continuación. Na extrusión o material a extruir é empuxado ou estirado a través dunha matriz que teña o perfil de sección transversal desexado. O proceso pode usarse para fabricar seccións transversais complexas cun excelente acabado superficial e para traballar material fráxil. Pódese producir pezas de calquera lonxitude usando este proceso. Para simplificar os pasos do proceso: 1.) Nas extrusións quentes ou quentes o material quéntase e cárgase nun recipiente na prensa. O material é presionado e empuxado fóra da matriz. 2.) O extruido producido é estirado para alisar, tratado térmicamente ou traballado en frío para mellorar as súas propiedades. Por outra banda COLD EXTRUSION ten lugar a temperatura ambiente e ten as vantaxes dunha menor oxidación, alta rapidez, boa resistencia e acabado superficial. A EXTRUSIÓN QUEnte realízase por encima da temperatura ambiente pero por debaixo do punto de recristalización. Ofrece un compromiso e equilibrio para as forzas necesarias, a ductilidade e as propiedades do material e, polo tanto, é a opción para algunhas aplicacións. HOT EXTRUSION ten lugar por riba da temperatura de recristalización do material. Deste xeito, é máis fácil empurrar o material a través da matriz. Non obstante, o custo do equipamento é elevado. Canto máis complexo sexa un perfil extruido, máis custosa é a matriz (utillaje) e menor é a taxa de produción. As seccións transversais da matriz así como os espesores teñen limitacións que dependen do material a extruir. As esquinas afiadas nas matrices de extrusión son sempre indesexables e deben evitarse a menos que sexa necesario. Segundo o material que se está a extruir, ofrecemos: • METAL EXTRUSIONS : os máis comúns que producimos son aluminio, latón, cinc, cobre, aceiro, titanio e magnesio • EXTRUSIÓN DE PLÁSTICO : o plástico fúndese e fórmase nun perfil continuo. Os nosos materiais comúns procesados son polietileno, nailon, poliestireno, cloruro de polivinilo, polipropileno, plástico ABS, policarbonato e acrílico. Os produtos típicos que fabricamos inclúen tubos e tubos, marcos de plástico. No proceso, as pequenas contas de plástico/resina son alimentadas por gravidade desde a tolva ata o barril da máquina de extrusión. Con frecuencia tamén mesturamos colorantes ou outros aditivos na tolva para darlle ao produto as especificacións e propiedades requiridas. O material que entra no barril quente é forzado polo parafuso xiratorio para deixar o barril ao final e moverse a través do paquete de pantalla para eliminar os contaminantes do plástico fundido. Despois de pasar o paquete de pantalla, o plástico entra na matriz de extrusión. A matriz dálle ao plástico brando en movemento a súa forma de perfil ao pasar. Agora o extruido pasa por un baño de auga para arrefriar. Outras técnicas que AGS-TECH Inc. leva empregando durante moitos anos son: • PIPE & TUBING EXTRUSION : os tubos e tubos de plástico fórmanse cando os plásticos se extruyen a través dunha matriz de conformación redonda e se arrefrían nun baño de auga, despois córtanse ao longo ou se enrollan/enrollan. Transparente ou de cores, a raias, de parede simple ou dobre, flexible ou ríxida, PE, PP, poliuretano, PVC, nylon, PC, silicona, vinilo ou ben, temos de todo. Temos abastecemento de tubos, así como a capacidade de producir segundo as súas especificacións. AGS-TECH fabrica tubos segundo os requisitos da FDA, UL e LE para aplicacións médicas, eléctricas e electrónicas, industriais e outras. • OVERJACKET / OVER JACKETING EXTRUSION : esta técnica aplica unha capa exterior de plástico sobre o fío ou o cable existente. Os nosos fíos de illamento están fabricados con este método. • COEXTRUSION : extrúense simultáneamente varias capas de material. As múltiples capas son entregadas por varias extrusoras. Os distintos espesores de capa pódense axustar para atender ás especificacións do cliente. Este proceso fai posible utilizar varios polímeros que teñen cada un unha funcionalidade diferente no produto. Como resultado, pódese optimizar unha variedade de propiedades. • EXTRUSIÓN DE COMPOSTOS: mestúranse un ou varios polímeros con aditivos para obter un composto plástico. As nosas extrusoras de dobre parafuso producen extrusións de composto. As matrices de extrusión son xeralmente máis baratas en comparación cos moldes metálicos. Se estás pagando moito máis que uns poucos miles de dólares por unha matriz de extrusión de tamaño pequeno ou medio extrusionado de aluminio, probablemente estea pagando demasiado. Somos expertos en determinar que técnica é a máis rendible, a máis rápida e a máis adecuada para a súa aplicación. Ás veces, extruir e despois mecanizar unha peza pode aforrarche moito diñeiro. Antes de tomar unha decisión firme, pregúntanos primeiro a nosa opinión. Axudamos a moitos clientes a tomar as decisións correctas. Para algunhas extrusións metálicas moi utilizadas, podes descargar os nosos folletos e catálogos facendo clic no texto coloreado a continuación. Se se trata dun produto que cumpre coas túas necesidades, será máis económico. Descarga as nosas capacidades de extrusión de tubos e tubos médicos Descarga os nosos disipadores de calor extrusionados • PROCESOS SECUNDARIOS DE FABRICACIÓN E DE FABRICACIÓN PARA EXTRUSIÓNS : Entre os procesos de valor engadido que ofrecemos para produtos extruídos están: -Dobrado, conformación e conformación de tubos e tubos personalizados, corte de tubos, conformación de extremos de tubos, bobinado de tubos, mecanizado e acabado, perforación e perforación de buratos e perforación, -Conxuntos de tubos e tubos personalizados, ensamblaxe tubular, soldadura, soldadura e soldadura. -Dobrado, conformado e conformado por extrusión a medida -Limpeza, desengraxado, decapado, pasivación, pulido, anodizado, chapado, pintura, tratamento térmico, recocido e endurecemento, marcado, gravado e etiquetado, envasado personalizado. CLICK Product Finder-Locator Service PÁXINA ANTERIOR
- Casting and Machined Parts, CNC Manufacturing, Milling, Turning, Swiss
Casting and Machined Parts, CNC Manufacturing, Milling, Turning, Swiss Type Machining, Die Casting, Investment Casting, Lost Foam Cast Parts from AGS-TECH Inc. Fundición e mecanizado As nosas técnicas de fundición e mecanizado personalizados son fundición prescindible e non prescindible, fundición férrica e non ferrosa, area, matriz, centrífuga, molde continuo, cerámico, investimento, escuma perdida, forma case rede, molde permanente (fundición por gravidade), xeso. moldes (fundición de xeso) e fundición de casca, pezas mecanizadas producidas por fresado e torneado utilizando equipos convencionais e CNC, mecanizado de tipo suízo para pezas pequenas e baratas de alta precisión, mecanizado de parafusos para elementos de fixación, mecanizado non convencional. Teña en conta que, ademais de metais e aliaxes metálicas, mecanizamos compoñentes de cerámica, vidro e plástico, nalgúns casos cando fabricar un molde non é atractivo ou non é a opción. O mecanizado de materiais poliméricos require da experiencia especializada que temos polo reto que presentan os plásticos e o caucho pola súa suavidade, non rixidez...etc. Para o mecanizado de cerámica e vidro, consulte a nosa páxina sobre Fabricación non convencional. AGS-TECH Inc. fabrica e fornece pezas de fundición lixeiras e pesadas. Estivemos a subministrar fundicións metálicas e pezas mecanizadas para caldeiras, intercambiadores de calor, automóbiles, micromotores, aeroxeradores, equipos de envasado de alimentos e moito máis. Recomendámosche que fagas clic aquí para DESCARGA as nosas ilustracións esquemáticas de procesos de mecanizado e fundición de AGS-TECH Inc. Isto axudarache a comprender mellor a información que che proporcionamos a continuación. Vexamos en detalle algunhas das diversas técnicas que ofrecemos: • FUNDACIÓN DE MOLDES EXPENDABLES: esta categoría ampla refírese aos métodos que implican moldes temporais e non reutilizables. Son exemplos de area, xeso, cuncha, revestimento (tamén chamado de cera perdida) e fundición de xeso. • FUNDACIÓN EN AREA: Proceso no que se utiliza area como material do molde. Un método moi antigo e aínda moi popular na medida en que a maioría das fundicións metálicas producidas son feitas por esta técnica. Baixo custo mesmo con produción en cantidade baixa. Adecuado para a fabricación de pezas pequenas e grandes. A técnica pódese usar para fabricar pezas en días ou semanas cun investimento moi reducido. A area húmida únase con arxila, aglutinantes ou aceites especiais. A area xeralmente está contida en caixas de moldes e o sistema de cavidades e portas créase compactando a area arredor dos modelos. Os procesos son: 1.) Colocación do modelo en area para facer o molde 2.) Incorporación de maqueta e area nun sistema de gating 3.) Eliminación do modelo 4.) Recheo da cavidade do molde con metal fundido 5.) Arrefriamento do metal 6.) Rotura do molde de area e retirada da fundición • FUNDACIÓN DE MOLDES DE xeso: Similar á fundición en area, e en lugar de area, utilízase o xeso de París como material do molde. Prazos de produción curtos como fundición en area e barato. Boas tolerancias dimensionales e acabado superficial. A súa principal desvantaxe é que só se pode usar con metais de baixo punto de fusión como o aluminio e o cinc. • FUNDACIÓN DE MOLDES DE CONCHAS : Tamén é semellante á fundición en area. Cavidade do molde obtida por casca de area endurecida e aglutinante de resina termoendurecible en lugar do matraz cheo de area como no proceso de fundición en area. Case calquera metal axeitado para ser fundido con area pode ser fundido mediante moldura de cuncha. O proceso pódese resumir como: 1.) Fabricación do molde de casca. A area utilizada é de gran tamaño moito menor en comparación coa area utilizada na fundición en area. A area fina mestúrase con resina termoendurecible. O patrón metálico está revestido cun axente de separación para facilitar a eliminación da cuncha. Despois diso, o patrón metálico quéntase e a mestura de area é porosa ou soplada sobre o patrón de fundición en quente. Na superficie do patrón fórmase unha capa fina. O grosor desta cuncha pódese axustar variando o tempo que a mestura de resina de area está en contacto co patrón metálico. Despois elimínase a area solta quedando o patrón cuberto de casca. 2.) A continuación, a casca e o patrón quéntanse nun forno para que a cuncha se endureza. Despois de completar o endurecemento, a cuncha é expulsada do patrón usando alfinetes incorporados ao patrón. 3.) Dúas cunchas deste tipo únense pegando ou abrazando e compoñen o molde completo. Agora o molde de cuncha insírese nun recipiente no que está sostido por area ou granalla metálica durante o proceso de fundición. 4.) Agora o metal quente pódese verter no molde de cuncha. As vantaxes da fundición de cunchas son produtos con moi bo acabado superficial, posibilidade de fabricar pezas complexas con alta precisión dimensional, proceso fácil de automatizar, económico para a produción de grandes volumes. As desvantaxes son que os moldes necesitan unha boa ventilación debido aos gases que se crean cando o metal fundido entra en contacto co produto químico aglutinante, as resinas termoendurecibles e os patróns metálicos son caros. Debido ao custo dos patróns metálicos, é posible que a técnica non se adapte ben a producións de baixa cantidade. • FUNDACIÓN POR INVESTIMENTO (tamén coñecida como FUNDA A CERA PERDIDA ): técnica tamén moi antiga e apta para fabricar pezas de calidade con gran precisión, repetibilidade, versatilidade e integridade a partir de moitos metais, materiais refractarios e aliaxes especiais de alto rendemento. Pódense producir pezas pequenas e grandes. Un proceso caro en comparación con algúns dos outros métodos, pero a principal vantaxe é a posibilidade de producir pezas cunha forma case neta, contornos e detalles complicados. Polo tanto, o custo vese algo compensado coa eliminación de reelaboración e mecanizado nalgúns casos. Aínda que pode haber variacións, aquí tes un resumo do proceso xeral de fundición de investimento: 1.) Creación dun patrón mestre orixinal a partir de cera ou plástico. Cada fundición necesita un patrón xa que estes son destruídos no proceso. Tamén é necesario un molde a partir do que se fabrican os patróns e a maioría das veces o molde é fundido ou mecanizado. Debido a que non é necesario abrir o molde, pódense conseguir fundicións complexas, moitos patróns de cera pódense conectar como as ramas dunha árbore e verter xuntos, permitindo así a produción de varias pezas a partir dunha única vertida do metal ou da aliaxe metálica. 2.) A continuación, o patrón é mergullado ou vertido cunha suspensión refractaria composta de sílice de gran fino, auga e aglutinantes. Isto dá lugar a unha capa de cerámica sobre a superficie do patrón. A capa refractaria do patrón déixase secar e endurecer. Este paso é de onde provén o nome de fundición de investimento: o lodo refractario inviste sobre o patrón de cera. 3.) Neste paso, o molde de cerámica endurecida bótase boca abaixo e quéntase para que a cera se derrita e saia do molde. Déixase unha cavidade para a fundición de metal. 4.) Despois de que a cera está fóra, o molde de cerámica quéntase ata unha temperatura máis alta, o que resulta no fortalecemento do molde. 5.) A fundición de metal bótase no molde quente enchendo todas as seccións complicadas. 6.) Permítese solidificar a fundición 7.) Finalmente rómpese o molde de cerámica e córtanse partes manufacturadas da árbore. Aquí tes unha ligazón ao folleto da planta de fundición de investimento • FUNDACIÓN DE PATRÓN EVAPORATIVO: O proceso utiliza un patrón feito a partir dun material como a espuma de poliestireno que se evapora cando se vierte metal fundido quente no molde. Existen dous tipos deste proceso: FUNDACIÓN DE ESPUMA PERDIDA que utiliza area sen unir e FUNDACIÓN DE MOLDES COMPLETOS que utiliza area adherida. Aquí están os pasos xerais do proceso: 1.) Fabrica o patrón a partir dun material como o poliestireno. Cando se fabriquen grandes cantidades, o patrón é moldeado. Se a parte ten unha forma complexa, é posible que teñan que unir varias seccións deste material de escuma para formar o patrón. Moitas veces recubrimos o patrón cun composto refractario para crear un bo acabado superficial na fundición. 2.) O patrón é entón colocado en area de moldeo. 3.) O metal fundido bótase no molde, evaporando o patrón de escuma, é dicir, poliestireno na maioría dos casos mentres flúe pola cavidade do molde. 4.) O metal fundido déixase no molde de area para endurecer. 5.) Despois de que estea endurecido, retiramos a fundición. Nalgúns casos, o produto que fabricamos require un núcleo dentro do patrón. Na fundición por evaporación, non hai necesidade de colocar e asegurar un núcleo na cavidade do molde. A técnica é axeitada para a fabricación de xeometrías moi complexas, pódese automatizar facilmente para a produción de gran volume e non hai liñas de separación na peza fundida. O proceso básico é sinxelo e económico de implementar. Para a produción de grandes volumes, xa que se necesita unha matriz ou un molde para producir os patróns a partir de poliestireno, isto pode ser algo custoso. • FUNDACIÓN DE MOLDES NON EXPANDIBLES: esta categoría ampla refírese aos métodos nos que o molde non precisa ser reformado despois de cada ciclo de produción. Exemplos son a fundición permanente, a matriz, continua e centrífuga. Conséguese repetibilidade e as pezas pódense caracterizar como NEAR NET SHAPE. • FUNDACIÓN DE MOLDES PERMANENTES: Os moldes reutilizables feitos de metal utilízanse para varias fundicións. Un molde permanente xeralmente pódese usar decenas de miles de veces antes de que se desgaste. A gravidade, a presión do gas ou o baleiro úsanse xeralmente para encher o molde. Os moldes (tamén chamados troqueles) están feitos xeralmente de ferro, aceiro, cerámica ou outros metais. O proceso xeral é: 1.) Mecanizar e crear o molde. É habitual mecanizar o molde a partir de dous bloques metálicos que encaixan e que se poden abrir e pechar. Tanto as características da peza como o sistema de compuerta son xeralmente mecanizados no molde de fundición. 2.) As superficies internas do molde están recubertas cunha suspensión que incorpora materiais refractarios. Isto axuda a controlar o fluxo de calor e actúa como lubricante para facilitar a eliminación da parte fundida. 3.) A continuación, péchanse as metades do molde permanente e quéntase o molde. 4.) O metal fundido bótase no molde e déixase quieto para a solidificación. 5.) Antes de que se produza moito arrefriamento, retiramos a peza do molde permanente mediante expulsores cando se abren as metades do molde. Usamos con frecuencia a fundición permanente en moldes para metais de baixo punto de fusión como o cinc e o aluminio. Para as fundicións de aceiro, usamos grafito como material do molde. Ás veces obtemos xeometrías complexas utilizando núcleos dentro de moldes permanentes. Vantaxes desta técnica son as fundicións con boas propiedades mecánicas obtidas por arrefriamento rápido, uniformidade nas propiedades, boa precisión e acabado superficial, baixas taxas de rexeitamento, posibilidade de automatizar o proceso e producir grandes volumes de xeito económico. As desvantaxes son os altos custos de configuración inicial que o fan inadecuado para operacións de baixo volume e as limitacións no tamaño das pezas fabricadas. • FUNDACIÓN A PRESIÓN: mecanízase unha matriz e empúxase o metal fundido a alta presión nas cavidades do molde. Son posibles fundicións tanto de metais non férreos como férreos. O proceso é adecuado para tiradas de produción en grandes cantidades de pezas pequenas e medianas con detalles, paredes extremadamente finas, consistencia dimensional e bo acabado superficial. AGS-TECH Inc. é capaz de fabricar espesores de paredes tan pequenos como 0,5 mm usando esta técnica. Do mesmo xeito que na fundición de moldes permanentes, o molde debe constar de dúas metades que se poidan abrir e pechar para eliminar a parte producida. Un molde de fundición a presión pode ter varias cavidades para permitir a produción de varias fundicións con cada ciclo. Os moldes de fundición son moi pesados e moito máis grandes que as pezas que producen, polo que tamén son caros. Reparamos e substituímos matrices desgastadas de xeito gratuíto para os nosos clientes, sempre que nos soliciten de novo as súas pezas. Os nosos troqueles teñen unha longa vida útil no rango de varios centos de miles de ciclos. Aquí están os pasos básicos do proceso simplificado: 1.) Produción do molde xeralmente a partir de aceiro 2.) Molde instalado na máquina de fundición a presión 3.) O pistón obriga o metal fundido a fluír nas cavidades da matriz enchendo as características complicadas e as paredes finas 4.) Despois de encher o molde co metal fundido, a fundición déixase endurecer a presión 5.) Ábrese o molde e elimínase a fundición coa axuda de pasadores expulsores. 6.) Agora a matriz baleira lubricase de novo e fíxase para o seguinte ciclo. Na fundición a presión, usamos frecuentemente moldaxe de inserción onde incorporamos unha parte adicional ao molde e fundimos o metal ao seu redor. Despois da solidificación, estas pezas pasan a formar parte do produto fundido. As vantaxes da fundición a presión son boas propiedades mecánicas das pezas, posibilidade de características complexas, detalles finos e bo acabado superficial, altas taxas de produción, fácil automatización. As desvantaxes son: non moi axeitado para volumes baixos debido ao alto custo do troquel e do equipamento, limitacións nas formas que se poden fundir, pequenas marcas redondas nas pezas de fundición derivadas do contacto dos pasadores do expulsor, un brillo fino de metal espremido na liña de separación, necesidade. para ventilacións ao longo da liña de separación entre a matriz, necesidade de manter as temperaturas do molde baixas usando circulación de auga. • FUNDACIÓN CENTRÍFUGA: bótase metal fundido no centro do molde rotativo no eixe de rotación. As forzas centrífugas arroxan o metal cara á periferia e déixase solidificar mentres o molde segue xirando. Pódense utilizar rotacións de eixe tanto horizontais como verticais. Pódense fundir pezas con superficies internas redondas, así como outras formas non redondas. O proceso pódese resumir como: 1.) O metal fundido bótase nun molde centrífugo. O metal é entón forzado ás paredes exteriores debido ao xiro do molde. 2.) A medida que o molde xira, a fundición de metal endurece A fundición centrífuga é unha técnica axeitada para a produción de pezas cilíndricas ocas como tubos, sen necesidade de sprues, risers e elementos de compuerta, bo acabado superficial e características detalladas, sen problemas de encollemento, posibilidade de producir tubos longos con diámetros moi grandes, alta capacidade de produción. . • FUNDACIÓN CONTINUA ( STRAND CASTING ): Úsase para fundir unha lonxitude continua de metal. Basicamente, o metal fundido é fundido nun perfil bidimensional do molde pero a súa lonxitude é indeterminada. Novo metal fundido introdúcese constantemente no molde mentres a fundición viaxa cara abaixo coa súa lonxitude aumentando co tempo. Os metais como o cobre, o aceiro e o aluminio son fundidos en longas cadeas mediante un proceso de fundición continua. O proceso pode ter varias configuracións, pero a común pódese simplificar como: 1.) O metal fundido bótase nun recipiente situado moi por riba do molde en cantidades e caudals ben calculados e flúe a través do molde arrefriado por auga. A fundición metálica vertida no molde solidifícase ata formar unha barra de arranque situada na parte inferior do molde. Esta barra de inicio dálle aos rolos algo ao que agarrarse inicialmente. 2.) A longa cadea metálica é levada por rolos a unha velocidade constante. Os rolos tamén cambian a dirección do fluxo de fío metálico de vertical a horizontal. 3.) Despois de que a fundición continua percorreu unha certa distancia horizontal, un facho ou serra que se move coa fundición córtaa rapidamente ás lonxitudes desexadas. O proceso de fundición continua pódese integrar co PROCESO DE LAMINACIÓN, onde o metal de fundición continua pode ser alimentado directamente nun laminador para producir vigas en I, vigas en T... etc. A fundición continua produce propiedades uniformes en todo o produto, ten unha alta taxa de solidificación, reduce o custo debido á moi baixa perda de material, ofrece un proceso onde a carga de metal, o vertido, a solidificación, o corte e a eliminación da fundición teñen lugar nunha operación continua e resultando así unha alta taxa de produtividade e alta calidade. Non obstante, unha consideración importante é o alto investimento inicial, os custos de instalación e os requisitos de espazo. • SERVIZOS DE MECANIZADO: Ofrecemos mecanizado de tres, catro e cinco eixos. O tipo de procesos de mecanizado que utilizamos son TORNEADO, FRESADO, PERFORADO, MANDRADO, BROCHADO, CESPILADO, ASERRADO, AFILADO, LAPEADO, PULIDO e MECANIZADO NON TRADICIONAL que se elabora máis adiante nun menú diferente da nosa web. Para a maior parte da nosa fabricación, usamos máquinas CNC. Non obstante, para algunhas operacións as técnicas convencionais encaixan mellor e, polo tanto, tamén confiamos nelas. As nosas capacidades de mecanizado alcanzan o nivel máis alto posible e algunhas pezas máis esixentes están fabricadas nunha planta certificada AS9100. As palas de motores a reacción requiren unha experiencia de fabricación altamente especializada e o equipo axeitado. A industria aeroespacial ten estándares moi estritos. Algúns compoñentes con estruturas xeométricas complexas fabrícanse máis facilmente mediante un mecanizado de cinco eixes, que só se atopa nalgunhas plantas de mecanizado, incluída a nosa. A nosa planta certificada aeroespacial ten a experiencia necesaria cumprindo os requisitos de documentación extenso da industria aeroespacial. Nas operacións de TORNEADO, unha peza de traballo é xirada e móvese contra unha ferramenta de corte. Para este proceso estase a utilizar unha máquina chamada torno. En FRESADO, unha máquina chamada fresadora ten unha ferramenta xiratoria para levar os bordos cortantes a unha peza de traballo. As operacións de perforación implican unha fresa xiratoria con bordos cortantes que produce buracos ao contacto coa peza. En xeral utilízanse perforadoras, tornos ou molinos. Nas operacións de ABADURADO, unha ferramenta cunha única punta de punta dobrada móvese a un burato áspero dunha peza de traballo xirando para ampliar lixeiramente o burato e mellorar a precisión. Utilízase para fins de acabado fino. O BROCHADO consiste nunha ferramenta dentada para eliminar o material dunha peza de traballo nunha pasada da brocha (ferramenta dentada). No brochado lineal, a brocha corre linealmente contra unha superficie da peza de traballo para efectuar o corte, mentres que no brochado rotativo, a brocha é xirada e presionada na peza de traballo para cortar unha forma simétrica do eixe. O MECANIZADO DE TIPO SUÍZO é unha das nosas valiosas técnicas que utilizamos para a fabricación de grandes volumes de pezas pequenas de alta precisión. Usando un torno de tipo suízo transformamos pezas pequenas, complexas e de precisión a un prezo económico. A diferenza dos tornos convencionais, nos que a peza se mantén estacionaria e a ferramenta en movemento, nos centros de torneado de tipo suízo, a peza pode moverse no eixe Z e a ferramenta está estacionaria. No mecanizado de tipo suízo, o stock de barras mantense na máquina e avanza a través dunha casquiña guía no eixe z, deixando só ao descuberto a parte a mecanizar. Deste xeito, garante un agarre firme e a precisión é moi alta. A dispoñibilidade de ferramentas activas ofrece a oportunidade de fresar e perforar a medida que o material avanza dende o buxo guía. O eixe Y dos equipos de tipo suízo ofrece capacidades de fresado completas e aforra moito tempo na fabricación. Ademais, as nosas máquinas dispoñen de brocas e ferramentas de mandrinar que operan sobre a peza cando se suxeita no subfuso. A nosa capacidade de mecanizado de tipo suízo ofrécenos unha oportunidade de mecanizado completo totalmente automatizado nunha soa operación. O mecanizado é un dos maiores segmentos do negocio de AGS-TECH Inc. Utilizámolo como operación principal ou como operación secundaria despois da fundición ou extrusión dunha peza para que se cumpran todas as especificacións do deseño. • SERVIZOS DE ACABADO DE SUPERFICIES: Ofrecemos unha gran variedade de tratamentos de superficie e acabados de superficies, como o acondicionamento de superficies para mellorar a adhesión, a deposición de fina capa de óxido para mellorar a adhesión do revestimento, chorro de area, película química, anodizado, nitruración, recubrimento en po, recubrimento por pulverización. , varias técnicas avanzadas de metalización e revestimento, incluíndo sputtering, feixe de electróns, evaporación, recubrimentos, recubrimentos duros como o diamante como o carbono (DLC) ou o revestimento de titanio para ferramentas de perforación e corte. • SERVIZOS DE MARCADO E ETIQUETADO DE PRODUTOS: Moitos dos nosos clientes requiren marcado e etiquetado, marcado con láser, gravado en pezas metálicas. Se tes algunha necesidade, imos discutir cal é a mellor opción para ti. Aquí tes algúns dos produtos de fundición metálica de uso común. Dado que estes están dispoñibles, pode aforrar en custos de moldes no caso de que algún destes se adapte ás súas necesidades: PREME AQUÍ PARA DESCARGAR as nosas caixas de aluminio fundido da serie 11 de AGS-Electronics CLICK Product Finder-Locator Service PÁXINA ANTERIOR
- Custom Manufactured Parts, Assemblies, Plastic Mold, Casting,Machining
Custom Manufactured Parts, Assemblies, Plastic Mold, Rubber Molding, Metal Casting, CNC Machining, Turning, Milling, Electrical Electronic Optical Assembly PCBA Pezas e conxuntos e produtos personalizados Le máis Moldes e moldes de plástico e caucho Le máis Fundición e mecanizado Le máis Extrusións, Produtos extruídos Le máis Estampación e fabricación de chapas Le máis Forxa de metais e pulvimetalurxia Le máis Formación de fíos e resortes Le máis Formación e conformación de vidro e cerámica Le máis Fabricación aditiva e rápida Le máis Fabricación de materiais compostos e compostos Le máis Procesos de unión e montaxe e fixación Producimos pezas e conxuntos para ti e ofrecémosche os seguintes procesos de fabricación: • Moldes e pezas moldeadas de plástico e caucho. Moldeo por inxección, termoformado, moldeado termoestable, conformado ao baleiro, moldeo por soplado, moldaxe rotacional, moldaxe por vertedura, moldaxe por inserción e outros. • Extrusións de plástico, caucho e metal • Fundicións ferrosas e non ferrosas e pezas mecanizadas producidas mediante técnicas de fresado e torneado, mecanizado tipo suízo. • Pezas de pulvimetalurxia • Estampacións metálicas e non metálicas, conformación de chapa metálica, conxuntos de chapa soldada • Forxa en frío e en quente • Arames, conxuntos de arames soldados, conformación de arames • Varios tipos de resortes, formando resortes • Fabricación de engrenaxes, caixa de cambios, acoplamento, sinfín, redutor de velocidade, cilindro, correas de transmisión, cadeas de transmisión, compoñentes de transmisión • Vidro temperado e antibalas personalizado conforme aos estándares militares e da OTAN • Bolas, rodamentos, poleas e conxuntos de poleas • Válvulas e compoñentes pneumáticos como junta tórica, arandela e selos • Pezas e conxuntos de vidro e cerámica, compoñentes herméticos e estancos ao baleiro, unión metal-cerámica e cerámica-cerámica. • Varios tipos de conxuntos mecánicos, optomecánicos, electromecánicos, optoelectrónicos. • Unión metal-goma, metal-plástico • Tubos e tubos, conformación de tubos, dobrado e conxuntos de tubos personalizados, fabricación de fol. • Fabricación de fibra de vidro • Soldadura mediante diversas técnicas como soldadura por puntos, soldadura láser, MIG, TIG. Soldadura por ultrasóns para pezas plásticas. • Gran variedade de tratamentos de superficie e acabados superficiais, como o acondicionamento de superficies para mellorar a adhesión, a deposición de fina capa de óxido para mellorar a adhesión do revestimento, chorro de area, película química, anodizado, nitruración, recubrimento en po, revestimento por pulverización, varias técnicas avanzadas de metalización e revestimento. incluíndo pulverización catódica, feixe de electróns, evaporación, recubrimentos duros como o diamante como o carbono (DLC) ou o titanio para ferramentas de corte e perforación. • Marcado e rotulación, marcado con láser en pezas metálicas, impresión en pezas de plástico e caucho Descarga o folleto dos termos comúns de enxeñaría mecánica empregados por deseñadores e enxeñeiros Construímos produtos segundo as súas especificacións e requisitos particulares. Para ofrecerche a mellor calidade, entrega e prezos, fabricamos produtos a nivel mundial en China, India, Taiwán, Filipinas, Corea do Sur, Malaisia, Sri Lanka, Turquía, Estados Unidos, Canadá, Alemaña, Reino Unido e Xapón. Isto fainos moito máis fortes e competitivos a nivel mundial que calquera outro custom manufacturer. Os nosos produtos están fabricados en ambientes certificados ISO9001:2000, QS9000, ISO14001, TS16949 e posúen a marca CE, UL e cumpren outros estándares da industria. Unha vez que sexamos designados para o seu proxecto, podemos encargarnos de toda a fabricación, montaxe, probas, cualificación, envío e aduanas como desexe. Se o prefires, podemos almacenar as túas pezas, montar kits personalizados, imprimir e etiquetar o nome e a marca da túa empresa e enviar o envío aos teus clientes. Noutras palabras, tamén podemos ser o teu centro de almacenamento e distribución se o prefire. Dado que os nosos almacéns están situados preto dos principais portos marítimos, ofrécenos vantaxes loxísticas. Por exemplo, cando os teus produtos chegan a un porto marítimo importante dos EUA, podemos transportalos directamente a un almacén próximo onde podemos almacenar, montar, fabricar kits, reetiquetar, imprimir, empaquetar segundo a túa elección e soltar. enviar aos seus clientes. Non só fornecemos produtos. A nosa empresa traballa en contratos personalizados nos que chegamos ao teu sitio, avaliamos o teu proxecto in situ e desenvolvemos unha proposta de proxecto deseñada a medida para ti. Despois enviamos o noso equipo experimentado para implementar o proxecto. Podes atopar máis información sobre o noso traballo de enxeñería en http://www.ags-engineering.com -Levamos proxectos pequenos e grandes a escala industrial. Como primeiro paso, podemos conectarte por teléfono, teleconferencia ou MSN Messenger cos membros do noso equipo de expertos, para que poidas comunicarte directamente cun experto, facer preguntas e discutir o teu proxecto. Chámanos e se é necesario viremos visitarte. PÁXINA ANTERIOR