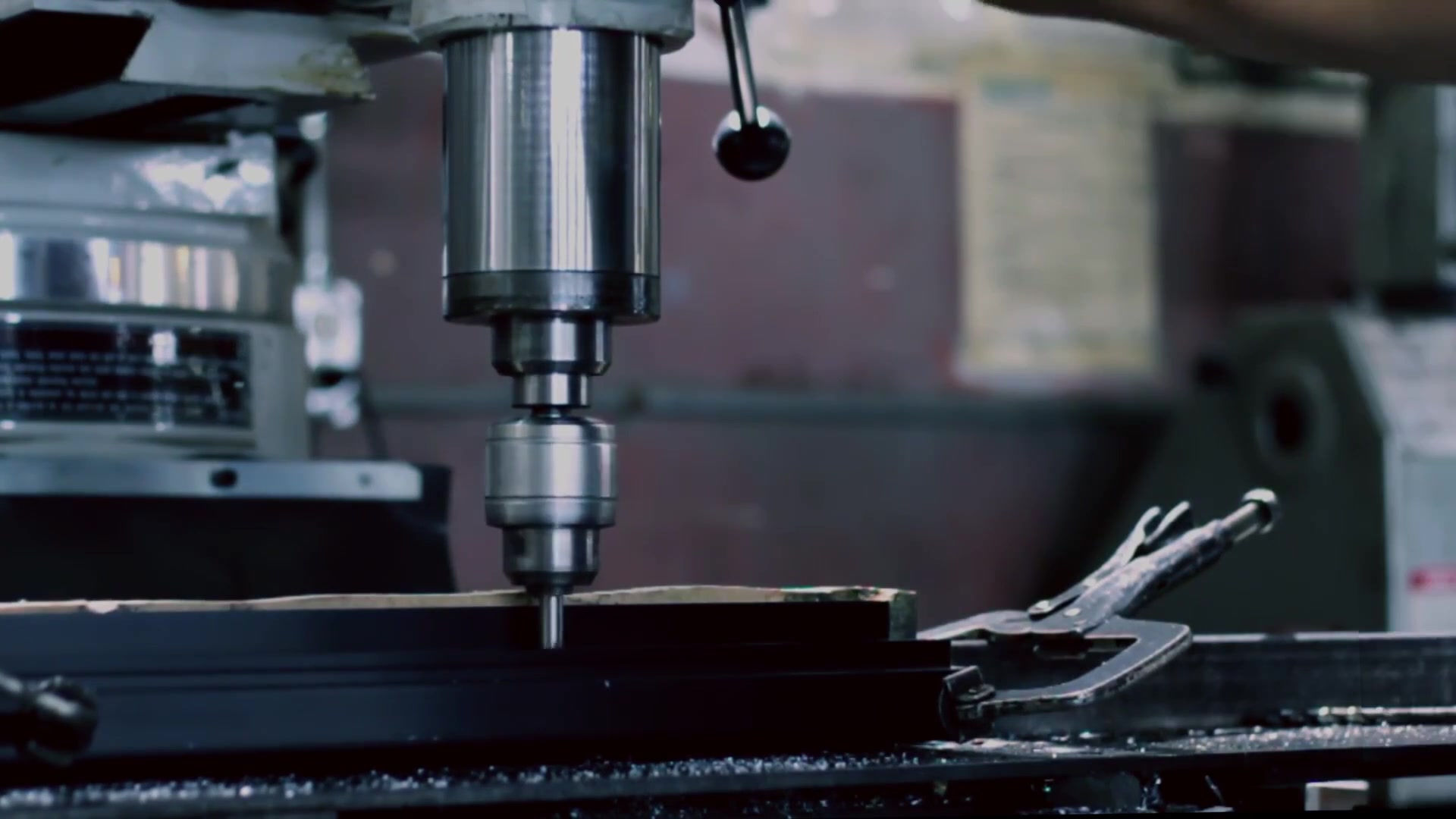
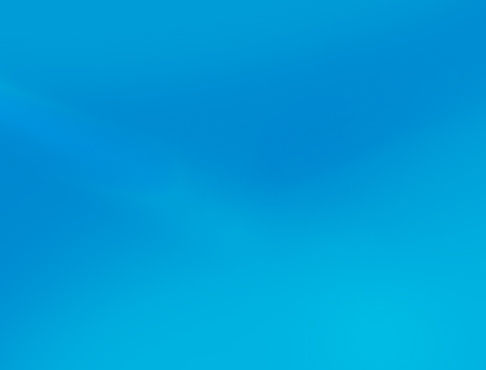
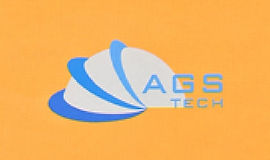
Fabricante global personalizado, integrador, consolidador, socio de outsourcing para unha ampla variedade de produtos e servizos.
Somos a súa fonte única para a fabricación, fabricación, enxeñaría, consolidación, integración e subcontratación de produtos e servizos fabricados a medida e dispoñibles.
Escolla o seu idioma
-
Fabricación personalizada
-
Fabricación por contrato nacional e global
-
Outsourcing de Manufactura
-
Compras domésticas e globais
-
Consolidación
-
Integración de enxeñería
-
Servizos de Enxeñaría
Search Results
164 results found with an empty search
- Mesomanufacturing,Mesoscale Manufacturing,Miniature Device Fabrication
Mesomanufacturing - Mesoscale Manufacturing - Miniature Device Fabrication - Tiny Motors - AGS-TECH Inc. - New Mexico Fabricación a Mesoescala / Mesofabricación Con técnicas de produción convencionais producimos estruturas a "macroescala" relativamente grandes e visibles a simple vista. Con MESOMANUFACTURING non obstante, producimos compoñentes para dispositivos en miniatura. Mesomanufacturing tamén se coñece como MESOSCALE MANUFACTURING or_cc781905-9400-05-05-05-05-05-05-05-05-13 A mesofabricación se solapa tanto á macro como á microfabricación. Exemplos de mesofabricación son audífonos, stents, motores moi pequenos. O primeiro enfoque na mesofabricación é reducir os procesos de macrofabricación. Por exemplo un pequeno torno cunhas dimensións nas poucas ducias de milímetros e un motor de 1,5 W que pesa 100 gramos é un bo exemplo de mesofabricación onde se produciu a redución de escala. O segundo enfoque é escalar os procesos de microfabricación. Como exemplo, os procesos LIGA pódense ampliar e entrar no ámbito da mesofabricación. Os nosos procesos de mesofabricación están cubrindo a brecha entre os procesos MEMS baseados en silicio e o mecanizado en miniatura convencional. Os procesos a mesoescala poden fabricar pezas bidimensionais e tridimensionais con características de tamaño de micras en materiais tradicionais como aceiro inoxidable, cerámica e vidro. Os procesos de mesofabricación que temos actualmente dispoñibles inclúen pulverización catódica con feixe iónico enfocado (FIB), microfresado, microtorneado, ablación con láser excimer, ablación con láser de femtosegundo e mecanizado de micro electrodescarga (EDM). Estes procesos de mesoescala empregan tecnoloxías de mecanizado subtractivo (é dicir, eliminación de material), mentres que o proceso LIGA é un proceso de mesoescala aditivo. Os procesos de mesofabricación teñen diferentes capacidades e especificacións de rendemento. As especificacións de rendemento de mecanizado de interese inclúen o tamaño mínimo das características, a tolerancia das características, a precisión da localización das características, o acabado superficial e a taxa de eliminación de material (MRR). Temos a capacidade de mesofabricar compoñentes electromecánicos que requiren pezas a mesoescala. As pezas de mesoescala fabricadas mediante procesos de mesofabricación substractiva teñen propiedades tribolóxicas únicas debido á variedade de materiais e ás condicións de superficie producidas polos diferentes procesos de mesofabricación. Estas tecnoloxías de mecanizado de mesoescala sustractivos achégannos preocupacións relacionadas coa limpeza, a montaxe e a triboloxía. A limpeza é vital na mesofabricación porque a sucidade a mesoescala e o tamaño das partículas de restos creados durante o proceso de mesomecanizado poden ser comparables ás características de mesoescala. O fresado e o torneado a mesoescala poden crear virutas e rebabas que poden bloquear buratos. A morfoloxía superficial e as condicións de acabado superficial varían moito dependendo do método de mesofabricación. As pezas a mesoescala son difíciles de manexar e aliñar, o que fai da montaxe un desafío que a maioría dos nosos competidores non poden superar. As nosas taxas de rendemento na mesofabricación son moi superiores ás dos nosos competidores, o que nos dá a vantaxe de poder ofrecer mellores prezos. PROCESOS DE MECANIZADO A MESOSCALA: As nosas principais técnicas de mesofabricación son Focused Ion Beam (FIB), microfresado e microtorneado, mesomecanizado con láser, microEDM (mecanizado de electrodescarga). Mesofabricación mediante feixe iónico enfocado (FIB), microfresado e microtorneado: o FIB pulveriza material dunha peza de traballo mediante un bombardeo de feixe de iones de galio. A peza de traballo está montada nun conxunto de etapas de precisión e colócase nunha cámara de baleiro debaixo da fonte de galio. As etapas de traslación e rotación na cámara de baleiro fan que o feixe de ións Galio dispoña de varias localizacións na peza de traballo para a mesofabricación FIB. Un campo eléctrico sintonizable explora o feixe para cubrir unha área proxectada predefinida. Un potencial de alta tensión fai que unha fonte de ións galio acelere e choque coa peza de traballo. As colisións eliminan átomos da peza de traballo. O resultado do proceso de meso-mecanizado FIB pode ser a creación de facetas case verticais. Algúns FIB dispoñibles teñen diámetros de feixe tan pequenos como 5 nanómetros, o que fai que o FIB sexa unha máquina capaz de mesoescala e incluso microescala. Montamos microfresadoras en fresadoras de alta precisión para mecanizar canles en aluminio. Usando FIB podemos fabricar ferramentas de microtorneado que logo se poden usar nun torno para fabricar varillas de rosca fina. Noutras palabras, FIB pódese usar para mecanizar ferramentas duras ademais de funcións de mesomecanizado directamente sobre a peza final. A baixa taxa de eliminación de material fixo que o FIB sexa pouco práctico para mecanizar directamente grandes características. As ferramentas duras, con todo, poden eliminar o material a un ritmo impresionante e son o suficientemente duradeiros para varias horas de tempo de mecanizado. Non obstante, o FIB é práctico para mecanizar directamente formas complexas tridimensionais que non requiren unha taxa de eliminación substancial de material. A lonxitude de exposición e o ángulo de incidencia poden afectar moito á xeometría das características mecanizadas directamente. Mesofabricación con láser: os láseres excímeros úsanse para a mesofabricación. O láser excimer mecaniza o material pulsándoo con pulsos de nanosegundos de luz ultravioleta. A peza de traballo está montada en etapas de traslación de precisión. Un controlador coordina o movemento da peza de traballo en relación ao raio láser UV estacionario e coordina o disparo dos pulsos. Pódese utilizar unha técnica de proxección de máscara para definir xeometrías de mesomecanizado. A máscara insírese na parte expandida do feixe onde a fluencia do láser é demasiado baixa para eliminar a máscara. A xeometría da máscara é desamplificada a través da lente e proxéctase sobre a peza de traballo. Este enfoque pódese usar para mecanizar múltiples buratos (matriz) simultaneamente. Os nosos láseres excimer e YAG pódense usar para mecanizar polímeros, cerámicas, vidro e metais con tamaños tan pequenos como 12 micras. Un bo acoplamento entre a lonxitude de onda UV (248 nm) e a peza de traballo na mesofabricación / mesomecanizado con láser resulta en paredes de canle verticais. Un enfoque de meso-mecanizado con láser máis limpo é utilizar un láser de femtosegundo Ti-zafiro. Os restos detectables de tales procesos de mesofabricación son partículas de tamaño nanométrico. Pódense microfabricar características profundas dunha micra usando o láser de femtosegundo. O proceso de ablación con láser de femtosegundo é único en que rompe enlaces atómicos en lugar de ablación térmica do material. O proceso de mesomecanizado/micromecanizado con láser de femtosegundo ten un lugar especial na mesofabricación porque é máis limpo, capaz de micras e non é específico de material. Mesofabricación mediante Micro-EDM (mecanizado por electro-descarga): o mecanizado por electro-descarga elimina o material mediante un proceso de erosión por chispa. As nosas máquinas de micro-EDM poden producir características tan pequenas como 25 micras. Para o sumidoiro e a máquina de micro-EDM de fío, as dúas consideracións principais para determinar o tamaño da característica son o tamaño do electrodo e o espazo de sobre-bum. Están a utilizarse electrodos de pouco máis de 10 micras de diámetro e con sobrepeso de poucas micras. Crear un electrodo cunha xeometría complexa para a máquina de electroerosión con sumidoiro require coñecementos técnicos. Tanto o grafito como o cobre son populares como materiais de electrodos. Unha forma de fabricar un complicado electrodo EDM sinker para unha peza mesoescala é utilizar o proceso LIGA. O cobre, como material do electrodo, pode ser chapado en moldes LIGA. O eléctrodo LIGA de cobre pódese montar na máquina de electroerosión de cobre para a mesofabricación dunha peza nun material diferente, como aceiro inoxidable ou kovar. Ningún proceso de mesofabricación é suficiente para todas as operacións. Algúns procesos de mesoescala teñen un alcance máis amplo que outros, pero cada proceso ten o seu nicho. Na maioría das veces necesitamos unha variedade de materiais para optimizar o rendemento dos compoñentes mecánicos e estamos cómodos con materiais tradicionais como o aceiro inoxidable porque estes materiais teñen unha longa historia e foron moi ben caracterizados ao longo dos anos. Os procesos de mesofabricación permítennos utilizar materiais tradicionais. As tecnoloxías de mecanizado de mesoescala sustractiva amplían a nosa base de materiais. O desgaste pode ser un problema con algunhas combinacións de materiais na mesofabricación. Cada proceso particular de mecanizado a mesoescala afecta de forma única a rugosidade e a morfoloxía da superficie. O microfresado e o microtorneado poden xerar rebabas e partículas que poden causar problemas mecánicos. Micro-EDM pode deixar unha capa de refundición que pode ter características particulares de desgaste e fricción. Os efectos de fricción entre pezas a mesoescala poden ter puntos de contacto limitados e non están modelados con precisión polos modelos de contacto de superficie. Algunhas tecnoloxías de mecanizado a mesoescala, como a micro-EDM, están bastante maduras, en oposición a outras, como o meso-mecanizado con láser de femtosegundo, que aínda requiren un desenvolvemento adicional. CLICK Product Finder-Locator Service PÁXINA ANTERIOR
- Fasteners including Anchors, Bolts, Nuts, Pin Fasteners, Rivets, Rods
Fasteners including Anchors, Bolts, Nuts, Pin Fasteners, Rivets, Rods, Screws, Sockets, Springs, Struts, Clamps, Washers, Weld Fasteners, Hangers from AGS-TECH Fabricación de Suxeidores Fabricamos FASTENERS under TS16949, sistema de xestión de calidade ISO9001 segundo estándares internacionais como ISO, DIN, MIL, DIN, MIL. Todos os nosos elementos de fixación son enviados xunto con certificacións de materiais e informes de inspección. Fornecemos elementos de suxeición para uso comercial e de fabricación personalizada segundo os seus debuxos técnicos no caso de precisar algo diferente ou especial. Ofrecemos servizos de enxeñería no deseño e desenvolvemento de fixadores especiais para as súas aplicacións. Algúns dos principais tipos de fixación que ofrecemos son: • Áncoras • Parafusos • Hardware • Unhas • Froitos secos • Suxeidores de pasadores • Remaches • Varas • Parafusos • Suxeicións de seguridade • Parafusos de fixación • Enchufes • Mananciais • Puntales, abrazaderas e colgadores • Lavadoras • Suxeidores de soldadura - PREME AQUÍ para descargar o catálogo de porcas de remache, remaches cegos, porcas de inserción, porcas de nylon, porcas soldadas, porcas de brida - PREME AQUÍ para descargar información adicional-1 sobre porcas de remache - PREME AQUÍ para descargar información adicional-2 sobre porcas de remache - PREME AQUÍ para descargar o catálogo dos nosos parafusos e porcas de titanio - FAI CLIC AQUÍ para descargar o noso catálogo que contén algúns elementos de fixación e hardware populares dispoñibles para a industria electrónica e informática. Os nosos THREADED FASTENERS pódense enroscar tanto internamente como externamente e teñen varias formas, incluíndo: - Rosca métrica ISO - ACME - Rosca de parafuso nacional americana (tamaños de polgadas) - Rosca de parafuso nacional unificada (tamaños de polgadas) - Verme - Praza - Artigo - Contraforte Os nosos fixadores roscados están dispoñibles con roscas para dereitas e zurdas, así como con roscas simples e múltiples. Tanto roscas de polgadas como roscas métricas están dispoñibles para fixadores. Para fixadores roscados en polgadas están dispoñibles as clases de rosca exterior 1A, 2A e 3A, así como as clases de rosca interna 1B, 2B e 3B. Estas clases de rosca en polgadas difiren na cantidade de tolerancias e tolerancias. Clases 1A e 1B: Estes fixadores producen o axuste máis solto na montaxe. Utilízanse onde se necesita facilidade de montaxe e desmontaxe, como parafusos da cociña e outros parafusos e porcas. Clases 2A e 2B: Estes elementos de fixación son aptos para produtos comerciais comúns e pezas intercambiables. Os parafusos e parafusos típicos da máquina son exemplos. Clases 3A e 3B: Estes fixadores están deseñados para produtos comerciais de calidade excepcional onde se require un axuste perfecto. O custo dos fixadores con fíos nesta clase é maior. Para fixadores de rosca métrica, temos dispoñibles rosca gruesa, rosca fina e unha serie de pasos constantes. Serie de rosca gruesa: Esta serie de fixadores está pensada para o seu uso en traballos de enxeñería xeral e aplicacións comerciais. Serie de rosca fina: Esta serie de fixadores é para uso xeral onde se necesita unha rosca máis fina que a rosca grosa. En comparación co parafuso de rosca grosa, o parafuso de rosca fina é máis forte tanto en resistencia á tracción como á torsión e é menos probable que se afrougue baixo a vibración. Para o paso de fixación e o diámetro da cresta, temos unha serie de graos de tolerancia, así como posicións de tolerancia dispoñibles. ROSCAS DE TUBO: Ademais dos elementos de fixación, podemos mecanizar roscas en tubos segundo a designación proporcionada por vostede. Asegúrate de indicar o tamaño do fío nos teus planos técnicos para tubos personalizados. CONXUNTOS ROSCADOS: Se nos proporcionas debuxos de montaxes roscadas, podemos utilizar as nosas máquinas para fabricar elementos de fixación para mecanizar os teus conxuntos. Se non está familiarizado coas representacións de rosca de parafuso, podemos preparar os planos para vostede. SELECCIÓN DE FIXADORS: A selección do produto debería comezar idealmente na fase de deseño. Determina os obxectivos do teu traballo de fixación e consúltanos. Os nosos expertos en fixadores revisarán os seus obxectivos e circunstancias e recomendarán os fixadores axeitados ao mellor custo no lugar. Para obter a máxima eficiencia do parafuso de máquina, é necesario un coñecemento profundo das propiedades tanto dos parafusos como dos materiais fixados. Os nosos expertos en fixadores teñen estes coñecementos dispoñibles para axudarche. Precisaremos de vostede algunha información como as cargas que deben soportar os parafusos e parafusos, se a carga dos parafusos e parafusos é de tensión ou cizallamento e se o conxunto suxeito estará suxeito a choques ou vibracións. Dependendo de todos estes e doutros factores, como a facilidade de montaxe, o custo, etc., proporase o tamaño recomendado, a resistencia, a forma da cabeza, o tipo de rosca dos parafusos e fixadores. Entre os nosos parafusos roscados máis comúns atópanse TORNILLOS, PARAFÚS e TÁNS. PARAFUSOS DE MÁQUINA: Estes parafusos teñen fíos finos ou grosos e están dispoñibles cunha variedade de cabezas. Os parafusos de máquina pódense usar en buratos roscados ou con porcas. PARAFUSOS DE TAPA: Son fixadores roscados que unen dúas ou máis pezas pasando por un orificio libre nunha parte e atornillando nun orificio roscado na outra. Os parafusos tamén están dispoñibles con varios tipos de cabeza. PARAFUSOS CATIVOS: Estes fixadores permanecen unidos ao panel ou ao material principal aínda que a parte de acoplamento estea desenganchada. Os parafusos cautivos cumpren os requisitos militares, para evitar que se perdan os parafusos, para permitir unha montaxe/desmontaxe máis rápida e evitar que os parafusos soltos caian nas pezas móbiles e nos circuítos eléctricos. PARAFUSOS DE ROSCADO: Estes parafusos cortan ou forman unha rosca de acoplamento cando se introducen nos buratos preformados. Os parafusos de rosca permiten unha instalación rápida, xa que non se usan porcas e só se require o acceso desde un lado da unión. A rosca de acoplamento producida polo parafuso de rosca encaixa estreitamente coas roscas do parafuso e non é necesario espazo libre. O axuste próximo adoita manter os parafusos axustados, mesmo cando hai vibración. Os parafusos autoperforantes teñen puntos especiais para perforar e despois tocar os seus propios buratos. Non é necesario perforar nin perforar para os parafusos autoperforantes. Os parafusos de rosca utilízanse en fundición a presión de aceiro, aluminio (fundido, extruído, laminado ou moldeado), fundición, forxa, plásticos, plásticos reforzados, madeira compensada impregnada de resina e outros materiais. PARALUÑOS: Estes son parafusos roscados que pasan por orificios de separación nas pezas ensambladas e se enroscan nas porcas. ESTUCHES: Estes fixadores son eixes roscados nos dous extremos e utilízanse en montaxes. Dous tipos principais de cravos son os de dobre extremo e os continuos. En canto a outros elementos de fixación, é importante determinar que tipo de grao e acabado (chapado ou revestimento) é o máis adecuado. NUTS: Están dispoñibles porcas métricas de estilo 1 e estilo 2. Estes fixadores úsanse xeralmente con parafusos e cravos. As porcas hexagonales, as porcas hexagonales e as porcas hexagonales son populares. Tamén hai variacións dentro destes grupos. ARANDELAS: Estes fixadores realizan moitas funcións variadas en conxuntos fixados mecánicamente. As funcións das arandelas poden ser abarcar un orificio de separación de gran tamaño, proporcionar un mellor soporte para porcas e caras de parafuso, distribuír cargas en áreas máis grandes, servir como dispositivos de bloqueo para fixadores roscados, manter a presión de resistencia do resorte, protexer as superficies contra roturas, proporcionar función de selado e moito máis. . Hai moitos tipos destes elementos de fixación dispoñibles, como arandelas planas, arandelas cónicas, arandelas de resorte helicoidais, tipos de bloqueo de dentes, arandelas de resorte, tipos de propósitos especiais... etc. TORNILLOS DE PRESA: Usanse como fixadores semipermanentes para suxeitar un colar, polea ou engrenaxe nun eixe contra as forzas de rotación e translación. Estes fixadores son basicamente dispositivos de compresión. Os usuarios deben atopar a mellor combinación de forma de parafuso, tamaño e estilo de punto que proporcione o poder de suxeición necesario. Os parafusos están clasificados polo seu estilo de cabeza e o estilo de punto desexado. PORCAS DE BLOQUEO: Estes parafusos son porcas con medios internos especiais para agarrar os fixadores roscados para evitar a rotación. Podemos ver as porcas de bloqueo basicamente como porcas estándar, pero cunha función de bloqueo engadida. As porcas de bloqueo teñen moitas áreas de aplicación moi útiles, incluíndo a suxeición tubular, o uso de porcas de bloqueo en abrazaderas de resorte, o uso de porcas de bloqueo onde a montaxe está sometida a movementos vibratorios ou cíclicos que poden causar afrouxamentos, para conexións montadas por resorte onde a porca debe permanecer estacionaria ou está suxeita a axustes. . PORCAS CATIVAS OU AUTORETENTES: Esta clase de fixadores proporciona unha suxeición permanente, forte e de múltiples roscas en materiais finos. As porcas cautivas ou autosuxetivas son especialmente boas cando hai lugares cegos e pódense unir sen danar os acabados. INSERTOS: Estes parafusos son porcas de forma especial deseñadas para cumprir a función dun burato roscado en lugares cegos ou pasantes. Hai diferentes tipos dispoñibles, como insercións moldeadas, insercións autorroscantes, insercións roscadas externas e internas, insercións prensadas e insercións de material fino. FIXADORS DE SELADO: Esta clase de fixadores non só mantén dúas ou máis pezas xuntas, senón que poden ofrecer simultaneamente función de selado para gases e líquidos contra fugas. Ofrecemos moitos tipos de fixadores de selado, así como construcións de xuntas seladas deseñadas a medida. Algúns produtos populares son parafusos de selado, remaches de selado, porcas de selado e arandelas de selado. REMACHES: O remache é un método de fixación rápido, sinxelo, versátil e económico. Os remaches considéranse fixadores permanentes en oposición aos fixadores extraíbles como parafusos e parafusos. Simplemente descritos, os remaches son pasadores metálicos dúctiles inseridos a través de buratos en dúas ou máis partes e que teñen os extremos formados para suxeitar de forma segura as pezas. Dado que os remaches son fixadores permanentes, as pezas remachadas non se poden desmontar para o seu mantemento ou substitución sen tirar o remache e instalar un novo no lugar para a súa montaxe. O tipo de remaches dispoñibles son remaches grandes e pequenos, remaches para equipos aeroespaciais, remaches cegos. Como con todos os elementos de fixación que vendemos, axudamos aos nosos clientes no proceso de deseño e selección de produtos. Desde o tipo de remache axeitado para a súa aplicación, ata a velocidade de instalación, os custos no lugar, o espazamento, a lonxitude, a distancia ao bordo e moito máis, somos capaces de axudarche no proceso de deseño. Código de referencia: OICASRET-GLOBAL, OICASTICDM CLICK Product Finder-Locator Service PÁXINA ANTERIOR
- Functional Decorative Coatings - Thin Film - Thick Films - AR Coating
Functional & Decorative Coatings, Thin Film, Thick Films, Antireflective and Reflective Mirror Coating - AGS-TECH Inc. Revestimentos funcionais / Revestimentos decorativos / Película fina / Película gruesa A COATING é unha cuberta que se aplica á superficie dun obxecto. Coatings can be in the form of THIN FILM (less than 1 micron thick) or THICK FILM ( máis de 1 micra de espesor). En función da finalidade de aplicar o revestimento podemos ofrecerlle DECORATIVOS COATINGS e/ou_cc781905-58d_CC781905-5cde-3194-bb3b-136bad5cf58d_e/ou_cc781905-05-02-05-05-05 Ás veces aplicamos revestimentos funcionais para cambiar as propiedades da superficie do substrato, como a adhesión, a moxabilidade, a resistencia á corrosión ou a resistencia ao desgaste. Noutros casos, como na fabricación de dispositivos semicondutores, aplicamos os revestimentos funcionais para engadir unha propiedade completamente nova, como a magnetización ou a condutividade eléctrica, que se converten nunha parte esencial do produto acabado. Os nosos máis populares FUNCTIONAL COATINGS son: Revestimentos adhesivos: exemplos son a cinta adhesiva, o tecido de ferro. Aplícanse outros revestimentos adhesivos funcionais para cambiar as propiedades de adhesión, como tixolas antiadherentes revestidas de PTFE, imprimacións que fomentan que os revestimentos posteriores se adhiran ben. Revestimentos tribolóxicos: estes revestimentos funcionais están relacionados cos principios de fricción, lubricación e desgaste. Calquera produto onde un material desliza ou roza sobre outro vese afectado por complexas interaccións tribolóxicas. Produtos como implantes de cadeira e outras próteses artificiais lubrican de certa maneira, mentres que outros produtos están sen lubricar, como nos compoñentes deslizantes a alta temperatura onde non se poden usar lubricantes convencionais. Probouse que a formación de capas de óxido compactadas protexe contra o desgaste destas pezas mecánicas deslizantes. Os revestimentos funcionais tribolóxicos teñen enormes beneficios na industria, minimizando o desgaste dos elementos da máquina, minimizando o desgaste e as desviacións de tolerancia en ferramentas de fabricación como matrices e moldes, minimizando os requisitos de enerxía e facendo que a maquinaria e os equipos sexan máis eficientes enerxéticamente. Revestimentos ópticos: son exemplos os revestimentos antirreflectantes (AR), os revestimentos reflectantes para espellos, os revestimentos absorbentes UV para a protección dos ollos ou para aumentar a vida útil do substrato, as tintas utilizadas nalgunha iluminación de cores, os cristais tintados e as lentes de sol. Revestimentos catalíticos tales como aplicados en vidro autolimpador. Revestimentos sensibles á luz usado para facer produtos como películas fotográficas Revestimentos protectores: pódense considerar que as pinturas protexen os produtos ademais de ser decorativas. Os revestimentos antiarañazos duros en plásticos e outros materiais son un dos nosos revestimentos funcionais máis utilizados para reducir os arañazos, mellorar a resistencia ao desgaste, etc. Tamén son moi populares os revestimentos anticorrosivos como o revestimento. Outros revestimentos funcionais protectores colócanse en tecidos e papel impermeables, revestimentos de superficie antimicrobianos en ferramentas cirúrxicas e implantes. Revestimentos hidrófilos/hidrófobos: as películas finas e grosas funcionais mollantes (hidrofílicas) e deshumectantes (hidrófobas) son importantes en aplicacións nas que a absorción de auga se desexa ou non se desexa. Usando tecnoloxía avanzada podemos alterar as superficies dos seus produtos, para que sexan facilmente mollables ou non. As aplicacións típicas son en téxtiles, apósitos, botas de coiro, produtos farmacéuticos ou cirúrxicos. A natureza hidrófila refírese a unha propiedade física dunha molécula que pode unirse transitoriamente coa auga (H2O) mediante enlaces de hidróxeno. Isto é termodinámicamente favorable e fai que estas moléculas sexan solubles non só en auga, senón tamén noutros disolventes polares. As moléculas hidrófilas e hidrófobas tamén se coñecen como moléculas polares e moléculas non polares, respectivamente. Revestimentos magnéticos: estes revestimentos funcionais engaden propiedades magnéticas como é o caso dos disquetes magnéticos, casetes, bandas magnéticas, almacenamento magnetoóptico, soportes de gravación indutivos, sensores magnetoresist e cabezas de película fina dos produtos. As películas delgadas magnéticas son láminas de material magnético con espesores de poucos micrómetros ou menos, utilizadas principalmente na industria electrónica. As películas delgadas magnéticas poden ser recubrimentos funcionais monocristalino, policristalino, amorfo ou multicapa na disposición dos seus átomos. Utilízanse películas ferromagnéticas e ferrimagnéticas. Os revestimentos funcionais ferromagnéticos adoitan ser aliaxes a base de metais de transición. Por exemplo, o permalloy é unha aliaxe de níquel e ferro. Os revestimentos funcionais ferrimagnéticos, como os granates ou as películas amorfas, conteñen metais de transición como ferro ou cobalto e terras raras e as propiedades ferrimagnéticas son vantaxosas en aplicacións magnetoópticas onde se pode acadar un momento magnético global baixo sen un cambio significativo na temperatura de Curie. . Algúns elementos sensores funcionan no principio de cambio nas propiedades eléctricas, como a resistencia eléctrica, cun campo magnético. Na tecnoloxía de semicondutores, o cabezal magnetoresist usado na tecnoloxía de almacenamento en disco funciona con este principio. Obsérvanse sinais magnetoresist moi grandes (magnetorresistencia xigante) en multicapas magnéticas e compostos que conteñen un material magnético e non magnético. Revestimentos eléctricos ou electrónicos: estes revestimentos funcionais engaden propiedades eléctricas ou electrónicas como a condutividade para fabricar produtos como resistencias, propiedades de illamento como no caso dos revestimentos de fíos magnéticos utilizados nos transformadores. RECUBRIMIENTOS DECORATIVOS: Cando falamos de revestimentos decorativos as opcións só están limitadas pola túa imaxinación. Tanto os revestimentos de tipo película grosa como fina foron deseñados e aplicados con éxito no pasado aos produtos dos nosos clientes. Independentemente da dificultade da forma xeométrica e do material do substrato e das condicións de aplicación, sempre somos capaces de formular a química, aspectos físicos como o código Pantone exacto de cor e o método de aplicación para os revestimentos decorativos desexados. Tamén son posibles patróns complexos que inclúen formas ou cores diferentes. Podemos facer que as súas pezas de polímero de plástico parezan metálicas. Podemos colorear extrusións anodizadas con varios patróns e nin sequera parecerá anodizada. Podemos revestir de espello unha parte de forma estraña. Ademais pódense formular revestimentos decorativos que tamén actuarán como revestimentos funcionais ao mesmo tempo. Calquera das técnicas de deposición de películas finas e grosas que se mencionan a continuación usadas para revestimentos funcionais pódese utilizar para revestimentos decorativos. Aquí tes algúns dos nosos revestimentos decorativos populares: - Revestimentos decorativos de película fina PVD - Revestimentos decorativos electrochapados - Revestimentos decorativos de película fina CVD e PECVD - Revestimentos Decorativos por Evaporación Térmica - Revestimento decorativo roll-to-roll - Revestimentos decorativos de interferencia de óxidos E-Beam - Revestimento iónico - Evaporación de arco catódico para revestimentos decorativos - PVD + Fotolitografía, chapado en oro pesado sobre PVD - Revestimentos en aerosois para a cor de vidro - Revestimento antideslucido - Sistemas decorativos de cobre-níquel-cromo - Pintura decorativa en polvo - Pintura decorativa, formulacións de pintura a medida usando pigmentos, recheos, dispersante de sílice coloidal... etc. Se nos contactas cos teus requisitos de revestimentos decorativos, podemos ofrecerche a nosa opinión de expertos. Temos ferramentas avanzadas como lectores de cores, comparadores de cores... etc. para garantir unha calidade constante dos seus revestimentos. PROCESOS DE REVESTIMIENTO DE PELÍCULA FINA E GROSA: Aquí están as nosas técnicas máis utilizadas. Electrochapado/Chapado químico (cromo duro, níquel químico) A galvanoplastia é o proceso de enchapamento dun metal sobre outro por hidrólise, con fins decorativos, prevención da corrosión dun metal ou outros fins. A galvanoplastia permítenos utilizar metais económicos como o aceiro ou o cinc ou os plásticos para a maior parte do produto e despois aplicar distintos metais no exterior en forma de película para unha mellor aparencia, protección e outras propiedades desexadas para o produto. O revestimento electroless, tamén coñecido como revestimento químico, é un método de revestimento non galvánico que implica varias reaccións simultáneas nunha solución acuosa, que ocorren sen o uso de enerxía eléctrica externa. A reacción realízase cando un axente reductor libera hidróxeno e se oxida, producindo así unha carga negativa na superficie da peza. As vantaxes destas películas finas e grosas son a boa resistencia á corrosión, a baixa temperatura de procesamento, a posibilidade de depositarse en orificios, ranuras... etc. As desvantaxes son a limitada selección de materiais de revestimento, a natureza relativamente branda dos revestimentos, os baños de tratamento contaminantes que son necesarios. incluíndo produtos químicos como cianuro, metais pesados, fluoruros, aceites, precisión limitada da replicación superficial. Procesos de difusión (nitruración, nitrocarburación, boro, fosfatación, etc.) Nos fornos de tratamento térmico, os elementos difusos adoitan orixinarse de gases que reaccionan a altas temperaturas coas superficies metálicas. Esta pode ser unha reacción térmica e química pura como consecuencia da disociación térmica dos gases. Nalgúns casos, os elementos difusos orixínanse de sólidos. As vantaxes destes procesos de revestimento termoquímico son unha boa resistencia á corrosión, unha boa reproducibilidade. As desvantaxes destes son os revestimentos relativamente brandos, a selección limitada do material base (que debe ser adecuado para a nitruración), os longos tempos de procesamento, os riscos ambientais e para a saúde implicados, a esixencia do tratamento posterior. CVD (Deposición Química en Vapor) CVD é un proceso químico usado para producir revestimentos sólidos de alta calidade e alto rendemento. O proceso tamén produce películas finas. Nunha CVD típica, os substratos están expostos a un ou máis precursores volátiles, que reaccionan e/ou se descompoñen na superficie do substrato para producir a película delgada desexada. As vantaxes destas películas finas e grosas son a súa alta resistencia ao desgaste, o potencial de producir de xeito económico revestimentos máis grosos, a súa idoneidade para orificios, ranuras, etc. As desvantaxes dos procesos CVD son as súas altas temperaturas de procesamento, a dificultade ou imposibilidade de revestimentos con múltiples metais (como TiAlN), o redondeo de bordos, o uso de produtos químicos perigosos para o medio ambiente. PACVD / PECVD (Deposición de vapor químico asistido por plasma) PACVD tamén se denomina PECVD, que significa CVD mellorada por plasma. Mentres que nun proceso de revestimento PVD os materiais de película fina e grosa se evaporan dunha forma sólida, no PECVD o revestimento resulta dunha fase gaseosa. Os gases precursores rachan no plasma para estar dispoñibles para o revestimento. As vantaxes desta técnica de deposición de película fina e grosa é que son posibles temperaturas de proceso significativamente máis baixas en comparación co CVD, deposítanse revestimentos precisos. As desvantaxes do PACVD son que só ten unha idoneidade limitada para orificios, ranuras, etc. PVD (Deposición física de vapor) Os procesos PVD son unha variedade de métodos puramente físicos de deposición ao baleiro que se usan para depositar películas finas mediante a condensación dunha forma vaporizada do material de película desexado sobre as superficies das pezas de traballo. Os revestimentos por pulverización evaporativa son exemplos de PVD. As vantaxes son que non se producen materiais e emisións prexudiciais para o medio ambiente, pódense producir unha gran variedade de revestimentos, as temperaturas do revestimento están por debaixo da temperatura final de tratamento térmico da maioría dos aceiros, revestimentos finos reproducibles con precisión, alta resistencia ao desgaste, baixo coeficiente de fricción. As desvantaxes son orificios, ranuras...etc. só se pode recubrir ata unha profundidade igual ao diámetro ou ancho da abertura, resistente á corrosión só en determinadas condicións, e para obter espesores de película uniformes, as pezas deben ser rotadas durante a deposición. A adhesión dos revestimentos funcionais e decorativos depende do substrato. Ademais, a vida útil dos revestimentos de película fina e grosa depende de parámetros ambientais como a humidade, a temperatura... etc. Por iso, antes de considerar un revestimento funcional ou decorativo, póñase en contacto connosco para a nosa opinión. Podemos escoller os materiais de revestimento e a técnica de revestimento máis axeitados para os seus substratos e aplicación e depositalos baixo os máis estritos estándares de calidade. Póñase en contacto con AGS-TECH Inc. para obter detalles sobre as capacidades de deposición de películas finas e grosas. Necesitas axuda de deseño? Necesitas prototipos? Necesitas fabricación en masa? Estamos aquí para axudarche. CLICK Product Finder-Locator Service PÁXINA ANTERIOR
- Display, Touchscreen, Monitors, LED, OLED, LCD, PDP, HMD, VFD, ELD
Display - Touchscreen - Monitors - LED - OLED - LCD - PDP - HMD - VFD - ELD - SED - Flat Panel Displays - AGS-TECH Inc. Fabricación e montaxe de pantallas e pantallas táctiles e monitores Ofrecemos: • Pantallas personalizadas, incluíndo LED, OLED, LCD, PDP, VFD, ELD, SED, HMD, Laser TV, pantalla plana das dimensións necesarias e especificacións electroópticas. Fai clic no texto destacado para descargar folletos relevantes para os nosos produtos de pantalla, pantalla táctil e monitor. Paneles de visualización LED Módulos LCD Descarga o noso folleto para monitores multitáctiles TRu. Esta liña de produtos de monitores consta dunha gama de pantallas multitáctiles de escritorio, marco aberto, delgada e de gran formato, de 15" a 70". Creados para ofrecer calidade, capacidade de resposta, atractivo visual e durabilidade, os monitores multitáctiles TRu complementan calquera solución interactiva multitáctil. Fai clic aquí para ver o prezo Se desexa ter módulos LCD deseñados e fabricados especialmente segundo os seus requisitos, enche e envíenos un correo electrónico: Formulario de deseño personalizado para módulos LCD Se desexa ter paneis LCD deseñados e fabricados especialmente segundo os seus requisitos, enche e envíenos un correo electrónico: Formulario de deseño personalizado para paneis LCD • Pantalla táctil personalizada (como o iPod) • Entre os produtos personalizados que desenvolveron os nosos enxeñeiros están: - Unha estación de medición de contraste para pantallas de cristal líquido. - Un centro de centrado informatizado para lentes de proxección de televisión Os paneis/pantallas son pantallas electrónicas utilizadas para ver datos e/ou gráficos e están dispoñibles nunha variedade de tamaños e tecnoloxías. Aquí están os significados dos termos abreviados relacionados cos dispositivos de visualización, pantalla táctil e monitor: LED: Diodo emisor de luz LCD: Pantalla de cristal líquido PDP: Panel de pantalla de plasma VFD: Pantalla fluorescente ao baleiro OLED: diodo emisor de luz orgánico ELD: Pantalla electroluminiscente SED: Pantalla de emisor de electróns de condución superficial HMD: Pantalla montada en cabeza Un beneficio significativo da pantalla OLED sobre a pantalla de cristal líquido (LCD) é que o OLED non require unha luz de fondo para funcionar. Polo tanto, a pantalla OLED consume moita menos enerxía e, cando se alimenta cunha batería, pode funcionar máis tempo en comparación coa LCD. Debido a que non hai necesidade de retroiluminación, unha pantalla OLED pode ser moito máis delgada que un panel LCD. Non obstante, a degradación dos materiais OLED limitou o seu uso como pantalla, pantalla táctil e monitor. ELD funciona excitando átomos facendo pasar unha corrente eléctrica a través deles, e facendo que ELD emita fotóns. Variando o material que se excita, pódese cambiar a cor da luz emitida. ELD constrúese usando tiras de electrodos planas e opacas que corren paralelas entre si, cubertas por unha capa de material electroluminiscente, seguidas por outra capa de electrodos, perpendiculares á capa inferior. A capa superior debe ser transparente para que a luz pase e escape. En cada intersección, o material ilumina, creando así un píxel. Os ELD úsanse ás veces como retroiluminación nos LCDs. Tamén son útiles para crear unha luz ambiental suave e para pantallas de cores baixas e de alto contraste. Unha pantalla emisora de electróns de condución de superficie (SED) é unha tecnoloxía de pantalla plana que utiliza emisores de electróns de condución de superficie para cada píxel de visualización individual. O emisor de condución superficial emite electróns que excitan un revestimento de fósforo no panel de visualización, semellante aos televisores con tubo de raios catódicos (CRT). Noutras palabras, os SED usan pequenos tubos de raios catódicos detrás de cada píxel en lugar dun tubo para toda a pantalla, e poden combinar o factor de forma delgado de LCDs e pantallas de plasma cos ángulos de visión, contraste, niveis de negro, definición de cor e píxeles superiores. tempo de resposta dos CRT. Tamén se afirma que os SED consomen menos enerxía que as pantallas LCD. Unha pantalla montada na cabeza ou pantalla montada en casco, ambas abreviadas como 'HMD', é un dispositivo de visualización, que se usa na cabeza ou como parte dun casco, que ten unha pequena óptica de visualización diante dun ou de cada ollo. Un HMD típico ten unha ou dúas pequenas pantallas con lentes e espellos semitransparentes incorporados nun casco, lentes ou visor. As unidades de visualización son pequenas e poden incluír CRT, LCDs, cristal líquido sobre silicio ou OLED. Ás veces, se despregan varias micropantallas para aumentar a resolución total e o campo de visión. Os HMD difiren en se poden mostrar só unha imaxe xerada por ordenador (CGI), mostrar imaxes en directo do mundo real ou unha combinación de ambos. A maioría dos HMD mostran só unha imaxe xerada por ordenador, ás veces chamada imaxe virtual. Algúns HMD permiten superpoñer un CGI a unha visión do mundo real. Isto ás veces denomínase realidade aumentada ou realidade mixta. A combinación da visión do mundo real con CGI pódese facer proxectando o CGI a través dun espello parcialmente reflectivo e vendo o mundo real directamente. Para espellos parcialmente reflectores, consulte a nosa páxina sobre Compoñentes ópticos pasivos. Este método adoita chamarse óptico transparente. A combinación da visión do mundo real con CGI tamén se pode facer electrónicamente aceptando vídeo dunha cámara e mesturándoo electrónicamente con CGI. Este método adoita chamarse Video See-Through. As principais aplicacións HMD inclúen militares, gobernamentais (incendios, policía, etc.) e civís/comerciales (medicina, videoxogos, deportes, etc.). Os militares, a policía e os bombeiros usan HMD para mostrar información táctica como mapas ou datos de imaxes térmicas mentres ven a escena real. Os HMD están integrados nas cabinas de helicópteros e avións de combate modernos. Están totalmente integrados co casco de voo do piloto e poden incluír viseiras protectoras, dispositivos de visión nocturna e pantallas doutros símbolos e información. Os enxeñeiros e científicos usan HMD para proporcionar vistas estereoscópicas de esquemas CAD (Computer Aided Design). Estes sistemas tamén se usan no mantemento de sistemas complexos, xa que poden darlle a un técnico unha "visión de raios X" de forma eficaz combinando gráficos por ordenador, como diagramas de sistemas e imaxes, coa visión natural do técnico. Tamén hai aplicacións en cirurxía, onde se combinan unha combinación de datos radiográficos (TAC e resonancia magnética) coa visión natural da operación do cirurxián. Pódense ver exemplos de dispositivos HMD de menor custo con xogos 3D e aplicacións de entretemento. Estes sistemas permiten que oponentes "virtuais" asomarse desde fiestras reais mentres un xogador se move. Outros desenvolvementos interesantes en tecnoloxías de visualización, pantalla táctil e monitor interesan a AGS-TECH: TV láser: A tecnoloxía de iluminación con láser seguía sendo demasiado cara para ser utilizada en produtos de consumo comercialmente viables e demasiado pobre en rendemento para substituír as lámpadas, excepto nalgúns raros proxectores de gama ultra-alta. Non obstante, máis recentemente, as empresas demostraron a súa fonte de iluminación láser para pantallas de proxección e un prototipo de "televisión láser" de retroproxección. O primeiro comercial Laser TV e posteriormente outros foron presentados. As primeiras audiencias ás que se lles mostraron clips de referencia de películas populares informaron de que quedaron abraiadas pola destreza ata agora inédita de pantallas en cor dun televisor láser. Algunhas persoas incluso o describen como demasiado intenso ata o punto de parecer artificial. Algunhas outras tecnoloxías de visualización futuras probablemente inclúen nanotubos de carbono e pantallas de nanocristais usando puntos cuánticos para facer pantallas vibrantes e flexibles. Como sempre, se nos proporcionas detalles sobre a túa esixencia e aplicación, podemos deseñar e fabricar pantallas, pantallas táctiles e monitores personalizados por ti. Fai clic aquí para descargar o folleto dos nosos medidores de panel - OICASCHINT Descarga o folleto para o noso PROGRAMA DE COLABORACIÓN DE DESEÑO Podes atopar máis información sobre o noso traballo de enxeñería en: http://www.ags-engineering.com CLICK Product Finder-Locator Service PÁXINA ANTERIOR
- Filters & Filtration Products & Membranes, USA, AGS-TECH
AGS-TECH supplies off-the-shelf and custom manufactured filters, filtration products and membranes including air purification filters, ceramic foam filters, activated carbon filters, HEPA filters, pre-filtering media and coarse filters, wire mesh and cloth filters, oil & fuel & gas filters. Filtros e produtos de filtración e membranas Ofrecemos filtros, produtos de filtración e membranas para aplicacións industriais e de consumo. Os produtos inclúen: - Filtros a base de carbón activado - Filtros planos de malla de arame feitos segundo as especificacións do cliente - Filtros de malla de arame de forma irregular feitos segundo as especificacións do cliente. - Outro tipo de filtros como filtros de aire, aceite, combustible. - Filtros de escuma cerámica e membrana cerámica para diversas aplicacións industriais en petroquímica, fabricación química, farmacéutica...etc. - Sala limpa de alto rendemento e filtros HEPA. Dispoñemos de filtros por xunto, produtos de filtración e membranas dispoñibles con varias dimensións e especificacións. Tamén fabricamos e subministramos filtros e membranas segundo as especificacións dos clientes. Os nosos produtos de filtro cumpren as normas internacionais como as normas CE, UL e ROHS. Fai clic nos links abaixo_cc781905-5cde-3194-bb3b-3194-bb3b-58d6_para seleccionar o produto que che interese. Filtros de carbón activado O carbón activado tamén chamado carbón activado é unha forma de carbón procesada para ter poros pequenos e de baixo volume que aumentan a superficie dispoñible para a adsorción ou as reaccións químicas. Debido ao seu alto grao de microporosidade, só un gramo de carbón activado ten unha superficie superior a 1.300 m2 (14.000 pés cadrados). Un nivel de activación suficiente para unha aplicación útil de carbón activado pódese acadar só desde unha superficie elevada; porén, o tratamento químico adicional adoita mellorar as propiedades de adsorción. O carbón activado úsase amplamente en filtros para purificación de gases, filtros para descafeinación, extracción de metais & purification, filtración e purificación de auga, medicamentos, tratamento de sumidoiros, filtros de aire en máscaras de gas e respiradores, filtros de aire comprimido , filtrado de bebidas alcohólicas como vodka e whisky a partir de impurezas orgánicas que poden afectar gusto,_381905-5cde-3194-bb3b-136bad5cf58d_gusto,_381905_05_05_05_05_05_05_05_05_05_05_05_05_05_05_05_05_05_05_05_05_05_05_06 -5cde-3194-bb3b-136bad5cf58d_O carbón activado é usado en varios tipos de filtros, máis habitualmente en filtros de panel, tecido non tecido, filtros tipo cartucho... etc. Podes descargar folletos dos nosos filtros de carbón activado nas seguintes ligazóns. - Filtros de purificación de aire (inclúe filtros de aire de carbón activado tipo plegado e en forma de V) Filtros de membrana cerámica Os filtros de membrana cerámica son inorgánicos, hidrófilos e son ideais para aplicacións extremas de nano, ultra e microfiltración que requiren lonxevidade, superior tolerancias de presión/temperatura e resistencia a disolventes agresivos. Os filtros de membrana cerámica son basicamente filtros de ultrafiltración ou microfiltración, utilizados para tratar augas residuais e augas a temperaturas máis elevadas. Os filtros de membrana cerámica prodúcense a partir de materiais inorgánicos como óxido de aluminio, carburo de silicio, óxido de titanio e óxido de circonio. O material do núcleo poroso da membrana fórmase primeiro mediante un proceso de extrusión que se converte na estrutura de soporte da membrana cerámica. Despois aplícanse revestimentos á cara interna ou á cara filtrante coas mesmas partículas cerámicas ou ás veces con partículas diferentes, dependendo da aplicación. Por exemplo, se o seu material principal é óxido de aluminio, tamén usamos partículas de óxido de aluminio como revestimento. O tamaño das partículas cerámicas utilizadas para o revestimento, así como o número de revestimentos aplicados determinarán o tamaño dos poros da membrana así como as características de distribución. Despois de depositar o revestimento no núcleo, prodúcese a sinterización a alta temperatura dentro dun forno, facendo que a capa de membrana sexa integrante da the estructura de soporte do núcleo. Isto ofrécenos unha superficie moi duradeira e dura. Esta unión sinterizada garante unha vida útil moi longa para a membrana. Podemos personalizar os filtros de membrana cerámica cc781905-5cde-3194-bb3b-136bad5cf58d_desde o intervalo de microfiltración ata o de ultrafiltración, variando o número de partículas de revestimento e o tamaño adecuados para o revestimento. Os tamaños de poros estándar poden variar entre 0,4 micras e 0,01 micras. Os filtros de membrana cerámica son como o vidro, moi duros e duradeiros, a diferenza das membranas poliméricas . Polo tanto, os filtros de membrana cerámica ofrecen unha resistencia mecánica moi elevada. Os filtros de membrana cerámica son químicamente inertes e pódense usar a un fluxo moi alto en comparación coas membranas poliméricas. Os filtros de membrana cerámica pódense limpar vigorosamente e son térmicamente estables. Os filtros de membrana cerámica teñen unha vida útil moi longa, aproximadamente de tres a catro veces máis en comparación coas membranas poliméricas. En comparación cos filtros poliméricos, os filtros cerámicos son moi caros, porque as aplicacións de filtración cerámica comezan onde rematan as aplicacións poliméricas. Os filtros de membrana cerámica teñen varias aplicacións, sobre todo no tratamento de augas e augas residuais moi difíciles de tratar, ou onde interveñen operacións a alta temperatura. Tamén ten amplas aplicacións en petróleo e gas, reciclaxe de augas residuais, como pretratamento para RO e para eliminar metais precipitados de calquera proceso de precipitación, para separación de auga e aceite, industria de alimentos e bebidas, microfiltración de leite, clarificación de zumes de froitas. , recuperación e recollida de nanopos e catalizadores, na industria farmacéutica, na minería onde hai que tratar os estanques de residuos desperdiciados. Ofrecemos filtros de membrana cerámica con forma de canle único e varios. AGS-TECH Inc ofréceche tanto a fabricación propia como a personalizada. Filtros de espuma cerámica Filtro de espuma cerámica is a tough escuma feito a partir de cerámica . As espumas de polímero de células abertas están impregnadas internamente con cerámica purín e despois despedido in a_cc781905-5cde-3194-bb3b-58d_badforno , deixando só material cerámico. As escumas poden consistir en varios materiais cerámicos como óxido de aluminio , unha cerámica común para altas temperaturas. Ceramic foam filters get_cc781905-5cde-bad5cf58d_Ceramic foam filters get_cc781905-5cde-bad5cf58d_Ceramic Foam Filters get_cc781905-5cde-bad5cf58d_Ceramic Foam Filters Os filtros de escuma cerámica úsanse para filtración de aliaxes de metal fundido, absorción de contaminantes ambientais , e como substrato para catalizadores requiring large internal surface area. Ceramic foam filters are hardened ceramics with pockets of air or other gases trapped in_cc781905-5cde-3194-bb3b -136bad5cf58d_poros en todo o corpo do material. Estes materiais pódense fabricar entre un 94 e un 96 % de aire en volume con resistencias a altas temperaturas, como 1700 °C. Dende que most ceramics xa son_cc781905-5cde-3194-bb3b-5836_badóxidos ou outros compostos inertes, non hai perigo de oxidación ou redución do material nos filtros de escuma cerámica. - Folleto de filtros de espuma cerámica - Guía do usuario do filtro de espuma cerámica Filtros HEPA HEPA é un tipo de filtro de aire e a abreviatura significa High-Efficiency Particulate Arrestance (HEPA). Os filtros que cumpren o estándar HEPA teñen moitas aplicacións en salas limpas, instalacións médicas, automóbiles, avións e fogares. Os filtros HEPA deben cumprir certos estándares de eficiencia, como os establecidos polo Departamento de Enerxía dos Estados Unidos (DOE). Para cualificar como HEPA segundo os estándares gobernamentais dos Estados Unidos, un filtro de aire debe eliminar do aire que pasa 99,97 % das partículas de tamaño_cc781905-5cde-3194-bb3b-136µm_0cf358d_0cf3. A resistencia mínima do filtro HEPA ao fluxo de aire, ou caída de presión, é xeralmente especificada como 300 pascais (0,044 psi) ao seu caudal nominal. A filtración HEPA funciona por medios mecánicos e non se parece aos métodos de filtración iónica e ozono que usan ións negativos e gas ozono respectivamente. Polo tanto, as posibilidades de posibles efectos secundarios pulmonares, como asma e alerxias, son moi inferiores cos sistemas de filtrado HEPA. Os filtros HEPA tamén se usan nas aspiradoras de alta calidade de forma eficaz para protexer aos usuarios da asma e as alerxias, porque o filtro HEPA atrapa partículas finas como poles e feces de ácaros do po que provocan síntomas de alerxia e asma. Póñase en contacto connosco se desexa obter a nosa opinión sobre o uso de filtros HEPA para unha aplicación ou proxecto en particular. Pode descargar os folletos dos nosos produtos HEPA. a continuación. Se non atopa o tamaño ou a forma adecuados que precisa, estaremos encantados de deseñar e fabricar filtros HEPA personalizados para a súa aplicación especial. - Filtros de purificación de aire (inclúe filtros HEPA) Filtros gruesos e medios de prefiltración Os filtros grosos e os medios de prefiltración utilízanse para bloquear grandes residuos. Son de importancia crítica porque son baratos e protexen os filtros de grao superior máis caros de que se contaminen con partículas grosas e contaminantes. Sen filtros grosos e medios de prefiltración, o custo do filtrado sería moito máis elevado xa que teriamos que cambiar os filtros finos con moita máis frecuencia. A maioría dos nosos filtros grosos e medios de prefiltración están feitos de fibras sintéticas con diámetros e tamaños de poros controlados. Os materiais filtrantes grosos inclúen o popular material poliéster. O grao de eficiencia do filtrado é un parámetro importante para comprobar antes de escoller un medio de filtrado/prefiltrado groso en particular. Outros parámetros e características que hai que comprobar son se o medio de filtrado previo é lavable, reutilizable, valor de detención, resistencia ao fluxo de aire ou fluído, fluxo de aire nominal, po e partículas capacidade de retención, resistencia á temperatura, inflamabilidade , características de caída de presión, dimensional e especificación relacionada coa forma... etc. Póñase en contacto connosco para obter unha opinión antes de escoller os filtros grosos e os medios de prefiltrado adecuados para os seus produtos e sistemas. - Folleto de malla de arame e tea (inclúe información sobre as nosas capacidades de fabricación de filtros de tea e malla de arame. As teas metálicas e non metálicas pódense utilizar como filtros grosos e medios de prefiltración nalgunhas aplicacións) - Filtros de purificación de aire (inclúe filtros gruesos e medios prefiltrantes para o aire) Filtros de aceite, combustible, gas, aire e auga AGS-TECH Inc. deseña e fabrica filtros de aceite, combustible, gas, aire e auga segundo os requisitos do cliente para maquinaria industrial, automóbiles, lanchas a motor, motocicletas... etc. Os filtros de aceite están deseñado para eliminar contaminantes de aceite de motor , aceite de transmisión , aceite lubricante , aceite hidráulico . Os filtros de aceite utilízanse en moitos tipos diferentes de maquinaria hidráulica . A produción de petróleo, a industria do transporte e as instalacións de reciclaxe tamén empregan filtros de aceite e combustible nos seus procesos de fabricación. Os pedidos OEM son benvidos, etiquetamos, serigrafía, marcamos con láser aceite, combustible, gas, aire e auga. filtros segundo as súas necesidades, poñemos os seus logotipos no produto e paquete segundo as súas necesidades e requisitos. Se o desexa, pódense personalizar os materiais de carcasa dos seus filtros de aceite, combustible, gas, aire e auga dependendo da súa aplicación particular. A continuación pódese descargar información sobre os nosos filtros estándar de aceite, combustible, gas, aire e auga. - Aceite - Combustible - Gas - Aire - Folleto de selección de filtros de auga para automóbiles, motocicletas, camións e autobuses - Filtros de purificación de aire Membranas A membrane é unha barreira selectiva; permite que unhas cousas pasen pero para outras. Tales cousas poden ser moléculas, ións ou outras partículas pequenas. Xeralmente, as membranas poliméricas utilízanse para separar, concentrar ou fraccionar unha gran variedade de líquidos. As membranas serven como unha delgada barreira entre fluídos miscibles que permiten o transporte preferente dun ou máis compoñentes da alimentación cando se aplica unha forza motriz, como un diferencial de presión. Ofrecemos un conxunto de membranas de nanofiltración, ultrafiltración e microfiltración deseñadas para proporcionar fluxo e rexeitamento óptimos e que se poden personalizar para satisfacer os requisitos exclusivos de aplicacións específicas de procesos. Os sistemas de filtración son o corazón de moitos procesos de separación. A selección de tecnoloxía, o deseño de equipos e a calidade da fabricación son factores críticos para o éxito final dun proxecto. Para comezar, debe seleccionarse a configuración adecuada da membrana. Contacta connosco para axudar nos teus proxectos. PÁXINA ANTERIOR
- Microwave Components & Subassembly, Microwave Circuits, RF Transformer
Microwave Components - Subassembly - Microwave Circuits - RF Transformer - LNA - Mixer - Fixed Attenuator - AGS-TECH Fabricación e montaxe de compoñentes e sistemas de microondas Fabricamos e subministramos: Electrónica de microondas, incluíndo díodos de microondas de silicio, díodos de punto de contacto, díodos schottky, díodos PIN, díodos varactor, díodos de recuperación de pasos, circuítos integrados de microondas, divisores/combinadores, mesturadores, acopladores direccionais, detectores, moduladores I/Q, filtros, atenuadores fixos, RF transformadores, desfasadores de simulación, LNA, PA, interruptores, atenuadores e limitadores. Tamén fabricamos subconxuntos e conxuntos de microondas personalizados segundo as necesidades dos usuarios. Descarga os nosos folletos de compoñentes e sistemas de microondas nas seguintes ligazóns: Compoñentes de RF e microondas Guías de ondas de microondas - Compoñentes coaxiais - Antenas de ondas milimétricas 5G - LTE 4G - LPWA 3G - 2G - GPS - GNSS - WLAN - BT - Combo - Antena ISM - Folleto Ferritas suaves - Núcleos - Toroides - Produtos de supresión EMI - Folleto de transpondedores e accesorios RFID Descarga o folleto para o noso PROGRAMA DE COLABORACIÓN DE DESEÑO As microondas son ondas electromagnéticas con lonxitudes de onda que varían de 1 mm a 1 m, ou frecuencias entre 0,3 GHz e 300 GHz. O rango de microondas inclúe frecuencia ultraalta (UHF) (0,3–3 GHz), frecuencia súper alta (SHF) (3–3 GHz). 30 GHz) e sinais de frecuencia extremadamente alta (EHF) (30–300 GHz). Usos da tecnoloxía de microondas: SISTEMAS DE COMUNICACIÓN: Antes da invención da tecnoloxía de transmisión por fibra óptica, a maioría das chamadas telefónicas de longa distancia facíanse mediante enlaces punto a punto de microondas a través de sitios como AT&T Long Lines. A partir de principios da década de 1950, utilizouse a multiplexación por división de frecuencia para enviar ata 5.400 canles telefónicas en cada canle de radio de microondas, con ata dez canles de radio combinadas nunha antena para o salto ao seguinte sitio, que estaba a 70 km de distancia. . Os protocolos de LAN sen fíos, como Bluetooth e as especificacións IEEE 802.11, tamén usan microondas na banda ISM de 2,4 GHz, aínda que 802.11a usa frecuencias de banda ISM e U-NII na franxa de 5 GHz. Os servizos de acceso a Internet sen fíos de longo alcance con licenza (ata uns 25 km) pódense atopar en moitos países no rango de 3,5 a 4,0 GHz (non en Estados Unidos). Redes de área metropolitana: protocolos MAN, como WiMAX (Worldwide Interoperability for Microwave Access) baseado na especificación IEEE 802.16. A especificación IEEE 802.16 foi deseñada para operar entre frecuencias de 2 a 11 GHz. As implementacións comerciais están nos rangos de frecuencia de 2,3 GHz, 2,5 GHz, 3,5 GHz e 5,8 GHz. Acceso sen fíos de banda ancha móbil de área ampla: os protocolos MBWA baseados en especificacións estándares como IEEE 802.20 ou ATIS/ANSI HC-SDMA (por exemplo, iBurst) están deseñados para funcionar entre 1,6 e 2,3 GHz para proporcionar mobilidade e características de penetración no edificio similares aos teléfonos móbiles. pero cunha eficiencia espectral moito maior. Parte do espectro de frecuencias de microondas inferior úsase na televisión por cable e no acceso a Internet por cable coaxial, así como na televisión. Tamén algunhas redes de telefonía móbil, como GSM, tamén usan frecuencias de microondas máis baixas. A radio de microondas emprégase nas transmisións de radiodifusión e telecomunicacións porque, debido á súa curta lonxitude de onda, as antenas altamente directivas son máis pequenas e, polo tanto, máis prácticas do que serían a frecuencias máis baixas (longitudes de onda máis longas). Tamén hai máis ancho de banda no espectro de microondas que no resto do espectro radioeléctrico; o ancho de banda utilizable por debaixo de 300 MHz é inferior a 300 MHz mentres que moitos GHz poden usarse por riba dos 300 MHz. Normalmente, os microondas úsanse nos telexornais para transmitir un sinal desde un lugar remoto a unha estación de televisión nunha furgoneta especialmente equipada. As bandas C, X, Ka ou Ku do espectro de microondas utilízanse no funcionamento da maioría dos sistemas de comunicacións por satélite. Estas frecuencias permiten un gran ancho de banda ao mesmo tempo que evitan as frecuencias UHF ateigadas e mantéñense por debaixo da absorción atmosférica das frecuencias EHF. A televisión por satélite funciona na banda C para o tradicional servizo de satélite fixo de antena grande ou na banda Ku para a transmisión directa por satélite. Os sistemas de comunicación militares funcionan principalmente sobre enlaces X ou Ku Band, e a banda Ka se usa para Milstar. DETECCIÓN REMOTA: Os radares usan a radiación de frecuencia de microondas para detectar o alcance, a velocidade e outras características dos obxectos remotos. Os radares úsanse amplamente para aplicacións que inclúen o control do tráfico aéreo, a navegación de barcos e o control do límite de velocidade do tráfico. Ademais dos decices ultrasónicos, ás veces úsanse osciladores de diodos Gunn e guías de ondas como detectores de movemento para abridores automáticos de portas. Gran parte da radioastronomía utiliza tecnoloxía de microondas. SISTEMAS DE NAVEGACIÓN: Os sistemas globais de navegación por satélite (GNSS), incluíndo o sistema de posicionamento global (GPS) estadounidense, o Beidou chinés e o GLONASS ruso emiten sinais de navegación en varias bandas entre aproximadamente 1,2 GHz e 1,6 GHz. POTENCIA: Un forno de microondas fai pasar a radiación de microondas (non ionizante) (a unha frecuencia próxima a 2,45 GHz) a través dos alimentos, provocando quecemento dieléctrico pola absorción de enerxía na auga, as graxas e o azucre contidos nos alimentos. Os fornos de microondas fixéronse comúns despois do desenvolvemento de magnetróns de cavidade económicos. O quecemento por microondas úsase amplamente nos procesos industriais para secar e curar produtos. Moitas técnicas de procesamento de semicondutores usan microondas para xerar plasma con fins como o gravado con ións reactivos (RIE) e a deposición química de vapor potenciada por plasma (PECVD). Os microondas pódense utilizar para transmitir enerxía a longas distancias. A NASA traballou na década de 1970 e principios dos 80 para investigar as posibilidades de usar sistemas de satélites de enerxía solar (SPS) con grandes matrices solares que transmitirían enerxía ata a superficie terrestre a través de microondas. Algunhas armas lixeiras usan ondas milimétricas para quentar unha fina capa de pel humana a unha temperatura intolerable para que a persoa obxecto de aprendizaxe se afasta. Unha ráfaga de dous segundos do feixe enfocado de 95 GHz quenta a pel a unha temperatura de 130 °F (54 °C) a unha profundidade de 1/64 de polgada (0,4 mm). A Forza Aérea e os Marines dos Estados Unidos usan este tipo de Sistema de Denegación Activa. Se o teu interese está na enxeñería e a investigación e desenvolvemento, visita o noso sitio de enxeñería http://www.ags-engineering.com CLICK Product Finder-Locator Service PÁXINA ANTERIOR
- Computer Networking Equipment, Intermediate Systems, InterWorking Unit
Computer Networking Equipment - Intermediate Systems - InterWorking Unit - IWU - IS - Router - Bridge - Switch - Hub available from AGS-TECH Inc. Equipos de rede, dispositivos de rede, sistemas intermedios, Unidade de Intertraballo OS DISPOSITIVOS DE REDES DE COMPUTADORES son equipos que median datos en redes informáticas. Os dispositivos de redes informáticas tamén se denominan EQUIPOS DE REDE, SISTEMAS INTERMEDIOS (IS) ou UNIDADE DE INTERFUNCIONAMENTO (IWU). Os dispositivos que son o último receptor ou que xeran datos chámanse HOST ou EQUIPO TERMINAL DE DATOS. Entre as marcas de alta calidade que ofrecemos están ATOP TECHNOLOGIES, JANZ TEC, ICP DAS e KORENIX. Descarga a nosa ATOP TECHNOLOGIES folleto do produto compacto (Descargar o produto ATOP Technologies List 2021) Descarga o noso folleto de produtos compactos da marca JANZ TEC Descarga o noso folleto de produtos compactos da marca KORENIX Descarga o noso folleto de produtos de comunicación industrial e redes da marca ICP DAS Descarga o noso conmutador Ethernet industrial da marca ICP DAS para ambientes resistentes Descarga o noso folleto de controladores integrados e DAQ de PACs da marca ICP DAS Descarga o noso folleto Industrial Touch Pad da marca ICP DAS Descarga o noso folleto sobre Módulos IO remotos e unidades de expansión IO da marca ICP DAS Descarga as nosas placas PCI e tarxetas IO da marca ICP DAS Para escoller un dispositivo de rede de grao industrial axeitado para o seu proxecto, vai á nosa tenda de informática industrial facendo CLIC AQUÍ. Descarga o folleto para o noso PROGRAMA DE COLABORACIÓN DE DESEÑO A continuación móstrase información fundamental sobre os dispositivos de rede que pode resultar útil. Lista de dispositivos de rede de ordenadores / Dispositivos de rede básicos comúns: ENRUTADOR: Este é un dispositivo de rede especializado que determina o seguinte punto de rede onde pode reenviar un paquete de datos cara ao destino do paquete. A diferenza dunha pasarela, non pode interactuar con protocolos diferentes. Funciona na capa OSI 3. PONTE: este é un dispositivo que conecta varios segmentos de rede ao longo da capa de enlace de datos. Funciona na capa OSI 2. SWITCH: este é un dispositivo que asigna o tráfico dun segmento de rede a determinadas liñas (destinos previstos) que conectan o segmento a outro segmento de rede. Polo tanto, a diferenza dun concentrador, un interruptor divide o tráfico da rede e envíao a diferentes destinos en lugar de a todos os sistemas da rede. Funciona na capa OSI 2. HUB: conecta varios segmentos Ethernet xuntos e fai que actúen como un único segmento. Noutras palabras, un concentrador proporciona ancho de banda que se comparte entre todos os obxectos. Un concentrador é un dos dispositivos de hardware máis básicos que conecta dous ou máis terminais Ethernet nunha rede. Polo tanto, só un ordenador conectado ao concentrador é capaz de transmitir á vez, ao contrario dos interruptores, que proporcionan unha conexión dedicada entre nodos individuais. Funciona na capa OSI 1. REPETITOR: É un dispositivo para amplificar e/ou rexenerar os sinais dixitais recibidos mentres os envía dunha parte a outra dunha rede. Funciona na capa OSI 1. Algúns dos nosos dispositivos de REDE HÍBRIDA: INTERRUPTOR MULTI CAPA: Este é un interruptor que, ademais de activar a capa OSI 2, ofrece funcionalidade en capas de protocolo superiores. CONVERTIDOR DE PROTOCOLOS: Este é un dispositivo de hardware que converte entre dous tipos diferentes de transmisións, como as asíncronas e as síncronas. BRIDGE ROUTER (B ROUTER): este equipo combina funcionalidades de enrutador e ponte e, polo tanto, funciona nas capas OSI 2 e 3. Estes son algúns dos nosos compoñentes de hardware e software que a maioría das veces se colocan nos puntos de conexión de diferentes redes, por exemplo, entre redes internas e externas: PROXY: este é un servizo de rede informática que permite aos clientes realizar conexións de rede indirectas con outros servizos de rede FIREWALL: Trátase dunha peza de hardware e/ou software colocada na rede para evitar o tipo de comunicacións que están prohibidas pola política de rede. TRADUCTOR DE ENDREZOS DE REDE: Servizos de rede proporcionados como hardware e/ou software que converten enderezos de rede internos a externos e viceversa. Outro hardware popular para establecer redes ou conexións de acceso telefónico: MULTIPLEXOR: Este dispositivo combina varios sinais eléctricos nun único sinal. CONTROLADOR DE INTERFAZ DE REDE: Unha peza de hardware do ordenador que permite que o ordenador conectado se comunique por rede. CONTROLADOR DE INTERFAZ DE REDE INALÁMBRICA: unha peza de hardware do ordenador que permite que o ordenador conectado se comunique mediante WLAN. MÓDEM: Este é un dispositivo que modula un sinal portador analóxico (como o son), para codificar información dixital, e que tamén demodula ese sinal portador para decodificar a información transmitida, como un ordenador que se comunica con outro ordenador a través da rede telefónica. ADAPTADOR DE TERMINAL ISDN (TA): Esta é unha pasarela especializada para a rede dixital de servizos integrados (RDSI) LINE DRIVER: Este é un dispositivo que aumenta as distancias de transmisión mediante a amplificación do sinal. Só redes de banda base. CLICK Product Finder-Locator Service PÁXINA ANTERIOR
- Micromanufacturing, Surface & Bulk Micromachining, Microscale, MEMS
Micromanufacturing - Surface & Bulk Micromachining - Microscale Manufacturing - MEMS - Accelerometers - AGS-TECH Inc. Fabricación a Microescala / Microfabricación / Micromecanizado / MEMS MICROMANUFACTURING, MICROSCALE MANUFACTURING, MICROFABRICATION or MICROMACHINING refers to our processes suitable for making tiny devices and products in the micron or microns of dimensions. Ás veces, as dimensións xerais dun produto microfabricado poden ser maiores, pero aínda usamos este termo para referirnos aos principios e procesos implicados. Usamos o enfoque de microfabricación para fabricar os seguintes tipos de dispositivos: Dispositivos microelectrónicos: exemplos típicos son os chips de semicondutores que funcionan baseándose en principios eléctricos e electrónicos. Dispositivos micromecánicos: son produtos de natureza puramente mecánica, como engrenaxes e bisagras moi pequenas. Dispositivos microelectromecánicos: utilizamos técnicas de microfabricación para combinar elementos mecánicos, eléctricos e electrónicos a escalas de lonxitude moi pequenas. A maioría dos nosos sensores están nesta categoría. Sistemas microelectromecánicos (MEMS): estes dispositivos microelectromecánicos tamén incorporan un sistema eléctrico integrado nun produto. Os nosos produtos comerciais populares nesta categoría son os acelerómetros MEMS, os sensores de airbag e os dispositivos de microespellos dixitais. Dependendo do produto que se vaia fabricar, implementamos un dos seguintes métodos principais de microfabricación: Micromecanizado a granel: este é un método relativamente máis antigo que utiliza gravados dependentes da orientación sobre silicio monocristal. O enfoque do micromecanizado a granel baséase en gravar nunha superficie e deterse en certas caras de cristal, rexións dopadas e películas gravables para formar a estrutura necesaria. Os produtos típicos que podemos microfabricar mediante a técnica de micromecanizado a granel son: - Pequenos voladizos - Groves en V en silicona para aliñamento e fixación de fibras ópticas. MICROMECANIZADO DE SUPERFICIE: Desafortunadamente, o micromecanizado a granel está restrinxido a materiais monocristalinos, xa que os materiais policristalinos non se mecanizarán a diferentes velocidades en diferentes direccións usando gravadores húmidos. Polo tanto, o micromecanizado de superficies destaca como unha alternativa ao micromecanizado a granel. Un separador ou unha capa de sacrificio como o vidro de fosfosilicato deposítase mediante o proceso CVD sobre un substrato de silicio. En xeral, as capas estruturais de película fina de polisilicio, metal, aliaxes metálicas, dieléctricos deposítanse sobre a capa espaciadora. Usando técnicas de gravado en seco, as capas estruturais de película fina son estampadas e utilízase o gravado en húmido para eliminar a capa de sacrificio, o que resulta en estruturas independentes como cantilevers. Tamén é posible utilizar combinacións de técnicas de micromecanizado a granel e de superficie para converter algúns deseños en produtos. Produtos típicos axeitados para a microfabricación mediante unha combinación das dúas técnicas anteriores: - Microlámparas de tamaño submilimétrico (da orde de tamaño de 0,1 mm) - Sensores de presión - Microbombas - Micromotores - Actuadores - Dispositivos de microfluído Ás veces, para obter estruturas verticais altas, realízase a microfabricación en grandes estruturas planas horizontalmente e despois as estruturas rótanse ou róganse en posición vertical mediante técnicas como a centrifugación ou o microensamblaxe con sondas. Non obstante, pódense obter estruturas moi altas en silicio monocristalino usando enlaces por fusión de silicio e gravado con ións reactivos profundos. O proceso de microfabricación Deep Reactive Ion Etching (DRIE) realízase en dúas obleas separadas, despois aliñadas e unidas por fusión para producir estruturas moi altas que doutro xeito serían imposibles. PROCESOS DE MICROMANUFACTURA LIGA: O proceso LIGA combina litografía de raios X, electrodeposición, moldeado e, en xeral, implica os seguintes pasos: 1. Sobre o substrato primario deposítanse unha capa de resistencia de polimetilmetacrilato (PMMA) de centos de micras de espesor. 2. O PMMA desenvólvese mediante raios X colimados. 3. O metal é electrodepositado sobre o substrato primario. 4. O PMMA desprázase e queda unha estrutura metálica independente. 5. Utilizamos a estrutura metálica restante como molde e realizamos o moldeado por inxección de plásticos. Se analizas os cinco pasos básicos anteriores, utilizando as técnicas de microfabricación/micromecanizado de LIGA podemos obter: - Estruturas metálicas independentes - Estruturas plásticas moldeadas por inxección - Usando a estrutura moldeada por inxección como bruto podemos investir pezas de metal fundido ou pezas de cerámica de fundición deslizante. Os procesos de microfabricación/micromecanizado de LIGA son lentos e caros. Non obstante, o micromecanizado LIGA produce estes moldes de precisión submicrométricos que se poden usar para replicar as estruturas desexadas con distintas vantaxes. A microfabricación LIGA pódese usar, por exemplo, para fabricar imáns en miniatura moi fortes a partir de po de terras raras. Os po de terras raras mestúranse cun aglutinante epoxi e preséntanse no molde de PMMA, curan a alta presión, magnetízanse baixo fortes campos magnéticos e, finalmente, o PMMA disólvese deixando atrás os pequenos imáns fortes de terras raras que son unha das marabillas de microfabricación / micromecanizado. Tamén somos capaces de desenvolver técnicas de microfabricación/micromecanizado MEMS multinivel mediante a unión de difusión a escala de obleas. Basicamente podemos ter xeometrías sobresaíntes dentro dos dispositivos MEMS, utilizando un procedemento de unión e liberación por difusión por lotes. Por exemplo, preparamos dúas capas de PMMA modeladas e electroformadas co PMMA liberado posteriormente. A continuación, as obleas alíñanse cara a cara con pasadores de guía e encaixan nunha prensa en quente. A capa de sacrificio dun dos substratos está gravada, o que dá como resultado unha das capas unidas á outra. Outras técnicas de microfabricación non baseadas en LIGA tamén están dispoñibles para a fabricación de varias estruturas complexas multicapa. PROCESOS DE MICROFABRICACIÓN DE FORMA LIBRE DE SÓLIDOS: a microfabricación aditiva úsase para a creación rápida de prototipos. Con este método de micromecanizado pódense obter estruturas 3D complexas e non se produce ningunha eliminación de material. O proceso de microestereolitografía utiliza polímeros termoestables líquidos, fotoiniciador e unha fonte láser altamente enfocada a un diámetro tan pequeno como 1 micra e grosores de capa de aproximadamente 10 micras. Non obstante, esta técnica de microfabricación limítase á produción de estruturas poliméricas non condutoras. Outro método de microfabricación, o “enmascaramento instantáneo” ou tamén coñecido como “fabricación electroquímica” ou EFAB, consiste na produción dunha máscara elastomérica mediante fotolitografía. A máscara é presionada contra o substrato nun baño de electrodeposición para que o elastómero se axuste ao substrato e exclúa a solución de recubrimento nas áreas de contacto. As áreas que non están enmascaradas son electrodepositadas como a imaxe especular da máscara. Usando un recheo de sacrificio, microfábricas formas complexas en 3D. Este método de microfabricación/micromecanizado de "enmascaramento instantáneo" tamén permite producir salientes, arcos... etc. CLICK Product Finder-Locator Service PÁXINA ANTERIOR
- Electromagnetic Components Manufacturing and Assembly, Selenoid
Electromagnetic Components Manufacturing and Assembly, Selenoid, Electromagnet, Transformer, Electric Motor, Generator, Meters, Indicators, Scales,Electric Fans Solenoides e compoñentes e conxuntos electromagnéticos Como fabricante personalizado e integrador de enxeñería, AGS-TECH pode fornecerche os seguintes COMOÑENTES E CONXUNTOS ELECTROMAGNÉTICOS: • Conxuntos de selenoide, electroimán, transformador, motor eléctrico e xerador • Medidores electromagnéticos, indicadores, básculas fabricados especificamente para adaptarse ao seu dispositivo de medida. • Conxuntos sensor electromagnético e actuador • Ventiladores e refrixeradores eléctricos de varios tamaños para dispositivos electrónicos e aplicacións industriais • Montaxe doutros sistemas electromagnéticos complexos Fai clic aquí para descargar o folleto dos nosos medidores de panel - OICASCHINT Ferritas suaves - Núcleos - Toroides - Produtos de supresión EMI - Folleto de transpondedores e accesorios RFID Descarga o folleto para o noso PROGRAMA DE COLABORACIÓN DE DESEÑO Se estás interesado principalmente nas nosas capacidades de enxeñería e investigación e desenvolvemento en lugar das capacidades de fabricación, invitámosche a visitar o noso sitio de enxeñería http://www.ags-engineering.com CLICK Product Finder-Locator Service PÁXINA ANTERIOR
- Industrial Servers, Database Server, File Server, Mail Server, Print
Industrial Servers - Database Server - File Server - Mail Server - Print Server - Web Server - AGS-TECH Inc. - NM - USA Servidores industriais Cando se refire á arquitectura cliente-servidor, un SERVIDOR é un programa informático que se executa para atender as solicitudes doutros programas, tamén considerados como ''clientes''. Noutras palabras, o ''servidor'' realiza tarefas computacionais en nome dos seus ''clientes''. Os clientes poden executarse no mesmo ordenador ou estar conectados a través da rede. No entanto, no uso popular, un servidor é un ordenador físico dedicado a executar como host un ou máis destes servizos e atender as necesidades dos usuarios dos outros ordenadores da rede. Un servidor pode ser un SERVIDOR DE BASE DE DATOS, SERVIDOR DE FICHEIROS, SERVIDOR DE CORREO, SERVIDOR DE IMPRESIÓN, SERVIDOR WEB ou ben dependendo do servizo informático que ofreza. Ofrecemos as marcas de servidores industriais da mellor calidade dispoñibles como ATOP TECHNOLOGIES, KORENIX e JANZ TEC. Descarga a nosa ATOP TECHNOLOGIES folleto do produto compacto (Descargar o produto ATOP Technologies List 2021) Descarga o noso folleto de produtos compactos da marca JANZ TEC Descarga o noso folleto de produtos compactos da marca KORENIX Descarga o noso folleto de produtos de comunicación industrial e redes da marca ICP DAS Descarga o noso folleto Tiny Device Server e Modbus Gateway da marca ICP DAS Para escoller un servidor de grao industrial axeitado, vai á nosa tenda de informática industrial facendo clic AQUÍ. Descarga o folleto para o noso PROGRAMA DE COLABORACIÓN DE DESEÑO SERVIDOR DE BASE DE DATOS: Este termo úsase para referirse ao sistema de fondo dunha aplicación de base de datos que usa a arquitectura cliente/servidor. O servidor de base de datos back-end realiza tarefas como análise de datos, almacenamento de datos, manipulación de datos, arquivo de datos e outras tarefas específicas non do usuario. SERVIDOR DE FICHEROS : No modelo cliente/servidor, trátase dun ordenador encargado do almacenamento e xestión centralizada dos ficheiros de datos para que outros equipos da mesma rede poidan acceder a eles. Os servidores de ficheiros permiten aos usuarios compartir información nunha rede sen transferir fisicamente ficheiros mediante disquete ou outros dispositivos de almacenamento externos. En redes sofisticadas e profesionais, un servidor de ficheiros pode ser un dispositivo dedicado de almacenamento conectado á rede (NAS) que tamén serve como unidade de disco duro remota para outros ordenadores. Así, calquera persoa da rede pode almacenar ficheiros nel como no seu propio disco duro. SERVIDOR DE CORREO: Un servidor de correo, tamén chamado servidor de correo electrónico é un ordenador dentro da súa rede que funciona como a súa oficina de correos virtual. Consiste nunha área de almacenamento onde se almacena o correo electrónico para os usuarios locais, un conxunto de regras definidas polo usuario que determinan como debe reaccionar o servidor de correo ao destino dunha mensaxe específica, unha base de datos de contas de usuario que o servidor de correo recoñecerá e tratará. con módulos de comunicación local e que se encargan da transferencia de mensaxes a e dende outros servidores e clientes de correo electrónico. Os servidores de correo están deseñados xeralmente para funcionar sen intervención manual durante o funcionamento normal. SERVIDOR DE IMPRESIÓN: ás veces chamado servidor de impresoras, este é un dispositivo que conecta impresoras a ordenadores cliente a través dunha rede. Os servidores de impresión aceptan traballos de impresión dos ordenadores e envían os traballos ás impresoras adecuadas. O servidor de impresión pon os traballos en cola localmente porque o traballo pode chegar máis rápido do que a impresora pode xestionalo. SERVIDOR WEB: son ordenadores que entregan e serven páxinas web. Todos os servidores web teñen enderezos IP e xeralmente nomes de dominio. Cando introducimos a URL dun sitio web no noso navegador, este envía unha solicitude ao servidor web cuxo nome de dominio é o sitio web introducido. Despois, o servidor obtén a páxina chamada index.html e envíaa ao noso navegador. Calquera ordenador pódese converter nun servidor web instalando o software do servidor e conectando a máquina a Internet. Hai moitas aplicacións de software de servidor web, como paquetes de Microsoft e Netscape. CLICK Product Finder-Locator Service PÁXINA ANTERIOR
- Brazing, Soldering, Welding, Joining Processes, Assembly Services
Brazing - Soldering - Welding - Joining Processes - Assembly Services - Subassemblies - Assemblies - Custom Manufacturing - AGS-TECH Inc. - NM - USA Soldadura e soldadura Entre as moitas técnicas de UNIÓN que implementamos na fabricación, dáselle especial énfase á SOLDADURA, SOLDADURA, SOLDADURA, ENLACE ADHESIVO e MONTAXE MECÁNICO PERSONALIZADO porque estas técnicas son amplamente utilizadas en aplicacións como a fabricación de conxuntos herméticos, fabricación de produtos de alta tecnoloxía e selado especializado. Aquí concentrarémonos nos aspectos máis especializados destas técnicas de unión xa que están relacionados coa fabricación de produtos e conxuntos avanzados. SOLDADURA POR FUSIÓN: Utilizamos a calor para fundir e unir materiais. A calor é subministrada por electricidade ou vigas de alta enerxía. Os tipos de soldadura por fusión que implantamos son SOLDADURA POR GAS OXICOMBUSTIBLE, SOLDADURA POR ARCO, SOLDADURA POR FACES DE ALTA ENERXÍA. SOLDADURA EN ESTADO SÓLIDO: Unimos pezas sen fundir e fusión. Os nosos métodos de soldadura en estado sólido son FRÍO, ULTRASONS, RESISTENCIA, FRICCIÓN, SOLDADURA POR EXPLOSIÓN e ENLACE POR DIFUSIÓN. SOLDADURA E SOLDADURA: Empregan metais de recheo e dannos a vantaxe de traballar a temperaturas máis baixas que na soldadura, polo que menos danos estruturais aos produtos. A información sobre a nosa instalación de soldadura que produce accesorios de cerámica a metal, selado hermético, pasaxes ao baleiro, baleiro alto e ultraalto e compoñentes de control de fluídos pódese atopar aquí:Folleto de Brazing Factory ENLACE ADHESIVO: debido á diversidade de adhesivos utilizados na industria e tamén á diversidade de aplicacións, temos unha páxina dedicada para iso. Para ir á nosa páxina sobre unión adhesiva, prema aquí. MONTAXE MECÁNICA PERSONALIZADA: utilizamos unha variedade de elementos de fixación como parafusos, parafusos, porcas, remaches. Os nosos fixadores non se limitan a fixadores estándar fóra de estante. Deseñamos, desenvolvemos e fabricamos fixadores especiais que están feitos de materiais non estándar para que poidan cumprir os requisitos para aplicacións especiais. Ás veces é desexable a non condutividade eléctrica ou térmica, mentres que ás veces a condutividade. Para algunhas aplicacións especiais, un cliente pode querer fixadores especiais que non se poden quitar sen destruír o produto. Hai infinitas ideas e aplicacións. Temos todo para ti, se non está dispoñible, podemos desenvolvelo rapidamente. Para ir á nosa páxina sobre montaxe mecánica, prema aquí . Examinemos con máis detalle as nosas diversas técnicas de unión. SOLDADURA CON GAS OXICOMBUSTIBLE (OFW): Utilizamos un gas combustible mesturado con osíxeno para producir a chama de soldadura. Cando usamos o acetileno como combustible e osíxeno, chamámoslle soldadura con gas oxiacetileno. No proceso de combustión de gas oxicombustible ocorren dúas reaccións químicas: C2H2 + O2 ------» 2CO + H2 + Calor 2CO + H2 + 1,5 O2--------» 2 CO2 + H2O + Calor A primeira reacción disocia o acetileno en monóxido de carbono e hidróxeno ao tempo que produce preto do 33% da calor total xerada. O segundo proceso anterior representa unha maior combustión do hidróxeno e do monóxido de carbono mentres produce preto do 67% da calor total. As temperaturas na chama están entre 1533 e 3573 Kelvin. A porcentaxe de osíxeno na mestura de gases é importante. Se o contido de osíxeno é máis da metade, a chama convértese nun axente oxidante. Isto é indesexable para algúns metais pero desexable para outros. Un exemplo cando é desexable a chama oxidante son as aliaxes a base de cobre porque forman unha capa de pasivación sobre o metal. Por outra banda, cando se reduce o contido de osíxeno, a combustión total non é posible e a chama convértese nunha chama redutora (cementadora). As temperaturas nunha chama redutora son máis baixas e, polo tanto, é adecuada para procesos como a soldadura e a soldadura. Outros gases tamén son potenciais combustibles, pero teñen algunhas desvantaxes sobre o acetileno. Ocasionalmente subministramos metais de recheo á zona de soldadura en forma de varillas de recheo ou fío. Algúns deles están recubertos de fundente para retardar a oxidación das superficies e protexer así o metal fundido. Un beneficio adicional que nos proporciona o fluxo é a eliminación de óxidos e outras substancias da zona de soldadura. Isto leva a unha unión máis forte. Unha variación da soldadura con gas oxicombustible é a SOLDADURA POR GAS A PRESIÓN, onde os dous compoñentes quentan na súa interface usando soplete de gas oxiacetileno e unha vez que a interface comeza a fundirse, retírase o soplete e aplícase unha forza axial para presionar as dúas partes xuntas. ata que se solidifique a interface. SOLDADURA POR ARCO: Utilizamos enerxía eléctrica para producir un arco entre a punta do electrodo e as pezas a soldar. A fonte de alimentación pode ser AC ou DC mentres que os electrodos son consumibles ou non. A transferencia de calor na soldadura por arco pódese expresar coa seguinte ecuación: H/l = ex VI/v Aquí H é a entrada de calor, l é a lonxitude da soldadura, V e I son a tensión e corrente aplicada, v é a velocidade de soldadura e e é a eficiencia do proceso. Canto maior sexa a eficiencia "e", máis beneficiosa é a enerxía dispoñible para fundir o material. A entrada de calor tamén se pode expresar como: H = ux (Volumen) = ux A xl Aquí u é a enerxía específica para fundir, A a sección transversal da soldadura e l a lonxitude da soldadura. Das dúas ecuacións anteriores podemos obter: v = ex VI / u A Unha variación da soldadura por arco é a SOLDADURA POR ARCO METÁLICO APINTADO (SMAW) que constitúe preto do 50% de todos os procesos de soldadura industrial e de mantemento. A SOLDADURA CON ARCO ELÉCTRICO (SOLD WELDING) realízase tocando a punta dun electrodo revestido coa peza de traballo e retirándoa rapidamente a unha distancia suficiente para manter o arco. Chamámoslle a este proceso tamén soldadura por varillas porque os electrodos son varas finas e longas. Durante o proceso de soldadura, a punta do electrodo fúndese xunto co seu revestimento e o metal base nas proximidades do arco. Unha mestura de metal base, metal do electrodo e substancias do revestimento do electrodo solidificase na zona de soldadura. O revestimento do electrodo desoxidase e proporciona un gas protector na rexión de soldadura, protexendo así do osíxeno do ambiente. Polo tanto, o proceso denomínase soldadura por arco metálico blindado. Usamos correntes entre 50 e 300 amperios e niveis de potencia xeralmente inferiores a 10 kW para un rendemento óptimo da soldadura. Tamén é importante a polaridade da corrente continua (dirección do fluxo de corrente). A polaridade recta onde a peza é positiva e o eléctrodo negativo é preferible na soldadura de chapas metálicas pola súa penetración pouco profunda e tamén para xuntas con fendas moi amplas. Cando temos polaridade inversa, é dicir, o electrodo é positivo e a peza negativa podemos conseguir penetracións de soldadura máis profundas. Con corrente alterna, xa que temos arcos pulsantes, podemos soldar seccións grosas utilizando electrodos de gran diámetro e correntes máximas. O método de soldadura SMAW é axeitado para espesores de pezas de 3 a 19 mm e aínda máis utilizando técnicas de múltiples pasadas. A escoura formada na parte superior da soldadura debe ser eliminada mediante un cepillo de arame, para que non haxa corrosión e falla na zona de soldadura. Isto, por suposto, engádese ao custo da soldadura por arco de metal blindado. Non obstante, o SMAW é a técnica de soldadura máis popular na industria e nos traballos de reparación. SOLDADURA POR ARCO SUMMERXIDO (SAW): Neste proceso protexemos o arco de soldadura utilizando materiais de fluxo granular como cal, sílice, floruro de calcio, óxido de manganeso... etc. O fluxo granular introdúcese na zona de soldadura mediante un fluxo por gravidade a través dunha boquilla. O fluxo que cobre a zona de soldadura fundida protexe significativamente de chispas, fumes, radiación UV... etc. e actúa como illante térmico, deixando así que a calor penetre profundamente na peza de traballo. O fluxo non fundido é recuperado, tratado e reutilizado. Unha bobina desnuda úsase como eléctrodo e lévase a través dun tubo ata a zona de soldadura. Usamos correntes entre 300 e 2000 Amperios. O proceso de soldadura por arco mergullado (SAW) está limitado a posicións horizontais e planas e soldaduras circulares se é posible a rotación da estrutura circular (como tubos) durante a soldadura. As velocidades poden alcanzar os 5 m/min. O proceso SAW é axeitado para placas grosas e dá como resultado soldaduras de alta calidade, resistentes, dúctiles e uniformes. A produtividade, é dicir, a cantidade de material de soldadura depositado por hora é de 4 a 10 veces a cantidade en comparación co proceso SMAW. Outro proceso de soldadura por arco, a saber, a SOLDADURA POR ARCO DE GAS METAL (GMAW) ou alternativamente denominada SOLDADURA DE GAS INERTE METAL (MIG) baséase en que a zona de soldadura está protexida por fontes externas de gases como helio, argón, dióxido de carbono, etc. Pode haber desoxidantes adicionais presentes no metal do electrodo. O fío consumible é alimentado a través dunha boquilla na zona de soldadura. A fabricación de metais tanto férreos como non férreos realízase mediante soldadura por arco de metal con gas (GMAW). A produtividade da soldadura é aproximadamente 2 veces a do proceso SMAW. Empréganse equipos de soldadura automatizados. O metal transfírese dun dos tres xeitos neste proceso: a "Transferencia de pulverización" implica a transferencia de varios centos de pequenas gotas de metal por segundo desde o electrodo á zona de soldadura. En "Transferencia Globular", por outra banda, utilízanse gases ricos en dióxido de carbono e glóbulos de metal fundido son impulsados polo arco eléctrico. As correntes de soldadura son altas e a penetración da soldadura máis profunda, a velocidade de soldadura maior que na transferencia de pulverización. Así, a transferencia globular é mellor para soldar seccións máis pesadas. Finalmente, no método de "Curtocircuíto", a punta do electrodo toca o baño de soldadura fundido, curtocircuítao xa que o metal a velocidades superiores a 50 gotas/segundo transfírese en gotas individuais. Utilízanse correntes e voltaxes baixas xunto cun fío máis fino. As potencias utilizadas son duns 2 kW e as temperaturas relativamente baixas, o que fai que este método sexa adecuado para chapas finas de menos de 6 mm de espesor. Outra variación do proceso de SOLDADURA POR ARCO DE NÚCLEO FLUXANTE (FCAW) é similar á soldadura por arco metálico con gas, excepto que o electrodo é un tubo cheo de fluxo. As vantaxes de usar electrodos de fluxo con núcleo é que producen arcos máis estables, dannos a oportunidade de mellorar as propiedades dos metais de soldadura, a natureza menos fráxil e flexible do seu fluxo en comparación coa soldadura SMAW, os contornos de soldadura mellorados. Os electrodos con núcleo autoprotexidos conteñen materiais que protexen a zona de soldadura contra a atmosfera. Usamos uns 20 kW de potencia. Do mesmo xeito que o proceso GMAW, o proceso FCAW tamén ofrece a oportunidade de automatizar procesos para a soldadura continua, e é económico. Pódense desenvolver diferentes químicas de metal de soldadura engadindo varias aliaxes ao núcleo de fluxo. En SOLDADURA ELECTROGÁS (EGW) soldamos as pezas colocadas bordo a bordo. Ás veces tamén se lle chama SOLDADURA A BORDE. O metal de soldadura colócase nunha cavidade de soldadura entre dúas pezas a unir. O espazo está pechado por dúas presas refrixeradas por auga para evitar que a escoura fundida se derrame. As presas son movidas cara arriba mediante accionamentos mecánicos. Cando se pode xirar a peza de traballo, tamén podemos utilizar a técnica de soldadura electrogás para soldar circunferenciais de tubos. Os electrodos son alimentados a través dun conduto para manter un arco continuo. As correntes poden ser duns 400 amperios ou 750 amperios e os niveis de potencia duns 20 kW. Os gases inertes orixinados a partir dun electrodo con núcleo de fluxo ou dunha fonte externa proporcionan protección. Utilizamos a soldadura por electrogás (EGW) para metais como aceiros, titanio….etc con espesores de 12 mm a 75 mm. A técnica é adecuada para grandes estruturas. Porén, noutra técnica chamada ELECTROSLAG WELDING (ESW) encéndese o arco entre o electrodo e a parte inferior da peza e engádese fluxo. Cando a escoura fundida chega á punta do electrodo, o arco apágase. A enerxía é continuamente subministrada a través da resistencia eléctrica da escoura fundida. Podemos soldar chapas con espesores entre 50 mm e 900 mm e incluso superiores. As correntes son duns 600 amperios mentres que as tensións están entre 40 e 50 V. As velocidades de soldadura son de 12 a 36 mm/min. As aplicacións son similares á soldadura por electrogás. Un dos nosos procesos de electrodos non consumibles, a SOLDADURA POR ARCO DE TUNGSTENO (GTAW) tamén coñecida como SOLDADURA DE GAS INERTE DE TUNGSTENO (TIG) implica a subministración dun metal de recheo mediante un fío. Para xuntas axustadas ás veces non usamos o metal de recheo. No proceso TIG non usamos fluxo, senón que usamos argón e helio para a blindaxe. O volframio ten un alto punto de fusión e non se consume no proceso de soldadura TIG, polo que se pode manter a corrente constante así como os espazos de arco. Os niveis de potencia están entre 8 e 20 kW e as correntes de 200 amperios (CC) ou 500 amperios (CA). Para o aluminio e o magnesio utilizamos corrente alterna para a súa función de limpeza de óxidos. Para evitar a contaminación do electrodo de wolframio, evitamos o seu contacto con metais fundidos. A soldadura por arco de tungsteno con gas (GTAW) é especialmente útil para soldar metais finos. As soldaduras GTAW son de moi alta calidade cun bo acabado superficial. Debido ao maior custo do gas hidróxeno, unha técnica de uso menos frecuente é a SOLDADURA ATÓMICA DE HIDRÓGENO (AHW), onde xeramos un arco entre dous electrodos de wolframio nunha atmosfera de protección de gas hidróxeno en fluxo. O AHW tamén é un proceso de soldadura de electrodos non consumibles. O gas hidróxeno diatómico H2 descompón a súa forma atómica preto do arco de soldadura onde as temperaturas superan os 6273 Kelvin. Mentres se rompe, absorbe gran cantidade de calor do arco. Cando os átomos de hidróxeno chocan contra a zona de soldadura que é unha superficie relativamente fría, recombínanse en forma diatómica e liberan a calor almacenada. A enerxía pódese variar cambiando a peza de traballo á distancia do arco. Noutro proceso de electrodos non consumibles, a SOLDADURA POR ARCO DE PLASMA (PAW), temos un arco de plasma concentrado dirixido cara á zona de soldadura. As temperaturas alcanzan os 33.273 Kelvin en PAW. Un número case igual de electróns e ións compoñen o gas do plasma. Un arco piloto de baixa corrente inicia o plasma que está entre o electrodo de wolframio e o orificio. As correntes de funcionamento son xeralmente arredor dos 100 amperios. Pódese alimentar un metal de recheo. Na soldadura por arco de plasma, a blindaxe realízase mediante un anel de protección exterior e utilizando gases como argón e helio. Na soldadura por arco de plasma, o arco pode estar entre o electrodo e a peza de traballo ou entre o electrodo e a boquilla. Esta técnica de soldadura ten as vantaxes sobre outros métodos de maior concentración de enerxía, capacidade de soldadura máis profunda e estreita, mellor estabilidade do arco, velocidades de soldadura máis altas de ata 1 metro/min, menos distorsión térmica. Normalmente utilizamos soldadura por arco de plasma para espesores inferiores a 6 mm e ás veces ata 20 mm para aluminio e titanio. SOLDADURA POR FAIS DE ALTA ENERXÍA: Outro tipo de método de soldadura por fusión con soldadura por feixe de electróns (EBW) e soldadura con láser (LBW) como dúas variantes. Estas técnicas son de especial valor para o noso traballo de fabricación de produtos de alta tecnoloxía. Na soldadura por feixe de electróns, os electróns de alta velocidade golpean a peza e a súa enerxía cinética convértese en calor. O feixe estreito de electróns viaxa facilmente na cámara de baleiro. Xeralmente usamos alto baleiro na soldadura por feixe electrónico. Pódense soldar placas de 150 mm de grosor. Non se necesitan gases de protección, fundentes ou materiais de recheo. As pistolas de feixe Elecron teñen unha capacidade de 100 kW. Son posibles soldaduras profundas e estreitas con relacións de aspecto altas de ata 30 e pequenas zonas afectadas pola calor. As velocidades de soldadura poden alcanzar os 12 m/min. Na soldadura por raio láser utilizamos láseres de alta potencia como fonte de calor. Os raios láser de tan pequenos como 10 micras con alta densidade permiten unha penetración profunda na peza de traballo. Coa soldadura con láser é posible unha relación de profundidade a ancho de ata 10. Usamos tanto láseres de ondas pulsadas como continuas, sendo o primeiro en aplicacións para materiais finos e o segundo principalmente para pezas grosas de ata uns 25 mm. Os niveis de potencia son de ata 100 kW. A soldadura por raio láser non é adecuada para materiais ópticamente moi reflectores. Tamén se poden utilizar gases no proceso de soldadura. O método de soldadura por raio láser é adecuado para a automatización e a fabricación de gran volume e pode ofrecer velocidades de soldadura entre 2,5 m/min e 80 m/min. Unha das principais vantaxes que ofrece esta técnica de soldadura é o acceso a zonas onde non se poden utilizar outras técnicas. Os raios láser poden viaxar facilmente a rexións tan difíciles. Non se necesita baleiro como na soldadura por feixe de electróns. Soldaduras con boa calidade e resistencia, baixa contracción, baixa distorsión e baixa porosidade pódense obter coa soldadura con láser. Os raios láser pódense manipular e dar forma facilmente mediante cables de fibra óptica. Así, a técnica é moi adecuada para soldar conxuntos herméticos de precisión, paquetes electrónicos, etc. Vexamos as nosas técnicas de SOLDADURA DE ESTADO SÓLIDO. A SOLDADURA EN FRÍO (CW) é un proceso no que se aplica presión en lugar de calor mediante matrices ou rolos ás pezas que se acoplan. Na soldadura en frío, polo menos unha das partes de acoplamento debe ser dúctil. Os mellores resultados obtéñense con dous materiais similares. Se os dous metais a unir coa soldadura en frío son diferentes, poderemos ter xuntas débiles e quebradizas. O método de soldadura en frío é moi adecuado para pezas brandas, dúctiles e pequenas, como conexións eléctricas, bordos de recipientes sensibles á calor, tiras bimetálicas para termostatos... etc. Unha variación da soldadura en frío é a unión de rolos (ou soldadura de rolos), onde a presión se aplica a través dun par de rolos. Ás veces realizamos soldadura en rolo a temperaturas elevadas para unha mellor resistencia da interface. Outro proceso de soldadura en estado sólido que utilizamos é a SOLDADURA ULTRASÓNICA (USW), onde as pezas están sometidas a unha forza normal estática e esforzos cortantes oscilantes. Os esforzos de cizallamento oscilante aplícanse a través da punta dun transdutor. A soldadura ultrasónica desprega oscilacións con frecuencias de 10 a 75 kHz. Nalgunhas aplicacións, como a soldadura de costura, usamos un disco de soldadura xiratorio como punta. Os esforzos de cizallamento aplicados ás pezas provocan pequenas deformacións plásticas, rompen capas de óxido, contaminantes e conducen a unión en estado sólido. As temperaturas implicadas na soldadura por ultrasóns están moi por debaixo das temperaturas do punto de fusión dos metais e non se produce fusión. Usamos frecuentemente o proceso de soldadura ultrasóns (USW) para materiais non metálicos como plásticos. Nos termoplásticos, as temperaturas alcanzan puntos de fusión. Outra técnica popular, na SOLDADURA POR FRICCIÓN (FRW) a calor xérase a través da fricción na interface das pezas a unir. Na soldadura por fricción mantemos unha das pezas de traballo estacionaria mentres que a outra peza se mantén nun dispositivo e xira a unha velocidade constante. A continuación, as pezas póñense en contacto baixo unha forza axial. A velocidade de rotación da superficie na soldadura por fricción pode alcanzar 900 m/min nalgúns casos. Despois dun contacto interfacial suficiente, a peza de traballo xiratoria deténse de forma súbita e aumenta a forza axial. A zona de soldadura é xeralmente unha rexión estreita. A técnica de soldadura por fricción pódese usar para unir pezas sólidas e tubulares feitas de diversos materiais. Algún flash pode desenvolverse na interface en FRW, pero este flash pódese eliminar mediante mecanizado secundario ou rectificado. Existen variacións no proceso de soldadura por fricción. Por exemplo, a "soldadura por fricción por inercia" implica un volante cuxa enerxía cinética de rotación se utiliza para soldar as pezas. A soldadura está completa cando o volante se detén. A masa xiratoria pode ser variada e, polo tanto, a enerxía cinética rotacional. Outra variación é a "soldadura por fricción lineal", onde se impón o movemento alternativo lineal de polo menos un dos compoñentes a unir. Na soldadura por fricción lineal as pezas non teñen que ser circulares, poden ser rectangulares, cadradas ou doutra forma. As frecuencias poden estar en decenas de Hz, amplitudes no rango de milímetros e presións en decenas ou centos de MPa. Finalmente a "soldadura por fricción" é algo diferente ás outras dúas explicadas anteriormente. Mentres que na soldadura por fricción por inercia e na soldadura por fricción lineal o quecemento das interfaces conséguese por fricción frotando dúas superficies de contacto, no método de soldadura por fricción axitada un terceiro corpo frotase contra as dúas superficies que se van unir. Ponse en contacto coa xunta unha ferramenta rotativa de 5 a 6 mm de diámetro. As temperaturas poden aumentar a valores entre 503 e 533 Kelvin. Prodúcese o quecemento, mestura e axitación do material na unión. Usamos a soldadura por fricción nunha variedade de materiais, incluíndo aluminio, plásticos e compostos. As soldaduras son uniformes e a calidade é alta con mínimos poros. Non se producen fumes nin salpicaduras na soldadura por fricción e o proceso está ben automatizado. SOLDADURA POR RESISTENCIA (RW): A calor necesaria para a soldadura prodúcese pola resistencia eléctrica entre as dúas pezas a unir. Non se utilizan fluxos, gases de protección nin electrodos consumibles na soldadura por resistencia. O quecemento Joule ten lugar na soldadura por resistencia e pódese expresar como: H = (Cadro I) x R xtx K H é a calor xerada en joules (vatios-segundos), I a corrente en amperios, R a resistencia en ohmios, t é o tempo en segundos que atravesa a corrente. O factor K é menor que 1 e representa a fracción de enerxía que non se perde pola radiación e a condución. As correntes nos procesos de soldadura por resistencia poden alcanzar niveis tan altos como 100.000 A pero as tensións son normalmente de 0,5 a 10 voltios. Os electrodos son normalmente feitos de aliaxes de cobre. Pódense unir tanto materiais similares como distintos mediante soldadura por resistencia. Existen varias variacións para este proceso: a "soldadura por puntos por resistencia" implica que dous electrodos redondos opostos entran en contacto coas superficies da unión de solapa das dúas follas. Aplícase presión ata que se desconecte a corrente. A pepita de soldadura adoita ter un diámetro de ata 10 mm. A soldadura por puntos por resistencia deixa marcas de sangría lixeiramente descoloridas nos puntos de soldadura. A soldadura por puntos é a nosa técnica de soldadura por resistencia máis popular. Na soldadura por puntos utilízanse varias formas de electrodos para chegar a zonas difíciles. O noso equipo de soldadura por puntos está controlado por CNC e ten varios electrodos que se poden usar simultaneamente. Outra variación "soldadura de costura por resistencia" realízase con electrodos de roda ou rolo que producen soldaduras por puntos continuas sempre que a corrente alcanza un nivel suficientemente alto no ciclo de alimentación de CA. As unións producidas pola soldadura de costura por resistencia son estancas a líquidos e gases. Velocidades de soldadura de aproximadamente 1,5 m/min son normais para chapas finas. Pódense aplicar correntes intermitentes para que as soldaduras por puntos se produzan nos intervalos desexados ao longo da costura. En "soldadura por proxección por resistencia" gravamos unha ou varias proxeccións (coviñas) nunha das superficies da peza a soldar. Estas proxeccións poden ser redondas ou ovaladas. Nestes puntos en relevo alcánzanse altas temperaturas localizadas que entran en contacto coa parte de apareamento. Os electrodos exercen presión para comprimir estas proxeccións. Os electrodos na soldadura por proxección por resistencia teñen puntas planas e son aliaxes de cobre refrixeradas por auga. A vantaxe da soldadura por proxección por resistencia é a nosa capacidade para realizar varias soldaduras nun só golpe, polo que a vida útil prolongada do electrodo, a capacidade de soldar follas de varios grosores, a capacidade de soldar porcas e parafusos a follas. A desvantaxe da soldadura por proxección de resistencia é o custo adicional de gravar as coviñas. Outra técnica máis, na "soldadura por flash" xérase calor a partir do arco nos extremos das dúas pezas cando comezan a facer contacto. Este método tamén pode considerar alternativamente a soldadura por arco. A temperatura na interface sobe e o material ablandase. Aplícase unha forza axial e fórmase unha soldadura na rexión suavizada. Despois de completar a soldadura flash, a unión pódese mecanizar para mellorar o aspecto. A calidade da soldadura obtida mediante soldadura flash é boa. Os niveis de potencia son de 10 a 1500 kW. A soldadura por flash é adecuada para a unión de bordo a bordo de metais similares ou disímiles de ata 75 mm de diámetro e chapas de entre 0,2 mm e 25 mm de espesor. A "soldadura por arco de pernos" é moi similar á soldadura por flash. O espárrago, como un parafuso ou varilla roscada, serve como un electrodo mentres se une a unha peza de traballo como unha placa. Para concentrar a calor xerada, evitar a oxidación e reter o metal fundido na zona de soldadura, colócase un anel de cerámica desbotable arredor da unión. Finalmente "soldadura por percusión" outro proceso de soldadura por resistencia, utiliza un capacitor para subministrar a enerxía eléctrica. Na soldadura por percusión, a potencia descárgase en milisegundos de tempo moi rapidamente desenvolvendo unha elevada calor localizada na unión. Usamos amplamente a soldadura por percusión na industria de fabricación de produtos electrónicos onde se debe evitar o quecemento de compoñentes electrónicos sensibles nas proximidades da unión. Unha técnica chamada SOLDADURA POR EXPLOSIÓN consiste na detonación dunha capa de explosivo que se coloca sobre unha das pezas a unir. A moi alta presión exercida sobre a peza produce unha interface turbulenta e ondulada e ten lugar un enclavamiento mecánico. As forzas de unión na soldadura explosiva son moi altas. A soldadura por explosión é un bo método para o revestimento de placas con metais diferentes. Despois do revestimento, as placas pódense enrolar en seccións máis finas. Ás veces usamos soldadura por explosión para tubos de expansión para que queden selados firmemente contra a placa. O noso último método dentro do dominio da unión en estado sólido é o ENLACE POR DIFUSIÓN ou SOLDADURA POR DIFUSIÓN (DFW) na que se consegue unha boa unión principalmente por difusión de átomos pola interface. Algunha deformación plástica na interface tamén contribúe á soldadura. As temperaturas implicadas son ao redor de 0,5 Tm onde Tm é a temperatura de fusión do metal. A forza de unión na soldadura por difusión depende da presión, temperatura, tempo de contacto e limpeza das superficies en contacto. Ás veces usamos metais de recheo na interface. A calor e a presión son necesarias na unión por difusión e son subministradas por resistencia eléctrica ou forno e pesos mortos, prensa ou ben. Pódense unir metais similares e disímiles coa soldadura por difusión. O proceso é relativamente lento debido ao tempo que tardan os átomos en migrar. DFW pódese automatizar e úsase amplamente na fabricación de pezas complexas para as industrias aeroespacial, electrónica e médica. Os produtos fabricados inclúen implantes ortopédicos, sensores e membros estruturais aeroespaciais. A unión por difusión pódese combinar con SUPERPLÁSTIC FORMING para fabricar estruturas complexas de chapa metálica. Os lugares seleccionados das follas son primeiro unidos por difusión e despois as rexións non unidas son expandidas nun molde usando presión de aire. As estruturas aeroespaciais con altas relacións de rixidez-peso son fabricadas mediante esta combinación de métodos. O proceso combinado de soldadura por difusión/formado superplástico reduce o número de pezas necesarias eliminando a necesidade de fixadores, resultando en pezas moi precisas de baixo estrés de xeito económico e con curtos prazos de entrega. SOLDADURA: As técnicas de soldadura forte implican temperaturas máis baixas que as necesarias para a soldadura. Non obstante, as temperaturas de soldadura son máis altas que as de soldadura. Na soldadura colócase un metal de recheo entre as superficies a unir e as temperaturas elévanse ata a temperatura de fusión do material de recheo por encima de 723 Kelvin pero por debaixo das temperaturas de fusión das pezas de traballo. O metal fundido enche o espazo entre as pezas de traballo. O arrefriamento e a posterior solidificación do metal de lima produce xuntas fortes. Na soldadura por soldadura, o metal de recheo deposítase na unión. Úsase considerablemente máis metal de recheo na soldadura por soldadura en comparación coa soldadura. O soplete de oxiacetileno con chama oxidante úsase para depositar o metal de recheo na soldadura por soldadura. Debido ás temperaturas máis baixas na soldadura, os problemas nas zonas afectadas pola calor como a deformación e as tensións residuais son menores. Canto menor é o espazo libre na soldadura, maior é a resistencia ao corte da unión. Non obstante, a máxima resistencia á tracción conséguese nun intervalo óptimo (un valor máximo). Por debaixo e por riba deste valor óptimo, a resistencia á tracción na soldadura diminúe. Os xogos típicos en soldadura poden estar entre 0,025 e 0,2 mm. Usamos unha variedade de materiais de soldadura con diferentes formas, como performs, po, aneis, arame, tiras... etc. e pode fabricar estes traballos especialmente para o seu deseño ou xeometría do produto. Tamén determinamos o contido dos materiais de soldadura segundo os seus materiais de base e aplicación. Usamos con frecuencia fundentes nas operacións de soldadura para eliminar as capas de óxido non desexadas e evitar a oxidación. Para evitar a corrosión posterior, os fluxos son xeralmente eliminados despois da operación de unión. AGS-TECH Inc. usa varios métodos de soldadura, incluíndo: - Soldadura con soplete - Soldadura ao forno - Soldadura por indución - Soldadura por resistencia - Soldadura por inmersión - Soldadura por infravermellos - Soldadura por difusión - Feixe de alta enerxía Os nosos exemplos máis comúns de unións soldadas están feitos de metais diferentes con boa resistencia, como brocas de carburo, insercións, paquetes herméticos optoelectrónicos, selos. SOLDADURA: Esta é unha das nosas técnicas máis utilizadas onde a soldadura (metal de recheo) enche a unión como na soldadura entre compoñentes que se axustan. As nosas soldaduras teñen puntos de fusión inferiores a 723 Kelvin. Implementamos soldadura manual e automatizada nas operacións de fabricación. En comparación coa soldadura, as temperaturas de soldadura son máis baixas. A soldadura non é moi adecuada para aplicacións de alta temperatura ou de alta resistencia. Usamos soldaduras sen chumbo, así como aliaxes de estaño-chumbo, estaño-zinc, chumbo-prata, cadmio-prata, cinc-aluminio ademais doutras para soldar. Tanto a base de resinas non corrosivas como os ácidos e sales inorgánicos úsanse como fundente na soldadura. Usamos fluxos especiais para soldar metais con baixa soldabilidade. Nas aplicacións nas que temos que soldar materiais cerámicos, vidro ou grafito, primeiro chapamos as pezas cun metal axeitado para aumentar a soldabilidade. As nosas técnicas de soldadura populares son: - Soldadura por reflujo ou pasta - Soldadura por onda - Soldadura ao forno - Soldadura con soplete - Soldadura por indución - Soldadura de ferro - Soldadura por resistencia - Soldadura por inmersión - Soldadura por ultrasóns - Soldadura por infravermellos A soldadura por ultrasóns ofrécenos unha vantaxe única pola que se elimina a necesidade de fluxos debido ao efecto de cavitación ultrasónica que elimina as películas de óxido das superficies que se unen. A soldadura por refluxo e por onda son as nosas técnicas destacadas industrialmente para a fabricación de grandes volumes en electrónica e, polo tanto, merece a pena explicarlas con máis detalle. Na soldadura por refluxo, usamos pastas semisólidas que inclúen partículas de metal de soldadura. A pasta colócase sobre a unión mediante un proceso de cribado ou stencil. En placas de circuíto impreso (PCB) utilizamos con frecuencia esta técnica. Cando os compoñentes eléctricos se colocan sobre estas almofadas a partir de pasta, a tensión superficial mantén os paquetes de montaxe en superficie aliñados. Despois de colocar os compoñentes, quentamos o conxunto nun forno para que se produza a soldadura por refluxo. Durante este proceso, os disolventes na pasta evaporan, o fluxo na pasta actívase, os compoñentes prequentanse, as partículas de soldadura fúndense e mollan a unión e, finalmente, o conxunto de PCB arrefríase lentamente. A nosa segunda técnica popular para a produción de placas de PCB en grandes cantidades, a saber, a soldadura por ondas, baséase no feito de que as soldaduras fundidas mollan as superficies metálicas e forman boas unións só cando o metal se quenta previamente. Unha onda laminar estacionaria de soldadura fundida é xerada por primeira vez por unha bomba e os PCB precalentados e prefluxados son transportados sobre a onda. A soldadura só molla superficies metálicas expostas, pero non molla os paquetes de polímero IC nin as placas de circuíto revestidas de polímero. Un chorro de auga quente de alta velocidade expulsa o exceso de soldadura da unión e impide a ponte entre os cables adxacentes. Na soldadura por onda de paquetes de montaxe en superficie, primeiro unímolos de forma adhesiva á placa de circuíto antes de soldar. De novo utilízase cribado e esténcil pero esta vez para epoxi. Despois de colocar os compoñentes nos seus lugares correctos, o epoxi se cura, as placas invírtense e prodúcese a soldadura por onda. CLICK Product Finder-Locator Service PÁXINA ANTERIOR
- Mesh & Wire, USA, AGS-TECH Inc.
We supply wire and wire mesh, galvanized wires, metal wire, black annealed wire, wire mesh filters, wire cloth, perforated metal mesh, wire mesh fence and panels, conveyor belt mesh, wire mesh containers and customized wire mesh products to your specifications. Malla e arame Ofrecemos produtos de arame e malla, incluíndo fíos de ferro galvanizado, fíos de unión de ferro revestido de PVC, malla de arame, rede de arame, fencing, malla de cinta transportadora, malla metálica perforada. Ademais dos nosos produtos de malla de arame estándar, facemos malla de fabricación personalizada e produtos de fío metálico metal segundo as súas especificacións e necesidades. Cortamos ao tamaño desexado, etiquetamos e embalamos segundo os requisitos do cliente. Fai clic nos submenús a continuación para ler máis sobre un produto específico de malla e arame. Arames galvanizados e fíos metálicos Estes fíos úsanse en numerosas aplicacións en toda a industria. Por exemplo, os fíos de ferro galvanizado utilízanse con frecuencia para fins de atadura e fixación, como cordas de considerable resistencia á tracción. Estes fíos metálicos poden estar galvanizados en quente e ter un aspecto metálico ou poden estar revestidos de PVC e estar coloreados. Os arames de púas teñen varios tipos de navalla e utilízanse para manter os intrusos fóra das zonas restrinxidas. Hai varios calibres de arame dispoñibles no stock. Fios longos veñen en bobinas. Se as cantidades o xustifican, podemos fabricalos coa lonxitude e dimensións da bobina desexadas. É posible a etiquetaxe e embalaxe personalizados dos nosos arames galvanizados, Metal Wires, Barbed Wire. Descargar folletos: - Cables metálicos - Galvanizados - Recocidos en negro Filtros de malla de arame Estes están feitos na súa maioría de malla fina de arame de aceiro inoxidable e moi utilizados na industria como filtros para filtrar líquidos, po, po... etc. Os filtros de malla de arame teñen espesores de poucos milímetros. AGS-TECH conseguiu fabricar mallas de arame con diámetros de arame inferiores a 1 mm para apantallamento electromagnético dos sistemas militares de iluminación naval. Fabricamos filtros de malla de arame cunhas dimensións segundo as especificacións do cliente. O cadrado, o redondo e o oval son xeometrías de uso habitual. Podes escoller ti o diámetro do fío e o número de mallas dos nosos filtros. Cortámolas a medida e enmarcamos os bordos para que a malla do filtro non se deforme nin se dane. Os nosos filtros de malla de arame posúen alta resistencia, longa vida útil, bordos fortes e fiables. Algunhas áreas de uso dos nosos filtros de malla de arame son industria química, industria farmacéutica, cervexa, bebidas, blindaxe electromagnética, industria do automóbil, aplicacións mecánicas, etc. - Folleto de malla de arame e tea (inclúe filtros de malla de arame) Malla metálica perforada As nosas follas de malla metálica perforada prodúcense a partir de aceiro galvanizado, aceiro baixo en carbono, aceiro inoxidable, placas de cobre, placas de níquel ou segundo o solicite vostede, o cliente. Varios Formas e patróns de buratos pódense estampar como queiras. A nosa malla metálica perforada ofrece suavidade, planitude superficial perfecta, resistencia e durabilidade e é adecuada para moitas aplicacións. Ao proporcionar malla metálica perforada, cumprimos as necesidades de moitas industrias e aplicacións, incluíndo illamento acústico interior, fabricación de silenciadores, minería, medicina, procesamento de alimentos, ventilación, almacenamento agrícola, protección mecánica e moito máis. Chámanos hoxe. Con gusto cortaremos, estamparemos, dobraremos e fabricaremos a súa malla metálica perforada segundo as súas especificacións e necesidades. - Folleto de malla de arame e tea (inclúe malla metálica perforada) Cerca de malla de arame e paneis e reforzo A malla de arame é amplamente utilizada na construción, deseño de xardíns, mellora do fogar, xardinería, construción de estradas, etc., con aplicacións populares de malla de arame como cercado e paneis de reforzo na construción._cc781905-5cde-31 bb3b-136bad5cf58d_Consulta os nosos folletos descargables a continuación para escoller o teu modelo preferido de abertura de malla, calibre de cable, cor e acabado. Todos os nosos valos e paneis de arame e produtos de reforzo cumpren cos estándares internacionais da industria. Hai unha variedade de estruturas de valado de arame dispoñibles no stock. - Folleto de malla de arame e tea (inclúe información sobre o noso valado, paneis e reforzo) Malla de cinta transportadora A nosa malla de cinta transportadora está feita xeralmente de fío de aceiro inoxidable de malla reforzada, fío de ferro inoxidable, fío de nicromo, fío de bala. petróleo, metalurxia, industria alimentaria, farmacéutica, industria do vidro, entrega de pezas dentro dunha planta ou instalación..., etc. O estilo de tecido da maioría das mallas de cinta transportadora é a preflexión para o resorte e despois a inserción do fío. Os diámetros do fío son xeralmente: 0,8-2,5 mm Os espesores do fío son xeralmente: 5-13,2 mm As cores comúns son xeralmente: Silver Xeralmente o ancho é de entre 0,4 m e 3 m e a lonxitude está entre 0,5 e 100 m. A malla da cinta transportadora é resistente á calor O tipo de cadea, o ancho e a lonxitude da malla da cinta transportadora están entre os parámetros personalizables. - Folleto de malla de arame e tea (inclúe información xeral sobre as nosas capacidades) Produtos personalizados de malla de arame (como bandexas de cables, estribos, etc.) A partir de malla de arame e malla metálica perforada podemos fabricar unha variedade de produtos personalizados, como bandexas de cables, axitadores, gaiolas de Faraday e estruturas de blindaxe EM, cestas e bandexas de arame, obxectos arquitectónicos, obxectos de arte, luvas de malla de aceiro utilizadas na industria cárnica. para protección contra lesións...etc. A nosa malla de arame personalizada, metais perforados e metais expandidos pódense cortar ao tamaño e aplanar para a súa aplicación desexada. A malla de arame aplanada úsase habitualmente como protectores de máquinas, pantallas de ventilación, pantallas de queimadores, pantallas de seguridade, pantallas de drenaxe de líquidos, paneis de teito e moitas outras aplicacións. Podemos crear metais perforados personalizados con formas e tamaños de buratos para satisfacer os requisitos do seu proxecto e produto. Os metais perforados son versátiles no seu uso. Tamén podemos proporcionar malla de arame revestida. Os revestimentos poden mellorar a durabilidade dos seus produtos personalizados de malla de arame e tamén proporcionar unha barreira resistente á ferruxe. Os revestimentos de malla de arame personalizados dispoñibles inclúen revestimento en po, electropulido, galvanizado por inmersión en quente, nailon, pintura, aluminización, electrogalvanizado, PVC, Kevlar, etc. Xa sexa tecido a partir de arame como malla de arame personalizada, ou estampado e perforado e aplanado a partir de chapa metálica como follas perforadas, póñase en contacto con AGS-TECH para obter os requisitos de produtos personalizados. - Folleto de malla de arame e tea (inclúe moita información sobre as nosas capacidades de produción personalizadas de malla de arame) - Folleto de bandexas e cestas de malla de arame (Ademais dos produtos deste folleto podes obter bandexas de cables personalizadas segundo as túas especificacións) - Formulario de deseño de cotización de contedores de malla de arame (faga clic para descargar, cubrir e enviarnos un correo electrónico) PÁXINA ANTERIOR