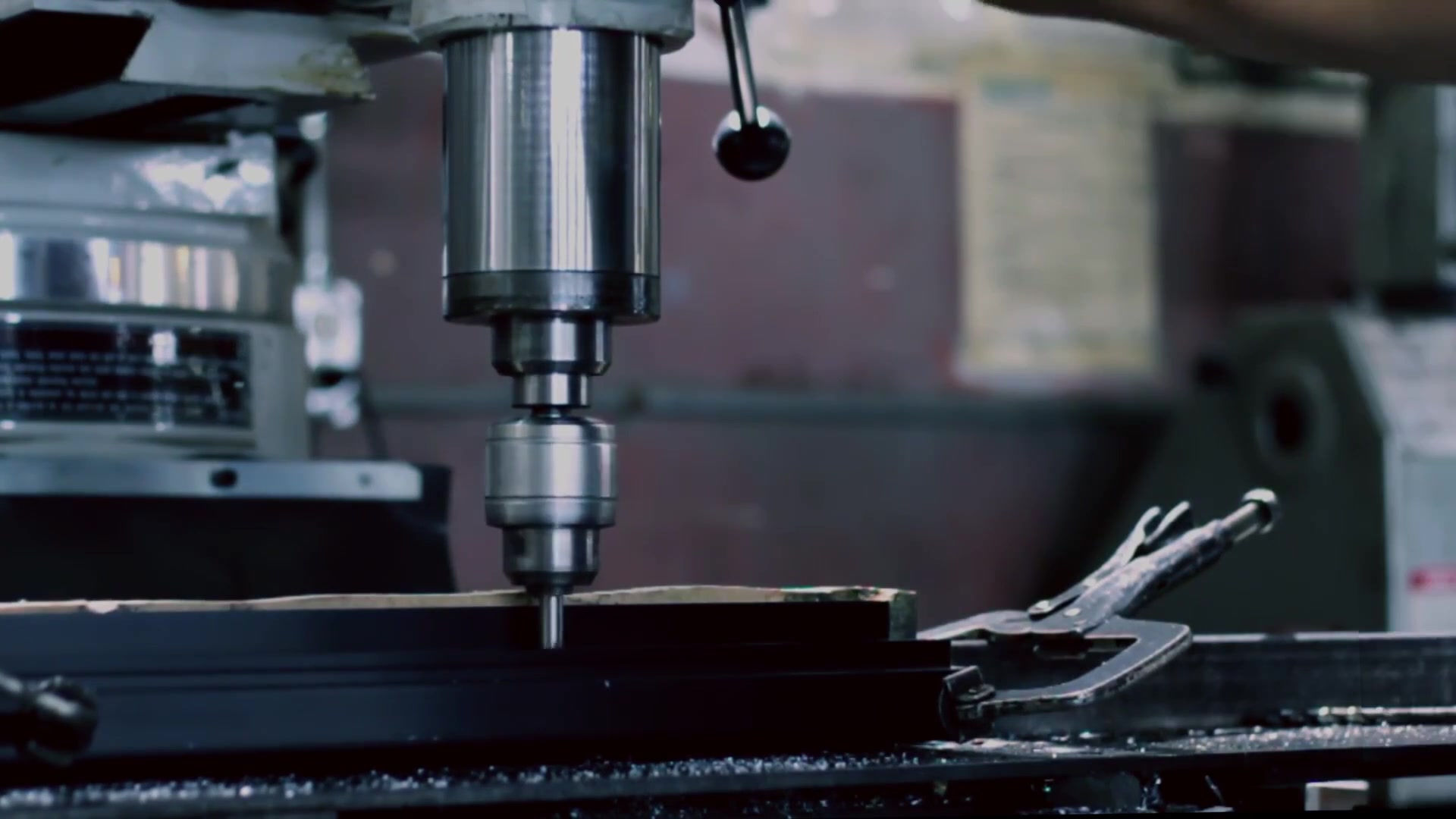
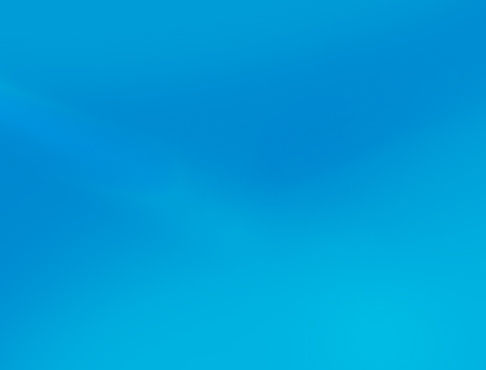
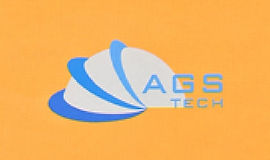
Fabricante global personalizado, integrador, consolidador, socio de outsourcing para unha ampla variedade de produtos e servizos.
Somos a súa fonte única para a fabricación, fabricación, enxeñaría, consolidación, integración e subcontratación de produtos e servizos fabricados a medida e dispoñibles.
Escolla o seu idioma
-
Fabricación personalizada
-
Fabricación por contrato nacional e global
-
Outsourcing de Manufactura
-
Compras domésticas e globais
-
Consolidación
-
Integración de enxeñería
-
Servizos de Enxeñaría
Search Results
164 results found with an empty search
- Electron Beam Machining, EBM, E-Beam Machining & Cutting & Boring
Electron Beam Machining, EBM, E-Beam Machining & Cutting & Boring, Custom Manufacturing of Parts - AGS-TECH Inc. - NM - USA Mecanizado EBM e mecanizado de feixe electrónico En ELECTRON-BEAM MACHINING (EBM) temos electróns de alta velocidade concentrados nun feixe estreito, creando o material de calor e que se dirixe cara o traballo. Así, EBM é unha especie de High-ENERGY-BEAM MACHINING technique. O mecanizado por feixe de electróns (EBM) pódese usar para cortar ou perforar con moita precisión unha variedade de metais. O acabado superficial é mellor e o ancho da corte é máis estreito en comparación con outros procesos de corte térmico. Os feixes de electróns dos equipos EBM-Machining xéranse nun canón de feixe de electróns. As aplicacións do mecanizado con feixe de electróns son similares ás do mecanizado con feixe láser, agás que a EBM require un bo baleiro. Así, estes dous procesos clasifícanse como procesos electro-óptico-térmicos. A peza que se vai mecanizar co proceso EBM sitúase baixo o feixe de electróns e mantense ao baleiro. Os canóns de feixe de electróns das nosas máquinas EBM tamén están provistos de sistemas de iluminación e telescopios para o aliñamento do feixe coa peza de traballo. A peza de traballo está montada nunha mesa CNC para que se poidan mecanizar buratos de calquera forma usando o control CNC e a funcionalidade de desviación do feixe da pistola. Para conseguir a rápida evaporación do material, a densidade plana da potencia no feixe debe ser o máis alta posible. Pódense acadar valores de ata 10exp7 W/mm2 no lugar do impacto. Os electróns transfieren a súa enerxía cinética en calor nunha área moi pequena, e o material impactado polo feixe evaporase en moi pouco tempo. O material fundido na parte superior da fronte, é expulsado da zona de corte pola alta presión de vapor nas partes inferiores. Os equipos EBM constrúense de forma similar ás máquinas de soldadura por feixe de electróns. As máquinas de feixe de electróns adoitan utilizar voltaxes no rango de 50 a 200 kV para acelerar os electróns ata un 50 a 80% da velocidade da luz (200.000 km/s). Para enfocar o feixe de electróns á superficie da peza de traballo utilízanse lentes magnéticas cuxa función se basea nas forzas de Lorentz. Coa axuda dun ordenador, o sistema de deflexión electromagnética sitúa o feixe segundo sexa necesario para que se poidan perforar buratos de calquera forma. Noutras palabras, as lentes magnéticas dos equipos de mecanizado de feixes electrónicos dan forma ao feixe e reducen a diverxencia. Por outra banda, as aberturas permiten que só pasen os electróns converxentes e capten os electróns diverxentes de baixa enerxía das franxas. A apertura e as lentes magnéticas en EBM-Machines melloran así a calidade do feixe de electróns. A arma en EBM úsase en modo pulsado. Os buratos pódense perforar en láminas finas cun só pulso. Non obstante, para as placas máis grosas, serían necesarios varios pulsos. Normalmente úsanse duracións de pulso de conmutación de tan baixo como 50 microsegundos a 15 milisegundos. Para minimizar as colisións electrónicas coas moléculas de aire que producen a dispersión e manter a contaminación ao mínimo, utilízase o baleiro na EBM. O baleiro é difícil e caro de producir. Especialmente obter un bo baleiro dentro de grandes volumes e cámaras é moi esixente. Polo tanto, EBM é o máis adecuado para pezas pequenas que encaixan en cámaras de baleiro compactas de tamaño razoable. O nivel de baleiro dentro da arma do EBM está na orde de 10EXP(-4) a 10EXP(-6) Torr. A interacción do feixe de electróns coa peza de traballo produce raios X que supoñen un perigo para a saúde, polo que o persoal ben adestrado debe manexar os equipos EBM. En xeral, EBM-Machining utilízase para cortar buratos de tan pequenos como 0,025 milímetros de diámetro e ranuras tan estreitas como 0,001 polgadas en materiais de ata 0,250 polgadas (6,25 milímetros) de espesor. A lonxitude característica é o diámetro sobre o que está activo o feixe. O feixe de electróns en EBM pode ter unha lonxitude característica de decenas de micras a mm dependendo do grao de enfoque do feixe. Xeralmente, o feixe de electróns enfocado de alta enerxía incide na peza de traballo cun tamaño de punto de 10 a 100 micras. O EBM pode proporcionar orificios de diámetros no intervalo de 100 micras a 2 mm cunha profundidade de ata 15 mm, é dicir, cunha relación profundidade/diámetro de arredor de 10. No caso de feixes de electróns desenfocados, as densidades de potencia baixarían ata 1. vatios/mm2. Non obstante, no caso de feixes focalizados, as densidades de potencia poderían aumentarse ata decenas de kW/mm2. Como comparación, os raios láser pódense enfocar nun tamaño de punto de 10 a 100 micras cunha densidade de potencia de ata 1 MW/mm2. A descarga eléctrica normalmente proporciona as densidades de potencia máis altas con tamaños de puntos máis pequenos. A corrente do feixe está directamente relacionada co número de electróns dispoñibles no feixe. A corrente do feixe en Electron-Beam-Machining pode ser tan baixa como 200 microamperios a 1 amperio. Aumentar a corrente do feixe e/ou a duración do pulso do EBM aumenta directamente a enerxía por pulso. Usamos pulsos de alta enerxía superiores a 100 J/pulso para mecanizar buratos máis grandes en placas máis grosas. En condicións normais, o mecanizado EBM ofrécenos a vantaxe de produtos sen rebabas. Os parámetros do proceso que afectan directamente ás características de mecanizado en Electron-Beam-Machining son: • Tensión de aceleración • Corrente do feixe • Duración do pulso • Enerxía por pulso • Potencia por pulso • Corrente da lente • Tamaño do punto • Densidade de potencia Tamén se poden obter algunhas estruturas fantásticas usando Electron-Beam-Machining. Os buratos poden ser estreitos ao longo da profundidade ou en forma de barril. Ao enfocar o feixe debaixo da superficie, pódense obter conos inversos. Unha ampla gama de materiais como aceiro, aceiro inoxidable, superligas de titanio e níquel, aluminio, plásticos e cerámica pódense mecanizar mediante mecanizado por vigas electrónicas. Pode haber danos térmicos asociados a EBM. Non obstante, a zona afectada pola calor é estreita debido á curta duración do pulso na EBM. As zonas afectadas pola calor son xeralmente de 20 a 30 micras. Algúns materiais como o aluminio e as aliaxes de titanio son máis fáciles de mecanizar en comparación co aceiro. Ademais, o mecanizado EBM non implica forzas de corte nas pezas de traballo. Isto permite o mecanizado de materiais fráxiles e fráxiles mediante EBM sen ningún tipo de suxeición ou suxeición significativa como é o caso das técnicas de mecanizado mecánico. Os buratos tamén se poden perforar en ángulos moi pouco profundos, como entre 20 e 30 graos. As vantaxes de Electron-Beam-Machining: EBM proporciona taxas de perforación moi altas cando se perforan pequenos buratos con alta relación de aspecto. EBM pode mecanizar case calquera material independentemente das súas propiedades mecánicas. Non se implican forzas de corte mecánicas, polo que os custos de suxeición, suxeición e fixación do traballo son ignorables e pódense procesar materiais fráxiles/fráxiles sen problemas. As zonas afectadas pola calor en EBM son pequenas debido aos pulsos curtos. EBM é capaz de proporcionar calquera forma de buratos con precisión utilizando bobinas electromagnéticas para desviar os feixes de electróns e a mesa CNC. As desvantaxes de Electron-Beam-Machining: os equipos son caros e o funcionamento e mantemento dos sistemas de baleiro require de técnicos especializados. EBM require períodos de bombeo de baleiro significativos para acadar as baixas presións necesarias. Aínda que a zona afectada pola calor é pequena en EBM, a formación da capa de refundición ocorre con frecuencia. Os nosos moitos anos de experiencia e coñecementos axúdanos a aproveitar este valioso equipo no noso entorno de fabricación. CLICK Product Finder-Locator Service PÁXINA ANTERIOR
- Tanks and Containers, USA, AGS-TECH Inc.
AGS-TECH offers off-shelf and custom manufactured tanks and containers of various sizes. We supply wire mesh cage containers, stainless, aluminum and metal tanks and containers, IBC tanks, plastic and polymer containers, fiberglass tanks, collapsible tanks. Tanques e contedores Subministramos recipientes de almacenamento de produtos químicos, po, líquidos e gas e depósitos feitos de polímeros inertes, aceiro inoxidable....etc. Temos envases plegables, enrollables, apilables, abatibles, envases con outras funcionalidades útiles atopando aplicacións en moitas industrias como a construción, a alimentación, a farmacéutica, a química, a petroquímica....etc. Fálanos da túa aplicación e recomendarémosche o recipiente máis axeitado. Os envases de aceiro inoxidable ou outros materiais de gran volume están feitos por encargo e segundo as súas especificacións. En xeral, os envases máis pequenos están dispoñibles fóra da estantería e tamén se fabrican a medida se as súas cantidades o xustifican. Se as cantidades son importantes, podemos soplar ou rotar envases de plástico e tanques segundo as súas especificacións. Aquí están os principais tipos dos nosos tanques e contedores: Recipientes de gaiola de malla de arame Temos unha variedade de envases de gaiola de malla de arame en stock e tamén podemos fabricalos personalizados segundo as súas especificacións e necesidades. Os nosos contedores de gaiola de malla de arame inclúen produtos como: Palés de gaiola apilables Contenedores plegables de rolo de malla de arame Contenedores plegables de malla de arame Todos os nosos envases de gaiola de malla de arame están feitos de materiais de aceiro inoxidable ou de aceiro suave da máis alta calidade e as versións non inoxidables están recubertas contra a corrosión e a descomposición xeralmente usando_cc781905-5cde-3194-bb35cde-5cde-3194-bb3b5c95-136-bb3b5c-58d 3194-bb3b-136bad5cf58d_inmersión en quente ou revestimento en po. A cor do acabado é xeralmente zinc: branco ou amarelo; ou revestido en po segundo a súa solicitude. Os nosos contenedores de gaiolas de malla de arame son montados baixo estritos procedementos de control de calidade e probados por impactos mecánicos, capacidade de carga, durabilidade, resistencia e fiabilidade a longo prazo. Os nosos contedores de gaiola de malla de arame axústanse aos estándares internacionais de calidade, así como aos estándares estadounidenses e internacionais da industria do transporte. Os contedores de gaiola de malla de arame úsanse xeralmente como caixas de almacenamento e papeleiras, carros de almacenamento, carros de transporte, etc. Ao elixir un recipiente de gaiola de malla de arame, teña en conta parámetros importantes como a capacidade de carga, o peso do propio recipiente, as dimensións da reixa, as dimensións exteriores e interiores, se precisa un recipiente que se dobra plano para aforrar espazo e almacenamento, e Por favor, considere tamén cantos contedores se poden cargar nun contedor de 20 ou 40 pés. A conclusión é que os envases de gaiola de malla de arame son unha alternativa duradeira, económica e respectuosa co medio ambiente aos envases desbotables. Abaixo amósanse folletos descargables dos nosos produtos de envases de malla de arame. - Formulario de deseño de cotización de contedores de malla metálica (faga clic para descargar, enche e envíenos un correo electrónico) Depósitos e recipientes metálicos e inoxidables Os nosos depósitos e recipientes de aceiro inoxidable e doutro metal son ideais para almacenar cremas e líquidos. Son ideais para a cosmética, industrias farmacéuticas e de alimentos e bebidas e outras. Cumpre coas directrices europeas, americanas e internacionais. Os nosos tanques de aceiro inoxidable e metálicos son fáciles to_cc781905-5cf58d_bb35-cc781905-9430-bb35-943-bb305-943-bb305-5cde 136bad5cf58d_Estes recipientes teñen unha base estable e pódense desinfectar sen zona de retención. Podemos equipar os nosos depósitos e recipientes metálicos e inoxidables con todo tipo de accesorios, como integración dun cabezal de lavado. Os nosos envases son presurizables. Adáptanse facilmente á súa planta e lugar de traballo. As presións de traballo dos nosos contedores varían, así que asegúrate de comparar as especificacións coas túas necesidades. Os nosos recipientes e tanques de aluminio tamén son moi populares na industria. Algúns modelos son móbiles con rodas, outros son apilables. Temos depósitos de almacenamento de po, gránulos e pellets aprobados por UN para o transporte de produtos perigosos. UN. e especificacións. As dimensións interiores e exteriores, o grosor das paredes dos nosos tanques e recipientes metálicos e inoxidables pódense variar segundo as súas necesidades. Depósitos e recipientes de aluminio e inoxidable Tanques e contedores apilables Tanques con rodas e contedores IBC & GRV Tanks Tanques de almacenamento de po, gránulos e pellets Tanques e contedores de deseño e fabricación a medida Fai clic nas ligazóns a continuación para descargar os nosos folletos para Depósitos e contedores de metal e inoxidable: Tanques e contedores IBC Tanques e contedores de plástico e polímero AGS-TECH ofrece tanques e contedores dunha gran variedade de materiais plásticos e polímeros. Animámoslle a que se poña en contacto connosco coa súa solicitude e que especifique o seguinte para poder cotizarlle o produto máis axeitado. - Aplicación - Grao do material - Dimensións - Rematar - Requisitos de embalaxe - Cantidade Por exemplo, os materiais plásticos de calidade alimentaria aprobados pola FDA son importantes para algúns recipientes que almacenan bebidas, grans, zumes de froitas... etc. Por outra banda, se necesitas depósitos e recipientes de plástico e polímero para almacenar produtos químicos ou farmacéuticos, a inercia do material plástico fronte ao contido é de máxima importancia. Póñase en contacto connosco para a nosa opinión sobre os materiais. Tamén podes pedir depósitos e recipientes de plástico e polímeros dispoñibles nos nosos folletos below. Fai clic nas seguintes ligazóns para descargar os nosos folletos para tanques e recipientes de plástico e polímeros: Tanques e contedores IBC Tanques e contedores de fibra de vidro Ofrecemos tanques e contedores feitos de fibra de vidro materials. Os nosos depósitos e contedores de fibra de vidro meet US e internacionalmente_cc781905-5cde-3194-5cde-3194-bb3b35-cf58d_costrución estándar Os tanques e recipientes de fibra de vidro están fabricados con laminados moldeados por contacto conforme á norma ASTM 4097 e laminados enrolados de filamento conforme á norma ASTM 3299. Resinas especiais utilizadas na fabricación de tanques de fibra de vidro sobre a concentración, a temperatura e o comportamento corrosivo do produto que se almacena. As resinas ignífugas aprobadas pola FDA e as están dispoñibles para aplicacións especiais. Animámoslle a que se poña en contacto connosco coa súa solicitude e especifique o seguinte para que poidamos cotizarlle o depósito e recipiente de fibra de vidro máis axeitados. - Aplicación - Especificacións e expectativas materiais - Dimensións - Rematar - Requisitos de embalaxe - Cantidade necesaria Con gusto daremos a nosa opinión. Tamén podes pedir fiberglass tanks e contedores dispoñibles nos nosos folletos below. Se ningún dos tanques e recipientes de fibra de vidro da nosa carteira fóra de estante lle satisface, infórmenos e poderemos considerar a fabricación personalizada segundo as súas necesidades. Tanques e contedores plegables Os depósitos e recipientes de auga abatibles son a mellor opción para almacenar líquidos en aplicacións onde barrís de plástico e outros recipientes son demasiado pequenos ou pouco prácticos. Ademais, cando necesitas grandes cantidades de auga ou líquido rapidamente sen construír un tanque de formigón ou metálico, os nosos tanques e recipientes plegables son ideais. Como o seu nome indica, os depósitos e envases abatibles son plegables, é dicir, pódense encoller despois do uso, enrolar e facelos moi compactos e de pequeno volume, fáciles de almacenar e transportar cando estean baleiros. Son reutilizables. Podemos proporcionarche calquera tamaño e modelo e segundo as túas especificacións. Características xerais dos nosos tanques e contedores plegables: - Cor: Azul, laranxa, gris, verde escuro, negro,.....etc. - Material: PVC - Capacidade: Xeralmente entre 200 a 30000 litros - Peso lixeiro, fácil operación. - Tamaño mínimo de embalaxe, fácil de transportar e almacenar. - Sen contaminación de water - Alta resistencia do tecido revestido, adherencia ata 60 lb/in. - A alta resistencia das costuras está asegurada con o fundido de alta frecuencia e selado co mesmo poliuretano que o corpo do tanque, polo que os tanques teñen unha excelente capacidade evitando_cc781905-5cde-3194-3194-bb3513d6air seguro para a auga. Aplicacións para tanques e contedores plegables: · Almacenamento temporal · Recollida de augas pluviais · Almacenamento Residencial e Público de Auga · Aplicacións de almacenamento de auga de defensa · Tratamento de augas · Almacenamento e socorro de emerxencia · Rego · As construtoras elixen tanques de auga de PVC para probar a carga máxima da ponte · Loita contra incendios Tamén aceptamos pedidos OEM. Está dispoñible a etiquetaxe personalizada, embalaxe e impresión de logotipos. PÁXINA ANTERIOR
- Micro Assembly & Packaging - Micromechanical Fasteners - Self Assembly
Micro Assembly & Packaging - Micromechanical Fasteners - Self Assembly - Adhesive Micromechanical Fastening - AGS-TECH Inc. - New Mexico - USA Micromontaxe e embalaxe Xa resumimos os nosos MICRO ASSEMBLY & PACKAGING services e produtos relacionados especificamente coa microelectrónica na nosa páxina_cc781905-bb3bd315-bb3bd3_cc75cf58dFabricación de Microelectrónica / Fabricación de Semicondutores. Aquí concentrarémonos en técnicas de microensamblaxe e envasado máis xenéricas e universais que utilizamos para todo tipo de produtos, incluíndo sistemas mecánicos, ópticos, microelectrónicos, optoelectrónicos e híbridos que consisten nunha combinación destes. As técnicas que comentamos aquí son máis versátiles e pódense considerar que se usan en aplicacións máis pouco habituais e non estándar. Noutras palabras, as técnicas de microensamblaxe e embalaxe que se comentan aquí son as nosas ferramentas que nos axudan a pensar "fóra da caixa". Aquí tes algúns dos nosos extraordinarios métodos de microensamblaxe e envasado: - Micromontaxe e embalaxe manual - Micromontaxe e envasado automatizados - Métodos de autoensamblaxe como a autoensamblaxe fluídica - Microconxunto estocástico mediante forzas vibratorias, gravitatorias ou electrostáticas ou non. - Emprego de fixadores micromecánicos - Fijación micromecánica adhesiva Exploremos algunhas das nosas versátiles técnicas extraordinarias de microensamblaxe e envasado con máis detalle. MICROMONTAXE E EMBALAXE MANUAL: As operacións manuais poden ser prohibitivas e requiren un nivel de precisión que pode resultar pouco práctico para un operador debido á tensión que provoca nos ollos e ás limitacións de destreza asociadas á montaxe de pezas en miniatura baixo un microscopio. Non obstante, para aplicacións especiais de baixo volume, a micromontaxe manual pode ser a mellor opción porque non require necesariamente o deseño e construción de sistemas de microensamblaxe automatizados. MICRO-MONTAXE E EMBALAXE AUTOMATIZADO: Os nosos sistemas de micro-ensamblaxe están deseñados para facer a montaxe máis fácil e rendible, permitindo o desenvolvemento de novas aplicacións para tecnoloxías de micro-máquina. Podemos micro-ensamblar dispositivos e compoñentes en dimensións de nivel de micras mediante sistemas robóticos. Aquí tes algúns dos nosos equipos e capacidades de microensamblaxe e envasado automatizados: • Equipos de control de movemento de primeira calidade, incluíndo unha célula de traballo robótica con resolución de posición nanométrica • Células de traballo controladas por CAD totalmente automatizadas para microensamblaxe • Métodos ópticos de Fourier para xerar imaxes de microscopio sintético a partir de debuxos CAD para probar rutinas de procesamento de imaxes con diferentes aumentos e profundidades de campo (DOF) • Capacidade de deseño e produción personalizados de micro pinzas, manipuladores e actuadores para a micromontaxe e envasado de precisión. • Interferómetros láser • Extensométricas para realimentación de forza • Visión por ordenador en tempo real para controlar servomecanismos e motores para o micro-alineamento e micro-ensamblaxe de pezas con tolerancias submicronicas. • Microscopios electrónicos de barrido (SEM) e microscopios electrónicos de transmisión (TEM) • Nanomanipulador de 12 graos de liberdade O noso proceso de micromontaxe automatizado pode colocar varias engrenaxes ou outros compoñentes en varios postes ou localizacións nun só paso. As nosas capacidades de micromanipulación son enormes. Estamos aquí para axudarche con ideas extraordinarias non estándar. MÉTODOS DE AUTOMONTAXE MICRO E NANO: nos procesos de autoensamblaxe un sistema desordenado de compoñentes preexistentes forma unha estrutura ou patrón organizado como consecuencia de interaccións específicas e locais entre os compoñentes, sen dirección externa. Os compoñentes que se ensamblan só experimentan interaccións locais e normalmente obedecen a un conxunto simple de regras que rexen como se combinan. Aínda que este fenómeno é independente da escala e pode utilizarse para sistemas de autoconstrución e fabricación a case todas as escalas, o noso foco está na micro autoensamblaxe e na nanoautoensamblaxe. Para construír dispositivos microscópicos, unha das ideas máis prometedoras é explotar o proceso de autoensamblaxe. Pódense crear estruturas complexas combinando bloques de construción en circunstancias naturais. Para dar un exemplo, establécese un método para a microensamblaxe de múltiples lotes de microcomponentes nun único substrato. O substrato prepárase con sitios de unión de ouro revestidos hidrófobos. Para realizar a micromontaxe, aplícase un aceite hidrocarburo ao substrato e molla exclusivamente os sitios de unión hidrófobo en auga. Despois engádense microcomponentes á auga e reúnense nos sitios de unión mollados con aceite. Aínda máis, a microensamblaxe pódese controlar para que teña lugar nos sitios de unión desexados mediante un método electroquímico para desactivar sitios específicos de unión ao substrato. Ao aplicar repetidamente esta técnica, pódense ensamblar secuencialmente diferentes lotes de microcomponentes nun único substrato. Despois do procedemento de microensamblaxe, prodúcese a galvanoplastia para establecer conexións eléctricas para os compoñentes micro ensamblados. MICROCONXUNTO ESTOCÁSTICO: No micromontaxe paralelo, onde as pezas se ensamblan simultáneamente, existe un microconxunto determinista e estocástico. No microconxunto determinista coñécese de antemán a relación entre a peza e o seu destino sobre o substrato. No microconxunto estocástico, por outra banda, esta relación é descoñecida ou aleatoria. As pezas autoensamblan en procesos estocásticos impulsados por algunha forza motriz. Para que se produza a micro autoensamblaxe, é necesario que haxa forzas de unión, a unión debe producirse de forma selectiva e as pezas de microensamblaxe deben poder moverse para que poidan xuntarse. A micromontaxe estocástica vai moitas veces acompañada de vibracións, forzas electrostáticas, microfluídicas ou outras que actúan sobre os compoñentes. A micromontaxe estocástica é especialmente útil cando os bloques de construción son máis pequenos, porque o manexo dos compoñentes individuais convértese nun desafío máis. A autoensamblaxe estocástica tamén se pode observar na natureza. FIXACIÓNS MICROMECÁNICAS: a microescala, os tipos convencionais de fixadores como parafusos e bisagras non funcionarán facilmente debido ás limitacións de fabricación actuais e ás grandes forzas de fricción. Por outra banda, os micro fixadores a presión funcionan máis facilmente en aplicacións de microensamblaxe. Os micro fixadores de presión son dispositivos deformables que consisten en pares de superficies de acoplamento que se unen durante a micromontaxe. Debido ao movemento de montaxe simple e lineal, os peches a presión teñen unha ampla gama de aplicacións en operacións de micromontaxe, como dispositivos con compoñentes múltiples ou en capas, ou micro enchufes optomecánicos, sensores con memoria. Outros elementos de fixación de microconxuntos son as xuntas de "bloqueo de chave" e as xuntas de "interbloqueo". As unións de bloqueo de chave consisten na inserción dunha "chave" nunha microparte, nunha ranura de acoplamento doutra microparte. O bloqueo na posición conséguese trasladando a primeira microparte dentro da outra. As xuntas de bloqueo son creadas pola inserción perpendicular dunha microparte cunha fenda, noutra microparte cunha fenda. As fendas crean un axuste de interferencia e son permanentes unha vez que se unen as micropartes. FIXACIÓN MICROMECÁNICA ADHESIVO: a fixación mecánica adhesiva úsase para construír microdispositivos 3D. O proceso de fixación inclúe mecanismos de autoalineación e unión adhesiva. Os mecanismos de auto-alineamento están implantados no microconxunto adhesivo para aumentar a precisión de posicionamento. Unha microsonda unida a un micromanipulador robótico recolle e deposita adhesivo con precisión nos lugares obxectivo. A luz de curado endurece o adhesivo. O adhesivo curado mantén as pezas micromontadas nas súas posicións e proporciona xuntas mecánicas fortes. Usando adhesivo condutor, pódese obter unha conexión eléctrica fiable. A suxeición mecánica do adhesivo só require operacións sinxelas e pode dar lugar a conexións fiables e altas precisións de posicionamento, que son importantes na micromontaxe automática. Para demostrar a viabilidade deste método, moitos dispositivos MEMS tridimensionais foron microensamblados, incluíndo un interruptor óptico rotativo 3D. CLICK Product Finder-Locator Service PÁXINA ANTERIOR
- Thermal Infrared Test Equipment, Thermal Camera, Differential Scanning
Thermal Infrared Test Equipment, Thermal Camera, Differential Scanning Calorimeter, Thermo Gravimetric Analyzer, Thermo Mechanical Analyzer, Dynamic Mechanical Equipos de proba térmica e IR CLICK Product Finder-Locator Service Entre os moitos EQUIPOS DE ANÁLISE TÉRMICA, centramos a nosa atención nos máis populares da industria, a saber, o EQUIPO DE ANÁLISE TÉRMICO, TERMÉTICO -ANÁLISE MECÁNICA ( TMA ), DILATOMETRÍA, ANÁLISE MECÁNICA DINÁMICA ( DMA ), ANÁLISE TÉRMICA DIFERENCIAL ( DTA). O noso EQUIPO DE PROBA DE INFRAVERMELLOS inclúe INSTRUMENTOS DE IMAXE TÉRMICA, TERMÓGRAFOS INFRAVERMELLOS, CÁMARAS INFRAVERMELLOS. Algunhas aplicacións dos nosos instrumentos de imaxe térmica son a inspección de sistemas eléctricos e mecánicos, a inspección de compoñentes electrónicos, danos por corrosión e adelgazamento de metais, detección de defectos. CALORÍMETROS DIFERENCIAIS DE EXPLORACIÓN (DSC) : técnica na que se mide a diferenza na cantidade de calor necesaria para aumentar a temperatura dunha mostra e referencia en función da temperatura. Tanto a mostra como a referencia mantéñense case á mesma temperatura durante todo o experimento. O programa de temperatura para unha análise DSC establécese para que a temperatura do soporte da mostra aumente linealmente en función do tempo. A mostra de referencia ten unha capacidade calorífica ben definida no intervalo de temperaturas a analizar. Os experimentos DSC proporcionan como resultado unha curva do fluxo de calor en función da temperatura ou do tempo. Os calorímetros de varrido diferencial úsanse con frecuencia para estudar o que ocorre cos polímeros cando se quentan. As transicións térmicas dun polímero pódense estudar mediante esta técnica. As transicións térmicas son cambios que teñen lugar nun polímero cando se quentan. A fusión dun polímero cristalino é un exemplo. A transición vítrea tamén é unha transición térmica. A análise térmica DSC realízase para determinar os cambios de fase térmica, a temperatura de transición térmica do vidro (Tg), as temperaturas de fusión cristalina, os efectos endotérmicos, os efectos exotérmicos, as estabilidades térmicas, as estabilidades de formulación térmica, as estabilidades oxidativas, os fenómenos de transición, as estruturas de estado sólido. A análise DSC determina a temperatura de transición vítrea Tg, temperatura á que os polímeros amorfos ou unha parte amorfa dun polímero cristalino pasan dun estado fráxil duro a un estado gomoso brando, punto de fusión, temperatura á que se funde un polímero cristalino, Hm Enerxía absorbida (joules). /gramo), cantidade de enerxía que absorbe unha mostra ao fundirse, Tc Punto de cristalización, temperatura á que un polímero cristaliza ao quentarse ou arrefriarse, Hc Enerxía liberada (joules/gramo), cantidade de enerxía que libera unha mostra ao cristalizar. Os calorímetros de varrido diferencial pódense utilizar para determinar as propiedades térmicas de plásticos, adhesivos, selantes, aliaxes metálicas, materiais farmacéuticos, ceras, alimentos, aceites e lubricantes e catalizadores, etc. ANALIZADORES TÉRMICOS DIFERENCIAIS (DTA): Unha técnica alternativa ao DSC. Nesta técnica é o fluxo de calor á mostra e a referencia que permanecen igual en lugar da temperatura. Cando a mostra e a referencia se quentan de forma idéntica, os cambios de fase e outros procesos térmicos provocan unha diferenza de temperatura entre a mostra e a referencia. DSC mide a enerxía necesaria para manter tanto a referencia como a mostra á mesma temperatura, mentres que o DTA mide a diferenza de temperatura entre a mostra e a referencia cando ambas se someten á mesma calor. Polo tanto, son técnicas similares. ANALIZADOR TERMOMECÁNICO (TMA) : O TMA revela o cambio nas dimensións dunha mostra en función da temperatura. Pódese considerar a TMA como un micrómetro moi sensible. O TMA é un dispositivo que permite medicións precisas de posición e pode calibrarse contra estándares coñecidos. Un sistema de control de temperatura composto por un forno, un disipador de calor e un termopar rodea as mostras. Os accesorios de cuarzo, invar ou cerámica suxeitan as mostras durante as probas. As medicións de TMA rexistran os cambios causados por cambios no volume libre dun polímero. Os cambios no volume libre son cambios volumétricos no polímero causados pola absorción ou liberación de calor asociada a ese cambio; a perda de rixidez; aumento do fluxo; ou polo cambio no tempo de relaxación. Sábese que o volume libre dun polímero está relacionado coa viscoelasticidade, o envellecemento, a penetración de disolventes e as propiedades de impacto. A temperatura de transición vítrea Tg nun polímero corresponde á expansión do volume libre permitindo unha maior mobilidade da cadea por riba desta transición. Visto como unha inflexión ou flexión na curva de expansión térmica, este cambio no TMA pódese ver para cubrir un rango de temperaturas. A temperatura de transición vítrea Tg calcúlase mediante un método acordado. A concordancia perfecta non se constata inmediatamente no valor da Tg ao comparar diferentes métodos, porén, se examinamos coidadosamente os métodos acordados para determinar os valores de Tg, entendemos que realmente hai un bo acordo. Ademais do seu valor absoluto, o ancho da Tg tamén é un indicador de cambios no material. A TMA é unha técnica relativamente sinxela de levar a cabo. A TMA utilízase a miúdo para medir a Tg de materiais como polímeros termoestables altamente reticulados para os que é difícil de usar o calorímetro de varrido diferencial (DSC). Ademais da Tg, o coeficiente de expansión térmica (CTE) obtense da análise termomecánica. O CTE calcúlase a partir das seccións lineais das curvas TMA. Outro resultado útil que nos pode proporcionar o TMA é coñecer a orientación dos cristais ou das fibras. Os materiais compostos poden ter tres coeficientes de expansión térmica distintos nas direccións x, y e z. Ao rexistrar o CTE nas direccións x, y e z pódese entender en que dirección se orientan predominantemente as fibras ou os cristais. Para medir a expansión masiva do material pódese utilizar unha técnica chamada DILATOMETRY . A mostra é inmersa nun fluído como aceite de silicio ou po de Al2O3 no dilatómetro, transcorre polo ciclo de temperatura e as expansións en todas as direccións convértense nun movemento vertical, que é medido polo TMA. Os modernos analizadores termomecánicos facilitan isto aos usuarios. Se se usa un líquido puro, o dilatómetro énchese con ese líquido en lugar do aceite de silicio ou óxido de alúmina. Usando TMA de diamante, os usuarios poden executar curvas de tensión, experimentos de relaxación do estrés, recuperación de fluencia e exploracións dinámicas de temperatura mecánica. O TMA é un equipo de proba indispensable para a industria e a investigación. ANALIZADORES TERMOGRAVIMÉTRICOS ( TGA ) : A análise termogravimétrica é unha técnica na que se controla a masa dunha substancia ou mostra en función da temperatura ou do tempo. A mostra está sometida a un programa de temperatura controlada nunha atmosfera controlada. O TGA mide o peso dunha mostra mentres se quenta ou arrefría no seu forno. Un instrumento TGA consiste nunha bandexa de mostras que está apoiada por unha balanza de precisión. Esa tixola reside nun forno e quéntase ou arrefríase durante a proba. A masa da mostra é monitorizada durante a proba. O ambiente da mostra é purgado cun gas inerte ou reactivo. Os analizadores termogravimétricos poden cuantificar a perda de auga, disolvente, plastificante, descarboxilación, pirólise, oxidación, descomposición, % en peso de material de recheo e % en peso de cinzas. Segundo o caso, pódese obter información ao quentar ou arrefriar. Unha curva térmica TGA típica móstrase de esquerda a dereita. Se a curva térmica TGA descende, indica unha perda de peso. Os TGA modernos son capaces de realizar experimentos isotérmicos. Ás veces, o usuario pode querer usar unha mostra reactiva de gases de purga, como o osíxeno. Cando use osíxeno como gas de purga, o usuario pode querer cambiar os gases de nitróxeno a osíxeno durante o experimento. Esta técnica utilízase con frecuencia para identificar a porcentaxe de carbono nun material. O analizador termogravimétrico pódese usar para comparar dous produtos similares, como ferramenta de control de calidade para garantir que os produtos cumpran as súas especificacións materiais, para garantir que os produtos cumpran os estándares de seguridade, para determinar o contido de carbono, identificar produtos falsificados, identificar temperaturas operativas seguras en varios gases, para mellorar os procesos de formulación do produto, para facer enxeñaría inversa dun produto. Finalmente, cabe mencionar que están dispoñibles combinacións dun TGA cun GC/MS. GC é a abreviatura de Gas Chromatography e MS é a abreviatura de Mass Spectrometry. ANALIZADOR MECÁNICO DINÁMICO ( DMA) : Trátase dunha técnica onde se aplica unha pequena deformación sinusoidal a unha mostra de xeometría coñecida de forma cíclica. A continuación estúdase a resposta dos materiais a tensión, temperatura, frecuencia e outros valores. A mostra pode estar sometida a un estrés controlado ou a unha tensión controlada. Para unha tensión coñecida, a mostra deformarase unha certa cantidade, dependendo da súa rixidez. O DMA mide a rixidez e o amortiguamento, estes indícanse como módulo e delta do bronceado. Como estamos aplicando unha forza sinusoidal, podemos expresar o módulo como un compoñente en fase (o módulo de almacenamento) e un compoñente desfasado (o módulo de perdas). O módulo de almacenamento, E' ou G', é a medida do comportamento elástico da mostra. A relación entre a perda e o almacenamento é o tan delta e chámase amortecemento. Considérase unha medida da disipación de enerxía dun material. O amortecemento varía segundo o estado do material, a súa temperatura e a frecuencia. A DMA ás veces chámase DMTA standing for_cc781905-5cde-3194-bb3b-3194-bb3b-3194-5cde-3194-bb3b-136bad5cf58d_standing for_cc781905-5cde-3194-bb3b-3194-bb3b-3194-b3b3b-3194-b3b3b-3194-b3b3b-3194. A análise termomecánica aplica unha forza estática constante a un material e rexistra os cambios dimensionales do material a medida que varía a temperatura ou o tempo. O DMA, por outra banda, aplica unha forza oscilatoria a unha frecuencia establecida á mostra e informa de cambios na rixidez e na amortiguación. Os datos DMA ofrécennos información sobre o módulo mentres que os datos TMA dannos o coeficiente de expansión térmica. Ambas técnicas detectan transicións, pero o DMA é moito máis sensible. Os valores do módulo cambian coa temperatura e as transicións dos materiais pódense ver como cambios nas curvas E' ou tan delta. Isto inclúe a transición vítrea, a fusión e outras transicións que se producen na meseta vítrea ou gomosa que son indicadores de cambios sutís no material. INSTRUMENTOS DE IMAXE TÉRMICA, TERMÓGRAFOS DE INFRARROJOS, CÁMARAS DE INFRARROXOS : Son dispositivos que forman unha imaxe mediante radiación infravermella. As cámaras diarias estándar forman imaxes usando luz visible no rango de lonxitude de onda de 450-750 nanómetros. Non obstante, as cámaras infravermellas funcionan no intervalo de lonxitudes de onda infravermellos ata 14.000 nm. Xeralmente, canto maior sexa a temperatura dun obxecto, máis radiación infravermella se emite como radiación do corpo negro. As cámaras de infravermellos funcionan mesmo na escuridade total. As imaxes da maioría das cámaras infravermellas teñen unha única canle de cor porque as cámaras xeralmente usan un sensor de imaxe que non distingue diferentes lonxitudes de onda da radiación infravermella. Para diferenciar lonxitudes de onda os sensores de imaxe en cor requiren unha construción complexa. Nalgúns instrumentos de proba, estas imaxes monocromáticas móstranse en pseudocor, onde se usan cambios de cor en lugar de cambios de intensidade para mostrar os cambios no sinal. As partes máis brillantes (máis cálidas) das imaxes adoitan estar de cor branca, as temperaturas intermedias teñen cor vermella e amarela, e as partes máis tenues (máis frías) teñen cor negra. Xeralmente móstrase unha escala xunto a unha imaxe de cor falsa para relacionar as cores coas temperaturas. As cámaras térmicas teñen resolucións considerablemente inferiores á das cámaras ópticas, con valores próximos a 160 x 120 ou 320 x 240 píxeles. As cámaras infravermellos máis caras poden acadar unha resolución de 1280 x 1024 píxeles. Existen dúas categorías principais de cámaras termográficas: SISTEMAS DE DETECCIÓN DE IMAXE INFRAVERMELLO REFRIGERADO and_INFRAVERMELLO_DETECTORES_DETECTORES_DE_INFRAVERMELLOS DETECTORES As cámaras termográficas arrefriadas teñen detectores contidos nunha caixa pechada ao baleiro e están arrefriadas crioxenicamente. O arrefriamento é necesario para o funcionamento dos materiais semicondutores utilizados. Sen arrefriamento, estes sensores veríanse inundados pola súa propia radiación. Con todo, as cámaras infravermellos arrefriadas son caras. O arrefriamento require moita enerxía e leva moito tempo, xa que require varios minutos de tempo de arrefriamento antes de traballar. Aínda que o aparello de refrixeración é voluminoso e caro, as cámaras infravermellos arrefriadas ofrecen aos usuarios unha calidade de imaxe superior en comparación coas cámaras sen arrefriar. A mellor sensibilidade das cámaras arrefriadas permite o uso de lentes con maior distancia focal. O gas nitróxeno embotellado pódese usar para arrefriar. As cámaras térmicas sen arrefriar utilizan sensores que funcionan a temperatura ambiente ou sensores estabilizados a unha temperatura próxima á ambiente mediante elementos de control de temperatura. Os sensores infravermellos sen arrefriar non se arrefrían a baixas temperaturas e, polo tanto, non requiren refrixeradores crioxénicos voluminosos e caros. Non obstante, a súa resolución e calidade de imaxe son inferiores en comparación cos detectores arrefriados. As cámaras termográficas ofrecen moitas oportunidades. Os puntos de sobrequecemento é que as liñas eléctricas pódense localizar e reparar. Pódense observar circuítos eléctricos e puntos inusualmente quentes poden indicar problemas como curtocircuítos. Estas cámaras tamén son moi utilizadas en edificios e sistemas enerxéticos para localizar lugares onde hai unha perda de calor importante para que se poida considerar un mellor illamento térmico neses puntos. Os instrumentos de imaxe térmica serven como equipos de proba non destrutivos. Para obter máis información e outros equipos similares, visite o noso sitio web de equipos: http://www.sourceindustrialsupply.com PÁXINA ANTERIOR
- Optical Displays, Screen, Monitors Manufacturing - AGS-TECH Inc.
Optical Displays, Screen, Monitors, Touch Panel Manufacturing Fabricación e montaxe de pantallas ópticas, pantallas, monitores Descarga o folleto para o noso PROGRAMA DE COLABORACIÓN DE DESEÑO CLICK Product Finder-Locator Service PÁXINA ANTERIOR
- Nanomanufacturing, Nanoparticles, Nanotubes, Nanocomposites, CNT
Nanomanufacturing - Nanoparticles - Nanotubes - Nanocomposites - Nanophase Ceramics - CNT - AGS-TECH Inc. - New Mexico Fabricación a nanoescala / Nanofabricación As nosas pezas e produtos a escala nanométrica prodúcense mediante NANOSCALE MANUFACTURING/NANOMANUFACTURING. Esta zona aínda está na súa infancia, pero ten grandes promesas para o futuro. Dispositivos de enxeñaría molecular, medicamentos, pigmentos... etc. están a desenvolverse e estamos traballando cos nosos socios para manternos á fronte da competencia. Os seguintes son algúns dos produtos dispoñibles comercialmente que ofrecemos actualmente: NANOTUBOS DE CARBONO NANOPARTÍCULAS CERÁMICA NANOFASE REFORZO NEGRO CARBONO para caucho e polímeros NANOCOMPOSITOS en pelotas de tenis, bates de béisbol, motocicletas e bicicletas NANOPARTÍCULAS MAGNÉTICAS para almacenamento de datos NANOPARTICLE conversores catalíticos Os nanomateriais poden ser calquera dos catro tipos, é dicir, metais, cerámicas, polímeros ou compostos. Xeralmente, NANOSTRUCTURES son menos de 100 nanómetros. Na nanofabricación adoptamos un dos dous enfoques. Como exemplo, no noso enfoque de arriba abaixo tomamos unha oblea de silicio, usamos métodos de litografía, gravado en húmido e en seco para construír pequenos microprocesadores, sensores e sondas. Por outra banda, no noso enfoque de nanofabricación ascendente usamos átomos e moléculas para construír pequenos dispositivos. Algunhas das características físicas e químicas que presenta a materia poden experimentar cambios extremos a medida que o tamaño das partículas se aproxima ás dimensións atómicas. Os materiais opacos no seu estado macroscópico poden facerse transparentes na súa escala nanométrica. Os materiais químicamente estables no macroestado poden converterse en combustibles na súa escala nanométrica e os materiais eléctricamente illantes poden converterse en condutores. Actualmente, os seguintes están entre os produtos comerciais que podemos ofrecer: DISPOSITIVOS DE NANOTUBO DE CARBONO (CNT) / NANOTUBO: Podemos visualizar os nanotubos de carbono como formas tubulares de grafito a partir das cales se poden construír dispositivos a nanoescala. CVD, ablación con láser de grafito, descarga de arco de carbono pódese usar para producir dispositivos de nanotubos de carbono. Os nanotubos clasifícanse como nanotubos de parede simple (SWNT) e nanotubos de parede múltiple (MWNT) e pódense dopar con outros elementos. Os nanotubos de carbono (CNT) son alótropos de carbono cunha nanoestrutura que pode ter unha relación lonxitude-diámetro superior a 10.000.000 e ata 40.000.000 e incluso superior. Estas moléculas de carbono cilíndricas teñen propiedades que as fan potencialmente útiles en aplicacións en nanotecnoloxía, electrónica, óptica, arquitectura e outros campos da ciencia de materiais. Presentan unha resistencia extraordinaria e propiedades eléctricas únicas, e son condutores eficientes da calor. Os nanotubos e as buckyballs esféricas son membros da familia estrutural dos fullerenos. O nanotubo cilíndrico adoita ter polo menos un extremo tapado cun hemisferio da estrutura buckyball. O nome nanotubo deriva do seu tamaño, xa que o diámetro dun nanotubo é da orde duns poucos nanómetros, cunha lonxitude de polo menos varios milímetros. A natureza da unión dun nanotubo descríbese mediante a hibridación orbital. O enlace químico dos nanotubos está composto enteiramente por enlaces sp2, semellantes aos do grafito. Esta estrutura de enlace, é máis forte que os enlaces sp3 que se atopan nos diamantes, e proporciona ás moléculas a súa forza única. Os nanotubos alíñanse naturalmente en cordas unidas polas forzas de Van der Waals. A alta presión, os nanotubos poden fusionarse, intercambiando algúns enlaces sp2 por enlaces sp3, dando a posibilidade de producir fíos fortes e de lonxitude ilimitada mediante a conexión de nanotubos de alta presión. A forza e flexibilidade dos nanotubos de carbono fai que sexan de uso potencial para controlar outras estruturas a nanoescala. Producíronse nanotubos de parede única con resistencias á tracción entre 50 e 200 GPa, e estes valores son aproximadamente unha orde de magnitude maiores que para as fibras de carbono. Os valores do módulo elástico son da orde de 1 tetrapascal (1000 GPa) con tensións de fractura entre un 5% e un 20%. As excelentes propiedades mecánicas dos nanotubos de carbono fan que os utilicemos en roupa duras e roupa deportiva, chaquetas de combate. Os nanotubos de carbono teñen unha forza comparable ao diamante, e están tecidos na roupa para crear roupa a proba de puñaladas e a proba de balas. Ao cruzar moléculas de CNT antes da incorporación nunha matriz polimérica podemos formar un material composto de súper alta resistencia. Este composto CNT podería ter unha resistencia á tracción da orde de 20 millóns de psi (138 GPa), revolucionando o deseño de enxeñería onde se require un peso baixo e unha alta resistencia. Os nanotubos de carbono tamén revelan mecanismos de condución de corrente pouco habituais. Dependendo da orientación das unidades hexagonais no plano do grafeno (é dicir, as paredes do tubo) co eixe do tubo, os nanotubos de carbono poden comportarse como metais ou semicondutores. Como condutores, os nanotubos de carbono teñen unha capacidade de transporte de corrente eléctrica moi elevada. Algúns nanotubos poden transportar densidades de corrente máis de 1000 veces a da prata ou do cobre. Os nanotubos de carbono incorporados aos polímeros melloran a súa capacidade de descarga de electricidade estática. Isto ten aplicacións en liñas de combustible de automóbiles e avións e produción de tanques de almacenamento de hidróxeno para vehículos impulsados por hidróxeno. Os nanotubos de carbono demostraron que presentan fortes resonancias electrón-fonón, o que indica que baixo determinadas condicións de polarización e dopaxe de corrente continua (DC) a súa corrente e a velocidade media dos electróns, así como a concentración de electróns no tubo oscilan en frecuencias de terahercios. Estas resonancias pódense usar para facer fontes ou sensores de terahercios. Demostráronse transistores e circuítos de memoria integrada de nanotubos. Os nanotubos de carbono úsanse como recipiente para transportar drogas ao corpo. O nanotubo permite que a dosificación do fármaco se rebaixa localizando a súa distribución. Isto tamén é económicamente viable debido a que se usan cantidades máis baixas de fármacos. O fármaco pode estar unido ao lado do nanotubo ou arrastrado por detrás, ou o fármaco pódese colocar dentro do nanotubo. Os nanotubos a granel son unha masa de fragmentos de nanotubos bastante desorganizados. Os materiais de nanotubos a granel poden non alcanzar resistencias á tracción semellantes á dos tubos individuais, pero tales compostos poden, non obstante, producir resistencias suficientes para moitas aplicacións. Os nanotubos de carbono a granel estanse a utilizar como fibras compostas en polímeros para mellorar as propiedades mecánicas, térmicas e eléctricas do produto a granel. Están considerando películas transparentes e condutoras de nanotubos de carbono para substituír ao óxido de indio e estaño (ITO). As películas de nanotubos de carbono son mecánicamente máis robustas que as películas ITO, polo que son idóneas para pantallas táctiles de alta fiabilidade e pantallas flexibles. Deséxanse tintas imprimibles a base de auga de películas de nanotubos de carbono para substituír a ITO. As películas de nanotubos son prometedoras para o seu uso en pantallas de ordenadores, teléfonos móbiles, caixeiros automáticos... etc. Utilizáronse nanotubos para mellorar os ultracondensadores. O carbón activado utilizado nos ultracondensadores convencionais ten moitos pequenos espazos ocos cunha distribución de tamaños, que crean xuntos unha gran superficie para almacenar cargas eléctricas. Non obstante, como a carga se cuantifica en cargas elementais, é dicir, electróns, e cada unha destas necesita un espazo mínimo, unha gran fracción da superficie do electrodo non está dispoñible para almacenar porque os espazos ocos son demasiado pequenos. Con electrodos feitos de nanotubos, os espazos están previstos para adaptarse ao tamaño, sendo só uns poucos demasiado grandes ou demasiado pequenos e, en consecuencia, a capacidade de aumentar. Unha célula solar desenvolvida usa un complexo de nanotubos de carbono, feito de nanotubos de carbono combinados con pequenas bólas de carbono (tamén chamadas fullerenos) para formar estruturas similares a serpes. As Buckyballs atrapan electróns, pero non poden facer fluír os electróns. Cando a luz solar excita os polímeros, os buckyballs collen os electróns. Os nanotubos, comportándose como fíos de cobre, poderán entón facer que os electróns ou a corrente fluyan. NANOPARTÍCULAS: As nanopartículas pódense considerar unha ponte entre os materiais a granel e as estruturas atómicas ou moleculares. Un material a granel xeralmente ten propiedades físicas constantes independentemente do seu tamaño, pero a escala nanométrica adoita non ser así. Obsérvanse propiedades dependentes do tamaño como o confinamento cuántico en partículas semicondutoras, a resonancia plasmática superficial nalgunhas partículas metálicas e o superparamagnetismo en materiais magnéticos. As propiedades dos materiais cambian a medida que o seu tamaño se reduce a nanoescala e a porcentaxe de átomos na superficie se fai significativa. Para materiais a granel superiores a un micrómetro, a porcentaxe de átomos na superficie é moi pequena en comparación co número total de átomos do material. As diferentes e destacadas propiedades das nanopartículas débense en parte aos aspectos da superficie do material que dominan as propiedades en lugar das propiedades a granel. Por exemplo, a flexión do cobre a granel ocorre co movemento de átomos/cúmulos de cobre a unha escala de 50 nm. As nanopartículas de cobre inferiores a 50 nm considéranse materiais súper duros que non presentan a mesma maleabilidade e ductilidade que o cobre a granel. O cambio de propiedades non sempre é desexable. Os materiais ferroeléctricos inferiores a 10 nm poden cambiar a súa dirección de magnetización usando enerxía térmica a temperatura ambiente, o que os fai inútiles para o almacenamento da memoria. As suspensións de nanopartículas son posibles porque a interacción da superficie das partículas co disolvente é o suficientemente forte como para superar as diferenzas de densidade, que para partículas máis grandes adoitan dar lugar a que un material se afunda ou flote nun líquido. As nanopartículas teñen propiedades visibles inesperadas porque son o suficientemente pequenas como para limitar os seus electróns e producir efectos cuánticos. Por exemplo, as nanopartículas de ouro aparecen de vermello profundo a negro en solución. A gran relación entre superficie e volume reduce as temperaturas de fusión das nanopartículas. A moi alta relación entre superficie e volume das nanopartículas é unha forza motriz para a difusión. A sinterización pode ter lugar a temperaturas máis baixas, en menos tempo que para as partículas máis grandes. Isto non debería afectar á densidade do produto final, pero as dificultades de fluxo e a tendencia das nanopartículas a aglomerarse poden causar problemas. A presenza de nanopartículas de dióxido de titanio imparte un efecto de autolimpeza e, sendo o tamaño nanoranaxa, as partículas non se poden ver. As nanopartículas de óxido de zinc teñen propiedades de bloqueo UV e engádense ás loções solares. As nanopartículas de arxila ou o negro de carbón cando se incorporan ás matrices de polímero aumentan o reforzo, ofrecéndonos plásticos máis resistentes, con temperaturas de transición vítrea máis altas. Estas nanopartículas son duras e imparten as súas propiedades ao polímero. As nanopartículas unidas ás fibras téxtiles poden crear roupa intelixente e funcional. CERÁMICA NANOFASE: Usando partículas a nanoescala na produción de materiais cerámicos podemos ter un aumento simultáneo e importante tanto da resistencia como da ductilidade. As cerámicas de nanofase tamén se utilizan para a catálise debido ás súas altas relacións superficie-área. As partículas cerámicas nanofase como o SiC tamén se usan como reforzo en metais como a matriz de aluminio. Se se che ocorre unha aplicación de nanofabricación útil para a túa empresa, avísanos e recibe a nosa aportación. Podemos deseñar, prototipar, fabricar, probar e entregarche. Valoramos moito a protección da propiedade intelectual e podemos facer arranxos especiais para garantir que non se copien os seus deseños e produtos. Os nosos deseñadores de nanotecnoloxía e enxeñeiros de nanofabricación son algúns dos mellores do mundo e son as mesmas persoas que desenvolveron algúns dos dispositivos máis avanzados e pequenos do mundo. CLICK Product Finder-Locator Service PÁXINA ANTERIOR
- Industrial & Specialty & Functional Textiles, Hydrophobic - Hydrophillic Textile Materials, Flame Resistant, Antibasterial, Antifungal, Antistatic Fabrics, Filtering Cloths, Biocompatible Fabric
Industrial & Specialty & Functional Textiles, Hydrophobic - Hydrophillic Textile Materials, Flame Resistant Textiles, Antibasterial, Antifungal, Antistatic, UC Protective Fabrics, Filtering Clothes, Textiles for Surgery, Biocompatible Fabric Téxtiles industriais e especiais e funcionais Só nos interesan os téxtiles e tecidos especiais e funcionais e os produtos feitos con eles que serven para unha aplicación concreta. Trátase de téxtiles de enxeñería de gran valor, tamén denominados en ocasións téxtiles e tecidos técnicos. Tecidos e tecidos non tecidos e panos están dispoñibles para numerosas aplicacións. A continuación móstrase unha lista dalgúns tipos principais de téxtiles industriais, especiais e funcionais que están dentro do noso ámbito de desenvolvemento e fabricación de produtos. Estamos dispostos a traballar contigo no deseño, desenvolvemento e fabricación dos teus produtos feitos de: Materiais téxtiles hidrófobos (repelentes de auga) e hidrófilos (absorbentes de auga). Téxtiles e tecidos de extraordinaria resistencia, durabilidade e resistencia a condicións ambientais severas (como a proba de balas, alta resistencia á calor, resistente a baixas temperaturas, resistente á chama, inerte ou resistente a fluídos e gases corrosivos, resistente ao mofo). formación...) Antibacteriano e antifúngico téxtiles e tecidos Protección UV Tecidos e tecidos eléctricamente condutores e non condutores Tecidos antiestáticos para control ESD... etc. Téxtiles e tecidos con propiedades ópticas e efectos especiais (fluorescentes... etc.) Téxtiles, tecidos e panos con capacidades especiais de filtrado, fabricación de filtros Téxtiles industriais como tecidos para conductos, entretelas, reforzos, correas de transmisión, reforzos para caucho (cintas transportadoras, mantas estampadas, cordóns), téxtiles para cintas e abrasivos. Téxtil para a industria do automóbil (mangueiras, correas, airbags, entretelas, pneumáticos) Téxtiles para produtos de construción, construción e infraestruturas (tecido de formigón, xeomembranas e tecido interior) Tecidos compostos multifuncionais que teñen diferentes capas ou compoñentes para diferentes funcións. Téxtiles feitos con carbón activado infusion on fibras de poliéster para proporcionar sensación de algodón, liberación de olores e funcións de xestión da humidade e protección UV. Téxtiles feitos de polímeros con memoria de forma Téxtiles para cirurxía e implantes cirúrxicos, tecidos biocompatibles Teña en conta que deseñamos, deseñamos e fabricamos produtos segundo as súas necesidades e especificacións. Podemos fabricar produtos segundo as súas especificacións ou, se o desexa, podemos axudarche a escoller os materiais adecuados e a deseñar o produto. PÁXINA ANTERIOR
- Microelectronics Manufacturing, Semiconductor Fabrication, Foundry, IC
Microelectronics Manufacturing, Semiconductor Fabrication - Foundry - FPGA - IC Assembly Packaging - AGS-TECH Inc. Fabricación e fabricación de microelectrónica e semicondutores Moitas das nosas técnicas e procesos de nanofabricación, microfabricación e mesofabricación que se explican nos outros menús pódense usar para MICROELECTRONICS MANUFACTURING_cc781905-943bd3b3b5-5cde-3194 Non obstante, debido á importancia da microelectrónica nos nosos produtos, aquí concentrarémonos nas aplicacións específicas destes procesos. Os procesos relacionados coa microelectrónica tamén son coñecidos como SEMICONDUCTOR FABRICATION processes. Os nosos servizos de deseño e fabricación de enxeñaría de semicondutores inclúen: - Deseño, desenvolvemento e programación de placas FPGA - Servizos de fundición de microelectrónica: deseño, creación de prototipos e fabricación, servizos de terceiros - Preparación de obleas de semiconductor: cortado en dados, esmerilado, adelgazamento, colocación de retículas, clasificación de matrices, selección e colocación, inspección - Deseño e fabricación de paquetes microelectrónicos: deseño e fabricación tanto dispoñibles como personalizados - Montaxe e empaquetado e proba de IC Semiconductor: Unión de matrices, cables e chips, encapsulación, montaxe, marcado e marcado - Marcos de chumbo para dispositivos semicondutores: deseño e fabricación tanto dispoñibles como personalizados - Deseño e fabricación de disipadores de calor para microelectrónica: deseño e fabricación tanto dispoñibles como personalizados - Deseño e fabricación de sensores e actuadores: deseño e fabricación tanto dispoñibles como personalizados - Deseño e fabricación de circuítos optoelectrónicos e fotónicos Imos examinar as tecnoloxías de proba e fabricación de microelectrónica e semicondutores con máis detalle para que poida comprender mellor os servizos e produtos que ofrecemos. Deseño e desenvolvemento e programación da placa FPGA: as matrices de portas programables en campo (FPGA) son chips de silicio reprogramables. Ao contrario dos procesadores que atopas nos ordenadores persoais, a programación dunha FPGA reconecta o propio chip para implementar a funcionalidade do usuario en lugar de executar unha aplicación de software. Usando bloques lóxicos preconstruídos e recursos de enrutamento programables, os chips FPGA pódense configurar para implementar unha funcionalidade de hardware personalizada sen usar unha placa de proba e un soldador. As tarefas de computación dixital realízanse en software e compílanse nun ficheiro de configuración ou fluxo de bits que contén información sobre como deben conectarse os compoñentes. Os FPGA pódense usar para implementar calquera función lóxica que poida realizar un ASIC e son completamente reconfigurables e pódense dar unha "personalidade" completamente diferente recompilando unha configuración de circuíto diferente. Os FPGA combinan as mellores partes dos circuítos integrados específicos de aplicacións (ASIC) e dos sistemas baseados en procesadores. Estes beneficios inclúen os seguintes: • Tempos de resposta de E/S máis rápidos e funcionalidade especializada • Superar a potencia de cálculo dos procesadores de sinal dixitais (DSP) • Prototipado rápido e verificación sen o proceso de fabricación de ASIC personalizado • Implantación de funcionalidades personalizadas coa fiabilidade do hardware determinista dedicado • Actualizable no campo eliminando o gasto de redeseño e mantemento personalizados de ASIC As FPGA proporcionan velocidade e fiabilidade, sen requirir grandes volumes para xustificar o gran gasto inicial do deseño ASIC personalizado. O silicio reprogramable tamén ten a mesma flexibilidade que o software que se executa en sistemas baseados en procesadores e non está limitado polo número de núcleos de procesamento dispoñibles. A diferenza dos procesadores, as FPGA son de natureza realmente paralela, polo que as operacións de procesamento diferentes non teñen que competir polos mesmos recursos. Cada tarefa de procesamento independente está asignada a unha sección dedicada do chip e pode funcionar de forma autónoma sen ningunha influencia doutros bloques lóxicos. Como resultado, o rendemento dunha parte da aplicación non se ve afectado cando se engade máis procesamento. Algunhas FPGA teñen características analóxicas ademais de funcións dixitais. Algunhas funcións analóxicas comúns son a velocidade de rotación programable e a forza de impulsión en cada pin de saída, o que permite ao enxeñeiro establecer velocidades lentas en pinos con carga lixeira que, doutro xeito, sonarían ou acoplarían de forma inaceptable, e establecer taxas máis fortes e máis rápidas en pinos moi cargados a alta velocidade. canles que doutro xeito correrían demasiado lentamente. Outra característica analóxica relativamente común son os comparadores diferenciais nos pinos de entrada deseñados para conectarse a canles de sinalización diferencial. Algúns FPGA de sinal mixto teñen integrados conversores analóxico a dixital (ADC) e conversores dixital a analóxico (DAC) con bloques de acondicionamento de sinal analóxico que lles permiten funcionar como un sistema nun chip. Brevemente, os 5 principais beneficios dos chips FPGA son: 1. Bo rendemento 2. Tempo curto no mercado 3. Baixo custo 4. Alta fiabilidade 5. Capacidade de mantemento a longo prazo Bo rendemento: coa súa capacidade de acomodar o procesamento paralelo, os FPGA teñen unha mellor potencia de cálculo que os procesadores de sinal dixitais (DSP) e non requiren execución secuencial como DSP e poden realizar máis ciclos por reloxo. O control de entradas e saídas (E/S) a nivel de hardware proporciona tempos de resposta máis rápidos e funcionalidades especializadas para adaptarse aos requisitos das aplicacións. Tempo de comercialización curto: as FPGA ofrecen flexibilidade e capacidades de creación rápida de prototipos e, polo tanto, un tempo de comercialización máis curto. Os nosos clientes poden probar unha idea ou concepto e verificalo no hardware sen pasar polo longo e caro proceso de fabricación do deseño personalizado ASIC. Podemos implementar cambios incrementais e iterar nun deseño FPGA en cuestión de horas en lugar de semanas. O hardware comercial dispoñible tamén está dispoñible con diferentes tipos de E/S xa conectados a un chip FPGA programable polo usuario. A crecente dispoñibilidade de ferramentas de software de alto nivel ofrece núcleos IP valiosos (funcións preconstruídas) para control avanzado e procesamento de sinal. Baixo custo: os gastos de enxeñaría non recorrente (NRE) dos deseños personalizados ASIC superan os das solucións de hardware baseadas en FPGA. O gran investimento inicial en ASIC pódese xustificar para os OEM que producen moitos chips ao ano, porén moitos usuarios finais necesitan unha funcionalidade de hardware personalizada para os moitos sistemas en desenvolvemento. O noso FPGA de silicio programable ofrécelle algo sen custos de fabricación nin longos prazos de montaxe. Os requisitos do sistema cambian con frecuencia co paso do tempo, e o custo de facer cambios incrementais nos deseños de FPGA é insignificante en comparación co gran gasto que supón a reactivación dun ASIC. Alta fiabilidade: as ferramentas de software proporcionan o ambiente de programación e os circuítos FPGA son unha verdadeira implementación da execución do programa. Os sistemas baseados en procesadores xeralmente implican múltiples capas de abstracción para axudar a programar tarefas e compartir recursos entre múltiples procesos. A capa de controladores controla os recursos de hardware e o SO xestiona a memoria e o ancho de banda do procesador. Para calquera núcleo de procesador, só se pode executar unha instrución á vez, e os sistemas baseados en procesadores corren continuamente o risco de que as tarefas críticas de tempo se adelantan entre si. As FPGA, non usan sistemas operativos, presentan problemas mínimos de fiabilidade coa súa verdadeira execución paralela e hardware determinista dedicado a cada tarefa. Capacidade de mantemento a longo prazo: os chips FPGA poden actualizarse no campo e non requiren o tempo e o custo que implica o redeseño de ASIC. Os protocolos de comunicación dixitais, por exemplo, teñen especificacións que poden cambiar co paso do tempo, e as interfaces baseadas en ASIC poden provocar problemas de mantemento e compatibilidade cara adiante. Pola contra, os chips FPGA reconfigurables poden manterse ao día coas modificacións futuras potencialmente necesarias. A medida que os produtos e sistemas maduran, os nosos clientes poden facer melloras funcionais sen gastar tempo en redeseñar o hardware e modificar os deseños da placa. Servizos de fundición de microelectrónica: os nosos servizos de fundición de microelectrónica inclúen deseño, creación de prototipos e fabricación, servizos de terceiros. Ofrecemos aos nosos clientes asistencia ao longo de todo o ciclo de desenvolvemento de produtos, desde soporte de deseño ata soporte de prototipado e fabricación de chips semicondutores. O noso obxectivo nos servizos de apoio ao deseño é permitir un enfoque correcto por primeira vez para deseños dixitais, analóxicos e de sinal mixto de dispositivos semicondutores. Por exemplo, están dispoñibles ferramentas de simulación específicas de MEMS. Os Fabs que poden manexar obleas de 6 e 8 polgadas para CMOS e MEMS integrados están ao teu servizo. Ofrecemos aos nosos clientes soporte de deseño para todas as principais plataformas de automatización de deseño electrónico (EDA), proporcionando modelos correctos, kits de deseño de procesos (PDK), bibliotecas analóxicas e dixitais e soporte para deseño para a fabricación (DFM). Ofrecemos dúas opcións de prototipado para todas as tecnoloxías: o servizo Multi Product Wafer (MPW), onde se procesan varios dispositivos en paralelo nunha mesma oblea, e o servizo Multi Level Mask (MLM) con catro niveis de máscara debuxados na mesma retícula. Estes son máis económicos que o conxunto completo de máscaras. O servizo MLM é moi flexible en comparación coas datas fixas do servizo MPW. As empresas poden preferir terceirizar produtos de semicondutores a unha fundición de microelectrónica por varias razóns, entre elas a necesidade dunha segunda fonte, o uso de recursos internos para outros produtos e servizos, a vontade de non facer fábulas e diminuír o risco e a carga de executar unha fábrica de semicondutores, etc. AGS-TECH ofrece procesos de fabricación de microelectrónica de plataforma aberta que se poden reducir para pequenas tiradas de obleas así como para a fabricación en masa. En determinadas circunstancias, as túas ferramentas de fabricación de microelectrónica ou MEMS existentes ou conxuntos completos de ferramentas pódense transferir como ferramentas enviadas ou vendidas desde a túa fábrica ao noso sitio de fabricación, ou os teus produtos de microelectrónica e MEMS existentes pódense redeseñar utilizando tecnoloxías de proceso de plataforma aberta e portalos a un proceso dispoñible na nosa fábrica. Isto é máis rápido e económico que unha transferencia de tecnoloxía personalizada. Se o desexa, pódense transferir os procesos de fabricación de microelectrónica/MEMS existentes do cliente. Preparación de obleas de semicondutores: Se o desexan os clientes despois de que as obleas sexan microfabricadas, realizamos operacións de cortado, esmerilado, adelgazamento, colocación de retículas, clasificación de matrices, selección e colocación, operacións de inspección en obleas de semicondutores. O procesamento de obleas de semicondutores implica metroloxía entre os distintos pasos de procesamento. Por exemplo, os métodos de proba de película delgada baseados en elipsometría ou reflectometría úsanse para controlar estreitamente o espesor do óxido de porta, así como o grosor, o índice de refracción e o coeficiente de extinción do fotorresistente e outros revestimentos. Usamos equipos de proba de obleas de semicondutores para verificar que as obleas non foron danadas por etapas de procesamento anteriores ata a proba. Unha vez que se completaron os procesos front-end, os dispositivos microelectrónicos de semicondutores son sometidos a unha variedade de probas eléctricas para determinar se funcionan correctamente. Referímonos á proporción de dispositivos microelectrónicos que se atopan na oblea que funcionan correctamente como o "rendemento". As probas dos chips microelectrónicos na oblea realízanse cun probador electrónico que presiona pequenas sondas contra o chip semicondutor. A máquina automatizada marca cada chip microelectrónico defectuoso cunha pinga de colorante. Os datos das probas de obleas rexístranse nunha base de datos central de ordenador e os chips de semicondutores clasifícanse en contenedores virtuais segundo límites de proba predeterminados. Os datos de agrupación resultantes pódense representar gráficamente ou rexistrarse nun mapa de obleas para rastrexar defectos de fabricación e marcar chips defectuosos. Este mapa tamén se pode usar durante a montaxe e envasado de obleas. Nas probas finais, os chips microelectrónicos son probados de novo despois do empaquetado, porque poden faltar fíos de unión ou o rendemento analóxico pode verse alterado polo paquete. Despois de probar unha oblea de semicondutores, normalmente redúcese o seu espesor antes de que a oblea sexa marcada e despois dividida en matrices individuais. Este proceso chámase corte de obleas de semicondutores. Usamos máquinas automáticas de selección e colocación especialmente fabricadas para a industria microelectrónica para clasificar as matrices de semicondutores boas e malas. Só se empaquetan os chips de semicondutores bos e sen marcar. A continuación, no proceso de envasado de plástico ou cerámica microelectrónica montamos a matriz de semicondutores, conectamos as almofadas de matriz aos pasadores do paquete e selamos a matriz. Utilízanse pequenos fíos de ouro para conectar as almofadas aos pinos mediante máquinas automatizadas. O paquete de escala de chip (CSP) é outra tecnoloxía de envasado de microelectrónica. Un paquete de plástico dual en liña (DIP), como a maioría dos paquetes, é varias veces máis grande que a matriz de semicondutores real colocada no seu interior, mentres que os chips CSP teñen case o tamaño da matriz microelectrónica; e pódese construír un CSP para cada matriz antes de cortar a oblea de semicondutores. Os chips microelectrónicos empaquetados volven probar para asegurarse de que non se danen durante o envasado e de que o proceso de interconexión entre morre e pin se completou correctamente. Usando láseres gravamos os nomes e números de chip no paquete. Deseño e fabricación de paquetes microelectrónicos: ofrecemos deseño e fabricación de paquetes microelectrónicos tanto fóra de estante como personalizados. Dentro deste servizo tamén se realiza a modelización e simulación de paquetes microelectrónicos. O modelado e a simulación garanten o deseño virtual de experimentos (DoE) para lograr a solución óptima, en lugar de probar paquetes no campo. Isto reduce o custo e o tempo de produción, especialmente para o desenvolvemento de novos produtos en microelectrónica. Este traballo tamén nos dá a oportunidade de explicar aos nosos clientes como afectarán a montaxe, a fiabilidade e as probas nos seus produtos microelectrónicos. O obxectivo principal dos envases microelectrónicos é deseñar un sistema electrónico que satisfaga os requisitos dunha determinada aplicación a un custo razoable. Debido ás moitas opcións dispoñibles para interconectar e albergar un sistema microelectrónico, a elección dunha tecnoloxía de envasado para unha determinada aplicación precisa dunha avaliación experta. Os criterios de selección dos paquetes de microelectrónica poden incluír algúns dos seguintes controladores tecnolóxicos: -Filabilidade -Rendemento -Custo -Propiedades de disipación da calor -Rendemento de apantallamento electromagnético - Resistencia mecánica - Fiabilidade Estas consideracións de deseño para paquetes de microelectrónica afectan a velocidade, funcionalidade, temperaturas de unión, volume, peso e moito máis. O obxectivo principal é seleccionar a tecnoloxía de interconexión máis rendible pero fiable. Usamos sofisticados métodos de análise e software para deseñar paquetes de microelectrónica. Os envases de microelectrónica tratan sobre o deseño de métodos para a fabricación de sistemas electrónicos en miniatura interconectados e a fiabilidade deses sistemas. En concreto, a embalaxe microelectrónica implica o enrutamento dos sinais mantendo a integridade do sinal, a distribución de terra e enerxía a circuítos integrados de semicondutores, a dispersión da calor disipada mantendo a integridade estrutural e material e a protección do circuíto dos perigos ambientais. Xeralmente, os métodos para empaquetar circuitos integrados microelectrónicos implican o uso dun PWB con conectores que proporcionan as E/S do mundo real a un circuíto electrónico. Os enfoques tradicionais de envasado microelectrónico implican o uso de paquetes individuais. A principal vantaxe dun paquete dun só chip é a capacidade de probar completamente o IC microelectrónico antes de interconectalo co substrato subxacente. Estes dispositivos de semicondutores empaquetados están montados en orificios pasantes ou en superficie no PWB. Os paquetes de microelectrónica montados en superficie non precisan de orificios de paso para atravesar toda a placa. Pola contra, os compoñentes microelectrónicos montados na superficie pódense soldar a ambos os dous lados do PWB, o que permite unha maior densidade de circuítos. Este enfoque chámase tecnoloxía de montaxe en superficie (SMT). A adición de paquetes tipo matriz de área, como matrices de reixa esférica (BGA) e paquetes a escala de chip (CSP) está facendo que SMT sexa competitiva coas tecnoloxías de envasado de microelectrónica de semicondutores de maior densidade. Unha tecnoloxía de envasado máis nova implica a conexión de máis dun dispositivo semicondutor nun substrato de interconexión de alta densidade, que despois se monta nun paquete grande, proporcionando tanto pines de E/S como protección ambiental. Esta tecnoloxía de módulo multichip (MCM) caracterízase ademais polas tecnoloxías de substrato utilizadas para interconectar os IC conectados. MCM-D representa metal de película fina depositada e multicapas dieléctricas. Os substratos MCM-D teñen as densidades de cableado máis altas de todas as tecnoloxías MCM grazas ás sofisticadas tecnoloxías de procesamento de semicondutores. MCM-C refírese a substratos "cerámicos" de varias capas, cocidos a partir de capas alternas apiladas de tintas metálicas filtradas e follas de cerámica sen cocer. Usando MCM-C obtemos unha capacidade de cableado moderadamente densa. MCM-L refírese a substratos multicapa feitos de "laminados" PWB metalizados apilados, que se estampan individualmente e despois laminan. Antes era unha tecnoloxía de interconexión de baixa densidade, pero agora MCM-L achégase rapidamente á densidade das tecnoloxías de envasado de microelectrónica MCM-C e MCM-D. A tecnoloxía de empaquetado de microelectrónica de conexión directa (DCA) ou chip-on-board (COB) implica montar os IC microelectrónicos directamente no PWB. Un encapsulante de plástico, que se "globa" sobre o IC espido e despois cura, proporciona protección ambiental. Os circuitos integrados microelectrónicos pódense interconectar ao substrato mediante métodos de unión de flip-chip ou de cable. A tecnoloxía DCA é particularmente económica para sistemas que están limitados a 10 ou menos IC de semicondutores, xa que un número maior de chips pode afectar o rendemento do sistema e os conxuntos DCA poden ser difíciles de reelaborar. Unha vantaxe común ás opcións de empaquetado DCA e MCM é a eliminación do nivel de interconexión do paquete IC de semicondutores, que permite unha proximidade máis estreita (retrasos de transmisión de sinal máis curtos) e unha reducida inductancia do chumbo. A principal desvantaxe de ambos os métodos é a dificultade para mercar circuitos integrados microelectrónicos totalmente probados. Outras desvantaxes das tecnoloxías DCA e MCM-L inclúen unha mala xestión térmica grazas á baixa condutividade térmica dos laminados PWB e a unha pobre coincidencia do coeficiente de expansión térmica entre a matriz de semicondutores e o substrato. Resolver o problema de desaxuste da expansión térmica require un substrato interposto como molibdeno para a matriz unida por cable e un epoxi de recheo inferior para a matriz flip-chip. O módulo portador multichip (MCCM) combina todos os aspectos positivos de DCA coa tecnoloxía MCM. O MCCM é simplemente un pequeno MCM nun soporte metálico fino que se pode unir ou unirse mecánicamente a un PWB. O fondo metálico actúa tanto como un disipador de calor como como un intermediario de tensión para o substrato MCM. O MCCM ten cables periféricos para unir cables, soldar ou unir pestanas a un PWB. Os circuitos integrados de semicondutores desnudos están protexidos mediante un material glob-top. Cando se poña en contacto connosco, comentaremos a súa aplicación e os requisitos para escoller a mellor opción de embalaxe de microelectrónica para vostede. Montaxe e embalaxe e proba de IC de semicondutores: como parte dos nosos servizos de fabricación de microelectrónica, ofrecemos unión de matrices, fíos e chips, encapsulación, montaxe, marcado e marcado, probas. Para que funcione un chip de semicondutores ou un circuíto microelectrónico integrado, debe estar conectado ao sistema que controlará ou ao que proporcionará instrucións. O conxunto de microelectrónica IC proporciona as conexións para a transferencia de enerxía e información entre o chip e o sistema. Isto conséguese conectando o chip microelectrónico a un paquete ou conectándoo directamente á PCB para estas funcións. As conexións entre o chip e o paquete ou a placa de circuíto impreso (PCB) realízanse mediante unión de fíos, orificios pasantes ou conxunto de chip flip. Somos líderes na industria na busca de solucións de envasado de IC microelectrónicos para satisfacer os complexos requisitos dos mercados sen fíos e internet. Ofrecemos miles de formatos e tamaños de paquetes diferentes, que van desde os paquetes tradicionais de microelectrónicos de leadframe para montaxe en superficie e orificios pasantes, ata as máis recentes solucións de escala de chip (CSP) e matriz de reixa de bolas (BGA) necesarias en aplicacións de alta densidade e número de pins. . Hai unha gran variedade de paquetes dispoñibles en stock, incluíndo CABGA (Chip Array BGA), CQFP, CTBGA (Chip Array Thin Core BGA), CVBGA (Very Thin Chip Array BGA), Flip Chip, LCC, LGA, MQFP, PBGA, PDIP, PLCC, PoP - Paquete en paquete, PoP TMV - A través de moldes, SOIC/SOJ, SSOP, TQFP, TSOP, WLP (Paquete de nivel de oblea)…..etc. A conexión de fíos que usa cobre, prata ou ouro está entre os populares en microelectrónica. O fío de cobre (Cu) foi un método para conectar matrices de semicondutores de silicio aos terminais do paquete microelectrónico. Co recente aumento do custo do fío de ouro (Au), o fío de cobre (Cu) é unha forma atractiva de xestionar o custo global do paquete en microelectrónica. Tamén se asemella ao fío de ouro (Au) debido ás súas propiedades eléctricas similares. A autoinductancia e a autocapacitancia son case as mesmas para o fío de ouro (Au) e de cobre (Cu) e o fío de cobre (Cu) ten menor resistividade. En aplicacións de microelectrónica onde a resistencia debido ao fío de enlace pode afectar negativamente o rendemento do circuíto, o uso de fío de cobre (Cu) pode ofrecer melloras. Os fíos de aliaxe de cobre, cobre revestido de paladio (PCC) e prata (Ag) xurdiron como alternativas aos fíos de enlace de ouro debido ao custo. Os fíos a base de cobre son baratos e teñen baixa resistividade eléctrica. Non obstante, a dureza do cobre dificulta o seu uso en moitas aplicacións, como aquelas con estruturas de almofadas de unión fráxiles. Para estas aplicacións, Ag-Alloy ofrece propiedades similares ás do ouro mentres que o seu custo é similar ao do PCC. O fío de aliaxe Ag-Alloy é máis suave que o PCC, o que provoca un menor Al-Splash e un menor risco de danos na almofada de unión. O fío Ag-Alloy é o mellor reemplazo de baixo custo para aplicacións que precisan de unión de matrices, enlaces en cascada, paso de almofada de unión ultrafino e aberturas de almofada de unión pequenas, altura de bucle ultra baixa. Ofrecemos unha gama completa de servizos de proba de semicondutores, incluíndo probas de obleas, varios tipos de probas finais, probas a nivel de sistema, probas de tiras e servizos completos de fin de liña. Probamos unha variedade de tipos de dispositivos semicondutores en todas as nosas familias de paquetes, incluíndo radiofrecuencia, sinal analóxico e mixto, dixital, xestión de enerxía, memoria e varias combinacións como ASIC, módulos multichip, System-in-Package (SiP) e envases 3D apilados, sensores e dispositivos MEMS como acelerómetros e sensores de presión. O noso hardware de proba e equipos de contacto son axeitados para o tamaño de paquete personalizado SiP, solucións de contacto de dúas caras para paquete en paquete (PoP), TMV PoP, tomas FusionQuad, MicroLeadFrame de varias filas, Pilar de cobre de paso fino. Os equipos de proba e os pisos de proba están integrados con ferramentas CIM/CAM, análise de rendemento e seguimento do rendemento para ofrecer un rendemento de eficiencia moi alto a primeira vez. Ofrecemos numerosos procesos de proba de microelectrónica adaptativa para os nosos clientes e ofrecemos fluxos de proba distribuídos para SiP e outros fluxos de ensamblaxe complexos. AGS-TECH ofrece unha gama completa de servizos de consulta, desenvolvemento e enxeñería de probas ao longo de todo o ciclo de vida do seu produto microelectrónico e semicondutores. Entendemos os mercados exclusivos e os requisitos de proba para SiP, automoción, redes, xogos, gráficos, informática, RF/sen fíos. Os procesos de fabricación de semicondutores requiren solucións de marcaxe rápidas e controladas con precisión. Velocidades de marcado superiores a 1000 caracteres/segundo e profundidades de penetración de material inferiores a 25 micras son comúns na industria de microelectrónica de semicondutores mediante láseres avanzados. Somos capaces de marcar compostos de moldes, obleas, cerámicas e moito máis cunha entrada de calor mínima e unha repetibilidade perfecta. Usamos láseres con alta precisión para marcar ata as pezas máis pequenas sen danos. Marcos de chumbo para dispositivos semicondutores: son posibles tanto o deseño e fabricación personalizados como dispoñibles. Os cadros de chumbo utilízanse nos procesos de ensamblaxe de dispositivos semicondutores e son esencialmente finas capas de metal que conectan o cableado desde minúsculos terminais eléctricos da superficie da microelectrónica de semicondutores aos circuítos a gran escala dos dispositivos eléctricos e PCB. Os marcos de chumbo úsanse en case todos os paquetes de microelectrónica de semicondutores. A maioría dos paquetes de microelectrónicos IC realízanse colocando o chip de silicio semicondutor nun cadro de chumbo, despois unindo o chip cos cables metálicos dese cadro de chumbo e, posteriormente, cubrindo o chip microelectrónico cunha tapa de plástico. Este envase microelectrónico sinxelo e relativamente baixo custo segue sendo a mellor solución para moitas aplicacións. Os marcos de chumbo prodúcense en tiras longas, o que permite procesalas rapidamente en máquinas de montaxe automatizadas, e xeralmente utilízanse dous procesos de fabricación: fotograbado dalgún tipo e estampación. En microelectrónica, o deseño de cadros de plomo adoita ser demandado por especificacións e características personalizadas, deseños que melloren as propiedades eléctricas e térmicas e requisitos específicos de tempo de ciclo. Temos unha profunda experiencia na fabricación de marcos de plomo microelectrónicos para unha gran variedade de clientes utilizando gravado fotográfico e estampado asistido por láser. Deseño e fabricación de disipadores de calor para microelectrónica: deseño e fabricación tanto fóra de estante como personalizados. Co aumento da disipación de calor dos dispositivos microelectrónicos e a redución dos factores de forma xerais, a xestión térmica convértese nun elemento máis importante do deseño de produtos electrónicos. A coherencia no rendemento e a esperanza de vida dos equipos electrónicos están inversamente relacionadas coa temperatura dos compoñentes do equipo. A relación entre a fiabilidade e a temperatura de funcionamento dun dispositivo semicondutor de silicio típico mostra que unha redución da temperatura corresponde a un aumento exponencial da fiabilidade e da esperanza de vida do dispositivo. Polo tanto, pódese conseguir unha longa vida útil e un rendemento fiable dun compoñente microelectrónico de semicondutores controlando eficazmente a temperatura de funcionamento do dispositivo dentro dos límites establecidos polos deseñadores. Os disipadores de calor son dispositivos que melloran a disipación da calor desde unha superficie quente, xeralmente a carcasa exterior dun compoñente xerador de calor, a un ambiente máis frío como o aire. Para as seguintes discusións, suponse que o aire é o fluído de refrixeración. Na maioría das situacións, a transferencia de calor a través da interface entre a superficie sólida e o aire de refrixeración é a menos eficiente dentro do sistema, e a interface de aire sólido representa a maior barreira para a disipación de calor. Un disipador de calor reduce esta barreira principalmente aumentando a superficie que está en contacto directo co refrixerante. Isto permite que se disipe máis calor e/ou rebaixa a temperatura de funcionamento do dispositivo semicondutor. O obxectivo principal dun disipador de calor é manter a temperatura do dispositivo microelectrónico por debaixo da temperatura máxima permitida especificada polo fabricante do dispositivo semicondutor. Podemos clasificar os disipadores de calor en función dos métodos de fabricación e das súas formas. Os tipos máis comúns de disipadores de calor refrixerados por aire inclúen: - Estampacións: as chapas de cobre ou aluminio están estampadas nas formas desexadas. utilízanse na refrixeración tradicional por aire de compoñentes electrónicos e ofrecen unha solución económica aos problemas térmicos de baixa densidade. Son axeitados para a produción de grandes cantidades. - Extrusión: Estes disipadores de calor permiten a formación de elaboradas formas bidimensionais capaces de disipar grandes cargas de calor. Pódense cortar, mecanizar e engadir opcións. Un corte transversal producirá disipadores de calor de aletas rectangulares omnidireccionais e incorporar aletas dentadas mellora o rendemento entre un 10 e un 20% aproximadamente, pero cunha taxa de extrusión máis lenta. Os límites de extrusión, como o grosor das aletas entre a altura da aleta e a separación, adoitan ditar a flexibilidade nas opcións de deseño. Con técnicas de extrusión estándar, pódense conseguir unha relación de aspecto típica entre a altura da aleta e a brecha de ata 6 e un espesor mínimo de aleta de 1,3 mm. Pódense obter unha relación de aspecto de 10 a 1 e un grosor de aleta de 0,8″ con funcións especiais de deseño de matrices. Non obstante, a medida que aumenta a relación de aspecto, a tolerancia de extrusión vese comprometida. - Aletas adheridas/fabricadas: a maioría dos disipadores de calor refrixerados por aire están limitados á convección, e o rendemento térmico global dun disipador de calor arrefriado por aire a miúdo pódese mellorar significativamente se se pode expoñer máis superficie ao fluxo de aire. Estes disipadores de calor de alto rendemento utilizan epoxi recheo de aluminio condutor térmicamente para unir aletas planas nunha placa base de extrusión ranurada. Este proceso permite unha relación de aspecto entre 20 e 40 entre a altura da aleta e a brecha, aumentando significativamente a capacidade de refrixeración sen aumentar a necesidade de volume. - Fundición: Área, cera perdida e procesos de fundición para aluminio ou cobre/bronce están dispoñibles con ou sen axuda ao baleiro. Usamos esta tecnoloxía para a fabricación de disipadores de calor de aletas de pin de alta densidade que proporcionan o máximo rendemento cando se usa o arrefriamento por impacto. - Aletas plegadas: a chapa ondulada de aluminio ou cobre aumenta a superficie e o rendemento volumétrico. O disipador de calor fíxase entón a unha placa base ou directamente á superficie de calefacción mediante epoxi ou soldadura. Non é adecuado para disipadores de calor de alto perfil debido á dispoñibilidade e á eficiencia das aletas. Polo tanto, permite fabricar disipadores de calor de alto rendemento. Ao seleccionar un disipador de calor axeitado que cumpra os criterios térmicos necesarios para as súas aplicacións de microelectrónica, necesitamos examinar varios parámetros que afectan non só ao rendemento do disipador de calor en si, senón tamén ao rendemento xeral do sistema. A elección dun tipo particular de disipador de calor en microelectrónica depende en gran medida do orzamento térmico permitido para o disipador de calor e das condicións externas que rodean o disipador de calor. Nunca hai un único valor de resistencia térmica asignado a un disipador de calor dado, xa que a resistencia térmica varía coas condicións de refrixeración externas. Deseño e fabricación de sensores e actuadores: están dispoñibles tanto deseño e fabricación personalizados como dispoñibles. Ofrecemos solucións con procesos listos para usar para sensores inerciales, sensores de presión e presión relativa e dispositivos sensores de temperatura IR. Ao usar os nosos bloques IP para acelerómetros, sensores IR e de presión ou aplicando o seu deseño segundo as especificacións dispoñibles e as regras de deseño, podemos enviarche dispositivos de sensor baseados en MEMS en poucas semanas. Ademais de MEMS, pódense fabricar outros tipos de estruturas de sensores e actuadores. Deseño e fabricación de circuítos optoelectrónicos e fotónicos: un circuíto integrado fotónico ou óptico (PIC) é un dispositivo que integra múltiples funcións fotónicas. Pódese asemellar aos circuítos electrónicos integrados en microelectrónica. A principal diferenza entre os dous é que un circuíto integrado fotónico proporciona funcionalidade para os sinais de información impostas en lonxitudes de onda ópticas no espectro visible ou no infravermello próximo 850 nm-1650 nm. As técnicas de fabricación son similares ás utilizadas nos circuítos integrados de microelectrónica onde se usa a fotolitografía para modelar obleas para gravar e depositar material. A diferenza da microelectrónica de semicondutores onde o dispositivo primario é o transistor, non existe un único dispositivo dominante na optoelectrónica. Os chips fotónicos inclúen guías de ondas de interconexión de baixa perda, divisores de potencia, amplificadores ópticos, moduladores ópticos, filtros, láseres e detectores. Estes dispositivos requiren unha variedade de materiais e técnicas de fabricación diferentes e, polo tanto, é difícil realizalos todos nun só chip. As nosas aplicacións dos circuítos integrados fotónicos atópanse principalmente nas áreas de comunicación por fibra óptica, informática biomédica e fotónica. Algúns exemplos de produtos optoelectrónicos que podemos deseñar e fabricar para ti son LED (diodos emisores de luz), láseres de diodos, receptores optoelectrónicos, fotodiodos, módulos de distancia láser, módulos láser personalizados e moito máis. CLICK Product Finder-Locator Service PÁXINA ANTERIOR