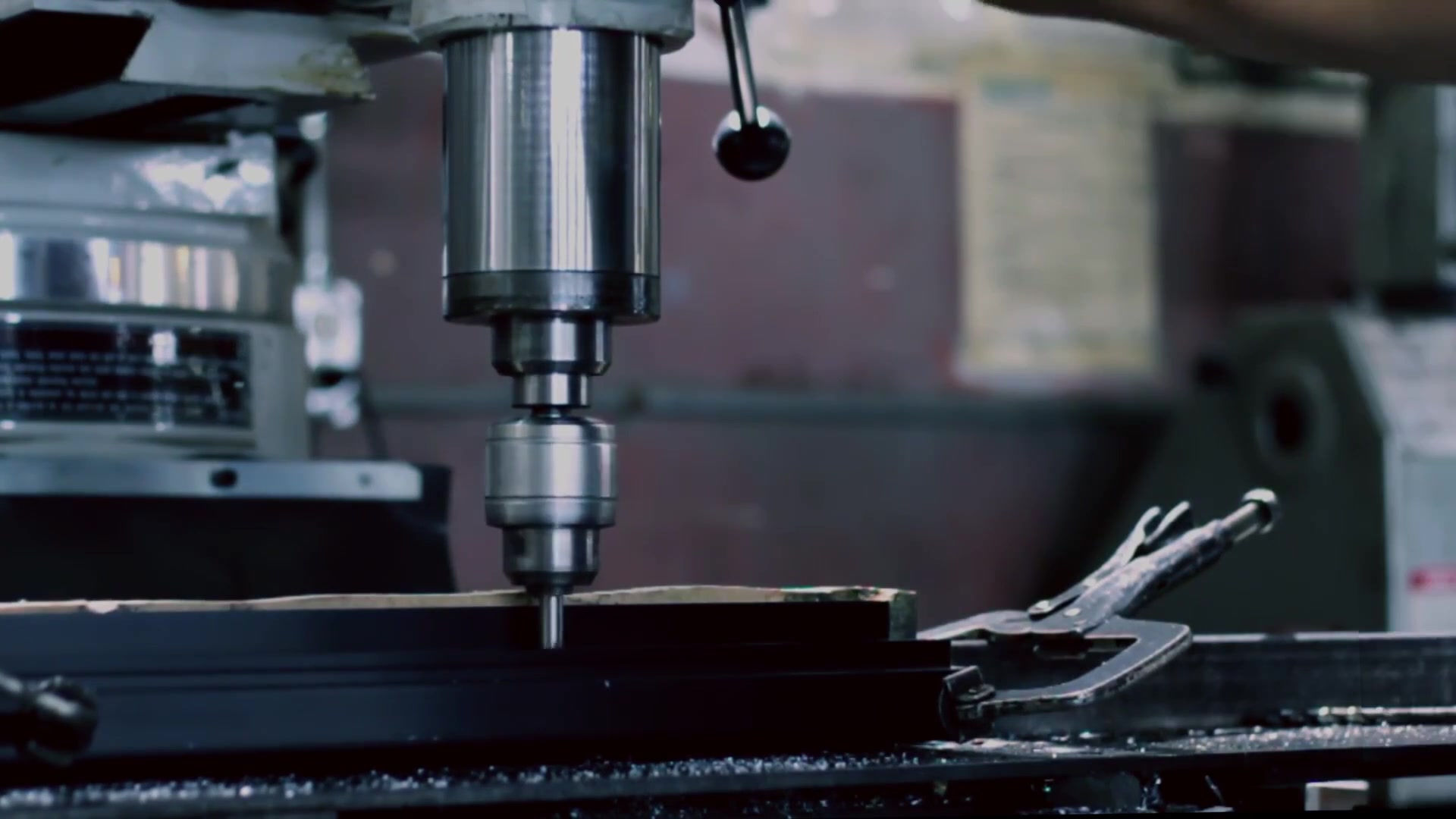
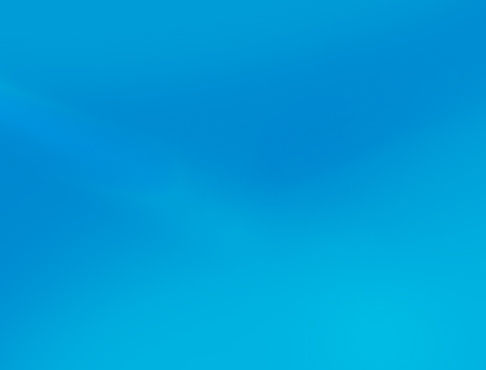
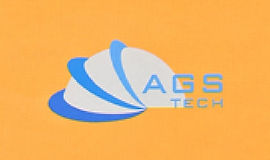
Fabricante global personalizado, integrador, consolidador, socio de outsourcing para unha ampla variedade de produtos e servizos.
Somos a súa fonte única para a fabricación, fabricación, enxeñaría, consolidación, integración e subcontratación de produtos e servizos fabricados a medida e dispoñibles.
Escolla o seu idioma
-
Fabricación personalizada
-
Fabricación por contrato nacional e global
-
Outsourcing de Manufactura
-
Compras domésticas e globais
-
Consolidación
-
Integración de enxeñería
-
Servizos de Enxeñaría
Search Results
164 results found with an empty search
- Global Product Finder Locator for Off Shelf Products
Global Product Finder Locator for Off Shelf Products AGS-TECH, Inc. é o teu Fabricante global personalizado, integrador, consolidador, socio de outsourcing. Somos a súa fonte única de fabricación, fabricación, enxeñaría, consolidación e subcontratación. If you exactly know the product you are searching, please fill out the table below If filling out the form below is not possible or too difficult, we do accept your request by email also. Simply write us at sales@agstech.net Get a Price Quote on a known brand, model, part number....etc. First name Last name Email Phone Product Name Product Make or Brand Please Enter Manufacturer Part Number if Known Please Enter SKU Code if You Know: Your Application for the Product Quantity Needed Do You have a price target ? If so, please let us know: Give us more details if you want: Condition of Product Needed New Used Does Not Matter If you have any, upload product relevant files by clicking at the below link. Don't worry, the link below will pop up a new window for downloading your files. You will not navigate away from this current window. After uploading your files, close ONLY the Dropbox Window, but not this page. Make sure to fill out all spaces and click the submit button below. CLICK HERE TO UPLOAD FILES Request a Quote Thanks! We’ll send you a price quote shortly. PREVIOUS PAGE Somos AGS-TECH Inc., a súa fonte única de fabricación e fabricación e enxeñería, subcontratación e consolidación. Somos o integrador de enxeñería máis diverso do mundo que che ofrece fabricación, subconxunto, montaxe de produtos e servizos de enxeñería personalizados.
- Custom Made Products Data Entry
Custom Made Products Data Entry, Custom Manufactured Parts, Assemblies, Plastic Molds, Casting, CNC Machining, Extrusion, Metal Forging, Spring Manufacturing, Products Assembly, PCBA, PCB AGS-TECH, Inc. é o teu Fabricante global personalizado, integrador, consolidador, socio de outsourcing. Somos a súa fonte única de fabricación, fabricación, enxeñaría, consolidación e subcontratación. Fill In your info if you you need custom design & development & prototyping & mass production: If filling out the form below is not possible or too difficult, we do accept your request by email also. Simply write us at sales@agstech.net Get a Price Quote on a custom designed, developed, prototyped or manufactured product. First name Last name Email Phone Product Name Your Application for the Product Quantity Needed Do you have a price target ? If you do have, please let us know your expected price: Give us more details if you want: Do you accept offshore manufacturing ? YES NO If you have any, upload product relevant files by clicking at the below link. Don't worry, the link below will pop up a new window for downloading your files. You will not navigate away from this current window. After uploading your files, close ONLY the Dropbox Window, but not this page. Make sure to fill out all spaces and click the submit button below. Files that will help us quote your specially tailored product are technical drawings, bill of materials, photos, sketches....etc. You can download more than one file. CLICK HERE TO UPLOAD FILES Request a Quote Thanks! We’ll send you a price quote shortly. PREVIOUS PAGE Somos AGS-TECH Inc., a súa fonte única de fabricación e fabricación e enxeñería, subcontratación e consolidación. Somos o integrador de enxeñería máis diverso do mundo que che ofrece fabricación, subconxunto, montaxe de produtos e servizos de enxeñería personalizados.
- Camera Systems & Components, Optic Scanner, Optical Readers, CCD
Camera Systems - Components - Optic Scanner - Optical Readers - Imaging System - CCD - Optomechanical Systems - IR Cameras Fabricación e montaxe de sistemas de cámara personalizados AGS-TECH ofrece: • Sistemas de cámaras, compoñentes de cámaras e conxuntos de cámaras personalizados • Escáneres ópticos, lectores e conxuntos de produtos de seguridade óptica deseñados e fabricados a medida. • Conxuntos ópticos, opto-mecánicos e electro-ópticos de precisión que integran ópticas de imaxe e non, iluminación LED, fibra óptica e cámaras CCD • Entre os produtos que desenvolveron os nosos enxeñeiros ópticos están: - Periscopio omnidireccional e cámara para aplicacións de vixilancia e seguridade. Imaxe de alta resolución de campo de visión de 360 x 60º, sen necesidade de costuras. - Cámara de vídeo gran angular cavidade interior - Videoendoscopio flexible súper delgado de 0,6 mm de diámetro. Todos os acopladores de vídeo médico encaixan sobre os oculares de endoscopio estándar e están completamente selados e empapables. Para os nosos sistemas de cámaras e endoscopios médicos, visite: http://www.agsmedical.com - Cámara de vídeo e acoplador para endoscopio semiríxido - Sonda de vídeo Eye-Q. Videosonda zoom sen contacto para máquinas de medición de coordenadas. - Espectrógrafo óptico e sistema de imaxe IR (OSIRIS) para satélite ODIN. Os nosos enxeñeiros traballaron na montaxe, aliñamento, integración e proba da unidade de voo. - Interferómetro de imaxe do vento (WINDII) para o satélite de investigación da atmosfera superior (UARS) da NASA. Os nosos enxeñeiros traballaron en consultoría en montaxe, integración e proba. O rendemento e a vida útil de WINDII superaron con creces os obxectivos e requisitos de deseño. Dependendo da súa aplicación, determinaremos que dimensións, número de píxeles, resolución e sensibilidade á lonxitude de onda require a súa aplicación de cámara. Podemos construír sistemas para ti adecuados para lonxitudes de onda infravermellos, visibles e outras. Póñase en contacto connosco hoxe para obter máis información. Descarga o folleto para o noso PROGRAMA DE COLABORACIÓN DE DESEÑO Tamén asegúrate de descargar o noso completo catálogo de compoñentes eléctricos e electrónicos para produtos dispoñibles facendo clic AQUÍ. CLICK Product Finder-Locator Service PÁXINA ANTERIOR
- Computer Chassis, Racks, Shelves, 19 inch Rack, 23 inch Rack, Case
Computer Chassis - Racks - Shelves - 19 inch Rack - 23 inch Rack - Computer and Instrument Case Manufacturing - AGS-TECH Inc. - New Mexico - USA Chasis, bastidores, soportes para ordenadores industriais We offer you the most durable and reliable INDUSTRIAL COMPUTER CHASSIS, RACKS, MOUNTS, RACK MOUNT INSTRUMENTS and RACK MOUNTED SYSTEMS, SUBRACK, SHELF, 19 INCH & 23 INCH RACKS, FULL SİZE and HALF RACKS, OPEN and CLOSED RACK, MOUNTING HARDWARE, STRUCTURAL AND SUPPORT COMPONENTS, RAILS and SLIDES, TWO andFOUR POST RACKS that meet international and industry standards. Ademais dos nosos produtos dispoñibles, podemos construírche calquera chasis, bastidores e soportes especialmente adaptados. Algunhas das marcas que temos en stock son BELKIN, HEWLETT PACKARD, KENDALL HOWARD, GREAT LAKES, APC, RITTAL, LIEBERT, RALOY, SHARK RACK, UPSITE TECHNOLOGIES. Fai clic aquí para descargar o noso chasis industrial da marca DFI-ITOX Fai clic aquí para descargar o noso chasis enchufable da serie 06 de AGS-Electronics Fai clic aquí para descargar o noso 01 Series Instrument Case System-I de AGS-Electronics Fai clic aquí para descargar o noso 05 Series Instrument Case System-V de AGS-Electronics Para escoller un chasis, bastidor ou soporte de grao industrial axeitado, vai á nosa tenda de informática industrial facendo clic AQUÍ. Descarga o folleto para o noso PROGRAMA DE COLABORACIÓN DE DESEÑO Aquí tes algunhas terminoloxías clave que deberían ser útiles como referencia: A RACK UNIT or U (menos comunmente denominada RU) é unha unidade de medida que se utiliza para describir a altura dos equipos destinados ao montaxe en a_cc758-bbde35 -136bad5cf58d_19-inch rack or a 23-inch rack (The 19-inch or 23-inch dimension refers to the width of the equipment marco de montaxe no bastidor é dicir, o ancho do equipo que se pode montar dentro do bastidor). Unha unidade de rack mide 1,75 polgadas (44,45 mm) de alto. O tamaño dun equipo montado en bastidor descríbese con frecuencia como un número en "U". Por exemplo, unha unidade de rack adoita denominarse ''1U'', 2 unidades de rack como ''2U'' e así por diante. Un típico full size rack is 44U, o que significa que contén algo máis de 6 pés de equipo. En informática e tecnoloxía da información, porén, half-rack normalmente describe unha unidade que ten unha altura de 1U e a metade da rede de rack , enrutador, conmutador KVM ou servidor), de forma que se poidan montar dúas unidades en 1U de espazo (unha montada na parte frontal do bastidor e outra na parte traseira). Cando se usa para describir o propio gabinete de rack, o termo medio-rack normalmente significa un gabinete de rack de 24U de altura. Un panel frontal ou un panel de recheo nun rack non é un múltiplo exacto de 1,75 polgadas (44,45 mm). Para permitir espazo entre os compoñentes adxacentes montados en rack, un panel ten unha altura de 1⁄32 polgada (0,031 polgada ou 0,79 mm) menos do que implicaría o número total de unidades de rack. Así, un panel frontal 1U tería unha altura de 1,719 polgadas (43,66 mm). Un rack de 19 polgadas é un marco ou carcasa estandarizado para montar varios módulos de equipos. Cada módulo ten un panel frontal de 19 polgadas (482,6 mm) de ancho, incluíndo bordos ou orellas que sobresaen a cada lado que permiten fixar o módulo ao marco do rack con parafusos. O equipo deseñado para colocarse nun bastidor descríbese normalmente como montaxe en bastidor, instrumento de montaxe en bastidor, un sistema de montaxe en bastidor, un chasis de montaxe en bastidor, subrack, montaxe en bastidor ou, ocasionalmente, simplemente en estante. Un rack de 23 polgadas úsase para albergar teléfono (principalmente), ordenador, audio e outros equipos, aínda que é menos común que o rack de 19 polgadas. O tamaño indica o ancho da placa frontal para o equipo instalado. A unidade de rack é unha medida de espazamento vertical e é común aos bastidores de 19 e 23 polgadas (580 mm). O espazo entre orificios é en centros de 1 polgada (25 mm) (estándar de Western Electric) ou o mesmo que para bastidores de 19 polgadas (480 mm) (espazo de 0,625 polgadas / 15,9 milímetros). CLICK Product Finder-Locator Service PÁXINA ANTERIOR
- Laser Machining, LM, Laser Cutting, CO2 Laser Processing, Nd-YAG Cut
Laser Machining - LM - Laser Cutting - Custom Parts Manufacturing - CO2 Laser Processing - Nd-YAG - Cutting - Boring Mecanizado e corte con láser e LBM LASER CUTTING is a HIGH-ENERGY-BEAM MANUFACTURING HIGH-ENERGY-BEAM MANUFACTURING_cc781905-5cde-3194-958d_cc781905-5cde-3194-b3b3b-31cf58d_fabricación_cc781905-5cde-31cf58d_de corte con láser para aplicacións industriais e técnicas de corte con láser. En LASER BEAM MACHINING (LBM), unha fonte láser enfoca a enerxía óptica na superficie da peza. O corte con láser dirixe a saída altamente enfocada e de alta densidade dun láser de alta potencia, por ordenador, cara ao material que se vai cortar. A continuación, o material obxectivo se funde, queima, vaporiza ou é expulsado por un chorro de gas, de forma controlada, deixando un bordo cun acabado superficial de alta calidade. As nosas cortadoras con láser industriais son adecuadas para cortar material de folla plana, así como materiais estruturais e de tubos, pezas metálicas e non metálicas. Xeralmente non se require baleiro nos procesos de mecanizado e corte con raio láser. Hai varios tipos de láseres utilizados no corte e fabricación con láser. A onda pulsada ou continua CO2 LASER é adecuada para cortar, perforar e gravar. The NEODYMIUM (Nd) and neodymium yttrium-aluminum-garnet (Nd-YAG) LASERS are identical no estilo e só difiren na aplicación. O Nd de neodimio úsase para aburrir e onde se require alta enerxía pero pouca repetición. Por outra banda, o láser Nd-YAG úsase onde se require unha potencia moi elevada e para aburrir e gravar. Tanto os láseres de CO2 como de Nd/Nd-YAG pódense usar para SOLDADURA LÁSER. Outros láseres que usamos na fabricación inclúen Nd:GLASS, RUBY e EXCIMER. En Laser Beam Machining (LBM), os seguintes parámetros son importantes: A reflectividade e a condutividade térmica da superficie da peza e a súa calor específica e calor latente de fusión e evaporación. A eficiencia do proceso de Laser Beam Machining (LBM) aumenta coa diminución destes parámetros. A profundidade de corte pódese expresar como: t ~ P / (vxd) Isto significa que a profundidade de corte "t" é proporcional á potencia de entrada P e inversamente proporcional á velocidade de corte v e ao diámetro do punto do raio láser d. A superficie producida con LBM é xeralmente rugosa e ten unha zona afectada pola calor. CORTE E MECANIZADO POR LÁSER DE DIÓXIDO DE CARBONO (CO2): os láseres de CO2 excitados por CC son bombeados facendo pasar unha corrente a través da mestura de gas, mentres que os láseres de CO2 excitados por RF usan enerxía de radiofrecuencia para a excitación. O método RF é relativamente novo e fíxose máis popular. Os deseños de CC requiren electrodos dentro da cavidade e, polo tanto, poden ter erosión de electrodos e recubrimento de material de electrodos na óptica. Pola contra, os resonadores de RF teñen electrodos externos e, polo tanto, non son propensos a eses problemas. Usamos láseres de CO2 no corte industrial de moitos materiais como aceiro suave, aluminio, aceiro inoxidable, titanio e plásticos. CORTE LÁSER YAG and MACHINING: Usamos láseres YAG para cortar e trazar metais e cerámica. O xerador de láser e a óptica externa requiren arrefriamento. A calor residual é xerada e transferida por un refrixerante ou directamente ao aire. A auga é un refrixerante común, normalmente circula a través dun enfriador ou un sistema de transferencia de calor. CORTE E MECANIZADO CON LÁSER EXCIMER: un láser excimer é unha especie de láser con lonxitudes de onda na rexión ultravioleta. A lonxitude de onda exacta depende das moléculas utilizadas. Por exemplo, as seguintes lonxitudes de onda están asociadas ás moléculas mostradas entre parénteses: 193 nm (ArF), 248 nm (KrF), 308 nm (XeCl), 353 nm (XeF). Algúns láseres excimer son sintonizables. Os láseres excímeros teñen a atractiva propiedade de que poden eliminar capas moi finas de material de superficie case sen quentarse nin cambiar o resto do material. Polo tanto, os láseres excimer son moi axeitados para o micromecanizado de precisión de materiais orgánicos como algúns polímeros e plásticos. CORTE LÁSER ASISTIDO POR GAS: ás veces usamos raios láser en combinación cunha corrente de gas, como osíxeno, nitróxeno ou argón para cortar materiais de láminas finas. Isto faise usando a LASER-BEAM TORCH. Para o aceiro inoxidable e o aluminio utilizamos o corte con láser de alta presión asistido por gas inerte con nitróxeno. Isto resulta en bordos libres de óxidos para mellorar a soldabilidade. Estes fluxos de gas tamén expulsan o material fundido e vaporizado das superficies das pezas de traballo. En a LASER MICROJET CUTTING temos un láser guiado por chorro de auga no que se acopla un raio láser de chorro de auga pulsado a baixa presión. Utilizámolo para realizar cortes con láser mentres utilizamos o chorro de auga para guiar o raio láser, de forma similar a unha fibra óptica. As vantaxes do microjet láser son que a auga tamén elimina os restos e arrefría o material, é máis rápido que o corte láser "seco" tradicional con velocidades de corte máis altas, corte paralelo e capacidade de corte omnidireccional. Implementamos diferentes métodos de corte mediante láser. Algúns dos métodos son vaporización, fusión e soplado, fusión e queimadura, rachadura por estrés térmico, trazado, corte e queima en frío, corte con láser estabilizado. - Corte por vaporización: o feixe enfocado quenta a superficie do material ata o seu punto de ebulición e crea un burato. O buraco leva a un aumento repentino da absorción e afonda rapidamente o burato. A medida que o buraco se afonda e o material ferve, o vapor xerado erosiona as paredes fundidas expulsando o material e agrandando aínda máis o burato. Os materiais que non se funden como madeira, carbono e plásticos termoestables adoitan cortarse por este método. - Corte por fusión e soplado: Utilizamos gas a alta presión para soplar material fundido da zona de corte, diminuíndo a potencia necesaria. O material quéntase ata o seu punto de fusión e despois un chorro de gas expulsa o material fundido da corte. Isto elimina a necesidade de aumentar aínda máis a temperatura do material. Cortamos metais con esta técnica. - Fisuras por tensión térmica: Os materiais fráxiles son sensibles á fractura térmica. Un feixe céntrase na superficie causando quecemento localizado e expansión térmica. Isto dá lugar a unha greta que despois pode ser guiada movendo a viga. Usamos esta técnica no corte de vidro. - Corte en dados furtivos de obleas de silicio: a separación de chips microelectrónicos das obleas de silicio realízase mediante o proceso de corte en dados sigilosos, utilizando un láser Nd:YAG pulsado, a lonxitude de onda de 1064 nm está ben adoptada para a banda intercalada electrónica do silicio (1,11 eV ou 1117 nm). Isto é popular na fabricación de dispositivos semicondutores. - Corte reactivo: Tamén chamado corte de chama, esta técnica pode asemellarse ao corte con soplete pero cun raio láser como fonte de ignición. Utilizámolo para cortar aceiro ao carbono en grosores superiores a 1 mm e incluso chapas de aceiro moi grosas con pouca potencia de láser. LÁSER PULSADO proporcionanos unha ráfaga de enerxía de gran potencia durante un curto período de tempo e son moi eficaces nalgúns procesos de corte con láser, como a perforación, ou cando se precisan orificios moi pequenos ou velocidades de corte moi baixas. Se se usase un raio láser constante, a calor podería chegar ao punto de fundir toda a peza que se está a mecanizar. Os nosos láseres teñen a capacidade de pulsar ou cortar CW (onda continua) baixo o control do programa NC (control numérico). Usamos DOUBLE PULSE LASERS emitindo unha serie de pares de pulsos para mellorar a taxa de eliminación do material e a calidade do burato. O primeiro pulso elimina o material da superficie e o segundo pulso evita que o material expulsado se adhira ao lado do burato ou corte. As tolerancias e o acabado superficial no corte e mecanizado con láser son destacables. Os nosos modernos cortadores con láser teñen unha precisión de posicionamento de preto de 10 micrómetros e repetibilidades de 5 micrómetros. As rugosidades estándar Rz aumentan co grosor da folla, pero diminúen coa potencia do láser e a velocidade de corte. Os procesos de corte e mecanizado con láser son capaces de acadar tolerancias estreitas, a miúdo ata dentro de 0,001 polgadas (0,025 mm) a xeometría da peza e as características mecánicas das nosas máquinas están optimizadas para acadar as mellores capacidades de tolerancia. Os acabados superficiais que podemos obter mediante o corte con láser poden oscilar entre 0,003 mm e 0,006 mm. En xeral, conseguimos buracos de 0,025 mm de diámetro facilmente, e en varios materiais producíronse buratos de tan só 0,005 mm e proporcións de profundidade a diámetro do burato de 50 a 1. As nosas cortadoras con láser máis simples e estándar cortarán metal de aceiro carbono de 0,51 a 13 mm (0,020-0,5 polgadas) de espesor e poden ser facilmente ata trinta veces máis rápido que o serrado estándar. O mecanizado con feixe láser úsase amplamente para perforar e cortar metais, non metais e materiais compostos. As vantaxes do corte con láser fronte ao corte mecánico inclúen unha maior suxeición do traballo, limpeza e redución da contaminación da peza (xa que non hai un filo de corte como no fresado ou torneado tradicional que poida contaminarse polo material ou contaminar o material, é dicir, acumulación de bue). A natureza abrasiva dos materiais compostos pode dificultar o mecanizado por métodos convencionais, pero fácil mediante o mecanizado con láser. Debido a que o raio láser non se desgasta durante o proceso, a precisión obtida pode ser mellor. Dado que os sistemas láser teñen unha pequena zona afectada pola calor, tamén hai menos posibilidades de deformar o material que se está cortando. Para algúns materiais, o corte con láser pode ser a única opción. Os procesos de corte con feixe láser son flexibles e a entrega de feixe de fibra óptica, a fixación sinxela, os tempos de configuración curtos e a dispoñibilidade de sistemas CNC tridimensionais permiten que o corte e o mecanizado con láser compitan con éxito con outros procesos de fabricación de chapa metálica como a perforación. Dito isto, a tecnoloxía láser ás veces pódese combinar coas tecnoloxías de fabricación mecánica para mellorar a eficiencia xeral. O corte con láser de chapas metálicas ten as vantaxes sobre o corte por plasma de ser máis preciso e empregar menos enerxía, non obstante, a maioría dos láseres industriais non poden cortar o maior grosor de metal que pode facer o plasma. Os láseres que operan con potencias máis altas como 6000 vatios achéganse ás máquinas de plasma na súa capacidade para cortar materiais grosos. Non obstante, o custo de capital destas cortadoras con láser de 6000 vatios é moito maior que o das máquinas de corte por plasma capaces de cortar materiais grosos como chapas de aceiro. Tamén hai desvantaxes do corte e mecanizado con láser. O corte con láser implica un alto consumo de enerxía. A eficiencia do láser industrial pode variar entre o 5% e o 15%. O consumo de enerxía e a eficiencia dun láser en particular variará dependendo da potencia de saída e dos parámetros de funcionamento. Isto dependerá do tipo de láser e do ben que o láser se axuste ao traballo a man. A cantidade de potencia de corte con láser necesaria para unha tarefa en particular depende do tipo de material, o grosor, o proceso (reactivo/inerte) utilizado e a velocidade de corte desexada. A taxa máxima de produción no corte e mecanizado con láser está limitada por unha serie de factores, incluíndo a potencia do láser, o tipo de proceso (reactivo ou inerte), as propiedades do material e o espesor. In LASER ABLATION eliminamos o material dunha superficie sólida irradiándoo cun raio láser. A baixo fluxo de láser, o material quéntase pola enerxía do láser absorbida e evapora ou sublima. A alto fluxo de láser, o material normalmente convértese nun plasma. Os láseres de alta potencia limpan un punto grande cun só pulso. Os láseres de menor potencia usan moitos pequenos pulsos que se poden escanear nunha zona. Na ablación con láser eliminamos o material cun láser pulsado ou cun raio láser de onda continua se a intensidade do láser é suficientemente alta. Os láseres pulsados poden perforar buratos moi pequenos e profundos a través de materiais moi duros. Os pulsos láser moi curtos eliminan o material tan rápido que o material circundante absorbe moi pouca calor, polo que a perforación con láser pódese facer en materiais delicados ou sensibles á calor. A enerxía do láser pode ser absorbida selectivamente polos revestimentos, polo que os láseres pulsados de CO2 e Nd:YAG pódense usar para limpar superficies, eliminar pintura e revestimento ou preparar superficies para pintar sen danar a superficie subxacente. We use LASER ENGRAVING and LASER MARKING to engrave or mark an object. Estas dúas técnicas son de feito as aplicacións máis utilizadas. Non se empregan tintas nin se trata de brocas de ferramenta que entran en contacto coa superficie gravada e se desgastan, como ocorre cos métodos tradicionais de gravado e marcado mecánicos. Os materiais especialmente deseñados para gravar e marcar con láser inclúen polímeros sensibles ao láser e novas aliaxes especiais de metal. Aínda que os equipos de marcado e gravado con láser son relativamente máis caros en comparación con alternativas como punzóns, alfinetes, estiletes, selos de gravado... etc., fixéronse máis populares debido á súa precisión, reproducibilidade, flexibilidade, facilidade de automatización e aplicación en liña. nunha gran variedade de ambientes de fabricación. Finalmente, usamos raios láser para outras operacións de fabricación: - SOLDADURA LÁSER - TRATAMENTO TERMICO LÁSER: Tratamento térmico a pequena escala de metais e cerámicas para modificar as súas propiedades mecánicas e tribolóxicas da superficie. - TRATAMIENTO / MODIFICACIÓN DA SUPERFICIE LÁSER: Os láseres utilízanse para limpar superficies, introducir grupos funcionais, modificar superficies co fin de mellorar a adhesión antes da deposición de revestimentos ou procesos de unión. CLICK Product Finder-Locator Service PÁXINA ANTERIOR
- Electric Discharge Machining, EDM, Spark Machining, Die Sinking
Electric Discharge Machining - EDM - Spark Machining - Die Sinking - Wire Erosion - Custom Manufacturing - AGS-TECH Inc. Mecanizado por electroerosión, fresado de descarga eléctrica e rectificado ELECTRICAL DISCHARGE MACHINING (EDM), also referred to as SPARK-EROSION or ELECTRODISCHARGE MACHINING, SPARK ERODING, DIE SINKING_cc781905-5cde-3194-bb3b -136bad5cf58d_or WIRE EROSION, is a NON-CONVENTIONAL MANUFACTURING process where erosion of metals takes place and desired shape is obtained using electrical discharges in the form de chispas. Tamén ofrecemos algunhas variedades de electroerosión, a saber, NO-WEAR EDM, WIRE EDM (WEDM), EDM GRINDING (EDG), DIE-SINKING EDM, ELECTRICAL-DISCHARGE MILLING, micro-EDMcc78190_5, -5cde-3194-bb3b-136bad5cf58d_and TRITURADO POR DESCARGA ELECTROQUÍMICA (ECDG). Os nosos sistemas EDM consisten en ferramentas/electrodos conformados e a peza de traballo conectada a fontes de alimentación de CC e inserida nun fluído dieléctrico non condutor. Despois de 1940, o mecanizado de descarga eléctrica converteuse nunha das tecnoloxías de produción máis importantes e populares nas industrias manufactureras. Cando se reduce a distancia entre os dous eléctrodos, a intensidade do campo eléctrico no volume entre os electrodos faise maior que a forza do dieléctrico nalgúns puntos, que se rompe, formando finalmente unha ponte para que a corrente fluya entre os dous electrodos. Xérase un intenso arco eléctrico que provoca un importante quecemento para fundir unha parte da peza de traballo e parte do material da ferramenta. Como resultado, o material é eliminado de ambos os electrodos. Ao mesmo tempo, o fluído dieléctrico quéntase rapidamente, o que provoca a evaporación do fluído no espazo do arco. Unha vez que o fluxo de corrente se detén ou se detén, a calor é eliminada da burbulla de gas polo fluído dieléctrico circundante e a burbulla cavita (colapso). A onda de choque creada polo colapso da burbulla e o fluxo de fluído dieléctrico expulsan os restos da superficie da peza de traballo e arrastran calquera material fundido da peza ao fluído dieléctrico. A taxa de repetición destas descargas está entre 50 e 500 kHz, tensións entre 50 e 380 V e correntes entre 0,1 e 500 Amperios. O novo dieléctrico líquido, como aceites minerais, queroseno ou auga destilada e desionizada, adoita transportarse ao volume entre electrodos levando as partículas sólidas (en forma de restos) e restablecen as propiedades illantes do dieléctrico. Despois dun fluxo de corrente, a diferenza de potencial entre os dous electrodos restablece ao que era antes da avaría, polo que pode ocorrer unha nova avaría dieléctrica líquida. As nosas modernas máquinas de descarga eléctrica (EDM) ofrecen movementos controlados numéricos e están equipadas con bombas e sistemas de filtrado dos fluídos dieléctricos. O mecanizado por descarga eléctrica (EDM) é un método de mecanizado utilizado principalmente para metais duros ou aqueles que serían moi difíciles de mecanizar con técnicas convencionais. A electroerosión normalmente funciona con calquera material que sexa condutor eléctrico, aínda que tamén se propuxeron métodos para mecanizar cerámicas illantes con electroerosión. O punto de fusión e a calor latente de fusión son propiedades que determinan o volume de metal eliminado por descarga. Canto máis altos sexan estes valores, menor será a taxa de eliminación do material. Debido a que o proceso de mecanizado por descarga eléctrica non implica ningunha enerxía mecánica, a dureza, resistencia e tenacidade da peza non afectan á taxa de eliminación. A frecuencia de descarga ou enerxía por descarga, a tensión e a corrente varíanse para controlar as taxas de eliminación de material. A taxa de eliminación do material e a rugosidade da superficie aumentan co aumento da densidade de corrente e a diminución da frecuencia de faíscas. Podemos cortar contornos ou cavidades complicados en aceiro pre-endurecido mediante electroerosión sen necesidade de tratamento térmico para suavizar e volver a endurecer. Podemos usar este método con calquera metal ou aliaxe metálica como titanio, hastelloy, kovar e inconel. As aplicacións do proceso de electroerosión inclúen a conformación de ferramentas de diamante policristalino. EDM considérase un método de mecanizado non tradicional ou non convencional xunto con procesos como o mecanizado electroquímico (ECM), o corte por chorro de auga (WJ, AWJ), o corte con láser. Por outra banda, os métodos de mecanizado convencionais inclúen torneado, fresado, rectificado, perforación e outros procesos cuxo mecanismo de eliminación de material baséase esencialmente en forzas mecánicas. Os electrodos para mecanizado por descarga eléctrica (EDM) están feitos de grafito, latón, cobre e aliaxe de cobre-tungsteno. Son posibles diámetros de electrodos de ata 0,1 mm. Dado que o desgaste da ferramenta é un fenómeno non desexado que afecta negativamente á precisión dimensional na electroerosión, aproveitamos un proceso chamado NO-WEAR EDM, invertendo a polaridade e utilizando ferramentas de cobre para minimizar o desgaste da ferramenta. Idealmente falando, o mecanizado de descarga eléctrica (EDM) pode considerarse unha serie de ruptura e restauración do líquido dieléctrico entre os electrodos. En realidade, con todo, a eliminación dos restos da zona entre electrodos é case sempre parcial. Isto fai que as propiedades eléctricas do dieléctrico na zona entre electrodos sexan diferentes dos seus valores nominais e varíen co tempo. A distancia inter-electrodos, (gapa de chispa), axústase polos algoritmos de control da máquina específica utilizada. Desafortunadamente, a fenda de chispa en EDM pode ser curtocircuitada polos restos. É posible que o sistema de control do eléctrodo non reaccione con suficiente rapidez para evitar que os dous electrodos (ferramenta e peza) se produzan un curtocircuíto. Este curtocircuíto non desexado contribúe á eliminación de material de forma diferente ao caso ideal. Prestamos a máxima importancia á acción de lavado para restablecer as propiedades illantes do dieléctrico para que a corrente se produza sempre no punto da zona inter-electrodo, minimizando así a posibilidade de cambios non desexados de forma (danos) da ferramenta-electrodo. e peza de traballo. Para obter unha xeometría específica, a ferramenta EDM é guiada polo camiño desexado moi preto da peza de traballo sen tocala, Prestamos a máxima atención ao rendemento do control de movemento en uso. Deste xeito, prodúcense un gran número de descargas / chispas de corrente, e cada unha contribúe á eliminación de material tanto da ferramenta como da peza de traballo, onde se forman pequenos cráteres. O tamaño dos cráteres é unha función dos parámetros tecnolóxicos establecidos para o traballo específico a que se refire e as dimensións poden variar desde a nanoescala (como no caso das operacións de microEDM) ata algúns centos de micrómetros en condicións de desbaste. Estes pequenos cráteres na ferramenta provocan unha erosión gradual do electrodo chamado "desgaste da ferramenta". Para contrarrestar o efecto prexudicial do desgaste na xeometría da peza substitúese continuamente o electrodo da ferramenta durante unha operación de mecanizado. Ás veces conseguimos isto usando un fío continuamente substituído como electrodo (este proceso de electroerosión tamén se chama WIRE EDM ). Ás veces usamos a ferramenta-electrodo de tal xeito que só unha pequena parte del está realmente implicada no proceso de mecanizado e esta parte cámbiase regularmente. Este é, por exemplo, o caso cando se usa un disco xiratorio como electrodo de ferramenta. Este proceso chámase EDM GRINDING. Outra técnica que implementamos consiste en utilizar un conxunto de electrodos con diferentes tamaños e formas durante a mesma operación de electroerosión para compensar o desgaste. Chamamos a esta técnica de electrodos múltiples, e úsase máis habitualmente cando o electrodo da ferramenta replica en negativo a forma desexada e avanza cara ao branco ao longo dunha única dirección, normalmente a dirección vertical (é dicir, o eixe z). Isto aseméllase ao sumidoiro da ferramenta no líquido dieléctrico no que está inmersa a peza de traballo e, polo tanto, denomínase DIE-SINKING EDM_cc781905-5cde-3194-bb3b5cf5805-5cde-3194 3194-bb3b-136bad5cf58d_CONVENTIONAL EDM or RAM EDM). As máquinas para esta operación chámanse SINKER EDM. Os electrodos para este tipo de electroerosión teñen formas complexas. Se a xeometría final se obtén mediante un electrodo de forma xeralmente simple movido en varias direccións e tamén está suxeito a rotacións, chamámoslle EDM MILLING. A cantidade de desgaste depende estritamente dos parámetros tecnolóxicos utilizados na operación (polaridade, corrente máxima, tensión de circuíto aberto). Por exemplo, in micro-EDM, tamén coñecido como m-EDM, estes parámetros adoitan establecerse en valores que xeran un desgaste severo. Polo tanto, o desgaste é un problema importante nesa área que minimizamos utilizando o noso coñecemento acumulado. Por exemplo, para minimizar o desgaste dos electrodos de grafito, un xerador dixital, controlable en milisegundos, inverte a polaridade a medida que se produce a electroerosión. Isto dá como resultado un efecto similar ao galvanoplastia que deposita continuamente o grafito erosionado de volta no electrodo. Noutro método, un circuíto denominado ''Zero Wear'', minimizamos a frecuencia con que se inicia e se detén a descarga, mantendo acendida o maior tempo posible. A taxa de eliminación de material no mecanizado con descarga eléctrica pódese estimar a partir de: MRR = 4 x 10 exp(4) x I x Tw exp (-1,23) Aquí MRR está en mm3/min, I é a corrente en Amperios, Tw é o punto de fusión da peza en K-273.15K. Exp significa expoñente. Por outra banda, a taxa de desgaste Wt do electrodo pódese obter a partir de: Peso = ( 1,1 x 10exp(11) ) x I x Ttexp(-2,38) Aquí Wt está en mm3/min e Tt é o punto de fusión do material do electrodo en K-273.15K Finalmente, a relación de desgaste da peza de traballo respecto ao electrodo R pódese obter a partir de: R = 2,25 x Trexp (-2,38) Aquí Tr é a relación entre os puntos de fusión da peza a traballar co electrodo. SINKER EDM : Sinker EDM, tamén coñecido como CAVITY TYPE EDM or_cc781905-5cde-bad5cf58d_cavity TYPE EDM or_cc781905-5cde-bad5cf58d_emersión e submersión de líquidos e pezas de submersión e submersión de líquidos e 3cf1905-5cde-emersión e pezas de electroerosión. O electrodo e a peza de traballo están conectados a unha fonte de alimentación. A fonte de alimentación xera un potencial eléctrico entre ambos. A medida que o electrodo se achega á peza de traballo, prodúcese a ruptura dieléctrica no fluído, formando unha canle de plasma e salta unha pequena chispa. As faíscas adoitan caer unha a unha porque é moi improbable que diferentes localizacións do espazo entre electrodos teñan idénticas características eléctricas locais que permitan que unha faísca se produza en todas esas localizacións simultaneamente. Centos de miles destas faíscas ocorren en puntos aleatorios entre o electrodo e a peza por segundo. A medida que o metal base se erosiona e a fenda de chispa aumenta posteriormente, o electrodo baixa automaticamente pola nosa máquina CNC para que o proceso poida continuar sen interrupcións. O noso equipo dispón de ciclos de control coñecidos como ''on time'' e ''off time''. A configuración de tempo de activación determina a duración ou a duración da faísca. Un tempo máis longo produce unha cavidade máis profunda para esa faísca e todas as faíscas posteriores para ese ciclo, creando un acabado máis rugoso na peza de traballo e viceversa. O tempo de apagado é o período de tempo que unha chispa é substituída por outra. Un tempo de apagado máis longo permite que o fluído dieléctrico pase a través dunha boquilla para limpar os restos erosionados, evitando así un curtocircuíto. Estes axustes axústanse en microsegundos. WIRE EDM : In WIRE ELECTRICAL DISCHARGE MACHINING (WEDM), also called WIRE-CUT EDM or WIRE CUTTING, we feed a fío metálico fino dun só fío de latón a través da peza de traballo, que está mergullada nun tanque de fluído dieléctrico. Wire EDM é unha variación importante da EDM. Ocasionalmente usamos electroerosión con fío para cortar placas de ata 300 mm de grosor e para fabricar punzóns, ferramentas e matrices a partir de metais duros que son difíciles de mecanizar con outros métodos de fabricación. Neste proceso, que se asemella ao corte de contornos cunha serra de cinta, o fío, que se alimenta constantemente dunha bobina, mantéñense entre as guías de diamante superior e inferior. As guías controladas por CNC móvense no plano x–y e a guía superior tamén pode moverse de forma independente no eixe z–u–v, dando lugar á capacidade de cortar formas cónicas e de transición (como círculo na parte inferior e cadrado no a parte superior). A guía superior pode controlar os movementos do eixe en x–y–u–v–i–j–k–l–. Isto permite que o WEDM corte formas moi complicadas e delicadas. O corte medio de corte dos nosos equipos que consegue o mellor custo económico e tempo de mecanizado é de 0,335 mm utilizando fío de latón, cobre ou wolframio de Ø 0,25. Non obstante, as guías de diamante superior e inferior dos nosos equipos CNC teñen unha precisión de aproximadamente 0,004 mm e poden ter unha traxectoria de corte ou un corte de tan pequeno como 0,021 mm utilizando un fío de 0,02 mm de Ø. Polo tanto, os cortes moi estreitos son posibles. O ancho de corte é maior que o ancho do fío porque prodúcese chispa desde os lados do fío ata a peza de traballo, causando erosión. Este ''sobrecorte'' é necesario, para moitas aplicacións é previsible e, polo tanto, pódese compensar (no micro-EDM non adoita ser o caso). As bobinas de fío son longas: unha bobina de 8 kg de fío de 0,25 mm ten algo máis de 19 quilómetros de lonxitude. O diámetro do fío pode ser tan pequeno como 20 micrómetros e a precisión xeométrica é de aproximadamente +/- 1 micrómetro. Xeralmente usamos o fío só unha vez e reciclámolo porque é relativamente barato. Viaxa a unha velocidade constante de 0,15 a 9 m/min e mantense unha ranura (ranura) constante durante o corte. No proceso de electroerosión por fío utilizamos auga como fluído dieléctrico, controlando a súa resistividade e outras propiedades eléctricas con filtros e unidades desionizadoras. A auga elimina os restos cortados fóra da zona de corte. O lavado é un factor importante para determinar a taxa de alimentación máxima para un determinado espesor de material e, polo tanto, mantemos consistente. A velocidade de corte na electroerosión por fío indícase en termos da área de sección transversal cortada por unidade de tempo, como 18.000 mm2/h para o aceiro para ferramentas D2 de 50 mm de espesor. A velocidade de corte lineal para este caso sería 18.000/50 = 360 mm/h. A taxa de eliminación de material na electroerosión por fío é: MRR = Vf xhxb Aquí MRR está en mm3/min, Vf é a velocidade de avance do fío na peza de traballo en mm/min, h é o grosor ou altura en mm e b é o corte, que é: b = dw + 2s Aquí dw é o diámetro do fío e s é a distancia entre o fío e a peza en mm. Xunto con tolerancias máis estritas, os nosos modernos centros de mecanizado de corte de fíos por electroerosión de eixes múltiples engadiron funcións como cabezas múltiples para cortar dúas pezas ao mesmo tempo, controis para evitar a rotura do fío, funcións automáticas de rosca automática en caso de rotura de fíos e funcións programadas. estratexias de mecanizado para optimizar o funcionamento, as capacidades de corte recto e angular. Wire-EDM ofrécenos baixas tensións residuais, porque non precisa de altas forzas de corte para a eliminación de material. Cando a enerxía/potencia por pulso é relativamente baixa (como nas operacións de acabado), espérase un pequeno cambio nas propiedades mecánicas dun material debido ás baixas tensións residuais. MOLIADORA DE DESCARGA ELÉCTRICA (EDG) : As moas non conteñen abrasivos, son de grafito ou latón. As faíscas repetitivas entre a roda xiratoria e a peza de traballo eliminan o material das superficies da peza. A taxa de eliminación do material é: MRR = K x I Aquí MRR está en mm3/min, I é a corrente en amperes e K é o factor de material da peza en mm3/A-min. Adoitamos usar o rectificado de descarga eléctrica para cortar fendas estreitas nos compoñentes. Algunhas veces combinamos o proceso EDG (Electrical-Discharge Grinding) co proceso ECG (Electrochemical Grinding) no que o material é eliminado por acción química, as descargas eléctricas da roda de grafito rompen a película de óxido e lavadas polo electrólito. O proceso chámase MOLIADO POR DESCARGA ELECTROQUÍMICA (ECDG). Aínda que o proceso ECDG consume relativamente máis enerxía, é un proceso máis rápido que o EDG. Amolamos principalmente ferramentas de carburo usando esta técnica. Aplicacións do mecanizado de descarga eléctrica: Produción de prototipos: Usamos o proceso de electroerosión na fabricación de moldes, ferramentas e matrices, así como para facer prototipos e pezas de produción, especialmente para as industrias aeroespacial, automotriz e electrónica nas que as cantidades de produción son relativamente baixas. En Sinker EDM, un electrodo de grafito, tungsteno de cobre ou cobre puro é mecanizado na forma desexada (negativa) e introdúcese na peza de traballo no extremo dun pistón vertical. Fabricación de troqueles de moeda: Para a creación de matrices para a produción de xoias e insignias mediante o proceso de acuñación (estampación), o master positivo pode estar feito de prata esterlina, xa que (con axustes de máquina adecuados) o master está significativamente erosionado e úsase só unha vez. A matriz negativa resultante endurece e úsase nun martelo para producir planos estampados a partir de follas en branco recortadas de aliaxe de bronce, prata ou ouro de baixa resistencia. Para os distintivos, estes pisos poden ter unha forma adicional nunha superficie curva mediante outro troquel. Este tipo de electroerosión adoita realizarse mergullada nun dieléctrico a base de aceite. O obxecto acabado pódese refinar aínda máis mediante esmaltado duro (vidro) ou brando (pintura) e/ou galvanoplastia con ouro puro ou níquel. Os materiais máis suaves, como a prata, poden ser gravados a man como un refinamento. Perforación de pequenos buratos: Nas nosas máquinas de electroerosión con fío, usamos electroerosión con perforación de pequenos buratos para facer un burato pasante nunha peza de traballo a través do cal pasar o fío para a operación de electroerosión con fío. Nas nosas máquinas cortadoras de fío están montadas cabezas EDM separadas específicamente para perforacións de pequenos buratos, o que permite que as placas endurecidas grandes poidan erosionar as pezas acabadas delas segundo sexa necesario e sen perforación previa. Tamén usamos EDM de pequenos buratos para perforar filas de buratos nos bordos das palas das turbinas utilizadas nos motores a reacción. O fluxo de gas a través destes pequenos orificios permite que os motores usen temperaturas máis altas do posible. As aliaxes monocristais de alta temperatura e moi duras das que están feitas estas láminas fai que o mecanizado convencional destes buratos cunha relación de aspecto elevada sexa extremadamente difícil e mesmo imposible. Outras áreas de aplicación para EDM de pequenos buratos son a creación de orificios microscópicos para os compoñentes do sistema de combustible. Ademais dos cabezales de electroerosión integrados, implantamos máquinas de electroerosión de pequenos buratos autónomos con eixes x–y para mecanizar buratos cegos ou pasantes. EDM perfora orificios cun electrodo longo de tubo de latón ou cobre que xira nun portabrocas cun fluxo constante de auga destilada ou desionizada que flúe polo eléctrodo como axente de lavado e dieléctrico. Algúns EDM de perforación de pequenos buratos son capaces de perforar 100 mm de aceiro brando ou incluso endurecido en menos de 10 segundos. Nesta operación de perforación pódense conseguir buratos entre 0,3 mm e 6,1 mm. Mecanizado de desintegración de metais: Tamén contamos con máquinas de electroerosión especiais para o propósito específico de eliminar ferramentas rotas (brocas ou machos) das pezas de traballo. Este proceso denomínase ''mecanizado de desintegración de metal''. Vantaxes e inconvenientes Mecanizado de descarga eléctrica: As vantaxes da electroerosión inclúen o mecanizado de: - Formas complexas que doutro xeito serían difíciles de producir con ferramentas de corte convencionais - Material extremadamente duro con tolerancias moi estreitas - Pezas de traballo moi pequenas onde as ferramentas de corte convencionais poden danar a peza por exceso de presión da ferramenta de corte. - Non hai contacto directo entre a ferramenta e a peza de traballo. Polo tanto, as seccións delicadas e os materiais débiles pódense mecanizar sen ningunha distorsión. - Pódese obter un bo acabado superficial. - Os buratos moi finos pódense perforar facilmente. As desvantaxes da EDM inclúen: - A baixa taxa de eliminación do material. - O tempo e o custo adicionais utilizados para crear electrodos para electroerosión ram/sinker. - Reproducir cantos afiados na peza de traballo é difícil debido ao desgaste dos electrodos. - O consumo de enerxía é elevado. - Fórmase ''Sobrecorte''. - Durante o mecanizado prodúcese un desgaste excesivo da ferramenta. - Os materiais eléctricamente non condutores só se poden mecanizar cunha configuración específica do proceso. CLICK Product Finder-Locator Service PÁXINA ANTERIOR
- Embedded Systems, Embedded Computer, Industrial Computers, Janz Tec
Embedded Systems, Embedded Computer, Industrial Computers, Janz Tec, Korenix, Industrial Workstations, Servers, Computer Rack, Single Board Computer Sistemas embebidos e ordenadores industriais e panel PC Le máis Sistemas e ordenadores integrados Le máis Panel PC, pantallas multitáctiles, pantallas táctiles Le máis PC industrial Le máis Estacións de traballo industriais Le máis Equipos de Rede, Dispositivos de Rede, Sistemas Intermedios, Unidade de Interfuncionamento Le máis Dispositivos de almacenamento, matrices de discos e sistemas de almacenamento, SAN, NAS Le máis Servidores industriais Le máis Chasis, bastidores, soportes para ordenadores industriais Le máis Accesorios, módulos, placas portadoras para ordenadores industriais Le máis Automatización e sistemas intelixentes Como provedor de produtos industriais ofrecémosche algúns dos máis indispensables ordenadores e servidores industriais e dispositivos de rede e almacenamento, ordenadores e sistemas integrados, ordenadores de placa única, panel PC, PC industrial, ordenador resistente, pantalla táctil ordenadores, estación de traballo industrial, compoñentes e accesorios de ordenadores industriais, dispositivos de E/S dixitais e analóxicas, enrutadores, ponte, equipos de conmutación, concentrador, repetidor, proxy, firewall, módem, controlador de interface de rede, conversor de protocolos, matrices de almacenamento conectado á rede (NAS) , matrices de rede de área de almacenamento (SAN), módulos de relé multicanle, controlador CAN completo para tomas MODULbus, placa portadora MODULbus, módulo codificador incremental, concepto de enlace PLC intelixente, controlador de motor para servomotores de CC, módulo de interface serie, placa de prototipado VMEbus, intelixente Interface escrava profibus DP, software, electrónica relacionada, soportes para bastidores de chasis. Traemos o mellor de t os produtos informáticos industriais do mundo desde a fábrica ata a súa porta. A nosa vantaxe reside en poder ofrecerche diferentes marcas como Janz Tec and_cc781905-95905-95905-05-05-05-05-05-05-05-05-05-05-05-05-05-05-05-05-05-02 Tamén o que nos fai especiais é a nosa capacidade de ofrecerlle variacións de produtos / configuracións personalizadas / integración con outros sistemas que non pode adquirir doutras fontes. Ofrecémosche equipos de marca de alta calidade polo prezo de lista ou inferior. Hai descontos significativos nos prezos publicados se a túa cantidade de pedido é importante. A maioría dos nosos equipos están en stock. Se non está en stock, xa que somos un revendedor e distribuidor preferido, aínda podemos subministralo nun prazo de entrega máis curto. Ademais dos artigos en stock, podemos ofrecerche produtos especiais deseñados e fabricados segundo as túas necesidades. Simplemente indícanos cales son as diferenzas que necesitas no teu sistema informático industrial e conseguirémolo de acordo coas túas necesidades e solicitudes. We offer you CUSTOM MANUFACTURING and ENGINEERING INTEGRATION capability. We also build CUSTOM AUTOMATION SYSTEMS, MONITORING and PROCESS CONTROL SYSTEMS by integrating ordenadores, etapas de tradución, etapas rotativas, compoñentes motorizados, brazos, tarxetas de adquisición de datos, tarxetas de control de procesos, sensores, actuadores e outros compoñentes de hardware e software necesarios. Independentemente da súa localización na terra, enviamos ata a súa porta nuns días. Temos acordos de envío con desconto con UPS, FEDEX, TNT, DHL e aéreo estándar. Podes pedir en liña usando opcións como tarxetas de crédito coa nosa conta de PayPal, transferencia bancaria, cheque certificado ou xiro postal. Se queres falar connosco antes de tomar unha decisión ou se tes algunha dúbida, só tes que chamarnos e un dos nosos experimentados enxeñeiros en informática e automatización axudarache. Para estar máis preto de ti, temos oficinas e almacéns en varios lugares globais. Fai clic nos submenús correspondentes arriba para ler máis sobre os nosos produtos na categoría de ordenadores industriais. Descarga o folleto para o noso PROGRAMA DE COLABORACIÓN DE DESEÑO Para obter información máis detallada, tamén te invitamos a visitar a nosa tenda de informática industrialhttp://www.agsindustrialcomputers.com CLICK Product Finder-Locator Service PÁXINA ANTERIOR
- Microfluidic Devices, Microfluidics,Micropumps,Microvalves,Lab-on-Chip
Microfluidic Devices - Microfluidics - Micropumps - Microvalves - Lab-on-a-Chip Systems - Microhydraulic - Micropneumatic - AGS-TECH Inc.- New Mexico - USA Dispositivos microfluídicos Manufacturing As nosas FABRICACIÓN DE DISPOSITIVOS MICROFLUÍDICOS operations están dirixidas á fabricación de dispositivos e sistemas nos que se manexan pequenos volumes de fluídos. Temos a capacidade de deseñar dispositivos microfluídicos para ti e ofrecer prototipos e microfabricación personalizados para as túas aplicacións. Exemplos de dispositivos microfluídicos son os dispositivos de micropropulsión, os sistemas lab-on-a-chip, os dispositivos microtérmicos, os cabezales de impresión de inxección de tinta e moito máis. En MICROFLUIDICS temos que ocuparnos do control e manipulación precisos de fluídos restrinxidos a rexións submilimétricas. Os fluídos son movidos, mesturados, separados e procesados. Nos sistemas microfluídicos, os fluídos móvense e contrólanse de forma activa mediante pequenas microbombas e microválvulas e similares ou ben aproveitando pasivamente as forzas capilares. Cos sistemas lab-on-a-chip, os procesos que normalmente se realizan nun laboratorio miniaturizan nun só chip para mellorar a eficiencia e a mobilidade, así como para reducir os volumes de mostra e reactivos. Algunhas das principais aplicacións dos dispositivos e sistemas microfluídicos son: - Laboratorios nun chip - Detección de drogas - Probas de glicosa - Microrreactor químico - Refrixeración por microprocesador - Micro pilas de combustible - Cristalización de proteínas - Cambio rápido de fármacos, manipulación de células individuais - Estudos de células unicelulares - Arrays de microlentes optofluídicos sintonizables - Sistemas microhidráulicos e micropneumáticos (bombas de líquidos, válvulas de gas, sistemas de mestura, etc.) - Sistemas de alerta temperá con biochip - Detección de especies químicas - Aplicacións bioanalíticas - Análise de ADN e proteínas en chip - Dispositivos de pulverización de boquillas - Células de fluxo de cuarzo para a detección de bacterias - Chips de xeración de gotas dobres ou múltiples Os nosos enxeñeiros de deseño teñen moitos anos de experiencia no modelado, deseño e proba de dispositivos microfluídicos para unha variedade de aplicacións. A nosa experiencia en deseño na área da microfluídica inclúe: • Proceso de enlace térmico a baixa temperatura para microfluídica • Gravado húmido de microcanles con profundidades de grabado de nm a mm de profundidade en vidro e borosilicato. • Esmerilado e pulido para unha ampla gama de espesores de substrato desde 100 micras ata máis de 40 mm. • Capacidade de fusionar varias capas para crear complexos dispositivos microfluídicos. • Técnicas de perforación, troceado e mecanizado por ultrasóns aptas para dispositivos microfluídicos • Técnicas de corte en dados innovadoras con conexión de bordo precisa para a interconexión de dispositivos microfluídicos • Aliñación precisa • Variedade de revestimentos depositados, chips microfluídicos pódense pulverizar con metais como platino, ouro, cobre e titanio para crear unha ampla gama de características, como RTD, sensores, espellos e electrodos incorporados. Ademais das nosas capacidades de fabricación personalizadas, temos centos de deseños de chips microfluídicos estándar dispoñibles con revestimentos hidrófobos, hidrófilos ou fluorados e unha ampla gama de tamaños de canles (de 100 nanómetros a 1 mm), entradas, saídas e xeometrías diferentes, como cruz circular. , matrices de pilares e micromesturadoras. Os nosos dispositivos microfluídicos ofrecen unha excelente resistencia química e transparencia óptica, estabilidade a altas temperaturas de ata 500 centígrados, rango de alta presión de ata 300 bar. Algúns chips microfluídicos populares son: CHIPS DE GOTAS MICROFLUÍDICOS: están dispoñibles chips de gotas de vidro con diferentes xeometrías de unión, tamaños de canle e propiedades de superficie. Os chips de gotas microfluídicas teñen unha excelente transparencia óptica para obter imaxes claras. Os tratamentos de revestimento hidrofóbicos avanzados permiten xerar gotas de auga en aceite, así como gotas de aceite en auga formadas nas virutas sen tratar. CHIPS MISCELADORES MICROFLUÍDICOS: permitindo a mestura de dous fluxos de fluídos en milisegundos, os chips micromezcladores benefician a unha ampla gama de aplicacións, incluíndo cinética de reacción, dilución de mostras, cristalización rápida e síntese de nanopartículas. CHIPS DE CANAL MICROFLUÍDICO ÚNICO: AGS-TECH Inc. ofrece chips de microfluídico de canle único cunha entrada e unha saída para varias aplicacións. Están dispoñibles dúas dimensións de chip diferentes (66x33mm e 45x15mm). Tamén temos soportes de chip compatibles. CHIPS CRUZADO DE CANLES MICROFLUÍDICOS: Tamén ofrecemos chips microfluídicos con dúas canles simples que se cruzan. Ideal para aplicacións de xeración de gotas e foco de fluxo. As dimensións estándar do chip son 45x15 mm e temos un soporte para chip compatible. CHIPS T-JUNCTION: A T-Junction é unha xeometría básica utilizada en microfluídica para o contacto con líquidos e a formación de gotas. Estes chips microfluídicos están dispoñibles en varias formas, incluíndo versións de capa fina, cuarzo, revestidas de platino, hidrófobas e hidrófilas. CHIPS Y-JUNCTION: son dispositivos microfluídicos de vidro deseñados para unha ampla gama de aplicacións, incluíndo estudos de contacto líquido-líquido e difusión. Estes dispositivos microfluídicos presentan dúas unións en Y conectadas e dúas canles rectas para a observación do fluxo de microcanles. CHIPS DE REACTOR MICROFLUÍDO: Os chips de microrreactor son dispositivos microfluídicos de vidro compactos deseñados para a mestura e reacción rápidas de dous ou tres fluxos de reactivos líquidos. CHIPS WELLPLATE: Esta é unha ferramenta para investigación analítica e laboratorios de diagnóstico clínico. Os chips Wellplate serven para manter pequenas gotas de reactivos ou grupos de células en pozos de nanolitros. DISPOSITIVOS DE MEMBRANA: Estes dispositivos de membrana están deseñados para ser utilizados para a separación líquido-líquido, contacto ou extracción, filtración de fluxo cruzado e reaccións químicas de superficie. Estes dispositivos benefician dun volume morto baixo e dunha membrana desbotable. CHIPS RESELABLES MICROFLUÍDICOS: Deseñado para chips microfluídicos que se poden abrir e volver selar, os chips resellables permiten ata oito conexións fluídicas e oito eléctricas e a deposición de reactivos, sensores ou células na superficie da canle. Algunhas aplicacións son o cultivo e análise celular, a detección de impedancia e as probas de biosensores. CHIPS DE MEDIOS POROSOS: este é un dispositivo microfluídico de vidro deseñado para a modelización estatística dunha estrutura de rocha arenisca porosa complexa. Entre as aplicacións deste chip microfluídico están a investigación en ciencias da terra e enxeñaría, industria petroquímica, probas ambientais e análise de augas subterráneas. CHIP DE ELECTROFORESE CAPILAR (chip CE): Ofrecemos chips de electroforese capilar con e sen electrodos integrados para análise de ADN e separación de biomoléculas. Os chips de electroforese capilar son compatibles con encapsulados de dimensións 45x15 mm. Temos chips CE, un con cruce clásico e outro con cruce en T. Todos os accesorios necesarios, como soportes para chips, conectores están dispoñibles. Ademais dos chips microfluídicos, AGS-TECH ofrece unha ampla gama de bombas, tubos, sistemas microfluídicos, conectores e accesorios. Algúns sistemas microfluídicos dispoñibles son: SISTEMAS DE INICIO DE GOTAS MICROFLUÍDICOS: O sistema de arranque de gotas baseado en xiringa proporciona unha solución completa para a xeración de gotas monodispersas que varían de 10 a 250 micras de diámetro. Operando en amplos intervalos de caudal entre 0,1 microlitros/min e 10 microlitros/min, o sistema de microfluídica químicamente resistente é ideal para o traballo inicial e a experimentación. O sistema iniciador de gotas baseado en presión, por outra banda, é unha ferramenta para traballos preliminares en microfluídica. O sistema ofrece unha solución completa que contén todas as bombas, conectores e chips microfluídicos necesarios que permiten a produción de gotículas altamente monodispersas de 10 a 150 micras. Operando nun amplo rango de presión entre 0 e 10 bares, este sistema é resistente químicamente e o seu deseño modular fai que sexa facilmente ampliable para futuras aplicacións. Ao proporcionar un fluxo de líquido estable, este kit de ferramentas modular elimina o volume morto e os residuos de mostras para reducir eficazmente os custos de reactivos asociados. Este sistema microfluídico ofrece a capacidade de proporcionar un cambio rápido de líquido. Unha cámara de presión con bloqueo e unha innovadora tapa de cámara de 3 vías permiten bombear simultáneamente ata tres líquidos. SISTEMA DE GOTAS MICROFLUÍDICOS AVANZADO: un sistema microfluídico modular que permite a produción de gotas, partículas, emulsións e burbullas de tamaños extremadamente consistentes. O avanzado sistema de gotas microfluídicas usa tecnoloxía de enfoque de fluxo nun chip microfluídico cun fluxo de líquido sen pulso para producir gotas monodispersas entre nanómetros e centos de micras de tamaño. Adecuado para a encapsulación de células, a produción de esferas, o control da formación de nanopartículas, etc. O tamaño das pingas, as taxas de fluxo, as temperaturas, as unións de mestura, as propiedades da superficie e a orde das adicións pódense variar rapidamente para optimizar o proceso. O sistema microfluídico contén todas as pezas necesarias, incluíndo bombas, sensores de fluxo, chips, conectores e compoñentes de automatización. Tamén están dispoñibles accesorios, incluíndo sistemas ópticos, depósitos máis grandes e kits de reactivos. Algunhas aplicacións de microfluídica para este sistema son a encapsulación de células, ADN e perlas magnéticas para investigación e análise, a entrega de fármacos a través de partículas de polímero e a formulación de fármacos, a fabricación de precisión de emulsións e escumas para alimentos e cosméticos, a produción de pinturas e partículas de polímero, a investigación de microfluídica en gotas, emulsións, burbullas e partículas. SISTEMA MICROFLUÍDICO DE GOTAS PEQUENAS: Un sistema ideal para producir e analizar microemulsións que ofrecen maior estabilidade, maior área interfacial e capacidade para solubilizar compostos tanto acuosos como solubles en aceite. Os chips microfluídicos de pequenas gotas permiten a xeración de microgotas altamente monodispersas que van de 5 a 30 micras. SISTEMA DE GOTAS PARALELAS MICROFLUÍDICOS: Un sistema de alto rendemento para a produción de ata 30.000 microgotas monodispersas por segundo que van de 20 a 60 micras. O sistema de gotas paralelas microfluídicas permite aos usuarios crear gotas estables de auga en aceite ou aceite en auga, facilitando unha ampla gama de aplicacións na produción de medicamentos e alimentos. SISTEMA DE RECOLLIDA DE GOTAS MICROFLUÍDICOS: Este sistema é moi axeitado para a xeración, recollida e análise de emulsións monodispersas. O sistema de recollida de gotas microfluídicas presenta o módulo de recollida de gotas que permite recoller as emulsións sen interrupción do fluxo nin coalescencia de gotas. O tamaño das gotas microfluídicas pódese axustar con precisión e cambiar rapidamente o que permite un control total sobre as características da emulsión. SISTEMA MICROFLUÍDICO MICROMIXER: Este sistema está formado por un dispositivo microfluídico, bombeo de precisión, elementos microfluídicos e software para obter unha excelente mestura. Un dispositivo microfluídico de vidro micromezclador compacto baseado en laminación permite a mestura rápida de dous ou tres fluxos de fluídos en cada unha das dúas xeometrías de mestura independentes. Con este dispositivo microfluídico pódese conseguir unha mestura perfecta tanto en relacións de caudal altas como baixas. O dispositivo microfluídico e os seus compoñentes circundantes ofrecen unha excelente estabilidade química, alta visibilidade para a óptica e unha boa transmisión óptica. O sistema micromezclador funciona de xeito excepcionalmente rápido, funciona en modo de fluxo continuo e pode mesturar completamente dous ou tres fluxos de fluídos en milisegundos. Algunhas aplicacións deste dispositivo de mestura de microfluídicos son a cinética de reacción, a dilución da mostra, a selectividade de reacción mellorada, a cristalización rápida e a síntese de nanopartículas, a activación celular, as reaccións enzimáticas e a hibridación de ADN. SISTEMA MICROFLUÍDICO DE GOTAS A DEMANDA: Este é un sistema microfluídico de gotas baixo demanda compacto e portátil para xerar gotas de ata 24 mostras diferentes e almacenar ata 1000 gotas con tamaños de ata 25 nanolitros. O sistema microfluídico ofrece un excelente control do tamaño e frecuencia das gotas, ademais de permitir o uso de múltiples reactivos para crear ensaios complexos de forma rápida e sinxela. As gotículas microfluídicas pódense almacenar, ciclos térmicamente, fusionarse ou dividirse de gotitas de nanolitro a picolitro. Algunhas aplicacións son, a xeración de bibliotecas de cribado, a encapsulación celular, a encapsulación de organismos, a automatización de probas ELISA, a preparación de gradientes de concentración, a química combinatoria, os ensaios celulares. SISTEMA DE SÍNTESE DE NANOPARTÍCULAS: as nanopartículas son máis pequenas que 100 nm e benefician a unha serie de aplicacións como a síntese de nanopartículas fluorescentes baseadas en silicio (puntos cuánticos) para etiquetar biomoléculas con fins de diagnóstico, entrega de fármacos e imaxes celulares. A tecnoloxía microfluídica é ideal para a síntese de nanopartículas. Reducindo o consumo de reactivos, permite distribucións de tamaño de partículas máis estritas, un mellor control dos tempos de reacción e das temperaturas, así como unha mellor eficiencia de mestura. SISTEMA DE FABRICACIÓN DE GOTAS MICROFLUÍDAS: Sistema microfluídico de alto rendemento que facilita a produción de ata unha tonelada de gotas, partículas ou emulsións moi monodispersadas ao mes. Este sistema microfluídico modular, escalable e altamente flexible permite montar ata 10 módulos en paralelo, permitindo condicións idénticas para ata 70 unións de gotas de chip microfluídico. É posible a produción en masa de gotículas microfluídicas altamente monodispersadas que oscilan entre 20 micras e 150 micras que poden fluír directamente fóra dos chips ou dentro de tubos. As aplicacións inclúen a produción de partículas: PLGA, xelatina, alxinato, poliestireno, agarosa, entrega de fármacos en cremas, aerosois, fabricación de precisión a granel de emulsións e escumas en alimentos, cosméticos, industrias de pinturas, síntese de nanopartículas, micromesturas paralelas e microreaccións. SISTEMA DE CONTROL DE FLUXO MICROFLUÍDICO IMPULSADO POR PRESIÓN: o control de fluxo intelixente de bucle pechado proporciona control de caudais desde nanolitros/min ata mililitros/min, a presións desde 10 bar ata o baleiro. Un sensor de caudal conectado en liña entre a bomba e o dispositivo microfluídico facilita aos usuarios introducir un obxectivo de caudal directamente na bomba sen necesidade dun PC. Os usuarios obterán suavidade de presión e repetibilidade do fluxo volumétrico nos seus dispositivos microfluídicos. Os sistemas pódense estender a varias bombas, que controlarán o caudal de forma independente. Para funcionar no modo de control de caudal, o sensor de caudal debe conectarse á bomba mediante a pantalla do sensor ou a interface do sensor. CLICK Product Finder-Locator Service PÁXINA ANTERIOR
- Micromanufacturing, Nanomanufacturing, Mesomanufacturing AGS-TECH Inc.
Micromanufacturing, Nanomanufacturing, Mesomanufacturing - Electronic & Magnetic Optical & Coatings, Thin Film, Nanotubes, MEMS, Microscale Fabrication Fabricación a nanoescala, microescala e mesoescala Le máis Our NANOMANUFACTURING, MICROMANUFACTURING and MESOMANUFACTURING processes can be categorized as: Tratamentos Superficiais e Modificación Revestimentos funcionais / Revestimentos decorativos / Película delgada / Película gruesa Fabricación a nanoescala / Nanofabricación Fabricación a Microescala / Micromanufactura / Micromecanizado Fabricación a Mesoescala / Mesofabricación Microelectrónica & Fabricación de semiconductores e Fabricación Dispositivos microfluídicos Manufacturing Fabricación de Micro-Óptica Micromontaxe e embalaxe Litografía suave En cada produto intelixente deseñado hoxe, pódese considerar un elemento que aumentará a eficiencia, a versatilidade, reducirá o consumo de enerxía, reducirá o desperdicio, aumentará a vida útil do produto e, polo tanto, será respectuoso co medio ambiente. Para este fin, AGS-TECH está a centrarse nunha serie de procesos e produtos que se poden incorporar a dispositivos e equipos para acadar estes obxectivos. Por exemplo, low-friction FUNCTIONAL COATINGS pode reducir o consumo de enerxía. Outros exemplos de revestimentos funcionais son os revestimentos resistentes a arañazos, anti-humectación SURFACE TREATMENTS revestimento hidrofóbico, revestimento antifúngico (revestimento hidrofóbico, revestimento hidrofóbico) Revestimentos de carbono tipo diamante para ferramentas de corte e trazado, THIN FILRevestimentos electrónicos, revestimentos magnéticos de película fina, revestimentos ópticos multicapa. In NANOMANUFACTURING or_cc781905-5cde-3194-3194-5cde-3194-bb3b-136bad5cf58d_or_cc781905-5cde-3194-5cde-3194-3194-5cde-3194-bb3b-136bad5cf58d-136bad5cf58d Na práctica refírese a operacións de fabricación por debaixo da escala micrométrica. A nanofabricación aínda está na súa infancia en comparación coa microfabricación, pero a tendencia é nesa dirección e a nanofabricación é definitivamente moi importante para o futuro próximo. Algunhas aplicacións da nanofabricación hoxe en día son os nanotubos de carbono como fibras de reforzo para materiais compostos en cadros de bicicletas, bates de béisbol e raquetas de tenis. Os nanotubos de carbono, dependendo da orientación do grafito no nanotubo, poden actuar como semicondutores ou condutores. Os nanotubos de carbono teñen unha capacidade de transporte de corrente moi elevada, 1000 veces maior que a prata ou o cobre. Outra aplicación da nanofabricación é a cerámica nanofase. Usando nanopartículas na produción de materiais cerámicos, podemos aumentar simultaneamente tanto a resistencia como a ductilidade da cerámica. Fai clic no submenú para obter máis información. MICROSCALE MANUFACTURING or MICROMANUFACTURING_cc781905-136bad5cf58d_or MICROMANUFACTURING_cc781905-5cde-3194-5cde-3194-5cde-3195-5cde-3194-5cde-3194 Os termos microfabricación, microelectrónica, sistemas microelectromecánicos non se limitan a escalas tan pequenas de lonxitude, senón que suxiren unha estratexia de material e fabricación. Nas nosas operacións de microfabricación algunhas técnicas populares que usamos son a litografía, o gravado en seco e húmido, o revestimento de película fina. Unha gran variedade de sensores e actuadores, sondas, cabezales de disco duro magnético, chips microelectrónicos, dispositivos MEMS como acelerómetros e sensores de presión, entre outros, son fabricados utilizando estes métodos de microfabricación. Atoparás información máis detallada sobre estes nos submenús. MESOSCALE MANUFACTURING or MESOMANUFACTURING refers to our processes for fabrication of miniature devices such as hearing aids, medical stents, medical valves, mechanical watches and extremely small motores. A fabricación a mesoescala se solapa tanto coa macrofabricación como coa microfabricación. Fabricáronse tornos en miniatura, con motor de 1,5 vatios e dimensións de 32 x 25 x 30,5 mm e pesos de 100 gramos mediante métodos de fabricación a mesoescala. Usando tales tornos, o latón foi mecanizado a un diámetro tan pequeno como 60 micras e as rugosidades da superficie da orde dunha ou dúas micras. Outras máquinas-ferramentas en miniatura como fresadoras e prensas tamén se fabricaron mediante mesofabricación. En FABRICACIÓN DE MICROELECTRONICS empregamos as mesmas técnicas que na microfabricación. Os nosos substratos máis populares son o silicio, e tamén se utilizan outros como arseniuro de galio, fosfuro de indio e xermanio. Na fabricación de dispositivos e circuítos microelectrónicos utilízanse películas/revestimentos de moitos tipos e, especialmente, revestimentos de película fina condutores e illantes. Estes dispositivos adoitan obterse a partir de varias capas. As capas illantes obtéñense xeralmente por oxidación como o SiO2. Os dopantes (tanto p como n) son comúns e partes dos dispositivos están dopadas para alterar as súas propiedades electrónicas e obter rexións de tipo p e n. Usando litografías como a fotolitografía ultravioleta, ultravioleta profunda ou ultravioleta extrema, ou a litografía de raios X con feixe de electróns, transferimos patróns xeométricos que definen os dispositivos desde unha fotomáscara/máscara ás superficies do substrato. Estes procesos de litografía aplícanse varias veces na microfabricación de chips microelectrónicos para conseguir as estruturas requiridas no deseño. Tamén se realizan procesos de gravado mediante os cales se eliminan películas enteiras ou seccións particulares de películas ou substrato. Brevemente, mediante o uso de varios pasos de deposición, gravado e múltiples litografías obtemos as estruturas multicapa sobre os substratos semicondutores de soporte. Despois de procesar as obleas e microfabricar nelas moitos circuítos, córtanse as pezas repetitivas e obtéñense matrices individuais. Despois diso, cada matriz está unida por cable, empaquetada e probada e convértese nun produto microelectrónico comercial. Podes atopar algúns detalles máis sobre a fabricación de microelectrónica no noso submenú, non obstante o tema é moi extenso e, polo tanto, recomendámosche que te poñas en contacto connosco no caso de que necesites información específica sobre o produto ou máis detalles. As nosas MICROFLUIDICS MANUFACTURING operacións están dirixidas á fabricación de dispositivos e sistemas nos que se manipulan pequenos volumes de fluídos. Exemplos de dispositivos microfluídicos son os dispositivos de micropropulsión, os sistemas lab-on-a-chip, os dispositivos microtérmicos, os cabezales de impresión de inxección de tinta e moito máis. En microfluídica temos que tratar co control preciso e a manipulación de fluídos restrinxidos a rexións submilimétricas. Os fluídos son movidos, mesturados, separados e procesados. Nos sistemas microfluídicos, os fluídos móvense e contrólanse de forma activa mediante pequenas microbombas e microválvulas e similares ou ben aproveitando pasivamente as forzas capilares. Cos sistemas lab-on-a-chip, os procesos que normalmente se realizan nun laboratorio miniaturizan nun só chip para mellorar a eficiencia e a mobilidade, así como para reducir os volumes de mostra e reactivos. Temos a capacidade de deseñar dispositivos microfluídicos para ti e ofrecer prototipos de microfluídicos e microfabricación personalizados para as túas aplicacións. Outro campo prometedor na microfabricación é MICRO-OPTICS MANUFACTURING. A micro-óptica permite a manipulación da luz e a xestión de fotóns con estruturas e compoñentes a escala micrónica e submicrónica. A microóptica permítenos relacionar o mundo macroscópico no que vivimos co mundo microscópico do procesamento de datos optoelectrónicos e nanoelectrónicos. Os compoñentes e subsistemas micro-ópticos atopan aplicacións amplas nos seguintes campos: Tecnoloxías da información: en micropantallas, microproxectores, almacenamento de datos ópticos, microcámaras, escáneres, impresoras, copiadoras... etc. Biomedicina: Diagnóstico mínimamente invasivo/punto de atención, seguimento do tratamento, sensores de microimaxe, implantes retinianos. Iluminación: Sistemas baseados en LED e outras fontes de luz eficientes Sistemas de seguridade e seguridade: sistemas de visión nocturna por infravermellos para aplicacións de automoción, sensores ópticos de pegadas dixitais, escáneres de retina. Comunicación óptica e telecomunicacións: en interruptores fotónicos, compoñentes pasivos de fibra óptica, amplificadores ópticos, sistemas de interconexión de ordenadores persoais e mainframe. Estruturas intelixentes: en sistemas de detección baseados en fibra óptica e moito máis Como o provedor de integración de enxeñaría máis diverso, estamos orgullosos da nosa capacidade de ofrecer unha solución para case todas as necesidades de consultoría, enxeñaría, enxeñería inversa, prototipado rápido, desenvolvemento de produtos, fabricación, fabricación e montaxe. Despois de microfabricar os nosos compoñentes, moitas veces temos que continuar con MICRO ASSEMBLY & PACKAGING. Isto implica procesos como a fixación de matrices, unión de fíos, conectorización, selado hermético de paquetes, sondaxe, probas de produtos envasados para a fiabilidade ambiental... etc. Despois de fabricar dispositivos de microfabricación nunha matriz, unimos a matriz a unha base máis resistente para garantir a fiabilidade. Con frecuencia usamos cementos epoxi especiais ou aliaxes eutécticas para unir a matriz ao seu envase. Despois de que o chip ou matriz estea unido ao seu substrato, conectámolo eléctricamente aos cables do paquete mediante unión por cable. Un método é usar fíos de ouro moi finos do paquete que conduce a almofadas de unión situadas ao redor do perímetro da matriz. Por último, necesitamos facer o empaquetado final do circuíto conectado. Dependendo da aplicación e do ambiente operativo, hai dispoñibles unha variedade de paquetes estándar e personalizados para dispositivos electrónicos, electro-ópticos e microelectromecánicos microfabricados. Outra técnica de microfabricación que usamos é LITOGRAFÍA SUAVE, un termo usado para unha serie de procesos para a transferencia de patróns. Un molde mestre é necesario en todos os casos e está microfabricado utilizando métodos de litografía estándar. Usando o molde principal, producimos un patrón / selo elastomérico. Unha variación da litografía suave é a "impresión de microcontacto". O selo de elastómero está recuberto cunha tinta e presionado contra unha superficie. Os picos do patrón entran en contacto coa superficie e transfírese unha fina capa de aproximadamente 1 monocapa de tinta. Esta monocapa de película fina actúa como máscara para o gravado húmido selectivo. Unha segunda variación é o "moldeo por microtransferencia", no que os recesos do molde de elastómero son cheos de precursor de polímero líquido e empuxados contra unha superficie. Unha vez curado o polímero, despegamos o molde, deixando atrás o patrón desexado. Por último, unha terceira variación é o "micromoldeo en capilares", onde o patrón de selo de elastómero consiste en canles que usan forzas capilares para introducir un polímero líquido no selo dende o seu lado. Basicamente, unha pequena cantidade do polímero líquido colócase xunto ás canles capilares e as forzas capilares tiran do líquido cara ás canles. Elimínase o exceso de polímero líquido e permítese curar o polímero dentro das canles. O molde do selo quítase e o produto está listo. Podes atopar máis detalles sobre as nosas técnicas de microfabricación de litografía suave facendo clic no submenú relacionado ao lado desta páxina. Se estás principalmente interesado nas nosas capacidades de enxeñería e investigación e desenvolvemento en lugar das capacidades de fabricación, invitámosche a visitar tamén o noso sitio web de enxeñería http://www.ags-engineering.com Le máis Le máis Le máis Le máis Le máis Le máis Le máis Le máis Le máis CLICK Product Finder-Locator Service PÁXINA ANTERIOR
- Soft Lithography - Microcontact Printing - Microtransfer Molding
Soft Lithography - Microcontact Printing - Microtransfer Molding - Micromolding in Capillaries - AGS-TECH Inc. - NM - USA Litografía suave LITOGRAFÍA SUAVE é un termo usado para unha serie de procesos para a transferencia de patróns. Un molde mestre é necesario en todos os casos e está microfabricado utilizando métodos de litografía estándar. Usando o molde principal, producimos un patrón / selo elastomérico para ser usado en litografía suave. Os elastómeros utilizados para este fin deben ser químicamente inertes, ter unha boa estabilidade térmica, resistencia, durabilidade, propiedades de superficie e ser higroscópicos. A goma de silicona e o PDMS (polidimetilsiloxano) son dous bos materiais candidatos. Estes selos pódense utilizar moitas veces na litografía suave. Unha variación da litografía suave é MICROCONTACT PRINTING. O selo de elastómero está recuberto cunha tinta e presionado contra unha superficie. Os picos do patrón entran en contacto coa superficie e transfírese unha fina capa de aproximadamente 1 monocapa de tinta. Esta monocapa de película fina actúa como máscara para o gravado húmido selectivo. Unha segunda variación é MOLDURA DE MICROTRANSFERENCIA, na que as cavidades do molde de elastómero se enchen de precursor de polímero líquido e se empurran contra unha superficie. Unha vez que o polímero cura despois do moldeado por microtransferencia, despegamos o molde, deixando atrás o patrón desexado. Por último, unha terceira variación é MICROMOLDING IN CAPILLARIES, onde o patrón de selo de elastómero consiste en canles que usan forzas capilares para introducir un polímero líquido no selo dende o seu lado. Basicamente, unha pequena cantidade do polímero líquido colócase xunto ás canles capilares e as forzas capilares tiran do líquido cara ás canles. Elimínase o exceso de polímero líquido e permítese curar o polímero dentro das canles. O molde do selo quítase e o produto está listo. Se a relación de aspecto da canle é moderada e as dimensións da canle permitidas dependen do líquido utilizado, pódese asegurar unha boa replicación do patrón. O líquido usado no micromoldeo en capilares pode ser polímeros termoestables, sol-xel cerámico ou suspensións de sólidos dentro de disolventes líquidos. A técnica de micromoldeo en capilares utilizouse na fabricación de sensores. A litografía suave utilízase para construír elementos medidos a escala de micrómetro a nanómetro. A litografía suave ten vantaxes sobre outras formas de litografía como a fotolitografía e a litografía con feixe de electróns. As vantaxes inclúen as seguintes: • Menor custo na produción en masa que a fotolitografía tradicional • Adecuación para aplicacións en biotecnoloxía e electrónica plástica • Adecuación para aplicacións que impliquen superficies grandes ou non planas (non planas). • A litografía suave ofrece máis métodos de transferencia de patróns que as técnicas tradicionais de litografía (máis opcións de "tinta"). • A litografía suave non precisa dunha superficie fotorreactiva para crear nanoestruturas • Coa litografía suave podemos conseguir detalles máis pequenos que a fotolitografía en ambientes de laboratorio (~30 nm vs ~100 nm). A resolución depende da máscara utilizada e pode alcanzar valores de ata 6 nm. LITOGRAFÍA SUAVE MULTICADA é un proceso de fabricación no que se moldean cámaras, canles, válvulas e vías microscópicas dentro de capas unidas de elastómeros. Usando dispositivos de litografía branda multicapa que consisten en varias capas pódense fabricar a partir de materiais brandos. A suavidade destes materiais permite que as áreas do dispositivo se reduzan en máis de dúas ordes de magnitude en comparación cos dispositivos baseados en silicio. As outras vantaxes da litografía branda, como a rápida creación de prototipos, a facilidade de fabricación e a biocompatibilidade, tamén son válidas na litografía branda multicapa. Usamos esta técnica para construír sistemas microfluídicos activos con válvulas de on-off, válvulas de conmutación e bombas totalmente fóra de elastómeros. CLICK Product Finder-Locator Service PÁXINA ANTERIOR
- Electrochemical Machining and Grinding - ECM - Reverse Electroplating
Electrochemical Machining and Grinding - ECM - Reverse Electroplating - Custom Machining - AGS-TECH Inc. - NM - USA Mecanizado ECM, mecanizado electroquímico, rectificado Some of the valuable NON-CONVENTIONAL MANUFACTURING processes AGS-TECH Inc offers are ELECTROCHEMICAL MACHINING (ECM), SHAPED-TUBE ELECTROLYTIC MACHINING (STEM) , MECANIZADO ELECTROQUÍMICO PULSADO (PECM), TRITURADO ELECTROQUÍMICO (ECG), PROCESOS DE MECANIZADO HÍBRIDO. MECANIZADO ELECTROQUÍMICO (ECM) é unha técnica de fabricación non convencional na que se elimina o metal mediante un proceso electroquímico. ECM é normalmente unha técnica de produción en masa, utilizada para mecanizar materiais extremadamente duros e materiais que son difíciles de mecanizar mediante os métodos de fabricación convencionais. Os sistemas de mecanizado electroquímico que utilizamos para a produción son centros de mecanizado de control numérico con altas taxas de produción, flexibilidade, perfecto control das tolerancias dimensionais. O mecanizado electroquímico é capaz de cortar ángulos pequenos e de formas estrañas, contornos complicados ou cavidades en metais duros e exóticos como aluminuros de titanio, Inconel, Waspaloy e aliaxes de alto níquel, cobalto e renio. Pódense mecanizar tanto xeometrías externas como internas. As modificacións do proceso de mecanizado electroquímico utilízanse para operacións como torneado, fresado, ranurado, trepanado, perfilado onde o electrodo convértese na ferramenta de corte. A taxa de eliminación de metal é só unha función da taxa de cambio iónico e non se ve afectada pola resistencia, dureza ou tenacidade da peza de traballo. Desafortunadamente, o método de mecanizado electroquímico (ECM) está limitado a materiais eléctricamente condutores. Outro punto importante a considerar ao despregar a técnica ECM é comparar as propiedades mecánicas das pezas producidas coas producidas por outros métodos de mecanizado. O ECM elimina o material en lugar de engadilo e, polo tanto, ás veces denomínase "galvanización inversa". Parécese nalgúns aspectos ao mecanizado de descarga eléctrica (EDM) en que se fai pasar unha alta corrente entre un eléctrodo e a peza, a través dun proceso de eliminación de material electrolítico que ten un electrodo cargado negativamente (cátodo), un fluído condutor (electrólito) e un peza condutora (ánodo). O electrólito actúa como portador de corrente e é unha solución salina inorgánica altamente condutora como o cloruro de sodio mesturado e disolto en auga ou nitrato de sodio. A vantaxe do ECM é que non hai desgaste da ferramenta. A ferramenta de corte ECM é guiada polo camiño desexado preto da obra pero sen tocar a peza. A diferenza do EDM, non obstante, non se crean faíscas. Con ECM son posibles altas taxas de eliminación de metal e acabados de superficie de espello, sen que se transfiran tensións térmicas ou mecánicas á peza. O ECM non causa ningún dano térmico na peza e ao non haber forzas da ferramenta non hai deformación da peza nin desgaste da ferramenta, como sería o caso das operacións típicas de mecanizado. No mecanizado electroquímico a cavidade producida é a imaxe de acoplamento feminino da ferramenta. No proceso ECM, unha ferramenta de cátodo móvese nunha peza de ánodo. A ferramenta en forma xeralmente está feita de cobre, latón, bronce ou aceiro inoxidable. O electrólito presurizado é bombeado a un ritmo elevado a unha temperatura establecida a través dos pasaxes da ferramenta ata a zona que se está a cortar. A taxa de avance é a mesma que a taxa de "licuación" do material, e o movemento do electrólito no espazo entre a ferramenta e a peza de traballo lava os ións metálicos lonxe do ánodo da peza antes de que teñan a posibilidade de colocarse na ferramenta do cátodo. A brecha entre a ferramenta e a peza varía entre 80-800 micrómetros e a fonte de alimentación de CC no rango de 5 a 25 V mantén densidades de corrente entre 1,5 e 8 A/mm2 de superficie mecanizada activa. A medida que os electróns atravesan a brecha, o material da peza de traballo disólvese, xa que a ferramenta forma a forma desexada na peza de traballo. O fluído electrolítico leva o hidróxido metálico formado durante este proceso. Dispoñibles máquinas electroquímicas comerciais con capacidades de corrente entre 5 A e 40.000 A. A taxa de eliminación de material no mecanizado electroquímico pódese expresar como: MRR = C x I xn Aquí MRR=mm3/min, I=intensidade en amperes, n=eficiencia de corrente, C=a constante do material en mm3/A-min. A constante C depende da valencia dos materiais puros. Canto maior sexa a valencia, menor será o seu valor. Para a maioría dos metais está entre 1 e 2. Se Ao indica a área da sección transversal uniforme que se está a mecanizar electroquímicamente en mm2, a velocidade de avance f en mm/min pódese expresar como: F = MRR / Ao A velocidade de avance f é a velocidade coa que o electrodo penetra na peza de traballo. No pasado houbo problemas de escasa precisión dimensional e residuos contaminantes para o medio ambiente das operacións de mecanizado electroquímico. Estes foron en gran parte superados. Algunhas das aplicacións do mecanizado electroquímico de materiais de alta resistencia son: - Operacións de afundimento. O afundimento é o mecanizado de cavidades de forxa. - Perforación de palas de turbina, pezas de motores a reacción e toberas. - Perforación de pequenos buratos múltiples. O proceso de mecanizado electroquímico deixa unha superficie sen rebabas. - As palas das turbinas de vapor pódense mecanizar dentro de límites próximos. - Para desbarbado de superficies. No desbarbado, o ECM elimina as proxeccións metálicas que quedan dos procesos de mecanizado e, así, embota os bordos afiados. O proceso de mecanizado electroquímico é rápido e moitas veces máis cómodo que os métodos convencionais de desbarbado manual ou procesos de mecanizado non tradicionais. MECANIZADO ELECTROLÍTICO DE TUBO CON FORMA (TAO) é unha versión do proceso de mecanizado electroquímico que usamos para perforar buratos profundos de pequeno diámetro. Utilízase un tubo de titanio como ferramenta que está revestido cunha resina illante eléctrica para evitar a eliminación de material doutras rexións como as caras laterais do burato e do tubo. Podemos perforar orificios de 0,5 mm con relacións de profundidade a diámetro de 300:1 MECANIZADO ELECTROQUÍMICO PULSADO (PECM): Utilizamos densidades de corrente pulsada moi elevadas da orde de 100 A/cm2. Ao usar correntes pulsadas eliminamos a necesidade de altas taxas de fluxo de electrólitos, o que supón limitacións para o método ECM na fabricación de moldes e matrices. O mecanizado electroquímico pulsado mellora a vida á fatiga e elimina a capa de refundición que deixa a técnica de mecanizado por descarga eléctrica (EDM) nas superficies de moldes e matrices. En TRITURADO ELECTROQUÍMICO (ECG) combinamos a operación de rectificado convencional co mecanizado electroquímico. A moa é un cátodo xiratorio con partículas abrasivas de diamante ou óxido de aluminio que están unidas ao metal. As densidades de corrente oscilan entre 1 e 3 A/mm2. Similar ao ECM, un electrólito como o nitrato de sodio flúe e a eliminación de metal na moenda electroquímica está dominada pola acción electrolítica. Menos do 5% da eliminación de metal é por acción abrasiva da roda. A técnica de ECG é moi adecuada para carburos e aliaxes de alta resistencia, pero non tanto para afundir matrices ou facer moldes porque a moedora pode non acceder facilmente ás cavidades profundas. A taxa de eliminación de material na moenda electroquímica pódese expresar como: MRR = GI/d F Aquí MRR está en mm3/min, G é a masa en gramos, I é a corrente en amperios, d é a densidade en g/mm3 e F é a constante de Faraday (96.485 Coulombs/mol). A velocidade de penetración da moa na peza de traballo pódese expresar como: Vs = (G / d F) x (E / g Kp) x K Aquí Vs está en mm3/min, E é a tensión da cela en voltios, g é a distancia entre a roda e a peza en mm, Kp é o coeficiente de perda e K é a condutividade do electrólito. A vantaxe do método de moenda electroquímica sobre a moenda convencional é un menor desgaste da roda porque menos do 5% da eliminación de metal é por acción abrasiva da roda. Hai semellanzas entre EDM e ECM: 1. A ferramenta e a peza están separadas por un espazo moi pequeno sen contacto entre elas. 2. Tanto a ferramenta como o material deben ser condutores da electricidade. 3. Ambas técnicas necesitan un alto investimento de capital. Utilízanse modernas máquinas CNC 4. Ambos métodos consomen moita enerxía eléctrica. 5. Utilízase un fluído condutor como medio entre a ferramenta e a peza de traballo para ECM e un fluído dieléctrico para EDM. 6. A ferramenta aliméntase continuamente cara á peza para manter un espazo constante entre elas (a electroerosión pode incorporar retirada da ferramenta intermitente ou cíclica, normalmente parcial). PROCESOS DE MECANIZADO HÍBRIDO: Adoitamos aproveitar as vantaxes dos procesos de mecanizado híbrido onde hai dous ou máis procesos diferentes como ECM, EDM….etc. úsanse en combinación. Isto dános a oportunidade de superar as deficiencias dun proceso por outro, e beneficiarnos das vantaxes de cada proceso. CLICK Product Finder-Locator Service PÁXINA ANTERIOR
- Industrial Chemicals, Industrial Consumables, Aerosols, Sprays, Industrial Chemical Agents
Industrial Chemicals, Industrial Consumables, Aerosols, Sprays, Industrial Chemical Agents Téxtiles industriais e especiais e funcionais Só nos interesan os téxtiles e tecidos especiais e funcionais e os produtos feitos con eles que serven para unha aplicación concreta. Trátase de téxtiles de enxeñería de gran valor, tamén denominados en ocasións téxtiles e tecidos técnicos. Tecidos e tecidos non tecidos e panos están dispoñibles para numerosas aplicacións. A continuación móstrase unha lista dalgúns tipos principais de téxtiles industriais, especiais e funcionais que están dentro do noso ámbito de desenvolvemento e fabricación de produtos. Estamos dispostos a traballar contigo no deseño, desenvolvemento e fabricación dos teus produtos feitos de: Materiais téxtiles hidrófobos (repelentes de auga) e hidrófilos (absorbentes de auga). Téxtiles e tecidos de extraordinaria resistencia, durabilidade e resistencia a condicións ambientais severas (como a proba de balas, alta resistencia á calor, resistente a baixas temperaturas, resistente á chama, inerte ou resistente a fluídos e gases corrosivos, resistente ao mofo). formación...) Antibacteriano e antifúngico téxtiles e tecidos Protección UV Tecidos e tecidos eléctricamente condutores e non condutores Tecidos antiestáticos para control ESD... etc. Téxtiles e tecidos con propiedades ópticas e efectos especiais (fluorescentes... etc.) Téxtiles, tecidos e panos con capacidades especiais de filtrado, fabricación de filtros Téxtiles industriais como tecidos para conductos, entretelas, reforzos, correas de transmisión, reforzos para caucho (cintas transportadoras, mantas estampadas, cordóns), téxtiles para cintas e abrasivos. Téxtil para a industria do automóbil (mangueiras, correas, airbags, entretelas, pneumáticos) Téxtiles para produtos de construción, construción e infraestruturas (tecido de formigón, xeomembranas e tecido interior) Tecidos compostos multifuncionais que teñen diferentes capas ou compoñentes para diferentes funcións. Téxtiles feitos con carbón activado infusion on fibras de poliéster para proporcionar sensación de algodón, liberación de olores e funcións de xestión da humidade e protección UV. Téxtiles feitos de polímeros con memoria de forma Téxtiles para cirurxía e implantes cirúrxicos, tecidos biocompatibles Teña en conta que deseñamos, deseñamos e fabricamos produtos segundo as súas necesidades e especificacións. Podemos fabricar produtos segundo as súas especificacións ou, se o desexa, podemos axudarche a escoller os materiais adecuados e a deseñar o produto. PÁXINA ANTERIOR