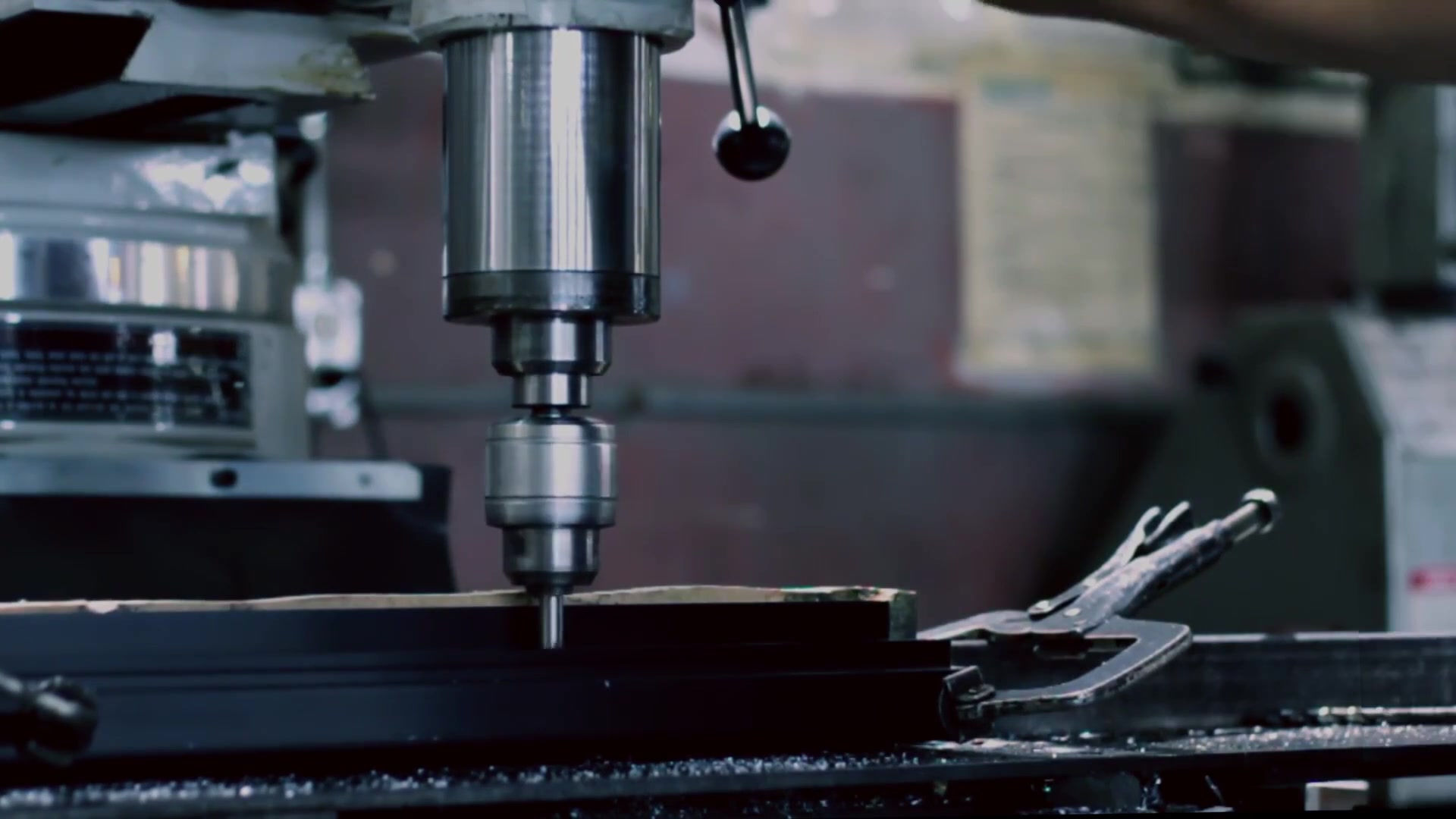
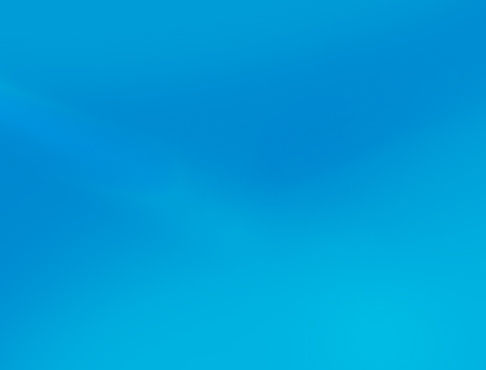
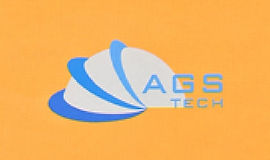
ગ્લોબલ કસ્ટમ મેન્યુફેક્ચરર, ઈન્ટિગ્રેટર, કોન્સોલિડેટર, પ્રોડક્ટ્સ અને સેવાઓની વિશાળ વિવિધતા માટે આઉટસોર્સિંગ પાર્ટનર.
અમે મેન્યુફેક્ચરિંગ, ફેબ્રિકેશન, એન્જિનિયરિંગ, કન્સોલિડેશન, ઇન્ટિગ્રેશન, કસ્ટમ ઉત્પાદિત અને ઑફ-શેલ્ફ પ્રોડક્ટ્સ અને સેવાઓના આઉટસોર્સિંગ માટે તમારા વન-સ્ટોપ સ્ત્રોત છીએ.
તમારી ભાષા પસંદ કરો
-
કસ્ટમ મેન્યુફેક્ચરિંગ
-
સ્થાનિક અને વૈશ્વિક કરાર ઉત્પાદન
-
મેન્યુફેક્ચરિંગ આઉટસોર્સિંગ
-
સ્થાનિક અને વૈશ્વિક પ્રાપ્તિ
-
એકીકરણ
-
એન્જિનિયરિંગ એકીકરણ
-
એન્જિનિયરિંગ સેવાઓ
ELECTRICAL DISCHARGE MACHINING (EDM), also referred to as SPARK-EROSION or ELECTRODISCHARGE MACHINING, SPARK ERODING, DIE SINKING_cc781905-5cde-3194-bb3b -136bad5cf58d_or WIRE EROSION, is a NON-CONVENTIONAL MANUFACTURING process where erosion of metals takes place and desired shape is obtained using electrical discharges in the form તણખા ની. અમે EDM ની કેટલીક જાતો પણ ઑફર કરીએ છીએ, જેમ કે NO-WEAR EDM, WIRE EDM (WEDM), EDM ગ્રાઇન્ડિંગ (EDG), DIE-SINKING EDM, ઇલેક્ટ્રીકલ-ડિસ્ચિંગ, એમસીસીએમએલએલએમડીએમ5, માઈક્રો-ડિસ્ચિંગ, એમ. -5cde-3194-bb3b-136bad5cf58d_and ELECTROCHEMICAL-DISCHARGE ગ્રાઇન્ડીંગ (ECDG). અમારી EDM સિસ્ટમમાં આકારના ટૂલ્સ/ઇલેક્ટ્રોડ અને વર્કપીસનો સમાવેશ થાય છે જે DC પાવર સપ્લાય સાથે જોડાયેલ છે અને ઇલેક્ટ્રિકલી નોન-કન્ડક્ટિંગ ડાઇલેક્ટ્રિક પ્રવાહીમાં દાખલ કરવામાં આવે છે. 1940 પછી ઇલેક્ટ્રિકલ ડિસ્ચાર્જ મશીનિંગ એ ઉત્પાદન ઉદ્યોગોમાં સૌથી મહત્વપૂર્ણ અને લોકપ્રિય ઉત્પાદન તકનીકોમાંની એક બની ગઈ છે.
જ્યારે બે ઇલેક્ટ્રોડ વચ્ચેનું અંતર ઓછું થાય છે, ત્યારે ઇલેક્ટ્રોડ્સ વચ્ચેના વોલ્યુમમાં ઇલેક્ટ્રિક ફિલ્ડની તીવ્રતા કેટલાક બિંદુઓમાં ડાઇલેક્ટ્રિકની મજબૂતાઈ કરતાં વધુ બને છે, જે તૂટી જાય છે, જે આખરે બે ઇલેક્ટ્રોડ્સ વચ્ચે પ્રવાહ માટે પ્રવાહ માટે પુલ બનાવે છે. એક તીવ્ર વિદ્યુત ચાપ ઉત્પન્ન થાય છે જેના કારણે વર્કપીસનો એક ભાગ અને કેટલીક ટૂલિંગ સામગ્રી પીગળી જાય છે. પરિણામે, બંને ઇલેક્ટ્રોડમાંથી સામગ્રી દૂર કરવામાં આવે છે. તે જ સમયે, ડાઇલેક્ટ્રિક પ્રવાહી ઝડપથી ગરમ થાય છે, જેના પરિણામે આર્ક ગેપમાં પ્રવાહીનું બાષ્પીભવન થાય છે. એકવાર વર્તમાન પ્રવાહ બંધ થઈ જાય અથવા તે બંધ થઈ જાય તે પછી આસપાસના ડાઇલેક્ટ્રિક પ્રવાહી દ્વારા ગેસના બબલમાંથી ગરમી દૂર કરવામાં આવે છે અને બબલ પોલાણ કરે છે (ભંગી પડે છે). પરપોટાના પતન અને વર્કપીસની સપાટી પરથી ડાઇઇલેક્ટ્રિક ફ્લુઇડ ફ્લશ કચરાના પ્રવાહ અને કોઈપણ પીગળેલી વર્કપીસ સામગ્રીને ડાઇલેક્ટ્રિક પ્રવાહીમાં પ્રવેશવાથી સર્જાયેલી આઘાત તરંગ. આ ડિસ્ચાર્જનો પુનરાવર્તન દર 50 થી 500 kHz, 50 થી 380 V વચ્ચેના વોલ્ટેજ અને 0.1 અને 500 Amperes વચ્ચેનો પ્રવાહ છે. નવા પ્રવાહી ડાઇલેક્ટ્રિક જેમ કે ખનિજ તેલ, કેરોસીન અથવા નિસ્યંદિત અને ડીયોનાઇઝ્ડ પાણી સામાન્ય રીતે આંતર-ઇલેક્ટ્રોડ વોલ્યુમમાં પહોંચાડવામાં આવે છે જે ઘન કણો (કાટમાળના સ્વરૂપમાં) દૂર કરે છે અને ડાઇલેક્ટ્રિકની ઇન્સ્યુલેટીંગ પ્રોપરાઇટી પુનઃસ્થાપિત થાય છે. વિદ્યુતપ્રવાહના પ્રવાહ પછી, બે ઇલેક્ટ્રોડ વચ્ચેનો સંભવિત તફાવત જે તે ભંગાણ પહેલા હતો તેના પર પુનઃસ્થાપિત થાય છે, તેથી નવું પ્રવાહી ડાઇલેક્ટ્રિક ભંગાણ થઇ શકે છે. અમારા આધુનિક ઇલેક્ટ્રિકલ ડિસ્ચાર્જ મશીનો (EDM) આંકડાકીય રીતે નિયંત્રિત હલનચલન પ્રદાન કરે છે અને તે ડાઇલેક્ટ્રિક પ્રવાહી માટે પંપ અને ફિલ્ટરિંગ સિસ્ટમ્સથી સજ્જ છે.
ઇલેક્ટ્રિકલ ડિસ્ચાર્જ મશીનિંગ (EDM) એ એક મશીનિંગ પદ્ધતિ છે જેનો ઉપયોગ મુખ્યત્વે સખત ધાતુઓ માટે થાય છે અથવા જે પરંપરાગત તકનીકો સાથે મશીન માટે ખૂબ જ મુશ્કેલ હોય છે. EDM સામાન્ય રીતે કોઈપણ સામગ્રી સાથે કામ કરે છે જે વિદ્યુત વાહક હોય છે, જો કે EDM સાથે ઇન્સ્યુલેટિંગ સિરામિક્સને મશિન કરવાની પદ્ધતિઓ પણ પ્રસ્તાવિત કરવામાં આવી છે. ગલનબિંદુ અને ગલનનો સુષુપ્ત ગરમી એ એવા ગુણધર્મો છે જે સ્રાવ દીઠ દૂર કરાયેલી ધાતુની માત્રા નક્કી કરે છે. આ મૂલ્યો જેટલું ઊંચું છે, સામગ્રી દૂર કરવાની દર ધીમી. કારણ કે વિદ્યુત ડિસ્ચાર્જ મશીનિંગ પ્રક્રિયામાં કોઈપણ યાંત્રિક ઉર્જાનો સમાવેશ થતો નથી, વર્કપીસની કઠિનતા, તાકાત અને કઠિનતા દૂર કરવાના દરને અસર કરતી નથી. ડિસ્ચાર્જ ફ્રીક્વન્સી અથવા ડિસ્ચાર્જ દીઠ ઊર્જા, વોલ્ટેજ અને વર્તમાન સામગ્રી દૂર કરવાના દરને નિયંત્રિત કરવા માટે વિવિધ છે. વર્તમાન ઘનતામાં વધારો અને સ્પાર્કની આવર્તન ઘટવા સાથે સામગ્રીને દૂર કરવાનો દર અને સપાટીની ખરબચડી વધે છે. અમે પૂર્વ-કઠણ સ્ટીલમાં જટિલ રૂપરેખા અથવા પોલાણને EDM નો ઉપયોગ કરીને તેમને નરમ અને ફરીથી સખત કરવા માટે હીટ ટ્રીટમેન્ટની જરૂર વગર કાપી શકીએ છીએ. અમે આ પદ્ધતિનો ઉપયોગ કોઈપણ ધાતુ અથવા ધાતુના એલોય જેમ કે ટાઇટેનિયમ, હેસ્ટેલોય, કોવર અને ઇનકોનલ સાથે કરી શકીએ છીએ. EDM પ્રક્રિયાના કાર્યક્રમોમાં પોલીક્રિસ્ટલાઇન ડાયમંડ ટૂલ્સને આકાર આપવાનો સમાવેશ થાય છે. EDM એ ઇલેક્ટ્રોકેમિકલ મશીનિંગ (ECM), વોટર જેટ કટીંગ (WJ, AWJ), લેસર કટીંગ જેવી પ્રક્રિયાઓ સાથે બિન-પરંપરાગત અથવા બિન-પરંપરાગત મશીનિંગ પદ્ધતિ ગણવામાં આવે છે. બીજી તરફ પરંપરાગત મશીનિંગ પદ્ધતિઓમાં ટર્નિંગ, મિલિંગ, ગ્રાઇન્ડિંગ, ડ્રિલિંગ અને અન્ય પ્રક્રિયાઓનો સમાવેશ થાય છે જેની સામગ્રી દૂર કરવાની પદ્ધતિ આવશ્યકપણે યાંત્રિક દળો પર આધારિત છે. ઇલેક્ટ્રિકલ-ડિસ્ચાર્જ મશીનિંગ (EDM) માટેના ઇલેક્ટ્રોડ્સ ગ્રેફાઇટ, પિત્તળ, તાંબુ અને કોપર-ટંગસ્ટન એલોયથી બનેલા છે. ઇલેક્ટ્રોડ વ્યાસ 0.1mm સુધી શક્ય છે. ટૂલ વેર એ EDM માં પરિમાણીય ચોકસાઈને પ્રતિકૂળ અસર કરતી અનિચ્છનીય ઘટના હોવાથી, અમે ધ્રુવીયતાને ઉલટાવીને અને કોપર ટૂલ્સનો ઉપયોગ કરીને ઓછામાં ઓછા પહેરવા માટે, અમે NO-WEAR EDM નામની પ્રક્રિયાનો લાભ લઈએ છીએ.
આદર્શ રીતે કહીએ તો, ઇલેક્ટ્રિકલ-ડિસ્ચાર્જ મશીનિંગ (EDM) એ ઇલેક્ટ્રોડ્સ વચ્ચેના ડાઇલેક્ટ્રિક પ્રવાહીના ભંગાણ અને પુનઃસ્થાપનની શ્રેણી ગણી શકાય. જોકે વાસ્તવમાં, આંતર-ઇલેક્ટ્રોડ વિસ્તારમાંથી કાટમાળને દૂર કરવાનું લગભગ હંમેશા આંશિક હોય છે. આના કારણે આંતર-ઇલેક્ટ્રોડ્સ વિસ્તારમાં ડાઇલેક્ટ્રિકની ઇલેક્ટ્રિકલ પ્રોપરાઇટી તેમના નજીવા મૂલ્યોથી અલગ હોય છે અને સમય સાથે બદલાય છે. ઇન્ટર-ઇલેક્ટ્રોડ અંતર, (સ્પાર્ક-ગેપ), વપરાયેલ ચોક્કસ મશીનના નિયંત્રણ અલ્ગોરિધમ્સ દ્વારા ગોઠવવામાં આવે છે. EDM માં સ્પાર્ક-ગેપ કમનસીબે ક્યારેક કાટમાળ દ્વારા શોર્ટ-સર્કિટ થઈ શકે છે. ઇલેક્ટ્રોડની કંટ્રોલ સિસ્ટમ બે ઇલેક્ટ્રોડ્સ (ટૂલ અને વર્કપીસ) ને શોર્ટ સર્કિટિંગથી રોકવા માટે પૂરતી ઝડપથી પ્રતિક્રિયા કરવામાં નિષ્ફળ થઈ શકે છે. આ અનિચ્છનીય શોર્ટ સર્કિટ આદર્શ કેસથી અલગ રીતે સામગ્રીને દૂર કરવામાં ફાળો આપે છે. અમે ડાઇલેક્ટ્રિકના ઇન્સ્યુલેટીંગ પ્રોપર્ટીઝને પુનઃસ્થાપિત કરવા માટે ફ્લશિંગ એક્શનને ખૂબ મહત્વ આપીએ છીએ જેથી કરંટ હંમેશા ઇન્ટર-ઇલેક્ટ્રોડ એરિયાના પોઈન્ટમાં થાય છે, જેનાથી ટૂલ-ઇલેક્ટ્રોડના આકારમાં અનિચ્છનીય ફેરફાર (નુકસાન) થવાની શક્યતા ઓછી થાય છે. અને વર્કપીસ. ચોક્કસ ભૂમિતિ મેળવવા માટે, EDM ટૂલને વર્કપીસને સ્પર્શ કર્યા વિના ઇચ્છિત પાથ સાથે માર્ગદર્શન આપવામાં આવે છે, અમે ઉપયોગમાં લેવાતા ગતિ નિયંત્રણના પ્રદર્શન પર ખૂબ ધ્યાન આપીએ છીએ. આ રીતે, મોટી સંખ્યામાં વર્તમાન ડિસ્ચાર્જ / સ્પાર્ક થાય છે, અને દરેક ટૂલ અને વર્કપીસ બંનેમાંથી સામગ્રીને દૂર કરવામાં ફાળો આપે છે, જ્યાં નાના ક્રેટર્સ રચાય છે. ક્રેટર્સનું કદ એ હાથ પરના ચોક્કસ કામ માટે સેટ કરેલા તકનીકી પરિમાણોનું કાર્ય છે અને પરિમાણો નેનોસ્કેલ (જેમ કે માઇક્રો-ઇડીએમ ઓપરેશન્સના કિસ્સામાં) થી રફિંગ સ્થિતિમાં કેટલાક સેંકડો માઇક્રોમીટર્સ સુધીના હોઈ શકે છે. ટૂલ પરના આ નાના ક્રેટર્સ "ટૂલ વેર" તરીકે ઓળખાતા ઇલેક્ટ્રોડના ધીમે ધીમે ધોવાણનું કારણ બને છે. વર્કપીસની ભૂમિતિ પર વસ્ત્રોની હાનિકારક અસરનો સામનો કરવા માટે અમે મશીનિંગ ઓપરેશન દરમિયાન ટૂલ-ઇલેક્ટ્રોડને સતત બદલીએ છીએ. કેટલીકવાર આપણે ઇલેક્ટ્રોડ તરીકે સતત બદલાતા વાયરનો ઉપયોગ કરીને આ પ્રાપ્ત કરીએ છીએ (આ EDM પ્રક્રિયાને WIRE EDM પણ કહેવાય છે). કેટલીકવાર આપણે ટૂલ-ઇલેક્ટ્રોડનો ઉપયોગ એવી રીતે કરીએ છીએ કે તેનો માત્ર એક નાનો ભાગ જ વાસ્તવમાં મશીનિંગ પ્રક્રિયામાં રોકાયેલ હોય છે અને આ ભાગ નિયમિતપણે બદલાય છે. દાખલા તરીકે, ટૂલ-ઇલેક્ટ્રોડ તરીકે ફરતી ડિસ્કનો ઉપયોગ કરતી વખતે આ કેસ છે. આ પ્રક્રિયાને EDM ગ્રાઇન્ડીંગ કહેવામાં આવે છે. હજુ સુધી અમે જમાવટ કરીએ છીએ તે બીજી તકનીકમાં વસ્ત્રોની ભરપાઈ કરવા માટે સમાન EDM ઑપરેશન દરમિયાન વિવિધ કદ અને આકારો સાથેના ઇલેક્ટ્રોડ્સનો ઉપયોગ કરવાનો સમાવેશ થાય છે. અમે આને બહુવિધ ઇલેક્ટ્રોડ ટેકનિક કહીએ છીએ, અને જ્યારે ટૂલ ઇલેક્ટ્રોડ ઇચ્છિત આકારની નકારાત્મક નકલ કરે છે અને એક જ દિશામાં, સામાન્ય રીતે ઊભી દિશા (એટલે કે z-અક્ષ) સાથે ખાલી તરફ આગળ વધે છે ત્યારે તેનો સૌથી વધુ ઉપયોગ થાય છે. આ ડાઇલેક્ટ્રિક પ્રવાહીમાં ટૂલના સિંક જેવું લાગે છે જેમાં વર્કપીસને ડૂબવામાં આવે છે, અને તેથી તેને DIE-SINKING EDM_cc781905-5cbb6-31-31_5cde-31_time5cde-31_5cde-31-58d_DIE તરીકે ઓળખવામાં આવે છે. 3194-bb3b-136bad5cf58d_CONVENTIONAL EDM or_cc781905-5cde-3194-bb3b-136bad5cf58d). આ કામગીરી માટેના મશીનોને SINKER EDM કહેવામાં આવે છે. આ પ્રકારના EDM માટેના ઇલેક્ટ્રોડ્સ જટિલ સ્વરૂપો ધરાવે છે. જો અંતિમ ભૂમિતિ સામાન્ય રીતે સરળ આકારના ઇલેક્ટ્રોડનો ઉપયોગ કરીને મેળવવામાં આવે છે જે ઘણી દિશાઓમાં ખસેડવામાં આવે છે અને તે પરિભ્રમણને પણ આધિન છે, તો અમે તેને EDM મિલિંગ કહીએ છીએ. વસ્ત્રોની માત્રા ઓપરેશનમાં ઉપયોગમાં લેવાતા તકનીકી પરિમાણો પર સખત રીતે નિર્ભર છે (ધ્રુવીયતા, મહત્તમ વર્તમાન, ઓપન સર્કિટ વોલ્ટેજ). ઉદાહરણ તરીકે, in micro-EDM, જેને m-EDM તરીકે પણ ઓળખવામાં આવે છે, આ પરિમાણો સામાન્ય રીતે ગંભીર જેન મૂલ્યો પર સેટ કરવામાં આવે છે. તેથી, તે ક્ષેત્રમાં વસ્ત્રો એ એક મોટી સમસ્યા છે જેને આપણે આપણી સંચિત જાણકારીનો ઉપયોગ કરીને ઘટાડી નાખીએ છીએ. ઉદાહરણ તરીકે, ગ્રેફાઇટ ઇલેક્ટ્રોડના વસ્ત્રોને ઘટાડવા માટે, ડિજિટલ જનરેટર, મિલિસેકન્ડમાં નિયંત્રિત કરી શકાય તેવું, ઇલેક્ટ્રો-ઇરોશન થાય છે ત્યારે ધ્રુવીયતાને ઉલટાવી દે છે. આના પરિણામે ઈલેક્ટ્રોપ્લેટિંગ જેવી જ અસર થાય છે જે સતત ધોવાઈ ગયેલા ગ્રેફાઈટને ઈલેક્ટ્રોડ પર પાછા જમા કરે છે. બીજી પદ્ધતિમાં, કહેવાતા ''ઝીરો વેર'' સર્કિટમાં આપણે શક્ય તેટલા લાંબા સમય સુધી તેને ચાલુ રાખીને ડિસ્ચાર્જ કેટલી વાર શરૂ થાય અને બંધ થાય તે ઘટાડી નાખીએ છીએ. ઇલેક્ટ્રિકલ-ડિસ્ચાર્જ મશીનિંગમાં સામગ્રી દૂર કરવાના દરનો અંદાજ આના પરથી લગાવી શકાય છે:
MRR = 4 x 10 exp(4) x I x Tw exp (-1.23)
અહીં MRR mm3/min માં છે, I એમ્પીયરમાં કરંટ છે, Tw એ K-273.15K માં વર્કપીસ મેલ્ટિંગ પોઈન્ટ છે. એક્સ્પોનન્ટનો અર્થ થાય છે.
બીજી બાજુ, ઇલેક્ટ્રોડનો પહેરવાનો દર Wt આમાંથી મેળવી શકાય છે:
Wt = ( 1.1 x 10exp(11) ) x I x Ttexp(-2.38)
અહીં Wt mm3/min માં છે અને Tt K-273.15K માં ઇલેક્ટ્રોડ સામગ્રીનો ગલનબિંદુ છે
છેલ્લે, વર્કપીસ અને ઇલેક્ટ્રોડ R ના વસ્ત્રો ગુણોત્તર આમાંથી મેળવી શકાય છે:
R = 2.25 x Trex(-2.38)
અહીં Tr એ વર્કપીસ અને ઇલેક્ટ્રોડના ગલનબિંદુનો ગુણોત્તર છે.
SINKER EDM :
Sinker EDM, also referred to as CAVITY TYPE EDM or VOLUME EDM, consists of an electrode and workpiece submerged in an insulating liquid. ઇલેક્ટ્રોડ અને વર્કપીસ પાવર સપ્લાય સાથે જોડાયેલા છે. પાવર સપ્લાય બંને વચ્ચે વિદ્યુત સંભવિતતા પેદા કરે છે. જેમ જેમ ઇલેક્ટ્રોડ વર્કપીસની નજીક આવે છે તેમ, પ્રવાહીમાં ડાઇલેક્ટ્રિક ભંગાણ થાય છે, પ્લાઝ્મા ચેનલ બનાવે છે અને એક નાનો સ્પાર્ક કૂદકો મારે છે. તણખા સામાન્ય રીતે એક સમયે એક સાથે પ્રહાર કરે છે કારણ કે આંતર-ઈલેક્ટ્રોડ સ્પેસમાં વિવિધ સ્થાનો સમાન સ્થાનિક વિદ્યુત લક્ષણો ધરાવે છે જે એક સાથે આવા તમામ સ્થળોએ સ્પાર્ક થવા માટે સક્ષમ બનાવે છે તેવી શક્યતા નથી. આમાંથી સેંકડો હજારો સ્પાર્ક પ્રતિ સેકન્ડે ઇલેક્ટ્રોડ અને વર્કપીસ વચ્ચેના રેન્ડમ બિંદુઓ પર થાય છે. જેમ જેમ બેઝ મેટલ ક્ષીણ થાય છે, અને ત્યારબાદ સ્પાર્ક ગેપ વધે છે, ત્યારે અમારા CNC મશીન દ્વારા ઇલેક્ટ્રોડને આપમેળે નીચું કરવામાં આવે છે જેથી પ્રક્રિયા અવિરત ચાલુ રહી શકે. અમારા સાધનોમાં ''ઓન ટાઇમ'' અને ''ઓફ ટાઇમ'' તરીકે ઓળખાતા નિયંત્રણ ચક્ર છે. સમયસર સેટિંગ સ્પાર્કની લંબાઈ અથવા અવધિ નક્કી કરે છે. લાંબો સમય તે સ્પાર્ક માટે વધુ ઊંડો પોલાણ અને તે ચક્ર માટે અનુગામી તમામ સ્પાર્ક ઉત્પન્ન કરે છે, વર્કપીસ પર વધુ રફ ફિનિશ બનાવે છે અને તેનાથી વિપરીત. બંધ સમય એ સમયનો સમયગાળો છે જેમાં એક સ્પાર્ક બીજા દ્વારા બદલવામાં આવે છે. લાંબો સમય વિક્ષેપિત કાટમાળને સાફ કરવા માટે ડાઇલેક્ટ્રિક પ્રવાહીને નોઝલ દ્વારા ફ્લશ કરવાની પરવાનગી આપે છે, તેથી શોર્ટ સર્કિટ ટાળે છે. આ સેટિંગ્સ માઇક્રો સેકન્ડમાં ગોઠવાય છે.
વાયર EDM :
In WIRE ELECTRICAL DISCHARGE MACHINING (WEDM), also called WIRE-CUT EDM or WIRE CUTTING, we feed a વર્કપીસ દ્વારા પિત્તળનો પાતળો સિંગલ-સ્ટ્રેન્ડ મેટલ વાયર, જે ડાઇલેક્ટ્રિક પ્રવાહીની ટાંકીમાં ડૂબી જાય છે. વાયર EDM એ EDM ની મહત્વપૂર્ણ વિવિધતા છે. અમે અવારનવાર વાયર-કટ EDM નો ઉપયોગ 300mm જેટલી જાડી પ્લેટો કાપવા અને અન્ય ઉત્પાદન પદ્ધતિઓ સાથે મશીન માટે મુશ્કેલ હોય તેવી સખત ધાતુઓમાંથી પંચ, ટૂલ્સ અને ડાઈઝ બનાવવા માટે કરીએ છીએ. આ પ્રક્રિયામાં જે બેન્ડ સો સાથે કોન્ટૂર કટીંગ જેવું લાગે છે, વાયર, જે સતત સ્પૂલમાંથી ખવડાવવામાં આવે છે, તે ઉપરના અને નીચલા હીરા માર્ગદર્શિકાઓ વચ્ચે રાખવામાં આવે છે. CNC-નિયંત્રિત માર્ગદર્શિકાઓ x–y પ્લેનમાં આગળ વધે છે અને ઉપલા માર્ગદર્શિકા z–u–v અક્ષમાં પણ સ્વતંત્ર રીતે આગળ વધી શકે છે, જે ટેપર્ડ અને સંક્રમણ આકારોને કાપવાની ક્ષમતાને જન્મ આપે છે (જેમ કે તળિયે વર્તુળ અને ચોરસ ટોચ). ઉપલા માર્ગદર્શિકા x–y–u–v–i–j–k–l– માં ધરીની ગતિવિધિઓને નિયંત્રિત કરી શકે છે. આ WEDM ને ખૂબ જ જટિલ અને નાજુક આકારો કાપવા દે છે. Ø 0.25 પિત્તળ, તાંબા અથવા ટંગસ્ટન વાયરનો ઉપયોગ કરીને શ્રેષ્ઠ આર્થિક ખર્ચ અને મશીનિંગ સમય હાંસલ કરતા અમારા સાધનોનો સરેરાશ કટીંગ કર્ફ 0.335 મીમી છે. જો કે અમારા CNC સાધનોના ઉપલા અને નીચલા હીરા માર્ગદર્શિકાઓ લગભગ 0.004 mm સુધી સચોટ છે, અને તેમાં Ø 0.02 mm વાયરનો ઉપયોગ કરીને 0.021 mm જેટલો નાનો કટીંગ પાથ અથવા કેર્ફ હોઈ શકે છે. તેથી ખરેખર સાંકડા કાપ શક્ય છે. કટીંગની પહોળાઈ વાયરની પહોળાઈ કરતા વધારે છે કારણ કે વાયરની બાજુઓથી વર્કપીસ સુધી સ્પાર્કિંગ થાય છે, જેના કારણે ધોવાણ થાય છે. આ ''ઓવરકટ'' જરૂરી છે, ઘણી એપ્લિકેશનો માટે તે અનુમાનિત છે અને તેથી તેની ભરપાઈ કરી શકાય છે (માઈક્રો-EDM માં આવું વારંવાર થતું નથી). વાયર સ્પૂલ લાંબા હોય છે - 0.25 મીમી વાયરના 8 કિલો સ્પૂલની લંબાઈ માત્ર 19 કિલોમીટરથી વધુ હોય છે. વાયરનો વ્યાસ 20 માઇક્રોમીટર જેટલો નાનો હોઇ શકે છે અને ભૂમિતિની ચોકસાઇ +/- 1 માઇક્રોમીટરની પડોશમાં છે. અમે સામાન્ય રીતે વાયરનો ઉપયોગ ફક્ત એક જ વાર કરીએ છીએ અને તેને રિસાયકલ કરીએ છીએ કારણ કે તે પ્રમાણમાં સસ્તું છે. તે 0.15 થી 9m/મિનિટના સતત વેગથી પ્રવાસ કરે છે અને કટ દરમિયાન સતત કેર્ફ (સ્લોટ) જાળવવામાં આવે છે. વાયર-કટ EDM પ્રક્રિયામાં અમે પાણીનો ઉપયોગ ડાઇલેક્ટ્રિક પ્રવાહી તરીકે કરીએ છીએ, તેની પ્રતિરોધકતા અને અન્ય વિદ્યુત ગુણધર્મોને ફિલ્ટર અને ડી-આયનાઇઝર એકમો સાથે નિયંત્રિત કરીએ છીએ. પાણી કાપેલા કાટમાળને કટીંગ ઝોનથી દૂર ફ્લશ કરે છે. આપેલ સામગ્રીની જાડાઈ માટે મહત્તમ ફીડ રેટ નક્કી કરવા માટે ફ્લશિંગ એ એક મહત્વપૂર્ણ પરિબળ છે અને તેથી અમે તેને સુસંગત રાખીએ છીએ. વાયર EDM માં કાપવાની ઝડપ એકમ સમય દીઠ ક્રોસ-સેક્શનલ એરિયા કટના સંદર્ભમાં દર્શાવવામાં આવી છે, જેમ કે 50mm જાડા D2 ટૂલ સ્ટીલ માટે 18,000 mm2/hr. આ કેસ માટે લીનિયર કટીંગ સ્પીડ 18,000/50 = 360mm/hr હશે વાયર EDM માં સામગ્રી દૂર કરવાનો દર છે:
MRR = Vf xhxb
અહીં MRR mm3/min માં છે, Vf એ mm/min માં વર્કપીસમાં વાયરનો ફીડ રેટ છે, h એ mm માં જાડાઈ અથવા ઊંચાઈ છે, અને b એ કેર્ફ છે, જે છે:
b = dw + 2s
અહીં dw એ વાયરનો વ્યાસ છે અને s એ mm માં વાયર અને વર્કપીસ વચ્ચેનું અંતર છે.
ચુસ્ત સહિષ્ણુતા સાથે, અમારા આધુનિક મલ્ટી એક્સિસ EDM વાયર-કટીંગ મશીનિંગ કેન્દ્રોએ એક જ સમયે બે ભાગો કાપવા માટે મલ્ટી હેડ્સ, વાયર તૂટવાથી બચવા માટે નિયંત્રણો, વાયર તૂટવાના કિસ્સામાં સ્વચાલિત સ્વ-થ્રેડીંગ સુવિધાઓ અને પ્રોગ્રામ્ડ જેવી સુવિધાઓ ઉમેરી છે. ઑપરેશનને ઑપ્ટિમાઇઝ કરવા માટે મશીનિંગ વ્યૂહરચના, સીધી અને કોણીય કટીંગ ક્ષમતાઓ.
વાયર-EDM અમને ઓછા અવશેષ તણાવ પ્રદાન કરે છે, કારણ કે તેને સામગ્રીને દૂર કરવા માટે ઉચ્ચ કટિંગ દળોની જરૂર નથી. જ્યારે પલ્સ દીઠ ઉર્જા/શક્તિ પ્રમાણમાં ઓછી હોય છે (જેમ કે અંતિમ કામગીરીમાં), ત્યારે ઓછા અવશેષ તણાવને કારણે સામગ્રીના યાંત્રિક ગુણધર્મોમાં થોડો ફેરફાર અપેક્ષિત છે.
ઇલેક્ટ્રીકલ-ડિસ્ચાર્જ ગ્રાઇન્ડીંગ (EDG) : ગ્રાઇન્ડીંગ વ્હીલ્સમાં ઘર્ષણ નથી હોતું, તે ગ્રેફાઇટ અથવા પિત્તળના બનેલા હોય છે. ફરતા વ્હીલ અને વર્કપીસ વચ્ચે પુનરાવર્તિત સ્પાર્ક વર્કપીસ સપાટીઓમાંથી સામગ્રીને દૂર કરે છે. સામગ્રી દૂર કરવાની દર છે:
MRR = K x I
અહીં MRR mm3/min માં છે, I amperes માં કરંટ છે, અને K એ mm3/A-min માં વર્કપીસ મટીરીયલ ફેક્ટર છે. ઘટકો પર સાંકડી સ્લિટ્સ જોવા માટે અમે વારંવાર ઇલેક્ટ્રિકલ-ડિસ્ચાર્જ ગ્રાઇન્ડીંગનો ઉપયોગ કરીએ છીએ. અમે કેટલીકવાર EDG (ઇલેક્ટ્રિકલ-ડિસ્ચાર્જ ગ્રાઇન્ડીંગ) પ્રક્રિયાને ECG (ઇલેક્ટ્રોકેમિકલ ગ્રાઇન્ડીંગ) પ્રક્રિયા સાથે જોડીએ છીએ જ્યાં રાસાયણિક ક્રિયા દ્વારા સામગ્રીને દૂર કરવામાં આવે છે, ગ્રેફાઇટ વ્હીલમાંથી ઇલેક્ટ્રિકલ ડિસ્ચાર્જ ઓક્સાઇડ ફિલ્મને તોડીને ઇલેક્ટ્રોલાઇટ દ્વારા ધોવાઇ જાય છે. પ્રક્રિયાને ELECTROCHEMICAL-DISCHARGE GRINDING (ECDG) કહેવામાં આવે છે. ભલે ECDG પ્રક્રિયા પ્રમાણમાં વધુ પાવર વાપરે છે, તે EDG કરતાં ઝડપી પ્રક્રિયા છે. અમે મોટે ભાગે આ ટેકનિકનો ઉપયોગ કરીને કાર્બાઇડ સાધનોને ગ્રાઇન્ડ કરીએ છીએ.
ઇલેક્ટ્રિકલ ડિસ્ચાર્જ મશીનિંગની એપ્લિકેશન્સ:
પ્રોટોટાઇપ ઉત્પાદન:
અમે EDM પ્રક્રિયાનો ઉપયોગ મોલ્ડ-મેકિંગ, ટૂલ અને ડાઇ મેન્યુફેક્ચરિંગ તેમજ પ્રોટોટાઇપ અને પ્રોડક્શન પાર્ટ્સ બનાવવા માટે કરીએ છીએ, ખાસ કરીને એરોસ્પેસ, ઓટોમોબાઈલ અને ઈલેક્ટ્રોનિક્સ ઈન્ડસ્ટ્રીઝ કે જેમાં ઉત્પાદનની માત્રા પ્રમાણમાં ઓછી હોય છે. સિંકર EDM માં, ગ્રેફાઇટ, કોપર ટંગસ્ટન અથવા શુદ્ધ કોપર ઇલેક્ટ્રોડને ઇચ્છિત (નકારાત્મક) આકારમાં મશીન કરવામાં આવે છે અને વર્ટિકલ રેમના છેડે વર્કપીસમાં ખવડાવવામાં આવે છે.
સિક્કાઓનું નિર્માણ:
સિક્કા (સ્ટેમ્પિંગ) પ્રક્રિયા દ્વારા દાગીના અને બેજના ઉત્પાદન માટે ડાઈઝ બનાવવા માટે, સ્ટર્લિંગ સિલ્વરમાંથી પોઝિટિવ માસ્ટર બનાવવામાં આવી શકે છે, કારણ કે (યોગ્ય મશીન સેટિંગ્સ સાથે) માસ્ટર નોંધપાત્ર રીતે ક્ષીણ થઈ જાય છે અને તેનો ઉપયોગ ફક્ત એક જ વાર થાય છે. પરિણામી નકારાત્મક ડાઇને પછી સખત બનાવવામાં આવે છે અને બ્રોન્ઝ, સિલ્વર અથવા લો-પ્રૂફ ગોલ્ડ એલોયના કટઆઉટ શીટ બ્લેન્ક્સમાંથી સ્ટેમ્પ્ડ ફ્લેટ બનાવવા માટે ડ્રોપ હેમરમાં ઉપયોગમાં લેવાય છે. બેજ માટે આ ફ્લેટને અન્ય ડાઇ દ્વારા વળાંકવાળી સપાટી પર આકાર આપી શકાય છે. આ પ્રકારનું EDM સામાન્ય રીતે તેલ આધારિત ડાઇલેક્ટ્રિકમાં ડૂબીને કરવામાં આવે છે. ફિનિશ્ડ ઑબ્જેક્ટને વધુ સખત (કાચ) અથવા નરમ (પેઇન્ટ) ઇનેલિંગ અને/અથવા શુદ્ધ સોના અથવા નિકલથી ઇલેક્ટ્રોપ્લેટેડ દ્વારા વધુ શુદ્ધ કરી શકાય છે. ચાંદી જેવી નરમ સામગ્રીને સંસ્કારિતા તરીકે હાથથી કોતરવામાં આવી શકે છે.
નાના છિદ્રો ડ્રિલિંગ:
અમારા વાયર-કટ EDM મશીનો પર, અમે વર્કપીસમાં થ્રુ હોલ બનાવવા માટે નાના છિદ્ર ડ્રિલિંગ EDMનો ઉપયોગ કરીએ છીએ જેના દ્વારા વાયર-કટ EDM ઑપરેશન માટે વાયરને થ્રેડ કરી શકાય છે. અમારા વાયર-કટ મશીનો પર ખાસ કરીને નાના હોલ ડ્રિલિંગ માટે અલગ EDM હેડ લગાવવામાં આવે છે જે મોટી કઠણ પ્લેટોને જરૂરીયાત મુજબ અને પ્રી-ડ્રિલિંગ વિના તેમનામાંથી તૈયાર ભાગોને ભૂંસી નાખવાની મંજૂરી આપે છે. અમે જેટ એન્જિનમાં ઉપયોગમાં લેવાતા ટર્બાઇન બ્લેડની કિનારીઓમાં છિદ્રોની પંક્તિઓને ડ્રિલ કરવા માટે નાના છિદ્ર EDM નો પણ ઉપયોગ કરીએ છીએ. આ નાના છિદ્રોમાંથી ગેસનો પ્રવાહ એન્જિનને અન્યથા શક્ય કરતાં વધુ તાપમાનનો ઉપયોગ કરવાની મંજૂરી આપે છે. ઉચ્ચ-તાપમાન, ખૂબ જ સખત, સિંગલ ક્રિસ્ટલ એલોયથી બનેલા આ બ્લેડ આ છિદ્રોની પરંપરાગત મશીનિંગને ઉચ્ચ પાસા ગુણોત્તર સાથે અત્યંત મુશ્કેલ અને અશક્ય પણ બનાવે છે. નાના છિદ્ર EDM માટે અન્ય એપ્લિકેશન વિસ્તારો ઇંધણ સિસ્ટમ ઘટકો માટે માઇક્રોસ્કોપિક ઓરિફિસ બનાવવા માટે છે. સંકલિત EDM હેડ ઉપરાંત, અમે એકલા નાના છિદ્ર ડ્રિલિંગ EDM મશીનોને x–y અક્ષો સાથે મશીન બ્લાઈન્ડ અથવા છિદ્રો દ્વારા તૈનાત કરીએ છીએ. EDM ડ્રીલ્સ લાંબા પિત્તળ અથવા કોપર ટ્યુબ ઇલેક્ટ્રોડ સાથે છિદ્રો બોર કરે છે જે ફ્લશિંગ એજન્ટ અને ડાઇલેક્ટ્રિક તરીકે ઇલેક્ટ્રોડમાંથી વહેતા નિસ્યંદિત અથવા ડીયોનાઇઝ્ડ પાણીના સતત પ્રવાહ સાથે ચકમાં ફરે છે. કેટલાક નાના-છિદ્ર ડ્રિલિંગ EDMs 10 સેકન્ડથી ઓછા સમયમાં 100 mm નરમ અથવા તો સખત સ્ટીલને ડ્રિલ કરવામાં સક્ષમ છે. આ ડ્રિલિંગ ઓપરેશનમાં 0.3 mm અને 6.1 mm વચ્ચેના છિદ્રો મેળવી શકાય છે.
મેટલ વિઘટન મશીનિંગ:
કામના ટુકડામાંથી તૂટેલા સાધનો (ડ્રિલ બિટ્સ અથવા નળ) દૂર કરવાના ચોક્કસ હેતુ માટે અમારી પાસે ખાસ EDM મશીનો પણ છે. આ પ્રક્રિયાને ''ધાતુના વિઘટન મશીનિંગ'' કહેવાય છે.
ઇલેક્ટ્રિકલ-ડિસ્ચાર્જ મશીનિંગના ફાયદા અને ગેરફાયદા:
EDM ના ફાયદાઓમાં મશીનિંગનો સમાવેશ થાય છે:
- જટિલ આકારો કે જે અન્યથા પરંપરાગત કટીંગ ટૂલ્સ સાથે ઉત્પન્ન કરવા મુશ્કેલ હશે
- ખૂબ જ નજીકની સહનશીલતા માટે અત્યંત સખત સામગ્રી
- ખૂબ નાના કામના ટુકડાઓ જ્યાં પરંપરાગત કટીંગ ટૂલ્સ વધુ પડતા કટીંગ ટૂલના દબાણથી ભાગને નુકસાન પહોંચાડી શકે છે.
- ટૂલ અને વર્ક પીસ વચ્ચે સીધો સંપર્ક નથી. તેથી નાજુક વિભાગો અને નબળી સામગ્રી કોઈપણ વિકૃતિ વિના મશીન કરી શકાય છે.
- સારી સરફેસ ફિનીશ મેળવી શકાય છે.
- ખૂબ જ બારીક છિદ્રો સરળતાથી ડ્રિલ કરી શકાય છે.
EDM ના ગેરફાયદામાં શામેલ છે:
- સામગ્રી દૂર કરવાની ધીમી દર.
- રેમ/સિંકર EDM માટે ઇલેક્ટ્રોડ બનાવવા માટે વપરાતો વધારાનો સમય અને ખર્ચ.
- ઇલેક્ટ્રોડના વસ્ત્રોને કારણે વર્કપીસ પર તીક્ષ્ણ ખૂણાઓનું પુનઃઉત્પાદન કરવું મુશ્કેલ છે.
- પાવર વપરાશ વધારે છે.
- ''ઓવરકટ'' રચાય છે.
- મશીનિંગ દરમિયાન ટૂલનો વધુ પડતો ઘસારો થાય છે.
- ઇલેક્ટ્રિકલી બિન-વાહક સામગ્રીને પ્રક્રિયાના ચોક્કસ સેટ-અપ સાથે જ મશીન કરી શકાય છે.