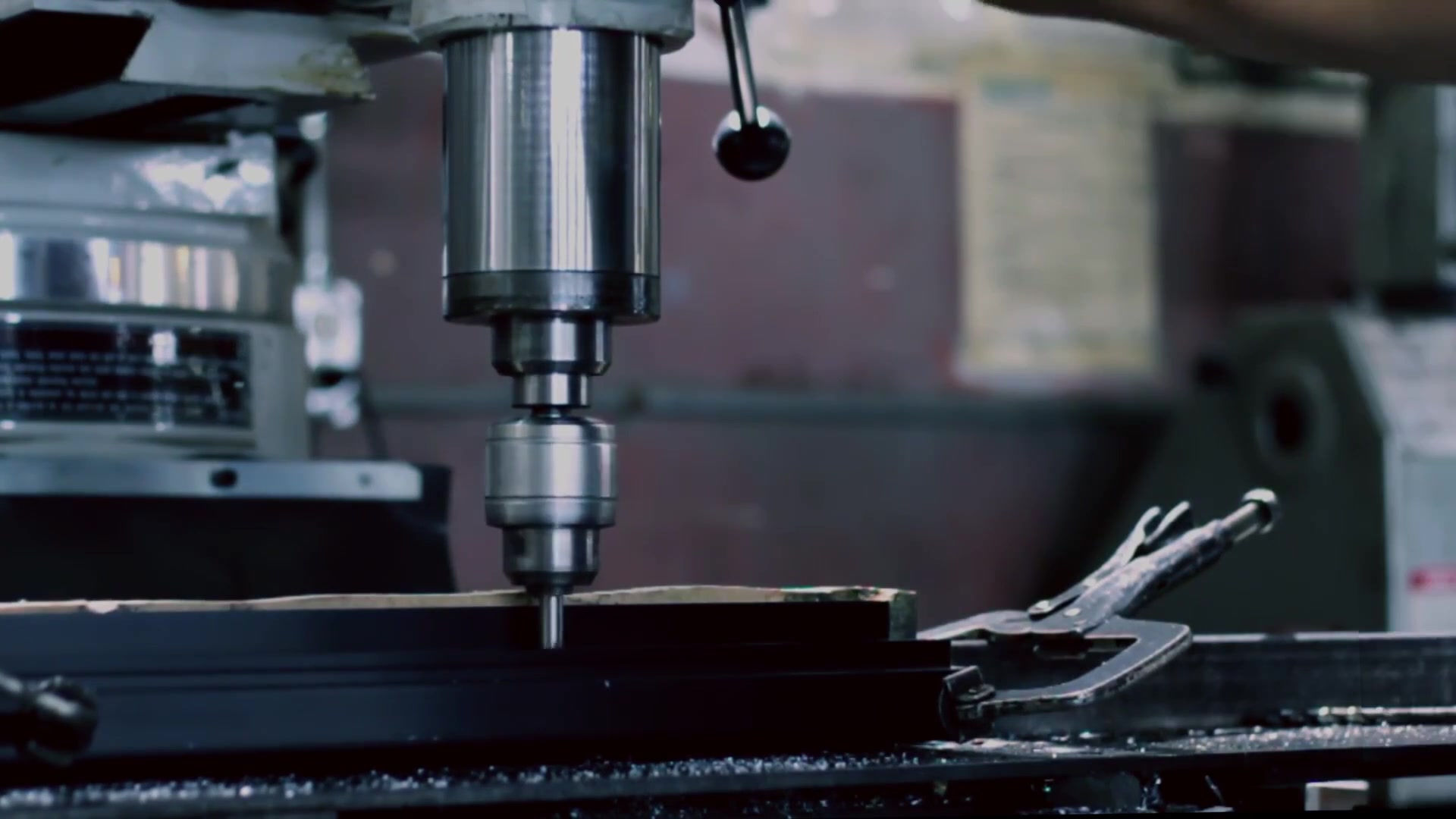
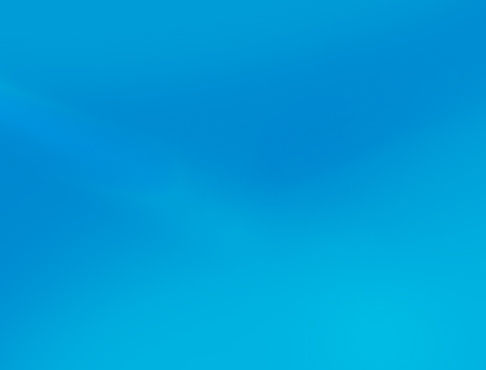
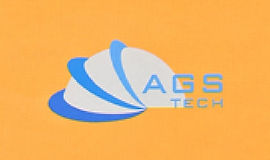
ગ્લોબલ કસ્ટમ મેન્યુફેક્ચરર, ઈન્ટિગ્રેટર, કોન્સોલિડેટર, પ્રોડક્ટ્સ અને સેવાઓની વિશાળ વિવિધતા માટે આઉટસોર્સિંગ પાર્ટનર.
અમે મેન્યુફેક્ચરિંગ, ફેબ્રિકેશન, એન્જિનિયરિંગ, કન્સોલિડેશન, ઇન્ટિગ્રેશન, કસ્ટમ ઉત્પાદિત અને ઑફ-શેલ્ફ પ્રોડક્ટ્સ અને સેવાઓના આઉટસોર્સિંગ માટે તમારા વન-સ્ટોપ સ્ત્રોત છીએ.
તમારી ભાષા પસંદ કરો
-
કસ્ટમ મેન્યુફેક્ચરિંગ
-
સ્થાનિક અને વૈશ્વિક કરાર ઉત્પાદન
-
મેન્યુફેક્ચરિંગ આઉટસોર્સિંગ
-
સ્થાનિક અને વૈશ્વિક પ્રાપ્તિ
-
એકીકરણ
-
એન્જિનિયરિંગ એકીકરણ
-
એન્જિનિયરિંગ સેવાઓ
Search Results
164 results found with an empty search
- Transmission Components, Belts, Chains, Cable Drives, Pulleys,AGS-TECH
Transmission Components, Belts, Chains and Cable Drives, Conventional & Grooved or Serrated, Positive Drive, Pulleys બેલ્ટ અને ચેઇન્સ અને કેબલ ડ્રાઇવ એસેમ્બલી AGS-TECH Inc. તમને બેલ્ટ અને ચેઇન્સ અને કેબલ ડ્રાઇવ એસેમ્બલી સહિત પાવર ટ્રાન્સમિશન ઘટકો પ્રદાન કરે છે. વર્ષોના રિફાઇનમેન્ટ સાથે, અમારી રબર, ચામડું અને અન્ય બેલ્ટ ડ્રાઇવ હળવા અને વધુ કોમ્પેક્ટ બની ગયા છે, જે ઓછા ખર્ચે વધુ ભાર વહન કરવા સક્ષમ છે. એ જ રીતે, અમારી ચેઈન ડ્રાઈવો સમયાંતરે ઘણા વિકાસમાંથી પસાર થઈ છે અને તે અમારા ગ્રાહકોને ઘણા ફાયદા આપે છે. ચેઇન ડ્રાઇવનો ઉપયોગ કરવાના કેટલાક ફાયદાઓ તેમના પ્રમાણમાં અનિયંત્રિત શાફ્ટ સેન્ટર અંતર, કોમ્પેક્ટનેસ, એસેમ્બલીની સરળતા, સ્લિપ અથવા ક્રીપ વિના તણાવમાં સ્થિતિસ્થાપકતા, ઉચ્ચ-તાપમાન વાતાવરણમાં કામ કરવાની ક્ષમતા છે. અમારી કેબલ ડ્રાઈવો અન્ય પ્રકારના ટ્રાન્સમિશન ઘટકો પર કેટલીક એપ્લિકેશન્સમાં સરળતા જેવા ફાયદા પણ આપે છે. ઑફ-શેલ્ફ બેલ્ટ, ચેઇન અને કેબલ ડ્રાઇવ્સ તેમજ કસ્ટમ ફેબ્રિકેટેડ અને એસેમ્બલ વર્ઝન બંને ઉપલબ્ધ છે. અમે આ ટ્રાન્સમિશન ઘટકોને તમારી એપ્લિકેશન માટે યોગ્ય કદમાં અને સૌથી યોગ્ય સામગ્રીમાંથી બનાવી શકીએ છીએ. બેલ્ટ અને બેલ્ટ ડ્રાઇવ્સ: - પરંપરાગત ફ્લેટ બેલ્ટ: આ દાંત, ગ્રુવ્સ અથવા સીરેશન વિનાના સાદા ફ્લેટ બેલ્ટ છે. ફ્લેટ બેલ્ટ ડ્રાઈવો લવચીકતા, સારા શોક શોષણ, ઉચ્ચ ઝડપે કાર્યક્ષમ પાવર ટ્રાન્સમિશન, ઘર્ષણ પ્રતિકાર, ઓછી કિંમત આપે છે. મોટા બેલ્ટ બનાવવા માટે બેલ્ટને સ્પ્લિસ અથવા કનેક્ટ કરી શકાય છે. પરંપરાગત ફ્લેટ બેલ્ટના અન્ય ફાયદા એ છે કે તે પાતળા હોય છે, તે ઉચ્ચ કેન્દ્રત્યાગી ભારને આધિન નથી (તેને નાની પુલી સાથે હાઇ સ્પીડ કામગીરી માટે સારી બનાવે છે). બીજી બાજુ તેઓ ઉચ્ચ બેરિંગ લોડ લાદે છે કારણ કે ફ્લેટ બેલ્ટને ઉચ્ચ તાણની જરૂર હોય છે. ફ્લેટ બેલ્ટ ડ્રાઈવના અન્ય ગેરફાયદામાં સ્લિપિંગ, ઘોંઘાટીયા ઓપરેશન અને કામગીરીની નીચી અને મધ્યમ ઝડપે પ્રમાણમાં ઓછી કાર્યક્ષમતા હોઈ શકે છે. અમારી પાસે બે પ્રકારના પરંપરાગત બેલ્ટ છે: પ્રબલિત અને બિન-પ્રબલિત. પ્રબલિત પટ્ટાઓ તેમની રચનામાં તાણયુક્ત સભ્ય ધરાવે છે. પરંપરાગત ફ્લેટ બેલ્ટ ચામડા, રબરયુક્ત ફેબ્રિક અથવા કોર્ડ, બિન-પ્રબલિત રબર અથવા પ્લાસ્ટિક, ફેબ્રિક, પ્રબલિત ચામડા તરીકે ઉપલબ્ધ છે. ચામડાના બેલ્ટ લાંબા આયુષ્ય, લવચીકતા, ઘર્ષણના ઉત્તમ ગુણાંક, સરળ સમારકામ આપે છે. જો કે ચામડાના બેલ્ટ પ્રમાણમાં મોંઘા હોય છે, બેલ્ટને ડ્રેસિંગ અને સફાઈની જરૂર હોય છે અને વાતાવરણના આધારે તે સંકોચાઈ શકે છે અથવા ખેંચાઈ શકે છે. રબરયુક્ત ફેબ્રિક અથવા કોર્ડ બેલ્ટ ભેજ, એસિડ અને આલ્કલીસ માટે પ્રતિરોધક છે. રબરાઈઝ્ડ ફેબ્રિક બેલ્ટ કપાસના પ્લાઈસ અથવા રબરથી ગર્ભિત કૃત્રિમ બતકના બનેલા હોય છે અને તે સૌથી વધુ આર્થિક હોય છે. રબરાઈઝ્ડ કોર્ડ બેલ્ટમાં રબર-ઈમ્પ્રેગ્નેટેડ કોર્ડની શ્રેણીનો સમાવેશ થાય છે. રબરવાળા કોર્ડ બેલ્ટ ઉચ્ચ તાણ શક્તિ અને સાધારણ કદ અને સમૂહ આપે છે. નોન-રિઇનફોર્સ્ડ રબર અથવા પ્લાસ્ટિક બેલ્ટ લાઇટ-ડ્યુટી, ઓછી-સ્પીડ ડ્રાઇવ એપ્લિકેશન માટે યોગ્ય છે. બિન-રિઇનફોર્સ્ડ રબર અને પ્લાસ્ટિકના પટ્ટાઓ તેમની ગરગડી પર સ્થાને ખેંચી શકાય છે. રબર બેલ્ટની સરખામણીમાં પ્લાસ્ટિક નોન-રિઇનફોર્સ્ડ બેલ્ટ વધુ પાવર ટ્રાન્સમિટ કરી શકે છે. પ્રબલિત ચામડાના બેલ્ટમાં ચામડાના ઉપરના અને નીચેના સ્તરો વચ્ચે સેન્ડવીચ કરાયેલા પ્લાસ્ટિક ટેન્સાઈલ મેમ્બરનો સમાવેશ થાય છે. છેલ્લે, અમારા ફેબ્રિક બેલ્ટમાં કપાસનો એક ટુકડો અથવા ડક ફોલ્ડ અને રેખાંશ ટાંકાઓની પંક્તિઓ સાથે સીવેલું હોઈ શકે છે. ફેબ્રિક બેલ્ટ એકસરખી રીતે ટ્રેક કરવા અને ઊંચી ઝડપે ઓપરેટ કરવામાં સક્ષમ છે. - ગ્રુવ્ડ અથવા સેરેટેડ બેલ્ટ્સ (જેમ કે V-બેલ્ટ): આ અન્ય પ્રકારના ટ્રાન્સમિશન પ્રોડક્ટના ફાયદા પ્રદાન કરવા માટે સુધારેલા મૂળભૂત ફ્લેટ બેલ્ટ છે. આ સપાટ બેલ્ટ છે જેની નીચે રેખાંશ પાંસળી હોય છે. Poly-V બેલ્ટ એ ટેન્સાઈલ સેક્શન સાથે રેખાંશ રૂપે ગ્રુવ્ડ અથવા સેરેટેડ ફ્લેટ બેલ્ટ છે અને ટ્રેકિંગ અને કમ્પ્રેશન હેતુઓ માટે નજીકના V-આકારના ગ્રુવ્સની શ્રેણી છે. પાવર ક્ષમતા બેલ્ટની પહોળાઈ પર આધારિત છે. વી-બેલ્ટ એ ઉદ્યોગનો વર્કહોર્સ છે અને લગભગ કોઈપણ લોડ પાવરના ટ્રાન્સમિશન માટે વિવિધ પ્રમાણભૂત કદ અને પ્રકારોમાં ઉપલબ્ધ છે. વી-બેલ્ટ ડ્રાઈવ 1500 થી 6000 ફૂટ/મિનિટની વચ્ચે સારી રીતે કામ કરે છે, જો કે સાંકડા વી-બેલ્ટ 10,000 ફૂટ/મિનિટ સુધી કામ કરશે. વી-બેલ્ટ ડ્રાઈવો 3 થી 5 વર્ષ જેવા લાંબા જીવનની ઓફર કરે છે અને મોટા સ્પીડ રેશિયોને મંજૂરી આપે છે, તે સ્થાપિત કરવા અને દૂર કરવા માટે સરળ છે, શાંત કામગીરી, ઓછી જાળવણી, બેલ્ટ ડ્રાઈવર અને ચાલિત શાફ્ટ વચ્ચે સારી શોક શોષણ ઓફર કરે છે. વી-બેલ્ટનો ગેરલાભ એ તેમની ચોક્કસ સ્લિપ અને ક્રીપ છે અને તેથી જ્યાં સિંક્રનસ સ્પીડની આવશ્યકતા હોય તે શ્રેષ્ઠ ઉકેલ ન હોઈ શકે. અમારી પાસે ઔદ્યોગિક, ઓટોમોટિવ અને કૃષિ બેલ્ટ છે. સ્ટોક કરેલ પ્રમાણભૂત લંબાઈ તેમજ બેલ્ટની કસ્ટમ લંબાઈ ઉપલબ્ધ છે. તમામ પ્રમાણભૂત વી-બેલ્ટ ક્રોસ સેક્શન સ્ટોકમાંથી ઉપલબ્ધ છે. ત્યાં કોષ્ટકો છે જ્યાં તમે બેલ્ટની લંબાઈ, પટ્ટા વિભાગ (પહોળાઈ અને જાડાઈ) જેવા અજાણ્યા પરિમાણોની ગણતરી કરી શકો છો, જો કે તમે તમારી સિસ્ટમના કેટલાક પરિમાણો જેમ કે ડ્રાઇવિંગ અને સંચાલિત ગરગડીના વ્યાસ, ગરગડી વચ્ચેનું કેન્દ્ર અંતર અને ગરગડીની રોટેશનલ સ્પીડ જાણતા હોવ. તમે આવા કોષ્ટકોનો ઉપયોગ કરી શકો છો અથવા અમને તમારા માટે યોગ્ય V-બેલ્ટ પસંદ કરવાનું કહી શકો છો. - પોઝિટિવ ડ્રાઇવ બેલ્ટ (ટાઇમિંગ બેલ્ટ): આ બેલ્ટ પણ સપાટ પ્રકારના હોય છે જેમાં અંદરના પરિઘ પર સમાન અંતરે દાંતની શ્રેણી હોય છે. પોઝિટિવ ડ્રાઈવ અથવા ટાઈમિંગ બેલ્ટ ફ્લેટ બેલ્ટના ફાયદાઓને ચેઈન અને ગિયર્સની પોઝિટિવ-ગ્રિપ લાક્ષણિકતાઓ સાથે જોડે છે. પોઝિટિવ ડ્રાઈવ બેલ્ટ કોઈ સ્લિપેજ અથવા ઝડપ ભિન્નતા દર્શાવે છે. સ્પીડ રેશિયોની વિશાળ શ્રેણી શક્ય છે. બેરિંગ લોડ ઓછા છે કારણ કે તે ઓછા તાણ પર કામ કરી શકે છે. જો કે તેઓ ગરગડીમાં ખોટી ગોઠવણી માટે વધુ સંવેદનશીલ હોય છે. - પલ્લીઓ, શીવ્સ, બેલ્ટ માટે હબ: ફ્લેટ, રિબ્ડ (સેરેટેડ) અને પોઝિટિવ ડ્રાઈવ બેલ્ટ સાથે વિવિધ પ્રકારની ગરગડીનો ઉપયોગ થાય છે. અમે તે બધાનું ઉત્પાદન કરીએ છીએ. અમારી મોટાભાગની ફ્લેટ બેલ્ટ પુલી લોખંડના કાસ્ટિંગ દ્વારા બનાવવામાં આવે છે, પરંતુ સ્ટીલ વર્ઝન વિવિધ રિમ અને હબ સંયોજનોમાં પણ ઉપલબ્ધ છે. અમારી ફ્લેટ-બેલ્ટ પુલીમાં નક્કર, સ્પોક્ડ અથવા સ્પ્લિટ હબ હોઈ શકે છે અથવા અમે તમારી ઈચ્છા મુજબ ઉત્પાદન કરી શકીએ છીએ. રિબ્ડ અને પોઝિટિવ-ડ્રાઈવ બેલ્ટ વિવિધ સ્ટોક સાઈઝ અને પહોળાઈમાં ઉપલબ્ધ છે. ડ્રાઇવ પર બેલ્ટ રાખવા માટે ટાઇમિંગ-બેલ્ટ ડ્રાઇવ્સમાં ઓછામાં ઓછી એક ગરગડી ફ્લેંજ કરેલી હોવી આવશ્યક છે. લાંબી સેન્ટર ડ્રાઇવ સિસ્ટમો માટે, બંને પુલીને ફ્લેંજવાળી રાખવાની ભલામણ કરવામાં આવે છે. શીવ એ ગરગડીના ગ્રુવ્ડ વ્હીલ્સ છે અને સામાન્ય રીતે આયર્ન કાસ્ટિંગ, સ્ટીલ ફોર્મિંગ અથવા પ્લાસ્ટિક મોલ્ડિંગ દ્વારા બનાવવામાં આવે છે. ઓટોમોટિવ અને એગ્રીકલ્ચરલ શેવ્સ બનાવવા માટે સ્ટીલની રચના યોગ્ય પ્રક્રિયા છે. અમે નિયમિત અને ઊંડા ગ્રુવ્સ સાથે શેવ્સનું ઉત્પાદન કરીએ છીએ. ડીપ-ગ્રુવ શીવ્સ સારી રીતે યોગ્ય છે જ્યારે વી-બેલ્ટ શીવમાં એક ખૂણા પર પ્રવેશ કરે છે, જેમ કે ક્વાર્ટર-ટર્ન ડ્રાઇવ્સમાં કેસ છે. ડીપ ગ્રુવ્સ વર્ટિકલ-શાફ્ટ ડ્રાઈવો અને એપ્લીકેશન માટે પણ યોગ્ય છે જ્યાં બેલ્ટના કંપન એક સમસ્યા હોઈ શકે છે. અમારી નિષ્ક્રિય ગરગડી એ ગ્રુવ્ડ શીવ્સ અથવા ફ્લેટ ગરગડી છે જે યાંત્રિક શક્તિને પ્રસારિત કરતી નથી. આઈડલર પુલીનો ઉપયોગ મોટાભાગે બેલ્ટને કડક કરવા માટે થાય છે. - સિંગલ અને મલ્ટીપલ બેલ્ટ ડ્રાઈવો: સિંગલ બેલ્ટ ડ્રાઈવમાં સિંગલ ગ્રુવ હોય છે જ્યારે મલ્ટીપલ બેલ્ટ ડ્રાઈવમાં બહુવિધ ગ્રુવ હોય છે. નીચેના સંબંધિત રંગીન ટેક્સ્ટ પર ક્લિક કરીને તમે અમારા કેટલોગ ડાઉનલોડ કરી શકો છો: - પાવર ટ્રાન્સમિશન બેલ્ટ્સ (વી-બેલ્ટ્સ, ટાઇમિંગ બેલ્ટ્સ, રો એજ બેલ્ટ્સ, રેપ્ડ બેલ્ટ્સ અને સ્પેશિયાલિટી બેલ્ટ્સનો સમાવેશ થાય છે) - કન્વેયર બેલ્ટ - વી-પુલીઝ - ટાઇમિંગ પુલી સાંકળો અને સાંકળ ડ્રાઈવો: અમારી પાવર ટ્રાન્સમિશન સાંકળોમાં કેટલાક ફાયદા છે જેમ કે પ્રમાણમાં અપ્રતિબંધિત શાફ્ટ સેન્ટર અંતર, સરળ એસેમ્બલી, કોમ્પેક્ટનેસ, સ્લિપ અથવા ક્રીપ વિના તણાવ હેઠળ સ્થિતિસ્થાપકતા, ઊંચા તાપમાને કાર્ય કરવાની ક્ષમતા. અહીં અમારી સાંકળોના મુખ્ય પ્રકારો છે: - અલગ પાડી શકાય તેવી સાંકળો: અમારી અલગ પાડી શકાય તેવી સાંકળો કદ, પીચ અને અંતિમ શક્તિની શ્રેણીમાં અને સામાન્ય રીતે નબળું પાડી શકાય તેવા આયર્ન અથવા સ્ટીલમાંથી બનાવવામાં આવે છે. નિષ્ક્રિય સાંકળો 0.902 (23 mm) થી 4.063 ઇંચ (103 mm) પિચ અને અંતિમ તાકાત 700 થી 17,000 lb/ચોરસ ઇંચ સુધીના કદની શ્રેણીમાં બનાવવામાં આવે છે. બીજી તરફ અમારી અલગ કરી શકાય તેવી સ્ટીલની સાંકળો પિચમાં 0.904 ઇંચ (23 મીમી) થી લગભગ 3.00 ઇંચ (76 મીમી) સુધીના કદમાં બનાવવામાં આવે છે, જેમાં અંતિમ તાકાત 760 થી 5000 lb/ચોરસ ઇંચ છે._cc781905-5cde-3194-3194-3bb 136bad5cf58d_ - પિન્ટલ ચેઇન્સ: આ સાંકળોનો ઉપયોગ ભારે લોડ અને થોડી વધુ ઝડપે લગભગ 450 ફીટ/મિનિટ (2.2 એમ/સેકંડ) માટે થાય છે. પિન્ટલ ચેઇન્સ વ્યક્તિગત કાસ્ટ લિંક્સથી બનેલી હોય છે જેમાં સંપૂર્ણ, રાઉન્ડ બેરલ એન્ડ ઓફસેટ સાઇડબાર હોય છે. આ સાંકળની કડીઓ સ્ટીલની પિન સાથે એકબીજા સાથે જોડાયેલી છે. આ સાંકળો પિચમાં લગભગ 1.00 ઇંચ (25 મીમી) થી 6.00 ઇંચ (150 મીમી) અને અંતિમ શક્તિ 3600 થી 30,000 એલબી/ચોરસ ઇંચની વચ્ચે હોય છે. - ઓફસેટ-સાઇડબાર ચેઇન્સ: આ કન્સ્ટ્રક્શન મશીનરીની ડ્રાઇવ ચેઇન્સમાં લોકપ્રિય છે. આ સાંકળો 1000 ફૂટ/મિનિટની ઝડપે કામ કરે છે અને લગભગ 250 એચપી સુધી લોડ ટ્રાન્સમિટ કરે છે. સામાન્ય રીતે દરેક લિંકમાં બે ઓફસેટ સાઇડબાર હોય છે, એક બુશિંગ, એક રોલર, એક પિન, કોટર પિન. - રોલર ચેઇન્સ: તે 0.25 (6 mm) થી 3.00 (75 mm) ઇંચની પિચમાં ઉપલબ્ધ છે. સિંગલ-પહોળાઈવાળી રોલર ચેઈન્સની અંતિમ તાકાત 925 થી 130,000 lb/ચોરસ ઈંચની વચ્ચે હોય છે. રોલર ચેઈનના બહુવિધ-પહોળાઈ વર્ઝન ઉપલબ્ધ છે અને વધુ ઝડપે વધુ પાવર ટ્રાન્સમિટ કરે છે. મલ્ટીપલ-પહોળાઈની રોલર ચેઈન પણ ઓછા અવાજ સાથે સરળ ક્રિયા પ્રદાન કરે છે. રોલર સાંકળો રોલર લિંક્સ અને પિન લિંક્સમાંથી એસેમ્બલ કરવામાં આવે છે. કોટર પિનનો ઉપયોગ ડિટેચેબલ વર્ઝન રોલર ચેઈન્સમાં થાય છે. રોલર ચેઇન ડ્રાઇવની ડિઝાઇન માટે વિષયની કુશળતાની જરૂર છે. જ્યારે બેલ્ટ ડ્રાઈવો લીનિયર સ્પીડ પર આધારિત હોય છે, તો ચેઈન ડ્રાઈવ નાના સ્પ્રૉકેટની રોટેશનલ સ્પીડ પર આધારિત હોય છે, જે મોટાભાગના ઈન્સ્ટોલેશનમાં ચાલતા સભ્ય હોય છે. હોર્સપાવર રેટિંગ અને રોટેશનલ સ્પીડ ઉપરાંત, ચેઇન ડ્રાઇવની ડિઝાઇન અન્ય ઘણા પરિબળો પર આધારિત છે. - ડબલ-પિચ ચેઇન્સ: મૂળભૂત રીતે રોલર ચેઇન્સ જેવી જ છે સિવાય કે પિચ બમણી લાંબી હોય. - ઇન્વર્ટેડ ટૂથ (સાઇલન્ટ) ચેઇન્સ: હાઇ સ્પીડ ચેઇન્સનો ઉપયોગ મોટે ભાગે પ્રાઇમ મૂવર, પાવર-ટેકઓફ ડ્રાઇવ માટે થાય છે. ઇન્વર્ટેડ ટૂથ ચેઇન ડ્રાઇવ 1200 એચપી સુધીની શક્તિઓનું પ્રસારણ કરી શકે છે અને તે દાંતની લિંક્સની શ્રેણીથી બનેલી હોય છે, જે વૈકલ્પિક રીતે પિન અથવા સંયુક્ત ઘટકોના સંયોજન સાથે એસેમ્બલ થાય છે. કેન્દ્ર-માર્ગદર્શિકા સાંકળમાં સ્પ્રૉકેટમાં ગ્રુવ્સને જોડવા માટે માર્ગદર્શિકા લિંક્સ હોય છે, અને સાઇડ-ગાઇડ શૃંખલામાં સ્પ્રૉકેટની બાજુઓને જોડવા માટે માર્ગદર્શિકાઓ હોય છે. - મણકો અથવા સ્લાઇડર ચેઇન્સ: આ સાંકળોનો ઉપયોગ ધીમી ગતિની ડ્રાઇવ માટે અને મેન્યુઅલ કામગીરીમાં પણ થાય છે. નીચેના સંબંધિત રંગીન ટેક્સ્ટ પર ક્લિક કરીને તમે અમારા કેટલોગ ડાઉનલોડ કરી શકો છો: - ડ્રાઇવિંગ ચેઇન્સ - કન્વેયર સાંકળો - મોટી પિચ કન્વેયર સાંકળો - સ્ટેનલેસ સ્ટીલ રોલર ચેઇન્સ - સાંકળો ફરકાવવી - મોટરસાયકલ સાંકળો - કૃષિ મશીન સાંકળો - સ્પ્રોકેટ્સ: અમારા પ્રમાણભૂત સ્પ્રોકેટ્સ ANSI ધોરણોને અનુરૂપ છે. પ્લેટ સ્પ્રોકેટ્સ ફ્લેટ, હબલેસ સ્પ્રોકેટ્સ છે. અમારા નાના અને મધ્યમ કદના હબ સ્પ્રૉકેટ્સ બાર સ્ટોક અથવા ફોર્જિંગમાંથી ફેરવવામાં આવે છે અથવા બાર-સ્ટોક હબને હોટ-રોલ્ડ પ્લેટમાં વેલ્ડિંગ કરીને બનાવવામાં આવે છે. AGS-TECH Inc. ગ્રે-આયર્ન કાસ્ટિંગ, કાસ્ટ સ્ટીલ અને વેલ્ડેડ હબ કન્સ્ટ્રક્શન્સ, સિન્ટર્ડ પાવડર મેટલ, મોલ્ડેડ અથવા મશીન્ડ પ્લાસ્ટિકમાંથી મશિન કરેલા સ્પ્રૉકેટ્સ સપ્લાય કરી શકે છે. ઉચ્ચ ઝડપે સરળ કામગીરી માટે, સ્પ્રોકેટ્સના કદની યોગ્ય પસંદગી જરૂરી છે. અવકાશની મર્યાદાઓ એ એક પરિબળ છે જેને આપણે સ્પ્રોકેટ પસંદ કરતી વખતે અવગણી શકતા નથી. એવી ભલામણ કરવામાં આવે છે કે ડ્રાઇવર સ્પ્રૉકેટ્સ અને ડ્રાઇવરનો ગુણોત્તર 6:1 કરતાં વધુ ન હોવો જોઈએ, અને ડ્રાઇવર પરની સાંકળની લપેટી 120 ડિગ્રી હોવી જોઈએ. નાના અને મોટા સ્પ્રોકેટ્સ વચ્ચેનું કેન્દ્ર અંતર, સાંકળની લંબાઈ અને સાંકળના તાણને પણ કેટલીક ભલામણ કરેલ ઇજનેરી ગણતરીઓ અને માર્ગદર્શિકાઓ અનુસાર પસંદ કરવી જોઈએ અને અવ્યવસ્થિત રીતે નહીં. નીચે રંગીન ટેક્સ્ટ પર ક્લિક કરીને અમારા કેટલોગ ડાઉનલોડ કરો: - Sprockets અને પ્લેટ વ્હીલ્સ - ટ્રાન્સમિશન બુશિંગ્સ - સાંકળ કપલિંગ - સાંકળ તાળાઓ કેબલ ડ્રાઇવ્સ: કેટલાક કિસ્સાઓમાં બેલ્ટ અને ચેઇન ડ્રાઇવ્સ પર આના ફાયદા છે. કેબલ ડ્રાઈવો બેલ્ટ જેવા જ કાર્યને પરિપૂર્ણ કરી શકે છે અને કેટલીક એપ્લિકેશનોમાં અમલ કરવા માટે સરળ અને વધુ આર્થિક પણ હોઈ શકે છે. ઉદાહરણ તરીકે, સિંક્રોમેશ કેબલ ડ્રાઇવ્સની નવી શ્રેણી પરંપરાગત દોરડાં, સાદા કેબલ અને કોગ ડ્રાઇવ્સને બદલવા માટે હકારાત્મક ટ્રેક્શન માટે ડિઝાઇન કરવામાં આવી છે, ખાસ કરીને ચુસ્ત જગ્યાઓમાં. નવી કેબલ ડ્રાઈવ ઈલેક્ટ્રોનિક સાધનો જેમ કે કોપીંગ મશીન, પ્લોટર, ટાઈપરાઈટર, પ્રિન્ટર વગેરેમાં ઉચ્ચ ચોકસાઈપૂર્વક સ્થિતિ પ્રદાન કરવા માટે રચાયેલ છે. નવી કેબલ ડ્રાઈવની મુખ્ય વિશેષતા એ છે કે તે 3D સર્પેન્ટાઈન કન્ફિગરેશનમાં ઉપયોગમાં લેવાની ક્ષમતા છે જે તેને સક્ષમ કરે છે. અત્યંત લઘુચિત્ર ડિઝાઇન. સિંક્રોમેશ કેબલનો ઉપયોગ દોરડા સાથે સરખામણી કરવામાં આવે ત્યારે ઓછા તાણ સાથે થઈ શકે છે જેથી વીજ વપરાશમાં ઘટાડો થાય છે. બેલ્ટ, ચેઈન અને કેબલ ડ્રાઈવ પર પ્રશ્નો અને અભિપ્રાય માટે AGS-TECH નો સંપર્ક કરો. CLICK Product Finder-Locator Service પાછલું પૃષ્ઠ
- Composites, Composite Materials Manufacturing, Fiber Reinforced
Composites, Composite Materials Manufacturing, Particle and Fiber Reinforced, Cermets, Ceramic & Metal Composite, Glass Fiber Reinforced Polymer, Lay-Up Process સંયુક્ત અને સંયુક્ત સામગ્રી ઉત્પાદન સરળ રીતે વ્યાખ્યાયિત કરવામાં આવે તો, કમ્પોઝિટ અથવા કમ્પોઝિટ મટિરિયલ્સ એ એવી સામગ્રી છે જેમાં વિવિધ ભૌતિક અથવા રાસાયણિક ગુણધર્મો સાથે બે અથવા બહુવિધ સામગ્રીનો સમાવેશ થાય છે, પરંતુ જ્યારે તેઓ એકીકૃત થાય છે ત્યારે તે સામગ્રી બને છે જે ઘટક સામગ્રી કરતાં અલગ હોય છે. આપણે એ નિર્દેશ કરવાની જરૂર છે કે બંધારણમાં ઘટક સામગ્રી અલગ અને અલગ રહે છે. સંયુક્ત સામગ્રીના ઉત્પાદનમાં ધ્યેય એ ઉત્પાદન મેળવવાનું છે જે તેના ઘટકો કરતાં શ્રેષ્ઠ હોય અને દરેક ઘટકની ઇચ્છિત વિશેષતાઓને જોડે. ઉદાહરણ તરીકે; મજબૂતાઈ, ઓછું વજન અથવા નીચી કિંમત સંયુક્ત ડિઝાઇન અને ઉત્પાદન પાછળ પ્રેરક હોઈ શકે છે. અમે ઑફર કરીએ છીએ તે પ્રકારના કંપોઝીટમાં પાર્ટિકલ-રિઇન્ફોર્સ્ડ કમ્પોઝિટ, ફાઇબર-રિઇનફોર્સ્ડ કમ્પોઝિટ છે જેમાં સિરામિક-મેટ્રિક્સ/પોલિમર-મેટ્રિક્સ/મેટલ-મેટ્રિક્સ/કાર્બન-કાર્બન/હાઇબ્રિડ કમ્પોઝિટ, સ્ટ્રક્ચરલ અને લેમિનેટેડ અને સેન્ડવિચ-સ્ટ્રક્ચર્ડ કમ્પોઝિટ અને નેનોકોમ્પોઝિટનો સમાવેશ થાય છે. કમ્પોઝિટ મટિરિયલ મેન્યુફેક્ચરિંગમાં અમે જે ફેબ્રિકેશન ટેકનિકનો ઉપયોગ કરીએ છીએ તે છે: પલ્ટ્રુઝન, પ્રીપ્રેગ પ્રોડક્શન પ્રોસેસ, એડવાન્સ્ડ ફાઈબર પ્લેસમેન્ટ, ફિલામેન્ટ વિન્ડિંગ, ટેલર્ડ ફાઈબર પ્લેસમેન્ટ, ફાઈબરગ્લાસ સ્પ્રે લે-અપ પ્રોસેસ, ટફ્ટિંગ, લેન્ક્સાઈડ પ્રોસેસ, ઝેડ-પિનિંગ. ઘણી સંયુક્ત સામગ્રીઓ બે તબક્કાઓથી બનેલી હોય છે, મેટ્રિક્સ, જે સતત હોય છે અને બીજા તબક્કાની આસપાસ હોય છે; અને વિખરાયેલો તબક્કો જે મેટ્રિક્સથી ઘેરાયેલો છે. અમે ભલામણ કરીએ છીએ કે તમે અહીં ક્લિક કરોAGS-TECH Inc દ્વારા સંયુક્ત અને સંયુક્ત સામગ્રીના ઉત્પાદનના અમારા યોજનાકીય ચિત્રો ડાઉનલોડ કરો. આ તમને અમે નીચે આપેલી માહિતીને વધુ સારી રીતે સમજવામાં મદદ કરશે. • પાર્ટિકલ-રિઇન્ફોર્સ્ડ કમ્પોઝીટઃ આ કેટેગરીમાં બે પ્રકારના હોય છે: મોટા-કણ કોમ્પોઝીટ્સ અને ડિસ્પર્સન-સ્ટ્રેન્થ્ડ કમ્પોઝીટ. અગાઉના પ્રકારમાં, કણ-મેટ્રિક્સ ક્રિયાપ્રતિક્રિયાઓ પરમાણુ અથવા પરમાણુ સ્તર પર સારવાર કરી શકાતી નથી. તેના બદલે સાતત્ય મિકેનિક્સ માન્ય છે. બીજી બાજુ, વિક્ષેપ-મજબૂત સંયોજનોમાં કણો સામાન્ય રીતે દસ નેનોમીટર રેન્જમાં ઘણા નાના હોય છે. મોટા પાર્ટિકલ કમ્પોઝિટનું ઉદાહરણ પોલિમર છે જેમાં ફિલર ઉમેરવામાં આવ્યા છે. ફિલર્સ સામગ્રીના ગુણધર્મોને સુધારે છે અને કેટલાક પોલિમર વોલ્યુમને વધુ આર્થિક સામગ્રી સાથે બદલી શકે છે. બે તબક્કાઓના વોલ્યુમ અપૂર્ણાંક સંયુક્તના વર્તનને પ્રભાવિત કરે છે. ધાતુઓ, પોલિમર અને સિરામિક્સ સાથે મોટા પાર્ટિકલ કમ્પોઝિટનો ઉપયોગ થાય છે. CERMETS એ સિરામિક/ધાતુના સંયોજનોના ઉદાહરણો છે. અમારું સૌથી સામાન્ય પ્રમાણપત્ર સિમેન્ટેડ કાર્બાઇડ છે. તેમાં કોબાલ્ટ અથવા નિકલ જેવી ધાતુના મેટ્રિક્સમાં ટંગસ્ટન કાર્બાઇડ કણો જેવા પ્રત્યાવર્તન કાર્બાઇડ સિરામિકનો સમાવેશ થાય છે. આ કાર્બાઇડ કમ્પોઝીટનો વ્યાપકપણે સખત સ્ટીલના કટીંગ ટૂલ્સ તરીકે ઉપયોગ થાય છે. કઠણ કાર્બાઇડ કણો કાપવાની ક્રિયા માટે જવાબદાર છે અને તેમની કઠિનતા ડક્ટાઇલ મેટલ મેટ્રિક્સ દ્વારા વધારે છે. આમ અમે એક જ સંયુક્તમાં બંને સામગ્રીના ફાયદા મેળવીએ છીએ. અમે ઉપયોગ કરીએ છીએ તે મોટા પાર્ટિકલ કમ્પોઝિટનું બીજું એક સામાન્ય ઉદાહરણ છે જે કાર્બન બ્લેક પાર્ટિક્યુલેટ્સને વલ્કેનાઈઝ્ડ રબર સાથે મિશ્રિત કરીને ઉચ્ચ તાણ શક્તિ, કઠિનતા, આંસુ અને ઘર્ષણ પ્રતિકાર સાથે સંયોજન મેળવવા માટે છે. વિક્ષેપ-મજબૂત સંયુક્તનું ઉદાહરણ ધાતુઓ અને ધાતુના એલોય છે જે ખૂબ જ કઠણ અને જડ પદાર્થના સૂક્ષ્મ કણોના એકસરખા વિક્ષેપ દ્વારા મજબૂત અને સખત બને છે. જ્યારે એલ્યુમિનિયમ મેટલ મેટ્રિક્સમાં ખૂબ જ નાના એલ્યુમિનિયમ ઓક્સાઈડ ફ્લેક્સ ઉમેરવામાં આવે છે ત્યારે અમે સિન્ટર્ડ એલ્યુમિનિયમ પાવડર મેળવીએ છીએ જેમાં ઉન્નત ઉચ્ચ-તાપમાન શક્તિ હોય છે. • ફાઇબર-રિઇનફોર્સ્ડ કમ્પોઝીટઃ કમ્પોઝીટ્સની આ શ્રેણી હકીકતમાં સૌથી મહત્વપૂર્ણ છે. હાંસલ કરવાનો ધ્યેય એકમ વજન દીઠ ઉચ્ચ તાકાત અને જડતા છે. આ સામગ્રીના ગુણધર્મો અને ઉપયોગિતા નક્કી કરવા માટે આ મિશ્રણોમાં ફાઇબરની રચના, લંબાઈ, દિશા અને સાંદ્રતા મહત્વપૂર્ણ છે. અમે ઉપયોગ કરીએ છીએ તે તંતુઓના ત્રણ જૂથો છે: મૂછો, તંતુઓ અને વાયર. WHISKERS ખૂબ જ પાતળા અને લાંબા સિંગલ ક્રિસ્ટલ છે. તેઓ સૌથી મજબૂત સામગ્રી પૈકી એક છે. કેટલાક ઉદાહરણ વ્હીસ્કર સામગ્રી ગ્રેફાઇટ, સિલિકોન નાઇટ્રાઇડ, એલ્યુમિનિયમ ઓક્સાઇડ છે. બીજી તરફ FIBERS મોટે ભાગે પોલિમર અથવા સિરામિક્સ હોય છે અને પોલીક્રિસ્ટલાઇન અથવા આકારહીન સ્થિતિમાં હોય છે. ત્રીજું જૂથ ફાઇન વાયર્સ છે જેનો વ્યાસ પ્રમાણમાં મોટો હોય છે અને તેમાં વારંવાર સ્ટીલ અથવા ટંગસ્ટન હોય છે. વાયર રિઇનફોર્સ્ડ કમ્પોઝિટનું ઉદાહરણ કારના ટાયર છે જે રબરની અંદર સ્ટીલના વાયરને સમાવિષ્ટ કરે છે. મેટ્રિક્સ સામગ્રીના આધારે, અમારી પાસે નીચેના સંયોજનો છે: પોલિમર-મેટ્રિક્સ કમ્પોઝિટ: આ મજબૂતીકરણ ઘટક તરીકે પોલિમર રેઝિન અને ફાઇબરથી બનેલું છે. ગ્લાસ ફાઇબર-રિઇનફોર્સ્ડ પોલિમર (GFRP) કમ્પોઝિટ નામના પેટાજૂથમાં પોલિમર મેટ્રિક્સની અંદર સતત અથવા અવિચ્છેદિત ગ્લાસ ફાઇબર હોય છે. ગ્લાસ ઉચ્ચ શક્તિ પ્રદાન કરે છે, તે આર્થિક, ફાઇબરમાં બનાવવું સરળ છે અને રાસાયણિક રીતે નિષ્ક્રિય છે. ગેરફાયદા તેમની મર્યાદિત કઠોરતા અને જડતા છે, સેવાનું તાપમાન માત્ર 200 - 300 સેન્ટિગ્રેડ સુધી છે. ફાઇબરગ્લાસ ઓટોમોટિવ સંસ્થાઓ અને પરિવહન સાધનો, દરિયાઈ વાહન સંસ્થાઓ, સંગ્રહ કન્ટેનર માટે યોગ્ય છે. તેઓ મર્યાદિત કઠોરતાને કારણે એરોસ્પેસ કે પુલ બનાવવા માટે યોગ્ય નથી. અન્ય પેટાજૂથને કાર્બન ફાઇબર-રિઇનફોર્સ્ડ પોલિમર (CFRP) કમ્પોઝિટ કહેવામાં આવે છે. અહીં, પોલિમર મેટ્રિક્સમાં કાર્બન એ આપણી ફાઇબર સામગ્રી છે. કાર્બન તેના ઉચ્ચ વિશિષ્ટ મોડ્યુલસ અને તાકાત અને ઊંચા તાપમાને તેને જાળવી રાખવાની તેની ક્ષમતા માટે જાણીતું છે. કાર્બન ફાઇબર્સ અમને પ્રમાણભૂત, મધ્યવર્તી, ઉચ્ચ અને અલ્ટ્રાહાઇ ટેન્સાઇલ મોડ્યુલી ઓફર કરી શકે છે. વધુમાં, કાર્બન તંતુઓ વિવિધ ભૌતિક અને યાંત્રિક લાક્ષણિકતાઓ પ્રદાન કરે છે અને તેથી વિવિધ વૈવિધ્યપૂર્ણ અનુરૂપ એન્જિનિયરિંગ એપ્લિકેશનો માટે યોગ્ય છે. રમતગમત અને મનોરંજનના સાધનો, દબાણ જહાજો અને એરોસ્પેસ માળખાકીય ઘટકોના ઉત્પાદન માટે CFRP કમ્પોઝીટ ગણી શકાય. તેમ છતાં, અન્ય પેટાજૂથ, એરામિડ ફાઇબર-રિઇનફોર્સ્ડ પોલિમર કમ્પોઝીટ પણ ઉચ્ચ-શક્તિ અને મોડ્યુલસ સામગ્રી છે. તેમની તાકાત અને વજનના ગુણોત્તરમાં અસાધારણ રીતે ઉચ્ચ છે. એરામિડ રેસાને વેપારી નામો કેવલર અને નોમેક્સ દ્વારા પણ ઓળખવામાં આવે છે. તણાવ હેઠળ તેઓ અન્ય પોલિમેરિક ફાઇબર સામગ્રી કરતાં વધુ સારી કામગીરી કરે છે, પરંતુ તેઓ સંકોચનમાં નબળા છે. એરામિડ રેસા કઠિન, અસર પ્રતિરોધક, સળવળાટ અને થાક પ્રતિરોધક, ઊંચા તાપમાને સ્થિર, મજબૂત એસિડ અને પાયા સિવાય રાસાયણિક રીતે નિષ્ક્રિય હોય છે. રમતગમતના સામાન, બુલેટપ્રૂફ વેસ્ટ, ટાયર, દોરડા, ફાઈબર ઓપ્ટિક કેબલ શીટ્સમાં એરામીડ ફાઈબરનો વ્યાપક ઉપયોગ થાય છે. અન્ય ફાઇબર મજબૂતીકરણ સામગ્રી અસ્તિત્વમાં છે પરંતુ તેનો ઉપયોગ ઓછા પ્રમાણમાં થાય છે. આ મુખ્યત્વે બોરોન, સિલિકોન કાર્બાઈડ, એલ્યુમિનિયમ ઓક્સાઇડ છે. બીજી બાજુ પોલિમર મેટ્રિક્સ સામગ્રી પણ મહત્વપૂર્ણ છે. તે સંયુક્તનું મહત્તમ સેવા તાપમાન નક્કી કરે છે કારણ કે પોલિમરમાં સામાન્ય રીતે ગલન અને અધોગતિનું તાપમાન ઓછું હોય છે. પોલિએસ્ટર અને વિનાઇલ એસ્ટર્સનો પોલિમર મેટ્રિક્સ તરીકે વ્યાપકપણે ઉપયોગ થાય છે. રેઝિનનો પણ ઉપયોગ થાય છે અને તેમાં ઉત્તમ ભેજ પ્રતિકાર અને યાંત્રિક ગુણધર્મો છે. ઉદાહરણ તરીકે પોલિમાઇડ રેઝિન લગભગ 230 ડિગ્રી સેલ્સિયસ સુધી વાપરી શકાય છે. મેટલ-મેટ્રિક્સ કમ્પોઝીટસ : આ સામગ્રીઓમાં આપણે નમ્ર ધાતુના મેટ્રિક્સનો ઉપયોગ કરીએ છીએ અને સેવાનું તાપમાન સામાન્ય રીતે તેમના ઘટક ઘટકો કરતા વધારે હોય છે. જ્યારે પોલિમર-મેટ્રિક્સ કમ્પોઝીટ્સની તુલના કરવામાં આવે છે, ત્યારે આનું સંચાલન તાપમાન વધારે હોઈ શકે છે, તે બિન-જ્વલનશીલ હોઈ શકે છે અને કાર્બનિક પ્રવાહી સામે વધુ સારી રીતે અધોગતિ પ્રતિકાર હોઈ શકે છે. જો કે તેઓ વધુ ખર્ચાળ છે. મજબૂતીકરણ સામગ્રી જેમ કે મૂછો, રજકણો, સતત અને અખંડ તંતુઓ; અને કોપર, એલ્યુમિનિયમ, મેગ્નેશિયમ, ટાઇટેનિયમ, સુપરએલોય જેવી મેટ્રિક્સ સામગ્રીનો સામાન્ય રીતે ઉપયોગ કરવામાં આવે છે. ઉદાહરણ એપ્લીકેશન એ એલ્યુમિનિયમ ઓક્સાઇડ અને કાર્બન ફાઇબરથી પ્રબલિત એલ્યુમિનિયમ એલોય મેટ્રિક્સના બનેલા એન્જિન ઘટકો છે. સિરામિક-મેટ્રિક્સ કમ્પોઝિટ: સિરામિક સામગ્રીઓ તેમની ઉત્કૃષ્ટ સારી ઉચ્ચ તાપમાન વિશ્વસનીયતા માટે જાણીતી છે. જો કે તેઓ ખૂબ જ બરડ છે અને અસ્થિભંગની કઠિનતા માટે ઓછા મૂલ્યો ધરાવે છે. એક સિરામિકના રજકણો, તંતુઓ અથવા મૂછોને બીજાના મેટ્રિક્સમાં એમ્બેડ કરીને આપણે ઉચ્ચ અસ્થિભંગની કઠિનતા સાથે સંયોજનો હાંસલ કરવામાં સક્ષમ છીએ. આ જડિત સામગ્રી મૂળભૂત રીતે મેટ્રિક્સની અંદર તિરાડોના પ્રસારને અમુક મિકેનિઝમ્સ દ્વારા અટકાવે છે જેમ કે ક્રેકની ટીપ્સને વિચલિત કરવી અથવા ક્રેક ફેસ પર પુલ બનાવવું. ઉદાહરણ તરીકે, એસઆઈસી વ્હિસ્કર સાથે પ્રબલિત એલ્યુમિનાનો ઉપયોગ હાર્ડ મેટલ એલોયને મશિન કરવા માટે કટીંગ ટૂલ ઇન્સર્ટ તરીકે થાય છે. આ સિમેન્ટેડ કાર્બાઇડ્સની તુલનામાં વધુ સારી કામગીરી જાહેર કરી શકે છે. કાર્બન-કાર્બન સંયોજનો : મજબૂતીકરણ અને મેટ્રિક્સ બંને કાર્બન છે. તેમની પાસે 2000 સેન્ટિગ્રેડથી વધુ ઊંચા તાપમાને ઉચ્ચ તાણયુક્ત મોડ્યુલી અને શક્તિઓ, ક્રીપ પ્રતિકાર, ઉચ્ચ અસ્થિભંગની કઠિનતા, નીચા થર્મલ વિસ્તરણ ગુણાંક, ઉચ્ચ થર્મલ વાહકતા છે. આ ગુણધર્મો તેમને થર્મલ શોક પ્રતિકારની જરૂર હોય તેવા કાર્યક્રમો માટે આદર્શ બનાવે છે. કાર્બન-કાર્બન કમ્પોઝીટની નબળાઈ જોકે ઊંચા તાપમાને ઓક્સિડેશન સામે તેની નબળાઈ છે. ઉપયોગના વિશિષ્ટ ઉદાહરણો છે હોટ-પ્રેસિંગ મોલ્ડ, અદ્યતન ટર્બાઇન એન્જિન ઘટકોનું ઉત્પાદન. હાઇબ્રિડ કમ્પોઝીટ : એક મેટ્રિક્સમાં બે કે તેથી વધુ વિવિધ પ્રકારના ફાઇબર મિશ્રિત થાય છે. આ રીતે વ્યક્તિ ગુણધર્મોના સંયોજન સાથે નવી સામગ્રીને અનુરૂપ બનાવી શકે છે. એક ઉદાહરણ એ છે કે જ્યારે કાર્બન અને ગ્લાસ ફાઇબર બંનેને પોલિમેરિક રેઝિનમાં સમાવિષ્ટ કરવામાં આવે છે. કાર્બન તંતુઓ ઓછી ઘનતાની જડતા અને શક્તિ પ્રદાન કરે છે પરંતુ તે ખર્ચાળ છે. બીજી બાજુ કાચ સસ્તો છે પરંતુ તેમાં કાર્બન ફાઇબરની જડતા નથી. ગ્લાસ-કાર્બન હાઇબ્રિડ કમ્પોઝિટ વધુ મજબૂત અને સખત છે અને ઓછા ખર્ચે ઉત્પાદન કરી શકાય છે. ફાઇબર-રિઇનફોર્સ્ડ કમ્પોઝીટ્સની પ્રક્રિયા: સમાન દિશામાં સમાનરૂપે વિતરિત ફાઇબર સાથે સતત ફાઇબર-રિઇનફોર્સ્ડ પ્લાસ્ટિક માટે અમે નીચેની તકનીકોનો ઉપયોગ કરીએ છીએ. પલ્ટ્રુઝન: સળિયા, બીમ અને સતત લંબાઈ અને સતત ક્રોસ-સેક્શનની નળીઓ બનાવવામાં આવે છે. સતત ફાઇબર રોવિંગ્સને થર્મોસેટિંગ રેઝિનથી ફળદ્રુપ કરવામાં આવે છે અને તેને ઇચ્છિત આકાર આપવા માટે સ્ટીલ ડાઇ દ્વારા ખેંચવામાં આવે છે. આગળ, તેનો અંતિમ આકાર મેળવવા માટે તેઓ ચોકસાઇવાળા મશિન ક્યોરિંગ ડાઇમાંથી પસાર થાય છે. ક્યોરિંગ ડાઇ ગરમ હોવાથી, તે રેઝિન મેટ્રિક્સને મટાડે છે. પુલર્સ ડાઈઝ દ્વારા સામગ્રી દોરે છે. દાખલ કરેલા હોલો કોરોનો ઉપયોગ કરીને, અમે ટ્યુબ અને હોલો ભૂમિતિ મેળવવા માટે સક્ષમ છીએ. પલ્ટ્રુઝન પદ્ધતિ સ્વયંસંચાલિત છે અને અમને ઉચ્ચ ઉત્પાદન દર આપે છે. ઉત્પાદનની કોઈપણ લંબાઈનું ઉત્પાદન શક્ય છે. પ્રેપ્રેગ પ્રોડક્શન પ્રક્રિયા : પ્રીપ્રેગ એ આંશિક રીતે સાધ્ય પોલિમર રેઝિન સાથે પ્રીપ્રેગ્નેટેડ સતત-ફાઇબર રિઇન્ફોર્સમેન્ટ છે. તે માળખાકીય કાર્યક્રમો માટે વ્યાપકપણે ઉપયોગમાં લેવાય છે. સામગ્રી ટેપ સ્વરૂપમાં આવે છે અને ટેપ તરીકે મોકલવામાં આવે છે. ઉત્પાદક તેને સીધું જ મોલ્ડ કરે છે અને કોઈપણ રેઝિન ઉમેરવાની જરૂર વગર તેને સંપૂર્ણ રીતે મટાડે છે. પ્રીપ્રેગ્સ ઓરડાના તાપમાને ઉપચારાત્મક પ્રતિક્રિયાઓમાંથી પસાર થતા હોવાથી, તેઓ 0 સેન્ટિગ્રેડ અથવા નીચલા તાપમાને સંગ્રહિત થાય છે. ઉપયોગ કર્યા પછી, બાકીની ટેપ નીચા તાપમાને પાછા સંગ્રહિત થાય છે. થર્મોપ્લાસ્ટિક અને થર્મોસેટિંગ રેઝિનનો ઉપયોગ કરવામાં આવે છે અને કાર્બન, એરામિડ અને કાચના મજબૂતીકરણ રેસા સામાન્ય છે. પ્રીપ્રેગ્સનો ઉપયોગ કરવા માટે, કેરિયર બેકિંગ પેપરને પહેલા દૂર કરવામાં આવે છે અને પછી ટૂલવાળી સપાટી (લે-અપ પ્રક્રિયા) પર પ્રીપ્રેગ ટેપ બિછાવીને ફેબ્રિકેશન હાથ ધરવામાં આવે છે. ઇચ્છિત જાડાઈ મેળવવા માટે કેટલાક પ્લાઈસ નાખવામાં આવી શકે છે. વારંવાર પ્રેક્ટિસ એ ક્રોસ-પ્લાય અથવા એંગલ-પ્લાય લેમિનેટ બનાવવા માટે ફાઇબર ઓરિએન્ટેશનને વૈકલ્પિક કરવાનો છે. અંતમાં ઉપચાર માટે ગરમી અને દબાણ લાગુ કરવામાં આવે છે. પ્રિપ્રેગ અને લે-અપ કાપવા માટે હાથની પ્રક્રિયા તેમજ સ્વચાલિત પ્રક્રિયા બંનેનો ઉપયોગ થાય છે. ફિલામેન્ટ વિન્ડિંગ : હોલો અને સામાન્ય રીતે ચક્રાકાર આકારને અનુસરવા માટે સતત રિઇન્ફોર્સિંગ ફાઇબર ચોક્કસ રીતે પૂર્વનિર્ધારિત પેટર્નમાં સ્થિત હોય છે. તંતુઓ પહેલા રેઝિન બાથમાંથી પસાર થાય છે અને પછી ઓટોમેટેડ સિસ્ટમ દ્વારા મેન્ડ્રેલ પર ઘા કરવામાં આવે છે. વિન્ડિંગના અનેક પુનરાવર્તનો પછી ઇચ્છિત જાડાઈ મેળવવામાં આવે છે અને ઓરડાના તાપમાને અથવા પકાવવાની નાની ભઠ્ઠીની અંદર ક્યોરિંગ કરવામાં આવે છે. હવે મેન્ડ્રેલ દૂર કરવામાં આવે છે અને ઉત્પાદનને તોડી નાખવામાં આવે છે. ફિલામેન્ટ વિન્ડિંગ તંતુઓને પરિઘ, હેલિકલ અને ધ્રુવીય પેટર્નમાં વિન્ડિંગ કરીને ખૂબ જ ઉચ્ચ તાકાત-થી-વજન ગુણોત્તર પ્રદાન કરી શકે છે. પાઇપ્સ, ટાંકીઓ, કેસીંગ્સ આ તકનીકનો ઉપયોગ કરીને બનાવવામાં આવે છે. • માળખાકીય સંયોજનો : સામાન્ય રીતે આ એકરૂપ અને સંયુક્ત બંને સામગ્રીથી બનેલા હોય છે. તેથી આના ગુણધર્મો તેના ઘટકોની ઘટક સામગ્રી અને ભૌમિતિક ડિઝાઇન દ્વારા નક્કી કરવામાં આવે છે. અહીં મુખ્ય પ્રકારો છે: લેમિનાર કમ્પોઝીટ : આ માળખાકીય સામગ્રી બે પરિમાણીય શીટ્સ અથવા પેનલ્સથી બનેલી હોય છે જેમાં પસંદગીની ઉચ્ચ-શક્તિ દિશાઓ હોય છે. સ્તરો એકસાથે સ્ટેક અને સિમેન્ટ કરવામાં આવે છે. બે લંબરૂપ અક્ષોમાં ઉચ્ચ-શક્તિની દિશાઓને વૈકલ્પિક કરીને, અમે એક સંયુક્ત મેળવીએ છીએ જે દ્વિ-પરિમાણીય સમતલમાં બંને દિશામાં ઉચ્ચ-શક્તિ ધરાવે છે. સ્તરોના ખૂણાઓને સમાયોજિત કરીને તમે પસંદગીની દિશામાં મજબૂતાઈ સાથે સંયુક્ત બનાવી શકો છો. આધુનિક સ્કી આ રીતે બનાવવામાં આવે છે. સેન્ડવીચ પેનલ્સ : આ માળખાકીય સંયોજનો ઓછા વજનના હોય છે પરંતુ તેમ છતાં તેમાં ઉચ્ચ કઠોરતા અને શક્તિ હોય છે. સેન્ડવીચ પેનલ્સમાં એલ્યુમિનિયમ એલોય, ફાઈબર રિઇનફોર્સ્ડ પ્લાસ્ટિક અથવા સ્ટીલ જેવી સખત અને મજબૂત સામગ્રીથી બનેલી બે બાહ્ય શીટ્સ અને બાહ્ય શીટ્સની વચ્ચે એક કોર હોય છે. કોરનું વજન ઓછું હોવું જરૂરી છે અને મોટા ભાગના સમયે સ્થિતિસ્થાપકતાનું મોડ્યુલસ ઓછું હોય છે. લોકપ્રિય મુખ્ય સામગ્રી સખત પોલિમરીક ફીણ, લાકડું અને મધપૂડો છે. બાંધકામ ઉદ્યોગમાં છત સામગ્રી, ફ્લોર અથવા દિવાલ સામગ્રી તરીકે અને એરોસ્પેસ ઉદ્યોગોમાં પણ સેન્ડવિચ પેનલનો વ્યાપકપણે ઉપયોગ થાય છે. • NANOCOMPOSITS : આ નવી સામગ્રીમાં મેટ્રિક્સમાં જડિત નેનોસાઇઝ્ડ કણોના કણોનો સમાવેશ થાય છે. નેનોકોમ્પોઝીટ્સનો ઉપયોગ કરીને અમે રબર સામગ્રીઓનું ઉત્પાદન કરી શકીએ છીએ જે હવાના પ્રવેશ માટે ખૂબ જ સારી અવરોધો છે જ્યારે તેમના રબર ગુણધર્મોને યથાવત જાળવી રાખે છે. CLICK Product Finder-Locator Service પાછલું પૃષ્ઠ
- Machine Elements Manufacturing, Gears, Gear Drives, Bearings, Keys, Splines
Machine Elements Manufacturing, Gears, Gear Drives, Bearings, Keys, Splines, Pins, Shafts, Seals, Fasteners, Clutch, Cams, Followers, Belts, Couplings, Shafts મશીન એલિમેન્ટ્સ મેન્યુફેક્ચરિંગ વધુ વાંચો બેલ્ટ અને ચેઇન્સ અને કેબલ ડ્રાઇવ એસેમ્બલી વધુ વાંચો ગિયર્સ અને ગિયર ડ્રાઇવ એસેમ્બલી વધુ વાંચો કપલિંગ અને બેરિંગ્સ મેન્યુફેક્ચરિંગ વધુ વાંચો કી અને સ્પ્લાઈન્સ અને પિનનું ઉત્પાદન વધુ વાંચો કેમ્સ અને ફોલોઅર્સ અને લિંકેજ અને રેચેટ વ્હીલ્સ મેન્યુફેક્ચરિંગ વધુ વાંચો શાફ્ટ મેન્યુફેક્ચરિંગ વધુ વાંચો યાંત્રિક સીલ ઉત્પાદન વધુ વાંચો ક્લચ અને બ્રેક એસેમ્બલી વધુ વાંચો ફાસ્ટનર્સ મેન્યુફેક્ચરિંગ વધુ વાંચો સરળ મશીનો એસેમ્બલી MACHINE ELEMENTS મશીનના પ્રાથમિક ઘટકો છે. આ તત્વો ત્રણ મૂળભૂત પ્રકારો ધરાવે છે: 1.) માળખાકીય ઘટકો જેમાં ફ્રેમના સભ્યો, બેરિંગ્સ, એક્સેલ્સ, સ્પ્લાઈન્સ, ફાસ્ટનર્સ, સીલ અને લુબ્રિકન્ટ્સનો સમાવેશ થાય છે. 2.) ગિયર ટ્રેન, બેલ્ટ અથવા ચેઇન ડ્રાઇવ્સ, લિન્કેજ, કેમ અને ફોલોઅર સિસ્ટમ્સ, બ્રેક્સ અને ક્લચ જેવી વિવિધ રીતે હિલચાલને નિયંત્રિત કરતી મિકેનિઝમ્સ. 3.) બટનો, સ્વીચો, સૂચકો, સેન્સર્સ, એક્ટ્યુએટર અને કમ્પ્યુટર નિયંત્રકો જેવા નિયંત્રણ ઘટકો. અમે તમને ઑફર કરીએ છીએ તે મોટાભાગના મશીન તત્વો સામાન્ય કદમાં પ્રમાણિત છે, પરંતુ કસ્ટમ મેડ મશીન તત્વો તમારી વિશિષ્ટ એપ્લિકેશનો માટે પણ ઉપલબ્ધ છે. મશીન તત્વોનું કસ્ટમાઇઝેશન હાલની ડિઝાઇન પર થઈ શકે છે જે અમારા ડાઉનલોડ કરી શકાય તેવા કેટલોગમાં છે અથવા તદ્દન નવી ડિઝાઇન પર છે. એકવાર ડિઝાઇન બંને પક્ષો દ્વારા મંજૂર થઈ જાય પછી મશીન તત્વોનું પ્રોટોટાઇપિંગ અને ઉત્પાદન આગળ વધારી શકાય છે. જો નવા મશીન તત્વોને ડિઝાઇન અને ઉત્પાદન કરવાની જરૂર હોય, તો અમારા ગ્રાહકો કાં તો અમને તેમની પોતાની બ્લુપ્રિન્ટ્સ ઇમેઇલ કરે છે અને અમે મંજૂરી માટે તેમની સમીક્ષા કરીએ છીએ, અથવા તેઓ અમને તેમની એપ્લિકેશન માટે મશીન તત્વો ડિઝાઇન કરવા કહે છે. પછીના કિસ્સામાં અમે અમારા ગ્રાહકોના તમામ ઇનપુટનો ઉપયોગ કરીએ છીએ અને મશીન તત્વોને ડિઝાઇન કરીએ છીએ અને મંજૂરી માટે અમારા ગ્રાહકોને અંતિમ બ્લૂપ્રિન્ટ મોકલીએ છીએ. એકવાર મંજૂર થયા પછી, અમે પ્રથમ લેખો બનાવીએ છીએ અને ત્યારબાદ અંતિમ ડિઝાઇન અનુસાર મશીન તત્વોનું ઉત્પાદન કરીએ છીએ. આ કાર્યના કોઈપણ તબક્કે, જો કોઈ ચોક્કસ મશીન એલિમેન્ટ ડિઝાઇન ક્ષેત્રમાં અસંતોષકારક રીતે કાર્ય કરે છે (જે દુર્લભ છે), તો અમે સમગ્ર પ્રોજેક્ટની સમીક્ષા કરીએ છીએ અને જરૂરિયાત મુજબ અમારા ગ્રાહકો સાથે સંયુક્ત રીતે ફેરફારો કરીએ છીએ. જ્યારે પણ જરૂર હોય અથવા જરૂર હોય ત્યારે મશીન તત્વો અથવા અન્ય કોઈપણ ઉત્પાદનની ડિઝાઇન માટે અમારા ગ્રાહકો સાથે નોનડિસ્કલોઝર એગ્રીમેન્ટ્સ (NDA) પર હસ્તાક્ષર કરવાની અમારી પ્રમાણભૂત પ્રથા છે. એકવાર ચોક્કસ ગ્રાહક માટેના મશીન તત્વો કસ્ટમ ડિઝાઇન અને ઉત્પાદિત થઈ ગયા પછી, અમે તેને ઉત્પાદન કોડ સોંપીએ છીએ અને માત્ર ઉત્પાદન અને ઉત્પાદનની માલિકી ધરાવતા અમારા ગ્રાહકને તેને વેચીએ છીએ. અમે વિકસિત ટૂલ્સ, મોલ્ડ અને પ્રક્રિયાઓનો ઉપયોગ કરીને અને જ્યારે પણ અમારા ગ્રાહક તેમને પુનઃક્રમાંકિત કરે છે ત્યારે ઘણી વખત મશીન તત્વોનું પુનઃઉત્પાદન કરીએ છીએ. બીજા શબ્દોમાં કહીએ તો, એકવાર તમારા માટે કસ્ટમ મશીન એલિમેન્ટ તૈયાર થઈ જાય અને તેનું ઉત્પાદન થઈ જાય, પછી બૌદ્ધિક સંપત્તિ તેમજ તમામ ટૂલિંગ અને મોલ્ડ તમારા માટે અમારા દ્વારા અનિશ્ચિત સમય માટે અનામત રાખવામાં આવે છે અને તમારી ઈચ્છા મુજબ ઉત્પાદનોનું પુનઃઉત્પાદન કરવામાં આવે છે. અમે અમારા ક્લાયન્ટ્સને એન્જિનિયરિંગ સેવાઓ પણ ઓફર કરીએ છીએ કે મશીન ઘટકોને એક ઘટક અથવા એસેમ્બલીમાં રચનાત્મક રીતે જોડીને જે એપ્લિકેશન સેવા આપે છે અને અમારા ગ્રાહકોની અપેક્ષાઓ પૂરી કરે છે અથવા તેનાથી વધુ છે. અમારા મશીન તત્વો બનાવતા છોડ ISO9001, QS9000 અથવા TS16949 દ્વારા લાયકાત ધરાવે છે. વધુમાં, અમારા મોટાભાગના ઉત્પાદનોમાં CE અથવા UL માર્ક હોય છે અને તે ISO, SAE, ASME, DIN જેવા આંતરરાષ્ટ્રીય સ્તરે સંબંધિત ધોરણોને પૂર્ણ કરે છે. અમારા મશીન તત્વો સહિતની વિગતવાર માહિતી મેળવવા માટે કૃપા કરીને સબમેનુસ પર ક્લિક કરો: - બેલ્ટ, ચેઈન અને કેબલ ડ્રાઈવ - ગિયર્સ અને ગિયર ડ્રાઇવ્સ - કપ્લિંગ્સ અને બેરિંગ્સ - કી અને સ્પ્લાઈન્સ અને પિન - કેમ્સ અને લિંકેજ - શાફ્ટ - યાંત્રિક સીલ - ઔદ્યોગિક ક્લચ અને બ્રેક - ફાસ્ટનર્સ - સરળ મશીનો અમે અમારા ગ્રાહકો, ડિઝાઇનર્સ અને મશીન તત્વો સહિત નવા ઉત્પાદનોના વિકાસકર્તાઓ માટે સંદર્ભ પુસ્તિકા તૈયાર કરી છે. તમે મશીન ઘટકોની ડિઝાઇનમાં સામાન્ય રીતે ઉપયોગમાં લેવાતા કેટલાક શબ્દોથી તમારી જાતને પરિચિત કરી શકો છો: ડિઝાઇનર્સ અને એન્જિનિયરો દ્વારા ઉપયોગમાં લેવાતી સામાન્ય મિકેનિકલ એન્જિનિયરિંગ શરતો માટે બ્રોશર ડાઉનલોડ કરો અમારા મશીન તત્વો ઔદ્યોગિક મશીનરી, ઓટોમેશન સિસ્ટમ્સ, ટેસ્ટ અને મેટ્રોલોજીના સાધનો, પરિવહન સાધનો, બાંધકામ મશીનો અને વ્યવહારીક રીતે જ્યાં પણ તમે વિચારી શકો ત્યાં જેવા વિવિધ ક્ષેત્રોમાં એપ્લિકેશન શોધે છે. AGS-TECH એપ્લિકેશનના આધારે વિવિધ સામગ્રીમાંથી મશીન તત્વો વિકસાવે છે અને તેનું ઉત્પાદન કરે છે. મશીન તત્વો માટે વપરાતી સામગ્રી રમકડાં માટે વપરાતા મોલ્ડેડ પ્લાસ્ટિકથી માંડીને ઔદ્યોગિક મશીનરી માટે સખત અને ખાસ કોટેડ સ્ટીલ સુધીની હોઈ શકે છે. અમારા ડિઝાઈનરો અત્યાધુનિક પ્રોફેશનલ સોફ્ટવેર અને ડિઝાઈન ટૂલ્સનો ઉપયોગ મશીન એલિમેન્ટ્સ વિકસાવવા માટે કરે છે, જેમ કે ગિયર દાંતમાં કોણ, સામેલ તણાવ, વસ્ત્રોના દરો….વગેરે વિગતોને ધ્યાનમાં લઈને. કૃપા કરીને અમારા સબમેનુસ દ્વારા સ્ક્રોલ કરો અને અમારી પ્રોડક્ટ બ્રોશરો અને કેટલોગ ડાઉનલોડ કરો કે તમે તમારી એપ્લિકેશન માટે ઑફ-ધ-શેલ્ફ મશીન તત્વો શોધી શકો છો કે કેમ. જો તમે તમારી અરજી માટે સારો મેળ શોધી શકતા નથી, તો કૃપા કરીને અમને જણાવો અને અમે તમારી સાથે મશીન તત્વોના વિકાસ અને ઉત્પાદન માટે કામ કરીશું જે તમારી જરૂરિયાતોને પૂર્ણ કરશે. જો તમને ઉત્પાદન ક્ષમતાઓને બદલે અમારી એન્જિનિયરિંગ અને સંશોધન અને વિકાસ ક્ષમતાઓમાં રસ હોય, તો અમે તમને અમારી વેબસાઇટ ની મુલાકાત લેવા આમંત્રણ આપીએ છીએ.http://www.ags-engineering.com જ્યાં તમે અમારી ડિઝાઇન, ઉત્પાદન વિકાસ, પ્રક્રિયા વિકાસ, એન્જિનિયરિંગ કન્સલ્ટિંગ સેવાઓ અને વધુ વિશે વધુ વિગતવાર માહિતી મેળવી શકો છો. CLICK Product Finder-Locator Service પાછલું પૃષ્ઠ
- Joining & Assembly & Fastening Processes, Welding, Brazing, Soldering
Joining & Assembly & Fastening Processes, Welding, Brazing, Soldering, Sintering, Adhesive Bonding, Press Fitting, Wave and Reflow Solder Process, Torch Furnace જોડાવું અને એસેમ્બલી અને ફાસ્ટનિંગ પ્રક્રિયાઓ અમે તમારા ઉત્પાદિત ભાગોને જોડીએ છીએ, એસેમ્બલ કરીએ છીએ અને બાંધીએ છીએ અને વેલ્ડિંગ, બ્રેઝિંગ, સોલ્ડરિંગ, સિન્ટરિંગ, એડહેસિવ બોન્ડિંગ, ફાસ્ટનિંગ, પ્રેસ ફિટિંગનો ઉપયોગ કરીને તેને તૈયાર અથવા અર્ધ-તૈયાર ઉત્પાદનોમાં ફેરવીએ છીએ. અમારી કેટલીક સૌથી લોકપ્રિય વેલ્ડીંગ પ્રક્રિયાઓ આર્ક, ઓક્સિફ્યુઅલ ગેસ, રેઝિસ્ટન્સ, પ્રોજેક્શન, સીમ, અપસેટ, પર્ક્યુસન, સોલિડ સ્ટેટ, ઈલેક્ટ્રોન બીમ, લેસર, થર્મીટ, ઈન્ડક્શન વેલ્ડીંગ છે. અમારી લોકપ્રિય બ્રેઝિંગ પ્રક્રિયાઓ ટોર્ચ, ઇન્ડક્શન, ફર્નેસ અને ડિપ બ્રેઝિંગ છે. અમારી સોલ્ડરિંગ પદ્ધતિઓ આયર્ન, હોટ પ્લેટ, ઓવન, ઇન્ડક્શન, ડીપ, વેવ, રિફ્લો અને અલ્ટ્રાસોનિક સોલ્ડરિંગ છે. એડહેસિવ બોન્ડિંગ માટે અમે વારંવાર થર્મોપ્લાસ્ટિક્સ અને થર્મો-સેટિંગ, ઇપોક્સીસ, ફિનોલિક્સ, પોલીયુરેથીન, એડહેસિવ એલોય તેમજ કેટલાક અન્ય રસાયણો અને ટેપનો ઉપયોગ કરીએ છીએ. છેલ્લે અમારી ફાસ્ટનિંગ પ્રક્રિયાઓમાં નેઇલિંગ, સ્ક્રૂઇંગ, નટ્સ અને બોલ્ટ્સ, રિવેટિંગ, ક્લિન્ચિંગ, પિનિંગ, સ્ટીચિંગ અને સ્ટેપલિંગ અને પ્રેસ ફિટિંગનો સમાવેશ થાય છે. • વેલ્ડીંગ : વેલ્ડીંગમાં કામના ટુકડાને પીગળીને અને ફિલર મટીરીયલ રજૂ કરીને સામગ્રીને જોડવાનો સમાવેશ થાય છે, જે પીગળેલા વેલ્ડ પૂલમાં પણ જોડાય છે. જ્યારે વિસ્તાર ઠંડુ થાય છે, ત્યારે અમે મજબૂત સાંધા મેળવીએ છીએ. કેટલાક કિસ્સાઓમાં દબાણ લાગુ પડે છે. વેલ્ડીંગથી વિપરીત, બ્રેઝિંગ અને સોલ્ડરિંગ કામગીરીમાં વર્કપીસ વચ્ચે નીચા ગલનબિંદુ ધરાવતી સામગ્રીને માત્ર પીગળવાનો સમાવેશ થાય છે અને વર્કપીસ ઓગળતા નથી. અમે ભલામણ કરીએ છીએ કે તમે અહીં ક્લિક કરોAGS-TECH Inc દ્વારા વેલ્ડીંગ પ્રક્રિયાઓના અમારા યોજનાકીય ચિત્રો ડાઉનલોડ કરો. આ તમને અમે નીચે આપેલી માહિતીને વધુ સારી રીતે સમજવામાં મદદ કરશે. ARC વેલ્ડીંગમાં, અમે ધાતુઓને પીગળતા ઇલેક્ટ્રિક આર્ક બનાવવા માટે પાવર સપ્લાય અને ઇલેક્ટ્રોડનો ઉપયોગ કરીએ છીએ. વેલ્ડીંગ પોઈન્ટનું રક્ષણ ગેસ અથવા વરાળ અથવા અન્ય સામગ્રી દ્વારા કરવામાં આવે છે. આ પ્રક્રિયા ઓટોમોટિવ ભાગો અને સ્ટીલ સ્ટ્રક્ચર્સને વેલ્ડીંગ કરવા માટે લોકપ્રિય છે. શેલ્ડેડ મેટલ આર્ક વેલ્ડીંગ (SMAW) અથવા તેને સ્ટીક વેલ્ડીંગ તરીકે પણ ઓળખવામાં આવે છે, ઈલેક્ટ્રોડ સ્ટીકને બેઝ મટીરીયલની નજીક લાવવામાં આવે છે અને તેમની વચ્ચે ઈલેક્ટ્રીક આર્ક જનરેટ થાય છે. ઇલેક્ટ્રોડ સળિયા ઓગળે છે અને ફિલર સામગ્રી તરીકે કાર્ય કરે છે. ઇલેક્ટ્રોડમાં ફ્લક્સ પણ હોય છે જે સ્લેગના સ્તર તરીકે કાર્ય કરે છે અને વરાળને બહાર કાઢે છે જે રક્ષણાત્મક ગેસ તરીકે કાર્ય કરે છે. આ વેલ્ડ વિસ્તારને પર્યાવરણીય દૂષણથી સુરક્ષિત કરે છે. અન્ય કોઈ ફિલરનો ઉપયોગ કરવામાં આવતો નથી. આ પ્રક્રિયાના ગેરફાયદા તેની ધીમીતા છે, ઇલેક્ટ્રોડને વારંવાર બદલવાની જરૂર છે, પ્રવાહમાંથી ઉદ્ભવતા શેષ સ્લેગને દૂર કરવાની જરૂર છે. સંખ્યાબંધ ધાતુઓ જેમ કે આયર્ન, સ્ટીલ, નિકલ, એલ્યુમિનિયમ, તાંબુ... વગેરે. વેલ્ડિંગ કરી શકાય છે. તેના ફાયદા તેના સસ્તા સાધનો અને ઉપયોગમાં સરળતા છે. ગેસ મેટલ આર્ક વેલ્ડીંગ (GMAW) જેને મેટલ-ઇનર્ટ ગેસ (MIG) તરીકે પણ ઓળખવામાં આવે છે, અમારી પાસે ઉપભોજ્ય ઇલેક્ટ્રોડ વાયર ફિલર અને એક નિષ્ક્રિય અથવા આંશિક રીતે નિષ્ક્રિય ગેસ છે જે વેલ્ડ પ્રદેશના પર્યાવરણીય દૂષણ સામે વાયરની આસપાસ વહે છે. સ્ટીલ, એલ્યુમિનિયમ અને અન્ય બિન-ફેરસ ધાતુઓને વેલ્ડિંગ કરી શકાય છે. MIG ના ફાયદા ઉચ્ચ વેલ્ડીંગ ઝડપ અને સારી ગુણવત્તા છે. ગેરફાયદા એ તેના જટિલ સાધનો અને પવનની બહારના વાતાવરણમાં પડકારોનો સામનો કરવો પડે છે કારણ કે આપણે વેલ્ડીંગ વિસ્તારની આસપાસના રક્ષણાત્મક ગેસને સ્થિર રાખવાનો હોય છે. GMAW ની વિવિધતા એ ફ્લક્સ-કોર્ડ આર્ક વેલ્ડીંગ (FCAW) છે જેમાં ફ્લક્સ સામગ્રીઓથી ભરેલી ઝીણી ધાતુની નળીનો સમાવેશ થાય છે. કેટલીકવાર ટ્યુબની અંદરનો પ્રવાહ પર્યાવરણીય દૂષણથી રક્ષણ માટે પૂરતો હોય છે. ડૂબેલું આર્ક વેલ્ડીંગ (SAW) વ્યાપકપણે સ્વયંસંચાલિત પ્રક્રિયા છે, જેમાં સતત વાયર ફીડિંગ અને આર્કનો સમાવેશ થાય છે જે ફ્લક્સ કવરના સ્તર હેઠળ અથડાય છે. ઉત્પાદન દર અને ગુણવત્તા ઊંચી છે, વેલ્ડિંગ સ્લેગ સરળતાથી બંધ થઈ જાય છે, અને અમારી પાસે ધૂમ્રપાન મુક્ત કાર્ય વાતાવરણ છે. ગેરલાભ એ છે કે તેનો ઉપયોગ માત્ર parts ને અમુક ચોક્કસ સ્થિતિમાં વેલ્ડ કરવા માટે થઈ શકે છે. ગેસ ટંગસ્ટન આર્ક વેલ્ડીંગ (GTAW) અથવા ટંગસ્ટન-ઇનર્ટ ગેસ વેલ્ડીંગ (TIG) માં આપણે અલગ ફિલર અને નિષ્ક્રિય અથવા નજીકના નિષ્ક્રિય વાયુઓ સાથે ટંગસ્ટન ઇલેક્ટ્રોડનો ઉપયોગ કરીએ છીએ. જેમ આપણે જાણીએ છીએ કે ટંગસ્ટનનું ગલનબિંદુ ઊંચું છે અને તે ખૂબ ઊંચા તાપમાન માટે ખૂબ જ યોગ્ય ધાતુ છે. TIG માં ટંગસ્ટનનો ઉપયોગ ઉપર વર્ણવેલ અન્ય પદ્ધતિઓથી વિપરીત થતો નથી. ધીમી પરંતુ ઉચ્ચ ગુણવત્તાવાળી વેલ્ડીંગ ટેકનિક પાતળા સામગ્રીના વેલ્ડીંગમાં અન્ય તકનીકો કરતાં ફાયદાકારક છે. ઘણી ધાતુઓ માટે યોગ્ય. પ્લાઝ્મા આર્ક વેલ્ડીંગ સમાન છે પરંતુ ચાપ બનાવવા માટે પ્લાઝ્મા ગેસનો ઉપયોગ કરે છે. પ્લાઝ્મા આર્ક વેલ્ડીંગમાં ચાપ જીટીએડબલ્યુની તુલનામાં પ્રમાણમાં વધુ કેન્દ્રિત છે અને તેનો ઉપયોગ ધાતુની જાડાઈની વિશાળ શ્રેણી માટે ઘણી ઊંચી ઝડપે થઈ શકે છે. GTAW અને પ્લાઝ્મા આર્ક વેલ્ડીંગ વધુ કે ઓછા સમાન સામગ્રી પર લાગુ કરી શકાય છે. OXY-FUEL / OXYFUEL વેલ્ડીંગ જેને ઓક્સીસીટીલીન વેલ્ડીંગ પણ કહેવાય છે, ઓક્સી વેલ્ડીંગ, ગેસ વેલ્ડીંગ વેલ્ડીંગ માટે ગેસ ઇંધણ અને ઓક્સિજનનો ઉપયોગ કરીને હાથ ધરવામાં આવે છે. ઇલેક્ટ્રિક પાવરનો ઉપયોગ થતો ન હોવાથી તે પોર્ટેબલ છે અને જ્યાં વીજળી નથી ત્યાં તેનો ઉપયોગ કરી શકાય છે. વેલ્ડીંગ ટોર્ચનો ઉપયોગ કરીને અમે પીગળેલા મેટલ પૂલ બનાવવા માટે ટુકડાઓ અને ફિલર સામગ્રીને ગરમ કરીએ છીએ. વિવિધ ઇંધણનો ઉપયોગ કરી શકાય છે જેમ કે એસીટીલીન, ગેસોલિન, હાઇડ્રોજન, પ્રોપેન, બ્યુટેન... વગેરે. ઓક્સિ-ઇંધણ વેલ્ડીંગમાં આપણે બે કન્ટેનરનો ઉપયોગ કરીએ છીએ, એક ઇંધણ માટે અને બીજો ઓક્સિજન માટે. ઓક્સિજન બળતણને ઓક્સિડાઇઝ કરે છે (તેને બાળે છે). રેઝિસ્ટન્સ વેલ્ડીંગ: આ પ્રકારનું વેલ્ડીંગ જ્યુલ હીટિંગનો લાભ લે છે અને ચોક્કસ સમય માટે જ્યાં વિદ્યુત પ્રવાહ લાગુ કરવામાં આવે છે તે સ્થાન પર ગરમી ઉત્પન્ન થાય છે. ઉચ્ચ પ્રવાહો મેટલમાંથી પસાર થાય છે. આ સ્થાન પર પીગળેલા ધાતુના પૂલ રચાય છે. પ્રતિકાર વેલ્ડીંગ પદ્ધતિઓ તેમની કાર્યક્ષમતા, ઓછી પ્રદૂષણની સંભાવનાને કારણે લોકપ્રિય છે. જો કે ગેરફાયદા એ છે કે સાધનસામગ્રીનો ખર્ચ પ્રમાણમાં નોંધપાત્ર છે અને પ્રમાણમાં પાતળા કામના ટુકડાઓ માટે સહજ મર્યાદા છે. સ્પોટ વેલ્ડીંગ એ પ્રતિકારક વેલ્ડીંગનો એક મુખ્ય પ્રકાર છે. અહીં આપણે બે કે તેથી વધુ ઓવરલેપિંગ શીટ્સ અથવા વર્ક પીસને બે કોપર ઈલેક્ટ્રોડનો ઉપયોગ કરીને શીટ્સને એકસાથે ક્લેમ્પ કરીને જોડીએ છીએ અને તેમાંથી ઉચ્ચ પ્રવાહ પસાર કરીએ છીએ. કોપર ઇલેક્ટ્રોડ વચ્ચેની સામગ્રી ગરમ થાય છે અને તે સ્થાન પર પીગળેલા પૂલનું નિર્માણ થાય છે. પછી પ્રવાહ બંધ થઈ જાય છે અને કોપર ઇલેક્ટ્રોડ ટીપ્સ વેલ્ડ સ્થાનને ઠંડુ કરે છે કારણ કે ઇલેક્ટ્રોડ પાણી ઠંડું કરવામાં આવે છે. યોગ્ય સામગ્રી અને જાડાઈ પર યોગ્ય માત્રામાં ગરમી લાગુ કરવી આ તકનીક માટે ચાવીરૂપ છે, કારણ કે જો ખોટી રીતે લાગુ કરવામાં આવે તો સાંધા નબળા પડી જશે. સ્પોટ વેલ્ડીંગમાં વર્કપીસમાં કોઈ નોંધપાત્ર વિકૃતિ ન થવાના ફાયદા છે, ઉર્જા કાર્યક્ષમતા, ઓટોમેશનની સરળતા અને ઉત્કૃષ્ટ ઉત્પાદન દરો અને કોઈપણ ફિલરની જરૂર નથી. ગેરલાભ એ છે કે વેલ્ડીંગ સતત સીમ બનાવવાને બદલે ફોલ્લીઓ પર થાય છે, અન્ય વેલ્ડીંગ પદ્ધતિઓની તુલનામાં એકંદર શક્તિ પ્રમાણમાં ઓછી હોઈ શકે છે. બીજી તરફ સીમ વેલ્ડીંગ સમાન સામગ્રીની ફેઇંગ સપાટી પર વેલ્ડનું ઉત્પાદન કરે છે. સીમ બટ્ટ અથવા ઓવરલેપ સંયુક્ત હોઈ શકે છે. સીમ વેલ્ડીંગ એક છેડેથી શરૂ થાય છે અને ક્રમશઃ બીજા તરફ જાય છે. આ પદ્ધતિ વેલ્ડ પ્રદેશમાં દબાણ અને પ્રવાહ લાગુ કરવા માટે તાંબામાંથી બે ઇલેક્ટ્રોડનો પણ ઉપયોગ કરે છે. ડિસ્ક આકારના ઇલેક્ટ્રોડ્સ સીમ લાઇન સાથે સતત સંપર્ક સાથે ફરે છે અને સતત વેલ્ડ બનાવે છે. અહીં પણ, ઇલેક્ટ્રોડને પાણી દ્વારા ઠંડુ કરવામાં આવે છે. વેલ્ડ ખૂબ જ મજબૂત અને વિશ્વસનીય છે. અન્ય પદ્ધતિઓ પ્રોજેક્શન, ફ્લેશ અને અપસેટ વેલ્ડીંગ તકનીકો છે. સોલિડ-સ્ટેટ વેલ્ડીંગ એ ઉપર વર્ણવેલ અગાઉની પદ્ધતિઓ કરતાં થોડી અલગ છે. સંકલન ધાતુઓના ગલન તાપમાનથી નીચેના તાપમાને થાય છે અને મેટલ ફિલરનો ઉપયોગ થતો નથી. કેટલીક પ્રક્રિયાઓમાં દબાણનો ઉપયોગ થઈ શકે છે. વિવિધ પદ્ધતિઓ કોએક્સટ્રુઝન વેલ્ડીંગ છે જ્યાં એક જ ડાઇ દ્વારા વિભિન્ન ધાતુઓ બહાર કાઢવામાં આવે છે, કોલ્ડ પ્રેશર વેલ્ડીંગ જ્યાં આપણે સોફ્ટ એલોયને તેમના ગલનબિંદુઓથી નીચે જોડીએ છીએ, ડિફ્યુઝન વેલ્ડીંગ એક દૃશ્યમાન વેલ્ડ લાઇન વગરની ટેકનિક, વિસ્ફોટ વેલ્ડીંગ, વિભિન્ન ધાતુઓ સાથે જોડાવા માટે વિસ્ફોટ વેલ્ડિંગ સ્ટીલ્સ, ઈલેક્ટ્રોમેગ્નેટિક પલ્સ વેલ્ડીંગ જ્યાં આપણે ઈલેક્ટ્રોમેગ્નેટિક દળો દ્વારા ટ્યુબ અને શીટ્સને વેગ આપીએ છીએ, ફોર્જ વેલ્ડીંગ જેમાં ધાતુઓને ઊંચા તાપમાને ગરમ કરવા અને તેમને એકસાથે હેમરીંગનો સમાવેશ થાય છે, ઘર્ષણ વેલ્ડીંગ જ્યાં પર્યાપ્ત ઘર્ષણ સાથે વેલ્ડીંગ કરવામાં આવે છે, ઘર્ષણ જે રોટીંગને અટકાવે છે. સંયુક્ત લાઇનને પાર કરતા ઉપભોક્તા સાધન, હોટ પ્રેશર વેલ્ડીંગ જ્યાં આપણે વેક્યૂમ અથવા નિષ્ક્રિય વાયુઓમાં ગલન તાપમાનથી નીચેના એલિવેટેડ તાપમાને ધાતુઓને એકસાથે દબાવીએ છીએ, હોટ આઇસોસ્ટેટિક પ્રેશર વેલ્ડીંગ એવી પ્રક્રિયા છે જ્યાં આપણે જહાજની અંદર નિષ્ક્રિય વાયુઓનો ઉપયોગ કરીને દબાણ લાગુ કરીએ છીએ, રોલ વેલ્ડીંગ જ્યાં આપણે જોડાઈએ છીએ. તેમની વચ્ચે દબાણ કરીને અલગ સામગ્રી બે ફરતા વ્હીલ્સ, અલ્ટ્રાસોનિક વેલ્ડીંગ જ્યાં પાતળી ધાતુ અથવા પ્લાસ્ટિકની શીટ્સને ઉચ્ચ આવર્તન કંપન ઊર્જાનો ઉપયોગ કરીને વેલ્ડિંગ કરવામાં આવે છે. અમારી અન્ય વેલ્ડીંગ પ્રક્રિયાઓ ઈલેક્ટ્રોન બીમ વેલ્ડીંગ છે જેમાં ઊંડા ઘૂંસપેંઠ અને ઝડપી પ્રક્રિયા છે પરંતુ ખર્ચાળ પદ્ધતિ હોવાને કારણે અમે તેને ખાસ કિસ્સાઓમાં ધ્યાનમાં લઈએ છીએ, ઈલેક્ટ્રોસ્લેગ વેલ્ડીંગ એ ભારે જાડી પ્લેટો અને સ્ટીલના કામના ટુકડાઓ માટે યોગ્ય પદ્ધતિ છે, ઇન્ડક્શન વેલ્ડીંગ જ્યાં આપણે ઈલેક્ટ્રોમેગ્નેટિક ઇન્ડક્શનનો ઉપયોગ કરીએ છીએ. અમારા વિદ્યુત વાહક અથવા ફેરોમેગ્નેટિક વર્કપીસને ગરમ કરો, લેસર બીમ વેલ્ડીંગ પણ ઊંડા ઘૂંસપેંઠ અને ઝડપી પ્રક્રિયા સાથે પરંતુ એક ખર્ચાળ પદ્ધતિ, લેસર હાઇબ્રિડ વેલ્ડીંગ જે એલબીડબ્લ્યુને જીએમએડબલ્યુ સાથે સમાન વેલ્ડીંગ હેડમાં જોડે છે અને પ્લેટો વચ્ચે 2 મીમીના અંતરને પુલ કરવા સક્ષમ છે. ઇલેક્ટ્રીક ડિસ્ચાર્જ અને ત્યારબાદ લાગુ દબાણ સાથે સામગ્રીને ફોર્જ કરીને, થર્મિટ વેલ્ડિંગ જેમાં એલ્યુમિનિયમ અને આયર્ન ઓક્સાઇડ પાવડર વચ્ચે એક્ઝોથર્મિક પ્રતિક્રિયાનો સમાવેશ થાય છે., ઉપભોક્તા ઇલેક્ટ્રોડ સાથે ઇલેક્ટ્રોગાસ વેલ્ડિંગ અને ઊભી સ્થિતિમાં માત્ર સ્ટીલ સાથે વપરાય છે, અને અંતે સ્ટડ સાથે બેઝમાં જોડાવા માટે STUD ARC વેલ્ડિંગનો સમાવેશ થાય છે. ગરમી અને દબાણ સાથે સામગ્રી. અમે ભલામણ કરીએ છીએ કે તમે અહીં ક્લિક કરોAGS-TECH Inc દ્વારા બ્રેઝિંગ, સોલ્ડરિંગ અને એડહેસિવ બોન્ડિંગ પ્રક્રિયાઓના અમારા યોજનાકીય ચિત્રો ડાઉનલોડ કરો આ તમને અમે નીચે આપેલી માહિતીને વધુ સારી રીતે સમજવામાં મદદ કરશે. • બ્રેઝિંગ : અમે બે કે તેથી વધુ ધાતુઓને તેમની વચ્ચેના ગલનબિંદુઓ ઉપર ગરમ કરીને અને કેશિલરી ક્રિયાનો ઉપયોગ કરીને ફેલાવીએ છીએ. પ્રક્રિયા સોલ્ડરિંગ જેવી જ છે પરંતુ ફિલરને ઓગાળવામાં સામેલ તાપમાન બ્રેઝિંગમાં વધુ હોય છે. વેલ્ડીંગની જેમ, ફ્લક્સ ફિલર સામગ્રીને વાતાવરણીય દૂષણથી સુરક્ષિત કરે છે. ઠંડક પછી વર્કપીસ એકસાથે જોડાય છે. પ્રક્રિયામાં નીચેના મુખ્ય પગલાઓનો સમાવેશ થાય છે: સારી ફિટ અને ક્લિયરન્સ, આધાર સામગ્રીની યોગ્ય સફાઈ, યોગ્ય ફિક્સરિંગ, યોગ્ય પ્રવાહ અને વાતાવરણની પસંદગી, એસેમ્બલીને ગરમ કરવી અને અંતે બ્રેઝ્ડ એસેમ્બલીની સફાઈ. અમારી કેટલીક બ્રેઝિંગ પ્રક્રિયાઓ ટોર્ચ બ્રેઝિંગ છે, જે મેન્યુઅલી અથવા ઓટોમેટેડ રીતે કરવામાં આવતી લોકપ્રિય પદ્ધતિ છે. તે ઓછા વોલ્યુમ ઉત્પાદન ઓર્ડર અને વિશિષ્ટ કેસ માટે યોગ્ય છે. સાંધાને બ્રેઝ કરવામાં આવતા નજીક ગેસની જ્વાળાઓનો ઉપયોગ કરીને ગરમી લાગુ કરવામાં આવે છે. ફર્નેસ બ્રેઝિંગ માટે ઓછા ઓપરેટર કૌશલ્યની જરૂર છે અને તે ઔદ્યોગિક મોટા પાયે ઉત્પાદન માટે યોગ્ય અર્ધ-સ્વચાલિત પ્રક્રિયા છે. ભઠ્ઠીમાં તાપમાનનું નિયંત્રણ અને વાતાવરણનું નિયંત્રણ બંને આ ટેકનિકના ફાયદા છે, કારણ કે પહેલાની પદ્ધતિ આપણને ગરમીના ચક્રને નિયંત્રિત કરવા અને સ્થાનિક ગરમીને દૂર કરવા સક્ષમ બનાવે છે જેમ કે ટોર્ચ બ્રેઝિંગમાં થાય છે, અને બાદમાં ભાગને ઓક્સિડેશનથી સુરક્ષિત કરે છે. જિગિંગનો ઉપયોગ કરીને અમે ઉત્પાદન ખર્ચને ન્યૂનતમ ઘટાડવા માટે સક્ષમ છીએ. ગેરફાયદા ઉચ્ચ પાવર વપરાશ, સાધનોના ખર્ચ અને વધુ પડકારરૂપ ડિઝાઇન વિચારણાઓ છે. વેક્યૂમ બ્રેઝિંગ શૂન્યાવકાશની ભઠ્ઠીમાં થાય છે. તાપમાનની એકરૂપતા જાળવવામાં આવે છે અને અમે ખૂબ ઓછા શેષ તણાવ સાથે પ્રવાહ મુક્ત, ખૂબ જ સ્વચ્છ સાંધા મેળવીએ છીએ. વેક્યૂમ બ્રેઝિંગ દરમિયાન હીટ ટ્રીટમેન્ટ થઈ શકે છે, કારણ કે ધીમી ગરમી અને ઠંડક ચક્ર દરમિયાન ઓછા અવશેષ તણાવ હાજર છે. મુખ્ય ગેરલાભ એ તેની ઊંચી કિંમત છે કારણ કે શૂન્યાવકાશ વાતાવરણનું નિર્માણ એક ખર્ચાળ પ્રક્રિયા છે. બીજી તકનીક ડીપ બ્રેઝિંગ ફિક્સ્ડ ભાગોને જોડે છે જ્યાં સમાગમની સપાટી પર બ્રેઝિંગ સંયોજન લાગુ કરવામાં આવે છે. ત્યારબાદ ફિક્સ્ડ ભાગોને સોડિયમ ક્લોરાઇડ (ટેબલ મીઠું) જેવા પીગળેલા મીઠાના સ્નાનમાં ડૂબાડવામાં આવે છે જે હીટ ટ્રાન્સફર માધ્યમ અને પ્રવાહ તરીકે કામ કરે છે. હવાને બાકાત રાખવામાં આવે છે અને તેથી ઓક્સાઇડની રચના થતી નથી. ઇન્ડક્શન બ્રેઝિંગમાં અમે ફિલર મેટલ દ્વારા સામગ્રીને જોડીએ છીએ જેનો ગલનબિંદુ બેઝ મટિરિયલ કરતાં ઓછો હોય છે. ઇન્ડક્શન કોઇલમાંથી વૈકલ્પિક પ્રવાહ એક ઇલેક્ટ્રોમેગ્નેટિક ક્ષેત્ર બનાવે છે જે મોટાભાગે ફેરસ ચુંબકીય પદાર્થો પર ઇન્ડક્શન હીટિંગને પ્રેરિત કરે છે. પદ્ધતિ પસંદગીયુક્ત ગરમી, માત્ર ઇચ્છિત વિસ્તારોમાં વહેતા ફિલર સાથેના સારા સાંધા, થોડું ઓક્સિડેશન પ્રદાન કરે છે કારણ કે કોઈ જ્વાળાઓ હાજર નથી અને ઠંડક ઝડપી, ઝડપી ગરમી, સુસંગતતા અને ઉચ્ચ વોલ્યુમ ઉત્પાદન માટે યોગ્યતા છે. અમારી પ્રક્રિયાઓને ઝડપી બનાવવા અને સુસંગતતાની ખાતરી આપવા માટે અમે વારંવાર પ્રીફોર્મ્સનો ઉપયોગ કરીએ છીએ. સિરામિકથી મેટલ ફિટિંગ, હર્મેટિક સીલિંગ, વેક્યૂમ ફીડથ્રૂઝ, ઉચ્ચ અને અલ્ટ્રાહાઈ વેક્યૂમ અને પ્રવાહી નિયંત્રણ ઘટકો ઉત્પાદન કરતી અમારી બ્રેઝિંગ સુવિધા વિશેની માહિતી અહીં મળી શકે છે:_cc781905-5cf58d_.બ્રેઝિંગ ફેક્ટરી બ્રોશર • સોલ્ડરિંગ : સોલ્ડરિંગમાં કામના ટુકડાઓનું ગલન થતું નથી, પરંતુ સંયુક્તમાં વહેતા જોડાવાના ભાગો કરતાં નીચું ગલનબિંદુ ધરાવતી ફિલર મેટલ હોય છે. સોલ્ડરિંગમાં ફિલર મેટલ બ્રેઝિંગ કરતા ઓછા તાપમાને ઓગળે છે. અમે સોલ્ડરિંગ માટે લીડ-ફ્રી એલોયનો ઉપયોગ કરીએ છીએ અને RoHS અનુપાલન કરીએ છીએ અને વિવિધ એપ્લિકેશનો અને જરૂરિયાતો માટે અમારી પાસે સિલ્વર એલોય જેવા અલગ અને યોગ્ય એલોય છે. સોલ્ડરિંગ અમને સાંધા આપે છે જે ગેસ અને પ્રવાહી-ચુસ્ત હોય છે. સોફ્ટ સોલ્ડરિંગમાં, આપણી ફિલર મેટલનો ગલનબિંદુ 400 સેન્ટિગ્રેડથી નીચે હોય છે, જ્યારે સિલ્વર સોલ્ડરિંગ અને બ્રેઝિંગમાં આપણને ઊંચા તાપમાનની જરૂર પડે છે. સોફ્ટ સોલ્ડરિંગ નીચા તાપમાનનો ઉપયોગ કરે છે પરંતુ એલિવેટેડ તાપમાને એપ્લિકેશનની માંગ માટે મજબૂત સાંધામાં પરિણમતું નથી. બીજી બાજુ, સિલ્વર સોલ્ડરિંગ માટે, ટોર્ચ દ્વારા પ્રદાન કરવામાં આવેલા ઊંચા તાપમાનની જરૂર છે અને અમને ઉચ્ચ તાપમાનના ઉપયોગ માટે યોગ્ય મજબૂત સાંધા આપે છે. બ્રેઝિંગ માટે સૌથી વધુ તાપમાનની જરૂર પડે છે અને સામાન્ય રીતે ટોર્ચનો ઉપયોગ કરવામાં આવે છે. બ્રેઝિંગ સાંધા ખૂબ જ મજબૂત હોવાથી, તે ભારે લોખંડની વસ્તુઓના સમારકામ માટે સારા ઉમેદવારો છે. અમારી મેન્યુફેક્ચરિંગ લાઇનમાં અમે મેન્યુઅલ હેન્ડ સોલ્ડરિંગ તેમજ ઓટોમેટેડ સોલ્ડર લાઇનનો ઉપયોગ કરીએ છીએ. INDUCTION સોલ્ડરિંગ ઇન્ડક્શન હીટિંગની સુવિધા માટે કોપર કોઇલમાં ઉચ્ચ આવર્તન એસી કરંટનો ઉપયોગ કરે છે. કરંટ સોલ્ડર કરેલ ભાગમાં પ્રેરિત થાય છે અને પરિણામે ઉચ્ચ પ્રતિકાર joint પર ગરમી ઉત્પન્ન થાય છે. આ ગરમી ફિલર મેટલને ઓગળે છે. ફ્લક્સનો પણ ઉપયોગ થાય છે. ઇન્ડક્શન સોલ્ડરિંગ એ સોલ્ડરિંગ સાયક્લિન્ડર અને પાઈપોને સતત પ્રક્રિયામાં તેમની આસપાસ કોઇલ વીંટાળીને સારી પદ્ધતિ છે. ગ્રેફાઇટ અને સિરામિક્સ જેવી કેટલીક સામગ્રીને સોલ્ડરિંગ કરવું વધુ મુશ્કેલ છે કારણ કે તેને સોલ્ડરિંગ પહેલાં યોગ્ય ધાતુ સાથે વર્કપીસની પ્લેટિંગની જરૂર છે. આ ઇન્ટરફેસિયલ બોન્ડિંગને સરળ બનાવે છે. અમે ખાસ કરીને હર્મેટિક પેકેજિંગ એપ્લીકેશન માટે આવી સામગ્રીને સોલ્ડર કરીએ છીએ. અમે મોટાભાગે વેવ સોલ્ડરિંગનો ઉપયોગ કરીને અમારા પ્રિન્ટેડ સર્કિટ બોર્ડ્સ (PCB)નું ઉચ્ચ વોલ્યુમમાં ઉત્પાદન કરીએ છીએ. માત્ર થોડી માત્રામાં પ્રોટોટાઈપિંગ હેતુઓ માટે અમે સોલ્ડરિંગ આયર્નનો ઉપયોગ કરીને હેન્ડ સોલ્ડરિંગનો ઉપયોગ કરીએ છીએ. અમે થ્રુ-હોલ તેમજ સરફેસ માઉન્ટ PCB એસેમ્બલીઝ (PCBA) બંને માટે વેવ સોલ્ડરિંગનો ઉપયોગ કરીએ છીએ. કામચલાઉ ગુંદર સર્કિટ બોર્ડ સાથે ઘટકોને જોડાયેલ રાખે છે અને એસેમ્બલી કન્વેયર પર મૂકવામાં આવે છે અને પીગળેલા સોલ્ડર ધરાવતા સાધનોમાંથી આગળ વધે છે. પહેલા પીસીબી ફ્લક્સ થાય છે અને પછી પ્રીહિટીંગ ઝોનમાં પ્રવેશ કરે છે. પીગળેલું સોલ્ડર તપેલીમાં હોય છે અને તેની સપાટી પર ઊભેલા મોજાની પેટર્ન હોય છે. જ્યારે PCB આ તરંગો પર ખસે છે, ત્યારે આ તરંગો PCB ના તળિયે સંપર્ક કરે છે અને સોલ્ડરિંગ પેડ્સને વળગી રહે છે. સોલ્ડર ફક્ત પીન અને પેડ્સ પર જ રહે છે અને પીસીબી પર જ નહીં. પીગળેલા સોલ્ડરમાં તરંગો સારી રીતે નિયંત્રિત હોવા જોઈએ જેથી કોઈ સ્પ્લેશિંગ ન થાય અને તરંગોની ટોચ બોર્ડના અનિચ્છનીય વિસ્તારોને સ્પર્શતી નથી અને દૂષિત કરતી નથી. રિફ્લો સોલ્ડરિંગમાં, અમે બોર્ડમાં ઇલેક્ટ્રોનિક ઘટકોને અસ્થાયી રૂપે જોડવા માટે સ્ટીકી સોલ્ડર પેસ્ટનો ઉપયોગ કરીએ છીએ. પછી બોર્ડને તાપમાન નિયંત્રણ સાથે રિફ્લો ઓવન દ્વારા મૂકવામાં આવે છે. અહીં સોલ્ડર ઓગળે છે અને ઘટકોને કાયમી રૂપે જોડે છે. અમે આ ટેકનિકનો ઉપયોગ સપાટીના માઉન્ટ ઘટકો તેમજ થ્રુ-હોલ ઘટકો બંને માટે કરીએ છીએ. બોર્ડ પરના ઈલેક્ટ્રોનિક ઘટકોને તેમની મહત્તમ તાપમાન મર્યાદાથી વધુ ગરમ કરીને તેમના વિનાશને ટાળવા માટે ઓવનના તાપમાનનું યોગ્ય નિયંત્રણ અને ગોઠવણ જરૂરી છે. રિફ્લો સોલ્ડરિંગની પ્રક્રિયામાં આપણી પાસે વાસ્તવમાં અલગ-અલગ થર્મલ રૂપરેખા સાથે અનેક પ્રદેશો અથવા તબક્કાઓ હોય છે, જેમ કે પ્રીહિટીંગ સ્ટેપ, થર્મલ સોકીંગ સ્ટેપ, રીફ્લો અને કૂલીંગ સ્ટેપ્સ. પ્રિન્ટેડ સર્કિટ બોર્ડ એસેમ્બલીઝ (PCBA) ના નુકસાન મુક્ત રીફ્લો સોલ્ડરિંગ માટે આ વિવિધ પગલાં આવશ્યક છે. ULTRASONIC સોલ્ડરિંગ એ અનન્ય ક્ષમતાઓ સાથે વારંવાર વપરાતી બીજી તકનીક છે- તેનો ઉપયોગ કાચ, સિરામિક અને નોન-મેટાલિક સામગ્રીને સોલ્ડર કરવા માટે થઈ શકે છે. ઉદાહરણ તરીકે, ફોટોવોલ્ટેઇક પેનલ્સ કે જે બિન-ધાતુ હોય છે તેને ઇલેક્ટ્રોડની જરૂર હોય છે જે આ તકનીકનો ઉપયોગ કરીને જોડી શકાય છે. અલ્ટ્રાસોનિક સોલ્ડરિંગમાં, અમે ગરમ સોલ્ડરિંગ ટિપ ગોઠવીએ છીએ જે અલ્ટ્રાસોનિક સ્પંદનો પણ ઉત્સર્જન કરે છે. આ સ્પંદનો પીગળેલા સોલ્ડર સામગ્રી સાથે સબસ્ટ્રેટના ઇન્ટરફેસ પર પોલાણ પરપોટા ઉત્પન્ન કરે છે. પોલાણની વિસ્ફોટક ઊર્જા ઓક્સાઇડની સપાટીને સુધારે છે અને ગંદકી અને ઓક્સાઇડને દૂર કરે છે. આ સમય દરમિયાન એલોય સ્તર પણ રચાય છે. બોન્ડિંગ સપાટી પર સોલ્ડર ઓક્સિજનનો સમાવેશ કરે છે અને કાચ અને સોલ્ડર વચ્ચે મજબૂત વહેંચાયેલ બોન્ડની રચનાને સક્ષમ કરે છે. ડીપ સોલ્ડરિંગને માત્ર નાના પાયે ઉત્પાદન માટે યોગ્ય વેવ સોલ્ડરિંગના સરળ સંસ્કરણ તરીકે ગણી શકાય. પ્રથમ સફાઈ પ્રવાહ અન્ય પ્રક્રિયાઓની જેમ લાગુ પડે છે. માઉન્ટ થયેલ ઘટકો સાથેના PCB ને મેન્યુઅલી અથવા અર્ધ-સ્વચાલિત રીતે પીગળેલા સોલ્ડર ધરાવતી ટાંકીમાં ડૂબાડવામાં આવે છે. પીગળેલું સોલ્ડર બોર્ડ પર સોલ્ડર માસ્ક દ્વારા અસુરક્ષિત ખુલ્લા ધાતુના વિસ્તારોમાં ચોંટી જાય છે. સાધનસામગ્રી સરળ અને સસ્તું છે. • એડહેસિવ બોન્ડિંગ : આ બીજી લોકપ્રિય ટેકનિક છે જેનો આપણે વારંવાર ઉપયોગ કરીએ છીએ અને તેમાં ગુંદર, ઇપોક્સી, પ્લાસ્ટિક એજન્ટો અથવા અન્ય રસાયણોનો ઉપયોગ કરીને સપાટીઓનું બોન્ડિંગ સામેલ છે. બોન્ડિંગ કાં તો દ્રાવકને બાષ્પીભવન કરીને, ગરમીના ઉપચાર દ્વારા, યુવી પ્રકાશ ક્યોરિંગ દ્વારા, દબાણયુક્ત ઉપચાર દ્વારા અથવા ચોક્કસ સમયની રાહ જોઈને પૂર્ણ થાય છે. અમારી ઉત્પાદન રેખાઓમાં વિવિધ ઉચ્ચ પ્રદર્શન ગુંદરનો ઉપયોગ થાય છે. યોગ્ય રીતે એન્જિનિયર્ડ એપ્લિકેશન અને ક્યોરિંગ પ્રક્રિયાઓ સાથે, એડહેસિવ બોન્ડિંગ ખૂબ જ ઓછા સ્ટ્રેસ બોન્ડ્સમાં પરિણમી શકે છે જે મજબૂત અને વિશ્વસનીય છે. એડહેસિવ બોન્ડ પર્યાવરણીય પરિબળો જેમ કે ભેજ, દૂષકો, કાટરોધક પદાર્થો, કંપન... વગેરે સામે સારા સંરક્ષક બની શકે છે. એડહેસિવ બોન્ડિંગના ફાયદાઓ છે: તે એવી સામગ્રી પર લાગુ કરી શકાય છે જે અન્યથા સોલ્ડર, વેલ્ડ અથવા બ્રેઝ કરવા મુશ્કેલ હશે. વેલ્ડીંગ અથવા અન્ય ઉચ્ચ તાપમાન પ્રક્રિયાઓ દ્વારા નુકસાન પામેલ ગરમી સંવેદનશીલ સામગ્રી માટે પણ તે પ્રાધાન્યક્ષમ હોઈ શકે છે. એડહેસિવ્સના અન્ય ફાયદા એ છે કે તેઓ અનિયમિત આકારની સપાટી પર લાગુ કરી શકાય છે અને અન્ય પદ્ધતિઓની તુલનામાં એસેમ્બલીનું વજન ખૂબ જ ઓછી માત્રામાં વધારી શકે છે. ભાગોમાં પરિમાણીય ફેરફારો પણ ખૂબ ઓછા છે. કેટલાક ગુંદરમાં ઇન્ડેક્સ મેચિંગ પ્રોપર્ટીઝ હોય છે અને પ્રકાશ અથવા ઓપ્ટિકલ સિગ્નલ સ્ટ્રેન્થને નોંધપાત્ર રીતે ઘટાડ્યા વિના ઓપ્ટિકલ ઘટકોની વચ્ચે વાપરી શકાય છે. બીજી તરફ ગેરફાયદા લાંબા સમય સુધી ઉપચાર સમય છે જે મેન્યુફેક્ચરિંગ લાઇન, ફિક્સરિંગ જરૂરિયાતો, સપાટીની તૈયારીની જરૂરિયાતો અને પુનઃકાર્યની જરૂર હોય ત્યારે ડિસએસેમ્બલ કરવામાં મુશ્કેલીને ધીમી કરી શકે છે. અમારી મોટાભાગની એડહેસિવ બોન્ડિંગ કામગીરીમાં નીચેના પગલાં શામેલ છે: -સરફેસ ટ્રીટમેન્ટ: ડીયોનાઇઝ્ડ વોટર ક્લિનિંગ, આલ્કોહોલ ક્લિનિંગ, પ્લાઝમા અથવા કોરોના ક્લિનિંગ જેવી ખાસ સફાઈ પ્રક્રિયાઓ સામાન્ય છે. સફાઈ કર્યા પછી અમે શક્ય શ્રેષ્ઠ સાંધાઓની ખાતરી કરવા માટે સપાટી પર સંલગ્નતા પ્રમોટર્સ લાગુ કરી શકીએ છીએ. -પાર્ટ ફિક્સ્ચરિંગ: એડહેસિવ એપ્લિકેશન તેમજ ક્યોરિંગ બંને માટે અમે કસ્ટમ ફિક્સ્ચર ડિઝાઇન અને ઉપયોગ કરીએ છીએ. -એડહેસિવ એપ્લિકેશન: અમે કેટલીકવાર મેન્યુઅલનો ઉપયોગ કરીએ છીએ, અને કેટલીકવાર કેસ ઓટોમેટેડ સિસ્ટમ્સ જેમ કે રોબોટિક્સ, સર્વો મોટર્સ, લીનિયર એક્ટ્યુએટર્સ પર આધાર રાખીને એડહેસિવ્સને યોગ્ય સ્થાન પર પહોંચાડવા માટે અને અમે તેને યોગ્ય વોલ્યુમ અને જથ્થા પર પહોંચાડવા માટે ડિસ્પેન્સર્સનો ઉપયોગ કરીએ છીએ. -ક્યોરિંગ: એડહેસિવ પર આધાર રાખીને, અમે સરળ સૂકવણી અને ક્યોરિંગ તેમજ યુવી લાઇટ્સ હેઠળ ક્યોરિંગનો ઉપયોગ કરી શકીએ છીએ જે ઉત્પ્રેરક અથવા પકાવવાની નાની ભઠ્ઠીમાં હીટ ક્યોરિંગ તરીકે કામ કરે છે અથવા જીગ્સ અને ફિક્સર પર માઉન્ટ થયેલ પ્રતિકારક હીટિંગ તત્વોનો ઉપયોગ કરે છે. અમે ભલામણ કરીએ છીએ કે તમે અહીં ક્લિક કરોAGS-TECH Inc દ્વારા ફાસ્ટનિંગ પ્રક્રિયાઓના અમારા યોજનાકીય ચિત્રો ડાઉનલોડ કરો. આ તમને અમે નીચે આપેલી માહિતીને વધુ સારી રીતે સમજવામાં મદદ કરશે. • ફાસ્ટનિંગ પ્રક્રિયાઓ : અમારી યાંત્રિક જોડાવાની પ્રક્રિયાઓ બે બ્રાડ કેટેગરીમાં આવે છે: ફાસ્ટનર્સ અને ઈન્ટિગ્રલ જોઈન્ટ્સ. અમે ઉપયોગ કરીએ છીએ તે ફાસ્ટનર્સના ઉદાહરણો સ્ક્રૂ, પિન, નટ્સ, બોલ્ટ્સ, રિવેટ્સ છે. અમે ઉપયોગમાં લઈએ છીએ તેવા અભિન્ન સાંધાના ઉદાહરણો સ્નેપ અને સંકોચાઈને ફિટ, સીમ, ક્રિમ્પ્સ છે. ફાસ્ટનિંગની વિવિધ પદ્ધતિઓનો ઉપયોગ કરીને અમે ખાતરી કરીએ છીએ કે અમારા યાંત્રિક સાંધા ઘણા વર્ષોના ઉપયોગ માટે મજબૂત અને વિશ્વસનીય છે. સ્ક્રૂ અને બોલ્ટ એ વસ્તુઓને એકસાથે પકડી રાખવા અને પોઝિશનિંગ માટે સૌથી વધુ ઉપયોગમાં લેવાતા ફાસ્ટનર્સ છે. અમારા સ્ક્રૂ અને બોલ્ટ ASME ધોરણોને પૂર્ણ કરે છે. હેક્સ કેપ સ્ક્રૂ અને હેક્સ બોલ્ટ્સ, લેગ સ્ક્રૂ અને બોલ્ટ્સ, ડબલ એન્ડેડ સ્ક્રૂ, ડોવેલ સ્ક્રૂ, આઇ સ્ક્રૂ, મિરર સ્ક્રૂ, શીટ મેટલ સ્ક્રૂ, ફાઇન એડજસ્ટમેન્ટ સ્ક્રૂ, સેલ્ફ-ડ્રિલિંગ અને સેલ્ફ-ટેપિંગ સ્ક્રૂ સહિત વિવિધ પ્રકારના સ્ક્રૂ અને બોલ્ટ્સ ગોઠવવામાં આવ્યા છે. , સેટ સ્ક્રૂ, બિલ્ટ-ઇન વોશર સાથેના સ્ક્રૂ,…અને વધુ. અમારી પાસે કાઉન્ટરસંક, ડોમ, રાઉન્ડ, ફ્લેંજ્ડ હેડ અને સ્લોટ, ફિલિપ્સ, સ્ક્વેર, હેક્સ સોકેટ જેવા વિવિધ સ્ક્રુ હેડ પ્રકારો છે. બીજી તરફ A RIVET એ કાયમી યાંત્રિક ફાસ્ટનર છે જેમાં એક તરફ સરળ નળાકાર શાફ્ટ અને એક માથું હોય છે. દાખલ કર્યા પછી, રિવેટનો બીજો છેડો વિકૃત થાય છે અને તેનો વ્યાસ વિસ્તારવામાં આવે છે જેથી તે સ્થાને રહે. બીજા શબ્દોમાં કહીએ તો, ઇન્સ્ટોલેશન પહેલાં રિવેટનું એક માથું હોય છે અને ઇન્સ્ટોલેશન પછી તેની પાસે બે હોય છે. અમે એપ્લિકેશન, તાકાત, સુલભતા અને કિંમતના આધારે વિવિધ પ્રકારના રિવેટ્સ ઇન્સ્ટોલ કરીએ છીએ જેમ કે સોલિડ/રાઉન્ડ હેડ રિવેટ્સ, સ્ટ્રક્ચરલ, સેમી-ટ્યુબ્યુલર, બ્લાઇન્ડ, ઓસ્કર, ડ્રાઇવ, ફ્લશ, ફ્રિકશન-લોક, સેલ્ફ-પિયર્સિંગ રિવેટ્સ. રિવેટીંગને એવા કિસ્સાઓમાં પ્રાધાન્ય આપી શકાય છે જ્યાં ગરમીની વિકૃતિ અને વેલ્ડીંગ ગરમીને કારણે સામગ્રીના ગુણધર્મોમાં ફેરફાર ટાળવાની જરૂર છે. રિવેટિંગ હળવા વજન અને ખાસ કરીને સારી તાકાત અને શીયર ફોર્સ સામે સહનશક્તિ પણ આપે છે. ટેન્સાઈલ લોડ્સ સામે જો કે સ્ક્રૂ, નટ્સ અને બોલ્ટ વધુ યોગ્ય હોઈ શકે છે. CLINCHING પ્રક્રિયામાં અમે ખાસ પંચનો ઉપયોગ કરીએ છીએ અને શીટ મેટલ્સ વચ્ચે મિકેનિકલ ઇન્ટરલોક રચવા માટે મૃત્યુ પામે છે. પંચ શીટ મેટલના સ્તરોને ડાઇ કેવિટીમાં ધકેલે છે અને પરિણામે કાયમી સાંધાની રચના થાય છે. ક્લિન્ચિંગમાં કોઈ હીટિંગ અને ઠંડકની જરૂર નથી અને તે ઠંડા કામ કરવાની પ્રક્રિયા છે. તે એક આર્થિક પ્રક્રિયા છે જે કેટલાક કિસ્સાઓમાં સ્પોટ વેલ્ડીંગને બદલી શકે છે. પિનિંગમાં આપણે પીનનો ઉપયોગ કરીએ છીએ જે મશીન તત્વો છે જેનો ઉપયોગ મશીનના ભાગોને એકબીજાની તુલનામાં સુરક્ષિત કરવા માટે થાય છે. મુખ્ય પ્રકારો છે ક્લેવિસ પિન, કોટર પિન, સ્પ્રિંગ પિન, ડોવેલ પિન, અને સ્પ્લિટ પિન. સ્ટેપલિંગમાં અમે સ્ટેપલિંગ ગન અને સ્ટેપલ્સનો ઉપયોગ કરીએ છીએ જે બે-પાંખવાળા ફાસ્ટનર્સ છે જેનો ઉપયોગ સામગ્રીને જોડવા અથવા બાંધવા માટે થાય છે. સ્ટેપલિંગના નીચેના ફાયદા છે: આર્થિક, સરળ અને ઝડપી ઉપયોગ, સ્ટેપલનો તાજ એકસાથે બટેડ સામગ્રીને પુલ કરવા માટે વાપરી શકાય છે, સ્ટેપલનો તાજ કેબલ જેવા ટુકડાને પુલ કરવા અને પંચર કર્યા વિના તેને સપાટી પર બાંધવામાં સરળતા આપે છે. નુકસાનકારક, પ્રમાણમાં સરળ દૂર. પ્રેસ ફિટિંગ ભાગોને એકસાથે દબાણ કરીને કરવામાં આવે છે અને તેમની વચ્ચેનું ઘર્ષણ ભાગોને જોડે છે. મોટા કદના શાફ્ટ અને અંડરસાઈઝ્ડ હોલ ધરાવતા પ્રેસ ફિટ ભાગોને સામાન્ય રીતે બેમાંથી એક પદ્ધતિ દ્વારા એસેમ્બલ કરવામાં આવે છે: કાં તો બળનો ઉપયોગ કરીને અથવા ભાગોના થર્મલ વિસ્તરણ અથવા સંકોચનનો લાભ લઈને. જ્યારે પ્રેસ ફિટિંગ બળ લગાવીને સ્થાપિત કરવામાં આવે છે, ત્યારે અમે કાં તો હાઇડ્રોલિક પ્રેસ અથવા હાથથી સંચાલિત પ્રેસનો ઉપયોગ કરીએ છીએ. બીજી તરફ જ્યારે થર્મલ વિસ્તરણ દ્વારા પ્રેસ ફિટિંગ સ્થાપિત કરવામાં આવે છે ત્યારે અમે પરબિડીયુંના ભાગોને ગરમ કરીએ છીએ અને જ્યારે ગરમ હોય ત્યારે તેમને તેમની જગ્યાએ ભેગા કરીએ છીએ. જ્યારે તેઓ ઠંડુ થાય છે ત્યારે તેઓ સંકુચિત થાય છે અને તેમના સામાન્ય પરિમાણો પર પાછા ફરે છે. આનાથી સારી પ્રેસ ફિટ થાય છે. અમે તેને વૈકલ્પિક રીતે SHRINK-FITTING કહીએ છીએ. આ કરવાની બીજી રીત એ છે કે એસેમ્બલી પહેલાં પરબિડીયુંવાળા ભાગોને ઠંડું કરીને અને પછી તેમને સમાગમના ભાગોમાં સરકાવીને. જ્યારે એસેમ્બલી ગરમ થાય છે ત્યારે તે વિસ્તરે છે અને અમે ચુસ્ત ફિટ મેળવીએ છીએ. આ પછીની પદ્ધતિ એવા કિસ્સાઓમાં પ્રાધાન્યક્ષમ હોઈ શકે છે જ્યાં ગરમીથી સામગ્રીના ગુણધર્મોમાં ફેરફાર થવાનું જોખમ રહેલું હોય. તે કિસ્સાઓમાં ઠંડક વધુ સુરક્ષિત છે. વાયુયુક્ત અને હાઇડ્રોલિક ઘટકો અને એસેમ્બલીઝ • વાલ્વ, હાઇડ્રોલિક અને વાયુયુક્ત ઘટકો જેમ કે ઓ-રિંગ, વોશર, સીલ, ગાસ્કેટ, રિંગ, શિમ. વાલ્વ અને વાયુયુક્ત ઘટકો વિશાળ વિવિધતામાં આવતા હોવાથી, અમે અહીં બધું સૂચિબદ્ધ કરી શકતા નથી. તમારી અરજીના ભૌતિક અને રાસાયણિક વાતાવરણના આધારે, અમારી પાસે તમારા માટે વિશેષ ઉત્પાદનો છે. કૃપા કરીને અમને એપ્લિકેશન, ઘટકનો પ્રકાર, વિશિષ્ટતાઓ, પર્યાવરણીય પરિસ્થિતિઓ જેમ કે દબાણ, તાપમાન, પ્રવાહી અથવા વાયુઓ કે જે તમારા વાલ્વ અને વાયુયુક્ત ઘટકોના સંપર્કમાં હશે તેનો ઉલ્લેખ કરો; અને અમે તમારા માટે સૌથી યોગ્ય ઉત્પાદન પસંદ કરીશું અથવા તમારી એપ્લિકેશન માટે ખાસ ઉત્પાદન કરીશું. CLICK Product Finder-Locator Service પાછલું પૃષ્ઠ
- Rapid Prototyping, Desktop Manufacturing, Additive Manufacturing, FDM
Rapid Prototyping, Desktop Manufacturing, Additive Manufacturing, Stereolithography, Polyjet, Fused Deposition Modeling, Selective Laser Sintering, FDM, SLS એડિટિવ અને ઝડપી ઉત્પાદન તાજેતરના વર્ષોમાં, અમે રેપિડ મેન્યુફેક્ચરિંગ અથવા રેપિડ પ્રોટોટાઇપિંગની માંગમાં વધારો જોયો છે. આ પ્રક્રિયાને ડેસ્કટોપ મેન્યુફેક્ચરિંગ અથવા ફ્રી-ફોર્મ ફેબ્રિકેશન પણ કહી શકાય. મૂળભૂત રીતે ભાગનું નક્કર ભૌતિક મોડલ સીધું ત્રિ-પરિમાણીય CAD ડ્રોઇંગમાંથી બનાવવામાં આવે છે. અમે આ વિવિધ તકનીકો માટે એડિટિવ મેન્યુફેક્ચરિંગ શબ્દનો ઉપયોગ કરીએ છીએ જ્યાં અમે સ્તરોમાં ભાગો બનાવીએ છીએ. સંકલિત કોમ્પ્યુટર સંચાલિત હાર્ડવેર અને સોફ્ટવેરનો ઉપયોગ કરીને અમે એડિટિવ મેન્યુફેક્ચરિંગ કરીએ છીએ. અમારી ઝડપી પ્રોટોટાઇપિંગ અને ઉત્પાદન તકનીકો છે સ્ટીરિયોલિથોગ્રાફી, પોલિજેટ, ફ્યુઝ્ડ-ડિપોઝિશન મોડલિંગ, સિલેક્ટિવ લેસર સિન્ટરિંગ, ઇલેક્ટ્રોન બીમ મેલ્ટિંગ, થ્રી-ડાયમેન્શનલ પ્રિન્ટિંગ, ડાયરેક્ટ મેન્યુફેક્ચરિંગ, આર. અમે ભલામણ કરીએ છીએ કે તમે અહીં ક્લિક કરોAGS-TECH Inc. દ્વારા એડિટિવ મેન્યુફેક્ચરિંગ અને રેપિડ મેન્યુફેક્ચરિંગ પ્રક્રિયાઓના અમારા યોજનાકીય ચિત્રો ડાઉનલોડ કરો આ તમને અમે નીચે આપેલી માહિતીને વધુ સારી રીતે સમજવામાં મદદ કરશે. રેપિડ પ્રોટોટાઇપિંગ અમને પ્રદાન કરે છે: 1.) 3D / CAD સિસ્ટમનો ઉપયોગ કરીને મોનિટર પર વૈચારિક ઉત્પાદન ડિઝાઇનને વિવિધ ખૂણાઓથી જોવામાં આવે છે. 2.) નોનમેટાલિક અને મેટાલિક સામગ્રીમાંથી પ્રોટોટાઇપ્સનું ઉત્પાદન અને કાર્યાત્મક, તકનીકી અને સૌંદર્યલક્ષી પાસાઓથી અભ્યાસ કરવામાં આવે છે. 3.) ખૂબ જ ઓછા સમયમાં ઓછા ખર્ચે પ્રોટોટાઈપિંગ પૂર્ણ થાય છે. એડિટિવ મેન્યુફેક્ચરિંગને એકબીજાની ઉપર વ્યક્તિગત સ્લાઇસેસને સ્ટેક કરીને અને બોન્ડિંગ કરીને બ્રેડની રોટલીના નિર્માણ સાથે સામ્યતા આપી શકાય છે. બીજા શબ્દોમાં કહીએ તો, ઉત્પાદન સ્લાઇસ દ્વારા સ્લાઇસ બનાવવામાં આવે છે, અથવા સ્તર દ્વારા સ્તર એકબીજા પર જમા કરવામાં આવે છે. મોટાભાગના ભાગો કલાકોમાં ઉત્પન્ન કરી શકાય છે. જો ભાગો ખૂબ જ ઝડપથી જરૂરી હોય અથવા જો જરૂરી માત્રા ઓછી હોય અને મોલ્ડ અને ટૂલિંગ બનાવવું ખૂબ ખર્ચાળ અને સમય લે તો આ તકનીક સારી છે. જો કે મોંઘા કાચા માલના કારણે એક ભાગની કિંમત મોંઘી છે. • સ્ટીરિયોલિથોગ્રાફી : આ ટેકનિક STL તરીકે પણ સંક્ષિપ્ત છે, જે પ્રવાહી ફોટોપોલિમરને તેના પર લેસર બીમ ફોકસ કરીને ચોક્કસ આકારમાં ક્યોરિંગ અને સખત બનાવવા પર આધારિત છે. લેસર ફોટોપોલિમરને પોલિમરાઇઝ કરે છે અને તેને ઇલાજ કરે છે. ફોટોપોલિમર મિશ્રણની સપાટી પર પ્રોગ્રામ કરેલા આકાર અનુસાર યુવી લેસર બીમને સ્કેન કરીને ભાગ નીચેથી ઉપરથી એકબીજાની ટોચ પર કાસ્કેડ કરાયેલ વ્યક્તિગત સ્લાઇસેસમાં ઉત્પન્ન થાય છે. સિસ્ટમમાં પ્રોગ્રામ કરેલ ભૂમિતિઓ પ્રાપ્ત કરવા માટે લેસર સ્પોટનું સ્કેનિંગ ઘણી વખત પુનરાવર્તિત થાય છે. ભાગ સંપૂર્ણ રીતે તૈયાર થઈ ગયા પછી, તેને પ્લેટફોર્મ પરથી દૂર કરવામાં આવે છે, અલ્ટ્રાસોનિક રીતે અને આલ્કોહોલ બાથ સાથે બ્લોટ અને સાફ કરવામાં આવે છે. આગળ, પોલિમર સંપૂર્ણ રીતે સાજો અને સખત છે તેની ખાતરી કરવા માટે તે થોડા કલાકો માટે યુવી ઇરેડિયેશનના સંપર્કમાં આવે છે. પ્રક્રિયાનો સારાંશ આપવા માટે, ફોટોપોલિમર મિશ્રણ અને યુવી લેસર બીમમાં ડૂબેલું પ્લેટફોર્મ ઇચ્છિત ભાગના આકાર અનુસાર સર્વો-કંટ્રોલ સિસ્ટમ દ્વારા નિયંત્રિત અને ખસેડવામાં આવે છે અને પોલિમર સ્તરને સ્તર દ્વારા ફોટોક્યોર કરીને ભાગ મેળવવામાં આવે છે. અલબત્ત ઉત્પાદિત ભાગના મહત્તમ પરિમાણો સ્ટીરીઓલિથોગ્રાફી સાધનો દ્વારા નક્કી કરવામાં આવે છે. • પોલીજેટ : ઇંકજેટ પ્રિન્ટીંગની જેમ જ, પોલીજેટમાં અમારી પાસે આઠ પ્રિન્ટ હેડ છે જે બિલ્ડ ટ્રે પર ફોટોપોલિમર જમા કરે છે. જેટની સાથે મૂકવામાં આવેલ અલ્ટ્રાવાયોલેટ પ્રકાશ દરેક સ્તરને તરત જ મટાડે છે અને સખત બનાવે છે. પોલિજેટમાં બે સામગ્રીનો ઉપયોગ થાય છે. પ્રથમ સામગ્રી વાસ્તવિક મોડેલના ઉત્પાદન માટે છે. બીજી સામગ્રી, જેલ જેવી રેઝિનનો ઉપયોગ આધાર માટે થાય છે. આ બંને સામગ્રીને સ્તર દ્વારા જમા કરવામાં આવે છે અને એક સાથે ઉપચાર કરવામાં આવે છે. મોડલ પૂર્ણ થયા પછી, સપોર્ટ સામગ્રીને જલીય દ્રાવણ વડે દૂર કરવામાં આવે છે. વપરાયેલ રેઝિન સ્ટીરીઓલિથોગ્રાફી (STL) જેવા જ છે. સ્ટીરીઓલિથોગ્રાફી કરતાં પોલિજેટના નીચેના ફાયદા છે: 1.) ભાગોને સાફ કરવાની જરૂર નથી. 2.) પોસ્ટપ્રોસેસ ક્યોરિંગની જરૂર નથી 3.) નાના સ્તરની જાડાઈ શક્ય છે અને આમ આપણે વધુ સારું રિઝોલ્યુશન મેળવી શકીએ છીએ અને ઝીણા ભાગોનું ઉત્પાદન કરી શકીએ છીએ. • ફ્યુઝ્ડ ડિપોઝિશન મોડલિંગ : સંક્ષિપ્તમાં FDM તરીકે પણ ઓળખાય છે, આ પદ્ધતિમાં રોબોટ-નિયંત્રિત એક્સ્ટ્રુડર હેડ ટેબલ પર બે સિદ્ધાંત દિશાઓમાં ફરે છે. કેબલને જરૂર મુજબ નીચે અને ઊંચો કરવામાં આવે છે. માથા પર ગરમ ડાઇના ઓરિફિસમાંથી, થર્મોપ્લાસ્ટિક ફિલામેન્ટ બહાર કાઢવામાં આવે છે અને ફોમ ફાઉન્ડેશન પર પ્રારંભિક સ્તર જમા કરવામાં આવે છે. આ એક્સ્ટ્રુડર હેડ દ્વારા પરિપૂર્ણ થાય છે જે પૂર્વનિર્ધારિત માર્ગને અનુસરે છે. પ્રારંભિક સ્તર પછી, કોષ્ટક નીચે કરવામાં આવે છે અને અનુગામી સ્તરો એકબીજાની ટોચ પર જમા થાય છે. કેટલીકવાર જટિલ ભાગનું ઉત્પાદન કરતી વખતે, સપોર્ટ સ્ટ્રક્ચર્સની જરૂર પડે છે જેથી ડિપોઝિશન ચોક્કસ દિશામાં ચાલુ રહી શકે. આ કિસ્સાઓમાં, આધાર સામગ્રીને સ્તર પર ફિલામેન્ટના ઓછા ગાઢ અંતર સાથે બહાર કાઢવામાં આવે છે જેથી તે મોડેલ સામગ્રી કરતાં નબળી હોય. આ સપોર્ટ સ્ટ્રક્ચર્સ પાછળથી ઓગાળી શકાય છે અથવા ભાગ પૂર્ણ થયા પછી તોડી શકાય છે. એક્સ્ટ્રુડર ડાઇ પરિમાણો બહિષ્કૃત સ્તરોની જાડાઈ નક્કી કરે છે. એફડીએમ પ્રક્રિયા ત્રાંસી બાહ્ય વિમાનો પર સ્ટેપવાળી સપાટી સાથે ભાગોનું ઉત્પાદન કરે છે. જો આ ખરબચડી અસ્વીકાર્ય હોય, તો તેને સરળ બનાવવા માટે રાસાયણિક વરાળ પોલિશિંગ અથવા ગરમ સાધનનો ઉપયોગ કરી શકાય છે. આ પગલાંને દૂર કરવા અને વાજબી ભૌમિતિક સહિષ્ણુતા પ્રાપ્ત કરવા માટે પોલિશિંગ મીણ પણ કોટિંગ સામગ્રી તરીકે ઉપલબ્ધ છે. • સિલેક્ટિવ લેસર સિન્ટરિંગ : SLS તરીકે પણ સૂચવવામાં આવે છે, પ્રક્રિયા પોલિમર, સિરામિક અથવા મેટાલિક પાઉડરને પસંદ કરીને ઑબ્જેક્ટમાં સિન્ટરિંગ પર આધારિત છે. પ્રોસેસિંગ ચેમ્બરના તળિયે બે સિલિન્ડર છે: એક પાર્ટ-બિલ્ડ સિલિન્ડર અને પાવડર-ફીડ સિલિન્ડર. પહેલાના ભાગને ક્રમિક રીતે નીચે કરવામાં આવે છે જ્યાં સિન્ટર્ડ ભાગ બનાવવામાં આવે છે અને બાદમાં રોલર મિકેનિઝમ દ્વારા પાર્ટ-બિલ્ડ સિલિન્ડરને પાવડર સપ્લાય કરવા માટે વધતા જતા વધારો કરવામાં આવે છે. પહેલા પાર્ટ-બિલ્ડ સિલિન્ડરમાં પાવડરનો પાતળો પડ જમા કરવામાં આવે છે, પછી લેસર બીમ તે સ્તર પર ફોકસ કરવામાં આવે છે, ચોક્કસ ક્રોસ સેક્શનને ટ્રેસિંગ અને પીગળવું/સિન્ટરિંગ કરવામાં આવે છે, જે પછી નક્કર બની જાય છે. પાવડર એ વિસ્તારો છે જે લેસર બીમ દ્વારા અથડાતા નથી તે છૂટક રહે છે પરંતુ હજુ પણ નક્કર ભાગને ટેકો આપે છે. પછી પાવડરનો બીજો સ્તર જમા કરવામાં આવે છે અને ભાગ મેળવવા માટે પ્રક્રિયા ઘણી વખત પુનરાવર્તિત થાય છે. અંતે, છૂટક પાવડરના કણોને હલાવી દેવામાં આવે છે. આ તમામ પ્રક્રિયા-નિયંત્રણ કમ્પ્યુટર દ્વારા ઉત્પાદિત ભાગના 3D CAD પ્રોગ્રામ દ્વારા જનરેટ કરાયેલ સૂચનાઓનો ઉપયોગ કરીને હાથ ધરવામાં આવે છે. પોલિમર (જેમ કે ABS, PVC, પોલિએસ્ટર), મીણ, ધાતુઓ અને યોગ્ય પોલિમર બાઈન્ડર સાથે સિરામિક્સ જેવી વિવિધ સામગ્રીઓ જમા કરી શકાય છે. • ELECTRON-BEAM MELTING : પસંદગીના લેસર સિન્ટરિંગ જેવું જ છે, પરંતુ વેક્યૂમમાં પ્રોટોટાઇપ બનાવવા માટે ટાઇટેનિયમ અથવા કોબાલ્ટ ક્રોમ પાઉડરને ઓગળવા માટે ઇલેક્ટ્રોન બીમનો ઉપયોગ કરીને. સ્ટેનલેસ સ્ટીલ, એલ્યુમિનિયમ અને કોપર એલોય પર આ પ્રક્રિયા કરવા માટે કેટલાક વિકાસ કરવામાં આવ્યા છે. જો ઉત્પાદિત ભાગોની થાકની શક્તિ વધારવાની જરૂર હોય, તો અમે ગૌણ પ્રક્રિયા તરીકે ભાગોના ઉત્પાદન પછી ગરમ આઇસોસ્ટેટિક પ્રેસિંગનો ઉપયોગ કરીએ છીએ. • થ્રી-ડાયમેન્શનલ પ્રિન્ટિંગ : 3DP દ્વારા પણ સૂચવવામાં આવે છે, આ તકનીકમાં પ્રિન્ટ હેડ અકાર્બનિક બાઈન્ડરને નોનમેટાલિક અથવા મેટાલિક પાવડરના સ્તર પર જમા કરે છે. પાઉડર બેડ વહન કરતો પિસ્ટન ધીમે ધીમે નીચે કરવામાં આવે છે અને દરેક પગલા પર બાઈન્ડરને layer દ્વારા સ્તરમાં જમા કરવામાં આવે છે અને બાઈન્ડર દ્વારા ફ્યુઝ કરવામાં આવે છે. ઉપયોગમાં લેવાતી પાવડર સામગ્રી પોલિમર મિશ્રણો અને રેસા, ફાઉન્ડ્રી રેતી, ધાતુઓ છે. એકસાથે વિવિધ બાઈન્ડર હેડ અને વિવિધ કલર બાઈન્ડરનો ઉપયોગ કરીને આપણે વિવિધ રંગો મેળવી શકીએ છીએ. પ્રક્રિયા ઇંકજેટ પ્રિન્ટીંગ જેવી જ છે પરંતુ રંગીન શીટ મેળવવાને બદલે આપણે રંગીન ત્રિ-પરિમાણીય પદાર્થ મેળવીએ છીએ. ઉત્પાદિત ભાગો છિદ્રાળુ હોઈ શકે છે અને તેથી તેની ઘનતા અને શક્તિ વધારવા માટે સિન્ટરિંગ અને ધાતુની ઘૂસણખોરીની જરૂર પડી શકે છે. સિન્ટરિંગ બાઈન્ડરને બાળી નાખશે અને મેટલ પાવડરને એકસાથે જોડશે. ધાતુઓ જેમ કે સ્ટેનલેસ સ્ટીલ, એલ્યુમિનિયમ, ટાઇટેનિયમનો ઉપયોગ ભાગો બનાવવા માટે થઈ શકે છે અને ઘૂસણખોરી સામગ્રી તરીકે આપણે સામાન્ય રીતે તાંબા અને કાંસાનો ઉપયોગ કરીએ છીએ. આ તકનીકની સુંદરતા એ છે કે જટિલ અને મૂવિંગ એસેમ્બલીઓ પણ ખૂબ જ ઝડપથી ઉત્પાદન કરી શકાય છે. ઉદાહરણ તરીકે, ગિયર એસેમ્બલી, સાધન તરીકે રેન્ચ બનાવી શકાય છે અને તેમાં મૂવિંગ અને ટર્નિંગ ભાગો વાપરવા માટે તૈયાર હશે. એસેમ્બલીના વિવિધ ઘટકો વિવિધ રંગો સાથે અને બધા એક જ શોટમાં બનાવી શકાય છે. અમારી બ્રોશર આના પર ડાઉનલોડ કરો:મેટલ 3D પ્રિન્ટીંગ બેઝિક્સ • ડાયરેક્ટ મેન્યુફેક્ચરિંગ અને રેપિડ ટૂલિંગ : ડિઝાઇન મૂલ્યાંકન ઉપરાંત, મુશ્કેલીનિવારણ અમે ઉત્પાદનોના સીધા ઉત્પાદન અથવા ઉત્પાદનોમાં સીધા એપ્લિકેશન માટે ઝડપી પ્રોટોટાઇપિંગનો ઉપયોગ કરીએ છીએ. બીજા શબ્દોમાં કહીએ તો, ઝડપી પ્રોટોટાઇપિંગને પરંપરાગત પ્રક્રિયાઓમાં વધુ સારી અને વધુ સ્પર્ધાત્મક બનાવવા માટે સામેલ કરી શકાય છે. ઉદાહરણ તરીકે, ઝડપી પ્રોટોટાઇપિંગ પેટર્ન અને મોલ્ડ બનાવી શકે છે. ઝડપી પ્રોટોટાઇપિંગ કામગીરી દ્વારા બનાવવામાં આવેલ ગલન અને બર્નિંગ પોલિમરના પેટર્નને રોકાણ કાસ્ટિંગ માટે એસેમ્બલ કરી શકાય છે અને રોકાણ કરી શકાય છે. ઉલ્લેખ કરવા માટેનું બીજું ઉદાહરણ સિરામિક કાસ્ટિંગ શેલ બનાવવા અને શેલ કાસ્ટિંગ કામગીરી માટે તેનો ઉપયોગ કરવા માટે 3DP નો ઉપયોગ કરવાનું છે. ઇન્જેક્શન મોલ્ડ અને મોલ્ડ ઇન્સર્ટ પણ ઝડપી પ્રોટોટાઇપિંગ દ્વારા ઉત્પન્ન કરી શકાય છે અને વ્યક્તિ મોલ્ડ બનાવવાના લીડ ટાઇમના ઘણા અઠવાડિયા કે મહિનાઓ બચાવી શકે છે. ફક્ત ઇચ્છિત ભાગની CAD ફાઇલનું વિશ્લેષણ કરીને, અમે સોફ્ટવેરનો ઉપયોગ કરીને ટૂલ ભૂમિતિ બનાવી શકીએ છીએ. અહીં અમારી કેટલીક લોકપ્રિય ઝડપી ટૂલિંગ પદ્ધતિઓ છે: RTV (રૂમ-ટેમ્પરેચર વલ્કેનાઇઝિંગ) મોલ્ડિંગ / યુરેથેન કાસ્ટિંગ : ઝડપી પ્રોટોટાઇપિંગનો ઉપયોગ કરીને ઇચ્છિત ભાગની પેટર્ન બનાવવા માટે વાપરી શકાય છે. પછી આ પેટર્નને વિભાજન એજન્ટ સાથે કોટેડ કરવામાં આવે છે અને મોલ્ડના અર્ધભાગ બનાવવા માટે પેટર્ન પર પ્રવાહી RTV રબર રેડવામાં આવે છે. આગળ, આ મોલ્ડ અર્ધભાગનો ઉપયોગ મોલ્ડ લિક્વિડ યુરેથેન્સને ઇન્જેક્શન કરવા માટે થાય છે. મોલ્ડ લાઇફ ટૂંકી છે, માત્ર 0 અથવા 30 ચક્રની જેમ પરંતુ નાના બેચના ઉત્પાદન માટે પૂરતી છે. ACES (Acetal Clear Epoxy Solid) ઈન્જેક્શન મોલ્ડિંગ : સ્ટીરીઓલિથોગ્રાફી જેવી ઝડપી પ્રોટોટાઈપિંગ તકનીકોનો ઉપયોગ કરીને, અમે ઈન્જેક્શન મોલ્ડ બનાવીએ છીએ. ઇપોક્સી, એલ્યુમિનિયમથી ભરેલા ઇપોક્સી અથવા ધાતુઓ જેવી સામગ્રીઓથી ભરવાની મંજૂરી આપવા માટે આ મોલ્ડ ખુલ્લા છેડાવાળા શેલ છે. ફરીથી મોલ્ડ જીવન દસ અથવા મહત્તમ સેંકડો ભાગો સુધી મર્યાદિત છે. સ્પ્રેડ મેટલ ટૂલિંગ પ્રક્રિયા : અમે ઝડપી પ્રોટોટાઇપિંગનો ઉપયોગ કરીએ છીએ અને પેટર્ન બનાવીએ છીએ. અમે પેટર્નની સપાટી પર ઝીંક-એલ્યુમિનિયમ એલોય સ્પ્રે કરીએ છીએ અને તેને કોટ કરીએ છીએ. મેટલ કોટિંગ સાથેની પેટર્ન પછી ફ્લાસ્કની અંદર મૂકવામાં આવે છે અને ઇપોક્સી અથવા એલ્યુમિનિયમથી ભરેલા ઇપોક્સી સાથે પોટ કરવામાં આવે છે. અંતે, તેને દૂર કરવામાં આવે છે અને આવા બે મોલ્ડ અર્ધભાગ બનાવીને આપણે ઈન્જેક્શન મોલ્ડિંગ માટે સંપૂર્ણ મોલ્ડ મેળવીએ છીએ. આ મોલ્ડ લાંબા સમય સુધી જીવે છે, કેટલાક કિસ્સાઓમાં સામગ્રી અને તાપમાનના આધારે તેઓ હજારોમાં ભાગો ઉત્પન્ન કરી શકે છે. કીલટૂલ પ્રક્રિયા: આ તકનીક 100,000 થી 10 મિલિયન ચક્ર જીવન સાથે મોલ્ડ ઉત્પન્ન કરી શકે છે. ઝડપી પ્રોટોટાઇપિંગનો ઉપયોગ કરીને અમે આરટીવી મોલ્ડ બનાવીએ છીએ. પછી બીબામાં A6 ટૂલ સ્ટીલ પાઉડર, ટંગસ્ટન કાર્બાઈડ, પોલિમર બાઈન્ડર અને લેટ ટુ ક્યોર ધરાવતા મિશ્રણથી ભરવામાં આવે છે. આ મોલ્ડ પછી પોલિમરને બાળી નાખવા અને ધાતુના પાવડરને ફ્યુઝ કરવા માટે ગરમ કરવામાં આવે છે. આગલું પગલું અંતિમ ઘાટ બનાવવા માટે તાંબાની ઘૂસણખોરી છે. જો જરૂરી હોય તો, વધુ સારી પરિમાણીય ચોકસાઈ માટે મોલ્ડ પર મશીનિંગ અને પોલિશિંગ જેવી ગૌણ કામગીરી કરી શકાય છે. _cc781905-5cde-3194-bb3b-1358cd5 CLICK Product Finder-Locator Service પાછલું પૃષ્ઠ
- Glass and Ceramic Manufacturing, Hermetic Packages, Seals, Bonding
Glass and Ceramic Manufacturing, Hermetic Packages Seals and Bonding, Tempered Bulletproof Glass, Blow Moulding, Optical Grade Glass, Conductive Glass, Molding ગ્લાસ અને સિરામિક ફોર્મિંગ અને શેપિંગ અમે કન્ટેનર ગ્લાસ, ગ્લાસ બ્લોઇંગ, ગ્લાસ ફાઇબર અને ટ્યુબિંગ અને સળિયા, ઘરેલું અને ઔદ્યોગિક કાચનાં વાસણો, લેમ્પ અને બલ્બ, ચોકસાઇવાળા ગ્લાસ મોલ્ડિંગ, ઓપ્ટિકલ ઘટકો અને એસેમ્બલીઝ, ફ્લેટ અને શીટ અને ફ્લોટ ગ્લાસ જેવા કાચ ઉત્પાદનનો પ્રકાર ઓફર કરીએ છીએ. અમે હાથ બનાવવાની સાથે સાથે મશીનની રચના પણ કરીએ છીએ. અમારી લોકપ્રિય તકનીકી સિરામિક ઉત્પાદન પ્રક્રિયાઓ છે ડાઇ પ્રેસિંગ, આઇસોસ્ટેટિક પ્રેસિંગ, હોટ આઇસોસ્ટેટિક પ્રેસિંગ, હોટ પ્રેસિંગ, સ્લિપ કાસ્ટિંગ, ટેપ કાસ્ટિંગ, એક્સટ્રુઝન, ઇન્જેક્શન મોલ્ડિંગ, ગ્રીન મશીનિંગ, સિન્ટરિંગ અથવા ફાયરિંગ, ડાયમંડ ગ્રાઇન્ડિંગ, હર્મેટિક એસેમ્બલી. અમે ભલામણ કરીએ છીએ કે તમે અહીં ક્લિક કરો AGS-TECH Inc દ્વારા કાચની રચના અને આકાર આપવાની પ્રક્રિયાના અમારા યોજનાકીય ચિત્રો ડાઉનલોડ કરો. AGS-TECH Inc દ્વારા ટેકનિકલ સિરામિક મેન્યુફેક્ચરિંગ પ્રક્રિયાઓના અમારા યોજનાકીય ચિત્રો ડાઉનલોડ કરો. ફોટા અને સ્કેચ સાથેની આ ડાઉનલોડ કરી શકાય તેવી ફાઇલો અમે તમને નીચે આપેલી માહિતીને વધુ સારી રીતે સમજવામાં મદદ કરશે. • કન્ટેનર ગ્લાસ મેન્યુફેક્ચર: અમે મેન્યુફેક્ચરિંગ માટે સ્વચાલિત પ્રેસ અને બ્લો તેમજ બ્લો અને બ્લો લાઇન્સ છે. ફટકો અને ફૂંકવાની પ્રક્રિયામાં આપણે ખાલી ઘાટમાં ગોબ નાખીએ છીએ અને ઉપરથી સંકુચિત હવાનો ફટકો લગાવીને ગરદન બનાવીએ છીએ. આને તરત જ અનુસરીને, બોટલનું પૂર્વ-સ્વરૂપ બનાવવા માટે કન્ટેનરની ગરદન દ્વારા બીજી દિશામાં સંકુચિત હવાને બીજી વખત ફૂંકવામાં આવે છે. આ પૂર્વ-સ્વરૂપને પછી વાસ્તવિક ઘાટમાં સ્થાનાંતરિત કરવામાં આવે છે, તેને નરમ કરવા માટે ફરીથી ગરમ કરવામાં આવે છે અને પ્રી-ફોર્મને તેના અંતિમ પાત્રનો આકાર આપવા માટે સંકુચિત હવા લાગુ કરવામાં આવે છે. વધુ સ્પષ્ટ રીતે, તે દબાણ કરે છે અને તેનો ઇચ્છિત આકાર લેવા માટે બ્લો મોલ્ડ કેવિટીની દિવાલો સામે દબાણ કરવામાં આવે છે. છેલ્લે, ઉત્પાદિત કાચના કન્ટેનરને અનુગામી ફરીથી ગરમ કરવા અને મોલ્ડિંગ દરમિયાન ઉત્પન્ન થતા તાણને દૂર કરવા માટે એનેલીંગ ઓવનમાં સ્થાનાંતરિત કરવામાં આવે છે અને તેને નિયંત્રિત રીતે ઠંડુ કરવામાં આવે છે. પ્રેસ અને બ્લો પદ્ધતિમાં, પીગળેલા ગોબ્સને પેરિઝન મોલ્ડ (ખાલી મોલ્ડ) માં નાખવામાં આવે છે અને પેરિઝન આકાર (ખાલી આકાર) માં દબાવવામાં આવે છે. પછી બ્લો મોલ્ડમાં બ્લોક્સ ટ્રાન્સફર કરવામાં આવે છે અને "બ્લો એન્ડ બ્લો પ્રોસેસ" હેઠળ ઉપર વર્ણવેલ પ્રક્રિયાની જેમ જ ફૂંકાય છે. અનુગામી પગલાં જેવા કે એનેલીંગ અને તાણ રાહત સમાન અથવા સમાન છે. • ગ્લાસ બ્લોઇંગ : અમે પરંપરાગત હેન્ડ બ્લોઇંગનો ઉપયોગ કરીને તેમજ ઓટોમેટેડ સાધનો સાથે કોમ્પ્રેસ્ડ એરનો ઉપયોગ કરીને કાચના ઉત્પાદનોનું ઉત્પાદન કરીએ છીએ. કેટલાક ઓર્ડર માટે પરંપરાગત બ્લોઇંગ જરૂરી છે, જેમ કે ગ્લાસ આર્ટ વર્ક સાથે સંકળાયેલા પ્રોજેક્ટ્સ અથવા એવા પ્રોજેક્ટ કે જેમાં છૂટક સહિષ્ણુતાવાળા ભાગોની નાની સંખ્યાની જરૂર હોય, પ્રોટોટાઇપિંગ / ડેમો પ્રોજેક્ટ્સ….વગેરે. પરંપરાગત કાચ ફૂંકવામાં હોલો મેટલ પાઇપને પીગળેલા કાચના વાસણમાં ડૂબવું અને કાચની સામગ્રીનો થોડો જથ્થો એકત્ર કરવા માટે પાઇપને ફેરવવાનો સમાવેશ થાય છે. પાઇપની ટોચ પર એકત્ર કરાયેલ કાચને સપાટ લોખંડ પર ફેરવવામાં આવે છે, તેને ઇચ્છિત આકાર આપવામાં આવે છે, વિસ્તરેલ, ફરીથી ગરમ કરવામાં આવે છે અને હવા ફૂંકાય છે. જ્યારે તૈયાર થાય છે, ત્યારે તેને ઘાટમાં દાખલ કરવામાં આવે છે અને હવા ફૂંકાય છે. ધાતુ સાથે કાચના સંપર્કને ટાળવા માટે ઘાટની પોલાણ ભીની છે. પાણીની ફિલ્મ તેમની વચ્ચે ગાદી જેવું કામ કરે છે. મેન્યુઅલ બ્લોઇંગ એ શ્રમ-સઘન ધીમી પ્રક્રિયા છે અને માત્ર પ્રોટોટાઇપિંગ અથવા ઉચ્ચ મૂલ્યની વસ્તુઓ માટે યોગ્ય છે, જે સસ્તી પ્રતિ પીસ ઉચ્ચ વોલ્યુમ ઓર્ડર માટે યોગ્ય નથી. • ઘરેલું અને ઔદ્યોગિક કાચનાં વાસણોનું ઉત્પાદન: વિવિધ પ્રકારની કાચની સામગ્રીનો ઉપયોગ કરીને કાચનાં વાસણોની વિશાળ વિવિધતા બનાવવામાં આવી રહી છે. કેટલાક ચશ્મા ગરમી પ્રતિરોધક હોય છે અને પ્રયોગશાળાના કાચના વાસણો માટે યોગ્ય હોય છે જ્યારે કેટલાક ડીશવોશરને ઘણી વખત ટકી શકે તેટલા સારા હોય છે અને ઘરેલું ઉત્પાદનો બનાવવા માટે યોગ્ય હોય છે. વેસ્ટલેક મશીનોનો ઉપયોગ કરીને દરરોજ પીવાના ગ્લાસના હજારો ટુકડાઓ બનાવવામાં આવે છે. સરળ બનાવવા માટે, પીગળેલા કાચને શૂન્યાવકાશ દ્વારા એકત્રિત કરવામાં આવે છે અને પૂર્વ-સ્વરૂપ બનાવવા માટે મોલ્ડમાં દાખલ કરવામાં આવે છે. પછી હવાને મોલ્ડમાં ફૂંકવામાં આવે છે, તે બીજા ઘાટમાં સ્થાનાંતરિત થાય છે અને હવા ફરીથી ફૂંકાય છે અને કાચ તેનો અંતિમ આકાર લે છે. હાથ ફૂંકવાની જેમ, આ મોલ્ડને પાણીથી ભીના રાખવામાં આવે છે. વધુ સ્ટ્રેચિંગ એ અંતિમ કામગીરીનો એક ભાગ છે જ્યાં ગરદનની રચના કરવામાં આવી રહી છે. વધારાનો કાચ બળી જાય છે. ત્યારબાદ ઉપર વર્ણવેલ નિયંત્રિત રી-હીટિંગ અને કૂલિંગ પ્રક્રિયા નીચે મુજબ છે. • ગ્લાસ ટ્યુબ અને રોડ ફોર્મિંગ : ગ્લાસ ટ્યુબના ઉત્પાદન માટે આપણે જે મુખ્ય પ્રક્રિયાઓનો ઉપયોગ કરીએ છીએ તે ડેનર અને વેલો પ્રક્રિયાઓ છે. ડેનર પ્રક્રિયામાં, ભઠ્ઠીમાંથી કાચ વહે છે અને પ્રત્યાવર્તન સામગ્રીથી બનેલી ઢાળવાળી સ્લીવ પર પડે છે. સ્લીવને ફરતી હોલો શાફ્ટ અથવા બ્લોપાઇપ પર લઈ જવામાં આવે છે. પછી કાચને સ્લીવની આસપાસ વીંટાળવામાં આવે છે અને સ્લીવની નીચે અને શાફ્ટની ટોચ પર વહેતો એક સરળ સ્તર બનાવે છે. ટ્યુબના નિર્માણના કિસ્સામાં, હોલો ટીપ સાથે બ્લોપાઇપ દ્વારા હવા ફૂંકાય છે, અને સળિયાના નિર્માણના કિસ્સામાં આપણે શાફ્ટ પર નક્કર ટીપ્સનો ઉપયોગ કરીએ છીએ. પછી ટ્યુબ અથવા સળિયા વહન રોલરો પર દોરવામાં આવે છે. દિવાલની જાડાઈ અને કાચની નળીઓના વ્યાસ જેવા પરિમાણોને સ્લીવનો વ્યાસ સેટ કરીને અને હવાના દબાણને ઇચ્છિત મૂલ્યમાં ફૂંકીને, તાપમાન, કાચના પ્રવાહનો દર અને ચિત્રની ઝડપને સમાયોજિત કરીને ઇચ્છિત મૂલ્યો સાથે ગોઠવવામાં આવે છે. બીજી તરફ વેલો ગ્લાસ ટ્યુબ ઉત્પાદન પ્રક્રિયામાં કાચનો સમાવેશ થાય છે જે ભઠ્ઠીમાંથી બહાર નીકળે છે અને હોલો મેન્ડ્રેલ અથવા બેલ સાથે બાઉલમાં જાય છે. કાચ પછી મેન્ડ્રેલ અને બાઉલ વચ્ચેની હવાની જગ્યામાંથી પસાર થાય છે અને નળીનો આકાર લે છે. ત્યારપછી તે રોલરો ઉપરથી ડ્રોઈંગ મશીનમાં જાય છે અને ઠંડુ થાય છે. કૂલિંગ લાઇનના અંતે કટીંગ અને અંતિમ પ્રક્રિયા થાય છે. ટ્યુબના પરિમાણોને ડેનર પ્રક્રિયાની જેમ જ એડજસ્ટ કરી શકાય છે. વેલો પ્રક્રિયા સાથે ડેનરની સરખામણી કરતી વખતે, અમે કહી શકીએ કે વેલો પ્રક્રિયા મોટા જથ્થાના ઉત્પાદન માટે વધુ યોગ્ય છે જ્યારે ડેનર પ્રક્રિયા ચોક્કસ નાના વોલ્યુમ ટ્યુબ ઓર્ડર માટે વધુ યોગ્ય હોઈ શકે છે. • શીટ અને ફ્લેટ અને ફ્લોટ ગ્લાસની પ્રક્રિયા: અમારી પાસે સબમિલીમીટર જાડાઈથી લઈને કેટલાક સેન્ટિમીટર સુધીની જાડાઈમાં ફ્લેટ ગ્લાસનો મોટો જથ્થો છે. અમારા ફ્લેટ ચશ્મા લગભગ ઓપ્ટિકલ પરફેક્શનના છે. અમે ઓપ્ટિકલ કોટિંગ્સ જેવા વિશિષ્ટ કોટિંગ્સ સાથે કાચની ઑફર કરીએ છીએ, જ્યાં રાસાયણિક વરાળ ડિપોઝિશન તકનીકનો ઉપયોગ એન્ટિ-રિફ્લેક્શન અથવા મિરર કોટિંગ જેવા કોટિંગ્સ મૂકવા માટે થાય છે. પારદર્શક વાહક કોટિંગ પણ સામાન્ય છે. કાચ પરના હાઇડ્રોફોબિક અથવા હાઇડ્રોફિલિક કોટિંગ્સ અને કોટિંગ જે કાચની સ્વ-સફાઈ કરે છે તે પણ ઉપલબ્ધ છે. ટેમ્પર્ડ, બુલેટપ્રૂફ અને લેમિનેટેડ ચશ્મા હજી અન્ય લોકપ્રિય વસ્તુઓ છે. અમે ઇચ્છિત સહિષ્ણુતા સાથે કાચને ઇચ્છિત આકારમાં કાપીએ છીએ. અન્ય ગૌણ કામગીરી જેમ કે વળાંક અથવા ફ્લેટ ગ્લાસ બેન્ડિંગ ઉપલબ્ધ છે. • પ્રિસિશન ગ્લાસ મોલ્ડિંગ : અમે આ ટેકનિકનો ઉપયોગ મોટાભાગે ગ્રાઇન્ડિંગ, લેપિંગ અને પોલિશિંગ જેવી વધુ ખર્ચાળ અને સમય લેતી તકનીકોની જરૂર વગર ચોકસાઇવાળા ઓપ્ટિકલ ઘટકોના ઉત્પાદન માટે કરીએ છીએ. શ્રેષ્ઠ ઓપ્ટિક્સમાંથી શ્રેષ્ઠ બનાવવા માટે આ ટેકનિક હંમેશા પર્યાપ્ત નથી, પરંતુ ગ્રાહક ઉત્પાદનો, ડિજિટલ કેમેરા, મેડિકલ ઓપ્ટિક્સ જેવા કેટલાક કિસ્સાઓમાં તે ઉચ્ચ વોલ્યુમ ઉત્પાદન માટે ઓછો ખર્ચાળ સારો વિકલ્પ બની શકે છે. તેમજ તે કાચ બનાવવાની અન્ય તકનીકો પર એક ફાયદો ધરાવે છે જ્યાં જટિલ ભૂમિતિ જરૂરી હોય છે, જેમ કે એસ્ફિયર્સના કિસ્સામાં. મૂળભૂત પ્રક્રિયામાં અમારા ઘાટની નીચેની બાજુને કાચની ખાલી સાથે લોડ કરવી, ઓક્સિજન દૂર કરવા માટે પ્રક્રિયા ચેમ્બરને ખાલી કરવી, ઘાટ બંધ થવાની નજીક, ઇન્ફ્રારેડ લાઇટ સાથે ડાઇ અને ગ્લાસને ઝડપી અને ઇસોથર્મલ હીટિંગ, મોલ્ડના અડધા ભાગને વધુ બંધ કરવાનો સમાવેશ થાય છે. નરમ પડેલા કાચને ધીમે ધીમે નિયંત્રિત રીતે ઇચ્છિત જાડાઈ સુધી દબાવવા માટે, અને અંતે કાચને ઠંડુ કરીને અને ચેમ્બરને નાઈટ્રોજનથી ભરીને ઉત્પાદનને દૂર કરવું. ચોક્કસ તાપમાન નિયંત્રણ, ઘાટ બંધ થવાનું અંતર, ઘાટ બંધ થવાનું બળ, મોલ્ડના વિસ્તરણના ગુણાંક અને કાચની સામગ્રી સાથે મેળ આ પ્રક્રિયામાં ચાવીરૂપ છે. • ગ્લાસ ઓપ્ટિકલ ઘટકો અને એસેમ્બલીઓનું ઉત્પાદન : ચોકસાઇવાળા ગ્લાસ મોલ્ડિંગ ઉપરાંત, અમે ઉચ્ચ ગુણવત્તાવાળા ઓપ્ટિકલ ઘટકો અને એસેમ્બલીની માંગણી માટે ઉપયોગ કરવા માટે ઘણી મૂલ્યવાન પ્રક્રિયાઓનો ઉપયોગ કરીએ છીએ. ઓપ્ટિકલ ગ્રેડના ચશ્માને ઝીણી ખાસ ઘર્ષક સ્લરીઝમાં ગ્રાઇન્ડીંગ, લેપિંગ અને પોલિશ કરવું એ ઓપ્ટિકલ લેન્સ, પ્રિઝમ, ફ્લેટ અને વધુ બનાવવા માટે એક કળા અને વિજ્ઞાન છે. સપાટીની સપાટતા, વેવિનેસ, સ્મૂથનેસ અને ખામી રહિત ઓપ્ટિકલ સપાટીઓને આવી પ્રક્રિયાઓમાં ઘણો અનુભવ જરૂરી છે. પર્યાવરણમાં નાના ફેરફારો સ્પષ્ટીકરણ ઉત્પાદનોમાં પરિણમી શકે છે અને ઉત્પાદન લાઇનને બંધ કરી શકે છે. એવા કિસ્સાઓ છે કે જ્યાં સ્વચ્છ કપડાથી ઓપ્ટિકલ સપાટી પર એક જ લૂછવાથી ઉત્પાદન સ્પષ્ટીકરણોને પૂર્ણ કરી શકે છે અથવા પરીક્ષણમાં નિષ્ફળ જઈ શકે છે. ઉપયોગમાં લેવાતી કેટલીક લોકપ્રિય કાચ સામગ્રી ફ્યુઝ્ડ સિલિકા, ક્વાર્ટઝ, BK7 છે. ઉપરાંત આવા ઘટકોની એસેમ્બલી માટે વિશિષ્ટ વિશિષ્ટ અનુભવની જરૂર છે. કેટલીકવાર ખાસ ગુંદરનો ઉપયોગ કરવામાં આવે છે. જો કે, કેટલીકવાર ઓપ્ટિકલ કોન્ટેક્ટીંગ તરીકે ઓળખાતી ટેકનિક શ્રેષ્ઠ પસંદગી હોય છે અને તેમાં જોડાયેલા ઓપ્ટિકલ ચશ્મા વચ્ચે કોઈ સામગ્રીનો સમાવેશ થતો નથી. તેમાં ગુંદર વિના એકબીજા સાથે જોડવા માટે ભૌતિક રીતે સપાટ સપાટીઓનો સંપર્ક કરવામાં આવે છે. કેટલાક કિસ્સાઓમાં યાંત્રિક સ્પેસર્સ, ચોકસાઇવાળા કાચના સળિયા અથવા બોલ, ક્લેમ્પ્સ અથવા મશિન મેટલ ઘટકોનો ઉપયોગ ચોક્કસ અંતર પર અને ચોક્કસ ભૌમિતિક અભિગમ સાથે ઓપ્ટિકલ ઘટકોને એકબીજા સાથે એસેમ્બલ કરવા માટે કરવામાં આવે છે. ચાલો હાઇ એન્ડ ઓપ્ટિક્સના ઉત્પાદન માટે અમારી કેટલીક લોકપ્રિય તકનીકોનું પરીક્ષણ કરીએ. ગ્રાઇન્ડિંગ અને લેપિંગ અને પોલિશિંગ : ઓપ્ટિકલ કમ્પોનન્ટનો ખરબચડો આકાર એક ગ્લાસ બ્લેન્કને ગ્રાઇન્ડ કરીને મેળવવામાં આવે છે. ત્યારપછી ઓપ્ટિકલ ઘટકોની ખરબચડી સપાટીને ઇચ્છિત સપાટીના આકારવાળા ટૂલ્સ સામે ફેરવીને અને ઘસીને લેપિંગ અને પોલિશિંગ હાથ ધરવામાં આવે છે. ઓપ્ટિક્સ અને આકાર આપવાના સાધનો વચ્ચે નાના ઘર્ષક કણો અને પ્રવાહી સાથે સ્લરી રેડવામાં આવી રહી છે. આવા સ્લરીઝમાં ઘર્ષક કણોનું કદ ઇચ્છિત સપાટતાની ડિગ્રી અનુસાર પસંદ કરી શકાય છે. ઇચ્છિત આકારમાંથી નિર્ણાયક ઓપ્ટિકલ સપાટીઓના વિચલનો ઉપયોગ કરવામાં આવતા પ્રકાશની તરંગલંબાઇના સંદર્ભમાં વ્યક્ત કરવામાં આવે છે. અમારા ઉચ્ચ ચોકસાઇવાળા ઓપ્ટિક્સમાં તરંગલંબાઇનો દસમો ભાગ (તરંગલંબાઇ/10) સહનશીલતા હોય છે અથવા તેનાથી પણ વધુ ચુસ્ત શક્ય છે. સપાટીની રૂપરેખા ઉપરાંત, નિર્ણાયક સપાટીઓ સ્કેન કરવામાં આવે છે અને અન્ય સપાટીના લક્ષણો અને ખામીઓ જેમ કે પરિમાણો, સ્ક્રેચ, ચિપ્સ, ખાડાઓ, સ્પેક્સ... વગેરે માટે મૂલ્યાંકન કરવામાં આવે છે. ઓપ્ટિકલ મેન્યુફેક્ચરિંગ ફ્લોરમાં પર્યાવરણીય પરિસ્થિતિઓનું ચુસ્ત નિયંત્રણ અને અત્યાધુનિક સાધનો સાથે વ્યાપક મેટ્રોલોજી અને પરીક્ષણ આવશ્યકતાઓ આને ઉદ્યોગની એક પડકારરૂપ શાખા બનાવે છે. • ગ્લાસ મેન્યુફેક્ચરિંગમાં સેકન્ડરી પ્રક્રિયાઓ: ફરીથી, જ્યારે કાચની સેકન્ડરી અને ફિનિશિંગ પ્રક્રિયાઓની વાત આવે છે ત્યારે અમે ફક્ત તમારી કલ્પના સાથે મર્યાદિત છીએ. અહીં અમે તેમાંના કેટલાકને સૂચિબદ્ધ કરીએ છીએ: -કાચ પર કોટિંગ્સ (ઓપ્ટિકલ, ઇલેક્ટ્રિકલ, ટ્રાઇબોલોજિકલ, થર્મલ, ફંક્શનલ, મિકેનિકલ...). ઉદાહરણ તરીકે આપણે કાચની સપાટીના ગુણધર્મોને બદલી શકીએ છીએ, ઉદાહરણ તરીકે તે ગરમીને પ્રતિબિંબિત કરે છે જેથી તે મકાનના આંતરિક ભાગોને ઠંડુ રાખે, અથવા નેનો ટેકનોલોજીનો ઉપયોગ કરીને એક બાજુ ઇન્ફ્રારેડ શોષી શકે. આ ઇમારતોની અંદરના ભાગને ગરમ રાખવામાં મદદ કરે છે કારણ કે કાચની સૌથી બહારની સપાટીનું સ્તર ઇન્ફ્રારેડ કિરણોત્સર્ગને ઇમારતની અંદર શોષી લેશે અને તેને અંદરથી પાછું રેડિયેટ કરશે. -એચિંગ on કાચ -એપ્લાઇડ સિરામિક લેબલીંગ (ACL) - કોતરણી - ફ્લેમ પોલિશિંગ - કેમિકલ પોલિશિંગ - સ્ટેનિંગ ટેકનિકલ સિરામિક્સનું ઉત્પાદન • ડાઇ પ્રેસિંગ : ડાઇમાં બંધાયેલા દાણાદાર પાવડરના અક્ષીય કોમ્પેક્શનનો સમાવેશ થાય છે • હોટ પ્રેસિંગ: ડાઇ પ્રેસિંગ જેવું જ છે પરંતુ ઘનતા વધારવા માટે તાપમાનના ઉમેરા સાથે. પાઉડર અથવા કોમ્પેક્ટેડ પ્રીફોર્મ ગ્રેફાઇટ ડાઇમાં મૂકવામાં આવે છે અને ડાઇને 2000 સે. જેવા ઊંચા તાપમાને રાખવામાં આવે છે ત્યારે અક્ષીય દબાણ લાગુ કરવામાં આવે છે. સિરામિક પાવડરની પ્રક્રિયાના પ્રકારને આધારે તાપમાન અલગ અલગ હોઈ શકે છે. જટિલ આકારો અને ભૂમિતિઓ માટે અન્ય અનુગામી પ્રક્રિયા જેમ કે ડાયમંડ ગ્રાઇન્ડીંગની જરૂર પડી શકે છે. • આઇસોસ્ટેટિક પ્રેસિંગ : દાણાદાર પાવડર અથવા ડાઇ પ્રેસ્ડ કોમ્પેક્ટને હવાચુસ્ત કન્ટેનરમાં અને પછી અંદર પ્રવાહી સાથે બંધ દબાણ જહાજમાં મૂકવામાં આવે છે. ત્યારબાદ તેઓ દબાણયુક્ત જહાજના દબાણને વધારીને કોમ્પેક્ટ કરવામાં આવે છે. જહાજની અંદરનું પ્રવાહી હવાચુસ્ત કન્ટેનરની સમગ્ર સપાટીના વિસ્તાર પર દબાણ દળોને એકસરખી રીતે સ્થાનાંતરિત કરે છે. આમ સામગ્રી એકસરખી રીતે કોમ્પેક્ટ કરવામાં આવે છે અને તેના લવચીક કન્ટેનર અને તેની આંતરિક પ્રોફાઇલ અને સુવિધાઓનો આકાર લે છે. • હોટ આઇસોસ્ટેટિક પ્રેસિંગ : આઇસોસ્ટેટિક પ્રેસિંગ જેવું જ, પરંતુ દબાણયુક્ત ગેસ વાતાવરણ ઉપરાંત, અમે ઉચ્ચ તાપમાને કોમ્પેક્ટને સિન્ટર કરીએ છીએ. ગરમ આઇસોસ્ટેટિક દબાવવાથી વધારાની ઘનતા અને શક્તિ વધે છે. • સ્લિપ કાસ્ટિંગ / ડ્રેઇન કાસ્ટિંગ : અમે માઇક્રોમીટરના કદના સિરામિક કણો અને વાહક પ્રવાહીના સસ્પેન્શન સાથે મોલ્ડ ભરીએ છીએ. આ મિશ્રણને "સ્લિપ" કહેવામાં આવે છે. ઘાટમાં છિદ્રો હોય છે અને તેથી મિશ્રણમાંનું પ્રવાહી ઘાટમાં ફિલ્ટર થાય છે. પરિણામે, ઘાટની આંતરિક સપાટી પર કાસ્ટ રચાય છે. સિન્ટરિંગ પછી, ભાગોને ઘાટમાંથી બહાર લઈ શકાય છે. • ટેપ કાસ્ટિંગ : અમે ફ્લેટ મૂવિંગ કેરિયર સપાટી પર સિરામિક સ્લરી કાસ્ટ કરીને સિરામિક ટેપનું ઉત્પાદન કરીએ છીએ. સ્લરીમાં બંધન અને વહન હેતુ માટે અન્ય રસાયણો સાથે મિશ્રિત સિરામિક પાવડર હોય છે. જેમ જેમ દ્રાવકનું બાષ્પીભવન થાય છે તેમ સિરામિકની ગાઢ અને લવચીક શીટ્સ પાછળ રહી જાય છે જેને ઈચ્છા મુજબ કાપી અથવા રોલ કરી શકાય છે. • એક્સ્ટ્રુઝન ફોર્મિંગ : અન્ય એક્સટ્રુઝન પ્રક્રિયાઓની જેમ, બાઈન્ડર અને અન્ય રસાયણો સાથે સિરામિક પાવડરનું નરમ મિશ્રણ તેનો ક્રોસ-સેક્શનલ આકાર પ્રાપ્ત કરવા માટે ડાઈમાંથી પસાર થાય છે અને પછી ઇચ્છિત લંબાઈમાં કાપવામાં આવે છે. પ્રક્રિયા ઠંડા અથવા ગરમ સિરામિક મિશ્રણ સાથે કરવામાં આવે છે. • લો પ્રેશર ઈન્જેક્શન મોલ્ડિંગ : અમે બાઈન્ડર અને સોલવન્ટ્સ સાથે સિરામિક પાવડરનું મિશ્રણ તૈયાર કરીએ છીએ અને તેને એવા તાપમાને ગરમ કરીએ છીએ જ્યાં તેને સરળતાથી દબાવી શકાય અને ટૂલ કેવિટીમાં દબાણ કરી શકાય. એકવાર મોલ્ડિંગ ચક્ર પૂર્ણ થઈ જાય, તે ભાગને બહાર કાઢવામાં આવે છે અને બંધનકર્તા રસાયણને બાળી નાખવામાં આવે છે. ઈન્જેક્શન મોલ્ડિંગનો ઉપયોગ કરીને, અમે આર્થિક રીતે ઉચ્ચ વોલ્યુમ પર જટિલ ભાગો મેળવી શકીએ છીએ. છિદ્રો જે 10 મીમી જાડા દિવાલ પર મિલિમીટરનો નાનો અપૂર્ણાંક છે તે શક્ય છે, આગળના મશીનિંગ વિના થ્રેડો શક્ય છે, +/- 0.5% જેટલી ચુસ્ત સહનશીલતા શક્ય છે અને મશીનના ભાગો પણ ઓછા હોય ત્યારે , 0.5mm થી 12.5 mm લંબાઈના ક્રમમાં દિવાલની જાડાઈ શક્ય છે તેમજ 6.5mm થી 150mm લંબાઈની દિવાલની જાડાઈ શક્ય છે. • ગ્રીન મશીનિંગ : સમાન ધાતુના મશીનિંગ ટૂલ્સનો ઉપયોગ કરીને, અમે દબાવવામાં આવેલી સિરામિક સામગ્રીને મશીન કરી શકીએ છીએ જ્યારે તે હજી પણ ચાકની જેમ નરમ હોય છે. +/- 1% ની સહનશીલતા શક્ય છે. વધુ સારી સહિષ્ણુતા માટે અમે હીરા ગ્રાઇન્ડીંગનો ઉપયોગ કરીએ છીએ. • સિન્ટરિંગ અથવા ફાયરિંગ : સિન્ટરિંગ સંપૂર્ણ ઘનતા શક્ય બનાવે છે. ગ્રીન કોમ્પેક્ટ ભાગો પર નોંધપાત્ર સંકોચન થાય છે, પરંતુ આ કોઈ મોટી સમસ્યા નથી કારણ કે જ્યારે આપણે ભાગ અને ટૂલિંગની રચના કરીએ છીએ ત્યારે આ પરિમાણીય ફેરફારોને ધ્યાનમાં લઈએ છીએ. પાવડર કણો એકબીજા સાથે જોડાયેલા હોય છે અને કોમ્પેક્શન પ્રક્રિયા દ્વારા પ્રેરિત છિદ્રાળુતા ઘણી હદ સુધી દૂર થાય છે. • ડાયમંડ ગ્રાઇન્ડીંગ: વિશ્વની સૌથી સખત સામગ્રી "હીરા" નો ઉપયોગ સિરામિક્સ જેવી સખત સામગ્રીને ગ્રાઇન્ડ કરવા માટે કરવામાં આવે છે અને ચોક્કસ ભાગો મેળવવામાં આવે છે. માઇક્રોમીટર શ્રેણીમાં સહનશીલતા અને ખૂબ જ સરળ સપાટીઓ પ્રાપ્ત કરવામાં આવી રહી છે. તેના ખર્ચને લીધે, અમે ફક્ત ત્યારે જ આ તકનીકને ધ્યાનમાં લઈએ છીએ જ્યારે અમને ખરેખર તેની જરૂર હોય. • હર્મેટિક એસેમ્બલીઓ એવી છે કે જે વ્યવહારીક રીતે કહીએ તો ઇન્ટરફેસ વચ્ચે દ્રવ્ય, ઘન, પ્રવાહી અથવા વાયુઓના કોઈપણ વિનિમયને મંજૂરી આપતા નથી. હર્મેટિક સીલિંગ હવાચુસ્ત છે. ઉદાહરણ તરીકે હર્મેટિક ઈલેક્ટ્રોનિક એન્ક્લોઝર્સ એવા છે કે જે પેકેજ્ડ ડિવાઈસની સંવેદનશીલ આંતરિક સામગ્રીને ભેજ, દૂષકો અથવા વાયુઓથી અસુરક્ષિત રાખે છે. કંઈપણ 100% હર્મેટિક નથી, પરંતુ જ્યારે આપણે હર્મેટીસીટી વિશે વાત કરીએ છીએ ત્યારે અમારો અર્થ એ છે કે વ્યવહારિક દ્રષ્ટિએ, ત્યાં હર્મેટીસીટી એટલી હદે છે કે લીક દર એટલો ઓછો છે કે ઉપકરણો ખૂબ લાંબા સમય સુધી સામાન્ય પર્યાવરણીય પરિસ્થિતિઓમાં સુરક્ષિત છે. અમારી હર્મેટિક એસેમ્બલીમાં મેટલ, ગ્લાસ અને સિરામિક ઘટકો, મેટલ-સિરામિક, સિરામિક-મેટલ-સિરામિક, મેટલ-સિરામિક-મેટલ, મેટલથી મેટલ, મેટલ-ગ્લાસ, મેટલ-ગ્લાસ-મેટલ, ગ્લાસ-મેટલ-ગ્લાસ, ગ્લાસ- મેટલ અને ગ્લાસથી ગ્લાસ અને મેટલ-ગ્લાસ-સિરામિક બોન્ડિંગના અન્ય તમામ સંયોજનો. અમે ઉદાહરણ તરીકે સિરામિક ઘટકોને મેટલ કોટ કરી શકીએ છીએ જેથી તેઓ એસેમ્બલીમાં અન્ય ઘટકો સાથે મજબૂત રીતે બંધાઈ શકે અને ઉત્તમ સીલિંગ ક્ષમતા ધરાવે છે. અમારી પાસે ઓપ્ટિકલ ફાઇબર અથવા ફીડથ્રુને મેટલ સાથે કોટિંગ કરવાની અને સોલ્ડરિંગ અથવા તેમને બિડાણમાં બ્રેઝિંગ કરવાની જાણકારી છે, જેથી કોઈ વાયુઓ બિડાણમાં પસાર થતા નથી અથવા લીક થતા નથી. તેથી તેનો ઉપયોગ સંવેદનશીલ ઉપકરણોને સમાવી લેવા અને બાહ્ય વાતાવરણથી રક્ષણ કરવા માટે ઇલેક્ટ્રોનિક બિડાણના ઉત્પાદન માટે થાય છે. તેમની ઉત્કૃષ્ટ સીલિંગ લાક્ષણિકતાઓ ઉપરાંત, અન્ય ગુણધર્મો જેમ કે થર્મલ વિસ્તરણ ગુણાંક, વિરૂપતા પ્રતિકાર, બિન-આઉટગેસિંગ પ્રકૃતિ, ખૂબ લાંબી આયુષ્ય, બિન-વાહક પ્રકૃતિ, થર્મલ ઇન્સ્યુલેશન ગુણધર્મો, એન્ટિસ્ટેટિક પ્રકૃતિ... વગેરે. કાચ અને સિરામિક સામગ્રીને ચોક્કસ એપ્લિકેશન માટે પસંદગી બનાવો. સિરામિકથી મેટલ ફિટિંગ, હર્મેટિક સીલિંગ, વેક્યૂમ ફીડથ્રૂ, હાઈ અને અલ્ટ્રાહાઈ વેક્યુમ અને ફ્લુઈડ કંટ્રોલ ઘટકો ઉત્પાદન કરતી અમારી સુવિધા વિશેની માહિતી અહીં મળી શકે છે:હર્મેટિક ઘટકો ફેક્ટરી બ્રોશર CLICK Product Finder-Locator Service પાછલું પૃષ્ઠ
- Wire & Spring Forming, Shaping, Welding, Assembly of Wires, Coil, CNC
Wire & Spring Forming, Shaping, Welding, Assembly of Wires, Coil Compression Extension Torsion Flat Springs, Custom Wires, Helical Springs at AGS-TECH Inc. વાયર અને સ્પ્રિંગ રચના અમે કસ્ટમ વાયર, વાયર એસેમ્બલી, ઇચ્છિત 2D અને 3D આકારમાં બનેલા વાયર, વાયર નેટ, જાળી, બિડાણ, બાસ્કેટ, વાડ, વાયર સ્પ્રિંગ, ફ્લેટ સ્પ્રિંગનું ઉત્પાદન કરીએ છીએ; ટોર્સિયન, કમ્પ્રેશન, ટેન્શન, ફ્લેટ સ્પ્રિંગ્સ અને વધુ. અમારી પ્રક્રિયાઓ છે વાયર અને સ્પ્રિંગ ફોર્મિંગ, વાયર ડ્રોઇંગ, શેપિંગ, બેન્ડિંગ, વેલ્ડિંગ, બ્રેઝિંગ, સોલ્ડરિંગ, પિઅરિંગ, સ્વેઝિંગ, ડ્રિલિંગ, ચેમ્ફરિંગ, ગ્રાઇન્ડિંગ, થ્રેડિંગ, કોટિંગ, ફોરસ્લાઇડ, સ્લાઇડ ફોર્મિંગ, વાઇન્ડિંગ, કોઇલિંગ, અપસેટિંગ. અમે ભલામણ કરીએ છીએ કે તમે અહીં ક્લિક કરો AGS-TECH Inc દ્વારા વાયર અને સ્પ્રિંગ ફોર્મિંગ પ્રક્રિયાઓના અમારા યોજનાકીય ચિત્રો ડાઉનલોડ કરો. ફોટા અને સ્કેચ સાથેની આ ડાઉનલોડ કરી શકાય તેવી ફાઇલ અમે તમને નીચે આપેલી માહિતીને વધુ સારી રીતે સમજવામાં મદદ કરશે. • વાયર ડ્રોઈંગ : તાણયુક્ત દળોનો ઉપયોગ કરીને આપણે મેટલ સ્ટોકને ખેંચીએ છીએ અને વ્યાસ ઘટાડવા અને તેની લંબાઈ વધારવા માટે તેને ડાય દ્વારા દોરીએ છીએ. કેટલીકવાર આપણે મૃત્યુની શ્રેણીનો ઉપયોગ કરીએ છીએ. અમે વાયરના દરેક ગેજ માટે ડાઈ બનાવવા સક્ષમ છીએ. ઉચ્ચ તાણ શક્તિની સામગ્રીનો ઉપયોગ કરીને આપણે ખૂબ જ પાતળા વાયર દોરીએ છીએ. અમે ઠંડા અને ગરમ બંને વાયર ઓફર કરીએ છીએ. • વાયર ફોર્મિંગ : ગેજ્ડ વાયરનો રોલ વાળીને ઉપયોગી ઉત્પાદનમાં આકાર આપવામાં આવે છે. અમારી પાસે તમામ ગેજમાંથી વાયર બનાવવાની ક્ષમતા છે, જેમાં પાતળા ફિલામેન્ટ્સ તેમજ ઓટોમોબાઈલ ચેસીસ હેઠળ સ્પ્રીંગ્સ તરીકે ઉપયોગમાં લેવાતા જાડા વાયરનો સમાવેશ થાય છે. વાયર બનાવવા માટે અમે જે સાધનોનો ઉપયોગ કરીએ છીએ તે મેન્યુઅલ અને CNC વાયર ફોરમર્સ, કોઇલર, પાવર પ્રેસ, ફોરસ્લાઇડ, મલ્ટી-સ્લાઇડ છે. અમારી પ્રક્રિયાઓ ડ્રોઇંગ, બેન્ડિંગ, સ્ટ્રેટનિંગ, ફ્લેટનિંગ, સ્ટ્રેચિંગ, કટીંગ, અપસેટિંગ, સોલ્ડરિંગ અને વેલ્ડિંગ અને બ્રેઝિંગ, એસેમ્બલી, કોઇલિંગ, સ્વેજીંગ (અથવા વિંગિંગ), વેધન, વાયર થ્રેડિંગ, ડ્રિલિંગ, ચેમ્ફરિંગ, ગ્રાઇન્ડિંગ, કોટિંગ અને સપાટીની સારવાર છે. અમારા અત્યાધુનિક સાધનો કોઈપણ આકાર અને ચુસ્ત સહનશીલતાની ખૂબ જ જટિલ ડિઝાઇન વિકસાવવા માટે સેટ-અપ કરી શકાય છે. અમે તમારા વાયર માટે ગોળાકાર, પોઈન્ટેડ અથવા ચેમ્ફર્ડ છેડા જેવા વિવિધ પ્રકારો ઓફર કરીએ છીએ. અમારા મોટાભાગના વાયર બનાવવાના પ્રોજેક્ટમાં ન્યૂનતમથી શૂન્ય ટૂલિંગ ખર્ચ હોય છે. સેમ્પલ ટર્નઅરાઉન્ડ સમય સામાન્ય રીતે દિવસો હોય છે. વાયર સ્વરૂપોની ડિઝાઇન/રૂપરેખાંકનમાં ફેરફાર ખૂબ જ ઝડપથી કરી શકાય છે. • સ્પ્રિંગ ફોર્મિંગ : AGS-TECH ઝરણાની વિશાળ વિવિધતા બનાવે છે જેમાં નીચેનાનો સમાવેશ થાય છે: -ટોર્સિયન / ડબલ ટોર્સિયન સ્પ્રિંગ -ટેન્શન / કમ્પ્રેશન સ્પ્રિંગ -કોન્સ્ટન્ટ / વેરીએબલ વસંત -કોઇલ અને હેલિકલ સ્પ્રિંગ -ફ્લેટ અને લીફ સ્પ્રિંગ -સંતુલિત વસંત -બેલેવિલે વોશર - નેગેટર સ્પ્રિંગ -પ્રોગ્રેસિવ રેટ કોઇલ સ્પ્રિંગ - વેવ વસંત -વોલ્યુટ સ્પ્રિંગ - ટેપર્ડ સ્પ્રિંગ્સ -સ્પ્રિંગ રિંગ્સ -ક્લોક સ્પ્રિંગ્સ -ક્લિપ્સ અમે વિવિધ સામગ્રીમાંથી ઝરણાનું ઉત્પાદન કરીએ છીએ અને તમારી અરજી અનુસાર તમને માર્ગદર્શન આપી શકીએ છીએ. સૌથી સામાન્ય સામગ્રી સ્ટેનલેસ સ્ટીલ, ક્રોમ સિલિકોન, ઉચ્ચ-કાર્બન સ્ટીલ, ઓઇલ-ટેમ્પર્ડ લો-કાર્બન, ક્રોમ વેનેડિયમ, ફોસ્ફર બ્રોન્ઝ, ટાઇટેનિયમ, બેરિલિયમ કોપર એલોય, ઉચ્ચ-તાપમાન સિરામિક છે. અમે ઝરણાના ઉત્પાદનમાં વિવિધ તકનીકોનો ઉપયોગ કરીએ છીએ, જેમાં CNC કોઇલિંગ, કોલ્ડ વિન્ડિંગ, હોટ વિન્ડિંગ, હાર્ડનિંગ, ફિનિશિંગનો સમાવેશ થાય છે. વાયર ફોર્મિંગ હેઠળ ઉપર જણાવેલી અન્ય તકનીકો પણ અમારી વસંત ઉત્પાદન કામગીરીમાં સામાન્ય છે. • વાયર અને સ્પ્રિંગ્સ માટે ફિનિશિંગ સર્વિસીસ : અમે તમારી પસંદગી અને જરૂરિયાતોને આધારે તમારા ઉત્પાદનોને ઘણી રીતે સમાપ્ત કરી શકીએ છીએ. કેટલીક સામાન્ય પ્રક્રિયાઓ અમે ઑફર કરીએ છીએ: પેઇન્ટિંગ, પાવડર કોટિંગ, પ્લેટિંગ, વિનાઇલ ડિપિંગ, એનોડાઇઝિંગ, સ્ટ્રેસ રિલિવ, હીટ ટ્રીટમેન્ટ, શૉટ પીન, ટમ્બલ, ક્રોમેટ, electroless નિકલ, પાસિવેશન, પ્લાસ્ટિક કોટિંગ , પ્લાઝમા સફાઈ. CLICK Product Finder-Locator Service પાછલું પૃષ્ઠ
- Forging and Powdered Metallurgy, Die Forging, Heading, Hot Forging
Forging and Powdered Metallurgy, Die Forging, Heading, Hot Forging, Impression Die, Near Net Shape, Swaging, Metal Hobbing, Riveting, Coining from AGS-TECH Inc. મેટલ ફોર્જિંગ અને પાવડર મેટલર્જી અમે જે પ્રકારની મેટલ ફોર્જિંગ પ્રક્રિયાઓ ઑફર કરીએ છીએ તે છે ગરમ અને ઠંડા ડાઇ, ઓપન ડાઇ અને ક્લોઝ્ડ ડાઇ, ઇમ્પ્રેશન ડાઇ અને ફ્લેશલેસ ફોર્જિંગ, cogging, ફુલરિંગ, એજિંગ અને પ્રિસિઝન ફોર્જિંગ, હેડ શેપ, નેટ , સ્વેજિંગ, અપસેટ ફોર્જિંગ, મેટલ હોબિંગ, પ્રેસ એન્ડ રોલ અને રેડિયલ અને ઓર્બિટલ અને રિંગ અને આઇસોથર્મલ ફોર્જિંગ, કોઈનિંગ, રિવેટિંગ, મેટલ બોલ ફોર્જિંગ, મેટલ પિઅરિંગ, સાઈઝિંગ, હાઈ એનર્જી રેટ ફોર્જિંગ. અમારી પાઉડર મેટલર્જી અને પાઉડર પ્રોસેસિંગ તકનીકો પાવડર પ્રેસિંગ અને સિન્ટરિંગ, ગર્ભાધાન, ઘૂસણખોરી, ગરમ અને ઠંડા આઇસોસ્ટેટિક પ્રેસિંગ, મેટલ ઇન્જેક્શન મોલ્ડિંગ, રોલ કોમ્પેક્શન, પાવડર રોલિંગ, પાવડર એક્સટ્રુઝન, લૂઝ સિન્ટરિંગ, સ્પાર્ક હોટ સિન્ટરિંગ, છે. અમે ભલામણ કરીએ છીએ કે તમે અહીં ક્લિક કરો AGS-TECH Inc. દ્વારા ફોર્જિંગ પ્રક્રિયાઓના અમારા યોજનાકીય ચિત્રો ડાઉનલોડ કરો AGS-TECH Inc. દ્વારા પાવડર મેટલર્જી પ્રક્રિયાઓના અમારા યોજનાકીય ચિત્રો ડાઉનલોડ કરો ફોટા અને સ્કેચ સાથેની આ ડાઉનલોડ કરી શકાય તેવી ફાઇલો અમે તમને નીચે આપેલી માહિતીને વધુ સારી રીતે સમજવામાં મદદ કરશે. મેટલ ફોર્જિંગમાં, સંકુચિત દળો લાગુ કરવામાં આવે છે અને સામગ્રી વિકૃત થાય છે અને ઇચ્છિત આકાર પ્રાપ્ત થાય છે. ઉદ્યોગમાં સૌથી સામાન્ય બનાવટી સામગ્રી લોખંડ અને સ્ટીલ છે, પરંતુ અસંખ્ય અન્ય જેમ કે એલ્યુમિનિયમ, કોપર, ટાઇટેનિયમ, મેગ્નેશિયમ પણ વ્યાપકપણે બનાવટી છે. બનાવટી ધાતુના ભાગોએ સીલબંધ તિરાડો અને બંધ ખાલી જગ્યાઓ ઉપરાંત અનાજની રચનામાં સુધારો કર્યો છે, આમ આ પ્રક્રિયા દ્વારા મેળવેલા ભાગોની મજબૂતાઈ વધારે છે. ફોર્જિંગ એવા ભાગોનું ઉત્પાદન કરે છે જે કાસ્ટિંગ અથવા મશીનિંગ દ્વારા બનાવેલા ભાગો કરતાં તેમના વજન માટે નોંધપાત્ર રીતે વધુ મજબૂત હોય છે. બનાવટી ભાગોને ધાતુના પ્રવાહને તેના અંતિમ આકારમાં બનાવીને આકાર આપવામાં આવતો હોવાથી, ધાતુ એક દિશાત્મક અનાજ માળખું લે છે જે ભાગોની શ્રેષ્ઠ શક્તિ માટે જવાબદાર છે. બીજા શબ્દોમાં કહીએ તો, ફોર્જિંગ પ્રક્રિયા દ્વારા મેળવેલા ભાગો સાદા કાસ્ટ અથવા મશીનવાળા ભાગોની તુલનામાં વધુ સારી યાંત્રિક ગુણધર્મો દર્શાવે છે. મેટલ ફોર્જિંગનું વજન નાના હળવા ભાગોથી માંડીને હજારો પાઉન્ડ સુધીનું હોઈ શકે છે. અમે મોટાભાગે યાંત્રિક રીતે માગણી કરતી એપ્લિકેશનો માટે ફોર્જિંગનું ઉત્પાદન કરીએ છીએ જ્યાં ઓટોમોટિવ પાર્ટ્સ, ગિયર્સ, વર્ક ટૂલ્સ, હેન્ડ ટૂલ્સ, ટર્બાઇન શાફ્ટ્સ, મોટરસાઇકલ ગિયર જેવા ભાગો પર વધુ ભાર મૂકવામાં આવે છે. કારણ કે ટૂલિંગ અને સેટ-અપ ખર્ચ પ્રમાણમાં વધારે છે, અમે આ ઉત્પાદન પ્રક્રિયાની ભલામણ માત્ર ઉચ્ચ જથ્થાના ઉત્પાદન માટે અને નીચા જથ્થાના પરંતુ ઉચ્ચ મૂલ્યના નિર્ણાયક ઘટકો જેમ કે એરોસ્પેસ લેન્ડિંગ ગિયર માટે કરીએ છીએ. ટૂલિંગની કિંમત ઉપરાંત, મોટા જથ્થાના બનાવટી ભાગો માટે ઉત્પાદનનો સમયગાળો કેટલાક સરળ મશીનવાળા ભાગોની સરખામણીમાં લાંબો હોઈ શકે છે, પરંતુ ટેકનિક એવા ભાગો માટે નિર્ણાયક છે કે જેઓ અસાધારણ શક્તિની જરૂર હોય છે જેમ કે બોલ્ટ, નટ્સ, ખાસ એપ્લિકેશન. ફાસ્ટનર્સ, ઓટોમોટિવ, ફોર્કલિફ્ટ, ક્રેન ભાગો. • હોટ ડાઇ અને કોલ્ડ ડાઇ ફોર્જિંગ : હોટ ડાઇ ફોર્જિંગ, નામ પ્રમાણે, ઊંચા તાપમાને હાથ ધરવામાં આવે છે, તેથી તેની નમ્રતા વધારે છે અને સામગ્રીની તાકાત ઓછી છે. આ સરળ વિરૂપતા અને ફોર્જિંગની સુવિધા આપે છે. તેનાથી વિપરિત, કોલ્ડ ડાઇ ફોર્જિંગ નીચા તાપમાને હાથ ધરવામાં આવે છે અને ઉચ્ચ બળની જરૂર પડે છે જેના પરિણામે તાણ સખત, સારી સપાટી પૂર્ણ અને ઉત્પાદિત ભાગોની ચોકસાઈ થાય છે. • ઓપન ડાઈ અને ઈમ્પ્રેશન ડાઈ ફોર્જિંગ : ઓપન ડાઈ ફોર્જિંગમાં, ડાઈઝ સંકુચિત થઈ રહેલી સામગ્રીને અવરોધતા નથી, જ્યારે ઈમ્પ્રેશન ડાઈ ફોર્જિંગ ડાઈઝની અંદરના પોલાણને સામગ્રીના પ્રવાહને પ્રતિબંધિત કરે છે જ્યારે તે ઇચ્છિત આકારમાં બનાવટી હોય છે. અપસેટ ફોર્જિંગ અથવા તેને UPSETTING પણ કહેવાય છે, જે વાસ્તવમાં સમાન નથી પરંતુ ખૂબ સમાન પ્રક્રિયા છે, એ એક ઓપન ડાઇ પ્રક્રિયા છે જ્યાં વર્ક પીસને બે ફ્લેટ ડાઈઝ વચ્ચે સેન્ડવીચ કરવામાં આવે છે અને સંકોચનશીલ બળ તેની ઊંચાઈ ઘટાડે છે. જેમ જેમ ઊંચાઈ reduced છે, વર્ક પીસની પહોળાઈ વધે છે. હેડિંગ, અપસેટ ફોર્જિંગ પ્રક્રિયામાં નળાકાર સ્ટોકનો સમાવેશ થાય છે જે તેના અંતમાં અસ્વસ્થ હોય છે અને તેનો ક્રોસ સેક્શન સ્થાનિક રીતે વધે છે. હેડિંગમાં સ્ટોકને ડાઇ, બનાવટી અને પછી લંબાઈમાં કાપવામાં આવે છે. ઓપરેશન ઝડપથી ફાસ્ટનર્સની ઉચ્ચ માત્રા ઉત્પન્ન કરવામાં સક્ષમ છે. મોટે ભાગે તે કોલ્ડ વર્કિંગ ઓપરેશન છે કારણ કે તેનો ઉપયોગ નખના છેડા, સ્ક્રુ છેડા, નટ્સ અને બોલ્ટ બનાવવા માટે થાય છે જ્યાં સામગ્રીને મજબૂત કરવાની જરૂર હોય છે. અન્ય ઓપન ડાઇ પ્રક્રિયા કોગિંગ છે, જ્યાં વર્ક પીસને દરેક સ્ટેપ સાથે શ્રેણીબદ્ધ સ્ટેપ્સમાં બનાવટી બનાવવામાં આવે છે જેના પરિણામે સામગ્રીનું સંકોચન થાય છે અને વર્ક પીસની લંબાઈ સાથે ઓપન ડાઈની અનુગામી ગતિ થાય છે. દરેક પગલા પર, જાડાઈ ઓછી થાય છે અને લંબાઈ થોડી માત્રામાં વધે છે. આ પ્રક્રિયા એક નર્વસ વિદ્યાર્થી જેવી લાગે છે જે તેની પેન્સિલને નાના પગલામાં કરડે છે. ફુલરિંગ નામની પ્રક્રિયા એ બીજી ઓપન ડાઇ ફોર્જિંગ પદ્ધતિ છે જે અમે ઘણીવાર અન્ય મેટલ ફોર્જિંગ કામગીરી થાય તે પહેલાં વર્ક પીસમાં સામગ્રીને વિતરિત કરવા માટે અગાઉના પગલા તરીકે ઉપયોગ કરીએ છીએ. અમે તેનો ઉપયોગ ત્યારે કરીએ છીએ જ્યારે વર્ક પીસને અનેક ફોર્જિંગ operationsની જરૂર હોય. ઓપરેશનમાં, બહિર્મુખ સપાટીઓ વિકૃત સાથે મૃત્યુ પામે છે અને બંને બાજુઓમાંથી ધાતુના પ્રવાહનું કારણ બને છે. ફૂલરિંગ જેવી જ પ્રક્રિયા, બીજી તરફ EDGINGમાં વર્ક પીસને વિકૃત કરવા માટે અંતર્મુખ સપાટી સાથે ઓપન ડાઇનો સમાવેશ થાય છે. એજિંગ એ અનુગામી ફોર્જિંગ કામગીરી માટે પણ એક પ્રારંભિક પ્રક્રિયા છે, જે સામગ્રીને બંને બાજુથી કેન્દ્રમાંના વિસ્તારમાં પ્રવાહિત કરે છે. ઇમ્પ્રેશન ડાઇ ફોર્જિંગ અથવા ક્લોઝ્ડ ડાઇ ફોર્જિંગ કારણ કે તેને ડાઇ / મોલ્ડનો ઉપયોગ પણ કહેવામાં આવે છે જે સામગ્રીને સંકુચિત કરે છે અને તેના પ્રવાહને પોતાની અંદર પ્રતિબંધિત કરે છે. ડાઇ બંધ થાય છે અને સામગ્રી ડાઇ/મોલ્ડ કેવિટીનો આકાર લે છે. પ્રિસિશન ફોર્જિંગ, એક પ્રક્રિયા જેમાં ખાસ સાધનો અને ઘાટની જરૂર હોય છે, તેમાં કોઈ અથવા બહુ ઓછા ફ્લેશ વગરના ભાગોનું ઉત્પાદન થાય છે. બીજા શબ્દોમાં કહીએ તો, ભાગો પાસે અંતિમ પરિમાણો હશે. આ પ્રક્રિયામાં સારી રીતે નિયંત્રિત સામગ્રીને કાળજીપૂર્વક દાખલ કરવામાં આવે છે અને ઘાટની અંદર મૂકવામાં આવે છે. અમે આ પદ્ધતિને પાતળા વિભાગો, નાના સહિષ્ણુતા અને ડ્રાફ્ટ એંગલ સાથે જટિલ આકારો માટે અને જ્યારે મોલ્ડ અને સાધનસામગ્રીના ખર્ચને ન્યાયી ઠેરવવા માટે પૂરતી મોટી હોય ત્યારે આ પદ્ધતિનો ઉપયોગ કરીએ છીએ. • ફ્લેશલેસ ફોર્જિંગ : વર્કપીસને ડાઈમાં એવી રીતે મૂકવામાં આવે છે કે કોઈ પણ સામગ્રી પોલાણમાંથી ફ્લૅશ બનાવવા માટે બહાર નીકળી ન શકે. આમ કોઈ અનિચ્છનીય ફ્લેશ ટ્રિમિંગની જરૂર નથી. તે એક ચોકસાઇ ફોર્જિંગ પ્રક્રિયા છે અને તેથી વપરાયેલી સામગ્રીની માત્રા પર નજીકથી નિયંત્રણની જરૂર છે. • મેટલ સ્વેગિંગ અથવા રેડિયલ ફોર્જિંગ : વર્ક પીસ પર પરિઘ પર ડાઇ અને બનાવટી દ્વારા કાર્યવાહી કરવામાં આવે છે. મેન્ડ્રેલનો ઉપયોગ આંતરિક વર્ક પીસ ભૂમિતિ બનાવવા માટે પણ થઈ શકે છે. સ્વેજીંગ ઓપરેશનમાં વર્ક પીસ સામાન્ય રીતે સેકન્ડ દીઠ અનેક સ્ટ્રોક મેળવે છે. સ્વેજીંગ દ્વારા ઉત્પાદિત લાક્ષણિક વસ્તુઓ પોઈન્ટેડ ટીપ ટૂલ્સ, ટેપર્ડ બાર, સ્ક્રુડ્રાઈવર્સ છે. • મેટલ પિયરસીંગ : અમે આ ઓપરેશનનો ઉપયોગ ભાગોના ઉત્પાદનમાં વધારાના ઓપરેશન તરીકે વારંવાર કરીએ છીએ. વર્ક પીસની સપાટી પર તેને તોડ્યા વગર વેધન સાથે છિદ્ર અથવા પોલાણ બનાવવામાં આવે છે. મહેરબાની કરીને નોંધ કરો કે વેધન ડ્રિલિંગ કરતાં અલગ છે જે છિદ્ર દ્વારા પરિણમે છે. • હોબિંગ : ઇચ્છિત ભૂમિતિ સાથેનો પંચ વર્ક પીસમાં દબાવવામાં આવે છે અને ઇચ્છિત આકાર સાથે પોલાણ બનાવે છે. અમે આ પંચને HOB કહીએ છીએ. ઓપરેશનમાં ઉચ્ચ દબાણનો સમાવેશ થાય છે અને તે ઠંડા સમયે હાથ ધરવામાં આવે છે. પરિણામે સામગ્રી ઠંડા કામ કરે છે અને તાણ સખત બને છે. તેથી આ પ્રક્રિયા અન્ય ઉત્પાદન પ્રક્રિયાઓ માટે મોલ્ડ, ડાઇ અને કેવિટીના ઉત્પાદન માટે ખૂબ જ યોગ્ય છે. એકવાર હોબનું ઉત્પાદન થઈ જાય પછી, એક પછી એક મશીનની જરૂર વગર ઘણી સમાન પોલાણ સરળતાથી બનાવી શકે છે. • રોલ ફોર્જિંગ અથવા રોલ ફોર્મિંગ : મેટલના ભાગને આકાર આપવા માટે બે વિરોધી રોલનો ઉપયોગ કરવામાં આવે છે. વર્ક પીસને રોલ્સમાં ખવડાવવામાં આવે છે, રોલ્સ ફેરવે છે અને કામને ગેપમાં ખેંચે છે, પછી કામને રોલ્સના ગ્રુવ્ડ ભાગ દ્વારા ખવડાવવામાં આવે છે અને સંકુચિત દળો સામગ્રીને તેનો ઇચ્છિત આકાર આપે છે. તે રોલિંગ પ્રક્રિયા નથી પરંતુ ફોર્જિંગ પ્રક્રિયા છે, કારણ કે તે સતત કામગીરીને બદલે અલગ છે. રોલ્સ ગ્રોવ્સ પરની ભૂમિતિ સામગ્રીને જરૂરી આકાર અને ભૂમિતિમાં બનાવે છે. તે ગરમ કરવામાં આવે છે. ફોર્જિંગ પ્રક્રિયા હોવાને કારણે તે ઉત્કૃષ્ટ યાંત્રિક ગુણધર્મો ધરાવતા ભાગોનું ઉત્પાદન કરે છે અને તેથી અમે તેનો ઉપયોગ ઓટોમોટિવ ભાગોના ઉત્પાદન માટે કરીએ છીએ જેમ કે શાફ્ટ કે જેને સખત કામના વાતાવરણમાં અસાધારણ સહનશક્તિ હોવી જરૂરી છે. • ઓર્બિટલ ફોર્જિંગ: વર્ક પીસને ફોર્જિંગ ડાઇ કેવિટીમાં મૂકવામાં આવે છે અને ઉપલા ડાઇ દ્વારા બનાવટી કરવામાં આવે છે જે ભ્રમણકક્ષાના માર્ગમાં મુસાફરી કરે છે કારણ કે તે એક વળેલી ધરી પર ફરે છે. દરેક ક્રાંતિ વખતે, ઉપલા ડાઇ સમગ્ર વર્ક પીસ પર સંકુચિત દળોનો ઉપયોગ પૂર્ણ કરે છે. આ ક્રાંતિને ઘણી વખત પુનરાવર્તિત કરીને, પર્યાપ્ત ફોર્જિંગ કરવામાં આવે છે. આ મેન્યુફેક્ચરિંગ ટેકનિકના ફાયદા એ છે કે તેની ઓછી અવાજની કામગીરી અને નીચા દળોની જરૂર છે. નાના દળો સાથે બીજા શબ્દોમાં કહીએ તો, ડાઇના સંપર્કમાં હોય તેવા વર્ક પીસના ભાગ પર મોટા દબાણને લાગુ કરવા માટે એક ધરીની આસપાસ ભારે ડાઇને ફેરવી શકાય છે. ડિસ્ક અથવા શંકુ આકારના ભાગો ક્યારેક આ પ્રક્રિયા માટે યોગ્ય છે. • રિંગ ફોર્જિંગ : અમે વારંવાર સીમલેસ રિંગ્સ બનાવવા માટે ઉપયોગ કરીએ છીએ. સ્ટોક લંબાઈમાં કાપવામાં આવે છે, અસ્વસ્થ થાય છે અને પછી કેન્દ્રિય છિદ્ર બનાવવા માટે સમગ્ર રીતે વીંધવામાં આવે છે. પછી તેને મેન્ડ્રેલ પર મૂકવામાં આવે છે અને ફોર્જિંગ ડાઇ તેને ઉપરથી હેમર કરે છે કારણ કે જ્યાં સુધી ઇચ્છિત પરિમાણો પ્રાપ્ત ન થાય ત્યાં સુધી રિંગ ધીમે ધીમે ફેરવવામાં આવે છે. • રિવેટીંગ : ભાગોને જોડવાની એક સામાન્ય પ્રક્રિયા, ભાગો દ્વારા પહેલાથી બનાવેલા છિદ્રોમાં દાખલ કરવામાં આવેલા સીધા ધાતુના ટુકડાથી શરૂ થાય છે. ત્યારપછી ધાતુના ટુકડાના બે છેડા ઉપર અને નીચલા ડાઈ વચ્ચેના સાંધાને સ્ક્વિઝ કરીને બનાવટી બનાવવામાં આવે છે. • કોઈનિંગ : યાંત્રિક પ્રેસ દ્વારા કરવામાં આવતી બીજી લોકપ્રિય પ્રક્રિયા, ટૂંકા અંતર પર મોટા બળનો ઉપયોગ કરે છે. "સિક્કા" નામ ધાતુના સિક્કાઓની સપાટી પર બનાવટી બનેલી બારીક વિગતો પરથી આવે છે. તે મોટાભાગે ઉત્પાદન માટે અંતિમ પ્રક્રિયા છે જ્યાં ડાઇ દ્વારા લાગુ કરાયેલા મોટા બળના પરિણામે સપાટી પર સરસ વિગતો મેળવવામાં આવે છે જે આ વિગતોને વર્ક પીસમાં સ્થાનાંતરિત કરે છે. • મેટલ બૉલ ફોર્જિંગ : બૉલ બેરિંગ જેવી પ્રોડક્ટને ઉચ્ચ ગુણવત્તાવાળા ચોક્કસ રીતે ઉત્પાદિત મેટલ બૉલ્સની જરૂર પડે છે. SKEW ROLLING નામની એક ટેકનિકમાં, અમે બે વિરોધી રોલનો ઉપયોગ કરીએ છીએ જે સતત ફરતા રહે છે કારણ કે સ્ટોકને રોલ્સમાં સતત ખવડાવવામાં આવે છે. બે રોલ્સના એક છેડે ધાતુના ગોળા ઉત્પાદન તરીકે બહાર કાઢવામાં આવે છે. મેટલ બોલ ફોર્જિંગ માટેની બીજી પદ્ધતિ એ ડાઇનો ઉપયોગ કરી રહી છે જે મોલ્ડ કેવિટીનો ગોળાકાર આકાર લઈને તેમની વચ્ચે મૂકવામાં આવેલા મટિરિયલ સ્ટોકને સ્ક્વિઝ કરે છે. ઘણી વખત ઉત્પાદિત બોલને ઉચ્ચ ગુણવત્તાની પ્રોડક્ટ બનવા માટે ફિનિશિંગ અને પોલિશિંગ જેવા કેટલાક વધારાના પગલાંની જરૂર પડે છે. • ISOTHERMAL ફોર્જિંગ / હોટ ડાઇ ફોર્જિંગ : એક ખર્ચાળ પ્રક્રિયા ત્યારે જ કરવામાં આવે છે જ્યારે લાભ / કિંમત મૂલ્ય વાજબી હોય. ગરમ કામ કરવાની પ્રક્રિયા જ્યાં ડાઇને વર્ક પીસ જેટલા જ તાપમાને ગરમ કરવામાં આવે છે. મૃત્યુ અને કાર્ય બંને લગભગ સમાન તાપમાન હોવાથી, ત્યાં કોઈ ઠંડક નથી અને ધાતુના પ્રવાહની લાક્ષણિકતાઓમાં સુધારો થયો છે. સુપર એલોય અને હલકી કક્ષાની ફોર્જેબિલિટી અને સામગ્રીઓ માટે આ ઓપરેશન યોગ્ય છે જેની યાંત્રિક ગુણધર્મો નાના તાપમાનના ઘટકો અને ફેરફારો માટે ખૂબ જ સંવેદનશીલ હોય છે. • મેટલ સાઈઝિંગ : તે કોલ્ડ ફિનિશિંગ પ્રક્રિયા છે. બળ લાગુ કરવામાં આવે છે તે દિશામાં અપવાદ સિવાય સામગ્રીનો પ્રવાહ બધી દિશામાં અનિયંત્રિત છે. પરિણામે, ખૂબ સારી સપાટી પૂર્ણાહુતિ અને સચોટ પરિમાણો પ્રાપ્ત થાય છે. • HIGH એનર્જી રેટ ફોર્જિંગ : ટેકનિકમાં પિસ્ટનના હાથ સાથે જોડાયેલ ઉપલા મોલ્ડનો સમાવેશ થાય છે જે spark દ્વારા ઇંધણ-હવા મિશ્રણને સળગાવવામાં આવે ત્યારે ઝડપથી ધકેલવામાં આવે છે. તે કારના એન્જિનમાં પિસ્ટનની કામગીરી જેવું લાગે છે. ઘાટ કામના ટુકડાને ખૂબ જ ઝડપથી અથડાવે છે અને પછી બેકપ્રેશરને કારણે ખૂબ જ ઝડપથી તેની મૂળ સ્થિતિ પર પાછા ફરે છે. કામ થોડી મિલીસેકંડમાં બનાવટી થઈ જાય છે અને તેથી કામ ઠંડુ થવા માટે કોઈ સમય નથી. આ ખૂબ જ તાપમાન સંવેદનશીલ યાંત્રિક ગુણધર્મો ધરાવતા ભાગોને બનાવટી બનાવવા માટે ઉપયોગી છે. બીજા શબ્દોમાં કહીએ તો પ્રક્રિયા એટલી ઝડપી છે કે ભાગ સતત તાપમાન હેઠળ રચાય છે અને મોલ્ડ/વર્ક પીસ ઇન્ટરફેસ પર તાપમાનના ગ્રેડિએન્ટ્સ હશે નહીં. • DIE ફોર્જિંગમાં, મેટલને બે બંધબેસતા સ્ટીલ બ્લોક્સ વચ્ચે પીટવામાં આવે છે જેમાં ખાસ આકાર હોય છે, જેને ડાઈઝ કહેવાય છે. જ્યારે ધાતુને ડાઇની વચ્ચે હેમર કરવામાં આવે છે, ત્યારે તે ડાઇમાંના આકાર જેવો જ આકાર ધારણ કરે છે. જ્યારે તે તેના અંતિમ આકાર પર પહોંચે છે, ત્યારે તેને ઠંડુ થવા માટે બહાર કાઢવામાં આવે છે. આ પ્રક્રિયા મજબૂત ભાગો બનાવે છે જે ચોક્કસ આકારના હોય છે, પરંતુ વિશિષ્ટ મૃત્યુ માટે મોટા રોકાણની જરૂર પડે છે. અપસેટ ફોર્જિંગ ધાતુના ટુકડાને સપાટ કરીને તેનો વ્યાસ વધારે છે. તેનો ઉપયોગ સામાન્ય રીતે નાના ભાગો બનાવવા માટે થાય છે, ખાસ કરીને બોલ્ટ અને નખ જેવા ફાસ્ટનર્સ પર હેડ બનાવવા માટે. • પાઉડર ધાતુશાસ્ત્ર / પાઉડર પ્રોસેસિંગ : નામ પ્રમાણે, તેમાં પાઉડરમાંથી ચોક્કસ ભૂમિતિ અને આકારોના નક્કર ભાગો બનાવવા માટેની ઉત્પાદન પ્રક્રિયાઓનો સમાવેશ થાય છે. જો આ હેતુ માટે ધાતુના પાવડરનો ઉપયોગ કરવામાં આવે તો તે પાવડર ધાતુશાસ્ત્રનું ક્ષેત્ર છે અને જો બિન-ધાતુના પાવડરનો ઉપયોગ કરવામાં આવે તો તે પાવડર પ્રક્રિયા છે. ઘન ભાગો દબાવીને અને સિન્ટર કરીને પાવડરમાંથી ઉત્પન્ન થાય છે. પાઉડર પ્રેસિંગનો ઉપયોગ પાવડરને ઇચ્છિત આકારમાં કોમ્પેક્ટ કરવા માટે થાય છે. પ્રથમ, પ્રાથમિક સામગ્રી ભૌતિક રીતે પાવડર છે, તેને ઘણા નાના વ્યક્તિગત કણોમાં વિભાજિત કરે છે. પાવડરનું મિશ્રણ ડાઇમાં ભરવામાં આવે છે અને એક પંચ પાવડર તરફ જાય છે અને તેને ઇચ્છિત આકારમાં કોમ્પેક્ટ કરે છે. મોટેભાગે ઓરડાના તાપમાને કરવામાં આવે છે, પાવડર દબાવવાથી ઘન ભાગ પ્રાપ્ત થાય છે અને તેને ગ્રીન કોમ્પેક્ટ કહેવામાં આવે છે. બાઈન્ડર અને લુબ્રિકન્ટનો ઉપયોગ સામાન્ય રીતે કોમ્પેક્ટેબિલિટી વધારવા માટે થાય છે. અમે કેટલાક હજાર ટન ક્ષમતા સાથે હાઇડ્રોલિક પ્રેસનો ઉપયોગ કરીને પાવડર પ્રેસ બનાવવા માટે સક્ષમ છીએ. સાથે જ અમારી પાસે વિરોધી ટોપ અને બોટમ પંચ સાથે ડબલ એક્શન પ્રેસ તેમજ અત્યંત જટિલ ભાગ ભૂમિતિ માટે બહુવિધ એક્શન પ્રેસ છે. એકરૂપતા જે ઘણા પાવડર ધાતુશાસ્ત્ર/પાઉડર પ્રોસેસિંગ પ્લાન્ટ્સ માટે એક મહત્વપૂર્ણ પડકાર છે તે AGS-TECH માટે કોઈ મોટી સમસ્યા નથી કારણ કે ઘણા વર્ષોથી આવા ભાગોના કસ્ટમ ઉત્પાદનમાં અમારા વ્યાપક અનુભવને કારણે. જાડા ભાગો સાથે પણ જ્યાં એકરૂપતા એક પડકાર છે અમે સફળ થયા છીએ. જો અમે તમારા પ્રોજેક્ટ માટે પ્રતિબદ્ધ છીએ, તો અમે તમારા ભાગો બનાવીશું. જો અમને કોઈ સંભવિત જોખમો દેખાય, તો અમે તમને માં જાણ કરીશું. અગાઉથી. પાઉડર સિન્ટરિંગ, જે બીજું પગલું છે, તેમાં તાપમાનને ચોક્કસ ડિગ્રી સુધી વધારવા અને ચોક્કસ સમય માટે તે સ્તર પર તાપમાનની જાળવણીનો સમાવેશ થાય છે જેથી દબાયેલા ભાગમાં પાવડરના કણો એકબીજા સાથે બંધાઈ શકે. આના પરિણામે વધુ મજબૂત બોન્ડ્સ અને વર્ક પીસ મજબૂત થાય છે. સિન્ટરિંગ પાવડરના ગલન તાપમાનની નજીક થાય છે. સિન્ટરિંગ દરમિયાન સંકોચન થાય છે, સામગ્રીની શક્તિ, ઘનતા, નરમતા, થર્મલ વાહકતા, વિદ્યુત વાહકતા વધે છે. અમારી પાસે સિન્ટરિંગ માટે બેચ અને સતત ભઠ્ઠીઓ છે. અમારી ક્ષમતાઓમાંની એક એ છે કે અમે ઉત્પાદન કરીએ છીએ તે ભાગોના છિદ્રાળુતાના સ્તરને સમાયોજિત કરવું. ઉદાહરણ તરીકે અમે ભાગોને અમુક અંશે છિદ્રાળુ રાખીને મેટલ ફિલ્ટર ઉત્પન્ન કરવામાં સક્ષમ છીએ. IMPREGNATION નામની તકનીકનો ઉપયોગ કરીને, અમે ધાતુના છિદ્રોને તેલ જેવા પ્રવાહીથી ભરીએ છીએ. અમે ઉદાહરણ તરીકે ઓઇલ ગર્ભિત બેરિંગ્સનું ઉત્પાદન કરીએ છીએ જે સ્વ-લુબ્રિકેટિંગ છે. ઘૂસણખોરીની પ્રક્રિયામાં આપણે ધાતુના છિદ્રોને આધાર સામગ્રી કરતાં નીચા ગલનબિંદુની બીજી ધાતુથી ભરીએ છીએ. મિશ્રણને બે ધાતુઓના ગલન તાપમાન વચ્ચેના તાપમાને ગરમ કરવામાં આવે છે. પરિણામે કેટલાક વિશેષ ગુણો મેળવી શકાય છે. અમે વારંવાર ગૌણ કામગીરી પણ કરીએ છીએ જેમ કે પાવડર ઉત્પાદિત ભાગો પર મશીનિંગ અને ફોર્જિંગ જ્યારે વિશેષ સુવિધાઓ અથવા ગુણધર્મો મેળવવાની જરૂર હોય અથવા જ્યારે ઓછા પ્રક્રિયાના પગલાં સાથે ભાગનું ઉત્પાદન કરી શકાય. આઇસોસ્ટેટિક પ્રેસિંગ : આ પ્રક્રિયામાં ભાગને કોમ્પેક્ટ કરવા માટે પ્રવાહી દબાણનો ઉપયોગ કરવામાં આવે છે. ધાતુના પાઉડરને સીલબંધ લવચીક કન્ટેનરમાંથી બનેલા મોલ્ડમાં મૂકવામાં આવે છે. આઇસોસ્ટેટિક પ્રેસિંગમાં, પરંપરાગત પ્રેસિંગમાં જોવા મળતા અક્ષીય દબાણથી વિપરીત, ચારેબાજુથી દબાણ લાગુ કરવામાં આવે છે. આઇસોસ્ટેટિક પ્રેસિંગના ફાયદા એ ભાગની અંદર સમાન ઘનતા છે, ખાસ કરીને મોટા અથવા જાડા ભાગો માટે, શ્રેષ્ઠ ગુણધર્મો. તેનો ગેરલાભ એ લાંબો ચક્ર સમય અને પ્રમાણમાં ઓછી ભૌમિતિક ચોકસાઈ છે. કોલ્ડ આઇસોસ્ટેટિક પ્રેસિંગ ઓરડાના તાપમાને હાથ ધરવામાં આવે છે અને લવચીક ઘાટ રબર, પીવીસી અથવા યુરેથેન અથવા સમાન સામગ્રીથી બનેલો છે. પ્રેશર અને કોમ્પેક્ટીંગ માટે વપરાતો પ્રવાહી તેલ અથવા પાણી છે. ગ્રીન કોમ્પેક્ટનું પરંપરાગત સિન્ટરિંગ આને અનુસરે છે. બીજી તરફ હોટ આઇસોસ્ટેટિક પ્રેસિંગ ઊંચા તાપમાને હાથ ધરવામાં આવે છે અને મોલ્ડ સામગ્રી શીટ મેટલ અથવા સિરામિક છે જે તાપમાનનો પ્રતિકાર કરે છે તેટલા ઊંચા ગલનબિંદુ સાથે. દબાણયુક્ત પ્રવાહી સામાન્ય રીતે નિષ્ક્રિય ગેસ છે. પ્રેસિંગ અને સિન્ટરિંગ કામગીરી એક પગલામાં કરવામાં આવે છે. છિદ્રાળુતા લગભગ સંપૂર્ણપણે દૂર થઈ ગઈ છે, એક સમાન grain માળખું પ્રાપ્ત થાય છે. હોટ આઇસોસ્ટેટિક પ્રેસિંગનો ફાયદો એ છે કે તે કાસ્ટિંગ અને ફોર્જિંગને જોડીને તુલનાત્મક ભાગોનું ઉત્પાદન કરી શકે છે જ્યારે કાસ્ટિંગ અને ફોર્જિંગ માટે યોગ્ય ન હોય તેવી સામગ્રીનો ઉપયોગ કરી શકાય છે. ગરમ આઇસોસ્ટેટિક પ્રેસિંગનો ગેરલાભ એ તેનો ઉચ્ચ ચક્ર સમય અને તેથી ખર્ચ છે. તે ઓછા વોલ્યુમના જટિલ ભાગો માટે યોગ્ય છે. મેટલ ઇન્જેક્શન મોલ્ડિંગ: પાતળી દિવાલો અને વિગતવાર ભૂમિતિ સાથે જટિલ ભાગો બનાવવા માટે ખૂબ જ યોગ્ય પ્રક્રિયા. નાના ભાગો માટે સૌથી યોગ્ય. પાઉડર અને પોલિમર બાઈન્ડર મિશ્ર, ગરમ અને બીબામાં ઇન્જેક્ટ કરવામાં આવે છે. પોલિમર બાઈન્ડર પાવડર કણોની સપાટીને કોટ કરે છે. મોલ્ડિંગ પછી, બાઈન્ડરને દ્રાવકનો ઉપયોગ કરીને ઓગળેલા નીચા તાપમાને ગરમ કરીને દૂર કરવામાં આવે છે. રોલ કોમ્પેક્શન / પાઉડર રોલિંગ : પાવડરનો ઉપયોગ સતત સ્ટ્રીપ્સ અથવા શીટ બનાવવા માટે થાય છે. પાવડરને ફીડરમાંથી ખવડાવવામાં આવે છે અને શીટ અથવા સ્ટ્રીપ્સમાં બે ફરતા રોલ દ્વારા કોમ્પેક્ટ કરવામાં આવે છે. ઓપરેશન ઠંડા હાથ ધરવામાં આવે છે. શીટને સિન્ટરિંગ ભઠ્ઠીમાં લઈ જવામાં આવે છે. સિન્ટરિંગ પ્રક્રિયા બીજી વખત પુનરાવર્તિત થઈ શકે છે. પાઉડર એક્સટ્રુઝન : મોટી લંબાઈથી વ્યાસના રેશિયોવાળા ભાગો પાવડર સાથે પાતળા શીટ મેટલ કન્ટેનરને બહાર કાઢીને બનાવવામાં આવે છે. લૂઝ સિન્ટરિંગ : નામ પ્રમાણે, તે દબાણ રહિત કોમ્પેક્શન અને સિન્ટરિંગ પદ્ધતિ છે, જે મેટલ ફિલ્ટર્સ જેવા ખૂબ છિદ્રાળુ ભાગો બનાવવા માટે યોગ્ય છે. પાવડરને કોમ્પેક્ટ કર્યા વિના મોલ્ડ કેવિટીમાં ખવડાવવામાં આવે છે. લૂઝ સિન્ટરિંગ : નામ પ્રમાણે, તે દબાણ રહિત કોમ્પેક્શન અને સિન્ટરિંગ પદ્ધતિ છે, જે મેટલ ફિલ્ટર્સ જેવા ખૂબ છિદ્રાળુ ભાગો બનાવવા માટે યોગ્ય છે. પાવડરને કોમ્પેક્ટ કર્યા વિના મોલ્ડ કેવિટીમાં ખવડાવવામાં આવે છે. સ્પાર્ક સિન્ટરિંગ : પાવડરને મોલ્ડમાં બે વિરોધી પંચ દ્વારા સંકુચિત કરવામાં આવે છે અને પંચ પર ઉચ્ચ શક્તિનો ઇલેક્ટ્રિક પ્રવાહ લાગુ કરવામાં આવે છે અને તેમની વચ્ચે સેન્ડવિચ કરેલા કોમ્પેક્ટેડ પાવડરમાંથી પસાર થાય છે. ઉચ્ચ પ્રવાહ પાવડર કણોમાંથી સપાટીની ફિલ્મોને બાળી નાખે છે અને ઉત્પન્ન થતી ગરમીથી તેમને સિન્ટર કરે છે. પ્રક્રિયા ઝડપી છે કારણ કે ગરમી બહારથી લાગુ પડતી નથી પરંતુ તેના બદલે તે ઘાટની અંદરથી ઉત્પન્ન થાય છે. હોટ પ્રેસિંગ : પાઉડરને ઊંચા તાપમાને ટકી શકે તેવા ઘાટમાં એક જ પગલામાં દબાવવામાં આવે છે અને સિન્ટર કરવામાં આવે છે. જેમ જેમ ડાઇ કોમ્પેક્ટ થાય છે તેમ પાવડર ગરમી તેના પર લાગુ થાય છે. સારી સચોટતા અને યાંત્રિક ગુણધર્મો આ પદ્ધતિ દ્વારા પ્રાપ્ત થાય છે તે તેને આકર્ષક વિકલ્પ બનાવે છે. પ્રત્યાવર્તન ધાતુઓ પણ ગ્રેફાઇટ જેવા ઘાટ સામગ્રીનો ઉપયોગ કરીને પ્રક્રિયા કરી શકાય છે. CLICK Product Finder-Locator Service પહેલાનું મેનુ
- Sheet Metal Forming Fabrication, Stamping, Punching, Deep Drawing, CNC
Sheet Metal Forming and Fabrication, Stamping, Punching, Bending, Progressive Die, Spot Welding, Deep Drawing, Metal Blanking and Slitting at AGS-TECH Inc. સ્ટેમ્પિંગ્સ અને શીટ મેટલ ફેબ્રિકેશન અમે શીટ મેટલ સ્ટેમ્પિંગ, શેપિંગ, ફોર્મિંગ, બેન્ડિંગ, પંચિંગ, બ્લેન્કિંગ, સ્લિટિંગ, પોર્ફોરેટિંગ, નોચિંગ, નિબલિંગ, શેવિંગ, પ્રેસવર્કિંગ, ફેબ્રિકેશન, સિંગલ પંચ / સિંગલ સ્ટ્રોક ડાઈઝનો ઉપયોગ કરીને ડીપ ડ્રોઈંગ તેમજ પ્રોગ્રેસિવ ડાઈઝ અને સ્પિનિંગ, રબર ફોર્મિંગ અને હાઇડ્રોફોર્મિંગ; વોટર જેટ, પ્લાઝ્મા, લેસર, કરવત, જ્યોતનો ઉપયોગ કરીને શીટ મેટલ કટીંગ; વેલ્ડીંગ, સ્પોટ વેલ્ડીંગનો ઉપયોગ કરીને શીટ મેટલ એસેમ્બલી; શીટ મેટલ ટ્યુબ મણકાની અને બેન્ડિંગ; ડીપ અથવા સ્પ્રે પેઇન્ટિંગ, ઇલેકટ્રોસ્ટેટિક પાવડર કોટિંગ, એનોડાઇઝિંગ, પ્લેટિંગ, સ્પટરિંગ અને વધુ સહિત શીટ મેટલની સપાટીનું ફિનિશિંગ. અમારી સેવાઓ ઝડપી શીટ મેટલ પ્રોટોટાઇપિંગથી લઈને ઉચ્ચ વોલ્યુમ ઉત્પાદન સુધીની છે. અમે ભલામણ કરીએ છીએ કે તમે અહીં ક્લિક કરોAGS-TECH Inc દ્વારા શીટ મેટલ ફેબ્રિકેશન અને સ્ટેમ્પિંગ પ્રક્રિયાઓના અમારા યોજનાકીય ચિત્રો ડાઉનલોડ કરો. આ તમને અમે નીચે આપેલી માહિતીને વધુ સારી રીતે સમજવામાં મદદ કરશે. • શીટ મેટલ કટીંગ : અમે કટઓફ અને પાર્ટીંગ ઓફર કરીએ છીએ. કટઓફ શીટ મેટલને એક સમયે એક પાથ પર કાપી નાખે છે અને તેમાં મૂળભૂત રીતે સામગ્રીનો કોઈ બગાડ થતો નથી, જ્યારે વિભાજન સાથે આકાર ચોક્કસ રીતે બાંધી શકાતો નથી અને તેથી સામગ્રીનો ચોક્કસ જથ્થો વેડફાઈ જાય છે. અમારી સૌથી લોકપ્રિય પ્રક્રિયાઓમાંની એક પંચિંગ છે, જ્યાં શીટ મેટલમાંથી ગોળ અથવા અન્ય આકારની સામગ્રીનો ટુકડો કાપવામાં આવે છે. જે ટુકડો કાપવામાં આવે છે તે કચરો છે. પંચિંગનું બીજું સંસ્કરણ સ્લોટિંગ છે, જ્યાં લંબચોરસ અથવા વિસ્તૃત છિદ્રો પંચ કરવામાં આવે છે. બીજી તરફ બ્લેન્કિંગ એ પંચિંગ જેવી જ પ્રક્રિયા છે, જેમાં ભાગને કાપી નાખવામાં આવે છે તે જ કાર્ય છે અને તેને રાખવામાં આવે છે. ફાઇન બ્લેન્કિંગ, બ્લેન્કિંગનું શ્રેષ્ઠ સંસ્કરણ, નજીકની સહનશીલતા અને સીધી સરળ કિનારીઓ સાથે કટ બનાવે છે અને વર્કપીસની સંપૂર્ણતા માટે ગૌણ કામગીરીની જરૂર નથી. બીજી પ્રક્રિયા અમે વારંવાર ઉપયોગ કરીએ છીએ તે છે SLITTING, જે એક શીયરિંગ પ્રક્રિયા છે જ્યાં શીટ મેટલને બે વિરોધી ગોળાકાર બ્લેડ દ્વારા સીધા અથવા વળાંકવાળા માર્ગમાં કાપવામાં આવે છે. કેન ઓપનર એ સ્લિટિંગ પ્રક્રિયાનું એક સરળ ઉદાહરણ છે. અમારા માટે અન્ય એક લોકપ્રિય પ્રક્રિયા PERFORATING છે, જ્યાં ચોક્કસ પેટર્નમાં શીટ મેટલમાં ઘણા છિદ્રો રાઉન્ડ અથવા અન્ય આકારને પંચ કરવામાં આવે છે. છિદ્રિત ઉત્પાદન માટેનું એક વિશિષ્ટ ઉદાહરણ પ્રવાહી માટે ઘણા છિદ્રો સાથે મેટલ ફિલ્ટર છે. નૉચિંગમાં, શીટ મેટલ કાપવાની બીજી પ્રક્રિયા, અમે વર્ક પીસમાંથી સામગ્રી દૂર કરીએ છીએ, ધારથી અથવા અન્ય જગ્યાએથી શરૂ કરીને અને ઇચ્છિત આકાર ન મળે ત્યાં સુધી અંદરની તરફ કાપીએ છીએ. તે એક પ્રગતિશીલ પ્રક્રિયા છે કે જ્યાં સુધી ઇચ્છિત સમોચ્ચ પ્રાપ્ત ન થાય ત્યાં સુધી દરેક ઓપરેશન બીજા ભાગને દૂર કરે છે. નાના પ્રોડક્શન રન માટે અમે કેટલીકવાર NIBBLING નામની પ્રમાણમાં ધીમી પ્રક્રિયાનો ઉપયોગ કરીએ છીએ જેમાં મોટા વધુ જટિલ કટ બનાવવા માટે ઓવરલેપિંગ છિદ્રોના ઘણા ઝડપી પંચનો સમાવેશ થાય છે. પ્રગતિશીલ કટીંગમાં આપણે એક કટ અથવા ચોક્કસ ભૂમિતિ મેળવવા માટે વિવિધ કામગીરીની શ્રેણીનો ઉપયોગ કરીએ છીએ. છેવટે ગૌણ પ્રક્રિયાને શેવ કરવાથી અમને પહેલાથી જ કરવામાં આવેલ કટની કિનારીઓ સુધારવામાં મદદ મળે છે. તેનો ઉપયોગ શીટ મેટલ વર્ક પર ચીપ્સ, રફ કિનારીઓ કાપવા માટે થાય છે. • શીટ મેટલ બેન્ડિંગ : કટીંગ ઉપરાંત, બેન્ડિંગ એ એક આવશ્યક પ્રક્રિયા છે જેના વિના આપણે મોટા ભાગના ઉત્પાદનોનું ઉત્પાદન કરી શકતા નથી. મોટે ભાગે ઠંડા કામનું ઓપરેશન પરંતુ ક્યારેક ગરમ અથવા ગરમ હોય ત્યારે પણ કરવામાં આવે છે. અમે આ ઓપરેશન માટે મોટાભાગે ડાઈઝનો ઉપયોગ કરીએ છીએ અને દબાવીએ છીએ. પ્રગતિશીલ બેન્ડિંગમાં આપણે સિંગલ બેન્ડ અથવા ચોક્કસ ભૂમિતિ મેળવવા માટે વિવિધ પંચ અને ડાઇ ઓપરેશન્સની શ્રેણીનો ઉપયોગ કરીએ છીએ. AGS-TECH વિવિધ પ્રકારની બેન્ડિંગ પ્રક્રિયાઓનો ઉપયોગ કરે છે અને વર્કપીસની સામગ્રી, તેના કદ, જાડાઈ, વળાંકનું ઇચ્છિત કદ, ત્રિજ્યા, વળાંક અને વળાંકનું કોણ, વળાંકનું સ્થાન, કામગીરીની અર્થવ્યવસ્થા, ઉત્પાદન કરવાના જથ્થાને આધારે પસંદગી કરે છે. વગેરે અમે V-BENDING નો ઉપયોગ કરીએ છીએ જ્યાં V આકારનો પંચ શીટ મેટલને V આકારના ડાઇમાં દબાણ કરે છે અને તેને વાળે છે. 90 ડિગ્રી સહિત ખૂબ જ તીવ્ર અને સ્થૂળ ખૂણા અને વચ્ચે બંને માટે સારું. વાઇપિંગ ડાઈઝનો ઉપયોગ કરીને અમે એજ બેન્ડિંગ કરીએ છીએ. અમારા સાધનો અમને 90 ડિગ્રી કરતા પણ મોટા ખૂણા મેળવવા માટે સક્ષમ બનાવે છે. એજ બેન્ડિંગમાં વર્કપીસને પ્રેશર પેડ અને ડાઈ વચ્ચે સેન્ડવીચ કરવામાં આવે છે, બેન્ડિંગ માટેનો વિસ્તાર ડાઈ એજ પર સ્થિત છે અને વર્કપીસનો બાકીનો ભાગ સ્પેસ જેવા કેન્ટીલીવર બીમ પર રાખવામાં આવે છે. જ્યારે પંચ કેન્ટીલીવર ભાગ પર કાર્ય કરે છે, ત્યારે તે ડાઇની ધાર પર વળેલું હોય છે. ફ્લેંગિંગ એ ધાર વાળવાની પ્રક્રિયા છે જે 90 ડિગ્રીના ખૂણોમાં પરિણમે છે. ઓપરેશનના મુખ્ય ધ્યેયો તીક્ષ્ણ ધારને દૂર કરવા અને ભાગોને જોડવામાં સરળતા માટે ભૌમિતિક સપાટીઓ મેળવવાનો છે. બીડિંગ, અન્ય સામાન્ય ધાર વાળવાની પ્રક્રિયા ભાગની ધાર પર કર્લ બનાવે છે. બીજી તરફ હેમિંગ શીટની એક ધાર સાથે પરિણમે છે જે તેના પર સંપૂર્ણપણે વળેલું છે. સીમિંગમાં, બે ભાગોની કિનારીઓ એકબીજા પર વળેલી હોય છે અને જોડાય છે. બીજી તરફ ડબલ સીમિંગ વોટરટાઈટ અને એરટાઈટ શીટ મેટલ સાંધા પૂરા પાડે છે. એજ બેન્ડિંગની જેમ જ, રોટરી બેન્ડિંગ નામની પ્રક્રિયા ઇચ્છિત એંગલ કાપીને પંચ તરીકે સેવા આપતા સિલિન્ડરને જમાવે છે. જેમ જેમ બળ પંચમાં પ્રસારિત થાય છે, તે વર્કપીસ સાથે બંધ થાય છે. સિલિન્ડરનો ગ્રુવ કેન્ટિલવર ભાગને ઇચ્છિત કોણ આપે છે. ગ્રુવમાં 90 ડિગ્રી કરતા નાનો અથવા મોટો કોણ હોઈ શકે છે. એર બેન્ડિંગમાં, કોણીય ગ્રુવ રાખવા માટે આપણને નીચલા ભાગની જરૂર નથી. શીટ મેટલને બે સપાટીઓ વિરુદ્ધ બાજુઓ અને ચોક્કસ અંતરે આધારભૂત છે. પંચ પછી યોગ્ય સ્થાન પર બળ લાગુ કરે છે અને વર્કપીસને વાળે છે. ચેનલ બેન્ડિંગ ચેનલ આકારના પંચ અને ડાઇનો ઉપયોગ કરીને કરવામાં આવે છે, અને U-BEND એ U-આકારના પંચ દ્વારા પ્રાપ્ત થાય છે. ઑફસેટ બેન્ડિંગ શીટ મેટલ પર ઑફસેટ્સ ઉત્પન્ન કરે છે. રોલ બેન્ડિંગ, જાડા કામ અને મેટલ પ્લેટના મોટા ટુકડાને વાળવા માટે સારી તકનીક, પ્લેટોને ઇચ્છિત વળાંકો પર ખવડાવવા અને વાળવા માટે ત્રણ રોલનો ઉપયોગ કરે છે. રોલ્સ ગોઠવવામાં આવે છે જેથી કામની ઇચ્છિત વળાંક પ્રાપ્ત થાય. રોલ્સ વચ્ચેનું અંતર અને કોણ ઇચ્છિત પરિણામ મેળવવા માટે નિયંત્રિત થાય છે. મૂવેબલ રોલ વક્રતાને નિયંત્રિત કરવાનું શક્ય બનાવે છે. ટ્યુબ ફોર્મિંગ એ અન્ય એક લોકપ્રિય શીટ મેટલ બેન્ડિંગ ઑપરેશન છે જેમાં બહુવિધ મૃત્યુનો સમાવેશ થાય છે. ટ્યુબ બહુવિધ ક્રિયાઓ પછી મેળવવામાં આવે છે. કોરુગેશન બેન્ડિંગ ઓપરેશન દ્વારા પણ કરવામાં આવે છે. મૂળભૂત રીતે તે શીટ મેટલના સમગ્ર ભાગ પર નિયમિત અંતરાલો પર સપ્રમાણતાવાળી બેન્ડિંગ છે. લહેરિયું માટે વિવિધ આકારોનો ઉપયોગ કરી શકાય છે. લહેરિયું શીટ મેટલ વધુ કઠોર છે અને બેન્ડિંગ સામે વધુ સારી પ્રતિકાર ધરાવે છે અને તેથી બાંધકામ ઉદ્યોગમાં તેનો ઉપયોગ થાય છે. શીટ મેટલ રોલ ફોર્મિંગ, એક સતત મેન્યુફેક્ચરિંગ પ્રક્રિયા રોલનો ઉપયોગ કરીને ચોક્કસ ભૂમિતિના ક્રોસ સેક્શનને વાળવા માટે ગોઠવવામાં આવે છે અને અંતિમ કાર્ય પૂર્ણ કરીને કામ ક્રમિક તબક્કામાં વળેલું છે. કેટલાક કિસ્સાઓમાં એક જ રોલ અને કેટલાક કિસ્સાઓમાં શ્રેણીબદ્ધ રોલનો ઉપયોગ કરવામાં આવે છે. • સંયુક્ત શીટ મેટલ કટિંગ અને બેન્ડિંગ પ્રક્રિયાઓ : આ એવી પ્રક્રિયાઓ છે જે એક જ સમયે કાપે છે અને વાળે છે. પીરસીંગમાં, પોઈન્ટેડ પંચનો ઉપયોગ કરીને એક છિદ્ર બનાવવામાં આવે છે. જેમ જેમ પંચ શીટમાં છિદ્રને પહોળું કરે છે તેમ, સામગ્રી એક સાથે છિદ્ર માટે આંતરિક ફ્લેંજમાં વળે છે. મેળવેલ ફ્લેંજમાં મહત્વપૂર્ણ કાર્યો હોઈ શકે છે. બીજી તરફ LANCING ઑપરેશન ઊભેલી ભૂમિતિ બનાવવા માટે શીટને કાપે છે અને વાળે છે. • ધાતુની ટ્યુબ બલ્જીંગ અને બેન્ડિંગ : બલ્જીંગમાં હોલો ટ્યુબના કેટલાક આંતરિક ભાગ પર દબાણ આવે છે, જેના કારણે ટ્યુબ બહારની તરફ ફૂંકાય છે. ટ્યુબ ડાઇની અંદર હોવાથી, બલ્જની ભૂમિતિ ડાઇના આકાર દ્વારા નિયંત્રિત થાય છે. સ્ટ્રેચ બેન્ડિંગમાં, ધાતુની નળીને ટ્યુબની ધરીની સમાંતર અને નળીને ફોર્મ બ્લોક પર ખેંચવા માટે બેન્ડિંગ ફોર્સનો ઉપયોગ કરીને ખેંચવામાં આવે છે. ડ્રો બેન્ડિંગમાં, અમે ટ્યુબને તેના છેડાની નજીકના ફરતા ફોર્મ બ્લોકમાં ક્લેમ્પ કરીએ છીએ જે ફરતી વખતે ટ્યુબને વાળે છે. છેલ્લે, કમ્પ્રેશન બેન્ડિંગમાં ટ્યુબને બળ વડે નિશ્ચિત સ્વરૂપના બ્લોકમાં જકડી રાખવામાં આવે છે, અને ડાઇ તેને ફોર્મ બ્લોક પર વાળે છે. • ડીપ ડ્રોઈંગ: અમારા સૌથી લોકપ્રિય ઓપરેશનમાંના એકમાં, એક પંચ, મેચિંગ ડાઈ અને ખાલી હોલ્ડરનો ઉપયોગ કરવામાં આવે છે. શીટ મેટલ બ્લેન્ક ડાઇ ઓપનિંગ પર મૂકવામાં આવે છે અને પંચ ખાલી ધારક દ્વારા રાખવામાં આવેલ ખાલી જગ્યા તરફ જાય છે. એકવાર તેઓ સંપર્કમાં આવ્યા પછી, પંચ શીટ મેટલને ઉત્પાદન બનાવવા માટે ડાઇ કેવિટીમાં દબાણ કરે છે. ડીપ ડ્રોઇંગ ઓપરેશન કટીંગ જેવું લાગે છે, જો કે પંચ અને ડાઇ વચ્ચેનું ક્લિયરન્સ શીટને કાપતા અટકાવે છે. શીટને ઊંડી દોરેલી અને કાપવામાં આવતી નથી તે સુનિશ્ચિત કરતું બીજું પરિબળ એ ડાઇ અને પંચ પરના ગોળાકાર ખૂણાઓ છે જે શીરીંગ અને કટીંગને અટકાવે છે. ડીપ ડ્રોઈંગની વધુ માત્રા હાંસલ કરવા માટે, એક રીડ્રોઈંગ પ્રક્રિયા ગોઠવવામાં આવી રહી છે જ્યાં અનુગામી ડીપ ડ્રોઈંગ એવા ભાગ પર થાય છે જે પહેલાથી ડીપ ડ્રોઈંગ પ્રક્રિયામાંથી પસાર થઈ ચૂક્યું છે. રિવર્સ રીડ્રોઈંગમાં, ઊંડા દોરેલા ભાગને પલટીને વિરુદ્ધ દિશામાં દોરવામાં આવે છે. ડીપ ડ્રોઇંગ અનિયમિત આકારની વસ્તુઓ પ્રદાન કરી શકે છે જેમ કે ગુંબજ, ટેપર્ડ અથવા સ્ટેપ્ડ કપ, EMBOSSING માં અમે ડિઝાઇન અથવા સ્ક્રિપ્ટ સાથે શીટ મેટલને પ્રભાવિત કરવા માટે પુરુષ અને સ્ત્રી ડાઇ જોડીનો ઉપયોગ કરીએ છીએ. • SPINNING : એક ઓપરેશન જ્યાં સપાટ અથવા પ્રિફોર્મ્ડ વર્કપીસને ફરતી મેન્ડ્રેલ અને પૂંછડીના સ્ટોક વચ્ચે રાખવામાં આવે છે અને એક સાધન કામ પર સ્થાનિક દબાણ લાગુ કરે છે કારણ કે તે ધીમે ધીમે મેન્ડ્રેલ ઉપર જાય છે. પરિણામે, વર્કપીસ મેન્ડ્રેલ પર લપેટી છે અને તેનો આકાર લે છે. અમે આ ટેકનિકનો ઉપયોગ ડીપ ડ્રોઈંગના વિકલ્પ તરીકે કરીએ છીએ જ્યાં ઓર્ડરનો જથ્થો નાનો હોય, ભાગો મોટા હોય (20 ફૂટ સુધીનો વ્યાસ) અને અનન્ય વળાંકો હોય. જો કે પીસ દીઠ કિંમતો સામાન્ય રીતે વધારે હોય છે, ડીપ ડ્રોઈંગની સરખામણીમાં CNC સ્પિનિંગ ઓપરેશન માટે સેટ-અપ ખર્ચ ઓછો હોય છે. તેનાથી વિપરિત, ડીપ ડ્રોઇંગને સેટ-અપ માટે ઉચ્ચ પ્રારંભિક રોકાણની જરૂર પડે છે, પરંતુ જ્યારે પાર્ટસની ઊંચી માત્રાનું ઉત્પાદન કરવામાં આવે ત્યારે પ્રતિ ટુકડો ખર્ચ ઓછો હોય છે. આ પ્રક્રિયાનું બીજું સંસ્કરણ શીયર સ્પિનિંગ છે, જ્યાં વર્કપીસની અંદર ધાતુનો પ્રવાહ પણ છે. ધાતુનો પ્રવાહ વર્કપીસની જાડાઈને ઘટાડશે કારણ કે પ્રક્રિયા હાથ ધરવામાં આવે છે. હજુ સુધી અન્ય સંબંધિત પ્રક્રિયા ટ્યુબ સ્પિનિંગ છે, જે નળાકાર ભાગો પર લાગુ થાય છે. આ પ્રક્રિયામાં પણ વર્કપીસની અંદર ધાતુનો પ્રવાહ છે. આમ જાડાઈ ઓછી થાય છે અને ટ્યુબની લંબાઈ વધે છે. ટ્યુબની અંદર અથવા બહાર સુવિધાઓ બનાવવા માટે સાધનને ખસેડી શકાય છે. • શીટ મેટલનું રબર બનાવવું : રબર અથવા પોલીયુરેથીન સામગ્રીને ડાઇમાં મુકવામાં આવે છે અને વર્ક પીસ રબરની સપાટી પર મૂકવામાં આવે છે. ત્યારબાદ વર્ક પીસ પર પંચની કાર્યવાહી કરવામાં આવે છે અને તેને રબરમાં દબાણ કરે છે. રબર દ્વારા ઉત્પન્ન થયેલ દબાણ ઓછું હોવાથી, ઉત્પાદિત ભાગોની ઊંડાઈ મર્યાદિત છે. ટૂલિંગ ખર્ચ ઓછો હોવાથી, પ્રક્રિયા ઓછા જથ્થાના ઉત્પાદન માટે યોગ્ય છે. • હાઇડ્રોફોર્મિંગ : રબરની રચનાની જેમ, આ પ્રક્રિયામાં શીટ મેટલ વર્કને પંચ દ્વારા ચેમ્બરની અંદર દબાણયુક્ત પ્રવાહીમાં દબાવવામાં આવે છે. શીટ મેટલ વર્ક પંચ અને રબર ડાયાફ્રેમ વચ્ચે સેન્ડવીચ કરવામાં આવે છે. ડાયાફ્રેમ વર્કપીસને સંપૂર્ણ રીતે ઘેરી લે છે અને પ્રવાહીનું દબાણ તેને પંચ પર રચવા દબાણ કરે છે. આ ટેકનીક વડે ડીપ ડ્રોઈંગ પ્રોસેસ કરતા પણ ડીપ ડ્રો મેળવી શકાય છે. અમે તમારા ભાગના આધારે સિંગલ-પંચ ડાઈઝ તેમજ પ્રોજેસીવ ડાઈઝનું ઉત્પાદન કરીએ છીએ. સિંગલ સ્ટ્રોક સ્ટેમ્પિંગ ડાઈઝ એ મોટા જથ્થામાં સરળ શીટ મેટલ ભાગો જેમ કે વોશર ઝડપથી ઉત્પન્ન કરવા માટે ખર્ચ અસરકારક પદ્ધતિ છે. પ્રોગ્રેસિવ ડાઈઝ અથવા ડીપ ડ્રોઈંગ ટેકનિકનો ઉપયોગ વધુ જટિલ ભૂમિતિના ઉત્પાદન માટે થાય છે. તમારા કેસના આધારે, વોટરજેટ, લેસર અથવા પ્લાઝ્મા કટીંગનો ઉપયોગ તમારા શીટ મેટલના ભાગોને સસ્તી, ઝડપી અને સચોટ રીતે બનાવવા માટે કરી શકાય છે. ઘણા સપ્લાયરો આ વૈકલ્પિક તકનીકો વિશે કોઈ જાણતા નથી અથવા તેમની પાસે નથી અને તેથી તેઓ ડાઈઝ અને સાધનો બનાવવાની લાંબી અને ખર્ચાળ રીતોમાંથી પસાર થાય છે જે ફક્ત ગ્રાહકોના સમય અને નાણાંનો વ્યય કરે છે. જો તમને કસ્ટમ બિલ્ટ શીટ મેટલ ઘટકો જેવા કે એન્ક્લોઝર, ઈલેક્ટ્રોનિક હાઉસિંગ...વગેરે દિવસોની અંદર જેટલી ઝડપથી જરૂર હોય, તો અમારી રેપિડ શીટ મેટલ પ્રોટોટાઈપિંગ સેવા માટે અમારો સંપર્ક કરો. CLICK Product Finder-Locator Service પહેલાનું મેનુ
- Plastic Rubber Metal Extrusions, Extrusion Dies, Aluminum Extruding
Plastic Rubber Metal Extrusions, Extrusion Dies, Aluminum Extruding, Pipe Tube Forming, Plastic Profiles, Metal Profiles Manufacturing, PVC at AGS-TECH Inc. એક્સટ્રુઝન્સ, એક્સટ્રુડેડ પ્રોડક્ટ્સ, એક્સટ્રુડેટ્સ અમે નળીઓ અને હીટ પાઈપ્સ જેવા નિશ્ચિત ક્રોસ સેક્શનલ પ્રોફાઈલ સાથે ઉત્પાદનો બનાવવા માટે EXTRUSION process નો ઉપયોગ કરીએ છીએ. ભલે ઘણી બધી સામગ્રીને બહાર કાઢી શકાય છે, આપણા સૌથી સામાન્ય એક્સટ્રુઝન ધાતુ, પોલિમર/પ્લાસ્ટિક, સિરામિકમાંથી બનેલા હોય છે જે ઠંડા, ગરમ અથવા ગરમ એક્સટ્રુઝન પદ્ધતિ દ્વારા મેળવવામાં આવે છે. અમે બહિષ્કૃત ભાગોને એક્સ્ટ્રુડેટ અથવા એક્સ્ટ્રુડેટ્સ જો બહુવચન કહીએ છીએ. અમે પણ કરીએ છીએ તે પ્રક્રિયાના કેટલાક વિશિષ્ટ સંસ્કરણો ઓવરજેકેટિંગ, કોએક્સ્ટ્રુઝન અને કમ્પાઉન્ડ એક્સટ્રુઝન છે. અમે ભલામણ કરીએ છીએ કે તમે અહીં ક્લિક કરો AGS-TECH Inc દ્વારા મેટલ સિરામિક અને પ્લાસ્ટિક એક્સટ્રુઝન પ્રક્રિયાઓના અમારા યોજનાકીય ચિત્રો ડાઉનલોડ કરો. આ તમને અમે નીચે આપેલી માહિતીને વધુ સારી રીતે સમજવામાં મદદ કરશે. એક્સટ્રુઝન સામગ્રીમાં જે ઇચ્છિત ક્રોસ-સેક્શનલ પ્રોફાઇલ હોય છે તે ડાઇ દ્વારા દબાણ અથવા દોરવામાં આવે છે. પ્રક્રિયાનો ઉપયોગ શ્રેષ્ઠ સપાટી પૂર્ણાહુતિ સાથે જટિલ ક્રોસ-સેક્શન બનાવવા અને બરડ સામગ્રી પર કામ કરવા માટે થઈ શકે છે. વ્યક્તિ આ પ્રક્રિયાનો ઉપયોગ કરીને કોઈપણ લંબાઈના ભાગોનું ઉત્પાદન કરી શકે છે. પ્રક્રિયાના પગલાંને સરળ બનાવવા માટે: 1.) ગરમ અથવા ગરમ એક્સટ્રુઝનમાં સામગ્રીને ગરમ કરવામાં આવે છે અને પ્રેસમાં કન્ટેનરમાં લોડ કરવામાં આવે છે. સામગ્રી દબાવવામાં આવે છે અને ડાઇમાંથી બહાર ધકેલવામાં આવે છે. 2.) ઉત્પાદિત એક્સ્ટ્રુડેટ તેના ગુણધર્મોને વધારવા માટે સીધા કરવા, ગરમીની સારવાર અથવા ઠંડા કામ માટે ખેંચાય છે. બીજી તરફ COLD EXTRUSION ઓરડાના તાપમાનની આસપાસ સ્થાન લે છે અને તેના ફાયદાઓ છે અને ઓછી મજબૂતાઈ, સપાટીને સારી રીતે સમાપ્ત કરવા, વધુ ઝડપી ઓક્સિડેશનના ફાયદા છે. WARM EXTRUSION ઓરડાના તાપમાને ઉપર પરંતુ પુનઃસ્થાપન બિંદુથી નીચે કરવામાં આવે છે. તે જરૂરી દળો, નમ્રતા અને ભૌતિક ગુણધર્મો માટે સમાધાન અને સંતુલન પ્રદાન કરે છે અને તેથી કેટલીક એપ્લિકેશનો માટે પસંદગી છે. HOT EXTRUSION સામગ્રીના પુનઃસ્થાપન તાપમાનથી ઉપર સ્થાન લે છે. આ રીતે ડાઇ દ્વારા સામગ્રીને દબાણ કરવું સરળ છે. જો કે સાધનોની કિંમત વધારે છે. એક્સ્ટ્રુડેડ પ્રોફાઈલ જેટલી જટિલ છે, તેટલું વધુ ખર્ચાળ છે ડાઈ (ટૂલિંગ) અને ઉત્પાદનનો દર ઓછો છે. ડાઇ ક્રોસ સેક્શન તેમજ જાડાઈમાં મર્યાદાઓ હોય છે જે બહાર કાઢવાની સામગ્રી પર આધાર રાખે છે. એક્સટ્રુઝન ડાઈઝમાં તીક્ષ્ણ ખૂણા હંમેશા અનિચ્છનીય હોય છે અને જ્યાં સુધી જરૂરી હોય ત્યાં સુધી ટાળવા જોઈએ. બહાર કાઢવામાં આવી રહેલી સામગ્રી અનુસાર, અમે ઑફર કરીએ છીએ: • મેટલ એક્સટ્રુઝન : સૌથી સામાન્ય અમે એલ્યુમિનિયમ, પિત્તળ, જસત, તાંબુ, સ્ટીલ, ટાઇટેનિયમ, મેગ્નેશિયમ ઉત્પન્ન કરીએ છીએ • પ્લાસ્ટિક EXTRUSION : પ્લાસ્ટિક પીગળીને સતત પ્રોફાઇલમાં બને છે. અમારી પ્રક્રિયા કરવામાં આવતી સામાન્ય સામગ્રી પોલિઇથિલિન, નાયલોન, પોલિસ્ટરીન, પોલિવિનાઇલ ક્લોરાઇડ, પોલીપ્રોપીલિન, ABS પ્લાસ્ટિક, પોલીકાર્બોનેટ, એક્રેલિક છે. અમે જે ઉત્પાદનોનું ઉત્પાદન કરીએ છીએ તેમાં પાઈપો અને ટ્યુબિંગ, પ્લાસ્ટિક ફ્રેમનો સમાવેશ થાય છે. પ્રક્રિયામાં નાના પ્લાસ્ટિક મણકા/રેઝિનને હોપરમાંથી એક્સટ્રુઝન મશીનના બેરલમાં ગુરુત્વાકર્ષણ આપવામાં આવે છે. અવારનવાર અમે ઉત્પાદનને જરૂરી વિશિષ્ટતાઓ અને ગુણધર્મો આપવા માટે કલરન્ટ્સ અથવા અન્ય ઉમેરણોને હોપરમાં ભેળવીએ છીએ. ગરમ બેરલમાં પ્રવેશતી સામગ્રીને ફરતા સ્ક્રૂ દ્વારા બેરલને છેડે છોડી દેવા અને પીગળેલા પ્લાસ્ટિકમાંના દૂષકોને દૂર કરવા માટે સ્ક્રીન પેકમાંથી આગળ વધવાની ફરજ પાડવામાં આવે છે. સ્ક્રીન પેક પસાર કર્યા પછી પ્લાસ્ટિક એક્સટ્રુઝન ડાઇમાં પ્રવેશે છે. જ્યારે તે પસાર થાય છે ત્યારે ડાઇ મૂવિંગ સોફ્ટ પ્લાસ્ટિકને તેનો પ્રોફાઇલ આકાર આપે છે. હવે એક્સ્ટ્રુડેટ ઠંડક માટે પાણીના સ્નાનમાંથી પસાર થાય છે. AGS-TECH Inc. ઘણા વર્ષોથી ઉપયોગ કરે છે તે અન્ય તકનીકો છે: • PIPE & TUBING EXTRUSION : પ્લાસ્ટિકની પાઈપો અને ટ્યુબ બને છે જ્યારે પ્લાસ્ટિકને ગોળાકાર આકારની ડાઇ દ્વારા બહાર કાઢવામાં આવે છે અને પાણીના સ્નાનમાં ઠંડુ કરવામાં આવે છે, પછી લંબાઈમાં કાપવામાં આવે છે અથવા કોઇલ/સ્પૂલ કરવામાં આવે છે. સ્પષ્ટ અથવા રંગીન, પટ્ટાવાળી, સિંગલ અથવા ડ્યુઅલ દિવાલ, લવચીક અથવા કઠોર, PE, PP, પોલીયુરેથીન, PVC, નાયલોન, PC, સિલિકોન, વિનાઇલ અથવા બીજું, અમારી પાસે તે બધું છે. અમારી પાસે ટ્યુબનો સ્ટોક છે તેમજ તમારી વિશિષ્ટતાઓ અનુસાર ઉત્પાદન કરવાની ક્ષમતા છે. AGS-TECH તબીબી, ઇલેક્ટ્રિક અને ઇલેક્ટ્રોનિક, ઔદ્યોગિક અને અન્ય એપ્લિકેશનો માટે FDA, UL અને LE જરૂરિયાતો માટે ટ્યુબિંગનું ઉત્પાદન કરે છે. • ઓવરજેકેટીંગ / ઓવર જેકેટીંગ EXTRUSION : આ ટેકનીક હાલના વાયર અથવા કેબલ પર પ્લાસ્ટિકના બાહ્ય પડને લાગુ કરે છે. અમારા ઇન્સ્યુલેશન વાયર આ પદ્ધતિથી બનાવવામાં આવે છે. • COEXTRUSION : સામગ્રીના બહુવિધ સ્તરો એકસાથે બહાર કાઢવામાં આવે છે. બહુવિધ સ્તરો બહુવિધ એક્સ્ટ્રુડર્સ દ્વારા વિતરિત કરવામાં આવે છે. ગ્રાહકના સ્પષ્ટીકરણોને પહોંચી વળવા માટે વિવિધ સ્તરની જાડાઈને સમાયોજિત કરી શકાય છે. આ પ્રક્રિયા ઉત્પાદનમાં અલગ અલગ કાર્યક્ષમતા ધરાવતા બહુવિધ પોલિમરનો ઉપયોગ કરવાનું શક્ય બનાવે છે. પરિણામે, વ્યક્તિ ગુણધર્મોની શ્રેણીને ઑપ્ટિમાઇઝ કરી શકે છે. • સંયોજન એક્સ્ટ્ર્યુઝન: પ્લાસ્ટિક સંયોજન મેળવવા માટે એક અથવા બહુવિધ પોલિમરને ઉમેરણો સાથે મિશ્રિત કરવામાં આવે છે. અમારા ટ્વીન-સ્ક્રુ એક્સટ્રુડર્સ કમ્પાઉન્ડિંગ એક્સટ્રુઝન બનાવે છે. મેટલ મોલ્ડની સરખામણીમાં એક્સટ્રુઝન ડાઈઝ સામાન્ય રીતે સસ્તું હોય છે. જો તમે નાના અથવા મધ્યમ કદના એક્સ્ટ્રુઝન ડાઇ એક્સટ્રુડિંગ એલ્યુમિનિયમ માટે થોડા હજાર ડોલર કરતાં વધુ ચૂકવણી કરી રહ્યાં છો, તો તમે કદાચ ખૂબ જ ચૂકવણી કરી રહ્યાં છો. તમારી અરજી માટે કઈ ટેકનિક સૌથી વધુ સસ્તી, ઝડપી અને સૌથી યોગ્ય છે તે નક્કી કરવામાં અમે નિષ્ણાત છીએ. ક્યારેક એક્સ્ટ્રુડિંગ અને પછી કોઈ ભાગને મશિન કરવાથી તમે ઘણી બધી રોકડ બચાવી શકો છો. મક્કમ નિર્ણય લેતા પહેલા, પહેલા અમારો અભિપ્રાય પૂછો. અમે ઘણા ગ્રાહકોને યોગ્ય નિર્ણય લેવામાં મદદ કરી છે. કેટલાક વ્યાપકપણે ઉપયોગમાં લેવાતા મેટલ એક્સટ્રુઝન માટે, તમે નીચે આપેલા રંગીન ટેક્સ્ટ પર ક્લિક કરીને અમારા બ્રોશર અને કેટલોગ ડાઉનલોડ કરી શકો છો. જો તે તમારી જરૂરિયાતોને પૂર્ણ કરતી ઑફ-શેલ્ફ પ્રોડક્ટ છે, તો તે વધુ આર્થિક હશે. અમારી મેડિકલ ટ્યુબ અને પાઇપ એક્સટ્રુઝન ક્ષમતાઓ ડાઉનલોડ કરો અમારા એક્સટ્રુડેડ હીટ સિંક ડાઉનલોડ કરો EXTRUSIONS માટે સેકન્ડરી મેન્યુફેક્ચરિંગ અને ફેબ્રિકેશન પ્રક્રિયાઓ: એક્સટ્રુડેડ ઉત્પાદનો માટે અમે જે મૂલ્યવર્ધિત પ્રક્રિયાઓ ઓફર કરીએ છીએ તેમાં આ છે: -કસ્ટમ ટ્યુબ અને પાઇપ બેન્ડિંગ, ફોર્મિંગ અને શેપિંગ, ટ્યુબ કટઓફ, ટ્યુબ એન્ડ ફોર્મિંગ, ટ્યુબ કોઇલિંગ, મશીનિંગ અને ફિનિશિંગ, હોલ ડ્રિલિંગ અને પિઅરિંગ અને પંચિંગ, - કસ્ટમ પાઇપ અને ટ્યુબ એસેમ્બલી, ટ્યુબ્યુલર એસેમ્બલી, વેલ્ડીંગ, બ્રેઝિંગ અને સોલ્ડરિંગ - કસ્ટમ એક્સટ્રુઝન બેન્ડિંગ, ફોર્મિંગ અને શેપિંગ -સફાઈ, ડિગ્રેઝિંગ, અથાણું, પેસિવેશન, પોલિશિંગ, એનોડાઇઝિંગ, પ્લેટિંગ, પેઇન્ટિંગ, હીટ ટ્રીટિંગ, એનિલિંગ અને સખ્તાઇ, માર્કિંગ, કોતરણી અને લેબલિંગ, કસ્ટમ પેકેજિંગ. CLICK Product Finder-Locator Service પાછલું પૃષ્ઠ
- Casting and Machined Parts, CNC Manufacturing, Milling, Turning, Swiss
Casting and Machined Parts, CNC Manufacturing, Milling, Turning, Swiss Type Machining, Die Casting, Investment Casting, Lost Foam Cast Parts from AGS-TECH Inc. કાસ્ટિંગ અને મશીનિંગ અમારી કસ્ટમ કાસ્ટિંગ અને મશીનિંગ તકનીકો ખર્ચપાત્ર અને બિન-ખર્ચપાત્ર કાસ્ટિંગ, ફેરસ અને નોન-ફેરસ કાસ્ટિંગ, સેન્ડ, ડાઇ, સેન્ટ્રીફ્યુગલ, સતત, સિરામિક મોલ્ડ, ઇન્વેસ્ટમેન્ટ, લોસ્ટ ફોમ, નજીક-નેટ-આકાર, કાયમી ઘાટ (ગ્રેવિટી ડાઇ કાસ્ટિંગ), પ્લાસ્ટર છે. મોલ્ડ (પ્લાસ્ટર કાસ્ટિંગ) અને શેલ કાસ્ટિંગ, પરંપરાગત તેમજ CNC સાધનોનો ઉપયોગ કરીને મિલિંગ અને ટર્નિંગ દ્વારા ઉત્પાદિત મશીનવાળા ભાગો, ઉચ્ચ થ્રુપુટ સસ્તા નાના ચોકસાઇવાળા ભાગો માટે સ્વિસ પ્રકારની મશીનિંગ, ફાસ્ટનર્સ માટે સ્ક્રુ મશીનિંગ, બિન-પરંપરાગત મશીનિંગ. મહેરબાની કરીને ધ્યાનમાં રાખો કે ધાતુઓ અને ધાતુના એલોય ઉપરાંત, અમે સિરામિક, કાચ અને પ્લાસ્ટિકના ઘટકો તેમજ કેટલાક કિસ્સાઓમાં જ્યારે મોલ્ડનું ઉત્પાદન આકર્ષક ન હોય અથવા વિકલ્પ ન હોય ત્યારે મશીન બનાવીએ છીએ. પોલિમર મટીરીયલ્સનાં મશીનિંગ માટે અમારી પાસે વિશિષ્ટ અનુભવની જરૂર છે કારણ કે પ્લાસ્ટિક અને રબર તેમની નરમાઈ, બિન-કઠોરતા... વગેરેને કારણે પડકારરૂપ છે. સિરામિક અને કાચના મશીનિંગ માટે, કૃપા કરીને બિન-પરંપરાગત ફેબ્રિકેશન પર અમારું પૃષ્ઠ જુઓ. AGS-TECH Inc. હળવા અને ભારે કાસ્ટિંગનું ઉત્પાદન અને સપ્લાય કરે છે. અમે બોઈલર, હીટ એક્સ્ચેન્જર્સ, ઓટોમોબાઈલ, માઈક્રોમોટર્સ, વિન્ડ ટર્બાઈન, ફૂડ પેકેજિંગ ઈક્વિપમેન્ટ અને વધુ માટે મેટલ કાસ્ટિંગ અને મશીનિંગ પાર્ટ્સ સપ્લાય કરતા આવ્યા છીએ. અમે ભલામણ કરીએ છીએ કે તમે અહીં ક્લિક કરો AGS-TECH Inc દ્વારા મશીનિંગ અને કાસ્ટિંગ પ્રક્રિયાઓના અમારા યોજનાકીય ચિત્રો ડાઉનલોડ કરો. આ તમને અમે નીચે આપેલી માહિતીને વધુ સારી રીતે સમજવામાં મદદ કરશે. ચાલો આપણે વિગતવાર ઓફર કરીએ છીએ તે કેટલીક વિવિધ તકનીકો જોઈએ: • એક્સપેન્ડેબલ મોલ્ડ કાસ્ટિંગ : આ વ્યાપક કેટેગરી એવી પદ્ધતિઓનો સંદર્ભ આપે છે જેમાં કામચલાઉ અને બિન-પુનઃઉપયોગી મોલ્ડનો સમાવેશ થાય છે. ઉદાહરણો રેતી, પ્લાસ્ટર, શેલ, રોકાણ (લોસ્ટ-વેક્સ પણ કહેવાય છે) અને પ્લાસ્ટર કાસ્ટિંગ છે. • રેતી કાસ્ટિંગ : એક પ્રક્રિયા જેમાં રેતીનો ઉપયોગ ઘાટની સામગ્રી તરીકે થાય છે. ખૂબ જ જૂની પદ્ધતિ અને હજુ પણ એ હદે ખૂબ જ લોકપ્રિય છે કે મોટાભાગની મેટલ કાસ્ટિંગ આ તકનીક દ્વારા બનાવવામાં આવે છે. ઓછા જથ્થાના ઉત્પાદનમાં પણ ઓછી કિંમત. નાના અને મોટા ભાગોના ઉત્પાદન માટે યોગ્ય. ટેકનિકનો ઉપયોગ બહુ ઓછા રોકાણ સાથે દિવસો કે અઠવાડિયામાં ભાગો બનાવવા માટે કરી શકાય છે. ભેજવાળી રેતીને માટી, બાઈન્ડર અથવા ખાસ તેલનો ઉપયોગ કરીને એકસાથે જોડવામાં આવે છે. રેતી સામાન્ય રીતે મોલ્ડ બોક્સમાં સમાયેલ હોય છે અને કેવિટી અને ગેટ સિસ્ટમ મોડેલોની આસપાસ રેતીને કોમ્પેક્ટ કરીને બનાવવામાં આવે છે. પ્રક્રિયાઓ છે: 1.) મોલ્ડ બનાવવા માટે મોડેલને રેતીમાં મૂકવું 2.) ગેટિંગ સિસ્ટમમાં મોડેલ અને રેતીનો સમાવેશ 3.) મોડેલ દૂર કરવું 4.) પીગળેલી ધાતુથી મોલ્ડ કેવિટી ભરવા 5.) ધાતુની ઠંડક 6.) રેતીના ઘાટને તોડવું અને કાસ્ટિંગને દૂર કરવું • પ્લાસ્ટર મોલ્ડ કાસ્ટિંગ : રેતીના કાસ્ટિંગની જેમ જ, અને રેતીને બદલે, પ્લાસ્ટર ઑફ પેરિસનો ઉપયોગ ઘાટની સામગ્રી તરીકે કરવામાં આવે છે. ટૂંકા ઉત્પાદન લીડ ટાઇમ જેમ કે રેતી કાસ્ટિંગ અને સસ્તું. સારી પરિમાણીય સહિષ્ણુતા અને સપાટી પૂર્ણાહુતિ. તેનો મુખ્ય ગેરલાભ એ છે કે તેનો ઉપયોગ એલ્યુમિનિયમ અને ઝીંક જેવી નીચા ગલનબિંદુ ધરાવતી ધાતુઓ સાથે જ થઈ શકે છે. • શેલ મોલ્ડ કાસ્ટિંગ : રેતી કાસ્ટિંગ જેવું જ. રેતીના કઠણ શેલ અને થર્મોસેટિંગ રેઝિન બાઈન્ડર દ્વારા મેળવવામાં આવેલ મોલ્ડ કેવિટી રેતીની કાસ્ટિંગ પ્રક્રિયાની જેમ રેતીથી ભરેલા ફ્લાસ્કને બદલે. રેતી દ્વારા નાખવા માટે યોગ્ય લગભગ કોઈપણ ધાતુને શેલ મોલ્ડિંગ દ્વારા કાસ્ટ કરી શકાય છે. પ્રક્રિયાનો સારાંશ આ પ્રમાણે કરી શકાય છે: 1.) શેલ મોલ્ડનું ઉત્પાદન. રેતીના કાસ્ટિંગમાં વપરાતી રેતીની સરખામણીમાં વપરાયેલી રેતી ઘણી નાની દાણાની હોય છે. ઝીણી રેતીને થર્મોસેટિંગ રેઝિન સાથે મિશ્રિત કરવામાં આવે છે. શેલને દૂર કરવાનું સરળ બનાવવા માટે મેટલ પેટર્નને વિભાજન એજન્ટ સાથે કોટેડ કરવામાં આવે છે. ત્યારબાદ મેટલ પેટર્નને ગરમ કરવામાં આવે છે અને રેતીના મિશ્રણને હોટ કાસ્ટિંગ પેટર્ન પર છિદ્રિત અથવા ફૂંકવામાં આવે છે. પેટર્નની સપાટી પર પાતળા શેલ રચાય છે. આ શેલની જાડાઈ રેતીના રેઝિન મિશ્રણના મેટલ પેટર્નના સંપર્કમાં હોય તે સમયની લંબાઈને બદલીને ગોઠવી શકાય છે. પછી છૂટક રેતી શેલ ઢંકાયેલ પેટર્ન બાકી સાથે દૂર કરવામાં આવે છે. 2.) આગળ, શેલ અને પેટર્નને પકાવવાની નાની ભઠ્ઠીમાં ગરમ કરવામાં આવે છે જેથી શેલ સખત થઈ જાય. સખ્તાઇ પૂર્ણ થયા પછી, પેટર્નમાં બનેલ પિનનો ઉપયોગ કરીને શેલને પેટર્નમાંથી બહાર કાઢવામાં આવે છે. 3.) આવા બે શેલને ગ્લુઇંગ અથવા ક્લેમ્પિંગ દ્વારા એકસાથે એસેમ્બલ કરવામાં આવે છે અને સંપૂર્ણ ઘાટ બનાવે છે. હવે શેલ મોલ્ડને એક કન્ટેનરમાં દાખલ કરવામાં આવે છે જેમાં તેને કાસ્ટિંગ પ્રક્રિયા દરમિયાન રેતી અથવા મેટલ શૉટ દ્વારા સપોર્ટ કરવામાં આવે છે. 4.) હવે ગરમ ધાતુને શેલ મોલ્ડમાં રેડી શકાય છે. શેલ કાસ્ટિંગના ફાયદાઓમાં ખૂબ જ સારી સપાટીની પૂર્ણાહુતિ, ઉચ્ચ પરિમાણીય ચોકસાઈ સાથે જટિલ ભાગોના ઉત્પાદનની શક્યતા, સ્વયંસંચાલિત કરવા માટે સરળ પ્રક્રિયા, મોટા જથ્થાના ઉત્પાદન માટે આર્થિક છે. ગેરફાયદા એ છે કે મોલ્ડને સારી વેન્ટિલેશનની જરૂર પડે છે કારણ કે જ્યારે પીગળેલી ધાતુ બાઈન્ડર કેમિકલ, થર્મોસેટિંગ રેઝિન અને મેટલ પેટર્નનો સંપર્ક કરે છે ત્યારે ઉત્પન્ન થાય છે. મેટલ પેટર્નની કિંમતને લીધે, ઓછી માત્રાના ઉત્પાદન માટે આ ટેકનિક સારી રીતે અનુકૂળ ન હોઈ શકે. • ઇન્વેસ્ટમેન્ટ કાસ્ટિંગ (લોસ્ટ-વેક્સ કાસ્ટિંગ તરીકે પણ ઓળખાય છે): ઘણી જૂની ટેકનિક અને ઘણી ધાતુઓ, પ્રત્યાવર્તન સામગ્રી અને વિશેષ ઉચ્ચ પ્રદર્શન એલોયમાંથી ઉચ્ચ ચોકસાઈ, પુનરાવર્તિતતા, વર્સેટિલિટી અને અખંડિતતા સાથે ગુણવત્તાયુક્ત ભાગોના ઉત્પાદન માટે યોગ્ય. નાના તેમજ મોટા કદના ભાગોનું ઉત્પાદન કરી શકાય છે. અન્ય કેટલીક પદ્ધતિઓની સરખામણીમાં ખર્ચાળ પ્રક્રિયા છે, પરંતુ મુખ્ય ફાયદો એ છે કે નજીકના ચોખ્ખા આકાર, જટિલ રૂપરેખા અને વિગતો સાથે ભાગો બનાવવાની શક્યતા છે. તેથી કેટલાક કિસ્સાઓમાં પુનઃકાર્ય અને મશીનિંગને નાબૂદ કરવાથી ખર્ચ કંઈક અંશે સરભર થાય છે. તેમ છતાં તેમાં વિવિધતા હોઈ શકે છે, અહીં સામાન્ય રોકાણ કાસ્ટિંગ પ્રક્રિયાનો સારાંશ છે: 1.) મીણ અથવા પ્લાસ્ટિકમાંથી મૂળ માસ્ટર પેટર્નનું નિર્માણ. દરેક કાસ્ટિંગને એક પેટર્નની જરૂર છે કારણ કે આ પ્રક્રિયામાં નાશ પામે છે. ઘાટ કે જેમાંથી પેટર્ન બનાવવામાં આવે છે તે પણ જરૂરી છે અને મોટાભાગે મોલ્ડ કાસ્ટ અથવા મશિન કરવામાં આવે છે. કારણ કે ઘાટને ખોલવાની જરૂર નથી, જટિલ કાસ્ટિંગ પ્રાપ્ત કરી શકાય છે, ઘણી મીણ પેટર્નને ઝાડની શાખાઓની જેમ જોડી શકાય છે અને એકસાથે રેડવામાં આવી શકે છે, આમ ધાતુ અથવા ધાતુના મિશ્ર ધાતુના એક જ ઠાલવવાથી બહુવિધ ભાગોનું ઉત્પાદન સક્ષમ બને છે. 2.) આગળ, પેટર્નને ખૂબ જ બારીક દાણાદાર સિલિકા, પાણી, બાઈન્ડરથી બનેલી પ્રત્યાવર્તન સ્લરી વડે ડુબાડવામાં આવે છે અથવા રેડવામાં આવે છે. આ પેટર્નની સપાટી પર સિરામિક સ્તરમાં પરિણમે છે. પેટર્ન પરના પ્રત્યાવર્તન કોટને સૂકવવા અને સખત થવા માટે છોડી દેવામાં આવે છે. આ પગલું તે છે જ્યાંથી રોકાણ કાસ્ટિંગ નામ આવે છે: રીફ્રેક્ટરી સ્લરીનું વેક્સ પેટર્ન પર રોકાણ કરવામાં આવે છે. 3.) આ પગલા પર, સખત સિરામિક મોલ્ડને ઊંધો કરીને ગરમ કરવામાં આવે છે જેથી મીણ ઓગળે અને ઘાટમાંથી બહાર નીકળી જાય. મેટલ કાસ્ટિંગ માટે પાછળ એક પોલાણ બાકી છે. 4.) મીણ નીકળી ગયા પછી, સિરામિક મોલ્ડને વધુ તાપમાને ગરમ કરવામાં આવે છે જેના પરિણામે ઘાટ મજબૂત થાય છે. 5.) તમામ જટિલ વિભાગોને ભરીને ગરમ મોલ્ડમાં મેટલ કાસ્ટિંગ રેડવામાં આવે છે. 6.) કાસ્ટિંગને મજબૂત કરવાની મંજૂરી છે 7.) અંતે સિરામિક મોલ્ડ તૂટી જાય છે અને ઉત્પાદિત ભાગો ઝાડમાંથી કાપવામાં આવે છે. અહીં ઇન્વેસ્ટમેન્ટ કાસ્ટિંગ પ્લાન્ટ બ્રોશરની લિંક છે • બાષ્પીભવનકારી પેટર્ન કાસ્ટિંગ : પ્રક્રિયા પોલિસ્ટરીન ફીણ જેવી સામગ્રીમાંથી બનાવેલ પેટર્નનો ઉપયોગ કરે છે જે જ્યારે ગરમ પીગળેલી ધાતુને ઘાટમાં રેડવામાં આવે ત્યારે બાષ્પીભવન થાય છે. આ પ્રક્રિયાના બે પ્રકાર છે: લોસ્ટ ફોમ કાસ્ટિંગ જે અનબોન્ડેડ રેતીનો ઉપયોગ કરે છે અને ફુલ મોલ્ડ કાસ્ટિંગ જે બોન્ડેડ રેતીનો ઉપયોગ કરે છે. અહીં સામાન્ય પ્રક્રિયા પગલાં છે: 1.) પોલિસ્ટરીન જેવી સામગ્રીમાંથી પેટર્ન બનાવો. જ્યારે મોટી માત્રામાં ઉત્પાદન કરવામાં આવશે, ત્યારે પેટર્ન મોલ્ડ કરવામાં આવે છે. જો ભાગ જટિલ આકાર ધરાવે છે, તો પેટર્ન બનાવવા માટે આવા ફીણ સામગ્રીના કેટલાક ભાગોને એકસાથે વળગી રહેવાની જરૂર પડી શકે છે. કાસ્ટિંગ પર સારી સપાટીની પૂર્ણાહુતિ બનાવવા માટે અમે વારંવાર પેટર્નને પ્રત્યાવર્તન સંયોજન સાથે કોટ કરીએ છીએ. 2.) પેટર્ન પછી મોલ્ડિંગ રેતીમાં મૂકવામાં આવે છે. 3.) પીગળેલી ધાતુને ઘાટમાં રેડવામાં આવે છે, જે ફીણની પેટર્નનું બાષ્પીભવન કરે છે, એટલે કે મોટા ભાગના કિસ્સાઓમાં પોલિસ્ટરીન કારણ કે તે ઘાટની પોલાણમાંથી વહે છે. 4.) પીગળેલી ધાતુને સખત થવા માટે રેતીના ઘાટમાં છોડી દેવામાં આવે છે. 5.) તે સખત થઈ ગયા પછી, અમે કાસ્ટિંગ દૂર કરીએ છીએ. કેટલાક કિસ્સાઓમાં, અમે જે ઉત્પાદનનું ઉત્પાદન કરીએ છીએ તેને પેટર્નની અંદર કોરની જરૂર હોય છે. બાષ્પીભવનકારી કાસ્ટિંગમાં, ઘાટની પોલાણમાં કોર મૂકવાની અને સુરક્ષિત કરવાની જરૂર નથી. આ તકનીક ખૂબ જટિલ ભૂમિતિના ઉત્પાદન માટે યોગ્ય છે, તે ઉચ્ચ વોલ્યુમ ઉત્પાદન માટે સરળતાથી સ્વચાલિત થઈ શકે છે, અને કાસ્ટ ભાગમાં કોઈ વિદાય રેખાઓ નથી. મૂળભૂત પ્રક્રિયા અમલ કરવા માટે સરળ અને આર્થિક છે. મોટા જથ્થાના ઉત્પાદન માટે, પોલિસ્ટરીનમાંથી પેટર્ન બનાવવા માટે ડાઇ અથવા મોલ્ડની જરૂર હોવાથી, આ કંઈક અંશે ખર્ચાળ હોઈ શકે છે. • નોન-એક્સપાન્ડેબલ મોલ્ડ કાસ્ટિંગ : આ વ્યાપક શ્રેણી એવી પદ્ધતિઓનો ઉલ્લેખ કરે છે જ્યાં દરેક ઉત્પાદન ચક્ર પછી ઘાટને સુધારવાની જરૂર નથી. ઉદાહરણો કાયમી, મૃત્યુ પામે છે, સતત અને કેન્દ્રત્યાગી કાસ્ટિંગ છે. પુનરાવર્તિતતા પ્રાપ્ત થાય છે અને ભાગોને NEAR NET SHAPE તરીકે દર્શાવી શકાય છે. • કાયમી મોલ્ડ કાસ્ટિંગ : ધાતુમાંથી બનેલા ફરીથી વાપરી શકાય તેવા મોલ્ડનો ઉપયોગ બહુવિધ કાસ્ટિંગ માટે થાય છે. કાયમી ઘાટનો સામાન્ય રીતે હજારો વખત ઉપયોગ થઈ શકે તે પહેલાં તે ખસી જાય છે. ગુરુત્વાકર્ષણ, ગેસનું દબાણ અથવા શૂન્યાવકાશ સામાન્ય રીતે ઘાટ ભરવા માટે વપરાય છે. મોલ્ડ (જેને ડાઇ પણ કહેવાય છે) સામાન્ય રીતે લોખંડ, સ્ટીલ, સિરામિક અથવા અન્ય ધાતુઓથી બનેલા હોય છે. સામાન્ય પ્રક્રિયા છે: 1.) મશીન અને મોલ્ડ બનાવો. એકસાથે બંધબેસતા અને ખોલી અને બંધ કરી શકાય તેવા બે ધાતુના બ્લોકમાંથી મોલ્ડને મશીન બનાવવું સામાન્ય છે. બંને ભાગની વિશેષતાઓ તેમજ ગેટીંગ સિસ્ટમ સામાન્ય રીતે કાસ્ટિંગ મોલ્ડમાં મશિન કરવામાં આવે છે. 2.) આંતરિક ઘાટની સપાટીઓ પ્રત્યાવર્તન સામગ્રીનો સમાવેશ કરતી સ્લરી સાથે કોટેડ હોય છે. આ ગરમીના પ્રવાહને નિયંત્રિત કરવામાં મદદ કરે છે અને કાસ્ટ ભાગને સરળતાથી દૂર કરવા માટે લુબ્રિકન્ટ તરીકે કાર્ય કરે છે. 3.) આગળ, કાયમી મોલ્ડ અર્ધભાગ બંધ કરવામાં આવે છે અને ઘાટ ગરમ થાય છે. 4.) પીગળેલી ધાતુને ઘાટમાં રેડવામાં આવે છે અને તેને ઘનતા માટે સ્થિર થવા દો. 5.) વધુ ઠંડક આવે તે પહેલાં, જ્યારે મોલ્ડના અડધા ભાગ ખોલવામાં આવે ત્યારે અમે ઇજેક્ટરનો ઉપયોગ કરીને કાયમી ઘાટમાંથી ભાગને દૂર કરીએ છીએ. અમે વારંવાર ઝીંક અને એલ્યુમિનિયમ જેવી ઓછી ગલનબિંદુ ધાતુઓ માટે કાયમી મોલ્ડ કાસ્ટિંગનો ઉપયોગ કરીએ છીએ. સ્ટીલ કાસ્ટિંગ માટે, અમે મોલ્ડ સામગ્રી તરીકે ગ્રેફાઇટનો ઉપયોગ કરીએ છીએ. અમે કેટલીકવાર કાયમી મોલ્ડમાં કોરોનો ઉપયોગ કરીને જટિલ ભૂમિતિ મેળવીએ છીએ. ઝડપી ઠંડક, ગુણધર્મોમાં એકરૂપતા, સારી સચોટતા અને સપાટી પૂર્ણાહુતિ, નીચા અસ્વીકાર દર, પ્રક્રિયાને સ્વચાલિત કરવાની સંભાવના અને આર્થિક રીતે ઉચ્ચ વોલ્યુમનું ઉત્પાદન કરીને સારી યાંત્રિક ગુણધર્મો ધરાવતી કાસ્ટિંગ આ તકનીકના ફાયદા છે. ગેરફાયદામાં ઉચ્ચ પ્રારંભિક સેટઅપ ખર્ચ છે જે તેને ઓછા વોલ્યુમની કામગીરી માટે અયોગ્ય બનાવે છે અને ઉત્પાદિત ભાગોના કદ પરની મર્યાદાઓ છે. • ડાઇ કાસ્ટિંગ : ડાઇને મશિન કરવામાં આવે છે અને પીગળેલી ધાતુને મોલ્ડ કેવિટીમાં ઉચ્ચ દબાણ હેઠળ ધકેલવામાં આવે છે. બંને નોનફેરસ તેમજ ફેરસ મેટલ ડાઇ કાસ્ટિંગ શક્ય છે. વિગતો, અત્યંત પાતળી દિવાલો, પરિમાણીય સુસંગતતા અને સારી સપાટીની પૂર્ણાહુતિ સાથે નાનાથી મધ્યમ કદના ભાગોના ઉચ્ચ જથ્થાના ઉત્પાદન માટે પ્રક્રિયા યોગ્ય છે. AGS-TECH Inc. આ તકનીકનો ઉપયોગ કરીને 0.5 મીમી જેટલી નાની દિવાલની જાડાઈનું ઉત્પાદન કરવા સક્ષમ છે. કાયમી મોલ્ડ કાસ્ટિંગની જેમ, મોલ્ડમાં બે ભાગો હોવા જોઈએ જે ઉત્પાદિત ભાગને દૂર કરવા માટે ખુલી અને બંધ થઈ શકે. દરેક ચક્ર સાથે બહુવિધ કાસ્ટિંગના ઉત્પાદનને સક્ષમ કરવા માટે ડાઇ કાસ્ટિંગ મોલ્ડમાં બહુવિધ પોલાણ હોઈ શકે છે. ડાઇ કાસ્ટિંગ મોલ્ડ ખૂબ જ ભારે હોય છે અને તેઓ બનાવેલા ભાગો કરતા ઘણા મોટા હોય છે, તેથી તે ખર્ચાળ પણ હોય છે. જ્યાં સુધી તેઓ અમારી પાસેથી તેમના ભાગોને ફરીથી ગોઠવે ત્યાં સુધી અમે અમારા ગ્રાહકો માટે વિનામૂલ્યે જર્જરીત મૃત્યુનું સમારકામ અને બદલી કરીએ છીએ. આપણા મૃત્યુનું જીવન લાખો હજાર ચક્ર શ્રેણીમાં લાંબુ હોય છે. અહીં મૂળભૂત સરળીકૃત પ્રક્રિયા પગલાં છે: 1.) સામાન્ય રીતે સ્ટીલમાંથી ઘાટનું ઉત્પાદન 2.) ડાઇ કાસ્ટિંગ મશીન પર મોલ્ડ ઇન્સ્ટોલ કરેલું 3.) પિસ્ટન જટિલ લક્ષણો અને પાતળી દિવાલોને ભરીને પીગળેલી ધાતુને ડાઇ કેવિટીમાં વહેવા દબાણ કરે છે. 4.) પીગળેલી ધાતુથી ઘાટ ભર્યા પછી, દબાણ હેઠળ કાસ્ટિંગને સખત થવા દેવામાં આવે છે. 5.) ઇજેક્ટર પિનની મદદથી મોલ્ડ ખોલવામાં આવે છે અને કાસ્ટિંગ દૂર કરવામાં આવે છે. 6.) હવે ખાલી ડાઇને ફરીથી લ્યુબ્રિકેટ કરવામાં આવે છે અને આગામી ચક્ર માટે ક્લેમ્પ કરવામાં આવે છે. ડાઇ કાસ્ટિંગમાં, અમે વારંવાર ઇન્સર્ટ મોલ્ડિંગનો ઉપયોગ કરીએ છીએ જ્યાં અમે મોલ્ડમાં વધારાનો ભાગ સામેલ કરીએ છીએ અને તેની આસપાસ મેટલ કાસ્ટ કરીએ છીએ. નક્કરતા પછી, આ ભાગો કાસ્ટ પ્રોડક્ટનો ભાગ બની જાય છે. ડાઇ કાસ્ટિંગના ફાયદા એ ભાગોના સારા યાંત્રિક ગુણધર્મો, જટિલ લક્ષણોની શક્યતા, સરસ વિગતો અને સારી સપાટી પૂર્ણાહુતિ, ઉચ્ચ ઉત્પાદન દર, સરળ ઓટોમેશન છે. ગેરફાયદાઓ છે: ઉચ્ચ ડાઇ અને સાધનોના ખર્ચને કારણે ઓછા વોલ્યુમ માટે ખૂબ જ યોગ્ય નથી, કાસ્ટ કરી શકાય તેવા આકારોમાં મર્યાદાઓ, ઇજેક્ટર પિનના સંપર્કના પરિણામે કાસ્ટ ભાગો પર નાના ગોળાકાર નિશાનો, વિભાજન રેખા પર ધાતુની પાતળી ફ્લેશ સ્ક્વિઝ્ડ, જરૂરિયાત ડાઇ વચ્ચેની વિભાજન રેખા સાથેના વેન્ટ માટે, પાણીના પરિભ્રમણનો ઉપયોગ કરીને ઘાટનું તાપમાન ઓછું રાખવાની આવશ્યકતા. • સેન્ટ્રીફ્યુગલ કાસ્ટિંગ : પીગળેલી ધાતુ પરિભ્રમણની ધરી પર ફરતા ઘાટના કેન્દ્રમાં રેડવામાં આવે છે. કેન્દ્રત્યાગી દળો ધાતુને પરિઘ તરફ ફેંકી દે છે અને તેને ઘન થવા દેવામાં આવે છે કારણ કે ઘાટ ફરતો રહે છે. બંને આડી અને ઊભી અક્ષ પરિભ્રમણનો ઉપયોગ કરી શકાય છે. ગોળ આંતરિક સપાટીઓ તેમજ અન્ય બિન-ગોળાકાર આકાર ધરાવતા ભાગોને કાસ્ટ કરી શકાય છે. પ્રક્રિયાનો સારાંશ આ પ્રમાણે કરી શકાય છે: 1.) પીગળેલી ધાતુને સેન્ટ્રીફ્યુગલ મોલ્ડમાં રેડવામાં આવે છે. ધાતુને પછી ઘાટની સ્પિનિંગને કારણે બાહ્ય દિવાલો પર દબાણ કરવામાં આવે છે. 2.) જેમ જેમ ઘાટ ફરે છે, મેટલ કાસ્ટિંગ સખત થાય છે સેન્ટ્રીફ્યુગલ કાસ્ટિંગ એ પાઈપો જેવા હોલો નળાકાર ભાગોના ઉત્પાદન માટે યોગ્ય ટેકનિક છે, સ્પ્રૂ, રાઈઝર અને ગેટીંગ એલિમેન્ટ્સની જરૂર નથી, સારી સપાટીની પૂર્ણાહુતિ અને વિગતવાર લક્ષણો, સંકોચનની કોઈ સમસ્યા નથી, ખૂબ મોટા વ્યાસવાળા લાંબા પાઈપો બનાવવાની શક્યતા, ઉચ્ચ દર ઉત્પાદન ક્ષમતા. . • સતત કાસ્ટિંગ (સ્ટ્રેન્ડ કાસ્ટિંગ): મેટલની સતત લંબાઈને કાસ્ટ કરવા માટે વપરાય છે. મૂળભૂત રીતે પીગળેલી ધાતુને ઘાટની બે પરિમાણીય રૂપરેખામાં નાખવામાં આવે છે પરંતુ તેની લંબાઈ અનિશ્ચિત હોય છે. નવી પીગળેલી ધાતુને સતત ઘાટમાં ખવડાવવામાં આવે છે કારણ કે કાસ્ટિંગ સમય સાથે તેની લંબાઈ વધવાની સાથે નીચે તરફ જાય છે. તાંબુ, સ્ટીલ, એલ્યુમિનિયમ જેવી ધાતુઓને સતત કાસ્ટિંગ પ્રક્રિયાનો ઉપયોગ કરીને લાંબા સેરમાં નાખવામાં આવે છે. પ્રક્રિયામાં વિવિધ રૂપરેખાંકનો હોઈ શકે છે પરંતુ સામાન્યને આ રીતે સરળ બનાવી શકાય છે: 1.) પીગળેલી ધાતુને મોલ્ડની ઉપર સ્થિત કન્ટેનરમાં સારી રીતે ગણતરી કરેલ માત્રામાં અને પ્રવાહ દરે રેડવામાં આવે છે અને પાણીના ઠંડા મોલ્ડમાંથી વહે છે. બીબામાં નાખવામાં આવેલ ધાતુનું કાસ્ટિંગ બીબાના તળિયે મૂકવામાં આવેલ સ્ટાર્ટર બારમાં ઘન બને છે. આ સ્ટાર્ટર બાર રોલર્સને શરૂઆતમાં પકડવા માટે કંઈક આપે છે. 2.) લાંબા મેટલ સ્ટ્રાન્ડને રોલર્સ દ્વારા સતત ઝડપે વહન કરવામાં આવે છે. રોલોરો મેટલ સ્ટ્રાન્ડના પ્રવાહની દિશાને ઊભીથી આડી તરફ પણ બદલી નાખે છે. 3.) સતત કાસ્ટિંગ ચોક્કસ આડી અંતરની મુસાફરી કર્યા પછી, એક ટોર્ચ અથવા સો જે કાસ્ટિંગ સાથે ફરે છે તે ઝડપથી તેને ઇચ્છિત લંબાઈ સુધી કાપી નાખે છે. સતત કાસ્ટિંગ પ્રક્રિયાને રોલિંગ પ્રક્રિયા સાથે સંકલિત કરી શકાય છે, જ્યાં I-Bems, T-Beams….વગેરે પેદા કરવા માટે સતત કાસ્ટ મેટલને સીધી રોલિંગ મિલમાં ખવડાવી શકાય છે. સતત કાસ્ટિંગ સમગ્ર ઉત્પાદનમાં એકસમાન ગુણધર્મો ઉત્પન્ન કરે છે, તે ઉચ્ચ ઘનતા દર ધરાવે છે, સામગ્રીના ખૂબ જ ઓછા નુકસાનને કારણે ખર્ચ ઘટાડે છે, એક પ્રક્રિયા પ્રદાન કરે છે જેમાં ધાતુનું લોડિંગ, રેડવું, ઘનકરણ, કટીંગ અને કાસ્ટિંગ દૂર કરવું બધું જ સતત કામગીરીમાં થાય છે અને આમ ઉચ્ચ ઉત્પાદકતા દર અને ઉચ્ચ ગુણવત્તામાં પરિણમે છે. જોકે મુખ્ય વિચારણા એ ઉચ્ચ પ્રારંભિક રોકાણ, સેટઅપ ખર્ચ અને જગ્યાની જરૂરિયાતો છે. • મશીનિંગ સેવાઓ: અમે ત્રણ, ચાર અને પાંચ - ધરી મશીનિંગ ઓફર કરીએ છીએ. અમે ટર્નિંગ, મિલિંગ, ડ્રિલિંગ, બોરિંગ, બ્રોચિંગ, પ્લાનિંગ, સોઇંગ, ગ્રાઇન્ડિંગ, લેપિંગ, પોલિશિંગ અને નોન-પરંપરાગત મશીનિંગનો ઉપયોગ કરીએ છીએ જે અમારી વેબસાઇટના અલગ મેનૂ હેઠળ વધુ વિગતવાર છે. અમારા મોટાભાગના ઉત્પાદન માટે, અમે CNC મશીનોનો ઉપયોગ કરીએ છીએ. જો કે કેટલીક કામગીરી માટે પરંપરાગત તકનીકો વધુ યોગ્ય છે અને તેથી અમે તેમના પર પણ આધાર રાખીએ છીએ. અમારી મશીનિંગ ક્ષમતાઓ શક્ય ઉચ્ચતમ સ્તર સુધી પહોંચે છે અને કેટલાક સૌથી વધુ માંગવાળા ભાગો AS9100 પ્રમાણિત પ્લાન્ટમાં બનાવવામાં આવે છે. જેટ એન્જિન બ્લેડ માટે ઉચ્ચ વિશિષ્ટ ઉત્પાદન અનુભવ અને યોગ્ય સાધનોની જરૂર હોય છે. એરોસ્પેસ ઉદ્યોગમાં ખૂબ જ કડક ધોરણો છે. જટિલ ભૌમિતિક બંધારણવાળા કેટલાક ઘટકો પાંચ અક્ષ મશીનિંગ દ્વારા સૌથી વધુ સરળતાથી બનાવવામાં આવે છે, જે ફક્ત આપણા સહિત કેટલાક મશીનિંગ પ્લાન્ટ્સમાં જ જોવા મળે છે. અમારા એરોસ્પેસ સર્ટિફાઇડ પ્લાન્ટ પાસે એરોસ્પેસ ઉદ્યોગની વ્યાપક દસ્તાવેજીકરણ આવશ્યકતાઓનું પાલન કરવાનો આવશ્યક અનુભવ છે. ટર્નિંગ ઑપરેશનમાં, વર્કપીસને ફેરવવામાં આવે છે અને કટીંગ ટૂલની સામે ખસેડવામાં આવે છે. આ પ્રક્રિયા માટે લેથ નામના મશીનનો ઉપયોગ કરવામાં આવી રહ્યો છે. મિલિંગમાં, મિલિંગ મશીન નામના મશીનમાં વર્કપીસની સામે કટીંગ કિનારીઓ લાવવા માટે ફરતું સાધન હોય છે. ડ્રિલિંગ કામગીરીમાં કટીંગ કિનારીઓ સાથે ફરતા કટરનો સમાવેશ થાય છે જે વર્કપીસના સંપર્ક પર છિદ્રો બનાવે છે. સામાન્ય રીતે ડ્રિલ પ્રેસ, લેથ્સ અથવા મિલ્સનો ઉપયોગ થાય છે. કંટાળાજનક કામગીરીમાં, છિદ્રને સહેજ મોટું કરવા અને ચોકસાઈને સુધારવા માટે એક જ વળાંકવાળા ટિપવાળા સાધનને સ્પિનિંગ વર્કપીસમાં રફ હોલમાં ખસેડવામાં આવે છે. તેનો ઉપયોગ ફાઇન ફિનિશિંગ હેતુઓ માટે થાય છે. બ્રોચિંગમાં બ્રોચ (દાંતવાળું ટૂલ) ના એક પાસમાં વર્કપીસમાંથી સામગ્રીને દૂર કરવા માટે દાંતાળું સાધનનો સમાવેશ થાય છે. રેખીય બ્રોચિંગમાં, કટને અસર કરવા માટે બ્રોચ વર્કપીસની સપાટીની સામે રેખીય રીતે ચાલે છે, જ્યારે રોટરી બ્રોચિંગમાં, અક્ષ સપ્રમાણ આકારને કાપવા માટે બ્રોચને વર્કપીસમાં ફેરવવામાં આવે છે અને દબાવવામાં આવે છે. SWISS TYPE MACHINING એ અમારી મૂલ્યવાન તકનીકોમાંની એક છે જેનો ઉપયોગ અમે નાના ઉચ્ચ ચોકસાઇવાળા ભાગોના ઉચ્ચ વોલ્યુમના ઉત્પાદન માટે કરીએ છીએ. સ્વિસ પ્રકારના લેથનો ઉપયોગ કરીને અમે નાના, જટિલ, ચોકસાઇવાળા ભાગોને સસ્તામાં ફેરવીએ છીએ. પરંપરાગત લેથ્સથી વિપરીત જ્યાં વર્કપીસને સ્થિર રાખવામાં આવે છે અને સાધનને ખસેડવામાં આવે છે, સ્વિસ-પ્રકારના ટર્નિંગ કેન્દ્રોમાં, વર્કપીસને Z-અક્ષમાં ખસેડવાની મંજૂરી છે અને સાધન સ્થિર છે. સ્વિસ-પ્રકારની મશીનિંગમાં, બાર સ્ટોકને મશીનમાં રાખવામાં આવે છે અને z-અક્ષમાં માર્ગદર્શિકા બુશિંગ દ્વારા આગળ વધારવામાં આવે છે, ફક્ત તે ભાગને ખુલ્લી પાડે છે જે મશીન કરવા માટે હોય છે. આ રીતે ચુસ્ત પકડ સુનિશ્ચિત થાય છે અને ચોકસાઈ ખૂબ ઊંચી છે. લાઇવ ટૂલ્સની ઉપલબ્ધતા માર્ગદર્શિકા બુશિંગમાંથી સામગ્રી આગળ વધવાથી મિલ અને ડ્રિલ કરવાની તક પૂરી પાડે છે. સ્વિસ-પ્રકારના સાધનોનો Y-અક્ષ સંપૂર્ણ મિલિંગ ક્ષમતાઓ પ્રદાન કરે છે અને ઉત્પાદનમાં ઘણો સમય બચાવે છે. વધુમાં, અમારા મશીનોમાં કવાયત અને કંટાળાજનક સાધનો છે જે જ્યારે તે સબ સ્પિન્ડલમાં રાખવામાં આવે છે ત્યારે તે ભાગ પર કાર્ય કરે છે. અમારી સ્વિસ-પ્રકારની મશીનિંગ ક્ષમતા અમને એક જ કામગીરીમાં સંપૂર્ણ સ્વચાલિત સંપૂર્ણ મશીનિંગ તક આપે છે. મશીનિંગ એ AGS-TECH Inc. બિઝનેસના સૌથી મોટા સેગમેન્ટમાંનું એક છે. અમે તેનો ઉપયોગ કાં તો પ્રાથમિક કામગીરી તરીકે અથવા તો ભાગને કાસ્ટ કર્યા પછી અથવા બહાર કાઢ્યા પછી ગૌણ કામગીરી તરીકે કરીએ છીએ જેથી તમામ ડ્રોઇંગ સ્પષ્ટીકરણો પૂર્ણ થાય. • સરફેસ ફિનિશિંગ સેવાઓ: અમે સપાટીની સારવાર અને સરફેસ ફિનિશિંગની વિશાળ વિવિધતા પ્રદાન કરીએ છીએ જેમ કે સંલગ્નતા વધારવા માટે સપાટીની કન્ડિશનિંગ, કોટિંગને સંલગ્નતા વધારવા માટે પાતળા ઓક્સાઈડ સ્તર જમા કરવી, સેન્ડ બ્લાસ્ટિંગ, કેમ-ફિલ્મ, એનોડાઇઝિંગ, નાઇટ્રાઇડિંગ, પાવડર કોટિંગ, સ્પ્રે કોટિંગ. , વિવિધ અદ્યતન મેટાલાઈઝેશન અને કોટિંગ તકનીકો જેમાં સ્પુટરિંગ, ઈલેક્ટ્રોન બીમ, બાષ્પીભવન, પ્લેટિંગ, હાર્ડ કોટિંગ્સ જેમ કે કાર્બન જેવા ડાયમંડ (DLC) અથવા ડ્રિલિંગ અને કટીંગ ટૂલ્સ માટે ટાઇટેનિયમ કોટિંગનો સમાવેશ થાય છે. • ઉત્પાદન માર્કિંગ અને લેબલિંગ સેવાઓ: અમારા ઘણા ગ્રાહકોને ધાતુના ભાગો પર માર્કિંગ અને લેબલિંગ, લેસર માર્કિંગ, કોતરણીની જરૂર પડે છે. જો તમને આવી કોઈ જરૂરિયાત હોય, તો ચાલો ચર્ચા કરીએ કે તમારા માટે કયો વિકલ્પ શ્રેષ્ઠ રહેશે. અહીં સામાન્ય રીતે ઉપયોગમાં લેવાતી કેટલીક મેટલ કાસ્ટ પ્રોડક્ટ્સ છે. આ ઑફ-ધ-શેલ્ફ હોવાથી, જો આમાંથી કોઈપણ તમારી જરૂરિયાતોને બંધબેસતું હોય તો તમે મોલ્ડ ખર્ચમાં બચત કરી શકો છો: AGS-Electronics પરથી અમારા 11 સિરીઝના ડાઇ-કાસ્ટ એલ્યુમિનિયમ બોક્સ ડાઉનલોડ કરવા માટે અહીં ક્લિક કરો CLICK Product Finder-Locator Service પાછલું પૃષ્ઠ
- Custom Manufactured Parts, Assemblies, Plastic Mold, Casting,Machining
Custom Manufactured Parts, Assemblies, Plastic Mold, Rubber Molding, Metal Casting, CNC Machining, Turning, Milling, Electrical Electronic Optical Assembly PCBA કસ્ટમ મેન્યુફેક્ચર્ડ પાર્ટ્સ અને એસેમ્બલીઝ અને પ્રોડક્ટ્સ વધુ વાંચો પ્લાસ્ટિક અને રબરના મોલ્ડ અને મોલ્ડિંગ વધુ વાંચો કાસ્ટિંગ અને મશીનિંગ વધુ વાંચો એક્સટ્રુઝન્સ, એક્સટ્રુડેડ પ્રોડક્ટ્સ વધુ વાંચો સ્ટેમ્પિંગ્સ અને શીટ મેટલ ફેબ્રિકેશન વધુ વાંચો મેટલ ફોર્જિંગ અને પાવડર મેટલર્જી વધુ વાંચો વાયર અને સ્પ્રિંગ રચના વધુ વાંચો ગ્લાસ અને સિરામિક ફોર્મિંગ અને શેપિંગ વધુ વાંચો એડિટિવ અને ઝ ડપી ઉત્પાદન વધુ વાંચો સંયુક્ત અને સંયુક્ત સામગ્રી ઉત્પાદન વધુ વાંચો જોડાવું અને એસેમ્બલી અને ફાસ્ટનિંગ પ્રક્રિયાઓ અમે તમારા માટે ભાગો અને એસેમ્બલીઓનું ઉત્પાદન કરીએ છીએ અને નીચેની ઉત્પાદન પ્રક્રિયાઓ પ્રદાન કરીએ છીએ: • પ્લાસ્ટિક અને રબરના મોલ્ડ અને મોલ્ડેડ ભાગો. ઇન્જેક્શન મોલ્ડિંગ, થર્મોફોર્મિંગ, થર્મોસેટ મોલ્ડિંગ, વેક્યુમ ફોર્મિંગ, બ્લો મોલ્ડિંગ, રોટેશનલ મોલ્ડિંગ, પોર મોલ્ડિંગ, ઇન્સર્ટ મોલ્ડિંગ અને અન્ય. • પ્લાસ્ટિક, રબર અને મેટલ એક્સટ્રુઝન • ફેરસ અને નોનફેરસ કાસ્ટિંગ અને મિલિંગ અને ટર્નિંગ તકનીકો, સ્વિસ-પ્રકારની મશીનિંગ દ્વારા ઉત્પાદિત મશીનવાળા ભાગો. • પાઉડર મેટલર્જી ભાગો • મેટલ અને નોનમેટલ સ્ટેમ્પિંગ, શીટ મેટલ ફોર્મિંગ, વેલ્ડેડ શીટ મેટલ એસેમ્બલી • ઠંડા અને ગરમ ફોર્જિંગ • વાયર, વેલ્ડેડ વાયર એસેમ્બલી, વાયર બનાવવું • વિવિધ પ્રકારના ઝરણા, સ્પ્રિંગ ફોર્મિંગ • ગિયર મેન્યુફેક્ચરિંગ, ગિયરબોક્સ, કપલિંગ, વોર્મ, સ્પીડ રીડ્યુસર, સિલિન્ડર, ટ્રાન્સમિશન બેલ્ટ, ટ્રાન્સમિશન ચેન, ટ્રાન્સમિશન ઘટકો • કસ્ટમ ટેમ્પર્ડ અને બુલેટપ્રૂફ ગ્લાસ નાટો અને લશ્કરી ધોરણો સાથે સુસંગત છે • બોલ્સ, બેરિંગ્સ, ગરગડી અને ગરગડી એસેમ્બલી • વાલ્વ અને વાયુયુક્ત ઘટકો જેમ કે ઓ-રિંગ, વોશર અને સીલ • ગ્લાસ અને સિરામિક ભાગો અને એસેમ્બલીઓ, વેક્યૂમ પ્રૂફ અને હર્મેટિક ઘટકો, મેટલ-સિરામિક અને સિરામિક-સિરામિક બોન્ડિંગ. • વિવિધ પ્રકારની યાંત્રિક, ઓપ્ટોમિકેનિકલ, ઈલેક્ટ્રોમિકેનિકલ, ઓપ્ટોઈલેક્ટ્રોનિક એસેમ્બલી. • મેટલ-રબર, મેટલ-પ્લાસ્ટિક બોન્ડિંગ • પાઇપ અને ટ્યુબ, પાઇપ બનાવવી, બેન્ડિંગ અને કસ્ટમ પાઇપ એસેમ્બલી, બેલો મેન્યુફેક્ચરિંગ. • ફાઇબરગ્લાસ ઉત્પાદન • સ્પોટ વેલ્ડીંગ, લેસર વેલ્ડીંગ, MIG, TIG જેવી વિવિધ તકનીકોનો ઉપયોગ કરીને વેલ્ડીંગ. પ્લાસ્ટિક ભાગો માટે અલ્ટ્રાસોનિક વેલ્ડીંગ. • સપાટીની સારવાર અને સરફેસ ફિનીશની વિશાળ વિવિધતા જેમ કે સંલગ્નતા વધારવા માટે સરફેસ કન્ડીશનીંગ, કોટિંગને સંલગ્નતા વધારવા માટે પાતળા ઓક્સાઇડ લેયર જમા કરાવવું, સેન્ડ બ્લાસ્ટિંગ, કેમ-ફિલ્મ, એનોડાઇઝિંગ, નાઇટ્રાઇડિંગ, પાવડર કોટિંગ, સ્પ્રે કોટિંગ, વિવિધ અદ્યતન મેટાલાઇઝેશન અને કોટિંગ તકનીકો. સ્પુટરિંગ, ઇલેક્ટ્રોન બીમ, બાષ્પીભવન, પ્લેટિંગ, કટિંગ અને ડ્રિલિંગ ટૂલ્સ માટે ડાયમંડ જેવા કાર્બન (ડીએલસી) અથવા ટાઇટેનિયમ જેવા સખત કોટિંગ્સ સહિત. • માર્કિંગ અને લેબલિંગ, મેટલ ભાગો પર લેસર માર્કિંગ, પ્લાસ્ટિક અને રબરના ભાગો પર પ્રિન્ટિંગ ડિઝાઇનર્સ અને એન્જિનિયરો દ્વારા ઉપયોગમાં લેવાતી સામાન્ય મિકેનિકલ એન્જિનિયરિંગ શરતો માટે બ્રોશર ડાઉનલોડ કરો અમે તમારા ચોક્કસ વિશિષ્ટતાઓ અને જરૂરિયાતો અનુસાર ઉત્પાદનો બનાવીએ છીએ. તમને શ્રેષ્ઠ ગુણવત્તા, ડિલિવરી અને કિંમતો ઓફર કરવા માટે, અમે ચીન, ભારત, તાઇવાન, ફિલિપાઇન્સ, દક્ષિણ કોરિયા, મલેશિયા, શ્રીલંકા, તુર્કી, યુએસએ, કેનેડા, જર્મની, યુકે અને જાપાનમાં વૈશ્વિક સ્તરે ઉત્પાદનોનું ઉત્પાદન કરીએ છીએ. આ અમને કોઈપણ અન્ય કસ્ટમ ઉત્પાદક કરતાં વધુ મજબૂત અને વૈશ્વિક સ્તરે વધુ સ્પર્ધાત્મક બનાવે છે. અમારા ઉત્પાદનો ISO9001:2000, QS9000, ISO14001, TS16949 પ્રમાણિત વાતાવરણમાં ઉત્પાદિત થાય છે અને CE, UL માર્ક ધરાવે છે અને અન્ય ઉદ્યોગ ધોરણોને પૂર્ણ કરે છે. એકવાર અમે તમારા પ્રોજેક્ટ માટે નિયુક્ત થઈ ગયા પછી, અમે તમારી ઇચ્છા મુજબ સમગ્ર ઉત્પાદન, એસેમ્બલી, પરીક્ષણ, લાયકાત, શિપિંગ અને કસ્ટમ્સનું ધ્યાન રાખી શકીએ છીએ. જો તમે ઇચ્છો તો, અમે તમારા ભાગોને વેરહાઉસ કરી શકીએ છીએ, કસ્ટમ કિટ્સ એસેમ્બલ કરી શકીએ છીએ, તમારી કંપનીનું નામ અને બ્રાન્ડ પ્રિન્ટ અને લેબલ કરી શકીએ છીએ અને તમારા ગ્રાહકોને શિપ ડ્રોપ કરી શકીએ છીએ. બીજા શબ્દોમાં કહીએ તો, જો પ્રાધાન્ય હોય તો અમે તમારું વેરહાઉસિંગ અને વિતરણ કેન્દ્ર બની શકીએ છીએ. અમારા વેરહાઉસ મુખ્ય બંદરોની નજીક આવેલા હોવાથી, તે અમને લોજિસ્ટિકલ લાભ આપે છે. ઉદાહરણ તરીકે, જ્યારે તમારા ઉત્પાદનો મુખ્ય યુએસએ બંદર પર આવે છે, ત્યારે અમે તેને સીધું નજીકના વેરહાઉસમાં ટ્રાન્સપોર્ટ કરી શકીએ છીએ જ્યાં અમે તમારી પસંદગી અને ડ્રોપને સ્ટોર કરી, એસેમ્બલ કરી, કિટ બનાવી શકીએ, રિબેલ કરી શકીએ, પ્રિન્ટ કરી શકીએ. તમારા ગ્રાહકોને મોકલો. અમે માત્ર ઉત્પાદનો જ સપ્લાય કરતા નથી. અમારી કંપની કસ્ટમ કોન્ટ્રાક્ટ્સ પર કામ કરે છે જ્યાં અમે તમારી સાઇટ પર આવીએ છીએ, સાઇટ પર તમારા પ્રોજેક્ટનું મૂલ્યાંકન કરીએ છીએ અને તમારા માટે ડિઝાઇન કરાયેલ પ્રોજેક્ટ પ્રસ્તાવ કસ્ટમ વિકસાવીએ છીએ. ત્યારપછી અમે અમારી અનુભવી ટીમને પ્રોજેક્ટના અમલીકરણ માટે મોકલીએ છીએ. અમારા એન્જિનિયરિંગ કાર્ય વિશે વધુ માહિતી પર મળી શકે છે http://www.ags-engineering.com -અમે ઔદ્યોગિક ધોરણે નાના પ્રોજેક્ટ તેમજ મોટા પ્રોજેક્ટ્સ લઈએ છીએ. પ્રથમ પગલા તરીકે, અમે તમને અમારી નિષ્ણાત ટીમના સભ્યો સાથે ફોન, ટેલિકોન્ફરન્સિંગ અથવા MSN મેસેન્જર દ્વારા કનેક્ટ કરી શકીએ છીએ, જેથી તમે સીધા નિષ્ણાત સાથે વાતચીત કરી શકો, પ્રશ્નો પૂછી શકો અને તમારા પ્રોજેક્ટની ચર્ચા કરી શકો. અમને કૉલ કરો અને જો જરૂર હોય તો અમે તમારી મુલાકાત લઈશું. પાછલું પૃષ્ઠ