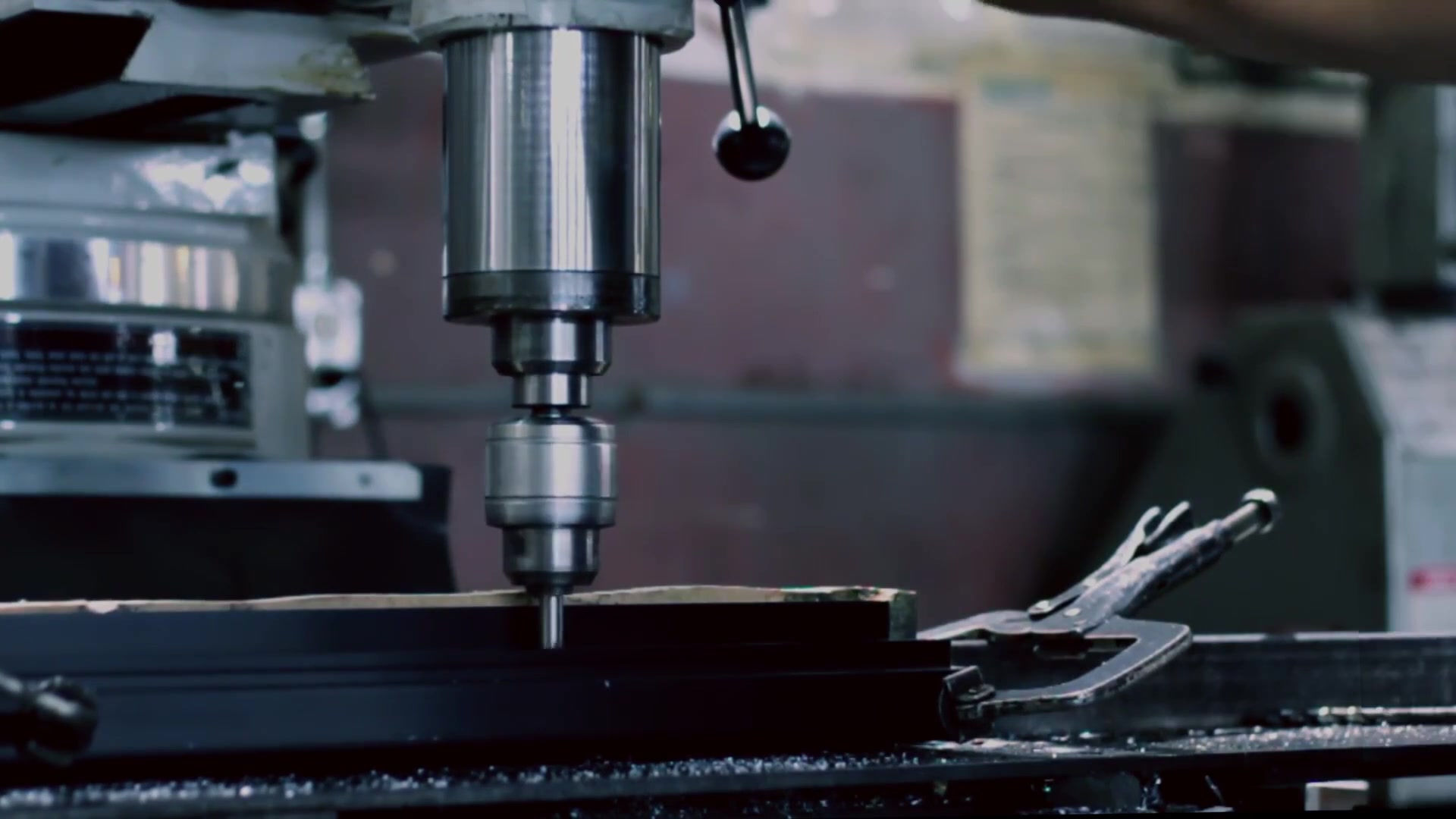
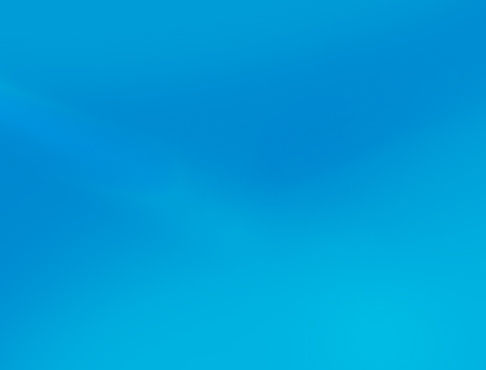
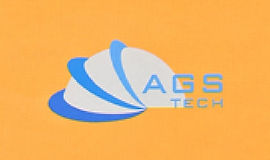
יצרן מותאם אישית גלובלי, אינטגרטור, מאחד, שותף מיקור חוץ עבור מגוון רחב של מוצרים ושירותים.
אנחנו המקור היחיד שלך לייצור, ייצור, הנדסה, איחוד, אינטגרציה, מיקור חוץ של מוצרים ושירותי מדף מיוצרים בהתאמה אישית.
בחר את השפה שלך
-
ייצור בהתאמה אישית
-
ייצור חוזים מקומי וגלובלי
-
מיקור חוץ של ייצור
-
רכש מקומי וגלובלי
-
Consolidation
-
אינטגרציה הנדסית
-
שרותי הנדסה
בין טכניקות ההצטרפות הרבות שאנו נוקטים בייצור, ניתן דגש מיוחד על ריתוך, הלחמה, הלחמה, הדבקה דבקה והרכבה מכנית מותאמת אישית מכיוון שטכניקות אלו נמצאות בשימוש נרחב ביישומים כמו ייצור של מכלולים הרמטיים, ייצור מוצרי היי-טק ואיטום מיוחד. כאן נתרכז בהיבטים המיוחדים יותר של טכניקות הצטרפות אלה, שכן הם קשורים לייצור מוצרים ומכלולים מתקדמים.
ריתוך היתוך: אנו משתמשים בחום כדי להמיס ולהתלכד חומרים. החום מסופק על ידי חשמל או קרני אנרגיה גבוהה. סוגי ריתוך היתוך שאנו פורסים הם ריתוך גז OXYFUEL, ריתוך קשת, ריתוך קרן גבוה.
ריתוך במצב מוצק: אנו מחברים חלקים ללא התכה והיתוך. שיטות הריתוך במצב מוצק שלנו הן COLD, ULTRASonic, התנגדות, חיכוך, ריתוך פיצוץ והדבקה בפיזור.
הלחמה והלחמה: הם משתמשים במתכות מילוי ומעניקים לנו את היתרון של עבודה בטמפרטורות נמוכות יותר מאשר בריתוך, ובכך פחות נזק מבני למוצרים. מידע על מתקן ההלחמה שלנו לייצור אביזרי קרמיקה למתכת, איטום הרמטי, הזנת ואקום, ואקום גבוה ואולטרה גבוה ורכיבי בקרת נוזלים ניתן למצוא כאן:חוברת מפעל הלחמה
הדבקת דבק: בגלל מגוון הדבקים המשמשים בתעשייה וגם מגוון היישומים, יש לנו דף ייעודי לכך. למעבר לדף שלנו בנושא הדבקה, אנא לחץ כאן.
הרכבה מכנית מותאמת אישית: אנו משתמשים במגוון מחברים כגון ברגים, ברגים, אומים, מסמרות. המחברים שלנו אינם מוגבלים למחברי מדף סטנדרטיים. אנו מתכננים, מפתחים ומייצרים מחברים מיוחדים העשויים מחומרים לא סטנדרטיים כדי שיוכלו לעמוד בדרישות ליישומים מיוחדים. לפעמים רצויה אי מוליכות חשמלית או חום ולפעמים מוליכות. עבור יישומים מיוחדים מסוימים, ייתכן שלקוח ירצה מחברים מיוחדים שלא ניתן להסירם מבלי להרוס את המוצר. יש אינסוף רעיונות ויישומים. יש לנו הכל בשבילך, אם לא מהמדף נוכל לפתח אותו במהירות. למעבר לעמוד שלנו בנושא הרכבה מכנית, אנא לחץ כאן. הבה נבחן את טכניקות ההצטרפות השונות שלנו בפירוט רב יותר.
ריתוך גז OXYFUEL (OFW): אנו משתמשים בגז דלק מעורבב עם חמצן כדי לייצר את להבת הריתוך. כאשר אנו משתמשים באצטילן כדלק וחמצן, אנו קוראים לזה ריתוך גז אוקסיאצטילן. שתי תגובות כימיות מתרחשות בתהליך שריפת גז החמצן:
C2H2 + O2 ------» 2CO + H2 + חום
2CO + H2 + 1.5 O2--------» 2 CO2 + H2O + חום
התגובה הראשונה מפרקת את האצטילן לפחמן חד חמצני ומימן תוך הפקת כ-33% מסך החום שנוצר. התהליך השני לעיל מייצג בעירה נוספת של המימן והפחמן החד חמצני תוך הפקת כ-67% מכלל החום. הטמפרטורות בלהבה הן בין 1533 ל-3573 קלווין. אחוז החמצן בתערובת הגז חשוב. אם תכולת החמצן היא יותר ממחצית, הלהבה הופכת לחומר מחמצן. זה לא רצוי עבור מתכות מסוימות אך רצוי עבור אחרות. דוגמה כאשר רצוי להבה מחמצנת היא סגסוגות על בסיס נחושת מכיוון שהיא יוצרת שכבת פסיבציה על המתכת. לעומת זאת, כאשר תכולת החמצן מצטמצמת, לא מתאפשרת בעירה מלאה והלהבה הופכת ללהבה מצמצמת (מקרבת). הטמפרטורות בלהבה מפחיתה נמוכות יותר ולכן היא מתאימה לתהליכים כמו הלחמה והלחמה. גזים אחרים הם גם דלקים פוטנציאליים, אבל יש להם כמה חסרונות על פני אצטילן. מדי פעם אנו מספקים מתכות מילוי לאזור הריתוך בצורה של מוטות מילוי או חוט. חלקם מצופים בשטף כדי לעכב חמצון של משטחים ובכך להגן על המתכת המותכת. יתרון נוסף שהשטף נותן לנו הוא סילוק תחמוצות וחומרים אחרים מאזור הריתוך. זה מוביל לחיבור חזק יותר. וריאציה של ריתוך גז oxyfuel היא ריתוך גז PRESSURE, שבו שני הרכיבים מחוממים בממשק שלהם באמצעות לפיד גז אוקסיאצטילן וברגע שהממשק מתחיל להימס, הלפיד נסוג ומופעל כוח צירי כדי ללחוץ את שני החלקים יחד. עד שהממשק מתמצק.
ריתוך קשת: אנו משתמשים באנרגיה חשמלית כדי לייצר קשת בין קצה האלקטרודה לחלקים שיש לרתך. ספק הכוח יכול להיות AC או DC בעוד האלקטרודות הן מתכלות או בלתי מתכלות. ניתן לבטא העברת חום בריתוך קשת באמצעות המשוואה הבאה:
H / l = ex VI / v
כאן H הוא קלט החום, l הוא אורך הריתוך, V ו-I הם המתח והזרם המופעלים, v היא מהירות הריתוך ו-e היא יעילות התהליך. ככל שהיעילות "e" גבוהה יותר, כך נעשה שימוש מועיל יותר באנרגיה הזמינה להמסת החומר. ניתן לבטא את כניסת החום גם כך:
H = ux (נפח) = ux A xl
כאן u היא האנרגיה הספציפית להתכה, A חתך הריתוך ו-l אורך הריתוך. משתי המשוואות לעיל נוכל לקבל:
v = ex VI / u A
וריאציה של ריתוך קשת הוא ריתוך מתכת SHIELDED METAL ARC WELDING (SMAW) המהווה כ-50% מכלל תהליכי הריתוך התעשייתי והתחזוקה. ריתוך חשמלי בקשת (ELECTRIC WELDING) מתבצע על ידי נגיעה בקצה האלקטרודה המצופה בחומר העבודה ומשיכתו במהירות למרחק מספיק כדי לשמור על הקשת. אנו קוראים לתהליך הזה גם ריתוך מקל מכיוון שהאלקטרודות הן מקלות דקים וארוכים. במהלך תהליך הריתוך, קצה האלקטרודה נמס יחד עם הציפוי שלה והמתכת הבסיסית בסביבת הקשת. תערובת של המתכת הבסיסית, מתכת האלקטרודה וחומרים מציפוי האלקטרודה מתמצקת באזור הריתוך. ציפוי האלקטרודה משחרר את החמצון ומספק גז מגן באזור הריתוך ובכך מגן עליו מפני החמצן בסביבה. לכן התהליך מכונה ריתוך קשת מתכת מוגנת. אנו משתמשים בזרמים בין 50 ל-300 אמפר וברמות הספק בדרך כלל פחות מ-10 קילוואט לביצועי ריתוך מיטביים. ישנה חשיבות גם לקוטביות של זרם ה-DC (כיוון זרימת הזרם). קוטביות ישרה שבה חומר העבודה חיובי והאלקטרודה שלילית מועדפת בריתוך של מתכות בגלל חדירתה הרדודה וגם לחיבורים עם מרווחים רחבים מאוד. כאשר יש לנו קוטביות הפוכה, כלומר האלקטרודה היא חיובית וחומר שלילי, נוכל להשיג חדירות ריתוך עמוקות יותר. עם זרם AC, מכיוון שיש לנו קשתות פועם, אנו יכולים לרתך קטעים עבים באמצעות אלקטרודות בקוטר גדול וזרמים מקסימליים. שיטת ריתוך SMAW מתאימה לעוביים של 3 עד 19 מ"מ ואף יותר באמצעות טכניקות ריבוי מעברים. את הסיגים שנוצרו על גבי הריתוך יש להסיר באמצעות מברשת תיל, כדי שלא תהיה קורוזיה וכשל באזור הריתוך. זה כמובן מוסיף לעלות של ריתוך בקשת מתכת מסוככת. עם זאת, ה-SMAW היא טכניקת הריתוך הפופולרית ביותר בתעשייה ובעבודות תיקונים.
ריתוך קשת שקוע (מסור): בתהליך זה אנו מגנים על קשת הריתוך באמצעות חומרי שטף גרגירים כמו סיד, סיליקה, סידן פלוריד, תחמוצת מנגן וכו'. השטף הגרגירי מוזן לאזור הריתוך על ידי זרימת כוח הכבידה דרך זרבובית. השטף המכסה את אזור הריתוך המותך מגן באופן משמעותי מפני ניצוצות, אדים, קרינת UV וכו' ופועל כמבודד תרמי, ובכך נותן לחום לחדור עמוק לתוך חלק העבודה. השטף שלא התמזג מוחזר, מטופל ועושה שימוש חוזר. סליל חשוף משמש כאלקטרודה ומוזן דרך צינור לאזור הריתוך. אנו משתמשים בזרמים בין 300 ל-2000 אמפר. תהליך ריתוך קשת שקוע (SAW) מוגבל למצבים אופקיים ושטוחים ולריתוכים מעגליים אם סיבוב המבנה העגול (כגון צינורות) אפשרי במהלך הריתוך. המהירויות יכולות להגיע ל-5 מ' לדקה. תהליך ה-SAW מתאים לצלחות עבות ומביא לריתוך איכותי, קשיח, רקיע ואחיד. הפרודוקטיביות, כלומר כמות חומר הריתוך המופקד בשעה היא פי 4 עד 10 מהכמות בהשוואה לתהליך SMAW.
תהליך ריתוך קשת נוסף, כלומר ריתוך גז מתכת GAS (GMAW) או לחילופין המכונה METAL INERT GAS WELDING (MIG) מבוסס על אזור הריתוך המוגן על ידי מקורות חיצוניים של גזים כמו הליום, ארגון, פחמן דו חמצני וכו'. יתכנו חומרים משחררי חמצון נוספים במתכת האלקטרודה. חוט מתכלה מוזן דרך זרבובית לתוך אזור הריתוך. ייצור הכולל מתכות ברזליות כמו גם מתכות לא ברזליות מתבצע באמצעות ריתוך גז מתכת קשת (GMAW). פרודוקטיביות הריתוך היא בערך פי 2 מתהליך SMAW. נעשה שימוש בציוד ריתוך אוטומטי. מתכת מועברת באחת משלוש דרכים בתהליך זה: "העברת ספריי" כוללת העברה של כמה מאות טיפות מתכת קטנות בשנייה מאלקטרודה לאזור הריתוך. ב"העברה כדורית" לעומת זאת, נעשה שימוש בגזים עשירים בפחמן דו חמצני וכדוריות של מתכת מותכת מונעות על ידי הקשת החשמלית. זרמי ריתוך גבוהים וחדירת ריתוך עמוקה יותר, מהירות ריתוך גבוהה יותר מאשר בהעברת ריסוס. לפיכך ההעברה הכדורית טובה יותר לריתוך קטעים כבדים יותר. לבסוף, בשיטת "קצר חשמלי", קצה האלקטרודה נוגע בבריכת הריתוך המותך, מקצר אותה כמתכת בקצבים של מעל 50 טיפות לשנייה מועברת בטיפות בודדות. זרמים ומתחים נמוכים משמשים יחד עם חוט דק יותר. ההספקים המשמשים הם כ-2 קילוואט והטמפרטורות נמוכות יחסית, מה שהופך שיטה זו למתאימה ליריעות דקות בעובי של פחות מ-6 מ"מ.
וריאציה נוספת של תהליך FLUX-CORED ARC WELDING (FCAW) דומה לריתוך קשת מתכת בגז, אלא שהאלקטרודה היא צינור מלא בשטף. היתרונות של שימוש באלקטרודות עם שטף ליבות הוא שהן מייצרות קשתות יציבות יותר, נותנות לנו את ההזדמנות לשפר את המאפיינים של מתכות ריתוך, אופי פחות שביר וגמיש של השטף שלה בהשוואה לריתוך SMAW, קווי מתאר ריתוך משופרים. אלקטרודות מכוסות ליבה עצמיות מכילות חומרים המגנים על אזור הריתוך מפני האטמוספרה. אנו משתמשים בהספק של כ-20 קילוואט. כמו תהליך GMAW, גם תהליך FCAW מציע הזדמנות להפוך תהליכים לריתוך מתמשך לאוטומטי, וזה חסכוני. ניתן לפתח כימיות שונות של מתכת ריתוך על ידי הוספת סגסוגות שונות לליבת השטף.
ב- ELECTROGAS WELDING (EGW) אנו מרתכים את החלקים הממוקמים מקצה לקצה. לפעמים זה נקרא גם ריתוך בטן. מתכת ריתוך מוכנסת לתוך חלל ריתוך בין שני חלקים לחיבור. החלל מוקף בשני סכרים מקוררים במים כדי למנוע מהסיגים המותכים לשפוך החוצה. הסכרים מוזזים על ידי כוננים מכניים. כאשר ניתן לסובב חומר עבודה, אנו יכולים להשתמש בטכניקת ריתוך אלקטרוגז גם לריתוך היקפי של צינורות. אלקטרודות מוזנות דרך צינור כדי לשמור על קשת רציפה. זרמים יכולים להיות בסביבות 400 אמפר או 750 אמפר ורמות הספק בסביבות 20 קילוואט. גזים אינרטיים שמקורם מאלקטרודה עם ליבת שטף או מקור חיצוני מספקים מיגון. אנו משתמשים בריתוך אלקטרוגז (EGW) עבור מתכות כגון פלדה, טיטניום וכו' בעוביים של 12 מ"מ עד 75 מ"מ. הטכניקה מתאימה למבנים גדולים.
עם זאת, בטכניקה אחרת הנקראת ELECTROSLAG WELDING (ESW) הקשת מוצתת בין האלקטרודה לתחתית חומר העבודה ומתווסף שטף. כאשר סיגים מותכים מגיעים לקצה האלקטרודה, הקשת נכבית. אנרגיה מסופקת באופן רציף דרך ההתנגדות החשמלית של הסיגים המותכים. אנו יכולים לרתך צלחות בעוביים שבין 50 מ"מ ל-900 מ"מ ואף יותר. הזרמים הם בסביבות 600 אמפר בעוד המתחים הם בין 40 - 50 וולט. מהירויות הריתוך נעות בסביבות 12 עד 36 מ"מ לדקה. יישומים דומים לריתוך אלקטרוגז.
אחד מתהליכי האלקטרודה הבלתי מתכלים שלנו, GAS TUNGSTEN ARC WELDING (GTAW) הידוע גם בשם TUNGSTEN INERT GAS WELDING (TIG) כולל אספקה של מתכת מילוי באמצעות חוט. עבור מפרקים בהתאמה הדוקה, לפעמים אנחנו לא משתמשים במתכת המילוי. בתהליך TIG אנחנו לא משתמשים בשטף, אלא משתמשים בארגון והליום למיגון. לטונגסטן יש נקודת התכה גבוהה ואינו נצרך בתהליך ריתוך TIG, לכן ניתן לשמור על זרם קבוע כמו גם פערי קשת. רמות ההספק נעות בין 8 ל-20 קילוואט וזרמים של 200 אמפר (DC) או 500 אמפר (AC). עבור אלומיניום ומגנזיום אנו משתמשים בזרם AC לפונקציית ניקוי התחמוצת שלו. כדי למנוע זיהום של אלקטרודת הטונגסטן, אנו נמנעים ממגע שלה עם מתכות מותכות. ריתוך קשת טונגסטן בגז (GTAW) שימושי במיוחד לריתוך מתכות דקות. ריתוך GTAW הם באיכות גבוהה מאוד עם גימור משטח טוב.
בשל העלות הגבוהה יותר של גז מימן, טכניקה שפחות נפוצה היא ריתוך מימן אטומי (ATOMIC HYDROGEN WELDING), שבו אנו יוצרים קשת בין שתי אלקטרודות טונגסטן באווירת מיגון של גז מימן זורם. ה-AHW הוא גם תהליך ריתוך אלקטרודות שאינו מתכלה. גז המימן הדיאטומי H2 מתפרק לצורתו האטומית ליד קשת הריתוך שבה הטמפרטורות הן מעל 6273 קלווין. בזמן פירוק, הוא סופג כמות גדולה של חום מהקשת. כאשר אטומי המימן פוגעים באזור הריתוך שהוא משטח קר יחסית, הם מתחברים מחדש לצורה דו-אטומית ומשחררים את החום המאוחסן. ניתן לשנות את האנרגיה על ידי שינוי חומר העבודה למרחק קשת.
בתהליך אחר של אלקטרודה שאינה מתכלה, ריתוך PLASMA ARC (PAW) יש לנו קשת פלזמה מרוכזת המכוונת לכיוון אזור הריתוך. הטמפרטורות מגיעות ל-33,273 קלווין ב-PAW. מספר כמעט שווה של אלקטרונים ויונים מרכיבים את גז הפלזמה. קשת פיילוט עם זרם נמוך יוזמת את הפלזמה שנמצאת בין אלקטרודת הטונגסטן לפתח. זרמי הפעולה הם בדרך כלל סביב 100 אמפר. ניתן להזין מתכת מילוי. בריתוך קשת פלזמה, המיגון מתבצע על ידי טבעת מיגון חיצונית ושימוש בגזים כגון ארגון והליום. בריתוך קשת פלזמה, הקשת עשויה להיות בין האלקטרודה לחומר העבודה או בין האלקטרודה והזרבובית. לטכניקת ריתוך זו היתרונות על פני שיטות אחרות של ריכוז אנרגיה גבוה יותר, יכולת ריתוך עמוקה וצרה יותר, יציבות קשת טובה יותר, מהירויות ריתוך גבוהות יותר עד 1 מטר/דקה, פחות עיוות תרמי. בדרך כלל אנו משתמשים בריתוך קשת פלזמה בעוביים של פחות מ-6 מ"מ ולעיתים עד 20 מ"מ עבור אלומיניום וטיטניום.
ריתוך קרן אנרגיה גבוהה: סוג נוסף של שיטת ריתוך היתוך עם ריתוך קרן אלקטרונים (EBW) וריתוך לייזר (LBW) כשתי גרסאות. לטכניקות אלו יש ערך מיוחד עבור עבודת ייצור מוצרי ההייטק שלנו. בריתוך קרן אלקטרונים, אלקטרונים במהירות גבוהה פוגעים בחומר העבודה והאנרגיה הקינטית שלהם מומרת לחום. אלומת האלקטרונים הצרה נעה בקלות בתא הוואקום. בדרך כלל אנו משתמשים בוואקום גבוה בריתוך קרן אלקטרוני. ניתן לרתך צלחות בעובי של עד 150 מ"מ. אין צורך בגזי מגן, שטף או חומר מילוי. לתותחי אלקרון יש קיבולת של 100 קילוואט. ריתוכים עמוקים וצרים עם יחסי גובה-רוחב גבוהים של עד 30 ואזורים קטנים מושפעי חום אפשריים. מהירויות ריתוך יכולות להגיע ל-12 מ' לדקה. בריתוך קרן לייזר אנו משתמשים בלייזרים בעלי הספק גבוה כמקור החום. קרני לייזר קטנות עד 10 מיקרון עם צפיפות גבוהה מאפשרות חדירה עמוקה לתוך חומר העבודה. יחסי עומק לרוחב אפשריים עד 10 עם ריתוך קרן לייזר. אנו משתמשים בלייזר גלים פולסים ורציפים, כאשר הראשון ביישומים לחומרים דקים והשני בעיקר עבור חלקי עבודה עבים עד כ-25 מ"מ. רמות ההספק הן עד 100 קילוואט. ריתוך קרן הלייזר אינו מתאים לחומרים מחזירי אור אופטית. גזים עשויים לשמש גם בתהליך הריתוך. שיטת הריתוך בקרן הלייזר מתאימה היטב לאוטומציה וייצור בנפח גבוה ויכולה להציע מהירויות ריתוך בין 2.5 מ' לדקה ל-80 מ' לדקה. יתרון מרכזי אחד שטכניקת ריתוך זו מציעה הוא גישה לאזורים שבהם לא ניתן להשתמש בטכניקות אחרות. קרני לייזר יכולות להגיע בקלות לאזורים קשים כאלה. אין צורך בוואקום כמו בריתוך קרן אלקטרונים. ניתן להשיג ריתוכים עם איכות וחוזק טוב, התכווצות נמוכה, עיוות נמוך, נקבוביות נמוכה עם ריתוך בקרן לייזר. ניתן לתפעל ולעצב בקלות קרני לייזר באמצעות כבלי סיבים אופטיים. לכן הטכניקה מתאימה היטב לריתוך של מכלולים הרמטיים מדויקים, אריזות אלקטרוניות וכו'.
הבה נבחן את טכניקות הריתוך שלנו במצב מוצק. ריתוך קר (CW) הוא תהליך שבו לחץ במקום חום מופעל באמצעות קוביות או גלילים על החלקים המשודכים. בריתוך קר, לפחות אחד מהחלקים המתואמים צריך להיות רקיע. התוצאות הטובות ביותר מתקבלות עם שני חומרים דומים. אם שתי המתכות שיש לחבר בריתוך קר אינן דומות, אנו עלולים לקבל חיבורים חלשים ושבירים. שיטת הריתוך הקרה מתאימה היטב לחלקי עבודה רכים, רקיעים וקטנים כגון חיבורי חשמל, קצוות מיכלים רגישים לחום, פסים דו-מתכתיים לתרמוסטטים וכו'. וריאציה אחת של ריתוך קר היא ריתוך גליל (או ריתוך גליל), כאשר הלחץ מופעל דרך זוג גלילים. לפעמים אנו מבצעים ריתוך גליל בטמפרטורות גבוהות לחוזק הממשק טוב יותר.
תהליך ריתוך מוצק נוסף שאנו משתמשים בו הוא הריתוך האולטראסוני (USW), שבו חלקי העבודה נתונים לכוח נורמלי סטטי ולמתחי גזירה מתנודדים. מתחי הגזירה המתנודדים מופעלים דרך קצהו של מתמר. ריתוך אולטראסוני פורס תנודות עם תדרים מ-10 עד 75 קילו-הרץ. ביישומים מסוימים כגון ריתוך תפר, אנו משתמשים בדיסק ריתוך מסתובב כקצה. מתחי הגזירה המופעלים על חלקי העבודה גורמים לעיוותים פלסטיים קטנים, מפרקים שכבות תחמוצת, מזהמים ומובילים להדבקה במצב מוצק. הטמפרטורות המעורבות בריתוך קולי הן הרבה מתחת לטמפרטורות נקודת ההיתוך עבור מתכות ולא מתרחש היתוך. אנו משתמשים לעתים קרובות בתהליך ריתוך קולי (USW) עבור חומרים לא מתכתיים כמו פלסטיק. עם זאת, בתרמופלסטיים, הטמפרטורות אכן מגיעות לנקודות התכה.
טכניקה פופולרית נוספת, בריתוך FRICTION (FRW) החום נוצר באמצעות חיכוך בממשק של חלקי העבודה שיש לחבר. בריתוך חיכוך אנו שומרים על אחד מחלקי העבודה נייח בעוד החלק השני מוחזק במתקן ומסובב במהירות קבועה. לאחר מכן מביאים את חלקי העבודה למגע תחת כוח צירי. מהירות סיבוב פני השטח בריתוך חיכוך עשויה להגיע ל-900 מטר לדקה במקרים מסוימים. לאחר מגע מספיק משטחי, חומר העבודה המסתובב נעצר בפתאומיות והכוח הצירי מוגבר. אזור הריתוך הוא בדרך כלל אזור צר. ניתן להשתמש בטכניקת ריתוך החיכוך לחיבור חלקים מוצקים וצינוריים העשויים ממגוון חומרים. הבזק מסוים עשוי להתפתח בממשק ב-FRW, אך ניתן להסיר הבזק זה על ידי עיבוד משני או שחיקה. קיימות וריאציות של תהליך ריתוך החיכוך. לדוגמה "ריתוך חיכוך אינרציה" כולל גלגל תנופה שהאנרגיה הקינטית הסיבובית שלו משמשת לריתוך החלקים. הריתוך הושלם כאשר גלגל התנופה נעצר. ניתן לגוון את המסה המסתובבת ובכך את האנרגיה הקינטית הסיבובית. וריאציה נוספת היא "ריתוך חיכוך ליניארי", כאשר תנועה הדדית ליניארית מוטלת על לפחות אחד מהרכיבים שיש לחבר. בריתוך חיכוך ליניארי חלקים לא חייבים להיות מעגליים, הם יכולים להיות מלבניים, מרובעים או בעלי צורה אחרת. תדרים יכולים להיות בעשרות הרץ, אמפליטודות בטווח המילימטרים ולחצים בעשרות או מאות MPa. לבסוף "ריתוך בוחשת חיכוך" שונה במקצת מהשניים האחרים שהוסברו לעיל. בעוד בריתוך חיכוך אינרציה וריתוך חיכוך ליניארי חימום ממשקים מושג באמצעות חיכוך על ידי שפשוף שני משטחים מגע, בשיטת ריתוך בחיכוך ערעור גוף שלישי משופשף בשני המשטחים שיש לחבר. כלי מסתובב בקוטר של 5 עד 6 מ"מ מובא במגע עם המפרק. הטמפרטורות יכולות לעלות לערכים שבין 503 ל-533 קלווין. מתבצע חימום, ערבוב וערבוב של החומר במפרק. אנו משתמשים בריתוך בחיכוך על מגוון חומרים כולל אלומיניום, פלסטיק וחומרים מרוכבים. הריתוכים אחידים והאיכות גבוהה עם מינימום נקבוביות. לא מיוצרים אדים או ניתזים בריתוך בחיכוך והתהליך הוא אוטומטי היטב.
ריתוך התנגדות (RW): החום הנדרש לריתוך מופק על ידי ההתנגדות החשמלית בין שני חלקי העבודה שיש לחבר. אין שימוש בשטף, גזי מגן או אלקטרודות מתכלות בריתוך התנגדות. חימום ג'ול מתרחש בריתוך התנגדות ויכול להתבטא כך:
H = (ריבוע I) x R xtx K
H הוא חום שנוצר בג'אול (וואט-שניות), זרם I באמפר, התנגדות R באוהם, t הוא הזמן בשניות שהזרם זורם דרכו. הגורם K קטן מ-1 ומייצג את חלק האנרגיה שלא אובד בקרינה והולכה. זרמים בתהליכי ריתוך התנגדות יכולים להגיע לרמות גבוהות של 100,000 A אך המתחים הם בדרך כלל 0.5 עד 10 וולט. אלקטרודות עשויות בדרך כלל מסגסוגות נחושת. ניתן לחבר חומרים דומים ולא דומים על ידי ריתוך התנגדות. קיימות מספר וריאציות לתהליך זה: "ריתוך נקודתי התנגדות" כולל שתי אלקטרודות עגולות מנוגדות המגעות עם המשטחים של מפרק הברכיים של שתי היריעות. לחץ מופעל עד כיבוי הזרם. קוטר גוש הריתוך הוא בדרך כלל עד 10 מ"מ. ריתוך נקודתי התנגדות משאיר סימני חריטה מעט דהויים בנקודות הריתוך. ריתוך נקודתי היא טכניקת ריתוך ההתנגדות הפופולרית ביותר שלנו. צורות אלקטרודות שונות משמשות בריתוך נקודתי על מנת להגיע לאזורים קשים. ציוד הריתוך הנקודתי שלנו נשלט CNC ויש לו מספר אלקטרודות שניתן להשתמש בהן בו זמנית. וריאציה נוספת של "ריתוך תפר התנגדות" מתבצעת עם אלקטרודות גלגל או רולר המייצרות ריתוכים נקודתיים רציפים בכל פעם שהזרם מגיע לרמה גבוהה מספיק במחזור הספק AC. המפרקים המיוצרים על ידי ריתוך תפר התנגדות הם אטומים לנוזל ולגז. מהירויות ריתוך של כ-1.5 מ' לדקה נורמליות עבור יריעות דקות. אפשר להחיל זרמים לסירוגין כך שריתוכים נקודתיים מיוצרים במרווחים רצויים לאורך התפר. ב"ריתוך הקרנת התנגדות" אנו מטביעים הבלטה אחת או יותר (גומות) על אחד ממשטחי העבודה שיש לרתך. הקרנות אלו עשויות להיות עגולות או סגלגלות. מגיעים לטמפרטורות מקומיות גבוהות בנקודות המובלטות הללו הבאות במגע עם חלק ההזדווגות. אלקטרודות מפעילות לחץ כדי לדחוס את ההקרנות הללו. לאלקטרודות בריתוך הקרנת התנגדות יש קצוות שטוחים והן סגסוגות נחושת מקוררות במים. היתרון של ריתוך הקרנת התנגדות הוא היכולת שלנו לבצע מספר ריתוכים במכה אחת, ובכך הארכת חיי האלקטרודה, יכולת ריתוך יריעות בעוביים שונים, יכולת ריתוך אוומים וברגים ליריעות. החיסרון של ריתוך הקרנת התנגדות הוא העלות הנוספת של הבלטה של הגומות. טכניקה נוספת, ב"ריתוך הבזק" נוצר חום מהקשת בקצות שני חלקי העבודה כשהם מתחילים ליצור מגע. שיטה זו עשויה גם לשקול לחילופין ריתוך קשת. הטמפרטורה בממשק עולה, והחומר מתרכך. מופעל כוח צירי ונוצר ריתוך באזור המרוכך. לאחר השלמת ריתוך הבזק, ניתן לעבד את המפרק לשיפור המראה. איכות הריתוך המתקבלת על ידי ריתוך הבזק טובה. רמות ההספק הן 10 עד 1500 קילוואט. ריתוך הבזק מתאים לחיבור מקצה לקצה של מתכות דומות או שונות בקוטר של עד 75 מ"מ ויריעות בעובי של 0.2 מ"מ עד 25 מ"מ. "ריתוך קשת חתיכים" דומה מאוד לריתוך הבזק. החתך כגון בורג או מוט הברגה משמש כאלקטרודה אחת בזמן שהוא מחובר לחומר עבודה כגון צלחת. כדי לרכז את החום שנוצר, למנוע חמצון ולשמור על המתכת המותכת באזור הריתוך, מונחת טבעת קרמית חד פעמית סביב המפרק. לבסוף "ריתוך הקשה" תהליך ריתוך התנגדות נוסף, משתמש בקבל כדי לספק את האנרגיה החשמלית. בריתוך הקשה הכוח נפרק תוך אלפיות שניות של זמן במהירות רבה ומפתח חום מקומי גבוה במפרק. אנו משתמשים בריתוך כלי הקשה נרחב בתעשיית ייצור האלקטרוניקה שבה יש להימנע מחימום של רכיבים אלקטרוניים רגישים בקרבת המפרק.
טכניקה הנקראת EXPLOSION WELDING כוללת פיצוץ של שכבת חומר נפץ המונחת על אחד מחלקי העבודה שיש לחבר. הלחץ הגבוה מאוד המופעל על חומר העבודה מייצר ממשק סוער וגלי ומתרחשת חיבור מכני. חוזק הקשר בריתוך נפץ גבוה מאוד. ריתוך פיצוץ הוא שיטה טובה לחיפוי לוחות עם מתכות שונות. לאחר החיפוי, ניתן לגלגל את הצלחות לחלקים דקים יותר. לפעמים אנו משתמשים בריתוך פיצוץ להרחבת צינורות כך שהם ייאטמו בחוזקה כנגד הצלחת.
השיטה האחרונה שלנו בתחום של הצטרפות מצב מוצק היא DIFFUSION BONDING או DIFFUSION WELDING (DFW) שבה חיבור טוב מושג בעיקר על ידי דיפוזיה של אטומים על פני הממשק. דפורמציה פלסטית מסוימת בממשק תורמת גם היא לריתוך. הטמפרטורות המעורבות הן בסביבות 0.5 Tm כאשר Tm היא טמפרטורת ההיתוך של המתכת. חוזק הקשר בריתוך דיפוזיה תלוי בלחץ, טמפרטורה, זמן מגע וניקיון משטחי מגע. לפעמים אנו משתמשים במתכות מילוי בממשק. חום ולחץ נדרשים בחיבור דיפוזיה והם מסופקים על ידי התנגדות חשמלית או תנור ומשקולות מתות, מכבש או אחר. ניתן לחבר מתכות דומות ולא דומות באמצעות ריתוך דיפוזיה. התהליך איטי יחסית בגלל הזמן שלוקח לאטומים להגירה. DFW יכול להיות אוטומטי ונמצא בשימוש נרחב בייצור חלקים מורכבים לתעשיות התעופה והחלל, האלקטרוניקה והרפואה. המוצרים המיוצרים כוללים שתלים אורטופדיים, חיישנים, חלקי מבנה תעופה וחלל. ניתן לשלב הדבקת דיפוזיה עם SUPERPLASTIC FORMING לייצור מבני מתכת מורכבים. מיקומים נבחרים על היריעות מחוברים תחילה בדיפוזיה ולאחר מכן מורחבים האזורים הלא מלוכדים לתוך תבנית באמצעות לחץ אוויר. מבני תעופה וחלל בעלי יחסי קשיחות-משקל גבוהים מיוצרים בשילוב שיטות זה. התהליך המשולב של ריתוך דיפוזיה / יצירת סופר-פלסטיק מפחית את מספר החלקים הנדרשים על-ידי ביטול הצורך במחברים, גורם לחלקים בעלי מתח נמוך ומדויק ביותר מבחינה כלכלית ועם זמני אספקה קצרים.
הלחמה: טכניקות ההלחמה וההלחמה כרוכות בטמפרטורות נמוכות מאלה הנדרשות לריתוך. עם זאת, טמפרטורות ההלחמה גבוהות יותר מטמפרטורות ההלחמה. בהלחמה מונחת מתכת מילוי בין המשטחים לחיבור והטמפרטורות מועלות לטמפרטורת ההיתוך של חומר המילוי מעל 723 קלווין אך מתחת לטמפרטורות ההיתוך של חלקי העבודה. המתכת המותכת ממלאת את החלל המתאים בין חלקי העבודה. הקירור וההתמצקות לאחר מכן של מתכת הפילטר מביאים למפרקים חזקים. בריתוך הלחמה מתכת המילוי מופקדת במפרק. הרבה יותר מתכת מילוי משמשת בריתוך הלחמה בהשוואה להלחמה. לפיד אוקסיאצטילן עם להבה מחמצנת משמש להפקדת מתכת המילוי בריתוך הלחמה. בשל טמפרטורות נמוכות יותר בהלחמה, הבעיות באזורים מושפעי חום כמו עיוות ומתחים שיוריים פחותות. ככל שפער המרווח בהלחמה קטן יותר חוזק הגזירה של המפרק גבוה יותר. חוזק מתיחה מרבי עם זאת מושג בפער אופטימלי (ערך שיא). מתחת ומעל לערך אופטימלי זה, חוזק המתיחה בהלחמה פוחת. מרווחים אופייניים בהלחמה יכולים להיות בין 0.025 ל-0.2 מ"מ. אנו משתמשים במגוון של חומרי הלחמה בעלי צורות שונות כגון ביצועים, אבקה, טבעות, חוט, רצועה וכו'. והוא יכול לייצר ביצועים אלה במיוחד עבור העיצוב או הגיאומטריה של המוצר שלך. אנו גם קובעים את תכולת חומרי ההלחמה בהתאם לחומרי הבסיס והיישום שלך. אנו משתמשים לעתים קרובות בשטפים בפעולות הלחמה כדי להסיר שכבות תחמוצת לא רצויות ולמנוע חמצון. כדי למנוע קורוזיה לאחר מכן, שטפים מוסרים בדרך כלל לאחר פעולת ההצטרפות. AGS-TECH Inc משתמשת בשיטות הלחמה שונות, כולל:
- הלחמת לפיד
- הלחמת תנור
- הלחמת אינדוקציה
- הלחמת התנגדות
- הלחמת טבילה
- הלחמת אינפרא אדום
- הלחמת דיפוזיה
- קרן אנרגיה גבוהה
הדוגמאות הנפוצות ביותר שלנו לחיבורים מולחמים עשויות ממתכות שונות בעלות חוזק טוב כגון מקדחי קרביד, תוספות, אריזות הרמטיות אופטואלקטרוניות, אטמים.
הלחמה: זוהי אחת הטכניקות הנפוצות ביותר שלנו, שבה ההלחמה (מתכת המילוי) ממלאת את המפרק כמו בהלחמה בין רכיבים מתאימים. להלחמות שלנו יש נקודות התכה מתחת ל-723 קלווין. אנו פורסים הלחמה ידנית ואוטומטית בפעולות ייצור. בהשוואה להלחמה, טמפרטורות ההלחמה נמוכות יותר. הלחמה אינה מתאימה במיוחד ליישומים בטמפרטורה גבוהה או חוזק גבוה. אנו משתמשים בהלחמות ללא עופרת וכן בסגסוגות בדיל-עופרת, בדיל-אבץ, עופרת-כסף, קדמיום-כסף, אבץ-אלומיניום מלבד אחרים להלחמה. גם חומצות ומלחים לא-קורוזיביות, כמו גם חומצות אורגניות, משמשות כשטף בהלחמה. אנו משתמשים בשטפים מיוחדים להלחמת מתכות עם יכולת הלחמה נמוכה. ביישומים בהם עלינו להלחים חומרים קרמיים, זכוכית או גרפיט, אנו מצפים תחילה את החלקים במתכת מתאימה להגברת הלחמה. טכניקות ההלחמה הפופולריות שלנו הן:
- הלחמה מחדש או הדבקה
-הלחמת גל
-הלחמת תנור
-הלחמת לפיד
-הלחמת אינדוקציה
-הלחמת ברזל
-הלחמת התנגדות
-הלחמת טבילה
-הלחמה אולטרה-סונית
-הלחמה אינפרא אדום
הלחמה אולטראסונית מעניקה לנו יתרון ייחודי לפיו הצורך בשטפים מתבטל עקב אפקט קוויטציה אולטרסאונד אשר מסיר סרטי תחמוצת מהמשטחים המחוברים. זרימה חוזרת והלחמת גל הן הטכניקות הבולטות שלנו מבחינה תעשייתית לייצור בנפח גבוה באלקטרוניקה, ולכן כדאי להסביר בפירוט רב יותר. בהלחמה חוזרת, אנו משתמשים במשחות מוצקות למחצה הכוללות חלקיקי הלחמה-מתכת. את המשחה מניחים על המפרק באמצעות תהליך הקרנה או שבלונה. במעגלים מודפסים (PCB) אנו משתמשים לעתים קרובות בטכניקה זו. כאשר מרכיבים חשמליים מונחים על רפידות אלה מהדבקה, מתח פני השטח שומר על אריזות ההרכבה על פני השטח מיושרות. לאחר הנחת הרכיבים, אנו מחממים את המכלול בכבשן כך שההלחמה החוזרת מתרחשת. במהלך תהליך זה, הממיסים שבמשחה מתאדים, השטף במשחה מופעל, הרכיבים מחוממים מראש, חלקיקי ההלחמה מומסים ומרטיבים את המפרק, ולבסוף מכלול ה-PCB מתקרר באיטיות. הטכניקה הפופולרית השנייה שלנו לייצור בנפח גבוה של לוחות PCB, כלומר הלחמת גלים מבוססת על העובדה שהלחמות מותכות מרטיבות משטחי מתכת ויוצרות קשרים טובים רק כאשר המתכת מחוממת מראש. גל למינרי עומד של הלחמה מותכת נוצר תחילה על ידי משאבה וה-PCB שחומם מראש ושטף מראש מועברים על הגל. ההלחמה מרטיבת רק משטחי מתכת חשופים אך אינה מרטיבת את אריזות הפולימר IC וגם לא את לוחות המעגלים המצופים בפולימר. מהירות גבוהה של סילון מים חמים מוציאה עודפי הלחמה מהמפרק ומונעת גישור בין מובילים סמוכים. בהלחמת גלים של חבילות מותקן על פני השטח, אנו מחברים אותן תחילה בהדבקה ללוח המעגלים לפני ההלחמה. שוב נעשה שימוש בסינון ובשבלונות אבל הפעם לאפוקסי. לאחר הנחת הרכיבים במיקומים הנכונים, האפוקסי מתרפא, הלוחות הופכים ומתבצעת הלחמת גלים.