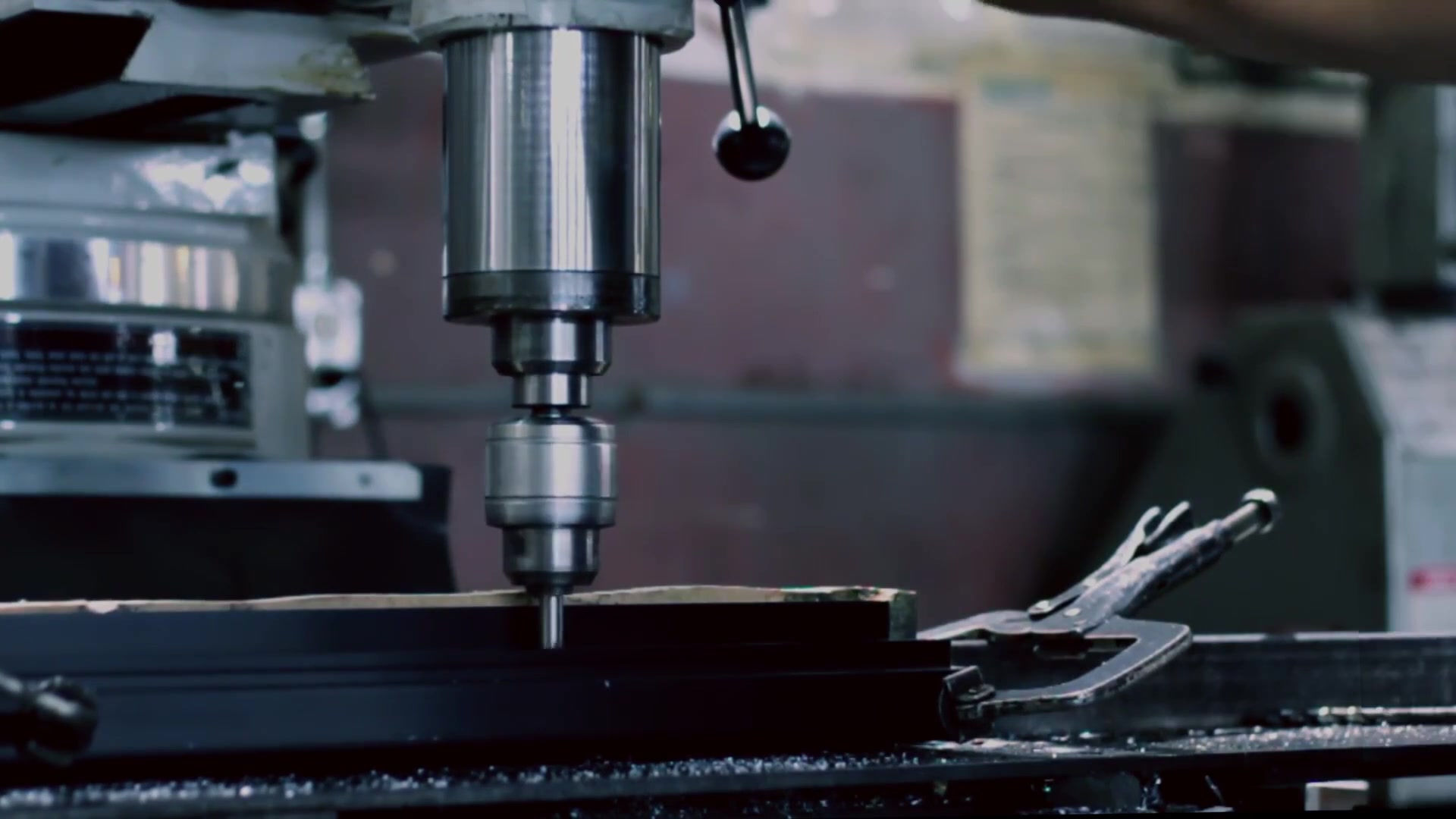
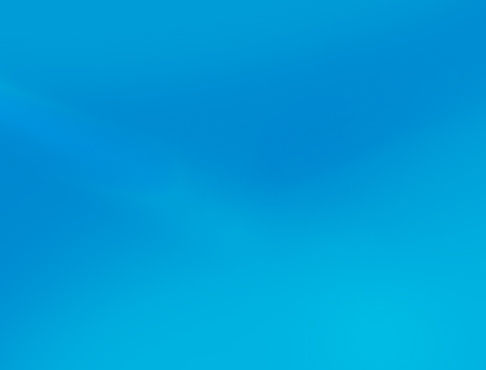
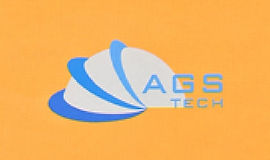
יצרן מותאם אישית גלובלי, אינטגרטור, מאחד, שותף מיקור חוץ עבור מגוון רחב של מוצרים ושירותים.
אנחנו המקור היחיד שלך לייצור, ייצור, הנדסה, איחוד, אינטגרציה, מיקור חוץ של מוצרים ושירותי מדף מיוצרים בהתאמה אישית.
בחר את השפה שלך
-
ייצור בהתאמה אישית
-
ייצור חוזים מקומי וגלובלי
-
מיקור חוץ של ייצור
-
רכש מקומי וגלובלי
-
Consolidation
-
אינטגרציה הנדסית
-
שרותי הנדסה
ELECTRICAL DISCHARGE MACHINING (EDM), also referred to as SPARK-EROSION or ELECTRODISCHARGE MACHINING, SPARK ERODING, DIE SINKING_cc781905-5cde-3194-bb3b -136bad5cf58d_or WIRE EROSION, is a NON-CONVENTIONAL MANUFACTURING process where erosion of metals takes place and desired shape is obtained using electrical discharges in the form של ניצוצות. אנו מציעים גם כמה סוגים של EDM, כלומר NO-WEAR EDM, WIRE EDM (WEDM), EDM GRINDING (EDG), EDM-Sinking EDM, EDM-Sinking EDM, ELECTRICAL-DESCHARGE TILLING, mc-19EDMcc, micro-EDM_cc -5cde-3194-bb3b-136bad5cf58d_and ELECTROCHEMICAL-DISCHARGE GRINDING (ECDG). מערכות ה-EDM שלנו מורכבות מכלים/אלקטרודה מעוצבים ומחומר העבודה המחוברים לספקי כוח DC ומוכנסים בנוזל דיאלקטרי שאינו מוליך חשמלית. לאחר 1940 הפכה עיבוד שבבי פריקה חשמלית לאחת מטכנולוגיות הייצור החשובות והפופולריות ביותר בתעשיות הייצור.
כאשר המרחק בין שתי האלקטרודות מצטמצם, עוצמת השדה החשמלי בנפח בין האלקטרודות הופכת גדולה יותר מחוזק הדיאלקטרי בחלק מהנקודות, אשר נשבר, ובסופו של דבר יוצר גשר לזרימת זרם בין שתי האלקטרודות. נוצרת קשת חשמלית עזה הגורמת לחימום משמעותי להמיס חלק מחומר העבודה וחלק מחומר העבודה. כתוצאה מכך, חומר מוסר משתי האלקטרודות. במקביל, הנוזל הדיאלקטרי מחומם במהירות, וכתוצאה מכך אידוי של הנוזל במרווח הקשת. ברגע שזרימת הזרם נעצרת או שהיא נעצרת חום מוסר מבועת הגז על ידי הנוזל הדיאלקטרי שמסביב והבועה מתנתקת (קורסת). גל ההלם שנוצר כתוצאה מהתמוטטות הבועה וזרימת הנוזל הדיאלקטרי שוטף פסולת ממשטח היצירה ומכניס כל חומר מותך של חומר העבודה לתוך הנוזל הדיאלקטרי. קצב החזרות לפריקות אלו הוא בין 50 ל-500 קילו-הרץ, מתחים בין 50 ל-380 וולט וזרמים בין 0.1 ל-500 אמפר. דיאלקטרי נוזלי חדש, כגון שמנים מינרליים, נפט או מים מזוקקים ודה-יוניים, מועברים בדרך כלל לתוך נפח הבין-אלקטרודות כשהוא נושא את החלקיקים המוצקים (בצורה של פסולת) ותכונות הבידוד של הדיאלקטרי משוחזרות. לאחר זרימת זרם, הפרש הפוטנציאלים בין שתי האלקטרודות משוחזר למה שהיה לפני ההתמוטטות, כך שיכול להתרחש התמוטטות דיאלקטרי נוזלי חדש. מכונות הפריקה החשמליות המודרניות שלנו (EDM) מציעות תנועות מבוקרות מספרית ומצוידות במשאבות ומערכות סינון לנוזלים הדיאלקטריים.
עיבוד פריקה חשמלית (EDM) היא שיטת עיבוד המשמשת בעיקר למתכות קשות או כאלה שיהיה קשה מאוד לעבד אותן בטכניקות קונבנציונליות. EDM עובד בדרך כלל עם כל חומר שהם מוליכים חשמליים, אם כי הוצעו גם שיטות לעיבוד קרמיקה בידודית עם EDM. נקודת ההיתוך והחום הסמוי של ההיתוך הם מאפיינים שקובעים את נפח המתכת שהוצאה בכל פריקה. ככל שערכים אלו גבוהים יותר, כך קצב הסרת החומר איטי יותר. מכיוון שתהליך עיבוד הפריקה החשמלית אינו כרוך באנרגיה מכנית כלשהי, הקשיות, החוזק והקשיחות של חומר העבודה אינם משפיעים על קצב ההסרה. תדירות פריקה או אנרגיה לכל פריקה, המתח והזרם משתנים כדי לשלוט בקצבי הסרת החומר. קצב הסרת החומר וחספוס פני השטח גדלים עם הגדלת צפיפות הזרם וירידה בתדירות הניצוץ. אנו יכולים לחתוך קווי מתאר או חללים מורכבים בפלדה מוקשה מראש באמצעות EDM ללא צורך בטיפול בחום כדי לרכך ולהקשיח אותם מחדש. אנו יכולים להשתמש בשיטה זו עם כל מתכת או סגסוגות מתכת כמו טיטניום, hastelloy, kovar, ו-inconel. יישומים של תהליך EDM כוללים עיצוב של כלי יהלום רב גבישי. EDM נחשבת לשיטת עיבוד שבבי לא מסורתית או לא קונבנציונלית יחד עם תהליכים כמו עיבוד אלקטרוכימי (ECM), חיתוך סילון מים (WJ, AWJ), חיתוך לייזר. מצד שני שיטות העיבוד הקונבנציונליות כוללות חריטה, כרסום, שחיקה, קידוח ועוד תהליך שמנגנון הסרת החומרים שלהם מבוסס בעיקרו על כוחות מכניים. אלקטרודות לעיבוד עיבוד חשמלי (EDM) עשויות גרפיט, פליז, נחושת וסגסוגת נחושת-טונגסטן. קוטרים של אלקטרודה עד 0.1 מ"מ אפשריים. מכיוון שחיקת הכלים היא תופעה לא רצויה המשפיעה לרעה על דיוק הממדים ב-EDM, אנו מנצלים את היתרונות של תהליך שנקרא NO-WEAR EDM, על ידי היפוך קוטביות ושימוש בכלי נחושת כדי למזער את שחיקת הכלים.
באופן אידיאלי, עיבוד פריקה חשמלית (EDM) יכול להיחשב כסדרה של התמוטטות ושיקום של הנוזל הדיאלקטרי בין האלקטרודות. אולם במציאות, הסרת הפסולת מאזור הבין-אלקטרודות היא כמעט תמיד חלקית. זה גורם לתכונות החשמליות של הדיאלקטרי באזור הבין-אלקטרודות להיות שונות מהערכים הנומינליים שלהן ומשתנות עם הזמן. המרחק בין האלקטרודות, (פער ניצוץ), מותאם על ידי אלגוריתמי הבקרה של המכונה הספציפית שבה נעשה שימוש. פער הניצוצות ב-EDM יכול למרבה הצער לפעמים להיות קצר על ידי הפסולת. מערכת הבקרה של האלקטרודה עלולה להיכשל בתגובה מהירה מספיק כדי למנוע משתי האלקטרודות (כלי וחומר עבודה) לקצר. קצר חשמלי לא רצוי זה תורם להסרת חומר באופן שונה מהמקרה האידיאלי. אנו מקדישים חשיבות מרבית לפעולת השטיפה על מנת לשחזר את תכונות הבידוד של הדיאלקטרי כך שהזרם יתרחש תמיד בנקודה של אזור הבין-אלקטרודות, ובכך למזער את האפשרות של שינוי צורה (נזק) לא רצוי של הכלי-אלקטרודה. וחומר עבודה. כדי להשיג גיאומטריה ספציפית, כלי ה-EDM מונחה לאורך הנתיב הרצוי קרוב מאוד לחומר העבודה מבלי לגעת בו, אנו מקדישים תשומת לב מרבית לביצועי בקרת התנועה בשימוש. כך מתרחשות מספר רב של פריקות/ניצוצות זרם, וכל אחת מהן תורמת להסרת החומר הן מהכלי והן מחומר העבודה, שם נוצרים מכתשים קטנים. גודל המכתשים הוא פונקציה של הפרמטרים הטכנולוגיים שנקבעו לעבודה הספציפית שעל הפרק, והממדים עשויים לנוע בין ננו-סקאלה (כגון במקרה של פעולות מיקרו-EDM) ועד כמה מאות מיקרומטרים בתנאי חיספוס. המכתשים הקטנים הללו על הכלי גורמים לשחיקה הדרגתית של האלקטרודה הנקראת "בלאי הכלים". כדי לנטרל את ההשפעה המזיקה של הבלאי על הגיאומטריה של חומר העבודה, אנו מחליפים ללא הרף את האלקטרודה של הכלי במהלך פעולת עיבוד שבבי. לפעמים אנו משיגים זאת על ידי שימוש בחוט שהוחלף ברציפות כאלקטרודה (תהליך EDM זה נקרא גם WIRE EDM ). לפעמים אנו משתמשים בכלי-אלקטרודה בצורה כזו שרק חלק קטן ממנה עוסק בפועל בתהליך העיבוד והחלק הזה משתנה על בסיס קבוע. זה, למשל, המקרה כאשר משתמשים בדיסק מסתובב כאלקטרודה לכלי. תהליך זה נקרא EDM GRINDING. טכניקה נוספת שאנו פורסים מורכבת משימוש בסט של אלקטרודות בגדלים וצורות שונות במהלך אותה פעולת EDM כדי לפצות על שחיקה. אנו קוראים לזה טכניקת אלקטרודות מרובות, והיא משמשת לרוב כאשר אלקטרודת הכלי משכפלת בשלילה את הצורה הרצויה ומתקדמת לעבר הריק לאורך כיוון יחיד, בדרך כלל הכיוון האנכי (כלומר ציר z). זה דומה לשקוע של הכלי בנוזל הדיאלקטרי שבו טבול חומר העבודה, ולכן הוא מכונה DIE-SINKING EDM_cc781905-5cde-3194-bb3b-15scde 3194-bb3b-136bad5cf58d_CONVENTIONAL EDM or RAM EDM). המכונות לפעולה זו נקראות SINKER EDM. לאלקטרודות לסוג זה של EDM יש צורות מורכבות. אם הגיאומטריה הסופית מתקבלת באמצעות אלקטרודה בעלת צורה פשוטה בדרך כלל הנעה לאורך מספר כיוונים ונתונה גם לסיבובים, אנו קוראים לזה EDM MILLING. כמות הבלאי תלויה אך ורק בפרמטרים הטכנולוגיים המשמשים בפעולה (קוטביות, זרם מרבי, מתח מעגל פתוח). לדוגמה, in micro-EDM, הידוע גם בשם m-EDM, פרמטרים אלו נקבעים בדרך כלל בערכים חמורים שיוצרים שחיקה חמורה. לכן, בלאי הוא בעיה מרכזית באותו תחום שאנו ממזערים באמצעות הידע המצטבר שלנו. לדוגמה, כדי למזער שחיקה של אלקטרודות גרפיט, גנרטור דיגיטלי, הניתן לשליטה תוך אלפיות שניות, הופך את הקוטביות כאשר מתרחשת שחיקה אלקטרו. כתוצאה מכך נוצרת השפעה דומה לציפוי האלקטרוני שמפקיד את הגרפיט הנשחק בחזרה על האלקטרודה. בשיטה אחרת, מעגל שנקרא ''Zero Wear'' אנו ממזערים את התדירות שבה הפריקה מתחילה ונפסקת, ומשאירים אותה דולקת למשך זמן רב ככל האפשר. ניתן להעריך את קצב הסרת החומר בעיבוד שבבי פריקה חשמלית מתוך:
MRR = 4 x 10 exp(4) x I x Tw exp (-1.23)
כאן MRR הוא ב-mm3/min, I הוא זרם באמפר, Tw הוא נקודת התכה של חלקי העבודה ב-K-273.15K. ה-ex מייצג אקספוננט.
מצד שני, ניתן לקבל את קצב הבלאי Wt של האלקטרודה מ:
Wt = ( 1.1 x 10exp(11) ) x I x Ttexp(-2.38)
כאן Wt הוא ב-mm3/min ו-Tt היא נקודת ההתכה של חומר האלקטרודה ב-K-273.15K
לבסוף, ניתן לקבל את יחס הבלאי של חומר העבודה לאלקטרודה R מ:
R = 2.25 x Trexp(-2.38)
כאן Tr הוא היחס בין נקודות ההתכה של חלק העבודה לאלקטרודה.
SINKER EDM :
Sinker EDM, המכונה גם CAVITY TYPE EDM or_cc781905-94cde-electronic work an-5cde31905-94cde, EDM or_cc781905-94cde-electronic workflow an-f3d3d5111905-94cde-5cde האלקטרודה וחומר העבודה מחוברים לאספקת חשמל. ספק הכוח מייצר פוטנציאל חשמלי בין השניים. כאשר האלקטרודה מתקרבת לחומר העבודה, מתרחשת התמוטטות דיאלקטרית בנוזל, ויוצרת תעלת פלזמה, וניצוץ קטן קופץ. הניצוצות בדרך כלל פוגעים בזה אחר זה מכיוון שאין זה סביר ביותר שלמיקומים שונים בחלל הבין-אלקטרודות יש מאפיינים חשמליים מקומיים זהים שיאפשרו לניצוץ להתרחש בכל המיקומים הללו בו זמנית. מאות אלפי ניצוצות אלו קורים בנקודות אקראיות בין האלקטרודה לחומר העבודה בשנייה. כאשר המתכת הבסיסית נשחקת, ומרווח הניצוץ גדל לאחר מכן, האלקטרודה יורדת אוטומטית על ידי מכונת ה-CNC שלנו כך שהתהליך יכול להמשיך ללא הפרעה. לציוד שלנו יש מחזורי שליטה הידועים כ''בזמן'' ו''זמן כבוי''. הגדרת זמן ההפעלה קובעת את אורך או משך הניצוץ. זמן ארוך יותר מייצר חלל עמוק יותר עבור אותו ניצוץ וכל הניצוצות הבאים עבור אותו מחזור, יוצר גימור גס יותר על חומר העבודה ולהיפך. זמן הכיבוי הוא פרק הזמן שבו ניצוץ אחד מוחלף באחר. זמן הפסקה ארוך יותר מאפשר לנוזל הדיאלקטרי לשטוף דרך זרבובית כדי לנקות את הפסולת הנשחקת, ובכך למנוע קצר חשמלי. הגדרות אלו מותאמות תוך מיקרו שניות.
WIRE EDM :
In WIRE ELECTRICAL DISCHARGE MACHINING (WEDM), also called WIRE-CUT EDM or WIRE CUTTING, we feed a חוט מתכת דק של פליז דרך חומר העבודה, שקוע במיכל נוזל דיאלקטרי. Wire EDM הוא וריאציה חשובה של EDM. מדי פעם אנו משתמשים ב-EDM בחיתוך חוט כדי לחתוך צלחות בעובי של עד 300 מ"מ וליצור חבטות, כלים וקוביות ממתכות קשות שקשה לעבד אותן בשיטות ייצור אחרות. בתהליך זה הדומה לחיתוך קווי מתאר עם מסור פס, החוט, המוזן כל הזמן מסליל, מוחזק בין מובילי יהלום עליונים ותחתונים. המנחים הנשלטים על ידי CNC נעים במישור x–y והמוביל העליון יכול גם לנוע באופן עצמאי בציר z–u–v, מה שמוביל ליכולת לחתוך צורות מחודדות ומעבר (כגון עיגול בתחתית וריבוע ב החלק העליון). המנחה העליון יכול לשלוט בתנועות הציר ב-x–y–u–v–i–j–k–l–. זה מאפשר ל-WEDM לחתוך צורות מאוד מורכבות ועדינות. חוט החיתוך הממוצע של הציוד שלנו המשיג את העלות הכלכלית ואת זמן העיבוד הטובים ביותר הוא 0.335 מ"מ באמצעות Ø 0.25 חוטי פליז, נחושת או טונגסטן. עם זאת, מובילי היהלומים העליונים והתחתונים של ציוד ה-CNC שלנו מדוייקים עד ל-0.004 מ"מ בערך, ויכולים להיות בעלי נתיב חיתוך או חוט קטן עד 0.021 מ"מ באמצעות חוט Ø 0.02 מ"מ. אז אפשר לחתוך ממש צר. רוחב החיתוך גדול מרוחב החוט מכיוון שנוצר ניצוצות מצידי החוט לחומר העבודה, הגורם לשחיקה. ''חיתוך יתר'' זה הכרחי, עבור יישומים רבים הוא ניתן לחיזוי ולכן ניתן לפצות עליו (במיקרו-EDM זה לא קורה לעתים קרובות). סלילי החוטים ארוכים - סליל של 8 ק"ג של חוט 0.25 מ"מ באורך של קצת יותר מ-19 ק"מ. קוטר החוט יכול להיות קטן עד 20 מיקרומטר ודיוק הגיאומטריה הוא בסביבה של +/- 1 מיקרומטר. בדרך כלל אנו משתמשים בחוט רק פעם אחת וממחזרים אותו מכיוון שהוא זול יחסית. הוא נוסע במהירות קבועה של 0.15 עד 9 מ'/דקה ונשמר חריץ (חריץ) קבוע במהלך החתך. בתהליך חיתוך תיל אנו משתמשים במים כנוזל הדיאלקטרי, שולטים בהתנגדות שלו ובתכונות חשמליות אחרות באמצעות מסננים ויחידות דה-יוניזטור. המים שוטפים את הפסולת החתוכה מאזור החיתוך. שטיפה היא גורם חשוב בקביעת קצב ההזנה המקסימלי עבור עובי חומר נתון ולכן אנו שומרים על עקביות. מהירות חיתוך ב-EDM של חוט מצוינת במונחים של שטח חתך חתך ליחידת זמן, כגון 18,000 מ"מ לשעה עבור פלדת כלי D2 בעובי 50 מ"מ. מהירות החיתוך הליניארית עבור מקרה זה תהיה 18,000/50 = 360 מ"מ לשעה. קצב הסרת החומר ב-EDM חוט הוא:
MRR = Vf xhxb
כאן MRR הוא ב-mm3/min, Vf הוא קצב ההזנה של החוט לתוך חלק העבודה ב-mm/min, h הוא עובי או גובה ב-mm, ו-b הוא ה-cerf, כלומר:
b = dw + 2s
כאן dw הוא קוטר החוט ו-s הוא הפער בין החוט לחומר העבודה במ"מ.
יחד עם סובלנות הדוקה יותר, מרכזי העיבוד הרב-ציריים המודרניים שלנו לחיתוך חוט EDM הוסיפו תכונות כמו רב ראשים לחיתוך שני חלקים בו-זמנית, בקרות למניעת שבירת חוט, תכונות הברגה עצמית אוטומטית במקרה של שבירת חוט, ומתוכנתות אסטרטגיות עיבוד כדי לייעל את הפעולה, יכולות חיתוך ישר וזוויתי.
Wire-EDM מציע לנו מתחים שיוריים נמוכים, מכיוון שהוא אינו דורש כוחות חיתוך גבוהים להסרת החומר. כאשר האנרגיה/הספק לפולס נמוכים יחסית (כמו בפעולות גימור), צפוי שינוי קטן בתכונות המכניות של חומר עקב מתחים שיוריים נמוכים.
שחיקה חשמלית (EDG) : גלגלי השחזה אינם מכילים חומרים שוחקים, הם עשויים גרפיט או פליז. ניצוצות חוזרים ונשנים בין הגלגל המסתובב לחומר העבודה מסירים חומר ממשטחי העבודה. קצב הסרת החומר הוא:
MRR = K x I
כאן MRR הוא ב-mm3/min, I הוא זרם באמפר, ו-K הוא גורם חומרי עבודה ב-mm3/A-min. אנו משתמשים לעתים קרובות בטחינת פריקה חשמלית כדי לנסר חריצים צרים ברכיבים. לעיתים אנו משלבים תהליך EDG (Electrical-Discharge Grinding) עם תהליך ECG (Electrochemical Grinding) שבו חומר מוסר על ידי פעולה כימית, הפרשות החשמליות מגלגל הגרפיט מפרקות את סרט התחמוצת ונשטפות על ידי האלקטרוליט. התהליך נקרא ELECTROCHEMICAL-DISCHARGE GRINDING (ECDG). למרות שתהליך ה-ECDG צורך יחסית יותר חשמל, זהו תהליך מהיר יותר מה-EDG. אנו טוחנים בעיקר כלי קרביד בטכניקה זו.
יישומים של עיבוד שבבי פריקה חשמלית:
ייצור אב טיפוס:
אנו משתמשים בתהליך ה-EDM בייצור תבניות, ייצור כלים ומוות, כמו גם לייצור אב טיפוס וחלקי ייצור, במיוחד עבור תעשיות התעופה והחלל, הרכב והאלקטרוניקה שבהן כמויות הייצור נמוכות יחסית. ב-Sinker EDM, אלקטרודת גרפיט, נחושת טונגסטן או נחושת טהורה מעובדת במכונה לצורה הרצויה (שלילית) ומוכנסת לחומר העבודה בקצה כבש אנכי.
יצירת קוביות מטבעות:
ליצירת קוביות לייצור תכשיטים ותגים בתהליך המטבעות (הטבעה), המאסטר החיובי עשוי להיות עשוי מכסף סטרלינג, שכן (עם הגדרות מכונה מתאימות) המאסטר נשחק באופן משמעותי ונעשה בו שימוש פעם אחת בלבד. לאחר מכן, התבנית הנגטיבית שנוצרה מוקשחת ומשמשת בפטיש טיפה לייצור חלקים מוטבעים מחלקי גיליון חתוכים של ברונזה, כסף או סגסוגת זהב בעלת הוכחה נמוכה. עבור תגים ניתן לעצב את הדירות הללו למשטח מעוקל על ידי קובייה אחרת. סוג זה של EDM מבוצע בדרך כלל שקוע בדיאלקטרי מבוסס שמן. האובייקט המוגמר עשוי להיות מעודן יותר על ידי אמייל קשיח (זכוכית) או רך (צבע) ו/או מצופה אלקטרוניקה בזהב טהור או ניקל. חומרים רכים יותר כגון כסף עשויים להיות חרוטים ביד כעידון.
קידוח חורים קטנים:
במכונות EDM לחתוך חוט שלנו, אנו משתמשים ב-EDM לקידוח חורים קטנים כדי ליצור חור דרך בחומר עבודה שדרכו ניתן להשחיל את החוט לפעולת ה-EDM החתוכה. ראשי EDM נפרדים במיוחד עבור קידוח חורים קטנים מותקנים על מכונות החיתוך החוט שלנו המאפשרות לצלחות גדולות מוקשחות לשחוק מהן חלקים מוגמרים לפי הצורך וללא קידוח מוקדם. אנו משתמשים גם ב-EDM עם חורים קטנים כדי לקדוח שורות של חורים בקצוות של להבי טורבינה המשמשים במנועי סילון. זרימת גז דרך החורים הקטנים הללו מאפשרת למנועים להשתמש בטמפרטורות גבוהות יותר ממה שאפשר אחרת. הסגסוגות החד-גבישיות בטמפרטורה גבוהה, קשיחה מאוד, מהן עשויים להבים, הופכת את העיבוד הקונבנציונלי של חורים אלה עם יחס רוחב-גובה לקשה ביותר ואף בלתי אפשרי. אזורי יישום אחרים עבור חור קטן EDM הוא ליצור פתחים מיקרוסקופיים עבור רכיבי מערכת הדלק. מלבד ראשי ה-EDM המשולבים, אנו פורסים מכונות EDM לקידוח חורים קטנים עצמאיים עם צירי x-y למכונה עיוורת או דרך חורים. קדחי EDM מקדחים חורים עם אלקטרודה ארוכה של צינור פליז או נחושת המסתובבת בצ'אק עם זרימה קבועה של מים מזוקקים או דה-יוניונים הזורמים דרך האלקטרודה כחומר שטיפה ודיאלקטרי. כמה EDMs לקידוח חורים קטנים מסוגלים לקדוח דרך 100 מ"מ של פלדה רכה או אפילו מוקשה בפחות מ-10 שניות. ניתן להשיג חורים בין 0.3 מ"מ ל-6.1 מ"מ בפעולת קידוח זו.
עיבוד שבבי לפירוק מתכת:
יש לנו גם מכונות EDM מיוחדות למטרות ספציפיות של הסרת כלים שבורים (מקדחים או ברזים) מחתיכות עבודה. תהליך זה נקרא ''עיבוד עיבוד מתכת''.
יתרונות וחסרונות עיבוד שבבי פריקה חשמלית:
היתרונות של EDM כוללים עיבוד שבבי של:
- צורות מורכבות שאחרת יהיה קשה לייצר עם כלי חיתוך קונבנציונליים
- חומר קשה במיוחד לסובלנות קרובה מאוד
- חלקי עבודה קטנים מאוד שבהם כלי חיתוך קונבנציונליים עלולים לגרום נזק לחלק כתוצאה מלחץ יתר של כלי החיתוך.
- אין מגע ישיר בין הכלי לפריט העבודה. לכן ניתן לעבד קטעים עדינים וחומרים חלשים ללא כל עיוות.
- ניתן לקבל גימור משטח טוב.
- ניתן לקדוח בקלות חורים עדינים מאוד.
החסרונות של EDM כוללים:
- הקצב האיטי של הסרת החומר.
- הזמן והעלות הנוספים המשמשים ליצירת אלקטרודות ל-RAM/Sinker EDM.
- קשה לשחזר פינות חדות על חומר העבודה עקב בלאי אלקטרודות.
- צריכת החשמל גבוהה.
- נוצר ''חיתוך יתר''.
- בלאי יתר של הכלים מתרחש במהלך העיבוד.
- חומרים שאינם מוליכים חשמלית ניתנים לעיבוד רק עם הגדרה ספציפית של התהליך.