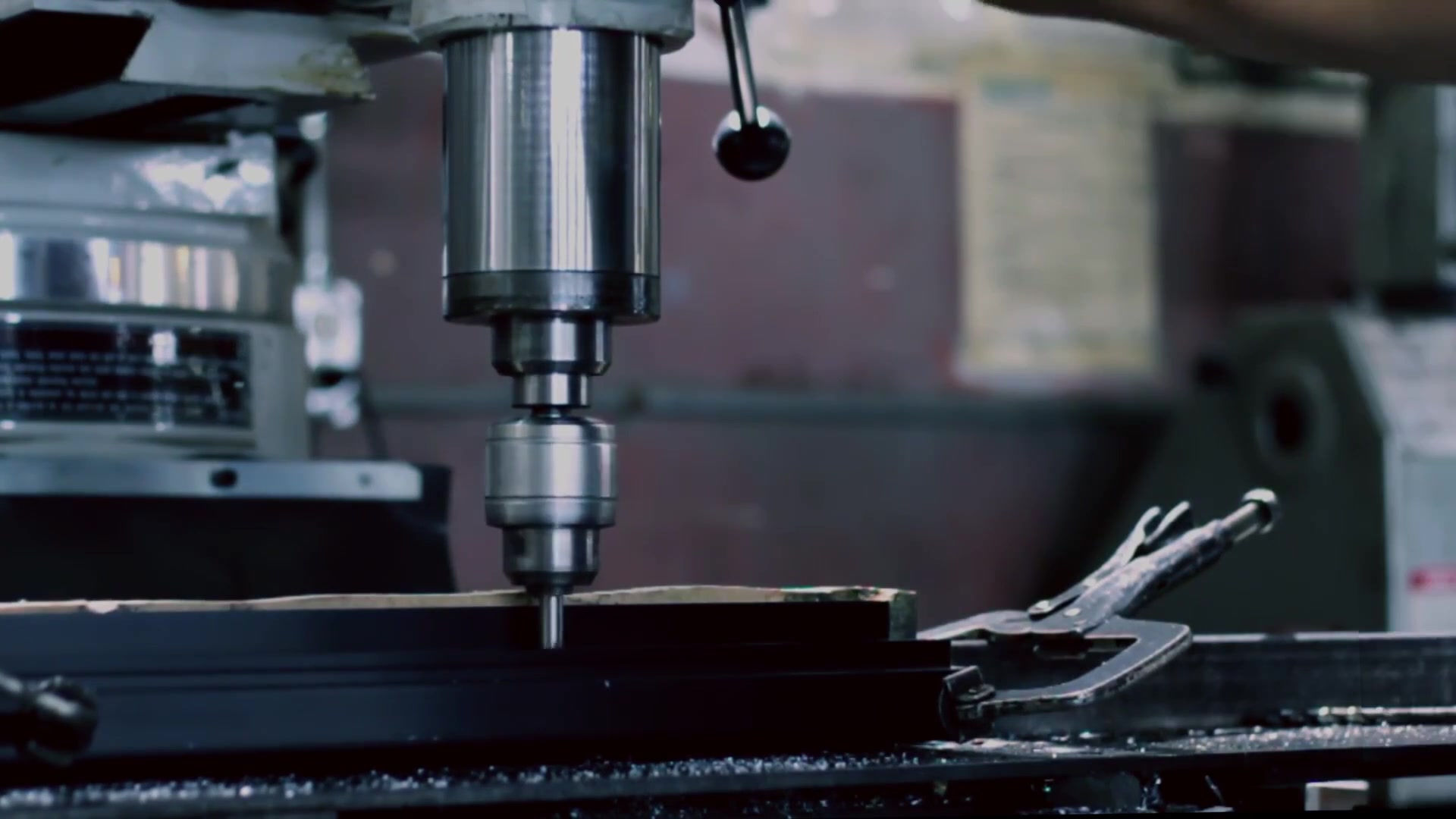
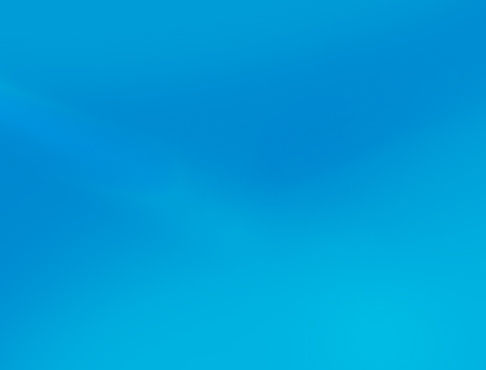
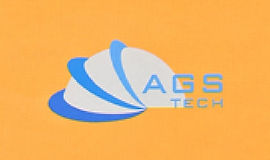
יצרן מותאם אישית גלובלי, אינטגרטור, מאחד, שותף מיקור חוץ עבור מגוון רחב של מוצרים ושירותים.
אנחנו המקור היחיד שלך לייצור, ייצור, הנדסה, איחוד, אינטגרציה, מיקור חוץ של מוצרים ושירותי מדף מיוצרים בהתאמה אישית.
בחר את השפה שלך
-
ייצור בהתאמה אישית
-
ייצור חוזים מקומי וגלובלי
-
מיקור חוץ של ייצור
-
רכש מקומי וגלובלי
-
Consolidation
-
אינטגרציה הנדסית
-
שרותי הנדסה
Search Results
נמצאו 164 תוצאות בלי מונחי חיפוש
- Transmission Components, Belts, Chains, Cable Drives, Pulleys,AGS-TECH
Transmission Components, Belts, Chains and Cable Drives, Conventional & Grooved or Serrated, Positive Drive, Pulleys חגורות ושרשראות ומכלול כונן כבלים AGS-TECH Inc. מציעה לך רכיבי הילוך כוח, לרבות חגורות ושרשראות ומכלול הנעה בכבלים. עם שנים של עידון, כונני הגומי, העור ושאר הרצועות שלנו הפכו קלים וקומפקטיים יותר, המסוגלים לשאת עומסים גבוהים יותר בעלות נמוכה יותר. באופן דומה, כונני השרשרת שלנו עברו התפתחות רבה לאורך זמן והם מציעים ללקוחותינו מספר יתרונות. כמה יתרונות של שימוש בהנעי שרשרת הם מרחקי מרכז הפיר הבלתי מוגבלים יחסית, הקומפקטיות, קלות ההרכבה, גמישות המתיחה ללא החלקה או זחילה, יכולת הפעולה בסביבות בטמפרטורה גבוהה. כונני הכבלים שלנו מציעים גם יתרונות כמו פשטות ביישומים מסוימים על פני סוגים אחרים של רכיבי תמסורת. זמינים גם כונני חגורת מדף, שרשרת וכבלים וגם גרסאות מותאמות ומורכבות. אנו יכולים לייצר רכיבי תמסורת אלו בגודל המתאים ליישום שלך ומהחומרים המתאימים ביותר. כונני חגורות וחגורות: - חגורות שטוחות קונבנציונליות: אלו חגורות שטוחות רגילות ללא שיניים, חריצים או שיניים. כונני חגורה שטוחים מציעים גמישות, בלימת זעזועים טובה, העברת כוח יעילה במהירויות גבוהות, עמידות בפני שחיקה, עלות נמוכה. ניתן לחבר או לחבר חגורות כדי ליצור חגורות גדולות יותר. יתרונות נוספים של חגורות שטוחות קונבנציונליות הן שהן דקות, הן אינן כפופות לעומסים צנטריפוגליים גבוהים (מה שהופך אותן טובות לפעולות במהירות גבוהה עם גלגלות קטנות). מצד שני הם מטילים עומסי נשיאה גבוהים מכיוון שחגורות שטוחות דורשות מתח גבוה. חסרונות נוספים של כונני רצועה שטוחה יכולים להיות החלקה, פעולה רועשת ויעילות נמוכה יחסית במהירויות פעולה נמוכות ומתונות. יש לנו שני סוגים של חגורות קונבנציונליות: מחוזקות ולא מחוזקות. לחגורות מחוזקות יש איבר מתיחה במבנה שלהן. חגורות שטוחות קונבנציונליות זמינות כעור, בד או חוט מגומי, גומי לא מחוזק או פלסטיק, בד, עור מחוזק. חגורות עור מציעות חיים ארוכים, גמישות, מקדם חיכוך מצוין, תיקון קל. עם זאת חגורות עור יקרות יחסית, צריכות חבישה וניקוי חגורות, ובהתאם לאווירה הן עלולות להתכווץ או להימתח. חגורות בד או חוטים מגומיים עמידות בפני לחות, חומצה ואלקליות. חגורות בד מגומי מורכבות משכבות כותנה או ברווז סינטטי ספוג גומי והן החסכוניות ביותר. חגורות חבל מגומי מורכבות מסדרה של שכבות של חבלים ספוגים בגומי. חגורות חוט מגומי מציעות חוזק מתיחה גבוה וגודל ומסה צנועים. חגורות גומי או פלסטיק לא מחוזקות מתאימות ליישומי הנעה קלים ומהירות נמוכה. ניתן למתוח חגורות גומי ופלסטיק לא מחוזקות למקומן מעל הגלגלות שלהן. חגורות פלסטיק לא מחוזקות יכולות להעביר כוח גבוה יותר בהשוואה לחגורות גומי. חגורות עור מחוזקות מורכבות מאיבר מתיחה מפלסטיק המחובר בין שכבות העור העליונות והתחתונה. לבסוף, חגורות הבד שלנו עשויות להיות מורכבות מחתיכת כותנה או ברווז בודדת מקופלת ותפורה בשורות של תפרים אורכיים. חגורות בד מסוגלות לעקוב בצורה אחידה ולפעול במהירות גבוהה. - חגורות מחורצות או משוננות (כגון רצועות V): אלו הן חגורות שטוחות בסיסיות ששונו כדי לספק את היתרונות של סוג אחר של מוצר תיבת הילוכים. אלו חגורות שטוחות עם צד תחתון מצולע לאורך. חגורות פולי-V הן חגורה שטוחה מחורצת לאורך או משוננת עם חתך מתיחה וסדרה של חריצים סמוכים בצורת V למטרות מעקב ודחיסה. קיבולת הכוח תלויה ברוחב החגורה. חגורת V היא סוס העבודה של התעשייה וזמינות במגוון גדלים וסוגים סטנדרטיים להעברה של כמעט כל כוח עומס. כונני רצועות V פועלים היטב בין 1500 ל-6000 רגל/דקה, אולם רצועות V צרות יפעלו עד 10,000 רגל/דקה. כונני רצועות V מציעים חיים ארוכים כגון 3 עד 5 שנים ומאפשרים יחסי מהירות גדולים, הם קלים להתקנה והסרה, מציעים פעולה שקטה, תחזוקה נמוכה, בלימת זעזועים טובה בין מנע הרצועה לצירים המונעים. החיסרון של רצועות V הוא החלקה וזחילה מסויימת שלהן ולכן הן לא יכולות להיות הפתרון הטוב ביותר כאשר נדרשות מהירויות סינכרוניות. יש לנו חגורות תעשייתיות, רכב וחקלאות. זמינים אורכים סטנדרטיים מצוידים כמו גם אורכים מותאמים אישית של חגורות. כל החתכים הסטנדרטיים של חגורת V זמינים מהמלאי. יש טבלאות שבהן אתה יכול לחשב פרמטרים לא ידועים כמו אורך רצועה, חתך רצועה (רוחב ועובי) בתנאי שאתה יודע כמה פרמטרים של המערכת שלך כגון קוטרי גלגלות הנעה ומונעות, מרחק מרכז בין גלגלות ומהירויות סיבוב של הגלגלות. אתה יכול להשתמש בטבלאות כאלה או לבקש מאיתנו לבחור את רצועת ה V המתאימה לך. - רצועות הנעה חיוביות (רצועת טיימינג): רצועות אלו הן גם מסוג שטוח עם סדרה של שיניים מרווחות באופן שווה בהיקף הפנימי. רצועות הנעה חיוביות או תזמון משלבות את היתרונות של חגורות שטוחות עם מאפייני האחיזה החיובית של שרשראות וגלגלי שיניים. רצועות הנעה חיוביות לא חושפות החלקה או שינויים במהירות. טווח רחב של יחסי מהירות אפשרי. עומסי המיסבים נמוכים מכיוון שהם יכולים לפעול במתח נמוך. עם זאת, הם רגישים יותר לאי-יישור בגלגלות. - גלגלות, אלומות, רכזות לחגורות: סוגים שונים של גלגלות משמשים עם חגורות הנעה שטוחות, מצולעות (משוננות) וחיוביות. אנחנו מייצרים את כולם. רוב גלגלות הרצועה השטוחות שלנו עשויות מיציקת ברזל, אך גרסאות פלדה זמינות גם בשילובי חישוק ורכזת שונים. לגלגלות החגורה השטוחה שלנו עשויות להיות רכזות מוצקות, חישוריות או מפוצלות, או שנוכל לייצר כרצונך. רצועות עם צלעות והנעה חיובית זמינות במגוון גדלים ורוחב מלאי. לפחות גלגלת אחת בהנעי רצועת טיימינג חייבת להיות מאובטחת כדי לשמור על הרצועה על הכונן. עבור מערכות הנעה מרכזיות ארוכות, מומלץ להחזיק את שתי הגלגלות עם אוגן. אלומות הן הגלגלים המחורצים של גלגלות ומיוצרות בדרך כלל על ידי יציקת ברזל, יצירת פלדה או יציקת פלסטיק. יצירת פלדה היא תהליך מתאים לייצור אלומות רכב וחקלאות. אנו מייצרים אלומות עם חריצים רגילים ועמוקים. אלומות עם חריצים עמוקים מתאימות היטב כאשר חגורת V נכנסת לאלמה בזווית, כמו שקורה בהנעות של רבע פנייה. חריצים עמוקים מתאימים גם להנעי גל אנכי ויישומים שבהם רטט של חגורות יכול להוות בעיה. גלגלות הסרק שלנו הן אלומות מחורצות או גלגלות שטוחות שאינן משרתות כוח מכני מעביר. גלגלות סרק משמשות בעיקר להידוק חגורות. - כונני רצועה בודדים ומרובים: כונני רצועה בודדים הם בעלי חריץ בודד ואילו כונני רצועה מרובים כוללים חריצים מרובים. על ידי לחיצה על הטקסט הצבעוני הרלוונטי למטה תוכל להוריד את הקטלוגים שלנו: - רצועות הילוך כוח (כולל רצועות V, רצועות טיימינג, חגורות קצה גלם, חגורות עטופות וחגורות מיוחדות) - מסועים - גלגלות V - גלגלות תזמון שרשראות והנעי שרשרת: לשרשראות העברת הכוח שלנו יש כמה יתרונות כגון מרחקי מרכז פיר בלתי מוגבלים יחסית, הרכבה קלה, קומפקטיות, גמישות תחת מתח ללא החלקה או זחילה, יכולת פעולה בטמפרטורות גבוהות. להלן הסוגים העיקריים של הרשתות שלנו: - שרשראות ניתנות להסרה: השרשראות הניתנות להסרה שלנו עשויות במגוון גדלים, גובה וחוזק אולטימטיבי, ובדרך כלל מברזל או פלדה ניתנים להסרה. שרשראות ניתנות לעיבוד מיוצרות במגוון גדלים מ-0.902 (23 מ"מ) עד 4.063 אינץ' (103 מ"מ) ועוצמה אולטימטיבית מ-700 עד 17,000 פאונד/אינץ' מרובע. שרשראות הפלדה הניתנות להסרה שלנו מיוצרות בגדלים מ-0.904 אינץ' (23 מ"מ) עד כ-3.00 אינץ' (76 מ"מ), עם חוזק אולטימטיבי מ-760 עד 5000 פאונד/אינץ' מרובע._cc781905-5cde-3194-bb3b- 136bad5cf58d_ - שרשראות פינטל: שרשראות אלו משמשות לעומסים כבדים יותר ולמהירויות מעט גבוהות יותר לכ-450 רגל/דקה (2.2 מ'/שנייה). שרשראות פינטל עשויות מחוליות יצוק בודדות בעלות קצה קנה מלא ועגול עם מוטות צד מאופזים. חוליות שרשרת אלו מחוברות זו לזו עם פיני פלדה. שרשראות אלו נעות בגובה הגובה בין כ-1.00 אינץ' (25 מ"מ) ל-6.00 אינץ' (150 מ"מ) וחוזק אולטימטיבי בין 3600 ל-30,000 פאונד/אינץ' מרובע. - שרשראות אופסט-צדדיות: אלה פופולריות בשרשראות הנעה של מכונות בנייה. שרשראות אלו פועלות במהירויות של עד 1000 רגל/דקה ומעבירות עומסים לכ-250 כ"ס. בדרך כלל לכל חוליה יש שני מוטות צד מאופזים, תותב אחד, רולר אחד, סיכה אחת, סיכת חוצה. - שרשראות רולר: הן זמינות במגרשים מ-0.25 (6 מ"מ) עד 3.00 (75 מ"מ) אינץ'. החוזק האולטימטיבי של שרשראות רולר ברוחב יחיד נע בין 925 ל-130,000 פאונד/אינץ' מרובע. גרסאות ברוחב מרובות של שרשראות גלילה זמינות ומשדרות כוח רב יותר במהירויות גבוהות יותר. שרשראות גלגלות ברוחב מרובות מציעות גם פעולה חלקה יותר עם רעש מופחת. שרשראות רולר מורכבות מחוליות רולר ומחוליות סיכות. סיכות קוטר משמשות בשרשראות גלילה ניתנות להסרה. העיצוב של כונני שרשרת רולר דורש מומחיות בנושא. בעוד שהנעי רצועה מבוססים על מהירויות ליניאריות, כונני שרשרת מבוססים על מהירות הסיבוב של גלגל השיניים הקטן יותר, שהוא ברוב המתקנים האיבר המונע. מלבד דירוג כוח סוס ומהירות סיבוב, העיצוב של כונני שרשרת מבוסס על גורמים רבים אחרים. - שרשראות Double-Pitch: זהה בעצם לשרשראות רולר פרט לכך שהמגרש ארוך פי שניים. - שרשראות שן הפוכות (שקטות): שרשראות במהירות גבוהה המשמשות בעיקר עבור כוננים ראשוניים, כונני המראה כוח. כונני שרשרת שיניים הפוכים יכולים להעביר הספקים של עד 1200 כ"ס והם מורכבים מסדרה של חוליות שיניים, המורכבות לסירוגין עם פינים או שילוב של רכיבי מפרקים. לשרשרת המובילה המרכזית יש חוליות מובילות לשילוב חריצים בגלגל השיניים, ולשרשרת המובילה הצדדית יש מובילים לחיבור הצדדים של גלגל השיניים. - שרשראות חרוזים או סליידר: שרשראות אלו משמשות להנעות במהירות איטית וגם בפעולות ידניות. על ידי לחיצה על הטקסט הצבעוני הרלוונטי למטה תוכל להוריד את הקטלוגים שלנו: - שרשראות נהיגה - שרשראות מסועים - שרשראות מסוע גדולות - שרשראות רולר מנירוסטה - שרשראות הרמה - שרשראות לאופנועים - שרשראות מכונות חקלאיות - גלגלי שיניים: גלגלי השיניים הסטנדרטיים שלנו תואמים לתקני ANSI. גלגלי שיניים מלוחים הם גלגלי שיניים שטוחים ללא רכזת. גלגלי השיניים הקטנים והבינוניים שלנו הופכים ממלאי מוט או פרזול או מיוצרים על ידי ריתוך רכזת מוטות לצלחת מגולגלת חמה. AGS-TECH בע"מ יכולה לספק גלגלי שיניים מעובדים מיציקות ברזל אפור, פלדה יצוקה וקונסטרוקציות רכזות מרותכות, מתכת אבקת סינטרה, פלסטיק יצוק או מעובד. לפעולה חלקה במהירויות גבוהות, בחירה נכונה של גודל גלגלי השיניים היא חיונית. מגבלות המקום הן כמובן גורם שאנו לא יכולים להתעלם ממנו בעת בחירת גלגל שיניים. מומלץ שהיחס בין הנהג לגלגלי שיניים מונעים יהיה לא יותר מ-6:1, ועטיפת השרשרת על הנהג היא 120 מעלות. יש לבחור גם מרחקי מרכז בין גלגלי השיניים הקטנים לגדולים יותר, אורכי השרשרת ומתח השרשרת לפי כמה חישובים הנדסיים מומלצים והנחיות ולא באופן אקראי. הורד את הקטלוגים שלנו על ידי לחיצה על טקסט צבעוני למטה: - גלגלי שיניים וגלגלי לוח - תותבי הילוכים - צימוד שרשרת - מנעולי שרשרת כונני כבלים: יש להם את היתרונות שלהם על פני רצועות והנעי שרשרת במקרים מסוימים. כונני כבלים יכולים לבצע את אותה פונקציה כמו חגורות ועשויים להיות פשוטים וחסכוניים יותר ליישום ביישומים מסוימים. לדוגמה, סדרה חדשה של כונני כבלים של Synchromesh מיועדת למשיכה חיובית כדי להחליף חבלים קונבנציונליים, כבלים פשוטים והנעי שיניים, במיוחד במקומות צרים. כונן הכבלים החדש נועד לספק מיקום דיוק גבוה בציוד אלקטרוני כגון מכונות צילום, פלוטרים, מכונות כתיבה, מדפסות וכו'. תכונה מרכזית של כונן הכבלים החדש היא היכולת שלו לשמש בתצורות סרפנטין תלת מימדיות המאפשרות עיצובים מיניאטוריים במיוחד. ניתן להשתמש בכבלי סינכרום עם מתח נמוך יותר בהשוואה לחבלים ובכך להפחית את צריכת החשמל. צרו קשר עם AGS-TECH לשאלות וחוות דעת על רצועות, שרשרת וכבלים. CLICK Product Finder-Locator Service עמוד קודם
- Joining & Assembly & Fastening Processes, Welding, Brazing, Soldering
Joining & Assembly & Fastening Processes, Welding, Brazing, Soldering, Sintering, Adhesive Bonding, Press Fitting, Wave and Reflow Solder Process, Torch Furnace תהליכי הצטרפות והרכבה והידוק אנו מצטרפים, מרכיבים ומהדקים את החלקים המיוצרים שלך והופכים אותם למוצרים מוגמרים או חצי מוגמרים באמצעות ריתוך, הלחמה, הלחמה, הלחמה, הדבקת הדבקה, הידוק, התאמת לחיצה. חלק מתהליכי הריתוך הפופולריים ביותר שלנו הם קשת, גז חמצן, התנגדות, הקרנה, תפר, עצבנות, הקשה, מצב מוצק, קרן אלקטרונים, לייזר, טרמיט, ריתוך אינדוקציה. תהליכי ההלחמה הפופולריים שלנו הם הלחמה לפיד, אינדוקציה, תנור וטבילה. שיטות ההלחמה שלנו הן ברזל, פלטה, תנור, אינדוקציה, טבילה, גל, זרימה חוזרת והלחמה על-קולית. להדבקת דבק אנו משתמשים לעתים קרובות בתרמופלסטיים ובתרמו-הגדרה, אפוקסי, פנולים, פוליאוריטן, סגסוגות דבקות כמו גם כמה כימיקלים וסרטים אחרים. לבסוף תהליכי ההידוק שלנו מורכבים ממסמר, הברגה, ברגים ואומים, ריתוק, ליטוש, הצמדה, תפירה והידוק והתאמת לחיצה. • ריתוך: ריתוך כרוך בחיבור חומרים על ידי המסת חלקי העבודה והחדרת חומרי מילוי, המצטרפים גם לבריכת הריתוך המותך. כאשר האזור מתקרר, אנו מקבלים מפרק חזק. לחץ מופעל במקרים מסוימים. בניגוד לריתוך, פעולות ההלחמה וההלחמה כוללות רק התכה של חומר עם נקודת התכה נמוכה יותר בין חלקי העבודה, וחלקי העבודה אינם נמסים. אנו ממליצים ללחוץ כאן כדיהורד את האיורים הסכמטיים שלנו של תהליכי ריתוך מאת AGS-TECH Inc. זה יעזור לך להבין טוב יותר את המידע שאנו מספקים לך למטה. ב-ARC WELDING, אנו משתמשים בספק כוח ובאלקטרודה כדי ליצור קשת חשמלית הממיסה את המתכות. נקודת הריתוך מוגנת על ידי גז מגן או אדים או חומר אחר. תהליך זה פופולרי לריתוך חלקי רכב ומבני פלדה. בריתוך קשת מתכת מכוסה (SMAW) או המכונה גם ריתוך מקל, מקל אלקטרודה מקרב לחומר הבסיס ונוצר קשת חשמלית ביניהם. מוט האלקטרודה נמס ופועל כחומר המילוי. האלקטרודה מכילה גם שטף שפועל כשכבת סיגים ומוציא אדים המשמשים כגז המגן. אלה מגנים על אזור הריתוך מפני זיהום סביבתי. לא נעשה שימוש בחומרי מילוי אחרים. החסרונות של תהליך זה הם האיטיות שלו, הצורך להחליף אלקטרודות לעתים קרובות, הצורך לשבש את שאריות הסיגים שמקורם בשטף. מספר מתכות כגון ברזל, פלדה, ניקל, אלומיניום, נחושת וכו'. ניתן לרתך. היתרונות שלו הם הכלים הזולים וקלות השימוש. ריתוך גז מתכת קשת (GMAW) הידוע גם בשם מתכת אינרטי (MIG), יש לנו הזנה רציפה של מילוי חוטי אלקטרודה מתכלה וגז אינרטי או אינרטי חלקי שזורם סביב החוט נגד זיהום סביבתי של אזור הריתוך. ניתן לרתך פלדה, אלומיניום ומתכות לא ברזליות אחרות. היתרונות של MIG הם מהירויות ריתוך גבוהות ואיכות טובה. החסרונות הם הציוד המסובך והאתגרים העומדים בפניו בסביבות חיצוניות סוערות מכיוון שעלינו לשמור על יציבות גז המגן סביב אזור הריתוך. וריאציה של GMAW היא ריתוך קשת עם ליבות שטף (FCAW) המורכב מצינור מתכת עדין מלא בחומרי שטף. לפעמים השטף בתוך הצינור מספיק להגנה מפני זיהום סביבתי. ריתוך קשת שקוע (SAW) הוא תהליך אוטומטי באופן נרחב, הכולל הזנת תיל רציפה וקשת שנפגעת מתחת לשכבת כיסוי שטף. קצבי הייצור והאיכות גבוהים, סיגי ריתוך יורד בקלות, ויש לנו סביבת עבודה נטולת עשן. החיסרון הוא שניתן להשתמש בו רק לריתוך parts במיקומים מסוימים. בריתוך גז טונגסטן בקשת (GTAW) או ריתוך גז אינרטי של טונגסטן (TIG) אנו משתמשים באלקטרודת טונגסטן יחד עם חומר מילוי נפרד וגזים אינרטים או קרובים לאנרטיים. כידוע לטונגסטן נקודת התכה גבוהה והיא מתכת מתאימה מאוד לטמפרטורות גבוהות מאוד. הטונגסטן ב-TIG אינו נצרך בניגוד לשיטות האחרות שהוסבר לעיל. טכניקת ריתוך איטית אך איכותית מועילה על פני טכניקות אחרות בריתוך של חומרים דקים. מתאים למתכות רבות. ריתוך קשת פלזמה דומה אך משתמש בגז פלזמה ליצירת הקשת. הקשת בריתוך קשת פלזמה מרוכזת יותר באופן יחסי בהשוואה ל-GTAW וניתן להשתמש בה למגוון רחב יותר של עובי מתכת במהירויות גבוהות בהרבה. ניתן ליישם ריתוך GTAW וקשת פלזמה על אותם חומרים פחות או יותר. OXY-FUEL / OXYFUEL WELDING נקרא גם ריתוך אוקסיאצטילן, ריתוך אוקסי, ריתוך גז מתבצע באמצעות דלקי גז וחמצן לריתוך. מכיוון שלא נעשה שימוש בחשמל הוא נייד וניתן להשתמש בו היכן שאין חשמל. באמצעות לפיד ריתוך אנו מחממים את החלקים ואת חומר המילוי כדי לייצר בריכת מתכת מותכת משותפת. ניתן להשתמש בדלקים שונים כמו אצטילן, בנזין, מימן, פרופאן, בוטאן וכו'. בריתוך דלק חמצן אנו משתמשים בשני מיכלים, אחד עבור הדלק והשני עבור חמצן. החמצן מחמצן את הדלק (שורף אותו). ריתוך התנגדות: סוג זה של ריתוך מנצל את חימום הג'אול וחום נוצר במקום בו מופעל זרם חשמלי למשך זמן מסוים. זרמים גבוהים עוברים דרך המתכת. במקום זה נוצרות בריכות של מתכת מותכת. שיטות ריתוך התנגדות פופולריות בשל יעילותן, פוטנציאל הזיהום המועט. עם זאת, החסרונות הם שעלויות הציוד משמעותיות יחסית והמגבלה המובנית לחתיכות עבודה דקות יחסית. ריתוך נקודתי הוא סוג מרכזי אחד של ריתוך התנגדות. כאן אנו מחברים שניים או יותר יריעות או חלקי עבודה חופפים על ידי שימוש בשתי אלקטרודות נחושת כדי להדק את היריעות יחד ולהעביר זרם גבוה דרכן. החומר בין אלקטרודות הנחושת מתחמם ובמקום זה נוצרת בריכה מותכת. לאחר מכן נעצר הזרם וקצות אלקטרודת הנחושת מצננים את מיקום הריתוך מכיוון שהאלקטרודות מקוררות במים. הפעלת כמות החום הנכונה על החומר והעובי הנכונים היא המפתח לטכניקה זו, מכיוון שאם מיושמים בצורה לא נכונה המפרק יהיה חלש. לריתוך נקודתי יש את היתרונות בכך שהוא אינו גורם לעיוות משמעותי לחלקי העבודה, יעילות אנרגטית, קלות אוטומציה ושיעורי ייצור יוצאי דופן, ואינו מצריך חומרי מילוי. החיסרון הוא שמכיוון שהריתוך מתבצע בנקודות במקום יצירת תפר רציף, החוזק הכולל יכול להיות נמוך יחסית בהשוואה לשיטות ריתוך אחרות. ריתוך תפר, לעומת זאת, מייצר ריתוכים במשטחים הנפולים של חומרים דומים. התפר יכול להיות מפרק תחת או חפיפה. ריתוך התפר מתחיל בקצה אחד ועובר בהדרגה לקצה השני. שיטה זו משתמשת גם בשתי אלקטרודות מנחושת כדי להפעיל לחץ וזרם על אזור הריתוך. האלקטרודות בצורת דיסק מסתובבות במגע קבוע לאורך קו התפר ויוצרות ריתוך רציף. גם כאן, אלקטרודות מקוררות במים. הריתוכים מאוד חזקים ואמינים. שיטות נוספות הן טכניקות הקרנה, הבזק וריתוך נסער. ריתוך במצב מוצק מעט שונה מהשיטות הקודמות שהוסברו לעיל. ההתאחדות מתרחשת בטמפרטורות הנמוכות מטמפרטורת ההיתוך של המתכות המחוברות וללא שימוש במילוי מתכת. ניתן להשתמש בלחץ בתהליכים מסוימים. שיטות שונות הן COEXTRUSION WELDING שבו מתכות שונות נשלחות דרך אותה תבנית, ריתוך בלחץ קר שבו אנו מחברים סגסוגות רכות מתחת לנקודות ההיתוך שלהן, DIFFUSION WELDING טכניקה ללא קווי ריתוך גלויים, ריתוך פיצוץ לחיבור חומרים לא דומים, למשל סגסוגות עמידות בפני קורוזיה. פלדות, ריתוך דופק אלקטרומגנטי שבו אנו מאיצים צינורות ויריעות על ידי כוחות אלקטרומגנטיים, ריתוך FORGE המורכב מחימום המתכות לטמפרטורות גבוהות ולחיצתן יחד, FRICTION WELDING שבו מתבצע ריתוך חיכוך מספיק, FRICTION STIR WELDING הכולל ריתוך שאינו מסתובב כלי מתכלה שחוצה את קו המפרק, ריתוך בלחץ חם שבו אנו מצמידים מתכות יחד בטמפרטורות גבוהות מתחת לטמפרטורת ההיתוך בוואקום או בגזים אינרטיים, ריתוך בלחץ חם ISOSTATIC תהליך שבו אנו מפעילים לחץ באמצעות גזים אינרטיים בתוך כלי, ריתוך ROLL בו אנו מצטרפים חומרים לא דומים על ידי אילוץ ביניהם שני גלגלים מסתובבים, ריתוך ULTRASONIC שבו מרותכים יריעות מתכת דקות או פלסטיק באמצעות אנרגיית רטט בתדר גבוה. תהליכי הריתוך האחרים שלנו הם ELECTRON BEAM WELDING עם חדירה עמוקה ועיבוד מהיר אך בהיותנו שיטה יקרה אנו רואים אותה למקרים מיוחדים, ELECTROSLAG WELDING שיטה המתאימה ללוחות עבים כבדים וחתיכות עבודה מפלדה בלבד, INDUCTION WELDING בה אנו משתמשים באינדוקציה אלקטרומגנטית ו לחמם את חלקי העבודה המוליכים החשמליים או הפרומגנטיים שלנו, ריתוך קרן LASER גם עם חדירה עמוקה ועיבוד מהיר אבל שיטה יקרה, ריתוך LASER HYBRID WELDING המשלב LBW עם GMAW באותו ראש ריתוך ומסוגל לגשר על פערים של 2 מ"מ בין לוחות, PERCUSSION WELDING כי כולל פריקה חשמלית ולאחריה חישול החומרים בלחץ מופעל, THERMIT WELDING הכוללת תגובה אקסותרמית בין אבקות אלומיניום ותחמוצת ברזל., ELECTROGAS WELDING עם אלקטרודות מתכלות ומשמש רק עם פלדה במיקום אנכי, ולבסוף STUD ARC WELDING לחיבור חתך לבסיס חומר עם חום ולחץ. אנו ממליצים ללחוץ כאן כדיהורד את האיורים הסכמטיים שלנו של תהליכי הלחמה, הלחמה והדבקה על ידי AGS-TECH Inc. זה יעזור לך להבין טוב יותר את המידע שאנו מספקים לך למטה. • הלחמה: אנו מחברים שתי מתכות או יותר על ידי חימום מתכות מילוי ביניהן מעל נקודות ההיתוך שלהן ושימוש בפעולה נימית להתפשטות. התהליך דומה להלחמה אך הטמפרטורות הכרוכות בהמסת חומר המילוי גבוהות יותר בהלחמה. כמו בריתוך, השטף אכן מגן על חומר המילוי מפני זיהום אטמוספרי. לאחר הקירור מחברים את חלקי העבודה יחד. התהליך כולל את השלבים המרכזיים הבאים: התאמה ופינוי טובים, ניקוי נכון של חומרי בסיס, קיבוע נכון, בחירת שטף ואווירה נכונה, חימום המכלול ולבסוף ניקוי מכלול המולחם. חלק מתהליכי ההלחמה שלנו הם TORCH BRAZING, שיטה פופולרית המתבצעת באופן ידני או באופן אוטומטי. זה מתאים להזמנות ייצור בנפח נמוך ומקרים מיוחדים. חום מופעל באמצעות להבות גז ליד המפרק המולחם. הלחמת תנור דורש פחות מיומנות מפעיל והוא תהליך חצי אוטומטי המתאים לייצור המוני תעשייתי. גם בקרת הטמפרטורה וגם בקרת האטמוספירה בתנור הם יתרונות של טכניקה זו, מכיוון שהראשונה מאפשרת לנו מחזורי חום מבוקרים ולבטל חימום מקומי כפי שקורה בהלחמת לפידים, והאחרון מגן על החלק מפני חמצון. באמצעות ג'יגינג אנו מסוגלים להפחית את עלויות הייצור למינימום. החסרונות הם צריכת חשמל גבוהה, עלויות ציוד ושיקולי עיצוב מאתגרים יותר. הלחמת ואקום מתבצעת בכבשן של ואקום. אחידות הטמפרטורה נשמרת ואנו משיגים חיבורים נקיים מאוד ללא שטף עם מעט מאוד מתחים שיוריים. טיפולי חום יכולים להתקיים במהלך הלחמה בוואקום, בגלל הלחצים הנמוכים הקיימים במהלך מחזורי חימום וקירור איטיים. החיסרון העיקרי הוא העלות הגבוהה שלו מכיוון שיצירת סביבת ואקום היא תהליך יקר. טכניקה נוספת DIP BRAZING מצטרפת לחלקים קבועים שבהם תרכובת הלחמה מוחלת על משטחי הזדווגות. לאחר מכן, החלקים המקושרים נטבלים באמבט של מלח מותך כגון Sodium Chloride (מלח שולחן) הפועל כתווך ושטף להעברת חום. אוויר אינו נכלל ולכן לא מתרחשת היווצרות תחמוצת. ב-INDUCTION BRAZING אנו מצטרפים חומרים על ידי מתכת מילוי בעלת נקודת התכה נמוכה יותר מחומרי הבסיס. זרם החילופין מסליל האינדוקציה יוצר שדה אלקטרומגנטי אשר משרה חימום אינדוקציה על חומרים מגנטיים ברזליים בעיקר. השיטה מספקת חימום סלקטיבי, חיבורים טובים עם חומרי מילוי הזורמים רק באזורים רצויים, חמצון מועט מכיוון שאין להבות והקירור מהיר, חימום מהיר, עקביות והתאמה לייצור בנפח גבוה. כדי להאיץ את התהליכים שלנו ולהבטיח עקביות אנו משתמשים לעתים קרובות ב-preforms. מידע על מתקן ההלחמה שלנו המייצר אביזרי קרמיקה למתכת, איטום הרמטי, הזנת ואקום, ואקום גבוה ואולטרה גבוה ורכיבי בקרת נוזלים ניתן למצוא כאן:_cc781905-91633dcbcd-5cde_cc781905-9163dcbcfc5cdeחוברת מפעל הלחמה • הלחמה : בהלחמה אין לנו התכה של חלקי העבודה, אלא מתכת מילוי עם נקודת התכה נמוכה יותר מהחלקים המחברים שזורמת לתוך המפרק. מתכת המילוי בהלחמה נמסה בטמפרטורה נמוכה יותר מאשר בהלחמה. אנו משתמשים בסגסוגות נטולות עופרת להלחמה ומתאימות ל-RoHS וליישומים ודרישות שונות יש לנו סגסוגות שונות ומתאימות כגון סגסוגת כסף. הלחמה מציעה לנו חיבורים אטומים לגז ולנוזלים. בהלחמה רכה, למתכת המילוי שלנו יש נקודת התכה מתחת ל-400 צלזיוס, בעוד שבהלחמת כסף והלחמה אנו זקוקים לטמפרטורות גבוהות יותר. הלחמה רכה משתמשת בטמפרטורות נמוכות יותר אך אינה גורמת לחיבורים חזקים עבור יישומים תובעניים בטמפרטורות גבוהות. הלחמת כסף לעומת זאת, דורשת טמפרטורות גבוהות המסופקות על ידי לפיד ונותנת לנו חיבורים חזקים המתאימים ליישומים בטמפרטורה גבוהה. הלחמה דורשת את הטמפרטורות הגבוהות ביותר ובדרך כלל נעשה שימוש בלפיד. מכיוון שמפרקי הלחמה חזקים מאוד, הם מועמדים טובים לתיקון חפצי ברזל כבדים. בקווי הייצור שלנו אנו משתמשים גם בהלחמה ידנית וגם בקווי הלחמה אוטומטיים. INDUCTION SOLDERING משתמש בזרם AC בתדר גבוה בסליל נחושת כדי להקל על חימום אינדוקציה. זרמים מושרים בחלק המולחם וכתוצאה מכך נוצר חום בהתנגדות הגבוהה joint. חום זה ממיס את מתכת המילוי. נעשה שימוש גם בשטף. הלחמת אינדוקציה היא שיטה טובה להלחמת מחזורים וצינורות בתהליך מתמשך על ידי כריכת הסלילים סביבם. הלחמה של חומרים מסוימים כמו גרפיט וקרמיקה היא קשה יותר מכיוון שהיא מצריכה ציפוי של חלקי העבודה במתכת מתאימה לפני ההלחמה. זה מקל על התקשרות הממשק. אנו מלחמים חומרים כאלה במיוחד עבור יישומי אריזה הרמטית. אנו מייצרים את המעגלים המודפסים שלנו (PCB) בנפח גבוה בעיקר באמצעות הלחמת גל. רק למטרות של כמות קטנה של אב טיפוס אנו משתמשים בהלחמה ידנית באמצעות מלחם. אנו משתמשים בהלחמת גל הן למכלולי PCB להתקנה על פני השטח (PCBA). דבק זמני שומר על הרכיבים מחוברים למעגל המעגל והמכלול מונח על מסוע ועובר דרך ציוד המכיל הלחמה מותכת. תחילה מזרימים את ה-PCB ואז נכנס לאזור החימום המוקדם. ההלחמה המותכת נמצאת במחבת ועל פני השטח שלה תבנית של גלים עומדים. כאשר ה-PCB נע על הגלים הללו, גלים אלו יוצרים קשר עם החלק התחתון של ה-PCB ונצמדים לרפידות ההלחמה. ההלחמה נשארת על פינים ורפידות בלבד ולא על ה-PCB עצמו. יש לשלוט היטב על הגלים בהלחמה המותכת כך שאין התזות וצמרות הגלים לא נוגעות ומזהמות אזורים לא רצויים של הלוחות. ב-REFLOW SOLDERING, אנו משתמשים במשחת הלחמה דביקה כדי לחבר זמנית את הרכיבים האלקטרוניים ללוחות. לאחר מכן מעבירים את הלוחות דרך תנור זרימה חוזרת עם בקרת טמפרטורה. כאן ההלחמה נמסה ומחברת את הרכיבים לצמיתות. אנו משתמשים בטכניקה זו הן עבור רכיבי הרכבה על פני השטח והן עבור רכיבים דרך חורים. בקרת טמפרטורה נכונה והתאמה של טמפרטורות התנור חיוניים כדי למנוע הרס של רכיבים אלקטרוניים על הלוח על ידי התחממות יתר מעל גבולות הטמפרטורה המקסימלית שלהם. בתהליך של הלחמת זרימה חוזרת יש לנו למעשה מספר אזורים או שלבים שלכל אחד מהם פרופיל תרמי מובהק, כגון שלב חימום מוקדם, שלב השרייה תרמית, שלבי זרימה מחדש וקירור. השלבים השונים הללו חיוניים להלחמת זרימה חוזרת ללא נזק של מכלולי מעגלים מודפסים (PCBA). ULTRASONIC SOLDERING היא עוד טכניקה בשימוש תכוף עם יכולות ייחודיות- ניתן להשתמש בה להלחמת זכוכית, חומרים קרמיים ולא מתכתיים. למשל פאנלים פוטו-וולטאיים שאינם מתכתיים זקוקים לאלקטרודות שניתן להצמיד אותן בטכניקה זו. בהלחמה על-קולית, אנו פורסים קצה הלחמה מחומם שגם פולט רעידות על-קוליות. תנודות אלו מייצרות בועות קוויטציה בממשק המצע עם חומר ההלחמה המותכת. האנרגיה המפורקת של הקוויטציה משנה את פני התחמוצת ומסירה את הלכלוך והתחמוצות. במהלך הזמן הזה נוצרת גם שכבת סגסוגת. ההלחמה במשטח ההדבקה משלבת חמצן ומאפשרת יצירת קשר משותף חזק בין הזכוכית להלחמה. ניתן להתייחס ל-DIP SOLDERING כגרסה פשוטה יותר של הלחמת גל המתאימה לייצור בקנה מידה קטן בלבד. שטף ניקוי ראשון מוחל כמו בתהליכים אחרים. לוחות PCB עם רכיבים מורכבים טובלים ידנית או בצורה חצי אוטומטית לתוך מיכל המכיל הלחמה מותכת. ההלחמה המותכת נדבקת לאזורים המתכתיים החשופים ללא הגנה על ידי מסכת הלחמה על הלוח. הציוד פשוט ולא יקר. • הדבקת דבק: זוהי טכניקה פופולרית נוספת שאנו משתמשים בה לעתים קרובות והיא כוללת הדבקה של משטחים באמצעות דבקים, אפוקסים, חומרים פלסטיים או כימיקלים אחרים. ההדבקה מתבצעת על ידי אידוי הממס, על ידי ריפוי בחום, על ידי ריפוי באור UV, על ידי ריפוי בלחץ או המתנה לזמן מסוים. בקווי הייצור שלנו נעשה שימוש בדבקים בעלי ביצועים גבוהים שונים. עם תהליכי יישום וריפוי מהונדסים כהלכה, הדבקה דבק יכולה לגרום לקשרי מתח נמוכים מאוד שהם חזקים ואמינים. קשרי דבק יכולים להוות מגנים טובים מפני גורמים סביבתיים כגון לחות, מזהמים, חומרים קורוזיביים, רעידות וכו'. היתרונות של הדבקת דבק הם: ניתן ליישם אותם על חומרים שאחרת יהיה קשה להלחם, לרתך או להלחים. כמו כן, זה יכול להיות עדיף עבור חומרים רגישים לחום שייפגעו על ידי ריתוך או תהליכים אחרים בטמפרטורה גבוהה. יתרונות נוספים של דבקים הם שניתן ליישם אותם על משטחים בעלי צורה לא סדירה ולהגדיל את משקל ההרכבה בכמויות קטנות מאוד בהשוואה לשיטות אחרות. כמו כן, שינויים ממדיים בחלקים הם מאוד מינימליים. לחלק מהדבקים יש תכונות התאמת אינדקס וניתן להשתמש בהם בין רכיבים אופטיים מבלי להפחית את עוצמת האור או האות האופטי באופן משמעותי. החסרונות לעומת זאת הם זמני אשפרה ארוכים יותר אשר עלולים להאט את קווי הייצור, דרישות מתקן, דרישות הכנת פני השטח וקושי בפירוק כאשר יש צורך בעיבוד חוזר. רוב פעולות הדבקת הדבק שלנו כוללות את השלבים הבאים: -טיפול פני השטח: נהלי ניקוי מיוחדים כגון ניקוי מים מופחתים, ניקוי אלכוהול, ניקוי פלזמה או קורונה נפוצים. לאחר הניקוי אנו עשויים ליישם מקדמי הדבקה על המשטחים כדי להבטיח את החיבורים הטובים ביותר האפשריים. -קיבוע חלק: הן עבור יישום דבק והן עבור ריפוי אנו מעצבים ומשתמשים במתקנים מותאמים אישית. -יישום דבק: לפעמים אנו משתמשים במערכות אוטומטיות ידניות, ולפעמים בהתאם למקרה, כגון רובוטיקה, מנועי סרוו, מפעילים ליניאריים כדי לספק את הדבקים למקום הנכון ואנו משתמשים במכשירים כדי לספק אותו בנפח ובכמות הנכונים. - אשפרה: בהתאם לדבק, אנו עשויים להשתמש בייבוש וריפוי פשוטים, כמו גם בריפוי תחת נורות UV הפועלות כזרז או ריפוי חום בתנור או באמצעות גופי חימום התנגדות המורכבים על ג'יג'ים ומתקנים. אנו ממליצים ללחוץ כאן כדיהורד את האיורים הסכמטיים שלנו של תהליכי הידוק מאת AGS-TECH Inc. זה יעזור לך להבין טוב יותר את המידע שאנו מספקים לך למטה. • תהליכי הידוק: תהליכי החיבור המכאניים שלנו מתחלקים לשתי קטגוריות ברד: מחברים וחיבורים אינטגרליים. דוגמאות למחברים בהם אנו משתמשים הם ברגים, פינים, אומים, ברגים, מסמרות. דוגמאות למפרקים אינטגרליים בהם אנו משתמשים הם התאמות הצמד וכיווץ, תפרים, כיווץ. באמצעות מגוון שיטות הידוק אנו מוודאים שהחיבורים המכניים שלנו יהיו חזקים ואמינים למשך שנים רבות של שימוש. ברגים וברגים הם חלק מהמחברים הנפוצים ביותר להחזקת חפצים יחד ולמיקום. הברגים והברגים שלנו עומדים בתקני ASME. סוגים שונים של ברגים וברגים נפרסים כולל ברגים משושה וברגי משושה, ברגים וברגים לאחור, בורג כפול, בורג דיבל, בורג עין, בורג מראה, בורג מתכת, בורג כוונון עדין, ברגים לקידוח עצמי וברגים. , בורג סט, ברגים עם דסקיות מובנות,...ועוד. יש לנו סוגים שונים של ראשי ברגים כגון שקוע, כיפה, ראש עגול, אוגן וסוגי הברגים שונים כגון חריץ, פיליפס, ריבוע, שקע משושה. RIVET לעומת זאת הוא אטב מכני קבוע המורכב מפיר גלילי חלק וראש מצד אחד. לאחר ההחדרה, הקצה השני של המסמרת מעוות וקוטרה מורחב כך שיישאר במקומו. במילים אחרות, לפני ההתקנה למסמרת יש ראש אחד ואחרי ההתקנה יש לה שניים. אנו מתקינים סוגים שונים של מסמרות בהתאם ליישום, חוזק, נגישות ועלות כגון מסמרות ראש מוצק/עגול, מסמרות מבניות, חצי צינוריות, עיוור, אוסקר, הנעה, סומק, חיכוך נעילת, מסמרות חודרות עצמיות. ניתן להעדיף ריתוך במקרים בהם יש להימנע מעיוות חום ושינוי בתכונות החומר עקב חום הריתוך. המרתקת מציעה גם משקל קל ובעיקר חוזק וסיבולת טובים נגד כוחות גזירה. כנגד עומסי מתיחה אולם ברגים, אומים וברגים עשויים להיות מתאימים יותר. בתהליך ה-CLINCHING אנו משתמשים בפאנצ'ים מיוחדים כדי ליצור חיבור מכני בין מתכות הפח המצורפות. האגרוף דוחף את שכבות הפח לתוך חלל התבנית וגורם להיווצרות מפרק קבוע. אין צורך בחימום ואין צורך בקירור בקלינצ'ינג וזהו תהליך עבודה קר. זהו תהליך חסכוני שיכול להחליף ריתוך נקודתי במקרים מסוימים. ב-PINNING אנו משתמשים בפינים שהם רכיבי מכונה המשמשים לאבטחת מיקומים של חלקי מכונה זה ביחס לזה. הסוגים העיקריים הם סיכות סכין, סיכת סיכה, סיכת קפיץ, סיכות דיבל, וסיכה מפוצלת. ב- STAPLING אנו משתמשים ברובי הידוק והידוק שהם מחברים דו-כיוניים המשמשים לחיבור או קשירת חומרים. להידוק היתרונות הבאים: חסכוני, פשוט ומהיר לשימוש, ניתן להשתמש בכתר המהדקים לגישור בין חומרים שחוברים זה לזה, הכתר של המהדק יכול להקל על גישור חתיכה כמו כבל והצמדתו למשטח ללא ניקוב או מזיק, הסרה קלה יחסית. PRESS FITTING מתבצע על ידי דחיפת חלקים יחד והחיכוך ביניהם מהדק את החלקים. חלקי התאמה בלחיצה המורכבים מפיר גדול מדי וחור קטן מדי מורכבים בדרך כלל באחת משתי שיטות: או על ידי הפעלת כוח או ניצול התרחבות תרמית או כיווץ של החלקים. כאשר נוצרת התאמה באמצעות הפעלת כוח, אנו משתמשים במכבש הידראולי או במכבש המופעל ביד. מצד שני כאשר התאמה לחיצה נוצרת על ידי התפשטות תרמית אנו מחממים את החלקים העוטפים ומרכיבים אותם למקומם בעודם חמים. כשהם מתקררים הם מתכווצים וחוזרים לממדים הרגילים שלהם. זה מביא להתאמה לחיצה טובה. אנחנו קוראים לזה לחילופין SHRINK-FITTING. הדרך האחרת לעשות זאת היא על ידי קירור החלקים העטופים לפני ההרכבה ולאחר מכן החלקתם לתוך החלקים המתואמים שלהם. כאשר המכלול מתחמם הם מתרחבים ואנחנו מקבלים התאמה הדוקה. שיטה אחרונה זו עשויה להיות עדיפה במקרים בהם חימום מהווה סיכון לשינוי תכונות החומר. הקירור בטוח יותר במקרים אלה. רכיבים ומכלולים פניאומטיים והידראוליים • שסתומים, רכיבים הידראוליים ופנאומטיים כגון O-ring, מכונת כביסה, אטמים, אטם, טבעת, shim. מכיוון שסתומים ורכיבים פנאומטיים מגיעים במגוון גדול, איננו יכולים לפרט כאן הכל. בהתאם לסביבה הפיזית והכימית של היישום שלך, יש לנו מוצרים מיוחדים עבורך. אנא ציין לנו את היישום, סוג הרכיב, המפרטים, תנאי הסביבה כגון לחץ, טמפרטורה, נוזלים או גזים שיהיו במגע עם השסתומים והרכיבים הפנאומטיים שלך; ואנו נבחר את המוצר המתאים ביותר עבורך או ניצור אותו במיוחד עבור היישום שלך. CLICK Product Finder-Locator Service עמוד קודם
- Machine Elements Manufacturing, Gears, Gear Drives, Bearings, Keys, Splines
Machine Elements Manufacturing, Gears, Gear Drives, Bearings, Keys, Splines, Pins, Shafts, Seals, Fasteners, Clutch, Cams, Followers, Belts, Couplings, Shafts ייצור רכיבי מכונה קרא עוד חגורות ושרשראות ומכלול כונן כבלים קרא עוד מכלול הילוכים וגלגלי שיניים קרא עוד ייצור צימודים ומסבים קרא עוד ייצור מפתחות וסיכות ופינים קרא עוד ייצור מצלמות ועוקבים והצמדות וייצור גלגלי ראצ'ט קרא עוד ייצור פירים קרא עוד ייצור אטמים מכניים קרא עוד מכלול מצמד ובלם קרא עוד ייצור מחברים קרא עוד הרכבת מכונות פשוטות MACHINE ELEMENTS הם רכיבים יסודיים של מכונה. אלמנטים אלה מורכבים משלושה סוגים בסיסיים: 1.) רכיבים מבניים לרבות איברי מסגרת, מיסבים, סרנים, קווים, מחברים, אטמים וחומרי סיכה. 2.) מנגנונים השולטים בתנועה בדרכים שונות כגון רכבות גלגלי שיניים, הנעות רצועות או שרשרת, קישורים, מערכות פקה ועוקב, בלמים ומצמדים. 3.) רכיבי בקרה כמו לחצנים, מתגים, מחוונים, חיישנים, מפעילים ובקרי מחשב. רוב רכיבי המכונה שאנו מציעים לך הם סטנדרטיים לגדלים נפוצים, אך רכיבי מכונה בהתאמה אישית זמינים גם עבור היישומים המיוחדים שלך. התאמה אישית של רכיבי מכונה יכולה להתבצע על עיצובים קיימים שנמצאים בקטלוגים להורדה שלנו או על עיצובים חדשים לגמרי. אב טיפוס וייצור של רכיבי מכונה יכולים להתבצע לאחר אישור עיצוב על ידי שני הצדדים. אם יש צורך לתכנן ולייצר רכיבי מכונה חדשים, הלקוחות שלנו או לשלוח לנו אימייל עם השרטוטים שלהם ואנו בודקים אותם לאישור, או שהם מבקשים מאיתנו לתכנן רכיבי מכונה עבור היישום שלהם. במקרה האחרון אנו משתמשים בכל הקלט של הלקוחות שלנו ומתכננים את רכיבי המכונה ושולחים את השרטוטים הסופיים ללקוחותינו לאישור. לאחר האישור, אנו מייצרים פריטים ראשונים ובהמשך מייצרים את רכיבי המכונה בהתאם לתכנון הסופי. בכל שלב של עבודה זו, במקרה שתכנון רכיבי מכונה מסוים מתפקד בצורה לא מספקת בשטח (וזה נדיר), אנו בוחנים את כל הפרויקט ומבצעים שינויים במשותף עם לקוחותינו לפי הצורך. זהו הנוהג המקובל שלנו לחתום על הסכמי סודיות (NDA) עם לקוחותינו לעיצוב רכיבי מכונה או כל מוצר אחר בכל עת שצריך או נדרש. ברגע שרכיבי מכונה עבור לקוח מסוים מתוכננים ומיוצרים בהתאמה אישית, אנו מקצים לו קוד מוצר ומייצרים ומוכרים אותם רק ללקוח שלנו שבבעלותו המוצר. אנו משכפלים את רכיבי המכונה באמצעות הכלים, התבניות והנהלים שפותחו כמה פעמים לפי הצורך ובכל פעם שהלקוח שלנו מזמין אותם מחדש. במילים אחרות, ברגע שרכיב מכונה בהתאמה אישית מתוכנן ומיוצר עבורכם, הקניין הרוחני כמו גם כל כלי העבודה והתבניות נשמרים ומצוידים אצלנו ללא הגבלת זמן עבורכם והמוצרים משוכפלים כרצונכם. אנו גם מציעים ללקוחותינו שירותי הנדסה על ידי שילוב יצירתי של רכיבי מכונות לרכיב או מכלול המשרתים אפליקציה ועונה על ציפיות הלקוחות שלנו או עולה עליהן. מפעלים המייצרים את רכיבי המכונה שלנו מוסמכים לפי ISO9001, QS9000 או TS16949. בנוסף, לרוב המוצרים שלנו יש סימן CE או UL ועומדים בתקנים רלוונטיים בינלאומיים כגון ISO, SAE, ASME, DIN. אנא לחץ על תפריטי משנה כדי לקבל מידע מפורט על רכיבי המכונה שלנו כולל: - חגורות, שרשראות והנעי כבלים - גלגלי שיניים וכונני הילוכים - צימודים ומסבים - מפתחות & Splines & סיכות - מצלמות והצמדות - פירים - אטמים מכניים - מצמד ובלם תעשייתי - מחברים - מכונות פשוטות הכנו חוברת עזר ללקוחותינו, המעצבים והמפתחים של מוצרים חדשים כולל רכיבי מכונה. אתה יכול להכיר כמה מונחים נפוצים בתכנון רכיבי מכונה: הורד חוברת למונחים נפוצים של הנדסת מכונות המשמשים מעצבים ומהנדסים רכיבי המכונות שלנו מוצאים יישומים במגוון תחומים כמו מכונות תעשייתיות, מערכות אוטומציה, ציוד בדיקה ומטרולוגיה, ציוד תחבורה, מכונות בנייה וכמעט בכל מקום שתעלה על דעתך. AGS-TECH מפתחת ומייצרת רכיבי מכונות מחומרים שונים בהתאם ליישום. חומרים המשמשים לרכיבי מכונות יכולים לנוע מפלסטיק יצוק המשמש לצעצועים ועד פלדה מוקשחת ומצופה במיוחד עבור מכונות תעשייתיות. המעצבים שלנו משתמשים בתוכנה מקצועית מתקדמת ובכלי עיצוב לפיתוח רכיבי מכונה, תוך התחשבות בפרטים כגון זוויות בשיני הילוכים, מתחים מעורבים, שיעורי שחיקה וכו'. אנא גלול בתפריטי המשנה שלנו והורד את חוברות המוצרים והקטלוגים שלנו כדי לראות אם אתה יכול לאתר רכיבי מכונה מהמדף עבור היישום שלך. אם אינך יכול למצוא התאמה טובה ליישום שלך, אנא הודע לנו ואנו נעבוד איתך על מנת לפתח ולייצר רכיבי מכונה שיענו על הצרכים שלך. אם אתה מתעניין בעיקר ביכולות ההנדסה והמחקר והפיתוח שלנו במקום ביכולות הייצור, אז אנו מזמינים אותך לבקר באתר האינטרנט שלנו http://www.ags-engineering.com שם תוכל למצוא מידע מפורט יותר על העיצוב שלנו, פיתוח מוצר, פיתוח תהליכים, שירותי ייעוץ הנדסי ועוד CLICK Product Finder-Locator Service עמוד קודם
- Composites, Composite Materials Manufacturing, Fiber Reinforced
Composites, Composite Materials Manufacturing, Particle and Fiber Reinforced, Cermets, Ceramic & Metal Composite, Glass Fiber Reinforced Polymer, Lay-Up Process ייצור חומרים מרוכבים וחומרים מרוכבים בהגדרה פשוטה, קומפוזיטים או חומרים מרוכבים הם חומרים המורכבים משני או מספר חומרים בעלי תכונות פיזיקליות או כימיות שונות, אך בשילובם הם הופכים לחומר שונה מהחומרים המרכיבים אותם. עלינו לציין שהחומרים המרכיבים נשארים נפרדים ונבדלים במבנה. המטרה בייצור חומר מרוכב היא להשיג מוצר עדיף על מרכיביו ומשלב את התכונות הרצויות של כל מרכיב. לדוגמא; חוזק, משקל נמוך או מחיר נמוך יותר עשויים להיות המניע מאחורי עיצוב וייצור קומפוזיט. סוג החומרים המרוכבים שאנו מציעים הם חומרים מרוכבים מחוזקים בחלקיקים, חומרים מרוכבים מחוזקים בסיבים כולל קרמיקה-מטריקס / פולימר-מטריקס / מתכת-מטריקס / פחמן-פחמן / מרוכבים היברידיים, חומרים מרוכבים מבניים ולמינים וכריכים וננו-מרוכבים. טכניקות הייצור שאנו מפעילים בייצור חומרים מרוכבים הן: Pultrusion, תהליכי ייצור prepreg, מיקום סיבים מתקדם, סיפוף נימה, מיקום סיבים מותאם, תהליך הנחת ריסוס פיברגלס, ציוץ, תהליך lanxide, Z-pinning. חומרים מרוכבים רבים מורכבים משני שלבים, המטריצה, שהיא רציפה ומקיפה את השלב השני; והפאזה המפוזרת אשר מוקפת במטריקס. אנו ממליצים ללחוץ כאן כדיהורד את האיורים הסכמטיים שלנו של ייצור חומרים מרוכבים וחומרים מרוכבים על ידי AGS-TECH Inc. זה יעזור לך להבין טוב יותר את המידע שאנו מספקים לך למטה. • חומרים מרוכבים מחוזקים בחלקיקים: קטגוריה זו מורכבת משני סוגים: מרוכבים בעלי חלקיקים גדולים וחומרים מרוכבים מחוזקים בפיזור. בסוג הקודם, לא ניתן לטפל באינטראקציות של חלקיקים-מטריקס ברמה האטומית או המולקולרית. במקום זאת, מכניקת הרצף תקפה. מצד שני, בחלקיקים מרוכבים המחוזקים בפיזור הם בדרך כלל הרבה יותר קטנים בעשרות טווחי ננומטר. דוגמה לרכיבים מרוכבים של חלקיקים גדולים היא פולימרים שאליהם נוספו חומרי מילוי. חומרי המילוי משפרים את תכונות החומר ועשויים להחליף חלק מנפח הפולימר בחומר חסכוני יותר. שברי הנפח של שני השלבים משפיעים על התנהגות המרוכב. מרוכבים חלקיקים גדולים משמשים עם מתכות, פולימרים וקרמיקה. ה-CERMETS הם דוגמאות לרכבי קרמיקה/מתכת. הצרמט הנפוץ ביותר שלנו הוא קרביד צמנט. הוא מורכב מקרמיקה קרביד עקשן כגון חלקיקי טונגסטן קרביד במטריצה של מתכת כגון קובלט או ניקל. חומרי קרביד אלה נמצאים בשימוש נרחב ככלי חיתוך לפלדה מוקשה. חלקיקי הקרביד הקשים אחראים לפעולת החיתוך והקשיחות שלהם מוגברת על ידי מטריצת המתכת המתכתית. כך אנו משיגים את היתרונות של שני החומרים במרוכב אחד. דוגמה נפוצה נוספת לקומפוזיט של חלקיקים גדולים שאנו משתמשים בהם היא חלקיקי פחמן שחור מעורבבים עם גומי מגופר לקבלת חומר מרוכב בעל חוזק מתיחה גבוה, קשיחות, עמידות בפני קריעה ושחיקה. דוגמה לחומר מרוכב מחוזק בפיזור היא מתכות וסגסוגות מתכת שמחוזקות ומתקשות על ידי פיזור אחיד של חלקיקים עדינים מחומר קשה ואינרטי מאוד. כאשר מוסיפים פתיתי תחמוצת אלומיניום קטנים מאוד למטריצת מתכת אלומיניום, אנו משיגים אבקת אלומיניום סנטרית בעלת חוזק משופר בטמפרטורה גבוהה. • חומרים מרוכבים מחוזקים בסיבים: קטגוריה זו של חומרים מרוכבים היא למעשה החשובה ביותר. המטרה להשיג היא חוזק ונוקשות גבוהים ליחידת משקל. הרכב הסיבים, האורך, הכיוון והריכוז בחומרים מרוכבים אלה הם קריטיים בקביעת התכונות והתועלת של חומרים אלה. ישנן שלוש קבוצות של סיבים שאנו משתמשים: שפם, סיבים וחוטים. WHISKERS הם גבישים בודדים דקים וארוכים. הם בין החומרים החזקים ביותר. כמה חומרי שפם לדוגמה הם גרפיט, סיליקון ניטריד, תחמוצת אלומיניום. FIBERS לעומת זאת הם בעיקר פולימרים או קרמיקה והם במצב פולי-גבישי או אמורפי. הקבוצה השלישית היא WIRES עדינים בעלי קטרים גדולים יחסית ומורכבים לעתים קרובות מפלדה או טונגסטן. דוגמה לקומפוזיט מחוזק תיל הוא צמיגי רכב המשלבים חוטי פלדה בתוך גומי. בהתאם לחומר המטריצה, יש לנו את החומרים המרוכבים הבאים: פולימר-מטריקס מורכבים: אלה עשויים משרף פולימרי וסיבים כמרכיב החיזוק. תת-קבוצה של אלה הנקראת חומרי פולימר מחוזקים בסיבי זכוכית (GFRP) מכילה סיבי זכוכית רציפים או לא רציפים בתוך מטריצת פולימר. זכוכית מציעה חוזק גבוה, היא חסכונית, קלה לייצור לסיבים והיא אינרטית מבחינה כימית. החסרונות הם הקשיחות והקשיחות המוגבלת שלהם, טמפרטורות השירות הן רק עד 200 - 300 צלזיוס. פיברגלס מתאים למרכבי רכב וציוד תחבורה, מרכבי רכב ימיים, מכולות אחסון. הם אינם מתאימים לתעופה וחלל ולא לייצור גשרים בגלל קשיחות מוגבלת. תת-הקבוצה השנייה נקראת Composite Carbon Fiber-Reinforced Polymer (CFRP). כאן, פחמן הוא חומר הסיבים שלנו במטריצת הפולימר. פחמן ידוע במודולוס ובחוזק הספציפיים הגבוהים שלו וביכולתו לשמור על אלה בטמפרטורות גבוהות. סיבי פחמן יכולים להציע לנו מודולי מתיחה סטנדרטיים, בינוניים, גבוהים ואולטרה-גבוהים. יתר על כן, סיבי פחמן אכן מציעים מאפיינים פיזיים ומכאניים מגוונים ולכן מתאימים ליישומים הנדסיים מותאמים אישית שונים. חומרים מרוכבים CFRP יכולים להיחשב לייצור ציוד ספורט ופנאי, כלי לחץ ורכיבים מבניים תעופה וחלל. עם זאת, תת-קבוצה נוספת, חומרי הפולימרים המחוזקים בסיבים אראמיד הם גם חומרים בעלי חוזק גבוה ומודולוס. יחסי החוזק והמשקל שלהם גבוהים להפליא. סיבי ארמיד ידועים גם בשמות המסחריים KEVLAR ו-NOMEX. תחת מתח הם מתפקדים טוב יותר מחומרי סיבים פולימריים אחרים, אך הם חלשים בדחיסה. סיבי ארמיד קשים, עמידים בפני פגיעות, עמידים לזחילה ועייפות, יציבים בטמפרטורות גבוהות, אינרטי כימית למעט חומצות ובסיסים חזקים. סיבי ארמיד נמצאים בשימוש נרחב במוצרי ספורט, אפודים חסיני כדורים, צמיגים, חבלים, כיסויי כבל סיבים אופטיים. חומרי חיזוק סיבים אחרים קיימים אך משמשים במידה פחותה. אלה הם בורון, סיליקון קרביד, תחמוצת אלומיניום בעיקר. חומר המטריצה הפולימרי מצד שני הוא גם קריטי. זה קובע את טמפרטורת השירות המקסימלית של המרוכב מכיוון שלפולימר יש בדרך כלל טמפרטורת התכה ופירוק נמוכה יותר. פוליאסטרים ואסטרים ויניל נמצאים בשימוש נרחב כמטריצת הפולימר. נעשה שימוש גם בשרף ויש להם עמידות מצוינת ללחות ותכונות מכניות. למשל שרף פוליאמיד יכול לשמש עד כ-230 מעלות צלזיוס. חומרים מרוכבים של מתכת-מטריקס: בחומרים אלו אנו משתמשים במטריצת מתכת רקיעה וטמפרטורות השירות גבוהות בדרך כלל מהרכיבים המרכיבים אותם. בהשוואה לחומרים מרוכבים של פולימר-מטריקס, אלה יכולים להיות בעלי טמפרטורות עבודה גבוהות יותר, להיות לא דליקים ועשויים להיות בעלי עמידות טובה יותר להתפרקות נגד נוזלים אורגניים. עם זאת הם יקרים יותר. חומרי חיזוק כגון שפם, חלקיקים, סיבים רציפים ובלתי רציפים; וחומרי מטריקס כגון נחושת, אלומיניום, מגנזיום, טיטניום, סגסוגות-על נמצאים בשימוש נפוץ. יישומים לדוגמה הם רכיבי מנוע העשויים ממטריקס מסגסוגת אלומיניום מחוזקת בתחמוצת אלומיניום וסיבי פחמן. תרכובות קרמיקה-מטריקס: חומרים קרמיים ידועים באמינותם הטובה ביותר בטמפרטורות גבוהות. עם זאת הם שבירים מאוד ויש להם ערכים נמוכים עבור קשיחות שבר. על ידי הטבעת חלקיקים, סיבים או שפם של קרמיקה אחת לתוך המטריצה של אחר, אנו מסוגלים להשיג חומרים מרוכבים בעלי קשיחות שבר גבוהה יותר. חומרים מוטבעים אלה בעצם מעכבים את התפשטות הסדקים בתוך המטריצה על ידי כמה מנגנונים כגון הסטת קצות הסדקים או יצירת גשרים על פני הסדקים. כדוגמה, אלומיניום המחוזקים בשפם SiC משמשים כתוספות לכלי חיתוך לעיבוד סגסוגות מתכת קשות. אלה יכולים לחשוף ביצועים טובים יותר בהשוואה לקרבידים מוצקים. פחמן-פחמן מרוכבים: גם החיזוק וגם המטריצה הם פחמן. יש להם מודולי מתיחה גבוהים וחוזק בטמפרטורות גבוהות מעל 2000 צלזיוס, עמידות לזחילה, קשיחות גבוהה לשברים, מקדמי התפשטות תרמית נמוכים, מוליכות תרמית גבוהה. מאפיינים אלה הופכים אותם לאידיאליים עבור יישומים הדורשים עמידות בפני זעזועים תרמיים. החולשה של חומרים מרוכבים פחמן-פחמן היא עם זאת פגיעותו בפני חמצון בטמפרטורות גבוהות. דוגמאות אופייניות לשימוש הן תבניות בכבישה חמה, ייצור רכיבי מנועי טורבינה מתקדמים. חומרים מרוכבים היברידיים: שני סוגים שונים או יותר של סיבים מעורבבים במטריצה אחת. כך ניתן להתאים חומר חדש עם שילוב של תכונות. דוגמה לכך היא כאשר גם סיבי פחמן וגם סיבי זכוכית משולבים בשרף פולימרי. סיבי פחמן מספקים קשיחות וחוזק בצפיפות נמוכה אך הם יקרים. הזכוכית לעומת זאת זולה אך חסרה את הקשיחות של סיבי פחמן. הקומפוזיט ההיברידי מזכוכית-פחמן חזק וקשיח יותר וניתן לייצרו בעלות נמוכה יותר. עיבוד של חומרים מרוכבים מחוזקים בסיבים: עבור פלסטיק רציף מחוזק בסיבים עם סיבים בפיזור אחיד המכוונים לאותו כיוון, אנו משתמשים בטכניקות הבאות. PULTRUSION: מוטות, קורות וצינורות באורך רציף וחתכים קבועים מיוצרים. רצועות סיבים רציפים מוספגים בשרף תרמוסטי ונמשכים דרך תבנית פלדה כדי ליצור אותם מראש לצורה הרצויה. לאחר מכן, הם עוברים דרך תבנית ריפוי במכונה מדויקת כדי להגיע לצורתה הסופית. מכיוון שתבנית הריפוי מחוממת, היא מרפאה את מטריצת השרף. מושכים שואבים את החומר דרך הקוביות. באמצעות ליבות חלולות מוכנסות, אנו מסוגלים להשיג צינורות וגיאומטריות חלולות. שיטת ה-pultrusion היא אוטומטית ומציעה לנו קצבי ייצור גבוהים. ניתן לייצר כל אורך של מוצר. תהליך ייצור PREPREG: Prepreg הוא חיזוק סיבים רציפים הספוג מראש בשרף פולימרי שנרפא חלקית. זה נמצא בשימוש נרחב עבור יישומים מבניים. החומר מגיע בצורת קלטת ונשלח כקלטת. היצרן מעצב אותו ישירות ומרפא אותו במלואו ללא צורך בהוספת שרף. מכיוון שהפרפרים עוברים תגובות ריפוי בטמפרטורת החדר, הם מאוחסנים בטמפרטורות של 0 מעלות צלזיוס או נמוכות יותר. לאחר השימוש שאר הקלטות מאוחסנות בחזרה בטמפרטורות נמוכות. נעשה שימוש בשרף תרמופלסטי ותרמוסטי ונפוצים סיבי חיזוק של פחמן, ארמיד וזכוכית. כדי להשתמש ב-prepregs, תחילה מסירים את נייר הגיבוי של הנשא ולאחר מכן מבוצעת הייצור על ידי הנחת סרט ה-prepreg על משטח מנוצל (תהליך ה-lay-up). ניתן להניח מספר שכבות כדי להשיג את העובי הרצוי. תרגול תכוף הוא להחליף את כיוון הסיבים כדי לייצר לרבד צולב או זווית. לבסוף מופעלים חום ולחץ לצורך ריפוי. גם עיבוד ידני וגם תהליכים אוטומטיים משמשים לחיתוך prepregs והנחת. פיתול נימה: סיבי חיזוק רציפים ממוקמים במדויק בתבנית קבועה מראש כדי לעקוב אחר צורה חלולה ובדרך כלל מחזורית. הסיבים עוברים תחילה אמבט שרף ולאחר מכן נרפפים על גבי ציר על ידי מערכת אוטומטית. לאחר מספר חזרות פיתולים מתקבלים עוביים רצויים ומתבצע אשפרה או בטמפרטורת החדר או בתוך תנור. כעת מסירים את המדרל ומפרקים את המוצר. פיתול נימה יכול להציע יחסי חוזק למשקל גבוהים מאוד על ידי סלילה של הסיבים בדפוסים היקפיים, סלילניים וקוטביים. צינורות, מיכלים, מארזים מיוצרים בטכניקה זו. • חומרים מרוכבים מבניים: בדרך כלל אלה מורכבים מחומרים הומוגניים ומרוכבים כאחד. לכן המאפיינים של אלה נקבעים על ידי החומרים המרכיבים והעיצוב הגיאומטרי של האלמנטים שלו. להלן הסוגים העיקריים: חומרים מרוכבים למינריים: חומרים מבניים אלה עשויים מיריעות או לוחות דו מימדיים עם כיוונים מועדפים בעלי חוזק גבוה. השכבות מוערמות ומוצקות יחד. על ידי החלפת כיווני החוזק הגבוה בשני הצירים הניצבים, נקבל קומפוזיט בעל חוזק גבוה בשני הכיוונים במישור הדו-ממדי. על ידי התאמת זוויות השכבות ניתן לייצר קומפוזיט בעל חוזק בכיוונים המועדפים. סקי מודרני מיוצר בדרך זו. לוחות סנדוויץ': חומרים מרוכבים מבניים אלה הם קלים אך עם זאת יש להם קשיחות וחוזק גבוהים. לוחות סנדוויץ' מורכבים משתי יריעות חיצוניות העשויות מחומר קשיח וחזק כמו סגסוגות אלומיניום, פלסטיק מחוזק בסיבים או פלדה וליבה בין היריעות החיצוניות. הליבה צריכה להיות קלת משקל ורוב הזמן בעלת מודול גמישות נמוך. חומרי ליבה פופולריים הם קצף פולימרי קשיח, עץ וחלות דבש. לוחות סנדוויץ' נמצאים בשימוש נרחב בתעשיית הבנייה כחומר קירוי, חומר רצפה או קירות, וגם בתעשיות התעופה והחלל. • ננו-מרוכבים: חומרים חדשים אלה מורכבים מחלקיקי חלקיקים בגודל ננו המשובצים במטריצה. באמצעות ננו מרוכבים נוכל לייצר חומרי גומי שהם מחסומים טובים מאוד לחדירת אוויר תוך שמירה על תכונות הגומי שלהם ללא שינוי. CLICK Product Finder-Locator Service עמוד קודם
- Rapid Prototyping, Desktop Manufacturing, Additive Manufacturing, FDM
Rapid Prototyping, Desktop Manufacturing, Additive Manufacturing, Stereolithography, Polyjet, Fused Deposition Modeling, Selective Laser Sintering, FDM, SLS ייצור תוסף וייצור מהיר בשנים האחרונות אנו רואים עלייה בביקוש ל-RAPID MANUFACTURING או RAPID PROTOTYPING. תהליך זה עשוי להיקרא גם ייצור שולחני או ייצור חופשי. בעיקרון מודל פיזי מוצק של חלק עשוי ישירות משרטוט CAD תלת מימדי. אנו משתמשים במונח ADDITIVE MANUFACTURING עבור הטכניקות השונות הללו בהן אנו בונים חלקים בשכבות. באמצעות חומרה ותוכנה מונעי מחשב משולבים אנו מבצעים ייצור תוסף. טכניקות אבות הטיפוס והייצור המהירה שלנו הן סטריאוליטוגרפיה, פוליג'ט, מודלים בהתמזגות, סינון לייזר סלקטיבי, התכת קרן אלקטרונים, הדפסה תלת מימדית, ייצור ישיר, כלי עבודה מהיר. אנו ממליצים ללחוץ כאן כדיהורד את האיורים הסכמטיים שלנו של ייצור תוסף ותהליכי ייצור מהירים מאת AGS-TECH Inc. זה יעזור לך להבין טוב יותר את המידע שאנו מספקים לך למטה. אב טיפוס מהיר מספק לנו: 1.) עיצוב המוצר הרעיוני נצפה מזוויות שונות על גבי צג באמצעות מערכת תלת מימד / CAD. 2.) אבות טיפוס מחומרים לא מתכתיים ומטאליים מיוצרים ונלמדים מהיבטים פונקציונליים, טכניים ואסתטיים. 3.) יצירת אב טיפוס בעלות נמוכה תוך זמן קצר מאוד מושגת. ניתן לדמות ייצור תוסף לבניית כיכר לחם על ידי ערימה והדבקה של פרוסות בודדות זו על גבי זו. במילים אחרות, המוצר מיוצר פרוסה אחר פרוסה, או שכבה אחר שכבה מונחת זה על זה. ניתן לייצר את רוב החלקים תוך שעות. הטכניקה טובה אם יש צורך בחלקים מהר מאוד או אם הכמויות הנדרשות נמוכות והכנת תבנית וכלי עבודה היא יקרה מדי ולוקחת זמן. עם זאת העלות של חלק יקרה בגלל חומרי הגלם היקרים. • STEREOLITHOGRAPHY : טכניקה זו המכונה גם בקיצור STL, מבוססת על ריפוי והתקשות של פוטופולימר נוזלי לצורה ספציפית על ידי מיקוד קרן לייזר עליו. הלייזר מפילמר את הפוטופולימר ומרפא אותו. על ידי סריקת קרן הלייזר UV לפי הצורה המתוכנתת לאורך פני השטח של תערובת הפוטופולימר, החלק מיוצר מלמטה למעלה בפרוסות בודדות המשולבות זו על גבי זו. הסריקה של נקודת הלייזר חוזרת על עצמה פעמים רבות כדי להשיג את הגיאומטריות שתוכנתו במערכת. לאחר ייצור מלא של החלק, הוא מוסר מהפלטפורמה, סופג ומנקה באולטרסאונד ובאמבט אלכוהול. לאחר מכן, הוא נחשף לקרינת UV למשך מספר שעות כדי לוודא שהפולימר נרפא במלואו והתקשה. לסיכום התהליך, פלטפורמה שנטבלת בתערובת פוטופולימר וקרן לייזר UV נשלטת ומועברת דרך מערכת בקרה סרוו לפי צורת החלק הרצוי והחלק מתקבל על ידי צילום פולימר שכבה אחר שכבה. כמובן שהמידות המקסימליות של החלק המיוצר נקבעות על ידי ציוד הסטריאוליטוגרפיה. • POLYJET: בדומה להדפסת הזרקת דיו, ב-polyjet יש לנו שמונה ראשי הדפסה שמפקידים פוטופולימר על מגש הבנייה. אור אולטרה סגול המוצב לצד הסילונים מרפא ומקשיח מיד כל שכבה. שני חומרים משמשים בפוליג'ט. החומר הראשון מיועד לייצור הדגם בפועל. החומר השני, שרף דמוי ג'ל משמש לתמיכה. שני החומרים הללו מופקדים שכבה אחר שכבה ומתרפאים בו זמנית. לאחר השלמת הדגם, חומר התמיכה מוסר עם תמיסה מימית. שרפים המשמשים דומים לסטריאוליטוגרפיה (STL). לפוליג'ט יש את היתרונות הבאים על פני סטריאוליטוגרפיה: 1.) אין צורך בניקוי חלקים. 2.) אין צורך בריפוי לאחר תהליך 3.) אפשריים עובי שכבה קטנים יותר וכך אנו מקבלים רזולוציה טובה יותר ויכולים לייצר חלקים עדינים יותר. • FUSED DEPOSITION MODELING: גם בקיצור FDM, בשיטה זו ראש אקסטרודר נשלט על ידי רובוט נע בשני כיוונים עקרוניים מעל שולחן. הכבל מורד ומורם לפי הצורך. מתוך הפתח של תבנית מחוממת על הראש, נימה תרמופלסטית מוחלפת ושכבה ראשונית מונחת על בסיס קצף. זה מושג על ידי ראש האקסטרודר שעוקב אחר נתיב קבוע מראש. לאחר השכבה הראשונית, השולחן מורידים והשכבות הבאות מופקדות זו על גבי זו. לפעמים בעת ייצור חלק מסובך, יש צורך במבני תמיכה כדי שתצהיר יוכל להמשיך בכיוונים מסוימים. במקרים אלה, חומר תמיכה מוחלף עם מרווח פחות צפוף של נימה על שכבה כך שהוא חלש יותר מחומר הדגם. מבני תמיכה אלו יכולים להיות מומסים או לשבור מאוחר יותר לאחר השלמת החלק. מימדי קוביות האקסטרודר קובעות את עובי השכבות המחולצות. תהליך FDM מייצר חלקים עם משטחים מדורגים במישורים חיצוניים אלכסוניים. אם החספוס הזה אינו מקובל, ניתן להשתמש בליטוש אדים כימי או בכלי מחומם להחלקת אלה. אפילו ווקס פוליש זמין כחומר ציפוי כדי לבטל את השלבים הללו ולהשיג סובלנות גיאומטריות סבירות. • סינון לייזר סלקטיבי: מסומן גם כ-SLS, התהליך מבוסס על סינון של אבקות פולימר, קרמיקה או מתכתי באופן סלקטיבי לתוך אובייקט. בתחתית תא העיבוד יש שני צילינדרים: צילינדר בנוי חלקית וגליל הזנת אבקה. את הראשון מורידים בהדרגה למקום שבו נוצר החלק הסינטר והאחרון מורם בהדרגה כדי לספק אבקה לגליל הבנוי החלק באמצעות מנגנון רולר. תחילה מופקדת שכבה דקה של אבקה בצילינדר הבנוי לחלקי, לאחר מכן קרן לייזר ממוקדת בשכבה זו, מתחקה וממיסה / חותכת חתך רוחב מסוים, אשר לאחר מכן מתמצק למוצק. האבקה היא אזורים שאינם נפגעים מקרן הלייזר נשארים רופפים אך עדיין תומכים בחלק המוצק. לאחר מכן מונחת שכבה נוספת של אבקה והתהליך חוזר על עצמו פעמים רבות לקבלת החלק. בסוף מנערים את חלקיקי האבקה הרופפים. כל אלה מבוצעים על ידי מחשב בקרת תהליכים תוך שימוש בהוראות המופקות על ידי תוכנית ה-3D CAD של החלק המיוצר. ניתן להפקיד חומרים שונים כגון פולימרים (כגון ABS, PVC, פוליאסטר), שעווה, מתכות וקרמיקה עם קלסרים פולימריים מתאימים. • ELECTRON-BEAM MELTING : דומה לסינטרינג לייזר סלקטיבי, אך באמצעות קרן אלקטרונים להמסת אבקות טיטניום או קובלט כרום לייצור אבות טיפוס בוואקום. נעשו כמה פיתוחים לביצוע תהליך זה על פלדות אל חלד, אלומיניום וסגסוגות נחושת. אם יש צורך להגביר את חוזק העייפות של החלקים המיוצרים, אנו משתמשים בכבישה איזוסטטית חמה לאחר ייצור החלקים כתהליך משני. • הדפסה תלת מימדית: מסומן גם ב-3DP, בטכניקה זו ראש הדפסה מפקיד קלסר אנאורגני על שכבה של אבקה לא מתכתית או מתכתית. בוכנה הנושאת את מיטת האבקה יורדת בהדרגה ובכל שלב מפקידים את הקלסר שכבה אחר שכבה ומתמזג על ידי הקלסר. חומרי אבקה המשמשים הם תערובות פולימרים וסיבים, חול יציקה, מתכות. באמצעות ראשי קלסר שונים בו זמנית ובקלסרים בצבעים שונים נוכל להשיג צבעים שונים. התהליך דומה להדפסת הזרקת דיו אך במקום לקבל דף צבעוני נקבל אובייקט תלת מימדי צבעוני. החלקים המיוצרים עשויים להיות נקבוביים ולכן עשויים לדרוש סינטר וחדירת מתכת כדי להגביר את הצפיפות והחוזק שלה. סינטרינג ישרוף את הקלסר ויתיך את אבקות המתכת יחד. ניתן להשתמש במתכות כגון נירוסטה, אלומיניום, טיטניום לייצור החלקים וכחומרי הסתננות אנו משתמשים בדרך כלל בנחושת וברונזה. היופי בטכניקה זו הוא שגם מכלולים מסובכים ונעים ניתן לייצר במהירות רבה. לדוגמא מכלול גלגלי שיניים, מפתח ברגים ככלי יכול להתבצע ויהיה בו חלקים נעים ומסתובבים מוכנים לשימוש. ניתן לייצר רכיבים שונים של המכלול בצבעים שונים והכל בצילום אחד. הורד את החוברת שלנו ב:יסודות הדפסת תלת מימד מתכת • ייצור ישיר ועיבוד מהיר: מלבד הערכת עיצוב, פתרון בעיות אנו משתמשים באב טיפוס מהיר לייצור ישיר של מוצרים או יישום ישיר במוצרים. במילים אחרות, ניתן לשלב אב טיפוס מהיר בתהליכים קונבנציונליים כדי להפוך אותם לטובים יותר ותחרותיים יותר. לדוגמה, אב טיפוס מהיר יכול לייצר דפוסים ותבניות. ניתן להרכיב דפוסים של פולימר נמס ובוער שנוצר על ידי פעולות אב טיפוס מהירות ליציקה ולהשקיע. דוגמה נוספת שיש להזכיר היא שימוש ב-3DP כדי לייצר מעטפת יציקה קרמית ולהשתמש בה לפעולות יציקת מעטפת. אפילו תבניות הזרקה ותוספות תבניות יכולות להיות מיוצרות על ידי יצירת אב טיפוס מהיר ואפשר לחסוך שבועות או חודשים רבים של זמן אספקת עובש. רק על ידי ניתוח קובץ CAD של החלק הרצוי, נוכל לייצר את גיאומטריית הכלי באמצעות תוכנה. להלן כמה משיטות הכלים המהירים הפופולריות שלנו: יציקת RTV (חפירת טמפרטורת חדר) / יציקת URETHANE: ניתן להשתמש באב-טיפוס מהיר כדי ליצור את התבנית של החלק הרצוי. לאחר מכן מצפים את התבנית הזו בחומר פרידה וגומי RTV נוזלי יוצקים על התבנית כדי לייצר את חצאי התבנית. לאחר מכן, חצאי עובש אלה משמשים להזרקת uretans נוזלי. חיי התבנית קצרים, רק כמו 0 או 30 מחזורים אבל מספיק לייצור אצווה קטנה. דפוס הזרקה ACES (Acetal Clear Epoxy Solid) : באמצעות טכניקות של אב טיפוס מהיר כגון סטריאוליטוגרפיה, אנו מייצרים תבניות הזרקה. תבניות אלו הן קונכיות בעלות קצה פתוח על מנת לאפשר מילוי בחומרים כגון אפוקסי, אפוקסי במילוי אלומיניום או מתכות. שוב חיי העובש מוגבלים לעשרות או מקסימום מאות חלקים. תהליך כלי מתכת מרוסס: אנו משתמשים באב-טיפוס מהיר ויוצרים דפוס. אנו מרססים סגסוגת אבץ-אלומיניום על משטח הדפוס ומצפים אותו. לאחר מכן מניחים את התבנית עם ציפוי המתכת בתוך בקבוקון ומכניסים לעציץ אפוקסי במילוי אפוקסי או אלומיניום. לבסוף מוציאים אותה ועל ידי ייצור שני חצאי תבניות כאלה נקבל תבנית שלמה להזרקה. לתבניות אלו יש חיים ארוכים יותר, במקרים מסוימים בהתאם לחומר ולטמפרטורות הן יכולות לייצר חלקים באלפים. תהליך KEELTOOL: טכניקה זו יכולה לייצר תבניות עם 100,000 עד 10 מיליון חיי מחזור. באמצעות אב טיפוס מהיר אנו מייצרים תבנית RTV. לאחר מכן ממלאים את התבנית בתערובת המורכבת מאבקת פלדת כלי A6, טונגסטן קרביד, חומר מקשר פולימרי ומניחים להתרפא. לאחר מכן מחממים את התבנית הזו כדי לגרום לפולימר לשרוף ואבקות המתכת להתמזג. השלב הבא הוא חדירת נחושת לייצור התבנית הסופית. במידת הצורך, ניתן לבצע פעולות משניות כגון עיבוד שבבי וליטוש על התבנית לדיוק ממדים טוב יותר. _cc781905-5cde-3194-bb3b-136bad_5cf58 CLICK Product Finder-Locator Service עמוד קודם
- Glass and Ceramic Manufacturing, Hermetic Packages, Seals, Bonding
Glass and Ceramic Manufacturing, Hermetic Packages Seals and Bonding, Tempered Bulletproof Glass, Blow Moulding, Optical Grade Glass, Conductive Glass, Molding עיצוב ועיצוב זכוכית וקרמיקה סוג ייצור הזכוכית שאנו מציעים הם זכוכית מיכל, ניפוח זכוכית, סיבי זכוכית וצינורות ומוטות, כלי זכוכית ביתיים ותעשייתיים, מנורה ונורה, יציקת זכוכית מדויקת, רכיבים ומכלולים אופטיים, זכוכית שטוחה ויריעות וזכוכית צפה. אנו מבצעים הן גיבוש ביד והן יצירה במכונה. תהליכי ייצור הקרמיקה הטכניים הפופולריים שלנו הם לחיצת קוביות, כבישה איזוסטטית, כבישה איזוסטטית חמה, כבישה חמה, יציקת החלקה, יציקת קלטת, אקסטרוזיה, הזרקה, עיבוד שבבי ירוק, סינטה או שריפה, טחינת יהלומים, מכלולים הרמטיים. אנו ממליצים ללחוץ כאן כדי הורד את האיורים הסכמטיים שלנו של תהליכי יצירת ועיצוב זכוכית מאת AGS-TECH Inc. הורד את האיורים הסכמטיים שלנו של תהליכי ייצור קרמיקה טכניים מאת AGS-TECH Inc. קבצים אלה להורדה עם תמונות וסקיצות יעזרו לך להבין טוב יותר את המידע שאנו מספקים לך למטה. • ייצור זכוכית מכולות: יש לנו קווי לחיצה ונשיפה אוטומטיים כמו גם קווי נשיפה ונשיפה לייצור. בתהליך הנשיפה והנשיפה אנו מפילים גוב לתוך תבנית ריקה ויוצרים את הצוואר על ידי הפעלת מכה של אוויר דחוס מלמעלה. מיד לאחר מכן, אוויר דחוס נשף פעם שנייה מהכיוון השני דרך צוואר המיכל כדי ליצור את הצורה המוקדמת של הבקבוק. הצורה המוקדמת הזו מועברת לתבנית הממשית, מחוממת מחדש כדי לרכך ואוויר דחוס מופעל כדי לתת לתבנית המוקדמת את צורת המיכל הסופית שלה. באופן מפורש יותר, הוא נלחץ ונדחף אל הדפנות של חלל תבנית המכה כדי לקבל את צורתו הרצויה. לבסוף, מיכל הזכוכית המיוצר מועבר לתנור חישול לחימום חוזר והסרת הלחצים שנוצרו במהלך היציקה ומקורר בצורה מבוקרת. בשיטת העיתונות והנשיפה מכניסים גובסים מותכים לתבנית פריזון (תבנית ריקה) ולוחצים לצורת הפריזון (צורת ריק). לאחר מכן מעבירים את החסר לתבניות נשיפה ומפוצצים בדומה לתהליך המתואר לעיל תחת "תהליך נשיפה ונפוח". השלבים הבאים כמו חישול והפגת מתח דומים או זהים. • ניפוח זכוכית: אנו מייצרים מוצרי זכוכית באמצעות ניפוח יד קונבנציונלי וכן באמצעות אוויר דחוס עם ציוד אוטומטי. עבור הזמנות מסוימות נחוצה ניפוח קונבנציונלי, כגון פרויקטים הכוללים עבודות אמנות זכוכית, או פרויקטים הדורשים מספר קטן יותר של חלקים עם סובלנות רופפת, יצירת אב טיפוס / פרויקטי הדגמה... וכו'. ניפוח זכוכית קונבנציונלי כולל טבילה של צינור מתכת חלול לתוך סיר של זכוכית מותכת וסיבוב הצינור לאיסוף כמות מסוימת של חומר הזכוכית. הזכוכית שנאספת על קצה הצינור מגולגלת על ברזל שטוח, מעוצבת לפי הרצוי, מוארכת, מחוממת מחדש ומנשבת אוויר. כשהוא מוכן, מכניסים אותו לתבנית ומנשבים אוויר. חלל התבנית רטוב כדי למנוע מגע של הזכוכית עם מתכת. סרט המים פועל כמו כרית ביניהם. ניפוח ידני הוא תהליך איטי עתיר עבודה ומתאים רק ליצירת אב טיפוס או פריטים בעלי ערך גבוה, לא מתאים להזמנות זולות ליחידה בנפח גבוה. • ייצור של כלי זכוכית ביתיים ותעשייתיים: באמצעות סוגים שונים של חומרי זכוכית מיוצר מגוון גדול של כלי זכוכית. חלק מהכוסות עמידות בחום ומתאימות לכלי זכוכית מעבדה בעוד שחלקן מספיק טובות לעמידה במדיחי כלים פעמים רבות ומתאימות לייצור מוצרים ביתיים. באמצעות מכונות Westlake מיוצרות עשרות אלפי חתיכות של כוסות שתייה ביום. כדי לפשט, זכוכית מותכת נאספת על ידי ואקום ומוכנסת לתבניות כדי ליצור את הטפסים המוקדמים. לאחר מכן מפריחים אוויר לתוך התבניות, אלו מועברים לתבנית אחרת ושוב נושבים אוויר והזכוכית מקבלת את צורתה הסופית. כמו בניפוח יד, תבניות אלו נשמרות רטובות במים. מתיחה נוספת היא חלק מפעולת הגמר שבה נוצר הצוואר. עודפי זכוכית נשרפים. לאחר מכן יופיע תהליך החימום והקירור המבוקר המתואר לעיל. • יצירת צינורות זכוכית ומוטות: התהליכים העיקריים שבהם אנו משתמשים לייצור צינורות זכוכית הם תהליכי DANNER ו-VELLO. בתהליך דנר, זכוכית מתנור זורמת ונופלת על שרוול משופע העשוי מחומרים עמידים. השרוול נישא על מוט חלול מסתובב או צינור נשיפה. לאחר מכן, הזכוכית נכרכת סביב השרוול ויוצרת שכבה חלקה הזורמת במורד השרוול ומעל קצה הפיר. במקרה של יצירת צינורות, אוויר נשף דרך צינור נשיפה עם קצה חלול, ובמקרה של יצירת מוט אנו משתמשים בקצות מוצקות על הפיר. לאחר מכן נמשכים הצינורות או המוטות מעל גלילי נשיאה. המידות כמו עובי הדופן והקוטר של צינורות הזכוכית מותאמים לערכים הרצויים על ידי קביעת קוטר השרוול ונשיפת לחץ אוויר לערך רצוי, התאמת הטמפרטורה, קצב זרימת הזכוכית ומהירות השרטוט. תהליך ייצור צינורות הזכוכית של Vello, לעומת זאת, כולל זכוכית שעוברת החוצה מתנור לתוך קערה עם ציר חלול או פעמון. לאחר מכן הכוס עוברת דרך חלל האוויר שבין הציר לקערה ומקבלת צורה של צינור. לאחר מכן הוא עובר על גלילים למכונת ציור ומתקרר. בסוף קו הקירור מתבצע חיתוך ועיבוד סופי. ניתן להתאים את מידות הצינור בדיוק כמו בתהליך דאנר. כאשר משווים את תהליך Danner ל-Vello, אנו יכולים לומר שתהליך וולו מתאים יותר לייצור כמויות גדולות בעוד שתהליך Danner עשוי להתאים יותר להזמנות מדויקות של צינורות בנפח קטן יותר. • עיבוד של זכוכית שטוחה וזכוכית שטוחה: יש לנו כמויות גדולות של זכוכית שטוחה בעוביים הנעים בין עובי תת-מילימטרים למספר סנטימטרים. המשקפיים השטוחים שלנו הם בעלי שלמות אופטית כמעט. אנו מציעים זכוכית עם ציפויים מיוחדים כגון ציפויים אופטיים, כאשר טכניקת שקיעת אדים כימית משמשת כדי לשים ציפויים כגון אנטי-השתקפות או ציפוי מראה. כמו כן ציפויים מוליכים שקופים נפוצים. זמינים גם ציפויים הידרופוביים או הידרופיליים על זכוכית, וציפוי שהופך את הזכוכית לניקוי עצמי. משקפיים מחוסמים, חסיני כדורים ולמינציה הם פריטים פופולריים נוספים. חתכנו זכוכית לצורה הרצויה עם סובלנות רצויה. זמינות פעולות משניות אחרות כגון עיקול או כיפוף זכוכית שטוחה. • יציקת זכוכית מדויקת: אנו משתמשים בטכניקה זו בעיקר לייצור רכיבים אופטיים מדויקים ללא צורך בטכניקות יקרות יותר וגוזלות זמן כמו השחזה, ליטוש וליטוש. טכניקה זו לא תמיד מספיקה להפיק את המיטב מהאופטיקה הטובה ביותר, אך במקרים מסוימים כמו מוצרי צריכה, מצלמות דיגיטליות, אופטיקה רפואית היא יכולה להיות אפשרות טובה פחות יקרה לייצור בנפח גבוה. כמו כן יש לו יתרון על פני שאר טכניקות יצירת הזכוכית שבהן נדרשות גיאומטריות מורכבות, כמו במקרה של אספרות. התהליך הבסיסי כולל העמסת הצד התחתון של התבנית שלנו עם ריק הזכוכית, פינוי תא התהליך להסרת חמצן, סמוך לסגירה של התבנית, חימום מהיר ואיזוטרמי של תבנית וזכוכית באור אינפרא אדום, סגירה נוספת של חצאי התבנית. ללחוץ את הזכוכית המרוככת באיטיות בצורה מבוקרת לעובי הרצוי, ולבסוף קירור הכוס ומילוי החדר בחנקן והוצאת המוצר. בקרת טמפרטורה מדויקת, מרחק סגירת התבנית, כוח סגירת התבנית, התאמת מקדמי ההתפשטות של התבנית וחומר הזכוכית הם המפתח בתהליך זה. • ייצור רכיבים ומכלולים אופטיים מזכוכית: מלבד יציקת זכוכית מדויקת, ישנם מספר תהליכים בעלי ערך שאנו משתמשים בהם לייצור רכיבים ומכלולים אופטיים באיכות גבוהה עבור יישומים תובעניים. שחיקה, חיכוך והברקה של משקפיים בדרגה אופטית בתמיסות שוחקות משובחות הן אמנות ומדע לייצור עדשות אופטיות, פריזמות, שטוחות ועוד. שטוחות פני השטח, גליות, חלקות ומשטחים אופטיים ללא פגמים דורשים ניסיון רב בתהליכים כאלה. שינויים קטנים בסביבה עלולים לגרום למוצרים מחוץ למפרט ולהפסיק את קו הייצור. ישנם מקרים בהם ניגוב בודד על המשטח האופטי עם מטלית נקייה יכול לגרום למוצר לעמוד במפרטים או להיכשל בבדיקה. כמה חומרי זכוכית פופולריים המשמשים הם סיליקה מתמזגת, קוורץ, BK7. כמו כן, הרכבה של רכיבים כאלה דורשת ניסיון נישה מיוחד. לפעמים משתמשים בדבקים מיוחדים. עם זאת, לפעמים טכניקה הנקראת מגע אופטי היא הבחירה הטובה ביותר ואינה כוללת חומר בין משקפיים אופטיות מחוברות. זה מורכב ממגע פיזי עם משטחים שטוחים כדי להצמד זה לזה ללא דבק. במקרים מסוימים משתמשים במרווחים מכניים, מוטות או כדורי זכוכית מדויקים, מלחציים או רכיבי מתכת מעובדים כדי להרכיב את הרכיבים האופטיים במרחקים מסוימים ובכיוונים גיאומטריים מסוימים זה לזה. הבה נבחן כמה מהטכניקות הפופולריות שלנו לייצור אופטיקה מתקדמת. שחיקה & ליטוש וליטוש: הצורה הגסה של הרכיב האופטי מתקבלת עם שחיקה של ריק מזכוכית. לאחר מכן הליפוף והליטוש מתבצעים על ידי סיבוב ושפשוף המשטחים הגסים של הרכיבים האופטיים כנגד כלים בעלי צורות פני שטח רצויות. תמיסות עם חלקיקים שוחקים ונוזל זעירים מוזגים בין האופטיקה לכלי העיצוב. ניתן לבחור את גדלי החלקיקים השוחקים בתמיסות כאלה בהתאם למידת השטיחות הרצויה. הסטיות של משטחים אופטיים קריטיים מצורות רצויות מתבטאות במונחים של אורכי גל של האור בשימוש. האופטיקה שלנו בעלת דיוק גבוה יש סובלנות של עשירית אורך הגל (אורך גל/10) או אפילו הדוקה יותר אפשרית. מלבד פרופיל פני השטח, המשטחים הקריטיים נסרקים ומוערכים עבור תכונות ופגמים אחרים של פני השטח כגון מידות, שריטות, שבבים, בורות, כתמים וכו '. השליטה ההדוקה של תנאי הסביבה ברצפת הייצור האופטית ודרישות מטרולוגיה ובדיקות נרחבות עם ציוד חדיש הופכים את זה לענף מאתגר בתעשייה. • תהליכים משניים בייצור זכוכית: שוב, אנו מוגבלים רק עם הדמיון שלך בכל הנוגע לתהליכים משניים וגימורים של זכוכית. הנה רשימה של כמה מהם: -ציפויים על זכוכית (אופטי, חשמלי, טריבולוגי, תרמי, פונקציונלי, מכאני...). כדוגמה, אנו יכולים לשנות את תכונות פני השטח של זכוכית ולגרום לה למשל לשקף חום כך שהיא תשמור את פנים הבניין קריר, או להפוך את צד אחד לספוג אינפרא אדום באמצעות ננוטכנולוגיה. זה עוזר לשמור על חום הפנים של הבניינים מכיוון ששכבת הזכוכית החיצונית ביותר תספוג את קרינת האינפרא אדום בתוך הבניין ותקרין אותה בחזרה פנימה. -Etching on glass -תיוג קרמי יישומי (ACL) -חריטה -ליטוש להבה -ליטוש כימי -הכתמה ייצור קרמיקה טכנית • דחיסה חד-צירית של אבקות גרגיריות כלואות בתבנית • כבישה חמה: דומה ללחיצת קוביות אך עם תוספת של טמפרטורה להגברת הצפיפות. אבקה או תבנית דחוסה מוכנסת לתוך תבנית גרפיט ולחץ חד-ציר מופעל בזמן שהמתה נשמרת בטמפרטורות גבוהות כגון 2000 C. הטמפרטורות יכולות להיות שונות בהתאם לסוג האבקה הקרמית המעובדת. עבור צורות וגיאומטריות מסובכות, ייתכן שיהיה צורך בעיבוד אחר אחר כגון השחזה של יהלומים. • דחיסה ISOSTATIC: אבקה גרגירית או קוביות דחוסות מונחות במיכלים אטומים ואז לתוך מיכל לחץ סגור עם נוזל בפנים. לאחר מכן הם נדחסים על ידי הגברת הלחץ של כלי הלחץ. הנוזל בתוך הכלי מעביר את כוחות הלחץ באופן אחיד על פני כל שטח הפנים של המיכל האטום. החומר נדחס בצורה אחידה ומקבל את צורת המיכל הגמיש שלו ואת הפרופיל הפנימי והתכונות שלו. • כבישה איזוסטטית חמה: בדומה לכבישה איזוסטטית, אך בנוסף לאטמוספרה של גז בלחץ, אנו חונטים את הקומפקטי בטמפרטורה גבוהה. לחיצה איזוסטטית חמה מביאה לצפיפות נוספת ולחוזק מוגבר. • יציקת החלקה / יציקת ניקוז: אנו ממלאים את התבנית בתרחיף של חלקיקי קרמיקה בגודל מיקרומטר ונוזל נשא. תערובת זו נקראת "החלקה". לתבנית יש נקבוביות ולכן הנוזל בתערובת מסונן לתוך התבנית. כתוצאה מכך, נוצר יציקה על המשטחים הפנימיים של התבנית. לאחר הסינטר, ניתן להוציא את החלקים מהתבנית. • יציקת קלטות: אנו מייצרים סרטי קרמיקה על ידי יציקת תפוחים קרמיים על משטחי מנשא נעים שטוחים. התמיסות מכילות אבקות קרמיקה מעורבות עם כימיקלים אחרים למטרות קשירה ונשיאה. כאשר הממסים מתאדים נותרות מאחור יריעות קרמיקה צפופות וגמישות אותן ניתן לחתוך או לגלגל כרצונך. • יצירת שחול: כמו בתהליכי שחול אחרים, תערובת רכה של אבקה קרמית עם קלסרים וכימיקלים אחרים מועברת דרך תבנית כדי לרכוש את צורת החתך שלה ולאחר מכן נחתכת באורכים הרצויים. התהליך מתבצע עם תערובות קרמיות קרות או מחוממות. • הזרקה בלחץ נמוך: אנו מכינים תערובת של אבקה קרמית עם קלסרים וממיסים ומחממים אותה לטמפרטורה שבה ניתן ללחוץ אותה בקלות ולהכניס אותה לחלל הכלי. לאחר השלמת מחזור הדפוס, החלק נפלט והכימיקל הקושר נשרף. באמצעות הזרקה, אנו יכולים להשיג חלקים מורכבים בנפחים גבוהים מבחינה כלכלית. חורים שהם שבריר זעיר של מילימטר על דופן בעובי 10 מ"מ אפשריים, הברגים אפשריים ללא עיבוד נוסף, סובלנות הדוקה עד +/- 0.5% אפשריות ואף נמוכות יותר כאשר חלקים מתאפשרים במכונה. , אפשריים עובי דופן בסדר גודל של 0.5 מ"מ עד אורך של 12.5 מ"מ וכן עובי דופן של 6.5 מ"מ עד אורך של 150 מ"מ. • עיבוד ירוק: באמצעות אותם כלי עיבוד מתכת, נוכל לעבד חומרים קרמיים דחוסים כשהם עדיין רכים כמו גיר. אפשריות סובלנות של +/- 1%. לקבלת סובלנות טובה יותר אנו משתמשים בשחיקת יהלומים. • SINTERING או FIRING: סינטה מאפשרת ציפוף מלא. הצטמקות משמעותית מתרחשת בחלקים הקומפקטיים הירוקים, אך זו לא בעיה גדולה מכיוון שאנו לוקחים בחשבון את השינויים הממדים הללו כאשר אנו מתכננים את החלק והכלים. חלקיקי אבקה נקשרים יחד והנקבוביות הנגרמת על ידי תהליך הדחיסה מוסרת במידה רבה. • טחינת יהלומים: החומר הקשה ביותר בעולם "יהלום" משמש לטחינת חומרים קשים כמו קרמיקה ומתקבלים חלקים מדויקים. מושגות סובלנות בטווח המיקרומטר ומשטחים חלקים מאוד. בשל הוצאותיה, אנו שוקלים את הטכניקה הזו רק כאשר אנו באמת זקוקים לה. • מכלולים הרמטיים הם אלו שבאופן מעשי אינם מאפשרים כל חילוף של חומר, מוצקים, נוזלים או גזים בין ממשקים. איטום הרמטי אטום. לדוגמה, מארזים אלקטרוניים הרמטיים הם אלה ששומרים על התוכן הפנימי הרגישה של מכשיר ארוז ללא פגע מלחות, מזהמים או גזים. שום דבר אינו הרמטי ב-100%, אבל כשמדברים על הרמטיות מתכוונים לכך מבחינה מעשית, שיש הרמטיות במידה ששיעור הדליפה כל כך נמוך עד שהמכשירים בטוחים בתנאי סביבה רגילים למשך זמן ארוך מאוד. המכלולים הרמטיים שלנו מורכבים מרכיבי מתכת, זכוכית וקרמיקה, מתכת-קרמיקה, קרמיקה-מתכת-קרמיקה, מתכת-קרמית-מתכת, מתכת למתכת, מתכת-זכוכית, מתכת-זכוכית-מתכת, זכוכית-מתכת-זכוכית, זכוכית- מתכת וזכוכית לזכוכית וכל שאר השילובים של מליטה מתכת-זכוכית-קרמית. אנחנו יכולים למשל לצפות במתכת את הרכיבים הקרמיים כך שיוכלו להיות מחוברים חזק לרכיבים אחרים במכלול ובעלי יכולת איטום מצוינת. יש לנו את הידע של ציפוי סיבים אופטיים או הזנה במתכת והלחמתם או הלחמתם למארזים, כך שאף גזים לא עוברים או דולפים לתוך המתחמים. לכן הם משמשים לייצור מארזים אלקטרוניים כדי לכלול מכשירים רגישים ולהגן עליהם מהאטמוספרה החיצונית. מלבד מאפייני האיטום המצוינים שלהם, תכונות אחרות כגון מקדם ההתפשטות התרמית, עמידות בפני דפורמציה, אופי ללא גז, אורך חיים ארוך מאוד, אופי לא מוליך, תכונות בידוד תרמי, אופי אנטי סטטי... וכו'. להפוך זכוכית וקרמיקה לבחירה עבור יישומים מסוימים. מידע על המתקן שלנו לייצור אביזרי קרמיקה למתכת, איטום הרמטי, הזנת ואקום, ואקום גבוה ואולטרה גבוה ורכיבי בקרת נוזלים ניתן למצוא כאן:חוברת מפעל רכיבים הרמטיים CLICK Product Finder-Locator Service עמוד קודם
- Wire & Spring Forming, Shaping, Welding, Assembly of Wires, Coil, CNC
Wire & Spring Forming, Shaping, Welding, Assembly of Wires, Coil Compression Extension Torsion Flat Springs, Custom Wires, Helical Springs at AGS-TECH Inc. יצירת תיל וקפיצים אנו מייצרים חוטים מותאמים אישית, הרכבת חוטים, חוטים שנוצרו לצורות דו-ממדיות ותלת-ממדיות רצויות, רשתות תיל, רשת, מארזים, סל, גדר, קפיץ תיל, קפיץ שטוח; פיתול, דחיסה, מתח, קפיצים שטוחים ועוד. התהליכים שלנו הם יצירת תיל וקפיצים, שרטוט תיל, עיצוב, כיפוף, ריתוך, הלחמה, הלחמה, ניקוב, הנחתה, קידוח, שיוף, שחיקה, השחלה, ציפוי, ארבע שקופיות, יצירת שקופיות, סלילה, סלילת, שיבושים. אנו ממליצים ללחוץ כאן כדי הורד את האיורים הסכמטיים שלנו של תהליכי יצירת תיל וקפיצים מאת AGS-TECH Inc. קובץ זה להורדה עם תמונות וסקיצות יעזור לך להבין טוב יותר את המידע שאנו מספקים לך למטה. • ציור תיל : בעזרת כוחות מתיחה אנו מותחים את מלאי המתכת ומושכים אותו דרך תבנית כדי להקטין את הקוטר ולהגדיל את אורכו. לפעמים אנחנו משתמשים בסדרה של מתות. אנו מסוגלים לייצר קוביות עבור כל מד חוט. באמצעות חומר בעל חוזק מתיחה גבוה אנו מציירים חוטים דקים מאוד. אנו מציעים חוטים קרים וחמים כאחד. • יצירת חוט: גליל של חוט מדורג מכופף ומעצב למוצר שימושי. יש לנו את היכולת ליצור חוטים מכל המדידות, כולל חוטים דקים, כמו גם חוטים עבים כמו אלה המשמשים כקפיצים מתחת לשלדת הרכב. הציוד שאנו משתמשים בו ליצירת חוטים הם יוצרי חוטים ידניים ו-CNC, קוילרים, מכבשי כוח, ארבע מגלשות, רב-שקופיות. התהליכים שלנו הם שרטוט, כיפוף, יישור, שיטוח, מתיחה, חיתוך, שיבוץ, הלחמה וריתוך והלחמה, הרכבה, פיתול, סילוף (או כנף), ניקוב, השחלת חוטים, קידוח, שיוף, השחזה, ציפוי וטיפולי משטח. ניתן להגדיר את הציוד המתקדם שלנו לפיתוח עיצובים מורכבים מאוד בכל צורה וסובלנות הדוקה. אנו מציעים סוגי קצה שונים כמו קצוות כדוריים, מחודדים או משופשפים עבור החוטים שלך. לרוב הפרויקטים שלנו ליצירת תיל יש עלויות כלי עבודה מינימליות עד אפסיות. זמני אספקה לדוגמה הם בדרך כלל ימים. ניתן לבצע שינויים בעיצוב/תצורה של טפסי תיל במהירות רבה. • SPRING Forming: AGS-TECH מייצרת מגוון גדול של קפיצים הכוללים: -קפיץ פיתול / כפול פיתול -קפיץ מתח / דחיסה -קפיץ קבוע / משתנה -סליל וקפיץ סליל -קפיץ שטוח ועלים -איזון אביב מכונת כביסה בלוויל -מעיין השלילה -קפיץ סליל בקצב מתקדם -אביב גל -אביב כרך -מעיינות מחודדים -טבעות אביב -קפיצי שעון -קליפים אנו מייצרים קפיצים ממגוון חומרים ויכולים להדריך אותך בהתאם ליישום שלך. החומרים הנפוצים ביותר הם נירוסטה, סיליקון כרום, פלדה בעלת פחמן גבוה, פחמן נמוך מחוסמת שמן, כרום ונדיום, ברונזה זרחנית, טיטניום, סגסוגת נחושת בריליום, קרמיקה בטמפרטורה גבוהה. אנו משתמשים בטכניקות שונות בייצור קפיצים, לרבות סלילת CNC, סלילה קרה, סלילה חמה, התקשות, גימור. טכניקות אחרות שכבר הוזכרו לעיל תחת יצירת תיל נפוצות גם בפעולות ייצור הקפיץ שלנו. • שירותי גימור עבור חוטים וקפיצים: אנו יכולים לסיים את המוצרים שלך בדרכים רבות בהתאם לבחירתך ולצרכים שלך. כמה תהליכים נפוצים שאנו מציעים הם: צביעה, ציפוי אבקה, ציפוי, טבילת ויניל, אילגון, הפגת מתחים, טיפול בחום, shot peen, נפילה, כרומט, ניקל נטול חשמל, פסיבציה, אמייל אפוי, פלסטיק , ניקוי פלזמה. CLICK Product Finder-Locator Service עמוד קודם
- Sheet Metal Forming Fabrication, Stamping, Punching, Deep Drawing, CNC
Sheet Metal Forming and Fabrication, Stamping, Punching, Bending, Progressive Die, Spot Welding, Deep Drawing, Metal Blanking and Slitting at AGS-TECH Inc. הטבעות וייצור פחים אנו מציעים הטבעה, עיצוב, גיבוש, כיפוף, ניקוב, הרס, חיתוך, ניקוב, חריצים, נישנושים, גילוח, עיבוד בלחיצה, ייצור, שרטוט עמוק תוך שימוש במות אגרוף יחיד/מכה בודדת, כמו גם מתכות פרוגרסיביות וספינינג, יצירת גומי ו הידרופורמינג; חיתוך מתכת באמצעות סילון מים, פלזמה, לייזר, מסור, להבה; הרכבה מתכת מתכת באמצעות ריתוך, ריתוך נקודתי; צינור מתכת מתכת בולט וכיפוף; גימור משטח מתכת מתכת כולל טבילה או צביעה בהתזה, ציפוי אבקה אלקטרוסטטי, אילגון, ציפוי, התזת ועוד. השירותים שלנו נעים בין אב טיפוס מהיר של גיליונות לייצור בנפח גבוה. אנו ממליצים ללחוץ כאן כדיהורד את האיורים הסכמטיים שלנו של תהליכי ייצור והטבעה של פחים על ידי AGS-TECH Inc. זה יעזור לך להבין טוב יותר את המידע שאנו מספקים לך למטה. • חיתוך מתכת: אנו מציעים חתכים ופרידות. חתכים חותכים את הפח על פני נתיב אחד בכל פעם ואין בעצם בזבוז של חומר, ואילו עם פרידות לא ניתן לקנן את הצורה במדויק ולכן כמות מסוימת של חומר מתבזבזת. אחד התהליכים הפופולריים ביותר שלנו הוא PUNCHING, שבו חתיכת חומר עגולה או צורה אחרת נחתכת מפח. החתיכה שנחתכת היא פסולת. גרסה נוספת של ניקוב היא SLOTTING, שבה מחוררים חורים מלבניים או מוארכים. BLANKING לעומת זאת הוא אותו תהליך כמו ניקוב, כאשר ההבחנה של היצירה הנחתכת היא העבודה ונשמרת. FINE BLANKING, גרסה מעולה של הבלקה, יוצרת חיתוכים עם סובלנות קרובה וקצוות חלקים ישרים ואינה דורשת פעולות משניות לשלמות של חומר העבודה. תהליך נוסף שאנו משתמשים בו לעתים קרובות הוא SLITTING, שהוא תהליך גזירה שבו מתכת נחתכת על ידי שני להבים מעגליים מנוגדים בנתיב ישר או מעוקל. פותחן קופסאות שימורים הוא דוגמה פשוטה לתהליך החריכה. עוד תהליך פופולרי עבורנו הוא PERFORATING, שבו חורים רבים עגולים או צורה אחרת מחוררים בפח מתכת בדוגמה מסוימת. דוגמה טיפוסית למוצר מחורר היא מסנני מתכת עם חורים רבים לנוזלים. ב-NOCHING, תהליך נוסף של חיתוך פח, אנו מסירים חומר מחומר עבודה, מתחילים בקצה או במקום אחר וחותכים פנימה עד לקבלת הצורה הרצויה. זהו תהליך פרוגרסיבי שבו כל פעולה מסירה חלק נוסף עד לקבלת קו המתאר הרצוי. עבור ריצות ייצור קטנות אנו משתמשים לפעמים בתהליך איטי יותר יחסית שנקרא NIBBLING אשר מורכב מחבטות מהירות רבות של חורים חופפים כדי לבצע חיתוך גדול יותר מורכב. ב-PROGRESSIVE CUTTING אנו משתמשים בסדרה של פעולות שונות כדי להשיג חיתוך בודד או גיאומטריה מסוימת. לבסוף תהליך גילוח משני עוזר לנו לשפר קצוות של חתכים שכבר נעשו. הוא משמש לחיתוך השבבים, קצוות מחוספסים בעבודת מתכת. • כיפוף פחים: מלבד חיתוך, כיפוף הוא תהליך חיוני שבלעדיו לא נוכל לייצר את רוב המוצרים. לרוב פעולת עבודה קרה אך לעיתים מבוצעת גם כשהוא חם או חם. אנו משתמשים במות ולוחצים רוב הזמן עבור הפעולה הזו. ב-PROGRESSIVE BENDING אנו משתמשים בסדרה של פעולות אגרוף וקוביות שונות כדי להשיג כיפוף בודד או גיאומטריה מסוימת. AGS-TECH משתמשת במגוון תהליכי כיפוף ועושה את הבחירה בהתאם לחומר העבודה, גודלו, עוביו, גודל הכיפוף הרצוי, רדיוס, עקמומיות וזווית הכיפוף, מיקום הכיפוף, חסכון הפעולה, כמויות לייצור... וכו ' אנו משתמשים ב-V-BENDING שבו אגרוף בצורת V כופה את מתכת הגיליון לתוך התבנית בצורת V ומכופף אותה. טוב גם לזוויות חדות מאוד וגם קהות וביניהן, כולל 90 מעלות. באמצעות קוביות ניגוב אנו מבצעים כיפוף EDGE BENDING. הציוד שלנו מאפשר לנו להשיג זוויות אפילו יותר מ-90 מעלות. בכיפוף קצה חומר העבודה מוחזק בין כרית לחץ לבין התבנית, האזור לכיפוף ממוקם על קצה התבנית ושאר חומר העבודה מוחזק מעל space כמו קורה שלוחה. כאשר האגרוף פועל על החלק שלוחה, הוא כפוף על קצה הקוביה. FLANGING הוא תהליך כיפוף קצה המביא לזווית של 90 מעלות. המטרות העיקריות של הפעולה הן ביטול קצוות חדים והשגת משטחים גיאומטריים כדי להקל על חיבור החלקים. BEADING, תהליך נפוץ נוסף של כיפוף קצה יוצר סלסול על קצה של חלק. HEMMING לעומת זאת תוצאה עם קצה של הסדין שכופף לגמרי על עצמו. ב-SEAMING, הקצוות של שני חלקים מכופפים זה על זה ומחברים אותם. תפירה כפולה לעומת זאת מספקת חיבורי פחים אטומים למים ואטומים. בדומה לכיפוף קצה, תהליך הנקרא ROTARY BENDING פורס צילינדר עם הזווית הרצויה חתוכה ומשמש כאגרוף. כאשר הכוח מועבר אל האגרוף, הוא נסגר עם חומר העבודה. החריץ של הגליל נותן לחלק שלוחה את הזווית הרצויה. החריץ יכול לקבל זווית קטנה או גדולה מ-90 מעלות. ב-AIR BENDING, אנחנו לא צריכים את התבנית התחתונה כדי שיהיה חריץ זווית. גיליון המתכת נתמך על ידי two משטחים בצדדים מנוגדים ובמרחק מסוים. לאחר מכן האגרוף מפעיל כוח במיקום הנכון ומכופף את חומר העבודה. CHANNEL BENDING מתבצע באמצעות אגרוף בצורת תעלה, ו-U-BEND מושג עם אגרוף בצורת U. OFFSET BENDING מייצר קיזוזים על הפח. ROLL BENDING, טכניקה טובה לעבודה עבה וכיפוף של חתיכות גדולות של לוחות מתכת, משתמשת בשלושה גלילים להזנה ולכיפוף של הלוחות לעקמומיות הרצויות. רולים מסודרים כך שמתקבל העיקול הרצוי של העבודה. המרחק והזווית בין הגלילים נשלטים כדי להשיג את התוצאה הרצויה. גליל נייד מאפשר לשלוט בעקמומיות. TUBE FORMING היא עוד פעולת כיפוף מתכת פופולארית הכוללת מספר מתכות. צינורות מתקבלים לאחר מספר פעולות. CORRUGATION מתבצע גם על ידי פעולות כיפוף. בעיקרון זה הכיפוף הסימטרי במרווחים קבועים על פני פיסת מתכת שלמה. ניתן להשתמש בצורות שונות לגלי. מתכת גלי היא קשיחה יותר ובעלת עמידות טובה יותר בפני כיפוף ולכן יש לה יישומים בענף הבנייה. גליל גליל מתכת מתכת, תהליך ייצור מתמשך נפרס לכיפוף חתכים של גיאומטריה מסוימת באמצעות גלילים והעבודה מכופפת בשלבים עוקבים, כשהגליל הסופי משלים את העבודה. במקרים מסוימים משתמשים בגליל בודד ובמקרים מסוימים בסדרה של גלילים. • תהליכי חיתוך וכיפוף משולבים בפח: אלו הם התהליכים החותכים ומתכופפים בו-זמנית. ב-PIERCING, נוצר חור באמצעות אגרוף מחודד. כאשר האגרוף מרחיב את החור בסדין, החומר מכופף בו זמנית לאוגן פנימי עבור החור. לאוגן המתקבל עשויות להיות פונקציות חשובות. פעולת ה-LANCING לעומת זאת חותכת ומכופפת את הסדין ליצירת גיאומטריה מוגבהת. • בליטה וכיפוף של צינור מתכת: בבליטה חלק פנימי של צינור חלול מופעל בלחץ, מה שגורם לצינור לבלוט החוצה. מכיוון שהצינור נמצא בתוך קובייה, גיאומטריית הבליטה נשלטת על ידי צורת התבנית. ב- STRETCH BENDING, צינור מתכת נמתח באמצעות כוחות מקבילים לציר הצינור וכוחות כיפוף כדי למשוך את הצינור מעל גוש צורה. ב-DRAW BENDING, אנו מהדקים את הצינור ליד הקצה שלו לבלוק צורה מסתובב שמכופף את הצינור תוך כדי סיבוב. לבסוף, ב-COMPRESSION BENDING הצינור מוחזק בכוח אל גוש צורה קבוע, וקוביה מכופפת אותו על גוש הצורה. • ציור עמוק: באחת הפעולות הפופולריות ביותר שלנו, נעשה שימוש באגרוף, קובייה תואמת ומחזיק ריק. את ריק המתכת מניחים מעל פתח התבנית והאגרוף נע לעבר הריק המוחזק על ידי מחזיק הריק. ברגע שהם באים במגע, האגרוף מאלץ את המתכת לתוך חלל התבנית כדי ליצור את המוצר. פעולת ציור עמוק מזכירה חיתוך, אולם המרווח בין האגרוף לתבנית מונע את חיתוך הסדין. גורם נוסף המבטיח שהיריעה נמשכת לעומק ואינה חתוכה הן הפינות המעוגלות על התבנית והאגרוף שמונעים את הגזירה והחיתוך. כדי להשיג גודל גדול יותר של ציור עמוק, נפרס תהליך REDRAWING שבו מתרחש ציור עמוק שלאחר מכן על חלק שכבר עבר תהליך ציור עמוק. ב-REVERSE REDRAWING, החלק המצויר עמוק מתהפך ומצויר בכיוון ההפוך. ציור עמוק יכול לספק חפצים בעלי צורה לא סדירה כגון כוסות כיפות, מחודדות או מדורגות. • SPINNING : פעולה שבה מוחזק חומר עבודה שטוח או מעוצב מראש בין ציר מסתובב ומק זנב וכלי מפעיל לחץ מקומי על העבודה כשהיא נעה בהדרגה במעלה הציר. כתוצאה מכך, חומר העבודה עטוף על המדרל ולוקח את צורתו. אנו משתמשים בטכניקה זו כחלופה לשרטוט עמוק כאשר כמות ההזמנה קטנה, החלקים גדולים (בקוטר של עד 20 רגל) ובעלי קימורים ייחודיים. למרות שהמחירים ליחידה גבוהים יותר בדרך כלל, עלויות ההתקנה עבור פעולת ספינינג CNC נמוכות בהשוואה לשרטוט עמוק. להיפך, ציור עמוק דורש השקעה ראשונית גבוהה להתקנה, אך העלויות ליחידה נמוכות כאשר מייצרים כמות גדולה של חלקים. גרסה נוספת של תהליך זה היא SHEAR SPINNING, כאשר ישנה גם זרימת מתכת בתוך חומר העבודה. זרימת המתכת תפחית את עובי חומר העבודה תוך כדי ביצוע התהליך. תהליך נוסף קשור הוא TUBE SPINNING, אשר מיושם על חלקים גליליים. גם בתהליך זה יש זרימת מתכת בתוך חומר העבודה. כך מצטמצם העובי ואורך הצינור גדל. ניתן להזיז את הכלי כדי ליצור תכונות בחלק הפנימי או החיצוני של הצינור. • יצירת גומי של גיליון מתכת: גומי או חומר פוליאוריטן מונחים בתבנית מיכל ומניחים את חתיכת העבודה על פני הגומי. לאחר מכן מופעל אגרוף על חלק העבודה ודוחף אותו לתוך הגומי. מכיוון שהלחץ שנוצר על ידי הגומי נמוך, עומק החלקים המיוצרים מוגבל. כיוון שעלויות הכלים נמוכות, התהליך מתאים לייצור בכמות נמוכה. • HYDROFORMING : בדומה ליצירת גומי, בתהליך זה עבודת מתכת נלחצת על ידי אגרוף לתוך נוזל בלחץ בתוך תא. עבודת הפח מתוחה בין האגרוף לבין דיאפרגמת גומי. הסרעפת מקיפה את חומר העבודה לחלוטין ולחץ הנוזל מאלץ אותה להיווצר על האגרוף. ניתן להשיג רישומים עמוקים מאוד אפילו עמוק יותר מאשר בתהליך הציור העמוק בטכניקה זו. אנו מייצרים מתנות עם אגרוף בודד כמו גם מתנות פרוגסיביות בהתאם לחלק שלך. מתכות הטבעה חדות הן שיטה חסכונית לייצור כמויות גדולות של חלקי מתכת פשוטים כגון מכונות כביסה במהירות. תבניות פרוגרסיביות או טכניקת השרטוט העמוק משמשות לייצור גיאומטריות מורכבות יותר. בהתאם למקרה שלך, ניתן להשתמש בחיתוך סילון מים, לייזר או פלזמה לייצור חלקי הפח שלך בזול, מהיר ומדויק. לספקים רבים אין מושג לגבי טכניקות אלטרנטיביות אלו או שאין להם ולכן הם עוברים דרכים ארוכות ויקרות של ייצור מתנות וכלים שרק מבזבזים ללקוחות זמן וכסף. אם אתה זקוק לרכיבי מתכת בנויים בהתאמה אישית כגון מארזים, מארזים אלקטרוניים וכו' תוך כמה ימים, צור איתנו קשר לשירות RAPID SHEET METAL PROTOTYPING שלנו. CLICK Product Finder-Locator Service התפריט הקודם
- Forging and Powdered Metallurgy, Die Forging, Heading, Hot Forging
Forging and Powdered Metallurgy, Die Forging, Heading, Hot Forging, Impression Die, Near Net Shape, Swaging, Metal Hobbing, Riveting, Coining from AGS-TECH Inc. פרזול מתכת ומטלורגיית אבקה סוג התהליכים של METAL FORGING שאנו מציעים הם תבנית חמה וקרה, תבנית פתוחה ותבנית סגורה, תבנית התרשמות וחיתולים ללא הבזק, cogging, מלאות, חישול קצה ודיוק, צורה כמעט נטו, כותרת , חישולים, פרזול, חישול מתכת, חישול לחיצה אנד רול ורדיאלי ואורביטלי וטבעת & איזותרמיים, טבעה, ריתוק, חישול כדורי מתכת, פירסינג מתכת, חישול מידות, חישול בקצב אנרגיה גבוה. טכניקות ה-POWDER METALLURGY ו-POWDER PROCESSING שלנו הן כבישה וסינטר אבקה, הספגה, הסתננות, כבישה איזוסטטית חמה וקרה, הזרקת מתכת, דחיסה של גלילים, גלגול אבקה, שחול אבקה, סינטה רופפת, סינון ניצוץ, כבישה חמה. אנו ממליצים ללחוץ כאן כדי הורד את האיורים הסכמטיים שלנו של תהליכי חישול מאת AGS-TECH Inc. הורד את האיורים הסכמטיים שלנו של תהליכי מטלורגיית אבקה מאת AGS-TECH Inc. קבצים אלה להורדה עם תמונות וסקיצות יעזרו לך להבין טוב יותר את המידע שאנו מספקים לך למטה. בפרזול מתכת מופעלים כוחות לחיצה ומתעוות החומר ומתקבלת הצורה הרצויה. החומרים המחושלים הנפוצים ביותר בתעשייה הם ברזל ופלדה, אך רבים אחרים כגון אלומיניום, נחושת, טיטניום, מגנזיום מחושלים גם הם באופן נרחב. לחלקי מתכת מזויפים יש מבני גרגר משופרים בנוסף לסדקים אטומים וחללים ריקים סגורים, ולכן חוזקם של חלקים המתקבלים בתהליך זה גבוה יותר. פרזול מייצר חלקים שהם חזקים משמעותית למשקלם מאשר חלקים שנעשו על ידי יציקה או עיבוד שבבי. מכיוון שחלקים מחושלים מעוצבים על ידי זרימת המתכת לצורתה הסופית, המתכת מקבלת מבנה גרגר כיווני המהווה את החוזק המעולה של החלקים. במילים אחרות, חלקים המתקבלים בתהליך חישול מגלים תכונות מכניות טובות יותר בהשוואה לחלקים יצוקים או מעובדים פשוטים. משקלם של פרזול מתכת יכול לנוע בין חלקים קטנים וקלים למאות אלפי פאונד. אנו מייצרים פרזול בעיקר ליישומים תובעניים מבחינה מכנית בהם מופעלים מתחים גבוהים על חלקים כגון חלקי רכב, גלגלי שיניים, כלי עבודה, כלי עבודה ידניים, פירי טורבינה, ציוד לאופנועים. מכיוון שעלויות הכלים וההקמה גבוהות יחסית, אנו ממליצים על תהליך ייצור זה רק לייצור בנפח גבוה ולרכיבים קריטיים בנפח נמוך אך בעל ערך גבוה כגון ציוד נחיתה בתעופה וחלל. מלבד עלות הכלים, זמני הייצור של חלקים מזויפים בכמות גדולה יכולים להיות ארוכים יותר בהשוואה לחלקים פשוטים מעובדים, אך הטכניקה חיונית עבור חלקים ש דורשים חוזק יוצא דופן כגון ברגים, אומים, יישום מיוחד מחברים, רכב, מלגזה, חלקי מנוף. • HOT DIE ו-COLD DIE FORGING : חישול קוביות חמות, כפי שהשם מרמז, מתבצע בטמפרטורות גבוהות, לכן השיכות גבוהה וחוזק החומר נמוך. זה מקל על עיוות וזיוף קל. להיפך, חישול תבנית קרה מתבצע בטמפרטורות נמוכות יותר ודורש כוחות גבוהים יותר מה שגורם להתקשות מתח, גימור משטח טוב יותר ודיוק של החלקים המיוצרים. • חישול קוביות פתוחות ו-IMPRESSION: בחישול קוביות פתוחות, הקוביות אינן מגבילות את החומר הנדחס, ואילו בחישול קוביות הדפסה, החללים בתוך התבנית מגבילים את זרימת החומר בזמן שהוא מחושל לצורה הרצויה. UPSET FORGING או שנקרא גם UPSETTING, שלמעשה אינו זהה אלא תהליך דומה מאוד, הוא תהליך קובייה פתוחה שבו חתיכת העבודה נדחסת בין שני קוביות שטוחות וכוח דחיסה מפחית את גובהו. ככל שהגובה הוא reduced, רוחב חתיכת העבודה גדל. HEADING, תהליך פרזול מעורער כרוך במלאי גלילי שמתקלקל בקצהו וחתך הרוחב שלו גדל באופן מקומי. בכותרת המניות מוזנות דרך התבנית, מחושלות ואז חותכות לאורך. הפעולה מסוגלת לייצר כמויות גבוהות של מחברים במהירות. לרוב מדובר בפעולת עבודה קרה מכיוון שהיא משמשת לייצור קצוות מסמרים, קצוות ברגים, אומים וברגים שבהם צריך לחזק את החומר. תהליך תבנית פתוחה נוסף הוא COGGING, כאשר חלק העבודה מחושל בסדרה של שלבים כאשר כל שלב מביא לדחיסה של החומר ולתנועה שלאחר מכן של התבנית הפתוחה לאורך חלקת העבודה. בכל שלב, העובי מצטמצם והאורך גדל בכמות קטנה. התהליך דומה לתלמיד עצבני הנושך את העיפרון שלו לאורך כל הדרך בצעדים קטנים. תהליך שנקרא FULLERING הוא עוד שיטת חישול מתכת פתוחה שאנו מפרסים לעתים קרובות כשלב מוקדם יותר להפצת החומר בחתיכת העבודה לפני שמתבצעות פעולות חישול מתכת אחרות. אנו משתמשים בו כאשר חלק העבודה דורש מספר פעולות חישול operations. בניתוח, מתים עם משטחים קמורים עיוותים וגורמים לזרימת מתכת החוצה לשני הצדדים. תהליך דומה למלאות, EDGING לעומת זאת כולל תבנית פתוחה עם משטחים קעורים כדי לעוות את חלק העבודה. שולים גם תהליך הכנה לפעולות פרזול עוקבות גורם לחומר לזרום משני הצדדים לאזור במרכז. IMPRESSION DIE FORGING או CLOSED DIE FORGING כפי שהוא נקרא גם עושה שימוש בתבנית / תבנית שדוחסת את החומר ומגבילה את זרימתו בתוך עצמה. התבנית נסגרת והחומר מקבל את הצורה של חלל התבנית / התבנית. PRECISION FORGING, תהליך הדורש ציוד מיוחד ועובש, מייצר חלקים ללא הבזק או מעט מאוד. במילים אחרות, לחלקים יהיו ממדים כמעט סופיים. בתהליך זה כמות חומר מבוקרת היטב מוכנסת בקפידה וממוקמת בתוך התבנית. אנו פורסים שיטה זו עבור צורות מורכבות עם חתכים דקים, סובלנות קטנות וזוויות טיוטה וכאשר הכמויות גדולות מספיק כדי להצדיק את עלויות העובש והציוד. • פרזול ללא הבזקים: חומר העבודה ממוקם בתבנית בצורה כזו ששום חומר לא יכול לזרום החוצה מהחלל כדי ליצור הבזק. לכן אין צורך בגזירת פלאש לא רצויה. זהו תהליך פרזול מדויק ולכן דורש שליטה צמודה על כמות החומר בשימוש. • חישול מתכת או חישול רדיאלי: חלקת עבודה מושפעת היקפית על ידי תבנית ומחושלת. ניתן גם להשתמש במדרל כדי לזייף את הגיאומטריה של חלק העבודה הפנימי. בפעולת ההחלקה, חתיכת העבודה מקבלת בדרך כלל מספר תנועות בשנייה. פריטים אופייניים המיוצרים על ידי חלוקה הם כלים מחודדים, מוטות מחודדים, מברגים. • פירסינג מתכת: אנו משתמשים בפעולה זו לעתים קרובות כפעולה נוספת בייצור חלקים. נוצר חור או חלל עם פירסינג על משטח היצירה מבלי לפרוץ דרכו. שימו לב שפירסינג שונה מקידוח שגורם לחור עובר. • HOBBING : אגרוף עם הגיאומטריה הרצויה נלחץ לתוך חלק העבודה ויוצר חלל עם הצורה הרצויה. אנחנו קוראים לאגרוף הזה כיריים. הפעולה כרוכה בלחצים גבוהים ומתבצעת בקור. כתוצאה מכך החומר מעובד בקור ומתקשה. לכן תהליך זה מתאים מאוד לייצור תבניות, תבנית וחללים לתהליכי ייצור אחרים. לאחר יצירת הכיריים, ניתן לייצר בקלות חללים זהים רבים ללא צורך בעיבודם אחד אחד. • חישול גליל או יצירת גליל: שני גלילים מנוגדים משמשים לעיצוב חלק המתכת. חלק העבודה מוכנס לתוך הגלילים, הגלילים מסתובבים ומושכים את העבודה לתוך הרווח, לאחר מכן העבודה מוזנת דרך החלק המחורץ של הגלילים וכוחות הלחיצה נותנים לחומר את צורתו הרצויה. זה לא תהליך גלגול אלא תהליך חישול, כי מדובר בפעולה בדיד ולא מתמשכת. הגיאומטריה על חורשות הגלילים מחשלת את החומר לצורה ולגיאומטריה הנדרשת. זה מבוצע חם. בגלל היותו תהליך פרזול הוא מייצר חלקים בעלי תכונות מכניות יוצאות דופן ולכן אנו משתמשים בו עבור ייצור חלקי רכב כגון פירים שצריכים להיות בעלי סיבולת יוצאת דופן בסביבות עבודה קשות. • חישול מסלולי: חלק העבודה מוכנס לחלל תבנית חישול ומחושל על ידי תבנית עליון שנוסע בנתיב מסלולי כשהוא מסתובב על ציר משופע. בכל סיבוב, התבנית העליונה משלימה את הפעלת כוחות הלחיצה על כל חלקת העבודה. על ידי חזרה על מהפכות אלו מספר פעמים, מבוצע חישול מספק. היתרונות של טכניקת ייצור זו הם פעולת הרעש הנמוכה שלה וכוחות נמוכים יותר הדרושים. במילים אחרות עם כוחות קטנים אפשר לסובב קובייה כבדה סביב ציר כדי להפעיל לחצים גדולים על קטע של חלק העבודה שנמצא במגע עם התבנית. חלקים בצורת דיסק או חרוט מתאימים לפעמים לתהליך זה. • חישול טבעות: אנו משתמשים לעתים קרובות לייצור טבעות ללא תפרים. המאגר נחתך לאורך, נסער ואז מחורר עד הסוף כדי ליצור חור מרכזי. לאחר מכן מניחים אותו על ציר ותבנית חישול מפטישת אותו מלמעלה כשהטבעת מסובבת לאט עד לקבלת המידות הרצויות. • RIVETING : תהליך נפוץ לחיבור חלקים, מתחיל בחתיכת מתכת ישרה המוכנסת לחורים שנעשו מראש דרך החלקים. לאחר מכן, שני הקצוות של חלק המתכת מחושלים על ידי סחיטת המפרק בין תבנית עליונה לתחתונה. • מטבעות: תהליך פופולרי נוסף המתבצע על ידי לחיצה מכנית, מפעיל כוחות גדולים על פני מרחק קצר. השם "טבעה" מגיע מהפרטים העדינים המחושלים על משטחי מטבעות מתכת. לרוב מדובר בתהליך גימור למוצר בו מתקבלים פרטים עדינים על המשטחים כתוצאה מהכוח הרב המופעל על ידי התבנית המעביר את הפרטים הללו אל חלקת העבודה. • חישול כדורי מתכת: מוצרים כגון מיסבים כדוריים דורשים כדורי מתכת המיוצרים במדויק באיכות גבוהה. בטכניקה אחת שנקראת SKEW ROLLING, אנו משתמשים בשני גלילים מנוגדים המסתובבים ברציפות כשהמלאי מוזן ברציפות לתוך הגלילים. בקצה האחד של שני הגלילים נפלטים כדורי מתכת כתוצר. שיטה שנייה לזיוף כדורי מתכת היא שימוש בתבנית שסוחטת את מלאי החומר הממוקם ביניהם בצורת כדורית של חלל התבנית. לעתים קרובות כדורים המיוצרים דורשים כמה שלבים נוספים כגון גימור וליטוש על מנת להפוך למוצר באיכות גבוהה. • חישול איזוטרמי / חישול חם : תהליך יקר המתבצע רק כאשר התועלת / העלות מוצדקת. תהליך עבודה חם שבו התבנית מחוממת לאותה טמפרטורה בערך כמו חלק העבודה. מכיוון שגם התבנית וגם העבודה הם בערך אותה טמפרטורה, אין קירור ומאפייני הזרימה של המתכת משתפרים. הפעולה מתאימה היטב לסגסוגות ולחומרים בעלי יכולת חישול נחותה וחומרים ש שלהם מאפיינים מכניים רגישים מאוד לשיפועים קטנים ושינויים בטמפרטורה. • גודל מתכת: זהו תהליך גימור קר. זרימת החומר אינה מוגבלת לכל הכיוונים למעט הכיוון בו מופעל הכוח. כתוצאה מכך מתקבל גימור משטח טוב מאוד ומידות מדויקות. • חישול HIGH ENERGY RATE FORGING: הטכניקה כוללת תבנית עליונה המחוברת לזרוע של בוכנה שנדחפת במהירות כאשר תערובת דלק-אוויר נדלקת על ידי מצת. זה דומה לפעולה של בוכנות במנוע של מכונית. התבנית פוגעת ביצירה מהר מאוד ואז חוזרת למקומה המקורי מהר מאוד הודות ללחץ האחורי. העבודה מחושלת תוך אלפיות שנייה בודדות ולכן אין זמן להתקררות העבודה. זה שימושי עבור חלקים קשים לזיוף שיש להם תכונות מכניות מאוד רגישות לטמפרטורה. במילים אחרות התהליך כל כך מהיר שהחלק נוצר בטמפרטורה קבועה לאורך כל הדרך ולא יהיו שיפועים טמפרטורה בממשקי התבנית/חלק העבודה. • ב- DIE FORGING מכים מתכת בין שני גושי פלדה תואמים ובהם צורות מיוחדות, הנקראות קוביות. כאשר המתכת נלחצת בין הקוביות, היא לובשת את אותה צורה כמו הצורות בתבנית. כאשר הוא מגיע לצורתו הסופית, מוציאים אותו להתקרר. תהליך זה מייצר חלקים חזקים בעלי צורה מדויקת, אך מצריך השקעה גדולה יותר עבור המתחות המיוחדות. פרזול נסער מגדיל את הקוטר של פיסת מתכת על ידי שיטוחה. הוא משמש בדרך כלל לייצור חלקים קטנים, במיוחד ליצירת ראשים על מחברים כמו ברגים ומסמרים. • מתכת אבקה / עיבוד אבקה: כפי שהשם מרמז, זה כרוך בתהליכי ייצור להכנת חלקים מוצקים של גיאומטריות וצורות מסוימות מאבקות. אם משתמשים באבקות מתכת למטרה זו זה תחום מטלורגיית האבקה ואם משתמשים באבקות שאינן מתכת זה עיבוד אבקה. חלקים מוצקים מיוצרים מאבקות על ידי לחיצה וסינטר. לחיצת אבקה משמשת לדחיסת אבקות לצורות רצויות. ראשית, החומר העיקרי הוא אבקה פיזית, מחלק אותו לחלקיקים בודדים קטנים רבים. תערובת אבקה ממולאת לתוך התבנית ואגרוף נע לעבר האבקה ודוחס אותה לצורה הרצויה. מבוצע בעיקר בטמפרטורת החדר, בלחיצת אבקה מתקבל חלק מוצק והוא נקרא ירוק קומפקטי. קלסרים וחומרי סיכה משמשים בדרך כלל כדי לשפר את יכולת הדחיסה. אנו מסוגלים ליצור לחיצת אבקה באמצעות מכבשים הידראוליים בעלי קיבולת של כמה אלפי טונות. כמו כן, יש לנו לחיצות כפולות עם חבטות מנוגדות עליון ותחתון, כמו גם לחיצות מרובות עבור גיאומטריות חלקים מורכבות ביותר. אחידות המהווה אתגר חשוב עבור מפעלי מתכות/עיבוד אבקות רבים אינה בעיה גדולה עבור AGS-TECH בגלל הניסיון הרב שלנו בייצור מותאם אישית של חלקים כאלה במשך שנים רבות. גם עם חלקים עבים יותר שבהם האחידות מהווה אתגר הצלחנו. אם אנחנו מתחייבים לפרויקט שלך, אנחנו ניצור את החלקים שלך. אם אנו רואים סיכונים פוטנציאליים, נודיע לך ב advance. POWDER SINTERING, שהוא השלב השני, כולל העלאת הטמפרטורה לדרגה מסוימת ושמירה על הטמפרטורה באותה רמה למשך זמן מסוים, כך שחלקיקי האבקה בחלק הדחוס יוכלו להיקשר זה לזה. זה מביא לקשרים הרבה יותר חזקים וחיזוק של חלק העבודה. הסינטר מתרחש קרוב לטמפרטורת ההיתוך של האבקה. במהלך סינטר תתרחש כיווץ, חוזק החומר, צפיפות, משיכות, מוליכות תרמית, מוליכות חשמלית גדלים. יש לנו תנורים אצווה ורציפים לסינטר. אחת היכולות שלנו היא התאמת רמת הנקבוביות של החלקים שאנו מייצרים. לדוגמה, אנו מסוגלים לייצר מסנני מתכת על ידי שמירה על החלקים נקבוביים במידה מסוימת. באמצעות טכניקה הנקראת IMPREGNATION, אנו ממלאים את הנקבוביות במתכת בנוזל כמו שמן. אנחנו כן מייצרים למשל מיסבים ספוגים בשמן שהם משמנים עצמיים. בתהליך INFILTRATION אנו ממלאים את נקבוביות המתכת במתכת אחרת בעלת נקודת התכה נמוכה יותר מחומר הבסיס. התערובת מחוממת לטמפרטורה בין טמפרטורות ההיתוך של שתי המתכות. כתוצאה מכך ניתן לקבל כמה מאפיינים מיוחדים. כמו כן, אנו מבצעים לעיתים קרובות פעולות משניות כגון עיבוד שבבי ופרזול בחלקים שיוצרו באבקה כאשר יש צורך להשיג תכונות או מאפיינים מיוחדים או כאשר ניתן לייצר את החלק בפחות שלבי תהליך. לחיצה איזוסטטית: בתהליך זה נעשה שימוש בלחץ נוזלים כדי לדחוס את החלק. אבקות מתכת מונחות בתבנית עשויה מכל גמיש אטום. בלחיצה איזוסטטית מופעל לחץ מכל עבר, בניגוד ללחץ צירי הנראה בכבישה קונבנציונלית. היתרונות של לחיצה איזוסטטית הם צפיפות אחידה בתוך החלק, במיוחד עבור חלקים גדולים או עבים יותר, תכונות מעולות. החיסרון שלו הוא זמני מחזור ארוכים ודיוקים גיאומטריים נמוכים יחסית. כבישה איזוסטטית קרה מתבצעת בטמפרטורת החדר והתבנית הגמישה עשויה מגומי, PVC או אוריתן או חומרים דומים. הנוזל המשמש ללחץ ודחיסה הוא שמן או מים. סינטר קונבנציונלי של הקומפקט הירוק עוקב אחר כך. לחיצה חמה איזוסטטית לעומת זאת מתבצעת בטמפרטורות גבוהות וחומר התבנית הוא מתכת מתכת או קרמיקה עם נקודת התכה גבוהה מספיק העומדת בטמפרטורות. נוזל לחץ הוא בדרך כלל גז אינרטי. פעולות הלחיצה והסינטר מתבצעות בשלב אחד. נקבוביות מתבטלת כמעט לחלוטין, מתקבל מבנה uniform grain. היתרון של כבישה איזוסטטית חמה הוא בכך שהיא יכולה לייצר חלקים דומים ליציקה ולפרזול בשילוב תוך מתן אפשרות לשימוש בחומרים שאינם מתאימים ליציקה ולפרזול. החיסרון של כבישה איזוסטטית חמה הוא זמן המחזור הגבוה שלה ולכן העלות. זה מתאים לחלקים קריטיים בעלי נפח נמוך. הזרקת מתכת: תהליך מתאים מאוד לייצור חלקים מורכבים בעלי קירות דקים וגיאומטריות מפורטות. מתאים ביותר לחלקים קטנים יותר. אבקות וחומר קלסר פולימרי מערבבים, מחממים ומזריקים לתבנית. קלסר הפולימר מצפה את המשטחים של חלקיקי האבקה. לאחר הדפוס, הקלסר מוסר על ידי חימום בטמפרטורה נמוכה או מומס באמצעות ממס. דחיסה של גליל / גלגול אבקה: אבקות משמשות לייצור רצועות או יריעות רציפות. אבקה מוזנת ממזין ונדחסת על ידי שני גלילים מסתובבים לגיליון או לרצועות. הפעולה מתבצעת קר. הסדין נישא לתוך תנור סינטר. ניתן לחזור על תהליך הסינטר פעם שניה. שחול אבקה: חלקים בעלי יחסי אורך לקוטר גדולים מיוצרים על ידי הוצאת מיכל מתכת דק עם אבקה. SINTERING רופף: כפי שהשם מרמז, זוהי שיטת דחיסה וסינטר ללא לחץ, המתאימה לייצור חלקים נקבוביים מאוד כגון מסנני מתכת. אבקה מוזנת לתוך חלל התבנית מבלי להידחס. SINTERING רופף: כפי שהשם מרמז, זוהי שיטת דחיסה וסינטר ללא לחץ, המתאימה לייצור חלקים נקבוביים מאוד כגון מסנני מתכת. אבקה מוזנת לתוך חלל התבנית מבלי להידחס. SPARK SINTERING: האבקה נדחסת בתבנית על ידי שני אגרוף מנוגדים וזרם חשמלי בעל הספק גבוה מופעל על האגרוף ועובר דרך האבקה הדחוסה הסמויה ביניהם. הזרם הגבוה שורף את סרטי השטח מחלקיקי האבקה ומחטא אותם עם החום שנוצר. התהליך מהיר מכיוון שלא מופעל חום מבחוץ אלא הוא נוצר מתוך התבנית. כבישה חמה: האבקות נלחצות ומסינטרות בצעד אחד בתבנית העומדת בטמפרטורות הגבוהות. כאשר התבנית נדחסת מופעל עליה חום האבקה. דיוק טוב ותכונות מכניות המושגות בשיטה זו הופכים אותה לאופציה אטרקטיבית. אפילו מתכות עקשנות ניתן לעבד על ידי שימוש בחומרי עובש כגון גרפיט. CLICK Product Finder-Locator Service התפריט הקודם
- Plastic Rubber Metal Extrusions, Extrusion Dies, Aluminum Extruding
Plastic Rubber Metal Extrusions, Extrusion Dies, Aluminum Extruding, Pipe Tube Forming, Plastic Profiles, Metal Profiles Manufacturing, PVC at AGS-TECH Inc. שחול, מוצרים שחול, אקסטרודטים אנו משתמשים בתהליך EXTRUSION לייצור מוצרים עם פרופיל חתך קבוע כגון צינורות, צינורות וגופי קירור. למרות שניתן להוציא חומרים רבים, השחולים הנפוצים ביותר שלנו עשויים מתכת, פולימרים/פלסטיק, קרמיקה המתקבלת בשיטת שחול קרה, חמה או חמה. אנו קוראים לחלקים שחולצו extrudate או extrudates אם רבים. כמה גרסאות מיוחדות של התהליך שאנו גם מבצעים הן מעיל-יתר, קו-אקסטרוזיה ושיחול מורכב. אנו ממליצים ללחוץ כאן to הורד את האיורים הסכמטיים שלנו של תהליכי שחול מתכת קרמיקה ופלסטיק מאת AGS-TECH Inc. זה יעזור לך להבין טוב יותר את המידע שאנו מספקים לך למטה. בשיחול חומר לשיחול נדחף או נמשך דרך תבנית בעלת פרופיל החתך הרצוי. התהליך יכול לשמש לייצור חתכים מורכבים עם גימור משטח מעולה ולעבודה על חומר שביר. אפשר לייצר כל אורך של חלקים באמצעות תהליך זה. כדי לפשט את שלבי התהליך: 1.) בשחולים חמים או חמים החומר מחומם ומוטען למיכל במכבש. החומר נלחץ ונדחק החוצה מהקוביה. 2.) אקסטרודאט המיוצר נמתח ליישור, מטופל בחום או עיבוד קר לשיפור תכונותיו. מצד שני COLD EXTRUSION מתרחש בסביבות טמפרטורת החדר ויש לו את היתרונות של פחות חוזק משטח, מהירות גימור גבוהה, מהירות חמצון טובה יותר של משטח. WARM EXTRUSION מתבצע מעל טמפרטורת החדר אך מתחת לנקודת התגבשות מחדש. הוא מציע פשרה ואיזון עבור כוחות נדרשים, משיכות ותכונות חומר ולכן הוא הבחירה עבור יישומים מסוימים. HOT EXTRUSION מתרחש מעל טמפרטורת ההתגבשות מחדש של החומר. כך קל יותר לדחוף את החומר דרך התבנית. עם זאת עלות הציוד גבוהה. ככל שפרופיל שחול מורכב יותר, כך התבנית (כלי עבודה) יקרה יותר וקצב הייצור נמוך יותר. לחתכי הרוחב, כמו גם לעוביים, יש מגבלות התלויות בחומר לשיחול. פינות חדות במות אקסטרוזיה הן תמיד לא רצויות ויש להימנע מהן, אלא אם כן יש צורך. בהתאם לחומר שחולץ אנו מציעים: • מתכת EXTRUSIONS : הנפוצים ביותר שאנו מייצרים הם אלומיניום, פליז, אבץ, נחושת, פלדה, טיטניום, מגנזיום • PLASTIC EXTRUSION : פלסטיק נמס ויוצר לפרופיל רציף. החומרים הנפוצים שלנו המעובדים הם פוליאתילן, ניילון, פוליסטירן, פוליוויניל כלוריד, פוליפרופילן, פלסטיק ABS, פוליקרבונט, אקריליק. מוצרים אופייניים שאנו מייצרים כוללים צינורות וצינורות, מסגרות פלסטיק. בתהליך זה, חרוזי פלסטיק קטנים / שרף מוזנים מהכבידה לחבית של מכונת האקסטרוזיה. לעתים קרובות אנו גם מערבבים חומרי צבע או תוספים אחרים לתוך הופר כדי לתת למוצר את המפרטים והמאפיינים הנדרשים. החומר הנכנס לחבית המחוממת נאלץ על ידי הבורג המסתובב לעזוב את הקנה בקצה ולנוע דרך אריזת המסך להסרת מזהמים בפלסטיק המותך. לאחר העברת חבילת המסך, הפלסטיק נכנס למות האקסטרוזיה. התבנית מעניקה לפלסטיק הרך הנע את צורת הפרופיל שלו בזמן שהוא עובר דרכו. כעת האקסטרודט עובר אמבט מים לקירור. טכניקות אחרות ש-AGS-TECH Inc. משתמשת במשך שנים רבות הן: • EXTRUSION PIPE & TUBING : צינורות וצינורות פלסטיק נוצרים כאשר פלסטיק מוחלף דרך תבנית עגולה ומתקרר באמבט מים, ולאחר מכן חותכים לאורכם או מפותלים/סלולים. שקוף או צבעוני, פסים, קיר בודד או כפול, גמיש או קשיח, PE, PP, פוליאוריטן, PVC, ניילון, PC, סיליקון, ויניל או אחר, יש לנו הכל. יש לנו מלאי צינורות כמו גם את היכולת לייצר לפי המפרט שלך. AGS-TECH מייצרת צינורות לפי דרישות ה-FDA, UL ו-LE ליישומים רפואיים, חשמליים ואלקטרוניים, תעשייתיים ואחרים. • OVERJACKETING / OVER JACKETING EXTRUSION : טכניקה זו מיישמת שכבה חיצונית של פלסטיק על חוט או כבל קיימים. חוטי הבידוד שלנו מיוצרים בשיטה זו. • COEXTRUSION : שכבות מרובות של חומר מופקעות בו-זמנית. השכבות המרובות מועברות על ידי מכבשים מרובים. ניתן להתאים את עובי השכבה השונים בהתאם למפרטי הלקוח. תהליך זה מאפשר להשתמש במספר פולימרים שלכל אחד מהם פונקציונליות שונה במוצר. כתוצאה מכך, ניתן לבצע אופטימיזציה של מגוון מאפיינים. • שחול תרכובים: פולימרים בודדים או מרובים מעורבבים עם תוספים לקבלת תרכובת פלסטית. מכבשי הברגים הכפולים שלנו מייצרים אקסטרוזיות מורכבות. מתכות שחול הן בדרך כלל זולות בהשוואה לתבניות מתכת. אם אתה משלם הרבה יותר מכמה אלפי דולרים עבור תבנית שחול קטנה או בינונית בגודל אלומיניום, כנראה שאתה משלם יותר מדי. אנו מומחים בקביעת הטכניקה היעילה ביותר, המהירה והמתאימה ביותר ליישום שלך. לפעמים שחול ולאחר מכן עיבוד של חלק יכול לחסוך לך כסף רב. לפני קבלת החלטה נחרצת, שאלו אותנו קודם כל לדעתנו. עזרנו ללקוחות רבים לקבל את ההחלטות הנכונות. עבור כמה שחול מתכת בשימוש נרחב, אתה יכול להוריד את החוברות והקטלוגים שלנו על ידי לחיצה על הטקסט הצבעוני למטה. אם מדובר במוצר מדף העונה על הדרישות שלך, זה יהיה חסכוני יותר. הורד את יכולות שחול הצינורות והצינורות הרפואיים שלנו הורד את גופי הקירור המוחלטים שלנו • תהליכי ייצור וייצור משניים עבור אקסטרוזיות : בין תהליכי הערך המוסף שאנו מציעים עבור מוצרים שחולפים הם: -כיפוף, צורה ועיצוב של צינורות וצינורות בהתאמה אישית, חיתוך צינורות, גיבוש קצה צינור, סלילת צינורות, עיבוד שבבי וגימור, קידוח חורים, ניקוב וניקוב, -מכלולי צנרת וצינורות בהתאמה אישית, הרכבת צינורות, ריתוך, הלחמה והלחמה -כיפוף, צורה ועיצוב שחול מותאם אישית -ניקוי, הסרת שומנים, כבישה, פסיבציה, הברקה, אילגון, ציפוי, צביעה, טיפול בחום, חישול והתקשות, סימון, חריטה ותיוג, אריזה בהתאמה אישית. CLICK Product Finder-Locator Service עמוד קודם
- Casting and Machined Parts, CNC Manufacturing, Milling, Turning, Swiss
Casting and Machined Parts, CNC Manufacturing, Milling, Turning, Swiss Type Machining, Die Casting, Investment Casting, Lost Foam Cast Parts from AGS-TECH Inc. יציקה ועיבוד שבבי טכניקות היציקה והעיבוד המותאמות אישית שלנו הן יציקות מתכלות ולא מתכלות, יציקה ברזלית ולא ברזלית, חול, מת, צנטריפוגלי, רציף, תבנית קרמית, השקעה, קצף אבוד, צורה כמעט נטו, תבנית קבועה (יציקת כבידה), טיח יציקות תבניות (יציקת גבס) וקונכיות, חלקים מעובדים המיוצרים על ידי כרסום וחריטה באמצעות ציוד קונבנציונלי כמו גם CNC, עיבוד שבבי מסוג שוויצרי עבור חלקים דיוק קטנים זולים בתפוקה גבוהה, עיבוד בורג למחברים, עיבוד שבבי לא קונבנציונלי. אנא זכור שמלבד מתכות וסגסוגות מתכת, אנו מכינים רכיבי קרמיקה, זכוכית ופלסטיק גם במקרים מסוימים כאשר ייצור תבנית אינו מושך או אינו אופציה. עיבוד של חומרים פולימריים מצריך את הניסיון המיוחד שיש לנו בגלל האתגר שמציבים הפלסטיק והגומי בשל רכותם, אי קשיחותם... וכו'. לעיבוד של קרמיקה וזכוכית, אנא עיין בעמוד שלנו בנושא ייצור לא קונבנציונלי. AGS-TECH Inc מייצרת ומספקת יציקות קלות וכבדות כאחד. אנו מספקים יציקות מתכת וחלקים מעובדים עבור דוודים, מחליפי חום, מכוניות, מיקרו-מנועים, טורבינות רוח, ציוד לאריזת מזון ועוד. אנו ממליצים ללחוץ כאן to הורד את האיורים הסכמטיים שלנו של תהליכי עיבוד ויציקה מאת AGS-TECH Inc. זה יעזור לך להבין טוב יותר את המידע שאנו מספקים לך למטה. בואו נסתכל על כמה מהטכניקות השונות שאנו מציעים בפירוט: • יציקת עובש מתכלה: קטגוריה רחבה זו מתייחסת לשיטות הכוללות תבניות זמניות ובלתי ניתנות לשימוש חוזר. דוגמאות לכך הן חול, טיח, מעטפת, השקעה (נקראת גם שעווה אבודה) ויציקת גבס. • יציקת חול: תהליך שבו חול משמש כחומר התבנית. שיטה ישנה מאוד ועדיין מאוד פופולרית במידה שרוב יציקות המתכת המיוצרות נעשות בטכניקה זו. עלות נמוכה אפילו בייצור בכמות נמוכה. מתאים לייצור חלקים קטנים וגדולים. ניתן להשתמש בטכניקה לייצור חלקים תוך ימים או שבועות עם מעט מאוד השקעה. החול הלח נקשר יחדיו באמצעות חימר, קלסרים או שמנים מיוחדים. חול כלול בדרך כלל בקופסאות תבניות ומערכת חלל ושער נוצרות על ידי דחיסת החול סביב דגמים. התהליכים הם: 1.) הנחת הדגם בחול להכנת התבנית 2.) שילוב דגם וחול במערכת שערים 3.) הסרת דגם 4.) מילוי חלל עובש במתכת מותכת 5.) קירור המתכת 6.) שבירת תבנית החול והסרת היציקה • יציקת תבנית גבס: בדומה ליציקת חול, ובמקום חול, נעשה שימוש בגבס של פריז כחומר התבנית. זמני ייצור קצרים כמו יציקת חול ולא יקר. סובלנות מידות טובה וגימור פני השטח. החיסרון העיקרי שלו הוא שניתן להשתמש בו רק עם מתכות בנקודת התכה נמוכה כמו אלומיניום ואבץ. • יציקת מעטפת: דומה גם ליציקת חול. חלל עובש מתקבל על ידי קליפה מוקשה של חול וחומר מקשר שרף תרמוסטי במקום בקבוק מלא בחול כמו בתהליך יציקת חול. כמעט כל מתכת המתאימה ליציקה בחול ניתנת ליציקה באמצעות יציקת מעטפת. ניתן לסכם את התהליך כך: 1.) ייצור תבנית המעטפת. החול המשמש הוא בגודל גרגר קטן בהרבה בהשוואה לחול המשמש ליציקת חול. החול הדק מעורבב עם שרף תרמוסטי. תבנית המתכת מצופה בחומר פרידה כדי להקל על הסרת המעטפת. לאחר מכן מחממים את תבנית המתכת ותערובת החול עוברת נקבוביות או מפוצצת על תבנית היציקה החמה. קליפה דקה נוצרת על פני התבנית. ניתן להתאים את העובי של מעטפת זו על ידי שינוי משך הזמן שבו תערובת שרף החול נמצאת במגע עם תבנית המתכת. לאחר מכן מסירים את החול הרופף כשנותרת הדפוס המכוסה בקליפה. 2.) לאחר מכן, הקליפה והתבנית מחוממים בתנור כך שהקליפה מתקשה. לאחר השלמת ההתקשות, הקליפה נפלטת מהתבנית באמצעות סיכות המובנות בתבנית. 3.) שתי קונכיות כאלה מורכבות יחד על ידי הדבקה או הידוק ומרכיבות את התבנית השלמה. כעת תבנית המעטפת מוכנסת למיכל בו היא נתמכת בחול או זריקת מתכת במהלך תהליך היציקה. 4.) כעת ניתן לשפוך את המתכת הלוהטת לתוך תבנית המעטפת. היתרונות של יציקת מעטפת הם מוצרים בעלי גימור משטח טוב מאוד, אפשרות לייצור חלקים מורכבים עם דיוק ממדי גבוה, תהליך קל לאוטומטי, חסכוני לייצור בנפח גדול. החסרונות הם שהתבניות מחייבות אוורור טוב בגלל גזים שנוצרים כאשר מתכת מותכת נוגעת בכימיקל הקושר, השרפים התרמוסטיים ודפוסי המתכת יקרים. בשל העלות של דפוסי מתכת, ייתכן שהטכניקה לא תתאים היטב לריצות ייצור בכמות נמוכה. • יציקת השקעה (הידועה גם בשם LOST-WAX CASTING): גם טכניקה ותיקה מאוד ומתאימה לייצור חלקים איכותיים עם דיוק גבוה, חזרתיות, צדדיות ושלמות ממתכות רבות, חומרים עקשנים וסגסוגות מיוחדות עם ביצועים גבוהים. ניתן לייצר חלקים קטנים כגדולים. תהליך יקר בהשוואה לכמה מהשיטות האחרות, אך היתרון העיקרי הוא האפשרות לייצר חלקים בעלי צורה כמעט נטו, קווי מתאר ופרטים מורכבים. אז העלות מתקזזת במידת מה על ידי ביטול עיבוד מחדש ועיבוד שבבי במקרים מסוימים. למרות שיכולות להיות וריאציות, הנה סיכום של תהליך יציקת ההשקעה הכללי: 1.) יצירת דפוס מאסטר מקורי משעווה או פלסטיק. כל יציקה צריכה דפוס אחד שכן אלה נהרסים בתהליך. יש צורך גם בתבנית שממנה מייצרים דוגמאות ולרוב התבנית מיוצקת או במכונה. מכיוון שאין צורך לפתוח את התבנית, ניתן להגיע ליציקות מורכבות, ניתן לחבר דפוסי שעווה רבים כמו ענפי עץ ולצקת יחד ובכך לאפשר ייצור של מספר חלקים מיציקה אחת של המתכת או סגסוגת המתכת. 2.) לאחר מכן, התבנית נטבלת או יוצקת עליה עם תמיסת עקשן המורכבת מסיליקה עדינה מאוד, מים, קלסרים. כתוצאה מכך נוצרת שכבת קרמיקה על פני התבנית. הציפוי העמיד על התבנית נשאר לייבוש ולהתקשות. שלב זה הוא המקום ממנו מגיע השם יציקת השקעה: תמיסת עקשן מושקעת על תבנית השעווה. 3.) בשלב זה הופכים את תבנית הקרמיקה המוקשה ומחממים כך שהשעווה נמסה ונשפכת מהתבנית. נותר חלל עבור יציקת המתכת. 4.) לאחר יציאת השעווה, מחממים את התבנית הקרמית לטמפרטורה גבוהה אף יותר מה שגורם לחיזוק התבנית. 5.) יציקת מתכת מוזגת לתוך התבנית החמה וממלאת את כל החלקים המורכבים. 6.) מותר ליציקה להתמצק 7.) לבסוף נשברת תבנית הקרמיקה וחלקים מיוצרים נחתכים מהעץ. הנה קישור לחוברת מפעל יציקה להשקעות • יציקת דפוס אידוי: בתהליך נעשה שימוש בתבנית העשויה מחומר כמו קצף פוליסטירן שיתנדף כאשר יוצקים מתכת מותכת חמה לתוך התבנית. ישנם שני סוגים של תהליך זה: LOST FOAM CASTING המשתמשת בחול לא מלוכד ויציקת FULL MOLD CASTING המשתמשת בחול מלוכד. להלן שלבי התהליך הכלליים: 1.) לייצר את התבנית מחומר כגון פוליסטירן. כאשר ייוצרו כמויות גדולות, התבנית מיוצרת. אם לחלק יש צורה מורכבת, ייתכן שיהיה צורך להדביק כמה חלקים של חומר קצף כזה כדי ליצור את התבנית. לעתים קרובות אנו מצפים את הדפוס בתרכובת עקשנית כדי ליצור גימור משטח טוב על היציקה. 2.) לאחר מכן מכניסים את התבנית לתוך חול דפוס. 3.) את המתכת המותכת יוצקים לתוך התבנית, ומאדים את תבנית הקצף, כלומר פוליסטירן ברוב המקרים תוך כדי זורם דרך חלל התבנית. 4.) המתכת המותכת נשארת בתבנית החול להתקשות. 5.) לאחר שהוא מתקשה, אנו מסירים את היציקה. במקרים מסוימים, המוצר שאנו מייצרים דורש ליבה בתוך התבנית. ביציקה באידוי, אין צורך להניח ולאבטח ליבה בחלל התבנית. הטכניקה מתאימה לייצור גיאומטריות מורכבות מאוד, ניתן לבצע אוטומטית בקלות לייצור בנפח גבוה, ואין קווי פרידה בחלק היצוק. התהליך הבסיסי פשוט וחסכוני ליישום. עבור ייצור בנפח גדול, מכיוון שיש צורך בתבנית או תבנית כדי לייצר את הדפוסים מפוליסטירן, זה עשוי להיות מעט יקר. • יציקת תבנית שאינה ניתנת להרחבה: קטגוריה רחבה זו מתייחסת לשיטות שבהן אין צורך לחדש את התבנית לאחר כל מחזור ייצור. דוגמאות לכך הן יציקה קבועה, מתה, יציקה רציפה וצנטריפוגלית. מתקבלת יכולת חזרה וניתן לאפיין חלקים כ-NEAR NET SHAPE. • יציקת תבנית קבועה: תבניות לשימוש חוזר עשויות מתכת משמשות ליציקות מרובות. בדרך כלל ניתן להשתמש בתבנית קבועה עשרות אלפי פעמים לפני שהיא מתבלה. כבידה, לחץ גז או ואקום משמשים בדרך כלל למילוי התבנית. תבניות (הנקראות גם למות) עשויות בדרך כלל מברזל, פלדה, קרמיקה או מתכות אחרות. התהליך הכללי הוא: 1.) מכונות ויוצרות את התבנית. מקובל לעבד את התבנית משני גושי מתכת המשתלבים זה בזה וניתנים לפתיחה וסגירה. גם תכונות החלק וגם מערכת השער מעובדות בדרך כלל לתוך תבנית היציקה. 2.) משטחי התבנית הפנימיים מצופים בתרחיץ המשלב חומרים עקשן. זה עוזר לשלוט בזרימת החום ופועל כחומר סיכה להסרה קלה של החלק היצוק. 3.) לאחר מכן סוגרים את חצאי התבנית הקבועה ומחממים את התבנית. 4.) מתכת מותכת יוצקים לתבנית ומניחים עדיין להתמצקות. 5.) לפני שמתרחש קירור רב, אנו מסירים את החלק מהתבנית הקבועה באמצעות מפלטים כאשר חצאי התבנית נפתחים. אנו משתמשים לעתים קרובות ביציקת תבנית קבועה עבור מתכות בנקודת התכה נמוכה כגון אבץ ואלומיניום. עבור יציקות פלדה, אנו משתמשים בגרפיט כחומר תבנית. לעתים אנו משיגים גיאומטריות מורכבות באמצעות ליבות בתוך תבניות קבועות. היתרונות של טכניקה זו הם יציקות בעלות תכונות מכניות טובות המתקבלות על ידי קירור מהיר, אחידות בתכונות, דיוק וגימור משטח טוב, שיעורי פסילה נמוכים, אפשרות לאוטומציה של התהליך והפקת נפחים גבוהים בצורה חסכונית. החסרונות הם עלויות התקנה ראשוניות גבוהות אשר הופכות אותו ללא מתאים לפעולות בנפח נמוך, ומגבלות על גודל החלקים המיוצרים. • יציקת מתות: תבנית מעובדת ומתכת מותכת נדחפת בלחץ גבוה לתוך חללי עובש. הן יציקות מתכת אל ברזליות כמו גם ברזליות אפשריות. התהליך מתאים להרצות ייצור בכמות גדולה של חלקים קטנים עד בינוניים עם פרטים, קירות דקים במיוחד, עקביות ממדית וגימור משטח טוב. AGS-TECH Inc. מסוגלת לייצר עובי דופן קטן עד 0.5 מ"מ באמצעות טכניקה זו. כמו ביציקת תבנית קבועה, התבנית צריכה להיות מורכבת משני חצאים שיכולים להיפתח ולהיסגר לצורך הסרת החלק המיוצר. לתבנית יציקה עשויה להיות מספר חללים כדי לאפשר ייצור של יציקות מרובות בכל מחזור. תבניות יציקה הן כבדות מאוד וגדולות בהרבה מהחלקים שהן מייצרות, ולכן גם יקרות. אנו מתקנים ומחליפים מתבלות בלויות ללא תשלום עבור לקוחותינו כל עוד הם מזמינים מאתנו את החלקים שלהם מחדש. למות שלנו יש תקופות חיים ארוכים בטווח של כמה מאות אלפי מחזורים. להלן שלבי התהליך הפשוטים הבסיסיים: 1.) ייצור התבנית בדרך כלל מפלדה 2.) עובש מותקן על מכונת יציקת למות 3.) הבוכנה מאלצת מתכת מותכת לזרום בחללי התבנית וממלאת את התכונות המורכבות והקירות הדקים 4.) לאחר מילוי התבנית במתכת המותכת, נותנים ליציקה להתקשות בלחץ 5.) פותחים תבנית ומסירים את היציקה בעזרת פיני מפלט. 6.) כעת משמנים שוב את התבנית הריקה ומהודקים למחזור הבא. ביציקת הדפסה, אנו משתמשים לעתים קרובות ב-Insert Device כאשר אנו משלבים חלק נוסף לתוך התבנית ויוצקים את המתכת סביבה. לאחר התמצקות, חלקים אלו הופכים לחלק מהמוצר היצוק. היתרונות של יציקת גזר הם תכונות מכניות טובות של החלקים, אפשרות לתכונות מורכבות, פרטים עדינים וגימור משטח טוב, שיעורי ייצור גבוהים, אוטומציה קלה. החסרונות הם: לא מאוד מתאים לנפח נמוך בגלל עלות התבנית והציוד הגבוהה, מגבלות בצורות שניתן ליצוק, סימנים עגולים קטנים על חלקי יציקה הנובעים ממגע של פיני מפלט, הבזק דק של מתכת שנדחט החוצה בקו הפרידה, צורך עבור פתחי אוורור לאורך קו ההפרדה בין התבנית, הכרח לשמור על טמפרטורות עובש נמוכות באמצעות זרימת מים. • יציקה צנטריפוגלית: מתכת מותכת יוצקים למרכז התבנית המסתובבת בציר הסיבוב. כוחות צנטריפוגליים זורקים את המתכת לעבר הפריפריה ונותנים לה להתמצק כשהתבנית ממשיכה להסתובב. ניתן להשתמש בסיבובי ציר אופקיים ואנכיים. ניתן ליצוק חלקים עם משטחים פנימיים עגולים כמו גם צורות לא עגולות אחרות. ניתן לסכם את התהליך כך: 1.) מתכת מותכת מוזגת לתוך תבנית צנטריפוגלית. לאחר מכן, המתכת נאלצת אל הקירות החיצוניים עקב ספינינג של התבנית. 2.) כשהתבנית מסתובבת, יציקת המתכת מתקשה יציקה צנטריפוגלית הינה טכניקה מתאימה לייצור חלקים גליליים חלולים כמו צינורות, אין צורך במפתחים, מפלסים ואלמנטי שער, גימור משטח טוב ומאפיינים מפורטים, ללא בעיות התכווצות, אפשרות לייצר צינורות ארוכים בקטרים גדולים מאוד, יכולת ייצור בקצב גבוה . • יציקה רציפה (יציקה רצועה): משמש ליציקת מתכת באורך מתמשך. בעיקרון המתכת המותכת מיוצקת לפרופיל דו מימדי של התבנית אך אורכה אינו מוגדר. מתכת מותכת חדשה מוזנת כל הזמן לתוך התבנית כאשר היציקה נעה כלפי מטה כאשר אורכה עולה עם הזמן. מתכות כגון נחושת, פלדה, אלומיניום נוצקות לגדילים ארוכים באמצעות תהליך יציקה מתמשכת. לתהליך עשויות להיות תצורות שונות, אך ניתן לפשט את המשותף כ: 1.) מתכת מותכת מוזגת למיכל הממוקם גבוה מעל התבנית בכמויות ובקצבי זרימה מחושבים היטב וזורמת דרך התבנית המקוררת במים. יציקת המתכת שנשפכת לתבנית מתמצקת לבר סטרטר המונח בתחתית התבנית. בר המתנע הזה נותן לרולים משהו לאחוז בו בהתחלה. 2.) גדיל המתכת הארוך נישא על ידי גלילים במהירות קבועה. הגלילים גם משנים את כיוון זרימת גדיל המתכת מאנכי לאופקי. 3.) לאחר שהיציקה הרציפה עברה מרחק אופקי מסוים, לפיד או מסור שנעים עם היציקה חותכים אותו במהירות לאורכים הרצויים. ניתן לשלב תהליך יציקה רציפה עם ROLLING PROCESS, כאשר המתכת היצוקה ברציפות יכולה להיות מוזנת ישירות לתוך מכבש מתגלגל לייצור I-Beams, T-Beams... וכו'. יציקה רציפה מייצרת תכונות אחידות לכל אורך המוצר, היא בעלת קצב התמצקות גבוה, מפחיתה עלויות עקב אובדן חומר נמוך מאוד, מציעה תהליך בו העמסת מתכת, יציקה, התמצקות, חיתוך ופינוי יציקה מתרחשים כולם בפעולה רציפה ו ובכך מביא לשיעור פרודוקטיביות גבוה ואיכות גבוהה. אולם שיקול מרכזי הוא ההשקעה הראשונית הגבוהה, עלויות ההתקנה ודרישות השטח. • שירותי עיבוד שבבי: אנו מציעים עיבוד של שלושה, ארבעה וחמישה צירים. סוג תהליכי העיבוד שאנו משתמשים בהם הם פנייה, כרסום, קידוח, משעמם, חטיף, הקצעה, ניסור, שחיקה, חיכוך, ליטוש ועיבוד שבבי לא מסורתי אשר מפורט יותר תחת תפריט אחר של האתר שלנו. עבור רוב הייצור שלנו, אנו משתמשים במכונות CNC. עם זאת עבור פעולות מסוימות טכניקות קונבנציונליות מתאימות יותר ולכן אנו מסתמכים עליהן גם כן. יכולות העיבוד שלנו מגיעות לרמה הגבוהה ביותר האפשרית וחלק מהחלקים התובעניים ביותר מיוצרים במפעל מוסמך AS9100. להבי מנועי סילון דורשים ניסיון בייצור מיוחד וציוד מתאים. לתעשייה האווירית יש תקנים מחמירים מאוד. חלק מהרכיבים בעלי מבנים גיאומטריים מורכבים מיוצרים בצורה הקלה ביותר על ידי עיבוד חמישה צירים, המצוי רק בחלק ממפעלי העיבוד כולל שלנו. למפעל המוסמך לתעופה וחלל שלנו יש את הניסיון הדרוש בעמידה בדרישות התיעוד הנרחבות של תעשיית התעופה והחלל. בפעולות TURNING, חומר עבודה מסובב ומזיז כנגד כלי חיתוך. לתהליך זה נעשה שימוש במכונה הנקראת מחרטה. ב-MILLING, למכונה הנקראת מכונת כרסום יש כלי מסתובב כדי להביא קצוות חיתוך להיצמד לחומר עבודה. פעולות הקידוח כוללות חותך מסתובב עם קצוות חיתוך היוצר חורים במגע עם חומר העבודה. בדרך כלל משתמשים במכבשי מקדחה, מחרטות או כרסום. בפעולות BORING מעבירים כלי עם קצה מחודד יחיד כפוף לתוך חור גס בחומר מסתובב כדי להגדיל מעט את החור ולשפר את הדיוק. הוא משמש למטרות גימור עדינות. BROACHING כרוך בכלי בעל שיניים כדי להסיר חומר מחומר עבודה במעבר אחד של הסיכה (כלי שיניים). בפריצה ליניארית, הסיכה פועלת באופן ליניארי כנגד משטח של חומר העבודה כדי לבצע את החיתוך, בעוד שבפריחה סיבובית, הפשפש מסובב ונלחץ לתוך חומר העבודה כדי לחתוך צורה סימטרית של ציר. עיבוד שבבי מסוג SWISS היא אחת מהטכניקות החשובות שלנו בהן אנו משתמשים לייצור בנפח גבוה של חלקים קטנים ברמת דיוק גבוהה. באמצעות מחרטה מסוג שוויצרי אנו הופכים חלקים קטנים, מורכבים ודיוקים בזול. בניגוד מחרטות קונבנציונליות שבהן חומר העבודה נשמר נייח והכלי נע, במרכזי סיבוב מסוג שוויצרי, מותר ליצירה לנוע בציר Z והכלי נייח. בעיבוד שבבי מסוג שוויצרי, מלאי המוט מוחזק במכונה ומתקדם דרך תותב מוביל בציר ה-Z, רק חושף את החלק המיועד לעיבוד. כך מובטחת אחיזה הדוקה והדיוק גבוה מאוד. זמינות של כלים חיים מספקים את ההזדמנות לכרסום ולקדוח כשהחומר מתקדם מהתותב המנחה. ציר ה-Y של הציוד מסוג שוויצרי מספק יכולות כרסום מלאות וחוסך זמן רב בייצור. יתר על כן, למכונות שלנו יש מקדחות וכלים משעממים הפועלים על החלק כאשר הוא מוחזק בציר המשנה. יכולת העיבוד השוויצרי שלנו מעניקה לנו הזדמנות עיבוד מלאה אוטומטית לחלוטין בפעולה אחת. עיבוד שבבי הוא אחד מהמגזרים הגדולים ביותר בעסקי AGS-TECH Inc. אנו משתמשים בו כפעולה ראשית או כפעולה משנית לאחר יציקה או חילוץ של חלק כך שכל מפרטי השרטוט יתקיימו. • שירותי גימור משטחים: אנו מציעים מגוון עצום של טיפולי משטח וגימור משטחים כגון מיזוג פני השטח כדי לשפר את ההדבקה, הנחת שכבת תחמוצת דקה כדי לשפר את ההדבקה של הציפוי, התזת חול, כימי-פילם, אילגון, ניטרידינג, ציפוי אבקה, ציפוי ריסוס , טכניקות מתכת וציפוי מתקדמות שונות לרבות קישוט, אלומת אלקטרונים, אידוי, ציפוי, ציפויים קשים כגון יהלום כמו פחמן (DLC) או ציפוי טיטניום עבור כלי קידוח וחיתוך. • שירותי סימון ותיוג מוצרים: רבים מלקוחותינו דורשים סימון ותיוג, סימון לייזר, חריטה על חלקי מתכת. אם יש לך צורך כזה, תן לנו לדון באיזו אפשרות תהיה הטובה ביותר עבורך. להלן כמה ממוצרי יצוק מתכת נפוצים. מכיוון שאלו הם מהמדף, אתה יכול לחסוך בעלויות עובש במקרה שאחד מאלה מתאים לדרישות שלך: לחץ כאן כדי להוריד את 11 קופסאות האלומיניום שלנו מבית AGS-Electronics CLICK Product Finder-Locator Service עמוד קודם
- Custom Manufactured Parts, Assemblies, Plastic Mold, Casting,Machining
Custom Manufactured Parts, Assemblies, Plastic Mold, Rubber Molding, Metal Casting, CNC Machining, Turning, Milling, Electrical Electronic Optical Assembly PCBA חלקים ומכלולים ומוצרים בהתאמה אישית קרא עוד תבניות ודפוס פלסטיק וגומי קרא עוד יציקה ועיבוד שבבי קרא עוד אקסטרוזיה, מוצרים שחולפים קרא עוד הטבעות וייצור פחים קרא עוד פרזול מתכת ומטלורגיית אבקה קרא עוד יצירת תיל וקפיצים קרא עוד עיצוב ועיצוב זכוכית וקרמיקה קרא עוד ייצור תוסף וייצור מהיר קרא עוד ייצור חומרים מרוכבים וחומרים מרוכבים קרא עוד תהליכי הצטרפות והרכבה והידוק אנו מייצרים עבורכם חלקים ומכלולים ומציעים את תהליכי הייצור הבאים: • תבניות פלסטיק וגומי וחלקים יצוקים. הזרקה, תבנית תרמו, יציקה תרמוסית, יצירת ואקום, יציקת מכה, יציקה סיבובית, יציקת יציקה, יציקת הוספה ועוד. • שחול פלסטיק, גומי ומתכת • יציקות ברזליות ולא ברזליות וחלקים מעובדים המיוצרים בטכניקות כרסום וחריטה, עיבוד שבבי מסוג שוויצרי. • חלקי מתכות אבקה • הטבעות מתכת ולא מתכת, יצירת גיליונות מתכת, מכלולי מתכת מרותכים • פרזול קר וחם • חוטים, מכלולי תיל מרותכים, יצירת חוטים • סוגים שונים של קפיצים, יצירת קפיצים • ייצור ציוד, תיבת הילוכים, צימוד, תולעת, מפחית מהירות, צילינדר, רצועות הילוכים, שרשראות הילוכים, רכיבי הילוכים • זכוכית מחוסמת וחסינת כדורים בהתאמה אישית תואמת לתקנים של נאט"ו וצבא • כדורים, מיסבים, גלגלות ומכלולי גלגלות • שסתומים ורכיבים פנאומטיים כגון טבעת O, מכונת כביסה ואטמים • חלקים ומכלולים מזכוכית וקרמיקה, רכיבים עמידים בוואקום ורכיבים הרמטיים, הדבקה מתכת-קרמית וקרמיקה-קרמית. • סוגים שונים של מכלולים מכניים, אופטו-מכניים, אלקטרו-מכאניים, אופטו-אלקטרוניים. • מליטה מתכת-גומי, מתכת-פלסטיק • צינורות וצינורות, יצירת צינורות, כיפוף ומכלולי צינורות בהתאמה אישית, ייצור מפוח. • ייצור פיברגלס • ריתוך בטכניקות שונות כגון ריתוך נקודתי, ריתוך לייזר, MIG, TIG. ריתוך אולטרסאונד לחלקי פלסטיק. • מגוון עצום של טיפולי משטח וגימור משטח כגון מיזוג פני השטח להגברת ההדבקה, הנחת שכבת תחמוצת דקה להגברת ההדבקה של הציפוי, התזת חול, כימי-פילם, אילגון, ניטרידינג, ציפוי אבקה, ציפוי בהתזה, טכניקות מתכת וציפוי מתקדמות שונות כולל קיצוץ, אלומת אלקטרונים, אידוי, ציפוי, ציפויים קשים כגון יהלום כמו פחמן (DLC) או טיטניום עבור כלי חיתוך וקידוח. • סימון ותיוג, סימון לייזר על חלקי מתכת, הדפסה על חלקי פלסטיק וגומי הורד חוברת למונחים נפוצים של הנדסת מכונות המשמשים מעצבים ומהנדסים אנו בונים מוצרים בהתאם למפרטים ולדרישות הספציפיות שלך. על מנת להציע לך את האיכות, המשלוח והמחירים הטובים ביותר, אנו מייצרים מוצרים ברחבי העולם בסין, הודו, טייוואן, הפיליפינים, דרום קוריאה, מלזיה, סרי לנקה, טורקיה, ארה"ב, קנדה, גרמניה, בריטניה ויפן. זה הופך אותנו להרבה יותר חזקים ותחרותיים בעולם מכל יצרן custom אחר. המוצרים שלנו מיוצרים בסביבות מוסמכות ISO9001:2000, QS9000, ISO14001, TS16949 והם בעלי תו CE, UL ועומדים בתקנים אחרים בתעשייה. לאחר שנתמנה לפרויקט שלך, נוכל לטפל בכל הייצור, ההרכבה, הבדיקה, ההסמכה, המשלוח והמכס כרצונך. אם אתה מעדיף, נוכל לאחסן את החלקים שלך, להרכיב ערכות מותאמות אישית, להדפיס ולתייג את שם החברה והמותג שלך ולהעביר משלוח ללקוחות שלך. במילים אחרות, אנחנו יכולים להיות גם מרכז האחסנה וההפצה שלך אם תעדיף. מכיוון שהמחסנים שלנו ממוקמים ליד נמלי ים מרכזיים, זה נותן לנו יתרון לוגיסטי. לדוגמה, כאשר המוצרים שלך מגיעים לנמל ימי גדול בארה"ב, אנו יכולים להעביר אותם ישירות למחסן סמוך בו נוכל לאחסן, להרכיב, להכין ערכות, לסמן מחדש, להדפיס, לארוז לפי בחירתך ולשחרר לשלוח ללקוחות שלך. אנחנו לא רק מספקים מוצרים. החברה שלנו עובדת על חוזים מותאמים אישית שבהם אנחנו מגיעים לאתר שלך, מעריכים את הפרויקט שלך באתר ומפתחים הצעת פרויקט בהתאמה אישית עבורך. לאחר מכן אנו שולחים את הצוות המנוסה שלנו ליישם את הפרויקט. מידע נוסף על עבודת ההנדסה שלנו ניתן למצוא ב http://www.ags-engineering.com -אנו לוקחים פרויקטים קטנים כמו גם פרויקטים גדולים בקנה מידה תעשייתי. כצעד ראשון, נוכל לחבר אותך בטלפון, שיחות ועידה או מסנג'ר MSN לחברי הצוות המומחים שלנו, כך שתוכל לתקשר ישירות למומחה, לשאול שאלות ולדון בפרויקט שלך. התקשר אלינו ובמידת הצורך נבוא לבקר אותך. עמוד קודם